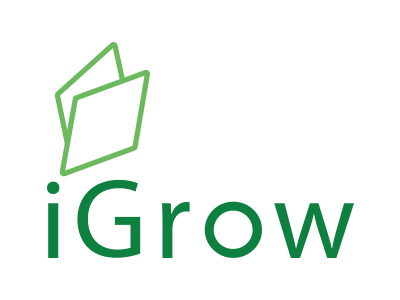
Welcome to iGrow News, Your Source for the World of Indoor Vertical Farming
Sowing Season For Vertical Farms
Growing fresh produce in a controlled indoor environment using technology inputs has, in some cases, been around for almost two decades. But it has only recently started to gain traction linked to climate change and sustainability concerns. However, can it be profitable and competitive?
June 29, 2021
Concerns over climate change and food security have fuelled optimism over controlled-environment farming but operators face questions over their forecasts for profitability. Simon Harvey digs into the sector’s prospects.
Growing fresh produce in a controlled indoor environment using technology inputs has, in some cases, been around for almost two decades. But it has only recently started to gain traction linked to climate change and sustainability concerns. However, can it be profitable and competitive?
Indoor or controlled-environment farming is a niche yet expanding sector, but questions have been raised over whether these operations are profitable, and are able to compete with traditional field-grown crops, given the capital-intensive nature of the industry.
Much, however, depends on individual operations, and the objectives in terms of scale – whether it be targeting mass-market consumers or local buyers, the geographical location, etc – whether the farm is in a hot or cold climate, along with the types of crops grown and, most importantly, the technologies employed to replicate the natural environment at the lowest cost possible.
Vertical farming, per se, is the most popular system where crops are grown on stacked units in a warehouse, underground tunnel, or even in shipping containers, requiring artificial lighting, usually through expensive LEDs to mimic sunlight. But some operators, particularly in hot countries such as the Middle East and Asia, are growing crops in high-tech greenhouses using mostly natural light.
Nonetheless, even the companies in those hot climates need LED lighting to supplement the daylight hours, and, generally speaking, all operators within controlled-environment farming are similar in terms of the inputs such as labour, ventilation, irrigation, and cooling. And all require huge capital investment to purchase land, build the farm, put in the appropriate technology, and run it.
Despite the costs, indoor farming is viewed through a longer-term lens to address environmental concerns like the decreasing availability of land, unpredictable weather patterns and climate change, and the limited resources on hand to feed the world’s growing population.
Securing future harvests
Fraser Black, the CEO of UK-based Crop Health and Protection (CHAP), one of the country’s Aagri-tech centres and funded by Innovate UK, a government-backed agency, gives his interpretation of the current landscape.
“I think it is going to be a while before you see millionaires in vertical farming,” Black says. “It's still at that point where you are justifying the costs and developing the market.
"I think there are enough people around now that are breaking even and starting to become profitable, but we are not there yet. Look at electric cars, we are sort of following that same trajectory.”
Controlled-environment farming comes with advantages: less water than regular agriculture and without the need for pesticides, and higher yields linked to year-round production. And, from the consumer perspective, better-quality produce because the nutrient inputs can be controlled, and freshness, because the crops tend to be grown close to source.
For food importers like those in the Middle East and some parts of Asia, the technology offers food security, too.
All those benefits stack up through the eyes of private equity and venture-capital funds, which are ploughing vast sums of money into the sector.
This is no doubt in the hope of reaping profits when indoor farming has reached scale and matured beyond the current leafy greens and herbs – although soft fruits such as strawberries and blueberries, and tomatoes, cucumbers, and mushrooms, are starting to emerge.
I think it is going to be a while before you see millionaires in vertical farming.
Black also addresses the consumer angle and how controlled-environment farming is likely to develop over the coming years.
“The first decades are going to see people getting involved, learning how to do it, and leading the charge, and it will be niche. But, as they learn and as they build, and they learn how to get the costs down, and control the costs, the more mainstream it will become, and then more people pile in and the bigger the scale.
“There are other points of differentiation people are picking up on, which I think will project it forward until such time that the volume is big enough and people recognise all of the benefits that it will become profitable like other systems.
“Trying to compete with the major growers and put it all in the major supermarkets right now is more difficult because they don't have the volume. But I think those sort of trends are starting to shift.’”
Sky Greens in Singapore is one of the oldest vertical-farming businesses in Asia, founded in 2012 by Jack Ng to grow leafy greens under glasshouses using hydroponic systems and natural light. While Ng points out that labour is the biggest operational cost, he also says that Sky Greens saves money by not employing LEDs, enabling the business to focus on yield and productivity.
“Our energy use is similar to traditional farming, so we can save about 75% on labour,” Ng says. “Our running costs are cheaper than traditional farming, the only thing is the investment cost. Because our output is ten times higher than traditional farming, the investment costs average out.”
He adds: “We have proven in Singapore that we can grow and sell mass-market vegetables. The reason many vertical farms aren't competitive is because they are using artificial lighting, which is a high energy cost, so your payback is high and your overheads are high, plus you have the replacement costs because LED lights only have a two to three-year lifespan.”
Harvesting time at the Sky Greens farm. Credit: Sky Greens
Ng says that the price of locally-grown crops is important given that Singapore is an import-dependent economy when it comes to food, having to contend with cheap products coming in from Malaysia, Indonesia, and China, but its optimum yield gives Sky Greens the ability to compete.
“Our farm operation is profitable. Using our system, based on studies, the payback is about five years but your crop price has to be at a certain level. Therefore, what we produce is usually the higher-end vegetables like pak choi, which is, in a sense, a smaller market.”
Indicative of the costs, Plenty Unlimited in California, a vertical-farming business set up in 2014, has raised $500m to date from investors as it seeks to scale up production of leafy greens such as lettuce, kale, and rocket, along with tomatoes and strawberries.
Others, like AeroFarms, established in 2004 in New Jersey, and Infarm in Berlin founded in 2013, are turning to special purpose acquisition companies, or SPACs, to raise funds and gain public listings.
AeroFarms, which grows leafy greens, herbs, blueberries, and raspberries using aeroponic systems, recently entered a SPAC deal with Spring Valley Acquisition Company valued at $1.2bn, which will give the business access to more than $300m in cash to invest.
Infarm is also proposing a SPAC, said to be valued at $1bn, to expand from herbs and greens into chillies, mushrooms, and tomatoes, all grown using hydroponic technology. The company has so far raised around $400m.
Expensive seeds to sow
Nonetheless, the chief executive of Intelligent Growth Solutions (IGS) in Scotland, a tech-firm that designs and patents controlled-environment platforms using artificial intelligence and robotics, with a particular focus on productivity and efficiencies, is critical of the sums being raised relative to the individual revenues generated, and the technologies employed.
IGS CEO David Farquhar says that many of the vertical-farm operators “are still a long way from being profitable”.
“The first important thing is to get our positioning in the market right. There are a lot of very big and noisy companies that have had to raise a huge amount of money because they are trying to reinvent the wheel,” he explains.
“There is no one magic bullet that makes these things economically competitive. It is a combination of about six subsystems. There are two major costs in commercial agriculture in an enclosed environment.
"One is energy and the other one is labour. If you can take the labour out, and we've managed to reduce it by about 80%, that is a major cost-saving and will make you much more economically efficient.”
Farquhar argues that there is no need to have numerous people tending to these farms, as is depicted on many a website, if AI technology and robotics are employed, which reduce costs and ultimately helps with profitability.
He continues: “We give recipes of weather to the AI and the computer does all that work and the mechanical handling system does all that work. Once you have put the seed into the substrate, in the inserts that go into the growth trays, there is really no need for human intervention at all.
“And if you don't put humans in, you are not going to introduce bugs and disease and things, and therefore you don't need to use fungicides and herbicides, whatever. That means you don't need to wash the crop, which means that you are saving more money but also you are going to increase the shelf life by about 50%-100% and you are also going to reduce waste.”
The IGS ‘Growth Towers’ use a multitude of technologies. Credit: IGS
Dr. Nate Storey, a co-founder of Plenty, says it’s surprising how quickly a vertical farm operator can become profitable, compared to those in field crops, but it’s more difficult for a “company that's raised a couple of hundred million dollars – it takes time for them to grow into that investment than it does for a farm that you just stood up”.
“Agriculture has historically been a low-margin industry, especially field production. And one thing we want to correct as we move into a new era of agriculture is to make it much more profitable. Having a better margin also makes you more investable.
“If we can get the flywheel spinning, we can drive costs out of the business faster and pull capital into the business in a way that allows us to expand much more quickly than you could probably imagine today,” Storey suggests.
“We are on a cost curve, more so than some of the other folks in the space, because we have invested very heavily in R&D. That builds our own internal cost curve, which allows us to drive yield up by seven times and costs out by 50% over the course of two years. So we have this kind of crazy economic curve that we get to ride towards higher profitability.”
Storey says that Plenty is competitive with field crops: “I know that's not true for everyone but again, people have some catch up to play. People are just waiting for these external cost curves to drive their costs down.”
Jonathan Webb, the CEO who founded US vertical-farming business AppHarvest in 2017, says that scale is key to profitability.
The company, based in Kentucky, grows a wide range of tomatoes in glass houses and has recently invested $60m to buy artificial intelligence and robotics firm Root AI, which has the technology to predict yields and evaluate crop health.
While Webb admits that one of its farms in the city of Morehead is a user of LED lighting, it mainly uses natural sunlight, and it also recycles rainwater to save on costs.
“If you are just in a warehouse then you can't use sunlight. So, for us, the two free inputs would be sunlight and rainwater. We are only adding in technology when we need it,” Webb says.
“If you package all that and go at scale, which ends up getting our construction costs down and our operating costs down, we can compete with conventional pricing today. If you are not using sunlight and you are not using rainwater how are you possibly going to compete with conventional crops and keep your costs low? It doesn't make sense.”
Webb adds AppHarvest’s new Morehead facility is going through the ramp-up stage and costs usually level out in year two. “Year three on is where you really start to drive profitability,” he concedes.
