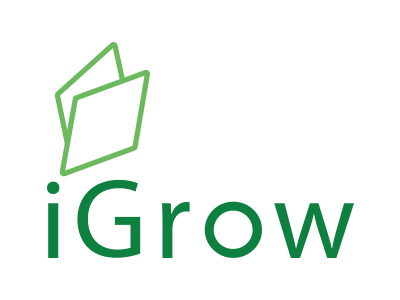
Welcome to iGrow News, Your Source for the World of Indoor Vertical Farming
Grow Strong: African Farmers, Entrepreneurs Revamp Agriculture Norms Through Purdue Partnership
Scott Massey, a Purdue University graduate and founder of Heliponix, a company that makes an appliance that fits under a kitchen counter and grows produce year-round, is hoping to change that by bringing sustainable agriculture methods in Cameroon.
January 28, 2019
Scott Massey, founder of hydroponics startup Heliponix, discusses agricultural innovations with Togonese students as a part of his first Mandela Washington Fellowship. In 2019, Massey will workshop at Cameroonian universities, empowering students interested in agricultural innovation and entrepreneurship. (Photo provided) Download image
WEST LAFAYETTE, Ind. – Many farmers in the Republic of Cameroon usually grow just enough food to feed their families due to limited fertilizer and high-yield seeds, coupled with poor soil quality and lack of irrigation.
Scott Massey, a Purdue University graduate and founder of Heliponix, a company that makes an appliance that fits under a kitchen counter and grows produce year-round, is hoping to change that by bringing sustainable agriculture methods in Cameroon.
Massey has been selected for a second Mandela Washington Fellowship to lead educational workshops at Cameroonian universities this month. Approximately 200 million hectares of suitable land remains unfarmed across Africa, causing many observers to wonder how African nations can unlock their full agricultural potential.
The Mandela Washington Fellowship seeks to promote agricultural development through the academic and entrepreneurial empowerment of African peoples.
“African entrepreneurs have immeasurable economic opportunities to market solutions using new agricultural technologies,” Massey said. “Our overall goal is to provide these resilient people the means to their own production and permanently break the cycle of dependency on foreign aid.”
Massey has used his extensive knowledge in hydroponic systems and agricultural engineering to develop GroPod, an in-home appliance that grows produce year-round. His background also gives him the unique expertise to teach innovative and sustainable farming techniques in Cameroon.
“In these workshops, we are implementing a new vertical farming technique that utilizes an adaption of the proprietary vertical farming technology also used in GroPod,” Massey said. “Not only will we be teaching the students about these advanced technologies that they can use to start their own businesses, but we will also be building model farms that they can incorporate into their curriculums to grow clean food.”
On this trip, Massey will travel with Daliwa Joseph Bainamndi, another Mandela Washington fellow, to give Cameroonian farmers vital information on developing and incorporating innovative farming practices into their work. The pair will lead lectures on hydroponic farming, entrepreneurship, 3D printing and computer-assisted design at the University of Ngaoundéré, University of Ngoa-ékélé and the agriculture school of Institut Superieur des Sciences et Techniques de Yaounde.
In general, African farmers struggle against nonexistent agricultural infrastructure and poor farming conditions, making subsistence farming the most advantageous practice. However, Massey and Bainamndi’s work could empower Cameroonian students and farmers to expand operations sustainably and successfully through entrepreneurship and innovation.
Massey’s work aligns with Purdue's Giant Leaps celebration of the university’s global advancements made in health, space, artificial intelligence and sustainability as part of Purdue’s 150th anniversary. Those are the four themes of the yearlong celebration’s Ideas Festival, designed to showcase Purdue as an intellectual center solving real-world issues.
Massey received his first Mandela Washington Fellowship in 2018 when he traveled to Togo, Africa, to teach farmers there about the farming usages of hydroponics systems. Read more about his first trip here.
“This diplomatic humanitarian mission will fight the war against hunger on its front line and expand the addressable technology market to maximize global impact,” he said. “I look forward to the day that Africa becomes an environmentally and economically sustainable farming model.”
About Purdue Foundry
The Purdue Foundry is an entrepreneurship and commercialization accelerator in Discovery Park's Burton D. Morgan Center for Entrepreneurship whose professionals help Purdue innovators create startups. Managed by the Purdue Research Foundation, the Purdue Foundry was co-named a top recipient at the 2016 Innovation and Economic Prosperity Universities Designation and Awards Program by the Association of Public and Land-grant Universities for its work in entrepreneurship. For more information about funding and investment opportunities in startups based on a Purdue innovation, contact the Purdue Foundry at foundry@prf.org.
Writer: Kelsey Henry, 765-588-3342, kehenry@prf.org
Purdue Research Foundation Contact: Tom Coyne, 765-558-1044, tjcoyne@prf.org
Source: Scott Massey, scott@heliponix.com
Detecting and Understanding Stray Voltage
Spark Your Electrical Vocabulary
All stray voltage is unintentional and undesirable, yet it is extremely common. In fact, it would be rare to find a farm or home without it, usually not in a good location. The main culprit, even though there are several variations of causation, is that with all standard 120 volt wiring we only have one hot wire, one neutral wire and a ground wire.
If the neutral wire is inadequate or if there is a weak or failed connection, the electrical current arriving on the hot wire must return to the source in some manner, which means it will try to go through any and all other objects that will conduct electricity. This undesirable flow of electrons can be via the earth, metal buildings, metal stanchions, fences or other objects.
The motor on a center pivot irrigation tower had been experiencing a tiny short in the wiring recently on a Midwestern farm. It had been this way for several weeks, but it was still working, and as you know there’s never enough time to do everything on the farm. However, the sand filter on the irrigator was also full, and this function needed emptying. The farmer was up on a metal ladder opening the overflowing trap to clean it out. It was safe, because all the pumps were switched off — except for what he did next, which was to instruct his wife to turn on the pump in order to flush the sand. It was a fatal mistake, as 480 volts surged through the system, instantly killing the farmer.
Another farmer had a grinder in the shop with a minor short in the motor; when it was turned on, it would give out a little shock. He “cured” the problem by turning on the grinder switch with a wooden broomstick. Who hasn’t done something like that?
On another farm there was a series of five livestock water fountains all connected to the electrical line. The first four fountains seemed normal, and the cattle were approaching them casually and drinking water normally. However, the cattle seemed to sense something was wrong with the fifth fountain, and they avoided it. Thirsty, two young heifers approached the fifth fountain, which was also overflowing slightly and creating a small puddle they were standing in. Within seconds after touching the water in the fountain, both heifers were instantly killed.
I heard many stories like this from Jerry Lush, a professional stray voltage consultant and ag engineer from Sioux Falls. After decades in the field of electrical energy, Lush can recount many horror stories of the abundant, and usually safe, power supply that we can’t seem to live without. Even folks who do not allow commercial electricity on their farm can encounter problems. I’m talking about stray voltage, a potential evader that can sneak onto any farm or barn.
What is Stray Voltage?
This is a very aptly named problem, in that it applies to any two objects that have electrical potential between them that ideally should not have any voltage difference between them. How much does it take? In general, we are always hoping for zero voltage, however, almost any animal can easily feel anything at 0.5 volts or higher. We could feel it too, but we usually have shoes or boots on and sometimes gloves. Lush says he finds this all too often and has even seen it run as high as 9 volts of current. Just imagine touching your tongue to a 9 volt battery.
Spark Your Electrical Vocabulary
Amperage: A measurement of the amount (strength) of current that is flowing through a wire.
Current: As stated above, current (flow of electricity) is measured in amps.
Induced voltage: A form of stray voltage that comes from other nearby circuits. This is more difficult to diagnose, but commonly runs through head stanchions or milk lines. It can be diagnosed and cured by a professional.
Resistance: This is something like a heater or light bulb; it is anything that holds back the current. It is measured in ohms.
Single-phase wiring: Brings 120-240 volts via one to two hot wires.
Three-phase wiring: (High voltage for large motors) brings in three hot lines.
Voltage: A unit of measurement of the pressure that pushes the amps through the wire.
Wattage: The sum of volts X amps and equal to power, as in the horsepower of an electric motor, for example. High voltage lines can adjust current flow by vastly increasing the voltage, which simultaneously lowers the flow of current and reduces line loss. Many transmission lines carry 7200 volts (this is what linemen work with) whereas coast-to-coast lines can carry 35,000 volts or more.
Potentially dangerous stray voltage was just diagnosed in our own home because the neutral wire coming from some “professionally installed” wiring, which had been put into our house by licensed electricians during remodeling, had actually been spliced into the ancient knob-and-tube neutral wire that runs through most of the walls and ceilings.
Jerry Lush has nearly 40 years of experience in the field of electrical energy.
Lush states that a big part of the problem is that electricians and linemen may see electricity in a different way than engineers trained in electricity (I’m generalizing here; there are some very knowledgeable technicians, likewise engineers are frequently so specialized they just don’t know everything, some engineers have no electrical training at all). But typically, the linemen have not been trained in household or farm wiring. Sometimes they can barely visualize the flow at all; their job is to get the power to the site.
Electrical engineers, including agricultural engineers, are trained to see electrical current wherever it is, quite like the rest of us might see water flowing. We could hardly expect to see water flowing into a structure without knowing where and how this water will exit. With voltage, if the neutral wire is not fat enough, or if the distance is too far, there’s no way it can keep up with electrical flow so that current “spills” into other areas in order for it to eventually get back to the source.
Stray voltage can come from any electrical device that is malfunctioning. Even properly installed wiring or devices can be damaged by moisture, lightning, or mice, squirrels and rats. Most commonly afflicted are barn fans in the summer and water tank heaters in the winter. Lastly, there can often be problems coming onto your farm from the utility service. Wherever the source, proper diagnosis is a critical starting point.
Symptoms of Stray Voltage
The key word is mysterious. Many farmers think they must be bad farmers or bad managers, or that they must have poor-quality livestock, not realizing there is a hidden cause. Electricity is essentially invisible, and we are usually focused on visible issues. Every single farm, ranch barn, garage or home can have stray voltage problems — we have seen it with dairy, beef, swine, sheep, goats, poultry or horses, but most often electrical problems are most clear in a dairy. In general, dairy animals drink more (to make milk), and they are quite often indoors and being handled, in a place where we can watch them.
Animals that are plagued with stray voltage will most frequently manifest specific problems such as mastitis, or high somatic cell count (pus in the milk), or they are jumpy when they come in to be milked. In many cases they just will not let down their milk flow. Watch your animals when they drink; they will tell you. Frequently they will only drink just enough to satisfy their thirst but not enough to maintain adequate production, which soon falls off even worse. Instead of taking a steady intake of water, they merely lap at the water, bobbing their heads.
Humans are more likely to feel the voltage themselves when walking barefoot on wet concrete, even more so when touching plumbing or metal when they are somewhat grounded by being wet. People have even been known to keep a dry rag around so that they can shut off their shower faucet without getting a mild shock.
Diagnosing Stray Voltage
Ideally, hire a pro! Lush is one of several in the United States. He comes by his skills honestly with two degrees in ag engineering and years of service working for rural electric utilities and co-op extension services. He has focused exclusively on stray voltage problems since 2007. Having worked both for the utility and for the farmer, he understands both sources of problems. He says his main tool of the trade is a simple volt meter, one that can measure micro voltage. At times he will hold a metal rod in one hand as he explores with the leads from a volt meter. He also uses a device that converts electrical current into an audible signal which emits a buzz if there is current flow. Quite often he can instantly spot wiring design errors or find loose connections. By the use of all these devices he can pinpoint sources of the problem.
