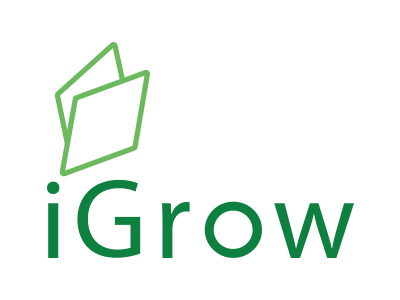
Welcome to iGrow News, Your Source for the World of Indoor Vertical Farming
Indoor Ag Sci Cafe Talks About Propagation And Transplants
This presentation ‘Precision Indoor Propagation for High Quality Transplants’ was given by Dr. Ricardo Hernandez (North Carolina State University) during our 32nd cafe forum on August 3rd, 2021
August 5, 2021
This presentation ‘Precision Indoor Propagation for High Quality Transplants’ was given by Dr. Ricardo Hernandez (North Carolina State University) during our 32nd cafe forum on August 3rd, 2021.
Upcoming Cafes:
September 21st (Tuesday), 11AM Eastern – ‘Introduction to Aquaponics‘ by Dr. Paul Brown and Dr. Cary Mitchell (Purdue University)
October 26th (Tuesday), 11AM Eastern – ‘Vertical Farming – Past, Present and Future‘ by Robert Colangelo (Green Sense Farms)
November TBA
December 7th (Tuesday), 11AM Eastern – ‘Plant-Made Pharmaceuticals under Controlled Environment‘ by Dr. Nobuyuki Matoba (University of Louisville)
Interested in giving a talk to share your thoughts and experiences? Please contact Chieri Kubota
Babylon Micro-Farms Partners With Harvest Table, Providing Fresher, Hyper-Local Food Options To Top Universities Across America
Babylon Micro-Farms, the intelligent, accessible and market-leading indoor micro-farm company, is excited to announce their partnership with Harvest Table Culinary Group, the pioneering collegiate food service company.
July 30, 2021
Babylon Micro-Farms, the intelligent, accessible and market-leading indoor micro-farm company, is excited to announce their partnership with Harvest Table Culinary Group, the pioneering collegiate food service company. To kick off the partnership, Babylon installed their micro-farms in Harvest Table colleges and universities, including University of Virginia, Wake Forest University, Elon University, and Springfield College, serving over 40,000 students.
With the food hall climate continuing to evolve year to year, several universities are beginning to increase the amount of sustainable and healthy food options for their students across campus. Babylon is stepping in to help make university life more sustainable and healthy, with the installation of their micro-farms in the food halls. These micro-farms produce the freshest, high-quality selection of crops for kitchens to use in preparing their menus. Food from Babylon Micro-Farms is not only good for your health, but also for the environment, as they grow food locally with few pollutants, less water, food waste, and is pesticide free.
Harvest Table Culinary Group has a track record of culinary excellence, taking pride in their fresh and responsibly-sourced ingredients. President of Harvest Table, Mary Thornton comments, “Our partnership with Babylon Micro-Farms enables us to bring the Harvest Table effect to life for our students and their guests across the country. As we return to a new normal in the fall, there is a ripe opportunity for collaboration with student groups to further support the cause of local foods.”
Since 2017, Babylon Micro-Farms has delivered a simple, yet engaging indoor growing experience, helping companies such as hospitals, senior living communities and universities showcase their commitment to providing fresh, nutritious produce and sustainability to their students and other customers. The goal through their on-site farming service is to make growing simple for anyone. Babylon is the most affordable, efficient, and advanced vertical farming platform available, remotely managed through the cloud with unparalleled customer service. To date, the company operates a network of 45 farms in the Mid-Atlantic region of the USA with a further 106 farms due to be installed by Q1 2022.
Babylon’s CEO, Alexander Olesen shares, “Harvest Table represents the thought leader in the education space and we're extremely happy to partner with them. This partnership demonstrates how we can grow at scale and this is the first step in our plan to get into as many universities as possible.”
What’s Real And What’s Hype With Controlled Environment Agriculture?
The flourishing development of Controlled Environment Agriculture and how retailers and consumers view this emerging segment of fresh produce production will be the topic of an educational session at Organic Produce Summit 2021.
July 27, 2021
The flourishing development of Controlled Environment Agriculture and how retailers and consumers view this emerging segment of fresh produce production will be the topic of an educational session at Organic Produce Summit 2021. The Growth of CEA—What’s Real and What’s Hype from a Retail and Consumer Perspective will feature leadership from a pair of recognized retailers and one of the fresh produce industry’s most progressive grower-shippers, offering their insight on how indoor-grown fresh produce items come to market, pricing and marketing challenges, and how consumers are reacting to them.
Moderated by Walter Robb, former CEO of Whole Foods, the session is the second of a two-part educational series at OPS offering a retailer and consumer perspective on the growth of indoor growing. Among the topics to be discussed in the session are the impact of indoor-grown products on the supply chain, the messaging and labeling of these various items, and the ramifications of what CEA production means for the organic fresh produce industry.
Panelists for the session include Frances Dillard, vice president of brand and product marketing at Driscoll’s; Victor Savanello, vice president produce and floral at Spartan Nash; and Shawn Peery, vice president produce and floral at Albertsons.
Production of fresh produce in CEA has become a $100 billion-plus industry, showcasing how growing indoors uses less water and no pesticides, while incorporating innovative and efficient technologies to provide fresher produce to consumers. “CEA is changing the landscape of food production and providing consumers a variety of new items that will continue to evolve in the years ahead,” said Susan Canales, president of Organic Produce Summit. “OPS attendees will have the chance to hear from retail leadership on how these products are marketed and learn about the challenges and opportunities these new items offer consumers.”
This second educational workshop follows a session exploring the growth of CEA from leaders actively involved in the production of indoor growing. The panelists for the first session include Philip Karp, president of Shenandoah Growers; Marc Oshima, co-founder of AeroFarms; and Caitlin Tierney, director of business development for Mastronardi Produce.