“As the industry matures and scales, we are going to see our costs for lighting come down, you'll see costs for steel and glass come down, and then it becomes that self-fulfilling prophecy because, as the industry scales, your material costs are going to be lower and the business models themselves will be fine-tuned to better perform.”
Smart applications of technology
In the Middle East, Pure Harvest is growing tomatoes and strawberries in high-tech glass houses using natural sunlight and only uses LEDs to a small degree because they have more daylight hours and more intense sunlight than other parts of the world.
The business, founded in 2016 in Abu Dhabi, is about to move into leafy greens, with capsicums, cucumbers, and other berry fruits in the pipeline.
Majed Halawi, the vice president for growth at Pure Harvest, says that “it's completely uneconomical” to use artificial lighting, although LEDs are used for “control and steering… but only to supplement the natural light”.
However, Pure Harvest doesn’t use stacked units like vertical-farm operators, and the company is very different in its objective, which is mainly to address food security and reduce the Emirates’ reliance on food imports.
Over the next ten years, our estimation is you will see tens of billions of dollars flood into controlled-environment agriculture.
“Where we compete and where we position ourselves is that we are this local, very high-quality product that is at a discounted price to what comes from Europe and outside of the market,” Halawi explains.
“We have a lot of similarities to a vertical farm in terms of climate management, however, our operating strategy and our set up of the greenhouses and the facilities is different. We find we have a more efficient set-up.
“Vertical farms bank on selling their produce at a very high cost, assuming the customers would pay them a premium for the fact they are grown on a vertical farm.
"However, what we find in this market in the Middle East is it doesn't make any sense to be growing using vertical farms because firstly, the consumer is very price-conscious, so you need to be able to compete with your traditional farms and imports, and, secondly, we have such an abundance of natural light.”
AppHarvest’s Webb believes that controlled-environment farming has a bright future, given the unpredictability of the weather and climate change, and will eventually become a necessity to ensure the long-term supply of fresh produce. As the sector expands and scales, the cost of borrowing is likely to come down too, he says.
“We feel we are really at that tipping point. Over the next ten years, our estimation is you will see tens of billions of dollars flood into controlled-environment agriculture globally, and it's because of the need. You will see scale and you will see profitability immediately because the industry can be profitable if you design the right facility in the right region.”
For BrightFarms, Indoor Farming Model Brings Big Growth
The company is unique among producers for its indoor hydroponic farming model, which is highly sustainable and cost efficient, allowing the company to offer its greens at an affordable price point
By Bridget McCusker -
June 28, 2021
Unlike most large lettuce and greens providers, BrightFarms is not a West Coast company. Instead, it’s headquartered in the village of Irvington. Its greenhouses are more remote, on the East Coast and in the Midwest, and provide fresh produce to nearby major metro areas, cities and towns.
Lightfoot
The company’s founder, Paul Lightfoot, is a former tech and software CEO for BSG, a company that operated software businesses to improve distribution and productivity in retail. About a decade ago, he decided to bring his supply-chain management expertise to the mission of providing healthy, local, sustainably grown food to stores at an accessible price point.
“Through my career in supply-chain management, I had been programmed to live, breathe and eat efficiency,” Lightfoot said. “As I approached my 40th birthday, I had an epiphany that I needed to follow my passion, making sure people have access to delicious and nutritious food … I dug into the produce supply chain and found a system that seemed like it was at odds with itself and not as efficient as it could be. I was compelled to build a better supply chain that helps deliver fresher, tastier and more nutritious leafy greens at an accessible price point.”
The company is unique among producers for its indoor hydroponic farming model, which is highly sustainable and cost efficient, allowing the company to offer its greens at an affordable price point.
“We implement environmentally friendly practices, first, by relying almost entirely on natural sunlight for energy,” Lightfoot said. “This keeps energy bills and carbon emissions low. In fact, our costs are much lower than vertical farming methods for that very reason. Our greenhouse model also uses 85% less light, 90% less land and 95% less water than conventional farming methods.”
If you’ve ever tried BrightFarms products around the Westchester and Fairfield region, available at its regional partner Stop & Shop supermarkets, they likely came from the company’s greenhouse in Selinsgrove, Pennsylvania, its 280,000-square foot facility that’s about a three-hour drive from the New York metro area.
Another benefit of indoor growth is a high level of control over pests and disease that could affect the crops. This means that no pesticides are necessary and none are used; nor are any insecticides, herbicides or fungicides, which is a step further than USDA organic standards.
BrightFarms’ greenhouse.
With no pesticides used and a hydroponic model, which means the plants are grown from water and sunlight — no soil — there is no need to wash the produce after picking or at home, eliminating another usual step before packaging. And even though it is just water used to grow the greens, the process actually uses much less water than typical farming practices, about seven times less, and produces no runoff.
The proximity of greenhouses to their targeted markets makes it possible for the greens to be delivered and become available to consumers less than a day after being harvested. Compare that to greens shipped in from the West Coast, which can take up to a week to make it to shelves across the country. Over 98% of leaf lettuces in the country are grown in just two states, California and Arizona.
Aside from the need for freshness, this short transport time saves on both costs and total energy used.
Usually, to find locally grown produce, consumers have to go to farmers markets or order directly, but BrightFarms partners with grocery stores, making products accessible to consumers who primarily buy produce at the grocery store. Likely, this model is also part of what will position the company to become a national brand.
The setup is also easily replicable; according to Lightfoot, it can be created anywhere in the country, which allows BrightFarms to expand into, essentially, any market it chooses.
The North Carolina greenhouse.
The most recent expansion was sizable, bringing BrightFarms into the southeast with a greenhouse in Hendersonville, North Carolina. The new facility is as large as its greenhouse in Pennsylvania, which was its biggest one so far. BrightFarms estimates that it will produce up to 2 million pounds of produce per year for its markets in the Carolinas.
The new greenhouse will up their customer base significantly, but the company intends to keep growing in new markets nationwide. Its last round of funding in the fall of 2020 brought in over $100 million with which to work.
“Our smart greenhouse model can be replicated anywhere across the country, and we have big plans to expand into every region in the next few years,” Lightfoot said.
“Next up, we’ll be expanding in New England, and move onto Texas later this year. By the end of 2021, we will double in size and production and surpass availability in over 3,500 stores — the most of any indoor farming player.”
The 5th AVF International Summit - The International Vertical Farming And New Food System Conference & Exhibition - 2nd - 3rd September, 2021 In Munich, Germany.
A hybrid event, it is designed to welcome back delegates and participants for in-person meetings, networking, and exchanges relating to innovations, investments, business opportunities, strategic partnerships, and cooperation in our vertical farming industry across the globe
The Association for Vertical Farming (AVF) in official partnership with the German State of Bavaria through its Ministry of Economy and Ministry of Food, Agriculture & Forestry announces the 5th AVF International Summit – The International Vertical Farming and New Food System Conference & Exhibition -- on 2-3 September 2021 in Munich, Germany.
A hybrid event, it is designed to welcome back delegates and participants for in-person meetings, networking, and exchanges relating to innovations, investments, business opportunities, strategic partnerships, and cooperation in our vertical farming industry across the globe.
We have prepared a two-day program of world-class keynotes, panels, roundtables, break-out sessions, and startup pitches to get everyone up to speed with the latest crucial developments and emerging trends in the various subsectors of our dynamic global industry. In addition, we are also organizing workshops on artificial intelligence, insect protein, robotics, automation, and sustainability certification.
And what’s more the city of Munich -- with its centuries-old culture, gastronomy, art, and architecture together with its vibrant, contemporary, and fun-loving modern incarnation – is eagerly awaiting your visit.
See You All In September
Click Here To Reserve Your Early Bird Tickets!
USA: VIRGINIA - Maker of Hydroponic Farming Systems Gets $1 Million Grant, Relocates Headquarters To Scott's Addition
The grant will help the company move further into commercialization. The company had been awarded a $225,000 Phase 1 grant in 2019 to conduct scientific trials of its technology
June 24, 2021
A startup company that makes indoor, hydroponic farming systems has opened its new headquarters and production site in the Scott’s Addition area of Richmond.
The opening of the Babylon Micro-Farms Inc. office comes after the company received a $1 million grant from the National Science Foundation with the potential for $750,000 in follow-on funding to continue development of BabylonIQ, its technology platform designed to operate decentralized, automated micro-farms.
The grant will help the company move further into commercialization. The company had been awarded a $225,000 Phase 1 grant in 2019 to conduct scientific trials of its technology.
Babylon Micro-Farms also completed a $3 million investment round in the first quarter of this year. Investors include Virginia’s Center for Innovative Technology, Hull Street Capital, Venture South, and the CAV Angels Group.
The capital raised “helped us move here [to Richmond] and build our team,” Alexander Oleson, the company’s CEO who co-founded the business with Graham Smith, said Thursday as Babylon Micro-Farms hosted an open house at the headquarters.
“A lot of it is about switching from an R&D organization to a sales organization,” Oleson said. “We have a backlog of orders to fill.”
Babylon Micro-Farms was founded in Charlottesville in 2017 by Oleson and Smith, who were University of Virginia students. The company announced plans to move its headquarters to Richmond earlier this year.
The company now has more than 30 employees working in a renovated 7,700-square-foot building on Carlton Street. The facility serves as the company’s main office as well as a research and development site for its indoor farming units designed to grow more than 40 different types of leafy greens, herbs and flowers.
From the Scott’s Addition site, the company staff also can remotely monitor the functioning of more than 40 of its indoor farming units that have been installed at customer sites including retirement communities, universities, and corporate cafeterias.
Several of the company’s 8-foot-tall, climate-controlled farming units stand in the main lobby of the headquarters, growing plants such as basil, kale, lettuce, and bok choy.
In a research area of the building, Babylon Micro-Farms is testing growing other produce such as strawberries and peppers in its hydroponic systems.
