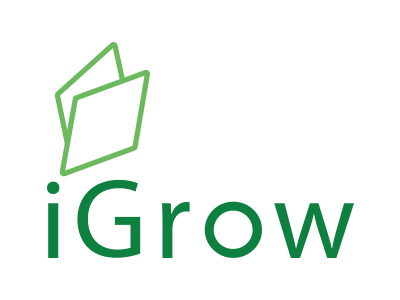
Welcome to iGrow News, Your Source for the World of Indoor Vertical Farming
USA: Big Ideas Grow In Wisconsin
Fork Farms has created a unique hydroponic growing system, called the Flex Farm, that allows consumers to grow up to 394 pounds of fresh food a year in just nine square feet of space
May 25, 2021
WEDC
Wisconsin Economic Development Corporation (WEDC) Secretary and CEO Missy Hughes visited Green Bay’s Fork Farms with a simple message: Wisconsin can help businesses and entrepreneurs bring big ideas to life.
“With our state’s talent, workforce and top-ranked university system, Wisconsin businesses are creating solutions for today’s problems and opportunities for tomorrow,” Hughes said. “Innovation is one of the keys to recovering from the COVID-19 pandemic and building a more prosperous economy for everyone.”
In April, Fork Farms was certified as a Qualified New Business Venture by WEDC. That certification allows investors in the company to receive tax credits up to 25% of the value of the investment made.
Fork Farms has created a unique hydroponic growing system, called the Flex Farm, that allows consumers to grow up to 394 pounds of fresh food a year in just nine square feet of space. CEO and co-founder Alex Tyink, who at the time was an opera singer in New York City, was inspired to start the company after working at a Brooklyn rooftop garden and discovering the physical and mental health benefits to eating and growing one’s own food.
“WEDC’s QNBV designation will provide Fork Farms significant lift to our organization's mission,” Tyink said. “It will aid us in growing our business and focusing on ways that we can create transformative social benefit. Overall, we believe their support of the local startup community is critical to building a vibrant Wisconsin state economy."
The company, which is headquartered at Green Bay’s TitletownTech, continues to spread its message of fresh food and environmental sustainability by partnering with nonprofit groups such as community centers and schools to inspire a new generation of growers and creators.
3 Challenges of Vertical Farming And Their Solutions
The world is continuing to grow. By the year 2050, researchers estimate that there will be nearly 10 billion people on the planet. As the population increases, the demand for food and food security also increases
Source: Shannon Flynn, ReHack
05/26/21
The world is continuing to grow. By the year 2050, researchers estimate that there will be nearly 10 billion people on the planet. As the population increases, the demand for food and food security also increases.
Traditional farming methods won’t be able to sustainably keep up with the necessary food production to feed the population. That’s why farmers and researchers have been developing new means of feeding people, especially in urban areas.
The advent of vertical farming has taken the agricultural industry by storm. Although it has proven to be beneficial to farmers and the environment alike, there are some challenges that vertical farmers face. Below are three challenges of vertical farming and their solutions. As long as the solutions are available, vertical farming can still be a reliable way to feed the population.
Vertical Farming Basics
Vertical farming takes traditional farming to new levels — literally. Instead of conventional horizontal, soil-based farming, vertical farming implements hydroponics into vertical buildings. Crops grow upwards instead of outwards.
The buildings use a combination of climate and light-controlled areas to grow the plants. It creates a perfect environment for plants to thrive. This type of farming is optimal in urban areas because it takes up much less space than a traditional farm.
Therefore, populations in cities and urban communities have the opportunity to get fresh produce a few blocks away from their homes. Since most of the world’s population will reside in urban areas, this provides greater food security for them.
Vertical farming has evolved over the years to include more than just fruits and vegetables. Seafood producers wanted a more sustainable approach to seafood production, so they have also implemented vertical farming techniques. Seafoods like mussels, scallops, and seaweed grow vertically on ropes, which creates a more biodiverse and resilient seafood system.
Challenges of Vertical Farming and Their Solutions
Unfortunately, there are challenges that vertical farmers face that they must solve to meet those future food needs and to remain sustainable. Here are some of the challenges, along with potential solutions, of vertical farming.
Location
Although vertical farms can go almost anywhere, farmers have to choose the correct location. If it’s too far from potential consumers, then it won’t be a lucrative business. One could have the best place, but if there isn’t a demand for food there, then they won’t be able to sell the produce.
Plus, land in cities can be a bit more expensive. Smaller vertical farms have a more difficult time finding land they can afford, along with permits and insurance.
The solution is to research the considered location for a vertical farm. What kinds of food are the people there looking for? Can a vertical farm provide that for them? Will they be a loyal customer to the farm? Without a good location, a vertical farm won’t get far. Fundraising, loans, and grants are great options for farmers who may not have the funds for a location, too.
Temperature and Humidity Control
The next challenge is temperature and humidity control. These two need to be spot on to produce vegetables and fruits. Managing them can take a while to overcome. Farmers often have to try various recipes of cooling, dehumidification and heating. Vertical farms are usually well-insulated, so when the weather gets warmer, the farmer must cool it and remove humidity.
Before installing an HVAC system, it’s wise to ask for professional help to know how large of a system will be needed for the building. This is the best solution to this challenge, and it will save a lot of headaches in the future.
Multitasking
Another challenge is ensuring proper management of the entire vertical farm. Many farmers who set out to start their industry in vertical farming rely on themselves and possibly a couple of other people to get all of the work done. Vertical farms attempt to do too many things simultaneously, like growing food and selling technology, and managing day-to-day tasks.
New vertical farmers should focus on one thing, like growing food and selling it. This helps build a solid customer base. Choosing either growing and selling or developing technology so allows the farmer to put their best effort into it.
Farming of the Future
Vertical farming has become a popular solution to the growing problem of food security. However, there are challenges within the industry that must first be addressed and overcome to remain a sustainable business. These challenges and solutions are excellent learning tools to grow a thriving vertical farm.
Tags: Indoor & Vertical Farming, Processing & Supply Chain | Business Development, vertical farming
Jungle Aims To Supply 2000 Supermarkets In The EU By 2025
Jungle is a vertical farming company that first began in a 15-square meter container installed near a supermarket in Lisbon, Portugal
Expanding Throughout France,
With Another Two Farms
In The Pipeline
“In France, associating technology to food production can be challenging since the country has a really strong agricultural culture. We figured that if we manage to succeed in France, then we can do it anywhere,” says Gilles Dreyfus, President & co-founder at Jungle.
Jungle is a vertical farming company that first began in a 15-square meter container installed near a supermarket in Lisbon, Portugal. However, founders Gilles Dreyfus and Nicholas Séguy both dreamed of establishing the company in France due in part to the challenges posed by the French agri-food sector.
In March 2021, Jungle announced that it had raised €42 million to expand across the United Kingdom and Europe, with plans to supply more than 2,000 points of sale by 2024.
Gilles Dreyfus
Expanding throughout France
By Q2 of 2022, Jungle plans to have an even larger production facility in southern France, in close proximity to the food distribution and logistics centers. Next to that, the company has another farm in the pipeline at an unknown location. “We’ll be delivering our products to the supermarkets’ logistics centers and they will deliver it to their stores. We won’t be delivering store-to-store, which further reduces our carbon footprint,” says Gilles.
After spending 2.5 years researching the optimal growing recipes, Jungle partnered with a French retailer in Lisbon and built its team in Lisbon over the course of three years. In Portugal, Jungle expanded from being available in one store to ten stores. Despite the obvious market opportunities in Lisbon, Gilles explains that a primary inconvenience of establishing a vertical farm in Lisbon is the distance from consumers, with the country’s 10 million people being dispersed across the country which makes it more difficult to tackle a large consumer base. In contrast, Paris’s metropolitan area has roughly 14 million people.
First Lisbon, then France
Jungle’s productivity in Lisbon paid off, as the company soon attracted the interest of major French retail chain Monoprix in mid-2019. In response, Gilles and Nicholas created Jungle France in August 2019 and began with a small unit as a pilot project in January 2020. After demonstrating impressive KPIs over a few months, Jungle signed an agreement with Monoprix in October 2020 to supply 120 stores.
Jungle France has secured its first farm location in Château-Thierry in September 2019. roughly 80 km from Paris. The Château-Thierry farm has a total footprint of 3,800 m2, of which half is dedicated to growing while the other half is used for germination, equipment washing, packaging, delivery and administration. The floor area for cultivation is thus roughly 1,800 m2 and the room is 10 m tall, bringing the net production area to 5,500 m2, according to Gilles.
Bringing vertical farming to France
As Gilles mentions, establishing a vertical farm in France can be challenging due to the strong agricultural culture in the country, which has somewhat disfavored hydroponics and alternative forms of agriculture. This has not made marketing impossible for Jungle; rather, the company has simply taken different approaches to ensure that their products are understood and accepted. One of the key elements of Jungle’s approach has been to remain humble and not attempt to completely revolutionize the agricultural sector.
“Our branding doesn’t focus on the fact that our products have been grown vertically; we’re not trying to hide anything, but our market research has shown that highlighting technology isn’t always appealing to the customers,” says Gilles.
He compares it to the introduction of organic agriculture in the 1980s, which was poorly received and took several decades to be widely accepted as environmentally superior to conventional agriculture.
Jungle's products
“Nowadays, information travels much faster so the time taken to educate the population about vertical farming is much shorter, maybe 4-5 years. But Jungle’s position is not to educate people; it is to produce healthy plants on an industrial level and at reasonable prices for the masses. So for marketing and branding, we have taken a simple route,” explains Gilles.
In supermarkets, Jungle products are sold in company-provided displays. So far, the reception has been good as people are beginning to understand the benefits of vertical farming with respect to efficient energy and water use, lack of pesticides, and overall environmental sustainability. According to Gilles, it also helps that Jungle products are roughly 20% less expensive than their organic counterparts.
More partnerships and avenues ahead in 2021
While Jungle currently produces herbs, salads, microgreens, and flowers, the company is planning to expand its portfolio and its consistent research on different vine crops. Jungle is also excited about impending partnerships that will be announced in the coming months, which will allow the company to further expand its client base and possibly access cosmetic industries.
For more information:
Gilles Dreyfus, Co-Founder
Jungle
gdreyfus@jungle.bio
www.jungle.bio/old-home
Publication date: Tue 25 May 2021
Author: Rebekka Boekhout
© VerticalFarmDaily.com
VIDEO: California Farmers Leave Fields Fallow As Drought Grows More Dire In West
Northern California reservoirs contain only half the water they normally do in late spring.
