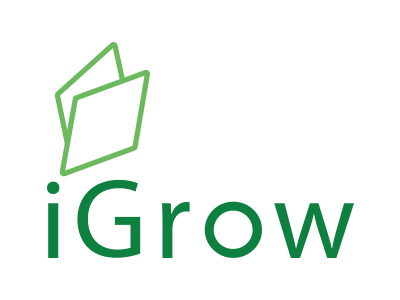
Welcome to iGrow News, Your Source for the World of Indoor Vertical Farming
iUNU Meets U.S. House Agriculture Committee & Highlights Importance of CEA To U.S. Food Supply
Chairman David Scott (GA) held a Congressional Hearing Thursday morning to increase public awareness of the critical importance of the CEA (Controlled Environment Agriculture) industry to promote food safety, nutritious produce, and food security for the American people
Chairman David Scott (GA) held a Congressional Hearing Thursday morning to increase public awareness of the critical importance of the CEA (Controlled Environment Agriculture) industry to promote food safety, nutritious produce, and food security for the American people.
Adam Greenberg | CEO | IUNU LLC
“While a global pandemic certainly magnified our food supply chain issues, one of the issues we can cover today is how to ensure a supply of fresh fruits and vegetables from all sources,” Chairman Scott asserted in his opening statement. “Controlled environment agriculture has the ability to fill in gaps where there are food deserts, reduce emissions from transportation of produce, and very importantly, limit our reliance on imports to fill our needs for fresh produce. We have an opportunity today to be on the cutting edge of technologies and the ability to provide affordable food to more households that need it.”
iUNU, an AI and computer vision-based technology platform that is employed by large commercial growers to enhance productivity is working with Congress and the USDA to ensure nutritious produce is available to all Americans.
“iUNU is an integral part of the solution to these issues as the leading provider of Artificial Intelligence and machine learning to help indoor growers rapidly expand their operations,” stated CEO Adam Greenberg at the Hearing. “The fact that 87% of the imported tomatoes come from one country, Mexico, leaves the U.S. population highly susceptible to food insecurity whether it is from a pandemic or other forces we can’t control. The CEA industry can significantly reduce these risks.”
Representative Jim McGovern (MA) expressed deep concerns about the need to recognize that food security is a national security issue in terms of ensuring the availability of healthy, nutritious produce for all Americans. “Every child in America deserves fresh, nutritious, contaminant-free fruits and vegetables they can trust.”
iUNU provides indoor growers with an AI and machine learning technology that gives growers the ability to see a plant from the time it sprouts until the time it is harvested in real-time.
“Our LUNA system can see where a problem is when it is happening and what is causing it, which significantly reduces the time it takes to identify any potential outbreak,” Mr. Greenberg said. “By catching a pest or pathogen issue as early as possible, we help growers reduce the need for pesticides. In short, we help reduce a grower’s risks and increase their productivity.”
Representative Jim Costa (CA) reiterated his concern with the nation’s food supply. “The sustainability of our food supply is critical,” he stated. “Focusing on protecting America's food supply chain is a national security issue. We need to focus on innovation as we move forward.”
Later in the afternoon, both Chairman Scott (GA) and Ranking Member Thompson (PA) issued a joint statement urging Congress to address the expansion of Broadband Internet so Americans living in rural areas and food deserts will have the same access as those living in urban areas. The lack of access hampers the ability of businesses such as growers to optimize their facilities through the use of AI and computer vision.
Dairy Container Costs "Going Crazy"
The skyrocketing cost of shipping containers is hitting the margins of Victorian pulse, grain, dairy and meat processors and exporters
30 Jul 2021
Andrew Miller
CONTAINER PAIN: Wimpak, Minyip, general manager James French says margins are being squeezed by the price of containers.
The skyrocketing cost of shipping containers is hitting the margins of Victorian pulse, grain, dairy and meat processors and exporters.
Thomas Elder Markets analyst Andrew Whitelaw said containers (boxes) were used to export pulses, grains, meat, and wool from Victoria.
"The box market has gone crazy this year," Mr. Whitelaw said.
Rates were at their highest since 2001, with the cost of hiring a 40-foot container to export products to India now sitting at $4000, (A$7700).
That compared with the first week in June 2019 when the rate was US$1300.
The top five agricultural containerized export destinations are China, Japan, the USA, Vietnam, and South Korea.
READ MORE: Rising port costs being passed back to the farmer
Port of Melbourne figures show wheat accounts for 10 percent of all agricultural exports, with hay, chaff and fodder coming in a close second.
Other cereals, barley, lentils, and chickpeas comprise nearly 20 percent of all exports.
Dried milk and processed dairy products make up more than 12pc of exports.
Huge demand
Mr. Whitelaw said part of the problem was the huge demand for containers, from Chinese manufacturers.
"Everyone seems to have much more disposable income, and most of the western world isn't able to spend that money on leisure or travel activities," Mr Whitelaw said.
"This has resulted in huge volumes and gadgets and gizmos shipped out of China."
Sea freight broker Anchor Logistics director Bob Brittles said a combination of factors had resulted in supply and demand pressures.
The blockage of the Suez Canal, when the Ever Given ran aground earlier this month, had a massive effect.
"When the Ever Given was freed, 350 ships followed her through and dumped about 350,000 containers in Europe and just after that there were unloading delays in China.
"Those delays held up 650,000 containers."
He said the Australian market was serviced by about 12 major shipping lines.
"They have been influenced by the coronavirus situation and closures of various ports, over the last year and a half."
That had resulted in congestion and delays in unloading in many south-east Asian ports, which was contributing to the container shortages.
"The containers are in the wrong place, the ships are in the wrong place," Mr Brittles said.
Rising prices
Grain cleaning and packing service Wimpak, Minyip, general manager James French said container prices to ship to most overseas ports had risen dramatically.
"The Bangladesh rates are very similar to India and the shipping lines are making a move (on prices) every four to six weeks," Mr. French said.
He said grower pricing might have to reflect the freight cost.
"Normally we are putting work on, six to eight weeks out, but we are struggling to do that, knowing what our freight rates are going to be," he said.
"It makes us more reluctant to buy more product when we don't know what the price will be at the other end."
READ MORE: Food-grade container shortages hitting Victorian exporters hard
Burra Foods exports most of its dairy products and chief executive Stewart Carson said there was a direct container cost, as well as timing and availability.
"You might have a vessel booked to leave on Friday, then you're told the vessel won't be available until Tuesday or Wednesday," Mr. Carson said.
"What do you do with that container? In some cases, you have to put it on power, which costs you money."
Mr. Carson said the company carried the cost or sought to recoup it from the market.
"Everyone is paying a competitive milk price, you can't say sorry I'll pay 10 cents less because the container price has gone up," Mr. Carson said.
Companies could not pass the cost back to the farmer, which was only right.
"I think that's great, it gives an assurance to the farmer," he said.
He said Burra was in the same position as all other processors.
Southern Grain Storage director Campbell Brumby said his company was fortunate that his company had finished its export program before the price increases hit.
"I was speaking to a colleague who was paying $1750 for a box to a particular destination, and was now looking at $4250 if they can get the container," he said.
He put the price increase down to the state government's lease of the Port of Melbourne.
"We've been doing containers for about 10 years and when we first started, charges were negligible," he said.
"Since the lease was sold to DP World, the rates have gone through the roof - we just have to pay them and the market absorbs the cost.
"As long as all our competitors and all the people we are trying to trade with are working on the same cost basis, the market tends to absorb it.
"Whether its pulses or cereals, the market will be the market."
How To Maximize Resource Efficiency In Controlled Environment Ag Operations
Join Meena Sankara, KETOS CEO, and Tinia Pina, Re-Nuble CEO, for a discussion about the most significant challenges and opportunities facing Controlled Environment Agriculture operations
Tuesday, August 3 @ 12:30 pm ET / 9:30 am PT
Wednesday, August 4 @ 9:00 am ET / 1 pm GMT
Meena Sankara, KETOS CEO
Join Meena Sankara, KETOS CEO, and Tinia Pina, Re-Nuble CEO, for a discussion about the most significant challenges and opportunities facing Controlled Environment Agriculture operations. In this webinar you will learn:
Tinia Pina, Re-Nuble CEO
Why water management is important in the CEA industry
Challenges soilless/indoor farms face when improving water management efficiency
How soilless operations (including vertical farms and greenhouses) can be more resource-efficient
Strategies for the nutrient wastewater recovery
Which waste recovery solutions are best for your operation
August 3rd Webinar Registration
August 4th Webinar Registration
Optimizing Resource Use Efficiency In CEA System
An important factor affecting the profitability of vertical farming is a grower’s ability to consistently deliver a predictable product
Date: July 29, 2021
Time: 2 p.m. - 3 p.m. EDT
Presented by: Murat Kacira (The University of Arizona)
Click Here To Register
Webinar Description
An important factor affecting the profitability of vertical farming is a grower’s ability to consistently deliver a predictable product. To achieve this, growers must create an environment that supplies all the crop’s needs over its entire growth cycle by identifying and co-optimizing environmental variables such as CO2, light, humidity, airflow, and other parameters. This presentation will focus on real-time sensing, monitoring, and climate control strategies with system designs for environmental uniformity leading to enhanced resource use efficiency in CEA system.
Dr. Murat Kacira (Professor)
Murat Kacira is director of the Controlled Environment Agriculture Center and he is a professor in the Biosystems Engineering Department at the University of Arizona. He received his B.S. degree in Agricultural Engineering in Cukurova University in Turkey and M.Sc. and Ph.D. degrees from Food, Agricultural and Biological Engineering from The Ohio State University in USA. His research involves automation, environmental control, alternative energy integrated CEA systems and resource use optimization in controlled environment agriculture systems including greenhouses and vertical farming-based plant factories with artificial lighting. He is a member of American Society of Agricultural and Biological Engineers (ASABE), American Society of Horticultural Sciences (ASHS), and International Society for Horticultural Science (ISHS). He serves as Chair of the Division Precision Horticulture Engineering under ISHS.
Special thanks to our Industry partners
Join Today
If you have any questions or would like to know more about GLASE, please contact its executive director Erico Mattos at em796@cornell.edu
No Soil. No Growing Seasons. Just Add Water And Technology
A New Breed of Hydroponic Farm, Huge And High-tech, is Popping Up in Indoor Spaces All Over America, Drawing Celebrity Investors And Critics
A New Breed of Hydroponic Farm, Huge And High-tech, is Popping Up in Indoor Spaces All Over America, Drawing Celebrity Investors And Critics.
By Kim Severson
July 6, 2021
MOREHEAD, Ky. — In this pretty town on the edge of coal country, a high-tech greenhouse so large it could cover 50 football fields glows with the pinks and yellows of 30,600 LED and high-pressure sodium lights.
Inside, without a teaspoon of soil, nearly 3 million pounds of beefsteak tomatoes grow on 45-feet-high vines whose roots are bathed in nutrient-enhanced rainwater. Other vines hold thousands of small, juicy snacking tomatoes with enough tang to impress Martha Stewart, who is on the board of AppHarvest, a start-up that harvested its first crop here in January and plans to open 11 more indoor farms in Appalachia by 2025.
In a much more industrial setting near the Hackensack River in Kearny, N.J., trays filled with sweet baby butterhead lettuce and sorrel that tastes of lemon and green apple are stacked high in a windowless warehouse — what is known as a vertical farm. Bowery, the largest vertical-farming company in the United States, manipulates light, humidity, temperature, and other conditions to grow produce, bankrolled by investors like Justin Timberlake, Natalie Portman, and the chefs José Andrés and Tom Colicchio.
“Once I tasted the arugula, I was sold,” said Mr. Colicchio, who for years rolled his eyes at people who claimed to grow delicious hydroponic produce. “It was so spicy and so vibrant, it just blew me away.”
