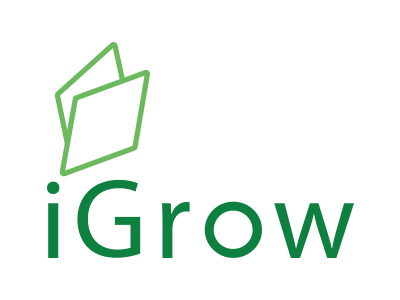
Welcome to iGrow News, Your Source for the World of Indoor Vertical Farming
Large-Scale Automated Vertical Farm Near Tokyo by Spread And ENEOS Partnership
Techno Farm Narita is Spread’s first partnership project and the first to be located in Eastern Japan
July 14, 2021, Spread Co., Ltd. (HQ: Kyoto, Japan; CEO: Shinji Inada, hereinafter “Spread”)’s partner, and a member of ENEOS Group, J Leaf Corporation (HQ: Chiba, Japan; President: Jun Uehara, hereinafter “J Leaf”) started operating the automated vertical farm “Techno Farm Narita” (Chiba, Japan) on 30th of June.
Spread’s Large-Scale Vertical Farming Partnership with ENEOS Group’s J Leaf Starts Operations near Tokyo
Spread owns and operates two vertical farms in Western Japan (Kyoto), the Kameoka Plant and Techno Farm Keihanna. Techno Farm Narita is Spread’s first partnership project, and the first to be located in Eastern Japan. The most significant feature of Techno Farm Narita is the increased efficiency in the use of land. This has been achieved by increasing the number of cultivation racks levels to 28, double that of Techno Farm Keihanna. Techno Farm Narita will produce 30,000 heads of lettuce daily, building on the know-how accumulated through the operation of Techno Farm Keihanna to deliver increasingly sustainable food production.
Unique Features of Techno Farm Narita
Even more efficient land saving through 28-level cultivation rack system (roughly 2 times more efficient than Techno Farm Keihanna)
Located in the Greater Tokyo Area, allowing for local production and consumption
Transforming idle land to efficient and sustainable agriculture ・
The utilization of renewable energy generated from solar panels
Techno Farm Narita also retains other features of Spread’s next-generation food production system, Techno Farm™, including pesticide-free, stable cultivation, integrated automation, specialized LED lighting, and Spread’s proprietary IoT-based cultivation management system, Techno Farm Cloud.
Techno Farm Narita’s Cultivation Room Opening Ceremony
About the Partners
ENEOS Group is one of Japan's leading corporate groups, with revenue in excess of 10 trillion yen. *1
The Group has the largest market share in oil refinery and petrochemicals distribution in Japan and is centered around ENEOS Holdings.
Spread’s vision is to create a sustainable society where future generations can live with peace of mind. On the way to this objective, Spread plans to reach a total production capacity of 100 tons per day domestically by 2030, through the expansion of its Techno Farm™. With the collaboration at Techno Farm Narita as a foundation, both parties are considering further partnership projects. The green business market is expected to continue growing, and Spread strives to become a leading vertical farming company globally.
Spread will continue to pursue further business opportunities through technological innovation both in Japan and overseas. Spread aims to provide solutions for the global problems of climate change and food security and the delivery of a truly sustainable society.
*1 FY2019 results (announced on May 20, 2020)
*2 ENEOS Techno Materials Corporation is a member of ENEOS Group
Applying Automated Warehouse Systems To Indoor Farming
“At Swisslog, we don’t have standard solutions in place for vertical farms yet. But due to our long-lasting expertise both in the food industry and in the distribution of fresh products to the point of sale, we understand the supply chain processes and linked to that shelf life considerations.”
“History is written in circles as we observe similar drive for automation in indoor farming, as we saw years ago in the intralogistics sector. There are yet few important differences,” says Timo Landener, product innovator at Swisslog.
Swisslog, with the vision to shape the future of intralogistics, not only develops warehouse automation and software solutions to reduce costs and introduce flexibility to warehouse-based operations but also looks into innovative future-proof approaches. In March 2021, Swisslog announced its foray into the vertical farming market. While Swisslog has not specifically designed systems for vertical farming, its vast portfolio of automation solutions can be adapted to vertical farms, whether pre-existing or purpose-built.