“Indoor agriculture is increasingly playing a more meaningful role in our fresh produce supply, in terms of volume, variety, and geographical footprint,” said Robb. “The ability of indoor ag to provide predictability and resiliency for supply, coupled with its lower impact on both the environment and resource use, is drawing substantial interest from both investors and consumers. Clearly, the future will be a hybrid one and our panels will explore how quickly and responsibly this will happen.”
Organic Produce Summit 2021 is a live and in-person two-day event specifically designed to bring together organic fresh produce growers, shippers, and processors with retailer and buying organizations from across North America. Over 1,000 attendees will meet Sept. 15-16 in Monterey, CA, to exchange ideas, information and insights into the organic fresh produce industry.
In addition to the educational sessions focused on CEA, a session looking at the organic industry in a post-COVID-19 environment and a keynote presentation by Jim Donald, co-chairman of Albertsons, have also been announced. OPS 2021 also includes a selection of field tours for retailers and buyers, a gala opening night reception, and a sold-out trade show floor featuring over 150 producers and processors of organic fresh produce from across North America and the globe.
SINGAPORE: High-Five: Developing “The World’s First Vertical Aquaculture Farm”
Singapore-based entrepreneur John Diener is committed to developing a series of urban aquaculture facilities that are able to produce shrimp, whitefish and seaweeds in high tech five-story farming systems
by Rob Fletcher
24 November 2020
Singapore-based entrepreneur John Diener is committed to developing a series of urban aquaculture facilities that are able to produce shrimp, whitefish, and seaweeds in high tech five-story farming systems.
John Diener aims to produce shrimp, tilapia, and seaweeds in five-tier facilities that can be fitted into the footprint of a standard warehouse. © Akualogix
The last decade of Diener’s career has seen him involved in a number of aquaculture-related ventures, as well as agritech startups, and the concept of a completely novel farming system came to him in 2016 when he was researching how machine learning could benefit aquaculture during a part-time MSc in aquaculture at St Andrews University.
“I have a lot of experience in data science and I wanted to find out what would happen if you reassessed the whole concept of aquaculture,” he explains.
Diener’s research led him to believe that vertical farms using cutting-edge technologies had the capacity to produce – for their footprint – an impressive amount of seafood, making them suitable for urban settings.
Three pillars
Diener describes the development of the system as resting on three pillars – biological, mechanical and digital. The biological side relates to investigating the most productive integrated-multitrophic (IMTA) system, with vannamei shrimp as the primary species.
“The business plan has been developed around shrimp – they’re a unique product in terms of their flavour profile, much like salmon are, which makes it very hard to produce substitutes. And they can also be raised at high densities,” Diener notes.
“We’ve also incorporated a filter-feeding fish – we’re currently using tilapia because they’re very robust, but will probably trial milkfish too,” he adds.
The bottom of the IMTA pyramid is taken up by sea grapes – called umibudo in Japan, where they are considered something of a delicacy.
“These are known as ‘the green caviar’ in parts of Asia, so have the potential to be sold as food. They can also be used as an ingredient in shrimp feeds, as we’re aiming to produce our own, sustainable feeds, while they also help to remove nitrates and phosphates from the water,” says Diener.
Technology
The second pillar consists of the engineering, and Diener intends to develop raceway systems four or five levels high, which are equipped with modular autonomous devices to optimise factors such as measuring water quality. The third pillar relates to the digital side of operations.
“We’re investing time and effort to develop advanced technology to manage feeding – both in terms of studying shrimp behaviour so we know when to feed and in terms of measuring the biomass in the systems, so we know how much to feed. We will also be looking to manage the water quality by feeding information into a deep learning algorithm that can control factors like pump speeds and the addition of minerals to the water,” he says.
The digital side also covers the farm’s “Aqua OS” [operational systems], ensuring all the technology works together, to simplify the management of all the tanks, Diener explains.
Launch
John Diener, founder of Akualogix
Four years after coming up with the concept Diener launched his own company, called Akualogix, in August, after finding a suitable site for a pilot-scale facility, in a building owned by the Marine Aquaculture Centre, on St John’s island in Singapore. This will, he notes, be perfect for securing proof-of-concept, before he looks to expand into a commercial-scale facility.
Initially self-funded, by Diener and the company’s co-founder, they are now looking into securing pre-series A funding in order to build a larger scale production unit.
Funding opportunities have remained robust in the agri-food sector, despite the outbreak of Covid. And as our systems are designed for an urban environment, and food security is increasingly important in Singapore and other cities around the world, we see strong investor interest
“Funding opportunities have remained robust in the agri-food sector, despite the outbreak of Covid. And as our systems are designed for an urban environment, and food security is increasingly important in Singapore and other cities around the world, we see strong investor interest,” Diener reflects.
The current farm has – he predicts – the capacity to produce 500-600 kg of shrimp per cycle, but he’s not yet sure what the yields of the tilapia or sea grapes will be – pointing out that no one has undertaken a mass balance study in such a system.
A juvenile shrimp at the pilot facility in Singapore. © Akualogix
“Our business economics is based on shrimp – making any money from the tilapia would be the icing on the cake – but the main reason we have the fish is part of the multi-trophic system and benefit the overall environment, they’re part of the filtration system,” he explains.
We will be looking at establishing commercial farms that can produce in the region of 1,000 to 1,500 tonnes of shrimp a year. It might not sound like much compared to some of the commercial salmon RAS that are now being established, but if we’re operating 20 or 30 farms that would make us one of the biggest shrimp producers in the world
Next steps
Once the pilot facility has fulfilled its potential Diener aims to establish a farm – and ultimately a network of farms – that use Akualogix’s design and equipment, establishing partnerships in a range of countries, primarily in Asia, as the concept takes off.
“We will be looking at establishing commercial farms that can produce in the region of 1,000 to 1,500 tonnes of shrimp a year. It might not sound like much compared to some of the commercial salmon RAS that are now being established, but if we’re operating 20 or 30 farms that would make us one of the biggest shrimp producers in the world,” he points out.
Diener is also looking to develop a unique, sustainable feed that’s designed specifically for producing shrimp in RAS facilities.
