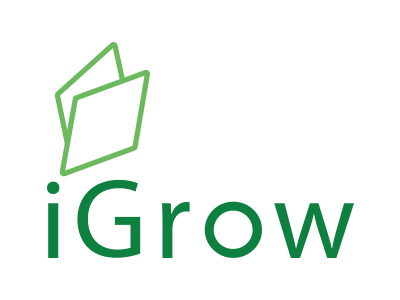
Welcome to iGrow News, Your Source for the World of Indoor Vertical Farming
Signify’s Expanded GrowWise Control System Helps Growers Boost Operational Efficiencies
Signify has expanded its GrowWise Control System, allowing for higher levels of automation and reducing manual labor and operational costs
Signify has expanded its GrowWise Control System, allowing for higher levels of automation and reducing manual labor and operational costs. This can be achieved by automating the lighting planning for their crop’s full growth cycle, up to one year ahead. The software tool brings dynamic lighting to greenhouses and vertical farms and fits seamlessly with modern climate computers and greenhouse management systems. This enables growers to automatically adjust light levels to maintain consistent levels on cloudy days, save energy on sunny days and simulate sunrise and sunset throughout the day or season.
Growers, like the Italian vertical farm, Planet Farms, and the Belgium greenhouse, De Glastuin, are already using the expanded system providing additional value within their growing facility.
“Using the GrowWise Control System is ideal for us,” says Luca Travaglini, co-founder of Planet Farms. “We want to automate as many aspects of our operations as possible to become more cost efficient. Now we can easily create custom light recipes and set them to run year-round to provide the right light recipe with the right light intensity at the right time throughout the crop’s growth cycle. By automating our full light strategy during the growth cycle, for the whole year, we can run our operations very efficiently and keep our manual labor costs low. That makes it easier for us to maintain consistent quality as we scale up our production.”
The demand for the GrowWise Control System is increasing for greenhouse applications as well. “The lighting can be used much more efficient, since it gives us the flexibility to reduce light levels at any moment we need to,” says Wouter de Bruyn, owner at De Glastuin. Lettuce grower De Glastuin is using the GrowWise Control System to control the Philips GreenPower LED toplighting compact grow lights via its climate control system. “The climate computer is equipped with a daylight sensor that sends actual light measurements to the GrowWise Control System so we can adapt our light levels automatically to ensure an even light level throughout the day and season. This results in a continuous high-quality crop. In case the electricity is the limiting factor, we are still able to use the LEDs evenly for the whole greenhouse in a lesser intensity.”
“Dynamic lighting in a greenhouse is the next step in improving the cost-efficiency and quality for the cultivation process,” says Udo van Slooten, Business leader Horticulture LED solutions at Signify. “It allows growers to effortlessly maintain a consistent level of light throughout the day to produce the best possible crops. The system compensates for cloudy weather and creates a more controlled growing environment for your crop.”
For more information about the GrowWise Control System and our Philips-banded horticulture lighting, visit our horticulture pages.
Or please contact:
Global Marcom Manager Horticulture at Signify
Daniela Damoiseaux
Tel: +31 6 31 65 29 69
E-mail: daniela.damoiseaux@signify.com
About Signify
Signify (Euronext: LIGHT) is the world leader in lighting for professionals and consumers and lighting for the Internet of Things. Our Philips products, Interact connected lighting systems and data-enabled services, deliver business value and transform life in homes, buildings and public spaces. With 2019 sales of EUR 6.2 billion, we have approximately 37,000 employees and are present in over 70 countries. We unlock the extraordinary potential of light for brighter lives and a better world. We achieved carbon neutrality in 2020, have been in the Dow Jones Sustainability World Index since our IPO for four consecutive years and were named Industry Leader in 2017, 2018 and 2019. News from Signify is located at the Newsroom, Twitter, LinkedIn and Instagram. Information for investors can be found on the Investor Relations page.
The One Thing You’re Probably Overlooking In Your Greenhouse
We often overlook the value of light in southern parts of the continent.
The cost of natural sunlight is an important thing for producers to understand because there is an economic value that they should be placing on sunlight. It’s one of the main inputs to production!
If you ask a good greenhouse operator, “What is your cost of natural gas? Electricity? Building cost per square foot? Operational cost per square foot?”, he’ll give you detailed answers.
Ask him, “What is the value of the light you receive?” and you’ll get a different response.
“…Uh, what?” he might respond.
You clarify. “The light, the sunlight. What is the value of the sunlight?
“I don’t know.” He will be taken off guard because he’s never thought about it before. Why?
Because people take light for granted. After all, sunlight is free. Why place a value on it?
But light is a “free” resource!
The cost of natural sunlight is an important thing for producers to understand because there is an economic value that they should be placing on sunlight. It’s one of the main inputs to production! If they’re placing an economic value on supplemental lighting, then they should be placing an economic value on natural light.
Why do they make that mistake? Because it’s free. Most people don’t put a value on free things.
And if a person places no value on a thing, they’re not going to use it efficiently. When something is free you don’t think about trying to use it in the most economical sense. When something is free you just use it.
Why would you try to conserve something that’s free? Why would you try to maximize the value of something that’s free? In your mind, it has no value.
This is true with sunlight. Because it’s (supposedly) a free resource, people don’t place an economic value on it and then they don’t build their model to maximize that value. The problem with this is that light does have a cost that can act as a limiting factor on your operation. This inefficiency poses a significant problem.
For instance, say you want to grow in Alaska. You want to grow year round but in the middle of the winter you might only have an hour of daylight – all of a sudden the economic value of that light becomes alarmingly apparent. Because you actually have to pay to replace it in the wintertime. So if you’re growing in Alaska in the wintertime, you’re freaking out about how you get the maximum value out of that light. You’re may choose to use red and blue LEDs instead of white because you can get more efficiency from them – even if it’s at a higher initial cost. You’re going to do everything you can to maximize the value of that resource.
We often overlook the value of light in southern parts of the continent.
And that’s why, even though light is a resource like everything else, no one actually figures it into any of their calculations, including the cost of goods sold. This mistake often limits growers to much lower production, or missing out on key observations that inform their model. (Among other things.)
In reality, the value of light is high
Note that the value and the cost of light are very comparable here. The value of something can be defined by it’s cost. Keep that in mind.
If you did think about light use efficiency, you would probably find yourself at the same destination that we did: volumetric farming, and much higher production because of it.
How to Place a Value on Light
If you don’t have light, then the easiest way to calculate it is by calculating the cost of replacing that light. What is the cost of replacing it with LEDs or HID or whatever supplemental lighting you choose?
If you do have light, then you’re probably growing in a greenhouse. In that case, you can find the cost of light by comparing the cost of growing in a greenhouse (which is how you are acquiring that light) with the cost of growing in a facility without that sunlight. (So the value of the sunlight is essentially the difference in operational cost between a warehouse of the same size and a greenhouse.)
These operating costs are going to include things like replacing a covering, heating (heating a greenhouse is always a lot more expensive), and maybe things like building permits.
