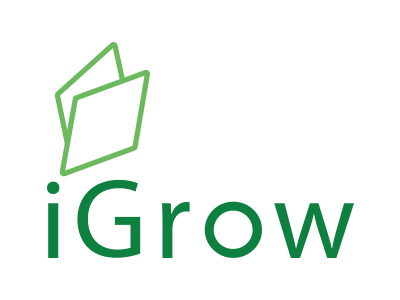
Welcome to iGrow News, Your Source for the World of Indoor Vertical Farming
USA: This Colorado Company Is Building Farms In Shipping Containers To Help Feed People In Need
FarmBox Foods wants people to be able to farm anywhere, allowing them to access fresh food they otherwise wouldn't be able to
Author: Jeremy Moore
April 19, 2021
FarmBox Foods Wants People To Be Able To Farm
Anywhere, Allowing Them To Access Fresh Food
They Otherwise Wouldn't Be Able To
SEDALIA, Colo. — A three-year-old Colorado company has an ambitious goal: to bring food security, safety, and sustainability to communities in need around the world.
FarmBox Foods aims to achieve that goal by connecting those communities to sustainably sourced food that's grown locally inside one of their container farms.
Their first product was a vertical hydroponic farm, or VHF, built inside a shipping container.
The company has since developed a second product: a gourmet mushroom farm, or GMF.
So far, customers in Colorado include Centura Health, Vitamin Cottage Natural Food Markets, and the C Lazy U Ranch in Granby.
FarmBox CEO Rusty Walker and COO Jake Savageau joined 9NEWS to talk about how they hope to change the way the world thinks about farming.
9NEWS also spoke with a prospective customer of FarmBox, Cori Hunt of the Denver restaurant group Edible Beats.
(Editor’s note: Responses have been edited for context and clarity.)
As a mission-driven company, what is the mission of FarmBox Foods?
Walker: Our goal and our mission is to get our products out into the communities where we can help develop food security programs. We’re looking to get into food deserts, opportunities where folks in the world might not have access to good, clean nutritional food. And so we kind of strive as a company that’s driven to feed the world one container at a time. And we’re ready to go out and manufacture thousands of these if we can.
We’re able to decentralize growing food by being mobile – being able to deploy these by just having a semi come in. We can then lift it up on a flatbed and take it to anywhere in the world. We’ve got two containers going to islands. We’ve got our first container that took off for the island of Jamaica. It’s going to Montego Bay where it’s going to be used behind mega marts on the island. And then we have another container which is our gourmet mushroom farm that’s going to be going to Tahiti where they’re going to be using that to feed the island population which does not have access to that type of food.
One big area that we’re really focusing on is the urban areas throughout the U.S. where they don’t have a lot of land to grow. These farms can go right into the parking lots, behind a church for example. We’re working with a community church on the south side of Chicago that’s looking at placing two of these containers – a vertical hydroponic farm and a mushroom farm – right outside in the parking lot outside the church.
And we think we could bring an educational spin to this where we can have the community grow their own food and supply the community themselves with highly nutritional food that ordinarily they just would not be able to get their hands on. So, we’re thinking that if this pilot program goes well this would be an application that would apply to every inner city throughout the U.S.
Farmbox Foods grows vegetables in shipping containers. Credit: Jeremy Moore, KUSA
Savageau: The mission’s always been to create products that are for the decentralized food insecurity industry. So, we want to create a product that can be deployed anywhere in the world, can run off-grid, and can feed communities. So, we have two different products – the VHF and the GMF. Every product that we develop gets us one step closer to being able to feed a community with everything they need, because you can’t feed communities forever just on leafy greens.
So mushrooms, they’re more nutrient dense, that gets us one step closer. There’s other products that we’re going to develop to get us to that point. But, I think the mission for the company is to be able to deploy these farms into communities where they’re needed, whether that’s a rural area, a food desert in the U.S., an inner city, or somewhere in Africa like Ghana or the Sudan.
We want to align with big ag and we want to help the industry get better. So we want to get food to where it’s needed. We’re looking at doing stuff with food insecurity and food inequality. That’s big with what we’re doing. So, that kind of aligns with our mission. If you look at our food system – just take for instance – you know if you look at a SNAP program or food subsidy program – you’re taking food and giving it to somebody or they’re purchasing it.
But, a lot of that food that they’re purchasing is processed, sugar – I mean, it’s poison. And if you go on a military base anywhere in the U.S., there’s fast food on the base. It’s really what you see. So, there’s a lot of reasons why we’re doing this I think. We can help fix our food system. And we can help educate the youth on how they should eat. We’re doing some stuff with an Inuit community in Alaska. They don’t necessarily know how to fix this food or prepare it or use it. So, I think education is a big part of what we’re doing.
How do these container farms work?
Savageau: When people think of farms, they don’t think of agriculture like this. Vertical hydroponics and indoor ag and controlled environments – it’s been around for a long time. I think that the way that this one works is pretty simple. The water gets fed into a tube system and the water trickles down and goes back into the tank. And where you’re standing – the seedling tray area – the water goes into a tank, into the seedling trays, gets flooded, and then back into the tank.
There’s a software that we use called Agrotech that monitors the temperature, the humidity, the lights – basically, all automated. So, it’s fairly easy to run. You need about 15 to 20 hours a week to run one farm. The GMF farms takes about 25 hours a week. It’s a little bit more intensive. The VHF is the vertical hydroponic farm and that’s the farm that we’re standing in. The GMF is the gourmet mushroom farm, which is the one that you went through earlier. You want to just keep things as clean as possible. The cleaner that you keep it the better it’s going to run.
So, we have a standard SOP, you know, that we implement with our training. Cleaning the floors. Cleaning the tubes. You don’t clean them every time. But, usually, every couple harvests you’ll take the tubes out, wash them out. You’re cleaning the tanks about every 60 days.
But, on average it’s pretty easy to maintain if you’re doing the daily checklist. The seeds are going to be in the seedling tray for about two weeks. Then, they go into the wall. And then they get harvested about 60 days after they start in the seedling tray. So, on average you’re about 60 days from seedling to harvest depending on what you’re growing.
And this farm is really setup for vertical hydroponics. So, it’s leafy greens. You can do hundreds of different types of lettuce. You can do cherry tomatoes, strawberries and peppers. There’s a lot of different things that you can grow in here. Most of our clients are only growing a couple things at one time. You don’t have to worry about weather. You don’t have to worry about if this is in a cold climate like the arctic. You know, they can’t grow food. If it’s in a desert, they can’t grow food. If it’s on an island, they can’t grow food. So, these can be deployed anywhere. And they grow 365, all day, every day. Also, the yield is very high for the square footage. So, you can put these on top of a building, inside of a building. It only takes up 320-square feet. You don’t have any pesticides. So, you don’t have to worry about pests, bugs, mildew, stuff like that’s going to effect the plant as it’s growing. It’s also decentralizing the food system.
So, you’re not having to ship food hundreds of thousands of miles from point A to point B. So, the food is right there. And the nutrients that we use are organic plant-based nutrients. And there’s no pesticides. So, the nutrient density is extremely high compared to something that you would buy – even organic – in a store.
Walker: We grow a variety of vegetables and lettuces. I believe that we’re somewhere in the area of 30 to 40 different types of vegetables and lettuces that we can grow in our farms. And, then of course we’ve got our gourmet mushroom farm which we’re currently growing anywhere from eight to nine different varieties of mushrooms. We’re in the startup phase of running that farm ourselves. So, we’re exploring the different types of mushrooms that we can grow. But, we’re very proud of the folks that are actually running these farms – our staff, very knowledgeable and they do a great job. We’re going upwards to 300 to 400 pounds a week now. We’re not competing with traditional farming. We’re actually a compliment.
Who are your customers?
Walker: One of our first customers is Centura Health. They purchased their first container – which is now sitting at St. Mary’s in Pueblo. They ordered two more containers after seeing how the first container behind their hospital worked. We actually started up a pilot program with Centura Health where we’re now running them as the FarmBox family.
We’re working with Centura Health in identifying not only their hospitals and the patients who are going to be fed through our vertical farm – but then we’re also identifying where the food deserts are and Centura Health will then help us with what we’re going to be growing, and then the communities that we’re going to be serving from those, those particular crops.
We do have a couple that’s looking at doing some farming right here in Sedalia. They’re going to use it to supplement their traditional farming, which will be an interesting pilot program for us to work with them on. We’re working with C Lazy U Ranch out of Granby, Colorado. They’ve ordered a hydroponic farm and we’re going to be manufacturing that. And they’re going to place that at the ranch. They don’t really have access to a lot of good food as far as having it grown right there on the property. So, this will be a nice compliment to the services and the customer experience that they provide their customers by having one of our farms right on site.
Centura Health is one of FarmBox Foods' first customers. Credit: Jeremy Moore, KUSA
One big area that we’re really focusing on is the urban areas throughout the U.S. where they don’t have a lot of land to grow. These farms can go right into the parking lots, behind a church for example. We’re working with a community church in the south side of Chicago that’s looking at – we’re looking at placing two of these containers – a vertical hydroponic farm and a mushroom farm right outside in the parking lot outside the church.
We can have the community grow their own food and supply the community themselves with highly nutritional food that ordinarily they just would not be able to get their hands on. So, we’re thinking that if this pilot program goes well this would be an application that would apply to every inner city throughout the United States.
Savageau: We have a customer here in Lakewood that’s going to put one in their backyard. They run a small organic farm. We’re looking all the way up into federal government and military, and everything in between.
So, Rusty was talking about FEMA, the UN, UNICEF, those are the big customers that take a long time to build a relationship with. And then we have customers that are all the way down to just an individual that wants one for their property or maybe a couple of people are going to run one for a restaurant or a developer wants one for a small development that he’s doing.
We’re working with a group in New Mexico and they’re building a huge development of about 45,000 houses. So, we’re talking about 100 of these units that are going to be deployed in that area right outside Albuquerque to feed those communities within that area over the course of about two years. We work with a grocer that’s regional. And we work with some other customers that are kind of at a government, federal government level.
