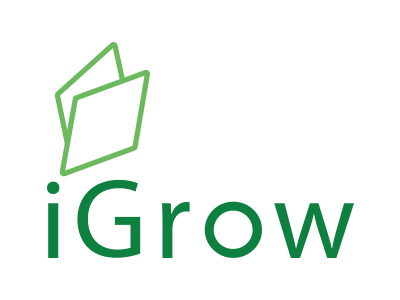
Welcome to iGrow News, Your Source for the World of Indoor Vertical Farming
Opening Large Vertical Farming Facilities in Europe
Infarm has signed a contract for a new Growing Centre in Bedford which will measure 9,760 sqm in size, offering more than 5500 sqm of growing space in Infarm’s cloud-connected farming units.
August 9, 2021
Infarm has signed a contract for a new Growing Centre in Bedford which will measure 9,760 sqm in size, offering more than 5500 sqm of growing space in Infarm’s cloud-connected farming units.
Jeremy Byfleet, UK Country Director at Infarm, said: “Infarm has a clear goal to expand in the UK market. Our second UK Growing Centre located in the “golden triangle” allows us to significantly increase the amount of fresh produce grown year-round in the UK.
When fully equipped, the units - each occupying 25 sqm of ground space and 10 metres in height - are able to produce up to 18 million plants per year and generate the crop equivalent of 360,000 sqm of farmland. The Growing Centre is currently in construction and on track for a first harvest in Q4 of 2021.
Each Infarm Growing Centre can save up to ten million liters of water per year, reducing water consumption by 95% versus traditional agricultural methods. Pentadel, appointed by Infarm to select a site as well as design and manage the construction of the new Growing Centre, has also integrated rainwater harvesting into the design of Infarm's new facility. Implementing rainwater harvesting is expected to capture a further 2.5 million litres of water per year, which will be used for conditioning plants.
Infarm will continue to operate its existing Growing Centre in Edmonton, North London and is currently hiring. “We have already opened up new positions for our locations in London and Bedford and will continue to do so as we expand our Bedford operation,” said Byfleet. To establish this large vertical farming facility, Infarm has partnered with Pentadel Project Management.
The location of the facility enables us to serve 90% of the UK population within four hours, bringing the freshest plants just on time to our clients. Consequently, food mileage is substantially reduced. One of the largest indoor vertical farming facilities in Europe to date is going to deliver millions of plants and provide fresh and locally grown produce to even more consumers via our retail partners, restaurants and online food retailers.”
James Kemp, Managing Director of Pentadel, said: “We are thrilled to be supporting Infarm with the delivery of this innovative facility that we believe represents the future of sustainable, scalable and resilient farming. We are passionate about delivering projects just like this – projects that place the future of people and the planet at their heart – and I know the whole team is proud to play a part in Infarm's revolutionary story.” Pentadel has identified a suitable UK site, negotiated terms and is now designing and managing the construction of the facility.
In the UK, Infarm’s herbs and leafy greens are currently found at Whole Foods Market, Selfridges, Marks & Spencer, Fortnum & Mason and Budgens as well at online retailers Weezy and Farmdrop. The new Growing Centre will join Infarm’s expanding global network of vertical farms that all connect to a central farming brain that gathers data constantly to improve plant yield, taste, and nutritional value, while further reducing the use of natural resources. By the end of 2025, Infarm plans to expand to 100 locations worldwide.
For more information:
Infarm
press@infarm.com
www.infarm.com
"We’re Hoping For A More Domestic Type of Farming”
“Whilst living in a 9-square meter student residence, the idea of being able to use this really small space to sustain myself with well packed nutritious food was what sparked the idea of Vita” Walid Brahim, CEO with Élever Group explains.
By Jenneken Schouten
August 9, 2021
“Whilst living in a 9-square meter student residence, the idea of being able to use this really small space to sustain myself with well packed nutritious food was what sparked the idea of Vita” Walid Brahim, CEO with Élever Group explains.
A small personal farm for everyone, a revolutionary product that combines aesthetic looks and the implementation of the most advanced technologies to date. That is the idea behind Vita that Élever Group recently launched.
The main aim of creating Vita was to bring a new level of transparency to food production, powered by blockchain technology, permitting users to safely buy and sell their harvest within small-scale communities. “We noticed that France, despite being a nation known for its agricultural scene, has experienced somewhat of a downfall regarding the people’s confidence when buying or consuming the goods grown in their own country. With Vita, we aim to rebuild this confidence,” Walid explains.
Read the rest of the article here
“We Can Put 90 Strawberry Plants Per m2 Where A Greenhouse Would Put Only 10-12”
“I spent my first 25 years on a farm and the next 25 years in technology. Vertical farming is the bridge between those worlds,” says Yves Daoust, chief operating officer and founder of Ferme d’Hiver. The company was founded in 2018 and aims to develop a network of indoor farms and become a global hub for vertical farming.
By Rebekka Boekhout
August 9, 2021
“I spent my first 25 years on a farm and the next 25 years in technology. Vertical farming is the bridge between those worlds,” says Yves Daoust, chief operating officer and founder of Ferme d’Hiver. The company was founded in 2018 and aims to develop a network of indoor farms and become a global hub for vertical farming.
In May 2021, Ferme d’Hiver announced that it had secured $5 million in funding from Investissement Québec, Haystack and Mavrik during its most recent funding. This funding will help Ferme d’Hiver build its first commercial indoor strawberry farm, which will cover roughly 1000 square meters and be located in Vaudreuil, Québec. Winterberry production is expected to begin in October 2021.
Read the rest of the article here
AmplifiedAg Inc. Completes $40MM In Capital Raise, Expanding Global Technologies And Vertical Roots Indoor Farms Across The Southeast
AmplifiedAg Inc.™, fast-growing agtech industry leader on a mission to provide global access to safe food, announced today that the company has completed $40 million in equity financing.
August 9, 2021
CHARLESTON, S.C., /PRNewswire/ -- AmplifiedAg Inc.™, fast-growing agtech industry leader on a mission to provide global access to safe food, announced today that the company has completed $40 million in equity financing. The funding will support the continued expansion of the company's world-leading hydroponic container farm, Vertical Roots and further development of the company's holistic operating system, AmpEDGE™, which uniquely combines environment monitoring and controls with business operations for end-to-end indoor farm management.
"Our demonstrated ability to scale our indoor farms and technology is leading to discussions with strategic and financial partners, and we expect to consummate additional financing later this year to further accelerate Vertical Roots' presence across the Country," said Don Taylor, CEO of AmplifiedAg.
Vertical Roots' rapid success exemplifies the time, profitability, operational growth efficiency, and superior product quality AmplifiedAg farms and technology achieve. In less than four years, Vertical Roots has grown to be the largest hydroponic container farm in the world growing multiple varieties of mature, fresh leafy greens. The company currently operates three farm sites in Charleston, S.C., Columbia, S.C., and Atlanta, Ga. with produce available at 1,700 major grocery stores across 12 states including retailers such as Publix, Harris Teeter and Whole Foods, as well as schools, universities, and restaurants.
The current round of funding will support the installation of farms in north and central Florida, extending Vertical Roots' dominant position as the leading CEA and vertical farming business in the southeast market.
AmplifiedAg implements a distinctive strategy to operate Vertical Roots farms directly at distribution facilities, eliminating a massive leg of produce transportation in order to reduce emissions and provide communities with fresh, locally grown produce. Vertical Roots current focus is on nutritious, mature lettuce varieties that are celebrated for their flavor, freshness and being 100% pesticide-free.
Taylor added, "We're dually focused to deploy Vertical Roots farms across the country as close to the point of consumption as possible, while advancing and expanding AmplifiedAg's global network of proven technologies and farms to others in the CEA industry."
About AmplifiedAg, Inc.
AmplifiedAg, Inc.™ is an agtech industry visionary on a mission to provide global access to safe food. The company manufactures indoor vertical container farms, hydroponic systems, and disruptive seed-to-sale SaaS-based technologies. AmplifiedAg provides holistic indoor farming solutions to sustainably grow and distribute food anywhere in the world.
AmplifiedAg owns and operates Vertical Roots, the largest hydroponic container farm in the World with produce in over 1,700 grocery stores nationwide. Learn more at www.amplifiedaginc.com. Growing Food for a Growing World.
80 Acres Farms Secures $160 Million In Series B Led by General Atlantic To Accelerate Global Farm Expansion & Product Development
80 Acres Farms' vertical farm systems grow the widest variety of produce commercially sold at scale by any vertical farm to-date, including leafy greens, herbs, tomatoes, cucumbers, and microgreens
August 9, 2021
HAMILTON, OH / ACCESSWIRE / 80 Acres Farms, the industry-leading vertical farming company, has secured $160 million in additional funding in a round led by General Atlantic and joined by Siemens Financial Services, Inc. (the U.S. financing arm of global technology company Siemens). The company intends to utilize the capital for continued expansion and product development, building from its current footprint of vertical farms that yield a diverse offering of high-quality produce.
The funding round also included Blue Earth (formerly PG Impact Investments) and General Atlantic's Beyond Net Zero team, in addition to participation from existing investors including Barclays and Taurus.
80 Acres Farms' vertical farm systems grow the widest variety of produce commercially sold at scale by any vertical farm to-date, including leafy greens, herbs, tomatoes, cucumbers, and microgreens. The company's breakthrough growing technologies and advanced data analytics capabilities have enabled this industry-leading product breadth, driving over 450% revenue growth since the end of 2020. 80 Acres Farms now services over 600 retail and food service locations, including its recent expansion with Kroger, announced earlier this year to 316 stores in the U.S. Midwest and to the e-commerce channel powered by Kroger - Ocado Solutions' partnership. With farms co-located near customers, 80 Acres Farms' produce travels significantly fewer food miles, shortening the farm-to-table footprint and reducing overall food waste. Growing methods at 80 Acres Farms use 97% less water than traditional farming practices and are powered by renewable energy.
- ADVERTISEMENT -
To date, 80 Acres Farms operates eight indoor farms and is committed to supporting and building high-tech production facilities close to regions where fresh produce is consumed. The company has transformed a former factory in Hamilton, Ohio, to a world-class tomato indoor farm, and in 2020, 80 Acres Farms completed construction on a new, 64,000-square-foot, state-of-the art farm with 10 levels of cultivating space. 80 Acres Farms is currently engaged in identifying new farm locations for additional commercial farms to operate at similar scale.
