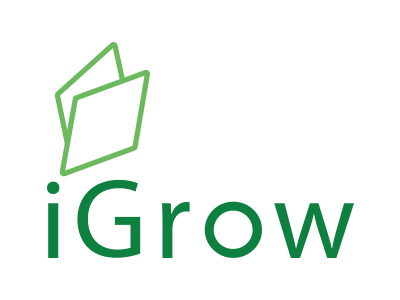
Welcome to iGrow News, Your Source for the World of Indoor Vertical Farming
Register For ERASMUS + ECVET PONICS VET LAUNCH - Friday, October 16th
Erasmus plus helps the CEA industry grow with free online vocational training courses in hydroponics for the technician level profile
ERASMUS DAYS PUBLIC LAUNCH
October 16th, 2020
Register for ERASMUS+ ECVET PONICS VET
LAUNCH:
Erasmus plus helps the CEA industry grow with free online vocational training courses in hydroponics for the technician level profile
PONICS VET:
Hydroponics Technician is an Erasmus + project. It aims to service agriculture communities and future growers from outside the industry. It provides essential basic training and an introduction into practices and the use of technology in the soilless growing of plants. Hydroponic systems have a proven track record in resource efficiency and resilience in the age of climate change. It also provides an attractive solution for existing farm operations that are not economical anymore and create new income streams for growers and would-be farmers.
The PONICS VET training services an innovative professional profile, the hydroponics technician, and delivers credentials for such a profile in a commercial context. The course will introduce system definitions, various technical insights, and important proficiencies in practical growing, including pest control, food safety, and certification information. Also included are case studies and ample supporting material. The micro-credential rules are drawn from the ECVET (the European credit system for VET) methodology, which will allow recognition of applied learning outcomes in the EU and beyond.
As the development of workforce pathways in times of CoVid19 and for the agriculture, communities has become a critical demand, FTS and its industry-based membership was selected as a critical partner in the development and deployment of PONICS VET project. Stay tuned for further modules and languages.“Workforce development in Agriculture has been underserviced in new and innovative agriculture practices and needs to be the main focus by the industry as well as the policymaker, PONICS VET is a great start for the Controlled Environment Agriculture sector as there currently no accredited vocational training courses online outside of the NL/BE greenhouse cluster. “ ~ FarmTech Society
HOW TO JOIN THIS EVENT:
Registration Page
INTERESTED IN JOINING THE COURSE:
Link to FREE ONLINE COURSE (Guest)
About FTSFarmTech Society (FTS) ASBL is an international non-profit association that unites and supports the Controlled Environment Agriculture (CEA) industry, seeking to strengthen the sector through the development and implementation of resilient and future-proof methods and technologies for indoor growing. A prime focus area of the FTS is education, by developing training and education courses and creating credentials for graduates facilitating certification that meets industry needs. Secondly, the FTS engages with lawmakers in order to help promote policies and regulations that foster innovation and propel businesses in CEA. Thirdly, the FTS supports the establishment of standards to help the industry grow and innovate. Lastly, the FTS also provides an international network for the CEA industry.
Project Partners:
1 Latvia University of Lifesciences and Technology (Lativia)
2 Eurocrea Merchant Srl (Italy)
3 IDEC (Greece)
4 BIC Innobridge (Bulgaria)
5 FarmTech Society ASBL (Belgium)
6 zemniekusaeima (Lativa)
US: Vertical Harvest To Open New Farm in Maine
“We want to grow as much food as possible. We want to employ as many people as possible. We want to do both year-round
An outside shot of Vertical Harvest's Wyoming farm. | Photo: Allison Kreig
The Facility is Expected to be 70,000 Square Feet And Produce 1 Million Pounds of Food in a Year.
August 24, 2020
Posted by Chris Manning
According to story from News Center Maine, vertical farming company Vertical Harvest is expanding to Westbrook, Maine with a 70,000 square foot vertical farm.
“We want to grow as much food as possible. We want to employ as many people as possible. We want to do both year-round. That’s what gave us the idea to go up. So at its heart, we want to be able for these farms to serve the community in which it sits, so that means being in the heart of our urban centers,” said co-founder Nona Yehia, per the article.
Related story: Vertical Harvest takes a new approach to CEA
Vertical Harvest is based out of Jackson Hole, Wyoming. Earlier in 2020, Yehia told Produce Grower that the company had plans to build a farm in Lancaster, Pennsylvania.
Irish Vertical Farming Technology Startup Farmony Signs European Distribution Agreement With US LED Horticultural Lighting And Vertical Farming Equipment Provider Sananbio
Irish Agtech company Farmony has signed a European distribution deal with Sananbio for their vertical farming Radix systems. The Dublin based startup, established in 2018, will incorporate Sananbio’s technology into their controlled environment vertical farming solutions
Dublin, Ireland | May 19th, 2020
SANANBIO, a global leader provider in LED horticulture lighting and vertical farm technology, announces strategic distribution partnership with Dublin based startup for European markets. Farmony will build a network of interconnected, controlled environment vertical farms across Europe.
Irish Agtech company Farmony has signed a European distribution deal with Sananbio for their vertical farming Radix systems. The Dublin based startup, established in 2018, will incorporate Sananbio’s technology into their controlled environment vertical farming solutions.
“As our climate continues to change and populations across the globe expand, food production must evolve in order to keep pace with these unprecedented changes. We are delighted to announce our partnership with Sananbio; global leaders in cutting-edge vertical farming technology developed to empower the modern farmer and spur sustainable local food production. Sananbio is the ideal technology partner to complement our own customized, automated controlled environment software & hardware solution. ”- John Paul Prior, Strategy and Sales Director, Farmony
Farmony: Left to right: John Paul Prior (Strategy Director), Dan O’Brien (CEO), Rodrigo Andrade (Operations Director)
“Farmony provides Sananbio with the ideal partner to expand our industry leading technology into the European markets. With over one million square feet of commercial vertical farms currently using RADIX, farmers, and investors in more than 10 countries believe in our company's highly engineered grow technology. In Farmony we have a partner that adds significant value to our product offering through exceptional sales & marketing, IOT focus and new product development. " -Michael Yates, Vice President Sales, Sananbio
ABOUT Sananbio®
SANANBIO is a leading Ag-tech company backed by one of the world’s largest LED chip manufacturers. Supported by an elite R&D team comprised of plant scientists, researchers, and engineers; SANANBIO utilizes state-of-the-art technology that enables growers worldwide in the horticulture industry to increase the quality and quantity of their yields. Years of extensive research and real-world deployment and operations allow SANANBIO to offer its customers proven, scalable, efficient and cost-effective solutions in LED horticulture lighting and Controlled Environment Agriculture (CEA) vertical farming grow system; as well as turn-key vertical farm solutions including building, transfer, financing, and training of staff for both large and small-scale farming facilities. SANANBIO empowers growers with the technology and knowledge to achieve unprecedented results in farming operations.
Learn more: SANANBIO
Farmony build controlled environment Vertical Farming solutions: Left to right: Rodrigo Andrade, Dan O’Brien, John Paul Prior
John Paul Prior asks will vertical farming mean that Irish horticulture finally gets its 'day in the sun'?
ABOUT Farmony
With offices in Dublin & mainland Europe; Farmony provides an operating system for Controlled Environment Farms through a combination of software and hardware, customized specifically for vertical farming applications. The Farmony operating system provides producers with grow recipes, real time alerts, and feedback on the efficiencies of their farm, while also automating dosage, irrigation, and lighting.
Through the aggregation of the associated growing data from their network of producers, Farmony can then optimize yields and, through machine learning technology, ensure that the network is constantly improving it’s output for its network of users, establishing a growing efficiency algorithm.
Their partnership with Sananbio, facilitates all-year-round pesticide-free growth of leafy greens, microgreens, and herbs from a footprint of 55 Square Meters, producing the output equivalent of 5 acres of traditional farmland. Farmony has recently opened a facility in Poland to support their European expansion.
Learn More: www.farmony.ie www.farmony.pl
Media Contact: John Paul Prior +353 86 8116708
VIDEO: Babylon Harvested Here - Remotely Managed Micro-Farm
Babylon is often asked how our remotely managed, but locally supported micro-farms work
International Manufacturing and Distribution,
Sales and Marketing Management, Connector.