Electric fencing is rarely a problem, in general, but if wired wrong it can be devastating. Lush says that it is of utmost importance to create a grounding system that is as good as or better than that of the rest of the farm. The fence should have its own individual ground and it should never be attached to any other ground. Place the ground far away from barns or other electrical systems.
Can Stray Voltage Be Cured?
Absolutely! However, Lush admits there are a few mysterious challenges over a lifetime of work. He recalls a few farms that defy logic such as an Amish farm he once investigated that haunts him. They were having barn issues of serious stray voltage in the metal stanchions yet were hundreds of yards from power lines, buried lines, transformers or substations. In some of these cases, even though no source can be detected, the professionals can build a circular passageway around the farm buildings using highly conductive materials.
Most of the time however, he says he can diagnose and cure almost every farm within four hours’ time, and most diagnoses come in the first half hour. Even if the problem is coming from the utility, a power pole/transformer neutral isolator can be installed. Since many problems come from inadequate grounding, this is a cure that can be rewired in a proper manner and without much cost. With 240 volt wiring there are fewer problems because there are two hot wires, and the current will arrive via one hot line and go back to the source via the other hot wire.
However, it’s not always that easy to settle disputes if questions arise with regard to the sources of the problem. If the utility will not accept responsibility for causing the problem or for the cost of fixing it, many farmers can feel left in the lurch. In fact, many institutions practically deny the existence of the problem, some even insinuating that the farmer must either be crazy or just a whiner.
Here in my state of Minnesota alone there are currently at least six pending lawsuits between farmers and the utilities with little hope of resolution in sight. However, the tide is slowly beginning to shift toward more accountability and more willingness to admit that the problem exists. Is it worth fighting? One dairy farmer in Minnesota suing the power utility estimates the voltage running through his dairy cost him over $700,000 in lost production, last year alone. Another Minnesota suit was settled, awarding $3 million to the damaged parties.
ZipGrow Helping To Transform Indoor Agriculture
A dedicated team of farming pioneers based in Cornwall are helping to bring local fresh food to the table in a growing number of communities.
December 13, 2018
By Bob Peters
Cornwall Ontario – A dedicated team of farming pioneers based in Cornwall are helping to bring local fresh food to the table in a growing number of communities.
ZipGrow manufactures vertical growing systems in Cornwall and works with farmers in external markets to install the technology and build economically viable indoor farms.
Essentially plants are grown from seeds in rows that are oriented vertically as opposed to on a traditional horizontal plane. Light, water and nutrients are supplied via a system that maximizes efficiency and crop yield.
“Our towers are designed by farmers for use by farmers,” says Eric Lang, President and Co-Founder of ZipGrow. “Going vertical allows you to grow crops in a relatively small physical area, which makes it ideal for indoor locations.”
The system is scaleable as well, which means that restaurants can grow their own greens, students can learn about agriculture and entrepreneurs can build commercial farm operations are that are climate-proof.
The ZipGrow method of farming is versatile and can accommodate different crops. Indoor farmers have had success with leafy greens such as lettuce, kale and arugula while herbs like basil, mint, and rosemary are perfect matches for growing vertically. With a little extra planning and preparation, you can also successfully grow fruiting plants such as strawberries, cucumbers, and bell peppers.
ZipGrow is located on Fourth Street West in the middle of Cornwall. Demand for their product has led to continuing increases in production, requiring the company to expand its physical footprint. The company now employs 15 people.
“We are selling ZipGrow systems in North, Central and South America and demand continues to increase quarter after quarter,” says Eric Lang. “Each sale paves the way for another as people become familiar and comfortable with the technology.”
Mr. Lang is partners with Eric Bergeron who first brought the concept of indoor farming to Cornwall with SmartGreens in 2014.
“Indoor farming offers solutions to problems that conventional agriculture struggles with – namely environmental impact, timely transportation of perishable goods to distant markets, climate change and more,” says Mr. Bergeron, Co-Founder and Chief Marketing Officer for ZipGrow. “We believe that with right knowledge and the right technology, individuals and communities can help bring farmers and consumers much closer together for the benefit of all.”
About ZipGrow
ZipGrow designs and builds vertical farming technology for installations around the world. Its team of proven leaders in the field educate, equip, and empower local farmers to grow better food for their communities and operate successful vertical indoor farms.
Web: ZipGrow.com
Singapore Aiming To Become Region's Urban Agriculture Technology Hub: Koh Poh Koon
January 15, 2019
SINGAPORE - Singapore has the "right ingredients" to make it the urban agriculture and aquaculture technology hub in the region, Dr Koh Poh Koon, Senior Minister of State for Trade and Industry, said on Tuesday (Jan 15).
In a keynote speech at the Indoor Ag-Con Asia conference at Marina Bay Sands Expo and Convention Centre, which is being held in Singapore for the fourth time, Dr Koh said Singapore is in a strong position to "catalyse technological and business innovations", as it has a climate for innovation, strong talent base and strategic location which can transform agriculture and aquaculture in the Asia-Pacific region.
"Where arable land is scarce, innovating how we produce food is critical in helping us overcome our farming constraints and better contribute to our food sustainability and traceability efforts," he said.
Senior Minister of State for Trade and Industry Koh Poh Koon said Singapore is in a strong position to "catalyse technological and business innovations".PHOTO: LIANHE ZAOBAO
"Investments in agri-tech can also help to reduce our reliance on food imports and allow us to enjoy seasonal produce while lowering our carbon footprint."
To boost the agri-tech sector, Dr Koh announced that Enterprise Singapore, through its investment arm Seeds Capital, has appointed seven investment partners under Startup SG Equity - a scheme that encourages private sector investment for start-ups.
Seeds Capital aims to spur the growth of emerging and strategic sectors such as agri-tech, by stimulating investment in innovative local start-ups.
Under this partnership, more than S$90 million worth of investments will go into early-stage tech start-ups with food and agri-tech solutions.
The appointed partners are AgFunder, Hatch, ID Capital, Openspace, The Yield Lab, Trendlines and VisVires New Protein.
With Seeds Capital, the partners will assist early-stage start-ups, such as by introducing new business partners and providing support to enter new markets.
Seeds Capital will also provide co-funding of up to $4 million per deep tech start-up under Startup SG Equity.
Dr Koh said: "We are building a vibrant agri-tech start-up environment to uncover more talent, anchor experts, partners, investors and accelerators into our ecosystem, and expand the pool of knowledge and resources.
"We are developing relevant research capabilities in areas such as seed formulation and fish nutrition, advanced biotech-based protein production and food safety science. (Furthermore) we are establishing a high-tech physical cluster in Kranji to support operations in urban agriculture and aquaculture."
One of the Singapore agri-tech companies at the conference was Protenga, an insect farming company that produces animal feed. It has incorporated data sensors into its farms to help determine the right feeding frequency and amount, increasing the quality and volume of produce.
Another company VertiVegies, an indoor vertical farming firm, also displayed its modular planting system that uses technology to ensure efficient plant growth, while taking up minimal space and giving Singapore the potential to achieve food security.
"Singapore's journey to become a leader in agriculture technology is still in the early days, and there is much more for us to do," added Dr Koh. "I encourage industry representatives and leaders to carry on your good work in leading the development of solutions and standards for the sector, to provide fertile ground for the germination of new ideas, technology matching and transfer, capability development."
Spotlighting Women In AG
Female Growers and Innovators Are Featured At 2019 EcoFarm Conference
By Amy Wu
Even in the 21st century, the image of the modern-day farmer often centers on overalls, pitchforks, and the image of the “farmer” as a man steering the tractor. While the image remains reality to an extent, agriculture is fast extending into a new generation of women growers and innovators, who are carving a path in agtech, science, and research while others are running their own enterprise.
As a journalist, who specializes in telling stories about women leaders in farming, I am delighted that this year’s EcoFarm features a wide range of women-focused events, and many more feature female panelists and keynote speakers. There is also a plethora of amazing women spotlighted on the "Equity, Food Justice, Sovereignty" track.
The “Women in Food & Ag Mixer” that traditionally bookends the conference on Friday also returns. And one of this year’s keynote speaker on the final conference day is social expert Nikki Silvestri founder and CEO of Soil and Shadow, which works to create systems change towards economic development and ecosystem restoration. Silvestri’s impressive background also includes being co-founder of Live Real and former executive director of People's Grocery and Green for All that focus on food justice.
In the past year, discussion over food and farming has also morphed into the intersection of environment, agriculture and climate change. Case in point regenerative agriculture, loosely defined as using a variety of farming techniques and land practices to improve soil health and improve water cycles.
To be sure, for a second year in a row there is an entire day devoted to “Women in Regenerative Agriculture Field Day” at Paicines Ranch in San Benito County, where attendees will have a chance to connect with female farmers, ranchers, scientists, physicians and advocates, bookended with a wine tasting.
The uptick in women panelists and speakers can only be positive since it directly touches the critical area of land equity; how many farms are owned and operated by underserved communities whether that be women or people of color? A January 23 workshop is devoted to discussion surrounding the importance and ways to increase diversity on farms and in the food system and “address root causes of inequity, and explore strategies for moving forward in healthy relationships with one another and the land,” according to the program description.
The opportunities and potential surrounding ownership are immense for women, especially as more farms struggle to stay afloat. Many farms across the country are being squeezed by severe labor shortage, limited water and land supply, skyrocketing costs of doing business, the ongoing trade wars, and the reality that the next generation might not be interested in farming. The upshot is a growing number of women are managing farms in the capacity of owner or operator; I recently had the pleasure of spending a morning with Jacky Vasquez one of the few if not only female farm operators in Monterey County. On any given day you’ll find Jacky in the vast landscape of berries on the farm where she runs, walking through the fields and reviewing the berry quality, on a tractor, or directing field crews. She is proud to be boots on the ground. She has a passion for agriculture that transcends gender and demographics.
“I like the mix of it. Yesterday I was in heels and speaking in a conference and today I am about to walk the fields and check strawberries for their qualities. It’s from eating gourmet catered meals to tacos from a truck,” Jacky shared. My personal hope is that down the road I will find more women like Jacky and female farm operators will no longer be an anomaly.
This appears possible as a silver lining emerges with the current landscape; an estimated 1 million women are now farm operators and over a half-million own and lease land to farmers, and a third of farmland in the U.S. is farmed or co-farmed by women, and women own 87 million acres.
Finally, last but not least there is a powerhouse panel of women, Malaika Bishop co-director of Sierra Harvest, Denisa Livingston of Diné Community Advocacy Alliance and Karen Washington co-founder of Black Urban Growers (BUGS), who will take a deep dive in “Engaging & Empowering our Communities to Transform the Food System.”
Having documented and profiled some amazing women leaders in farming, I am excited to participate in the discussion and dialogue at EcoFarm 2019. My hope is that in years to come women will no longer be spotlighted, but will simply be a part of the landscape of discussion of agriculture.
To learn more and register for EcoFarm Conference 2019 visit www.eco-farm.org/conference
Amy Wu is the founder and chief content director of “From Farms to Incubators,” a resident company inside the WG Center for Innovation and Technology. She previously reported on ag for The Salinas Californian. She considers herself bicoastal and splits her time between New York and California.
