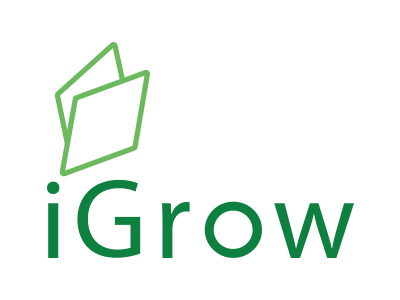
Welcome to iGrow News, Your Source for the World of Indoor Vertical Farming
US (MA): MIT Halts Work On The Controversial Open Agriculture Initiative Food Project
MIT has closed down much of its Open Agriculture Initiative following allegations of academic dishonesty and improper dumping of wastewater, according to an article published in the NY Times
MIT has closed down much of its Open Agriculture Initiative following allegations of academic dishonesty and improper dumping of wastewater, according to an article published in the NY Times. Late last week, MIT’s vice president of research, Maria Zuber, closed down all offsite work on the project, though she has allowed researchers to continue doing some design and document work.
The project, often simply referred to as “OpenAg,” is known for its food computers — small, high-tech containers meant to grow plants in controlled environments and without any soil. OpenAg also operated larger farms it called “food servers” in shipping containers housed outside the MIT campus in Middleton, Massachusetts.
Project leader Caleb Harper also had a vision that owners of these food computers would be able to share data on the perfect combinations of light, water, nutrient, and temperature levels with one another, creating a kind of open-source framework for high-tech indoor farming. “As an open-source project, we believe the more Food Computers we all build, the more data we all have to play with, and the more we can radically alter the future of food,” states a page on the Open Ag site.
Read the full article at The Spoon (Jennifer Marston)
The Economics of Container Farming In Nauru
You might be excused for not knowing much about the country of Nauru. It’s a small island in the Pacific Ocean that’s only ten times larger than Microsoft’s campus in Redmond with one-fifth the people. The 11,000 citizens of Nauru occupy a footprint of about 8.1 square miles (21.98 sq. kilometers) out in the middle of absolutely nowhere where the waters are so deep they never have to worry about tsunamis
People from countries we refer to as frontier markets must roll their eyes when some people in America talk about how “oppressed” they are. The same people complaining about how bad it is in the States probably think Africa is a country when in fact it’s 54 countries. A lot of Africans actually are oppressed because about half of the continent’s countries are run by dictators. If you can go into your local store and buy some fresh lettuce at any hour of the day, 365 days a year, you’re not oppressed. Most people around the world don’t have access to a large selection of fresh vegetables or the means to purchase them. Take Nauru for instance.
You might be excused for not knowing much about the country of Nauru. It’s a small island in the Pacific Ocean that’s only ten times larger than Microsoft’s campus in Redmond with one-fifth the people. The 11,000 citizens of Nauru occupy a footprint of about 8.1 square miles (21.98 sq. kilometers) out in the middle of absolutely nowhere where the waters are so deep they never have to worry about tsunamis. About once a month, a ship will cruise into the harbor dropping off loads of food and supplies. Vegetables are all flown in by air. With its pleasant island breezes, Nauru is a hidden gem that happens to be the least visited place in the world. As a result of not having to deal with obnoxious tourists, the citizens are some of the kindest people you’ll ever meet. They’re also the world’s most portly. You would be too if you had to pay these prices for vegetables.
Produce prices in a Nauru supermarket in AUD – Credit: Nanalyze
We did the math for you on those numbers. If you want to buy a head of lettuce in Nauru, you can’t. They don’t have any right now. If they did, you would pay $3.29 a pound or $7.25 a kilo in greenbacks. That’s more than three times the retail price of lettuce in the United States which sits at around $1.09 a pound. In order to solve the obesity problem which commonly afflicts island nations like Nauru, we need to make healthy food more affordable. Maybe we can use something Nauru has a whole lot of already – shipping containers.
In a previous article, we wrote about the newly sprouted industry of “vertical farming.” Also called indoor farming, the eleven startups we looked at have collectively raised more than $900 million in venture capital so far. The appeal is in the delicious numbers. Indoor farming uses 95% less water and yields 400 times more output than the same land footprint when compared to traditional farming methods. That’s what it says on the tin, but the experts are skeptical when it comes to indoor farming using shipping containers like the one seen below.
The Greenery from Freight Farms – Credit: Freight Farms
Container Farming Economics
We’re not interested in the “farm to table” marketing spin being put on container farming, we’re solely interested in the economics. For that we can turn to Peter Tasgal, a man who used to work as an investment banker before he managed to turn his life around and became the CFO of a $100 million consumer packaged goods company. Today, he’s an agriculture consultant, and this past February he penned a piece on “What is the Future of Container Farming?” in which he talks about how it’s largely a niche business applicable to applications like “restaurants, traditional farmers seeking to maintain year-round customers, clean rooms, and areas of extreme climate.” This table pulled from his article compares various methods of farming:
Source: Agfunder News
Container farming has the “highest cost per delivered pound” with Mr. Tasgal stating that it’s “at best four times as expensive per pound to grow in a container farm and more likely over 10.0x as expensive as compared to traditional farming methods.” He proposed that either technology can be used to reduce the cost per pound (nothing on the horizon yet) or people can pay a price premium for “better quality produce.” Since the people of Nauru already pay a price premium, this isn’t exactly a showstopper.
Some Initial Concerns
We shipped one of our MBAs over to Nauru to visit with Mathew Batsiua, former Health Minister of Nauru, and someone who has spent the last 4 years of his life fighting his own version of an African dictatorship with the local government. He thinks that container farming might be able to provide the Nauruan people with an alternative to purchasing over-priced greens at the supermarket. Aside from being able to offer cheaper and fresher greens, container farming could be used as part of a school program to get the country’s youth eating healthier. An additional benefit would be creating some local jobs. If the initial implementation works out, Nauru could act as a model for other Pacific Island countries that all have a similar obesity problem for all the same reasons.
Some initial concerns he raised around container farming:
Support and training
Durability of the components in the unique climate of Nauru
Consumption of electricity
The need for solar integration
Availability of consumables required to operate the farm
In order to gauge the suitability of container farming for the country of Nauru, we’re turning to “the world’s leading manufacturer of container farming technology,” a startup called Freight Farms.
Freight Farms
Founded in 2013, aptly named startup Freight Farms hails out of Bahstun Massachusetts and has raised $11.4 million in funding so far to develop “high-volume crop production units made from upcycled shipping containers to support farming in any climate.” Their container farming solution can produce over 500 types of lettuces, herbs, leafy greens, and small root vegetables at a commercial scale. As of January 2019, their hydroponic container farms can be found in 38 U.S. states and 15 countries. Their latest growing platform, The Greenery, costs $104,000.
Credit: Freight Farms
It’s a significant price increase over their previous container solution, The Leafy Green Machine, which ran just $76,000. That’s because The Greenery has over 70% more growing space than the Leafy Green Machine.
If we’re going to deploy The Greenery on Nauru, we need to get it there first. Let’s say that’s an additional $8,000 in shipping costs. With an initial capital outlay of $112,000, we can begin to crunch some numbers. Firstly, let’s look at the operational requirements:
Credit: Freight Farms
Nothing too alarming here. Water is clearly in short supply for Nauru but 5 gallons a day is manageable. One gigabyte of data a month is affordable. We need to consider that electricity in this part of the world is more costly as well. Consumables like peat moss plugs, seeds, and nutrient solutions will all need to be imported by ship. Let’s do some back-of-the-napkin math and see how much time it might take to recoup our initial investment.
Container Farming Yields
According to an article by the University of Saskatchewan on hydroponic lettuce, “all it takes to grow one lettuce is 1 g of fertilizer, 1 L water, 1 seed, and 1 Jiffy-7 peat pellet, at a cost of as little as 10 cents per plant.” Now we have an estimated cost per head of lettuce. “With an average plant success rate of 95%, you can plan on harvesting about 940 plants a week,” says Freight Farms. They’re talking about harvesting lettuce at a 4-week maturity and we’re estimating the weight of each lettuce head to be 4 ounces based on an estimate given from Bright Agrotech in their article on How Much Can Container Farms Really Grow? That gives us 235 pounds of lettuce a week or 12,220 pounds of lettuce a year (just over 6 tons). If we sold that lettuce at $1.64 a pound – about half the price of lettuce on Nauru today – that gives us about $20,040 in revenues a year. For consumables, let’s assume ten cents per plant (48,880 plants = $4,888). For electricity, the company states that power consumption for a Greenery ranges from 150-165 kWh per day. Here’s an idea of electricity rates on Nauru in AUD.
Credit: Nauru Utilities Corporation
Unless we can convince the government to cut us a break, the math works out to $21,900 a year AUD which is $15,064 a year USD in electricity costs. Subtracting our costs ($15,064 + $4,888) from our revenues ($20,040) we get a meager profit of $88 and we haven’t even considered labor or the cost of support. Barring any serious errors in our assumptions, it doesn’t look like container farming would be very economically viable for the country of Nauru. Even with electricity subsidized at the lowest domestic rate, we’re still looking at 10 years before we can receive a return on our initial capital outlay and that’s without considering the time value of money.
Conclusion
Container farming shouldn’t just be about producing better tasting “farm to table” produce for over-priced restaurants to sell at a premium to well-off diners, it should do something better than that for mankind. Our back of the napkin calculations don’t quite add up. Sure, we might be able to negotiate down the price a bit, or the Government of Nauru might subsidize the operation, but as we’ve said before, subsidizing the world’s problems won’t scale. The operation needs to be self-sustaining, generate a profit, and provide an ROI in a reasonable amount of time. If you think your container farming startup can provide a solution to Nauru’s obesity problem, Mr. Batsiua would like to have a chat with you. Just drop us a line and we’ll put you in touch with him. Stay tuned for our next article on container farming where we look at all the players in this space in addition to Freight Farms.
Pressure To Revoke Certification of Containers Continues At Fall NOSB Meeting
Multiple groups push USDA to revoke certification for organic production systems with containers during most recent National Organic Standards Board meeting cycle
Multiple groups push USDA to revoke certification for organic production systems with containers during most recent National Organic Standards Board meeting cycle
The June 3 USDA memo summarizing the land-use history requirements has not slowed down the efforts of opponents to organic production systems incorporating containers into their farms. Several organizations including retail organizations belonging to the National Organic Coalition in their written and verbal comments for the Fall NOSB meeting continued to call for revocation of certifications of operations using containers. Multiple members of the NOSB went so far as to call for the decertification of seedling facilities that produce transplants for vegetable growers if those facilities rotate greenhouses where raised tables are located during the course of the year between organic and non-organic potting soils in the containers. However, USDA continues to stand firm on the June 3 memo and has not placed the issue of containers on the work agenda of the NOSB nor USDA staff.
