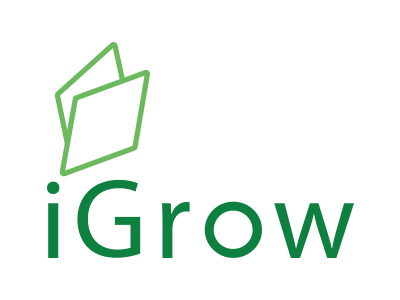
Welcome to iGrow News, Your Source for the World of Indoor Vertical Farming
A Method To Monitor Indoor Crop Health No Matter What Planet You're On
A user-friendly, cost-effective protocol to use SI-NDVI imaging for early, remote detection of plant stress.
PUBLIC RELEASE: 17-DEC-2018
BOTANICAL SOCIETY OF AMERICA
IMAGE: SINGLE-IMAGE NORMALIZED DIFFERENCE VEGETATION INDEX (SI-NDVI) ANALYSIS ENABLES EARLY DETECTION OF PLANT RESPONSE TO STRESS, PRIOR TO WHITE LIGHT-VISIBLE DETECTION. SI-NDVI IMAGES OF ARABIDOPSIS PLANTS SHOW RESPONSE TO SALT STRESS... view more
CREDIT: NICOLE S. BEISEL, JORDAN B. CALLAHAM, NATASHA J. SNG, DYLAN J. TAYLOR, ANNA-LISA PAUL, AND ROBERT J. FERL. 2018. UTILIZATION OF SINGLE-IMAGE NORMALIZED DIFFERENCE VEGETATION INDEX (SI-NDVI) FOR EARLY PLANT...
As the world urbanizes and technologies such as LED grow lights bring down costs, indoor farming is becoming an increasingly important part of the food supply. Eventually, indoor farming techniques could help humans maintain a healthy diet in space. However, because of the completely closed systems in which indoor crops are grown, imbalances in soil nutrients, salinity, temperature, and other factors must be caught quickly to avoid losing a whole crop. In work published in a recent issue of Applications in Plant Sciences, Dr. Robert Ferl and colleagues at the University of Florida Space Plants Lab developed a light-based tool to assess plant health quickly, accurately, and inexpensively.
Not surprisingly for work coming from the Space Plants Lab, this study was conducted with an eye toward extraterrestrial farming. "Imagine a greenhouse being robotically maintained on Mars," said Dr. Ferl, corresponding author on the study. "The only data we can get back from that greenhouse is electronic. No sample return. Under those conditions it becomes really beneficial to derive as much data as possible from the photons that are coming off the leaves of plants." These photons make distinctive light signatures that can tell quite a bit about how a plant is doing, when analyzed using the normalized difference vegetation index (NDVI).
The NDVI is a widely used metric of plant health and photosynthetic rate that was originally developed for satellite-based monitoring of plant growth. This metric compares the plants' absorption of different spectra of light; healthy plants give off an identifiable light signature, absorbing light in the photosynthetically active region of light spectra, and reflecting near-infrared light. "[NDVI] proved to be an interesting starting point for the project simply because there is a large dataset and collective understanding that underpins the idea of using different spectral components to understand plant health," said Dr. Ferl. They adapted single-image NDVI (SI-NDVI), a low-cost version of this analysis, to see if it would be practical for monitoring crop health in indoor farming conditions.
Dr. Ferl and colleagues assessed the efficacy of this monitoring technique by exposing two different plants (arugula and the model plant Arabidopsis thaliana) to two different stressors (salinity and a high-concentration ammonium nitrate treatment) that create distinctive and well-understood stress responses. "Using these well-controlled stresses that have a well-defined biochemical basis for their responses is allowing us to probe the root causes of NDVI difference detections of stress or health responses," said Dr. Ferl. They were able to detect stress signatures from both treatments well before stress was visible to the naked eye, proving the utility of these techniques as early monitoring systems that can be deployed remotely and relatively inexpensively.
While these authors were primarily motivated by an interest in growing plants in space, the monitoring technique they developed could prove useful here on earth for indoor farmers looking to catch problems in the grow room quickly. "Single-image NDVI offers the opportunity to derive spectral character from a single RGB image. This keeps costs down," said Dr. Ferl. "It also opens the door to a large community of citizen scientists and applications developers that are interested in using SI-NDVI concepts commercially." This means that this method could be adapted to monitor a variety of crops grown under indoor conditions, which could mean less expensive, healthier salad greens on your table, whether that table be here or on Mars.
Why Choosing Automated Dosing Systems Is A Profitable Investment
by Mia Godfrey | Technology, Materials & Equipment
Automated dosing systems can be expensive, which means they’re often an intimidating investment for small farmers. However, many growers note that their upfront investment pays off once they start saving on time and labor costs, especially if they’re beginning to scale their farm or hire employees.
If you’re a hydroponic or aquaponic farmer, you are likely familiar with the time-intensive process of manually testing and dosing nutrients and pH adjustments in your system. As business owners, we know that time is money, and if there’s any way to save on both, we’re likely to jump on it.
We’ll discuss what automated dosing systems are, how they work, and how they can benefit your farm and business. This information will help you decide whether or not you’d like to take the leap and purchase one.
What do automated dosing systems do?
At a high level, automated systems reduce the manual workload of managing your nutrients: measuring, dosing, and testing pH, EC, and temperature*. When done by hand, these tasks can take up a sizeable portion of your highly valuable time, or that of an employee, increasing your labor costs. These systems can also help you reduce human error: you’ll cut down on over- or under-dosing and shocking your plants by accidentally adding an incorrect amount of nutrient.
Now, you might be thinking “I have an aquaponic system, so I don’t need to manage nutrients in the same way, and therefore, I don’t need an automated dosing system.” Don’t be too hasty. These automated systems can benefit aquaponic growers just as much as they benefit others. While aquaponic systems do not require the same inputs, it is often—if not always—the case that you’ll consistently be supplementing chelated iron. You can use automated dosing systems to monitor and adjust pH and iron in aquaponics the same way you would in hydroponics!
*It is important to note, however, that while automated dosing systems will measure the amount of nutrient in your reservoir, they will not measure and mix your nutrients for you. Learn more about this in the next sections.
How does it work?
Depending on the type of automated dosing system you’re looking at, it’ll come with a number ofsensors or probes. These measure water chemistry parameters like pH, EC, and temperature. Some more advanced systems include environmental sensors that will monitor conditions like air temperature, humidity, and CO2 concentration.
These sensors and probes work the same way that your handheld meters do, only they’re all connected to one computing system. Since the system is automated, it allows the user to set determined parameters which the computer will compare to the real-time measurements it’s taking from the reservoir.
In response to those measurements, the computer makes adjustments by operating a series of pumps. These pumps are connected to lines that are placed in buckets, which contain nutrient mixes and pH adjusters.
In our system, we had a series of 3 5-gallon buckets for the nutrient mixes:
part A (N-P-K + CaNO3),
part B (magnesium sulfate),
and a pH adjuster (pH down)
Pay attention to whether your system trends upward or downward in pH—you may want to switch to pH up if there is a consistent downward trend. Read more about pH here.
In small intervals, the system pulls solution from the appropriate bucket into the nutrient water until the readings on the meter meet the programmed target parameters.
Systems like the IntelliDose allow the user to set alarms for when something goes awry and include a host of other useful features. Some auto-dosing systems allow growers to set different parameters for different systems within the same farm.
How much can I save with an auto-dosing system?
Most growers can save upward of 15–30 minutes a day by using an auto dosing system. Multiply that by the wage that you’re paying a system manager, add it all up to the lifetime of the auto-doser, and you’ll see your savings potential.
However, the benefits of an automated dosing system stretch beyond “minutes saved.” Auto-dosing systems can help prevent costly events like crop loss due to human error, and can even lead to more beneficial results, such as increased yield.
Growers have several options for auto-dosing systems. Aquaponic growers may use only pH and iron dosers, for example. Small-scale growers may decide that a monitoring unit serves their purposes just as well as a full auto-dosing system. Whichever direction you decide to go, always balance the price of labor and time against the price of an auto-dosing system.
Monitoring-only units will typically cost between $250 and $400. For instance, an all-in-one handheld meter may run at $280. When you add dosing and remote login capabilities, the price runs closer to $2,000. Systems like Growlink can be customized for your farm, but they’ll likely run you a pretty penny.
