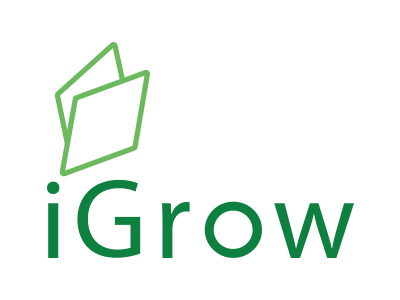
Welcome to iGrow News, Your Source for the World of Indoor Vertical Farming
The Evolution of The Vertical Hydroponic Container Farm
On April 11th we hosted our most popular webinar ever: The Evolution of the Vertical Hydroponic Container Farm! We explored how the Greenery has reimagined controlled environment agriculture to bring farmers increased yields, customization, and control.
Don’t have a full hour? No worries! We went ahead and summarized our conversation in this blog post. We’re going to follow along with the webinar’s structure with an overview of CEA and an introduction to hydroponics, followed by a look at the evolution of the container farm: how we got started, where we’ve been, where we’re going with our new Greenery farm!Don’t have a full hour? No worries! We went ahead and summarized our conversation in this blog post. We’re going to follow along with the webinar’s structure with an overview of CEA and an introduction to hydroponics, followed by a look at the evolution of the container farm: how we got started, where we’ve been, where we’re going with our new Greenery farm!
OUR SPEAKERS
CAROLINE KATSIROUBAS
Director of Marketing & Community Engagement
DEREK BAKER
Industrial Designer
WHAT IS CONTROLLED ENVIRONMENT AGRICULTURE (CEA)?
CEA uses an enclosed space (in our case, a container) to bring farmers control over components such as lights, heating, ventilation, AC, pumps, etc. to create the perfect growing environment in any climate, 365 days a year. Hydroponics, specifically, uses nutrient enriched water to replace soil. Here at Freight Farms we use hydroponic techniques because they’re extremely water-efficient and can be adapted to many environments and crop varieties.
In our farms, we use:
A vertical drip system: This system pumps water up to the top of the vertical channel, and gravity allows it to drip down that channel so the roots can access it. Any excess water runs out the bottom and is returned in the reservoir where it is recycled.
An ebb & flow system: This is a horizontal system where nutrient rich water floods a shallow trough to saturate the plants’ roots, then drains back into the reservoir to be recycled.
Read about other systems in Hydroponics 101.
THE EVOLUTION OF THE CONTAINER FARM
The container farm’s story begins in 2009 when Freight Farms co-founders Jon and Brad set out to bring farming into urban centers in an effort to decrease the distance food travels to the people that are eating it. Although they were always certain CEA was the way to do it, their initial focus was in rooftop hydroponic farming.
Rooftop hydroponic farming had several pros, such as activating abundant yet unused space, and taking advantage of sunlight. However, they quickly ran into several cons. For one, they were constantly dealing with red tape and difficult zoning boards. There was also too much customization involved: Each new rooftop setup needed to be created with unique specifications, which led to extreme upfront costs.
Jon and Brad decided to pursue a method of CEA that was easier to standardize while still allowing people to activate unused space in their cities. That’s when the aha moment happened: What about shipping containers?
It was clear from the start that containers could be the perfect modular vessel for the farms. Plus, there was an abundance of decommissioned containers sitting around waiting to be used. The question then was, can you grow in them?
In 2012, Jon and Brad got a container and built the first prototype by hand. After months of testing and refinement, the world’s first container farm–the Leafy Green Machine–came on the market in 2013.
The next five years were spent iterating on the Leafy Green Machine as we learned more and more from our expanding customer base. We made subtle but important changes, resulting in 8 total versions of the Leafy Green Machine. Today, we have 200 farms operating in 39 states and 15 countries. Each has their own unique story, whether it’s a school uses their farms as learning labs, or operating in tandem with a traditional farm to extend their growing season and create revenue year round. All of them are positively impacting their communities 365 days a year.
The Greenery
“We knew that we had to develop a farm that could not only be a leader in production, but could be flexible in suiting the needs of all it’s users”
— Derek Baker
GREENERY EXTERIOR
In the past, we sourced used containers and modified them. Now we’re building new containers to our specifications, giving us unmatched control over weather-proofing and R-28 U.S. Department of Energy insulation rating. The R value is the capacity of an insulating material to resist heat flow. The higher the number, the better the insulative properties. This high value lets us operate in all kinds of harsh weather conditions by maintaining the perfect indoor temperatures.
The new Greenery design features an in-set rear so that all the components fit within the ‘standard’ 40 ft x 8 ft container boundaries. This makes is as easy to ship as possible.
At the back, you can find a 100-amp main breaker to accommodate any additional power draws, and a 36,000 BTU climate control unit with a built in dehumidifier and economizer. The economizer is a simple feature that helps the energy efficiency of the farm. Senses outdoor air and–if it’s below the set temperature in the farm–pulls it in instead of running the A/C (therefore conserving energy).
Audience Q&A with Derek
What’s the maximum temperatures that the Greenery can withstand?
DB: We haven’t seen anything yet that it can’t withstand! We have our previous generation farms operating in 120ºF in Dubai and various negative temperatures in places like Halifax, Colorado, Alaska…and that’s just with the Leafy Green Machine’s R-16 insulation.
How can you protect and secure the Greenery in aversive weather conditions, like hurricanes?
DB: The good thing about shipping containers is that we’re very familiar with them–we know how to secure them down, be it on a ship, on a truck, or on the ground. There is lots of standardized equipment available to lock the container in place as long as you put it on the right foundation. Plus, they weigh a lot–each container is about 8 tons–so they’re not typically going anywhere.
GREENERY SEEDLING AREA
The seedling area features a seedling station that doubles as a worktable. Mounted on the wall above it are dosers and reservoirs that monitor the seedling tank and the main tanks with smart, IoT connected sensors that tell the dosers to pull nutrient and pH solutions from their respective reservoirs to maintain the right water nutrient conditions. The seedling tank is arranged vertically on the right side of the station to make it easy to access and clean.
The seedling table itself is built of food-grade stainless steel and consists of two independently controlled ebb and flow troughs that, combined, hold up to 4,608 plant sites. The troughs were built independently so you can use one for seedlings and one for microgreens, or not use it at all, in which case you don’t end up wasting energy or water.
Audience Q&A with Derek
There is a lot of moisture inside these containers… is there any risk of rusting?
DB: We have chosen specific materials–stainless steel and aluminum–that don’t oxidize the same way as regular steel to avoid rust in the farm.
Can you reuse the water?
DB: Hydroponics in general is a super a water-efficient system. Compared to traditional agriculture we’re using about 95% less water. On a daily basis, you’re using 5-10 gallons. But, when the weather is hot and humid, we’re able to actually generate water. So, yes, the system is built to save and reuse water.
Is the seedling tank easy to move?
DB: The reason we put the tank where it is and made it vertical is so you don’t have to move it. We have all the hookups on the side of the tank along with an app-connected water level sensor. The lid is very accessible if you do have to get in there to clean it… the idea is that you don’t have to move it to perform any of your regular farming activities.
GREENERY MAIN GROWING AREA
The main growing area in the farm is where you can see the most innovative design improvements in the Greenery. Below we’ll first explain the features themselves, and then we’ll dive into the thought process behind the changes.
For one, individual hanging string lights have been replaced with 112 Freight-Farms-developed LED arrays that line the walls and hang between the growing rows and emit directional red and blue light onto the plants.
Our legacy 256 crop columns have been replaced with 88 plant panels that are designed to adapt to multiple crop types and maximize growing space. Combined, the panels have 7,480 potential growing sites.
Finally, both the LED arrays and the plant panels hang on a sliding rack system that allows you to configure the farms layout to best suit your harvesting and maintenance workflow.
Audience Q&A with Derek
Do you only use red and blue lights?
