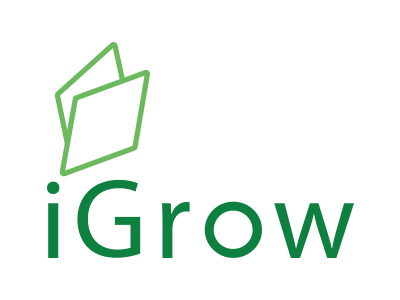
Welcome to iGrow News, Your Source for the World of Indoor Vertical Farming
$1.8 Million Dollar Alaska Micro-Grant Opportunity
Both individuals and organizations can apply; the definition is very broad: all individuals, Indian Tribes or tribal organizations, non-profit organizations, and federally funded educational facilities in the State of Alaska
State of Alaska, Division of Agriculture
Micro-Grants For Food Security 2021
Important: February 15th Scoping Pre-Application Deadline
There is a two-step process to apply:
1) Submit a simple, two-page application by the February 15th deadline.
2) Applications meeting the criteria, will be notified to submit a full proposal.
More Details and Dates
The Department of Natural Resources Division of Agriculture has complete Micro-Grants for Food Security information.
February 15: The simple two-page Scoping Pre-Application is due.
Grant Award Scoping Applications and Full Applications are to be submitted to dnr.ag.grants@alaska.gov or by mail at Division of Agriculture, Attn: Grants Coordinator, 1801 S. Margaret Drive, Palmer, Alaska 99645.
March 1, 2021: Notification of selection for full proposal submissions. Qualified, unfunded applications will be given priority in 2022.
April (TBD), 2021 - Announcement of final awards
Overview
Alaskans have a huge opportunity to increase their food security and resilience through a $1.8 million dollar mini-grant offered through the State of Alaska Division of Agriculture in 2021.
VH Hydroponics is offering guidance and estimates for interested clients who would like to apply. Email iinfo@vhhydroponics.com or (907) 782-4420.
Who Can Apply?
Both individuals and organizations can apply; the definition is very broad: all individuals, Indian Tribes or tribal organizations, non-profit organizations, and federally funded educational facilities in the State of Alaska. Therefore, everyone in the State of Alaska who has a project which will meet the requirements of the program are eligible to participate.
How much?
$1.8 million dollars for 2021. There will be additional funding in 2022 and 2023.
Individuals
Individuals may apply for up to $5,000 per year for up to 3 years. The maximum of $15,000 over 3 years.
Organizations
Organizations may apply for up to $10,000 per year for up to 3 years. Maximum of $30,000 over 3 years.
Multiple Awards For The Same
Project Are Allowed | 10% Matching
Awards may be granted for two or more eligible entities to carry out the same project. 10% match is required; but for individual grants, a waiver may be requested which will be considered for approval.
Purpose And Use of Grant Funds
To engage in activities that will increase the quantity and quality of locally grown food for food insecure individuals, families, neighborhoods, and communities, including by:
Purchasing tools, equipment, soil, soil amendments, seeds, plants, animals, canning equipment, refrigeration, or other items necessary to grow and store food;
Expanding areas under cultivation to grow food or to qualify for an EQUIP high tunnel to extend the growing season;
Hydroponic and aeroponic farming;
Building, buying, erecting, or repairing fencing for livestock, poultry, or reindeer;
Purchasing and equipping a slaughter and processing facility;
Traveling to participate in agricultural education
Paying for shipping of items related to growing or raising food;
Creating or expanding avenues for the sale of local food, increasing the availability of local nutritious food, and engaging in other activities related to increasing food security (including subsistence)
Scoping Pre-Application Project Scoring
An independent Review Committee will evaluate the scoping pre-applications with the following criteria:
Eligibility of the proposal per the farm bill legislation
The ability of the proposed activity to increase the production and/or storage capacity in the local community
The level of food insecurity in the applicant’s region
Other relevant information as to the capacity and purpose of the applicants
VH Hydroponics is Here to Help
Contact VH Hydroponics to learn more about pricing and possibilities
Email: VH Hydroponics for More Information
VH Hydroponics | (907) 782-4420 | https://vhhydroponics.com
2020 Shone A New Light On The Need For Container Farming
For us here at Freight Farms, the COVID-19 pandemic became a pivotal moment
Even A Pandemic Couldn’t Stop Us!
When the COVID-19 pandemic came to a head in March, we all felt a deep sense of trepidation. At the time, the future looked beyond bleak. We were all at the forefront of a completely new experience and it was up to us to figure out how to stay safe and continue to thrive in the ‘new normal’ world. For us here at Freight Farms, the COVID-19 pandemic became a pivotal moment. Would people still care about their source of food in the midst of a health crisis? Would individuals be looking to shift careers and lifestyles during such uncertainty?
The answer came right away: yes. The pandemic shone a spotlight on the key flaws within our food system and the need for a workplace revolution. We saw a tremendous growth of interest from people looking to make a positive and needed impact on their communities. We reflect on the year with immense gratitude for our community of farmers that continue to help us address pressing issues of sustainability and food security–we can’t wait to see all we can accomplish together in 2021!
E. coli Strikes Again
On November 10th, the CDC issued a statement alerting us that E.coli has struck again, this time in a pre-packaged single-head romaine after several people became ill from eating E. coli contaminated lettuce
The World Is Scary Enough Without Our Lettuce Trying To Kill Us.
On November 10th, the CDC issued a statement alerting us that E.coli has struck again, this time in a pre-packaged single-head romaine after several people became ill from eating E. coli contaminated lettuce.
This calls us back to the past two Novembers where salad mix and commercial romaine were mass-recalled surrounding the most popular eating holiday in the US: Thanksgiving.
You might remember, the shelves all looked like this:
No lettuce as far as the eye can see. Photo: Washington State University
Lucky for us, the food system is slowly changing (too slowly), so that when E.coli strikes some lucky consumers can turn to small-scale indoor farmers in their area for salad greens that are not only safe, but also very tasty.
We know E. coli is bad... but what, exactly, is it?
