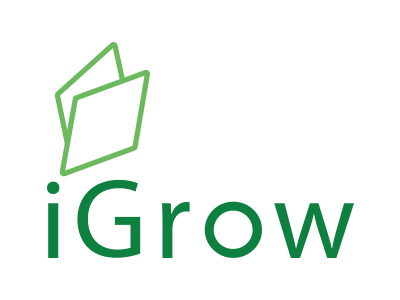
Welcome to iGrow News, Your Source for the World of Indoor Vertical Farming
3 Challenges of Vertical Farming And Their Solutions
The world is continuing to grow. By the year 2050, researchers estimate that there will be nearly 10 billion people on the planet. As the population increases, the demand for food and food security also increases
Source: Shannon Flynn, ReHack
05/26/21
The world is continuing to grow. By the year 2050, researchers estimate that there will be nearly 10 billion people on the planet. As the population increases, the demand for food and food security also increases.
Traditional farming methods won’t be able to sustainably keep up with the necessary food production to feed the population. That’s why farmers and researchers have been developing new means of feeding people, especially in urban areas.
The advent of vertical farming has taken the agricultural industry by storm. Although it has proven to be beneficial to farmers and the environment alike, there are some challenges that vertical farmers face. Below are three challenges of vertical farming and their solutions. As long as the solutions are available, vertical farming can still be a reliable way to feed the population.
Vertical Farming Basics
Vertical farming takes traditional farming to new levels — literally. Instead of conventional horizontal, soil-based farming, vertical farming implements hydroponics into vertical buildings. Crops grow upwards instead of outwards.
The buildings use a combination of climate and light-controlled areas to grow the plants. It creates a perfect environment for plants to thrive. This type of farming is optimal in urban areas because it takes up much less space than a traditional farm.
Therefore, populations in cities and urban communities have the opportunity to get fresh produce a few blocks away from their homes. Since most of the world’s population will reside in urban areas, this provides greater food security for them.
Vertical farming has evolved over the years to include more than just fruits and vegetables. Seafood producers wanted a more sustainable approach to seafood production, so they have also implemented vertical farming techniques. Seafoods like mussels, scallops, and seaweed grow vertically on ropes, which creates a more biodiverse and resilient seafood system.
Challenges of Vertical Farming and Their Solutions
Unfortunately, there are challenges that vertical farmers face that they must solve to meet those future food needs and to remain sustainable. Here are some of the challenges, along with potential solutions, of vertical farming.
Location
Although vertical farms can go almost anywhere, farmers have to choose the correct location. If it’s too far from potential consumers, then it won’t be a lucrative business. One could have the best place, but if there isn’t a demand for food there, then they won’t be able to sell the produce.
Plus, land in cities can be a bit more expensive. Smaller vertical farms have a more difficult time finding land they can afford, along with permits and insurance.
The solution is to research the considered location for a vertical farm. What kinds of food are the people there looking for? Can a vertical farm provide that for them? Will they be a loyal customer to the farm? Without a good location, a vertical farm won’t get far. Fundraising, loans, and grants are great options for farmers who may not have the funds for a location, too.
Temperature and Humidity Control
The next challenge is temperature and humidity control. These two need to be spot on to produce vegetables and fruits. Managing them can take a while to overcome. Farmers often have to try various recipes of cooling, dehumidification and heating. Vertical farms are usually well-insulated, so when the weather gets warmer, the farmer must cool it and remove humidity.
Before installing an HVAC system, it’s wise to ask for professional help to know how large of a system will be needed for the building. This is the best solution to this challenge, and it will save a lot of headaches in the future.
Multitasking
Another challenge is ensuring proper management of the entire vertical farm. Many farmers who set out to start their industry in vertical farming rely on themselves and possibly a couple of other people to get all of the work done. Vertical farms attempt to do too many things simultaneously, like growing food and selling technology, and managing day-to-day tasks.
New vertical farmers should focus on one thing, like growing food and selling it. This helps build a solid customer base. Choosing either growing and selling or developing technology so allows the farmer to put their best effort into it.
Farming of the Future
Vertical farming has become a popular solution to the growing problem of food security. However, there are challenges within the industry that must first be addressed and overcome to remain a sustainable business. These challenges and solutions are excellent learning tools to grow a thriving vertical farm.
Tags: Indoor & Vertical Farming, Processing & Supply Chain | Business Development, vertical farming
Aquaponics Is Complex: ‘It’s Everything, Anything You Can Really Think Of’
The needs of the fish, bacteria, and plants must be addressed to get and maintain conditions for success
The needs of the fish, bacteria, and plants must be addressed to get and maintain conditions for success.
May 16, 2021
Unlike other agricultural techniques that focus on a single product, aquaponics growers must consider both the fish and the plants when altering the conditions of the system.
Aquaponic systems are often described as their own ecosystems. Everything from the types of organisms in the system to the bacteria breaking down waste impact the productivity and success of the system.
Fish meal is the major source of nutrients in the entire system. What the fish are fed, and how much, plays a role in determining which nutrients will be available for the plants further down the line.
“(The fish meal) will break down into the fundamental components of the fertilizer, which will then be broken down further by beneficial bacteria in the system,” says Trevor Kenkel, owner of Springworks aquaponics farm in Lisbon. “It will go on to then generate the major macronutrients for the plants, but also the micronutrients as well.”
Kenkel said they also monitor the amount of food they feed the fish to prevent excess nutrients in the system.
“The amount of nutrients that are thrown off out of a system is really significant, and it’s so concentrated,” he said. “If we weren’t running a system to capture this afterward, you would either be dumping those into a local ecosystem, or you’d have to find some other way to treat them, which can be very expensive.”
Managing the greenhouse environment can also be difficult, particularly in Maine. Growing produce in the summer and winter is very different, Kenkel said.
Springworks’ greenhouses have lights that supplement the sun on cloudy, gray days. Additionally, a system helps control the temperature within the greenhouses.
Paul Brown, a professor at Purdue University who studies aquaponics, said many factors are involved. For instance, different types of fish provide different kinds of nutrients, and different plants require more of some nutrients than others.
Even the kinds of microorganisms breaking waste down into fertilizer play a part in this complex system. At times, Brown said, it can become necessary to add additional nutrients to make up for deficiencies in the system. The acidity and salinity of the water can also be major factors.
Springworks has plants growing to maturity constantly, allowing Kenkel and his team to measure different qualities and environmental factors: the location in the greenhouse the plant grew in, the density of the leaves, and the effects of different temperatures, for example.
“It’s everything, anything you can really think of,” said Kenkel, who studied plant physiology at Bowdoin College.
Jungle Aims To Supply 2000 Supermarkets In The EU By 2025
Jungle is a vertical farming company that first began in a 15-square meter container installed near a supermarket in Lisbon, Portugal
Expanding Throughout France,
With Another Two Farms
In The Pipeline
“In France, associating technology to food production can be challenging since the country has a really strong agricultural culture. We figured that if we manage to succeed in France, then we can do it anywhere,” says Gilles Dreyfus, President & co-founder at Jungle.
Jungle is a vertical farming company that first began in a 15-square meter container installed near a supermarket in Lisbon, Portugal. However, founders Gilles Dreyfus and Nicholas Séguy both dreamed of establishing the company in France due in part to the challenges posed by the French agri-food sector.
In March 2021, Jungle announced that it had raised €42 million to expand across the United Kingdom and Europe, with plans to supply more than 2,000 points of sale by 2024.
Gilles Dreyfus
Expanding throughout France
By Q2 of 2022, Jungle plans to have an even larger production facility in southern France, in close proximity to the food distribution and logistics centers. Next to that, the company has another farm in the pipeline at an unknown location. “We’ll be delivering our products to the supermarkets’ logistics centers and they will deliver it to their stores. We won’t be delivering store-to-store, which further reduces our carbon footprint,” says Gilles.
After spending 2.5 years researching the optimal growing recipes, Jungle partnered with a French retailer in Lisbon and built its team in Lisbon over the course of three years. In Portugal, Jungle expanded from being available in one store to ten stores. Despite the obvious market opportunities in Lisbon, Gilles explains that a primary inconvenience of establishing a vertical farm in Lisbon is the distance from consumers, with the country’s 10 million people being dispersed across the country which makes it more difficult to tackle a large consumer base. In contrast, Paris’s metropolitan area has roughly 14 million people.
First Lisbon, then France
Jungle’s productivity in Lisbon paid off, as the company soon attracted the interest of major French retail chain Monoprix in mid-2019. In response, Gilles and Nicholas created Jungle France in August 2019 and began with a small unit as a pilot project in January 2020. After demonstrating impressive KPIs over a few months, Jungle signed an agreement with Monoprix in October 2020 to supply 120 stores.
Jungle France has secured its first farm location in Château-Thierry in September 2019. roughly 80 km from Paris. The Château-Thierry farm has a total footprint of 3,800 m2, of which half is dedicated to growing while the other half is used for germination, equipment washing, packaging, delivery and administration. The floor area for cultivation is thus roughly 1,800 m2 and the room is 10 m tall, bringing the net production area to 5,500 m2, according to Gilles.
