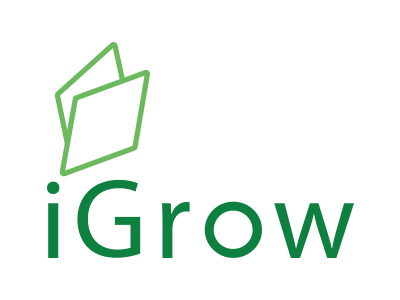
Welcome to iGrow News, Your Source for the World of Indoor Vertical Farming
Unfold Expands, Adds Research Facility For Vertical Farming
Unfold, a company that combines leading seed genetics with crop growing and agronomic expertise to advance the vertical farming industry welcomes Minos Athanassiadis as a company advisor and breaks ground on its new state-of-the-art R&D vertical farm facility in Davis, California
April 15, 2021
Unfold, a company that combines leading seed genetics with crop growing and agronomic expertise to advance the vertical farming industry welcomes Minos Athanassiadis as a company advisor and breaks ground on its new state-of-the-art R&D vertical farm facility in Davis, California.
Minos Athanassiadis, one of the foremost leaders in the produce space, working at brands such as Dole Fresh Vegetables, Underwood Ranches, and Fresh Link Group, will leverage his expertise to help Unfold develop products of value to produce retailers and consumers.
“Consumer demands are propelling changes in the food supply that are safe, transparent, personalized, and sustainable,” said Athanassiadis. “As an advisor to Unfold, I look forward to working with their fast-growing team to help them discover and develop products that will meet this criteria for retailers and consumers alike.”
Since launching, Unfold has doubled in size, bringing on diverse talent expertise from software engineers who will build digital agronomic services for vertical farm operators to the computational biology experts that will breed tomorrow’s seeds.
For vertical farms to have an impact on our food system, production can't begin and end with leafy greens. The industry’s success will require new products to be brought to market to supplement what can be produced by traditional farms and greenhouses. With the opening of their new R&D facility, Unfold will leverage expertise in AI, machine learning, and plant biology to test new varieties of fruits and vegetables faster and to develop the digital tools that will speed up plant optimization for Unfold’s customers.
“As we look to bring seeds to market in the next year, Minos’ rich history in the produce industry will be invaluable,” said John Purcell, Ph.D., President, and CEO of Unfold. “Another variable to this equation is finally being able to open the doors to our R&D facility in Davis where we’ll be able to push the boundaries of our plant breeding in controlled environments that leverage state-of-the-art digital tools.”
For additional information about Unfold or to hear about potential career opportunities, please visit our website at https://unfold.ag/.
Lead photo and logo courtesy Unfold
GREECE: 15 Hectare Semi-Closed Hydroponic Greenhouse
With the second round of financing expected to conclude by September 2021, Aurarius first facility is planned to be operational in the first quarter of 2023
Greece Investment Group Closes Funding On
Hydroponic Greenhouse
The Aurarius Investment Group successfully closed its first round of financing in the first quarter of 2021 covering development activities for Aurarius’ inaugural hydroponic greenhouse/energy plant in Greece. With the second round of financing expected to conclude by September 2021, Aurarius first facility is planned to be operational in the first quarter of 2023.
The facility will be composed of a ~15-hectare semi-closed hydroponic greenhouse farm combined with a ~10 MWh CHP facility. Aurarius intends to develop a portfolio of hydroponic farms combined with energy plants across Greece and other Southern European Countries, aiming to grow high-quality vegetables using the most modern and safe hydroponic greenhouse technology – with an eye both to social impact and sound economic returns.
For more information:
Aurarius Investment Group
https://www.aurariusgroup.com/
This Weeks Episode - Season 3 Episode 31
Niko is the CEO of Netled, an organization that designs and builds the high-tech platform for the world's smartest vertical farms
Join Harry Duran, host of Vertical Farming Podcast, as he welcomes to the show Niko Kivioja. Niko is the CEO of Netled, an organization that designs and builds the high-tech platform for the world's smartest vertical farms. Niko spent the first part of his career in controlled-environment-agriculture as a grower and has spent the last decade in high-tech closed-environment and vertical farming technology development.
In this episode, Harry and Niko discuss the Niko’s familial history of entrepreneurship and the inspiration to start Netled. Niko speaks to the proprietary Vera vertical farming platform development that he’s recently been managing, how the global pandemic impacted the food supply chain, and what excites him the most about the future of Netled and the vertical farming industry as a whole.
Listen & Subscribe
Season 3 Title Sponsor
If you are starting a vertical farm and don't know where to begin, or which technology would suit your needs, Cultivatd can help. As indoor farm brokers, they help connect you to the right technology and ensure your project is successful. Best of all, their service is free. They work on behalf of their partners.
Take a closer look
CubicFarm Systems Corp. Announces International Expansion Into Australia
Food production in Australia has been significantly impacted year over year by devastating wildfires and major flooding. Farming currently covers 385 million hectares, or 58 percent of Australia, and accounts for 59 percent of the water extracted
USD $2.7M Sale of Commercial
Scale Indoor Growing Systems
VANCOUVER, B.C., April 23, 2021 – CubicFarm® Systems Corp. (TSXV:CUB) (“CubicFarms” or the “Company”), a local chain agricultural technology company, today announced the sale of 18 modules of the CubicFarm System onsite indoor growing technology at a sale price of USD$2.7M. BoomA Food Group will operate the first commercial-scale vertical farm in Australia, positioning the company as a market leader BoomA Food Group will use these modules to grow commercial-scale amounts of produce in New South Wales, specializing in herbs and microgreens.
Food production in Australia has been significantly impacted year over year by devastating wildfires and major flooding. Farming currently covers 385 million hectares, or 58 percent of Australia, and accounts for 59 percent of the water extracted¹. Crops and horticulture in Australia are generally concentrated near the coast, while areas of New South Wales have been cleared at more than double the rate of the previous decade—and agriculture was responsible for more than half the area cleared.
“We searched the world over for the right sustainable growing technology to serve our communities in New South Wales and beyond. Australia has experienced the challenges of climate change, the devastating effects of drought, and significant impacts on our food production. CubicFarms’ patented technology is superior to other vertical farming options because it provides commercial-scale output while minimizing environmental impact and maximizing cost efficiencies,” said Cory Robertson, Managing Director, BoomA Food Group.
The CubicFarm System was purchased by BoomA Food Group with funding provided by Baillie Asset Management as trustee for the Pokolbin Vertical Farm Infrastructure Fund.
“I’m thrilled to announce our newest farmer partner in Australia, as the initial launch of our global markets expansion, bringing our technologies to another continent,” said Dave Dinesen, CEO, CubicFarms. “For a region that’s been devastated by natural disasters and food scarcity, our local chain ag-tech will empower local farmers to improve independent food production with predictable fresh produce 365 days a year. Our technology was founded by farmers as a solution to help farmers to succeed despite unpredictable outdoor growing conditions.”
Cory Robertson, Managing Director, BoomA Food Group, is an Australian Aboriginal social entrepreneur and business owner, as well as the Services Director of Goanna Services PTY Ltd. (“Goanna”), a company providing direct community access to contracts employing Indigenous peoples for environmental, government, and construction services.
Kevin Chandler, Chairman, BoomA Food Group, has extensive experience using business principles and practices to address community needs and improve opportunities for Indigenous youth. He is a psychologist and management consultant who founded and grew the Chandler Macleod Group into an AUD$1.5B company. Previously, Chandler was the director of Australian venture capital firm Nanyang Ventures.
Ben Macauley, CEO, Baillie Asset Management, has over 25 years of experience in accounting, finance, and C-level management across financial services, family office, not-for-profit, and banking/finance sectors. Baillie Asset Management has extensive experience in Australian agricultural innovations.
Footnote
¹According to the Government of Australia: https://www.agriculture.gov.au/abares/products/insights/ snapshot-of-australian-agriculture-2021#agricultural-production-is-growing.
About CubicFarms
CubicFarms is a local chain, agricultural technology company developing and deploying technology to feed a changing world. Its proprietary ag-tech solutions enable growers to produce high quality, predictable produce and fresh livestock feed with HydroGreen Nutrition Technology, a division of CubicFarm Systems Corp. The CubicFarms™ system contains patented technology for growing leafy greens and other crops onsite, indoors, all year round. CubicFarms provides an efficient, localized food supply solution that benefits our people, planet, and economy.
For more information, please visit www.cubicfarms.com.
On behalf of the Board of Directors
“Dave Dinesen”
Dave Dinesen, Chief Executive Officer
Neither the TSX Venture Exchange nor its Regulation Services Provider (as that term is defined in the policies of the TSX Venture Exchange) accepts responsibility for the adequacy or accuracy of this release. Certain statements in this release may constitute “forward-looking statements” or “forward-looking information” within the meaning of applicable securities laws including, but not limited to, statements with respect to CubicFarms’ expected revenue recognition and the completion of the sale and installation of the modules by the customer. Forward-looking statements are not guarantees of future performance and actual results may vary materially from those statements. General business conditions are factors that could cause actual results to vary materially from forward-looking statements.
For more information, please visit www.cubicfarms.com.
Media Contact:
Andrea Magee
T: 236.885.7608
E: andrea.magee@cubicfarms.com
Investor Contact:
Tom Liston
T: 416.721.9531
E: tom.liston@cubicfarms.com
Barton Breeze Launches Bank Guarantee For Hydroponic Farms
In an attempt to make hydroponic farming attractive to those interested in farming, Barton Breeze, a Gurugram-based agritech firm, has come up with an assured return plan with a bank guarantee
New Delhi | April 21, 2021
TV Jayan
In an attempt to make hydroponic farming attractive to those interested in farming, Barton Breeze, a Gurugram-based agritech firm, has come up with an assured return plan with a bank guarantee.
