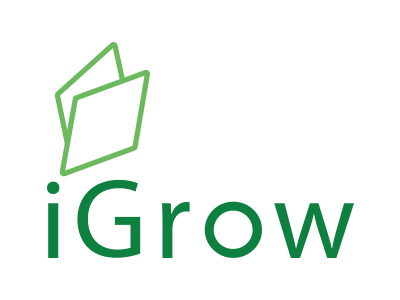
Welcome to iGrow News, Your Source for the World of Indoor Vertical Farming
AI Is Learning To Understand How Vegetables Taste
With the global demand for food escalating, vertical farms are becoming a critical component of agriculture's future. They use robotics, machine learning and artificial intelligence (AI) to automate farming and perfect the growing of greens and vegetables.
By Jennifer Kite-Powell
July 20, 2021
With the global demand for food escalating, vertical farms are becoming a critical component of agriculture's future. They use robotics, machine learning and artificial intelligence (AI) to automate farming and perfect the growing of greens and vegetables. With steady growth, the vertical farming market was had an estimated value of $4.4 billion in 2019 and is expected to reach $15.7 billion by 2025.
Fifth Season is a vertical farm in Pittsburgh that uses super-stack software and robotics to run their fully automated farming systems. And, by combining big data and AI, they have created the optimal grow recipe that determines the best flavor for the plants they grow.
"The role of AI in determining flavor is to leverage big data and AI to ensure you achieve the target flavor — sweetness, spiciness, bitterness, total degree of flavor and texture," said Austin Webb, CEO of Fifth Season.
"Our plant's individualized grow recipe is the unique mix of the different LED lights," said Webb. "The plants go through the grow room with a QR code that communicates that plant's route and tells the automated system where each plant needs to be throughout the process."
Webb says their super stack system, which serves as 'the brain' of the vertical farm maps, maps out each plant's route through the grow room based on its grow recipe and then moves the plants where they need to go.
"We use AI and data to find improvements in all aspects of crop quality, even beyond what humans think they know about flavor profiles. We call this proactive, deterministic growing compared to traditional farming, including greenhouse growing, where you have to be reactive based on weather and sunlight conditions," said Webb. "We then leverage human/chef feedback on what tastes the best and what texture is best and [..] combine that qualitative data with the 26K quantitative data points for every tray of greens per lifecycle."
"From there, we tweak our grow recipes to build the best flavor. For some vegetables, like tomatoes, experts have leveraged Brix scores, but [..] we measure flavor quality based on these factors: sweetness, spiciness, bitterness, the total degree of flavor, texture and color," said Webb. "Humans don't need to guess what iron content or Brix score is best; the brain in our farms can do that. Humans tell the grain what tastes best, and the brain will compute and tweak the grow recipes from there."
Darryn Keiller, CEO and founder of WayBeyond, says that to impact flavor, you either have to change the genetics of the crop or alter the existing biochemical profile.
"For example, growers can impact flavor by adjusting light and nutrients, which can then enhance the texture (crunch, thickness) or flavor (increased sweetness or bitterness)," said Keiller. "Once you determine the key characteristics you want in a crop, you then use machine learning or AI to automate and optimize the production process for consistent growth and be responsive to changing consumer preferences."
"Currently, vertical farms utilize seed stock bred for outdoor farming. Using AI technology, they can create their breeding stock (or lines) better suited for indoor environments. It's about refining your research and development and creating genetics perfect for your environment and management practices while ensuring continuous improvement of commercial production. The potential is huge."
Webb adds that many indoor growers sought to build an outdoor farming system that can thrive indoors; however, Fifth Season chose to apply smart manufacturing principles to agriculture that would enable them to grow food in a new way.
"We grow more than 15K pounds a week of fresh food with 90% less water than what would be required to grow that amount of fresh food on a traditional outdoor farm - and that is done on a footprint of just 25,000 square feet," added Webb.
Webb believes that scaling viable vertical farming operations that can crack code on both the technology and the consumer experience to deliver consistently fresh, nutritious and clean produce changes the consumer shopping significantly.
"It changes our entire definition of what fresh can and should taste like; it changes the ease of access and availability and convenience to fresh food, which brings so much value to consumers," said Webb. "It's another avenue for shoppers to access the freshest, highest-quality food at retail with produce that has a much longer shelf life than we're accustomed.”
Lead Photo: Greens leaving the grow environment on route to harvesting and packaging in Fifth Season's vertical farm in Pittsburgh.
Will Tomatoes Be The Next Big Commercial Crop For Vertical Farms?
Researchers at University of California-Riverside are using CRISPR technology to develop miniature tomato plants for production in vertical farms and on the International Space Station.
By David Kuack
July 22, 2021
Researchers at the University of California-Riverside are using CRISPR technology to develop miniature tomato plants for production in vertical farms and on the International Space Station.
What crops come to mind when you think of vertical farm production? Leafy greens, microgreens and herbs are likely the most common answer. How about tomatoes?
University of California researchers Robert Jinkerson and Martha Orozco-Cárdenas are using CRISPR-Cas9 gene-editing technology to develop short tomato plants that have the potential to be grown in vertical farms and on the International Space Station. Orozco-Cárdenas initially used CRISPR technology to reduce the size of normal tomato plants, including the number of leaves and stems, without significantly reducing the size and yield of the fruit.
