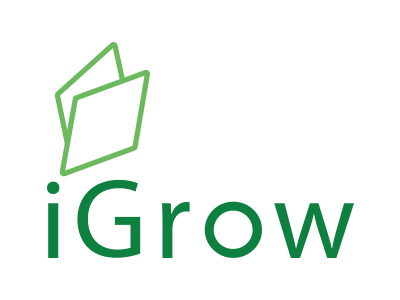
Welcome to iGrow News, Your Source for the World of Indoor Vertical Farming
USA - KENTUCKY: AppHarvest Announces Ground-Breaking For Fourth And Fifth High-Tech Indoor Farms
The high-tech Somerset farm marks the company’s expansion into growing berry crops. The Somerset indoor farm will be 30 acres
The Company’s Newest Large-Scale Controlled Environment Facilities, Located In Somerset and Morehead, Ky., Will Grow Strawberries And Leafy Greens, Respectively
June 21, 2021
Source: AppHarvest
MOREHEAD, Ky., June 21, 2021 (GLOBE NEWSWIRE) -- AppHarvest, Inc. (NASDAQ: APPH, APPHW), a leading AgTech company, public benefit corporation and Certified B Corp focused on farming more sustainably using up to 90% less water than open-field agriculture and only recycled rainwater, today announced the start of construction for two new high-tech indoor farms in Central Appalachia. The company’s new farms, located in Somerset and Morehead, Ky., will grow berries and leafy greens, respectively.
The high-tech Somerset farm marks the company’s expansion into growing berry crops. The Somerset indoor farm will be 30 acres.
The high-tech Morehead, Ky. farm is the second AppHarvest farm in Rowan County to date. The new Morehead facility will produce leafy greens and will be about 15 acres.
AppHarvest’s newest indoor farms in Morehead and Somerset are preceded by the company’s flagship 2.76-million-square-foot facility growing tomatoes in Morehead; a 15-acre facility in Berea that will grow leafy greens; and a 60-acre facility in Richmond that will grow vine crops.
"These new facilities place us exactly where we want to be at the forefront of AgTech. With today’s dual announcement, we put ourselves ahead of our development schedule,” said AppHarvest Founder & CEO Jonathan Webb. “Our Somerset and Morehead farms will build on the success of our flagship farm to provide higher quality produce using cutting-edge technology at a large scale.”
AppHarvest’s goal is to operate 12 high-tech indoor farms by the end of 2025, and today’s announcement means five of those now have been put on the map. Construction for both the Somerset and Morehead facility is anticipated to finish by the end of 2022.
“AppHarvest has positioned Kentucky as a leader in the AgriTech industry, created hundreds of good-paying jobs for our people and pushed through and thrived during some of our most difficult times,” said Gov. Beshear. “Even as a pandemic raged, Jonathan Webb and his team built one of the biggest indoor farming operations anywhere using one of the most advanced LED-lighting systems ever created. We know the jobs and investments of the future will flow to those who can meet these challenges, so why not us? AppHarvest is making it happen.” AppHarvest’s newest facilities will provide hundreds of well-paying jobs to Eastern Kentuckians in and around Somerset-Pulaski and Rowan Counties.
Both the Somerset-Pulaski and Rowan County facilities will produce non-GMO fruits and vegetables free of harsh chemical pesticides, to be distributed to top U.S. grocers and restaurants. Because of the company’s strategic location in Appalachia, AppHarvest can reach nearly 70% of the U.S. population in a day’s drive, with up to 80% less diesel fuel compared to existing growers in Mexico and the Southwestern U.S.
Supporting Quotes
Congressman Hal Rogers: “I am excited to welcome AppHarvest to Pulaski County and the Lake Cumberland area. Our rich farming history and skilled workforce makes southern Kentucky a prime partner for this innovative AgTech industry. As AppHarvest expands efforts to farm for our future, they are also inspiring a new generation of ingenuity and stellar work ethic that will benefit our region for generations to come.”
Somerset Mayor Alan Keck: “AppHarvest is breaking ground literally and imaginatively across Southern and Eastern Kentucky, and the company’s record growth creates a beautiful synergy with the record growth we are seeing in Somerset and Pulaski County. We share a vision for what this community and this region of Kentucky can become, that it can grow and thrive with the right nurturing and investment. We are thrilled AppHarvest chose Somerset and Pulaski County to expand and are honored to partner with this visionary company.”
Morehead Mayor Laura White-Brown: “This groundbreaking continues to highlight the progression of Eastern Kentucky and Appalachia. AppHarvest continues to pave the way for communities in this region by contributing to the workforce and economic development and at the same time helping to combat world hunger.”
Pulaski County Judge-Executive Steve Kelley: "What an exciting time this is to witness up-close an industry disruption. Who would have imagined that Southern and Eastern Kentucky could be an industry leader in produce supply? With AppHarvest’s vision and determination, we have that chance. We welcome AppHarvest to our county with open arms, and we can’t wait to see its prosperity here. It is victories like these that make me proud of my county."
About AppHarvest
AppHarvest is an applied technology company building some of the world’s largest high-tech indoor farms in Appalachia that grow non-GMO, chemical pesticide-free produce using up to 90% less water than open-field agriculture and only recycled rainwater while producing yields up to 30 times that of traditional agriculture on the same amount of land with zero agricultural runoff. The Company combines conventional agricultural techniques with cutting-edge technology including artificial intelligence and robotics to improve access for all to nutritious food, farming more sustainably, building a domestic food supply, and increasing investment in Appalachia. The Company’s 60-acre Morehead, Ky. facility is among the largest controlled environment agriculture facilities in the U.S. For more information, visit https://www.appharvest.com/.
Forward-Looking Statements
Certain statements included in this press release that are not historical facts are forward-looking statements for purposes of the safe harbor provisions under the United States Private Securities Litigation Reform Act of 1995. Forward-looking statements generally are accompanied by words such as “believe,” “may,” “will,” “estimate,” “continue,” “anticipate,” “intend,” “expect,” “should,” “would,” “plan,” “predict,” “potential,” “seem,” “seek,” “future,” “outlook,” and similar expressions that predict or indicate future events or trends or that are not statements of historical matters. All statements, other than statements of present or historical fact included in this press release, regarding Novus Capital’s proposed acquisition of AppHarvest, Novus Capital’s ability to consummate the transaction, the benefits of the transaction and the combined company’s future financial performance, as well as the combined company’s growth plans and strategy, future operations, estimated financial position, estimated revenues and losses, projected costs, prospects, plans and objectives of management are forward-looking statements. These statements are based on various assumptions, whether or not identified in this press release, and on the current expectations of AppHarvest’s management and are not predictions of actual performance. These forward-looking statements are provided for illustrative purposes only and are not intended to serve as, and must not be relied on as, a guarantee, an assurance, a prediction, or a definitive statement of fact or probability. Actual events and circumstances are difficult or impossible to predict and will differ from assumptions. Many actual events and circumstances are beyond the control of AppHarvest. These forward-looking statements are subject to a number of risks and uncertainties, including those discussed in Novus Capital’s registration statement on Form S-4, filed with the SEC on October 9, 2020 (the “Registration Statement”), under the heading “Risk Factors,” and other documents Novus Capital has filed, or will file, with the SEC. If any of these risks materialize or our assumptions prove incorrect, actual results could differ materially from the results implied by these forward-looking statements. In addition, forward-looking statements reflect AppHarvest’s expectations, plans, or forecasts of future events and views as of the date of this press release. AppHarvest anticipates that subsequent events and developments will cause its assessments to change. However, while AppHarvest may elect to update these forward-looking statements at some point in the future, AppHarvest specifically disclaims any obligation to do so. These forward-looking statements should not be relied upon as representing AppHarvest’s assessments of any date subsequent to the date of this press release. Accordingly, undue reliance should not be placed upon the forward-looking statements.
Important Information for Investors and Stockholders
In connection with the proposed transaction, Novus Capital has filed the Registration Statement with the SEC, which includes a preliminary proxy statement to be distributed to holders of Novus Capital’s common stock in connection with Novus Capital’s solicitation of proxies for the vote by Novus Capital’s stockholders with respect to the proposed transaction and other matters as described in the Registration Statement, as well as the prospectus relating to the offer of securities to be issued to AppHarvest’s stockholders in connection with the proposed transaction. After the Registration Statement has been declared effective, Novus Capital will mail a definitive proxy statement, when available, to its stockholders. Investors and security holders and other interested parties are urged to read the proxy statement/prospectus, any amendments thereto and any other documents filed with the SEC carefully and in their entirety when they become available because they will contain important information about Novus Capital, AppHarvest and the proposed transaction. Investors and security holders may obtain free copies of the preliminary proxy statement/prospectus and definitive proxy statement/prospectus (when available) and other documents filed with the SEC by Novus Capital through the website maintained by the SEC at http://www.sec.gov, or by directing a request to: Novus Capital Corporation, 8556 Oakmont Lane, Indianapolis, IN 46260. The information contained on, or that may be accessed through, the websites referenced in this press release is not incorporated by reference into, and is not a part of, this press release.
Participants in the Solicitation
Novus Capital and its directors and officers may be deemed participants in the solicitation of proxies of Novus Capital’s shareholders in connection with the proposed business combination. Security holders may obtain more detailed information regarding the names, affiliations and interests of certain of Novus Capital’s executive officers and directors in the solicitation by reading the Registration Statement and other relevant materials filed with the SEC in connection with the business combination when they become available. Information concerning the interests of Novus Capital’s participants in the solicitation, which may, in some cases, be different than those of their stockholders generally, is set forth in the Registration Statement.
MEDIA CONTACT: blair.carpenter@appharvest.com
INVESTOR CONTACT: kaveh.bakhtiari@appharvest.com
IMAGE/VIDEO GALLERY: Available here
Robotic Warehouse Farms Will Save The World
CEA technology is just getting started. Like the Tesla Cybertruck, we have a working concept that promises a more-than-Jetson’s-level future many of us can see the benefits of and actively want―it’s just not quite available to the masses yet
by Elle Griffin
Four years ago, Ritch Wood was looking for a better way to grow plants. As the CEO of global skincare company Nu Skin, he ran into ingredient shortages every winter when fields went dormant―and when he moved grow operations to the equator he ran into water and land shortages, along with a host of quality control issues.
Nu Skin needed reliable, quality ingredients for their skincare products. But farming was too unpredictable an industry. “If there was a way to grow indoors,” he thought, “and be able to do that 24 hours a day, 365 days a year―if we could guarantee that it was grown without any herbicides or pesticides and in a sustainable way that uses less water and land―that would be really helpful.”
At the time, controlled-environment agriculture (CEA) was in its infancy and grow-light technology had yet to take a turn for the more affordable. When he learned of an agricultural system that promised to use a fraction of the land and water used by traditional agriculture methods and had the potential to make it more affordable, Wood made an investment.
Nu Skin paid $3 million for 70 percent of the company and rights to its IP―and Grōv Technologies was born.
Grōv grass grown in the Olympus machine at the Bateman Mosida Farms. Photo from Grōv Technologies
Controlled-environment agriculture is on the rise
The theory behind CEA is that by controlling the environment in which it grows, we can control everything about a plant and what it grows into by micro-tweaking one of a thousand different characteristics―including temperature, humidity, light duration, light wavelength, dissolved oxygen in the water, and carbon dioxide saturation in the air. By tweaking the growing cycle, we can control the caloric content as well as the nutrient content and density of the plant.
“What we’ve learned through controlled-environment agriculture,” Benjamin Swan, co-founder and CEO at Sustenir in Singapore, once told National Geographic, “[is] we can actually emphasize certain characteristics of the plants. So, without using GMO, we can make our kale softer, we can actually make it sweet.”
The theoretical use cases for this technology are endless―from being able to grow in places where water is scarce (like in much of Africa), or where water is overly abundant (like Hawaii), or in places where labor is scarce (like in parts of Asia), or even in places that have long winters (like Northern Europe). Theoretically, we could have grow towers in every town and feed the whole of it no matter its natural environment.
We could even grow those foods to those cities’ exact nutritional needs―more vitamin D-rich foods in wintery places, for example. Dr. Lee Mun Wei, a senior manager at the Food Innovation and Resource Centre (FIRC) in Singapore aims to predict and prevent illness in a given population by tracking their biometric data using Apple watch-like wearables, then 3D printing nutrient-specific foods that could mitigate imbalances.
