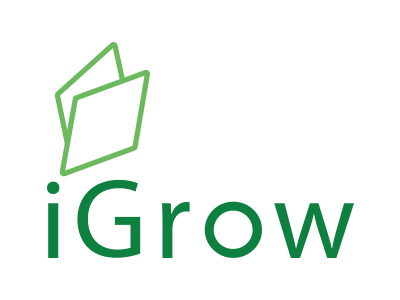
Welcome to iGrow News, Your Source for the World of Indoor Vertical Farming
Greenroofs.com Featured Project
Sky View Parc
Flushing, NY, USA
55,000 sf. Greenroof
April 15, 2019
Wow, this awesome project looks like something you’d see in pro-environmental design Singapore with its highrises, beautifully landscaped park, and living architecture, right? But it’s not – the lucky location is in the New York City borough of Queens.
Image: Sempergreen
Due to its undeniable scale and multi-color presence, the distinctive Sky View Parc green roof benefits not only condominium’s residents and the environment, but developers and marketers, too. It’s as a great sales tool for eco-friendly design!
Read the entire article here
The Future of Farming
Darren Handschuh - May 7, 2019
Naomi LaFrance has a vision.
She wants to feed not only people from her first nation in Saskatchewan, but other nations as well.
And she wants to do it all with as little impact on the planet as possible so she turned to the Aquaponics Training Institute in Vernon for help.
Aquaponics is the marriage of hydroponics and aquaculture where the best of both systems are used to grow plants with very little harm to Mother Earth.
“Right now we have a hockey arena that is not being used so maybe we will be able to convert that into a growing operation,” said LaFrance. “I didn't realize how big it can become. I just came here to learn and the more I am learning, the bigger the vision is becoming and it's pretty exciting.”
The Aquaponics Training Institute is located in the BX area and is the brain child of Shawn Bonnough who teaches classes on aquaponics.
One of the big advantages of aquaponics is the food will grow 24 hours a day, 365 days a year with a minimal environmental footprint.
“The fish are fertilizing the water for the plants and the plants are filtering the water for the fish,” said Bonnough. “In between those two living systems is the bacteria that breaks everything down and creates natural fertilizer which is not harmful to the environment. This is the only system that is working on 10 percent of the water of traditional farming but is producing 10 times as much food.”
LaFrance said she will take what she has learned at the institute back her Cree nation in Saskatchewan.
The Aquaponics Training Institute offers courses online as well as at the institute itself.
Boston, MA - It Happens Here: Hands-Off, Year Round Farming At Little Leaf Farms In Devens
By Kate Merrill April 26, 2019 Filed Under: Boston News, Devens News, It Happens Here, Little Leaf Farms
DEVENS (CBS) – It happens here in Devens, a region made up of sections of Shirley and nearby Ayer. It’s a decommissioned army base named for Union Army General Charles Devens. It is now a residential and business community that is home to a small company helping New Englanders eat fresh, locally grown greens year-round.
Welcome to Little Leaf Farms. It’s not what most of us picture when we think of farming.
“It’s an automated system,” explained founder and CEO Paul Sellew.
It’s a massive greenhouse where green leaf, red leaf, and arugula are neatly planted in gutters. They are irrigated with rainwater collected from the roof, and an automatic shading system on the roof makes sure it doesn’t get too hot.
Lettuce grows in gutters at Little Leaf Farms in Devens. (WBZ-TV)
Each gutter slowly moves across the massive greenhouse at a pace so slow, you don’t even notice it. After about three weeks, the gutter drops onto a conveyer belt where it heads into the packing room where it feeds through a pair of circular cutters and then through a sorting system before it’s packaged into plastic bins.
While not officially organic, Sellew says there are no chemical pesticides.
“We use something called biological control,” he explains.
Little Leaf Farms uses lady bugs to eat the insects that threaten crops. (WBZ-TV)
They use lady bugs to eat the insects that threaten the crop.
“Because no human hands touch it, there’s no need to wash it. It’s ready to eat,” Sellew said.
With a farming background, (he also created Backyard Tomatoes from Maine) Sellew built a massive greenhouse back in 2015. His goal was to provide New England shoppers with an alternative to produce that’s shipped from the west coast.
“They were relying on stuff that’s grown in California that is trucked across the country and by the time we get it, it’s 10 days old,” he said.
Little Leaf Farms products are boxed at their Devens facility. (WBZ-TV)
The company believes the hydroponic method of growing also cuts down on the risk of disease like the romaine E.coli outbreak last fall.
“What we are doing has nothing in common with that is being done in California where they have cattle ranches and dairy farms next to lettuce fields,” Sewell said.
Greens from Little Leaf are packaged within minutes of harvest and can be at the store that same day.
Sellew says customers are loyal and demand is constantly increasing which is why they are building another massive greenhouse on their Devens campus.
Their next project? A new romaine variety. No word on when you’ll see it in your local supermarket.
KATE MERRILL
Emmy award winning journalist Kate Merrill is a news anchor for WBZ-TV News weekday morning and noon newscasts.
CO2 GRO Inc (CVE:GROW) Proprietary Foliar Spray System Boosts Yields By 25 Percent
By MIDASLETTER LIVE | APRIL 24, 2019
CO2 GRO INC
CO2 GRO Inc (CVE:GROW) (OTCMKTS:BLONF) (FRA:4O21) is developing advanced carbon dioxide technologies to accelerate plant growth. COO Aaron Archibald explains that carbon dioxide is beneficial for growth, resulting in larger and quicker-growing plants. The company’s proprietary process dissolves carbon dioxide into water, which is then applied to the foliage of plants using CO2 GRO’s foliar spray system.
Typically, growers use gas deployment systems that result in significant carbon dioxide loss as a result of venting; CO2 GRO’s foliar sprays ensure each plant receives the necessary carbon dioxide. Unlike gas deployment systems, the company’s foliar spray technology can be applied to outdoor grows and greenhouses.
Archibald reveals that using CO2 GRO’s foliar sprays regularly results in yields 25 to 30 percent higher than yields produced by using gas deployment systems. Archibald anticipates that the company’s technology will be adopted by cannabis LPs in Canada, as Health Canada is in the process of reviewing applicable regulations. CO2 GRO currently has licensing agreements in both Canada and the US, and has seen broad interest from the American hemp space since the passage of the Farm Bill.
Transcript:
Narrator: CO2 GRO is a Toronto based, precision agriculture technology company. GRO offers CO2 foliar spray systems to both indoor and outdoor growers for increasing their crop yields, safely and naturally.
The company has over 66 million shares outstanding, with management ownership at 26 percent. CO2 GRO Inc is listed on the TSX-Venture under the symbol GROW.
James West: I’m joined now by Aaron Archibald, Chief Operating Officer of CO2 Grow, trading on the TSX Venture under the symbol GROW. That’s a good symbol.
Aaron Archibald: It is, thanks!
James West: Aaron, so your business is essentially creating foliar CO2 sprays, and so just to refresh the memory of our audience, or to enlighten them for those who might not know, what is the benefit of CO2 as a foliar spray?
Aaron Archibald: Well, any grower knows that adding CO2 to plants is beneficial, and they’ll grow faster and grow bigger; it’s difficult to get CO2 to plants, though. So what we do is, we dissolve CO2 into water and apply it to the foliage of the plant. That makes it 100 percent bioavailable, and it’s driven into the plant by osmotic pressure.
James West: Okay. So interestingly, most greenhouses that beneficiate with CO2 use gas deployment systems.
