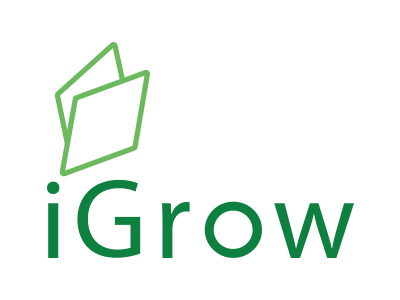
Welcome to iGrow News, Your Source for the World of Indoor Vertical Farming
Vertical Indoor Farms Make Sense
Nate Storey, founder of a startup in the burgeoning agtech sector, which applies high-tech solutions to agriculture and farming, is convinced that the future of vegetable production is vertical and indoor cultivation, an approach that allows crops to be grown anywhere in the world to supply local markets
Enrique Dans Senior Contributor
Teaching and consulting in the innovation field since 1990
Nate Storey, founder of a startup in the burgeoning agtech sector, which applies high-tech solutions to agriculture and farming, is convinced that the future of vegetable production is vertical and indoor cultivation, an approach that allows crops to be grown anywhere in the world to supply local markets. His company, Plenty, has just demonstrated that about two acres laid out vertically and growing hydroponically, produces more than a conventional farm covering some 720 acres.
The company, which makes intensive use of robots and algorithms for watering and providing nutrients for fruit and vegetables, closed a $140 million funding round in October, bringing total investment to $500 million and reflecting the growing interest in this type of technology. Other companies also in the San Francisco area, such as Iron Ox Robotic Farms, also rely on robotization throughout the process, from planting to plant feeding and harvesting, and report similar yields.
High-density cultivation and control throughout the production cycle reduce the incidence of pests and diseases, along with reduced transportation costs, meaning the main expense is labor (hence the need for robotization), along with the initial installation investment and energy, which is increasingly cheaper and more efficient thanks to the development of solar energy and LED technology for lighting.
Another company, Finland’s iFarm, founded three years ago, , raised $4 million in an initial investment round in August. The company provides technology to about 50 projects in Europe and the Middle East covering a total of 11,000 square meters, and is capable of automating the care of about 120 varieties of plants, with the goal of reaching 500 by 2025 (the firm says it adds 10 new varieties each month).
Others, such as Rise Gardens, which raised $2.6 million in seed capital at the end of May, provide hardware and software kits for home hydroponics, which can be assembled in less than an hour and come in three different sizes, IKEA style, which also has a similar product. Others, such as Germany’s Infarm, offer these facilities to businesses such as stores and restaurants and have also attracted investors’ interest.
And there are many more: Eden Green, Bowery Farming, BrightFarms, Freight Farms, AeroFarms… a fast-growing sector that points to a future for vertical and indoor farming. A completely different model from that of conventional farms (which are also being heavily technologized), and that can be installed in any industrial building or even in containers (or in space, if need be), and that promises a transformation similar to that from growing crops under plastic. Will the vegetables we consume in the future come from this type of innovative farms?
Lead photo: (Brandon Wade/AP Images for Eden Green) ASSOCIATED PRESS
Never Forget The Horizontal In Vertical Farming
Vertical farming is all about how high you can go, how you can repurpose the space you have in ways you never thought possible before
Vertical farming is all about how high you can go, how you can repurpose the space you have in ways you never thought possible before.
But what sometimes gets lost in these conversations about vertical farming is the horizontal. To take advantage of all that high-density mobile grow rack systems like Montel’s GROW&ROLL have to offer, to truly maximize your space and your yield, always remember that it’s just as much about growing out as it is about growing up.
Whether you’re cultivating leafy greens, herbs, mushrooms, or cannabis, both the vertical and horizontal axes must work together to optimize space in grow rooms and reliably produce the healthiest crops month after month, year after year.
WHAT WE ALREADY KNOW ABOUT VERTICAL FARMING
We’ve spoken a lot about how multi-tier vertical farming benefits indoor growers, but it never hurts to go over the basics.
First and foremost, vertical farming capitalizes on the space you have, not the space you wish you had. Growing two, three, four times more plants without an inch of additional space is only limited by your imagination.
Montel’s mobile vertical farming racks can outfit your grow op with ventilation, lighting, and watering systems built right into each mobile carriage—no wasted power or resources, no plants missing out on what they need to thrive. And because of its collapsible design, mobile racking for indoor farms lower the risk of unauthorized handling, chemical contamination, or spreading disease.
HERE’S WHAT YOU MIGHT NOT KNOW ABOUT HORIZONTAL FARMING
We’ll take vertical farming out of the picture for a moment—how does horizontal farming contribute to the goals of high-density mobile racking for indoor grow ops?
Let’s look at rolling benches, another popular mobile racking option for indoor farmers. Traditional rolling benches leave about seven inches between each bench, enough room to slip a hand between to shift one bench open. Sure, that’s lost space, but it isn’t that much, right?
Actually, when the goal is to maximize canopy yield with only the space you have, it absolutely is.
Montel’s mobile benches were designed with special handles that don’t require the gap between benches. The result of this small change? You can fit sixteen Montel benches in the space needed for fourteen traditional benches. That’s two more benches of plants, two more benches of crop, and two more benches of profit.
Even when the conversation in agriculture focuses on the vertical in vertical farming, Montel always remembers the horizontal.
KUWAIT: "Up To 550 kg of Lettuce Per Day Thanks To Faster Growth Cycles"
Instead of traveling 5,000 kilometers between German growing areas and consumers, lettuce from vertical farming company &ever in Kuwait travels less than 100 kilometers
Hamburg-Based Start-Up &ever Makes Big Strides In Kuwait
Instead of traveling 5,000 kilometers between German growing areas and consumers, lettuce from vertical farming company &ever in Kuwait travels less than 100 kilometers. With its first commercial farm in the middle of the Kuwaiti desert, the Hamburg-based company supplies regionally grown leaf lettuce to local restaurants and grocers. These are grown on more than 3,000 m2 of cultivation area and taste like they were picked fresh from the field. "Thanks to faster-growing cycles, we can produce up to 550 kilograms of lettuce per day," Mark Korzilius, founder of &ever, told IT Zoom.de
Hypermodern cultivation technology / Image: &ever
"In the process, our newly developed Dryponics cultivation technology reduces water consumption by 90 percent and fertilizer use by 60 percent when compared to traditional cultivation methods." The company also eliminates the use of crop protection products.
For more information: https://and-ever.com
22 Dec 2020
Hort Innovation To Explore High-Tech Solutions
In a release, Hort Innovation said the use of technology, such as vertical farm systems and hydroponics, in food production and delivery systems have the potential to redefine horticulture by optimising yield, quality, and supply
17th December 2020, Melbourne
Six-month project to assess potential of emerging production technology and its uses in Australian urban landscape
A modular farm in Brisbane using high-tech horticulture.
Hort Innovation has announced it has teamed up with a consortium led by agricultural consultancy RMCG in partnership with University of Technology Sydney (UTS) and global urban agriculture consultancy Agritecture, to assess the potential of emerging production technology and its application in the Australian urban landscape as part of a six-month project.
In a release, Hort Innovation said the use of technology, such as vertical farm systems and hydroponics, in food production and delivery systems have the potential to redefine horticulture by optimising yield, quality, and supply.
“High-technology horticulture is being implemented in urban areas across the globe using vertical farm systems, hydroponics and aquaponic systems and nearly fully automated production as well as rooftop, underground and floating farms,” it said in a statement.
