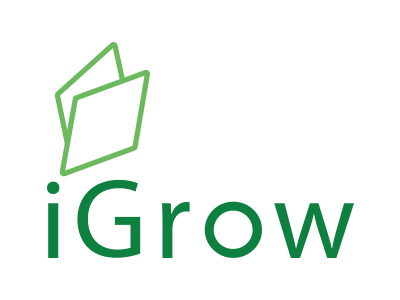
Welcome to iGrow News, Your Source for the World of Indoor Vertical Farming
Dutch PlantLab Raises € 20 Million In First External Investment Round
’This injection of capital will enable us to open up additional production sites and further perfect our technology’, explains Michiel Peters, CEO of PlantLab
Production Sites For Vertical Farming Rolled Out On a Global Scale
Den Bosch (the Netherlands), 22 July 2020 – Dutch scale-up PlantLab has raised a first external investment of € 20 million from De Hoge Dennen Capital. The company has developed a globally patented technology for ‘vertical farming’, a hyper-efficient method for growing vegetables and fruits. It will use the injection of capital to open indoor production sites in various countries, including the Netherlands, US, and the Bahamas.
PlantLab management team: Leon van Duijn (founder), Marcel Kers (founder), Michiel Peters (CEO), John van Gemert (founder) and Frank Roerink (CFO)
Over the last 10 years, PlantLab has succeeded in developing an innovative and revolutionary technology for hyper-efficient urban farming, which is already being successfully applied in a commercial production site in Amsterdam. The new technology makes it possible to grow fresh, healthy, and delicious vegetables on a large scale very close to the consumer without using any chemical crop protection agents. On a surface area the size of only two football fields, it is now possible to produce enough crops to feed a city of 100,000 residents with 200 g of vegetables each on a daily basis.
Innovative solutions
’This injection of capital will enable us to open up additional production sites and further perfect our technology’, explains Michiel Peters, CEO of PlantLab. ‘The increasing population of the planet and the climate crisis are posing new and enormous challenges to the production of food for the world’s population. We have no choice but to grow our food more sustainably and efficiently, and that demands innovative and revolutionary solutions.’
Left: Michiel Peters, right: Plant Production Unit Manager Tobias Glimmerveen pinching tomato plants
PlantLab’s production sites can be set up anywhere in the world, even on barren land or urban areas. Thanks to optimized temperature, moisture, and light control, the crops grow to their full potential, while water use is reduced by as much as 95%. Light is provided by specially developed LEDs that provide the specific wavelength needed by the plant for photosynthesis. ‘Our technology makes it possible to grow crops anywhere in the world very close to the consumer. The crops then no longer need to be transported over long distances. The result: less CO2 emissions, lower cost, and less food waste’, says Peters.
Making a difference
De Hoge Dennen is part of the investment company founded by the De Rijcke family, the former owners of Kruidvat. The company has made previous investments in the online supermarket Picnic, the salad producer De Menken Keuken, and the electric bicycle brand QWIC. CFO Jelle Roodbeen: ‘We are convinced that PlantLab’s technology will make a real difference on a global level. It will make healthy and delicious vegetables affordable and accessible to everyone, in an environmentally friendly and sustainable fashion’.
In addition to the injection of capital by De Hoge Dennen, CFO Frank Roerink and CEO Michiel Peters are joining the scale-up company to strengthen the management team, which also includes the founding partners Leon van Duijn, Marcel Kers and John van Gemert. PlantLab has its vertical farming R&D centre, the biggest of its kind anywhere in the world, in Den Bosch, and a commercial production site in Amsterdam. PlantLab already employs over 60 people.
About PlantLab
PlantLab specializes in technology for innovative urban farming and aims to supply the planet with a sustainable source of food for the future. The company was founded in 2010 in Den Bosch with the goal of revolutionizing the production of food for our planet. Over the last 10 years, the company has already invested € 50 million in the development of technology that makes it possible to grow healthy, day fresh vegetables close to the consumer anywhere in the world without the use of chemical crop agents sustainably and environmentally friendly, while at the same time reducing water consumption to an absolute minimum. Enough crops can be grown on an area no bigger than two football fields to supply a city of 100,000 residents with 200 g of fresh vegetables every day. As the new technology can be used all year all over the world, it also makes it possible to radically rethink and restructure the logistics chain. The benefits: superior product quality, longer shelflife, much less food wastage, and no CO2 emissions or nuisance associated with long-distance transport. PlantLab aims to make its revolutionary technology accessible to everyone and therefore bring fresh and sustainably grown food within reach for everyone.
For more information:
PlantLab www.plantlab.com
info@plantlab.com
Feeding The World With Controlled Environments
The fallout from increasing global temperatures, a worldwide pandemic, and political unrest is causing projection reductions for crop yields in some countries as much as 50% this year, and small-scale farmers are the most affected with crop net revenues falling by as much as 90% by 2100
This case study, written by Gene Giacomelli and Eric Roth for Agritecture, takes a look at how CEA has emerged as a viable, contemporary agricultural practice over the past 50 years. Here’s how it happened!
The fallout from increasing global temperatures, a worldwide pandemic, and political unrest is causing projection reductions for crop yields in some countries as much as 50% this year, and small-scale farmers are the most affected with crop net revenues falling by as much as 90% by 2100. The consumer preference for consistent, year-round availability of produce has expanded because of the Controlled Environment Agriculture (CEA) industry, even surviving the recession of 2008. “That indicates to me, that no matter what the next recession brings, CEA food production systems will be firmly entrenched in U.S. agriculture production practices,” says Gene Giacomelli, Professor of Biosystems Engineering and former Director of CEAC at The University of Arizona.
CEA has emerged as a viable, contemporary agricultural practice over the past 50 years. There have been dramatic improvements in efficiency metrics including overall crop yield per square unit and reduction of wastage due to disease, nutrient deficiency, or damage to the product. From Space to Antarctica; from rooftop greenhouses to rural farms worldwide, CEA has proven itself to be not only a complement to open field crop production, but in some instances, a competitive alternative (or in the case of Space and Antarctica the ONLY) approach. Today, more than 60% of all fresh tomatoes consumed in the U.S. are grown in controlled environments and that number approaches 100% during the North American winter. Here’s how it happened...
In the 1990s, the U.S. greenhouse production shifted from its infancy to a steady supplier of fresh produce. While greenhouses use the sun as their main source of light, they can also make use of supplemental lighting for additional growth. This advantage, along with the ability to control and protect the growing environment, encouraged large farming corporations to enter the space in the Northeast, Arizona, Colorado, California, and Texas. Environmental control enabled these early adopters to produce crops like tomatoes, cucumbers, and lettuces year-round. During the same time, small family farms were often adding greenhouses to complement their traditional open-field production.
During the next decade, the major suppliers of field-grown vegetables in Canada and Mexico also began focusing on greenhouse production. The 2000’s firmly established CEA vegetable production as a viable commercial growing method.
In the 2010’s, vertical farming became more mainstream when Dr. Dickson Despommier published the book, The Vertical Farm: Feeding the World in the 21st Century. Vertical farms are essentially plant factories, with multi-level grow systems in insulated buildings using only electrical light instead of sunlight for plant growth. Although there were most likely small scale vertical farms before it, Sky Greens in Singapore was the first vertical farm to begin large scale commercial operations in 2012. Vertical farming became more commercially viable largely because of the advancing technology of Light Emitting Diodes (LED). These distributed light sources are less energy-intensive than the industry standard high-intensity discharge lamps, but more importantly, allow growers to move lights closer to the crop without burning or overheating. This enabled business developers to stack hydroponic grow systems, producing significantly more greens in increasingly smaller spaces. Now confined urban areas where arable land is very limited, could become producers of locally-grown, fresh food.
Protected cultivation has been in America at some level for two centuries, but what technological advancements made feeding the world with controlled environments possible?
Plastics
Polymer plastics such as polyethylene began providing a low-cost, energy-efficient film covering for greenhouses. This lowered the financial barrier to entry by creating more affordable greenhouses, thereby allowing unestablished growers to gain experience with a much lower investment than traditional glass-covered greenhouses. The plastic films dropped the investment cost significantly, while the more rigid, molded plastics improved operational metrics like production capacity, labor efficiency, and biosecurity.
Molded plastics also provided light-weight,easily-sanitized crop handling with trays, pots/flats, and clamshells for the packaging, among other things. Molded plastics further created light-weight structural channels, containers and benches which supported the plant and its root zone within hydroponic nutrient delivery systems, and even provided transport systems for improved labor and logistics management. Fully outfitted climate-controlled CEA plastic film boxes provided lettuce and greens production for the International Space Station.
