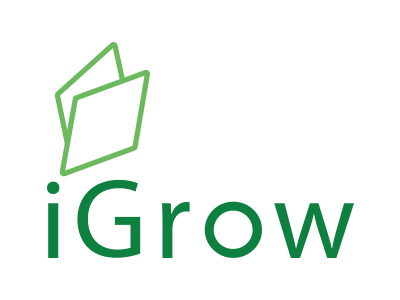
Welcome to iGrow News, Your Source for the World of Indoor Vertical Farming
Strengthening Ties With Qatar To Grow In The Middle East
At iFarm, we will remember June 2021 as the month of Qatar! We announced an agreement to build a vertical farm based on our technology in Doha, hosted two high-profile delegations from Qatar at a lettuce farm, and held a series of important discussions regarding cooperation in the country
August 3, 2021
At iFarm, we will remember June 2021 as the month of Qatar! We announced an agreement to build a vertical farm based on our technology in Doha, hosted two high-profile delegations from Qatar at a lettuce farm, and held a series of important discussions regarding cooperation in the country.
Background information on the Middle East region
The Arabian Peninsula has an extremely hot and arid climate (it’s one of the hottest places on the planet), and Qatar is no exception. There are sands and dunes in the north, sandy hills in the south — with a rocky desert in the middle. In the summer months, temperatures can reach 50 °C. The country has no rivers and obtains most of its freshwater by desalinating seawater. As a result, Qatar has extremely unfavourable conditions for growing edible plants such as vegetables, berries, and herbs. However, where tomato plants wither, date palms thrive. The “Queen of the Oasis” has been bearing excellent fruit throughout the entire Middle East region for thousands of years. It’s just, you can’t live on dates alone.
99,1 %
Qatar’s urbanisation rate
(one of the highest in the world)
90 %
of food in Qatar is imported
Although Qatar ranks among the richest countries in the world in terms of per capita income, it relies heavily on imports to feed its population. Local agriculture only covers 10% of the country’s needs, and food security remains high on Qatar’s agenda. With its abundant financial resources, the country can use state-of-the-art technology to grow crops. Due to this, we believe local, year-round cultivation of vegetables, berries, and herbs on vertical farms is one of the best solutions for this region.
“By working with iFarm, Qatar increases its share of locally grown products, and we can showcase how our technology can be used in a region with extreme climatic conditions. The use of translucent greenhouses can be a problem given the hot climate: they need to be shaded and cooled. Vertical farming, on the other hand, is a perfect match. This is an excellent tool that can help Qatar achieve its ambitious food security goals.”
Alex Lyskovsky
president of iFarm
As you may recall, Qatar has adopted a National Food Security Strategy under which the country aims to reach 70% self-sufficiency in food production by 2023.
Cooperation with Agrico
Our first talks about building vertical farms powered by iFarm technology in Qatar go back to 2019. The Qataris are very cautious in choosing partners, but once they get involved, you can be sure it’s going to be serious and long-lasting. We recently announced a joint project with Sadarah that includes building a commercial pilot farm based on the Agrico Farm in Al Khor, 50 km from Doha. iFarm supplies hardware and software, and will oversee the farm once it goes live and help the partners manage the technology. The second phase of this joint effort involves the commercial distribution of products to the local market and the extension of vertical cultivation technology to other farms in Qatar and neighboring countries. Contractors are currently erecting a purpose-built environment specifically for this vertical “plant factory” project.
Cooperation with Lulu Group International
LuLu Group International is iFarm’s signature partner in the Middle East. It is a multinational corporation that operates one of the largest retail chains in Asia and the Persian Gulf. LuLu is among the fastest-growing chains in the world and employs more than 57,000 people around the world. We are in talks with LuLu Group’s representative office in Qatar regarding building vertical farms right in the supermarkets. At least one side of the pilot farm is designed using transparent material, so that customers can see the process of growing and harvesting plants from “smart” beds. In early June 2021, the project was discussed at the International Economic Forum in St. Petersburg. It is of great importance to us because it can be scaled up throughout the entire chain, covering more than 200 stores in 22 countries.
Qatari delegations visit farms powered by iFarm technology
Indoor cultivation in a fully controlled environment still attracts a lot of attention and investment due to its obvious benefits, including land and water conservation, reduction of CO2 emissions, absence of pesticides, etc. Vertical farming is a sustainable method of farming, and although it won’t replace conventional farming everywhere, in many regions it is, perhaps, the only way to harvest high-quality fresh vegetables, berries, and herbs locally throughout the whole year.
Two delegations from Qatar visited a farm powered by iFarm technology in June. The head of the country’s investment promotion agency (IPA Qatar), Sheikh Ali Al-Walid Al-Thani, was one of our guests. The agency aims to attract direct investment in Qatar and assists entrepreneurs throughout the entire investment process providing services on a ‘one-stop shop’ basis.
We also had the pleasure of welcoming Masoud Jarallah al-Marri, Director of the Food Security Department at the Ministry of Municipality and Environment. He is responsible for the national certification of agricultural products and takes special care to verify the performance of any technology that is going to be introduced in Qatar.
Both guests inspected all of the production areas at the vertical farm, saw how the engineering equipment and software work, tasted a range of products grown on the farm, and left satisfied!
“Qatar is developing rapidly, and I am amazed at the pace of change in this country, which is literally turning into a huge beautiful oasis in the middle of the desert. Doha, for example, has a state-of-the-art, fully automated subway running under the city’s skyscrapers. Qatar has welcomed many foreign investors and businesses in recent years, thanks to its national vision, efforts to diversify the economy and the country’s role as hosts of the FIFA World Cup in 2022. We are happy that iFarm technology will provide guests and locals with delicious greens, vegetables and berries, and will enhance the country’s food security in the long term.”
Alex Lyskovsky, president of iFarm
Source and All Photo Courtesy of iFarm
Smart Farms: Getting To the Heart of The Matter
Labour costs account for up to 50% of the market price of vegetables, berries, and herbs. However, just like the tractor that once transformed agriculture, the new technological revolution greatly reduces the need for manual, skilled and specialist labour
August 3, 2021
Take a look behind the scenes of vertical plant automation and find out what it takes to bring a smart farm to life with exciting exploded-view diagrams.
Labour costs account for up to 50% of the market price of vegetables, berries, and herbs. However, just like the tractor that once transformed agriculture, the new technological revolution greatly reduces the need for manual, skilled and specialist labour. Today, the work is done by a team of robots, sensors, artificial intelligence, and a core team of highly skilled professionals who manage hundreds of farms at once using special software. As a result, we witness the “battle for the harvest” moving into the IT domain.
A vertical farm functions as an organism, and its equipment can be compared to human organ systems. Its sensors and senders are the nervous system, its air conditioners and dehumidifiers act as the respiratory system, while the solution supply pipeline represents the circulatory system. We can compare the nutrient mixing unit to the endocrine system, tray conveyors and lifts to muscles. Naturally, this organism has a “brain” — the Growtune IT platform.
The degree to which the brain can accurately and confidently “take control” determines how ready various systems, nodes, and technologies are to operate without human intervention. Below, we describe all of the tech that lies inside a vertical farm. How, where, and at what production stages does the automation work? For this purpose, we’ll leverage the somewhat forgotten “exploded-view diagram” style. This way, we'll be able to show all the devices the farm uses to take care of the plants.
1. Breathing: ventilation and air conditioning
Let’s remember biology classes. Plants use photosynthesis to turn light, water and CO2 into oxygen and energy. By doing so, they can consume far more CO2 than is normally present in the air. Since the farm, like a space station, uses a closed-loop air exchange system, with no air inflow from the street, creating an optimal environment and climate for plants is purely an engineering challenge. This includes purifying, conditioning, and adding some CO2 to the room to allow plants breathe freely and grow intensively.
“People who walk into a vertical farm for the first time notice how nice and clean the air is. That’s no surprise because it doesn’t contain any dust — there’s nowhere dust can appear from in the closed-loop circuit of the farm.
Alexey Novokreshchenko, Head of Automation at iFarm
The farm has multiple air conditioning units. It’s not just a matter of maintaining a certain temperature and humidity. We need to make sure that the climate is as homogeneous as possible throughout the entire arm, including at different heights. So, instead of one super-powerful unit, we install several medium-sized devices. This provides the right air circulation and creates a failure-proof system.
Hydroponic technologies tend to create a lot of moisture, and the farm air typically needs to be dehumidified (iFarm has developed and patented a dehumidification system that allows you to reuse this water to feed your plants). There are times, though, when you need to do the opposite: for example, you may need to humidify the air, especially at the initial stage of starting a farm when you don’t have a lot of plants.
2. Energy: grow lights
Photosynthesis, that is the conversion of light energy into chemical energy, only occurs when there is light. Agronomists call artificial lighting of plants “supplemental lighting”. It may vary from one area of the farm to another, depending on the crop and its cultivation phase. The light control unit creates “day” and “night” conditions for plants. The most frequent setup resembles a nice summer day: 14–16 hours of light and 8–10 hours of darkness. Darkness is crucial: the night is when cellular respiration occurs and other important processes take place.
“The plant depends on the day-and-night schedule. Its structure and maturation phases vary depending on the light cycle. Keep the microgreen sprouts in the dark a little longer, and they'll stretch out but will become coarser. By changing the lighting, you can experiment with taste. For example, if you keep sunflower microgreens in the dark for 10 days and then expose them to the light for a full day, you’ll get long and very sweet sprouts.”
Nikolai Podvigin, Head of the Agrolaboratory at iFarm
Agronomists at pilot farms refine cultivation flow charts. For example, they are currently experimenting with variable brightness to grow pine strawberries: the lamps are equipped with a dimmer so you can gradually add brightness. It seems that the agronomists’ hypothesis holds true — the berry evidently "enjoys" long dawns. Through smooth, incremental changes in lighting, the osmotic pressure in the stem and leaves grows gradually, whereas its surge upon sudden light exposure can have a tissue-damaging effect.
Sometimes you have to focus not only on what the plants need but also on organisational or purely economic factors. For example, the cost of electricity. True, the lamps we manufacture and install in racks are highly energy-efficient: they convert every watt of electricity into 0.6 watts of photosynthetically active radiation (FAR). Still, energy costs make up a large portion of the costs of growing herbs indoors. Automation can (and should) be leveraged to ensure optimal load distribution. If the farm can use a night rate, we change “days” with “nights” and reschedule the supplemental lighting for the nighttime to minimise operating costs.
3. Nutrition: irrigation and nutrient solution supply
The nutrient solution is made from several components stored in individual containers which can easily be replaced. The solution is prepared in the mixing unit, a sophisticated automated system capable of mixing dozens of litres of stock solutions with high precision and in the right proportions.
The nutrient solution is delivered to the roots of the plants through a tube system. Since the specific recipe depends on the type of the plant and its cultivation stage, the system continuously monitors (and sometimes adjusts) the composition of the solution.
“Plants eat and plants drink. We provide them with both by mixing nutrition with water. This water continuously runs through the rack. To create an individual “menu” for each plant type, we divide the farm into different watering areas and install an additional storage tank in each of them. Each area is equipped with an additional set of sensors that dynamically monitor the changes in the solution. In fact, these sensors control whether the plant “ate well” today and whether they have everything they need.”
Alexey Novokreshchenko, Head of Automation at iFarm
The water used for preparing the solution is added to the system after it is properly treated with a reverse osmosis filter. This removes contaminants, such as minerals, heavy metals, bacteria and viruses, leaving the water virtually pure.