CSO reaffirms sensible application of USDA organic standards in Washington and at the NOSB meetings
Members of the CSO met with members of Congress and the USDA as well as testified in front of the NOSB over the last few weeks to reiterate the importance of containers to help meet their obligations as growers under the organic requirements of conserving natural resources. CSO members and staff reminded officials on the importance of organic containers in conserving wildlands by reducing the footprint of fruit and vegetable production, minimizing nutrient runoff from farming operations, increasing the efficiency of water use, enhancing the effectiveness of beneficial insects and generally helping growers properly respond to the site-specific conditions on their farms.
Frankel urged USDA and the NOSB to avoid making false statements regarding the production practices of container growers, especially when making policy decisions. Frankel also presented data showing that the June 3 memo was not raising prices yet was stifling supply increases as growers and marketers are withdrawing investment, promotion, and research necessary to build fresh produce categories as a result of uncertainty surrounding how policy is interpreted and made.
FOR SALE: 2016 Computer Controlled "Modular Farm" - Hydroponic Grow System - Canada
The “Modular Farm” is a complete hydroponic growing system built entirely inside a shipping container with all the components needed for commercial food production. The system is designed and engineered for easy operation, allowing users of all backgrounds to immediately start growing.
Location: Canada
Price: $59,000 USD
Exterior Farm Dimensions: 40' x 10' x 10'.
AutoGrow technology with IntelliGrow support. This allows for remote control of the farm (climate, lights, nutrients, etc.) from anywhere using your mobile phones or computer. Also, gives a history report.
Upstart University, a Facebook group, has been a great resource tool to connect with other hydroponic growers or Upstart personnel, for assistance in whatever it may be.
There are four (4) cameras installed to remotely view the interior of the farm.
240 x 8' zipgrow towers allowing for 2800+ plants. This is in 4 rows (2 sections) with 60 towers in each. As you can see in the picture with the table.
Farm labor is 15-20 hours per week for harvesting and upkeep.
There is a large 9' x 3', stainless steel working table accessible on 3 sides. 4 adults working can work in the farm at one time with plenty of space.
The farm has been able to maintain a healthy climate in the middle of the Alberta winters. The farm’s first winter experienced -40 Celsius for 2 weeks.
US: BrightFarms Investing $21M In North Carolina
November 1, 2019
The packaged salads company will create 54 jobs at a hydroponic greenhouse in Etowah, NC.
(Photo: BrightFarms)
BrightFarms, a packaged salads company, will create 54 jobs in Henderson County, NC. The company will invest $21 million to operate a hydroponic greenhouse in Etowah.
“Today’s consumers are searching for produce that’s fresher, safer and responsibly grown. It’s the reason that locally grown food has become the #1 purchase driver in produce for supermarkets,” said Steve Platt, CEO of BrightFarms. “We are incredibly grateful for the support from Governor Cooper and the North Carolina Department of Commerce and look forward to bringing local, pesticide-free leafy greens to North Carolina and neighboring states.”
BrightFarms grows leafy salad greens and herbs including spring mix, spinach, baby kale, romaine and arugula. The company describes its local greens, which are grown in a safe, secure and clean indoor environment without the use of pesticides, as beyond organic. By growing produce close to its consumers, BrightFarms’ produce is delivered to supermarkets in as little as 24 hours of harvest, about a week faster than leafy greens grown on the West Coast.
BrightFarms’ North Carolina greenhouse will be the company’s sixth and one of its largest locations to date. At full production, the 280,000-square-foot, state-of-the-art greenhouse in Hendersonville could produce up to two million pounds of leafy greens each year.
“Agriculture has always been a strong driver in North Carolina, and BrightFarms’ expansion is good for our state,” said Governor Roy Cooper. “They are committed to conserving water, land and energy resources while growing their business–green economic development that is good for the company, the community and the workers who will support them.”
The North Carolina Department of Commerce led the state’s support for the company’s decision. A performance-based grant of $55,000 from the One North Carolina Fund will help facilitate BrightFarms’s operation in Henderson County. The One NC Fund provides financial assistance to local governments to help attract economic investment and to create jobs. Companies receive no money upfront and must meet job creation and capital investment targets to qualify for payment. All One NC grants require a matching grant from local governments and any award is contingent upon that condition being met.
“North Carolina is a great location for innovators like BrightFarms to do business,” said North Carolina Commerce Secretary Anthony M. Copeland. “The company will join more than 1,000 food and beverage manufacturers in our state and will have their local produce available to a large supply chain along the East Coast.”
In addition to North Carolina Commerce and the Economic Development Partnership of North Carolina, other key partners in the project include the North Carolina Community College System, Agribusiness Henderson County, and Henderson County.
Want to learn more about North Carolina corporate expansion?
Considering North Carolina for your company’s relocation or expansion project? Check out all the latest news related to North Carolina economic development, corporate relocation, corporate expansion, and site selection.
Farming Goes Underground In Seoul Subway Station
The project is called Metro Farm, and the Sangdo location is the first of five subway farms slated to open by the end of the year in a partnership between the Seoul Metropolitan Government and Farm8, a South Korean agriculture company
SEOUL, Nov. 1 (UPI) — For the past month, commuters at Seoul’s Sangdo subway station have been met with a surprising sight: a fully functioning farm growing leafy lettuce, sprouts and microgreens.
This underground farm doesn’t rely on soil and sunlight but uses special LED lighting, hydroponic growing trays and a smart network that controls factors such as temperature, humidity, CO2 levels and light intensity.
The project is called Metro Farm, and the Sangdo location is the first of five subway farms slated to open by the end of the year in a partnership between the Seoul Metropolitan Government and Farm8, a South Korean agriculture company.
The Sangdo farm opened in late October, and a second branch recently opened in Dapsimni Station.
The farms highlight the changing face of agriculture in rapidly urbanizing societies, said Kim Sung-un, senior manager of Farm8.
“As South Korea is aging and the rural population is rapidly shrinking, this is the future direction of farming,” he said. “These farms use less space and take less time to grow vegetables.”
The operation in Sangdo certainly looks like something from the future, more space station than a subway station.
Lettuce is grown on vertical shelves in the main facility, a brightly lit glass-encased 4,240-square-foot) cleanroom that must be entered through an airlock. The Sangdo farm produces around 66 pounds of greens per day, with seeding and harvesting the only human interaction necessary.
Growing times are reduced in this hydroponic system, taking around 38 days to grow lettuce from seed to harvesting, as opposed to more than 50 days in soil. The farm also absorbs CO2 and pumps out oxygen, contributing to the air quality in the subway station.
A smaller space nearby contains a fully automated robot farm that grows sprouts and microgreens, while a Farm Café sells salads made from the plants at the Metro Farm. The station also hosts an experience center that offers tours and interactive demonstrations of the farm to families and schools.
Kim said that only three employees are needed to maintain the farms across all five subway locations, and these positions are being filled by retirees and disabled workers.
“The best thing about urban farming is that it can improve the lives of people who are socially excluded,” Kim said.
The benefits of the subway farm for Seoul are widespread, said Choen So-young, who heads the Smart Farm initiative in the city government, ranging from minimizing transportation to providing a stable food supply.
“As the vegetables produced in the stations can be distributed right away, we can minimize the cost of distribution and logistics,” she said. “And the farms are located in urban areas so we can have an easy supply of manpower. In addition, as the smart farms are not affected by climate change including fine dust, they can have a stable production to supply clean and safe vegetables.”
While interest in vertical and urban farming has been on the rise in cities around the world, questions remain about its economic viability on a broad scale. One study in Japan last year found that 60 percent of indoor farm operators are unprofitable because of the cost of electricity to run their facilities.
However, South Korea, with limited available land, extreme seasons that make growing year-round difficult and electricity prices that are among the lowest in the world among developed nations, could prove an ideal urban farm market.
“Compared to the traditional outdoor farming, the vertical type of smart farming can maximize the production volume per unit area throughout the year with a stable condition,” Choen said. “So the cost efficiency is the strongest point.”
What is certain is that the coming decades are going to require radical new approaches to feeding the world.
A United Nations report from 2013 predicted that the world will need to sustainably produce 70 percent more food by the year 2050 to feed a population of nearly 10 billion. And an August report from the U.N.’s Intergovernmental Panel on Climate Change warned that arable land, which has been declining globally for decades, is under critical pressure from climate change and human development.
In the meantime, commuters at Sangdo Station are getting a taste of the future.
Kim Jie-eun, a 30-year-old teacher, said she lived nearby and was intrigued by the new addition.
“I come through the station often and I noticed the farm,” she said while eating a salad from the Farm Café with a friend.
“It was the first time I had ever seen something like this and I wanted to try it, especially because I eat a lot of salads. I like the fact that it’s really fresh. And the idea is really new, innovative and creative. I hope more residents will try it.”
Element Farms Unveils New State-of-The-Art Greenhouse
New Facility Will 20x Company’s Current Capacity for Growing
Pesticide-Free, Local, and Sustainable Leafy Greens Year-Round
New York, NY -- October 31, 2019 -- Element Farms, one of the only companies capable of growing pesticide-free, local, and sustainable spinach year-round, has announced that it will begin operations at its new 70,000 square foot Lafayette, New Jersey, greenhouse facility in the coming weeks. The company will outfit its new site, once home to a horticulture company, with proprietary technology and supplemental lighting to produce a wider variety of leafy greens at a higher yield and lower cost than most competitors. At full capacity, Element Farms will produce over half a million pounds each year of pesticide-free baby spinach, arugula, baby lettuces, pea shoots, beet greens, and more.
The new facility is an evolution from Element Farms’ current home: the structure is made entirely of glass, which allows for more efficient transmission of sustainable natural sunlight, and the hilltop location moderates temperatures, bringing heating and cooling costs down during the company’s year-round production.
Most of the operation’s everyday tasks will be automated with Element Farms’ custom machinery, like seeders and harvesters, to increase yield per square foot. The new greenhouse is ideally situated on delivery routes for New York, New Jersey, and Pennsylvania’s population-dense and produce-hungry cities. As before, greens will be delivered directly to retailers within 24 hours of harvest for maximum shelf life.
“We couldn’t be more excited for our new greenhouse. We’re customizing every aspect for operational efficiencies, integrated pest management, and sustainability,” said company founder Serdar Mizrakci. “We’re also thrilled that we’ll be able to meet our ever-increasing demand and bring more pesticide-free, safe, and delicious greens to the retailers and customers who have been clamoring for it.”
The new greenhouse will have dedicated areas for research and development and fully climate-controlled space for both growing and packing. As the company grows, so will the facility: the rest of the property is similarly zoned for agriculture and can support more acres of greenhouse space. Element Farms expects to double its greenhouse team after launch and bring jobs to the surrounding area.