Aaron Archibald: Absolutely.
James West: And that’s got to be a little bit more wasteful, because obviously the air is being changed in the environment?
Aaron Archibald: Yeah. Most of it gets vented; it’s very difficult to create a homogenic environment and get all the CO2 to every plant. It’s like HVAC systems are extremely difficult in building; most people have a forced air furnace in their home know that they have a room in the winter that’s always colder than the other ones.
James West: Sure.
Aaron Archibald: So by putting it directly into the water and putting that directly onto the plant, every plant gets CO2, and it’s just the most bioavailable means of doing it.
James West: Cool. Then, you guys, when you were last here, we were talking about this issue where Health Canada had not approved foliar-sprayed CO2 for use in commercial gardens by licensed producers in Canada. Has that changed?
Aaron Archibald: Of cannabis. They haven’t changed their regulations necessarily; they have let us know that we’re approved by GFIA, and that we don’t contravene anything. We’re not a pesticide, we’re not a herbicide. I look at it and say we’re just a novel means of applying water and CO2 at the same time. Any LP is allowed to water their plant, and allowed to use CO2.
James West: Okay, so there’s no barrier to any of the LPs using the product.
Aaron Archibald: I think it’s a matter of how you interpret the legislation, and where and when they can use it in their facilities.
James West: Okay, let me ask you this another way.
Aaron Archibald: All right.
James West: How soon till LPs are using your product over gas-delivered CO2?
Aaron Archibald: I’d say very soon. I think that Health Canada is having a long, hard look at some of their regulations, and I think they did it very quickly and did it with a broad brush. You know, you can water or foliar spray cuttings, or clones, right now; it’s just more mature plants you can’t. I think when they recognize that there’s no added pesticides, anything harmful, there wouldn’t be a problem with spraying water on a plant.
James West: Sure. So I’m curious: how do you get CO2 dissolved in water?
Aaron Archibald: We use a proprietal technology that does it very efficiently. I mean, there’s a number of different ways to put dissolved gases into liquids; we just happen to have experience doing it efficiently. We don’t need to chill it, we don’t need to compress it. You know, some of that’s proprietal, so I won’t tell everyone exactly how we do it, but we can do it extremely efficiently, at high, high levels.
James West: Wow. Okay, so then, how often does a greenhouse or a, say, cannabis plant, need to be treated with foliar CO2 in order to optimize the growth cycle?
Aaron Archibald: The more times you can apply it, the better. So what we have worked on with people is applying extremely small volumes of water more times per day, because you get more CO2 delivered to the plant that way.
James West: Okay. So is this something that you could actually create an automated misting system within a environment that would be a beneficial way to approach it?
Aaron Archibald: Absolutely. Some of our customers do that now.
James West: Oh, okay, great.
Aaron Archibald: So you – most overhead booms, you can control the volume of water, the speed of the boom, and the number of times per day that it runs, so it’s easily automatable.
James West: And your process, as you say, is proprietary, but is it patented?
Aaron Archibald: Patent pending.
James West: Patent pending. Great. So at this point, who is using your product?
Aaron Archibald: Well, a number of different growers in the States and Canada.
James West: Okay.
Aaron Archibald: Generally we do sign a non-disclosure agreement; lots of people don’t necessarily want their name put out there, but we –
James West: They don’t want their competitors to know that they’re using this secret weapon.
Aaron Archibald: Exactly, but we currently have commercial operations in Canada and the US.
James West: Uh-huh. Okay, and how much does it cost? I mean, let’s pick a unit of square footage; let’s say, per thousand square feet, is it easy to say, well, this is how much the cost is going to be per month, per thousand square feet?
Aaron Archibald: It is pretty easy. You know, we do a scoping survey with them; we have an engineering group that works with them and looks at whether or not their infrastructure is set up to use the technology, what might need to be tweaked, and then we come to a commercial arrangement. And we usually charge by the square foot per month. We can do it quarterly as well, but it’s a per square foot, or per square metre in Europe, charge.
James West: So unlike software as a service, this is like CO2 as a service, model? [laughter]
Aaron Archibald: Yes it is, yeah. We – it’s a site license/lease model that we’re doing.
James West: Very interesting. And at some point, will you have a retail option available for those growing at home?
Aaron Archibald: I could see that in the future. It would be a matter of engineering it down to a small enough size and a price point where a home grower could use it. Right now, I think it’s not very feasible, but I could see it in the near future.
James West: Really? Okay.
Aaron Archibald: Just from a cost standpoint –
James West: This is me with my hand up. I would like to grow. Heading to my NDI, this is my garden in my own home right now that is growing hydroponically, and I would love the opportunity to treat two plants with foliar spray and two plants without and see how the difference is in a measured basis.
Aaron Archibald: Well, as we talked about before we got on air, I’ll get you some equipment used for a trial. So you just have to share the data with me.
James West: Great! Yeah, of course, I’d be happy to. Okay, Aaron, then how does the revenue model, the business model, of the company work, then? You’re saying you have a per square foot plus a licensing; how does that sort of, what per user, how much – what’s your – I guess I’m babbling now. What is the projected growth of the revenue in the company?
Aaron Archibald: That’s hard to say. The market is so big. You know, the plant for food market is $9 trillion per year; you know, the focus is cannabis right now in Canada, it’s very popular, but we can help all plants grow. So whether it’s peppers or lettuce, it’s almost hard to measure what our revenues are going to be like in two years, simply because we have so much opportunity in front of us.
James West: Sure. What’s to stop me from just spraying club soda on my plants?
Aaron Archibald: You could. Technically, you’d be in violation of the process patent, but also the cost to buy club soda and spray it on your plants would be –
James West: Pretty high.
Aaron Archibald: High. Extremely high.
James West: Interesting.
Aaron Archibald: Extremely inefficient.
James West: And is the carbon content of club soda equal or similar to that, and the bioavailability, does it even apply?
Aaron Archibald: Well, not really. I mean, they chill soft drinks and put it under extreme pressure; that’s why you see bubble nucleation, so you know, if you shake it and open it, it explodes. So that’ll tend to drive the CO2 out of it, and that’s part of the experience of drinking a carbonated drink, is you like the sense of the bubbles in it.
James West: The fizz.
Aaron Archibald: What we do is different in that you won’t actually see bubbles, and bubbles won’t nucleate out; it’s done on a molecular level, and it stays in solution so that it can be utilized. If it comes out of solution, it’s just not bioavailable anymore.
James West: Sure. What kind of increase in yield, in percentage terms, can one expect from applying foliar CO2 relative to not applying any CO2?
Aaron Archibald: I’d say on average we’ve seen between 25 and 30 percent increase versus standard gassing, so 800 to 1,200 ppm in a room.
James West: Then, now with Health Canada reconsidering some of its regulations over foliar applied, let’s call it a nutrient for lack of a better descriptor – is that something that they now have to specifically give you the ability, or an LP the ability, to say, okay, you can use that now without risk of it resulting in a negative test result from your product? Is there any risk of that?
Aaron Archibald: There isn’t. See, plants take in CO2, and they keep the C, which is the carbon, which is a building block for plants, and they respire out O2, much the same way we breathe in air with O2 and respire out CO2. So there’ll be no residual CO2 left in a plant because it becomes carbon, becomes the plant. So there really is no way to test for CO2 in a plant.
James West: Right. I guess as carbon-based life forms, we have no problem dealing with carbon in our cannabis.
Aaron Archibald: Exactly right. And that’s why CO2 makes plants grow bigger and faster and yield more.