4. Well-being: IoT sensors
The purity of the source water, the ratio of nutrients in the solution, its acidity, the brightness of the light, the amount of carbon dioxide in the air, temperature, and humidity — you need to control all these things with precision. A large farm can have hundreds of sensors.
Based on sensor measurements, the farm's central processing unit controls the equipment and hardware in real-time, always keeping climatic and biochemical parameters within the limits set by the cultivation flow chart.
If these limits are exceeded, it triggers an alarm and remote technicians are alerted. The algorithm helps identify potential human errors, among other things. For example, it will immediately alert you if a technician incorrectly replaces the cans with the source materials for the solution.
“Plants can be extremely sensitive, some may “dislike” even a one-degree deviation from the usual temperature. We covered the racks with sensors and cameras so we could understand what a crop is sensitive to during cultivation. Now we’ve stabilised the process by defining the optimal number of devices to ensure accurate environment control.
Nikolai Podvigin, Head of the Agrolaboratory at iFarm
5. Analytics: computer processing of Big Data
The “head” of the system is a cloud server. It collates and computes data indirectly from the array of actual measurements collected. For example, it calculates the efficiency of air circulation across the farm based on the data from all of the climatic sensors. What’s even more important is the ability of Growtune, the farm management software platform, to process all of the Big Data collected on the farm.
“The algorithms we use to prepare nutrient solutions are based both on recipes and on the processing of collected data. The outcomes of plant nutrition in previous cycles affect future mixing. The controller monitors the plants’ reaction to “dinner” on the previous day and adjusts the solution accordingly. And, after reviewing the combined data from different farms, we gradually optimise the flow charts.”
Alexey Novokreshchenko, Head of Automation at iFarm
Farms are increasingly using machine vision in their “nervous system”. Images from the cameras installed on the racks are analysed by a neural network trained to determine if the plants are healthy. Technicians can also use this neural network by uploading a picture of plants through a chatbot to gain critical information about its health. Another neural network calculates the dynamics of herbage mass accumulation using the same stationary video cameras or drone cameras.
6. Movement: automation of tray movements
Problems usually dealt with by rare and expensive specialists, agronomists, biochemists, and phytopathologists can be solved using artificial intelligence, special equipment, or remote consultants. But, until recently, there hasn’t been a fully automatic farm where electronics also handle routine manual work, such as moving trays.
In February 2021, iFarm engineers implemented and tested a design prototype of a fully automated vertical farm. It features a conveyor belt that moves trays with pots through the planting, germination, growth, ripening, and cutting areas. The farm can also be equipped with individual robot modules for packaging products and preparing trays for the next cycle.
7. A human helping hand
As with any sophisticated modern equipment, an automated farm has special service message protocols. Naturally, these protocols are intended for a person, such as an employee of a certified service provider. Automatic warnings about errors, worn-out nodes, or the need for consumables to be replaced translate into assignments for replenishment or troubleshooting.
The reports of deviations in the growth of herbs are handled by an iFarm agronomist. The first thing this expert does is double-check that the actual conditions match the ones in the flow chart. They then go through a list of tasks almost identical to the sections of this article. So, what’s happening with the air, climate, energy, and nutrition of the plants on the farm? Do the sensors provide correct data? When suspecting a technical failure, the agronomist connects a service employee to the diagnostic interface with one click. They can also connect to the technician’s camera or AR glasses if the employee is already on site.
“We have several continuous operation circuits, millions of second-by-second measurements, sensors, robots, conveyors, drones, cameras, and neural networks. It seems we’ve automated almost everything we can. The only thing you can’t automate is the R&D process itself. This is why people in the company focus on this process. And this is exactly why we are fighting for strategic investments.”
AppHarvest: Management Estimates Vs. The Market
APPH's management projects appealing unit economics and a long runway for future growth. If management's projections are accurate, in five years APPH will be generating over $100mm in annual free cash flow and be able to reinvest 100% of that cash at a rate of return over 15%.
By Carleton Hanson
July 28, 2021
Summary
AppHarvest is a vertical farming company that is ramping up its operations.
AppHarvest's management has rosy projections for profitability and growth, but the market is skeptical about the company's future.
If management's estimates are accurate, AppHarvest looks appealing on a future cash flow basis.
AppHarvest has meaningful downside risk.
I am considering starting a small, "coffee can" position in the company.
I look for companies that generate consistent free cash flow and that can reinvest cash at a high rate of return. AppHarvest (APPH) does not fit the bill in its current state. The company only started to generate revenue in 2021 and is years away from generating free cash flow. APPH's management projects appealing unit economics and a long runway for future growth. If management's projections are accurate, in five years APPH will be generating over $100mm in annual free cash flow and be able to reinvest 100% of that cash at a rate of return over 15%. APPH's business model is unproven but I would be excited to own shares in a company with their projected return profile.
What is AppHarvest?
APPH is an indoor farming company based in Appalachia. The company grows tomatoes in a 60-acre indoor farm located in Morehead, KY. By growing their produce indoors, APPH is able to avoid using pesticides, recycle water, and optimize the controlled environment for higher crop yields. APPH can grow 365 days a year and crops are protected from adverse weather events. The company reports that it can produce yields as high 30x those of conventional outdoor farms while using 90% less water and a fraction of the soil and fertilizer. APPH sells exclusively to Mastronardi Produce Limited, another indoor farming company that has an extensive distribution network across the United States.
APPH is a new company, and only began harvesting from their Morehead facility this year; there isn't much data yet on their operational metrics. As of Q1, the company had about $300mm in cash on their balance sheet, but APPH is investing heavily into building additional farms. There are two farms currently under construction in KY and six additional sites have been identified as future farm locations. APPH's goal is to have 12 farms completed or under construction by the end of 2025. A standard 60-acre facility costs about $120mm to build and APPH estimates that a fully functional farm can bring in annual revenues above $40mm with gross margins as high as 40% and EBITDA margins around 35%.
(Source: Analyst Presentation)
Management raised facility EBIDTA estimates to over $23mm on the Q1 conference call, with the excess coming from increases revenue and lower input costs. Some of this upward revision is also due to the acquisition of robotics company Root AI, which management expects to improve farm efficiency and automation in the future.
Putting together the farm unit economics and the target number of farms, five-year projections look like this:(Source: Analyst Presentation)
APPH has a market cap of $1.2 billion. If the projections above are accurate, APPH will be generating more than $100mm in free cash flow by 2026 and have a proven, profitable model that they can leverage to build more farms with an expected cash return above 15%. $1.2 billion is a cheap enough price to pay for a company with that return profile.
Let's Take Management's Projections at Face Value; How Much Should We Pay For APPH?
The big question is: Are management's estimates accurate? I will talk more about this risk later in the article, but for now let's say that the future plays out exactly as management projects. In this scenario, what would be a fair price to pay for APPH shares today? Using company estimates, we can put together a rough 5-year DCF. I am going to use a 15% discount rate in my equation. This might be controversial, but there are a number of other companies that I own that I expect to return at least 15% a year. If I am going to tie up capital in APPH while I wait for management to execute their plan, I am going to treat the opportunity cost as 15% a year. The results look like this:
The netted cash amount is inconsequential for just five years. In the scenario where management's estimates have been accurate, the company would be in a great position at the end of 2026. They have a proven business model, are generating ample free cash flow, and could continue to expand their operations by building more farms. I think a multiple of 25-30x FCF is reasonable in this scenario, resulting in a market cap of between $1.4-$1.6 billion and a share price between $14-$16. Due to a fairly steady decline in APPH's share price over the last month, a $14 price target is a 16% premium to the current price and $16 would be a 33% premium. For this scenario, I'll split the difference, slap a $15 price target on the stock, and estimate the company is undervalued by 25%.
The Market is Skeptical
Using management's estimates and my DCF assumptions, my "base case" price target for APPH is around $15/share. Despite some initial excitement about the company when it came public via a SPAC, the market is skeptical about this base case:(Source: Seeking Alpha)
APPH is trading more than 70% below its 52-week high and has significant short interest; why might the market be pessimistic about APPH's future? I think the market has two main concerns. First, APPH is only just beginning their operations; the unit economics and long-term growth plans presented by management are just projections at this point. Perhaps the farms will have higher maintenance costs than expected or produce a lower yield over a prolonged period. Interest rate changes could make future expansion projects more expensive. APPH might incur greater than expected SG&A costs. With no operating history, investors are forced to rely on management estimates or make their own projections with limited information. In this case, uncertainty about the future works against APPH's share price in the short term.
Secondly, despite their advanced indoor farm technology and investments in artificial intelligence software, at the end of the day APPH sells commodity products (tomatoes and eventually other produce). It is hard to find a convincing competitive advantage that is unique to APPH that will help them stand out in the market place. There are dozens of other indoor farming companies in various stages of development and production, so APPH's technology isn't unique. Companies like Plenty, AeroFarms, and Local Bounti come to mind, but there are many others as well. APPH's location (Kentucky), cited by the company as a large competitive advantage, will be diminished by the growth in indoor farming. Kentucky might be closer to New York than Mexico or California, but if other companies have the ability to start up small urban farms (like Plenty), then in not too many years I could see more farms popping up closer to major urban areas and reducing APPH's location advantage. SA author Jamie Louko recently did a deeper dive on APPH vs the competition in this article, and I think he brings up good points, especially around APPH's scale and progress in building their farms and securing funding for future work. I'm not sure the market is convinced these advantages will be enough, especially in today's market where traditional farming remains the primary competition.
Investment Thesis (and Risks)
Is the market right to be skeptical about APPH's future, or is the market being short-sighted and creating a favorable investment opportunity? I think the answer to both questions is yes. On the one hand, it is reasonable to remain cautious about APPH's unit economics until the company has been operating multiple farms for multiple years. Without a strong unit economic base, I see limited downside protection for investors. APPH still has a sizable cash position on their balance sheet and owns their one operating farm, but much of the cash is already allocated to completing their two in-progress farms, and their existing farm won't be of much value if the unit economics end up being a lot worse than anticipated. APPH needs to complete more than three farms to overcome their overhead costs, so their long-term success is going to be dependent on a successful progression of new farm construction. New farm construction will be impacted by the future availability of credit and/or the company's share price (if they decide to an equity raise). Finally, APPH would be negatively impacted by short-term drops in vegetable commodity pricing. Tomato pricing has been relatively stable over the last 15-20 years, but swings of 15-25% or more have happened regularly and will likely continue to happen. An APPH investment has real risks that the market is keenly aware of.
On the other hand, I see a lot to like about the company if management is able to execute on their plans. In this scenario, APPH is only a few years away from consistent cash flow generation and will have a long runway for reinvestment at high rates of return. It is rare to find a company today that can reinvest 100% of their free cash flow to grow their business; often companies resort to paying a dividend or buying back shares with excess cash. These outcomes are "fine" for investors, but aren't going to generate the same 15-20% ROI that APPH would be able to get from additional farm construction. The most optimistic outlook makes me think of investing in Walmart or McDonalds in their early stages, when they were building new stores or opening new franchises at a brisk pace and reaping solid returns on those investments.
I can also envision scenarios where APPH makes an unexpected leap forward and expands into an adjacent industry. Company president David Lee made a comment on the Q1 conference call that suggested he sees the potential of their in-house AI and robotic solutions to be licensed to other companies. This would provide another source of high-margin revenue. He even went as far as to say that APPH's solution could be what "AWS is to Amazon" (source). APPH's investment in Root AI shows their commitment to solving technological problems presented by indoor farming and to continuing to optimize their day-to-day operations. If APPH expands into a true tech-focused company that is able to build a platform of tools that other future companies will want to use, that would be a huge and unexpected win for the company. I would take this projection with a huge grain of salt and say it is unlikely to materialize, but I think APPH's technology has value and at least has the potential to be monetized in the future.