“The tomatoes originally were under investigation by my collaborator Dr. Orozco-Cárdenas, who is director of the UC-Riverside Plant Transformation Research Center,” Jinkerson said. “I was touring her research facility and saw tomato plants that were fruiting in vitro. The plants were incredibly small. I thought these tomatoes would have a lot of different applications, particularly for NASA. We also determined that the tomatoes could be well suited for vertical farming. It started out as a basic science project investigating gene function and we expanded it to look toward other applications where genes could be mutated to control plant architecture for vertical farming and for space flight applications.
“For the first iteration, Dr. Orozco-Cárdenas took an existing dwarf tomato plant variety and used CRISPR gene editing to further shrink the plants. Currently we are working on using the CRISPR technology to stack more mutations on top of the original variety. We are also performing gene editing in a commercial indeterminate variety to determine if we can alter the plant architecture and size so that they would be suitable for vertical farm production.”
University of California researchers are studying how to grow tomato plants to the smallest size and still produce the highest fruit yield.
Limits to plant size
Jinkerson said the CRISPR gene-editing technology can be used to create mutations that affect the inflorescence, number of flowers, and branching architecture. Initially plant size was the trait the two researchers were interested in changing, but Jinkerson said he has expanded the studies to include the impact on fruit size and yields.
“We are looking primarily at how we can grow the plants to the smallest size and still produce the highest fruit yield to maximize the harvest index,” Jinkerson said. “The harvest index is the amount and weight of the fruit vs. the weight of the total plant biomass, including the fruit. If there was 100 percent fruit then the harvest index would be 100 percent. But because plants need leaves, stems, and roots, the harvest index can’t be 100 percent.
“There is a point where the plant becomes so small that there are not enough leaves to perform photosynthesis and the plant won’t be able to support the fruit that it is trying to produce. This is something we have to keep in mind as we try to balance the plant size and how much vegetative biomass is needed to produce the fruit. Currently, we are investigating this relationship. We think we are starting to hit the lower limit of size where we cannot make the plants much smaller without negatively affecting the fruit yields.”
University of California researcher Robert Jinkerson is looking to work with commercial controlled environment growers to determine how the short tomatoes work in their production systems.
Overcoming vertical farm limitations
Jinkerson’s tomato research is being funded by a $450,000 New Innovator grant from the Foundation for Food & Agriculture Research. Even though Jinkerson’s background is in engineering and algae, he saw the potential that vertical farming could have on future food supplies.
“Most commercial crops are grown outdoors and there really are not any restrictions on size,” he said. “For vertical farming there is a lot of work that needs to be done to customize crops for this new production environment. For instance, the plants can only be a certain size and should have a quick production time to reach harvest. They should also be very efficient with the way they utilize artificial light for photosynthesis because electricity for lighting is one of the largest operating costs.”
Part of the FFAR grant is for Jinkerson to work with commercial growers to determine how the short tomatoes that are developed work in their production systems.
“We are interested in finding commercial growers who are operating vertical farms or a commercial partner who can help trial and evaluate the lines that we have already produced and future lines we will be developing,” he said. “Another aspect of the research grant is to take other tomato varieties and try to optimize their architecture for vertical farms in order to have a greater variety of fruit that can be grown in these systems.”
Although Jinkerson does not have a vertical farm set up at the university, he is trialing the plants in a greenhouse and a controlled environment room equipped with fluorescent lights.
“The grow room with fluorescent lighting that we are using is not like a high-tech vertical farm equipped with LEDs,” he said. “The plants have been grown with a photon flux of a few hundred μmol m−2 s−1 PAR at a 16-hour photoperiod. The temperature and humidity have been maintained at normal room conditions. We haven’t tried to optimize environmental conditions for plant growth yet. We haven’t pushed the plants under any extreme conditions, but these are future areas of research we are interested in exploring.”
Jinkerson and his students are also collecting data related to the amount of light that is needed for the plants to flower and fruit under artificial light.
“We have fruit yield data,” he said. “We have done a lot of calculations on fruit yield per volume. This is an important metric for vertical farms. With our data, we can estimate what type of yields we could expect with the plants. Depending on the vertical spacing distance, the yield per volume for the plants we have developed could be anywhere between 1.5 to three times higher compared to greenhouse yields.”
Future crops for vertical farms, space travel
While Jinkerson’s current research is focused on tomatoes he said there is the potential to apply the gene-editing technology being developed to other vertical farm crops.
“We are going to start with other Solanaceae crops, including peppers, eggplant and potatoes,” he said. “We think that many of the findings we have identified with tomato will be able to translate to these other crops because they are closely related to tomato.”
University of California researcher Robert Jinkerson (above) wants to expand the study of CRISPR gene-editing technology beyond tomatoes to other Solanaceae crops, including peppers, eggplant and potatoes.
Part of the research on the tomatoes is being funded by NASA and will be used to conduct a seed-to-seed experiment in space.
“The goal is to grow tomato plants on the International Space Station to fruit and have the astronauts harvest the seed,” Jinkerson said. “The astronauts will then take the seed and grow them for the next crop to have them fruit again. This process is essential in order to have a sustainable crop system for food production. This has never been demonstrated before with tomatoes on the space station.”
The astronauts are currently producing leafy greens on the space station.
“There is very limited physical space on the space station so trying to maximize the harvest index is essential,” Jinkerson said. “This is a very good analog for vertical farms on Earth. With leafy greens the astronauts are able to eat everything but the roots, making these plants perfect for space travel. However, NASA is interested in growing other crops in space. There is an experiment planned for peppers coming up in the next year and our experiment with tomatoes in the next two to three years. Just like vertical farm growers on Earth, astronauts will be trying to produce different types of crops in space.”