Both the State Water Project and the federal Central Valley Project have announced they intend to deliver only 5% of requested supplies this year
By TYNE MORGAN May 28, 2021
As rains drop needed moisture for areas of the country dealing with drought and in need of relief, the situation is growing more dire in the West.
The latest U.S. Drought Monitor shows improvement in the Plains, especially in the Southern Plains. Heavy rains also falling across western portions of the High Plains this week, lessening the drought conditions in the western Dakotas. Those moisture improvements also pilling over into western Nebraska and Kansas.
The drought has become a mainstay in California. The Drought Monitor released Thursday shows exceptional drought growing, including Kern County, one of the top ranked counties for ag production in the nation.
Northern California reservoirs contain only half the water they normally do in late spring.
Both the State Water Project and the federal Central Valley Project have announced they intend to deliver only 5% of requested supplies this year.
As California farmers rely on Mother Nature and ground water this year, one farmer says it won't be enough to even grow a crop, with some farmers choosing to not plant at all. Some producers are even pulling out trees.
"There are land areas out here that are going to get one acre foot of water from the ground. That's what they're allocated," says Tyler Ribeiro, a dairy farmer in Tulare, California. "Good luck growing cactus on one acre foot. You're not going to be able to feed with that you can't grow trees out there. And we align with a lot of these tree guys in a sense of we feed their byproduct, I need those all almond hulls, I need those orange peels. I need a lot of those things. That's how we stay efficient [as a day farmer]."
USDA meteorologists telling AgDay there's not much relief in sight for California and the West. Forecasters expect the drought west of the Rockies to only get worse.
Greta Thunberg Aims To Change How Food Is Produced
The Global Center on Adaptation, which works to accelerate climate resilience, said in January climate change could depress global food production by up to 30%, while rising seas and more intense storms could force hundreds of millions of people in coastal cities out of their homes
By REUTERS May 28, 2021
STOCKHOLM (Reuters) - Swedish climate activist Greta Thunberg has set her sights on changing how the world produces and consumes food in order to counteract a trio of threats: carbon emissions, disease outbreaks and animal suffering.
In a video posted on Twitter on Saturday, Thunberg said the environmental impact of farming as well as disease outbreaks such as COVID-19, which is believed to have originated from animals, would be reduced by changing how food was produced.
"Our relationship with nature is broken. But relationships can change," Thunberg said in the video marking the International Day of Biological Diversity.
A focus on agriculture and linking the climate crisis to health pandemics is a new angle for Thunberg who has typically focused her ire on policy-makers and carbon emissions from fossil fuels.
"The climate crisis, ecological crisis, and health crisis, they are all interlinked," she said.
Thunberg said the spillover of diseases from animals to humans was caused by farming methods, adding that a move to a plant-based diet could save up to 8 billion tonnes of CO2 each year.
The World Health Organization has said the coronavirus was probably transmitted from bats to humans through another animal, while scientists say 60% of the infectious human diseases that emerged from 1990 to 2004 came from animals.
Meanwhile, demand for alternatives to regular meat is surging worldwide due to concerns about health, animal welfare, and the environment.
More than two dozen firms are testing lab-grown fish, beef, and chicken, hoping to break into an unproven segment of the alternative meat market, which Barclays estimates could be worth $140 billion by 2029.
The Global Center on Adaptation, which works to accelerate climate resilience, said in January climate change could depress global food production by up to 30%, while rising seas and more intense storms could force hundreds of millions of people in coastal cities out of their homes.
(Reporting by Colm Fulton; Editing by Alison Williams)
Lead photo: Greta Thunberg (Reuters)
Purpose At Work: How Square Roots Is Growing A Sustainable Food Movement
How can we reduce the climate impacts of our food system? How can we get the freshest produce to people in urban areas? How can we offer fulfilling jobs to today’s youth? These are all issues that Square Roots is working to address
May 24, 2021
Purpose At Work: How Square Roots Is Growing A Sustainable Food Movement
PHOTO PROVIDED BY SQUARE ROOTS
How can we reduce the climate impacts of our food system? How can we get the freshest produce to people in urban areas? How can we offer fulfilling jobs to today’s youth? These are all issues that Square Roots is working to address.
“The mission of the company is to bring locally grown food to people in cities, all across the world while empowering the next generation of leaders in urban agriculture,” Tobias Peggs, Co-founder, and CEO of Square Roots, tells We First.
The agriculture startup’s modular and technology-first design is transforming how food is grown and distributed in amazing ways. The scalability and data-driven approach make Square Roots an excellent example of a company demonstrating how to scale business growth and impact.
Founding story
Before Square Roots, Tobias received a Ph.D. in machine learning and had worked for a number of successful startups, one of which was acquired by Walmart. “I worked as a data scientist there for a year. One of the projects they had me do was study global grocery buying behaviors.” With around 300 million customers, Tobias had a massive amount of data to pull insights from.
“That's a lot of bananas flying all over the world,” he says. “You begin to think about the impact of transportation on the planet. “As food is traveling, nutrients are breaking down and maybe the quality of food isn't as good at the end of long supply chains as it would be for local food. Customers don't have any idea of where that food comes from. The sense of community around food was just lost.”
MORE FOR YOU
Vertical Indoor Farms Make Sense
The insights Peggs was having lit a spark in his entrepreneurial engine. “People want food from all over the world. That's not going to change,” he says. “Instead of shipping food, how about we ship environmental data from one part of the world to the other?” By collecting data on the best growing conditions, Tobias could hypothetically grow anything at any time of year in a controlled indoor environment made from repurposed shipping containers and deliver that to a nearby retail store on the day it’s picked. “It looks and smells amazing, which also means all the nutrients are intact,” he says. “That was the idea behind Square Roots.”
Peggs cofounded the company with Kimbal Musk, “He would say, ‘Can it feed the world? And are we going to make a massive positive impact? If so, let's figure out how to get this done,’” Peggs recalls. The two innovators began by working together in a WeWork office. “With the experience of being involved in a number of startup companies before—some successful, some failure—I know for sure that if you don't get started, you're going to fail.”
In the two-man brainstorming sessions, Peggs and Musk would visualize the business at scale. “We saw these modular farms in every city across the world. That is the way that we're able to think about feeding every consumer on the planet with locally-grown food,” Peggs says. “There was a missing piece of the puzzle. There wouldn't be enough farmers to hire to staff all of those farms.” That realization was the foundation of the second pillar of Square Roots’ purpose, “To provide pathways for young people to come into the farming industry and become the future leaders,” he shares.
Leading with purpose
Purpose At Work: How Square Roots Is Growing A Sustainable Food Movement
PHOTO PROVIDED BY SQUARE ROOTS
Square Roots’ core business was structured to address some of the world’s biggest challenges. Food is interconnected with climate, which also poses risks on outdoor crops. It is also fundamental to public health and prosperity. As the global population rises, our planet’s carrying capacity will be tested. We need to innovate to meet that rising global demand for food.
The model relies on able-bodied young people to tend to the crops. The talent pool of skilled farmers in the U.S. is aging. The average farmer is 58 years old. “Who the hell is going to grow all the food when our current farmers retire in five or 10 years’ time? ” Tobias proposes. “We had to figure out a way to bring young people into the industry and train them quickly so they could be not just productive farmers, but feel infused about a career in a completely new industry.”
To overcome the hurdle, the founders developed hardware, software and teaching methods. “We had an investment banker who was bored sitting behind a spreadsheet all day. He quit his job to join Square Roots because he wanted to make an impact on the world. He was growing the most delicious kale, you've ever tasted in your life,” Peggs says. “That was six months after making the transition, it was magic to see that.” Within a year they trained 10 people, many with no previous farming experience.
In addition to creating purpose-driven employment opportunities, Square Roots is addressing climate through transportation and waste. “Forty percent of food from industrial systems is wasted. We waste around 3%,” Tobias says. A significant portion of wasted food is discarded before it even hits the shelf, due to damages during shipping or spoiling quickly. “Because we're indoor, there's a lot of precision, a lot of control. We can grow food for demand.”
Modular design
Square Roots’ structure allows it to be replicated and optimized from a systems approach. It's a distributed model. “We deploy clusters of these modular farms together so there's some operational scale and the business economics work,” Peggs explains. “Each farm serves its local market and runs its own independent business entity, set on top of a standard technology platform.” Every compound grows, harvests packages and delivers produce to local retailers. “We look after everything from seed to shelf.”
The growing startup has set up operations in Brooklyn, New York, and Grand Rapids, Michigan with plans for expansion across the Midwest, the North East in cities around the world where demand is large enough. People can see inside the shipping containers and when Covid-19 is under control, you can schedule a farm tour. “While its a very scalable platform, the consumer experience is a hyper-local one.”
Leveraging data & technology
When it comes to deciding what to grow, Square Roots focuses on crops that require the least amount of energy. “Walk into a supermarket. Lineup every single fruit and vegetable from the lightest to the heaviest. And that's essentially our product roadmap for the next 20 years,” Peggs says.
They also choose crops based on economic yields based on competitive market prices. “This is where data science and technology marry,” Tobias says. “Outdoor farmers can’t suddenly look at the sun, make it twice as efficient and reduce costs or double their yield. Indoor farmers can.”
Integration of AI machine learning empowers Square Roots to optimize at scale. “We're building a network of cloud-connected modular farms,” Tobias says. The company monitors and collects data from each of those farms every second. “We’re looking at temperature, humidity, nutrients, yield, taste and texture,” Peggs says. “ If in one particular box, a farmer did something or we changed an environmental parameter that increased yield or improves efficiency, we can spot that information from the data and push that new instruction out across the whole network. The whole network is learning how to farm better as we go about building the business.”
Building community
Food has the potential to unite people. While Square Roots farms are indoors, they connect and share knowledge with outdoor farmers. “ I'll give you an example,” Tobias says. “A good technique in organic farming is known as integrated pest management, where a farmer might release beneficial insects onto the crop, essentially ridding the nasty insects that we don't want. We use that technique inside the farm.”
“The farmers that we work with are very much on the same mission, which is how do we get people more connected with where their food comes from? How do we build that sense of community around food? And I think the common enemy is the industrial food system,” Peggs says. That common enemy also resonates with employees, consumers and other key stakeholders who join together around a set of core values.
“I know pretty much every founder or CEO of every indoor farming company. There's remarkable alignment around that mission,” Tobias says. “Everybody understands that we've got to change the food system and if we're helping each other out, it's better for all of us,” Tobias mentions companies like Gotham Greens and Oishii that are also innovating in the indoor farming space.
Purpose also informs Square Roots’ investor strategy. “We’re a venture-backed company. When we're talking with investors, we want to make sure that they're mission aligned. I can’t tell you how many investors have talked to me about considering cannabis. It’s not aligned with our mission.” A lot of people don't realize that the power of purpose is just as compelling in terms of what you don't do, as opposed to what you do.