Timo Landener
“At Swisslog, we don’t have standard solutions in place for vertical farms yet. But due to our long-lasting expertise both in the food industry and in the distribution of fresh products to the point of sale, we understand the supply chain processes and linked to that shelf life considerations. Moreover, our portfolio can be easily adapted to indoor farming since the payload is fairly light, the throughput is not critical and the automation operations demand low power compared to the needs of the intralogistics automation,” explains Timo. “Nevertheless, we already learned, that we can't just adopt the same requirements, because plants are living organisms. And we have to respect that.”
Although unable to reveal their clients, Swisslog has reportedly demonstrated its technologies in the vertical farming industry with success to allow growers to reduce operational costs and increase scalability. Examples of innovative systems applicable to vertical farming include the PowerStore high-density storage system, the AGV based good-to-person order fulfillment solution CarryPick, the Tornado mini-load crane and the Vectura stacker crane.
When does automation become economically feasible?
Automation can be applied to multiple processes in an indoor farm including seeding, harvesting, packaging, tray manipulation, etc. However, Timo explains that automation is capital-intensive and best suited for large-scale indoor farms. A higher production level introduces more opportunities to increase operational efficiency and reduce labor requirements.
“Even Amazon began in a small space with little automation. Then, they reached a level where automation made sense. In the vertical farming industry, we need to discuss with clients where the tipping point is for needing automation,” says Timo.
To determine which automation solutions are right for the grower, Swisslog’s automation experts work directly with clients to identify opportunities for increased operational efficiency and customize solutions according to the farm’s architecture. Additionally, the close relation with KUKA as the parental company allows collaboration opportunities to automate and incorporate the sub-processes in an Indoor Farm to a more turnkey solution.
Harvest-on-demand
Timo explains that despite the relatively short distance between urban indoor farms and retailers, a major challenge to indoor farming is the logistics of transporting farm-grown products to retailers while maintaining crop quality.
“After the plants have grown in a perfect environment, they are cut and immediately begin to lose quality. The current challenge is to speed up the process of getting the products to the retailer. Pursuing the innovative approach of harvesting-on-demand, we can make sure that the end customer receives fresh and rich nutrition vegetables. With a palette of automated solutions this is finally possible,” says Timo.
Swisslog’s ties with global retailers started long ago as the Swiss Company delivered solutions for huge automated projects (distribution centers) as well as smaller, more local applications, known as Micro-Fulfillment Centers. Harvesting-on-demand differs from mainstream distribution models by supplying retailers with living plants, which can continue growing until they are purchased.
This process can be carried out in retailers’ “back shops” and would support additionally retailers to fulfill three major sales channels: in-store sales, home delivery and BOPIS (buy online, pick up in-store). Swisslog is certain that we are at the edge of a revolution in food the supply chain: There will be the need for Indoor Farms at the point of sales: a “fresh food on the demand-supply grid”. We see automation as a means for leveraging the indoor farms and help them deliver efficiency that will lower the entry threshold for further investments.
Retailers are a fundamental part of this revolution. “Many indoor farms are currently selling to retailers. Due to the fact, that the retailers sell the crops, they determine how the supply chain will look like. Thus, the power of re-designing the process of the supply chain and ensuring consistency in the circular economy lies in their hands. As for today, the complexity and ramifications of the matter inspire us to join forces with retailers and find out how to react in the best way to changing needs of the customers and the industry. We are on the verge of something new and powerful. Swisslog, an intralogistics automation leader, together with retailers and farming experts, we can deliver a great added value for consumers” explains Timo.
For more information:
Timo Landener, product innovator
Swisslog
timo.landener@swisslog.com
www.swisslog.com
Publication date: Thu 3 Jun 2021
Author: Rebekka Boekhout
© VerticalFarmDaily.com
Pontus Files International Patent Application For Automated Vertical Farm Harvesting Robot
Pontus' initial crop, water lentils, is the fastest-growing leafed plant.* Pontus' CEVAS helps accelerate the growth of Pontus' water lentils, requiring the plant to be harvested every 24 hours
NEWS PROVIDED BY
Jun 09, 2021, VANCOUVER, BC, June 9, 2021 /CNW/ - Pontus Protein Ltd. (TSXV: HULK) (OTCQB: HLKKF) (FSE: 8YC) ("Pontus" or the "Company"), is pleased to announce that it has filed an international patent application through the Patent Coordination Treaty with the World Intellectual Property Organization for Pontus' proprietary Harvesting Automated Robotic Vehicle or "HARV" for short. HARV is a vertical farm rack system and automated plant tending and harvesting robot designed to work alongside and assist Pontus' Closed Environment Vertical Aquaponics System or CEVAS system.
