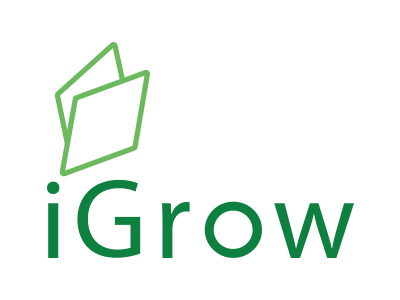
Welcome to iGrow News, Your Source for the World of Indoor Vertical Farming
Signify Expands Philips Horticulture Research Partner Network In China By Adding Yunnan AiBiDa Greenhouse Technology Co., Ltd. To Serve The Chinese Floriculture Business
The partnership will further promote the use of LED applications in floriculture production in greenhouses. "We need high quality products for our customers in China. Philips Horticulture LED lighting technology is what we need for our greenhouse crop production," said Li Qin, founder and CEO of Yunnan AiBiDa."
On Aug. 28, 2020, Signify signed a cooperation agreement with Yunnan AiBiDa Greenhouse Technology Co., LTD, to formally become a research partner using Philips GreenPower LED products as supplementary lighting for its greenhouse floriculture production improving crop growth efficiency and quality in western China.
"We are pleased to welcome AiBiDa to our horticultural network,” said Udo van Slooten, Business Leader Horticulture at Signify. "Yunnan AiBiDa is committed to integrating advanced European Horticulture technology and facilities to China’s developing floriculture market. AiBiDa’s flowers such as cut rose enjoy a high reputation in the Chinese market. Signify will provide AiBiDa with advanced horticulture LED lighting technology and services to improve the quality and yield of their greenhouse crops.”
The partnership will further promote the use of LED applications in floriculture production in greenhouses. "We need high-quality products for our customers in China. Philips Horticulture LED lighting technology is what we need for our greenhouse crop production," said Li Qin, founder and CEO of Yunnan AiBiDa."
Signify and Yunnan AiBiDa have already cooperated in the Linxia International (Sino-Dutch) Floriculture Port project located in Gansu province. In May this year, a three-party joint laboratory (Signify, Baiyi Group, and Yunnan AiBiDa) was officially set up at the project location. Meanwhile, Yunnan AiBiDa was awarded as ambassador of Philips Horticulture LED lighting solutions globally and locally in China’s Floriculture market. Signify will continue to expand its partner network in China to better serve the Chinese Horticulture market with innovative Philips grow lights and services.
A Whole Season of Hybrid Tomato Cultivation Den Berk Delice & Bryte Confirm: “LED Ensures Controllability”
A stronger plant, higher fruit weight, and more uniformity in growth; these are the results of a lit tomato crop when combining Philips GreenPower LED toplighting compact and HPS lighting in a hybrid lighting solution
September 9, 2020
A stronger plant, higher fruit weight, and more uniformity in growth; these are the results of a lit tomato crop when combining Philips GreenPower LED toplighting compact and HPS lighting in a hybrid lighting solution. The growers, the world-renowned tomato cultivators Bryte from the Netherlands and Den Berk Délice from Belgium share their experiences with hybrid lighting during the first cultivation season in this article. Both projects were installed at the end of 2019
Both entrepreneurs were very positive about their experiences after a year of tomato cultivation with hybrid grow light. The combination, which resulted in a more uniform fruit and crop growth and a more controllable greenhouse climate, asks for more. Cultivation with hybrid lighting, in which LED lighting is combined with HPS lighting, however, requires a different approach than cultivation with only HPS lighting. “The big advantage of LED lighting is that there is much less radiant heat from the light, which gives us more control over the climate in the greenhouse. Since light and temperature can be controlled more independently from each other with hybrid lighting, we have to change the way we approach the climate differently and that requires a new way of thinking, where the experience of the Signify plant specialists comes in handy, ”says Zwinkels.
Heat differences in the greenhouse
Where heat is mostly the deciding factor with traditional HPS illumination - but also plays a major role as an unavoidable by-product for cultivation control - this is no longer the case with hybrid illumination. LED leads to much less excess heat in the greenhouse, which makes it possible to control light and temperature separately. It is thus easier to control the growing conditions. For example, Den Berk Délice chooses to grow generatively up to 28° C in winter and from March more vegetatively to keep a strong crop. Lucas: "We noticed that we are much more in control with LED." The cultivation experts at both companies carefully thought about how they could anticipate on the changing temperature situation in the greenhouse. Erik: "With us, the position of the growth tube could be at the expense of the fruit weight. In our case, the best solution was to introduce extra heat from the bottom of the greenhouse. We also noticed that control errors were less likely to be made due to better control over the climate and that the climate became more constant. We saw positive crop development and were satisfied with the fruit weight and the crop growth."
