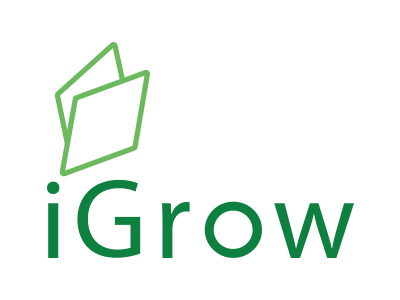
Welcome to iGrow News, Your Source for the World of Indoor Vertical Farming
Wageningen University Announces Course On Lighting In Greenhouses And Vertical Farms
By: urbanagnews -
October 30, 2018
In 2019, the Horticulture & Product Physiology group, together with Wageningen Plant Research, again will organize a course on lighting in greenhouses and vertical farms. In this course WageningenUR scientists share their unique knowledge with international students, researchers, and horticultural and light experts.
The course is held in Wageningen, The Netherlands.
Registration for the course in February 2019 is now possible.
The course consists of a mixture of interactive classroom lectures, group discussions, demonstrations, and an excursion day.
The lectures will be given by a team of experts of Wageningen University & Research. Lecturers include Prof. Leo Marcelis, Dr. Cecilia Stanghellini, Dr. Ep Heuvelink, Dr. Anja Dieleman, and Prof. Ernst Woltering.
This excellent and intensive course is meant for professionals in lighting, greenhouse production and vertical farms as well as MSc and PhD students, post-docs and junior scientists from all over the world.
For more detailed information on the course content, please visit the corresponding web page: Course Lighting 2019
Samsung Electronics Expands Horticulture LED Lineups To Advance Greenhouse And Vertical Farming
Samsung Newsroom 11.20.18
New horticulture LEDs are designed to promote healthier plant growth and enhance farming conditions for indoor growers
SEOUL, Korea – Nov. 21, 2018 – Samsung Electronics Co., Ltd., a world leader in advanced digital component solutions, today announced new horticulture LED lineups, including full-spectrum packages and modules as well as color (monochromatic) LEDs. Optimized for lighting in greenhouses and vertical farming*, the new LEDs provide a broader spectrum of light for healthier plant growth, enhanced farming environments and reduced lighting system costs.
Full-spectrum light encompasses a continuous range of wavelengths from blue and green to red, creating a light blend suitable for horticultural uses. Compared to narrow spectrum lighting, Samsung’s full-spectrum-based LEDs encourage healthier and more balanced plant growth by stimulating photosynthesis, enhancing plant immunity and increasing nutritional value. Additionally, the LEDs can help to improve the overall farming environment by enabling growers to observe plant conditions more easily and spot diseases, like damping-off, at an earlier stage under bright white lighting. As high-efficiency and cost-effective alternatives to higher-priced red LEDs, full-spectrum LEDs can help lower the costs of a grower’s entire lighting system.
“Samsung’s full-spectrum-based horticulture LEDs present a new way of using LED lighting to improve plant cultivation at reduced system costs,” said Un Soo Kim, senior vice president of LED Business Team at Samsung Electronics. “We plan to further expand our horticulture offerings by integrating the latest in smart LED lighting technology, including Samsung’s leading sensor and connectivity solutions.”
In addition to its full-spectrum white LEDs, Samsung has added blue, red and far-red LEDs to its horticulture family to offer an extensive variety of wavelength combinations and meet the different design needs of horticulture lighting manufacturers.
Built on Samsung’s market-proven LED technologies, the new full spectrum and color LED lineups feature a high degree of reliability, making them well-suited to withstand high temperatures and humidity levels as well as agricultural chemicals used in greenhouses and vertical farming.
Samsung’s horticulture LED packages are now in mass production for lighting manufacturers and growers worldwide. The modules will become available in the first quarter of 2019.
* Vertical farming is the practice of growing crops in vertically stacked layers and usually takes place in controlled, indoor environments.
** PPF (photosynthetic photon flux) indicates the total amount of photons in the photosynthetically active radiation (PAR) range – a spectral range between 400 and 700nm – that can enhance plant photosynthesis and is measured in micromoles per second (μmol/s).
*** PE (photon efficacy) indicates the light efficacy level for photosynthesis in plants and is measured in micromoles per joule (μmol/J).
Green Life Farms Announces Innovative Partnership with Hydronov for Sustainable Ag-Tech Greenhouse
Flagship hydroponic farm will feature Hydronov’s industry-leading deep-water floating raft technology to grow premium baby greens year-round
Boynton Beach, FL (November 19, 2018) – Green Life Farms has selected Hydronov, a Pranger Company, to design, construct and provide technology for its state-of-the-art hydroponic farm in Boynton Beach, FL. This agreement marks an important milestone as Green Life Farms prepares to begin commercial operation in the first half of 2019. Green Life Farms will grow premium baby leafy greens year-round from its Boynton Beach facility.
Green Life Farms has selected Hydronov, a Pranger Company, to design, construct and provide technology for its state-of-the-art hydroponic farm in Boynton Beach, FL. Green Life Farms will use Hydronov’s pioneering deep-water floating raft technology (pictured above), which is cost effective and environmentally friendly.
Green Life Farms has selected Hydronov, a Pranger Company, to design, construct and provide technology for its state-of-the-art hydroponic farm in Boynton Beach, FL. Green Life Farms will use Hydronov’s pioneering deep-water floating raft technology (pictured above), which is cost effective and environmentally friendly.
Green Life Farms will use Hydronov’s deep-water floating raft technology (FRT) to grow baby leafy greens for supermarkets, restaurants, cruise ships, and other customers from its state-of-the-art hydroponic greenhouse in South Florida. Hydronov is a pioneer in the hydroponic sector, leading the way with this cost-effective and environmentally-friendly method of hydroponic growing.
“Partnering with Hydronov and leveraging the company’s leading technology will help us realize our vision for Green Life Farms – growing sustainable and delicious leafy greens for consumers in South Florida and beyond,” said Mike Ferree, Vice President, Green Life Farms. “Green Life Farms will grow baby leafy greens that are good for your body, family, community, and planet. Creating a sustainable facility by using leading Ag-Tech methodology, along with green energy and other environmentally-friendly practices, brings our mission to life.”
FRT helps to conserve water, allowing a buffer for fertilization and oxygen control, and provides an integrated Harvest Transportation System which uses the water in which the plants grow as a conveyer system, eliminating the costs and maintenance associated with mechanical conveyers. No water is lost through soil or growing media; there is no direct evaporation by the sun, no dumping of growing solution and no dripping gutters. The FRT system leads to higher productivity, producing up to 18 crop harvests per year versus the five harvests per year with soil-based greenhouse growers.
Hydronov is an industry leader in the design and construction of hydroponic growing facilities. With more than 30 years of experience in hydroponics and aquaponics, the company brings industry-leading expertise to the innovative project with Green Life Farms.
“We’re excited to partner with Green Life Farms on this state-of-the-art project,” said Gabe Pranger, owner of Hydronov. “Growing leafy greens in South Florida presents a number of unique challenges, but we’re confident that the combination of Hydronov’s technology and construction management expertise with Green Life Farms’ strategy will result in great success.”