Bringing vertical farming to France
As Gilles mentions, establishing a vertical farm in France can be challenging due to the strong agricultural culture in the country, which has somewhat disfavored hydroponics and alternative forms of agriculture. This has not made marketing impossible for Jungle; rather, the company has simply taken different approaches to ensure that their products are understood and accepted. One of the key elements of Jungle’s approach has been to remain humble and not attempt to completely revolutionize the agricultural sector.
“Our branding doesn’t focus on the fact that our products have been grown vertically; we’re not trying to hide anything, but our market research has shown that highlighting technology isn’t always appealing to the customers,” says Gilles.
He compares it to the introduction of organic agriculture in the 1980s, which was poorly received and took several decades to be widely accepted as environmentally superior to conventional agriculture.
Jungle's products
“Nowadays, information travels much faster so the time taken to educate the population about vertical farming is much shorter, maybe 4-5 years. But Jungle’s position is not to educate people; it is to produce healthy plants on an industrial level and at reasonable prices for the masses. So for marketing and branding, we have taken a simple route,” explains Gilles.
In supermarkets, Jungle products are sold in company-provided displays. So far, the reception has been good as people are beginning to understand the benefits of vertical farming with respect to efficient energy and water use, lack of pesticides, and overall environmental sustainability. According to Gilles, it also helps that Jungle products are roughly 20% less expensive than their organic counterparts.
More partnerships and avenues ahead in 2021
While Jungle currently produces herbs, salads, microgreens, and flowers, the company is planning to expand its portfolio and its consistent research on different vine crops. Jungle is also excited about impending partnerships that will be announced in the coming months, which will allow the company to further expand its client base and possibly access cosmetic industries.
For more information:
Gilles Dreyfus, Co-Founder
Jungle
gdreyfus@jungle.bio
www.jungle.bio/old-home
Publication date: Tue 25 May 2021
Author: Rebekka Boekhout
© VerticalFarmDaily.com
VIDEO: California Farmers Leave Fields Fallow As Drought Grows More Dire In West
Northern California reservoirs contain only half the water they normally do in late spring.
Both the State Water Project and the federal Central Valley Project have announced they intend to deliver only 5% of requested supplies this year
By TYNE MORGAN May 28, 2021
As rains drop needed moisture for areas of the country dealing with drought and in need of relief, the situation is growing more dire in the West.
The latest U.S. Drought Monitor shows improvement in the Plains, especially in the Southern Plains. Heavy rains also falling across western portions of the High Plains this week, lessening the drought conditions in the western Dakotas. Those moisture improvements also pilling over into western Nebraska and Kansas.
The drought has become a mainstay in California. The Drought Monitor released Thursday shows exceptional drought growing, including Kern County, one of the top ranked counties for ag production in the nation.
Northern California reservoirs contain only half the water they normally do in late spring.
Both the State Water Project and the federal Central Valley Project have announced they intend to deliver only 5% of requested supplies this year.
As California farmers rely on Mother Nature and ground water this year, one farmer says it won't be enough to even grow a crop, with some farmers choosing to not plant at all. Some producers are even pulling out trees.
"There are land areas out here that are going to get one acre foot of water from the ground. That's what they're allocated," says Tyler Ribeiro, a dairy farmer in Tulare, California. "Good luck growing cactus on one acre foot. You're not going to be able to feed with that you can't grow trees out there. And we align with a lot of these tree guys in a sense of we feed their byproduct, I need those all almond hulls, I need those orange peels. I need a lot of those things. That's how we stay efficient [as a day farmer]."
USDA meteorologists telling AgDay there's not much relief in sight for California and the West. Forecasters expect the drought west of the Rockies to only get worse.
USA: Vertical Harvest Maine And Sodexo
In a partnership announced last week, Sodexo, also one of Maine's largest employers, committed to serving our produce on collegiate campuses from Canadian border-hugging Fort Kent to South Portland
Vertical Harvest Farms is thrilled to announce a partnership with Sodexo, a global food service provider, to source as much as 80-percent of its lettuce products from our new Westbrook, Maine farm. The 70,000-square-foot farm, scheduled to break ground later this summer, will grow over 1-million pounds of greens.
In a partnership announced last week, Sodexo, also one of Maine's largest employers, committed to serving our produce on collegiate campuses from Canadian border-hugging Fort Kent to South Portland. "The partnership with Vertical Harvest will be a game-changer for Sodexo’s ability to buy fresh produce twelve months per year,” says Varun Avasthi, Director of Strategic Partnerships, Sodexo.
Read the story on our blog by clicking the button below.
Read Now
CANADA - MONTREAL: Indoor Farming Technology Seeks To Localize Agriculture
“The goal is to have the first crops in the system in August of this year,” Zeman said. “It’s going to take a pretty serious pull from everyone involved to get us there.” Whereas traditional agriculture grows in outdoor fields or gardens, Interius Farms uses hydroponics and vertical farming to grow plants indoors, offering a climate-controlled environment and artificial lighting in place of sunlight.
A Canadian company is pioneering new technology for growing produce indoors, utilizing hydroponics to provide year-round, cost-effective food production. Interius Farms, based in Montreal, developed the innovative system as a means to localize agriculture in a country where fresh produce is imported at least seven months a year from other parts of the U.S. and North America.
Founded in 2018 by longtime friends Jonnie Lawson and Tristan Zeman, the company is taking vertical farming to the next level with its 8-foot rotating rack design—exposing plants to a single light fixture saving on both space and energy demand.
More efficiency
While the project is currently in its beta stage, Interius Farms is ambitiously ramping up to commercial scale, moving into a 14,000-square-foot facility to grow leafy greens, including lettuce, kale, cilantro, parsley, and basil.
The rotating rack eliminates the need for additional lighting systems, maximizing energy efficiency. Zeman said the system requires 40-80% less lighting and 92% less land than traditional agriculture. The original proof of concept was done in the corner of Zeman’s Chicago apartment. Now, he said they are zeroing in on a commercial facility where Interius Farms can grow a significant amount of food. “5,000 square feet of growing space produces over a million heads of lettuce,” he said.
Growing with hydroponics is inherently more expensive, Zeman said, with higher costs of inputs. He knows they cannot compete on direct cost with field lettuce. However, where the technology proves especially valuable is how it insulates against seasonal price fluctuations of produce and other shocks in the supply chain, such as disease outbreaks and natural disasters in other parts of the world.
Collaboration
Interius Farms is also working with urban-gro, a Colorado-based company that focuses on engineering efficient and profitable controlled environment agriculture facilities. Though urban-gro is traditionally rooted in cannabis, the business is expanding its expertise to work with innovators in other areas of farming. “We are excited to be working with Interius Farms and their innovative and patented approach to growing fresh and sustainable foods for the Canadian market,” said Jim Dennedy, urban-gro’s president and chief operating officer.
The mission of Interius Farms, according to Zeman, is to localize Canadian agriculture through its platform. Buyers will have access to locally grown food even in harsh winter months while at the same time giving themselves an “insurance policy” against volatile prices caused by supply chain disruptions.
“We offer a fresher and more sustainable product, and we introduce price and business sustainability into the Canadian food market, especially in those import months,” Zeman said.
Seasonal fluctuations can increase the price of field lettuce by as much as 85% during the non-growing months, Zeman said. “When the vast majority of the Canadian supply chain in the winter is coming from the American Southwest, you’re very exposed, and you’re not getting very high-quality produce by the time it’s been shipped up here,” Zeman added.
The fresh produce
More control
Looking ahead, Zeman said he has heard from some consumers who question whether indoor agriculture produces healthy, natural food. That is a perception the company will battle, he said, though he points out Interius Farms can offer enhanced traceability with its design. “Everyone wants to know exactly where their food came from,” he said. “And we can tell you, from the seed, exactly what nutrients it has received. For every second of the plant’s life, we can tell you exactly what the plant has received, whereas if you’re in the field, many factors are out of your control.”
Over the next six months, Zeman said Interius Farms and urban-gro will be joined at the hip, testing their commercial facility’s design, vendors, lighting fixtures and other options. “Through our engagement with urban-gro, we gain the advantage of supplementing our internal expertise with the urban-gro team that has spent decades working with complex systems. We can rely on urban-gro to guide us in developing the right solutions for our unique application. The ultimate goal is to be in that facility, to have that anchor customer—which we feel like we’re very close to having in place—and growing very soon in our first facility,” Zeman said.
Lead photo: From the left: Brady Deslippe (Chief Technology Officer) and Tristan Zeman (Founder/President)
For more information:
Publication date: Thu 27 May 2021
Author: Andrea Di Pastena
© HortiDaily.com
Noor III is The Newest Stage of The Ouarzazate Solar Power Station in Ouarzazate, Morocco
The Noor III CSP tower can produce and then store enough energy to provide continuous power to the surrounding area for ten days
Noor III is the newest stage of the Ouarzazate Solar Power Station in Ouarzazate, Morocco. This site utilizes a concentrated solar power (CSP) tower design with 7,400 heliostat mirrors that focus the sun’s thermal energy toward the top of an 820-foot-high (250 meters) tower at its center.
At the top of the tower, there is molten salt, which is used in this process due to its ability to get very hot (500–1022°F / 260–550°C). The molten salt then circulates from the tower to a storage tank, where it is used to produce steam and generate electricity.