Using automated dosing systems
In ZipGrow systems, the sump tank acts as a “collect-all” for system water before it is redirected to the mixing tank and sent to irrigate the towers again.
Here, the tank is equipped with an IntelliDose system. Like most auto-dosing systems, it consists of a controller where the user programs their desired parameters. The EC and pH probes are placed in a small basket-like contraption inside of the reservoir. At the bottom of the reservoir, there is a pump that keeps the water moving so that the probes are always taking an accurate reading. If the water is too still, it is possible for the nutrients to settle along the bottom of the tank. As you can imagine, probes at the top of the tank, in this case, would read differently than if they were at the bottom. It is ideal to have aconsistent concentration of nutrients throughout the reservoir.
We like to hang the IntelliDose controller, pumps, nutrient buckets, and a small electronics box to hold cords on the side of our mixing tank (we use an IBC). This allows us to remove and replace nutrient buckets quickly as well as keep the floor clear for cleaning. The electronics box keeps cords out of the tripping and dripping zones to avoid accidents and improves the safety of the farm.
While this may seem like a “set-it-and-forget-it” type of system, we would like to discourage you from thinking that way. As a part of your daily or weekly farm maintenance, you should take a few moments to ensure that everything is working as it should. Additionally, you will need to calibrate the probesabout once a week and occasionally check the water manually.
Ready to get an auto dosing system?
If you’re ready to take the plunge into auto-dosing, we recommend systems from Hydrofarm, BlueLab, and Autogrow. Begin your exploration with a needs assessment to determine exactly what you need before you purchase a system so you get one that fits your operation.
We chose the IntelliDose System from Autogrow because it is well-made and comes with great customer support.
“I work with four different production facilities, and so I can save quite a bit of time. But that is not the reason I went with an IntelliDose system. I went with IntelliDose out of necessity. I want everything to be done right, and to remove the human error from the system.” -Mark Germino
Learn more about hydroponic farming
Anyone can run a profitable local farm, and at Upstart University, we’re dedicated to unlocking that possibility. At Upstart University, aspiring farmers can learn the tricks of the trade from building a business plan and securing funding, to managing a hydroponic or aquaponic system and achieving high crop yields.
New York Vertical Farm Aims To Instill Consumer Trust With Transparency
Starting today, consumers can just point their camera app at the QR code, or type in the lot number, found on all Square Roots food packaging to trace their food’s path from seed to sale.
By Laura Drotleff| December 19, 2018
Consumers can simply scan the QR code with the camera on their phones to get the full story on when, where, and how Square Roots’ herbs are produced in Brooklyn, NY.
In the wake of the romaine lettuce recall, Square Roots, a Brooklyn, NY-based vertical farm with famous co-founders, has launched new labeling that will allow consumers to access the full backstory for when, where, how, and by whom their food was grown with a simple scan.
Starting today, consumers can just point their camera app at the QR code, or type in the lot number, found on all Square Roots food packaging to trace their food’s path from seed to sale, with the aim of bringing a “whole new level of transparency” to the food chain.
Co-founded by Tobias Peggs and Kimbal Musk (yes, Elon’s brother), Square Roots is a seed-to-sale indoor urban farm that produces a variety of fresh, pesticide-free herbs that are hand-harvested, self-packaged, and same-day-delivered to retail stores in New York City. The company was built on the premise of reconnecting city dwellers with the “comfort, nourishment, and taste of food and the people who grow it.” In addition to growing and selling herbs, Square Roots has taken it upon itself to groom next-generation farmers and future leaders in urban farming through its training platform that requires a one-year commitment to the company.
The Why Behind Square Roots’ Transparency Timeline
Musk wrote in a blog-post revealing Square Roots’ reason for launching its new scan-able label is that the operation wants to provide consumers with the transparency they’re demanding about where and how their food is grown.
Following the E. coli outbreak that resulted in the recall of all romaine lettuce grown in the U.S., consumers were put at risk, and the complexities and lack of traceability in the agricultural supply chain resulted in it taking weeks for federal agencies to track down the source of the bacteria.
Meanwhile, by growing in controlled environments, indoor food producers can provide advantages to minimizing the occurrence of outbreaks. Musk says by promoting this, Square Roots’ customers can enjoy the operation’s locally grown products “with the comfort and confidence of being able to see exactly how and where your food was grown and who grew it.”
Grown hydroponically inside climate-controlled, refurbished shipping containers, Square Roots’ end-to-end system monitors and controls every aspect of the production process, Musk says. The operation’s technology stack surrounds its farmers with data, tools, and insights to make smart decisions in real time, allowing them to sustainably produce food year-round.
Musk says while there’s a lot of excitement around the possibilities that blockchain offers for food traceability that could improve the current supply chain, consumers are turning to locally grown produce because there are fewer steps and less time involved from farm to fork.
“We, like many local farmers, don’t need to utilize blockchain architecture to give the consumer what they want today – total transparency, without the buzzword BS.”
Read Musk’s full article on the Square Roots blog, and learn about the company on its website. Stay tuned for more stories on how indoor producers are promoting food safety and transparency on GreenhouseGrower.com.
How Sustainable Farming Stacks Up
A look at the initiatives undertaken across the UAE to promote sustainable agriculture.
Published: December 04, 2018 14:38 Suparna Dutt D’ Cunha, Special to GN Focus
Emirates Flight Catering’s 130,000-sq-ft facility will harvest 2,700kg of herbicide- and pesticide-free leafy greens a day at full production.Image Credit: Supplied
In a country where it’s common to find apples from South Africa, potatoes from India and carrots from Australia — all marked at a price to cover the import costs — in supermarkets, some farming initiatives in recent years are bringing to reality a new breed of green agriculture that seeks to produce more crops in less space and water, and is efficient, easier and kinder on the natural environment.
It is hard not to be dazzled by the current pace of technological change in agriculture in the country. An ambitious manifestation of agricultural technology is coming to fruition next year. Emirates Flight Catering and US-based Crop One Holdings are building what they say will be the world’s largest vertical farm, producing 2,700kg of pesticide-free leafy greens daily, in Dubai.
The greens will be manufactured using hydroponics, a technique in which crops are grown in vertical stacks of plant beds, without soil, sunlight or pesticides. Above each bed of greens will be columns of LED lights, which when plants photosynthesise will convert light of certain wavelengths into chemical energy and store it for future use.
Proponents of new-age farming tout the potential of such technology to address the country’s largely hostile desert landscapes, its reliance on the global food trade, importing more than 80 per cent of its food needs, and food shortages as the population continues to grow.
“It is encouraging to see the initiatives that are underway, including some of the larger scale projects, using highly advanced technologies,” says Nicholas Lodge, Managing Partner at Abu Dhabi-based agriculture consultancy Clarity. “Developing sustainable farming with smart use of water will not only provide improved supplies for the local market but also potentially create viable businesses for export to neighbouring countries. Furthermore, technology and an ecological approach will contribute to food diversity and security as it will enhance crop production and lower its cost.”
For Omar Al Jundi, Founder and CEO of Badia Farms, the Middle East’s first commercial vertical farm in Dubai, sustainable farming is a solution for more pressing and concrete concerns such as land — less than 5 per cent of the total land area being arable in the UAE — and water shortages, meeting the demand for locally grown greens, and climate change. Growing and selling locally means emissions associated with transportation are reduced.
“The only solution is to grow smart. Sustainable farming is the future. It is time for the country and the region to become food producers rather than just consumers, since ensuring food security will be challenging in the future due to impacts of climate change.”
Using hydroponics technology on an 800-square-metre plot of land in Dubai, Badia Farms grows gourmet leafy greens for sale 365 days of the year.
Hydroponics brings some important benefits, explains Amjad Omar, Farm Manager at Emirates Hydroponics Farms (EHF). “Because crops are grown in a controlled environment there is no need for chemicals; it allows farming without soil. Most importantly, [hydroponics] uses 90 per cent less water than traditional open-field farming, although the tech uses water as a medium to grow plants, and the yield is six times more from the same amount of land.”
Situated halfway between Dubai and Abu Dhabi, EHF has adapted modern technology to grow lettuce and other herb crops year-round as well. The produce, which it sells both online and offline, is not only cheaper than imported goods but fresher too, adds Omar.