Conclusion
An APPH investment is a departure from my usual style; I tend to focus more heavily on protecting against the downside than shooting for home-run returns with a favorable risk/reward ratio. That being said, I see APPH as an intriguing opportunity. APPH's potential to invest 100% of ample free cash flow at high rates of return is the most appealing part of this equation, and after the slow fall of the company's share price I think today's market cap looks fairly reasonable. Even with a 15% discount rate APPH is trading slightly below "fair value", assuming management estimates are close to reality. If I were to invest in APPH, I would make it a small portfolio position and plan on holding it "forever" to let the long-term investment thesis play out.
Paul Mastronardi of Mastronardi Produce® And Caitlin Tierney of Mastronardi Produce West® Discuss CEA For Upcoming Organic Produce Summit
Now, with the Organic Produce Summit (OPS) on the horizon, Paul Mastronardi, President and Chief Executive Officer, Mastronardi Produce® and Caitlin Tierney, Business Director, Mastronardi Produce West®, join me to discuss the impact of a growing area of investment in organics—controlled environment agriculture (CEA)—and how it is primed to accelerate fresh produce’s advantages and benefits in organics, conventional, and the greater food industry.
By Jordan Okumura
July 28, 2021
KINGSVILLE, ON - The dynamic, challenging, and volatile nature of the recent year and a half has revealed quite a few things about fresh produce to me—and one of them is that organics are not only here to stay, but continue to be an area of incredible growth opportunities. Now, with the Organic Produce Summit (OPS) on the horizon, Paul Mastronardi, President and Chief Executive Officer, Mastronardi Produce® and Caitlin Tierney, Business Director, Mastronardi Produce West®, join me to discuss the impact of a growing area of investment in organics—controlled environment agriculture (CEA)—and how it is primed to accelerate fresh produce’s advantages and benefits in organics, conventional, and the greater food industry.
Caitlin Tierney, Business Director of Western Operations, Mastronardi Produce®
“Consumer demand for flavorful fresh produce that is sustainably and locally grown is rising. As our population continues to grow, so too does the need for fresh, nutrient-rich produce. Traditional farming simply cannot keep up with this increasing demand,” Caitlin reflects, adding that to meet supply and reduce dependence on imported goods, CEA in greenhouses offers a more viable solution. “Greenhouses are also ten to twenty times more efficient and use up to ten times less water than conventional field farms.”
Caitlin leads me down the CEA path, sharing how consumers have come to expect a “season-less” pantry, and as a result of high-flavor, year-round varieties like Campari® and Flavor Bombs™, the company is seeing more retailers and foodservice operators move toward greenhouse-grown produce grown with innovative methods.
“By increasing quality, reducing the use of pesticides, growing locally, and bringing year-round supply, we can meet the needs of both consumers and retailers. A great example of this is our greenhouse in Coldwater, Michigan. Here, we use CEA techniques—such as Integrated Pest Management (IPM)—which significantly reduce the need for pesticides and provides local retailers and foodservice operators high-quality, flavorful produce that is grown year-round and is closer to them and their consumers,” Caitlin asserts.
Consumer demand for flavorful fresh produce that is sustainably and locally grown is rising, and SUNSET is helping to respond to that need
Costs also play a major role in how the conversation around CEA has progressed—a big topic that will be at play during OPS' "Growth of CEA: What's Real and What's Hype? - Part 1" panel during the September 15-16 show, where Caitlin will be a panelist. To register for OPS, please click here!
“As we all know, produce has a shelf-life that impacts the entire supply chain. If you are a retailer located on the East Coast, your fresh produce could take up to a week to get to the closest distribution center. Transportation relies on liquid fuels, which are predicted to rise in price faster than the U.S. economic inflation rate,” Caitlin reveals. “Production in CEA facilities relies on electricity and natural gas, and these prices are predicted to remain on par with inflation. With CEA, you will get fresher, more reliable produce that’s not only grown closer to where consumers are buying it, but is also cost-sustainable for the supplier.”
A win-win, in Caitlin’s words.
To get an idea of the difference and the dynamic between greenhouse and CEA, Paul breaks it down for me this way.
Paul Mastronardi, President and Chief Executive Officer, Mastronardi Produce®
“CEA can be produced in several sectors of the agricultural industry: fish, dairy, produce, etc. It’s essentially the production of food while controlling certain aspects of the environment in order to reduce pest or disease, increase efficiencies, become more sustainable, and save costs,” he says.
Using technology and data, food can be produced with quality and flavor.
“Greenhouse farming does all of this with a focus on controlled variables. Variables like temperature, humidity, and sunlight are considered carefully when growing produce in greenhouses,” he adds. “And, while CEA and greenhouse growing are two separate methods of quality food production, CEA is regularly used in greenhouses because it adds significant benefits to crop production, sustainability, and increased quality and flavor.”
Mark your calendars for the Organic Produce Summit’s "Growth of CEA: What's Real and What's Hype? -Part 1" session where Caitlin Tierney will be a panelist.
It is at this point in the conversation that he pauses to bring in the impact of vertical farming as well.
“Vertical farming, which is the process of growing crops in vertically stacked layers, is a relatively novel concept and has some significant headwinds to overcome before commercially viable. It’s currently a very small part of the market with significantly higher pricing, so it won’t replace, but will complement, existing food production with local, sustainably grown food,” Paul expresses.
This leads me to inquire how one would define the differences between vertical farming and greenhouse, and Paul details how a primary difference between vertical farming and greenhouse growing is output costs.
“Fully automated vertical farms rely exclusively on artificial lighting, which results in higher operating costs and capital expenditures. Our greenhouses, on the other hand, provide nutrient-dense produce grown sustainably, year-round without the high costs associated with energy. Why? Because we draw a lot of value from the fact that the production surfaces are mostly illuminated by the sun,” he shares.
And as Paul Mastronardi always says to his team, “there’s something magical about the sun.”
As OPS draws near, mark your calendars, build your schedule, and add Educational Breakout Session: "Growth of CEA: What's Real and What's Hype? -Part 1" for September 15!
La Sierra University Celebrates First Hydroponics Harvest
The Freight Farms container arrived on March 30, 2021, hoisted by a crane and set down on a slab of recycled concrete and asphalt. Three months later, the Enactus team harvested its first crops — approximately 540 heads of red leaf lettuce on July 12 and roughly 550 heads on July 19, a first bounty donated to campus and community members.
By La Sierra University News
July 27, 2021
During La Sierra University’s beginnings in the early 20th century, the school farm, especially its dairy, alfalfa fields, and watermelon patch, was a critical source of income for the institution and its student laborers. In 2021, farming returned to the campus in Riverside, California, United States — on a big rig.
During the 2019-2020 school year, the university’s student Enactus team based in the Zapara School of Business began work on its Freight2Table project through the Boston-based Freight Farms program. The project involves growing varieties of lettuce and leafy green vegetables, herbs, flowers, and roots inside a 40-foot shipping container repurposed and designed with hydroponics technology.
The Freight Farms container arrived on March 30, 2021, hoisted by a crane and set down on a slab of recycled concrete and asphalt. Three months later, the Enactus team harvested its first crops — approximately 540 heads of red leaf lettuce on July 12 and roughly 550 heads on July 19, a first bounty donated to campus and community members. The team also planted baby leaf lettuce, Swiss chard, and butter lettuce in various growth stages. The Enactus team aims to establish produce-supplier agreements with local businesses and organizations and is communicating with markets in Riverside and with the university’s Dining Commons.
Nancy and Hermogenes Guerpo arrive to pick up containers of fresh red leaf lettuce during the Enactus team’s distribution event in the Sierra Vista Chapel parking lot on July 12, 2021. [Photo: La Sierra University]
A crane lifts the Freight Farms shipping container onto a slab at La Sierra University on March 30, 2021. [Photo: Natan Vigna, La Sierra University]
Megan Eisele (left), president of La Sierra’s Enactus team, and Aaron DesJardins, team marketing vice president, plant the first tiny lettuce seeds on May 17, 2021, inside the Freight Farms hydroponics container. [Photo: La Sierra University]
Enactus member Max Proebstle, a health-care management and finance graduate student, describes the transplanting process for red leaf lettuce seedlings shown in vertical growing panels. [Photo: La Sierra University]
Red leaf lettuce continues to mature in vertical panels inside the Freight Farms hydroponics container. [Photo: La Sierra University]
Enactus members left to right, Brandon Ching, Max Proebstle, and Aaron DesJardins conduct the first harvest of red leaf lettuce on July 12, 2021. [Photo: La Sierra University]
La Sierra Enactus team members Natasha Thomas (left) and Andrew Léon package freshly harvested red leaf lettuce on July 12, 2021, for distribution to campus and community. [Photo: La Sierra University]
Packages of Freight2Table lettuce branded with the Enactus team’s “Two-Bit’s Best” product labels. [Photo: La Sierra University]
The growing process involves a reverse osmosis water filtration system purchased and installed inside the container. A timed and regulated supply of electricity and nutrient-infused water along with growing lights for plant photosynthesis forms the basis for how the hydroponic farm operates. University faculty and staff oversee the system processes and container technology. Freight Farms in Boston has real-time virtual access to the container’s systems for providing assistance if needed. For students, the hydroponics farming venture has provided a plethora of learning opportunities, starting with an introduction to hydroponics agriculture.
“While I had heard that term thrown around in the past, I was never really quite sure what it meant, but after having spent so many hours tending to a hydroponic garden, I feel I have a pretty clear picture of how the whole system operates,” Aaron DesJardins, a dual marketing and graphic design major, who this year serves as the Enactus team’s marketing vice president, said. His efforts include designing the farm’s logo and branding as “Two-Bit’s Best,” in reference to the hill overlooking the university campus known as Two-Bit Mountain.
“Another big thing I've learned while working with the Freight2Table project has been the importance of coordination, communication, and team management,” DesJardins said. “There is a much higher likelihood that the crop will not turn out good if it is not managed correctly.”
Since May, DesJardins and his teammates have dedicated several hours each week working with crops in the container and in team meetings planning produce distribution. Inside the container, they wear masks for health and safety purposes, as well as gloves and protective lab coats, to reduce the risk of contamination to the plants and growing system.
Marvin Payne, associate biochemistry professor and project director for the Title V grant-funded Guided Pathways to Success program, and Richard Rakijian, summer program coordinator and chemistry/biochemistry lab manager, oversee the operations of the hydroponics farm. “Dr. Payne and Richard have been a huge help in being there to help us navigate the freight operations,” DesJardins said. “They have also been a big help in helping us decide which crops to plant and scheduling things such as harvests and transplant dates.”
The new Title V program, Guided Pathways to Success in STEM, incorporates STEM education into a summer curriculum designed to help incoming first-year students become inspired to pursue STEM degrees and succeed in college. Botanist and university biology professor John Perumal will lead activities in germinating seeds for experiments under different conditions and in plant growth and development assessments. The Enactus team has developed partnerships with other campus groups and programs, such as the Hispanic Business Incubator.
The Enactus Freight2Table project will also offer agricultural technology education to elementary students in local school districts.
