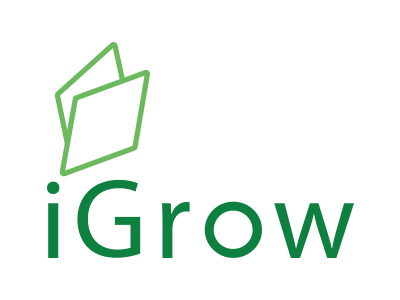
Welcome to iGrow News, Your Source for the World of Indoor Vertical Farming
CropKing Partners With Urban Crop Solutions To Grow Vertical Container Farm Showcase
CropKing, a full-service hydroponic company located in Lodi, OH, specializing in controlled-environment agriculture and hydroponic growing, will operate the Urban Crop Solutions’ FarmPro vertical container farm as a showcase, continued research, and testing facility
March 4, 2020
CropKing and Urban Crop Solutions have announced plans to collaborate on a controlled-environment agriculture project in the U.S., leveraging the extensive hydroponic experience of CropKing with the high-quality controlled-environment technology in vertical farming of Urban Crop Solutions.
CropKing, a full-service hydroponic company located in Lodi, OH, specializing in controlled-environment agriculture and hydroponic growing, will operate the Urban Crop Solutions’ FarmPro vertical container farm as a showcase, continued research, and testing facility. The first FarmPro container arrives in March at the Lodi headquarters, where CropKing will start testing it with the help of in-house plant scientists.
“We are excited to be working with Urban Crop Solutions and for the opportunity to validate the effectiveness of automated container farming,” said CropKing President Paul Brentlinger in a press release from Urban Crop Solutions. “
Their personal and custom-made approach could fulfill the needs of many clients. The shipping container system offers advantages like climate control, irrigation system, and automated growing process, which has captured our interest for the past few years.”
Urban Crop Solutions, a turn-key solutions provider that offers biological know-how in the indoor vertical farming industry, recently celebrated its 5th anniversary and already has 28 active projects across the world. In the last five years, it has developed more than 200 plant growing recipes, for a variety of industries, through its in-house research center.
Paulina Murrath, Business Development Manager of Urban Crop Solutions, will serve as a point of contact for the North American market at the company’s offices in Miami, FL.“
It’s a great honor to start a collaboration with CropKing and Paul Brentlinger, who is a controlled-environmental agriculture expert with extensive knowledge of growing high-quality food products,” Murrath said in the press release. “CropKing shares the same values that we consider as important, like bringing higher yields, nutritional value, food security, local production, and consumption, to different industries. That’s why we believe our collaboration will be rewarding.
”The Vertical Farming Industry Needs Proven Technology
CropKing will put the FarmPro vertical container through a rigorous testing process, which includes assessing items such as plant pathology and system yield, as well as validating the true return on investment (ROI) of the unit, according to Brecht Stubbe, Global Sales Director at Urban Crop Solutions.
The FarmPro vertical container CropKing will receive is a fully automated and climate-controlled 40-foot freight container with a four-layer, state-of-the-art growing system for leafy greens and herbs. The insulated container includes features such as climate control and an irrigation system, continuous monitoring, custom-made LEDs, a handling area and technical room, as well as online crop and process management. Plants grow in a nutrient film technique (NFT) hydroponic system.“
Technological failures and resulting bankruptcies have been a problem in the vertical farming industry,” Stubbe says. “With CropKing’s 30 years of experience in the greenhouse industry, we can prove that this technology and our growing recipes can provide the ROI to growers. We don’t want this technology to fail for our clients.”
Collaboration a Strong Match for Exploring New Markets, Including Floriculture
This collaboration is only phase one for CropKing and Urban Crop Solutions. Stubbe says the companies hope to work together on more projects to explore new markets and opportunities in the vertical farming sphere
.Urban Crop vertical farming technology is already being used for research into medical plants for compound extraction. On the floriculture side, Stubbe says Urban Crop Solutions is currently conducting some promising research in Belgium. The latest growth trials with strawberries, for example, resulted in sweet fruits with a Brix value averaging between 11 and 16.“
They are growing azaleas at the trialing facility and now to a very high extent can control the temperature and bring crops just to the point of flowering, which helps increase their shelflife when they go to retail,” Stubbe says. “This type of technology could allow flowers to be grown across the globe, instead of shipped internationally to supply those markets.”
When asked about how the unit might be integrated into a controlled-environment greenhouse operation, Stubbe said he sees several applications and benefits, two being maximizing germination space with multilayer growing and eliminating risk factors involved with plant handling. For people growing in high tunnels or the field, the unit could help them diversify their operation into new crop segments. A grower could also use the unit to provide products locally on a year-round basis.
Janeen Wright is managing editor for Greenhouse Grower. You can email her at jwright@meistermedia.com. See all author stories here.
SCOTLAND: City Hydroponics Company Growing Fast
The company says that its vertical farms will grow up to five times as many greens as traditional ones
February 24, 2020
An Edinburgh based start-up is going to fastback indoor ‘vertical farms’ across the UK.
The company says that its vertical farms will grow up to five times as many greens as traditional ones. Shockingly Fresh have just obtained planning permission for a 1.2ha site near Offenham in Worcestershire for their low cost naturally-lit ‘vertical farm’ – which uses special hydroponic towers to grow multiple crop cycles of green veg such as salads and herbs.
Saturn Bioponics’ CEO Alex Fisher at a farm near Stratford-upon-Avon, Warwickshire, 31st August 2017.
The specialist firm has approval from Wychavon District Council to build a state-of-the-art 11,899 square meter greenhouse on the site in partnership with indoor farming specialists Saturn Bioponics and nationwide salad growers Valefresco. The farm will be completed this summer and will then start producing crops shortly thereafter. The increased output will offset the setup costs, and the enclosed environment leads to cleaner crops and less pesticide use.
Dr. Garth Bryans COO of Shockingly Fresh.
The team then plans a rapid roll-out of 40 more indoor farms in the next 5 years. Dr. Garth Bryans COO at Shockingly Fresh said: “The Midlands are ideal for vertical farming and we are really excited about delivering our first site.“
The climate is good, there is a well-established horticulture sector and it is close to major markets and road networks, so it makes sense for us to begin our rollout plans there.“
We have identified a significant market – particularly around the early and late season ‘shoulder months’ – which is currently filled by imported crops from Europe. We believe a raft of sites across the country will enable British growers to compete on a level field.“
We have partnered with hydroponic specialists Saturn Bioponics which supplies all of the equipment and we are focussed on raising finance, finding sites and securing planning consent. If our plans develop as we hope then vertical farms will become an important part of the UK vegetable supply chain.”
How To Start A Container Farm Business
Using stacked farming to produce food in vertical spaces, vertical farming is an attractive option to traditional methods of farming, opening more opportunities for year-round freshly grown and locally accessed food
Have You Ever Wondered How To Start A Container Farm Business?
Vertical farming continues to grow with increased interest for both beginners and seasoned professional farmers. In this guide, Pure Greens helps new growers navigate the business side of container farming, with helpful steps to get started, such as:
How to create customer personas
Investment planning and funding
How to grow and harvest your crops
How to sell and brand your container farm business
Check Out The Guide Here
Living Wall Garden Bringing Tranquility To Historic Downtown San Bernardino
Thanks to a grant from the Arbor Day Foundation in conjunction with BNSF, SistersWe and Viva La Boba owners David Friedman and Tansu Philip are planting a living wall garden on the side of a vacant brick building near the Breezeway in the heart of downtown San Bernardino
'This green area will be somewhere people can go and breathe fresh air,' Viva La Boba owner David Friedman says
By BRIAN WHITEHEAD | bwhitehead@scng.com
San Bernardino Sun
A garden is being planted in San Bernardino, but not where you might expect.