Shaw Joseph, Managing Director of General Atlantic, said: "80 Acres Farms is building an incredibly exciting vertical farming business that provides high-quality produce through innovative practices. With global food consumption increasing and growing threats impacting supply chains and food security, there is a pressing need for healthy, fresh and local foods that are grown in more sustainable and cost-effective ways. We look forward to working closely with Mike, Tisha and the broader 80 Acres Farms' team as they scale."
Jason Thompson, Vice President of Sustainability and Growth Equity at Siemens Financial Services, said, "We are committed to help scale sustainable vertical farming technology. 80 Acres has demonstrated their ability to build and operate profitable farms, and Siemens is enthusiastic about the opportunity to support its global expansion with both our capital and technical know-how, including our recently established Center of Competence dedicated to supporting companies in realizing their digital transformation."
Kayode Akinola, Head of Private Equity Directs at Blue Earth Capital, said, "We are excited to be partnering with General Atlantic and Siemens to provide growth capital and support to Mike, Tisha and the entire 80 Acres team to help scale their operations within existing and new markets."
Mike Zelkind, CEO of 80 Acres Farms, said: "We are proud of what our team has been able to accomplish and enthusiastic about the road ahead. We are also honored to be supported by such a high caliber group of strategic investors who are enabling us to continue to lead this evolving and fast-growing industry. The investment is a quantum leap for the business to build more farms both nationally and globally.
Tisha Livingston, CEO of Infinite Acres, and Co-founder of 80 Acres Farms, said: "The new investment positions the company as the leading proven and profitable technology provider prepared for rapid expansion. In addition, this enables 80 Acres to focus on their operational expertise and deep research and development capabilities beyond leafy greens."
As part of this funding round, Shaw Joseph will join the 80 Acres Farms board. Eli Aheto, former 80 Acres Farms board member, led BeyondNetZero's contributions to this round. "I am pleased to be able to continue and grow my support of 80 Acres with this contribution from the BeyondNetZero team. 80 Acres has proven a farm design that is poised to reduce food miles, food waste and the resulting negative carbon emissions that exist within our food supply chain," said Eli Aheto.
Barclays acted as sole placement agent to 80 Acres on the capital raise.
About 80 Acres Farms
80 Acres Farms is a vertical farming leader providing customers with the freshest, and most nutritious fruits and vegetables at affordable prices. Utilizing world-class technology and analytics, the Company offers customers a wide variety of pesticide-free food with a longer shelf-life that exceeds the highest standards in food safety. Consumers can find 80 Acres' products of just-picked salads, tomatoes, cucumbers, herbs, and microgreens at Kroger, Whole Foods, The Fresh Market, Dorothy Lane Markets, Jungle Jim's Markets, and key National Foodservice Distributors including Sysco and US Foods.
Media Contact
Rebecca Haders / rebecca.haders@eafarms.com / +1 513-910-9089
About General Atlantic
General Atlantic is a leading global growth equity firm with more than four decades of experience providing capital and strategic support for over 400 growth companies throughout its history. Established in 1980 to partner with visionary entrepreneurs and deliver lasting impact, the firm combines a collaborative global approach, sector specific expertise, a long-term investment horizon and a deep understanding of growth drivers to partner with great entrepreneurs and management teams to scale innovative businesses around the world. General Atlantic currently has over $65 billion in assets under management and more than 175 investment professionals based in New York, Amsterdam, Beijing, Hong Kong, Jakarta, London, Mexico City, Mumbai, Munich, Palo Alto, São Paulo, Shanghai, Singapore and Stamford. For more information on General Atlantic, please visit the website: www.generalatlantic.com
General Atlantic also recently formed its BeyondNetZero (BnZ) team to seek out growth companies delivering innovative climate solutions. BnZ looks to identify entrepreneurs with technologies that enable companies to meet and exceed Net Zero emissions targets, with a focus on de-carbonization, energy efficiency, resource conservation and emissions management.
Media Contacts
Mary Armstrong & Emily Japlon / General Atlantic media@generalatlantic.com
Faustine Rohr-Lacoste / Spendesk faustine@spendesk.com
About Siemens Financial Services
Siemens Financial Services (SFS) - the financing arm of Siemens - provides business-to-business financial solutions. A unique combination of financial expertise, risk management and industry know-how enable SFS to create tailored innovative financial solutions. With these, SFS facilitates growth, creates value, enhances competitiveness and helps customers access new technologies. SFS supports investments with equipment and technology financing and leasing, corporate lending, equity investments and project and structured financing. Trade and receivable financing solutions complete the SFS portfolio. With an international network, SFS is well adapted to country-specific legal requirements and able to provide financial solutions globally. Within Siemens, SFS is an expert adviser for financial risks. Siemens Financial Services has its global headquarters in Munich, Germany, and has around 2,800 employees worldwide. www.siemens.com/finance.
About Blue Earth Capital
Blue Earth Capital is a global investment firm focused on sustainability and impact investing. Headquartered in Zug, Switzerland, with operations in New York, London, Singapore, Luxembourg and Guernsey, Blue Earth Capital seeks to invest in businesses that address pressing environmental and social challenges, whilst generating market-rate financial returns. Initiated in 2015 by Urs Wietlisbach, one of the founders of Partners Group, and backed by the Wietlisbach Foundation, Blue Earth Capital was incubated and built up with the support of Partners Group.
Media Contacts
Urs Baumann / CEO Blue Earth Capital urs.baumann@blueearth.capital
Geoponica Greens, Indoor Vertical Farm, To Open Facility In Hamilton Twp.
Geoponica Greens, an indoor hydroponics vertical farm business based in Chesilhurst, is expanding its existing operations to the historic Mill One warehouse in Hamilton Township this fall, the company announced.
August 4, 2021
Geoponica Greens, an indoor hydroponics vertical farm business based in Chesilhurst, is expanding its existing operations to the historic Mill One warehouse in Hamilton Township this fall, the company announced.
Desmond Hayes, founder and owner of Geoponica Greens, said the company utilizes hydroponics, an agricultural practice of growing plants without soil, using only water and nutrients — while avoiding the use of pesticides or insecticides.
By delivering the nutrients straight to the plants’ roots, this grow method is also able to shorten crop cycles, produce the best flavors and level of nutrition and increase the lifespan of the crop, he said.
“Geoponica Greens is dedicated to changing the way food is both grown and realized through our low-waste model and our hyperlocal interaction within nearby areas,” Hayes said.
“New Jersey is strategically located between New York City and Philadelphia, making it the perfect place to reimagine farming. We are especially excited to reach minority communities, Opportunity Zones and food deserts, and introduce our sustainable methods of agriculture to new areas.”
The new warehouse space will support Geoponica Greens’ efforts to provide fresh microgreens, leafy greens and herbs to the local communities, with plans to hire three to five employees and interns in the first year.
Because the produce will be grown in an indoor farm, it is not subjected to the effects of climate seasonality, so the facility will be able to harvest 2-3 tons of greens per year at full capacity, Hayes said.
Geoponica Greens also plans to create a local Community Supported Agriculture program aimed at bringing a subscription-based model to customers.
A minority business owner, Hayes founded Geoponica Greens in 2014.
Choose New Jersey provided Geoponica Greens with state resources information, economic development connections and site selection assistance and will continue to support the company’s success in New Jersey.
Choose New Jersey CEO Jose Lozano said his group was happy to keep such an innovative company within the state.
“True to our nickname as the Garden State and the most densely populated state in the country, it is no surprise that New Jersey is on the forefront of the urban farm movement,” he said.
“Geoponica Greens is an integral part of that movement, and Choose New Jersey is proud to support their continued growth in our state as they bring agricultural innovation to Hamilton and its surrounding communities.”
Geoponica Greens, an indoor hydroponics vertical farm business based in Chesilhurst, is expanding its existing operations to the historic Mill One warehouse in Hamilton Township this fall, the company announced.
Desmond Hayes, founder and owner of Geoponica Greens, said the company utilizes hydroponics, an agricultural practice of growing plants without soil, using only water and nutrients — while avoiding the use of pesticides or insecticides.
By delivering the nutrients straight to the plants’ roots, this grow method is also able to shorten crop cycles, produce the best flavors and level of nutrition and increase the lifespan of the crop, he said.
“Geoponica Greens is dedicated to changing the way food is both grown and realized through our low-waste model and our hyperlocal interaction within nearby areas,” Hayes said.
“New Jersey is strategically located between New York City and Philadelphia, making it the perfect place to reimagine farming. We are especially excited to reach minority communities, Opportunity Zones and food deserts, and introduce our sustainable methods of agriculture to new areas.”
The new warehouse space will support Geoponica Greens’ efforts to provide fresh microgreens, leafy greens and herbs to the local communities, with plans to hire three to five employees and interns in the first year.
Because the produce will be grown in an indoor farm, it is not subjected to the effects of climate seasonality, so the facility will be able to harvest 2-3 tons of greens per year at full capacity, Hayes said.
Geoponica Greens also plans to create a local Community Supported Agriculture program aimed at bringing a subscription-based model to customers.
About Mill One and Geoponica Greens
The historic Mill One warehouse was once home to notable Atlantic Products Corp. during the World War II era in the Trenton area. The 2,000-square-foot warehouse was selected because of its important features that will support Geoponica Greens’ hydroponics operations. With high ceilings, skylights and exposed brick walls, the impressive existing warehouse is being renovated to become a modern, sustainable space.
A minority business owner, Hayes founded Geoponica Greens in 2014.
Choose New Jersey provided Geoponica Greens with state resources information, economic development connections and site selection assistance and will continue to support the company’s success in New Jersey.
Choose New Jersey CEO Jose Lozano said his group was happy to keep such an innovative company within the state.
“True to our nickname as the Garden State and the most densely populated state in the country, it is no surprise that New Jersey is on the forefront of the urban farm movement,” he said.
“Geoponica Greens is an integral part of that movement, and Choose New Jersey is proud to support their continued growth in our state as they bring agricultural innovation to Hamilton and its surrounding communities.”
Lead Photo: Geoponica greens uses hydroponic techniques to grow produce. - Geoponica Greens
SRUC To Build Vertical Farm
Scotland’s Rural College (SRUC) will be the first higher education institute in Scotland to open a vertical farm for research and education.
By Michael Barker
August 9, 2021
Scotland’s Rural College (SRUC) will be the first higher education institute in Scotland to open a vertical farm for research and education.
The project, which has received a £200,000 grant from the Scottish Government, will be used in key research into plant and crop science, and will also be used by students. SRUC will build the half million-pound facility at its King’s Buildings campus in Edinburgh next year.