Babylon is often asked how our remotely managed,
but locally supported micro-farms work
The new video below should answer some of your questions but please contact us for any additional information. (www.babylonmicrofarms.com)
AeroFarms Reveals To California North Coast Food Producers Its High-Tech Controlled Environment Agriculture
Imagine a farming method so efficient that you could grow a variety of leafy greens in half the time it traditionally takes — without any pesticides, herbicides or fungicides — and where the sun has no role
NORTH BAY BUSINESS JOURNAL March 2, 2020
CHERYL SARFATY
Imagine a farming method so efficient that you could grow a variety of leafy greens in half the time it traditionally takes — without any pesticides, herbicides or fungicides — and where the sun has no role.
It’s all done indoors, and it’s a growing trend known as controlled environment agriculture (CEA). The biggest player in the space is AeroFarms, a Newark, New Jersey-based operation that was among the businesses that participated at the Feb. 25 North Coast Specialty Food & Beverage Conference.
“We track everything that happens to the plants, from its genetics all the way to harvest. And by measuring along the way, we can use that data to learn more about what makes plants grow,” said AeroFarms Chief Financial Officer Guy Blanchard. “The ability to do this is transformative, it’s brand new if you think of the difference with field farming, where you can’t control the temperature and you can’t control the weather. You’re really reacting and trying to respond to the things that Mother Nature is throwing at you.”
In addition to AeroFarms, which is privately held, there are a variety of CEA players in the marketplace, including Bright Farms, Little Leaf Farms, Bowery Farms, Revol Greens and Plenty, which is based in South San Francisco. The majority of these businesses are headquartered in the Midwest and further east, where bad weather makes it impossible to grow the greens outdoors.
There are a variety of growing methods within the CEA category, the two most common being hydroponics and aeroponics. With hydroponics, plants are grown with mineral nutrients in a water base rather than in soil. Aeroponics, which is AeroFarms’ method, also uses no soil, instead of planting seeds in fabric and misting them with mineral nutrients.
AeroFarms grows 800 varieties of edible greens, such as lettuce, arugula, and spinach. The plants require 95% less water than on farms and are completely grown in 12 to 14 days, rather than 30 to 45 days in the field. The company’s retail brand, Dream Greens, is sold in grocery stores in New Jersey and New York.
Blanchard declined to disclose the company’s financial metrics. According to ROI-NJ, a New Jersey business publication, AeroFarms raised $40 million in 2017.
The vertical farming market size was valued at $2.23 billion in 2018 and projected to hit $12.77 billion by 2026, according to Allied Marketing Research.
There’s going to be change, but I don’t want to lose our small farmers.
Pegi Ball, Santa Rosa Original Certified Farmers Market
Pegi Ball and Janet Ciel, who each run farmers markets in the North Bay, said at the conference they wonder how the CEA industry might someday impact the region’s farmers“.
There’s going to be change, but I don’t want to lose our small farmers,” said Ball, who manages the Santa Rosa Original Certified Farmers Market at the Luther Burbank Center for the Arts. “It’s more than just lettuce and that sort of thing. It’s the culture, it’s the tradition, it’s our community, so that’s what concerns me.”Ciel, who manages the Healdsburg Certified Farmers Market and also works with the Agricultural Institute of Marin’s Stonestown Farmers Market in San Francisco, came away impressed by Blanchard’s presentation, but also curious about how traditional farming and controlled environment agriculture could potentially coexist.
“I think the technology is brilliant,” Ciel said.
“I just think the small farmer is … dealing with the weather and pests and (various other factors), and they don’t have the funding or the education to pull something like this off. Is there something there that is for them?”
Blanchard views the growing CEA industry to be more comparable to — and therefore more competitive with — commercial food-processing operations than traditional farming because of the costs involved, from investing in capital equipment to staffing, of which AeroFarms employs about 160 people.
“If you’re going to have a farm manager, a safety manager, a shipping manager and a maintenance manager (among the staff), you may be up to like $600,000 a year in wages and benefits before you’ve even gotten to anything really related to the farm,” Blanchard said. “In many ways, even though the processes are different, this isn’t different than some other food-processing (businesses) necessarily, and you’ve got to manage it.”
I’m certain we’ll continue to see new and different commodities take advantage of innovative growing techniques of a controlled environment.
Mary Coppola, United Fresh Produce Association
Another reason CEA poses little to no threat to farmers, at least at this point in time, is because food grown in this vertical indoor environment is limited primarily to leafy greens. Greenhouses have more latitude.
“There are a number of companies who are growing greenhouse strawberries, peppers, cucumbers and tomatoes with much success,” said Mary Coppola, vice president for marketing and communications at United Fresh Produce Association. The Washington, D.C.-based organization was founded in 1904 and advocates for companies in the fresh produce supply chain. “I’m certain we’ll continue to see new and different commodities take advantage of innovative growing techniques of a controlled environment.”
And where agriculture industry experts laud controlled environment agriculture for its renewable and sustainable efforts, such as conserving land and water, there are other cost concerns.“
They rely a lot on artificial lighting, so obviously energy consumption is an issue,” said Humberto Izquierdo, agricultural commissioner, and sealer of weights and measures for Napa County. “I think the economics have to be there.”
Guy Blanchard, chief financial officer of AeroFarms, explains how the New Jersey-based startup gets dozens of turns of fresh produce annually through its vertical indoor farm, speaking at North Bay Business Journal’s North Coast Specialty Food and Beverage Industry Conference on Tuesday, Feb. 25, 2020, at Doubletree Hotel by Hilton Sonoma Wine Country in Rohnert Park. (Jeff Quackenbush / North Bay Business Journal)
Blanchard said he doesn’t view energy consumption as a challenge for AeroFarms.“I think when people think about energy or environmental footprint, it’s tough to see how much is really embedded in traditional agriculture when you have all the energy going to root watering, soil and soil degradation, and the energy that goes into fertilizers and harvesting a field,” Blanchard said, as well as transporting, cooling and washing.
Marc Oshima, AeroFarms co-founder, and chief marketing officer said the company and its competitors are focused on strengthening the overall agriculture industry, such as sharing their expertise about how to grow greens safely to avoid contamination. They also formed their own group, called the Controlled Environment Agriculture Food Safety Coalition.
“(It) was a critical step to establishing best practices and educating the FDA and customers on why indoor farming has so many more safeguards versus traditional field farming, and less exposure that often occurs with co-mingling at the major leafy greens processors, who are sourcing from multiple growing regions both domestically and internationally,” he said.
The coalition also has partnered with Foundation for Food and Agriculture Research on a $2 million, three-year program to identify stressors of leafy greens in order to optimize taste and nutrition, he said.
Staff Writer Cheryl Sarfaty covers tourism, hospitality, health care, and education. Reach her at cheryl.sarfaty@busjrnl.com or 707-521-4259.
FOR SALE - 2018 Freight Farm Computer Controlled Hydroponic Grow System - Atlanta, Georgia
The Leafy Green Machine is a complete hydroponic growing system built entirely inside a shipping container with all the components needed for commercial food production. The system is designed and engineered for easy operation, allowing users of all backgrounds to immediately start growing.
Make & Model - 2018 Freight Farm Computer Controlled Hydroponic Grow System
Manufacturer - Freight Farms
Location - Atlanta, Georgia
Price - $75,000
Description
Well maintained 2018 LGM purchased from Freight Farms.
This LGM has been a reliable producer of healthy produce.
The Leafy Green Machine is a complete hydroponic growing system built entirely inside a shipping container with all the components needed for commercial food production. The system is designed and engineered for easy operation, allowing users of all backgrounds to immediately start growing.
Current Uses
• Perfect for starting a small produce business, growing for restaurants or supplementing existing produce production.
• Restauranter who wants to grow custom greens for rotating menus 365 days a year. Farm to Table? How about Parking Lot to Table!
• Universities and schools have created programs for students to learn to grow while supplementing dining facilities with fresh greens.
The Highest Standard in Controlled Environment Agriculture
• Pre-built system designed to maximize operational efficiency and streamline workflow
• Perfect environment is achievable 365 days a year, regardless of geographic location
• Automated scheduling reduces the amount of labor required to operate
• Remote monitoring & control capabilities through the Farmhand AppTM
Operation Requirements
Space- The LGM dimensions are 40’ x 8’ x 9.5’. We suggest putting the farm on either trap rock or a concrete pad.
Electrical- 60 amp, 120/240-volt single phase or 120/208V three phase connection.
Water- A designated water source is suggested such as a garden hose or hardline water plumbing.
Labor- 15 to 20 hours a week for farming and upkeep.
It is recommended growing smaller compact crops with a high turnover rate, like head and loose leaf lettuces, herbs and heartier greens like kale and swiss chard.
LGM Accessories
Replaced sink with a 4 row, direct lighting microgreen station.