Here, there is no lush green space, no playground nearby for children to burn off energy. The spot gets, at most, four hours of sunlight a day and can easily be missed by even the most observant passersby.
And yet, San Bernardino-born-and-raised sisters Adrienne Thomas, Vanessa Dean, and Nedra Myricks could not have found a better place for their nonprofit’s latest community project.
Thanks to a grant from the Arbor Day Foundation in conjunction with BNSF, SistersWe and Viva La Boba owners David Friedman and Tansu Philip are planting a living wall garden on the side of a vacant brick building near the Breezeway in the heart of downtown San Bernardino.
David Friedman, Viva La Boba owner, right, looks back while mounting vertical wall planters to a 100-foot-long, 18-foot-tall brick wall with SisterWe sisters, from left, Nedra Myricks, Vanessa Dean, and Adrienne Thomas during The Historic Downtown San Bernardino Living Pocket Park Project in downtown San Bernardino on Wednesday, Jan. 15, 2020. (Photo by Watchara Phomicinda, The Press-Enterprise/SCNG)
“Bringing San Bernardino back to life (with this project) is what I’m looking forward to, making it a little more people-friendly,” said Thomas, SistersWe president. “I’m really excited to see the wall coming in and things happening around San Bernardino. It’s been too long without anything to do or places to go.“This wall will bring and attract people to San Bernardino.”Pitched in 2018 as an environmental beautification project, “The Historic Downtown San Bernardino Living Pocket Park Project” and a second SistersWe project in Muscoy received grant funding last year, in part, for their health and environmental benefits.
On Wednesday, Jan. 15, a handful of volunteers and about two dozen fifth-grade students from nearby Jones Elementary School helped Thomas, Dean, Myricks, and Friedman bolt vertical planters to a 100-foot-long, 18-foot-tall brick wall near Fourth and E streets.
In the coming weeks, a hydroponics system will be woven through the felt planters and succulents and other plants will take their place in the living wall garden, a stone’s throw from the Rosa Parks State Memorial Building.
And keeping with the art theme permeating the area, local artist Nathaniel Gelston plans to paint a mural in the alleyway.
Friedman, who owns several buildings downtown, sees such investment in the once-bustling entertainment corridor as the catalyst for the revitalization of San Bernardino.“My generation, we want to live in an urban culture, one that’s more sustainable,” he said. “We want to walk, bike. You see the youth rallying around downtown, and with the preservation of historical artifacts, historical buildings, comes a sense of art, and artists seem to want to congregate around this area.“
This green area,” Friedman added, “will be somewhere people can go and breathe fresh air. Somewhere they can take a break and go back to work or go back to their house. That’s important to have in any urban environment.”
In addition to their work this week, Thomas, Dean, and Myricks will add 15 more trees to green space at California and Nolan streets in Muscoy at 8 a.m. Wednesday, Jan. 22.
The trio’s “Muscoy Pocket Park Project” includes plans to add 20 raised-bed family garden plots, a farmer’s market, movie nights and other family activities throughout the year.
Myricks, the oldest sister at age 71, joked Wednesday she and her siblings are busier now, in retirement, than they ever were as professionals.“These are things all of us need to really embrace,” Thomas said. “San Bernardino really needs something. It needs a spark of life, and with all the young people involved in this, I’m really looking forward to the future.”
Coalition For Sustainable Organics Disappointed in Latest Attempts Center For Food Safety To Restrict Supplies Organic Foods through Lawsuit
Lee Frankel, the executive director of the CSO stated, “It is disappointing to see groups target pioneering organic farmers that use the most appropriate organic growing methods adapted to their site-specific conditions on their farms to meet the needs of consumers
SAN DIEGO, CALIFORNIA March 3, 2020 – The Coalition for Sustainable Organics (CSO) is saddened by the latest attempts by the Center for Food Safety and their allies to limit fair competition and organic supplies in the market through legal action.
Lee Frankel, the executive director of the CSO stated, “It is disappointing to see groups target pioneering organic farmers that use the most appropriate organic growing methods adapted to their site-specific conditions on their farms to meet the needs of consumers. The members of the CSO are strongly committed to the integrity of organic standards and the organic label. The groups behind the lawsuit failed to convince the members of the National Organic Standards Board (NOSB) to prohibit container and hydroponic production methods after significant industry debate and submission of public comments. Instead of unifying the industry after the decision made by representatives of the organic community at the NOSB, the CFS is seeking to eliminate public input to achieve their goals of restricting competition to drive up the price of organics for organic consumers to allow favored producers to increase their profit margins.”
Frankel continued, “Growers using containers adhere to the U.S. Department of Agriculture organic standards under the National Organic Program (NOP) and have been allowed to grow certified organic produce since the initiation of the NOP more than 25 years ago. After extensive study in 2010, the USDA through the NOP opted not to change these high standards for certifying organic produce – and affirmed that organic produce can be grown through containerized methods. After additional review in 2015-2017, the National Organic Standards Board voted to reject a proposed prohibition on container and hydroponic systems.”
Karen Archipley of Archi’s Acres of Escondido, California added “Our production systems are managed in accordance with the federal organic law. We chose to incorporate hydro-organic methods at our operations since it is the most appropriate way to promote ecological balance by drastically reducing our water use, conserve biological diversity by preserving valuable habitat while still incorporating the microbial processes described by organic pioneers to recycle nutrients to nourish our crops. Every choice we make and every input we use must be audited and approved by USDA-accredited certifying agents like any other Organic Farmer.”
Archipley continued “Changing the rules now would limit the amount of organic produce available to the public – just as the public is demanding more organic produce. This is not an issue that should be settled in the courts or politicized. If a grower meets USDA standards for organic certification, they should be able to market organic produce, whether they grow in soil or any other sustainable, certified organic growing media.
Israeli-Founded Urban Farming Startup to Expand To Japan
Israeli-founded urban farming platform Infarm, the startup that combines vertical farms with IoT technologies and machine learning, announced last week that the company has raised funding from JR East, the East Japan Railway Company, to expand into the Japanese market, Japanese and English tech news website Bridge reported
Infarm's urban farming system in Germany. Photo via Kroger
Israeli-founded urban farming platform Infarm, the startup that combines vertical farms with IoT technologies and machine learning, announced last week that the company has raised funding from JR East, the East Japan Railway Company, to expand into the Japanese market, Japanese and English tech news website Bridge reported.
Erez Galonska, one of the three founders of the Berlin-based startup, announced the news at the TOA World Tour Tokyo meet-up in Tokyo last Thursday. Infarm will establish a local subsidiary called Infarm Japan to enable to the expansion. Galonska also said Infarm is expected to launch its service this summer at Kinokuniya premium supermarket, a subsidiary of JR East. Sales at the Kinokuniya supermarket will be the company’s first in the Asia region.
Japanese cold supply chain company Muroo will partner with Infarm to help roll out their facilities across Japan, Bridge reported.
Founded in 2013 by Osnat Michaeli and brothers Erez and Guy Galonska to cultivate greens in the dead of German winter, Infarm has grown into a multinational brand that has raised over $134 million, including $100 million in a Series B round led by London-based VC firm Atomico last year. They also partnered with Kroger, the highest-grossing American supermarket chain and are poised to rapidly expand in the American market.
Infarm has also expanded into France, Switzerland, Luxembourg, the UK, Denmark, and Canada with supermarkets such as Irma (Denmark), Marks and Spencer (UK), Metro (Europe) and Edeka (Germany) to sell locally-grown vegetable products.