Though these technologies exist, they are still in their infancy. Singapore leads much of the research and development out of necessity. With limited land and water resources, the county is forced to import 90 percent of their food and 40 percent of their water from outside the country. As a result, they have no option but to grow vertically and desalinate water from the ocean.
Elsewhere, the industry has been slow to catch on, largely due to exorbitant startup costs, low returns, and lack of urgent need. According to a 2017 State of Farming report by L.E.K., only 27 percent of indoor, vertical farms are profitable compared with 50 percent of container farms and 75 percent of greenhouses. But one thing has spurred the industry on in recent years: cannabis.
Legalized in 39 states, demand for cannabis has created a $13.6 billion industry and enough capital to fund CEA-enabled grow operations. “When you have a crop that fetches up to $2,400 or $2,500 a pound, you need to be able to dial everything in and make it consistent and repeatable,” says Dashiel Kulander, co-founder and CEO at Boojum Group. “If the temperature swings five to 10 degrees on a cannabis plant, that will change the plant’s various cannabinoids. The goal is to create a medicine that is consistent batch after batch.”
It’s only recently that there has been some financial incentive to use CEA technologies for food use―largely driven by Big Ag players hoping to hedge out the competition. Berry farming giant Driscoll’s, for one, led a $500 million round to fund Plenty, a 2.2-acre vertical farm in California they hope will help them fulfill a contract with Albertsons. The Ingka Group, for another, led a $100 million round to fund AeroFarms, a 2.4-acre vertical farm in New Jersey that will help them fulfill a contract with Singapore Airlines.
Grōv tent at the Bateman Mosida Farms. Photo from Grōv Technologies
Grōv Tech is building CEA prototypes in Utah
By investing in Grōv Tech, Nu Skin hopes to do something similar, getting ahead of the supply chain that fuels their skincare products before the competition can beat them to it, or before climate change makes traditional methods more difficult, all while shoring up technology that could provide a farming model that is more sustainable―if only it were more economical.
“The purpose was always, can we build a better product for Nu Skin?” Wood says. “We think there’s a huge story around the ingredient sustainability, and there were a lot of ingredients we felt we could grow, but the challenge was: could we do it in an economical way?”
Grōv Tech started out with a prototype: a tower that pairs hydroponic growing technology with grow lights. But like all CEA startups, a lot of the growing process was manual and the technology was prohibitively expensive. To make something that was scalable and profitable the whole thing needed to be automated and it needed to be cheap.
With this goal in mind, Wood decided they would start by growing animal feed for Bateman’s Dairy farm. Having grown up on a dairy farm himself, Wood figured this would allow the company to scale the product while refining and automating the technology to the point that it could be replicated. And all of this would have a fortuitous effect on Nu Skin’s bottom line.
“One of our bestselling products is a weight-loss protein powder which uses whey protein,” Wood says. “So again, a very nice connection there is if the animal is eating a more sustainable product and producing better milk with better protein and it’s being done in a sustainable way―certainly that can be a benefit to Nu Skin down the road.”
One year into feeding the 20,000 animals at Bateman, the company has learned a lot. For instance: cows need a lot of magnesium, but they don’t like eating it. Now, Grōv Tech puts magnesium in the water so it’s directly absorbed into the plant and then becomes bioavailable to the cow upon eating it. And because the growing process only takes seven days, data scientists can analyze the results in real-time and adjust the components to optimize production for the next batch of feed.
According to Grōv Tech president Steven Lindsley, it’s not far off that we’ll be looking at milk production (butter, fats, and proteins) and optimizing a herd’s diet for taste, quality, and nutritional value―not to mention the wellbeing of the animal. We’ll be able to look at how many trips from the veterinarian an animal gets when they’re fed certain nutrients in their diet, and whether they can have more calves and produce the same amount of dairy on less, better quality feed. (So far, the answer to this last question is yes. When animals are fed better quality food they need less of it―just like humans.)
And if we hook all of the cows up to robotic milking equipment and connect everything to artificial intelligence, machine learning, and the Internet of Things―Lindsley’s far-flung goal―then we might be able to collect enough data to not only feed cows to their optimum health and performance ability, but humans too. And that could have ramifications not only for feeding the world, but nourishing it― just like Dr. Wei hopes to do in Singapore.
“Last year was about starting to feed animals and get data and prove out the hypothesis we have while continuing to perfect the technology and get confidence there,” Wood says. “And now we’re really to a point where we’ve got data that proves that it works and that financially it’ll be a good thing for a farmer. So now we can really take that proposition to farmers and start to scale.”
Olympus Tower Farm at Bateman Farms in Mosida, UT. Photo from Grōv Technologies
CEA technology could feed the world
Right now, Grōv Tech is focused on refining its technology right here in our own backyard. But once they do that, the plan is to expand internationally.
“Saudi Arabia has actually passed a law where you cannot use water to grow fodder or feed for animals, so all of that now has to be imported. China imports one-third of their alfalfa feed for their dairy animals because they don’t have the capability of growing it,” Wood says. “So there are countries that will probably benefit more than the US would. But we’ve got to refine the technology and get that built to where it’s ready to scale before we start spreading ourselves all around the globe.”
CEA technology is just getting started. Like the Tesla Cybertruck, we have a working concept that promises a more-than-Jetson’s-level future many of us can see the benefits of and actively want―it’s just not quite available to the masses yet. But with more than a billion dollars invested in the technology in just the past few years alone―we’re getting there. And the “there” we are heading toward is rosy indeed.
“To put it in perspective, one tower that is about 875 square feet on the ground will replace 35 to 50 acres of land,” says Lindsley. “And that will feed the animals on roughly five percent of the amount of water. The UN says that that the world will add about 2.5 billion people in the next 30 years. And we have to find a way to feed them on arguably less arable land and water. The good news is the technology is coming along to help solve that equation.”
If COVID-19 taught us anything, it’s that our food supply chain is fragile. But that’s only because our supply chain was built to grow food in California, refrigerate it so it stays fresh, then transport it 1,500 miles so we can eat a salad in the winter in Chicago. In the future, that might not be a thing. “We’re having a dry year now,” Lindsley tells me in February. “But a year ago we were in a blizzard, and even in the middle of a blizzard in February in Utah, we’re pumping out fresh, beautiful, safe green grass for animals. It’s a paradigm shift.”
“Four years ago it was a good idea,” Wood tells me of his company’s investment in CEA technology, “But four years from now it’s going to be required.”
Elle Griffin
Elle is the editor-in-chief of Utah Business and a freelance writer for Forbes, The Muse, and The Startup. She is also a literary novelist and the author of a weekly newsletter called The Novelleist. Learn more at ellegriffin.com.
VIDEO: Tortuga Raises $ 20m To Build Hundreds of Harvesting Robots
Last year Tortuga launched a strawberry harvesting robot. This platform is flexible, according to Tortuga it can be adapted to work on other crops like indoor-grown tomatoes or outdoor table grapes
23-04-2021
Harvest automation start-up Tortuga completed a $ 20 million Series A funding. The money will be used to build hundreds of robots to deploy in 2022.
Last year Tortuga launched a strawberry harvesting robot. This platform is flexible, according to Tortuga it can be adapted to work on other crops like indoor-grown tomatoes or outdoor table grapes.
Picking robots
“For many years, the story behind harvesting robotics has been a lot of promise but really companies have struggled to deliver on that promise for the customer. That’s because this is one of the hardest problems there is to solve,” Eric Adamson, co-founder of Tortuga AgTech told AgFunder News. “Not only are we doing autonomous robotics but we are also doing picking robotics and we are doing them together in really unstructured environments.”
Robots-as-a-service
The $ 20 million in new capital will be used to build hundreds of robots to deploy in 2022. Some of the funding will also go towards building out the operating model and making sure there are enough employees to operate the robot fleets.
Tortuga currently offers its technology through a robots-as-a-service model, getting paid by the kilo for the produce that its robots pick.
Additional services
“On top of that, as we provide other services that are close to harvest, like data-driven forecasting and other types of cultivation services, those will also be service-based although they may not be quite so specific to a kilogram. We are charging for some of these additional services on a monthly or per-hectare basis,” Adamson told AFN.
Web editor for Future Farming
The Farm Of The Future Might Be In Compton. Inside A Warehouse. And Run Partly By Robots
Plenty wants to build at least 500 of these vertical farms around the planet, especially in densely populated cities of at least 1 million people
BY STEFAN A. SLATER IN FOOD
OCTOBER 6, 2020
Lettuce grows in a vertical farm at Urban Crop Solutions in Waregem, Belgium, on September 20, 2016. (JOHN THYS/AFP via Getty Images)
From the outside, the gray and white warehouse near the corner of Oris Street and Mona Boulevard seems like a thousand other mundane Southern California buildings. But the interior, once completed, will resemble a sketch from a futurist's daydreams. If all goes well, the 95,000-square-foot Compton facility will house rows of hydroponic towers organized into emerald walls of non-GMO, pesticide-free leafy greens. These plants won't rely on sunlight in order to grow. Gleaming LED lamps will provide all the light the crops could ever want. Robots will transport seedlings while other machines move the towers as part of an orchestrated production process. Picture a grow room in a futuristic Martian colony and you're probably on the right track.
The exterior of Plenty's vertical farming facility in Compton. (Stefan Slater for LAist)
The operation is run by Plenty, a San Francisco-based startup that uses vertical farming to create high-quality, nutritious plants "you'd actually want to eat" (their words). Stated another way, they grow crops, often without natural light or soil, in vertically stacked beds in enclosed and controlled environments.
Plenty wants to build at least 500 of these vertical farms around the planet, especially in densely populated cities of at least 1 million people.
The first Plenty farm, in South San Francisco, went into production in 2018 and was upgraded in the summer of 2019 to increase production. For its agricultural second act, the company chose Compton.
A farm operations associate in front of leafy greens growing in vertical towers at Plenty's vertical farming facility in South San Francisco. (Spencer Lowell/Courtesy of Plenty)
Plenty's long-term goals go beyond tasty salad greens. It wants to combat food apartheid by bringing healthy, locally-grown crops to communities that lack access to nutritious produce.
"We want to invest in places where we can serve a large number of people," says Shireen Santosham, the company's head of strategic initiatives. "Compton can help us better serve Los Angeles while also allowing us to invest in a community with a long history of farming."
The goal for Plenty's Compton outpost, once it's running at full capacity, will be to create enough produce to make regular deliveries to hundreds of grocery stores. In early August, the company reached an agreement with Albertsons to provide 430 of its California stores with assorted leafy greens.
Company reps say the Compton site will initially focus on producing kale, arugula, fennel, and bok choy before adding strawberries to its repertoire. They expect prices to be similar to organic leafy greens currently on grocery store shelves.
The company was hoping its Compton farm would be able to bring produce to market by the end of 2020 but the coronavirus pandemic altered that timeline. Plenty now hopes to start its first customer deliveries sometime in 2021.
A view of the grow space at Plenty's vertical farming facility in South San Francisco as seen through the vestibule window. (Spencer Lowell/Courtesy of Plenty)
WHY COMPTON?
Los Angeles has for centuries been a land of citrus groves, peaches, olives, and even vineyards, and Compton was no exception. In the late 1860s, Reverend Griffith Dickenson Compton led roughly 30 people from Stockton to settle in and cultivate the area. Rough weather and tremendous floods nearly destroyed their dreams, but they persisted, and their agricultural efforts eventually began to thrive.
A drawing of the Compton farm and Star Cheese Dairy of Omri J. Bullis in 1880. It was located on Alameda Street, north of El Segundo Blvd. (Security Pacific National Bank Collection/Los Angeles Public Library Collection)
In 1888, Compton donated his land and the area was incorporated as the city of Compton under the condition that a swath of it be zoned for agriculture. That particular area — a 10-block neighborhood sandwiched between downtown Compton and what's now the 91 Freeway — became Richland Farms, known for a variety of crops including pumpkins, sugar beets, and cauliflower. By the 1940s and '50s, Compton had become a working-class suburb. African American families, many of whom had moved to the West Coast to work in military production during World War II, settled there and were drawn to the Richland Farms neighborhood. With its large lots and agricultural zoning, residents could grow crops and raise livestock to provide for their families and their community.