DB: Yes–This is a big debate in the hydroponic and general indoor ag world but we’ve done extensive research and...had great success with the 5:1 red-to-blue ratio lights. In the Greenery, you also have the opportunity to isolate the red and blue lights to create different light environments for different crops.
Can you remove the plant panels to clean them, and how does the hanging/removing process work?
DB: Yes, they are removable. And, to make them easier to hang, they include ribbing on the back that acts as a haptic feedback guide for when you go to hook them onto the racks.
How do you protect plants while you’re moving the rows?
DB: There are a few ways to do that. First is to come up with a compatible planting schedule where you have seedlings and mature plants on opposite walls of the farm so you have space to shift the rows. Then, there’s also spacers built into the racks themselves to maintain a minimum distance that protects most standard sized plants.
THE DESIGN PROCESS
“This design is really the culmination of two years of research, testing, and general gleanings. The Greenery takes the feedback that we’ve received from our customers and combines it with the most recent technology to build a farm that’s focused on creating greater yields, allowing more crop variety, and reducing labor.”
— Derek Baker
Achieving greater yields
THE PLANT PANEL
We upgraded to the plant panel to take advantage of unused space that was going to waste with the individual crop columns. This way, we’ve reduced the number of growing fixtures while drastically increasing the amount of food you can grow.
By planting in channels 1, 3, and 5 (option 1), you’re able to mimic the same row cropping techniques used with the crop columns. This is a great option for large head plants, like lettuce, Swiss chard, and kale. From there, you can also activate channels 2, 4 (option 2) for mixing in small crops, like turnips or radishes, between the larger ones growing in channels 1,3, and 5.
A different planting method involves using all five channels for one plant. This is called linear cropping, and it is very effective for smaller greens and herbs and allows you take advantage of the entire panel.
“I’m very excited to see how each farmer takes advantage of the plant panels and the different cropping techniques they develop in their own farms.”
— Derek Baker
THE LED ARRAY
Our new rigid LED board is specifically designed to create a powerful and uniform lighting environment to accelerate the rate of photosynthesis, the result of which are heavier, fuller, and richer plants.
To understand the value of the new LEDs, we first need to understand PPFD!
PPFD (Photosynthetic Photon Flux Density… say that five times fast) measures the amount of light energy that reaches the canopy. It’s important to understand that it refers to the amount of photons in the visible light spectrum that flow over a square meter in one second. That means that this value does not measure the power of the light fixture itself, but the amount of light that actually reaches the intended surface (in this case, your plants). For that reason, PPFD measurements always need to be paired with a distance measurement.
So, the Greenery’s lights generate 200 PPFD at a distance of 18 inches from the canopy, compared to the LGM, which generate 100 PPFD at 9 inches. This means that the Greenery has double the PPFD at double the distance!
This graph shows that increasing the PPFD in this way results in more than double the rate of photosynthesis. Doubling the PPFD results in more than double the rate of photosynthesis.
We specifically identified 200 PPFD as our preferred light intensity for the Greenery because, as you can see on the graph, anything over 200 PPFD results in a plateau in the rate of photosynthesis. What we wanted to avoid was putting unnecessary energy into our lights that would not be directly translated into a dramatic difference in growth.
More Variety, Simpler Workflow
The moving racks allow you to transform the space based on your needs. This can mean growing exciting new crops that require more space to grow. By moving the grow rows and center LED fixture you have the flexibility to organize the space for any crop type.
Default Position
Harvesting Position
Position 2 - Inner plants receive more intense light, outer plants have more room.
Position 3 - Inner plants have more room, outer plants receive more intense light.
You can space it evenly to allow small to medium crops or move them to any other position to allow for a combination of crop types and sizes (as seen in positions 2 and 3).
Mobile rows also lets you create walkways where you need them. This lets you harvest, transplants, and maintain directly in the rows.
“We wanted to create a space that suits everyone’s needs and could be configured to adapt to each individual’s workflow preference.”
— Derek Baker
There you have it!
For more details about the Greenery, Freight Farms, and our entire 30 minute live Q&A session, check out the complete webinar recording. You can also view more webinars in our portal!
Want information relating to a specific project? Contact our team!
Superior Fresh Expanding Their Aquaponics Operation
Superior Fresh utilizes aquaponics to raise seafood and leafy greens for retailers across the Midwest.They are now expanding their greenhouse footprint from six acres to 13 acres and their aquaculture center from 40,000 square feet to 100,000 square feet
Mike Beiermeister
Hixton, Wis. (WXOW) — Superior Fresh utilizes aquaponics to raise seafood and leafy greens for retailers across the Midwest.
To View The Video, Please Click Here
They are now expanding their greenhouse footprint from six acres to 13 acres and their aquaculture center from 40,000 square feet to 100,000 square feet.
“Most people wouldn’t think that you could grow organic vegetables in the middle of Wisconsin in the middle of the winter,” said Brandon Gottsacker, president of Superior Green.
The company was founded back in 2011. Since the creation, Superior Fresh has become the first indoor Atlantic Salmon farm in the United States. They are also able to grow leafy greens year-round thanks to their aquaponics system and sustainable practices.
“You know you’re doing something for not just us, for the rest of the world and leading the harvest of the first Atlantic Salmon in the United States, right here,” said Kyle Woolever, aquaculture manager for Superior Fresh.
Aquaponics integrates fish and plant growth to create a symbiotic environment. Superior Fresh utilizes these practices to produce around 4,000 pounds of leafy greens per day and around 4,000 pounds of Atlantic Salmon each week. By this time next year, they plan to produce 25,000 pounds of Atlantic Salmon each week. Right now, they have 200,000 Atlantic Salmon swimming in their tank.
“We’re probably the most sustainable farm on the planet when you talk about how many pounds of fish and produce were producing on the volume of water,” said Gottsacker.
The company uses the bulk of summer sun to shed light on their produce with the help of diffused glass. They use LED lighting for winter months. Their produce is pesticide-free, non-GMO, and constantly controlled for perfect growing.
“Our goal is to locate these farms all over the world, so in theory, you could build a facility like this in the desert, you could build it right outside of a city where food is scarce, or it has travel really far to get there,” said Gottsacker. “Our goal is to provide really good, high quality, safe, healthy food for everyone.”
Mike Beiermeister
WXOW Weekend Anchor and Reporter
Detroit Organization Uses Shipping Containers As Farms Providing Food For Soup Kitchen, Restaurant
The farming being done inside the shipping container is the equivalent of almost two acres of land
By Amy Lange
December 2, 2019
DETROIT (FOX 2) - At the new Three Cats restaurant in Clawson, co-owner and Chef Matt Prentice is serving up the Cass Community arugula salad and the beet stack with Cass basil.
Prentice, a big fan of farm to table, says this is as close and as fresh as you can get.
Shipping container farm is as close to fresh as it gets
It comes from the Freight Farm at Cass Community Social Services in Detroit where seeds are watered in trays then transferred to hangers farming vertically inside a shipping container"It gets harvested two, three, four days a week.
The arugula that I get from California -- I mean it's fine, but it's two weeks old before I get it. Here it's sometimes two hours old," he said.
That's because it comes from the Freight Farm at Cass Community Social Services in Detroit, where seeds are watered in trays then transferred to hangers, farming vertically inside a shipping container."So you can see everything's dated - what it is and when it was started so they'll know," said Faith Fowler, Cass Community Social Services. "It comes down almost like drip irrigation so that you're wasting very little water at all."
This is a great solution to having fresh good food year-round.
"Donated by the Ford Fund about a year ago, the Freight Farm is now producing fresh produce year-round for the soup kitchen at Cass and at Three Cats."
It means his restaurant is able to have farm to table, table to farm in a really good way and to support the work we're doing here, with hungry people and homeless people and others," said Rev. Faith Fowler with Cass Community Social Services. Fowler runs Cass Community Social Services, where serving the homeless and getting them work and housing is also about health and the environment."It tastes really good and it is good for you," she said. "We're using solar for here and considerably less water so it ties in with sustainability which is a theme at Cass.
