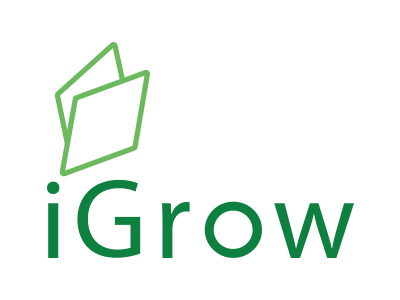
Welcome to iGrow News, Your Source for the World of Indoor Vertical Farming
Videos: Freight Farms - Container Farming
To learn more about how to get started with your own Freight Farm go to Freight Farms, or to inquire about a pre-owned Freight Farm Container go to iGrow News
FREIGHT FARMER SPOTLIGHT: PATRICK STOFFER
In a lot of ways, Patrick Stoffer isn't your average 28-year old. To start with, he is a hydroponic farmer, but perhaps even more unusual, he is roommates with a 90-year old, Harrie, just one of the members of his community he is passionate about serving. Patrick lives at Humanitas Independent Senior Living Facility in Deventer, The Netherlands. In exchange for room and board, Patrick spends time with the residents, who help him grow, harvest and prepare the fresh produce from his Freight Farms operation, Grow Local. To learn more about how to get started with your own Freight Farm go to Freight Farms, or to learn more about pre-owned Freight Farm LGM container, got to iGrow News.
GROW FOOD HERE: SPRINGDALE, ARKANSAS | VET VEGGIES
4 STEPS TO GROWING IN OUR CONTAINER FARM
FREIGHT FARMER SUPPORT
MEET THE FARMERS AT AGORA GREENS
2015 LEAFY GREEN MACHINE BY FREIGHT FARMS
INSIDE A SHIPPING CONTAINER VERTICAL HYDROPONIC FARM
INTRODUCTION TO THE LEAFY GREEN MACHINE
FREIGHT FARMS X KARMA FARM
THE STORY BEHIND FREIGHT FARMS
INSIDE THE LEAFY GREEN MACHINE
Crop One Grows Food Hydroponically With Unique Formulas For Each Plant
Crop One is a vertical farming holding company for two subsidiaries – FreshBox Farms, Millis, Mass., and a joint venture with Emirates Flight Catering, Dubai South, United Emirates
Crop One is hardware agnostic but develops its own proprietary software and data analytics platform that governs its growing process as well as it farms.
Hydroponic Technology and Data Analytics in Vertical Farming
Dave Vosberg, CFO & SVP Strategy | Crop One
07/30/19 Indoor & Vertical Farming
Tell us about Crop One and your role with the company.
Crop One is a vertical farming holding company for two subsidiaries – FreshBox Farms, Millis, Mass., and a joint venture with Emirates Flight Catering, Dubai South, United Emirates. Crop One has been in commercial production longer than any other major vertical farmer in the U.S. It produces the highest crop yield per square foot, at 25% of the capital cost, of any vertical farm, due to its unique combination of proprietary technology platform and best-in-class plant science. For more information about Crop One and vertical farming follow the link to CropOneHoldings.com. Crop One’s mission is to solve the world’s food problems one crop at a time. The first crop we are successful with is leafy greens, but soon we will be growing fruits, proteins, some cereals and many specialty crops. My role with the company is as CFO and SVP Strategy, helping to provide the vision for corporate financial success.
Please tell us what advantages and benefits Crop One provides?
Crop One Holdings is transforming the ag tech industry, using advanced hydroponic technology and proprietary data analytics to provide pure, safe and consistent produce year round. Crop One’s differentiated technology stack and growing process make it the most advanced company in the vertical farming space. The company delivers industry-leading environmental benefits with technology that is centered around lowering costs and increasing yields. Additionally, the company is also actively experimenting with growing new crop types and cultivars, and has partnered with leading seed and research companies to develop seeds specifically bred for the controlled indoor environment.
Since sustainably feeding a growing population is a paramount interest globally, what type of international interest do you have for your farms?
Crop One Holdings, the world’s leading vertical farm operator through its FreshBox Farms brand and Emirates Flight Catering (EKFC), announced a $40 million joint venture the build the world’s largest vertical farm in Dubai, United Arab Emirates. The 130,000 square foot controlled environment facility will produce three US tons (6,000 pounds) of high quality, herbicide and pesticide-free leafy greens, harvested daily, using 99 percent less water than outdoor fields. Its location will enable quick delivery of fresh products within hours of harvest, maintaining the food’s nutritional value and reducing carbon emissions associated with transportation.
How big of an issue is distribution?
Distribution is the key issue. Crops are now grown far from the point of consumption often times traveling weeks before reaching supermarkets and are vulnerable to disruptions related to climate, pathogens, and chemical intervention. Addressing these challenges will require a combination of plant science, AI, agtech, software analytics, environmental sustainability and operations management to address. Crop One’s differentiated technology stack and grow process makes it the most scalable company in the vertical farming space, delivering industry-leading environmental and economic benefits.
What role have Sensors and LEDs played?
Vertical farming that can control the environment in which it grows can be liberated from climate and geography enabled by the advent of cheap LED lighting and cheap sensors. Both have allowed us to improve economics of leafy greens and will continue to allow us to permanently change the infrastructure of agriculture, one crop at a time.
What are the innovative aspects or the technological advances that make Crop One unique?
Crop One grows food hydroponically with unique formulas for each plant. Crop One is hardware agnostic but develops its own proprietary software and data analytics platform that governs its growing process as well as it farms. Crop One is technology enabled and plant science forward - it has a strong plant science team led by Dr. Deane Falcone, enabling the company to manage its cost and increase yields. The company’s plants are supported by more than 250M+ data points for maximum growth and give the exact, correct amount of water, light, and nutrients, all grown without the use of soil. The final products (leafy greens) are fresher, safer and cleaner.
What are the biggest hurdles currently facing Vertical Farming and its expansion?
To date, the biggest hurdle facing Vertical Farming has been operators who can demonstrate consistent operational and financial success in order to attract debt financing. This is an asset-heavy industry, and without debt or third-party project capital, the business is un-scalable. Crop One has consistently proven its operations and financial performance being the only vertical farm that has consistently delivered product every week for the past four years, and at positive gross margins the past two and a half years. As such, Crop One is now on a growth trajectory to significantly expand production.
Where do you see Vertical Farming and Crop One 5 years down the road?
5-10 years from now, Vertical Farming will supply roughly 50% of the value of the leafy greens market. It will also have made inroads into fruits, proteins, cereals and specialty crops. Similar to data centers, we are at the beginning of this industry and vertical farms will soon become as plentiful. Crop One will be a leader in this space, but this is a multi-winner market. Crop One will be distinguished by its leadership in plant science, technology and business model innovation.
About David Vosburg, CFO & SVP Strategy
Dave has spent his life's work founding, growing and scaling technology businesses. Crop One Holdings, trading as FreshBox Farms, is his fifth successful startup he has lead at the CXO level. As CFO and SVP Strategy for Crop One, Dave leads the finance and strategy of the company.
Dave is passionate about businesses which use technology to disrupt markets while creating significant social value. Previously, Dave was CFO of Southern Africa's largest money transfer company, outside of South Africa, CEO of Zambia's leading HR consulting and outsourcing company and CCO of an Ed-Tech startup which translated the entire Zambian primary curriculum into 5,000 flash-animated lessons.
Mr. Vosburg also served as the past President of the American Chamber of Commerce in Zambia and holds a BA from the University of Notre Dame and an MBA from Yale University."
The content & opinions in this article are the author’s and do not necessarily represent the views of AgriTechTomorrow
Fresh Produce, Brought To You By Robots
IN SAN CARLOS, CALIFORNIA, UNDER LED lighting in a controlled, 8,000-square-foot environment, a team of autonomous robots is whirring night and day between rows of leafy greens
A Family-Owned Market In California
Is Now Selling Robot-Reared Leafy Greens
BY LUKE FATER AUGUST 08, 2019
An industrial robotic arm with custom gripper and sensors constantly reorganizes plants as they grow. IRON OX
IN SAN CARLOS, CALIFORNIA, UNDER LED lighting in a controlled, 8,000-square-foot environment, a team of autonomous robots is whirring night and day between rows of leafy greens. There is no dirt, there are no pesticides, and on this indoor farm, the only humans work behind screens. This is one of the world’s first autonomously operated commercial farms, and their produce is now flying off the shelves.
As a child, roboticist Brandon Alexander spent summers in Oklahoma helping his grandfather grow potatoes, peanuts, and cotton on a 6,000-acre farm. But as CEO of Iron Ox, the start-up company behind the automated farm, he says traditional farming is now his biggest competition—and granddad understands. “He knows that for farming to survive, this is almost inevitable,” says Alexander.
At Bianchini’s Market, a family-owned grocery in the San Francisco Bay Area, the two worlds are competing for the first time. As it stands, the robots are holding their own: Between retail buyers and several local restaurants, including San Francisco’s Trace, Iron Ox saw sales more than double last quarter.