Lead Photo: University of California-Riverside researchers Martha Orozco-Cárdenas (above) and Robert Jinkerson are using CRISPR gene-editing technology to develop short tomato plants that have the potential to be grown in vertical farms and on the International Space Station. Photos courtesy of Robert Jinkerson, Univ. of Calif.-Riverside Photos courtesy of Robert Jinkerson, Univ. of Calif.-Riverside
FI Report Preview: Vertical Farming Concept Experiencing Immense Growth
Vertical farming is growing by leaps and bounds. In fact, the evolving form of agriculture has become a multibillion-dollar industry and is expected to reach $12.77 by 2026, growing at a compound annual growth rate of nearly 25%, according to Allied Market Research.
By Kelly Beaton
July 19, 2021
Vertical farming is growing by leaps and bounds. In fact, the evolving form of agriculture has become a multibillion-dollar industry and is expected to reach $12.77 by 2026, growing at a compound annual growth rate of nearly 25%, according to Allied Market Research.
Quite simply, the concept “has gone viral,” said Dr. Dickson Despommier, a professor at Columbia University.
And Despommier should know. After all, he’s credited with conceiving the concept, back in 1999, during an especially spirited Medical Ecology course.
The Food Institute recently interviewed Despommier at length, in advance of its in-depth report on vertical farming, which is set to be published Tuesday (you can eventually download the report here). Here’s some exclusive content from that interview, which discussed numerous aspects of indoor farming, also known as controlled-environment agriculture (or CEA):
HOW WOULD YOU PERSONALLY DEFINE INDOOR FARMING AND VERTICAL FARMING?
Despommier: “Indoor farming includes all indoor farms, including vertical farms, and it also includes greenhouses. The only difference between a vertical farm and a greenhouse is height, because you can’t just set greenhouses on top of each other.
“Vertical farms have grow lights. If you use grow lights … you get more nutritious plants as a result of that, because you can tweak those lights to cause the plants to produce more things that we need, like vitamins.”
IN YOUR OPINION, WHAT’S A KEY BENEFIT PROVIDED BY VERTICAL FARMING?
Despommier: “By manipulating the indoor lighting systems … you can create plants that you could never grow outside. That’s one of the advantages.”
WHICH COUNTRIES ARE EMBRACING VERTICAL FARMING THE MOST?
Despommier: “The country that’s really got the most [vertical farming facilities] is Japan – Japan now has hundreds of vertical farms throughout the country, and they’re doing quite well. Taiwan has about 150, last I heard. Singapore has countrywide demand for locally produced food. The United States has a fair number, I would say in the neighborhood of 100, to 150.
HOW DO YOU ENVISION VERTICAL FARMING GROWING IN THE NEXT 5-10 YEARS?
Despommier: “I think the next issue will be, how can we franchise ourselves into a complete grocery store. And I know companies that are already doing that, so that’s in the wings. And, I think in another 5 years you’re going to see a versatility of crop selection that will force everything else into competition, and therefore [vertical farming] will succeed. That’s in the next 5 to 10 years.”
Startup Raises Millions for Vertical Green Production
Now the Danish startup Nabo Farm has received DKK 3 million. from investors to expand their version of an "urban agriculture" and will open farm number two in the capital, rather on Amager, it says in a press release.
By Torben Salomonsen
June 25, 2021
The production of vegetables in vertical farms is gaining ground all over the globe and in Denmark, indoor agriculture with coastal light has also found a market.
Now the Danish startup Nabo Farm has received DKK 3 million from investors to expand their version of an "urban agriculture" and will open farm number two in the capital, rather on Amager, it says in a press release.
Since 2018, Nabo Farm has had production of green from a disused car workshop in northwestern Copenhagen, but will now expand with another farm, which will simply be the first in a series of several, according to the founders Sebastian Dragelykke and Jens Juul Krogshede.
"For us as a start-up company, it is a great thing that we have succeeded in raising such a significant amount, because it means that we can now focus on scaling the Neighbor Farm concept further by opening another farm. At the same time, The investment from Danban and Vækstfonden also means that we can, at a societal level, help to spread the knowledge of sustainable food production," says Sebastian Dragelykke.
The 3 mio. As mentioned, this comes from the business angel network DanBan and Vækstfonden, and Nabo Farm currently sells green on a subscription to a clientele that includes canteens, catering companies and restaurants such as Compass Group, Aamanns, Meyers and Alchemist.
The goal of the company is to attract "more and larger investors" to fold the ambitions to produce even more food via LED lamps and a self-developed automatic irrigation system.
Lead Photo: The company Nabo Farm has raised capital to build a new indoor green production in Copenhagen.
An Urban's Rural View - Vertical Farming Is Looking Up
It looks like some of the big boys in agriculture are finally taking vertical farming seriously
11/2/2020
By Urban C Lehner , Editor Emeritus
Connect with Urban: @urbanize
It looks like some of the big boys in agriculture are finally taking vertical farming seriously.
Last month one of the biggest, the berry behemoth Driscoll's, became an investor in and joint venture partner of Plenty Unlimited, an indoor vertical-farming startup. (https://www.businesswire.com/…) (https://agfundernews.com/…) From Driscoll's and Japanese tech investor SoftBank, Plenty is getting $140 million, bringing its total funding to $500 million. More importantly, it's getting to work with Driscoll's on growing strawberries indoors.