The tomatoes at AppHarvest were delicious enough to attract an investment from Martha Stewart.Credit...Luke Sharrett for The New York Times
The two operations are part of a new generation of hydroponic farms that create precise growing conditions using technological advances like machine-learning algorithms, data analytics and proprietary software systems to coax customized flavors and textures from fruits and vegetables. And they can do it almost anywhere.
These farms arrive at a pivotal moment, as swaths of the country wither in the heat and drought of climate change, abetted in part by certain forms of agriculture. The demand for locally grown food has never been stronger, and the pandemic has shown many people that the food supply chain isn’t as resilient as they thought.
But not everyone is on board. These huge farms grow produce in nutrient-rich water, not the healthy soil that many people believe is at the heart of both deliciousness and nutrition. They can consume vast amounts of electricity. Their most ardent opponents say the claims being made for hydroponics are misleading and even dangerous.
“At the moment, I would say the bad guys are winning,” said Dave Chapman, a Vermont farmer and the executive director of the Real Organic Project. “Hydroponic production is not growing because it produces healthier food. It’s growing because of the money. Anyone who frames this as food for the people or the environment is just lying.”
The sprawling Kentucky farm is one of a dozen that AppHarvest hopes to open across Appalachia.Credit...Luke Sharrett for The New York Times
The technical term for hydroponic farming is controlled environmental agriculture, but people in the business refer to it as indoor farming. What used to be simply called farms are now referred to as land-based farms or open-field agriculture.
“We’ve perfected mother nature indoors through that perfect combination of science and technology married with farming,” said Daniel Malechuk, the chief executive of Kalera, a company that sells whole lettuces, with the roots intact, in plastic clamshells for about the same price as other prewashed lettuce.
In March, the company opened a 77,000-square-foot facility south of Atlanta that can produce more than 10 million heads of lettuce a year. Similar indoor farms are coming to Houston, Denver, Seattle, Honolulu, and St. Paul, Minn.
The beauty of the process, Mr. Malechuk, and other executives say, is that it isn’t limited by seasons. The cost and growing period for a crop can be predicted precisely and farms can be built wherever people need fresh produce.
“We can grow in the Antarctic,” he said. “We can be on an island. We can be on the moon or in the space station.”
That’s easy to picture: The farms are staffed by a new breed of young farmers who wear lab coats instead of overalls and prefer computers to tractors.
Today, the more than 2,300 farms growing hydroponic crops in the United States make up only a sliver of the country’s $5.2 billion fruit and vegetable market. But investors enamored of smart agriculture are betting heavily on them.
Lettuces at a Kalera vertical farm destined for nutrient-filled water begin in small plugs of growing medium.
Credit...Courtesy of Kalera
In 2020, $929 million poured into U.S. indoor-farming ventures, more than double the investments in 2019, according to PitchBook data. Grocery chains and California’s biggest berry growers are partnering with vertical farms, too.
“There is no question we are reinventing farming, but what we are doing is reinventing the fresh-food supply chain,” said Irving Fain, the founder, and chief executive of Bowery, which is based in Manhattan and has the indoor farm in New Jersey and one in Maryland, another under construction in Pennsylvania, and two research farms in New Jersey.
Mr. Fain said his farms are 100 times as productive as traditional ones and use 95 percent less water. Other companies claim they can grow as much food on a single acre as a traditional farm can grow on 390.
Vertical farms can be built next to urban centers, so lettuce, for example, doesn’t have to sit inside a truck for days as it makes its way from California to the East Coast, losing both quality and nutritional value. Vegetables can be bred for flavor rather than storage and yield.
The new systems are designed to produce a sanitary crop, grown without pesticides in hygienic buildings monitored by computers, so there is little risk of contamination from bacteria like E. coli, which forced large recalls of romaine lettuce in 2019 and 2020.
Bowery, the largest vertical-farm company in the United States, is growing hydroponic vegetables that have attracted the attention of chefs. Credit...Brian Fraser for The New York Times
Still, many farmers and scientists remain unpersuaded. Mr. Chapman, of the Real Organic Project, served on a U.S. Department of Agriculture hydroponics task force five years ago, and is leading an effort to get the agency to stop allowing hydroponic farmers to certify their produce as organic. The very definition of organic farming, he and others say, rests on building healthy soil. In May, the Center for Food Safety, an environmental advocacy group, led an appeal of a federal court ruling that upheld the agency’s policy.
Although the nutritional profile of hydroponic produce continues to improve, no one yet knows what kind of long-term health impact fruits and vegetables grown without soil will have. No matter how many nutrients indoor farmers put into the water, critics insist that indoor farms can never match the taste and nutritional value, or provide the environmental advantages, that come from the marriage of sun, a healthy soil microbiome, and plant biology found on well-run organic farms.
“What will the health outcomes be in two generations?” Mr. Chapman asked. “It’s a huge live experiment, and we are the rats.”
The divide between soil loyalists and ag-tech futurists is playing out on a much more intimate scale between two influential brothers: Dan and David Barber, who founded and own the organic farm Blue Hill and its restaurants in Greenwich Village and at Stone Barns in Pocantico Hills, N.Y.
In 2018, David Barber created an investment fund to support new food tech companies, including Bowery. But Dan Barber, a chef whose 2014 book “The Third Plate: Field Notes on the Future of Food” devotes an entire section to soil, believes that truly delicious food can come only from the earth.
“I am not buying any of it,” Dan Barber said of the hydroponic fever.
The chef Dan Barber, a soil loyalist, is skeptical of the claims made for hydroponic farms.
Credit...James Estrin/The New York Times
Trying to enhance water with nutrients to mimic what soil does is virtually impossible, he said, in part because no one really knows how the soil microbiome works.
“We know more about the stars and the sky than we do about soil,” he said. “We don’t know a lot about nutrition, actually.”
There is a cultural cost, too. For centuries, cuisines have been developed based on what the land and the plants demanded, he said. Regional Mexican diets built on corn and beans came about because farmers realized that beans fixed nitrogen in soil, and corn used it to grow strong.
“The tech-farming revolution is turning this equation on its head,” Mr. Barber said. It aids efficiency in the name of feeding more people but divorces food from nature.
His brother, David, had long been skeptical of hydroponics, too. “Most of my career was about good soil leads to good agriculture and good systems and ultimately good flavor,” David Barber said.
But the environmental advantages of next-generation hydroponic food production can’t be ignored, he said. Nor can the improvements in taste over earlier hydroponic produce. “They are combining outdoor and indoor thinking, and science and history, to create something special,” he said. “There are not going to be many winners in this space, but it is going to be a part of our food system.”
At Bowery, “there is no question we are reinventing farming, but what we are doing is reinventing the fresh-food supply chain,” said Irving Fain, its founder, and chief executive. Credit...Brian Fraser for The New York Times
Indoor farm companies view their competition as the large, industrial growers that produce fruits and vegetables bred to withstand processing and shipping — not smaller farmers using more natural growing techniques. The battle, they say, is against monoculture, not farmers who maintain healthy soil and feed their communities. Hydroponic farms can help develop new and more diverse plants, and reduce overall pesticide use.
“The only thing we are trying to do is get as good as farmers were 100 years ago,” said Mr. Malechuk, the hydroponic lettuce grower.
Indoor farming is a bet on the nation's agriculture, said Jonathan Webb, the Kentucky-born founder and chief executive of AppHarvest.
“The American farmer is already obsolete,” he said, pointing out that the United States imports four billion pounds of tomatoes from Mexico every year. “Our hope is we can get farmers back on U.S. shelves.”
Even Mr. Colicchio, who led a campaign against genetically modified food and has long been a champion of small farmers, said the two styles of farming can coexist. “We’re going to need a lot of tools in the toolbox,” he said.
Ouita Michel, a chef in Kentucky, likes AppHarvest because the company is creating jobs and growing tomatoes she is happy to use in her restaurants.
But technology, she said, will never trump the magic of soil. “Nothing will ever replace my summer Kentucky tomatoes.”
Lead photo: AppHarvest, the nation’s largest hydroponic greenhouse, opened in January in Morehead, Ky. — one in a new breed of huge indoor produce farms that use technology to fine-tune flavor, texture, and other attributes. Credit...Luke Sharrett for The New York Times
CEA Producers Join To Support Data-Driven USDA Project
AppHarvest (Ky.) and Revol Greens (Texas) are vanguards of modern greenhouse cultivation, while Elevate Farms (N.J.) and Fifth Season (Penn.) are pioneers in vertical farming
Four agricultural producers have joined with nonprofit Resource Innovation Institute (RII) under the banner of its USDA Conservation Innovation Grant-funded project: Data-Driven Market Transformation for Efficient, Sustainable Controlled Environment Agriculture.
AppHarvest (Ky.) and Revol Greens (Texas) are vanguards of modern greenhouse cultivation, while Elevate Farms (N.J.) and Fifth Season (Penn.) are pioneers in vertical farming. The producers will serve as initial pilot partners in support of the USDA-funded project that aims to transform the controlled environment agriculture (CEA) market sector toward more efficient production through coordinated research on energy and water practices spearheaded by RII and the American Council for an Energy-Efficient Economy (ACEEE).
“We are thrilled to unite with these categories in the name of innovation and agricultural resilience,” said Derek Smith, Executive Director of RII. “Working together with these initial pilot partners and others to follow, we can unlock basic knowledge about performance metrics that will serve as beacons of efficiency and productivity for CEA producers globally.” In addition to geographic diversity, the producers represent an expanding global market growing a range of crops in indoor environments, from microgreens to tomatoes to berries.
Resource Innovation Institute’s PowerScore resource benchmarking platform enables CEA producers to confidentially validate their innovative practices. Using standardized key performance indicators, PowerScore helps producers gain powerful insights into their operational performance while protecting strategic business interests.
“RII is trusted throughout the supply chain to provide data analysis and peer-reviewed guidance to producers, vendors, governments and utilities. Our consortium of members and partners are committed to collaboratively study the most sustainable horticultural practices across climate zones, building types, technologies and techniques to guide decision-makers on how to advance agricultural resilience,” said RII’s Smith.
To ensure the highest level of PowerScore data protection, RII has engaged Management Science Associates (MSA), global companies in data security and analytics, with expertise in HIPAA compliance and benchmarking for associations across industries. Together with producers, investors, and supply chain partners, RII continues to develop protocols that clearly define access, use, and ownership of data.
“We believe that the only way to fundamentally build an industry starts with data capture and accountability,” said Travis Kanellos, Chief Strategy Officer, Elevate Farms. “Our approach from day one has been to drive yields and profitability through metrics and KPIs. We believe RII will validate our approach."
For more information:
Resource Innovation Center
www.resourceinnovation.org
23 June 2021
Can Vertical Farms Be Profitable?
Basically, we’re skeptical of both the economics and the save-the-world ethos that many companies preach. We enlisted an industry insider to help us separate the wheat from the chaff
Earlier this year, we covered a couple of indoor farming companies going public through mergers with special purpose acquisition companies (SPACs). Neither seemed very appetizing for retail investors, with negligible revenues to date. As we predicted, more indoor farming startups (referring to both large-scale greenhouses and vertical farming operations) are jumping on the SPAC crazy train. The latest is a Montana company called Local Bounti that had generated little buzz until this month’s announcement, which included news that Cargill is providing $200 million in debt financing in the deal.
In this article, we want to take a step back and look a little more closely at the indoor farming industry, sometimes referred to as controlled environment agriculture (CEA), particularly on the vertical farming side of things. Basically, we’re skeptical of both the economics and the save-the-world ethos that many companies preach. We enlisted an industry insider to help us separate the wheat from the chaff.