The company has more than 600 farming units in stores and distribution centers around the world and ships more than 250,000 plants a month.
Texas A&M AgriLife Expands Urban Agriculture Research
Niu’s research is in urban horticulture specifically. This can conjure images of community and backyard gardens, or rooftop and balcony plant installations, but her focus is producing quality food in controlled environments
A living, vertical salad bar in the employee break room is more than just a novelty at the Texas A&M AgriLife Center at Dallas. It is a small, and delicious, sign of the comprehensive urban agriculture research ramping up at the center in 2020.
Genhua Niu, Ph.D. Texas A&M AgriLife Research professor of controlled environment agriculture, with an indoor vertical garden system at the Texas A&M AgriLife Center at Dallas (Texas A&M AgriLife photo by Patricia Moran)
The purple-glowing installation arrived at Dallas with Genhua Niu, Ph.D., and Texas A&M AgriLife Research professor of controlled environment agriculture. Her research team represents one component of an overarching push by Texas A&M AgriLife to realize sustainable production of nutritious food within cities — the next frontier in commercial agriculture.
Niu’s research is in urban horticulture specifically. This can conjure images of community and backyard gardens, or rooftop and balcony plant installations, but her focus is producing quality food in controlled environments. Her studies are especially relevant in Dallas — of which certain communities are urban food deserts — and they carry promising implications for agriculture industries across rural Texas, too.
“AgriLife’s substantial investments in urban agriculture innovation reflect our commitment to better human nutrition and health at every interval along the food supply chain,” said Patrick Stover, Ph.D., vice chancellor and dean of Texas A&M’s College of Agriculture and Life Sciences and director of AgriLife Research. “In addressing these obstacles, we can bring to bear the considerable research and extension resources of the Texas A&M University System.”
Bringing urban horticulture to Dallas
Niu comes to Dallas from the AgriLife Center at El Paso, where her work since 2004 hinged on research conducted in varying greenhouse settings. Now, controlled environments at the renovated urban center at Dallas allow her to direct innovation toward vertical farming systems housed fully indoors.
Niu earned her doctorate in horticultural engineering at Chiba University in Japan as controlled environment agriculture there gained momentum in the 1980s. The research area has seen rapid growth in recent years on the heels of climate change concern and increasing limitations of global open-field production.
Greenhouses, the focus of much of Niu’s research to date, also pose obstacles to agricultural economics and environmental sustainability.
Niu said plants utilize about 43% of sunlight to grow; the surplus becomes heat. And glass and clear plastics — typical greenhouse covers — can make temperature control difficult during harsher outdoor conditions. Consequently, these systems require energy-intensive heating and cooling in winter and summer.
“There are still problems to economic feasibility, like very high upfront investment and operational expenditures,” Niu said.
But opportunity for controlled environment agriculture, or CEA development, is ripe across Texas.
Niu peers into vertical grow rack. (Texas A&M AgriLife photo by Patricia Moran)
On the horizon: Seedlings
For example, she said, many open-field crop producers — who comprise the majority of Texas farmers — acquire transplant seedlings from out-of-state sellers who grow them in controlled environments. Valuable Texas examples include tomato and pepper transplants produced in winter. Dollars for out-of-state seedlings might be kept in Texas down the line by bolstering the state’s own urban production capacity, and by delivering emerging knowledge to farmers and urban upstarts via the Texas A&M AgriLife Extension Service.
On the practical side of implementation, Niu said, “In my opinion, it would be easier to do in Texas because we have high temperatures, which means lower heating costs in winter than northern states.”
Better technology: Controlled environment agriculture
She also seeks opportunities for improving controlled environmental agriculture technology.
“How can we design lighting systems in a way that the plants use most efficiently?” she asked. “How do we use less energy and produce more lumens? Can we reduce labor costs through automation? Do we need to heat the whole greenhouse or just the nutrient solution? How do we control temperature efficiently while improving quality and productivity?”
These are the questions her team works to answer in Dallas. At the same time, the second edition of Niu’s co-edited and co-authored textbook, Plant Factory: An Indoor Vertical Farming System for Efficient Quality Food Production, is available following its publication in late 2019.
LED light fixtures in a vertical grow rack at Dallas (Texas A&M AgriLife photo by Patricia Moran)
The 33-chapter text is a collaboration with Niu’s Chiba University mentor Toyoki Kozai, Michiko Takagaki and other contributors to the CEA field. It covers the latest information on each area of controlled environment horticulture: plant-light responses, advances in LED technology, environmental effects on plants as well as production for pharmaceuticals and transplant production among a range of other CEA topics.
Niu’s research in Dallas over the next year aims to expand emerging knowledge in these areas. Her laboratories now house controlled environment studies of leafy greens, and she will pursue future research on specialty greens, pharmaceutical-grade plant production and a range of other controlled environment agriculture systems.
“It is a field of innumerable possibilities,” Niu said.
Find urban horticulture program information, a curriculum vitae and listing of Niu’s publications at dallas.tamu.edu/urbanhort.
Source: AgriLife Today (Gabe Saldana)
Publication date: Wed 19 Feb 2020
This Brooklyn Farm Company Is Training A New Generation of Urban Farmers
In old shipping containers, the shoots of a new way of urban farming are starting to emerge, which could help meet the demand of a growing urban population
February 7, 2020, by World Economic Forum
(Credit: Unsplash)
This article is brought to you thanks to the collaboration of The European Sting with the World Economic Forum.
Author: Kate Whiting, Senior Writer, Formative Content
The average age of an American farmer is 57.5 years.
Just under 70% of the world’s population will live in urban areas by 2050.
Square Roots is teaching young city farmers how to grow food sustainably.
Among the high-rise buildings and concrete sidewalks of Brooklyn, there’s a quiet green revolution taking place.
In old shipping containers, the shoots of a new way of urban farming are starting to emerge, which could help meet the demand of a growing urban population.
Square Roots is an indoor urban farming company, which not only grows food sustainably without soil but is teaching a new generation of farmers how to do it too.
“We realized there were tens of thousands of young people who were as passionate about changing the food system as we were, but just didn’t know how to get started,” says Tobias Peggs, CEO of Square Roots.
Feeding the future
Square Roots is tackling several issues in one go: the need to use less water and other resources in agriculture, the aging of farmers, the global population rise and, in particular, the growing urban population.
Farmers in the US aren’t getting any younger, with an average age at 57.5, according to census data, up 1.2 years from 2012.
A new way of farming. Image: WWF/Netflix
And it’s a similar story in other places around the world. In Kenya, the average farmer is 60. In Japan, 67.
By 2050, 68% of the world’s population is expected to live in urban areas, so that’s where much of the focus of food growing will need to be.
“Younger generations are really interested in making sure we’re all eating healthy food that’s nutritious and grown in sustainable ways, but they’re less interested in living in the middle of the country,” says Peggs.
The future of farming
The Next-Gen Farmer Training Program teaches would-be farmers how to grow leafy greens in a high-tech hydroponic system that it says uses up to 95% less water than traditional farms.
They study plant science, to find out what’s happening at a molecular level as the plant grows, they learn about the business side and engage with the local community and agriculture ecosystems.
Food
What is the World Economic Forum doing to help ensure global food security?
Two billion people in the world currently suffer from malnutrition and according to some estimates, we need 60% more food to feed the global population by 2050. Yet the agricultural sector is ill-equipped to meet this demand: 700 million of its workers currently live in poverty, and it is already responsible for 70% of the world’s water consumption and 30% of global greenhouse gas emissions.
