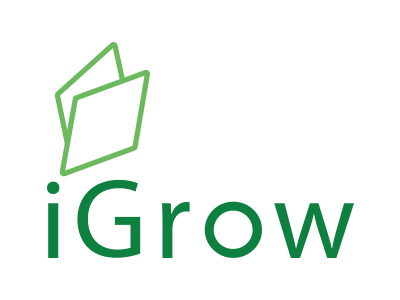
Welcome to iGrow News, Your Source for the World of Indoor Vertical Farming
US (MA): Hydroponic Growing Graduates Learned With Lettuce, Seek Jobs in Cannabis
"The skills they learn in the (shipping containers) are transferable to the cannabis industry," Morse said.
Ernesto Hernandez Martin graduated Thursday from the Freight Farms Hydroponic Growing apprenticeship program at Holyoke Community College, having learned how to grow lettuce in the controlled environment of two shipping containers. But that’s not all he can grow.
“I’m looking forward to getting a job in the new industries, either in marijuana or in growing vegetables,” Hernandez Martin said while leading a tour of Freight Farms on Race Street in the city’s industrial Flats neighborhood and adjacent to the HCC MGM Culinary Arts Institute.
Neither college officials or Holyoke Mayor Alex Morse were shy Thursday about linking the hydroponic program with the city’s new marijuana industry and its need for skilled labor. They also said the program has the potential to help feed Holyokers who have trouble affording healthy meals.
"The skills they learn in the (shipping containers) are transferable to the cannabis industry," Morse said.
The college has no plans to grow anything but vegetables. The city, though, has embraced the newly legal cannabis industry.
Just this month, seed-to-sale marijuana company Trulieve Cannabis Corp., formerly Life Essence, bought a 150-year-old mill building at 56 Canal St. for $3.2 million with plans to build a 126,000-square-foot growing, processing, testing and retail operation there.
Source: MassLive (Jim Kinney)
Publication date: 7/1/2019
Last Week, People From All Over North America Came To Participate In Our Hydroponic Crop Production Seminar
Upcoming Events: July 18th Free Webinar "Hydroponic Farming Indoors" | August 22nd and 23rd Hydroponic Crop Production Seminar (5 spots left!) | October 24th and 25th Hydroponic Crop Production Seminar
Recently, American Hydroponics hosted their popular
“Hydroponic Crop Production Seminar” in Eureka, California
Focused on hands on experience, this 2 day seminar teaches hydroponic students not only how to grow hydroponically, but how to run a successful business while doing so.
American Hydroponics will host 2 additional seminars this year.
Get your spot now!”
Email: maya@amhydro.com to sign up!
Hydroponic Recap
Take yourself there....
The fans blow the warm 70 degree breeze through the billowing leafy greens, the sound of flowing water surrounds the 4320 sq. ft greenhouse and the aroma of fresh basil wafts through the air.
It's Friday morning, day 2 of our seminar, and the greenhouse is bustling with excitement. The students are beaming as they prepare to get to work in our greenhouse breakout sessions.
Station 1: Seeding Techniques
Joe Swartz, leading hydroponic consultant and VP of AmHydro, shows our students the seeding tray technique for planting. Using Oasis growing cubes and the EZ Seeder, growers are able to seed hundreds of plants at once.
Station 2: Nutrient Solution and Transplanting
Students transplant arugula from nursery channels to finishing channels. This exemplifies AmHydro's space saving Crop Turn Technology which allows for the highest producing NFT system on the market. And...it's lots of fun!
Back to the recirculating system for 2 more weeks before harvest.
Station 3: Harvest Time
Students perform quality control by scrutinizing each plant to ensure market standards are met. Here, they are harvesting basil in 5 lb boxes to be delivered fresh to local grocery stores and restaurants in Humboldt County.
Station 4: Tending Vine Crops
AmHydro's grower, Chris, leads the students in suckering tomatoes and training cucumbers to grow up and not out. He explains his daily growers' log and shows the students how to grow happy productive vine crops.
Other topics covered during the seminar:
General & hydroponic plant growth
Operating a hydroponic business
Marketing a hydroponic business
Components and building of a greenhouse
Environmental controls and nutrient dosing
Biological pest control & plant disease
Watch our Facebook Live Video
Upcoming Events:
July 18th Free Webinar "Hydroponic Farming Indoors"
August 22nd and 23rd Hydroponic Crop Production Seminar (5 spots left!)
October 24th and 25th Hydroponic Crop Production Seminar
email maya@amhydro.com to sign up!
Tradeoffs In Aquaponics Vs Hydroponics, By The Numbers
Enhanced flavor and higher consumer preference for ecologically grown products make aquaponics better aligned with consumer and operator interests
Part two in our “Lean manufacturing for indoor agriculture” series
Nov 26, 2017
In our previous blog post, we made the case that aquaponics enables better capacity management for indoor agriculture than hydroponics. The basis of our argument is that aquaponics is a “just-in-time” manufacturing system — multiple SKUs with different nutrient requirements can be produced in the same aquaponic system simultaneously without sacrificing quality or yield, whereas multiple hydroponic systems with different nutrient recipes would be required to achieve similar quality and yield.
This is one of the key reasons that we believe aquaponics is the future of indoor farming.
But what if you stripped away all the benefits of aquaponics? Is aquaponics still competitive with hydroponics on cost if you assumed the same yield, quality, and breadth of product with no fish sales? Unwinding this is the purpose of this blog post, and we find that aquaponics is slightly more expensive with costs 2% higher than those in hydroponics as a percentage of revenue. To compensate for this, aquaponic operators will need to utilize the capacity management methods discussed in our previous blog post to achieve throughputs ~2% higher than their hydroponic counterparts. Below, we break down how we got to these numbers.
But first, there are trade offs besides cost in choosing aquaponics over hydroponics. Let’s start with aquaponics’ unique barriers to entry.
Nonstarters
The first two tradeoffs with aquaponics are existential. The inability to overcome these first two tradeoffs will make it highly unlikely the aquaponic farm will get off the ground.
Lack of off-the-shelf systems and expertise. If you want to be a commercial hydroponics operator, there are dozens of top-notch hydroponic design and consulting firms who can construct turnkey, state-of-the-art hydroponic farms anywhere in the world and even bring in an experienced grower to run the operation. If you’re a hobbyist, you can buy an off the shelf hydroponic system, along with the hydroponic bible, Howard Resh’s Hydroponic Food Production, and get yourself 80% of the way there (it’s great — aquaponic hobbyists should buy it too and get themselves 50% of the way there). In short, hydroponic education and expertise is accessible.
In aquaponics, while there are experts who have designed large scale commercial operations, these experts are few and far between. Scaling an aquaponic farm relies on finding these people, most of whom are not in the US. On the education front, while there are books on aquaponics, the true leaders of the movement are PhD-level researchers who have published narrowly focused academic papers as opposed to accessible, comprehensive, authoritative guidebooks. It’s on operators to find the right people, design a stable system, and implement a comprehensive operating plan.
Keeping the fish and plants healthy, at the same time. This is a big one. Each piece of the aquaponic ecosystem — the fish that supply manure, the bacteria that break down the manure into nutrients that are bioavailable to the plants, and the plants that absorb those nutrients and drive revenue — requires slightly different environmental conditions. Optimizing for plant health, as a result, requires monitoring three different systems as opposed to one.
Even if you were to install a well-designed aquaponic system and manage the operational tradeoffs, black swan events happen. If the fish develop an infection, if you develop a fly infestation, or if pythium (a common fungus that wreaks havoc on plants) takes root, the standard remedies of antibiotics for fish or toxic pesticides for crops won’t cut it in a traditional aquaponic design.
Your production is entirely dependent on maintaining a healthy ecosystem and plant microbiome. When you kill the bad microbes through antibiotics or pesticides, they tend to kill the good microbes too. Most pesticides, even organic ones, are not “fish safe” — fish are particularly chemical sensitive. For aquaponic farmers, the ecological approach to farming doesn’t just apply when yields are steady. It applies 24/7, 365 days a year, barring traditional, toxic, pesticidal approaches to solving these problems.
All that said, hydroponic and aquaponic operations are converging towards similar operating constraints due to technology improvements and consumer demand. One of the most sought after labels in produce is “pesticide free”. As a result, many of the latest generation of hydroponic operators have taken up the label, limiting themselves to the same biological and ecological remedies aquaponic operators are inherently restricted too. At the same time, “decoupled” aquaponic systems, where water only flows in one direction — from the fish to the plants (and not back again) — are growing in popularity due to their ability to treat the plants without worrying about the effect on fish. The result is the ability to use the same plant treatments as a traditional hydroponic facility.
Luckily for all camps, there are plenty of ways to remedy these issues in pesticide free facilities that are more cost effective than traditional approaches. In indoor farms especially, the incidence of most issues can be reduced through rigorous standard operating procedures for both day to day practices and early detection of and response to ecological stress.
If you’re confident that you have the expertise to design a stable aquaponic system and to handle both the operating basics and ecological considerations during black swan events, then it’s worth digging into the operating costs of aquaponics and hydroponics.
Comparing operating costs
There are certain added costs associated with aquaponics — there’s no free lunch, so growing all those fish has to be accounted for somewhere. For aquaponics to be a better business than hydroponics, the added costs must be compensated for by either higher throughput of salad greens or fish. In our previous blog post, we showed how aquaponics can achieve higher throughput than hydroponics. In this analysis, assuming fish are never sold, we show that throughput needs to be ~2% higher in order for aquaponics to beat hydroponics on cost, which is well within aquaponics’ potential.
We have put these tradeoffs in a spreadsheet for a more convenient comparison. You can see the spreadsheet here, while reading below for context. The numbers here are not reflective of Edenworks’ designs and projections. We’re basically asking “if we ran our competitor’s farms aquaponically instead of hydroponically, what would the business look like?” For example, Gotham Greens projected an EBITDA for their first facility at “greater than 15%,” and so we’ve targeted a 15% EBITDA margin for the hydroponic facility, then made a few changes based on industry-standard assumptions to back out the aquaponic cost analysis.
source: Edenworks spreadsheet analysis
The following line items are the largest cost differences:
Added expense of fish feed. While hydroponic fertilizer is most often composed of mined mineral salts, fish feed for aquaponics has the fat and protein that the fish need along with the minerals that both plants and fish need. For aquaponics in a recirculating shallow water culture system, we calculate¹ the expense of fish feed to be about 9 cents per pound of harvested greens, a 7 cent premium over synthetic hydroponic fertilizer. Assuming best in class yields for both systems, this comes out to a 1.4% difference in nutrient costs between the two systems, as a percentage of revenue. However, with the world farming more fish than ever before, new technologies are coming online that are expected to substantially lower the price of fish feed, while also making the feed more sustainable.
Added labor. Most indoor farming facilities have a long way to go until they can be considered highly automated. Despite incorporating automation and machine learning techniques for things like climate control and disease detection, modern indoor farms still complete many tasks, such as harvesting, by hand. The biggest labor efficiency gains are fertilizer (i.e. hydroponic / aquaponic) agnostic. Those gains come from automating the movement of plants through the production system, along with the unit tasks of seeding, transplanting, harvesting, packaging, and cleaning. This is where Edenworks has invested substantially in IP, but that’s a story for another post.
All that said, raising fish does require someone who knows how to spot potential health issues, how to harvest fish, and how to maintain aquaculture equipment. None of this is time intensive, but it does require hiring an aquaculture specialist at each facility.
Space for the fish. Aquaponic fish tanks and hydroponic nutrient reservoirs require similar space. However, aquaponic systems require a bit more space overall for the extra pumps, sumps, and biofilters for converting fish waste into nutrition for the plants — an additional 1.7% more space in our analysis of an approximately 70,000 square foot hydroponic facility. Assuming rent for warehouse space is $10 per square foot, this comes out to a difference of 0.1% of revenue.