Hort Innovation chief executive Matt Brand said bringing the technology to Australia would help attract capital as well as new investment to the sector with new ideas, approaches and mindsets.
“It gives us the opportunity to grow more from less and to keep demonstrating the good work that Australian growers do, day in day out, providing food to families both here and overseas,” explained Brand.
“Urban also means regional areas and hubs. Growers will use the technology as part of the overall production mix. It’s another production system that will be part of the diversity and variety that is Aussie horticulture.
“High technology horticulture may have the potential to play a significant role in increasing Australia’s horticulture sector value and help achieve Australia’s target of a A$30bn industry by 2030,” he added.
The feasibility study aims to identify opportunities and challenges for high technology horticulture in urban Australia. It will identify a range of high technology systems and assess their suitability to urban Australia by considering four key areas.
This includes how the technology fits within current regulations and planning requirements, farm input and waste, supply chain logistics and social, environmental and economic requirements.
Hort Innovation said the project will include a high-level literature review, modelling of the social, economic and environmental impacts and detailed analysis of how the economics of high technology urban systems compare to traditional farming systems.
The outcomes of the study will identify future priorities for research, development and extension activities and investment into Australian high technology horticulture in urban areas.
The study is being guided by an industry-led reference group including growers and emerging commercial leaders engaged in urban high technology horticulture in Brisbane and Sydney, members of local city councils, and subject-matter experts in protected cropping.
Enjoyed this free article from Produce Plus Magazine and its team of editors? Don't miss out on even more in-depth analysis, plus all the latest news from the fresh produce business. Subscribe now to Produce Plus Magazine.
PODCAST: Building A Sustainable Future By Falling In Love With The Solution, Not The Science
In this episode, Harry and John discuss John’s previous work at Bayer and Monsanto, which led to innovations and diverse technologies for important global crops. John opens up about the passion he has for sustainability, the respect he has for farmers, and his family ranching operation in Montana
Join Harry Duran as he welcomes to the show President and CEO of Unfold, Dr. John Purcell. John has dedicated his life to helping farmers safely and sustainably grow food using less of the earth’s natural resources. In his new role as President and CEO of Unfold Bio, John is continuing this same mission to improve the food ecosystem with more sustainable, fresher, and better-tasting fruits and vegetables.
In this episode, Harry and John discuss John’s previous work at Bayer and Monsanto, which led to innovations and diverse technologies for important global crops. John opens up about the passion he has for sustainability, the respect he has for farmers, and his family ranching operation in Montana.
VERTICAL FARMING PODCAST
Listen & Subscribe
Autogrow Officially Launches European Office With The Appointment of James Croy
With over 15 years’ experience in the agricultural sector, James is looking forward to introducing cutting-edge technology to one of the largest exporting areas in the world
8 December 2020: Netherlands based James Croy has joined Autogrow to support the growth of their digital solutions, Folium, and FarmRoad, in the region. With over 15 years’ experience in the agricultural sector, James is looking forward to introducing cutting-edge technology to one of the largest exporting areas in the world.
“There’s a tangible shift in the mindset of growers here in Europe who understand the importance of capturing data and how it can be used for improving operations. It’s not just the younger generation but growers of all ages, crops and business sizes,” explains James.
“The way crops are managed today is through visual inspection and judgement based on varying degrees of grower knowledge and experience. Data allows for more advanced analytics and understanding of what is driving physiological responses in the plant.”
One of the unique things about James is he also happens to be a New Zealander.
“I left New Zealand in 2006 and was based in London for a time before moving to the Netherlands in 2009. 11 years and three children later, I am firmly embedded in the culture and the environment of the region and love being in such a historically significant and accessible location.”
“It’s ironic how I moved over 18,000 kilometers away from New Zealand and now find myself working for a New Zealand headquartered company again. It’s also great to be representing such great solutions and a business that invests in products that continuously develop in line with the evolving market.”
James will be the key contact for any customers based in Europe interested in FarmRoad and Folium. To contact James – james.croy@farmroad.io
For more information on Folium Network Sensor - https://autogrow.com/products/folium
For more information on FarmRoad - https://www.farmroad.io
MEDIA QUERIES
Kylie Horomia, Head of Brand & Communications
(e) Kylie.horomia@autogrow.com
(w) www.autogrow.com www.farmroad.io
Sales queries – sales@farmroad.io
About Autogrow
Autogrow leverages the power of technology, data science, and plant biology to provide indoor growers affordable, accessible, and easy-to-use innovation – 24/7, anywhere in the world.
Our hardware, software, and data solutions support growers and resellers in over 40 countries producing over 100 different crop types.
We are the experts in Controlled Environment Agriculture (CEA) and continue to stay ahead of a rapidly evolving landscape.
Autogrow, Building 3, Level 1, 61 Constellation Drive, Mairangi Bay, Auckland, Auckland 0632, New Zealand
RotoGro Executes Binding $10 Million Technology License Agreement With Verity Greens
The agreement is designed to provide RotoGro with a foothold in the expanding indoor urban vertical farming space as a technology and services provider
RotoGro executes binding $10 million technology license agreement with Verity Greens
RotoGro executed a binding Technology License Agreement with Verity Greens Inc. for the granting of manufacturing and technology use licenses. The agreement provides RotoGro with a foothold in the expanding indoor urban vertical farming space as a technology and services provider globally.
The agreement also facilitates the payment of annual software licensing fees and a long-term net profit share from the sale (by Verity) of perishable foods cultivated at facilities utilizing RotoGro technology for the initial 20-year term of the agreement. All of which are expected to generate long-term sustained recurring for RotoGro.
The agreement is designed to provide RotoGro with a foothold in the expanding indoor urban vertical farming space as a technology and services provider. It facilitates RotoGro providing Verity Greens with the opportunity to use and manufacture the company's patented and proprietary cultivation technology in the perishable foods field, consistent with the company's strategy to engage in less capital-intensive business partnerships and collaborations.
Read the complete agreement here.
For more information:
RotoGro
info@rotogro.com
www.rotogro.com
3 Dec 2020
VeggiTech Inspires People To Grow Crops Sustainably
VeggiTech is an agro-tech organization focused on disrupting the agriculture industry to create sustainable and eco-friendly farms
How VeggiTech Is Changing UAE's
Agriculture Sector With Innovative Farming-Tech
November 18, 2020
Hatim Morbiwala, Head of Learning and Development,VeggiTech, controls and monitors eco systems with VeggiTech IoTImage Credit: Supplied
VeggiTech is an agro-tech organization focused on disrupting the agriculture industry to create sustainable and eco-friendly farms. Its tech-enabled solutions are:
VeggiTech digital operating system (V-DOS)
This is a scalable, repeatable set of solutions that are focused on the controlled environment agriculture as well as farming as a service (FAAS) model for its customers and investors.
Grow operating system
VeggiTech deploys the latest technology in terms of grow lights that provide the right amount of spectrum of light frequency to a plant-based on its type and growth cycle. This light is tuned to the grow cycle and creates the optimum environment for it to grow, coupled with the right nutrition and water quality for the plants. Internet of Things (IoT)-based sensors manage the environment and are linked to the data models that track the yield per unit of input resource so that it continually improves the quality of yield per sqm of grow space.
Farm operating system
All of VeggiTech’s business activities are managed in an enterprise resource planning (ERP) solution that provides complete control of the unit economics while creating a unique QR code for every crop being grown on its farms.