Green Life Farms produce will set new standards for cleanliness, freshness, and taste. Grown locally, using sustainable farming practices combined with the most advanced AgTech practices, and kept free from pesticides and contaminants, Green Life Farms baby leafy greens are good for your body, family, community, and planet.
For more information about Green Life Farms, visit GreenLifeFarms.ag. Please contact Elayne@GreenLifeFarms.ag for sales and Ray@GreenLifeFarms.ag for investor relations.
About Green Life Farms
Green Life Farms is constructing a 100,000 square foot state-of-the-art hydroponic greenhouse in Boynton Beach, Florida, with additional expansion planned in Florida and beyond. Commercial operation is expected to begin in the first half of 2019. By incorporating agriculture with technology, Green Life Farms will provide consumers with premium-quality, fresh, local, flavorful and clean baby leafy greens that are good for their bodies, families, communities and planet – year-round.
About Hydronov
Hydronov LLC was purchased by Nick Pranger and Gabe Pranger in 2017. Since its beginnings in the 1980s with founder Luc DeRochers, Hydronov has focused on innovation in the greenhouse industry. The success of a small research project developed into Hydronov’s unique growing system, Deep Water Floating Raft Technology. Today, Hydronov’s technology is a cost-effective, environmentally friendly, and profitable way to grow hydroponic lettuce, herbs, and produce. Hydronov is headquartered in Ashley, Indiana. Learn more about Hydronov’s floating raft technology at www.hydronov.com.
CAN (BC): Bevo Agro Taken Over By Cannabis Grower, Changes Name To Zenabis
Combined entity will have 3.5 million square feet of growing space
CAN (BC): Bevo Agro Taken Over By Cannabis Grower, Changes Name To Zenabis
Bevo Agro has signed an Arrangement Agreement dated October 4, 2018 with Sun Pharm for a reverse take-over of Bevo.
The Transaction involves three main elements:
the amalgamation of Sun Pharm with a wholly-owned subsidiary of Bevo, with Sun Pharm shareholders receiving Bevo shares representing 86% of the outstanding Bevo shares (the expected exchange ratio being one Bevo share for each Sun Pharm share) and the existing Bevo shareholders continuing to hold Bevo shares representing a 14% interest in Bevo.
a plan of arrangement under which Bevo will distribute its interest in Cubic to the shareholders of Bevo, with Bevo shareholders expected to receive one common share of Cubic for every Bevo share held.
Bevo changing its name to Zenabis Global Inc. (“Zenabis,” being one of Sun Pharm’s established brands in the cannabis industry).
The transaction was unanimously approved by the board of directors of Bevo. Shareholders holding approximately 58% of Bevo’s common shares have entered into voting agreements committing to vote their Bevo common shares in favour of the transaction.
Zenabis
Sun Pharm is currently a privately-held cannabis company which has one of the largest, federally licensed indoor medical cultivation footprints in Canada, operating two licensed production facilities in British Columbia and New Brunswick, with a third expected to be coming online shortly in Nova Scotia. These facilities encompass 660,000 square feet of indoor pharmaceutical grade cannabis production space, strategically positioned on Canada’s coasts, facilitating national distribution and access to international markets. Sun Pharm has received purchase agreements for recreational cannabis from each of the British Columbia Liquor Distribution Branch, New Brunswick Liquor Corporation, Nova Scotia Liquor Corporation, and Yukon Liquor Corporation.
Following the completion of the Transaction, Bevo’s greenhouse facilities in Langley are intended to be expanded and retrofitted to integrate advanced propagation technologies and state-of-the-art lighting and ventilation systems. On completion of the expected expansion of these greenhouse facilities, Zenabis will have 660,000 square feet of indoor space and 2.8 million square feet of state-of-the-art greenhouse space in three provinces – British Columbia, New Brunswick and Nova Scotia.
Proposed management team
It is currently anticipated that the management of the resulting issuer will include each of Rick Brar (Chief Executive Officer), Leo Benne (Chief Growing Officer), John Hoekstra (Chief Financial Officer), Mike McGinty (Chief Administrative Officer) and Kevin Coft (Chief Facilities Officer).
Rick Brar – Chief Executive Officer
Mr. Rick Brar is an experienced business leader in the cannabis, nutraceutical, beverage, consumer packaged goods, agriculture, land development and construction sectors. Mr. Brar has international expertise in emerging market sectors, having incubated and grown several companies over his career. He is experienced in sales and marketing, with demonstrated success in corporate sales growth, new market penetration, new product development, and long range planning. Mr. Brar was previously the Chief Executive Officer of International Herbs Limited, where he led one of the largest herb companies in North America for nine years.
Leo Benne – Chief Growing Officer
Mr. Leo Benne is currently Vice President and a Director of Bevo, and the General Manager of Bevo Farms Ltd., the company’s wholly owned subsidiary. Mr. Benne gained advanced knowledge of modern horticultural methods at Rijks Middelbare Tuinbouwschool in Holland. Mr. Benne has overseen every stage of the company’s operations, from planting to shipping. He has been with Bevo for over 25 years.
John Hoekstra – Chief Financial Officer
Mr. John Hoekstra is the Executive Vice President and Chief Financial Officer of Bevo Agro, where he oversees all finance, administration and accounting activities. He joined Bevo in 2004, shortly after the company went public. Prior to joining Bevo, Mr. Hoekstra worked as Supply Chain Manager at Air Liquide Canada, and at Unitor Ships Service as Branch Manager. He is a Chartered Professional Accountant (CPA, CGA) and holds a Business Administration degree from Redeemer University.
Mike McGinty – Chief Administrative Officer
Mr. Mike McGinty has extensive experience in large-scale coordination and planning. Previously, he was a post-graduate tutor in leadership and planning for senior government and military staff from Canada and over 25 allied nations worldwide. Mr. McGinty was a senior officer in the British Army and served widely overseas, including in Iraq and Afghanistan, where he was responsible for more than 1,000 people with $2 billion in capital assets. Mike remains an active member of the Canadian Armed Forces. He also served as the Head of Risk and Security for UBC Okanagan.
Kevin Coft – Chief Facilities Officer
Mr. Kevin Coft is an operational and supply chain professional with over 30 years of Canadian and international procurement, facility operations, and managerial experience. His industrial expertise covers a wide range of functions including navigating Health Canada’s regulatory licensing, team development, facility construction, strategic analysis, import/export operations, logistics, warehousing, customer relationship management, benchmarking, and business systems analysis.
“Our primary goal with this merger is to expand Zenabis’ capacity to supply high-quality cannabis for worldwide distribution. We will achieve this by taking advantage of Bevo’s greenhouse growing expertise to cultivate high-quality cannabis,” said Mr. Brar. “This is a unique partnership that gives Zenabis a significant advantage among Canadian producers as we continue to grow our business to meet Canadian and international demand.”
“This transaction represents a positive growth opportunity for Bevo Agro, as Zenabis intends to invest up to $100 million to expand our greenhouse facility to provide state-of-the-art cannabis production capacity, while maintaining our existing propagation and floral business,” said Mr. Benne. “This partnership will bring new jobs and economic opportunities to the communities in which we operate, while we continue to support the local and international food and floral markets.”
