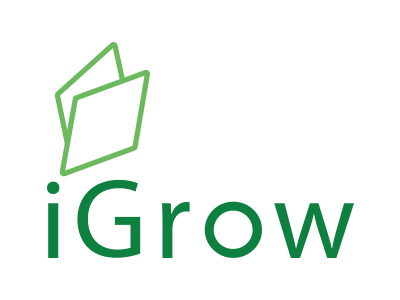
Welcome to iGrow News, Your Source for the World of Indoor Vertical Farming
Q & A With Jake Counne, Founder, Wilder Fields
Jake Counne, founder, Wilder Fields shares greens with Calumet City Mayor Michelle Markiewicz Qualkinbush
Jake Counne, founder, Wilder Fields shares greens with Calumet City Mayor Michelle Markiewicz Qualkinbush. Pictured announcing Wilder Fields’ commitment to build and operate a full-scale commercial vertical farm in a former Super Target store in Calumet City, Ill.
When Jake Counne established Backyard Fresh Farms as an incubator in 2016, he knew that most large-scale vertical farming operations were large-scale financial disappointments.
So rather than attempting to patch up the prevailing model, he and his team chose to build something new from the ground up. “Other start-ups had tried scaling their operations with antiquated greenhouse practices,” he says. “We realized that to solve the massive labor and energy problems that persist with indoor vertical farming. We needed to look to other industries that had mastered how to scale.”
That vision, and several years of persistent innovation, came to fruition in 2019 when Counne announced he would transplant the successful pilot farm—now renamed Wilder Fields—into a full-scale commercial vertical farm. It is currently under construction in an abandoned Super Target store, with an uninterrupted expanse of three acres under its roof in Calumet City, just outside Chicago.
Wilder Fields is designed to supply supermarkets and restaurants in the Chicago metro trade area,. It is scheduled to sell its first produce in the spring of 2021. It will provide fresh produce to those living in nearby food deserts in Illinois and Northwest Indiana. In this Q & A With Jake Counne, Indoor Ag-Con will share more about Jake’s vision and plans for the future.
According to an Artemis survey, only 27 percent of indoor vertical farms are profitable despite attracting $2.23 billion in investments in 2018. Why do you think a small start-up like Wilder Fields can succeed where so many have yet to earn a profit?
We started four years ago by investing our own resources. We were also working on a very limited scale in a small incubator space. I think those constraints pushed us to be more discerning about what we should tackle first. In that time, we developed an array of proprietary software and hardware, many of which have patents pending. And we refined a new paradigm for vertical farming, moving from the greenhouse model to lean manufacturing.
We also had the good fortune of starting up just as many first-wave indoor farms were closing down. So we looked at those case studies to understand what went wrong. And, what they could have done differently—what was needed to succeed. In fact, the founder of one of those first-wave farms now serves on our advisory board and really helped us identify the right blend of automation and labor.
With traditional vertical farming, the bigger you get, the more your labor costs increase. It seemed to us that the first generation of large-scale commercial vertical farms thought they could simply scale-up labor as they grew.
But we realized that operational excellence and efficiencies are essential to marry growth and profitability. It’s very hard to control a wide variety of factors using a 100 percent human workforce; for the most part, our industry has realized we need to recalibrate and find ways to automate.
This 135 thousand square foot former Super Target store in Calumet City, Ill. will soon be transformed into one of the world’s largest vertical farms. This former retail space will house 24 clean rooms with the capacity to produce 25 million leafy green plants each year.
So automation solves the problem? It’s not as simple as that.
Now the problem that the pendulum has swung a little too far in the other direction. The industry is almost hyper-focused on automation—as if automation is the answer to all of the vertical farming’s problems. It’s not. Remember when Elon Musk tried using too much automation to produce the Model 3? I believe he called his big mistake “excessive automation” and concluded that humans are underrated.
We believe well-run vertical farms, and the most profitable ones will achieve the right balance of human labor and automation. And that’s been our laser-focused goal from day one—to bring down labor costs in an intelligent way, in order to make vertical farming economically sustainable.
We also reduced costs by repurposing an existing structure rather than building a new one. We located a vacant, 135,000-square-foot Super Target in the Chicago suburb of Calumet City. What better way to farm sustainably than to build our farm in a sustainable way? Along with City leaders, we think we can help revitalize the depressed retail corridor where it is located.
To my knowledge, converting a big-box space to an indoor vertical farm has never been done before. So we also are creating a blueprint for how to impart new life to empty, expansive buildings.
We also will provide opportunities for upwardly mobile jobs and environmentally sound innovations, and produce food that promotes community health.
Vertical farming is a fairly new development. How does it fit into the history of modern agriculture?
I make an analogy with the automobile industry. Field agriculture is sort of like the combustion engine. It came first and was easy to scale up, making it available to more and more people. There were obvious downsides to it, but soon the whole world was using the combustion engine, so we kept churning them out.
But as the detrimental effects began to accumulate, we started asking ourselves how to reduce the negative impact. That’s when the auto industry came up with hybrid cars—they’re the greenhouses in this analogy—and while they were certainly a less bad solution, they weren’t really the solution.
And now we have the fully electric car and it has started outperforming combustion engines on many different levels—just as indoor vertical farming is now beginning to outperform field agriculture
Today’s business mantra holds that the more you automate, the more efficient you become. So why is vertical farming any different?
There are certain efficiencies that don’t require specialized robotics, especially if these tasks can be accomplished in other ways that sustain quality and reduce costs. For example, instead of our workers going among the plants to tend them, the plants come to the workers in an assembly-line fashion that requires fewer harvesters. So it’s always a balance between the investment in specialized machinery and the cost of the labor that it will eliminate.
And while there’s definitely room for automation, it doesn’t always require new specialized robotics. In our industry, plenty of mature automation already exists that can be used to good effects, such as automated transplanting and automated seeding: both employ proven, decades-old technology.
So when I see some other start-ups trying to reinvent these processes, it’s hard to understand. They design and build new, expensive equipment—something possible with an unlimited budget—but in fact, a more affordable, simple solution already is available.
Start-up costs are notoriously difficult to finance. How were you able to get off the ground? What advice would you have for others in the industry?
There’s no easy way to bootstrap from a small start-up to a large scale without that big infusion of capital. You’ve got to decide early on if you should try to secure venture capital from institutional folks or search out more, smaller checks from friends and family and accredited investors.
As I see it, venture capitalists look to the founders’ background and education more than a business model that needs to be tested. If you don’t have that pedigree out of the gate, it’s an uphill battle.
We chose to take a different path, one that has proven successful for me in the past. It’s one where I led a group of investors who acquired overlooked residential properties on Chicago’s South Side. We brought stability to neighborhoods and now manage a large portfolio of quality rental properties. There was no white paper when we embarked on that venture, but we shared a vision for revitalizing good housing stock.
I also tell people to explore equipment financing, which thanks to the cannabis industry has opened up more and more. It’s definitely possible to finance some of this equipment. That seems to be a good route as well.
How will vertical farming impact the types of the crops you grow?
Wilder Fields grows and will continue to grow a wonderful variety of leafy greens. Many will be new to people because they can’t be efficiently raised in a field. So we are building our product line around flavor and texture as opposed to supply-chain hardiness.
But remember, the indoor vertical farming industry is in its very early days. Soon we will have a whole new frontier of applications and crops to grow. Especially now that certain companies are offering indoor-specific seeds. We’ve seen this movie before. When greenhouse-style vertical farms first came on the scene, they used seeds that were really bred for the field. They were doing okay. But, as soon as seeds were bred specifically for that greenhouse environment, yield and quality shot through the roof.
Now that we’re on the cusp of having specialized seeds bred specifically for our purposes, I think we’re going to see that same leap in yield and quality as well.
Of course, your initial planning could not have factored in a global pandemic and ailing economy. How have the ramifications of COVID-19 affected Wilder Fields, and your industry at large?
This is a time for us to champion the benefits of indoor agriculture because vertical farming is doing really well. Any farms primarily serving restaurants obviously had a problem. Companies that pivoted away from restaurants have been able to reach consumers more than ever. They’re capitalizing on their indoor-grown—and therefore much cleaner—product.
Supermarkets are our primary market. With people cooking more at home and looking for fresher and healthier choices, they’re eating more leafy greens. This is another positive phenomenon.