“The current range of commercial shrimp feeds are not great for use in RAS, and we’re looking to produce a next generation shrimp feed using sustainable ingredients. And we’re looking for a flavour enhancing additive as a finishing diet – potentially one that comes from algae,” he says.
Given the technology involved and the emphasis on sustainable feed ingredients Diener is aware that production costs are going to be considerably higher than conventional shrimp farms.
“We estimate that our cost of production will be 40-50 percent higher than shrimp produced in a pond in, say, India. But we’re close to market and can charge a premium for a fresh product that’s so sustainably produced,” he says.
Operational experience
The pilot facility holds 30,000 shrimp per cohort and 1,000 tilapia. The former are housed in a two-stage grow-out system and he aims to take them from the end of the nursery stage to harvest in 60 days, while achieving survival rates of roughly 90 percent.
However, as Diener admits, the design concepts of the system are still evolving, and there are other issues that have caused setbacks.
“It turned out that our first batch of PL [post-larvae] had pathogenic vibrio and we started seeing mortalities related to vibriosis,” he explains.
It was an unfortunate start, but a useful reminder of the importance of biosecurity.
“We decided to implement a full biosecurity package [once operating commercially], which will include our own hatcheries to prevent the introduction of pathogens,” he says.
Should the pilot facility prove productive, and investment forthcoming, Diener then aims to roll out the concept across some of Asia’s most populous coastal cities.
“There’s currently a lot of investment in salmon RAS and I think shrimp are the next species to go in that direction. If we can be a pioneer of shrimp RAS it will be a game-changer,” he concludes.
Why We Believe Vertical, Urban Farming Can Help Save The Planet!
Conventional industrial farming contributes significantly to issues such as deforestation, biodiversity loss and the release of carbon emissions
Sophie | 2020
Our vertical, hydroponic farm based in Paddington, London.
Increasingly, we are all becoming aware of the negative impact of our food system on the environment. As individuals many of us are taking action to reduce the environmental impact of our diets, whether we’re reducing our meat and dairy consumption by trying out ‘meat-free Mondays’ or ‘veganuary’, buying zero waste foods, trying to buy more locally produced food or even growing our own.
Ultimately, we are looking for ways to minimize the negative environmental impacts of our food system. At Square Mile Farms, we believe that urban farming can play an important role in building a sustainable food system. Not only can we reduce food miles and prevent natural habitats from being converted for growing, we can also re-engage people to help them understand how food reaches their plates, which we believe is essential to enact real change going forward.
How does the current food system negatively impact the environment?
Conventional industrial farming contributes significantly to issues such as deforestation, biodiversity loss, and the release of carbon emissions. According to the Food Climate Research Network, the global food system is responsible for around 20-30% of greenhouse gas emissions. The WWF notes that food is responsible for 60% of global biodiversity loss and the UNFAO records that food production accounts for 70% of freshwater withdrawals.
The clearing of forests for livestock or growing crops is doubly concerning: not only do these practices have their own environmental impacts, e.g. methane emissions and issues related to fertilizer run-off, but they are also destroying forests which are important ‘carbon sinks’, absorbing approximately 2 billion tonnes of carbon dioxide yearly according to the UN.
Clearly, our current food system is flawed and this is only set to worsen as demands increase.
Infographic from: FCRN, ‘What is the food system’s contribution to the global GHG emissions total?’
Growing pressures on the food system
By 2050 the UN predicts the world population will grow to 9 billion: this is expected to require 60% more food and increase demand for water by 20% in the agriculture sector alone. So we need to find ways of making the food system more sustainable. We need to increase food production, while minimizing the environmental impact, or ideally making it negligible.
How can hydroponic farming in offices lessen the environmental impact of our food system?
We believe hydroponic, vertical farming is part of the solution to this issue. This method of growing food uses around 90% less water than conventional agricultural systems and can increase crop yields by up to 500%. So we can tackle two key problems in our current food system, the demand for water (by using considerably less) and the spatial impact (growing vertically allows a much more efficient use of space). By using existing urban spaces, such as workplaces, we can grow veg and herbs without converting more land for agricultural purposes.
Growing in offices also has the benefit of reducing food miles. By bringing food production to population centers, and further to that, by bringing it to people’s workplaces we are able to provide fresh produce where people are. If you’re taking home fresh produce once a week from work, there are virtually no food miles involved as you’d be traveling to and from work anyway!
Our office farm installations.
Another important way in which office farming can help improve our food system is by re-engaging consumers in cities. Writing for the World Economic Forum, Ellen MacArthur, a champion of Circular Economy, emphasized the important role cities will have in achieving a sustainable food system, especially because “80% of all food is expected to be consumed in cities by 2050”. She notes that cities should source food locally where possible and that they should avoid being “passive consumers” and instead, use their demand power to reward responsible farming practices. Office farming allows us to bring food production to the forefront of people’s minds, driving engagement, and encouraging conversation around our food system. We believe this is vital in order to educate and to inspire the change that we need to secure a sustainable future.
We believe that individual action is important when it comes to enacting change, but to achieve this we need innovative ideas that make it achievable for consumers to make such changes a reality. That’s why we bring urban farming to offices. We install farm walls and displays to improve employee wellbeing, drive engagement, and of course, provide fresh, nutritious produce. If you’d like to find out more about our offering click here.
You can also sign up for our newsletter to receive weekly tips and advice on sustainable living, as well as a round-up of relevant news.
Sources:
Bradley, P. and Marulanda, C., ‘Simplified Hydroponics to Reduce Global Hunger’, Acta Hortic. 554, 289-296.
Innovate UK, ‘Predictions - The Future of Food’.
MacArthur, Ellen, ‘Our food system is no longer fit for the 21st century’.
FCRN, ‘What is the food system’s contribution to the global GHG emissions total?'
UNFAO, ‘Water’.
UNFAO, ‘Water Use’.
UN News, ‘Climate Change’.
WWF, ‘Why we’re working on food’.
UNESCO World Water Assessment Programme, ‘The United Nations world water development report, 2016’.