Those costs can add up, and you’ll find that light is a costly resource even if you don’t think about it much. When you understand the costs of light, you will begin to use it more efficiently. You’ll start thinking about maximizing light use the same way that you maximize water and electrical and natural gas and other resources.
Initially this will result in lower overall costs, but we think you’ll find that your efforts toward efficiency will lead to even more benefits.
Once you do understand the value of your light, how do you get more out of it?
To increase light use efficiency, you first have to identify the main areas of waste and eliminate them. To do that, you start by identifying what’s happening with most of the light that enters your greenhouse: absorption and reflection.
ZipGrow Towers were designed to reflect light through the mass of towers to reduce shadowing and light waste.
Absorption is happening either when the light hits photosynthesizing plants or when it hits another absorptive surface and is either used by plants or turns to heat. Reflection happens when light hits a surface and bounces back. This is what you want, because if it’s not being absorbed by plants, then we reflect it to be absorbed by plants. (The less light energy that’s converted to heat, the more is conserved for use by your plants.)
The most obvious way to promote reflectance is to use reflective surfaces wherever possible. This doesn’t necessarily mean using silver or mirror finish, but it does mean white finishes to reflect that light. It also means that we think about growing plants on multiple planes, and arranging the production apparatus to conserve light within the greenhouse through reflection as opposed to reflecting it out of the greenhouse.
If you’re growing on a horizontal plane, know that if that light doesn’t hit a plant, oftentimes light will just be reflected back up and out of your greenhouse. When we switch the plane around so that the photons are conserved to the bottom of the mass, our absorption rates are higher, we have more plants absorbing energy rather than energy just being reflected up and out of the greenhouse. That’s the idea behind volumetric farming with ZipGrow™ Towers.
Source and Photo Courtesy of Agritech Tomorrow
IPO Planned To Improve Revenues Indoors
Light Science Technologies has gained the funding from Intuitive Investments Group plc (IIG), ahead of going public on the London Stock Exchange in the next six months.
8-01-2021| Business Live
“We believe that there is no better time to be involved in both agritech and medtech." A company which makes technology to improve indoor crop yields has received a £1 million investment ahead of a planned IPO.
Light Science Technologies has gained the funding from Intuitive Investments Group plc (IIG), ahead of going public on the London Stock Exchange in the next six months.
The business, based on the Hilton Business Park, Derby, provides lighting and plant growing and monitoring technology for agriculture in partnership with university research teams.
Its agricultural tech can be used in three main indoor settings – vertical farming (where crops such as tomatoes are grown in vertically stacked layers), greenhouses and medicinal plants.
Its patent-pending, sustainable light unit combines interchangeable LEDs, power and technology to help reduce costs and generate maximum yields over 25 years.
Its real-time monitoring and control technology can also be used to link technicians, farmers, and facility managers with their crops to provide instant production data.
Management said that with better light quality and energy savings, its light, science and technology products increase cycles.
It also supplies technology to clients in the electronics, audio, automotive, AI technology and pest control sectors.
The move to become a publicly listed company follows significant investment in its team and operations over the past few years which, the business said, has “brought to market a fully updateable, bespoke and intelligent lighting solution that provides optimal yield”.
The company is also due to launch its own in-house growth and laboratory service in the spring, focusing on plant growth and performance to help farmers with their crops.
Chief executive Simon Deacon said: “We believe that there is no better time to be involved in both agritech and medtech as two rapidly expanding sectors which are going to be responsible for spearheading some of the most significant global developments over the coming decade and beyond.
“IIG’s investment is not just a reflection of its commitment to LSTH as a fast-growing business backed by almost 30 years’ expertise in light technology but also of its awareness of the importance in achieving a better, more sustainable approach to agricultural production as well as pioneering potential life-saving solutions in digital health innovation.”
Light Science Technologies is IIG’s first investment following its own successful IPO and admission to AIM in December, as it seeks to attract investors with its life sciences portfolio.
IIG chairman David Evans said: “LSTH has the key ingredients for success; it has an excellent management team, a deep knowledge of the light spectrum and the application of that knowledge to areas where substantial growth can be obtained.
“I am personally excited about the potential diagnostic applications in the digital health sector, such as non-invasive haemoglobin measurement, as well as the developments in vertical farming technology that will underpin the long-term growth of LSTH.”
The investment follows recent funding for Light Science Technologies from Innovate UK which will see it work over the next six months with Nottingham Trent University to develop a growing sensor and transmission node for vertical farms.
Photo: Light Science Technologies designs lighting, science and plant monitoring technology.
Source and Photo Courtesy of BusinessLive
Combining Hydroponic And Aeroponic In Vertical Farming
Growers are finding new ways to drive the efficiency up and the cost down, and one of these solutions is vertical farming.
Generally speaking, horticulture operations can be quite expensive to operate; yet, growers can rely on hundreds of years of knowledge to improve the efficiency, so that those costs go down. At the same time, indoor farming cannot rely on such knowledge, and it is not uncommon to see cultivation facilities with huge bills at the end of the month. As the industry matures, growers are finding new ways to drive the efficiency up and the cost down, and one of these solutions is vertical farming.
LED technology
Nowadays, LED technology has made a huge leap forward, and Alvis Ma, the CEO of GrowSpec claims they are the industry standard. “Growers generally make the switch from HPS to LED for three reasons: increased yield, improved cannabinoid, and terpene content, and energy efficiency,” he explains. Thus, LEDs allow for vertical cultivation, which has a host of benefits, especially when it comes to space optimization.
“The VetriAero Planter system uses a mobile planting rack that reduces the ‘required’ indoor grow space area and extends the plant cultivation space by multiple tiers, maximizing growth space, increasing the yield and thus the profit,” Alvis Ma points out. “And if a grower wants to use one rack only initially, other tiers can be added later on: the helves can be connected to one another so that growers can modify the VetriAero Planter system length according to the size of the room.”
A very peculiar feature of this system is the integration of both aeroponic and hydroponic methods. “Instead of growing in soil, the roots are suspended in mid-air and surrounded by oxygen,” he adds. “The plant roots get misted directly with a nutrient-dense solution that gets sprayed to the roots every 3-5 minutes. At the same time, the remaining liquid at the bottom of our container ensures that, in the event of an emergency, there is still enough nutrient-dense liquid to sustain your plants for up to 48 hours.”
“Commercial indoor cultivation operations can be very expensive,” says Alvis Ma with GrowSpec. “And if you look at the cost of the real estate, added on top of substantial
power bills and staffing requirements, it becomes critical to find a way to increase profit and reduce overhead costs.” Exactly to respond to such a demand, GrowSpec has developed the VertiAero Planter system, a new vertical growing system. “One of the primary reasons why vertical farming is so attractive for growers is the improved performance of current LEDs,” Alvis Ma continues. “This is something that could not happen back in the day, as HPS has been the go-to lights for decades, and they produce a lot of heat; generally speaking, the plants have to be placed a couple of feet away from light to stay safe and healthy.”
Controlling the environment
Indoor growing, especially vertical growing, requires a particularly efficient airflow system to guarantee healthy growth for the plants. This has direct consequences on the growing environment. “Maintaining optimum temperature, humidity, and air circulation is challenging for all cannabis operations,” Alvis Ma remarks. “But in vertical growing, there is even more variability in macro and micro environmental conditions, because more plants make control more difficult.
