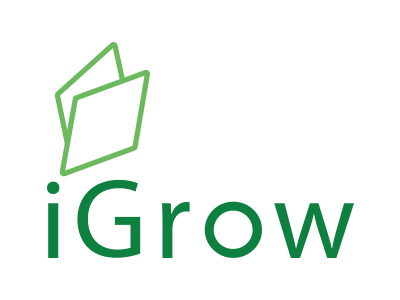
Welcome to iGrow News, Your Source for the World of Indoor Vertical Farming
Indoor Farming Technology Leader, SANANBIO®, Debuts UPLIFT Vertical Farming System
SANANBIO firmly believes that agriculture technology should be based on science paired with input from farmers. Michael Yates, SANANBIO's VP of Sales said, "Advanced knowledge of plant physiology and photobiology are fundamental to success in the vertical farming industry
The System Offers Customers A Fully
Automated Indoor Growing Process
LAS VEGAS, NEVADA (September 25, 2019) – SANANBIO®, a leading provider in LED horticulture lighting and vertical farm equipment and technology, announces the commercial release of its fully automated vertical farming system, UPLIFT (Unmanned Platform of Lean and Intelligent Farming Technology). Decades of manufacturing and automation experience, combined with successful multi-year vertical farm operations through parent company Sanan Optoelectronics has given SANANBIO the expertise in designing and operating the UPLIFT system to offer its customers a proven, fully automated indoor growing process.
SANANBIO firmly believes that agriculture technology should be based on science paired with input from farmers. Michael Yates, SANANBIO's VP of Sales said, "Advanced knowledge of plant physiology and photobiology are fundamental to success in the vertical farming industry. Through employing one of the world's largest teams focused on advancing vertical farming technology, UPLIFT is the solution born from the efforts of over 100 plant scientists and engineers."
The UPLIFT automated solution is based on SANANBIO's highly successful manual vertical farming grow system being used in farms today, RADIX. "With over 1M square feet of commercial vertical farms currently using RADIX, farmers and investors in more than 10 countries believe in our company's highly engineered grow technology. The proof is in the plants as our customers like to say," said Yates.
SANANBIO designed and installed the first pilot UPLIFT farm in April 2018 at its facility in Xiamen, China. After 18 months of operation and optimization, the UPLIFT system is now available for commercial deployment globally.
UPLIFT offers a full suite of automation for growing vertically. From seeding and germination to transplanting and harvesting, the high-stack, high-cube configuration offers the latest advancements in vertical farming solutions that reduce labor while achieving higher yields. The UPLIFT farming platform also benefits from an industry-standard production and inventory management system facilitating crop management, farm production planning, and crop traceability.
"Labor costs continue to be a major challenge for vertical farm operators while also maintaining profitability," stated Dr. Charlie Wang, SANANBIO CEO. "The UPLIFT system will help operators significantly reduce labor costs so they can sell more fresh and healthy produce, and therefore receive better returns on their investment. The system also provides an open platform to integrate technology that enables farms with more intelligence and controls allowing for maximized yields and profitability," said Wang.
SANANBIO's engineers and sales teams are prepared to work with leading farmers and investors in the industry who share the same passion to build ground-breaking projects in controlled environment agriculture using this cutting-edge technology.
SANANBIO® is a trademark carried and backed by Sanan Sino-science Photobiotech, a company invested in by Sanan Optoelectronics, one of the world’s largest LED chip manufacturers. Supported by an elite R&D team comprised of plant scientists, researchers, and engineers; SANANBIO utilizes state-of-the-art technology that enables growers worldwide in the horticulture industry to increase the quality and quantity of their yields. Years of extensive research and real-world deployment and operations allow SANANBIO to offer its customers proven, scalable, efficient and cost-effective solutions in LED horticulture lighting and Controlled Environment Agriculture (CEA) vertical farming grow systems. SANANBIO empowers growers with the technology and knowledge to achieve unprecedented results in farming operations.
To learn more visit: https://sananbious.com/
###
The Scottish Innovations Tackling The World’s Food Shortage
Invergowrie-based Intelligent Growth Solutions (IGS) has created Scotland’s first vertical farm, pictured here, and the company has recently harvested a £5.4 million cash boost from the Scottish Investment Bank, agri-food investor S2G and online venture capital firm AgFunder
Intelligent Growth Solutions' purpose-built facility is being constructed at the James Hutton Institute near Dundee.
SARAH DEVINE
19 September 2019
Scotland’s agriculture sector is changing rapidly, with rural businesses across the country driving forward groundbreaking innovations in attempts to address the myriad challenges of the land.
Globally, some 113 million people across 53 countries reportedly experienced food poverty last year, and it is expected that the world’s population will reach 9.8 billion by 2050, according to the UN.
However, inventive organizations across Scotland are devising new and creative ways to tackle the global food shortage.
Invergowrie-based Intelligent Growth Solutions (IGS) has created Scotland’s first vertical farm, pictured here, and the company has recently harvested a £5.4 million cash boost from the Scottish Investment Bank, agri-food investor S2G and online venture capital firm AgFunder.
The firm, which is based at the James Hutton Institute situated on the outskirts of Dundee, provides vertical farming technology to enable efficient food production through indoor crops around the world, having built its demonstration facility at Invergowrie last year.
It features stacked layers, LED lights and app-controlled air vents to create the perfect conditions for crops to thrive all year round.
The early-stage company states that its patented Internet of Things-enabled power and communications platform is able to reduce an organization’s energy usage by up to 50 percent and labor costs by up to 80 percent, in comparison to other indoor growing environments, and can produce yields of 225 percent compared to crops that have been grown under glass.
IGS experimented with colored LED lights, growing basil plants at the indoor facility in an impressive 20 days.
Its chief executive, David Farquhar, explains that such developments are urgently needed because at present an astonishing 30 percent of the world’s food is put to waste.
“Vertical farming allows experimentation to take place in order to impact the yield or cost of production, flavor, nutrients, appearance or a combination of those things,” he says.
“Producers want consistency, assurance of supply, and to know they are going to fill supermarket shelves or supply those Michelin-starred restaurants every day of the week. Those are things that farmers struggle with all the time.”
Farquhar adds: “If there is a forecast for bad weather and a supermarket decides to only take half of their delivery, what are they going to do with the rest of the produce?”
Using the vertical farm, a crop’s growth can be slowed down or sped up to prevent waste.
“People have been talking about vertical farms for several years, but we are now at the starting point. Over the next six months, we will get going with the first technology in the world that is capable of delivering this on an industrial scale.”
The firm, which was formed in 2013, plans to use this recent funding to create jobs in areas such as software development, engineering, robotics, and automation.
Investment into such areas is also needed across Scotland because dietary demand is changing, according to David Ross, chief executive of Edinburgh-based Agri-EPI Centre.
“Environmental sustainability is personal now for everyone and therefore there are challenges for primary producers to adapt to the needs of the consumer, the needs of society and the overall sustainability of the planet,” he says.
DASCOM Americas Announces Contained Environment Horticulture Systems To Be Globally Marketed And Jointly-Branded As HYVETM and EPONICTM
According to Ken Bryant, Marketing Director for DASCOM Americas: “The joint-branding effort will provide consistency and logistical advantages for our clients and prospects worldwide
August 22, 2019, Verona, Virginia – DASCOM Americas, a worldwide diversified technology leader today announced a joint branding initiative for its complete indoor hydroponic farming systems. Going forward the systems will be developed, marketed, and sold as either HYVETM (www.growhyve.com) or EPONICTM (www.eponicagriculture.com) depending on the geographic region of the globe.
HYVETM is led by Ron Acorn, President of DASCOM Americas and has its offices and grow lab facilities approximately 2 1⁄2 hours southwest of Washington, D.C.
EPONICTM is a brand of Eponic Agriculture Company, Ltd. Based in Zhuhai, Guangdong, China. Eponic Agriculture is led by Liu Guowei, a noted developer, engineer, entrepreneur, and horticulture system specialist. The company has enjoyed success throughout Asia and Europe with its innovative hydroponic growing systems and has developed a branded following with the EPONICTM name.
The respective farming systems consist of scalable product offerings including a comprehensive solution for commercial growing which includes vertical racking, irrigation, fertigation, LED grow lighting, robotics, programmable logic control, and other ancillary system components that provide industrial growers with a “complete solution” from one source.
Acorn says of the commercial vertical system: “Our complete solution is different than any system in the market because we combine all elements of contained environment horticulture into one product system offering. Our vertical racking offering is designed to provide growers with a great return on investment and consumers with a choice for the healthiest and freshest plants in the market. Indoor farming cuts down on transportation and spoilage costs, limits the exposure to diseased plants, and is safer largely because of no need for herbicides or pesticides.”
The brands are also offering a smaller home hydroponic unit that is a solid offering for education, residential, or small business use. The “LF-ONE” allows users to grow up to 54 mature plants per grow cycle and is programmable and automated much like the larger system. It is easy to assemble and use and provides fresh produce and the opportunity to grow 365 days a year.
