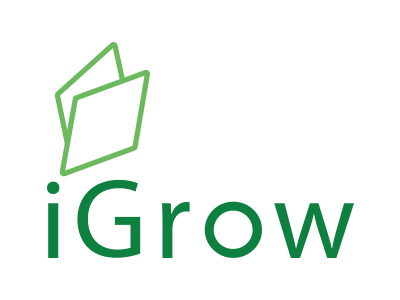
Welcome to iGrow News, Your Source for the World of Indoor Vertical Farming
Nigeria: Farming Without Soil
Farmers are growing crops without soil.
They are on a national campaign to promote this type of agriculture, DANIEL ESSIET writes.
In a room in Anifowoshe, Ikeja, Lagos, kale, romaine, lettuce, oregano, thyme, arugula and basil are grown in trays under energy bulbs.
The seeds are cultivated without soil. You are greeted by the pleasant sight of rows of young maize leaves growing out of pipes filled with water and saw dust –no soil.
Though they are growing in a protected environment, the leaves are thick, lush green, and free of dust particles, giving them a clean and healthy look.
BIC Farms Concept Chief Executive, Pastor Debo Onafowora, believes hydroponics – growing plants without soil – is the best way to go.
Hydroponics, he explained, involves growing plants without soil.
An Associate Pastor with Living Faith Church (aka Winners’ Chapel), Ota in Ogun State, Onafowora grows crops hydroponically. The most common are tomatoes, peppers, cucumbers and maize. The seeds are placed in trays and watered several times daily with a nutrient solution.
Onafowora added that hydroponics is better than conventional farming.
He emphasised that a plant only need some nutrients, water, and sunlight to grow.
He listed the advanges of hydroponics as high quality products, less space, and consumes fewer resources.
He harvests his vegetables just after 25 days, half the time needed with regular planting.
Besides farming, he teaches agriculturists how to apply the technology. He helps his customers to set up farms and provides consultation and training.
A small scale vegetable hydroponic farm requires an investment of N500,000. This will give a 10 ft X 20ft greenhouse hydroponics farm with hydroponics with systems for growing 250 kilogrammes ( KG) of tomatoes or 350 kg of cucumber.
One can make net profits of 40 to N50,000 monthly. He has established over 100 farms across the country.
By growing cattle fodder off the fields, he said hydroponics could offer a solution to the frequent violent clashes between farmers and herdsmen over arable farmland that is disappearing due to desertification.
Onafowora advocated the use of hydroponic fodder as the best option for livestock feed, adding that this would help reduce the cost of the product by over 20 per cent.
He said the fodder could be grown within nine days and that it saves about 95 per cent of land.
Onafowora noted that hydroponics fodder production technology is a climate-controlled crop growing system, which guaranteed daily production of highly nutritious livestock feeds.
“It is grown from grains. We convert one kilogramme of grain to 5kg of fodder within nine days. Normally, on the soil, it will take up to 90 days.
“What you need is 100 hectares of land to grow. In terms of fodder quantity, we will do that on one hectare of land and we are doing that saving about 90 per cent of water,” he added.
He is partnering Landmark University, Omu-Aran, Kwara State.
Universities of Lagos, Ibadan, Federal University of Agriculture Abeokuta, Lead City University have also picked the technology.
To boost food production, Samson Ogbole is employing aeroponics- a process of growing plants in the air.
He became involved in soilless farming in 2014. Two years later, he founded PS Nutraceuticals, a firm that applies agricultural technologies to boost food production.
The firm Nutracueuticals deploys various technologies, including hydroponics (plants in water), aquaponics (use of waste produce of fishes to feed plants) and aeroponics (plants grown in air) to grow crops all year round.
To him, aeroponics is a better alternative for growing crops indoors.
Experts say aeroponics is similar to hydroponics and that it uses water. The roots are suspended in a dark chamber and sprayed with nutrient-rich solution.
To Fresh Direct Produce and Agro-Allied Services CEO/founder Angel Adelaja, urban agriculture has brought a new hope. She uses old shipping containers for farming.
A self-taught hydroponics expert, Adelaja appears to be making headway. The entrepreneur, who has a background in biostatistics and epidemiology, learnt hydroponics online.
She created a stackable container farm in Abuja, which is essentially an aggregation of vertical farming and hydroponics.
She is campaigning for the transformation of old shipping containers into miniature hydroponic farms.
The containers are retrofitted with growing platforms where beds of lettuce are grown with their roots in water.
Adelaja and her team grow those vegetables using only nutrient, water and LED light.
The method makes it possible to grow crops all year round.
Adelaja encourages farmers to use abandoned shipping containers in their farms.
Her company, Fresh Direct, has several divisions one of which produces stackable containers.
She is passionate about creating awareness among other farmers.
Green Life Farms Erects Framing For Flagship Hydroponic Greenhouse
Innovative project prepares to begin commercial operations in the first half of 2019
Boynton Beach, FL (February 15, 2019) – Green Life Farms has begun erecting the steel structure of its state-of-the-art hydroponic greenhouse in Boynton Beach, FL, an important construction milestone as the company prepares to begin commercial operations in the first half of 2019. Once operational, the hydroponic greenhouse, slated to be the largest indoor hydroponic produce grower in the southeast, will offer baby leafy greens to supermarkets, restaurants, cruise ships and other distributors throughout the region year-round.
“Excitement continues to build as we work towards beginning commercial operations in the next few months,” said Mike Ferree, Vice President, Green Life Farms. “Grocery partners, consumers, local officials, and other future clients are impressed with the construction progress. We can’t wait to ‘open our doors’ to this larger community. Demand is very strong for produce that is grown locally using sustainable farming practices and free from pesticides and contaminants.”
Construction of the Green Life Farms’ flagship facility began in 2018; when complete, the greenhouse and packing facility will occupy nearly three acres and produce approximately 750,000 pounds of premium leafy green produce per year.
Green Life Farms’ hydroponic greenhouse will feature innovative Deep-Water Floating Raft Technology (FRT) from Hydronov, an industry leader in the hydroponic space with more than 30 years of experience. FRT helps to conserve water, using the oxygenated clean water in which the plants grow as a conveyer system, eliminating the costs and maintenance associated with mechanical conveyers. The FRT system leads to higher productivity, producing up to 18 crop harvests per year versus the five harvests per year with soil-based greenhouse growers.
In preparation for commercial operations, Green Life Farms recently hired its sales director and head grower. Once operational, the hydroponic greenhouse will employ approximately 16 additional people in the state-of-the-art facility.
Green Life Farms produce will set new standards for cleanliness, freshness, and taste. Grown locally, using sustainable farming practices combined with the most advanced AgTech practices, and kept free from pesticides and contaminants, Green Life Farms baby leafy greens are good for the body, family, community, and planet.
For more information about Green Life Farms, visit GreenLifeFarms.ag. Please contact Elayne Dudley at Elayne@GreenLifeFarms.ag for sales and Raymond John at Ray@GreenLifeFarms.ag for investor relations.
Caption: Green Life Farms has begun erecting the steel structure of its state-of-the-art hydroponic greenhouse in Boynton Beach, FL, an important construction milestone as the company prepares to begin commercial operations in the first half of 2019. Pictured above, an aerial view of the construction site showcases the two greenhouses (top and bottom), which will each total 54,00 square feet, with a packing facility in the middle.
About Green Life Farms
Green Life Farms is constructing a 100,000 square foot state-of-the-art hydroponic greenhouse in Boynton Beach, Florida, with additional expansion planned in Florida and beyond. Commercial operation is expected to begin in the first half of 2019. By incorporating agriculture with technology, Green Life Farms will provide consumers with premium-quality, fresh, local, flavorful and clean baby leafy greens that are good for their bodies, families, communities and planet – year-round.
About Hydronov
Hydronov LLC was purchased by Nick Pranger and Gabe Pranger in 2017. Since its beginnings in the 1980s with founder Luc DeRochers, Hydronov has focused on innovation in the greenhouse industry. The success of a small research project developed into Hydronov’s unique growing system, Deep Water Floating Raft Technology. Today, Hydronov’s technology is a cost-effective, environmentally friendly, and profitable way to grow hydroponic lettuce, herbs, and produce.
“Access To Equity Capital is a Competitive Advantage”
Equilibrium Capital on Revol Greens & Houwelings investments
There’s a new kid on the block investing in the greenhouse industry. Early this year, Revol Greens announced a facility equity partnership with Equilibrium Capital - and just two weeks later Houweling’s Group was connected to the same investment company. Then there's a third investment, in a yet to-be-named hydroponic berry producer. Time for a chat with David Chen, CEO with the firm. “We definitely look for more opportunities to expand in the greenhouse industry.”
'Strategic advantage'
"Something that's hard to understand for a lot of farmers is that when an industry starts to accelerate, the access to several forms of capital, especially equity capital, becomes a strategic advantage. Most growers and operators have been used to access to bank debt, and have interpreted that as all they needed. What we see is that the growth has accelerated in the US, following a growing market demand. The expansion is no longer five hectares, ten hectares, the expansion is now twenty, thirty hectares, maybe fifty hectares. In this accelerating industry, growers are discovering that access to all forms of equity capital is a competitive advantage,” David Chen with Equilibrium Capital explains when asked about the growing role of investors and foreign capital in horticulture.