With Freight2Table, the Enactus team is entering an agricultural technology market that is expected to grow substantially in coming years. Food producers are looking to feed the planet's burgeoning population in more controlled and easily accessible ways in the face of extreme weather and drought, and as individual growers seek alternatives to traditional gardens. Hydroponics agriculture comprised about half of the vertical farming marketing in the U.S. in 2018, according to an industry outlook and forecast through Research and Markets in Dublin, Ireland. It is forecasted to grow 22 percent during the period of 2019 to 2024. The report states that the overall U.S. vertical farming market is projected to reach a value of around US$3 billion by 2024.
Hydroponic agriculture’s water-conserving process is an important consideration in drought-prone regions, including the western U.S. and, in particular, California, where a years-long, historic drought is stoking anxiety over water supplies. Hydroponic farming systems capture and re-use water, and as such, can use as much as 10 times less water than what is used with field crops, according to Powerhouse Hydroponics.
Currently, Enactus students are volunteering their time to establish and maintain Freight2Table. In the future, the team aims to hire students to manage the container farm as it increases production. The eight-week crop-growing process is labor intensive. During the first week, tiny seeds are planted by hand in small peat pods and then germinated in seedling trays in a top trough. In the second and third weeks, the germinates mature in the seedling trays in a bottom trough. During the fourth week, hundreds of juvenile plants are transplanted to vertical growing panels one at a time and left to grow and mature four to five weeks before harvesting. The moveable vertical growing panels, which occupy most of the shipping container space, provide four sides for growing plants, with each side accommodating between 576 and 990 plants, depending on the variety.
The hydroponics farming project and its results are included in the team’s Enactus annual report and multi-media presentation during annual Enactus competitions. Enactus, a global non-profit organization based in Springfield, Missouri, is focused on economic and educational empowerment through business innovation and collaboration. It has teams at 1,730 campuses in 36 countries. Since joining in 1991, the La Sierra team has won seven Enactus national championships and two world cups. During national competitions in April, which were held virtually, the La Sierra team placed among the top eight teams in the nation and received the Excellence in Project Management Award from the U.S. Enactus organization.
La Sierra Enactus member Max Proebstle will enter his second year of graduate study this fall and served as part of the presentation team this past school year during competitions. He is earning dual MBAs in health-care management and finance and has been involved in the hydroponics farm since October 2020. Going forward, he will work with other students in maintaining a steady flow of crops from the farm and building up its customer base.
“Before this project, I didn’t even know that hydroponics existed. So, everything has been relatively new for me. It’s been quite the experience learning how to grow plants in this way,” Proebstle said. “The hardest part is learning the system and then getting a feel for nutrient and pH levels. Another thing I’ve learned is that more people care about this form of sustainable farming and food production than I would have thought. We’ve gotten such great feedback from donors, sponsors, the school, and the community; it’s really been a blessing.”
Lead Photo: Freight2Table recasts the Adventist school’s century-old tradition of farming.
The original version of this story was posted by La Sierra University.
Will Tomatoes Be The Next Big Commercial Crop For Vertical Farms?
Researchers at University of California-Riverside are using CRISPR technology to develop miniature tomato plants for production in vertical farms and on the International Space Station.
By David Kuack
July 22, 2021
Researchers at the University of California-Riverside are using CRISPR technology to develop miniature tomato plants for production in vertical farms and on the International Space Station.
What crops come to mind when you think of vertical farm production? Leafy greens, microgreens and herbs are likely the most common answer. How about tomatoes?
University of California researchers Robert Jinkerson and Martha Orozco-Cárdenas are using CRISPR-Cas9 gene-editing technology to develop short tomato plants that have the potential to be grown in vertical farms and on the International Space Station. Orozco-Cárdenas initially used CRISPR technology to reduce the size of normal tomato plants, including the number of leaves and stems, without significantly reducing the size and yield of the fruit.
“The tomatoes originally were under investigation by my collaborator Dr. Orozco-Cárdenas, who is director of the UC-Riverside Plant Transformation Research Center,” Jinkerson said. “I was touring her research facility and saw tomato plants that were fruiting in vitro. The plants were incredibly small. I thought these tomatoes would have a lot of different applications, particularly for NASA. We also determined that the tomatoes could be well suited for vertical farming. It started out as a basic science project investigating gene function and we expanded it to look toward other applications where genes could be mutated to control plant architecture for vertical farming and for space flight applications.
“For the first iteration, Dr. Orozco-Cárdenas took an existing dwarf tomato plant variety and used CRISPR gene editing to further shrink the plants. Currently we are working on using the CRISPR technology to stack more mutations on top of the original variety. We are also performing gene editing in a commercial indeterminate variety to determine if we can alter the plant architecture and size so that they would be suitable for vertical farm production.”
University of California researchers are studying how to grow tomato plants to the smallest size and still produce the highest fruit yield.
Limits to plant size
Jinkerson said the CRISPR gene-editing technology can be used to create mutations that affect the inflorescence, number of flowers, and branching architecture. Initially plant size was the trait the two researchers were interested in changing, but Jinkerson said he has expanded the studies to include the impact on fruit size and yields.
“We are looking primarily at how we can grow the plants to the smallest size and still produce the highest fruit yield to maximize the harvest index,” Jinkerson said. “The harvest index is the amount and weight of the fruit vs. the weight of the total plant biomass, including the fruit. If there was 100 percent fruit then the harvest index would be 100 percent. But because plants need leaves, stems, and roots, the harvest index can’t be 100 percent.
“There is a point where the plant becomes so small that there are not enough leaves to perform photosynthesis and the plant won’t be able to support the fruit that it is trying to produce. This is something we have to keep in mind as we try to balance the plant size and how much vegetative biomass is needed to produce the fruit. Currently, we are investigating this relationship. We think we are starting to hit the lower limit of size where we cannot make the plants much smaller without negatively affecting the fruit yields.”
University of California researcher Robert Jinkerson is looking to work with commercial controlled environment growers to determine how the short tomatoes work in their production systems.
Overcoming vertical farm limitations
Jinkerson’s tomato research is being funded by a $450,000 New Innovator grant from the Foundation for Food & Agriculture Research. Even though Jinkerson’s background is in engineering and algae, he saw the potential that vertical farming could have on future food supplies.
“Most commercial crops are grown outdoors and there really are not any restrictions on size,” he said. “For vertical farming there is a lot of work that needs to be done to customize crops for this new production environment. For instance, the plants can only be a certain size and should have a quick production time to reach harvest. They should also be very efficient with the way they utilize artificial light for photosynthesis because electricity for lighting is one of the largest operating costs.”
Part of the FFAR grant is for Jinkerson to work with commercial growers to determine how the short tomatoes that are developed work in their production systems.
“We are interested in finding commercial growers who are operating vertical farms or a commercial partner who can help trial and evaluate the lines that we have already produced and future lines we will be developing,” he said. “Another aspect of the research grant is to take other tomato varieties and try to optimize their architecture for vertical farms in order to have a greater variety of fruit that can be grown in these systems.”
Although Jinkerson does not have a vertical farm set up at the university, he is trialing the plants in a greenhouse and a controlled environment room equipped with fluorescent lights.
“The grow room with fluorescent lighting that we are using is not like a high-tech vertical farm equipped with LEDs,” he said. “The plants have been grown with a photon flux of a few hundred μmol m−2 s−1 PAR at a 16-hour photoperiod. The temperature and humidity have been maintained at normal room conditions. We haven’t tried to optimize environmental conditions for plant growth yet. We haven’t pushed the plants under any extreme conditions, but these are future areas of research we are interested in exploring.”
Jinkerson and his students are also collecting data related to the amount of light that is needed for the plants to flower and fruit under artificial light.
“We have fruit yield data,” he said. “We have done a lot of calculations on fruit yield per volume. This is an important metric for vertical farms. With our data, we can estimate what type of yields we could expect with the plants. Depending on the vertical spacing distance, the yield per volume for the plants we have developed could be anywhere between 1.5 to three times higher compared to greenhouse yields.”
Future crops for vertical farms, space travel
While Jinkerson’s current research is focused on tomatoes he said there is the potential to apply the gene-editing technology being developed to other vertical farm crops.
“We are going to start with other Solanaceae crops, including peppers, eggplant and potatoes,” he said. “We think that many of the findings we have identified with tomato will be able to translate to these other crops because they are closely related to tomato.”
University of California researcher Robert Jinkerson (above) wants to expand the study of CRISPR gene-editing technology beyond tomatoes to other Solanaceae crops, including peppers, eggplant and potatoes.
Part of the research on the tomatoes is being funded by NASA and will be used to conduct a seed-to-seed experiment in space.
“The goal is to grow tomato plants on the International Space Station to fruit and have the astronauts harvest the seed,” Jinkerson said. “The astronauts will then take the seed and grow them for the next crop to have them fruit again. This process is essential in order to have a sustainable crop system for food production. This has never been demonstrated before with tomatoes on the space station.”
The astronauts are currently producing leafy greens on the space station.
“There is very limited physical space on the space station so trying to maximize the harvest index is essential,” Jinkerson said. “This is a very good analog for vertical farms on Earth. With leafy greens the astronauts are able to eat everything but the roots, making these plants perfect for space travel. However, NASA is interested in growing other crops in space. There is an experiment planned for peppers coming up in the next year and our experiment with tomatoes in the next two to three years. Just like vertical farm growers on Earth, astronauts will be trying to produce different types of crops in space.”
Lead Photo: University of California-Riverside researchers Martha Orozco-Cárdenas (above) and Robert Jinkerson are using CRISPR gene-editing technology to develop short tomato plants that have the potential to be grown in vertical farms and on the International Space Station. Photos courtesy of Robert Jinkerson, Univ. of Calif.-Riverside Photos courtesy of Robert Jinkerson, Univ. of Calif.-Riverside
Center To Announce First Winners of Its “Best In Class” Awards
The Center of Excellence for Indoor Agriculture, a U.S. based company that supports the growth and development of the vertical and indoor farming industry, will announce the first winners of its Center of Excellence “Best in Class”TM Awards for indoor farm manufacturers at a virtual event scheduled for August 4th with Indoor Ag-Con.
By July 23, 2021
The Center of Excellence for Indoor Agriculture, a U.S. based company that supports the growth and development of the vertical and indoor farming industry, will announce the first winners of its Center of Excellence “Best in Class” TM Awards for indoor farm manufacturers at a virtual event scheduled for August 4th with Indoor Ag-Con. The goal of the “Best in Class” Awards is to recognize operational excellence in the indoor agriculture industry through an analysis of KPI’s on indoor farm operations and the supporting equipment.
The announcement will take place in the context of a virtual panel discussion on the importance of metrics to indoor farm sustainability and future investment in indoor agriculture. Finalists and industry thought leaders will sit on the panel. Those interested may register for the event at: indoor.ag/webinar.
The winners will be announced virtually in two categories: commercial indoor production systems and indoor farm lighting fixtures. Indoor production systems are turnkey systems that are optimized for the production of leafy greens and other vegetables in indoor vertical farm facilities. The top systems use the least amounts of water, energy, labor, and other resources to produce the greatest yield. The top lighting fixtures are energy-efficient, affordable, and yield-optimizing.
“We are really excited to recognize excellence among the Agtech manufacturers supporting the indoor and vertical farming industry. Our finalists offer solutions that help indoor farms achieve operational efficiency and sustainability. We believe the awards can help spur innovation in this space,” stated Eric W. Stein, Ph.D., founder and Executive Director of the Center of Excellence.
The winning products were selected through a process that includes being nominated and then evaluated according to technical and operational merits in several categories. The Center performs a quality check on the data before being input into a proprietary weighted multi-criteria model. Products are also evaluated based on interviews and an analysis of online data.