Saving the World from BS
Mark Korzilius
Mark Korzilius is the founder and chief strategy officer of &ever, a vertical farming startup based in Germany, with its first mega-farm located in the desert of Kuwait. Korzilius was also the co-founder in 2002 of a chain of fast-casual Italian restaurants, Vapiano, with more than 200 locations in about 30 countries. He reached out to us, as founders sometimes do after reading a story that didn’t include them, to tell us about all of the cool things their company is doing. In the case of Korzilius, he also wanted to set the record straight on all of the things that competitors like AeroFarms and other indoor vertical farming companies aren’t doing despite claims to the contrary.
Obviously, Mr. Korzilius is biased, but he also confirmed one of our chief suspicions: Many indoor farming companies claim they are on a mission to help feed the world, which seems incongruous with the fact that most are growing leafy greens, herbs, berries, and maybe tomatoes. Hardly the sorts of staples that are going to keep the estimated 800 million people in the world from going hungry at the end of the day. He also argues that claims of automation using artificial intelligence and sensor-rich environments are also overblown.
“We truly believe to become farmers and to be successful farmers for some crops, we can prove that [vertical farming] is, in the end, a way forward,” he says. “Hopefully, we can find some technologies to really overcome some issues that have been created by others … that will help solve problems that have been the result of technologies that have been created 50 years ago.”
In the second half of that comment, Korzilius is obviously referring to the modern industrial farming system, with its reliance on pesticides, herbicides, and fertilizers that deplete and poison soils and water supplies. That’s why you see so many companies developing natural fertilizers using microbes or biomanufacturing solutions for non-chemical pesticides. Outdoor agriculture is also water intensive, especially for products like almonds, which require one gallon of water per nut. Various technologies are in development to use water more efficiently, from soil sensors to aerial imagery from drones and satellites. Vertical farming gets at the root of the problem by moving the growing operation indoors, employing LED lights and hydroponics to deliver nutrients using only water rather than soil. That eliminates both pesticides and many traditional fertilizers, and reportedly cuts down on water usage by as much as 95%. Let’s take a look at the specific technology behind Korzilius’ company.
Creating the Right Climate for Vertical Farms
Founded in 2015, &ever (formerly known as Farmers Cut) has raised an undisclosed amount of money, originally through bootstrapping and Seed funding, before raising a Series A from partners in Kuwait for its mega-farm, a joint venture with a local investment company called NOX Management. Korzilius said &ever is currently raising a Series B but declined to offer any details.
There are two key parts to the company’s technology, as we understand it: Dryponics and climate cells.
Dryponics is a new riff on hydroponics, which involves growing plants without soil. The company uses a proprietary growth substrate to keep the roots dry. In effect, the root system stays on top of the substrate, while absorbing the nutrients in the water. This setup reportedly has several advantages, including using 68% less water than common hydroponic systems and 37% less water than aeroponic systems, which grow plants in the air using a mist environment or similar system. Less water means the basins underneath the substrates are flatter, allowing more compact layering of crops.
Each crop requires different growing conditions, Korzilius explains, so his team developed climate cells – microenvironments optimized for temperature, light, humidity, and CO2, among other factors. Controlling the environment also helps control energy costs, especially in the large structures that house many of today’s vertical farms, including the company’s flagship facility in Kuwait.
Credit: &ever
“Within the same premises, we can create different climates. In our Kuwait farm, we have four climate cells next to each other. So, we could potentially create California climate next to Denmark climate next to Singapore climate,” he explains. “By creating climate cells within one premise, we save energy [and] only climatize what needs to be climatized.”
Take spinach, a notoriously difficult plant to grow indoors that took the company two years to figure out the right combination of substrate and climate. But that work has paid off by reducing the amount of growth time by 15%, which translates into 18 grow cycles a year, which is good enough for Popeye to be an investor (if only he hadn’t blown his retirement on canned spinach).
Betting the Farm on Indoor Farming
The value proposition is that products from &ever leave the farm as living plants with the roots intact, continuing to grow while staying fresh and retaining maximum freshness, according to Korzilius. The Kuwait farm is the first large-scale effort to prove the business model, though the company also has smaller grow towers for on-site retail locations like grocery stores, including one in Munich. A second mega-farm is in development in Singapore.
A &ever grow tower. Credit: &ever
The Kuwait farm, which went live shortly before the Rona hit, is designed to grow up to 250 varieties of greens and herbs. The 30,000-square-foot facility can reportedly produce up to 1,200 pounds of green stuff. Korzilius says the pandemic continues to hinder full-scale operations of the farm, which is overseen by just six employees. However, he claims the vertical farm is profitable from an operations standpoint (in other words, without accounting for the original capital expenditure). “So, we are not selling below cost. Yes, it’s a prototype, but it’s working nicely.”
Tasty greens from a vertical farm in Kuwait. Credit: &ever
However, there is a reason why the mega-farm is located in Kuwait and not in Munich or elsewhere in Europe. Energy is simply cheaper in the Middle East, so it was a no-brainer to plug into the grid there. In Singapore, where electricity doesn’t come as cheaply, the local government has stepped in with grant money to subsidize the project. Currently, Singapore imports more than 90% of its food, so the government is motivated to find ways to be more self-sufficient, especially in the wake of the pandemic.
The bigger implication is that vertical farms will require cheap sources of energy to be economically viable. That goes against the current narrative of locating large-scale operations in the middle of big urban centers where electricity is usually pretty expensive. Of course, there are other economics to consider: Centrally located growing facilities will incur lower shipping costs and can theoretically deliver fresher, tastier products to consumers, who may be willing to pay the premium for what Korzilius calls harvest on demand.
“I strongly believe in consumers being at the center of all activities,” he says. “The consumer, in the end, has to pay for this. And, if he doesn’t, then all of this is just a stupid bubble.”
Conclusion
The bubble is certainly ballooning. The three indoor farming companies that are going (or have gone) public that we are aware of are valued at nearly $4 billion. Last year, the top three indoor farming startups in 2020 funding brought in more than $400 million between them, according to AgFunder News. These companies claim to be building a sustainable food system, but it seems unlikely that a business built on microgreens can be sustainable at that scale and cost. As always, the market will decide which model will succeed.
Tech investing is extremely risky. Minimize your risk with our stock research, investment tools, and portfolios, and find out which tech stocks you should avoid. Become a Nanalyze Premium member and find out today!
What Is Driving The UK’s CEA boom?
The main findings of the panel were that the UK has been lucky with its well-established greenhouse industry which offers a great foundation for vertical farmers to understand the CEA space
“In the UK, fruits and vegetables are quite cheap in comparison to other European countries and other parts of the world. In the UK, the market has been squeezed by supermarkets that squeeze out the margins of the supply chain,” said Andrew Lloud, COO at Intelligent Growth Solutions, during a panel at the Indoor AgTech Innovation Summit.
During the session, three UK-supplier panelists elaborated on the topic. Joining were, Andrew Lloud, COO at IGS, Ben Crowther, Co-founder and CTO at LettUs Grow, Jen Bromley, Head of Plant R&D at Vertical Future, and Oscar Brennecke with Rethink Events who led the conversation.
The main findings of the panel were that the UK has been lucky with its well-established greenhouse industry which offers a great foundation for vertical farmers to understand the CEA space.
However, at the same time, it's quite costly to produce indoors given the high electricity and transport costs. This might change over time, due to several renewable energies coming into the market that will allow for cheaper production. Later on, the panelists will elaborate on the differences between the US and Europe, being monocropping whereas EU farmers grow more different varieties at the same time.
What makes the UK CEA space unique?
Andrew noted that UK consumers are willing to pay a certain price for fruits and vegetables. However, indoor ag bring along high electricity costs, whereas UK transport costs are high as well. Next to that, the economic and political dynamic being post-Brexit and currently battling the pandemic has highlighted its challenges. “Technology can economically viable grow a wide variety of crops, forming part of the food mix in the UK and in other parts of the world.”
73% of the surface area available for farming, said Ben Crowther, Co-Founder and CTO at LettUs Grow, a UK-vertical farming supplier, however, the UK still imports half of the produce.” He claimed that there’s an opportunity to make things more sustainable and efficient. Jen Bromley, Head of Plant R&D at Vertical Future, said that it’s not always about growing at a large scale, but that it differs per crop. “It’s always about pushing boundaries to see where the economics can work for the crop.”
Opportunities
More renewables and power generation are coming in, so there’s the opportunity to drop in things like vertical farms according to Andrew. “The real trick is to see if you can get a tariff from the energy provider so that the price per kw/h consumed is optimized to grow plants in the cheapest way.
Jen added that there are some obvious low-hanging fruits that can be taken within the market. Such as leafy greens, herbs, and fruits, given they work really well with the infrastructure. “However, there are also markets we can go deeper into, such as proteins, high-care products that can all be managed very well in the vertical farming space.”
Andrew added that a wide variety of crops will eventually be important, depending on your location. The difference in the US is that it’s a lot about monocropping, but they don’t tend to have the same diversity as seen in the UK or other European countries. I’ve seen it here, but I expect it to come to America as well.”
UK greenhouse- vs vertical farming market
Ben notes that “because of the well-established UK greenhouse industry, we can better understand the vertical farming market.” Berries are a great example, in the UK there has been a 10% market growth. It drives how people are looking for rootstock in these markets, specifically in greenhouses. As well as looking into year-round growing to complement their off-season. The idea translates into more traditional farmers, looking for a more consistent, lower-risk way to make their business more resilient.
Jen said that a traditional farm is a long-term play as they’re handed down by generations. In a vertical farming system, it’s an infrastructure that has to last. Whereas, Andrew claimed that the seasonal variation will be smoothed out by multi-tenant farmers using the same facility for different crops for different points in the year.
Consumer perception
“On the whole, there’s a growing understanding I think,” says Ben. He explains that there are some products available at various retailers already. Jen noted that branding is far more developed in the US, given the produce brands they have. Whereas Andrew affirmed that the elephant in the room in the UK and Europe is the use of the word organic. In the US, vertically farmed produce can be labeled as organic, however, in Europe, we’re still looking at what post-organic looks like. It’s confusing for the consumers, however, we’re at the beginning of educating people, starting with kids.
Other topics discussed were subsidies and barriers in vertical farming in the UK.
For more information:
Intelligent Growth Solutions
www.intelligentgrowthsolutions.com
For more information:
Vertical Future
info@verticalfuture.co.uk
www.verticalfuture.co.uk
For more information:
LettUs Grow
info@lettusgrow.com
lettusgrow.com
For more information:
Indoor AgTech Innovation Summit
www.indooragtechnyc.com
29 Jun 2021
Author: Rebekka Boekhout
© HortiDaily.com
OptimIA Program Analyzes Fruitfulness of US Vertical Farms
In a research fact sheet, a USDA Specialty Crop Initiative team outlines results with a model for calculating profitability potential against various factors that impact the return on investment of CEA operations
In a research fact sheet, a USDA Specialty Crop Initiative team outlines results with a model for calculating profitability potential against various factors that impact the return on investment of CEA operations.
May 21st, 2021
Image created with Adobe Spark using Pixabay free library. Data from OptimIA fact sheet, "Potential Profitability and Economic Success of Indoor Agriculture in the United States."
As we have heard from many industry speakers and reported in horticultural lighting coverage, global urbanization and population growth will continue to put a strain on the food supply. Such wide-scale concerns also breed opportunities for innovative research which will ultimately support technology development that helps improve the food supply.
I recently learned of Optimizing Indoor Agriculture (OptimIA), a Specialty Crop Research Initiative (SCRI) supported by the US Department of Agriculture (USDA). The larger objective is to extend the knowledge base regarding controlled environment agriculture (CEA) — often referred to as indoor farming, vertical farming, and indoor agriculture — to support long-term goals of:
Increasing uptake of CEA practices
Addressing food supply — quality, quantity, and availability, particularly in areas where food inequities are prevalent
Bringing sustainable, profitable operations and techniques to CEA growers
The initiative draws from team members across education and commercial horticultural/agricultural organizations: Dr. Greenhouse, Inc.; Michigan State University; Ohio State University; Purdue University; University of Arizona; and the USDA Agricultural Research Service (USDA-ARS). Some of the participants are familiar names from speaking at past LEDs Magazine events, such as Purdue’s Cary Mitchell, MSU’s Erik Runkle, and Dr. Greenhouse president Nadia Sabeh.