James West: Right. So I guess, then, the inflection point for your company is going to be when widespread adoption of foliar-sprayed CO2 at the commercial level takes root – the pun intended – in the cannabis industry broadly?
Aaron Archibald: Yes. Yeah, and you know, like many Canadian technologies, sometimes you go abroad before you get adoption at home. It’s an unfortunate thing, but you see it a lot. We have a phenomenal amount of interest internationally; you know, US hemp growers can’t keep up with the number of phone calls we’re getting right now. Since it’s been legalized federally in the States, they’re really, really interested, especially outdoor growers. It’s the only means to apply CO2 to a plant outdoors, is by putting it in water first and applying it to the plant.
James West: Right. Either that, or putting a coal-fired hydroelectric plant next door!
Aaron Archibald: It’d be pretty inefficient to blow it on, because the wind would just take it away. So by putting it in water, we can supply outdoor growers with CO2, hoop houses, shade houses, things that historically – like, structures that have historically not been able to use CO2 in them.
James West: Right. What about competitors? Do you have – who do you have in the competitive realm?
Aaron Archibald: Touch wood as I say it: Right now, there are no competitors! You know, it’s a novel technology. No one had ever thought to do it before, so we’re first to market with it, and you know, that’s why we’ve gone through the process of getting the IP, but I think more importantly it’s going to be first to market, having some trade secrets and penetrating the market, and becoming the company that’s known as the CO2 foliar spray technology.
James West: Interesting as ever, Aaron. We’re going to continue to follow the story, and I can’t wait to try it out on my own plants. Thanks for joining me today.
Aaron Archibald: Okay! All right, thanks very much.
‘We Are Right At The Starting Gate’: Vertical Farming Could Change The Food System
08-May-2019 By Katy Askew
Intelligent Growth Solutions (IGS) talks vertical farming, demand growth and its unique technological proposition.
To Read the Article and View the Video, Please Click Here
DelFrescoPure Introduces The LivingCube
Our exciting partnership between DelFrescoPure and CubicFarms has resulted in the LivingCube -- a system of automated vertical farming growing machines that continuously produces living lettuce, living basil and microgreens all year long
Our exciting partnership between DelFrescoPure and CubicFarms has resulted in the LivingCube -- a system of automated vertical farming growing machines that continuously produces living lettuce, living basil and microgreens all year long.
LivingCube - Vertical Growing System
LivingCube is powered by DelFrescoPure, which produces power by using an off-the-grid electrical cogeneration system. The growing chambers are all individually climate controlled to optimize the environment for each crop to create an independent growing facility.
"We wanted to offer our retail partners innovative and local commodities and the ideal solution was to partner with CubicFarms," stated Carl Mastronardi, President of DelFrescoPure.
The LivingCube living lettuce, living basil and microgreens are always fresh, nutritious and flavor-filled. LivingCube finally offers you the freshness you love without sacrificing nutrition and flavor!
Living Lettuce
Who says you need to compromise quality for flavor? Our LivingCube allows our living lettuce to be vertically grown without pesticides in multiple varieties. Available in a 3-count lettuce bag, our living lettuce is convenient and delicious; you can grow it in your fridge or on your counter. Lettuce grow for you!
Basil Microgreens
With 12x the nutrients of mature leaves, LivingCube microgreens are a small way you can add health benefits to food! We offer multiple varieties and customized packaging combinations. Our LivingCube machines are flexible -- allowing quick crop changes that adjust seasonally. It's convenience with flavor!
"Our LivingCube microgreens allow you to add flavor, quality and fresh health benefits to your food without having to put in hard work to get it," stated Fiona McLean, Marketing Manager of DelFrescoPure.
Our packaging is made from 100% post-consumer recycled PET and comes in 50g and 100g, making our microgreens versatile and easy to buy, store and use. No need to chop, just sprinkle!
Trending: Are Shipping Container Farms The Future of The Industry?
BY LUKIE PIETERSE ON APRIL 19, 2019
Could shipping containers be the future of farming? According to Cleveland Containers in the UK, they can. The company states that shipping containers could provide an answer to the rapid demand for local produce.
According to the company, the trend for local food has risen over the last few years and as a result, the demand for local produce is showing no signs of slowing down. With this in mind, farmers are being forced to get creative in how they can deliver the volume needed for local supermarkets, whilst still keeping hold of the nutritional value in its fruit and veg.
So, how could container farms shape the future of the industry? Johnathan Bulmer, Managing Director of Cleveland Containers, explains.
“Many are unaware that containers can be fitted with heating and water systems, as well as gas and electrics and therefore offer a whole host of benefits for crops and farmers alike.”
“Creating your own farming space inside a container enables you to grow crops all year round and once modified, allows you to control growing conditions such as climate, soil quality and heat and light exposure.”
Read the full article in Future Farming here
Related article: Indoor farming technology market to grow to $ 40.25 billion
Jury Convicts Former South Dakota Aquaponics Company Official of Fraud
APRIL 29, 2019
THE ASSOCIATED PRESS
SIOUX FALLS, S.D.
A federal jury has convicted a former executive of a South Dakota company accused of defrauding investors in a scheme to build an $11 million fish farm.
The jury Monday found Timothy Burns guilty of five charges of wire fraud for his role in soliciting investors for Global Aquaponics in Brookings. He will be sentenced later.
Burns was the one-time chief operating officer of Global Aquaponics. The company sought investors to build an indoor fish farm and hydroponics facility.
But the Argus Leader reports construction on the fish farm never started. Investors who put a minimum of $25,000 each in the project lost hundreds of thousands of dollars.
Businessman Tobias Ritesman earlier pleaded guilty to all 18 counts against him in the alleged scheme. Ritesman also awaits sentencing.
Pittsburg State University Showcases Aquaponics Project On Campus
Project Creates Sustainable, Healthy Food
By: Chris Warner
April 24, 2019
PITTSBURG, Kan. - Hydroponics involves growing plants in water instead of soil, and a project at Pittsburg State University has turned that into aquaponics by adding another element.
"It started out as a hydroponics operation so, it's basically growing lettuce primarily, but other food through water rather than soil, with the aquaponics, that incorporates fish into the system so it's more of a closed loop." Erin Kruse is one of two students giving tours at Pitt State to showcase their new aquaponics project.
Aquaponics, as Kruse mentioned, incorporates fish, in this case, tilapia, into the hydroponics system. Kruse says "So the fish actually generate the nutrients for the plants and then the plants actually clean the water for the fish."
And it's this unique system that officials like Matt O'Malley with Live Well Crawford County, are excited to see. O'Malley says "We are hoping to increase access to healthy foods for everyone in the county and thought this could be a really neat way to get that in communities that might not be able to do a garden project or something like that."
Kruse says the Students 4 Sustainability group, agree. "We really think, as students for sustainability, that local food production, sustainable food production is something that's always going to be paramount, especially in rural communities."
For O'Malley, he says he's looking at an even bigger picture. O'Malley says "We like to dream big and how cool would it be if every high school in Crawford County had an aquaponics system and they grew their own lettuce for their own school lunch salad bar, and so that's what we're kinda dreaming about with this project."
The project is still in it's early stages but Kruse says they hope to see it continue to grow and expand to serve the county.
The project was originally started by another group on campus before the students for sustainability group took over.