Quantifying the total trade-off.
Assumptions are based on commonly used designs, equipment, and raw material suppliers, which are noted in the spreadsheet. Furthermore, in order to get close to an apples to apples comparison, we assumed the following:
Both systems sell baby greens for the same price.
Revenue from fish, and the associated costs of selling fish are not included.
Both systems are vertically stacked, indoor farms.
Yields for both hydroponic and aquaponic systems are the same. For the purpose of this study, we use our yield estimate for AeroFarms. AeroFarms has projected yields of 2 million lbs of greens at their Newark facility. Looking at the size of their facility (69,000 s.f.) and their geometry, we estimate their growing space is ~160,000 s.f.² in vertically stacked beds. This gives AeroFarms 12.5 lbs yield / s.f. / year, which is in line with other best-in-class yields for hydroponic and aquaponic indoor leafy greens farm.
Both systems have similar needs, and therefore costs, for the following line items: energy, packaging, growing medium, seeds, delivery, rent, cleaning and other general farm supplies, and merchandising.
This leaves just three significant differences between the costs of the two systems: nutrients (fish feed vs synthetic fertilizer), labor (employing an aquaculture specialist vs. having one less employee), and rent (extra space needed to break down organic nutrients vs. not needing extra space).
Given the assumptions behind these hypothetical facilities, we estimate aquaponic systems’ costs as a percentage of revenue are 2 percentage points higher than hydroponics’. In order to compensate for these added costs, aquaponic facilities need to sell 2% more of their capacity than hydroponic facilities. As explained in our previous post, with typical per-SKU sales swings in packaged salad of up to 20% week on week, hydroponic farms that cannot grow different crops in the same production system suffer from significant capacity constraints. Aquaponics, on the other hand, can grow wide varieties of crops in the same production system, enabling them to sell higher percentage of their capacity (certainly higher than 2% more).
To top it all off, enhanced flavor and higher consumer preference for ecologically grown products make aquaponics better aligned with consumer and operator interests. It is for these reasons, in addition to its competitiveness with hydroponics on cost, that we believe aquaponics will become the primary fertilization technology for indoor operators as the market continues to grow.
¹ This calculation is based on standard aquaponic feed ratios from Dr. James Rakocy and hydroponic feed ratios from Howard Resh’s book Hydroponic Food Production. These calculations are in the third tab of the spreadsheet and are what we used in this analysis. Comparing one “standard” feed rate to another “standard” feed rate seemed apples to oranges to us though, so we also compared feed costs based on nitrogen content of each feed, and came up with very similar cost ratios. These are presented in the fourth tab of the spreadsheet.
² Aerofarms’ bedspace estimation comes from public websites. For bed width and length, see (a) and (b). For number of beds, see (b) and (c).
(a) https://patentimages.storage.googleapis.com/pdfs/US8533992.pdf
(b) http://www.foxbusiness.com/features/2015/07/28/farming-in-sky-inside-wall-street-backed-vertical-farm.html
(c) https://www.nytimes.com/2015/04/08/realestate/commercial/in-newark-a-vertical-indoor-farm-helps-anchor-an-areas-revival.html
Part of Something Bigger - Promote Jobs And Improve Diets
February 1, 2018
Growers Create Community Partnerships And Educational Programs to
Promote Jobs And Improve Diets.
From left to right: Traders Hill Farm's Nichole Curry, Tracy Nazzaro and Victoria Caba
When it comes to doing good, some growers set a high bar. They form integral community partnerships and educate people about health and nutrition through offering locally grown produce, all the while creating jobs and committing to strict food safety and environmental standards. These growers exude a sense of altruism, and their passion provides clear benefits to their and other communities.
Although it is rare to succeed in these many ways, examples are being set by Traders Hill Farm, an aquaponics and leafy greens operation in Hilliard, Florida; and the Rid-All Green Partnership, a nonprofit urban farm in Cleveland.
Beta steps
Traders Hill Farm began small and is now a commercial agribusiness, says company president Tracy Nazzaro. The operation built its aquaponics beta system in a retrofitted chicken barn in 2013. “The structure itself was in pretty good shape, but it had that tin roof to it, so we cut out sections of the roof and put in corrugated plastic just to let the light in,” Nazzaro says. Traders Hill no longer grows produce in the former chicken barn, but it plans to turn it into an aquaculture hatchery in 2018.
The greenhouse operation specializes in romaine lettuce — both red and green varieties — but also grows Bibb, Lollo Rossa, Oscarde, frisée and a spring mix. It sells fresh produce to mostly restaurants, but also a handful of retail stores.
To fuel growth and advance food safety protocols, Traders Hill built a 10,000-square-foot commercial structure in 2015, and the following year, built a larger 40,000-square foot structure. It also began another major development in 2016 — its internship program.
Traders Hill’s aquaculture team measures feed amounts and dissolved oxygen in fish tanks.
Students in the Sunshine State
For the past two summers, paid interns have shadowed growers and their colleagues at Traders Hill. Working with the aquaculture team, the interns measured greenhouse temperatures, as well as feed amounts and dissolved oxygen in the fish tanks for the operation’s approximately 10,000 tilapia. Afterward, the students mapped the data they gathered.
In their internships, students have worked in Traders Hill’s aquaculture, horticulture, general farm and office environments. All high school interns so far have been local, and college interns have come from the University of North Florida, Jacksonville University, Southern Illinois University, Auburn University and Valdosta State University in Georgia.
Nazzaro suspects many young people are drawn to this work because it is technical. “This is a different farming from what we think of as traditional ag — although traditional ag isn’t what it used to be either,” she says. “But it’s not tractors and hoes and garden tools. This is a much smaller footprint. There are a lot more moving parts. I think that they gravitate toward that.”
Victoria Caba worked at Traders Hill as an intern in 2017 and was subsequently hired in the farm's aquaculture department.
Traders Hill awarded a full scholarship to a local student who worked at the farm during his senior year of high school and is now a sophomore at Southern Illinois University studying agricultural systems and education. Looking ahead, the operation is considering offering partial scholarships to benefit a greater number of students.
The greenhouse has hired interns following completion of their internships. In September 2017, the farm hired Victoria Caba, an intern from that summer and a Jacksonville University marine science and sustainability graduate, to work in its aquaculture department. And the farm hired summer 2017 intern Nichole Curry, a freshman studying finance and accounting at the University of North Florida, to work part-time while she attends college.
Traders Hill participates in community partnerships, such as working with the Nassau County School District to supply students with lettuce, engage them in health fairs and invite them on tours. Additionally, it works with professors at nearby Jacksonville University and provides tours for students in the university’s marine science program.
“One of our core values is developing people,” Nazzaro says. “So we seek out and hire people who are a good fit for our company and our culture, and then we’ll provide them with opportunities and training.”
Emphasizing local produce
Traders Hill Farm sells its popular romaine lettuce to markets spanning the area from Daytona, Florida, to the south; to Tallahassee, Florida, to the west; and Savannah, Georgia, to the north. “Where we’re located on the East Coast, that’s a pretty big deal,” Nazzaro says. “From being in the ag industry, almost all romaines are grown either in Yuma [Arizona] or Salinas [California].” But Traders Hill’s customers can expect their produce to be grown within 130 miles and delivered promptly.
Local produce is one of many benefits the Nassau County School District sees in partnering with Traders Hill. The 16-school district previously received its lettuce from a national supplier at a low price. But Traders Hill conducted a test whose results convinced the district to switch lettuce providers to its nearby aquaponics farm.
“We took what they got from their supplier and we took ours, and over a week we looked at what kind of shrink we had,” Nazzaro says. “The commercial stuff was getting between 40 and 50 percent shrink, which was just not usable product, and ours was in the 5 percent range. They were like, ‘Wow.’”
In many ways, local produce is healthier than that which has traveled a long distance. Produce with fewer miles on it contains more nutrients and nutrient variety, according to Kathleen Frith of the Harvard School of Public Health. And children have something to gain from eating local produce, because according to the Mayo Clinic, they need the same types of nutrients as adults, just in different amounts.
Traders Hill visits the district schools to discuss the greenhouse's process and the importance of eating healthy eating. “We are really proud of the fact that we provide the cleanest food possible, both from a food safety standpoint — we take our food safety very, very seriously — and that we aren’t adding anything into this food supply that doesn’t need to be there, just from a pure health standpoint — no pesticides, no herbicides, no fungicides.”
One of roughly 10,000 tilapia at Traders Hill
Photo courtesy of Traders Hill Farm
Fulfilling consumer demand
Valuing health and safety, Nazzaro and her colleagues at Traders Hill Farm were excited when the National Organic Standards Board voted in November 2017 to allow USDA Organic certification for hydroponic and aquaponic produce operations. Prior to the decision, Nazzaro says, hydroponic and aquaponic growers found themselves in a precarious position in declaring certification.
Traders Hill joined the debate to ensure aquaponics would be certified USDA Organic. “We had six team members write arguments for why we should be allowed to do that,” Nazzaro says. “I reached out to my local university professors. They also wrote arguments. We delivered verbal comments at the recent hearing, and we were really pleased about that.” Within the next year and a half, Nazzaro says Traders Hill plans to determine if USDA Organic certification is viable for the operation — aiming to officialize the practices it already intently follows.
Also, in the future, Traders Hill will consider adding other types of produce. “We’re a regional player,” Nazzaro says. “We developed this regional market and they’re buying all our leafy greens. Then it’s like, ‘Okay, what else would you guys like that grows well in our system?’”
Produce markets might need more greenhouses like Traders Hill to step up their output. The United Nations Department of Economic and Social Affairs expects the world population to reach 8.6 billion by 2030, 9.8 billion by 2050 and 11.2 billion in 2100, according to the report, 2017 Revision of World Population Prospects.
“We’re feeding people,” Nazzaro says. “This is part of a bigger plan, and we need more food. This is really important, because on a global scale our food production needs to exponentially increase. I don’t know if we need a lot of lettuce, but on a lot of levels it needs to exponentially increase. It’s fun to be a part of something that’s bigger.”
From left to right: Rid-All Green Partnership’s David Hester, Keymah Durden, Damien Forshe, Randell McShepard and Marc WhitePhoto: Gary Yasaki | From forthcoming “Soil Brothers” documentary
Meet the Soil Brothers
Another grower creating jobs and improving diets is the Rid-All Green Partnership, a nonprofit urban farm thriving in Cleveland’s Kinsman neighborhood. Produce Grower first featured Rid-All’s work in the community in the December 2014 issue (Editor’s note: Read the story here). But we decided to provide an update as the farm has continued expanding over the past several years, in part through strengthening its aquaponics and composting efforts, and by influencing urban farmers outside of Cleveland.
Childhood friends Damien Forshe, Keymah Durden and Randell McShepard began Rid-All Green Partnership in 2009 with broad ambitions to clean up and revitalize toxic soils, develop meaningful community partnerships and provide fresh produce to city residents.
Operating in an area known as the “Forgotten Triangle” for its history of illegal dumping and burned-out cars, Rid-All cuts through the area’s discord to bring community members together. “We encourage everybody to come and get involved,” Forshe says, “because that’s what we all have in common — food.”
Rid-All’s output includes lettuce; heirloom tomatoes; kale greens; collard greens; chili, ghost and cayenne peppers; rosemary; lavender; thyme; basil; beets; and Swiss chard. On 1.3 acres, Rid-All runs one 30-by-80-square-foot hoop house, two 30-by-60-square-foot hoop houses, two 30-by-60-square-foot greenhouses, a treehouse office and a teepee (used for events such as weddings and concerts, as well as relaxation for the farmers). In 2017, Rid-All expanded its aquaponics footprint by 7,200 square feet and added a five-acre compost facility.