Mizrakci started Element Farms as an MBA student at Cornell University’s Johnson School of Management after learning that most leafy greens consumed on the east coast make a week-long trek from California and lose freshness and nutrients in transport. He envisioned and executed a better process based on his independent study work with co-founder Danny Janeczko at the College of Agriculture and Life Sciences at Cornell, his own expertise as an industrial engineer, and his passion for good food.
The Lafayette greenhouse is just the first part of Element Farms’ growth plan. The company is currently pursuing greenhouse projects in two other states where the markets for year-round local produce are ripe for disruption. Element Farms expects to announce these projects in the coming year.
About Element Farms
Element Farms launched in 2016 with a single goal: to grow the purest, best-tasting greens for the most people possible. Element Farms is one of the only indoor controlled-agriculture companies that can produce local, pesticide-free, hydroponic spinach at scale year-round.
Founder Serdar Mizrakci has solved the biggest issues in indoor agriculture--inconsistency, plant disease, and high operational costs--by bringing farming back to its most basic elements: the plant, light, nutrients, and water. The company uses proprietary technology and renewable energy to seed, grow, and harvest its produce and higher yields and lower costs than most competitors.
The Element Farms greenhouse is located in Lafayette, New Jersey. The brand’s current product line includes baby spinach, baby arugula, crispy lettuce, salad mixes, and more.
Learn more about the company at www.element-farms.com.
Images by Element Farms
Health Check Kids: Leafy Green Machine Planted At West Warwick High School
With permission and funding from the school district, a 40-foot climate-controlled container was planted just outside the cafeteria doors more than a year ago. And that's when the science department got on board
by BARBARA MORSE, NBC 10 NEWS
Thursday, October 31, 2019
A Leafy Green Machine planted at West Warwick High School. (WJAR)
To View The Video, Please Click Here
Sodexo — the school district’s food service company — seeing it in action at a University in Massachusetts.
"And we figured, gee, what a great idea. Local food, right on site. Why don't we just bring it in," said Donna Walker, general manager of Sodexo food services for the West Warwick School District.
With permission and funding from the school district, a 40-foot climate-controlled container was planted just outside the cafeteria doors more than a year ago. And that's when the science department got on board.
"We learned how to run the machine, how to seed and transplant and harvest the lettuce," said Gina Poulos, a science teacher at the high school.
Then they got students involved -- forming the leafy green club.
"I'm super interested in plants and all type of agriculture and it's a nice, relaxing thing to do after school or even in the middle of school when we have advisory and I can kind of just plant stuff and get to learn and talk to other people," said Joshua Dick, a junior at the high school.
"I love salads and I always thought plants were so cool. I always love going to botanical gardens and just thought it was so cool and was like why not," said Gabrielle Dascoli, a senior.
The plants, most leafy green lettuce, are grown -- chock full of nutrients -- vertically, which is a space saver. Special lights are programmed remotely. And the process uses minimal water and electricity.
Harvested and turned into salads within hours.
"I think it tastes amazing. you can taste the nutrients. You can tell it's really thought out. It's great," said Gascoli.
"We're trying different things,” said Walker. "We've done tomatoes, we've done some herbs, we've done kale for soups and stuff."
The leafy green machine can produce up to two acres' worth of greens. The modified shipping containers are re-purposed into green machines by Freight Farms in Boston.
Rise Gardens Helps You Grow The Perfect Tomato In Your Living Room
After becoming frustrated with growing fruits and veggies outdoors, Hank Adams tried his hand at building his own in-home hydroponic system, a device that grows plants in a reservoir of moving water and organic materials
October 31, 2019
Maintaining a garden in Chicago is difficult. Not only is the region plagued with a short growing season and unpredictable weather, but figuring out how to provide fruits and vegetables with the perfect amount of water, sunlight and nutrients can be confusing.
After becoming frustrated with growing fruits and veggies outdoors, Hank Adams tried his hand at building his own in-home hydroponic system, a device that grows plants in a reservoir of moving water and organic materials.
“It was a really frustrating experience,” Adams said. “It actually took a fair amount of research to figure it out. And what I ended up with was a system that really belonged in my basement.”
The system was “ugly,” he said. “It was nothing I wanted to show off.”
A Rise Gardens system (Photo via Katherine Davis)
But the experience led to Adams launching Rise Gardens, a Chicago startup creating an indoor, IoT-connected hydroponic system that is attractive enough to put in your living room and simple enough for anyone to grow a perfect head of lettuce.
Adams began making prototypes for Rise Gardens in 2017, working out of Chicago startup incubators 1871 and mHub, and began selling the final product in August. Adams is a board member of 1871 and also the former CEO of Sportsvision, a Chicago-based graphics company best known for inventing the yellow first-down marker in football broadcasts.
Rise Garden systems can be bought online or in the startup’s pop-up shop at 20 W. Kinzie St., which opened in early October.
The modular system is made out of hardwood and heavy-gauge, powder-coated steel. It has a built-in water pump, seed sockets and a programmed LED light system that automatically shifts on and off to give plants the perfect amount of light.
Once consumers purchase their hydroponic system, they are encouraged to subscribe to Rise Gardens’ subscription service, which sends them seed pods every month and gives them access to the company’s mobile app that reminds users when to add water or nutrients. The startup sells seeds for a range of vegetables and herbs, including kale, lettuce, tomatoes, peppers, basil, and rosemary.
“We’ve made it simple,” Adams said. “If you follow the instructions, it grows really robustly.”
Adams said plants grow 20 percent faster in his system than they could in soil or outdoors, adding that users can expect to grow arugula in 14 days and a head of lettuce in 25 days.
A Rise Garden system (Photo via Katherine Davis)
Though small, counter-top hydroponic systems are common, Adams says Rise Gardens’ large size allows for users to actually grow a significant amount of fresh food.
Since launching, Adams said he has sold 70 systems and is now working with retailers to sell the device in more locations. The system starts at $549 for one level and goes up to nearly $950 for three.
In his own Rise Gardens system at home, Adams grows lettuce, carrots, beets, tomatoes, peppers, and strawberries. Often times, he says he uses his produce in homemade salads, pastas and pizzas.
“It’s really nutritious and it tastes great,” Adams said. “Compared to a lot stuff that we’re used to getting in grocery stores, you’re surprised by the taste.”
Hank Adams, founder of Rise Gardens, with his hydroponic system (Photo via Rise Gardens)
Misconceptions About Hydroponics Yield
There are many reasons why gardeners choose to grow their crops using soil-less hydroponic methods instead of traditional soil-based methods. Some of hydroponics key advantages include more space-saving, more energy/water efficient, less weeding, and fewer pests to contend with
Hydroponics Yield
There are many reasons why gardeners choose to grow their crops using soil-less hydroponic methods instead of traditional soil-based methods. Some of the hydroponics key advantages include more space-saving, more energy/water efficient, less weeding, and fewer pests to contend with. Hydroponics also allows the grower more control and creativity their crops so that they may provide the most ideal conditions for plants. However, the single most compelling reason for gardeners to switch to soil-less gardening is its ability to significantly increase crop yield. Let’s review the factors that influence hydroponics yield in order to demonstrate why this type of gardening is better than soil in nearly every respect.
Misconceptions about Hydroponics Yield
Some people are under the impression that hydroponics will produce much larger plants than soil. This isn’t necessarily the case. Each seed has its own genetic code which determines the plant’s size, flavor, and yield potential. In other words, you can’t transform a cherry tomato into a Roma tomato, but you can turn a cherry tomato seed into the genetically best possible cherry tomato plant if you provide the perfect growing conditions. Hydroponics gardening gives plants the best opportunity to reach their full genetic potential. More often than not, this translates into healthier, larger, and more flavorful crops.
Hydroponics Yield vs. Soil Yield
It can be difficult for plants to reach their highest genetic potential in common soil. This is because there are hundreds of variables in soil’s makeup that can influence a plant’s growth. Hydroponics, on the other hand, gives the grower the ability to micromanage and control the growing conditions so there are no surprises from Mother Nature. Soil-based plants use a lot of energy to seek out their food source, while hydroponics plants are given exactly what they need when they need it. Thus, hydroponically-grown plants can direct all their energy into producing higher yields, denser vegetation, faster growth, and more flavorful crops. It is more likely that hydroponic crops reach their genetic potential, and thus, is often considered a superior form of agriculture.
Hydroponics Yield: Lessons from Dr. Howard Resh
In his book “Hydroponic Food Production,” hydroponics pioneer Dr. Howard M. Resh makes a compelling case for ditching the dirt and going soil-less. He discusses the main advantages of hydroponics over soil culture, especially for regions of the world that have non-arable land. Resh outlines the efficiency of regulating the nutrients and water, the low cost and ease-of-use to sterilize the medium, as well as how hydroponics allows for higher density planting and – ultimately – increased yields per acre.
In the table below, Resh compares the yields per acre in soil vs. soil-less culture:
As you can see, his findings are quite dramatic. It is no surprise that urban planners and policymakers are often proponents of hydroponic gardening. Hydroponic gardening has wide implications for the future of practical, efficient, and cost-effective farming across the world. Because crop yields of hydroponically-grown plants can be up to an astounding 100 times higher than crops grown in the field, hydroponics yield is the clear winner.
Hydroponics Yield Factors
So why exactly are the crop yields so much greater for hydroponics? Let’s look at the most important factors of hydroponics yield.
1. Year-Round Gardening Means More Crops Per Year
One of the most important factors influencing hydroponics yield is its ability to grow crops indoors and year-round. Field crops are often limited to one harvest per year because of frost and other weather variations. Since greenhouse and hydroponic crops are grown indoors – away from Nature’s elements – you can cultivate 12 one-month crops, 5 seventy-day crops, or whatever crop harvesting time frame you choose. As a result, you can increase crop yield each year by a factor of 2x to 8x by growing indoors and year-round with hydroponics.
See our Hydroponics System, Best Grow Tent, Grow Tent Kits, and Hydroponic Weed System, pages for the tools to grow successful hydroponic crops.
2. Higher Plant Density Allows for More Crops Per Acre
Hydroponics allows for higher plant density in one or more of the following ways: hydroponic crops can be grown 1. closer together than in soil, 2. grown vertically as opposed to horizontally, 3. in layers, and 4. with much less walking space between rows. Employing any one of these methods can increase crop yields, but incorporating several can result in even more plant density. Overall, you can increase plant density by a factor of 4x to 16x with hydroponics.