Learning Hub
VeggiTech also manages its Learning Hub using a state-of-the-art learning management platform that has online and offline features to interact with the learners. This has proven to be a very useful tool during the Covid-19 times as it continues to enable the future leaders – students – with the knowledge to grow their own food.
New launches
“With our vision to create the next one billion farmers, we are delighted to announce the launch of two new products that have been conceived, designed, and developed in the UAE,” says Hatim Morbiwala, Head of Learning and Development at VeggiTech. “We have developed a mobile app – Grow App – that will enable everybody to grow their own food and they can interact with the VeggiTech agronomist in case they need support with their plants. The app also has the ability to diagnose issues with the plants and recommend solutions using a machine learning database.”
Grow Kit is another unique product, developed by VeggiTech. “This is a physical kit which will inspire everybody to start their journey of growing their own food. We believe this is a life skill and should be part of the curriculum of every citizen on the planet,” says Morbiwala.
For more information, visit Veggitech.com
Call 058 263 1317 and 06 881 1861
email: info@veggitech.com
Folium 2.0 Hits The Market Ahead of Schedule
“F2 gives growers that next level microclimate data. Traditionally, microclimates described the farm, then it was the greenhouse, but now with F2 it is down to the level of the plant itself. Each sensor can gather a monumental amount of data making it the most comprehensive sensor network on the market.”
19 November 2020
Autogrow has launched the second generation of its Folium Smart Sensor Network, ahead of schedule to meet customer demand for greater access to data in the cloud.
“Since the initial launch of Folium in February we have had fantastic feedback from customers requesting further features. Because of our focus on usability and our approach to design; we have been able to deliver F2 significantly ahead of our timeline and incorporate the most requested items which is incredibly exciting,” says Chief Technology Officer Jonathan Morgan.
“F2 gives growers that next level microclimate data. Traditionally, microclimates described the farm, then it was the greenhouse, but now with F2 it is down to the level of the plant itself. Each sensor can gather a monumental amount of data making it the most comprehensive sensor network on the market.”
The Autogrow team focused on the most requested features for F2 including the addition of plant temperature readings, substrate moisture readings, and actual VPD (Vapor Pressure Deficit).
“With the release of our Folium public API (Application Programming Interface) in August, we were able to integrate other sensor technology like Plant Temperature sensors and Substrate Moisture Sensors to the platform. Growers don’t need to buy seven or eight different sensors any longer to get all of these readings. Everything is available in F2.”
F2 introduces new features including:
Connecting a Plant Temperature Sensor
Connecting a Substrate Moisture Sensor
Receiving actual VPD (Vapor Pressure Deficit) readings as opposed to estimated.
Dew Point calculation.
As well as delivering the existing readings for:
Climate Temperature
Relative Humidity
CO2
PAR (Photosynthetically Active Radiation)
RAD (Radiation)
Barometric pressure
“All of the readings and microclimate visualization are presented in the cloud on one platform. When you’re looking for precision in agriculture you need to understand the levers you can pull to further increase your yield and F2 is what’s going to get you there.”
For more information on F2 - https://autogrow.com/products/folium-f2
MEDIA QUERIES
Kylie Horomia, Head of Brand & Communications
(e) Kylie.horomia@autogrow.com
(w) www.autogrow.com www.farmroad.io
Sales queries – sales@autogrow.com
About Autogrow
Autogrow leverages the power of technology, data science, and plant biology to provide indoor growers affordable, accessible, and easy-to-use innovation – 24/7, anywhere in the world.
Our hardware, software, and data solutions support growers and resellers in over 40 countries producing over 100 different crop types.
We are the experts in Controlled Environment Agriculture (CEA) and continue to stay ahead of a rapidly evolving landscape.
Autogrow, Building 3, Level 1, 61 Constellation Drive, Mairangi Bay, Auckland, Auckland 0632, New Zealand
VIDEO: This 2-Acre Vertical Farm Out-Produces 750 Acre ‘Flat Farms’
According to Nate Storey, the future of farms is vertical. It’s also indoors, can be placed anywhere on the planet, is heavily integrated with robots and AI, and produces better fruits and vegetables while using 95% less water and 99% less land
John Koetsier Senior Contributor
November 20, 2020 Consumer Tech
John Koetsier is a journalist, analyst, author, and speaker
Farming is going vertical, thanks to startups like San Francisco-based Plenty.
PHOTO BY ALEX WIGAN ON UNSPLASH
According to Nate Storey, the future of farms is vertical. It’s also indoors, can be placed anywhere on the planet, is heavily integrated with robots and AI, and produces better fruits and vegetables while using 95% less water and 99% less land.
But the future of farms is also personal, emotional, and deeply meaningful.
“The objective of all technology really should be to enable human joy, right?” Storey asked me on the recent episode of the TechFirst podcast. “For me, it’s the memory of being a child in the garden and eating a carrot that my grandfather gave me that still has the grit on it, and the snap and the crunch and the flavor and the aroma, or a tomato from my grandmother’s garden.”
Plenty is an ag-tech startup in San Francisco that is reinventing farms and farming. Storey is the co-founder and chief science officer in a time when farming is going high-tech.
Despite getting a bad rep in much of popular culture over the last few decades for lack of education, farmers have always been stealthily technical, fixing tractors, constructing buildings, and innovating new tools to making farming better or easier. Recently drones and robots are invading the world of “flat farming,” as Storey calls it, and the space is legitimately hot, with over 1,600 startups and tens of billions of dollars of investment.
Plenty is one of those startups, but it’s taking a novel path.
Necessity, as per usual, is the mother of invention.
“The reality is, there are five places in the world where you can grow fresh fruits and vegetables really economically, and all of that land is used up at this point,” Storey says. “Vertical farming exists because we want to grow the world’s capacity for fresh fruits and vegetables, and we know it’s necessary.”
Americans are only eating half of the fresh fruit and veggies they should be, and globally it’s even worse: an average of 30%. In richer nations a lack of a healthy diet means increased levels of obesity, diabetes, and other health concerns; in poorer nations, there may not be enough food of any kind to go around.
Plus, some nations with limited land or poor growing conditions such as deserts face existential risks when they can’t control their own food supply.
“If you are a nation in this world that has limited food security, you have to import everything, the value of your food is quite different than it is here in the United States,” Storey says. “Which means that what you’re willing to pay for it is quite different. And what you’re willing to pay for that independence and that control is quite different.”
Indeed.
In fact, one of the lessons Covid-19 has taught us is the fragility of the interconnected global economy.
Listen to the interview behind this story on the TechFirst podcast:
So Plenty takes the flat farm and performs an Inception transformation on it: ripping up horizontal rows of plants and hanging them vertically from the ceilings. Sunlight from above is replaced by full-spectrum LED lights from all sides. Huge robots grab large hanging racks of growing vegetables and moves them where they’re needed. Artificial intelligence manages all the variables of heat and light and water, continually optimizing and learning how to grow faster, bigger, better crops. Water lost by transpiration is recaptured and reused. And all of it happens not 1,000 miles away from a city, but inside or right next to the place where the food is actually needed.
It turns out that growing, while natural, is also hard. At least at scale.
One key: de-stressing plants.
Nate Storey, chief science officer and co-founder of Plenty | NATE STOREY
“Our problem is that we have to push yields and we have to push quality to an extent that we need to eliminate all plant stress,” Storey say. “That’s really hard, it turns out. Anyone can grow plants at low yield levels, that is not hard. Plants are set up to withstand a lot. But trying to grow them at some of these just, I guess unprecedented growth rates, unprecedented qualities … that is really hard, it turns out.”