Website of previous owner being sold at additional cost. The website is currently set up for the business of this local farmer, and upon purchase can be changed to the meet the purchaser’s new brand.
Crop Examples
Butterhead lettuce, Oakleaf lettuce, Swiss Chard, Mustard Greens, Cabbage Leaves, Arugula, Cilantro, Mint, Dill, Oregano, Kale, Endive, Basil, Chives and Thyme
Yields
800+ heads of lettuce weekly
12 heads per tower (256 vertical towers)
1 LGM= 1.8 acres
Numerous additional extras included.
Numerous warranties still in effect
Training, website and ongoing support available through Freight Farms.
Visit Freight Farms (Website) for more information.
2018 - Freight Farms LGM Information Booklet
For Additional Information And To Arrange A Viewing:
(909) 942-9594
Spencer.Hoff@iGrow.News
1. ALL-WEATHER CONSTRUCTION
Steel frame with stainless interior, 40' x 8' x 9.6' overall footprint.
2. AUTOMATIC DOSING
Programmable nutrient & pH dosing for perfect growing conditions.
3. CUSTOM WORKBENCH
TIG-welded stainless workbench with integrated seedling growth stage.
4. COMMERCIAL VOLUME
Thousands of growing sites across 256 irrigated vertical towers.
5. HIGH-EFFICIENCY LED ARRAY
5:1 red / blue LED lighting optimized for green leafy growth.
6. INSULATED ENTRY
Padlock-proof safety door with controlled-environment insulation.
All information is from sources deemed reliable but is subject to errors, omissions, changes in price, prior sale or withdrawal without notice.
No representation is made as to the accuracy of any description.
All measurements, yields and square footages are approximate and all information should be confirmed by the customer.
Safe, Not Sorry
There are certainly many reasons why agriculture is making a big move indoors. It can be argued that CEA offers more local and sustainable food production and that it requires less water than field growing and doesn’t impact topsoil or lead to erosion
By Leslie F. Halleck
Food poisoning is not something you wish on anyone.
It’s horrible, miserable and downright deadly.
If you’ve ever had an E. coli or Salmonella infection, then you probably take food safety seriously. I know I do. Outbreaks of E. coli have plagued the field-grown leafy greens industry for the past three years in a row, with the most recent outbreaks sending romaine lettuce to the garbage bins across the country. With each recall, consumers are forced to focus more closely on where and how their food is grown.
With animal feces and surface water contamination for field-grown produce at the center of most of the leafy greens recalls, some food companies and restaurants are making shifts to buy from hydroponic and CEA producers. While this is a great opportunity for those of you growing under glass or in controlled environments, don’t make the mistake of thinking that you won’t come under the same safety and transparency scrutiny, or liability.
There are certainly many reasons why agriculture is making a big move indoors. It can be argued that CEA offers more local and sustainable food production and that it requires less water than field growing and doesn’t impact topsoil or lead to erosion. Controlled growing may also create conditions where fewer, or no, pesticides or herbicides are used. And when you’re growing local, with potentially less pest pressure, you can grow edible varieties that offer up better flavor and nutritional value, versus having to grow varieties or use harvesting methods that cater to shipability.
While there may be a perception that the boundaries created by greenhouses or controlled environments mean safer produce, we all know that there are still plenty of ways contamination can happen. Growing in a controlled environment means you lose the benefits of nature’s sanitizers: air and sunlight. Close monitoring of all environmental conditions is a must in hydroponics and controlled environments. Anywhere there is water involved, pathogens can spread. And of course, any time you have people involved in your production process, there’s ample opportunity for all sorts of contamination.
With venture capitalists jumping into the CEA game, and new operations launching left and right, we can also argue that this is a very young industry with a lot of learning and growing to do. Mistakes are bound to happen. Many CEA growers may not even have a good understanding of what translates to safe, or not safe, growing or processing procedures. Technology is changing rapidly, influencing a variety of production techniques utilized differently by different growers. You do have much better opportunities for authentic transparency and traceability as a CEA, but collective standard protocols aren’t yet where we need them to be.
This is a very young industry with a lot of learning and growing to do.
Enter, the CEA Food Safety Coalition (FSC). This new independent and member-governed organization debuted in 2018 and just recently announced the appointment of its first executive director. The goal of the organization is to bring together CEA growers of leafy greens to self-submit to external audits of their production processes. Then, thorough evaluation to develop appropriate food safety standards and consumer education.
If you grow leafy greens using any sort of controlled environment, be it hydroponics, aeroponics or aquaponics, and you’re willing to submit to a third-party food safety audit, then you are welcome to join the CEA FSC.
If you grow produce, do you have a Farm Food Safety Plan (FFSP) in place? If not, it’s time to get your house in order. You need to make sure you’re keeping a detailed record of your operation’s procedures and adherence to growing and processing safe greens or other produce. I suspect the CEA FSC will be working with members to develop FFSPs that help them fine-tune their safety measures and comply with federal regulations.
Good news if you’ll be attending the United Fresh 2020 Convention & Expo, because they’ve just partnered with the CEA FSC to create a new Controlled Environmental Pavilion at the show. The Pavilion will showcase thought leaders and foster discussions between experienced and new growers, as well as highlight new technologies and food safety issues. If you’re a CEA or service provider, you can now book booths both inside and adjacent to the Pavilion.
No one likes getting food poisoning, and we already throw away far too much food in this country. Growing as a CEA offers up the ability to not only limit waste of resources but also produce safer and contamination-free food. Consumers are willing to pay you a bit more for your produce when you can be totally transparent about your methods and food safety concerns. But it’s going to take a lot more research, learning, communication, and community standards before CEAs can truly take the lead on produce safety.
Lead photo: PHOTO: © freshidea | Adobe stock
Leslie (CPH) owns Halleck Horticultural, LLC, through which she provides horticultural consulting, business and marketing strategy, product development and branding, and content creation for green industry companies. lesliehalleck.com
International Partnership For New Certificate For CEA-Grown Produce
The FarmTech Society and GlobalGAP recognize each other in their membership programs, initiating a new open partnership to develop and implement a certification specifically for new “indoor” high tech systems with natural and artificial lights
The FarmTech Society and GlobalGAP recognize each other in their membership programs, initiating a new open partnership to develop and implement a certification specifically for new “indoor” high tech systems with natural and artificial lights.
The partnership is open to all industry stakeholders small and large to help advance a comprehensive new certificate for innovative production systems.
Innovative production systems in CEA require new standards
The partners have identified the need for all stakeholders active in the production of produce in CEA systems to form a working group at a pre-competitive level to address critical challenges, such as climate change, consumer trust and food security facing the industry. The partnership will develop best-practice standards for the certification process, recognizing the need for a multidisciplinary/multi-stakeholder approach in developing a certificate – by and for industry stakeholders in CEA.
The partnership will strengthen the existing well-established foundation of the GlobalGAP Integrated Farm Assurance (IFA) process by adding criteria for new technologies and cultivation methods, inserting dynamic data collection applications and adapting to the potential of the digital era, keeping future options valid.
The main goal of the GlobalGAP revision process is to deliver a standard that will take into account producers’ practices and the risks presented. The unique challenges presented by vertical farming or more generally, produce grown in controlled environments will be addressed to ensure appropriate user experience. Additionally, the group will focus on implementing real-time monitoring and data-driven solutions to facilitate the certification process, enabling transparency and traceability.
Taking into consideration the limits in technology by engaging with growers, retail, innovators and proven experts in the supply chain, the certification target will enhance the advantages of the end products and differentiate them in the marketplace.
The development roadmap will have three milestones: The first phase “open call for design and information gathering” will be kicked-off with a press conference at Fruit Logistica 2020, on February 6th, 2020. The second phase commences in June 2020 with the conclusion of the public consultations with multiple partners, and extensive international stakeholder meetings. The third phase is scheduled for the fall of 2020 with pilot testing in key supply chains followed by a market-wide peer review and introduction in 2021.
For more information:
www.globalgap.org
www.farmtechsociety.org
www.ukuat.org
www.cultinova.com
www.integar.de
Publication date: Mon 3 Feb 2020
FOR SALE - 2014 Freight Farm - Computer Controlled Hydroponic Grow System - Texas
The Leafy Green Machine is a complete hydroponic growing system built entirely inside a shipping container with all the components needed for commercial food production. The system is designed and engineered for easy operation, allowing users of all backgrounds to immediately start growing.