That’s why the GrowSpec VertiAero’s multi-layer airflow solution improves the airflow rate in the micro-environment of the plant canopy by maintaining consistent plant canopy temperature and humidity, reducing the cultivation potential of harmful pathogens, and increasing the rate of photosynthesis by evenly distributing CO2 over the plant canopy. The system utilizes various sensors to detect crucial data points such as moisture change, for instance.”
Although such a system might sound complicated to use, user-friendliness and easiness of use are very well implemented. “The VertiAero Planter system integrates intelligent control and touchscreen control system so that your business can save up exponentially on overhead costs,” Alvis Ma points out. “At our core, we operate according to the highest standard, combining this with technology that respects our planet.”
For more information:
GrowSpec
Yuxin Industry Zone, Shishan Town, Nanhai, Foshan, Guangdong, China
+86-15914220731
Signify And RIAT Pioneer Growing Tomatoes And Cucumbers In A Vertical Farm Without Daylight
RIAT’s indoor farm is located in the center of the Ivanovo region, enabling the company to distribute its tomatoes, cucumbers, and 19 types of green crops to its own RIAT stores within an hour after harvesting. RIAT has a special technique to fold the long stems, allowing it to grow the 3.5m high plants indoors
Eindhoven, the Netherlands – Signify (Euronext: LIGHT), the world leader in lighting, and RIAT, an innovative farming enterprise located in Russia, have together pioneered the growing of tomatoes and cucumbers in a vertical farm without daylight. During the research phase in 2019, RIAT achieved a yield comparable to advanced traditional greenhouses using Philips GreenPower LED grow lights.
“We already had facilities of sufficient height at our disposal, therefore there was no need to invest in building a glass construction. But as the building had no windows, we needed a high-quality lighting system to fulfill the intensive lighting requirements of tomatoes and cucumbers,” says Vladimir Bukharev, director at RIAT. “In 2019, Signify provided it’s Philips GreenPower LED grow lighting, helping us to achieve a yield performance comparable to traditional greenhouse operations.”
RIAT’s indoor farm is located in the center of the Ivanovo region, enabling the company to distribute its tomatoes, cucumbers, and 19 types of green crops to its own RIAT stores within an hour after harvesting. RIAT has a special technique to fold the long stems, allowing it to grow the 3.5m high plants indoors.
“With a harvest of 2.7 to 3.2 kg of cucumbers per m2 every week, and 1.7 kg per m2 of tomatoes, we started making a profit as of the second year of operation,” Bukharev added. “In addition to that, the quality of the product is very high, there’s hardly any waste and we sell 99% of what is being grown.”
“To mimic nature as much as possible, RIAT has chosen a combination of different kinds of Philips GreenPower LED toplighting and interlighting, bringing light both from the top and right in the canopy where the light is needed the most for photosynthesis. While using different kinds of lights, the light recipe can be adjusted based on the crop that is grown,” said Sergey Khokhrin, business Development Manager CEE/Russia & CIS at Signify.
Signify, in collaboration with several research partners, discovered that the red spectrum in light stimulates growth of plant cells and tissues, while the blue spectrum influences the processes of cytodifferentiation (racemes initiation, bines and root formation, flowering). The combination of red and blue with the addition of white and other colors in Philips LED grow lights creates lighting conditions that are as close to natural daylight as possible. Additionally, RIAT is using bumblebees for pollination, as in traditional greenhouses. The bees don’t experience difficulties due to the absence of natural light.
When choosing a lighting supplier, RIAT tested LED modules from different manufacturers from around the globe. “By using Philips LED lighting modules, we managed to achieve maximum stability and a light output of 18 g/mol. This is why we chose Signify. The area equipped with LED lamps is currently 3,800 m2. Soon, we are going to launch a new area of 700 m2 to grow lettuce which will also be equipped with Philips LED lighting,” Bukharev added.
--- END ---
For further information, please contact:
Global Marcom Manager Horticulture at Signify
Daniela Damoiseaux
Tel: +31 6 31 65 29 69
E-mail: daniela.damoiseaux@signify.com
Signify Corporate Communications and Government Affairs in Russia and CIS
Natalia Neverskaya
Tel.: +7 (495) 937-93-30; fax +7 (495) 937-93-59
E-mail: natalia.neverskaya@signify.com
About Signify
Signify (Euronext: LIGHT) is the world leader in lighting for professionals and consumers and lighting for the Internet of Things. Our Philips products, Interact connected lighting systems and data-enabled services, deliver business value, and transform life in homes, buildings, and public spaces. With 2019 sales of EUR 6.2 billion, we have approximately 38,000 employees and are present in over 70 countries. We unlock the extraordinary potential of light for brighter lives and a better world. We have been named Industry Leader in the Dow Jones Sustainability Index for three years in a row. News from Signify is located at the Newsroom, Twitter, LinkedIn, and Instagram. Information for investors can be found on the Investor Relations page.
About RIAT
RIAT is a holding in the Ivanovo region, Russia, which owns the world's first indoor production of tomatoes and cucumbers, as well as 10 supermarkets in Ivanovo and 2 in the Ivanovo region (in the cities of Ples and Kineshma).
Japanese Autotech Giant Denso Invests in Certhon
Denso, the second-largest advanced automotive technology supplier in the world, has announced its investment in Certhon, to expand horticulture business in the global market
Denso, the second-largest advanced automotive technology supplier in the world, has announced its investment in Certhon, to expand horticulture business in the global market. Denso and Certhon will collaborate to develop and provide greenhouse solutions.
Through this capital alliance, and combined with Certhon’s horticulture business knowledge, Denso will develop next-generation greenhouse technologies, such as fully automated indoor farming, and sell greenhouse package solutions tailored to the diverse needs of countries across the world.
Denso’s Long-term Policy 2030 launched in 2017 has identified the non-automotive business as one of its four focus areas and has defined agriculture as a key pillar under the non-automotive field. Until now, Denso has contributed to the improvement of productivity in the agricultural field and the stabilization of cultivation environments through climate control technologies.
As part of that, AgriD, established in 2018 with Asai Nursery, has built one of the largest greenhouses in Japan to realize greenhouse operations 24/7 through cooperation between farmers and robots to reduce the amount of work. Moreover, Denso has started the demonstration of the automatic harvesting robot “Faro” developed by Denso.
In the future, Denso will contribute to sustainable agricultural production through industrialization, and will provide new value to the agri-food sector by establishing an integrated food value chain business.
For more information:
Certhon
www.certhon.com
Denso
www.denso.com
Publication date: Wed 1 Apr 2020
Leo Marcelis: LED Light Recipe Can Enhance Rooting of Stem Cuttings in Medical Cannabis
Uniformity of the plants and predictability of the crop are key factors for the successful production of medicinal cannabis
LED light recipe can enhance rooting of stem cuttings
Uniformity of the plants and predictability of the crop are key factors for the successful production of medicinal cannabis. Growing medicinal cannabis, therefore, requires a high level of control over the production process, which is possible in greenhouses but even more so in indoor farms. LED lighting may be used to control the different developmental stages of the cannabis crop. Wageningen University and Signify have now made the next steps in a research program that aims to control the different developmental and growth processes, such as rooting, canopy establishment, flower induction and formation of secondary metabolites in the inflorescences.