The Noor III CSP tower can produce and then store enough energy to provide continuous power to the surrounding area for ten days.
–
31.059494°, -6.870344°
Greta Thunberg Aims To Change How Food Is Produced
The Global Center on Adaptation, which works to accelerate climate resilience, said in January climate change could depress global food production by up to 30%, while rising seas and more intense storms could force hundreds of millions of people in coastal cities out of their homes
By REUTERS May 28, 2021
STOCKHOLM (Reuters) - Swedish climate activist Greta Thunberg has set her sights on changing how the world produces and consumes food in order to counteract a trio of threats: carbon emissions, disease outbreaks and animal suffering.
In a video posted on Twitter on Saturday, Thunberg said the environmental impact of farming as well as disease outbreaks such as COVID-19, which is believed to have originated from animals, would be reduced by changing how food was produced.
"Our relationship with nature is broken. But relationships can change," Thunberg said in the video marking the International Day of Biological Diversity.
A focus on agriculture and linking the climate crisis to health pandemics is a new angle for Thunberg who has typically focused her ire on policy-makers and carbon emissions from fossil fuels.
"The climate crisis, ecological crisis, and health crisis, they are all interlinked," she said.
Thunberg said the spillover of diseases from animals to humans was caused by farming methods, adding that a move to a plant-based diet could save up to 8 billion tonnes of CO2 each year.
The World Health Organization has said the coronavirus was probably transmitted from bats to humans through another animal, while scientists say 60% of the infectious human diseases that emerged from 1990 to 2004 came from animals.
Meanwhile, demand for alternatives to regular meat is surging worldwide due to concerns about health, animal welfare, and the environment.
More than two dozen firms are testing lab-grown fish, beef, and chicken, hoping to break into an unproven segment of the alternative meat market, which Barclays estimates could be worth $140 billion by 2029.
The Global Center on Adaptation, which works to accelerate climate resilience, said in January climate change could depress global food production by up to 30%, while rising seas and more intense storms could force hundreds of millions of people in coastal cities out of their homes.
(Reporting by Colm Fulton; Editing by Alison Williams)
Lead photo: Greta Thunberg (Reuters)
USA - WISCONSIN: Planet to Plate To Launch Pilot Food-Tech Incubator, Hundred Acre, In Milwaukee's 30th Street Industrial Corridor
Hundred Acre Farm is creating an entire ecosystem that brings together food businesses, non-profits, educational institutions, and the surrounding Milwaukee community
Hundred Acre Farm is creating an entire ecosystem that brings together food businesses, non-profits, educational institutions, and the surrounding Milwaukee community.
Milwaukee, May 19, 2021 – Beginning this Summer, Hundred Acre will grow fresh greens in Milwaukee while improving supply-chain resilience and offering an educational pathway to local employment. The initial product offering includes seven varieties of greens including holy basil, spring mix, and baby kale.
The specialized farm will utilize a 5,000-square-foot controlled environmental system with vertical hydroponics, creating secure and traceable non-GMO produce grown without pesticides or herbicides, available year-round and harvested weekly.
Hundred Acre’s goal is to improve access to fresh, healthy food while also revitalizing a light manufacturing employment hub. The 30th Street Industrial Corridor could become one of the next major innovation hubs for food tech in America, providing a blueprint for other inner-city areas struggling with food insecurity.
“A year ago, the world found itself disconnected and communities isolated. Our routines and our relationships were interrupted, as were businesses and access to vital resources. The pandemic highlighted what was fragile in our food systems, and what wasn’t working,” says Planet to Plate Founder Chris Corkery. “The pandemic also highlighted what was working, and what was demanded: hyperlocal food. Now we are reemerging cautiously from our shells, strengthened by a reassessment of our values and priorities. Hundred Acre is uniquely situated to rebuild more resilient local communities through the power of fresh food. In doing this, it’s all about the little wins together as we look ahead.”
2020 was a year that brought to light the serious shortcomings of the food supply chain in the United States and around the world. Everything from ingredients to packaging saw fulfillment challenges, leaving businesses and consumers scratching their heads. Now, perhaps more than ever is the time for localized solutions to emerge for reliable, fresh food. As Dr. Michael Carriere, Associate Professor of the Milwaukee School of Engineering deftly puts it: "As global populations continue to grow, we must figure out new ways to feed such people. At the same time, the damages wrought by climate change have severely impacted traditional agricultural models. We must develop sustainable agricultural systems that take into account these developments. Institutions of higher learning have a vital role to play here, as they are able to pull together a myriad of partners to create innovative agricultural solutions." Hundred Acre aims to play just this role by bringing together like-minded partners who share the common goal of agricultural innovation and local resilience.
How can leveraging the power of fresh food, new agricultural technologies, and light manufacturing revitalize an underserved area and usher in a renaissance that creates new jobs? This is the question that Hundred Acre will explore every day through strategic partnerships with key Milwaukee stakeholders, including local policy-makers, educators, and businesses. Residing between two marginalized neighborhoods, the Century City building is a prime location to bring these partnerships to life.
"The Century City Business Park and its tenants are pleased to welcome Hundred Acre to the Century City 1 building”, said building landlord Kyle Stephens of Good City Brewing. “Their focus on supporting the local food supply chain and its impact on underserved communities, especially those lacking access to healthy foods, is a complement to the original intention of this real estate development. We're excited to see the project activated -- it is the next step in building a food, beverage, and tech hub in the 30th Street Industrial Corridor."
Partnering with Building2Learn, MSOE, Milwaukee Public Schools, and the 30th Street Corridor, Hundred Acre will serve as the education site for Milwaukee-area students to get excited about and involved with the agricultural systems of tomorrow. High school students and young adults interested in STEM will have the opportunity to learn about hydroponic farming, sustainable food systems, supply chains, and distribution channels. This will serve as a foundation that can lead student participants into local light industrial employment or careers in the food tech industry.
Hundred Acre will host an exclusive walk-through of the farm site at Century City this June. To learn more and to stay up to date on the project’s progress, visit hundred-acre.org.
About Hundred Acre
Hundred Acre is a unique urban farm providing a rapid response solution to food insecurity in the heart of Milwaukee. Workforce development and student apprenticeship programs are integrated to grow consistent, premium greens sold directly to local food businesses year-round. A consortium of growers, technologists, and community partners ensures that the farm remains a sustainable local business. Now, buyers can increase reliable local sourcing and provide community support.
Learn more at hundred-acre.org and follow @hundredacre_mke.
About Planet to Plate
Planet to Plate is a community developer specializing in green infrastructure that cultivates reliable fresh food and vital jobs in urban markets. Their goal is to reinforce local supply chains and access to nutrient-rich food by bringing together social entrepreneurs, nonprofits and the surrounding neighborhood. Planet to Plate offers a platform that encourages discovery, conversation, and learning around fresh, accessible food, which they believe is the first step in creating healthier communities.
Learn more at planet2plate.org and follow @planet2plate.
Indoor Ag Science Cafe’s Latest Video Checks Out How To Turn A Smart Phone Into A Sensor
Dr. Krishna Nemali, Assistant Professor and Extension Specialist at Purdue University, has developed an easy-to-use, affordable smart sensor that’s proving valuable to indoor farmers for improving farm productivity and crop quality
Purdue University professor turns smartphones into smart sensors
Dr. Krishna Nemali, Assistant Professor and Extension Specialist at Purdue University, has developed an easy-to-use, affordable smart sensor that’s proving valuable to indoor farmers for improving farm productivity and crop quality.
Using only a smartphone and a connection to Dr. Nemali’s apps, users can quickly and precisely monitor/measure a wide variety of production and growth parameters including light efficiency, germination rate, plant size (area, height, weight), color (intensity, progression), damage (nutrient deficiency, insect), biochemistry (chlorophyll, nitrogen and other micronutrients), and stress index.
Dr. Nemali plans to make his smart sensor tool available in January 2022 for a nominal annual fee, which will support the development of future applications.
For more information: http://scri-optimia.org/showcafe.php?ID=111113
Indoor Ag Science Café is an outreach program of the OptimIA project, funded by the USDA SCRI grant program.
Interested parties can join the free café forums, live or recorded (http://www.scri-optimia.org).
The café forum is designed to serve as a communication platform among scientists and indoor farming professionals.
Indoor Vertical Farming Startup Bowery Farming Raises $300 Million
Vertical farming grows its produce in stacked arrangements in technologically controlled environments, reducing the need for vast expanses of land and bringing mass production right in to urban areas
MAY 25, 202
(Reuters) - New York-based indoor vertical farming startup Bowery Farming said on Tuesday it raised $300 million in its latest funding round, valuing the company at $2.3 billion as the pandemic shed light on the importance of securing the local food supply.
Vertical farming grows its produce in stacked arrangements in technologically controlled environments, reducing the need for vast expanses of land and bringing mass production right in to urban areas.
While the new industry has struggled to break even in the past, the drop in technology costs, such as LED lights, is changing the economics and fueling investor interest.
According to PitchBook data, nearly $1.9 billion of global venture capital was invested in indoor farming in 2020, nearly tripling investment in 2019. (Graphic: Global VC Funding in Indoor Farming, )
Bowery’s latest funding round, led by Fidelity Management & Research Company LLC, would be the largest vertical farming deal on record, based on previous such deals listed by PitchBook.