Storey says, without irony, that it’s like “building a space shuttle.” There are millions of parts, millions of genes, and plants tend to do “all sorts of wild stuff.”
“It’s kind of our modern human arrogance that thinks we’ve got that under control,” he adds.
The potential benefits are massive.
400X greater yield per acre of ground is not just an incremental improvement, and using almost two orders of magnitude less water is also critical in time of increasing ecological stress and climate uncertainty. All of these are truly game-changers, but they’re not the only goals, Storey says.
The key goal: great produce that tastes amazing.
The startup is fairly early in its mission to reinvent how produce is grown. It has a farm in San Francisco, dubbed Tigris, and another under construction in Compton, California. (Just think about that statement: a farm under construction.) Plus, the company has plans for much more expansion, using $400 million in capital injected by investors including Softbank, Amazon’s Jeff Bezos, and former Google chairman Eric Schmidt.
Commercialization is well underway, with a deal inked to supply 430 Albertsons stores in California.
But there’s also plenty of competition, and that’s not just from the flat farms of Iowa, Nebraska, and California. AeroFarms and BrightFarms are two American competitors in indoor farming, while InFarm and Agricool are among the European competitors. Others, like FreightFarms, focus on growing food in shipping containers.
A growing industry can support multiple players, however.
And growing better food in more places with less environmental cost is something that’s positive for everyone.
“The future will be quite remarkable,” Storey told me. “And I think the size of the global fresh fruit and vegetable industry will be multiples of what it is today.”
Follow me on Twitter or LinkedIn. Check out my website or some of my other work here.
I forecast and analyze trends affecting the mobile ecosystem. I've been a journalist, analyst, and corporate executive, and have chronicled the rise of the mobile economy. I built the VB Insight research team at VentureBeat and managed teams creating software for partners like Intel and Disney. In addition, I've led technical teams, built social sites and mobile apps, and consulted on mobile, social, and IoT. In 2014, I was named to Folio's top 100 of the media industry's "most innovative entrepreneurs and market shaker-uppers.” I live in Vancouver, Canada with my family, where I coach baseball and hockey, though not at the same time
PODCAST: Joe Swartz & Nick Greens
Our new podcast called Polygreens with Joe Swartz from AmHydro and Nick Greens from Nick Greens Grow Team brings agriculture and technology together in educational episodes. With this episode you'll learn about tips on operating a greenhouse
11/20/2020
Our new podcast called Polygreens with Joe Swartz from AmHydro and Nick Greens from Nick Greens Grow Team brings agriculture and technology together in educational episodes. With this episode, you'll learn about tips on operating a greenhouse.
Breakthrough Biological Innovation – The Key To Profitable And Sustainable Vertical Farming
Vertical farming, first conceptualized in the late ’90s, is premised on the idea of “a farm within a skyscraper” where environmental conditions, nutrition, and lighting can be optimized
Algae-Based Biostimulants Improve Growth Velocity, Yield, And Quality
In Hydroponic And Aeroponic Indoor Farming
The rapid growth of urban agglomerations across the planet presents serious food security challenges. The US Census Bureau estimated that 80% of Americans lived in cities in 2015. Vertical farming is generally regarded as the most promising approach to supplying cities with fresh leafy greens, vegetables, and small fruits, but skeptics point out that we still have a long way to go before indoor “plant factories” can reach the scale and efficiencies that would make them a truly sustainable source of nutrition for millions of people.
Vertical farming, first conceptualized in the late ’90s, is premised on the idea of “a farm within a skyscraper” where environmental conditions, nutrition, and lighting can be optimized. Growing crops in layers instead of rows, usually employing hydroponics, is a concept that has seduced investors globally. We all see the advantages of growing our food locally - in shipping containers, in warehouses and maybe even in skyscrapers to reduce the need for trans-continental shipping, to generate employment and limit pesticide and chemical-input intensive outdoor farming.
The major barrier to the upscale of vertical farming is economic sustainability and this is mainly related to the energy costs associated with artificial lighting. Can local, vertically grown produce be sold affordably? Despite remarkable technological advances in lighting technology and automation and the availability of renewable energy, there is still an urgent need to develop innovative solutions to get vertical farming over the “tipping point” from a promising food security approach and into a real, long- term and indispensable part of urban food systems.
Doing More with Less
How can vertical farms use less energy and produce more and better? In Chicago, Back of the Yards Algae Sciences, a sustainable industrial biotechnology company, has been working on a simple but elegant solution; grow in less time. After almost 2 years of intensive research, they just published a paper demonstrating that an algae-derived biostimulant (a formulated biological material for improving plant growth) shortened the time between planting and harvesting hydroponically grown red leaf and green leaf lettuce by six days. Since traditionally farmed, outdoor-gown lettuce is currently three-to-five times less expensive to grow than vertically farmed lettuce, a shortened growing period may have significant implications for the economic sustainability of vertical farming as it reduces energy inputs and labor costs.
This breakthrough research was based on the concept of trying to translate the amazing interaction between plants and their soil environments into hydroponic and aeroponic systems. The team was already developing a proprietary Spirulina (blue-green algae) extract for the food and alternative protein markets and began to explore whether phycocyanin, a protein-pigment complex that acts as a key regulator of photosynthesis in blue-green algae, could play a similar role in plants growth.
A series of experiments produced evidence that a phycocyanin-rich Spirulina extract worked as a biostimulant in hydroponics, improving growth, yield, and quality of lettuce while cutting maturation time by 6 days-or 21%-compared to control groups. The faster-growing treatment groups also produced 12.5% more lettuce and were 22% better at photosynthesis than control groups. The treated lettuce was more robust; a mean increase of 2.6cm in leaf length and 2.2cm in basal stem diameter compared to the untreated lettuce was observed and. In the shelf-life test, wilting was seen 2-3 days after it was observed in control groups.
Treatment groups were brighter green (specifically 17% brighter and 75% greener) and better tasting. They had firmer texture, a stronger aroma, and more intense flavor than the untreated group, according to an independent certification company. Using analytical chemistry techniques, the team also examined nutrient content by comparing flavonoid-antioxidant levels in control and experimental groups. Their findings suggested experimental groups were more nutrient-rich, where one flavonoid, Quercetin, had a mean increase of 30% in the treated lettuce.
What it Means
Back of the Yards Algae Sciences was working to cut growing time in hydroponically grown lettuce using a biostimulant to give vertical farmers a new avenue for reducing energy inputs. They were successful and also happened to find that Spirulina extract biostimulants improved color, vigor, nutrient content, and preservation. These product quality findings will support vertical farming in improving profitability by ensuring better selling prices. But perhaps the most exciting aspect of developing natural biostimulants specifically for vertical farming is the possibility to extend the indoor farming sector into row crops as food staples (wheat, soy, corn), ensuring not only better and more secure food supplies for urban populations, but also protecting the environment.
This research is available at: https://www.preprints.org/manuscript/202011.0354/v1
For further information – www.algaesciences.com
Autogrow Challenges Other Industry Players To Publish APIs
“To date, large industry players have not publicly published APIs’, but our argument is that it’s your data - you should be able to do what you want with it,” says Chief Technology Officer Jonathan Morgan
Autogrow is calling for more public APIs (Application Programming Interface), giving increased access for growers to their own data, and fostering faster innovation in the Controlled Environment Agriculture industry.
“To date, large industry players have not publicly published APIs’, but our argument is that it’s your data - you should be able to do what you want with it,” says Chief Technology Officer Jonathan Morgan.