Light to control your crop growth
Often the variability of plants is already present at the start of the crop, which makes crop uniformity challenging. Therefore, certain measures can be taken to minimize the plant differences and grow a uniform crop. LED lighting can help enhance plant uniformity and quality when the right light recipe is applied. A LED light recipe is defined by the light spectrum, intensity, the photoperiod and the timing of that period.
Plant hormones are affected by LED light
Medicinal cannabis is commonly propagated by stem cuttings, which is usually preferred over propagation by seeds because it is a low-cost method and it delivers genetically uniform plants. Auxins and carbohydrates are plant hormones and play a key role in adventitious rooting in cannabis: a critical process in the propagation of stem cuttings. A powder containing synthetic auxins is often applied because it improves rooting and uniformity among plants. When no rooting powders with synthetic auxin can be used, the rooting is rather slow and very variable. Important to know is that auxins and carbohydrates are both affected by LED light. Preliminary results now indicate that the rooting of stem cuttings can be enhanced by using the right light recipe.
The perfect light recipe for rooting
Now, the rooting process of medicinal cannabis is being studied in detail. Cuttings from the tops of the stems are put in pots and placed in rooms with a controlled environment. In a series of experiments, a range of spectra and intensities are tested for their effects on the formation of adventitious roots of cuttings treated with and without auxins. Subsequently, the effects of light are assessed on the development of the cuttings as well as on the morphology of the formed canopy. Thereafter, we investigate the effects of the light regime on flower induction.
In June 2019, Signify and WUR expanded their ongoing research program to determine the effects of Philips LED lighting on compounds and plant characteristics of medicinal cannabis crops. In this unique research project, they develop specific light recipes for medicinal cannabis based on a fundamental understanding of the influence of light on crops to enhance the purity and composition of cannabinoids. In this series of articles, Leo Marcelis from Wageningen University explains what the effects of LED lighting are on improved yield, flowering, and other plant characteristics.
Leo Marcelis is a professor of Horticulture and Product Physiology at Wageningen University, The Netherlands. Leo has a vast experience in researching the physiology, growth and product formation of plants in order to improve sustainability and quality of crop production in greenhouses and vertical farms. Plant responses to LED lighting is a focal point of his research.
Valoya Announces Addition of A Former Conviron VP To Its Board of Directors
Its Board of Directors will now be strengthened with the addition of Mr. Bill Mukanik, former VP Client Services at Conviron, one of the world’s leading growth chamber manufacturers and also Valoya’s long term partner
Valoya, the Finnish LED grow lights manufacturer has been steadily growing since its founding 11 years ago. Its Board of Directors will now be strengthened with the addition of Mr. Bill Mukanik, former VP Client Services at Conviron, one of the world’s leading growth chamber manufacturers and also Valoya’s long term partner. Mr. Mukanik brings to Valoya’s Board of Directors team over 40 years of experience in the crop science market.
I look forward to working with Valoya to expand their presence and market share in North America. Having successfully integrated their LEDs for many years, I witnessed firsthand their ability to understand a client’s needs and then provide proven research-driven solutions. I am confident that this capability, along with their desire to provide exceptional value, will lead to even greater success. – Bill Mukanik
Mr. Mukanik’s longlasting experience in the crop science market will help Valoya solidify its position as the global leader of horticultural LED lighting solutions for this segment. As a highly respected and seasoned executive with a valuable understanding of the needs of the crop science customers, Mr. Mukanik will help Valoya serve this market even better. This addition to the Board of Directors comes at the stage of the company’s rapid development.
“I am very pleased and honored, that Bill joins our Board of Directors. He brings very valuable and relevant knowledge and vision to Valoya. He has an extensive global network and unsurpassed insight into the North American indoor growing and plant research markets. I have had the pleasure of working with him already many years in another capacity and now I am happy to continue working with him in his role as a Valoya board member” comments Lars Aikala, the CEO and Co-Founder of Valoya.
About Valoya
Valoya is a provider of high end, energy-efficient LED grow lights for use in crop science, vertical farming, and medicinal plants cultivation. Valoya LED grow lights have been developed using Valoya's proprietary LED technology and extensive plant photobiology research. Valoya's customer base includes numerous vertical farms, greenhouses and research institutions all over the world (including 8 out of 10 world’s largest agricultural companies).
Additional information:
Valoya Oy, Finland
Tel: +358 10 2350300
Email: sales@valoya.com
Web: www.valoya.com
Facebook: https://www.facebook.com/valoyafi/
Twitter: https://twitter.com/valoya
VIDEO: April Indoor Science Cafe Recording Is Now Available! Photons = Flavor The Case Study of Basil
This presentation 'Photons = Flavor, The case study of basil' was given by Dr. Roberto Lopez and Kellie Walters (Michigan State University) during our 18th cafe forum on April 14th, 2020
This presentation 'Photons = Flavor, The case study of basil' was given by Dr. Roberto Lopez and Kellie Walters (Michigan State University) during our 18th cafe forum on April 14th, 2020. Indoor Ag Science Cafe is organized by the OptimIA project team funded by USDA SCRI grant program.
Webinar: Developing A Light Spectrum – A Balancing Act
The webinar is free-of-charge and will be held on May 27th at 15.00 EET. It will be presented by Ms. Stefanie Linzer, Plant R&D Director and Mr. Harri Ekdahl, Product Manager at Valoya
In an ocean of LED companies with conflicting claims, which one can be trusted for their horticultural lighting expertise? How can a grower understand which spectrum his/her plants would mostly benefit from? In this free webinar, we will breakdown the spectrum development process so as to enable growers and researchers to better understand what kind of light is best for them.
Valoya, the research-driven LED manufacturer from Finland, has conducted over 600 plant trials in the past decade in search for the highest quality light for cultivation and research purposes. In this process, it has amassed over 100 patents and developed over 60 spectra of which only 5 were commercialized.
Choosing wavelengths such as blue, red, far-red, UV and manipulating ratios such as red:far-red and blue: green are some of the factors that go into account in the spectrum development process. In the plant trials conducted we observe parameters that are of importance to growers such as plant biomass and morphology, secondary metabolite accumulation, etc. Additionally, growers need lights that achieve their cultivation targets efficiently, so spectrum development always includes economic considerations so that the minimal amount of Watts gets the desired output.
The webinar is free-of-charge and will be held on May 27th at 15.00 EET. It will be presented by Ms. Stefanie Linzer, Plant R&D Director and Mr. Harri Ekdahl, Product Manager at Valoya.
To learn more about the webinar and register for it, please click here.