E. coli is a bacteria found in the intestines of humans and animals.
That’s right...it’s inside of us.
Before you freak out, most strains of the bacteria are completely harmless. Unfortunately, the bad one that makes you sick (E. coli 0157:H7) is the one that’s currently in our lettuce. Womp-womp.
E. coli makes its way into the outside world… through poop. If the poop makes contact with food, you’ve got an E. coli contamination. If the poop makes contact with a lot of food, it becomes a full-on outbreak.
This isn’t just gross, it's dangerous. E. coli 0157:H7 causes intestinal infections (read: diarrhea, abdominal pain, nausea, vomiting, fever, and fatigue). In severe cases it can cause bloody diarrhea (*silent scream*), dehydration, kidney failure… even death.
This is awful. How the heck did it get on our lettuce?
The best explanation we have is animal or human poop infected the soil or water source at a big romaine farm. The scary thing is, this is only an educated guess. Since people might not start getting sick until several weeks after harvest, it’s hard to go back and try to figure out what actually happened at Ground Zero (or even where Ground Zero is).
Feel like you’re having deja-vu?
That’s because this happened literally the past two years! In 2018 we had three E. coli outbreaks in romaine alone, the worst of which was in the spring: There were reported outbreaks in 36 states with 210 infected, 96 hospitalized and 5 dead. Only months later, another outbreak struck 12 states with 43 infected and 19 hospitalized just after Thanksgiving. Since then, romaine-related Ecoli has been popping up all over the place. The most frustrating part is that it usually takes the CDC months to investigate, meaning we don’t even hear about these outbreaks until well after the dangerous food is long-forgotten.
By now you’re probably thinking…
Before you denounce all salad, forever, we may have a solution.
The problem is with the system as a whole.
The reason that E. coli outbreaks are so widespread is because we source 95 percent of our leafy greens from a few farms in California and Arizona. Those greens (romaine included), get harvested and amassed at big distribution points before making their way cross-country to stores and restaurants. This means zero transparency into where the E. coli originated, making it difficult to eradicate. Not to mention, a lack of regulations prevents any actual accountability. The result? We keep eating the nasty stuff, and more people get sick.
One solution is surprisingly simple… decentralization.
This problem wouldn’t exist if we moved away from a centralized food system to a distributed one with small indoor farms. Here's why:
(1) Small, indoor farms create total environmental control with all types of fancy filters and regular water tests. Plus, this prevents exposure to two common sources of E. coli: contaminated soil and animal waste.
(2) Decentralization = transparency. Lettuce from small farmers isn’t changing hands, like, a million times. In the event of an outbreak, we can easily trace it back to its source to confirm that it’s safe to eat. With a shorter supply chain, this process take days, not months.
(3) While chances of contamination in a small indoor farm are much, much, much smaller… it is theoretically possible. Distributed production means, even if you do have one contaminated small farm, the exposure is contained, so it’s still safe to eat lettuces from other local farms.
Cultivar Boston | Massachusetts, @chefmarydumont @cultivarboston
These are all things we know a lot of our farmers' customers appreciate about the Leafy Green Machine. Throughout this whole ordeal, they've had access to safe greens in their neighborhoods.
It’s always rattling to see how fragile our food system can be, and we hope this whole hoopla motivates policymakers, wholesalers, and shoppers to think more about how we source our food.
Want to be the change you want to see in the world?
Become a farmer
VIDEO: Reviving Urban Life - An Innovative Soil-Based Indoor Vertical Farm That Brings The Production of Food to The Place It Is Consumed
One revolutionary agro-tech company, Vertical Field (www.verticalfield.com), is harnessing the power of geoponic technology, agricultural expertise, and smart design to tackle all of these issues and more
VERTICAL FIELD’S NEW PORTABLE FARMS ARE MAKING
THE WORLD MORE SUSTAINABLE – AND BETTER FED
Consistent Supply
Reduces Inventory Waste
Less Human Handling
More Sterile Environment
[DEC 9, 2020, New York/Rana’na, Israel] – Urban areas contain more than half the world’s population and contribute to some 70% of the planet’s energy emissions. Cities guzzle the bulk of Earth’s resources and produce more waste. Many residents live in “urban food deserts.” And buildings are literally making their occupants sick.
Vertical Field’s Urban Crops offers an ideal alternative to traditional agriculture. The soil-based platform can grow hundreds of types of crops – pesticide-free, indoors or outdoors – and requires no training to operate.
Our planet is home to some 7.7 billion people. In many places, hunger is a reality. Unpredictable climate patterns are threatening the availability and stability of fresh produce. Yet the global population is rising. How will we feed the world by the mid-21st century, when an expected 10 billion of us need food? And now in-light of the COVID-19 pandemic, the food supply chain is in jeopardy more than ever before -- the need to bring food easier and faster directly to consumers is more important than ever.
One revolutionary agro-tech company, Vertical Field (www.verticalfield.com), is harnessing the power of geoponic technology, agricultural expertise, and smart design to tackle all of these issues and more. The Israeli startup – cited by Silicon Review as a “50 Innovative Companies to Watch in 2019” and named by World Smart City in 2019 as “Best Startup” – produces vertical agricultural solutions that help the environment, improve human health conditions, cut down on human handling, reduce waste, and make fresh, delicious and more produce available 365 days a year locally and directly to consumers and other end users.
“Vertical Fields offers a revolutionary way to eat the freshest greens and herbs, by producing soil based indoor vertical farms grown at the very location where food is consumed,” said Vertical Field’s Chief Executive Officer, Guy Elitzur of Ra’anana, Israel who is hoping to place his ‘vertical farms’ in retail chains and restaurants establishments in cities throughout the US.
“Not only do our products facilitate and promote sustainable life and make a positive impact on the environment, we offer an easy to use real alternative to traditional agriculture. Our Urban farms give new meaning to the term ‘farm-to-table,’ because one can virtually pick their own greens and herbs at supermarkets, restaurants or other retail sites,” he adds.