Completion of the transaction is subject to a number of conditions, including but not limited to, TSXV acceptance and if applicable, disinterested shareholder approval. Where applicable, the transaction cannot close until the required shareholder approval is obtained. There can be no assurance that the transaction will be completed as proposed or at all.
Acquisition of additional greenhouse operations and land
Bevo has also entered into a purchase agreement with an arm’s length third party to acquire 10.4 acres of greenhouse operations on 50 acres of land in Aldergrove, British Columbia. Post-amalgamation, Zenabis intends to use this greenhouse acreage to ensure continuity for existing Bevo propagation customers. The greenhouse acquisition is subject to customary closing conditions and is expected to close prior to December 31, 2018.
For more information:
Zenabis
info@zenabis.com
www.zenabis.com
Bevo Agro
www.bevofarms.com
Publication date : 10/5/2018
Life Support System Greenhouses To Be Launched To Space
At 19:31 CET on 19 November 2018, the German Aerospace Center (Deutsches Zentrum für Luft- und Raumfahrt; DLR) Eu:CROPIS mission was launched into space from Vandenberg Air Force Base in California.
A Falcon 9 from the US aerospace company SpaceX will carry two biological life support systems comprising greenhouses, dwarf tomato seeds, single-celled algae and synthetic urine on a satellite up to a near-Earth orbit at an altitude of 600 kilometres. The aim is for the seeds to germinate in space and continue to grow due to the successful conversion of urine into a fertiliser solution. The mission is intended to show how biological life support systems can be used to supply food on long-term missions. The Eu:CROPIS satellite, which is approximately one cubic metre in size and weighs 230 kilograms with its biological payload, was designed and built by DLR and the Friedrich Alexander University (FAU) in Erlangen–Nuremberg.
"With the Eu:CROPIS mission, DLR is making a significant contribution towards future long-term missions, showing whether and how a closed biological life support system can function and produce food far away from Earth. In the process, DLR has once again demonstrated its systems expertise in the design and construction of satellites," says Hansjörg Dittus, DLR Executive Board Member for Space Research and Technology. The satellite will separate from the Falcon 9 carrier rocket 35 minutes after the launch in its orbit. The DLR German Space Operations Center (GSOC) in Oberpfaffenhohen, which will control the satellite, expects first radio contact about one and a half hours after the launch.
A closed life support system
Eu:CROPIS stands for 'Euglena and Combined Regenerative Organic-food Production in Space'. "This mission seeks to show that urine can be converted into nutrients even under lunar and Martian gravity conditions," says Jens Hauslage of the DLR Institute of Aerospace Medicine in Cologne. Inside the satellite are two greenhouses, each maintained as a pressurised closed loop system. The core elements of these systems are a biofilter and green algae (Euglena gracilis). The biofilter consists of a 400-millilitre chamber filled with lava stones. Bacteria have settled on and within these porous stones, which convert the urine flowing over them into nitrate in a water cycle.
"The nutrient solution obtained is used to cultivate the tomatoes. This is, so to speak, an indicator that our experiment is proceeding successfully in space," says Hauslage. The single-celled Euglena gracilis, also known as green algae, which will be carried into space as a 500-millilitre 'green solution', also play a key role in the system. Firstly, they can produce oxygen, which will prove particularly important at the start of the experiment, when the tomatoes are not yet generating oxygen via photosynthesis. Secondly, the Euglena can detoxify the system and protect it against excessive levels of ammonia, which can occur if the biofilter is not functioning properly. "We use the properties of communities of organisms to apply purely organic methods for transforming waste into substances that we need to grow crop plants, in this case tomatoes. As such, we are preparing the vital groundwork for supplying astronauts with food on future long-term missions," explains Hauslage. He and Michael Lebert (FAU in Erlangen) are the scientific instigators behind the project, and are now leading the Eu:CROPIS mission.
The processes at play inside the greenhouses are recorded by cameras and transmitted to the GSOC and the Microgravity User Support Center (MUSC). LED light provides a day-and-night rhythm, while a pressure tank ensures atmospheric pressure of one bar, which corresponds with that of Earth's. Also on board the Eu:CROPIS satellite are two RAMIS (Radiation Measurement in Space) devices, developed by the Institute of Aerospace Medicine. These will measure radiation levels both inside and outside the satellite during the mission. DLR is also sending the on-board computer SCORE (SCalable On-BoaRd Computing Experiment), developed by the Institute of Space Systems, to test the principle of a COBC (Compact On-Board Computer) in space for the first time. The computer will process the images taken by the on-board cameras. NASA will also be running a PowerCell experiment relating to the production of useful substances in space using bacteria.
Gravitational conditions as on the Moon or Mars
During the mission, the satellite will rotate around its longitudinal axis. Depending on the rotation rate, this generates a specific level of altered gravity. During the first part of the experimental phase, gravitational conditions like those on the Moon will be created (0.16 times Earth's gravitational pull), with 20 rotations per minute. This will last for around 23 weeks. The first greenhouse will be put into operation during this phase. In the second research phase, the satellite will simulate gravity on Mars (0.38 times that of Earth) by rotating 32 times per minute. Experiments will now take place in the second life support system.
Systems expertise in satellite construction
The satellite was built at the DLR Institute of Space Systems in Bremen. The DLR Institute of Composite Structures and Adaptive Systems in Braunschweig developed the frame structure and the pressure tank. Power is supplied via four solar panels, each with a surface area of one square metre. DLR scientists were able to draw on their experience of developing standard components for satellites in the run-up to the mission. Depending on the payload, they are able to design and construct satellites of different sizes quickly and flexibly. "In its efforts towards this mission, DLR has shown that it can develop satellites efficiently and cost-effectively. This component-oriented design is a unique feature of DLR, enabling us to support lots of different research missions," says Hartmut Müller, Project Manager for the satellite’s construction at the DLR Institute of Space Systems.
Benefits for Earth
Fresh vegetables that thrive in space thanks to converted organic waste products are not only a prerequisite for long-term space travel, but the research findings from such projects can also be useful on Earth. If urine or manure can be recycled into fresh water and nutrients usable by plants, this could improve living conditions in overcrowded areas or in places that have an extreme shortage of drinking water, while providing relief for soil and groundwater – another of DLR’s areas of research.
Source: DLR
Publication date : 11/16/2018
Mums To Marijuana: Pequannock, New Jersey, Family Farm Applies For License To Grow Medical Pot
Jai Agnish, North Jersey Record
2018
(Photo: Jai Agnish/Northjersey.com)
Ken VandeVrede, of Gro-Rite Garden Center & Florist and CEO of Hillview Med in Pequannock discusses applying for license to farm medical marijuana. Jai Agnish, Staff Writer, @jaiagnish
Fifty years ago the VanderVrede family delivered tomatoes from the farm in Pequannock to customers in Paterson. If the state allows, the family may soon replace the tomatoes with medical marijuana.
Gro-Rite Garden Center & Florist has applied for one of six available state licenses to grow medical marijuana on its 150 acres of farmland in Pequannock and Belvidere under the name Hillview Med.
"It's very competitive," said Ken VandeVrede, the CEO of Hillview Med in Pequannock.
The farming family is among 147 statewide applicants, 49 in North Jersey, including Evergreen Cultivation in West Milford, who want to cultivate, process, and sell medical marijuana. Two licenses will be awarded in North Jersey, two in Central Jersey and two in South Jersey. There are currently six active state licences in circulation.