Compact spacing techniques unique to hydroponic farms allow Iron Ox to grow 30 times the yield per acre compared to outdoor farming, according to Alexander. IRON OX
The San Carlos operation is not completely automated just yet. Human staff still plant the initial seed and handle post-harvest packaging. But the rest is left to robots.
Angus, a half-ton aluminum porter, roams the “field” of trays, or pallets, 24/7 with an overhead camera. On traditional farms, plants need space for their roots to absorb nutrients; on hydroponic farms, however, seeds can be planted in their trays mere inches apart. As they grow and begin crowding each other, though, this does require more attention from, say, a sleepless robot. Angus carries the 800-pound pallets in need of rearranging to a separate, industrial robotic arm that gently re-shuffles the growing pods into new compact rows. Angus is also responsible for IPM (integrated pest management) and scanning for aphids, mildew, and browning.
The robotic arm’s stereo-camera (“two cameras that kind of mimic your eyes,” Alexander casually explains) creates a 3-D model of at-risk produce that’s run through a machine algorithm to diagnose the issue and quarantine or prune accordingly. “The Brain,” a cloud-based AI software, coordinates all these autonomous functions while monitoring light, nitrogen, and water levels. “It’s a neighborhood farm,” says Alexander.
A 1,000-pound aluminum porter named Angus scans for crowding, carrying plant pallets to a separate robotic arm for rearranging. IRON OX
He’s not wrong. Produce from Iron Ox travels less than a mile to reach Bianchini’s—itself a mere 25 miles from downtown San Francisco. In fact, evening shoppers at Bianchini can buy produce robo-picked that morning, and at price points that compete with outdoor farms: A bunch of basil sells for $2.99; four heads of baby lettuce for $4.99; and a bunch of red-veined sorrel for $2.99.
Typically, the cost of human labor required for indoor hydroponic farms has made their produce inaccessibly expensive. Jake Counne of Backyard Fresh Farms, a similarly autonomously assisted farm in Chicago, told the Chicago Tribune that employing robotics reduced his labor costs by 80 percent. For this reason, building a farm around robotics and A.I. could crack the code of making indoor farms feasible. And while Alexander’s leafy greens remain local, the consequences of Iron Ox’s success may not.
Using robotics to make indoor hydroponic farms practical could alleviate a host of agricultural problems. In 2016, World Water Forum cited farming as a major contributor to global water scarcity. But farms like Iron Ox use 90 percent less water than outdoor farms. In a 2019 report on the challenges of feeding 10 billion people by 2050, The World Resources Institute cites concern over “the difference between global agricultural land area in 2010 and the area required in 2050 … if crop yields continue to grow at past rates.” According to Alexander, Iron Ox yields 30 times more produce per acre over the course of a year than conventional farms, and without using any arable land. A 2016 report from the National Center for Biotechnology on Chemical Pesticides urged a “drastic reduction in the use of agrochemicals,” and indoor farms alleviate the need for herbicides and pesticides.
This vision-enabled robot runs 3-D scanned models of the plants through a machine learning algorithm for quality control. IRON OX
For now, Iron Ox’s goals are more pointed. “How can we make your salad pop? We try to prioritize that,” Alexander says. Following the success of the San Carlos location, he does plan to set up robotic farms near other U.S. cities, though he’s not announcing anything yet. Iron Ox is, however, hiring humans for plant science and growing teams.
Gastro Obscura covers the world’s most wondrous food and drink.
Sign up for our email, delivered twice a week
VIDEO: How To Feed 10 Billion People?
The American news platform Bloomberg launched a new video ‘How to feed 10 billion people’ in the series called ‘Problem Solved’
The American news platform Bloomberg launched a new video ‘How to feed 10 billion people’ in the series called ‘Problem Solved’. These videos focus on how scientists are trying to solve some of the biggest challenges the world faces.
How to feed 10 billion people by 2050? That is one of the questions to which NPEC research can contribute. Photosynthesis is at the heart of plant production, and while we thought this cannot be improved, we now know it can. If only one can measure photosynthesis accurately and at high-throughput, which is exactly what NPEC will provide for several crops.
For more information:
NPEC
www.npec.nl
Publication date: 8/20/2019
Can Vertical Farming Feed The World And Change The Agriculture Industry?
Can Vertical Farming Feed The World And Change The Agriculture Industry?
Year after year, cities expand and pristine natural habitats are turned into farms and pastures to support the world’s growing population. But despite our encroachment into the environment, we still struggle to feed everyone. Vertical farms could offer a solution by producing higher crop yields year-round in less space than conventional agriculture.
What Is Vertical Farming?
With land for crops and pastures growing scarce — plus the threat of pesticides and herbicides taking a toll on our health and the environment — people are exploring new ways to grow food, such as urban agriculture. In general, this is the process of growing food within city limits – whether on rooftops, in backyards or on balconies. The goal is to provide families with fresh, healthy food that isn’t laced with chemicals — and when you grow your own crops, you can control these elements.
Vertical farming is a type of urban agriculture – but vertical farms are often constructed indoors in extremely controlled environments. Crops are grown on shelves that extend upward instead of outward, and the environment is carefully monitored, so crops grow year-round.
In addition to growing crops, some vertical farmers have developed ways to grow fish in a self-sustaining system. Water from the plants is recycled into fish tanks, and the waste from the fish becomes fertilizer for the plants. Then, both the plants and fish can be harvested for food.
The benefits of vertical farming
The benefits of vertical farming are numerous. Farmers can control the crops’ environment in vertical farms, so the plants aren’t subjected to nasty weather conditions or droughts. Humidity, nutrients and water are administered to growing plants to achieve optimum growing conditions. Because of the controlled environment, crops can be harvested more than once a year, resulting in higher yields than traditional farming.
Related: The GCC’s first commercial vertical farm launches in Dubai
Vertical farms are more sustainable than conventional farms because they use less water (which is often recycled through the system), they take up less space and they use less fossil fuels because they don’t rely on heavy machinery such as tractors and harvesters.
Technology helps vertical farmers get the best output from the farm. Tailored lamps help plants get more light exposure, which encourages them to grow faster than crops that rely on the sun. Vertical farms also provide greater protection from insects, thus decreasing the need for harmful chemical products.
Downsides to vertical farming
While vertical farms can help with local hunger issues and sustainability, there are some barriers that may keep them from gaining worldwide traction. The cost of setting up a vertical farm can be prohibitive. Conservative estimates put the initial start-up cost at around $110,000, but there are estimates upward of millions of dollars.
Finding an abandoned warehouse or building in an urban setting for a reasonable price might be difficult. Since vertical farms rely on electricity for growing lamps and strict environmental controls, the location has to have reliable power — not just any old abandoned building will do. Vertical farms also depend heavily on technology, which can be costly. Keeping the lights on and the environmental controls running will impact energy use — and your budget.
Not every crop that is grown traditionally can be raised successfully in a vertical farm. Leafy greens and herbs do the best in an indoor environment, while staple crops like wheat and potatoes are difficult to grow indoors, as are some fruits and vegetables. The crops that can be harvested from a vertical garden are limited.
Growing food to feed the hungry is a noble gesture, but it also has to be profitable, especially when the initial cost to set up a vertical farm is so high. If there isn’t a market in your area, it’s a waste of time to grow large amounts of food that you won’t be able to sell.
The Verdict
Despite the downsides, the positives are plentiful. In addition to embracing sustainability and helping combat hunger, vertical farms can also encourage support for local economies. These farms can create jobs, turn a profit and provide a healthy source of food for locals.
As technology continues to advance, new approaches will improve the efficiency and productivity of vertical farms. If nothing else, the idea sparks the conversation about changing the agricultural industry and gives us a place to start for finding better, more sustainable ways to grow food.
Images via Depositphotos, Aqua Mechanical and Mike Chino for Inhabitat
under Agriculture, Features, Innovation, Sustainable Food, Urban Farming
The Future of Food: Why Farming Is Moving Indoors
A car park opposite the infamous New York City housing estate where rapper Jay-Z grew up seems an unlikely place for an agricultural revolution. Ten shipping containers dominate a corner of the Brooklyn parking area, each full of climate control tech, growing herbs that are distributed to local stores on bicycles. This is urban farming at its most literal
By Russell Hotten BBC News, New York
August 22, 2019
Tobias Peggs says the fledgling industry is still developing the right business models. SQUARE ROOTS
A car park opposite the infamous New York City housing estate where rapper Jay-Z grew up seems an unlikely place for an agricultural revolution.
Ten shipping containers dominate a corner of the Brooklyn parking area, each full of climate control tech, growing herbs that are distributed to local stores on bicycles. This is urban farming at its most literal.
The containers are owned by Square Roots, part of America's fast-expanding vertical farming industry, a sector run by many tech entrepreneurs who believe food production is ripe for disruption.
The world's best basil reputedly comes from Genoa, Italy. Square Roots grows Genovese seeds in a container that recreates the city's daylight hours, humidity, Co2 levels - and all fed hydroponically in nutrient-rich water.
"Rather than ship food across the world, we ship the climate data and feed it into our operating system," says co-founder Tobias Peggs.