Meanwhile, to grow tomatoes, Abu Dhabi-based Pure Harvest Smart is using a fully climate-controlled high-tech, water-efficient greenhouse, which is yielding ten times more food per metre using one-seventh the water.
As the movement continues to evolve, some are experimenting with novel ways to make local agriculture an integral part of urban life. At this year’s World Future Energy Summit in Abu Dhabi, Maha Al Muhairi displayed her innovative energy-efficient automated system, FreshFridge, which lets you grow a wide range of herbs and microgreens in your kitchen. “The FreshFridge allows users to grow more than 50 varieties of microgreens in 10-15 days. People can grow whatever they want in any season,” says Al Muhairi.
Technology is fundamental to the future of agricultural production in the region, says Lodge. “Whether in the form of vertical farm, or through the research and development work of organisations such as the the International Centre for Biosaline Agriculture in Dubai. The region will not enjoy an increase in water availability in our lifetime, so we must use what we have carefully and intelligently.”
But growing crops sustainably isn’t always easy. “Steep costs of acquiring cutting-edge technologies and unavailability of raw materials locally for production are among the challenges,” says Omar.
While according to Al Jundi, the concept of vertical farming is still in its infancy in the region. “Governments and the private sector need to invest heavily to accelerate learning and development in this sector,” he says.
Although these new-age farming initiatives will not change the UAE’s reliance on food imports drastically, it certainly represents a better way of growing produce and a future of continually increasing food supplies in ever more sophisticated manipulation of agro-ecosystems.
Osram Presents New Near-Infrared LED for Smart Farming Application
Oslon Black SFH 4736 near-infrared LED (NIRED) helps farmers harvest at the right time.
12/12/18, 10:38 AM | Indoor & Vertical Farming, Monitoring & Growing
Osram, a leader in the optoelectronic industry, today announced its new Oslon Black SFH 4736 near-infrared LED (NIRED). When installed in a smartphone or tablet, the NIRED offers a simple way for farmers to scan fruit, vegetable or grain crops, generating reliable information about the sugar, water and fat content. One of the most important decisions for farmers and vineyard owners is picking the right time to harvest. This not only ensures that the produce has the best possible taste, but also saves precious time and money during the processing and shipment stages.
Determining ripeness is made possible by near-infrared spectroscopy. This process involves scanning the content of various types of fruit, vegetables and grains - and takes only a few seconds. For example, a farmer would select a random ear of wheat, scan it with a smartphone, and just a few seconds later read the results on the display.
The NIRED irradiates the sample with a defined spectrum of light. Depending on its precise composition, the sample will reflect only a certain proportion of that light. The spectrometer then processes the information and integrates it into the smartphone or tablet. The reflected light can be considered a kind of "photometric fingerprint." These measurements indicate the existence and quantity of certain nutrients, allowing farmers to take samples and easily monitor the progress of their crops in real time so they can plan the ideal time for harvest.
"By focusing on making progress for farmers, the new Oslon Black SFH 4736 near-infrared LED takes farming technology to the next frontier," said Karl Leahy, Director of Emitters, Lasers and Sensors at Osram Opto Semiconductors. "Our unique NIRED allows farmers to optimize their crop yield, as well as enhance harvest efficiency while keeping costs down."
In late 2016, Osram Opto Semiconductors unveiled the SFH 4735 as the worlds first broadband emitter of its kind. The previous model is being used in various applications including in SCiO, one of the first near-infrared micro-spectrometers for the consumer market from Consumer Physics. The SFH 4736, which achieves almost twice the output thanks to its newly integrated lens, is also suitable for use in the professional sector and can provide valuable assistance to farmers.
ABOUT OSRAM
OSRAM, based in Munich, is a leading global high-tech company with a history dating back more than 110 years. Primarily focused on semiconductor-based technologies, our products are used in highly diverse applications ranging from virtual reality to autonomous driving and from smartphones to smart and connected lighting solutions in buildings and cities. OSRAM uses the endless possibilities of light to improve the quality of life for individuals and communities. OSRAMs innovations enable people all over the world not only to see better, but also to communicate, travel, work and live better. OSRAM has approximately 27,400 employees worldwide as of end of fiscal 2018 (September 30) and generated revenue of more than €4.1 billion. The company is listed on the stock exchanges in Frankfurt and Munich (ISIN: DE000LED4000; WKN: LED 400; trading symbol: OSR). Additional information can be found at www.osram.com.
Disruptive 'Precision Farming' Spells Opportunities for This AgTech Company
The world is going to run out of food. Don't worry, the best minds are on it. They are using robots, better seeds, lighting and irrigation systems to reimagine farming.
Jon Markman Dec 19, 2018 9:00 AM EST
The world is going to run out of food. Don't worry, the best minds are on it. They are using robots, better seeds, lighting and irrigation systems to reimagine farming.
Bowery Farming Inc. calls the process precision farming. According to a report from Bloomberg, the indoor agriculture technology company is about to secure $90 million in funding.
It is a larger opportunity for investors with vision.
Like many technology startups, Bowery founders are determined to solve the big problems confronting the world. The United Nations projects that the world population will swell to 10 billion people by 2050. To keep up, global farmers will have to produce 70% more food. Unfortunately, most of the world's water resources are used for food production, and 30% of arable agricultural land has been lost to poor planning, pesticides and urbanization.
There is not enough water or land to possibly meet future demand.
Engineers are Bowery set out to do more with less. The solution began with controlling as many variables as possible. Crops are grown indoors under ideal conditions, without pesticides. Complex, LED lighting mimics the full spectrum of the sun. Irrigation systems deliver nutrients with exact specificity, resulting in 95% less water use than traditional farming and a 100x improvement in crop yields.
The urban farm company is using all of the tools of modern technology -- robotics, machine learning, computer vision and data science - to fine tune the entire process.
Bowery is not the only company in the game. Last year, Plenty, another indoor farm company from made headlines when it secured $200 million in financing from Softbank (SFTBY) , the Japanese firm led by billionaire Masayoshi Son, and investment companies associated with former Alphabet chairman Eric Schmidt and Amazon founder Jeff Bezos.
The gigantic investment in the tiny San Francisco startup sent shockwaves through the burgeoning ag-tech community. Early investors understood the potential of marrying sensors, robotics and data science with agriculture. The Softbank vote of confidence underscored the urgency.
The latest $90 million round was led by GV, the new name of Google Ventures. Alphabet (GOOGL- Get Report) , the parent company of Google, has made a cottage industry out of developing businesses models around machine learning. Its investment in Bowery is on brand.
Farming has not changed much in centuries. Yes, there are now self-driving tractors and even drones to monitor the growing process, but the basic premise still involves sowing seeds and waiting patiently for mother nature to bless the soil with bountiful crops. Companies like Bowery and Plenty completely disrupt that notion.
They want to control every aspect of the growing environment. They are cutting mother nature out of the loop in an effort to reduce costs, speed up growing cycles and reduce the footprint of farms. It's a revolution made possible by automation, better information and data science.
Even five years ago the economics of this revolution did not make sense. However, falling prices for cloud computing, robotics, sensors and machine learning have opened new doors. Information technology is being commoditized, just like fruits, vegetables and livestock.
Cognex Corp. (CGNX - Get Report) is the leading maker of sensors and vision systems for smart, industrial robots.
For a long time, truly smart machines were a pipe dream. Robots were impressive for their might. They stamped or welded or pushed items along a precision conveyor belt. But they were dumb. They didn't have eyes. They could not make sense of their place in the process.
The Cognex Insight Vision system gave industrial robots eyes. Machine learning and better software systems gave them intelligence. These attributes that are in high demand as factories get smarter, and ambitious startups push the limits of ag-tech.
The Massachusetts company has an impressive history of growth. Since 2013, sales are up 2.2x to $748 million. During fiscal 2017, the last full year of financial data, revenues shot up 43.5% while income ballooned 18% to $177 million. These metrics are certain to increase as more industrial robots gain sight, and smarts.
Cognex shares have been cut in half amid concern about the health of the global economy. The stock has fallen from a high of $73 in October 2017, to the lower $40s, bringing the market capitalization to only $7.2 billion.
At 29x forward earnings, Cognex shares are still expensive, but not ridiculous, for a unique, patent-protected, cutting-edge tech company in a growing field. Long-term investors with vision should consider using weakness in the weeks ahead to establish positions.