Microprocessors
The microprocessor with its accuracy, consistency, data storage and simultaneous interpretation of multiple types and number of sensors has allowed the grower to tend more to plant production and much less to environmental control. No longer must the grower walk the greenhouse each morning to adjust the ventilation openings based on a guess of the day to be sunny, rainy or cold. Sensors are available to determine critical environmental plant needs and to make precise responses to air temperature and humidity for VPD (vapor pressure deficit) which affects plant transpiration and photosynthesis; light intensity with quantum sensors to determine DLI (daily light integral) which is directly related to desired growth or production rates; and, pH and EC which affects plant nutrient availability. When all combined, the grower is provided an improved understanding of the plant response to its environment. All this can be obtained on request in real-time by cellphone or within a report upon early morning arrival of the grower to the greenhouse each day.
Even more valuable is the capability of the computer to save data and further process it into useful information, which directs better grower decisions. Expect additional sensor development and implementation in the future to provide higher quality information about the food products, such as its flavor, sweetness, or nutritional quality.
The automation of information, although critically important, may become second in importance to labor-saving automation. Labor is often a farm’s biggest expense and the agricultural talent pool is limited nearly everywhere, but a high-tech farm’s food safety and security are dramatically enhanced when human contact with the edible product is reduced or eliminated. Production system automation that removes the need for people to work in groups on production lines is becoming crucial within this new world of viral pandemics.
There are still many advancements to be made in CEA. Technologies and experiences were transferred from the established greenhouse industry and applied to the developing indoor vertical farming industry. From LED lighting ‘recipes’ to plant nutrition under those recipes; from materials handling and logistics to labor management, years of R&D are required to reach optimal solutions for the plethora of combinations of plant cultivars, stages of growth, and harvest expectations within each type of CEA system.
The challenges remain for educating the people managing and operating the controlled environments. Educated employees working within a production process that is logistically sound, labor efficient, and task friendly are critical considerations for successful CEA businesses. Even with automation, the required work of skilled employees will remain, but at a higher educational level and a lower quantity.
In the future, it’s entirely possible that a CEA system will be able to autonomously program itself, or modify the plant environment without being directed, but for now, the plant production experience of an educated grower or crop manager is still required even in the most high-tech operations. Additional developments for successful CEA businesses include breeding of plant cultivars optimized for CEA production; emphasizing the importance of marketing; valuing employee education and experience; accepting that growing plants is a skill and an art; and, understanding basic physical principles that follow the laws of physics and biology!
CEA is still in such an early stage of commercial viability, but the blueprints for successful ventures continue to be created by intelligent and increasingly well-equipped entrepreneurs. As we look at the timeline of its commercial origins, to the critical technologies that made it work, we can see how far it's come, but also the potential the future holds for feeding the world with controlled environments.
Have you participated in the 2020 Global CEA Census? Autogrow and Agritecture Consulting have launched their 2nd Annual Global CEA Census, focusing on understanding the impact of the COVID-19 pandemic on controlled environment agriculture (CEA) operations around the world. The 2020 Global Census runs from July 7th to August 10th. Those who complete the census are entered to win different prizes from Agritecture and Autogrow.
Publication date: Fri 24 Jul 2020
UAE: Smart Acres Plans To Open R&D Lab For Local Produce Amid AgTech Growth
Abu Dhabi vertical farming start-up Smart Acres is looking to raise at least Dh20 million to fund a research and development center to produce a local variety of potato as agriculture technology gathers pace in the UAE
Vertical farming start-up aims to raise as much as Dh20m to fund the project
Abu Dhabi vertical farming start-up Smart Acres is looking to raise at least Dh20 million to fund a research and development center to produce a local variety of potato as agriculture technology gathers pace in the UAE.
“The future is green. The Hope probe has headed to Mars, why shouldn’t the UAE be the first to put a container farm on the planet?” Abdulla Al Kaabi, founder and chief executive, told The National.
The entrepreneur is part of a team of three working in partnership with a Korean AgTech platform called N.thing, to adapt the technology to the harsh arid climate of the Emirates on an Abu Dhabi farm gifted to him two years ago by his father.
Smart Acres has designed vertical farms in shipping containers using the IoT-based technology system that monitors water, carbon dioxide, and nutrient levels. The system sends a push notification to one of the team's iPhones or iPads if levels need to be adjusted, but it allows the process to happen largely unmonitored. The farm is empty most of the time, Mr. Al Kaabi said. The growing process also consumes up to 90 percent less water than traditional farming methods and grows premium and cost-competitive lettuces.
Food security and innovation in agriculture is a priority of the Abu Dhabi government, which has earmarked Dh1 billion for an agri-tech incentive program as part of the government’s Ghadan 21 accelerator initiative.
In April, Abu Dhabi Investment Office (Adio) invested $100 million (Dh367m) to bring four agriculture technology companies to the emirate as part of government efforts to attract high-skilled talent and cutting-edge research. The country’s 24,000 farms are set to benefit if new technology can be applied to drive efficiencies in crop yield and water usage.
The Covid-19 pandemic has only underscored the need to achieve greater food security in the UAE. Between 80 and 90 percent of the food in the GCC is imported, according to Chatham House.
While the figure is high, UAE residents are starting to see signs of progress: locally-harvested tomatoes and greens at the market or on dining menus are now a common sight. All of this has sprung up in the last several years as vertical and hydroponic farming ventures and research, as well as cloud-seeding, bear fruit.
Mr Al Kaabi wants the Smart Acres Institute of Food Security & Agriculture “to have Emirati hands” build the project. He is looking to attract recent graduates in environmental sciences and technology to the R&D lab to customize seeds to grow in this region in a controlled environment.
Potatoes, one of the most common crops in the world with consistent growing demand year-on-year, will be his first target. The team also wants to develop robots to help with harvesting and packing.
In addition to the R&D lab, Mr. Al Kaabi is aiming to increase the annual yield capacity at the farm more than tenfold, from the 40 tonnes of lettuces that it currently produces.
Mr. Al Kaabi was well-versed with the food industry even before he struck out on his own. His family owns the exclusive distribution license for a popular Korean ramen brand called Samyang Noodles as well as Tom’s Farm almonds.
While he learned a lot from the family trading business, his father encouraged him to build something on his own. After seeing how difficult the last several months have been on the imported food business, he is glad he did so.
With Smart Acres, Mr. Al Kaabi said, "I'm finally doing something right. Now my father asks me every two weeks what is going on at the farm”.
Updated: July 21, 2020 06:52 PM
Lead Photo: Farming via smartphone in Abu Dhabi. Courtesy Smart Acres
UAE Agricultural Firm Uses Technology To Help With Food Security
Smart Acres aims to support the UAE’s food security program by using high-tech vertical farming to produce approximately 8,000 kilograms of lettuce per cycle
KATERYNA KADABASHY
July 13, 2020 | DUBAI
Smart Acres aims to support the UAE’s food security program by using high-tech vertical farming to produce approximately 8,000 kilograms of lettuce per cycle.“
In the expansion phase, we will have 78 modules, which comes to a total of 88,320 pots. Each lettuce, for example, will weigh 100 grams. So, that is approximately 8,000 kilograms of crops per cycle,” the company’s CEO Abdulla Al-Kaabi told Arab News.
The vertical farm — currently in the proof-of-concept stage — is expected to launch in the third quarter of 2020, producing 12 cycles of crops annually and expanding from Abu Dhabi to the rest of the country. In this type of farming, plants are stocked vertically, providing more produce per area and resembling something similar to the green walls sometimes seen in malls.
Smart Acres collaborated with South Korean vertical farming technology n.thing in their farming processes. (Supplied)
The company collaborated with South Korean vertical farming technology n.thing to employ the Internet of Things in their farming so as to efficiently use water and monitor humidity, temperature, and nutrients.“
Vertical farms, in general, save over 90 percent of water compared to traditional farming methods. There is constant water flow across all the little pots, and the water is filled with all the nutrients necessary for the plant to grow,” Lead Project Manager Aphisith Joe Phongsavanh said.
The high-tech design of the farm allows Smart Acres to produce clean crops without any pesticides and with minimal intervention.“
Since we are growing our crops in a 100 percent closed environment, we don’t have to use pesticides at all. That’s exactly what we mean by clean food: non-adulterated food products that go through minimal processing,” Phongsavanh said.
However, this closed environment in which the plants grow requires staff and visitors to wear protective gear before entering the premises in order to preserve the sterility of the area.“
It is almost like going into a very high-tech factory. You have to wear lab coats and go through an air shower, where one door is closed and the other door only opens after 10 seconds of disinfection,” Director of Smart Acres Sean Lea said.
Currently, the company does not have any investors, but Al-Kaabi said that the expansion phase “of course will require an investment,” expected to cost around AED16.7 million ($4.5 million).
It will not just include a larger number of crops, but also a research and development center with a vision to start cultivating baby spinach, mature spinach, baby arugula, strawberries, and potato seeds.