“Our hope is to be in hundreds of locations by the end of next year, mostly in Virginia, but really casting our footprint nationally,” Oleson said.
Photos: John Reid Blackwell
Karen Sizer, an account manager for Babylon Micro-Farms Inc., spoke with visitors on Thursday about the company’s hydroponic, indoor farming systems. The company, founded in Charlottesville in 2017, hosted an open house at its new headquarters in Scott’s Addition.
Alexander Oleson, co-founder, and CEO of Babylon Micro-Farms stands by one of the company’s 8-foot-tall, climate-controlled hydroponic farming units.
Babylon Micro-Farms Inc., a maker of indoor farming systems, has its headquarters and research facility on Carlton Street in the Scott’s Addition area of Richmond
(804) 775-8123
GreenFire Energy June Updates: How Geothermal Energy Could Power The Future
We are excited to share the new CNBC video “How Geothermal Energy Could Power the Future
We are excited to share the new CNBC video “How Geothermal Energy Could Power the Future.” Katie Brigham, a CNBC producer, reached out to Joseph Scherer, CEO, GreenFire Energy, in early April to learn about geothermal and GreenFire Energy’s solutions. The powerful video features Joseph Scherer and other industry experts: Jamie Beard, GEO, University of Texas at Austin; Catherine Hickson, Geothermal Canada; Tim Latimer, Fervo Energy; John Redfern, Eavor Technologies; and Barbara Burger, Chevron Technology Ventures.
From the video: “Geothermal anywhere is futuristic. Geothermal in great locations is a present opportunity that can be expanded dramatically. And with retrofits, the capital expenditures are relatively low and the payback is relatively fast because you don’t need to drill a well,” says Joseph Scherer. “Geothermal at scale, leveraging the entire oil and gas industry, literally solves energy,” says Jamie Beard.
Our View of the Industry
In May the International Energy Agency released its roadmap to Net Zero by 2050. Getting to net zero requires a “massive deployment of all available clean energy technologies–such as renewables, EVs, and energy efficient building retrofits–between now and 2030 and clean energy investment to more than triple by 2030.”
The effort to propel geothermal is making headway in many countries. Japan’s government is relaxing regulations to push geothermal forward, as part of a broader renewable energy initiative. The UK is looking at the decarbonization opportunities of geothermal energy. Geothermal energy can make a significant contribution to reducing CO2 according to a study released by researchers of the University of Bayreuth in Bavaria, Germany.
While we are seeing significant interest in geothermal investment, geothermal energy, with its tremendous potential to produce clean energy, is currently underutilized. Here is a cogent article on the issues that the industry needs to address.
Hollis Chin - hollis.chin@greenfireenergy.com
Read Geothermal Energy Is Critical to Biden’s 100% Carbon-Free Grid, Why Is It Currently Underutilized?
UNITED KINGDOM: The Secret Underground Farm In The Middle of Sheffield With An Important Mission
Mr. Ellis, from Sheffield, has been growing greens beneath the streets of Sheffield's Kelham Island since last December, after developing an interest in sustainable hydroponic growing techniques
June 20, 2021
Luke Ellis Grows Plants Underground
Using Hydroponics And Artificial Light
Sheffield has its very own underground farm growing microgreens and veg (Image: coloboque (Pixabay)
Luke Ellis used to be a builder, but now he spends his days underground growing sustainable vegetables.
Mr. Ellis, from Sheffield, has been growing greens beneath the streets of Sheffield's Kelham Island since last December, after developing an interest in sustainable hydroponic growing techniques.
Hydroponics replace the need for a conventional soil and sunlight approach to growing vegetables, using water-based growing techniques instead.
This inventive method of growing means that Mr Ellis can produce a huge amount of leafy greens year-round, without needing to wait for the right season or growing conditions to become available.
Mr. Ellis' business, named 'Leaf + Shoot', now grows a wealth of leafy greens, microgreens, herbs, houseplants, and mushrooms for the people of Sheffield to enjoy - with very little food miles, zero pesticides, and no water waste.
On his business website, Mr. Ellis said: "We are a vertical bioponic farm in the heart of Sheffield, underneath 92 Burton Rd, Kelham in an old spring factory.
"Sustainability is at the heart of everything we do, in fact, it's why we started in the first place. Born out of a desire to produce nutrient-dense, tasty produce with minimum food miles and zero water waste.
"We grow 10 x as much food in the same space as traditional farming twice as quickly, year-round. Reducing the need to import seasonal produce and increasing the nutrient density and freshness."
All of Leaf + Shoot's produce is grown with organic principles, which means that there are no pesticides, herbicides, fertilizers or other chemicals used.
And the delicious and eco-friendly produce is sold around the city, with many businesses benefitting from Mr. Ellis' innovative underground farm.
And individuals can also purchase the fresh produce as Leaf + Shoot regularly sell their harvested greens at pop-up shops outside their farm on Burton Road, where people can bag freshly harvested salad mixes and house plants.
Have you ever tried Leaf + Shoot greens? Let us know in the comments!
How A Malaysian Company Born During The Pandemic Is Championing Harvest-To-Table In Kuala Lumpur
The brainchild of founders Shawn Ng, 28, and Sha G.P., 27, The Vegetable Co. aims to deliver fresh greens within three to four hours after harvest to their customers in various parts of Klang Valley
27 June 2021
BY KENNY MAH
Harvest-to-table vegetables have arrived in Malaysia, courtesy of The Vegetable Co. — Picture courtesy of The Vegetable Co.
PUCHONG, June 27 — The vegetables we eat and where we get them from can be a quagmire of questions: Is it organic? Local or imported? Is it safe? Is it fresh?
Getting your daily intake of healthy greens shouldn’t be this stressful, I reckon.
Enter The Vegetable Co. This fledgling harvest-to-table startup was launched early last year and is based on sustainable vertical farming concepts and in-house, customized technology.
The Vegetable Co. founders Shawn Ng (left) and Sha G.P. (right). — Picture courtesy of The Vegetable Co.
The brainchild of founders Shawn Ng, 28, and Sha G.P., 27, The Vegetable Co. aims to deliver fresh greens within three to four hours after harvest to their customers in various parts of Klang Valley.
Quality is a major differentiator. Ng explains, “Our vegetables are meant to be better than what’s available in the market due to their freshness and growing method. The indoor farming method ensures that they are delicious and pesticide-free while still reaching optimal size, taste, and nutritional value.”
Through their Controlled-Environment Agriculture farming method, the startup has devised and built an indoor, environment-controlled chamber that saves significantly on land and water consumption.
This indoor environment approach differs from conventional farming practices as they grow vegetables utilizing LED lights, vertical stacks, hydroponic systems, and environmental control to keep the internal atmosphere at an optimal constant that encourages optimal plant growth.
Ng adds, “The chamber is also an isolated environment, which prevents external contaminants from entering and as such mitigates the need for pesticide usage. Basically, we are farmers in lab coats, or plant scientists. Our aim is to grow food in the best possible environment to get the most nutrition and freshness onto your table.”
As with many startups, The Vegetable Co.’s overall ambitions and strategy are heavily influenced by the founders. The duo first met when they were doing their A-levels, and have been friends for well over a decade.
This meant they understood each other’s strengths and differences — Sha has a BSc in Economics from The University of Manchester while Ng received a Masters in Green Management and Sustainability from the University of Bocconi in Italy — and how best to complement each other.
Ng recalls, “Since college, we have always been young idealists who spent countless nights debating on the many ways in which we could contribute to the nation’s development. Generally, Sha is always pragmatic in nature, while I’m a bit of an optimist who dreams of a better future for the Malaysian people.”
Therefore, unlike many businesses that are driven solely by profit making, the two friends started their venture due to their burning need to drive change in a significant and tangible manner.
A sense of purpose was crucial, as Ng observes: “We both had work experiences prior to this, and they never fully aligned to our overarching goals and principles. By working on the business, we were given the opportunity to pursue and craft our own paths forward.”
But why vegetables?
Loyal customers have the 2015 film The Martian to thank. Ng explains, “It really intrigued Sha as the astronaut had to find a way to grow food in an extreme environment to survive. He began considering whether it could be feasible and commercially viable in the Malaysian context. He approached me with the idea, and the rest is history.”
Assembling their team was another piece of the puzzle they had to solve early on.
Ng says, “One of our most important hires remains our first farm operator, Bryan Lee. We hired him back in late 2019 when he was 19, and he has been with us since. Combining his love for plants with his mechanical and electrical engineering skills has made him essential for the work here, especially during the early stages.”
Plenty of care is taken in growing the vegetables, with the latest vertical farming technology. — Picture courtesy of The Vegetable Co.
The Vegetable Co. also has an in-house Research & Technology team — comprising young Malaysians below the age of 30 from varying backgrounds — working to optimise their automated systems, fit-for-purpose farm designs, as well as the quality and nutritional value of their produce.
That last attribute, Ng notes, is a crucial factor to market acceptance: “Our customers can smell the fragrance of the basil when they first open the box. This, combined with the springiness of our lettuce, really drives a good impression on people.”
The key to the freshness of their produce lies in their harvest-to-table approach, typically within a three- to four-hour window.
Ng explains, “Our intention is to move away from mass industrial agriculture and long supply chains. Research has shown that vegetables travelling far distances tend to lose nutritional value over time, some as fast as within 48 hours. There are also the concerns of food waste, as a third of all food stuff is usually discarded in the beginning, generating methane through open decomposition and exacerbating climate change.”
A typical subscription box contains seven types of freshly harvested vegetables. — Picture courtesy of The Vegetable Co.
As a result, The Vegetable Co. strives to grow within 20 kilometres of high populated districts within the Klang Valley, such as Kuala Lumpur, Petaling Jaya, Subang, Puchong, and Shah Alam.
In doing so, Ng claims this will help preserve the maximum nutrients possible, cut down on transport emissions and increase transparency as they minimise the number of unknown variables between the farm and the consumers.
