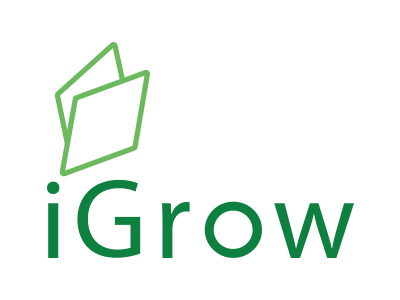
Welcome to iGrow News, Your Source for the World of Indoor Vertical Farming
Recycling Solar Energy for Indoor Farming Use
New patented technology that recycles renewable energy is ready to revolutionize CEA (Controlled Environment Agriculture) and make indoor farming both more profitable and more attainable in remote rural areas. This upgrade in solar technology offers benefits for farmers, consumers, businesses, environmentalists and local governments
New patented technology that recycles renewable energy is ready to revolutionize CEA (Controlled Environment Agriculture) and make indoor farming both more profitable and more attainable in remote rural areas. This upgrade in solar technology offers benefits for farmers, consumers, businesses, environmentalists and local governments.
Two businesses are building a prototype of the vertical farm of the future in Marquette, Kansas (pop. 620.) The indoor farm will recycle its own solar energy at night and during storms by absorbing LED light energy when it’s used to illuminate the interior growing spaces. The 60-unit, 11-acre prototype development will function independently of the local power grid using technology designed and built by Kansas native David Hinson, CTO of TSO Greenhouses.
Image from: Hortidaily
This technology will reduce burdensome costs of power, water, financing, real estate acquisitions, and property taxes. Such hurdles have often been the downfall of previous vertical farms, especially in urban areas. The forward-thinking pair’s plan addresses and solves all of these challenges.
The duo’s “ag tech campus” model includes accelerated growing of all-natural, clean food and protein fodder as well as reliable 5G internet for rural farmers, citizens and businesses. The entire system will be powered by renewable energy and make digital telecom deployment more practical.
Image from: Hortidaily
Hinson’s technology enables roof-mounted “solar trackers” to capture LED energy at night from the light reflected inside the structures that house hydroponic crops growing inside. These trackers rotate East to West when the sun is shining and then flip inward at night and during bad weather.
As a result, farmers can harness the energy generated “off-hours” to grow a variety of crops 24 hours a day in multiple vertical “stacks” based on bespoke microclimates. Growing by “zones” inside a multi-level structure boosts crop production and horticulture flexibility. Traditional indoor farms and rudimentary greenhouses usually grow only 1-2 crops for local distribution.
In contrast, these new farms will be able to produce 10-15 different plant species simultaneously. Increased agility and production speed will also improve vertical farmers' ability to react to sudden demand shifts.
Image from: Hortidaily
5G Adds Lucrative Tech Payoff to Growth Cycle
Since the new 24/7/365 solar energy recycling technology only needs 33 percent to 40 percent of the harnessed energy, developers and farmers can sell excess energy for additional revenue. The local clean energy will power wireless 5G with the help of small rotating solar trackers with batteries. These trackers can be placed on community buildings, water towers, grain elevators, farm silos, bridge spans, existing cell towers and other permanent objects to ensure uptime and reliability.
This new source of 5G will create emerging markets for renewable energy, boosting rural economies. In the past, 5G telecom has been difficult to install and deploy in remote areas.
Path Diversity will be a game-changer
The pair plan to locate data centers near 100GB digital fiber trunks to further reduce the cost and time required to deploy 5G wireless. High-end data processing groups pay premium rates for 5G, which is rated as Tier 5 (aka T5 or always-on) based on its reliability. T5 is far less subject to outages and service disruptions.
Such state-of-the-art data centers are expected to attract the largest data processing groups in the world based on their enhanced functionality and amenities. This market also provides another lucrative revenue stream for farmers and tax-equity entrepreneurs interested in sustainability.
Investors Can Support Sustainability with “free money”
Freedom Farms CEO Geist and TSO Greenhouses Hinson have already raised nearly half a million dollars for Phase One, which will be the prototype of the vertical farming headquarters. They’re seeking an additional $2.5 million to finish the prototype by summer 2021.
Phase Two will be devoted to building 12 larger campuses that will fan out statewide from the headquarters in McPherson, Kansas. The entire $2 billion hub-and-spoke sustainability system is targeted for completion by 2030. Yields are expected to feed nearly 3 million residents statewide including many school lunch programs. Local hospitals, restaurants, colleges, universities, assisted living centers and public agencies are expected to become customers of the same-day harvests.
Investors will be able to reap these profits without ever risking their own money. Thanks to little-known U.S tax credit programs and clean-energy incentives, these projects don’t require a cash infusion. VC firms can "pool" their tax obligations, converting them to credits. This structure sets the project apart from previous urban farms or sluggish VC-funded startups.