I think we’ve done a lot in the last three years. I mean we haven’t gone out and raised any capitol. So, we’ve self-funded it. And I think from that point of view you know we’ve done a lot. We’re kind of at the point right now where we’re just starting to scale. So, we’ve just started our social media. You know SEO (search engine optimization), SEM (search engine marketing). We have a sales team. And orders are starting to come in. We’ve partnered with RK which is manufacturing our units. That’s giving us the ability to scale. Because before that we were building these one or two at a time in Sedalia and now we can build 100 of them. So, that’s really been a huge part of us being able to scale is the manufacturing side.
How much does it cost to purchase and operate the farms?
Jake: This VHF farm – vertical hydroponic farm – starts at $140,000. The GMF starts at $150,000. Then, you have training and deploy, getting it there. So, usually, you’re over $150,000 for a farm. So, your ROI (return on investment) in this product is going to be about 12 months to 24 months depending on what you’re growing and where it is in the world.
The GMF is going to be closer to 12 months because mushrooms tend to be more expensive – again – depending on where it’s going. We have a unit that’s going to Tahiti for example. That ROI is going to be extremely fast because they ship everything in. If there’s a market for mushrooms there, which there is with a grocer, it’s going to be quick. So, the cost of running it with labor and everything you need to grow the plants, usually around $20,000 to $40,000 a year. We’re a mission-driven company. So, money isn’t the first thing that’s important. We want to build a certain amount of these and then every x amount that we build, we build one for free and we send it to a community that maybe our social media has engaged with or given us an idea that ‘hey, this would be a good community.’ And then, we send it there. We pay for it. We train people. And that’s something that we want to do. We can’t do it yet. But, I think that’s coming in the next year.
Why is Edible Beats interested in working with FarmBox?
Hunt: We try to be as local and organic as possible and that’s what brought us here to FarmBox. We can put a box behind a restaurant and have lettuces cut and washed and put on the plate the next day.
Just to have that connection with our food and know exactly where it’s coming from and how it was produced. It’s going to be better quality because it’s not traveling. It’s not ripening in a truck coming from Mexico. Economically, what we can do to not pay the mileage on the vehicles and the gas, the inputs, the emissions, the extra packaging, the plastics.
That’s one of the best things about FarmBox – that what we can do is – if we produce food for our restaurant group – I’m not going to have to buy packaging that’s going to go into a landfill or even need to be recycled. It’ll go directly into the vessels that we’re going to store them in the cooler. We don’t have to worry about marketing and labeling and you know stickers and plastics and all this extra stuff – this hoopla that we don’t need – because FarmBox is a possibility now.
The Farmbox Foods containers allow leafy greens to grow vertically, maximizing space.
Credit: Jeremy Moore, KUSA
We are looking at lettuces and herbs, leafy greens. So yeah, like basils, sage, leaf lettuces, butter lettuces, arugula – these kinds of things that we use that could greatly help our impact. Essentially it’s a self-contained box that you can grow fruits and vegetables in – most likely leafy greens – and it’s a soilless or near soilless medium.
So, essentially you plant your seed in a very small amount of coconut core or soil or peat moss – something to hold the root structure – and that, according to with FarmBox, they’re system is a vertical farming.
So, they have vertical towers and then they put the lettuces in the towers in their small soil medium and then they drip water with enhanced nutrients mixed into the water specifically built for those vegetables. It doesn’t have a lot of soil waste.
For the amount of the surface area you can get way more production out of it and the water that goes through is recycled. Per plant, it uses far less water than any other type of growing system.
RELATED: Why Colorado agriculture groups oppose Initiative 16, an animal cruelty proposal
Foundation Farms Corp., Announces Vertical Farm Out For Delivery
The turnkey farm package has left the ZipGrow manufacturing facility for arrival at the Red Deer area site this week
April 20, 2021
NEW YORK, NY / ACCESSWIRE / April 20, 2021 / Foundation Farms, Corp., ("Foundation Farms") a subsidiary of GME Innotainment, Inc. (OTC PINK:GMEV) today announced confirmation of delivery and installation dates for the first of its many vertical farms. The turnkey farm package has left the ZipGrow manufacturing facility for arrival at the Red Deer area site this week. The installation crew is scheduled to arrive on-site next Monday and assembly and commissioning will be completed next week. Production of the first crop will begin on May 1.
Management is also excited to report that each of the company's vertical farms will become local community food hubs known as E-ROOTS CENTRES. In addition to selling its own vertical farm produce, each E-ROOTS CENTRE will buy other locally grown food products from farmers wholesale and then package, market, and distribute the locally grown food products to corporations, families, schools, restaurants, caterers, sports teams, and stores, maintaining economic growth in the community. These E-ROOTS CENTRES will develop health food brands utilizing local produce to promote nutritious diets. Mechanisms for dispatch and delivery logistics are included.
Ed Kroeker, CEO of Foundation Farms stated, "The installation and startup of our first E-ROOTS CENTRE is a wonderful milestone achievement but what I am even more excited about is the interest we are getting throughout North America from prospective joint venture partners and host communities. Demand is even greater than we anticipated. Projects are aggressively underway in Minneapolis-our important entry point for the United States as well as Regina, the Greater Vancouver Region, and the Greater Toronto Area, with the list of projects growing weekly."
Yves R. Michel, GMEV CEO applauded the milestone achievement this week and further added, "Food sustainability and reliability have become two of the most important goals within North American communities today. Foundation Farms has developed a business strategy that provides the components as well as the assembly, packaging, and distribution systems to achieve those goals in every community serviced by E-ROOTS CENTRES."
Yves R. Michel
Chief Executive Officer and Director
208 East 51st St., Suite 170
New York, NY 10022
Source: GME Innotainment, Inc. ("GMEV")
www.srcorpgroup.com/
Released April 20, 2021
OTCPink:GMEV
This press release may include certain statements that are forward-looking in nature and that involve a number of uncertainties and risks. Such forward-looking statements are within the meaning of that term in Section 27A of the Securities Act of 1933, as amended, and Section 21E of the Securities Exchange Act of 1934, as amended. The forward-looking statements in this press release are based on GME Innotainment, Inc., current expectations and projections regarding future events, which are based on currently available information. The forward-looking statements in this press release may also include statements relating to GME Innotainment, Inc.'s anticipated new developments, business prospects, financial performance, strategies and similar matters. GME Innotainment, Inc. disclaims any obligation to update any of its forward-looking statements, except as may be required by law.
SOURCE: GME Innotainment, Inc.
GME Innotainment, Inc.
USA: FLORIDA - The Villages Grown Passes On Expertise
By Michael Salerno
Daily Sun Senior Writer
April 20, 2021
The intersection of agriculture and wellness is now expanding. The Villages Grown, the community’s farm-to-table initiative, is building on its relationship with the University of Florida through its agricultural, health, and culinary programs. Villages Grown Executive Director Jennifer Waxman recently announced The Villages Grown became the local produce supplier for UF’s campus in Gainesville. Both The Villages Grown and UF’s Institute of Food and Agricultural Sciences
(UF/IFAS) are working together on research concerning controlled-environment agriculture, which involves crops growing in climate-controlled settings for the best possible growing conditions. Waxman described The Villages Grown as a leader in this practice.
She also revealed plans are in the works to train master gardener volunteers from UF/IFAS’s extension office, who would pass on expertise to residents on how to use hydroponic gardening to cultivate nutrient-dense produce.
“This is really going to help us grow the most nutrient-dense crops you can have access to, to strengthen the food as medicine approach,” Waxman said. “The partnership with UF will help extend our educational offerings with health and gardening to fulfill that thirst for knowledge that we don’t have the bandwidth for.”
Fresh and Local on Campus
The Villages Grown’s produce is now a part of the menu offerings of UF’s on-campus dining through a partnership with the university’s Gator Dining Services.
Diners may expect the full line of produce including microgreens, lettuce, herbs, tomatoes, and cucumbers, Waxman said.
“It’s really bridging agriculture, culinary, and health together, which is what The Villages Grown’s model was built after,” she said.
Gator Dining’s partnership with The Villages Grown builds on a food service program that already was Florida-centric.
Its other Florida suppliers include the Hilliard aquaponics facility Traders Hill Farm, Orlando milk factory T.G. Lee Dairy, Ormond Beach plant-based food producer PAOW! and Lake Mary sausage maker Nettles Sausage.
Agriculture Industry Research
The Villages Grown’s position as a leader in controlled-environment agriculture, also known by its acronym CEA, allows it to be at the forefront of research on the subject.
And that’s what’s happening now, as UF/IFAS researchers seek to learn more about the processes involved and whether it’s economically viable for large farms.
There’s a great interest in controlled-environment agriculture in the private sector, said Jeanna Mastrodicasa, UF/IFAS associate vice president of operations. That interest translates to abundant research opportunities with The Villages Grown and other CEA agribusinesses.
“I’d like to see how well it works,” she said. “We simply don’t know well enough about it, most of agriculture in Florida has been in open fields.”
The Villages Grown depends on controlled-environment greenhouses utilizing vertical hydroponics — a process that uses vertically stacked towers to plant and grow more crops on less land — to grow its line of crops.
It also operates a nutrient tank system that sends a recipe of nutrients from a tank in a utility room through a drip irrigation system, said Adam Wright, The Villages Grown’s director of operations.
Waxman described The Villages Grown as the Southeast’s largest controlled-environment agriculture operation of its kind, made possible by the diversification of its crop offerings.
“There’s a lot of large CEAs that only grow lettuce,” she said.
Expanding Education
But people don’t need large greenhouses to grow vegetables and herbs hydroponically.
That’s something Waxman thinks master gardeners could teach residents. She said she’s working with UF/IFAS on training master gardener volunteers about concepts such as hydroponic growing to cultivate nutritious food.
The commercial needs of The Villages Grown don’t allow its staff much time to teach residents about hydroponic gardening. That’s where trained volunteers would come in, Waxman said.
“We want them to be an extension of The Villages Grown and help them get info out to them on their behalf,” she said.
It’s a philosophy echoed by local UF/IFAS staff, who see trained master gardeners as an extension of themselves, on a mission of helping their communities.
“Having volunteers associated, that will be a great part of it,” said Jim Davis, extension director with the UF/IFAS Sumter County Extension Office.