The farm sells produce to restaurants and caterers, and directly to end consumers. “We operate a CSA — community-supported agricultural program — where members from the community can sign up for one of three tiers — gold, silver or bronze,” Durden says. “Based on their membership, they can come and pick up food weekly that they take home and consume.”
Rid-All established Soil Brothers, a soil compost business, in 2016.Photo: Matt McClellan
Overcoming the unknown
Rid-All, whose partners include the Cleveland Metropolitan School District, Ohio State University and Central State University in Wilberforce, Ohio, places a strong emphasis on job creation. The farm’s main staff consists of six people, but they require help with tasks such as growing, groundskeeping, landscaping and driving to pick up food waste. “Since our beginning we have created over 15 to 20 jobs for local residents,” Durden says. “Some only stay with us for a short time before moving on to manage their own project.” Over the course of a year, the operation adds around 300 volunteers.
Durden stresses the importance of educating people about healthy eating habits. “Most days, many folks, particularly in low-income areas, are making food choices with their wallet — ‘I can buy what I can afford’ — instead of making an educated choice based on knowledge of the food that they’re consuming,” he says. “We believe that if we can educate folks about how to make healthy choices, then that fear of the unknown won’t be as prevalent.”
But, Durden says, people are more educated about food choices now than they ever were in the past. When organizations like Rid-All teach children to develop healthy eating habits, those children will retain those habits as they transition into adulthood. Simultaneously, Rid-All teaches children and other community members about making smart decisions in other aspects of life, from the TV they watch to the environment they find themselves in.
Many of the partnership’s educational offerings are specific to growing produce, but a generous portion of them extend into other areas as well. “Our main tracks deal with our composting, our aquaponics operations and urban farming as our main core of classes that we teach,” Durden says. “But that branches out anywhere to wastewater management, it goes into animal husbandry, dealing with trees and agriculture. But then we spin off even further into arts and entertainment, where we engage local students and residents about how to become creative again.”
Rid-All’s work isn’t limited to Cleveland, either. When Columbus, Ohio’s Linden neighborhood was facing many of the same issues as Kinsman, its Saint Stephen’s Community House decided to address them. In 2014-15, the community house linked with Rid-All, which built it a greenhouse with aquaponic tanks, a compost bin and double-wide hoop houses. Since then, the community house, like Rid-All, has been providing educational programs, creating jobs and making compost. It even has its own teepee.
To make good happen in the community, growers need to put in “manpower and blood, sweat and tears,” says David Hester, Forshe and McShepard’s cousin and a farmer at Rid-All. “When you’re not getting paid, or anything that you still have the passion with, keep on moving it forward, as long as you’re doing something,” he says. “Don’t just talk about it — actually do something. For us, a lot of times, we recommend starting with the soil, because that makes the hugest difference in how your place is going to turn out.”
“Since our beginning we have created over 15 to 20 jobs for local residents,” says Rid-All co-founder Keymah Durden.Photo: Gary Yasaki | From forthcoming “Soil Brothers” documentary
Remediating the soil
The soil is a major component of the Rid-All Green Partnership. The toxins that saturated the former dump site created a challenge for the urban farmers, who had to improve soil conditions. They tried remediation via clay, as well as using soil they received from a rural area. Ultimately, they succeeded when they layered the ground with wood chips. “What I found out is that wood chips are the best remediation that you can use for lead, arsenic, things like that, so we were layering our ground [with them],” Forshe says. “Wood chips eventually break down from a carbon to a soil.”
With a commitment to minimize food waste, Rid-All established a soil compost business with the name Soil Brothers in 2016. As a whole, Rid-All has produced more than 500 tons of compost since 2011. In 2014, Soil Brothers became the only compost facility in Greater Cleveland to earn a Class II Compost Facility license through the EPA. The soil business is one of Rid-All's biggest revenue streams, working with local Starbucks stores, the Greater Cleveland Food Bank, AVI Foodsystems and other partners.
In June 2017, former Ambassador to the United Nations and civil rights activist Andrew Young visited Rid-All for the purpose, Young says, of partnering with Soil Brothers. A Cleveland public broadcasting station filmed Young telling an audience at the event, “I think it’s our calling to kind of pull the world together in peace, and peace starts with a good, balanced diet.”
“The Soil Brothers’ whole concept is relative to fortifying our bodies with nutritionally rich soil first,” says Marc White, Rid-All’s operations manager. “If [nutrients] are not in the soil, they can’t get in the food. We’ve been eating empty food for the last 20 years. That’s why everybody’s sick.”
Over the past eight years, the urban farm has helped redefine the area and even earn it a new name. “As society has shifted and the economies have changed, a lot of neighborhoods got left behind,” Durden says. “We believe that we can go into those neighborhoods and transform them from desolate to places of hope. This area that we’re in now, the Kinsman area, which was called the ‘Forgotten Triangle’ is now referred to as the ‘Urban Agriculture Innovation Zone.’”
We're excited to see what Rid-All does in the future. Look out for the forthcoming “Soil Brothers” documentary for more coverage.
Vertical Farming For Cannabis Gets Trial Run in Langley
Leo Benne, chief growing officer of Zenabis, with the converted shipping container that will become a testbed for a vertical cannabis farm. (Matthew Claxton/Langley Advance Times)
Grower Zenabis Will Start With Industrial Hemp And May Move to
Commercial Marijuana
Jun. 6, 2019
Zenabis, which merged with longtime Langley greenhouse firm Bevo last year, has received a hemp cultivation license from Health Canada, with growing to take place in Langley, Pitt Meadows, and Aldergrove facilities.
“We expect the seed to come in this week,” said Leo Benne, chief growing officer for Zenabis.
A small portion of that seed will be planted not in one of the greenhouses facilities, but in a converted shipping container, as a test on whether cannabis can be vertically farmed.
Bevo has already helped develop a vertical farming system through CubicFarms, a Pitt Meadows-based spin off.
Vertical farming involves growing large amounts of crops on small amounts of space, indoors, and usually without any soil.
Plants are reared in racks, stacked as high as the building or container can accommodate, and grown either hydroponically or aeroponically.
Energy efficient LED lights allow the plants to grow 24 hours, seven days a week, in any weather.
In theory, the cost of the equipment and intensive rearing is offset by the ability to grow non-stop and to place the growing site much closer to the end-consumer. Rather than trucking lettuce from California or Mexico, it could be grown just a few miles outside of Canadian cities and shipped just a few kilometres.
The hemp vertical farm is just a test at this point, said Benne. A single converted shipping crate has been hauled into one of the Zenabis greenhouses in Langley and will be ready for its test run at about the same time as 20 acres of industrial hemp is planted in the three facilities, from Langley to Pitt Meadows.
While most crops planted in vertical farms are extremely low-growing, allowing for many racks close together, cannabis is usually a tall-growing crop.
Benne said that a combination of the plants chosen and growing practices is expected to keep the plants shorter for the vertical farm project.
If the project goes well, vertical farming facilities could be used for growing commercial marijuana, said Zenabis CEO Andrew Grieve.
The industrial hemp isn’t being grown for commercial marijuana sales. Instead, the hemp will be processed into CBD oil, fibre, or other derivatives. The project is separate from Zenabis’s plans for growing commercial cannabis in Langley.
While Langley’s other large cannabis cultivator has caused controversy in Aldergrove over smell issues, Benne doesn’t believe that will be an issue for Zenabis.
“We’re doing things a lot differently,” he said. “First of all, we’re constructing a closed greenhouse facility. We’re able to keep most of the air inside the greenhouse.”
There are to be no roof vents, which should not only control odour, it helps the growers control humidity and other issues.
“Because we don’t have that exchange of air with the outside, we don’t have a lot of pest issues,” he said.
Air exhaust is to be controlled through carbon filters, and if those aren’t sufficient, biofiltration. That means basically pumping all the air exhaust through a big box full of bark and cedar chips to absorb the smell.
Vertical Roots Innovation Emerges
BY KATHY HARRELSON | MAY 15, 2019
Imagine growing conditions when weather, disease and insects come as second thoughts.
Enter the enclosed, controlled world of hydroponics — farming indoors with vertical or horizontal root preparations.
The indoor farming involves nourishing roots by placing them in a liquid nutrient solution. There is no soil.
One 3-year-old, start-up company, based in Summerville, SC, Vertical Roots, has just completed a hydroponics farm in Charleston, SC, which includes 24 grow pods and has started the construction of a farm in Columbia, SC, which will have more than 120 grow pods.
It takes a committed staff to nurture the Vertical Roots crops. Bottom: Vertical Roots keeps its plants in pods, in a controlled environment, growing indoors with nutrient-enhanced water channels.
Hydroponic systems are touted for using up to 98 percent less water than traditional agriculture, and at Vertical Roots, the company aims to be as sustainable as possible.
Labor and maintenance are also minimized.
Vertical Roots grows leafy greens — green and red oak, Bibb, romaine, red butter and arugula.
“We consider ourselves to be the future of farming, so everything we do is innovative and focused on technology that monitors and controls our farms,” said Shelby Weimer, marketing strategist for the company.
The system has had its skeptics relative to scalability, Weimer said, but being on the ground floor of development has the company and team excited and optimistic.
“We truly feel that we have a model that will set us up for success,” Weimer said. “We are here to change the game.”
A key factor is turnaround time in distribution.
About 95 percent of leafy greens come from California and Arizona, she said.
“We aim to bring lettuce as close to distribution as possible, sometimes with a turnaround of 24 hours from harvest to table, compared to weeks on a truck,” she said.
In what she referred to as “hyper-local,” she said the company could distribute lettuce that is fresher, tastier and safer.
“We also want to provide the next generation of farmers with a sustainable living for years to come and open the ag-tech world to a new way of farming,” Weimer said.
In that sense, the company clings to a list of values within its mission. They are:
• Empowerment for every team member to have a voice.
• Precision in paying attention to detail.
• Fun, with a positive attitude.
• Consistency. Do it the right way, every time.
• Respect.
• Integrity, by being trustworthy and honest.
Vertical Roots also sees its role within the community as significant. It promotes the model within schools, in restaurants and in local businesses.
“We offer tours of our facility and educational opportunities to learn about our growing methods,” Weimer said. “As a company, we are focused on sustainability, so we try to educate our customers and community as much as possible.”
There is also a flair for philanthropy and zero tolerance for waste. The company donated about 7,000 pounds of lettuce to those in need earlier this year, and routinely gives excess to the hungry.
The company takes the future and innovation seriously as well, company co-owner Andrew Hare said.
“We never want to stop learning and growing, so at any given time we have a variety of test products in our panels,” he said.
Automation For Hydroponics
One of the biggest costs for any hydroponic business, regardless of the crops they produce, is labor
Incorporating Automation Can Help Hydroponic Operations Become
More Efficient And Grow More Productively
March 25, 2019
Fig. 1. Rafts for deep-flow technique (DFT) systems are quickly and effectively sanitized using this wash station.Photo: Christopher J. Currey
One of the biggest costs for any hydroponic business, regardless of the crops they produce, is labor. Mechanizing processes to reduce the amount of labor required for crop production is a sure way one way to reduce input costs. While the primary reason for using mechanization and automating processes is to reduce labor costs, there are other benefits to automation.
For example, in addition to saving on labor costs, it can also make more labor available for other jobs in the greenhouse, make certain tasks easier to execute and increase employee productivity. But benefits of automating extend beyond labor. Automation also reduces the time it takes to accomplish tasks and expedites processes and may open additional space in your facility and help you turn crops.
Regardless of what scale you are producing on, there are steps you can take to improve your efficiencies by integrating automation and mechanization to improve productivity. Plus, there are some relatively easy steps to take to start automating processes in your greenhouse. Investing in a seeder is going to be one of the first things any producer should do. A vacuum seeder is going to be one of the first and easiest ways to incorporate equipment to improve productivity. Manifold seeders seed one row of plugs at a time, whereas plate seeders will seed an entire flat at once; large facilities may benefit from using the larger drum or cylinder seeders.