Going forward HYVETM will direct its primary focus and brand in the North America and LAT regions of the globe. EPONICTM will be the brand name for systems marketed in EMEA and most of China and select other Asia-Pacific Regions. The exception in the China market will be that XiaMen New Green Ecological Technology Company LTD will utilize the HYVETM brand name as part of an exclusive distributorship agreement.
According to Ken Bryant, Marketing Director for DASCOM Americas: “The joint-branding effort will provide consistency and logistical advantages for our clients and prospects worldwide. EPONIC Agriculture is an expert company in development of products for contained horticulture systems. Our collaboration from day one has been extremely strong. Together this will allow us to capitalize on the strong EPONICTM brand in select markets while we build the HYVETM brand in our region of the world, while assuring our combined customers and prospects will experience consistency in equipment advances, customer service, and pricing.”
####
Ontario Greenhouse Growers Look At Cutting-Edge Advances
“As a vertically integrated grower, we’re using all the latest technologies available to us to grow the best possible vegetables,” said Chris Veillon, chief marketing officer for Pure Hothouse Foods Inc. in Leamington, ON
In an effort to contend with labor shortages, pests, food safety, and other challenges, Ontario’s greenhouse growers are tapping into a number of innovations.
“As a vertically integrated grower, we’re using all the latest technologies available to us to grow the best possible vegetables,” said Chris Veillon, chief marketing officer for Pure Hothouse Foods Inc. BB #:170379 in Leamington, ON.
Some growers use high-pressure sodium lights to supplement natural sunlight.
Pure Hothouse Foods installed the lights in a few facilities, and Carl Mastronardi, president and CEO of Del Fresco Produce Ltd. BB #:194101 in Kingsville, ON, said this the type of light used in Del Fresco’s strawberry greenhouses.
Automation is another increasingly common theme.
“Automation to offset the growing shortage of general farm labor is constantly added where it makes good financial sense,” said Ray Wowryk, director of business development with Nature Fresh Farms Sales Inc. BB #:274537 in Leamington, ON, adding that many growers are using upgraded artificial intelligence (AI) and other technologies to assist in crop management.
Some growers are also exploring indoor vertical farming, including Del Fresco.
“Our vertical farming is a very unique system—it doesn’t work like others where you’re growing in a warehouse on shelves,” Mastronardi said.
Called the LivingCube, he said it’s a very efficient growing method “where the plants actually get bathed by the light in the container. We’re going to grow microgreens and lettuce this way.”
The system produces living lettuce, basil, and microgreens all year, featuring 12 mechanized growing, germination, and irrigation machines, each built inside a proprietary insulated, 40-foot, stainless-steel growing chamber. The growing machines are individually climate controlled to optimize the environment and create a complete standalone growing system and independent growing facility.
Next, is packaging, and recent years have seen an uptick in demand for sustainability.
“Consumers are requesting more sustainable packaging,” Wowryk said.
In response, Nature Fresh has been working with retail partners to provide more eco-friendly options.
“Recently, we introduced a compostable tray for our mini cucumbers. Response has been very positive from our retail community, and customers have expressed gratitude through our social channels welcoming the change.”
Pure Hothouse Foods is also striving to reduce its carbon footprint with packaging alternatives.
“We’re transitioning our snacking tomato line to packaging that uses lidding film, which can reduce up to 25 percent of the plastic,” Veillon said. “The use of alternative bases such as palm fiber or sugarcane are emerging solutions that can be recyclable, biodegradable, or even compostable.”
Tagged greenhouse, ontario
US: Chicago - Vertical Farming Brings High-Tech Approach To Metropolitan Agriculture
"We're doing for farming what Henry Ford did for the automobile," said entrepreneur Jake Counne
A Local Entrepreneur Has A High-Tech Take
On Agriculture That Could Change What Ends Up On Our Plates
By Meghan Kluth
Thursday, August 15, 2019 CHICAGO (WLS)
You could call it farming for the future.
A local entrepreneur has a high-tech take on agriculture that could change what ends up on our plates.
"We're doing for farming what Henry Ford did for the automobile," said entrepreneur Jake Counne.
Counne has found a way to grow produce locally, even when it's below 50 outside. He said the answer is using cameras, software and a conveyor belt in what's called a vertical farm.
"I came across vertical farming and I was just enamored with the ability to exponentially out produce the natural ability of that land," said Counne, who is the founder and CEO of Backyard Fresh Farms.
Six types of lettuce are stacked on a four level tower under the glow of purple LED lights in his Back of the Yards facility.
The farm produces three tons of greens in one year's time, which is what a farmer could do with Soldier Field but in just four parking spaces.
Counne's vertical farm reduces costs of energy, labor, and his produce has proven to last weeks.
"We've already beat the cost of a field farmed equivalent products," Counne said.
An automatic lift collects trays of ready plants and brings them to an assembly line of workers for harvest. It has reduced labor by 80% compared to the first vertical farms of its kind.
"We are quite literally building an assembly line of greens," Counne said.
Counne has nine patents pending that are helping him create the perfect environment for a plant every day of its life.
"The software here is looking to try to figure out what the optimal amount of light. It's also looking for early signs of stress in the new growth," said Counne.
Some of the cities high end restaurants are already using Counne's produce and when put to the taste test, it's clear this is not your average lettuce.
Counne's plan is to expand and open 100,000 square foot facilities near every major metropolitan area around the country
Competitors Join Forces to Push The Industry Forward
“FarmRoadTM was conceived to fulfil two broad purposes. A platform for autonomous farming and secondly as a way of bringing together all disparate technologies that farmers use into one unified management tool,” explains Darryn
Autogrow and Ridder
In order for the industry to move forward, collaboration is necessary. That’s what Darryn Keiller, CEO with Autogrow, is convinced of. “Everybody is innovating, but innovating in silos. There’s no real sharing of advantages created for the broader industry - and that’s the only way of speeding up innovation.”
Launching FarmRoad on the Indoor AgTech yesterday!
To change this, Autogrow launched a new farm management platform: FarmRoad. The new platform was launched yesterday at the Indoor AgTech Summit in New York.
“FarmRoadTM was conceived to fulfil two broad purposes. A platform for autonomous farming and secondly as a way of bringing together all disparate technologies that farmers use into one unified management tool,” explains Darryn.
Autogrow aren’t just talking - they are doing what they say they are - and have also announced a collaboration with their competitor Ridder Group, which will make it possible for growers to connect their Ridder climate control and irrigation systems to the FarmRoadTM platform.
“To be truly unified you need to be open and work collaboratively across the industry with buy-in from existing major players. It’s a concept we advocated two years ago when we came out with the first open API (Application Programming Interface) and I’m pleased to be in a position to say the dream is now tangible.”
“We are ecstatic that Ridder has shown the foresight and faith in us, to support what we are doing and join us in showing the industry what is possible when true collaboration occurs.”
Both Autogrow and Ridder market automation solutions for Controlled Environment Agriculture (CEA) and both will be able to integrate with FarmRoadTM. Ridder Group, will make it possible for growers to connect their Ridder climate control and irrigation systems to the FarmRoadTM platform.
“The Ridder Group, developer of the HortiMaX greenhouse control systems for over 40 years, supports the initiative of Autogrow,” says Joep van den Bosch, Chief Innovation Officer, Ridder Group. “Ridder believes strongly in a connected future where systems and data is shared for the benefit of optimizing the plants growing conditions and more efficient and sustainable greenhouse operations.”
There are various developments in the industry causing Autogrow to start innovating in this direction. Darryn explains how there are roadblocks in the way when it comes to the adoption of Agtech including the knowledge base – with the average age of the farming community going up and limited knowledge sharing tools available.
In order to transfer knowledge and systemise it, making it possible to utilise new technology, they developed FarmRoadTM, making it possible to share knowledge and collaborate.
Autogrow CEO Darryn Keiller at the Auckland, NZ office
“There are many applications growers have to deal with at their farm. If it’s the cultivars or heating, or energy consumption - traceability, environmental effects, finance, labor. Part of our journey is unifying farm information and data for different farms and crops, including machine learning techniques, into one platform.”
Alongside Ridder Group, Autogrow will also be collaborating with New York based Start-Up NATIVE.
“Equally as important as an established player showing vision, is new entrants to the industry who are also bringing innovation. What NATIVE are creating delivers a fundamental industry building block, which we will integrate with FarmRoadTM,” says Darryn.
The NATIVE platform connects farms with local buyers, maximizing the value of their harvests and helping both buyers and restaurants deliver on the promise and demand of locally sourced food.
“Our partnership with Autogrow will most benefit the growers and the farmers,” says Frank Pica, co-founder, NATIVE. “FarmRoadTM users can provide NATIVE with real-time data that verifies the quantity and quality of their harvests, and Native will return the true market value of the products. NATIVE then provides an outlet for growers to bring their products to premium markets within their region.”
Autogrow will work closely with Ridder Group and NATIVE over the coming months during the pilot phase. The beginning of the journey in working collaboratively with producers and growers.
