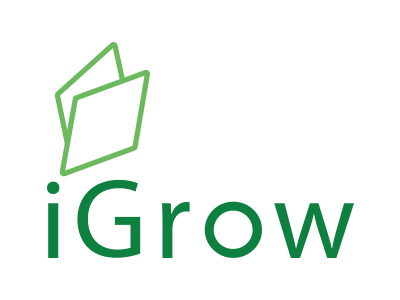
Welcome to iGrow News, Your Source for the World of Indoor Vertical Farming
US - OHIO: Thinking And Growing Inside The Box
A brother-sister team has taken the mechanics of farming out of the field and into a freight container. “We are growing beautiful plants without the sun; there’s no soil, and so it’s all a closed-loop water system,” Britt Decker, co-owner of Fifth Season FARM, said
A brother-sister team has taken the mechanics of farming out of the field and into a freight container.
“We are growing beautiful plants without the sun; there’s no soil, and so it’s all a closed-loop water system,” Britt Decker, co-owner of Fifth Season FARM, said. “We use non-GMO seeds, completely free of herbicides and pesticides, so the product is really, really clean. In fact, we recommend people don’t even wash it, because there’s no reason to.”
Fifth Season FARM is unique in many ways; the 3-acre hydroponic farm is contained in a 320-square-foot freight container that sits along 120 S. Main St. in Piqua, with everything from varying varities of lettuce, to radishes, to kale and even flowers in a climate-controlled smart farm that allows Decker and his sister, Laura Jackson, to turn crops in a six- to eight-week cycle. The crops spend 18 hours in “daytime” every day, and the farm uses 90% less water than traditional farming.
“It’s tricky because we’re completely controlling the environment in here. It’s kind of a laboratory more than a farm,” Decker said. “I think there’s about 50 of them around the world right now. These are really international, and they’re perfect for places that are food deserts where they can’t grow food because of climate or other reasons. It gives them a way to grow food in the middle of nowhere.”
Image from: Sidney Daily News
Decker and Jackson, along with their brother Bill Decker, also do traditional farming and grow corn, wheat and soybeans, but Decker said they were looking for a new venture that would help lead them to a healthier lifestyle and learn something new.
“Just with the whole local food movement becoming more and more important and food traceability, we just thought it would be a great thing to bring to our community to help everyone have a healthier lifestyle,” Decker said. “People love food that’s grown right in their hometown and the shelf-life on it, when you get it home, is remarkable. It’ll keep for two weeks.”
Image from: AgFunder News
Currently, Decker and Jackson are growing a half-dozen variety of specialty lettuces that include arugula, butterhead and romaine, as well as specialty greens like kale and Swiss chard, and even radishes and flowers. They received their freight container at the end of July and set up their indoor farm over two weeks; while the farm has been in operation for less than six months, Decker says that they’re growing beautiful product.
They have also started growing micro-greens, said Decker. Micro-greens are immature plants which are 1 to 3 inches tall and are in a 5-inch by 5-inch container.
“People will use them as garnishments and in smoothies,” said Decker. “Since they are immature plants, they have an intense flavor.”
Decker said they are growing wheat germ, broccoli and spicy salad mixes.
They’ve also started moving forward with sales and marketing. Fifth Season FARM has partnered with the Miami County Locally Grown Virtual Market to sell their products to the community. They also take orders through their website, customers can opt to pick up their orders between 4 and 6 p.m. on Wednesdays, or Decker and Jackson will deliver products up to five miles from the farm. Decker said that Fifth Season FARM is also in discussions with three restaurants in the area about including their specialty greens on their menus.
Decker said they also plan to attend the Sidney Farmers Market when it opens for the spring/summer season.
“We’re really just getting going,” Decker said. “While we were learning to grow products, we didn’t want to overcommit to a restaurant or grocery store before we knew we could really grow beautiful product, so we’ve been donating product every week to the food pantry at the Presbyterian Church. It feels good to plant the seeds and watch them grow, and it feels good to make sure that people who aren’t getting the proper nutrition are getting some.”