Fig. 2. This leaf lettuce grown in nutrient-film technique (NFT) troughs is planted in one location in the greenhouse and, throughout production, the trough moves throughout the facility until it is fully grown, after which the trough moves down a conveyor to be harvested.Photo: Christopher J. Currey
In the greenhouse, regardless of size, automation can be key to maintaining a productive growing environment. Nutrient solutions for recirculating systems require adjustment to keep the pH and electrical conductivity within target ranges. This can be achieved by hand, spot-checking nutrient solution EC and pH and making the adjustments as-needed. However, automated pH and EC measurement of nutrient solution properties and subsequent adjustments moderates root-zone conditions and minimizes unwanted fluctuations. Sanitizing the troughs for nutrient-film technique (NFT) systems and rafts for deep-flow technique (DFT) or raceway systems can also be a laborious process. The opportunity to sanitize NFT channels and DFT rafts keep your system clean and reduces disease incidences and increases food safety, but it can be a laborious task. Equipment simplifying routine sanitation reduces labor costs and helps maintain best management practices (Fig. 1).
The larger the scale an operation and production, the possibilities to automate become even greater; the return on investment increases with the scale of production. In order to centralize labor, from planting to harvest, in the same part of the facility, some production systems are designed to move crops through a growing environment throughout production.
For instance, the lettuce grown in the NFT system in Fig. 2 is planted in the same area of the greenhouse where it is harvested. The NFT troughs move throughout the greenhouse and returns to be harvested. There are also opportunities to automate post-harvest processing and packaging. For common Dutch cucumbers produced hydroponically, conveyor belts facilitate transporting fruits from harvesting carts to shrink-wrapping machines, then onto cardboard containers for bulk packaging.
And there are some very exciting robots in the CEA industry. Grafted tomato plants are increasingly popular, but grafting is a very labor-intensive process. While these grafting robots still require labor to operate, they can complete up to 800 grafts per hour, greatly improving productivity. On the other end of production, we are not far from having automated harvesting as well! There are robots designed to selectively harvest hydroponically grown fruits such as cucumbers and strawberries.
Christopher (ccurrey@iastate.edu) is an assistant professor in the Department of Horticulture at Iowa State University.
Automation Hydroponics NFT pH EC Employees Labor Harvesting
DFT Robotics
Homegrown Hydroponics Project Spreads Around The World
May 14, 2019 - Mike Enright '88 (CLAS), University Communications
Christian Heiden ’20 (ENG), center, started a non-profit organization Levo International to bring hydroponics to those in need in Haiti.
The idea began when UConn junior Christian Heiden ’20 (ENG) was working on his Eagle Scout project in high school. It has developed into a non-profit organization that is helping the poor of Haiti and inspiring the curiosity of students in the UConn Child Development Labs.
Through his scout work, Heiden, of Bloomfield, Connecticut, first built a hydroponic greenhouse for his high school, Northwest Catholic in West Hartford. Then, Heiden and his father, Bill, and brother, Nathaniel, traveled to Haiti and built a demonstration hydroponic greenhouse for a community in that nation.
Hydroponics is a method of growing plants without the use of soil and instead relying solely on mineral nutrient solvents in water. While it has been used on a large-scale basis for growing vegetables like tomatoes and lettuce, Heiden says, he has broken it down for the most simplified use yet.
“We wanted something that would only cost a few dollars a day to operate, so we designed our Babylon System which is a 5-by-2 foot system and grows 16 plants at a time,” said Heiden. “It allows people not just to grow produce for their family, but also at market. So they are gaining a way not to just eat but gain money for their family.”
Heiden started the non-profit organization Levo International in his freshman year at UConn to bring hydroponics to those in need in both Haiti and in Connecticut. He soon reached out to Jonathan Moore, an instructor at the operations and information management department (OPIM) in the School of Business.
“Through our emerging tech initiative OPIM Innovate, we have worked on a number of projects,” said Moore. “Christian reached out to me looking for advice on how we could incorporate technology into this work and what the cost would be. He also brought up the path of wanting to develop the for-profit side of the business in order to fund the non-profit side.
“I thought it would be a great idea for him to donate a prototype right here on campus and the Child Development Labs was a natural choice.”
The Child Development Labs are run by the Department of Human Development and Family Sciences and provide care for children up to five years old. Much of its staffing includes UConn students in the early childhood development and education program.
Anne Bladen, director of the Child Development Labs, said she liked the idea of situating a hydroponics greenhouse there for several reasons, including that the student-teachers would be able to see what happen when you increase nature experiences in your young students.
“We have a big commitment to having our children being outside in nature and being active,” said Bladen. “Having the hydroponic greenhouse at the Child Lab helps us get the children invested in learning where their food comes at a young age. It also gives us the opportunity to talk about Haiti and those less fortunate.”
UConn senior Eli Udler ’19 (CLAS) has been assisting Heiden and his company in the use of 3D printing in hydroponics as part of his work as a member of the team at OPIM Innovate.
“The goal is to make hydroponics more accessible in terms of cost and how easy the greenhouses are to build from ready made components,” said Udler. “I am interested in exploring this with the use of biodegradable material.”
Heiden sees a great future for the hydroponic greenhouses all over the world.
“Our goal is to bring sustainability into the agriculture system on a global scale,” said Heiden. “We think we have a really unique product that will allow us to leverage and accomplish that both here in the United States and the worldwide market.”
“Growing In Hydroponics Saves 90% Water”
At MedFEL, the company Les Halles Mandar presented aromatic herbs grown in hydroponics and with the label “Zero Pesticide Residue” (ZPR). “The range currently includes four herbs - basil, chives, cilantro and mint - which we started marketing at large retailers in 2018,” explains Camille Le Large, product manager of the company.
Hydroponics, a cultivation technique with many advantages
According to Camille, the cultivation above ground, where roots are permanently immersed in water, presents many advantages. “Hydroponics has the particularity of being able to reduce water intake by 90% compared to traditional cultivation. Additionally, we grow with pesticides or chemical products, because the plant feeds on mineral fertilizers added to the water.”
The consumer will easily be able to recognize the aromatic plants grown in hydroponics. Everything will be explained on the back of the packaging. “The plant cultivated in hydroponics has roots, which have been preserved and are visible under a small pile of substrate. This gives a significant advantage to the product that will stay fresh longer, on the shelves but also after the consumers bring it back home. They have three options. They can put it in a new pot or replant it directly in the ground, or keep it the way it is in the fridge, or even immerse the roots again in water so the herb can continue to grow.”
Alain Pissavy of Les Halles Mandar, at the booth with Camille Le Large, at MedFEL
About Les Halles Mandar
Les Halles Mandar is a family business created in 1973 and specialized in the selection and distribution of fruits and vegetables, as well as aromatic herbs. The company also started producing more than 10 years ago, thanks to its production site in the Loiret. It markets its range of constantly evolving fresh aromatic herbs to restaurant professionals and large retailers.
For more information:
Serge FARUCH
Les Halles Mandar
20 Avenue de la Villette
94637 Rungis Cedex
serge.faruch@mandar.fr
www.mandar.fr
Publication date: 5/21/2019
© HortiDaily.com
Aquaponics Adapted For Africa
Colin Bremner, Kleinskuur Aquaponics
A South African aquaponics grower has tweaked the techniques he has learned from Australia’s Dr Murray Hallam for African conditions and his design is being installed in an increasing number of African locations.
Colin Bremner’s Kleinskuur Aquaponics system in Donkerhoek, outside Pretoria, last year functioned for up to a week without electricity (when their transformer was hit by lightning), exhibiting minimal stress.
The water surface between the floating vegetables is completely covered by duckweed, which retards evaporation and is fed to the fish in the system
Kleinskuur Aquaponics produces greens, microgreens and herbs to packhouses that supply all of South Africa’s retailers and to a few restaurants, around 50,000 plants a month.
“This system has been running for three and a half years, during which we’ve never cleaned the system. It’s still the same water we started with. We just clean the outlet holes every three or four months,” Colin says.
In all respects he has tried to minimise reliance on electricity, using some quite interesting techniques along the way. The water temperature is maintained at 23°C despite winter cold that has dipped to -7°C and summer temperatures into the mid-thirties. In fact, he notes, at one of the Kleinskuur sites in west Africa, daytime temperatures can climb as high as 47°C but the water remains at 23°C.
Geothermal piping, running along the outlines of the beds three metres underground, maintain the water temperature within this narrow band. The piping runs for a length of 160m in the commercial size of his aquaponic design.
Furthermore the system has only one water pump and one air pump. The surface is covered with duckweed, reducing evaporation and removing nitrates from the water, as well as being fed to the fish.
The fish come when he whistles, Colin says, as he scoops a handful of duckweed from the surface of the deepwater beds for them
The fish he uses – and the species that he recommends or provides along with his system design implemented in African projects – are the males of four tilapia species, all highly tolerant to pH and temperatures fluctuations, low oxygen levels and high nitrite levels.
Seedlings are placed in ordinary sponges in which he cuts a slit (“our Pacman system”, he calls it), holding stems upright as the plant is lowered in its hole in the floating polystyrene plate.
The sponges (pictured left) are re-used many times, while plastic seed nets often tear when the plant is removed and besides, can cost up to R2 for one.
His own gravel bucket design
Regarding gravel beds, he solved the problem of anaerobic bacteria proliferating in areas that are not drained, which would usually necessitate a clean-out, with his own patent on a gravel bucket. These buckets house an individual plant (typically a fruiting plant), so that should the plant need to be removed, others are undisturbed.
“The gravel barrels, to which I hold the mould and design patent, is a manageable size, one person can carry it, and it doesn’t have to perfectly fit over a hole, it can be settled over a trench. Water runs in at the top and drains out, five cycles an hour. When the water drains out it takes with it the particles that are not eaten by earthworms. This drainage movement cools the gravel and the water down, from the approximately 28°C at which it leaves the fish to 23°C, the optimal temperature for roots.”
The gravel bucket system needs earthworms in the capillaries between the 20mm gravel pebbles, with other biota like nematodes and fungi also present, making it philosophically very different from the striving for sterile conditions in hydroponics.
“When you work with nature you have none of the problems they have in hydroponics,” opines Colin, who practised hydroponics for a few years in Port Elizabeth. “In hydroponic systems bacteria are removed with UV lights and ozone. We encourage other forms of wildlife, like dragonflies, lady bugs and other beneficial insects. Nature has been doing everything right.”
One drawback to the system is that under current legislation, such produce can’t, despite the complete absence of insecticides and other poisons that would of course be lethal to the fish, be marketed as organic because it does not grow in soil, Colin explains.
Expansion into Africa
His design is being built in Zimbabwe, Botswana and Namibia to provide fresh vegetables within the hospitality sector, while mining countries in remote areas in countries like Burkina Faso are also interested in its ability to produce in harsh environments.
Kleinskuur Aquaponics regularly offers training courses in his system of aquaponics. The next course is on 25 May 2019.
For more information:
Colin Bremner
Publication date: 5/22/2019
Author: Carolize Jansen
© FreshPlaza.com
Puerto Rico Governor Ricardo Rosselló Nevares to Attend Ribbon Cutting Ceremony of Fusion Farms Facility
MAYAGUEZ , PUERTO RICO, USA
May 17, 2019 /EINPresswire.com/
The husband-and-wife team behind Fusion Farms, a hurricane-protected aquaponics farming initiative, are finally celebrating a hard-earned success. This Tuesday, May 21st 2019, Kendell Lang and Lisa Jander together with the island of Puerto Rico will be celebrating the ribbon cutting ceremony at their pilot facility in Mayagüez, and Puerto Rico Governor Ricardo Rosselló Nevares will be attending.