Square Roots Implements “Transparency Timeline” for Greens
An indoor farm in Brooklyn, N.Y., wants to do its part to restore consumer confidence in greens.
Tom Karst December 19, 2018
Urban farm Square Roots has unveiled what they call a transparency timeline, accessed via QR code on their packaging.
( Square Roots )
An indoor farm in Brooklyn, N.Y., wants to do its part to restore consumer confidence in greens.
Urban farm Square Roots has unveiled a new food packaging system that the company says will give consumers a comprehensive story of how the firm’s basil, sage, chives, and mint traveled from seed to the retail shelf.
In a Dec. 19 blog post by co-founder Kimbal Musk (younger brother of Elon Musk) headlined “After the Romaine recall nightmare, here’s how Square Roots is going to get Americans to trust their food again," the company said it was introducing a labeling program that would allow consumers to see “the complete story of where and how their food was grown, and who grew it, with a simple #knowyourfarmer scan.”
“By simply scanning a QR code or typing in the lot number found on every package of Square Roots fresh produce, you are now able to see the complete story of where and how your food was grown and who grew it — tracing the entire path from seed-to-store,” Musk said in the blog post.
The QR code scan — readable by most smartphone cameras — informs consumers of what Musk called the “transparency timeline” for the commodity. The timeline includes information about the crop’s development, including:
Seeding: the scan tells where the seeds were sourced from, when and where they were seeded and the first name of the worker who seeded the commodity;
Nursery: The date the commodity was placed in the company’s climate-controlled nursery in the specified farm and the first name of the individual that transferred the tray;
Transplant: The date the seedlings were moved from the nursery to the hydroponic grow towers i in the specified farm, and the name of the worker who moved them;
Harvest: The date the herb commodity was hand-harvested and the first name of the worker that harvested it;
Packing: Date of packing and first name of the worker who packed it; and
Delivery: Date of delivery to retail store, with a note that delivery was done with “low impact transport.”
Musk said future versions of the transparency timeline could add information about the specific climate that food was grown in, recycling information relevant to the packaging for the product and perhaps other data. “If you would like see any other information added to the timeline, just let us know,” he said in the post.
With recent the recent E. coli outbreak linked to romaine lettuce — the third outbreak in two years — Musk said that consumers are at risk from foodborne illnesses.
“The situation was compounded by opaque supply chains in the Industrial Food System, making it ridiculously difficult to accurately trace the source of guilty pathogens,” he said in the blog post. “To their credit, the big lettuce producers did eventually react, and agreed to start labeling their products with a mark of the state in which their products are grown. But that’s not enough. Consumers demand — and deserve — to know more.”
Musk said that indoor climate-controlled farming “has many advantages” over open field growing when it comes to minimizing the risk of such outbreaks. He said that Square Roots’ distributed, modular farm network reduces that risk even further.
“Square Roots customers can enjoy our products not just because they taste great and are grown hyper-locally, but also because they come with the comfort and confidence of being able to see exactly how and where your food was grown and who grew it,” he said.
Musk said blockchain technology has created buzz but so far hasn’t delivered much information to consumers.
“We’re optimistic on that long-term vision (of blockchain), and we know many of the people working hard on blockchain solutions right now,” he said in the post. “But the reality is that initial implementations, while heavily buzzword-compliant, have been distinctly underwhelming in terms of the information they provide.”
Applied Technology: Putting The Hyper In Local
December 21, 2018
For some retailers and restaurants, proximity to local food is key—like next door, on the next floor, or on the roof— and you can’t get much fresher than that.
This technology is already gaining traction across the nation and worldwide with vertical farms in skyscrapers, vegetable and herb gardens at restaurants or near retailers, and container farms in areas where growing can be nearly impossible.
Local Roots, a Los Angeles-based startup, has created a twist on greenhouse growing. The company does grow produce and herbs in a protected setting, but instead of a greenhouse, the indoor farms are in 40-foot shipping containers.
The four student founders say that by using robotics, microbiology, and data analytics, their indoor container “TerraFarms” produce up to 300 times higher per square foot densities than traditional farms.
The containers “have also achieved cost parity with greens and other produce grown out in the field,” says Gary Hawkins, founder and CEO of the Los Angeles, CA-based Center for Advancing Retail & Technology, LLC.
Better yet, he says, “they use a fraction of the water and no pesticides or herbicides.”
Local Roots believes it has eliminated many hazards of the supply chain and is partnering with area businesses, restaurants, and retailers, notably Walmart.
And if a retailer or processor has the desire, Local Roots will not only sell and set up a TerraFarm, but oversee the entire growing process from seed to harvest for the freshest, local vegetables and herbs.
Samson Ogbole Is A Nigerian Farmer Who Wants To Bring Aeroponics To The World
Ogbole says that there are many advantages to aeroponics, the biggest being that you can grow crops at any time of the year.
by Perry Miller
Samson Ogbole is a Nigerian farmer who is trying to solve the problem of land shortages in his native country. Nigeria’s population has now reached 190 million, but there isn’t enough land in the country to grow the food needed for the ever-growing population. So, Ogbole has found a solution — aeroponics.
This unconventional method is the process of growing plants in the air without using soil. Ogbole first got involved with soilless farming in 2014, and just two years later founded PS Nutraceuticals, a company that puts cutting-edge agricultural technologies into action to improve the efficiency of food production and to ensure food security.
“Soilless growing entails removing the soil component, bringing in substitutes, and applying fertilizer to enable the plants to grow,” Ogbole says. “With soilless farming, we have been able to push for what you call urban farming, where we now have farms in cities such that we are able to cut off the middlemen and marketers.”
Ogbole says that there are many advantages to aeroponics, the biggest being that you can grow crops at any time of the year. The method has also allowed them to eliminate pathogens that naturally exist in the soil and affect crops.
Nigeria needs an estimated 78.5 million hectares of land to produce enough food for the population. But, right now there are only 30 million hectares of farmland under cultivation, according to the International Trade Administration of the United States.
And, Ogbole says that only 46 percent of Nigerian soil is fertile to grow crops, so the country needs to take steps towards self-sustainability in food production and let technology play a more prominent role. He believes that the “war of the future will be fought through agriculture.”
“We’re bringing in technology into agriculture so that the youth can actually see this as a viable option,” explains Ogbole. “We also want to ensure that food production is no longer seasonal, and we’re also bringing in smart sensor technologies into agriculture so that you’re able to get feedback from your plants.”
The farmer added that the future of the economy depends on a few people who have bright ideas and can think outside the box. It is ideas, not money, that solves problems.
Via CNN
Images via Shutterstock
Urban Farm In Brooklyn Looking To Attract Young Farmers
Located in a former Pfizer factory in the Williamsburg district, the company said one of its main aims is to offer young people careers in agriculture.
So-called 'urban', or 'vertical', farms have been making their way into some US cities over the past few years. With limited land in major metropolitan areas, indoor urban farms offer the chance for city stores and restaurants to get their hands on locally-grown produce. Square Roots in Brooklyn, New York, is one of these next generation indoor farms. Located in a former Pfizer factory in the Williamsburg district, the company said one of its main aims is to offer young people careers in agriculture.
"The average age of the American farmer is 58," noted Karsten Ch'ien of Square Roots. "With more young people living in cities, we bought shipping containers into the city because that is where many of them live. Young people are very technology literate, and with the rise in demand for healthy, locally-grown foods, this is the perfect combination for them to get involved in the produce industry. As a result, the average age of our farmers is just 24."
Ch'ien said that Square Roots offers training and skill building as part of helping young farmers establish a firm foundation in the industry. "At the heart of Square Roots is the Next-Gen farmer training program, which creates opportunities for more people to become farmers—and future leaders in urban farming—through a year-long commitment on the Square Roots team."
Produce is grown in modified shipping containers. Ch'ien is on the far right.
Growing in shipping containers
Produce at Square Roots is grown in shipping containers, which have been climate controlled and fitted with the latest in vertical farming gadgetry. All the operations are controlled in the company's offices overlooking the parking lot where the ten containers lie. The shipping container model gives the company great flexibility.
"Growing in shipping containers requires less upfront capital to establish and maintain," Ch'ien explained. "They are easy to retrofit and move if we need to. Additionally, it's very simple to expand the farm. Instead of remodeling or building an extension, we simply add another shipping container and fit it out in the same manner. Here in the parking lot, we have plenty of room to grow horizontally. At this stage, it's not practical for us to stack containers due to the need for climbing up and down ladders with produce."