CO2 GRO Provides A 2018 Review And 2019 Outlook
TORONTO, ON – January 15, 2019 – Toronto based CO2 GRO Inc. (“GROW”) (TSX-V: GROW, OTCQB: BLONF, Frankfurt: 4021) is pleased to provide a 2018 Review and 2019 Outlook:
2018 Grow Trials and 2019 Commercial Revenue
During 2018, GROW conducted scientific and commercial grow trials using CO2 Foliar Spray on high value plants including cannabis, flowers, lettuce, micro greens and peppers. All trials led to major value improvements in plant size, quality and growth speed.
GROW’s accumulated positive data was sufficient for our first two customers to sign Commercial Agreements to install CO2 Foliar Spray equipment in mid-Q1, 2019. Data to August 2018 was filed to take a provisional PCT CO2 Foliar Spray patent to pending status.
Site technology leasing revenue is expected start in late Q1, 2019.
GROW’s 2019 pipeline of companies and plant growers includes US hemp growers that can now grow unlimited acres as the US decriminalized US hemp growth in 2019.
Targeted geographic areas for CO2 Foliar Spray commercial development are primarily the Southwest, Southeast and Midwest US and Eastern Canada. In 2020, potential international CO2 Foliar Spray trials and commercial installations are being considered in the EU, South America and Africa.
Year-End 2019 Revenue and EBITDA Expectations
GROW is forecasting a site license lease revenue run rate of C$10M/year entering 2020 with EBITDA margins of 50%.
Use of Q4 2018 Equity Financing
In October 2018, $1.427M was raised from the exercise of 7.135M of GROW’s $0.20 warrants. Proceeds are being used to:
1) Retire a $200,000 secured three-year note resulting in the Company having no debt outstanding.
2) Hire key US and Canadian personnel to accelerate GROW’s CO2 Foliar Spray technology leasing revenue growth and,
3) General corporate purposes.
Business Development and Scientific Staff Appointments
US Appointments
1) Michigan based US Midwest Representative with 35 years of flower and vegetable based grower and greenhouse experience.
2) Florida based US Southeast and parts of Southwest Reperesentative with extensive hemp and medical cannabis market development expertise.
3) California based Market Representative with a plant micronutrient background.
4) Minnesota based Dr. Matt Julius who is a Biology Professor at St. Cloud State University, Minnesota – he will start as acting Chief Science Officer from April to December 2019
Canadian Appointments
5) Ontario based Representative for Ontario, Quebec and New York State with extensive greenhouse experience.
6) Ontario based Manager of Project Engineering.
John Archibald, CEO, commented “2018 was a pivotal year as we completed GROW’s restructuring and reorganization, conducted successful scientific and commercial trials and signed our first two site license agreements. For 2019, we are now staffed to execute on our highest impact trials and provide CO2 Foliar Spray solutions to customers that want to proceed directly to installations as our first two customers did.“
About CO2 GRO Inc.
GROW's mission is to accelerate all indoor and outdoor value plant growth naturally, safely, and economically using its patent pending CO2 Foliar Spray technology. GROW’s global target retail plant markets are food at $8 trillion per year (Plunkett Mar 2017), non-food at an estimated $1.2 trillion per year with retail tobacco at $760 billion (BA Tobacco 2017), floriculture at $100 billion by 2022 (MarketResearch.Biz estimate). Legal cannabis at $52.5 billion per year by 2023 (Statista) and legal US hemp CBD at $22B per year by 2022 (the Brightfield Group).
GROW's CO2 technologies are commercially proven, scalable and easily adopted into existing irrigation systems.
The CO2 technologies work by transferring CO2 gas into water and foliar spraying water across the entire plant leaf surface which is a semi permeable membrane. The dissolved concentrated CO2 then penetrates a leaf's surface area naturally like nicotine dissolves through human skin from a soluble nicotine patch.
Foliar spraying of water, dissolved nutrients and chemicals on plant leaves has been used for over 60 years by millions of indoor and outdoor growers. To date, outdoor growers have not had any way to enhance plant CO2 gas uptake for faster growth.
Indoor CO2 gassing has enhanced plant yields for over 60 years but 60% of the CO2 gas used is typically lost from ventilation. Current greenhouse CO2 gassing levels of up to 1500 PPM are not ideal for worker health and safety. GROW's safer infused CO2 Foliar Spray can be used by both indoor and outdoor plant growers with minimal dissolved CO2 gas lost and much greater CO2 plant bioavailability resulting in higher plant yields than both CO2 gassing and no gassing plant yields.
Forward-Looking Statements This news release may contain forward-looking statements that are based on CO2GRO's expectations, estimates and projections regarding its business and the economic environment in which it operates. These statements are not guarantees of future performance and involve risks and uncertainties that are difficult to control or predict. Therefore, actual outcomes and results may differ materially from those expressed in these forward-looking statements and readers should not place undue reliance on such statements. Statements speak only as of the date on which they are made, and the Company undertakes no obligation to update them publicly to reflect new information or the occurrence of future events or circumstances, unless otherwise required to do so by law.
Neither the TSX Venture Exchange nor its Regulation Services Provider (as that term is defined in the policies of the TSX Venture Exchange) accepts responsibility for the adequacy or accuracy of this release.
For more information, please visit www.co2gro.ca or contact Sam Kanes, VP Business Development at 416-315-7477.
What Bowery’s Latest Funding Round Says About Indoor Farming
The new investment round brings Bowery’s total funding to $117.5 million.
By
December 13, 2018
New Jersey-based indoor-farming startup Bowery announced yesterday that it has raised $90 million in fresh funding. The round was led by Alphabet Inc.’s GV with participation from Temasek and Almanac Ventures, General Catalyst and GGV Capital (Bowery’s Series A investors), and various seed investors.
Bowery produces what founder Irving Fain calls “post-organic produce.” Or to put it more plainly, Bowery produces leafy greens in an indoor environment it controls with proprietary software. The FarmOS system, as it’s called, helps farmers manage crops by collecting data about water flow, light levels, humidity, and other environmental factors that impact the taste of greens. And because the farm is indoors, Bowery can grow its crops without soil, pesticides, or chemicals.
This new investment round brings Bowery’s total funding to $117.5 million. That sounds like a lot until you compare it to Softbank’s $200 million investment in Bowery’s West Coast competitor Plenty, which took place in July of 2017.
Both companies’ raises illustrate the enormous amount of interest in indoor and vertical farming right now. The latter field is expected to have a market valuation of more than $13 billion by 2024, and there are dozens of other companies working on various iterations of indoor farming today.
AeroFarms grows leafy greens inside a 70,000-square-foot facility in New Jersey and has backing from IKEA and Momofuku’s David Chang. Crop One Holdings and Emirates Flight Catering are building what they call “the world’s largest vertical farm.” And Ford Motors operates a farm in Detroit that helps feed the homeless.
Okay, but will leafy greens really feed the homeless? Will butter lettuce and fresh basil help alleviate the global food shortage we’re expected to face as the population nears 9 billion people?
By itself, indoor farming can’t do either of those things, at least not adequately. But that doesn’t render indoor farming an overhyped segment. What it does mean, though, is that we need to start moving beyond the leafy greens and start producing foods with a little more substance. Plenty says cucumbers and strawberries are next on its list. Meanwhile, it’s possible to grow root vegetables like turnips, beets, and sweet potatoes using hydroponics. It’s just more expensive and more challenging than basil.
Bowery says its new capital will go towards “scale its operation in new cities across the country and open multiple farms by the end of 2019.” There’s no word yet on whether those new farms will stick to leafy greens or branch out, though Fain did say Bowery is working on “scalable solutions for an impending climate and food crisis.”
We’ll hopefully see Bowery put those words into action by figuring out how to widen the possibilities of what we can grow with indoor farming.
The 3 Most Important Factors for a Profitable Farm
Regardless of how you grow, the profitability of your farm will depend on three main factors: demand, viability, and profit margin.
by Mia Godfrey | Nov 9, 2018 | Farm Management | 1 comment
Regardless of how you grow, the profitability of your farm will depend on three main factors: demand, viability, and profit margin. Lots of new farmers focus the majority of their efforts on their ability to grow a single crop and forget to do research on the other factors. In this article, learn how to appropriately address questions like the following:
What can you sell a lot of? What does your market want?
What are you good at growing?
What has a good profit margin?
For a profitable farm, you must consider all three. Let’s start with how you know you can sell something well.
What can you sell a lot of?
This is the most important thing: if people don’t want it, you won’t make money off of it. It may seem obvious, but it’s easy to get excited and overlook the importance of demand.
Imagine that you’ve just invested a lot of money in starting up a farm. You’ve tried a few different crops but discovered that you’ve been able to grow cilantro especially well. Since you can grow it so successfully, you decided to overhaul your whole farm and plant tons of cilantro. Then you discover that your market does not want to buy cilantro. Now, your whole farm is taken up by rows and rows of cilantro, and you’ve got nothing to do with it. You’re out of money and have no way to make it back.
This is why market research is so crucial. You need to know what people will buy from you not just once, but many times. You also need to know how much they want to consume on a regular basis so you don’t end up with a lot of wasted produce. This is called market volume. Aim for high market volume—lots of people want to consume lots of what you’re growing.
But market research isn’t just looking at numbers. Spend a little bit of time talking to buyers and looking at what other people are growing. Is there a gap you could fill with your unique product? Could you alleviate customers’ pain points by offering a better product at a better price? Take the Market Research for Farmers course to learn more about effective strategies.
In addition to high market volume, you want to choose a product that has low supply competition. If everybody grows cilantro and sells it at the market, you probably don’t want to depend on cilantro for the success of your farm, even if you can grow it well.
Insider tip: Wholesale retailers—think grocery stores and restaurants—are great places to find information on demand because they’ll have consistent records where you can get an idea of what they’ve had success with in the past. This information is slightly more difficult to find in something like a farmers’ market, where different vendors will have different experiences based on a variety of factors.
Low supply competition means that there are fewer people in your area growing it. This leads us to what you can grow well.
What can you grow well?
In your particular climate, with your particular capabilities, what grows best? Are you good at it? Do you understand it well? Are you excited about it?
Now that you know what people want, you’ll need to successfully execute production. Say you find out that the market in your area has a high demand for spinach. You figure it’s a pretty good bet, and throw everything you’ve got into growing spinach but you just cannot get the little buggers to grow. You are not going to make money.
You won’t know what you’re good at growing—or even if you like it—until you give it a try. You will likely experience some error, so when you’re starting out keep it fairly small in order to minimize cost and risk.
That said, this type of success isn’t just dependent on your personal farming abilities. It will largely be influenced by where you farm, what type of farm environment you have, and what type of system you’re growing in.
Additional factors to consider are the costs and resources that are available to you. Do you have affordable access to the resources you need to build a successful farm? Unreliable or inconsistent availability of resources—like nutrients, plugs, and system repair parts—can throw a wrench in your production as well as your relationships with your customers.
Even if you can get reliable access, think about the total cost. Whether or not you have great profitability, you’ll still need to make sure your costs are as low as possible.
Finally, if you don’t like doing it, even if all the other factors are there, it’s possible that you won’t do it well. Find something that you enjoy!
What has a good profit margin?
First of all, what is profit margin?