The family sees the connection to Paterson as a natural one, VanderVrede said, after all that is where his grandfather started off delivering his tomatoes in the early days of the business after immigrating from Holland.
The New Jersey Board of Health is expected to announce which applicants will receive a license on Nov. 1.
"It would be absolutely amazing," VanderVrede said of landing one of the coveted licenses. "For us to get in on the ground floor of the medical cannabis market in New Jersey would be amazing."
Why medical marijuana?
The Hillview Med proposal results from Gov. Phil Murphy’s early-summer move to double the state’s marijuana providers to meet growing demand. With more than 28,000 registered patients by early July, the state program is on track to double its numbers in 2018, state records show.
"We consider this as the next evolving space in the agriculture space," VandeVrede said.
Hillview Med is also trying to be ready if recreational marijuana is legalized in the state, VanderVrede said. A bill to create a legal marijuana marketplace in New Jersey is nearly complete.
Based on what's happened in other states, medical marijuana growers will likely be grandfathered in and have a foot in the door to grow legal recreational marijuana, VandeVrede said.
The distinction between medicinal versus recreational use marijuana is determined at the consumer end, VanderVrede explained. It's just taxed differently.
"We feel we have a very, very strong application," VandeVrede said.
The move from growing mums to marijuana could be made in seven months, he said.
Gro-Rite ships hundreds of thousands of plants and flowers on a weekly basis to supermarkets including ShopRite, Whole foods, and others in a number of states including Virginia and Pennsylvania.
Among the products are hydroponic basil, which is grown in state-of-the-art greenhouses. The company has 750,000 square feet of greenhouse space on the two farms and is permitted to build 2.2 million square feet more. That's the equivalent of 13 football fields with the potential for 38 more, he said.
"We can expand quickly," VandeVrede said.
The other plus, the CEO said, is the farm can get an affordable product to market.
Hillview Med can produce a pound of marijuana for under $400, VanderVrete said on Thursday. He said applicants who plan to open a warehouse and use electricity will find it difficult to get below $1,000 a pound.
"The lowest cost producers are the ones with high-tech greenhouses," he said.
These are computer- and sensor-based systems to control temperature, humidity, and water metrics. Also, the use of a sealed, closed-loop temperature system avoids having to vent out stinky marijuana odors during production.
"I don't have many neighbors but I wouldn't even want to go there," VandeVrede said.
In addition to sustainably cultivated agriculture products, Gro-Rite's food and herb lines are certified organic. This approach would carry over to marijuana even though VanderVrede said certified organic cannabis is not a thing yet.
"We know how to grow food at the highest level that there is, so for us to move into the cannabis space, this is automatic production that we do already," he said.
It's a vertical integration license meaning Hillview Med would grow the plant, extract it into oils, edibles, pills, vapes, and distribute products to dispensaries.
Ken VandeVrede, of Gro-Rite Garden Center & Florist, and CEO of Hillview Med in Pequannock. (Photo: Courtesy of Ken VandeVrede)
Why the Paterson market?
Hillview Med chose Paterson for several reasons, one being the family's history of delivering produce to the "Silk City" going back 50 years. More recently Gro-Rite has provided fresh produce to food banks there and has forged relationships with community groups. He said the company would hire Paterson residents to work in the dispensary.
"We've done a lot of exciting stuff in Paterson," he said.
Another reason is the diversity of the city's population. Having a marijuana dispensary in an urban city helps fulfill the licensing goal to promote inclusivity with minorities, VandeVrede said.
Hillview Med/Gro-Rite Garden Center & Florist in Pequannock applied for a license to grow and distribute medical marijuana. (Photo: Jai Agnish/Northjersey.com)
Gro-Rite's expansion into the cannabis market would be a remarkable change for the family, said VandeVrede during a recent tour of the farm. He reminisced about when he worked on the Pequannock farm as a child. His father was in charge then and he expanded to farm into Belvidere.
VandeVrede, a non-active private pilot, said it would be fun to one day fly a helicopter from nearby Lincoln Park Airport to the grass strip at the Belvidere farm. Such a costly flight may not be so out of reach if his company secures one of the lucrative medical marijuana farming licenses.
Staff writer David M. Zimmer contributed to this article.
Follow Jai Agnish on Twitter: @JaiAgnish. Email: agnish@northjersey.com.
CAN (ON): How Cannabis Is Transforming The Tomato Capital of Canada
Located around Canada’s southernmost point, the Leamington and Kingsville area has one of the warmest climates in Canada.
The town of 30,000 people has seen 21 of its approximately 120 greenhouse growers convert entirely to cannabis production or be acquired by a larger firm, according to James Cox, Leamington’s manager of economic development.
Meanwhile, an additional 35 greenhouses are planning to add capacity to existing facilities to produce marijuana alongside crops like tomatoes, peppers and cucumbers.
Additionally, the area’s growers have the technical expertise to handle a highly-regulated agricultural sector like cannabis, according to Mike Dixon, environmental science professor and director of the Controlled Environment Systems Research Facility at the University of Guelph.
“This is not gum boots and garden hoses in a plastic greenhouse,” Dixon said.
“[Leamington has] serious technology in terms of computer automated, environmentally controlled, hydroponic systems, disinfection protocol – a long laundry list of horticultural practices for cucumbers, tomatoes and peppers. It’s a logical home for a new commodity that promises significantly larger margins than food or even ornamental [plants].”
That was something Aphria’s Cacciavillani saw in 2012, after Canada changed the regulatory framework around medical cannabis and paved the way for the plant to be grown commercially. At the time, Cacciavillani Farms was already the “oddball” of Leamington’s growers, Cacciavillani says, bucking the trend of growing fruits and vegetables for more vertically-integrated holiday plants, such as poinsettias and Easter lilies. He fully converted the greenhouses to grow cannabis in 2016.
Second Greenhouse Heated by Cryptocurrency Mining
UnitedCorp's technology uses the heat from cryptocurrency mining to support greenhouse agricultural operations
Miami-based United American Corp announces the completion of its second BlockchainDome and the full commissioning of 1,500 additional miners for a total of 2,500 miners (3.8 megawatts) now in service in two BlockchainDomes. Pre-installation of 1.5 megawatts of electrical service for adjacent greenhouses heated by the BlockchainDomes is now also complete.
The latest BlockchainDome incorporates a number of improvements in construction and deployment from the first dome which includes mass pre-fabrication of a number of dome components and in-house CNC manufacturing of the mining rig docking stations. Construction logistics have also been refined to include pre-installation of foundations and utilities for future domes resulting in overall lower construction costs and shorter construction timelines.
"We have taken everything we have learned from the construction of the first BlockchainDome and used this knowledge to make the implementation of this subsequent BlockchainDomes faster, cheaper and of better quality," stated UnitedCorp CEO Benoit Laliberte. "Along with the generation of heat from the BlockchainDomes for agricultural purposes, our goal remains to be the low cost and environmentally sustainable standard for the industry."