"I think the first wave were a number of large tomato operators that took on some outside investors”, he continues. “But I think the real start of this was when the leader in the greenhouse tomato market started to expand and accelerate the amount of acreage that they partnered with and owned in their corporation. And then when they took on some private equity, I think that that signalled the next chapter of this industry.”
In January Revol Greens, a Minnesota greenhouse farm, announced a facility equity partnership with Equilibrium Capital to drive expansion in 2019.
Landlord
And now Equilibrium Capital has taken its first steps in this business as well. The company has an extensive portfolio in wastewater, energy facilities and permanent crops, and has recently expanded into the horticultural industry. “Investing in agricultural infrastructure”, he calls their strategy, explaining that the company has no ambition to be involved in the day-to-day running of the companies they invest in. Rather than participating in the company, they extend the greenhouse operator’s balance sheet.
To make it concrete: Equilibrium is not investing in greenhouse operating companies, but is buying greenhouses and building out future greenhouses. By now, they've invested over $100 million in three large-scale greenhouse operations in California, Utah, and Minnesota and they plan to commit $2 billion to indoor food production over the next five years.
“Our objective is to acquire or build a set of greenhouses and hold onto them for a long period of time. To growers, we operate like a landlord. We give the grower, the operator of the farm, more options to accelerate and manage their growth.”
For example, in the Revol Greens investment, the company bought the existing greenhouse, making it possible for Revol to lease these premises and free up capital and begin plans for expansion. “We do not own any part of Revol. We own the greenhouse and financed the expansion of the greenhouse itself”, he says, comparing it to when companies like FedEx or DHL expand. “They don’t own their distribution center real estate. They own the business and operate the business inside the real estate. Airlines don’t own their terminals, Microsoft don’t own their data centers buildings.
The main advantage of the Equilibrium business model, David explains, is that a grower remains independent: “We just get him some fuel in the tank – and upgrade his motor at the same time!”
To Equilibrium themselves, it provides a safe solution. “In agriculture, putting too much debt is always dangerous. That's why our strategy has been to stay an equity investor, and to hold to very tight debt equity ratios, where the investment is still dominated by the equity."
Portfolio expansion
Having gotten a taste of the market with their recent acquisitions, Equilibrium is looking to expand their portfolio in the horticultural industry, in both existing greenhouses and expansion. Looking at the industry in general, David sees tremendous growth ahead in the next decade. "I can't emphasize enough what a driver climate is in the development of horticulture in non-Mediterranean growing climates. Even the regions that normally have stable weather have to get used to less table weather. Then there's the desire for regionality and for greater variation in the food that we eat. All together this is pushing and propelling indoor agriculture forward. Over the next decade, we're going to see acquisitions, mergers. You're going to see food companies outside of horticulture begin to invest in this area", he speaks. “We not only want to participate in that movement, but to be a leader and pioneer in the financing of that growth. We're believers that a horizontal high-tech greenhouse is going to become a mainstay of vegetable and fruit growing in this next decade, also outside of northern Europe.”
Like many participants in the industry, David emphasizes the importance of knowledge of farming. “Because greenhouses are hot right now, everybody reads about it and says, 'oh, I can do that'. The only caution that we have is: if you don't have experience, then at least have humility! The common belief seems to be there’s three pipes at one end of the greenhouse – putting in seed, water and fertilizers, and a fourth one on the other side, where the tomatoes come out. Well, we know there’s a lot more going on. That’s why we’re looking for the best, most experienced operators in the category, and like to be partners with them for their growth.”
In this outlook, he’s not afraid to cross the US borders. “If some of the Dutch growers were interested in expansion outside of Northern Europe, we would be a great partner for them to expand into Asia, North America, or even South America. Let’s put it like this: if experienced growers bring their knowledge to the table, Equilibrium provides the necessary capital.”
For more information:
Equilibrium
971-352-8430
info@eq-cap.com
eq-cap.com
Publication date : 2/18/2019
Author: Arlette Sijmonsma
© FreshPlaza.com
Controlled-Environment Growers Power Their Operations With Cogeneration Systems
Cogeneration systems can deliver the electricity, heat and supplemental carbon dioxide that controlled-environment growers can use to produce edible, ornamental and medical cannabis crops more efficiently and more profitably.
January 30, 2019
By David Kuack
The highest density of cogeneration systems in greenhouses is in the Netherlands. Cogeneration systems in Dutch greenhouses represent almost 25 percent of the electricity produced in the country.
“Cogeneration is a technology that converts natural gas into useful energy for greenhouses, which includes inside power generation to heat the greenhouses and the production of supplemental carbon dioxide that can be used to increase plant growth,” said Dick Kramp, founder and CEO of AB Greenhouse Power Netherlands. AB GPN is acting as a vertical cultivation center of excellence for the global AB organization. Over the last three decades AB GPN developed a standardized cogeneration solution for greenhouses which is fully integrated with the cultivation system.
“The cogeneration system purifies the exhaust gases to produce carbon dioxide. The carbon dioxide can be used to supplement atmospheric carbon dioxide for the production of vegetables, ornamentals and medical cannabis. For the production of cannabis, cogeneration is being used to generate electricity to operate the grow lights. Also, heat from the cogeneration system can be converted into chilled water to cool the greenhouses.”
The majority of greenhouse operations that have installed cogeneration systems have done so to support the electrical power they cannot get from the grid.
Photo courtesy of AB Greenhouse Power Netherlands
The cogeneration system is based on the burning of natural gas.
“Fortunately natural gas is relatively cheap at this time,” Kramp said. “Right now cogeneration is the most economical way of producing energy. The founders of AB GPN started with this technology in Europe and have done over 1,000 unit installations in greenhouses.
“In greenhouses the two major costs are labor and energy. Cogeneration is an additional income stream by selling electricity to the grid and/or energy savings for growers to reduce their price of growing. To operate grow lights growers have to purchase electrical power from the grid. They have to have boilers to heat the greenhouses. They have to have chillers to cool down/dehumidify the greenhouses. With cogeneration on site growers can produce electricity so that they don’t have to buy it from the grid and they can produce the electricity themselves for a lower price. Growers save on their energy bill thereby lowering their cost of production. This enables growers to be more competitive.”
Greenhouse, indoor farm applications
Cogeneration systems can be used in greenhouses and in indoor farms.
“A cogeneration system is not just an engine and a generator,” Kramp said “It’s a total system that is integrated into a greenhouse or building. Ninety percent or higher of every Btu of natural gas is converted into useful energy. Cogeneration is the most economical way of converting natural gas into energy.
“With an indoor farm, it’s more energy intensive because it is not making use of sunlight. On the other hand, an indoor farm allows for the creation of its own climate because the building is more controlled. But it is more expensive to create that climate because it is not making use of the sunlight and grow lights have to be installed to light the crops.”
Kramp said the majority of greenhouse operations are using cogeneration to support the power that they cannot get from the grid.
“In Canada, we have sold more than 50 megawatts of cogeneration in Ontario,” he said. All of the cogeneration systems there are supplying power back to the grid as intermittent power.
“Cogeneration was driven by the need for flexible power supplied to the grid. There is a lot of wind-generated electricity in Ontario and there was a need for integrated flexible power. Cogeneration systems were installed in greenhouses to supply electricity back to the grid when it was needed when there was no wind.”
The carbon dioxide produced by cogeneration systems can be used to supplement atmospheric carbon dioxide for the production of vegetables, ornamentals and medical cannabis. Photo courtesy of SunSelect Produce
A vegetable greenhouse in California has a contract with its utility company to supply electricity back into the grid. The electricity generated by the company’s cogeneration system produces heat, carbon dioxide and enough electricity to power its 64-acre operation plus an additional 2,300 homes.
“This greenhouse is creating an income stream out of selling power to the grid,” Kramp said. “The cogeneration engines run during the day to produce electricity. The heat that is generated is captured and stored in a heat storage tank. This heat can be extracted from the tank at night when the engines are not operating. The engines also produce carbon dioxide that can be used during the day to increase crop productivity.”
Need for more electricity
Kramp said many medical cannabis growers in the U.S. and Canada are installing cogeneration systems.
“The biggest driver of cogeneration in this industry is the shortage of power,” he said. “Right now in the U.S. and Canada they are installing cogeneration systems because they cannot get the electricity from the grid that they need to light their crops. Many growers are installing cogeneration systems in order to guarantee that they have enough power.”
Kramp said growers who have installed cogeneration systems will see the value of the systems as the price of produce begins to drop.
“Currently growers are not really interested in reducing their energy bills by generating electricity at a cheaper price,” he said. “The value of medical cannabis will eventually decrease and will become a commodity like other crops. When it becomes a commodity, then the growers will have to lower their energy bills by installing cogeneration to stay competitive.”
Financial incentives
Kramp said the amount of money growers can save using cogeneration depends on the price of natural gas and electricity.