Richland Farms — home of the Compton Cowboys — remains a living link to Compton's agricultural past. Drawing on that history, Plenty began designing and developing its Compton vertical farm (located a few miles north of Richland) in the summer of 2019.
"There is just a rich tradition of farming in Compton, and to have Plenty come back in an innovative way is exciting for our community," Compton Mayor Aja Brown says.
City officials are working with the company to connect its facility with nearby schools so kids can learn about vertical farming and the technologies associated with it.
A farm operations associate tends to plants in the grow space at Plenty's vertical farming facility in South San Francisco. (Spencer Lowell/Courtesy of Plenty)
OK, BUT WHAT EXACTLY IS A VERTICAL FARM?
Compared to traditional field agriculture, which humanity first started tinkering with approximately 12,000 years ago, vertical farming is in its infancy.
One of the first vertical farms was a hydroponic system built-in Armenia sometime before the early 1950s, although there's not much information about it.
The modern vertical farm, at least in the way we think of it, was popularized two decades ago by Dickson Despommier, an emeritus professor of public and environmental health at Columbia University.
Baby kale is grown at AeroFarms on February 19, 2019, in Newark, New Jersey. (ANGELA WEISS/AFP via Getty Images)
In 1999, he wanted students in his medical ecology class to explore ways they could feed New York's residents on crops grown entirely within the city. They started with rooftop gardens but those barely made a dent in the amount of food they needed. Then, Despommier remembered the city's abandoned buildings. "What if you could fill up those buildings with the grow system that you've instituted on the rooftop and just increase food production?" he says.
The result was a multi-level, urban farm featuring layers of crops stacked on top of one another.
Greens growing at Bowery Farming, a vertical farm in Kearny, New Jersey, on January 28, 2019. (DON EMMERT/AFP via Getty Images)
Until the 21st century, commercial vertical farming seemed like the stuff of utopias, a grand if impractical dream evangelized by a handful of futurists and agricultural techies. But the last few years have seen a jump in interest — and venture capital. Between 2016 and 2017, investments in vertical farming grew nearly eightfold.
In 2017, Plenty received $200 million from several high-profile investors including Alphabet chairman Eric Schmidt and Amazon founder Jeff Bezos. One of its East Coast competitors, Bowery Farming, received a $90 million investment from Google Ventures.
The UAE's Badia Farms in Dubai, seen on August 4, 2020, uses hydroponic technology and vertical growing towers to produce fruits and vegetables year-round. (KARIM SAHIB/AFP via Getty Images)
AeroFarms, which uses aeroponics to grow produce, scored $40 million from IKEA and Sheikh Mohammed bin Rashid of Dubai. The United Arab Emirates is also hoping vertical farming will boost the country's limited domestic food production. The Abu Dhabi Investment Office sunk $100 million into four ag-tech companies, including Aerofarms, which plans to build a new vertical farm and R&D center in Abu Dhabi.
Two farm operations associates tend to plants in the grow space at Plenty's vertical farming facility in South San Francisco. (Spencer Lowell/Courtesy of Plenty)
WHY DO WE NEED THEM?
Vertical farming is all about efficiency. The process allows growers to control and monitor light, oxygen, nutrients, temperature, humidity, and carbon dioxide levels. In a vertical farm, you don't need to wait for the right season. Growth and harvesting can occur year-round.
Plenty's approach relies on automation, intricate sensors, machine learning and hydroponic grow towers where plants are cultivated in a nutrient-rich water solution instead of soil. With this method, the company claims it can grow 350 times as much produce, per square foot, as a conventional, outdoor farm — all while consuming a fraction of the water.
"[Vertical farms] are much more water-use efficient than field production," Neil Mattson, associate professor of plant science at Cornell University, says.
Santosham claims Plenty's vertical farms will use "about 1% of the land and 5% of the water" required by a comparable traditional farm.
Producing more food with less land is a must if we want to keep humanity fed.
A worker tends to basilicum plants at an indoor vertical farm at Colruyt Group in Halle, Belgium on March 3, 2020. (THIERRY ROGE/BELGA MAG/AFP via Getty Images)
By 2050, Earth will have 9.8 billion residents and two-thirds of them will probably live in a city. In places like Los Angeles or New York, where real estate doesn't come cheap, vertical farms could be installed without taking up much space.
Produce from vertical farms would also be less likely to spoil since it would, in theory, only travel a few miles to the nearest grocery store, market or restaurant, instead of sitting on a plane or cargo ship for hundreds or thousands of miles.
Plus, vertical farms could help make our food supply chain more resilient.
Since March, the pandemic has impacted everything from beans to strawberries. When the hospitality industry shut down, some farmers had buyers for only half of their crops, so they had to let them rot or plow them back into the soil. Dairy farmers dumped millions of gallons of milk. Meat plants have had to shut down due to COVID-19 outbreaks. Plus, the workers who pick the crops, raise the cows and run the slaughterhouses have been ravaged by the virus. And all of this has been happening while hunger skyrockets. In the last six months, food banks have seen a surge in demand, in some cases by as much as 600% percent.
"I don't think all of our food is going to come from urban production," Mattson says. "It does add diversity to our food supply chain to have some of our produce — the nutrient-dense foods — come from close to where they're consumed."
With COVID-19 exposing the weaknesses in our food supply chain, Mattson believes indoor growing (which includes vertical farming and greenhouses) and more localized production might get their moment in the high-intensity LED spotlight: "We're going to see these trends happen even quicker than if we hadn't encountered COVID."
The central processing area at Plenty's vertical farming facility in South San Francisco. (Spencer Lowell/Courtesy of Plenty)
A PEEK INSIDE
The Compton farm is still under construction but the company is using its existing South San Francisco facility as a template.
That facility, which started in 2015 as a container farm, features 50,000 square feet of production space and a roughly 10,000-square foot grow room. It provides produce to approximately 40 grocery stores and runs entirely on solar and wind power.
The Compton farm will feature a similar grow system. Employees, referred to as growers, will oversee the process of cultivating seeds into seedlings. Robotics will transfer the seedlings to large vertical grow towers, arranged to form what looks like a vast, green wall.
The amount of time produce spends in the grow room depends on the crop. Nate Storey, chief science officer and co-founder of Plenty, explains that one leafy green crop might go through the entire process from seedling production to harvesting in two to three weeks. That's significantly less time than if those crops were grown via traditional agriculture.
Laborers harvest romaine lettuce using a machine with heavy plastic dividers that separate them from each other on April 27, 2020, in Greenfield, Monterey County, California. (Brent Stirton/Getty Images)
On a large, outdoor farm in the Salinas Valley, baby kale would typically require 35 to 50 days, depending on the time of year, before it was ready for harvest, according to Richard Smith, a University of California Cooperative Extension vegetable advisor for the Central Coast.
"For something like lettuce, where you might be waiting for several weeks in the field, we're carving a significant amount of time off that production schedule," Storey says.
A post-harvest associate inspects produce for packaging at Plenty's vertical farming facility in South San Francisco. (Spencer Lowell/Courtesy of Plenty)
Once the plants spend some time in Plenty's grow room, robots pick up the towers and retrieve the produce, which is moved to a processing area where it's packaged. Through it all, human hands never touch the food.
"We're able to create an environment that's so favorable to plants and not pathogens or pests that we can deliver a product without ever applying pesticides, which is a big win," says Nick Kalayjian, senior vice president of engineering at Plenty.
In fact, without bugs or human contact, he claims Plenty's produce doesn't need to be washed. Kalayjian also says the small adjustments in temperature, water, nutrients and light result in produce that's at the peak of flavor.
Plenty sent me samples of their baby kale, baby arugula and Sweet Sunrise mix, a combo of fennel, beet leaves and other greens. Did visions of tree stars seize me and shatter all perception of space and time? No. But they did taste exceptionally fresh. The flavors were strong, clean and... just good. I found myself snacking on the Sunrise mix straight from the package, something I never do with greens.
A farm operations associate tends to plants in the grow space at Plenty's vertical farming facility in South San Francisco. (Spencer Lowell/Courtesy of Plenty)
WHERE DO WE GROW FROM HERE?
Vertical farms aren't cheap to build. They also require a lot of energy to run, much more than conventional field agriculture or greenhouses. "That, to me, is one of the big sticking points," Mattson says.
In a 2020 study, Mattson and other Cornell University researchers studied the economic and environmental impacts of bringing leaf lettuce to U.S. cities via field-based agriculture vs. CEA (controlled environmental agriculture) supply chains such as greenhouses and vertical farms.
"We had almost the same carbon footprint of growing in a greenhouse in New York City as compared to field growing and shipping 3,000 miles. The vertical farm had about twice the carbon footprint of either of those," Mattson says.
In Plenty's case, making sure their farms operate on sustainable, renewable power is a priority. The South San Francisco facility has a power purchase agreement in place with a renewable provider to supply the farm with sustainable energy. Plenty wants its Compton farm to run entirely on clean energy but that won't happen until some undetermined point in the future. Company reps couldn't offer a more precise timeline on when that might happen.
Various leafy greens grow in vertical towers at Plenty's vertical farming facility in South San Francisco. (Spencer Lowell/Courtesy of Plenty)
Warehouse-sized vertical farms may someday be common sights in major cities but it'll take time to scale up to that level. No one, except maybe the most optimistic futurists, thinks vertical farming is going to overtake field agriculture anytime soon.
"We're an additive technology, not a replacement technology. We simplify the supply chain and allow domestic production in places that don't currently have it," Kalayjian says.
A worker tends to lettuce under artificial lights at the Pink Farms warehouse in Sao Paulo, Brazil, on August 28, 2020. (JONNE RORIZ/AFP via Getty Images)
Although vertical farming is still in its earliest stages, Despommier urges us to imagine how it might work in 50 years. "We're looking at a sort of Stanley Steamer [car], not even a Ford Model T," he says, "We're looking at the early trials and tribulations of an industry that wants to supply all of your food. Look how fast it took America to go from no cars to two cars per person."
Maybe by the time humanity has figured out how to colonize other planets and build Star Trek-style replicators, the urban dwellers of earth will rely on skyscraper-style vertical farms. Maybe thousand-acre fields of fruit and vegetables will someday look as obsolete as rotary phones. Until then, we'll be playing in the dirt, just as we've done for thousands of years.
Meet Angus: A Robotic Field Hand For The Autonomous Farming Revolution
Angus rolls through the Iron Ox warehouse hoisting trays into position for robotic-arms that can plant crops, add nutrients, transplant crops as they grow, harvest and ultimately package their bounty
The farm robot is part of Iron Ox’s aim to build hyper-efficient farms in the urban centers where most food is consumed.
By Carl Engelking December 23, 2019
Angus in action. (Credit: Iron Ox)
For centuries, farmers cajoled Earth’s bounty with oxen and plow. But eventually, grass-fed power gave way to steel workhorses fueled by steam and diesel — and a new era of agricultural efficiency followed. Now, rays of light from a new agricultural dawn are splintering the bucolic horizon: autonomous indoor farms tended by fleets of robots connected to hyper-efficient agro-hiveminds.
For a glimpse at this new twist on the farm workhorse, look no further than Iron Ox’s robotic farmhand nicknamed Angus. Angus’ job on the “farm” — a warehouse in Silicon Valley, technically — is to transport 1,000-pound trays of leafy greens growing in a perfectly-balanced hydroponic bath. Angus rolls through the Iron Ox warehouse hoisting trays into position for robotic-arms that can plant crops, add nutrients, transplant crops as they grow, harvest and ultimately package their bounty.
But Angus isn’t really “Angus” the individual. Rather, Angus is just one appendage of an entire robotic-software-sensor system controlled by “The Brain.” It’s a central computer that monitors the entire operation, from Angus’ next move to the nitrogen levels in tray 2. It’s all part of Iron Ox’s aim to build hyper-efficient farms in the urban centers where most food is consumed.
By locating autonomous farms closer to consumption, you already cut down on the fuel and labor costs needed to get plants from point A to B. But Iron Ox isn’t doing too bad on the productivity side, either. Their farm, on a foot-to-foot comparison, is about five times as productive as a traditional farm.
That’s because Iron Ox monitors every single facet of the growing cycle. Plants are given just the right amount of space, sun (the warehouse allows natural light in) and nutrients to grow. Because computers can run 24/7, the plants are constantly monitored and conditions adjusted to optimize growth. With the aid of machine learning algorithms, every additional crop improves the ability of “The Brain” to grow the next crop. Of course, it also helps that Angus doesn’t need to eat, sleep or collect a wage for his labor.