High costs
An artificial intelligence expert, Mr Peggs founded Square Roots with investor Kimball Musk (Elon's brother) two years ago. They've signed a deal with one of America's big distribution companies, Gordon Food Service, to locate herb-growing containers at some its 200 warehouses.
He says the deal represents everything about indoor farming's potential: locally grown, quick-to-market, fresh produce that can be harvested year-round and is free of pesticides and harsh weather.
Bowery is set to open its third industrial-sized indoor farm. BOWERY FARMING
"Indoor farming can answer many of the questions being asked by today's consumers about the provenance, sustainability and health of the food they eat," he says.
Jeffery Landau, director of business development at Agritecture Consulting estimates the global value of the vertical farming market will rise to about $6.4bn by 2023, from $403m in 2013, with almost half that attributed to growth in the US.
Despite the sector's high costs and limited food range, the potential is not lost on investors. Recently, AeroFarms, a producer of lettuce and other leafy greens, raised $100m, including from Ingka Group, Ikea's parent company. Bowery Farming raised $90m in a funding round backed by Google Ventures and Uber boss Dara Khosrowshahi.
Plenty, another major US player, raised funds from Softbank chief executive Masayoshi Son and former Google head Eric Schmidt. The company has ambitions to build hundreds of vertical farms in China. In the UK, food delivery and robotics company Ocado is investing in indoor farming.
But there have also been failures. "Vertical farms are a highly intensive capital expenditure," says Mr Landau. "Your lighting system will be one of your highest capital costs." And then there's ventilation, air conditioning, irrigation and harvesting. "Make a mistake and you will have one costly upgrade on the horizon," he adds.
Mr Peggs chose a modular system based around shipping containers because he says it is quickly scalable according to demand. "We can put a herb farm in new city for less than $500,000 and be growing within two months. We just press the 'basil button' - or mint, or tarragon - and the box configures itself to grow in optimum climate conditions."
In neighbouring New Jersey, however, Bowery Farming, takes a different approach. The five-year-old company runs industrial-sized farms. Outside one huge, grey windowless warehouse a heat haze shimmers off the concrete. It's a sharp contrast to the chilly interior where an aroma of fresh farm produce hits you immediately.
Robots
Produce is grown on trays stacked ceiling-high to maximise acreage. Everything from the automatic seeding machine to harvesting is run by Bowery's proprietary operating system (OS) which controls light, adjusts water nutrients and takes camera images of each plant to monitor its health.
"The OS is our central nervous system. There are millions of data points," says founder Irving Fain. "The artificial intelligence is constantly learning and predicting how to produce the best quality product."
Irving Fain hopes to soon start producing radishes and turnips commercially. Michael BACA Image
Running the farm manually would be difficult, he says. Staff operate things from computer screens and iPads. In the cavernous farm room itself, the only sound is robots moving the shelves.
Growing food indoors has been around for decades, but the industry got a kick-start from advances in the performance of lower cost LED lighting. Combine that with robotics, innovations and AI, and you have an industry that Mr Fain says is both viable and scalable.
"The big question was, how can we grow in large volumes at a consistently high quality? Suddenly, the economics changed," he says. "We can grow 365 days a year - a major departure from thousands of years of agriculture. Unlike outdoor farming, our yield is virtually 100% guaranteed."
Vertical farmers talk with a zeal you'd expect of entrepreneurs with tech world backgrounds. With population growth and climate change putting pressure on food production, they think they may have answers.
Square Roots' herbs are delivered to customers by bike. SQUARE ROOTS
But this highlights one of the industry's limitations. You can't feed the world on leafy greens. That said, for Mr Fain, if Bowery only ever grew lettuce or kale, "it's still a win". But his ambitions are greater. Bowery is growing radishes and turnips that he expects to come to market with two years.
Square Roots hopes to soon start commercial production of beetroots and strawberries, and is experimenting with so-called heirloom produce from rare and long-forgotten seeds.
Carbon footprint
Mr Peggs says: "It makes sense to grow perishable produce in the same neighbourhood as the consumer - stuff that doesn't travel well. A lot of produce - tomatoes, strawberries - are grown for travel, not for taste. It doesn't make sense to vertically farm food with a long shelf life."
But different produce presents different challenges, says Mr Landau. Where plants are concerned, not all light is created equal. Fruiting and flowering crops such as tomatoes, strawberries and peppers have different needs.
QR codes on the food packaging can tell customers the history of the produce. SQUARE ROOTS
"Lights for these types of crops will generally be more expensive, require more electricity, and produce more heat, meaning additional cooling," says Mr Landau. "Harvesting these crops can be a significant operational cost."
But it is being done. In the US, Oishii vertically farms the much-prized Japanese Omakase strawberry year-round. And Farm One produces more than 200 products, including 34 edible flowers. Plenty is experimenting with watermelons. As technology costs fall and R&D intensifies, the crop variety will expand.
That may also ease criticism of the industry's carbon footprint. In the artificial light versus sunlight debate, the latter often has the upper hand. But, then, indoor farmers point to the transportation costs and waste in traditional agriculture.
For the moment, Mr Landau says, the carbon footprint concerns are valid, although he expects indoor farms to increasingly draw on renewable energy.
"And when you look at markets located in extreme climate environments or island nations where they import a majority of food, indoor farming could be a viable option," he says.
Mr Peggs stresses that industry is still young are trying to work out the right business models and direction. The entrepreneurs don't agree on everything, though they certainly agree on this: vertical farming has the potential to transform global food production as we know it.
US: Chicago - Vertical Farming Brings High-Tech Approach To Metropolitan Agriculture
"We're doing for farming what Henry Ford did for the automobile," said entrepreneur Jake Counne
A Local Entrepreneur Has A High-Tech Take
On Agriculture That Could Change What Ends Up On Our Plates
By Meghan Kluth
Thursday, August 15, 2019 CHICAGO (WLS)
You could call it farming for the future.
A local entrepreneur has a high-tech take on agriculture that could change what ends up on our plates.
"We're doing for farming what Henry Ford did for the automobile," said entrepreneur Jake Counne.
Counne has found a way to grow produce locally, even when it's below 50 outside. He said the answer is using cameras, software and a conveyor belt in what's called a vertical farm.
"I came across vertical farming and I was just enamored with the ability to exponentially out produce the natural ability of that land," said Counne, who is the founder and CEO of Backyard Fresh Farms.
Six types of lettuce are stacked on a four level tower under the glow of purple LED lights in his Back of the Yards facility.
The farm produces three tons of greens in one year's time, which is what a farmer could do with Soldier Field but in just four parking spaces.
Counne's vertical farm reduces costs of energy, labor, and his produce has proven to last weeks.
"We've already beat the cost of a field farmed equivalent products," Counne said.
An automatic lift collects trays of ready plants and brings them to an assembly line of workers for harvest. It has reduced labor by 80% compared to the first vertical farms of its kind.
"We are quite literally building an assembly line of greens," Counne said.
Counne has nine patents pending that are helping him create the perfect environment for a plant every day of its life.
"The software here is looking to try to figure out what the optimal amount of light. It's also looking for early signs of stress in the new growth," said Counne.
Some of the cities high end restaurants are already using Counne's produce and when put to the taste test, it's clear this is not your average lettuce.
Counne's plan is to expand and open 100,000 square foot facilities near every major metropolitan area around the country
Mastronardi, DeJoria Launch GIVE Partnership In Middle East
Mastronardi Produce Ltd.®, North America's leading grower and distributor of greenhouse produce, and visionary John Paul DeJoria have selected the Middle East as the first market in which to develop the world's largest and most technologically advanced indoor farming project.
NEWS PROVIDED BY
Aug 19, 2019
KINGSVILLE, ON, Aug. 19, 2019 /PRNewswire/ - Mastronardi Produce Ltd.®, North America's leading grower and distributor of greenhouse produce, and visionary John Paul DeJoria have selected the Middle East as the first market in which to develop the world's largest and most technologically advanced indoor farming project.
Green International Ventures LLC (GIVE)'s Middle East location will be the world's largest and most technologically advanced indoor farming project. (CNW Group/Mastronardi Produce Ltd.)
John Paul DeJoria (CNW Group/Mastronardi Produce Ltd.)
.Paul Mastronardi (CNW Group/Mastronardi Produce Ltd.)
The newly formed company, Green International Ventures LLC (GIVE), will make locally grown fresh produce more widely available around the globe via its proprietary Advanced High-Density Farming System. This will be the first project for the groundbreaking GIVE venture, and it will reduce the Middle East's dependence on imported food, create a sustainable source of local employment, and significantly increase the region's non-petroleum-based exports.
"As pioneers in the greenhouse industry, we are passionate about increasing access to local, sustainably grown fruits and vegetables," says Paul Mastronardi, President and CEO, and the fourth-generation family member to lead Mastronardi Produce. "Our first location in the Middle East will allow us to reach over half the world's population in less than 8 hours, and this is just the start. Look for more global locations as we continue to scale to meet the growing need for food security, safety, and sustainability."
GIVE will also support the integration of modern AgTech initiatives into the local farming community and expand knowledge of sustainable agricultural techniques by establishing a permanent Research and Development facility in the region.