Vertical Field’s Urban Crops offers an ideal alternative to traditional agriculture, especially in urban settings where space is scarce. The soil-based platform can grow hundreds of types of crops – pesticide-free, indoors or outdoors – and requires no training to operate.
From Wall to Fork
Vertical farming in cities is an energy-efficient, space-saving, farming alternative to traditional crops grown in acres and fields. Thanks to Vertical Field, everyone from city planners and architects to restaurants, supermarkets, hotels are using vertical farming to create lush, green edible spaces in congested areas around the world.
Portable Urban Farm
An alternative to the living wall is Vertical Field’s unique Vertical Field®, which can be placed in either a 20-ft or 40-ft. container equipped with advanced sensors that provide a controlled environment. This technology constantly monitors, irrigates, and fertilizes crops throughout every growth stage. Healthy, high-quality fruits and vegetables flourish in soil beds that contain a proprietary mix of minerals and nutrients.
Advantages of Vertical Field’s Vertical Farm:
Bug-free and pesticide-free – healthy, fresh, and clean produce
Less waste – uses 90% less water
Shorter growing cycles, longer shelf life
Plants are “in season” 365 days/year - grow whatever you want, no matter the weather or climate conditions of the geography
Consistent quality
Modular, expandable, and moveable farm
Automated crop management
More Sterile Environment
Less Human Contact
Creating a more sustainable way of life in cities across the globe has never been more urgent. Vertical Field is responding to the challenge today. Green cities will enrich life in urban areas, provide healthier and better food, and shorten the distance between consumers and their food.
About Vertical Field: Vertical Field is a leading agro-tech provider of vertical farming and living green wall solutions for urban environments and smart cities. The company is operated by professionals, agronomists, researchers, and a multi-disciplinary team, enabling the development of smart walls that combine the best of design and manufacturing, smart computerized monitoring, soil-based technology, water and lighting technology, and more. Vertical Field delivers next-generation vertical farming systems for a global clientele, including Facebook, Intel, Apple, Isrotel, Microsoft, and many more.
Israeli Supermarket Employs Vertical Farm Start-Up For Selling Produce
Vertical Fields, a Ra'anana based agri-tech start-up that creates vertical, sustainable farms using geoponic technology, agricultural expertise, and smart design, teamed up with BIOLED, a Tzuba-based eco-lighting start-up that uses LED lights to create more sustainable, profitable crops in order to erect the growing container
The new technologies eliminate the need to rely on outdoor growers and suppliers while also providing a fresher, more eco-friendly product which needs much less water and land to grow.
NOVEMBER 21, 2020
Produce growing under BIOLED lights. (photo credit: BIOLED)
Rami Levy, one of Israel's largest supermarket chains, has been cooperating with two Israeli agri-tech start-ups to erect large containers to grow fruit and vegetables, which will be sold in the chain's stores.
Vertical Fields, a Ra'anana based agri-tech start-up that creates vertical, sustainable farms using geoponic technology, agricultural expertise, and smart design, teamed up with BIOLED, a Tzuba-based eco-lighting start-up that uses LED lights to create more sustainable, profitable crops in order to erect the growing containers.
According to BIOLED, the first container is already in the process of being set up in Rami Levy's Ayalon Mall branch in Tel Aviv.
Thanks to the rapidly growing worldwide population, the amount of produce must grow by 60% to keep up with demand and overpopulation trends. Current methods of farming require too much water and land to meet that demand.
The new technologies eliminate the need to rely on outdoor growers and suppliers while also providing a fresher, more eco-friendly product that needs significantly less water and land to grow.
BIOLED already produces eco-friendly LED lighting for a wide variety of purposes for companies in Israel and plan to expand to Europe and the rest of the global market. Recently they breezed through their crowdfunding goal, nearly two months before their funding deadline expires in January 2021.
BIOLED also provides agricultural lighting for most of Israel's medical cannabis companies, most famously for the largest cannabis farm in the country, grown by medical cannabis giant INDOOR.
One of the main reasons for this is BIOLED's ability to shorten and stabilize horticultural growth cycles regardless of season, while also eliminating the need for pesticides and the logistical issues that comes with supplying fresh produce to urban areas,
Vertical Fields is a slightly younger company. They recently burst onto the Israeli agri-tech scene with their technology, which allows for produce to be farmed vertically within containers big enough to fit in a parking lot, using only one-tenth the amount of water usually needed.
Tags startup ecology hi-tech israel tech israel technology for agriculture rami levy agriculture Hunger start-up supermarket Farming
A Couple of Showrooms In Europe Need To Get The Ball Rolling For Verde Compacto - Shipping Container Farm
"People Are Immediately Enthusiastic When They See It"
"People Are Immediately Enthusiastic When They See It"
He, partly joking, calls himself ‘a born and raised’ city dweller from the heart of Amsterdam: Olivier Kappetein. As a representative of Mexican vertical farming company Verde Compacto in Europe, this is not ideal; will people be willing to listen to him given his background and his not yet widely undisputed product?
"Unfortunately not always, but that is why I’m looking for partners to start showrooms within Europe where we can display our cultivation systems. If people could actually see what we do, they would also see the potential in it. Of this, I’m sure. And yes, I know very well that vertical farming is not the solution to the global food problem, but I do believe there are many situations in which our systems would come in handy.”
The team of Verde Compacto that develops the container farm Huvster and the smaller Veggiebox cultivation variety
Advancing a Mexican family-run company
Before going further into the systems (such as the cultivation containers), we need to go back to where it all began. How does a young man from Amsterdam end up at a Mexican company active in vertical farming? “I was introduced to a Mexican through my dad a few years ago. It turns out he worked at Verde Compacto where he developed fertilizers. Through those fertilizers, they came into contact with vertical farming and decided to continue in that field.
I went to Mexico myself and got to know the family-run business better. They are ambitious and want to expand their brand in Europe and were looking for someone who could help them with that. With my degree in Business Administration, I can take on that role, and after doing my research to understand the relatively young market better, I now want to take some real steps forward.”