Crop One Holdings Wins Best Innovation In Indoor Farming Award For Joint Venture With Emirates Flight Catering
Crop One Holdings, the world’s leading vertical farm operator through its FreshBox Farms brand, has won the Best Innovation in Indoor Farming Award at the 2019 Global Forum for Innovations in Agriculture (GFIA) conference in Abu Dhabi, UAE
Oakland, Calif., April 29, 2019 -- Crop One Holdings, the world’s leading vertical farm operator through its FreshBox Farms brand, has won the Best Innovation in Indoor Farming Award at the 2019 Global Forum for Innovations in Agriculture (GFIA) conference in Abu Dhabi, UAE. Crop One Holdings was recognized for being a leader in confronting core environmental, economic, and social issues, combining spatial optimization with resource efficiency to grow leafy greens year round.
The company announced a $40 million joint venture agreement with Emirates Flight Catering last year, to build the world’s largest vertical farming facility in Dubai, UAE. The controlled environment facility in Dubai, will be 130,000 square feet and use 99 percent less water than traditional fields to produce three US tons of high-quality, herbicide- and pesticide-free leafy greens daily.
“This award is a testament to our commitment to responsibly feed our planet’s 7.4 billion people,” said Sonia Lo Crop One Holdings chief executive officer. “We are firm believers in building a more sustainable world, and aim to continue being a thought leader in this industry.”
Seven years after its founding in 2012, Crop One is now the world’s largest vertical farmer and the only one to consistently maintain a gross profit. The company’s patented grow process, created and augmented by top plant scientists and systems engineers, allows its farm to grow 400 acres worth of outdoor-grown produce in 1 acre of warehouse space. The GFIA judging criteria was on four main criteria: environmental sustainability, innovation, productivity and impact.
“The GFIA Innovation Awards celebrates some of the world’s most pioneering developments in agriculture,” said GFIA Event Director David Stradling. “Crop One has a proven dedication to providing innovative solutions to one of the world’s most complex problems by combining soilless hydroponic growing technology with advanced plant science to produce local, fresh greens globally.”
GFIA was founded in 2014 and is the global authority on innovative, sustainable agriculture practices and food production. Its Innovation Awards are designed to celebrate innovations that help to improve global food security while maintaining and improving sustainable agriculture practices.
About Crop One Holdings
Oakland, California - based Crop One is a vertical farming holding company for two subsidiaries – FreshBox Farms, Millis, Massachusetts, and a joint venture with Emirates Flight Catering, Dubai South, United Emirates. Crop One has been in commercial production longer than any other major vertical farmer in the U.S. It produces the highest crop yield per square foot, at 25% of the capital cost, of any vertical farm, due to its unique combination of proprietary technology platform and best-in-class plant science.
For more information about Crop One and vertical farming follow the link to cropone.ag.
About Emirates Flight Catering
Emirates Flight Catering is one of the world’s largest catering operations. Offering airline, events and VIP catering as well as ancillary services including laundry, food production and airport lounge food & beverage, Emirates Flight Catering is a trusted partner of over 100 airline customers, hospitality groups and UAE government entities. Each day, the company’s 11,000 dedicated employees prepare an average of 225,000 meals and handle 210 tonnes of laundry.
INDIA - VIDEO: A Vertical-Farming Startup Cultivating Organic, Healthy Greens in Space-Crunched Mumbai
The hyper-local farm delivering freshly-harvested,
leafy greens right to your doorstep
A vertical-farming startup cultivating organic, healthy greens in space-crunched Mumbai. Watch the journey of Herbivore Farms in the video below:
Mumbai Couple Grows Organic Produce through Hydroponics on
Commercial Level
25 April, 2019
By: Dr. Sangeeta Soi
A Mumbai based couple - Oshua Lewis and Sakina Rajkotwala decided to take the leap after a visit to Auroville in Puducherry in 2017 where they got inspired by Krishna Mckenzie, a native of England, who’s “honouring Mother Nature through local food.”
They named it as Herbivore Farms, Mumbai’s first hyperlocal, hydroponic farm. Today, the farm grows 2,500 plants, and sells fresh, organic vegetables to customers across Mumbai.
As told to Mumbai Foodie, the couple said, “Herbivore Farms is Mumbai’s first hyperlocal farm located in Andheri East. We grow super-healthy varieties of leafy green vegetables like Swiss chard, kale, rocket, and lettuce using hydroponic methods of cultivation.”
The farm is actually made at a place which was earlier used as a warehouse in an old industrial estate. It is spread over 1,000 sq ft, and houses over 2,500 kinds of plants in a temperature-controlled indoor setting.
According to the couple, the hydroponic method they use to grow their vegetables sets their produce apart. They also stated that there is no real-time solution to all the questions that they had in hydroponic farming so the trial and error methods usually works.
The irrigation system used here is re-circulating type which uses 80 percent lesser water to grow the produce. Other than this no pesticides are used in order to keep the environment sterile and safe completely. The water in which the plants are grown contains macro and micro-nutrients that facilitate the growth of the plant. Growing the plants in a vertical format has helped the couple to grow five times more the normal produce their farm would have otherwise done.
The couple also makes sure that they can deliver their products through home delivery, maintaining freshness, nutrition, and flavour.
They also reported that in spite of the higher cost of boxes the fresh organic produce are always in demand among customers.
#Mumbai #hydroponics #OshuaLewisandSakinaRajkotwala #Herbivorefarms#hydroponicfarm #recirculating
Italy: Thirteen Hectares of Lettuce Grown On A Floating System
All types of lettuce are grown with the floating system on an area of 13 hectares. The whole system is automated to produce salad marketed under the brand name Ninfa. The location is Standiana, (Ravenna), near the large amusement park Mirabilandia, famous in Italy. "Here we also have fun with water - and we produce lettuce with water", entrepeneur Gianluca Rossi says.
The owner Gianluca Rossi
High quality
A production site of this size, with these technologies is not often seen in Europe. According to Rossi he gets positive responds on his systems, even from the major seed companies in the world.
"The 13 hectares are part of a 100-hectare farm. The design took more than six years to complete and I did it myself together with the leading experts. I made many trips abroad before it was done", he recalls.
Here is how the roots appear in the support, just removed from the water
On the track, oriented in the direction of the processing warehouse, the panels with the lettuce.
Gianluca shows how everything is done with utmost care. "Our greenhouses only serve as protection, not to anticipate cycles. The production runs from mid-April to December, while in the winter months it is suspended."
The cultivation takes place with floating panels certified for contact with food. The roots are immersed in water. Nutrition is carried out with the classic triad of elements N, K, P and microelements. Weed killers are not needed, of course. Defence follows the technique of integrated control.
Watch the video!
The positioning of the panels with lettuce on the railroad.
180 hectare land
"With traditional methods, adds Rossi - considering also the rotations, in the open field - it would take 180 hectares of land to produce what we can do in 13 hectares of floating system. In our case, the rotation is nothing more than the replacement of the "old" water that is not wasted but returned to the fields of the remaining 87 hectares of our company".
No water waste
At first glance, it might seem that there is a waste of water, but that is not the case. "Careful management allows for prolonged and waste-free use. With the same number of plants produced, the reduction in water consumption varies between 70 and 80% compared to a traditional method".
Here are some other numbers: 9 million cultivated plants expected in 2019, 4000 tons of products and 169,000 floating support panels. "Our history goes back a long way, Rossi points out, because it was my father, from a very young age, who dedicated himself to the trade in vegetables. At a national level, we are already known for our activity as traditional producers, and now we want to make ourselves known for this new reality".