FOR SALE - 2014 Freight Farm - Computer Controlled Hydroponic
Grow System - Texas
Manufacturer - Freight Farms
Model - 2014 Leafy Green Machine (LGM)
Price - $29,950
Location: Texas
The Leafy Green Machine is a complete hydroponic growing system built entirely inside a shipping container with all the components needed for commercial food production. The system is designed and engineered for easy operation, allowing users of all backgrounds to immediately start growing.
Current Uses
• Perfect for starting a small produce business, growing for restaurants or supplementing existing produce production.
• Restauranter who wants to grow custom greens for rotating menus 365 days a year. Farm to Table? How about Parking Lot to Table!
• Universities and schools have created programs for students to learn to grow while supplementing dining facilities with fresh greens.
The Highest Standard in Controlled Environment Agriculture
• Pre-built system designed to maximize operational efficiency and streamline workflow
• Perfect environment is achievable 365 days a year, regardless of geographic location
• Automated scheduling reduces the amount of labor required to operate
• Remote monitoring & control capabilities through the Farmhand AppTM
Operation Requirements
Space- The LGM dimensions are 40’ x 8’ x 9.5’. We suggest putting the farm on either trap rock or a concrete pad.
Electrical- 60 amp, 120/240-volt single phase or 120/208V three phase connection.
Water- A designated water source is suggested such as a garden hose or hardline water plumbing.
Labor- 15 to 20 hours a week for farming and upkeep.
It is recommended growing smaller compact crops with a high turnover rate, like head and loose leaf lettuces, herbs and heartier greens like kale and swiss chard.
Crop Examples
Butterhead lettuce, Oakleaf lettuce, Swiss Chard, Mustard Greens, Cabbage Leaves, Arugula, Cilantro, Mint, Dill, Oregano, Kale, Endive, Basil, Chives and Thyme
Yields
800+ heads of lettuce weekly
12 heads per tower (256 vertical towers)
1 LGM= 1.8 acres
Freight Farms technology makes it easy to bring farming closer to where people live. The result is local, year-round production featuring fresh, sustainably-grown, and flavorful greens.
Freight Farms is exactly what it sounds like–a farm in a repurposed freight container.
These old containers are retrofitted with vertical, hydroponic components to make farming possible anywhere in the world, regardless of the outside climate.
LGM Included Accessories:
2 (two) new Freight Farm chem panels; with AgrowDose pumps. Pumps where primed with water but never used. New sensors also.
2 (two) A/C units: Unit #1 is Factory the other is a MrCool Oasis ES Series Ductless Mini-
Split Heat Pump System 230V 19 SEER - 24,000 BTU. If you don’t need 2nd A/C unit remove it & reinstall exhaust fan. All tubing, wires where run into the farm through exhaust port hole so as to keep farm integrity.
1 Dehumidifier Model HCWH-90 Whole Home Dehumidifier
1 (one) ClearView pump to manage the condensate.
2 (two) (Floor fan tubes (2ea. for both sides)
2 (two) 800cfm fans; only one installed
4 (four) Westpointe fans not installed
2 (two) Co2 Generators, 1 MiniGen; 1 Autopilot
1 (one) Evolution RO1000 High Flow Reverse Osmosis Water Filter by HydroLogic
1 (one) BIGboy Ultra Violet Sterilizer Kit by HydroLogic.
2 (two) Seedling Doser Panel & Main Doser Panel w/sensors
2 (two) sets pH probe - EC probe - Temp probe -
Seedling & Main delivery tanks; replaced All of them 8 are new
Illumitex - Eclipse Gen2 8 LED Grow lights & Eclipse Gen2 12 LED Grow lights - 3ea. Over the seedlings area NEW
10 LED light strips 7 replacements
Agrowtek – Hydro Transmitter and sensors; (All New)
Cradle Point (AT&T) Cell for Internet into LGM has ??? router that works with Farmhand.
4 port switch
Laptop cradle w/swing arm not installed
Lots of spare parts
Misc. PVC fittings most treaded a few slip on
2 aux pumps, small volume, 2 air pumps,
Training, website and ongoing support available through Freight Farms.
Visit www.freightfarms.com for more information.
Everything You Will Need To Grow Seedling And Microgreens And Then Some
Materials For Growing Hydroponic Plants - Additional $7,500.00 USD
Seedling Cart & Racks (DIY) 6 trays, 1 sump, lights (mix of LED’s & T5) Bright Agrotech design ($500)
Illumitex - Eclipse Gen2 8 LED Grow lights & Eclipse Gen2 12 LED Grow lights** ($4,000)
20 (twenty) K5 fluorescents lights 4’
Agrobrite 2’x1’ 4 bulbs
Multiponics High-End Cycle Timer in waterproof box ($250)
Multiponics Aquatec CDP 8800 pump w/psi guage in waterproof box ($300)
ProSeries 5 stage Reverse Osmosis Water Filter System 1 ea. w/expansion tank (5gal.); 50GPD ($350)
4 stage Reverse Osmosis Water Filter System 1 ea. w/expansion tank (4.4gal) ($250)
Trays w/holes 50 ea. Trays w/ holes (diamond pattern)
Trays seedling (200ea. cells) 20ea. Trays w/o holes $20 ea.
Q Plugs 20/60 4K per case 1ea. case by IHort
Microgreen grow Pads & roll
Propagating Chamber model PC-22 by PRO-GROW ($2,200)
Zipgrow Farm Walls: 2ea. 4’ & 1ea. 8’ complete by Bright Agrotech ($1,500)
Tower Garden growing system ($500)
1ea. 30”x30”x6” tub
Pumps; Aerators; Timers; Tubing and fittings (1/4” / 3/8” / ½”)
PSI gauges
pH & EC probes handheld w/solution
Light Meter (Apogee Instruments) Full-Spectrum Quantum sensor ($500)
** (Seeds Included 1 Year Old)
Attached Documents:
Freight Farm Twitter Feed
LGM Cut Sheets
See All Photos And Videos Here
All information is from sources deemed reliable but is subject to errors, omissions, changes in price, prior sale or withdrawal without notice.
No representation is made as to the accuracy of any description.
All measurements, yields and square footages are approximate and all information should be confirmed by the customer.
Disclaimer of Warranty - The 2017 Freight Farms LGM hydroponic farming container is being sold “as is” and the Seller disclaims all warranties of quality, whether express or implied, including the warranties of merchantability and fitness for particular purpose.
US - OHIO: Great Lakes Ag-Tech Summit - September 23, 2019
Join Urban Ag News, Hort Americas and Current, powered by GE, for the inaugural Great Lakes Ag Tech Summit on September 23rd
Don't miss the opportunity to hear from this year keynote speakers, Austin Webb (Robotany) and Chieri Kubota (The Ohio State University.)
Join Urban Ag News, Hort Americas and Current, powered by GE, for the inaugural Great Lakes Ag-Tech Summit on September 23rd. Held at the historic Nela Park campus in Cleveland, the one-day event features keynotes and panel discussions from leading researchers and innovative growers in the Great Lakes region. Connect with growers, scientists, researchers and entrepreneurs as we shape the future of food and move controlled environment agriculture forward.
Register Now!
We have added a panel to the agenda!
Hear Michel Doss, Paul Brentlinger, Dr. Chieri Kubota, Dr. Ariana Torres, Austin Webb and Chris Higgins at the end of the day as they recap and take your questions!
Location
The Institute at Nela Park
1975 Noble Rd. Cleveland, OH 44112
When
Monday, September 23, 2019
9 am to 4pm
Cost
Early bird ticket cost is $30 if you register before September 16.
Regular admission $50.
Keynotes
Optimizing Plant Production Under a Controlled Environment – Research and Education Programs at the Ohio State University
Dr. Chieri Kubota – Ohio State University
Dr. Kubota’s research mission is to serve in the development of science and technology in the area of controlled environment agriculture (CEA). Her projects are in an interdisciplinary area that encompasses plant physiology and horticultural engineering to enhance understanding and efficiency of CEA plant production systems such as greenhouses, warehouses (vertical farms), and growth chambers.
Are Consumers and Growers Putting Dollars in the Local Food Industry? Insights on Technologies and Preferences
Dr. Ariana Torres – Purdue University
Dr. Torres’ background combines field experience in agriculture with theoretical and applied research on agricultural economics. She has worked on projects looking at the impact of marketing choices on technology adoption for fruit and vegetable growers; the economic implications of social capital on entrepreneurship; and the role of community support on the resilience of small business after disasters.
Dr. Torres uses economic analysis to support the economic viability of the horticulture industry. Her research focuses on the intersection between the horticulture industry and marketing decisions. Her goal is to conduct innovative outreach and applied research in Specialty Crops Marketing, with the end of promoting economic sustainability for horticultural businesses.