Iron Ox isn’t the only enterprise taking autonomous, robotic farming to the city. There are now dozens of startups putting their vision of urban farming to the test, and indoor farming is expected to be a $40 billion industry within a decade. Some are vertical farms that bathe walls of plants in LED lights. Aquaponic farms raise fish and veggies in a circular system: the fish poop and feed the plants, and the plants filter the water for the fish. But even old-school farms are getting a hand from robotic labor.
While there’s a lot of buzz about autonomous vehicles on highways, it’s the endless rows of farm fields that will likely first play host to widespread autonomous vehicle operations.
Already, precision-ag giants like John Deere are testing autonomous planters, sprayers and harvesters that chart daily routes and interventions based on data gathered by self-directed drones flying over fields and other real-time sensors. Indeed, though tractors still rule the farm, their days of dominance may be numbered.
Fresh Produce, Brought To You By Robots
IN SAN CARLOS, CALIFORNIA, UNDER LED lighting in a controlled, 8,000-square-foot environment, a team of autonomous robots is whirring night and day between rows of leafy greens
A Family-Owned Market In California
Is Now Selling Robot-Reared Leafy Greens
BY LUKE FATER AUGUST 08, 2019
An industrial robotic arm with custom gripper and sensors constantly reorganizes plants as they grow. IRON OX
IN SAN CARLOS, CALIFORNIA, UNDER LED lighting in a controlled, 8,000-square-foot environment, a team of autonomous robots is whirring night and day between rows of leafy greens. There is no dirt, there are no pesticides, and on this indoor farm, the only humans work behind screens. This is one of the world’s first autonomously operated commercial farms, and their produce is now flying off the shelves.
As a child, roboticist Brandon Alexander spent summers in Oklahoma helping his grandfather grow potatoes, peanuts, and cotton on a 6,000-acre farm. But as CEO of Iron Ox, the start-up company behind the automated farm, he says traditional farming is now his biggest competition—and granddad understands. “He knows that for farming to survive, this is almost inevitable,” says Alexander.
At Bianchini’s Market, a family-owned grocery in the San Francisco Bay Area, the two worlds are competing for the first time. As it stands, the robots are holding their own: Between retail buyers and several local restaurants, including San Francisco’s Trace, Iron Ox saw sales more than double last quarter.
Compact spacing techniques unique to hydroponic farms allow Iron Ox to grow 30 times the yield per acre compared to outdoor farming, according to Alexander. IRON OX
The San Carlos operation is not completely automated just yet. Human staff still plant the initial seed and handle post-harvest packaging. But the rest is left to robots.
Angus, a half-ton aluminum porter, roams the “field” of trays, or pallets, 24/7 with an overhead camera. On traditional farms, plants need space for their roots to absorb nutrients; on hydroponic farms, however, seeds can be planted in their trays mere inches apart. As they grow and begin crowding each other, though, this does require more attention from, say, a sleepless robot. Angus carries the 800-pound pallets in need of rearranging to a separate, industrial robotic arm that gently re-shuffles the growing pods into new compact rows. Angus is also responsible for IPM (integrated pest management) and scanning for aphids, mildew, and browning.
The robotic arm’s stereo-camera (“two cameras that kind of mimic your eyes,” Alexander casually explains) creates a 3-D model of at-risk produce that’s run through a machine algorithm to diagnose the issue and quarantine or prune accordingly. “The Brain,” a cloud-based AI software, coordinates all these autonomous functions while monitoring light, nitrogen, and water levels. “It’s a neighborhood farm,” says Alexander.
A 1,000-pound aluminum porter named Angus scans for crowding, carrying plant pallets to a separate robotic arm for rearranging. IRON OX
He’s not wrong. Produce from Iron Ox travels less than a mile to reach Bianchini’s—itself a mere 25 miles from downtown San Francisco. In fact, evening shoppers at Bianchini can buy produce robo-picked that morning, and at price points that compete with outdoor farms: A bunch of basil sells for $2.99; four heads of baby lettuce for $4.99; and a bunch of red-veined sorrel for $2.99.
Typically, the cost of human labor required for indoor hydroponic farms has made their produce inaccessibly expensive. Jake Counne of Backyard Fresh Farms, a similarly autonomously assisted farm in Chicago, told the Chicago Tribune that employing robotics reduced his labor costs by 80 percent. For this reason, building a farm around robotics and A.I. could crack the code of making indoor farms feasible. And while Alexander’s leafy greens remain local, the consequences of Iron Ox’s success may not.
Using robotics to make indoor hydroponic farms practical could alleviate a host of agricultural problems. In 2016, World Water Forum cited farming as a major contributor to global water scarcity. But farms like Iron Ox use 90 percent less water than outdoor farms. In a 2019 report on the challenges of feeding 10 billion people by 2050, The World Resources Institute cites concern over “the difference between global agricultural land area in 2010 and the area required in 2050 … if crop yields continue to grow at past rates.” According to Alexander, Iron Ox yields 30 times more produce per acre over the course of a year than conventional farms, and without using any arable land. A 2016 report from the National Center for Biotechnology on Chemical Pesticides urged a “drastic reduction in the use of agrochemicals,” and indoor farms alleviate the need for herbicides and pesticides.
This vision-enabled robot runs 3-D scanned models of the plants through a machine learning algorithm for quality control. IRON OX
For now, Iron Ox’s goals are more pointed. “How can we make your salad pop? We try to prioritize that,” Alexander says. Following the success of the San Carlos location, he does plan to set up robotic farms near other U.S. cities, though he’s not announcing anything yet. Iron Ox is, however, hiring humans for plant science and growing teams.
Gastro Obscura covers the world’s most wondrous food and drink.
Sign up for our email, delivered twice a week
Indoor Farmers Bet On Robots, AI
While the first versions of modern vertical farms sprouted about a decade ago, in recent years the introduction of automation and the tracking of data to regulating light and water has allowed them to get out of lab mode and into stores. Now they are trying to scale up
Erik Groszyk, 30, used to spend his day as an investment banker working on spreadsheets. Now, he blasts rapper Kendrick Lamar while harvesting crops from his own urban farm out of a shipping container in a parking lot in Brooklyn, New York, US. REUTERS/Mike Segar/Files
Leafy salad greens grown under banks of LED lights, with mist or drips of water are having their day in the sun. Several top US indoor farms, stacked with plants from floor to ceiling, tell Reuters they are boosting production to a level where they can now supply hundreds of grocery stores.
Plenty, Bowery, Aerofarms, and 80 Acres Farms are among young companies that see a future in salad greens and other produce grown in what are called vertical farms that rely on robotics and artificial intelligence, along with LED lights.
While the first versions of modern vertical farms sprouted about a decade ago, in recent years the introduction of automation and the tracking of data to regulating light and water has allowed them to get out of lab mode and into stores. Now they are trying to scale up.
Plenty and others say their customized, controlled lighting — some more blue light here, some more red light there — makes for tastier plants compared to sun-grown leaves and that they use 95 percent less water than conventional farms, require very little land, and use no pesticides, making them competitive with organic farms.
And because vertical farms exist in windowless buildings that can be located in the heart of urban areas, produce does not have to travel far by fossil-fuel-guzzling trucks to reach stores.
The companies’ expansion comes as plant-based burger makers Beyond Meat Inc and Impossible Foods captivate investors and make inroads in high-end restaurants and fast-food chains.
But whether the sunless farms can compete financially with their field-grown brethren, given big upfront investments and electric bills, remains a question.
“We’re competitive with organic today and we’re working very hard to continue to make more and more crops grocery store competitive,” said Matt Barnard, chief executive and co-founder of Plenty, which is based in Silicon Valley.
Plenty’s salads sell on organic grocery delivery site Good Eggs for 99 cents an ounce, while a leading brand, Organic Girl, on grocery chain Safeway’s online site was priced at 80 cents an ounce.
Plenty said its new farm, dubbed “Tigris,” can produce enough leafy greens to supply over 100 stores, compared with its previous farm that could only supply three stores and some restaurants.
The technology world is paying attention. In its last round in 2017 Plenty raised about $200 million from investors including Japan’s Softbank, Amazon founder and CEO Jeff Bezos and former Alphabet Chairman Eric Schmidt. New York City-based Bowery raised $95 million in a fund-raising round led by Google Ventures and Temasek last year.
LED lights glow from a cluster of 10 hydroponic climate-controlled farms housed in repurposed 320-square-foot metal shipping containers where entrepreneur farmers enrolled in the "Square Roots" farming program are growing and selling a variety of organic greens in the parking lot of a former Pfizer factory in Brooklyn, New York, US. REUTERS/Mike Segar/Files
Bowery said its third farm coming online soon will help it supply hundreds of stores from dozens today, and Aerofarms, in New Jersey, said it is doubling its space to meet demand.
None of the three companies would give details about costs.
Former Vertical Farm CEO Matt Matros is sceptical that sunless farms can make economic sense. He invested in and ran Chicago-based FarmedHere in 2015, but changed its business into food processing.
“The issue with indoor farming was that you could really only grow a couple things efficiently — namely basil and micro greens. But the problem is the world just doesn’t need that much basil and micro greens,” Matros said.
80 Acres Farms in Cincinnati says it already grows and sells tomatoes and cucumbers, and Plenty is testing cherry tomatoes and strawberries in the lab.
Agriculture technology investor Michael Rose says vertical sunless farms are more expensive to run than modern greenhouses that rely on sunlight, supplemented by LED lights. He sees limited areas where it makes sense, such as the Middle East, where much of the food is imported, or China’s mega-cities where pollution and urban sprawl limit the availability of premium fresh food.
At Plenty’s new farm, robots put seedlings in tall, vertically hung planters. The planters move along a wall of LED lights for 10 days and are then put through a harvesting machine that shaves off the leafy greens.
The machines minimize labour needs, and Plenty says the speed of production also helps control pests.
“We use no pesticides,” said Nate Storey, co-founder and chief scientist at Plenty. “We don’t even have to use things like ladybugs, because we go so fast in our production that we out-race the pests themselves.”
Will America's Future Farmers Be Robots?
Iron Ox Start-Up
Angus possibly will be America’s farmer of the future. He's heavyset, weighing in at nearly 1,000 pounds, and he is a bit slow. But he's strong enough to hoist 800-pound pallets of maturing vegetables and can move them from place to place on his own. Angus is a robot.
To Brandon Alexander, Angus and other robots are key to a new wave of local agriculture that aims to raise lettuce, basil and other produce in metropolitan areas while conserving water and sidestepping the high costs of human labor. It's a big challenge, and some earlier efforts have flopped.
After raising $6 million and tinkering with autonomous robots for two years, Alexander's startup Iron Ox says it's ready to start delivering crops of its robotically grown vegetables to people's salad bowls.
As reported by cbsnews.com, Iron Ox planted its first robot farm in an 8,000-square-foot warehouse in San Carlos, California, a suburb located 25 miles south of San Francisco. Although no deals have been struck yet, Alexander says Iron Ox has been talking to San Francisco Bay area restaurants interested in buying its leafy vegetables and expects to begin selling to supermarkets next year.
Publication date : 10/4/2018
Vertical Farms Tended By Robots To Make Harvesting More Efficient
- MARK BLUNDEN August 17, 2018
Clapham underground is home to 'Growing Underground', the UKs first underground farm. ( Getty Images )
Vertical urban farms tended by robots that grow vegetables — and even rear chickens, fish, and lobsters — in hundreds of stacked boxes have been designed by online grocer Ocado.
It has drawn up plans for a “mechanized growing system” to rival existing projects by London salad farmers, such as one at Clapham North Tube station.
According to a European patent, Ocado’s intensive warehouse system could grow plants using LED lights, and its stacking concept would do away with “large areas of land” normally needed for crops such as herbs.
The patent even suggests that in addition to fruits and vegetables, Ocado’s system could battery-farm “living organisms” such as poultry and fish.
The firm believes “vertical farming” will be cheaper, more efficient, higher-yielding and need fewer people than traditional methods. Produce would be grown in trays inside stacked boxes tended by wheeled, wifi-connected robo-pickers on rails, which winch up the trays when the produce is ripe and dispatch them to another robot for picking and packing.