Solar panels rotate with the sun so direct sunlight can reach inside the CEA facility and stimulate photosynthesis. Software allows the indoor farmer to create direct sun exposure on certain plants while creating shade for others, all based on each plant’s DNA preference.
The solar panels (modules) can be fully closed facing outward to create 100% shade inside if desired for any length of time controlled by the grower. By using TSO Greenhouses’ technology, vertical farmers and greenhouse growers can control and optimize sun and shade exposure simultaneously. This allows different crops to grow in zones inside the structure tailored precisely to receive the ideal light and shade to maximize plant life and production.
This 11-acre greenhouse will eventually serve as a headquarters to 12 smaller greenhouse hubs across Kansas. What makes this greenhouse unique is its ability to recycle solar energy to grow crops 24 hours a day while powering lucrative 5G data centers.
TURKEY: Vegetables Will Be Grown In The Geothermal Greenhouse Established on 60 Decares In Sivasta
The first seedlings were planted for the products to be grown in the geothermal greenhouse established on 60 decares of land in Sivasta Hot Çermik region
The first seedlings were planted for the products to be grown in the geothermal greenhouse established on 60 decares of land in Sivasta Hot Çermik region.
120 thousand tomato seedlings were planted in a 60-acre glass greenhouse, which was started to be built a year ago in the region and will be heated by geothermal water, which cost about 40 million lira. Sivas Governor Salih Ayhan, Mayor Hilmi Bilgin and former Sivas Mayor businessperson Sami Aydın Stating that Sivas has gained a great value, Ayhan said: “I congratulate our company, which has brought a very high technology and a seminal service to Sivas, for its courage,”.
I can say that it is one of the projects that excites me the most. Sivas is developing in every field, but there is a completely different development in agriculture. I can say that Sivas has gained a very good momentum in agriculture. We use Thermal not only for health tourism but also for visual and cultural purposes. This place almost added value to the region. Saying that the greenhouse will open a vision for Sivas, Bilgin thanked Sami Aydın for bringing a modern, world-class greenhouse to Sivas. The Çermik Region has been distributing healing for years. I hope Sivas will be a cluster with this greenhouse project.
Sami Aydın also said that they have accomplished a first in Sivas and implemented the thermal smart greenhouse project. Stating that he was happy to realise the first seedling planting of such a facility, Aydın said, This is the first greenhouse project in Sivas, a smart greenhouse. While hot Çermik water has been healing for health until today, it will also be healing for agriculture from now on.
In the seedling planting done in accordance with the social distance rules, the protocol members passed through the disinfectant cabin one by one and were taken to the greenhouse area.
Fifth Season Takes Vertical Farming to a Whole New Level
Fifth Season’s verdant baby spinach screams farm fresh even though it’s grown nowhere near traditional farmland. The sweet and slightly crunchy greens are grown in a Braddock warehouse on racks stacked 30 feet high. Located just a stone’s throw from U.S. Steel’s Mon Valley Works Edgar Thomson Plant, it is urban farming at its core
Image from: Pittsburgh Post-Gazzette
Fifth Season’s verdant baby spinach screams farm fresh even though it’s grown nowhere near traditional farmland. The sweet and slightly crunchy greens are grown in a Braddock warehouse on racks stacked 30 feet high. Located just a stone’s throw from U.S. Steel’s Mon Valley Works Edgar Thomson Plant, it is urban farming at its core.
What makes the vertical farming operation especially unique is that it is automated and robots call the shots. About 40 to 60 machines are involved in every step of the life of the spinach and other leafy greens, from planting the seed to providing nutrients to the final packing.
Fifth Season does employ local “farm workers” to assist the robots in seeding, harvesting, packaging, quality assurance and control using computer software, but there is no human touch involved through it all.
“The first time someone ever touches the spinach leaf with a finger is when the package is opened,” says Grant Vandenbussche, chief category officer.
Co-founded by brothers Austin and Brac Webb and Austin Lawrence, Fifth Season started a year ago. Within months it was rolling out its baby spinach, leafy greens and salad kits.
“We wanted a name that represents what we are doing,” says Austin Webb, 32, who also is the CEO. “It is a call to the fact we have created an entirely new season. It is 24/7, 365 with the technology we have built.”
None of them planned to become modern farmers, says the Carnegie Mellon University grad, but they turned to vertical farming because it was an efficient, economically sustainable way to solve land and water woes.
Image from: thespoon.tech
‘Fields’ of Greens
Fifth Season grows an equivalent production of 200 acres in 25,000 square feet of grow space. Its “fields” are stacked on top of one another in vertical shelves. When you add up all that surface area of grow space, it is more like 126,000 square feet.