3. The Crops you Choose May Increase Yield
Which variety of crops you decide to grow can influence the hydroponics yield. While you can cultivate nearly any crop in a hydroponics system, some will give you better results and a higher yield. For example, leafy crops – like lettuce, chard, kale, and arugula – produce great results, as do herbs like basil, chives, parsley, and sage. Tomatoes, peppers, and cucumbers can also result in high yields with hydroponics. Certain crops present more of a challenge – like watermelons and strawberries – but with special attention, they can also produce great results. On the other hand, root vegetables, corn, and plants that vine are not recommended for hydroponic gardening. Depending on the crop variety you choose, hydroponics can increase yields by 2x – 4x over soil farming.
4. Proper Lighting is Key
Plant growth is dependent on adequate lighting. They tend to do best with a light of wavelengths in the 360 – 760 nm (nanometers) range. Plant photosynthesis responds to blue light (around 430 nm) and red light (around 660 nm). Plant germination, stem, and flower growth thrive when red light is around 660 nm and infrared light wavelength is around 735 nm. White fluorescent lights provide a light spectrum that includes these preferred wavelengths. While field-grown crops depend entirely on the sunlight for their growth, greenhouse or indoor hydroponic crops utilize grow lights to mimic the sun’s natural light. With the proper grow lights, hydroponics plants will receive the optimal spectrum of light throughout the year regardless of what the sun is doing outside. Good lighting can increase hydroponics yield by 1x – 2x.
5. Water Plays an Important Role in Crop Yield
Water is clearly one of the most important factors influencing crop yield. After all, the water-weight of fruits and vegetables is 86% and 90%, respectively. Field-grown crops are susceptible to droughts and inconsistent rain patterns – too much or too little water can wreak havoc on crops. Water can be managed much more efficiently with hydroponic and greenhouse crops. The proper water management can translate to a 1x – 2x increase in yield.
6. The Efficiency of Hydroponic Fertilizer
In hydroponics, a fertilizer is mixed with water to create the nutrient solution. This nutrient solution is typically pumped into the grow bed to feed the plant’s roots. Hydroponics allows plants to get the correct nutrients they need when they need it. Soil grown crops don’t have it as easy. If they don’t get the proper nutrients at the right time, crops will suffer. Hydroponics provides a much more efficient way of delivering nutrients to plants. Yield can be multiplied by a factor of 1x – 2x if greenhouse or hydroponic crops are feed properly.
7. Managing Temperature and CO2 can Increase Yield
Temperature and CO2 are important factors in plant growth. Each crop variety has its own preferred temperature, and this varies depending on its phase of growth. However, most plants respond best when temperatures are kept in the 75F to 85F range. With hydroponics, the yield can be multiplied by 1x – 2x if temperatures are kept within ideal levels.
As for carbon dioxide, the more CO2 in the air, the faster a plant grows. Dr. Howard Resh proposes that two to five-time the normal amount of carbon dioxide may be the optimal amount. He states that tomato and cucumber growth rates can be increased by up to 20% – 40%, while the faster growth rates in lettuce can allow for an extra crop grown each year. Carbon dioxide enrichment can increase yield in hydroponically-grown crops by 1x-2x.
8. Other Factors that Influence Hydroponics Yield
There are several other factors that affect plant growth. These include relative humidity in the growing environment, the amount of oxygen the plant’s roots are exposed to, and the proper pollination. Hydroponics allows you to control all of these things to the ideal levels, but it requires close attention to get it right. Another clear advantage to growing crops indoors and without soil is the protection from storms and bad weather, as well as the near elimination of pests. While insects, mammals, birds, pathogens, and weeds can destroy around 33% of field crops, indoor hydroponic and greenhouse crops experience very few of these problems.
One issue hydroponics gardeners must prevent is waterborne disease, as this can devastate an entire crop. Grow media should be sterilized after each grow so as to prevent diseases from one grow to the next. Certain organic soil fertilizers – like manure and waste – can also introduce disease, whereas a hydroponic nutrient solution mix of water and fertilizer eliminates this risk. In total, all of these “other factors” can increase hydroponics yield by 1x -2x.
Hydroponics Yield – The Clear Winner
When you multiply all of these factors together, the crop yields of hydroponically-grown plants can be up to an astounding 100 times higher than crops grown in the field. The benefit of controlled-environment agriculture and vertical systems have wide implications for not only at-home gardeners and commercial growers, but also for global hunger advocates, policy makers, and urban planners. Since hydroponic farms can be built on low-cost and/or non-arable land, greenhouses and hydroponic farms can be built in areas where conventional soil farming is not possible. Urban hydroponic farms can provide jobs for city residents, a source of healthy, locally-grown produce, and minimize the environmental costs associated with shipping produce around the world.
Hydroponic grown-crops nearly eliminates the problems associated with soil-based agriculture – it is not weather dependent, it’s more space-saving and water/energy efficient, and there are fewer pests to deal with. And most compelling, hydroponics provides higher yields and a more reliable food source due to its year-round growing and frequent harvesting. Make the switch to hydroponics!
Thanks for reading and best of luck with your hydroponics garden! For more helpful articles on hydroponics and aquaponics, feel free to browse through other pages on uPONICS.com.
Green Automation Is Bringing Automation And Efficiency To New Greenhouse Operation In Texas
Green Automation Group is proud to announce the latest project realization in the North American market – hydroponic lettuce producer TrueHarvest Farms in Belton, Texas. The 50,000 square feet greenhouse is equipped with growing automation technology from Green Automation
October 24, 2019, Wellington, FL, USA
Green Automation Group is proud to announce the latest project realization in the North American market – hydroponic lettuce producer TrueHarvest Farms in Belton, Texas. The 50,000 square feet greenhouse is equipped with growing automation technology from Green Automation. Riding on the steadily increasing demand for locally grown produce, TrueHarvest Farms will grow fresh and pesticide-free head lettuce locally in the controlled environment of a greenhouse 365 days a year. The farm is strategically located in the “Texaplex Triangle”, which is formed between the cities, Dallas-Fort Worth, Houston, San Antonio, and Austin. With a population of around 20 million people and having 80% of the state’s population growth since 2000 as well as generating up to 70% of the Texas economy, this area is the ideal location for new, innovative and sustainable production of leafy greens.
“The climate here in Texas makes year-round field growing of leafy greens impossible and the area has so far, as the rest of the USA, relied heavily on having lettuce trucked into the state from California and Arizona for a substantial part of the year”, says Marshall McDaniel, Managing Member at TrueHarvest Farms. “We will be distributing truly fresh, nutritious, safe and locally grown lettuce to stores within a 250 miles radius of our operations. The lettuce will be available to the customer in less than 24 hours of harvesting”.
TrueHarvest Farms, rooted in Belton, TX, is ready to supply fresh, nutritious and safe leafy greens to the Texaplex Triangle.
Recent food safety scares in the lettuce industry has led to an increased interest in and call for safe and clean lettuce produced in a controlled environment. The greenhouse is a closed system, controlling what comes into the greenhouse, making it possible to not only keep the lettuce clean but also to grow them without using any chemical pesticides. The irrigation water, the air, and the growing medium are controlled, monitored and clean - keeping consumers safe and the environment protected.
“There is an enormous demand for locally grown and safe lettuce today”, confirms Jason Maks, Managing Member, and Grower at TrueHarvest Farms. “Our facility is in the final stage of obtaining PrimusGFS certification and we are dedicated to meeting the highest safety standards in the food industry. TrueHarvest Farms will be a reliable source for locally grown and safe produce for the Texas markets. We are ramping up our production right now and expect to reach full capacity in January 2020. At the moment we are growing Butterhead, Crisp and Romaine varieties”, explains Maks.
TrueHarvest Farms is using the automated growing system optimized for head lettuce production. “When growing leafy greens in tough climates it is imperative to operate the greenhouse with the highest efficiency and to generate the highest yields per square foot, therefore TrueHarvest Farms decided to use the automated growing system from Green Automation”, says Patrik Borenius, CEO, Green Automation Americas. “Throughout the entire growing process maximal space efficiency is achieved through automatic movement and adjustment of gutters, giving the plants as much space as needed, but as little as possible”.
In addition to maximizing yield through space efficiency, labor efficiency is an essential key component in a profitable operation. The system has a highly automated and versatile medium filling and seeding line arrangement using stackable trays and supporting both net pots as well as Ellepots. After seeding and germination, the plants are placed onto the automatic growing system, featuring adjustable and movable growing lines, where they will soak up the natural sunlight. As the plants grow, they are moved automatically through the greenhouse toward the harvesting station.
TrueHarvest Farms did multiple trips to reference operators in Europe, including to such remote locations as Joensuu, Finland, before making a decision. “It is a proven system and on par with our earth-conscious commitment. We are looking forward to growing and providing the Texas market with the highest quality lettuce”, says Marshall McDaniel. “This is only the beginning, we have room to grow and our head house as well as the irrigation system are designed for future expansions,” McDaniel explains.
Contact:
Patrik J. Borenius
Green Automation Americas LLC
13833 Wellington Trace, Suite #E4-203
Wellington, Florida 33414
About Green Automation Group
Green Automation Group Ltd, headquartered in Finland, and it’s subsidiary Green Automation Americas LLC, based in Florida, develop, manufacture and market the most advanced greenhouse automation systems for lettuce and herb production. The systems are designed for commercial greenhouse operations with a growing area of 1 acre / 0.4 hectares and above. www.greenautomation.com
About TrueHarvest Farms
TrueHarvest Farms, LLC is a controlled environment hydroponic farm specializing in leafy greens. Founded in 2017, the company is focused on rapid growth through the production and distribution of high-quality lettuce and other leafy greens. TrueHarvest Farms is the evolution of a family hay and pecan farm now 40 years old. So, whether it is the “family roots” or the “plant roots,” we are truly “Rooted in Belton, Texas”.
https://www.facebook.com/trueharvestfarms
Westcore Lands Vertical Farmer Plenty Unlimited at Industrial Asset
Bay Area-based Plenty Unlimited signed a 10-year lease to take Westcore Properties’ entire 94,875-square-foot warehouse development project currently under construction in Compton, CA
October 29, 2019
Bay Area-based Plenty Unlimited signed a 10-year lease to take Westcore Properties’ entire 94,875-square-foot warehouse development project currently under construction in Compton, CA. The vertical indoor farming company will take occupancy at 126 E. Oris St., which is slated for completion next month.
The Class A building’s ceilings soar to 32 feet making the facility a good match for the vertical rows of sustainably grown, leafy greens, like kale, Plenty will cultivate at the property.
Plenty will make a multi-million-dollar investment into the build out and technology for the farm at the Compton property. The farmers growing technique requires a tiny fraction of the water and land of conventional farms, and allows plants to grow independent of seasonal or weather variations through use of hydroponics and LED lights. The controlled environment also eliminates the need for pesticides.