According to the company, each shipping container yields between 50 and 70 pounds of produce each week. The containers have been engineered to be environmentally friendly and food safe. "The mineral nutrient system cycles and recycles, so each container only requires eight to ten gallons of water per day. Any kind of food safety issue can be contained in each farm," Ch'ien said.
Culinary herbs the focus
Vertical farms still have a way to go to become a mainstream source of produce. Currently, they are typically restricted to leafy greens and other plants that have minimal energy requirements. Square Roots focuses on culinary herbs. The herbs are grown and packed inside the container and then delivered to local independent retailers on one of the company's tricycles.
"Leafy greens are the easiest to grow vertically," Ch'ien observed. "We can also grow things like grape tomatoes and other small vegetables. It really depends on the energy requirements of each plant. Here at Square Roots, we focus on culinary herbs, with each container specializing in a herb. Typically, the timeframe of maturity to harvest is four to six weeks, depending on the herb. We grow in sections and harvest each container twice per week, so that there is always produce that is ready to be picked."
Square Roots uses these tricycles to deliver their produce direct to customers in the NYC area.
Ch'ien notes that growing more energy-intensive commodities such as tomatoes and small root vegetables is not economical at this stage but said that this may soon become viable as technology continues to improve. "Outside of leafy greens and herbs, it's very challenging to grow other crops economically right now. However, technology is improving each year, providing us with increased opportunities to scale and moderate costs. Additionally, we want to ensure we balance sellable yields with quality."
As to the question of whether vertical farming is a threat to traditional farming, Ch'ien believes the two are not mutually exclusive, but rather the whole system can work side by side. "We don't see it as a competition between traditional land-based farming and urban, vertical farming. All growers have the same goal which is to deliver the freshest, best quality produce to customers. We believe vertical farming can work in tandem with traditional farming, each serving a useful purpose in the industry."
For more information:
Karsten Ch'ien
Square Roots
Ph: +1 (740) 337-6687
karsten@squarerootsgrow.com
www.squarerootsgrow.com
Publication date : 12/18/2018
Author: Dennis Rettke
© FreshPlaza.com
The Technology of Berries
High-tech strawberries are flourishing in Paris. French urban tech farming start-up Agricool has just picked up a cool €25m to grow more fruit
High-tech strawberries are flourishing in Paris. French urban tech farming start-up Agricool has just picked up a cool €25m to grow more fruit. It plans to use the cash to establish more growing operations in the centre of Paris and to expand across France, as well as to launch in Dubai.
Argricool has been using old shipping containers in the heart of Paris to grow its produce. There’s no pesticide use and the method requires 90% less water and nutrients than regular strawberry rearing. It also leans solely on renewable energy.
The outfit claims it is 120 times more productive than conventional farming. Its output is currently available in four supermarkets in the French capital and in one on the outskirts.
Container farms are sprouting everywhere right now. One high-profile venture is Square Roots operated by Kimbal Musk – brother of Elon – which propagates fresh herbs for stores across New York City. The company has just launched new packaging featuring a QR code which unlocks the story of how and where the food item was grown. The goal is to boost food supply chain transparency.
How Osram Is Investing in Horticulture Technology Partnerships
The deal was a key part of Osram’s mission of moving beyond its role as a lighting company, and becoming a leading provider of intelligent plant growth solutions.
By Brian D. Sparks|December 3, 2018
Hällnäs Handelsträdgård in Northern Sweden is using Fluence’s VYPRx PLUS with PhysioSpec Greenhouse spectrum for full-cycle plant growth and development, along with Fluence’s VYPRx PLUS with AnthoSpec as a finishing spectrum to increase anthocyanin accumulation in lettuce. This has resulted in a deep-red color and higher antioxidant properties, which were previously impossible to produce under HPS or sunlight.
Photo courtesy of Osram
Earlier this year, Osram, a Munich, Germany-based tech company, acquired Fluence Bioengineering, which specializes in LED-based horticulture lighting systems. The deal was a key part of Osram’s mission of moving beyond its role as a lighting company, and becoming a leading provider of intelligent plant growth solutions.
Osram’s 110-year history in lighting is based on four pillars:
Mobility
Security and safety
Connectivity, particularly in smart buildings and cities
Health and well-being
Initially focused on the automotive and entertainment industries, the company became more engaged in horticulture when old traditional light sources were disrupted by the growth of LEDs.
“Our products changed over to LEDs for many of the same original applications, in addition to use in the medical and horticulture industries,” says Timo Bongartz, Senior Innovation Manager for Smart Farming at Osram. Now, Bongartz says, we are seeing the next industry disruptor: the Internet of Things.
“Light source alone is not enough anymore,” Bongartz says. “We saw a need to create more value around lighting, and that’s why we are shifting more from a lighting company to a technology company. We do not just want to provide components, but lighting solutions for all types of indoor production, from ornamental greenhouses to vertical farms to cannabis production facilities.”
This innovative mission was the basis behind Osram’s acquisition of Fluence, as well as its partnership with Motorleaf, a software service solutions provider.
“We want to allow growers to make more efficient use of their time, so we’re looking to provide tools for microclimate management and disease and yield prediction,” Bongartz says. “If growers know early how their yields will be, they can hopefully get higher prices.”
Bongartz says Osram also wants to stay in the loop on when a grower’s production system or crop mix may be changing, so it can place lights accordingly.
We see growers wanting to bring more intelligence and cloud-based control into their intelligent lighting systems,” he says. “On a light prediction level, we are making lights connectible and controllable through the cloud. This is how we are bringing more value to lighting solutions.”
Phytofy RL is an LED horticultural lighting system for research applications with real-time control and scheduling features for each individual channel. The calibrated system is capable of delivering light treatments with varying spectra (wavelength and intensity) for horticulture research, including far-red end-of-day treatment, brief UV light, night interruption lighting, etc.
Photo courtesy of Osram
Osram and Fluence Partner on New Lighting Systems
RAZR4 Array
From seed germination and cutting propagation to full-cycle microgreen and leafy green cultivation, RAZR4 is optimized to decrease consumption and increase production for vertical farm applications. At 2.3 µmol/J, RAZR4 is 169% more energy efficient than standard vertical farm lighting systems, while providing up to 350% more photosynthetic photon flux.VYPRx PLUS
With energy efficiency reaching 2.3 μmol/J and output surpassing 1,190 μmol/s, VYPRx PLUS is key to establishing a path to sustainability and productivity in a greenhouse. Whether extending the day or growing season for low daily light integral (DLI) crops, VYPR has the power, energy efficiency, and longevity to grow consistent crops year-round.SPYDR 2i
The SPYDR series is designed for controlled environment horticulture applications requiring efficient, precise, and uniform levels of photosynthetic photon flux density (PPFD). The SPYDR 2i is streamlined to quickly deploy in multi-tier vertical farm applications for high-DLI crops and single-tier applications including growth chambers, adjacent aisle tables, and tents.
NASA is studying lighting combinations and recipes that it can then apply to crops grown in the International Space Station.
Photo courtesy of Osram
New Research Is Out of This World
While it is focused on offering growers new lighting systems and components, Osram is also doing its own research to help growers become more innovative by enabling them to develop their own light recipes. Using a tool called Phtyofy, growers can set up trials, changing light spectrums throughout the day based on how the plants are reacting.
This tool has also been developed through partnerships with Michigan State University (MSU) and even NASA. When MSU horticultural lighting expert Dr. Erik Runkle was planning a new controlled environment lighting lab, he reached out to Osram’s Semiconductors division. Partnering with Runkle gave Osram access to plant science from a horticulture perspective, while enabling MSU students to carry out lighting research on the wavelengths and light quality that may be optimal for certain crops.
The NASA partnership started through HortAmericas, whom NASA approached when it was looking for a lighting source. At Cultivate’18, one of the NASA researchers visited with the Osram team, who provided them with three lighting units for use in NASA’s advanced plant habitat lab. The objective of NASA’s research is to study lighting combinations and recipes that it could apply for crops grown in the International Space Station.