New technologies could help our food systems become more sustainable and efficient, but unfortunately, the agricultural sector has fallen behind other sectors in terms of technology adoption.
Launched in 2018, the Forum’s Innovation with a Purpose Platform is a large-scale partnership that facilitates the adoption of new technologies and other innovations to transform the way we produce, distribute and consume our food.
With research, increasing investments in new agriculture technologies and the integration of local and regional initiatives aimed at enhancing food security, the platform is working with over 50 partner institutions and 1,000 leaders around the world to leverage emerging technologies to make our food systems more sustainable, inclusive and efficient.
Learn more about Innovation with a Purpose’s impact and contact us to see how you can get involved.
Each shipping container at the company’s campus in Brooklyn’s Bed-Stuy neighborhood can produce up to 45kg of fresh basil, chive or mint leaves per week, which is grown without pesticides and uses data to optimize flavor and nutrition.
“Successful companies in the 21st century have to be doing well – and doing good at the same time,” says Peggs.
“We’re growing food and selling food, that’s how we make money. But we’re doing that in a sustainable way, which is better for the planet and we’re empowering the next generation of leaders in urban farming.”
The Influence of Temperature And Daily Light Integral on Culinary Herb Production
Greenhouse average daily temperature (ADT) and daily light integral (DLI) can be adjusted to improve crop timing, maximize biomass production, and increase crop quality
Date: March 12, 2020
Time: 2 p.m. - 3 p.m. EST
Presented by: Roberto Lopez and Kellie Walters
Register here
Greenhouse average daily temperature (ADT) and daily light integral (DLI) can be adjusted to improve crop timing, maximize biomass production, and increase crop quality. In this webinar, Michigan State University researchers will discuss how the growth, development, and color of culinary herbs is influenced by ADT and DLI. They will share research on crops including sweet basil, purple basil, sage, and spearmint, giving research-backed tips on how to use these environmental parameters to improve crop yield and quality.
Join today
If you have any questions or would like to know more about GLASE, please contact its executive director Erico Mattos at em796@cornell.edu
Special thanks to our Industry partners
US: Florida - Kalera Opens New Vertical Farming Facility In Orlando
Built in record time, the new farm has the highest production volume capacity in the Southeastern United States
March 03, 2020 | Source: Kalera
Kalera, a technology-driven vertical farming company, announced the opening of its new state-of-the-art growing facility in Orlando, Florida. Daniel Malechuk, CEO of Kalera, believes the company is leading the way in defining what pick-to-plate means for the future.
Kalera’s New Facility Is The Highest Production
Volume Vertical Farm In the Southeast
ORLANDO, Fla., March 03, 2020 (GLOBE NEWSWIRE) -- Today, technology-driven vertical farming company Kalera announced the opening of its new state-of-the-art growing facility in Orlando, Florida. This new facility is the highest production volume vertical farm in the Southeast.
The rapidly constructed facility also demonstrates Kalera’s ability to quickly build and open farms around the US and the world. This new facility complements Kalera’s initial HyCube growing facility located at the Orlando World Center Marriott and is centrally located in the heart of Florida, one of the largest tourist destinations in the world. The new facility has the capacity to supply millions of heads of leafy greens per year to consumers while also providing dozens of new high-quality jobs.
Originally announced at the end of August, Kalera was able to get its new growing facility up and running in less than six months due to a streamlined design and construction process that illustrates the company’s ability to quickly scale and expand its vertical farms. Kalera was able to retrofit the existing building with its proprietary technology to create the highest production volume vertical farming facility in the Southeastern United States. As Kalera accelerates its growth over the next few years, it will build additional facilities, expanding production capacity throughout the US and internationally.
“Adding a large-scale vertical farm to Central Florida was the next logical step for us as a company. We’ve spent years perfecting and fine-tuning our technology to place us as industry leaders in the local farming ag-tech revolution," said Daniel Malechuk, CEO of Kalera. “Right now, we are leading the way in defining what pick-to-plate means for the future. In a sense, we are trying to perfect Mother Nature indoors by combining science and technology with farming.”
The new facility has the capacity to supply millions of heads of leafy greens per year to consumers while also providing dozens of new high-quality jobs.
"Kalera's business is built on good science. We’re planting non-GMO seed, and over the past several years we have perfected plant and data science-driven methods to optimize the growing environment, nutrient mixes, and distribution that make plants thrive,” said Cristian Toma, Chief Technology Officer of Kalera. “We’re excited to be able to meet customers’ demands for cleaner, safer, non-GMO, pesticide-free leafy greens that are fresher, boast a longer shelf life and higher nutritional value, and are grown locally with consistently high yields.”
The company utilizes cleanroom technology and processes to eliminate the use of chemicals and remove exposure to pathogens. With indoor facilities situated right where the demand is, Kalera is able to supply an abundance of produce locally, eliminating the need to travel long distances when shipping perishable products. This means Kalera can ensure the highest quality and freshness by delivering product to customers within hours of harvest rather than days or weeks. Kalera's plants grow while consuming 95% less water compared to field farming.
Kalera opened its first vertical farm in 2018, the HyCube growing center, on the premises of the Orlando World Center Marriott to bring fresh, local produce to the hotel’s visitors and customers. This farm has served as a successful model illustrating the place of vertical farms in the sustainable food movement.
About Kalera
Kalera is a technology-driven vertical farming company with unique growing methods combining optimized nutrients and light recipes, precise environmental controls, and cleanroom standards to produce safe, highly nutritious, pesticide-free, non-GMO vegetables with consistently high quality and longer shelf life year-round. The company’s high-yield, automated, data-driven hydroponic production facilities have been designed for rapid rollout with industry-leading payback times to grow vegetables faster, cleaner, at a lower cost, and with less environmental impact.
Media Contact:
Elka Karl
Phone: 510-508-7328
Email: elka@dadascope.com
Darragh McCullough: Vertical Farming Is All The Rage, But The Downsides Will Limit Its Potential
There are so many stories about this tech that you would be forgiven for thinking that there is going to be a vertical farm at every traffic light next time you make it into the city
What grows up, must come down: Vertical farming presents interesting possibilities, but it has its limits
Darragh McCullough
February 20, 2020
Vertical farming is all the rage. It makes great click-bait by combining key buzz words: 'technology' in the form of new LED lighting; 'novelty' food that some celebrity chef can shout about producing beside their New York restaurant, and 'sustainability' courtesy of zero food miles and a low carbon footprint.
Your phone's news feed is probably similar to my own.
There are so many stories about this tech that you would be forgiven for thinking that there is going to be a vertical farm at every traffic light next time you make it into the city.
But beyond the low-energy LED lights in colours tailored to turbo-charge plant growth even in the depths of winter, you realise that we've had vertical farms for decades.
More recently, I've seen production in tunnels and glass take on vertical formats. Modern glasshouses are now so tall that each line of tomatoes or peppers is tended to via nifty little scissor lifts. I see the same trend in tunnels, with 4m high tunnels now standard in new soft fruit set-ups.
When I visited the Farmony vertical farm in Ballycoolin, west Dublin for Ear to the Ground this year, we all had to gown up before being allowed access to the growing unit.
It might have appeared a bit over-the-top given that we were just stepping into a converted refrigerated truck container that has a few pumps, fans and extra sockets fitted.
But by manipulating every single aspect of this growing environment - and maintaining near-sterile conditions - the people behind Farmony claim that their 80 square metre unit can produce the same amount as a 5ac field. That's a 250-fold increase in the productivity per square metre, which is impressive by any measure.
Farmony is focusing on the unit's ability to grow leafy salads and herbs, especially the baby and micro-leaved versions that are so beloved of chefs and foodies.