"It has long been my passion to help feed the world's population," says John Paul DeJoria. "The introduction of this revolutionary model in the Middle East is the first step of many towards increasing global access to sustainably grown fruits and vegetables."
All GIVE projects use innovative Advanced High-Density Farming Systems that incorporate a multitude of cutting-edge growing systems, such as water-saving irrigation and energy-efficient lighting, and they take advantage of advanced automation and robotic devices, AI processes for predictive analysis, and real-time crop and soil monitoring.
Produce grown in these innovative AgTech systems will be marketed under the SUNSET® brand. Known for award-winning flavor, innovation, and packaging, SUNSET's many exclusive labels include Campari®, the world's first branded tomato, and the uniquely colorful Aloha™ pepper.
SUNSET of Holland® will be the first distributor for the GIVE partnership.
About Paul Mastronardi and Mastronardi Produce Limited
Paul Mastronardi is the President and CEO of Mastronardi Produce, which recently received the prestigious honor of being named one of "Canada's Best Managed Companies" for the 10th consecutive year. In 2016, Paul was named Produce Person of the Year at the United Fresh Convention & Exposition in Chicago, USA, and in 2013, he was named Ernst & Young's "Entrepreneur of the Year" for Ontario.
Mastronardi Produce, the leading greenhouse company in North America, grows and sells flavorful, world-class tomatoes, peppers, cucumbers, and berries under the Sunset® brand. As pioneers in revolutionary greenhouse technology, they focus on sustainable non-GMO growing practices, recognizing that what is good for the environment, is good for business.
About John Paul DeJoria
John Paul DeJoria is a serial entrepreneur, philanthropist, business leader, and mentor with a true rags-to-riches story. Once homeless, he overcame adversity, and went on to build two billion-dollar brands—leading professional hair care manufacturer, John Paul Mitchell Systems, and Patrón Spirits—and several global enterprises. He started his first company, John Paul Mitchell Systems, with partner Paul Mitchell and a borrowed $700. He remains true to his motto, "success unshared is failure," and dedicates himself to numerous charitable causes through his philanthropy hub, JP's Peace, Love & Happiness Foundation, and he has committed to donate more than half of his wealth to philanthropy through his signing of Bill Gates and Warren Buffet's "The Giving Pledge."
SOURCE Mastronardi Produce Ltd.
Related Links
'Lettuce' Start A New Container Farming Venture
Essentially the company manufacturer purpose-built containers (sea containers don't work) housing a hydroponics system to vertically grow any number of products.
Ken Wilson 17 August 2019
Modular Farms Australia director James Pateras.
ON the surface you might think hydroponics farming is for somebody else to try.
But at last week's TECHSPO, Modular Farms Australia director James Pateras, laid out a tantalising case for the technology to be a niche business on any Australian farm.
A former Victorian dairy farmer and a Deakin University graduate majoring in economics and finance, Mr Pateras is now firmly ensconced in a vertical farming system, growing herbs, and making money.
He also is a director of Modular Farms Australia, which is linked to its Canadian parent in Ontario.
Essentially the company manufacturer purpose-built containers (sea containers don't work) housing a hydroponics system to vertically grow any number of products.
Being modular, additional modules are available for multiple uses.
"One of the secrets of producing quality product is lighting and our company has partnered with world-leading experts in LED lighting, plant health sciences, and indoor agriculture to re-think the container farm from scratch," Mr Pateras said.
"We focus entirely on plant health and farmer return on investment (ROI), which was one of the first questions Mr Pateras answered after his talk.
"The downside is we use a lot of energy in our enterprise but balancing the costs is the fact we are producing a high value product which we can supply virtually on demand year-round," he said.
"And to mitigate power costs it could be supplemented by on-farm energy, either solar or biomass.
His company also supplied cold storage units to maintain freshness until product was transported to clients.
"It's a closed loop system and we have a particular LED light recipe that enhances the quality of produce we market," he said.
Mr Pateras also reiterated the diminishing amount of arable land available throughout the world for farming practices.
"So, for example, we can grow 44,000 lettuce heads a year in a 36 square metre space," he said.
"The land needed to achieve that would be 1000 square metres.
"So vertical farming is making more efficient use of land with year-round supply and scalability.
"There already is work going on to produce rice by hydroponics so as technology improves there may be a way to grow our main line crops the same way.
"But at the moment opportunities exist to grow fresh produce and compete on quality and timing."
Another business opportunity for farmers existed with using biomass.
Department of Primary Industry and Regional Development (DPIRD) researcher Ron Masters said biomass was a realistic cash crop for farmers.
"Biomass on farms would mainly come from animal waste, crop residues or purpose-grown crops," he said.
"It's a renewable resource which reduces the carbon footprint and has the potential to be a substitutive product.
"For example, it could be used for carbon offsets or as a substitution for diesel and ethanol fuels.
"Biomass can be used to create steam for industrial uses or for a generator, bio-hydrogen, biochar and plastics.
"But I think the big winner for farmers will be using it for high value chemicals."
Though Mr Masters didn't expand on this subject, it is well known that sugar constitutes 75 per cent of all biomass, and it can be obtained from many different sources such as cane, beet and corn.
Even wood and straw can be processed into sugars that can be converted to chemicals.
Mr Masters also said renewable diesel would "probably" be the next big thing before renewable chemicals.
"The hidden gem is oil mallees," he said.
"Things have changed since the early days and we now have a commercial operator in Kochi Oil at Darkan which is processing the oil mallees.
"The resultant biomass is there to collect to power a greenhouse system, for example."
Have a commercial operator in the State makes such a proposition more viable."
Mr Masters said that overseas, biomass was a big business in making bio-hydrogen, nitrogenous fertilisers, plastics and used as a wood replacement.
When asked about the potential for canola oil, Mr Masters said there was "massive investment" internationally in canola as a first generation biofuel.
"WA has ignored this area for a long, long time but the opportunities are there," he said.
BREAKING NEWS: Crop One Holdings And Sananbio Announce Strategic Partnership To Jointly Develop Vertical Farms
Crop One Holdings (Crop One), a leading global vertical farm operator, and Sino-Science North America Photobiotech (SNAP), one of the largest vertical farm technology providers in the world, have formed a strategic partnership to jointly develop future vertical farm projects. SNAP is the owner of SANANBIO®, affiliated and supported by the largest producer of top-quality, ultra-high bright LED wafers and chips
August 20, 2019
OAKLAND, Calif.--(BUSINESS WIRE)--Crop One Holdings (Crop One), a leading global vertical farm operator, and Sino-Science North America Photobiotech (SNAP), one of the largest vertical farm technology providers in the world, have formed a strategic partnership to jointly develop future vertical farm projects. SNAP is the owner of SANANBIO®, affiliated and supported by the largest producer of top-quality, ultra-high bright LED wafers and chips.
For future projects developed jointly, Crop One will lead project development and plant operations, contributing its best-in-class plant science and controls technology, and SNAP will provide LED lighting and its proprietary modular growing systems and next-generation, fully automated vertical farm system, UPLIFTTM (Unmanned Platform of Lean & Intelligent Farming Technology). Crop One will license its plant science and controls technology to projects and both parties will contribute technology, equipment, know-how and financing.
Sonia Lo, Crop One’s Chief Executive Officer, commented, “We are thrilled to collaborate with SNAP in developing our combined pipeline of vertical farming projects. This partnership is a validation of our company and strategy, and significantly expands both Crop One and SNAP’s breadth and reach in the vertical farming sector while leveraging our respective strengths. We are long time, happy users of SNAP’s LED lights and believe its growing suite of best-in-breed hardware solutions is the perfect complement to our software, controls and plant science technology. Importantly, we share the same approach to pursuing an asset-light model to building vertical farms that is focused on scale, cost and energy efficiency.
“Successful vertical farms require a broad array of expertise and capabilities to operate efficiently and effectively, and we expect strategic partnerships between market participants with best-in-class complementary resources will become an increasingly important way for the leaders in the space to accelerate growth. Most vertical farm assets are owned by infrastructure investors, and technology companies such as Crop One and SNAP are enabling those owners to achieve the best return on their assets without the burden of technology development and management.”
Michael Yates, Sananbio U.S.’s Vice President of Technology Sales, added, “On a combined basis, we believe Crop One and SNAP’s pipeline in vertical farms is the largest in North America, with the potential to serve a full range from large wholesale to specialty retail customers across the continent with mega-farms capable of producing three or more tons of crops per day. As a proven leader in the vertical farming sector, Crop One is the ideal partner for us. They have a demonstrated track record of success in operating vertical farms at scale. The company’s partnership with Emirates Flight Catering to build the world’s largest vertical farm underscores the success of Crop One’s model and plant science technology, which address the most critical issue in vertical farming – optimizing plant growth with higher yields, at lower costs.
“Our LED products and growing systems are backed by many years of research in plant physiology and semiconductors and supported by a team of professionals with deep expertise in manufacturing, quality control, and sales and marketing. In combination, Crop One and SNAP will be able to provide a complete suite of solutions, from growing systems and technologies to crop development and production, which we believe is a significant competitive advantage. We are very excited about this strategic partnership with Crop One and look forward to starting our first project soon.”