“Substantial savings can be achieved by installing cogeneration,” he said. “Depending on the price of gas, a kilowatt of electricity can usually be produced for a lower price than buying it from the grid. It really depends on the price of natural gas. The exact savings will be determined in a feasibility study that is done before a cogeneration system is advised.”
In addition to the savings that growers will realize from generating their own electricity, Kramp said many states offer financial incentives for installing cogeneration systems. Both the U.S. Department of Energy and EPA promote incentive programs related to cogeneration, which is referred to as combined heat and power.
“Each state has its own cogeneration program where there are different rebate programs available,” Kramp said. “The incentive program in Massachusetts is called Mass Save. The Department of Energy is supporting cogeneration. The agency has a special group that is available to do feasibility studies for growers interested in installing cogeneration systems.
“Massachusetts is also offering rebates for the installation of LED lights. To apply for these rebates a feasibility study has to be submitted. This is usually done by an engineering company. The state is only awarding the rebates when it is supported by a feasibility study that shows the savings from installing LED lights. Growers can work with the lighting companies to determine what types of rebates are available with the state. Combining LED lights with cogeneration is a great way to maximize efficiency.”
For more: AB Greenhouse Power Netherlands, (31) 631635065; dick.kramp@gruppoab.com; https://www.gruppoab.com/en/greenhouse.
David Kuack is a freelance technical writer in Fort Worth, Texas; dkuack@gmail.com.
New Greenhouse Concept: Multispan, Foil and Semi-Closed
During this year's Sival, a new greenhouse concept was launched by CMF Groupe. The GreenPush BioActive is a semi-closed multispan concept. "We want to limit the pest pressure and offer a more homogeneous climate", Corenthin (Felix) Chassouant with CMF Groupe explains.
IPM
As shown at the Sival and in the video above, the GreenPush BioActive is equipped with insect nets, in the roof and windows. A constant airflow into the greenhouses creates over-pressure, making it impossible for insects to enter the greenhouse and thus creating favorable conditions for IPM.
The air entering into the greenhouse is controlled by a high-tech climate management system, offering extra control over the greenhouse air. "Temperature, humidity and CO2 can be optimized in an easy way, offering growers extra tools to control their climate", Felix continues. "Since the air is dehumidified before it enters the greenhouse anyhow, it offers opportunities to recycle the air various times and create a homogeneous, favorable climate for the crop while ensuring optimal heating conditions and using the energy to the best. In warmer periods and with the use of cooling pads, it's also possible to cool the outside air being brought into the greenhouse."
The GreenPush BioActiv is equipped with the oval tubes - like the GreenPush concept that was launched last year. The ovalized tube makes higher widths possible and thus more volume in the greenhouse. "This concept is for both glass as well as foil greenhouses", Felix tells us. "The larger widths & higher volume gives a better humidity and temperature control within the greenhouse, whereas the amount of shadow is significantly lower thanks to the larger distance between posts. With the GreenPush BioActiv we take the next step."
Like CMF's other options, the CMF’s GreenPush BioActiv turnkey solution can be adapted to all climatic conditions to obtain more homogeneous crops by reducing or even eliminating chemical products.
For more information:
Author: Arlette Sijmonsma
© HortiDaily.com
Ozone Technology For Greenhouse Water Treatment
"Proper Greenhouse Water Recycling Is The Key To Increasing Your Profitability"
“Proper greenhouse water recycling is the key to increasing your profitability, year after year. Without adequate control of your nutrient feed solution, the entire process of fertigation can prove harmful for your crop’s steady growth.” Speaking is Christopher Labbate with Climate Control. The company offers ozone water treatment to eliminate pathogens spreading through water. “Water recycling has become a popular trend in the agricultural industry. As more greenhouse operations are in need of treating their nutrient wastewater on site. Growers are recognizing that using quality water has substantial benefits in many areas of production, including plant health and quality control.”
Although using a hydroponics system may eliminate soil borne pests, there are other pathogens that spread through water. Pathogens and other water bacteria are a cause for concern in water quality. Most greenhouses today use some type of recycled water treatment in their irrigation systems or use chlorination. Sometimes multiple solutions are combined to answer the problem of crop management.
Climate Control offers Ozone solutions. “Ozone is a powerful oxidant gas that is injected in the water to kill microorganisms, bacteria, and break down other plant pathogens by oxidation. This occurs immediately at point of contact and continues to disinfect your nutrient solution. Some of the ozone reverts back into oxygen in the treated storage tank and this can be a large advantage to growers as it is beneficial to growth”, Christopher explains.
Ozone generators create ozone through an electric discharge of sparking Oxygen (O2) to create Ozone (O3). This can be controlled by software to increase or decrease the concentration of ozone, to output the desired amount for optimal plant health.
“Monitoring and control of pH and Electrical Conductivity (EC) have become standard practice, for improving plant health and quality throughout growers. By measuring these two simple factors, most nutritional problems can be avoided.”
According to Christopher, the measurement of Dissolved Oxygen (DO) is also proving to be just as critical to plant growth. “Minimum levels of dissolved oxygen are also required for a healthy plant. Most growers do not have the sensors to read this important quality of the water. Ozone water treatment not only kills 99.9% of bacteria in your irrigation water, but also gives added benefit. By providing dissolved oxygen for the root zone of the plants, you will see a 10% increase in crop yields.”
Ozone is effective in getting rid of odors in the water as well, like from iron and manganese. “It's the gold standard for drinking water, and used in many municipal water treatment plants around the world.”
Currently many growers might doubt between UV Sterilization. This technique inactivates microorganisms and stunts pathogen growth with UV light. Christopher believes this is not sufficient. “This happens while the water is in the UV chamber only, and as long as the water has sufficient contact time. And it’s also interesting to note that UV disinfects the water by sterilizing the contaminants so they can no longer replicate. Whereas ozone will destroy the contaminants completely by breaking them down. Then Ozone dissolves back into oxygen, which is very beneficial to the rootzone of the plant.”
Christian concludes: “Our mission at Climate Control Systems has always been, to help growers stay profitable by offering cutting edge automation and control technology. You can also expect to save 35% on water costs and 40% on fertilizer expenses with this industrial grade ozone water sterilization equipment.”
For more information:
Climate Control Systems
Christopher M. Labbate
1-519-322-2515
Chris@climatecontrol.com
www.climatecontrol.com
Publication date : 2/5/2019
"Labor Is The Number One Topic In All The Conversations We Are Currently Having"
“…Being a wholesaler and being constantly aware of the need to add value to our customers’ businesses, we are focused on finding the winning innovation of tomorrow”
As we begin 2019, the moment is here to take a general look at the industry, and who better to discuss today’s topics with than Chris Higgins? With Hort Americas continually competing to be one of the leading wholesalers in North America, and Chris being a complete horti-geek, he’s on top of the industry’s topics of today and tomorrow. And there’s much to cover at the moment. “For us, Hort Americas, the only constant thing we see is change. Being a wholesaler and being constantly aware of the need to add value to our customers’ businesses, we are focused on finding the winning innovation of tomorrow”, he explains.
Drew Demler (State Fair of Texas), Chris Higgins and Stephen Ritz (Green Bronx Machine) (photo Hort Americas)
Anniversary
It's been almost a decade since Hort Americas was founded. In April 2009, a group of young American entrepreneurs united with the Dutch suppliers of Horticoop and started bringing horticultural products to the quickly growing horticultural industry of the USA and Canada. Operating as a wholesaler, the company made many products accessible to bigger and smaller companies.
Within their client base you can find vegetable growers, ornamental growers as well as a wide variety of growers implementing a wide variety of innovative techniques used to produce an even wider variety of crops. However, there are various topics that unite them. “Labor is the number one topic in all the conversations we are currently having. It does not seem to matter if we are talking about commercial horticulture, field agriculture or vertical farming. This trend seems constant. In vegetable production as well as in ornamental horticultural production – the quality, availability and cost of labor is the number one topic in North America”, Chris explains. To the company, being on top of these trends and offering solutions to them is key.
“We have a fairly narrow focus on a niche market and we are in contact with our client base daily. This allows us to understand their needs intimately and find and deliver solutions that make our customers more profitable and more successful.” He continues, “This includes new emerging markets as well as established industries that are evolving to meet demand and stay relevant, like indoor farming of medicinal crops and the hydroponic production of soft fruits.”
On a side note he offers, “I do believe that out of these new or evolving grower populations, we are going to see some all stars: people that do things differently - apply new technology, or operate their business in a different way - and become the leaders. But, as common throughout history, it will only be a small percentage of the companies that change the industry. And it is not our desire nor our goal to pick winners. To us, the focus is the complete industry: seeing the similarities between the companies and the way trends and novelties impact their operation. Within these topics, we select products that are winners to us: that can add value to most growers' businesses. That’s how we’re serving the industry and how we are on the look-out for our own product range.”