Pontus' Harvesting Automated Robotic Vehicle or “HARV” for short. HARV is a vertical farm rack system and automated plant tending and harvesting robot (CNW Group/Pontus Protein Ltd.)
Pontus' initial crop, water lentils, is the fastest-growing leafed plant.* Pontus' CEVAS helps accelerate the growth of Pontus' water lentils, requiring the plant to be harvested every 24 hours. Pontus developed the HARV technology to allow the crop to be automatically harvested daily. In addition, due to its low profile, HARV will enable Pontus to stack nine levels of vertical farming at its Surrey, British Columbia production facility.
Steve McArthur, Chief Technology Officer, Pontus, stated, "Talking with the experienced team at Automation Experts (an automation and innovation company based in Calgary, Canada), we were able to identify that there was no robot out there that handled everything we needed it to do. By harvesting the crop in situ, using HARV, we will reduce the space between the water beds and increase the number of levels, increasing efficiency and the yield. We are beyond excited about pairing HARV with our CEVAS system, as we see CEVAS as a greener, more ecologically sustainable way of producing high nutrition food products."
Stephen Bruce Wong, CEO, Automation Experts, added, "HARV is more than a mechanical tool for harvesting. It will manage the farm and give us critical insight and data regarding the optimization of the growing environment. The robotics in HARV will allow Pontus to eliminate moving parts from the structure thus lowering the cost to build Pontus' vertical farms as the water beds can be dumb and do not need the technology built into them. It also uses machine learning and artificial intelligence to support all aspects of the growing process."
The patent filing is part of the technology leadership in the aquaponic space that Pontus continues to secure.
About Pontus Protein Ltd.
Pontus Protein Ltd. is a Vancouver, B.C. based technology company that grows water lentil protein for commercial use. Pontus is reinventing agriculture with their proprietary Closed Environment Vertical Aquaponic System (CEVAS) – the farming of the future. Pontus specializes in the indoor vertical farming of water lentils that use 95% less water than traditional agriculture and no pesticides or chemicals. Pontus is committed to solving the global food crisis by providing access to sustainable indoor biosecure pure plant-based proteins. Pontus' water lentils can be harvested every 24 hours, exceed organic certification, and can be grown in any climate in a relatively small area. Our water lentil protein is filled with antioxidants, minerals, vitamins, and all the amino acids, making a complete protein food source. Pontus aims to revolutionize the plant-based sector as the entire sector is currently based on two main protein sources: soy and pea. Water lentil protein is far superior to pea and soy protein. It contains over 40% protein vs. 5-36% protein*, and Pontus aims to be the base protein for nutrition-rich plant-based food products and nutraceuticals to support the movement transitioning the world from meat-based to plant-based proteins.
To learn more, please visit pontuswaterlentils.com.
*https://www.infood.net/visitor/collection/75?portion_size=100
*https://www.zmescience.com/science/fastest-growing-plant-02022021/
On behalf of the Board of Directors
"Connor Yuen"
Connor Yuen, CEO
Pontus Protein Ltd.
Contact Information
For more information, please contact:
Connor Yuen
Chief Executive Officer
https://pontuswaterlentils.com/company/#contact
Forward-Looking Information
Certain statements in this release are forward-looking statements, which reflect the expectations of management regarding the Company. Forward-looking statements consist of statements that are not purely historical, including any statements regarding beliefs, plans, expectations or intentions regarding the future, including but not limited to Pontus' ability to revolutionize the plant based sector. Such statements are subject to risks and uncertainties that may cause actual results, performance or developments to differ materially from those contained in the statements, including risks related to factors beyond the control of the Company. These risks include, but are not limited to, the following: the unknown magnitude and duration of the effects of the COVID-19 pandemic, the failure of Pontus to receive the necessary approvals from the Canadian Food Inspection Agency for its products and facilities, the inability to complete Pontus' Surrey-based production facility, as well as other general business, economic, or market related risks beyond the director control of the Company and which may affect the Company's business, operations, or products. No assurance can be given that any of the events anticipated by the forward-looking statements will occur or, if they do occur, what benefits the Company will obtain from them. The Company undertakes no obligation to update forward-looking information if circumstances or management's estimates or opinions should change, unless required by law. The reader is cautioned not to place undue reliance on forward-looking information.