Savills’ Zack Jamail and David Gordon represented the tenant. Kidder Mathews’ Marc Bonando and Brad Connors advised the landlord.
VIDEO: Boys & Girls Club Introduces Kids To Hydroponic Farming
The Freight Farm will allow students to learn about science and agriculture. It will also act as revenue for the BGCCA
by: Justina Latimer
October 30, 2019
TROY, N.Y. (NEWS10) — The Boys & Girls Clubs of the Capital Area are introducing kids to high-tech hydroponic farming.
The Freight Farm will allow students to learn about science and agriculture. It will also act as revenue for the BGCCA.
The farm was donated by SEFCU with CDPHP and Brown’s Brewing Company also partnering to support the cause.
Entrepreneurs And Government Are Teaming Up To Boost Food Security In The United Arab Emirates - And Beyond
This approach to indoor agriculture, known as vertical farming, has been gaining popularity in many parts of the world recently — the business consulting firm Grand View Research, Inc., estimates the global market will reach US$9.96 billion by 2025
From vertical farms to fish caves, new
technologies aim to boost food production and vanquish hunger
Photo courtesy of Masdar Farms
WRITERRabiya Jaffery
@rabiyasdfghjkl Freelance journalist
October 29, 2019 — Tucked away in Masdar City, a quiet planned neighborhood in the emirate of Abu Dhabi that combines earth-tone Arabic architecture with wind turbines and other innovative technology, is a cluster of container-style buildings.
These containers are the site of Madar Farms, co-founded by Abdulaziz Al Mulla, a Kuwaiti entrepreneur now based in the United Arab Emirates. Al Mulla began getting interested in food security while at the management consulting firm McKinsey & Co., where he worked with several of the region’s governments addressing a variety of national risk challenges. He left McKinsey after one particular project introduced him to the national security threats food and water challenges will bring to the region. He decided he wanted to do something about it, and ended up purchasing old shipping containers and transforming them into these indoor farms as a way to increase local food production. Today lettuce, basil, kale and other leafy greens grow without soil in trays that sit under red and blue LED lights, stacked in levels much like floors in a building.
“I was overwhelmed by the numbers: less than 5% of land in the Arabian Gulf is arable farmland. Despite this, over 80% of water use in our drier climate is used for agriculture. If we keep going at the same pace, we will deplete a significant amount of our natural resources in the next 50 years,” says Al Mulla. “This didn’t make sense to me, and I knew there had to be a better way. A week after this project, I resigned and began Madar Farms.”
This approach to indoor agriculture, known as vertical farming, has been gaining popularity in many parts of the world recently — the business consulting firm Grand View Research, Inc., estimates the global market will reach US$9.96 billion by 2025 — but is still an emerging concept in the Middle East. Madar Farms — along with many other innovations attempting to lead to sustainable agriculture in the region — represents the humble beginnings of a new bid the UAE is taking on to end food shortage globally.
Home Grown
Although the UAE currently is not short on food, its harsh climate and limited supplies of water and arable land offer little opportunity for agriculture, and over 80% of its food is imported. With increasing uncertainty around food production in the face of climate change and global political instability, the Middle Eastern country is looking to take on more of its own food production.
In November 2018, UAE minister for food security Mariam Al Mheiri launched a national food security strategy that aims to implement resilient agricultural practices that increase productivity and production. This primarily involves increasing investment in research and development of agriculture technologies and facilitating a market that supports agribusinesses.
Hina Kamal, a UAE-based food and nutrition researcher at United Arab Emirates University, explains that much of the focus is on boosting the use of agricultural technology required in both indoor and outdoor farming to increase homegrown produce. Kamal has been studying which produce is best suited for growth in UAE’s climate.
While Madar Farms is one of the first companies capitalizing on this interest, it isn’t the only one catching onto the trend. A growing number of companies, including more traditional outdoor farms, see similar opportunities.
Drones flying over fruit farms in Abu Dhabi provide aerial images researchers and farmers can use to improve food production practices. Photo © iStockphoto.com | ZambeziShark
Fruit farms in Abu Dhabi, UAE’s oil-rich capital, and Ras Al Khaimah, another emirate, for example, have already started testing and implementing drones to map farming areas that supply farmers as well as farming researchers with images, from bird’s-eye views of the fields to up-close images of individual plants. According to Fatima Al Hantoubi, head of environmental protection and natural reserves at Dibba Al Fujairah Municipality, a few organic farms in Ras Al Khaimah have started using sensors and artificial intelligence to improve seed selection, determine the amount of fertilizer needed for specific crops in specific soils and detect early signs of diseases.
In the Khor Fakkan area, meanwhile, the Ministry of Climate Change and the Environment has installed artificial caves in the Persian Gulf. The hope is to further contribute to food security by boosting fish stocks and promote sustainable fish farming.
Al Hantoubi explains that the caves were built out of eco-friendly materials and then placed along a stretch of the coast using cranes.
The initiative also includes the establishment of coral gardens over 850 square meters (9,100 square feet) along the coast to help rehabilitate natural marine ecosystems in the area and to promote research and studies in marine biodiversity, which will also enhance the fisheries stock.
Food Waste
While Al Mulla and others are using agriculture technology to boost food security, other approaches are also helping the UAE become self-reliant with respect to food.
Among them are efforts to address the issue of food waste. On average, each UAE resident wastes an estimated 197 kilograms (434 pounds) of food per year. Over 30% of that waste happens in restaurants, and another 30% is leftovers that get thrown out after family and corporate celebrations.
One of the UAE Ministry of Climate Change and the Environment’s newest projects is encouraging the use of artificial intelligence (AI) in kitchens, particularly in hotels and restaurants, to track food waste and guide kitchens on how to minimize it.
A monitor developed by food tech company Winnow lets restaurant kitchens characterize wasted food as a first step toward reducing it. Photo courtesy of Winnow
Huzaifa Waheed, an entrepreneur and a developer for food-waste-tracking software that is to hit the market soon, says that one of the main reasons this technology can prove to be effective is because it is offering businesses a major cost-saving incentive. “And it helps the government meet its sustainability targets, making it a win-win,” he adds.
Over 100 of the biggest kitchens in the country, including major hotel groups such as Emaar and Majid Al Futtaim, are already using AI to reduce food waste.
The computer vision-based product, launched in the UAE by the government and made by a food tech company called Winnow, uses a camera that sits over the kitchen’s bin to take pictures before and after food is thrown away. It then runs a classification algorithm to identify the discarded food, as well as its weight and cost. That information can be used to identify and address specific sources of food waste, such as spillage or preparation techniques.
The AI program was launched as a proof-of-concept project in 2018. Through this program, the government is encouraging UAE’s lavish hospitality sector to save the equivalent of 2 million meals’ worth of wasted food in 2019 and 3 million in 2020, thanks to better decision making based on data. Several significant public and private entities in the UAE, including Dubai Municipality, Etihad Airways and Hilton Hotels, have already pledged to incorporate the program in their operations.
International Cuisines
An issue that the UAE has yet to tackle is how to accommodate the discerning palate for international cuisines in a country that is currently home to over 200 nationalities and that has a high per capita consumption of staples such as rice, which require acres of tropical land to flourish.
“The major emphasis must be in increasing local production by focusing on targeted major staple foods and enhanced efficiency in the agriculture sector through constant investments in agricultural research and development for modern farming techniques,” Kamal says.
What this means is that in order to most effectively become self-reliant, the UAE needs to have an accurate sense of what food needs to be grown and how to do it at competitive prices.
According to Kamal, a more “holistic food security” is the only way UAE can proceed toward this goal. Government bodies, research institutions, and commercial ventures, Kamal adds, need to work together to address the issues of research, technology, human capital and other factors that arise through the process.
“And perhaps not keep a specific year as the end-all target that has to be reached because it is not a realistic way to conduct research and development — at least not in a sustainable way,” Kamal says.
Overall, while the UAE’s efforts to tackle its food dependence can boost food security in the region and diversify its economy, the success of its strategies will depend on how it tackles the many challenges in a sustainable way.
Editor’s note: Rabiya Jaffery wrote this story as a participant in the Ensia Mentor Program. The mentor for the project was Rachel Cernansky.
History of The Tower Garden®
I applied for a patent on the Tower Garden on August 11, 2004. I also applied for the trademark “Tower Garden” at the same time. I was successful in selling the Tower Garden to the local market, mostly in Greenville, Spartanburg and Anderson, SC
By urbanagnews
October 30, 2019
By Morris Bryan, Inventor of the Tower Garden
In 1974, I graduated from The Georgia Institute of Technology like the majority of the men in my family – my grandfather, father, two uncles, and three brothers – with a diploma I thought would change my life, but it wasn’t until that summer when I visited my mother in Athens, GA that I would stumble upon the beginnings of my true passion.
The very first Tower Garden in 1974
As we reminisced and she congratulated me on my hard-earned degree, I looked through her window into the backyard and saw flowers and vegetables growing out of concrete blocks and pipes and stacked terra cotta pots. Even though I had spent the past four years studying engineering, the landscape appeared entirely alien and almost mystical. My mother credited the growing systems behind her flourishing garden to her friend named Michael Dillon of Flowers, Inc.
Not long after, I met Michael at his nursery and our friendship sparked instantly. In addition to his innovative mind, I admired his foresight and the convictions that fueled his “towers.” Long before climate change and sustainability became a major global concern, Michael believed that the world was running out of usable land for crops and that future human survival depended on growing food differently or as he saw it, vertically. Together we made hydroponic towers from pots, concrete, used tires, garbage bins, and anything we found that we could stack and plant.
It’s important to note that while Michael introduced me to the concept of hydroponic growing, the practice itself was not new. However, what made Michael’s approach unique was the way he utilized existing structures as vessels and modified contemporary fertilizers by crushing them into extremely fine particles and put them into solution. He documented his nuanced approach to hydroponics within “The Dollars and Sense of Tower Gardening,” a text that became my lifeline to a new way of thinking about gardening. Michael passed away in 1987 but I would continue to carry the impact of our intellectual companionship and his vision for the rest of my life.
Although by that time tinkering with towers began to take on a smaller role in my life as I devoted myself to the family business of textiles, I never stopped growing and so too did the hydroponic industry. Companies like American Hydroponics, General hydroponics, and others evolved and released new and exciting growing systems and nutrient solutions that were ready-made for the consumer. The network of hydroponic engineers expanded internationally with the Dutch and Israeli markets leading the way. Hydroponic nutrient quality improved dramatically, and indoor gardening became popular thanks to the equally overwhelming rise in marijuana use.