The facility will grow nutrient-dense fruit and vegetables that have specific human health qualities. It will also analyse crop yield and growth rates with all resource inputs to compare their carbon footprint to other production systems.
It will operate on renewable energy sources from the national grid, supported by battery technology to manage peaks in energy demand. The project will be going out to tender in the coming weeks.
With only a handful of commercial vertical farms in Scotland, the facility will be important for demonstration and knowledge exchange with farmers, growers and small businesses, giving vital support and promoting innovation, SRUC said.
Mairi Gougeon, cabinet secretary for rural affairs and islands, said: “As we look to produce more fruits and vegetables locally, vertical farming could provide us with a way to make better use of our land. It’s an exciting and innovative field that could bring us real benefits and it is important that we have the skills in Scotland to take advantage of this technology.
“By supporting the industry at an early stage, we can assess these benefits and help to focus our long-term strategy. We will also be reaching out to the wider industry to explore in further detail the opportunities low-carbon vertical farming offers. We will work together to establish the future of vertical farming in Scotland.”
Lead Photo: New facility will grow nutrient-dense fruit and vegetables that have specific human health qualities
Why Lettuce Greenhouse Sector's Growth Is Focused In The U.S.
Greenhouses for lettuce and leafy greens are being built at a rapid pace across the U.S. In contrast, in neighboring Mexico there is no similar greenhouse production and in Canada there is very little — the primary exception being 11-acre Whole Leaf Farms located in Coaldale, Alberta.
By Peter Tasgal
August 10, 2021
Greenhouses for lettuce and leafy greens are being built at a rapid pace across the U.S. In contrast, in neighboring Mexico there is no similar greenhouse production and in Canada there is very little — the primary exception being 11-acre Whole Leaf Farms located in Coaldale, Alberta.
Based on my research, the primary driver for this U.S. phenomenon is investor comfort in making U.S.-based investments in leafy greens greenhouses, which are more expensive to build compared to tomato, cucumber and pepper greenhouses.
For example, AppHarvest’s latest tomato greenhouse is expected to be 63 acres and valued at $139 million — just over $50 per square foot. In contrast, Bright Farms’ 280,000-square-foot leafy greens greenhouse in North Carolina cost $21 million, or $75 per square foot. Gotham Greens built a 100,000-square-foot leafy greens greenhouse in Providence, Rhode Island, that cost $12.2 million, or $122 per square foot.
In addition to investor interest in the U.S. market, other potential factors affecting this phenomenon include:
Temperature variance;
Pricing certainty;
Equilibrium capital leading the charge; and
Generational knowledge in Canada.
Temperature variance
Lettuce and leafy greens perform best at cooler temperatures, up to 70 degrees Fahrenheit. Tomatoes, cucumbers and peppers, in comparison, grow best at temperatures in excess of 70 degrees Fahrenheit.
As the U.S. has a more moderate climate than either Canada or Mexico, a band of greenhouses across the U.S. takes advantage of the more temperate climate. Historically, leafy greens greenhouses have been built in the middle and upper sections of the U.S. However, boundaries have moved. Revol Greens, for example, has a 10-acre greenhouse in Minnesota and is expected to build a 20-acre greenhouse in Austin, Texas, to be completed in 2022.
Historically it has been more costly to keep a greenhouse cool rather than to heat it. However, alternative sources of energy and energy pricing incentives in parts of the southern U.S. have made it increasingly cost competitive to build greenhouses in this area.
Pricing certainty
The cost to build a leafy greens greenhouse is more than a tomato, pepper or cucumber greenhouse on a per square foot basis and on a per pound basis. As a reference, the cost of AppHarvest’s tomato greenhouse is approximately $3 per one year’s production of pounds of tomatoes. In comparison, Bright Farms’ recent leafy greens greenhouse is over $10 per one year’s production of pounds of lettuce and leafy greens.
This large cost structure variance requires greenhouse-grown lettuce to be priced at a premium. In contrast, greenhouse-grown tomatoes can and are priced directly with field-grown tomatoes. In the U.S. today, greenhouse-grown tomatoes make up the majority of fresh tomato sales.
The risk for an investor in a premium product is demand fluctuation. Economic and other market conditions will have a greater effect on premium product demand compared to product with more commodity-like traits.
Equilibrium Capital leading the charge
Equilibrium Capital is a leading investor in the North American controlled environment agriculture sector. It closed its second fund (CEFF II) this past month, with a capacity of $1.022 billion. Its first fund, CEFF I, had a capacity of $336 million. Recent investments made by Equilibrium include:
AppHarvest: $91 million non-dilutive investment to support the building of its second tomato greenhouse in Kentucky.
FINKA: Expansion capital for the Mexican greenhouse company, which operates tomato, pepper and cucumber greenhouses, the product of which is primarily sold into the U.S. and Canada. This was Equilibrium’s first investment outside of the U.S.
Little Leaf Farms: $90 million of debt and equity financing for the company, which is currently building a lettuce and leafy greens facility in Pennsylvania and is expected to follow with a facility in North Carolina.
Revol Greens: $110 million of debt and equity capital to support its building of a large lettuce and leafy greens greenhouse in Texas.
FINKA is Equilibrium’s only investment outside of the U.S. to-date.
Generational knowledge in Canada
According to the Ontario Greenhouse Vegetable Growers’ website, the organization formed in 1967 has “220 members who grow greenhouse tomatoes, cucumbers and peppers on over 3,000 acres.”
Two of the largest growers in Canada, Mastronardi Produce and Mucci Farms, have invested primarily in building their current greenhouses. To the extent each has branched out, it has been primarily to berries and eggplants. Mastronardi and Mucci have little to no owned lettuce and leafy greens production across North America.
Of note, in 2019 AppHarvest entered into a Purchase and Marketing Agreement with Mastronardi, under which “Mastronardi will be the sole and exclusive marketer and distributor of all tomatoes, cucumbers, peppers, berries and leafy greens” at its Morehead, Ky., facility (currently producing only tomatoes).
Per the 10-year agreement, Mastronardi has a right of first refusal for any additional facilities established in Kentucky or West Virginia. The take-away is Mastronardi is willing to distribute and market greenhouse-grown leafy greens, venturing a reputational risk, but has not yet chosen the investment risk of operating its own greenhouses.
Speaking to the OGVG, most greenhouse operators in Ontario have chosen to put their resources into products they already know. When asked specifically about lettuce and leafy greens, OGVG said the cost to build this type of greenhouse is very expensive per unit of output.
Recap
Some of the most seasoned greenhouse operators in North America are growing a range of produce types in the Ontario, Canada, area largely focused on tomatoes, cucumbers and peppers.
Each of these products grows best at higher temperatures than lettuce and leafy greens. Canadian operators who have been in the business for generations are potentially willing to distribute and market leafy greens, yet they have not been willing to make significant investments in the area.
While leafy greens were once only grown in the Northern parts of the U.S., Revol Greens, backed by Equilibrium Capital, is building one of the largest greenhouses in Texas. Equilibrium Capital, the “smart money,” has only invested in U.S. CEA companies to-date. The exception is FINKA, which operates in Mexico but sells exclusively to the U.S. and Canada.
Based on my research, until lettuce and leafy greens greenhouse production can be priced competitively with field-grown product, it will continue to be a U.S. phenomenon. At least until that time, Canadian and Mexican operators will leave greenhouse lettuce and leafy greens production to U.S. operators.
Peter Tasgal is a Boston-area food agriculture consultant focused on controlled environment agriculture.
80 Acres CEO Reflects on Vertical Farming Post $160m Raise: ‘There Will Be Losers With Very Big Names’
For Mike Zelkind, CEO at Ohio-based vertical ag operation 80 Acres Farms, not everyone will make it to the finish line.
By Lauren Manning
August 11, 2021
The indoor farming sector is dazzling investors and attracting its fair share of nine-figure deals. But as the space grows more crowded and competitive, questions are sprouting up regarding market saturation, the right business models, and whether indoor mega-farms like the one Minnesota’s Revol Greens is planning are the way to go.
For Mike Zelkind, CEO at Ohio-based vertical ag operation 80 Acres Farms, not everyone will make it to the finish line.
“This is the way the market works. There will be winners and losers and there will be losers with very big names,” he tells AFN.
“But the world needs this and even the losers [will have been] very well-intentioned. My heart will go out to everyone who does not win because I know they fought the good fight.”
80 Acres just announced the close of a $160 million Series B round led by US growth equity firm General Atlantic.
Other investors in the round included Siemens Financial Services — the US financing arm of German tech giant Siemens — as well as Barclays, Blue Earth, Taurus Investment Holdings, and General Atlantic’s impact-focused BeyondNetZero team.
Although Zelkind views the indoor farming space as big enough for many players to do well, he thinks some recent valuations are exaggerated.
In his opinion, 80 Acres sets itself apart through its partnerships, like its joint venture with e-grocer Ocado and tech provider Priva. The trio formed the venture, Infinite Acres, in 2019 to help growers enter the tech-enabled indoor farming space.
Staying close to the consumer
80 Acres takes a decentralized approach to getting its produce on consumers’ tables, building its farms close to areas where its customers are located. The startup runs eight farms, and sells its products in around 600 retail and foodservice locations. Without sharing specific figures, it claims to have posted 450% growth in revenue since the end of last year.
Building close to its customer base has also been a foundational aspect of 80 Acres’ business model, Zelkind suggests.
“I don’t think there are any other farming operations today that have built a farm as close to the distribution center of their customer,” he says. “Just getting a little closer to the customer is not good enough.”
Zelkind claims that 80 Acres had a lot of options when it came to choosing investors for its Series B round but that funders with strategic angles were the winning choice. General Atlantic focuses on world-changing technologies, including foodtech, while Siemens can assist with continued industrialization of the startup’s capabilities, he adds.
80 Acres will use the new funding to expand its footprint while supporting product development. Based on his own observations of rival startups’ activities and claims, Zelkind argues that his company offers the widest variety of produce in the vertical farming industry, selling leafy greens, herbs, tomatoes, cucumbers, and microgreens, among others.
“I’m not aware of anybody even making a claim that they are commercially growing these items, and we’ve had the product in the marketplace for the last four years,” he says. “It’s not a claim – it’s a fact.”
Lead Photo: Mike Zelkind, CEO, 80 Acres Farms. Photo credit: 80 Acres Farms Facebook page.
Urban Crop Solutions Awarded As Best-In-Class Vertical Farming Solution Provider
Urban Crop Solutions has been awarded a ‘Best-in-Class’ award for their production systems by the Center of Excellence for Indoor Agriculture. They were selected as the winners for the category of ‘systems starting between $250k-$500k’.