Neither the TSX Venture Exchange nor its Regulation Services Provider (as that term is defined in policies of the TSX Venture Exchange) accepts responsibility for the adequacy or accuracy of this release.
SOURCE Pontus Protein Ltd.
For further information: Investor Relations or Media enquiries: invest@pontuswaterlentils.com, (403) 589-7992
Organization Profile
Pontus Protein Ltd.
"We’re Retrofitting With The Variables We Have In Place"
Planted Detroit introduces new 20.000 sq. ft. growing facility
“The Square Room is a big block of pink lights with eight levels, where all our growing is done. Everything after germination is done in the same room, both harvesting of our baby greens and microgreens. Because we’re almost done with our PARS (Planted Automated Racking System), which is the big automation,” says Megan Burritt, Managing partner at Planted Detroit.
From a mix-fused downtown neighborhood in Detroit, daily deliveries of ready-to-eat salads and fresh greens are transported to local retailers and restaurants. Planted Detroit makes a large contribution to the city’s share of fresh produce.
New facility
Planted Detroit has been in the middle of the construction of its new 20.000 sq. ft growing facility. The growing space has been a massive update to the company compared to its previous 6-level growing facility which was between 1500-2000 sq. ft. The same room was used for processing, packaging, harvesting, and so on. “It was rather crowded, says Megan, but the main goal was to keep everything tight for the construction to continue in the near surrounding. We’re very serious about biosecurity and we have a daily procedure for everyone who sets foot in our grow room to go through. Making sure our greens don’t come into contact with pathogens is our top priority.
The new growing room
The Square Room, one of our growing rooms, is highly automated, including an automatic harvester to ensure work-efficiency. Once everything is big enough to be transplanted out of their plug trays, PARS (Planted Automated Racking System) will be transplanted with gutters and then go into harvesting. On the other side of PARS, the gutters are taken down and harvested through Planted’s new automatic harvester.
Delivering directly to consumers
The company wants to reach a higher volume of customers as it’s aiming to obtain a consumer brand status. Next to that, the company is always on the lookout for finding more customers through other venues. “We want to go directly to consumers via our web-store to shorten food miles as much as possible, delivering the freshest and most delicious greens,” Megan says. In order to do that the company needed to have a bit more scale, trying to maximize the space they already had.
She adds: “Our farm maybe isn’t the square footage which we could have built from scratch, but we’re retrofitting with the variables we have in place. That is why we have done a combination of a microgreen vertical nursery and PARS for baby greens. Our direct customers wanted meal solutions and we’ve been able to deliver them that. We’ve been doing everything from seed to plate basically.”
Megan Burritt, Managing partner
New projects coming up
On the same campus, 10 meters away, a new farm will be constructed, under the company's office space. In this farm herbs and edible flowers will be grown in response to different customers' demands. Megan says that Planted Detroit’s wholesale customers got them to this point as they were very interested in herbs and edible flowers. “However we weren’t able to perfect these as well in the systems that our baby greens were in perfectly. That’s why we’ve been leaning into R&D lately because once finishing the construction of Farm 2 it will have excellent growing conditions that are better than they have been for those crops.”
Edible flowers are an interesting thing, says Megan, but the company has gotten so much interest in it. According to Megan there aren’t many farms in the US that are growing them. “They’re high priced at this point. It sort of sticks to our original innovation, namely what exists here in the food system and what does not. Where can we fill the ‘does not exist niche’ and satisfy the needs of our customers.”
The company is rolling out a subscription program sometime this year and figuring out where it fits into the fresh food subscription system and how they can partner with other parties in order to get produce closer to society. “It’s great to have this ag job, applied science to be able to do. In all the things we’ve been doing is hiring these Detroiters and showing that we can really create a really great culture of work. It’s really great to see we’re contributing to a better Detroit and a better tomorrow,” Megan states.