“We also quickly turn crops at the farm,” Mr. Vandenbussche says.
While spinach takes about 40 days to grow outdoors and can be harvested only twice during its peak season, it takes the crop only three or four weeks to grow in the controlled environment and is harvested 19 times. Once the plants are harvested, a new cycle of reseeding begins with fresh media, seeds and nutrients.
“That’s why we get so much more productivity,” he says. “We are immediately reseeding our ‘land.’”
This controlled environment yields quality produce because it is always peak season at Fifth Season, says Chris Cerveny, who heads the Grow R&D division. Greens are grown in the same conditions year-round, getting the exact amount of nutrients and water they need. Because pests and airborne toxins also are kept at bay, crops can be produced without pesticides.
All that TLC comes through in the slightly curled baby spinach, which is sweet and not grassy. The leaf doesn’t wilt or get slimy or lose its slight crunch even after two weeks of refrigeration.
A lot of thought was given even for the curl, which gives the spinach a stronger volume, making it look full and bountiful. The curl also makes the spinach more forkable unlike its flat-leaf counterpart that is hard to stab on a plate.
Other leafy greens such as kale, mustard, Chinese cabbage, green tatsoi and purple pac choi are featured in two blends — Bridge City and Three Rivers. Fifth Season plans to roll out its Romaine lettuce in spring.
The greens also are found in four types of salad kits — Sweet Grains (blended greens, quinoa, chickpeas, corn, feta and poppy seed dressing), Crunchy Sesame (blended greens, farro, sesame sticks, dried cranberries and ginger-mandarin dressing), Toasted Tuscan (spinach, lentils, sun-dried tomatoes, bagel chips and vinaigrette), and Spiced Southwest (blended greens, black beans, pepitas, cotija cheese, corn-salsa sticks and chipotle ranch dressing) — which are available online and in Giant Eagle stores. A fifth salad kit is in the works and is being called “a shakeup of one of the most classic salads.”
While machines are a big part of what Fifth Season does, it seeks to keep human connection alive. It recently launched a recipe blog for those who have an appetite for cooking and writing, The Green Room is devoted to cataloging personal memories, dream meals and recipes via short stories.
Fifth Season also has partnered with the Penguins and is providing greens for the team’s pregame meals for the 2020-21 season.
“We want people in Pittsburgh to be able to eat the exact same delicious blend of greens that Sidney Crosby and company are eating,” Mr. Webb says. “We want people to know that there’s a new way to grow food and to eat and experience it.”
Image from: Next Pittsburgh
It’s All Under Control
Everything from seeding to packaging is done in four rooms. The process starts in the seeding and processing room, where seeds and growing media are placed inside black planter-like boxes called inserts. Each has a unique code that’s traced by a software system. The inserts go on white trays that pass through a photo station, feeding information to the computer system, and then glide into the bio dome.
There are two rooms in the bio dome, each with a grow space of 12,500 square feet. They’re lit up with a pinkish-purplish glow from high-efficiency LED light bulbs that mimic the different seasons of the year.
“They are positioned over the plants at different heights depending on stage of growth,” Mr. Cerveny says. “This is partly how we can provide consistently ideal growing conditions.”
As the plants grow, they are moved by a robot to optimize their growth cycle. Full-grown crops are transferred to the harvesting room by another robot.
“Harvesting is where it becomes like a Willy Wonka factory,” Mr. Vandenbussche says.
Long rows of trays filled with tiny plants are sent on a conveyor system to a station where workers inspect them for quality with surgical tools. After inspection, the plants are harvested by a robot and then immediately ride up a tall conveyor to be packaged and sealed in a 34- to 36-degree room so they remain fresh.
“Every crop we grow gets evaluated for maximum flavor, volume, crunch and color,” he says.
The plants’ intense, dark color is controlled by LED light bulbs, which are dialed up or down to get the correct hue. Although they never see the sun, the greens don’t get into a funk as humans might.
“What humans see in terms of light and how chlorophyll responds during photosynthesis are two different things,” Mr. Cerveny says. “Plants really only need red and blue light to grow effectively. We include some additional colors to help bring out other quality aspects of our crops, but providing the full sunlight spectrum is effectively a waste of energy, especially indoors.
“To the human eye, it looks like the plants live in a land of purple and pink lights, but they are perfectly happy there.”
Even though the environment is controlled and the software system is constantly updated, no two plants are exactly the same. Some fight for light more than others. Some might fail the quality control test and end up in a compost waste facility if their flavor is off or their color is not right.
“That is what is so amazing. We have more control than any other farmer, and yet we have limitations. Every seed is different,” Mr. Vandenbussche says. “They are plants. They are real living organisms.”