Entrepreneurs have been trying to make a go of indoor vertical farming since 1999 when Columbia University professor Dickson Despommier and his students developed the concept. It seemed like a no-brainer to grow food close to where it would be consumed, with high yields on minimal acreage, with less water and fewer if any chemicals, without soil in some iterations, and without fear of droughts, fires, floods, frost or high winds.
The disadvantages were less obvious -- but debilitating. For conventional farms, the sun provides free photosynthesis. For farms inside buildings, the cost of artificial lighting is horrific, and the cost of climate control makes matters worse. An Irish researcher contends that in the United Kingdom, indoor farms require more than ten times the energy of heated greenhouses. He recommends rooftops for those who want to grow food in cities. (https://theconversation.com/…)
Other disadvantages include high costs for labor, rent, and capital-equipment depreciation. "Despite the advances that have been made in controlled environment agriculture, it isn't quite ready for prime time and many opportunities for innovation remain," a Cambridge Consultants paper concluded. (https://www.cambridgeconsultants.com/…)
Vertical farmers, venture capitalists, consultants, academics, and others are doing cartwheels trying to solve these problems. Plenty Unlimited uses wind power and solar cells to generate its electricity and has developed special forms of plastic LED lights. A University of Florida researcher is working on pulsing light -- five seconds on, 10 or 20 seconds off -- and seeing signs that it cuts lighting costs substantially without hindering plant growth. (https://theconversation.com/…)
While depreciation costs are high, capital is available; fearless investors are hurling money at the sector. Rent costs could start coming down, too. With the pandemic encouraging more work from home, there will be surplus space in office buildings. (On the other hand, some vertical farms sell directly to restaurants, which the pandemic has been hard on.)
Though making progress, vertical farming remains a tiny corner of the multi-trillion-dollar agriculture and food business. A market research firm estimated it at $212 million in 2019 and predicted it would hit $1.4 billion by 2027. (https://www.prnewswire.com/…) When I last covered this subject in 2015, many vertical farms were still losing money. It's likely many lose money today. (https://www.dtnpf.com/…)
All that said, vertical farming has come a long way in the last few years. Hundreds of operations have germinated and sprouted in countries around the world. There have been innovations in lighting and climate control.
After years of growing mostly leafy greens and herbs, vertical farms are preparing to add crops like potatoes, tomatoes, and blueberries. As vertical-farm pioneer Despommier wrote in the Wall Street Journal recently, "Vertical farms are no longer some futuristic fantasy." (https://www.wsj.com/…)
As an example, Despommier cited Infarm, a company that was started in Israel, is now headquartered in Berlin and employs 400 people in 40 countries, mostly European. According to Despommier, who serves as an unpaid adviser to Infarm, the company provides grocery stores with automated, hydroponic systems that allow them to grow food in their produce aisles.
"Each store selects its own mix of greens and herbs, and consumers are encouraged to choose, taste and harvest from a menu growing right in front of them," he wrote. You can't cut transportation costs much more or provide much greater freshness.
And now, to move the sector further forward, comes Driscoll's and Plenty.
You can see the benefits to Plenty in this deal. They go beyond the $140 million and the expansion into a new and promising product, strawberries. They're hitching their wagon to a company that controls about a third of the $6 billion U.S. berry market. It has proprietary genetics and a team of geneticists developing new products. It has a recognized brand name and marketing muscle; the "clamshell" berry package was its idea. (https://www.newyorker.com/…)
What does Driscoll's get out of the arrangement? Plenty, too, has plenty to offer a partner. It says its Laramie, Wyoming, farm -- where Driscoll's berries will be grown -- is "the largest privately-owned vertical farm research and development center in the world." Plenty says it's "currently building the world's highest-output, vertical, indoor farm in Compton, California." https://www.businesswire.com/…)
But why vertical farming in the first place? Bloomberg emphasized Driscoll's desire to learn robotics from Plenty, whose farms are highly automated. Labor is a big part of Driscoll's cost structure and immigrant labor is becoming scarcer in the U.S. (https://www.bloomberg.com/…)
The Financial Times pointed to the fires in Driscoll's home state of California. A Driscoll's executive told the FT that instead of moving a whole farm farther up the mountain to get away from them, it can move to vertical farms. (https://www.ft.com/…)
The FT also mentioned "deglobalization," by which it apparently meant that in the future there may be less cross-border trade in food. That would encourage big players like Driscoll's to produce locally. The FT noted that two of Driscoll's biggest markets are in Hong Kong and the Arab world. It won't grow berries outside in either place but could grow them vertically indoors.
Whatever the reasons, what Driscoll's has done is big. Of all the progress vertical farming has made over the last several years, getting the big boys in ag to take it seriously is arguably the most important.
Urban Lehner can be reached at urbanize@gmail.com
Agtech Startup Nordetect Wins €10,000 Prize For Portable Nutrient Sensor
Nordetect, which is also a part of the SOSV portfolio, won the challenge for its portable device that measures nutrients in soil, water, and plant tissue so growers can more precisely use fertilizer in crops and get better yields and less waste
There are plenty of reasons food producers are considering indoor agriculture these days, including the potential for better crops and yields thanks to tech integrations and the ability to keep farmworkers safer (ie, not laboring in the thick of wildfire smoke). However, to make indoor farming as efficient as possible, and thereby cut down on food waste, more precision around plant nutrients, water, and other elements is needed.
Denmark-based startup Nordetect is one such company tackling this challenge. The precision-agriculture-focused company just nabbed the top spot (and €10,000) of agtech company Priva’s recent Horti Heroes challenge, which showcased companies innovating in the horticulture space.