Profit margin is the money you have left over after you pay to cover all of your costs. Some crops can provide better profit margins than others. Think of it this way:
When you set up a farm, you pay capital expenses (CapEx) to acquire all of your system components, like media, lights, and structural components. Then, when your farm is running, you have operating expenses (OpEx) like water, electricity, and nutrients. The CapEx plus the OpEx is what you pay to create your product (the plants). You then sell the product, and the money you receive in return should be a larger amount than what you originally paid. The difference (what you sold your product for minus what you paid to create it) is your profit margin. Ideally, you have a positive profit margin.
During your market research process, you should also consider discovering what the possible profit margins are for a variety of crops. Research the nutrient and water demand of the crop in addition to the market demand.
Essentially, you want a crop that is cheap to produce, but that people will pay more for. Fortunately, being a hydroponic or aquaponic grower gives you a unique advantage because your product is likely higher in quality than what your customers have had previously.
All of your profit margins contribute to your net profit, which is the total amount of money you’ll keep as a result of your sales. Much of the profit you make from selling your produce will need to be put back into your farm to keep it running and producing.
Business is about trade-offs and compromises, and you get to play the exciting game of finding the most profitable compromise for your business. For example, you could grow and sell a high volume of produce at a lower price, or more specialized produce at lower volumes and higher prices.
There are ways to make all of these cases work, and it will depend on your business model.
Decide based on your business model
Different markets and market types will provide different pros and cons when it comes to profit margin. Think carefully about the trade-offs between high volume versus high prices, and do your research—which works best for you?
Making decisions
If you do decide to focus your farming efforts on a single crop, ensure that:
your market wants it,
that you can grow it well,
and that you can make money off it.
Say you discover that you are really good at growing hydroponic cucumbers, for example, and you have a lot of market demand for them. You may be able to get away with only growing and selling cucumbers. While these are three critical decisions that can lead your farm to profitable success, there are other factors you’ll need to consider as well, such as inputs, seasons, and environmental controls.
Interested in learning more? Take these courses:
Going To Fruit Logistica? See Motorleaf On Stage And Drop By Our Stand
WILL YOU BE AT THE FRUIT LOGISTICA TRADE SHOW?
See Motorleaf on stage presenting greenhouse automation technology
Fruit Logistica will take place in Berlin, Germany this February 6th to 8th. This event is a great opportunity to rub shoulders with leaders in the agri-food industry, including the team at Motorleaf.
Check out our presentation and exhibition stand
Motorleaf was one of 20 new agriculture technology companies selected from an international pool of applicants to demonstrate our greenhouse technology services on stage
Happening on Friday, February 8th, the theme for the series of presentations is 'disrupt agriculture', where innovative products, projects and ideas will be in the limelight. We will present the application of our artificial intelligence technology to automate greenhouse tasks, such as harvest forecasting and disease scouting.
Future Farming Hub Is Creating A One-Stop-Shop Vertical Farming System For ‘Anyone’
January 15, 2019
The Vertical Farming Development Centre at Stockbridge Technology Centre (a Liberty Produce consortium member)
For a company less than one year old, Liberty Produce has already taken some big strides along its path to make vertical farming a more scalable, economically feasible reality. Specifically, the UK-based agtech company hopes to not just grow food, but also create an end-to-end, automated vertical farm system that, according to founder Zeina Chapman, “anybody” could use.
On vertical farming in the UK, Chapman notes there are “really great things happening . . . but they’re all siloed.” In other words, LED companies aren’t talking to those who make HVAC systems, and thus the development of these products happens independent of one another. As technologies by themselves, they work, but when put together in one environment, are they creating the most energy- and resource-efficient way to grow the best crop yield?
It’s a question Liberty will address with its new project, the Future Farming Hub. For the £1.3 million (~$1,652,000 USD) project, Liberty will lead a consortium of 11 different partners, each focusing on a different capability of the vertical farm. Chapman wouldn’t name specific names over the phone, but she did note there were partners in Taiwan, where vertical farming is a huge industry, a major LED company, as well as companies working on sensors, nutrient delivery (for the plants), and the growbeds themselves. For the latter, a partner will redesign growbeds to reduce the amount of bacterial growth that can sometimes hinder plant growth or damage plants. Sensor technology, meanwhile, would immediately tip the grower off to there being a bacterial problem in the growbed.
Underscore that word “immediately,” as that’s the other point Liberty and the Future Farming Hub are pushing. The project will also focus on a developing a system that gives growers real-time data about the farming operation
All of this rolls up under one goal focused on, according to a press release, reducing operational costs of vertical farms by 25 percent, increasing crop yield by 30 percent, and cutting down the amount of decisions growers themselves have to make when it comes to caring for plants.
“There’s lots we don’t know about growing plants in this artificial environment and we’re not giving them optimal conditions,” says Chapman. She cites lighting as one example: “With lighting, there isn’t an option to control it in a way that maximizes plant growth. So we might be putting plants under stress.”
Chapman also wants to make it easier for virtually anybody to operate a vertical farm. When I asked if that includes an open-source framework for growing, as others have suggested, she noted this project goes a step beyond open source. “If you decide you’re going to grow basil, you just press the button and the system will take care of that,” she said. In theory, at least, Liberty will have already developed the formula for growing optimal basil and programmed it into the system, effectively taking the guesswork out of growing.
Automated vertical farming is slowly gaining momentum around the globe, and other proprietary farm systems abound. Stateside, AeroFarms’ patented system can create light “recipes” to give each plant the exact spectrum and intensity it needs to grow. Bowery, too, uses a mix of hardware, analytics, and proprietary software to produce greens year-round. They also just got a $90 million shot of fresh investment. Over on the West Coast, Plenty more than doubled that figure last year, when Softbank invested $200 million in the company’s system.
But no one’s yet come out with a one-stop-shop system that you need neither an agricultural or engineering background to operate and which relies on real-time data to do the heavy lifting.
The project doesn’t kick off until April of 2019, which makes all of this somewhat abstract at the moment. But Chapman’s optimistic. “One of the greatest things we want to achieve is to pull together a system that’s fully integrated and get all these systems to talk to each other,” she says. “We hope it can reduce the costs, which is a huge barrier to entry and also increase yield. As we increase yield, more and more products become viable.”
Chapman and Liberty aim to have a full product ready for market at the end of the 27-month project, and along with it, a more accessible, scalable approach to vertical farming.
Digestate As Alternative Substrate For Soil-Less Lettuce Farming
Researchers from Modena University and Reggio Emilia University – in collaboration with the Foggia’s CRA – evaluated the digestate as an alternative and sustainable substrate for farming and as a nutritive solution in the hydroponic farming of lettuce.
The consumption of ready-to-eat salad has been growing over the last 20 years in the European market. The annual growth rate is at 4%. That's why this food category is renowned as one of the most profitable horticultural segments.
As a result of a growing trend, the lettuce and chicory are farmed over a 1.2 million hectares surface globally. The global production is of 27 million tons, almost.
Italy occupies the fourth place in the world, with 38.542 hectares farmed with lettuce and chicory (31.7% in the north, 10% in the Centre, and 58,3% in the South) for a total production of 8.1 million tons. Additionally, greenhouse production is important as well, for a total surface of 4.549 hectares (37.3% in the North, 31.9% in the Centre and 30.8 in the South).
Leafy produce is considered to be one of the most exposed to microbiological risks. The ready-to-eat lettuce is often connected to food poisoning. The Escherichia Coli O157: H7 has been often associated with lettuce.
Researchers from Modena University and Reggio Emilia University – in collaboration with the Foggia’s CRA – evaluated the digestate as an alternative and sustainable substrate for farming and as a nutritive solution in the hydroponic farming of lettuce. In three different experiments, nine hydroponic combinations of substrate and fertilization (agriperlite + standard solution, agri-perlite + liquid digestate, solid digestate + standard solution, solid digestate + liquid digestate, soil + standard solution, peat + standard solution, peat + liquid digestate, digested pelleted + standard solution and digested pelleted + liquid digestate) were tested and compared for the cultivation of baby leaf lettuce.
During crop cycles, the yield and other agronomic and microbiological parameters have been studied. In all the experiments, the combination of agri-perlite + liquid digestate, solid digestate + standard solution and pelleted digestate + standard solution improved the plant growth by influencing roots (+ 32%), buds (+ 40%), total dry weight (+ 29%) and SPAD parameters (+ 17%).
As the results illustrate, the digestate represents a nutritive sustainable solution and an alternative for the soilless baby leaf lettuce farming.
Source: Domenico Ronga, Leonardo Setti, Chiara Salvarani, Riccardo De Leo, Elisa Bedin, Andrea Pulvirenti, Justyna Milc, Nicola Pecchioni, Enrico Francia, 'Effects of solid and liquid digestate for hydroponic baby leaf lettuce (Lactuca sativa L.) cultivation', 2019, Scientia Horticulturae, Vol. 244, pag. 172-181.
Publication date : 12/12/2018
Evansville, A Home For Business
Back text: “E — Scenic View of Ohio River, V — Reitz Memorial High School, A — Vandenburgh County Courthouse, N — Adm. Bldg., Evansville College, S — Evansville National Guard Armory, V — Dade Park Race Track, I — Electric Fountain, Garvin Park, L — Greyhound Bus Station, L — Lions Den, Mesker Park Zoo, E — Dress Plaza”
After graduating from Purdue University in May 2017, I continued to rent co-work space on campus in West Lafayette working for Heliponix full-time until my apartment lease ended at August 2017. At the time, I was hyper focused on the engineering design tasks at hand for Heliponix to debut a new prototype GroPod™ at the Forbes AgTech Summit. After the summit ended, I brought all of my possessions back to Evansville. It occurred to me I was once again living in Evansville only after I had moved back home. Upon moving back, I was asked to speak at Evansville’s Tech on Tap weekly entrepreneurial meetup where I was asked why I came back. I answered, “Evansville is home, and I can continue working on my company without paying myself by living with my parents.” This seemingly obvious answer spurred a new found sense of urgency that if I were to scale a technology company, than I must leave southern Indiana for greener pastures. I then began to look for every possible reason why I should move away from Evansville for the benefit of Heliponix. I identified the following four reasons why I could not headquarter Heliponix in Evansville, Indiana.
Early adopter customers for new technologies do not live in the midwest.
Tech companies need investors. Evansville did not have venture funds.
Tech companies need top tier software engineering talent. Evansville did not have individuals with this skill set on hand.
Hardware companies such as Heliponix need to manufacture overseas to be cost competitive in the marketplace.
Customers
Heliponix (formerly Hydro Grow) team picture after winning first place at the Schurz Innovation Prize at Purdue University. Left to Right: Scott Massey (CEO), Jimmy Carlson (Software Engineering Intern), Ivan Ball (CTO)
Starting a company without experience or the money needed is comparable to charging into a battle unarmed and unaware of the terrain with dangers ahead. I was acutely aware of my limitations, and spent my senior year at Purdue University delivering newspapers at night for about $9/hour, and competing in business plan competitions between classes for cash awards. Although we were very lucky to have successfully secured over $80k over the course my senior year and a little under $100k from competitions post graduation, the money was the second most valuable aspect of winning these pitch competitions. For every competition we won, at least two or three articles from local media publications would cover the story with our name on the front title. We jumped at every opportunity to showcase our prototypes at schools, STEM career fairs, and also leveraged my position as the lowly delivery boy to publish articles in the Exponent to grasp as much publicity as possible for an early stage company.