"The farming being done inside the shipping container is the equivalent of almost two acres of land.
"It's a lot better product but it also gets the Cass name out there," said Prentice. "I mean, this little kitchen here feeds hundreds of thousands of people every year."
Prentice should know. As a longtime volunteer at Cass who then became the director of food services, serving up fresh produce to clients at the soup kitchen and customers here at Three Cats - it's about more than just good food."
The bottom line is, the fresher the produce is, the better it is for you - it's just that simple," he said. "There's a lot of advantages to it but the biggest thing is just making people aware of what we're doing down here."
CANADA: Lettuce Crop Planted In Old School Library As Couple Turn Building Into A Farm
A Quebec couple have moved to the tiny community of Saint-Léolin in northeastern New Brunswick with plans to turn a former school into a large, indoor vertical farm, capable of producing 750,000 heads of lettuce a year
Chantal Gagnon and Daniel Ratté plan to hire 20 people for their indoor farm in Saint-Léolin
Gabrielle Fahmy · CBC News · Posted: Dec 17, 2019
A Quebec couple have moved to the tiny community of Saint-Léolin in northeastern New Brunswick with plans to turn a former school into a large, indoor vertical farm, capable of producing 750,000 heads of lettuce a year.
The opportunity for the farm cropped up after the village of 600 saw its school close in 2012. Saint-Léolin was dealing with a problem experienced by many rural communities: there weren't enough students to keep the school open.
Saint-Léolin Mayor Guy Cormier started looking for someone to purchase the 2,200-square-metre building after the doors closed.
About a year ago, he met Chantal Gagnon and Daniel Ratté, who were living in the United States at the time. The couple were looking to come back to Canada and for a new project to keep them busy.
They'd been inspired by a visit to a vertical farm in Florida a few months earlier.
The couple grow lettuce and other leafy greens in the room where the school's library used to be. (CBC)
"This is when we decided this is what we're going to do," said Gagnon.
"I was very excited. I grew up on a farm."
The mayor gave them a tour of the school by video chat and the rest is history.
Gagnon grew up in the Matapedia Valley of eastern Quebec, just across the border from Campbellton. And so after looking at buildings all across the country, she was drawn by the prospect of returning to a place close to home.
Vertical farming is similar to other methods of indoor farming, such as hydroponics, in that the plants are grown without soil.
Can't keep up with demand
But cultivating them in "trees" allows producers to use the space, and resources, more efficiently.
Instead of rays of sunshine, LED lights are used.
If a purple hue often radiates from these farms, it's because the lights' blue and red wavelengths provide the plants what they need.
The plants get their nutrients through a water system that constantly reuses the supply.
The couple invested $55,000 of their own money in the equipment, and right now, lettuce and other leafy greens, herbs and microgreens are being grown in the school's old library.
What was initially supposed to be just the pilot project has gotten the community so excited that Gagnon and Ratté are having a hard time keeping up with the demand.
The only sign of the couple's indoor farm right now is the purple hue coming from one of the windows, where the library was. (CBC)
"We are amazed," said Gagnon.
"We didn't think that people would respond so well."
Every Saturday morning, when they open their doors to the public, people have been lining up to buy the produce, and the crops usually sell out in a couple of hours.
Chantal Gagnon and Daniel Ratté moved to Saint-Léolin in northeastern New Brunswick last year. (Gabrielle Fahmy/CBC)
Watch - This former school was transformed into an indoor vertical farm
A Quebec couple bought a building that used to be a school in Saint-Léolin and turned it into an indoor vertical farm, capable of producing 750,000 heads of lettuce a year. 1:00
The vertical farm began selling its produce on Oct. 29 and the couple are selling at grocery store prices. Customers can pick up a head of romaine lettuce for $2.99.
Romaine troubles
Ratté is not surprised. He thinks ongoing troubles with romaine lettuce coming from California has played a big role in driving people to find alternatives produced closer to home.
He also thinks with climate change and other threats to traditional agriculture, this type of farming will only become more common.
"There's no more land anymore to grow anything," said Ratté.
"And the one we have right now, there's a lot of issues with the pesticides, with the chemicals."
Ratté said if their plants ever get sick, they are treated with vinegar and hydrogen peroxide.
Daniel Ratté thinks this type of indoor farming is part of the solution to worldwide threats to traditional agriculture. (CBC)
The couple hopes to attract investors and fill every classroom with plants so they can supply customers, grocery stores and restaurants in northern New Brunswick year-round, a project estimated at $4.5 million.
Saint-Léolin's mayor said the prospect of new life being injected into the village is helping to spread the word.
"I think it's the future," said Cormier.
"I talk with other friends from other towns around, and they say you're lucky to get that in your town."
Another E. coli Outbreak – A New Solution to Help
Another continent-wide romaine lettuce recall from an outbreak of E. coli is underway with 67 people reported sick in 19 states
CO2GRO
December 6, 2019
Another continent-wide romaine lettuce recall from an outbreak of E. coli is underway with 67 people reported sick in 19 states. The source of the latest outbreak was found in irrigation reservoir sediments. The chief suspect is wild animal feces entering the irrigation reservoir. The last several outbreaks began on farms in Monterrey, Santa Barbara, Salinas, and Santa Maria, California growing romaine lettuce.
The economic impact including costs of shipping returns, taking the lettuce off shelves, plant destruction, medical care costs and increases in retail prices due to shrinking supply can be up to $350 million. The Center for Disease Control (CDC) estimates that 265,000 STEC infections occur each year in the United States. E. coli O157:H7 causes more than 36% of these infections.
E. coli are bacteria that typically live in the intestines of healthy humans and animals. Most types of E. coli bacteria are harmless but some can cause severe diarrhea and urinary tract infections while more severe strains can cause kidney failure in children and other severe symptoms.
Leafy greens are highly regulated in California but vulnerable to bacterial infections. The primary method for preventing E. coli is good hygiene in the grow facility and monitoring bacterial levels. Beyond these practices, there is little that growers can do to inhibit the spread of E. coli, especially once an infection has taken to a crop in the facility or in areas where there are several grow facilities.
CO2 Delivery Solutions’ Success Inhibiting the Spread of E. coli
CO2 Delivery Solutions has been demonstrated to inhibit the spread of E. coli by up to 99% in trials on pepper plants and Cannabis. CO2 Delivery Solutions dissolves and saturates CO2 gas into the water to form an aqueous CO2 solution that is misted on to plant leaves.
The microdroplets create a thin aqueous film around the leaf surface isolating the leaf from the atmosphere. Gradient diffusion allows CO2 molecules to move into the leaf. This CO2 transfer occurs within 90 seconds and the moisture evaporates in minutes. Misting is done for a few seconds up to four times an hour during the light cycle.
The inhibition of single-cell pathogens such as E. coli on plants is caused by the frequent aqueous CO2 misting. Aqueous CO2 is acidic therefore dropping the pH on the plant surface for a few seconds. Once the CO2 is transferred the pH rebounds back up towards neutral. This continual fluctuation in pH makes for an unfavorable environment for single-cell pathogens such as E. coli, powdery mildew, and others to thrive, thus inhibiting their growth and spread.
This pH volatility process is 100% natural without the requirement for any chemical sprays. Increasing the efficiency of CO2 uptake in plants from using CO2 Delivery Solutions also increases and accelerates indoor and outdoor crop growth resulting in higher biomass yields, faster cycle time for more harvests and reducing crop loss, all adding to grower profitability and consumer safety.
Urban Crop Solutions Celebrates it's 5th Anniversary
The company is a total solution provider and offers container farms and plant factories and all products and services that growers need to grow healthy crops in an indoor farm
Today, Urban Crop Solutions celebrates its 5th anniversary. On this occasion, a movie was released with testimonials from customers around the globe. Urban Crop Solutions is proud to be a pioneer in the emerging market of indoor vertical farming with a unique business model. The company is a total solution provider and offers container farms and plant factories and all products and services that growers need to grow healthy crops in an indoor farm.