Team expansion
During 2020 most of the team stayed on by moving around working hours, so the farm could come back in full force. By the time all equipment was in place, 10 to 12 people were added to the team to have them fully trained before the system would be functioning. “It has been really wonderful to expand the team to see what our capacity is,” says Megan.
“Luckily we’ve been able to develop systems that have been resilient. We’ve seen so many different patterns in consumer behavior but they seem to have fallen in our favor. People are eating more at home, shopping for groceries more, and that triggered our pivot focusing on direct consumers. But now, it’s perfectly in line with our strategy on how we go to market. As long as we can supply our customer needs we’ll be on the right path. Nothing but bright hopes for the future right now,” Megan affirms.
For more information:
Planted Detroit
Megan Burritt, Managing partner
megan@planteddetroit.com
www.planteddetroit.com
Author: Rebekka Boekhout
© VerticalFarmDaily.com
IDTechEx: How to Succeed in Vertical Farming
Vertical farming is an emerging technique within agriculture that involves growing crops indoors under controlled environmental conditions
NEWS PROVIDED BY IDTechEx
May 26, 2020
BOSTON, May 26, 2020,/PRNewswire/ -- Vertical farming is an emerging technique within agriculture that involves growing crops indoors under controlled environmental conditions. By carefully tailoring the environment to the exact requirements of the crop, such as through using LED lighting to produce the exact light spectrum needed for optimal photosynthesis, it is possible to obtain yields hundreds of times higher than traditional agriculture.
Vertical farms can be set up almost anywhere, making it possible to grow crops in the middle of populous urban centers, meaning that it is possible for crops to reach consumers within minutes of harvest. This contrasts with traditional agriculture, where fresh produce can take weeks to reach consumers, losing the freshness, and increasing contamination risk along the way. The recent IDTechEx report, "Vertical Farming: 2020-2030" explores the technologies and markets around the fast-growing vertical farming industry.
Vertical farms use artificial lighting and carefully controlled climates to grow crops at far higher yields than conventional agriculture. Source: Intelligent Growth Solutions (PRNewsfoto/IDTechEx)
Vertical farming has been the subject of a lot of hype in recent years, with supporters claiming it could revolutionize food production. Industry advocates, such as Columbia University Professor Dickson Despommier, have presented visions of a future world where fresh food is grown inside skyscrapers to feed giant, high-tech metropolises (for further visions of the cities of the future, see the IDTechEx report, "Smart City Opportunities: Infrastructure, Systems, Materials 2019-2029"). Investors are also feeling the hype, with vertical farming start-ups raising over a billion dollars in investment in the last five years alone.
However, despite this optimism, the industry does face some major challenges and the sector has more than its fair share of bankruptcies. PodPonics, once the most well-funded vertical farming company in the world, and FarmedHere, which once operated what remains the largest vertical farm ever built, both went bankrupt. David Rosenberg, Chief Executive of New Jersey-based vertical farming outfit AeroFarms, recently said he wouldn't be surprised if 90% of the players in the industry went out of business within the next three years.
Broadly, many vertical farms struggle for the same reasons. As well as costing a lot of money to set up, vertical farms can be very expensive to run, largely because they require continuously running artificial lighting and climate controls. This is compounded by high labor costs and logistical difficulties that often get more difficult as the vertical farm gets larger. This all makes it very difficult to compete on price with produce grown on conventional farms, which typically have razor-thin profit margins.
Because of these challenges, vertical farmers generally only grow crops where the whole of the plant can be consumed, in order to maximize space efficiency and avoid wasting energy on growing inedible stems and leaves. Therefore, almost all vertical farmers are restricted to growing herbs and leafy greens. These are still a large market but fall somewhere short of the lofty claims made by some supporters of the industry.
It is certainly possible to run a successful vertical farming business, as fast-growing players such as Bowery Farming and InFarm will attest to, however, it requires a carefully planned out strategy and consideration of all the variables and trade-offs involved in vertical farming, in addition to a fair amount of investor capital.