Earlier in July, Abu Dhabi’s Crown Prince Mohammed bin Zayed Al-Nahyan visited some local farms and met with agricultural entrepreneurs.“
I was pleased to meet some of the UAE’s aspiring agricultural entrepreneurs who are pioneering sustainable and resilient farming practices using modern technology,” Al-Nahyan tweeted.
The UAE is pushing for local production of crops and livestock.
According to Khaleej Times, the Abu Dhabi Agriculture and Food Safety Authority provided over $174 million to “138,000 families, 30,632 breeders and farmers, and 259 small-scale producers and commercial animal farms in Abu Dhabi” to support the industry in June.
Lead Photo: Smart Acres’ vertical farming technology enables it to produce approximately 8 tons of lettuce per cropping cycle. (Supplied)
The "AgrarCycle" Network is Intended to Give Vertical Agriculture a Major Boost
In vertical agriculture, vegetables and fruits are grown in multi-story buildings. This system does not require direct sunlight or arable land because the plants grow in nutrient solutions under artificial light or daylight
Osnabrück University of Applied Sciences
July 3, 2020
In October of the previous year, the Osnabrück University of Applied Sciences announced that a new research center "Agricultural Systemys of the Future" would be created on the Haste campus. The expertise from the research center will also be incorporated into the ZIM network "AgrarCycle". Graphics: Hüdepohl.Ferner Architektur- und Ingenieurges.mbH
In the network for agricultural systems development, the university works closely with research and development institutions, small and medium-sized companies, and start-ups. Cooperation with partners from the IT, engineering, and agricultural sectors should result in highly innovative approaches for food production.
(Osnabrück, July 2nd, 2020) In the coming months and years, a research team from Osnabrück University of Applied Sciences wants to set up a highly innovative network of science and business under the name "AgrarCycle" in order to sustainably promote vertical agriculture in Germany. The project is being funded with more than 120,000 euros from the Innovation Program for Small and Medium-Sized Enterprises (ZIM) of the Federal Ministry for Economic Affairs and Energy.
In vertical agriculture, vegetables and fruits are grown in multi-story buildings. This system does not require direct sunlight or arable land because the plants grow in nutrient solutions under artificial light or daylight. In addition to efficient use of space at height, food can be produced in an indoor vertical farm (IVF) in reliable, weather-independent quality. In addition, the use of pesticides can largely be dispensed within production in closed and controllable agricultural systems of an IVF. "This will make it possible for people in urban areas to be supplied with locally produced food in the future," says Prof. Dr. Andreas Ulbrich, professor of vegetable production and processing.
Further project partners are welcome
Food from an indoor vertical farm is still too expensive, partly because of the higher electricity consumption. With regard to an IVF, for example, the project proposal states: "Apart from additional costs, the costs of energy consumption of 7 kWh per kilogram of leaf lettuce are already over one euro." To significantly reduce production costs, there is above all a lack of innovative power electronics. With the help of the ZIM network, that should change. "With the various project partners, we want to find ways to reduce emissions and use resources more efficiently," explains Prof. Dr. Hans-Jürgen Pfisterer, Professor of Electrical Drives and Fundamentals. "We want to meet the requirements of nutrition and health-conscious consumer groups and bring new herbal product innovations to the market",
This should succeed both with partners who support the network financially and with associated partners who ideally support the network. The time for the project seems favorable in many ways: In July of last year, the Faculty of Agricultural Sciences at the University of Göttingen published a study that concluded that every second consumer would buy products from vertical agriculture.
Additional project partners from science and industry are being sought for the "AgrarCycle" network. "The vision of the ZIM network AgrarCycle is the further development of closed and controllable agricultural systems with all components and stakeholders along the entire agri-food value chain so that they are climate-resilient, efficient, quality-oriented and economical, and energy and material cycles are optimized and closed can ”, says the project application.
Further information:
Prof. Dr. Hans-Jürgen Pfisterer
Phone: 0541 969-3664
Email: j.pfisterer@hs-osnabrueck.de
Prof. Dr. Andreas Ulbrich
Phone: 0541 969-5116
email: a.ulbrich@hs-osnabrueck.de
Background: The ZIM network "AgrarCycle - Network for agricultural system developments to increase efficiency and climate-secure production of vegetable raw materials through energy and material cycles" is large. Regular partners are: DIL German Institute for Food Technology; ISFH - Institute for Solar Energy Research; DH Light - Professional Lighting; RAM measurement and control technology; Gefoma; Thissen Analytics; Cultinova Experior Microtech; Ingenieurbüro Mencke & Tegtmeyer; Anedo and Hagedorn Software Engineering. Associated partners are: Seedhouse - InnovationsCentrum Osnabrück; Knowledge networking Weser-Ems - bioeconomy Landkreis Osnabrück; Mählmann vegetable growing; ELEA; ELO eG; Vrielmann; K + S and TROX HGI.
By: Holger Schleper | Jasmin Schulte
CubicFarms Announces Sale of 16-Machine Commercial-Scale System in Armstrong, BC
"We invite growers to contact us for a visit to our facility in Pitt Meadows, BC to get a first-hand view of our technology and learn how we can help them scale up their business
VANCOUVER, BC, July 10, 2020,/CNW/
CubicFarm® Systems Corp. (CUB.V) ("CubicFarms" or the "Company") is pleased to announce that its automated, controlled-environment system has been selected by a new customer to grow commercial quantities of leafy greens for retail markets in the Okanagan region in British Columbia, Canada .
The Company has finalized an agreement for the sale of 16 CubicFarms machines, and received a deposit from a British Columbia -based agriculture industry expert specialized in equipment sales in Western Canada.
CubicFarms CEO Dave Dinesen commented: "We are excited to be working with our new customer who plans to supply commercial-scale greens in the Okanagan region. While the Okanagan Valley is a great location for growing fresh produce, the weather can affect growing seasons. CubicFarms allows our customers to eliminate the weather variable and grow locally, all year round.
"We invite growers to contact us for a visit to our facility in Pitt Meadows, BC to get a first-hand view of our technology and learn how we can help them scale up their business. Interested parties can also opt for tours via live video calls, or receive the same in-person tour experience through our virtual tour available on our website. We look forward to continue serving our customers and sales leads to help them supply their markets with fresh produce and nutritious livestock feed."
The system includes 14 growing machines, two propagation machines, and an irrigation system, representing a total of US$2,145,000 (excluding installation and shipping) in anticipated sales revenues to the Company. The system is expected to be installed by the end of the year in Armstrong, BC.
The Company has a current backlog of approximately US$20 million representing 161 machines under deposit and awaiting installation – demonstrating continued sales momentum due in part to the growing demand for its systems. The current backlog is anticipated to be recognized in revenue in late-2020 to mid-2022.
Neither the TSX Venture Exchange nor it’s Regulation Services Provider (as that term is defined in the policies of the TSX Venture Exchange) accepts responsibility for the adequacy or accuracy of this release.
About CubicFarm® Systems Corp.
CubicFarm Systems Corp. ("CubicFarms") is a technology company that is developing and deploying technology to feed a changing world. Its proprietary technologies enable growers around the world to produce high-quality, predictable crop yields. CubicFarms has two distinct technologies that address two distinct markets. The first technology is its patented CubicFarm™ System, which contains patented technology for growing leafy greens and other crops. Using its unique, undulating-path growing system, the Company addresses the main challenges within the indoor farming industry by significantly reducing the need for physical labour and energy, and maximizing yield per cubic foot. CubicFarms leverages its patented technology by operating its own R&D facility in Pitt Meadows, British Columbia, selling the System to growers, licensing its technology, and providing vertical farming expertise to its customers.
The second technology is CubicFarms' HydroGreen System for growing nutritious livestock feed. This system utilizes a unique process to sprout grains, such as barley and wheat, in a controlled environment with minimal use of land, labour and water. The HydroGreen System is fully automated and performs all growing functions including seeding, watering, lighting, harvesting, and re-seeding – all with the push of a button – to deliver nutritious livestock feed without the typical investment in fertilizer, chemicals, fuel, field equipment, and transportation. The HydroGreen System not only provides superior nutritious feed to benefit the animal but also enables significant environmental benefits to the farm.
Cautionary statement on forward-looking information
Certain statements in this release constitute "forward-looking statements" or "forward-looking information" within the meaning of applicable securities laws, including, without limitation, statements with respect to the customer's ability to supply leafy greens to the Okanagan region, CubicFarms' expected revenue recognition, and installation of the system by the end of the year. Such statements involve known and unknown risks, uncertainties, and other factors including evolving market conditions, which may cause the actual results, performance, or achievements of CubicFarm Systems Corp., or industry results, to be materially different from any future results, performance, or achievements expressed or implied by such forward-looking statements or information including the Company obtaining the approval of the Offering from the TSX Venture Exchange. Such statements can be identified by the use of words such as "may", "would", "could", "will", "intend", "expect", "believe", "plan", "anticipate", "estimate", "scheduled", "forecast", "predict", and other similar terminology, or state that certain actions, events, or results "may", "could", "would", "might", or "will" be taken, occur, or be achieved.