The company’s leafy greens are sold in over 800 grocery stores and it has two commercial farms in New York and Maryland, and a third coming online this year in Pennsylvania, said Irving Fain, Bowery’s CEO and Founder. Fain said the products are the same or lower in price than their organic rivals, but declined to say whether Bowery was selling them at a profit.
“The real benefit of what we’re growing at Bowery is, first of all, it’s completely pesticide-free,” said Fain, adding that a large part of the power used for the farms is renewable with an aim to eventually make it fully renewable.
He said the new funds will be used to expand farms across the United States, looking for global expansion opportunities, and developing new crops and technology to grow things like strawberries, tomatoes, and carrots indoors and near consumers as well.
Bowery’s investors include GV, formerly known as Google Ventures, General Catalyst, GGV Capital, and Temasek.
Reporting By Jane Lanhee Lee; Editing by Sam Holmes
Image Credits: Bowery Farming
Our Standards: The Thomson Reuters Trust Principles.
BRITISH COLUMBIA: Whistler Harvest Corp. Announces Launch of Operations
The Company was founded in March 2021 and began growing its signature microgreens, salad mixes, and gourmet mushrooms in early April. The Company provides its customers with microgreens and mushrooms the same day that they are harvested all year-round
Pemberton, BC Canada - May 20, 2021 - Whistler Harvest Corp., an indoor vertical farming company based in the Sea-to-Sky region of British Columbia, is pleased to announce that is launched and harvesting its first crops.
The Company was founded in March 2021 and began growing its signature microgreens, salad mixes, and gourmet mushrooms in early April. The Company provides its customers with microgreens and mushrooms the same day that they are harvested all year-round. Our products are available at our Pemberton farm, selected farmer markets, restaurants, and online.
The microgreens market is driven by chefs that use them as flavor enhancements and as colorful garnishes on their plates but there is another niche industry that pushes new growth within this segment, cosmetics. These microgreens are processed into oils and ingredients for consumer items like shampoo and skincare products. Microgreens contain a lot of vitamin A&B in addition to many other micro-elements, making them very attractive ingredients for personal care product manufacturers.
Local. Fresh. Now. Our mission to create meaningful relationships with the food we nurture and to strive on providing locally grown, healthy food for our communities. Every day is a perfect day inside our farm.
Whistler Harvest Corp.
(phone) 778.569.0717
(email) sales@whistlerharvest.ca
P A D D Y S M Y T H
RSVP - Indoor Ag Science Cafe June 1st
Indoor Ag Science Cafe is an open discussion forum, planned and organized by OptimIA project team supported by USDA SCRI grants
June Indoor Ag Science Cafe
June 1st Tuesday 11:00 AM Eastern
Please sign up, thank you!
"All Season Oishii Berry:
America's first vertical strawberry farm"
by Hiroki Koga
Oishii
Please register to receive your Zoom link.
The recording will not be available for this cafe.
Indoor Ag Science Cafe is an open discussion forum, planned and organized by OptimIA
project team supported by USDA SCRI grants.
Register here
Vertical Farming: Disrupting Agriculture
A New Agricultural Revolution Could Forever Change The Planet
24 May 2021
Vertical farming leverages cutting-edge technology to grow food in a new and better way.
One of its many benefits is that it can increase crop yield by 700 percent.
Vertical farming can help relieve pressure on scarce resources and boost Earth's biodiversity.
One day soon, you could eat bananas grown in downtown Manhattan.
It's a way of growing food that turns traditional agriculture on its head. With the required technologies now rapidly maturing, vertical farming is sprouting across the globe.
While there are still unresolved issues with this marriage of technology and agriculture, its promise may be irresistible. If it gets off the ground — literally — in a major way, it could solve the problem of feeding the Earth's 7.9 billion people. And that's just one of the benefits its proponents promise.
Vertical farms could take over the world | Hard Reset by Freethink www.youtube.com
Agriculture through time
When humankind began planting crops for nutrition about 12,000 years ago, the nature of our hunter-gatherer species fundamentally shifted. For the first time, it's believed, people began staying put.
With agriculture as their central mission, communities formed, with the now-familiar arrangement of residential areas surrounded by land dedicated to growing food. Even today, with modern transportation making the widespread consumption of non-local foods common, this land-allocation model largely survives: population centers surrounded by large areas for growing vegetables and fruit and raising livestock.
Credit: Genetics4Good / Wikimedia
Challenges facing traditional agriculture
As our population has grown, traditional agriculture has begun facing some big challenges:
Farmland takes up a lot of space and destroys biodiversity. Our World in Data reports that half of all habitable land is used for agriculture. As Nate Storey of Plenty, Inc., a vertical farming startup, puts it, "It is probably one of the most defining acts of humanity: We literally changed the ecosystem of the entire planet to meet our dietary needs."
The demand for farmland — both for produce and livestock — has led to a dangerous deforestation in several parts of the world. This also results in biodiversity loss and contributes to an increase in the greenhouse gases that drive climate change.
Degradation of farmland, such as through soil erosion, poses a threat to agricultural productivity.
Agriculture consumes copious amounts of water, which exacerbates water shortages. (Obviously, water shortages also reduce agricultural productivity.)
Fertilizer run-off causes substantial environmental damage, such as algal blooms and fish kills.
Pesticides can degrade the environment by affecting non-target organisms.
The effects of climate change are already making agriculture more challenging due to significant shifts in weather, changes to growing seasons, and realignment of water supplies. Our climate is continuing to change in unexpected ways, and the only predictable aspect of what lies ahead is unpredictability.
Vertical farming proponents expect that a re-think of how we grow food can ultimately solve these problems.
What is vertical farming?
Credit: Freethink Media / Plenty, Inc.
Vertical farming is a form of agriculture that grows plants indoors in floor-to-ceiling, tower-like walls of plant-holding cells. Instead of growing plants in horizontal fields on the ground, as in traditional farming, you can think of vertical farming's "fields" as standing on the edge and extending upward toward the ceiling. The plants need no soil or other aggregate medium in which to grow; their roots are typically held in a cell lining, often composed of coconut fiber.
Vertical flora is grown either aeroponically, in which water and nutrients are delivered to plants via misting, or hydroponically, in which plants are grown in nutrient-rich water. These are incredibly efficient systems, requiring 95% less irrigation than soil-grown plants. With vertical farming, Storey says that 99 percent of the moisture transpired by plants can be recaptured, condensed, and recirculated.
Plants, of course, also need light to grow, and vertical farms use increasingly efficient LED bulbs to keep plants thriving.
Vertical farms can increase crop yields by 700 percent
Credit: pressmaster / Adobe Stock
If vertical farming takes off the way its supporters believe it should and will, it may solve many of the aforementioned challenges facing agriculture.
Crop yields with vertical farming far exceed what's possible with traditional agriculture. Plenty, Inc.'s Shireen Santosham notes that the highly controlled growing environment of vertical farming has allowed her company to reduce the growing time for some crops to as little as 10 days. Without needing to consider whether or even sunlight, combined with the ability to operate 365 days a year, their system increases the potential annual yield by about 700 percent.
The land requirement for vertical farming is a mere fraction of that for traditional agriculture. Santosham says it can be done in a building the size of a big-box retail store that can be built pretty much anywhere that has adequate utilities, including within major urban centers. The tightly controlled environment of a vertical farm should also eliminate the need for applied pesticides.
Yet another benefit of vertical farming is the return of land currently needed for food production back to the planet. This could help facilitate Earth's recovery from deforestation and return much-needed habitat to threatened or endangered species. Of course, if we ever colonize the moon or Mars, vertical farming will be the go-to option for feeding the colonists.
Several vertical farming company pioneers are already getting their high-quality crops into the hands, and mouths, of consumers. Plenty, Inc. has an eponymous line of greens, and Aerofarms has their FlavorSpectrum line. Both companies claim that their products are exceptionally tasty, a result of their carefully controlled growing environments in which computer-controlled lighting can be optimized to bring out the most desirable qualities of each crop.
Credit: Alesia Berlezova / Adobe Stock
The history of vertical farming
The idea of vertical farming isn't new, and experts have been questioning its viability since the term was first coined in 1915 by Gilbert Ellis Bailey, who was obviously way ahead of the available technology at the time. The first attempt to grow produce in a constructed environment was a Danish farmhouse factory that was built to grow cress, a peppery green related to mustard, in the 1950s.
The modern concept of a vertical farm arose in the New York classroom of Columbia University's Dickson Despommier in 1999. He presented the idea as a theoretical construct, a mental/mathematical exercise imagining how to farm in an environmentally sound manner. His class began with the notion of a rooftop garden before considering a "high-rise" version that might theoretically be able to grow enough rice to feed two percent of Manhattan's population at the time. The eureka moment was a question Dispommier asked: "If it can't be done using rooftops, why don't we just grow the crops inside the buildings? We already know how to cultivate and water plants indoors."
With the technological advances of the last few decades, vertical farming is now a reality. Our sister site, Freethink, recently paid Plenty, Inc. a visit. (See video above.)
Vertical farming today
Credit: Nelea Reazanteva / Adobe Stock
Today, growers across the globe are developing vertical farms. While the U.S. has more vertical farms than any other country, the industry is blooming everywhere.