Dr. Torres is currently working on a project evaluating the market, economics, and potential barriers to produce export-quality dried apricots from smallholders of southern Tajikistan. She is also working on evaluating the adoption of solar dehydrator for selected dried specialty crops in Indiana and Georgia. Lastly, she is collecting foundational data and establishing long-term pricing reports for Indiana farmers’ markets.
Agenda
Start: 9 am 09/23/19
9-9:30 am Introduction from Current
Brief history of Nela Park and Thomas Edison’s Institute
9:30-10 am Introduction from Hort Americas/Current
Chris Higgins, Owner of Urban Ag News and President of Hort Americas, LLC
Michel Doss, General Manager of Specialty at Current, powered by GE
10-10:45 am Keynote: Hear from a New Vertical Farming Company
10:45-11 am Break
11-11:45 am Panel discussion
Participants and topic TBD
11:45-1pm Lunch
1-1:45 pm Keynote: Ohio State University
Dr. Chieri Kubota
Dr. Kubota’s research mission is to serve in the development of science and technology in controlled environment agriculture (CEA). Her projects are in an interdisciplinary area that encompasses plant physiology and horticultural engineering to enhance understanding and efficiency of CEA plant production systems such as greenhouses, warehouses (vertical farms), and growth chambers.
1:45-2:30 pm Keynote: Purdue University
Dr. Ariana Torres
Ag economist focused on the marketing and economics of specialty crops, especially those grown in controlled environments. Courses instructed center on entrepreneurship, marketing and the economics of specialty crop production. Researches technology adoption for specialty crop operations, and how consumers perceive grower technologies.
2:30-2:45 pm Break
2:45-3:30 pm Panel discussion
Participants and topic TBD
3:30-3:45 pm Closing remarks
Hort Americas and Current, powered by GE
USDA - NIFA Conference Sept. 9 - 12, 2019
Developing sustainable and strategic plans to feed the future in the face of growing global challenges will demand interdisciplinary vision, collaboration and innovation
USDA - NIFA Conference At Biosphere 2
September 9 - 12, 2019
Developing sustainable and strategic plans to feed the future in the face of growing global challenges will demand interdisciplinary vision, collaboration and innovation. Controlled environment agriculture (CEA) implemented as fully enclosed, multi-level indoor agricultural food production systems, Vertical Farms (VF), will complement future greenhouse (GH) plant production systems and will offer innovative technological solutions for issues at the food-energy-water nexus.
The purpose of the conference is to Plan an Interdisciplinary Controlled Environment Indoor Agriculture R&D Roadmap and Coordinated Research Plan. It is supported by USDA/NIFA-AFRI program and is hosted by the Controlled Environment Agriculture Center at the University of Arizona, Tucson, AZ and Biosphere 2, Oracle, AZ
This conference (September 9 – 12) will facilitate interdisciplinary discussions centered on several major thematic R&D areas for CEA/VF/GH, each of which will interface with the others to identify cross-disciplinary areas of synergy, opportunity and need. Thematic areas include:
Economics: focus questions and discussions will include: what are good metrics of success in these systems from both industry and community perspectives? Can we develop a pipeline to quantify environmental and social benefits of these systems in a Benefit-Cost Analysis framework? How scalable are these systems? What are environmental impacts, life cycle analyses?
Engineering: focus questions and discussions will include: how to increase lighting efficacy, light use efficiency, and reduce cost? How to control and modulate CO2? How to design and enhance air circulation and to optimize HVAC? How to minimize labor input and integrate innovative automation and robotic systems? How to improve water use efficiency and cycling?
Production Systems: focus questions and discussions will include: how to manage crops to integrate with improve environmental controls, nutrient delivery and automation. How to improve plant architecture to enhance crop productivity and reduce waste? How to improve logistics and enhance labor efficiency?
Plant Breeding: focus questions and discussions will include: what makes a crop a good candidate for indoor farming/what are priority candidate crops for these systems beyond what is currently grown? What traits should be privileged in breeding programs for indoor farming? How can gene editing and genomic techniques be leveraged to integrate novel financial opportunities into these growing systems, such as increased nutritional content, enhanced water, nutrients and light use efficiencies, or pharmaceutical production? How CEA production systems can alter the structure of microbial communities associated with plants, growing media, and determine how the alterations affect plant nutrient and water uptake and utilization?
Pest and Disease Management: focus questions and discussions will include: what are the major viral, fungal, and insect pathogens in these systems and how are they best addressed? Integrate Pest Management for reduced chemical control? How to develop and implement a rapid and simple digital imaging system for pest and disease diagnosis? How to improve the efficiency of pest and disease management while not harming beneficial insects and pollinators?
Food Nutrition and Safety: focus questions and discussions will include: how alterations to growing media and environment will impact food quality, flavor, nutrition content and food safety? How do indoor growing conditions alter the microbial communities of plants? How do they impact product quality and shelf life?
Industrial Ecology in Closed Systems: focus questions will include: how can we better design more energy and resource efficient systems? Can we build holistic energy models? Can we create industrial ecosystems where one industry’s effluent is another’s intake? How would we model/quantify the ecosystem services provided by a functioning ‘closed loop industrial ecosystem’?
Conference participants are additionally welcome to join writing teams and collaborate on a proposal for a coordinated agricultural project (CAP) grant on VF that builds off of conference discussions. Writing teams may also choose to develop proposals for relevant funding programs at USDA-NIFA SAS, SCRI, NSF/USDA/DOE INFEWS, and NSF
Deadlines
Pre-registration ends June 30th
invitation to attend conference July 15th
Final registration, room reservations and payment due August 1st;
Conference events begin Monday September 9th
For more information about the conference please read the Project Summary.
For more information about conference activities please read the Conference Program Schedule and Format.
Conference Program Schedule & Format.pdf
For more information about Biosphere 2 please read the following document.
Want to make the most of your time in Tucson? Go to Visit Tucson to discover things to do during your visit!
What Is Hydronic Cooling?
“As Surna’s projects have become larger and more complex, we have added several products to our fan coil product family to meet the climate control needs of our customers”
Boulder, Colorado, August 27, 2019 — Surna Inc. (OTCQB: SRNA) introduces a full line of purpose- built fan coil products providing a wide range of choices for both ducted and ductless applications for small to large commercial indoor cannabis cultivation facilities.
“As Surna’s projects have become larger and more complex, we have added several products to our fan coil product family to meet the climate control needs of our customers”. These new products are part of our strategy to enhance our position as a trusted climate control advisor to our customers and offer more products and services to meet their specific requirements,” said Troy Rippe, Surna’s Director of Engineering and R&D.
The introduction of the IsoStreamTM product family allows Surna to serve:
Ductless environments where climate control systems circulate water, not air.
Ducted environments that provide economical solutions while still serving multiple grow
rooms.
Surna provides efficient and economical environmental control systems across a larger array of indoor cannabis cultivation facilities. Our new, whisper quiet fan coil units use electronically commutated motors to optimize airflow while specialized chilled water modulating valves are used to fine-tune for minimizing energy consumption.
If you want to learn more about our full line of Surna IsoStreamTM fan coils, please contact us at
www.surna.com
About Surna
Surna Inc. (www.surna.com) designs, engineers and manufactures application-specific environmental control and air sanitation systems for commercial, state- and provincial-regulated indoor cannabis cultivation facilities in the U.S. and Canada. Our engineering and technical team provides energy and water efficient solutions that allow growers to meet the unique demands of a cannabis cultivation environment through precise temperature, humidity, and process controls and to satisfy the evolving code and regulatory requirements being imposed at the state, provincial and local level.
With Founder Gone, U. Vertical Farming Project's Main Farm Closes, But Forbes Offshoot Will Remain
After two years of operation, the Princeton Vertical Farming Project (PVFP), which introduced students to sustainable farming practices and provided fertile ground for research, has come to an end
By Katie Tam | August 12, 2019
A taste test set up at the Forbes College vertical farm for Akiti's thesis project.
Photo Courtesy of Kor Akiti
After two years of operation, the Princeton Vertical Farming Project (PVFP), which introduced students to sustainable farming practices and provided fertile ground for research, has come to an end.
The PVFP was launched in April of 2017 by Paul Gauthier, who served as an associate research scholar in plant physiology and environmental plant metabolism in the Department of Geosciences beginning in 2012, in a windowless room in Moffett Laboratory. With support from the Office of Sustainability, Gauthier and student collaborators built and maintained the hydroponic vertical farm, where peppers, strawberries, herbs, and other plants were grown only with water and nutrient solutions—no soil.