About Crop One Holdings
California-based Crop One Holdings is a vertical farming technology company that enables fresh produce to be grown in a sustainable manner for its customers. It operates two subsidiaries: FreshBox Farms in Millis, Mass., and a joint venture with Emirates Flight Catering in Dubai South, United Arab Emirates. Crop One has been in continuous commercial production longer than any other vertical farmer in North America. The company’s proprietary technology and plant science put it ahead of its competitors, producing crop yields among the highest of the industry, but at 25% to 50% of the capital cost of other vertical farming companies. To learn more, visit https://cropone.ag/.
About Sino-science North America Photobiotech Inc.
SANANBIO® is a trademark carried and backed by Sanan Sino-Science Photobiotech, a company invested by Sanan Optoelectronics, one of the world’s largest LED chip manufacturers. Supported by an elite R&D team comprised of plant scientists, researchers and engineers, Sananbio utilizes state-of-the-art technology that enables growers worldwide in the horticulture industry to increase the quality and quantity of their yields. Years of extensive research and real-world deployment and operations allow Sananbio to offer its customers proven, scalable, efficient and cost-effective solutions in LED horticulture lighting and Controlled Environment Agriculture vertical farming grow systems. Sananbio empowers growers with the technology and knowledge to achieve unprecedented results in farming operations. To learn more visit: http://sananbious.com/.
Meet Tigris, Our Largest Farm to Date
Plenty brought the farm indoors to create a better future for people and our planet. We need to triple the production of fruits and vegetables if we want to provide a healthy diet to everyone on the planet
August 2nd, 2019 By Plenty Farms
PLENTY - TIGRIS FARM
Plenty brought the farm indoors to create a better future for people and our planet. We need to triple the production of fruits and vegetables if we want to provide a healthy diet to everyone on the planet. This is an eye-opening statistic based on a Harvard study and data from the United Nations. Decades of research and development in outdoor farming have solved primarily for calories through yield gains while largely neglecting nutrients and flavor. This has led to the predominant global diet being low in nutrients and high in calories, driving the global pandemics of obesity and diabetes.
Farmers have relatively little control over the crops they grow. They select which seed, when to plant, and when to harvest. They can apply water, fertilizers, and chemicals to encourage growth and fend off pests. For crops to be profitable, they are typically chosen and grown to survive travel on trucks and for easy storage. Crops from different climates are shipped thousands of miles to customers. The end result is expensive, lower quality, and less delicious fruits and vegetables.
Plenty’s goal is to grow the best possible produce and to make it more accessible than ever before. We want to sustainably offer people the healthiest, happiest lives possible. Our new farm, code named Tigris, represents our largest and most ambitious leap forward. It demonstrates our ability to grow delicious produce using less than 5% of the water and less than 1% of the land compared to outdoor farms. By developing reliable, indoor, vertical farms that control everything our plants experience, we can reach people around the world with nutrient-rich fruits and vegetables that consumers will actually crave.
In order to change consumers expectations and to compete with flavorful processed foods, we grow the most delicious version of every crop that we sell. Can kale be decadent? Can mustard greens create the same binge response that we find in a bag of Doritos? Can we do this without genetic modification or pesticides? The short answer is a resounding yes. If you control the growing environment, you can find the world’s most delicious varieties and remove geography and seasonality as limitations.
Strawberries are more delicious in California because California is one of five Mediterranean climates in the world that has the ideal environment in which to grow produce. The Italian tomato isn’t the best because Italian farmers are magical, but because Italian tomatoes benefit from the most perfect tomato-growing environment in nature. Inside the walls of our indoor farms, Plenty is able to create the perfect environment for almost anyfruit or vegetable to create the perfect flavor. We can build local farms and replicate the ideal environment near any city in the world. By eliminating long-distance transportation, we can harvest and put these foods in consumer’s hands the same day.
Most importantly, Plenty can grow produce that people want to eat. The human brain evolved to associate flavor with nutrients. Many processed foods are engineered to have the flavors our brains crave, but lack the nutrients that our bodies need. The intense artificial flavors don’t actually satisfy our bodies and our cravings drive us to eat more calories than we need. There are many communities around the world where there is enough food, but without balanced nutrition the result is excess consumption that leads to obesity and related diseases. Plenty is reestablishing the connection between flavor and nutrients to put an end to this cycle.
Building a new form of agriculture at a scale that can impact people around the world while using fewer resources and delivering mind-blowing flavor and nutrition is incredibly difficult. At Plenty, we have assembled an amazing team of the world’s leading Plant Scientists, Flavor Experts, Hardware and Software Engineers, Growers, Operations experts, and people from many related fields. We have built dozens of farm prototypes to attack this challenge from every angle. We have grown hundreds of varieties of plants to find the highest yielding plants with flavors that will change expectations. Tigris isn’t just a story about robots or climate control or LED lights or hydroponics. It is the first instance of a new way of feeding people that can deliver on the promise of each of these individual technologies when every detail is optimized.
Inside Tigris is the technological opportunity to revolutionize human health. We give plants the perfect environment to be the best and most craveable versions of themselves, so that we can all be the best, most nourished versions of ourselves. I hope people enjoy the photos and videos of Tigris, but I really can’t wait for people to taste our amazing produce.
Nick Kalayjian
SVP of Engineering, Plenty
The Only Way Is Up: Will Vertical Farms Tackle The World's Growing Food Crisis?
In an unassuming white shed on the outskirts of Dundee lies what could be the most futuristic farm in the world. It’s not reached by trundling down miles of country roads, but by going through a pressurised air lock designed to keep the uncontrolled outside out
David Farquhar inside his vertical farm CREDIT: STUART NICOL/STUART NICOL PHOTOGRAPHY
15 AUGUST 2019
In an unassuming white shed on the outskirts of Dundee lies what could be the most futuristic farm in the world.
It’s not reached by trundling down miles of country roads, but by going through a pressurised air lock designed to keep the uncontrolled outside out.
And the crops - towering stacks of vegetables and fruit grown in metal trays under coloured LED lights - are not tended to by rugged farmers in overalls.
Instead they are overseen by robots, who carefully manage every environmental parameter: from light to temperature to CO2 to humidity, in a totally closed system without a handful of soil or ray of sunlight.
It might sound like a dystopian scene from science fiction, but this demonstration farm, run by Scottish technology firm Intelligent Growth Solutions (IGS), is not a vision of the future. It’s a look inside one of a growing number of indoor vertical farms sprouting up around the world in old factories, skyscrapers, warehouses and disused highway tunnels.
Plants grown under LED lighting CREDIT: STUART NICOL/STUART NICOL PHOTOGRAPHY
But why are we growing upwards rather than outwards? The answer lies mostly in our dwindling natural resources and growing population, particularly in Africa which is undergoing a youth boom.
According to the United Nations, by 2050 the amount of arable land per person could be one third of the amount that was available in 1970. The earth’s population meanwhile will have more than doubled to 10 billion in the same period.
While there’s still more land that could be brought under cultivation doing so would also mean destroying more forests and wild areas.
The farmland that is available is not evenly distributed. That’s why densely-packed places like New York, Hong Kong and Singapore are looking at farming upwards. It’s why China too, which has to feed one-fifth of the world’s population with one-tenth of its farmland, is turning to vertical farms.
The challenge is complicated by an increasingly unpredictable climate that can take out a crop in a matter of days.
“If you can have a system that’s independent of the climate, the weather and availability of land you’ve got a very disruptive new food supply system and that’s what indoor vertical farming can potentially do,” says Professor Colin Campbell of the James Hutton Institute, a Scottish research centre that works alongside IGS to build technology for vertical farms. “It takes the weather and puts it inside a box.”
But it is not cheap and it is why most vertical farms are currently in wealthy countries despite the fact that most of the additional people the planet will need to feed by 2050 will live in the developing world.
According to proponents of vertical farming such as David Farquhar, the serial entrepreneur who runs IGS, while the technology is still at the starting gate, the potential global environmental and societal benefits of vertical farming are huge.
“It can do a huge amount of good. You can help to feed people, improve the quality of produce people get, reduce food miles and reduce the use of chemicals,” he says.
Those in favour of vertical farms argue that if you keep pests and diseases locked out, there’s no need for pesticides and other toxic chemicals.
Vertical farms also use a fraction of the water of conventional farms. It takes just two to four litres of water to grow a kilogram of vegetables in a vertical farm compared to 16 litres in a Dutch greenhouse and 60 litres in a Mediterranean field.
By bringing food production to cities, close to where most of it is consumed, you avoid gas-guzzling transport. And by growing upwards, land is saved.
And the benefits are not just environmental. Taking out the variability of light, soil, rainfall and everything else that can’t be controlled outdoors, also takes out the variability out of the crop.
“All the plants are exactly the same height - there’s no wonky veg in there,” says Prof Campbell.
By experimenting with light scientists can change how a plant tastes and feels without any genetic modification.
“By changing the wavelength of light you can change the chemistry of the plant,” says Prof Campbell. “You can increase things like flavour and taste, and you can increase the concentration of health promoting chemicals.”
Others maintain however, that recreating nature indoors comes at a cost.