Since their first visit to the Caribbean island of Puerto Rico several years ago, Kendell and Lisa dreamed about moving there to establish a sustainable agricultural initiative that would contribute to the island’s recovery from financial insolvency and hurricane damage.
In 2018, they made the move from San Diego, California and after more than a year of hard toil against the monumental tasks of fund-raising, interpreting government grants and incentives, and completing bank applications, they managed to secure the first Fusion Farms facility in Mayagüez, a municipality in western Puerto Rico. With the help of #PRIDCO, #USDA and the Department of Agriculture, to name a few, Fusion Farms is well on the way to pioneering a sustainable indoor agriculture model for the island.
The Ribbon Cutting Ceremony
The ribbon cutting ceremony is scheduled to take place on Tuesday, May 21st 2019 at 1:30 PM where community members will be able to see the vision for the indoor farm.
“We are pleased to announce that Governor Ricardo Rosselló Nevares is scheduled to come to the Fusion Farms facility in Mayagüez,” says CEO and co-founder Kendell Lang. “He will be doing a site visit, tour of the building, presentation, and ribbon cutting ceremony to officially welcome Fusion Farms to Puerto Rico. Fusion Farms is proud to be at the forefront of what the Department of Economic Development is incentivizing for innovative agriculture solutions, specifically our hurricane-protected aquaponic vertical farm.”
Also in attendance will be the Secretary of the Department of Economic Development and Commerce, who will be discussing their delivery of $9 million USD to the Programa de Hidroponicos (Program of Hydroponics) and Pymes Innovadoras (Innovative Small to Medium Enterprises) in an effort to advance the agriculture sector of Puerto Rico.
“Fusion Farms is excited to create jobs and work with the University of Puerto Rico, Mayagüez, Department of Agriculture. By working together, we can address the needs of the community and begin to establish food security for the island. The current incentives offered to all farmers are making it possible for agriculture to thrive,” says Lisa Jander, co-founder and Director of Operations of Fusion Farms.
“We are incredibly grateful for this opportunity and look forward to welcoming everyone to our ribbon cutting ceremony!”
To attend, please visit the Facebook Event page, click “Number of Spots”, and then “Reserve” to secure a spot at this ground-breaking ceremony.
About Fusion Farms
Cultivando buena comida para buenas personas / Growing good food for good people
Fusion Farms is the first indoor aquaponic farm of its kind on the Caribbean island of Puerto Rico. The concept seeks to transform the unused Puerto Rico Industrial Development Company (PRIDCO) buildings that are scattered across the island into hurricane-protected, vertical #aquaponic farms. Within this contained and controlled environment, vegetables, micro-greens, and herbs can be grown and supplied to the island, greatly reducing its dependence on imported fresh produce. Furthermore, Fusion Farms will be able to supply a fresh, #sustainable source of fish protein, since Tilapia are an essential component of aquaculture.
For more information about Fusion Farms and to become an investor in this opportunity, go to http://www.fusionfarmspr.com
Andrew Braithwaite
Distributed by: Release-News.com
+44 7532285902
email us here
Pittsburg State University Showcases Aquaponics Project On Campus
Project Creates Sustainable, Healthy Food
By: Chris Warner
April 24, 2019
PITTSBURG, Kan. - Hydroponics involves growing plants in water instead of soil, and a project at Pittsburg State University has turned that into aquaponics by adding another element.
"It started out as a hydroponics operation so, it's basically growing lettuce primarily, but other food through water rather than soil, with the aquaponics, that incorporates fish into the system so it's more of a closed loop." Erin Kruse is one of two students giving tours at Pitt State to showcase their new aquaponics project.
Aquaponics, as Kruse mentioned, incorporates fish, in this case, tilapia, into the hydroponics system. Kruse says "So the fish actually generate the nutrients for the plants and then the plants actually clean the water for the fish."
And it's this unique system that officials like Matt O'Malley with Live Well Crawford County, are excited to see. O'Malley says "We are hoping to increase access to healthy foods for everyone in the county and thought this could be a really neat way to get that in communities that might not be able to do a garden project or something like that."
Kruse says the Students 4 Sustainability group, agree. "We really think, as students for sustainability, that local food production, sustainable food production is something that's always going to be paramount, especially in rural communities."
For O'Malley, he says he's looking at an even bigger picture. O'Malley says "We like to dream big and how cool would it be if every high school in Crawford County had an aquaponics system and they grew their own lettuce for their own school lunch salad bar, and so that's what we're kinda dreaming about with this project."
The project is still in it's early stages but Kruse says they hope to see it continue to grow and expand to serve the county.
The project was originally started by another group on campus before the students for sustainability group took over.
Hydroponics To Aquaponics: How University Students Are Learning To Master Sustainable Food Production — On The Roof
PSU
April 18, 2019
Pittsburg, KS
Fish soon will be living on the roof of the science building at Pittsburg
State University.
And those fish will be helping to grow plants.
It’s a forward-thinking project by Students for Sustainability (S4S), a student organization at PSU, in cooperation with Enactus, another student organization, and the PSU Biology Department.
S4S has gained a reputation for its recycling efforts: each Fall, members collect as much recyclable material as they can during the move-in process at the residence halls. At each Spring, they collect reusable items students don’t want to take with them when they leave campus to head home — hair dryers, brooms, microwaves, you name it. Those, they sell at the SEK Recycling Center.
The group’s latest initiative, hydroponics and soon to be aquaponics, is one that’s trending: they’re promoting sustainability by developing a sustainable food production project they have installed in a greenhouse on the roof of Heckert-Wells Hall.
“Trial phase”
One recent afternoon saw a group of students there tending plants; they're growing without soil in a “garden” built of PVC pipe and covered with mosquito netting to diffuse sunlight.
Among them was Charlie Beetch, who moved his family from Hutchinson, Kansas, to Pittsburg to pursue a bachelor’s degree in Sustainability, Society, and Resource Management (SSRM); it’s the only program of its kind in Kansas.
“We’re still in the trial phase,” Beetch said. “Th fish ought to be here next week. Then, it will be a full system.”
As he checked the health of the plants, a classmate, Cecily Stephens, a non-traditional graduate student from Pittsburg, harvested greens she considered using in a salad later.
“We’re growing arugula, red kale, romaine, collard greens, and butter lettuce,” said Stephens, who dreams of becoming an environmental journalist. “I’m pushing for starting herbs, and we could use them for fresh pesto!”
“Perfect fit”
The project was borne of conversations between S4S advisors and students during last year’s Earth Day celebration in the Overman Student Center. Enactus member Dodge Mattingly was displaying a booth that described his group’s trip to Haiti to set up a hydroponic system at an orphanage to help them grow fresh produce.
S4S members had been dreaming of a food production project — especially one that would provide a learning laboratory experience. Enactus was wanting to give away their prototype hydroponic set-up. And S4S
President Erin Kruse, a Girard, Kansas, native, had experience with aquaponics, hydroponics, and farm-to-table production at Johnson County Community College before transferring here.
“It seemed like a perfect fit,” said Jim Triplett, who volunteers as the Special Assistant to the President for Sustainability — a position created last year as part of the university’s focus on sustainability.
Enactus also gave S4S the fertilizer, seeds, and other supplies needed, and offered to share what they had learned to help S4S get up and running.
“Enactus had worked out the hydroponic side of the project, but the aquaponics portion is a new dimension, because it involves growing fish,” said Triplett, who for decades taught in the PSU Biology Department and served as its chair.
“The waste from the fish will break down and provide nutrients for the plants that will use the nutrients to grow, cleaning the water before it’s returned to the fish,” he explained. “When properly balanced, the system provides extremely efficient food production in terms of resources, energy and space.”
The biggest challenge? Fitting the PVC pipes and other supplies into the elevator.
Networking
Last month, their project took another step forward with a visit to Nile Valley Aquaponics, in inner Kansas City, Missouri, where they toured the facility and gained insight into its closed loop system.
The trip was organized by Kruse, who works at the Student Assistant for Sustainability in the President’s Office, and is majoring in SSRM.
Joining her on the trip were several S4S members, SSRM majors, faculty members including Catherine Hooey (Geography), June Freund (Economics), Tim Bailey (Geography), and staff including Jesse Briscoe (Housing), Elliott Rowland (Physical Plant).
Nile Valley provided inspiration: it features three, six-foot deep, lined trenches that house more than 60,000 tilapia. The water from the fish-rearing troughs is pumped up to the top of a stack of four growing beds that sit on top of the trenches and run their full length, Triplett said.
The nutrient-laden water travels through each bed and drops to the bed below until it is returned to the fish trough. In addition to plants and fish, the facility raises soldier flies to feed the fish and goats to eat the vegetative leftovers from production.
The trip also included a visit to Johnson County Community College, which created a Center for Sustainability in 2003.
“A composting operation there takes in all of the food waste from the facility and runs it through a hot tumbler and, with the addition of wood chips and sawdust, it develops into a compostable mix in about 10 days,” Triplett said.
The mix then is moved to aeration piles and is used as a soil amendment on the campus farm.
A greenhouse there houses the aquaponics project, which features a fish tank that holds 60 tilapia. They provide the nutrients for the hydroponic production of leafy greens and larger plants in media beds. All of the material grown from the system is used in JCCC dining services.
“It’s an amazing system and is reflective of future sustainable food production. We hope some of these ideas can be applied to future projects at PSU,” Triplett said. “There is a lot more to do before our system is fully operational, but this project has caught the imagination and interest of an active and enthusiastic group of students who are investing their time and energy to forge a new path in sustainable food production."
Learn more about the SSRM degree at https://bit.ly/2Og4STx
Canada: Using Hydroponics To Provide Northern Communities With Fresh Produce All Year Long
Alexander Wilkinson, research analyst on the University of Calgary’s Sustainability Studies team, is developing a database so that UCalgary has an inventory of its sustainability-related researchers, providing the ability to build an interdisciplinary sustainability community of practice.
“We want to bring researchers together and be leaders for interdisciplinary sustainability research. Currently I’m cataloguing all sustainability and sustainability-related research being done across campus,” says Wilkinson.
In addition to the community of practice, Wilkinson also conducts applied sustainability research as a PhD student through UCalgary’s Faculty of Environmental Design. In his PhD, Wilkinson is conducting research on two case studies with a focus on community health and well-being, sustainable development, resilience and capacity development for effective local responses to change.
The first case study is a project in partnership with the Artic Institute of North America (AINA), amongst other external partners. Together, Alex, AINA and external partners are implementing a food security intervention project where they are using a containerized hydroponic system, with a complementary renewable energy system, to sustainably grow fresh produce in rural northern communities.
“One goal of this research is to use hydroponics to provide northern communities with fresh produce all year long,” says Wilkinson. “We’re trying to determine if we can produce food in an off-grid scenario in the middle of winter in the Yukon when it’s -40 degrees and there is only one hour of sunlight.”
A Beginner’s Guide To Help You Grow Plants Indoors
In the last 5 to 10 years, a number of exciting technologies have come forward that may change the way people garden forever
Do you ever feel like your garden just won’t grow right, no matter how many nutrients, pesticides, or hours of care you throw at it?
If you answered yes, you are not alone! Growing up, many of us have seen our parents or teachers work magic with plants in their garden, dealing with cold weather, frost, bugs, animal invasions, and other tedious garden tasks. Many of us are left wondering how dealing with the elements and bugs can be worth it for anyone!
In the last 5 to 10 years, a number of exciting technologies have come forward that may change the way people garden forever. No longer do gardeners have to brave the elements and deal with cold winters where nothing grows. Indoor gardening has gained global attention, and there are countless innovators working on indoor growing solutions for the home and office.
Here are a few of these technologies. We hope these tips can empower you grow more food for more of the year!