“There can be a protectionist approach to development to dissuade people from building their own versions or integrating other products. But you will never keep up with all the customer requests or in the same timeframe as the 15 other companies working on the same improvements in the market. Access equals innovation - simple as that.”
Autogrow's FarmRoad has launched their public API on a new Developer Portal which is product agnostic and welcomes all industry players. This will allow growers to use the platform to build a ‘best of breed’ solution for their operation, no matter what their current technology providers are.
“You don’t have to rip and replace your existing technology. You just need to use an API to connect it to FarmRoad and then see all your information in one place. You can also give third parties secure access to specific areas of your information – keeping control of what you want them to see.”
“As innovation accelerates it creates a unique challenge of being able to centralize all of your data in one place – regardless of the source. We’ve been offering public APIs for over three years and are certainly the leaders when it comes to cloud technology,” notes Mr. Morgan.
Initially, the FarmRoad Developer Portal will give access to:
Measurements: Over 39 different measurement data types related to the environment and crop registration.
Events: Capturing key events or notes for example pest detection or spray regimes.
Farms/compartments/sectors: Get the full picture from different areas of the farm. Giving comparative studies, trends or with permission-based access.
“This is just the beginning for what FarmRoad will be able to offer. With API availability, growers will be able to create their own custom applications alongside the work we are doing. It’s a great developer community which can evolve and scale as businesses and the industry changes.”
For more information on the FarmRoad Developer Portal - https://farmroad.io/developer
For more information on the API documentation - https://developer.farmroad.io/
For more information on Yield Prediction by FarmRoad - https://www.farmroad.io/
11 Nov 2020
CANADA: Vertical Farming Is On The Rise In Ontario
According to Elevate’s chief strategy officer, Travis Kanellos, the farm’s goal, for now, is to produce and market leafy greens, such as lettuce, arugula and basil; eventually, it will branch out to more products
November 2, 2020
Experts Say That A Technology Developed
For Space Travel Could Help Good Things Grow Right Here At Home
WELLAND — The technology behind vertical farming was originally developed with space travel in mind. Researchers, attempting to minimize the amount of real estate and materials needed for interplanetary travellers to grow food on long-haul trips, found that the tech could work on Earth. Despite the seemingly futuristic possibilities, vertical farming is becoming a practical reality in southern Ontario: a new vertical farm in Welland’s Industrial Zone had its first harvest last week. The facility, which opened in September, practises a high-tech way of growing food indoors that proponents say saves energy and will help improve food security and safety.
The vertical farm in Welland is about 1,860 square metres. (Courtesy of Amin Jadavji)
Whereas traditional farming involves planting across a wide area, vertical farms build upwards, stacking plants in layers. Run by Elevate Farms, a company that grows and sells produce in vertical farms, the facility in Welland is about 1,860 square metres, 465 of which is growing space. Plants are stacked 13 layers high (about 7.5 metres) and grow with their roots in water, rather than soil. They get their light from LEDs, which can be adjusted to produce changes in the plants’ colours and nutrients.
According to Elevate’s chief strategy officer, Travis Kanellos, the farm’s goal, for now, is to produce and market leafy greens, such as lettuce, arugula and basil; eventually, it will branch out to more products. Kanellos says the farm should be able to produce an estimated 454,000 kilograms of greens per year: “That facility will have a capacity of 1 million pounds annually out of a 5,000 square-foot box. And that’s our quote-unquote standard facility.”
McGill University professor Mark Lefsrud, an expert in food security and urban agriculture, says that, while vertical farming currently accounts for less than 1 per cent of all farming in Canada, within 20 years, “I’d expect it to slowly creep up to around 20 per cent of the total market.”
In a March report, Ontario’s Greenbelt Foundation identifies vertical farming as a priority to expand fruit and vegetable growth in the region and lists six vertical farms operating in Ontario (not including Elevate Farms): one in Kingsville, two in Guelph, and three in Toronto. All grow leafy greens, herbs, and microgreens (such as kale). The report notes that global investment in vertical farms is estimated at US$3.1 billion; about a third of that takes place in North America.
To Youbin Zheng, a professor and expert in controlled environment facilities at the University of Guelph, building more vertical farms in southern Ontario makes sense: “If you look at the Greenbelt and Golden Horseshoe, our land is limited, very limited, but our population has been increasing. If you grow vegetables in the field, there are only a few months in a year you can produce outside. If you grow inside with vertical farming, what you can get is just enormous.” The Greenbelt Foundation report states that, by building up, a vertical farm can produce the equivalent of more than 4,000 square metres of greenhouse space using just 185 square metres of floor space.
Proponents also cite the significant benefits of vertical farming when it comes to food security and safety. The farms can be close to major population centres, reducing the need for transportation. In the case of Elevate Farms, Welland’s easy access to transportation routes means lower transportation costs and fresher, more nutrient-rich food for the consumer. Closer monitoring of produce and the fact that it stays within one country’s border may also reduce the risk of contamination. Before the pandemic, Kanellos says, “we had numerous outbreaks of E. coli and salmonella in different products across the supply chain — and we're going to eliminate that.”
Despite the significant savings when it comes to land and energy, nobody is suggesting that vertical farms will replace traditional farms anytime soon. For Elevate Farms, Kanellos says, “the play is not to try and replace traditional agriculture” but to supplement the existing market with what the farm produces.
At the vertical farm in Welland, plants are stacked 13 layers high and grow with their roots in water. (Courtesy of Josh Siteman)
University of Guelph professor Mike Dixon is a leading expert in vertical farming who also works with space agencies including the Canadian Space Agency and NASA. Dixon leads the school’s Controlled Environment Systems Research Facility and advises Intravision Group, the research and development company behind Elevate Farms. “I've been long quoted as saying the next worst place after the surface of the moon to try to grow plants is a snowbank in northern Canada,” he says. While food-insecure communities such as First Nations in Ontario’s north could benefit from vertical farms, experts point out that building them is costly. Labour is expensive, and energy costs are high: lighting accounting for about 40 per cent of capital costs, as the Greenbelt Foundation notes. “First Nations communities have a hard time covering this without serious subsidies from the government,” Lefsrud says.
Another hurdle for vertical farms is diversifying what they produce. Josh Siteman, the Canadian managing director of Intravision Group, calls leafy greens the “tipping point for vertical farming,” which proved there was a market. Zheng notes that greens are relatively easy to produce and have short growth cycles, meaning that if something goes wrong, it’s not a huge loss to start over. But there are only so many greens a person can eat.
“I'm kind of sick and tired of people growing lettuce,” Dixon says jokingly. “Lettuce is not food until you add the ranch dressing. But everybody and their dog — I would say 95 per cent of the entrepreneurial ventures in horticulture [within] controlled environments — are growing lettuce or some variation on a salad green that has marginal nutritional value, in most cases.” Other popular produce, such as fruits and legumes, take more time to grow and require more nutrition, Dixon says, and harvesting them is more challenging and costly.
Lefsrud notes that there are companies working to produce berries and legumes in vertical farms, and Kanellos says Elevate Farms will eventually move in that direction. He also says the business plans to expand to more Canadian locations but declines to share which ones.
Dixon says that artificial-intelligence systems will be the next big game-changer for vertical farms, allowing growers to work more efficiently and precisely, thereby opening up more possibilities. “The imaging technology that we can bring to bear even now can detect nutrient imbalances, water stress, all kinds of abiotic and biotic stress responses in plants, and affect a management strategy to mitigate those problems long before you and I would ever know that there was a problem. Even a skilled horticulturist would not detect some of the kinds of nutrient imbalances,” he says. “We’ll evolve away from lettuce.”