August 2021
Urban Crop Solutions has been awarded a ‘Best-in-Class’ award for their production systems by the Center of Excellence for Indoor Agriculture. They were selected as the winners for the category of ‘systems starting between $250k-$500k’. Each finalist went through a rigorous review process and was evaluated according to several criteria. Emphasis was given to sustainable farms and equipment manufacturers that efficiently use resources such as land, energy, labour and water to produce the highest yields at an affordable price in indoor farm settings.
“The award is definitely a recognition for our team that is continuously working on state-of-the art growing solutions which optimise the sustainability of our industry, whether this is in an existing building or for a greenfield project.” says Maarten Vandecruys, Founder and CTO, Urban Crop Solutions.
“Today we are rewarded with a prize for our approach, but to be successful for our customers, the knowledge of the plant science is as equally important as the engineering part. We keep on striving for a more sustainable impact, not just on the consumption of our natural resources, but also the yield, which positively impacts the financial sustainability” he adds.
"We are enormously proud of the entire team! A team that works together for the future. A team that is there for each other, to give the best of themselves. Looking at our latest realisations, the ModuleX and the FarmLab, and our 24/7 support both technically and biologically, as a team leader you can look forward with a broad smile!" says Jean-Pierre Coene, CEO, Urban Crop Solutions.
Jean-Pierre Coene operating the ModuleX
ABOUT UCS
Urban Crop Solutions is a Belgium based pioneer in the fast-emerging technology of indoor vertical farming. It has developed over the past six years, 220+ plant growth recipes in its research centre in Waregem, Belgium. To date, UCS has delivered over 25 projects in multiple global locations. Their farms are being operated both for commercial and research purposes. Uses range from the production of leafy greens, microgreens and herbs for food retail, service and industrial use, and scientific research across multiple institutions.
Website: www.urbancropsolutions.com
Facebook: www.facebook.com/urbancropsolutions
Twitter: www.twitter.com/U_C_Solutions
LinkedIn: www.linkedin.com/company/urbancropsolutions
CONTACT
Filip Meeuws – Sales Director, Urban Crop Solutions
fime@urbancropsolutions.com
Maarten Vandecruys – Co-founder & CTO, Urban Crop Solutions
maarten.vandecruys@urbancropsolutions.com
Jean-Pierre Coene – CEO, Urban Crop Solutions
jpco@urbancropsolutions.com
Lead Photo: Maarten Vandecruys in the UCS Research Centre
Growing Up: The Next Frontier In Farming Is Vertical And It Could Cut Canada's Reliance on Imported Food
The spicy mustard micro green begins its short life in a plastic tray of mud, filed away in a germination warehouse at an industrial park on the outskirts of Guelph, Ont. It spends several days in hot and humid darkness, using all its energy to open itself, push through the top layer of soil and unfurl its first two tender leaves
By Jake Edmiston
July 30, 2021
The spicy mustard micro green begins its short life in a plastic tray of mud, filed away in a germination warehouse at an industrial park on the outskirts of Guelph, Ont. It spends several days in hot and humid darkness, using all its energy to open itself, push through the top layer of soil and unfurl its first two tender leaves.
In the germination room, trays of mustard greens all sit on shelves the size of ping pong tables, stacked in rows up to the roof. The plants are ready after about two days and the automated growing system comes to retrieve them, pulling the shelf from its stack and ejecting it through a slot in the warehouse wall.
Soaring crop prices will catch up to consumers
Next, they enter another, larger warehouse, with more shelves stacked up three to four storeys high. Here, the spicy mustard greens feel light for the first time. More than 14,000 LED lamps shine for 14 to 20 hours a day, using only the part of the light spectrum that the plants will need: red and blue. So the warehouse is always a thick, glowing magenta.
After spending two days in the darkness of the germination room, a large flat of spicy mustard greens is moved into the 45,000 square foot vertical farming grow room. PHOTO BY GLENN LOWSON FOR NATIONAL POST
“It’s always a beautiful, spring day,” says Juanita Moore, the executive director of operations at GoodLeaf Farms, which owns this indoor farm in Guelph.
It is incredibly important that these mustard greens survive, not just for GoodLeaf — the company uses them for its Spicy Mustard Medley and Ontario Spring Mix — but also for the long-term stability of the Canadian food system.
Canadian agriculture scholars are warning that the country’s dependence on California and other southern growing regions for fresh produce through the winter has become a national security risk.
“We have to really ask the question, ‘How secure are we?'” said Evan Fraser, director of the University of Guelph’s Arrell Food Institute. “On fruits and vegetables, we are not secure at all.”
On fruits and vegetables, we are not secure at all
EVAN FRASER
The pandemic has given companies and consumers a glimpse at how a global crisis can stymie supply chains and push trading partners to hold back exports. And the extreme drought and wildfires that have threatened California’s vast crop production this summer are just the latest example of a glaring vulnerability in the Canadian food chain, which relied on $11.2-billion worth of imported vegetables, fruits and nuts last year. Farmers in the United States supplied $5.4 billion of that produce — $3.1 billion of which came from California.
“Suddenly this idea that California might not be able to provide food is not that farfetched at all — to the point I’m actively kind of worried about it,” said Lenore Newman, director of the Food and Agriculture Institute at the University of the Fraser Valley. “My worry is, we’re going to start having shortages, because California’s production is going to fall. They don’t have the water.”
Fraser and Newman are part of a growing chorus of professors and industry leaders calling for Canada to stop relying on imports from the U.S. and Mexico and start feeding itself, fast. The best hope to do that, in a country with only five or six good growing months, is to farm indoors.
Juanita Moore, the executive director of operations at GoodLeaf Farm, in Guelph, Ont. PHOTO BY GLENN LOWSON FOR NATIONAL POST
“If the trends continue, we’re in real trouble in North America,” Newman said. “Growing all of this food intensively in one location and moving it all over the continent is not going to work. So we may as well start now. I mean, we should have started five years ago but now is good too.”
This ambition for Canada to grow its own supply of fresh produce in the dead of winter isn’t as implausible as it might sound. The country actually isn’t bad at growing things indoors. Canada’s greenhouse industry is already proficient at growing tomatoes, cucumbers and peppers — to the point that 81.2 per cent of the domestically grown supply of cucumbers come from a greenhouse, according to Statistics Canada.
Historically, the problem with greenhouses has been that they rely on the sun, which means production dips in the darker, winter months. They’re also expensive to heat. Even in summer, the sun can be confounding, as Newman put it. It’s bright one day, obscured by clouds the next. It hits the plants unevenly, making it tougher to produce the sort of uniform crops that the market demands.
The new frontier in farming, Newman said, is to sideline the sun. Advancements in more efficient LED light technology have reduced the cost of growing plants indoors, allowing greenhouses to add lights to augment the sun and effectively extend their growing season.
Cheaper LED technology has also made it possible to farm without any sun at all, in the sort of windowless warehouses “you’d put a Costco in,” Newman said.
LED lights are calibrated to only emit the red and blue of the light spectrum. PHOTO BY GLENN LOWSON FOR NATIONAL POST
This new generation of indoor crop factory can pump out more production per acre because the farmer doesn’t have to worry about sun exposure, droughts or pests. In vertical farming — a common method in the rapidly changing world of closed environment agriculture — the plants are stacked one on top of another, in soil trays or in hydroponic fluid, with LED lights in between.
“You can take a 100-acre farm, compress it into a one-acre farm, and put the rest back into wilderness,” Newman said.
Vertical farms can recycle much of the water they use, and often cost little to heat through winter thanks to warmth from the LED lamps and the plants themselves. But possibly the most important perk, she said, is that “everything will taste better.”
The general vision, for Newman and others, is to have vertical farming operations supplying produce to every region in the country. That would drastically reduce the distance between farm and market, so producers would be able to focus on making varieties that taste good instead of the “wooden” varieties preferred in California because they travel thousands of kilometres without bruising.
Major food and technology companies have been funnelling capital into the indoor farming sector, including French fry giant McCain Foods Ltd.’s roughly $65-million investment to become the single largest shareholder in GoodLeaf.
A sampling of three of the six varieties of leafy greens GoodLeaf cultivates in it’s indoor 45,000 square foot vertical farming operation in Guelph, Ont. PHOTO BY GLENN LOWSON FOR NATIONAL POST
But vertical farming hasn’t quite proven itself to be a profitable option yet, according to one analyst who follows the sector. The building costs for new vertical farms and other large-scale indoor models can range as high as $30 million to $50 million per site. Even when the facilities are built, high energy bills and labour costs make it difficult for the farms to make consistent profits. So most operations focus on crops that grow quickly, can be packed into tight spaces and sell at a premium.
“A lot of these groups are still losing money,” said Steve Hansen, managing director at Raymond James Ltd. “The big challenge is, ultimately, getting to profitability.”
And the goal isn’t just to reach profitability by competing with organic farms on expensive niche products like spicy mustard greens. If the true purpose is to replace Canada’s $11.2-billion reliance on imported produce, indoor operations need to be able to reach the sort of scale that will allow them to compete in the broader fruit and vegetable market. More advancement in LED lighting and automation inside the farms are expected to keep tamping down energy and labour costs.
“The vertical industry is still not quite yet on par with field-grown product,” Hansen said. “They’re getting down there and they’re getting closer but they’re still not there.”
Hansen estimated that globally, capital investments into vertical farms and next-generation indoor farming technology are now in the “billions of dollars” globally.
“It’s become a large sector very quickly,” he said, adding that some established operations are finally starting to reach a scale where they’re able to make a profit. “The development we’ve seen on the indoor space has really happened in the last five years.”
Samples of the latest daily crop of leafy greens are taken for testing before shipping to customers at GoodLeaf. PHOTO BY GLENN LOWSON FOR NATIONAL POST
Still, vertical farms are mostly confined to growing salad greens, which grow within a matter of days and allow the farms to constantly be turning over product.
Branching out to other crops will be a challenge, Hansen said. Tomatoes and cucumbers, for example, can be too tall for vertical farming, which means the farm has to pack fewer rows into the space before hitting the ceiling. (Interestingly, greenhouses actually benefit from the height of cucumbers and tomatoes because they’re essentially vertical farms in and of themselves, Newman said.)
Other vegetables that take months to reach market size mean months’ worth of energy costs have to be included in the price — which Newman suggested could lead to potatoes that cost $20 per pound.