Opportunities, among others for apocalyptic bunkers
In the beginning, Olivier planned to aim all of his efforts in the Netherlands at first, but due to, among other things, the coronavirus, getting to know the market better, and the reservations against vertical farming in the Netherlands, he had to look in other places as well. “I want to build a couple of showrooms where people can see our products both in the Netherlands and in other European countries. We make cultivation systems in various sizes, from container to fridge-sized systems, always according to the vertical farming principle with a high productivity per square meter of 253 kilograms. I see a potential for these systems in, for example, Scandinavia, Germany, and the United Kingdom, countries with large urban areas or difficult growing climates. The younger generations in those places have a demand for sustainable, local products.”
But Olivier also has his eyes set outside of Europe, like in the Middle East. He is also looking into bunkers. Actual bunkers. “It is currently trendy for rich people worldwide to build apocalypse bunkers out of fear for the end of the world. Those people want to be self-sufficient in those bunkers, which is where our systems come into play. A great niche market with requests from the United States, Australia, and New Zealand, to name a few.”
Realistic due to size
In any case, Olivier is a realist: replacing large, traditional cultivation companies with vertical farms in whatever way can not be justified anywhere. “To give you an indication of our system size: recently, we started working together with The Goat Project, an Italian vertical farming project. Up to an investment amount of 30 million euros, we will be delivering together, but after that, they take on everything up to an investment amount of 3 billion euros.”
That is why Olivier aims first and foremost on restaurants and supermarkets, where the consumer can choose how the product they will eat is grown. But, the systems can just as well be used for ornamental cultivation or cannabis cultivation, both medical and recreational. “For that latter type of cultivation, we developed a specialized system which could also be used to cultivate tomatoes, though on such a small scale that would not be very profitable.”
Strawberry yogurt
However, it would be profitable for an Icelandic producer of strawberry yogurt. Importing fresh strawberries to the island is more expensive than growing them yourself in a vertical farm. “The energy comes from the earth in Iceland due to the geysers, but there are many more situations in which, with a bit of thinking and using the local circumstances, a generally more expensive system works. The ROI of our systems is about one to three years, with a very high productivity per square meter (5700 plants in a 12-meter container named Huvster), the second-highest for container cultivation on the market.”
Rotating LED lighting increases energy efficiency
Critics often point out the high energy input of vertical farming. Olivier recognizes that, but refers to the clever use of local circumstances, and the technological innovations developed by Verde Compacto meant to increase efficiency. Rotating lights, for instance, a unique system compared to many other vertical farming systems. “Instead of cultivating in layers, we work with cultivating in standing tubes with LED strips rotating around them so that every plant gets the light it needs, but the energy input in kilowatt-hours is 50% lower per square meter and the production per square meter higher.”
Make them enthusiastic
Back to the restaurants, which is what Olivier focuses on in Europe first. He imagines one of the cultivation containers walls being see-through so that the consumers can take a peek at the cultivation facility. “Especially large groups of young consumers who want to, for instance, eat vegetarian or vegan, I expect will be very enthusiastic, and so will the investors. It is also easier to talk about something if it is physically there and allows fresh and healthy foods to be sourced closer to home.”
However, Olivier is aware of the disadvantage that European supermarkets are not yet able to sell products grown in vertical farms under an organic quality mark. According to him, that hampers the growth of vertical farming. “At the moment, they lose their organic quality mark as soon as they cultivate on water because the standards are pretty outdated when compared to the technological cultivation developments.”
Win-win situation
But it is not an insurmountable problem, especially given the worldwide increase in demand for local products during the pandemic. But is this true given the fact that Verde Compacto is Mexican, and in the Netherlands, many well-known players are active in offering cultivation solutions? “I don’t think that matters all too much these days. Price-wise we don’t differ much from European or North American systems. Every system has its pros and cons. I am very open about that. A well-thought-out calculation is always required, but both parties can create a win-win situation when it happens. Of this, I, and hopefully my future partners as well, am sure. I'm looking forward to discussing it with them.”
For more information:
Verde Compacto
www.verdecompacto.com
Olivier Kappetein
olivier.kappetein@verdecompacto.com
+316 14 62 13 10
SINGAPORE: Port CEO Wants To Stop Food Rotting On Ships
The food industry accounts for almost a quarter of global carbon emissions. Yet 30% of production is wasted because it doesn’t arrive in an edible form — caused by “logistical failures” that can be addressed using information technology, said Tan Chong Meng, the chief executive officer of PSA International Group in Singapore
Port CEO Wants To Stop Food Rotting On Ships
October 28, 2020
One of the largest container port operators is calling on the shipping industry to tackle a growing yet often overlooked major environmental problem: spoiled food from hauling produce around the world.
The food industry accounts for almost a quarter of global carbon emissions. Yet 30% of production is wasted because it doesn’t arrive in an edible form — caused by “logistical failures” that can be addressed using information technology, said Tan Chong Meng, the chief executive officer of PSA International Group in Singapore.
Reducing that wastage through “digitalization” to move food more efficiently is “a huge opportunity” for the freight industry, which emits about 800 million tons of carbon dioxide, Tan told the Singapore International Energy Week conference.
The shipping companies that move 90% of the world’s goods including food have pledged to decarbonize in the next 30 years by curbing fossil-fuel emissions. That commitment focuses on the pollution caused by fuel, but doesn’t include the indirect emissions from food waste. About 1.3 billion tons of global food production is lost before reaching consumers’ plates every year, according to the Food and Agriculture Organization of the United Nations.
Supply disruptions caused by the coronavirus pandemic have put the spotlight on food security, prompting calls for reduced wastage to boost self-sufficiency. In August, China’s President Xi Jinping introduced a “Clean Plates Campaign” to tackle the “shocking and distressing” problem of food waste.
In Singapore, which relies on imports for more than 90% of its food and increased wastage by 20% over the past decade, President Halimah Yacob urged citizens to help overcome the problem.