Role as a wholesaler
The company's vision sounds clear - but there’s challenges in the market. In 2018 Horticoop, the Dutch partner of Hort Americas, announced it would resign their wholesale activities and focus on production only. Whilst this does not affect the Hort Americas business, it did urge the company to rethink their role as a wholesaler. Adding value is key, Chris explains. “Being a distributor is more than just selling or providing products. To us it is offering growers solutions to better their business in both the short and the long term.” To do so, HortAmericas puts a lot of effort in helping growers with their specific challenges and, if needed, educate them about the solutions. “Before, being a supplier meant supplying products. Now it’s about understanding what our growers need and value, then finding ways to fulfill those needs as a service: educating, improving the crop(s) quality, creating a better more efficient work environment, and eventually helping growers find ways to become more profitable.”
Demo Greenhouse
It’s not just a vision to Hort Americas. Besides being active continuously in educating growers and researching a lot, the company (which two years ago started their own demo greenhouse) is focused on creating positive change within their community while at the same time improving the knowledge of the Hort Americas team and their ability to communicate that knowledge with both their vendors and their grower partners.
“Thanks to our relationship with the State Fair of Texas (better known as Big Tex Urban Farms), who’ve continuously supported our business, we’ve been able to combine our efforts, energies and resources to create a demo greenhouse at the fairgrounds based in Dallas, Texas. As long as you have scheduled an appointment, it is open for both the community and growers year round. It is in production year round. It is in a constant state of learning and development. But most importantly it is contributing free, safe and healthy food to members of the south Dallas community in need.”
Night time before the start of the Texas State Fair, where more than 200 thousand people are estimated to visit the greenhouse each year. This pond uses Current, Powered by GE LED Top Lights and the Moleaer Nanobubble Generator. (photo Hort Americas)
Hot summer
When asked why Dallas, Texas, Higgins responds, “We are testing products and trying to prove their value. The hot Texas summers offer a tough and difficult environment to grow in. If we can make it work in Dallas, we are confident in the quality of these products and their abilities to perform in some of the most harsh circumstances.” From their commitment to have a positive social impact to their commitment to playing an important role in both the success of their vendors and their grower partners, Higgins is excited and enthusiastic about the future.Then there’s the social aspect: adding value to the local community.
Chilling the rootzone
In the demo greenhouse the Moleaer system is shown - one of Hort Americas' most talked about products at the moment. “We’ve focused on the limiting factors in producing the best possible crops 12 months of the year. One of the biggest issues in Dallas turned out to be controlling temperature of the root-zone. Chilling the rootzone is not cost-effective in most scenarios. Adding dissolved oxygen to it, turned out to do the trick.”
To Chris, the Moleaer product range offered a typical Hort Americas solution. “It can benefit many growers in an affordable, easy way and it is applicable in a wide area of the countries we service”, he explains. “With Hort Americas, we want to be there for a large group of growers. Products that are only accessible to a small part of the market are not a good fit to us. We are looking for the products that help the average grower in their business.”
Add value by specializing
He explains how the North American industry on one hand consists of big companies, in need of tailor-made solutions. “Then there is a large amount of smaller scale customers. These farming operations do not follow the same pattern of upscaling or monocropping. Instead they add value by specializing in specific groups of products, serving local communities with locally grown product or whatever business model proves them to be right. Whilst we are capable of supplying the large customers, we also want to bring suitable products and services to the farms and greenhouses of all shapes and sizes.”
The Sudlac product portfolio is another example of a product line that is effective for large and small greenhouse ranges as well as hydroponic vegetable production and ornamental horticulture. The demand for the various shading solutions has been on the rise. “Creating a better production climate is of course important to growers everywhere in the world. The added value at the moment is in innovative second generation shading products that not only reduce the amount of light in the greenhouse, but can manipulate and improve light in ways that can enhance crop quality.”
USDA Fresh Herbs Grant Planning Meeting held during the 2018 Texas State Fair. (photo Hort Americas)
Relationships with suppliers
The importance of a good and stable relationship isn’t a one way road. Relationships with suppliers are of high importance to Hort Americas. “Obviously the product itself is important in our selection, but it’s not just that... it cannot be just that. Trust between us and our valued suppliers has continued to evolve into a vital part of our business model. We look for specific relationships with suppliers. We look for companies that we can count on and trust, and vice versa. We ask ourselves, ‘Can the manufacturer add value to the chain? Can we help them market their products in the better ways? Do the manufacturers understand the needs of the market?’ Again we want to create partnerships. Partnerships lead to better business for everyone involved.”
A perfect example of this is Hort Americas' relationship with Current by GE (LED grow light solutions). Adding lighting to the crop is an important topic for many growers wanting to lengthen their season and increase their production. “This goes for vegetables, but for sure is not exclusive to vegetable crops. Managing light intensity, light quality and photoperiod is important in all crop production. LED lighting has helped everyone from tree nurseries (for example) becoming more efficient in growing maple trees to tissue culture facilities producing ornamental and medicinal crops.
"Investing in LED is all about effectiveness and efficiency - making it a perfect Hort Americas product catalog. And the engineering team at Current has helped us to develop a variety of fixtures perfect for many (not all) applications. We are working towards that.” Higgins’ excitement about the GE partnership carries over to other partners that are helping them produce innovative fertilizers and have provided them with opportunities to explore new technologies like 30MHZ (sensor products offering growers a better control and more insights on their crop).
Leafy Greens being grown under Current, Powered by GE LED Grow Lights (Arize Lynk LED Grow Lights) (photo Hort Americas)
Keeping up is a challenge
With the Hort Americas client base being super diverse, staying on top of the various needs in the industry is of vital importance. “Keeping up with all the issues along with the wide range of crops and topics indeed is a challenge”, Chris confirms. “On the other hand, trends are similar across the categories. Labor (again) is something affecting the complete industry: the quality, availability and cost of it is the number one topic in North America at the moment. The biggest difference between the various sub-segments within industries are access finance and the pace of developments and investments - depending on both the maturity of the sectors and what their opportunity for profits look like. But in the end the demand of growers is the same in all crops. It all comes down to the smart use of technology and how that technology lets the grower achieve a sound ROI. That’s the main question we are all trying to answer. This will always be the question we are trying to answer.”
For more information:
Hort Americas
Chris Higgins
chiggins@hortamericas.com
www.hortamericas.com
Publication date : 1/15/2019
Author: Arlette Sijmonsma
© HortiDaily.com
Greenhouse In An Auchan Hypermarket
In Italy, Auchan is testing the installation of a greenhouse in a hypermarket. Fresh herbs and salads grow directly on the shelves and customers do their own “harvesting”.
In Italy, Auchan is testing the installation of a greenhouse in a hypermarket. Fresh herbs and salads grow directly on the shelves and customers do their own “harvesting”.
Agricooltur, a young company from the Turin region, is the originator of this scheme. The neighboring Auchan hypermarket placed the installation in its market area at the end of November; it is a spectacular complex of about thirty meters square. The plants are grown by aeroponics: the roots are hanging loose and are sprinkled with a nutrient solution.
Also in late November, Casino installed a showcase in which an assortment of fresh herbs were grown in its supermarket in La-Varenne-Saint-Hilaire, France.
Source: internationalsupermarketnews.com
Publication date : 1/17/2019
University of Arizona Greenhouse Crop Production & Engineering Design March 2019 Short Course
By urbanagnews - January 25, 2019
Combine lectures with hands-on workshops at the Controlled Environment Agriculture Center of the University of Arizona on March 11-15, 2019.
Three days of lectures from prominent Controlled Environment Agriculture experts from Arizona and around the country.
A full day of hands-on workshops that focus on different aspects of Controlled Environment Agriculture.
Great Networking Opportunities with peers, industry experts, and educators from all over the world.
Like tending to the vine closest to the wet-wall on a hot day, CEAC’s Short Course may be exactly what your operation needs for relief! Get your questions answered and increase your hydroponic growing know-how at the Greenhouse Crop Production & Engineering Design Short Course – A four day conference, put on by the University of Arizona Controlled Environment Agriculture Center, including three full days of lecture, one day of hands-on training workshops at CEAC, and an optional commercial greenhouse tour at NatureSweet Tomatoes.
Hydroponic Crop Production
Greenhouse Structure & Design
Greenhouse Site Selection
Developing Urban Ag Systems
Medicinal Crops & CEA
Emerging Greenhouse Crops
Sole-source Electric Lighting
Energy Conservation
Environmental Controls
Greenhouse Plant Lighting
Plant Physiology & Nutrition
Crop Layout, Care & Maintenance
Integrated Pest Management
Greenhouse Structure & Design
Organic Hydroponics
Myco-culture & Mushrooms
Business Considerations
Click here for more information and to register!
VIDEO: EPIC Urban Farming On Top of a Whole Foods | Gotham Greens Tour 🏙️🌿
A mythical urban farm on top of a Whole Foods in Brooklyn, NY, where they grow 13+ different types of greens and herbs.
It was called Gotham Greens, which is just about the best name for a hydroponic greenhouse you'll ever hear. They use nutrient film technique (NFT) channels to grow basil, arugula, leaf lettuce, and more. And better yet, it's all automated, down to CO2 monitoring, shade clothes, and more. They even make their own line of salad dressings, pestos, and other value-added products with the produce they grow!