About Valoya
Valoya is a provider of high end, energy-efficient LED grow lights for use in crop science, vertical farming, and medicinal plants cultivation. Valoya LED grow lights have been developed using Valoya's proprietary LED technology and extensive plant photobiology research. Valoya's customer base includes numerous vertical farms, greenhouses and research institutions all over the world (including 8 out of 10 world’s largest agricultural companies).
Additional information:
Valoya Oy, Finland
Tel: +358 10 2350300
Email: sales@valoya.com
Web: www.valoya.com
Facebook: https://www.facebook.com/valoyafi/
Twitter: https://twitter.com/valoya
Signify Installs Poland’s First FULL LED Lighting In A Pink Tomato Greenhouse
Signify provides growers horticulture LEDs, which allow them to increase growth predictability, quality, and yield, and which allows growers to grow fruit and vegetables in their greenhouses all year round
April 8, 2020
Warsaw, Poland – Signify (formerly Philips Lighting), (Euronext: LIGHT), the world leader in lighting, has installed LED lamps in a Tomimaru Muchoo pink tomato greenhouse for the first time in Poland. This innovative full LED system was implemented on a 2ha plantation belonging to Łukasz Budyta Greenhouse Complex, which was fitted with Philips GreenPower LED toplighting modules and Philips GreenPower LED interlighting modules. Electrical installation design works on the project were carried out by Philips Horti LED Partner – company Lek/Habo.
Modern greenhouse lighting
Signify provides growers horticulture LEDs, which allow them to increase growth predictability, quality, and yield, and which allows growers to grow fruit and vegetables in their greenhouses all year round. As LEDs are more energy-efficient than high-pressure sodium (HPS) lamps, it also helps growers to reduce electricity consumption.
“When designing the greenhouse lighting, we wanted to minimize the installed grid power while maintaining levels of light that are appropriate for the plant’s need. LED lighting is the most energy-efficient, and at the same time – which is equally important to us – the most environmentally friendly solution,” said Łukasz Budyta, owner of Łukasz Budyta Greenhouse Complex.
Compared to 1000W HPS lights, Philips GreenPower LED lighting produces the same amount of light while consuming 50% less energy and producing little radiation heat. This allows growers to independently control the temperature and amount of light deployed, and thus more effectively control climate conditions in their greenhouse. The use of LED modules can shorten production cycles, increase yields and allow better use of growing space. Modern lighting ensures economical and at the same time eco-friendly greenhouse cultivation.
“Philips GreenPower LED lighting is an innovative approach to year-round cultivation of vegetables and fruit in greenhouses. We are constantly following the trends and trying to meet the requirements of our business partners, and our technology for grow light with LEDs in greenhouses is perfectly in line with the eco-friendly approach of modern farms,” said Maciej Król, Horti LED C&EE Business Development Expert, Signify.
Pink tomatoes all year round
Łukasz Budyta Greenhouse Complex focuses on growing pink tomatoes. As the first farm in Poland, it uses LED lighting in a greenhouse in Piotrowice near Karczew.
The greenhouse is illuminated with a full LED system, providing a light intensity of 140 µmol/s/m2 from toplighting modules and 60 µmol/s/m2 from interlighting modules, which allows intensive and energy-efficient winter cultivation.
The setup of their lighting installation is the result of successful trials carried out in 2015-2017 at the micro-greenhouses of the Warsaw University of Life Sciences (SGGW). In their own full-size production facility located in Piotrowice, Łukasz Budyta Greenhouse Complex wanted to repeat the results achieved in the test installation.
Łukasz Budyta Greenhouse Complex is located near Warsaw, providing easy, direct access to the vast market of the Polish capital and the rest of the country. The first pink tomatoes grown using Signify’s Philips LED fixtures are now available in stores in Warsaw
--- END ---
For further information, please contact:
Global Marcom Manager Horticulture at Signify
Daniela Damoiseaux
Tel: +31 6 31 65 29 69
E-mail: daniela.damoiseaux@signify.com
Signify Press Officer in Poland
Dorota Sławińska
Tel: +48 605 342 517
E-mail: dorota.slawinska@signify.com
About Signify
Signify (Euronext: LIGHT) is the world leader in lighting for professionals and consumers and lighting for the Internet of Things. Our Philips products, Interact connected lighting systems and data-enabled services, deliver business value and transform life in homes, buildings and public spaces. With 2019 sales of EUR 6.2 billion, we have approximately 32,000 employees and are present in over 70 countries. We unlock the extraordinary potential of light for brighter lives and a better world. We have been named Industry Leader in the Dow Jones Sustainability Index for three years in a row. News from Signify is located at the Newsroom, Twitter, LinkedIn, and Instagram. Information for investors can be found on the Investor Relations page.
You Are Invited To Join A GLASE Webinar: Lighting Approaches To Maximize Profits
Supplemental lighting is often necessary for year-round greenhouse production of ornamentals and vegetables
Date: April 16, 2020
Time: 2 p.m. - 3 p.m. EST
Presented by: Marc van Iersel
Register here
Supplemental lighting is often necessary for year-round greenhouse production of ornamentals and vegetables. However, the cost of providing supplemental light is high. It is therefore important that supplemental light is provided in a way that provides the greatest benefits for the crop, at the lowest possible price. To do so, it is important to understand the cost of providing supplemental light as well as how plants use that light. Accurate weather predictions can help minimize the risk of providing more excess light than is required by a specific crop. Learn how to account for these factors to help grow high-quality, profitable crops.
Special thanks to our Industry partners
Join today
If you have any questions or would like to know more about GLASE, please contact its executive director Erico Mattos at em796@cornell.edu
The Value of Third-Party Verification For Horticultural Lighting
Horticultural lighting comprises the largest percentage of power demand in controlled environment agriculture (CEA) facilities for fruit and vegetable production
By urbanagnews
February 24, 2020
By Leora Radetsky
The US vertical farming market is projected to reach $3 billion by 2024, exhibiting a compound annual growth rate of over 24 percent, according to a February 2019 report. Another report, by the US Department of Energy’s Office of Energy Efficiency and Renewable Energy, put the annual electricity consumption of US horticultural lighting installations at 5.9 terawatt hours – equal to the annual usage of about 550,000 US households, and projected that to increase 15 to 25 percent annually.
Horticultural lighting comprises the largest percentage of power demand in controlled environment agriculture (CEA) facilities for fruit and vegetable production. A 2019 study by Toronto’s Independent Electricity System Operator (IESO) found, for example, that “a lit vegetable greenhouse consumes 10 times as much electricity as an unlit vegetable greenhouse, with essentially all the additional electricity used for lighting”.
Clearly, getting a handle on facility efficiency, including horticultural lighting, is a must-have if individual states and the US as a whole hope to rein in carbon emissions and meet energy reduction goals. This increase in electricity usage comes as states, provinces, and cities across North America are confronting the impacts of climate change and working to reduce – not grow – greenhouse gas (GHG) emissions from the electrical generation sector. In the US, 23 states and the District of Columbia have adopted specific GHG reduction targets. Massachusetts law, for example, requires the state to reduce GHG emissions by 80 percent below 1990 levels by 2050, and California is under a statutory mandate to cut emissions by 40 percent below 1990 levels by 2030.