UnitedCorp's technology uses the heat from cryptocurrency mining to support greenhouse agricultural operations through the BlockchainDome Heat Station system which keeps greenhouses at 20oC year-round. This represents a simple design solution compared to various alternatives whereby the cost of generating this heat from a single source is shared between multiple use cases.
Commercial greenhouses in cooler climates like in the Province of Quebec typically require a significant amount of thermal energy to supplement daytime solar energy, particularly during the period of September to May, and many older greenhouses utilize inefficient heating systems for this purpose. The dry heat produced by the BlockchainDome Heat Station is also used in the summer to reduce greenhouse mold and fungus caused by condensation thereby reducing or eliminating the need for chemicals to treat this problem and creating a more organic growth environment.
UnitedCorp believes this "Heat Campus" approach for heat generation and utilization is the future for agriculture and any other industry that can make use of low-cost heat with the ultimate goal being to get as close zero waste as possible. This is not only good economically but allows businesses to "green" their operations by significantly reducing the amount of electricity the combined operations require from the grid.
For more information:
UnitedCorp
5201 Blue Lagoon Drive, 8th floor,
Miami FL 33126
www.unitedcorp.com
Get The Free Report On The Investment Potential Of Greenhouse Business In Russia 2018
Last year was one of the most successful years for Russia’s greenhouse industry. Over 250 ha new commercial greenhouses were commissioned, the number of 5-gen greenhouses increased. Further expansion of greenhouse area is expected – new projects are set to be launched in different regions across the country.
Last year was one of the most successful years for Russia’s greenhouse industry. Over 250 ha new commercial greenhouses were commissioned, the number of 5-gen greenhouses increased. Further expansion of greenhouse area is expected – new projects are set to be launched in different regions across the country.
Prior to the International Investment Forum and Exhibition “Greenhouse Complexes Russia 2018”, Vostock Capital team of analysts has conducted a research on the investment potential of Russian greenhouse industry, which covers:
the information about the prospects for the development of Russian greenhouse industry
new investment greenhouse projects (construction and modernisation)
criteria for the selection of technology and equipment by the decision-makers of greenhouse companies and agriholdings and many other important results.
Request the report:
The research involved over 250 respondents, including the C-suite of agroindustrial holdings and greenhouse complexes, suppliers of latest technologies and equipment, regulators, project operators, representatives of financial institutions and investors, independent market experts.
The international Forum and Exhibition “Greenhouse Complexes Russia 2018” is the high-class professional platform to unlock investment in Russian greenhouse industry, discuss industry development strategy, share experiences between key market players and conclude new lucrative contracts.
The Event spans investors from the CIS, Europe, and Asia, initiators of investment projects from across Russia, decision-makers of federal and regional agriholdings, dedicated ministries and agencies, heads of regions, retail chain executives, service providers, presidents of national unions and associations.
Contact: Elvira Sakhabutdinova, Project Director
ESakhabutdinova@vostockcapital.com Tel. +7 499 505 1 505
Website: http://www.greenhousesforum.com/en/
Prestigious Professional Platform For Decision-Makers of CIS And Russian Greenhouse Industry
We are very pleased to announce that the “Greenhouse Complexes of Russia” has already attracted confirmed attendance from over 700 leaders of the greenhouse industry. But, as the number of places in Moscow’s Baltchug Kempinsky hotel is limited, registration for participation will now close before the previously established date. If you still hope to join us – to present your products, technologies, or services, we ask that you let us know now. Two remaining booth spaces will be made available to the participants who respond first.
Gold Sponsor: Grodan. Silver Sponsor: Signify, Svetogor, Green Automation Group. Bronze Sponsors: Royal Brinkman, Rijk Zwaan, Mir Stekla, AWETA, Lider-Pak. Video Promotion Sponsors: Uralchem, RICHEL Group, AHPS.
Request a Call
Among the honoured guests and presenters of 2018:
Aleksandr Rudakov, President, APH ECO-Culture
Sergey Rukin, President, Greenhouse Growth Technologies
Dmitry Lashin, Chairman of the Council of Directors, TK Lipetskagro
Nurbek Adaev, Director, TK YugAgroHolding
David Bondarenko, Director, CHINAR
Viktor Ovchinnikov, Executive Director, Greenhouse Complex Podosinki
Sergei Kirillov, General Director, Greenhouse Plant Tatarinovo (STK) and many others.
Register Now
I will be very pleased to respond to all possible questions and receive your comments.
Elvira Sakhabutdinova
Project Director
Tel: +44 207 394 3 090
Fax: +44 207 231 1600
Email: ESakhabutdinova@vostockcapital.com
Web: http://www.greenhousesforum.com/en/
Investment Projects For The Construction and Modernization of Greenhouse Complexes Will Be Presented at the 3rd Annual Forum and Exhibition
“Greenhouse Complexes Russia 2018”
Date: 5-6 December 2018
Venue: Moscow, Baltschug Kempinski Hotel
Organiser: Vostock Capital
Website: https://www.greenhousesforum.com/
The 3rd annual international Forum and Exhibition “Greenhouse Complexes Russia 2018” is the high-level professional platform to unlock investment in Russian greenhouse industry, discuss development strategies, share experiences, and conclude new lucrative contracts.
The Forum gathers investors from the CIS, Europe, and Asia, initiators of greenhouse investment projects from all Russian regions, decision-makers of federal and regional agro holdings, dedicated ministries and agencies, heads of regions, retail chain executives, service providers, presidents of national unions and associations.
Among Forum attendees 2017:
Alexander Tkachev, Ministry of Agriculture of the Russian Federation
Jambulat Khatuov, First Deputy Minister of Agriculture of the Russian Federation
Sergey Dankvert, Head of the Federal Service for Veterinary and Phytosanitary Control
Vladimir Vladimirov, Governor of the Stavropol Territory
Sergey Korolev, President, National Union of Fruit and Vegetable Producers
Sergey Rukin, General Director, Greenhouse Growth Technology
Viktor Semenov, Chairman of the Supervisory Board, Belaya Dacha
Alexander Rudakov, Chairman of the Board of Directors, APH Eco-culture
Alexander Zaklyepkin, General Director, Vyborgec Agrofirm
Irina Meshkova, General Director, Agro-Inwest
Nurlan Adilkhan, Director, BRB APK
Anatoly Tarasov, General Director, Teplitsy Belogoria
Andrey Volkov, General Director, Udmurt Flowers and many others.
Greenhouse Complexes Russia 2017 in facts and figures:
500+ participants representing flagship greenhouse complexes and agro holdings from Russia and the CIS – Greenhouse Growth Technology, Udmurt Flowers, YugAgroholding, TK Rodina, Ivanisovo Agrocomplex, Teplitsy Belogoria, Yuzhny Agrokombinat, BRB APK, Agrokultura Group, Teplichny Agrokombinat, Volzhsky Agrocomplex, Grodnenskaya Ovoschnaya Fabrika, Kaskad Mushroom Complex, Iftikhari, ECOS, RoseHill, Chekhov Garden, EcoProduct and many others.