Aerial view of the Standiana farm. There are 13 hectares of greenhouses with lettuce grown in floating systems
Minerals
Water, like the earth, does not of itself, contain enough nutrients, but they are both a means of mixing, holding and conveying them. Unlike traditional methods, in the tank, the mineral salts are available only to plants that absorb according to their daily needs, excluding leaching, waste and dispersion into the surrounding environment or in the aquifers.
"More yields, less waste of nutrients, less water consumption, no forcing, concludes Rossi. There is a difference, even from an organoleptic point of view. The panel tests carried out on the Ninfa salad have shown a higher percentage of mineral salts than traditional crops, with a significant increase in shelf life.
Oceanix City: This Concept Of Floating City Includes Food Production And Farming
Linked by Michael Levenston
“Every island has 3,000 square metres of outdoor agriculture that will also be designed so that it can be enjoyed as free space,” said Ingels.
By Katharine Schwab
Fast Company
Apr 4, 2019
Excerpt:
For Oceanix’s idea to work, all the food needed to feed every person living in the floating city would need to be grown there. What does that mean? There’s certainly no meat involved, mostly because beans are a far more efficient way of getting protein. Some crops would be grown outdoors–an estimated 32,000 square feet on each hexagon would be devoted to food cultivation. Much of that would be outdoors, since the sun uses the least amount of stored energy, and the crops would double as green space for residents.
But according to Clare Miflin, the cofounder of the Center for Zero Waste Design, a floating city would also need to experiment with other ways of growing food. One possibility: outdoor vertical farming for crops like lettuce. Then there’s hydroponics and aeroponics, the latter of which uses 10 times less water than traditional farming simply by spraying plant roots with mist. Aquaponics, in which plants grow hydroponically and are fertilized with fish waste, has a deep precedent–the Aztecs used aquaponic farming on their own floating agricultural islands many centuries ago.
With food comes food waste. Miflin wants to create a circular system where all food waste is turned into nutrients for the soil through composting. Food waste would go through a pneumatic system of pipes directly to an anaerobic digester to start the composting process. But there’s also the problem of packaging. Miflin believes that it would be crucial for the floating city to only use reusable food containers, with centrally located drop-off points for people to put their empty containers; from there, they could be cleaned centrally and reused.
Read the complete article here.
Students Compete For Plant Growth Chamber
Plantae and Conviron have collaborated to launch the Seeding Discovery Competition.
The competition is aimed to equip a successful university or college student with a high-performing GEN1000 plant growth chamber that will enable them to fulfill a meaningful research program in the field of plant sciences, biology, and biotechnology.
The Seeding Discovery Competition provides students with the opportunity to define and submit a proposal for a study that:
Aligns with personal and departmental objectives
Enables them to work with faculty and administration on planning and logistics
Contribute to their institution’s infrastructure with new research equipment at no cost
To be eligible, applicants must be students enrolled in a post-secondary program related to plant science. For further eligibility criteria and competition rules visit www.plantae.org/seedingdiscovery.
For more information:
Plantae
plantae.org
Conviron
Publication date: 4/10/2019
Are Container Farms The Future of The Industry?
The trend for local food has risen over the last few years and as a result, the demand for local produce is showing no signs of slowing down
29 March 2019
Could Shipping Containers Be The Future of
Farming? According To Cleveland Containers,
They Can.
In the UK alone, over half a million people still rely on food parcels, and overall around 3 billion people in the world live below the poverty line, according to Cleveland Containers.
The company states that shipping containers could be the future of farming and could provide an answer to the rapid demand for local produce.
Trend for local food
According to British Cleveland Containers The trend for local food has risen over the last few years and as a result, the demand for local produce is showing no signs of slowing down.
"Creating your own farming space inside a container enables you to grow crops all year round and once modified, allows you to control growing conditions such as climate, soil quality and heat and light exposure," says Johnathan Bulmer. - Photo: Cleveland Containers
“The problem that farmers have with this rising demand is that they are faced with the challenge of providing seasonal produce all year round, with no control over weather conditions,” says the company.
Farmers forced to be creative
With this in mind, farmers are being forced to get creative in how they can deliver the volume needed for local supermarkets, whilst still keeping hold of the nutritional value in its fruit and veg.
So, how could container farms shape the future of the industry? Johnathan Bulmer, Managing Director of Cleveland Containers, explains.
“Many are unaware that containers can be fitted with heating and water systems, as well as gas and electrics and therefore offer a whole host of benefits for crops and farmers alike.”
Control growing conditions
“Creating your own farming space inside a container enables you to grow crops all year round and once modified, allows you to control growing conditions such as climate, soil quality and heat and light exposure.”
Bulmer claims that container farms can produce up to 4,000 heads of lettuce every 10 days, using no soil and 97% less water than a conventional farm.
Eliminating the need for pesticides
“Shipping container farms also mean that crops are protected from nasty pests, therefore eliminating the need for pesticides which can cause health problems in those who consume them.”
Johnathan Bulmer:
Farmers won’t need to empty their pockets and fork out for extra land to expand
By removing the need for pesticides the produce will be healthier and, according to Bulmer, research shows that UK buyers find products free from pesticides more desirable.
Farm anywhere
Container farms are also easily scalable, as they can be stacked, says Bulmer. “What this means for farmers is they won’t need to empty their pockets and fork out for extra land to expand. You also have the flexibility to be located anywhere you want as containers are designed to be easily relocated, so farmers no longer need to be based out in the sticks.”
A 40 foot container could equate to approximately 5 acres of farming land and can be easily transported almost anywhere with minimal effort, says Bulmer.
Cut down on costs
“We are seeing more and more farmers deciding to opt for container farms in the UK. The flexibility and ability to mass produce fruit and vegetables within a short space of time alongside the savings on water usage means farmers can cut down on costs and produce seasonal fruit and vegetables all year round, and on a much grander scale.”
Also read: Indoor farming technology market to grow to $ 40.25 billion
DelFrescoPure Introduces The LivingCube
BY DELFRESCOPURE | APRIL 19, 2019
Our exciting partnership between DelFrescoPure and CubicFarms has resulted in the LivingCube -- a system of automated vertical farming growing machines that continuously produces living lettuce, living basil and microgreens all year long.
LivingCube - Vertical Growing System
LivingCube is powered by DelFrescoPure, which produces power by using an off-the-grid electrical cogeneration system. The growing chambers are all individually climate controlled to optimize the environment for each crop to create an independent growing facility.
"We wanted to offer our retail partners innovative and local commodities and the ideal solution was to partner with CubicFarms," stated Carl Mastronardi, President of DelFrescoPure.
The LivingCube living lettuce, living basil and microgreens are always fresh, nutritious and flavor-filled. LivingCube finally offers you the freshness you love without sacrificing nutrition and flavor!
Living Lettuce
Who says you need to compromise quality for flavor? Our LivingCube allows our living lettuce to be vertically grown without pesticides in multiple varieties. Available in a 3-count lettuce bag, our living lettuce is convenient and delicious; you can grow it in your fridge or on your counter. Lettuce grow for you!
Basil Microgreens
With 12x the nutrients of mature leaves, LivingCube microgreens are a small way you can add health benefits to food! We offer multiple varieties and customized packaging combinations. Our LivingCube machines are flexible -- allowing quick crop changes that adjust seasonally. It's convenience with flavor!
"Our LivingCube microgreens allow you to add flavor, quality and fresh health benefits to your food without having to put in hard work to get it," stated Fiona McLean, Marketing Manager of DelFrescoPure.