Robots would also be used for planting, pruning, and spraying pesticides. The patent shows two levels of about 300 growing containers, each about 1m wide by 1.4m high, which would be supplied with water, fertilizer, light, and heat.
Each tray would be tall enough to “allow the plants to grow to their natural harvesting height”, the patent says, and the boxes could be stacked 20m high or more. The patent says growing the plants upside-down, lit from below, “would reduce the energy expended by the plant to move water and nutrients against gravity and may make some species grow faster”.
The idea is based on an automated system used in Ocado’s warehouses.
Dr Nick Palmer, of Compassion in World Farming, said he was “extremely worried” that Ocado envisaged raising fish, chickens, oysters, and lobsters in the system. He said: “A factory farming system where animals are likely to be crammed together with little space, natural light or stimuli would be a step backwards.”
Why You Should Hope Your Next Tomato’s Grown Indoors by Robots
Why You Should Hope Your Next Tomato’s Grown Indoors by Robots
Kevin Maney is a journalist, author, and advisor. His most recent book, written with Hemant Taneja, is Unscaled: How AI and a New Generation of Upstarts Are Creating the Economy of the Future.
If you were inventing the farm today, why would you put it outside, on a giant plot of land?
OK, there’s the sunlight thing, but then you get droughts and frosts and plant-munching insects that have to be battled with harmful pesticides. And because outdoor farms need so much acreage, they’re usually far from most of their customers — which means that by the time a tomato gets to you in a city, it tastes like a baseball.
But now, upstarts such as Bowery farming, AeroFarms, and Lettuce Networks are doing something different. They’re growing food indoors. They’re using data and artificial intelligence to operate more efficiently than traditional farms. And they’re staying small and close to population centers. The new generation of farming promises to feed more people while doing less environmental damage.
Photograph by AeroFarms
This kind of distributed farming fits with a larger 21st-century movement that venture capitalist Hemant Taneja and I call “unscaling.” We document the economic trend in our book, Unscaled: How AI and a New Generation of Upstarts Are Creating the Economy of the Future.
Massive scale was the goal throughout the 20th century. Mechanization and technologies such as the truck and telephone made it possible. Mass production, mass markets, and economies of scale ruled in every sector. So we ended up with giant companies, huge hospitals, big universities — and corporate mega-farms.
Today, industry after industry is unscaling. The cloud, mobile devices, big data, AI, and new technologies such as blockchain and 3D printing are making it possible to profitably customize products for smaller and smaller niches. Netflix is an unscaled version of mass-market cable networks like HBO, using data to make programs that appeal to specific types of viewers. Airbnb is a distributed hotel company. In an unscaled era, businesses can operate at smaller, more focused levels and beat giant enterprises.
So farms are unscaling, too. Bowery and AeroFarms both operate inside old industrial buildings in New Jersey and are a short drive from New York City. Inside these buildings, LED lights mimic natural sunlight. The crops grow in nutrient-rich water beds on trays stacked floor to ceiling. And sensors constantly monitor the plants and send data back to AI-driven software, which can learn what’s best for the plants and tweak lighting, water, and fertilizer to improve yields. Much of the “farming” is done by robots. “We get productivity hundreds of times greater than a traditional farm,” says AeroFarms CEO David Rosenberg. “And we use less water and no pesticides — because we’re indoors — and can grow 365 days a year.”
These unscaled farms can give consumers a better product than mega-farms, too. Food grown nearby doesn’t need to endure shipping — so it can ripen the way it’s supposed to. In the middle of winter, indoor-grown, local tomatoes will taste like tomatoes. As you can imagine, that’s what consumers prefer.
Photograph by AeroFarms
Since 2013, about US$2 billion has been invested in hundreds of agricultural technology startups, according to CB Insights senior analyst Zoe Leavitt, who spoke about the future of food at a recent Techonomy conference in New York. AeroFarms has raised more than $100 million and sells to Whole Foods and FreshDirect.
Boston-based Freight Farms is growing food in container cargo vessels, often selling to restaurants, hotels, and college campus eateries. New York-based BrightFarms says it “finances, designs, builds, and operates” indoor farms close to food retailers and has raised $11 million in funding. Edenworks is operating rooftop greenhouses that grow produce fertilized by ground tilapia and prawns, which are also grown at the mini-farm.
Lettuce Networks is trying another approach. It is using cloud and mobile technology to create a network of urban farms. Founder Yogesh Sharma calls it an Airbnb for farming. The company contracts with owners of small plots throughout a city and installs sensors that can monitor crops and the surrounding environment. Nearby residents can subscribe to the Lettuce service to get food delivered. The system knows what’s being grown all around the city and, from that network, assembles a basket of local produce for delivery. Owners of the plots make some money off their harvest, while subscribers get an assortment of fresh food grown nearby.
In an unscaled era, businesses can operate at smaller, more focused levels and beat giant enterprises. Distributed, indoor, AI-assisted farming should be good news for the environment. Scaled-up farming was the right answer for the past century, feeding a burgeoning population while making food relatively cheap. The percentage of disposable income used for food is lower today than it was in the 1970s, according to Pew Research Center. But by 2050, the planet is projected to have 2.2 billion more people to feed, just as global warming is expected to make weather less predictable and dry up previously fertile regions. If food can be grown indoors, in a cost-effective way, in or near cities, climate will be less of a concern, and far less carbon will be burned moving food thousands of miles via trucks, trains, and ships.
Whether unscaled farming is a net economic benefit remains to be seen. It’s a new industry, with techniques and business models that are works in progress. Analyst firm Market Research Future notes that urban farms cost a lot to start (a warehouse in New Jersey is more expensive than a plot of land in Saskatchewan) and don’t yet work for a lot of crops, such as corn or bananas. Sunlight is free and sustainable; LED lights require energy. But proponents believe that because these indoor farms are far more productive and are closer to consumers, once there are a lot of them and the techniques and technology get honed, more people will be fed for less cost than ever before.
As investment pours in and environmental conditions drive a need for new solutions, unscaled farming looks a lot more like the future of food than does a massive field baking under the sun.
Topics: agriculture, artificial intelligence, carbon, green technology, startups, sustainability, technology
African Agtech Market Map: 99 Technologies Changing the Future of Agriculture in Africa
African Agtech Market Map: 99 Technologies Changing the Future of Agriculture in Africa
FEBRUARY 14, 2018 LINA BELMAACHI
Editor’s Note: Lina Belmaachi is cofounder of The Seed Project, a non-profit think tank. The team spent time on-the-ground in Africa in order to do a diagnosis and identify pain points across the agricultural value chain before heading to worldwide innovation hubs to meet with start-ups and select the solutions best adapted to African specificities. Their goal is to contribute to the African agricultural progress towards a system with optimized resource allocation through technology. Here Belmaachi organizes 99 African Agrifood technologies.
There are seven billion people on the planet and more than one-quarter of them suffer from malnutrition, mostly in South Asia and sub-Saharan Africa. By 2050, the global population is expected to reach 9 billion people and the number of under-nourished children to increase by 25 million. We are now facing one of the biggest challenges of this century – how can we feed all these mouths?
Innovative solutions need to be implemented and technology and information sharing can help produce enough food and correctly distribute it around the planet.
The African continent has huge potential with 60% of world’s non-cultivated arable lands but still spends $25 billion annually on food imports. Africa could play a major role and take on future food challenges, yet it needs to leapfrog the innovation gap with other continents to produce enough food for its own population and work toward becoming a food exporter.
Even though African farmers are attached to their traditions and quite reluctant to change, they are not immune to the technology revolution. Just like in the banking industry, where mobile money technologies have become pervasive regardless of the quasi-inexistent banking system, agriculture must follow suit.
Coming back to the basics of agriculture, farmers essentially have four main access challenges:
- Financing & Insurance
- Resources (inputs, equipment, labour)
- Knowledge & know-how (business and agronomic)
- Market (logistics, commercialization, transformation)
A representative and non-exhaustive selection of these companies have been visualized in this African Agtech market map, into nine categories by AgFunder and The Seed Project.
Financial Services
Financial services are not intuitively linked to agriculture, but they have a crucial role to play for African farmers. Smallholder farmers are seen as high-risk profile clients, dependent on climate, and with no collateral. This, combined with the lack of credit and risk-scoring capabilities, turns loan and insurance application processes into real hurdles for farmers. Different types of financial solutions are thus arising, such as:
- Micro-banking, with Oradian (Nigeria)
- Micro-insurance, with Mobbisurance (South Africa)
- Transaction services, with M-Pesa (Kenya)
- Data analytics for risk scoring with Acre Africa (Kenya) and credit scoring with Farm Drive (Kenya)
Ag Biotech Inputs
Farmers are using inputs (seeds, fertilizers, and pesticides) that are environmental detractors and not suited for their lands given their underdeveloped agronomic knowledge. There is room for start-ups to use advances in biotechnology such as plant breeding, gene editing, biologicals or microbiome research in order to propose more sustainable and efficient input solutions.
Wanda Organic is a Kenyan start-up providing organic bio-fertilizers to small and medium-sized farmers in order to improve their soil health and yields. Clients can order products by sending a simple SMS with their phone. Another company, InteliSeed from South Africa, partnered with Syngenta to provide farmers with optimized seeds that can offer them an butter output and quality for their crops. They are focused on vegetables, oil, and legumes and are starting to look at new varieties.
Resources Access
Smallholder farmers are operating on just a few acres of land, yet represent 80% of the food production in Africa. They are dispersed, landlocked and limited in cash, thus making it extremely difficult to access inputs or equipment. Marketplaces and sharing platforms aim at giving farmers the production tools they need.
Esoko is an information and communication service for agricultural markets in Africa that recently launched Tulaa, a marketplace for inputs. It combines mobile technology and last mile agent networks to connect input suppliers, financial service providers, and commodity buyers to smallholder farmers.
Apart from inputs, access to natural resources (i.e. water and energy) is a prerequisite for farming activity. Efficient management solutions are necessary to limit costs and waste. SunCulture, a start-up in Kenya is proposing an innovative solution. Their AgroSolar Irrigation Kit is a solar-powered irrigation system – a solar water pumping technology and a high-efficiency drip irrigation, bundled with a “pay-as-you-grow” financing service launched in 2016.
Farmers’ knowledge
With better agronomic practices and knowledge on value-add operations, farmers could obtain higher yields and better quality products. Yet the current farming system is based on traditional practices relayed from father to son. How can these isolated villagers have access and adopt best farming practices? This effort is commonly done by NGOs but a few other actors are also entering the field. For instance:
- Ojay Greene (Kenya) offers training, advisory services and market access for underserved smallholder farmers;
- ICT4Dev (Côte d’Ivoire) integrates ICT solutions for farmers’ problems through platform design, web management tools, mobile, SMS and voice;
- AgroSpaces (Cameroon) is a networking site connecting agricultural communities to share information and form valuable connections.
Farm Management Software, Sensing & IoT
As the saying goes, “what you measure, you optimize”. Farmers are operating in uncertain environments and are eager to obtain smart recommendations. UjuziKilimo is a Kenyan company that utilizes data science and machine learning to provide actionable agronomic insights to farmers. Data on soil and crops are obtained with sensors and farmers can get real-time information and advice by SMS. Sokopepe is another Kenyan startup offering market information and farm records management services through FARMIS, a farm management and diagnostic tool and SOKO+, a digital commodity trading and information system, linking small-scale farmers to end retailers and bulk purchasers of produce.
Farm Robotics, Mechanization & Equipment
Startups are working on automating many repetitive, tiring tasks in order for farmers to save time and energy. A good example is DroneScan, specially-designed drone attachments that can take inventory in food storage facilities and provide live feedback. The Institue for Grape and Wine Sciences is also working on a robot in South Africa for data gathering purposes on vineyards.
Midstream Technologies
Nowadays, consumers are increasingly looking at the life of products from “farm to fork” — they want to know the story behind the product. This is a great challenge in Africa, where logistics can be very tricky. Some Agtech start-ups are laying the foundation for a leaner supply chain, including quality testing devices, sensors for products’ traceability and safety, and smart logistics. iProcure is the largest agricultural supply chain platform in rural Africa. In addition to complete procurement and last-mile distribution services, the Kenyan company provides business intelligence and data-driven stock management across the supply chains. AfriSoft is a technology and software solutions provider in South Africa that addresses challenges such as warehouse management, quality, traceability and production tracking.