IGS Senior Team Expands Further As Technology Innovator Welcomes Head of HR
Inverness-born Donald joins IGS following more than 23 years working with Michelin in Dundee where he started out as a Trainee Industrial Engineer before moving through various people management positions
Donald Mackenzie Joins Edinburgh-Headquartered
Firm To Help Build Growing Team
Edinburgh, Scotland – 14 September 2020 – Senior HR leader, Donald Mackenzie, has joined IGS, the Scottish-based agritech and smart spaces business, as Head of HR. His appointment is the latest in a series undertaken to grow the company’s management team as it continues to expand to supply a growing customer base across the world.
Inverness-born Donald joins IGS following more than 23 years working with Michelin in Dundee where he started out as a Trainee Industrial Engineer before moving through various people management positions. He brings a wealth of Human Resources experience, as well as skills across learning and development, community engagement, and communications in a technical environment.
Most recently, Donald was responsible for the social plan that supported 850 employees impacted by the Michelin Dundee site closure, including developing programs to re-train, relocate, and find alternative employment opportunities for all those individuals. On joining IGS, Donald’s role will see him support a rapidly growing team as the company moves onto a global stage, all the while maintaining its ethos of continuous innovation and investment into research and development.
Preparing for his first day in the role, Donald Mackenzie commented: “IGS seems like a natural fit for me. The people, the organization, and the outlook all appeal to me: it feels like a positive environment with loads of exciting opportunities. The whole company is about learning and growth and expansion, ultimately driven by-products that the team is fully behind and that really works.
“Obviously in a field like HR, the people side of a business is always the most important, and for me there’s a real human opportunity which has been created at IGS by the development of products that could fundamentally change the way that society and whole populations live. The possibility of developing solutions able to tackle the whole food security issue is really enticing.”
IGS CEO David Farquhar commented: “Being able to attract an HR professional with Donald’s perspective is a major win for IGS, as we look to employ new people and offer the best possible support to the immensely skilled crew we already have. We are at a very exciting point in our company history right now, and it has never been more important that we are best placed to attract, nurture, and develop highly talented people.
“We are delighted to have the opportunity to welcome someone of Donald’s caliber to join us, and strongly believe that his wealth of experience – particularly with organizational development – is just what we need as we look to the future of the business.”
Ends
Notes to editors:
For more information: please contact Georgia Lea, IGS on georgia@intelligentgrowthsolutions.com or call +44 7897 539 954.
About IGS:
Founded in 2013, IGS brought together decades of farming and engineering experience to create an agritech business with a vision to revolutionize the indoor growing market. Its commitment to innovation has continued apace and it has evolved the applications of its technology beyond agriculture to create solutions for a wide variety of indoor environments that enhance life for plants and people alike.
IGS launched its first vertical farming demonstration facility in August 2018.
For more information visit www.intelligentgrowthsolutions.com or connect with us on Twitter and LinkedIn.
Scottish Agritech Firm Has The World In Its Sights With Appointment of Global Projects Director
Kathleen Honeyman joins IGS to drive vertical farm implementation worldwide
Kathleen Honeyman joins IGS to drive vertical farm implementation worldwide
Edinburgh, Scotland – 01 September 2020 – Edinburgh-based agritech and smart spaces business, IGS, has welcomed Kathleen Honeyman to its management team as Global Projects Director. Her appointment marks a significant step-change in the company’s development as it moves to deliver vertical farms to customers around the world.
The new role will see Kathleen take overall leadership of the successful delivery of each IGS-built vertical farm worldwide, engaging closely with our deployment and supply chain partners. Kathleen will build an international team of project managers to ensure the resource and skills within IGS to deliver extremely precise systems to a very high-quality threshold.
South African-born Kathleen has lived in Scotland for more than 18 years. She joins IGS from Edinburgh Airport where she was Senior Project Manager, taking overall responsibility for the end-to-end management of all IT Projects including a variety of strategic operational, financial, and compliance-specific assignments. Prior to that, she held project management roles at Royal Bank of Scotland and Scottish Water.
Reflecting on her decision to join IGS, Kathleen commented: “The chance to be part of this exciting sector, in a company as innovative and forward thinking as IGS, is an opportunity that I am delighted to accept. The team is ambitious and excited about its future ambitions, not just in the deployment of our solutions, but also the wider impact of supporting globally sustainable food supply chains. My role will be heavily focused on meeting those ambitions – something I am really proud to be able to support.”
IGS CEO, David Farquhar, continued: “Kathleen is a strategic hire for IGS and we’re delighted to have her join the team. We are currently facing what is simultaneously the most exciting and challenging phase of IGS’ history to date: rolling out our vertical farms to customers across the globe. Having a person of Kathleen’s calibre and experience to help drive our deployments forward, utilising globally recognised best practice, will provide confidence to our customers in committing to buying IGS farms. In turn, this will help support the supplier commitments to their off-takers.
“As an organisation, we’ve always prided ourselves on going above and beyond, continuously innovating and never resting on our laurels, and we want our customers to know that the same applies to the way in which we deliver farms in the field. Kathleen is ideally qualified to help us continue to deliver outstanding service on a global scale.”
About IGS:
Founded in 2013, IGS brought together decades of farming and engineering experience to create an agritech business with a vision to revolutionize the indoor growing market. Its commitment to innovation has continued apace and it has evolved the applications of its technology beyond agriculture to create solutions for a wide variety of indoor environments that enhance life for plants and people alike.
IGS launched its first vertical farming demonstration facility in August 2018.
For more information visit www.intelligentgrowthsolutions.com or connect with us on Twitter and LinkedIn.
Indoor Growing vs. Traditional Greenhouse Growing
Indoor growing offers some sustainability benefits because considerable savings can be made on water, nutrients and use of pesticides
Today, in theory, there is enough food on the planet to feed approximately 12 billion people, but the way it is distributed around the world is inefficient and unsustainable. As food is transported across the entire globe, its shelf life or freshness tends to deteriorate considerably and a lot of food often goes to waste. Indoor growing is a step closer to a new situation – one in which it is possible to grow locally produced, fresh food all year round, regardless of the weather and external conditions. It may even enable us to change the face of the food industry.