The story of the founding of Urban Crop Solutions starts in 2012 when the founders were experimenting with rooftop farming in urban areas. Only in 2014, the choice was made to focus on indoor vertical farming after some successful tests where done in the warehouse of one of the founders. Since then the company was taken on a rollercoaster and the company evolved from a local AgTech startup to an international scale-up with unique commercial products and services.
Link to the 5 years anniversary movie with testimonials from over the globe.
https://youtu.be/KnqLMtNrr7w
From its incorporation, the company’s vision was always that the knowledge of plant growth is key. Today, the company operates 10 labs, 1 demo plant factory and 1 demo container farm for its research operations.
“Over the last 5 years, we have conducted over 800 cultivar trials. Some tests with seeds failed miserably.” explains dr. Oscar Navarrete, chief plant scientist and the first employee of Urban Crop Solutions. “But through our continuous work to tweak seed selection, LED spectrum, irrigation, substrate and nutrition, we have developed more than 200 plant growth recipes that are available for our clients.”
The design of the plant growth infrastructure that Urban Crops Solutions is building for its clients is the result of the know-how the plant scientists transfer to the mechanical engineers to achieve optimal plant growth in an indoor vertical farm environment. In February 2016, the Flemish Minister-President Geert Bourgeois opened Urban Crop Solutions’ automated indoor farm which was the largest in Europe. This installation was built and is operated by Urban Crop Solutions for research purposes.
“We’ve been at the forefront of this emerging industry since the beginning. Some of our engineering concepts lacked robustness, but by listening to the feedback of our customers we’ve upgraded numerous components to improve the reliability, the operational efficiency, and food safety”, says Maarten Vandecruys, founder and CTO of Urban Crops Solutions. “We now have 24 containers in operation with our customers, of which about half in Europe and half in the USA. We are proud to have collaborations with large corporates and with several scientific institutions”.
Urban Crop Solutions caught in the past 5 years much attention by media, by trendwatchers, by large corporates, by politicians, and by royals. In November 2018, the company could present its technology to the French president Emmanuel Macron and the Belgian King Filip. In September 2019, the company realized a series A capital round, marking the start of the international commercialization of its products and services portfolio.
“It is clear that indoor vertical farming is still an early-stage industry. With the current high initial cost involved, it requires finding the right market niche for the right crop in order to achieve an attractive ROI.” Explains CEO and co-investor Tom Debusschere. “However, the world is changing very fast and besides the obvious food industry we see a lot potential for our products and services in some high-value end-markets like food supplements, fragrances, cosmetics, aromatics and phyto-pharmaceuticals.”
The technology and the products of Urban Crop Solutions are best explained as at “the crossroads between plant biology and factory engineering”. In the coming years, the company will continue to invest in products and services for ‘killer applications’ (revolutionizing market segments) and ‘moonshot crops’ (developing indoor plant growth recipes with large impact) in order to realize its mission: ‘Urban Crop Solutions contributes to the solutions for the challenges caused by global urbanization, the growing world population and the lack of agricultural land in the world’.
For more information on this press release, on Urban Crop Solutions or on the products and services of Urban Crop Solutions you can contact Tom Debusschere, Managing Director (tode@urbancropsolutions.com), or Maarten Vandecruys, Co-founder and CTO (mava@urbancropsolutions.com ) or visit our website ( www.urbancropsolutions.com ):
European headquarters: American headquarters:
Grote Heerweg 67 800 Brickell Avenue, 1100 Suite
8791 Beveren-Leie (Waregem) Miami (FL 33131)
Belgium Florida
(+32)56 96 03 06 +1 (786) 408-6027
Facebook: www.facebook.com/urbancropsolutions
Twitter: www.twitter.com/U_C_Solutions
LinkedIn: www.linkedin.com/company/urbancropsolutions
YouTube channel: http://www.youtube.com/c/UrbanCropSolutions
US: OHIO - 8,600 sq ft Indoor Aquaponics Facility Opened In Toledo
There's a new farm in Toledo, and it's located inside a building downtown. Balance Farms is an aquaponics farm in Downtown Toledo vertically integrated with parent restaurant Balance Grille
There's a new farm in Toledo, and it's located inside a building downtown. Balance Farms is an aquaponics farm in Downtown Toledo vertically integrated with parent restaurant Balance Grille.
Their restaurant has been active for nearly a decade, serving vegetable-focused Build-a-Bowls, Asian-inspired Tacos, and seasonal snacks to the Toledo and Cleveland communities
Balance Grille held a grand opening showcase Friday night for its state-of-the-art aquaponics farm, germinating right in the heart of downtown Toledo.
The new 8,600 square-foot facility uses waste from fish as a natural fertilizer for plants to grow in water, pesticide-free. The facility cultivates crops grown outside the soil, specializing in leafy greens, microgreens, living herbs, and fruiting vegetables such as peppers and tomatoes. Additionally, the farm utilizes LED lighting and energy-efficient climate control systems that reduce utility usage. The farm runs on the organic fish matter produced by its collection of tilapia and koi fish.
"In any Balance location, you will notice the open-kitchen concept that informs customers on how their food is being prepared. Opening the Balance Farms helps us take the concept of transparency to another level by showing customers where their food is coming from", they explain.
Scheduled tours are available for groups and individuals.
To View The Video, Please Click Here
Publication date: Mon 25 Nov 2019
INDIA: This MeitY-Backed Startup Has Built An Automated Farming Device To Grow Plants And Veggies Indoors
This MeitY-backed startup has built an automated farming device to grow plants and veggies indoors Delhi-based startup Agro2o is marrying hydroponics (soilless farming) and automation to bring a cool new gadget and a whole lot of good vibes to millennial households
This MeitY-backed startup has built an automated farming device to grow plants and veggies indoors Delhi-based startup Agro2o is marrying hydroponics (soilless farming) and automation to bring a cool new gadget and a whole lot of good vibes to millennial households.
Yash Vyas was working in a retail store in Dubai when he stumbled upon the concept of hydroponics in a newspaper.
Hydroponics (also known as ‘soilless farming’) is a practice where plants are grown indoors using mineral nutrient solutions in water solvents. It fascinated Yash instantly and also made him realize that Dubai’s harsh desert climate had made it difficult to grow farms.
“There was inefficiency of land and water, and almost no greenery either at home or outside. That formed my belief that hydroponics could be a fix. It is a clean and sustainable solution, unlike current farming techniques,” Yash tells YourStory. He then returned to India at the end of 2017 and started Agro2o in early 2018.
Yash Vyas, Founder & CEO, Agro2o (centre) with Ashish Goel, CTO, Agro2o (right)
Growing an indoor smart garden
The Delhi-based startup operates at the intersection of agritech and IoT. Agro2o has developed a proprietary smart garden using a fully automated indoor hydroponics system.
The plug-and-play solution allows anyone to grow fresh herbs, veggies, medicinal plants, and even flowers inside their homes. Because it is an IoT-enabled product, it requires little human attention on a daily basis. The Founder-CEO explains, “We call it automated hydroponics. Depending on the plant type, the system can intelligently judge and provide the level of light, water, and nutrients required, and create an ideal growing condition for the plant.
There are microcontrollers fitted into it. All you have to do is insert a nutrient cartridge depending on the plant you want to grow.” The smart garden is also enabled with a touchscreen and WiFi connectivity. It sends out alerts to users whenever the water has to be topped up. In the future, the system could even come with Alexa integrations, Yash shares.
Intersection of hydroponics and automation
He explains that this unique marriage between hydroponics and automation is a result of the startup’s two years of extensive R&D in plant science, for which it collaborated with the Delhi University’s Department of Plant Molecular Biology.
“We also acquired expertise in automation and AI to be able to perfect the technology and apply for design patents,” Yash reveals. While the product is yet to see a commercial launch (planned for early 2020), Agro2o showcased its technology at the Startup Expo held in September.