Derby Vertical Farming Startup Gets £500K Funding to Develop ‘All In One’ Sensor
Derby-based Light Science Technologies delivers lighting, science and research-proven plant monitoring technology and software in partnership with world-leading university research teams
INVESTMENT NEWS / 13 JAN 2021
Derby-based Light Science Technologies delivers lighting, science and research-proven plant monitoring technology and software in partnership with world-leading university research teams. It delivers the right solution across multiple indoor applications such as vertical farming, medicinal plants, and greenhouses. Its full turnkey solution for Controlled Environment Agriculture (CEA) applications for next-generation scalable farming helps customers grow more with less.
Investment to boost agricultural productivity
Light Science Technologies just secured part of the £90M government investment to support the most innovative technology to boost agricultural productivity and set food production systems towards net zero emissions by 2040.
Furthermore, it is one of the 23 feasibility projects that has been awarded up to £500,000 from £4.3M funding that is meant for Science and Technology into Practice feasibility competition, as part of UKRI’s £90 million Transforming Food Production (TFP) program. Innovate UK drives productivity and economic growth by supporting businesses to develop and realize the potential of new ideas. Notably, Innovate UK is part of UK Research and Innovation.
Simon Deacon, CEO of Light Science Technologies added: “This is an especially important boost to our business. To be selected by Innovate UK is confirmation of the urgent need for more sustainable, productive, and cost-effective solutions in farming. Investment in UK technology and innovation in this sector is crucial in achieving a better approach to agricultural production and reducing emissions.”
Innovate UK Executive Chair Dr Ian Campbell said: “There are many innovative projects in our latest feasibility competition showcasing ideas for improving productivity and cutting emissions that range across the whole agricultural sector, from arable, to livestock, to sensor technology and to new biopesticides. Our funding and support for these projects is ongoing.”
Groundbreaking sensor technology
Along with partnership with Nottingham Trent University, the company will lead the project to develop a growing sensor and innovative transmission node for vertical farms over the next six months, which is in synergy with their light and science offering.
The IoT precision data solution for vertical farming will help in boosting 0roductivity and efficiency, thereby reflecting the government’s drive to help the agricultural sector grow economically with less environmental impact.
Light Science Technologies’ ‘all in one’ indoor farm sensor will let farms to monitor and control their environment by measuring key areas such as light, water, air, temperature, humidity, oxygen and soil, thereby ensuring optimal plant productivity and yield. Also, this sensor will form a vital part of its bespoke offering, reducing energy and saving costs using technology and real-time data.
Demand for CEA market!
Of late, there is a growing demand for the Controlled Environment Agricultural (CEA) market, which is growing fast at a CAGR of 21%. The demand is mainly from AgTech CEA farmers looking to install or replace existing indoor farms to achieve a maximum yield on crops for optimum profitability. However, the high startup costs attract investment from stakeholders eyeing the potentially significant ROI opportunity.
Light Science Technologies provides custom-made solution for the CEA market, and works with growers to provide an integrated, cost-effective and low maintenance solution that can be used across different crops to achieve maximum yield. Eventually, it creates the full growing recipe of lighting, nutrients, and the environment.
Notably, Light Science Technologies is focused on becoming a technology-driven trailblazer in vertical farming innovation and technology over the next four years as it eyes to shape up the future of the CEA market.
Global CEA Census Report Shows Continued Positivity Despite COVID-19
Data captured over an 8-week period show 95% of growers have an optimistic outlook for the next 12 months with all types of operations including greenhouses, shipping containers, tunnel and vertical farms showing profitability
1 DECEMBER 2020
Autogrow and Agritecture Consulting have released the 2nd Annual CEA Census Report highlighting positive signs of growth despite the global pandemic.
Data captured over an 8-week period show 95% of growers have an optimistic outlook for the next 12 months with all types of operations including greenhouses, shipping containers, tunnel and vertical farms showing profitability.
“The optimism reflects what we have seen across many areas of the industry including increased technology adoption and increased consumer expenditure on fresh produce. And despite the challenges we’re seeing an overwhelming number of new entrants into the market,” says Autogrow CEO Darryn Keiller.
“What has not changed is the high percentage of new growers, almost 50%, that have no experience in agriculture before starting their business. That lack of experience has an impact on new technology solutions created and the need for more education to be available to support them. It also shows a real desire to make a difference considering their willingness to start during a pandemic.”