“A prospective investor will be able to get an assured annual return of 30 percent on his capital expenditure. We would operate the farm for them and sell the produce for them. If there is a shortfall in this return, the deficit would be paid by banks with whom we have entered into an agreement,” said Shivendra Singh, Founder, and CEO of the commercial hydroponic farming venture, which set up shop in India in 2017 after a successful run in West Asia.
Singh said the firm has already tied up with the State Bank of India and HDFC Bank for the bank guarantee scheme. Explaining the model further, Singh said not only progressive farmers, but HNIs and corporates would be able to reap benefits from this scheme.
“Hydroponic has several benefits for commercial farms. However, many customers are not completely aware of the environmental and financial contribution of it that makes them skeptical of investing in a hydroponic set-up. Our approach of providing a bank guarantee to B2B customers ensures a risk-free transaction. With this strategic step, we look forward to strengthening our relationship with customers,” said Singh.
“This a bit similar to contract farming, except that in this case, we take care of everything, including running of the farm. Unlike in contract farming where the farmer is having the liability and responsibility of growing the crop, we ensure that the crop is grown properly by being present at the farm on a continuous basis,” Singh told BusinessLine.
According to him, the capital expenditure involved in setting a one-acre hydroponic farm is around ₹1.1 crore, and with the government subsidies, this comes further down to around ₹85 lakh.
To make this attractive for urban dwellers interested in investing in farming, Barton Breeze plans to make it possible to invest as little as ₹5 lakh. He said a bunch of people can together and start a hydroponic farm, which his firm can help set up. There is no need to purchase the land as it can be taken on long lease, say, of 10 to 12 years. “We will ensure that they would get 30 percent or more returns on the investment annually,” said Singh. The bank guarantee will be available to the investors for three years initially, but this can be further renewed.
He said already a few farms are being planned in Delhi-NCR, Kolkata, and Indore in Madhya Pradesh under the bank guarantee scheme.
Singh said his young company has been growing exponentially in the last few years. Starting from a low base, the firm grew by eight times in 2017, six times each in two subsequent years. “Even in 2020, which was hit by Covid-19, we grew by 300 per cent,” he claimed.
Barton Breeze, which introduced hydroponic kits that can be used by city dwellers to grow vegetables in their terraces and balconies in the country a couple of years ago, normally grows off-season vegetables and greens to fetch a better price for their farmer customers.
Follow us on Telegram, Facebook, Twitter, Instagram, YouTube, and Linkedin.
You can also download our Android App or IOS App.
US: KENTUCKY - AppHarvest Continues To Expand Operations, Adds New Container Farm In Madison County
Some Central Kentucky high school students will soon be able to help grow food not only for themselves but the entire region
AppHarvest (WYMT)
By Brandon Robinson
Apr. 22, 2021
RICHMOND, Ky. (WYMT) - Some Central Kentucky high school students will soon be able to help grow food not only for themselves but the entire region.
On Thursday, officials with Morehead-based AppHarvest announced the expansion of their container farm program to Madison County High School in Richmond.
Watch Live Below:
Gov. Andy Beshear, who attended the event, appropriately held on Earth Day, said the move will not only provide food but help students prepare for possible careers in a field with growing demand.
“AppHarvest has been reimagining and reinventing sustainable food production at its state-of-the-art facility in Morehead. With the opening of the company’s container farm classroom at Madison Central High School, AppHarvest is showing its commitment to the Commonwealth runs both strong and deep,” said Gov. Andy Beshear. “This living, teaching lab will inspire and engage Kentucky students to learn about cutting-edge technology that will become the basis of the jobs of the future. Thank you to Founder & CEO Jonathan Webb and his team for making education and Kentucky students a priority in his plans for success.”
The container farm is 2,880 cubic feet, weighs 7.5 tons and includes space to grow up to 4,608 seedlings and 8,800 mature plants all at once using 440 vertical crop columns.
Each retrofitted shipping container serves as a hands-on agricultural classroom for students, allowing them to grow and provide fresh leafy greens to their classmates and those in need in their communities. The company has previously opened container farms in Eastern Kentucky at Breathitt High School in Jackson, Shelby Valley High School in Pikeville, and Rowan County Senior High School in Morehead, the site of the company’s flagship farm.
AppHarvest Founder & CEO Jonathan Webb said the latest expansion will not only help feed Kentuckians but will help Eastern Kentucky’s struggling economy.
“We knew long before opening our Morehead farm that we wanted to invest in the region to help grow our growers and build on the many outstanding community and education programs focused on creating a more resilient Appalachian economy,” Webb said. “The technology in each of these container farms is a good example of what AppHarvest’s modern farmers use daily on a larger scale.”
The Madison Central High School container program will be led by agriculture teacher and FFA adviser Derek Adams.
“Our students are looking forward to getting hands-on experience with state-of-the-art technology that will better prepare them for career opportunities in the agriculture industry,” Adams said. “They are especially eager to see the leafy greens come full circle from farm to table in their own school cafeteria.”
VIDEO: Growing Your Offtake With Minimal Marketing
The technology of the vertical farming industry is growing faster than the produce
The initial thoughts of any product-supplying business should answer the question; Who, what and where is my potential offtake?
You are about the produce the best product of current times. Marketing is key to grow businesses in ensuring success to those that sell their product and or services. “Marketing is to sales as plowing is to planting for a farmer”- Mary Ellen Bianco, well now, in vertical farming we don’t plow, is the necessity still applicable to extensively market the product?
The production approach at CAN-AGRI is focused on consumer satisfaction. We accomplish this with proper nutrient supply in turn producing a great tasting product with no harmful chemical sprays. Our hypothesis is; High-quality products with extended shelf-life and good presentation will sell themselves. We are proud to know that through our product we set new standards in quality and freshness, a fantastic product to use in restaurants and homes. It has been proven, growth cycle, after the growth cycle, with the greatest success.
The technology of the vertical farming industry is growing faster than the produce. There are many different target points, to name a few, i.e. lights, HVAC, vertical vs horizontal operations, stacking horizontal, and combinations thereof. The technology developers need to keep a continuous drive in the development and improvement. The fact that food insecurity becomes an ever more concerning issue aids in the justification why this should be one of the top fields in research and development.
The R&D outcome focus should enable the customer to produce an economically viable safe to consume fresh produce. CAN-AGRI’s (www.can-agri.com) approach to this is in the trailed and tested uniquely designed patented grow towers. The technology not only addresses the supply and demand orders but also achieves global targets in reducing the use of scarce resources coupled with a low carbon footprint accomplished by our “use of natural resources” approach.
Each facility is tailor-made to you, the clients’, comfortability, and needs. Depending on your conditions CAN-AGRI’s adaptability and flexibility in the facility make your system a success.
Farm 111, Klipkop, Graham Rd, Pretoria, South Africa.
Advances In Hydroponic Cultivation of Floriculture Crops
Advances In Commercial Hydroponic Cultivation of Floriculture Crops for International Markets
ITALY: Zero Farms Delivers Its Salads To Regional Supermarkets
This launch is proof that Zero farming is the solution to enable access to quality products for a wide range of consumers
After years of R&D by the company team, they're now aiming to create an ideal environment, combined with software and technologies for the aeroponically growing salads, arugula, aromatic herbs, and packaged microgreens. All crops are grown in a Pordenone-based production site. The formerly abandoned warehouse has a capacity of producing up to 30 tons per year.
"This launch is proof that Zero farming is the solution to enable access to quality products for a wide range of consumers." This is how Zero's CEO Daniele Modesto explains the entry into the Italian market. The company now presents its first products on the shelves of the Eurospesa supermarkets in Friuli Venezia Giulia and Veneto.
"We entered large-scale distribution starting with local groups, because we needed to take measures with some processes that were new to us. The processes had to be refined before going into national distribution groups," explains Daniele.
"It all started with a visit to the Expo Milano in 2015. What struck me most was a small glass cube that contained basil, arranged in multiple layers, illuminated by LED lights: the embryonic prototype of a vertical farm. From there on, I tracked down the designer and contacted him."
This appeared to be Paolo Battistel, one of Europe's greatest experts in soilless cultivation and today's scientific supervisor of Zero. He then told me what vertical farming comprised and that it would be a new frontier of agriculture. He said that it often clashes with the economic unsustainability of the project." Modesto then shared his idea with Andrea Alessio, owner of a company that deals with industrial photography with a strong passion for the product and the management of production processes."
In 2018, Zero was born in the Italian commune, Pordenone. Initially self-financed with the first partners, it later saw the first investments of other industrial companies in the area. At the beginning of 2021, the company entered the national and international agritech market as Zero Modular Architecture. This is a proprietary hardware-software technology to mass-produce, on an industrial scale, production plants in vertical farms. Namely, a transversal technological platform that involves the combination of standardized components, all produced independently by Zero, which is quickly assembled in disused industrial spaces regenerated into farms powered by clean energy.
Read more at Fruitbook Magazine (in Italian)
8 Apr 2021
Inside Inuvik’s New Hydroponic Greenhouse
Inuvik’s first all-season growing facility will soon be operational, offering residents year-round access to locally produced greens.
April 16, 2021
Inuvik’s first all-season growing facility will soon be operational, offering residents year-round access to locally produced greens.
Inuvik's hydroponic greenhouse is decorated with artwork by resident Adi Scott. Meaghan Brackenbury/Cabin Radio
The hydroponic greenhouse, in a trailer on land donated by Jesse and Keren Harder, is run by the Inuvik Community Greenhouse. Leafy veg like lettuce and herbs will grow using nutrient-rich water rather than soil.
“We have been working on this project for a long time, trying to get funding,” executive director Ray Solotki told Cabin Radio. “We want to be putting food in the community. We want to be hiring people in the community. We want to be doing things that are actually helpful to what our mandates are.