Our packaging is made from 100% post-consumer recycled PET and comes in 50g and 100g, making our microgreens versatile and easy to buy, store and use. No need to chop, just sprinkle!
Fusion Farms In Puerto Rico An Investment Opportunity With Brains, Heart, And Guts
It's an intelligent investment opportunity with a social conscious and serious punch and it's opened its arms to investors to go from start-up to success.
Apr. 15, 2019 / PRZen / MAYAGüEZ, Puerto Rico -- It's an intelligent IMPACT investment opportunity with a socially conscious and serious punch and it's opened its arms to investors who want to own a piece of a Hurricane-Protected Aquaponics Vertical Farm.
For the past year, husband-and-wife business partners Kendell Lang and Lisa Jander have worked tirelessly through government bureaucracy, the language barrier, and the tendency of things to grind along at "island time" in Puerto Rico to get their start-up to germinate and put down roots. Now, with milestone after milestone under their belts, Kendell and Lisa are presenting investors with a unique opportunity to contribute positively to the environment and help Puerto Rico rebuild itself after the devastating landfall of Hurricane Maria in September 2017, all the while benefiting from fund capital gains reduction and deferrals.
It's called Fusion Farms, a hurricane-protected, indoor, controlled environment aquaponics farm model that leverages the natural relationship between fish and vegetation to grow a quality, fresh, and reliable source of non-GMO, pesticide-free, all natural proteins and greens. This is particularly needed in Puerto Rico because it is estimated that the island imports upwards of 95% of their fresh produce, which, after weeks of travel, is not-so-fresh and not very nutritious when it arrives.
Learn more about Controlled Environment Aquaponics
Hurricane-protected agriculture
Read: Hurricane Protected Farming in Puerto Rico
The model can be applied anywhere, but Fusion Farms' "secret sauce" is its location inside one of the many unused Puerto Rico Industrial Development Company (PRIDCO) buildings that pepper the Island. The Pilot Project is in the Mayagüez district of Western Puerto Rico. These steel-reinforced concrete structures have withstood the ravages of hurricane season in the Caribbean, making them the perfect facility to house an indoor farming operation. And with farming encouraged in Puerto Rico – farming that is sheltered from even the most wrathful of storms – Fusion Farms aims to establish the island's food sovereignty, vastly reduce its reliance on imports, encourage local commerce and agriculture, and restore fresh, healthy, locally-grown produce to grocery store shelves.
"Importing is expensive and the final product lacks the labelled nutrient value," says Lisa Jander. "All those food miles also contribute immensely to the condition of the produce when it arrives. There are thousands of farmers and ancillary service providers that have taken a hit or even lost their jobs due to hurricane damage. Fusion Farms is here to contribute to Puerto Rico's food sovereignty, to give the people back their jobs, and to encourage prosperity on the island."
This is an IMPACT investment with a socially conscious, renewable energy, sustainable agriculture focus, and a heart.
A unique investment opportunity
And now: the brains. The start-up is offering investors a smart investment opportunity with a bevvy of attractive benefits, many of which stem from the start-up being in a Qualified Opportunity Zone and a Qualified Small Business Stock:
"We are a Qualified Opportunity Zone investment, as well as a Qualified Small Business Stock, both of which have tremendous capital gains tax benefits for investors," says Kendell Lang. "Additionally, investors can work directly with us without having to deal with a third party administrator, which gives them the benefit of the capital gains reduction and deferrals without the overhead/management fees that fund managers charge.
"In other words, investor dollars go further with us than with non-self qualified investments."
Another attractive aspect of Fusion Farms' equity investment opportunity is that it is being presented through an Online Public Offering. This eliminates the middleman and the pressures and costs associated with having an investment banker or broker sell and manage the opportunity for investors. Everything potential investors need to see is presented on Fusion Farms' Campaign Page and if they like it, they can go right ahead and invest. But this also means that investors have to take action so they don't miss out when offering closes.
The demand for what Fusion Farms is setting out to do is enormous and has been confirmed by several local food distributors and hospitality businesses. Lisa Jander provides an example of just one agricultural product that's in demand:
"We have upscale hotels, bars, and restaurants on the island begging for fresh mint because Puerto Rico's iconic drink is the mojito; you cannot make a mojito without mint," says Lisa. "What's currently available is expensive or wild grown, limited in supply, and isn't great quality, yet these establishments don't have much of a choice. If we can supply a dependable, fresh, local source of mint, we could support a large part of the tourism market."
Read: How a Holiday in Puerto Rico Became a Calling to Change its Future
Fusion Farms' outlook on fresh produce
Fusion Farms' choice of agricultural products reflects the need for crops that are in high in local demand, grow easily and prolifically, and are considered valuable, such as basil, butter lettuce, microgreens, cilantro, mint, and whole Tilapia fish. Year two would provide the opportunity for Fusion Farms to reconfirm market demand for its existing agricultural products while exploring the feasibility of expanding this portfolio. This could happen initially with the planting of fruit trees. Year three could see the introduction of strawberries, green beans, Swiss chard, peppers, and tomatoes.
"Our diversification is attractive to investors who might otherwise worry about their investment if anything were to go wrong with, for example, the lettuce crop," explains Kendell Lang. "Our plan offers diversity, stability and market flexibility."
Tax-free exports
A specific strategy and interesting twist to Fusion Farms' ultimate business plan is Kendell and Lisa's intention to apply for a Value Added Producer Grant for the purchase of equipment to extract essential oils from herbs such as basil and mint as an additional revenue stream. These oils are not only considered a highly valuable commodity but, more important to investors, they also qualify Fusion Farms as an Act 20 company under the Export Services Act.
Act 20 provides tax incentives for companies that establish and expand their export services businesses in Puerto Rico. Under Act 20, income from eligible services rendered for the benefit of non-resident individuals or foreign entities (Export Services Income, or EIS) is taxed at a reduced tax rate of 4%. Moreover, dividends or benefits distributed out of EIS are 100% exempt from Puerto Rico taxation.
This means that all of Fusion Farms' revenues derived from export sales would be tax-free.
"If there's uncertainty or price fluctuation in the local markets for basil or mint, we have a multi-tiered alternate plan model," says Kendell. "We can sell fresh farm-to-table leafy green vegetables, turn excess basil into pesto, excess mint into mint jelly, and both into essential oils."
The whole package
With its keen environmental awareness, warm social conscious, sharp and comprehensive business plan, and numerous investment benefits, it's clear that Fusion Farms presents the investment community with an opportunity with brains and heart, while Kendell and Lisa's fierce determination and ambition prove they have guts!
Learn more about this investment opportunity.
About Fusion Farms
Fusion Farms PR is CEA farming which allows crops to grow faster, all year round in a hurricane-protected, climate-controlled indoor facility, using less water and minimal labor while eliminating crop failures. Fusion Farms, in the beautiful Mayagüez district of Western Puerto Rico, is the ideal location to use an existing PRIDCO facility to grow mint, basil, cilantro, heirloom tomatoes, and leafy green vegetables, which are in high local and organic demand.
For more information about Fusion Farms and to become an investor in this opportunity, go to www.fusionfarmspr.com or email: Info@FusionFarmsPR.com
Media Contact
Kendell Lang
7604453315
Follow the full story here: https://przen.com/pr/33294020
Read more:http://www.digitaljournal.com/pr/4256802#ixzz5lFYOERki
How Can Controlled-Environment Growers Improve Energy Efficiency And Grow Light Optimization?
Greenhouse Lighting and Systems Engineering (GLASE) consortium researchers are looking for ways to reduce grow light electricity use and improve light uniformity to maximize controlled-environment crop yields.