Green Life Farms Hires Head Grower
Green Life Farms Hires Head Grower
Industry veteran brings more than 15 years of experience growing produce in indoor hydroponic greenhouses to team
Boynton Beach, FL (January 28, 2019) – Green Life Farms, the state-of-the-art hydroponic produce greenhouse under construction in Boynton Beach, FL, has hired Gregory Graft as its Head Grower. Graft will play a significant role in helping the organization prepare to begin commercial operations in the first half of 2019. Green Life Farms is slated to be the largest indoor hydroponic produce grower in the southeast.
“Gregory is a seasoned expert in all aspects of the hydroponic industry,” said Mike Ferree, Vice President, Green Life Farms. “His 17 years of hands-on experience in managing a hydroponic greenhouse makes him a vital addition to the Green Life Farms team, as we work to establish ourselves as an industry leader in sustainable farming practices.”
After serving in the United States Marine Corp, Graft was the Vice President and General Manager of Grateful Greens Hydroponic Farm in Clarksville, IN. There, he designed, built and maintained the hydroponic farm, managing every aspect from assessing plant health to developing client relationships. Graft also served as a production supervisor at Enjoy Life Foods in Jeffersonville, IN, assuming responsibility for product quality, planned volume and line efficiency.
As Head Grower for Green Life Farms, Graft will oversee the facility and lead the day-to-day operations. He will be directly involved with growing operations and maintaining the greenhouse’s infrastructure and hydroponic equipment. In addition to his immersion in the daily processes, Graft will take a holistic approach to managing the facility, analyzing data to evaluate its performance and recommending adjustments. He will also hire, train and supervise a staff of 16 greenhouse employees. Graft will work closely with the rest of the team to continue to drive sales.
Green Life Farms baby leafy greens will set new standards for cleanliness, freshness, and taste. Grown locally, using sustainable farming practices combined with the most advanced AgTech practices, and kept free from GMOs, pesticides and contaminants, Green Life Farms baby leafy greens are good for your body, family, community, and planet.
For more information about Green Life Farms, visit GreenLifeFarms.ag. Contact Elayne@GreenLifeFarms.ag for sales and Ray@GreenLifeFarms.ag for investor relations.
About Green Life Farms
Green Life Farms is constructing a 100,000 square foot state-of-the-art hydroponic greenhouse in Boynton Beach, Florida, with additional expansion planned in Florida and beyond. Commercial operation is expected to begin in the first half of 2019. By incorporating agriculture with technology, Green Life Farms will provide consumers with premium-quality, fresh, local, flavorful and clean baby leafy greens that are good for their bodies, families, communities and planet – year-round.
Netherlands: Additional Research Facilities At Delphy
The facility has now been extended with the addition of two climate cells.
For years, Delphy Improvement Centre in Bleijswijk and Certhon have shared the same ambition: to contribute to global solutions in the field of health, food safety and sustainability, through knowledge sharing and knowledge development. This is reflected in the Improvement Centre, which was opened a few years ago and has been used for various research projects since. The facility has now been extended with the addition of two climate cells.
Following the research facilities in the greenhouse, Delphy wanted to make an in-depth study of research and research methods. With the two climate cells realized by Certhon last summer, Delphy can gain more knowledge about daylight-free cultivation and physiological aspects of plants. This knowledge can also be applied in the greenhouse.
The two climate cells can be found in the reception area of the research centre. The doors of the cells are equipped with two small windows, so visitors can see which test set-up with which crops are inside. A few weeks ago, the first tomato and cucumber plants were placed and the research started. During the cultivation process there will be frequent consultation between Delphy and Certhon, to share advice and knowledge.
For more information:
Certhon
www.certhon.com
Publication date : 12/17/2018
Jardins Réunis And Cheminant First In France To Grow Cucumbers Year-Round With Full Philips GreenPower LED Lighting Installations
Eindhoven, Netherlands – Signify (Euronext: LIGHT), the world leader in lighting, today announced that Jardins Réunis and Cheminant have both installed Philips GreenPower LED toplighting and Philips GreenPower LED interlighting in their new cucumber greenhouses in the Nantes region of France. The growers are the first to grow high-wire cucumbers with LED lighting in the country, showing their leadership as members of the Océane grower cooperative.
“We have experience growing high-wire cucumbers under LED lighting in other parts of the world, and can predict quite well how much production will increase after installing our LEDs,” says Udo van Slooten, Business Leader Horticulture at Signify. “In general, cucumber production goes up with increased light levels. But with LEDs we can truly optimize production by steering light and heat separately. The Philips LEDs have the right spectrum for cucumber growth – the plants use this color spectrum for optimal photosynthesis, resulting in greater production of a high-quality crop.”
Unique benefits
Both growers expect an increase in production, but that’s not the only reason they’ve opted for full LED lighting. Unlike HPS lighting, LED enables growers to increase light levels without increasing heat. The ability to control light and temperature more precisely guarantees high-quality production as efficiently as possible throughout the year.
“LEDs give a better heat-light balance, generating a significant increase in production without the heat that you would get with HPS lighting,” explains Antoine Cheminant, co-owner of Cheminant. “As per Signify’s calculations, we’re aiming for 30% more production in our 20,000 m² semi-closed lit greenhouse compared to a traditional non-lit greenhouse.”
Productive partnerships
“Signify has worldwide experience in growing high-wire cucumbers under LED lighting, so they can provide us with good advice and support from their plant specialists,” says Vincent Olivon, co-owner of Jardins Réunis. “LED lighting will help us to improve energy efficiency and to reduce gaps in production, especially in the more profitable winter period. This is critical in sustaining our position in the market year-round.”
Like Cheminant, Jardins Réunis installed their lighting in a newly built semi-closed greenhouse. The 25,000 m² greenhouse will use LED toplighting (145 µmol/s/m2) and LED interlighting (67 µmol/s/m2). Installations for both greenhouses were carried out by the French certified Philips Horti LED Partner Eiffage Énergie Systèmes in November 2018. This is the first growing season for both companies to make use of the system.
Visit us at SIVAL 2019
Are you attending SIVAL 2019? Visit us at booth E226 from January 15–17 in Angers Exhibition Center to learn more about Philips Horticulture LED Solutions.
In case of any questions, pls let me know!
Regards.
Daniela Damoiseaux
Global MarCom Manager Horticulture
+31 6 31652969
High Tech Campus 7
5656 AE, Eindhoven, The Netherlands
2019 Virginia Innovation In Greenhouse And Vertical Farming Conference
By urbanagnews
January 12, 2019
Join us on Tuesday, March 12, and explore additional tools for expanding farm revenue through vertical farming innovations.
Virginia Tech and Virginia Cooperative Extension invite you to register at http://bit.ly/Register-2019-Vertical-Farming for the 2019 Virginia Innovation in Greenhouse and Vertical Farming Conference
Tuesday, March 12, 2019
Virginia Farm Bureau
12580 West Creek Parkway; Richmond, Virginia
Keynote Speaker
Neil Mattson, Ph.D., Cornell University
Special Guest Speaker
Chris Higgins, Hort Americas
In addition, you will hear from:
Jerry Conner, Four Oaks Farms
Travis Higginbothan, Fluence Bioengineering
John McMahon, Schulyer Greens
Ryan Pierce, Fresh Impact Farms
Join academic and industry experts in exploring the latest advances in vertical farming, greenhouse technology, sensor technology, lighting, and automation. Hear from technical experts and Virginia producers who have been successful in incorporating controlled environment agriculture into their business models.
Register by visiting http://bit.ly/Register-2019-Vertical-Farming before Thursday, February 28.
TAGS: Chris Higgins Conference Cornell University Education Hort Americas Neil Mattson
Denver, Colorado: A Look Inside Rino's Rooftop Urban Farm
January 8, 2019
If you’ve recently walked down Lawrence Street in RiNo, you have probably have been stopped in your tracks by the sight of a rooftop garden. At the very least, you’ve probably wondered what was going on above Uchi. This beautiful greenhouse space is home to Altius Farms. As one of the largest vertical aeroponic rooftop gardens in the country, Altius currently grows varieties of lettuce, herbs and edible flowers galore.
Part of the new S*Park condo community, Altius landed at the RiNo location where the land historically has been farmed since the 1930s. The greenhouse itself offers 8,000 square feet to run operations, and the community garden outside will double the growing space once the spring comes. S*Park and Altius are planning to team up for great farm-to-table events and community dinners come warmer temperatures.
Sally Herbert, co-founder of Altius, is excited to open the flagship location of Altius Farms in Denver and partner with S*Park to do so. Short for Sustainability Park, the condo community is an incubator for sustainable living and community development. Centered around wellness for human bodies and the earth, Altius Farms is a great addition to the RiNo living complex.
Herbert commented that their mission is to “bring urban farming back into our communities.” They are currently focusing on their partnerships with restaurants to do so. Altius works with some of Denver’s top-rated restaurants – including Beast + Bottle, Butcher’s Bistro and Urban Farmer. The team at Avanti Food & Beverage asked Herbert to grow a mix of greens to pair well with a particular dressing the restaurant is concocting for a special event.