Ontario Hubs are made possible by the Barry and Laurie Green Family Charitable Trust & Goldie Feldman.
Related tags: Food
Author: Justin Chandler
Justin Chandler is TVO.org's Hamilton-Niagara reporter.
CombaGroup SA Reveals Rebrand With New Name, Logo, and Products
The new name, CleanGreens, is synonymous with powering clean, sustainable solutions in the agrotech space. It also reflects the company's mission to represent more directly what they are bringing to the table: fresh, healthy, premium quality yields of their customers’ favorite crops
Molondin, Switzerland – 5 November 2020: On the 21st October 2020, CombaGroup SA has announced the company's complete rebranding and launch of its new website.
Last year, the company realized it was time to leverage its unique position in the field of mobile aeroponic growing solutions. This year, they've rebranded to solidify their stance, offering, and direction within the industry.
The new name, CleanGreens, is synonymous with powering clean, sustainable solutions in the agrotech space. It also reflects the company's mission to represent more directly what they are bringing to the table: fresh, healthy, premium quality yields of their customers’ favorite crops.
The rebranding is a response to accelerated company growth and a renewal of its corporate vision, subtly captured by its new
With six years of R&D and technology breakthroughs in mobile irrigation and agronomy expertise, CleanGreens is proud to offer CleanGreens Pro, a system designed to be as simple as A-B-C, with immediate support and maintenance as well as a technical hotline available in addition to the built-in resources.
As a platform, CleanGreens is expanding to welcome new communities of users and has gone even further in solidifying its global position going forward. It has released new product packages and features that allow its clients to build, manage, and deploy custom applications quickly with its own intuitive, integrated, cloud-based operating application, GURU by CleanGreens. The platform gives clients the ability to grow exactly what they want with the support they require whenever they need it.
Based on the experiences and feedback from CleanGreens’ agronomist team and customers, this new app assists in key tasks like sowing, harvesting, and preventive maintenance and also features built-in reminders, alerts, and real-time records. It’s like having your own personal CleanGreens agro-expert assistant at your fingertips.
Currently, there are seven cultivation lines in operation in three locations: Molondin and Geneva in Switzerland, and Châteauneuf-sur-Loire in France. More are in the pipeline for the future. The new improvements have allowed CleanGreens to meet elevated customer demands for more of its innovative products and technologies.
"Our complete solution is different from any system in the market and our re-branding is largely driven by our effort to reflect this for our products, mission, vision, and of course, our customers and consumers,” says Serge Gander, CEO.
He adds: ”We've taken a clean, modern approach to the name, the website's design and the user experience in our new look and rebrand. We purposefully set out to challenge the status quo in all aspects of our business and this redesign reflects that." logo with the notion of interaction and connectedness. These are core to the capabilities of scalable mobile aeroponic technology platforms that are a priority for both CleanGreens and its clients and partners.
Please visit the revamped website www.cleangreens.ch to explore the new website and learn more about the products and services offered.
About CleanGreens
CleanGreens is a Swiss agro-technology company that provides farmers and industrialists with innovative mobile aeroponic farming solutions for growing fresh, environmentally-friendly, nutrient-rich vegetables. A certified B Corp company CleanGreens’ patented technology significantly reduces water consumption and contamination risks while offering maximum productivity per square meter and minimizing environmental impact. Automated irrigation and mechanized spacing system produce clean, quality, pesticide-free salads, aromatic herbs, and medicinal plants all year round, thus providing consumers with healthy, responsible products.
For more information
info@cleangreens.ch +41 21 545 99 25 www.cleangreens.ch
Media information online
Media information and images can be downloaded directly from cleangreens.ch Journalists can subscribe to our media mailings to receive information on CleanGreens’ aeroponic solutions and technology.
For the latest updates on CleanGreens, visit www.cleangreens.ch, or follow on Instagram, Twitter @SmartLettuce, Pinterest, and LinkedIn.
Biggest Swiss Fruit And Vegetables Cooperative Invests In Vertical Farming
A major Swiss domestic supplier, fenaco Landesprodukte, is working on a pilot facility for vertical farming. They're investing in YASAI, a spin-off of public university ETH Zurich. With an investment of CHF 500,000 in YASAI AG, the fenaco cooperative is participating in the construction of the pilot facility in Zurich
Fenaco Collaborates With YASAI
A major Swiss domestic supplier, fenaco Landesprodukte, is working on a pilot facility for vertical farming. They're investing in YASAI, a spin-off of public university ETH Zurich. With an investment of CHF 500,000 in YASAI AG, the fenaco cooperative is participating in the construction of the pilot facility in Zurich.
"Consumer demands for healthy, safe and sustainably produced food require innovative solutions from the agricultural and food industry. By participating in a pilot facility for the novel Vertical Farming production method, fenaco Landesprodukte wants to verify the advantages of this cultivation method", the company explains. "Thanks to its stacked installation, it increases productivity by a factor of 10 to 15 per square meter. Water consumption can be reduced by 90%."
"In the future, we do not want to produce ourselves, but rather use our experience in the field of vertical farming to open up a new, profitable business segment for growers," says Daniel Schwab, Head of the Vegetable Category at fenaco Landesprodukte. To this end, a sounding board was set up with vegetable producers from the Seeland region.
No chemical crop protection is used, or very small amounts only. In addition, year-round indoor production allows growth 24 hours a day, 365 days a year and it is possible to increase the proportion of Swiss vegetables and herbs. "The aim is also to demonstrate the economic efficiency for various product categories and to reduce energy consumption by exploiting synergies", they explain.
A strong signal for innovation in the agricultural and food industry
fenaco entering the field of vertical farming is a strong signal for innovation in the Swiss agricultural and food industry. The partnership with the ETH spin-off enables fenaco to better understand the potential for vertical farming and, if positive, to exploit economies of scale with larger plants. On the one hand, the product portfolio will be tested in cultivation and marketing and on the other hand, central agronomic questions will be addressed in a research project in cooperation with Agroscope.
"We are working on the farm of the future and regard this investment as a preliminary work and a basis for decision-making for future investments of our producers", says Markus Hämmerli, Head of fenaco products and research cooperations. This means the commitment is based on the goals of the fenaco cooperative: to support Swiss growers in the economic development of their companies.
Industry and technology know-how go hand in hand
The ETH spin-off YASAI under the leadership of CEO Mark Essam Zahran is the ideal partner for fenaco. The four founders and majority shareholders have excellent know-how in the field of software and hardware as well as a large international network. After several successful financing rounds, fenaco's financial commitment and the associated construction of the first pilot plant in Switzerland is an important milestone for the still young company.
"Thanks to the cooperation with fenaco, we now have a strong industrial partner with a lot of market and customer knowledge from the agricultural sector on our side. This is extremely valuable when scaling up the technology and entering the Swiss market," says Mark Zahran of YASAI. The partnership with fenaco also enables YASAI to distribute the vegetables and herbs it produces nationally in the retail trade and in the catering trade.
For more information:
www.fenaco.com
www.yasai.ch
29 Oct 2020
GP Solutions, Inc. Enters Into Distribution Agreement With Advanced Container Technologies, Inc.