Some 10% of developed nations’ greenhouse gas emissions are created by producing food that’s never eaten, according to the UN Environment Programme. About 14% of the world’s food is lost after harvesting and before reaching the retail level, and good infrastructure and efficient trade logistics are key to preventing food losses, according to the UN Food and Agriculture Organization.
Lead photo: Photo: Bloomberg
Horticultural Team Sheds Light on Growing Sea Beans in Shipping Containers
Trident Technical College horticulture students Lindsey Clarke and Clara Wooters work at an unusual farm located inside 40-foot-long shipping containers
By Tony Bertauski
June 20, 2020
Sea beans grown in a hydroponic system which feeds the plants a layer of nutrient solution on a timed schedule. Lindsey Clarke/Provided
Trident Technical College horticulture students Lindsey Clarke and Clara Wooters work at an unusual farm located inside 40-foot-long shipping containers.
For more about Heron Farms, visit www.heronfarms.com.
Sam Norton is the founder of Heron Farms. He did his graduate research on halophytes, which includes sea beans, also known as sea pickle. He’s not your typical farmer. He wears a white lab coat and nitrile gloves. He’s more of a farming scientist and, like many good scientists, affectionately refers to the crop by its genus rather than common name, Salicornia.
Sea beans are succulent halophytes that don’t produce beans or pickles. The foliage is edible and salty. Succulents are plants that store water in their leaves. Halophytes tolerate saline conditions. And as halophytes go, sea beans are among the saltiest.
Sea beans grow in hypersaline soils that are uninhabitable for most plants. They are the first plant into a barren salty flat. As it pulls salt from the soil, it transforms the ground into a habitable region for other plants and, over time, sea beans are crowded out. As a crop, this makes it difficult to farm outdoors.
The halophytes pull salt from the soil, which transforms the ground into a habitable region for other plants. Lindsey Clarke/Provided
A shipping container can grow 4,800 plants. While sea beans are their main crop, they are growing four new halophytes and plan to grow as many as 35. They use a hydroponic system called nutrient film technique that only uses 20 gallons of water a week. Plugs of sea beans grow in plastic channels, or gutters, three inches apart. A thin layer of nutrient solution cycles through the channels on a timed schedule.
The foliage tips are harvested three times from seed to the final cut in 60 days. These are the fleshy parts that can be cooked or eaten raw. The stems are woody and don’t have much of a culinary use, but breweries have used them in gose-style beer for a salty flavor.
With a proficient research background, Sam is maximizing production within the confines of a shipping container. He and his team follow every plant, from seed to harvest, and study the effects of light, nutrients, spacing, and other environmental factors.
Vertical Farms: The Height of Sustainability In A Post-COVID World
Vertical farms are innovative soil-based indoor farms that bring production of food to the location where it is consumed: supermarkets, local distribution sites, and restaurants
Among the many indelible images of the COVID-19 crisis have been the photos of mountains of surplus produce rotting in fields while millions of Americans go hungry. Urban areas are especially hard hit as supply chains are disrupted due to coronavirus fallout.
Vertical farms are innovative soil-based indoor farms that bring production of food to the location where it is consumed: supermarkets, local distribution sites, and restaurants.
Vertical Field, an Israeli start-up, has a container up and running at a Poughkeepsie, New York, restaurant and arriving soon at Evergreen supermarket in Monsey, N.Y. Its global clientele for its next-gen vertical farming systems includes Facebook, Intel, Apple, Isrotel, Microsoft, and many more.
Benefits include:
Consistent Supply
Reduced Inventory Waste
Less Human Handling
More Sterile Environment
Modular, expandable, and moveable farm
Bug-free and pesticide-free – healthy, fresh, and clean produce
Uses 90% less water
For more information:
Vertical Field
www.verticalfield.com
The Future Of Farming Might Already Be Here, Inside A Shipping Container
"We are completely protected from any natural disasters, rainstorms, pests, weeds even -- there's no pollution because all of the air is filtered," the CEO of Sprout Stack said
Ali Donaldson
10 News First Senior Reporter, 25 Mar 2020
On Hugh McGilligan's farm, it's a perfect summer's day, 16 hours a day, every single day of the year.
"We are completely protected from any natural disasters, rainstorms, pests, weeds even -- there's no pollution because all of the air is filtered," the CEO of Sprout Stack said.
It's the farming of the future, packed inside converted shipping containers on Sydney's Northern beaches.
Sprout Stack runs five farms at Brookvale -- in five shipping containers --producing as much as five hectares of traditional mainland agriculture. The shipping container farms run as closed circuits, using about five percent of the water.
But it takes just five seconds to walk from one end to the other.
And depending on the crop, they can harvest within a week to five weeks.
"Here we have purple radish," Hugh says brushing his hand across the top of a miniature forest of lush leafy greens. "That's our fastest growing crop and it takes about a week from planting through to harvesting."
"That compares to traditional farming where it takes 40 percent longer to achieve the same results."
And they're not just saving on the environment.
Sprout Stack's Mick Harder has pulled off some amazing farming equipment hacks.
"I made a harvester out of a hedge trimmer from Bunnings and some steel offcuts lying around that only cost us $1000 instead of the industrial machine that's around $100,000," Mick said while feeding his ingenious machine with the latest crop.
They don't even use soil.
Instead, everything is planted into coconut husks, which are mulched in a concrete mixer -- another hack that has saved them thousands of dollars in equipment.
And they've even tinkered with Mother Nature and the precious light she provides.
Plants only use red and blue light -- mixed together it forms a beautiful fuchsia -- for all the protein and nutrients they need. So that's all that's used on these farms.
It's about customizing the best of nature in a box, including cutting out a big chunk of the rainbow.
The farms can even be controlled over a mobile phone.
Nestled in between Sprout Stack's plant beds is its "nervous system".
"It's a farm management system that tracks the environmental conditions of the farm and the computer keeps the CO2, the temperature and the humidity of the farm ideal for growing plants," Hugh said.
"It's all run by a computer so we don't have to make any decisions -- the computer is providing the plants with the ideal growing conditions."
As we talked, the lights inside the container started switching off.