At the end of June, Gauthier left for Delaware Valley University in Doylestown, PA, where he will start an appointment as Professor of Plant Science. Although an offshoot in Forbes College will remain, the main farm has been shuttered, with equipment in Moffett Laboratory dismantled and placed in storage.
As the global population continues to rise, vertical farming has grown in popularity, as the practice requires less water, space, and energy than traditional farms. Vertical farms can yield several harvests of fresh produce a year, which could help to feed growing urban centers.
According to Gauthier, although many start-ups have tried vertical farming, few have succeeded. Many have been forced to close after a few years due to lack of revenue and funding. In addition, he said, little research has been conducted on best practices, such as how water, nutrients, and the environment influence plant growth.
One of the primary motivations of the PVFP was to identify the problems and challenges associated with the technique and learn how to solve them — much like in traditional agriculture.
“People tend to forget that there is a ‘farming’ in ‘vertical farming,’” Gauthier said. “You are a farmer first.”
To that end, the farm experimented with different techniques, seeking to determine how to feed a family of four by quantifying nutrient usage, testing new technologies, and planting a variety of crops.
Another goal of the project was to create an on-campus “food hub,” where students could gain experience with farming and learn about food sustainability. Gauthier said that he wanted students to understand the commitment and responsibility that vertical farming entails.
“We want to train the next generation of vertical farmers,” he said.
Several students have taken on the burdens of both research and responsibility by conducting senior thesis projects with the PVFP. In the PVFP’s first year, projects ranged from a Department of Ecology and Evolutionary Biology (EEB) thesis comparing environmental impacts of vertical and conventional farming to a Wilson School thesis on the economic costs of running a vertical farm.
In her EEB thesis, Kor Akiti ’19 compared the palatability and nutritional quality of crops grown in the Vertical Farm to organic, soil-grown crops from a local grocer.
Akiti performed several “taste tests” in the Forbes dining hall and Frist Campus Center, asking passersby to taste and rank the produce – kale, peppers, and strawberries – on appearance, taste, and texture. She then asked tasters: which would you buy at the supermarket?
Using a technique called mass spectrometry, she was able to conclude that nutrient profiles of vertical farm and soil-grown crops were similar, but the hydroponic crops lacked visual appeal.
“One of the main takeaways was that the appearance of the hydroponic crops was significantly less satisfying than the appearance of the soil-grown crops across the board,” she said. “If vertical farming is going to be competitive, whether it’s in the context of Princeton, on campus, or in the larger urban market, farmers are going to have to find a way to make their produce more appealing, because appearance is such a critical point of purchase.”
Overall, her findings suggested the complexity of consumer choice and preference, hinting at challenges to come in not only growing crops in vertical farms but also in marketing them.
The impact of the PVFP has been considerable, not only in advancing research but also in contributing to outreach and education.
In September 2018, Gauthier partnered with Hopewell Elementary School in Hopewell, N.J., to develop a farm-to-cafeteria program. The initiative provides students with the opportunity to grow their own fresh produce, almost all of which is then used in school lunches.
Gauthier also co-founded his own indoor farming company, Ker Farms (pronounced “care”), in Hamilton, N.J., which grows and sells a variety of fruits and vegetables. According to Gauthier, the company is also training local educators in the hope of bringing vertical farming to more schools in the area.
“There is no question about it,” Gauthier said. “Vertical farming will be part of our lives.” Thus, Gauthier continued, it is essential that young people know how to grow, interact, and experiment with plants from a young age, so they can be prepared for the future.
Similar concerns motivated the establishment of an offshoot of the PVFP in the lobby of Forbes College in the fall of 2018. This mini-vertical farm was intended as a different kind of experiment – to see how farming could integrate into the daily life of a busy Princeton student, as Gauthier put it.
The conclusion, he said, was that taking care of plants was harder than it seemed.
Kaylin Xu ’22 played a leading role in maintenance of the Forbes College farm, changing the water, checking nutrient levels, and making adjustments to optimize conditions for growth. It was a labor-intensive job, Xu admitted, and although other students cycled in and out to help, she was one of the only people to consistently care for the plants. Xu hopes that the maintenance of the Forbes “farm” will become more communal.
“I want to get more of the Forbes community involved in having a hand in creating this green space, because I feel like that is really unique,” Xu said.
“Unfortunately, students are busy,” Xu continued, making it difficult to find dedicated members to join the team.
Gauthier also emphasized how important it was for future farmers to be dependable. “Plants are like babies,” Gauthier said. Just as a parent cannot ignore the cries of a hungry child, so a plant cannot go without water.
This past year, products from the Forbes offshoot and the main farm were featured in several “Meet What You Eat” dinners in the dining halls, where students could sample fresh produce incorporated into pastas, flatbreads, and more. In the fall, the Forbes farm will continue to grow crops for use in the Forbes kitchen and the Pink House food-share.
“I hope [the vertical farm in] Forbes will continue the spirit of sustainability,” Xu said, as the torch is passed from the original farm.
In his new position at Delaware Valley, Gauthier hopes to continue the work he started at Princeton, reproducing the vertical farm model on a larger scale and developing local projects and collaborations.
Although the Hopewell ES program and the Forbes offshoot will continue, the PVFP in its official capacity has ended – much like the start-ups and companies Gauthier was interested in when he began.
“I would have loved to continue,” Gauthier said of the project. “It’s important to start thinking and finding solutions for the future.” The University was a unique place for such an undertaking, he said, as it allowed for cross-pollination from a variety of fields of study.
“All different departments – computer science, MAE [Mechanical and Aerospace Engineering], EEB, business, architecture – students from all these departments were working on the vertical farm,” Gauthier said. “We can tackle the problem from very different disciplines.”
Gauthier did not rule out the possibility of reviving the PVFP.
“If there is demand, maybe the project will come back,” he said.
Lead Photo: Kor Akiti ’19 poses beside plants at the vertical farm in Moffet Laboratory. Photo Courtesy of Kor Akiti
Veggies Grown In Nevada's Massive Indoor Farm Are Now On Sale To Las Vegas Locals
Nevada does not have particularly fertile lands, but that didn't stop Oasis Biotech when they opened a 215,000-square-foot indoor farm to the public last July
by Phillip Moyer
July 30th 2019
The facility uses hydroponics and environmental control to reduce environmental impact. (PHOTO: Nathan O'Neal)
Nevada does not have particularly fertile lands, but that didn't stop Oasis Biotech when they opened a 215,000-square-foot indoor farm to the public last July.
Designed to be sustainable and environmentally-friendly, the facility uses hydroponics to use 90 percent less water than traditional farming, and have a completely controlled environment to eliminate the need for pesticides.
Guests had the chance to sample the vegetables after its openings, but until now, the food was only widely available to high-end restaurants in the Las Vegas Valley.
Today, the farm announced that they'll be selling eight-ounce bags of its baby leaf Spring Mix and Romaine Mix blends to consumers under its "Evercress" brand name.
“Over the last year, we have been working hard to perfect our crops and growing methods to bring the community and our customers the freshest salad greens in Las Vegas,” says Michelle Howell, Sales & Marketing Manager at Oasis Biotech. “We had over 1,000 people attend last year’s grand opening and the big question everyone asked us was “When can we buy it?” so we are thrilled to now offer the Evercress salad greens to Las Vegas locals."
The blends can beat Oasis Biotech's farming facility, located at at 6225 Annie Oakley Drive in Las Vegas.
In an effort to stay true to its mission to “Feed the World, Better.,” any product not sold to current customers or purchased by the public will be donated to local charities.
FarmTech Society Held First Constitutional Annual General Meeting
The Farm Tech Society (FTS) is an international non-profit industry association that unites and supports the Controlled Environment Agriculture (CEA) industry, seeking to strengthen the sector through the development and implementation of resilient and future proof methods and technologies for indoor growing
The Farm Tech Society (FTS) is an international non-profit industry association that unites and supports the Controlled Environment Agriculture (CEA) industry, seeking to strengthen the sector through the development and implementation of resilient and future proof methods and technologies for indoor growing.
The FarmTech Society (FTS) held its first constitutional annual general meeting at Greentech Amsterdam 2019. Also, FTS entered into a partnership with the vertical farm institute (vfi). Both organizations focus on value generation for the CEA industry and help the sector to grow together.