“It attracted a lot of interest from investors and general buyers,” claims the Founder. Agro2o has even opened pre-orders on its website.
It has also been incubated by Electropreneur Park, an initiative of the Ministry of Electronics and Information Technology (MeitY). The currently bootstrapped startup might even look to raise a seed round of Rs 1.5 crore to Rs 2 crore in 2020. Agro2o’s current device allows you to grow 10-12 crops at a time. These are categorized into Herbs, Greens, Veggies, and Ornamentals.
“Categories of crops cannot be mixed because the nutrients and conditions required for each are different,” Yash says. He adds that a 24-crop device is in the pipeline. The plan is to have three products for varying crop capacities in the price range of Rs 8,000 to Rs 18,000. “It is like any other consumer durable device that can last you for 4-5 years,” Yash adds. Also Read How DST-backed agritech incubator Indigram Labs is ushering in a new green revolution ‘
Key markets and growth plans
As could be expected, the demand for indoor hydroponics systems is much higher in the Gulf countries than in India.
The founder attributes this to severe climatic conditions and higher disposable incomes in these regions. Hence, to tap into this growing demand, Agro2o will launch in the Middle East along with its rollout in Delhi, Mumbai, Bengaluru, and Chennai. By 2025, the startup plans to sell two lakh units in India, and clock revenue of Rs 300 crore - Rs 350 crore. In the GCC countries, meanwhile, it hopes to sell about five lakh units in five years.
Yash observes, “I see two user profiles for our products. One is the value-conscious customer who wants something positive in their space.
The second is urban millennials who like cool gadgets and also love cooking with fresh veggies and herbs.” While smart homes is Agro2o’s immediate focus, the startup also has ambitions to venture into the smart farm segment. “Technology-enabled commercial soilless agriculture will soon become a reality,” says Yash. Also Read Stanford Seed startup Future Farms is out to solve India’s food crisis with clean, soil-less farming
Tech a facilitator for soilless agriculture
Hydroponics is a nascent sector in India. But globally, the market is expected to be worth $12.1 billion by 2025, with the Asia Pacific being the growth driver, according to Transparency Market Research.
Agro2o claims to be the first in Asia to launch a smart hydroponics product. “So, building awareness is both an opportunity and a challenge,” says the founder.
“Our nearest [undisclosed] competitor in the West is valued at only $120 million. This is a relatively new sector, but there is a large potential to be realized,” he explains. Does Agro2o want to be seen as an agritech or an IoT company? A bit of both perhaps. Or, as Yash puts it: an innovation company in the smart hydroponics sector. “Tech is just a facilitator to make soilless farming more accessible,” he signs off. (Edited by Evelyn Ratnakumar)
Read more at: https://yourstory.com/2019/12/meity-agritech-startup-hydroponics-smart-garden-automation-iot
"Montreal Will Be The Home of The World's Largest Rooftop Greenhouse"
Lufa Farms has announced the construction of their fourth commercial rooftop greenhouse, soon to be completed in the borough of Saint-Laurent, Montreal
Lufa Farms Announces Expansion
Lufa Farms has announced the construction of their fourth commercial rooftop greenhouse, soon to be completed in the borough of Saint-Laurent, Montreal. The greenhouse will measure 163,800 square feet (about 3 football fields), making it the largest rooftop farm in the world. Construction began in September of this year and is expected to be finished by March 2020. This milestone also coincides with the tenth anniversary of Lufa Farms' founding in 2009.
This greenhouse repurposes an existing industrial rooftop to further Lufa's vision of growing food where people live and doing so sustainably. "With each greenhouse, we hold ourselves to an ever-higher standard for sustainable design. Our new farm will be the most energy-efficient to-date and integrate all our learnings from the last ten years to responsibly grow more vegetables year-round," says Lauren Rathmell, Co-Founder and Greenhouse Director.
Responsible agriculture meets innovative greenhouse technology
The greenhouse will feature double-paned glass and two sets of energy-saving screens for improved insulation, and its integration with the building below provides additional thermal benefit to both structures. The greenhouse will also capture rainwater to be used in the closed-loop irrigation system, as well as offset waste with an on-site composting system. At this fourth and largest site, Lufa Farms will be growing eggplants and more than ten unique tomato varieties without the use of synthetic crop protection.
Scaling urban agriculture to feed Montreal
Lufa Farms' most recent greenhouse will have a greater surface area than their three current greenhouses combined. "This rooftop greenhouse will double our growing capacity and allow us to feed 2% of Montreal with fresh, local vegetables. It's an unbelievable step forward for hyper-local, sustainable urban farming," says Mohamed Hage, Co-Founder, and CEO.
Saint-Laurent's Mayor, Alan DeSousa, further stated that "as a sustainable municipal territory, Saint-Laurent is proud to welcome the fourth greenhouse for Lufa Farms. Located in the heart of Saint-Laurent's biodiversity corridor, this greenhouse will facilitate residents' access to local, sustainably-grown products and further promote healthy habits. It will also make it possible to fight against heat islands in our district, where more than 70% of the surface area is devoted to industrial and commercial activities. And lastly, it confirms Saint-Laurent's position at the forefront of the new 4.0, particularly innovative green technologies."
Lufa Farms' mission is to create a better food system by growing food sustainably on city rooftops and partnering with hundreds of farmers and food makers, to provide customers with fresh, local, responsible food via their online Marketplace.
See one of Lufa Farms' other rooftop greenhouses in action in the video below.
Lufa Farms
(514) 669-3559
info@lufa.com
montreal.lufa.com
Publication date: Mon 25 Nov 2019
QFCs In Bellevue And Kirkland To Begin Growing Produce In-Store
QFCs in Kirkland and Bellevue appear to be taking the whole farm to table concept to a new level, since the grocer will now be growing some of their own food as well. It’ll probably require a new aisle
BY MYNORTHWEST STAFF
DECEMBER 1, 2019
QFCs in Kirkland and Bellevue appear to be taking the whole farm to table concept to a new level, since the grocer will now be growing some of their own food as well. It’ll probably require a new aisle.
The Kroger Company has teamed up with urban farming network Infarm that would bring modular living produce farms to a few of their stores. This doesn’t mean there will be vast fields in the QFC parking lot; rather, they will allow some of their produce to grow onsite using hydroponic technology, potentially producing items like kale, cilantro, and lettuce, among others.
QFC’s new self-checkout cameras may send you back to human checkouts
“Kroger believes that everyone deserves to have access to fresh, affordable and delicious food, no matter who you are, how you shop or what you like to eat,” said Suzy Monford, Kroger’s group vice president of fresh. “Our partnership with Infarm allows us to innovate by combining ground-breaking in-store farming technology with our passion for fresh, local produce and ecological sourcing. Kroger is excited to be first to market and offer the best of the season, and we’re proud to lead the U.S. on this journey.”
Infarms are stackable and controlled through a cloud-based farming platform that adjusts lighting and temperature remotely. In addition to freshness, the idea is also intended to eliminate unnecessary transportation and storage.
Believe it or not, some people actually call QFC ‘The Q’
The two QFCs in Kirkland and Bellevue will be the first in the county to undertake such a partnership with Infarm, with the company planning to expand to 15 QFCs in Washington and Oregon by April, reports The Seattle Times. The new greens are expected to be ready within weeks at the two Washington locations.
Watch: 5 Acres of Greens In 55m²? No Imports…Hyper-Local Food
Two re-purposed shipping containers, fitted with a ‘Farmony’ – 55m² in size, can produce 55,000 heads of lettuce per year or 408 trays of micro greens per week
November 20, 2019
Two re-purposed shipping containers, fitted with a ‘Farmony’ – 55m² in size, can produce 55,000 heads of lettuce per year or 408 trays of microgreens per week.
John Paul Prior sees these “5ac farms” as a way to compliment an existing farming enterprise.
His vision is to have as many Farmony models across the country as possible, complementing an existing beef enterprise for example and providing another income, all while replacing food imports into this country.