The takeaway here is that building your community around shared purpose fosters goodwill amongst team members and customers. It also presents collaborative opportunities with other brands and organizations working towards the same goal.
Challenges and opportunities
With the opaque information in the industrial food system and increased health consciousness, consumers are looking for transparency. In addition to its open invitation to check out the farms, the company includes a QR code on each product. You can scan the code and learn all about where it's made and the value chain.
Purpose At Work: How Square Roots Is Growing A Sustainable Food Movement
PHOTO PROVIDED BY SQUARE ROOTS
Covid-19 has also presented challenges for businesses across sectors and Square Roots is no exception. Before the pandemic, they trained new hires to be farmers in classrooms. “If we didn't have our mission, it would have been easy to say, ‘We got to keep growing, forget this farmer training stuff. We're just going to go hire experienced people.’ Or we could have developed a robot to do part of the job of a farmer,” Tobias says.
“The mission allowed us to focus on solving issues with our current business model,” he continues. “It was already misaligned. Everyone was able to get behind it very quickly. And we were actually able to solve problems and put in place new programs and new policies ridiculously quickly. Never waste a good crisis.”
Despite adversity, the startup has started true to its mission and transitioned to digital and socially distanced training, and built a more robust system than before.
The future of food
Technology and data are a critical aspect of emerging agriculture trends. “Food is a $12 trillion industry,” Peggs states. “There's about 20 companies that have raised a bunch of money and are doing this stuff in America.”
“Indoor farming actually reminds me of the internet in the early '90s,” he says. “We know this thing is inevitable, but no one can quite yet tell you what shape it's going to take in the future. Indoor farming is like that. We're all helping each other figure out how this eventually feeds every consumer in the world.”
While innovation is budding, “The food system has to become a lot more responsible and sustainable,” Peggs says. “The current food system cannot feed the new future world, which has 10 billion people, 70% living in urban areas that are not near these industrial farms.”
We’ve seen changes over the last two decades with the organic food movement, which now grosses $25 to $30 billion annually, Tobias says. He thinks that Covid-19 will accelerate the shift towards healthy and sustainable food. “People were forced to stay at home and cook. You get more curious about the food that you're buying, and you observe how long it lasts in your refrigerator. You get more educated,” Tobias says. “We are in the first inning of indoor farming. We're just getting started.”
Lessons for entrepreneurs
With his experience from Square Roots and beyond, Tobias Peggs’ insights offer valuable lessons for entrepreneurs looking to Lead With We. Here are three teachings from Peggs on how to build a successful startup.
“Be prepared to be told, "No, we're not interested."
“You have to be a bit of a missionary and sign up for having a lot of stamina. Just be consistent with the drumbeat that this idea—no matter how crazy it might seem—you can do it.”
“There are going to be bumps in the road, there are going to be things that don't go quite right. If there's a shared purpose articulation of what the mission is, you move through those things and you make it happen. Purpose is a very powerful multiplier.”
Simon Mainwaring is the founder and CEO of We First, a strategic consultancy that accelerates growth and impact for purpose-driven brands by putting 'We' first. I specialize in brand strategy, culture building and impact storytelling for startups, high-growth companies, and Fortune 500 corporations. My national podcast is LeadWithWe.com on Spotify, Google and Apple. My book, We First: How brands and consumers use social media to build a better world is a New York Times, Wall Street Journal, and Amazon bestseller, and strategy+business named it the Best Business Marketing Book of the Year. I deliver keynotes, training, and workshops that help brands define, integrate and activate their purpose to drive growth and scale impact.
Visit SimonMainwaring.com for speaking and WeFirstBranding.com for consulting
A Lot of Promise’: Vertical Farming Takes Root In Virginia
Since its inception at the turn of the millennium, vertical farming — which in its simplest form is any system where plants are grown in vertical stacks — has promised to revolutionize yields by allowing producers to multiply their crop outputs by six to eight or even more times without expanding their footprint
May 24, 2021
Imagine a field of lettuce.
Say the lettuces are all buttercrunch, and they dot the field like crisp rosettes. Each has been seeded by a farmer, kept free of pests, watered for weeks, and finally cut at the base before being rinsed and packed for transport. Each is destined for a different meal: a lazy evening salad on the porch, an artfully arranged plate at a restaurant two-top, the vegetarian alternative at grandma’s 80th.
Now imagine six of these fields, all stacked on top of one another.
The idea isn’t far-fetched. In fact, it’s already a reality in Virginia, where a new, more technologically oriented form of agriculture known as vertical farming is quietly taking root.
“There’s a lot of promise,” said Tony Banks, senior assistant director of agriculture, development, and innovation for the Virginia Farm Bureau Federation. “As we continue to watch urban encroachment and we have this demand to have food produced closer to where people actually live, we’re going to see more and more of it.”
Since its inception at the turn of the millennium, vertical farming — which in its simplest form is any system where plants are grown in vertical stacks — has promised to revolutionize yields by allowing producers to multiply their crop outputs by six to eight or even more times without expanding their footprint.
“You’re trying to use an area more intensively. Because you’re limited by horizontal space, you want to maximize vertical space,” said Leonard Githinji, a professor of sustainable and urban agriculture at Virginia State University who also works with Virginia Cooperative Extension.
The concept is flexible and scalable. The stacks can be small, nothing more than a narrow shelf installed at a restaurant or in a convenience store to grow produce within a customer’s reach. Or they can fill a warehouse, bringing an industrial dimension to agriculture.
“There’s a wide range. On one end, it’s almost you have a greenhouse that’s highly automated,” said Banks. “On the other end, you could be in a warehouse and everything is grown on huge assemblies of racks and you have complete artificial lighting and hydroponics.”
The latter type of vertical farming is “high-tech manufacturing, essentially,” said Scott Lowman, director of the Controlled Environment Agriculture Innovation Center at the Institute for Advanced Learning and Research in Danville, where scientists and other experts are exploring the promise of various types of indoor agriculture can hold for Virginia.
Hopes are high, particularly in the historic tobacco region of Southside, where state officials have been working for several decades to encourage farmers who once depended on the golden leaf to diversify their enterprises. It’s no accident that the Controlled Environment Agriculture Innovation Center was sited in a region with a rich agricultural history and an abundance of old warehouses once devoted to tobacco and now empty.
Nor was it an accident that in 2019, Gov. Ralph Northam’s office announced that vertical farming company AeroFarms had decided to build a $42 million facility in an industrial park jointly operated by Danville and Pittsylvania County. Virginia aggressively courted the project with some $1.5 million in state grant funds and incentives. In exchange, AeroFarms promised to build the facility, employ 92 people and purchase roughly $20 million of Virginia agricultural or forest products.
But while AeroFarms’ Virginia location will be the largest vertical farm in the state once built, it won’t be the only one. Over the past few years, other operations have quietly been putting down roots. Shenandoah Farms in Rockingham operates a large-scale facility that grows herbs and lettuces. In Lorton, Beanstalk grows a range of greens. Fresh Impact Farms in Arlington, which grows herbs, greens, and edible flowers, announced an expansion this spring in conjunction with the governor’s office. Babylon Micro-Farms in Richmond is developing sophisticated technology to spread small-scale vertical farms around the country. Other efforts are underway.
“We’re in a great position on the East Coast in terms of population centers,” said Lowman. “And it’s a friendly environment for business, and we have a legacy of hard-working labor.”
Controlled environment agriculture
While vertical farming is relatively new, its lineage is much longer, nesting within the family tree of controlled environment agriculture, which encompasses any type of production that takes place within a structure.
From Roman orangeries to modern-day greenhouses, controlled environment agriculture offers the advantage embedded in its first descriptor: control.
Outdoors, farmers are at the whim of the weather, plagued by pests and disease, and caught in a never-ending struggle to keep water and fertilizer confined to their fields.
Indoors, the equation changes. Because of the precision-engineered systems, controlled environment agriculture tends to require less water, less fertilizer, and few or no pesticides compared to conventional agriculture. And, depending on a particular system’s design, it can allow producers to grow crops 24/7, 365 days a year. AeroFarms has said that its technology allows it to produce leafy greens “at a rate 390 times more productive than field-grown plants.”
A vertical micro-farm known as a cropbox. (Virginia State University)
“I can now schedule my crops,” said Michael Evans, director of Virginia Tech’s School of Plant and Environmental Sciences. “I can basically optimize the environment for that crop.”
There are, of course, drawbacks. Everything nature once provided to a plant must now be provided by a human — or a machine.
“With a greenhouse, you’re taking advantage of natural sunlight. You’re not paying for that,” said Evans. “But you’re paying quite a bit for heating and cooling. When you flip to an indoor vertical system, the disadvantage is that now you have to supply the light.” Other costs diminish at the same time: without the translucent walls of a greenhouse, “your heating and cooling can go down because it’s better insulated.”
For years, prohibitively high energy costs boxed out vertical farming as a viable option for producers working in controlled environment agriculture. What would change the playing field was a technological innovation: the high-powered and highly efficient LED.
“The thing that really changed that made indoor vertical farming work and become an economic possibility was really the development of LED lighting, because that changes the energy equation a lot,” said Evans. “It makes providing the light the crops need much economically viable.”
A new generation of farmers
Despite its promise, vertical farming won’t replace conventional agriculture, experts say. Many of Virginia’s biggest commodity crops — soybeans, corn, hay — are grown at such a large scale that trying to transport them indoors would be an exercise in absurdity.
Where controlled environment agriculture has found a growing niche is in the produce most familiar to the average Virginian: lettuces, herbs, tomatoes, cucumbers, peppers, herbs, microgreens, and more. Experiments in growing strawberries indoors are also underway, and Evans pointed out that once legalized, marijuana may not be far behind, although the federal government’s continued classification of the plant as illegal will keep institutions like Virginia Tech from working with it.
For consumers of these products, the idea of local food grown only a short distance away is increasingly appealing. That can be an argument in favor of controlled environment agriculture and vertical farming, said Banks.
“When we import food into this country, what we import is fruits and vegetables that require a lot of hand labor,” he said. “So there’s opportunity there to offset some of those imports and reduce our reliance on food produced overseas.”
Both Banks and Evans also noted an unusual aspect of vertical farming: its allure for younger and often more urban Virginians.
“It’s getting a whole new generation of folks interested in agriculture. It’s a different type of agriculture, but it’s getting a lot of students,” said Evans. At Virginia Tech’s School of Plant and Environmental Sciences, he added, “we have to change our curriculum for what we’re teaching to prepare students interested in controlled environment agriculture.”