FTS members also elected a new board of directors, as well as its new board of advisors. The new boards are elected for a period of two years, and the board of directors also appointed the daily management team:
Board of Directors
Chairman: Gus Van der Feltz (founding member)
Vice-chair: Yanni Garcia (founding member)
Vice-chair: Penny McBride (founding member)
Director: Adam Rosenbaum (founding member)
Director: Daniel Podmirseg - vertical farm institute
Director: Wythe Marschall - PhD candidate Harvard University
Director: Stefan Frey - FREYconsult
Board of Advisors
Maren Schoormanns - PRIVA
Nicole Thorpe - Cultinova
Enrico Costanzo - ILab AirLiquide
Stefanie Linzer - Valoya
Pierre Grootscholten - Grootscholten Consultancy
Ian Kanski - INTAG Systems
Daily management
Secretary-General: Thomas Zoellner (founding member)
Treasurer: Yanni Garcia (founding member)
Communication: Mark Horler - Soya Project / UKUAT
For more information:
FarmTech Society
Tom Zoellner
The Future of CEA And Urban Farming
Gearing up to the second Indoor AgTech Innovation Summit on June 19-20 in New York, the event organizers found out what the summit’s Research Partner Cornell University has been working on, with insights from Neil Mattson, CEA Director & Associate Professor, School of Integrative Plant Science, Horticulture.
Gearing up to the second Indoor AgTech Innovation Summit on June 19-20 in New York, the event organizers found out what the summit’s Research Partner Cornell University has been working on, with insights from Neil Mattson, CEA Director & Associate Professor, School of Integrative Plant Science, Horticulture.
What’s been your focus this year about CEA and Urban Farming?
A key project has been a collaboration between our FCEA group and Cornell economists Charles Nicholson and Miguel Gómez. Together we’ve produced a report focused on the economic and environmental footprint and viability to scale urban farming.
We looked at scenarios of producing leafy greens locally in New York and Chicago. For each city our three scenarios were:
Field production in CA and shipping to the city
Greenhouse production in a hypothetical facility with 1-acre crop canopy
Vertical farm production in a hypothetical warehouse facility with 1-acre crop canopy
In the New York City scenarios, we considered CEA production in the middle of the city and in the Chicago peri-urban CEA production about 50 miles outside the city.
The comparison led to some interesting discussion points around bottlenecks and priorities for the sector to scale. I’ll share more on that below, and in my presentation at the summit.
Aside from that important study, from a plant-science standpoint, Cornell CALS has also continued its work to improve energy-efficient leafy greens, tomatoes and strawberries using LED lighting strategies and CO2 enrichment to photosynthesize through its Greenhouse Lighting and Systems Engineering (GLASE) research efforts.
We’re also collaborating with Rensselaer Polytechnic Institute (RPI) to understand the nutritional content of CEA-grown kale vs field-grown kale.
How do the Greenhouse and Plant Factory compare economically with open field farming?
In terms of economics, our study found it was cheapest to produce in a field and ship thousands of miles with a landed cost of $3 per kilo of lettuce. The New York city greenhouse scenario cost $8 per kilo, including production and short shipping distance. Plant factory was slightly cheaper. In peri-urban Chicago, with cheaper land rates, greenhouse production gave a cost of $7 per kilo. Again, the plant factory cost came in slightly cheaper.
The lower plant factory cost in both scenarios unlocks potential opportunities in urban areas where a high land cost is a significant contributor to the overall cost. Plant factory is more efficient use of land due to its vertical stacking, with a smaller footprint overall.
Labor costs are a significant 50% of the high cost in our un-automated CEA scenarios. As a follow up to this study we’re looking at a scenario with automated production for seeding plants, moving channels through the greenhouse and harvest. We can reduce labor cost by two thirds to three quarters, bringing us much closer to field production costs overall.
Another option is to move to cheaper land rural production within a couple hundred miles outside the city. In this scenario, we can reduce cost of production by a further $1 per kilo. Taking automation and site selection into account CEA greenhouse production down to $4 per kilo may be possible which is very close field-grown and cuts 2,800 miles from transportation.
In all scenarios, CEA was much more water-efficient than any other field, of course really important in this time of climate change. Hydroponic systems are far more water-efficient by design, with water recapture and reuse.
Agtech Startup Agrilyst Is Now Artemis, Raises $8M Series A
May 22, 2019
Artemis, the agtech startup formerly known as Agrilyst, today announced that it has raised an $8 million Series A funding round. The round was co-led by Astanor Ventures and Talis Capital, with participation from iSelect Fund and New York State’s Empire State Development Fund. With this, the company, which won our 2015 Disrupt SF Battlefield competition, has now raised a total of $11.75 million.
When Agrilyst launched, the company mostly focused on helping indoor farmers and greenhouse operators manage their operations by gathering data about their crop yields and other metrics. Over the course of the last few years, that mission has expanded quite a bit, and today’s Artemis sees itself as an enterprise Cultivation Management Platform (CMP) that focuses on all aspects of indoor farming, including managing workers and ensuring compliance with food safety and local cannabis regulations, for example.
The expanded platform is meant to give these businesses a single view of all of their operations, and integrates with existing systems that range from climate control to ERP tools and Point of Sale systems.
Compliance is a major part of the expanded platform.
“When you look at enterprise operations, that risk is compounded because it’s not just that risk across many, many sites and many acres, so in 2018, we switched to almost entirely focusing on those operations and have gained a lot of momentum in that space,” CEO and founder Allison Kopf said. “And now we’re using the funding to expand from mainly focusing on managing that data to help with profitability to using that data to help you with everything from compliance down to the profitability element. We want to limit that exposure to controllable risk.”
With this new focus on compliance, the company also added Dr. Kathleen Merrigan to its board. Merrigan was the deputy secretary of Agriculture in the Obama administration and is the first executive director of the Swette Center for Sustainable Food Systems at Arizona State University . She is also a venture partner at Astanor Ventures .
“Technology innovation is rapidly transforming the agriculture sector. Artemis’ approach to using data as a catalyst for growth and risk management provides the company a significant advantage with enterprise-level horticulture operations,” said Merrigan.
Cannabis, it’s worth noting, was not something the company really focused on in its early years, but as Kopf told me, it now accounts for about half of the company’s revenue. Only a few years ago, many investors were also uncomfortable investing in a company that was in the cannabis business, but that’s far less of an issue today.
“When we raised our seed round in 2015, we were pitching to a lot of funds and a lot of funds told us that they had LPs that can’t invest in cannabis. So if you’re pitching that you’re going to eventually be in cannabis, we’re going to have to step away from the investment,” Kopf said. “Now, folks are saying: ‘If you’re not in cannabis, we don’t want to invest.’ ”
Today, Artemis’ clients are worth a collective $5 billion. The company plans to use the new funding to scale its sales and expand its team.
Image Credits: Ben McLeod / Getty Images
Ag Foundation Funds Groundbreaking Indoor Farming Research
April 08 , 2019
The Foundation for Food and Agriculture Research (FFAR) is pushing the boundaries of traditional agriculture with a new public-private partnership that will develop crops specifically suited for indoor environments.
To achieve this, the Precision Indoor Plants (PIP) Consortium is studying the environmental and genetic factors that help agriculture thrive indoors, says FFAR’s executive director Sally Rockey.
According to Rockey, this research will provide unique insight for the industry as most other studies on this type of farming focus on design elements for indoor systems, such as vertical productions facilities and lighting, rather than the plants themselves.
The PIP collaborative has joined together world-class indoor growers, breeders, genetics companies, and agricultural equipment leaders, including AeroFarms, BASF, and Benson Hill Biosystems, among others. These participants are pooling resources to fund research on the best means to present nutritious, flavorful crops that can grow anywhere, year-round, profitably.
Specifically, PIP says its research will explore how to improve nutrient content and yields, decrease the amount of energy needed for production, and help crops perform their best in indoor conditions.
So far, FFAR has committed to investing US$7.5 million in PIP, and with matching funds from participants, the consortium will grant a minimum of US$15 million to its studies.
This move is just part of the growing trend of indoor agriculture, also called controlled environmental agriculture (CEA).
The “booming” interest in this type of agriculture has been attributed to the new needs of our growing world. The challenge of feeding a rapidly rising global population in a sustainable way has influenced researchers to examine innovative food production approaches, says PR Newswire.
Producing crops indoors could also be a solution for challenges arising from a changing climate, adds the company.
Today, lettuce and other leafy greens have successfully become profitable CEA, while PIP’s research seeks to expand this to include a variety of other crops, such as herbs, tomatoes, strawberries and blueberries.
Initial PIP projects will focus on increasing nutritional content and changing the size and shape of the plant.