“This unit has been in the works with the hopes that we will produce enough food to see an actual tangible amount of difference in the communities, and also provide jobs here in Inuvik.”
Ray Solotki inside Inuvik’s community greenhouse in the summer of 2019. Ollie Williams/Cabin Radio
The greenhouse received more than $400,000 for the hydroponic facility from economic development agency CanNor last November. ColdAcre, a company that runs hydroponic greenhouses in Yukon, was contracted to construct it.
Another $100,000 from the territorial government will pay for a small solar farm to power the facility, which Solotki says will mean cheaper energy and lower-cost produce.
Solotki hopes the facility can grow as much as ColdAcre’s Whitehorse facility – about 500 lb of produce a month.
“If you consider how much spinach weighs, it’s not very heavy,” Solotki added. “That’s quite a lot of food to be bringing into the community.
Inside Inuvik’s hydroponic greenhouse. Plants are grown on shelves using nutrient-rich water that runs through a closed circuit. Meaghan Brackenbury/Cabin Radio
Kale, bok choy, Swiss chard, mizuna, and basil will be included in the greenhouse’s veggie box program, where members pay $20 a week and receive their share of the harvest. Some will be available at local grocery stores.
“I want this to be a case of once a week you get something that’s so fresh it was picked this morning, even when it’s minus-56 outside,” Solotki said.
Finding firm financial footing
The hydroponic unit will require a year-round staff member to operate it – a position Solotki said has been filled by an Inuvik resident – and offer more training opportunities for students and summer staff.
“We want to train kids from the ground up, literally, and teach them that this is a potential job,” she said.
The organization has received funding from the University of Saskatchewan for programs like bringing residents from smaller Beaufort Delta communities to teach them about hydroponics.
Shelving units inside the hydroponic greenhouse. Meaghan Brackenbury/Cabin Radio
“It doesn’t have to be in a shipping container,” Solotki explained. “You can take these out and put them in a school, you can put them in an office, you can do all sorts of things.
“But people need to understand how they work and see if it’s something they want to do.”
Meanwhile, produce sales from the hydroponic unit could help the greenhouse grow its commercial side.
Revenue that’s independently generated means less pressure to constantly fundraise, Solotki said, and could free up funding pots for other groups in the region.
“The amount of agricultural funding available per area is fixed, which means if I’m the one constantly tapping into it, other people can’t or might not have as many opportunities,” she said.
“If we could be utilizing it in better ways, and creating a better economy and creating more interesting things in the community, this is great for us.”
The greenhouse is currently seeking funding for an aeroponic facility – a system that suspends plants in the air and sprays them with nutrient-rich mist, which works well for heartier crops such as beans, potatoes, and peas.
Exploring what’s possible
Since the onset of the Covid-19 pandemic, agriculture and food security have become bigger discussions in the NWT.
Last June, a 50,000-pound donation of free potatoes to the NWT sparked debate about what northern food security should look like.
In February, three farmers in Hay River received funding for projects designed to help move the territory toward having an established agricultural sector. This month, the City of Yellowknife approved its latest food and agriculture plan after announcing a partnership with Wilfrid Laurier University to create a food hub in the city.
In Inuvik, Solotki concedes that leafy greens “won’t solve the problems of caloric intake and what you actually require for food security” – but she argues the hydroponic facility will allow the community to re-evaluate what is possible in the realm of Arctic agriculture.
“This is an idea that starts to change people’s mindsets: that we don’t have to buy from out-of-territory,” she said. “We don’t have to ship it in, we could actually do it ourselves.
“While the hydroponics is not going to be the be-all and end-all, wouldn’t it be cool to see community greenhouse hydroponics, sitting next to community greenhouse aeroponics, sitting next to the greenhouse chicken coop, sitting next to the pig barn, sitting next to the cow barn… having an actual agricultural sector that is utilizing what we need to work in our climates?”
New Freight Farms Greenery S Ushers In The Next Era of Smart Small-Space Farming
Five Specialized Systems Allow Farmers to Grow Food 365 Days a Year With Complete Control
Five Specialized Systems Allow Farmers
To Grow Food 365 Days A Year With
Complete Control
NEWS PROVIDED BY
April 21, 2021
BOSTON, April 21, 2021 /PRNewswire/ -- Earlier this month, Freight Farms, the world's leading manufacturer of container farming, unveiled its new container farm, the Greenery S. This latest model is the tenth generation of the technology since the company pioneered the small space farming concept in 2013.
The Greenery S features an exceptional new farm design which, when paired with seamless automation, unlocks powerful performance for all users. The Greenery S combines specialized space, light, air, water, and control systems to make it possible to grow 2.5 acres-worth of food in 320 square feet anywhere in the world.
Always keeping the farmer in mind, the Greenery S implements feedback drawn from in-depth customer research to execute an exceptional new farm design which, when paired with seamless automation, unlocks powerful performance for all users. The Greenery S combines specialized space, light, air, water, and control systems to make it possible to grow food anywhere in the world, thereby empowering individuals to grow food locally within their communities to decentralize the global food system.
"The Greenery S brings an entirely new level of design, control, robustness, and ease of use to our already industry-leading growing platform. It is built upon the technology we have developed over the past ten years while introducing a fresh suite of features. This farm is not just a refinement of our past models – it redefines what it means to be a farmer," said Freight Farms co-founder and COO Jon Friedman. "With the Greenery S, we hope to further simplify the process of farming to make the profession as accessible as possible to people around the world."
Industry-Leading Features for Design, Automation, and Performance
Of all the Greenery S features, the most notable are the re-imagined workspace, the enhanced farmhand® automation software, and the dynamic new proprietary LED technology.
All-New Workstation - User-Centric Design
As Freight Farms continues to define and refine what a farm can be, the company focuses specifically on optimizing workflow for their farmers with an all-new Workstation, a sleek, self-contained, and multi-functional farm command center.
Technical components – water and nutrient tanks, dosing panel, pumps – are hidden from view yet easily accessible with a simple push-to-open mechanism for instant access.
The 'Tabletop Riser' separates the workstation into two workzones, and includes an integrated, multi-functional LED bar (for tabletop illumination, plant spacing guidance, and task timing) and four full-range Bluetooth speakers.
Farmhand® Recipes - Network Learning & Automation
The latest release of Freight Farms' companion farming software–farmhand®–takes automation to the next level with the new Recipes feature.
Recipes allow farmers to achieve consistent harvests with the touch of a button: Operators simply choose the crop they wish to grow and farmhand automatically adjusts in-farm settings to optimize for that crop production.
Recipes are built by aggregating farmer network data and determining patterns that lead to exceptionally successful harvests; meaning the list of recipes will grow as the global Freight Farmer community continues to expand.
Dynamic Lighting Control - Power & Precision for Performance
The Greenery S takes a huge leap in LED technology by allowing farmers to customize the lighting spectrum, intensity, and duration of light to achieve their desired plant yields.
The Greenery S features Freight Farms' proprietary LEDs, which emit light with 60% greater intensity and 50% better efficiency compared to off-the-shelf options.
Farmers have precise control over their lights with brand new Eco (prioritizing farm efficiency by reducing power consumption), Performance (prioritizing plant growth for greater yields, and Standard (balances the two) modes.
The Most Versatile Platform in the Indoor Farming Industry
The accessibility and versatility of the Freight Farms platform allow customers to use it in a diverse range of locations and applications. The Greenery S is built with the same specifications as a standard 40-foot shipping container, making it possible to bring and install the farm in any location, such as a city center, tropical island, or area experiencing food insecurity. Once at its location, the 320 sq. ft. container becomes a commercial growing space, capable of producing 2.5 acres worth of fresh food every year. The farm's elite design, in combination with farmhand®, robust training, and access to an elite support team, ensures anyone can run a successful operation without any prior farming experience.
Freight Farms currently services more than 500 trained farmers across 48 U.S. states and more than 32 countries. For more information, visit freightfarms.com.
About Freight Farms:
In 2013, Freight Farms debuted the first vertical hydroponic farm built inside an intermodal shipping container with the mission of democratizing and decentralizing the local production of fresh, healthy food. Now with the Greenery S and integral IoT data platform, farmhand®, Freight Farms has the largest network of connected farms in the world, with global customers in 32 countries and 48 U.S. states ranging from entrepreneurs and small business farmers to corporate, hospitality, retail, education, and nonprofit sectors. To learn more, please visit freightfarms.com, or visit us on Instagram, Twitter, or Facebook.
Media Contact:
5WPR
Carinna Gano, Account Supervisor
cgano@5wpr.com
SOURCE Freight Farms
Related Links
USA: This Colorado Company Is Building Farms In Shipping Containers To Help Feed People In Need
FarmBox Foods wants people to be able to farm anywhere, allowing them to access fresh food they otherwise wouldn't be able to
Author: Jeremy Moore
April 19, 2021
FarmBox Foods Wants People To Be Able To Farm
Anywhere, Allowing Them To Access Fresh Food
They Otherwise Wouldn't Be Able To
SEDALIA, Colo. — A three-year-old Colorado company has an ambitious goal: to bring food security, safety, and sustainability to communities in need around the world.
FarmBox Foods aims to achieve that goal by connecting those communities to sustainably sourced food that's grown locally inside one of their container farms.
Their first product was a vertical hydroponic farm, or VHF, built inside a shipping container.
The company has since developed a second product: a gourmet mushroom farm, or GMF.
So far, customers in Colorado include Centura Health, Vitamin Cottage Natural Food Markets, and the C Lazy U Ranch in Granby.
FarmBox CEO Rusty Walker and COO Jake Savageau joined 9NEWS to talk about how they hope to change the way the world thinks about farming.
9NEWS also spoke with a prospective customer of FarmBox, Cori Hunt of the Denver restaurant group Edible Beats.