These statements reflect the Company's current expectations regarding future events, performance, and results and speak only as of the date of this news release. Consequently, there can be no assurances that such statements will prove to be accurate and actual results and future events could differ materially from those anticipated in such statements. Except as required by securities disclosure laws and regulations applicable to the Company, the Company undertakes no obligation to update these forward-looking statements if the Company's expectations regarding future events, performance, or results change.
SOURCE CubicFarm Systems Corp.
View original content to download multimedia: http://www.newswire.ca/en/releases/archive/July2020/10/c9695.html
OptimIA Free Indoor Ag Webinar - July 29, 2020 - 1 PM EST
OptimIA offers free indoor ag webinar on July 29, 2020. The OptimIA (Optimizing Indoor Agriculture) project team invites indoor farmers, allied trades, and professionals to their first annual meeting to share recent research results with leafy greens and discuss future activities
By urbanagnews
July 6, 2020
OptimIA offers free indoor ag webinar on July 29, 2020
The OptimIA (Optimizing Indoor Agriculture) project team invites indoor farmers, allied trades, and professionals to their first annual meeting to share recent research results with leafy greens and discuss future activities. OptimIA is a USDA-supported Specialty Crop Research Initiative project to advance the emerging indoor farming industry to become more profitable and sustainable through critical research and extension activities.
TENTATIVE AGENDA / TOPICS
Promotion of lettuce growth under an increasing daily light integral depends on the light intensity and photoperiod
Influence of light intensity and CO2 concentration on dill, parsley, and sage growth and development at harvest
Major energy savings during production of baby greens
Managing nutrient disorders of hydroponic leafy greens
Improving air distribution and humidity management in vertical farming systems
Critical elements of CEA economics
View the agenda and register at http://scri-optimia.org/stakeholder2020.php. The webinar is free, but space is limited and is on a first-come, first-served basis.
OptimIA Director and PIs
Erik Runkle, Michigan State University (Project Director)
Murat Kacira, University of Arizona
Chieri Kubota, The Ohio State University
Roberto Lopez, Michigan State University
Cary Mitchell, Purdue University
Simone Valle de Souza, Michigan State University
OptimIA Collaborators
Jennifer Boldt, USDA ARS
David Hamby, OSRAM
H. Christopher Peterson, Michigan State University
Nadia Sabeh, Dr. Greenhouse Inc.
US - VIRGINIA - What Does Governor Northam Have to Say About Babylon?
“Congratulations to Babylon Micro-Farms, an inspiring up and coming Virginia business, on its CRCF award. Babylon first received seed capital funding from CIT GAP Funds in August 2019
June 30, 2020
We are very excited to share the news that Governor Northam announced last week that Babylon has been awarded matching funds from the Center for Innovative Technology (CIT) for the Small Business Innovation Research (SBIR) grant we received from the National Science Foundation. The funding from the NSF made Babylon eligible for a highly competitive application process that CIT holds annually through the Commonwealth Research Commercialization Fund which provides additional support for SBIR recipients to foster ongoing innovation by Virginia-based companies.
“Congratulations to Babylon Micro-Farms, an inspiring up and coming Virginia business, on its CRCF award. Babylon first received seed capital funding from CIT GAP Funds in August 2019. I had the pleasure to get to know the team and learn about the vital work they are doing for indoor farming,” said Ed Albrigo, President and CEO of CIT. “They continue to move forward on research and development of their disruptive platform for hydroponic farming, which has now earned them funding support through CIT CRCF. The Babylon CRCF award, along with CIT GAP funding, is a prime example of how our programs work together to help sustain companies through the difficult first stages of the commercialization process. Sustainable urban agriculture technologies are among the most critical emerging technologies in the nation today, and thanks to Babylon, Virginia will play an essential role in the future of farming."
Babylon added Lansdowne Resort in Leesburg, VA to our portfolio of high-end resorts and we are happy to welcome them to the Babylon family. Lansdowne is very focused on the connection between food and health and has a history of being at the forefront of hospitality trends that incorporate wellness and mindfulness-based activity options. They offer their guests a carefully curated offering of dietary choices based on their commitment to providing them the highest possible quality available in every aspect of their experience. Babylon is proud to be part of that commitment.
The recently installed farm at Champion Brewing Company Pub is the first partnership between Babylon and our hometown pioneer of the rapidly growing craft beer movement. When founder Hunter Smith envisioned the Pub, he wanted to create a fun community space that was hip and cool, but truly more than that – a place for people to connect. Mission accomplished and since Babylon is all about connecting people to their food by growing it right in front of them, it was a natural fit. The synergy of two local startups working together to bring the best of local food and drink to the table is a winning combination. Stop by and have a cold beer, it's hot outside!
Podcast Agency FullCast Launches Vertical Farming Podcast with David Farquhar of Intelligent Growth Solutions
David Farquhar, CEO of Intelligent Growth Solutions (IGS), says Covid-19 has prompted a spike in interest in vertical farming, as retailers and governments scramble to improve supply chain resilience and lower their reliance on imported food
MINNEAPOLIS, May 6, 2020 /PRNewswire/ — In the inaugural interview of the Vertical Farming Podcast, David Farquhar, CEO of Intelligent Growth Solutions (IGS), says Covid-19 has prompted a spike in interest in vertical farming, as retailers and governments scramble to improve supply chain resilience and lower their reliance on imported food.
The vertical farming industry must ‘take a hard look at itself’ before it fulfills its promise of reliable, quality food, produced affordably and sustainably, says one of its leading figures.
Vertical Farming Podcast produced by FullCast
“But it will be fascinating to see what changes last on the back of this pandemic,” he says. “To what degree are we willing to invest to prepare ourselves to survive another one? We’re working with a lot of governments to think how this might happen.
“Yes, there are huge opportunities, but let’s be realistic. Vertical farming and indoor agriculture are young; making them work is a marathon task. Anyone who says otherwise is lying.”
“In three decades in the tech sector, I’ve never seen anything that’s attracted so much interest nor created so much misinformation.”
“A lot of people are telling a lot of lies. The industry must grow up. Many commentators and participants within the industry feel the same.”
A former British Army officer, Farquhar announced on the podcast that he’s committing the company to openly publish all its data – energy consumption, water usage and nutrient utilization – from its ‘in a box’ vertical farming systems, in a bid to demonstrate the industry-wide honesty and transparency that he believes is so sorely needed.
Headquartered in Scotland, IGS is currently working with commercial and government groups across Australasia, the Middle East, the Caribbean, and North America. Farquhar was interviewed for the first episode of Vertical Farming Podcast, a new show produced by FullCast and hosted by Harry Duran. Harry has launched VFP to engage with the leaders, founders, and visionaries of the evolving vertical farming industry, to bring their insights and knowledge to a wider audience.
Farquhar kicks off a line-up of guests that includes Agritecture’s Henry Gordon-Smith, Freight Farms Co-Founder & COO Jon Friedman, and AgTech journalist Louisa Burwood-Taylor of AgFunderNews.
Listeners are invited to subscribe today at: https://verticalfarmingpodcast.com
Contact InformationCompany: FullCast
Contact Name: Harry Duran
Email: harry@verticalfarmingpodcast.com
Phone: +1-323-813-6570
Address: 340 S Lemon Ave #5557 Walnut, CA 91789
Website: https://verticalfarmingpodcast.com
Source: PRNewsire
Ground Broken on New Hydroponic Facility To Serve The Marginalized Communities in Torrington CT.
The mission of the farm is to provide entry-level, safe, clean “green jobs” to members of the community
Published on July 6, 2020
Joe Swartz
Vice President/Lead Horticulturalist at AmHydro - 36 years as Controlled Environment Ag Consultant and Commercial Grower
June 30, 2020, was an exciting day for the local Connecticut organization, New Opportunities. http://www.newoppinc.org/ After years of planning, the ground was broken on a new hydroponic farm project called "CT Food4Thought" that is going to bring fresh, nutritious, pesticide-free food to local food banks, shelters, soup kitchens, and schools to communities throughout Connecticut. In addition to that, the farm will also supply retail grocery stores and co-ops with fresh produce as a way to generate income for programs through selling the produce grown. New Opportunities partnered with industry-leading Controlled Environment Agriculture Technology company AmHydro of Arcata, CA. (https://amhydro.com/ )
The groundbreaking marked the start of three greenhouses, containing AmHydro’s soilless hydroponic growing systems, being constructed in partner with Borghesi Engineering with plans to expand up to 12 greenhouses in the future. AmHydro VP Joe Swartz and the Commercial Growing Team at AmHydro will provide on-going support and grower training to ensure a successful project and economic sustainability.