Respondents from 58 countries shared their views on their farming practices, financials, and the impact of COVID-19. The report also gave insight on three key growth regions around the world – India, the UK, and MENA (Middle East & North Africa).
"The results of the 2020 Census confirmed our hypothesis that the UK, India, and MENA regions are the emerging hotspots for CEA, albeit for different reasons. In the UK, Brexit is driving investment towards CEA to combat supply chain risks, while in India rising population and increased premium consumer demand for clean food are driving CEA. In the MENA region, government responses to COVID-19 have accelerated policies and incentives for developing scalable CEA solutions,” explains Agritecture Consulting Founder Henry Gordon-Smith.
“All of these regions present great opportunities for the CEA industry to grow and make a meaningful impact on their respective local conditions.”
Other takeaways from the Census:
· CEA businesses showing optimism and resilience despite the COVID hurdles
· 88% of growers surveyed are below age 50
· 29% of respondents receive funding from multiple sources
RECEIVE THE FREE REPORT!
MEDIA QUERIES
Kylie Horomia, Head of Brand & Communications
(e) Kylie.horomia@autogrow.com
(m) +6421 733 025
(w) www.farmroad.io www.autogrow.com
Sales queries – info@farmroad.io
Briana Zagami, Agritecture Media Strategist
(e) briana@agritecture.com
About Autogrow
Autogrow leverages the power of technology, data science, and plant biology to provide indoor growers affordable, accessible, and easy-to-use innovation – 24/7, anywhere in the world.
Our solutions support growers and resellers in over 40 countries producing over 100 different crop types.
We are the experts in Controlled Environment Agriculture (CEA) and continue to stay ahead of a rapidly evolving landscape.
About Agritecture Consulting
Agritecture Consulting provides a comprehensive approach to CEA project development.
In operation since 2014, Agritecture has helped more than eighty organizations determine the feasibility of their ideas, validate their business strategies, recruit talent for their projects, and manage operational challenges.
Our job is to jumpstart your knowledge of CEA, help you navigate barriers to entry, make industry connections, and mitigate risk. Our consulting services are backed by several years of operations data and a team of experienced growers, engineers, and sustainability managers.
FURTHER READING:
AUTOGROW AND AGRITECTURE RELEASE FIRST-EVER GLOBAL CEA CENSUS REPORT
GLOBAL CEA CENSUS LAUNCHED TO HELP DRIVE AGRICULTURE INDUSTRY FORWARD
WEBINAR - Food Safety in CEA Systems - September 24, 2020 - 2:00 PM EDT
Data will be presented on space-grown leafy green vegetables, as well as from a study with market produce and ground-grown produce to compare
Date: September 24, 2020
Time: 2 p.m. - 3 p.m. EDT
Presented by: Gioia Massa (NASA) and Marni Karlin (CEA Food Safety Coalition)
Click here to register
Dr. Gioia Massa, plant scientist at NASA will highlight some of the unique aspects of space crop production and the microbial food safety considerations of space-grown produce. Data will be presented on space-grown leafy green vegetables, as well as from a study with market produce and ground-grown produce to compare. NASA's preliminary Hazard Analysis Critical Control Points (HACCP) Plan will be highlighted and future goals will be discussed.
Dr. Marni Karlin, executive director of the CEA Food Safety Coalition will provide a brief introduction to the unique opportunities and challenges for CEA leafy greens producers, vis-à-vis food safety. Dr. Karlin will identify the areas where a risk assessment may indicate increased controls needed to ensure food safety; as well as the areas where CEA processes enhance the ability to ensure food safety.
USA (CA) - Iron Ox Raises $20 Million To Grow Robotic Greenhouse Operations
The funding will be used to open additional robotic growing facilities in California and other parts of the U.S., according to company co-founder and CEO Brandon Alexander
Khari Johnson @kharijohnson
September 9, 2020
Robotics farming company Iron Ox today announced the close of a $20 million funding round. The funding will be used to open additional robotic growing facilities in California and other parts of the U.S., according to company co-founder and CEO Brandon Alexander. The funding will also be used to hire additional machine learning and robotics experts as well as growers and scientists who work with plants.