60+ major investment projects – Alania Greenhouses, Avasyuninsky, Prompark, Master-R, Agrocluster, and a lot more
20+ presentations with key information delivered by the heads of such companies as Vyborgec Agrofirm, APH Eco-culture, Dolina Solntsa, Demetra Technology, NPO BioGreen, LipetskAgro, Agro-Inwest and others
Delegations of the government and development corporations – Stavropol territory, Ulyanovsk region, Irkutsk region, Tyumen region, Kaliningrad region, Voronezh region, Oryol region, Moscow region, Bashkortostan Republic, Karachay-Cherkessia Republic, Tambov region and other regions across Russia
Forum Highlights 2018:
500+ decision-makers of flagship greenhouse complexes and agro holdings from Russia and the CIS – Kazakhstan, Uzbekistan, Belarus, Armenia, Azerbaijan, as well as investors, government officials, chief agronomists, retail chain executives, service providers
Presentation of 30+ greenhouse investment projects to be executed within 2019-2025 from across Russia and CIS countries
Leaders debate: Ministry of Agriculture of the Russian Federation, investors, initiators, agri holdings. How will the Russian greenhouse industry evolve beyond 2020?
NEW! AGRONOMY DAY – specialized workshops on growing tomatoes, cucumbers, lettuce. Modern techniques of working with hybrids, effective use of LED-lighting and hydroponics
STRATEGIC FOCUS: ASSORTMENT POLICY – diversification and new business areas. What niches are the most promising in the greenhouse industry?
Dedicated exhibition of modern equipment and technologies delivered by the lead companies from Holland, Israel, Germany, Italy, Spain, and other countries
IMPORTANT: FINANCING. Cooperation with investors and banks, project financing. How to get best credit conditions?
ROUNDTABLE ON MUSHROOM FARMING AND FLORICULTURE – explore peers’ practices and learn about industry development prospects
FOCUS-SESSION: ENERGY-SAVING – connection to the electricity network, on-site generation, distributed power. What tariffs are to be expected in 2019?
Fast and effcient! Roadshow of innovative technologies and equipment from the global leaders
SPECIAL SESSION: THE TALENTS MAKE ALL THE DIFFERENCE! How to find a prospective hire?
Contact: Elvira Sakhabutdinova, Project Director
ESakhabutdinova@vostockcapital.com Tel. +7 499 505 1 505
Website: http://www.greenhousesforum.com/
UPDATE:
440+ decision-makers of major greenhouse complexes, agriholdings, investment projects, regulators, and lead service and equipment providers have already confirmed their participation and will present their projects at the 3rd International Investment Forum “Greenhouse Complexes Russia 2018” (5-6 December, Moscow).
Gold sponsor: Grodan. Silver sponsors: Signify, Svetogor, GREEN AUTOMATION EXPORT. Bronze sponsors: Royal Brinkman, Rijk Zwaan, AWETA, Lider-Pak. Sponsor of video-promotion: Uralchem.
Request the full list of confirmed participants
Speakers and VIP-guests 2018 include:
Alexander Rudakov, President, APH Eco-culture
Irina Meshkova, General Director, TK AgroInwest
Gury Shilov, General Director, Greenhouse
Nurlan Adilkhan, General Director, BRB APK (Kazakhstan)
Yanis Galanidi, General Director, Dolina Solntsa
David Bondarenko, Director, CHINAR
Valery Astapchik, Director, Grodno Vegetable Factory (Belarus)
Alexey Soshnikov, General Director, Ecoresurs
Jamal Majidov, Greenhouse Director, Grow Group Azerbaijan (Azerbaijan) and many other leaders of greenhouse industry in Russia and the CIS.
Northeast Greenhouse Conference
November 7 & 8, 2018
Boxborough, MA
For more information go to negreenhouse.org
The NEGC will have more than 40 sessions delivered by nationwide experts.
Topics include disease management, IPM, water and nutrient management, greenhouse technologies, basic production techniques, buisiness and marketing.
Special sessions include greenhouse vegetables and perennials, and practical training for the Spanish-speaking workforce, and hands-on training sessions.
Pesticide Recertification Credits: A total of 12 hours of presentations (credits will vary by state) will be offered for the six New England states plus New York and Pennsylvania.
The updated New England Floriculture Guide will be available at a reduced price in the conference.
For more information about the program, go to:
https://www.negreenhouse.org/schedule.html
Register today at: https://www.negreenhouse.org/registration.html
US (MA): AmeriCann Releases Designs For 345,000 sq.ft. MJ Facility
The dedicated cultivation facilities are designed to utilize AmeriCann’s proprietary greenhouse system called Cannopy.
AmeriCann has released designs for Building 2 which includes 345,000 square feet of cannabis manufacturing and cultivation infrastructure at its 52-acre Massachusetts Medical Cannabis Center (MMCC) in Freetown, MA.
The configuration of Building 2 includes over 100,000 square feet of dedicated cannabis extraction, processing and product manufacturing space and approx. 245,000 sq. ft. of cultivation infrastructure. The dedicated cultivation facilities are designed to utilize AmeriCann’s proprietary greenhouse system called Cannopy.
The design of Building 2 of the MMCC, which is 345,000 square feet, will include three distinct units:
Unit A: 184,720 square foot cannabis cultivation facility
Unit B: 40,178 square foot extraction and product manufacturing facility; and
Unit C: 118,580 square foot cannabis cultivation facility cannabis
AmeriCann will own and operate Unit B which is designed to provide extraction and product manufacturing support to the entire MMCC project, as well as to other licensed cannabis farmers throughout Massachusetts. In addition to large-scale extraction of cannabis plant material, AmeriCann plans to produce branded consumer packaged goods including cannabis beverages, vaporizer products, edible products, non-edible products and concentrates at the state-of-the-art facility.
The company has already commenced construction on the first phase of the 1 million square foot multi-phase MMCC project with a 30,000 square foot cultivation facility.
AmeriCann plans to replicate the brands, technology and innovations developed at its MMCC project to new markets as a multi-state licensed operator.
For more information:
AmeriCann
3200 Brighton Blvd. Unit 114
Denver, CO 80216
(303) 862-9000
info@americann.co
www.americann.co
Publication date : 10/11/2018
Pure Flavor® Breaks Ground on New Georgia Distribution Center
Georgia greenhouse, Pure Flavor® announced recently that they have broken ground on a new 60,000 sq. ft distribution center just 10 minutes away from their new greenhouse facility off of I-75 in Peach County, GA.
Fort Valley, GA - November 1st, 2018
With fresh tomatoes coming to life in its new Fort Valley, Georgia greenhouse, Pure Flavor® announced recently that they have broken ground on a new 60,000 sq. ft distribution center just 10 minutes away from their new greenhouse facility off of I-75 in Peach County, GA.
“We are strategically growing our business across North America and in doing so, need to support this growth with regional facilities that reduce food miles for our greenhouse grown vegetables. Our new distribution center in Peach County will allow us to better serve our retail & foodservice customers throughout the southeast year-round”, said Jamie Moracci, President. As a vertically integrated vegetable company, Pure Flavor®’s family of growers produce greenhouse tomatoes, peppers, cucumbers, eggplants and a wide variety of USDA certified Organic items at farms in Canada, USA, and Mexico.
The new Georgia distribution center will serve as a consolidation point which will provide an opportunity for a greater assortment of Pure Flavor® greenhouse grown vegetables to retailers & foodservice partners in the southeastern US region starting in early 2019. Pure Flavor® operates distribution centers in Leamington, ON, Romulus, MI, and San Antonio, TX to support its vast network of growers throughout North America.