It helps that involvement in the master gardener program historically has been very strong in The Villages, Mastrodicasa said.
“New people to Florida want to learn about what they can grow in Florida,” she said. “There’s so much opportunity. Just the idea you can have more than one growing season in a year is different. Most places in the country have one.”
Building a Healthier Community
The ultimate goal of The Villages Grown and UF’s expanding relationship is simple: building a healthier community.
That may mean supplying the freshest and most nutrient-rich vegetables possible, or teaching people how they can grow them themselves.
It also explains why The Villages Grown develops blends of microgreens for hospitals, for example, to help those suffering from cardiovascular issues, Waxman said.
For The Villages Grown’s staff, relationships like those with UF make it possible to cultivate nutrient-dense produce in an affordable and accessible way, Waxman said.
“You can’t be a lone ranger,” she said. “Or you’ll be out of business.”
Senior writer Michael Salerno can be reached at 352-753-1119, ext. 5369, or michael.salerno@thevillagesmedia.com.
Lead photo: The Villages Grown assistant director of production, Rachel Skiles, checks the tomato plants to make sure everything is on track inside a greenhouse at the facility. Michael Johnson, Daily Sun
Feeding A City From The World’s Largest Rooftop Greenhouse
The world’s largest rooftop greenhouse is in Montreal, Canada. It measures more than 15,000m2 and produces more than 11,000kg of food per week. The company behind it had to hire 200 new employees due to pandemic-driven demand
The New Greenhouse Will Accelerate Lufa’s Mission To Grow Food
Image: REUTERS/Mariana Bazo
20 Apr 2021
Senior Writer
The world’s largest rooftop greenhouse is in Montreal, Canada.
It measures more than 15,000m2 and produces more than 11,000kg of food per week.
The company behind it had to hire 200 new employees due to pandemic-driven demand.
Can you grow enough produce for an entire city in rooftop greenhouses? Two entrepreneurs in Montreal, Canada, believe it might be possible.
Lauren Rathmell and Mohamed Hage cofounded Lufa in 2009. The company has four urban gardens in the Canadian city, all in rooftop greenhouses. Lufa’s most recent sits on top of a former warehouse and measures more than 15,000m2 – larger than the other three greenhouses combined. Its main crops are tomatoes and aubergines, producing more than 11,000kg of food per week. It is, the company says, the largest rooftop greenhouse in the world.
Lufa says its new rooftop greenhouse in Saint-Laurent, Montreal, is the largest in the world. Image: Lufa
An ambitious goal
Rathmell says the new greenhouse will accelerate Lufa’s mission to grow food where people live and help it to meet an “ever-growing demand for fresh, local, and responsible foods”.
The company – which says it’s not trying to replace local farms and food makers, acknowledging that not everything can be grown on rooftops – follows what it calls ‘responsible agriculture’ practices. These include capturing and recirculating rainwater, energy-saving glass panels, and an absence of synthetic pesticides. Any waste is composted and reused, and food is sold directly to customers on the day it is harvested. Lufa also has a fleet of electric vehicles to make those deliveries.
“Our objective at Lufa is to get to the point where we’re feeding everyone in the city,” Hage said in an interview in Fortune. Lufa’s fifth greenhouse is due to open later in 2021.
At the moment, Lufa grows food for around 2% of the city’s population. While that might sound like a modest proportion, interest in urban agriculture is on the rise. Presently, agriculture in urban areas tends to be more common in developing countries. But the UN Food and Agriculture Organization (FAO) favours an increase in urban agriculture, saying it can have “important benefits for food security”.
Urban farming is often more common among poorer members of society. Image: UN FAO
A growing global trend
Urban agriculture has been taking off in other parts of the world in recent years, too – from shipping containers in Brooklyn, New York City, to allotments in unused spaces in Brussels, Belgium.
And at 14,000 m2, there’s Nature Urbaine in Paris – which claims to be the world’s largest urban rooftop farm. Nature Urbaine rents out growing space to Parisians who want to grow their own crops. Tenant farmers pay around $450 per year per 1m2 sized plot. They get a welcome pack with everything they need to start growing, as well as regular access to the Nature Urbine gardening team who are on hand to offer advice and support.
Lufa produces more than 11,000kg of food per week, including tomatoes and aubergines. Image: Lufa
Lufa’s first greenhouse was opened in 2011, in Montreal’s Ahuntsic-Cartierville borough, to grow herbs, microgreens, cucumbers, and peppers. Two more were added in 2013 and 2017, with the fourth joining last year. It sits on top of a former Sears warehouse in the Saint-Laurent area of the city.
In addition to its own produce, Lufa also sells a selection of other locally made or grown food, including bread, cheese, and drinks to its customers. Rising demand for its service, in the wake of the pandemic, led to the company hiring an additional 200 people, and partnering with 35 new farmers and food makers.
Have you read?
This Belgian start-up allows anyone to become an urban farmer
This illuminated field isn't just pretty - it's helping to grow crops
Grow your own: Urban farming is flourishing during the coronavirus lockdowns
License and Republishing
World Economic Forum articles may be republished in accordance with the Creative Commons Attribution-NonCommercial-NoDerivatives 4.0 International Public License, and in accordance with our Terms of Use.
POLAND: The Only Way Is Up! Puławy Vertical Farm First In Europe To Supply Beauty And Health Industries With Plant Extract From Herbs
Vertigo Farms, located in the Puławy Science and Technology Park in the east of Poland grows 11, 000 plants on an area of 300 square metres using 4 metres high metal constructions resembling shelving units, a capacity which would require an area 100 times larger if using a traditional farm
BLANKA KONOPKA
APRIL 20, 2021
Established by the husband and wife team Anna and Dawid Drzewiecki after their observations of where different plant extracts came from in cosmetics and natural supplements, the company’s innovation is based on their unique form of production, combining the growth of plants and the production of extracts in one place.
An ‘experimental’ start-up has become the first in Europe to utilize a vertical farm to both grow herbs and produce plant extracts for the beauty, health, and pharmaceutical industries.
Vertigo Farms, located in the Puławy Science and Technology Park in the east of Poland grows 11, 000 plants on an area of 300 square metres using 4 metres high metal constructions resembling shelving units, a capacity which would require an area 100 times larger if using a traditional farm.
Vertigo Farms grows 11, 000 plants on an area of 300 square metres using 4 metres high metal constructions resembling shelving units, a capacity which would require an area 100 times larger if using a traditional farm. CC BY 4.0
Established by husband and wife team Anna and Dawid Drzewiecki after their observations of where different plant extracts came from in cosmetics and natural supplements, the company’s innovation is based on their focus on vertical farming for the cosmetics and pharmaceutical industry as well as their unique form of production, combining the growth of plants and the production of extracts in one place.
The two-processes of growth and production have hitherto been separate in other companies in the same field, with sites often large distances apart.
Dawid Drzewiecki told Puls Biznesu: “Our idea was to shorten the supply chain and make it independent of logistics.
The process starts from seeds which are first kept under lamps and with constant access to water before they sprout.Vertigo Farms/Facebook
“These needs were strongly highlighted by the pandemic. Last year, there were delays in production due to difficulties in transport due to closed borders.
“More importantly, climate change is more often disrupting the production of plants, which our method of cultivation enables us to avoid.”
The farm, which is the only vertical farm in Poland focusing on delivery to the cosmetics and pharmaceutical industry, currently produces three plant types: basil, coriander and bakuchi, the latter being a herb from Asia often used as a substitute of retinol, a popular ingredient used in anti-ageing and acne creams.
Plants are grown under violet lamps with the continual monitoring of various indicators.Vertigo Farms/Facebook
The process starts from seeds which are first kept under lamps and with constant access to water before they sprout when they are transferred to the 4m units whose shelves are comprised of gutters with peat plant pots where plants are grown under violet lamps with the continual monitoring of various indicators.
The plants are then picked, dried, and passed through a machine to extract extracts from them for use in creams, oils, and dietary supplements. The whole process requires the service of just four people.
The ambitious company, which sees themselves as filling a niche due to the small number of companies producing plant extracts for the cosmetics, health, and pharma sectors, has big expansion plans.
The oil from plants grown on vertical farms.Vertigo Farms/Facebook
Earlier this year, it signed an important deal for innovative vertical farming technology with a leading Finnish company specialising in the building of vertical farms.
The technology will enable the company to experiment with tropical plants and to grow a wider variety of herbs.
Their aim is to expand to 10-20 plant types by 2022-2023.
TAGS: TECHNOLOGY, START-UP, STARTUP, HERBS, PHARMACY, PLANTS, FARM, VERTICAL FARM, VERTIGO FARMS, DAWID DRZEWIECKI, ANNA DRZEWIECKA
Nature Fresh Farms Introduces New Program For Their Imperfect Produce
The Waste Me Nots program was recently created to leverage Nature Fresh Farms Tomatoes, Peppers, and Cucumbers that do not meet the criteria of their Quality Control team
Leamington, ON (April 13, 2021)
A recent loss-conscious program focuses on selling Nature Fresh Farms imperfect produce to reduce food waste.
The Waste Me Nots program was recently created to leverage Nature Fresh Farms Tomatoes, Peppers, and Cucumbers that do not meet the criteria of their Quality Control team. As most greenhouses hope to grow flawless quality produce, some product grows to be naturally bent or smaller in size. Although unique in shape and size, these vegetables still have the same nutritional value and flavor as their perfect counterparts. Nature Fresh Farms wants to put these pieces of produce in the spotlight, creating more of an opportunity to fight waste and give shoppers further access to nutritious foods.
‘We believe it’s important to ensure that nutritious and delicious produce does not go to waste,” shared Ray Wowryk, Director of Business Development. “By creating this program, we are helping our retailers with a ready-made waste reduction alternative.”
Since volume of this type of product is not predictable, the program cannot be guaranteed to supply specific quantities and will depend on the product grown. However, Nature Fresh Farm feels that the unpredictability is outweighed by the fact that their quality and freshness is worth rescuing and sharing with consumers, making the most of all their product grown.