New Opportunities is a social service organization that serves marginalized and low-income communities throughout Connecticut. The mission of the farm is to provide entry-level, safe, clean “green jobs” to members of the community. Specifically, CT Food4Thought wants to offer these job opportunities to those with developmental disabilities, those who have been previously incarcerated, and those who are unemployed as a way to provide a path to higher-level employment opportunities in both this industry and others, such as: the field of nutrition, food safety, environmental management, and horticulture.
Dr. James H. Gatling, Ph.D., CEO of New Opportunities, speaks prior to breaking ground.
New Opportunities Foundation had a vision and worked directly with hydroponic industry leader AmHydro to develop the most optimum growing system and production methods available. This hydroponic farm will use 90% less water than conventional field agriculture and will be able to produce more than 10 times the amount of produce that traditional growing methods yield. The farm will also be able to operate year-round due to the environmental controls inside the greenhouse that can simulate the perfect growing conditions for plants even in the dead of winter. This will allow people in Connecticut to have access to fresh, local produce all year in comparison to the normal outdoor growing season in the area that lasts approximately 120 days.
Bill Rybczyk, New Opportunities, Joe Swartz, AmHydro, Jon Jensen, the Corporate Advisory at the project site this Spring.
AmHydro is proud to partner with New Opportunities on their new project CT Food4Thought and is excited to continue to be a part of and support the project through providing training to members of New Opportunities and members of the community.
Quote, from Bill Rybczyk, Director of Research, Planning, and Development for New Opportunities Inc : “We’re planting seeds for lettuce and other herbs, but we’re also planting seeds into people’s lives, and they can then take that, and they begin to grow….and that impacts not only their lives but their children’s lives and their grandchildren’s lives into the future…..and that’s what this project is all about."
For more information, please contact Joe Swartz, VP, AmHydro at Joe@AmHydro.com
Published by
Vice President/Lead Horticulturalist at AmHydro - 36 years as Controlled Environment Ag Consultant and Commercial Grower
Please check out this amazing project that American Hydroponics is proud to be a part of. New Opportunities will be producing fresh, pesticide-free food, local "green jobs," and economic empowerment to marginalized communities.
Truly wonderful. hashtag#LocalFood hashtag#LocalFarms hashtag#WeGotThis hashtag#HelpingOthers hashtag#SustainableFarming
Farm Box Foods - Digital Farming Entrepreneurs
In 2017, an unlikely group of friends—a real estate agent, a solar energy entrepreneur, and a fabricator, decided to take action. From the drive to decentralize food supply chains and assist communities to produce more locally grown, healthy food, FarmBox Foods was born
OUR MISSION
We want to empower communities to produce their own locally grown produce year-round.
We strive to change the way people farm by merging technology and agriculture into a system that greatly reduces water usage and transportation costs while maximizing space.
We see a future where communities have achieved food independence by producing their own healthy food and distributing it locally – no longer relying on centralized food systems.
Our Story
Our planet is in trouble, and we need to find new, innovative approaches to food production.
In 2017, an unlikely group of friends—a real estate agent, a solar energy entrepreneur, and a fabricator, decided to take action. From the drive to decentralize food supply chains and assist communities to produce more locally grown healthy food, FarmBox Foods was born.
Our founders knew they had to search for agricultural innovations. At the heart of this new approach lies the shipping container. Our goal was to develop the most efficient, high-yielding container farm on the market. Early in our research and development, we saw the appeal of vertical farming—this design principle would allow us to maximize limited space. Bringing all these ideas together, FarmBox Foods created a hydroponic farm with an elegant and user-friendly design.
With our hydroponic farm on the market, FarmBox Foods is now looking for new ways to bring more healthy food options to communities. Enter mushrooms. With their myriad health benefits and culinary versatility, mushrooms are the perfect crop for sustainable food systems. Our first-of-its-kind gourmet mushroom farm will debut in 2020 and boost access to this superfood.
FarmBox Foods is changing the way we think about growing food, one shipping container at a time.
It comes down to what’s inside, the “Plant Force One” is built inside of a recycled 40-foot container. Helping the environment and help you change the way you farm
JPFA Webinar June 30 - The Challenges And Impact of COVID-19
The Japan Plant Factory Association (JPFA) is organizing its 138th online workshop. The workshop is free of charge
Japan Plant Factory Association / JPFA
Japan Plant Factory Association (JPFA) is a non-profit organization founded in 2010 and is devoted to academic and business advancements in the global industry of plant factory/controlled environment agriculture. Our mission is to develop and disseminate sustainable systems that can address global challenges: food, environment, energy, resource and people's health. With international industry-academia collaborations, we manage around 20 R&D projects, workshops, training courses, etc. based in a Chiba University campus in Kashiwanoha, a smart city in Japan.
Monthly workshops are one of our important education/knowledge sharing activities with JPFA members and others. We have been organizing workshops since 2010 on a wide variety of topics, including plant physiology, new technologies towards next generation, cultivation methodology on multiple crops, business case studies of commercial plant factory operations, to name just a few.
The Japan Plant Factory Association (JPFA) is organizing its 138th online workshop. The workshop is free of charge.
Some sessions include the presentation of 80 Acres Farms on tomato production in indoor farms, a survey report on the impact of COVID-19 by JPFA and a lively panel discussion with leading plant factory companies from Japan and China. Such as, 808 Factory, Greenland, Saladbowl, and Future Agro-Tech, all together with researchers on plant factory and indoor breeding from JPFA and Chiba University.
Date
Scheduled to be released on June 30, 2020.
Free viewing will be available from 13:00 (JST) on June 30 to 13:00 (JST) July 15, 2020.
Theme
As the coronavirus disease (COVID-19) creates challenges worldwide, we feel concerted effort is crucial to our sector more than ever before.
The global challenges/impacts of COVID-19 in the sector, the future role, possibilities and direction of plant factory will be discussed to rethink about what we can do together for our future.
Outline
I. Keynote: “beyond leafy greens: tomato crop production in indoor farms” by Mike Zelkind, 80 Acres Farms + Q & A Session
II. “Report on COVID-19 survey by JPFA” Eri Hayashi (JPFA)
III. Panel discussion: “the challenges and impact of COVID-19, future role and direction of Plant Factory”
*Please kindly note that some contents might be only in Japanese.
Panelists:
Bai Baosuo (Future Agro-Tech (Beijing)
Katashi Kai (Shinnippou, 808 Factory)
Susumu Tanaka (Saladbowl)
Toyoki Kozai (JPFA)
Toru Maruo (Chiba University)
Yuhei Shimada (greenLand)
Moderator: Eri Hayashi (JPFA)
Fee Free of charge
How to watch
Advanced registration is required.
Registration deadline: 13:00 (JST) on July 14, 2020
Please register at https://select-type.com/e/?id=n2duYvX-Gas
After the registration, you will receive the link with access to the workshop videos a day before the release. Please apply one by one. If you cannot access the registration website, please send us the email with your "name", "organization", "country" and "questions to the webinar speaker/panelists (optional)" to info.english@npoplantfactory.org
For more information on the workshop:
JPFA Workshop website
https://select-type.com/s/JPFA-Training
https://npoplantfactory.org/information/1499/
If you have not joined the survey yet, please take the survey, Urgent Survey on the Impact of COVID-19 (Vol.1) before the workshop/online viewing starts.
For more information:
Japan Plant Factory Association (JPFA) International Relations & Consulting
Nozomi Hiramatsu, Eri Hayashi
info.english@npoplantfactory.org
Exelon Invests In Reducing Indoor Ag Energy Needs And Costs With GrowFlux
“GrowFlux specifically can increase yields in indoor farming making it more economical for city centers and where it can serve often underserved communities fresh and healthier foods.”
June 11, 2020
A welcome impact from the Covid-19 pandemic has been clearer skies and returning wildlife to usually polluted areas after industry, transport systems, and more shut down across the world, reducing carbon emissions.
Today marks two months since the UK’s electricity industry last used coal; the longest period since the Industrial Revolution began more than 200 years ago and well beyond the 18 days, 6 hours and 10 minutes record which was set in June last year, according to the BBC. Renewable and nuclear energy have stepped in to make up the shortfall in a trend that’s been particularly pronounced in the US where renewables supplied more energy than coal for the first time ever this year.
Agriculture’s impact on the environment, particularly surrounding its carbon emissions, has been flung into the spotlight in recent years, particularly by alternative meat and animal products startups keen to promote the environmental credentials of their plant-based or cultivated alternatives. But of course, even a plant-based diet has carbon emissions associated with it, from the fertilizer and pesticides applied in the production process, to its transport to end markets. Plant-based products and diets are also not always affordable or accessible to certain demographics who may live in food deserts.