Andrew Jenkins, a researcher at Queen's University Belfast believes vertical farming has potential for countries like the UK that import a lot of food, but cautions that the current high energy costs of artificial lighting could outweigh the benefits.
“Growing crops that require four to five times the energy means we [in the UK] are in a worse position than with imports,” says Dr Jenkins.
A technician tends to plants in a vertical growing facility CREDIT: STUART NICOL
Vertical farming’s champions are nevertheless, confident that scientists are already cracking the energy question. Among them is Mr Farquhar, who says IGS’s technology has reduced the typical energy use in a vertical farm by 50 per cent.
Dickson Despommier, emeritus professor of microbiology and public health at Columbia University, is something of a vertical farm visionary. When he published his seminal book on the subject in 2010 there were no such farms in existence.
“Now everyone is into vertical farming,” says Prof Despommier.
Mr Farquhar agrees. He says there’s been more media interest in his vertical farm in the year since it launched than in all the other enterprises in his more than 25-year career in technology.
Leo Marcelis, an expert on indoor farms at Wageningen University in the Netherlands, agrees that interest in vertical farming is global but believes that the high cost is stopping the spread of the technology to poorer countries, where it is needed most.
“In developing countries, there’s a lot of interest in this but it’s too early for them as it’s a relatively expensive system,” says Prof Marcelis. “At the moment high investment and running costs will stop it expanding faster.”
Plants growing under LED lighting at the vertical farm in Dundee CREDIT: STUART NICOL
Although most interest in his technology is from richer countries Mr Farquhar says that in the last few weeks alone he has received inquiries from places including the Ghana, Botswana, Ethiopia and India.
Among the countries pursuing vertical farming with a vengeance is China where a 250-acre district of urban and vertical farms is being planned in Shanghai.
Africa is also growing and rapidly urbanising. Vertical farming advocate, Dr Esther Ngumbi, a Kenyan researcher at the University of Illinois, is pushing the idea of growing upwards in Africa - albeit with smaller, cheaper, lower tech versions that borrow some of the land and water saving principles from vertical farms in the wealthy world.
Although from the point of view of the science almost any crop could be grown in a vertical farm, it’s currently only cost-effective to grow leafy greens and herbs - light, high value crops that don’t need long periods of time under costly artificial lights to mature. They are also short enough to stack in many layers.
Given the energy costs, Prof Marcelis is doubtful that vertical farming will be used to grow the cheap, non-perishable crops such as corn, rice and wheat that form the bulk of our diets.
“I don’t think that staple crops will be grown. That’s just not economically feasible,” he says. “What we see most is fresh vegetables where there is an advantage of having it near consumers”.
Since the leafy greens and herbs on which most commercial vertical farms are focusing only make up a tiny proportion of our daily calorie needs, skeptics argue that such farms will play a limited role in meeting food security needs, particularly in poorer countries.
Others also question the claims that growing fresh produce near urban populations will make us healthier, even for those who can afford it. A recent study of indoor vertical farms in New York found that the typically grown crops of lettuce and basil did little to improve diets and nutritional intake.
Prof Marcelis is however, optimistic that more nutritious crops, even though lacking in calories, will eventually be grown in vertical farms. “More and more initiatives are coming up with growing tall crops like tomatoes and peppers that are grown over a long duration so we’ll see it gradually expanding,” he says.
One way vertical farms might be able to help produce energy dense staples is by allowing quicker production of better seedlings for things like potatoes.
According to Prof Campbell this is one way field agriculture and indoor vertical farms can work together. The Dundee facility is working on “speed breeding” better varieties of basic crops in half the time it would take outdoors.
“Conventional field agriculture will continue to be the main way to provide staple crops for the future but indoor vertical farming can help with that as you can use indoor vertical farms to mass propagate the plants you plant out in the field,” he says.
Growing efficiently indoors what’s grown inefficiently outdoors also frees up valuable land for things like rice and wheat, says Mr Farquhar.
“There’s a lot of land being used inefficiently at the moment. If we can bring that inside and make that land available for growing staple crops then surely that’s a good thing,” he says.
But growing fruit and vegetables indoors is not just a way of helping us grow more energy rich foods outdoors. For Prof Despommier indoor vertical farming is one of the keys to addressing climate change.
“Farming is the worst thing we’ve ever turned loose on nature,” he says. “If you grow your food indoors and grow your trees outdoors it slows down climate change.
“Farming outdoors is failing, so indoor farming has to succeed.”
Protect yourself and your family by learning more about Global Health Security
Related Topics
Hong Kong Start-Ups Are Using Hydroponic Technology And Vertical Farming To Bring Fresh And Healthy Food To Citizens
The green movement is a growing revolution across the world and particularly Hong Kong. A part of this change is the ground-breaking farming technology that cuts lengthy supply chains to allow easy access to fresh produce rich in nutrients and bursting with flavour
Hong Kong Growing Urban Farming Tech
The green movement is a growing revolution across the world and particularly Hong Kong. A part of this change is the ground-breaking farming technology that cuts lengthy supply chains to allow easy access to fresh produce rich in nutrients and bursting with flavour.
A Hong Kong-based urban farming technology company launched in January 2018, has been offering herbs, microgreens, and edible flowers to restaurants, hotels and home cooks. It will take things to the next level in a couple of weeks with the launch of its first “mobile farm”.
Using hydroponic technology, the greens will grow in-store so that consumers know exactly where their food is coming from – they can actually see their vegetables as they grow. The pilot mobile farm will be launched in mid-August at an organic convenience store in Sai Kung.
Hydroponic basically refers to the way that the plants absorb nutrients, which is through water instead of soil. The start-up uses organic nutrients bought from the United States which has US Federal Drug Administration approval and adds it to water. An advantage of indoor farming is that it is extremely sanitary and water-saving.
Soil-based farming often sees the loss of a lot of water (which goes underground), hydroponic farming saves 90 per cent more water.
Hong Kong imports an astounding 98.3 per cent of its vegetables, with 70 per cent of the imports coming from China and 28 per cent flown in from around the world. All the emissions involved in getting our greens into Hong Kong is a massive black mark in terms of sustainability – and it’s also bad for health.
Another issue is that as soon as produce is harvested, the roots stop supplying water to the leaves and stem and the plant start losing their nutrient content. A benefit of a mobile farm is the ability to buy greens with the roots still intact, take the produce home and use it while it’s still fresh.
The start-up’s team have been using the Causeway Bay operation for research and development and a base in Cyberport to develop the mobile farm technology.
Beyond the hydroponic technology, the team is developing even more sustainable and efficient farming technology, but they’ve taken it slow the first year to develop their understanding of the crops they are growing.
According to an earlier report, a hi-tech vegetable farm in Hong Kong’s Tai Po district is thriving inside a converted factory building and produces four tonnes of lettuce, wild rocket, endive and cabbage for salads each month.
Its workers, most of them in their 20s and 30s, tend to neat rows of racks, each 30cm tall and 10 tiers high, filled with potted greens lit by low-energy light-emitting diode (LED) lamps and connected to fish tanks on the floor.
Instead of shovels and hoes, they work with computers and drones. The farm’s co-founder noted that they farm with technology, not ploughs. This is farming 4.0.
This start-up offers a glimpse of the future of farming by harnessing technology and using less space than traditional, long regarded a sunset industry in Hong Kong.
Primary industries, mainly comprising farming, fishing, mining and quarrying, accounted for HK$502 million last year, a tiny fraction of the city’s total gross domestic product of HK$2.65 trillion.
But the start-up’s co-founder, who is optimistic about the prospects for aqua-farming, said that Hong Kong is a service-based city, but still needs healthy food. This is a viable business in Hong Kong because of the demand for healthy produce and the growing awareness of food safety.
Fresh Out of The Box
Shipping containers, the vectors of globalisation that were forged in the first instance to ferry goods thousands of miles around the earth, are now being used to grow fresh produce that will be consumed in their immediate vicinity
Wednesday 14th August 2019, London
As interest in urban farming continues to grow, modular, closed-loop production units could spark a horticultural revolution
A growing phenomenon that is reshaping fresh produce supply chains. Shipping containers, the vectors of globalisation that were forged in the first instance to ferry goods thousands of miles around the earth, are now being used to grow fresh produce that will be consumed in their immediate vicinity. What’s more, having made international markets more accessible to all, the containers now house technology so advanced that even someone with the most basic, rudimentary knowledge of horticulture can control and oversee the cultivation within.
Excitement about the potential of urban farming continues to build, with the idea of producing closer to market – using fewer resources and arguably boosting quality in the process – attracting plenty of interest, not to mention investment. Earlier this year, Italian start-up Planet Farms unveiled a plan to build Europe’s largest and most advanced vertical farm by spring 2020 in Cavenago, halfway between Milan and Bergamo. The farm will eventually extend across 9,000m2 and supply 40,000 packs of residue-free produce per day.
It’s a trend that is by no means confined to Europe or North America. In Shanghai, a group called Orisis is working with joint venture Infinite Acres – comprising British online retailer Ocado, Dutch horticultural tech specialist Priva and US plant science firm 80 Acres Farms – to build what it says will be the city’s first indoor vertical farm, producing lettuce and other leafy greens.