“We’re now competing on price with field farms, but we think we can do even better and take this to more people,” he said.
Iron Ox employs a 1,000-pound mobile transport system roughly the size of a car to move trays of growing vegetables and tend to plants using a robotic grasper while computer vision systems monitor the plant growth cycle. The semi-autonomous system still relies on humans for a part of its seeding, pruning, and inspection process, Alexander said, but the goal is for Iron Ox to someday be fully autonomous.
While startups like Bowery practice indoor vertical farming in urban facilities near New York and Baltimore, Iron Ox has turned its focus toward greenhouse farming since the company was founded in 2015 as a way to lower energy costs. Earlier this year, Iron Ox opened its first greenhouse, a 10,000-square foot facility in Gilroy, California, the company’s second location. Iron Ox currently provides produce to 15 Whole Foods stores in the San Francisco Bay Area.
Though Gilroy is known as the garlic capital of the world, Iron Ox does not currently grow any garlic. Instead, the company focuses on leafy green vegetables like lettuce and some herbs.
Alexander said Iron Ox’s biggest challenge is how to use data collected by sensors to train AI systems that produce higher yields at lower costs.
“I would say in agriculture as a whole it’s not just collecting data, it’s not just taking an image, but it’s actually how do you include that data into the decision making process?” Alexander said. “I would say that is the biggest challenge in ag is how do you respond to these each individual plants and the variety and all these little variables.”
The $20 million funding round was led by Pathbreak Ventures with participation from Crosslink Capital, Amplify Partners, Eniac Ventures, R7 Partners, Tuesday Ventures, and At One Ventures. Iron Ox is based in San Carlos, California. The company currently has 30 employees and has raised $45 million to date.
Field farming today is still the most efficient way to grow produce. However, concern about shrinking field yields and instability due to climate change has spurred interest in indoor farming. In 2018, international teams from companies like Microsoft and Tencent competed against each other to find out who could grow the highest yield of cucumbers inside a greenhouse using AI and automation. (Spoiler: The Microsoft team won.)
In other AI and agriculture news, last month the startup iFarm raised $4 million for its AI-driven urban farming solution, and in June the startup Burro began rolling out its autonomous farm robot in southern California to assist in grape harvesting.
Image credits: Iron Ox
CANADA: Local Leaf Farms To Open Vertical Farming Site In Kingston
Purchasing local produce will become easier year-round after Local Leaf Farms opens their newest vertical farming site on Innovation Drive. Their innovative take on farming removes the need for a lot of land, and our Canadian dependency on weather
Credit: localleaffarms.com
Purchasing local produce will become easier year-round after Local Leaf Farms opens their newest vertical farming site on Innovation Drive. Their innovative take on farming removes the need for a lot of land, and our Canadian dependency on weather.
Local Leaf Farms is on a mission to change the way food is produced and distributed in Canada, growing superior quality food that’s safer, fresher, and more sustainable. Using vertical farming technology first invented by NASA, they are able to provide Canadians with pesticide and herbicide-free, hyper-local produce (grown within the city it is sold) year-round. With a model that has them delivering the product directly to store shelves within hours of harvest, they ensure maximal freshness of the product, while reducing both food waste and the carbon footprint of transportation.
Packed in 100% plastic-free, compostable containers, their innovative technology provides retailers & consumers with a fully traceable food source, via a QR code on the package, that allows instant access to all details about how the product in a specific package was grown, when and by whom.
Kingston Economic Development and the City of Kingston are pleased to welcome this new business to our community in the St. Lawrence Business Park. “I’m absolutely delighted to welcome Local Leaf Farms to Kingston,” says Mayor Paterson. “This is a company that brings an exciting and innovative approach to local food that will bring great benefits to our residents, and will further position Kingston as a leader in food security and sustainability.”
The Local Leaf facility will be located in a new development at 800 Innovation Drive and is anticipated to open in late October of this year. This business is a $450,000 investment in the Kingston community in terms of start-up costs and is expected to create seven (7) full-time jobs locally.