(Editor’s note: Responses have been edited for context and clarity.)
As a mission-driven company, what is the mission of FarmBox Foods?
Walker: Our goal and our mission is to get our products out into the communities where we can help develop food security programs. We’re looking to get into food deserts, opportunities where folks in the world might not have access to good, clean nutritional food. And so we kind of strive as a company that’s driven to feed the world one container at a time. And we’re ready to go out and manufacture thousands of these if we can.
We’re able to decentralize growing food by being mobile – being able to deploy these by just having a semi come in. We can then lift it up on a flatbed and take it to anywhere in the world. We’ve got two containers going to islands. We’ve got our first container that took off for the island of Jamaica. It’s going to Montego Bay where it’s going to be used behind mega marts on the island. And then we have another container which is our gourmet mushroom farm that’s going to be going to Tahiti where they’re going to be using that to feed the island population which does not have access to that type of food.
One big area that we’re really focusing on is the urban areas throughout the U.S. where they don’t have a lot of land to grow. These farms can go right into the parking lots, behind a church for example. We’re working with a community church on the south side of Chicago that’s looking at placing two of these containers – a vertical hydroponic farm and a mushroom farm – right outside in the parking lot outside the church.
And we think we could bring an educational spin to this where we can have the community grow their own food and supply the community themselves with highly nutritional food that ordinarily they just would not be able to get their hands on. So, we’re thinking that if this pilot program goes well this would be an application that would apply to every inner city throughout the U.S.
Farmbox Foods grows vegetables in shipping containers. Credit: Jeremy Moore, KUSA
Savageau: The mission’s always been to create products that are for the decentralized food insecurity industry. So, we want to create a product that can be deployed anywhere in the world, can run off-grid, and can feed communities. So, we have two different products – the VHF and the GMF. Every product that we develop gets us one step closer to being able to feed a community with everything they need, because you can’t feed communities forever just on leafy greens.
So mushrooms, they’re more nutrient dense, that gets us one step closer. There’s other products that we’re going to develop to get us to that point. But, I think the mission for the company is to be able to deploy these farms into communities where they’re needed, whether that’s a rural area, a food desert in the U.S., an inner city, or somewhere in Africa like Ghana or the Sudan.
We want to align with big ag and we want to help the industry get better. So we want to get food to where it’s needed. We’re looking at doing stuff with food insecurity and food inequality. That’s big with what we’re doing. So, that kind of aligns with our mission. If you look at our food system – just take for instance – you know if you look at a SNAP program or food subsidy program – you’re taking food and giving it to somebody or they’re purchasing it.
But, a lot of that food that they’re purchasing is processed, sugar – I mean, it’s poison. And if you go on a military base anywhere in the U.S., there’s fast food on the base. It’s really what you see. So, there’s a lot of reasons why we’re doing this I think. We can help fix our food system. And we can help educate the youth on how they should eat. We’re doing some stuff with an Inuit community in Alaska. They don’t necessarily know how to fix this food or prepare it or use it. So, I think education is a big part of what we’re doing.
How do these container farms work?
Savageau: When people think of farms, they don’t think of agriculture like this. Vertical hydroponics and indoor ag and controlled environments – it’s been around for a long time. I think that the way that this one works is pretty simple. The water gets fed into a tube system and the water trickles down and goes back into the tank. And where you’re standing – the seedling tray area – the water goes into a tank, into the seedling trays, gets flooded, and then back into the tank.
There’s a software that we use called Agrotech that monitors the temperature, the humidity, the lights – basically, all automated. So, it’s fairly easy to run. You need about 15 to 20 hours a week to run one farm. The GMF farms takes about 25 hours a week. It’s a little bit more intensive. The VHF is the vertical hydroponic farm and that’s the farm that we’re standing in. The GMF is the gourmet mushroom farm, which is the one that you went through earlier. You want to just keep things as clean as possible. The cleaner that you keep it the better it’s going to run.
So, we have a standard SOP, you know, that we implement with our training. Cleaning the floors. Cleaning the tubes. You don’t clean them every time. But, usually, every couple harvests you’ll take the tubes out, wash them out. You’re cleaning the tanks about every 60 days.
But, on average it’s pretty easy to maintain if you’re doing the daily checklist. The seeds are going to be in the seedling tray for about two weeks. Then, they go into the wall. And then they get harvested about 60 days after they start in the seedling tray. So, on average you’re about 60 days from seedling to harvest depending on what you’re growing.
And this farm is really setup for vertical hydroponics. So, it’s leafy greens. You can do hundreds of different types of lettuce. You can do cherry tomatoes, strawberries and peppers. There’s a lot of different things that you can grow in here. Most of our clients are only growing a couple things at one time. You don’t have to worry about weather. You don’t have to worry about if this is in a cold climate like the arctic. You know, they can’t grow food. If it’s in a desert, they can’t grow food. If it’s on an island, they can’t grow food. So, these can be deployed anywhere. And they grow 365, all day, every day. Also, the yield is very high for the square footage. So, you can put these on top of a building, inside of a building. It only takes up 320-square feet. You don’t have any pesticides. So, you don’t have to worry about pests, bugs, mildew, stuff like that’s going to effect the plant as it’s growing. It’s also decentralizing the food system.
So, you’re not having to ship food hundreds of thousands of miles from point A to point B. So, the food is right there. And the nutrients that we use are organic plant-based nutrients. And there’s no pesticides. So, the nutrient density is extremely high compared to something that you would buy – even organic – in a store.
Walker: We grow a variety of vegetables and lettuces. I believe that we’re somewhere in the area of 30 to 40 different types of vegetables and lettuces that we can grow in our farms. And, then of course we’ve got our gourmet mushroom farm which we’re currently growing anywhere from eight to nine different varieties of mushrooms. We’re in the startup phase of running that farm ourselves. So, we’re exploring the different types of mushrooms that we can grow. But, we’re very proud of the folks that are actually running these farms – our staff, very knowledgeable and they do a great job. We’re going upwards to 300 to 400 pounds a week now. We’re not competing with traditional farming. We’re actually a compliment.
Who are your customers?
Walker: One of our first customers is Centura Health. They purchased their first container – which is now sitting at St. Mary’s in Pueblo. They ordered two more containers after seeing how the first container behind their hospital worked. We actually started up a pilot program with Centura Health where we’re now running them as the FarmBox family.
We’re working with Centura Health in identifying not only their hospitals and the patients who are going to be fed through our vertical farm – but then we’re also identifying where the food deserts are and Centura Health will then help us with what we’re going to be growing, and then the communities that we’re going to be serving from those, those particular crops.
We do have a couple that’s looking at doing some farming right here in Sedalia. They’re going to use it to supplement their traditional farming, which will be an interesting pilot program for us to work with them on. We’re working with C Lazy U Ranch out of Granby, Colorado. They’ve ordered a hydroponic farm and we’re going to be manufacturing that. And they’re going to place that at the ranch. They don’t really have access to a lot of good food as far as having it grown right there on the property. So, this will be a nice compliment to the services and the customer experience that they provide their customers by having one of our farms right on site.
Centura Health is one of FarmBox Foods' first customers. Credit: Jeremy Moore, KUSA
One big area that we’re really focusing on is the urban areas throughout the U.S. where they don’t have a lot of land to grow. These farms can go right into the parking lots, behind a church for example. We’re working with a community church in the south side of Chicago that’s looking at – we’re looking at placing two of these containers – a vertical hydroponic farm and a mushroom farm right outside in the parking lot outside the church.
We can have the community grow their own food and supply the community themselves with highly nutritional food that ordinarily they just would not be able to get their hands on. So, we’re thinking that if this pilot program goes well this would be an application that would apply to every inner city throughout the United States.
Savageau: We have a customer here in Lakewood that’s going to put one in their backyard. They run a small organic farm. We’re looking all the way up into federal government and military, and everything in between.
So, Rusty was talking about FEMA, the UN, UNICEF, those are the big customers that take a long time to build a relationship with. And then we have customers that are all the way down to just an individual that wants one for their property or maybe a couple of people are going to run one for a restaurant or a developer wants one for a small development that he’s doing.
We’re working with a group in New Mexico and they’re building a huge development of about 45,000 houses. So, we’re talking about 100 of these units that are going to be deployed in that area right outside Albuquerque to feed those communities within that area over the course of about two years. We work with a grocer that’s regional. And we work with some other customers that are kind of at a government, federal government level.
I think we’ve done a lot in the last three years. I mean we haven’t gone out and raised any capitol. So, we’ve self-funded it. And I think from that point of view you know we’ve done a lot. We’re kind of at the point right now where we’re just starting to scale. So, we’ve just started our social media. You know SEO (search engine optimization), SEM (search engine marketing). We have a sales team. And orders are starting to come in. We’ve partnered with RK which is manufacturing our units. That’s giving us the ability to scale. Because before that we were building these one or two at a time in Sedalia and now we can build 100 of them. So, that’s really been a huge part of us being able to scale is the manufacturing side.
How much does it cost to purchase and operate the farms?
Jake: This VHF farm – vertical hydroponic farm – starts at $140,000. The GMF starts at $150,000. Then, you have training and deploy, getting it there. So, usually, you’re over $150,000 for a farm. So, your ROI (return on investment) in this product is going to be about 12 months to 24 months depending on what you’re growing and where it is in the world.
The GMF is going to be closer to 12 months because mushrooms tend to be more expensive – again – depending on where it’s going. We have a unit that’s going to Tahiti for example. That ROI is going to be extremely fast because they ship everything in. If there’s a market for mushrooms there, which there is with a grocer, it’s going to be quick. So, the cost of running it with labor and everything you need to grow the plants, usually around $20,000 to $40,000 a year. We’re a mission-driven company. So, money isn’t the first thing that’s important. We want to build a certain amount of these and then every x amount that we build, we build one for free and we send it to a community that maybe our social media has engaged with or given us an idea that ‘hey, this would be a good community.’ And then, we send it there. We pay for it. We train people. And that’s something that we want to do. We can’t do it yet. But, I think that’s coming in the next year.