A key component of the agreement is ACT's exclusivity to market GP Solutions "Grow Pods." GP Solutions "Grow Pods" has become a popular and trusted technology in the agriculture industry. Subsequently, ACT completed a share exchange on October 9th, 2020, with Medtainer, Inc., (MDTRD). Medtainer, Inc. is a California based company that specializes in manufacturing, branding, sales and marketing consultation
NEWS PROVIDED BY
Oct 27, 2020
CORONA, Calif., Oct. 27, 2020,/PRNewswire/ -- On August 6th, 2020, GP Solutions, Inc. (GWPD) finalized a distribution agreement with California-based Advanced Container Technologies, Inc., (ACT). The agreement states ACT has the exclusive right to market, sell, and distribute GP's products in the United States and its territories. This agreement has an initial term that expires on December 31, 2025, and is renewable indefinitely as long as ACT meets prescribed sales targets. GP manufactures fully insulated, food-grade shipping containers that are specifically modified to provide an optimally controlled environment for growing a wide range of horticultural and agricultural products in all environments and climates.
A key component of the agreement is ACT's exclusivity to market GP Solutions "Grow Pods." GP Solutions "Grow Pods" have become a popular and trusted technology in the agriculture industry. Subsequently, ACT completed a share exchange on October 9th, 2020, with Medtainer, Inc., (MDTRD). Medtainer, Inc. is a California based company that specializes in manufacturing, branding, sales, and marketing consultation.
GP Solutions, Inc. President, George Natzic, stated, "We are very excited about the prospects of this agreement allowing ACT to use its expertise to market and sell GP Solutions' Grow Pods." Also stating, "This also allows GP Solutions to focus on manufacturing new products and executing our business model into new industries and territories."
GrowPods are controlled environment micro-farms with a sealed eco-system, utilizing filtered air and water while maintaining a pest-free environment to eliminate pathogens. Grow Pods offers farmers a high-margin niche to expand into and gives consumers access to safe, tested, and nutritious "Super Foods."
For more information, call: (855) 247-8054 or visit: www.growpodsolutions.com.
Connect:
Website: www.growpodsolutions.com
Facebook: facebook.com/GrowPodTechnology
Twitter: @GrowPodSolution
Forward-Looking Statements
This release includes predictions or information that might be considered "forward-looking" within securities laws. These statements represent Company's current judgments, but are subject to uncertainties that could cause results to differ. Readers are cautioned to not place undue reliance on these statements, which reflect management's opinions only as of the date of this release. The Company is not obligated to revise any statements in light of new information or events.
SOURCE GP Solutions
Related Links
https://www.growpodsolutions.com
Also from this source
Vertical Farm Market Projected to Reach $7.3 Billion...
Test Results Show Lettuce Grown in GrowPods to be Pathogen Free...
VIDEOS: Vertical Farming Goes High-Tech And Underground
Vertical Farms Are Evolving Into A Major
Food Industry Powered by Sophisticated
Technologies And Production Methods
Growing fresh produce in underground areas
Transforming a tunnel into a vertical farming operation
Infarm allows customers to pick the produce themselves
Vertical farming companies are facing an array of challenges
Technology and lower costs are critical for the industry’s sustainability
Innovation is vital to solving the world’s greatest challenges
Farmers around the world are heading towards an uncertain future. Apart from the prospect of feeding the global population that’s set to reach around 10.9 billion by 2100, they are also facing climate change-induced floods, droughts, and heatwaves. Fertile land is in ever shorter supply as soil erosion intensifies. Farming is also to blame for some of these problems as the CO2 footprint of food accounts for 17 percent of total global emissions. And by the time plants get transported to supermarkets, they lose 45 percent of their nutrients. As it becomes increasingly apparent that traditional agriculture is unsustainable, growing food in an artificial environment is emerging as a potentially better way forward.
Instead of plowing fields, farmers would produce food in vertically stacked trays. Soil would be replaced by nutrient-rich water, while LED lights would act as the sun to ensure plants photosynthesize. This practice, known as vertical farming, offers many benefits. The indoor environment protects crops from extreme weather events and pests, which means that food grows fast and there’s no need for pesticides. Also, food is grown close to cities, which not only reduces food miles and the related carbon footprint but also provides consumers with fresh and tasty crops.
However, vertical farming faces certain challenges as well. Companies have to constantly innovate to cut production costs and turn a profit, which is vital for the survival of this industry. But entrepreneurs remain optimistic. The global vertical farming market is forecasted to reach $12.77 billion by 2026 and people are becoming increasingly aware that there’s a better way to feed the populGrowing fresh produce in underground areas
High rents and the lack of space have prompted some modern urban farmers to go underground. In London, for instance, a farm called Growing Underground operates from a World War II bomb shelter located 33 metres below Clapham High Street. Owned by Stephen Dring and Richard Ballard, the vertical farming facility produces an array of herb and salad mixes, including parsley, red mustard, coriander, and pea shoots. Fresh produce is then sold through Marks & Spencer, Waitrose, Ocado, and several other retailers. Some restaurants have also expressed interest in buying fresh produce, says Ballard.
He also points to many advantages of vertical farming. For instance, his farm delivers 60 harvests a year, compared with around seven that can be achieved in traditional agriculture. Furthermore, Growing Underground is carbon neutral and uses 70 percent less water than typical farms. The only major cost he’s trying to reduce is the electricity that powers the lights. And his ambitions are global. “The UK is the hardest market for growing salad. We’ve got very low prices in the supermarket, so if we can make it work here we can make it work anywhere,” says Ballard.
Underground vertical farming is thriving in other British cities as well. The Liverpool-based social enterprise Farm Urban, for example, provides customers with a weekly box of living salad leaves, edible flowers, and fragrant herbs. Jens Thomas, the company’s technical director, says that the product is pesticide-free and “it’s grown using 90% less water than if it was grown in a field; it’s zero-waste; and it’s hyper-local.” Farm Urban is trying to promote healthy and sustainable living. For each box of greens customers buy, the company delivers a box of greens to a local school. This activity is part of the Greens for Good campaign that aims to reconnect people with locally-grown food.
In New York, the vertical farming business Farm. One is also growing. Its underground farms produce over 500 different herbs, edible flowers, and microgreens year-round, using specialized software to manage multiple operations, such as seed, harvest, and flavor optimization. Founded by Rob Laing, the company supplies fresh produce to various New York-based restaurants, including Atera, Ai Fiori, Benno, and Flora Bar. All deliveries are made by bike and subway. Also, visitors can book a tour of the farm or take a class in hydroponics to learn how to grow vegetables in a soil-free environment.
Transforming a tunnel into a vertical farming operation
Successful vertical farming businesses can also be launched outside of cities. NEXTON, a South Korea-based startup, has built vertical farms in a former highway tunnel, located 190 kilometres south of the capital city of Seoul. Growing salads, leafy greens, and strawberries beneath mountains has many advantages. For one, the 6,500-square-metre facility naturally maintains a temperature that ranges between 10 to 20 degrees Celsius, which translates into lower energy spend for cooling or heating. Furthermore, labor costs are reduced by automating various operations. And as farming is done without pesticide or herbicide, with sensors monitoring humidity and CO2 concentrations, customers receive both healthy and affordable products.
Choi Jae-bin, the CEO of NextOn, also uses non-tech tactics to boost production. For instance, the music of Beethoven and Schubert is played in the 600-metre-long tunnel as Jae-bin believes it will help plants to grow faster. And his plan is to build more farms in urban areas. “Plants easily grow at home, at nearby stores, at hamburger restaurants, or even at metro stations. I think the system to grow crops far away from a city and transporting it will disappear,” he says.