“Sustainability is at the center of everything we do at Nature Fresh Farms. Not only does this encompass our packaging and growing processes but also that the food we grow gets utilized completely,” explained the Director of Sales, Matt Quiring. “The Waste Me Nots program helps us to reduce waste while allowing us to better service the price-focused shoppers looking for quality tasting products at a discounted price and let our retail partners bring in some incremental sales to the category.”
Nature Fresh Farms wants to bring more cost-effective options to its consumers and bring the focus back to the taste and freshness of the produce, not solely the look of it. They hope to break the cycle of imperfect food waste by offering discounted misshapen vegetables that there would normally not be a market for and expand the consumer’s knowledge of the type of produce they purchase.
-30-
About Nature Fresh Farms
Continuously expanding, Nature Fresh Farms has become one of the largest independent, vertically integrated greenhouse vegetable farms in North America. As a year-round grower with farms in Leamington, ON, Delta, OH, and Mexico, Nature Fresh Farms prides itself on consistently delivering exceptional flavor and quality to key retailers throughout North America, while continuing to innovate and introduce more viable and sustainable growing and packaging solutions.
SOURCE:
Nature Fresh Farms | info@naturefresh.ca T: 519 326 1111 | www.naturefresh.ca
FDA’s Warning Shot For Leafy Greens
I hope it will serve as a call to urgent action that gets to the root of the problem of the persistent presence of dangerous E. coli in the growing environment for leafy greens and other fresh produce
On April 6, the Food and Drug Administration fired an unmistakable warning shot at the leafy greens industry. I hope it will serve as a call to urgent action that gets to the root of the problem of the persistent presence of dangerous E. coli in the growing environment for leafy greens and other fresh produce.
Carefully using the regulatory language in its produce safety rule (21 CFR 112.11) and citing the recurring nature of the E. coli hazard in the Salinas and Santa Maria growing area, FDA declared the recurring strain implicated in the 2020 outbreak to be a “reasonably foreseeable hazard,” which FDA attributed to the presence of cattle on land adjacent to growing fields.
This finding seems obvious and shouldn’t be surprising. The surprise, however, is that FDA used regulatory language to express its finding and spelled out the implications: farms covered by the FSMA produce safety rules “are required to implement science and risk-based preventive measures” to minimize the risk of serious illness or death from the E. coli hazard.
Make no mistake, however, FDA’s message is aimed not only at farms but at every entity involved in the commercial production, processing, and sale of leafy greens coming from the California Central Coast Growing Region. The message is that, without effective preventive measures, such leafy greens are in violation of federal food safety regulatory standards.
I do not anticipate FDA taking judicial action to enforce its April 6 finding, absent egregious practices or clear negligence in a particular leafy green growing situation. I do see, however, a heightened sense of urgency at FDA and frustration that efforts to date have not solved the leafy greens safety problem. I share that frustration.
Fifteen years ago, the disastrous spinach outbreak caused by E. coli O157:H7 was linked by the Centers for Disease Control and Prevention (CDC) to run-off from nearby grazing land. Since then, we’ve had outbreak after outbreak associated with E. coli in leafy greens and other fresh produce. And the outbreaks are just the tip of the public health iceberg. The federal government estimates that 60 percent of all food-related E. coli O157:H7 illnesses are associated with fresh produce. The vast majority of these illnesses are not part of an identified outbreak.
The E. coli outbreaks and illnesses persist despite a lot of hard work by a lot of people in the leafy greens industry, researchers, the California Department of Food and Agriculture (CDFA), the FDA and its federal partners. Stop Foodborne Illness, the organization of illness victims and their families whose board I co-chair, works with the California LGMA on the common cause of strengthening food safety culture in the leafy green industry. We also advise the Leafy Greens Safety Coalition, a group of leading retailers working to strengthen safety practices. I have participated in the California Agricultural Neighbors Workgroup convened by CDFA Secretary Karen Ross. So, I know serious people are at work on the problem.
What then is the urgent call to action? What do consumers expect of the leafy greens industry, especially those individuals and families who know first-hand the devastating human impact E. coli infections can have? What does the public health demand?
At one level, the answer to all three questions is the same. The leafy greens industry and all those across the leafy greens supply chain and in government should be doing urgently everything they reasonably can to minimize the now well-known risk posed by E. coli O157:H7. According to FDA, the law requires no less. Certainly, this includes prevention measures within the leafy greens production system, such as strict implementation of rigorous water quality and irrigation standards, improved compost management, sanitation of harvesting equipment, and pre-harvest test-and-hold programs.
But the prevention strategy must go deeper. Modern food safety best practices dictate that prevention should begin at the root of the problem. As long as leafy greens are grown outdoors in the vicinity of cattle operations, I believe the food safety problem will persist until the shedding by cattle and the release of dangerous E. coli into the environment is minimized at its source. Effective vaccines are available. Changed feeding practices have promise. Perhaps containment measures can reduce risk.
The experts need to determine what combination of measures works best, but it is clear that no responsible food manufacturer would today deem it acceptable to produce food in an environment in which dangerous bacteria are being released or are present on a sustained basis. The same principle should apply to leafy greens and other fresh produce grown outdoors.
The important difference, of course, is that the leafy greens producer has no direct control over the source of the hazard. And the cattle producer isn’t responsible for where leafy greens are grown. That is why FDA Deputy Commissioner Frank Yiannas calls for “industry leadership and collaboration among growers, processors, retailers, state partners and the broader agricultural community,” including cattle producers.
I am glad FDA is sounding the alarm, but I know from experience that the kind of leadership and collaboration that is urgently needed is easier said than done in an industry and government structure that is notoriously fragmented and often works in silos. And the obstacles to solving the problem are not just technical. They include the need for creative solutions on such matters as who pays for interventions needed in cattle production to make leafy greens safe.
But too much is at stake for all concerned to let such obstacles stand in the way. Now is the time for leaders from all across the commercial value chain and government to act together, with greater urgency, to get to the root of the problem and prevent it.
Mike Taylor
About the author: Mike Taylor is co-chair of the board of the non-profit consumer advocacy group Stop Foodborne Illness, which is a 25-year-old group supporting and representing foodborne illness victims and their families in efforts to keep other people from getting sick. Before that Taylor served as FDA’s Deputy Commissioner for Foods and Veterinary Medicine from 2010 to mid-2016. His first tour in government began as a staff attorney at FDA, where he worked on seafood safety and nutrition labels. Later Taylor worked for USDA’s Food Safety and Inspection Service, where he became acting under secretary for food safety. Taylor was the government official who, after the deadly 1992-93 Jack in the Box hamburger outbreak, ruled that the pathogen E. coli O157:H7 is an adulterant in meat. Taylor also practiced law in the private sector.
(To sign up for a free subscription to Food Safety News, click here.)
Finland: College Grows Strawberries Indoors
The Kainuu college makes use of Netled's technology for the growing facility. Their technology takes care of the HVAC and lighting solutions
At the Kainuu Vocational College in Finland, strawberries are cultivated under LED lights in the school's warehouse. Kari Komulainen, CEO of Peuraniemen Taimitarha gives a farm tour. Ever since 1996, Peuraniemen Nursery is producing certified strawberry seedlings. In 2002 the company expanded into cranberry seedling production.
Now the company is collaborating with the College to grow strawberry seedlings on multiple levels in a controlled environment. "Strawberries have extremely sensitive roots. That means that in these conditions we have to be able to find the optimal balance between watering and humidity so the plants can transpire. As strawberries like lots of light, we noticed that they are lush under LED lights," Kari notes.
The Kainuu college makes use of Netled's technology for the growing facility. Their technology takes care of the HVAC and lighting solutions. "Nature and external conditions do not affect our vertical farm in any way, Kari adds.
Click on the video below to see the complete story.
For more information:
Netled
netled.fi
Publication date: Fri 9 Apr 2021
Author: Rebekka Boekhout
© VerticalFarmDaily.com
“I’m Opting For Localized Franchised Farming”
Natalie, an 18-year-old engineering student, is determined to run her own farm in the future. It all started with finding a research project . . .
Engineering student wants to start her own farm in New Jersey
“In the States, the food system is so inefficient both in the way it’s produced, at a massive scale and in terms of quality,” says Natalie Radu. "The problem is that consumers are left in the dark. They don’t know what pesticide is used on the food they’re eating. GM foods are not labeled. Let aside the waste this industry has.” Natalie says that many don’t have access to healthy food. When walking around in the Bronx for instance, on the lookout for a grocery store, it’s so much easier to buy a pack of soda for half the price of fresh produce.
‘Localized franchised farming’
“McDonald's is known for real estate. If only we could do a Wholefoods / McDonalds franchise where customers could walk in and snip off lettuce, directly available to consumers. I’m opting for localized franchised farming. I have been trying to figure out a location in terms of real estate, but, from the perspective of a small business, New Jersey and New York prices are very high. I would have to start out in a place that’s cheaper on average. However, I would definitely apply for grants to fund the initial infrastructure for the farms."
Natalie Radu in action on her channel
Natalie has her passion for writing and her engineering study to her advantage when starting a farm. “I think because of this intersection I will be able to work with the science and also have the ability to convey that science. I can make the lettuce we’ll be growing feel personal for someone that’s in their own house, miles away or even across the world. That’s the biggest thing, you have to get people excited about vertical farming, at least as excited as you are. However, when it comes down to engineering I’m going to need some help.”
“My family immigrated from Moldova to the US around the collapse of the Soviet Union,” says Natalie. “My grandparents used to grow several fruits in the backyards and my affection for farming started right about there, it’s in my blood.” Natalie, an 18-year-old engineering student has been determined to run her own farm in the future. It all started with finding a proper research topic, which turned into her biggest passion nowadays.
As Natalie’s based in New Jersey, she is surrounded by several vertical farms. She wanted to pass by some farms near her to visit and stumbled upon Good Feeling Farms. Eventually, Natalie was able to do an internship at Good Feeling Farms to get a better understanding of every aspect of a vertical farm, from seeding to growing to harvesting. Good Feeling Farms is a New Jersey-based wholesale micro greenery that specializes in microgreens and hydro lettuce. The farm is run by a team of three, taking care of the cultivation and harvesting process.