“The next iterations of FarmRoadTM include flower and fruiting identification through Machine Vision and AI to provide pollination rates and flower to fruit conversion performance. We will be extending the 3rd party integration to include finance, labor management, food security and more,” says Darryn.
For more information:
Kylie Horomia
Autogrow
kylie.horomia@autogrow.com
www.farmroad.io
Automation For Hydroponics
One of the biggest costs for any hydroponic business, regardless of the crops they produce, is labor
Incorporating Automation Can Help Hydroponic Operations Become
More Efficient And Grow More Productively
March 25, 2019
Fig. 1. Rafts for deep-flow technique (DFT) systems are quickly and effectively sanitized using this wash station.Photo: Christopher J. Currey
One of the biggest costs for any hydroponic business, regardless of the crops they produce, is labor. Mechanizing processes to reduce the amount of labor required for crop production is a sure way one way to reduce input costs. While the primary reason for using mechanization and automating processes is to reduce labor costs, there are other benefits to automation.
For example, in addition to saving on labor costs, it can also make more labor available for other jobs in the greenhouse, make certain tasks easier to execute and increase employee productivity. But benefits of automating extend beyond labor. Automation also reduces the time it takes to accomplish tasks and expedites processes and may open additional space in your facility and help you turn crops.
Regardless of what scale you are producing on, there are steps you can take to improve your efficiencies by integrating automation and mechanization to improve productivity. Plus, there are some relatively easy steps to take to start automating processes in your greenhouse. Investing in a seeder is going to be one of the first things any producer should do. A vacuum seeder is going to be one of the first and easiest ways to incorporate equipment to improve productivity. Manifold seeders seed one row of plugs at a time, whereas plate seeders will seed an entire flat at once; large facilities may benefit from using the larger drum or cylinder seeders.
Fig. 2. This leaf lettuce grown in nutrient-film technique (NFT) troughs is planted in one location in the greenhouse and, throughout production, the trough moves throughout the facility until it is fully grown, after which the trough moves down a conveyor to be harvested.Photo: Christopher J. Currey
In the greenhouse, regardless of size, automation can be key to maintaining a productive growing environment. Nutrient solutions for recirculating systems require adjustment to keep the pH and electrical conductivity within target ranges. This can be achieved by hand, spot-checking nutrient solution EC and pH and making the adjustments as-needed. However, automated pH and EC measurement of nutrient solution properties and subsequent adjustments moderates root-zone conditions and minimizes unwanted fluctuations. Sanitizing the troughs for nutrient-film technique (NFT) systems and rafts for deep-flow technique (DFT) or raceway systems can also be a laborious process. The opportunity to sanitize NFT channels and DFT rafts keep your system clean and reduces disease incidences and increases food safety, but it can be a laborious task. Equipment simplifying routine sanitation reduces labor costs and helps maintain best management practices (Fig. 1).
The larger the scale an operation and production, the possibilities to automate become even greater; the return on investment increases with the scale of production. In order to centralize labor, from planting to harvest, in the same part of the facility, some production systems are designed to move crops through a growing environment throughout production.
For instance, the lettuce grown in the NFT system in Fig. 2 is planted in the same area of the greenhouse where it is harvested. The NFT troughs move throughout the greenhouse and returns to be harvested. There are also opportunities to automate post-harvest processing and packaging. For common Dutch cucumbers produced hydroponically, conveyor belts facilitate transporting fruits from harvesting carts to shrink-wrapping machines, then onto cardboard containers for bulk packaging.
And there are some very exciting robots in the CEA industry. Grafted tomato plants are increasingly popular, but grafting is a very labor-intensive process. While these grafting robots still require labor to operate, they can complete up to 800 grafts per hour, greatly improving productivity. On the other end of production, we are not far from having automated harvesting as well! There are robots designed to selectively harvest hydroponically grown fruits such as cucumbers and strawberries.
Christopher (ccurrey@iastate.edu) is an assistant professor in the Department of Horticulture at Iowa State University.
Automation Hydroponics NFT pH EC Employees Labor Harvesting
DFT Robotics
Robot Farming Startup Iron Ox Sells First Produce In California
Robot farming startup Iron Ox has announced that it’s selling robot-reared leafy greens in a single location in California. The firm, which launched last October, is offering three varieties of greens at the San Carlos branch of Bianchini’s Market, a family-owned grocery store that specializes in local and organic produce.
Iron Ox is one of a number of companies trying to automate the human-intensive work of agriculture. It uses a combination of robotic picking arms, hydroponic vats, and self-driving porters to grow vegetables. But despite its repeated claims that its farming is “autonomous,” humans are still needed for a lot of the work. Laborers plant seedlings and package plants when they’re ready to eat: robots just tend them while they’re growing.
One benefit is that robot farms can be located nearer to customers because of their smaller physical footprint. Iron Ox says the greens it’s producing for Bianchini’s travel just 0.6 miles to get there, which is half the distance traveled by a typical head of lettuce. This means lower transportation costs and fewer food miles, a big factor when it comes to the environmental impact of what you put on your plate.
But the scale of Iron Ox’s operation is limited. It’s selling just three varieties of leafy greens and delivering them to Bianchini’s just once a week. The prices aren’t exorbitant, but they are on the expensive side. A two-ounce box of red-veined sorrel will go for $2.49, a two-ounce box of Genevieve basil will cost $2.99, and four heads of baby lettuce will be $4.99.
Source: www.theverge.com
Publication date: 5/3/2019
Automation: The Final Frontier of Vertical Farming
Article Blurb: Vertical indoor farming is poised to become a transformational and indispensable part of our food system — and system-wide automation is the key to unlocking its full potential.
By: Sam Bertram, Co-Founder & CEO of OnePointOne
It’s no secret that the world’s food system needs help. Our growing global population is urbanizing at a rapid rate – it’s estimated that 9 billion people will live in cities by 2100 – and traditional food sources will fall woefully short of being able to meet their needs. Vertical indoor farming is poised to become a transformational and indispensable part of our food system as we face the challenge of feeding those people. We’ve begun to see the first glimpse of successful vertical farming in the market, and system-wide automation will be the key to unlocking its full potential.
Already, urban dwellers around the world are enjoying freshly harvested produce grown locally on spare rooftops, in old shipping containers, and in repurposed warehouses. These farms provide tremendous benefits to consumers and producers: they can grow pesticide-free, nutritious leafy greens year-round in a controlled, space-, time- and resource-efficient way. The industry has experienced a rapid acceleration of growth and interest, with the likes of Jeff Bezos and Eric Schmidt placing early bets on the potential of this industry. Along with substantial investments, major partnerships with airlines, retailers, and governments are increasing the presence of vertically grown produce in our day-to-day lives.
However, despite the demonstrable consumer demand and investment around vertical farming, there is a significantly low volume of vertically farmed produce in the market. Why would this be? These farms are offering fresher and cleaner food than urban consumers have traditionally had access to before, and these products are arriving at a time when the local and organic food industries are positively booming.
What it comes down to is a simple fact that vertical farming is currently not a profitably scalable venture. In 2017, 73% of vertical farms were not profitable, even considering the premium at which their products are often sold. The vast majority of vertical farms have not been able to successfully expand to different locations and different markets. Overcoming this hurdle is essential if vertical farming is to capture a meaningful share of the retail and food service market in the US and abroad. The only way that vertically farmed produce can become a mass-market product is through system-wide automation.
Currently, no vertical farm has automated sufficiently or successfully enough to scale effectively or be price competitive in the current mass-market supply chain. This is not due to a lack of intellectual or capital resources, but rather the tremendous inherent complexity of automating the growth of a living plant and replicating it continuously. An apt analogy is Tesla. Tesla has run into enormous difficulty with automating the fabrication of what should be a predictable assembly line. Even with substantial financial and human capital, Tesla went through hell to make robotically automated car production lines a reality. Now replace the car with living organisms, and the profound complexity of this effort becomes apparent. Given this incredibly high barrier to entry, why would developing system-wide automation be a worthwhile endeavor?
Agrilyst reported that in 2017, labor accounted for 56% of production costs for vertical farms. Labor remains the single highest operating cost for even the most well-capitalized vertical farms in the world. Vertical farms must find more efficient ways to operate through strategic and sparing use of human labor in order to overcome this tremendous barrier. Total system automation must be developed if vertical farms hope to deliver on current promises and change our global food system.
Vertical farming companies have known this for a long time. The phrase “automated vertical farming” has been touted for many years, although without a clear definition, standardization, or validation process. Below is the first proposed framework to standardize levels of automation in vertical farms. Taking principles from categories of car automation, the framework below can be used to categorize the current and future automation potential of vertical farming companies and technologies.