More Info: More detailed information on the Center’s awards can be found at https://indooragcenter.org/awards. Growers and manufacturers are invited to become nominated and begin the application process. Winners receive several benefits including industry recognition, social media exposure as well as participation in future panel discussions and conferences.
About the Center
The Center of Excellence for Indoor Agriculture provides insights about the economics of indoor farming based on a careful analysis of industry data and from thought leaders in industry and academia. As the first U.S.-based Center of Excellence dedicated to indoor farming, it promotes best practices, benchmarking, networking, knowledge development, and research. Its annual Best in Class Indoor Farming Awards (TM) recognizes top indoor growers and manufacturers. The Center is located in the Philadelphia metro region.
About Indoor Ag-Con
Indoor Ag-Con is an organization that hosts premier events centered around building the indoor agriculture community. They unite growers and engineers alike to create a prime networking opportunity through discussions, workshops, and exhibits enhancing the participants’ knowledge of growing crops in indoor systems.
Media Contact Information
Center of Excellence for Indoor Agriculture
indooragcenter.org
team@indooragcenter.org
BASF Venture Capital Invests In Indian Hydroponics Pioneer UrbanKisaan
Hyderabad, India, and Ludwigshafen, Germany – BASF Venture Capital GmbH (BVC) is investing in the Indian startup UrbanKisaan, which specializes in hydroponic cultivation of various types of vegetables, greens and herbs in tropical urban environments.
July 13, 2021
Hyderabad, India, and Ludwigshafen, Germany – BASF Venture Capital GmbH (BVC) is investing in the Indian startup UrbanKisaan, which specializes in hydroponic cultivation of various types of vegetables, greens and herbs in tropical urban environments. This is BVC’s first investment in an early stage business focusing on India. Conceptualized in 2017, UrbanKisaan operates several suburban greenhouses and vertical indoor farms in Hyderabad and Bangalore. The company sells the fresh produce, some of which is grown directly in the shops, in its franchise-owned brick-and-mortar stores and via an app and website. Both parties agreed not to disclose financial details of the investment.
UrbanKisaan has optimized hydroponics technology for use in tropical climates such as India. With only one tenth of the costs, the proprietary technology is significantly more efficient than conventional global standards in hydroponics cultivation. The company is also capitalizing on the trend of online food retailing, which is booming on the subcontinent. “Our approach in hydroponics enables us to produce our food cost-effectively and with relatively little effort,” said Vihari Kanukollu, co-founder and CEO at UrbanKisaan. “Our produce also contributes towards sustainability as it is grown in clean, hygienic farms in and around the city, thus minimizing the total carbon footprint. Use of IoT (Internet-of-Things)-enabled technology for monitoring the farms ensures pesticide-free produce. The growing demand from our customers shows that our idea is well-received,” he added.
UrbanKisaan’s farms are managed through their proprietary technology. Nutrient content, pH levels, atmospheric humidity, CO2 concentration, light concentration and other important parameters are controlled and adapted to the needs of the particular plants with an app. “UrbanKisaan, as a pioneer in the hydroponics space, has developed a unique growing method and combines this with a compelling business model for sales,” commented Markus Solibieda, Managing Director of BASF Venture Capital GmbH. He added: “AgTech is one of our key investment focus areas worldwide. This includes, in particular, our goal of supporting innovative agricultural and food-related businesses in Asia. We look forward to learning more about hydroponic farming and exploring its potential through a close collaboration between UrbanKisaan and BASF’s agriculture experts.”
With the investment from BASF, UrbanKisaan plans to further expand its market presence in India, deploy its farming technology to work with thousands of farmers, and bring fresh, local, sustainable produce to urban dwellers.
Hydroponic farming – an efficient way to use limited resources.
The world’s population is expected to reach 10 billion by 2050 1 while the area available for farming and freshwater reserves are becoming increasingly scarce. Hydroponics offers a sustainable way to grow crops without soil and using vertically stacked layers while reducing water usage by about 90 percent 2 . Especially in densely populated urban areas, this presents a more efficient way to use limited resources like water, space and manpower. Water that is not absorbed by the plants is captured, purified and fed back into the farm’s water circulation system, minimizing wastage significantly.
India is the second-largest producer of fruits and vegetables in the world, with a production value of about $64 billion 3 . It is also a large consumer of fruits and vegetables, and while much of this is through unorganized channels (local vegetable markets, hand-pulled carts and neighborhood stores), organized channels (modern trade and online retail) account for a little over 20 percent of the market 4 . Thus, hydroponics is a fast growing and efficient alternative to traditional supply chains in the organized fresh produce market.
About UrbanKisaan
UrbanKisaan was conceptualized in 2017 in Hyderabad, India. The company began as a farming enterprise but wanted to grow more than just fresh and nutritious food. They wanted to create a sustainable future for farming and feed the world in a way that is good for both people and planet. Today, with its hyper-local urban farms the company is creating a transparent supply chain with a low carbon footprint, leveraging on proprietary growing technology that helps save 90% of water yet grow 30 times more crops compared to traditional farms of similar area. Further information at www.urbankisaan.com.
About BASF Venture Capital
At BASF, we create chemistry for a sustainable future. BASF Venture Capital GmbH (BVC) also contributes to this corporate purpose. Founded in 2001, BVC has offices in Europe, the U.S., China, India, Brazil, and Israel. BVC’s goal is to generate new growth potential for current and future business areas of BASF by investing in young companies and funds. The focus of investment is on new materials, AgTech, Digitization and new, disruptive business models. Further information at www.basf-vc.com.
About BASF
At BASF, we create chemistry for a sustainable future. We combine economic success with environmental protection and social responsibility. More than 110,000 employees in the BASF Group contribute to the success of our customers in nearly all sectors and almost every country in the world. Our portfolio is organized into six segments: Chemicals, Materials, Industrial Solutions, Surface Technologies, Nutrition & Care and Agricultural Solutions. BASF generated sales of €59 billion in 2020. BASF shares are traded on the stock exchange in Frankfurt (BAS) and as American Depositary Receipts (BASFY) in the U.S. Further information at www.basf.com.
80 Acres Farms CEO Mike Zelkind Joins CEO Keynote Line-Up For In-Person Indoor Ag-Con In Orlando Oct. 4-5, 2021
80 Acres Farms CEO Mike Zelkind will lead the Day Two CEO Keynote Address for the in-person October 4-5, 2021 edition of Indoor Ag-Con at the Hilton Orlando.
July 23, 2021
80 Acres Farms CEO Mike Zelkind will lead the Day Two CEO Keynote Address for the in-person October 4-5, 2021 edition of Indoor Ag-Con at the Hilton Orlando. Themed “Growing Your Business,” the trade show and conference for indoor |vertical farming | controlled environment agriculture will give attendees the opportunity to explore new resources on the expo floor and hear from Zelkind, other CEOs, thought leaders and industry experts from today’s cutting-edge farms and innovative companies.
“80 Acres has been making headlines this year in a number of areas – from plans to expand its produce offerings to new research initiatives. We are so excited to be returning to our live, in-person format in October and offering a platform for forward-thinking industry leaders like Mike Zelkind to share the indoor farming innovations he and the 80 Acres team are working on,” says Brian Sullivan, co-owner, Indoor Ag-Con LLC.
Scheduled for day two, October 5, 2021, Mike Zelkind’s address will be held from 11:30 am – 12:20 pm. In addition to his CEO role with 80 Acres Farms, Mike is also Board Member of Infinite Acres (est. 2019), a vertical farming leader providing customers with fresh, nutritious fruits and vegetables at affordable prices.
Utilizing world-class technology and analytics, 80 Acres Farms offers customers pesticide-free food with a longer shelf-life and the highest food safety standards while using fewer natural resources to produce over 300x more food on less than 1% of the footprint. Winner of Fast Company’s eighth “Most Innovative Company in North America,” 80 Acres was also a finalist for Red Herring’s Top 100 North America award, featured two years in a row on Forbes “Best Start-up List,” and awarded the eleventh spot on the “FoodTech 500” list.
For more than 25 years, Mike has been working with top-tier food companies such as General Mills, Del Monte, Bumble Bee, and ConAgra Foods and top-tier consultancies and start-ups AT Kearney and ICG Commerce, focusing on the food industry. Over the last 15 years, he has worked with Private Equity (such as Oaktree Capital and Bain Capital’s Sankaty) to drive over $2.5B of shareholder value.
In addition to headliner keynote sessions from leaders like Mike Zelkind, other 2021 event highlights include:
ROBUST 2021 CONFERENCE SCHEDULE NOW IN DEVELOPMENT
The 2021 conference will include a full roster of keynote sessions, panel discussions, fireside chats and presentations offering a deep dive into three core tracks – Business & Marketing, Science & Technology and Alternative Crops. Other keynotes will be led by David Rosenberg, CEO, AeroFarms and Sonia Lo, CEO, Sensei Ag.
The extensive educational conference will be joined by other new initiatives and show highlights, including:
NEW LOCATION: HILTON ORLANDO – DISCOUNTED HOTEL RATES, TOO
Indoor Ag-Con’s Hilton Orlando venue makes it the perfect opportunity for a business vacation. Centrally located to all major theme parks and attractions, it is just minutes from the eclectic dining scene and entertainment of International Drive. What’s more, the Hilton Orlando resort sits on more than 26 acres of lush landscaping and tropical inspirations making it a true destination of its own. Indoor Ag-Con has arranged for discounted hotel rates for attendees and exhibitors starting as low as $129/night. Complete details are available on the show website.
EXPANDED EXHIBIT FLOOR & NETWORKING OPPORTUNITIES
The Indoor Ag-Con team is working to bring even more resources for farmers/growers to explore across all sectors – everything from IT, energy, AI and lighting solutions to substrates, vertical farming solutions, business services and much more. Attendees and exhibitors alike will also have even more networking opportunities with daily luncheon sessions and receptions on the show floor.
QUICK FACTS:
WHEN: Monday, October 4 – Tuesday, October 5 , 2021
WHERE: Hilton Orlando, 6001 Destination Pkwy, Orlando, FL 32819
INFO: For information on exhibiting or attending www.indoor.ag or e: suzanne@indoor.ag
ABOUT INDOOR AG-CON LLC
Founded in 2013, Indoor Ag-Con has emerged as the premier trade event for vertical farming | indoor agriculture, the practice of growing crops in indoor systems, using hydroponic, aquaponic and aeroponic techniques. Its events are crop-agnostic and touch all sectors of the business, covering produce, legal cannabis |hemp, alternate protein and non-food crops. In December 2018, three event industry professionals – Nancy Hallberg, Kris Sieradzki and Brian Sullivan – acquired Indoor Ag-Con LLC, setting the stage for further expansion of the events globally. More information:www.indoor.ag
ABOUT 80 ACRES FARMS
80 Acres Farms is a vertical farming leader providing customers with the freshest and most nutritious fruits and vegetables at affordable prices. Utilizing world-class technology and analytics, the Company offers customers a wide variety of pesticide-free food with a longer shelf life that exceeds the highest food safety standards. More information: www.eafarms.com
USA - VIRGINIA - Urban Farm In Newport News Aims To Reduce Food Insecurity. It’s Not A ‘Handout,’ It’s A ‘Hand Up.’
Graham was gardening on a recent Saturday morning in a farm run by Hampton Roads Urban Agriculture, which wants to create a healthy, sustainable food system in the neighborhood. The farm is a partnership between the church and the Newport News-based nonprofit, which is working to reduce food insecurity through farming and educational programming.