The success of your model relies heavily on your proprietary technology. Do you have any plans to eventually license your innovations—to make them available to others, for a fee?
That’s a question we’ve been asked a lot, not only from our industry but also from the cannabis industry. We may revisit that opportunity in the future, but it’s not something we’re immediately considering.
Here’s why. When I first entered the industry in 2016, I noticed there were so many consultants. Many people were licensing technology, but none of them were actually using that technology to grow leafy greens at scale. They’re like the folks who sell the pickaxes and the shovels instead of mining the gold.
My perspective is, “You’ve got to venture into the mine to know what sort of shovel and pickaxe you need”; in other words, that’s how to understand what models to create for logistics and ergonomics and what tools are needed to make them work. I did not want our company to be one of those that are just sort of camping outside the mine and hawking its wares.
I think the only way we can develop a solution that’s worth its weight is by operating our own technology and equipment at scale. And I haven’t seen anybody do that yet. Is it possible that we license our technology somewhere down the road once we’ve actually proven it out at scale? Maybe; but it’s not part of our business model right now.
So, along those lines, when will Wilder Fields deliver your first produce—grown in your first full-scale commercial vertical farm—to grocers in metro Chicago?
We have committed to the end of the first quarter of next year: March 2021. In addition to this Indoor Ag-Con Q & A with Jake Counne, you can learn more about Wilder Fields visit the company website
Farm Boy Deal Just The Beginning For Indoor Farming Startup
Within six months of completing construction on its Cornwall growing facility, Fieldless Farms’ produce could already be found on the shelves of more than 20 Farm Boy stores across Ontario
Cornwall’s Fieldless Farms Eyes Expansion Into New Markets
BY: Adam Langenberg
October 6, 2020
“We want to scale this very large – we want to be a national success story,” says Fieldless Farms CEO Jon Lomow.
Within six months of completing construction on its Cornwall growing facility, Fieldless Farms’ produce could already be found on the shelves of more than 20 Farm Boy stores across Ontario.
But armed with an aggressive expansion plan to bring more hydroponically grown vegetables to Canadians, CEO Jon Lomow says his company is just getting started. Fieldless currently supplies two types of lettuce mixes – Northern Crunch and Ontario Sweets – grown in its Cornwall indoor farming facility. Lomow wants to rapidly expand both the types of crops the startup grows as well as its physical footprint.
Fieldless uses just 20,000 square feet at its Cornwall facility for its current operations, but Lomow insists that will increase quickly, with the CEO also harbouring ambitions of building new growing facilities in Toronto, Montreal and even the country’s west coast by 2025.“We want to scale this very large – we want to be a national success story. We want to play a major role in shortening supply chains for Canadians using controlled environment agriculture,” Lomow says.
He says Fieldless will significantly increase its capacity to grow leafy greens in the next one to three years, increasing the yield of both its current lettuce mixes and other crops such as romaine lettuce, spinaches, and basil. From there, there are plans to expand to smaller vegetable crops, including baby tomatoes, cucumbers, and peppers, which the company is just on the cusp of being able to grow economically, Lomow says.
Agricultural evolution
That kind of aggressive growth may seem overly optimistic to some, but Lomow says rapid change is all the company has known since its inception. Fieldless, which secured its first round of private capital funding in June last year, has gone from finishing construction on its Cornwall facility to providing almost 2,000 packs of lettuce mixes to customers each week inside six months.
Initially just selling products through Burrow Shop, the Ottawa-based online retailer Lomow co-founded, as well as Ottawa’s Massine’s Your Independent Grocer, Fieldless achieved one of its early goals in August when it signed a deal with supermarket chain Farm Boy to supply its lettuce mixes to 16 stores spanning from Cornwall to Kingston. That number quickly jumped when Farm Boy asked weeks later if Fieldless could supply seven stores in the Toronto area, a number that is set to grow again in coming weeks. Farm Boy’s origin in Cornwall and its “obsessive focus” on reducing the amount of fresh produce wastage made it the perfect first retailer to partner with, Lomow says.
That early growth gives confidence to Lomow, who notes that Canada – reliant on $48 billion of food imports each year – needs to significantly increase its food production in future years.
Lomow is also buoyed by what he predicts will be a “trillion-dollar evolution in the agriculture industry,” powered by falling automation costs and efficiency improvements in lighting technologies.
Fieldless Farms’ indoor growing plant in Cornwall.
The thing that sets Fieldless apart is that it’s not trying to do it all, Lomow says. Before launching, it signed a deal with an unnamed Canadian partner that handles the hydroponic technology side of the equation, leaving Lomow and his team to focus on the supply chain as well as perfecting the taste of its products and getting the products into stores.“We’ll deploy core technologies for our growing platforms and then we’ll innovate inside the gaps, because there are tons of gaps still in indoor farming,” Lomow says. “We just won’t be developing the core technology.”
“We decided we were way better off to focus our efforts on evaluating that technology, in making sure that we had the right technology as opposed to starting from scratch. If you go down the wrong road you’re kind of stuck there.”
The current technology platform sees lettuce crops grow from seedlings inside a 20-day cycle in a way that Lomow says strikes “the right balance between automation and manual labour,” but Fieldless’ technology-agnostic approach means it will partner with other technology companies to build other facilities and grow other crops in the future.
ORGANIZATIONS: Fieldless Farms Farm Boy'
PEOPLE: Jon Lomow. PLACES: Cornwall TAGS: Agri-business
Autogrow Expands Into Europe With New Role And New Farm Solutions
CEO Darryn Keiller says, “this expansion into Europe is counter-intuitive during a pandemic however innovation and crop production doesn’t slow down, and the challenges growers face haven’t disappeared because of COVID-19
29 September 2020: Autogrow has ramped up their activity in the Northern Hemisphere by establishing a new Sales Director Europe and U.K. role based in the Netherlands supporting their expanding customer base for new digital farming solutions FarmRoad® and Folium®.
CEO Darryn Keiller says, “this expansion into Europe is counter-intuitive during a pandemic however innovation and crop production doesn’t slow down, and the challenges growers face haven’t disappeared because of COVID-19. In fact, they have been exacerbated by the pandemic. We think now is the perfect time to introduce solutions that will help growers with productivity, gain greater economic benefits, and transform the market. Added to which, with cross-border restrictions and travel limitations likely to remain in place in the foreseeable future, establishing a local presence is the right move.”
“The Netherlands has been recognized by the World Economic Forum as a leader in efficient and sustainable agriculture and, after the United States, is the second-largest exporter of agriculture in the world. By establishing a role in the region, we create strong ties with growers and, like our partnerships in the United States, introduce our new digital farming solutions FarmRoad and Folium.”
Autogrow has been working closely over the past few months with customers and distributors in the region including some of the largest tomato producers. They are delighted to be working alongside Van der Voort, a member of the Prominent farming cooperative, who share Autogrow's focus on sustainable farming practices.
“We have been growing tomatoes for over 50 years and technology has always played a pivotal role in our success. With multiple farms and increasing production, we look for solutions that are leading the AgTech market. The work the Autogrow team are doing with sensor technology and farm management solutions is cutting edge and we are excited to be working together,” says Van der Voort Co-Owner, Joost Van der Voort.
Although Autogrow’s headquarters is based in New Zealand, large geographical distances have never hindered the organization from successfully operating on the global stage. Their endeavors also have the support of the New Zealand Government.
“It’s exciting to see AgTech innovation developed in New Zealand supporting growers here,” says Ariane Gonzalez, New Zealand Trade Commissioner to the Netherlands.
“New Zealand is recognized on the global stage for producing efficient and effective agricultural solutions that work in a range of climates, and this is another great example of that in action,” says Ms Gonzalez.
In addition, Autogrow has assistance from InnovationQuarter, the regional economic development agency for the Province of Zuid-Holland.
"The Netherlands, and Rotterdam - The Hague area specifically, is the worldwide center of horticulture. We are eager to attract and facilitate innovators with exciting solutions as Autogrow. They are a great addition to our region and the sector and support our regional economy. Next to that they benefit and contribute to strengthening our ecosystem of innovative companies in horticulture, impacting the societal challenge for feeding and greening the mega-cities of the future,” explains Chris van Voorden, Head of Internationalization at InnovationQuarter.
Autogrow is currently recruiting for the new role with the expectation to have someone in place over the next few months.