AgriBusiness Marketplaces
In Africa, the food supply chain is highly dependent on middlemen that take advantage of smallholder farmers given their limited market connectivity. Margins are then split between all these intermediaries, to the detriment of farmers. Some companies thus enable farmers to sell their products online, reaching final customers and increasing their revenues. M-Farm is a Kenyan startup providing a platform to connect farmers directly to buyers and inform them of price trends to optimize planting and harvesting timing.
Novel Farming Systems
The decreasing percentage of arable lands along with increasing pressure of climate change calls for more sustainable processes to produce food with fewer resources. The most well-known alternative to current farming systems is indoor farming, by growing produce in high-tech greenhouses and automated vertical farms. This includes aquaponics and hydroponics along with production facilities for new living ingredients such as insects and algae. Fresh Direct Nigeria brings fresh premium organic produce closer to market with their container farm technology. Using hydroponics and vertical farming within a shipping container, the company is able to grow directly in urban areas.
Using fly larvae fed on existing organic waste, AgriProtein from South Africa has developed and tested a new large-scale and sustainable source of natural protein.
Africa has the potential to turn into the breadbasket of the world, but the way is still long and arduous. Bright minds should keep looking for solutions fitted to the needs and adapted to the African context. As pointed out by Sudanese billionaire and philanthropist Mo Ibrahim, “This is neither a good time for Afro-optimism nor for Afro-pessimism! Africa needs to move towards Afro-realism.”
Four Growers: Farming For The Future
Four Growers: Farming For The Future
Senior mechanical engineering major Dan Chi promotes Four Growers, a company started by Chi and his friend Brandon Contino that is devoted to creating tomato-harvesting robots to work in greenhouses. (Photo courtesy of Karen Woolstrum)
BRIAN SALVATO | Staff Writer
February 13, 2018
Imagine being able to open a door and go from biting winds and snow to a warm, climate-controlled greenhouse that carries the aroma of fresh tomatoes — being harvested by robots roaming through the aisles.
For Brandon Contino and Daniel Chi, this fantasy is turning into a reality through their company Four Growers, as they aim to develop automated tomato harvesting robots to work in greenhouses.
Contino, CEO of Four Growers and a Pitt 2016 alumnus, takes the spokesperson role for the company, while senior mechanical engineering major Chi focuses on the technical side. The idea developed in April of 2017 when Contino and Chi began talking to tomato growers and associations.
“Dan and I knew we wanted to do something in an indoor farming or hydroponic growing place, so we decided to learn from those who were successful at it,” Contino said.
The two saw firsthand the issues facing modern-day tomato growing when they had their first greenhouse visit a month later with MightyVine — a sustainable tomato growing company in the Chicago area. These issues include weather variability, crop loss and population growth.
Contino’s conversation with the tomato growers made it clear that greenhouses are becoming the future of produce farming. The pair say greenhouse growing is more sustainable, versatile and efficient than traditional farming.
“They require 90 percent less water and provide consistent, yearlong, local, high-yield production with near-zero herbicide and pesticide use,” Contino said. “In fact, over 50 percent of fresh U.S. tomatoes are greenhouse grown.”
Despite the advantages greenhouse farming can provide, Contino said the largest limiting factors growers face are the cost, accessibility and reliability of their labor force.
“There are increasing shortages in workers, and the workers that they are able to find are inconsistent,” Contino said. “Growers desperately need automation to keep providing healthy, local produce at competitive rates.”
This is where Contino hopes Four Growers can provide a solution. Once fully developed, Contino said the automated harvesting robot could replace the role of a human.
“The tomato harvesting robot is able to go down greenhouse aisles, accurately identify ripe versus unripe clusters, harvest them from the plant without damaging them and place them in a cart to get sent back to the packhouse,” Contino said.
The robot — according to Contino’s estimates — will be able to harvest as much as a human, but do it more consistently at a lower cost.
While implementing robots could be more efficient, Four Growers also had to consider what it would mean to replace human labor. But they say that their robot would enable farmers to expand labor resources.
“By enabling this industry we’ll be able to increase the amount of fresh, … pesticide free, local produce greenhouse farms can produce,” Contino said. “It’s a win for the consumer, the greenhouse and the worker.”
So far, the company has developed a vision system for the robot that allows it to learn using artificial intelligence as it works. The two are currently refining a prototype, which they hope to test at major greenhouses.
“We are working with six different farms who wish to beta test our robot, and these farms collectively represent 20 percent of the U.S. and Canadian greenhouse tomato acreage,” Contino said.
For Contino and Chi, reaching the next stage is possible with continued support from Pitt’s Innovation Institute. Susan Dorff — manager for student programs at the Innovation Institute — worked alongside Four Growers since their inception. She said the company became involved with the Institute through student programming.
“We help [students] practice, learn, compete and get funding to continue with their idea,” she said.
Four Growers has been involved with several of the Innovation Institute’s programs, as well as competitions such as the Randall Family Big Idea Competition — an experience-based learning opportunity for Pitt students with big ideas that offers $100,000 in cash prizes.
Babs Carryer — the director of education and outreach at the Innovation Institute — said she has noticed distinct qualities in Contino and Chi’s approach between now and when she first met them.
“I think that the entrepreneurial lead is really important. I view Brandon [Contino] as sort of the driver of this project,” Carryer said. “A lot of student projects don’t quite have that strong a driver. Brandon’s really committed to doing this.”
Carryer said she was amazed by the amount of customer discovery the duo had done and the interest from tomato growers they received. Usually, Carryer sees entrepreneurs get nonspecific, general interest from companies that acknowledge their idea but never move beyond that. She believes the difference in Four Growers is their passion.
“They haven’t just been sitting on their laurels thinking about this. They’ve been actually out there really doing the deep work that’s necessary to advance an idea towards reality,” Carryer said.
As with any early product, there are still more hurdles on the road to completion. Carryer pointed out the challenge of realistically getting a robot to consistently harvest tomatoes without a problem, as well as Four Growers likely having to expand their team as their idea grows. Nevertheless, she believes in what Contino and Chi can do.
“I think they should be one of our leading student spinout companies, and I can’t wait to keep working with them on that,” Carryer said. “They definitely have what it takes.”
Q&A: Driscoll’s Head of Emerging Technology On Harvesting Robotics and Open Innovation
Q&A: Driscoll’s Head of Emerging Technology On Harvesting Robotics and Open Innovation
FEBRUARY 7, 2018 EMMA COSGROVE
As head of R&D strategy and emerging technology at Driscoll’s, Nolan Paul has a unique view of the agtech startups in the specialty crop space.
The global berry seller has become known for its technological innovation in breeding and genetics, but the company’s focus on robotics is less well-known. Paul told AgFunderNews that Driscoll’s wants to support the development of automated strawberry harvest and is in contact with many if not all of the startups working in this area of robotics. That interest has led to investments in Harvest CROO and Agrobot and field trials with more.
Strawberry growing is long overdue for a shake-up and stakeholders know it. Robotic harvesting technologies are not quite ready for wide use. Labor is becoming more scarce as immigration uncertainty in the US continues and also because strawberry picking at ground level is a particularly grueling task. Some growers, inside and out, are raising up growing surfaces to waist-height to mitigate these issues and Driscoll’s is in the position to help and encourage its growers to keep up with the times.
We caught up with Paul ahead of the World Agri-Tech Innovation Summit, where he’ll play the shark in several startup pitch presentations, to discuss how Driscoll’s works with startups and lessons learned while trying to determine the future of strawberry growing.
Driscoll’s is constantly testing and verifying technologies, but can growers afford to make major investments in technology right now?
Nolan Paul
It depends on what we’re talking about. The startups are recognizing that this is an issue and moving to a service model where you de-risk the technology for the grower base. They’re not going to have to pay a half a million dollars for a piece of equipment. But at some point, we come in. I think it’s not going to be as simple as just the robotics, let’s say, for harvest. It’s a combination of the robotics and the growing system and actually the genetics too. In that combination of all three is where you’ll really see the success. So Driscoll’s will come in, certainly on the breeding, on the genetics side, we’ll optimize for traits like mechanization. But on the growing system too, we’re supporting our growers with that, we help them out. And of course, we’re dedicated to investing in the development of ag technologies on behalf of our growers.
What is your assessment of the harvesting robotics field? Are outdoor growers transitioning to waist-height tables as well as indoor growers? And does that mean that harvesting machinery could work indoors and outdoors?
The good news is that the last couple years have seen a crop of harvesting startups pop up. Honestly, I doubted that would happen so quickly but I’m glad I was wrong. So today Driscoll’s is currently in active conversations with six automated strawberry harvesting startups. And they’re all taking a unique approach, which is great.
The challenges are certainly different. I think when you look at the visioning systems, that will be the same, but the robustness, the durability, and the scale will be different. And I think that’s what we’re seeing — some startups perhaps don’t appreciate the scale that will be required for outdoor farms in the US. If you’re growing in a greenhouse or a glasshouse, you know that’s one thing. But when you need to be out on a 100-acre ranch, those robots, those harvesters need to cover a lot of space and it’s probably not a reasonable thing to assume that you can just have a bunch of these robots going through a field. It’s hard for a grower to manage that. So I think there is a certain fleet size that can only be so big.
I think that’s something we’ve found that perhaps some of the startups haven’t looked at. And I don’t think you’ll just see one winner, I think you’ll see different solutions going into indoor farming whether that’s greenhouse or glasshouse or vertical farm and solutions for outdoors. I think the ones that are successful have the vision to scale from strawberries to other crops and perhaps indoors that’s easier to do. I think that’s a big deal. I’m still skeptical that harvesting robots are going to be successful if you just focus on one crop. And that’s really where we want to work with the startups, to help them understand that narrative, so they’re able to raise VC money.
That’s fascinating coming from you. It seems like Driscoll’s has done a pretty good job of making a big market for strawberry technology.
Yeah, it’s an interesting space. We’ve certainly recognized in the last three years how we engage with startups has to change because there are a lot of people who give them lip service. But what we’ve realized is you have to really be structured the right way. It’s not even about the money — there’s plenty of money. You need people who can work alongside these startups and move at the same speed.
It’s easy to go pitch ideas to a CEO, but to actually execute on them is really tough. And certainly we’re learning and getting better at it. Some of these large companies almost want to own what the startup is doing – to have a competitive edge. A lot of times, unless you’re really big, it just doesn’t work and you almost end up killing the startup.
Why doesn’t it work?
Well, I think most of the companies aren’t big enough to justify exclusivity — certainly not in the specialty crop space. It’s a very high, high-value space, but we’re fragmented. There are a lot of one to five billion dollar crops in the US across grapes, strawberries, nuts, and vegetables. But in and of itself it’s not big enough for a startup to scale. It’s important for folks to focus. But you have to have the vision of how you’re going to scale. The right strategic corporate can be a good partner for startups. But they need to recognize that, if you’re working with a startup it’s great that you’re an anchor customer, but you want the startup to be around in two, four, six, 10 years. And the only way they’re going to be around in six to 10 years is if they’ve been able to scale up and either be acquired or maybe, they have to create that scale themselves. I think people are too short-term when they interact with startups.
Canon Electronics Plans Full Automation At Vegetable Factory
The Canon unit will convert empty space at a Gunma Prefecture facility into an indoor farm initially dedicated to growing lettuce and other green, leafy vegetables friendly to hydroponics.
December 28, 2017
Canon Electronics Plans Full Automation At Vegetable Factory
Robots may bring lower costs crucial to profit in growing but finicky sector
At this Gunma Prefecture plant, Canon aims to turn empty space into a roboticized indoor farm.
TOKYO -- Canon Electronics plans to open an entirely automated vegetable factory in 2019, seeking to lower costs by applying homegrown robotics technology to a burgeoning industry where stable profits remain tough to cultivate.
The Canon unit will convert empty space at a Gunma Prefecture facility into an indoor farm initially dedicated to growing lettuce and other green, leafy vegetables friendly to hydroponics. Robots will handle everything from planting seeds and transplanting seedlings to harvesting and packaging crops for shipment. Details such as annual production scale and sales targets will be settled later.
The company will partner with other businesses for know-how on managing the factory and building sales networks. Canon Electronics is also considering building a second such factory in western Japan.