April 3, 2019
By David Kuack
Are you using or thinking about using grow lights to produce your controlled environment crops? If so, would you be interested in how to reduce the amount of electricity needed to operate those lights?
Researchers with the Greenhouse Lighting and Systems Engineering (GLASE) consortium at Cornell University in Ithaca, N.Y., are studying the use of control algorithms to optimize the light used on controlled-environment crops while reducing the amount of electricity used to operate grow lights.
“These control algorithms that deal with lighting were developed over 20 years ago,” said research associate Dr. Kale Harbick. “Unfortunately, this technology, which was under patent until about four years ago, never achieved large scale commercial use.
“The algorithms are related to delivering a constant amount of light to the plants every day, which is called daily light integral (DLI). Controlled-environment crops like lettuce prefer to receive a constant amount of light every day. This enables the plants to maximize their growth and helps to avoid problems with tipburn, which can make the crops unsalable.”
Even though this technology is off patent, Harbick said some growers are still hesitant to incorporate it into their environmental control systems.
“As part of the GLASE research program we are putting this control technology into two commercial pilot facilities in New York,” he said. “We are going to run multi-year experiments so that the growers in those facilities can compare the performance under our control system with what they are currently using. Incorporating this technology, we are looking to demonstrate a large amount of energy savings for the crop yields produced.
“We’re specifically focused on lettuce, tomato and strawberry. The first two pilot facilities are growing leafy greens, primarily lettuce. Lettuce is the crop the Cornell controlled-environment agriculture group has studied the longest and we understand the best. Tomato and strawberry are newer crops to us so we are doing a lot of greenhouse experiments right now with these plants to analyze the relationship between light, carbon dioxide and growth. We have the information well established for lettuce, but it’s not as well established for fruiting crops. We would eventually like to roll out pilot programs for tomatoes as well. We have some tomato growers in the state who have expressed interest in using the technology.”
GLASE researcher Dr. Kale Harbick is studying the use of control algorithms to optimize light while reducing the amount of electricity used to operate grow lights.
Photos courtesy of Kale Harbick, Cornell Univ.
Harbick said New York State Energy Research and Development Authority (NYSERDA), which is financially supporting GLASE, is interested in trying to meet greenhouse gas emission production targets. CEA has the potential to use a lot of energy. Any energy savings that the GLASE research can realize has a corresponding large reduction in greenhouse gas emissions.
Lack of light uniformity
One of the problems that Harbick often sees with grow lights is growers don’t install enough fixtures.
“The most basic problem is light intensity,” he said. “We often see greenhouses where growers are trying to produce lettuce with grow lights, but they only have installed half the number of fixtures they should have in order to grow lettuce optimally. What that means is even if they ran those lights 24/7 they wouldn’t be able to achieve the DLI needed to reach the target amount.”
Harbick said the issue of not installing enough lights is related to measuring light.
“Trying to measure the light is not a trivial thing to assess,” he said. “If there is an array of lights that are regularly spaced in the same plane, the problem is the light is not uniform on the crop. It kind of has a bullseye effect where there is a lot of light in the center and not very much on the edges. Lighting manufacturers and designers often provide growers with designs that show the light intensity at the center of the space, which is not representative of the light that is received in the rest of the space. The lights might be sized according to that center spot which is just fine, but everything else is undersized. We hear regularly from growers who’ve spent a lot of money on a lighting system and then realize later that it was undersized.”
Harbick has done a lot of work on lighting uniformity to try to address this issue of undersizing.
“We’ve looked at techniques to change the positon of the lights to make it more uniform,” he said. “We’ve looked at changing the brightness of the lights depending on where they are in the space to make the light more uniform. We have a couple of greenhouse spaces at Cornell that have this uniformity optimization. These are the only greenhouses on campus to have uniform lighting.”
One of the common issues encountered by growers who have installed grow lights is the lack of light uniformity which can be caused by undersizing the number of fixtures.
Harbick said this lack of light uniformity is not often noticed because of the way humans see light distribution.
“We could look out at a crop and the lighting looks uniform to our eyes because our eyes are so good at attenuating brightness levels,” he said. We don’t notice these differences very easily. The brightness level differences have to be measured.”
Although the lack of light uniformity can be related to the number of light fixtures installed, Harbick said there could be other factors involved.
“In the research greenhouse that we have optimized light uniformity, initially we received a design from the manufacturer that called for 20 LED fixtures,” he said. “I modified the design using a computer program that I wrote that was able to reduce the number of fixtures to 16, but improved the light uniformity. The light is much more uniform and we were able to do it with fewer fixtures.
“It’s not always a case of installing more fixtures to increase light uniformity. It can also be things like changing the brightness of the fixtures or changing the position of the fixtures. There are other possibilities to improve uniformity besides the number of lights.”
Loss of crop yields
One of the reasons that there continues to be light uniformity issues is how the fixtures are spaced in greenhouses and indoor farms.
“It’s a status quo thing,” Harbick said. “Lights have always been placed in a plane and regularly spaced out. This is how it has always been done. Until recently most grow lights have had a fixed intensity. Under those conditions it is difficult to overcome this light uniformity problem.
“Lack of light uniformity is less of problem in large greenhouses because there is a lot of interior space and not much edge space. However, this is a major problem in indoor farms where there are long rows or shelves. These indoor farms don’t have the background natural light like greenhouses to mitigate some of these effects. I have seen warehouses where they were growing a high DLI crop and the plants in the center of the room were a foot taller than the plants on the edge. It was simply because the plants in the center were receiving more light. In indoor farms, whether it’s lettuce, tomatoes or other high DLI crops, that is where the payoff really comes for optimizing light uniformity. For indoor farms light uniformity is something that people aren’t looking at yet. They just kind of live with it. They just move plants around to try and even out the growth. But that creates a lot of extra labor and logistic issues. They’re not optimizing the total yield of the crops. Every plant on the edges that is shorter than the ones in the center of the room is lost sales.”
GLASE researchers are conducting greenhouse experiments on tomato and strawberry to analyze the relationship between light, carbon dioxide and plant growth.
Harbick said that the issues with light uniformity may improve as changes are made to lighting fixtures.
“As the lights become more capable in terms of adjusting brightness and spectrum, there are opportunities for GLASE researchers to share some of that optimization technology with lighting manufacturers to try to get these improvements out to the industry. But it’s going to take some time. We’re still doing a lot of the research ourselves. We don’t have an active grant in this area right now so this is something that I have been doing on my own. It’s definitely an opportunity for future study.”
For more: Kale Harbick, Cornell University, School of lntegrative Plant Science, Horticulture Section, Ithaca, NY 14853; kh526@cornell.edu.
David Kuack is a freelance technical writer in Fort Worth, Texas; dkuack@gmail.com.
First ICA Maxi Store in Sweden, One of 84 Grocery Locations, Launches Sale of Onsite-Grown Produce
Freight Farms customer ICA Maxi Högskolan now offers customers leafy greens grown onsite just steps from in-store shelves
NEWS PROVIDED BY Freight Farms
April 10, 2019
BOSTON, April 10, 2019 /PRNewswire/ -- Freight Farms is pleased to announce the launch of ICA Maxi Högskolan's own line of produce grown onsite for shoppers. Located in Halmstad Sweden, Freight Farms customer ICA Maxi Högskolan is one of ICA Gruppen's 1,300 grocery stores in the country. This month, the store began harvesting a range of hydroponically-grown greens for shoppers from Freight Farms' flagship container farm, the Leafy Green Machine.