To see the advertised role - https://www.ceresrecruitment.nl/en/vacancy/sales-director-uk-europe/CEBI03123-en
For more information on Folium Network Sensor - https://autogrow.com/products/folium
For more information on Yield Prediction by FarmRoad - https://www.farmroad.io/
MEDIA QUERIES
Kylie Horomia, Head of Brand & Communications
(e) Kylie.horomia@autogrow.com
(m) +6421 733 025
(w) www.autogrow.com www.farmroad.io
Sales queries – sales@autogrow.com
About Autogrow
Autogrow leverages the power of technology, data science, and plant biology to provide indoor growers affordable, accessible, and easy-to-use innovation – 24/7, anywhere in the world.
Our hardware, software, and data solutions support growers and resellers in over 40 countries producing over 100 different crop types.
We are the experts in Controlled Environment Agriculture (CEA) and continue to stay ahead of a rapidly evolving landscape.
How Space-Saving Retailers Can Bring Fresh Farming Indoors
Farm.One’s latest “mini-farm” in a Manhattan Whole Foods sets a precedent for other stores
SEP 23, 2020
Melissa Kvidahl Reilly | Sep 28, 2020
Retailers who pride themselves on using their own homegrown ingredients in foodservice operations previously looked to a rooftop or back lot for garden space. But New York’s Farm.One is changing the game, making it possible for even the most urban locations to optimize space and offer open, transparent, and clean food production.
Previously known for its restaurant partnerships, the brand recently opened a “mini-farm” at the new Whole Foods Market Manhattan West location. The custom-designed, 32-square-foot structure holds 150 plant sites on three growing levels. These plant sites provide the store’s food and beverage preparers with freshly grown and harvested blue spice basil. This type of structure will be a big part of Farm.One’s strategy going forward, and it’s currently on the hunt for new retail partners.
Farm.OneMini-farms can offer as many as 700 varieties of hydroponic-grown crops. “A display farm can have multiple crops, or just one as is the case in the Whole Foods Manhattan West farm,” says Michael Chin, the company’s vice president of corporate development. And, Farm.One can build, install, and train stores on using farms anywhere in the world.
The bottom line? This isn’t the indoor farming of decades past. “Indoor farming has come a long way, especially in the last few years,” says Chin. “We can now produce fresh, clean and healthy food and ingredients profitably, and in an environmentally responsible way. Developments in technology and new techniques will continue to help make onsite production even more accessible to retailers and other businesses in the years to come.”
TAGS: RETAILER AND DISTRIBUTOR
Crops Can Now 'Tell' Growers When They Are Stressed
All plants use internal electrical, mechanical, and chemical signaling networks to coordinate growth, reproduction, and defense – and Vivent is the first company in the world to launch a commercial crop health diagnostic system based on plant electrophysiology
Vivent, the Swiss biosignals analysis specialist, has closed a multi-million Euro Series A funding round. This first external investment from Astanor Ventures, will be used to expand sales of a unique plant electrophysiology system that diagnoses crop stress in real-time.
All plants use internal electrical, mechanical, and chemical signaling networks to coordinate growth, reproduction, and defense – and Vivent is the first company in the world to launch a commercial crop health diagnostic system based on plant electrophysiology.
Electrical signals are some of the fastest to transmit information throughout a plant – from roots to shoots. Vivent’s crop diagnostics system, called ‘PhytlSigns’, uses AI to interpret signals linked to plant stress and diagnoses pathogens and pests prior to the appearance of any visible symptoms. Early diagnosis increases yields, improves crop protection effectiveness, and encourages the adoption of environmentally preferable protection solutions.
“Growers are using PhytlSigns to monitor their crops in real-time. This additional information is improving their decision-making on climate control, irrigation, and crop protection,” explains Carrol Plummer, founder, and CEO.
“Thanks to low-cost powerful machine learning, we can give growers real-time information that results in safer, higher-quality, and tastier food with less reliance on preventive spraying and more focus on environmentally preferable crop protection. We are very excited to be working with Astanor, a top deep-tech venture fund, with ambitions to enhance food quality, security, and sustainability.”
Christina Ulardic, Partner at Astanor Ventures and new Vivent board member, explains that “Vivent is pioneering a new relationship with the crops we grow. It is remarkable to be able to see precisely how plants are responding to stressors in the environment and to learn how we can use these signals to provide treatments which improve plant husbandry.”
Vivent is already working with top global crop protection companies and growers in several countries to improve yields and product quality. Customers value early diagnosis of plant diseases, particularly those in roots, which are hard to identify using other methods.
For more information:
Vivent
www.phytlsigns.com
Publication date: Mon 28 Sep 2020
Netled And SweGreen Collaborate In Sweden – Netled’s Vertical Farming System Delivered To In-Store Farm In ICA Focus Supermarket
Netled is specialized in developing and selling high-technology vertical farming systems
7th September 2020 by johannak
We have delivered a vertical farming system to our partner SweGreen’s project in Sweden. SweGreen has agreed on providing ICA Focus, one of Sweden’s biggest supermarkets in Gothenburg, an automated in-store farming solution. The greens are grown within the store and harvested directly off the shelf. This kind of in-store farm is first-of-its-kind in Sweden and globally unique in size as well as production capacity.
Netled is specialized in developing and selling high-technology vertical farming systems. Our mission is to enhance vertical farming by providing the best technology, expertise, and guidance for vertical farming projects and actors all around the world. The collaboration with SweGreen has been outstanding and produced valuable next steps towards hyper-local vertical farming.
Netled’s CEO Niko Kivioja comments: “We have followed the markets for ultra-local vertical farming for quite some time now and seen that our technology has clearly many opportunities for the current markets. This first project we have executed with and according to the wishes of our Swedish partner SweGreen is a great reference for us. Their business model, Farming as a Service, is elegant and easy to implement by supermarkets. Our team is proud to be partners with SweGreen, making fresh production close to consumers possible.”
Photos: SweGreen & Netled
More photos in SweGreen’s post on LinkedIn >
Watch a video by ICA Gruppen on LinkedIn >
Read more from the article in Gothenburg’s local paper Göteborg’s Posten (in Swedish) >
Facebook Twitter LinkedIn Share
Filed Under: NewsTagged With: agtech, autonomous farming, indoor farming, indoor farming technology, indoor growing, vertical farming, vertical farming expertise, vertical farming technology
Ocado Boosts Stake In Vertical Farming Specialist Jones Food Co
The online grocery giant bought a 58% stake in Jones Food Co in November 2019 and is understood to have exercised an option in that deal to grow its ownership to approximately 70% of the company
By Alec Mattinson, George Nott
28 August 2020
Ocado Has Upped Its Stake In Vertical Farming Specialist
Jones Food Company To Help
Support The Building of More Farms Next Year
The online grocery giant bought a 58% stake in Jones Food Co in November 2019 and is understood to have exercised an option in that deal to grow its ownership to approximately 70% of the company.
Ocado’s investment will help the indoor produce grower build three more farms in the UK before the end of 2021.
CEO and founder, James Lloyd-Jones told The Grocer: “Their investment is helping us very keenly understand all aspects of the systems we’re building, so we can make sure we’ve got price parity with field and greenhouse-grown, year-round.”
Scunthorpe-based Jones Food Co is Europe’s largest vertical farm operation, with its 5,000 sq m facility stacking up 12 metres high over 17 layers of produce.
Ocado invested in the company as part of a wider £17m bet on vertical farming that also saw it form a joint venture Netherlands-based Priva and US-based 80 Acres called Infinite Acres.
Ocado does not currently list products from its vertical farm operations on its site but hopes to build vertical farms next to or within its CFCs and Ocado Zoom micro fulfillment centres and has mooted plans to open as many as 10 within five years.
The farm’s first crop was harvested in November 2018 and was sold to food-to-go specialist Greencore.
“We want to provide any sort of crop, grown at a value anyone can buy,” Lloyd-Jones said. “I want vertical farming to become boring and not exciting and techy because the minute it’s boring we’ve cracked it.”
Topics: Finance Mergers & acquisitions Ocado Technology
The Underwater Habitat With A Greenhouse
Swiss designer Yves Behar has unveiled his design for French ocean conservationist Fabien Cousteau's underwater pressurised research station that will be "the ocean's equivalent to the International Space Station".
29-07-2020 | Msn News/ India Block
Swiss designer Yves Behar has unveiled his design for French ocean conservationist Fabien Cousteau's underwater pressurised research station that will be "the ocean's equivalent to the International Space Station".