However, this requires a different way of thinking. “Indoor growing is different from growing in a greenhouse in several ways,” says Fred Ruijgt, Market Development Indoor Growing. “In an automated, glass greenhouse you have to deal with external influences such as wind, rain, and sun. These variables need to be managed as effectively as possible, with or without additional technology. The grower is constantly working to achieve a stable climate for the crop. Indoor growing allows you to create your own optimal climate. The grower determines the growing conditions, from light level to air circulation.”
Fred Ruijgt
Comparing apples with oranges
According to Fred, many investors try to compare indoor growing with traditional horticulture. “In terms of investment and profitability, it is difficult to compare them,” he says. “It’s like comparing apples with oranges. It’s important to understand the differences between traditional horticultural practices and indoor growing. You can’t simply calculate what a greenhouse yields per square meter and compare it to an indoor farm. In a greenhouse you have to consider the crop cycle and in which months you can harvest and thus what you can supply to your customers. With indoor growing you can supply all year round, creating more opportunities to reach supply agreements with customers. But you also need to invest.
Indoor growing offers some sustainability benefits because considerable savings can be made on water, nutrients and use of pesticides. But, compared to a traditional greenhouse, much more artificial lighting is required. Also, the location and local sales potential should be included in the comparison. After all, a traditional greenhouse is not even an option in some countries, whereas in the Netherlands, for example, it probably costs two to three times more to grow fresh produce in an indoor farm than it does in a greenhouse.” Another difference is that traditional horticulture has traditional sales channels such as auctions, traders and cooperatives. That’s not the case with indoor growing – it’s more important to understand and collaborate with the entire chain.
Food security and food safety
The fact that indoor growing doesn’t have traditional sales channels is precisely what makes it special. “Indoor growing is clean and pesticide-free, resulting in high-quality and plannable production. An indoor farm can also be built in urban areas, which means that there’s always fresh, locally grown produce available for consumers. The product is often shipped directly from the indoor farm to, for example, the supermarket, so the route to the consumer is shorter. Therefore, in the case of indoor growing, it is important that the facility is an integrated part of the total chain: from suppliers to customers. That keeps the route nice and short,” continues Fred.
An indoor farm can be situated anywhere in the world and in any type of climate, whereas it is often not possible to build a greenhouse in certain areas. Fred: “In Singapore, for example, no more greenhouses can be built because there’s no agricultural or horticultural land available. An indoor farm offers a solution because it can be set up inside an existing building. This is an efficient alternative and it greatly reduces the dependence on food imports.”
Down to the consumer
The technology has already been proven in a number of large-scale indoor growing projects. So why isn’t this way of growing more common? “That’s because of several factors,” explains Fred. “Right now, indoor farms are mainly being integrated into existing retail chains. In addition, the demand largely comes from areas with a high average income. The existing retail chains have a vision and they always want to deliver good-quality products, so it makes sense for them to invest in this. But what are consumers prepared to pay for a fresh head of lettuce, for example,? If consumers start to value fresh and good-quality food more, entrepreneurs will be more willing to invest in a more sustainable way of producing food.”
For more information:
Priva
www.priva.com
contact.priva@priva.nl
Publication date: Tue 18 Aug 2020
VIDEO: IGS Intelligent System Design – FTS Finds Out More
IGS has, as a company, focused from the outset on automation, intelligent system design, and the energy equation of CEA vertical farming
July 6, 2020
IGS has, as a company, focused from the outset on automation, intelligent system design, and the energy equation of CEA vertical farming. This has garnered them a reputation as one of the leading and most innovative companies in the industry. We took some time to have a chat with them and find out a bit more about how this all works in practice.
FTS: Hello and thanks for taking the time to talk with us. Can you briefly introduce IGS, its history as well as its outlook?
IGS: IGS was founded in 2013 bringing together decades of farming and engineering experience with a vision to revolutionize the indoor growing market. The two founders, farmer Henry Aykroyd and our CTO Dave Scott had an appetite for innovation and realized that there were significant gaps in the provision of scalable technology for the sector.
Henry knew how to grow and understood the challenges which faced traditional farming: Dave knew how to manage automation and power controls in an industrial environment. The opportunity to bring greater climate control to a growing environment was significant. The ability to manage power consumption was revolutionary. The simplicity of its implementation and use is pivotal.
We opened our first vertical farm demonstrator in Scotland in 2018. Artificial intelligence determines optimal nutritional input and the exact combination or ‘recipes’ of weather: lighting, watering, and ventilation. Data is collected continuously and machine learning used to make iterative adjustments, all of which is monitored through a web-based app. The whole Intelligent Growth platform is IOT-enabled to automate system control and management. Our degree of control is so fine that each 6m2 growth tray has its own microclimate. Technical simplicity is at the heart of our mechanical design.
Our commitment to innovation has continued apace and we have evolved the applications of our technology beyond agriculture to create solutions for a wide variety of indoor environments, developing the Intelligent Grid platform.
The Intelligent Grid uses the same IOT-enabled power and controls platform to manage and monitor lights, sensors, cameras, and communications for complete climate control and reporting. It too has a very simple, clean, and elegant design for application in any commercial building, greenhouse or livestock shed. In contrast to the vertical farm, we use our same core technology through the Intelligent Grid to create whole-space macroclimates.
Both IGS demonstrators are based at the James Hutton Institute, a world-renowned crop, and plant science research facility. IGS and the Hutton collaborate closely to help advance the understanding of plant science for indoor growing.
Until 2018 IGS had invested approximately £7m in R&D to ensure that its platforms offered the greatest levels of control and achieved levels of economic viability, scale, and minimal environmental impact compared to other systems on the market. In 2019 IGS raised £7 million in institutional capital to enter production and take its systems to global markets. We continue to invest over £1m per annum in R&D.
FTS: You have recently shared news of two reseller partnerships – one in the Middle East and one in the UK and Italy with TEP Renewables. Can you tell us briefly a bit more about them?