My daughter picking tabasco peppers from a prototype in 2002
Amidst these swift and vast changes, my life continued to evolve as well. In 1991 my daughter Samantha was born and not long after we moved to Anderson, South Carolina after selling our family textile business. There, I began working on a new type of vertical gardening system and this product would become the Tower Garden as recognized today. Samantha was the creative catalyst I needed. She would wander into the garage to inspect my latest prototype, shake her head with the finicky disapproval of a preteen. I took these rejections, although playful, to heart and stayed focused on improving the Tower until I finally got a nod of her head. With the support of my family, it was then I knew the tower was ready for the market.
I applied for a patent on the Tower Garden on August 11, 2004. I also applied for the trademark “Tower Garden” at the same time. I was successful in selling the Tower Garden to the local market, mostly in Greenville, Spartanburg and Anderson, SC. After selling a few hundred units, I enlisted Bloomington Wholesale Garden Supply or BWGS as the exclusive distributor of the Tower. They gave my invention great exposure and enabled me to participate in the indoor gardening expos held in San Francisco, Tampa, and other cities. It was there that I made many friends in the hydroponic industry and established valuable relationships that I still maintain today.
Shortly after I filed for my patent, J.B. Jones, my friend, fellow hydroponic enthusiast, and technology director at the Fayfard horticultural media company, took some information on the Tower to a seminar he planned to attend at the University of Mississippi in Oxford. When he returned, he informed me that a person from Disney was there and requested additional info on the Tower. That person was Tim Blank. It is important to note that I had filed my patent prior to Tim Blank having knowledge of the existence of the Tower Garden.
In late 2004, I sent a Tower to Tim at Disney World where it was displayed in the entrance to Epcot. This gave me a huge boost of confidence and faith in my idea that propelled me into the next few months as I continued to sell towers with BWGS and through my own personal efforts. I spent several weeks traveling throughout the South selling Tower Gardens to hydroponic retail stores and making numerous invaluable and lasting friendships that reminded me of my time with Mr. Dillon.
After almost 2 years from the 2004 filing date, the Tower Garden patent was issued to me on June 6th, 2006 (patent # 7,055,282).
The first Tower Garden order in 2005 from my distributor Bloomington Wholesale (left), and the our patent (right)
I did not hear from Tim for 2 years. Then, in early 2006, I received a phone call from Tim Blank, and he stated he had left Disney and had started a new company called Future Growing where he would be interested in being a distributor of the Tower. I agreed and Future Growing replaced BWGS as the exclusive selling agent for the Tower Garden. As is the case with most distributor/manufacturer relationships, Future Growing requested that changes be made to the Tower Garden, based on consumer feedback. Several modifications were made, and some were denied due to expense or feasibility. Future Growing continued to be the exclusive selling agent for the Tower Garden and was successful in generating sales and increasing the visibility of the Tower.
My beautiful wife Angela enjoying a Tower Garden in 2006
In 2010, I realized that for the Tower Garden to be a commercial success, I needed either a huge influx of capital or to sell the patent to an entity that could provide higher volume distribution channels than Future Growing was providing. By chance, Future Growing was introduced to the Juice Plus Company located in Collierville, TN and the sale of the patent occurred in 2011. I became the manufacturer of the Tower for Juice Plus at my facility in Anderson, SC and produced 30,000 units until they requested assistance to transfer the manufacturing to their own facility in Memphis, TN.
Now, with tens of thousands of distributors and an established place in the wellness industry, Juice Plus has been able to provide the critical mass necessary to carry the Tower Garden forward into the future driven by the same values that inspired its humble origins.
The long yet rewarding journey of the Tower Garden and the continued encouragement of my family and friends have stayed my inventive spirit and I have now received three additional patents on new hydroponic growing systems: The Solar Salad®, the Solar Salad®Pro series, and a modified Tower Garden for Juice Plus issued in February, 2019. In addition, I have continued to refine and develop the Tower with the additions of the Micropot, the grow clip, and the plastic dolly which I created and designed with Juice Plus.
The Farmshelf Corridor Dubbed The “Garden of Eden” by Katie Couric At The Next50 Event Celebrating The Work of José Andrés And World Central Kitchen
Farmshelf was honored to play a small part in an event that kicks off the next 50 years of World Central Kitchen and its mission to mobilize chefs after natural disasters to deliver a hot plate of food when it’s needed most
The Farmshelf corridor dubbed the “Garden of Eden” by Katie CouricOctober 4, 2019
Jean-Paul KyrillosFollow
Co-founder/ CRO at Farmshelf
Farmshelf is rolling into new cities and big events.
Next50 at The Shed, Hudson Yards, NY
Last week, guests of José Andrés got to enjoy tapas with Farmshelf greens harvested on-demand as they wandered through the Farmshelf corridor. Farmshelf was honored to play a small part in an event that kicks off the next 50 years of World Central Kitchen and its mission to mobilize chefs after natural disasters to deliver a hot plate of food when it’s needed most.
Stop Food Waste NYC at the Javits Center
Jacob K. Javits Convention Center, New York, NY
Our partners from Cultivated NY had their brand new Farmshelfs on display as part of their larger effort to showcase ways that their parent company Compass Group is fighting food waste. With Farmshelf, no greens or herbs are lost in transit and chefs harvest only what is needed, so food waste from spoilage is virtually eliminated.
Oh hey, CA...
Renaissance Esmeralda Resort & Spa, Indian Wells, CA
As we get ready for our west coast launch, Farmshelf was at the Society for Hospitality and Foodservice Management conference in Palm Springs, CA. While we had some fun being outdoors, this was just a cameo. Farmshelf is designed for onsite growing inside your restaurant, hotel or café.
Wondering when we arrive in your city?
Available Now: NYC, DC, Philadelphia, Texas
October 2019: Chicago, Milwaukee
January 2020: SF Bay Area, Boston, Florida
March 2020: Portland, Seattle
Summer 2020: Top 20 U.S. Markets
Farmshelf connects you to your food by making growing simple and enjoyable. Available now for businesses only.
Subscribe to our newsletter for more live updates on Farmshelf and our partners!
MIT Media Lab Scientist Used Syrian Refugees To Tout Food Computers That Didn't Work
Media Lab’s Caleb Harper claimed success for a deployment of food computers to a refugee camp in Jordan, but an investigation by IEEE Spectrum reveals that it never happened
Media Lab’s Caleb Harper claimed success for a deployment of food computers to a refugee camp in Jordan, but an investigation by IEEE Spectrum reveals that it never happened
Photos: Left: WFP Innovation Accelerator; Right: Andreas Gebert/picture-alliance/AP
Left: A food computer at the World Food Programme office in Amman, Jordan. Right: Caleb Harper speaks during a panel discussion of the DLD17 Conference on January 15, 2017 in Munich, Germany.
“So we just put these last week in a Syrian refugee camp in Amman, Jordan,” Caleb Harper of MIT’s Media Lab told an audience at the Georgia Technology Summit in late March 2017.
He was referring to machines developed by his Open Agriculture Initiative (OpenAg) at the Media Lab, where he is a principal research scientist. The machines had been delivered to a United Nations World Food Programme project that aimed to give refugees in the Azraq camp—located in the Jordanian desert 90 kilometers from the Syrian border—the means to grow their own food, right inside the camp.
The vehicle for this agricultural miracle is called a personal food computer (PFC): an enclosed chamber the size of a dorm-room refrigerator loaded with LEDs, sensors, pumps, fans, control electronics, and a hydroponic tray for growing plants. PFCs are programmed to control light, humidity, and other parameters within the chamber to create the perfect conditions for growing a variety of plants. It’s a simple yet potentially revolutionary idea: a portable box that can grow practically any kind of plant just by downloading a recipe and planting some seeds.
The refugees fleeing war in Syria, leaving their homes, loved ones and possessions behind, had no idea where or when they would leave this temporary desert encampment or how they would make do while they were there. But what the refugees really needed, Harper contended, was “to be connected to other growers to share knowledge.” He added: “So super proud that that’s happening.”
On its face, the project sounds like one of the most ambitious and altruistic uses of high-tech agriculture you could imagine. In his talk in Georgia and presentations elsewhere as recently as this year, Harper enthusiastically conveyed a vision for the PFC that mimics how regular digital computing is scaled: PFCs would find a home in classrooms and home kitchens; food-computer “servers” would be housed in shipping containers to supply, say, a restaurant; and data center–scale vertical farms would feed entire cities.
As the name of the OpenAg initiative suggests, the food computer’s hardware and software are entirely open-source—that is, the equipment specs and code are available free to anyone with the desire to experiment with indoor agriculture. “Nerd farmers,” the hashtaggable moniker given to members of the OpenAg maker community, build their own machines and then test their “recipes”—consisting of an array of controlled environmental parameters such as nutrient mix, temperature, carbon dioxide and pH levels, and light color and intensity. The recipe’s purpose is to arrive at a specific expression of a given plant’s phenome, which is an organism’s physical and biochemical traits expressed in response to the interaction of its genes and environment. Nerd farmers share their experiences via the OpenAg community forum and wiki, and can even upload their recipes to a Github repository, allowing others to replicate that exact plant phenome in their own machines.
Launched in 2015, OpenAg differed from other indoor farming efforts in both its ambition and its scope. While the operators of urban indoor farms are careful to locate them in areas that have access to water, electricity, and cheap real estate, often using proprietary software and equipment, open-source food computers could be built by anyone and would be deployable virtually anywhere. Data from food computers all over the world would be fed to machine learning algorithms to optimize recipes and help people grow, say, the most flavorful basil (the subject of this peer-reviewed PLoS-One paper authored by Harper et al.) or replicate an Aleppo pepper grown in Syria in a food computer in the Jordanian desert.
It’s a nice idea—if your food computer works.
But the situation on the ground never matched the fantastic claims that Harper made about the WFP project in public appearances during the spring of 2017 and in briefings for corporate patrons of the Media Lab in the spring and fall of 2017. Harper and a colleague also cited the personal food computer’s successful deployment in the Azraq camp in emails to potential partners and patrons for the Open Agriculture Initiative and for Fenome Inc., a spin-off company that Harper founded in 2016.
Even as Harper took the stage in Georgia, it was clear to those working with the food computer at the World Food Programme (WFP) and at Fenome that the project wasn’t progressing as the team had hoped. Indeed, in September 2017, the WFP project officially ended without any of the machines having completed a single grow cycle, according to the official in charge of the project. The WFP’s personal food computers weren’t even deployed at the Azraq camp, home to some 35,000 Syrian refugees, but rather at a facility run by Jordan’s National Center for Agricultural Research and Extension, in Mafraq, an hour’s drive from Azraq.
Harper did not respond to detailed questions about the WFP project sent to him by IEEE Spectrum for this article.
Photo: WFP Innovation Accelerator
May 2017 photograph of two food computers at the World Food Programme office in Amman, Jordan.