Why is Edible Beats interested in working with FarmBox?
Hunt: We try to be as local and organic as possible and that’s what brought us here to FarmBox. We can put a box behind a restaurant and have lettuces cut and washed and put on the plate the next day.
Just to have that connection with our food and know exactly where it’s coming from and how it was produced. It’s going to be better quality because it’s not traveling. It’s not ripening in a truck coming from Mexico. Economically, what we can do to not pay the mileage on the vehicles and the gas, the inputs, the emissions, the extra packaging, the plastics.
That’s one of the best things about FarmBox – that what we can do is – if we produce food for our restaurant group – I’m not going to have to buy packaging that’s going to go into a landfill or even need to be recycled. It’ll go directly into the vessels that we’re going to store them in the cooler. We don’t have to worry about marketing and labeling and you know stickers and plastics and all this extra stuff – this hoopla that we don’t need – because FarmBox is a possibility now.
The Farmbox Foods containers allow leafy greens to grow vertically, maximizing space.
Credit: Jeremy Moore, KUSA
We are looking at lettuces and herbs, leafy greens. So yeah, like basils, sage, leaf lettuces, butter lettuces, arugula – these kinds of things that we use that could greatly help our impact. Essentially it’s a self-contained box that you can grow fruits and vegetables in – most likely leafy greens – and it’s a soilless or near soilless medium.
So, essentially you plant your seed in a very small amount of coconut core or soil or peat moss – something to hold the root structure – and that, according to with FarmBox, they’re system is a vertical farming.
So, they have vertical towers and then they put the lettuces in the towers in their small soil medium and then they drip water with enhanced nutrients mixed into the water specifically built for those vegetables. It doesn’t have a lot of soil waste.
For the amount of the surface area you can get way more production out of it and the water that goes through is recycled. Per plant, it uses far less water than any other type of growing system.
RELATED: Why Colorado agriculture groups oppose Initiative 16, an animal cruelty proposal
Foundation Farms Corp., Announces Vertical Farm Out For Delivery
The turnkey farm package has left the ZipGrow manufacturing facility for arrival at the Red Deer area site this week
April 20, 2021
NEW YORK, NY / ACCESSWIRE / April 20, 2021 / Foundation Farms, Corp., ("Foundation Farms") a subsidiary of GME Innotainment, Inc. (OTC PINK:GMEV) today announced confirmation of delivery and installation dates for the first of its many vertical farms. The turnkey farm package has left the ZipGrow manufacturing facility for arrival at the Red Deer area site this week. The installation crew is scheduled to arrive on-site next Monday and assembly and commissioning will be completed next week. Production of the first crop will begin on May 1.
Management is also excited to report that each of the company's vertical farms will become local community food hubs known as E-ROOTS CENTRES. In addition to selling its own vertical farm produce, each E-ROOTS CENTRE will buy other locally grown food products from farmers wholesale and then package, market, and distribute the locally grown food products to corporations, families, schools, restaurants, caterers, sports teams, and stores, maintaining economic growth in the community. These E-ROOTS CENTRES will develop health food brands utilizing local produce to promote nutritious diets. Mechanisms for dispatch and delivery logistics are included.
Ed Kroeker, CEO of Foundation Farms stated, "The installation and startup of our first E-ROOTS CENTRE is a wonderful milestone achievement but what I am even more excited about is the interest we are getting throughout North America from prospective joint venture partners and host communities. Demand is even greater than we anticipated. Projects are aggressively underway in Minneapolis-our important entry point for the United States as well as Regina, the Greater Vancouver Region, and the Greater Toronto Area, with the list of projects growing weekly."
Yves R. Michel, GMEV CEO applauded the milestone achievement this week and further added, "Food sustainability and reliability have become two of the most important goals within North American communities today. Foundation Farms has developed a business strategy that provides the components as well as the assembly, packaging, and distribution systems to achieve those goals in every community serviced by E-ROOTS CENTRES."
Yves R. Michel
Chief Executive Officer and Director
208 East 51st St., Suite 170
New York, NY 10022
Source: GME Innotainment, Inc. ("GMEV")
www.srcorpgroup.com/
Released April 20, 2021
OTCPink:GMEV
This press release may include certain statements that are forward-looking in nature and that involve a number of uncertainties and risks. Such forward-looking statements are within the meaning of that term in Section 27A of the Securities Act of 1933, as amended, and Section 21E of the Securities Exchange Act of 1934, as amended. The forward-looking statements in this press release are based on GME Innotainment, Inc., current expectations and projections regarding future events, which are based on currently available information. The forward-looking statements in this press release may also include statements relating to GME Innotainment, Inc.'s anticipated new developments, business prospects, financial performance, strategies and similar matters. GME Innotainment, Inc. disclaims any obligation to update any of its forward-looking statements, except as may be required by law.
SOURCE: GME Innotainment, Inc.
GME Innotainment, Inc.
USA: FLORIDA - The Villages Grown Passes On Expertise
By Michael Salerno
Daily Sun Senior Writer
April 20, 2021
The intersection of agriculture and wellness is now expanding. The Villages Grown, the community’s farm-to-table initiative, is building on its relationship with the University of Florida through its agricultural, health, and culinary programs. Villages Grown Executive Director Jennifer Waxman recently announced The Villages Grown became the local produce supplier for UF’s campus in Gainesville. Both The Villages Grown and UF’s Institute of Food and Agricultural Sciences
(UF/IFAS) are working together on research concerning controlled-environment agriculture, which involves crops growing in climate-controlled settings for the best possible growing conditions. Waxman described The Villages Grown as a leader in this practice.
She also revealed plans are in the works to train master gardener volunteers from UF/IFAS’s extension office, who would pass on expertise to residents on how to use hydroponic gardening to cultivate nutrient-dense produce.
“This is really going to help us grow the most nutrient-dense crops you can have access to, to strengthen the food as medicine approach,” Waxman said. “The partnership with UF will help extend our educational offerings with health and gardening to fulfill that thirst for knowledge that we don’t have the bandwidth for.”
Fresh and Local on Campus
The Villages Grown’s produce is now a part of the menu offerings of UF’s on-campus dining through a partnership with the university’s Gator Dining Services.
Diners may expect the full line of produce including microgreens, lettuce, herbs, tomatoes, and cucumbers, Waxman said.
“It’s really bridging agriculture, culinary, and health together, which is what The Villages Grown’s model was built after,” she said.
Gator Dining’s partnership with The Villages Grown builds on a food service program that already was Florida-centric.
Its other Florida suppliers include the Hilliard aquaponics facility Traders Hill Farm, Orlando milk factory T.G. Lee Dairy, Ormond Beach plant-based food producer PAOW! and Lake Mary sausage maker Nettles Sausage.
Agriculture Industry Research
The Villages Grown’s position as a leader in controlled-environment agriculture, also known by its acronym CEA, allows it to be at the forefront of research on the subject.
And that’s what’s happening now, as UF/IFAS researchers seek to learn more about the processes involved and whether it’s economically viable for large farms.
There’s a great interest in controlled-environment agriculture in the private sector, said Jeanna Mastrodicasa, UF/IFAS associate vice president of operations. That interest translates to abundant research opportunities with The Villages Grown and other CEA agribusinesses.
“I’d like to see how well it works,” she said. “We simply don’t know well enough about it, most of agriculture in Florida has been in open fields.”
The Villages Grown depends on controlled-environment greenhouses utilizing vertical hydroponics — a process that uses vertically stacked towers to plant and grow more crops on less land — to grow its line of crops.
It also operates a nutrient tank system that sends a recipe of nutrients from a tank in a utility room through a drip irrigation system, said Adam Wright, The Villages Grown’s director of operations.
Waxman described The Villages Grown as the Southeast’s largest controlled-environment agriculture operation of its kind, made possible by the diversification of its crop offerings.
“There’s a lot of large CEAs that only grow lettuce,” she said.
Expanding Education
But people don’t need large greenhouses to grow vegetables and herbs hydroponically.
That’s something Waxman thinks master gardeners could teach residents. She said she’s working with UF/IFAS on training master gardener volunteers about concepts such as hydroponic growing to cultivate nutritious food.
The commercial needs of The Villages Grown don’t allow its staff much time to teach residents about hydroponic gardening. That’s where trained volunteers would come in, Waxman said.
“We want them to be an extension of The Villages Grown and help them get info out to them on their behalf,” she said.
It’s a philosophy echoed by local UF/IFAS staff, who see trained master gardeners as an extension of themselves, on a mission of helping their communities.
“Having volunteers associated, that will be a great part of it,” said Jim Davis, extension director with the UF/IFAS Sumter County Extension Office.
It helps that involvement in the master gardener program historically has been very strong in The Villages, Mastrodicasa said.
“New people to Florida want to learn about what they can grow in Florida,” she said. “There’s so much opportunity. Just the idea you can have more than one growing season in a year is different. Most places in the country have one.”
Building a Healthier Community
The ultimate goal of The Villages Grown and UF’s expanding relationship is simple: building a healthier community.
That may mean supplying the freshest and most nutrient-rich vegetables possible, or teaching people how they can grow them themselves.
It also explains why The Villages Grown develops blends of microgreens for hospitals, for example, to help those suffering from cardiovascular issues, Waxman said.
For The Villages Grown’s staff, relationships like those with UF make it possible to cultivate nutrient-dense produce in an affordable and accessible way, Waxman said.
“You can’t be a lone ranger,” she said. “Or you’ll be out of business.”