IGS: We have been talking to International Real Estate Partners (IREP), the international facilities management firm for some time in the Middle East, and we’re really pleased to recently sign this referral agreement which is specifically focused on indoor vertical farming for the UAE and Saudi Arabian markets.
We also have an opportunity to extend into Asian markets in the future. It gives us a greater capacity to service the Middle East market and secure and deploy vertical farming platforms across the region. IREP’s presence in this market is well established with many existing customers across agriculture, retail, and construction and it is a very positive development for both companies we believe.
The agreement with TEP Renewables is an MOU (Memorandum of Understanding) or a reseller-type partnership if we identify customers who would like to operate solar-powered vertical farms in Italy or the United Kingdom that we will work with them.
FTS: Fantastic! In the end, any vertical farm (indeed any farm!) is only as environmentally sustainable as its energy equations. But it is also only as financially sustainable as its energy cost. You have focused quite intensely on this energy cost question. As we see this dramatic collapse of fossil fuel energy production return on investment, it seems that NOW is the time to have renewable energy options on hand for CEA. Do you believe that renewable energy can be cost-competitive – both in terms of installation, sustainable life-cycle and with regard to the price of the final product for the consumer?
IGS: We consider a variety of power distribution and supply methods. Renewables can have considerable benefits from an environmental perspective and also specific to grants and other financial support for utilizing renewable energy resources.
The “virtual power plant” capabilities of our systems indicate strong Demand Side Response (DSR) potential. We can manipulate our growth cycles to respond to power availability and respond to inherent instabilities in power networks. This is already having an influence on our engagement in circular energy projects to utilize spare energy for growing and allows for more renewable power sources to be adopted.
FTS: Labor cost is the other biggest outlay for any vertical farm. You have invested heavily in automation. Is the trade-off of increased capital expenditure for automation worth the reduction in operational expenditure for labor, in your experience?
IGS: Absolutely. Driving down the farm gate price is the ultimate goal and while labor costs vary from region to region, we believe that this investment in the automation (and indeed the associated patents) within our growing operations is imperative and differentiates our systems considerably.
FTS: You’ve set about designing modular and intelligent systems. Such a bespoke system offers advantages of course, as we’ve seen above. But it can also present challenges if it cannot be integrated with other equipment and systems later. Do you future-proof your systems to be able to accommodate such updates and integrations over time?
IGS: We have thought about this from the outset, and our systems are designed in a plug and play model, rather than being bespoke as such. Scalability is paramount for our customers and this has been a consideration throughout our R&D development. Rather than using proprietary systems for processes such as sowing and harvesting, we use off-the-shelf equipment and components. This means we can keep startup and maintenance costs down by providing items with which farmers are already familiar. If a section of the vertical farming system needs to be replaced or upgraded, such as a water filter, a lighting panel or a tray, it can be done with almost no interruption.
However, what is also imperative to think about in terms of future proofing, and a hugely important part of our approach, is how we work so closely with the science community to better understand plant light interactions. The level of control we have designed into our hardware systems allows us to flex and adapt as we need to deploy the most up to date plant light information through our software development, which is continuously evolving.
The approach of our software development has also involved maximising security of our systems and ensuring simplicity of operation. This will be continuously updated, but with seamless integration for our customers.
FTS: Along with FTS, you’ve joined a number of other associations and similar collaborative groups. Why is this important to you as a company, and how do you balance the proprietary needs of your company against this desire to cooperate?
IGS: Collaboration and cooperation across this sector is essential. Our vision is that sustainable change will only be delivered not only when we collaborate, but when we are all open and honest about the limitations, as well as the opportunities for this sector. We want to work alongside technology vendors with complementary products, and with growers and producers, supported by science and greater understanding of growing plants indoors, all backed by far-sighted investors.
We firmly believe that through innovation, collaboration and investment we can create an economically and environmentally sustainable global indoor food industry.
FTS: Thanks so much for taking the time to talk with us today. We wish you every success and look forward to working with you in the future.
IGS: Thanks very much indeed. We look forward very much to be part of Farmtech Society as we all move forward in the development and innovation of agricultural technology.
For IGS
David Farquhar
CEO
Clima - Digital Publication and Podcast Launched by Agritech Specialist, IGS
Thought leadership brought to you by IGS. Sustainable Food Security - is a global supply chain a thing of the past?
Indoor agritech specialist IGS has launched Clima, its new digital publication and accompanying podcast series. Through Clima, IGS will welcome industry-leading interviewees and share thought pieces on some of the most fundamental issues facing the world, including supply chains, agricultural innovation, and indoor growing.
About IGS:
Founded in 2013, IGS brought together decades of farming and engineering experience to create an agritech business with a vision to revolutionize the indoor growing market. Its commitment to innovation has continued apace and it has evolved the applications of its technology beyond agriculture to create solutions for a wide variety of indoor environments that enhance life for people, plants, and animals.
IGS launched its first vertical farming demonstration facility in August 2018, based at the James Hutton Institute in Invergowrie.
To subscribe to Clima and to access the first edition, please visit www.igsclima.io.
For more information visit www.intelligentgrowthsolutions.com or connect with us on Twitter and LinkedIn.
The Indoor Farm Revolution
Coronavirus chaos has spurred a grow-your-own food movement — and space-age hydroponic technology is rising to meet it.
Coronavirus chaos has spurred a grow-your-own food movement — and space-age hydroponic technology is rising to meet it.
NOTE FOR 2020 READERS: This is the eleventh in a series of open letters to the next century, now just 80 years away. The series asks: What will the world look like at the other end of our kids' lives?
Dear 22nd Century,
For all the pain, grief and economic hardship the 2020 coronavirus pandemic has sown, a handful of green shoots seem to have taken root in its blighted soil.
Green being the operative word, because many of these developments could be a net positive for the planet. In lockdown, many of us are seeing what our cities look like without smog. Office workers are experiencing office life without the office; just last week, Twitter announced that most of its employees could work from home forever, while much of Manhattan is reportedly freaking out about what could happen to commercial real estate. Thousands of companies just discovered they can still function, and maybe even function better, when they don’t chain employees to desks or force them to make a soul-crushing, carbon-spewing commute 10 times a week.