Indoor agriculture has long been a potential solution to food deserts and many of the carbon emissions related to crop production, making it an interesting prospect for city planners and city-based corporates. But the energy consumption associated with the production system, specifically related to lighting and climate control systems, has left much to be desired; not least because the costs involved have stunted the growth of viable business models.
Further, energy demand from these indoor farms is only set to increase as the need for more localized production in certain regions across the world has been highlighted during the Covid-19’s disruption of traditional supply chains; Singapore is a case in point.
“With over 8.6 terrawatt hours of energy consumed by horticultural lighting systems in emerging indoor farms and greenhouses in the US in 2019, utility companies are hard-pressed for rapidly scalable energy management tools that meet the needs of growers,” says Eric Eisele, CEO of GrowFlux. GrowFlux is an agtech startup focused on smart lighting controls for the horticulture industry working to significantly reduce the cost of lighting automation and its energy needs.
GrowFlux, a Philadelphia-based startup, was therefore immediately of interest to Exelon, the nuclear energy provider that claims to have the largest number of electricity and natural gas customers in the US after it launched a new startup incubator late last year aimed at reducing greenhouse gas emissions and bolstering urban centers. GrowFlux is part of the first cohort of Exelon’s $20 million Climate Change Investment Initiative (2c2i) and recently received $100,000 in cash as well as in-kind services such as legal and advisory as part of the program.
“When we think about food & ag, we think about there being a mitigation and adaptation benefit from helping to advance the indoor ag industry for food. [By growing food close to city centers] there’s a climate change mitigation benefit from the decreased emissions related to traditional, carbon-intensive farming methods of harvesting, planting and transporting food from rural areas to cities,” Exelon Corp SVP Chris Gould told AFN. Indoor ag, where farming environments can be completely controlled, is also a good mechanism to adapt to climate change, he added.
“GrowFlux specifically can increase yields in indoor farming making it more economical for city centers and where it can serve often underserved communities fresh and healthier foods.”
GrowFlux says its technology allows even the smallest farms and upstarts to build advanced controlled environment agriculture automation without millions in venture funding. Its approach is different from the traditional high-level objective of optimizing climate control towards a constant set point; instead it aims to respond more dynamically to crops’ needs via distributed sensor data and cultivar specific crop models. “Crop responsive environmental controls have the potential to result in tremendous resource efficiency, creating opportunities to grow new crops in greenhouses, reducing the operating cost of existing CEA, and reducing the capital costs associated with CEA,” reads the company website.
“We reduce cost with cloud-based control (as opposed to cloud-connected control), which is new to the industry. This strategy is unique from our competition, which are essentially boutique engineering firms that do a full range of automation services using on-site controls that are slow to scale and come at a significantly higher cost,” added Eisele.
2c2i is a partnership between Exelon and its foundation and involves $10 million in funding from the foundation and $10 million in-kind contribution of pro-bono services from the corporation, such as mentorship and access to the company’s venture capital and R&D departments.
“Our partnership with Exelon Foundation will help GrowFlux advance its energy savings and energy management solutions, and allow our customers to drive down their operating costs and carbon footprint associated with greenhouse and indoor agriculture,” said Eisele about the investment. “We believe their guidance on energy management strategy is just as valuable, if not more valuable than the cash.”
2c2i is focused on innovations that will positively impact the cities in which Exelon operates, including Atlantic City, Chicago, Baltimore, Philadelphia, Washington, D.C., and Wilmington. Innovations must also have the potential to mitigate greenhouse gas emissions; boost the resiliency of urban infrastructure (e.g., the power grid, transportation systems, buildings, vacant land) against flood, stormwater, and rising temperatures; help cities, businesses and communities adapt to climate change; or help achieve a state or city’s specific sustainability and climate goals. External consultant Freshwater Advisors selected a shortlist to pitch in front of the Exelon team.
“We also consider and have selected startups from outside of our cities, but in that regard we ask them to have a line of sight on one of our cities, with hope of attracting them to region to set up an office,” said Gould.
Scaling Up Urban Farming Beyond COVID-19
More urban dwellers who usually rely on food that is sourced from farms away from the city are turning to urban farming now that COVID-19 has fractured and exposed how fragile the existing food supply chains are
by Esther Ngumbi | University of Illinois
9 June 2020
*Any views expressed in this opinion piece are those of the author and not of Thomson Reuters Foundation.
The world has seen an increase in urban farming amid the coronavirus and fragile food supply chains
Esther Ngumbi, Ph.D., is Assistant Professor in the Department of Entomology and African American Studies Department at the University of Illinois at Urbana-Champaign. She is a Senior Food security fellow with the Aspen Institute New Voices
More urban dwellers who usually rely on food that is sourced from farms away from the city are turning to urban farming now that COVID-19 has fractured and exposed how fragile the existing food supply chains are. Google trends reports show that searches for “gardens” are up and enterprises that sell plants and seeds report a spike in the number of customers. Across America, people are planting more vegetables.
Around the world, other countries have seen a sharp increase in urban farming, from Jakarta, to Singapore to Australia. This is a move in the right direction and the reinvigorating of the urban farming movement should be supported and nurtured.
What does urban farming look like? According to the United States Department of Agriculture and Food and Agriculture Organization, urban agriculture can take many forms, from roof-top gardens to farming on abandoned buildings and parking lots to backyard and balcony gardening. In many African countries, it often entails sack and stack farming and traditional gardening in backyards, and in some places like South Africa, it also includes rooftop gardens and small farm gardens.
There are many benefits to urban farming including condensing the mileage of food from the farm to the market to improving personal health, ecosystems, and food insecurity while promoting sustainable livelihoods. Most importantly, during the pandemic, urban farming has helped families to cope with food insecurities.
The urban farming movement is especially welcome in Africa, a continent that is rapidly urbanizing, with cities that are crowded and costly. At 3.5 percent per year, Africa’s urban growth rate is the highest in the world, and that number is expected to keep increasing. Supporting urban farming across Africa would allow the continent to be ready for any future pandemics. Moreover, at the moment, urban cities in Africa rely on rural areas to meet their food demands, because most of the food consumed is bought in markets and from vendors who source their food directly from farmers that are based in rural areas.
How do we then tap into the renewed attention to urban farming by city dwellers?
Well, to develop effective support systems while further nurturing urban agriculture, there is the need to first and foremost accurately capture and map the current state of things. How many new community and city gardens and farms have been planted? Who is doing it? What challenges have they faced? What kind of food are they growing? How did they finance their venture? Who are they distributing the products to? How big is the space and land they are using?
Creating databases and dashboard maps of this information is vital to growing the urban farming movement. This can be done by sending surveys by organizations that are already practicing urban farming, city governments or educational institutions that are based near urban cities. Creating these inventories would also serve to inform urban city planners and policy makers and governments while connecting urban farmers with each other, to potential funders and to consumers.
Second, farming and agriculture is knowledge-intensive. Consequently, there is a need to establish support systems for these farmers. Urban dwellers need current knowledge about recent growing methods, innovative business models, and other best practices to ensure they make the most out of their urban farming enterprise. The good thing is that there are ample resources such as on the sites of USDA, and UN FAO.
Moreover, as urban farming grows, a community and network of support would be key. Urban farmers living in the same cities and regions can form partnerships to support each other.
As we nurture the movement, we must also encourage many more urban dwellers who have not yet ventured into urban farming to give it a try. From university webpages to private organizations to associations YouTube videos including guiding African cities urban dwellers on how to successfully create a bag garden.
Food supplies disruptions due to another pandemic or other causes are likely to happen. This new appreciation for urban farming fostered during COVID-19 lockdowns should keep growing. We must continue to tap onto urban agriculture to grow fresh, healthy, and nutritious food for urban city dwellers.
THEMES CLIMATE (AIR POLLUTION, GREEN TRANSPORT, ZERO CARBON INITIATIVES ETC)
"After Summing Up All Production Costs, The Plants Cost Less Than 0.25$, Which is 2% of The Total Sum of Normal Farmers"
The growing process is fully automated, except for harvesting. “We purposely chose moveable walls, so when our containers are installed, people with disabilities can participate during projects.”
Cost-Effective Growing
We’re working with high efficiency LED lights and cooling systems, which basically are our only costs. Therefore, our produce is way cheaper than with traditional farming. ”After summing up all production costs, the plants cost less than 0.25$, which is 2% of the total sum of normal farmers”, Tony English, Founder and Visionary of FarmBox Foods says. If a grower spends 2 cents more per plant, they can deliver organic produce with FarmBox Foods growing containers. The seeding process starts in organic fiber where organic nutrients are used. Next to that you can use filtered water and cultivation without pests. But it’s all up to the grower what plants they choose.”