Nordetect, which is also a part of the SOSV portfolio, won the challenge for its portable device that measures nutrients in soil, water, and plant tissue so growers can more precisely use fertilizer in crops and get better yields and less waste.
On its website, Nordetect says this nanosensor can be used on anything from leaf samples to soil to manure. The system also integrates with any existing software the farm might be using, and a built in GPS keeps track of where each sample is located in the field or farm. A major differentiator Nordetect offers is its ability to measure nutrients within minutes, as opposed to the traditional process that can take weeks.
Speaking in today’s press release, Nordetect CEO Keenan Pinto said the company’s target market was high-value crop space — that is, areas that grow crops like leafy greens, tomatoes, and cucumbers. “These are crops that have a nutrient requirement change between their vegetative and generative phases… and if you can get the fertilization correct, you can also achieve a significantly higher flower rate and yield,“ he said.
Many indoor farms, whether tech-enabled greenhouses or vertical farms, now grow those crops. At the same time, the number of these indoor farming facilities keeps rising and their locations include everywhere from isolated warehouses to grocery store parking lots to food desserts.
Priva is something of a heavyweight in the world of indoor farming, which means its awarding of the prize to Nordetect and subsequent partnership with the company will lead to further technological innovation around precision agriculture inside the above farming locations.
FILED UNDER: AG TECH BUSINESS OF FOOD FEATURED FOODTECH MODERN FARMER VERTICAL FARMING
The Basis, A Homogeneous Climate, Is Already There" Artechno Doing New Cultivation Tests In VF Chamber
Previously, the Artechno industrial hall was mainly the place to build complete water management systems for the greenhouse or harvesting lines and turnkey systems for vertical farms and deep-float systems
"Together with another colleague, I am adding green thumbs to the team that is full of technicians here", Rick van Schie laughs. As the son of a tomato grower and next year's fourth-year horticulture student, he started cultivation research in the industrial hall of Artechno in De Lier. In a AVF+ Junior climate chamber Rick researches irrigation strategies for four different substrates and the effect that far-red light has on the stretching in lettuce.
Previously, the Artechno industrial hall was mainly the place to build complete water management systems for the greenhouse or harvesting lines and turnkey systems for vertical farms and deep-float systems. “The cultivation space with deep-float facility provided insight into growth and also important key figures for the business case. By testing and growing ourselves, we can now also better serve our customers in the vertical farm industry and provide them with better data and growth recipes.”
Rick started growing in the climate chamber in mid-June. "It is often wise for a grower to first do tests in a small chamber and to collect as much information as possible about lighting, climate and irrigation before scaling up to a larger system. That is why we also offer our chambers for rent to growers."
Cameras and LED
The AVF + Junior with which Rick is currently doing tests is equipped with Philips GEN3 LED luminaires, whereby both the spectrum and the light intensity are adjustable. The chamber is also equipped with special hyper-spectral cameras (and sensors), making it possible to monitor the crop and climate without having to enter the chamber.
Homogeneous climate
Anyone who would enter the chamber will notice, according to Rick, that the climate is remarkably homogeneous. "Or actually you do not notice that much and that is positive. To demonstrate that there really is air circulation, I have hung up an A4 sheet, but you do not notice it."
Art, general director: "The aim was to realize a delta T difference of less than 1 degree Celsius difference in a 10-layer climate chamber of about 8 meters high, and we succeeded."
All this is possible thanks to the air treatment units that were developed by Artechno itself. "You want to exclude as many variables as possible in your research, so a homogeneous climate is essential."
Study 1: irrigation strategies
The first study examines the effect of different irrigation strategies on four different substrates (stone wool, foam plug, glue plug, and soil mix with 10% wood fiber). This should become the basis for other studies with various types of lettuce, Rick says.
Study 2: far-red light
The second research is conducted into the addition of far-red light. Lighting is applied with 180 micromoles for a total of 18 hours and in the last hour, far-red light is added with 10%. There is also a control group (DRB LB) without the addition of far-red light.
"The purpose of the addition of far-red light is to achieve more stretching in the leaves so that the plant makes better use of the growing surface after transplanting. This could possibly also influence the bringing forward of the growth curve."
Germination
Rick is very satisfied with the results of the sowing tests in comparison to the tests carried out in the previous two years. "96-98% germination on the various substrates is a good result, but maybe this might be surpassed by an upcoming germination chamber."
Low input, high output
The results of the tests are assessed, among other things, by measurements of fresh and dry weight, growth percentage, quality, and kilo/m2. "From these results, certain trend lines are emerging, from which the crop growth rate can be calculated. This trend line also gives us insight into the smarter use of the LED light (grams of fresh weight per mole). The ultimate aim is to be consistent with the lowest possible input to achieve the highest output (kilo/m2/year)."
Rick knows that kg/m2/year is an important factor for customers to determine the profitability of their business case. "The results of our tests are used for this, among other things. The results and experiences with certain products we always provide feedback to our suppliers and customers, so that they remain up-to-date."
Soft fruit
Meanwhile, Rick and Artechno see that, in addition to demand for research for herbs and leafy crops, there is also an increasing demand for soft fruit. "This includes, for example, growing strawberries indoors and testing with the rooting phase in, for example, the propagation of blueberry plants.
We also want to be proactive in this, so we will certainly carry out tests ourselves. For ourselves, but also for growers or suppliers to whom we rent the chambers. In addition, I can mentor them and, in consultation, help to draw up a good research plan, always with a lot of literature as a foundation, so that you are not wasting time doing research that has already been done."