The Vegetable Farmer from the Antarctic
Paul Zabel from the German Aerospace Center operates a greenhouse in the Antarctic, where tomatoes, lettuce and cucumbers flourish
By Dirk Asendorpf
The greenhouse EDEN: tomatoes, cucumbers and lettuce grow up to -40 degrees outside. (DLR)
Paul Zabel from the German Aerospace Center operates a greenhouse in the Antarctic, where tomatoes, lettuce and cucumbers flourish. For future space missions, plant cultivation is to be tested under difficult conditions.
"Zabel. Hello. "- A call in Antarctica. Just started there the polar day.
"We have 24 hours of sunshine when we have no clouds. Today it is very nice. We have the second right summer week. It's only
about minus 13 degrees. " In recent months, Paul Zabel had to cope with significantly worse weather conditions. For one polar winter, he was responsible for the research greenhouse of the German Aerospace Center. This is located 300 meters from the German Neumeyer Station in a container.
"We had the lowest temperature with minus 43.4 degrees in August. There were a few days where there were stronger storms, and I did not go because that was just too dangerous. "
He has a satellite connection at all times in the greenhouse 13,500 kilometers away in the view. A dozen screens fill a wall of the control room.
"We can not touch the plant itself. But we could say for example: The container is now two degrees warmer, we put this here and then the container would be up to two degrees warmer. We could control the light and, for example, we could also give a different nutrient mix to the plant. We can control everything from here. "
A full greenhouse for the first visitors to Mars
The complete remote control of vegetable cultivation in a hermetically sealed container is the prerequisite for its application to future interplanetary space missions.
"Scenarios provide that the greenhouse system flies to Mars in advance, unfolds there automatically and already plants are grown automatically. And when the first humans come to Mars, they can almost find a fully grown greenhouse. That's the theory. "
The tomatoes and salad are well grown. Only the strawberries and peppers did not really thrive in the EDEN greenhouse. (DLR)
However, the practice was still a long way away. Almost every day Paul Zabel had to look to the right in the Antarctic greenhouse.
"For example, we had a broken LED lamp from the plant LEDs relatively early in the year. I could then replace it with a spare part. We had several failures of electrically controlled valves and pumps in our cooling system, which are now being replaced by other models. "
The repairs will be carried out by project manager Daniel Schubert personally in January. Then he also brings the seeds for the next test run, including seeds for ten different types of lettuce that Nasa has already tested on the International Space Station. In the Antarctic container they should germinate and grow as independently as possible. A gardener will not exist in the next polar winter.
The greenhouse should be completely remotely controlled
"We could not find anyone who would like to hibernate again. And then we thought: Could we do a self-sufficient mission? So really just observe and control the greenhouse system only from Bremen, out of our mission control center. And we say to the overwinterers: Only go in an emergency - or to harvest. "
Paul Zabel flies back in mid-December to Bremen. There he missed a century summer.
"I also talked regularly with my colleagues and then I was a bit jealous here and there. But I was just a year in the Antarctic. But chirping birds and being able to go out into the forest again, these are things that you just can not do here. And I'm definitely looking forward to that. "
Belgian Supermarket to Introduce In-Store Vertical Farms
The retail group sees multilayer cultivation as part of its wider aim of pursuing more sustainable products, shortened chains and innovation.
Colruyt Group is testing a system developed in-house for 'vertical farming' or multilayer cultivation in climate-controlled conditions. The retail group sees multilayer cultivation as part of its wider aim of pursuing more sustainable products, shortened chains and innovation. Colruyt Group aims to start stocking the shelves of its retail formula Bio-Planet with the first herbs from its vertical farm from the autumn of 2019, under its own label Boni Selection, which is strongly committed to a sustainable product range.
Ambition: herbs with a very small ecological footprint
Consumers are making increasing demands regarding responsible consumption. Colruyt Group wants to offer a possible solution using vertical farming. "Our multilayer cultivation creates the perfect conditions for plants", explains Stefan Goethaert, Director at Colruyt Group and responsible for product sustainability. "Air, light, water and nutrients are dosed in the ideal quantities. As a result, we only use the amount of energy and raw materials that is strictly necessary, whilst still allowing the plant to achieve optimum growth. And it's no longer necessary to use pesticides. The plants are therefore 100% natural. Moreover, they reach maturity twice as fast than when conventionally cultivated. And the quality remains high throughout the year, regardless of the weather conditions."
The first results after a year of testing confirm the story, says Stefan Goethaert. "We are already using 90% less water and 50% less nutrients than in conventional cultivation. We reuse all of the nutrients that the plant doesn't use. Moreover, we only work with filtered rainwater. Our LED lighting is twice as efficient as the current standard on the market. And the system runs on green electricity from our own wind turbines and solar panels." It is Colruyt Group's ambition to sell herbs that have a very small ecological footprint. That's why the entire lifecycle of the plants is looked at, from seed to consumer's home. The retailer is therefore also working on recyclable packaging and a long shelf life, and will minimise the number of kilometres driven by integrating the vertical farm in a distribution centre in the future.
Home-grown innovative technology
Colruyt Group is the first retailer in Belgium to test a vertical farm that was developed in-house. The technology used has been fully developed within its own R&D department. In the current test set-up, biotechnologists and engineers continue to work on optimising growing conditions.
For Colruyt Group, this project isn't a leap into the unknown: recent innovation projects around water purification, LED lighting, renewable energy, automation, eco-design and refrigeration have formed the basis. In addition, the R&D department works together with a number of knowledge institutions. "We are also in talks with potential partners", adds Stefan Goethaert. "We also want to make some of the plants available to innovative entrepreneurs who work on food trends. Together we can explore the possibilities for using our products."
First trial at Bio-planet in 2019
"We are still in the testing phase, but the goal is to sell the first herbs at Bio-planet within a year", says Jo Ghilain, business unit manager of Bio-planet. "Vertical farming fits perfectly with our brand positioning. Bio-Planet stands for healthy, natural and local products. Furthermore, our customers are early adopters and are looking for added value. They are the people demanding products with a sustainable story." The herbs are currently grown using certified organic seed and substrate. "That was a decisive argument, in addition to the sustainability score of the plants", says Jo Ghilain.
Meanwhile, Bio-Planet customers were the first to taste test basil plants in three stores: on 27 November in Uccle, on 28 November in Grimbergen and Jambes. Jo Ghilain emphasises the added value of this co-creation: "The people of Uccle, Grimbergen and Jambes will help us determine the eventual flavour of the plants. Based on their opinions, we will adjust the cultivation process and the taste. This means that our customers actually choose the end result themselves."
For more information:
Colruyt Group
www.colruytgroup.com
Publication date : 12/5/2018
Hydroponics System Compared Side-By-Side
Today we’re talking about an experiment which we ran to compare four of the most popular hydroponic techniques.
by Urban Leaf Team | Dec 3, 2018 | Getting Started, How to Keep Plants Alive |
Today we’re talking about an experiment which we ran to compare four of the most popular hydroponic techniques. Since these techniques are used in dozens of commercially available units, we decided to test them out for ourselves directly side-by-side to determine which is the most effective form of indoor gardening. If you’re new to hydroponics and want to learn a little bit more about the science behind the systems discussed here or how they work, check out our YouTube video which goes through each of them in detail.
THE EXPERIMENT
The test included five different systems: four hydroponics and one control sample. We ran this experiment for three months on a bench in a basement with grow lamps situated to shine directly onto the plants. Each of the five systems contained three different plants including: cherry tomatoes (a model for flowering fruity plants), lettuce (a model for leafy greens), and beets (to represent root crops). All of the containers were solid opaque plastic to keep the light out of the water reservoirs and reduce the amount of aloe growth.
Check out some time lapse videos on YouTube. This post will focus on the data of the plant sizes, fruit yield, quantity of water usage, and temperature of each of the different systems.
#1: The Drip System: First, we have a drip system. The drip system uses clay pebbles to anchor the plant and delivers the water through an HTPE gardening irrigation system with three emitters. This system delivers water three times per day for 15 minutes each time.
#2: The Deep-Water Culture (DWC): Next, is the Deep-Water Culture. In this trial, the water is aerated with bubbles delivered by an aquarium tube and air stone.
#3: Aeroponics: The third system contains one ultrasonic fogger. These foggers were purchased from a specialty supplier for around $30 each.
#4: The Kratky: The fourth set-up is the Kratky: basically just distilled water and nutrients.