For a younger generation increasingly concerned with social and political justice, the opportunity offered by controlled environment agriculture and vertical farming to fill food deserts and involve local workers in local food systems is an attractive prospect. Many students are eager to look beyond the existing agricultural structures, said Githinji, who recently received a $600,000 grant from the U.S. National Institute of Food and Agriculture to explore the use of “micro-farms,” which incorporate vertical farming systems, as a way to address food deserts in urban neighborhoods.
It’s not unusual for extension agents to get calls in which people are saying, “‘As much as I want to grow more food, I can’t afford to buy even another quarter acre,” he said. “So you get people asking what they can do with what they have.”
The other draw is the technology. While vertical farming can be small- or large-scale, its larger applications rely on evolving and increasingly sophisticated technology that has piqued interest among the startup community.
“This is a really exciting industry that’s rapidly entering the mainstream,” said Alexander Olesen, CEO, and co-founder of Babylon Micro-Farms, a Richmond-based startup that develops indoor growing systems for institutional food service settings, such as hospitals, schools, and universities. Babylon, which in 2020 was the recipient of a $75,000 grant from the Commonwealth Research Commercialization Fund that aims to support small businesses in emerging research and technology sectors, builds small-scale vertical farms “as a sustainable amenity for these locations.”
The field’s growing popularity is also driving a need for more workers, more expertise, and more training, said many of the people interviewed for this story. The Controlled Environment Agriculture Innovation Center in Danville, itself a recipient of $365,000 in state grant funds in 2020, is key to that effort. So too are plans announced by the governor’s office last month that will see hydroponic greenhouse startup Sunny Farms build a 1.2 million square foot greenhouse in Virginia Beach — one of the largest on the East Coast — and work with Virginia Tech and the Virginia community college system to develop educational training in controlled environment agriculture.
“Our goal is really to support the controlled environment agriculture industry in Virginia, but we’re also working on creating an innovative controlled environment agriculture ecosystem in Virginia,” said Evans.
These enterprises may be only the beginning.
“Once people see that it’s working, we’re going to see them flourishing all across the commonwealth,” said Githinji.
Lead photo: Controlled digital lights help produce high-density feed grass in a Grov Olympus vertical farming machine in Utah. The Olympus Tower Farm uses a controlled environment to grow sprouted wheat and barley grass in 857 square feet of space and uses 95 percent less water to produce 5,000 to 6,000 pounds of grass per day, replacing 35-50 acres of land. (Photo by George Frey/Getty Images)
Sarah covers environment and energy for the Mercury. Originally from McLean, she has spent over a decade in journalism and academic publishing. Most recently she covered environmental issues in Central Virginia for Chesapeake Bay Journal, and she has also written for the Progress-Index, the Caroline Progress, and multiple regional publications. In 2017, she was honored as one of Gatehouse’s Feature Writers of the Year, and she has been the recipient of numerous awards from the Virginia Press Association. She is a graduate of the College of William & Mary. Contact her at svogelsong@virginiamercury.com
5 Things To Check When Comparing Lighting Designs For LED Grow Lights
As a grower, you invest in supplemental LED grow lights because they power the yield and quality of your crops.
May 17, 2021
· When you compare different lighting designs, make sure to compare apples with apples.
· These are the 5 things to check when comparing lighting designs for LED grow lights.
Eindhoven, the Netherlands – As a grower, you invest in supplemental LED grow lights because they power the yield and quality of your crops. In fact, the rule of thumb is that 1% light output equals 1% crop yield. So, it is vital that your LED lighting investment delivers the full performance you paid for.
The performance is determined by the light intensity and light uniformity of the LED grow lights you use. If the installed light intensity is lower than what has been designed, there will be less yield. If the uniformity is inconsistent, individual plants will grow and develop at different rates and there will be uneven production in your greenhouse.
Before you start
When you compare different lighting designs, make sure to compare apples with apples. This means taking 3 things into account:
1. Verify the credibility of the performance claims that manufacturers make
2. Make sure that DIALux calculation software is used for the lighting design. This calculation software is independent and commonly used in the horticulture market.
3. Check which input parameters have been used for each lighting design. It is easy to tweak the input parameters and give the impression of a more positive light level and uniformity within the lighting design. So which parameters are crucial?
Most important input parameters to check
• Is the right product specified? Check if the exact product that you have selected for your project has been used in the lighting design; with the right light output (PPF in µmol/s) and spectrum (blue/red/white/far red/…)
• Are your specific design values used like the average light level at your crop (PPFD in µmol/m2/s) and the overall light uniformity?
• What are the standard settings? The height of the grow light and crop (free height), reflection factors, and size and position of the area that is used in the uniformity calculation have an impact on the average light level and overall uniformity.
#1 Check the free height
The first input parameter to check is the free height specifying the distance between the LED module and the head of the crop. The free height can seriously impact the overall uniformity value. In case of high-wire tomato crops, with a limited free height of 1.50 to 2.50m, realizing a good overall uniformity value can be a challenge. An optimistic free height or calculating uniformity on floor level as if there is no crop will positively impact the overall uniformity value.
The free height is calculated by measuring the eventual top of the crop and the mounting height of the LED grow light.
#2 Check the reflection factors
Another important parameter to check, are the reflection factors used in the lighting plan. A reflection factor indicates the amount of light that is reflected by walls and other objects in a space. DIALux calculation software has originally been designed for indoor spaces like offices, where you will get reflection off the walls, ceiling, and floors that impact the light level on your desk. To avoid being too optimistic about the outcome, the reflection values in DIALux are set at 0% for a greenhouse lighting design, because the glass in a greenhouse does not reflect the light from the grow lights.
#3 Check the area that has been used to make light intensity calculations.
The next thing to check is the defined calculation surface. The size of the calculation area and the position of the grow lights within that area will seriously impact the average amount of active photons that reaches the surface of the crop (PPFD value in µmol/m2/s). When comparing lighting design results from different manufacturers, make sure that the calculation surface shows an equal number of maximum (peaks) and minimum (dips) light intensity values. Only then you receive a realistic average PPFD value in the lighting design.
In the below example, you will see two positions of a calculation area within the same light plan, which will generate far better average light intensity values in the B situation, because the light intensity is calculated with an area that shows more grow light (peaks), and consequently less areas with the minimal amount of grow lights, which will not represent the reality after installation
Position of measurement grid defines the outcome of average light intensity
#4 Check the size of the calculation surface
Another important factor is the size of the calculation surface that will impact the overall uniformity value. When comparing lighting design results from different manufacturers, make sure the same calculation surface has been applied.
To represent a real-life situation, a calculation for the full compartment area should be made that includes the edges of the greenhouse. In case of a typical production area, a centred area is used. You may understand that a full compartment will generate lower uniformity levels, because of the lower light intensities at the edges. So, make sure you always compare either full compartments or smaller areas.
#5 Check the used uniformity
The final parameter to check is the uniformity being used. Uniformity can be expressed in different ways. When you run the DIALux lighting design software, it provides you with different types of uniformity. When comparing lighting design results from different manufacturers, make sure the same type of uniformity is applied. For a horticulture application, we prefer to express uniformity as the average light intensity divided by the maximum light intensity, which represents real-life situations best.
In Summary
When comparing lighting designs there are lots of tweaks that suppliers can possibly make to finetune their plan. In case you want to make a proper comparison, you have to take a few parameters into account.
- Is the specified product with the right spectrum and efficiency used in the calculations?
- Is the right light level for your crop used and the right overall light uniformity?
- Are the settings comparable:
o Is the free height correctly defined?
o Are the reflection factors set to 0%?
o Does the measurement grid have an even number of light and dark spots in it.
o Are you comparing full compartment or small centered area numbers?
o And is the defined uniformity similar in the lighting designs?
Read our other blog and learn how to evaluate the performance claims of an LED grow light.
Grow with the pros
You want to be sure to get a rapid return on your investment and have all aspects of your project carried out professionally. With Signify, your project is in experienced hands. Signify is the global leader in the lighting sector and has built up a substantial track record in more than 1000 projects in the horticultural lighting market since 1995. This includes over two decades of dedicated experience developing tailor-made, LED-based light recipes that help growers speed up growth, increase yield and improve the quality of plants. With cutting-edge LED innovations at our command, we can custom-build a science-based solution for you.
Pascal van Megen is an application engineer at Signify with a background in mechanical engineering. As an application engineer, Pascal ensures that growers are provided with high-end horticulture lighting designs. He is providing internal and external training to customers and partners in the application of the Philips LED Horticulture products and systems. He acts as a consultant to customers and engineers, to drive continuous improvement of Philips LED lighting solutions.
--- END ---
For further information, please contact:
Global Marcom Manager Horticulture at Signify
Daniela Damoiseaux
Tel: +31 6 31 65 29 69
E-mail: daniela.damoiseaux@signify.com
About Signify
Signify (Euronext: LIGHT) is the world leader in lighting for professionals and consumers and lighting for the Internet of Things. Our Philips products, Interact connected lighting systems, and data-enabled services, deliver business value and transform life in homes, buildings, and public spaces. With 2020 sales of EUR 6.5 billion, we have approximately 37,000 employees and are present in over 70 countries. We unlock the extraordinary potential of light for brighter lives and a better world. We achieved carbon neutrality in 2020, have been in the Dow Jones Sustainability World Index since our IPO for four consecutive years, and were named Industry Leader in 2017, 2018, and 2019. News from Signify is located at the Newsroom, Twitter, LinkedIn, and Instagram. Information for investors can be found on the Investor Relations page.
VIDEO: Vertical Farms Could Take Over The World
As the global population continues to increase, vertical farming is becoming a more widely recognized and viable solution to our food production problem
By JACK BERNING
May 22, 2021
Vertical Farming Offers Better Tasting,
More Sustainable Produce.
Will It Take Over Farming
As We Know It?
As the global population continues to increase, vertical farming is becoming a more widely recognized and viable solution to our food production problem. Vertical farming is a type of indoor farming where crops are grown in stacked layers, rather than spread out across large plots of land.
To View The Video, Please Click Here
These futuristic farms aren't just going to have an impact on how we survive here on Earth; they could also enable us to create a food source beyond our planet, without a dependence on the outdoor climate or arable land.
Although the task sounds unimaginable, developments in controlled environment agriculture are proving that it is very much possible. Adopting these sustainable farming practices could lead to a monumental shift in how we produce food, both for today and the future of humanity.
Vertical Farming Advantages
Vertical farms offer many benefits over traditional farming practices — an increased crop yield with a smaller land requirement, more control over the resulting flavor and cleanliness of crops, and the prospect of better access to healthy foods in underserved communities, to name a few.