There are currently over 2,000 vertical farms in the U.S. While more than 60 percent of these are owned by small growers, there are a few heavyweights as well. In addition to Wyoming's Plenty, Inc. and Newark's Aerofarms, there's also New York's Bowery Farming. There are also companies such as edengreen, based in Texas, whose mission is to help new entrants construct and operate vertical farms.
Japan comes in second, with about 200 vertical farms currently in operation. The largest vertical farming company there is SPREAD. Across Asia, vertical farms are operating in China, South Korea, Singapore, Thailand, and Taiwan. In Europe, vertical growers are in Germany, France, Netherlands, and the U.K. Germany is also home to the Association for Vertical Farming, "the leading global, non-profit organization that enables international exchange and cooperation in order to accelerate the development of the indoor/vertical farming industry."
In the Middle East, whose desert land and scarcity of water present a particularly challenging agricultural environment, vertical farming is taking root, so to speak. The United Arab Emirates' Badia Farms is now producing more than 3,500 kilograms of high-quality produce each day and expects to increase that yield going forward. In Kuwait, NOX Management launched in the summer of 2020 with plans to produce 250 types of greens, with a daily output of 550 kg of salads, herbs, and cresses.
The economics of vertical farming
Credit: meryll / Adobe Stock
Building and operating a vertical farm is a costly endeavor, requiring a substantial initial investment in state-of-the-art technology, real estate, and construction. AgFunderNews (AFN) estimates that it can cost $15 million to construct a modern vertical farm. Fortunately, investors see the potential in vertical farming, and the industry has attracted more than $1 billion in investments since 2015. That includes $100 million for Aerofarms. Plenty, Inc raised $200 million in 2017 from a fund backed by such respected forward-thinkers as Jeff Bezos and Alphabet chairman Eric Schmidt.
AFN is particularly excited by the potential of what they call second-generation vertical farming technology. They cite advances in LED technology — expected to increase energy efficiency by 70 percent by 2030 — and increasingly sophisticated automation that can streamline the operation of vertical farms. AFN anticipates operating cost reduction of 12 percent due to improvements in lighting and another 20 percent from advances in automation.
BusinessWire says that the vertical farming produce market was valued at nearly $240 million in 2019, and they expect it to grow 20 percent annually to over $1 billion by 2027.
A welcome disruption
Vertical farming will be disruptive.
Vertical farming would eliminate the need for the arduous work of harvesting crops by hand from vast tracts of farmland. Current picking jobs, the company says, can be replaced by better-paying, full-time jobs available 365 days a year in better working conditions — and in the variety of geographic locations in which vertical farms can operate.
There are two caveats, however. First, the number of people needed to manage and harvest vertical farm crops will be far fewer than the many farmworkers required for less efficiently planted traditional fields. Second, with automation becoming ever-more capable — and perhaps a key to eventual profitability — one wonders just how many new jobs ultimately will be created.
But the societal benefits far outweigh any costs. As Plenty's Storey muses, "Like most everything in the world, we can only save our species if it makes economic sense." Thankfully, it does make economic sense
Lead photo: Credit: Freethink Media / Plenty, Inc..
A Lot of Promise’: Vertical Farming Takes Root In Virginia
Since its inception at the turn of the millennium, vertical farming — which in its simplest form is any system where plants are grown in vertical stacks — has promised to revolutionize yields by allowing producers to multiply their crop outputs by six to eight or even more times without expanding their footprint
May 24, 2021
Imagine a field of lettuce.
Say the lettuces are all buttercrunch, and they dot the field like crisp rosettes. Each has been seeded by a farmer, kept free of pests, watered for weeks, and finally cut at the base before being rinsed and packed for transport. Each is destined for a different meal: a lazy evening salad on the porch, an artfully arranged plate at a restaurant two-top, the vegetarian alternative at grandma’s 80th.
Now imagine six of these fields, all stacked on top of one another.
The idea isn’t far-fetched. In fact, it’s already a reality in Virginia, where a new, more technologically oriented form of agriculture known as vertical farming is quietly taking root.
“There’s a lot of promise,” said Tony Banks, senior assistant director of agriculture, development, and innovation for the Virginia Farm Bureau Federation. “As we continue to watch urban encroachment and we have this demand to have food produced closer to where people actually live, we’re going to see more and more of it.”
Since its inception at the turn of the millennium, vertical farming — which in its simplest form is any system where plants are grown in vertical stacks — has promised to revolutionize yields by allowing producers to multiply their crop outputs by six to eight or even more times without expanding their footprint.
“You’re trying to use an area more intensively. Because you’re limited by horizontal space, you want to maximize vertical space,” said Leonard Githinji, a professor of sustainable and urban agriculture at Virginia State University who also works with Virginia Cooperative Extension.
The concept is flexible and scalable. The stacks can be small, nothing more than a narrow shelf installed at a restaurant or in a convenience store to grow produce within a customer’s reach. Or they can fill a warehouse, bringing an industrial dimension to agriculture.
“There’s a wide range. On one end, it’s almost you have a greenhouse that’s highly automated,” said Banks. “On the other end, you could be in a warehouse and everything is grown on huge assemblies of racks and you have complete artificial lighting and hydroponics.”
The latter type of vertical farming is “high-tech manufacturing, essentially,” said Scott Lowman, director of the Controlled Environment Agriculture Innovation Center at the Institute for Advanced Learning and Research in Danville, where scientists and other experts are exploring the promise of various types of indoor agriculture can hold for Virginia.
Hopes are high, particularly in the historic tobacco region of Southside, where state officials have been working for several decades to encourage farmers who once depended on the golden leaf to diversify their enterprises. It’s no accident that the Controlled Environment Agriculture Innovation Center was sited in a region with a rich agricultural history and an abundance of old warehouses once devoted to tobacco and now empty.
Nor was it an accident that in 2019, Gov. Ralph Northam’s office announced that vertical farming company AeroFarms had decided to build a $42 million facility in an industrial park jointly operated by Danville and Pittsylvania County. Virginia aggressively courted the project with some $1.5 million in state grant funds and incentives. In exchange, AeroFarms promised to build the facility, employ 92 people and purchase roughly $20 million of Virginia agricultural or forest products.
But while AeroFarms’ Virginia location will be the largest vertical farm in the state once built, it won’t be the only one. Over the past few years, other operations have quietly been putting down roots. Shenandoah Farms in Rockingham operates a large-scale facility that grows herbs and lettuces. In Lorton, Beanstalk grows a range of greens. Fresh Impact Farms in Arlington, which grows herbs, greens, and edible flowers, announced an expansion this spring in conjunction with the governor’s office. Babylon Micro-Farms in Richmond is developing sophisticated technology to spread small-scale vertical farms around the country. Other efforts are underway.
“We’re in a great position on the East Coast in terms of population centers,” said Lowman. “And it’s a friendly environment for business, and we have a legacy of hard-working labor.”
Controlled environment agriculture
While vertical farming is relatively new, its lineage is much longer, nesting within the family tree of controlled environment agriculture, which encompasses any type of production that takes place within a structure.
From Roman orangeries to modern-day greenhouses, controlled environment agriculture offers the advantage embedded in its first descriptor: control.
Outdoors, farmers are at the whim of the weather, plagued by pests and disease, and caught in a never-ending struggle to keep water and fertilizer confined to their fields.
Indoors, the equation changes. Because of the precision-engineered systems, controlled environment agriculture tends to require less water, less fertilizer, and few or no pesticides compared to conventional agriculture. And, depending on a particular system’s design, it can allow producers to grow crops 24/7, 365 days a year. AeroFarms has said that its technology allows it to produce leafy greens “at a rate 390 times more productive than field-grown plants.”
A vertical micro-farm known as a cropbox. (Virginia State University)
“I can now schedule my crops,” said Michael Evans, director of Virginia Tech’s School of Plant and Environmental Sciences. “I can basically optimize the environment for that crop.”
There are, of course, drawbacks. Everything nature once provided to a plant must now be provided by a human — or a machine.
“With a greenhouse, you’re taking advantage of natural sunlight. You’re not paying for that,” said Evans. “But you’re paying quite a bit for heating and cooling. When you flip to an indoor vertical system, the disadvantage is that now you have to supply the light.” Other costs diminish at the same time: without the translucent walls of a greenhouse, “your heating and cooling can go down because it’s better insulated.”
For years, prohibitively high energy costs boxed out vertical farming as a viable option for producers working in controlled environment agriculture. What would change the playing field was a technological innovation: the high-powered and highly efficient LED.
“The thing that really changed that made indoor vertical farming work and become an economic possibility was really the development of LED lighting, because that changes the energy equation a lot,” said Evans. “It makes providing the light the crops need much economically viable.”
A new generation of farmers
Despite its promise, vertical farming won’t replace conventional agriculture, experts say. Many of Virginia’s biggest commodity crops — soybeans, corn, hay — are grown at such a large scale that trying to transport them indoors would be an exercise in absurdity.
Where controlled environment agriculture has found a growing niche is in the produce most familiar to the average Virginian: lettuces, herbs, tomatoes, cucumbers, peppers, herbs, microgreens, and more. Experiments in growing strawberries indoors are also underway, and Evans pointed out that once legalized, marijuana may not be far behind, although the federal government’s continued classification of the plant as illegal will keep institutions like Virginia Tech from working with it.