The majority of commercial vertical farms exist in Level 2 (basic growth and automation). A small number of vertical farms – in pursuit of scale and improved margins – have managed to operate commercially in Level 3 (conveyor automation). Only a subset of the most well-capitalized vertical farms has attempted the jump from Level 3 to Level 4 (adaptive automation) – unfortunately with little commercial success. Here, complex logistics and decision-making will become the responsibility of the machine; it will be the most difficult of all the transitions. In addition, almost all vertical farms do not have the necessary ingredients to even attempt such a leap: patient investors, sufficient capital, plant science expertise, automation/robotics expertise, software expertise, etc. For those without sufficient resources, hundreds of profitable niche markets remain to be satisfied around the world. For those with sufficient resources, cost-competitiveness with the traditional supply chain awaits, along with multiple billion-dollar market opportunities.
Current farms are concentrated in technologically advanced and affluent cities. If they hope to expand their reach and become seriously competitive players in the mass market, they will need to drastically reduce operating costs with capital-efficient automation. Most consumers buy on price, and vertical farms will never compete on cost if they remain stagnant in Level 3. Incredible profit and scale await the vertical farms that can crack Level 4, as well as the capacity to feed people outside of the global top 1%. What’s exciting is that with the right combination of plant science and automation robotics, that future is sure to be right around the corner.
How Urban Indoor Farming Technology Is Changing
Lana Bandoim Contributor
Some of the crops are available to taste and buy during a tour at Square Roots Urban Growers in New York. Photo credit: DON EMMERT/AFP/Getty Images
As automation and data collection processes become more common, they are affecting more areas of the food industry. Urban indoor farming technology is also changing. Tobias Peggs, CEO and co-founder of Square Roots, shared more about how tech is transforming the industry.
Located in Brooklyn, Square Roots focuses on urban indoor farming. Its scalable “farmer first” technology platform brings fresh, healthy food to urban areas year-round, while simultaneously training future generations of farmers. The company recently announced its first major national expansion and partnership with Gordon Food Service.
"Gordon Food Service is one of North America's leading food service providers. It is a massive $15 billion per year food company with distribution operations spanning North America, as well as 175 retail locations in the U.S. Together, we will be building new campuses of our Square Roots indoor farms on or near Gordon Food Service distribution centers and retail stores across the continent," Peggs says.
Square Roots
Square Roots' technology focuses on data, insights and tools that help farmers learn to grow non-GMO, pesticide-free and delicious food all year round. Its platform also has a network of cloud-connected, modular farms, which are built inside shipping containers. Each farm has its own controlled climate that is optimized for growing certain crops.
"This means better speed to market. Using a modular container, we can open a new farm in three months and be very efficient with capital instead of taking years and spending millions of dollars to build a plant factory or a large scale industrial indoor farm or greenhouse. We can test a new market very quickly and can also be very creative with existing city infrastructure. We can pop up in a parking lot or take over a disused warehouse," Peggs explains.
The company's farms can be built in the same zip code as the end consumer. This means fresher products for the customers and more engaged urban communities. The setup can help customers feel connected to their local farm and farmers through events like regular farm tours. For example, in Brooklyn, Square Roots can go from harvest to store shelf in 24 hours or less.
Urban indoor farming is also easy to scale. To meet increasing customer demand in any market, they can simply add another container to any existing farm. Each of the container farms can grow 100 pounds per week of products, so they can add farms to meet the market needs when necessary.
Square Roots
"This means just-in-time capital deployment (very efficient) and also just-in-time technology deployment, which is important, as technology in this industry is improving fast, and you do not want to spend years and millions to open a big farm full of old tech," Peggs shares.
Another advantage is faster learning. The farms are cloud-connected and collect millions of data points in real-time that they can analyze with machine learning techniques to determine how changes in certain environmental parameters can impact the yield and taste of the final produce. More climates in more containers mean more feedback loops, which means faster learning. For example, the system has learned how to bring down the time to grow basil from 50 days to 28 days. That same system will also help them develop new "recipes" for new SKUs later this year, like strawberries or tomatoes, faster.
Peggs explains the company's mission is to bring local, real food to people in cities across the world and empower the next generation of leaders in urban farming. The company has plans to build, scale and expand, while training more farmers to grow delicious food on a global scale.
Lana Bandoim Contributor
I am a freelance writer and editor with more than a decade of experience. My work has appeared on Yahoo! News, Business Insider, The Huffington Post, The Week, MSN Money...
Read More
A Middle School Farm Team Is Automating Agriculture
Take me to your seeder: Behold, the FarmBot, an agricultural automaton that can plant, till, water, take pictures, check soil conditions and more, built and programmed by the young geniuses at Melville's West Hollow Middle School.
MARCH 14, 2019
By GREGORY ZELLER //
Meanwhile, back on the farm, the future was evolving.
The farm, in this case, is inside West Hollow Middle School, a forward-looking jewel of the Half Hollow Hills Central School District. And the future comes in the form of FarmBot, a kid-crafted, kid-coded automaton that could help feed future generations on this increasingly crowded planet – and even astronauts exploring distant worlds.
The robot, of course, tills its land on a relatively small scale: FarmBot measures 9 feet by 14 feet, an impressive achievement for middle-schoolers, if not quite ready to solve a global food crisis.
But as a blueprint for creative and sustainable agricultural innovations – a veritable must, with 7.5 billion hungry humans already seated and 3 billion additional dinner guests expected by the end of the century – FarmBot truly shines.
Described as “an open-source farming robot,” the mechanism slides on vertical and horizontal axes, carrying a camera, a small rake, a grasping tool and even soil-quality sensors that know when it’s time to make it rain, all designed and installed by ambitious sixth-, seventh- and eighth-graders (school maintenance professionals plugged in the electricity and water lines).
FarmBot knows what to do, and when, because of coding. “Kids who are interested in engineering” volunteered their time to build it, according to Half Hollow Hills CSD Public Relations Director Charles Parker, and now “different kids with interests in coding” are working on the programming side.
“Students came during their lunch periods and after school to build it,” Parker told Innovate LI. “And now students who are interested in coding are spending their time off in the school day to come work on it.
“These students are really doing phenomenal stuff.”
Part child, part machine, all farmer: West Hollow Middle School students help FarmBot work the land.
While the obvious goal is to automate the indoor growing process – interesting to overstuffed urban centers, future populations crowded into arctic regions and possibly space colonies – there are bigger themes at play.
Not only do students strengthen those increasingly important STEAM skills (for science, technology, engineering, art and math), they gain a wider understanding of alternative agricultural practices – also a priority, as farming environments shift, in many cases for the worse.
The effort even has a heart of gold: Hauppauge-based hunger-relief organization Island Harvest has donated seeds to the FarmBot project and will gather the fruits of the robo-labor for distribution to regional food-insecure families (other FarmBot produce will be used by the middle school’s Family and Consumer Science teaching staffs).
It’s a healthy crop of cross-disciplinary goodness, packed into a truly innovative 21st century educational effort, according to West Hollow Middle School science teacher Christopher Regini.
Life on MarsFarm: The crispy green fruits of hydroponic labor.
“The goal is to combine computational thinking, data collection and analysis, electronics and prototyping, and general good science practices to better understand plants, food production and the resources needed to reduce food insecurity,” Regini noted.
FarmBot, which was constructed and programmed this school year, follows in the virtual footsteps of another West Hollow Middle School future-farming foray: the MarsFarm, an indoor hydroponics farm already in its second year of operation.
Incorporating cutting-edge sensor technology into its soil-less system, MarsFarm allows students to remotely control systems and analyze data; via the education-focused Flipgrid videoconferencing network, they share their agricultural experiences with students in Acapulco and China, among other places.
Together, the STEAM-powered middle school farms are already producing healthy crops of cabbage, bok choy, bell peppers, basil and other herbs and vegetables, and there’s more on the way. Expect the tech to grow, too – according to the school, students are eager to begin 3D printing new tools for their prototype FarmBot system.
Regini – who noted the MarsFarm data is shared with Princeton University researchers and Growing Beyond Earth, a partnership between NASA and Florida’s Fairchild Tropical Botanical Garden – said the forward-thinking farming efforts are a critical tool for familiarizing young learners with science, art and engineering.
“The goal is to apply STEAM education in a way that is meaningful, allowing us to focus on topics already within the science curriculum,” the science teacher added, “while engaging students in a practice that equips them with the 21st century skills that make them future-ready.”
TOPICS: Charles Parker Christopher Regini Fairchild Tropical Botanical Garden FarmBot Flipgrid Half Hollow Hills Central School District Island Harvet LeadMarsFarm NASAPrinceton UniversityWest Hollow Middle School
Stop & Shop Sending Produce In Self-Driving Grocery Vehicles
The vehicles will bring a selection of Stop & Shop produce as well as meal kits.
JANUARY 16, 2019
Stop & Shop will launch driverless grocery vehicles in the greater Boston area beginning this spring. The vehicles will bring a selection of Stop & Shop produce as well as meal kits and convenience items directly to customers so they can shop right at their doorsteps.
Part of an engagement with San Francisco-based startup Robomart, the vehicles will address consumers’ growing interest in selecting their own fresh produce when shopping via online or mobile and will deliver an even more convenient grocery shopping experience for Stop & Shop customers in the Boston area. The new service will also offer the potential for the brand to expand beyond its existing brick-and-mortar stores.