LEDs
Horticultural LEDs have revolutionized indoor gardening in more ways than any other technology could. With access to controlled indoor light that isn’t too expensive to run, anyone can turn their soil or hydro container farm into an indoor set up, eliminating the need for sunlight and the risk of climate damage to crops. With the right LEDs giving your crops light, you can also expect way higher yields and fuller growth from your plants!
Hydroponics
This is the most popular of the indoor growing methods today. Hydroponics is the process of growing plants using no soil, suspending them in or over a nutrient rich solution for food and often using LEDs or artificial lighting to induce day/night cycles for plants and allow them the energy to photosynthesize. There are many kinds of hydroponic system designs and configuration, all of which carry out different approaches for different plants and outcomes.
Aquaponics
Similar to hydroponics, this growing method allows the user to grow plants without soil. Using slightly different irrigation and feeding methods, aquaponics takes fish waste from a fish tank and circulates it into the hydroponic root system, giving plants truly organic natural food. The plant roots then soak up the waste and clean the water, which can then be circulated back to the fish and the cycle repeats. This technology most closely mimics a natural energy cycle, and also has the added benefit of producing more than just plants, but seafood in your home too!
Container Gardening
Container gardens can be either indoor or outdoor, and are the lowest tech and oldest indoor gardening solution. Using a container with a water catching tray underneath, anyone can move their plants indoors, eliminating many of the pest and climate issues commonly associated with container gardening outdoors. Besides being the lowest cost indoor gardening solution, container gardens are a great way to transition from soil gardening outdoors to soilless gardening indoors using something like a hydroponic system. Whether using LEDs or natural light from a window, container gardening will keep you growing right through the winter months with a little less work and risk.
Smart Gardening
The newest of these options, smart gardening utilizes a plug and play growing appliance or device which controls lighting, feeding, watering, and monitoring your plants for you. This is the most effortless and failure free gardening option for homeowners anywhere. Whether you have a colder climate, a busy job, or a full social life, having a smart garden guarantees you the space and time to grow a garden without the hassle, time commitment, or pesticides. Smart gardens often utilize full climate control systems to guarantee your plants an optimal environment, and produce much less waste, toxins, and runoff than any other indoor gardening solution. Smart gardens come in all shapes and sizes, growing everything from herbs and greens to tomatoes and cannabis! If you are looking to up your gardening game for good, you can’t do better than a Smart Garden!
Many people we meet and talk to at Aeroasis agree on a few key things:
First, gardening is an incredibly rewarding experience, minus one or two very tedious and time consuming tasks. Second, limitations like seasonality make it hard to keep their garden up year after year, and this affects people’s willingness to garden over time. Third, everyone is looking for a better way to grow, spending more time and money on their plants directly and less on tertiary tasks like weeding, spraying, and watering their crops. With the option to garden inside, all of the more tedious aspects of growing become significantly less limiting, and seasonal plants are a thing of the past!
We at Aeroasis hope to keep empowering more people to grow their food indoors, and to spread the joy of controlled environment agriculture globally!
LEARN MORE ABOUT OASIS
Soilless Agriculture: An In-Depth Overview
Everything you need to know about soilless agriculture. Agriculture without soil? It sounds like another hipster trend that pops up in places like Berkeley and San Francisco. In reality, soilless agriculture is an agricultural method that enables a stable and sustainable food supply
February 11, 2019
Everything you need to know about soilless agriculture
Agriculture without soil? It sounds like another hipster trend that pops up in places like Berkeley and San Francisco. In reality, soilless agriculture is an agricultural method that enables a stable and sustainable food supply. It allows us to run high-yield grow operations in completely controlled indoor environments. So, why does that matter? Well, there are a few very important reasons that may enlighten you to the real potential in soilless agriculture.
No need to use pesticides (less poison sprinkled on plants means healthier food and less cost).
Extreme decrease in water use (you need 90% less than soil-based methods).
Flexibility in use (use it indoors or outdoors, and if indoors you can grow whatever you want, wherever you want, whenever).
Now, I want to focus on the flexibility of soilless agriculture and why this is so important in today’s world. As you know, people around the world are getting used to buying whatever kinds of produce they want — even if it’s not in season. This means importing a lot of produce from other countries. That’s a decent solution, but it has many side effects. First, it costs more money to buy food and have it shipped to your country than just growing it locally (you’re outsourcing taxable labor and covering transportation costs). Second, the emissions from whatever vehicles that are shipping the produce pollute the earth and bring us closer to climate catastrophe. Third, if a natural disaster occurs in the other country, you can’t import food from there for a while. If your country heavily depends on the damaged country for food, you may have a nationwide food shortage. Just think about what would happen to the world’s wheat supply if a disaster occured in North America. In summary, the extreme interconnectedness of the global food system creates an unsustainable and potentially unstable situation. Soilless agriculture helps to address this issue because it’s a perfect method for localizing agriculture and bringing food production closer to the consumer. This localization of food production stabilizes the food system and improves the freshness of the food.
Since we know the benefits of soilless agriculture, how did it come about? I thought it was invented by a Silicon Valley genius in midst of the current technological explosion, but it’s roots go much deeper than that. Primitive examples of soilless techniques were discovered at the Floating Gardens in China and the Hanging Gardens of Babylon! Ancient wisdom at work. <Image of either Chinese or hanging gardens>
Although soilless agriculture has been utilized throughout human history, the modern introduction to the technology was lead by William Frederick Gericke when he grew 25 foot high tomato vines without soil, using a nutrient rich water solution. This grand achievement drove more and more research to the technology, and its advantages were discovered on a mainstream level.
So, how do you actually implement hydroponics? Let’s start with the definition. According to Google, hydroponics is “the process of growing plants in sand, gravel, or liquid, with added nutrients but without soil.”. So basically hydroponics is the sciency way of saying soilless agriculture. Simple, right? Well… not so much when you get into the implementation details.
There are quite a few ways to implement hydroponics. The simplest way is to put a plant in a pot with a growing medium — a substance that doesn’t supply nutrients to the plants but supports the roots — and hand water it with a solution infused with the needed nutrients. This is the essence of soilless agriculture. All the plant needs is oxygen, a variety of nutrients, light, and it will grow. No need for soil or the constraints that come with it. While this may seem simple, getting an optimal yield requires knowing the intricacies of plant growth and applying this knowledge to each aspect of the hydroponic environment. For clarity, I’ll break down the different complexities associated with each part of hydroponic growth: The Solution, The Growing Medium, The Lighting, and The System.
The Solution
The solution is the lifeblood of your hydroponic system. The yield, health, and resilience of the crops you grow depends on a well-crafted solution. Sometimes it’s difficult to create a perfect solution, however, because the exact amount of specific nutrients in the solution depends on the plant you’re growing.
What are the steps to creating a balanced and fruitful solution for your system? It all starts with the water. Whether you’re using tap, filtered, or water from rain buckets (not recommended — I would filter it first) you should get a laboratory analysis of your water. In this analysis, pay close attention to the alkalinity of your base water — it will give you a good indication of how to devise your fertilizer strategy. If you have high alkalinity, the pH of your end solution will tend to be higher. The pH of your solution is one of the key factors in determining the health of your plants, and you want to keep it in the range of 5.5 to 6.5 for most plants.
After you have your water source figured out, you need to gather all the needed nutrients. The types of nutrients in your solution are primary and secondary nutrients (nutrients that plants need a lot of) and micronutrients (trace amounts of specific materials).
The primary nutrients are Potassium, Nitrogen, and Phosphorus. Without the a healthy dosage of these, your plants won’t grow correctly and will be more susceptible to disease. The role of each nutrient is as follows:
Nitrogen (N): Assists in protein manufacture, promotes plant strength, and makes use of the plant’s carbohydrates.
Phosphorus(P): Facilitates photosynthesis, controls cell division, and regulates use of sugars within the plant.
Potassium(K): Enforces disease resistance, helps metabolize nutrients, and regulates water usage.
Each primary nutrient plays an essential role in the health and yield of the plants, so make sure there is a balance of each one in your solution.
Secondary nutrients include Calcium, Magnesium, and Sulfur. These nutrients are needed in only moderate volume by plants, but are also essential for healthy growth. They play the following roles:
Calcium(Ca): Regulates internal pH, facilitates disease resistance, fuels cell division and cell wall formation.
Magnesium(Mg): Assists internal oil, sugar, and fat formation, boosts photosynthesis.
Sulfur(S): Assists seed production, adds flavor, is building block for proteins and amino acids.
Micronutrients are a bit different from primary and secondary nutrients in that they’re optional and applied in trace amounts. Usually you would only add extra micronutrients if your plants were showing signs of deficiency (discoloration, hollow fruits, limited growth, etc). There are quite a few micronutrients but the main players you’ll want to know about are zinc, copper, iron, manganese, chlorine, molybdenum, and boron. The cool thing with micronutrients is that they can boost absorption of other nutrients.
For the ongoing maintenance and fine-tuning of your solution, the two measurements to pay attention to are pH and electrical conductivity (EC). The pH should fall into the range of 5.5–6.5, and the electrical conductivity should be between 1.5 and 2.5. A high EC rating means your solution is too nutrient dense, so in this case add water until it comes under 2.5. Here’s a great article that gives a step-by-step breakdown on how to make your own solution.
The Growing Medium
Since hydroponics are systems without soil, you may need a static substance to support the roots of the plants. The vast variety of growing mediums and different mixes can overwhelm and confuse so i’ll just talk about the characteristics of different types of mediums and the circumstances in which you want them.
The key characteristics in your growing medium are water retention, aeration, and pH neutrality.
Water retention describes how slowly it takes for solution to filter through the medium, and how long it stays available to the plant. Use mediums with high water retention in drip systems, and lower water retention mediums in flood-and-drain type systems.
Aeration is an indicator of how much oxygen is getting to the roots of the plant. Roots need oxygen to convert their stored energy into growth, so it’s a super important characteristic. You can increase aeration by making the medium more porous, with cracks and slivers for oxygen to seep through. Aeration to the roots also makes them more effective at uptaking water, so if they don’t have space to breathe, the plant may show signs of water shortage.
pH neutrality tells you how the growing medium may affect the pH of a plant’s growing environment. Grow mediums should normally be neutral so they don’t have side effects on the solution or the environment
Common Growing Mediums
Coco Coir (The discarded husks of coconut) protects seedlings from harmful fungi and salt damage, has high water retention, and is biodegradable and cheap. These advantages make it perfect to use in drip or wick hydroponic systems, where water comes little by little. You won’t want to use it in flood systems though — it can have poor aeration if irrigated poorly. It also can draw down some of the calcium in the nutrient solution. To mitigate it’s high water retention, you can mix the fibers with a chunkier medium to create some drainage.
Best Use Case: When you want a cheap and sustainable medium with good water retention.
Expanded Clay Pellets are a great medium to use if you want fast drainage and an infinitely reusable medium. They also don’t affect the solution’s nutrient balance. They also have great aeration, although this can mean a plant’s roots dry out quickly. Another issue with clay pellets is that they’re sourced from strip mines, so the environment may have been harmed in their creation.
Best Use Case: When you’re worried about overwatering or nutrient disruption.
I decided to pair Perlite and Vermeculite together because they’re almost always mixed in use. Perlite is superheated volcanic rock. It’s a lightweight, neutral medium that will sometimes float on water when flooded. A downside of perlite is that it leaches nutrients easily, disrupting the delicate balance of solution. Vermiculite is very similar to perlite, a lightweight mineral that draws nutrients upwards and retains water at a high rate. When combined, these make a soil — like mixture with great oxygen and water retention. One thing you must be careful of is the particles of this mixture that can infiltrate your solution without a great filtration system.
Best Use Case: Same as Coco Coir, but will be a little bit more expensive.