For more information:
Artechno
www.artechno.nl
info@artechno.nl
Rick van Schie
rick@artechno.nl
Publication date: Fri 24 Jul 2020
© HortiDaily.com
This Sustainable Neighborhood of The Future Is Designed To Manage Both Climate Change And Pandemics
A proposal for a new city in China is designed to be as green as possible—and also makes it easy to isolate in the case of another outbreak
09-04-20
A proposal for a new city in China is designed to be as green as possible—and also makes it easy to isolate in the case of another outbreak.
[Image: courtesy Guallart Architects]
Eighty miles southwest of Beijing, the Chinese government is planning a new five-million person city as a model of sustainability—powered by clean energy, featuring huge green spaces, and unsullied by many cars. A new design shows what neighborhoods in the city, called Xiong’an New Area, might look like.
City blocks would surround courtyards with native plants and garden plots. Apartments, designed for people of all income levels and ages, have large balconies with built-in boxes for gardening; greenhouses with vertical farms sit on the roofs, next to rooftop homes with gardens of their own. The wooden buildings, designed to use 80% less energy than typical buildings, use on-site solar power. Most streets are designed to prioritize people on bikes and on foot, not cars.
Read More Here
VIDEO: Will This Y Combinator-Backed Startup’s Urban Home Farms Take Root In India?
UrbanKisaan leverages hydroponic technology for home growing kits, as well as a network of urban farms for online delivery and retail channels
Inc42 Staff
27 Aug'20
UrbanKisaan leverages hydroponic technology for home growing kits, as well as a network of urban farms for online delivery and retail channels
During the lockdown phase, the company claimed to have seen 10x growth in terms of demand for its fresh produce, compared to pre-Covid times.
Based in Hyderabad, UrbanKisaan has installed close to 30+ vertical farms and plans to expand to Bengaluru, Chennai among other cities
There’s a minor revolution underway in many of India’s biggest cities. We are talking about hydroponic farming and this soil-less method is fast becoming the answer to solving the problem of carbon footprint in food. Call it hydroponic farming, soilless farming, vertical farming or anything else — for many it is the long-awaited answer to responsible eating.
In this backdrop, agritech and hydroponics startups are quickly finding niches in various produce categories and cities. Despite their shared ethos for sustainable food production, the likes of UrbanKisaan, Barton Breeze, Hydrilla, Simply Fresh, Acqua Farms, Letcetra Agritech, BitMantis Innovations, Future Farms, Ela Sustainable Solutions, Agro2o, Junga FreshnGreen, Pindfresh are working in this field through different models and targeting different niches — from large-scale hydroponics farming in rural areas to small home farms for the cities.
Working on the philosophy of bringing farms closer to home is Hyderabad-based UrbanKisaan. With the vision of making hydroponic technology more affordable and accessible for the masses, UrbanKisaan offers home-grow kits or vertical hydroponic farms. And by creating mini-farms in cities and revitalizing farmlands with hydroponic technology, the startup also supplies fresh produce to customers through Swiggy, Zomato, Dunzo, and other retail channels as well as in the D2C model on subscription and on-demand basis.
“We are the only startup in the hydroponic landscape to have taken a hybrid approach, where we have 20,000 sq. ft. research and development facility, along with 15+ in-house scientists working on newer innovations and products,” claimed cofounder and CEO Vihari Kanukollu elaborating on how the company is looking to differentiate itself in the burgeoning hydroponic market.
However, UrbanKisaan is not alone in the game, Simply Fresh, another Hyderabad based agritech startup, also grows and supplies a line of medicinal plants and fresh produce from its greenhouses. Similarly, Chennai-based Future Farms works on hydroponic technology at a commercial level, where it designs integrated full-stack solutions for alternative farming in the country. The vibrancy of the hydroponic models and the large ground area that needs to be covered across cities and villages has made it possible for multiple startups to thrive in this space.
Needless to say, the market opportunity is huge, as ‘urban farming’ is catching up at a rapid pace globally. According to MarketsandMarkets, the global hydroponics market is expected to reach $16.6 Bn by 2025, growing at a compound annual growth rate of 11.9% from $9.5 Bn in 2020. The growth of the sector is said to be driven by the increase in population and the need for food security through alternative high-yield farming techniques, given the depletion of water across the globe.
Plus, the rise in awareness and demand for a healthier lifestyle is said to have opened doors for a plethora of possibilities for hydroponic startups to reap the benefits in the long run.
UrbanKisaan earns revenue from its multiple channels which allow it to reach all kinds of consumers — from those who want a taste of the hydroponic produce to those who want to grow it themselves. Its urban farms are strategically located next to retail stores to facilitate hyperlocal deliveries and its DIY home kits are for the latter set. Additionally, it is also supplying its technology to local farmers to reutilise farmland.
The startup was founded in 2017 by Kanukollu, Srinivas Chaganti, Dr Hari, Shiva Prasad and Dr Sai Ram, a scientist who has been instrumental in developing the nutrient solution for their state-of-the-art vertical farming technique. In March 2020, the company also raised $1.5 Mn in seed funding from Y Combinator.
Home Farming In The Times Of Covid
During the lockdown phase, the company claimed to have witnessed 10x growth in terms of demand for its fresh produce, compared to pre-Covid levels. Further, cofounder Kanukollu said that the disruption in the supply chain and consumers leveraging on the hyperlocal delivery modes, along with the change in consumer lifestyle, for the consumption of fresh, organic produce has resulted in the surge in demand.