Illuminate longer
“A big advantage of hybrid cultivation in comparison with HPS is the possibility to light the crop for a longer period of time", said Koen. “Especially in the winter months, a high crop yield is important to us; it is a period that we want to make the most of. We have seen that with hybrid cultivation you can illuminate earlier in the fall, but also until deeper in the spring, up to thirteen or fourteen hours a day. Of course, you have to keep looking at what extra lighting brings in terms of production and costs.”
Light advice
The plant experts of Signify are experts in using LED and know better than anyone else what LED lighting means for crop growing and climate. In the past growing season, they assisted the companies with light and climate advice. Both companies now have 180 µmol/s/m2 light, distributed across 90 µmol/s/m2 LED toplighting compact and 90 µmol/s/m2 HPS lighting. The Philips GreenPower LED toplighting compact was introduced to the market during the last growing season. "Signify talks a clear language", said Erik. "They are the right discussion partner for me, who regularly visits and discusses what we encounter in practice." Koen adds: “The specialists also have a large network. Via them, I managed to get into contact with other growers who also use LED. I look forward to the annual Tomato Community Event organized by Signify, where cultivators from around the world get together. This not only gives me the opportunity to share experiences with LED lighting, but also to expand my network that I can take advantage of in the future. We always see talking to like-minded people as very valuable.”
Does LED toplighting have a future?
Firstly, LED saves up to 60% on energy costs, but there is more. Erik: "As cultivator, I would like to bring the winter to the summer. LED lighting makes it possible to go to higher light levels and is the right way to do that. I prefer a hybrid solution with HPS, and then look at how we can regulate the heat in the greenhouse.” For Koen, the ideal cleaning conditions, where the modules do not have to be shielded, and the simple scaling options are reasons to choose a combination of HPS with LED toplighting compact luminaires. He refers to the plug-and-play ease of installation of the Philips GreenPower LED toplighting. Both consider future investments in a larger portion of LED in their greenhouses. They look forward to the development of LED in combination with higher light levels.
Create the correct balance to control your crops
Erik wondered if he, at his company, as he said, maybe loved the plants too much. In passing, he refers to the learning curve that you as a grower with LED go through. "You control it differently with hybrid lighting and that requires experience that you will gain through the years. You become wiser. Light and heat become more tangible and you are better able to control the right balance in your crop. I see it as an added value in which we can develop ourselves year after year, with better end results. Let the summer come during the winter!"
Erik and Mark Zwinkels are co-owners of Bryte; with 40 hectare - of which 60% is lit - one of the biggest players in the Dutch tomato cultivation. Koen Lauwerysen is one of the four business managers at Den Berk Délice, where Lucas Aertsen is the cultivation manager. With 60 hectares tomatoes - of which half is lit - their company is also one of the bigger ones in Belgium. Both share their experiences during the past cultivation season where they used the combination LED and HPS for the first time. Bryte installed it on eight hectares, and Den Berk Délice on ten.
For further information, please contact:
Global Marcom Manager Horticulture at Signify
Daniela Damoiseaux
Tel: +31 6 31 65 29 69
E-mail: daniela.damoiseaux@signify.com
Signify Global Media relations - Professional Lighting
Wendy Schellens
Tel: +31 6 51 863 401
Email: wendy.schellens@signify.com
About Signify
Signify (Euronext: LIGHT) is the world leader in lighting for professionals and consumers and lighting for the Internet of Things. Our Philips products, Interact connected lighting systems and data-enabled services, deliver business value, and transform life in homes, buildings, and public spaces. With 2019 sales of EUR 6.2 billion, we have approximately 36,000 employees and are present in over 70 countries. We unlock the extraordinary potential of light for brighter lives and a better world. We have been named Industry Leader in the Dow Jones Sustainability Index for three years in a row. News from Signify is located at the Newsroom, Twitter, LinkedIn, and Instagram. Information for investors can be found on the Investor Relations page.
4 Facts You Need to Know About Vertical Farming LED Lighting
One of the main components that make vertical farming possible is the evolution of light-emitting diodes (LEDs)
One of the main components that make vertical farming possible is the evolution of light emitting diodes (LEDs). As LEDs become more and more accessible and affordable, the futuristic idea of vertical farming becomes more realistic for cities all over the globe. In this article, we’re going to share four important facts regarding vertical farming led lighting and how these systems are important to the future of farming.