The unit makes some of the manufacturing machinery on the automated production lines in Canon's domestic camera business. Its delicate automation technology from that precision machinery will be put to use developing green-thumbed robots for the company's new factory plan.
Japan had 197 plant factories using artificial light as of February, roughly triple the count in 2011, a survey by the Japan Greenhouse Horticulture Association shows. But production costs run high at such factories, driving up retail prices and making it hard to turn steady profits. In 2016, 37% of the factories operated in the red, the association reported.
Those losses recently led some companies to back out. At the end of 2016, Toshiba closed one such facility in Kanagawa Prefecture. And in 2015, an agricultural startup and plant factory manager based in Miyagi Prefecture went bankrupt under a debt burden of 1 billion yen ($8.81 million at present rates).
Canon Electronics intends to wield its automated production to make operations profitable. Some domestic plant factories automate seed-planting or other processes, but virtually none are automated start to finish. Agricultural startup Spread is building a fully automated plant factory in Kyoto Prefecture, set to begin operations in summer 2018.
(Nikkei)
Tortuga AgTech Raises $2.4m Seed Round for Indoor Ag Robotics
BREAKING EXCLUSIVE: Tortuga AgTech Raises $2.4m Seed Round for Indoor Ag Robotics
DECEMBER 4, 2017 EMMA COSGROVE
Tortuga AgTech, a Denver-based robotics startup targeting controlled-environment fruit and vegetable growers has raised a $2.4 million Seed round.
Tortuga Agtech is developing robotic systems for harvesting fresh produce in controlled environments, from indoor hydroponics to greenhouses, starting with strawberries.
“Our products will enable advanced growing methods to compete with scale agriculture, which means growers will be able to grow better produce that’s also better for the planet,” says the company’s website.
The round was led by early-stage hardware VC Root Ventures and closed in September. Root Ventures is also an investor inMomentum Machines, San Francisco’s burger-making robot company, which raised $18.4 million in June.
Also participating in this round were Silicon Valley tech VCs Susa Ventures and Haystack, data-focused firm AME Cloud Ventures, AI and robotics VC Grit Labs, the Stanford-StartX Fund and SVG Partners, which runs the Salinas Valley-based Thrive Agtech Accelerator. AME Cloud is also an investor Zume Pizza, a pizza delivery company in the Bay Area with a robot for a chef, which raised $48 million in October.
Harvesting of row crops has been automated for decades, but harvesting of specialty crops, like nuts, fruits, and vegetables, remains an elusive skill for farm robotics startups. Not only do these crops vary greatly in size, height, and color, they can also be more delicate and require not just a light touch in picking, but immediate assessment and packing by size or quality.
Though high-tech indoor agriculture is ripe for robotics interventions because of the easier and more stable working conditions compared to the field, not many robotics startups have emerged servicing this kind of growing.
Spread is a Japanese indoor vertical farming company that will open an automated lettuce farm in early 2018 allowing for a 50% reduction in human labor, according to the company. Transplanting seedlings, managing the growth process, and harvesting will all be automated, according to the company’s website.
South San Francisco-based vertical farm Plenty’s CEO told Business Insider that the company uses tiny robots in its seeding process. Though the company is not yet commercially growing strawberries, CEO Matt Barnard told AgFunderNews this is in the works.
Most operating vertical farms today are growing only leafy greens and microgreens due to the short growing cycles and high yields. There are just a few growing strawberries such as Japan’s Ichigo Company.
Greenhouses, however, are gaining market share of strawberry cultivation worldwide. Though greenhouse-growing of strawberries in the US has not yet taken off, 24% of strawberries grown in the Netherlands, the worlds second-largest exporter of food (by value) grow in a greenhouse according to the Dutch Central Bureau of Statistics.
Also working on harvesting strawberries, but in outdoor environments, are Agrobot and Harvest Croo
This Robot Handles The Entire Process Of Growing Lettuce By Itself
This Robot Handles The Entire Process Of Growing Lettuce By Itself
By Adele Peters/ Nov 30, 2017
A new indoor farming startup called Iron Ox wants to staff its greenhouses with only automated workers.
[Photo: Iron Ox]
Inside a warehouse in the middle of the suburban office sprawl of San Carlos, a Silicon Valley town south of San Francisco, hundreds of heads of lettuce and herbs grow next to a mobile robot designed to move the plants as they get bigger. In a lab next door, engineers tweak robots that can handle every part of the growing process, from planting seeds to packaging harvested heads of lettuce for a grocery store.
By early 2018, Iron Ox, the startup behind the R&D farm, plans to open an 8,000 square foot production farm nearby–all fully automated, in a system that the company says can make local, pesticide-free food production as cheap as traditional agriculture in the field.
[Photo: Iron Ox]
When the co-founders decided to launch the startup, one was working on delivery drones at Alphabet’s X, and the other was building room service robots for hotels. They liked the work but wanted to do more with the available technology. “Robotics has come so far in the past few years–sensors have gotten cheaper, software has become more robust,” says co-founder and CEO Brandon Alexander. “We felt that we could be doing something with more impact.”
[Photo: Iron Ox]
They saw an opportunity in food production, where traditional farming faces multiple challenges. Most lettuce, for example, is grown in California and Arizona, two states that face an increasing risk of water shortages and stress from heat as the climate changes. A head of lettuce may be treated with nine different pesticides before it’s harvested and then shipped hundreds or thousands of miles across the country to consumers. As fewer people want to work on farms, producers also struggle with labor shortages.
Indoor farming, which uses a tiny fraction of the water and space, doesn’t require pesticides, and can happen within cities or suburbs, is often billed as a solution. But as Alexander and co-founder Jon Binney researched the market, they realized that cost was a challenge. “We loved the idea [of greenhouses],” Alexander says. “But our question was, if this is so much better, why is most produce grown outdoors? The biggest thing we found was that it costs significantly more–at least twice as much–to grow a head of lettuce indoors than outdoors.”
Other companies, such as Plenty–another farming startup based in Silicon Valley, which grows greens in vertical towers and recently raised $200 million in funding–say that it can produce lettuce at a cost that is competitive with traditional farms. Plenty uses a layout that maximizes yield in small spaces, and notes that the cost of key components for growing, like LED lights, have dropped dramatically. But Iron Ox’s approach is to focus on removing another cost: labor, which for some growers, can account for 50% of the cost of production.
Some greenhouse-grown lettuce might cost $3.99 now, versus $1.99 for the same head of lettuce from the field. “At the end of the day, if you’re always going to have to cost more, then you’re going to be this niche product,” says Alexander. “For the impact that we’re after, one of the biggest things for us is we need to make this produce accessible. Accessible doesn’t just mean affordable–that’s part of it–but it’s affordable and available. Ideally to everybody.”
In the company’s system, a robotic arm plants seeds in a tightly-packed tray, where the seeds germinate in nutrient-filled water. As the plants get bigger, the arm can transplant them to a tray with more space, and then transplant them again a couple of weeks later. Moving the plants maximizes the number of plants that can grow in a tight space.
The robotic arm also uses a camera to scan each plant and note any problems. “We can actually observe is it the right size, is it the right color, does it have any pest pressure or mildew or anything like that,” he says. Plants with mildew, which can easily spread, can be automatically removed. The robots can use machine learning over time to optimize how the plants are grown.
[Photo: Iron Ox]
The new production farm won’t be the first to grow lettuce with an automated system; a massive new factory in Japan uses robots to grow millions of heads of lettuce a year. But the new system in Silicon Valley is less like a traditional factory, and more flexible.
“That [Japanese farm] works well for a set process: ‘we’re going to grow this type of lettuce in this way, and we’re going to do that for the next 20 years,'” Alexander says. “We try to go with as little infrastructure as possible. All we really need is a concrete floor, at the end of the day. All of our modules, these hydroponic pallets, are portable. We have a mobile robot.” If the company later wants to use a slightly more efficient layout, or change its operation, it can make those changes through software.
As the first production farm in San Carlos scales up, the startup will sell to local chefs with an interest in the company’s sustainability; once output is high enough, it will sell to grocery stores. Ultimately, the company envisions building farms near consumers across the country, so someone shopping at a grocery store in Atlanta no longer buys week-old greens from California. It also plans to expand to other crops.
“We don’t want to be just a leafy green farm, at the end of the day,” says Alexander. “That is our initial focus–we want to nail that, we think that’s important to solve– but with our approach, this robotic system, we would like to be a fresh produce farm.”
The Hydroponic, Robotic Future of Farming in Greenhouses
Here in 2017, the automation revolution in agriculture is poised to take on a whole new life—thanks to robots. In a nondescript office park in Silicon Valley, a startup called Iron Ox is taking the first steps toward roboticizing greenhouse farming, which has so far stubbornly resisted automation.
The Hydroponic, Robotic Future of Farming in Greenhouses
WHEN YOU THINK of automation, you probably think of the assembly line, a dramatic dance of robot arms with nary a human laborer in sight. But that’s child’s play. The grandest, most disruptive automation revolution has played out in agriculture. First with horses and plows, and eventually with burly combines—technologies that have made farming exponentially cheaper and more productive. Just consider that in 1790, farmers made up 90 percent of the US workforce. In 2012, it was 1.5 percent, yet America still eats.
Here in 2017, the automation revolution in agriculture is poised to take on a whole new life—thanks to robots. In a nondescript office park in Silicon Valley, a startup called Iron Ox is taking the first steps toward roboticizing greenhouse farming, which has so far stubbornly resisted automation. In the very near future, then, the salad on your table may come from the hand of a robot.
Unlike a lot of indoor farming operations, Iron Ox isn’t joining the booming movement of LED-powered grow houses. It’s still very much interested in harnessing the energy of the sun (free energy!). So it’s invading the greenhouse instead. “The problem up until today is that greenhouse production costs around twice as much to grow a head of lettuce as the outdoor farm,” says Brandon Alexander, CEO of Iron Ox. “And one reason is there's no tractors or anything indoors.”
Iron Ox doesn't have a tractor, but it also doesn't need one. Its solution begins with a custom hydroponics tray filled with nutrient-rich water. Over that is a cover with a grid of holes, in which the plants sit in little pods. This is all designed so a custom robot—essentially an intelligent rectangular frame—can come along and slide lifters under the tray, then cart it to a different part of the greenhouse.
Why bother with all the shuttling around? Because they can. Out in a field, farmers have no choice but to leave plants where they planted them—and because plants grow, farmers have to space out seeds to accommodate their fully-grown dimensions. But Iron Ox doesn't have to waste that extra space.
Here in the greenhouse, they’re using different trays with different spacing of their holes, some farther apart than others. Leafy greens, in particular, need more horizontal room to expand, so baby plants start off in a more densely packed tray, then graduate to trays with more room as they grow. “This, combined with the fact that we don't have to worry about seasonality—we can always be seeding, always be harvesting—allows us to grow over 30X per acre compared to an outdoor farm,” says Alexander.
The problem then becomes transplanting between trays. That’s where the robotic arm comes in. It sees with stereo cameras on its wrist and grabs the plants with a gripper custom-designed to fit the pods (which the plants never outgrow, by the way). The arm sits between two trays of different densities, eyeballing the plants and moving them from one tray and to another.
Because it’s equipped with a camera, it can simultaneously build a 3-D image of each plant. “Is it the size that we expect?" says Jon Binney, CTO of Iron Ox. "Is it the shape that we expect? If it's going to fall one way or the other, that could be a lighting problem. Brown spots on the edges of the leaves could be too much light and not enough air coming through.”
So Iron Ox’s system not only automates greenhouse growing but supercharges it. The company is developing machine learning algorithms that will automatically detect diseased plants and kick them out of the system before the sickness spreads. Underdeveloped plants would also get the boot. What you end up with is a system that does the repetitive tasks of greenhouse farming faster and more precisely than a human, and uses that data to make the process all the more efficient.
Whether in the greenhouse or the field, it’s this kind of automation that will be essential to the future of humanity. Our species has to figure out how to feed a rapidly growing population on a planet that refuses to grow bigger. So we’ll have to get smarter about how we use the land we’ve got, or we’re going to have trouble. That and climate change will monkey with water supplies around the world, so the inefficiencies of traditional outdoor farming are going to start looking more and more untenable. (Iron Ox claims its hydroponics system uses 90 percent less water than outdoor farming. Studies of hydroponics, in general, have found about the same efficiencies.)