“This is one way in which we’re leveraging new technology to make shopping easier for our customers – by essentially bringing the store to them,” said Mark McGowan, Stop & Shop president. “We also recognize that many of our customers want the opportunity to make their own choices when it comes to fresh produce, and we're proud to be the first retailer to engage with Robomart to address our customers’ needs with their cutting-edge solution.”
Stop & Shop customers in the Boston area can summon a Robomart vehicle with a smartphone app. Upon the vehicle’s arrival, they head outside, unlock the vehicle’s doors and then personally select the fruits, vegetables and other products they would like to purchase. When finished shopping, they simply close the doors and send the vehicle on its way. The vehicles’ RFID and computer vision technology automatically records what customers select to provide for a checkout-free experience, with receipts emailed within seconds.
“For decades, consumers had the convenience of their local greengrocer and milkman coming door to door, and we believe that by leveraging driverless technology we can recreate that level of convenience and accessibility,” said Robomart founder and CEO Ali Ahmed. “We’re extremely excited to bring our vision to life with Stop & Shop, one of the most pioneering and forward-thinking grocery chains in the world.”
All Robomart vehicles are autonomous, electric and remotely piloted from a Robomart facility. Throughout their delivery journey, these refrigerated vehicles will be restocked with fresh Stop & Shop goods to ensure customers are provided with the best selection.
The collaboration with Robomart is the latest example of Stop & Shop’s efforts to tap technology to enhance the grocery shopping experience and increase efficiencies. The brand recently opened a mechanized micro-fulfillment center in the Hartford, CT, area in partnership with Takeoff Technologies and, along with Giant/Martin’s, is introducing hundreds of robots in its stores.
Other Ahold Delhaize brands are investing in innovation as well, including Albert Heijn with the upcoming launch of the first fully automated distribution center in the Netherlands. Further, Ahold Delhaize is partnering with universities through its Artificial Intelligence for Retail Lab to accelerate research in AI and robotics.
Young Fijian Makes Good Use Of Govt Scheme
A Fijian who studied in India has made the most of Government’s Young Entrepreneurship Scheme and embarked on a journey to combine engineering and agriculture.
September 22
18:56 2018
by SWASHNA CHAND , SUVA
Entrepreneur, Rinesh Sharma.
A Fijian who studied in India has made the most of Government’s Young Entrepreneurship Scheme and embarked on a journey to combine engineering and agriculture.
Rinesh Sharma, 25, is an entrepreneur living in Lautoka who has started up something unique.
“While studying in India, I came across a software engineer who had an indoor hydroponics farm in Goa,” he said.
“After reading his success story, I made up my mind to do the same back home.”
Hydroponics is a method of growing plants without soil by using mineral nutrient solutions in a water solvent.
“Engineering combined with agriculture allows me to grow plants in its special conditions and parameters, maximising faster yields,” he said.
“I grow include strawberries, mint, coriander, coral lettuce and butter crunch lettuce. The idea of hydroponics came to me in my third year of engineering.
“Since then, I have researched every day about executing this project on a commercial scale in Fiji.”
Mr Sharma said he came back to Fiji in May and started an automated hydroponics system, in which he grew green leafy vegetables in his backyard.
“This was a challenging process because it was almost impossible to find hydroponic system supplies in Fiji, but regardless I made a small prototype where I can harvest 372 plants per month,” he said.
“Doing farming is the best thing I have done and perception really does matter because we have a lot of people who left farms and moved to the urban life and this has created a huge gap to fill in the field of agriculture.”
Mr Sharma said for him it was a mission to feed the world and he was going to start with his country.
“Upon my arrival in Fiji, I had applied for the YES entrepreneurship scheme run by the Ministry of Trade, Tourism and Industry with the intention to begin an automated hydroponics farm in Fiji on a commercial scale and got a grant of $20,000,” he said.
He is thankful to the Government for providing him with the assistance.
“The assistance is motivating and encouraging for us the younger generation to do step forward and do something,” he said.
“I keep challenging myself with growing the most impossible edible items such as blueberries, raspberries and apples as well.
“It is important that people of Fiji are able to afford proper nutritional meals every day and that to at low cost.
“So, as a hydroponics farmer, I am able to control any device in my farm through a single touch on my phone via internet and I am also able to receive any data changes that may occur, such as change in PH, moisture, temperature.
“It was a privilege to be given a scholarship by the Indian High Commission where I got to learn so much.
“I came back to Fiji with the intention of working with the Government and their expertise to change and shape farming methods in Fiji.”
Edited by Epineri Vula
Feedback: swashna.chand@fijisun.com.fj
Urban Crop Solutions Offers A Glowing And Growing Global Future For Indoor Farming
A start-up that engineers and builds fully automated indoor vertical farms inside shipping containers and buildings.
by S. Virani
25 September 2018
“Imagine yourself standing inside a climate-controlled, high-ceiling warehouse. In front of you stands a tower with 8 irrigated levels, on each of which lettuces, herbs, micro greens, and baby greens grow under LED lights. Robotics move trays with young plants from outside this grow room into the right position in the grow tower, while on the other end fully grown crops are taken out, ready to be harvested. Can you see it? You are standing in Urban Crop Solutions' Plant Factory — the state-of-the-art in indoor vertical farming technology. A highly engineered manufacturing plant producing not goods, but crops.” — Urban Crop Solutions.
Meet Urban Crop Solutions: A start-up that engineers and builds fully automated indoor vertical farms inside shipping containers and buildings. They also provide clients that have bought a system with carefully selected and tested seeds, substrates, nutrients and comprehensive software grow recipes. The result: year-round production of fresh and healthy crops.
The start-up’s goal is to create an optimum environment for plants to grow, with the right combination of climate, lighting and nutrients throughout their growth cycle.
From left, Frederic Bulcaen, co-founder and chairman at Urban Crop Solutions, with Brecht Stubbe, global sales director and Maarten Vandecruys, co-founder and CEO with at European FoodNexus Award Ceremony
Headquartered in Belgium, with regional offices in Miami (USA) and Osaka (Japan) as well as a network of sales agents in various territories, Urban Crop Solutions will take part in the World Agri-Tech Innovation Summit to be held from October 16-17 in London, selected as one of the 13 start-ups to present their innovative solutions.
Produce Business UK sat down with Brecht Stubbe, global sales director of Urban Crop Solutions, to understand the technology that the start-up has developed, as well the growth of the vertical farming market in general, challenges that farmers face now and will face in the future, and Urban Crop Solutions’ formulas to combat food shortage in the future.
How did the Urban Crop Solution concept come about?
By 2050, more than 70 per cent of all people will live in cities. The population will grow from 2.5 billion to over 9.8 billion, leading to a need to produce 70 per cent more food. In 2012, 80 per cent of the land suitable for agriculture was already in use. Due to these facts, it was safe to say that something needed to change.
That is when our co-founder (Maarten Vandecruys) started thinking: “What if we could use technology to grow any plant, year-round and independent of local climate? What if we could do this using 95 per cent less fresh water? What if we could do this using zero pesticides and herbicides?” Together with Frédéric Bulcaen, the other co-founder who acted as a business angel, they set out to explore this further.
With the above goals in mind, modular solutions were developed at Urban Crop Solutions: A fully controlled and automated resolution that can be placed anywhere and which can grow any plant. Imagine a closed box or warehouse with crisp white walls in which plants are grown using LED lights, as well as without soil.
In lieu of the Agri-Innovation Summit, where you will present alongside a dozen or so other start-ups, what is it about your technology that stands out and set up apart? Essentially what is your unique selling point?
Urban Crop Solutions has a total turnkey solution, as well the latest technology in terms of indoor farming systems. A big difference with other competitors is the fact that we have plant scientists that develop recipes for more than 180 crop varieties. We also offer all the consumables — seeds, substrates, nutrients — to help you grow your crops.
Finally, we have experience all over the globe, from Belgium to Japan to Miami.
So when we look at our unique selling propositions, these would be the consistent high quality of produce combined with our biological know-how of how to grow them, as well as the use of automation to bring down labour costs.
Let’s talk about your clientele and the sorts of industries that you have worked with? Furthermore, would you say there has been a growth in demand for this over the years?
A first category of clients are the entrepreneurs, people who see the opportunity this technology offers and plan to start from scratch. For example, those who want to build a produce brand growing vertically and indoors.
Another category are R&D institutions and corporate departments as well as crop science companies that use our technology to conduct relevant research while being able to manage all variables precisely to their needs.
A third important category is the existing vertical farmers who are looking for a high-quality, third-party solution provider to help them scale.
We would also include the category of existing traditional farmers that are looking to capture the new market this technology offers by complementing their existing production methods. For example, open-field and greenhouse farming.
Do you see other start-ups competing in this space?
Not really. There are a lot of vertical farmers focused on growing and integrating technology themselves. However, they are not any qualitative total solution providers like Urban Crop Solutions, that have the ability to design and build a tailored, fully automated efficient solution the world over.