"I just go an alert," he laughs, peering through the dark at his phone.
"We turned off the air-conditioning and because we are in here the farm has got a little bit warmer and shut everything down, to ensure there are no deleterious effects on the plants."
Sprout Stack poses some interesting solutions to the modern plagues on our food bowls.
"We know that we need to provide an awful lot more food and we can't do that just throwing more resources at a strained system," Hugh says.
"We've got to get more efficient about the way that we produce food and use scarce resources like water, and we have got to produce our food closer to where it's consumed."
He then runs through the traditional vegetable supply chain -- or, as he says -- "the reason why the tomato you buy at the supermarket tends not to have very much flavour."
Hugh explains it's generally picked green about a week ago, transported cold chain from the country to the capital city you live in where it sits in a distribution centre for a day.
It then gets redistributed to another distribution centre that sends it out to your supermarket.
"At that point, it's often hit with ethylene to ripen -- basically it turns red -- but in ripening it's not really ripening it's just changing colour and in the meantime the nutritional quality of that product has declined."
He claims Sprout Stack's produce is fresher and tastier because they harvest closer to where it is being consumed.
"On average we take about 16 hours between our harvest to store, which compares to about a week for traditional agriculture."
Harvest Fresh Canteen Vegetables On-Site
In schools and universities in America, the catering and service provider Sodexo plans to produce fresh vegetables all year round via indoor farming. To this end, the company is cooperating with the US hydroponics provider Freight Farms. The salad should grow vertically in containers on campus
by Frauke Brodkorb-Kettenbach
February 15, 2020
In the container greenery of the US company Freight Farms, Sodexo grows fresh vegetables for its cafeterias directly on campus. CAROLINE KATSIROUBAS / FREIGHT FARMS
In schools and universities in America, the catering and service provider Sodexo plans to produce fresh vegetables all year round via indoor farming. To this end, the company is cooperating with the US hydroponics provider Freight Farms. The salad should grow vertically in containers on campus.
Over 500 vegetables, such as Salanova Green Butter Salad (pictured), can be grown on a commercial scale in Freight Farm’s containers with 320 square meters of vertical acreage - regardless of the season and without pesticides or herbicides. Delivery routes are also eliminated with this type of vegetable cultivation.
Save resources
With the cooperation, Sodexo is pursuing its strategy of operating as sustainably as possible and at the same time being precisely informed about the origin of its food for customers in the education segment.
In addition, students could monitor the stages of growing their food. For example, schools could integrate hydroponic farming into interactive curricula or school subjects such as technology, agriculture, nutrition, and economics, according to Freight Farms' approach. The vertical farming provider also sees similar advantages for employees when using the containers in companies.
CAROLINE KATSIROUBAS / FREIGHT FARMS
So far, vegetables grow in freight farm containers in 25 countries and 44 states in the US - in small and medium-sized businesses, hospitals, as well as in retail and non-profit organizations, the information says. 35 school facilities now work with the hydroponics system. By working with Sodexo, the number should grow rapidly.
SODEXO, USA
Sodexo USA offers building management and catering services to schools, universities, hospitals, senior citizens' communities, venues, and other key industries. The parent company Sodexo Quality of Life Services, with headquarters in Issy-les-Moulineaux, France, was founded in 1966. According to its own statements, the group offers Benefits and Rewards Services and Personal and Home Services daily for 100 million people in 72 countries. In 2019, it had an annual turnover of 22 billion euros with 460,000 employees worldwide. The portfolio includes reception, security, maintenance and cleaning services, catering, facility management, restaurant, and gift vouchers and fuel passes for employees.
Hamilton’s 80 Acres Farms To Grow Tons of Tomatoes On New York City’s Fifth Avenue
Hamilton-based 80 Acres Farms will grow tomatoes on one of the busiest streets in New York outside the Solomon R. Guggenheim Museum. The grow is part of “Countryside, The Future,” the Guggenheim’s new exhibition in collaboration with Rem Koolhaas, which opens to the public Feb. 20, and runs through Aug. 14
February 21, 2020
By Eric Schwartzberg, Staff Writer
HAMILTON —
80 Acres Farms will grow tomatoes on one of the busiest streets in New York outside the Solomon R. Guggenheim Museum.
The grow is part of “Countryside, The Future,” the Guggenheim’s new exhibition in collaboration with Rem Koolhaas, which opens to the public today and runs through Aug. 14.
Along with its commercial partner’s Infinite Acres and Priva Holding BV, 80 Acres Farms will grow cherry tomatoes in an indoor grow area right outside the museum on Fifth Avenue.
80 Acres Farms is a leader in indoor growing for retailers such as Kroger, Jungle Jim’s International Market, Whole Foods, Dorothy Lane Markets, and Giant Eagle.
MORE: ‘The perfect home’: Why 80 Acres chose Hamilton to move its headquarters and create 125 jobs
People in New York will be able to look through a large window in the indoor farm to view a crop of fresh tomatoes being grown continuously during the next six months. The first tomatoes grown will be ready for harvesting and consumption by late March.
The “Countryside, The Future” exhibition will examine political forces, social issues, and environmental factors altering landscapes across the world, including traditional farmlands.
“We believe that what we are doing is about the future of food,” said Mike Zelkind, chief executive officer of 80 Acres Farms. “We are changing the way fruits and vegetables are grown and harvested locally then delivered to grocers the very next day. There is an enormous market and consumer appetite around the world for produce that our crop scientists and other food experts have been perfecting during the past five years.”
MORE: Dilapidated Hamilton building transforms into an industry-changing grow facility
Zelkind said 80 Acres’ participation in the “Countryside, The Future” exhibition will allow New York residents and visitors to experience how “the freshest, tastiest locally-grown tomatoes” can be grown year-round indoors in one of the busiest cities in the world.
For the Guggenheim exhibition, 80 Acres Farms, Infinite Acres, and its Priva partners have collaborated on the 700-square-foot grow center, which is expected to grow 50,000 tomatoes in six months. Additional tomatoes will be donated to City Harvest, a New York City food rescue organization that recovers excess food and distributes it to people in need.