Seed companies, however, have started to turn their attention to breeding varieties of crops that will work well indoors, though the developments are still in the early stages, Hansen said. “Very little effort has been done on short, stubby plants that can produce really high volume, because why would you have ever wanted that?”
Fully grown spicy mustard greens await packaging at GoodLeaf. PHOTO BY GLENN LOWSON FOR NATIONAL POST
The GoodLeaf vertical farm in Guelph is currently able to produce more than 800,000 pounds of micro greens and baby greens annually, though it’s currently producing less than half that. Hospitality and restaurants were intended to make up half the business, so the pandemic-related shutdown in that sector has significantly impacted sales. But the business is able to break even at an output of around 400,000 to 500,000 pounds, selling boxes at $3.99 for micro greens and $4.99 for baby greens in major Ontario supermarkets , including Whole Foods Market Inc., Metro Inc., Loblaw Cos. Ltd.
But even a top capacity of 800,000 pounds of greens is considered light. A new GoodLeaf facility in development in Montreal is expected to reach up to 1.4 million pounds, with an expansion option that would double that output.
“We won’t build farms as small as this one going forward,” GoodLeaf’s Juanita Moore said during a tour of the Guelph plant last week. “Every generation of farm will have kind of perfected it a little bit more.”
Fully grown spicy mustard greens grown at GoodLeaf in Guelph, Ont. PHOTO BY GLENN LOWSON FOR NATIONAL POST
In Guelph, the spicy mustard greens spend about six days in the glowing purple growing room. In that time, they extend themselves to half a finger long. There are hundreds of them per tray, a mix of vibrant greens and purples, all of them never knowing the sun or a bug or a breeze.
The automated lifts move the shelves of plants from one end of the growing warehouse to the other end, a little bit at a time, gradually pushing the mustard greens through the stages of their lives. At the end of it all, there is what appears to be a blue garage door.
When the greens are ready, the blue door cranks open and white light shines in. A worker in an overcoat and hardhat pulls them out of the growing warehouse and into a cold, sterile room with a conveyor belt in the centre.
Here, the greens meet the man who made them. As the move along the conveyor, Cesar Cappa, the head grower at the Guelph plant, stands over them and stares.
Agronomist and head grower Cesar Cappa inspects spicy mustard greens at GoodLeaf Farms in Guelph, Ont. PHOTO BY GLENN LOWSON FOR NATIONAL POST
He calls them by their technical name, cotyledons — the first little leaves to sprout from a seed. He watches for deviations in the cotyledons, aware that any problem means the micro mustard greens could rot and spoil the lettuce when they’re together in the spring mix.
“It can be something small,” he says, dressed in a lab coat.
After the inspection, the mustard greens continue along the conveyor belt toward a vibrating blade at the end of the line. It saws back and forth at high speed, aimed at the necks of the mustard greens. The trays move closer and closer in a slow, inevitable march. Each stem meets the knife and it severs them, clean and quick. From there, the greens are packaged, and the trays of roots and dirt are sent for compost.
Afterward, in an open-concept office connected to the vertical farm, Moore passed around paper plates of micro greens and lettuces grown at the facility. Everything tasted of the outdoors.
“It takes me right back to my grandpa’s farm,” she said.
Lead Photo: A tray of spicy mustard greens grown at GoodLeaf’s vertical farm in Guelph, Ont. PHOTO BY GLENN LOWSON FOR NATIONAL POST
Strengthening Ties With Qatar To Grow In The Middle East
At iFarm, we will remember June 2021 as the month of Qatar! We announced an agreement to build a vertical farm based on our technology in Doha, hosted two high-profile delegations from Qatar at a lettuce farm, and held a series of important discussions regarding cooperation in the country
August 3, 2021
At iFarm, we will remember June 2021 as the month of Qatar! We announced an agreement to build a vertical farm based on our technology in Doha, hosted two high-profile delegations from Qatar at a lettuce farm, and held a series of important discussions regarding cooperation in the country.
Background information on the Middle East region
The Arabian Peninsula has an extremely hot and arid climate (it’s one of the hottest places on the planet), and Qatar is no exception. There are sands and dunes in the north, sandy hills in the south — with a rocky desert in the middle. In the summer months, temperatures can reach 50 °C. The country has no rivers and obtains most of its freshwater by desalinating seawater. As a result, Qatar has extremely unfavourable conditions for growing edible plants such as vegetables, berries, and herbs. However, where tomato plants wither, date palms thrive. The “Queen of the Oasis” has been bearing excellent fruit throughout the entire Middle East region for thousands of years. It’s just, you can’t live on dates alone.
99,1 %
Qatar’s urbanisation rate
(one of the highest in the world)
90 %
of food in Qatar is imported
Although Qatar ranks among the richest countries in the world in terms of per capita income, it relies heavily on imports to feed its population. Local agriculture only covers 10% of the country’s needs, and food security remains high on Qatar’s agenda. With its abundant financial resources, the country can use state-of-the-art technology to grow crops. Due to this, we believe local, year-round cultivation of vegetables, berries, and herbs on vertical farms is one of the best solutions for this region.
“By working with iFarm, Qatar increases its share of locally grown products, and we can showcase how our technology can be used in a region with extreme climatic conditions. The use of translucent greenhouses can be a problem given the hot climate: they need to be shaded and cooled. Vertical farming, on the other hand, is a perfect match. This is an excellent tool that can help Qatar achieve its ambitious food security goals.”
Alex Lyskovsky
president of iFarm
As you may recall, Qatar has adopted a National Food Security Strategy under which the country aims to reach 70% self-sufficiency in food production by 2023.
Cooperation with Agrico
Our first talks about building vertical farms powered by iFarm technology in Qatar go back to 2019. The Qataris are very cautious in choosing partners, but once they get involved, you can be sure it’s going to be serious and long-lasting. We recently announced a joint project with Sadarah that includes building a commercial pilot farm based on the Agrico Farm in Al Khor, 50 km from Doha. iFarm supplies hardware and software, and will oversee the farm once it goes live and help the partners manage the technology. The second phase of this joint effort involves the commercial distribution of products to the local market and the extension of vertical cultivation technology to other farms in Qatar and neighboring countries. Contractors are currently erecting a purpose-built environment specifically for this vertical “plant factory” project.
Cooperation with Lulu Group International
LuLu Group International is iFarm’s signature partner in the Middle East. It is a multinational corporation that operates one of the largest retail chains in Asia and the Persian Gulf. LuLu is among the fastest-growing chains in the world and employs more than 57,000 people around the world. We are in talks with LuLu Group’s representative office in Qatar regarding building vertical farms right in the supermarkets. At least one side of the pilot farm is designed using transparent material, so that customers can see the process of growing and harvesting plants from “smart” beds. In early June 2021, the project was discussed at the International Economic Forum in St. Petersburg. It is of great importance to us because it can be scaled up throughout the entire chain, covering more than 200 stores in 22 countries.
Qatari delegations visit farms powered by iFarm technology
Indoor cultivation in a fully controlled environment still attracts a lot of attention and investment due to its obvious benefits, including land and water conservation, reduction of CO2 emissions, absence of pesticides, etc. Vertical farming is a sustainable method of farming, and although it won’t replace conventional farming everywhere, in many regions it is, perhaps, the only way to harvest high-quality fresh vegetables, berries, and herbs locally throughout the whole year.
Two delegations from Qatar visited a farm powered by iFarm technology in June. The head of the country’s investment promotion agency (IPA Qatar), Sheikh Ali Al-Walid Al-Thani, was one of our guests. The agency aims to attract direct investment in Qatar and assists entrepreneurs throughout the entire investment process providing services on a ‘one-stop shop’ basis.
We also had the pleasure of welcoming Masoud Jarallah al-Marri, Director of the Food Security Department at the Ministry of Municipality and Environment. He is responsible for the national certification of agricultural products and takes special care to verify the performance of any technology that is going to be introduced in Qatar.
Both guests inspected all of the production areas at the vertical farm, saw how the engineering equipment and software work, tasted a range of products grown on the farm, and left satisfied!
“Qatar is developing rapidly, and I am amazed at the pace of change in this country, which is literally turning into a huge beautiful oasis in the middle of the desert. Doha, for example, has a state-of-the-art, fully automated subway running under the city’s skyscrapers. Qatar has welcomed many foreign investors and businesses in recent years, thanks to its national vision, efforts to diversify the economy and the country’s role as hosts of the FIFA World Cup in 2022. We are happy that iFarm technology will provide guests and locals with delicious greens, vegetables and berries, and will enhance the country’s food security in the long term.”
Alex Lyskovsky, president of iFarm
Source and All Photo Courtesy of iFarm
5 Ways Vertical Farming Is Improving Nutrition
Vertical farming has taken cities by storm, enabling urbanites to grow produce within their own homes and entrepreneurs to meet the growing demand for fresher and higher quantities of locally-grown produce
August 3, 2021
Vertical farming has taken cities by storm, enabling urbanites to grow produce within their own homes and entrepreneurs to meet the growing demand for fresher and higher quantities of locally-grown produce.
We often hear about vertical farms using water sustainably, 95% less than traditional open field harvesting, to provide superior tasting crops.
But, how is this soilless farming technique impacting human health?
#1: Harvesting On Demand At Peak Freshness
&ever’s Grow Tower; image sourced from &ever
With the power to farm vertically within one’s own home, consumers can now harvest their crops only moments before consumption, resulting in a higher nutritional value, better-tasting greens, and significantly less food waste.
&ever’s Grow Box is a one-stop-shop system for leafy greens and can even be operated by untrained staff, according to &ever. The proprietary technology of the climate cell creates a steady microenvironment to allow plants to grow independently of weather, seasons, and pests, plus the use of “dryponics” helps keep the plants alive until the consumer is ready to harvest.
The key here is the freshness of the crops. Produce no longer has to travel miles and miles through countries or states to get to your kitchen table. This time saved in travel is also nutritional value preserved in the crops. Another benefit is that no artificial preservatives, like wax coatings, are needed to keep the produce consumer-ready.
#2: Growing Under Perfect Conditions
Vertical farms generally use hydroponics or aeroponics to grow their plants in nutrient-enriched water that can be carefully monitored through digital sensors. This degree of control over plant nutrient supply means that the fertilization strategies are designed to match the plant needs for all 14 essential plant nutrients throughout the growth period.
Control mechanisms are also utilized to balance temperature, humidity, and carbon dioxide levels in the grow facility and deliver the optimal combination of these factors for the specific crop or crops being grown. With climatic conditions playing no part in the crop’s success, growers have reliable year-round production of greater quantity and the highest quality.