The good news is there are reliable, third-party lighting and safety standards to help indoor farmers make the leap from old-school lighting to state-of-the-art light-emitting diodes (LEDs) that use a fraction of the electricity and are increasingly effective for growing a variety of crops. Perhaps even better for farmers is the availability of a new industry-wide benchmark for horticultural lighting and a growing list of qualified products that are third-party certified to meet it.
More about the benchmark later – first, it’s useful to walk through the various lighting and safety standards specific to horticultural lighting.
Most lighting fixtures in the North American market go through rigorous inspection by certified labs. The first part of the check is for safety. An official UL safety standard tailored for the unique challenges of the greenhouse environment was recently released (UL 8800, the Standard for Horticultural Lighting Equipment and Systems). This standard and similar safety certifications at other major labs address wiring, environmental conditions, ingress protection, and worker safety related to prolonged photobiological exposure to the eyes and skin. Growers should always ask a lighting fixture manufacturer about safety certification specifically for horticultural environments.
Next on the standards checklist for horticultural lighting fixtures is performance testing. This often happens at the same labs that do safety testing but is designed to verify efficacy, output, spectrum, and other important performance variables. Commercial labs are certified for specific standards so that a test on a fixture is repeatable at any other lab certified to the same standard. This performance testing results in a report summarizing items such as photosynthetic photon flux (PPF), input power (watts), photosynthetic flux efficacy (PPE, measured in μmol/J or micromoles of photosynthetic photons per joule of electrical input power), and spectral content (flux per nanometer (nm) between 400 and 700 nm).
Then, there are flux maintenance standards for LEDs (such as IES LM-80 and IES TM-21) that help make sure the photosynthetic light output of LED products degrades at an acceptable rate to make a grower’s investment worthwhile. The testing and calculation methods that go into these standards were painstakingly developed through a consensus of knowledgeable lighting stakeholders. A key difference between general lighting and plant lighting, however, is how flux maintenance is measured and benchmarked – the bar is significantly higher for plants compared to people since their metabolism and growth are dependent on the light spectrum and amount.
Against this backdrop of standards and testing, lighting and related technologies are quickly evolving. For indoor growers, questions abound – from how long a fixture will last and whether a manufacturer’s claims about efficacy are accurate to the effectiveness of various wavelengths for growing particular crops. The tests described above produce a lot of important information, but it takes an informed reader to analyze and use it to select appropriate horticultural lighting. This is where our organization, the DesignLights Consortium (DLC), comes in. Through our Horticultural Lighting Program, the DLC strives to make the process of vetting lighting products easier, freeing up growers to focus on their core business.
Horticultural lighting specification is a relatively recent addition to the DLC’s work. The organization was founded in the early days of LED lighting to help electric utilities compare different lighting factors and reports to inform their energy efficiency rebate/incentive programs for commercial and industrial electric customers. The DLC began serving as a central clearinghouse for setting energy efficiency and other product performance minimum standards, and for evaluating products against those standards. Then and now, lighting products that pass review qualify for an online qualified products list (QPL) that utilities use to quickly and accurately incentivize high-performing products.
Back to the benchmark mentioned earlier, the goal of the DLC’s new minimum performance standards for horticultural light fixtures is to accelerate the adoption of new energy-saving LED fixtures in controlled agriculture environments. To be on the new DLC Horticultural QPL, an LED fixture must have a PPE of 1.9 micro mol/J, which means it will be at least 10 percent more efficacious than the best non-LED alternative – a 1,000-watt double-ended high-pressure sodium (HPS) fixture. It also must have a Q90 of 36,000 hours (the number of hours before the photon flux output depreciates to 90 percent), and its driver and fan (if included) must have a rated life of at least 50,000 hours.
Importantly, every product is listed online in a searchable, filterable database to help growers and controlled environment agriculture facility designers quickly narrow their options. For example, in a retrofit, a grower might know what PPF is needed from each fixture but might also need to stay within a power budget to avoid rewiring circuits. The DLC’s Horticultural QPL can be filtered to quickly find and compare conforming products.
For utilities and horticultural lighting users alike, trusted, third-party verification holds the same value as it does in other industries. It plays a critical role in ensuring the integrity of a growing array of products – providing assurance that an independent party has done the legwork and is vouching that a fixture can do the job and save electricity.
As the IESO study referenced above noted, horticultural lighting standards developed by the DLC, as well as the American Society of Agricultural and Biological Engineers, “should help to build trust between growers and lighting manufacturers and suppliers regarding performance information as LED technology continues to mature”.
Just over a year since it was unveiled, the DLC’s Horticultural QPL contains 58 products from 18 manufacturers, and additional products are reviewed and added regularly. We’re confident this growing roster of third-party certified products is expanding the options for farmers and providing a greater level of assurance about product performance, leading to quicker and wider adoption of advanced, energy-efficient horticultural lighting technology.
Leora Radetsky (lradetsky@designlights.org) is a Senior Lighting Scientist at the DesignLights Consortium.
2020 GLASE Summit - CANCELLED
GLASE will host its annual Summit in Leamington, Ont. Canada. Participants will discuss the latest GLASE research innovations, the CEA market trends and connect with Canadian greenhouse growers
2020 GLASE Summit
Leamington, Ont. Canada
Best Western Plus Conference Center
March 26 - 27, 2020
GLASE will host its annual Summit in Leamington, Ont. Canada. Participants will discuss the latest GLASE research innovations, the CEA market trends and connect with Canadian greenhouse growers.
Over 60% of Ontario's greenhouses can be found in Leamington/Kingsville area. With the largest concentration of greenhouses in North America (nearly 2,000 acres under cover) Leamington host some of the largest CEA facilities in Canada and US.
To learn more about it please contact GLASE director Erico Mattos at em796@cornell.edu
Stop Basil Downy Mildew With These Simple LED Strategies
Every basil grower’s worst nightmare is Basil Downy Mildew. You walk down the aisles, peer across the canopy, and then “Oh No!”. You see leaf yellowing and fuzzy purple growth. The once sweet smell of herbaceous goodness no longer smells so sweet knowing you have hours not days to react
"Every very basil grower’s worst nightmare is Basil Downy Mildew. You walk down the aisles, peer across the canopy, and then “Oh No!”. You see leaf yellowing and fuzzy purple growth. The once sweet smell of herbaceous goodness no longer smells so sweet knowing you have hours not days to react.
Image source: Cornell University
This awful gut feeling can be felt by any plant grower, and most know it too well. In cucumbers, it’s all about powdery mildew. In cannabis, white powdery mildew.
Traditional techniques call for using fungicides and adjusting your environment. These are still important methods given the severity of the situation, but there’s now a new promise of prevention strategies using light.
First, what is Basil Downy Mildew?
Basil that’s become infected with downy mildew will begin to turn yellow and may be mistaken for a problem with nutrition. This yellowing may be followed by dark brown or purple fuzz as sporulation continues to develop. Peronospora belbahrii is the Latin name for basil downy mildew.
The promise of using light to stop downy mildew in basil
Light has many effects on plants and other organisms’ physiology. In the case of downy mildew, disrupting the dark period with red light while managing temperature and humidity has been shown to prevent the production of spores in sweet basil.