Recently, the OpenAg initiative has come under scrutiny following the departure in September of Media Lab director Joichi Ito. He was a champion of the project, which started during his tenure and seemed to exemplify his “deploy or die” approach. (In a 2014 TED talk, Ito announced he was changing the lab’s motto from “demo or die” to “deploy or die,” focusing researchers’ efforts on real-world implementations of the technologies they were developing.) MIT is now investigating OpenAg, following allegations that staff were told to demonstrate food computers with plants that were not actually grown in them. Business Insider and the Chronicle of Higher Education first reported these allegations.
Perhaps the only unqualified success of OpenAg was Harper’s ability to sell his idea. His first big public unveiling of the food computer came in a 2015 TED talk that has been viewed more than 1.8 million times. Audiences and the press alike swooned. Glowing reports about the food computer, including one in Spectrum, quickly followed, and continued right up until the most recent revelations. And Harper helped raise the capital to start up his OpenAg spin-off, Fenome.
Last month, The New York Times reported that four former researchers connected to OpenAg have complained about some of the claims Harper makes in his talks, including that the average age of an apple in a U.S. grocery store is 11 months sometimes and 14 months other times, statements refuted by a U.S. Department of Agriculture official in an email reviewed by the Times.
It’s one thing to get an incidental fact wrong. It’s quite another to repeatedly state that refugees were benefiting directly from food computers and enjoying a taste of home, when they were doing no such thing.
The WFP project started off with the best intentions. According to Nina Schroeder, Head of Scale Up Enablement at the WFP Innovation Accelerator and the World Food Programme official in charge of the Jordanian hydroponics project in 2017, the long-term goal of the project was indeed to deploy food computers at refugee camps. “First we wanted to come up with a concept that we could bring to a larger scale that actually makes sense to deploy. For the early research phase, it wouldn’t have made sense to deploy it inside the refugee camp.”
As Schroeder described it, the pilot program would let researchers evaluate the technology and determine if it was appropriate to install PFCs at the camp. If everything went well with the pilot, then the Azraq camp would receive the food computers.
The project launched at the end of January 2017, when a team from Fenome went to Jordan to assemble and install the food computers. At the time the company was based in Salt Lake City, with a staff of 17 there plus two employees in Boston and one in Seattle. Four food computers were placed at the WFP’s office in the Jordanian capital of Amman and six at the National Center for Agricultural Research and Extension (NCARE) facility at Al-Khalydeha Salinity Research Station in Mafraq, about a one-hour drive from the Azraq refugee camp.
The plan was that after installation, the project would be monitored remotely from Utah via the Internet and by three NCARE staff on site in Jordan. The NCARE experiments focused on testing the technology using local water and changing the light spectrum of the food computers’ LEDs and the nutrient mix of the hydroponic solution, according to a person close to the project who spoke with Spectrum anonymously for fear of retaliation. Plants tested included cucumbers, basil, and baby lettuces. The source confirmed that Fenome’s team communicated regularly by phone with their Jordanian counterparts.
Photo: Joi Ito/Flickr (CC by 2.0)
November 2014 photograph of Caleb Harper (left) and Media Lab director of operations and strategy and Fenome board member Barak Berkowitz, taken by Joi Ito.
According to corporate filings and internal Fenome documents obtained by Spectrum, Harper had helped raise $4 million for his startup, where he was executive chairman and a director. Barak Berkowitz, director of operations and strategy at the Media Lab and Mitchell Baker, chairwoman of Mozilla, also served on the board. Other directors included representatives of two venture capital firms that funded Fenome: Lucas Mann from Campbell Soup’s VC arm Acre Venture Partners and Ignacio Martinez of Flagship Pioneering, founded by Noubar Afeyan, who is also a member of the MIT Corporation, as the school’s board of trustees is known.
Martinez declined to comment on the WFP project or Fenome. Berkowitz, Baker, and Mann did not respond to questions posed by Spectrum.
But despite all this money and brainpower, things soon went awry in Jordan. Schroeder, in a phone interview, told Spectrum that the conditions at the NCARE site were harsh, with a very dry desert climate and high indoor temperatures. The power frequently failed, which shut down the building’s air conditioning and the food computers’ LEDs. When the air conditioning conked out, it sometimes reached 45 °C (113 °F) inside the lab.
Worse, the Wi-Fi was unreliable. A Wi-Fi connection was necessary to remotely monitor some of the parameters inside the grow chambers, which were equipped with cameras and sensors that measured temperature, humidity, and pH levels. Whenever a food computer went down, it had to be connected to Wi-Fi so that the remote team could reboot it. The software was still quite buggy, so not all features could be controlled locally at the NCARE facility. The Fenome team returned a month after the initial deployment to modify the boxes and some functions, and to allow the machines to be rebooted locally, according to our source close to the project.
But while Fenome might have solved some problems, others cropped up, according to Schroeder. Algae grew inside the containers, possibly because of low-quality water and light shining through the food computers’ clear acrylic access doors. The doors also deformed due to the heat, creating gaps that let ambient air into the grow chamber and contaminated what is supposed to be a controlled environment.
In all, the Fenome support team visited NCARE four times to set up the food computers, train local teams, and adjust the personal food computers. The last visit was in May 2017.
In late April, just a few weeks after OpenAg Inc. officially changed its name to Fenome, Inc., 15 of its 17 employees in Utah were dismissed. In the fall of 2017, the company left Utah and relocated to offices at its VC partner Flagship Pioneering, in Cambridge, Mass.
“When they closed down the Utah office, that made it very difficult to continue the experiments that were going on,” says Schroeder. The WFP officially ended the Jordanian project in September 2017. Not a single grow cycle was successfully completed, Schroeder says.
“The food computer we tested there wasn’t ready for our purpose, and it was still in the development stage,” Schroeder says. Her team is now deploying lower tech, locally adapted hydroponic systems to food-insecure communities in Algeria, Chad, Jordan, Kenya, Namibia, Peru, and Sudan.
The concept of the food computer “is so attractive that you have the possibility to grow locally,” she says. “But you need to have the right kind of environment. That food computer version was too early.”
While it may have been the most high profile, the World Food Programme wasn’t the only Fenome partner left high and dry.
Photo: Charisa Moore
Charisa Moore (right) and her students experimented with three food computers.
In the fall of 2016, Charisa Moore, a biology teacher at Bainbridge Island High School in Washington state, watched a recording of Harper’s TED talk. The food computer sounded like just what Moore had been looking for to beef up her curriculum with content centered on ecology. Moore called Harper.
She says Harper told her he could talk about what OpenAg had done in putting food computers into Boston-area schools but warned her that they didn’t work in a lot of the schools where they were deployed.
“Well, I can make it work!” Moore told Harper. Harper invited Moore, another teacher, and a star student to MIT for a week to learn how to build, program, and troubleshoot the food computer and experiment with plant recipes. Fenome would provide Moore’s school with the hardware, help her and her students build the units on-site, and support them free of charge.
When she got home in late April 2017, Moore and her team decided to give a TED-esque talk themselves to about 400 people in the Bainbridge community about the project they were about to embark on with the help of Fenome.
“We did basically Caleb’s presentation using his Fenome team. And then that week we built the computers.”
Students and teachers started running experiments with the food computers. The food computer cameras and sensors sent data to Fenome in Utah, and the Utah team communicated with Moore on what they saw happening in the machines.
“And then it kind of got really weird,” Moore recalls. “We started not hearing very much. We used [the food computers] through the summer. Starting the next [school] year, we started to hear Fenome was going to go out of business. So that team was not able to then really troubleshoot any of our stuff.”
Without tech support from Fenome, software maintenance proved difficult. Moore struggled to push updated software that had been published on Github to the machines. “It’s very complicated,” she told Spectrum. “This is way beyond my expertise. I can only barely code in Python.”
Hardware bugs were even more difficult to fix. “The equipment is really not sustainable,” Moore says. “It corrodes. You have a cooling unit on it, the Freon comes out, it freezes—it just becomes messy. So to clean it, you have to go and order the stuff and replace those items. And good luck finding them.”
Her team did come up with a solution for one glaring, design-for-demo’s-sake specification: the food computer’s clear acrylic door, which let in ambient light and contributed to the algae problems in Jordan.
“The thing about the food computer that sort of didn’t make a lot of sense to me was that it’s open.... It’s not controlled,” says Moore. At her students’ urging, she went to Home Depot and bought some silver wrapping and clad the chassis with it to shut out unwanted light.
Photos: Charisa Moore
The students modified the food computer by wrapping the door. They added a flap on the small rectangle to keep all light out.
Moore says that she and her students continued to experiment with their food computers, uploading plant recipes to the OpenAg open source forum. They also set up an experiment to see which equipment grew microgreens more effectively: a food computer or a basic UV light bank shining down on plants potted in soil. Moore’s team found that the conventional indoor setup grew microgreens at four inches per week—twice the rate of the food computer.
Moore concluded that the food computers “are pretty much not usable, because they just are not user-friendly. They’re too hard to troubleshoot. Any Joe could not just walk up and figure out how to do it. You couldn’t market that to put in your pantry at home unless you knew how to do all that stuff.”
Moore found herself with three food computers on her hands. She gave the “most unusable” one to a student, who took it home and converted the box “into a kind of a simplistic one with [manual controls] instead of electronic ones.” He used it to earn a Boy Scout merit badge.
Even as Fenome and its partners were struggling, Harper continued to enchant audiences with his tales of nerd farmers around the world. Harper, who holds a master’s degree in architecture from MIT and is a member of the World Economic Forum and a National Geographic Explorer, managed to parlay the exposure from his TED talk into a lucrative side gig as a speaker. He earns $20,000 to $30,000 per talk, according to his agent’s website. He also used a version of the TED talk at a pitch meeting with investors in the summer of 2016 to help get his company its first series of funding according to an email obtained by Spectrum.
In May 2017, Harper repurposed his Georgia Technology Summit talk for a Red Hat conference. He again spoke about how a refugee camp in Jordan was using the food computers. He also described what the refugees grew and the significance they attached to the machines: “We didn’t tell them what to grow. They decided to grow things that they missed from home. Things that they can’t get any more.”
“The food computer,” he said, “became a cultural object more than just a manufacturing object.”
Meanwhile, Harper’s startup was laying off staff and planning its relocation to Massachusetts. Just days after the Red Hat appearance, Harper posted about Fenome to the OpenAg Community Forum: “hey guys—the startup (fenome) in its infancy has had a couple gaffes (oops) and obv communications is one of them.” He explained that the Fenome team was working to fix bugs and upgrade these “crazy expensive and not fully functional” “1st run prototypes” so that the company could start selling PFC kits. He told the forum that “after some development we all think its [sic] better to be based in Cambridge and is in the process of moving.”
Trouble at his startup did not derail Harper’s traveling show.