LEDs are the best lighting system for vertical farming
With their ability to be highly energy efficient, LEDs produce light at optimal power while being able to last a long time. These effective light solutions are able to last for nearly six years, which is quite longer than other lighting solutions. What makes LEDs perfect for vertical farming is that they’re able to be confined in tight spaces with vertical layered crops, and they don’t emit too much heat. Other lighting solutions such as HPS or MH lights will damage vertical farming systems because they release too much heat, which is harmful to the crops.
LEDs are a cost-effective, energy saving solution
HPS lighting systems consume too much power in order to emit the same light levels as LEDs, which is why LED lighting systems are paving the way toward an affordable indoor growing environment. One of the significant benefits of using LED lights is that these advanced lighting systems do not consume as much power, which leads to reduced energy costs and higher productivity.
They use a visible spectrum to match the plant’s grow cycle
The innovative uses behind vertical farming LED lighting is that these systems use wavelengths on a visible spectrum to promote plant growth. When you see those pink colored lighting systems, this means that the LED lighting system is using a minuscule wavelength between the red and blue spectra to produce the pink glow. Plants depend on blue lightwaves to enhance the leaf’s color and prevent stretching, and the red light waves optimize photosynthesis. LED lights are able to emit the wavelengths needed to grow healthy, bountiful plants by mimicking their required natural environment.
LEDs are sustainable solutions to growing foods
Farmers are learning to work with LED lights because of their sustainable, efficient solutions. These vertical farming LED lighting systems are able to provide controlled lighting all-year-round, which allows for optimal plant growth. Also, by having a controlled indoor LED lighting environment, crops are saved from yearly harsh environmental conditions such as flooding, drought, hurricanes, and more. By being able to mimic sunlight, LEDs are a cost-effective solution to growing sustainable and healthy foods all year round indoors.
We at the Nick Greens Grow team are always learning and sharing our advanced farming knowledge with our subscribers. If you want to always stay up-to-date with the newest innovative farming technology subscribe to our YouTube channel for weekly videos or subscribe to our blog to get the latest farming information sent straight to your inbox!
#LEDlighting #verticalfarming #growlights #growfoodwithleds #verticalfarminggrowlights #ledlights #ledgrowlights #verticalfarmingLEDlighting #leds #indoorfarming
Shenandoah Growers - Bringing Nature Indoors
At Shenandoah Growers, we believe in the power of technologically-controlled indoor environments to sustainably transform the future of fresh produce. As the only large scale USDA Certified Organic soil-based indoor growing system in the United States, we are passionate about leveraging cutting-edge science and technological innovation to ensure that our customers receive the freshest, healthiest, most affordable organic produce possible year-round.
Working with (not against) nature to create an optimal environment for plants to thrive
What Sets Us Apart?
At Shenandoah Growers, we believe in the power of technologically-controlled indoor environments to sustainably transform the future of fresh produce. As the only large scale USDA Certified Organic soil-based indoor growing system in the United States, we are passionate about leveraging cutting-edge science and technological innovation to ensure that our customers receive the freshest, healthiest, most affordable organic produce possible year-round. With twelve growing locations across the country, we couldn’t be prouder to provide organic, local produce to over 18,000 stores every day.
Why Indoor Controlled Agriculture?
There’s nothing quite like the great outdoors—at Shenandoah Growers, we know there’s something better. Our LED-powered indoor bioponic growing platform increases yields and reduces waste, enabling us to make fresh herbs available year-round across the country. Plus this proprietary system is environmentally conscious, conserving water and land, and avoiding harmful pesticides.
How Do We Do It?
Some call it “Know-How”. We call it “Grow-How”
Our proprietary bioponic growing process mimics nature but enhances it with carefully controlled temperatures, light levels, humidity, and water exposure. And because we use just what we need to keep our plants healthy and no more, we conserve valuable environmental resources and set our industry up for a sustainable future.
IDTechEx: How to Succeed in Vertical Farming
Vertical farming is an emerging technique within agriculture that involves growing crops indoors under controlled environmental conditions
NEWS PROVIDED BY IDTechEx
May 26, 2020
BOSTON, May 26, 2020,/PRNewswire/ -- Vertical farming is an emerging technique within agriculture that involves growing crops indoors under controlled environmental conditions. By carefully tailoring the environment to the exact requirements of the crop, such as through using LED lighting to produce the exact light spectrum needed for optimal photosynthesis, it is possible to obtain yields hundreds of times higher than traditional agriculture.