“There’s a real demand for produce that’s safe, nutritionally dense, that’s got good flavor, that doesn’t have 1,500 food miles on it,” Herbert explained. Most of Altius’ customers are located in the surrounding neighborhoods, so the produce is fresh when restaurants receive their orders. This cuts back on food waste both within the farm and in restaurants – however the produce that Altius can’t sell before its prime, they donate to We Don’t Waste and Denver Food Rescue.
“We are a for-profit company with a social impact mission,” Herbert commented. And in addition to engaging the community in learning more about their food, Altius operates on a sustainable business model. The aeroponic tower system uses 10 percent of the water and 10 percent of the space to produce 10 times the yield of a conventional soil farm. Herbert also gets to see an eye-level view of each plant every day – making it easy to identify the needs of particular plants throughout the greenhouse.
The greenhouse itself was designed to recognize the plants needs by pooling the environment. Sensors around the greenhouse cue the processing system to turn on fans or heaters, open up roof and side vents to adjust the humidity and temperatures to make the greenhouse the perfect environment for growing leafy greens.
The greenhouse also provides a controlled environment for their plants to grow. Altius Farms has a separate water system and a controlled environment that is not affected by the state of surrounding farms. In result, Altius was able to supply their customers with romaine when the rest of the country was having an e. coli scare.Transversely, if Altius had a scare in their own farm, it wouldn’t affect any growing site except the greenhouse location.
The horticulturalist for Altius, Don Dwyer, has been in the growing business since the 1970s. More and more he sees that people want to “establish a relationship with their food.” Altius helps facilitate a positive relationship with food by providing fresh produce with interesting flavor profiles to Denver residents. Dwyer also understands that so many Denverites want to support local farms and Altius gives residents a way to learn about growing food in an urban location.
As Altius approaches full growing capacity, they are looking forward to living into their mission and engaging the community in their work. “Food is important in [illness] recovery and in education and just having nutritious meals for our kids,” Herbert explained. Once they have the capacity, Altius hopes to serve the community beyond restaurants – including schools and medical centers.
For the time being, Altius takes great care of their restaurants. Herbert enjoys offering tours and tasting to their chef partners and helping them to design a menu around Altius greens. With flavors like wasabi arugula to mustard greens and a number of edible flowers, Altius Farms caters to many chefs and their various dish innovations.
These partnerships excite Herbert, who has never worked with chefs in this way. “What’s been interesting,” Herbert commented, “is that they are – pun intended – hungry for this kind of food. They want to have the conversation with us.” In the future, Altius wants to expand their produce and grow specific plants for restaurants – working with chefs from the inception of a dish idea to the culmination.
Altius Farms is located at 2500 Lawrence Street #200, Denver. Their restaurant customers in RiNo and LoDo are Urban Farmer, Uchi, Crema, HiTide Poke, Port Side, Stowaway, Famous Original J’s Pizza, Butcher’s Bistro, Goed Zuur, Beast + Bottle and Dio Mio. Altius greens are available in both Marczyk’s Fine Foods.
All photography by Evans Ousley.
ABOUT THE AUTHOR
When not working one of her three jobs, Evans walks the streets of Denver to discover more about the city's food scene. On the weekends, Evans loves to stroll around Denver's many parks – mostly to obsess over all the dogs she can't have.
Kamchatka Won’t Get Its Vegetables: Renova Greenhouse Project Is Frozen
“…It is hard to say what has caused the delay, but the project is not developing. Possibly it is related to the minimization of state support”
The Renova company, owned by a Russian billionaire, Victor Vekselberg, has stopped the construction of the greenhouse complex within the Kamchatka Priority Social and Economic Development Area. The decision is allegedly related to the fact that the ministry of agriculture are considering minimizing state support in the greenhouse construction sector.
The price of a kilo of tomatoes and cucumbers in the Kamchatka markets and trade chains has reached 10.60 euros. The local authorities during the presentation of the full-scale project of the greenhouse complex construction promised that the produce of Renova would cost significantly less. Thus, the cucumbers were supposed to cost no more than 1 euro and tomatoes up to 1.50 euros per kilo. The local administration shrug their shoulders.
“We had high hopes for the Renova project. The land plot is completely ready for the construction. It is hard to say what has caused the delay, but the project is not developing. Possibly it is related to the minimization of state support”, mentioned the minister of Food and Food Production for the Kamchatka region, Mr. Aleksandr Kurchenko.
Strangely enough, even the administration of the Kamchatka region are not aware of the actual reasons for freezing the project within the Priority Social and Economic Development Area. It seems that the resident company have not informed the authorities about their decision.
In April 2018 the governor of Kamchatka, Mr. Vladimir Ilyukhin, personally presented the project of the Renova greenhouse complex construction within the Priority Social and Economic Development Area to the general public.
“One of the companies within the GK Renova are ready to construct the greenhouse complex in the Elizovsky region on an acreage of 15-20 ha. According to the preliminary calculation made by the investor, a kilo of cucumbers produced there will cost 1 euro and a kilo of tomatoes up to 1.50 euros”, mentioned mister Ilyukhin in April.
It was intended that the greenhouse complex produce would cover the need for fresh vegetables in the region by 40-43%.
In addition to other favorable conditions, a certain amount of gas from a Kamchatka gas field was specifically reserved for the Renova project.
The news on freezing the project has been very negatively taken by the local residents.
“What do they mean 'frozen'? The electric power line alone costs more than 6 million euros. And now what?”
“We will never have cheap vegetables”, Kamchatka residents write on social media.
Unfortunately, the disappointment of not getting cheap vegetables is not the only bad news for the locals. The administration have ensured them that most likely they will not have cheap meat or milk either.
Source: k-vedomosti.ru
Publication date : 12/4/2018
How Do You Stop Diseases On Controlled Environment Edible Crops?
Controlling the environment is a key component of preventing diseases on edible crops.
As an increasing number of growers start growing edible crops in controlled environment structures they may be facing some diseases that they haven’t encountered before. For ornamental plant growers who are adding edible crops, they will not have as many or as effective chemical controls as they have access to with their ornamental crops.
“Growers currently don’t have a good complement of products for edible crops being grown in greenhouses or other controlled environment structures,” said Michigan State University plant pathologist Mary Hausbeck. “And if there are chemical controls available, growers may want to spray all of their herbs together. For instance, if the rosemary needs to be sprayed to protect against Botrytis, it’s wise to make sure that other nearby herbs are also listed on the fungicide label. Otherwise, growers need to make sure that their employees who are going to be spraying know which herbs they can and cannot spray with a particular product. Fungicides labels can be complicated.”
Hausbeck said growers should be cautious about using pesticides in greenhouses and other controlled environment structures like warehouses, vertical farms and plant factories.
“Previously, EPA required that use in greenhouses had to be specifically stated on a pesticide label in order for greenhouse growers to use it. But states varied in their interpretation and so usage was determined on a state-by-state situation. Several years ago EPA determined that if the label doesn’t restrict use in greenhouses, then a pesticide can be applied to a greenhouse-grown crop. In Michigan, our state agency views greenhouses and other controlled environment structures similarly. Just make sure that the label doesn’t prohibit the use of a fungicide in a greenhouse.”
Optimizing environmental control
Because of the limited number of chemicals available to greenhouse growers of edible crops, Hausbeck said it is critical for growers to use environmental control to limit disease.
“Environmental control has to be part of the equation,” she said. “Powdery mildew, downy mildew and Botrytis have a tremendous capability to reproduce in large numbers via spores. A microscope is needed to see one spore, but when there are many spores, the eye can see the fuzziness of the mildew or grey mold on the plants. The spores are moved around the greenhouse via air currents.
“Powdery mildew and downy mildew tend to be specific as to what plants they will infect. Powdery mildew is a problem on tomatoes, cucurbits and peppers. Downy mildew can be a problem on basil, cucumber and lettuce. Botrytis has a much broader host range.”
Botrytis is in a lot of growing environments because it can take advantage of plant tissue whether it is alive or dead. Downy mildew and powdery mildew won’t colonize dead plant tissue that is lying on the floor or sitting in a trash pile. Botrytis will infect plant parts that are still attached or have been discarded.
Powdery mildew, downy mildew and Botrytis prefer cooler temperatures.
“Occasionally I have seen Botrytis sporulate in coolers,” Hausbeck said. “Older leaves that are mature and are senescing may be in direct contact with moist growing media and may lead to Botrytis infection. Plants growing in a moist environment with high humidity and extended periods of leaf wetness are at particular risk of Botrytis infection. For instance, Botrytis can cause stem blight on rosemary and other herbs leading to significant losses.”
Hausbeck said Botrytis has a fairly broad temperature range in which it can infect plants.
“Growers who effectively use environmental control to keep conditions dry and unfavorable for Botrytis can get by without fungicides,” she said. “Botrytis needs leaf wetness to infect plants. Moisture is key.
“At 80-85 percent relative humidity even a small drop in temperature can lead to Botrytis issues. If the relative humidity is maintained at a low level, Botrytis won’t be successful in becoming established. Growers should do everything possible to keep Botrytis at low levels.”
Botrytis can cause stem blight on rosemary leading to significant losses.