He adds, “During the past year, we also observed interruptions in supply and knee-jerk reaction price hikes due to inter-state logistical issues associated with Covid-19 restrictions and we believe our solution helps address these challenges by farming right in the middle of population centres.”
By growing in vertical stacks within urban areas, The Vegetable Co. purportedly mitigates around 95 times the land use through conventional farming methods. In the future, the duo also plans to activate unused urban spaces to further increase land use efficiency.
Given the constraints of each individual farm being able to only service a certain radius around it, The Vegetable Co. will leverage both localisation and decentralisation to scale up in a sustainable manner.
Ng explains, “The modularity of our farms enables us to install farms in every urban centre where there is demand. This is how we envision the growth of our company and the vertical farming sector here in Malaysia.
Sounds like a reasonable and promising business model, no? But as any seasoned entrepreneur would tell you, the journey is never a smooth nor swift one.
The Vegetable Co. was self-funded by the two co-founders at the beginning. Ng says, “We really had to dig deep into our coffers and commit all our resources into the start of the company — scraping for whatever savings or equipment we have in order to make things work.”
Harvesting time. — Picture courtesy of The Vegetable Co.
Beyond a startup tendency to stay lean and agile, part of the scramble came from launching the business barely a month before the first movement control order (MCO) last year. Initial plans for pop-up booths and taste testing as a market education tool were immediately shelved.
With only a small number of early adopters, they decided to focus solely on promoting their subscription model. Ng explains, “This was what truly appealed to our first base of customers — those who were concerned about regular access to freshly-grown produce without needing to brave the supermarkets or fearing a shortage of supply.”
That gamble paid off handsomely as revenue grew by 300 per cent in the first few weeks alone. Both co-founders realised that customer satisfaction and confidence were critical for pushing the product to market, and have since made it part of their company promise: To reduce the time and distance for quality produce to reach their customers.
“Customers who took the chance on us in the early stages could immediately tell the difference,” Ng says, “From there the product sold itself by word-of-mouth. The popularity of the subscription service drove demand and allowed us to expand and to increase our capacity as we prepare for the launch of our next phase in July.”
Packing the just-harvested vegetables into subscription boxes. — Picture courtesy of The Vegetable Co.
Since then, the duo has gotten the support of an angel investor as they expanded their operations. Ng adds, “Although we have no immediate fundraising plans, we’re looking at raising a bridging round sometime Q3/Q4 this year to continue our business expansion and technology consolidation.”
Part of that expansion would include gradually doubling the number of their produce variants as production capacity increases. Currently The Vegetable Co. has about 10 variants; a standard box comes with about seven variants, making every delivery a little surprise, not unlike CSA (Community Supported Agriculture) boxes.
The Vegetable Co. aims to deliver fresh greens within three to four hours after harvest to their customers. — Picture courtesy of The Vegetable Co.
According to Ng, by having fresh vegetables delivered to them on a frequent basis, many of their customers have changed their diets for the better: “Some of our customers have taken to snacking on our veggies and moving away from the bad habit of eating junk food. Fundamentally, we are in the business of encouraging healthy habits and lifestyles.”
Are vertical farming and vegetable subscription boxes the future of our dining tables? It is early days yet but The Vegetable Co. certainly makes a strong and admirable case for Malaysian harvest-to-table.
To borrow from a classic jingle: Any fresher and you’d have to pick these greens yourself.
The Vegetable Co.
Lead photo: A typical subscription box contains seven types of freshly harvested vegetables. — Picture courtesy of The Vegetable Co.
Web: thevegetable.co
USA: NEW JERSEY - Newark Farm Trying To Change The World
If the current movement to grow more food in urban settings by high-tech indoor methods follows the path that some predict, Newark's vertical farm on Rome street is the largest indoor farm in the world and will be an important part of the history
June 21, 2021
By George E. Jordan | For NJ Advance Media
AeroFarms Uses Aeroponics And
LED Lights To Grow Its Products
The company leased a shuttered steel beam supply company on Rome Street, tore down a rusted warehouse, and built a 70,000-square-foot building. It filled it to the ceiling with grow tables 80 feet long and stacked 12 layers to a height of 36 feet.
AeroFarms uses aeroponics and LED lights to grow its products. The company says it can produce up to 2 million pounds annually of kale, bok choy, watercress, arugula, red-leaf lettuce, mizuna, and other baby salad greens. It's all done without soil, sun or pesticides, and the company claims to use 95% less water than outdoor farms.
AeroFarms-branded leafy vegetables are sold in the northeastern U.S. at retailers, including Whole Foods Market, ShopRite, Amazon Fresh, and FreshDirect.
If the current movement to grow more food in urban settings by high-tech indoor methods follows the path that some predict, Newark's vertical farm on Rome street is the largest indoor farm in the world and will be an important part of the history.
"The vision long term for the company is to take a new understanding of agriculture to a new height and then feed people and to apply that knowledge to grow better plants," said David Rosenberg, AeroFarms' chief executive, who recently announced plans to expand its Newark headquarters.
AeroFarms operates nine indoor farms in four Newark locations, and one in Virginia, and a growth and research facility in Abu Dhabi as part of a $100 million investment by the United Arab Emeritus.
Rosenberg said the company plans to build a network of new high-tech indoor farms across the United States. The first is currently under construction in Danville, Virginia, on the North Carolina border in close proximity to more than 1,000 food retailers and approximately 50 million people within a day's drive.
AeroFarms has more than 150 employees in Newark, including grow-house workers, horticulturists, engineers, and data scientists who represent a dramatic shift from the scrap-metal yards and chemical plants and breweries that dominated the Ironbound.
Marc Oshima, AeroFarms' co-founder, and spokesman said the company offers computer and financial literacy training programs, and the workforce includes former criminal offenders and homeless people.
"The biggest impact we've had on the city is inspiring other tech firms to come to Newark," he said, describing how AeroFarms donated offices to Newark Venture Partners, a business incubator funded by Don Katz, founder, and chief executive of Audible.
Aaron Price, president of TechUnited, a non-profit that lures startups to New Jersey, said technology companies like AeroFarms figure in luring jobs and students and new residents to New Jersey's largest city.
"By leveraging technology, cities can thrive. Newark has embraced incoming technology companies and they are embracing Newark," he said. "Newark is having real job growth."
In addition to selling crops, AeroFarms announced various partnerships with governments, universities and Fortune 500 companies to help solve agriculture supply chain problems. For instance, AeroFarms will publish a study to improve leafy green production, flavor and nutrition next year with the Foundation for Food and Agriculture Research, a non-partisan, non-profit funded out of the U.S. Farm Bill. The findings are aimed at helping the farming industry.
Agriculture is responsible for 15% of global greenhouse gas emissions, and accounts for one-fifth of U.S. fossil fuel use, mainly to run farm equipment, transport food and produce fertilizer, according to Columbia University's Climate School.
The United Nations Food and Agriculture Organization (FAO) says more than two-thirds of the world's freshwater is used for agriculture. And around the world, farmers are losing the battle for water for their crops as scarce water resources are increasingly being diverted to expanding cities.
Rosenberg compared AeroFarms' trajectory to the growth of Amazon, which began focused on books, and Tesla's development of batteries and focuses on autonomous vehicles after gaining a foothold in electric vehicles.
This press release was produced by the City of Newark. The views expressed here are the author's own.
Aquaponic Springworks Farm Expands With 26-Year-Old CEO
“I became interested in sustainable agriculture after seeing the impacts of agriculture in the ecosystems around me,” he said. “There was this visceral impact for me. A lot of people don’t get the opportunity to see some of the negative consequences of agriculture and the way that we eat.”
By AMY SOWDER
June 25, 2021
How A Teen-Now 26-Scaled Up His Aquaponics Firm, Springworks
Trevor Kenkel was 13 when the fish and frogs dying from nutrient pollution in his favorite creek by his Montana home motivated him to experiment with aquaponics.
His teenaged tinkering in the garage led to founding Springworks Farm in 2014, while he was a freshman at Bowdoin College in Brunswick, Maine, studying biology.
“I became interested in sustainable agriculture after seeing the impacts of agriculture in the ecosystems around me,” he said. “There was this visceral impact for me. A lot of people don’t get the opportunity to see some of the negative consequences of agriculture and the way that we eat.”
Today, Springworks is headquartered in Lisbon, Maine, and counts 200 Hannaford stores, Whole Foods distribution centers, restaurants, and other companies as customers of its leafy greens.
And on June 19, Kenkel, Springworks CEO and president, sliced the grand-opening ribbon with golden scissors on his third greenhouse, totaling about 45,000 square feet of commercial production using the aquaponic farming technique in which fish and plants support each other’s growth in a closed system.
His sister, Sierra Kenkel, was by his side as vice president of the company.
At their company, the nutrient-rich water from raising tilapia is pumped into growing beds, which feeds the leafy greens. The plants, in turn, clean the water and return it to the fish. No chemicals are needed.
“We’re taking what would otherwise be a waste stream and turning it into a positive, as fertilizer,” Kenkel said.
From the start, Springworks greens were U.S. Department of Agriculture-certified organic, but the products were replacing conventional greens at local restaurants.
“We had to be at a competitive price point, and we also had to be able to articulate what our value proposition was: better shelf life, better quality,” he said. “We’re not relying on the USDA-certified organic label to add value, so much as our product being better than what our customer was buying.”
By 2026, the Kenkels want half a million square feet of aquaponic greenhouse operations on the Lisbon site.
“We’re able to produce a little under a million heads of lettuce a year, and we’ll be a little more than doubling that with the new facility,” Kenkel said the day before the grand opening of the third greenhouse.
Knowing that a mistake on a large scale is much more expensive, Kenkel started small and progressively expanded. At each step, he dealt with the new challenges associated with the scale and made improvements.
“We’ve been very intentional over the years at scaling up as we feel comfortable managing that size system, with where the technology is at and with our customer base,” he said.
The first few years, Kenkel and his team focused on water quality, fertigation, how to link the systems and updating infrastructure.
The product line is growing too, as the emphasis has transitioned toward more retail.