For consumers of these products, the idea of local food grown only a short distance away is increasingly appealing. That can be an argument in favor of controlled environment agriculture and vertical farming, said Banks.
“When we import food into this country, what we import is fruits and vegetables that require a lot of hand labor,” he said. “So there’s opportunity there to offset some of those imports and reduce our reliance on food produced overseas.”
Both Banks and Evans also noted an unusual aspect of vertical farming: its allure for younger and often more urban Virginians.
“It’s getting a whole new generation of folks interested in agriculture. It’s a different type of agriculture, but it’s getting a lot of students,” said Evans. At Virginia Tech’s School of Plant and Environmental Sciences, he added, “we have to change our curriculum for what we’re teaching to prepare students interested in controlled environment agriculture.”
For a younger generation increasingly concerned with social and political justice, the opportunity offered by controlled environment agriculture and vertical farming to fill food deserts and involve local workers in local food systems is an attractive prospect. Many students are eager to look beyond the existing agricultural structures, said Githinji, who recently received a $600,000 grant from the U.S. National Institute of Food and Agriculture to explore the use of “micro-farms,” which incorporate vertical farming systems, as a way to address food deserts in urban neighborhoods.
It’s not unusual for extension agents to get calls in which people are saying, “‘As much as I want to grow more food, I can’t afford to buy even another quarter acre,” he said. “So you get people asking what they can do with what they have.”
The other draw is the technology. While vertical farming can be small- or large-scale, its larger applications rely on evolving and increasingly sophisticated technology that has piqued interest among the startup community.
“This is a really exciting industry that’s rapidly entering the mainstream,” said Alexander Olesen, CEO, and co-founder of Babylon Micro-Farms, a Richmond-based startup that develops indoor growing systems for institutional food service settings, such as hospitals, schools, and universities. Babylon, which in 2020 was the recipient of a $75,000 grant from the Commonwealth Research Commercialization Fund that aims to support small businesses in emerging research and technology sectors, builds small-scale vertical farms “as a sustainable amenity for these locations.”
The field’s growing popularity is also driving a need for more workers, more expertise, and more training, said many of the people interviewed for this story. The Controlled Environment Agriculture Innovation Center in Danville, itself a recipient of $365,000 in state grant funds in 2020, is key to that effort. So too are plans announced by the governor’s office last month that will see hydroponic greenhouse startup Sunny Farms build a 1.2 million square foot greenhouse in Virginia Beach — one of the largest on the East Coast — and work with Virginia Tech and the Virginia community college system to develop educational training in controlled environment agriculture.
“Our goal is really to support the controlled environment agriculture industry in Virginia, but we’re also working on creating an innovative controlled environment agriculture ecosystem in Virginia,” said Evans.
These enterprises may be only the beginning.
“Once people see that it’s working, we’re going to see them flourishing all across the commonwealth,” said Githinji.
Lead photo: Controlled digital lights help produce high-density feed grass in a Grov Olympus vertical farming machine in Utah. The Olympus Tower Farm uses a controlled environment to grow sprouted wheat and barley grass in 857 square feet of space and uses 95 percent less water to produce 5,000 to 6,000 pounds of grass per day, replacing 35-50 acres of land. (Photo by George Frey/Getty Images)
Sarah covers environment and energy for the Mercury. Originally from McLean, she has spent over a decade in journalism and academic publishing. Most recently she covered environmental issues in Central Virginia for Chesapeake Bay Journal, and she has also written for the Progress-Index, the Caroline Progress, and multiple regional publications. In 2017, she was honored as one of Gatehouse’s Feature Writers of the Year, and she has been the recipient of numerous awards from the Virginia Press Association. She is a graduate of the College of William & Mary. Contact her at svogelsong@virginiamercury.com
Blue Radix & Ecoation Join Forces With The World's 1st Autonomous Find & Fix Solution
May 19, 2021, Rotterdam, Netherlands and North Vancouver, Canada
Blue Radix, an independent Dutch AI-tech specialist for the international greenhouse industry, and Ecoation Innovative Solutions Inc. (ecoation), a Canadian developer of automated greenhouse management and crop health monitoring technologies, have signed an agreement.
The collaboration aims to identify new ways to automate decision-making and action in the greenhouse, using vision technology and algorithms. ecoation and Blue Radix are using the data collected by ecoation’s OKO and platform to enhance the impact of Blue Radix’ algorithms for autonomous growing. By combining data sets, algorithms, and analytical efforts the companies are able to create new insights and applications that help growers worldwide to improve their crop strategy, quality and yield.
Blue Radix and ecoation look forward to ongoing collaborative efforts where the duo explores the multitude of innovation opportunities that become available when you combine ecoation’s OKO and platform with Blue Radix’ Crop Controller. Collaborating across data and algorithms has the potential to create value across many avenues, including optimizing crop strategy, autonomous steering, IPM enhancement, and understanding spatial climate distribution.
The World’s 1st Autonomous Find & Fix Solution
The first project the duo is working on is enhanced autonomous growing with crop data visualization. ecoation’s OKO collects sensory data and information about climate, integrated pest management, and crop work at every row and post to an SqM granularity. These insights greatly contribute to a complete and accurate view on the state of the crop. The broad range of data points, including fruit count, fruit colouring, and stem density, will be combined with the smart steering algorithms of Blue Radix’ Crop Controller. Crop Controller will actively, continuously and autonomously control the greenhouse conditions with the grower’s crop strategy as its starting point and the optimal crop status as its goal. E.g. by optimizing the plant load, plant stress is reduced avoiding weak plants that are vulnerable to pests and diseases. In this way ecoation and Blue Radix find and fix imperfections before they impact yield or crop quality.
Support growers
“Collaborating with Blue Radix means pioneering the future of ag more effectively, at a pace that would be difficult to reach if we carried on separately,” shared ecoation CEO Dr. Saber Miresmailli. “Both teams are committed to the same goal: to support growers in making the best possible decisions. Working together means unlocking new ways to get the most from the data and providing better insights to our customers that inform their decisions.”
“Ecoation offers solutions which are important components in a fully autonomous greenhouse. Optimization and steering with algorithms depends on high quality data and a robust crop strategy. Vision technology and enhanced analytics from ecoation provides this data and the necessary input to improve the grower’s crop strategy even further,” emphasizes Blue Radix CEO Ronald Hoek. “We strive for open collaboration and partnerships. Growers should always be able to choose freely what they want to do with their data and benefit from the best combination of services & products for their greenhouse.”
The duo will only work with greenhouse data retrieved from the customers of ecoation and Blue Radix who provide full consent. Transparency and data security is paramount, and this collaboration will rely on growers who are looking to optimize their greenhouse operations with autonomous processes and are interested in contributing to the future of ag with their facility data and insights.
About Blue Radix
Blue Radix is an independent Dutch AI-tech specialist for the international greenhouse industry. Blue Radix creates solutions with artificial intelligence for daily decisions and actions in greenhouses. Greenhouses offer an efficient way to produce food and flowers in a sustainable manner. But the number of skilled people with expertise of growing crops in greenhouses is declining every year. This has a direct and negative impact on yield, costs, continuity, and product quality. Blue Radix offers solutions for these challenges: smart algorithms which optimize and steer climate, irrigation, and energy continuously and autonomously, supported by off-site
Autonomous Greenhouse Managers. Blue Radix offers growers a digital brain for their greenhouse. More information at blue-radix.com. Find Blue Radix on LinkedIn, Twitter, and Instagram.
About ecoation
ecoation is an award-winning grower-centric platform that combines Human knowledge and experience with Machine precision and automation to increase operational visibility, assist growers, and enhance their decisions. Commercially available since September 2019, ecoation products can be found in greenhouses across the United States, Canada, Mexico, and Europe. With an experienced team of 60+ growers, scientists, engineers, and business professionals from all over the globe, ecoation is passionate about enabling a cleaner future and supporting growers in making the best possible decisions. At ecoation, we are on a mission to empower growers because we believe in doing so, we win together.
More information at ecoation.com. Find ecoation on LinkedIn, Twitter, and Instagram.
For media inquiries, please contact:
Blue Radix
Marijke van Rongen
Manager Global Marketing & Communications
marijke.vanrongen@blue-radix.com
+31 6 53 43 38 39
ecoation
Marketing and Media Contact
Cameron Lust
USA - VIRGINIA: Fairfax Hydroponic Farm Expanding, Creating 29 Jobs In Herndon
Beanstalk, an indoor hydroponic farm in Fairfax County, plans to expand its operation, investing $2 million and creating 29 jobs, Gov. Ralph Northam announced Monday
Beanstalk Plans To Invest $2 Million In Project
MAY 24, 2021
BY KATE ANDREWS
Beanstalk, an indoor hydroponic farm in Fairfax County, plans to expand its operation, investing $2 million and creating 29 jobs, Gov. Ralph Northam announced Monday.