Behar designed the station, which is called Proteus, for the Fabien Cousteau Ocean Learning Center. It will have its own greenhouse to allow scientists to grow their own food 18 metres under the sea near Curaçao, an island in the Caribbean.
Up to 12 researchers and aquanauts – scientists who remain underwater breathing pressurised air for over 24 hours – will be able to live in Proteus at a time.
Like the International Space Station, Proteus will allow scientists to collaborate and make new discoveries in an inhospitable environment.
"The research station will enable the discovery of new species of marine life, create a better understanding of how climate change affects the ocean, and allow for the testing of advanced technologies for green power, aquaculture, and robotic exploration," Behar told Dezeen.
Living underwater in a pressurised environment, rather than just diving in, allows scientists to spend far more time in the water and only decompress at the end of their assignment.
Proteus is the result of Behar's studio Fuseproject being commissioned by Cousteau, and his non-profit the Fabien Cousteau Ocean Learning Center (FCOLC).
"We needed to understand the constraints that come from building underwater and the challenges of living in an underwater structure," Behar said.
"The social isolation, the humidity, the lack of light and lack of exercise all needed to be addressed," he explained. "I learned about these challenges from Fabien, who had the record as the person who lived longest in an underwater habitat."
© Provided by Dezeen Proteus by Yves Behar
Cousteau broke the record, previously set by his grandfather, with a 31-day-long stay in an underwater laboratory off the coast of Florida called Aquarius.
Behar used Cousteau's experience to inform the design of Proteus, which has two levels connected by a curving ramp with pods set around the edges.
Circular-shaped main spaces are designed to encourage teamwork and social interaction for the scientists. Pods around the perimeter are designed to hold specific laboratories, bathrooms and areas for sleeping.
"Both circular floors are offset to allow as much natural light as possible through skylights and portholes, and are connected by a sloping ramp which creates the opportunity for physical activity," said Behar.
Social spaces will be kept separate from the more humid areas of the wet labs and the moon pool – the space in an underwater habitat where occupants can access the water directly in a protected environment.
© Provided by Dezeen Proteus by Yves Behar
An underwater greenhouse will allow occupants to grow their own food, allowing them to stay underwater for longer and cope more comfortably with the confines of a pressurised environment where no open flames for cooking are allowed.
Behar deliberately gave the underwater habitat a retrofuturist vibe in keeping with the way science fiction has traditionally imagined underwater living.
"Fabien and I looked at many exploratory designs from the 60s and 70s, a golden era of interest for the oceans pioneered by the Cousteau family history," Behar told Dezeen.
"We felt that Proteus could incorporate a new visual language based on modern hull and composite building technology, as well as be a state-of-the-art scientific environment while delivering a comfortable social interior space."
In keeping with the Cousteau dynasty's ocean conservation goals, Proteus will be powered by renewable energy. The habitat will use a mixture of wind, solar, and Ocean Thermal Energy Conversion (OTEC), a process that produces electricity using the difference in temperature between warm water on the surface and cold water from the deep ocean.
Cousteau will head to Curaçao to map the site as soon the borders shut due to the coronavirus pandemic open, hopefully in September. Behar estimates it will then take 36 months to build and lower Proteus to the ocean floor.
Behar hopes Proteus will be one of a series of marine habitats dedicated to research and conservation. As well as scientists, the designer hopes the facility will be able to welcome civilian visitors.
"Proteus is designed to be a scientific environment, but also to create that desire in people to want to visit," he said.
"For me, it’s a lot more exciting to visit Proteus than going to Mars."
Behar embraces technology with his designs, which include plans for 3D-printed houses for impoverished farmers and a wearable UV sensor to protect against skin cancer.
The post Proteus is an underwater habitat with a greenhouse designed by Yves Behar appeared first on Dezeen.
Source: Msn News/ India Block
Photo Provided by Dezeen
Are Automated Indoor Growing Facilities The Future For Fresh Produce?
Can growing veg in urban units scale up to meet demand, or is vertical farming a cottage industry focussed on leafy greens? Interest in Controlled Environment Agriculture is increasing internationally. Agri-TechE bring together Controlled Environment Agriculture technologists, producers and investors to discuss the current landscape and promising developments
CEA-Lite is an online debate on precisely that question,
taking place on 10th Sept.
Agri-TechE bring together Controlled Environment Agriculture technologists, producers and investors to discuss the current landscape and promising developments
Can growing veg in urban units scale up to meet demand, or is vertical farming a cottage industry focussed on leafy greens? Interest in Controlled Environment Agriculture is increasing internationally. In the UK autonomous growing systems have attracted funding from the Government’s Transforming Food Production program and tens of millions are being invested in a new training and demonstration facility; but the industry still has many challenges.
Agri-TechE is hosting an event “CEA-lite”, which is discussing the drivers for innovation and investment with leading entrepreneurs, producers, and investors on 10th September 2020.
Are new business models emerging?
Dr Belinda Clarke, Director of Agri-TechE says new models of food production are gaining traction. “Year-round intensive cropping of high-value crops becomes economically viable if the technology can scale. The Transforming Food Production call focussed on big, inspirational projects and this will help de-risk the technology, particularly around automating the monitoring and harvesting, which are so problematic for open field production.”
Jock Richardson of Growpura agrees: “A lot of operators have some great technology but to grow bigger means a linear (or worse) growth in costs. Scale-up is vital but there are operational challenges of how we grow plants at scale and at low cost.”
Could scaled-up vertical farms create economic value in vacant retail units?
“I have seen repurposing of buildings for CEA but location remains vitally important”, says Investor Kiryon Skippen of Capital Agri International, “landlords of these buildings need to be realistic in their rent demands and preferably have a real interest in the vertical farming business and work with it, taking the longer term view.”
Jock has seen uplift in interest in localised crop production, but as their system requires cleanroom conditions, refitting an older building could be too costly. “We’ve been talking to major retailers and its clear there is real interest in the use of hydroponics (growing in water) to fulfil the demand for fresh produce but of course it has to be at a competitive cost and offer a reliable supply,” he says.
The company will announce funding for a large training and demonstration facility in the coming days, which may provide over 200 jobs and internships in the South East Midlands area. “A vibrant hydroponics industry is essential in the UK. On the licensing front there has been interest from a number of countries particularly in the UAE and Asia and also for non-food products which we are progressing keenly,” Jock continues.
Can the industry look beyond leafy greens?
This international interest is a trend David Farquar, of Intelligent Growth Solutions, has also seen. He says; “Interest from NW Europe, the Middle East, and SE Asia is increasing the diversity of the food grown under secure conditions to reflect local diets and cuisine; encouraging the CEA industry to look beyond leafy greens and salads. For example, we have seen more demand for roots and fruits over recent months and interest in re-localizing as much of the food supply chain as possible.”
Phytoponics has recently raised £0.5M to develop its next-generation deep-water culture modules that offer a sustainable more profitable alternative to hydroponics substrates, such as rock wool and coir, and the company has started a series of strawberry trials with Total Produce. CEO Andy Jones, says the funding environment is challenging but that investment is there for companies with the right solutions.
He continues: “For growers, costs remain the big issue and one of the biggest is labor. New approaches need to give growers an economic advantage by reducing those costs.”
Are we swapping a labor shortage for a skills shortage?
However Max McGavillray of Redfox Executive says Brexit, and then COVID-19, has resulted in a marked increase in protected cropping roles as the UK adapts to a new normal: “We’re seeing individuals with plenty of cash establishing vertical farms but with very little experience in agriculture and foods, so there’s a real need for those with growth expertise in controlled environment agriculture.”
CEA Lite is an online event being held
on 10th September 2020 15:00 – 17:00.
Register your interest at bit.ly/ATEeEvents
About Agri-TechE – www.agri-tech-e.co.uk
Agri-TechE is a business-focused membership organization that is supporting the growth of a vibrant agri-tech cluster of innovative farmers, food producers and processors, scientists, technologists, and entrepreneurs.
Agri-TechE brings together organizations and individuals that share a passion for improving the productivity, profitability, and sustainability of agriculture. It aims to help turn challenges into business opportunities and facilitate mutually beneficial collaboration.