“This research has implications for a wide variety of agricultural environments, including outdoor agriculture and space,” the entity said.
“For farmers planning outdoors, PIP’s research has the potential to reduce strain on the environment, make crops more resilient to stresses, bolster food and nutritional security and shorten the supply chain for producers.
“The research is also useful for government agencies and corporations interested in growing food in space for long-term space exploration.”
How Can Controlled-Environment Growers Improve Energy Efficiency And Grow Light Optimization?
Greenhouse Lighting and Systems Engineering (GLASE) consortium researchers are looking for ways to reduce grow light electricity use and improve light uniformity to maximize controlled-environment crop yields.
April 3, 2019
By David Kuack
Are you using or thinking about using grow lights to produce your controlled environment crops? If so, would you be interested in how to reduce the amount of electricity needed to operate those lights?
Researchers with the Greenhouse Lighting and Systems Engineering (GLASE) consortium at Cornell University in Ithaca, N.Y., are studying the use of control algorithms to optimize the light used on controlled-environment crops while reducing the amount of electricity used to operate grow lights.
“These control algorithms that deal with lighting were developed over 20 years ago,” said research associate Dr. Kale Harbick. “Unfortunately, this technology, which was under patent until about four years ago, never achieved large scale commercial use.
“The algorithms are related to delivering a constant amount of light to the plants every day, which is called daily light integral (DLI). Controlled-environment crops like lettuce prefer to receive a constant amount of light every day. This enables the plants to maximize their growth and helps to avoid problems with tipburn, which can make the crops unsalable.”
Even though this technology is off patent, Harbick said some growers are still hesitant to incorporate it into their environmental control systems.
“As part of the GLASE research program we are putting this control technology into two commercial pilot facilities in New York,” he said. “We are going to run multi-year experiments so that the growers in those facilities can compare the performance under our control system with what they are currently using. Incorporating this technology, we are looking to demonstrate a large amount of energy savings for the crop yields produced.
“We’re specifically focused on lettuce, tomato and strawberry. The first two pilot facilities are growing leafy greens, primarily lettuce. Lettuce is the crop the Cornell controlled-environment agriculture group has studied the longest and we understand the best. Tomato and strawberry are newer crops to us so we are doing a lot of greenhouse experiments right now with these plants to analyze the relationship between light, carbon dioxide and growth. We have the information well established for lettuce, but it’s not as well established for fruiting crops. We would eventually like to roll out pilot programs for tomatoes as well. We have some tomato growers in the state who have expressed interest in using the technology.”
GLASE researcher Dr. Kale Harbick is studying the use of control algorithms to optimize light while reducing the amount of electricity used to operate grow lights.
Photos courtesy of Kale Harbick, Cornell Univ.
Harbick said New York State Energy Research and Development Authority (NYSERDA), which is financially supporting GLASE, is interested in trying to meet greenhouse gas emission production targets. CEA has the potential to use a lot of energy. Any energy savings that the GLASE research can realize has a corresponding large reduction in greenhouse gas emissions.
Lack of light uniformity
One of the problems that Harbick often sees with grow lights is growers don’t install enough fixtures.
“The most basic problem is light intensity,” he said. “We often see greenhouses where growers are trying to produce lettuce with grow lights, but they only have installed half the number of fixtures they should have in order to grow lettuce optimally. What that means is even if they ran those lights 24/7 they wouldn’t be able to achieve the DLI needed to reach the target amount.”
Harbick said the issue of not installing enough lights is related to measuring light.
“Trying to measure the light is not a trivial thing to assess,” he said. “If there is an array of lights that are regularly spaced in the same plane, the problem is the light is not uniform on the crop. It kind of has a bullseye effect where there is a lot of light in the center and not very much on the edges. Lighting manufacturers and designers often provide growers with designs that show the light intensity at the center of the space, which is not representative of the light that is received in the rest of the space. The lights might be sized according to that center spot which is just fine, but everything else is undersized. We hear regularly from growers who’ve spent a lot of money on a lighting system and then realize later that it was undersized.”
Harbick has done a lot of work on lighting uniformity to try to address this issue of undersizing.
“We’ve looked at techniques to change the positon of the lights to make it more uniform,” he said. “We’ve looked at changing the brightness of the lights depending on where they are in the space to make the light more uniform. We have a couple of greenhouse spaces at Cornell that have this uniformity optimization. These are the only greenhouses on campus to have uniform lighting.”
One of the common issues encountered by growers who have installed grow lights is the lack of light uniformity which can be caused by undersizing the number of fixtures.
Harbick said this lack of light uniformity is not often noticed because of the way humans see light distribution.
“We could look out at a crop and the lighting looks uniform to our eyes because our eyes are so good at attenuating brightness levels,” he said. We don’t notice these differences very easily. The brightness level differences have to be measured.”
Although the lack of light uniformity can be related to the number of light fixtures installed, Harbick said there could be other factors involved.
“In the research greenhouse that we have optimized light uniformity, initially we received a design from the manufacturer that called for 20 LED fixtures,” he said. “I modified the design using a computer program that I wrote that was able to reduce the number of fixtures to 16, but improved the light uniformity. The light is much more uniform and we were able to do it with fewer fixtures.
“It’s not always a case of installing more fixtures to increase light uniformity. It can also be things like changing the brightness of the fixtures or changing the position of the fixtures. There are other possibilities to improve uniformity besides the number of lights.”
Loss of crop yields
One of the reasons that there continues to be light uniformity issues is how the fixtures are spaced in greenhouses and indoor farms.
“It’s a status quo thing,” Harbick said. “Lights have always been placed in a plane and regularly spaced out. This is how it has always been done. Until recently most grow lights have had a fixed intensity. Under those conditions it is difficult to overcome this light uniformity problem.
“Lack of light uniformity is less of problem in large greenhouses because there is a lot of interior space and not much edge space. However, this is a major problem in indoor farms where there are long rows or shelves. These indoor farms don’t have the background natural light like greenhouses to mitigate some of these effects. I have seen warehouses where they were growing a high DLI crop and the plants in the center of the room were a foot taller than the plants on the edge. It was simply because the plants in the center were receiving more light. In indoor farms, whether it’s lettuce, tomatoes or other high DLI crops, that is where the payoff really comes for optimizing light uniformity. For indoor farms light uniformity is something that people aren’t looking at yet. They just kind of live with it. They just move plants around to try and even out the growth. But that creates a lot of extra labor and logistic issues. They’re not optimizing the total yield of the crops. Every plant on the edges that is shorter than the ones in the center of the room is lost sales.”
GLASE researchers are conducting greenhouse experiments on tomato and strawberry to analyze the relationship between light, carbon dioxide and plant growth.
Harbick said that the issues with light uniformity may improve as changes are made to lighting fixtures.
“As the lights become more capable in terms of adjusting brightness and spectrum, there are opportunities for GLASE researchers to share some of that optimization technology with lighting manufacturers to try to get these improvements out to the industry. But it’s going to take some time. We’re still doing a lot of the research ourselves. We don’t have an active grant in this area right now so this is something that I have been doing on my own. It’s definitely an opportunity for future study.”
For more: Kale Harbick, Cornell University, School of lntegrative Plant Science, Horticulture Section, Ithaca, NY 14853; kh526@cornell.edu.
David Kuack is a freelance technical writer in Fort Worth, Texas; dkuack@gmail.com.
US (NY): Cornell University Hosts CEA Conference
April 22, 2019
Geneva, New York
Cornell University is hosting a CEA conference on Friday April 26. The Cornell Controlled Environment Agriculture (CEA) advisory/stakeholder group was formed to address the increasing demands of consumers for fresh, local, and year-round produce. In the Northeast, meeting this demand means incorporating various technologies to extend the growing season.
The CEA advisory/stakeholder meetings are designed to address this challenge with a multifaceted approach made possible by the diversity of its participants, which include: New York State producers, agribusiness professionals, supermarkets, government agencies, financial management companies, and Cornell faculty and faculty/staff from the Cornell AgriTech, the Charles S. Dyson School of Applied Economics and Management, the School of Integrative Plant Science, and the Department of Biological and Environmental Engineering.
The April 26, 2019 conference is designed to explore possibilities that could enable New York State to become a leader in the industry. Participants will hear from industry experts and leading academics about how they can create and capture economic synergies that will provide tremendous lasting value for New York State and beyond.
The meeting will be held at the Jordan Hall Auditorium at Cornell AgriTech, 614 W North St., Geneva, N.Y. Parking is free and located directly behind the building.