Digging into the OptimIA website, I saw the project team had posted a fact sheet of research highlights titled “Potential Profitability and Economic Success of Indoor Agriculture in the United States.” These highlights were collected in preparation for contributing a chapter to the upcoming book Plant Factory Basics, Applications, and Advances. The fact sheet offers a balanced summary regarding challenges to quantification of profitability, benchmarking data, and other factors. Researchers used a Japanese Plant Factory with Artificial Lighting (PFAL), base-case model, to perform their analysis of the profitability of US-based vertical farming.
The most interesting points I have included in the infographic above. But this general conclusion from the highlights comes as no surprise, really: “The changes with the most potential to increase profitability are those that focus on enhancing market price for the quality of product delivered, decreasing capital costs, and improving elements of biomass (plant size, density, and type of crop).” You can download the fact sheet from the OptimIA website.
That’s where the hands-on research will come in and why we continue to refine the program for HortiCann each year. We continue to pursue experts with scientific findings, case studies, and system developments that can decrease the capital costs of horticultural solid-state lighting (SSL) and AgTech systems and enhance grower operations with solid data and monitoring for buildable results. For example, look to last year’s HortiCann presentations on updated research findings on light spectra for various plant characteristics, data-driven automation, and our blog on the grower panel, which centered around end-user experiences in applying LED lighting to greenhouse operations — lessons learned and how they plan to evolve operations with future updates.
Watch the HortiCann Light + Tech website for updates to the program and register to join us for the free virtual event Sept. 28–29, 2021.
Visit the OptimIA website for more information on the project and other published research.
CEA Food Safety Coalition Details First Indoor-Farming Standards
Inspired by rising food safety concerns after the 2018 Thanksgiving romaine recalls, the CEA Food Safety Coalition is launching the first-ever food safety certification program specifically designed for indoor-grown leafy greens.
By AMY SOWDER June 2, 2021
(Photos courtesy CEA Food Safety Coalition)
Inspired by rising food safety concerns after the 2018 Thanksgiving romaine recalls, the CEA Food Safety Coalition is launching the first-ever food safety certification program specifically designed for indoor-grown leafy greens.
“The new standard champions CEA-grown produce as a critical component of safe and secure domestic food supply, especially in times of business disruption as experienced during the COVID-19 pandemic,” Marni Karlin, executive director of the CEA Food Safety Coalition, said in a news release.
Controlled Environment Agriculture, or CEA, has exploded with investment and sales the last few years, as more urban, indoor farms crop up to meet demand.
Soon after organizing in 2019, the coalition educated the Centers for Disease Control and Prevention and Food and Drug Administration about the limited risk of contamination from indoor-produced leafy greens, Karlin said.
“During the Thanksgiving 2019 romaine recall, those government agencies were transparent that CEA leafy greens were safe and did not extend the recall to them. This enabled retailers to keep CEA-produced greens on the shelves and consumers to safely buy CEA leafy greens for their families,” she said in the release.
The team had to create a standard that made sense across the board for the variety of production processes included in CEA — from greenhouses and vertical farming to aeroponic, hydroponic and aquaponic.
“Current food safety standards were written for the field, and many don't adequately address the unique attributes of controlled indoor environments,” Karlin said in the release. “Traditional food-safety risk profiles associated with conventional farming include examining the physical hazards and microbial hazards from water use, herbicide, and pesticide use, and impact from animals and animal byproducts. These do not impact CEA growers in the same way, if at all.”
As a result, a separate set of guidelines is needed.
This new certification process and the accompanying on-pack seal will spread awareness about CEA and unify these growers while differentiating them from traditional field growers, she said.
“It will allow producers to adhere to a standard tailored to indoor production and give incoming entrepreneurs guidance on the measures they'll need to meet to align with the existing industry,” Karlin said in the release.
The certification program is available to all CEA food safety coalition members for a small fee, and an external audit to the standard must be completed on an annual basis.
Growers are assessed across four key areas:
Hazard analysis: All potential hazards associated with a producer’s practices, including use of water, nutrients, growing media, seeds, inputs, and site control;
Water: Often used by CEA producers, recirculated water requires a continuing hazard analysis throughout its life cycle and zone-based environmental monitoring based on company-specific risk assessment, she said;
Site control: All food contact surfaces and adjacent food contact surfaces, including plant containers, must be considered and associated with potential farm physical hazards, including lighting, robotics, sensors, equipment, and utensils; and
Pesticide and herbicide use: Even though CEA-produced greens generally don’t use pesticides or herbicides, this module evaluates the potential risk of pesticide contamination and addresses if residue testing is required, she said.
“Consumer interest in food labels is high and shows a genuine desire to shop smarter,” Karlin said. “For consumers to truly make informed purchasing decisions, we need to explain what the labels mean, the process of certification and which labels they can trust.”
USDA Funds Composition of New CEA Market Characterization Report
. “This is the first such supply chain assessment in CEA. We appreciate these leaders for stepping forward to support this important effort.”
Resource Innovation Institute (RII) has assembled a senior level of its Technical Advisory Council to support its USDA-funded project titled Data-driven Market Transformation for Efficient, Sustainable Controlled Environment Agriculture. The new Controlled Environment Agriculture (CEA) Leadership Committee, composed of a range of subject matter experts in CEA, will advise the development of a Market Characterization Report that will analyze the emerging “controlled environment” horticultural supply chain to determine opportunities to increase energy and water efficiency in cultivation.
“Market characterization is a critical first step in a coordinated effort to transform an economic sector toward efficient production,” said Derek Smith, Executive Director of Resource Innovation Institute. “This is the first such supply chain assessment in CEA. We appreciate these leaders for stepping forward to support this important effort.”
The Market Characterization Report represents the first publication that RII will deliver as part of its work on a three-year USDA Conservation Innovation Grant designed to advance resource efficiency in CEA, a diverse, expanding market that includes greenhouses and vertical farms growing a range of crops, from microgreens to tomatoes to berries. RII is partnering with the American Council for an Energy-Efficient Economy (ACEEE) to deploy the grant.
The CEA Leadership Committee is providing input on key market characterization issues such as supply chain: describing key market actors, barriers to energy efficiency and the best leverage points for market interventions; energy use: describing the energy used by producers (including on-site renewable energy, microgrids, and back-up generation); advantages of efficiency; describing the energy and non-energy benefits realized through implementation of efficiency projects; and baseline identification: describing key market baselines to be used in evaluating the impact of the market transformation initiative over time.
The organizations represented on RII’s CEA Leadership Committee include:
American Society of Agricultural and Biological Engineers
American Society of Heating, Refrigerating and Air-Conditioning Engineers
CEA Consultancy
Ceres Greenhouses
Energy Solutions
Fifth Season
Fluence by OSRAM
Grodan
Midwest Energy Efficiency Alliance
Oregon Association of Nurseries
Priva
Resource Innovations
Schneider Electric
Signify
UVM Extension Services
Zartarian Engineering
For a complete roster, see www.ResourceInnovation.org/TAC.
For more information:
Resource Innovation Center
www.resourceinnovation.org
7 June 2021
Vertical Farming: Disrupting Agriculture
A New Agricultural Revolution Could Forever Change The Planet
24 May 2021
Vertical farming leverages cutting-edge technology to grow food in a new and better way.
One of its many benefits is that it can increase crop yield by 700 percent.
Vertical farming can help relieve pressure on scarce resources and boost Earth's biodiversity.
One day soon, you could eat bananas grown in downtown Manhattan.
It's a way of growing food that turns traditional agriculture on its head. With the required technologies now rapidly maturing, vertical farming is sprouting across the globe.
While there are still unresolved issues with this marriage of technology and agriculture, its promise may be irresistible. If it gets off the ground — literally — in a major way, it could solve the problem of feeding the Earth's 7.9 billion people. And that's just one of the benefits its proponents promise.
Vertical farms could take over the world | Hard Reset by Freethink www.youtube.com
Agriculture through time
When humankind began planting crops for nutrition about 12,000 years ago, the nature of our hunter-gatherer species fundamentally shifted. For the first time, it's believed, people began staying put.
With agriculture as their central mission, communities formed, with the now-familiar arrangement of residential areas surrounded by land dedicated to growing food. Even today, with modern transportation making the widespread consumption of non-local foods common, this land-allocation model largely survives: population centers surrounded by large areas for growing vegetables and fruit and raising livestock.
Credit: Genetics4Good / Wikimedia
Challenges facing traditional agriculture
As our population has grown, traditional agriculture has begun facing some big challenges:
Farmland takes up a lot of space and destroys biodiversity. Our World in Data reports that half of all habitable land is used for agriculture. As Nate Storey of Plenty, Inc., a vertical farming startup, puts it, "It is probably one of the most defining acts of humanity: We literally changed the ecosystem of the entire planet to meet our dietary needs."
The demand for farmland — both for produce and livestock — has led to a dangerous deforestation in several parts of the world. This also results in biodiversity loss and contributes to an increase in the greenhouse gases that drive climate change.
Degradation of farmland, such as through soil erosion, poses a threat to agricultural productivity.
Agriculture consumes copious amounts of water, which exacerbates water shortages. (Obviously, water shortages also reduce agricultural productivity.)
Fertilizer run-off causes substantial environmental damage, such as algal blooms and fish kills.
Pesticides can degrade the environment by affecting non-target organisms.
The effects of climate change are already making agriculture more challenging due to significant shifts in weather, changes to growing seasons, and realignment of water supplies. Our climate is continuing to change in unexpected ways, and the only predictable aspect of what lies ahead is unpredictability.
Vertical farming proponents expect that a re-think of how we grow food can ultimately solve these problems.
What is vertical farming?
Credit: Freethink Media / Plenty, Inc.
Vertical farming is a form of agriculture that grows plants indoors in floor-to-ceiling, tower-like walls of plant-holding cells. Instead of growing plants in horizontal fields on the ground, as in traditional farming, you can think of vertical farming's "fields" as standing on the edge and extending upward toward the ceiling. The plants need no soil or other aggregate medium in which to grow; their roots are typically held in a cell lining, often composed of coconut fiber.
Vertical flora is grown either aeroponically, in which water and nutrients are delivered to plants via misting, or hydroponically, in which plants are grown in nutrient-rich water. These are incredibly efficient systems, requiring 95% less irrigation than soil-grown plants. With vertical farming, Storey says that 99 percent of the moisture transpired by plants can be recaptured, condensed, and recirculated.
Plants, of course, also need light to grow, and vertical farms use increasingly efficient LED bulbs to keep plants thriving.
Vertical farms can increase crop yields by 700 percent
Credit: pressmaster / Adobe Stock
If vertical farming takes off the way its supporters believe it should and will, it may solve many of the aforementioned challenges facing agriculture.
Crop yields with vertical farming far exceed what's possible with traditional agriculture. Plenty, Inc.'s Shireen Santosham notes that the highly controlled growing environment of vertical farming has allowed her company to reduce the growing time for some crops to as little as 10 days. Without needing to consider whether or even sunlight, combined with the ability to operate 365 days a year, their system increases the potential annual yield by about 700 percent.
The land requirement for vertical farming is a mere fraction of that for traditional agriculture. Santosham says it can be done in a building the size of a big-box retail store that can be built pretty much anywhere that has adequate utilities, including within major urban centers. The tightly controlled environment of a vertical farm should also eliminate the need for applied pesticides.