The seedling table
Self-Sanitizing Farm
The growing process is fully automated, except for harvesting. “We purposely chose moveable walls, so when our containers are installed, people with disabilities can participate during projects.” The company uses peat moss plugs for the seedling table, alongside an ebb and flow system. “When the plants are two inches high, they’re transferred to the grow walls. When one batch is harvested, a new one goes in immediately to maintain a constant production cycle,” English adds. These containers are maintenance-friendly and self-sanitizing. The grow towers are cleaned with ozone, a bacteria and disease killing gas. “It works better than bleach or other commonly used sanitizing agents.” When watering the plants, ozone is added into the nutrient solution, allowing the grow walls to clean themselves.
The moveable grow walls
New Designs
The system development took about a year to complete; during this time, FarmBox Foods designed a grow tube which solved all the problems that they came across during the R&D phase. The team is currently testing and researching new crops and designs. The R&D prototype has been sold and is now in use in Georgia. “We build our containers one at a time, and when we think of doing something better, we apply it. For now, we have three containers placed, but we’re looking into manufacturers around the States to speed up the production process.”
The Self-Sanitizing Farm
“We were actually going to build containers for homeless people for the major US cities, as there’s a big shortage of fresh produce, especially for those who won’t have access to them. We bought land and designed a hydro system. When they told us it would take up to 5 years before they would even look at our proposal. It would have been insane to wait for that approval. Well, we had a great hydro system thus why not move them inside a shipping container that we can provide to homeless shelters, churches, and anyone who could grow food for the people who need it the most?” The start-up supplies fully-automated containers for vegetable farming in the US.
Increasing Demand
FarmBox noticed an increasing demand as a result of the COVID-19 pandemic. They now have a major hospital chain buying their farms. “We have a system suitable for schools, and at first we were donating them to schools. We are not going to do that anymore as we’re too busy with fulfilling the demand for our containers farms.”
For more information:
FarmBox Foods Tony English, CEO and Founder
tony@farmboxfoods.com
www.farmboxfoods.com
Publication date: Tue 16 Jun 2020
Author: Rebekka Boekhout
© HortiDaily.com
Research For Workforce Development in Controlled Environment Ag: What Makes a Successful Indoor Farm Manager?
As indoor agriculture has grown, finding, training, and retaining a skilled workforce has emerged as an important challenge to the industry. A unique combination of plant production, tech troubleshooting, and innovation is needed among employees managing these operations
By urbanagnews
June 8, 2020
As indoor agriculture has grown, finding, training, and retaining a skilled workforce has emerged as an important challenge to the industry. A unique combination of plant production, tech troubleshooting, and innovation is needed among employees managing these operations.
What are the critical skill sets, and how can we create a larger pipeline of individuals trained in these skills so that they can contribute to CEA business success?
At Cornell University, a group led by Professor Anu Rangarajan (Director, Small Farms Program) seeks to provide answers as part of a National Science Foundation-funded research project on CEA Viability in Metro Areas.
Rangarajan’s team has conducted extensive research to date in order to understand the workforce needs of the hydroponics industry, including greenhouses and indoor vertical farms—and the research continues.
With the long-term goal of creating robust curricula for training CEA employees in mind, a team from Cornell University conducted many in-depth interviews with professional CEA growers in 2018 and 2019.
The team then organized a workshop, in consultation with The Ohio State and Agritecture Consulting, that invited a focus group of CEA operations managers to model in detail the diverse activities that they perform on the job.
The resulting chart is a detailed, peer-reviewed list of duties (responsibilities) and tasks (activities, skills) that describe the work of the expert Indoor Farm Operations Manager.
The chart is currently being reviewed by peer growers worldwide, who are asked to verify how important each skill is, and how frequently it is conducted.
Based on this input, the Indoor Farm Operations Manager chart will be used as a starting point for prioritizing future CEA training modules. After that, a deeper analysis of key individual skills will be conducted in order to translate the foundational research into a teachable vocational curriculum.
Right now, however, Rangarajan’s team is actively seeking more responses to the verification survey.
“We need your help,” she emphasizes, speaking to professional CEA growers. “We want to learn your priorities for a CEA curriculum that will enhance the skills of current or future employees.”
The survey takes approximately thirty minutes to complete and can be completely anonymously. CEA growers who complete the survey will also be provided with an Amazon gift card for $25 as a token of appreciation, although they must provide their names and email addresses in order to receive this gift.
To take the survey, register here. The Cornell team will send a survey link directly from Qualtrics.
As Rangarajan notes, “Grower input will help us prioritize the core education and training relevant to indoor agriculture,” helping provide the industry with the skilled workforce it will need to scale.
For more information about this study regarding the future of the CEA workforce, please contact project lead Anu Rangarajan (ar47@cornell.edu) or research associate Wythe Marschall (wmarschall@fas.harvard.edu).
U.S. Department of Agriculture Secretary Sonny Perdue Visits Kalera
On Monday, June 8th, technology-driven vertical farming company Kalera welcomed Secretary of Agriculture Sonny Perdue to its Orlando facility
Perdue Visits Kalera For a Behind-The-Scenes Tour With Top Kalera Executives
June 09, 2020, | Source: Kaleraphoto-release
Secretary of Agriculture Sonny Perdue (l) stands next to Kalera CEO Daniel Malechuk (r) during a visit to the vertical farm's Orlando facility.
ORLANDO, Fla., June 09, 2020 (GLOBE NEWSWIRE) -- On Monday, June 8th, technology-driven vertical farming company Kalera welcomed Secretary of Agriculture Sonny Perdue to its Orlando facility. Secretary Perdue was greeted by Kalera’s top executives, including CEO Daniel Malechuk and CTO Cristian Toma, who, along with other staff members, escorted him on a private tour of the facility’s proprietary technology, providing a glimpse at the future of farming. Key takeaways included how Kalera:
eliminates the use of chemicals and removes exposure to pathogens through cleanroom technology.
is able to supply an abundance of produce locally, eliminating the need to travel long distances when shipping perishable products.
ensures the highest quality and freshness by delivering product to customers within hours of harvest rather than days or weeks
Is able to reduce water consumption by 95% compared to field farming.
During the tour, Perdue was able to sample the lettuce Kalera grows at the Orlando facility. Some of his positive reflections about the tour can be read in this Fox 35 Orlando news piece, “USDA Secretary visits Central Florida hydroponic farm, calls it a 'very innovative food production system'.”
Kalera recently announced its new Atlanta facility, which will open in early 2021. While Kalera’s Orlando farm, which Perdue visited on Monday, is currently the highest production volume vertical farm in the Southeast, the new Atlanta facility will be more than double the size and generate approximately 75 jobs for the local community. As was the case in Orlando, Kalera is able to quickly open its newest growing facility in Atlanta as a result of a streamlined design and construction process, further illustrating its ability to rapidly scale and expand its vertical farms.
After the tour, Daniel Malechuk, CEO of Kalera, addressed Secretary Perdue in front of assembled employees and press, saying, “Thank you very much on behalf of the Kalera staff for your time, and visiting us to discuss the future of agriculture, which is clean, healthy, sustainable, local and fresh. We look forward to helping the US stay on the cutting edge of agricultural innovation and feeding a hungry world with fewer natural resources.”
In addition to its R&D center, Kalera opened its first commercial vertical farm, the HyCube growing center, on the premises of the Orlando World Center Marriott to bring fresh, local produce to the hotel’s visitors and customers. In March this year, it announced the opening of its second facility in Orlando. The Atlanta facility is the third farm in Kalera’s portfolio, and will soon be joined by more in the United States. Kalera is currently sold in over 160 Publix stores.
About Kalera
Kalera is a technology-driven vertical farming company with unique growing methods combining optimized nutrients and light recipes, precise environmental controls, and cleanroom standards to produce safe, highly nutritious, pesticide-free, non-GMO vegetables with consistently high quality and longer shelf life year-round. The company’s high-yield, automated, data-driven hydroponic production facilities have been designed for rapid rollout with industry-leading payback times to grow vegetables faster, cleaner, at a lower cost, and with less environmental impact.
Kalera’s shares are traded on NOTC, a marketplace for unlisted shares managed by NOTC AS, which is owned 100% by Oslo Børs ASA, the Oslo Stock Exchange.
Further information about the company may be found at www.kalera.com and www.kalera.com/investor along with an introductory Kalera film: www.youtube.com/watch?v=2Crpph9w0hE
Kalera Contact:
Daniel Malechuk, CEO
Phone: +1 407 574 2382
Email: dmalechuk@kalera.com
Valoya Announces Its Spectrum Technology Licensing Program
Valoya’s extensive patent portfolio in the field of horticultural LED lighting is a result of significant innovation and investments into R&D over the past 11 years
Valoya, the research-driven LED grow light manufacturer has today announced a licensing program making their patented technology available to LED manufacturers and horticultural LED fixture providers.