Photos:
1 – Credit: Growpura / Caption: Growpura is set to create a hydroponic farm, training and demonstration facility in Bedford, UK
2 – Credit: IGS / Caption: IGS has seen more demand for root vegetables and fruits in recent months as vertically farmed crops diversify
3 – Credit: IGS / Caption: Phytoponics has recently won funding and is undertaking commercial trials of its deep-water hydroponics modules
The Origins of Hydroponics
If one of you went to your grandfather and told him that people are growing plants and crops solely using water and have eliminated the soil use, he would've probably sighed and thought "Is this why we spend money on this nalayak's education?
Adhyayan Panwar | 22 Jun 2020
If one of you went to your grandfather and told him that people are growing plants and crops solely using water and have eliminated the soil use, he would've probably sighed and thought "Is this why we spend money on this nalayak's education?".
However, this is actually a practice. Plants can be and have been grown (for a while now) using almost no soil and “hydroponics” is the name given to this practice. Plants' roots are submerged in a water-based liquid, with extra nutrients and minerals added which are essential for the growth of the plants. In some cases, a medium is used so that the roots can hold the plants' weight and keep them upright. This medium is porous so that it can hold moisture and oxygen that the plants will require. The most popular media are clay, coir, brick shards, etc.
The solution contains all important nutrients present in appropriate proportions which ensure optimal growth. The main constituents are Nitrogen (N), Potassium (K), Calcium (Ca), Magnesium (Mg), etc. These are just some of the sixteen elements that are required by plants. Growing systems that don't use a medium are called liquid hydroponic systems which includes NFT (nutrient film technique, in which plants are put in slits in a tube through which nutrient solution is pumped), floating hydroponics, etc. When a medium is used, it's called aggregate hydroponics system which is further divided into open and closed systems. Rockwool is the most widely used medium in open system hydroponics.
Hydroponics is not, by any means, a new technology. Let's trace this practice right back to its origins.
THE ORIGINS:
The origins of hydroponics can be traced back to the ancient city of Babylon, where present-day Iraq is located. The Hanging Gardens of Babylon, one of the Seven Wonders of the Ancient World, is the first known example of soil-less growth of plants. This was around 600 BC. Later on, around 1100 BC, the Aztec Indians got creative with their growing techniques and created gardens that seemed to be floating. These “floating gardens” were called 'chinampas', which had a strong combination of roots and lashes, laden with sediment from lake-bottoms, providing nutrients to the crops and plantations.
Similar floating plantations were discovered by Marco Polo on his visit to China, which left him bewildered as he hadn't seen anything like this ever before. The first scientific perspective towards this soil-less technique is attributed to the Italian genius, Leonardo da Vinci, who observed that plants and crops needed to absorb minerals to survive. His findings were published after his death, that implied his famous branching rule: "all the branches of a tree at every stage of its height when put together are equal in thickness to the trunk".
THE JOURNEY:
In 1627, Sylva Sylvarum was published. Written by Francis Bacon, Sylva Sylvarum contained the earliest work on growing terrestrial plants with soil-less techniques. Major discoveries were made in the 17th century. Jean Baptista van Helmont, a Belgian chemist, discovered and proved that plants obtain the necessary minerals and nutrients (he called them "substances") from water. He performed the willow tree experiment, where the tree gained 164 pounds or 74.4 kg but the soil amount remained the same throughout the experiment. John Woodward performed the spear-mint experiment, which showed that plants grow better in impure water than to distilled water. The first standardized nutrient solution was created in the 18th century by Julius von Schaps and Wilhelm Knop which laid the foundations of hydroponics as we know it today. This solution made it possible to grow roots without any medium. Knop went on to create yet another solution, which is still in use today.
The word “hydroponic” was first used in 1937, coined by Dr. William Frederick Gericke, aptly known as the “father of hydroponics” (he made news when he was able to grow tomato vines more than 7-meters long just using mineral-nutrients solutions, right in his backyard!). The word is a combination of the Greek words “hydro” (meaning water) and “ponos” ( meaning labour). This means water-work, literally. After leaving his University position, Gericke wrote and published ‘Complete Guide to Soil-less Gardening’ in 1940. Then came into the picture Dennis R. Hoagland, who created a nutrient formula that provided the plants with all the nutrients essential for growth and catered to a large diversity of plant species. The Hoagland solution still serves as the basis for most of the nutrient solutions that are being utilised even today. Alongside Daniel I. Aaron, Hoagland published ‘The Water Culture Method for Growing Plants without Soil’, which is considered the most important text in hydroponics culture. There are accounts of the US Army using hydroponics to grow fresh food for the troops stationed in the infertile Pacific Islands, during World War II.
As the hydroponics technology picked up the attention across the world and the usage grew, it’s inevitable commercialisation took place. Lawrence Brooks founded ‘General Hydroponics’ in 1976. Now, even after 40 years, GH remains one of the leaders of continuously expanding the market of hydroponic mineral-nutrient solutions. In 1982, a new area called ‘The Land Pavilion’ was opened in Disneyworld’s EPCOT Center, where a ride goes through “gardens of tomorrow”, which are grown using hydroponic technology.
When you think about hydroponics, aside from the typical applications of the practice, you may also think about its applications in space and space travel. NASA is actually quite heavily invested in the practice of hydroponics. A research department completely dedicated to hydroponics and bio-farming was developed by NASA where they researched the growing of plants in extreme environments and hydroponic technology was a big player in the research.
THE PRESENT:
There’s no other way to put it, hydroponics is thriving. As per a recent Hydroponics Market Research Report, it is projected that the hydroponics market will be worth $27.29 billion by the year 2022. Currently, almost 90 percent of lettuce and tomatoes that are being grown in the US and Canada are being grown using hydroponics. As the population of the world keeps growing, hydroponics becomes a more viable substitute for traditional farming. Hydroponically grown crops take only 25 percent of the area used by traditional soil growing, for the same amount of crops. We all know the harrowing threat of water scarcity in the coming years. With hydroponics, water usage can be cut down by 90 percent. This is just another reason why hydroponics is booming. Zero pesticides and herbicide involvement, growth rate twice as fast as traditional agriculture, nutrient solutions with perfect pH eliminating soil worries, and the list is never-ending, which is why hydroponics is need for the present.
Countries have already started dedicating acres of lands for commercial hydroponics, including 10,000 acres in Holland, Israel reserving 30,000 acres, Australia and New Zealand having 8,00 acres between them and Canada with hundreds of acres of land for large-scale commercial greenhouses, mainly growing tomatoes, peppers, and cucumber. In India, hydroponics is still a pretty new technology but initiatives are being taken. Many startups have taken it upon them to make hydroponics more popular, affordable and accessible. These startups use new technologies like IoT (Internet of Things), data analysis, etc to perfect the procedure and make it as efficient as possible.
THE UNKNOWN:
While we don’t know what the future holds exactly, we can make a couple of calculated predictions as a society. Statistics and reports already indicate that hydroponics will have a special place in the coming years. As the concept of space travel and exploration becomes closer to reality with each passing day, hydroponics will find a place in long flights across space, where agriculture is restricted due to area and soil-weight limits. Similarly, when Mars colonisation does become a reality (Elon, we are looking at you) we won’t have to suffer the infertile and barren lands of unexplored planets since hydroponics will allow basic levels of agriculture, which is said to be the foundational step of every human civilization. Several companies across the globe have also begun providing ways to grow vegetables at home as well. As technological advances are being made, it won’t be surprising to see people growing their own assortments of vegetables in their own houses. There are already plenty of homes today that have home hydroponic installations.
With the drastic need for more and more land for the ever increasing urban sprawl, which reduces the land available for agriculture, hydroponics will eventually creep into our daily lives and get infused with our culture. Startups, commercial giants and space agencies have already begun traversing into this field. So, don't be surprised, when in the coming years every edible thing you see has hydroponic origins and your neighbor in a high-rise skyscraper is a successful farmer.
Adhyayan Pan
Microgreens Launched By Vertical Farmer April Sun
Just in time for this year’s winter season, vertical farmer April Sun launched its range of sustainably grown microgreens from its new commercial-sized micro-farming facility in Melbourne
Food & Beverage | June 4, 2020
Just in time for this year’s winter season, vertical farmer April Sun launched its range of sustainably grown microgreens from its new commercial-sized micro-farming facility in Melbourne.
With a philosophy of true sustainability and paired with cutting-edge technology, the local farm wants to provide the community with a range of nutrient-packed microgreens available year-round to their nearby community.