Yet another benefit of vertical farming is the return of land currently needed for food production back to the planet. This could help facilitate Earth's recovery from deforestation and return much-needed habitat to threatened or endangered species. Of course, if we ever colonize the moon or Mars, vertical farming will be the go-to option for feeding the colonists.
Several vertical farming company pioneers are already getting their high-quality crops into the hands, and mouths, of consumers. Plenty, Inc. has an eponymous line of greens, and Aerofarms has their FlavorSpectrum line. Both companies claim that their products are exceptionally tasty, a result of their carefully controlled growing environments in which computer-controlled lighting can be optimized to bring out the most desirable qualities of each crop.
Credit: Alesia Berlezova / Adobe Stock
The history of vertical farming
The idea of vertical farming isn't new, and experts have been questioning its viability since the term was first coined in 1915 by Gilbert Ellis Bailey, who was obviously way ahead of the available technology at the time. The first attempt to grow produce in a constructed environment was a Danish farmhouse factory that was built to grow cress, a peppery green related to mustard, in the 1950s.
The modern concept of a vertical farm arose in the New York classroom of Columbia University's Dickson Despommier in 1999. He presented the idea as a theoretical construct, a mental/mathematical exercise imagining how to farm in an environmentally sound manner. His class began with the notion of a rooftop garden before considering a "high-rise" version that might theoretically be able to grow enough rice to feed two percent of Manhattan's population at the time. The eureka moment was a question Dispommier asked: "If it can't be done using rooftops, why don't we just grow the crops inside the buildings? We already know how to cultivate and water plants indoors."
With the technological advances of the last few decades, vertical farming is now a reality. Our sister site, Freethink, recently paid Plenty, Inc. a visit. (See video above.)
Vertical farming today
Credit: Nelea Reazanteva / Adobe Stock
Today, growers across the globe are developing vertical farms. While the U.S. has more vertical farms than any other country, the industry is blooming everywhere.
There are currently over 2,000 vertical farms in the U.S. While more than 60 percent of these are owned by small growers, there are a few heavyweights as well. In addition to Wyoming's Plenty, Inc. and Newark's Aerofarms, there's also New York's Bowery Farming. There are also companies such as edengreen, based in Texas, whose mission is to help new entrants construct and operate vertical farms.
Japan comes in second, with about 200 vertical farms currently in operation. The largest vertical farming company there is SPREAD. Across Asia, vertical farms are operating in China, South Korea, Singapore, Thailand, and Taiwan. In Europe, vertical growers are in Germany, France, Netherlands, and the U.K. Germany is also home to the Association for Vertical Farming, "the leading global, non-profit organization that enables international exchange and cooperation in order to accelerate the development of the indoor/vertical farming industry."
In the Middle East, whose desert land and scarcity of water present a particularly challenging agricultural environment, vertical farming is taking root, so to speak. The United Arab Emirates' Badia Farms is now producing more than 3,500 kilograms of high-quality produce each day and expects to increase that yield going forward. In Kuwait, NOX Management launched in the summer of 2020 with plans to produce 250 types of greens, with a daily output of 550 kg of salads, herbs, and cresses.
The economics of vertical farming
Credit: meryll / Adobe Stock
Building and operating a vertical farm is a costly endeavor, requiring a substantial initial investment in state-of-the-art technology, real estate, and construction. AgFunderNews (AFN) estimates that it can cost $15 million to construct a modern vertical farm. Fortunately, investors see the potential in vertical farming, and the industry has attracted more than $1 billion in investments since 2015. That includes $100 million for Aerofarms. Plenty, Inc raised $200 million in 2017 from a fund backed by such respected forward-thinkers as Jeff Bezos and Alphabet chairman Eric Schmidt.
AFN is particularly excited by the potential of what they call second-generation vertical farming technology. They cite advances in LED technology — expected to increase energy efficiency by 70 percent by 2030 — and increasingly sophisticated automation that can streamline the operation of vertical farms. AFN anticipates operating cost reduction of 12 percent due to improvements in lighting and another 20 percent from advances in automation.
BusinessWire says that the vertical farming produce market was valued at nearly $240 million in 2019, and they expect it to grow 20 percent annually to over $1 billion by 2027.
A welcome disruption
Vertical farming will be disruptive.
Vertical farming would eliminate the need for the arduous work of harvesting crops by hand from vast tracts of farmland. Current picking jobs, the company says, can be replaced by better-paying, full-time jobs available 365 days a year in better working conditions — and in the variety of geographic locations in which vertical farms can operate.
There are two caveats, however. First, the number of people needed to manage and harvest vertical farm crops will be far fewer than the many farmworkers required for less efficiently planted traditional fields. Second, with automation becoming ever-more capable — and perhaps a key to eventual profitability — one wonders just how many new jobs ultimately will be created.
But the societal benefits far outweigh any costs. As Plenty's Storey muses, "Like most everything in the world, we can only save our species if it makes economic sense." Thankfully, it does make economic sense
Lead photo: Credit: Freethink Media / Plenty, Inc..
Widespread Investment In CEA Is An Important Piece of The Food Security Puzzle
It has become increasingly clear that traditional agriculture is simply not meeting the food demands of the future
Sky Kurtz, CEO, and Co-Founder, Pure Harvest Smart Farms
There is a commonly quoted statistic estimating that by 2050, we will have nearly 10 billion people on the planet and, in turn, 10 billion hungry mouths to feed. Aside from population factors, the world’s climate is changing in ways human beings have never seen before. Across the globe, our water sources are being diminished and arable landmasses are shrinking. Food security and sustainability is becoming an ever-more pressing issue. There are a number of pioneering companies worldwide working hard to address these critical issues.
The Problem with Traditional Agriculture
It has become increasingly clear that traditional agriculture is simply not meeting the food demands of the future. Food production is heavily driven by significant freshwater consumption and can be both labour intensive and inefficient. Alongside this, changes in climate are negatively impacting yields. This is being witnessed across the board by the food production industry, investors, and governments alike.
The Power of the Consumer
Increased awareness of these issues has led to changes in consumer demands. Consumers have become more discerning about the quality of the products they buy, specifically when it comes to pesticide use, sustainability, freshness, food safety, variety, and brands. They are ever more interested in having knowledge of and creating a relationship with the foods they consume. This is evidenced by the huge organic growth rates of organics over the past 10 years. People care about quality and are voting strongly with their wallets.
Cultural and socio-economic demographics heavily influence what can and should be grown. Some crops such as premium quality leafy greens tend to target more affluent demographics and palates, whereas tomatoes, cucumbers, and a number of other greenhouse vegetables are staples of many diets and can be produced affordably in most places in the world.
The Promise of Controlled-Environment Agriculture
Controlled-Environment Agriculture (CEA) facilitates the growth of sustainable, high-quality produce but not at the expense of the consumer. CEA allows for consistent, high quality production by eliminating the environmental impacts on food production, allowing for more localized production, and reducing, or even eliminating, the use of pesticides.
Reducing Risk
Since early 2020, COVID-19 has woken the world to the risks and fragility of global fresh fruit and vegetable supply chains. Given perishability, the fruit & vegetable market is uniquely vulnerable vs. other crops e.g. the likes of corn, wheat, rice which can be stored & siloed. Controlled-environment agriculture is a solution that addresses these issues facilitating more localized production and supply, offering high output, resource-efficient production capabilities, while meeting the consumer’s changing demands.
In March, the world’s gaze turned to the Suez Canal where a container ship, the Ever Given, became lodged, blocking the canal. On a daily basis, the Suez Canal carries 12% of global trade, around one million barrels of oil and roughly 8% of liquefied natural gas. The cost of the blockage was reportedly $14m-$15m every day!
The Local Promise
The local unique selling point (USP) is now possible pretty much anywhere. Solutions like ours at Pure Harvest Smart Farms have made it possible to affordably produce year-round, even in the harshest climates in the world for example, the UAE, Kuwait, and Malaysia serving Singapore.
Large-scale solutions are necessary for the food to be economic, due to economies of scale in what is ultimately a manufacturing process. Large-scale greenhouses are particularly suitable for dense urban populations, as just 1 or 2 large production sites within 100 – 500 kilometers of the city or town can serve a large group of people affordably.
Unfortunately for more distributed, rural populations, this becomes more challenging. If you scale-down the solutions to hyper-localize, you often lose efficiency (in terms of both capital expenditure/ m2 and operational expenditure/ m2 for production. With more of the world’s population urbanizing, this is another trend that supports widespread investment in CEA as an important piece of the puzzle to serve future food demands.
The Future
The challenge of feeding nearly 10 billion people by 2050 MUST be solved on both the supply side and demand side. From the supply side, adopting technologies that augment output and resource-efficient growing methods. From the demand side, via changing what we consume, reducing waste, and environmental consciousness. Addressing these issues means we can produce more food with less and less resources.
High-tech agriculture presents a multi-decade investment opportunity to contribute to food security, water conservation, economic diversification, and a more sustainable future for all.
Join Sky at the virtual Indoor AgTech Innovation Summit on June 24 and tune into his live panel discussion on ‘Scaling at Speed: Delivering the Promises of a Mission-Led Industry’ at 16.50 EST.
For more information about Pure Harvest Smart Farms, follow them on Facebook, LinkedIn, Instagram and Twitter.
Recent Posts
Indoor AgTech Investment Landscape
Widespread Investment in CEA is an Important Piece of the Food Security Puzzle
Workshop: Food for the Next Frontier
Connecting Retailers, Buyers, and Growers Across Indoor Farming
IGS enters UAE market, signing deal with Madar Farms to enhance food security in the GCC region
Archive
Twitter: @IndoorAgTech
LinkedIn: Indoor AgTech
Hashtag: #IndoorAgTech
Robotic Warehouse Farms Will Save The World
CEA technology is just getting started. Like the Tesla Cybertruck, we have a working concept that promises a more-than-Jetson’s-level future many of us can see the benefits of and actively want―it’s just not quite available to the masses yet
by Elle Griffin
Four years ago, Ritch Wood was looking for a better way to grow plants. As the CEO of global skincare company Nu Skin, he ran into ingredient shortages every winter when fields went dormant―and when he moved grow operations to the equator he ran into water and land shortages, along with a host of quality control issues.
Nu Skin needed reliable, quality ingredients for their skincare products. But farming was too unpredictable an industry. “If there was a way to grow indoors,” he thought, “and be able to do that 24 hours a day, 365 days a year―if we could guarantee that it was grown without any herbicides or pesticides and in a sustainable way that uses less water and land―that would be really helpful.”
At the time, controlled-environment agriculture (CEA) was in its infancy and grow-light technology had yet to take a turn for the more affordable. When he learned of an agricultural system that promised to use a fraction of the land and water used by traditional agriculture methods and had the potential to make it more affordable, Wood made an investment.
Nu Skin paid $3 million for 70 percent of the company and rights to its IP―and Grōv Technologies was born.
Grōv grass grown in the Olympus machine at the Bateman Mosida Farms. Photo from Grōv Technologies
Controlled-environment agriculture is on the rise
The theory behind CEA is that by controlling the environment in which it grows, we can control everything about a plant and what it grows into by micro-tweaking one of a thousand different characteristics―including temperature, humidity, light duration, light wavelength, dissolved oxygen in the water, and carbon dioxide saturation in the air. By tweaking the growing cycle, we can control the caloric content as well as the nutrient content and density of the plant.
“What we’ve learned through controlled-environment agriculture,” Benjamin Swan, co-founder and CEO at Sustenir in Singapore, once told National Geographic, “[is] we can actually emphasize certain characteristics of the plants. So, without using GMO, we can make our kale softer, we can actually make it sweet.”
The theoretical use cases for this technology are endless―from being able to grow in places where water is scarce (like in much of Africa), or where water is overly abundant (like Hawaii), or in places where labor is scarce (like in parts of Asia), or even in places that have long winters (like Northern Europe). Theoretically, we could have grow towers in every town and feed the whole of it no matter its natural environment.