Photo courtesy of Mary Hausbeck, Mich. St. Univ.
Botrytis can also come in as a secondary problem. It may become a problem as a result of the plants undergoing an environmental stress that results in some leaf browning. Botrytis can take advantage of this dead tissue.
Hausbeck said Botrytis can be an issue with rosemary propagated by vegetative cuttings.
“Growers should try to lower the humidity immediately following taking cuttings from rosemary stock plants for 24 to 48 hours,” she said. “Botrytis infection can occur on the wounded stems of stocks plants leading to dieback. Growers can raise the temperature in the greenhouse by a degree or two to reduce the relative humidity. Growers should try to drop the humidity below 70 percent or as low as possible depending on the circumstances of the greenhouse. They should also provide good air movement around the plants. Having good airflow movement around the plants helps to prevent all types of diseases, including Botrytis, bacterial diseases, powdery mildew and downy mildew.
“It doesn’t take a lot of expensive technology to keep the relative humidity low and the plants dry. Avoid overwatering and keep the leaves dry by watering at a time of day when they can dry rapidly. Keep the air in the greenhouse moving so that there aren’t pockets of high humidity. Ensure there is good drainage so there is no standing water on the greenhouse floors. In areas of the greenhouse where there is standing water, the relative humidity in these areas can be increased by as much 15 percent.”
Correctly identifying the disease
Hausbeck has encountered times when some of the problems growers have reported were caused by environmental stress.
“In some cases growers have been able to send me really good pictures and I can make a diagnosis based on the photos,” she said. “If it appears the plants have a potential disease I’ll recommend that growers send samples to a diagnostic lab. There are some symptoms that don’t look like a pathogen at all. I ask the growers about their growing systems and to describe when the symptoms first appeared and the pattern they are seeing across the crop.”
Having good airflow movement around plants applies to preventing all types of diseases, including basil downy mildew. Photo courtesy of Mary Hausbeck, Mich. St. Univ.
Hausbeck said as more edible crops are being grown, she expects to see some “oddball” diseases showing up that she hasn’t seen before.
“Some of these are fungal pathogens,” she said. “I have seen Septoria, which is a fungal leaf blight, on a couple of herbs. As herbs are being grown in greater volume, it’s likely that we are going to see more problems develop just by the sheer amount of plant material being grown. It’s important for growers to recognize in some situations this is still a relatively new arena for plant disease.
“We don’t know everything about the range of crops that can be impacted and what the disease symptoms might look like. If growers see a problem with a crop they really should connect with a diagnostic lab sooner than later. In the case of a disease problem, the recommendation may be to toss the plants and not try to save them because there isn’t a good complement of fungicides. Growers may sit on a crop trying to nurse it along with different growing regimes, not recognizing that it is a pathogen that is destroying their crop. This could result in costing them more time and more money.”
More control options available
Hausbeck and her laboratory at Michigan State have developed a reference chart for “Registered Products for Common Greenhouse Diseases on Vegetables and Herbs.”
“We have compiled this “cheat sheet” for products that can be used on edible crops,” she said. “We have grouped the crops according to brassica, cucurbit, leafy greens, fruiting and herbs. It is only meant to be used as a guide. Growers must read the pesticide labels carefully.
“What we have learned is that there is not a blanket product that can be used on all herbs. If a product can be used on herbs, it may or may not include basil. The situation is getting better with these crops and registered products in terms of having more options.”
For more: Mary Hausbeck, Michigan State University, Plant Biology Laboratory; hausbec1@msu.edu; https://veggies.msu.edu.
Hort Americas works with a wide variety of vendors that help controlled environment gorwers manage the climate inside their greenhouses and vertical farms. Learn more about fan, ventilation equipment and other products available from Hort Americas.
This article is property of Hort Americas and was written by David Kuack, a freelance technical writer in Fort Worth, TX.
Playing "Happy Families" To Understand Urban Agriculture In France
We hear a lot about urban agriculture, but what is it exactly? How is it different from traditional agriculture? What is the difference between rural farms and urban farms?
11 December 2018
Agnès Lelièvre, lecturer in agronomy at AgroParisTech, Baptiste Grard, postdoctoral researcher at the Laboratory of Functional Ecology and Ecotoxicology of Agroecosystems (AgroParisTech/INRA), Christine Aubry, head of the Urban Agriculture research team at AgroParisTech, and Véronique Saint-Ges, economist at INRA, tell us about the different forms of urban agriculture.
We hear a lot about urban agriculture, but what is it exactly? How is it different from traditional agriculture? What is the difference between rural farms and urban farms?
New definitions of that concept have emerged in the past few years—including that of Canadian expert Luc J.A. Mougeot (2000) and French experts Paula Nahmias et Yvon Le Caro (2012)—, along with new typologies such as those of Cerema, Exp’AU and IAU. In the present case we will use Mougeot’s definition of urban agriculture:
“A production unit located within a city or metropolis (urban) or in its direct vicinity (peri-urban) that produces, raises, processes and distributes a diversity of food or non-food products by massively (re)using human and material resources, products and services from that urban area and its surroundings, and providing human and material resources, products and services to that same area.”
To depict the different forms of urban farming, we have chosen to use the analogy of “Happy Families”, where each category of urban agriculture is a family. For each family, we will relate the story of its ancestors and parents (the ancient forms) as well as that of its children (the current forms).
Without further ado, let’s get to know all these happy families.
1. The “Feet in the soil” family
This family has historically lived in an urban environment, while staying deeply connected to the soil. In today’s context, this category suffers from two recurring issues: access to land and pollution.
The ancestors of that category were the vegetable gardens of aristocrats, such as the well-known “King’s garden”, established in Versailles during the 17th century to provide fruit and vegetables to Louis XIV’s court.
In this family, the parents are a popular and commercial version of their ancestors. They are, for example, the marais ("swamps") at the heart of Paris, which have led to the French word maraîchage (“market gardening”). These farmers were great initiators and inventors of agricultural techniques that are still being used today. They practiced intensive agriculture on small areas using frames or glass domes to cultivate earlier in the season. Horse manure (which at that time was abundant in the city) and urban mud were some of the resources commonly used. This shows how helpful market gardeners were to city dwellers.
They have a large, varied descent that includes peri-urban farms, often pushed outside of the cities due to urban densification and hygienization. These farmers continue to sell their products to city dwellers, i.e. mainly vegetable produce and small animals (chickens, eggs, etc.). Over the past fifteen years, these farms have become increasingly popular through the development of short, local distribution networks such as AMAPs. These farms usually cover a few hectares each. In 2010, almost half of French farms producing vegetables and honey sold their produce through short distribution networks.
However, some farmers have managed to establish themselves within cities—or to maintain ancestral farms, although this is less common—by diversifying their activities. Some of them do community work, for instance for individuals that have been disconnected from the job market (such as the gardens of association Aurore), others do educational work (Veni Verdi for vegetable production, Bergers urbains for urban pastoralism) or organize cultural events (La ferme du bonheur).
The closest descendants of market gardeners work in production farms (such as Perma G’Rennes), located on former agricultural plots, or in schools or parks with plots from a few hundred m2 to 1 or 2 hectares.
The garden of the Pierre Mendès France college in Paris, overseen by the Veni Verdi association. (Michèle Foin/Vimeo, 2016).
2. The “Rooftop” family
This family has been around for centuries, as plants were already found on rooftop terraces in ancient Egypt, as shown in certain images of the book Palais et Maisons du Caire ("Palaces and houses of Cairo"), on the architecture of the 13th-16th centuries. Today urban honey is harvested from beehives installed on the roof of many public and private buildings.
There has been a growing interest in "green roofs" (i.e. not producing food) since the 1980s. Now the “agricultural descent” of this family includes farm that are community-oriented—to foster social interactions (Culticimes), for educational or experimental purposes (AgroParisTech‘s rooftop) or for event planning (Jardins suspendus). Some roofs also host farms for productive purposes (Aéromate, AgriPolis).
Interview of Louise Doulliet, co-founder of startup Aéromate. (Supbiotech/YouTube, 2017).
These “rooftop farms” have specific requirements as they have limited space compared to regular land farms. Today, rooftop vegetable gardens can be seen as a solution to issues related to land access and soil pollution, to the point that in a growing number of cities, new constructions anticipate their presence. Yet many questions remain unanswered, including about their design and the growing medium used.
3. The “Vertical” family
Growing produce on walls may seem risky... Yet Montreuil’s peach walls were renowned worldwide during the 19th century for the quality of their production: the fruits were exported as far as the Russian Tsar’s court. Vines have also been climbing on small walls and all kinds of arbors since antiquity.
Whether in museums, hospitals or malls, living walls designed for decorative purposes have become increasingly popular since the 90’s and 2000’s. Today living walls producing vegetables or hop are also found next to urban microbreweries. Farms specializing in event planning also use walls on rooftops. This family is less common than the two previous ones.
Paris hops will grow on the walls https://t.co/6XSGvftnTJ — Le Parisien | Paris (@LeParisien_75) 18 février 2018
4. The “Greenhouse” family
Greenhouse farming extends the production period of fruit and vegetables. The aristocracy was the first to reap its benefits through orangeries and winter gardens. During the 19th century, greenhouses were built in Auteuil and Paris’s Jardin des plantes to ensure the conservation of varieties and species constituting plant collections.