These salads, herbs and microgreens will be grown using hydroponic technology – no soil involved – and will be highly nutritious and free of pesticides.
That IT input into the farm provides a controlled environment.
Anyone who owns a Farmony solution can control it from anywhere in the world with a mobile device. The controlled environment means no pesticides are used and growth cycles are efficient.
Salads and microgreens are grown inside this controlled environment
“The growing season in Ireland is obviously from May to September. In a Farmony, a producer can grow all year round – 365 days a year,” John Paul explained.
This provides a whole new window of opportunity for Irish growers to have a continuous supply of fresh and local produce.
The business model allows for crops to be grown in small spaces. Restaurants could have their own source of salads and herbs all year round for example.
A restaurant’s beef supplier could provide the beef, the herbs to season it and the salad to accompany it.
“With microgreens your grow cycle is just six-to-seven days, so in terms of output one module can grow 24 trays of micro-greens per week and multiply that by 17 and you’re at 408 trays of micro-greens every week, so it’s an impressive output.”
Replacing Imports
At present, Ireland is heavily dependent on imports in this sector, which can be clearly seen on the supermarket shelves.
“We’re encouraging people to apply for the horticultural grant in 2020,” John Paul noted.
“The country imports about €300 million worth of produce, so we’re trying to basically offer a solution for producers to replace those imports.
You’re talking about hyper-local produce. These farms could be placed in urban centres or farmyards.
John Paul noted that while there are some farming sectors struggling at the minute, one of his company’s solutions could fit into a current farm business.
John Paul estimates a total workload of 25-30 hours/week and noted that there is a 40% grant available to set up the farm.
The system can also be used in an existing farm building. Mushroom houses, which are no longer in use for example, are ideal for these modules.
How Does It Work?
John Paul explained a small bit about how the farm works. The modules – which from the outside look like shelves – are basically flat-packs and can each be assembled in 45 minutes.
Water and nutrients flow through these modules feeding the plants. The gallery below shows the root structures of some of the plants and the water in the trays which is filled with artificial fertilisers.
“We use hydroponic technology so there’s a constant water flow throughout the module.
First of all the process is you seed sow. Then you transplant and the roots take the nutrients from the water solution that’s ebbing and flowing throughout the module.
Once the initial work of sowing and transplanting is carried out, the remainder of the work can be completed from a mobile device until harvest.
Lighting and temperature, as well as electrical conductivity and pH levels in the water, are all monitored and used to decide on the different “plant recipes”. The information is all sent to the master controller and sends nutrients to the plants accordingly.
Lights go on and off automatically, nutrients go in and out.
The irrigation system and lighting can all be changed from anywhere in the world. The amount of light hours can be changed for example, depending on the different plants.
Some plants like basil might require more white lights, while mustard or chard will have more blue lights.
As well as plant recipes, John Paul thinks he has the recipe to “supplement and compliment” current farming businesses, which he thinks can be made more sustainable and profitable by building a Farmony on site.
High-Tech Farm In Shipping Container Cutting Growth Time In Half
A shipping container and a lot of ingenuity -- is changing the way produce is grown. "It's a 3.4-acre farm inside a 320 square foot shipping container," explained Dale Speetjens, CEO & Co-founder ShipShape Urban Farms.
To View The Video, Please Click Here
MOBILE, Ala. (WALA) -- A shipping container and a lot of ingenuity -- is changing the way produce is grown.
"It's a 3.4 acre farm inside a 320 square foot shipping container," explained Dale Speetjens, CEO & Co-founder ShipShape Urban Farms.
Calling it a "Business in a Box" -- Speetjens gave us a tour. Inside the container garden was several varieties of lettuce in various stages of growth.
"Inside here right now it's a balmy 70 degrees and it's this temperature whether it's 100 degrees outside or 30 degrees," said Speetjens.
Every variable is controlled by a computer system.
"This here is I would say the brain of the container... This is actually the control," said Carlos Augusto, VP of Marketing ShipShape Urban Farms.
From the temperature, PH levels, lighting, and right amount of water -- Augusto manages the day to day operations using hydroponic technology.
They're able to recycle the water - using only 10% of what a traditional farm uses and cutting down the growth time from 10 weeks to five weeks. The process all starts with employees planting seeds into individuals cells.
While they're seeding each cell by hand -- machines will eventually take over the process. The seedlings are then placed into the nursery section of the container.
Each container is designed for one person to work about 15 to 20 hours a week. The containers producing 1,200 heads of lettuce weekly.
INFORMATION BOOK
"So one of the steps we did to help is to make more efficient. We developed these lids and all the farmer needs to do to harvest is to pull the lid out and they harvest all the lettuce at once," Augusto demonstrated.
Each container costs $95,000 and upward. Debuting their prototype in New Orleans at the Louisiana Restaurant Association Expo in August -- ShipShape Urban Farms generated a lot of interest.
"Over 3,000 people walked through garden close to 300 to 400 people say they were interested in becoming a ShipShape Urban farmer," said Speetjens. "Eventually we'd like to create a network of urban farmers where all of us work together to produce food for our local communities.
Because it's all done on the computer and backed up every 15 minutes on a server -- ShipShape can monitor every stage of growth and share success stories with other farmers. There's also an app that allows the farmers to control settings from their phones.
"We will be able to monitor all the urban farms through the computer system -- not only to assist them but if we have a container that is producing more than average -- we can contact that farmer and share their experience with other farmers," explained Augusto.
The company hopes to build about 850 over the next five years. So far they have more than 30 orders and say while their focus is on the southern region of the U.S. -- they've had interest from as far away as the Galapagos Islands, India, Canada, and South America.
Romaine Has Had A Tough Go. Here’s What Has To Happen To Make it Safe
The Centers for Disease Control alerted consumers on Nov. 22 to not eat romaine lettuce from California’s Salinas Valley due to E. coli contamination
To View The Video, Please Click Here
By Stephen M. Ostroff
November 26, 2019
Stephen M. Ostroff is a former deputy commissioner for foods and veterinary medicine at the Food and Drug Administration.
Exactly a year ago, during Thanksgiving week, I was involved in the government’s decision to recommend removing romaine lettuce from grocery store shelves and restaurants. We also advised people not to eat any romaine they had purchased and to throw it away instead.
Now, right before Thanksgiving, it’s happening again.
Nobody wants to scratch romaine off the nation’s Thanksgiving menu. But these recommendations were easy ones to make.
Last year, an outbreak of E. coli bacteria linked to romaine was sweeping the country. Contaminated romaine was likely still on the market. We were unsure where the contaminated product came from, so all of it had to be removed. Even if we knew its origin, romaine wasn’t labeled to allow consumers to determine where it was grown. At least the labeling has improved since last year. But more needs to change.
Romaine lettuce on the shelves of a grocery store in Simi Valley, Calif., in 2018. (Mark J. Terrill/AP)
During the 2018 Thanksgiving outbreak, the government’s actions clearly prevented additional illnesses. But, unfortunately, 62 people still became ill. Symptoms of an E. coli infection can include severe stomach cramps, bloody diarrhea, vomiting, and fever. Some people experience only mild symptoms, but for others, a severe infection can be life-threatening.
Fast forward to now, and there’s another outbreak of the same strain of E. coli linked to romaine, likely from California’s central coast. As of Nov. 22, 40 cases had been reported across 16 states, with 28 hospitalizations but no deaths. The Food and Drug Administration and Centers for Disease Control and Prevention are recommending that consumers avoid romaine from the Salinas region.
Remarkably, the specific E. coli strain (O157:H7) causing the new outbreak is genetically indistinguishable from last years and another one in late 2017. Last month, the FDA retroactively identified an outbreak involving romaine lettuce that occurred in late summer, causing 23 illnesses. The CDC has not posted information about that outbreak, so the epidemiologic patterns of illness and causative strain are unknown.