Owners Mike and Jack Ross, brothers from Alexandria, started the business in 2018 and sell fresh salad mixes and fresh herbs to grocery stores and at farmers’ markets. The new facility, to be built in Herndon, will produce specialty herbs and pesticide-free leafy greens year-round with its proprietary hydroponic technology, Northam’s office said in a news release. In 2018, Jack Ross won the state’s STEM Catalyst Award for developing an automated indoor growing prototype, which later led to Beanstalk’s automated production system.
“Fairfax County is the perfect place for a startup like Beanstalk to put down roots and grow their company,” Northam said in a statement. “We are pleased to support a project that blends agriculture, Virginia’s oldest and largest industry, with technology, one of the fastest-growing sectors of our economy. Innovative entrepreneurs like Mike and Jack Ross are demonstrating how STEM fields can help cultivate new techniques like hydroponics that make fresh produce more accessible.”
The Virginia Department of Agriculture and Consumer Services (VDACS) and the Virginia Economic Development Partnership (VEDP) worked with Fairfax County and the Fairfax County Economic Development Authority (FCEDA) to secure the project for the commonwealth. Northam also approved a $100,000 grant from the Governor’s Agriculture and Forestry Industries Development Fund, which Fairfax County will match with local funds. The Virginia Jobs Investment Program will support job creation and training at no cost to the company.
“Jack and I are incredibly proud to be developing our technology and growing local produce in Virginia,” Michael Ross said in a statement. “Being ‘Virginia Grown’ ourselves, we are excited to be bringing new technology to the industry and new jobs to our home state.
Bowery Farming Unveils Research And Breeding Hub, Farm X
Farm X is one of the largest and most sophisticated vertical farming R&D facilities in the world, and will further accelerate the commercialization of products specifically designed for Bowery’s indoor system
May 18, 2021
NEW YORK, May 18, 2021 /PRNewswire/ — Bowery Farming, the largest vertical farming company in the United States, today announced the opening of Farm X, its newest state-of-the-art innovation hub for plant science in Kearny, N.J., adjacent to Bowery’s original R&D Center of Excellence and first commercial farm.
Farm X is one of the largest and most sophisticated vertical farming R&D facilities in the world, and will further accelerate the commercialization of products specifically designed for Bowery’s indoor system.
From the cultivation of strawberries, root vegetables, tomatoes, peppers and beyond, to the discovery of the next generation of wildly flavorful leafy greens, Farm X expands Bowery’s R&D capacity by nearly 300%.
“We’re proud to be the largest vertical farming company in the United States that is consistently and reliably delivering our customers a wide variety of high quality, flavorful produce that’s local, safe and sustainable,” said Irving Fain, founder, and CEO of Bowery Farming.
“From day one, our R&D team has been working tirelessly to unlock the next frontier in agriculture, and Farm X enables us to expedite the discovery of new vibrant crops and pioneering technological advancements that will further accelerate our momentum as the category leader.”
Bowery’s world-class team of plant breeders, plant physiologists, biochemists, and more, are constantly innovating from seed-to-shelf. At Farm X, they will be able to test more, faster—ultimately accelerating the discovery of new crops, growing recipes, and efficiency improvements that can be replicated at scale across the company’s network of commercial farms.
Featuring proprietary, highly customizable, modular growing environments managed and monitored by new technology developed in-house, Farm X will further unlock the next phase of Bowery’s growth.
Farm X also features a sensory lab where Bowery will continue its quest for the perfect cultivars for indoor growing, as well as launch the first-ever on-site breeding program at a vertical farming company.
Under the new breeding program, Bowery’s team will be able to develop varieties that thrive in its unique growing conditions and evaluate each one for optimal taste, quality and yield, rather than to survive outdoors, pest-resistance, and long-haul transportation. While a traditional breeding program takes up to ten years, Bowery’s controlled indoor environment and 24/7 monitoring of crops will enable the company to bring new groundbreaking products to market at scale in a fraction of the time.
Bowery’s R&D team works year-round to uncover flavor-packed produce and bring new and exciting culinary experiences to consumers. Beyond the cultivation of new fruits and vegetables at Farm X, they are also developing the next generation of greens.
The Farmer’s Selection category, which launched in January 2021, emerged as a way to let consumers in on the process, bringing the thrill of discovering a new ingredient at your local farm stand to the grocery store. Bowery is launching a new small-batch green every four months under this new category.
The first greens released, Bowery Mustard Frills — hearty mustard greens with a tingly start and a fiery, wasabi-style finish — were available through April 2021. Green Sorrel, bright, tart baby greens with a zing and the next release in the series, is now available from May through August 2021.
Farm X also serves as an experimental space for innovation in farm design, data science, computer vision, autonomous robotics, hardware, and software that can be deployed in Bowery’s growing network of commercial farms.
As Bowery continues to advance the integration of proprietary smart farming technology, it recently announced Injong Rhee (formerly VP at Google and CTO of Samsung Mobile) as its Chief Technology Officer. Rhee will ensure that every farm continues to benefit from the collective intelligence of the BoweryOS, the company’s proprietary operating system which integrates software, hardware, sensors, computer vision systems, machine learning models and robotics to orchestrate and automate the entirety of operations.
Rhee’s team is ensuring the advanced technological learnings discovered at Farm X will be seamlessly integrated and applied at scale across Bowery’s network.
Bowery has experienced more than 750% brick-and-mortar sales growth, and more than quadrupled sales with e-commerce partners, including Amazon, since early 2020. Bowery’s newest commercial farm in Bethlehem, Pennsylvania, will bring local, pesticide-free produce, harvested year-round at peak freshness, to a surrounding population of 50 million people within a 200-mile radius, and will be its largest and most technologically-advanced commercial farm yet, further automating the growing process from seed to store.
About Bowery Farming
Bowery Farming, the Modern Farming Company, was founded in 2015 with the belief that technology and human ingenuity can grow better food for a better future. Propelled by its proprietary software system, the BoweryOS, Bowery builds smart indoor vertical farms that deliver a wide variety of Protected Produce — in little time, near cities they serve, for a truly local approach.
Bowery’s farms are growing the next generation of vibrant and flavorful produce. With BoweryOS, farms are 100 times more productive on the same footprint of land than traditional agriculture and grow traceable pesticide-free produce with a fraction of the water and land.
The largest vertical farming company in the U.S., Bowery’s produce is available in more than 850 grocery stores and via e-commerce platforms serving the Tri-state and Mid-Atlantic region, including Amazon Fresh, Giant Food, Walmart, Weis, Whole Foods Market, Albertsons Companies and specialty grocers.
Based in New York City, Bowery has raised more than $172.5 million from leading investors, including Temasek and GV (formerly Google Ventures), General Catalyst, GGV Capital, First Round Capital, Henry Kravis, Jeff Wilke, and Dara Khosrowshahi, as well as some of the foremost thought leaders in food, including Tom Colicchio, José Andres, and David Barber of Blue Hill.
Tagged greenhouse, research, technology, vertical farming
5 Things To Check When Comparing Lighting Designs For LED Grow Lights
As a grower, you invest in supplemental LED grow lights because they power the yield and quality of your crops.
May 17, 2021
· When you compare different lighting designs, make sure to compare apples with apples.
· These are the 5 things to check when comparing lighting designs for LED grow lights.
Eindhoven, the Netherlands – As a grower, you invest in supplemental LED grow lights because they power the yield and quality of your crops. In fact, the rule of thumb is that 1% light output equals 1% crop yield. So, it is vital that your LED lighting investment delivers the full performance you paid for.
The performance is determined by the light intensity and light uniformity of the LED grow lights you use. If the installed light intensity is lower than what has been designed, there will be less yield. If the uniformity is inconsistent, individual plants will grow and develop at different rates and there will be uneven production in your greenhouse.
Before you start
When you compare different lighting designs, make sure to compare apples with apples. This means taking 3 things into account:
1. Verify the credibility of the performance claims that manufacturers make
2. Make sure that DIALux calculation software is used for the lighting design. This calculation software is independent and commonly used in the horticulture market.
3. Check which input parameters have been used for each lighting design. It is easy to tweak the input parameters and give the impression of a more positive light level and uniformity within the lighting design. So which parameters are crucial?
Most important input parameters to check
• Is the right product specified? Check if the exact product that you have selected for your project has been used in the lighting design; with the right light output (PPF in µmol/s) and spectrum (blue/red/white/far red/…)
• Are your specific design values used like the average light level at your crop (PPFD in µmol/m2/s) and the overall light uniformity?
• What are the standard settings? The height of the grow light and crop (free height), reflection factors, and size and position of the area that is used in the uniformity calculation have an impact on the average light level and overall uniformity.
#1 Check the free height
The first input parameter to check is the free height specifying the distance between the LED module and the head of the crop. The free height can seriously impact the overall uniformity value. In case of high-wire tomato crops, with a limited free height of 1.50 to 2.50m, realizing a good overall uniformity value can be a challenge. An optimistic free height or calculating uniformity on floor level as if there is no crop will positively impact the overall uniformity value.
The free height is calculated by measuring the eventual top of the crop and the mounting height of the LED grow light.
#2 Check the reflection factors
Another important parameter to check, are the reflection factors used in the lighting plan. A reflection factor indicates the amount of light that is reflected by walls and other objects in a space. DIALux calculation software has originally been designed for indoor spaces like offices, where you will get reflection off the walls, ceiling, and floors that impact the light level on your desk. To avoid being too optimistic about the outcome, the reflection values in DIALux are set at 0% for a greenhouse lighting design, because the glass in a greenhouse does not reflect the light from the grow lights.