MORE: Hamilton’s large indoor growing operation is so advanced they want it around the world
Last year saw a massive year of growth for 80 Acres. It opened its automated facility on Enterprise Drive, a facility that grows leafy vegetables, herbs and strawberries, then a downtown Hamilton location on South 2nd St. that grows vine crops, including tomatoes, cucumbers, and peppers.
The company also launched Infinite Acres, an independent joint venture aimed at providing large-scale indoor farming facilities worldwide. The venture also includes UK-based Ocado Group, one of the world’s largest dedicated online grocery retailers, and Netherlands-based Priva Holding BV, a leading provider of technology solutions, services, and automation systems to horticultural and other industries.
That partnership is now building large-scale, fully automated indoor farms in the United States, Asia and Europe.
It also inked a deal to moved its headquarters from Cincinnati to Hamilton and was granted a tax credit for committing to create 125 new jobs and investing at least $26.9 million.
MORE: Innovative Hamilton indoor growing company part of a worldwide deal to supply food
Detroit Organization Uses Shipping Containers As Farms Providing Food For Soup Kitchen, Restaurant
The farming being done inside the shipping container is the equivalent of almost two acres of land
By Amy Lange
December 2, 2019
DETROIT (FOX 2) - At the new Three Cats restaurant in Clawson, co-owner and Chef Matt Prentice is serving up the Cass Community arugula salad and the beet stack with Cass basil.
Prentice, a big fan of farm to table, says this is as close and as fresh as you can get.
Shipping container farm is as close to fresh as it gets
It comes from the Freight Farm at Cass Community Social Services in Detroit where seeds are watered in trays then transferred to hangers farming vertically inside a shipping container"It gets harvested two, three, four days a week.
The arugula that I get from California -- I mean it's fine, but it's two weeks old before I get it. Here it's sometimes two hours old," he said.
That's because it comes from the Freight Farm at Cass Community Social Services in Detroit, where seeds are watered in trays then transferred to hangers, farming vertically inside a shipping container."So you can see everything's dated - what it is and when it was started so they'll know," said Faith Fowler, Cass Community Social Services. "It comes down almost like drip irrigation so that you're wasting very little water at all."
This is a great solution to having fresh good food year-round.
"Donated by the Ford Fund about a year ago, the Freight Farm is now producing fresh produce year-round for the soup kitchen at Cass and at Three Cats."
It means his restaurant is able to have farm to table, table to farm in a really good way and to support the work we're doing here, with hungry people and homeless people and others," said Rev. Faith Fowler with Cass Community Social Services. Fowler runs Cass Community Social Services, where serving the homeless and getting them work and housing is also about health and the environment."It tastes really good and it is good for you," she said. "We're using solar for here and considerably less water so it ties in with sustainability which is a theme at Cass.
"The farming being done inside the shipping container is the equivalent of almost two acres of land.
"It's a lot better product but it also gets the Cass name out there," said Prentice. "I mean, this little kitchen here feeds hundreds of thousands of people every year."
Prentice should know. As a longtime volunteer at Cass who then became the director of food services, serving up fresh produce to clients at the soup kitchen and customers here at Three Cats - it's about more than just good food."
The bottom line is, the fresher the produce is, the better it is for you - it's just that simple," he said. "There's a lot of advantages to it but the biggest thing is just making people aware of what we're doing down here."
Have You Ever Considered Turning A Shipping Container Into A Greenhouse?
Here Lucchini custom-made a BoxXLand container with Senmatic’s LED-fixtures, fertilizer mixer, and climate control to fit the specific needs at HAMK University
That is what happened at HAMK University in Finland. The entire project started when our partner and greenhouse-supplier Lucchini was contacted by HAMK University in Lepaa, Finland. They asked Lucchini to assist in building and supplying box container system with the aim of R&D of indoor farming.
Here Lucchini custom-made a BoxXLand container with Senmatic’s LED-fixtures, fertilizer mixer, and climate control to fit the specific needs at HAMK University.
At the university, they are doing trials on lettuce and herbs of all kinds – and so far, they have been very happy with the results from the first production cycle. The box container greenhouse brings several benefits such as being able to grow vegetables in locations, where the climate normally makes it impossible.
Read the full article here
GP Solutions' New Technologies Provide Cleaner Farming
The company developed what they call a 'GrowPod.' Essentially, a food-grade shipping container refurbished and outfitted with the latest technology to grow clean food in a controlled environment," the publication stated
COLTON, Calif., Dec. 4, 2019,/PRNewswire/ -- GP Solutions (OTC:GWPD), the developer of modular automated micro-farms, may help in solving the E.coli crisis that is sickening dozens across America according to Business Management News.
The article said dozens of people were infected across 19 states in the most recent E. coli outbreak stemming from lettuce harvested in California. The infected range from 3 to 89 years old. 39 were hospitalized. Six developed kidney failure.
While the publication says, "America's food chain is broken," there is "hope on the horizon."
"New indoor Controlled Environment Micro-Farms (CEMFs) have been developed by some forward-thinking companies," the article stated.
"One such company is GP Solutions. The company developed what they call a 'GrowPod.' Essentially, a food-grade shipping container refurbished and outfitted with the latest technology to grow clean food in a controlled environment," the publication stated. "Inside a GrowPod, the air and water are filtered, and since it is a sealed environment, there is little chance for contamination."
Moreover, the magazine noted, these pods are not just for existing farmers.
"They are easy to operate so almost any business, organization, hotel, farmer's market, or restaurant can have their own Pod and supply their customers with truly farm-fresh, clean, healthy food."
GrowPods empower anyone to grow food for their community or for profit. Being portable and modular, they can be placed almost anywhere, and stacked to expand operations or keep crops separated. Farmers can utilize GrowPods to cultivate a broader product line, and sustain revenues and employees over the winter.
The article also stated that growing greens inside a CEMF is efficient and produces a large crop yield equivalent to about two acres of outdoor farmland.