Wood Chips are a simple, cheap (probably free), and organic growing medium. Wood chips are a great way to grow hydroponics, and will leave your environmental conscience clean too! There are a few downsides, as wood chips can degrade over time and aren’t the most reusable medium. It also might not be sterile, and attract pests.
Best Use Case: When you want to save money, and are running an indoor grow operation where pests and diseases won’t be as much of an issue.
Those are some tried-and-true growing mediums that you can use in your systems. When selecting growing mediums, keep in mind the requirements and orientation of your system(see: The System). You need to customize a combination of mediums based on the irrigation methods, types of plants, and environment (inside or outside).
If you want to go into more depth on growing mediums read this article, this article, and this article.
The Lighting
There are a few different types of lighting for your hydroponic system with their own advantages and disadvantages. In lighting, you want to find the right balance of intensity, spectrum, and cost. The most useful types of lighting for hydroponics are Fluorescents, High intensity Discharge Lamps (HID lamps) and Light Emitting Diodes.
Fluorescents are great for the growers that are just starting out. They’re efficient, widely available, and produce a spectrum of light that is conducive to plant growth. But, they emit weaker intensity light — which makes them sub-optimal for larger plants and grow operations.
One type of fluorescent lamp is the Compact Fluorescent Lamp (CFL). This type of lamp is cheap, easy to install (just screw it in), and efficient. One downside of CFL’s is that they emit light in all directions, so you’ll have to use a reflector to make sure you’re not wasting light and energy.
Another type of fluorescent light is the regular Fluorescent lamp. These are a larger version of the CFL’s and they emit more focused but weaker intensity light — which makes it sub-optimal for larger plants. The advantages are the same as CFL’s, but they might require a little more set-up to get working properly. A disadvantage with these and the CFL’s is the life span. To keep the system working optimally, these lamps should be changed out every year. This increases costs overtime and brings upon the question of disposal, as fluorescent lights contain mercury and other harmful chemicals.
The final type of fluorescent is an induction fluorescent. These have the same advantages (efficiency, spectrum) and disadvantages (intensity) as the other fluorescents with one catch: the lifespan is 10X longer than the previous two lights!
High Intensity Discharge Lights are great for experienced growers with large operations. The frequency of their light closest matches sunlight compared to the other types. The high intensity characteristic makes them the go-to choice for growing large plants indoors. This high intensity also leads to higher heat production, which can be mitigated by putting them in an open space where the heat can dissipate
Metal halide (MH) HID’s emit a bluish light that benefits leafy and vegetative plants while high pressure sodium (HPS) lights emit an orange light that work best for flowering plants and fruits.
Light Emitting Diodes are the newest option out of the three. They are also the most expensive. However, this upfront cost will be paid off in the long run because of their industry leading efficiency (they use around ⅓ the energy of fluorescents) and lifespan. If you don’t have tight upfront budget constraints, I recommend these because of the long-term savings (around $5,000 a year in recouped energy spending). The spectrum is a bit less optimal than fluorescents, but the difference isn’t very significant.
As you can see, the correct lighting setup will be determined by your budget, the plants you’re growing, and the size of your operation. As we look to the future, LED costs will go down and this will drive adoption of them over fluorescents.
The System
Whew, I just went through A LOT of stuff (don’t worry, we’re almost done :) ). Now, let’s put it all together! All the different types of growing mediums, solutions, and lighting setups can be put together in different ways. It all depends on your circumstances, budget, and expertise. Here are all the different types of systems, what they look like, and which situations they work for.
Hand Watering
Use this system if: You are a beginner in hydroponics or growing in general who doesn’t have extra time or money to spend on setting up a complicated hydroponics system with a lot of equipment.
Setup: Mix together your growing medium and nutrient solution, then put the plants/seeds in the medium and start watering!
Best medium: A mix of vermeculite/perlite and coco coir.
Best Practices: Make sure your nutrient solution is stored in a stable place where levels of nutrients wont fluctuate and other living things can’t get into it. Also, remember to water the plants!
Deep Water Culture
Use This system If: You want a relatively simple hydroponic system that is more intricate than hand watering — and you have a small budget to get started.
Setup: As It would be incredibly tedious for me to write words about how to setup this system, a video would do a much better job. So watch this for setup instructions!
Best Medium: Expanded clay pellets, or a similar medium with ph neutrality
Best Practices: Make sure the nutrients in your solution are very accurately measured, as a little mistake can go a long way in this system. Check the ph and electrical conductivity of the solution thoroughly before setup.
Ebb and Flow
Use This system If: You want a lower cost, flexible homemade hydroponics system and want to put the time in to a more complex setup.
Setup: Epic Gardening on youtube does a great job making these hydroponic system setup tutorials. So watch this for setup instructions!
Best Medium: The exact medium depends on how often you want to flood your plants, but a heavier medium like coco coir or expanded clay pellets is highly recommended.
Best Practices: This method requires more attention after setup than the previous two. Make sure you’re flooding the plants at different intervals throughout the year to match the change in light exposure and temperature, as the water will evaporate at different rates. Also, make sure the grow tray (see diagram/setup video) is level so all the plants get the same level of nutrients.
Drip System
Image From: https://www.pinterest.com/pin/54887689187136114/
Use This system If: You want to grow larger, greedier plants with a simple setup but don’t want to use a lot of water doing it.
Setup: Epic Gardening on youtube does a great job making these hydroponic system setup tutorials. So watch this for setup instructions!
Best Medium: The exact medium depends on how often you want to flood your plants, but a heavier medium like coco coir or expanded clay pellets is highly recommended.
Best Practices: This method requires more attention after setup than the previous two. Make sure you’re flooding the plants at different intervals throughout the year to match the change in light exposure and temperature, as the water will evaporate at different rates. Also, make sure the grow tray (see diagram/setup video) is level so all the plants get the same level of nutrients.
Wick System
Use This system If: You are going to grow a relatively low-water plant (like rosemary or a fast-growing lettuce), and want to build the system quickly and simply.
Setup: Here’s a nice tutorial on wikibooks that explains what materials you need and how to put it all together!
Best Medium: With a wicking system, choose a medium that absorbs and retains water well, like coco coir, perlite, or vermeculite.
Best Practices: Make sure there are multiple wicks when you set this system up so you’re sure the plants get enough water and nutrients. Keep the water levels in the reservoir high and wash growing mediums frequently to prevent nutrient buildup.
Aeroponics
Note: Aeroponics is not hydroponics. It differs because it uses a spray to diffuse the mineral-rich water onto exposed roots instead of a model where the roots are submerged in water or a growing medium.
Use This system If: You’re an experienced with hydroponic or diy projects with hands-on and technical knowledge that’s ready to build a more complex system with some automated parts. Another good reason to use this system is if you need to grow stuff quickly, for commercial sale or to feed your family.
Setup: Check out this video series by Peter Stanley for a step-by-step instruction on how to set up a cheap aeroponics system.
Best Medium: No medium needed!
Best Practices: Since the roots are exposed, aeroponic growing presents a large opportunity for disease and nutrients clogging the root system. Make sure the roots stay clean on a daily basis. Also, the misters tend to clog as well, so keeping them clear of debris with frequent maintenance can mitigate that risk. Just be sure to keep close tabs on the most vulnerable parts of the system.
There you have it! Hopefully all of this knowledge on hydroponics helps you get started with your own growing operation or helps you transition to a new growing method that fits. I enjoyed learning about all the complexity and the advantages of unique technology, and I’m excited to see what advancements may be made in the future! Thanks for reading :)
Adam French
I love learning and writing about programming, agricultural innovation, and design.
Future of Food Is Fishy
Darren Handschuh - March 29, 2019
It's a marriage made in heaven.
One that produces food faster and uses far fewer resources than traditional growing methods – and it is happening right here in the Okanagan.
With the right equipment, aquaponics can be done just about anywhere.
“Aquaponics is the perfect marriage of hydroponics and aquaculture,” says Jeff Smith with the Aquaponics Training Institute in Vernon. “Aquaculture is the raising of aquatic species in a closed system, and hydroponics is a soilless growing of plants within a closed system.”
Put the two together, and you get a method of producing food that leaves almost no environmental footprint.
Smith will be hosting information sessions and workshops to teach people how to set up their own systems.
Information sessions will be held this Saturday, from 9 a.m. until noon, and then again on April 6.
From there, people can sign up for workshops on how to build their own system.
“That's a full hands on, face-to-face workshop here in our facility, so they will get to learn all about aquaponics,” said ATI's Barbara Bonnough.
“The workshops are geared toward people who want to run their own facility in their own home, up to someone who might want to do it in an outdoor greenhouse and set up an aquaponics facility that would feed a community.”
More information can be found at the Aquaponics Training Institute website.
Korean Company Starts Building Hydroponic Greens Houses in Northern Tajikistan
The use of the hydroponic system will help increase productivity, according to the Sughd regional administration.
8 January 2019 14:39 (UTC+04:00)
South Korea’s Myung Sung Placon Ltd has begun building hydroponic greenhouses in the northern Sughd province. The hydroponic system has an ancient history and was reportedly used for building of the Hanging Gardens of Babylon, Trend reports referring to news.tj.
The use of the hydroponic system will help increase productivity, according to the Sughd regional administration.
The building of the hydroponic greenhouses began in the Somgor area of the Bobojon-Ghafourov district on January 7.
An official source at the Sughd regional administration says local “Bars” Company is a contractor and specialists from South Korea are implementing the project.
Sughd authorities have invited Myung Sung Placon Ltd to build greenhouses in the province, taking into account the company’s experience of work in the neighboring Uzbekistan, the source added.
Hydroponic growing is growing a plant without using soil - usually in an inert substance like rockwool or perlite, which hold the roots for easy water and nutrient absorption. Hydroponics systems back several hundred years, and there is evidence that ancient civilizations grew plants in water. Nutrients are vital to hydroponic success: there are sixteen essential elements that a plant needs to grow, and the right balance of these nutrients must be maintained for each specific variety of plants. Equally as important as nutrition are the factors of light, temperature (heating and cooling), and carbon dioxide. Insects play a key role in pollination and pest management.
The Hanging Gardens of Babylon were one of the Seven Wonders of the Ancient World and were described as a remarkable feat of engineering with an ascending series of tiered gardens containing a wide variety of trees, shrubs, and vines, resembling a large green mountain constructed of mud bricks, and said to have been built in the ancient city of Babylon, near present-day Hillah, Babil province, in Iraq. Its name refers to trees being planted on a raised structure such as a terrace.
According to one legend, the Hanging Gardens were built alongside a grand palace known as The Marvel of Mankind, by the Neo-Babylonian King Nebuchadnezzar II (who ruled between 605 and 562 BC), for his Median wife Queen Amytis, because she missed the green hills and valleys of her homeland. The construction of the Hanging Gardens has also been attributed to the legendary queen Semiramis, who supposedly ruled Babylon in the 9th century BC, and they have been called the Hanging Gardens of Semiramis as an alternate name.
NMSU Helps Bring Hydroponic Gardens into Las Cruces Schools
The initiative involves placing hydroponic plant systems in classrooms, which brings gardens indoors and eliminates the need for soil — the biggest challenge in school gardens.
Carlos Andres López, For the Sun-NewsPublished 11:17 a.m. MT Dec. 28, 2018 | Updated 12:35 p.m. MT Dec. 30, 2018
LAS CRUCES - Even as the days were colder last fall and winter, the tomato garden in Adrian Gaytan’s classroom at Zia Middle School in Las Cruces continued to thrive, a feat that would have been impossible more than a year ago but is now a reality – thanks to an initiative launched by New Mexico State University’s Cooperative Extension Service in Doña Ana County.
The initiative involves placing hydroponic plant systems in classrooms, which brings gardens indoors and eliminates the need for soil — the biggest challenge in school gardens. Hydroponic plant systems use water-based, nutrient-rich solutions to cultivate plants without the use of soil, resulting in better quality plants and higher yields, among other benefits.