In this sense, vertical farms are able to spend more time enhancing nutritional value and less time worrying about the success of their harvest. The SKY HIGH program led by Dr. Leo Marcelis of Wageningen University in the Netherlands, is one such program exploring factors that increase crop nutrients.
#3: Tailoring The Development Of Genetic Varieties
Vindara argues that the difference is in the seeds.
By designing seeds specifically for indoor vertical farms - “entirely through analytics, not gene-editing or GMOs” - this company claims to amplify crop yield, appearance, nutrition, and flavor.
Their seed-design system takes a data-driven approach to deliver any kind of genetic variety, tailored to each customer’s needs. According to Vindara, each property is individually editable.
Today’s seeds are still being bred for resistance to disease and pests, designed for long storage and transportation that isn’t as relevant for indoor vertical farming operations. This results in genetic tradeoffs that reduce nutritional value. Vindara removes these limitations that traditional seeds impose by delivering nutrient-dense seeds to growers.
#4: Growing Foods Adapted To Dietary Needs
Alongside fresh and flavorful food, there has been a growing demand and need for foods adapted to specific dietary needs.
Prime Delica, for example, has conducted research with Tamagawa University, CCS, and Signify to determine the optimal light recipe to increase the vitamin levels and nutritional value of lettuce. Dr. Céline Nicole from the Philips Lighting Research team has similarly studied the effects of the daily light integral (DLI) and light quality on the nitrate levels of arugula and spinach, alongside the vitamin C levels of arugula and tomatoes.
Through vertical farming, the Korea Institute of Science and Technology (KIST) has also successfully produced low potassium kale with increased glucosinolate content as a novel dietary option for renal dysfunction patients.
Growing foods with adapted dietary needs could thus make a world of difference in ensuring that we receive greater control over our diets, and allow us to design food-as-medicine alternatives to conventional produce.
#5: Food Safety
In using controlled growing environments, vertical farms are intrinsically free of harmful pesticides. Because of implementing biological controls, there is no need to contaminate crops with potentially toxic chemicals.
According to the CEA Food Safety Coalition, “traditional food safety risk profiles associated with conventional farming include examining the physical hazards and microbial hazards from water use, herbicide, and pesticide use, and impact from animals and animal byproducts. These do not impact CEA growers in the same way, if at all.” Even though the risk of contamination isn’t zero within CEA facilities (as seen in this recent news), CEA-grown produce has a reduced risk of such occurrences.
Compared to traditional field-grown crops, we find that the EPA regulates pesticides individually and not collectively, meaning that the pesticides can have a cumulative toxic loading effect on human health.
Studies have shown that pesticides most impact farmworkers and pesticide applicators with symptoms like nausea, abdominal cramps, diarrhea, dizziness, anxiety, and confusion. This long list of side effects tells us that pesticides are not to be taken lightly. As a result, it’s best to avoid them at all costs. Fortunately, vertical farms help us do precisely this.
Click here for more information.
Source and Photo Courtesy of Agritecture
Smart Farms: Getting To the Heart of The Matter
Labour costs account for up to 50% of the market price of vegetables, berries, and herbs. However, just like the tractor that once transformed agriculture, the new technological revolution greatly reduces the need for manual, skilled and specialist labour
August 3, 2021
Take a look behind the scenes of vertical plant automation and find out what it takes to bring a smart farm to life with exciting exploded-view diagrams.
Labour costs account for up to 50% of the market price of vegetables, berries, and herbs. However, just like the tractor that once transformed agriculture, the new technological revolution greatly reduces the need for manual, skilled and specialist labour. Today, the work is done by a team of robots, sensors, artificial intelligence, and a core team of highly skilled professionals who manage hundreds of farms at once using special software. As a result, we witness the “battle for the harvest” moving into the IT domain.
A vertical farm functions as an organism, and its equipment can be compared to human organ systems. Its sensors and senders are the nervous system, its air conditioners and dehumidifiers act as the respiratory system, while the solution supply pipeline represents the circulatory system. We can compare the nutrient mixing unit to the endocrine system, tray conveyors and lifts to muscles. Naturally, this organism has a “brain” — the Growtune IT platform.
The degree to which the brain can accurately and confidently “take control” determines how ready various systems, nodes, and technologies are to operate without human intervention. Below, we describe all of the tech that lies inside a vertical farm. How, where, and at what production stages does the automation work? For this purpose, we’ll leverage the somewhat forgotten “exploded-view diagram” style. This way, we'll be able to show all the devices the farm uses to take care of the plants.
1. Breathing: ventilation and air conditioning
Let’s remember biology classes. Plants use photosynthesis to turn light, water and CO2 into oxygen and energy. By doing so, they can consume far more CO2 than is normally present in the air. Since the farm, like a space station, uses a closed-loop air exchange system, with no air inflow from the street, creating an optimal environment and climate for plants is purely an engineering challenge. This includes purifying, conditioning, and adding some CO2 to the room to allow plants breathe freely and grow intensively.
“People who walk into a vertical farm for the first time notice how nice and clean the air is. That’s no surprise because it doesn’t contain any dust — there’s nowhere dust can appear from in the closed-loop circuit of the farm.
Alexey Novokreshchenko, Head of Automation at iFarm
The farm has multiple air conditioning units. It’s not just a matter of maintaining a certain temperature and humidity. We need to make sure that the climate is as homogeneous as possible throughout the entire arm, including at different heights. So, instead of one super-powerful unit, we install several medium-sized devices. This provides the right air circulation and creates a failure-proof system.
Hydroponic technologies tend to create a lot of moisture, and the farm air typically needs to be dehumidified (iFarm has developed and patented a dehumidification system that allows you to reuse this water to feed your plants). There are times, though, when you need to do the opposite: for example, you may need to humidify the air, especially at the initial stage of starting a farm when you don’t have a lot of plants.
2. Energy: grow lights
Photosynthesis, that is the conversion of light energy into chemical energy, only occurs when there is light. Agronomists call artificial lighting of plants “supplemental lighting”. It may vary from one area of the farm to another, depending on the crop and its cultivation phase. The light control unit creates “day” and “night” conditions for plants. The most frequent setup resembles a nice summer day: 14–16 hours of light and 8–10 hours of darkness. Darkness is crucial: the night is when cellular respiration occurs and other important processes take place.
“The plant depends on the day-and-night schedule. Its structure and maturation phases vary depending on the light cycle. Keep the microgreen sprouts in the dark a little longer, and they'll stretch out but will become coarser. By changing the lighting, you can experiment with taste. For example, if you keep sunflower microgreens in the dark for 10 days and then expose them to the light for a full day, you’ll get long and very sweet sprouts.”
Nikolai Podvigin, Head of the Agrolaboratory at iFarm
Agronomists at pilot farms refine cultivation flow charts. For example, they are currently experimenting with variable brightness to grow pine strawberries: the lamps are equipped with a dimmer so you can gradually add brightness. It seems that the agronomists’ hypothesis holds true — the berry evidently "enjoys" long dawns. Through smooth, incremental changes in lighting, the osmotic pressure in the stem and leaves grows gradually, whereas its surge upon sudden light exposure can have a tissue-damaging effect.
Sometimes you have to focus not only on what the plants need but also on organisational or purely economic factors. For example, the cost of electricity. True, the lamps we manufacture and install in racks are highly energy-efficient: they convert every watt of electricity into 0.6 watts of photosynthetically active radiation (FAR). Still, energy costs make up a large portion of the costs of growing herbs indoors. Automation can (and should) be leveraged to ensure optimal load distribution. If the farm can use a night rate, we change “days” with “nights” and reschedule the supplemental lighting for the nighttime to minimise operating costs.
3. Nutrition: irrigation and nutrient solution supply
The nutrient solution is made from several components stored in individual containers which can easily be replaced. The solution is prepared in the mixing unit, a sophisticated automated system capable of mixing dozens of litres of stock solutions with high precision and in the right proportions.
The nutrient solution is delivered to the roots of the plants through a tube system. Since the specific recipe depends on the type of the plant and its cultivation stage, the system continuously monitors (and sometimes adjusts) the composition of the solution.
“Plants eat and plants drink. We provide them with both by mixing nutrition with water. This water continuously runs through the rack. To create an individual “menu” for each plant type, we divide the farm into different watering areas and install an additional storage tank in each of them. Each area is equipped with an additional set of sensors that dynamically monitor the changes in the solution. In fact, these sensors control whether the plant “ate well” today and whether they have everything they need.”
Alexey Novokreshchenko, Head of Automation at iFarm
The water used for preparing the solution is added to the system after it is properly treated with a reverse osmosis filter. This removes contaminants, such as minerals, heavy metals, bacteria and viruses, leaving the water virtually pure.
4. Well-being: IoT sensors
The purity of the source water, the ratio of nutrients in the solution, its acidity, the brightness of the light, the amount of carbon dioxide in the air, temperature, and humidity — you need to control all these things with precision. A large farm can have hundreds of sensors.
Based on sensor measurements, the farm's central processing unit controls the equipment and hardware in real-time, always keeping climatic and biochemical parameters within the limits set by the cultivation flow chart.
If these limits are exceeded, it triggers an alarm and remote technicians are alerted. The algorithm helps identify potential human errors, among other things. For example, it will immediately alert you if a technician incorrectly replaces the cans with the source materials for the solution.
“Plants can be extremely sensitive, some may “dislike” even a one-degree deviation from the usual temperature. We covered the racks with sensors and cameras so we could understand what a crop is sensitive to during cultivation. Now we’ve stabilised the process by defining the optimal number of devices to ensure accurate environment control.
Nikolai Podvigin, Head of the Agrolaboratory at iFarm
5. Analytics: computer processing of Big Data
The “head” of the system is a cloud server. It collates and computes data indirectly from the array of actual measurements collected. For example, it calculates the efficiency of air circulation across the farm based on the data from all of the climatic sensors. What’s even more important is the ability of Growtune, the farm management software platform, to process all of the Big Data collected on the farm.
“The algorithms we use to prepare nutrient solutions are based both on recipes and on the processing of collected data. The outcomes of plant nutrition in previous cycles affect future mixing. The controller monitors the plants’ reaction to “dinner” on the previous day and adjusts the solution accordingly. And, after reviewing the combined data from different farms, we gradually optimise the flow charts.”
Alexey Novokreshchenko, Head of Automation at iFarm
Farms are increasingly using machine vision in their “nervous system”. Images from the cameras installed on the racks are analysed by a neural network trained to determine if the plants are healthy. Technicians can also use this neural network by uploading a picture of plants through a chatbot to gain critical information about its health. Another neural network calculates the dynamics of herbage mass accumulation using the same stationary video cameras or drone cameras.