We could even grow those foods to those cities’ exact nutritional needs―more vitamin D-rich foods in wintery places, for example. Dr. Lee Mun Wei, a senior manager at the Food Innovation and Resource Centre (FIRC) in Singapore aims to predict and prevent illness in a given population by tracking their biometric data using Apple watch-like wearables, then 3D printing nutrient-specific foods that could mitigate imbalances.
Though these technologies exist, they are still in their infancy. Singapore leads much of the research and development out of necessity. With limited land and water resources, the county is forced to import 90 percent of their food and 40 percent of their water from outside the country. As a result, they have no option but to grow vertically and desalinate water from the ocean.
Elsewhere, the industry has been slow to catch on, largely due to exorbitant startup costs, low returns, and lack of urgent need. According to a 2017 State of Farming report by L.E.K., only 27 percent of indoor, vertical farms are profitable compared with 50 percent of container farms and 75 percent of greenhouses. But one thing has spurred the industry on in recent years: cannabis.
Legalized in 39 states, demand for cannabis has created a $13.6 billion industry and enough capital to fund CEA-enabled grow operations. “When you have a crop that fetches up to $2,400 or $2,500 a pound, you need to be able to dial everything in and make it consistent and repeatable,” says Dashiel Kulander, co-founder and CEO at Boojum Group. “If the temperature swings five to 10 degrees on a cannabis plant, that will change the plant’s various cannabinoids. The goal is to create a medicine that is consistent batch after batch.”
It’s only recently that there has been some financial incentive to use CEA technologies for food use―largely driven by Big Ag players hoping to hedge out the competition. Berry farming giant Driscoll’s, for one, led a $500 million round to fund Plenty, a 2.2-acre vertical farm in California they hope will help them fulfill a contract with Albertsons. The Ingka Group, for another, led a $100 million round to fund AeroFarms, a 2.4-acre vertical farm in New Jersey that will help them fulfill a contract with Singapore Airlines.
Grōv tent at the Bateman Mosida Farms. Photo from Grōv Technologies
Grōv Tech is building CEA prototypes in Utah
By investing in Grōv Tech, Nu Skin hopes to do something similar, getting ahead of the supply chain that fuels their skincare products before the competition can beat them to it, or before climate change makes traditional methods more difficult, all while shoring up technology that could provide a farming model that is more sustainable―if only it were more economical.
“The purpose was always, can we build a better product for Nu Skin?” Wood says. “We think there’s a huge story around the ingredient sustainability, and there were a lot of ingredients we felt we could grow, but the challenge was: could we do it in an economical way?”
Grōv Tech started out with a prototype: a tower that pairs hydroponic growing technology with grow lights. But like all CEA startups, a lot of the growing process was manual and the technology was prohibitively expensive. To make something that was scalable and profitable the whole thing needed to be automated and it needed to be cheap.
With this goal in mind, Wood decided they would start by growing animal feed for Bateman’s Dairy farm. Having grown up on a dairy farm himself, Wood figured this would allow the company to scale the product while refining and automating the technology to the point that it could be replicated. And all of this would have a fortuitous effect on Nu Skin’s bottom line.
“One of our bestselling products is a weight-loss protein powder which uses whey protein,” Wood says. “So again, a very nice connection there is if the animal is eating a more sustainable product and producing better milk with better protein and it’s being done in a sustainable way―certainly that can be a benefit to Nu Skin down the road.”
One year into feeding the 20,000 animals at Bateman, the company has learned a lot. For instance: cows need a lot of magnesium, but they don’t like eating it. Now, Grōv Tech puts magnesium in the water so it’s directly absorbed into the plant and then becomes bioavailable to the cow upon eating it. And because the growing process only takes seven days, data scientists can analyze the results in real-time and adjust the components to optimize production for the next batch of feed.
According to Grōv Tech president Steven Lindsley, it’s not far off that we’ll be looking at milk production (butter, fats, and proteins) and optimizing a herd’s diet for taste, quality, and nutritional value―not to mention the wellbeing of the animal. We’ll be able to look at how many trips from the veterinarian an animal gets when they’re fed certain nutrients in their diet, and whether they can have more calves and produce the same amount of dairy on less, better quality feed. (So far, the answer to this last question is yes. When animals are fed better quality food they need less of it―just like humans.)
And if we hook all of the cows up to robotic milking equipment and connect everything to artificial intelligence, machine learning, and the Internet of Things―Lindsley’s far-flung goal―then we might be able to collect enough data to not only feed cows to their optimum health and performance ability, but humans too. And that could have ramifications not only for feeding the world, but nourishing it― just like Dr. Wei hopes to do in Singapore.
“Last year was about starting to feed animals and get data and prove out the hypothesis we have while continuing to perfect the technology and get confidence there,” Wood says. “And now we’re really to a point where we’ve got data that proves that it works and that financially it’ll be a good thing for a farmer. So now we can really take that proposition to farmers and start to scale.”
Olympus Tower Farm at Bateman Farms in Mosida, UT. Photo from Grōv Technologies
CEA technology could feed the world
Right now, Grōv Tech is focused on refining its technology right here in our own backyard. But once they do that, the plan is to expand internationally.
“Saudi Arabia has actually passed a law where you cannot use water to grow fodder or feed for animals, so all of that now has to be imported. China imports one-third of their alfalfa feed for their dairy animals because they don’t have the capability of growing it,” Wood says. “So there are countries that will probably benefit more than the US would. But we’ve got to refine the technology and get that built to where it’s ready to scale before we start spreading ourselves all around the globe.”
CEA technology is just getting started. Like the Tesla Cybertruck, we have a working concept that promises a more-than-Jetson’s-level future many of us can see the benefits of and actively want―it’s just not quite available to the masses yet. But with more than a billion dollars invested in the technology in just the past few years alone―we’re getting there. And the “there” we are heading toward is rosy indeed.
“To put it in perspective, one tower that is about 875 square feet on the ground will replace 35 to 50 acres of land,” says Lindsley. “And that will feed the animals on roughly five percent of the amount of water. The UN says that that the world will add about 2.5 billion people in the next 30 years. And we have to find a way to feed them on arguably less arable land and water. The good news is the technology is coming along to help solve that equation.”
If COVID-19 taught us anything, it’s that our food supply chain is fragile. But that’s only because our supply chain was built to grow food in California, refrigerate it so it stays fresh, then transport it 1,500 miles so we can eat a salad in the winter in Chicago. In the future, that might not be a thing. “We’re having a dry year now,” Lindsley tells me in February. “But a year ago we were in a blizzard, and even in the middle of a blizzard in February in Utah, we’re pumping out fresh, beautiful, safe green grass for animals. It’s a paradigm shift.”
“Four years ago it was a good idea,” Wood tells me of his company’s investment in CEA technology, “But four years from now it’s going to be required.”
Elle Griffin
Elle is the editor-in-chief of Utah Business and a freelance writer for Forbes, The Muse, and The Startup. She is also a literary novelist and the author of a weekly newsletter called The Novelleist. Learn more at ellegriffin.com.
10 New Trends In CEA In 2021 And Beyond
The world of controlled environment agriculture (CEA) is continuing to develop at an accelerated rate. In line with Agritecture’s mission “to accelerate climate-smart agriculture strategies,” we’ve decided to share our top predictions for the future of CEA for 2021 and beyond
22-04-2021 | Agritecture
The world of controlled environment agriculture (CEA) is continuing to develop at an accelerated rate. In line with Agritecture’s mission “to accelerate climate-smart agriculture strategies,” we’ve decided to share our top predictions for the future of CEA for 2021 and beyond.
This post is a follow-up to Agritecture’s post on the “10 New Trends In Hydroponics: What To Expect In 2017 And Beyond”.
Here are our top 10 predictions:
#1: Strawberries
In a sea of vertical farmers producing leafy greens, we’ve noticed sights shifting to strawberry production. While strawberries were initially difficult to produce given on-the-ground concerns like pests, fungal diseases, and weeding, growing vertically has allowed for easier harvesting and limited damage to the fruit. According to Agritecture’s Founder & CEO, Henry Gordon-Smith, “Strawberries are the hot new product for indoor growers because they can charge a lot for the best ones, they’re desired year-round, and the freshness and flavor are very noticeable,” being made more achievable by vertical farming.
Image sourced from Oishii
As of late last year, Driscoll’s and Plenty announced a partnership to grow strawberries indoors. We’re seeing increasing interest in high-quality strawberries with Oishii Berry’s $50m Series A fundraising for bee-assisted, carbon-neutral strawberry cultivation. In response to this growing interest, Agritecture’s Director of Operations, Yara Nagi, comments that “there is an interesting opportunity for growing strawberries hydroponically, especially for countries that import a majority of their strawberries. In order for strawberries to be exported to another country, they typically have to be harvested early. So, being able to grow them locally and in a controlled environment translates to better quality strawberries with a longer shelf-life. Other than the fact that growing strawberries hydroponically has become more and more efficient, the price point for strawberries can be relatively high when compared to other products grown in an indoor environment.”
#2: Breeding Seeds For Vertical Farms
As of recently, we’ve noticed a growing interest in breeding seeds for vertical farms. In February 2021, Kalera acquired Vindara Inc., a company developing non-GMO seeds for vertical indoor farms. Kasveista’s story of producing high-quality seeds and seedlings of open-source varieties for vertical farming similarly showcases this change in the industry.
Agritecture’s Lead Agronomist, David Ceaser, comments that “to date, crops grown in vertical farms have been grown using plant genetics developed for outdoor or greenhouse production. Environmental conditions in vertical farms are quite different from those environments, and so, plants respond differently. As genetics for vertical farms are developed, yields of current crops will improve greatly, and new crops will be successfully introduced into the vertical farm platform.”
#3: Fully Automated Vertical Farms
If you know anything about vertical farming, you know that labor is expensive and that this form of intensive agriculture requires highly skilled labor. According to Gordon-Smith, “new fully automated vertical farms are emerging” to respond to this labor challenge. He questions whether they will actually work, given that costs are high and the technology is new. Does this development in vertical farming mean fewer jobs or a more skilled workforce? Fully automated vertical farms are inevitable but will they pay off?
In September 2020, Agritecture’s new equipment partner, Urban Crop Solutions, launched their Module-X Automated Vertical Farm.
#4: Floating Farms
It’s always a struggle to find open space for agriculture in built-up urban areas. In recent years, we’ve seen abandoned and unused spaces converted into urban farms. So, why not take farming to the waters too? While it may not seem like the most sensible place to run a farm, it severely reduces food miles and pollution caused by the transportation of food.
Image sourced from Oceanix
Aqua Ark is a company that has taken to the waters to create Amphibious Homes that integrate floating wetlands for food production. Oceanix is a similar company that creates modular and self-sustaining communities on the water for people who want to live sustainably across the nexus of energy, water, food, and waste. The Floating Farm in Rotterdam is a project designed “for a future where rising sea levels mean that farmland is increasingly out of action due to flooding”.
To learn more, check out Agritecture Studios, where ‘floating cities’ is a challenging area within our inaugural cohort of architects.
#5: New Financing Options For CEA Startups
Financing for CEA operations is incredibly challenging. These capital-intensive projects require a robust business plan, strong management team, and access to capital to ensure on-time delivery of construction. Within the last year, we’ve seen SPACs be the latest means for private companies to raise capital. For startups, SPACs aren’t exactly the best route. “A new wave of investment and crowdfunding platforms are providing startups with alternative access to capital,” says Agritecture’s Director of Business Development, Jeffrey Landau.
Through Agritecture Designer, we have a partnership with several of these financing vehicles whereby our software users can access unique discounts and other benefits with these platforms.