“We’re proud to have Local Leaf Farms joining the innovative businesses that will be sharing one roof at 800 Innovation Drive when it opens this fall,” says Ben Pilon, President of BPE Group. “Their focus on sustainability and food security aligns nicely with our business philosophy, making this agreement a natural fit. With tenants like Local Leaf, 800 Innovation Drive, will see job creation, strengthen our local economy, and show the world that good things grow in Ontario.”
“As we scale to build 20 production facilities across the country by 2025, Kingston was an obvious choice. As a gateway to eastern Ontario, Kingston represents the perfect mix of a City whose municipal government understands the importance of both innovation and the food sector, an Economic Development Office that is exceptional in supporting out of town businesses in their relocation and a community that values sustainable, quality food products. It was an obvious choice that we are excited to commence upon,” says Steve Jones, President, and CEO of Local Leaf Farms.
“We are excited that Local Leaf Farms selected Kingston as a new site for their 7,000 sq. ft. facility. Their business mission aligns with the City of Kingston’s vision for innovation, entrepreneurship, and food security making it a great fit in the community,” says Shelley Hirstwood, Business Development Officer, Attraction & Aftercare with Kingston Economic Development Corporation. “The Kingston Economic Development team is looking forward to continuing to work with Local Leaf Farms as they became established.”
While you’re here …
…Can we take two minutes of your time?
More Kingstonians than ever are relying on Kingstonist for their local news. But we need your help to keep it going.
A few years ago, two big media conglomerates, Torstar and Postmedia, “swapped assets” and promptly shuttered one of Kingston’s main newspapers. We saw talented journalists displaced and years of recorded Kingston history destroyed by a decision made in another city, with interests not grounded in what was best for the Kingston community.
And we resolved that we would not permit that to happen again.
That’s when we decided to take the Kingstonist, at that time a popular Kingston community blog, and reimagine it as the dedicated, independent local news provider you see now.
Today, businesses everywhere are struggling under the burdens of COVID-19, and we are no different. So we’re asking you to support us. Help us in our mission to: hold our local governments accountable; provide voices for those fighting against social injustice; fight against misinformation; and provide news not censored by the influence of corporate bias.
We believe that access to news is an integral component of a healthy community. If you believe the same, click here to subscribe to Kingstonist.
Bejing National Agricultural Science And Technology Innovation Park To Be Expanded
AgriGarden International is a Chinese provider of services covering the entire industry chain of horticulture
AgriGarden International: To Build a Platform of Innovation For global horticultural Industry
The Covid-19 pandemic that has been ongoing for months has affected China's horticulture industry to varying degrees, and many projects under construction had to be suspended. AgriGarden International is a Chinese provider of services covering the entire industry chain of horticulture. Liu, Manager of International Cooperation, said, “Since the outbreak of Covid-19 at the end of January this year, the construction of all of our ongoing projects has been forced to stop. Currently, projects in other provinces and cities have been able to resume, but due to the second wave of cases occurred in Beijing in mid-June, the construction of National Agricultural Science and Technology Innovation Park here had to be once again put on hold and is awaiting approval for the resumption of work.”
National Agricultural Science and Technology Innovation Park
Liu, Manager of the company’s marketing department, said, “The National Agricultural Science and Technology Innovation Park and the International Facility Horticulture Innovation Center that is to be expanded will serve as an exchange platform for the horticulture industry. By working with internationally renowned horticultural research institutions and companies, they will showcase the latest results of horticultural scientific research, and new technologies and equipment for facility horticulture to visitors at home and abroad, and promote exchanges, cooperation, and joint innovation among enterprises. The Innovation Park will also function as an investor and incubator. Since the establishment of the park, it has received nearly 40 heads of state and leading politicians.
Interior of the National Agricultural Science and Technology Innovation Park
About the Innovation Center
When talking about the International Facility Horticulture Innovation Center, Liu said, “AgriGarden International is an agricultural high-tech enterprise affiliated with the Chinese Academy of Agricultural Sciences. It is a benchmark enterprise for transforming scientific and technological achievements via in-depth integration of production, education, and research handpicked by the Ministry of Agriculture and Rural Affairs. We often receive domestic and foreign leaders with investment intentions. In the future, our Innovation Center can provide office space for domestic and foreign horticultural technology companies, and more importantly, provide a communication platform for these companies and help them open the Chinese market and bring more potential customers. We also hope to facilitate joint innovation of the horticulture industry in this center to create more innovative products for the Chinese market.”