Senior writer Michael Salerno can be reached at 352-753-1119, ext. 5369, or michael.salerno@thevillagesmedia.com.
Lead photo: The Villages Grown assistant director of production, Rachel Skiles, checks the tomato plants to make sure everything is on track inside a greenhouse at the facility. Michael Johnson, Daily Sun
Feeding A City From The World’s Largest Rooftop Greenhouse
The world’s largest rooftop greenhouse is in Montreal, Canada. It measures more than 15,000m2 and produces more than 11,000kg of food per week. The company behind it had to hire 200 new employees due to pandemic-driven demand
The New Greenhouse Will Accelerate Lufa’s Mission To Grow Food
Image: REUTERS/Mariana Bazo
20 Apr 2021
Senior Writer
The world’s largest rooftop greenhouse is in Montreal, Canada.
It measures more than 15,000m2 and produces more than 11,000kg of food per week.
The company behind it had to hire 200 new employees due to pandemic-driven demand.
Can you grow enough produce for an entire city in rooftop greenhouses? Two entrepreneurs in Montreal, Canada, believe it might be possible.
Lauren Rathmell and Mohamed Hage cofounded Lufa in 2009. The company has four urban gardens in the Canadian city, all in rooftop greenhouses. Lufa’s most recent sits on top of a former warehouse and measures more than 15,000m2 – larger than the other three greenhouses combined. Its main crops are tomatoes and aubergines, producing more than 11,000kg of food per week. It is, the company says, the largest rooftop greenhouse in the world.
Lufa says its new rooftop greenhouse in Saint-Laurent, Montreal, is the largest in the world. Image: Lufa
An ambitious goal
Rathmell says the new greenhouse will accelerate Lufa’s mission to grow food where people live and help it to meet an “ever-growing demand for fresh, local, and responsible foods”.
The company – which says it’s not trying to replace local farms and food makers, acknowledging that not everything can be grown on rooftops – follows what it calls ‘responsible agriculture’ practices. These include capturing and recirculating rainwater, energy-saving glass panels, and an absence of synthetic pesticides. Any waste is composted and reused, and food is sold directly to customers on the day it is harvested. Lufa also has a fleet of electric vehicles to make those deliveries.
“Our objective at Lufa is to get to the point where we’re feeding everyone in the city,” Hage said in an interview in Fortune. Lufa’s fifth greenhouse is due to open later in 2021.
At the moment, Lufa grows food for around 2% of the city’s population. While that might sound like a modest proportion, interest in urban agriculture is on the rise. Presently, agriculture in urban areas tends to be more common in developing countries. But the UN Food and Agriculture Organization (FAO) favours an increase in urban agriculture, saying it can have “important benefits for food security”.
Urban farming is often more common among poorer members of society. Image: UN FAO
A growing global trend
Urban agriculture has been taking off in other parts of the world in recent years, too – from shipping containers in Brooklyn, New York City, to allotments in unused spaces in Brussels, Belgium.
And at 14,000 m2, there’s Nature Urbaine in Paris – which claims to be the world’s largest urban rooftop farm. Nature Urbaine rents out growing space to Parisians who want to grow their own crops. Tenant farmers pay around $450 per year per 1m2 sized plot. They get a welcome pack with everything they need to start growing, as well as regular access to the Nature Urbine gardening team who are on hand to offer advice and support.
Lufa produces more than 11,000kg of food per week, including tomatoes and aubergines. Image: Lufa
Lufa’s first greenhouse was opened in 2011, in Montreal’s Ahuntsic-Cartierville borough, to grow herbs, microgreens, cucumbers, and peppers. Two more were added in 2013 and 2017, with the fourth joining last year. It sits on top of a former Sears warehouse in the Saint-Laurent area of the city.
In addition to its own produce, Lufa also sells a selection of other locally made or grown food, including bread, cheese, and drinks to its customers. Rising demand for its service, in the wake of the pandemic, led to the company hiring an additional 200 people, and partnering with 35 new farmers and food makers.
Have you read?
This Belgian start-up allows anyone to become an urban farmer
This illuminated field isn't just pretty - it's helping to grow crops
Grow your own: Urban farming is flourishing during the coronavirus lockdowns
License and Republishing
World Economic Forum articles may be republished in accordance with the Creative Commons Attribution-NonCommercial-NoDerivatives 4.0 International Public License, and in accordance with our Terms of Use.
USA: New Farm Brings Sustainable Farming To Northern Michigan
There's a new farm in northern Michigan that provides fresh and local produce all-year-round using environmentally friendly practices and high-tech resources. The container is home to Pine Hill Farms, a farm that uses a controlled environment agriculture system to grow produce
by Miya Ingle
April 16, 2021
To View The Video, Please Click Here:
Pine Hill Farms uses a controlled environment agriculture system to grow produce. (Miya Ingle/ WPBN)
KALKASKA COUNTY, Mich., (WPBN/WGTU) -- There's a new farm in northern Michigan that provides fresh and local produce all-year-round using environmentally friendly practices and high-tech resources.
If you're driving down Tower Road in Kalkaska, you might notice a big container.
The container is home to Pine Hill Farms, a farm that uses a controlled environment agriculture system to grow produce.
The produce is grown hydroponically instead of in the ground.
Staff at Pine Hill Farms say this growing method uses 95% fewer resources than traditional farming.
"Some of the biggest benefits to growing hydroponically versus in a traditional manner is number one; we can grow year-round, 365 days a year," Pine Hill Farms Founder Jeff Bickley said. "Number two, we're hyperlocal. Local is a really big deal. People want to support local businesses. They also benefit from the difference in freshness."
Pine Hill Farms is currently growing nine different kinds of lettuce but plans to expand its products in the future.
The farm is connecting with local restaurants to sell its produce to.
Early Bird Registration Now Open For In-Person Orlando 4-5, 2021 Edition
We're excited to return to our live, in-person format for the October 4-5, 2021 edition of the premier event for indoor|vertical farming and look forward to seeing all of our industry friends again!
Indoor Ag-Con
INDOOR AG-CON IS LIVE FOR 2021...
EARLY BIRD REGISTRATION IS, TOO!
We're excited to return to our live, in-person format for the October 4-5, 2021 edition of the premier event for indoor|vertical farming and look forward to seeing all of our industry friends again!
SAVE WITH EARLY BIRD REGISTRATION RATES!
EVERYTHING YOU NEED TO GROW YOUR BUSINESS
UNRIVALED EDUCATION
CEO keynotes. Well-rounded panel discussions. Take a deep dive into 3 comprehensive track topics: Business & Marketing, Science & Technology, Alternative Crops.
SEE SCHEDULE
EXPANDED EXPO FLOOR
Explore a show floor filled with industry innovations, breaking trends, and best-sellers from some of the biggest names in the indoor agriculture | CEA industry and emerging leaders, too.
EXHIBITORS
A BUSINESS VACATION!
Ready to get back out there?! Centrally located, our fabulous Hilton Orlando venue is the perfect place for a business vacation - and we've got some great hotel discounts for you, too!
HOTEL SAVINGS
BEST VALUE FOR YOUR TIME & MONEY!
We're so confident you will benefit from your experience that we guarantee your registration fee! Get your money's worth... or get your money back! This guarantee covers your registration fee but not travel, hotel, or any other expenses incurred. Learn more...
REGISTER NOW & LEARN MORE!
YOUR PASS INCLUDES
Access to all conference sessions and exhibition floor
Cocktail receptions
Lunch Daily
Access to Indoor Ag-Con Library
Mobile App
SPECIAL THANKS TO OUR INDOOR
AG-CON SPONSORS,
MEDIA & MARKETING ALLIES
Indoor Ag-Con, 950 Scales Road, Building #200, Suwanee, GA 30024, United States
Sustainable Impacts Indoor Farming May Have On Environment
This article identifies the potential environmental effects large-scale indoor farming may have on air, water, and soil. We begin with an overview of what indoor farming is with a focus on greenhouses and indoor vertical farms (eg, plant factories)
Mar 18, 2021, | Knowledge Base, Learning, Research Paper
By Center of Excellence
Figure 1. Map of research and knowledge domain of indoor farming.
Abstract
This article identifies the potential environmental effects large-scale indoor farming may have on air, water, and soil. We begin with an overview of what indoor farming is with a focus on greenhouses and indoor vertical farms (eg, plant factories). Next, the differences between these 2 primary methods of indoor farming are presented based on their structural requirements, methods of growing, media, nutrient sources, lighting requirements, facility capacity, and methods of climate control. We also highlight the benefits and challenges facing indoor farming. In the next section, an overview of research and the knowledge domain of indoor and vertical farming is provided. Various authors and topics for research are highlighted. In the next section, the transformative environmental effects that indoor farming may have on air, soil, and water are discussed. This article closes with suggestions for additional research on indoor farming and its influence on the environment.
Citation
Stein EW. The Transformative Environmental Effects Large-Scale Indoor Farming May Have On Air, Water, and Soil. Air, Soil and Water Research. January 2021. doi:10.1177/1178622121995819
Introduction
Open field farming has been practiced the same way for centuries as the primary means of growing food. Its origins can be traced back to wheat production 11 000 years ago in the Middle East, which later spread to the Mediterranean, North Africa, and elsewhere.1 Given limitations on the amount of arable land, water scarcity, increased awareness of sustainable development, and the well-documented environmental effects of open-field agriculture, other farming methods have been developed in the past few decades. The primary alternative to open field farming is referred to as indoor farming, which has received relatively little attention in terms of environmental impacts. The goal of this article is to introduce indoor farming in its many forms to environmental scientists, outline key areas of research, and highlight the effects large-scale indoor farming could have on the environment. Research needs to be done to better understand the cumulative and transformative environmental effects indoor farming methods may have on water, air, and soil as it realizes its potential to supply a significant portion of the population with fresh food.