Inside Good Feeling Farms' growing facility
Ever since her internship, Natalie is determined to run her own farm in the future. She currently runs a YouTube channel, where she experiments with indoor hydroponics. She recently spoke at a local TEDx event about the inefficacies in traditional food production and distribution systems.
Natalie says: “I’ve tried many growing conditions for plants and I think you can grow them under many different conditions. You have to work with your circumstances. Ideally, your indoor garden would be sustainable. The growth mediums could be sanitized and reused to lessen waste. Besides being water-efficient, vertical farming really shines in the areas of automation and data science. The ability to collect and analyze plant data constantly and instantly modify environmental factors has massive potential for produce cultivation as we know it.”
For more information:
Natalie Radu
natlydrad@gmail.com
Publication date: Fri 15 Jan 2021
Author: Rebekka Boekhout
© VerticalFarmDaily.com
Hydroponics In The GCC - History And Emerging Trends
During World War II the shipping of fresh vegetables to overseas remote islands was not possible; and also feeding the soldiers, where troops were stationed. They couldn’t be grown in the soil. Then, Hydroponic technology was tested as a viable source for fresh vegetables during this time
K.V.Bhaskar Rao
Grower - Hydroponics Specialist,
Consultant, Mentor, Faculty,
Trend Setter And Speaker
During World War II the shipping of fresh vegetables to overseas remote islands was not possible; and also feeding the soldiers, where troops were stationed. They couldn’t be grown in the soil. Then, Hydroponic technology was tested as a viable source for fresh vegetables during this time. US Air Force built one of the first large hydroponic farms on Ascension Island in the South Atlantic, followed by additional hydroponic farms on the islands of Iwo Jima and Okinawa in the Pacific, using crushed volcanic rock as the growing medium and, on Wake Island west of Hawaii, using gravel as the growing medium. These hydroponic farms helped fill the need for a supply of fresh vegetables for troops stationed in these areas.
The American Army and Royal Air Force built hydroponic units at various military bases to help feed troops. In 1952, the US Army's special hydroponics branch grew over 8,000,000 lbs. of fresh produce for military demand. Also established at this time was one of the world's largest hydroponic farms in Chofu, Japan, consisting of 22 hectares. History says that in 1945 during the II world war, the US Air Force built large hydroponic facilities in Habbaniya in Iraq, Bharain and the Persian Gulf, to support troops stationed near large oil reserves. So, we know that hydroponic cultivation of vegetables was prevalent during that time in the Middle East and GCC.
Climate change, water stress & environmental degradation are affecting large populations around the world & represent a major threat to international hunger, human security & wellbeing. Technology development, implementation, indigenization to suit local conditions (labour and capital) along with skill development for personnel is the key to the success of agriculture in a rapidly urbanizing world. Based on predicted population growth and urbanization, food and water demand will create greater challenges by 2050. The world will be required to produce more food, with less water and a declining rural workforce.
Urban agriculture (CEA which includes hydroponics/ rooftop/ aquaponics/ aeroponics) is the new culture that is catching up everywhere and more in the GCC. We do have far too many participants in this industry who have too little actual crop production knowledge and / or experience. This challenge can be met with training/skill development to generate employment and food security with rational use of resources and thus producing safe, healthy & nutritious food. Educate individuals and companies to the new farming technology as innovation and capacity building is the only accelerators to this new endeavour.
Increasing awareness regarding the risks of consumption of contaminated food is a driving demand for crops and vegetables that are cultivated in a safe and controlled environment. Hydroponic plants are an ideal choice in this scenario as hydroponic systems eliminate the need for soil, which is where pathogens incubate. Moreover, the increasing rate of urbanization in developed regions is expected to cause a major shift towards a preference for hydroponic vegetables. Consumers with changing tastes are willing to pay a premium for an assortment of produce offering freshness, quality, flavour, safety, and convenience. Young and affluent Western food-loving consumers are driving the growth and demand for imported foods in the Middle East.
Locally grown vegetables, indigenous/ native herbs, microgreens, wheatgrass, salad greens, and the concept of “farm to fork” are becoming increasingly common in the marketplaces of GCC. Thanks to alternative agricultural practices such as hydroponic farming. Most GCC countries are now taking definite steps towards being self-sustainable with certain food items that often are served at the dinner table. RTE salad mix or even the snacking section like cherry tomatoes, baby carrots, and the likes are hitting the hypermarket shelves.
Many Arab countries rely heavily on groundwater to meet their water requirements for economic and social development, such as Saudi Arabia, Oman, Jordan, and Libya, with more than 80% groundwater dependence. Even in countries with the relative abundance of surface water such as Syria, Egypt, and Iraq, which have flowing rivers, reliance on groundwater is increasing due to growing demand for water – sometimes due to up streams’ control of flow. Groundwater is facing depletion in many GCC countries, which threatens its sustainability and the existence of the sectors that depend on it.
Hydroponics in the GCC has the following “cut above the rest” pointers to establish long-term investment benefits in all ways. It is a “win-win” situation for all the stakeholders.
* Huge potential in areas with poor arable land like the Middle East. You do not have to use "New Technology" it is Proven.
* Offers the chance to Grow food 12 months of the year even in warm climates. Increased Yields - more product is grown and harvested per M2.
* A huge reduction in the quantity of water currently used in the food chain, reduction in the use of fertilizers and energy currently used to produce food.
* Opens immediate employment opportunities in harvesting, retailing, and distribution, thus, stimulates new markets locally and nationally.
* Satisfy local demand = less imports = greener solution thus zero carbon footprint. Increased turnover of produce - crops grow faster and more often.
* Harvesting takes place at a more comfortable height - no bending over and better ergonomics. Promote more favorable working conditions.
* A healthier crop using fewer pesticides provides health benefits to the consumer. Improved Quality of Yields - more nutritionally sound and therefore tastes superior.
* Complete control over nutrient balance - controlled growing creates a healthier crop.
* Closed recirculation irrigation system conserves water. Nutrient solutions may be re-used in other areas.
Few parameters that would enhance and enable the growth potential in this sector can be achieved by the following. 1. Single window clearances, without stringent regulations on the import of soil conditioners, hydroponic grow media (cocopeat), Plant Protection Chemicals (PPC), Seeds, grafted cuttings, rooted plants, tissue-cultured saplings, and all planting materials to enhance diversity and try incorporating new species for cultivation to feed the local population.
2. Create “Local” or locally grown stamp to help leverage local farmers for direct entry into co-operatives, supermarkets etc. First preference to locally grown produce.
3. Create “ugly produce” sections for local growers only (as unflavorable local weather conditions or other reasons lead to visual imperfections but with the same taste and nutritional values).
4. All local farms mandatory to adopt Global GAP methods of cultivation to ensure safe & hygienic food, instead of so-called “organic”. Training and educating farmers and cultivation labour to ensure food safety.
5. Source all farm-related services for infrastructure development like greenhouses, irrigation systems, cooling systems, indoor vertical farms, LED/grow lights etc from locally approved vendors – economy
gets stronger and remains within the country. According to a report, food consumption in the GCC is expected to grow at 4.2% CAGR, with cereals leading the regional numbers. A quick rundown of the fastest-growing categories, per country:
* Kuwait’s fastest-growing market is Fruits, at a 7.9% CAGR.
* Oman’s fastest-growing market is Dairy, at a 6.1% CAGR.
* Saudi Arabia’s fastest-growing market is Dairy, at a 5.7% CAGR.
* UAE’s fastest-growing market is Fruits, at a 5.3% CAGR.
* Qatar’s fastest-growing market is Meat, at a 3.7% CAGR.
* Bahrain’s fastest-growing market is Cereal, at a 3.5% CAGR.
With a booming population growth, expected to increase 6.5 million by 2021, and shifting demographics, some key trends are unlocking new opportunities in the market:
* Youth heavily exposed to western diets drive a growing demand for international foods.
*The rise of working women led to growth in ready and packaged meals.
* A more tech-savvy population open new opportunities in retail, with advancements in e-commerce and new outlet concepts such as hypermarkets and food trucks.
* With some of the highest overweight population rates in the world, all GCC countries are looking at healthier products. n
Email: kazabhaskar@gmail.com
April 2021 Floriculture Today
USA: New Farm Brings Sustainable Farming To Northern Michigan
There's a new farm in northern Michigan that provides fresh and local produce all-year-round using environmentally friendly practices and high-tech resources. The container is home to Pine Hill Farms, a farm that uses a controlled environment agriculture system to grow produce
by Miya Ingle
April 16, 2021
To View The Video, Please Click Here:
Pine Hill Farms uses a controlled environment agriculture system to grow produce. (Miya Ingle/ WPBN)
KALKASKA COUNTY, Mich., (WPBN/WGTU) -- There's a new farm in northern Michigan that provides fresh and local produce all-year-round using environmentally friendly practices and high-tech resources.
If you're driving down Tower Road in Kalkaska, you might notice a big container.
The container is home to Pine Hill Farms, a farm that uses a controlled environment agriculture system to grow produce.
The produce is grown hydroponically instead of in the ground.
Staff at Pine Hill Farms say this growing method uses 95% fewer resources than traditional farming.
"Some of the biggest benefits to growing hydroponically versus in a traditional manner is number one; we can grow year-round, 365 days a year," Pine Hill Farms Founder Jeff Bickley said. "Number two, we're hyperlocal. Local is a really big deal. People want to support local businesses. They also benefit from the difference in freshness."
Pine Hill Farms is currently growing nine different kinds of lettuce but plans to expand its products in the future.
The farm is connecting with local restaurants to sell its produce to.
Early Bird Registration Now Open For In-Person Orlando 4-5, 2021 Edition
We're excited to return to our live, in-person format for the October 4-5, 2021 edition of the premier event for indoor|vertical farming and look forward to seeing all of our industry friends again!
Indoor Ag-Con
INDOOR AG-CON IS LIVE FOR 2021...
EARLY BIRD REGISTRATION IS, TOO!
We're excited to return to our live, in-person format for the October 4-5, 2021 edition of the premier event for indoor|vertical farming and look forward to seeing all of our industry friends again!
SAVE WITH EARLY BIRD REGISTRATION RATES!