The Covid-19 pandemic temporarily halted the movement of produce across India and highlighted the gap in the food supply chain. This allowed agritech startups such as UrbanKisaan that specialise in hydroponic farming to tap a tremendous opportunity and bring efficiency in the supply chain.
With its hyperlocal urban farms model, Kanukollu claimed UrbanKisaan is not only bringing transparency to the vegetable supply chain but also lowering the carbon footprint, reducing food waste. Most importantly, their farming technique also claimed to save 95% water, and grow the produce 30x compared to traditional farms.
Its home kits are priced anywhere between INR 9,900 and INR 19,900 with about 50+ varieties of leafy vegetables and exotic vegetables supported by these kits, including spinach, coriander, mint, basil, bok choy, lettuce, parsley, fenugreek, capsicum, tomato and kale among others.
Further, the company claimed to have semi-automated the entire process and has designed the kits in such a way that it requires limited resources to manage it. “Once installed, it requires 15 min/week of effort to take care of the plants, thereby making it seamless for consumers to grow their own fresh produce,” said Kanukollu.
A Tech Upgrade For Rural Farmers
In addition to this, UrbanKisaan also works with local farmers who own greenhouses, where it helps them in setting up vertical farms from scratch to producing and supplying fresh fruits and vegetables.
Cost-wise, the poly house or greenhouse setup would typically cost farmers anywhere between INR 35 to INR 50 Lakhs per acre, of which, the government may subsidise up to 80%. Once this is installed, which is a fixed cost, for setting up of hydroponic setup, it would cost the farmer additionally INR 50 Lakhs. But, UrbanKisaan told Inc42 that it looks to reduce this cost at INR 15 to INR 20 Lakhs.
UrbanKisaan claims to have installed close to 30+ hydroponics farms in the state, across its various offerings. In the coming days, it plans to expand into other cities, including Bengaluru, Chennai among others, along with growing its team, adding newer varieties of hydroponic seeds, fruits and vegetables, and enhancing its technology capabilities.
Kanukollu is looking at creating a centralised monitoring system through UrbanKisaan for these various hubs and farms. “We are heavily investing in artificial and machine learning tools, where once the network of the urban farm increases, we will be able to monitor and control their farms remotely and provide a real-time update to customers.”
Biomimicry Helps Urban Farmers Scale Up
The Biomimicry Institute sat down virtually with Felipe Hernandez Villa-Roel, CEO and founder of Hexagro Urban Farming, to ask him about his experience as an entrepreneur and Biomimicry Launchpad participant
The Biomimicry Institute sat down virtually with Felipe Hernandez Villa-Roel, CEO and founder of Hexagro Urban Farming, to ask him about his experience as an entrepreneur and Biomimicry Launchpad participant.
What motivated you to start HEXAGRO?
Hexagro started as a bachelor’s thesis in Product Design when I started to analyze the problems that organic farmers in Costa Rica are facing in terms of productivity, sustainability, and health. These challenges are related to the high amounts of pesticides used by adjacent traditional farms, soil degradation, and climate change, so I began researching methods that didn’t use soil as a growing medium.
I analyzed the latest trends on soilless food production, starting from the indoor farming sector and through vertical farming, which proposes a more efficient way to grow food with less effort through new technologies like LED lighting and hydroponics in vertical configurations. I concluded that the main issue with these solutions was their scalability, since they followed a centralized model which is capital-intensive, requires infrastructure and expert personnel, and is difficult to set up and launch. The thesis made an analysis of nature’s strategies to reduce space while maximizing productivity with a modular structure that was then translated into the first version of Hexagro’s Living Farming Tree.
What was your experience in the Biomimicry Launchpad? What did you learn and how did you apply that to your business?
This project became a team and then a finalist in the Biomimicry Global Design Challenge, thanks to the inspiration taken from nature to develop the first product iteration. After that, we were invited to participate in the Launchpad program. From 2015-2016, we participated in many training sessions and had access to expert mentoring. This gave the team the tools to define a clear business model, which changed the approach of the first design iteration and led to a second design iteration that gave the basis for the current pre-industrial product. Today, the team continues to take inspiration from Nature’s Unifying Patterns to create solutions that follow the principles of biomimicry for every aspect, from product development to marketing and business development. Hexagro Urban Farming was incorporated as a for-benefit company in Milan, Italy, after the participation in the finals of the Launchpad in late 2016.
The Hexagro team
Tell us about your work to incorporate the Living Farming Tree in hotels and workplaces. What are you hoping to accomplish?
Our vision for Hexagro is a future in which anybody, anywhere, can access healthy food through urban farming. In order to get there, the team has determined a strategy to enter the market and launch its first product, the Living Farming Tree (LFT). Urbanization is booming, and at the same time we are spending around 90% of our time indoors where the conditions are not always meant for people’s well-being. This disconnection from nature within working spaces has direct consequences in employees’ health and psychology and can lead to lack of productivity and engagement, which could have direct consequences for companies. We are reconnecting employees to nature and their work through a “gamified” urban farming experience in which users follow the instructions from a digital interface to perform various maintenance tasks during the cultivation process, aiming to achieve a successful harvest of medicinal herbs for fresh infusions to improve well-being and productivity. Our LFT educates and increases the awareness of indoor farming technologies, while reducing the costs of office greenery maintenance. It engages people with their company and becomes a “gravitational center” for social gathering and relaxation.
The Living Farming Tree (LFT) utilizes a “gamification” strategy to engage employees in offices to become active participants in their own health.
What are the benefits to a modular, decentralized system?