Notably, the 2018 Thanksgiving outbreak was not the first one that year either. It was preceded by the biggest outbreak in the United States of E. coli illness in more than a decade, with 210 illnesses, including five deaths, linked to romaine from the winter growing region around Yuma, Ariz.
With five multistate outbreaks in less than two years, it’s clear there’s a serious continuing problem with E. coli O157:H7 and romaine lettuce. The natural reservoir for this pathogen is ruminant animals, especially cattle. Moreover, one particular strain of E. coli seems to have found a home in the growing regions of central coastal California, returning each fall near the end of the growing season.
It’s not clear where this strain is hiding. Cattle? Water sources? Elsewhere? What is clear is that additional steps must be taken to make romaine safer.
Other commodities such as meat and flour also cause foodborne illness. But at least with these, cooking and baking eliminate the risk. That isn’t the case with romaine. Washing the lettuce may remove surface contamination, but the crinkly leaves make eliminating all of it almost impossible.
The Food Safety Modernization Act, signed into law in 2011, places the responsibility on food producers to prevent contamination from occurring and to assure their product is safe. The leafy greens industry, with input from the FDA, the CDC, and others, has recently taken steps to meet this obligation. In September, an industry-led task force issued a set of recommendations to address the problem.
One of the most significant recommendations is that any open-source water in contact with edible lettuce in the three weeks before harvest should be treated to remove contamination. E. coli O157:H7 was found in untreated surface water in both the Yuma and 2018 Thanksgiving outbreaks.
The task force recommendations should be immediately adopted and implemented. But even more should be done. Surface water used for romaine irrigation should be treated throughout the growing cycle, not just in the three weeks before harvest. The FDA should also quickly issue agricultural water standards that have been postponed but are required by FSMA’s produce-safety rules.
Another concern that must be addressed: concentrated animal feeding operations, where tens of thousands of cattle potentially carrying E. coli O157:H7 are housed if they are located near leafy green growing areas. Buffers between the cattle operations and growing fields are required, but bigger ones may be needed.
E. coli can cause terrible illnesses. Just ask any of the victims of the five most recent outbreaks. The romaine lettuce market has managed to rebound from the outbreak after the outbreak. But consumer loyalty is unlikely to be limitless. The industry should not take this resilience as a given.
Read more:
Letters: Blame E. coli contamination on our agriculture policy
The Post’s View: A great first step to protect antibiotics for the future
VIDEO: Talking Fresh Summit And Indoor Farming Companies
Carlson, a 30-year veteran of PMA expos, said one thing that caught his eye was the growth of indoor farming companies at the show
by Tom Karst
October 28, 2019
The Packer’s Tom Karst visits with Craig Carlson of Carlson Produce Consulting Oct. 25 about the just-concluded 2019 Produce Marketing Association’s Fresh Summit.
Carlson, a 30-year veteran of PMA expos, said one thing that caught his eye was the growth of indoor farming companies at the show. Those firms are capitalizing on the appeal of local produce relative to metropolitan regions, and emphasizing the operations use less water, less land and less fuel than traditional farming operations. What does the future hold for indoor farming companies?
“They are really checking a lot of boxes that I think is exciting,” Carlson said. “My concern about this is that most everybody is throwing money at the same idea,” he said, noting that indoor companies may need to expand their range beyond leafy greens.
Packer Interview - Craig Carlson Oct 25
Brownstein: Montreal's Lufa Farms Reaches New Heights
Airplanes are buzzing above. Gridlock has set in below. One couldn’t possibly imagine a more unlikely agricultural setting, yet on top of a non-descript office building in St-Laurent, within a tomato’s throw of the Place Vertu mall, construction is underway on the world’s largest urban rooftop farm
The fourth Lufa rooftop installation — this one the size of three football fields — is to open in March in St-Laurent.
BILL BROWNSTEIN, MONTREAL GAZETTE
November 21, 2019
Airplanes are buzzing above. Gridlock has set in below. One couldn’t possibly imagine a more unlikely agricultural setting, yet on top of a non-descript office building in St-Laurent, within a tomato’s throw of the Place Vertu mall, construction is underway on the world’s largest urban rooftop farm.
This will be the fourth Lufa Farm around Montreal, and when it opens in March, it will measure nearly 164,000 square feet, or roughly three football fields. That’s a whole lot of tomatoes and eggplants.
The Lufa mantra is: “We grow food where people live, and grow it more sustainably.” And that it does.
The plan is that this gi-normous greenhouse will double Lufa’s growing capacity and the four farms combined will allow it to feed two per cent of Montreal with fresh veggies. The St-Laurent farm is intended to meet the ultimate standard in energy-saving greenhouse technology. And like the other farms, it, too, will operate without use of synthetic pesticides.
In addition to the produce, St-Laurent borough mayor Alan DeSousa is also pumped about the rooftop farm’s ecological benefits: “It will make it possible to fight against heat islands in our district, where more than 70 per cent of the surface area is devoted to industrial and commercial activities.“
The bottom floor of the St-Laurent office building serves as a distribution centre, wherein individual boxes of vegetables, fruits, breads and cheeses, among other goodies, are prepared for Lufavores, Lufa’s member individuals and restaurants. About 17,000 boxes are shipped every week to Lufavores at hundreds of pickup points around the city. Lufa also provides home delivery by, natch, electric-powered autos.
“We like to think of the distribution centre as a giant online farmers market,” Lufa co-founder and greenhouse director Lauren Rathmell says.
Rathmell and her husband, Lufa co-founder and CEO Mohamed Hage, started germinating their business 10 years ago. Their first farm sprouted in Ahuntsic. Then came rooftop farms in Laval and Anjou. The company now has 327 employees — and counting.
While allowing that the Ahuntsic farm cost $2.2 million, Rathmell is tight-lipped about the budget for the St-Laurent greenhouse, which is five times the size of the former. She does, however, note that Lufa Farms has been profitable since 2016 and is not ruling out more expansion, in Montreal and elsewhere.
“Our goal is to be ecologically and economically sustainable,” says Rathmell, a Vermonter who moved here to study biochemistry at McGill and stayed on after meeting Hage.
“Our first site was the world’s first commercial rooftop greenhouse. There are ground-level greenhouses and farms, but this concept had never been done — taking an industrial space and repurposing it for food production. There’s still not many doing what we’re doing. We wanted to create a local food engine, and to do so by following tenets of responsible agriculture with hydroponic farms and reducing our footprint in the process.”
The trick was in finding rooftops around Montreal that would have enough room and that would be structurally able to support a greenhouse.
“We literally surveyed the entire island of Montreal on Google maps to find the rooftops.”
Lufa, incidentally, is a squash/cucumber-like vegetable indigenous to Lebanon, where Hage was born. While the Lufa farms grow almost every kind of veggie, they don’t yet produce a lufa. “We probably should soon.” Rathmell concedes. “It’s very practical. You can eat it. It’s hollow inside, and when you dry it, it turns into a sponge that grows on walls and rooftops.”
The hustle-bustle of St-Laurent’s distribution centre is in marked contrast to the laid-back vibe of Lufa’s Laval rooftop farm.
Of course, like Lufa’s other facilities, one might be hard-pressed to spot the Laval farm, situated atop another nondescript office building, off a fairly gridlocked highway.
But once inside the sprawling, 43,000-square-foot Laval greenhouse, one is transported from the grey and the cold and the snow to a near-tropical setting. There is a glow hanging over the place and with temperatures in the low 20s, cheery-faced farmers, mostly attired in T-shirts and one even in shorts, are planting and harvesting tomatoes and eggplants. A couple of them appear to be actually whistling while they work. It is almost surreal.
It’s more than just talk about reducing footprints. In touring the Laval greenhouse, Rathmell points out how all the water employed is re-circulated and reused. Rainwater is also collected off the roof. And considerable energy is saved simply by being on a rooftop.
“Being on a rooftop also means we’re not using new land, and also keeping us as close as possible to urban centres,” Rathmell says.
On the other hand, trying to convince prospective landlords on setting up rooftop farms was initially difficult.