EVERYTHING YOU NEED TO GROW YOUR BUSINESS
UNRIVALED EDUCATION
CEO keynotes. Well-rounded panel discussions. Take a deep dive into 3 comprehensive track topics: Business & Marketing, Science & Technology, Alternative Crops.
SEE SCHEDULE
EXPANDED EXPO FLOOR
Explore a show floor filled with industry innovations, breaking trends, and best-sellers from some of the biggest names in the indoor agriculture | CEA industry and emerging leaders, too.
EXHIBITORS
A BUSINESS VACATION!
Ready to get back out there?! Centrally located, our fabulous Hilton Orlando venue is the perfect place for a business vacation - and we've got some great hotel discounts for you, too!
HOTEL SAVINGS
BEST VALUE FOR YOUR TIME & MONEY!
We're so confident you will benefit from your experience that we guarantee your registration fee! Get your money's worth... or get your money back! This guarantee covers your registration fee but not travel, hotel, or any other expenses incurred. Learn more...
REGISTER NOW & LEARN MORE!
YOUR PASS INCLUDES
Access to all conference sessions and exhibition floor
Cocktail receptions
Lunch Daily
Access to Indoor Ag-Con Library
Mobile App
SPECIAL THANKS TO OUR INDOOR
AG-CON SPONSORS,
MEDIA & MARKETING ALLIES
Indoor Ag-Con, 950 Scales Road, Building #200, Suwanee, GA 30024, United States
Podcast: On How High-Tech Hydroponic Leafy Greens Are A Revolution To The Industry
Jake Counne, founder and CEO of Wilder Fields, joined Steve Alexander to discuss how high-tech hydroponic leafy greens are revolutionizing the food and farming…
Jake Counne, founder and CEO of Wilder Fields, joined Steve Alexander to discuss how high-tech hydroponic leafy greens are revolutionizing the food and farming…
Sustainable Impacts Indoor Farming May Have On Environment
This article identifies the potential environmental effects large-scale indoor farming may have on air, water, and soil. We begin with an overview of what indoor farming is with a focus on greenhouses and indoor vertical farms (eg, plant factories)
Mar 18, 2021, | Knowledge Base, Learning, Research Paper
By Center of Excellence
Figure 1. Map of research and knowledge domain of indoor farming.
Abstract
This article identifies the potential environmental effects large-scale indoor farming may have on air, water, and soil. We begin with an overview of what indoor farming is with a focus on greenhouses and indoor vertical farms (eg, plant factories). Next, the differences between these 2 primary methods of indoor farming are presented based on their structural requirements, methods of growing, media, nutrient sources, lighting requirements, facility capacity, and methods of climate control. We also highlight the benefits and challenges facing indoor farming. In the next section, an overview of research and the knowledge domain of indoor and vertical farming is provided. Various authors and topics for research are highlighted. In the next section, the transformative environmental effects that indoor farming may have on air, soil, and water are discussed. This article closes with suggestions for additional research on indoor farming and its influence on the environment.
Citation
Stein EW. The Transformative Environmental Effects Large-Scale Indoor Farming May Have On Air, Water, and Soil. Air, Soil and Water Research. January 2021. doi:10.1177/1178622121995819
Introduction
Open field farming has been practiced the same way for centuries as the primary means of growing food. Its origins can be traced back to wheat production 11 000 years ago in the Middle East, which later spread to the Mediterranean, North Africa, and elsewhere.1 Given limitations on the amount of arable land, water scarcity, increased awareness of sustainable development, and the well-documented environmental effects of open-field agriculture, other farming methods have been developed in the past few decades. The primary alternative to open field farming is referred to as indoor farming, which has received relatively little attention in terms of environmental impacts. The goal of this article is to introduce indoor farming in its many forms to environmental scientists, outline key areas of research, and highlight the effects large-scale indoor farming could have on the environment. Research needs to be done to better understand the cumulative and transformative environmental effects indoor farming methods may have on water, air, and soil as it realizes its potential to supply a significant portion of the population with fresh food.
What Is Indoor Farming?
Indoor farming is a relatively new method of growing vegetables and other plants under controlled environmental conditions. These farm systems are variously referred to as indoor farms, vertical farms, vfarms, zfarms, greenhouses, controlled environment agriculture (CEA), and plant factories.2,3 Indoor farms are sometimes confused with urban farms, which typically represent small outdoor farms or gardens to grow vegetables that are located in urban areas. It also should be noted that mushrooms have been grown indoors in compost under controlled conditions without light for more than one hundred years.4 For the purposes of this article, we will focus on characteristics of controlled environment indoor vertical farms and greenhouses, which are the primary architectures used for the large-scale production of leafy greens and other vegetables that require natural or artificial light.
The many faces of indoor farming
Greenhouses have been the workhorse for indoor growers for decades, especially in the production of flowers and ornamental plants. The modern high-tech greenhouse designs were pioneered in the Netherlands and have since been embraced all over the world. Several examples of these farms are evident throughout the United States and the largest span hundreds of acres. For example, according to Greenhouse Grower,5 Altman Plants (CA) has almost 600 acres under glass followed by Costa Farms (FL) with 345 acres. These are mainly used in the production of ornamental plants.
For vegetables, greenhouses were originally designed for tomatoes but now are used in the production of kale, microgreens, lettuces, herbs, squash, and other types of fresh produce. These greenhouses, formerly located in rural areas, are now being positioned near urban and peri-urban areas to bring operations closer to population centers to save money and reduce the carbon footprint associated with transportation miles. For example, BrightFarms (brightfarms.com) has greenhouse operations located just outside of Philadelphia and Cincinnati to produce lettuces and other leafy greens. Gotham Greens (gothamgreens.com) situated its first greenhouse on top of a warehouse in Brooklyn, NY and has since expanded to other cities. AppHarvest (appharvest.com) is a venture located in Kentucky whose greenhouses cover more than 60 acres to produce tomatoes and other vegetables. What is common to greenhouse design is that all growing takes place on a single level, they are clothed in materials such as glass that transmit natural sunlight, and include climate control and irrigation equipment. They may also use a modest amount of supplemental artificial lighting during winter months.6
Growing leafy greens and other plants in buildings has emerged in the past 25 years whereby plants are grown vertically and hydroponically using artificial lights. Indoor vertical farms are typically located in warehouses or similar structures that have been retrofitted to provide superior heating, ventilation, and cooling (HVAC) for the benefit of plant production and racking systems to support the production systems.7-9 The PVC grow systems transport nutrient-rich water to the root zone of the plants, and the water is then returned to the main reservoir. Designed as closed re-circulating systems, indoor vertical farms only use a fraction of the amount of water as greenhouses or open-field methods (see also section “Water Use”). The advent of cost-effective LED lighting technologies has allowed farmers to provide the plants with just the right wavelengths of light, intensity, and photo-period to optimize growth.10 Other advances include automation, IoT, and artificial intelligence; ie, all of the information technologies that contribute to “smart farming.”11
Although modern LEDs are very efficient compared to HID, high-pressure sodium, or florescent lamps, the capital and operating costs of these artificial lighting systems are significant,10 as are the climate control systems that are also required. Greenhouses, for example, require significant investment in heating and cooling equipment to maintain stable temperatures and humidity, which results in significant operating costs in buildings with low R-value membranes (eg, glass). The chief benefit of this design is that the light comes free, although growing is limited to a single level. Indoor vertical farms, however, can benefit from well-insulated structures that reduce heating and cooling costs and growing can take place on multiple levels. That said, these savings come at the expense of relatively high electricity usage for artificial lighting.10 These operating costs can be mitigated with the increasing efficiencies of LED’s, sensing systems that modulate light to the maximum required for the plants, pairing indoor farms with renewable energy sources such as solar and geo-thermal, and architectures that favor energy efficiency.9
Methods of indoor farms
Indoor farms are characterized by several parameters:
Growing Method and Media
Source of Nutrients
Lighting Requirements
Facility Capacity
Climate Control
Economics
Most indoor farms use hydroponic methods of growing; i.e, plants are grown in water. Seeding takes place in an inert material such as stone-wool or peat, which is irrigated with nutrient–rich water. Water is administered using a variety of techniques ranging from fine mist sprayers (aeroponics), to shallow water (NFT) irrigation, to deep water culture (DWC) immersion to flood and drain methods.9 All are effective and have their pros and cons. Nutrients for larger-scale hydroponic production systems typically come from dissolved salts that ionize in the water. In some smaller systems, the nutrients come from the nutrient-rich water of fish farms (ie, aquaponic systems) that are proximate to and coupled with the plant production system.
In greenhouse production facilities, most lighting comes from the sun, which may be supplemented with artificial light, especially in the northern latitudes during winter. Plant factories and vertical farms, however, use only artificial lighting but are designed to maximize growing area using stacking methods. One common design is characterized by horizontal multi-tier growing systems starting at ground level that may include up to a dozen growing levels or tiers. Aerofarms (aerofarms.com) and Bowery Farms (boweryfarming.com) use this type of design for their production processes. An alternative is to use vertical drip irrigation grow systems. This design is characterized by vertical multi-site growing systems starting at ground level that extend upwards of 8 ft. In these systems, plants grow “sideways” toward artificial lights that are positioned at a right angle. Plenty, Inc. (plenty.ag) uses systems like these obtained in the acquisition of Bright Agrotech. Several examples of vertical farming ventures can also be found in Al-Kodmany.
All indoor farming methods share the characteristic of offering CEA. Controlled environment agriculture offers the grower complete control over several environmental variables including, but not limited to: light intensity and wavelength, photo-period, wind velocity, temperature, and humidity. Water culture is further managed to obtain optimal results based on nutrient levels, PH, and dissolved oxygen.9,12 In most cases, pesticides and herbicides are eliminated. More advanced farms such as Fifth Season (fifthseasonfresh.com) benefit from extensive use of sensors, IoT, robotics, automation, and control systems designed to optimize yields and minimize labor. Another valuable aspect of CEA farms is their ability to produce plants with certain desired morphologies and nutritional profiles based on the control of lighting wavelength, temperature, and nutrient levels. Sharath Kumar et al13 go so far as to suggest that with CEA, we are moving from genetic to environmental modification of plants.