For more information, visit: www.growpodsolutions.com, or call: (855) 247-8054.
To view the article, visit: https://businessmanagement.news/2019/12/01/e-coli-sickens-dozens-across-the-nation/
Forward-Looking Statements
This release includes predictions or information that might be considered "forward-looking" within securities laws. These statements represent the Company's current judgments but are subject to uncertainties that could cause results to differ. Readers are cautioned to not place undue reliance on these statements, which reflect management's opinions only as of the date of this release. The Company is not obligated to revise any statements in light of new information or events.
Connect:
Email: info@growpodsolutions.com
Website: www.growpodsolutions.com
Facebook: facebook.com/GrowPodTechnology
Twitter: @GrowPodSolution
US: Idaho - Family Farm Serves Mushrooms To Treasure Valley
Mason and Tia Groves built the entire farm from three shipping containers and now have their mushrooms shipped to five restaurants in the Treasure Valley, to Cliff’s Country Market in Caldwell and to the Nampa Farmers Market
By RACHEL SPACEK rspacek@idahopress.com
July 29, 2019
PARMA — Tia Groves described her husband, Mason Groves, as an “entrepreneurial person with passion oozing out of his pores.” Last fall, that passion took the form of a hand-built, family-run mushroom farm in Parma.
On Wednesday morning, Tia Groves walked in and out of the three shipping containers-turned-mushroom farms with baby Abel on her hip. Groves Country Mushroom Farm had its first full month of operation in November and plans to continue growing mushrooms year-round to keep up with the demand.
Mason and Tia Groves built the entire farm from three shipping containers and now have their mushrooms shipped to five restaurants in the Treasure Valley, to Cliff’s Country Market in Caldwell and to the Nampa Farmers Market. They are also in a number of community supported agriculture bundles, a service in which people can get local produce delivered to them on a regular basis.
Tia Groves said she believes there are at least two other mushroom farmers in the Treasure Valley. She said that the competition among the three is minimal since they see a demand for mushrooms in the valley.
The couple met at Vallivue High School in 2009. The couple spent a few years apart when Mason Groves spent time on a fishing boat in Alaska and Tia Groves went to school and worked in Chicago. They rekindled their relationship in 2014 back in the Treasure Valley.
After having their first child, Jett, the two realized they couldn’t raise a family on an Alaskan fishing boat and decided to move back to the valley.
When searching for a way to make a living in the valley, Mason Groves, who said he has always been fascinated by agriculture, came up with the idea of growing mushrooms after talking with his grandfather, a longtime crop farmer in Parma.
“After that I dove right in,” he said.
Mason Groves said he started reading books on how to grow mushrooms and starting small growing facilities to work it out in trial and error.
Still, to make a living, Mason Groves continues to work on a fishing boat in Alaska, away from his family. He said growing mushrooms started as a way to make money while also being with his family. He is trying to get out of the commercial fishing business.
While Mason Groves is away fishing, Tia Groves and Justis Kelly, the farm’s only other employee, work on harvesting and moving the mushrooms between shipping containers.
Kelly is living near the farm for the summer and helps harvest the mushrooms twice a day.
One of the greatest challenges, Mason Groves said, was the consistency involved in growing a product.
“This is a weekly crop — you are on a schedule, doing the same thing every week, and any hiccup that shows up impacts the clients that are expecting mushrooms every week,” he said.
THE PROCESS
Mushrooms, Tia Groves explained, typically thrive in the Pacific Northwest, where it is cold and moist nearly year-round.
“In order to grow them in a climate like this, we try to mimic the way they would grow there,” she said.
Groves Country Mushrooms are grown indoors, in three shipping containers, so the farmers can regulate the temperatures of the containers to keep them cool and moist despite the weather outdoors.
Currently, the farm is growing three different colors of oyster mushrooms, chestnut mushrooms and lion’s mane. Tia Groves said in the fall the farm can grow as many as 11 different types.
The first shipping container on the farm has a refrigerator where the harvested mushrooms are preserved and where they await being shipped to consumers.
The second shipping container contains bags of wood chips and the mushroom spawn, what the mushroom grows from. This shipping container acts as the incubation chamber for the bags of wood chips and spawn to form mycelium, the vegetative part of a fungus or fungus-like bacterial colony.
After the bags fill with mycelium, they go into the last shipping container, or the fruiting chamber, where the mushrooms eventually sprout. The fruiting chamber is the foggiest and most humid of the containers. Once in the fruiting chamber, a slit is made in the bags of mycelium, allowing oxygen and light in so the mushrooms can grow.
The mushrooms start sprouting as pin sets, miniature mushrooms, and then grow into full clusters.
Once the mushrooms are in full clusters, they are harvested and put in the refrigerator in the first shipping container.
The excess wood chips and used mycelium from the plastic bags gets composted onto a pile on the farm. The compost is used on other parts of the Groveses’ property, like vegetable and flower beds. Mason Groves said they would eventually like to use the compost to grow other vegetables.
Water is used throughout the shipping containers to clean the space and regulate the environments inside. Once the water is used, it drains into a settling tank and is used on the compost pile.
Mason Groves said what little water is used in the process doesn’t go to waste.
Tia Groves said the family hopes to introduce new types of mushrooms to their farm in the fall and spring. She said the small farm is still in a trial-and-error period.
According to a ResearchAndMarkets.com report, the global mushroom market accounted for $38 billion in 2017. In the United States, the value of mushroom production was $1.22 billion in 2017, an 8 percent increase in value since 2007, according to a report commissioned by the American Mushroom Institute. The total crop in the United States was 929 million pounds of mushrooms.
Groves Country Mushrooms is expecting to triple in size by the first of the year after they move into a new building and keep the three shipping containers.
Mason Groves said the Treasure Valley community has been helpful and nice as the couple’s mushroom operation has gone through some ups and downs. He said their customers are countable on one hand, and he has personal relationships with all of them.
Rachel Spacek is the Latino Affairs reporter for the Idaho Press. You can reach her at rspacek@idahopress.com. Follow her on twitter @RachelSpacek.