Our team took inspiration from nature to create a system that could adapt to any space available and provide the maximum diversity with the lowest inventory. The Living Farming Tree has a standard configuration, but our plug-and-play components, along with our 3D-printed node and IoT automation systems, allow our system to adapt to any space available indoors (horizontally or vertically) to make it productive.
What is your ultimate hope for Hexagro?
We envision a new and regenerative food system based on the circular and sharing economy, helping people to grow plants and make a profit through a Smart Urban Farming Network. This nature-inspired model can increase accessibility to healthy food, decentralize indoor farming production, create new economic opportunities, and reconnect people to people through food.
For more information:
Biomimicry Institute
info@biomimicry.org
biomimicry.org
Publication date: 7/5/2019
Video: Australian Gardener Harvests Over 400 Kilos of Food From Her Gardens
The garden is maintained with approximately half a day each week, though this is unevenly distributed throughout the season. Surplus is preserved using bottling, drying, freezing and fermenting to supply the kitchen during the leaner months
Kat Lavers describes her approach to gardening, including vertical and biointensive growing, and how important it is – and possible! – for city dwellers to be food resilient in the face of natural, financial and social crises.
Happen Films
Feb 22, 2019
(Must see film. Mike)
Excerpt:
In response to space constraints, Kat trades homegrown persimmons for an annual supply of pumpkins, and buys a bag of potatoes every year. Almost all other herbs, veg and fruit are grown onsite. Gifting and swapping with family and friends adds extra variety to the diet. The garden emphasizes highly productive, resilient fruit trees and perennial vegetables like wild rocket, perennial leeks and bunching onions that thrive with minimal maintenance.
In 2018 the site recorded 428 kg of fresh produce, a figure which the household believes could ultimately grow to around 500kg when the full design is implemented. About half this produce is from the 20m² kitchen garden (30m² including paths).
The garden is maintained with approximately half a day each week, though this is unevenly distributed throughout the season. Surplus is preserved using bottling, drying, freezing and fermenting to supply the kitchen during the leaner months.
A covey of Japanese quails provides the household with eggs and occasional meat. The small aviary has trigger feeders and waterers for easy maintenance, as well as a deep litter floor of thick wood chips and autumn leaves that eventually breaks down into compost for the kitchen garden.
Read the complete article here.
The Farmhouse Concept Combines Modular Homes With Vertical Farms
Precht – the architecture studio of Penda co-founder and Chris Precht and his wife Fei – has developed a concept for modular housing where residents would produce their own food in vertical farms
February 22, 2019
Precht – the architecture studio of Penda co-founder and Chris Precht and his wife Fei – has developed a concept for modular housing where residents would produce their own food in vertical farms.
Architects Fei and Chris Precht developed The Farmhouse as a way to reconnect people in cities with agriculture and help them live in a more sustainable way.
Precht designed The Farmhouse as populations around the world are increasingly becoming city dwellers who have lost touch with how their food is produced, while food transportation has an increasingly damaging effect on the environment.
The conceptual modular system would allow people to grow food in residential tower blocks to eat or share with their local community.
"I think we miss this physical and mental connection with nature and this project could be a catalyst to reconnect ourselves with the life-cycle of our environment," said Chris Precht.
Prefabricated A-frame housing modules made from cross-laminated timber (CLT) would be stacked to provide flexible living spaces.
CLT is more sustainable than other low-cost building materials such as concrete because it locks in the carbon absorbed by the trees that were grown to make it.
Each of the module's wall would be made of three layers. An inner layer, facing the home interior, would hold the electricity and pipes with the surface finishes.
A layer of structure and insulation would form the middle layer, and on the outside layer would hold all the gardening elements and a water supply.
Different modules would have different types of external systems, such as hydroponic units for growing without soil, waste management systems, or solar panels to harness sustainable electricity.
Single-family users would be able to build their own homes using as many modules as they chose, or taller housing blocks could be formed by arranging the A-frames into stacked duplexes.
Each duplex would have an open plan living and kitchen space on the ground floor, with tent-shaped bedrooms on the upper floors. On the outer edges of the tower residences could have balconies.
Growing gardens would be arranged so they are either private or communal, with the inverted gaps left between modules providing V-shaped buffer zones between apartments and giving the plants natural light and ventilation.
The smallest living configuration available is just nine square metres with a 2.5-square-metre balcony. Hypothetically, Precht said, the tower could be built as tall as a city would allow.
"The system doesn't limit the height of the tower, because it is adaptable to a different thickness of structure," Chris Precht told Dezeen.
"But national regulations can limit the use of wood. In some countries like Japan, Canada, Scandinavia, Austria, UK, you can construct 18 to 30 stories and building codes around the globe are adapting fast to the use of CLT."
An indoor food market would be located on the ground floor of the tower, along with a root cellar for storing food in winter and composting units for turning food waste back into growing material.
The Prechts were motivated to design The Farmhouse system by their own experience. Two years ago they relocated from central Beijing to the mountains of Austria, where they grow their own food.
"Our motivation for The Farmhouse is personal," said Fei Precht.
"We live and work now off the grid and try to be as self-sufficient as somehow possible. We grow most of the food ourselves and get the rest from neighbouring farmers," she continued.
"We have now a very different relation to food. We are aware that this lifestyle is not an option for everyone, so we try to develop projects, that brings food back to cities."
Working as Penda, Chris Precht worked on the design of a hypothetical CLT tower for Toronto with tree-covered balconies, and a concept for a house in Germany with an interlocking green roof.
Renderings courtesy of Precht.