Springworks is the exclusive provider of organic green leaf lettuce to 200 Hannaford locations, which also carry the organic bibb lettuce and organic romaine pouch, the first three products launched for retail customers.
“Springworks checks every box when it comes to our lettuce supply needs and Zero Food Waste goals,” Hannaford produce category manager Mark Jewell said in a news release. “We also are impressed by their consistent quality and ingenuity. These factors, combined with their exceptional food safety practices, year-round availability and proximity to our distribution centers, made it an easy decision.”
Trevor Kenkel of Springworks Farm (left) with Mike Vail of Hannaford. (Photos and illustration courtesy Springworks Farm)
The aquaponics company has expanded to offer single-cut products for more convenience.
“They cut them once at the base and package them in a clamshell. You can pull out those leaves individually and make a salad with them, make a wrap,” Kenkel said.
Springworks also makes a salad mix.
“Consumers who value quality and transparency are asking supermarkets for organic products from local food producers,” said Sierra Kenkel, who handles sales and marketing as vice president for Springworks.
Kenkel’s goal is to be competitive with the product coming from the Southwest and to eventually replace it for his East Coast customers.
During the supply chain issues early in the COVID-19 pandemic, Springworks was able to fill the orders for regional customers that normally sourced from California, Arizona or Mexico.
Within the next decade or so, Kenkel sees a shift in the leafy greens industry from 95% centralized production in the Southwest to a more regionalized approach.
The product is naturally fresher when it’s grown near shoppers.
“Both in terms of the carbon footprint and the economics of it, this is a win-win,” Kenkel said. “Pricing will continue to get more competitive.
“And I think all of that is going to lead to that 95% number ending up a lot lower than that in the next decade or so, as more of these hubs of production start to develop closer to where the product is consumed.”
And what about those fish?
They sell the tilapia at a local fish market in Portland, Maine.
“With this process, you get a lot more volume in greens than you do fish,” he said.
USA: INDIANA - Delaware County Moves Ahead With Economic Incentives For Vertical Farming Company
Living Greens Farm, an indoor produce farmer based out of Minnesota, is looking to turn the space into its next produce facility. The company uses an aeroponics process, also referred to as vertical farming, to produce greens for sale in grocery stores
Muncie Star Press
MUNCIE, Ind. — Delaware County is moving forward with economic incentives for a vertical farming company looking to buy the Industria Centre shell building along Fuson Road.
The shell building, measuring 200,000 square feet, was built in 2014 by Garmong Construction. The nearly $8 million county-funded shell building had been unable to find a tenant in seven years.
This building is officially owned by Garmong, a Terre Haute-based company that's been a frequent partner with the county on shell buildings in the past.
►PREVIOUS: Indoor farming company could purchase Delaware County Shell building
The building is funded by the county and built on county-owned land.
Living Greens Farm, an indoor produce farmer based out of Minnesota, is looking to turn the space into its next produce facility. The company uses an aeroponics process, also referred to as vertical farming, to produce greens for sale in grocery stores.
Modern Farming: Coronavirus Outbreak Spurs High-Tech Greenhouse Boom in China
The facility is one of the dozens sprouting up on the outskirts of China's megacities that utilise high-end technology to manage irrigation, temperature and lighting systems to grow vegetables within easy reach of a large and affluent consumer base
June 4, 2021
Emily Chow
SHANGHAI, June 4 (Reuters) - At Chongming Island just outside Shanghai, China’s most populous city, workers collect and pack tomatoes and cucumbers at a glass greenhouse operated by Dutch company FoodVentures, which harvested their first batch of produce at the site in May.
The facility is one of the dozens sprouting up on the outskirts of China's megacities that utilize high-end technology to manage irrigation, temperature, and lighting systems to grow vegetables within easy reach of a large and affluent consumer base.
"There is a trend towards more sustainable and professional supply," said FoodVentures director Dirk Aleven.
"We've seen a huge acceleration since (the) coronavirus, it is even more important now that fresh produce is produced at the spot where it's consumed. Before that, they were transported for thousands of kilometers, even within the borders of China."
By far the world's largest vegetable producer, China has used greenhouses for decades, but food supply disruptions sparked by coronavirus lockdowns in 2020 have accelerated the development of high-tech glass greenhouse facilities.
To avoid future disruptions, municipal governments have said they aim to build up reserves of critical staples, and develop distribution and logistics facilities.
A growing affluent middle class, willing to pay more for higher quality food produced with less pesticides, is also fueling the trend, said greenhouse developers.
The area used for glass greenhouses grew 28% in 2020, well above the 5.9% rise seen in 2019, and faster than the 6% growth seen last year in areas housing cheaper plastic greenhouses, according to consultancy Richland Sources.
Plastic greenhouses help shield crops, but are considered less efficient than glass greenhouses. The latter can churn out high quality produce that is sold directly to retailers, reducing reliance on traditional supply chains.
"We see an irreversible trend since the pandemic in consumers buying more of their groceries online, and spending more on healthier choices and agricultural brands they trust," said Lim Xin Yi, executive director of sustainability at Pinduoduo, China's largest e-commerce platform by users.
BYPASSING THE MIDDLE MAN
Historically, China's vegetable production was concentrated in certain areas and required complex cold chain logistics networks for food to reach major cities' wholesale markets.
The vulnerability of that hub-centric system became apparent in 2020. COVID-19 outbreaks at a seafood market in Wuhan - ground zero for China's coronavirus pandemic - and at a major fresh market in Beijing caused a breakdown in the flow of goods to consumers, leading to food shortage and crop spoilage.
"The pandemic has pushed the fresh food industry to reduce the number of intermediaries in its supply chain network," said Gayathree Ganesan, an analyst at the Economist Intelligence Unit.
A farmer gathers cucumbers at Hengda greenhouse in Shanghai, China May 25, 2021. REUTERS/Aly Song
Built within city limits to reduce distance to buyers, the greenhouses are usually collaborative ventures between Chinese property firms and greenhouse companies from the Netherlands, a key player in agriculture technology.
FoodVentures' greenhouse outside Shanghai is a typical example.
Over three football fields long and two storeys high, one of the facility's units nurtures uniform rows of cherry tomato plants that snake up towards the ceiling. It is capable of producing up to 120 tonnes a month of cherry tomatoes.
"Being healthy is already a first protection against any virus, so people care even more about what they eat," said Aleven. "Secondly, ... we want to get rid of the long logistics because we are not sure if it always works and that's what we've seen during this pandemic."
"Localising it as much as possible is the only answer," he added.
Greenshouse-grown produce is usually sold directly to e-commerce platforms and supermarkets, bypassing the many middlemen and wholesale markets that are a traditional feature of China's vegetable supply chain.
Carrefour China, which is 80% owned by Chinese retail giant Suning, said its cooperation with greenhouses around cities has grown steadily in the past two years to meet consumer demand.
SUSTAINED EXPANSION
Further growth in key cities is likely, with a recent government document showing Beijing aims to more than double its "high-efficiency facility agriculture land" to over 300 hectares by 2025.
That growth could further cement China’s status as top vegetable producer. The country already accounts for 75% or more of global output of cucumbers, green beans, spinach and asparagus.
Xu Dan, CEO of greenhouse operator Beijing HortiPolaris, said his business benefited last year when a second coronavirus wave hit Beijing in June, shutting down a major wholesale market and driving his daily orders up 300%.
"(At that time) supermarkets were looking for growers with the ability to deliver within 24 hours and they had no time to search for new suppliers," he said.
But Xu said China could face some obstacles as it leaps into modern farming.
"The biggest challenges are people, people who have the knowledge to manage greenhouses to produce quality vegetables," he said.
“Most farmers are getting old and their way of production also out of date, replacing such (a) big amount of farmers is really a big challenge.”
Reporting by Emily Chow in Shanghai, additional reporting by Sophie Yu and Dominique Patton in Beijing and Beijing newsroom; Editing by Ana Nicolaci da Costa
BrightFarms Forms Research And Development Innovation Hub BrightLabs; Steve Platt And Matt Lingard Comment
BrightLabs places a key focus on developing proprietary and patented ecosystems for plants to thrive, increasing their flavor, yields, and texture in the process
June 24th, 2021
by Jenna Plasterer
IRVINGTON, NY - A new launch and a new leader? Tell me more! These are just a couple of the titillating details included in BrightFarms’ most recent announcement. The indoor greens grower has formed a new research and development (R&D) hub called BrightLabs at its Ohio growing facility. Matt Lingard, PhD, a former Bayer plant scientist with over 15 years of experience in biotechnology and greenhouse science, will be leading the BrightLabs team as Vice President of Agriculture and Science.
Steve Platt, Chief Executive Officer, BrightFarms“
The indoor farming industry is at an inflection point as local, indoor-farmed produce becomes a priority for retailers and consumers. Among competitors, we’ve developed the most profitable model for the production of indoor leafy greens, but it’s essential that we maintain our market advantage to stay ahead of the curve,” said Steve Platt, Chief Executive Officer. “We’ve built up a team of the best minds in indoor agriculture to officially launch BrightLabs, where we’ll develop the next phase of game-changing products and technology solutions for our operations.”
BrightLabs places a key focus on developing proprietary and patented ecosystems for plants to thrive, increasing their flavor, yields, and texture in the process. The team will bring together experts in technology, microbiology, and plant science to deliver breakthrough innovations in the salad category and beyond.
BrightFarms has formed a new research and development (R&D) hub called BrightLabs at its Ohio growing facility
This multi-million dollar R&D investment is launching as part of the company’s $100 million Series E Fundraise led by Cox Enterprises and represents a significant increase in the company’s research capabilities. Ten percent of the company is now dedicated to developing complex, patented growing solutions to be applied to BrightFarms’ burgeoning network of greenhouses.