Scott Massey giving a STEAM (Science, technology, engineering, agriculture, and math) career talk about indoor agriculture to middle and high school students Our Lady of Providence School in New Albany, Indiana.
For every article and interview that was published, I received an email from random Indiana residents interested in purchasing a GroPod when it became available for purchase. I kept a running list of these potential customers, and reached out to collect a $500 pre-order deposit when we had finally landed on a GroPod design that worked reliably. We had definitively proven that a pre-revenue startup company could launch an expensive product in Indiana if they are able to achieve enough publicity to convert impressions into executed sales. Although there are many more wealthy individuals in major cities who could buy an early stage product; we did not yet have the production capabilities to meet this demand, and still had product development to refine before we would be ready for a massive user base.
Funding
Inside Indiana Business interview with Dr. K and Gerry Dick
Although we had been veryfortunate to secure some funding from business plan competitions for patents and prototype development, we had reached the ceiling of competition funding available in Indiana for an idea not yet generating revenue. My Co-Founder, Ivan Ball accepted a full-time, electrical controls engineering job offer upon graduation to pay off student loans at GPC (Grain Processing Corporation, an ethanol and grain alcohol processing plant in Washington, Indiana) after interning and co-oping as a student for several years prior. Together we worked exhausting hours for a full year to refine the GroPod design until we created a functional product able to generate revenue in Ivan’s garage.
One of many harvests from the fourth generation GroPod™. ALL RIGHTS RESERVED. HELIPONIX©
Ivan Ball at his electrical work station in an unheated garage assembling the fourth generation GroPod™. ALL RIGHTS RESERVED. HELIPONIX©
This marked a major turning point for the company after three generations of failed prototypes. When asked if we both worked on Heliponix full-time to this point, I would honestly say yes. Our individual hours spanned 50–70 hours weekly even though Ivan had a full-time day job that took 40–45 hours per week. At this time, we had spent almost all competition award winnings on patents, prototyping, travel for events, or other business expenses. We simply did not have the capital needed to cover materials to assemble the first GroPod betas. I then approached Eric Steele, my Entrepreneur in Residence with Elevate Ventures (Indiana’s state venture fund) seeking capital needed to fund inventory. Eric referred us to the ISBDC (Indiana Small Business Development Center) who advised the Vectren Foundation Grow Local loan program for small businesses. After working with Douglas Claybourn and Kim Howard, we sent an application to the Vectren Foundation board to build the first GroPods. After waiting patiently, we were approved for a loan needed to build these GroPods with very favorable terms for any company, let alone a startup with zero cash flow history. We used the loan to buy all the parts needed, and collected the remaining $1,500 left on each GroPod order with early adopters to sell out of the beta models assembled by hand. We 3D-printed all parts, wrote our own code, soldered our boards, assembled every aspect of the product Ivan and I had designed entirely by ourselves, and delivered each GroPod in person to the early adopters. There was so many GroPod parts laying around Ivan’s home, I had to deflate my air mattress to make more room, and slept on his couch for months.
Ivan Ball installing a camera on the fifth generation GroPod™. ALL RIGHTS RESERVED. HELIPONIX©
GroPod™ assemblies consuming every square foot of Ivan Ball’s home in Washington, Indiana. ALL RIGHTS RESERVED. HELIPONIX©
Ivan Ball (Left), Scott Massey (Right) with first functional GroPod. ALL RIGHTS RESERVED. HELIPONIX©
At this point Ivan quit his job at GPC, to work solely at Heliponix, and sold his house in Washington, Indiana to be fully committed to the company. Today, I am pleased to announce that the risk the Vectren Foundation took on us for funding the loan is being paid back in full plus interest. This market validation thrusted us into the long sought after post-revenue status, which did not go unnoticed by local and regional angel investors; however, this is a story for another day. Despite the undeniable fact that the largest investment funds are in major cities, very few early stage hardware companies receive those investments due to the amount of competitors who rarely manufacture products within these cities, let alone the state. It is much better to refine the product and user experience until a sizable MRR (monthly recurring revenue) is established before approaching these funds which are beginning to invest outside of their states to leverage the capital efficiency of a midwest startup.
Talent
Delivering the first GroPods was just the beginning of a long troubleshooting learning curve with paying customers… Internet connectivity with a connected, IoT (Internet of Things) device will come with many software bugs as well as faulty sensor failures when buying in low quantities from Chinese suppliers. The problems that you are both unaware of, and unable to solve are the hardest any startup will encounter. It is incredibly important to find these problems by getting your product in the hands of early adopters as soon as possible to identify and solve. The dilemma of an underfunded hardware startup company is that you will more than likely need to sell a product that doesn’t yet have all the features needed to make it “perfect” in order to stay cash flow positive. The reality is that no garage startup will be fully ready, and you will certainly find excuses to not be ready if you look for them. This is called the MVP (minimum viable product). Then something amazing happened, customers began to complain less each day as we solved problems one after another, until I began to hear feedback that their GroPods were growing more food than they could consume! This major milestone was met with interest from angel investors who provided the capital needed to hire a full-time software development lead. Unfortunately, there is not a plethora of software developers in Evansville at this time, so we needed to look for a remote employee. After interviewing several developers, Ivan and I decided to hire Bryan Lemon, a PhD computer scientist from West Virginia University living in South Carolina. Bryan’s experience with IoT device companies translated very well into solving problems, creating new features that kept customers happy, and attributed to our zero-percent churn rate. Despite never meeting Bryan in person, we were quickly able to determine his technical ability by first hiring him as an independent contractor for an agreed upon milestone. I strongly encourage that early stage technology companies consider remote software developers to save cost, expand your professional network, and reach a wider pool of candidates to only hire top talent. You do not need to go to the bay area or other major cities to find top talent, and the operational cost of your business will increase by multiples if you move to a larger city.
Manufacturing
Whirlpool Refrigeration Plant on Highway 41. Source: Courier and Press
I remember all too well the day that the Whirlpool plant in Evansville shut down for the last time, a major manufacturing hub for appliances that employed several thousand people. At a very young age, this instilled the idea that hardware manufacturing companies must leave the United States in order to find competitive manufacturing prices. That is why I took a flight to Shenzhen, China to tour contract manufacturing plants. This massive manufacturing city is often called the hardware capital of the world based upon its speed, competitive labor, and material rates. After returning and considering the cost of manufacturing overseas, I began to factor in the not-so-obvious costs of building products outside of Evansville. The language barriers requires a translator to be present, and often leads to misunderstandings that can be very costly mistakes. The logistical challenges, uncertain trade relationship, and intellectual property theft quickly amounted to a cost that far exceeded that of domestic contract manufacturers. Most startup companies fail by aimlessly pursuing random goals without strategy as capital dwindles.
I have discovered that the resources I need to prototype and manufacture are widely available within the Midwest ecosystem. We then began to look locally for contract manufacturers within the Evansville-Cincinnati-Louisville trifecta that had worked at GE and Whirlpool appliance manufacturing plants and engineering design centers. Without disclosing trade secrets, we can confirm that the midwest has manufacturing capabilities that are very competitive with international rates. In our case, we were able to source almost all parts needed in manufacturing from Indiana, Illinois, and Kentucky. In addition to Evansville and Louisville being the former appliance manufacturing capitals of the world; we have been able to find top tier talent and industry partners with relative ease. Eventually, most hardware companies manufacture overseas when they exceed 1,000–10,000 units per year, but automation is the equalizer in a world where labor can be bought for a few dollars per hour, or be subsidized by a country in the process of industrialization. Indiana is uniquely positioned to be an entrepreneurial hotbed with several investment groups, and countless angel investors in one of the top manufacturing states in total manufacturing GDP (Gross Domestic Product).
Conclusion
After speaking to countless successful and not-so-successful entrepreneurs; I believe that starting a company requires two things.
The drive to achieve your goals
The means to achieve your goals
This has led to a new revelation about Evansville; it is not a good place to start a company… it’s a great place to start a company. It is uniquely large enough to have the means to fund a startup company, but not so large that the means become unobtainable to newer companies. The cost of living combined with these resources will triple to quintuple how far your dollar will go as opposed to a startup in a major city.
I now proudly say that Heliponix is based in Evansville, and we intend to stay here for the foreseeable future. We will continue to directly and indirectly create new jobs as operations expand. This only leaves one question from me to you, “Why not stay in Evansville?”.
Indiana entrepreneurial resource map, courtesy of Drew Peyronnin.
Indiana entrepreneurial resource map, courtesy of Drew Peyronnin.
The infographic above shows just some of the many resources available for startups in Indiana that has helped Heliponix many times in the past, present, and future. Purdue Foundry, Elevate Ventures, Purdue Polytechnic Institute, Blue Sky Capital, CoWork Evansville, APPCOM/BIZCOM, SVBIG, Certificate Entrepreneurship and Innovation — Purdue University, Burton D Morgan Business Plan Competition, Foundry@WestGate, GAGE, Agrinovus, Centric, IU IP Clinic, E is for Everyone, SouthWest Indiana Chamber of Commerce, Innovation Connector, TedxWabashCollege, Schurz Innovation Prize, Center for Entrepreneurship — PNW, Vectren Foundation, iGrow.news, and prospectively the MakerStation which conveniently holds many of these resources in one building; Innovation Pointe.
Scott Massey
Founder and CEO of Heliponix™. Purdue University, class of 2017. Mandela Washington Fellowship Alumni.
Indoor Farming with Bowery Farming
Were reappropriating previously unusable industrial space to grow crops indoors, closer to the point of consumption, at a rate that is 100+ times more productive per square foot of land than that of traditional agriculture.
Tell us about Bowery Farming and what you do.
Bowery is growing food for a better future by revolutionizing agriculture. Our modern farming company combines the benefits of the best local farms with advances made possible by technology to grow produce you can feel good about eating. BoweryOS, our proprietary software system, uses vision systems, automation technology, and machine learning to monitor plants and all the variables that drive their growth 24/7. Bowery produce is currently available at select Whole Foods and Foragers stores in the Tristate area, at select sweetgreen and Dig Inn locations in New York, and featured on the menus of Tom Colicchio’s New York restaurants Craft and Temple Court.
What got you started in the search to improve your energy monitoring and consumption?
While Bowery farms offer vast improvements compared to traditional agriculture - using zero pesticides, 95% less water, and are 100+ times more productive on the same footprint of land - we knew there was an opportunity to make our farms even more efficient and sustainable. We began our search to improve energy monitoring and consumption so that we could reduce our Co2 emissions, which make up a meaningful majority of our energy usage.
Tell us about the microgrid system you will be installing at Bowery Farming.
Bowery’s microgrid system will use distributed energy resources (DER), including a rooftop solar array, a natural gas generator equipped with advanced emissions control technologies and Schneider Electric’s lithium-ion battery energy storage system (BESS) interconnected in a behind-the-meter configuration. The system will greatly reduce Co2 emissions by using sustainable energy to offset the electric grid, reducing the power load we put on the grid, and offsetting our power load during periods of peak demand.
The main drawback currently for Indoor Farming is energy expense from lighting, what are your expectations for overall energy savings you will see with this system?