Benefits and challenges of indoor vertical farms
Several benefits are associated with vertical farming,9 although the industry is not without its challenges (see Table 1). The principal sustainable benefits of indoor vertical farming are a large reduction in the use of water (see also section “Water Use”), the reduction or elimination of pesticides, and mitigation of the effects of excess fertilizer run-off. From an economic perspective, the ability to control the environment results in a stable supply chain, price stability, long-term contracts with distributors and retail markets, and high yields per square foot. The elimination of pesticides puts produce grown this way on par with organics, which command premium pricing. Indoor farms, if designed correctly, can reduce labor costs and may be located closer to urban centers. Some see a role for indoor farms to ameliorate food deserts, unemployment, and as a means to re-purpose abandoned buildings and lots.3,9,14-16 Finally, vertical farms provide resilience to climate change, flooding, droughts, etc.
However, the vertical farming industry is facing some key challenges. For instance, currently only a very small portion of fresh vegetables are produced indoors. The one exception is the mushroom industry, which represents a US$1.15 billion industry.17 Second, the USDA does not clearly identify vegetable production by method; eg, greenhouse, open field, vertical farm, etc, so data are not readily available. Third, profits have been elusive, especially for vertical farms.18 According to the 2019 Global CEA Census Report only 15% of shipping container farms and 37% of indoor vertical farms were profitable vs. 45% for greenhouse operations.19 Another limitation of indoor farming is that a relatively small number of cultivars can be grown using indoor farming methods.
The primary ones are leafy greens, herbs, microgreens, tomatoes, and peppers, although berries, root vegetables, and other more exotic plants are being trialed.19 Another challenge for indoor farm start-ups are the high capital costs, which can range from US$50-150/ft2 for greenhouses to US$150-400/ft2 for vertical farms. For example, AppHarvest had to raise over US$150 million to fund its 60-acre greenhouse complex.20 Aerofarms raised US$42 million for a 150 000 ft2 vertical farm,21 which equates to over US$280/ft2. Cosgrove22 further reports that access to capital is impeding the growth of indoor farming, especially for smaller farms. One reason that indoor vertical farms are not easily profitable is that they have to compete against conventional farms, which still enjoy a cost advantage.
As a result, indoor farms typically price product toward the high end and along the lines of pricing for organics,2 which limits market penetration. The 2 major factors contributing to the high costs of indoor and vertical farm operations are energy10,23,24 and labor, which account for nearly 3 quarters of the total.2,24 Despite these challenges, venture capital continues to pour money into indoor farming and agtech in the hopes of driving cost down and maintaining growth. Dehlinger25 reported that US$2.8 billion was invested by venture capitalists in Agtech companies in 2019.
Finally, the industry is struggling to share knowledge, establish standards, and create best practices, although progress is being made. For example, the Center of Excellence for Indoor Agriculture established a “Best in Class” award for growers and manufacturers (indoorgacenter.org). Indoor Ag-Con (indoor.ag) and the Indoor Agtech Innovation Summit (rethinkevents.com) hold online events and annual conferences to help promote knowledge sharing. Several specialized industry news outlets now exist including Vertical Farm Daily (verticalfarmdaily.com), Urban Ag News (urbanagnews.com), iGrow (igrow.news), Hortidaily (hortidaily.com), AgFunder Network (agfundernews.com), and others.
Read more >>>
Keywords: Indoor farming, vertical farming, vfarm, zfarm, plant factory, water, air, soil, sustainability, carbon cycles, drought, information technology, greenhouse gases, climate change, environment, agtech
Polygreens Podcast Episode 22 -Jenn Frymark From Gotham Greens
In this episode, Joe and Nick interview Jenn Frymark from Gotham Greens
In this episode, Joe and Nick interview Jenn Frymark from Gotham Greens
Green produce starts with green decisions. Gotham Greens indoor farming facilities are sun (and wind) powered, and climate-controlled for a year-round growing season. This means they can provide clean, sustainable, and quality food to the communities. Any time, anywhere.
Robotic Warehouse Farms Will Save The World
The theory behind CEA is that by controlling the environment in which it grows, we can control everything about a plant and what it grows into by micro-tweaking one of a thousand different characteristics―including temperature, humidity, light duration, light wavelength, dissolved oxygen in the water, and carbon dioxide saturation in the air
by Elle Griffin
Four years ago, Ritch Wood was looking for a better way to grow plants. As the CEO of global skincare company Nu Skin, he ran into ingredient shortages every winter when fields went dormant―and when he moved grow operations to the equator he ran into water and land shortages, along with a host of quality control issues.
Nu Skin needed reliable, quality ingredients for their skincare products. But farming was too unpredictable an industry. “If there was a way to grow indoors,” he thought, “and be able to do that 24 hours a day, 365 days a year―if we could guarantee that it was grown without any herbicides or pesticides and in a sustainable way that uses less water and land―that would be really helpful.”
At the time, controlled-environment agriculture (CEA) was in its infancy and grow-light technology had yet to take a turn for the more affordable. When he learned of an agricultural system that promised to use a fraction of the land and water used by traditional agriculture methods and had the potential to make it more affordable, Wood made an investment.
Nu Skin paid $3 million for 70 percent of the company and rights to its IP―and Grōv Technologies was born.
Grōv grass grown in the Olympus machine at the Bateman Mosida Farms. Photo from Grōv Technologies
Controlled-environment agriculture is on the rise
The theory behind CEA is that by controlling the environment in which it grows, we can control everything about a plant and what it grows into by micro-tweaking one of a thousand different characteristics―including temperature, humidity, light duration, light wavelength, dissolved oxygen in the water, and carbon dioxide saturation in the air. By tweaking the growing cycle, we can control the caloric content as well as the nutrient content and density of the plant.
“What we’ve learned through controlled-environment agriculture,” Benjamin Swan, co-founder and CEO at Sustenir in Singapore, once told National Geographic, “[is] we can actually emphasize certain characteristics of the plants. So, without using GMO, we can make our kale softer, we can actually make it sweet.”
The theoretical use cases for this technology are endless―from being able to grow in places where water is scarce (like in much of Africa), or where water is overly abundant (like Hawaii), or in places where labor is scarce (like in parts of Asia), or even in places that have long winters (like Northern Europe). Theoretically, we could have grow towers in every town and feed the whole of it no matter its natural environment.
We could even grow those foods to those cities’ exact nutritional needs―more vitamin D-rich foods in wintery places, for example. Dr. Lee Mun Wei, a senior manager at the Food Innovation and Resource Centre (FIRC) in Singapore aims to predict and prevent illness in a given population by tracking their biometric data using Apple watch-like wearables, then 3D printing nutrient-specific foods that could mitigate imbalances.
Though these technologies exist, they are still in their infancy. Singapore leads much of the research and development out of necessity. With limited land and water resources, the county is forced to import 90 percent of their food and 40 percent of their water from outside the country. As a result, they have no option but to grow vertically and desalinate water from the ocean.
Elsewhere, the industry has been slow to catch on, largely due to exorbitant startup costs, low returns, and lack of urgent need. According to a 2017 State of Farming report by L.E.K., only 27 percent of indoor, vertical farms are profitable compared with 50 percent of container farms and 75 percent of greenhouses. But one thing has spurred the industry on in recent years: cannabis.
Legalized in 39 states, demand for cannabis has created a $13.6 billion industry and enough capital to fund CEA-enabled grow operations. “When you have a crop that fetches up to $2,400 or $2,500 a pound, you need to be able to dial everything in and make it consistent and repeatable,” says Dashiel Kulander, co-founder and CEO at Boojum Group. “If the temperature swings five to 10 degrees on a cannabis plant, that will change the plant’s various cannabinoids. The goal is to create a medicine that is consistent batch after batch.”
It’s only recently that there has been some financial incentive to use CEA technologies for food use―largely driven by Big Ag players hoping to hedge out the competition. Berry farming giant Driscoll’s, for one, led a $500 million round to fund Plenty, a 2.2-acre vertical farm in California they hope will help them fulfill a contract with Albertsons. The Ingka Group, for another, led a $100 million round to fund AeroFarms, a 2.4-acre vertical farm in New Jersey that will help them fulfill a contract with Singapore Airlines.
Grōv tent at the Bateman Mosida Farms. Photo from Grōv Technologies
Grōv Tech is building CEA prototypes in Utah
By investing in Grōv Tech, Nu Skin hopes to do something similar, getting ahead of the supply chain that fuels their skincare products before the competition can beat them to it, or before climate change makes traditional methods more difficult, all while shoring up technology that could provide a farming model that is more sustainable―if only it were more economical.
“The purpose was always, can we build a better product for Nu Skin?” Wood says. “We think there’s a huge story around the ingredient sustainability, and there were a lot of ingredients we felt we could grow, but the challenge was: could we do it in an economical way?”
Grōv Tech started out with a prototype: a tower that pairs hydroponic growing technology with grow lights. But like all CEA startups, a lot of the growing process was manual and the technology was prohibitively expensive. To make something that was scalable and profitable the whole thing needed to be automated and it needed to be cheap.
With this goal in mind, Wood decided they would start by growing animal feed for Bateman’s Dairy farm. Having grown up on a dairy farm himself, Wood figured this would allow the company to scale the product while refining and automating the technology to the point that it could be replicated. And all of this would have a fortuitous effect on Nu Skin’s bottom line.
“One of our bestselling products is a weight-loss protein powder which uses whey protein,” Wood says. “So again, a very nice connection there is if the animal is eating a more sustainable product and producing better milk with better protein and it’s being done in a sustainable way―certainly that can be a benefit to Nu Skin down the road.”
One year into feeding the 20,000 animals at Bateman, the company has learned a lot. For instance: cows need a lot of magnesium, but they don’t like eating it. Now, Grōv Tech puts magnesium in the water so it’s directly absorbed into the plant and then becomes bioavailable to the cow upon eating it. And because the growing process only takes seven days, data scientists can analyze the results in real-time and adjust the components to optimize production for the next batch of feed.
According to Grōv Tech president Steven Lindsley, it’s not far off that we’ll be looking at milk production (butter, fats, and proteins) and optimizing a herd’s diet for taste, quality, and nutritional value―not to mention the wellbeing of the animal. We’ll be able to look at how many trips from the veterinarian an animal gets when they’re fed certain nutrients in their diet, and whether they can have more calves and produce the same amount of dairy on less, better quality feed. (So far, the answer to this last question is yes. When animals are fed better quality food they need less of it―just like humans.)