The keys to success in vertical farming are outlined in the recent IDTechEx report, "Vertical Farming: 2020-2030". The report discusses several factors that can contribute to the success or failure of a vertical farm, including:
Whether or not to automate. Automation can significantly reduce labor costs while streamlining the logistical processes. However, investing in advanced automation equipment can lead to extremely high start-up costs.
Choice of crops. Should vertical farming try to branch out beyond leafy greens, or should it corner the market it has? What about higher-value crops inaccessible to conventional agriculture?
How large is too large? Larger centralized facilities could lead to economies of scale but could also face spiraling logistical difficulties. However, smaller localized facilities may face much higher start-up costs relative to the output capacity.
The importance of location: is a city center location really the best place to set up a vertical farm?
The need for experience in the food industry. Crops are living organisms and are not always predictable. Despite this, there is a relative lack of food and agriculture experience in the vertical farming sector.
For more information on this report, please visit www.IDTechEx.com/vertfarm or for the full portfolio of Food & AgTech research available from IDTechEx please visit www.IDTechEx.com/research/agtech.
IDTechEx guides your strategic business decisions through its Research, Consultancy and Event products, helping you profit from emerging technologies. For more information on IDTechEx Research and Consultancy, contact research@IDTechEx.com or visit www.IDTechEx.com.
Media Contact:
Jessica Abineri
Marketing Coordinator
press@IDTechEx.com
+44-(0)-1223-812300
SOURCE IDTechEx
How A Winnipeg Company Wants To Change Agriculture
Conviron has provided plant growth chambers and technology to the top government research agencies, universities and AgBiotech companies in over 90 countries around the world
Here are some other interesting tidbits about Conviron. Founded in 1964 by the Kroft family, CEL Group of Companies is headquartered in Winnipeg, MB. CEL comprises Conviron Canada, USA and Australasia. It also includes Argus Controls, a supplier of plant-centric environmental controls and automation systems used in greenhouse and indoor growing facilities.
Conviron has provided plant growth chambers and technology to the top government research agencies, universities and AgBiotech companies in over 90 countries around the world.
CEO Steve Kroft, often refers to his company’s solutions as 'weather in a box' because they mimic outside conditions and changing seasons over time through the automated control of temperature, light, humidity, irrigation and nutrients. In effect, it's a specialized type of high-tech greenhouse or indoor farm with environmental factors that can be precisely controlled.
The company has also delivered equipment to biotech companies like Medicago for the incubation and germination of tobacco plants critical for their research into plant-based vaccines for Ebola and SARs. Medicago recently announced it has produced a virus-like particle of the novel coronavirus, a first step towards producing a vaccine, which will now undergo preclinical testing.
Chambers range in size from six sq. ft. to over 2,000 sq. ft. depending on the application and includes lighting, temperature and humidity systems as well as a user-friendly control system to create and manipulate any kind of climate regime.
Argus Controls makes controlled environments for plant growth. It provides systems that automate the monitoring and controlling of all horticulture operations through on-site, remote and mobile interfaces.
Dating back to the early 1990s, Conviron has provided NASA with several chambers to support its research related to growing plants in outer space. The University of Guelph uses Conviron chambers and Argus controls systems in their high-tech facility in their research aligned with the Canadian Space Agency and International Space programs.
Since 2005, the National Science Foundation's Amundsen-Scott South Pole Station in Antarctica has been using an Argus control system to operate its food growth chamber that provides fresh vegetables and some much needed light, humidity and green space for the staff and scientists who winter at the station. The system operates the lighting, temperature control, and hydroponic nutrient feeding systems in the chamber, which is programmed and managed remotely from the University of Arizona.
Researchers at University College Dublin in Ireland can reconstruct prehistoric atmospheres using Conviron chambers and investigate plant evolution throughout Earth's history.
When canola was first developed in the 1970s, part of the research was done in Conviron chambers. Canola is the world’s only “Made in Canada” crop. In response to the ban of trans-fatty acids in food products, canola was developed by researchers from Agriculture and Agri-Food Canada and the University of Manitoba in the 1970s, using traditional plant-breeding techniques.
Some of the turf used around the greens at Augusta National Golf Club was also developed in Conviron equipment.
Source: Economic Development Winnipeg.
Publication date: Fri 22 May 2020