Vertical farms can be set up almost anywhere, making it possible to grow crops in the middle of populous urban centers, meaning that it is possible for crops to reach consumers within minutes of harvest. This contrasts with traditional agriculture, where fresh produce can take weeks to reach consumers, losing the freshness, and increasing contamination risk along the way. The recent IDTechEx report, "Vertical Farming: 2020-2030" explores the technologies and markets around the fast-growing vertical farming industry.
Vertical farms use artificial lighting and carefully controlled climates to grow crops at far higher yields than conventional agriculture. Source: Intelligent Growth Solutions (PRNewsfoto/IDTechEx)
Vertical farming has been the subject of a lot of hype in recent years, with supporters claiming it could revolutionize food production. Industry advocates, such as Columbia University Professor Dickson Despommier, have presented visions of a future world where fresh food is grown inside skyscrapers to feed giant, high-tech metropolises (for further visions of the cities of the future, see the IDTechEx report, "Smart City Opportunities: Infrastructure, Systems, Materials 2019-2029"). Investors are also feeling the hype, with vertical farming start-ups raising over a billion dollars in investment in the last five years alone.
However, despite this optimism, the industry does face some major challenges and the sector has more than its fair share of bankruptcies. PodPonics, once the most well-funded vertical farming company in the world, and FarmedHere, which once operated what remains the largest vertical farm ever built, both went bankrupt. David Rosenberg, Chief Executive of New Jersey-based vertical farming outfit AeroFarms, recently said he wouldn't be surprised if 90% of the players in the industry went out of business within the next three years.
Broadly, many vertical farms struggle for the same reasons. As well as costing a lot of money to set up, vertical farms can be very expensive to run, largely because they require continuously running artificial lighting and climate controls. This is compounded by high labor costs and logistical difficulties that often get more difficult as the vertical farm gets larger. This all makes it very difficult to compete on price with produce grown on conventional farms, which typically have razor-thin profit margins.
Because of these challenges, vertical farmers generally only grow crops where the whole of the plant can be consumed, in order to maximize space efficiency and avoid wasting energy on growing inedible stems and leaves. Therefore, almost all vertical farmers are restricted to growing herbs and leafy greens. These are still a large market but fall somewhere short of the lofty claims made by some supporters of the industry.
It is certainly possible to run a successful vertical farming business, as fast-growing players such as Bowery Farming and InFarm will attest to, however, it requires a carefully planned out strategy and consideration of all the variables and trade-offs involved in vertical farming, in addition to a fair amount of investor capital.
The keys to success in vertical farming are outlined in the recent IDTechEx report, "Vertical Farming: 2020-2030". The report discusses several factors that can contribute to the success or failure of a vertical farm, including:
Whether or not to automate. Automation can significantly reduce labor costs while streamlining the logistical processes. However, investing in advanced automation equipment can lead to extremely high start-up costs.
Choice of crops. Should vertical farming try to branch out beyond leafy greens, or should it corner the market it has? What about higher-value crops inaccessible to conventional agriculture?
How large is too large? Larger centralized facilities could lead to economies of scale but could also face spiraling logistical difficulties. However, smaller localized facilities may face much higher start-up costs relative to the output capacity.
The importance of location: is a city center location really the best place to set up a vertical farm?
The need for experience in the food industry. Crops are living organisms and are not always predictable. Despite this, there is a relative lack of food and agriculture experience in the vertical farming sector.
For more information on this report, please visit www.IDTechEx.com/vertfarm or for the full portfolio of Food & AgTech research available from IDTechEx please visit www.IDTechEx.com/research/agtech.
IDTechEx guides your strategic business decisions through its Research, Consultancy and Event products, helping you profit from emerging technologies. For more information on IDTechEx Research and Consultancy, contact research@IDTechEx.com or visit www.IDTechEx.com.
Media Contact:
Jessica Abineri
Marketing Coordinator
press@IDTechEx.com
+44-(0)-1223-812300
SOURCE IDTechEx
We Want To Grow Every Lettuce Variety Without Having To Think About The Light Recipe
The construction of the greenhouse for lettuce growers From Boer in the Dutch town of Dinteloord is in full swing, while this is happening they are already thinking about equipping the greenhouse with the latest technology
The construction of the greenhouse for lettuce growers From Boer in the Dutch town of Dinteloord is in full swing, while this is happening they are already thinking about equipping the greenhouse with the latest technology. For instance, regarding the perfect light needed during cultivation. To figure these things out, Rofianda Lighting Solutions and Form Boer had a meeting. The plans changed a hand full of times, but they have now devised a complete plan.