#5: Control Sample: Lastly, basic soil. Miracle Grow potting mix was placed into three free-draining containers (aka water bottles with holes in them) to use as the control. This was watered by hand, but truthfully, some waterings were missed and it got too dry every once in awhile.
ISSUES WITH THE EXPERIMENT:
There were some limitations and problems which might skew the results, including:
(1) The plants in the DWC with the bubbles died early. This wasn’t intentional, but (as we learned) the system goes through water extremely rapidly.
(2) Some of the plants were not given enough time to reach their full potential. For example, the tomato plant in the drip system grew very large but was slower to flower. Unfortunately, the experiment ended before it was given enough time for all of its flowers to fully produce fruit.
(3) Finally, there was an element of human error. Life happens and occasionally the control system wasn’t watered as a result.
EXPERIMENT RESULTS
What did we learn from our experiment? The most consistent and comparable data ended up being for the tomato plants, so that is the data which will be compared here.
Plant weight: The drip system grew the biggest plant, by far, but was much slower to flower. Unfortunately, because it ran out of water the Deep-Water Culture tomato plant didn’t make it to the end.
Yield: The aeroponic fog-based system produced both the largest and greatest quantity of fruit. The most surprising result was that the Kratky was the second best in terms of fruit yield. Given the simplicity and low cost of a Kratky set-up, it punches well above its weight.
Temperature: (Remember that these were all sitting in the same room, side-by-side.) You’ll notice from the graph that the aeroponic system was very warm. This is due to the heat emitted by the electronic fogger. Meanwhile, the DWC system with the bubbler was by far the coolest because the constant evaporation of water forced by the system is an endothermic reaction which absorbs heat.
Water use: The major differences in these systems was how they related to water use. The DWC with the bubbler by far consumed the most water. The Kratky consumed the least because it’s a passive system which doesn’t really force the air out. With the aeroponics, which was quite close to the Kratky in water usage, the vaporized water is able to condense back into the system so it recirculates rather than constantly intaking new water.
WHICH SYSTEM WAS THE OVERALL BEST?
If overall cost and maintenance are not a constraint, you’re likely to get the best results from an aeroponic-based system. However, in terms of bang for your buck, ease of set-up and use, and the fact that there are no moving parts, the Krafty system is hard to beat.
Hopefully, this has been a useful overview. Don’t forget to head on over and check out our video explaining the science behind each of these four hydroponic systems.
To learn more about hydroponics, gardening, or growing your own food, don’t forget to subscribe to our YouTube channel, sign up for future emails from Urban Leaf, or leave a question in the comments below.
US (MA): Lettuce Grower Decreases Crop Cycle by 30%
Fresh Roots Greenhouse is a hydroponic lettuce, herb and leafy greens grower based in Chelmsford, Massachusetts. After 40 years in the pharmaceutical industry, Fresh Roots’ owner Bill Evans wanted to give back to his community during his retirement years. He found himself drawn to how cooperative-run greenhouses like Evergreen Cooperatives and WellSpring Cooperative created jobs for underserved members in addition to providing local produce, which inspired him to build Fresh Roots Greenhouse. Fresh Roots’ state-of-the-art Harnois greenhouse uses an AmHydro Nutrient Film Technique (NFT) system to grow arugula, kale, basil, and several varieties of lettuce.
The potential to direct plant growth
Since Bill’s goal is to run his greenhouse year-round, he needed the most energy-efficient lighting system possible. His experiences growing with HPS and fluorescent lights at other facilities had been suboptimal. While the fixtures grew plants, Bill could tell that the plants were not growing as quickly and that the red varieties were not coloring up as expected. Bill felt that LEDs were the most practical financial choice – while LEDs cost a bit more up front, they would save him money on electricity and labor in the long run. After Bill learned about spectrum and LumiGrow through Melanie Yelton, Vice President of LumiGrow Research, at a hydroponic tomato growing course at the University of Arizona, he was eager to learn more and stayed in touch. He was impressed with LumiGrow Research’s depth of knowledge and hands-on approach to helping customers implement the latest lighting strategy research. As a result, LumiGrow was top of mind for Bill when he began to search for the right LED lighting system for Fresh Roots Greenhouse.
“I really believe in the promise of spectral science,” says Bill, “From the time I met Melanie [at University of Arizona] and learned about LED lighting’s potential to direct plant growth, I’ve wanted to work with LumiGrow.”
Extending photoperiod to maximize growth
Bill implemented LumiGrow fixtures across the Fresh Roots entire greenhouse. He uses them for all NFT stages of plant growth. Bill was eager to start growing and immediately began using the lights to extend his plants’ photoperiod to 21 hours.
“Keeping the light on for 21 hours keeps the plants awake,” explains Bill, “If they’re kept awake, we maximize their growth period.”
Fresh Roots lettuce varieties reach harvest size about 30% faster than their typical light exposure seen in soil farming. The seed manufacturer reports a typical harvest after 50-55 days, whereas the LumiGrow-lit lettuce is ready after about 35-40 days. Bill has had success growing a wide variety of lettuces, from green butterhead to green leaf to romaine. Depending on the variety, the finished lettuce heads weigh between 7-10 oz. Each variety grows a bit differently under the LumiGrow lights.
Bill has also successfully reduced his basil’s crop cycle by over 35-40%. The basil plants reach harvest size in 35-42 days – unlit greenhouse-grown basil can take up to 56-68 days as reported by the seed manufacturer.
Additional savings using smartPAR Light Sensors
Bill has moved past simple daylight extension and is using LumiGrow fixtures to automate his lighting strategy to improve production. Bill is using LumiGrow smartPAR Light Sensors to constantly monitor the light levels inside the greenhouse and adjust the fixture intensity to achieve a daily light integral (DLI) of 17 μmol·m−2·s−1 over the course of each 21-hour photoperiod. Once the target DLI is reached, the LumiGrow smartPAR Wireless Control System turns down the fixtures’ light intensity to minimize electricity use while keeping the plants awake for the full photoperiod. Bill is happy to see that his plants are thriving under the LumiGrow fixtures.
Bill was even happier to discover that in addition to consistently reaching his lighting goals, the smartPAR Light Sensors are maximizing his LumiGrow fixtures’ energy efficiency. After Fresh Roots’ smartPAR Light Sensors were installed, Bill noticed that his electricity bill was significantly lower than when he was simply turning the fixtures on at the end of the day to extend photoperiod. Bill can rest easy knowing that he can rely on his smart lighting to deliver the appropriate amount of light every day while saving him money each month.
Bill also appreciates the flexibility that LumiGrow adjustable spectrum offers. While Bill prefers to use his LumiGrow smartPAR Light Sensors to automate his greenhouse’s lighting, he likes that the LumiGrow smartPAR Wireless Control System also gives him the option to adjust each spectral channel to create custom spectral strategies. His LumiGrow fixtures’ versatility and user-friendly software make it simple to fine-tune his spectral programs as leafy greens research continues to develop. Bill likes that smartPAR enables him to easily create new lighting zones, which opens the possibility of growing new varieties of leafy greens under different ratios of light spectrum
In the meantime, Bill will continue to provide high-quality, locally-grown leafy greens to the local community in Massachusetts and share his passion for LumiGrow technology.
“I love sharing the many properties of these lights with people, particularly the science and engineering behind them,” says Bill, “Year-round supplemental lighting is not something a lot of greenhouses in this area have yet.”
For more information:
LumiGrow
800-514-0487
info@lumigrow.com
www.lumigrow.com
Growing Underground: The Hydroponic Farm Hidden 33 Metres Below London
"We have a growing population and a finite amount of land. We've got to find other spaces to grow in"Steven Dring, founder, Growing Underground
Thursday 13 April 2017
Forget everything you were taught in biology – plants don't need sunlight to grow. Growing Underground is a farm 33 metres below Clapham, south London, swapping sunlight for LEDs. "Over the past three to five years, LED development has reached the stage where we can grow without any natural light whatsoever," says Steven Dring, who founded the project with fellow Bristolian Richard Ballard. "You can even change the light spectrum to cater to the different plants that you're growing."
Growing Underground's focus is on the leafier vegetables, from microherbs to baby leaf salad. They grow quickly and need little space. "What's new about the latest lights is that you can stack them very close to the crops, 25cm away, if not closer," says Dring, "so you can layer products and lights on top of products and lights." This means that spaces such as car parks, warehouses and Growing Underground's second world war tunnels are all commercially viable spaces.