In Gaytan’s classroom, the hydroponic plant system, at less than six feet in length, takes up minimal space and has been outfitted with overhead lights and an automatic timer, which enable it to operate on its own, a feature that allows for year-round gardening (even when students are out of school for extended periods of time).
Jeff Anderson, an agent for NMSU’s Cooperative Extension Service in Doña Ana County who specializes in agronomy and horticulture, believes hydroponic plant systems may be the answer in helping schools boost the number of gardens in classrooms.
“It’s hard to send teachers and students outside in the winter to pick weeds and water plants,” Anderson said, noting that conventional outdoor gardens in local schools have declined in recent years. “So, I thought to myself: How are we going to bring agriculture into the school system?”
The answer finally came to Anderson when gardeners began calling the Doña Ana County Extension Master Gardener Program to inquire about starting hydroponic plant systems in the Las Cruces area, he said. As Anderson researched the system, he determined it could a practical solution for school gardens — but only if he could develop a cost-effective system. He then turned his efforts to building an affordable structure.
By sourcing material locally, Anderson was able to build a system for just under $300.
“We were able to figure out the cost and developed the program from there,” he said.
A pilot system underwent testing for about a year at the Cooperative Extension Service office in Las Cruces before similar systems were constructed for five local middle schools — Lynn, Vista, Sierra Vista, Picacho and Zia — which began using the gardens at the start of the 2017-18 school year, with assistance from the Master Gardener Program.
Zia and Vista had very successful first years, Anderson said.
“When I heard there was going to be an opportunity to have a hydroponics system in my classroom, I said, ‘Yes,’” said Gaytan, a Project Lead the Way and Technology, or PLWY, teacher at Zia. “We got it, and I used it for sixth-graders. They were immediately hooked; every day they tended the garden, checking the water and testing the pH levels. They took complete ownership of it.”
The hydroponics garden in Adrian Gaytan's classroom at Zia Middle School started with assistance from New Mexico State University’s Cooperative Extension Service in Doña Ana County in 2017. (Photo11: Photo courtesy of Adrian Gaytan)
Those students are now seventh-graders, Gaytan said, and continue to maintain the garden. This semester, they’re focused on growing tomatoes — the type that’s used to make ketchup. Last month, their tomato seedlings started to sprout, an indication the students were weeks away from enjoying fresh-from-the-vine tomatoes.
For Anderson, the gardens offer many opportunities for “direct teachable moments.”
“You can bring in science, technology, engineering and math,” he said, “and teach healthy eating, energy efficiency, energy use, water recycling and other life science skills.”
He added: “The schools have had successes and failures, all of which have provided valuable lessons. When you have a failure, the kids have to learn — why did we fail, why did the plants die? The kids have to do research and they have to apply that research to their garden.”
The students also become more caring individuals, Anderson said. “There’s a big thing about caring for a plant and that translates to caring for anything when you’re older,’ he said.
Now, Anderson said he is exploring ways in which to expand the program, not just throughout Las Cruces and Doña Ana County, but also statewide.
“We’re trying to get more of this type of agriculture in schools across the state,” he said.
To learn more about the program, visit https://aces.nmsu.edu/county/donaana/.
Greg Kelly And Jake Isham Farm Greens In A Former Granite Shed
Greg Kelly (left) and Jacob Isham harvesting greens beneath colored LED lights at Ceres Greens | JEB WALLACE-BRODEUR
Greg Kelly and Jake Isham have come a long way together since they met in 2016. At the time, Kelly, 61, was trying to grow lettuce in the basement of a mutual friend of his and Isham's — and it was not going well.
"I was using LED lights, but I didn't realize they wouldn't grow at 50 degrees," Kelly admitted. "I didn't even grow house plants. I knew nothing."
Their mutual friend soon introduced the pair because "neither of us would shut up about vertical farming," Isham, 28, explained recently in the Barre headquarters of their 2-year-old company, Ceres Greens.
While the business partners have moved away from literal "vertical" farming, in which plants sprout out of tall planter walls often called "living walls," their indoor farm still has a vertical, space-saving component and follows the same principles of hydroponic growing, or "controlled-environment agriculture," as they call it.
By the end of this year, their converted 12,500-square-foot granite shed will hold about 100,000 leafy green plants on shelves layered eight high. The top layer will approach the 26-foot ceiling of the cement-floored industrial space, which evokes quite a different feeling than the average Vermont farm.
At Ceres Greens on an icy early February day, production manager Holly St. Jean was placing seeds from Wolcott's High Mowing Organic Seeds into compostable coconut-fiber plugs nestled into plastic trays. A warm, brightly lit germination room coaxes them into sprouting before they head out to the main floor, where orange metal shelves are filled with vibrant green and red lettuces and aromatic basil.
Electronic sensors closely monitor ideal temperature and humidity. Plants are sustained by LED lights and mechanically pumped water and nutrients. Their roots will never search the soil for nourishment and moisture. Their leaves will not be exposed to sunshine or dew; nor will they face hungry pests, flooding or frost.
"We're controlling for a perfect growing environment," Kelly explained.
Just-harvested romaine lettuce at Ceres Greens | JEB WALLACE-BRODEUR
Ceres Greens does not use pesticides or herbicides, and the system sterilizes and recirculates any water not taken up by the plants. Kelly and Isham estimate they're using 85 percent less water than soil-based farms. Electricity is a significant input, but they're working toward being 100 percent solar powered.
To some, this approach to agriculture is yet another sign of humans trying to distance themselves from the natural world and the impacts we have had on it. Others, like Kelly and Isham, believe it's a valuable, environmentally responsible way to help feed Earth's booming population in the face of depleted natural resources and increasingly extreme and unpredictable weather patterns.
Close to home, they want to provide fresh, locally grown greens to Vermonters year-round. "Consumers obviously have their choice. We're just providing a new option," Kelly said. "As humans, we've already divorced ourselves from nature."
Ceres Greens received a noteworthy vote of confidence in December when it was named one of two winners of Accel-VT Ag & Food Tech 2018. The three-month, Vermont-based business accelerator program is open to early-stage ventures throughout North America that address climate change in various ways.
Managed by the Vermont Sustainable Jobs Fund, Accel-VT's annual entrepreneurial boot camp supports startup or seed-stage enterprises in a broadly defined sector each year. Participants are selected through a competitive process, then all receive business-development support, mentorship and potential access to capital. The eight companies in the 2018 boot camp represented six states and a range of technology-based solutions to issues within the agriculture and food system.
At the end of the program, participants vote on two winning ventures, which each receive $25,000. In addition to Ceres Greens, the other 2018 winner was AgHelp, a Michigan-based company that has developed a mobile platform connecting agricultural workers, employers and support agencies. The 2019 Accel-VT program will focus on energy.
While Kelly and Isham were gratified by their win, simply participating in the program helped them build their network and validate their fledgling operation for potential investors. "It helped us clarify our business strategy," Kelly said.
The prize dollars made an appreciated but relatively small contribution to the $1 million budgeted for full build-out. Ceres Greens has raised about a third of that goal so far from a variety of sources, including crowdfunding $69,000 via StartEngine; personal funds from both cofounders; a private placement offering; and loans from Yankee Farm Credit, Community Capital of Vermont and the Central Vermont Economic Development Corporation.
Ceres Greens is part of Yankee Farm Credit's FarmStart program for new agricultural enterprises that lack the track record, capital or collateral required for most business loans, explained Yankee senior vice president Dave Lane. The maximum loan is $75,000 over a five-year term, and participants are assigned a business adviser. "Our goal is to get them ready for a more traditional lending program," Lane said.
Katy Coombs, who has worked closely with Kelly and Isham for the last year as their FarmStart adviser, had previously researched controlled-environment agriculture for another FarmStart loan in New Hampshire. "It's definitely a different way of growing," she acknowledged. "I think we're going to see a lot more of it going forward. It's still very local, and it's grown in a clean way using methods that are socially friendly."
Coombs was initially impressed by Kelly and Isham's thorough business plan and their complementary skill sets. "They don't come at it just from the idealistic standpoint," she said. "They are also driven by the numbers."
The cofounders' different backgrounds and perspectives also contributed to the way each landed on this type of agriculture as both a mission and a business opportunity.
From left: Jacob Isham, Holly St. Jean and Greg Kelly at Ceres Greens
JEB WALLACE-BRODEUR
Kelly is originally from Guam but moved to Vermont 24 years ago from San Francisco. "It was as far from Silicon Valley as I could get," he said with a wry smile. He did continue a career in technology, building a regional fiber-optic network company, TelJet, which he sold in 2013.
After the sale, Kelly started looking into various sectors for his next move. "Food is a business that's never going to go out of fashion. Everybody has to eat," he said, "and I remembered getting fresh, local produce year-round in California."
He dug into the environmental aspects of food production. "I looked at water, the global water crisis. I looked at air quality," Kelly said. "We have too many on the planet to rely on what a variable harvest produces," he concluded. "How do we have a predictable harvest and not be harming our environment? We need to take a technological approach."
Isham, an eighth-generation Vermonter, grew up in Winooski and graduated from Norwich University with a degree in political science. He was commissioned as an infantry officer in 2012 but was medically retired four years later due to a serious health condition.
While working in finance, Isham started an online master's degree in diplomacy and international terrorism. "I was studying how civil unrest and resource scarcities go together," he explained. "Water and food shortages lead to economic instability. Civil unrest and conflict often follow."
Isham looked at projected global population growth and determined, "we need to develop ways to grow more food everywhere. This is a kind of agriculture you can do almost anywhere."
Shortly after the two were introduced, they expanded Kelly's growing experiments into a small warehouse in Colchester. "We killed a lot of plants," Isham said, laughing. Their first big strides came after he participated in a three-month Veterans to Farmers program in Denver on controlled-environment agriculture.
The business partners balance each other: Kelly has focused on the technology, Isham on the business and marketing side. The more seasoned Kelly is happy to let his younger colleague take the lead. "I didn't want to be the boss anymore," he said. "Jake has a lot of energy and drive. He wanted to be the boss."
Isham, in turn, appreciates Kelly's depth of experience. "I needed somebody to show me the ropes," he said. "I needed someone to steer me in the right direction, calm me down sometimes."
Since the Barre space was renovated last spring, Kelly has had his hands full refining and scaling up their proprietary growing method. In the relatively new field, there are few turnkey systems or specialty suppliers. He is often repurposing parts from other industries, such as marine and recreational vehicle water pumps.
It's no small feat to reproduce what Mother Nature can do so well at her best but with a better track record for reliability. "I joke that I understand why religion is popular in farming communities," Kelly said. "We get to play God," his business partner interjected with a laugh.
Ceres Greens has so far sold only limited quantities of its harvest to a few local restaurants but is poised to quadruple production by the end of April. Its business plan is built on selling 80 percent bulk to restaurants and institutions and 20 percent to independent retail stores such as co-ops. Kelly and Isham expect their price point to fall between conventional and organic and will hang their hat on freshness and low environmental impact.
"Some small part of this is educating people," Kelly acknowledged.
In Vermont, they anticipate hiring eight to 10 employees, among whom Isham hopes to include fellow veterans. Longer term, they envision 10 Ceres Greens facilities across the eastern U.S. employing a total of 100.
Kelly and Isham believe that Ceres Greens will be part of a wave and that there's room for everyone in the burgeoning sector. "We're not trying to corner the market," Kelly said.
Isham noted that the 2018 U.S. Farm Bill includes several programs supportive of newer forms of agriculture, including what it calls "high-tech vertical technology farms."
More farmers growing more greens in a variety of ways makes sense to these entrepreneurs. "We should all be eating more greens," said Isham.
The original print version of this article was headlined "Salad Days"