'Without' thinking
Rofianda and From Boer met in the spring of 2019. Due to modernization, the re-locating, and the current technological developments, the lettuce growers are looking into the questions regarding lighting. The researches’ most important goal is to find a way to cultivate every variety of lettuce without having to think about strict lighting recipes.
“To achieve this goal, Rofianda Lighting Solutions full-spectrum sunlight lighting is perfect”, says Arjan Boer. “You only need to decide on the lighting level, and the plant will take care of the rest.”
'Sunlight lamps’ versus red and blue LEDs
In a testing greenhouse, the results for lighting lettuce under sunlight lamps were compared to the results of those same varieties under red and blue LEDs. The results for lighting under Rofianda Lighting Solution lamps were very noticeable. “The overall growth is close to how it is in nature, and the root forming is much better than when using the LEDs.”
Micromol discussion
Because Arjan and Leonard want to equip their new greenhouse with the latest technology, cultivation will happen in a most modern way. Ronald Gronsveld, owner of Rofianda Lighting Solutions, and the brothers Boer have invested a considerable amount of time in creating just the right lighting plan for the automated cultivation department.
“These types of challenges form the cornerstone of our existence”, says Ronald. “We don’t just supply a few lamps, but think along with the growers when it comes to questions regarding design, installation, costs, lighting levels, the impact of lighting on the cultivation as a whole and payback period. More is not always better, especially in the current discussion regarding micromole. The quality of the light is much more important than the quantity”, in Ronald’s opinion.
The right choices
Arjan confirms that the plans have changed a few times and that they eventually reached a complete plan. “The contact was abundant, and we managed to make the right choices together”, says Arjan.
In the middle of March, the signatures were placed, and the entire cultivation will be equipped with lighting technology that was designed in the Netherlands.
For more information:
From Boer
www.fromboer.nl
Rofianda
info@rofianda.nl
www.rofianda.nl
By Horti Daily | May 4, 2020
The Decarbonization Promise of Indoor Agriculture is Still in The Seed Stage
The data we do have shows that a combination of efficiency improvements and grid decarbonization can make indoor farms a much better environmental choice for some crops
By Jim Giles
May 21, 2020
Here’s a tale of two chefs.
Both are based in the Midwest and both are preparing a Caesar salad. One uses lettuce shipped from where much of our lettuce is grown: The fields around Monterey, California. The other sources her greens from a nearby indoor farm.
Out in Monterey, the farmer used diesel-powered machinery, pumped water, fertilizer, and pesticides. At the indoor farm, precision systems provided the lettuce with exactly the amount of water and nutrients the crop requires — and no more.
The pickers in California discarded lettuces that didn’t look perfect. That wasn't an issue indoors: Conditions are so well controlled that almost all the crops met consumers’ exacting standards. Finally, when the crop was packed and ready, the indoor farmer drove 20 miles or so to drop the lettuce at our chef’s restaurant. The Monterey produce had to travel 2,000 miles.
Which chef is preparing the more environmentally friendly salad?
Let’s start with the bad news. The story above about indoor farming, a tale about technology can produce dramatic environmental gains — it doesn’t hold true. The Monterey lettuce is currently the better bet, according to a new analysis from the WWF.
For places that are food-insecure, this could be a real game-changer.
The problem with indoor farming, also known as controlled environment agriculture, is the electric grid. Indoor farms use LEDs to light crops. In St. Louis, Missouri, the focus of the WWF study, two-thirds of electricity comes from fossil fuel plants that pump out health-damaging particulates and planet-warming carbon dioxide.
The WWF team combined these and other impacts into a single score that captures total environmental harm. Lettuce grown in St. Louis greenhouses, which supplement LEDs with natural light, scored twice as high as the conventional crop. In a vertical farm lit entirely by LEDs, the difference was threefold.
Now to the good news: Our chef who sources from a nearby indoor farm may not be making the best environmental choice today, but she likely will be soon.
That’s partly because if we look beyond energy use, indoor ag delivers clear benefits. Indoor systems require little or even no pesticides and generate 80 percent less waste. They use less space, which can free up land for biodiversity. The WWF study found that precision indoor water systems use 1 liter of water to produce a kilogram of lettuce; for field-grown lettuce, the figure is 150 liters.
Another reason is that indoor ag’s energy problem is likely to become less serious. Market forces are already adding renewables to the U.S. electricity mix and pushing out coal. Technology improvements in the pipeline also will cut energy use in indoor farms.
PlantLab, a Netherlands-based startup, has developed an LED that’s more efficient in indoor ag settings because it emits light at the exact wavelengths used for photosynthesis. New crop varieties from Precision Indoor Plants, a public-private partnership that is developing seeds specifically for indoor use, may require less light to grow.