Normally these are flown in from places like Africa, Israel and further afield at this time of year when it's just impossible to grow them commercially here in tunnels or glass.
The beauty about using refrigerated truck containers is that they are insulated, allowing the grower to maintain ideal temperatures at a relatively low cost.
They are also pretty secure and mobile so that they can be parked anywhere there's room for a truck container.
The idea is that they'll pop up in carparks, basements, and office block roofs, regardless of whether that's in baltic Belfast or boiling Beirut.
Farmony claims that the €87,000 price tag is a snip given that the herbs the container is capable of producing would pay that off after all costs in about two years.
The downsides? The unit should be able to work well for produce that is 95pc water and has a short growth cycle of just 1-3 weeks. These plants don't need a lot of heat and light to get to a saleable point. But if you wanted to grow a more carbohydrate-dense food - like any root crop, or even a strawberry where only a small fraction of the plant that you've poured light and heat energy into ends up being saleable - the calculations start to unravel.
And, much and all as we should be reducing our calorie intake, there's only so much salad that a body can take.
We'll certainly see more of the LED light tech being incorporated into existing production systems like tunnels and glass, and there are interesting possibilities for old mushroom tunnels to be repurposed as salad units.
But there's a lot to be said still for good old-fashioned horizontal farming.
Indo Farming
Gaby Miodownik Appointed Netafim's New CEO
"It is a great honor for me to be appointed CEO of Netafim after years of personal growth with the company
Gaby Miodownik has been appointed as the new CEO of Netafim, and will replace Ran Maidan, who announced his desire to retire from Netafim after six years as CEO. The company's board of directors has approved the appointment of Gaby Miodownik as CEO of Netafim, as of March 2020.
Gaby Miodownik, 46, married with 3 children, a CPA in his education, joined Netafim 16 years ago as CFO of the Latin American unit and then held a number of management positions in the company, including Head of the Mexican subsidiary, VP of EMEA division (Europe, Middle East, Africa) and most recently Senior Vice President and President of the Americas Division.
Daniel Martinez Vella, CEO of Orbia and Chairman of the Netafim Board of Directors: "I am proud and happy to appoint Gaby Miodownik as CEO of Netafim. Gaby has had a rich experience in Netafim, during which he gained extensive knowledge in agriculture and irrigation, extensive knowledge of the global market and the company's customers, and demonstrated high management, leadership, and impressive growth in all the roles he has played to date. I believe in Gaby and in his ability to lead Netafim to new heights, contributing to Orbia's vision to advance life around the world". Daniel added: "I want to thank Ran Maidan who led the company for the last 6 years taking it to unprecedented new heights and driving Netafim to significant sales and profit growth in recent years, along with developing growth engines and strengthening the company's competitive advantage".
Ran Maidan, CEO of Netafim: "I am grateful for the opportunity I have been given to lead Netafim for the past six years. I thank the management and employees for their great contribution to the success of the company and becoming a global market leader. From my long-standing acquaintance with Gaby, I am convinced that he is a great candidate and the best fit to move this great company forward".
Gaby Miodownik: "It is a great honor for me to be appointed CEO of Netafim after years of personal growth with the company. I would like to thank the Company's Board of Directors and Chairman of the Board Daniel Martinez Vella for the trust they have given me. Netafim is an excellent company with great potential, and I am convinced that together with the company's management and dedicated employees, we will continue to grow the company and further strengthen its position as the world's leading irrigation company."
For more information:
Netafim
www.netafim.com
Publication date: Mon 10 Feb 2020
Michigan State University’s Specialty Crop Research Initiative Grant Funded by The USDA
The initiative, OptimIA, which stands for Optimizing Indoor Agriculture, aims to improve the profitability and sustainability of indoor leafy-greens production
The initiative, OptimIA, which stands for Optimizing Indoor Agriculture, aims to improve the profitability and sustainability of indoor leafy-greens production.
February 11, 2020
A multi-university team of horticulturists, engineers and agricultural economists led by Michigan State University (MSU) has received a four-year, $2.7 million grant from the U.S. Department of Agriculture (USDA) to study indoor production of leafy greens. Industry partners have matched funding, bringing the project total to $5.4 million. The investigators on the grant include Erik Runkle, Roberto Lopez and Simone Valle de Souza of Michigan State University; Chieri Kubota of Ohio State University; Cary Mitchell of Purdue University and Murat Kacira of University of Arizona.
Leafy greens include commonly consumed vegetables such as lettuce, kale, and microgreens. Production challenges outdoors have led to interest in growing these specialty crops hydroponically in controlled environments, such as indoor farms. However, there is little information on whether this is economically viable. Capital and operating costs can be significant for startups, especially as it relates to light-emitting diodes (LEDs) and cooling systems. Leafy greens are a good candidate for indoor farming because they can be grown rapidly and in relatively small spaces. Indoor environments are heavily controlled, so growers aren’t constrained to a small geographic area within the U.S. There are, however, other geographic concerns.
The team and its collaborators have three major goals:
Defining optimal profitability based on yield and other high-value attributes of the plants, such as nutrition content.
Optimizing indoor environmental conditions, such as humidity, air movement, temperature, light and carbon dioxide concentration, to increase yield and high-value attributes.
Encouraging indoor farming stakeholders to collaborate with academic and industry groups that are working in controlled-environment agriculture.
The long-term project goals are to help integrate indoor farming into the specialty-crop segment of agriculture in the U.S.; to increase the sustainability and hence profitability of this rapidly emerging sector; and to locally produce leafy greens that have higher quality attributes.
To this end, economists will better understand operating and capital expenditures (capex), and define risk and production scenarios that are most profitable. Horticulturists and engineers will improve production efficiency, product quality and value-added attributes of leafy greens for reliable, consistent, year-round production. In addition, the team will design and test more effective localized air-distribution methods suitable for indoor production systems, as well as develop strategies to better manage humidity around plants to reduce tip burn.
While the project focuses on leafy greens, the results will also inform a wide range of controlled-environment growers through the development of growth recipes, strategies for nutritional content and anthocyanin enhancement, environmental management recommendations, and insights for economic sustainability as well as market and consumer perception of locally produced crops.
For more information, visit the project website here.
Leafy greens Sustainability USDA Microgreens Controlled Environment Agriculture
Farmers, Nonprofits Sue USDA, Saying Hydroponics Can't Be Organic
Center for Food Safety (CFS), along with a coalition of organic farms and stakeholders, filed a lawsuit challenging the United States Department of Agriculture's (USDA's) decision to allow hydroponic operations to be certified organic
Center for Food Safety (CFS), along with a coalition of organic farms and stakeholders, filed a lawsuit challenging the United States Department of Agriculture's (USDA's) decision to allow hydroponic operations to be certified organic.
The lawsuit claims that hydroponic operations violate organic standards for failing to build healthy soils, and asks the Court to stop USDA from allowing hydroponically-produced crops to be sold under the USDA Organic label. The plaintiff coalition includes some of the longest-standing organic farms in the United States including Swanton Berry Farm, Full Belly Farm, Durst Organic Growers, Terra Firma Farm, Jacobs Farm del Cabo, and Long Wind Farm, in addition to organic stakeholder organizations including organic certifier OneCert and the Maine Organic Farmers and Gardeners Association.
"Healthy soil is the foundation of organic farming," said Andrew Kimbrell, executive director of plaintiff Center for Food Safety, "Organic farmers and consumers believe that the Organic label means not just growing food in soil, but improving the fertility of that soil. USDA's loophole for corporate hydroponics to be sold under the Organic label guts the very essence of 'Organic'."