And what do more people do when they’re spending more time at home? Well, if you’re like my wife, you start literally planting green shoots. Our house is filling up with them as I write this: lettuce, chard, tomatoes, basil, strawberries, to name the first five shoots poking out of dozens of mason jars now taking up residence on every windowsill. She’s hardly alone; garden centers and seed delivery services are reporting as much as 10 times more sales since the pandemic began. Even the mighty Wal-Mart has sold out of seeds. If viral Facebook posts and Instagram hashtags are any guide, pandemic hipsters have moved on from once-fashionable sourdough starters to growing fresh fruit and veg.
Another one of our cyclical “back to the land” movements seems to be underway, just like during the 1960s and the Great Depression before that. Only this time, we don’t need land. We don’t need soil. We don’t need pesticide of any kind. We don’t even need natural light. Thanks to giant leaps forward in the science of hydroponics and LED lighting, even people in windowless, gardenless apartments can participate in the revolution. With a number of high-tech consumer products on the way, the process can be automated for those of us without green thumbs.
In previous letters I’ve discussed the inevitable rise of alternative meat, a process that has been accelerated by the pandemic. I talked about the smaller, more nutritious plant-based meals we're going to need for life extension; I assumed such meals would be delivered by drone. But now I see a future with no food deserts, in which every home is filled with rotating space-station-like hydroponics run by artificial intelligence — a cornucopia of push-button farming providing the side salad to your plant-based meat.
Even if you don’t grow your own, robot-run vertical farms and community “agrihoods,” now springing up everywhere, will make amazing-tasting produce abundant and cheap. The “locavores” of our era like to boast about their 100-mile diet. Yours will look more like a 100-yard diet.
Green, not soylent
It’s worth remembering that it wasn’t supposed to be this way. The 2020s, in fact, is when we were slated for starvation, food riots, and big business quietly processing our corpses into food.
That’s the plot of the 1973 movie Soylent Green, set in the year 2022. Fruit and veg have all but vanished. In one scene, Charlton Heston's detective hero smuggles home a single tomato and a wilted stick of celery, enough to reduce his roommate Sol (Edward G. Robinson) to tears. On the other end of the future, in a lighter but equally depressing vein, the 2006 comedy Idiocracy showed the Americans of 2500 running out of crops because they couldn’t figure out that water, not "Brawndo" (a spoof on colorful sports drinks), is “what plants crave.”
But these dismal future visions are receding thanks to the science of hydroponics — which dates back to the 19th century, no matter its present-day association with growing marijuana. By the 1930s, we’d figured out that what plants crave is surprisingly minimal: nitrogen, a handful of minerals, something to anchor the roots like rock wool or coconut husks, and H2O. Early hydroponic farms helped feed U.S. soldiers as they hopped through the Pacific during World War II.
Minimalist methods multiplied, and are still multiplying. We’re tweaking the spectrum of LED lights for maximum growth, and figuring out ways to use progressively less water and nutrients. My wife’s mason jar seedlings use something called the Kratky method, where you don't even need to change the water. It turns out this method was invented by a Hawaiian scientist as recently as 2009. And it’s the closest science has yet given us to a free lunch.
Reinventing the wheel
I’m nowhere near as excited by hydroponics as my wife is. But during our quarantine time, even my head has been turned — by the Rotofarm, which I’ve come to think of as the iPhone of gardening. It’s a beautiful device inspired by NASA research on growing plants in space. It uses anti-gravity — literally, when the wheel rotates around its LED light source and the plants are hanging upside down — to grow plants faster. A magnetic cover reduces the glare and increases the internal humidity. You manage it via an app.
Humankind’s oldest technology turns out to be the most efficient use of space for growing plants; even in this 15-inch-wide wheel, you can really pack them in. At the bottom of the wheel, plants dip their roots into the water and nutrient tanks. An owner’s only job is to refill the tanks every week or so, and to snip off their dinner with scissors a few weeks after germination. Some leafy greens, like my favorite salad base arugula, can be regrown without replanting.
Still, to be fully self-sufficient, a future apartment is going to need to have multiple Rotofarm-style devices on the go at once — but they’re designed to live anywhere you can plug in, on coffee tables, on desks, on walls, as eye-catching as artwork.
The main problem with the Rotofarm: It isn’t actually on sale yet. “It feels like we’ve done everything in reverse,” Rotofarm creator Toby Farmer said when I reached him via video chat from his home in Melbourne. “We’ve got the patents, we’ve got the design awards, we’ve got the customers. Now we need to finish the prototypes.” (One key tweak: reducing Rotofarm’s energy requirements, which as it stands could double many users’ household electricity bills.)
Still, orders have come from as far afield as Japan and the Netherlands, from retailers and regular users alike. Farmer’s biggest regret: When Ron Howard’s production company called, hoping to use eight Rotofarms in an upcoming Nickelodeon show set in space, Farmer didn’t have enough to spare.
Rotofarm has been in the works for a few years, but a crowdfunded Indiegogo campaign that closed last month exceeded its $15,000 goal by a third of a million dollars. Farmer, despite his name, had no experience in this area; just 23 years old, he had been a web designer since the age of 12. But he’s scaling up fast, hiring teams in LA and Singapore, soaking up their knowledge (he was keen to assure me he’d hired a lot of 40-somethings for this very reason).
After a projected 2021 release date, Rotofarm’s business model involves making money on proprietary seed pods — though Farmer admits that “there’s a DIY aspect” where customers can make their own. His hope is that official Rotofarm pods will be competitive because they’ll have fewer germination failures, but he'd rather see a world where more people own the device itself. In that spirit, he’s making it modular — the LED light bar can be upgraded separately, for example, rather than making customers buy a whole new device. (As for cost, Farmer says he can't comment yet — though Indiegogo backers were able to secure one for $900 a pop.)