By Sonia Rao
July 20, 2021
NEWPORT NEWS — Judge Graham knelt over a row of bare soil and the occasional yellow marigold, planting seeds. In a little over a month, he hopes, the bed near Zion Baptist Church will be bursting with ripe tomatoes. The tomatoes, and the rest of the food Graham and other volunteers are growing, will go to the surrounding community.
Graham was gardening on a recent Saturday morning in a farm run by Hampton Roads Urban Agriculture, which wants to create a healthy, sustainable food system in the neighborhood. The farm is a partnership between the church and the Newport News-based nonprofit, which is working to reduce food insecurity through farming and educational programming.
On Aug. 14, the farm will open its first farmers market, which will take EBT and SNAP payments.
“The ones that can afford to pay, fine, but I’m not gonna turn anybody away,” said Graham, who helped start the group. “Anybody that shows up is gonna go home with some groceries.”
The area around Zion Baptist is a food desert, said Renee Foster, founder of Hampton Roads Urban Agriculture. It has only one grocery store, a Piggly Wiggly, and many residents are low-income and don’t have transportation to drive elsewhere.
The garden has been around for four years and Hampton Roads Urban Agriculture has managed it for two. All of its workers are volunteers, including high school students, veterans and service members. This year, the farm is expected to grow about 3,500 pounds of produce. Graham and Foster also deliver food to older adults who can’t come out because of health concerns or a lack of transportation.
Graham said the farm is also a teaching garden, so he treats it as a place for visitors and volunteers to get hands-on experience.
On June 25, a group from the Coast Guard came to volunteer. This was the first time Petty Officer 2nd Class Stacey Maine gardened. But by the end of the hour, she was explaining how to weed and cut asparagus.
Coast Guard Petty Officer 2nd Class Stacey Maine weeds a vegetable bed in the urban garden near the intersection of Jefferson Avenue and 21st Street in Newport News. (Kaitlin McKeown/Virginia Media)
Some people drive from Norfolk, Chesapeake or Virginia Beach to volunteer.
On the left of the 34-by-100-foot garden is an orchard of peach, plum, apple, fig, pear, cherry and nectarine trees. Next to the orchard are rows of tomatoes, butternut squash, strawberries, asparagus and radishes, and a garden of herbs with basil, sage, lemongrass and stevia. At the back is a collection of chili, tabasco, habanero and ghost peppers. A sign says “Judge’s ’HOT Pepper Zone’ ” with an image of a skull and crossbones to warn children away. Children, Graham said, often mistake the peppers for strawberries.
Interspersed between the crops are bright pink, purple, red and yellow flowers. They bring in pollinators like bees and hummingbirds, Graham said.
The farm also has more than eight types of sweet potatoes, all donated by Clifton Slade, who owns Slade Farms in Surry. Slade donated 270 slips of sweet potatoes. Other donors include The Virginia Small Farm Resource Center, Tidewater Community College’s horticultural program and the Hampton Roads Agricultural Research and Extension Center. The farm gets the rest of its supplies from Norfolk Feed and Seed or Slade Farms. Everything the garden grows is organic, Graham said.
Foster said she’s excited to start hosting more events now that more people are vaccinated and pandemic restrictions have been lifted. The farm has been having movie nights when children can come to have fun and learn about the garden.
She hopes the market will turn enough of a profit so that she can put more food back into the ground. She’s also raising $10,000 to start a “Drones in Agriculture” program to introduce children to careers in agriculture, science, technology, engineering and math. Children will learn how to code and fly drones, which will be used for agriculture scanning — mapping out the layout of the garden and recording plant health.
Foster hopes eventually to raise enough money to hire a part-time farm manager and create more urban farms across Hampton Roads. She and the other board members of her group work full-time jobs, so managing even one is difficult.
“It takes many, many hands,” she said.
At the end of the day, the goal is to empower food-insecure communities to create and maintain access to healthy food.
“We don’t want to give them a handout,” Graham said. “We want to give them a hand up.”
Lead Photo: Volunteers weed a vegetable bed in a garden on Friday, June 25, 2021, near the intersection of Jefferson Avenue and 21st Street in Newport News, Va. The garden is a partnership between Hampton Roads Urban Agriculture and Zion Baptist Church. (Kaitlin McKeown/Virginia Media)
FI Report Preview: Vertical Farming Concept Experiencing Immense Growth
Vertical farming is growing by leaps and bounds. In fact, the evolving form of agriculture has become a multibillion-dollar industry and is expected to reach $12.77 by 2026, growing at a compound annual growth rate of nearly 25%, according to Allied Market Research.
By Kelly Beaton
July 19, 2021
Vertical farming is growing by leaps and bounds. In fact, the evolving form of agriculture has become a multibillion-dollar industry and is expected to reach $12.77 by 2026, growing at a compound annual growth rate of nearly 25%, according to Allied Market Research.
Quite simply, the concept “has gone viral,” said Dr. Dickson Despommier, a professor at Columbia University.
And Despommier should know. After all, he’s credited with conceiving the concept, back in 1999, during an especially spirited Medical Ecology course.
The Food Institute recently interviewed Despommier at length, in advance of its in-depth report on vertical farming, which is set to be published Tuesday (you can eventually download the report here). Here’s some exclusive content from that interview, which discussed numerous aspects of indoor farming, also known as controlled-environment agriculture (or CEA):
HOW WOULD YOU PERSONALLY DEFINE INDOOR FARMING AND VERTICAL FARMING?
Despommier: “Indoor farming includes all indoor farms, including vertical farms, and it also includes greenhouses. The only difference between a vertical farm and a greenhouse is height, because you can’t just set greenhouses on top of each other.
“Vertical farms have grow lights. If you use grow lights … you get more nutritious plants as a result of that, because you can tweak those lights to cause the plants to produce more things that we need, like vitamins.”
IN YOUR OPINION, WHAT’S A KEY BENEFIT PROVIDED BY VERTICAL FARMING?
Despommier: “By manipulating the indoor lighting systems … you can create plants that you could never grow outside. That’s one of the advantages.”
WHICH COUNTRIES ARE EMBRACING VERTICAL FARMING THE MOST?
Despommier: “The country that’s really got the most [vertical farming facilities] is Japan – Japan now has hundreds of vertical farms throughout the country, and they’re doing quite well. Taiwan has about 150, last I heard. Singapore has countrywide demand for locally produced food. The United States has a fair number, I would say in the neighborhood of 100, to 150.
HOW DO YOU ENVISION VERTICAL FARMING GROWING IN THE NEXT 5-10 YEARS?
Despommier: “I think the next issue will be, how can we franchise ourselves into a complete grocery store. And I know companies that are already doing that, so that’s in the wings. And, I think in another 5 years you’re going to see a versatility of crop selection that will force everything else into competition, and therefore [vertical farming] will succeed. That’s in the next 5 to 10 years.”
Providing Tailored Crop Recipes, So Clients Can Hit the Ground Running
“You could best divide our products and services into three parts, being: external research and in-house contract research in our R&D labs, providing total indoor farming solutions, and collaborating in research projects,” explains Maarten Vandecruys, co-founder and CTO at Urban Crop Solutions (UCS)
By Rebekka Boekhout
July 8, 2021
“You could best divide our products and services into three parts, being: external research and in-house contract research in our R&D labs, providing total indoor farming solutions, and collaborating in research projects,” explains Maarten Vandecruys, co-founder and CTO at Urban Crop Solutions (UCS).
The Plant Biology team
UCS, a Belgian pioneer company in the indoor farming scene, recently made headlines with the announcement that the research consortium with whom they are developing the next generation of bread products to support future space missions, SpaceBakery, won the Gold Prize at the Global Space Exploration Conference. But intergalactic missions aren’t the only thing on the company’s mind…
UCS's ModuleX growing solution in action
Tailored recipes
“We are already looking into expanding our Research Centre due to the high demand for our contract research services, and our indoor biology research expertise. Our added value is to provide a completely tailored plant recipe as part of our end-to-end solution offering,” said Maarten. Normally, a product will be delivered and it’s up to the customer to see how the product works. However, UCS firmly believes that aftercare delivers the best results.
Depending on the crops to be grown, the client first has to give certain specifics about the preferred crop. Then UCS will look into its existing growing recipes, and whether it fits their needs. Eventually, if it’s something new or deviating from it, then UCS starts research on finding the best growing envelope for the client. “We’d rather sit down with them, providing the right solution so clients can hit the ground running,” Maarten notes.
Read the complete article here
For more information:
Maarten Vandecruys, Co-founder & CTO
Urban Crop Solutions
maarten.vandecruys@urbancropsolutions.com
www.urbancropsolutions.com
An Affordable Solution To Monitor And Optimize Food Production
Ecobloom, a startup based in Stockholm, provides two different solutions to the vertical farming space. The first solution is a B2B product, namely an AI solution ensuring automated growing of the plant and monitors plant food production at the same time
By Rebekka Boekhout
July 9, 2021
“We’re helping farmers optimize their food production through more efficient yield management,” says Hamza Qadoumi, CEO and founder of Ecobloom. “Also, cost reduction comes in through a significant reduction in labor and yield increases up to 2 times more per year through accurate predictions. The system allows us to reduce food waste up to 20% through yield prediction and our deviation analysis.”
Ecobloom, a startup based in Stockholm, provides two different solutions to the vertical farming space. The first solution is a B2B product, namely an AI solution ensuring automated growing of the plant and monitors plant food production at the same time. With already a successful consumer product on the market, their focus is to offer smart technology solutions for the indoor farming market.
The pilot farm
Smart sensor - EcoSense
The company provides a software-connected plug-and-play solution named EcoSense. EcoSense is a small box that can basically be placed anywhere on the farm, such as above shelves to monitor plant growth. EcoSense comes in two formats: a camera for growth and plant analysis, sensors for water analysis and sensors for air analysis. Next to that the sensors predict yield, so lots of data can be gathered to keep improving this. Hamza notes, “We’re now looking at venturing with flowers and fruit greenhouse growers in Spain, Holland, The UK and the Middle East region.
The core solution of the device is hardware, sensors and cameras. Through these elements, the environmental sensors and plant environment is captured by data collectors and cameras throughout the plant’s life cycle. According to Hamza, farmers need about 1 device per 100m2. The wifi-connected cameras and sensors are modular solutions, using machine learning to constantly monitor and analyze plant development, health and stress. Through camera recognition, a certain yield outcome and deviations can be predicted.
Read the rest of the article here
For more information:
Hamza Qadoumi, CEO and founder
Ecobloom
hamza@ecobloom.se
www.ecobloom.se
US (IA): Removing Seasonality by Rolling Out Multiple Farms Throughout The State
“We want Nebullam Farms to be available in every city throughout the US, so we can fulfill our mission of creating access to reliable and local food for everyone, year-round,” says Clayton Mooney, founder of Nebullam
By Rebekka Boekhout
July 6, 2021
“We want Nebullam Farms to be available in every city throughout the US, so we can fulfill our mission of creating access to reliable and local food for everyone, year-round,” says Clayton Mooney, founder of Nebullam.
Over half of the Nebullam team is comprised of Iowa State University Alumni. Today, Nebullam HQ and its Nebullam Farm 1 in Ames, located in the Iowa State University Research Park. At the end of this year, the company will be launching Nebullam Farm 2, which will be in another location in Iowa.