Co-founder Darren Nichol, April Sun visionary of Australia’s cleanest and highest nutritional food supply who has a wealth of knowledge due to his agricultural background, says, “This is a particular focus of the Darebin Council. They have an actual goal to increase food production within its municipality.”
These super foods are grown without pesticides and utilise 95 percent less water than traditional farming methods due to a hydroponic based (closed loop) watering system. Co-founder Ty Dickson, April Sun technologist and facility designer, said this system guarantees the plants do not receive too little or too much water.
“The watering targets each individual plant or root system and is drained back to the holding tanks,” he said. “Traditional farming methods would see water being lost to the ground and you would use more water to achieve the same level of fertigation without the ability to recapture the excess.”
With custom-spectrum lights developed in-house, the microgreens are grown in their ideal conditions, allowing for year-round production and minimal waste.
“We use a combination of specific wavelengths of blue, red, far red and full spectrum light to stimulate the chlorophyll A and B of the plants, while giving the right signals to ensure proper colour, increased nutrients through stress and, above all, a very healthy plant,” Dickson said.
“We are a non-single use plastics company; we opt for PLA compostable packaging. Our facility uses the highest efficiency components and equipment available. We do run on electricity, although we are engaging in using 100% renewables, and are in preliminary talks with the Darebin Council to implement 100kW of solar panels on our warehouse roof.” said Dickson.
In traditional farming, external factors such as drought, pollution, soil erosion and more can impact crop success. However, the world of vertical farming is “most often done indoors in a controlled environment”, he adds. “Vertical farming when done sustainably has less impact on the environment, there are significant reductions in water usage, land usage, gas usage and many other resources. This is all achieved whilst controlling the indoor growing environment with minimal impact to it outside.”
“By controlling every factor in the plant’s environment, you end up with a high-quality product on a number of levels,” said Nichol.
“We can grow to a timeline and the removal of variables such as the weather allows us to more accurately forecast and grow to our customers’ demands. This can reduce the amount of waste and also increase consistency of supply to customers. This is a huge problem for traditional farming and is the cause for the large price jumps and shortages of produce on the market.”
To see more, click here.
This Vertical Farm Lets You Subscribe to Your Own Plot of Indoor-Grown Greens
At a new vertical farm inside a warehouse in San Jose, consumers can subscribe to their own “plot,” where kale and mizuna grow under LED lights. It’s the 21st-century version of a CSA: Greens grow in towers with no pesticides and almost no water—and when they’re harvested, they’re delivered directly to consumers living within a 20-mile radius
06-11-20
For $149 a month, Willo will manage a spot in an LED-powered indoor farm for you, delivering you enough greens for five salads a week.
At a new vertical farm inside a warehouse in San Jose, consumers can subscribe to their own “plot,” where kale and mizuna grow under LED lights. It’s the 21st-century version of a CSA: Greens grow in towers with no pesticides and almost no water, and when they’re harvested, they’re delivered directly to consumers living within a 20-mile radius.
Willo, the startup behind the farm, wants to push people to adopt healthier eating habits. “Diet kills more people than anything else every year in the United States,” says Samuel Bertram, Willo co-founder and CEO. The promise of indoor farming—that it’s possible to grow produce in any climate at any time, deliver that food locally while it’s at the peak of freshness, and eventually sell it for less than conventionally grown greens—is something that he thinks could help convince more people to eat vegetables regularly.
[Photo: Willo]
The startup is one of several that are developing technology to make warehouse-grown kale and lettuce compete with greens grown in fields, both to deliver the freshest possible produce and to shrink the environmental footprint of food since indoor farming uses little water, less land, and avoids the need for pesticides. Nearby, a startup called Plenty has developed a fully automated system for planting, growing, and harvesting produce. On the East Coast, startups like Bowery and Aerofarms are developing technology of their own.
[Photo: Willo]
Willo has its own approach, growing plants aeroponically—meaning that the roots are exposed in the air and sprayed with a mist of water—on vertical walls, which Bertram says is “faster and more resource-efficient than our hydroponic and horizontal-plane counterparts.” The company has also tweaked other parts of the system; LED lights, for example, can be robotically moved around the farm to provide the right spectrum of light to each plant at any given time. Each plant is monitored by cameras and sensors that help the company learn how to improve growth and nutrition over time.
[Photo: Willo]
The startup’s business model is also unique. Rather than relying solely on sales to restaurants and grocery stores, it’s betting on a subscription model. Consumers will pay $149 a month for their own plot, where the farm will grow the salad greens and herbs that a particular consumer has ordered, and will get five weekly custom salads. A $99 subscription delivers five salads every two weeks. (The cost will go down over time; the company claims that the technology it has designed makes the production system cheaper than other vertical farms.) Because the company wants to reconnect people with the origins of their food, customers will be able to take tours of the farm. The startup also plans to connect subscribers with an online portal that shows time-lapse images of their plot, with data about the plants and nutrition.
[Photo: Willo]
The new farm in San Jose will begin making deliveries to new subscribers in August. It hopes to expand to other West Coast cities, and eventually to cities globally. “As soon as we show farm-level profitability, which is what we expect to show in the next 12 months, we can plant these facilities in every city in the United States and around the world to feed people locally sourced, fresh and sustainable nutritious product,” Bertram says. “That is the goal.” Other indoor farming startups have made similar promises about rapid expansion that haven’t yet materialized. But as the technology continues to improve, that may begin to change.
ABOUT THE AUTHOR
Adele Peters is a staff writer at Fast Company who focuses on solutions to some of the world's largest problems, from climate change to homelessness. Previously, she worked with GOOD, BioLite, and the Sustainable Products and Solutions program at UC Berkeley, and contributed to the second edition of the bestselling book "Worldchanging: A User's Guide for the 21st Century."
Dr. Anu Rangarajan From Cornell University Joins The GLASE Webinar Series - Thursday, June 18 - 2 PM EDT
CEA Workforce Development Study: What Makes a Successful Indoor Farmer Operations Manager?
June 12, 2020
The National Science Foundation-funded research project entitled “Strategic FEW (food, energy, water) and Workforce Investments to Enhance Viability of Controlled Environment Agriculture in Metropolitan Areas” (CEA Viability in Metro Areas) seeks to help the CEA industry develop a skilled workforce that will allow it to scale.
As part of this project, Anu Rangarajan’s team has conducted research to understand the workforce/labor needs of the broader hydroponics industry (greenhouse and indoor vertical farms). The project has surveyed dozens of stakeholders. In 2019, twelve industry members were brought together in an intensive Designing a Curriculum (DACUM) workshop whereby participants reflected on the skill sets required to be an Indoor Farm Operations Manager.
The chart is currently being reviewed by peer growers worldwide, who are being asked to respond to how important each skill set is and how frequently it is conducted. Based on stakeholder input the chart will be used as a starting point for prioritizing training modules.
Next, a deeper analysis of each skill will be conducted in order to translate this research into a teachable vocational curriculum. In this presentation, we will share preliminary research findings, outline our ongoing efforts to develop a solid empirical basis for CEA workforce development training programs and invite GLASE webinar audience members to participate in this important study.
Title: CEA Workforce Development Study: What Makes a Successful Indoor Farmer Operations Manager?
Date: June 18, 2020
Time: 2 p.m. – 3 p.m. EST
Presented by: Anu Rangarajan and Whyte Marschall
Click here to register
Erico Mattos
Executive Director
Greenhouse Lighting and Systems Engineering (GLASE)
Phone: +1 302-290-1560
Email: em796@cornell.edu
TAGS Business GLASE Greenhouse Greenhouse Technology Indoor Farming Technology
Vertical Farming webinar
Special thanks to our Industry partners
U.S. Department of Agriculture Secretary Sonny Perdue Visits Kalera
On Monday, June 8th, technology-driven vertical farming company Kalera welcomed Secretary of Agriculture Sonny Perdue to its Orlando facility
Perdue Visits Kalera For a Behind-The-Scenes Tour With Top Kalera Executives
June 09, 2020, | Source: Kaleraphoto-release
Secretary of Agriculture Sonny Perdue (l) stands next to Kalera CEO Daniel Malechuk (r) during a visit to the vertical farm's Orlando facility.