#6: Labor Bottlenecks
According to Agritecture’s Director of Business Development, Jeffrey Landau, “the number of greenhouses and vertical farms is growing rapidly. Yet, the number of trained professionals with CEA operating experience is not keeping up with this increasing demand. Agritecture has been working with Cornell University through a National Science Foundation and Agriculture and Food Research Initiative grant to study solutions to this challenge.”
In production systems, workloads often arrive too quickly for the production process and labor to manage. Although seemingly a small problem, the inefficiencies brought about can create delays and result in higher production costs. As a result, we need a highly trained workforce and more workforce development programs for CEA growers.
#7: Singapore, The New Hub For Urban Agriculture
As a country that imports over 90% of its fresh produce and has severe land scarcity limiting its agricultural options, Singapore was in serious need of CEA. This changed when the Government launched the Sustainable Singapore Blueprint. The objective is to develop 200ha of high-rise greenery by 2050, incentivize developers to include urban farms in their developments, integrate farming in mixed-use districts, and encourage the adoption of technologically advanced infrastructure and smart systems. Today, they have the best funding and planning in the sector.
Image sourced from Citiponics
Citiponics is one of Singapore’s first hydroponic rooftop farms, located on top of a carpark, a structure that services almost every neighborhood in Singapore. Sustenir Agriculture is another company farming in Singapore, creating indoor vertical farms that can retrofit into existing buildings. Natsuki’s Garden is another example of successful CEA operations in Singapore. It’s a greenhouse in the center of the city, occupying reused space in a former schoolyard.
Learn more about Singapore’s efforts here. Additionally, Agritecture recently wrote about several other cities that are paving the way for urban agriculture to thrive here.
#8: Architecture
The global pandemic continues to reshape our relationship with food. Challenged by a lack of food access and the declining retail real estate market, individuals have taken a new interest in growing their own food, in the comfort of their own homes. This interest in bringing food production closer to people’s homes is empowering architects to transcend the boundaries of traditional food production to integrate urban agriculture and AgTech into cities. This innovative step will help solve food supply and food access quandaries globally.
Agritecture Studios is working to empower architects to continue on this mission and be key stakeholders in shaping our food-secure futures.
#9: “Alternative Products” x CEA
Image sourced from Smallhold
CEA has a rap for only growing leafy greens. However, several commercial growers have scaled up recently to produce a variety of other specialty crops, including Smallhold (mushrooms), We Are The New Farmers (spirulina), Ynsect (insects), and Pure Salmon (aquaculture).
AgFunderNews groups all of these producers under the category of “novel farming” in their annual funding reports. Per their most recent report, novel farming startups raised more than $1.3B in private investment in 2020, a 16x increase from 2015.
#10: Rise Of Energy Producing Commercial Greenhouses
The high energy use in controlled environment agricultural operations has been a cause for concern from the beginning. Commercial greenhouses, in particular, are reshaping how we think of energy by producing it themselves. ClearVue Technologies installed their energy-generating photovoltaic glazing panels on the world-first clear solar glass greenhouse. TSO Greenhouses is another AgriTech company with the primary objective of maximizing greenhouse light management. There is a lot more research happening here at the university level to investigate some of the tradeoffs between upfront cost, maintenance, energy production, and crop yields. Wide-spread commercial adoption will be multiple years away - but is it 3 years or 10+ years?
There’s no doubt that there’s more to come for the CEA industry. Here at Agritecture, we are constantly combing through the latest research papers, new technology releases, and industry trends to ensure that our clients and software users are able to get creative, build a competitive advantage, but still have realistic goals. Build your first urban farm model today, or get in touch with us to see how we help organizations around the world plan smarter through custom services.
Source and Photo Courtesy of Agritecture
May 18th, 9 am EST - Webinar On How To Invest In CEA With Confidence
Agritecture is hosting a series of webinars, starting with How to invest in CEA with confidence
Agritecture is hosting a series of webinars, starting with How to invest in CEA with confidence. The CEA sector is heating up and is expected to grow 5x over the next 10 years. Investment in CEA has surpassed $2.0B across North America and Europe. Join Henry Gordon-Smith, Founder & CEO at Agritecture, for this 1-hour live webinar to learn more about how to invest confidently in the CEA industry.
How To invest In Controlled
Environment Agriculture With
Confidence
May 18 - 9 am EST
The lineup of speakers include:
Louisa Burwood Taylor, Head of Media & Research at AgFunder
Robert Glanville, Senior Advisor at REG Consulting LLC
Andrew Carter, Co-Founder & CEO at Smallhold
Darren Thompson, CFO at Bowery Farming
Djavid Amidi Abraham, Director Of Consulting at Agritecture
Click Here To Register!
For more information, you can check out our events listing here.
Agritecture
www.agritecture.com
Explore The Sixth Edition of Clima, Powered by IGS
In this edition, we look at why precision farming and Controlled Environment Agriculture (CEA) techniques are becoming more mainstream, and the skills and talent required to make this approach a success
In this edition, we look at why precision farming and Controlled Environment Agriculture (CEA) techniques are becoming more mainstream, and the skills and talent required to make this approach a success. Technology is having a greater impact on agriculture than ever before, and this is only set to increase. It will bring with it a wider and more advanced agricultural ecosystem that requires a skilled, knowledgeable, and committed workforce, with as great an appetite for innovation and capacity to problem solve as any generation before.
Discover more on this topic in the sixth edition of Clima today.
Bringing future talent to Agriculture 4.0
We discuss the emerging influences on education and skills development across Agriculture and Horticulture with two senior leaders from Scotland’s Rural College (SRUC). We spoke to Professor Fiona Burnett, Head of Connect for Impact in SRUC’s Knowledge and Information Hub, and Ruth Vichos, Lecturer in Horticulture, about the evolution of Agriculture 4.0, and how technology is impacting skills evolution and teaching mechanisms.
Listen To The Full Interview
Can Vertical Farming Be A Viable Method Of Controlled Environment Production?
Fifth Season is using its fully integrated, automated operating system to crack the economics code for vertical farming with the potential to integrate with greenhouse operations.
Fifth Season is using its fully integrated, automated operating system to crack the economics code for vertical farming with the potential to integrate with greenhouse operations.
To say that controlled environment agriculture is drawing a lot of interest and dollars from the investment world would be an understatement. Austin Webb, co-founder, and CEO at Fifth Season, a vertical farm operation in Pittsburgh, Pa., estimates that over $3 billion has been invested in the CEA industry during the last four years alone, excluding debt and merger and accusations activities for greenhouse operations.
“For indoor ag overall, including both vertical farming and greenhouse, about half that equity investment has been for vertical farming,” Webb said. “There were a lot of dollars that came into this space early on. The unfortunate piece to that is there was a lot of overhype and false promises made in this space. A lot of those dollars came in too early for some of these companies and overall were wasted.
“There has been an industry-wide struggle to make the economics of vertical farming work. All of these companies talk about what they are going to do in the future, but the issue is they have negative unit economics. They lose money for every pound of produce they sell. In many cases, they will say that they will make the economics work in the future, but only after they build more production facilities.”
Webb said negative economics has had a major impact on the vertical farm industry.
“The false promises and the negative economics have held the industry back, overshadowed companies that are building substantial vertical farming solutions that work and pushed additional dollars to incremental greenhouse solutions,” he said. “Moving forward we will continue to see more dollars come into CEA and into vertical farming specifically. This will include public markets and SPAC (special purpose acquisition company) activity.
“Overall, there will be more money invested in CEA. This will include investments that are mediocre. The important element will be investments made into tech platforms designed for scalability and repeatability. This is the only way that volume requirements for wholesale buyers can be met to unlock indoor ag as a material participant in overall market share.”
Need for a mindset change
Even with additional investment dollars coming into the CEA industry, Webb doesn’t expect it to be enough to make traditional vertical farming companies a success.
“Unfortunately, even though significant dollars have been invested in vertical farming, much of it has been wasted,” he said. “The incremental mindset a lot of people in this industry have had is to simply convert farming from outdoors to indoors. In doing so, all they inevitably did was bring people from outdoors and put them indoors. The mindset was to create a growing platform to produce leafy greens and then sprinkle on some technology. The technology was sort of an afterthought.
“There were a lot of companies throwing out buzz words without having actual practicality in regards to robotics, artificial intelligence, and automation. All the money that has been invested has been going toward continued R&D, but at a level which has companies creating technical debt.”
The thing that has helped Fifth Season avoid the technology issues other vertical farms have encountered is the way the company developed and designed its operating system.
Fifth Season has created a manufacturing platform that is fully automated from end-to-end including growing, processing, and packaging.
“We had a completely different mindset,” Webb said. “We took a blank slate to really design this holistically from beginning to end. We think of this as manufacturing a living organism. As a result, we’ve created an IoT–connected smart manufacturing platform that is an industry-first, industry-only, fully end-to-end automated platform—not just growing, but also processing and packaging. There are other operations that have automation here or there, but nothing else truly automated from beginning to end.
“More importantly, we have integrated the system so it is completely run by our proprietary software platform. We don’t have a bunch of automated equipment that runs on its own controls. Instead, we have a combination of our own proprietary tech and some off-the-shelf equipment such as conveyors. All of the electromechanical systems sit within our software skin and are run by our in-house built firmware and software brain. We have a pathfinding algorithm where when we receive an order from a customer, our system is sequencing out the schedule completely on a daily, weekly and monthly basis.”
Fifth Season worked with Hort Americas and GE Current, a Daintree company, to develop its automated grow room.
“Partnering together on our solution helped us validate that there was a path for our vertical farm to have favorable economics,” Webb said. “Being able to bounce ideas and technologies off of the Hort Americas team allowed us to push the boundaries of innovative thinking in terms of our approach and how we wanted to use technology to solve the complex issues that are limiting vertical farming. We were able to think differently, knowing we had the Hort Americas team as both a check and enabler, which ultimately created a successful collaboration.”
Partnering with Hort Americas also gave Fifth Season the opportunity to incorporate Current’s LED technology into its unique growing platform.
“We did a lot of things differently with our proprietary design and in so doing there were certain things that we couldn’t necessarily handle ourselves,” Webb said. “Working with Hort Americas and Current enabled us to move very quickly while making smart, capital-efficient decisions, as opposed to designing the LEDs ourselves or over-paying for unnecessary functionality.
“We worked with Current in key areas that made big differences related to the integration of our design. We leveraged Current’s significant expertise in regards to light spectrum strategy and the corresponding impact on plant science and quality.”
Creating an economic advantage
Webb said Fifth Season’s unique platform has allowed the company to unlock positive unit economics where it can offer a market price that works for wholesalers and consumers.
“We have been able to make money per pound and make vertical farming economically sustainable,” he said. “Our platform has enabled us to make a stepwise function change in labor costs and efficiency and in energy costs. For labor, we have 2x+ less labor costs than other companies in this space. We also measure and track energy down to every individual bot. We have over 60 bots that are all integrated into one robotics system. We measure and track how to optimize energy utilization to all of those bots.
Fifth Season’s unique operating platform has allowed the company to unlock positive unit economics enabling it to offer a market price that works for wholesalers and consumers.
“Finally we have made a stepwise function change in pounds to fixed costs ratio. That’s because we have been able to remove large aisle ways and manual inefficient storage and retrieval. We have created a patent-pending solution around our automated storage retrieval, which ties to the rest of our system. In the end, we are able to remove all human involvement from the grow room and are able to achieve 2x+ the growing capacity.”
Another advantage of the platform Fifth Season has created is the need for raising additional capital compared to some other vertical farms.
“We have raised just over $40 million to date,” Webb said. “There are multiple vertical farm companies that have raised $200 to $400 million+. The reason we haven’t had to raise that much capital is because of our mindset about engineering, grow science, and operations in the same R&D pipeline. It has allowed us to catch up and to surpass the rest of the industry in a fraction of the time with a fraction of the capital.