While Bowery farms require energy to power LED lighting systems, LEDs are effective and have more than doubled in efficiency in the last five years, making them an energy efficient solution. The offerings provided by Schneider Electric and Scale Microgrid will help cover a meaningful amount of our energy consumption needs and set us up with the knowledge and experience to install significantly more sustainable solutions in future farms.
Bowery Farming is at the forefront of the indoor farming industry. Why is it important for you to continue to innovate and lead the industry?
We’re continuing to innovate and lead the industry because we believe technology applied at scale can solve difficult and important, global problems. Agriculture sits at the epicenter of many global issues; over 70% of our global water supply goes to agriculture, we use over 700 million pounds of pesticides each year in the U.S. alone, and industrial farming practices have caused a loss of over 30% of the arable farmland in the last 40 years. At the same time, our global population is growing to 9-10Bn people by 2050 and we will need 70% more food in order to feed a population of that size. The result is a world in which the current food system must support the needs of an expanded population with a rapidly dwindling set of resources.
At Bowery, we’re re-thinking the current agricultural system to address the needs of an ever-increasing population by growing produce in large scale indoor farms. We’re reappropriating previously unusable industrial space to grow crops indoors, closer to the point of consumption, at a rate that is 100+ times more productive per square foot of land than that of traditional agriculture. In addition, our proprietary software and work management system BoweryOS organizes and directs the entire workflow inside the farm, driving efficiency, collecting data and creating a highly scalable framework for our farms.
Where do you see the indoor farming and Bowery Farming 5 years down the road?
We believe that indoor farming will continue to be a great contributor to solving difficult and important global problems. Our goal is to build a Bowery farm in every major city of the world to address major global challenges around food supply, environmental degradation and food waste.
You're Invited Tuesday, February 5, 2019 - Ronald Reagan Building - Washington, DC
The Foundation for Food and Agriculture Research invites you to explore food and agriculture research at our all day event, Foster Our Future. Join FFAR to:
Demonstrate game-changing research technology and innovation
Bring scientific breakthroughs to life
Celebrate the impact food and agriculture has on consumers and producers
Showcase research talent
Highlight the importance of continued research investment
For event and registration information:
REGISTER NOW!
CLICK HERE to add event to calendar.
FFAR thanks our current sponsors as of January 7, 2019.
AgLaunch Initiative, Conagra Brands, Institute for Feed Education & Research, Select Milk Producers
Agritecture Consulting
American Society of Agronomy, Crop Science Society of America, Soil Science Society of America
Association of American Veterinary Medical Colleges
Biotechnology Innovation Organization
Commonwealth Scientific and Industrial Research Organization (CSIRO)
Corn Refiners Association
Food Marketing Institute Foundation
The Grange Foundation
International Fertilizer Development Center
McDonald's Corporation
Meridian Institute | AGree
National Pork Producers Council
NOBLE RESEARCH INSTITUTE, LLC
Potomac Grange #1
Soil Health Institute
The Sugar Association
Supporters of Agricultural Research (SoAR) Foundation
Weed Science Society of America
Special thanks to the American Dairy Science Association
and the American Society of Animal Science.
For more information on how to sponsor contact:
Renée Bullion, rbullion@foundationfar.org.
Foundation for Food and Agriculture Research | 401 9th St NW, Suite 630, Washington , DC 20004
Disruptive 'Precision Farming' Spells Opportunities for This AgTech Company
The world is going to run out of food. Don't worry, the best minds are on it. They are using robots, better seeds, lighting and irrigation systems to reimagine farming.
Jon Markman Dec 19, 2018 9:00 AM EST
The world is going to run out of food. Don't worry, the best minds are on it. They are using robots, better seeds, lighting and irrigation systems to reimagine farming.
Bowery Farming Inc. calls the process precision farming. According to a report from Bloomberg, the indoor agriculture technology company is about to secure $90 million in funding.
It is a larger opportunity for investors with vision.
Like many technology startups, Bowery founders are determined to solve the big problems confronting the world. The United Nations projects that the world population will swell to 10 billion people by 2050. To keep up, global farmers will have to produce 70% more food. Unfortunately, most of the world's water resources are used for food production, and 30% of arable agricultural land has been lost to poor planning, pesticides and urbanization.
There is not enough water or land to possibly meet future demand.
Engineers are Bowery set out to do more with less. The solution began with controlling as many variables as possible. Crops are grown indoors under ideal conditions, without pesticides. Complex, LED lighting mimics the full spectrum of the sun. Irrigation systems deliver nutrients with exact specificity, resulting in 95% less water use than traditional farming and a 100x improvement in crop yields.
The urban farm company is using all of the tools of modern technology -- robotics, machine learning, computer vision and data science - to fine tune the entire process.
Bowery is not the only company in the game. Last year, Plenty, another indoor farm company from made headlines when it secured $200 million in financing from Softbank (SFTBY) , the Japanese firm led by billionaire Masayoshi Son, and investment companies associated with former Alphabet chairman Eric Schmidt and Amazon founder Jeff Bezos.
The gigantic investment in the tiny San Francisco startup sent shockwaves through the burgeoning ag-tech community. Early investors understood the potential of marrying sensors, robotics and data science with agriculture. The Softbank vote of confidence underscored the urgency.
The latest $90 million round was led by GV, the new name of Google Ventures. Alphabet (GOOGL- Get Report) , the parent company of Google, has made a cottage industry out of developing businesses models around machine learning. Its investment in Bowery is on brand.
Farming has not changed much in centuries. Yes, there are now self-driving tractors and even drones to monitor the growing process, but the basic premise still involves sowing seeds and waiting patiently for mother nature to bless the soil with bountiful crops. Companies like Bowery and Plenty completely disrupt that notion.
They want to control every aspect of the growing environment. They are cutting mother nature out of the loop in an effort to reduce costs, speed up growing cycles and reduce the footprint of farms. It's a revolution made possible by automation, better information and data science.
Even five years ago the economics of this revolution did not make sense. However, falling prices for cloud computing, robotics, sensors and machine learning have opened new doors. Information technology is being commoditized, just like fruits, vegetables and livestock.
Cognex Corp. (CGNX - Get Report) is the leading maker of sensors and vision systems for smart, industrial robots.
For a long time, truly smart machines were a pipe dream. Robots were impressive for their might. They stamped or welded or pushed items along a precision conveyor belt. But they were dumb. They didn't have eyes. They could not make sense of their place in the process.
The Cognex Insight Vision system gave industrial robots eyes. Machine learning and better software systems gave them intelligence. These attributes that are in high demand as factories get smarter, and ambitious startups push the limits of ag-tech.
The Massachusetts company has an impressive history of growth. Since 2013, sales are up 2.2x to $748 million. During fiscal 2017, the last full year of financial data, revenues shot up 43.5% while income ballooned 18% to $177 million. These metrics are certain to increase as more industrial robots gain sight, and smarts.
Cognex shares have been cut in half amid concern about the health of the global economy. The stock has fallen from a high of $73 in October 2017, to the lower $40s, bringing the market capitalization to only $7.2 billion.
At 29x forward earnings, Cognex shares are still expensive, but not ridiculous, for a unique, patent-protected, cutting-edge tech company in a growing field. Long-term investors with vision should consider using weakness in the weeks ahead to establish positions.
Kamchatka Won’t Get Its Vegetables: Renova Greenhouse Project Is Frozen
“…It is hard to say what has caused the delay, but the project is not developing. Possibly it is related to the minimization of state support”
The Renova company, owned by a Russian billionaire, Victor Vekselberg, has stopped the construction of the greenhouse complex within the Kamchatka Priority Social and Economic Development Area. The decision is allegedly related to the fact that the ministry of agriculture are considering minimizing state support in the greenhouse construction sector.
The price of a kilo of tomatoes and cucumbers in the Kamchatka markets and trade chains has reached 10.60 euros. The local authorities during the presentation of the full-scale project of the greenhouse complex construction promised that the produce of Renova would cost significantly less. Thus, the cucumbers were supposed to cost no more than 1 euro and tomatoes up to 1.50 euros per kilo. The local administration shrug their shoulders.
“We had high hopes for the Renova project. The land plot is completely ready for the construction. It is hard to say what has caused the delay, but the project is not developing. Possibly it is related to the minimization of state support”, mentioned the minister of Food and Food Production for the Kamchatka region, Mr. Aleksandr Kurchenko.
Strangely enough, even the administration of the Kamchatka region are not aware of the actual reasons for freezing the project within the Priority Social and Economic Development Area. It seems that the resident company have not informed the authorities about their decision.
In April 2018 the governor of Kamchatka, Mr. Vladimir Ilyukhin, personally presented the project of the Renova greenhouse complex construction within the Priority Social and Economic Development Area to the general public.
“One of the companies within the GK Renova are ready to construct the greenhouse complex in the Elizovsky region on an acreage of 15-20 ha. According to the preliminary calculation made by the investor, a kilo of cucumbers produced there will cost 1 euro and a kilo of tomatoes up to 1.50 euros”, mentioned mister Ilyukhin in April.
It was intended that the greenhouse complex produce would cover the need for fresh vegetables in the region by 40-43%.
In addition to other favorable conditions, a certain amount of gas from a Kamchatka gas field was specifically reserved for the Renova project.
The news on freezing the project has been very negatively taken by the local residents.
“What do they mean 'frozen'? The electric power line alone costs more than 6 million euros. And now what?”
“We will never have cheap vegetables”, Kamchatka residents write on social media.
Unfortunately, the disappointment of not getting cheap vegetables is not the only bad news for the locals. The administration have ensured them that most likely they will not have cheap meat or milk either.
Source: k-vedomosti.ru
Publication date : 12/4/2018
The Next Frontier of Agriculture
I gave a TEDx Talk at Wabash College that gave a glimpse as to why I chose to co-found Heliponix. We could only fit so much content in a 10 minute segment, so I saw it fitting to provide a written explanation to tell the full story. Follow the link below to see the full talk.
I was extremely fortunate to receive an internship the summers of 2014 and 2015 after my freshman and sophomore years at Purdue University working as a mechanical engineer for a company in the oil and natural gas industry that manufactured fluid control equipment in my hometown of Evansville, Indiana of about 120,000 people. Although I was surrounded by great co-workers who enriched my technical knowledge, I did not feel like this industry was right for my career.
Then one day during my junior year (Jan. 2016), I received a mass email from my college about a job opening at the horticultural college looking for an engineer familiar with fluid control systems for a hydroponic research project. I responded out of curiosity to see if I could at least learn more about other industries to strength my project experience portfolio, but I knew absolutely nothing about plant science. With luck, my email with resume and cover letter was well received, and I was invited into an interview with Dr. Cary Mitchell.
Dr. Mitchell expressed concerns for my generation's ability to grow enough food to meet the growing, global demand. Global food outputs must increase by 70% as we exceed 9 billion people in 2050 according to the UN. Agriculture accounts for 50% of land use, and 80% of freshwater consumption in the USA. To put it simply, we will run out of the land and water needed to produce enough food with our current consumption/production rates within the next thirty years.