Image source: Cohen Y, Vaknin M, Ben-Naim Y, Rubin AE (2013) Light Suppresses Sporulation and Epidemics of Peronospora belbahrii. PLoS ONE 8(11): e81282. https://doi.org/10.1371/journal.pone.0081282
Researchers at Bar-IIan University in Israel found that low-intensity red light inhibited sporulation of Peronospora belbahrii on sweet basil when applied during the dark period while maintaining moderate temperatures and low humidity.
Infected basil leaves were exposed to 5 or 10 micromoles of blue, green, red, or incandescent light. They were incubated at 20°C in moist conditions for 20 hours in a growth chamber.
Results showed that red light (at a peak of 625 nanometers) inhibited 99.7% sporulation regardless of the leaf surface exposed to light! Light strongly inhibited sporulation on leaves incubated at 15-27°C, but not on leaves incubated at 10°C.
What to do about powdery mildew in cucumbers
In the case of powdery mildew cucumber diseases, blue light has been shown to prevent the spread of disease by preventing the release of fungal spores.
Researchers at the Department of Chemical Biological Sciences in the Women’s University of Tokyo found that blue light can prevent the release of powdery mildew spores from developed fungal bodies and prevent the spread of disease melons.
Melon plants, inoculated with Podosphaera xanthii were grown in growth chambers under purple, blue, green, orange, red and broad-spectrum light, as well as in complete darkness and in a greenhouse under solar light. Light treatments were used on the powdery mildew for 14 days under continuous illumination of 59.5 micromoles of light.
Results showed that, while conidium fungal spores were still produced under all light treatments, spores were not released from conidiospores (or reproductive fungal spores) under blue light in the growth chamber. This research proves promising for preventing the spread of mildew in cucumbers, melons, and other cucurbits.
What this means for the future of Basil Downy and Powdery Mildew
These researchers have shown that light quality has the potential to stop the spread of fungal pathogens. It’s possible that in many cases, light spectrum must be readily controlled to inhibit the spread of mildew and other disease types.
In the case of fungal pathogens, light has been shown to suppress disease by disrupting the pathogen’s reproductive cycle and by exploiting natural adaptations in its circadian rhythm.
Depending on the fungi and plant species in question, this disruption can be a response to specific light wavelengths, the duration of the light period, duration of the dark period, total light intensity or a combination of these factors.
Light can also suppress disease by increasing the plant’s secondary metabolite production, which enhances the plant’s ability to defend against attack.
Using light to suppress disease in your operation
Research on light’s ability to suppress plant disease is in its early stages, but there are some important findings that can help guide growers when trialing light treatments for disease suppression.
Light treatments are plant and pathogen-specific, so it’s important to seek out information for light treatments specific to your particular crop and pathogen.
Depending on whether a disease is suppressed by enhancing the plant’s defense system or disrupting the pathogen’s physiological processes, light treatments may need to be applied throughout the plant’s entire growth cycle, limited to a short exposure or applied during a specific growth period in order to be effective.
Like all crop production processes, light treatment is only one part of the integrated strategy. Environmental factors like temperature and humidity, as well as production processes like irrigation and crop management, should be considered as part of an integrated pest management plan.
For more information:
LumiGrow
800-514-0487
info@lumigrow.com
www.lumigrow.com
Publication date: Mon 9 Mar 2020
Signify Expands Collaboration With Planet Farms
Thanks to the latest agreement, Europe’s largest vertical farm will boost the quality and yield of the crops using the Philips GreenPower LED production module managed by the Philips GrowWise Control System
Signify is expanding its collaboration with Planet Farms, a European operator of vertical farms based in Italy. Thanks to the latest agreement, Europe’s largest vertical farm will boost the quality and yield of the crops using the Philips GreenPower LED production module managed by the Philips GrowWise Control System.
Signify has also reached an agreement to provide horticultural LED grow lights to an additional five vertical farms that Planet Farms is planning to build in different European countries in the coming years, including Switzerland and the UK.
The Philips Greenpower LED production module, Signify’s latest horticultural LED innovation for vertical farming, helps growers optimize multilayer crop cultivation. By managing the lights with Philips GrowWise Control System, growers can easily create and run custom light recipes on dimmable and color-controllable modules to meet the needs of different crops and growth phases. This gives growers the ability and flexibility to create and control their own time-based light recipes and improve crop results and operational efficiency in closed, climate-controlled cultivation facilities.
“We started working with Signify five years ago because of the company’s knowledge and expertise of horticultural LEDs and light recipes,” said Luca Travaglini, co-founder and co-CEO of Planet Farms. “Thanks to the collaboration we’re able to grow high-quality crops all year round and that’s why we’re now expanding our collaboration. The GrowWise Contol System helps us easily adjust light recipes and continuously enhance the taste of our crops, which is crucial for us.”
This year, Planet Farms will finish construction of Europe’s largest vertical farm in Cavenago, just north of Milan. The vertical farm will cover more than 9,000 m2, which is the equivalent size of 45 tennis courts. Planet Farms operates an innovative integrated growth process that starts with the seeds and ends with packaged products. The production process is entirely automated meaning that consumers are the first to touch the crops.
“We’re proud to provide Europe’s largest vertical farm with our innovative lighting products and knowledge and expertise of light recipes. This next step in our collaboration shows that we can really help vertical farmers around the globe to improve the quality, yield and taste of their produce,” said Udo van Slooten, Business Leader Horticulture lighting at Signify. “The plans to build another five farms across Europe shows that vertical farming is rapidly growing and evolving. It’s a thrilling time to be involved in vertical farming, and we’re excited to help shape its future.”
Signify and Planet Farms formalized their collaboration in 2018 when Planet Farms announced the construction of Italy’s first vertical farm research lab in Milan. This lab opened in 2019. Signify supported Planet Farms with its lighting expertise for vertical farming and by providing its Philips GreenPower LED production module Dynamic grow lights.
For more information:
Signify: www.philips.com/horti
The Influence of Temperature And Daily Light Integral on Culinary Herb Production
Greenhouse average daily temperature (ADT) and daily light integral (DLI) can be adjusted to improve crop timing, maximize biomass production, and increase crop quality
Date: March 12, 2020
Time: 2 p.m. - 3 p.m. EST
Presented by: Roberto Lopez and Kellie Walters
Register here
Greenhouse average daily temperature (ADT) and daily light integral (DLI) can be adjusted to improve crop timing, maximize biomass production, and increase crop quality. In this webinar, Michigan State University researchers will discuss how the growth, development, and color of culinary herbs is influenced by ADT and DLI. They will share research on crops including sweet basil, purple basil, sage, and spearmint, giving research-backed tips on how to use these environmental parameters to improve crop yield and quality.
Join today
If you have any questions or would like to know more about GLASE, please contact its executive director Erico Mattos at em796@cornell.edu
Special thanks to our Industry partners
What Are The Challenges To Running A Successful Indoor Farm?