Today, greenhouses are extensively used in agriculture—including in the well-known Dutch production units—but also in cities for productive purposes (Skygreen) or on rooftops (Les Fermes Lufa, The New Farm). They can also be used to educate or experiment on social reinsertion and food therapy (such as in the Cité maraîchère in Romainville).
Greenhouse kale crops in Montreal’s Loufa farms. Les Fermes Lufa Facebook page
Aquaponics is another form of greenhouse farming that combines raising fish and growing vegetables. Although this type of production can be done in tanks based on a living substrate (with fertilizing power for the plants), it is usually based on a neutral substrate in hydroponic systems where the necessary elements for plants—and fish, if any—are provided through water. This type of production is currently being studied as part of a national research project.
5. The “Shade” family
The ancestors of this family developed underground, in mushroom and endive farms. They are known as produits de cave (“basement products”) and are commonly found in the greater Paris area. The parents haven’t diversified their products, yet they have developed new production systems. The children took over the family business by diversifying the offer, through micro-sprouts in particular, and by reusing new types of waste generated by the city, such as coffee grounds. It is mostly production-oriented (Boîte à champignons, La Caverne).
The Boîte à champignons (mushroom box). Agnès Lelièvre
A high tech “parent” has appeared in the last few years with growth in a controlled environment (light, atmosphere, etc.) thanks to recent progress in spatial research. Its children are using existing buildings or recycled containers (Agricool, Farmbox). This family is strongly developing in some countries with high population density or facing intense climatic stress. In France, it has been used as an opportunity to reuse areas such as abandoned parking lots, and in certain cases, to establish mobile farms.
6. The “Sunday gardening” family
The ancestor of the individual garden has led to private gardens, but also to group gardening with allotment gardens, which emerged at the end of the 19th century.
The children of this family continue to maintain private gardens on balconies, terraces and actual gardens, which can be produce high yields. They also practice collective gardening which covers shared gardens, family gardens and multiple hybrid experiments. While private gardening is aimed at growing vegetables, collective gardening also has a social and educational purpose.
This family has grown a lot since the 20th century and it has become increasingly popular, especially in the case of collective gardening. There are over 1,000 collective gardens in Île-de-France, covering at least 900 hectares, in a context where professional vegetable production covers 5,000 hectares. It is a great success, even though obtaining a plot to cultivate in the city or its surroundings remains difficult, as evidenced by the long waiting lists to access a family or collective garden.
Family gardens in the Lilas public park in Vitry-sur-Seine (94). Agnès Lelièvre.
7. The “Self-service” family
Inspired my movements such as Guerrilla gardening, which, in the 70s, started reclaiming land that had been built and abandoned, this is a family of creative, conquering activists.
It has given birth to active offspring seeking to establish plant production in public spaces for everyone to enjoy. It includes international initiatives such as the Incredible edibles, as well as initiatives launched by cities themselves such as permis de végétaliser ("license to plant") and the reintroduction of fruit trees in public parks. Although still discreet, this family has a bright future, as it is an inspiration to local communities.
The original version of this article was published on The Conversation.
"Every Time We Are Surprised By The Ideas Of Our Clients"
Avner Shohet, TAPkit:
Why would you build a greenhouse on a roof in the middle of the city, with all the compromises and investments you have to make? Why not get out of the city, only 10 or 20 kilometers, to have a simple greenhouse with a smaller investment, and it gives the same solution.”
Indoor farming
With the TAP kit, Israeli company Teshuva Agricultural Projects Ltd. enables small farmers who cannot afford to invest one or two million dollars in a big greenhouse. They see themselves as a competitor of indoor farming. “We want to enable people to get into sophisticated farming without getting into big investments, so we are aiming to keep the price low”, says CEO Avner Shohet.
“Containers and other indoor farming ideas are nice, but we believe in a low cost greenhouse, just outside the city will be more efficient. Also, indoor farms like containers needs artificial light which costs energy. Our partner on lighting is the sun. It is providing us with very good conditions, not charging us at all. It seems the produce here is stronger and better than growing in a container, because of the natural light.”
Rapid expansion
Avner shows the greenhouse of one of his clients in Israel, who is growing a mix of lettuce and herbs. “He first started selling to his neighbors, then came the restaurants. They like the fact that they know the grower of the food they serve. They visit him regularly. In this 500 m2 greenhouse he produces 150-200kg a week. He grows by demand, which is the dream of every farmer.”
Currently the grower is supplying to seven restaurants. He supplies them every week so gradually planning is needed. A new unit is planned. “Only two months after the greenhouse was put in production, he came to me saying his clients wanted more production. Some of them are actually willing to support his investment of the second unit, in order for them to secure his supply.”
Climate system
To keep a constant climate in the greenhouse, a system of Roots is being used. “The temperature underground is stable and the average of summer and winter. They drill a hole in which they put two pipes, 6 meters deep. In summer we get cold, chilled water to cool down, and in winter it is a little bit warm. It is the perfect temperature year-round.” This climate system is not a must for every client of the TAP kit. “It is a valuable addition for places that have big difference between summer and winter. This month we started building two installations in South Korea. There we use the same system. They have even more extreme temperatures. In summer they reach 40 degrees Celsius, in winter below -15 degrees.”
Profitable solution
In a unit of 500 m2 the production of lettuce is 12 tons a year, or in case of herbs, 6 tons a year. This grower is mixing crops, so his production will be 8 tons a year. His turnover should be around 100- 120,000 euros per year. The cost of the unit, including a small plant nursery and packing equipment, is around 55,000 euros. The preparations for the unit will add another 10,000 – 15,000 euros. The return on investment is 1.5 years. This makes it a profitable solution for growers.”
Three modules
Depending on the climate, TAP provides three different modules. The one that is being used in Israel is suitable for sub-tropical countries. There is also one for tropical areas that has more ventilation. For cold countries double plastic is being used. “This unit will cost 80,000 Euros, because it has a different structure. Every three or four years the plastic has to be replaced, which costs a few hundred Euros. This is still a small investment in comparison to containers with automation and artificial lighting.”
Surprised by clients
When we started, we focused mainly on Africa and South America, thinking: ‘these people don’t have much money and with support of the World Bank they are able to grow in our self-assemble hydroponic greenhouse. But very soon we discovered our market was much bigger than that.
“Our first clients were from South Korea. There is one in the Philippines and 2 units are on the way to a resort in Mauritius. I think here in Israel we can sell a few dozen of them. There is also interest from USA, France, Ecuador, Mozambique and even from Gaza.” Most clients will have one or two TAP kits and they can supply the products to the supermarkets, restaurants and vegetable sellers in their neighborhood. “This way they really answer the need of local produce.” A small part of the greenhouse is usually for propagation.
“A client from Miami is to buy 3 to 5 units, which he aims lease to several people”, says Avner. “Another client from New York wants to put a TAP kit in a home for the elderly. There will be food for the kitchen and occupation for the people living there. It’s not a hard job. People don’t have to bend down. These are uses that we have never thought of before. Every time we are surprised by the ideas of our clients.”
For more information:
Teshuva Agricultural Projects
60 Nof Harim St., Olesh, 42855 Israel
+972-9-8940507
+972-50-7922579
+1-201-5803003
office@taprojects.com
www.taprojects.com
Publication date : 12/12/2018
Author: Jobke den Hertog
© FreshPlaza.com
New York City School Opens Greenhouse Classroom
On a snowy November morning Manhattan Borough President Gale Brewer, students, teachers, School Construction and other community members celebrated City As School High School new Greenhouse Classroom.
The fundraising efforts were led by City As School teacher and Alum Naima Freitas who will be using NY Sun Works curriculum with experiments and research that connect science to math, social studies and art. “I am especially excited about using this classroom as a demonstration site for local elementary and middle schools,” said Freitas, “and will be working with my students to plan Pay What You Can Farm Stands and Cooking Demos with their hydroponic harvests”
Guests enjoyed fresh mint tea, kale chips and pesto made by the students using their first harvest.
The greenhouse classroom will expand far beyond the educational auspices of the Urban farm: Students will learn about the science of sustainability and how to grow food with cutting edge technology. They will also learn about contamination, pollution, biodiversity, and conservation while understanding how their actions have an impact on the environment.
“In-school hydroponics labs are a great innovation that make real-life, hands-on, project-based science education a day-to-day part of students’ lives,” said Manhattan Borough President Gale A. Brewer. “Research and common sense both tell us that experiential education opportunities produce deeper learning and more meaningful experiences for students, and I’m thrilled we could fund and complete this project through my office’s urban agriculture initiative. Whether it’s hydroponics, aquaponics, greenhouses, kitchens, media labs, or recording studios, giving our students the facilities they need to do more than just memorize and recite is always the right thing to do.”
The Borough Presidents funding allowed for a complete gut renovation by NYC School Construction Authority to transform the previous space into a fully functioning urban farm in collaboration with NY Sun Works.