#3 Check the area that has been used to make light intensity calculations.
The next thing to check is the defined calculation surface. The size of the calculation area and the position of the grow lights within that area will seriously impact the average amount of active photons that reaches the surface of the crop (PPFD value in µmol/m2/s). When comparing lighting design results from different manufacturers, make sure that the calculation surface shows an equal number of maximum (peaks) and minimum (dips) light intensity values. Only then you receive a realistic average PPFD value in the lighting design.
In the below example, you will see two positions of a calculation area within the same light plan, which will generate far better average light intensity values in the B situation, because the light intensity is calculated with an area that shows more grow light (peaks), and consequently less areas with the minimal amount of grow lights, which will not represent the reality after installation
Position of measurement grid defines the outcome of average light intensity
#4 Check the size of the calculation surface
Another important factor is the size of the calculation surface that will impact the overall uniformity value. When comparing lighting design results from different manufacturers, make sure the same calculation surface has been applied.
To represent a real-life situation, a calculation for the full compartment area should be made that includes the edges of the greenhouse. In case of a typical production area, a centred area is used. You may understand that a full compartment will generate lower uniformity levels, because of the lower light intensities at the edges. So, make sure you always compare either full compartments or smaller areas.
#5 Check the used uniformity
The final parameter to check is the uniformity being used. Uniformity can be expressed in different ways. When you run the DIALux lighting design software, it provides you with different types of uniformity. When comparing lighting design results from different manufacturers, make sure the same type of uniformity is applied. For a horticulture application, we prefer to express uniformity as the average light intensity divided by the maximum light intensity, which represents real-life situations best.
In Summary
When comparing lighting designs there are lots of tweaks that suppliers can possibly make to finetune their plan. In case you want to make a proper comparison, you have to take a few parameters into account.
- Is the specified product with the right spectrum and efficiency used in the calculations?
- Is the right light level for your crop used and the right overall light uniformity?
- Are the settings comparable:
o Is the free height correctly defined?
o Are the reflection factors set to 0%?
o Does the measurement grid have an even number of light and dark spots in it.
o Are you comparing full compartment or small centered area numbers?
o And is the defined uniformity similar in the lighting designs?
Read our other blog and learn how to evaluate the performance claims of an LED grow light.
Grow with the pros
You want to be sure to get a rapid return on your investment and have all aspects of your project carried out professionally. With Signify, your project is in experienced hands. Signify is the global leader in the lighting sector and has built up a substantial track record in more than 1000 projects in the horticultural lighting market since 1995. This includes over two decades of dedicated experience developing tailor-made, LED-based light recipes that help growers speed up growth, increase yield and improve the quality of plants. With cutting-edge LED innovations at our command, we can custom-build a science-based solution for you.
Pascal van Megen is an application engineer at Signify with a background in mechanical engineering. As an application engineer, Pascal ensures that growers are provided with high-end horticulture lighting designs. He is providing internal and external training to customers and partners in the application of the Philips LED Horticulture products and systems. He acts as a consultant to customers and engineers, to drive continuous improvement of Philips LED lighting solutions.
--- END ---
For further information, please contact:
Global Marcom Manager Horticulture at Signify
Daniela Damoiseaux
Tel: +31 6 31 65 29 69
E-mail: daniela.damoiseaux@signify.com
About Signify
Signify (Euronext: LIGHT) is the world leader in lighting for professionals and consumers and lighting for the Internet of Things. Our Philips products, Interact connected lighting systems, and data-enabled services, deliver business value and transform life in homes, buildings, and public spaces. With 2020 sales of EUR 6.5 billion, we have approximately 37,000 employees and are present in over 70 countries. We unlock the extraordinary potential of light for brighter lives and a better world. We achieved carbon neutrality in 2020, have been in the Dow Jones Sustainability World Index since our IPO for four consecutive years, and were named Industry Leader in 2017, 2018, and 2019. News from Signify is located at the Newsroom, Twitter, LinkedIn, and Instagram. Information for investors can be found on the Investor Relations page.
VIDEO: Vertical Farms Could Take Over The World
As the global population continues to increase, vertical farming is becoming a more widely recognized and viable solution to our food production problem
By JACK BERNING
May 22, 2021
Vertical Farming Offers Better Tasting,
More Sustainable Produce.
Will It Take Over Farming
As We Know It?
As the global population continues to increase, vertical farming is becoming a more widely recognized and viable solution to our food production problem. Vertical farming is a type of indoor farming where crops are grown in stacked layers, rather than spread out across large plots of land.
To View The Video, Please Click Here
These futuristic farms aren't just going to have an impact on how we survive here on Earth; they could also enable us to create a food source beyond our planet, without a dependence on the outdoor climate or arable land.
Although the task sounds unimaginable, developments in controlled environment agriculture are proving that it is very much possible. Adopting these sustainable farming practices could lead to a monumental shift in how we produce food, both for today and the future of humanity.
Vertical Farming Advantages
Vertical farms offer many benefits over traditional farming practices — an increased crop yield with a smaller land requirement, more control over the resulting flavor and cleanliness of crops, and the prospect of better access to healthy foods in underserved communities, to name a few.
Because these farms are constructed completely indoors using LED lights, their output isn't subject to the natural elements that typically affect plant production such as adverse weather, insects, and seasons.
Vertical farms offer more control over the resulting flavor and cleanliness of crops, and the prospect of better access to healthy foods in underserved communities.
They're better for the environment because they require less energy and put out less pollution, without a need for heavy machinery, pesticides, or fertilizers. Vertical farms often use soil-less farming methods like aquaponics, hydroponics, and aeroponics, which requires just 10% of the amount of water consumed by conventional outdoor farms.
Think of a vertical farm as a plant factory — one that enables farmers to predictably grow anything, anywhere, from strawberries to kale. The idea was first introduced in 1999 by Dickson Despommier, a professor at Columbia University. Despommier and his students came up with designs for a "skyscraper farm" that could feed 50,000 people. Though the structure has yet to be built, they successfully managed to popularize the ideology behind vertical farming systems.
Output isn't subject to the natural elements that typically affect plant production such as adverse weather and insects.
So, why wasn't the skyscraper farm ever built? The answer sheds light on one of the most prominent vertical farming disadvantages — cost. A single farm can cost a hundred million dollars to construct, and a lack of data surrounding the long-term economic feasibility of vertical farms has caused some investors to shy away.
However, this hasn't stopped vertical farmers from persisting to disrupt the food production industry. Vertical farming has already been adopted in countries like China, Japan, and other parts of Asia. In fact, the market for vertical farming in that region is expected to increase 24% by 2026. And in the U.S., some vertical farming companies are already selling their produce in stores.
More Produce With Less Resources
One of those companies is Plenty, headquartered in San Francisco, California. Plenty was founded in 2014 by Matt Barnard and Nate Storey with a simple yet powerful mission to improve the lives of plants, people, and the planet.
Plenty already has established vertical farms in the San Francisco Bay Area, Wyoming, and Washington. These farms supply fresh produce including kale, arugula, and lettuce to major grocery stores like Whole Foods and Safeway.
The team at Plenty recently began construction on a new farm in the Bay Area that they call Tigris. Tigris will be its largest and most efficient farm yet, capable of growing a million plants at a time.
With Plenty's vertical farming technology, 700 acres of farmland can be condensed into a structure the size of a big-box store. Plenty's farms harvest 365 days per year and shrink growth cycles to about 10 days for many of their products.
This results in a yield increase of about 700% as compared to traditional farming, all while saving about a million gallons of water per week and using just one percent of the land that traditional farms use.
The secret to this astronomical efficiency lies in the technology. Plenty's farms are equipped with air handling units that capture transpired water, allowing them to recirculate 99% of the water back into the system. They also use LED light bulbs and, seeking to be as efficient as possible, the bulbs are designed in a grid format that maximizes the amount of energy absorbed by the plants.
These systems allow farm operators to have more control over their crop yield — all the way down to a plant's flavor profile. Blue LED lighting, for example, can create a crispier crunch in kale leaves. Additionally, without a need for pesticides, their products are completely organic.
Plenty's farm saves about a million gallons of water per week and uses just 1% of the land that traditional farms use.
"When you grow things outside, the elements are much more unpredictable," Shireen Santosham, the head of strategic initiatives for Plenty, explains. "If you grow indoors, you can control a lot of those factors in ways that are accessible to outdoor growers. And the result is that our produce can be hundreds of times cleaner."
Not only is the produce cleaner, it's also higher quality. Because Plenty's products are grown in urban areas and don't have to be shipped across the country, the brand doesn't have to prioritize shelf life. Less transportation needs also reduces their carbon footprint.
What could all of this mean for the future? That every place in the world, regardless of climate, could sustainably grow the same nutrient-rich and flavorful crops. And it could someday result in the colonization of other planets, as well.
"We can give the world back — a lot," says Storey. "We can give the world back land. We can give back the jungles of Borneo to the orangutans. We can give back the Amazon to the planet. We can give back the midwest to the buffalo. We can give back the things that we've taken. And we can be a lot less extractive."