We just did a piece about the new Emirates Airlines vertical farm. It provides an example of how other industries can apply and utilize the vertical farm. What are your thoughts on that?
This is a good example of disruptive new business opportunities and vertical integration into supply chains. Zooming out, the broader definition of this case can be defined as food catering companies (a subcategory of food processing companies) integrating produce farming into their business. The technology allows them to capture an additional margin by adding the value themselves as opposed to buying the produce from a third party and enables them to perform just-in-time production with reductions in waste and certainty of ability to deliver.
You have various solutions on your website: The Farmflex Container, The Farmpro Container? The Plant Factory. What are the main differences between all of them?
We have two different product categories:
Off-the-shelve product
This includes our FarmPro & FarmFlex container. These are mainly used as a first stepping stone/proof of concept for companies that would like to grow commercially or conduct research on a larger scale in the future.
FarmPro container: The Urban Crop Solutions FarmPro is a 40-foot, fully automated freight container with a state-of-the-art leafy green growing system. This system gives a four-layer growing solution. Its design is primarily focused on growing lettuce and individual herbs.
FarmFlex container: This system has a state-of-the-art leafy green growing rack setup. It gives a fully automated, four-layer growing solution with maximum flexibility as to what you can grow. For this reason, educational and research institutions have the highest demand for this product, as it allows growth of almost anything: lettuce, herbs, micro greens, baby greens and more.
Then we have custom-made large-scale solutions:
PlantFactory: Our Urban Crop Solutions PlantFactory allows you to grow in any available space, whether it is a basement or a warehouse. This way, you can produce leafy greens year-round on an industrial scale or set up complex large-scale R&D infrastructure.
In an Urban Crop Solutions PlantFactory, everything is designed and engineered according to the available space, as well as to the customers’ needs. For example, the cultivation area, our innovative LED growing technology, ingenious irrigation systems and climate control.
In terms of industries, what industries do you work with, and what would you say are the industries most relevant for now in 2018?
Agricultural food production and crop science research are the most relevant industries for 2018 based on the demand they produce for us.
As a B2B publication focused on produce, we are interested in how vertical farming truly can affect the industry as a whole. What are some predictions you might have about the effect of vertical farming on produce? Are there particular fruits or vegetables that will thrive in this environment and produce higher yields?
There exists a distinction between what we can grow from a technical standpoint (almost everything – even strawberries, cucumbers, tomatoes, peppers, etc.) Then, however, there is the commercial standpoint. The latter is more limited because obviously one needs a positive cash flow. The capital-investment cost and substantial operational costs (e.g. electricity) require that one selects a crop that has a short grow cycle, high density and harvests the full biomass created.
As a result, the current commercially viable food production crops are the leafy greens such as lettuce, herbs, baby greens and micro greens.
Just how good, just how efficient are these farms?
The farms can be tailored to include carefully selected and tested seeds, substrates, nutrients and a comprehensive software tool automatically providing the plants with the right combination of climate, lighting and nutrients throughout their growth cycle. Our solution leads to higher yields, higher nutritional value, food safety and security, higher water efficiency. This can actually be up to 95 per cent less than open-field farming.
On your home page, you make the following claim: “Urban Crop Solutions envisions to become the global independent reference of the fast-emerging vertical farming industry." How would you say this is possible?
At this time, vertical farmers are trying to juggle two widely different business plans: on the one hand, they spend capital developing and integrating an engineered solution and the biological corresponding know-how. On the other hand, they then apply this research to construct a vertical farm, operate it as farmers, and earn back the investment not only of the infrastructure, but also of the R&D that precedes it, as well as continues afterwards. In our opinion, this is a poor business plan because they have to earn back their R&D and their operational infrastructure investment with the sale of crops.
If we look at the more mature greenhouse industry, we get a sense of where the sector of vertical farming will eventually evolve. A greenhouse tomato grower that wants to set up a new production facility will not develop his own technology, but instead turn to the 15 best greenhouse project developers, ask for quotes, and select the one he feels most confident about. In that setup, we see technology companies focusing on providing systems, and growers focusing on farming. We start seeing a change in the mindset of vertical farmers along those lines today as well.
Let’s talk briefly about the upcoming World Agri-Tech Innovation Summit. What will you be presenting there?
We will begin with a company introduction, present our unique selling points, newest technology, projects and achievements.
While creating all these solutions, there indeed have to be challenges that need solutions. What would you then say are some of the actual challenges that farmers face today?
Traditional farmers are combating unreliable climate conditions, increased labor costs, crop diseases, crop pests, soil degradation and much more. Our solutions provide reliable alternatives to all of these concerns.
Existing vertical farmers from their end are struggling with the high labor costs associated with running non-automated vertical farms — requiring scissor lifts or stairs to harvest the higher levels of crop cultivation areas — as well as inconsistent quality in their production due to poor control of the different variables. Our fully automated and well-engineered system reduces labour costs and deviations from the ideal settings, respectively.
The vertical farm model is certainly a rising trend amongst start-ups. How did this movement come about?
Well, it’s like I said from the beginning. By 2050, more than 70 per cent of all people will live in cities. Added to that, in 2017 almost 300 million USD has been invested in vertical farming, creating more and more momentum.
To put things into perspective globally, which regions would you say have the biggest influence on the vertical farm boom?
In North America and South East Asia, we see the most vertical farms. In South East Asia, there is a lack of land to farm on and a variety of food safety issues. In North America, there are a lot of business opportunities with vertical farming technology due to the willingness of consumers to pay a premium for locally produced healthy crops.
First Automated Indoor Farm In The U.S. Will Grow Greens For Whole Foods
America is about to get its first fully automated indoor farm.
BY KRISTIN HUNT
1 MONTH AGO
America is about to get its first fully automated indoor farm. This one-of-a-kind site will use robotics and artificial intelligence to grow fresh produce for supermarkets across the United States, including national chains like Whole Foods.
The farm is underway in Hamilton, Ohio — a city just 20 miles away from Cincinnati, where the company behind this innovative project is based. 80 Acre Farms has been on the vertical indoor farming scene since 2015, but this expansion will mark a dramatic increase in production.
The new farm will span over 150,000 square feet, or roughly 3.4 acres, and grow crops ranging from microgreens to kale. Once construction is complete, 80 Acres Farms will supply Whole Foods, Jungle Jims, U.S. Foods, Dorothy Lane Markets, and other food sellers and distributors with veggies year-round.
"We already have demonstrated that we can provide to our customers the freshest, best-tasting and nutritious locally-grown produce, while using renewable energy, very little water, and no pesticides," Mike Zelkind, co-founder and CEO of 80 Acres Farms, said in a press release.
"With the Hamilton facility we will achieve the next-generation of indoor vertical farming using best of breed technology. This project will deliver our proof of concept that indoor farming can be fully-automated, commercially scalable, higher-yielding, and profitable.
"It will serve as a prototype for our ambitious plans to co-locate similar facilities with commercial customers in other parts of the country."
80 Acres Farms uses a hydroponic system that nourishes plants with minimal resources. Hydroponic farming typically requires no soil, no pesticides, and much less water than traditional growing methods, making it the technique of choice among many sustainable food makers.
Indoor farms also allow for better temperature control. With four walls and a roof, growers can keep the environment as warm, cool, or mild as they like — meaning no crop is ever out of season.
They’re also not an energy drain. Thanks to efficient LED lights that nurture the plants’ growth, 80 Acres can manage its power needs. That efficiency extends to the day-to-day operations, which will be bolstered by artificial intelligence, data analysis, robotics, monitors, and control systems.
Despite the robot assistance, the farm will create 40 jobs with an average $40,000 to $50,000 salary — plus benefits.
"Hamilton thanks 80 Acres Farms for its investment in our city," Pat Moeller, the mayor of Hamilton, said in the release.
"80 Acres' high-tech indoor farm efficiently grows fresh produce that will continue to be sold locally. I have had the opportunity to purchase 80 Acres produce and really enjoyed the fresh, flavorful taste."
According to CNBC, the farm’s projected cost is somewhere between $10 and $15 million. Hamilton officials and 80 Acres Farms expect the first phase of the project to wrap by the end of this year, with three additional phases to follow after that.
It’s unclear when the new farm will be open and ready for business, but once it is, it could have a significant impact on the way the U.S. grows and sells food.
If Farms Are to Survive, We Need to Think About Them as Tech Companies
We’re not experiencing a food shortage—it’s a shortage of people to farm it.
By Brandon Alexander October 3, 2018
CEO of Iron Ox and former engineer at Google X's drone-delivery program, Project Wing
Growing up on my granddad’s farm—he grows cotton, peanuts, and potatoes in Texas—I often heard that technologies like genetically modified crops were required to scale food production. My granddad believed that organic practices do not scale and will not feed the world at an affordable price point. Given the state of technology then, I believe he was right.
But the industry has changed with much more than the seasons, and we need more than an iterative improvement on past technologies. We are reaching a plateau in food production. According to research published in Nature, about one third of the world’s agricultural lands have maxed out the amount of rice, wheat, and corn farmers can grow.