Because these farms are constructed completely indoors using LED lights, their output isn't subject to the natural elements that typically affect plant production such as adverse weather, insects, and seasons.
Vertical farms offer more control over the resulting flavor and cleanliness of crops, and the prospect of better access to healthy foods in underserved communities.
They're better for the environment because they require less energy and put out less pollution, without a need for heavy machinery, pesticides, or fertilizers. Vertical farms often use soil-less farming methods like aquaponics, hydroponics, and aeroponics, which requires just 10% of the amount of water consumed by conventional outdoor farms.
Think of a vertical farm as a plant factory — one that enables farmers to predictably grow anything, anywhere, from strawberries to kale. The idea was first introduced in 1999 by Dickson Despommier, a professor at Columbia University. Despommier and his students came up with designs for a "skyscraper farm" that could feed 50,000 people. Though the structure has yet to be built, they successfully managed to popularize the ideology behind vertical farming systems.
Output isn't subject to the natural elements that typically affect plant production such as adverse weather and insects.
So, why wasn't the skyscraper farm ever built? The answer sheds light on one of the most prominent vertical farming disadvantages — cost. A single farm can cost a hundred million dollars to construct, and a lack of data surrounding the long-term economic feasibility of vertical farms has caused some investors to shy away.
However, this hasn't stopped vertical farmers from persisting to disrupt the food production industry. Vertical farming has already been adopted in countries like China, Japan, and other parts of Asia. In fact, the market for vertical farming in that region is expected to increase 24% by 2026. And in the U.S., some vertical farming companies are already selling their produce in stores.
More Produce With Less Resources
One of those companies is Plenty, headquartered in San Francisco, California. Plenty was founded in 2014 by Matt Barnard and Nate Storey with a simple yet powerful mission to improve the lives of plants, people, and the planet.
Plenty already has established vertical farms in the San Francisco Bay Area, Wyoming, and Washington. These farms supply fresh produce including kale, arugula, and lettuce to major grocery stores like Whole Foods and Safeway.
The team at Plenty recently began construction on a new farm in the Bay Area that they call Tigris. Tigris will be its largest and most efficient farm yet, capable of growing a million plants at a time.
With Plenty's vertical farming technology, 700 acres of farmland can be condensed into a structure the size of a big-box store. Plenty's farms harvest 365 days per year and shrink growth cycles to about 10 days for many of their products.
This results in a yield increase of about 700% as compared to traditional farming, all while saving about a million gallons of water per week and using just one percent of the land that traditional farms use.
The secret to this astronomical efficiency lies in the technology. Plenty's farms are equipped with air handling units that capture transpired water, allowing them to recirculate 99% of the water back into the system. They also use LED light bulbs and, seeking to be as efficient as possible, the bulbs are designed in a grid format that maximizes the amount of energy absorbed by the plants.
These systems allow farm operators to have more control over their crop yield — all the way down to a plant's flavor profile. Blue LED lighting, for example, can create a crispier crunch in kale leaves. Additionally, without a need for pesticides, their products are completely organic.
Plenty's farm saves about a million gallons of water per week and uses just 1% of the land that traditional farms use.
"When you grow things outside, the elements are much more unpredictable," Shireen Santosham, the head of strategic initiatives for Plenty, explains. "If you grow indoors, you can control a lot of those factors in ways that are accessible to outdoor growers. And the result is that our produce can be hundreds of times cleaner."
Not only is the produce cleaner, it's also higher quality. Because Plenty's products are grown in urban areas and don't have to be shipped across the country, the brand doesn't have to prioritize shelf life. Less transportation needs also reduces their carbon footprint.
What could all of this mean for the future? That every place in the world, regardless of climate, could sustainably grow the same nutrient-rich and flavorful crops. And it could someday result in the colonization of other planets, as well.
"We can give the world back — a lot," says Storey. "We can give the world back land. We can give back the jungles of Borneo to the orangutans. We can give back the Amazon to the planet. We can give back the midwest to the buffalo. We can give back the things that we've taken. And we can be a lot less extractive."
Sobeys Expanding In-Store Vertical Farms Across Canada
Grocery store chain Sobeys is expanding its unique Infarm vertical farming units to more stores across the country as it takes advantage of the growing consumer appetite for made local products
May 2, 2021
Grocery store chain Sobeys is expanding its unique Infarm vertical farming units to more stores across the country as it takes advantage of the growing consumer appetite for made local products.
Niluka Kottegoda, Vice President Customer Experience, Sobeys, said Infarm is a vertical farming company based out of Germany.
Niluka Kottegoda
“We searched far and wide to find a really great best-in-the-world, unique, innovative solution for our customers as we were looking for a vertical farming solution,” she said.
“Infarm provided us with an opportunity to get farms into our stores, with end-to-end service. So they made it very easy for our stores and most importantly our customers’ best experience when it came to vertical farming globally. Each unit that you’ll see in the stores is a farm unto itself. The plants grow right in that module and they control all of the nutrients, the amount of water, the amount of food our plants get, and the amount of light that they get from a central farming platform.
“Just before COVID hit, I had the opportunity to go and see their office. And it’s really very special. On a screen, you can see every farm that they have around the world. They know exactly the condition of that plant and what it needs and if there’s a problem they can quality control. It’s all managed through the cloud and each one of the farmers has a tablet and information is passed on to the units and the farmers through their central platform.”
Local farmers manage the vertical farming at the individual grocery stores, where a variety of herbs, microgreens, leafy greens, and lettuces are grown year-round. Produce is grown directly in-store in a controlled energy-friendly environment and harvested sustainably.
Sobeys first unveiled its partnership with Infarm in 2020 and began its national rollout by unveiling Infarm vertical farming units in Safeway and Thrifty Foods stores in Vancouver and Victoria, B.C.
Kottegoda said generally there are two units per store but in larger stores, more units can be added.
“Right now we have them across Vancouver and Victoria. We have one installed in Halifax with 25 more coming. We have two installed in Calgary with 22 more coming. And one installed in Edmonton with 18 more coming,” she said.
“Once these latest ones are installed we’ll be closing in on 100 stores across the country. At the moment, we’re probably about 55 percent of the way there. We’re expanding across seven cities in the country.”
Kottegoda said the company does an assessment of all of its stores across the country to see whether it’s viable to put a farm into certain locations.
“The reason we’re going city by city is to make sure that we have the farmers ready. You just can’t put a unit in the store and hope for the best. You have tons of farmers there to support it. We have to make sure the local infrastructure is there and then we can expand across the country which is why you see us going city by city,” she added.
The company said these crops are harvested using 95 percent less water, 90 percent less transportation, and 75 percent less fertilizer than industrial agriculture.
“One of the great appeals of them is you can get fresh herbs, and leafy greens, all year round even through the winters as fresh as possible in our stores,” said Kottegoda.
“We can change up the assortment every five weeks. So the five-week cycle is from when our herbs and leafy greens and plants grow from seedlings until they’re ready to harvest. We can switch up the assortment anytime we need to. We can be really relevant to all of our local customers which is pretty exciting.”
She said locally-grown products are very important for consumers these days and the company has seen the importance of partnering with local producers in its stores.
“It’s also about the freshness and the taste experience. All of our customers are always looking for the best in terms of food and we pride ourselves in being able to give that to them. This is the freshest possible product, locally grown all year long,” added Kottegoda.
“And it’s been an interesting journey because we have been expanding during the pandemic and we have seen incredible trends in terms of at-home cooking, getting more and more popular. Going along with that people are getting more adventurous with the ingredients that they use, and the different herbs that they use.”
Lead photo: Exterior of Sobeys grocery store. Photo: Supermarket News
Article Author
Mario Toneguzzi, based in Calgary, has more than 40 years experience as a daily newspaper writer, columnist, and editor. He worked for 35 years at the Calgary Herald covering sports, crime, politics, health, faith, city and breaking news, and business. He now works on his own as a freelance writer and consultant in communications and media relations/training.
[Upcoming Webinars] Communicating Sustainability, Financing Indoor Ag
This panel will explore the best practices for communicating and reporting on sustainability with the hopes of encouraging the industry to mature
Indoor Ag-Con
SUSTAINABILITY, FINANCING HEADLINE
MAY | JUNE INDOOR AG-CONVERSATIONS SCHEDULE
MAY 26, 2021 10:00 AM - 11:00 AM EDT
Indoor Ag-Con & Agritecture invite you to join us for this important session.
Despite a decade of innovation and funding in vertical farming, many businesses do not communicate accurate information about the sustainability of their technology or operations. Whether it's unsubstantiated claims of water savings, carbon reduction, circularity, or overall sustainability, many companies do not avoid greenwashing in their marketing. This panel will explore the best practices for communicating and reporting on sustainability with the hopes of encouraging the industry to mature.
Moderator:
Henry Gordon-Smith, Founder & CEO, Agritecture
Panelists:
Sara Segergren, Project Portfolio Leader, Sustainability Innovation and Development,
Ingka Group | IKEA
Sam Norton, Founder, Heron Farms
Lisa Causarano, International Accounts Manager, Schneider Electric
SAVE YOUR FREE SPOT!
JUNE 8 & 9, 2021 1:00 PM - 4:30 PM EDT EACH DAY
Join Indoor Ag-Con, Brad McNamara & FarmTech Society for this
2-day SPECIAL EDITION of Indoor Ag-Conversations.
DAY 1 | JUNE 8, 2021 -- 1:00 PM - 4:30 PM
During 3 in-depth panel discussions with successful entrepreneurs and their investors, host Brad McNamara will push for first-hand accounts of each round to pull back the curtain on what it takes to fund an idea and create an investment-grade business in CEA.
DAY 2 | JUNE 9, 2021 -- 1:00 PM - 4:30 PM
2020 was a big year for Controlled Environment Agriculture -- and the next two years are likely to see unprecedented growth and change in the sector.
On day 2 of our Indoor Ag-Conversations 'Seed to Scale' event, the host FarmTech Society will focus on the maturing of the industry as CEA "crosses the chasm" into mainstream adoption.
LEARN MORE & SAVE THE DATE
INDOOR AG-CON - IN PERSON!
OCTOBER 4-5, 2021
We can't wait to see our industry colleagues again in October! We've got an incredible program lined up from you. Check out our expo hall floor, which is filling up quickly. And, explore our educational offerings, including keynotes from top indoor ag CEOS, panel discussions diving deep into 3 tracks - business & marketing; science & technology; alternative crops & growing methods.
And, of course, a full roster of networking opportunities, too!
JOIN US!