And if we hook all of the cows up to robotic milking equipment and connect everything to artificial intelligence, machine learning, and the Internet of Things―Lindsley’s far-flung goal―then we might be able to collect enough data to not only feed cows to their optimum health and performance ability, but humans too. And that could have ramifications not only for feeding the world, but nourishing it― just like Dr. Wei hopes to do in Singapore.
“Last year was about starting to feed animals and get data and prove out the hypothesis we have while continuing to perfect the technology and get confidence there,” Wood says. “And now we’re really to a point where we’ve got data that proves that it works and that financially it’ll be a good thing for a farmer. So now we can really take that proposition to farmers and start to scale.”
Olympus Tower Farm at Bateman Farms in Mosida, UT. Photo from Grōv Technologies
CEA technology could feed the world
Right now, Grōv Tech is focused on refining its technology right here in our own backyard. But once they do that, the plan is to expand internationally.
“Saudi Arabia has actually passed a law where you cannot use water to grow fodder or feed for animals, so all of that now has to be imported. China imports one-third of their alfalfa feed for their dairy animals because they don’t have the capability of growing it,” Wood says. “So there are countries that will probably benefit more than the US would. But we’ve got to refine the technology and get that built to where it’s ready to scale before we start spreading ourselves all around the globe.”
CEA technology is just getting started. Like the Tesla Cybertruck, we have a working concept that promises a more-than-Jetson’s-level future many of us can see the benefits of and actively want―it’s just not quite available to the masses yet. But with more than a billion dollars invested in the technology in just the past few years alone―we’re getting there. And the “there” we are heading toward is rosy indeed.
“To put it in perspective, one tower that is about 875 square feet on the ground will replace 35 to 50 acres of land,” says Lindsley. “And that will feed the animals on roughly five percent of the amount of water. The UN says that that the world will add about 2.5 billion people in the next 30 years. And we have to find a way to feed them on arguably less arable land and water. The good news is the technology is coming along to help solve that equation.”
If COVID-19 taught us anything, it’s that our food supply chain is fragile. But that’s only because our supply chain was built to grow food in California, refrigerate it so it stays fresh, then transport it 1,500 miles so we can eat a salad in the winter in Chicago. In the future, that might not be a thing. “We’re having a dry year now,” Lindsley tells me in February. “But a year ago we were in a blizzard, and even in the middle of a blizzard in February in Utah, we’re pumping out fresh, beautiful, safe green grass for animals. It’s a paradigm shift.”
“Four years ago it was a good idea,” Wood tells me of his company’s investment in CEA technology, “But four years from now it’s going to be required.”
Elle is the editor-in-chief of Utah Business and a freelance writer for Forbes, The Muse, and The Startup. She is also a literary novelist and the author of a weekly newsletter called The Novelist.
Learn more at ellegriffin.com.
MALAYSIA: Turn Empty Spaces Into Urban Farms To Grow Food
WITH the Covid-19 pandemic highlighting the importance of food self-sufficiency, it is probably time for Malaysians to turn empty urban spaces into farms. Urban farming is the practice of cultivating, processing and distributing food in or around urban areas
17 Apr 2021
WITH the Covid-19 pandemic highlighting the importance of food self-sufficiency, it is probably time for Malaysians to turn empty urban spaces into farms. Urban farming is the practice of cultivating, processing, and distributing food in or around urban areas.
Although our country is rich in natural resources, we are still highly dependent on high-value imported foods. Currently, our self-sufficiency level (SSL) for fruits, vegetables, and meat products is 78.4%, 44.6%, and 22.9% respectively.
With a lower occupancy rate in both retail and office space after businesses folded due to the pandemic, property owners could perhaps be induced into redeveloping their buildings for urban or vertical farming. This is being done in Singapore with tremendous success.
According to the National Property Information Centre (Napic), the occupancy rate for shopping malls in Malaysia has dropped steadily for five consecutive years, declining from 79.2% in 2019 to 77.5% in 2020, the lowest level since 2003.
And, according to the Valuation and Property Services Department (JPPH), the occupancy rate for privately-owned office buildings is lower now compared to the pre-pandemic era.
Aquaponics, a pesticide-free farming method that combines aquaculture (raising fish) and hydroponics (growing plants without soil), would be one of the ways forward in food production. In aquaponics, the nutrient rich aquaculture water is fed to the hydroponic-grown plant.
This method of farming could be the economic livelihood for many, particularly the underprivileged and disabled communities as well as fresh graduates who are still struggling to secure a decent job.
Sunway FutureX Farm, Kebun-Kebun Bangsar (KKB) and Urban Hijau are examples of good urban farming initiatives in the Kuala Lumpur city centre.
Perhaps Malaysians could adopt Singapore’s approach by setting up aquaponics farming systems on roofs of car parks and opening urban farms in unused buildings.
The vertical rooftop system is another way of increasing our food production capacity. This system requires only a quarter of the size of a traditional farm to produce the same quantity of vegetables. At the same time, it also reduces the need to clear land for agricultural use.
The government should provide incentives for farmers and the relevant stakeholders who are interested in venturing into urban farming. This would enhance the supply and affordability of a wide range of minimally processed plant-based foods, as suggested under the latest Malaysia Economic Monitor “Sowing the Seeds” report by the World Bank.
With the current administration’s laudable commitment to tackling food security issues, this would provide the opportunity for Malaysia to review the current national food security policy by addressing productivity, optimization of resources, sustainable consumption, climate change, and water and land scarcity. By putting greater emphasis on urban farming, the government could encourage farmers to plant more nutritious and higher-value crops.
Given that the involvement of youths in the agriculture sector is only 240,000 or just 15% of the total number of farmers in Malaysia, as noted by Deputy Minister of Agriculture and Food Industries I Datuk Seri Ahmad Hamzah, the Entrepreneur Development and Cooperatives Ministry and Youth and Sports Ministry would need to come up with training programmes and develop grant initiatives to attract the younger generation to farming, in this case urban farming.
These ministries can also work with the Agriculture Department, Malaysian Agricultural Research and Development Institute (Mardi), and Federal Agricultural Marketing Authority (Fama) to develop more comprehensive urban farming initiatives.
The upcoming 12th Malaysia Plan (12MP) would also provide opportunities for the government to turn empty spaces into urban farming. In a nutshell, every Malaysian can do their part to help the country become more food resilient by converting empty spaces into farms.
Lead photo: Vertical farming systems can maximize use of space in an urban context.
AMANDA YEO
EMIR Research
Kuala Lumpur
TAGS / KEYWORDS: Letters & Opinion,
May 18th, 9 am EST - Webinar On How To Invest In CEA With Confidence
Agritecture is hosting a series of webinars, starting with How to invest in CEA with confidence
Agritecture is hosting a series of webinars, starting with How to invest in CEA with confidence. The CEA sector is heating up and is expected to grow 5x over the next 10 years. Investment in CEA has surpassed $2.0B across North America and Europe. Join Henry Gordon-Smith, Founder & CEO at Agritecture, for this 1-hour live webinar to learn more about how to invest confidently in the CEA industry.
How To invest In Controlled
Environment Agriculture With
Confidence
May 18 - 9 am EST
The lineup of speakers include:
Louisa Burwood Taylor, Head of Media & Research at AgFunder
Robert Glanville, Senior Advisor at REG Consulting LLC
Andrew Carter, Co-Founder & CEO at Smallhold
Darren Thompson, CFO at Bowery Farming
Djavid Amidi Abraham, Director Of Consulting at Agritecture
Click Here To Register!
For more information, you can check out our events listing here.
Agritecture
www.agritecture.com
BrightFarms Hosting Virtual Event To Open North Carolina Farm
BrightFarms is one of the latest, announcing that it will be hosting a grand opening of its new state-of-the-art farm in Hendersonville, North Carolina of May 7
April 14th, 2021
- by Lilian Diep
HENDERSONVILLE, NC - As spring creates a new liveliness in the air, companies across our industry are preparing to host events to inspire connection between members. BrightFarms is one of the latest, announcing that it will be hosting a grand opening of its new state-of-the-art farm in Hendersonville, North Carolina of May 7. In addition to industry members, the event will be open to the public and will educate those in attendance about BrightFarms’ vision to scale farming across the U.S.
Throughout the past year, BrightFarms has transformed the Hendersonville site to include sustainable, high-tech agricultural capabilities. The facility is one of the largest indoor salad farms in the Carolinas, expected to grow more than 2 million pounds of salad per year for supermarkets in the Carolinas and throughout the Southeast.
BrightFarms is hosting a grand opening ceremony for the unveiling of its new state-of-the-art farm in Hendersonville, North Carolina on May 7
The grand opening ceremony will be held via Zoom and will offer participants a first-hand look at the company’s most technologically advanced farm yet. According to a press release, the new greenhouse will add to BrightFarms’ network of sustainable greenhouse farms, serving markets including Charlotte, NC; Winston-Salem, NC; Greenville, SC; Spartanburg, SC; and Atlanta, GA. The grower already has existing farms in operation in Virginia, Pennsylvania, Ohio, and Illinois.
Featured at the event will be prominent speakers that include North Carolina Senator Thom Tillis; Sam Kass, former White House Chef and Senior Policy Advisor for Nutrition; and Steve Platt, BrightFarms CEO. The ceremony will begin with the speakers and conclude with a virtual tour hosted by Founder, Paul Lightfoot, and a ribbon-cutting ceremony.
BrightFarms has transformed the Hendersonville site to include sustainable, high-tech agricultural capabilities, making it one of the largest indoor salad farms in the Carolinas
To sign up to attend the event, click here.
As BrightFarms and other greenhouse growers across the industry continue to expand, AndNowUKnow will bring you the latest.
RSVP Reminder: April Indoor Ag Science Cafe - April 20th Tuesday 10:00 AM Eastern Daylight Time
Indoor Ag Science Cafe is an open discussion forum, planned and organized by OptimIA project team supported by USDA SCRI grants