Matt Lingard, PhD, Vice President of Agriculture and Science, BrightFarms“
No other indoor farming company is studying a plant’s microbiome, the naturally occurring bacteria that help determine its health, to the same degree that we are,” said Lingard. “Instead of pouring dollars into artificial lighting research, we’re developing cutting-edge biotechnology solutions to out-maneuver our competition with the most productive indoor farms in the industry. There’s no question that high-tech greenhouses that leverage natural sunshine have emerged as the most promising new generation of agriculture technologies, and optimizing the microbiome will allow us to unlock even more of a plant’s natural potential in our indoor farms.”
BrightLabs aims to double its production of its hydroponically grown spinach, and will build on the success of its best-selling Sunny Crunch variety with a new, antioxidant-rich lettuce, NutriGreens, set for release this June.
BrightLabs places a key focus on developing proprietary and patented ecosystems for plants to thrive, increasing their flavor, yields, and texture in the process
BrightOS, the company’s award-winning proprietary data system, will help the BrightLabs team accelerate their research with machine learning and advanced data analysis.
Stay tuned as we wait to see the incredible innovations to come.
Indoor Farming Indoor Ag BrightFarms Research Development Research and Development R&D Innovation Innovates Innovation Hub BrightLabs Launch New Launch BrightOS Steve Platt Matt Lingard
COMPANIES IN THIS STORY
BrightFarms
BrightFarms finances, designs, builds and operates greenhouse farms at or near supermarkets, cutting time, distance, and...
A SPAC Deal Sprouts For AgTech Company Local Bounti: What Investors Should Know
One of the company’s key investors is Cargill which is listed as a strategic partner and will invest in the company as part of the SPAC deal. Cargill will also provide a $200 million debt facility to help with Local Bounti’s expansion plans
Chris Katje, Benzinga Staff Writer
June 18, 2021
Agriculture technology continues to be a hot segment for companies seeking to go public with another SPAC deal in the sector announced Friday morning.
The SPAC Deal: Local Bounti announced a SPAC deal with Leo Holdings III Corp LIII 0.71% valuing the company at $1.1 billion.
One of the company’s key investors is Cargill which is listed as a strategic partner and will invest in the company as part of the SPAC deal. Cargill will also provide a $200 million debt facility to help with Local Bounti’s expansion plans.
Public LIII shareholders will own 24.8% of Local Bounti if the merger is approved. Shares will trade on the NYSE as LOCL.!
About Local Bounti: One of several companies in the controlled environment agriculture segment, Local Bounti is seeking to improve the production of fresh produce across the United States.
Controlled environment agriculture is the future of farming according to Local Bounti’s presentation. This practice includes year-round farming, using 90% less water, zero pesticides, and providing cost-competitive produce.
The company uses proprietary technology to grow leafy greens and herbs in an indoor environment. Current products include cut lettuce, living lettuce and living herbs such as basil and cilantro.
Local Bounti products are currently in more than 400 retail stores, according to the company.
Related Link: Indoor Farming Startup AppHarvest Aims For Wall Street With SPAC Deal
Growth Ahead: Local Bounti will use capital from the SPAC deal to build out its indoor farming facilities across the Western U.S.
It plans to double the size of its flagship Hamilton, Montana facility and to break ground on additional facilities by the end of 2021. The company’s pipeline includes eight facilities and a plan for 30 SKUs by the end of 2025.
Local Bounti lists the total addressable market size of $30 billion for vegetables and herbs in the U.S. with a $10.6 billion market in Western U.S.
“Today’s announcement takes Local Bounti to the next level in enabling local, sustainable production and delivery of fresh, delicious and nutritious produce, including in regions that traditionally don’t have access to local supply, starting in the Western U.S. and expanding globally,” Local Bounti co-founder and co-CEO Craig Hurlbert said.
Other long-term growth plans for Local Bounti include international expansion, subscription as a service, new products and franchising and licensing.
Local Bounti joins companies like Appharvest Inc APPH 1.29% and AeroFarms, merging with Spring Valley Acquisition Corp SV 0.1% to choose the SPAC route to go public.
Financials: Local Bounti highlights its low-cost operations and high yield thanks to a hybrid facility configuration and vertical farming.
The company hit its first revenue in 2020. Projections are for the company to hit $13 million in revenue for fiscal 2022 and $85 million for fiscal 2023.
By 2025, the company expects to hit over $400 million in annual revenue.
LIII Price Action: LIII shares are up 1.44% to $9.87 on Friday morning at publication.
(Photo: Local Bounti)
Vertical Harvest Collaborates Directly With Chefs Across Jackson
Since its inception, Vertical Harvest Farms has had a special relationship with the chefs of Jackson. The farm works closely with chefs to grow micro and petite greens specifically curated to each restaurant’s menus
06-21-21
Vertical Harvest Collaborates Directly With Chefs,
Finding Fresh Flavor To Elevate Any Dish
JACKSON, Wyo. — Chef Alejandra Peña nibbles a small green leaf and the spark in her eyes is unmistakable. Her customers at Persephone Westbank will soon find a similar tiny stalk in their morning granola bowl. “They’ll be surprised at the pop of citrus with their oats and yogurt,” said Peña. “ Tangerine cress is something people haven’t experienced as a taste before and it is really exciting to use microgreens like these in unexpected ways.”
Chef Alejandra Peña of Persephone Wesbank. Photo: Lindley Rust
It’s a fun day at the farm when a chef stops by the Vertical Harvest greenhouse. Geeking out over a microgreen’s flavor profile rings deeply sincere coming from the person who places it precisely on the plate. “Seeing the colors, tastes and textures helps me brainstorm my menus with something that is very tangible,” said Peña. “This is such a different experience than looking at a product list because being in the greenhouse and talking through the flavors with the growers helps the dish in my head come to life.”
Since its inception, Vertical Harvest Farms has had a special relationship with the chefs of Jackson. The farm works closely with chefs to grow micro and petite greens specifically curated to each restaurant’s menus. Chefs are welcome to book time to come and “shop” the greens with the Vertical Harvest grow and sales teams.
Persephone West Bank Chef Alejandra trying microgreens with Hannah Bouline (Product Manager) and Emily Peterson (Sales Director). Photo: Kyra Foley
“It’s satisfying to see the look in chefs eyes when we sample a new green with them. We always do a deep dive into how the flavors and textures can make other ingredients come alive,” said Hannah Bouline, Vertical Harvest Product Manager.
On her recent greenhouse visit, Peña was preparing for Persephone Westbank’s new 5-9 p.m. dinner service, which just started on June 17, 2021. She tasted radish microgreens, mustard frills, rock chive, and red veined sorrel. While the sorrel and tangerine cress are already breakfast and lunch menu staples, she was excited to play with the mustard frills for the dinner menu.
According to Peña, it’s important to have microgreens and petite greens that she can use for breakfast, lunch, and dinner but still have very different flavors and textures throughout the day. “Our goal is to avoid waste and use the freshest product possible.”
The overall vibe of the new dinner menu is fresh, floral, and citrus-like a French bistro, she says. “We’ll offer vegan dinner options and provide an experience that is casual and kid-friendly with a specific kid’s menu. I don’t want anything to be too heavy, but instead, have the entire family leave feeling like they could really enjoy the dishes and not be too full.”
The Salmon Tartine. Photo: Kyra Foley
Peña’s plan is to pair Vertical Harvest’s red-veined sorrel with dishes such as salmon tartine and use the tangerine cress across many dishes on the menu. She also hopes to make Vertical Harvest edible flowers a key part of the restaurant’s cocktail program.
She is most excited about the ½ roasted chicken with seasonal vegetables. “It’s so juicy and has a light yet flavorful cardamom glaze,” she said. “I’m so excited for everyone to try it!”
A group of Vertical Harvest team members visited opening night and were impressed with the atmosphere and the food. “It was so lovely to enjoy the light, yet flavorful, food on a warm afternoon,” said Emily Peterson, Vertical Harvest Sales Director. “The cocktails were spot on and I loved the salmon tartine with its pop of citrus supplied by the red-veined sorrel. The menu perfectly balances rich dimensions of flavor without being too heavy. Even the usually deep and earthy ratatouille had a fresh essence.”
Try the chicken, salmon tartine, and other wonderful new dinner menu items yourself this season. Dine at Persephone Westbank at 3445 N Pines Way in the Aspens, Wilson WY. Learn more about Vertical Harvest Farms and its freshly, locally grown produce on the company’s website here.
Lead photo: Vertical Harvest collaborates directly with chefs, finding fresh flavor to elevate any dish. Photo: Shannon Corsi
Sponsored by Vertical Harvest - Jackson Hole, Wyoming
Highlighting The Potential of Dutch Horticulture In Vertical Farming
Indoor Farming Holland aims to bring companies together to see where their knowledge can be developed and applied in the vertical farming space. “We’re focusing on the combination of technical solutions with plant science, where Holland has a great proposition.”
“The Dutch are falling behind when it comes to vertical farming,” says Judith van Heck, Community Builder at Indoor Farming Nederland. “As we’re so tremendously good at greenhouse growing there is relatively less interest in building vertical farms in the Netherlands. In comparison to countries such as the US, this has resulted in lower investments. That’s why we started the initiative Indoor Farming Nederland. We want to help the Dutch horticulture sector to develop the potentially very interesting sector, and we also want to highlight the international potential of Dutch horticulture in vertical farming.”
Indoor Farming Holland aims to bring companies together to see where their knowledge can be developed and applied in the vertical farming space. “We’re focusing on the combination of technical solutions with plant science, where Holland has a great proposition. We, therefore, believe that we can obtain optimal results from vertical farms and take the lead on that,” Judith notes.
“Due to many things happening around vertical farming and innovative solutions that are brought to market, we’ve created a government-backed organization to stimulate indoor farming amongst Dutch horticultural companies,” says Gus van der Feltz, project leader for the Fieldlab Vertical Farming. In the Fieldlab Vertical Farming, an important collaboration is established between South Holland knowledge institutions and companies that are engaged in the production of vertically grown products, the sale of vertically grown products, and suppliers of technologies for vertical farms.