However, it’s the arrival of closed-loop, container-based systems, which theoretically allow anyone to become a grower, that could really revolutionise this area of the fresh produce business. In June 2019, furniture retail giant Ikea revealed it was preparing to harvest its first hydroponically grown lettuces and serve them to customers at two of its in-store restaurants in Helsingborg and Malmö. The vegetables are grown under led lights inside specially retrofitted shipping containers using a so-called circular farming system developed by partner company Bonbio. Days later, Swedish supermarket chain ICA announced a similar venture at its Maxi Högskolan store in Halmstad, between Gothenburg and Helsingborg, using a container system called Greenery configured by Boston-based vertical farming start-up Freight Farms.
In this exclusive interview, fresh focus tech speaks to Freight Farms co-founder Brad McNamara about the company’s recent dramatic growth, about the trends he says are driving that expansion and about a future that might eventually see fresh produce cultivation become something that practically anyone with access to a laptop or smartphone can manage and control.
Brad, can you tell us what inspired you and co-founder Jon Friedman to create Freight Farms?
Brad McNamara: We were originally looking at how we could bring food production closer to the urban centre. We were looking at greenhouses, but really it came down to a better way to create accessibility and transparency in the food system. So for us, the idea was to move away from the constraints of a rooftop greenhouse to a more user-friendly model that allows a wider population to grow locally in a particular place. That’s really where it all came from.
Were you involved in horticulture in any way prior to that?
BM: Not specifically, although I had been growing on my own for some time. I got an undergrad degree from Northeastern University in Boston, then an MBA in sustainability and environmental science. Jon’s background was industrial design, so the two kind of married well. The big thing for us was, when we first started the market potential for local, transparent, sustainable, chemical-free was just at the beginning. Everybody was talking about it, but no-one had a solution for how to produce in those ways while increasing the quality and consistency of the supply chain.
The business you created, was it a fairly large operation from the start?
BM: No, at the start it was Jon and I plus a small team, very much your classic startup, starting in a simple parking lot. We knew we needed to build the technology from the ground up with the market and the farmer in mind, and we knew it had the potential to empower anyone to grow food anywhere. We built our first prototypes in 2012 and went into commercial manufacturing in 2014.
To whom did you show this original proof of concept?
BM: Well, anyone that would look in the early days! What we did was grow a wide variety of crops to test the stability and the flexibility of the system, as well as some of the concepts within it. I was constantly bringing people from the produce industry by, so we made a lot of connections with cold supply chain, produce distributors, regional specialists, as well as some of the markets around us. We talked to a lot of the wholesalers and asked them, ‘Is this product ready? or ‘Is this crop specifically what you would look for, or maybe something different?’ That was really the guiding light, to know what the market would accept. The feedback was phenomenal. Much of the time they would say ‘this is fresher, brighter, crisper than anything I’m getting now’ and they got very excited about that.
Were there any areas in which you needed to improve?
BM: Well, once we got the plants in their mouths, there weren’t really any doubts left. You know when you eat something and it’s really good? I think in the early days it was more about general education in the market, in terms of growing crops indoors, hydroponics and all of the more technical pieces which by now have been more established. On the institutional side, the concept of needing to supply more locally grown food was not something we had to explain. They were getting hammered by their customers to provide higher quality, locally sourced, clean, healthy and consistent produce.
Brad McNamara (left) with Freight Farms co-founder Jon Friedman
Around 2012, there was a lot of talk about vertical farming as a concept that might eventually see production centres constructed as entire buildings in cities. Were you aware of this trend bubbling away?
BM: We were right there at the early stage of vertical farming, so we had the benefit of building systems while seeing those conceptual drawings of space-age technology. That was great, because it was almost like watching a sci-fi movie while you’re doing it in real life. Some of those concepts did apply but we had that functional knowledge we needed to satisfy.
Many people at the time said it was science fiction, but we kept very quiet about the fact that we were already accomplishing it with our unit. That made us feel like we were on to something. We were early enough that we were growing, we had customers and we had market insight. Technology for technology’s sake wasn’t going to serve our customers appropriately.
With any transition to a new technology, there can be resistance from certain quarters. Did you encounter any concerns about bringing traditional horticulture into an urban, indoor environment?
BM: What people want to understand is about traceability – where exactly did it come from, who grew it, how was it grown. That’s been the driving question in the conversation, and less about whether it’s grown in soil or not. Indoor-grown, whether in a greenhouse, warehouse or decentralised module is pretty much mainstream at this point.
The full interview with Brad McNamara of Freight Farms is published in Fruitnet's annual fresh produce technology supplement Fresh Focus Tech.
To order your copy, contact subscriptions@fruitnet.com or +44 20 7501 0311.
Part two of this interview will be published on Monday 26 August.
New Life CA Selects AEssenseGrows’ Aeroponic System For Its Socially Conscious Cannabis Business
New Life is a vertically integrated, state-licensed cultivation, distribution and non-store front company based in Oakland, California
The East Bay Cannabis Producer Selected Complete AEssenseGrows Automated System for Precision Cruise Control of Indoor Sterile Grow Environments
SUNNYVALE, Calif., Aug. 12, 2019 -- AEssenseGrows, an AgTech company specializing in precision automated aeroponic platforms for consistent high-yield plant production, announced today that New Life CA, a socially conscious California cannabis company, has purchased the AEssenseGrows AEtrium system for its operations. New Life determined the AEssenseGrows equipment could best deliver the precision and controls needed to grow superior cannabis at its East Bay facility.
“We wanted a cultivation system that was easy to use and provided a great degree of control over and visibility into the grow environment,” said Carlton Williams, founder of New Life. “The cutting-edge AEssenseGrows system meets those requirements with the automation and precision delivered with its revolutionary Guardian Grow Manager software.”
Williams added: “In addition to our own cultivation, New Life is dedicated to fostering opportunities for those in our community considering entering the cannabis industry, and we’ve worked with non-profits to help individuals establish equity requirements and build business plans. I always encourage these budding entrepreneurs to consider an indoor platform like the AEssenseGrows system.”
New Life is a vertically integrated, state-licensed cultivation, distribution and non-store front company based in Oakland, Calif.
The AEssenseGrows AEtrium system delivers cruise-control automation to simplify aeroponics and amplify its inherent benefits. The company's Guardian Grow Manager central management software monitors grow conditions 24/7 and, if needed, automatically adjusts key variables such as lighting, nutrients, and environment to maintain optimal conditions for the grow recipe.
“The AEtrium System can help cultivators achieve breakthrough aeroponic yields and lowest cost of production at the same time,” said Phil Gibson, AEssenseGrows vice president of Marketing. “Whether for large corporation’s or smaller, community-based growers like New Life, we are committed to helping our customers gain a competitive advantage through the integration of plant science and advanced technology.”
About AEssenseGrows
AEssenseGrows (pronounced "essence grows"), founded in 2014, is a precision AgTech company based in Sunnyvale, CA. AEssenseGrows provides accelerated plant growth SmartFarm platforms and software automation delivering pure, zero pesticide, year-round, enriched growth to fresh produce and medicinal plant producers globally. With AEssenseGrows, you can precisely control your production operations at your fingertips from anywhere in the world.
CIT Gaps Funds Invests In Charlottesville, Va.-Based Babylon Micro-Farms
The provider of an on-demand indoor farming service said it will use the investment to expand operations with new hires in product, sale and marketing.
By Michelai Graham / STAFF
A Babylon Micro-Farms' location at Boar's Head Resort in Charlottesville, Va. (Photo via @BabylonMF on Twitter)
The Center for Innovative Technology (CIT) announced that CIT GAP Funds made an investment in Charlottesville, Va.-based Babylon Micro-Farms, provider of an on-demand indoor farming service.
Center for Innovative Technology - VA@CITorg
Very pleased to announce a new @CITGAPFunds investment in Babylon Micro-Farms! @BabylonMF provider of on-demand indoor farming services https://bit.ly/2KOe0Ky #UrbanFarming #MicroFarms #Cville #innovation
"Tech to inspire a new generation of urban farmers" #sustainability #food
See Center for Innovative Technology - VA's other Tweets
Founded in 2017, Babylon provides small growers and businesses with indoor agriculture modules through on-demand farming services using their patented IoT tech. The financial terms of the investment were not disclosed but Babylon said in a press release that it plans to use this investment from CIT GAP Funds to expand their operations with new hires in product, sales and marketing.
Alexander Olesen, co-founder and CEO of Babylon Micro-Farms, said the startup’s idea was born in a University of Virginia (UVA) classroom when he and co-founder Graham Smith were asked by their professor to develop a high impact, low cost product that could help refugees.
“I quickly discovered and became interested in hydroponics, a way to grow plants without soil, use less water, and grow crops faster,” Olesen said in a statement. “Our mission is to develop technology that will inspire a new generation of urban farmers to grow their own fresh, affordable, sustainable produce at the push of a button. We are grateful for the support of CIT GAP funds at this stage of our development.”