Valoya’s extensive patent portfolio in the field of horticultural LED lighting is a result of significant innovation and investments into R&D over the past 11 years. The patents are in the field of light spectra for plant cultivation and lighting applications. At the moment, the portfolio consists of over 100 patents, all of which can be reviewed at valoya.com/patents.
'We have always been curious about the possibilities of light and how its potential could be pushed further to make cultivation of crops we use for food or medicine production more efficient. When we started in 2009, LED meant piercing purple light produced by red and blue chips. We were the first to apply wide spectrum LED light to plants in our experiments and to introduce wide spectrum light to the market. We are now in a business phase where we can extend this intellectual property and know-how to other companies wishing to produce premium quality horticultural LED luminaires through our licensing program' comments Lars Aikala, the CEO and Co-Founder of Valoya.
The research and development at Valoya does not stop. ‘After having conducted over 600 plant trials on over 300 plant varieties/species, we have an understanding of plant response to light, unmatched by other LED companies in the market. The focus remains on advancing horticulture through developing even better spectra and helping our customers grow. We are happy we get to share this expertise with other companies now’, comments Nemanja Rodic, Marketing Director of Valoya.
To learn more about Valoya's patent licensing program,
please click here.
About Valoya
Valoya is a provider of high end, energy-efficient LED grow lights for use in crop science, vertical farming, and medicinal plants cultivation. Valoya LED grow lights have been developed using Valoya's proprietary LED technology and extensive plant photobiology research. Valoya's customer base includes numerous vertical farms, greenhouses, and research institutions all over the world (including 8 out of 10 world’s largest agricultural companies).
Additional information:f
Valoya Oy, Finland
Tel: +358 10 2350300
Email: sales@valoya.com
Web: www.valoya.com
Facebook: https://www.facebook.com/valoyafi/
Twitter: https://twitter.com/valoya
Aquaponics Firm Eyes A Green Future, With Water Lentils In A Starring Role
After a year of research and development on Vancouver Island, and a crowdfunding campaign that reached $750,000, a new agri-tech company is preparing to significantly expand its footprint and hit the market with a plant protein
Andrew Duffy / Times Colonist
MAY 30, 2020
Steve McArthur, CEO of Pontus Water Lentils, at the company's research and development site.
Photograph By ADRIAN LAM, TIMES COLONIST
After a year of research and development on Vancouver Island, and a crowdfunding campaign that reached $750,000, a new agri-tech company is preparing to significantly expand its footprint and hit the market with a plant protein.
Pontus Water Lentils, which has been doing research and development at a test farm run by Victoria’s Garden City Aquaponics, has developed an aquaponics system — a hybrid of aquaculture and hydroponics — to produce water lentils. It says those lentils pack an unrivaled protein punch.
Chief technology officer and co-founder Steve McArthur said Pontus has developed a grow and harvest system which, when installed in a new facility, will be capable of producing 100 metric tonnes of water lentils.
McArthur, who also founded Garden City Aquaponics, said the plan is to build a new 10,000 square foot facility for the closed-cycle system. It will also grow and nurture rainbow trout — the fish waste is converted by microbes into fertilizer for water plants, which in turn filter the water for the fish.“
It’s a grown-in-Victoria business,” said McArthur. They are considering sites for the facility in Langford or on the Lower Mainland.
He said the water lentils grown in the facility would be dried and turned into about 6.4 metric tonnes of protein powder that can be used as a supplement for protein shakes, a partial ingredient replacement in foods such as pasta, or to be used in manufacturing food such as protein bars and beverages.
The company intends to package the powder for sale to grocery stores and find partners to produce a line of products packed with the protein-rich powder, while the fish will be sold to local grocery stores and restaurants.
McArthur noted they have already had some success in producing fish and leafy greens at Garden City, as they sold fish to local restaurants and small-scale production of leafy greens to Red Barn Market and other grocers as well as local chefs.
Currently, Garden City, which produces two types of tilapia and the water lentils, is being used entirely for research and development for Pontus, but it may revert to producing small-scale food for local stores and restaurants when Pontus opens its facility.
McArthur said the high-protein water lentils add a protein boost to various products.“The final product is 42.1 percent protein by weight, that’s pretty significant,” he said, noting that is higher than both pea and pumpkin protein. “In terms of plant-based protein that’s one of the highest and we would be growing it aquaponically on a commercial scale.”
The next step for Pontus is the larger facility, which McArthur said they now have the money to build.
Pontus started a crowdfunding campaign on Frontfundr.com. It had hoped to raise at least $750,000 and as much as $1.25 million to build its first production farm. To date, it has raised just over $766,000; they are also raising private capital.
When built, the facility will be capable of producing 6.4 metric tonnes of dried and powdered lentils and about 11,000 trout every year.
McArthur said the market opportunity is big as the product ticks a lot of boxes in terms of its sustainable production, the massive demand for plant-based protein, and food security.
The facility is scalable, moveable could be built almost anywhere, and has a small environmental footprint, he said.
The company says the farm uses less than five percent of the water used in field farming and has none of the carbon footprint.
Agrihoods and Access To Healthy Food
Enter agrihoods: the community feeling of suburbia mixed with the progressive thinking of the city, sprinkled with the splendor of the country
May 13, 2020
Written by Tinia Pina | Re-Nuble
The question has always been there: city life or country life? However, in the 1850’s, in response to a rising urban population and as a result of improved transportation methods, the suburbs began to sprawl out from large metropolises. Now, roughly 80 percent of Americans live in urban areas. Yet, the demand for closed-loop food processes continues to increase. Urban area citizens still want access to sustainable and healthy food systems.
Defining Closed-loop Systems
By definition, a closed-loop system is one in which the operation is regulated by feedback. To clarify, feedback, in this sense, means that a portion of the output is fed back into the system to act as part of the excitation. The output cannot exist independent of the feedback.
Closed loop food systems produce high-quality, healthy foods using less energy and less water. When locally-sourced, their production and sale contributes positively to local economies and develops pride within the community.
Agrihoods and Access to Healthy Food
Enter agrihoods: the community feeling of suburbia mixed with the progressive thinking of the city sprinkled with the splendor of the country. There are several reasons people are drawn to this style of living. First and foremost is access to locally grown, sustainable food. A close second is the closed-loop process: the inhabitants enjoy the crop and the remains are composted for use as fertilizer. There is an eloquent beauty in the cyclical nature of closed-loop food processes.
In addition to providing sustainable, locally-sourced food, agrihoods provide steady work for farmers who gain access to affordable farmland in exchange for their services. Most farmers rarely enjoy a steady salary; this is not true for those employed by agrihoods. Most earn a salary of $35,000 to $100,000 annually and receive free or reduced housing.
While these little utopias are springing up all over the country, they remain out of reach for many Americans that either cannot afford the amenity of living in a neighborhood with a resident farmer or who simply prefer to live in the bright lights.
However, the opportunity for a closed-loop food process can exist even in the middle of Manhattan, giving urban areas access to healthy food. Soilless systems provide a closed-loop, sustainable method of food production that is as valuable to communities as it is to farmers. Soilless systems can be established indoors or out and can take on any size. Additionally, it requires less water to produce foods in a soilless system than in a traditional, soil-based system because water is continuously circulated; not lost to runoff.
Soilless Systems Provides Healthy Food Access for Urban Areas
Recent studies have shown that indoor, soilless systems require up to 90% less water than traditional farming methods. By keeping the plants at optimum conditions throughout the growth cycle, they are better able to utilize nutrients and produce more fruits and vegetables per gallon of water used.
Consumers reap the benefits of locally-sourced, organically grown produce while farmers enjoy a sustainable production method. These systems remedy some of the challenges presented to those that attempt to bring in healthy, locally-sourced produce to urban areas; such as zoning and infrastructure.
However, what has been missing in most soilless systems is true feedback. The fertilizers and growth nutrients used in most systems are petroleum-derived and chemical-based. They are produced in a lab and have nothing to do with repurposing food waste. They fail to take advantage of the nutrients that exist in food waste.
Access to high-quality, bio-derived agricultural materials is challenging, especially for farmers and hobbyists that utilize alternative growth methods. Re-Nuble was developed to meet this need. Re-Nuble products are 100% bio-based, sourced from vegetative food waste, meaning that everything that goes into making Re-Nuble comes from plants; there are no petroleum-based ingredients. As we continue to carry out our own R&D, we hope to identify even more ways to help soilless farms regulate their operations through feedback, providing urban areas with access to healthy food.
Photo source
Tags: agrihoods, healthy food, urban agriculture, urban food