A little over 14 months ago, Pure Flavor® broke ground on a 75-acre, $105 million-dollar greenhouse facility in Fort Valley, GA. Phase 1 of 25 acres is now complete with the first crop of Georgia Grown tomatoes to be picked in a few weeks’ time. Pure Flavor®’s Long English & Mini Cucumber crop will also be ready for picking in November.
“Our team has been hard at work building a state of the art, high tech greenhouse facility in Georgia. What has been accomplished in the past year has been remarkable”, said Moracci. “Our goal to grow greenhouse tomatoes & cucumbers in Georgia is becoming a reality, we look forward to promoting Georgia Grown vegetables this winter”, said Jamie Moracci.
To learn more about Pure Flavor®’s Georgia greenhouse project and to see photos of the construction of both projects, visit GeorgiaGrownFlavor.com.
Pure Flavor® is a family of greenhouse vegetable growers who share a commitment to bringing A Life of Pure Flavor™ to communities everywhere. Our passion for sustainable greenhouse growing, strong support for our retail & foodservice customers, and focus on engaging consumers is built on a foundation drawn from generations of growing expertise.
SOURCE: Chris Veillon | chris@pure-flavor.com
Chief Marketing Officer | Pure Flavor®
T: 519 326 8444
Vegetable Towers to Rise in Parisian Suburbs
The country has seen a boom in urban farming over the last couple of years.
The French sure like their cities green. The country has seen a boom in urban farming over the last couple of years. In various projects both the government and various private parties have been launching ideas and concepts, and building farms to grow vegetables in the cities. The latest project to be launched is nearby Paris. In the suburb Romainville, two vegetable towers will comprise an acreage of 1000 m2 to supply inhabitants with freshly grown vegetables.
© : Poltred Studio / Ilimelgo and Secousses architects
"Talking about urban farming, the French market is a very promising market, since the French value their food highly", Corenthin (Felix) Chassouant with CMF confirms. CMF is specialized in high-tech greenhouses and buildings and has been working for several years on a proposal for urban farming greenhouses all around the world. In France they're participating in the new project as well.
La Cite Maraichere
This urban agriculture building is to be realized as part of a city renovation program. "All floors above the ground floor will be dedicated to local production", Corenthin shows. "As for the subsurface, it will be intended to produce mushrooms. The building will consist of 2 wings of 7 m wide each, the eastern greenhouse on the 6th floor and the western greenhouse on the 3rd floor (the first vegetable towers in Europe)."
© : Poltred Studio / Ilimelgo and Secousses architects
© : Poltred Studio / Ilimelgo and Secousses architects
The building will also meet the latest environmental standards and will comply with public safety regulations. According to Corenthin though, the major challenge of this project was to combine aesthetics and technicality.
The project is to deliver a harvest of up to twelve tonnes per year. That consists of carrots, tomatoes and other products, all grown grown in circular economy substrates, mixing local compost, grinded green waste, coffee grounds. The vegetables are to be sold for small prices to local inhabitants and will also be used in the cafeteria on the ground floor.
© : Poltred Studio / Ilimelgo and Secousses architects
Residence with greenhouses
The new Parisian project isn't the only urban farming project in France being realized currently. Various projects are mushrooming. One of them is "5 ponts" in Nantes, Corenthin shows. "This residence will integrate two urban farming greenhouses (6th floor and 4th floor) as well as two private winter gardens built by CMF. These greenhouses will be equipped with shading screens, heating systems and climate control. "This ambitious and innovative project entails various constraints: occupant safety, climate management of glazed spaces, and cohabitation with agricultural activity in urban areas", Corenthin shows.
©Samo / TETRARC Nantes Project manager and architect
The project is proposed by “Les Eaux Vives" Association. It is supported by the City of Nantes, Nantes Métropole and the European Union as part of the UIA project (Urban Innovative Action).
"It is really cool to be a part of this", Corenthin confirms. "With CMF we've always supplied the traditional market - which is also interesting - but now we see we have the capability to imagine and develop innovative solutions that combine our greenhouse knowhow as a climate builder with architectural concepts, to meet the specific situation of an urban farmer."
For more information:
CMF
BP 10 001 - Varades
44370 Loireauxence
Tél. : +33 (0)2 40 98 34 00
Fax. : +33 (0)2 40 98 34 94
www.cmf-groupe.com
Publication date : 10/29/2018
Author: Arlette Sijmonsma
© HortiDaily.com
As Director of The New School of Plant and Environmental Sciences, Mike Evans Wants to Create an Environment Where Creative Collaborations Lead to Innovative Discoveries
As director of the new School of Plant and Environmental Sciences, Mike Evans wants to create an environment where creative collaborations lead to innovative discoveries.
Mike Evans grew up in rural Pittsylvania County, Virginia, where he spent his summers pulling tobacco and running a soybean drill for his grandparents and neighbors.
He saved enough money during those hot summers to buy his first car — a 1980 Ford Pinto — which he proudly parked in the Cage during his first year at Virginia Tech. He’d been exposed to the university through his high school’s Future Farmers of America program, which brought him to campus to take part in horticultural competitions.
As a student majoring in horticulture, he fell in love with researching the plants he’d been surrounded by his entire life. The intensive laboratory work he did during his undergraduate years at Virginia Tech prepared him well for the rigors of graduate school at the University of Minnesota, where he earned a master’s degree and a Ph.D.
Evans went on to a career in higher education that involved research to help industries thrive, Extension outreach programs that impacted local communities, and academic programs that prepared the next generation of students for the challenges of facing the world.
Now, the Hokie alumnus has returned to Virginia Tech to use all the skills he’s acquired to lead the College of Agriculture and Life Sciences’ latest strategic initiative.
Evans is the director of the newly formed School for Plant and Environmental Sciences, which combines three former departments — horticulture; crop and soil environmental sciences; and plant pathology, physiology, and weed sciences — under one administrative roof.
“When we bring people together you get something new called ‘creative collisions.’ These intersections lead to innovation on a level that changes the paradigm of what is possible,” Evans said. “We want to create an environment in the school where the silos are broken down and people are interacting in unique ways to allow opportunities for more of these creative collisions to occur. This benefits everyone from students and professors to industry leaders and local producers.”
Though faculty and administration have been involved in planning the school via committees, public forms, and other outlets for three years, it becomes officially operational on July 1.
“Mike’s experience makes him the perfect person to lead the school and help our faculty, staff, students, and Extension professionals find new ways to work together to make an even greater impact on our college, the state, and the world” said Alan Grant, dean of the college.
Evans most recently worked at the University of Arkansas, where he was an interim associate dean in the Dale Bumpers College of Agricultural, Food, and Life Sciences. Prior to Arkansas, Evans was a professor at Iowa State University. At both institutions, he was a horticulture faculty member, teacher, and researcher who focused on controlled agricultural environments, such as greenhouses, and how to use hydroponic techniques to increase yields of food crops. He started his career as a researcher at the Gulf Coast Research and Education Center with the University of Florida where he conducted research and Extension programs related to greenhouse crops and ornamental plants.
Evans points to projects he did as a horticultural researcher that show how collaboration can lead to greater impact.