SPECIAL THANKS TO INDOOR AG-CON 2021 SPONSORS & MEDIA ALLIES
Indoor Ag-Con, 950 Scales Road, Building #200, Suwanee, GA 30024, United States
CubicFarm Systems Corp. Appoints Technology Industry Executive Janet Wood to the Company’s Board of Directors
Janet Wood is recognized globally as a leader in the technology sector and as a successful executive who retired from a rewarding career with several major technology companies including IBM, Crystal Decisions, Business Objects, and SAP
VANCOUVER, B.C., May 14, 2021 – CubicFarm® Systems Corp. (TSXV:CUB) (“CubicFarms” or the “Company”), a local chain agricultural technology company, announced today that Janet Wood has been appointed to the Company’s Board of Directors.
Janet Wood is recognized globally as a leader in the technology sector and as a successful executive who retired from a rewarding career with several major technology companies including IBM, Crystal Decisions, Business Objects, and SAP. Her success in building global channel partnerships and alliances with leading technology companies will bring invaluable insight to CubicFarms’ Board of Directors.
“It’s clear that the automated indoor growing technologies developed by CubicFarms will empower farmers to grow produce and livestock feed locally, directly addressing critical food security issues,” said Wood. “CubicFarms’ unique patented technologies use less land, less water, and no pesticides or herbicides, using our natural resources respectfully and sustainably.”
“We’re thrilled to welcome Janet Wood, a strong Canadian technology leader, to our Board of Directors. Janet is a trailblazer in the tech industry and an influential leader within every organization fortunate enough to benefit from her vision and expertise,” said Jeff Booth, Chair, CubicFarms. “Her significant experience with large software and technology companies will help CubicFarms continue to grow, innovate, and expand internationally.”
“Janet has been instrumental in contributing to the impressive growth of several large multi-national tech giants like SAP, and her experience will be critical as we enter into the high-growth phase of our business in 2021 and beyond,” said Dave Dinesen, CEO, CubicFarms. “Janet is a proven leader and the exact type of person we need to guide our company as we scale our business globally.”
After joining SAP in 2008, Wood's executive roles included Global Human Resources leader for the Office of the CEO, Global Head of Talent and Leadership, Executive Vice President (EVP) of Global Strategic Partners, and EVP of Global Maintenance Go To Market. At Business Objects, she worked as Senior Vice President of Global Partnerships. Wood also served as Vice President of Business Development at Crystal Decisions and held various management positions during her 16-year tenure at IBM. Wood holds a Bachelor's degree in Business Administration from the University of Alberta, graduating with distinction.
Wood has been recognized with a YWCA Women of Distinction Award and is a past recipient of the Canadian Women's Executive Network Top 100 Women Award.
An active member of the technology community and known for her leadership skills, Wood served for a year as the interim President and CEO of Science World shortly after retiring from SAP in 2019. Science World is a world-class science centre in Vancouver, B.C., that typically welcomes
over 800,000 visitors annually and connects with an additional 140,000 students throughout B.C. to advance STEAM learning for science, technology, engineering, the arts, and mathematics.
Wood is active in her community as a partner in B.C. Social Venture Partners, a not-for-profit organization that supports children and families at risk. She is a Board member of ICBC, Pureweb Technologies, and Junior Achievement of B.C. She sits on the University of Alberta Business School Advisory Committee and is the Canadian Regional Member Engagement Officer for Young Presidents Organization – Gold.
Wood will replace John de Jonge, a founding member of the Company’s Board of Directors. He will continue providing guidance in a different capacity by joining the Company’s newly-formed HydroGreen Business Advisory Board.
“We would like to thank John for his many years of service and contributions to the Board of Directors,” said Dinesen. “The HydroGreen Business Advisory Board will benefit from his significant agriculture and dairy experience with Artex and his commitment to our automated indoor growing technologies for farmers and ranchers to produce fresh, nutritious green livestock feed for their animals.”
About CubicFarms
CubicFarms is a local chain, agricultural technology company developing and deploying technology to feed a changing world. Its proprietary ag-tech solutions enable growers to produce high quality, predictable produce and fresh livestock feed with HydroGreen Nutrition Technology, a division of CubicFarm Systems Corp. The CubicFarmsTM system contains patented technology for growing leafy greens and other crops onsite, indoors, all year round. CubicFarms provides an efficient, localized food supply solution that benefits our people, planet, and economy.
For more information, please visit www.cubicfarms.com
. On behalf of the Board of Directors
“Dave Dinesen”
Dave Dinesen, Chief Executive Officer
Neither the TSX Venture Exchange nor its Regulation Services Provider (as that term is defined in the policies of the TSX Venture Exchange) accepts responsibility for the adequacy or accuracy of this release. Certain statements in this release may constitute “forward-looking statements” or “forward-looking information” within the meaning of applicable securities laws. Forward-looking statements are not guarantees of future performance and actual results may vary materially from those statements. General business conditions are factors that could cause actual results to vary materially from forward-looking statements.
Media Contact:
Andrea Magee
T: 236.885.7608
E: andrea.magee@cubicfarms.com
Investor Contact:
Tom Liston
T: 416.721.9531
E: tom.liston@cubicfarms.com
RUSSIA: A Unique Vertical Farm Can Produce 10 Times More Seed Potatoes A Year
Less than a year after the opening of the World-class Scientific Center "Agrotechnologies for the Future", Russian scientists had a breakthrough: the first-ever vertical farm with dynamic LED lighting
Less than a year after the opening of the World-class Scientific Center "Agrotechnologies for the Future", Russian scientists had a breakthrough: the first-ever vertical farm with dynamic LED lighting.
FEDERAL RESEARCH CENTRE «FUNDAMENTALS OF BIOTECHNOLOGY» OF THE RUSSIAN ACADEMY OF SCIENCE
The pandemic has interfered with technological production chains in many areas of agriculture, making the restoration of the Russian seed bank a priority of national food safety. Furthermore, pests and weather conditions prevent the production of standardized raw materials in needed quantities every year. It is only economically efficient to grow high-value crops such as berries or herbs in automated greenhouses. Potatoes, peppers, tomatoes, and oilseeds which are needed much more do not fall into this group.
A team from the Federal Research Center for Biotechnology of the Russian Academy of Sciences rose to the challenge and presented the first pre-production prototype of a vertical farm. The prototype was developed in the framework of the "Smart City Farm" project initiated by the World-class Scientific Center "Agrotechnologies for the Future" that was opened in 2020. Scientists have grown healthy potato for further multiplication in the field.
The crop rapid seed reproduction facility combines state-of-the-art digital technology with organic farming techniques. The vertical City Farm has controlled conditions: dynamic lighting, an automatic irrigation system, pathogen-free air, and nutrients supplied to the plant from a special substrate. A unique feature of the innovative farm is the individually adjustable LED lighting with different spectral composition preferred for specific varieties and for different periods of plant growth.
The complex makes it possible to grow products with specified properties under controlled conditions on an industrial scale with more than ten times the productivity from 1 m2 per year. It has also managed to achieve six harvests a year on the City Farm. This is because of unlocking the natural potential of varieties under controlled vertical farm conditions that do not depend on climate, weather or seed contamination risks.
"Our goal was to develop a universal multifunctional tool that would tap into the natural potential of different varieties, increase their productivity, and improve quantitative parameters. We used nature-like technologies and adjustable LED lighting without adding any genetic modifications. Our complex is based on the extensive researches of the RAS Biotechnology Research Centre. It is economically viable for industrial cultivation of the crops in demand. In addition, it is completely environmentally friendly and waste-free," said Vasiliy Zotov, a Candidate of Biological Sciences, and the head of the project.
The vertical farm consists of module stands with automated watering and multichannel LED lighting systems, as well as a set of microclimate and substrate sensors. Currently, the team is developing databases and analyzes the effect of adjustable lighting on various crops at different stages: from in vitro to nursery plants and final products. In particular, the team studies the influence of adjustable lighting on the morphogenesis and production process (including the biosynthesis of secondary metabolites) in different varieties of plants, including future generations.
"Another important feature of the vertical farm and the controlled vegetation technology developed for it is their flexibility and universal nature. The system can be easily changed to fit a particular task. For example, lighting can be chosen and automatically adjusted to secure the growth of other plants: flowers, berries, potatoes, beetroots, or even wheat", said Dmitry Kravchenko, a Candidate of Agricultural Sciences, a senior researcher at the Federal Research Center for Biotechnology of the Russian Academy of Sciences, and a development and agricultural support specialist in the project.
The team has already received the first commercial orders from major agricultural producers and potato processing companies. In the future, the scientists plan to develop a technology for controlled vegetation of essential-oil-bearing plants and vegetables, such as tomatoes and peppers.
Lead Image: IMAGE: THE MODULE STAND WITH AUTOMATED WATERING AND MULTICHANNEL LED LIGHTING SYSTEMS. view more
CREDIT: FEDERAL RESEARCH CENTER FOR BIOTECHNOLOGY OF THE RUSSIAN ACADEMY OF SCIENCES
###
Disclaimer: AAAS and EurekAlert! are not responsible for the accuracy of news releases posted to EurekAlert! by contributing institutions or for the use of any information through the EurekAlert system.
VIDEO: Indoor Farming Biz AppHarvest Delivered Sales In First Earnings As Public Company
AppHarvest, the tech-forward indoor vertical farming company that went public in February, released its first earnings report showing Q1 net sales of $2.3 million for its tomato harvest
May 17, 2021
AppHarvest, the tech-forward indoor vertical farming company that went public in February, released its first earnings report showing Q1 net sales of $2.3 million for its tomato harvest. The stock ($APPH) was up on the news, rising to more than $13 a share in morning trading, but still well short of its closing high of $38.
Founder and CEO Jonathan Webb spoke to Cheddar about the company's challenges in building a facility and harvesting its product amid a pandemic and pointed to expanding in the future. "Our thesis is that controlled-environment agriculture will be growing almost all fruit and vegetable production at scale indoors," Webb said.
Squamish Nation Grows Plans For Food Security With A Hydroponic Farm
While the outside of this 40-foot container is rather striking, it’s what’s on the inside that counts. 🌱
While The Outside of This 40-Foot Container Is Rather Striking,
It’s What’s On The Inside That Counts. 🌱
May 19, 2021
By: Elisia Seeber
A big bright orange container has just landed in the Sḵwx̱wú7mesh Úxwumixw (Squamish Nation) community of X̱wemelch'stn in North Vancouver.
While the outside of the 40-foot container is rather striking, it’s what’s on the inside that counts.
The container is a Growcer hydroponic modular farm that will support the community's wellness by allowing them to grow a year-round supply of fresh produce, including leafy greens, herbs and traditional medicinal plants.