CFS's lawsuit cites the federal Organic Foods Production Act, which requires farms to build soil fertility in order to be certified organic. Hydroponics cannot comply with federal organic standards because hydroponic crops are not grown in soil, the CFS claims.
"The federal organic law unequivocally requires organic production to promote soil fertility," said Sylvia Wu, senior attorney at the Center for Food Safety and counsel for plaintiffs. "USDA's decision to allow mega-hydroponic operations that do nothing with soil to be sold as 'Organic' violates the law."
"Healthy soil is critical to producing nutrient-dense foods that benefit both people and the environment," said Paul Muller, one of the farm owners of plaintiff Full Belly Farm in Guinda, California, a diversified family farm that has been farmed organically since 1985. "Healthy soil increases and improves the availability of soil nutrients and beneficial microorganisms, and enhances the land's ability to sequester carbon and retain nutrients and water."
"While I welcome the work that my friends in the hydroponic industry are doing, hydroponic production does not conform to the soil-building precepts of organic farming," said Jim Cochran, owner of plaintiff Swanton Berry Farm, one of the oldest certified organic strawberry farms in California. "I would be perfectly happy to have my strawberries compete with properly distinguished hydroponically-grown strawberries, without the latter piggybacking on an Organic label that has taken more than 30 years to develop and establish in the minds of consumers. Certifying hydroponically-grown crops as organic devalues that label."
"The USDA's claim that hydroponics can be certified as organic is disingenuous and false," said Sam Welsch, president of plaintiff organic certifier OneCert, Inc. "Until the USDA started telling certifiers that they could ignore the parts of the law and rules that required fertility to come from organic matter in soil, no one was certifying hydroponic systems as organic."
For more information:
Center for Food Safety
www.centerforfoodsafety.org
Publication date: Tue 3 Mar 2020
Elon Musk's Brother Wants To Transform Farming
Vertical farming is an indoor farming method in which crops are grown in stacked layers, often without soil. The practice is becoming more popular and important as urban populations grow dramatically and available farmland decreases
February 28, 2020
New York (CNN Business)Plant-based foods are all the rage right now, and vertical farms are capitalizing on the trend.
Vertical farming is an indoor farming method in which crops are grown in stacked layers, often without soil. The practice is becoming more popular and important as urban populations grow dramatically and available farmland decreases.
While vertical farming isn't a new concept, these eco-friendly indoor farms are now rapidly expanding.
Elon Musk's younger brother, Kimbal Musk, who was named "Global Social Entrepreneur" of the year by the World Economic Forum in 2017, started Square Roots, an indoor urban farming company based in Brooklyn, in 2016. Square Roots' mission is to bring fresh, local food to cities around the world by empowering younger generations to participate in urban farming.
"When I was a kid, the only way I could get my family to sit down and connect was by cooking the meal," Musk, co-founder and executive chairman of Square Roots, told CNN Business in an email.
Kimbal Musk teaches students how to plant a vegetable garden in California.
"Getting involved with the internet, especially in the late '90s, was very exciting and I wouldn't change anything about those experiences, but my passion has always been food," Musk said. "The moment Elon and I sold Zip2, our first internet company, I knew I wanted to pursue food and become a trained chef." He moved to New York and enrolled at the International Culinary Center.
Musk said the company plans to open a Square Roots "Super Farm" — with 25 climate-controlled shipping containers, cold storage, biosecurity infrastructure and everything else needed to run a vertical farm at scale — in less than three months.
Since its inception, Square Roots has grown more than 120 varieties of crops, including greens, vegetables, and strawberries.
The company isn't the first of its kind. Startups like Silicon Valley's Plenty, which was founded in 2013 and is backed by Jeff Bezos, are also beginning to dominate the space.
"Environmentalists, urban farmers, architects, agronomists, and public health experts, among others, have been joining this mini-revolution as they partner to work out a way to salvage a food-scarce, ultra-urbanized future," Kheir Al-Kodmany, a professor of sustainable urban design at the University of Illinois at Chicago, said in a report.
It involves various techniques, such as hydroponics, which uses mineral nutrient solutions in a water solvent; aquaponics, which uses aquatic creatures -- such as fish and snails -- and cultivates plants in water; and aeroponics, which grows plants in the air.
As for job creation, rapid climate change will put millions of traditional farmers out of business, but vertical farmers won't be affected, according to microbiologist Dickson Despommier, an emeritus professor of public and environmental health at Columbia University.
Although vertical farming was first introduced in the early 1900s, it was recently popularized by Despommier. More than 20 years ago, he began teaching a class at Columbia called Medical Ecology.
Despommier spent a decade growing crops indoors with his students. "Ten years ago, there were no vertical farms," he said, noting that LED grow lights have vastly improved farming efficiency over the last five years, making indoor growing cheaper and more reliable.
Basil growing at the Square Roots farm in Brooklyn.
"People want local food because they've lost trust in the industrial food system that ships in high calorie, low nutrient food from thousands of miles away with little transparency as to who grew the food and how," said Peggs, the Square Roots CEO.
At the same time, the world population is growing and urbanizing rapidly. Peggs said climate change is threatening existing supplies of food, forcing the industry to figure out new ways to grow food quickly.
Peggs is optimistic about raising money for vertical farming. "A lot of smart money and capital is entering the space," he said. "The quality of food that can now be produced in these indoor systems is at least on par with the best organic field-grown food you can buy."
Despommier said that cities will eventually be able to grow "all they can eat" from indoor farms located within city limits. "If an outdoor farm fails, the farmer has to wait until next year to start again, he said. "Indoor farms fail too, but the indoor farmer can start again within weeks."
Freight Farms Is Now More Green
Freight Farms runs a network of smart farms across 44 states and 25 countries. Each smart farm called a “Greenery” is housed in a 320 -sq.-ft. hydroponic shipping container
The Boston startup that builds automated farm systems in shipping containers raised $15M in a Series B round led by New York City-based Ospraie Ag Science, which invests in agtech companies. Existing investor Spark Capital also participated in the round, which brings the company’s total funding to more than $28M.
Freight Farms runs a network of smart farms across 44 states and 25 countries. Each smart farm called a “Greenery,” is housed in a 320-sq.-ft. hydroponic shipping container. These vertical farming containers are all linked to the startup’s data platform, Farmhand.
The startup’s customers range from food distributors and grocery stores to educational institutions and corporate campuses. In the past, the company has worked with the Compas Group, Google and Federal Realty Investment Trust.
The 10-year-old startup claims its farms can grow more than 500 varieties of crops at a commercial scale by using 99.8% less water than traditional agriculture.
Read more: Freight Farms Raises $15M in Series B For New Partnerships and Expansion
Kyoto’s Spread Co., Ltd. Brings Large-Scale Expertise to the AVF
Established in 2006, SPREAD has grown to become the leading Japanese vertical farm operator, with two farms capable of producing over two tons of lettuce per day
MARCH 3, 2020
KYLE BALDOCK
Established in 2006, SPREAD has grown to become the leading Japanese vertical farm operator, with two farms capable of producing over two tons of lettuce per day. By focusing solely on large scale vertical farming systems, they are leading a huge domestic industry in terms of production and profitability. I spoke to JJ Price, Manager of International Business Development, about their pioneering strategy and plans for the future.
Kameoka Plant
Taking the lead in a large domestic market
If the vertical farming market has matured anywhere in the world, it would be in Japan: current market research shows that there are just over two hundred vertical farms in the country. In 2007, Spread began their journey by constructing the Kameoka Plant, a non-automated vertical farm that is capable of producing 21,000 heads of lettuce per day. This large scale operation became profitable in 2013, but Spread looked to grow even bigger. In 2015, they announced the concept for an even larger, automated vertical farm to be constructed in the Kansai Science City. Fast forward to today and the Techno Farm Keihanna is operational, capable of producing a further three tons or 30,000 heads of lettuce per day.