In recent years, more and more companies have transitioned from traditional agriculture to facility horticulture, which shows the huge potential of the Chinese market. However, foreign companies have to face a series of challenges such as the lack of customers and ignorance of local policies, even though they have advanced technologies and concepts. The Innovation Center will provide these companies with localized information and help them expand the Chinese market.
International Facility Horticulture Innovation Center
AgriGarden International
AgriGarden International is an agricultural high-tech enterprise affiliated with the Chinese Academy of Agricultural Sciences. It is a benchmark enterprise for transforming scientific and technological achievements via in-depth integration of production, education, and research handpicked by the Ministry of Agriculture and Rural Affairs. “We welcome companies in the industry that are interested in joining the International Facility Horticulture Innovation Center (Alliance) to contact us." Manager Liu said.
Lead photo: The core part of the National Agricultural Science and Technology Innovation Park
For more information:
Contact: JING (Laurie) LIU
Company: AgriGarden International BD
Tel.: 00491791229249
Email: laurie.liu@agri-garden.com
Publication date: Thu 23 Jul 2020
© HortiDaily.com
CANADA: Space-Age Tech Will Take Farming To New Heights in Welland
Intravision Group has shone a light on everything from cannabis to planet simulators, spanning across Kuwait, McMaster University, and the European Space Agency. Now, through Intravision Greens Niagara, its tech is taking veggies to new heights in Welland
Vertical Farming Facility Aims to Produce 1-Million Pounds of Produce
Intravision Group has shone a light on everything from cannabis to planet simulators, spanning across Kuwait, McMaster University, and the European Space Agency. Now, through Intravision Greens Niagara, its tech is taking veggies to new heights in Welland.
Starting in Norway, Intravision made its progression across the pond to the University of Guelph's Controlled Environment Systems Research Facility. In collaboration with the university, they honed in on how isolated plants in a hyper-controlled environment responded to everything from lighting spectrum, to airflow movements.
While the technology applies to plants grown in space, the fundamentals behind it aren’t rocket science.
Modern farming has drastically evolved to give farmers more control over their crops, but outside in the field, nature still has the upper hand.
Move the entire growing process inside into a controlled environment, and suddenly you have control over everything. For Intravision Greens, it’s a bit like getting to play God.
"It's a low-tech approach to a high-tech challenge," says Nic Keast, a senior project manager with Intravision. "You're growing plants, plants grow themselves, let's give them the right conditions and let them do their thing."
Non-GMO, certified and sterile seeds are planted in-house. Every stage of the plant’s growth, from germination to harvesting, is dialed in; from what spectrum of light the plant gets, to the temperature and amount of air circulated over a plant, to the spacing in a tray.
By the time produce makes its way out the door, there’s a traceable log of its entire journey.
Plants start off on the lower level of a vertical farming system and as they mature, they’re moved up higher. It’s a constant cycle of maturing plants moving up, replaced by seeds below.
Intravision Greens Niagara’s Neville D’Souza, one of the operation’s executive directors, said without insects to worry about, there won’t be pesticides or herbicides used; leafy greens like basil and arugula, are sent out the door ready-to-eat; and the facility will use significantly less land and water than a conventional farm.
Inside the 20,000 square-foot facility, one-acre of leaf cover will be grown, producing around 1-million pounds of plants, according to D’Souza.
Undeniably, there’s a lot of work and money going into only one acre, but Keast stresses it’s all about getting the most out of a bit of space.
The Welland facility, now being built, is based off of a pilot plant in Toronto where the concept was tested on a small scale.
For their produce to compete with commercial-scale productions, they’ll eventually have to scale, says Keast. There’s the potential for an additional two acres — by knocking down a few walls, they can replicate their current setup.
D’Souza says they aren’t trying to compete with local farms though. Their interest lies in the GTA market, where he says most produce is imported.
"What we are going to produce here, represents just two to give percent of what is imported, so that is what we are looking at, and the farmers are growing for three or four months, this is growing the other nine months when stuff is imported ... this is import substitution, and so it compliments what the farmer is growing and not treading on his toes," D'Souza said.