Creating a sustainable healthy source of produce and increasing food sovereignty has long been a goal for the Squamish Nation, and the hydroponic farm is another piece of the puzzle, said Kelley McReynolds, director of Squamish Nation’s Ayás Méńmen Child and Family Services.
“Part of the reason that we started to look at ways that we could [provide food] was working from our values as Squamish people and our values around food sharing,” she said.
“Traditionally, we as a community, and as families, would go out and hunt and we would gather out on the lands and the waters and we’d bring it back to our community and people would only take what they need, and the rest of it would be shared.”
Through the launch of a food distribution program about four years ago, McReynolds said the team began breaking down the stigmas and fears around food insecurity and shifting back to their traditional ways, to ensure everyone in the community felt comfortable receiving food.
“We didn't want to look at the food as being a form of charity, or only for those who don’t have food,” she said.
Hydroponic farm idea sprouts
When the COVID-19 pandemic hit, McReynolds said food security worries increased for some members and the team started thinking further outside of the box about how they could address future food scarcity.
That’s when the idea for the hydroponic farm sprouted.
Squamish Nation has looked at more traditional styles of farming, and also has 19 garden boxes set up outside of their office where they grow fruit and vegetables and a traditional medicine garden.
“We plant every year and we harvest that to give to community,” McReynolds said. “We do a lot of training with our youth and our families to help them understand the plants, gardening and harvesting."
She said a thought they always had was, “think what we could do if we had farmland, we could feed so many more people.”
“But, you know, we live in a city and you don't have access to that kind of open space,” McReynolds said.
“So, when we looked at this option of the hydroponic farm and saw that it's the size of a shipping container, we thought, ‘that's pretty cool.’ It comes with all the equipment you need inside there. And, you can get it set up and within five to six weeks you are ready to make your first harvest and it yields approximately 450 heads of produce per week. That's a lot.
“We thought, ‘wow, that's amazing.’”
The founders of the ingenious technology and social enterprise came up with the idea based on their firsthand experience of food insecurity in Nunavut in 2015 and wanted to create a system that allowed communities to grow fresh produce anytime, anywhere, in any climate.
The growing technology was first deployed in food insecure, remote communities, but has since expanded to partner with schools, non-profits, and non-remote communities who see value in growing food locally – like Squamish Nation.
The electronically run hydroponic farms cost around $180,000 to set up and will produce fresh food for around 30 years, according to Growcer.
How does the modular hydroponic farm work?
Hydroponics is a soil-free growing method that uses nutrient-rich water to grow plants using less space, time, and crop inputs.
“The modular farms are automated to provide full environmental control,” Growcer’s website states, adding that plant growth factors such as light, nutrients, temperature, humidity, carbon dioxide, and water are monitored in real-time.
Once set up, a range of 140 leafy green plants can be grown in as little as six weeks.
“It's all brand new to us,” McReynolds said, adding that Growcer would be training staff this week and continue to provide support through their hydroponic farming journey.
“We’re all really excited.”
Squamish Nation to open Food Pantry and Community Kitchen
Produce from the new farm will be shared with families serviced by Ayás Méńmen, the youth centre and the future Smeḵw'ú7ts (Food Sharing) Community Kitchen and S7ílhen (Food) Pantry, which is hoped to be up and running by the summertime.
“We will continue to do monthly food distribution, but we will also have food on our shelves and in the freezers for any of our members who are in need … whatever the situation may be,” McReynolds said.
The hope for the community kitchen is to build a healthy community by providing a safe place for members to learn and improve their food preparation and cooking skills through workshops, which may start on Zoom during the pandemic. Ayás Méńmen also plans to host a six-week program for community members to meet once a week to cook and take a meal home for their families.
“I think what excites me about that is we are such relational people,” McReynolds said. “To be able to come together and learn and share and grow and laugh and tell stories, that's so healthy and therapeutic and it brings joy to your heart just being able to be together.”
While there’s still a bit of work to be done before the hydroponic farm starts producing the goods, McReynolds has more big plans.
“I have this vision of us being able to do a Friday night or Saturday afternoon market where we can have the fresh produce, we can have music, we can maybe have food trucks and we can gather together,” she said.
“I just think it's just a great opportunity for us to celebrate who we are as farmers and come together as a community.”
Elisia Seeber is the North Shore News’ Indigenous and civic affairs reporter. This reporting beat is made possible by the Local Journalism Initiative.
"Together We Are Expanding Our Facility In Sweden"
"Our expansion will enable us to offer our sustainably-grown salads to more Swedish households throughout the year, so we are looking forward to an exciting time," says Andreas Wilhelmsson, CEO of Ljusgårda
"Our expansion will enable us to offer our sustainably-grown salads to more Swedish households throughout the year, so we are looking forward to an exciting time," says Andreas Wilhelmsson, CEO of Ljusgårda.
In April, the first batch of salads was harvested in the company's new premises – and already now, Ljusgårda can deliver significantly more locally-grown salad to Swedish households, all year round. When the new 7000-m2 indoor farm, of which 2500 m2 growing area, is completed in the summer, Ljusgårda will become one of Europe's largest vertical farms.
"We are delighted to help Ljusgårda to produce local, climate-smart salads, says Henrik Nørgaard, Nordic Commercial Director of Agriculture at Signify[1]. "Ljusgårda shares our vision of a sustainable transformation within agriculture and is focusing in particular on quality and flavor."
Supporting the expansion
Andreas continues, "Signify has extensive experience of advanced lighting solutions and works with other large-scale indoor farms. They provide us access to lighting experts who can help us to continuously improve production. Signify is also one of the few suppliers with the capacity to deliver in line with our growth plan. Together we are expanding our facility in Sweden. Signify’s controllable light spectrum enables us to optimize the light for cultivation and produce the highest quality crops," Andreas continues.
Andreas Wilhelmsson
More than 70% of the fruit and vegetables consumed in Sweden today are imported by truck, ship, or plane from other countries. With the aim of making food production more sustainable, Swedish vertical farmer and salad producer Ljusgårda plans to increase its production 20-fold and expand its cultivation capacity to produce at least 60 tons of salads a month, which is the equivalent of around 1 million bags.
Signify is helping the Swedish vertical growers to expand their production facility in Tibro. By expanding its cultivation area from 300 m2 to 2500 m2, Ljusgårda will be able to supply fresh, locally produced salad all year round. Signify is providing the company with its latest high-tech solutions: Philips GreenPower LED production modules and the Philips GrowWise control system. These allow the light spectrum and lighting levels to be controlled, resulting in improved quality and higher yields per square meter.
As a result, Ljusgårda can ensure that its salads are tasty and nutritious. LED lighting also makes it simpler to predict growth levels, which means that it is easier for Ljusgårda to adapt its production to market demand during the season. The lighting is managed by the Philips GrowWise control system to schedule growth cycles well in advance and to allow for greater automation.
Making an impact
Henrik adds, "This is important to Signify because of our strategic goal of helping our customers accelerate the use of sustainable farming to improve agriculture’s impact on climate change. By using the latest lighting systems in vertical farming, Ljusgårda can supply salads that meet the highest food safety standards. The right lighting also results in plants of a higher quality and a higher percentage of crops being consumed, reducing food waste.'
"Additionally, by helping Ljusgårda to grow locally we contribute to significantly reducing the food miles these salads have to travel before making it to Swedish consumers. We are therefore proudly taking part in the journey from the first green shoots to more consumers being able to enjoy Swedish salads all year round," Henrik states.
Today, Ljusgårda's salads are sold in more than 60 ICA supermarkets, mainly in the Swedish regions of Västra Götaland and Småland. With the expansion of the facility and production on a much larger scale, Ljusgårda aims to supply sustainable Swedish salads to stores throughout Sweden.
Supporting food availability through horticulture LEDs illustrates Signify's commitment to supporting good health and wellbeing (SDG3). It is key to Signify's commitment to doubling the percentage of our revenues for brighter lives, which benefit society, to 32%. "This is part of our Brighter Lives, Better World 2025 program, which was launched in September 2020."
For more information:
Signify
Daniele Damoiseaux, Global Marcom Manager Horticulture
For more information:
Ljusgårda
info@ljusgarda.se
www.ljusgarda.se
Sources used:
[1] Climate-smart agriculture is an integrated approach to managing landscapes—cropland, livestock, forests, and fisheries—that addresses the interlinked challenges of food security and accelerating climate change.
11 May 2021
Crisis Looming In Trucking And Shipping; Here Is What’s At Stake for Horticulture
Spear called on the Senate panel to advance a bipartisan surface transportation infrastructure bill this year, focused on roads and bridges, that’s responsibly funded with a modernized user-fee system
By American Trucking Associations
May 12, 2021
American Trucking Associations President and CEO Chris Spear told the Senate Commerce, Science & Transportation Committee this week that growing pressures on the U.S. supply chain are fast approaching crisis levels, and that immediate action from Congress is needed to ensure our economic recovery is not derailed by further disruptions.
In testimony before the Subcommittee on Surface Transportation, during a hearing titled “Freight Mobility: Strengthening America’s Supply Chains and Competitiveness,” Spear outlined the trucking industry’s key priorities on infrastructure, workforce, safety, and the environment, detailing specific legislative steps lawmakers must take to ensure the integrity and longevity of the nation’s supply lines as the economy climbs out of the COVID-19 crisis.
“Investments in our supply chain are desperately needed, including the roads and bridges that connect our ports, rail yards, and airports to the National Highway System. Do that, and you will witness measurable efficiencies, including gains in productivity and safety, job growth, and sustainable employment, and historic reductions in carbon emissions,” Spear told members of the committee in his opening remarks.
The trucking industry moves more than 72% of the nation’s freight tonnage, and over the next decade, trucks will be tasked with moving 2.4 billion more tons of freight than they do today. Breakdowns in surface transportation infrastructure, as well as a severe and widening truck driver and diesel technician shortage, threaten the industry’s ability to keep goods moving safely and on time.
Freight bottlenecks and congestion on the National Highway System already cost the trucking industry an annual 1.2 billion hours of lost productivity, which is equivalent to more than 425,000 drivers sitting idle for an entire year — adding $75 billion to the cost of freight transportation. In addition, the industry currently faces a shortfall of nearly 61,000 drivers and will need to hire roughly 1.1 million new drivers over the next decade to keep pace with the economy’s increased freight demands.
Spear called on the Senate panel to advance a bipartisan surface transportation infrastructure bill this year, focused on roads and bridges, that’s responsibly funded with a modernized user-fee system. He also called on lawmakers to pass the DRIVE-Safe Act, legislation to remedy the driver shortage by promoting opportunity and enhancing safety training for emerging members of the trucking workforce. The bipartisan bill is backed by more than 117 organizations representing all levels of the U.S. supply chain.