“As we move forward and look at raising additional capital, what’s different is we don’t have to use our equity capital to build more farms for all the hard costs associated with real estate, equipment and building facilities. We can if we want to and if it makes sense for our equity partners, but it is not required. We have been able to unlock positive unit economics which means we have been able to unlock non-dilutive capital to build additional facilities more capital efficiently. Overall, we have built a scalable, repeatable platform, which is what investors need to see.”
What’s ahead for vertical farming?
Webb said there will be a few select companies that have approached indoor ag and vertical farming with a solution that works and will thrive. There will also be a number of companies that are large and excessive that will eventually disappear.
“There will be some consolidation in this industry,” he said. “Some companies won’t be consolidated because they don’t have a tech platform that is investable in terms of the synergies of wanting to acquire that footprint. Consolidation will be selective in some cases.
“There is a lot of production regardless of footprint and money going into leafy greens. There are companies in this space that have no intention of doing anything different than that. I think that focus will run them into a leafy greens race to the bottom. It all comes down to no sustainable competitive advantage.”
Webb also sees the potential for synergy between vertical farms and greenhouses.
“We have built a scalable system that allows us to do a number of crops and then do asset management across different applications,” he said. “We also have the technology that is applicable from an asset management production operations standpoint that works for greenhouses as well.
“We will be able to unlock with this technology what many others won’t necessarily be able to do. Fifth Season will not only be a company that has vertical farm and greenhouse footprints but also is one that uses those footprints in a collaborative way for specific crops. For example, a crop could be in a vertical farm environment for part of its life and in a greenhouse for another part of its life. This will create cross-category and cross footprint combinations.”
For more: Fifth Season, (412) 899-2268; hello@fifthseasonfresh.com; https://www.fifthseasonfresh.com/
Lead photo: Austin Webb, co-founder, and CEO at Fifth Season, said even though significant dollars have been invested in vertical farming, much of it has been wasted. Photos courtesy of Fifth Season
This article is property of Urban Ag News and was written by David Kuack, a freelance technical writer in Fort Worth, Texas.
CHINA: $500 Billion To Bring All World Crop Farming Indoors
China will build 2 Million hectares (20 billion square meters) of controlled environment greenhouses by 2025 and this will produce half of their vegetables and crop needs
Brian Wang | April 3, 2021
China will build 2 Million hectares (20 billion square meters) of controlled environment greenhouses by 2025 and this will produce half of their vegetables and crop needs. Temperature, humidity, lighting would all be under controlled conditions. It would not matter if there were new extreme temperature swings outside or if there was drought. The needed food and water would be immune to any projected climate change over the next 500-1000 years.
Alibaba sells greenhouses for as little as 70 cents per square meter. The bulk, high volume cost to the manufacturer is about 50 cents per square meter. If installation labor costs are 50% of the 2 million hectare project then it would cost about $20 billion for the 2 million hectare project. $40 billion would be sufficient for China to make 40 billion square meters of climate-controlled greenhouses which could produce all vegetables and crops. It would cost $260 billion to make greenhouses for the food production of the entire world.
Indoor climate-controlled agriculture has almost no need for pesticides and uses 7% of the water. This would take up 3-5% of the total land area of open-air farming.
Additional funds could be provided for higher demand from population growth and for some level of automation, sensors and other systems.
There is an economic analysis of smaller scale greenhouse and vertical farming. The all-in delivered cost of a pound of greens grown in a commercial greenhouse is estimated to be $2.33 per pound. It cost $18.3 million to build 280,000 square feet (2.6 hectares) of commercial greenhouse in the USA. The total cost to grow would be just over $3.0 million per year for 2 million pounds of greens or $1.52 per pound. BrightFarms employs 165 people for the three greenhouses. $1.10 per pound consists of employee costs.
The cost estimates for greenhouses could be brought down to $1 per pound or less with large-scale construction. Below are costs for 2.8 hectare systems in the USA.
There is value to having national food security and not having to depend on imported food. Ten billion to twenty billion dollars per year in indoor farm subsidies closes the cost gap with open-air farming.
China’s controlled environment system will have a lot of automation and lower construction costs because of the massive scale and lower costs in China.
PNAS – Wheat yield potential in controlled-environment vertical farms
Wheat growing is vastly more land and water-efficient but costs are not yet competitive with open-air farming.
Wheat is the most important food crop worldwide, grown across millions of hectares. Wheat yields in the field are usually low and vary with weather, soil, and crop management practices. We show that yields for wheat grown in indoor vertical farms under optimized growing conditions would be several hundred times higher than yields in the field due to higher yields, several harvests per year, and vertically stacked layers. Wheat grown indoors would use less land than field-grown wheat, be independent of climate, reuse most water, exclude pests and diseases, and have no nutrient losses to the environment. However, given the high energy costs for artificial lighting and capital costs, it is unlikely to be economically competitive with current market prices. Wheat grown on a single hectare of land in a 10-layer indoor vertical facility could produce from 700 ± 40 t/ha (measured) to a maximum of 1,940 ± 230 t/ha (estimated) of grain annually under optimized temperature, intensive artificial light, high CO2 levels, and a maximum attainable harvest index. Such yields would be 220 to 600 times the current world average annual wheat yield of 3.2 t/ha. Independent of climate, season, and region, indoor wheat farming could be environmentally superior, as less land area is needed along with reuse of most water, minimal use of pesticides and herbicides, and no nutrient losses.
Meat production could also be brought under climate control. The feed for cows, pigs, chicken and fish could be either brought into greenhouses or converted to insects. Insect feed can be twenty to one hundred times more space and water-efficient.
Meat can be converted into cell-based production in large vats. This would be similar to the industrial production of beer.
There would be zero risk of mass starvation caused by temperature or drought-induced crop failure.
There may not be a need to bring all crops indoors. But if China brings half of all of their crops indoors in five years it clearly shows that civilization can bring all crops and farming indoors at any time. The cost as I have shown is less than 0.5% of global GDP for the crops and a few percent to deal with the meat and feed as well.
It is likely only truly economical (even with China’s mass production) to bring vegetable and fruit farming indoors. If China has indoor vegetable and fruit production at $1 per pound then other countries could follow at different levels based upon how cost-competitive indoor farming is against open-air farming for a particular crop. There is also the question if people will pay more for greenhouse crops. Greenhouses allow for year-round crop production. This means consistent prices and availability for fruits and vegetable year round. It also means indoor farms can be inside of cities for fruit and vegetables that are fresh from the tree and vine. The greenhouse crops would also be mostly or completely free of pesticides. Indoor farming share will grow as efficiency and costs are improved.
I think 20-60% of all crops (mainly higher-value fruits and vegetables) globally will go indoors by 2030 and gradually more as indoor becomes a lower cost and superior product to outdoor farming. Greenhouse farmed fruits and vegetables can have a higher quality versus outdoor grown fruits and vegetables.
Some of the advantages of protected culture greenhouse crops are:
Season extension is just one of the advantages gained from greenhouse growing. Protected crops are less apt to be damaged by wind, rain, and hail so the percentage of marketable products is higher. Yield is often higher as well, if you can provide optimum growing conditions for each crop. Greenhouses protect crops from many diseases, particularly those that are soilborne and splash onto plants in the rain. And greenhouse crops may be protected from common field pests. Of course, greenhouse crops have their own particular problems such as foliar disease, aphids, and whiteflies, so vigilance is still required.
SOURCES- Alibaba, PNAS, agfunder news
Oishii Sees Itself As ‘The Tesla of Vertical Farming.’ Here’s How It’s Cracking CEA Strawberries
“Strawberries are the hardest crop to grow in a vertical system and it’s been every vertical farmer’s dream to grow them. Conquering strawberries allows us to grow into other crops very quickly.”
March 31, 2021
Indoor farming is best known for leafy greens and micro-herbs. But New York’s Oishii is hoping to blaze a new trail and sweeten up the segment.
“A lot of people call strawberries the holy grail of vertical farming,” Oishii founder Hiroki Koga tells AFN. “Strawberries are the hardest crop to grow in a vertical system and it’s been every vertical farmer’s dream to grow them. Conquering strawberries allows us to grow into other crops very quickly.”
The startup announced a $50 million funding round this month led by Mirai Creation Fund, part of Tokyo-based SPARX Group. Additional investors included Sony Innovation Fund — the corporate venture arm of Japanese tech giant Sony — Tokyo-based AI company PKSHA Technology, and San Francisco-based VC Social Starts.
“We’ve had multiple offers from different funds but we ultimately decided to go with SPARX because they have a very strategically aligned mandate. They’re backed by Toyota, one of the largest manufacturing companies in the world [and] vertical farming is the intersection of agriculture and manufacturing,” Koga says.
Although it may seem odd for Toyota to be interested in agrifood tech, the carmaker is working on its Woven City project located at the base of Japan’s Mount Fuji. It’s a so-called “living laboratory” where researchers live and work full-time to imagine what future cities may look like through technological innovation.
Koga is no stranger to controlled environment ag (CEA). Six years ago, he was working as a CEA consultant in Japan, helping large corporations enter the space. While Koga views Japan as the birthplace of vertical farming, he moved to the US in 2015 – around the time that the method was becoming popular in the country.
Alongside the allure of being the first to crack indoor strawberry cultivation, Koga sees the fruit as a way to address what he calls the “unit economics problem” in indoor farming. He sees strawberries as providing a very strong revenue and profit model, as well as a crop that can further “democratize” vertical farming.
“In order to democratize it, I wanted to start with something that’s truly impactful — not products that people will buy because they are sustainable — [but] something that is superior compared to what is on the market, and that would completely change people’s experience,” Koga says.
He leveraged his personal network in Japan to collaborate with farmers and research institutions on the details of indoor strawberry cultivation – from seeding all the way to harvesting. It took “countless” iterations to get the formula right, he says.
“There’s probably 20 or 30 different things that you can tweak in a given cycle of the plant. So, let’s say there are five or six different stages of the plant life cycle – if you multiply all of those, there are millions of different combinations,” he explains.
“It’s a matter of tweaking those on a daily basis to figure out what the perfect mix is.”
However, this know-how isn’t what Koga considers to be Oishii’s “secret sauce.” Rather, that’s the bees that the startup’s using handle pollination.
While Koga won’t spill the ‘bees’ about how all this works in Oishii’s context, he claims to have found a way to replicate a natural environment within an indoor vertical farm that convinces the critters they’re outside.
“They live in harmony with our farmers and robots,” is all Koga will add.
The Tesla of vertical farming
With the initial R&D under its belt, Oishii is now turning its focus to consistency and quality of the product. Its current New Jersey facility spans a few tennis courts, Koga says; but its next one will be the size of an American football field. It currently sells direct-to-consumer through its website, and through traditional retail channels like supermarkets.
But its strawberries may be out of some consumers’ grocery budgets, retailing between $15 and $50 per pack depending on the size and the number of fruits. This price point puts Oishii’s berries in the luxury food category – for now, at least.
“If you think about how Tesla started with a Roadster or Nissan started with the LEAF, we like to think we are in the Roadster camp,” Koga says.
“Our current Omakase berry is our Roadster right now, but we already have developed multiple strawberry cultivars that we can produce much more cost-efficiently. Our Model S and Model 3 will be on the market soon,” he says, referring to the latter-day models now being sold by Elon Musk’s company.
Another US vertical farming startup, Plenty, is also trying to solve the strawberry equation. It recently added Driscoll’s to its list of backers and is collaborating with the major berry producer on indoor strawberry cultivation.
Koga welcomes competition in the space, particularly if it means branching beyond leafy greens.
“It’s generally a good thing that people are following in our footsteps and expanding out of the leafy green space. The more berries the better,” he says.
“Ten years ago, we only had Tesla, maybe a few other companies. But Tesla was the one who proved that it can be done, and now there are dozens and dozens of electric car manufacturers. [The electric car] become much more widely available.”