Might the Rotofarm fail? Of course, just like any other crowdfunded project. Much depends on its price point, as yet unannounced. But it’s far from the only next-level, set-it-and-forget-it hydroponic station taking aim at your kitchen. There’s a Canadian Kickstarter called OGarden that also grows food on a wheel, albeit a much larger wheel. The OGarden was funded in its first six minutes online and is set to cost around $1,000 per unit. There’s Farmshelf, a $4,900 pre-order hydroponic device that looks like a see-through refrigerator, backed by celebrity chef Jose Andres. Users will pay a $35 monthly subscription to get all the seeds they need.
One of these models is the future; maybe all of them are. Right now, these are high-end devices aimed at early adopters (and restaurants, which get a lot of benefit out of showing off how fresh their produce is as customers walk-in). But with scale, with time, and with the growing desire for grow-your-own food that Rotofarm and its brethren have revealed, they will get cheaper and more widespread.
After all, the first Motorola cellphone, in 1983, cost $4,000. It looked like a brick and had 30 minutes of talk time. Now sleek, supercomputer-driven smartphones are accessible to pretty much everyone. The same process will happen in-home hydroponics.
Rise of the vertical farm
Give it 80 years, and I can see apartments with built-in hydroponic farms provided as a standard utility, much as a fridge is seen as a standard feature today. As more humans move to urban environments — two out of every three people will be in cities by 2050, according to the latest UN estimate — the need for such devices will only grow.
“We strongly believe the future of gardening is indoor gardening and more individual gardens,” OGarden CEO Pierre Nibart told us last year. “Stopping mass agriculture and starting to produce their own little stuff at home.” He said this while demonstrating his family's daily OGarden routine: His kids harvest most of what they need for dinner from the spinning wheel.
Mass agriculture hasn’t exactly covered itself in glory where produce is concerned. And in the post-coronavirus age, we are surely going to become less tolerant of the disease its intensive farming methods have caused.
Food poisoning caused by romaine lettuce, which makes up a quarter of all leafy greens sold in the U.S., has become depressingly familiar. The 2018 E Coli outbreak was the worst — it sickened 240 people in 37 states, hospitalized almost half of them, and killed five. But the CDC has logged 46 E Coli outbreaks since 2006 and says that every reported case of infection is likely matched by 26 unreported ones. And they’re only just starting to figure out the most likely cause: groundwater contaminated by nearby cattle manure. There could also be an infection from passing birds, another major vector of bacteria.
Never mind the wet markets of Wuhan that likely caused the coronavirus pandemic. We’re already sickening ourselves on the regular with a problem that is baked directly into our food system — and it’s affecting vegans as much as meat-eaters.
I have no doubt you’ll look at our barbaric farming methods and shake your heads. Why did they use so much water? Why did they transport produce an average of 1,500 miles? Why did they grow it outdoors, where it’s vulnerable to pests, and then use pesticides that had to be washed off? Why did they think “triple washing” did anything to remove bacteria (it doesn’t)? Why did they bother using soil, for goodness’ sake? Didn’t they know what plants crave?
The force of legacy agriculture is strong, but an increasing number of companies are figuring out a better way: the vertical farm, so named because they can stack hydroponic produce in shelves or towers. As I write this, there are more than 20 vertical farm operations being constructed and tested around the country. They use around 90 percent less water than regular soil farms, can grow roughly 10 times more food per acre than regular soil farms, and using precision software they can harvest their produce 30 percent faster than regular soil farms.
Sure, they’re spending more on electricity, but they’re also spending nothing on pesticide. The economics seem irresistible.
Last year, less than 20 miles from where I write this, in highly urbanized South San Francisco, a company called Plenty unveiled its flagship operation, a vast vertical farm named Tigris. Its sheer scale invites the correct usage of California’s favorite word, “awesome.” Tigris can grow a million plants at once, harvesting 200 of them every minute. With $226 million in funding, Plenty says it has already farmed 700 varieties of produce. Right now, the cost to consumers is comparable to non-hydroponic products (I can get their baby arugula at my nearest Safeway for a dollar an ounce); in the long run, it should be cheaper.
And they are far from the only success story. A Chinese startup, Alesca Life, is turning disused parking lots into vertical farms as well as selling plug-and-play shipping container farms. Back in Silicon Valley, a company called Iron Ox is developing robot arms for indoor farmwork. The future looks green and bountiful, and mostly automated (which is yet another reason you’re going to need Universal Basic Income).
Fresh future: Inside Plenty's vast vertical farm in South San Francisco.PLENTY
Which is not to say that outdoor agriculture is going away completely; it’s just going to shrink to the size of a community garden. That’s the basis of new urban developments called “agrihoods,” or multi-home communities centered around a professionally managed farm; a just-published book called Welcome to the Agrihood represents their first directory.
Rooftop organic farms, urban allotments: These are places where city dwellers can connect to the land and feel the satisfaction of nurturing their seeds from scratch. Soil may not be necessary to feed us, but sometimes it’s good to feel the dirt in your fingers. Similarly, farmer's markets are unlikely to go away. In a world where grocery stores are increasingly becoming delivery centers for services like Instacart, there will still be value in meeting and buying direct from the growers of high-end produce.
With big agribusiness heading indoors, with our apartments growing much of what we need and vertical farms providing backup in every city, we’ll also be able to let most of our present-day farmland go fallow. That in itself should take care of a chunk of climate change, considering the amount of carbon-soaking vegetation that springs up on fallow land. Lab-grown and plant-made meat will remove the need for those disease-ridden feedlots. Aquaponics, another discipline where the science is expanding by leaps and bounds, may even let us grow our own fish for food, reducing the strain on our overfished oceans.
No doubt it won’t be all smooth sailing. No doubt we, as humans, will stumble upon fresh ways to mess up the planet and make life worse. But from where I’m sitting, surrounded by soilless germinating jars, the future looks very green and nutritious indeed.
Yours in leafy goodness,
2020
TOPICS: Tech, Tech, Food, Health & Fitness, dear 22nd century, Internet Of Yum, Indoor-gardening