This tech is at an early stage, which makes it tough to quantify the future impact. But the data we do have shows that a combination of efficiency improvements and grid decarbonization can make indoor farms a much better environmental choice for some crops. Cutting energy use also will lower costs, making indoor farms competitive on price. It’s fascinating to speculate about what would happen if both these trends came to fruition.
Indoor farms likely would diversify, for starters. At present, indoor farms in urban areas profitably can grow leafy greens but little else. If energy costs come down, cucumbers, berries, and tomatoes also might make financial sense, suggests Julia Kurnik, director of innovation startups for WWF.
When this project ends, key players will already be invested and ready to move ahead with building a pilot system that can be replicated worldwide ...
With more diverse output, the farms could become local hubs that would strengthen the food system’s resilience to extreme weather events and other shocks. "For places that are food-insecure, this could be a real game-changer," Kurnik added.
Venture capitalists already have seen this future; hundreds of millions of dollars have flowed to indoor farming companies in recent years. That’s essential if this industry is to grow, but it’s also great to see an organization such as the WWF in the mix.
After studying the potential, the WWF has convened a diverse group of stakeholders to map out the expansion of indoor ag in St. Louis. In addition to business execs and investors, the group includes civic and community leaders.
"By working as a group to make those decisions," explains the report, "when this project ends, key players will already be invested and ready to move ahead with building a pilot system that can be replicated worldwide, making food production more environmentally sustainable."
I’ll certainly be keeping tabs on progress in St. Louis, and with indoor ag more generally. If you know of a particular project or related technology that deserves a mention, drop me an email at jg@greenbiz.com.
This article was adapted from the GreenBiz Food Weekly newsletter.
Sign up here to receive your own free subscription.
The Basics Of Hydroponic Lighting
Choosing the best lights for your hydro system can be daunting for a beginner. There are tons of options out there and depending on your system size and type of plants you are growing; some types may be better or more efficient than others.
Hobbyists often take up hydroponics because they want to grow their own food but don’t have access to outdoor space. Although the sun is the ideal lighting source for growing plants, artificial lighting in indoor systems can provide a good substitute within the appropriate color spectrum.
Choosing the best lights for your hydro system can be daunting for a beginner. There are tons of options out there and depending on your system size and type of plants you are growing; some types may be better or more efficient than others.
Outside, a vegetable garden requires between four and six hours of direct sun per day, plus at least 10 hours of “bright light” or indirect sunlight. With artificial lighting in your hydroponic garden, the main goal is to imitate this. You should plan your system on having at least 14 to 16 hours of bright artificial light, followed by 10 to 12 hours of darkness every day. The darkness is just as important as the light—just like animals, plants need time to rest and metabolize.
If your plants are perennials, you will have to have a more strict and calculated lighting schedule to bring the plants through their vegetative (growth) and flowering (production) stages. The easiest way to maintain a lighting schedule is with an automatic electric timer. They are worth the investment because one small mistake or simply forgetting to turn the lights on or off has the potential to affect your plants' growth and production rates dramatically.
Different Plants, Different Needs
An electronic timer is especially necessary if you are growing a variety of different plants. Although you can follow the general guidelines above and have success, some plants do much better with longer or shorter periods of “daylight.” If you have a mix of these in your garden, you will need to figure out a custom schedule. An electric timer allows you to take care of this hassle-free and change it according to your needs as your garden evolves.
Short day plants: These require a long period of darkness to photosynthesize and produce flowers. If they are exposed to over 12 hours of light per day, they will not flower. Poinsettias, strawberries, cauliflower, and chrysanthemums are short-day plants. The short-day cycle mimics the environment in nature for plants the flower in the spring.
Long day plants: These require up to 18 hours of sunlight per day. They include wheat, lettuce, potatoes, spinach, and turnips. The long-day cycle mimics the natural environment of summer-flowering plants.
Day-neutral plants: These are the most flexible. They produce fruit no matter how much light they are exposed to. Some examples include rice, eggplant, roses, and corn.
If you must mix sort and long day plants, it is best to compromise their needs and pick a lighting schedule that is right in the middle, around fourteen hours of light per day.
Parts of the System
All hydro lighting systems have four main parts. These are the bulb, reflector hood, remote ballast, and timer.
Bulb: The most popular wattage for hydroponic bulbs is between 400-600 Watts. Most hydro gardeners use High-Intensity Discharge (HID) lights. HID bulbs produce light by sending an arc of electricity between two electrodes that are encased in glass with a mixture of gas and metal salts. The gas aids the creation of the arc, which then evaporates the metal salts, producing bright white light.