What Is Indoor Farming?
Indoor farming is a relatively new method of growing vegetables and other plants under controlled environmental conditions. These farm systems are variously referred to as indoor farms, vertical farms, vfarms, zfarms, greenhouses, controlled environment agriculture (CEA), and plant factories.2,3 Indoor farms are sometimes confused with urban farms, which typically represent small outdoor farms or gardens to grow vegetables that are located in urban areas. It also should be noted that mushrooms have been grown indoors in compost under controlled conditions without light for more than one hundred years.4 For the purposes of this article, we will focus on characteristics of controlled environment indoor vertical farms and greenhouses, which are the primary architectures used for the large-scale production of leafy greens and other vegetables that require natural or artificial light.
The many faces of indoor farming
Greenhouses have been the workhorse for indoor growers for decades, especially in the production of flowers and ornamental plants. The modern high-tech greenhouse designs were pioneered in the Netherlands and have since been embraced all over the world. Several examples of these farms are evident throughout the United States and the largest span hundreds of acres. For example, according to Greenhouse Grower,5 Altman Plants (CA) has almost 600 acres under glass followed by Costa Farms (FL) with 345 acres. These are mainly used in the production of ornamental plants.
For vegetables, greenhouses were originally designed for tomatoes but now are used in the production of kale, microgreens, lettuces, herbs, squash, and other types of fresh produce. These greenhouses, formerly located in rural areas, are now being positioned near urban and peri-urban areas to bring operations closer to population centers to save money and reduce the carbon footprint associated with transportation miles. For example, BrightFarms (brightfarms.com) has greenhouse operations located just outside of Philadelphia and Cincinnati to produce lettuces and other leafy greens. Gotham Greens (gothamgreens.com) situated its first greenhouse on top of a warehouse in Brooklyn, NY and has since expanded to other cities. AppHarvest (appharvest.com) is a venture located in Kentucky whose greenhouses cover more than 60 acres to produce tomatoes and other vegetables. What is common to greenhouse design is that all growing takes place on a single level, they are clothed in materials such as glass that transmit natural sunlight, and include climate control and irrigation equipment. They may also use a modest amount of supplemental artificial lighting during winter months.6
Growing leafy greens and other plants in buildings has emerged in the past 25 years whereby plants are grown vertically and hydroponically using artificial lights. Indoor vertical farms are typically located in warehouses or similar structures that have been retrofitted to provide superior heating, ventilation, and cooling (HVAC) for the benefit of plant production and racking systems to support the production systems.7-9 The PVC grow systems transport nutrient-rich water to the root zone of the plants, and the water is then returned to the main reservoir. Designed as closed re-circulating systems, indoor vertical farms only use a fraction of the amount of water as greenhouses or open-field methods (see also section “Water Use”). The advent of cost-effective LED lighting technologies has allowed farmers to provide the plants with just the right wavelengths of light, intensity, and photo-period to optimize growth.10 Other advances include automation, IoT, and artificial intelligence; ie, all of the information technologies that contribute to “smart farming.”11
Although modern LEDs are very efficient compared to HID, high-pressure sodium, or florescent lamps, the capital and operating costs of these artificial lighting systems are significant,10 as are the climate control systems that are also required. Greenhouses, for example, require significant investment in heating and cooling equipment to maintain stable temperatures and humidity, which results in significant operating costs in buildings with low R-value membranes (eg, glass). The chief benefit of this design is that the light comes free, although growing is limited to a single level. Indoor vertical farms, however, can benefit from well-insulated structures that reduce heating and cooling costs and growing can take place on multiple levels. That said, these savings come at the expense of relatively high electricity usage for artificial lighting.10 These operating costs can be mitigated with the increasing efficiencies of LED’s, sensing systems that modulate light to the maximum required for the plants, pairing indoor farms with renewable energy sources such as solar and geo-thermal, and architectures that favor energy efficiency.9
Methods of indoor farms
Indoor farms are characterized by several parameters:
Growing Method and Media
Source of Nutrients
Lighting Requirements
Facility Capacity
Climate Control
Economics
Most indoor farms use hydroponic methods of growing; i.e, plants are grown in water. Seeding takes place in an inert material such as stone-wool or peat, which is irrigated with nutrient–rich water. Water is administered using a variety of techniques ranging from fine mist sprayers (aeroponics), to shallow water (NFT) irrigation, to deep water culture (DWC) immersion to flood and drain methods.9 All are effective and have their pros and cons. Nutrients for larger-scale hydroponic production systems typically come from dissolved salts that ionize in the water. In some smaller systems, the nutrients come from the nutrient-rich water of fish farms (ie, aquaponic systems) that are proximate to and coupled with the plant production system.
In greenhouse production facilities, most lighting comes from the sun, which may be supplemented with artificial light, especially in the northern latitudes during winter. Plant factories and vertical farms, however, use only artificial lighting but are designed to maximize growing area using stacking methods. One common design is characterized by horizontal multi-tier growing systems starting at ground level that may include up to a dozen growing levels or tiers. Aerofarms (aerofarms.com) and Bowery Farms (boweryfarming.com) use this type of design for their production processes. An alternative is to use vertical drip irrigation grow systems. This design is characterized by vertical multi-site growing systems starting at ground level that extend upwards of 8 ft. In these systems, plants grow “sideways” toward artificial lights that are positioned at a right angle. Plenty, Inc. (plenty.ag) uses systems like these obtained in the acquisition of Bright Agrotech. Several examples of vertical farming ventures can also be found in Al-Kodmany.
All indoor farming methods share the characteristic of offering CEA. Controlled environment agriculture offers the grower complete control over several environmental variables including, but not limited to: light intensity and wavelength, photo-period, wind velocity, temperature, and humidity. Water culture is further managed to obtain optimal results based on nutrient levels, PH, and dissolved oxygen.9,12 In most cases, pesticides and herbicides are eliminated. More advanced farms such as Fifth Season (fifthseasonfresh.com) benefit from extensive use of sensors, IoT, robotics, automation, and control systems designed to optimize yields and minimize labor. Another valuable aspect of CEA farms is their ability to produce plants with certain desired morphologies and nutritional profiles based on the control of lighting wavelength, temperature, and nutrient levels. Sharath Kumar et al13 go so far as to suggest that with CEA, we are moving from genetic to environmental modification of plants.
Benefits and challenges of indoor vertical farms
Several benefits are associated with vertical farming,9 although the industry is not without its challenges (see Table 1). The principal sustainable benefits of indoor vertical farming are a large reduction in the use of water (see also section “Water Use”), the reduction or elimination of pesticides, and mitigation of the effects of excess fertilizer run-off. From an economic perspective, the ability to control the environment results in a stable supply chain, price stability, long-term contracts with distributors and retail markets, and high yields per square foot. The elimination of pesticides puts produce grown this way on par with organics, which command premium pricing. Indoor farms, if designed correctly, can reduce labor costs and may be located closer to urban centers. Some see a role for indoor farms to ameliorate food deserts, unemployment, and as a means to re-purpose abandoned buildings and lots.3,9,14-16 Finally, vertical farms provide resilience to climate change, flooding, droughts, etc.
However, the vertical farming industry is facing some key challenges. For instance, currently only a very small portion of fresh vegetables are produced indoors. The one exception is the mushroom industry, which represents a US$1.15 billion industry.17 Second, the USDA does not clearly identify vegetable production by method; eg, greenhouse, open field, vertical farm, etc, so data are not readily available. Third, profits have been elusive, especially for vertical farms.18 According to the 2019 Global CEA Census Report only 15% of shipping container farms and 37% of indoor vertical farms were profitable vs. 45% for greenhouse operations.19 Another limitation of indoor farming is that a relatively small number of cultivars can be grown using indoor farming methods.
The primary ones are leafy greens, herbs, microgreens, tomatoes, and peppers, although berries, root vegetables, and other more exotic plants are being trialed.19 Another challenge for indoor farm start-ups are the high capital costs, which can range from US$50-150/ft2 for greenhouses to US$150-400/ft2 for vertical farms. For example, AppHarvest had to raise over US$150 million to fund its 60-acre greenhouse complex.20 Aerofarms raised US$42 million for a 150 000 ft2 vertical farm,21 which equates to over US$280/ft2. Cosgrove22 further reports that access to capital is impeding the growth of indoor farming, especially for smaller farms. One reason that indoor vertical farms are not easily profitable is that they have to compete against conventional farms, which still enjoy a cost advantage.
As a result, indoor farms typically price product toward the high end and along the lines of pricing for organics,2 which limits market penetration. The 2 major factors contributing to the high costs of indoor and vertical farm operations are energy10,23,24 and labor, which account for nearly 3 quarters of the total.2,24 Despite these challenges, venture capital continues to pour money into indoor farming and agtech in the hopes of driving cost down and maintaining growth. Dehlinger25 reported that US$2.8 billion was invested by venture capitalists in Agtech companies in 2019.
Finally, the industry is struggling to share knowledge, establish standards, and create best practices, although progress is being made. For example, the Center of Excellence for Indoor Agriculture established a “Best in Class” award for growers and manufacturers (indoorgacenter.org). Indoor Ag-Con (indoor.ag) and the Indoor Agtech Innovation Summit (rethinkevents.com) hold online events and annual conferences to help promote knowledge sharing. Several specialized industry news outlets now exist including Vertical Farm Daily (verticalfarmdaily.com), Urban Ag News (urbanagnews.com), iGrow (igrow.news), Hortidaily (hortidaily.com), AgFunder Network (agfundernews.com), and others.