Dr. Mitchell explained a new concept to me called CEA, controlled environment agriculture. It is exactly as it sounds, the practice of making an fully automated, indoor farm that used hydroponics. Hydroponics is a method of growing plants using no dirt, but only nutrient rich water recycled over the roots in a closed loop. By keeping the nutrients dissolved in the water in near constant curriculation, plants could grow three times faster than they would in a field. To put this in perspective, a lettuce farmer can typically grow a full head outdoors in 90 days, but hydroponics could grow lettuce in just 30 days or less in some circumstance. Most hydroponic systems are in controlled greenhouses, so a hydroponic farmer could harvest every month of the year without any pesticides and 95% less water by eliminating runoff. CEA was essentially a twelve times increase in productivity compared to conventional soil farming methods limited to one season a year. Additionally, a vertical farm that stacked layers of growing planes could multiply yields even further!
Dr. Mitchell was seeking assistance in the fluid control design for a hydroponic research apparatus called the minitron 3 funded through a NASA grant. Within my lifetime, permanent space colonies will be established on Mars which creates a need for a sustainable food supply. It is not feasible to regularly ship tons of food shipments from Earth, so they must be able to grow their own food. However, there are still challenges holding back the industry’s fruition.
The main challenge to creating a crop-growth module for space travel has been the staggering energy cost of the 600- to 1,000-watt conventional high-pressure sodium lamps traditionally used to mimic sunlight and stimulate plant photosynthesis in contained environments. The lamps also scorch plants if placed too close and require a filtration system to absorb the excess heat they create.
"Lighting was taking about 90 percent of the energy demand," Poulet said. "You'd need a nuclear reactor to feed a crew of four people on a regular basis with plants grown under traditional electric lights."
The focus of the Purdue-NASA research study was to measure the carbon dioxide concentration of air going into the minitron, and concentrations of oxygen leaving the growth chamber. This allowed researchers to measure photosynthetic efficiency rates under different wavelengths of light under an addressable LED array. If you only used LEDs of the right color plants need to grow, then you could eliminate the colors that the plants are not uptaking. The goal was to provide valuable insights about which spectrum of LEDs would be the best to reduce the energy consumption of an indoor growing operation, a major operational cost. This is why many vertical farms have “pink” lights, plants primarily need red and blue light. LEDs have become much more efficient than previous lighting options, and release little heat to greatly improve the energy efficiency of growing indoors.
With the youthful naivety of a 20 year old, I applied to every commercial, hydroponic facility in the US with little to no responses. I quickly learned that the research study I was a part of was not just an attempt to reduce the operational cost of CEA, but it was trying to make it more profitable for more people to pursue. Most indoor farming operations have access to reduced agricultural rates which is 90% less than what most residential consumers pay for energy. Without these subsidies, the industry would be reduced to very low margins, so paying for an engineering intern was out of question.
So I went back to the career fairs at Purdue desperate to find an internship opportunity anywhere outside of my hometown to see new things. I finally found my break when I was given an internship offer as a project manager in Hawaii for the summer of 2016. I immediately accepted the offer, but was told by the HR manager to not worry about the “TBD” stamp on my location of the contract I signed in March.... For the rest of the spring semester, I was ignored on all communication channels to this HR manager until I was finally called back during dead week at the end of the semester after canceling all interviews with the expectation I would be in Hawaii. I was informed that I was reassigned to build section-8 low income, government housing in El Paso, TX along the border to Juarez, Mexico.
A quick google search informed me that Juarez was a murder capital and major drug corridor for Mexican cartels bringing narcotics into the United States. The movie Sicario is based on the cartel violence in Juarez in this exact location. With no other options on the table, I packed my bags for a cross country roadtrip to the desert.
At the time, I spoke virtually no spanish and grew my beard out to appear older to the laborers working on the construction sites. My primary responsibility was to oversee a Spanish-speaking workforce for labor jobs such as toxic asbestos removal. Many of the workers had previous gang affiliations, and narcotic use was rampant. The section of El Paso I managed was originally called the “Angel's Triangle”; a triangular shaped subdivision situated between the Franklin Mountains range, the US Army’s Fort Bliss, and the border wall to Mexico. However, this portion of town was called the “devil's triangle” due to the gang activity, narcotics and prostitution that now plagues the area.
One day I woke up, and envisioned this career defining my entire life, and realized that this was not the industry for me either. I then began to look at my time in the desert as an opportunity to build a business model that could solve the food desert I was living in. A food desert is defined as, an urban area in which it is difficult to buy affordable or good-quality fresh food. Residents (who often lacked private transportation) often resorted to buying highly processed, non-perishable foods which are cheap and readily available at the local corner stores. These corner stores had little to no fresh produce which contributed to a high obesity and abnormally high diabetic rate. I knew that indoor farming could account for the poor soil quality and limited amount of water in the desert to bring these residents the fresh produce they needed, but the following points prevented this from happening.
Indoor, vertical farms require huge amounts of capital from investors to build the infrastructure with a long ROI.
Energy costs for indoor lighting greatly reduced the profitability of the facilities. Without reduced agricultural energy rates, many of these facilities would not be profitable.
Labor rates can be variable, and pose new liabilities for workman’s comp claims in the event of a workplace injury using equipment such as scissor lifts to reach top shelves. Although automation is the best solution, this is a tradeoff for an even higher infrastructure cost, and recurring maintenance cost from skilled laborers.
These points in mind, I concluded that the likelihood of a twenty-one year old being funded to build a multi-million dollar vertical farm was very unlikely. But this revelation posed a new question, “Could the technology be broken up into decentralized devices?”.
Que my TEDx talk… For inspiration I looked towards the ice industry which up until the 1800’s was made up of ice harvesters who could only cut ice from frozen bodies of water when the climate allowed water to freeze. This seasonal availability was disrupted by ice factories that could deliver ice year round in any climate. Today, 99.9% of Americans now own their own personal ice factories called refrigerators.
Much like the early ice industry, agriculture has always been dependant on the narrow window of growing seasons restricted by climates for crops to grow once a year. Since the explosion of microcontrollers and LEDs drastically increasing efficiencies and decreasing prices, indoor vertical farming has become financially viable for the first time. Much like the ice industries continual decentralization, we believe that agriculture will follow suit for many vegetables. In addition, decentralized, hydroponic farms eliminated the three concerns that limit the scalability of massive vertical farms.
Customers buy into for the hardware, not the investor.
The energy cost could be greatly reduced through a new, innovative design.
Contract manufacturing is highly competitive, and keeps manufacturing labor prices low.
This theory in my mind was validated by the success of the keurig recurring k-cup business model that could be emulated with hydroponic appliances sending monthly shipments of seed pods™ and fertilizers directly to the consumers.
Initial concept of recurring seed pod to be produced in an automated production line.
I spent the remaining time I had in El Paso creating conceptual designs this hydroponic appliance called a GroPod™. I then filed the first provisional patents on the new design before building the first prototype, and entered into business plan competitions at Purdue University my senior year. I quickly recruited my purdue-NASA-hydroponic coworker, Ivan Ball to be my Co-Founder because he was a brilliant electrical and computer engineer to close the skills gap we needed to keep improving upon our design. What happened afterwards could be a series of articles on its own, but at least this article can provide a deeper explanation of where I started, and where we are growing!
Follow us on social media as we continue growing to become the world’s largest farm without owning a single acre of land!
Instagram, Facebook, Linkedin, and Twitter: @heliponix
Playing "Happy Families" To Understand Urban Agriculture In France
We hear a lot about urban agriculture, but what is it exactly? How is it different from traditional agriculture? What is the difference between rural farms and urban farms?
11 December 2018
Agnès Lelièvre, lecturer in agronomy at AgroParisTech, Baptiste Grard, postdoctoral researcher at the Laboratory of Functional Ecology and Ecotoxicology of Agroecosystems (AgroParisTech/INRA), Christine Aubry, head of the Urban Agriculture research team at AgroParisTech, and Véronique Saint-Ges, economist at INRA, tell us about the different forms of urban agriculture.
We hear a lot about urban agriculture, but what is it exactly? How is it different from traditional agriculture? What is the difference between rural farms and urban farms?
New definitions of that concept have emerged in the past few years—including that of Canadian expert Luc J.A. Mougeot (2000) and French experts Paula Nahmias et Yvon Le Caro (2012)—, along with new typologies such as those of Cerema, Exp’AU and IAU. In the present case we will use Mougeot’s definition of urban agriculture:
“A production unit located within a city or metropolis (urban) or in its direct vicinity (peri-urban) that produces, raises, processes and distributes a diversity of food or non-food products by massively (re)using human and material resources, products and services from that urban area and its surroundings, and providing human and material resources, products and services to that same area.”
To depict the different forms of urban farming, we have chosen to use the analogy of “Happy Families”, where each category of urban agriculture is a family. For each family, we will relate the story of its ancestors and parents (the ancient forms) as well as that of its children (the current forms).
Without further ado, let’s get to know all these happy families.
1. The “Feet in the soil” family
This family has historically lived in an urban environment, while staying deeply connected to the soil. In today’s context, this category suffers from two recurring issues: access to land and pollution.
The ancestors of that category were the vegetable gardens of aristocrats, such as the well-known “King’s garden”, established in Versailles during the 17th century to provide fruit and vegetables to Louis XIV’s court.
In this family, the parents are a popular and commercial version of their ancestors. They are, for example, the marais ("swamps") at the heart of Paris, which have led to the French word maraîchage (“market gardening”). These farmers were great initiators and inventors of agricultural techniques that are still being used today. They practiced intensive agriculture on small areas using frames or glass domes to cultivate earlier in the season. Horse manure (which at that time was abundant in the city) and urban mud were some of the resources commonly used. This shows how helpful market gardeners were to city dwellers.
They have a large, varied descent that includes peri-urban farms, often pushed outside of the cities due to urban densification and hygienization. These farmers continue to sell their products to city dwellers, i.e. mainly vegetable produce and small animals (chickens, eggs, etc.). Over the past fifteen years, these farms have become increasingly popular through the development of short, local distribution networks such as AMAPs. These farms usually cover a few hectares each. In 2010, almost half of French farms producing vegetables and honey sold their produce through short distribution networks.
However, some farmers have managed to establish themselves within cities—or to maintain ancestral farms, although this is less common—by diversifying their activities. Some of them do community work, for instance for individuals that have been disconnected from the job market (such as the gardens of association Aurore), others do educational work (Veni Verdi for vegetable production, Bergers urbains for urban pastoralism) or organize cultural events (La ferme du bonheur).
The closest descendants of market gardeners work in production farms (such as Perma G’Rennes), located on former agricultural plots, or in schools or parks with plots from a few hundred m2 to 1 or 2 hectares.
The garden of the Pierre Mendès France college in Paris, overseen by the Veni Verdi association. (Michèle Foin/Vimeo, 2016).
2. The “Rooftop” family
This family has been around for centuries, as plants were already found on rooftop terraces in ancient Egypt, as shown in certain images of the book Palais et Maisons du Caire ("Palaces and houses of Cairo"), on the architecture of the 13th-16th centuries. Today urban honey is harvested from beehives installed on the roof of many public and private buildings.
There has been a growing interest in "green roofs" (i.e. not producing food) since the 1980s. Now the “agricultural descent” of this family includes farm that are community-oriented—to foster social interactions (Culticimes), for educational or experimental purposes (AgroParisTech‘s rooftop) or for event planning (Jardins suspendus). Some roofs also host farms for productive purposes (Aéromate, AgriPolis).
Interview of Louise Doulliet, co-founder of startup Aéromate. (Supbiotech/YouTube, 2017).