Less than a month after Red Hat, he dusted off his talk and delivered it at the EAT Stockholm Food Forum. He repeated his claim that the food computers at the Azraq refugee camp had created much more than mere plants:
“We’ve deployed in the world with the World Food Programme in Amman in a Syrian refugee camp. We did not tell them what to grow. Turns out they wanted to grow things from home. It became a cultural object for them. They missed the flavor of the place that they were from and that creates their culture and creates happiness for them.”
Harper’s story about Azraq evolved further in an interview earlier this year with science journalist Miles O’Brien at a Purdue University event on 26 February. This time, he revealed how St. John’s Wort plants had been grown by a “person at the camp that happened to be a Ph.D. on St. John’s Wort.” Harper claimed that the person started a business selling the medicinal plant to treat a population “rife with depression”:
Besides these public claims posted to YouTube, documents obtained by Spectrum reveal that Harper and at least one associate also misrepresented the World Food Programme project in email correspondence with potential funders and partners.
In a February 2017 email chain that included Nest cofounder and iPod coinventor Tony Fadell, Harper and his assistant tried to arrange a meeting with Fadell, now principal at Future Shape LLC, an investment and advisory firm based in Paris. Harper sent links to a couple of blog posts, one from 2016 about his lab and another about the “2017 expansion of our ecosystem with a nonprofit and a venture.” He ended his 14 February 2017 email with “Btw we just deployed food computers to a Syrian refugee camp in Jordanon [sic] a contract with the UN. Pretty cool. C”.
And about five months after the project at NCARE had ended, OpenAg was in talks with a group at Google about supporting research at OpenAg, according to another email chain obtained by Spectrum. In an email dated 30 January 2018, Google’s Jess Holbrook, senior staff UX researcher and UX manager, asked several questions regarding food computers, including “Has anyone picked up the design and adapted it to specific use cases like edu, refugee groups (I know you mentioned Jordan), etc.”
Hildreth England, the OpenAg Initiative assistant director at the time and currently co-director of the Media Lab’s PlusMinus program, answered the next day, “...yes, the PFC v2.0 was deployed in a Syrian refugee camp with the World Food Program.” England declined Spectrum’s request to comment, citing “an open inquiry being led by MIT’s Office of the VP for Research.”
Around the same time as the exchange between England and Holbrook, Dr. Babak Babakinejad, then the lead researcher for OpenAg, was testing a food server being set up in a shipping container in Middleton, Mass., at MIT Bates Research and Engineering Center. Babakinejad told Spectrum that he documented several problems with the equipment, including differences in temperatures in various areas inside the food server, in what is supposed to be a controlled environment, and a lack of control over carbon dioxide levels, humidity, and temperature. He told Spectrum that he had reported these issues to the OpenAg team.
Photo: Babak Babakinejad
Food server set up in a shipping container at MIT Bates Research and Engineering Center.
Babakinejad showed Spectrum an email he sent on 16 April 2018 to officials with MIT Environment, Health and Safety to report that OpenAg was discharging nutrient solutions beyond state-permitted limits, a controversy that was examined last month in a joint report by ProPublica and WBUR. Babakinejad also took his concerns about OpenAg and Harper to Media Lab director Ito.
In an email to Ito on 5 May 2018, Babakinejad stated that Harper was making claims in public talks about “implementations of image processing, microbiome dosing, creating different climates and collecting credible data from bots across the world that are not true.”
In addition, Babakinejad wrote, “He [Harper] takes credit for deployment of PFC’s to schools and internationally including a refugee camp in Amman despite the fact that they have never been validated, tested for functionality and up to now we could never make it work i.e. to grow anything consistently, for an experiment beyond prototyping stage.”
Ito responded and asked Babakinejad if he could share these concerns with Harper. That’s the last Babakinejad says he heard from Ito on the matter. Within a month, Babakinejad had taken a leave of absence. He officially left the OpenAg project in September 2018. Two months later, Harper was promoted to principal research scientist at the Media Lab, a position that as of this writing, he still holds.
If you have any information about MIT’s Media Lab or its Open Agriculture Initiative (OpenAg), you can contact Harry Goldstein at h.goldstein@ieee.org or on Twitter (DMs open, ask for Signal number).
Special Brand Developed For Vertically-Grown Products
The first vertically grown products have recently become available at Van Gelder fruit & vegetables. This is the result of the collaboration between Van Gelder and vertical cultivation specialist PlantLab
The first vertically grown products have recently become available at Van Gelder fruit & vegetables. This is the result of the collaboration between Van Gelder and vertical cultivation specialist PlantLab. Joint efforts were made to grow and market-fresh vegetables with a lot of taste and high nutritional values as sustainably as possible.
Van Gelder Indoor
To market the vertically grown products, Van Gelder introduced the new "Van Gelder Indoor" line. This is an exclusive fresh line of vegetables available from Van Gelder. These quality products are produced locally and sustainably, irrespective of the season or climate, with consistent quality and a high level of food safety.
Leafy vegetables and lettuce varieties
The first products of the "Van Gelder Indoor" line will be available from 24 October: two salad mixes and five types of leafy vegetables. "We have deliberately chosen to start growing lettuce varieties and leafy vegetables because these products are currently largely imported from abroad," said Gerrit van Gelder, Managing Director. "With this, we shorten the chain which immediately saves on transport costs."
Vertical cultivation in Experience Center
In the meantime, PlantLab's two Plant Production Units (PPUs) have also been taken into use in the Experience Center in Ridderkerk. These PPUs offer inspiration in the field of vertical cultivation. "We will soon start the search for new products with special flavors in cooperation with our customers," explains Commercial Director; Anton van Gelder. “The demand from our customers in this search was the driving factor. Together with them, we will start experimenting. In this way, we want to continue to distinguish ourselves with exclusive and quality products."
For more information:
Van Gelder
Handelsweg 70
2988 DB Ridderkerk
T: +31 (0)180 42 50 77
E: info@vangeldernederland.nl
www.vangeldernederland.nl/indoor
Publication date: Fri 25 Oct 2019
US: Texas Schools Tap ‘Container Farms’ To Fill Cafeterias With Fresh Produce
Texas schools are using refrigerated freight containers converted into hydroponic farms as an extension of the classroom
Texas students are getting hands-on, high-tech experience growing fresh produce inside converted shipping containers. (Freight Farms)
Texas News Service October 25, 2019
SAN ANTONIO – Texas schools are using refrigerated freight containers converted into hydroponic farms as an extension of the classroom.
At IDEA charter schools, students learn how to grow leafy greens and other vegetables, and deliver their harvests directly to the school cafeteria.
Caroline Katsiroubas – director of community relations at Freight Farms, the company that developed the technology – says schools are using the farms in part to shift traditional food culture and improve health by giving students nutritious options.
“In the San Antonio IDEA school’s campus, they don’t use salt or pepper in their cafeteria,” says Katsiroubas. “And they’re growing herbs specifically in their farm to make a seasoning.”
The University of North Texas also is using the container farms as a lab for a wide range of hands-on learning opportunities in biology, organic chemistry, nutrition, and culinary arts, as well as business, computer science, and marketing.
Many schools have developed certificate programs and majors around sustainable food production, which gives graduates a leg up on joining the growing ag-tech field or starting their own farm.
Because the climate is controlled inside the container, food can be grown all school year long with a predictable commercial-scale output. Greenery units can support 13,000 plants at a time, producing harvests of up to 900 heads of lettuce per week.
Katsiroubas says the technology is useful in a state such as Texas and notes Houston freight farmers played a critical role in providing food during Hurricane Harvey.
“These container farms act as a way to control the food supply chain, and make it resistant to shocks like extreme weather patterns or hurricanes or drought,” says Katsiroubas.
Katsiroubas says the container farms also are helping lower schools’ overall carbon footprint. Harvests happen just steps from the dining hall, which all but eliminates transportation emissions and packaging.
She says the farms use 99% less water than a traditional farm, running with as little as five gallons per day, less than the average dishwasher.
Author: Eric Galatas, Public News Service (TX)
Ag Firm Signs Electric Works Lease Muncie Business Uses Fish Waste As Plant Fertilizer
This is the second tenant announcement for Electric Works featuring an agricultural technology company in two weeks. Last week, the developers announced that Sweetwater Urban Farms had signed a lease agreement. Sweetwater Urban Farms uses aeroponic technology to produce nutrient-rich greens and herbs
SHERRY SLATER | The Journal Gazette
A Muncie company that uses fish waste as plant fertilizer has signed a lease for space in Electric Works, officials announced Monday.
Balance Holdings Inc. is a commercial regenerative agriculture technology company that uses 1% of the water needed for traditional farming and less than 20% used in hydroponics, a process of growing plants without soil, officials said.
The company will grow fish and crayfish in tanks. The waste-filled water, which is full of nutrients, is channeled to plants that produce fruits and vegetables. The plants filter the water, which is then cycled back to the fish tanks, creating a closed-loop system with no waste.
Glynn Barber, the company's founder, said that “growing better food is more than just putting a better tomato into the grocery store – it's about growing a better future” for the next generation.
“We believe healthier food produces healthier people, which produce healthier communities – and we see an exciting and unique opportunity for ECSIA to make a profound impact on this community, partnering with healthcare providers and higher education institutions at Electric Works,” Barber said in a statement.
More than 300 varieties of fruits and vegetables have been grown using the company's patented system in Indiana, Texas, and Haiti.
Balance Holdings plans to sell fish, fruits, and vegetables to restaurants in the region and directly to the public at an on-site store in Electric Works.
Jeff Kingsbury, a partner in Electric Works developer RTM Ventures, said the new tenant checks a lot of boxes for the type of businesses RTM is trying to attract.
RTM Ventures, he said in a statement, is looking for “firms that are exploring new technologies and market-based solutions through strategic alliances and creative partnerships with other businesses, as well as healthcare and education institutions.”
“At the same time, (the company's) impact will be felt in the neighborhoods surrounding Electric Works – areas of the city that have struggled with access to healthy food in the past,” Kingsbury added.
This is the second tenant announcement for Electric Works featuring an agricultural technology company in two weeks. Last week, the developers announced that Sweetwater Urban Farms had signed a lease agreement.
Sweetwater Urban Farms uses aeroponic technology to produce nutrient-rich greens and herbs.
Aeroponic systems nourish plants with nothing more than nutrient-laden mist, according to the Modern Farmer website.
Electric Works is a mixed-use district of innovation, energy, and culture, developed as a public/private partnership between RTM Ventures and the city of Fort Wayne. The 39-acre campus just south of downtown is the former location of General Electric.
RTM Ventures plans to convert 1.2 million square feet in 18 historic buildings into space for office, educational, innovation, retail, residential, hotel, and entertainment uses.