There are two types of bulbs available: High-Pressure Sodium (HPS) and Metal Halide (MH). Conversion lamps allow you to switch between the two types of bulbs easily.
Metal Halide is a good all-around light, and for most vegetables, it will work very well. If you can only afford or only have room for one type of bulb, MH is a good choice. They cost on average $150 or less for 400 watts. These should be replaced at least every two years, but a decrease in efficiency after about fifteen months so may need replacing earlier.
High-Pressure Sodium bulbs are the best choice for the flowering or fruiting stage of your plants. They are more expensive, so are often used in combination with an MH bulb (used during vegetative state) to save money on replacement costs. Although they are more expensive initially, HPS bulbs last up to twice as long as MH, up to five years. But, like MH lights they do lose effectiveness with use and may need to be replaced as often as every two years based on how much use they get.
Reflector hood: The reflector hood is a reflective casing around the bulb. It increases the effectiveness and efficiency of the bulb by reflecting the light down onto the plants at multiple angles, giving a more effective spread. This also allows you to use lights that give off less heat, saving on electricity and cooling costs.
Remote ballast: The ballast is the power box that powers the light. Sometimes ballasts are sold as a part of the lamp assembly, but these are usually far too hot and heavy. Remote ballasts are much better for home systems. This is the most expensive element of the lighting system, so it must be kept off the ground to ensure that it never gets wet in case of a flood or leak. Flooding is risky with systems such as Ebb & Flow in case your drainage tube gets clogged. It is recommended to buy the ballast as a set with the bulb because they must match each other in wattage.
Timer: Timers are the most inexpensive piece of the lighting system, but they are incredibly important. They must be heavy duty and grounded (three-prong plug) but can be either manual or electric. Manual timers use pins and have two plugs on either side so that you can attach it to two lamps at once. Manual timers are more popular because they are less likely to break than electric.
By Christina D’Anna | the Spruce | July 4, 2019
A High-Yield Indoor Farming System Ideal For The City
According to Pollard, the evolution of new technology, such as LED grow lighting and the Internet of Things (IoT), has complemented the development of indoor soilless cultivation systems
As prolonged droughts occur more frequently in South Africa, some entrepreneurs are investing in and developing new technology and farming methods, such as indoor growing systems, that ensure consistent, high-quality food production. Juan-Griffith Pollard, CEO of Urban Cultivation International, spoke to Pieter Dempsey about his scaleable hydroponic farming system.
More frequent and long-lived droughts. Global warming. Water scarcity. Higher input costs.
These are some of the factors driving the growing interest in new technology that enables a farmer to produce the same quality and yields as conventional farming, but using indoor farming systems instead.
Hydroponics, or indoor soilless cultivation, as Urban Cultivation International (UCI) calls it, is a method of growing plants in a water-based, mineral- and nutrient-rich solution instead of soil, and under artificial LED lights instead of sunshine.
According to Juan-Griffith Pollard, the CEO of UCI, indoor farming uses up to 90% less water than traditional farming practices, and far less space. In addition, plants can be grown pesticide-free and closer to high-consumption areas, such as densely populated cities.
These reasons, and more, explain why an increasing number of growers have begun exploring indoor soilless cultivation.
Precision growing
The system provides the optimal growing conditions for plants, enabling them to develop much faster and be far healthier than is the case with traditional outdoor cultivation.
According to Pollard, the evolution of new technology, such as LED grow lighting and the Internet of Things (IoT), has complemented the development of indoor soilless cultivation systems.
“IoT can be used to automate and regulate indoor farming by monitoring water levels, nutrient levels, pH levels, and temperature and light requirements of plants. “A farmer can be in control of the harvest at all times, wherever he or she is physically present.
“One of the biggest benefits of indoor farming is that produce can be farmed at any time of the year. Thus, a farmer can sell produce at out of season prices, and supermarkets can stock fresh local produce all year around,” says Pollard.
No-soil farming
Pollard started investigating various methods of indoor soilless cultivation in 2016 and fine-tuned them in 2019 to create a healthy, productive indoor farming system.
An entrepreneur by nature, he took note of the various challenges in traditional South African agriculture, including water scarcity and security risks. He also noticed the demand for certain leafy greens and microgreens in cities.
Thereafter, he traveled to the US, Europe and Asia to research systems that could be applied in the South African agricultural environment.
He went on to establish UCI at the N4 Gateway Industrial Park in Pretoria East.