Gus van der Feltz and Judith van Heck
Increasing awareness
The Fieldlab is supported by the European Fund for Regional Development of the European Union and the Province of South Holland. Now, the organization’s activities consist of four different ‘packages’ which they’d like to elaborate on throughout the Dutch horticulture industry. Vertical Farming Zuid-Holland received a subsidy to develop a foundation for potential market entrants that consists of four different packages.
The Fieldlab, working together with Indoor Farming Nederland, wants to increase awareness of the added value of vertical farming. Firstly, by using market research to understand consumers, growers, retailers, and the supply chain’s perspective on vertical farming. “Through market research, we want to highlight the benefits and processes that could be improved,” says Gus. Secondly, the organization will do research and testing to generate knowledge on vertical farming and recipes through development and innovations by Dutch horticulture companies.
Thirdly, “we want to educate and train people,” says Gus. “We’re working on developing training programs specifically focusing on vertical farming. From the technical side of things to running a farm and selling your produce successfully.” Last but not least, a sector-related platform is to be constructed to create a long-term and sustainable network the industry can fall back to. In collaboration with Vertical Farming Fieldlab, for the industry to further develop knowledge in Dutch horticulture, the organization consists of multiple companies, such as Own Greens, Delphy, Signify, WUR Bleiswijk, Vertify, Logiqs, Proeftuin Westland, InHolland, WUR Wageningen, Future Crops (Poeldijk).
Judith explains that the community works with jointly formulated ambitions. “We help this cluster of companies to obtain as much knowledge as needed. We stimulate them to co-create on several challenges. One of the ambitions is to communicate the potential of the cluster and indoor farming products to various target groups. Amongst other things, we are creating a white paper regarding the general statements about vertical farming and the complex reality of it.” Next to that, the organization is exploring the feasibility of a collective market intelligence tool to see where vertical farming can add value internationally. However, the community aims to not only help Dutch entrepreneurs but the collective market. One of the ambitions, for instance, is to communicate the potential of the cluster to various target groups within, but especially also outside, the Netherlands.
Amongst other things, Indoor Farming Nederland will create a whitepaper that states all facts concerning vertical farming. Next to that, the organization is exploring the feasibility of a collective market intelligence tool to see where vertical farming can add value internationally. They’re doing so by looking at climate, population density, food patterns, availability of water, and energy. Also by analyzing where the most potential is for vertical farming, or hybrid solutions even, in combination with greenhouses.
For more information:
Indoor Farming Nederland
Gus van der Feltz, Project leader
gus@feltzwerk.nl
Judith van Heck, Community Builder
judith@imagro.nl
Publication date: Wed 16 Jun 2021
Author: Rebekka Boekhout
© HortiDaily.com
How To Grow Food In A Concrete Jungle
Building flourishing farms in the heart of cities used to be just a utopian fantasy. Now it's an important step towards developing a smart, diversified food system capable of feeding a growing world population.
Editor’s Note: The vertical farming industry continues to evolve as more operators come online. The diversity of operators and crops being grown will allow for new products to go to market and provide the consumer with fresher choices for their shopping carts. Agritecture’s client, Agricool, is one of many CEA operators leading the way.
BY DALIAH SINGER
Building flourishing farms in the heart of cities used to be just a utopian fantasy. Now it's an important step towards developing a smart, diversified food system capable of feeding a growing world population.
Guillaume Fourdinier has lived in Paris for six years, but he still misses the taste of the fresh cereal grains, beets, carrots, and more that grow on his family's farm in Verton. There, in northern France's countryside, eating locally is a way of life – not simply a trend or a sticker on an apple at the grocery store.
“Local food is everywhere when you are in the countryside. You get fruits and vegetables with better taste, more nutritional value,” he says. “When you are in Paris, what is local food? There is nothing coming from a local farm. I think for quality of life for people living in big cities this is a big problem.”
In 2015, Fourdinier co-founded Agricool, an urban farm that's now comprised of 11 recycled shipping containers on the north side of the city. Eight farmers plant, harvest, pack, and deliver the pesticide-free lettuces, herbs, and strawberries to 60 supermarkets (though Fourdinier expects that number to grow to at least 200 retailers by the end of 2021).
mage sourced from BBC
Urban farms like Agricool are part of a broad collection of metropolitan agricultural efforts including everything from vertical farms to greenhouses to aquaponics to community gardens. The idea of cultivating food in or near cities is not new (see the victory gardens of both world wars, for example), but these ventures have become increasingly popular in recent years as the local food movement strengthens. After the rise of the supermarkets led many people to feel disconnected from food production, consumers are again paying more attention to how and where their food is grown, along with how far ingredients must travel between field and plate.
From Brussels to Nigeria, entrepreneurs and farmers are reimagining what farms are and conceiving innovative technology to help grow food in smaller spaces and in more sustainable ways. They're attempting to fix existing food supply chain concerns, which we've all became intimately familiar with in the past year. Images of picked-over grocery shelves and farmers tossing out produce early in the Covid-19 pandemic broadcast the failures and fragility of our current systems.
By 2050, it's estimated that the global population will balloon to almost 10 billion, and 68% of those people will live in cities. That means we'll have to produce more food than ever before, to feed people who live farther from the rural areas where most crops and animals are cultivated. Bringing production closer to where consumption happens could increase food security, improve our health and lessen the industry's considerable impacts on the planet – if we're able to grow enough nutrient-rich grub, that is.
In the United States, it's estimated that urban and peri-urban farms account for almost 15% of the country's farms. Among them is 80 Acres Farms, a vertical farming operation based in Ohio but which has eight locations in four states, all of which use zero pesticides and require 97% less water consumption compared to traditional farms. (Vertical farming refers to growing crops in vertically stacked layers in a controlled environment, often incorporating soilless techniques.)
Co-founders Mike Zelkind and Tisha Livingston are trying to push the potential of this multi-billion-dollar industry further. To date, enterprises like theirs have primarily focused on easy-to-grow leafy greens – which won't sustain civilisation on their own – but with advancements in technology Zelkind and Livingston have been able to add more substantial crops like peppers, tomatoes and baby cucumbers. They explain how their farms have incorporated sophisticated technologies in the video below.
80 Acres is a year-round operation that optimises its growing environments based on the plants' genetics, harvests at the peak of ripeness, and relies on a smaller delivery radius to get food to customers within a day of its picking. It's “democratising high-quality food”.
“You can enable people, no matter where they live, to reconnect to the food supply,” Zelkind says.
Image sourced from BBC
Technology has made the duo's goals increasingly achievable – and made indoor farming both more efficient and more affordable. 80 Acres' farms are, on average, 300 to 400 times more productive than field farming, Zelkind says, because the vertical structure creates room for more crops in less space and because the produce grows faster.
At Agricool, which also relies on a tiered growing system, Fourdinier says his containers produce 120 times more sustenance per square meter than in traditional field growing and 15 times more than most greenhouses.
“Ten years ago, this was science fiction,” Zelkind says. “Tomorrow it's going to be so ubiquitous that everybody's going to be doing it and we will think, 'Oh my God, did we really ship our berries 2,000 miles a few years ago?'”
To that end, 80 Acres is commercializing what it's learned through Infinite Acres – a partnership with Netherlands-based horticulture technology firm Priva Holding BV and the UK's online grocery giant Ocado. The project provides the technology, operations help, and necessary infrastructure to help budding farmers and interested municipalities launch their own indoor farms. 80 Acres operates a reference design and demonstration farm in Hamilton, Ohio, that's capable of robotically planting, harvesting, and packaging around 1.5 million pounds (681 tonnes) of leafy greens annually. It proves the “economic feasibility of vertical farming indoors”, Livingston says. “We intend to build a farm like this farm all over the world.”
Which gets to the big question: Can a patchwork of metro area farms actually grow enough to feed future populations?
“To say that it is a solution to all of the ails? No, it's never going to be to me because we don't grow calorie crops in controlled spaces. I think it's a compliment. It can provide resilience on a very local level in that you have multiple [food] sources and you're not relying on just one supply chain,” says Anu Rangarajan, director of the Cornell Small Farms Program, which works to advance the viability of small farms. “It becomes part of a whole platform of food supply.”
In Paris, Agripolis recently opened Nature Urbain Farm on the seventh story of the Paris Expo Porte de Versailles. Five gardeners currently tend to the tomatoes, strawberries, eggplant, and even butternut squash growing on the world's largest rooftop farm using a closed-circuit, aeroponics system. The facility is only one-third complete, but there will be room for 20 gardeners to harvest up to 1.1 tons (1,000kg) of 35 varieties of fruit and vegetables every day. This surprising farm on a central Paris rooftop is already bearing fruits.
Image sourced from BBC
A Primer On Vertical Farming As The Industry Gains Steam
Nearly $1.9 billion of global venture capital was invested in indoor farming in 2020, nearly tripling investment in 2019. And just this week, New York-based vertical farming startup Bowery Farming raised $300 million in its latest funding round, valuing the company at $2.3 billion.
Rich Alternman
May 28, 2021
The modern concept of vertical farming was put forth in 1999 by Columbia University microbiologist Dickson Despommier, who along with his students, came up with a design of a skyscraper farm that could feed 50,000 people.
Since then, vertical farming has become a multi-billion-dollar industry. And it’s growing rapidly.
According to PitchBook data, nearly $1.9 billion of global venture capital was invested in indoor farming in 2020, nearly tripling investment in 2019. And just this week, New York-based vertical farming startup Bowery Farming raised $300 million in its latest funding round, valuing the company at $2.3 billion.
Vertical farming growth may be accelerating at the ideal time, as concerns about population growth and climate change push the food industry to innovate to meet tomorrow’s challenges.
By 2050, around 68% of the world population is expected to live in urban areas, and this growth will lead to an increased demand for food. The use of vertical farming could play a role in preparing for such a challenge. At the same time, it could help restore forests depleted by commercialized agriculture and curb planet-warming emissions caused by farming and transportation. Agriculture and forestry alone account for about a quarter of the world’s greenhouse gases.