Freight Farms' Scandinavian distributor, FutuFarm, installs a Leafy Green Machine at ICA Maxi Högskolan in Halmstad.
ICA Maxi Högskolan employees, Max Rydberg and Douglas Klang, now grow produce onsite for customers in Freight Farms' Leafy Green Machine.
"We're excited to be the first ICA Maxi store to implement an onsite farm," said Rikard Hillarp, owner ICA Maxi Högskolan. "By growing crops just steps from our shelves, we're able to offer our customers what are truly the freshest greens possible."
Freight Farms' containerized farming technology allows ICA Maxi Högskolan to create and maintain the optimal growing conditions to harvest produce year-round using less than 5 gallons of water per day. Beyond the store's initial offering of butterhead lettuce, spinach, and herbs, the farm's integrated IoT data platform, farmhand, will also allow the store to grow non-native crops otherwise unavailable in the region, regardless of seasonal limitations in Sweden's Nordic climate.
"Freight Farms' technology is especially helpful in Sweden, where our short growing seasons can limit crop availability throughout the year and increase our reliance on imported produce," added Hillarp. "We're now able to shorten the distance food travels to get to our customers from 2,000 kilometers to just 30 meters."
By removing the miles between the food source and consumers, produce maintains nutrient density and stays fresh for far longer, significantly reducing food waste for both retailers and consumers.
On March 29, ICA Maxi Högskolan kicked off its launch with a Harvest Festival for customers, selling produce and offering free samples of the newly-harvested greens and a Q&A with store employees Max Rydberg and Douglas Klang, now the newest onsite farmers.
"Our team innovated the technology to empower individuals and businesses all over the world to decentralize the food system in meaningful ways specific to their local community or environment," said Freight Farms CEO Brad McNamara. "We're thrilled to work with industry leaders like Rikard Hillarp and retailers like ICA Maxi, who together have the forward-thinking vision and reach to disrupt the grocery industry internationally."
About Freight Farms
In 2012, Freight Farms debuted the first vertical hydroponic farm built inside an intermodal shipping container—the Leafy Green Machine—with the mission of democratizing and decentralizing the local production of fresh, healthy food. Now with the Greenery and integral IoT data platform, farmhand®, Freight Farms has the largest network of connected farms in the world, with global customers ranging from small business farmers to corporate, hospitality, retail, education, and nonprofit sectors.
To learn more, please visit freightfarms.com, or visit us on Instagram, Twitter, or Facebook. For inquiries local to Scandinavia, please contact Freight Farms' official distributor, FutuFarm, for more information.
About ICA Gruppen, ICA Maxi
With a focus on food and health, ICA Gruppen is one of the Nordic region's main players in grocery retail, with 2,079 wholly-owned or retailer-owned stores and pharmacies. Its ethos is defined by three entrepreneurial values: drive, innovation and the desire to take on responsibility. ICA Gruppen believes it has a great responsibility—and great opportunity—to have a genuine impact on the value chain by conducting its operations in a climate-conscious manner. To ICA Gruppen, a commitment to community engagement and improvement in sustainability mean long-term success. ICA Maxi stores, individually owned by grocery industry entrepreneurs, are the largest food stores within ICA Gruppen, with 84 locations across Sweden.
SOURCE Freight Farms
Related Links
Student Farmers Get A Chance To Learn How Their Garden Grows
On April 19, Meier and Mital will present “The Grow Pod Lab: A UO Indoor Agriculture Experiment” at the food studies Food Talks series. UO and community members are invited to tour the pod and learn more about potential research, curriculum and community engagement opportunities associated with the Grow Pod
April 8, 2019
On the outside, it may look like an ordinary industrial shipping container, but on the inside it’s nothing short of extraordinary.
Step into the temperature-controlled environment — a virtual oasis of calm bathed in purple lights that emanate from dozens of overhead, state-of-the art LED lights — and breathe in the rich aroma of soil and take in the rows upon rows of grow trays teeming with verdant green plants and herbs.
First-year students in Bean Hall’s Community for Environmental Leaders academic residential community — many of whom have never grown plants from seeds before — have spent the last few months getting their hands dirty and raising their first crops of indoor tomatoes.
“The students just light up when they come into the pod,” said Briana Meir, a doctoral student in the environmental sciences, studies and policy program and graduate employee in the Office of Sustainability. “It smells like dirt and plants and soil, and it’s funny because it’s a shipping container: It’s gray, it’s metal, it’s sort of ugly on the outside and you walk inside and there’s all this light. They find it a relaxing place. They have formed friendships.”
Designed to promote ongoing research, learning and innovation for sustainable urban food production, the idea for bringing indoor agriculture to the UO campus came with the generous donation of a shipping container by Imagination International Inc. Additional help came from a $10,000 applied environmental science seed grant awarded to the food studies program and the UO Office of Sustainability to support the start-up.
“These young environmental leaders in their first year at the UO are helping to grow food,” said Steve Mital, UO’s sustainability director. “Access to and knowledge about food production are an important part of a sustainability-focused education, and we’re hopeful that some of them will really explore these issues more deeply while they are undergraduate students here at the university.”
As the first group of academic residential community students to tend to and nurture a crop of tomatoes in the Grow Pod, emulating inside a 20-foot-long metal box what naturally occurs outside comes with its own set of challenges. That includes everything from determining the correct amount and strength of light the plants get, how much water they get and the precise consistency of soil and nutrients to figuring out how the plants can pollinate if there is no wind or bees to carry the pollen from plant to plant.
When a student posed the pollination question, it led to an ingenious solution: electric toothbrushes. Applied gently to the plant’s blooms, the vibration releases the pollen into the enclosed environment allowing pollination to occur.
Meir said the learn-as-you go approach has evolved since they started last fall, and recently they brought in a master gardener to help.
“It’s been a collective effort to figure out things as we go along, but the students are doing a pretty good job of taking ownership over it,” she said.
Courtney Kaltenbach, a music major, and Sydney Gastman, who is majoring in landscape architecture, got involved in the Grow Pod project through the Environmental Leaders academic community and agree the experience has been amazing.
“The greatest satisfaction was seeing something grow and being a part of that and working with a team of people with the same goals,” Kaltenbach said.
“Understanding how plants grow and getting involved with the science of it all has been such a great learning experience,” Gastman said. “I may not have the opportunity to take biology classes, so it’s been a really good way to get my science fix.”
Look for students from the program selling a variety of plant starts at a table outside the Erb Memorial Union during Earth week, April 22-24.
The Office of Sustainability is also exploring a number of additional academic and co-curricular opportunities. They include computer science classes using data generated from the lab to study machine learning, and UO business classes identifying income-generating opportunities for crops raised in the pod.
The indoor, controlled-environment agriculture industry has grown dramatically in the past several years. Shipping containers outfitted for growing vegetables are being used by farm-to-table restaurants, to support experiential education programs and for niche social enterprises that increase local food production in areas where land-based farming is limited.
Mital said shipping containers might support urban homesteading or post-disaster recovery efforts in the future. “We’re hoping our faculty and local entrepreneurs help us explore the possibilities,” he said.
On April 19, Meier and Mital will present “The Grow Pod Lab: A UO Indoor Agriculture Experiment” at the food studies Food Talks series. UO and community members are invited to tour the pod and learn more about potential research, curriculum and community engagement opportunities associated with the Grow Pod.
—By Sharleen Nelson, University Communications