This past Friday, some of Intravision’s 2,340 lighting units were being installed above roller racks that will eventually hold plant trays. Keast and D’Souza point out that robotics, framing, the water system, harvesting equipment, and a future conveyor system are all locally sourced.
D’Souza claims that an operation like theirs will be the first in the world, and believes as the technology becomes more viable, there will be more vertical farms to compliment traditional ones.
It’s still early stages, and D’Souza admits it’s an ambitious goal, but he hopes for the operation to be up and running by the fourth quarter of this year, and sees an expansion within 24 months.
Photo Credits:
A vertical farming system is seen at an upcoming Intravision Greens Niagara facility in Welland on July 17, 2020.
A vertical farming system is seen at the “We the Roots” pilot plant in Toronto, in this undated photo provided by Intravision Light Systems. - Photo provided: Intravision Light
A vertical farming system is seen at an upcoming Intravision Greens Niagara facility in Welland on July 17, 2020. - Jordan Snobelen/Torstar
Feeding The World With Controlled Environments
The fallout from increasing global temperatures, a worldwide pandemic, and political unrest is causing projection reductions for crop yields in some countries as much as 50% this year, and small-scale farmers are the most affected with crop net revenues falling by as much as 90% by 2100
This case study, written by Gene Giacomelli and Eric Roth for Agritecture, takes a look at how CEA has emerged as a viable, contemporary agricultural practice over the past 50 years. Here’s how it happened!
The fallout from increasing global temperatures, a worldwide pandemic, and political unrest is causing projection reductions for crop yields in some countries as much as 50% this year, and small-scale farmers are the most affected with crop net revenues falling by as much as 90% by 2100. The consumer preference for consistent, year-round availability of produce has expanded because of the Controlled Environment Agriculture (CEA) industry, even surviving the recession of 2008. “That indicates to me, that no matter what the next recession brings, CEA food production systems will be firmly entrenched in U.S. agriculture production practices,” says Gene Giacomelli, Professor of Biosystems Engineering and former Director of CEAC at The University of Arizona.
CEA has emerged as a viable, contemporary agricultural practice over the past 50 years. There have been dramatic improvements in efficiency metrics including overall crop yield per square unit and reduction of wastage due to disease, nutrient deficiency, or damage to the product. From Space to Antarctica; from rooftop greenhouses to rural farms worldwide, CEA has proven itself to be not only a complement to open field crop production, but in some instances, a competitive alternative (or in the case of Space and Antarctica the ONLY) approach. Today, more than 60% of all fresh tomatoes consumed in the U.S. are grown in controlled environments and that number approaches 100% during the North American winter. Here’s how it happened...
In the 1990s, the U.S. greenhouse production shifted from its infancy to a steady supplier of fresh produce. While greenhouses use the sun as their main source of light, they can also make use of supplemental lighting for additional growth. This advantage, along with the ability to control and protect the growing environment, encouraged large farming corporations to enter the space in the Northeast, Arizona, Colorado, California, and Texas. Environmental control enabled these early adopters to produce crops like tomatoes, cucumbers, and lettuces year-round. During the same time, small family farms were often adding greenhouses to complement their traditional open-field production.
During the next decade, the major suppliers of field-grown vegetables in Canada and Mexico also began focusing on greenhouse production. The 2000’s firmly established CEA vegetable production as a viable commercial growing method.
In the 2010’s, vertical farming became more mainstream when Dr. Dickson Despommier published the book, The Vertical Farm: Feeding the World in the 21st Century. Vertical farms are essentially plant factories, with multi-level grow systems in insulated buildings using only electrical light instead of sunlight for plant growth. Although there were most likely small scale vertical farms before it, Sky Greens in Singapore was the first vertical farm to begin large scale commercial operations in 2012. Vertical farming became more commercially viable largely because of the advancing technology of Light Emitting Diodes (LED). These distributed light sources are less energy-intensive than the industry standard high-intensity discharge lamps, but more importantly, allow growers to move lights closer to the crop without burning or overheating. This enabled business developers to stack hydroponic grow systems, producing significantly more greens in increasingly smaller spaces. Now confined urban areas where arable land is very limited, could become producers of locally-grown, fresh food.