What is it?
Vertical farming is the practice of growing crops in vertically stacked layers as opposed to a single level, like a field or greenhouse.
Through the artificial control of temperature, light, humidity, and gases, food can be produced indoors in a way that optimizes plant growth and soilless farming techniques such as hydroponics, aquaponics, and aeroponics. The benefits of which are reliable, environmentally friendly, year-round crop production, significantly reduced water usage (by some estimates up to 95% less), efficient land use, and less exposure to chemicals and disease.
Among its downsides, vertical farms are costly to set up and operate and are too dependent on technologies that have yet to reach full maturity. Further, with its heavy reliance on electricity for lighting and climate control, it uses more energy than traditional farming methods and contributes to greenhouse gas emissions.
With that, the sector continues to innovate. And with vertical farming merely in its infancy, it’s reasonable to expect big things in the coming decades.
Investors certainly think so.
In fact, the global vertical farming market is projected to reach $12.77 billion by 2026, growing at a CAGR of 24.6%, according to Allied Market Research.
Some recent examples of vertical farming going mainstream include:
Newark, N.J.-based AeroFarms planning to double its product offering at Whole Foods and, for Amazon Fresh, expanding from one to five distribution centers, increasing availability throughout the New York metropolitan area.
Albertsons Cos. rolling out indoor-farmed produce from Bowery Farming to 275 Acme and Safeway stores in the Northeast and Mid-Atlantic.
The Kroger Co. rolling out produce from vertical farm 80 Acres Farms to more than 300 stores in Ohio, Indiana and Kentucky.
Giant Eagle introducing more packaged greens products from vertical- and robotic-farming specialist Fifth Season to supermarkets in Pennsylvania and Ohio.
Cost barriers
While investors and environmentalists alike are excited by the prospects of vertical farms, the cost barriers are significant, around 20% to 30% higher than traditional farms.
With that, investors may not be able to live up to the hype they’ve created around the industry, and see their bubble burst before they have a chance to prove themselves, said IDTechEx analyst Michael Dent, in a Bloomberg News article. “If people are expecting world-changing progress and they don’t see it in the first two or three years — and what they see is high-quality salad — there’s a chance they might pull out their investment on the field and move on to the next thing.”
AeroFarms Begins Construction On Research Center In Abu Dhabi
H.E. Dr. Tariq Bin Hendi, Director General of ADIO, said: “This important milestone for AeroFarms AgX is another step in the realization of Abu Dhabi’s mission to ‘turn the desert green’
JUNE 24, 2021
AeroFarms, a certified B Corporation and leader in indoor vertical farming based in Newark, announced that AeroFarms AgX LTD, its wholly-owned subsidiary in the United Arab Emirates (“AeroFarms AgX”), has started construction in Abu Dhabi on the company’s state-of-the-art Research Center focused on the latest developments for indoor vertical farming, innovation, and AgTech.
In partnership with the Abu Dhabi Investment Office (ADIO), which is focused on enabling investment opportunities in Abu Dhabi, AeroFarms AgX will bring innovative research and development to the UAE and the Middle East to advance sustainable controlled environment agriculture (CEA) and vertical farming and help address broader global agriculture supply chain issues.
Last year, ADIO announced that it is providing $150 million in incentives to bring global AgTech pioneers to Abu Dhabi, including its partnership with AeroFarms to build a vertical farming facility dedicated to developing next-generation agriculture in arid and desert climates. The transformational R&D conducted at AeroFarms AgX is expected to enable new business lines, technologies, and growth of the AeroFarms platform while serving as a hub for regional expansion. AeroFarms AgX is expected to be completed and operational in the first quarter of 2022.
H.E. Dr. Tariq Bin Hendi, Director General of ADIO, said: “This important milestone for AeroFarms AgX is another step in the realization of Abu Dhabi’s mission to ‘turn the desert green’. In line with this goal, ADIO is supporting innovative technology that has the potential to impact farming practices across the globe and improve the food production value chain worldwide. AeroFarms AgX will add to the growing capabilities of Abu Dhabi’s agriculture ecosystem while benefiting from the emirate’s plentiful land, natural heat, competitive energy prices, access to research universities, and skilled talent.”
At 54,000 square feet, AeroFarms AgX will be the largest indoor vertical farm of its kind for research and development in the world, leading the way in breakthrough innovation to solve some of the world’s most pressing agriculture challenges. AeroFarms AgX will employ a projected 60 highly skilled engineers, horticulturists, and scientists and will have high-tech laboratories conducting organoleptic research and precision phenotyping, phytochemical analysis, advanced speed breeding, as well as next-generation machine vision, machine learning, robotics, and automation. AeroFarms AgX will also play a key role in Abu Dhabi’s AgTech ecosystem by working with local universities on research projects to tackle problems of agriculture within desert and arid climates.
David Rosenberg, Co-Founder, and CEO of AeroFarms commented: “This is an important development for AeroFarms as we expand globally and leverage our R&D and growing expertise. AeroFarms has been the global leader for controlled environment agriculture since 2004, and we will utilize this cutting-edge R&D Center to conduct the latest research in plant science, vertical farming, and automation, accelerating innovation cycles and commercializing products. Our vision has always been to leverage our expertise in plant biology and build on our successful history of collaborating with government, universities, industry, and major international companies. We are pleased to take this step forward and proud to be a catalyst for helping to establish the Emirate of Abu Dhabi as a global hub for AgTech innovation.”
To access more business news, visit NJB News Now.
VIDEO: Sweden: Growing Food In Umeå In A Freight Farms Shipping Container
Ellen Bergström and Daniel Remes are growing food in Umeå, Sweden to create a resilient and sustainable local food system
Ellen Bergström And Daniel Remes Are Growing
Food in Umeå, Sweden To Create A Resilient
And Sustainable Local Food System.
Although they had little agriculture experience, the realization that their community needed a dependable food supply chain that offered fresh, quality produce even through the long, dark winter months, led them to start their Freight Farming business, MY Harvest.
Click on the video below to watch their story.
For more information:
Freight Farms
info@freightfarms.com
www.freightfarms.com
24 Jun 2021
Designing Future-Proof Substrate for CEA
“I believe that Horticubes® AeroMax will be the most relevant substrate in the industry,” says Dr. Vijay Rapaka, global research manager at OASIS® Grower Solutions, a division of Smithers-Oasis Company, about Horticubes AeroMax. This substrate is engineered for the precision growing of young plants for hydroponic farming of leafy greens and compact plants.
OASIS Grower Solutions Launches Horticubes AeroMax
“I believe that Horticubes® AeroMax will be the most relevant substrate in the industry,” says Dr. Vijay Rapaka, global research manager at OASIS® Grower Solutions, a division of Smithers-Oasis Company, about Horticubes AeroMax. This substrate is engineered for the precision growing of young plants for hydroponic farming of leafy greens and compact plants.
OASIS Grower Solutions was established in the mid-1950s and began with the development of ornamental growing media. Fast forward to the present day and the company has expanded its product offering to meet the demands of the ever-developing horticultural industry, which now includes vertical farms and highly automated greenhouses. OASIS Grower Solutions currently has manufacturing locations in 20 countries and develops new products through in-house research and customer feedback. The company introduced its Horticubes line in the 1980s, then added Horticubes XL in 2011. Now, OASIS Grower Solutions introduces Horticubes AeroMax for the hydroponic production of leafy greens.
The benefits
When designing the Horticubes AeroMax substrate, OASIS Grower Solutions focused on what they consider to be the three cardinal rules of horticultural substrate development. Firstly, a substrate should allow the grower to propagate healthy, uniform, and vigorous young plants. The second rule is that a substrate should support growers in modulating crop growth by facilitating the acceleration or deceleration of growth, or the use of wet and dry cycles. Finally, substrates should be able to withstand automated processes. This, according to Vijay, is especially important in controlled environment agriculture as automation is becoming increasingly used.
“With more LEDs, IoT, and automated processes, we knew that we needed a substrate that allowed us to precise control of young plant growth. We needed a smart substrate exclusively designed for precision hydroponic farming,” says Vijay.
The Horticubes AeroMax is engineered according to these cardinal rules and is unique from other substrates in five main ways. As denoted in its name, AeroMax is a very porous media that enhances the oxygenation of the root zone so that seeds can germinate quickly and uniformly. According to Vijay, more air in the root zone also increases root health and root branching. AeroMax is also different in that the substrate is low-density, low-strength which makes the substrate light and airy. As a result, roots can easily penetrate the substrate and express their full potential without expending much energy.
“With hydroponics, we need the roots to get to the nutrients as soon as possible. We don’t want the substrate to be a barrier,” explains Vijay.
The third advantage of Horticubes AeroMax is the good drainage which virtually eliminates any chance of overwatering because the excess water easily drains out. This also means that growers can achieve maximum nutrient refreshment rates. Fourthly, OASIS Grower Solutions tested multiple substrate colors but eventually selected black as this allows growers to increase the surface temperature of the substrate by a few degrees, thereby accelerating crop growth. A final benefit of Horticubes AeroMax is the reduction in algae growth on the substrate surface as the high drainage rate ensures that the top surface is dry.
According to Vijay, “these five key features weren’t present in our previous substrates. Overall, we achieved in making a substrate that will respond well to controlled growing environments, allowing the precision production of plants.”
The target market for Oasis Horticubes AeroMax
Horticubes AeroMax was primarily developed for leafy green production in vertical farms and was engineered to be future-proof, according to Vijay.
“This industry is progressing with LEDs, IoT, automation, etc. We developed Horticubes AeroMax with all of this in mind and believe it will be the most relevant substrate in the industry.”
OASIS Grower Solutions is currently developing Horticubes AeroMax applications for high-wire products and has another product coming to the floriculture industry.
For more information:
Vijay Rapaka, Global Research Manager
OASIS Grower Solutions
https://oasisgrowersolutions.com/aeromax
Publication date: Wed 16 Jun 2021
Author: Rebekka Boekhout
© HortiDaily.com