ORLANDO, Fla., June 09, 2020 (GLOBE NEWSWIRE) -- On Monday, June 8th, technology-driven vertical farming company Kalera welcomed Secretary of Agriculture Sonny Perdue to its Orlando facility. Secretary Perdue was greeted by Kalera’s top executives, including CEO Daniel Malechuk and CTO Cristian Toma, who, along with other staff members, escorted him on a private tour of the facility’s proprietary technology, providing a glimpse at the future of farming. Key takeaways included how Kalera:
eliminates the use of chemicals and removes exposure to pathogens through cleanroom technology.
is able to supply an abundance of produce locally, eliminating the need to travel long distances when shipping perishable products.
ensures the highest quality and freshness by delivering product to customers within hours of harvest rather than days or weeks
Is able to reduce water consumption by 95% compared to field farming.
During the tour, Perdue was able to sample the lettuce Kalera grows at the Orlando facility. Some of his positive reflections about the tour can be read in this Fox 35 Orlando news piece, “USDA Secretary visits Central Florida hydroponic farm, calls it a 'very innovative food production system'.”
Kalera recently announced its new Atlanta facility, which will open in early 2021. While Kalera’s Orlando farm, which Perdue visited on Monday, is currently the highest production volume vertical farm in the Southeast, the new Atlanta facility will be more than double the size and generate approximately 75 jobs for the local community. As was the case in Orlando, Kalera is able to quickly open its newest growing facility in Atlanta as a result of a streamlined design and construction process, further illustrating its ability to rapidly scale and expand its vertical farms.
After the tour, Daniel Malechuk, CEO of Kalera, addressed Secretary Perdue in front of assembled employees and press, saying, “Thank you very much on behalf of the Kalera staff for your time, and visiting us to discuss the future of agriculture, which is clean, healthy, sustainable, local and fresh. We look forward to helping the US stay on the cutting edge of agricultural innovation and feeding a hungry world with fewer natural resources.”
In addition to its R&D center, Kalera opened its first commercial vertical farm, the HyCube growing center, on the premises of the Orlando World Center Marriott to bring fresh, local produce to the hotel’s visitors and customers. In March this year, it announced the opening of its second facility in Orlando. The Atlanta facility is the third farm in Kalera’s portfolio, and will soon be joined by more in the United States. Kalera is currently sold in over 160 Publix stores.
About Kalera
Kalera is a technology-driven vertical farming company with unique growing methods combining optimized nutrients and light recipes, precise environmental controls, and cleanroom standards to produce safe, highly nutritious, pesticide-free, non-GMO vegetables with consistently high quality and longer shelf life year-round. The company’s high-yield, automated, data-driven hydroponic production facilities have been designed for rapid rollout with industry-leading payback times to grow vegetables faster, cleaner, at a lower cost, and with less environmental impact.
Kalera’s shares are traded on NOTC, a marketplace for unlisted shares managed by NOTC AS, which is owned 100% by Oslo Børs ASA, the Oslo Stock Exchange.
Further information about the company may be found at www.kalera.com and www.kalera.com/investor along with an introductory Kalera film: www.youtube.com/watch?v=2Crpph9w0hE
Kalera Contact:
Daniel Malechuk, CEO
Phone: +1 407 574 2382
Email: dmalechuk@kalera.com
Shenandoah Growers - Bringing Nature Indoors
At Shenandoah Growers, we believe in the power of technologically-controlled indoor environments to sustainably transform the future of fresh produce. As the only large scale USDA Certified Organic soil-based indoor growing system in the United States, we are passionate about leveraging cutting-edge science and technological innovation to ensure that our customers receive the freshest, healthiest, most affordable organic produce possible year-round.
Working with (not against) nature to create an optimal environment for plants to thrive
What Sets Us Apart?
At Shenandoah Growers, we believe in the power of technologically-controlled indoor environments to sustainably transform the future of fresh produce. As the only large scale USDA Certified Organic soil-based indoor growing system in the United States, we are passionate about leveraging cutting-edge science and technological innovation to ensure that our customers receive the freshest, healthiest, most affordable organic produce possible year-round. With twelve growing locations across the country, we couldn’t be prouder to provide organic, local produce to over 18,000 stores every day.
Why Indoor Controlled Agriculture?
There’s nothing quite like the great outdoors—at Shenandoah Growers, we know there’s something better. Our LED-powered indoor bioponic growing platform increases yields and reduces waste, enabling us to make fresh herbs available year-round across the country. Plus this proprietary system is environmentally conscious, conserving water and land, and avoiding harmful pesticides.
How Do We Do It?
Some call it “Know-How”. We call it “Grow-How”
Our proprietary bioponic growing process mimics nature but enhances it with carefully controlled temperatures, light levels, humidity, and water exposure. And because we use just what we need to keep our plants healthy and no more, we conserve valuable environmental resources and set our industry up for a sustainable future.
Indoor Farming: How Can You Ensure Success?
Any business can fail for any number of reasons, but indoor farming is an incredibly delicate organism that depends on many disparate factors being perfectly aligned and in balance
Any business can fail for any number of reasons, but indoor farming is an incredibly delicate organism that depends on many disparate factors being perfectly aligned and in balance. This increases the risk of failure for those unaware of the number of plates that need to be kept spinning in perfect time. This list is not definitive but gives you a good idea of the most common mistakes to avoid.
1. Avoid a Trial and Error Approach to Design
There are multitudes of factors that are naturally managed and balanced with indoor farming. The sun cannot be changed, irrigation to every plant is different as weather patterns can change from moment to moment and even the nutrition in the soil can vary across the area of the field. Planning your farm therefore gives you the ultimate control but also dramatically increases the variables that you can and must consider.
These variables start with the facility’s very layout, such as the size of growing space, plant distribution, airflow and more. Additionally, without having the right models in place to determine the exact light recipe and combination of CO₂, nutrients and water required to grow a successful crop, growers can find themselves wasting time and money on testing phases to try to maximize yield and revenue. Once you have developed a model for your vertical farm, you should then put it through a testing phase on a smaller scale to ensure it is viable.
2. Pick the Right Crop
It’s far easier to develop a profitable and scalable facility if you know the needs of your crop inside and out. That ideally means specializing in one type of crop that you can design your facility around, electing the right growth spectrum and studying that particular plant’s biology to better understand how to optimize irrigation, nutrition, air flow, CO₂ concentration and propagation in order to maximize elements such as taste, nutritional content, visual appeal, potency or shelf life.
Too many growers have tried to hedge against perceived risk by trying to grow multiple crops. By default, it is extremely difficult to have one installation that is optimized for a wide variety of plants, and therefore the returns from each crop are lower than they could have been. The facility then may have to suffer through downtime as the technology is tweaked and optimized for the next crop — eating into profitability and adding unnecessary costs.
3. Location, Location, Location
The old adage that location is half the battle has never been more relevant than in vertical farming today. Vertical farms have a key advantage in their ability to be located close to their customer, whether they are selling to food processors, supermarkets or local shops. Removing the vast transport logistics associated with today’s food supply chain slashes costs and helps appeal to an increasingly conscientious customer. The lack of transport costs also helps counter the higher production costs resulting from higher energy and labor inputs.
At city planning level, there are also many advantages of co-locating a vertical farm with other facilities such as office buildings, shops or residences — which could draw the vertical farm’s excess heat to reduce demands on other sources of energy.
4. Simplify Your Business Model
Proximity to customers and the ability to produce crops year-round at a sustainable rate is a strong advantage in the market, whether you’re growing for the food or pharmaceutical sectors. Therefore, consider the opportunities available through establishing exclusive contracts with customers at a fixed rate that will offer more financial security as you build your business.
5. Be Realistic About Operational Cost
Setup and fit-out costs represent a high initial outlay for any indoor farming entrepreneur, but the ongoing operational costs (energy, labor, inputs, maintenance, etc.) are also significant. Businesses not only need to find creative ways to mitigate these risks (e.g. growing through the night when energy tariffs are lower and the outdoor climate is cooler to assist HVAC systems’ efficiency), but also consider the cost-benefits of different configurations and process flow.
6. Set Prices Based on What Consumers Will Pay
At the 2017 inaugural AgLanta Conference11, PodPonics’ CEO admitted that the company missed out on higher potential margins as it priced its crops to compete with conventional growers, ignoring the price premium that food traceability, pesticide-free growing and local production can increasingly attract from consumers in some markets.