Protected cultivation has been in America at some level for two centuries, but what technological advancements made feeding the world with controlled environments possible?
Plastics
Polymer plastics such as polyethylene began providing a low-cost, energy-efficient film covering for greenhouses. This lowered the financial barrier to entry by creating more affordable greenhouses, thereby allowing unestablished growers to gain experience with a much lower investment than traditional glass-covered greenhouses. The plastic films dropped the investment cost significantly, while the more rigid, molded plastics improved operational metrics like production capacity, labor efficiency, and biosecurity.
Molded plastics also provided light-weight,easily-sanitized crop handling with trays, pots/flats, and clamshells for the packaging, among other things. Molded plastics further created light-weight structural channels, containers and benches which supported the plant and its root zone within hydroponic nutrient delivery systems, and even provided transport systems for improved labor and logistics management. Fully outfitted climate-controlled CEA plastic film boxes provided lettuce and greens production for the International Space Station.
Microprocessors
The microprocessor with its accuracy, consistency, data storage and simultaneous interpretation of multiple types and number of sensors has allowed the grower to tend more to plant production and much less to environmental control. No longer must the grower walk the greenhouse each morning to adjust the ventilation openings based on a guess of the day to be sunny, rainy or cold. Sensors are available to determine critical environmental plant needs and to make precise responses to air temperature and humidity for VPD (vapor pressure deficit) which affects plant transpiration and photosynthesis; light intensity with quantum sensors to determine DLI (daily light integral) which is directly related to desired growth or production rates; and, pH and EC which affects plant nutrient availability. When all combined, the grower is provided an improved understanding of the plant response to its environment. All this can be obtained on request in real-time by cellphone or within a report upon early morning arrival of the grower to the greenhouse each day.
Even more valuable is the capability of the computer to save data and further process it into useful information, which directs better grower decisions. Expect additional sensor development and implementation in the future to provide higher quality information about the food products, such as its flavor, sweetness, or nutritional quality.
The automation of information, although critically important, may become second in importance to labor-saving automation. Labor is often a farm’s biggest expense and the agricultural talent pool is limited nearly everywhere, but a high-tech farm’s food safety and security are dramatically enhanced when human contact with the edible product is reduced or eliminated. Production system automation that removes the need for people to work in groups on production lines is becoming crucial within this new world of viral pandemics.
There are still many advancements to be made in CEA. Technologies and experiences were transferred from the established greenhouse industry and applied to the developing indoor vertical farming industry. From LED lighting ‘recipes’ to plant nutrition under those recipes; from materials handling and logistics to labor management, years of R&D are required to reach optimal solutions for the plethora of combinations of plant cultivars, stages of growth, and harvest expectations within each type of CEA system.
The challenges remain for educating the people managing and operating the controlled environments. Educated employees working within a production process that is logistically sound, labor efficient, and task friendly are critical considerations for successful CEA businesses. Even with automation, the required work of skilled employees will remain, but at a higher educational level and a lower quantity.
In the future, it’s entirely possible that a CEA system will be able to autonomously program itself, or modify the plant environment without being directed, but for now, the plant production experience of an educated grower or crop manager is still required even in the most high-tech operations. Additional developments for successful CEA businesses include breeding of plant cultivars optimized for CEA production; emphasizing the importance of marketing; valuing employee education and experience; accepting that growing plants is a skill and an art; and, understanding basic physical principles that follow the laws of physics and biology!
CEA is still in such an early stage of commercial viability, but the blueprints for successful ventures continue to be created by intelligent and increasingly well-equipped entrepreneurs. As we look at the timeline of its commercial origins, to the critical technologies that made it work, we can see how far it's come, but also the potential the future holds for feeding the world with controlled environments.
Have you participated in the 2020 Global CEA Census? Autogrow and Agritecture Consulting have launched their 2nd Annual Global CEA Census, focusing on understanding the impact of the COVID-19 pandemic on controlled environment agriculture (CEA) operations around the world. The 2020 Global Census runs from July 7th to August 10th. Those who complete the census are entered to win different prizes from Agritecture and Autogrow.
Publication date: Fri 24 Jul 2020