Infarm allows customers to pick produce themselves
Infarm, a Berlin-based startup, has already achieved in several European countries what Jae-bin plans to do in South Korea. The German company builds modular farms that are placed in customer-facing locations, such as schools, grocery stores, restaurants, and shopping malls, enabling customers to pick the produce themselves. Clients can also add more modules if they want to increase the farming output, while the production is monitored and controlled through a cloud-based platform. Essentially, the whole thing functions as a ‘farming as a service’ operation that combines the IoT, Big Data, and cloud analytics.
The company is working with 25 major food retailers in Germany, France, and Switzerland, including Migros, Casino, Intermarche, Auchan, Selgros, and AmazonFresh. Furthermore, it has installed more than 200 in-store farms, as well as 150 farms in distribution centres. And in 2019, Infarm raised $100 million in Series B investment round. The funding will be used to expand research and development, sales, and operation teams. Also, the startup plans to increase its presence in the UK and negotiate partnerships with retailers in the US and Japan.
Vertical farming companies are facing an array of challenges
While the rise of vertical farming companies has been impressive, the industry is facing many challenges and its survival depends on reducing costs and increasing productivity. Take, for example, the fact that deploying even a small, low-tech vertical farm with the 1st generation technology costs around $280,000. On the other hand, the cost of setting up more complex farms with advanced tech can go over $15 million. There are also operating expenses such as lighting and labour that can further pressure companies’ bottom line, making it hard to compete with organic and traditional producers.
So it comes as no surprise that return on investment (ROI) in vertical farming projects is mediocre at best. The current market prices don’t make the situation any easier either. A kilogram of vertically-grown leafy greens is around $33, while organic produce costs $23. To gain a competitive edge, vertical farming startups need to take several measures.
Technology and lower costs are critical for the industry’s sustainability
The first step in ensuring the long-term profitability of vertical farms is transitioning to 2nd generation technology. This means that in addition to automatic control of irrigation, humidity, lighting, CO2, and other relevant parameters, farms should also be capable of autonomously collecting data and optimizing growing processes. They also need to implement cutting-edge machines that will autonomously run planting and weeding operations in the facility, and harvest sort and package produce for shipping. These improvements can enable the second generation of vertical farms to yield 55 times more produce than conventional farms.
Increased automation will also cut labour expenses. Intelligent Growth Solutions, a UK-based agritech business, has reportedly developed an automated farming system that uses modular structures to reduce labour needs by up to 80 percent. Furthermore, LED lighting efficiency is likely to improve by an additional 70 percent by 2030, reducing the energy spend. Boaz Toledano, a business consultant specializing in vertical farming, says that “lighting improvements should reduce OPEX [operating expenses] by 12%, and automation should cut OPEX by a further 20%+”.
Companies can also reduce costs by setting up farming operations underground. This would not only help them avoid the high cost of renting in urban centres but also enable them to enjoy the benefits of having a steady temperature. Underground facilities also offer better protection against natural disasters and can be more easily adapted to producers’ needs.
Innovation is vital to solving the world’s greatest challenges
New technologies are moving the food industry forward. Vertical farming, though still gaining traction, could help solve some of the world’s greatest challenges, such as food shortage. Tasked with feeding the growing global population, today’s agriculture producers still primarily rely on farming practices that hurt the environment. As it becomes clear that traditional farming is unsustainable, innovative entrepreneurs and scientists have come up with a potential solution. Vertical farming is increasingly hailed as an alternative food production method that can provide people with healthy and fresh produce. Thriving in undergrounds, stores, and restaurants around the world, vertical farms are becoming a major industry. But their survival depends on the ability of businesses to lower food production costs and increase productivity.
This article is written by Richard van Hooijdonk
Trendwatcher, futurist, and international keynote speaker Richard van Hooijdonk takes you to an inspiring future that will dramatically change the way we live, work, and do business. All lectures
VIDEO: Vertical Farming To Prevent Food Loss In A Disaster
Matt Barnard, co-founder, and chief executive officer of Plenty, Inc. discusses the company's series D funding round on "Bloomberg Technology."
October 17th, 2020
Indoor vertical farming startup Plenty Inc. is working to deliver year-round produce from its controlled, resilient farms to avoid food loss during disastrous flooding, droughts, or fires.
Matt Barnard, co-founder, and chief executive officer of Plenty, Inc. discusses the company's series D funding round on "Bloomberg Technology." (Source: Bloomberg)
Tech-Magnate Jack Ma Visits Dezhou Greenhouse
Jack Ma congratulated China on its achievements in the development of smart agriculture and said: At present, the modern agricultural industry, is similar to the Internet at the beginning of the 21st century, is undergoing tremendous changes, and there is still much room for future development
The Chinese horticultural industry might get ready to rumble as two major business magnates found their way into the greenhouse. Last week Jack Ma (Ma Yun), founder and CEO of Alibaba, and Sun Hongbin, CEO of Sunac, visited the Kaisheng Haofeng Facility. This is the largest greenhouse in the Shandong Province in the Lingcheng District, Dezhou City. They were joined by representatives of the Dezhou Financial Investment Group, Qingdao Haofeng Food Group, and Kaisheng Haofeng (Dezhou) Intelligent Agriculture.
Photograph source: Kaisheng Haofeng (Dezhou) Intelligent Agriculture Co., Ltd.
Technology in the greenhouse
With Alibaba Jack Ma has created one of the biggest technology multinationals in the world, specializing in e-commerce, retail, internet, and technology. Now he took a peek at the "high-quality" scientific and technological content behind a small tomato.
The committee members of the Dezhou Financial Investment Group and vice-CEO Yu Ruihua introduced the modern greenhouse, in what the control over temperature, light, water, carbon dioxide, and fertilizer is integrated via the automatic environmental-control system. The process, including seed selection, seedling raising, planting, pest control, irrigation, picking, packaging, etc., is designed based on the growth requirements of the tomato plants. Besides, standardized management is strictly implemented. The greenhouse uses an automatic screening line with the spectral system, the automatic weighting and screening can be carried out according to the color, weight, and defect degree of tomatoes, ensuring uniform product quality and uniform gram weight.
"The tomatoes planted in this way are not only high in value but also good in taste full of seeds, juice, and rich vitamins", the team explained. After that, the technical operation team reported in detail the variety selection, research, development, plant model construction, digital management, and standardization system of the smart greenhouse.
Second season
The smart greenhouse's second planting season has just finished. The intelligent farm is buzzing with energy and the plants flourish. Jack Ma paid close attention to the growing conditions of the tomato plants, including the coconut coir growth medium, drip irrigation, liquid fertilizer, and other innovative plantation technologies. The bumblebee pollination attracted particular attention. During the period when the tomato plants blossom, the farmers use bumblebees to pollinate the flowers. They do not add hormones, but improve fruit ratio naturally. The tomatoes are juicy and plump, and the flavor is excellent.
Photograph source: Kaisheng Haofeng (Dezhou) Intelligent Agriculture Co., Ltd.
The inspection tour was followed by a conference where the technical operation team provided a detailed report on the development and selection of product varieties in the smart greenhouse, plantation installations, digital management, and standardized systems.
Jack Ma congratulated China on its achievements in the development of smart agriculture and said: At present, the modern agricultural industry, is similar to the Internet at the beginning of the 21st century, is undergoing tremendous changes, and there is still much room for future development. The development of agriculture should pay attention to the input of talents and technology. He hopes to discuss more development possibilities about agriculture with everyone and jointly promote the progress of farmers, industries, and the whole society.
19 Oct 2020