Presently, Dring and Ballard are using a 550-square-metre area fitted with hydroponics that will produce about 20,000kg of greens every year. As the business grows, so will the farm – they have 20,000 square metres to expand into. And their produce will be exclusively for those within the M25. "We'll be cutting it at four in the afternoon and people will be eating it at the next lunch time," he says. "And there's a desire to do this in other cities."
Moving production underground frees up more space on the surface for bulkier crops or livestock. "We have a growing population and a finite amount of land," says Dring. "We've got to find other spaces to grow in."
This article was originally published in March 2016.
Aquaponics in STEM Breakout Discussions
The Aquaponics Association’s Putting Up Shoots conference in September, 2018 featured breakout discussion sessions for Aquaponics in STEM Education and for other sub-fields of aquaponics.
By Kevin Savage
The Aquaponics Association’s Putting Up Shoots conference in September, 2018 featured breakout discussion sessions for Aquaponics in STEM Education and for other sub-fields of aquaponics. These sessions allowed all conference participants to give input and discuss steps we can take together to advance aquaponics in our respective areas.
In September 2012, I attended my first Aquaponics Association conference in Denver, CO. I was new to aquaponics, and new to attempting to use aquaponics as a model for teaching science and agriculture in a high school setting. The conference was a bit overwhelming with technical presentations, conversations during breaks and at meals, and networking with aquaponics practitioners (many of whom are now close friends). I distinctly recall, however, that I met only one or two other individuals who were doing aquaponics in a secondary school setting.
At the 2013 Tucson conference, the number of educators and professional who were working with school had increased significantly, and by the 2016 and 2017 conferences (Austin, TX and Portland, OR), educators had dedicated presentation tracks to share with others how they were using aquaponics in elementary, middle, and high school, as well as college and university settings, to teach a myriad of science, agriculture, engineering, and mathematics principles.
In September 2018, members and friends of the Aquaponics Association gathered in Hartford, Connecticut for the Association’s “Putting Up Shoots” conference. The “Shoots” conference included a STEM (Science-Technology-Engineering-Mathematics) technical track each day for education-focused presentations. Each day also include STEM-focused breakout sessions, where educators and those interested in adding aquaponics to a school or classroom had the opportunity to gather and discuss such topics as “How do I get my administration on board with aquaponics?”, “How do I incorporate aquaponics into my biology/chemistry/botany curriculum?”, and “Where do I find funding to cover the costs of starting aquaponics?” Some questions were easily addressed, but many others remained open-ended or unanswered, reflecting both the challenges and the opportunities for educators with a passion for experiential learning through aquaponics. The most exciting part of these breakout sessions was that over the three days of the conference, nearly 40 different individuals attended at least one of these sessions, and 25 individuals attended at least two of them! The participation of members in aquaponics in education continues grow!
Significant outcomes of these breakout sessions included introductions and networking, creation of a STEM education email group, and a “handshake” agreement to work with the educators of the U.S. Aquaculture Society to develop a forum or outlet for educators to share ideas and lesson plans, and to have a community in which to ask questions or seek assistance.
STEM Education is a primary focus area for the 2018 and 2019 Board of Directors, with the goal of creating a STEM Education Working Group. This working group will be composed of Association Members with a passion to see aquaponics education continue to grow, and a willingness to contribute to this growth. More information on the creation of this working group will be sent out in the near future.
IKEA and Tom Dixon Announce Urban Farming Collection
The project aims to motivate and enable a healthier and sustainable lifestyle for people in cities by making "homes the new farmland".
Gunseli Yalcinkaya | 29 November 2018 4 comments
IKEA has teamed up with British designer Tom Dixon to launch an urban farming project that encourages city-dwellers to grow food locally.
Dixon and the homeware brand are developing a series of gardening products and tools that can be used by individuals in cities to grow their own food and medicinal plants at home, available in IKEA stores globally in 2021.
Collaboration aims to encourage growing food at home
The project aims to motivate and enable a healthier and sustainable lifestyle for people in cities by making "homes the new farmland".
It also aims to build awareness of where food comes from and show the ways in which growing produce can be introduced into the home. "Food is a crucial part of everyday life, and IKEA wants to inspire and enable a healthier and more sustainable life," said IKEA.
Renders of the two planned levels at the Tom Dixon and IKEA RHS Chelsea Flower Show installation in May 2019
"If more greens were to be grown in homes, it would have a positive impact on the planet with fewer transports, lower water usage and less food waste."
Presentation at Chelsea Flower Show will demonstrate possibilities
An experimental model for growing plants in urban environments will be presented in May 2019 at the annual RHS Chelsea Flower Show in Chelsea in London.
It will feature a garden that is divided into two levels. The base garden will include a "horticultural laboratory" where hydroponic technology will be used to grow "hyper-natural" plants.
The raised level – described as a "botanical oasis" – will have a canopy-like ecosystem of trees and plants chosen for their medicinal, health and environmental properties.
The installation aims to explore the difference between natural and technology-driven approaches to farming. "Gardening is unique in its universal appeal and its transformational power," said Dixon.
"Although we are not traditional garden designers, we think we can demonstrate ways that anybody could make a small difference and broadcast not only the beauty but also the functional importance of horticulture through both traditional knowledge and the latest in growing innovation," he explained.
IKEA builds on previous urban gardening products
This is not the first time IKEA has branched into urban farming products. In 2016, the Swedish brand launched an indoor gardening product, intended to bring home hydroponics to a larger market.
"For IKEA, this collaboration is about challenging the way society looks at growing in general and addressing that it’s both possible and rewarding to have a place to grow your own plants in the city," said James Futcher, creative leader at IKEA Range and Supply.
"Food is key to humanity and design can support with better solutions. Because at the end of the day we need people to feel inspired to grow and harvest their own edibles within their homes and communities."
IKEA and Tom Dixon's previous project together was a bed that launched earlier this year with a distinctive furry cover and modular elements that allowed customers to modify the product for their own needs.
Farms in the City: How a Chinese Firm Uses Tech to Boost Yield
In suburban Beijing, a number of plant factories built with innovative techniques have incorporated farming into urban growth.
By Feng Yilei
2018-12-01 08:01 GMT+8
Updated 2018-12-01 09:06 GMT+8
An appetite for clean, fresh greens is growing with the burgeoning population in Chinese cities and towns. But feeding the rising demand is a challenge, partly because of the country's massive shift from being an agrarian to urban economy.
In the next 15 years, over 200 million Chinese are expected to move from rural areas into urban and suburban environments. This will greatly reduce the labor force on China's arable lands, which some say calls for a revolution in farming methods in order to create sustainable food production.
Beijing COFCO wisdom farm. /COFCO Photo
In suburban Beijing, a number of plant factories built with innovative techniques have incorporated farming into urban growth.
Dr. Wei Lingling, a researcher at the Chinese Academy of Agricultural Sciences, said controlled environmental agriculture (CEA) aims to get the most output with the least resources at the highest efficiency. They use technology like artificial intelligence (AI) and the Internet of Things (IoT) to precisely control production.
On a small plot of indoor space, plants are rooted on layered shelves vertically and bathe in light continuously during the day. Sensors linked to automatic irrigation and temperature control systems provide optimal conditions for growing.
Planned production means a higher yield resource-wise, space optimization, and labor savings. Dr. Wei believes CEA technologies will be more accurate in the future to better balance cultivation and the environment with less energy consumption.
“And in this closed production system, we circulate water and fertilizer to cut emissions, and improve sustainability of agriculture,” she added.
Plant factory using artificial light. /VCG Photo
While many believe this industrialized and intelligent way of farming will gradually replace extensive farming, which relies heavily on manual work and land usage for mass production, ordinary Chinese may have to accept difficulties in their daily lives during the process of moving on to the next stage.
For individual farmers that own the country's hundreds of millions of small plots, some have temporarily transferred their leaseholds to these high-tech farms and are adapting to their new roles.
Villager Wang Xiangang said that he got paid for both his land and working on the farm as an employee meaning he no longer worries about natural disasters and has time to learn about organic farming. He doesn't make as much as he used to, but it is stable.
And when conditions are ripe – will consumers be ready to pay a higher price for the products? Experts say the public will recognize the value of these crops as awareness of food safety and environmental stewardship rises. And once the demand rises, more players are expected to use tech-based food production, which will drive down prices.