At the same time, the World Resources Institute suggests we will need to double our food production by 2050 to feed nearly 10 billion people. In order to boost yield, we need to systematically improve the entire grow process and maximize the potential of every plant. To enable this next age of agriculture, we will need to rely on two new advances: machine learning and robotics.
The amount of data available to farmers has skyrocketed. In addition to collecting data at a macro level from satellite or drone imagery, we can also capture data at the micro level, thanks to a combination of cheaper, lower-powered sensors. These sensors provide farmers with insights like hyperlocal measurements on soil conditions, for example.
AP PHOTO/RICH PEDRONCELLI
Farmers have already been using drones to spray crops for years—what tech will come next?
But a firehose of data does not equate to insights, and that’s where the newer methods of applied machine learning come in. Companies like Descartes Labs and Farm Logs are applying machine learning and computer vision to glean insights from these new data streams, providing farmers not just pretty graphs, but actionable information to increase yield.
Machine learning and computer vision enables us to scan each plant in acres of land, detecting plant diseases before they spread and significantly minimizing yield loss and the need for pesticides. For example, traditionally a farmer would inspect parts of a plot of land for plant diseases like powdery mildew or signs of pest pressure like aphids. Because it was physically impossible for them to inspect each plant on acres of land, they would have to extrapolate their findings across the entire plot. Now, modern computer-vision techniques can take multiple images of every plant and stitch them together for a full 3D reconstructed model of the produce.
Data may give us the information we need to improve yield, but something still needs to perform the action. And it’s increasingly not humans.
We are experiencing a growing labor-shortage epidemic. According to the US Census, the average farmer is 58.3 years old, and new generations are not inspired to take on the laborious task that their elders did—even those who have generations of farmers in their family, like myself. This issue isn’t a shortage of food: It’s of people. Crops are rotting on bushes and vines because there aren’t enough staff to maintain and pick them. Considering that one in nine people onEarth aren’t getting adequate nutrition every day, it’s devastating.
This means that though there are more mouths to feed than ever, there will be less land to provide them food, and less calloused hands to tend to the crops that will feed them. So what do you do when you have little land to work with and fewer hands to help? You turn to technology.
Automation allows for a more accurate work environment with little human oversight. It will involve hardware that is more agile than the human eye or hand, and it will be able to give each and every plant the unique attention it needs.
Recent advancements in computing power, dexterity, motion planning, and computer vision are enabling a new generation of robotic applications. Robotics excel at rapidly performing repetitive tasks, but combined with computer vision, robots can start making real-time decisions on a per plant basis, from adjusting the nutrients to pruning. Companies like Blue River have successfully automated tasks like weeding (a manual process for non-GMO crops) to great effect, which is why John Deere bought the company for over $300 million last year.
DAVE GERSHGORN/QUARTZ
A sample of Iron Ox’s automated grow operation.
At Iron Ox, we’ve designed the entire grow process with a robotics-first approach. That means not just adding a robot to an existing process, but designing everything, including our own hydroponic grow system, around the robotics. In an indoor farm, tasks like seeding or harvesting are happening thousands of a times a day. These labor intensive, repetitive tasks are perfect for robotics. And by integrating machine learning and computer vision, we’re able to have the robots respond to an individual plant’s needs. For example, our robot can quarantine a plant if it shows early signs of pest pressure before it contaminates others nearby or change the nutrition recipe for a plant based on phenotyping.
And we don’t even need arable land: By creating indoor farmhouses with these technologies, we can open farmhouses in any location. This means we will be able to control the weather and take chance out of the growing process; currently, we’re losing more and more crops every year to drought, extreme heat and cold, and spontaneous weather incidents. We will also be able to grow crops closer to the communities that need them, reducing the amount of miles travelled to consumers’ kitchens and the industry’s carbon footprint writ large—and for much cheaper.
If farms are to survive, we need to think about them as tech companies. And that means they should be taking advantage of what many other industries are already harnessing: automation.
This story is part of What Happens Next, our complete guide to understanding the future. Read more predictions about the Future of Food.
Leafy Greens are Grown by Machines at New, Automated Silicon Valley Farm
Called Iron Ox, the farm aims to produce leafy greens — romaine, butterhead, and kale, alongside various herbs
Luke Dormehl POSTED ON 10.13.18 - 1:00PM
Did you hear the one about the Google software engineer who packed it all in to start a farm? No, it’s not the setup for a joke. Nor is it the premise for some quirky Sundance comedy, probably telling the story of a stressed-out programmer who rediscovers their happiness by moving to the country. It’s a real, honest-to-goodness farm, which just opened in San Carlos, around 20 miles outside San Francisco. Called Iron Ox, the farm aims to produce leafy greens — romaine, butterhead, and kale, alongside various herbs — at a rate of roughly 26,000 heads per year. Oh yes, and it’s staffed almost exclusively by robots.
“This is a fundamentally different way of approaching farming,” CEO and co-founder Brandon Alexander, 33, told Digital Trends. “Traditionally, the farming process means that you seed, you wait a few months, you come back, you harvest, and you distribute. That hasn’t changed a whole lot in hundreds, if not thousands, of years.” Until now, at least.
Iron Ox’s indoor farm measures around 8,000-square-feet. That makes it paltry compared to the thousands of acres occupied by many traditional farms, but, through the use of some smart technology, it promises a production output that’s more in line with an outdoor farm five times its size. To achieve this, it has a few tricks up its sleeve. For starters, Iron Ox is a hydroponics farm, a method of growing plants without soil, using mineral nutrient solutions in a water solvent. Unlike a regular farm, hydroponic farms grow their produce in vertical and horizontal stacks; every element minutely controlled through the use of glowing LED lights and jets of water to affect the crops’ size, texture, and other characteristics.
In place of a farmer, Iron Ox employs a giant, 1,000 pound robot called Angus. It’s Angus’ job to move the heavy 800 pound, water-filled tubs of fresh produce without spilling them. A robot arm is used to tend the crops, making this the agricultural equivalent of Elon Musk’s automated Tesla factory in Fremont, CA.
“We’ve taken a robotics-first approach to the growing,” Alexander continued, in what can only be described as an understatement. “Everything is designed with that in mind.”
DISRUPTING THE FAMILY BUSINESS
When he was a kid, Alexander was shipped off each summer to his grandfather’s family farm in the Texas and Oklahoma area. Looking back at it today, it’s a cherished memory. At the time, not so much.
Iron Ox
“I’ll be honest: I hated it,” he said. “All my friends were going on vacation and I was the one who was stuck on a farm.” When his buddies were sleeping in, he was getting up at the crack of dawn. When they were on the beach, he was on a tractor. Years later, when he and his co-founder and CTO Jonathan Binney, 34, were busy planning out Iron Ox, he called his grandfather. Now 83 and still running a farm, Alexander told him about his plans for roboticizing the work that his family had done by hand for generations.
But this isn’t a story about a guy who decided to take revenge for summers of hard labor by disrupting the industry. Far from it. Alexander has a deep respect for farming, evident from the reverent way that he speaks about a profession that has looked after his family for years.
“[My grandad is] technophobic; he doesn’t know how to use an iPhone [or about machine learning or computer vision],” Alexander said. “But when I explained what I was doing, he said, ‘This is inevitable.’ That kind of surprised me, but it shouldn’t. When he was a kid, and his dad was farming, they managed 40 acres. Now him and his crew are managing 6,000 acres. He’s seen the progression.”
JUST-IN-TIME FARMING
Farming isn’t an industry that’s at the forefront of many people’s minds in Silicon Valley. It probably should be, though, because the emphasis on farm-to-table produce is only growing. When Alexander and Binney speak to chefs, they regularly hear stories about customers wanting to know exactly where a particular bit of produce has been sourced from, or how old it is.
That typically gets an unsatisfactory answer in the U.S., where the average distance travelled by fresh fruit and vegetables is around 2,000 miles. “There are relatively few places that have the right conditions for growing,” Alexander explained. “Everyone else gets week-old produce.”
Iron Ox
Iron Ox aims to change that by building farms within easy reach of cities. Using its autonomous technology, customers can get fresh greens grown in their neighborhood. Better yet, they can get it year round, since an indoor farm isn’t subject to the same seasonal conditions as traditional farms are.
“We call this just-in-time farming,” Alexander said. He is using terminology that is usually applied to manufacturing, pioneered by automaker Toyota in Japan during the 1960s and 70s. What makes just-in-time manufacturing special is that it focuses on making items to meet demand, rather than creating surplus in advance of need. It means less waste with overproduction, less waiting, and less excess inventory. That works well for cars, computers, or smartphones. The Iron Ox team hope it will work great for crops, too.
“In a traditional greenhouse, you’re committed to growing a thousand or tens of thousands of a particular varietal,” Alexander said. “Our systems gives us the ability to fine-tune the nutrients for each crop. We’re only committed to growing a hundred of something at a time. That’s important. Previously you would committed to, for example, kale. ‘Kale’s going great,’ you say. ‘Let’s go all-in on kale.’ But trends change. If we suddenly notice a big demand for purple bok choy or Italian basil, our system can adapt to that consumer demand very quickly.”