The amount of investments made in the vertical farming and controlled environment agriculture industries has been well documented. Those companies that successfully raise capital are seen as industry heroes and it’s quickly assumed that they must have all the answers. But, the big question is…do they?
October 3, 2019
(I had the opportunity to host the Great Lakes Ag-Tech Summit in Cleveland on Sept. 23, 2019.)
The amount of investments made in the vertical farming and controlled environment agriculture industries has been well documented. Those companies that successfully raise capital are seen as industry heroes and it’s quickly assumed that they must have all the answers. But, the big question is…do they?
In order to answer that question, it is important to be specific about the questions we are asking, the assumptions we are making and to understand that the answers will come from a wide variety of different perspectives.
List of questions
Examples of questions I am receiving and ones that we might want to ask include:
Can a farm using controlled environment agriculture techniques be profitable?
What crops have proven to be profitable in a greenhouse?
What crops have proven to be profitable in a warehouse?
What crops have proven to be profitable in a shipping container?
What segment of the produce industry are these farms capable of serving?
What defines a vertical farm?
What is the difference between a greenhouse and an indoor ag facility?
What makes controlled environment agriculture techniques and innovations unique?
Does geographic location play a role in designing a controlled environment agriculture facility?
Why invest in controlled environment agriculture?
What problems are we solving?
Is controlled environment agriculture environmentally sustainable?
The answers to all these questions are extremely important. The answers provide important insight on whether there are existing examples of multiple successful projects in a given region for a given set of crops to be produced in a controlled environment agriculture facility.
An example of how this plays out can be seen when looking at the greenhouse-grown vegetable industry. There are a number of Dutch greenhouse experts for those climates and crops that companies have proven successful over the past decades. But this does not mean that their expertise necessarily transfers to every situation. Any time ag technology and “experience” are taken to a new climate and introduced to a new market and crop there will be problems, mistakes, and failures. This has been proven time and time again.
Successful business models
It is also important to realize that it is highly likely that there are many different business models that can be successful as we look at innovation to solve growing problems within horticulture and agriculture. This can easily be seen in existing greenhouse industries.
For those of us close to the industry, we can acknowledge the fact that there are low-, medium- and high-tech greenhouse facilities that are capable of producing good quality crops consistently and profitably. The reason for this is that depending on where the greenhouse is built and the crops that are grown, the greenhouse and the technology within it are designed to serve different purposes based on labor and access to natural resources. It is likely that as the indoor ag industry matures, we will find similar models.
Hurdles to overcome
So, what are the hurdles the indoor ag industry needs to overcome in order to be successful? And how are we as an industry going to achieve this success?
Based on my conversations with many industry leaders, these are the top 11 topics we need to address:
Finally, how are we as an industry going to provide solutions to these challenges or other larger problems?
First, we need to agree on which challenges we should address first and which ones we have the best chance of overcoming. Second, we need to be self-critical. We need to determine if these challenges are caused by problems we created and determine if they really need to be solved?
We then need to learn from other industries that have come before us. This means we need some level of open collaboration. We will need some form of standardization. We will need to focus on education. And finally, we will need some luck.
“Alone we can do so little, together we can do so much.” – Helen Keller
If you are interested in taking this conversation to the next level, I encourage you to join me on social media, at one of the many upcoming events I will be participating in or through collaboration.
Written by Chris Higgins – Urban Ag News and Hort Americas.
Wasabi Japonica Grown Under GE LED Grow Lights
Contact Hort Americas if you are looking to learn more about using the Current LED grow lights to produce crops grown in tissue culture and micropropagation facilities
The “Hardest to Grow” Plant in the World
The Opportunity
Wasabi Japonica is widely accredited as the “hardest to grow” plant in the world. The plants are native to Japan and require a very specific set of environmental conditions to successfully produce healthy plants.
Wasabi is most commonly associated with Japanese food, where it is used as a unique spice and as a condiment on sushi, but many are now learning of its secondary metabolites that possess distinct health benefits including significant anti-cancer and antimicrobial properties. Unfortunately, few growers outside of Japan have successfully grown Wasabi Japonica commercially. This has led not only to a high global demand for fresh grown product, but also to an increasing amount of interest from commercial growers trying to tap into a market that now pays an estimated $325/£250 per kilo of rhizome.
The Possibilities and the Challenges
Successful field cultivation is difficult because of the specific parameters required for growth over a relatively long harvest period of up to 2 years. Wasabi is also highly susceptible to pests and disease. Although resistant strains are available in Asia, the West is restricted to two main varieties: Mazuma and Daruma. Vegetative propagation can be successful for F1 generations, but thereafter, endogenous fungal infection leads to poor yields and major crop loss. Therefore, it is important to grow from clean stock produced under controlled environmental conditions.
A small startup in Scotland called The Functional Plant Company is currently working with LED grow lights from GE Current, a Daintree company to grow wasabi. The Functional Plant Company is using a variety of hydroponic and micropropagation techniques to produce plantlets from tissue culture through to acclimation and eventually full maturity. They are proving that light intensity and spectrum are equally important factors in establishing new cuticle and stomatal development. Their aim to prove this can become more efficient and faster by using GE LED battens as compared to natural daylight.
Finding Success with LED Grow Lights
Trials show the plants have established good root production using the Arize Lynk LED Grow Lights at 60umols/m2/s, although they noted the leaf canopy growth is slower and darker than when using TLEDs at equal intensity. The Functional Plant Company added that interesting results also arose when trying other spectrums of the Arize LED grow lights. They have noted a darker callus at higher light levels with high percentage of red light, while lower intensity prevents leaf burn and dehydration during early acclimation.
They concluded by noting that the Arize LED grow lights are very energy efficient, generating little heat—which is perfect for Wasabi as even a small temperature increase can cause wilt and plant loss.
Contact Hort Americas if you are looking to learn more about using the Current LED grow lights to produce crops grown in tissue culture and micropropagation facilities.
GERMANY: February 12-14, Wageningen Lighting In Greenhouses And Vertical Farms 2020
Do you want to improve the use of LED lighting in greenhouse production or vertical farming?
Do you want to improve the use of LED lighting in greenhouse production or vertical farming? Would you like to know how to reduce energy use and carbon foot print, how to improve production, or how to improve quality? Do you want to understand the different characteristics of light and how they affect physiological plant processes? Then this course might be valuable for you.
In this course on lighting in greenhouses and vertical farms Wageningen UR scientists will share their unique knowledge with international students, researchers, and horticultural and light experts.
For whom?
This intensive course is meant for professionals in lighting, greenhouse production and vertical farms as well as MSc and PhD students, post-docs and junior scientists from all over the world.
Course objectives
The aim of this course is to learn the basic principles behind the effects of LED lighting on plant growth, yield, product quality, and energy use efficiency. It aims that participants also understand how to apply this information in their daily practice by developing strategies to optimize the use of lighting in relation to the whole production system.
Learning outcomes
This course gives participants an in-depth view on:
Perception of light by plants
Major plant physiological and morphological processes affected by light
How lighting can be used effectively in greenhouses and vertical farms
The different characteristics of light and how to measure.
Click here for more information and to register.
Publication date: Fri 20 Dec 2019