“It’s become much easier with proof of concept,” Rathmell says. “When we approached the owners of that first building in Ahuntsic, in their minds it was cows and soil and tractors and whatever. We were able to convince them that wasn’t the case. Plus that the greenhouse would be fully contained and help insulate their building. And that we’d take care of the construction and electricity.”
And, oh yeah, the landlords would also be able to feast on the freshest produce around.
Tomatoes in lieu of cash for rent?
Quips Rathmell: “That’s the next deal.”
For more information about Lufa Farms or becoming a Lufavore, go to montreal.lufa.com.
RELATED
Second Chances Farm Launches In Wilmington With New Trainees And A Hemp License
Ajit George and his team had a lot to announce at the launch of social impact startup Second Chances Farm, where it celebrated the official opening of its 47,500-square-foot facility in Wilmington with a “ladybug dedication.”
The 47,500-square-foot facility in Riverside is bringing on 17 returning citizens to help run the indoor urban farm.
By Holly Quinn / STAFF
Ajit George speaks next to one of the hydroponic towers that will soon fill the warehouse space in Riverside. (Photo by Holly Quinn)
Ajit George and his team had a lot to announce at the launch of social impact startup Second Chances Farm, where it celebrated the official opening of its 47,500-square-foot facility in Wilmington with a “ladybug dedication.”
That’s like a ribbon-cutting, but instead of wielding oversized scissors, the governor, New Castle County executive, mayor and City Council president (among others) released tiny bags of live ladybugs into a floor-to-ceiling vertical “fields” of hydroponic lettuce and herbs.
The urban farm in Riverside will soon also be growing hemp, which is processed into CBD oil, after receiving approval for a license to grow it. (Hemp, a strain of cannabis that has an extremely low level of THC — the substance that gets you high — was made legal in all 50 states with the passage of the 2018 Federal Farm Bill.)
The farm will also offer a few free services to people who live in the neighborhood, including a Crossfit gym and wireless WhyFly service via a connection on the top of the building.
Seventeen returning citizens who have completed their sentences of incarceration have been selected as the first trainee cohort and will receive 16 weeks of paid training.
“We believe those nearest to the solution have also been affected nearest to the problem,” said Saad Soliman, executive director of Peace by Piece, the organization that assists with the reentry program at Second Chances Farm. “Borrowing from my own experience having served 15 years in prison and overcoming boundaries, overcoming barriers, overcoming obstacles, I believe in the leadership of every single man and woman that we’re bringing in here. Let’s humanize the components of who these men and women really are.”
In addition to Second Chances Farm launch, George is also celebrating the launch of his new book, “The Magic of the Red Carpet,” which follows his journey from the founding of TEDxDelaware to Second Chances Farm. All proceeds of the book will go to Peace by Piece.
Watch Soliman introduce the new team members here:
€5 Million For Dutch Vertical Farming Research
"The increasing world population needs to be fed, while more and more people live in cities, there is often too little water, and we want our vegetables to have more and more nutritional value”
Wageningen University & Research (WUR) is to receive more than €8 million from the Dutch Research Council (NWO) and participating bodies for two major research programs, one involving tower garden systems using LEDs and the other focusing on improvements in the welfare of pigs and chickens. A third project, with WUR as a partner, is about sustainable freshwater management in the Dutch delta.
The recipients of the so-called Perspectief round 2019 funding were announced during the annual ‘Teknowlogy’ event hosted by NWO’s Applied and Engineering Sciences domain.
Tower gardens using LEDs
Sky High, a research program led by Professor of Horticulture & Product Physiology Leo Marcelis, which aims to bring about a revolution in vertical farming, received a total grant of €5 million.
"The increasing world population needs to be fed, while more and more people live in cities, there is often too little water, and we want our vegetables to have more and more nutritional value. By growing plants in layers on top of each other and illuminating them with special LED lights, you can produce fresh vegetables all year round, anywhere in the world, and under all weather and climate conditions," says program leader Prof. Leo Marcelis.
Researchers working on the Sky High program will cooperate with lighting specialists, plant breeding companies, growers, horticultural technology companies, architects and food suppliers to make vertical agriculture systems cheaper and more energy-efficient. Another aim is to produce vegetables and herbs that taste better, have longer shelf lives and provide more nutritional value, while using the absolute minimum of water and fertilizers and no pesticides.
Other participants
Amsterdam Institute for Advanced Metropolitan Solutions (AMS), Bayer, Bosman Van Zaal, Certhon, Fresh Forward, Grodan, GrowX, HAS University of Applied Sciences, OneFarm, Own Greens, Priva, Signify (Philips Lighting), Solynta, TU Delft, Eindhoven University of Technology, Unilever, Leiden University, Utrecht University, University of Amsterdam, and Van Bergen Kolpa Architecten.
Source: Wageningen University & Research
Publication date: Tue 12 Nov 2019
Bowery Expands Indoor Farming To Baltimore Area With An Eye Towards More Sustainable Production Globally
18-Nov-2019 By Elizabeth Crawford
Uncomfortable with the idea that agriculture is a necessary evil with the demand for food outweighing the negative environmental impact of traditional farming and ranching, the co-founder and CEO of Bowery is expanding his revolutionary approach to food production through indoor farms that use proprietary technology to improve sustainability and produce quality.
To Read The Entire Article, And View The Video, Please Click Here
Nick Greens Explains The Importance of Food Safety While Growing Microgreens Indoors
CCEA 2019, is the place to commit, learn and apply the bases of controlled environment agriculture (CEA) for owners and operators of greenhouses and vertical farms, and was held in Panama City from November 06 to 08, 2019
CCEA 2019, is the place to commit, learn and apply the bases of controlled environment agriculture (CEA) for owners and operators of greenhouses and vertical farms, and was held in Panama City from November 06 to 08, 2019
In This Finnish Farm, Strawberries Grow On Multiple Levels
Despite fall being in full bloom, the strawberry cultivation in Lappträsk, Finland is running full throttle. Robert Jordas believes it is interesting to try new cultivation methods
Robert Jordas Performs 'Secret' Experiment In His Greenhouse
Despite fall being in full bloom, the strawberry cultivation in Lappträsk, Finland is running full throttle. Robert Jordas believes it is interesting to try new cultivation methods.
One of the new methods is the vertical cultivation of strawberries: the strawberries grow on different levels. In the space, around 30 square meters in size, strawberry plants are hanging with flowers, unripe, and ripe fruit. Because of the colorful lighting, it reminds of a disco.
The high air humidity immediate fogs up your glasses, but the temperature is not tropical. it looks more like the Finnish Indian summer.
All plants are looking well, because every level has its own lighting. Jordas: "We want the plants to grow optimally and to keep the climate around the plant as optimal as can be."
Secrets, pink light, and the perfect cultivation circumstances
The optimal climate for a strawberry plant means the right light and the right heat and air humidity. The plant also requires CO2, nutrients, and water.
Jordas: "The interesting thing is that we, focused or the growth requirement, can control everything."
Much of the project is still secret. One of the secrets is LED lighting. The plants need a lot of light; LED lighting produces less heat than other lamps and can be placed closer to the plant so you can create more levels.
Jordas: "There are many advantages to growing on multiple levels: a larger harvest on a smaller surface, being able to control the spectrum of the lamps. We try to learn as much as possible and find the right cultivation method."
Robert Jordas wanted to grow strawberries because he likes them, but he is not completely satisfied with the taste his strawberries have at the moment.
Jordas: "We are going to test this cultivation method for a year. Continuous harvesting is possible, when one plant has flowers, the other has ripe fruits."
But is it environmentally friendly to grow strawberries in Finland in the middle of winter?
According to Jordas, that depends on how the electricity is generated. "If we use sustainable energy, it is better than importing vegetables and fruit from other countries. Also, strawberries are fresh products and it is important to consume them as soon as possible."
Source: Svenska
Publication date: Fri 8 Nov 2019
© HortiDaily.com