But automation means humans lose jobs though, right? Not in this industry. “We've talked to dozens of commercial farmers, outdoor and indoor, and the biggest issue by far is labor scarcity,” says Alexander. “So the truth is today, it doesn't matter what country, newer generations are not taking up farming. And so there's a significant labor shortage especially here in California.” (He ain’t lying— between 2002 and 2014, the number of full-time farm workers in the US plummeted by 20 percent.)
The solution is to hand the future of our food supply to the machines. There’s simply no other way to go about it. So be careful not to bite the robotic hand that feeds you.
Startup Iron Ox Mixes Robotics and Hydroponics to Futurize Farming
Silicon Valley-based startup Iron Ox is utilizing autonomous robotics to fundamentally change the nature of greenhouse-based agriculture. While the exterior of the Iron Ox greenhouse in San Carlos, California is far from remarkable, the cost-cutting integration of hydroponics, solar energy, robotics, and space-conscious farming is more than noteworthy.
Startup Iron Ox Mixes Robotics and Hydroponics to Futurize Farming
Photo Credit: Jirakan Jiherb/123RF
Silicon Valley-based startup Iron Ox is utilizing autonomous robotics to fundamentally change the nature of greenhouse-based agriculture. While the exterior of the Iron Ox greenhouse in San Carlos, California is far from remarkable, the cost-cutting integration of hydroponics, solar energy, robotics, and space-conscious farming is more than noteworthy.
Iron Ox
By using autonomous robots to plant, seed, water, and even harvest their hydroponically grown crops, Iron Ox’s system provides uniformity and rapidity which conventional, human-centric farming methods can’t match. Iron Ox greenhouses’ daily harvesting and proximity to urban centers, grocery stores and produce suppliers diminishes the nutrient loss and often bland taste which results from produce being shipped hundreds or thousands of miles from farm to store.
Founders Brandon Alexander, a former Google X engineer and John Binney, who holds a PhD in robotics, check all the boxes when it comes to consumer demand for non-GMO, pesticide-free produce. Alexander, Iron Ox’s CEO, is uniquely qualified as the leader of this farming revolution. His work on Google’s Project Wing included exploring and implementing ways for autonomous robots to work in combination. With the proper technology in place, Alexander estimates that set-up of one of Iron Ox’s urban greenhouses takes only three to four months, on average.
Luiz Ribeiro Ribeiro/123RF
The master plan is to expand Iron Ox greenhouses manned by autonomous robot-farmers to as many American cities as possible, providing a fresher, potentially cheaper source of produce that traditional farms located far from these cities would be hard-pressed to compete with. Consider that, according to Alexander, a single square-acre Iron Ox greenhouse can match the annual yield of 30 acres of traditional farmland. It also stands to reason that the products created in these robotic greenhouses are less vulnerable to insects and parasites, eliminating the need to use harmful chemicals used to protect outdoor-grown crops.
Like so many industries that have long been a staple of the American and world economies, the application of robotic technology in agriculture will likely mean a drastic shift away from dependence on human labor. The proliferation of companies like Iron Ox carries clear benefits, but it will almost certainly mean structural unemployment for those who depend on traditional means of agriculture as a livelihood. That said, it’s not a matter of if, but a matter of when we see this shift toward autonomous greenhouse farming on a mass scale.
This $40 Million Robotic 'Plantscraper' Will Feed over 5,000 People Per Year
By 2050, the world's population is expected to swell to 9.6 billion, with around 66% living in urban areas. This projection is leaving many cities wondering how they will feed all those people.
This $40 Million Robotic 'Plantscraper' Will Feed over 5,000 People Per Year
- Leanna Garfield
- Nov. 18, 2017
Plantagon
By 2050, the world's population is expected to swell to 9.6 billion, with around 66% living in urban areas. This projection is leaving many cities wondering how they will feed all those people.
A Swedish food-tech company called Plantagon is proposing that cities consider building what it calls "plantscrapers" — office towers that contain giant indoor farms. Plantagon is constructing its first plantscraper in Linköping, Sweden.
Called The World Food Building, the tower will operate hydroponically, meaning vegetables (mostly greens) will grow without soil in a nutrient-rich, water-based solution. The farm will largely be automated, Plantagon CEO Hans Hassle told Business Insider.
Construction of the $40 million building began in 2012, and it's set to open by early 2020.
Check out the plans below.
The World Food Building will produce approximately 550 tons of vegetables annually — enough to feed around 5,500 people each year.
Plantagon
Source: Helgi Analytics
The front of the 16-story tower will include the farm, while the back will include the offices.
Plantagon
About two-thirds of the building will be devoted to offices, while the other third will include a huge indoor farm.
Plantagon
Companies are now signing leases to move in when it's complete.
The crops will grow using both natural sunlight and LEDs.
Plantagon
The LEDs will be calibrated to specific light frequencies to maximize production.
Plantagon
Robots will perform many of the farm's processes. This will keep operational costs down.
Plantagon
Compared to an outdoor farm of the same size, the plantscraper will generate more food while using less land and water, Hassle said. He estimates the tower will save 1,100 tons of CO2 emissions and 13 million gallons of water annually.
Plantagon
Some meeting rooms, like the one below, will have a view of the farm.
Plantagon
In other areas of the tower, there will be eateries for office employees and the public.
Plantagon
In addition, the building will include a market where people can purchase veggies. Local restaurants and other food retailers will be able to buy directly from Plantagon, which will operate the farm, Hassle said.
Plantagon
Plantagon has designed another similar indoor farm with offices, though it's in the shape of a globe. There are no plans to build it yet.
Plantagon
This plantscraper will include a spiraled food production line, which automatically moves the plants from the bottom to the top and back again while they grow. The length of the cycle would depend on the crop, but would normally take around 30 days, Hassle said.
Plantagon
The designers hope Linköping's plantscraper will encourage other cities around the world to build large-scale indoor farms that have multiple uses.
Plantagon
Plantagon is in conversations with other developers in Sweden, Singapore, the United States, Hong Kong, and Shanghai to build similar structures.
Hassle believes that more cities should grow food closer to urban centers. "This project demonstrates how to feed cities of the future when they lack land, water, and other resources," he said.
Your Next Head of Lettuce, Grown By A Robot
Your Next Head of Lettuce, Grown By A Robot
You could drive past and never see the only farm in San Carlos, California. The tiny city of 30,000 that sits between San Francisco and Silicon Valley has all the charms of suburbia—sprawling office parks and single-story homes—but doesn’t seem a likely suspect for agriculture.
The farm, run by startup Iron Ox, is nestled between three stonemasons and a plumber in a nondescript office park building; there’s no greenhouse, no rows of freshly-tilled soil, or tractor parked outside. Only peeking in the large bay door reveals the building’s tenants: a few hundred plants and two brightly-colored robot farmers.
Iron Ox looks a lot like a tech company. One of its co-founder is an ex-Google engineer and it raised $1.5 million in pre-seed venture capital from Y Combinator, Pathbreaker, and Cherubic Ventures in April 2016. Instead of fake food, or plant-based meat meals, or even a food delivery service tethered to an app, Iron Ox is reinventing farming, raising real, not faux, food. Think hydroponically raised lettuce and basil, like what you’d get at an ordinary farmers market.
Iron Ox plans to build a network of autonomous, robot-run greenhouses near major US cities, complete with a fleet of trucks to ensure same-day delivery. Traditional outdoor farms don’t mesh with suburban sprawl, but the planned square-acre greenhouses have a small footprint that can easily fit into dense urban or suburban areas. The robots plant, raise, and harvest the crops.
Iron Ox founders Jon Binney, left, and Brandon Alexander. (Iron Ox)
Pod lettuce
Co-founder and CEO Brandon Alexander, who worked on Google’s Project Wing, figuring out how to make multiple robots work together, says it takes just three or four months to set up one of its farms. Plants take six weeks to mature. One of these modular, square-acre farms could provide the same yearly yield as 30 acres of traditional farmland, Alexander says.
“We want to have the most efficient farm out there,” says Alexander. “In some ways this is just the natural evolution of [farming].” Growing up, Alexander spent summers working on his grandfather’s peanut, potato, and cotton farm that straddles Texas and Oklahoma. He’s seen his grandfather adopt self-guided tractors and other new technologies, giving the ability to scale the family farm from 40 to 5,000 acres in one generation.
While raising crops has evolved from the time of small family farms, it’s still inefficient, Alexander says. Vegetables waste a large portion of their shelf lives traveling 2000 miles to get from farm to store. In addition, the pool of labor for existing centralized farms is aging and diminishing. The average US farmer is 55 years old, and the average crop worker is 33. “There’s just not enough labor to go around,” Alexander says.
Iron Ox isn’t the only company trying to revolutionize food production. Plenty, another Bay area startup, recently received $200 million from the Softbank Vision fund with a similar mission of distributed farms near metropolitan areas. Plenty’s buzzword isn’t automation, but vertical farming: growing crops up walls to save space. AeroFarmswants to disrupt hydroponics with nutrient-filled mist. Freight Farmswill grow crops in shipping containers.
The robots
Iron Ox plans to use three robots powered by artificial intelligence to work each square-acre of greenhouse. Two robots, without official names but referred to as transporters, will lift and ferry trays of plants over to the third robot, a robotic arm. The robotic arm will plant seeds, cycle juvenile plants into larger growing plots, image the plants to check for disease, and harvest the crop. Iron Ox plans to grow leafy greens like the lettuce and basil varieties it is testing now. Large-field crops like corn aren’t on the roadmap.
Iron Ox is using a hydroponic system called deep water culture; the plants, seated in plastic cones, float on a raft in a tray of water, their roots submerged in nutrient-rich water.
These trays are the key to Iron Ox’s indoor farm; while many deep water culture systems are built around large, stationary pools of water, these trays allow the plants to be moved to and from the robotic arm. The company developing the three components—robotic arm movement, transporter robot, and automated hydroponic system—separately. Humans now do the work slated for the robots, but the pre-robot farming provides a valuable runway of data for Iron Ox about optimal growing conditions.
Half a dozen data points are collected from each water tray per second, plus air temperature and quality, ambient light, humidity. The brains of the system are in the robotic arm. If it knows certain plants need more space, the transporter can be summoned to collect them for transplanting. If it’s time for harvest, the trays come to the arm.
The arm, which stands between two trays, moves with serpentine ease only occasionally interrupted by a mechanical lurch. As I watch, it’s controlled by CTO Jon Binney, but can be set to autonomously shuffle plants around from tray to tray. The goal is to only have one robot arm per acre of greenhouse, able to switch out its end effector, or hand, for specialized tools based on the task. Universal Robots is the arm’s manufacturer, but it runs custom code for motion planning. The stereoscopic cameras used to image the produce are installed and integrated by Iron Ox, and the end effectors used to inject and transplant are built custom-built by the company as well.
The transporter’s job is to hulk over a tray of plants, tuck the tray into its belly, and carefully transport it to a space next to the arm. It glides around the warehouse with a precise, mechanical grace, seemingly able to drift in any direction on its Mecanum wheels. These specialized wheels mean the trays can be just inches apart on the entirety of the greenhouse floor, since the transporter doesn’t need space to turn.
The process
The plants start as seeds, which are injected by the robotic arm into small, foam-like cubes seated in a plastic cone. The plastic cone protects the base of the plant from the robotic arm’s grippers, which giving each plant a standardized place to grip the plant while moving it around.
When the seeds have sprouted and grown for about two weeks, they are brought to the arm by the transporter. The robotic arm then picks up the plants and transplants them to a tray with more room between each plant. Each tray is outfitted with augmented reality tags (that allow the arm to recognize which tray it’s working with, and the bounds of where it can and can’t put plants.)
Two weeks later, the transplant process occurs again, and then again two weeks after that. Each time a plant is moved, two cameras on the arm build a 3D model of it, which is analyzed to check for disease and to ensure it’s growing normally. After the plant is fully grown, the arm pulls it—roots and all—from its plastic cone, and places it in a plastic clamshell container to be shipped.
The company has yet to launch its first fully-functioning greenhouse, and it currently donates its hydroponically-grown produce at a local San Carlos food bank in addition to supplying the company salad bar. IronOx wants to build the first greenhouse by the end of 2017, sell to local chefs in the Bay Area, and then scale to grocery stores in early 2018.