6. Movement: automation of tray movements
Problems usually dealt with by rare and expensive specialists, agronomists, biochemists, and phytopathologists can be solved using artificial intelligence, special equipment, or remote consultants. But, until recently, there hasn’t been a fully automatic farm where electronics also handle routine manual work, such as moving trays.
In February 2021, iFarm engineers implemented and tested a design prototype of a fully automated vertical farm. It features a conveyor belt that moves trays with pots through the planting, germination, growth, ripening, and cutting areas. The farm can also be equipped with individual robot modules for packaging products and preparing trays for the next cycle.
7. A human helping hand
As with any sophisticated modern equipment, an automated farm has special service message protocols. Naturally, these protocols are intended for a person, such as an employee of a certified service provider. Automatic warnings about errors, worn-out nodes, or the need for consumables to be replaced translate into assignments for replenishment or troubleshooting.
The reports of deviations in the growth of herbs are handled by an iFarm agronomist. The first thing this expert does is double-check that the actual conditions match the ones in the flow chart. They then go through a list of tasks almost identical to the sections of this article. So, what’s happening with the air, climate, energy, and nutrition of the plants on the farm? Do the sensors provide correct data? When suspecting a technical failure, the agronomist connects a service employee to the diagnostic interface with one click. They can also connect to the technician’s camera or AR glasses if the employee is already on site.
“We have several continuous operation circuits, millions of second-by-second measurements, sensors, robots, conveyors, drones, cameras, and neural networks. It seems we’ve automated almost everything we can. The only thing you can’t automate is the R&D process itself. This is why people in the company focus on this process. And this is exactly why we are fighting for strategic investments.”
A Vertical Farm In New Jersey May Be Transforming The Farm-to-Store Supply Chain
Bowery Farming in Kearny, New Jersey, is reimagining the farm-to-store supply chain. Bowery is the largest vertical farm in the United States, growing leafy greens, herbs, fruits, and vegetables inside a climate-controlled warehouse where crops grow in stacked trays under lights that mimic natural sunlight.
August 5, 2021
Bowery Farming in Kearny, New Jersey, is reimagining the farm-to-store supply chain. Bowery is the largest vertical farm in the United States, growing leafy greens, herbs, fruits, and vegetables inside a climate-controlled warehouse where crops grow in stacked trays under lights that mimic natural sunlight. “Marketplace” host Kai Ryssdal recently toured the research and development part of the farm, where Bowery fine-tunes the flavor of new produce such as radishes and strawberries with fewer threats of pests, water scarcity, or other challenges associated with traditional outdoor farming. Bowery also grows wasabi arugula and other hard-to-find vegetables that are difficult to cultivate using conventional growing methods.Because Bowery’s business model is based on growing crops in indoor sites near the cities they sell in, most products that would normally take two or three weeks to reach stores make it to market a day or two from harvest. Bowery Farming’s CEO Irving Fain sees vertical farming as nothing short of revolutionary, stating that it can “democratize access to high-quality fresh food” in cities. Bowery is growing in other ways: It has a second farm in Nottingham, Maryland, and a third is under construction in Bethlehem, Pennsylvania.
Indoor Ag Sci Cafe Talks About Propagation And Transplants
This presentation ‘Precision Indoor Propagation for High Quality Transplants’ was given by Dr. Ricardo Hernandez (North Carolina State University) during our 32nd cafe forum on August 3rd, 2021
August 5, 2021
This presentation ‘Precision Indoor Propagation for High Quality Transplants’ was given by Dr. Ricardo Hernandez (North Carolina State University) during our 32nd cafe forum on August 3rd, 2021.
Upcoming Cafes:
September 21st (Tuesday), 11AM Eastern – ‘Introduction to Aquaponics‘ by Dr. Paul Brown and Dr. Cary Mitchell (Purdue University)
October 26th (Tuesday), 11AM Eastern – ‘Vertical Farming – Past, Present and Future‘ by Robert Colangelo (Green Sense Farms)
November TBA
December 7th (Tuesday), 11AM Eastern – ‘Plant-Made Pharmaceuticals under Controlled Environment‘ by Dr. Nobuyuki Matoba (University of Louisville)
Interested in giving a talk to share your thoughts and experiences? Please contact Chieri Kubota
AeroFarms and Nokia Unveil Partnership for Next Generation AI-Enabled Plant Vision Technology
AeroFarms and Nokia Bell Labs today unveiled a groundbreaking multi-year partnership to combine their expertise and expand their joint capabilities in cutting-edge networking, autonomous systems, and integrated machine vision and machine learning technologies to identify and track plant interactions at the most advanced levels.
August 5, 2021
NEWARK, N.J.--(BUSINESS WIRE)--AeroFarms and Nokia Bell Labs today unveiled a groundbreaking multi-year partnership to combine their expertise and expand their joint capabilities in cutting-edge networking, autonomous systems, and integrated machine vision and machine learning technologies to identify and track plant interactions at the most advanced levels.
As part of this partnership, AeroFarms, a Certified B Corporation and global leader in indoor vertical farming, contributes its commercial growing expertise, comprehensive environmental controls, an agriculture-focused data platform, and machine vision core foundation. Nokia Bell Labs, the world-renowned industrial research arm of Nokia, contributes its groundbreaking autonomous drone control and orchestration systems, private wireless networks, robust image and sensor data pipelines, and innovative artificial intelligence (AI) enabled mobile sensor technologies. This combination of innovative technologies allows AeroFarms to reach the next level of imaging insights that further enhance its capabilities as an industry leading operator of world-class, fully-connected smart vertical farms that grow the highest quality plants all year round.
AeroFarms and Nokia Bell Labs have been working together since 2020 and have reached an important milestone of achieving a proof of concept for this state-of-the-art integrated system and testing the technologies with AeroFarms’ current commercial crop varieties. Together, they are now ready to scale this system to all of AeroFarms’ crops and future indoor vertical farms, including the next ones in Danville, Virginia and Abu Dhabi, UAE.
The integration of Nokia Bell Labs’ AI-enabled drone-based sensors and advanced machine learning, computer vision and data analytics technologies with AeroFarms’ existing machine vision tools enhances and elevates AeroFarms’ position as an agriculture platform and capabilities organization dedicated to solving food and agriculture supply chain challenges.
David Rosenberg, CEO at AeroFarms, said: “With Nokia Bell Labs, we have developed the next-generation system that can image every plant every day in a cost-effective way at scale. This level of detailed imaging and insights helps us be better farmers by monitoring our plant biology dynamically and allowing us to course correct as needed to ensure the highest level of quality all year round. When I watch the drones autonomously imaging our plants, I am blown away by how this truly represents the power of harnessing leading-edge technologies and bringing brilliant problem solvers together from diverse groups to grow the best plants possible.”
Roger Buelow, CTO at AeroFarms, said: “AeroFarms’ expert team of plant scientists and engineers have been working together for two years with Nokia Bell Labs’ top researchers and engineers to train these complex learning systems with a nuanced understanding of plant biology. We have created a cross-disciplinary understanding at an industrial scale to develop the latest imaging technology to help accelerate our ability to introduce new crops and ensure the highest quality for our commercial operations.”
Nokia Bell Labs’ machine vision technology has enabled the most precise data capture yet, down to the level of individual plants, using leaf size segmentation, quantification, and pixel-based scanning to identify consistency and variation. Going beyond what even the human eye can perceive, this state-of-the art imaging technology enables the gathering of immense insights about a plant including its leaf size, stem length, coloration, curvature, spotting, and tearing. The end-to-end system is flexible and robust, built to take advantage of Nokia’s industry-leading 5G private wireless network with cloud processing technology, designed for low latency and high privacy in an on-premises network. It also provides intelligent industrial analytics capabilities as an integrated service that can be deployed quickly and efficiently anywhere.
Thierry Klein, VP, Integrated Solutions and Experiences Research Lab at Nokia, said: “Nokia Bell Labs is driven to solve hard and impactful problems, and together with AeroFarms, we are building the ability to see and identify plant interactions at unprecedented levels. The fundamental technologies of this partnership are our strength, and vertical farming is just the beginning. With the AeroFarms platform, we are exploring the power of network driven intelligence for industrial outcomes. These capabilities can expand into a multitude of indoor industrial operations, including logistics, warehousing, distribution hubs, and manufacturing.”
The multi-year partnership between AeroFarms and Nokia is anchored on shared values as mission-driven companies with the vision to scale technologies for the greater good. AeroFarms’ vertical farming platform is more sustainable than traditional farming with up to 390 times greater productivity per square foot annually, while using up to 95% less water and zero pesticides. In addition, vertical farming provides local food options for communities, reducing the environmental impact of trucking and shipping produce long distances and helping combat food waste.
Additional resources
AeroFarms website
Nokia Bell Labs website
About Nokia
At Nokia, we create technology that helps the world act together. As a trusted partner for critical networks, we are committed to innovation and technology leadership across mobile, fixed and cloud networks. We create value with intellectual property and long-term research, led by the award-winning Nokia Bell Labs. Adhering to the highest standards of integrity and security, we help build the capabilities needed for a more productive, sustainable and inclusive world.
About AeroFarms
Since 2004, AeroFarms has been leading the way for indoor vertical farming and championing transformational innovation for agriculture. On a mission to grow the best plants possible for the betterment of humanity, AeroFarms is a Certified B Corporation with global headquarters in Newark, New Jersey. Named one of the World’s Most Innovative Companies by Fast Company two years in a row and one of TIME’s Best Inventions in Food, AeroFarms patented, award-winning indoor vertical farming technology provides the perfect conditions for healthy plants to thrive, taking agriculture to a new level of precision, food safety, and productivity while using up to 95% less water and no pesticides ever versus traditional field farming. AeroFarms enables local production to safely grow all year round, using vertical farming for elevated flavor. In addition, through its proprietary growing technology platform, AeroFarms has grown over 550 varieties and has developed multi-year strategic partnerships ranging from government to major Fortune 500 companies to help uniquely solve agriculture supply chain needs. For additional information, visit: https://aerofarms.com/.
On March 26, 2021, AeroFarms announced a definitive business combination agreement with Spring Valley Acquisition Corp. (Nasdaq: SV). Upon the closing of the business combination, AeroFarms will become publicly traded on Nasdaq under the new ticker symbol "ARFM". Additional information about the transaction can be viewed here: https://aerofarms.com/investors/.