Clayton Mooney, founder
Tomatoes as a cash cow
The company’s staple food is Red Butterhead Lettuce. Next to that, Nebullam grows Red Oakleaf lettuce, pea shoots, micro radish, broccoli sprouts, and cherry- and slicer tomatoes. “What we grow comes from direct feedback from our subscribers. Tomatoes are a great example, as we started trialing them in mid-2020, delivered samples to chefs, produce managers, and subscribers,” notes Clayton. He says that their feedback helped to bring the tomatoes to market 3 months earlier than expected, which has continued to add to Nebullam’s revenue. Now, the company is looking at peppers, cucumbers, strawberries, and spinach, which are subscriber requests.
Read the rest of the article here
For more information:
Clayton Mooney, founder
Nebullam
c@nebullam.com
www.nebullam.com
Is Hydroponics The Future of Farming In Bangladesh?
Bangladesh is known to have flat fertile land which is exceptionally good for cultivating crops and vegetables all year round, but with the rise in water levels, the southern regions of the delta are becoming less cultivation friendly.
By Tanveer Mohiuddin
July 10, 2021
Hydroponics uses just nutrient-rich water to grow crops
Farmers across the Khulna region have not been able to make good use of the land for the cultivation of crops and vegetables. This is due to the region being flood-prone and the salinity of the soil. “We can neither cultivate crops nor fishes,” says a 45-year-old farmer from Satkhira district in the southwestern part of the country.
Bangladesh is known to have flat fertile land which is exceptionally good for cultivating crops and vegetables all year round, but with the rise in water levels, the southern regions of the delta are becoming less cultivation friendly.
Most parts of the region are becoming prone to floods and water-logging due to the Ganga-Brahmaputra River tributaries that flow through the country and often change their course. In addition to that, the saline soil makes it impossible to grow the necessary produce. In order to tackle such a problem, experts have come up with newer farming technologies to help cope with such problems.
Dr A F M Jamal Uddin, a renowned professor of the Department of Horticulture at Sher-e-Bangla Agriculture University, has given much hope with the use of hydroponics for growing crops in places where using soil can be challenging.
This method is also applicable for promoting urban farming where land is scarce and can sometimes be extremely expensive and unfeasible for cultivation. He mentions the challenges of pursuing this method as Bangladesh is yet very far off from using the method for commercial usage as the setup cost is very high.
In order to make sure the process gives sufficient dividends with its crop yields; the crops need to be grown inside a greenhouse made out of specialized polythene which helps control the temperature inside. Rain and rough weather can be a huge challenge in this respect as they can damage the setup.
More durable polythene can be used but that is only made in Israel, and bringing them here in Bangladesh is next to impossible with no diplomatic ties between the two. However, there are many high-value leafy crops that can easily be grown with this technique.
It’s most fitting for fodder cultivation for livestock farms around the urban areas as the year-round grass can ensure a steady feed for the cattle in places where empty land is difficult to find. Growing cattle feed or even leafy vegetables can easily be done with very little setup costs.
Floating gardens of Bangladesh
As the drylands become scarce in the region, farmers are forced to use Dhaps, a local name for floating garden agriculture practice better known as hydroponics. Hydroponics is a type of horticulture that involves growing plants and crops without the use of soil.
This is a method used by farmers for generations. But the technique is far more superior now and can yield crops in a larger quantity than before. Due to salinity, this method of growing farm produce has become ever more necessary as high-value crops can be cultivated all year round without the use of soil.
The Bangladesh government has been trying to promote such farming methods to be more widely used especially in these regions where monsoon rains can easily cause floods. In 2013, the government-sanctioned a project worth $1.6 million to promote floating agriculture, the project covered 12,000 families in eight districts across 50 locations.
A similar project was also recently started a couple of years back after the success of the initial one. Farmers in these low-lying regions are benefitting tremendously as vegetables such as spinach, eggplant, bitter gourd and even spices like turmeric and ginger can be grown easily.
“Last month we sold fish worth Tk 9,000 and spinach worth Tk 1,200 in the local market,” says Rani—a farmer who cultivates using the “Aqua-cage culture” method. This process does not require any fertilizers or insecticides, as a result, the vegetables are fully organic and financially more viable as no additional costs are incurred.
Challenges of Hydroponics Farm
According to experts who are trying to develop this method to become more efficient so that it can be used commercially, there are a few challenges that need to be taken care of such as, farmers need to be trained so that they can figure out how much cooling, dehumidification and heating are required to manage the temperature and humidity of the space for growing. This is a challenge that is difficult to overcome as most farmers lack proper literacy.
In order to properly set up a system that local company ACI is currently doing in Gazipur, huge amounts of money need to be invested as the system requires HVAC equipment. An HVAC equipment can include air conditioners, dehumidifiers, circulation fans, ductwork, chillers, boilers, pumps and pipes which all sums up to a huge cost of production, which is impossible for the ordinary Bangladeshi farmers to take on.
However, more and more people are coming into this method of cultivation, one such example is a Dohar-based Mizanur Rahman, who is a textile businessman and an amateur hydroponic vegetable grower. He has a setup of around 3000 sq ft greenhouse in which he cultivates tomatoes. In order to make the model more commercially viable, more expertise needs to be made available.
In order to tackle climate change and the rise of water levels and salinity of the soil in many regions across Bangladesh, new farming techniques need to be adopted by the farmers, which needs proper knowledge to do properly. With the help of government research and funding, these new methods can enable higher crop yields using up much lesser space.
An Action Plan To Ensure Food Security In Kashmir
In Kashmir valley, where most farmers own less than an acre of land, any Government policy related to land acquisition, especially for “development projects”, needs to take into account the fragile mountainous environment and climatic conditions as well. At a time when the agricultural land is shrinking day by day and population on rise, what is the future of agriculture in Jammu & Kashmir especially the Kashmir valley?
By Dr Raja Muzaffar Bhat
July 9, 2021
The majority of the farmers in Jammu and Kashmir are officially recognized as marginal farmers because of very small land holdings. The agricultural landholdings in J&K was estimated at 0.55 hectares during the agriculture census 2015-16, but unofficially this is much smaller (around 0.45 hectares ). In Kashmir valley, the size is even smaller. During the 2010-2011 agriculture census, the average size of operational land holdings in India was 1.15 hectares. This figure was lower, at 0.62 hectares in Jammu and Kashmir. Districts in Kashmir valley had even lower landholding sizes than the state as a whole. Kulgam 0.39 hectares Anantnag 0.39 , Shopian 0.56, Pulwama 0.48, Srinagar 0.31, Budgam 0.43, Baramulla 0.51, Ganderbal 0.37, Kupwara 0.51, Bandipora 0.48. These figures again came down during the 2015-16 census. I have written in detail about it in past.
In Kashmir valley, where most farmers own less than an acre of land, any Government policy related to land acquisition, especially for “development projects”, needs to take into account the fragile mountainous environment and climatic conditions as well. At a time when the agricultural land is shrinking day by day and population on rise, what is the future of agriculture in Jammu & Kashmir especially the Kashmir valley?
World population by 2040
The world's overall population is expected to increase by another 2 billion by 2040. Feeding such a large population will be the most challenging task ? Scientific studies show earth has lost one- fourth of its arable lands over the last
50 years only? India has a huge population. Urbanization and industrialization is shrinking its agricultural land. The Vertical farming is the solution to these challenges. This type of farming is an innovative way of maintaining our agricultural practices. In India, vertical farming is mostly polyhouse-based farming. Poly-house farming is a protected way that gives higher productivity and yield of vegetables and fruits across India. Increasing food demand due to a growing population along with ever decreasing arable lands poses one of the greatest challenges for us. Many believe that vertical farming can be the answer to this challenge. It is believed that vertical farming is the future of agriculture. For a place like Kashmir it is indeed the solution to ensure food security in future
What Is Vertical Farming ?
Vertical farming is the practice of producing food on vertically inclined surfaces. Instead of farming vegetables and other foods on a single level, such as in a field or a greenhouse, this method produces foods in vertically stacked layers commonly integrated into other structures like a skyscraper, shipping container or repurposed warehouse. Using Controlled Environment Agriculture (CEA) technology. This modern idea uses indoor farming techniques. The artificial control of temperature, light, humidity, and gases makes producing foods and medicine indoor possible. In many ways, vertical farming is similar to greenhouses where metal reflectors and artificial lighting augment natural sunlight. The primary goal of vertical farming is maximizing crops output in a limited space.
Firstly, the primary goal of vertical farming is producing more foods per square meter. To accomplish this goal, crops are cultivated in stacked layers in a tower life structure. Secondly, a perfect combination of natural and artificial lights is used to maintain the perfect light level in the room. Technologies such as rotating beds are used to improve lighting efficiency. Thirdly, instead of soil, aeroponic, aquaponic or hydroponic growing mediums are used. Peat moss or coconut husks and similar non-soil mediums are very common in vertical farming. Finally, the vertical farming method uses various sustainability features to offset the energy cost of farming. In fact, vertical farming uses 95% less water.
Vertical farming in J&K
As discussed above the agricultural land holding in Jammu & Kashmir is very less. The government is in the process of acquiring more and more agricultural land for highways and transmission lines. More than than 800 acres of highly fertile agriculture land is being acquired for the Srinagar Ring Semi Road project. Budgam alone is loosing more than 600 acres of vegetable, paddy and orchard land (4800 kanals). Right to Fair compensation act which is applicable in J&K post article 370 abrogation is not applied as the 2017 notification has become null and void due to efflux of time. Dozens of villages in Pulwama, Budgam, Srinagar and Ganderbal are affected by the land acquisition process for this project. We already lost a lot of agricultural land during construction of Qazigund – Baramulla railway line. Due to urbanization a lot of paddy fields were converted into housing colonies around Srinagar, Budgam and Ganderbal districts. Shopping malls, hospitals, schools have come up on agricultural land. Have we ever thought about our future generation ? Will people in Kashmir valley be able to grow vegetables or paddy in 2050 ? No not at all. What is the solution? Why are our agri –scientists and researchers not coming forward and guiding people on vertical farming?
Advantages of Vertical farming
Vertical farming has a lot of advantages. However, there are some challenges as well. The advantages are listed below :
Preparation for the Future:
In the next 30 to 35 years around 70 % of the world population is expected to live in urban areas, and the population growth will demand more food. The efficient use of vertical farming may perhaps play a significant role in facing such challenges.Year-Round Crop Production:
The vertical farming ensures to produce more crops from the same square footage of growing area. In fact, 1 acre (8 kanals) of an indoor area offers equivalent production to at least 4-6 acres of outdoor capacity. According to an estimate, a 30-story building with a base area of 5 acres can potentially produce an equivalent of 2,400 acres of conventional horizontal farming. Additionally, year-round crop production is possible in a controlled indoor environment which is completely controlled by vertical farming technologies. This is indeed a very useful technique for a place like Kashmir in view of shrinking farm lands and harsh winter months. Vertical farming allows us to produce crops with 70% to 95% less water than required for normal cultivation.
Production of Organic Crops:
As crops are produced in a well-controlled indoor environment without the use of chemical pesticides, vertical farming allows us to grow pesticide-free and organic crops. Indoor vertical farming can significantly lessen the occupational hazards associated with traditional farming. Farmers are not exposed to hazards related to heavy farming equipment, diseases like malaria, poisonous chemicals and so on. As it does not disturb animals and trees inland areas, it is good for biodiversity as well
Challenges
Difficulties with Pollination
Vertical farming takes place in a controlled environment without the presence of insects. As such, the pollination process needs to be done manually, which will be labor intensive and costly.