Read more >>>
Keywords: Indoor farming, vertical farming, vfarm, zfarm, plant factory, water, air, soil, sustainability, carbon cycles, drought, information technology, greenhouse gases, climate change, environment, agtech
Polygreens Podcast Episode 22 -Jenn Frymark From Gotham Greens
In this episode, Joe and Nick interview Jenn Frymark from Gotham Greens
In this episode, Joe and Nick interview Jenn Frymark from Gotham Greens
Green produce starts with green decisions. Gotham Greens indoor farming facilities are sun (and wind) powered, and climate-controlled for a year-round growing season. This means they can provide clean, sustainable, and quality food to the communities. Any time, anywhere.
Robotic Warehouse Farms Will Save The World
The theory behind CEA is that by controlling the environment in which it grows, we can control everything about a plant and what it grows into by micro-tweaking one of a thousand different characteristics―including temperature, humidity, light duration, light wavelength, dissolved oxygen in the water, and carbon dioxide saturation in the air
by Elle Griffin
Four years ago, Ritch Wood was looking for a better way to grow plants. As the CEO of global skincare company Nu Skin, he ran into ingredient shortages every winter when fields went dormant―and when he moved grow operations to the equator he ran into water and land shortages, along with a host of quality control issues.
Nu Skin needed reliable, quality ingredients for their skincare products. But farming was too unpredictable an industry. “If there was a way to grow indoors,” he thought, “and be able to do that 24 hours a day, 365 days a year―if we could guarantee that it was grown without any herbicides or pesticides and in a sustainable way that uses less water and land―that would be really helpful.”
At the time, controlled-environment agriculture (CEA) was in its infancy and grow-light technology had yet to take a turn for the more affordable. When he learned of an agricultural system that promised to use a fraction of the land and water used by traditional agriculture methods and had the potential to make it more affordable, Wood made an investment.
Nu Skin paid $3 million for 70 percent of the company and rights to its IP―and Grōv Technologies was born.
Grōv grass grown in the Olympus machine at the Bateman Mosida Farms. Photo from Grōv Technologies
Controlled-environment agriculture is on the rise
The theory behind CEA is that by controlling the environment in which it grows, we can control everything about a plant and what it grows into by micro-tweaking one of a thousand different characteristics―including temperature, humidity, light duration, light wavelength, dissolved oxygen in the water, and carbon dioxide saturation in the air. By tweaking the growing cycle, we can control the caloric content as well as the nutrient content and density of the plant.
“What we’ve learned through controlled-environment agriculture,” Benjamin Swan, co-founder and CEO at Sustenir in Singapore, once told National Geographic, “[is] we can actually emphasize certain characteristics of the plants. So, without using GMO, we can make our kale softer, we can actually make it sweet.”
The theoretical use cases for this technology are endless―from being able to grow in places where water is scarce (like in much of Africa), or where water is overly abundant (like Hawaii), or in places where labor is scarce (like in parts of Asia), or even in places that have long winters (like Northern Europe). Theoretically, we could have grow towers in every town and feed the whole of it no matter its natural environment.
We could even grow those foods to those cities’ exact nutritional needs―more vitamin D-rich foods in wintery places, for example. Dr. Lee Mun Wei, a senior manager at the Food Innovation and Resource Centre (FIRC) in Singapore aims to predict and prevent illness in a given population by tracking their biometric data using Apple watch-like wearables, then 3D printing nutrient-specific foods that could mitigate imbalances.
Though these technologies exist, they are still in their infancy. Singapore leads much of the research and development out of necessity. With limited land and water resources, the county is forced to import 90 percent of their food and 40 percent of their water from outside the country. As a result, they have no option but to grow vertically and desalinate water from the ocean.
Elsewhere, the industry has been slow to catch on, largely due to exorbitant startup costs, low returns, and lack of urgent need. According to a 2017 State of Farming report by L.E.K., only 27 percent of indoor, vertical farms are profitable compared with 50 percent of container farms and 75 percent of greenhouses. But one thing has spurred the industry on in recent years: cannabis.
Legalized in 39 states, demand for cannabis has created a $13.6 billion industry and enough capital to fund CEA-enabled grow operations. “When you have a crop that fetches up to $2,400 or $2,500 a pound, you need to be able to dial everything in and make it consistent and repeatable,” says Dashiel Kulander, co-founder and CEO at Boojum Group. “If the temperature swings five to 10 degrees on a cannabis plant, that will change the plant’s various cannabinoids. The goal is to create a medicine that is consistent batch after batch.”
It’s only recently that there has been some financial incentive to use CEA technologies for food use―largely driven by Big Ag players hoping to hedge out the competition. Berry farming giant Driscoll’s, for one, led a $500 million round to fund Plenty, a 2.2-acre vertical farm in California they hope will help them fulfill a contract with Albertsons. The Ingka Group, for another, led a $100 million round to fund AeroFarms, a 2.4-acre vertical farm in New Jersey that will help them fulfill a contract with Singapore Airlines.
Grōv tent at the Bateman Mosida Farms. Photo from Grōv Technologies
Grōv Tech is building CEA prototypes in Utah
By investing in Grōv Tech, Nu Skin hopes to do something similar, getting ahead of the supply chain that fuels their skincare products before the competition can beat them to it, or before climate change makes traditional methods more difficult, all while shoring up technology that could provide a farming model that is more sustainable―if only it were more economical.
“The purpose was always, can we build a better product for Nu Skin?” Wood says. “We think there’s a huge story around the ingredient sustainability, and there were a lot of ingredients we felt we could grow, but the challenge was: could we do it in an economical way?”
Grōv Tech started out with a prototype: a tower that pairs hydroponic growing technology with grow lights. But like all CEA startups, a lot of the growing process was manual and the technology was prohibitively expensive. To make something that was scalable and profitable the whole thing needed to be automated and it needed to be cheap.
With this goal in mind, Wood decided they would start by growing animal feed for Bateman’s Dairy farm. Having grown up on a dairy farm himself, Wood figured this would allow the company to scale the product while refining and automating the technology to the point that it could be replicated. And all of this would have a fortuitous effect on Nu Skin’s bottom line.
“One of our bestselling products is a weight-loss protein powder which uses whey protein,” Wood says. “So again, a very nice connection there is if the animal is eating a more sustainable product and producing better milk with better protein and it’s being done in a sustainable way―certainly that can be a benefit to Nu Skin down the road.”
One year into feeding the 20,000 animals at Bateman, the company has learned a lot. For instance: cows need a lot of magnesium, but they don’t like eating it. Now, Grōv Tech puts magnesium in the water so it’s directly absorbed into the plant and then becomes bioavailable to the cow upon eating it. And because the growing process only takes seven days, data scientists can analyze the results in real-time and adjust the components to optimize production for the next batch of feed.
According to Grōv Tech president Steven Lindsley, it’s not far off that we’ll be looking at milk production (butter, fats, and proteins) and optimizing a herd’s diet for taste, quality, and nutritional value―not to mention the wellbeing of the animal. We’ll be able to look at how many trips from the veterinarian an animal gets when they’re fed certain nutrients in their diet, and whether they can have more calves and produce the same amount of dairy on less, better quality feed. (So far, the answer to this last question is yes. When animals are fed better quality food they need less of it―just like humans.)
And if we hook all of the cows up to robotic milking equipment and connect everything to artificial intelligence, machine learning, and the Internet of Things―Lindsley’s far-flung goal―then we might be able to collect enough data to not only feed cows to their optimum health and performance ability, but humans too. And that could have ramifications not only for feeding the world, but nourishing it― just like Dr. Wei hopes to do in Singapore.
“Last year was about starting to feed animals and get data and prove out the hypothesis we have while continuing to perfect the technology and get confidence there,” Wood says. “And now we’re really to a point where we’ve got data that proves that it works and that financially it’ll be a good thing for a farmer. So now we can really take that proposition to farmers and start to scale.”
Olympus Tower Farm at Bateman Farms in Mosida, UT. Photo from Grōv Technologies
CEA technology could feed the world
Right now, Grōv Tech is focused on refining its technology right here in our own backyard. But once they do that, the plan is to expand internationally.
“Saudi Arabia has actually passed a law where you cannot use water to grow fodder or feed for animals, so all of that now has to be imported. China imports one-third of their alfalfa feed for their dairy animals because they don’t have the capability of growing it,” Wood says. “So there are countries that will probably benefit more than the US would. But we’ve got to refine the technology and get that built to where it’s ready to scale before we start spreading ourselves all around the globe.”
CEA technology is just getting started. Like the Tesla Cybertruck, we have a working concept that promises a more-than-Jetson’s-level future many of us can see the benefits of and actively want―it’s just not quite available to the masses yet. But with more than a billion dollars invested in the technology in just the past few years alone―we’re getting there. And the “there” we are heading toward is rosy indeed.
“To put it in perspective, one tower that is about 875 square feet on the ground will replace 35 to 50 acres of land,” says Lindsley. “And that will feed the animals on roughly five percent of the amount of water. The UN says that that the world will add about 2.5 billion people in the next 30 years. And we have to find a way to feed them on arguably less arable land and water. The good news is the technology is coming along to help solve that equation.”
If COVID-19 taught us anything, it’s that our food supply chain is fragile. But that’s only because our supply chain was built to grow food in California, refrigerate it so it stays fresh, then transport it 1,500 miles so we can eat a salad in the winter in Chicago. In the future, that might not be a thing. “We’re having a dry year now,” Lindsley tells me in February. “But a year ago we were in a blizzard, and even in the middle of a blizzard in February in Utah, we’re pumping out fresh, beautiful, safe green grass for animals. It’s a paradigm shift.”
“Four years ago it was a good idea,” Wood tells me of his company’s investment in CEA technology, “But four years from now it’s going to be required.”
Elle is the editor-in-chief of Utah Business and a freelance writer for Forbes, The Muse, and The Startup. She is also a literary novelist and the author of a weekly newsletter called The Novelist.
Learn more at ellegriffin.com.