Techno Farm Keihanna
While the level of automation and key technologies differs between the farms, Spread is now one of the largest vertical farming companies in Japan to be operating multiple farms. Their flagship products, the Vegetus brands of lettuce, are in 2,500 supermarkets across Japan and they recently hit the benchmark of 60 million products sold in total. When it comes to market share of vertically-farmed products on supermarket shelves, Spread is, again, the leader. Crop wise, they only focus on lettuce for commercial development, although various other products are in the works. Currently, 70% of the Vegetus brand production goes to retail and 30% goes to foodservice and ready meal products.
Growing even bigger with a partnership business model
With two farms operational, Spread is hoping to expand further through a partnership business model. With multiple agreements already in place, Spread will work with the partner company and provide expertise, support sales activities, advise on technology and the business model. The first farm under this model was announced on June 24, 2019, with Spread’s partner and member of JXTG Group J Leaf starting construction on Techno Farm Narita, one of Japan’s largest automated vertical farms. Recently, Spread entered into partnership discussions with Kyushu Electric to build the world’s largest automated vertical farm with production capacity of 5 tons of lettuce per day. With this model, Spread hopes to have 10 farms completed by 2025.
Looking outside of Japan, Spread is focused in the shorter term on particular markets. JJ Price told me they are looking closely at the US, Europe, and the Middle East. With the scales growing ever larger, and their reach going global, Spread makes sure that its customers come first.
Connecting with the consumer
Vegetus is a strong brand with Japanese consumers. The Spread team told me that in Japan, most open-field lettuce is iceberg, or a red variety called Sunny; all the varieties that Spread provides are different, milder and sweeter. The packaging of Vegetus clearly demonstrates that the products come from vertical farms, and the advantages are listed: no pesticides during cultivation, better texture, and flavor. In the supermarket itself, the product is set apart from traditional lettuce. In order to overcome negative perceptions of the product, the sales team goes round the supermarkets, holding events to engage consumers and promote the products. Overall, the perception of vertically-farmed produce is much more positive in Japan than in Europe or the US.
Vegetus Brand
In the end, the price is what counts, and Spread has a major advantage because of its scale: 1 head of Vegetus retails for 158 yen (suggested retail price), only 10-20% more expensive than outdoor-grown lettuce. This is central to Spread’s strategy: they are not looking for niche or premium brand products. They want Vegetus to be accessible and affordable for as many people as possible. In order to maintain this market position, I wanted to find out how Spread is innovating to drive down costs.
Innovation and automation to drive down costs
Spread does the majority of its R&D in house, from crop research and development to technology development, trialing and implementation. It is this spirit of innovation that led them through six years of trial and error to become a fully profitable vertical farm. But they are not averse to working with other market-leading companies: they developed their automation equipment and lighting in collaboration with leading Japanese companies. They have been working with the NTT Group to develop IoT and AI technologies that will optimize the growing environment and production processes. In terms of driving down costs, JJ Price told me that they are always on the lookout to improve hardware and automate labor-intensive processes. Furthermore, they also focus on improving the efficiency of human operations. These are the keys to driving down costs and increasing profitability moving forward.
Partner with Spread Co.
Spread is eager to partner with companies in the AVF network. They have invited interested parties to visit the website and connect. Please write to info@vertical-farming.net and ask for an introduction to Spread and we will be happy to connect you.
CubicFarm Systems Announces Its Largest Sale To Date - A 100-Machine Commercial-Scale Vertical-Farming System in Surrey, BC
The Company has a current backlog at C$24.7 million representing 144 machines under deposit and awaiting installation - demonstrating continued sales momentum due in part to the growing demand for its systems. The current backlog is anticipated to be recognized in revenue in mid-2020 to mid-2022
March 2, 2020
VANCOUVER, BC / ACCESSWIRE / March 2, 2020, / CubicFarm® Systems Corp. (TSXV: CUB) ("CubicFarms" or the "Company") is pleased to announce that it has finalized an agreement for the sale of 100 CubicFarms growing machines, and received a deposit in the amount of C$1.2 million from a commercial grower and agricultural product wholesaler based in the province of British Columbia, Canada. The customer had previously provided a deposit for a 12-machine system and now has applied its deposit toward this revised order for 100 machines.
The 100-machine system represents a total of C$16.5 million in sales revenues to the Company, and is expected to be installed in two phases in Surrey, BC. The first phase, consisting of the installation of 26 growing machines and an irrigation system, is planned for installation this year, with the remaining machines planned for installation by mid-2022.
The Company has a current backlog at C$24.7 million representing 144 machines under deposit and awaiting installation - demonstrating continued sales momentum due in part to the growing demand for its systems. The current backlog is anticipated to be recognized in revenue in mid-2020 to mid-2022.
The sale represents CubicFarms' largest to date, following on its 21-machine sale to a customer in Montana, USA - its largest sale in the US - and its 23-machine sale to a customer in Calgary, Canada.
Due to the close proximity of the customer's Surrey site to CubicFarms' headquarters, CubicFarms will provide a turn-key solution to the customer, by facilitating and managing site preparation and installation of the CubicFarms system - leveraging the experience the Company has gained from its R&D and production facility in Pitt Meadows, BC.
CubicFarms CEO Dave Dinesen commented: "We are extremely encouraged by the growth in sales we've enjoyed and the trend toward increasingly larger facilities. It reflects the demand emerging around the world for commercial-scale growing technology. Once installed, the system in Surrey will be one of the world's largest automated vertical-farming systems.
"We are excited to be working with our customer, an established multi-industry group with investments and operations in the agriculture, technology and health space. Our customer understands the importance of using technology to significantly improve yields in an environmentally sustainable manner, and we look forward to helping them scale up production of fresh local vegetables for their market in southwest British Columbia and beyond.
"We are also pleased to receive ongoing feedback from our existing machine customers about the quality of produce from our systems and the resulting growth in demand for that produce."
Concurrent with the 100-machine sale, CubicFarms has entered into a Shareholders' Agreement with the customer and its associated companies with respect to a joint venture entity that will own and operate the 100-machine venture. As consideration for CubicFarms' 20% ownership in the joint venture, the Company will provide approximately C$342,000 in the form of a zero-interest loan.
Neither the TSX Venture Exchange nor it’s Regulation Services Provider (as that term is defined in the policies of the TSX Venture Exchange) accepts responsibility for the adequacy or accuracy of this release.
About CubicFarm® Systems Corp.
CubicFarm Systems Corp. ("CubicFarms") is a technology company that is developing and deploying technology to feed a changing world. Its proprietary technologies enable farmers around the world to grow high-quality, predictable crop yields. CubicFarms has two distinct technologies that address two distinct markets. The first technology is its patented CubicFarm™ System, which contains patented technology for growing leafy greens and other crops. Using its unique, undulating-path growing system, the Company addresses the main challenges within the indoor farming industry by significantly reducing the need for physical labor and energy, and maximizing yield per cubic foot. CubicFarms leverages its patented technology by operating its own R&D facility in Pitt Meadows, British Columbia, selling the System to farmers, licensing its technology and providing industry-leading vertical farming expertise to its customers.