Labor Costs
As high as energy costs are in vertical farming, labour costs can be even higher due to their concentration in urban centers where wages are higher, as well as the need for more skilled labor. Automation in vertical farms, however, may lead to the need for fewer workers. Manual pollination may become one of the more labor-intensive functions in vertical farms.
Conclusion
The constant shrinking of agriculture land is a big challenge at global level as discussed above. For a place like Kashmir valley the shrinking of agricultural land due to urbanization and population growth will lead to food crises in future. Vertical farming is the only hope now and our agriculture scientists, universities and research institutions need to shift their focus on vertical farming....
Disclaimer: The views and opinions expressed in this article are the personal opinions of the author. The facts, analysis, assumptions and perspective appearing in the article do not reflect the views of GK.
Lead Photo: Why are our agri-scientists not coming forward, and guiding people on vertical farming?
Startup Raises Millions for Vertical Green Production
Now the Danish startup Nabo Farm has received DKK 3 million. from investors to expand their version of an "urban agriculture" and will open farm number two in the capital, rather on Amager, it says in a press release.
By Torben Salomonsen
June 25, 2021
The production of vegetables in vertical farms is gaining ground all over the globe and in Denmark, indoor agriculture with coastal light has also found a market.
Now the Danish startup Nabo Farm has received DKK 3 million from investors to expand their version of an "urban agriculture" and will open farm number two in the capital, rather on Amager, it says in a press release.
Since 2018, Nabo Farm has had production of green from a disused car workshop in northwestern Copenhagen, but will now expand with another farm, which will simply be the first in a series of several, according to the founders Sebastian Dragelykke and Jens Juul Krogshede.
"For us as a start-up company, it is a great thing that we have succeeded in raising such a significant amount, because it means that we can now focus on scaling the Neighbor Farm concept further by opening another farm. At the same time, The investment from Danban and Vækstfonden also means that we can, at a societal level, help to spread the knowledge of sustainable food production," says Sebastian Dragelykke.
The 3 mio. As mentioned, this comes from the business angel network DanBan and Vækstfonden, and Nabo Farm currently sells green on a subscription to a clientele that includes canteens, catering companies and restaurants such as Compass Group, Aamanns, Meyers and Alchemist.
The goal of the company is to attract "more and larger investors" to fold the ambitions to produce even more food via LED lamps and a self-developed automatic irrigation system.
Lead Photo: The company Nabo Farm has raised capital to build a new indoor green production in Copenhagen.
Farm.One Cuts The Ribbon on New Urban Farm In Prospect Heights
Farm.One, a pioneer in New York City’s urban farming scene, opened the doors on its first neighborhood farm in Prospect Heights last Thursday. Located in a 10,000 square foot warehouse space on Bergen Street, the new farm will grow a wide variety of species including many microgreens, herbs and flowers available for purchase
By Jackson Ferrari Ibelle
June 29, 2021
Farm.One, a pioneer in New York City’s urban farming scene, opened the doors on its first neighborhood farm in Prospect Heights last Thursday.
Located in a 10,000 square foot warehouse space on Bergen Street, the new farm will grow a wide variety of species including many microgreens, herbs and flowers available for purchase.
The crops are grown using vertical farming techniques, where plants grow indoors, under artificial light, using water-based methods such as hydroponics. These practices allow for a controlled environment conducive to an urban setting, and have skyrocketed in popularity in recent years.
Scenes from Thursday’s ribbon cutting. Photos: Farm.One.
“When we started, vertical farming was really new,” Rob Laing, founder of Farm.One told BK Reader. “Nobody really knew if it was going to actually be a thing.”
Still, he isn’t all that surprised by the industry’s growth. “New York has acres of rooftop space, thousands of unused basement spaces. We have a lot of resources here and a lot of smart people — I think it’s inevitable that we have become a hub for urban agriculture,” he said.
In addition to the new farm, there is also an event space with a glass wall, allowing for a full viewing experience of the crops. This space will be used for tasting tours where over 100 unique plants can be sampled, as well as lectures on food and agriculture. There are also talks of a cocktail menu and daytime cafe service.
This ambitious undertaking was born out of changes made within Farm.One out of necessity during COVID-19. Originally founded in 2016 to grow rare and unusual plants for chefs at high end restaurants looking to locally source their menus, Farm.One saw its operations slow when the restaurant industry shut down in March 2020. As a result, last summer it began growing for consumers.
“Obviously it’s more difficult and time consuming, but it was something we really believed in,” Laing said.
He was particularly concerned about making operations even more sustainable than they already were. In October the team began selling plant products in reusable containers, which were delivered by bike and then picked up to be repackaged again. They sold out before the end of the month.
Greens are now being sold in reusable containers. Photo: Farm.One.
This left Laing and his team with a growing waitlist and a need for new farm space. They settled in Prospect Heights where they hope to establish themselves in the community and offer good paying jobs to people interested in careers in agriculture. Farm.One even recently hired a young person who had been trained by Teens for Food Justice (TFFJ), an organization that teaches kids hydroponic farming techniques in local schools.
Laing said he hoped to continue these types of connections with Brooklyn organizations, perhaps even formalizing the connection between TFFJ and Farm.One.
A rendering of the new farm. Image: Farm.One.
And TFFJ is right there for it.
“TFFJ looks forward to its continuing partnership with Farm.One as it brings good food and good urban agriculture jobs to New York City’s residents and creates a workforce pipeline for students who complete the TFFJ program at their schools,” Katherine Soll, founder of TFFJ, said.
Soll, along with Latoya Meaders, CEO of Brownsville’s Collective Fare, spoke at Thursday’s ribbon cutting, signalling the communal nature of urban farming.
“We are trying to make New York City a place where urban agriculture is really happening and is thriving and is helping people get access to good food,” Laing said. “It’s obviously not just one organization that can do that. It takes a bunch of different voices.”
Farm.One will begin planting seeds at the Brooklyn farm in the coming weeks, with the first deliveries going out in August.
Lead Photo: The 10,000 square foot Bergen Street farm marks another addition to Brooklyn's growing urban agriculture scene.
Singapore: Mega-Farm, Research Center To Open By December 2021
&ever is currently building a mega-farm in Singapore with support from the Singapore Food Agency, SFA, and the Economic Development Board, EDB, and will be launched by the end of 2021. The mega-farm will be 15m high and have an annual production capacity of up to 500,000 kg of leafy greens.
&ever
“We’re really happy to have launched in Munich and consumers really like our harvest-on-demand concept,” says Franz Drack, Chief Marketing Officer at &ever. "We just need to see how to increase the accessibility of our solutions. I’d love to see 200 vertical farms in Europe with this technology in the next five years."
Although it all started in Hamburg, &ever is currently headquartered in Munich which is also where the grow tower showroom is located. In 2020, &ever opened its first commercial farm in Kuwait, spanning 3,400 m2 and with a daily output capacity of 550 kg. The farm provides its leafy greens to Kuwaiti restaurants and retailers. The company also recently launched a grow tower in an EDEKA Stadler+Honner “Die Frisch-Nachbarn” supermarket in Unterfôhring near Munich.
Mega-farm and research center
&ever is currently building a mega-farm in Singapore with support from the Singapore Food Agency, SFA, and the Economic Development Board, EDB, and will be launched by the end of 2021. The mega-farm will be 15m high and have an annual production capacity of up to 500,000 kg of leafy greens.
In addition to the mega-farm, &ever will be establishing Singapore as its global R&D center to accelerate knowledge development and transfer to the mega-farm. The R&D center will focus on improving energy use efficiency through optimized lighting strategies and improving crop quality by evaluating different seed and substrate combinations. Moreover, &ever will be working to develop non-invasive crop monitoring processes through vision systems.
“We’re getting tremendous support from our local partners EDB, SFA and A*Star; everyone is keen to get this farm online. This farm is what we are most excited about this year,” Franz notes. To better address consumer demand, &ever conducted market research in Singapore by speaking with potential consumers and foodservice providers. This research has allowed &ever to explore the balance between western and eastern leafy green species to be grown in the mega-farm.
“Our team under the lead of our country manager, Kerstin Köhler, have worked with food service providers who are very good at telling us what products are needed and wanted. Some products are very interesting for certain segments of the value chain, so we try to talk to a lot of different people,” says Franz.
&ever is continuing to focus on leafy greens, microgreens and herbs for the time being. While there is a lot of interest in fruits (like strawberries), Franz explains that the company is focused on keeping its product range simple to perfect the growing process.
&ever's growing tower
Rebranding efforts
In recent months, the vertical farming industry has seen major players taking a new approach to product branding by using brightly colored packaging. &ever is also focused on bright, enticing packaging designed to represent the company’s values and production process.
“We will start using colors that represent what we’re actually doing. Yellow for the light, blue for the water and green for our greens. It allows the brand to stand out and visually signals to consumers that things are changing. This shows that we are a new type of agricultural company. Stay tuned for that in the second half of 2021.” explains Franz.
Franz also notes that &ever’s products are also sold living, whereas many indoor farms sell cut greens, packaged in clamshells or other packaging materials. Moreover, &ever is also looking into direct-to-consumer sales of leafy greens.
In building its mega-farm, putting its products on European shelves and rebranding, &ever is eager to continue growing by getting consumers excited and developing more farm projects across the world.
&ever is a German agtech company offering three growing solutions, each addressing a different level of production. The &ever grow box is a small-scale system that allows growers to produce 15-30 kg of leafy greens per day in a small footprint. The company’s medium-sized solution is the &ever grow tower which is a small room containing a circular cultivation module.
Young plants are first transplanted in the inner circle and are gradually pushed further to the outer circles as new plants are introduced to the system. In pushing the plants further, the older plants receive more available space to continue growing without crowding neighboring plants. The grow towers provide a customizable output of 20-50 kg of leafy greens per day. Finally, &ever also develops large-scaled production system which it calls mega-farms.
For more information:
Franz Drack, CMO
&ever
local@andever.de
www.and-ever.com
Publication date: Tue 8 Jun 2021
Author: Rebekka Boekhout
© VerticalFarmDaily.com
New Vertical Farm In Oshawa Will Harvest Fresh Greens Year-Round
Founder Derrik Stevenson started the business as a way to follow his passions after being laid off from an office job as a result of the pandemic.
May 22, 2021
A new vertical farm is open in Oshawa with plans to harvest local greens year-round.
Mighty Harvest Produce, located at 871 Wilson Rd. S., is growing leafy greens and herbs hydroponically, which means without the use of soil.
Founder Derrik Stevenson started the business as a way to follow his passions after being laid off from an office job as a result of the pandemic.
“I decided, I’m not going to look for a job. I’m going to create my own job,” says Stevenson, who is vegan and has an interest in sustainability and fresh food.
Right now you can find greens like kale and salad blends growing at Mighty Harvest as well as herbs such as parsley, marjoram, and anise basil.
Stevenson says growing greens indoors has benefits for the environment as well as the people who eat them.
“The ultra freshness is what sets us apart from the grocery store,” he says, explaining how greens sold in Ontario often make a long journey from California or Arizona. “I can harvest on a Wednesday night and be selling the product on Thursday.”
Vertical farming uses 90 per cent less water than conventional agriculture and Mighty Harvest does not use pesticides or herbicides.
Stevenson says customers may be surprised to learn Mighty Harvest Greens are not certified organic — it’s because Canadian regulations don’t allow certification for produce that’s not grown in soil.
Mighty Harvest is open Thursday and Friday from 1 to 6 p.m. and Saturday from 9 a.m. to 2 p.m. and can be found at the Whitby's Farmers Market on Wednesdays.