These “rooftop farms” have specific requirements as they have limited space compared to regular land farms. Today, rooftop vegetable gardens can be seen as a solution to issues related to land access and soil pollution, to the point that in a growing number of cities, new constructions anticipate their presence. Yet many questions remain unanswered, including about their design and the growing medium used.
3. The “Vertical” family
Growing produce on walls may seem risky... Yet Montreuil’s peach walls were renowned worldwide during the 19th century for the quality of their production: the fruits were exported as far as the Russian Tsar’s court. Vines have also been climbing on small walls and all kinds of arbors since antiquity.
Whether in museums, hospitals or malls, living walls designed for decorative purposes have become increasingly popular since the 90’s and 2000’s. Today living walls producing vegetables or hop are also found next to urban microbreweries. Farms specializing in event planning also use walls on rooftops. This family is less common than the two previous ones.
Paris hops will grow on the walls https://t.co/6XSGvftnTJ — Le Parisien | Paris (@LeParisien_75) 18 février 2018
4. The “Greenhouse” family
Greenhouse farming extends the production period of fruit and vegetables. The aristocracy was the first to reap its benefits through orangeries and winter gardens. During the 19th century, greenhouses were built in Auteuil and Paris’s Jardin des plantes to ensure the conservation of varieties and species constituting plant collections.
Today, greenhouses are extensively used in agriculture—including in the well-known Dutch production units—but also in cities for productive purposes (Skygreen) or on rooftops (Les Fermes Lufa, The New Farm). They can also be used to educate or experiment on social reinsertion and food therapy (such as in the Cité maraîchère in Romainville).
Greenhouse kale crops in Montreal’s Loufa farms. Les Fermes Lufa Facebook page
Aquaponics is another form of greenhouse farming that combines raising fish and growing vegetables. Although this type of production can be done in tanks based on a living substrate (with fertilizing power for the plants), it is usually based on a neutral substrate in hydroponic systems where the necessary elements for plants—and fish, if any—are provided through water. This type of production is currently being studied as part of a national research project.
5. The “Shade” family
The ancestors of this family developed underground, in mushroom and endive farms. They are known as produits de cave (“basement products”) and are commonly found in the greater Paris area. The parents haven’t diversified their products, yet they have developed new production systems. The children took over the family business by diversifying the offer, through micro-sprouts in particular, and by reusing new types of waste generated by the city, such as coffee grounds. It is mostly production-oriented (Boîte à champignons, La Caverne).
The Boîte à champignons (mushroom box). Agnès Lelièvre
A high tech “parent” has appeared in the last few years with growth in a controlled environment (light, atmosphere, etc.) thanks to recent progress in spatial research. Its children are using existing buildings or recycled containers (Agricool, Farmbox). This family is strongly developing in some countries with high population density or facing intense climatic stress. In France, it has been used as an opportunity to reuse areas such as abandoned parking lots, and in certain cases, to establish mobile farms.
6. The “Sunday gardening” family
The ancestor of the individual garden has led to private gardens, but also to group gardening with allotment gardens, which emerged at the end of the 19th century.
The children of this family continue to maintain private gardens on balconies, terraces and actual gardens, which can be produce high yields. They also practice collective gardening which covers shared gardens, family gardens and multiple hybrid experiments. While private gardening is aimed at growing vegetables, collective gardening also has a social and educational purpose.
This family has grown a lot since the 20th century and it has become increasingly popular, especially in the case of collective gardening. There are over 1,000 collective gardens in Île-de-France, covering at least 900 hectares, in a context where professional vegetable production covers 5,000 hectares. It is a great success, even though obtaining a plot to cultivate in the city or its surroundings remains difficult, as evidenced by the long waiting lists to access a family or collective garden.
Family gardens in the Lilas public park in Vitry-sur-Seine (94). Agnès Lelièvre.
7. The “Self-service” family
Inspired my movements such as Guerrilla gardening, which, in the 70s, started reclaiming land that had been built and abandoned, this is a family of creative, conquering activists.
It has given birth to active offspring seeking to establish plant production in public spaces for everyone to enjoy. It includes international initiatives such as the Incredible edibles, as well as initiatives launched by cities themselves such as permis de végétaliser ("license to plant") and the reintroduction of fruit trees in public parks. Although still discreet, this family has a bright future, as it is an inspiration to local communities.
The original version of this article was published on The Conversation.
Urban Farms Could Be Incredibly Efficient—But Aren’t Yet
In some ways, hyper-local food is a counterculture movement, focused on growing herbs and vegetables in the same dense urban environments where they will be eaten. It trades the huge efficiencies of modern agriculture for large savings in transportation and storage costs. But is urban farming environmentally friendly?
Casual Farmers Overwork, Buy Fertilizer, And Use Municipal Water.
JOHN TIMMER - 12/27/2018
The green revolution that transformed modern agriculture has generally increased its scale. There's tremendous potential for efficiencies in the large-scale application of mechanization, fertilization, and pesticide use. But operating at that level requires large tracts of land, which means sources of food have grown increasingly distant from the people in urban centers who will ultimately eat most of it.
In some ways, hyper-local food is a counterculture movement, focused on growing herbs and vegetables in the same dense urban environments where they will be eaten. It trades the huge efficiencies of modern agriculture for large savings in transportation and storage costs. But is urban farming environmentally friendly?
According to researchers at Australia's University of New England, the answer is pretty complex. Within their somewhat limited group of gardeners, urban agriculture is far more productive for the amount of land used, but isn't especially efficient with labor and materials use. But the materials issue could be solved, and the labor inefficiency may be a product of the fact that most urban farmers are hobbyists, and are doing it for fun.
Urban ag
The researchers—Robert McDougalla, Paul Kristiansena, and Romina Rader—defined urban agriculture as taking place within a kilometer of a densely built environment. Working in the Sydney area, they were able to find 13 urban farmers who were willing to keep detailed logs of their activity for an entire year. Labor and materials costs were tracked, as was the value of the produce it helped create. The energetic costs of the materials and labor were also calculated in order to assess the sustainability of urban farming.
The plots cultivated by these farmers were quite small, with the median only a bit over 10 square meters. Yet they were extremely productive, with a mean of just under six kilograms of produce for each of those square meters. That's about twice as productive as a typical Australian vegetable farm, although the output range of the urban farms was huge—everything from slightly below large farm productivity to five times as productive.
For the vast majority of crops, however, the urban farms weren't especially effective. They required far more labor than traditional farms and as a result the total value of the inputs into the crop exceeded the income from selling it. In other words, the urban farmers were losing money, at least by traditional accounting measures. And the farms weren't especially sustainable, with only about 10 percent of all the inputs coming from renewable resources. Again, labor was a major culprit, as it's not considered very renewable, and urban farming is very labor-intensive.
So that all sounds like a bit of a disaster, really. But as mentioned above, things quickly get complex. The urban farmers, as it turned out, bought compost and fertilizer, and used the municipal water supply. Cities, as the authors note, produce large quantities of organic waste that could be used to make compost. While it would require additional labor and land space, it would be easy to make the care of the crops far more sustainable. Combined with the use of collected rainwater, these could get the percentage of renewable contributions up to roughly 40 percent.
Laborious
Then there's the issue of the time spent on labor. The urban farmers don't seem to be especially efficient compared to regular farm laborers, and by all indications they don't necessarily want to be. For many of them, it's more a hobby than career; they put in more labor because they enjoy it or find it relaxing. If you start reducing the labor costs to reflect this, things start changing dramatically. If only the material costs of urban farming is considered (meaning labor was set to $0), then the apparent efficiency improves dramatically.
Not surprisingly, ignoring labor costs also makes a big difference financially, with the profit-to-cost ratio going from a mean of 0.62 up to 2.8, indicating that these urban farms would generally be quite profitable.
Labor also makes a big difference in terms of energy use. As they're now operating, these urban farms aren't very different from rural farms, which means they're not sustainable. Shifting to local sources of materials, like rainwater and compost, would drop the energy use dramatically, shifting the farms into territory that's typically considered sustainable. Eliminating labor considerations on top of that would make urban agriculture among the most efficient means of growing vegetables presently studied.
There are two obvious caveats to this work: the small number of farms sampled and the fact that they were all in a single urban area. This sort of study will obviously need to be replicated in other locations before we can start generalizing about hyper-local produce. But the role of labor in this sort of analysis makes conclusions difficult to generalize. Is it reasonable to discount some fraction of the labor costs when people are doing the farming for pleasure? Do we start considering a tomato plant on a balcony part of an urban farm?
While many of the details are unclear, the overall conclusion seems solid: while urban farms aren't yet there in terms of sustainability and energy use, the potential for them to outpace their larger urban cousins is definitely there. But it will take an entire sustainable support infrastructure for them to truly arrive.
PNAS, 2018. DOI: 10.1073/pnas.1809707115 (About DOIs).
How The Farm Bill Impacts Greenhouse And Indoor Growers
December 28, 2018
Photo taken by Allison Kopf
When President Trump signed the Farm Bill last week, it was the first time that indoor farmers have been included in the act’s provisions since its birth in 1933.
The Farm Bill, which will allocate $867 billion of federal money over the next ten years came about in reaction to the dust bowl years of the 1930s. That era of climate variability and unsustainable farming techniques left American farmers vulnerable, which the first farm bill attempted to help with. Today, facing our own era of climate change, Congress has begun to take an interest in how it can help indoor farmers. Here are four parts of the bill that we’re really excited about:
Office of Urban Agriculture and Innovative Production
Section 12302 of the bill opens a new office to aid urban and indoor farmers. The newly created Office of Urban Agricultural and Innovative Production will “ encourage and promote urban, indoor, and other emerging agricultural practices.”
We’ll have to wait and see what that encouragement and promotion actually means, but it’s certainly a plus for indoor and greenhouse growers to have a federal office learning where it can have the government add value to the indoor ecosystem.
Micro-Grants
Good news for farmers in food insecure places: the government wants to help. In order to feed citizens with real, healthy foods, provision 12616 of the bill authorizes small grants for farmers who want to build hydroponic and aeroponic farms.
A Census
In order to get a grasp on the indoor farming landscape, the government will conduct a census of existing indoor, rooftop, greenhouse, and hydroponic farming operations in both urban and rural areas.
This is great news. We’ve been conducting our own survey for a few years now since the ag census previously didn’t do much for highlighting indoor growers. We’re excited to see where this goes.
Help From the Government
Information from that census will help the government aid farmers in a couple ways under section 11122 of the bill. One of them is that the Federal Crop Insurance Corporation will research insurance plans to help farmers, particularly those in small-scale production to offer policies that are most beneficial. Currently, the government offers subsidized insurance for farmers in case of drought or hail or if prices fall. The primary crops covered under insurance are the most basic staples of American agriculture, such as wheat and corn. For indoor farms, the elements would not affect yield as they would outside, but there are still plenty of variables, including the price of crops, the cost of electricity, and others, which could benefit from some type of federal insurance.
We believe that greenhouse and indoor farming is the future of farming, and we’re glad to see that the U.S. government is thinking ahead and moving in the same direction. The farming industry faces some challenges before it. With climate changes, the patterns of planting will vary more and more, and extreme weather will become more normal. As our cities continue to support more people, it’s becoming more of a challenge to provide fresh, wholesome food to the neighborhoods that need it. The provisions in the farm bill provide the beginnings of some solutions for meeting those challenges, and for leading to a farming industry that’s equitable, sustainable, and healthy!