A transcript of his opening remarks is available here.
Leading European Vertical Farming Company Retains Strategic Advisor to Explore Strategic Options
Award-winning Belgian vertical farming and contract research company, Urban Crop Solutions (“UCS”) has retained Contain, Inc., to explore strategic options to elevate its status as a leading European technology player in the fast-emerging global indoor farming space
Urban Crop Solutions Tech
Vertical farm & contract research co Urban Crop Solutions has retained Contain to explore strategic options to elevate its status as a tech leader in indoor ag.
We have long realised that we would need to decide between remaining independent and joining a larger organization to scale...this is the optimal time to make this move.”— Frederic Bulcaen, Chairman and founder of UCS
Urban Crop Solutions Container Farm
RENO, NV, UNITED STATES, May 19, 2021 /EINPresswire.com/ -- Award-winning Belgian vertical farming and contract research company, Urban Crop Solutions (“UCS”) has retained Contain, Inc., to explore strategic options to elevate its status as a leading European technology player in the fast-emerging global indoor farming space.
“We are delighted to have been awarded this mandate by UCS”, says Nicola Kerslake, founder of Contain. “It is a mark of the UCS management’s professionalism and dedication that they are open to exploring options from merger or acquisition to adding strategic investors to take this industry-leading firm to the next level.”
Urban Crop Solutions Grow System
UCS’ clients range from global billion-dollar companies to research institutions and start-ups across multiple industries in Europe, North America, and Southeast Asia. The growth of the business is attributed to a strong management and scientific team who have created best-in-class products and services made possible by application expertise and trade secrets. UCS expects to more than triple its revenues and reach breakeven profitability this year.
UCS offers two key solution and product channels:
-Plant biotechnology research: capabilities to simulate any growth environment and create growth recipe applications to address business and market opportunities in all crop verticals for use across numerous industries. UCS has developed innovative research applications such as growth performance of wheat, tobacco and cotton plants in controlled environments, growth recipe for green roof succulent plants on substrates and use of residual flows from waste to grow food.
-Vertical farming technology: indoor growing installations of hydroponic modules with growing surface areas ranging from 70 to over 5,000 square meters with an end-to-end customer support model. UCS has 4 different classes of product size that can be customized to meet the size or configuration requirements of any customer.
Maarten Vandecruys, founder and CTO of UCS, comments, “Now that we have our solutions and services in place, it is important that we pursue the best strategic options for the future of our organisation and team.”
“As a Board, we have long realised that we would need to decide between remaining independent and joining a larger organization to scale. There is such great momentum in indoor farming that this is the optimal time to make this move”, explains Frederic Bulcaen, Chairman and founder of UCS.
Contain Contact info:
Marilyn Jentzen
marilyn@contain.ag
+1.404.353.3754
About Urban Crop Solutions
Urban Crop Solutions BV is a privately held Belgian company founded in 2014. It offers end-to-end solutions for indoor hydroponic vertical farming via full-service customized and scalable solutions to multi-industry customers in two key product and service areas. Plant research products and services help customers select the right plant varieties or create new growth recipes for specific client needs or market opportunities. Indoor plant growing solutions and services range from concept design through business planning, manufacturing, installation, training, and after-sales servicing and support.
https://urbancropsolutions.com
About Contain, Inc.
Contain Inc is a US-based fintech platform dedicated to indoor agriculture, growing crops in warehouses, greenhouses and container farms. The Company serves the controlled environment agriculture industry in several capacities; it works with leading equipment vendors and with a wide pool of lenders to aid indoor growers in finding funding for their farms. It is also home to microlearning platform Rooted Global, which works with majors such as Danone and Dole to enable employees to grow a little of their own food at home. Most recently, the Company launched a used equipment trading platform, Equipped, to take the drama out of buying and selling used indoor farming equipment. The Company graduated from the 2019 Techstars Farm to Fork program, backed by Cargill and Ecolab.
https://contain.ag
Marilyn Jentzen
Contain Inc
marilyn@contain.ag
Visit us on social media:
Twitter
LinkedIn
Modular Hydroponic Growing Spaces In Freight Containers For Local Food Production
Freight Farms’ design was the first containerized vertical growing environment using hydroponic technology
May 17, 2021
Southeastern Pennsylvania Correspondent
A Massachusetts company has developed a unique, hydroponic growing environment in closed 40-foot freight containers that are being used world-wide to grow produce in areas with bad soil or weather conditions not conducive to outdoor growing.
Bay State natives Jon Friedman and Brad McNamara were developing rooftop greenhouses in the early 2000s when they realized a modular, hydroponic container might be a more viable solution.
Hydroponics wasn’t something new. Historians believe this soilless gardening can be traced back to hanging gardens of Babylon in Iraq built by King Nebuchadnezzar about 600 BC. Nutrient-rich water was pumped to the gardens from the Euphrates river to sustain its plants. A water-based growing thread continued through history and in the 1930s a University of California scientist, William Gericke, coined the term from the Greek word “hydro” (water) and “ponics” (work).
Friedman and McNamara, who were building outdoor, roof-based gardens on older residential buildings, looked outside the box, and turned their focus to widely available shipping containers.
They thought they could provide the equivalent of 2 acres of growing space in traditional 40-foot-by-8-foot containers and extend growing seasons year-round everywhere — especially in areas that couldn’t support traditional outdoor agriculture or in parts of the world affected most by climate change.
They named their company Freight Farms and placed their first container less than a decade ago. Now the concept is catching on worldwide.
View Photos From Freight Farms
Freight Farms’ design was the first containerized vertical growing environment using hydroponic technology. It was initially funded by a Kickstarter campaign in 2012, where they raised the funds to build a prototype to allow local food production to be available to everyone, anywhere.
The first commercial unit was installed at Boston Latin School, the oldest public school in the U.S., to produce fresh produce for the school cafeteria as well as serving as a teaching classroom for high school students.
“The company has placed 350 units in 48 states and 32 foreign countries,” Friedman said.
The company also introduced proprietary software called “farmhand” to help automate many farm processes, and is manufacturing its 10th generation container, the Greenery S, incorporating the latest technology and automation for vertical, hydroponics growing.
Growing Strong
Hydroponic Operation Supplies High-End Restaurants
Art Petrosemolo, Southeastern Pennsylvania Correspondent
Although the Freight Farms container units are capable of growing a variety of produce, leafy greens are its specialty and the best choice for farmers looking to sell their harvests year-round.
Containers also have been embraced by educational institutions to supply fresh vegetables for cafeterias and serve as learning and teaching space.
St. Joseph College in Standish, Maine, has been operating a Freight Farms unit for years to both supply fresh vegetables to its dining facilities as well as for student employment.
The site also has been a tool for community involvement with St. Joseph students working with a town Institute for Local Food System Innovation utilizing the Freight Farms container in partnership with a large hydroponic farm and commercial processing kitchen for events and agritourism.
With a decade head start in the business, Freight Farms does not have major competition in hydroponics container gardening production, although, in recent years, it has seen significant growth in multiple indoor soil- and water-based farming formats including warehouses, greenhouses and pods that are addressing growing produce year-round.
Climate change has increased concern about food production for growing populations worldwide with extreme weather conditions and higher levels of carbon dioxide in the atmosphere.
Friedman and McNamara have always been aware that the challenge to expansion for stand-alone, container gardening is the cost of power and each new rendition of their growing units has addressed both power consumption and automation to be more efficient.
Their latest Greenery S model uses growing lights that are 50% more efficient than previous models and the technology allows farmers to choose pre-set growing modes to maintain higher yields — 20% higher than earlier models — while prioritizing energy use.
Addressing affordable and clean power for customers, Freight Farms recently partnered with Arcadia, a Washington, D.C., energy company to offer affordable, renewable power options for customers.
Going forward, Friedman said growing container units will continue to become more efficient, allowing owners to increase their growing yield while having more control of their energy use to power the unit.
Slide Show Photos:
Lights and plant arrangements in Freight Farms new Greenery S model container.
Photo provided by Freight Farms
Leafy greens grow in Freight Farms’ own Greenery Farm container.
Photo provided by Freight Farms
This Freight Farms container is ready for shipment.
Photo provided by Freight Farms
Freight Farms' containers under construction in their Vermont facility.
Photo provided by Freight Farms
Lexy Basquette, Freight Farm’s on-site farmer, checks on some of her growing plants.
Photo provided by Freight Farms
Greenhouses, Vertical Farming and Urban Ag: Controlled-Environment Agriculture Has Growth Potential
Paul Post, New York Correspondent
USA-VIRGINIA: New Moneta Farm Redefines Method of Growing Fresh Produce
A new veteran-owned farm in Moneta is revamping traditional farming with advanced technology to serve up the freshest greens all year long
Its Growing 6,000 Greens A Month In A 40-Foot Box
MONETA, Va. – A new veteran-owned farm in Moneta is revamping traditional farming with advanced technology to serve up the freshest greens all year long.
Ditching the soil and bringing in a laptop, there’s a new hydroponic farm in Moneta.
Using selective lighting, balancing pH and nutrient levels, and releasing water through a bar of foam, Vittone Farms is growing 6,000 greens a month in a 40-foot box.
“365 days a year is what we can do,” Jeff Vittone, owner of Vittone Farms, said. “Which is also busting some paradigms. Like, ‘how do you do this and why is it ready and why is it so green?’ And it’s like well, it’s all grown here.”
The farm also uses green power by using a solar panel to produce a variety of foods stemming from lettuce to radishes to even carrots.
A lover of salads, Vittone said he got into hydroponics after noticing major food waste after E. coli scares.
After serving eight years active duty in the Air Force and a total of 12 years in the Virginia Air National Guard, Vittone turned his hobby into a business to put more fresh food on local tables.
“I believe if you ask any veteran they will say that after my duty to my country was served,” he said. “It’s like going without water. You still want to serve to some capacity.”
Now, he is calling on other veterans to get into the business.
By using only about five gallons of water a day, he encourages people to try container farming if they don’t have much land.
“If you have two, three acres of land that is just not enough to produce to make money but that’s enough for this to be there…small local communities and food deserts need this kind of technology.”
Hosting the Smith Mountain Lake Farmer’s Market, Vittone plans to highlight other local businesses from now till the week before Thanksgiving.
The farmer’s market is open on Fridays from 2 p.m to 6 p.m and Saturdays from 10 a.m to 2 p.m.
ABOUT THE AUTHOR:
Alexus Davila
Alexus joined 10 News in October 2020.
email facebook
Copyright 2021 by WSLS 10 - All rights reserved.