Overseeing the farm, like a green-fingered HAL 9000 from 2001: A Space Odyssey, is what Alexander calls “The Brain.” This is a cloud-based, A.I. which constantly monitors information relating to nitrogen levels, temperature, and the location of robots. Over time, it will expand this to take into account data pertaining to food orders, or more general information about food-based trends.
Weighing up all this data, it can then make decisions about exactly what should be growing — and in what quantities — in each of the modular tanks.
THE ROAD FROM HERE
Right now, Iron Ox is starting to take chef’s orders for the two dozen-plus varieties of leafy greens that it is growing from the start. It aims to be in full production by the end of the year. This is still the beginning of the journey, but it’s one that Alexander and his co-founder are happy to be on.
“We had some pretty good, cushy jobs at Google and whatnot,” Alexander said. “We wanted to make sure that, when we took the next step, it was something we were passionate about. It’s not about staying passionate for one year; it’s about whether or not this was something we could put decades of our life into? That’s a different metric, for sure.”
How does he feel about the impact of automation on jobs in the farming community as a whole?
“I think farming is a fairly unique space in this regard,” he said. “Agriculture is one of the few industries right now where they can’t get enough help. That was something that surprised Jon and myself when we first started. When we quit our jobs, we spent four months roadtripping California, talking to farmers. We talked to dozens of outdoor and indoor farmers. One of the questions we asked was ‘what’s your biggest pain point?’ 100 percent of them said that it was labor scarcity. They could not get enough help for their farms.”
Added to this is the fact that, in the United States, the average age of a farmer is 58. “It’s a bell curve distribution, and it keeps shifting over to older and older,” he said.
Those jobs are not being replaced in equal numbers by the younger generation. “There simply aren’t enough people wanting to do this,” he continued. “And I don’t blame them. It’s hard, back-breaking work. It’s just where it’s going.”
Iron Ox isn’t the only startup applying the latest technology to farming. Other companies and researchers are building self-driving tractors for farms, using CRISPR gene editing to improve the efficacy of crops, and building robots that are capable of picking a variety of fresh produce without damaging it. But Iron Ox’s business model nevertheless represents an enormous step potential forward in U.S. agriculture and the way that it works.
In 1820, more than half of the United States population lived and worked on farms. Today, this is fewer than 2 percent of the population, with the overwhelming majority having moved to the city. Thanks to companies such Iron Ox, people may no longer have to choose between farm and city. If people won’t leave the city for farms, then the farms will just have to come to them.
Tackling the Food Crisis with a Borderless Collaboration
At Omron, opportunities to engage with new challenges are abundant
After graduating from university in London, Kassim Okara joined the largest specialist distributor of control and automation products in the UK, where he worked on numerous large-scale projects. He decided to leave however, to join Omron Electronics as field sales engineer in 2015, as he had always felt that he wanted to contribute to society from a business development standpoint.
At Omron, opportunities to engage with new challenges are abundant; the varying projects involve not only control equipment but also healthcare and mobility as well as initiatives to actively employ disabled persons.
At that time, Intelligent Growth Solutions (IGS) had begun working on automated vertical farming to optimize crop production. Based at the James Hutton Institute in Scotland a leading crop science and research institute, the opportunity to collaborate was one of the key considerations in this location. To advance the efforts to practical application level, IGS needed an automation solutions provider.
In search of a suitable provider, IGS found Omron. In addition to its solutions, Omron's commitment to social responsibility attracted them into collaboration.
With the addition of Omron's automation technology to the expertise and knowledge of the two organizations, the first-ever UK project for automated vertical farming using IoT was initiated. Kassim was assigned as project leader on Omron's side. His passion for his work increased by the day as he deepened his understanding of his partners' enthusiasm toward the project.
In the beginning, developing an understanding of the project was particularly challenging, as it was unprecedented so that previous case studies could not be found. Despite this, Kassim took on the project, led by his determination to respond to social needs through business.
Publication date : 10/29/2018
New Autonomous Farm Wants To Produce Food Without Human Workers
To View Video Please Click Here | COURTESY OF IRON OX
Down on a new robot farm, machines tend rows of leafy greens under the watch of software called “The Brain.”
by Erin Winick
October 3, 2018
Iron Ox isn’t like most robotics companies. Instead of trying to flog you its technology, it wants to sell you food.
As the firm’s cofounder Brandon Alexander puts it: “We are a farm and will always be a farm.”
But it’s no ordinary farm. For starters, the company’s 15 human employees share their work space with robots who quietly go about the business of tending rows and rows of leafy greens.
Today Iron Ox is opening its first production facility in San Carlos, near San Francisco. The 8,000-square-foot indoor hydroponic facility—which is attached to the startup’s offices—will be producing leafy greens at a rate of roughly 26,000 heads a year. That’s the production level of a typical outdoor farm that might be five times bigger. The opening is the next big step toward fulfilling the company’s grand vision: a fully autonomous farm where software and robotics fill the place of human agricultural workers, which are currently in short supply.
COURTESY OF IRON OX
Iron Ox isn’t selling any of the food it produces just yet (it is still in talks with a number of local restaurants and grocers). So for now, those tens of thousands of heads of lettuce are going to a local food bank and to the company salad bar. Its employees had better love eating lettuce.
The farm’s non-lettuce-consuming staff consists of a series of robotic arms and movers. The arms individually pluck the plants from their hydroponic trays and transfer them to new trays as they increase in size, maximizing their health and output—a luxury most outdoor farms don’t have. Big white mechanical movers carry the 800-pound water-filled trays around the facility.
COURTESY OF IRON OX
At first, making sure these different machines worked together was tricky. “We had different robots doing different tasks, but they weren’t integrated together into a production environment,” says Alexander.
So Iron Ox has developed software—nicknamed “The Brain”—to get them to collaborate. Like an all-seeing eye, it keeps watch over the farm, monitoring things like nitrogen levels, temperature, and robot location. It orchestrates both robot and human attention wherever it is needed.
Yes, although most of the operation is automated, it still does require a bit of human input. Currently, workers help with seeding and processing of crops, but Alexander says he hopes to automate these steps.
But why go to the trouble of automating farming at all?
Alexander sees it as solving two problems in one: the shortage of agricultural workers and the distances that fresh produce currently has to be shipped.
Rather than eliminating jobs, the company hopes, the robots will fill the gaps in the industry’s workforce. And he believes that by making it possible to grow crops close to urban areas without paying city-level salaries, the automated farms will enable stores to chose vegetables fresher than those that had to travel thousands of miles to get there. That is, assuming the startup can get its prices to match those of traditional competitors.
COURTESY OF IRON OX
“The problem with the indoor [farm] is the initial investment in the system,” says Yiannis Ampatzidis, an assistant professor of agricultural engineering at the University of Florida. “You have to invest a lot up front. A lot of small growers can’t do that.” This could risk creating a gap between the big farming institutions and smaller family-owned operations, in terms of gaining access to new technology.
To View Video Please Click Here | COURTESY OF IRON OX
Despite this, Ampatzidis says that bringing automation to both indoor and outdoor farming is necessary to help a wider swath of the agricultural industry solve the long-standing labor shortage.
“If we don’t find another way to bring people [to the US] for labor, automation is the only way to survive,” he says.
Erin Winick Associate Editor
I am the associate editor of the future of work at MIT Technology Review. I am particularly interested in automation and advanced manufacturing, spurring from my background in mechanical engineering. I produce our future of work e-mail… More
Ellepot And TTA Enter Strategic Alliance
Danish supplier of the world-leading paper pot system, Ellepot and the world-leading Dutch young plant handling and selection experts, TTA form key partnership targeting forestry sector worldwide.
Global suppliers to the horticulture industry, Ellepot and TTA, have formed a partnership to better serve professional forest nurseries. The partnership is a formalization of many projects which already have been executed in good cooperation. The announcement comes at a time when both companies are realizing the benefits of strategic partnering to achieve enhanced customer service and company growth.
Ellepot developed the unique Ellepot Propagation System – an integrated eco-friendly growing method for healthier roots and high-quality plants that eliminates the need for plastic. Known for their game-changing innovations, within advanced machines for sorting, grading and transplanting, TTA became a market leader and continuously invests in R&D to deliver the best in production equipment for the handling and selection of young plants.
GREATER CONTROL THROUGH THE ENTIRE CHAIN
The two industry pioneers will offer a fully automated system to forestry customers worldwide, where every process is designed to optimize efficiency and production.
“Teaming up with TTA means that we can offer customers an even broader automated package, giving them the opportunity to influence the handling of young tree plants completely,” says Ellepot CEO, Lars Steen Pedersen.
“It is an honour joining forces with such an exceptional global industry player as TTA. Ellepot and TTA can learn from each other and use this synergy to help forestry customers all over the world benefit from improved production processes and quality throughout the entire value chain. We both have a strong focus on creating customer value through increased control in production, and this is the ultimate goal to bring to customers in the future.”