The second technology is CubicFarms' HydroGreen System for growing nutritious livestock feed. This system utilizes a unique process to sprout grains, such as barley and wheat, in a controlled environment with minimal use of land, labor, and water. The HydroGreen System is fully automated and performs all growing functions including seeding, watering, lighting, harvesting, and re-seeding - all with the push of a button - to deliver nutritious livestock feed without the typical investment in fertilizer, chemicals, fuel, field equipment, and transportation. The HydroGreen System not only provides superior nutritious feed to benefit the animal but also enables significant environmental benefits to the farm.
Information contact
Kimberly Lim
kimberly@cubicfarms.com
Phone: +1-236-858-6491
www.cubicfarms.com
Cautionary statement on forward-looking information
Certain statements in this release constitute "forward-looking statements" or "forward-looking information" within the meaning of applicable securities laws, including, without limitation, statements with respect to the anticipated benefits to the customer; timing and the completion of machine installation by mid-2022; benefits to the Company of the sale; the anticipated revenue recognition in mid-2020 to mid-2022; and the joint venture that will own and operate the 100-machine venture. Such statements involve known and unknown risks, uncertainties, and other factors which may cause the actual results, performance, or achievements of CubicFarm Systems Corp., or industry results, to be materially different from any future results, performance, or achievements expressed or implied by such forward-looking statements or information. Such statements can be identified by the use of words such as "may", "would", "could", "will", "intend", "expect", "believe", "plan", "anticipate", "estimate", "scheduled", "forecast", "predict", and other similar terminology, or state that certain actions, events, or results "may", "could", "would", "might", or "will" be taken, occur, or be achieved.
These statements reflect the company's current expectations regarding future events, performance, and results and speak only as of the date of this news release. Consequently, there can be no assurances that such statements will prove to be accurate and actual results and future events could differ materially from those anticipated in such statements. Except as required by securities disclosure laws and regulations applicable to the company, the company undertakes no obligation to update these forward-looking statements if the company's expectations regarding future events, performance, or results change.
SOURCE: CubicFarm Systems Corp
Harvest Fresh Canteen Vegetables On-Site
In schools and universities in America, the catering and service provider Sodexo plans to produce fresh vegetables all year round via indoor farming. To this end, the company is cooperating with the US hydroponics provider Freight Farms. The salad should grow vertically in containers on campus
by Frauke Brodkorb-Kettenbach
February 15, 2020
In the container greenery of the US company Freight Farms, Sodexo grows fresh vegetables for its cafeterias directly on campus. CAROLINE KATSIROUBAS / FREIGHT FARMS
In schools and universities in America, the catering and service provider Sodexo plans to produce fresh vegetables all year round via indoor farming. To this end, the company is cooperating with the US hydroponics provider Freight Farms. The salad should grow vertically in containers on campus.
Over 500 vegetables, such as Salanova Green Butter Salad (pictured), can be grown on a commercial scale in Freight Farm’s containers with 320 square meters of vertical acreage - regardless of the season and without pesticides or herbicides. Delivery routes are also eliminated with this type of vegetable cultivation.
Save resources
With the cooperation, Sodexo is pursuing its strategy of operating as sustainably as possible and at the same time being precisely informed about the origin of its food for customers in the education segment.
In addition, students could monitor the stages of growing their food. For example, schools could integrate hydroponic farming into interactive curricula or school subjects such as technology, agriculture, nutrition, and economics, according to Freight Farms' approach. The vertical farming provider also sees similar advantages for employees when using the containers in companies.
CAROLINE KATSIROUBAS / FREIGHT FARMS
So far, vegetables grow in freight farm containers in 25 countries and 44 states in the US - in small and medium-sized businesses, hospitals, as well as in retail and non-profit organizations, the information says. 35 school facilities now work with the hydroponics system. By working with Sodexo, the number should grow rapidly.
SODEXO, USA
Sodexo USA offers building management and catering services to schools, universities, hospitals, senior citizens' communities, venues, and other key industries. The parent company Sodexo Quality of Life Services, with headquarters in Issy-les-Moulineaux, France, was founded in 1966. According to its own statements, the group offers Benefits and Rewards Services and Personal and Home Services daily for 100 million people in 72 countries. In 2019, it had an annual turnover of 22 billion euros with 460,000 employees worldwide. The portfolio includes reception, security, maintenance and cleaning services, catering, facility management, restaurant, and gift vouchers and fuel passes for employees.
Bowery Is Sprouting In Baltimore With A New Automated Indoor Farm
Using technology that allows farming to go beyond the limits that the land imposes, the company has a mission to democratize access to fresh produce. It initially opened two farms in Kearney, New Jersey, serving the tri-state area
With a mission to democratize food access, the indoor farming startup sees the White Marsh location as a mid-Atlantic hub.
By Stephen Babcock / STAFF / 2/20/20
Inside Bowery's indoor farming operation. (Courtesy photo)
On land in White Marsh that was once associated with a working farm, new growth is taking root. But it didn’t require clearing away the building on the site: All of the growing is done inside.
“We are turning what was once an industrial warehouse back into a modern farm,” said Katie Seawell, chief marketing officer of Bowery Farming.
In early November, Bowery Farming opened a new indoor farming operation inside the warehouse on Franklin Square Drive and has been ramping up operations.
First flagged by Fast Company, it’s the third and largest farm for the New York-based startup, which in 2018 raised $90 million in a round led by Google Ventures.
Using technology that allows farming to go beyond the limits that the land imposes, the company has a mission to democratize access to fresh produce. It initially opened two farms in Kearney, New Jersey, serving the tri-state area.
With the expansion to Baltimore, the company is seeking a wider foothold in the mid-Atlantic. Seawell said the White Marsh location will open up distribution into a 150-mile radius where it can reach a potential 25 million people.
The company looks to hire locally even as it thinks regionally, and Seawell said White Marsh proved to be a transit-accessible location.
When it is fully-staffed, Bowery Farming expects to have about 80 farmers working at the space, in a mix of hourly and supervisory roles. Even for folks with no prior farming experience, Bowery looks to offer opportunities for farmers to move up within the organization as they gain skills. The farmers rotate through different roles on the farm, learning different aspects. Seawell recalled one farmer whom she met in the early days of the Kearney farm when he had a role in the packing section.
“I just ran into him last week and he was now in a support role for the ag science team,” she said.
They also seek out opportunities to support growth. In New York, the engineering team recently taught a coding class.
Inside the farm itself, hydroponics — the process of growing plants without soil — is key to the vertical farming operation, and technology plays a big role, too. CEO Irving Fain teamed with cofounders to apply technology to a big mission area. The team devised a system called BoweryOS to run the farm, which uses visual systems, sensory systems and automation. With data-gathering techniques and machine learning, the company sees its farms as a network, so the data is helping to build on what’s been done at the other two locations.
“Even though it’s the newest farm, it’s the smartest farm we’ve ever had,” Seawell said.
Bowery Farming from above. (Courtesy photo)
When it comes to the crops themselves, the farm has leafy greens and herbs in the market now. They’re available through Amazon Fresh, and Bowery is working on developing retail partnerships in the region to bring produce in the spring and summer. The company is also working to move beyond the “leafy green” category, which is often a staple of indoor farms and is testing other crops. It also has a partnership to regularly deliver hundreds of pounds of produce to the Maryland Food Bank.
Vertical farming doesn’t only upend the traditional growing model. With a wider food system that often involves food being shipped long distances, Bowery’s indoor farming approach yields lots of promise to bring production closer to where it’s eaten, employ local folks and offer a pesticide-free product.
Still, indoor farming remains new, and it’s entering an existing market with plenty of other produce players. As such, it has to make a product that’s attractive to folks, as well, and Seawell said the company has also put a lot of time and care into not just the operations, but also how it tastes.
“We believe we have a great-tasting product,” Seawell said.