No Offer or Solicitation
This press release does not constitute an offer to sell or a solicitation of an offer to buy, or the solicitation of any vote or approval in any jurisdiction in connection with a proposed potential business combination among Spring Valley and AeroFarms or any related transactions, nor shall there be any sale, issuance or transfer of securities in any jurisdiction where, or to any person to whom, such offer, solicitation or sale may be unlawful. Any offering of securities or solicitation of votes regarding the proposed transaction will be made only by means of a proxy statement/prospectus that complies with applicable rules and regulations promulgated under the Securities Act of 1933, as amended (the “Securities Act”), and Securities Exchange Act of 1934, as amended, or pursuant to an exemption from the Securities Act or in a transaction not subject to the registration requirements of the Securities Act.
Forward Looking Statements
Certain statements included in this press release that are not historical facts are forward-looking statements for purposes of the safe harbor provisions under the United States Private Securities Litigation Reform Act of 1995. Forward-looking statements generally are accompanied by words such as “believe,” “may,” “might,” “will,” “estimate,” “continue,” “contemplate,” “anticipate,” “intend,” “expect,” “should,” “would,” “could,” “plan,” “predict,” “project,” “potential,” “seem,” “seek,” “future,” “outlook,” and similar expressions that predict or indicate future events or trends or that are not statements of historical matters. All statements, other than statements of present or historical fact included in this press release, including those regarding the expected benefits of the partnership, improvement of plant yields and quality and Spring Valley’s proposed acquisition of AeroFarms are forward-looking statements. These statements are based on various assumptions, whether or not identified in this press release, and on the current expectations of the respective management of AeroFarms and Spring Valley and are not predictions of actual performance. These forward-looking statements are provided for illustrative purposes only and are not intended to serve as, and must not be relied on as, a guarantee, an assurance, a prediction, or a definitive statement of fact or probability. Actual events and circumstances are difficult or impossible to predict and will differ from assumptions. Many actual events and circumstances are beyond the control of AeroFarms and Spring Valley. These forward-looking statements are subject to a number of risks and uncertainties, including changes in domestic and foreign business, market, financial, political, and legal conditions; the inability of the parties to successfully or timely consummate the proposed transaction, including the risk that any regulatory approvals are not obtained, are delayed or are subject to unanticipated conditions that could adversely affect the combined company or the expected benefits of the proposed transaction or that the approval of the stockholders of Spring Valley or AeroFarms is not obtained; failure to realize the anticipated benefits of the proposed transaction; risks related to the expansion of AeroFarms’ business and the timing of expected business milestones; the effects of competition on AeroFarms’ business; the ability of Spring Valley or AeroFarms to issue equity or equity-linked securities or obtain debt financing in connection with the proposed transaction or in the future, and those factors discussed in Spring Valley’s Annual Report on Form 10-K, Quarterly Report on Form 10-Q, final prospectus dated November 25, 2020 and definitive proxy statement/prospectus dated July 26, 2021 under the heading “Risk Factors,” and other documents Spring Valley has filed, or will file, with the SEC. If any of these risks materialize or our assumptions prove incorrect, actual results could differ materially from the results implied by these forward-looking statements. There may be additional risks that neither Spring Valley nor AeroFarms presently know, or that Spring Valley nor AeroFarms currently believe are immaterial, that could also cause actual results to differ from those contained in the forward-looking statements. In addition, forward-looking statements reflect Spring Valley’s and AeroFarms’ expectations, plans, or forecasts of future events and views as of the date of this press release. Spring Valley and AeroFarms anticipate that subsequent events and developments will cause Spring Valley’s and AeroFarms’ assessments to change. However, while Spring Valley and AeroFarms may elect to update these forward-looking statements at some point in the future, Spring Valley and AeroFarms specifically disclaim any obligation to do so. These forward-looking statements should not be relied upon as representing Spring Valley’s and AeroFarms’ assessments of any date subsequent to the date of this press release. Accordingly, undue reliance should not be placed upon the forward-looking statements.
Contacts
AeroFarms Contacts
Investor Relations:
Jeff Sonnek
ICR
Jeff.Sonnek@icrinc.com
1-646-277-1263
Media Relations:
Marc Oshima
AeroFarms
MarcOshima@AeroFarms.com
1-917-673-4602
Vertical Farming Congress Raises Expectations
The 2nd Vertical Farming World Congress on 20-22 September will now be held entirely online, to ensure complete certainty for participants and to avoid potential travel disruption.
August 4, 2021
The 2nd Vertical Farming World Congress on 20-22 September will now be held entirely online, to ensure complete certainty for participants and to avoid potential travel disruption.
“We have the most fantastic programme, featuring numerous industry leaders and innovators alongside awards, workshops, panels, exhibits and networking,” commented organiser Richard Hall, Chairman of food and drink consultancy Zenith Global.
Highlights include:
Industry leadership panel with Infarm, Kalera, Plenty and YesHealth
Future visions from 80 Acres, Bowery, CubicFarms, IGS, Vertical Field and Vertical Future
Market overview from Hort Americas and Rabobank
Regional pioneers from Chile, India and Japan
Retailer and investor panels with IKEA and Metro plus KPMG and S2G
Key innovators from the United States and United Kingdom to Malaysia and Sweden
Association leaders from North America, Europe, Africa and Japan.
“Our theme of Raising Expectations really does reach for the stars with a science briefing on space crop production from NASA. More stars will be celebrated by the first Vertical Farming World Awards. Future stars will be nurtured by an intensive half day workshop with Agritecture on Planning an Urban Farming Business,” added Richard Hall.
“We have also developed stellar new online features that worked so well last year, including virtual vertical farm visits, quick fire Vertical Venture delegate presentations and informal regional networking receptions. With the added advantages of time efficiency and recorded content, we feel the event should prove immensely valuable to any business wanting the latest insights on this rapidly taking off sector,” he concluded.
The Congress is sponsored by several leading industry suppliers including platinum sponsors Vertical Future and IGS Limited, gold sponsor CubicFarm Systems and silver sponsor Roto-Gro International.
Full programme and booking details are available online at www.zenithglobal.com/events/vfwc2021, with concessions for start-ups or company groups of 4 or more and early discounts up to 13 August. For further information, email events@zenithglobal.com.
Infarm Appoints Crop Genetics Specialist
Berlin-based urban farming specialist Infarm has appointed plant geneticist Pádraic Flood to lead its crop genetics team and help adapt various staple crops for vertical farming.
By Fred Searle
August 4, 2021
Berlin-based urban farming specialist Infarm has appointed plant geneticist Pádraic Flood to lead its crop genetics team and help adapt various staple crops for vertical farming.
A former research scientist at Wageningen University and the renowned Max Planck Institute for Plant Breeding Research, Flood will spearhead Infarm’s ongoing efforts to improve the quality, flavour and freshness of its vertically farmed produce.
Flood has a PhD from Wageningen in natural genetic variation in plant photosynthesis, and over the past decade he has used genetics to understand a range of key scientific questions ranging from photosynthesis to how plants adapt to extreme environments.
At Infarm he will lead the development of a breeding programme to adapt grains, legumes and other staple crops for vertical farming.
The company said the aim of the programme is to help return the land currently devoted to these staples to nature and biodiversity, while trying to have a positive impact on both people and the planet through more sustainable agriculture.
Infarm was founded in Berlin in 2013 by Osnat Michaeli and brothers Erez and Guy Galonska.
With a multinational team of more than 1,000 people globally, the vertical farming business has partnered with more than 30 major food retailers around the world.
To date, it has deployed more than 1,300 ‘in-store ‘farms’ as well as large-scale Growing Centres, producing various herbs, micro greens and leafy greens.
It claims to have saved more than 60 million litres of water and 60,000 square metres of land when compared with conventional production.
Lead Photo: Pádraic Flood will lead development of breeding programme to adapt grains, legumes and other staple crops for vertical farming
Vertical Gardening: A Modern Farming Method
Many of our communities are transforming into industrial and urban centres as the earth’s population increases. This growth, coupled with climate change, poses new challenges to the human populace to produce enough food as farmland acreage decreases and consumers’ demands increase.
July 25, 2021
Many of our communities are transforming into industrial and urban centres as the earth’s population increases. This growth, coupled with climate change, poses new challenges to the human populace to produce enough food as farmland acreage decreases and consumers’ demands increase.
Over the past decade, scientists and agronomists have been developing methods to produce double or triple the amount of food, using the same scale of land or less a farmer may cultivate. One of these approaches currently gaining much attention and adaptation is the vertical gardening or farming method.
NAREI staff harvesting and inspecting various crops planted in the vertical stack stand model, using PVC gutters
The notion of farming indoors is not strange to us, since greenhouse agricultural systems have been widely adopted for some time now. These houses have been used for years, providing conditions for numerous commercial crops (such as tomatoes, strawberries, peppers, and cucumbers) to thrive at its maximum production index. Cultivating under shaded facilities compared to outdoor farming fields can aid in year-round production, but few or none of these greenhouses have been constructed as multi-storey facilities.
Vertical farming is a method that uses vertically inclined surfaces to produce food, instead of the traditional method of growing vegetables on a single level in a greenhouse or open field. The National Agricultural Research and Extension Institute (NAREI) is currently evaluating the cost and productivity of various vertical-farming models. The experiment is being conducted at NAREI’s compound, Mon Repos, ECD.
NAREI staff harvesting and inspecting various crops planted in the vertical stack stand model, using PVC gutters
The vertical models installed under the tunnel house are: vertical stack stand using PVC gutters, vertical trellis made of nylon, barrel model using recycled plastic drums, and vertical wall using recycled plastic bottles.
Using vertical farming techniques have numerous advantages, such as: year-round production; reducing soil erosion and runoffs; maximising the use of abandoned structures or unused spaces; minimising crop failures due to harsh weather conditions and reduces the use of fossil fuels, since less farm mechanisation is needed. It also creates new urban employment openings; adds energy back to the grid via methane generation; returns farmlands to nature, aiding in restoring ecosystem functions; reduces pest and disease indices; reduces the need for abundant use of pesticides and herbicides, and offers the possibility of a sustainable food-production engine for our communities.
The experiment is being done to ascertain yields of a wide variety of crops needed to sustain large populations, without exhausting existing resources. With the success of this study, local households in Guyana can better utilise yard space to produce their foods at a cheaper cost and local farmers can increase productivity to reach consumer demand. In addition to that, this method can be utilised to combat major challenges faced due to climate variation in Guyana, such as flooding.