7. The Skills Gap
In many cases, those who have embraced the promise of indoor farming have not been traditional growers but rather tech entrepreneurs, engineers or hobbyists. Vertical farming requires a unique mix of skills to be successful: big data scientists, systems integrators, project managers, engineers, growers and plant scientists all have a role to play in addition to the core functions that any business needs to be successful (financial strategists, marketing and business development, etc.). From the leadership perspective, experience at replicating and scaling a business is critical. Ignoring any one of these functions leaves a serious gap in business capability that could undermine the overall success of the operation.
8. Remember What You’re Selling
In a bid to capitalize on the new technology and growth models offered by vertical farming, some growers have forgotten that their primary focus should be on growing and selling the highest quality food. Instead, they have tried to recoup their investment by trying to commercialize their vertical farm’s technology, process and methodology. Unfortunately, as we have seen, every vertical farm is different with potentially very different needs. The trick is to not to try and do many different things at once, but instead keep a clear focus on doing one thing as well as possible.
Source: www.currentbyge.com/ideas
USA: Nebullam Launches Farm-To-Door Program For Central Iowa Residents
“In the span of six days we decided to pivot from selling to restaurants to going from farm-to-door, offering fresh lettuce and microgreens direct to consumers weekly or bi-weekly,” said Clayton Mooney, co-founder of Nebullam. “We put up an e-commerce site, got everything set up, and launched.”
Screenshot from the shop section of Nebullam's website.
Nebullam, an emerging indoor farming company based in Ames, has launched a delivery service of its fresh food products to Central Iowa residents, to ensure that Iowans have access to locally grown lettuce, herbs, and microgreens during the COVID-19 pandemic, as well as year-round.
“In the span of six days we decided to pivot from selling to restaurants to going from farm-to-door, offering fresh lettuce and microgreens direct to consumers weekly or bi-weekly,” said Clayton Mooney, co-founder of Nebullam. “We put up an e-commerce site, got everything set up, and launched.”
Since pivoting, Nebullam has had its best month of revenue to date and is growing at almost ten percent month over month, Mooney told Clay & Milk.
“In some ways, the change has really been a blessing in disguise for our business model,” said Mooney.
Nebullam was founded in 2017 with a primary focus of improving indoor farming technologies to help indoor farm owners and operators become profitable, faster. Today, Nebullam owns and operates its own indoor farm within the Iowa State University Research Park.
“Prior to COVID, about 3/4 of Nebullam’s produce was going to Central Iowa restaurants with the remain 1/4 going to grocery stores,” said Mooney. “In early March, we began talking to friends on the west coast who are indoor farmers about restaurants shutting down there and felt like it was inevitably going to happen here as well.”
Nebullam’s indoor farm produces red butterhead lettuce and microgreens such as broccoli sprouts and micro radish. Through Nebullam’s site residents from Ames, Boone, Nevada, Ankeny, and Des Moines can subscribe to have fresh produce delivered directly to their door, every week or every other week. In addition to Nebullam’s website options, you can always find fresh Nebullam lettuce and broccoli sprouts at Wheatsfield Co-op in Ames.
“We do have two restaurant partners that have come back online. When our other restaurant partners are able to get back up and going again, we’ll have the production to meet their weekly needs,” said Mooney. “As for the direct-to-consumer, we’re pretty excited to continue to pursue that.”
VIDEO: The Future of Farming & Investing in Land - w/ Cubic Farms CEO Dave Dinesen
CubicFarms has developed and patented some of the most advanced automated growing machines for Fresh Vegetables and Nutritious Animal Feed that enable commercial-scale indoor farming, anywhere on earth
May 28, 2020
The Covid-19 pandemic exposed fragility in supply chains, such as labour shortages, disruptions in the packing and transportation sectors, and increasing uncertainty in the domestic and international markets. CubicFarms’ automated growing systems have emerged as a key solution to overcoming these challenges by allowing growers to localize food production and provide their markets with fresh produce and nutritious livestock feed reliably and consistently. What does this do to opportunities for land investment?
Speaker Bio:
Dave is the CEO of CubicFarms, one of the world’s leading Ag Tech companies that develops “Technology to Feed a Changing World”. CubicFarms has developed and patented some of the most advanced automated growing machines for Fresh Vegetables and Nutritious Animal Feed that enable commercial-scale indoor farming, anywhere on earth. Dave leads growth at CubicFarms and since inception, has raised over $23MM in capital.
Dave is the former CEO and founder of BackCheck, which became one of the world’s top ten largest background screening companies, where he advanced the company from a start-up to an industry-leading company operating on three continents with over 500 employees.
Recorded: Thursday, May 28, 2020,
**The information provided in this webinar and accompanying material is for informational purposes only. It should not be considered financial or professional advice.
You should consult with a professional to determine what may be best for your individual needs. http://addyinvest.com/
The First Online Dashboard For Aquaponics
“We’re about empowering people to be the best aquaponic growers possible. Tech is what gives people the tools to do awesome things.” - Jonathan Reyes, CEO, and Co-founder of Aquaponics AI
Aquaponics AI, a US-based aquaponic technology research company, just unleashed their software into the wild. It’s the system every aquaponic grower has been waiting for.
It has traditionally been difficult to get started in Aquaponics because of the steep learning curve but they are making it easy to get started and maintain a system with features like a project template that gets your system running with recommended maintenance schedules by big players in Aquaponics.
They’re bringing innovative usage of artificial intelligence and big data to Aquaponics for the betterment of the global aquaponics community. Their vision is to unleash your Aquaponic growing powers. You’re the beneficiary of high-quality produce and revenue streams created from your system.
In addition to being the forerunner in Aquaponic technology, they also have invaluable libraries for fish, plants, and diseases, as well as calculators for managing your system.
“We’re about empowering people to be the best aquaponic growers possible. Tech is what gives people the tools to do awesome things.” - Jonathan Reyes, CEO, and Co-founder of Aquaponics AI
You can see the latest developments on their website https://aquaponics.ai alongside invaluable resources and calculators that are available for free.
Digital Image Processing And Analysis For Plant Phenotyping
LemnaTec, based in Aachen, Germany, has been developing hardware and software for plant phenotyping since 1998
LemnaTec, based in Aachen, Germany, has been developing hardware and software for plant phenotyping since 1998. These systems use digital image processing for applications in research and development, which are used in breeding, science, agro- and biotechnology, as well as in the seed industry.
"Digital tools are the key to modern phenotyping", says Fred Corbett with LemnaTec. "Mendel's visual inspection of pea crosses has enabled groundbreaking discoveries in genetics and, even in the 21st century, phenotypic data is essential for plant research and breeding. Today, computer-aided analysis and machine learning are used for solution-oriented phenotyping."
In addition to tailor-made solutions for complex research questions - e.g. large installations for greenhouses and open field systems - LemnaTec supplies a range of products for routine applications in phenotyping and for seed testing.
"The classical "workhorses" for digital phenotyping are imaging sensors, in particular, high-resolution industrial cameras as known from other areas of image processing. These provide data on the size, shape, and color of the test objects", Fred explains.
"For the analysis of physiological properties, more complex sensor systems are also gaining in importance, such as fluorescence cameras that, in combination with special lighting and filters, provide data on the performance of the photosynthesis system of plants. Application-oriented analysis systems also include methods for evaluating plant diseases and pests."
Digital seed test
The digital seed test developed by LemnaTec is an application derived from phenotyping, which provides valuable services in the seed industry and for gene banks in determining germination capacity, germination quality, and seed quality.
"The experience gained from numerous large-scale installations and laboratory systems has been incorporated into a new product line that provides image recognition solutions for reliable documentation, analysis, and evaluation of data", Fred shows.
SeedaixpertThe Seedaixpert belongs to the new Aixpert product series and is suitable for paper-based germination and seedling emergence tests. "Unified imaging and analysis make data reproducible and standardizable. Modern image processing algorithms including machine learning provide reliable and comprehensive data, the quality and information content of which exceeds the classical visual assessment. In addition, the digital image data can be retrieved at any time so that complete documentation of the samples is guaranteed."
The Seedaixpert offers extensive accessories.
For more information:
Fred Corbett
LemnaTec GmbH
Nerscheider Weg 170
52076 Aachen, Germany
Phone: +49 2408 9818514
E-Mail: fred.corbett@lemnatec.de
Internet: http://www.lemnatec.com
Publication date: Tue 19 May 2020