The startup provides 24/7 farming support for the patented IoT system that remotely controls the customizable farming ecosystems. Babylon provides farmers with a guide to take them through the indoor farming process. Some of the startup’s customers include a UVA dining hall, The Boar’s Head’s Resort and Corner Juice.
“Being able to grow any kind of produce year round within our communities, such as for local food service industries, education and assisted living, or community farms to name a few, is a game changer for the state of sustainable urban agriculture. CIT is very confident in Babylon’s future success, and we look forward to being part of their journey,” Thomas Weithman, managing director of CIT GAP Funds and president and CEO of MACH37, said in a press release.
Companies: Center for Innovative Technology
Projects: CIT Gap Funds
CEA Food Safety Coalition Creates Board of Directors, Elects Officers And Seeks Members
The CEA Food Safety Coalition, comprised of leading controlled environment leafy greens producers, recently completed the formation of its governance structure and is taking steps to accept new members
By urbanagnews - August 13, 2019
Press Release – New York, NY – The CEA Food Safety Coalition, comprised of leading controlled environment leafy greens producers, recently completed the formation of its governance structure and is taking steps to accept new members. Controlled environment agriculture (“CEA”) is agricultural food production in environments that are indoors (such as in greenhouses and vertical farms) and controlled, providing crops with ideal growing conditions and protection from outdoor elements (such as weather and animals). The Coalition’s objective is to establish food safety standards, educate, and protect consumer health.
The Coalition, a tax exempt 501(c)(6), recently filed its articles of incorporation, adopted bylaws and elected the following individuals as the initial members of its board of directors: Michele Kubista (Revol Greens), Paul Lightfoot (BrightFarms), Christopher Livingston (Bowery Farming), Daniel Malech (Plenty), Marc Oshima (Aerofarms), Jack Seaver (Plenty), and Paul Sellew (Little Leaf Farms).
In addition, the Coalition elected the following officers:
Board Chairman – Paul Lightfoot (BrightFarms)
Acting Executive Director – Jack Seaver (Plenty)
Board Vice Chairman – Marc Oshima (AeroFarms)
Board Secretary – Christopher Livingston (Bowery Farming)
Board Treasurer – Paul Sellew (Little Leaf Farms)
Until the position is filled permanently, Jack Seaver of Plenty will serve as Acting Executive Director.
“The growing methods in our industry are different as compared to field-grown produce,” said the Coalition’s Chairman Paul Lightfoot. “This coalition provides an opportunity for all brands in the space to collaborate to further protect consumers by establishing standards and sharing insights.” “This is a critically important step in maintaining consumer confidence and supporting the growth of our industry,” he added.
“We frequently get questions from growers and buyers as to what food safety means in a CEA environment” said Dr. Jennifer McEntire, vice president for food safety at United Fresh Produce Association. “We look forward to helping the coalition develop appropriate food safety standards for this growing segment”
The Coalition is developing an enrollment process for admitting new members. All leafy greens growers employing controlled environment methods (including hydroponics, aquaponics and aeroponics), and who are willing to submit to third party food safety auditing, are encouraged to join the Coalition.
Interested parties can contact membership@ceafoodsafety.org. In addition, the Coalition seeks great candidates for a permanent Executive Director, and welcomes applications at info@ceafoodsafety.org.
Netled Oy And Astwood Infrastructure Collaborate To Build Industrial Scale Vertical Farms Worldwide
Netled Oy, Finnish specialists in vertical farming systems and greenhouse lighting solutions, have signed a long term frame
7th August 2019 by johannak
Netled Oy, Finnish specialists in vertical farming systems and greenhouse lighting solutions, have signed a long term framework agreement with Astwood Infrastructure to supply equipment for industrial scale vertical farms.
The agreement covers an initial four such farms, based predominantly in the UK, to be delivered over the next three years and provides a framework for serving global customers. The total value of the agreement, including all project options, reaches over 10 million euros. The rapidly growing vertical farming market has been predicted to grow to 10 billion USD by 2025.
Niko Kivioja, CEO, Netled Oy, confirmed: “We have been developing our technology for vertical farming for several years now. During this time the market for vertical farming has developed very fast. Now the technology and the economic figures are in the point, where industrial scale vertical farms beat the traditional ways to grow leafy greens. Green field projects require quite massive design work for infrastructure. We are more than happy to present our partner, Astwood Infrastructure. Together we have possibility to serve global market with an all-inclusive project offering.”
Netled designs, manufactures and sells world leading technology, equipment and related automation and software for vertical farming, where its vertical farm Vera® is the most advanced vertical farming system in the world.
Astwood Infrastructure is a technology company with a focus on sustainable design and engineering. The company has significant know-how in commercialising technologies. For vertical farming, the company has developed its own brand, Vertivore, based on 3 years’ worth of research into the sector. Astwood will be working with specialist technology providers like Netled to build a position as a market leading operator and supplier of vertical farm solutions.
Photo: Niko Kivioja, CEO of Netled (on the left) and Mike Capewell, CEO of Astwood Infrastructure.
A pilot facility, the first under the framework, is built and is in continuous use in Redditch, UK. The long term focus of Netled and Astwood is on industrial scale growing. The production volumes are planned to be millions of heads of lettuces and herbs annually.
Mike Capewell, CEO for Astwood Infrastructure, added: “We are incredibly excited about our new agreement with Netled Oy and the opportunity we now have in building and scaling a UK wide and potentially global vertical farm operation. Our pilot farm has shown some incredibly exciting results and we feel optimistic that we will be able to replicate this success at scale.”
“As issues like rising import costs and climate change continue to advance, vertical farming systems will become critical to production, where, through the Vertivore brand, we will be able to grow sustainable, local and clean produce without being impacted by any external sources such as weather conditions or pollution.”
Closed vertical farming systems, like the one currently being piloted by Astwood, are protected from extreme weather conditions, pollution and lack of freshwater resources as the growing conditions are created artificially. As a result, vertical farming makes cultivation possible in areas where production of traditional vegetables is impossible, and the freshwater resources are limited, whilst also improving quality, production speed and yield.
For more information, visit:
MEDIA CONTACT:
Netled Oy
Niko Kivioja CEO, Netled Oy
+358 50 3608121
niko.kivioja@netled.fi
Astwood Group
Hannah Haffield
hhaffield@makemorenoise.co.uk
0121 312 1177/ 07939 468 567
Editor’s Notes
Netled Oy
Netled offers vertical farming systems and innovative greenhouse lighting solutions. Netled’s vertical farms are sold under the brand name Vera®. The world leading technology has already been delivered to multiple producers for commercial use. Netled was founded in 2007 in Finland. It employs 10 multidisciplinary experts. For more information, please visit our website www.netled.fi.
Astwood Infrastructure
Astwood Infrastructure Limited is operating at the cutting edge of vertical farming technology. It has, along with specialist technology providers, developed, a sustainable, reliable indoor vertical food production facility that can be located virtually anywhere. For more information please visit our website https://www.vertivore.com/
Autogrow Appoints New Chief Technology Officer
Autogrow has named Jonathan Morgan as its new Chief Technology Officer responsible for continuing development of their innovation utilizing the latest technology, plant biological science and artificial intelligence
August 13, 2019: Autogrow has named Jonathan Morgan as its new Chief Technology Officer responsible for continuing development of their innovation utilizing the latest technology, plant biological science and artificial intelligence.
“We are very pleased to welcome Jonathan to the Autogrow family and look forward to seeing him put his talents to use to deliver world class products and customer experiences,” says CEO Darryn Keiller.
Jonathan brings to the role more than 18 years of commercial expertise in software and integrated technology solutions for customers. Leading teams in product development, continuous improvement and customer experience.
His previous role was as Ventures VP Engineering at EROAD, a global leader in road charging, compliance and telematics services across NZ, Australia and North America.
“I’m excited to join a progressive team like Autogrow who is leading disruptive innovation within the AgTech space and creating new and exciting solutions to help grow food. It’s an area I’m interested in exploring and seeing how we can make positive impacts in the pockets of farmers and on the planet,” explains Jonathan.
Over the past two years Autogrow has doubled their employee number and launched some of the most cutting-edge solutions for indoor growing including the first API (Application Programming Interface), the first SDK (Software Development Kit), the first indoor agtech hackathon – #CropsOnMars, and most recently the integrated farm management platform FarmRoad.
“It’s been a busy two years and we are only set to become bigger with more innovative solutions for farmers. Jonathan’s appointment will ensure that we continue to push forward within CEA (Controlled Environment Agriculture), an industry that is evolving at a rapid pace,” says Darryn.
Jonathan will begin his role 18 September and will be based at the Autogrow Head Office in Auckland, New Zealand.
AUDIO: Mounting Investor Interest In Agricultural Technology
As the earth warms and the world’s population grows, more and more companies are growing food indoors in greenhouses and vertical farms
Carole Zimmer
JulY 31, 2019
Investors are paying close attention to the rapidly growing sector that is agricultural technology, or ag-tech.
As the earth warms and the world’s population grows, more and more companies are growing food indoors in greenhouses and vertical farms.
Although demand is increasing, this segment of the agricultural industry faces high costs of both labor, energy costs and equipment, for things like lighting.
Lead image: Angela Weiss/AFP/Getty Images