“What makes UCI’s technology different from most other indoor systems is that a farmer can start small and expand by adding additional racks to the system. So there’s no need to commit to a huge capital investment to get started,” Pollard explains.
The UCI model enables the farmer to control the light hours, nutrients and moisture. It is automated to produce rapid harvest cycles with predictable results, and can be used in a small space. Crucially, it is also affordable.
A key advantage is that the plants can be grown without the use of insecticides and herbicides, as the crops are grown in a controlled environment.
Pollard predicts that farms of the future will be urban-based, and crop cultivation will have to become far more sensitive to water and energy usage. There are many cost-effective options for indoor, soilless cultivation, and these allow farmers to move from the fields to the city.
Indoor production is also an easier entry into farming; it can be started by any entrepreneur, or even a retiree, he adds.
A wide range
The options offered by UCI range from small household units to large-scale commercial systems. Regardless of size, they can deliver crop yields of up to 10kg/m2.
The household units are small, with just enough space to service the average household and to plant a variety of crops, such as leafy greens, microgreens and berries.
The household system was also developed for educational purposes and can be used as an entry into indoor soilless cultivation before a large capital investment is made in a commercial unit. UCI has developed a curriculum that explains the A to Z of indoor hydroponic farming.
The company’s industrial units include climate control and a lift system, which makes harvesting easier.
Depending on the type of crop, the return on investment is between two-and-a-half and five years, while high-value crops such as microgreens have a payback period of less than a year on capital investment.
Growing with ease
Plants can be grown from seed to harvest in 28 days, three times faster than that achieved with traditional farming.
“The plants are grown in a controlled environment under 12 to 16 hours of LED lights, giving you optimal harvest and zero wastage,” explains Pollard. In addition, produce grown in UCI’s systems has proved to be of excellent quality and offer good taste.
The entry commercial turnkey solution system contains a 10m-long and 1,9m-wide row, and the buyer can choose to fit between three and 12 levels.
For example, a 10m-row, five-level-high farm enables 100m2 to be planted in a floor space of only 20m2. “The higher you go, the more your yield per square metre,” says Pollard. The grow trays and spacing between plants are designed for optimal growing and yield. No sunlight is needed for this method; all the systems use LED grow lighting.
“LED technology provides the best energy efficiency, which saves you money in the long term,” says Pollard.
Production
A 10m-long unit can handle 54 plants per tray. At 12 trays per level and at five levels, this equates to 3 240 plants per unit.
The lighting is usually kept on for between 12 and 16 hours a day, depending on the requirements of the plants.
“The more light they get, the faster they grow,” says Pollard.
The system can handle a variety of crops such as lettuce, spinach, baby spinach, marog (imfino), cherry tomatoes, strawberries, basil, watercress, sage, zucchini, beans, fodder and a range of microgreens and herbs.
To illustrate potential crop yields, Pollard and his team have used the five-level demonstration system at UCI’s premises to grow 250g lettuce heads in 28 days under optimal growing conditions. A yield of more than 18kg per tray has been achieved.
“Compared with traditional farming, the only major cost drivers are electricity and wages,” he says.
Each tray contains about 20ℓ of constantly recirculated water, and total water use is approximately 1 250ℓ/month. The system is extremely water-friendly, as almost all the water is absorbed by the plant.
“No water is wasted, hence the saving of 90% compared with traditional farming,” says Pollard.
He adds that climate and temperature control is a key factor in the grow room, and even the water temperature is cooled or heated as the plants require.
“We can mimic the controlled growing environment of certain crops as they require. “The system works with any water, and tests are routinely conducted to see what nutrients the plants need, and all variables can be adjusted according to the needs of the plants.
“We have a nursery system that grows the plants from seed to seedlings. After about seven days, the seedlings can be transported into the commercial system; the fully grown plant is then ready to be harvested after another 21 days,” Pollard says.
Due to the way in which the system operates, the chances of a pest infestation are very low.
“Biosecurity is crucial and we prevent any pathogens and pests from entering the facility.”
Harvesting a system that is 10m long and has five levels requires about three hours with two people.
With rapid urbanization increasing the demand for food, UCI’s system offers a number of key advantages.
It brings the farm closer to the people, thereby improving food security, and it reduces transport costs, in turn lowering the carbon footprint of supplying food. The system also offers good potential as a job creator.
“Our aim is to get entrepreneurial farmers to start utilizing the empty spaces in cities, such as empty buildings in city centres. Such spaces can be used to grow food, provide jobs and supply retailers directly,” says Pollard.
Visit urbancultivation.co.za.
By Pieter Dempsey | Farmer’s Weekly | May 6, 2020