A few years ago, he was researching how lettuce is best grown in a controlled environment using hydroponics. He started to talk with a plant pathologist who was trying to find ways to combat powdery mildew on spinach. The two began to collaborate on ways to grow the spinach in a greenhouse, which allowed for faster growing cycles. This development in the greenhouse helped the plant pathologist do quicker scientific trials than it would have been possible in the field. The teamwork between disciplines was what made the solution possible.
“You never know what innovative, cross-disciplinary solutions are possible until you tear down the walls that exist and build a space where ideas can freely flow — and new ideas can be born,” he said.
Similarly, the school will merge three former departments and bring researchers, faculty, and staff together to use their diverse experiences and skillsets to tackle issues ranging from increased crop production to ways to grow healthier food throughout the world.
None of the majors or degrees offered by the three former departments will change, though Evans said the school will explore creating new majors that build upon the expertise of the faculty and meet the demands of students and industry. All clubs and student organizations will remain as they currently operate. The school also will focus on ways to expand the college’s physical footprint, such as constructing new greenhouses or the future Human and Agricultural Biosciences Building 2.
“I believe that by creating a space where new relationships can form and risk-taking in the name of innovation is encouraged, there is unlimited potential to make a lasting impact in plant and environmental sciences,” he said.
Contact:
Idrologica Proposes New Anti-Hail/Anti-Bugs System
V5: Anti-Hail System That Prevents Ice Accumulation
Increasingly devastating weather phenomena are now threatening even the anti-hail/anti-bug nets. Often, heavy hailstorms damage not only the nets but also break the poles. To avoid this, the European patented V5 system is a type of anti-hail cover characterized by an innovative ice discharge method which prevents the formation of dangerous build-ups on the nets.
Looking at the net's profile, you can notice two different slopes: the first one is relatively flat, while the second one has a strong slope so to make a funnel.
The technician continued, “Therefore, the net has great flexibility. In the case of a hailstorm, the slope increases thus immediately discharging the ice. The two net-cloths are tied in two parts: through an elastic between the intermediate supports, and through plaques between the external supports”. Eventually, the net looks like a triangle pointing downwards, where the hail is collected and discharged. It is also possible to close the net so to isolate it from the Asian bug.
“The Idrologica company proposes, develops and installs farming plants and machinery, for private and public gardens and for industries and large sports facilities. We contribute to the improvement of the agricultural and agri-food productions and to the increase of green areas. This is thanks to the experience of our specialised human resources who are capable to constantly support in specific technical matters”.
Info
Idrologica srl
via Soldata, 1
48018 Faenza (RA) - Italy
Mark Servadei
Technical office
Tel.: +39 0545 906274
Tel.: +39 333 9365933
Email: impiantistica@idrologica.it
Web: www.idrologica.it
Self-Assembly Greenhouse To Be Launched In USA
“North America is looking for better solutions for local produce, so-called farm to table produce”, says TAP’s CEO, Avner Shohet. “People are looking for fresh products that leave less of a carbon footprint.” He says there is a lot of effort going into urban farming in that country. “The TAPKIT is another solution. It can be used for suburban farming where the land is less expensive, making it a cheaper solution, with the added benefit of less energy consumption.”
The TAPKIT, a self-assembly hydroponic greenhouse, is to be launched in the USA for the first time later this month. This farming solution was developed by the Israeli company, Teshuva Agricultural Projects (TAP). This company builds commercial greenhouse installations throughout the world. The TAPKIT is to be introduced at the PMA fresh summit being held in Orlando on 19 and 20 October.
The TAPKIT is a 500 m2 hydroponic unit, which can produce 6-12 tons of leafy vegetables and fresh herbs per year. “We started with the idea of TAPKIT for small farmers to have their own hydroponic system, but since then the kit has been ordered by resorts for their kitchen supply and retailers for their own shops too”, says Shohet.
Wide range of interested parties
“Other clients have now also shown interest. These include organizational kitchens, retirees, schools and young people who are looking for ecologically-friendly, sustainable business opportunities”, he says. “We are continually surprised to learn from the market about another sector that finds the TAPKIT to be an affordable and efficient solution.”
The TAPKIT greenhouse was first presented at ’Agri-Tech Israel 2018’ in May. “This first unit has reported to us that their produce has been sold out”, reports the CEO. TAP has developed three different types of TAPKIT greenhouses. “For tropical, subtropical and cold weather”, explains Shohet. “The potential is, therefore, almost unlimited.
Growth technique has many advantages
These units can be operated by just two people and uses Nutrition Film Technique (NFT). This is a method of hydroponic growing in which the plant roots are placed in a shallow stream of re-calculating solution that contains all that is needed for maximum productivity. “NFT techniques are on the increase globally due to growing consumption of high-value and exotic crops and the increasing need for global food security by increasing yield in smaller spaces”, Shohet said in an earlier interview.
“Two units have already been shipped to South Korea and one to the Philippines. In two weeks, two units will also be shipped to a resort in Mauritius”, Shohet concludes.
For more information;
Avner Shohet
T.A.P / 2BFresh
Office: +972-9-8940507
Mobile: +972-50-7922579
Email: avner@taprojects.com
www.taprojects.com
Publication date : 10/12/2018
Author: nick@freshplaza.com
© HortiDaily.com
US (NC): Verdesian Opens New Greenhouse At Duke University
Verdesian Life Sciences has expanded its research pipeline by opening a greenhouse facility at Duke University to develop early technology validation screening for agricultural nutrient use efficiency (NUE) technologies.
The new Verdesian greenhouse is part of Verdesian’s Early Technology Validation (ETV) screening to facilitate the Verdesian Technology Advancement (VTA) pipeline. Improved pipeline efficiency through early testing of new concepts under small-scale, controlled conditions will allow Verdesian to better understand capabilities at an early stage, helping to define opportunities while mitigating risks and optimizing time and resources on viable candidates. The 1,000 square feet of greenhouse space at Duke University adds to Verdesian’s existing growth chambers in Research Triangle Park (RTP).
“Our greenhouse at Duke University supports our R&D as a science-backed company,” said Kenny Avery, CEO for Verdesian. “The greenhouse provides the necessary environment to support vetting and evaluating new technologies that meet grower needs.”
New technology opportunities vary drastically, requiring a customized ETV screening method that brings together various growth system components and methods for detecting differences in plant function.
Agricultural field trials are critical to product development but are time consuming and introduce unnecessary risks for untested products. The new Verdesian greenhouses at Duke University will allow Verdesian to efficiently and economically identify and classify new prospects, test viable technologies and prioritize and develop those opportunities into NUE technologies. Prospects passing ETV screening will continue down the VTA pipeline and on to field testing.
The new Verdesian greenhouse at Duke is overseen by the ETV team which is leading the effort to develop these new screening capabilities. The team was formed to build a robust and flexible screening platform in 2018, further expanding those capabilities with additional laboratory methods and instruments into early 2019.
Plant physiologist, Dr. Amy Burton, joined Verdesian in December of 2017 and leads the VTA pipeline. Prior to Verdesian, Dr. Burton was with Bayer CropScience in Research Triangle Park. She completed her post-doctoral work in plant stress physiology with the United States Department of Agriculture.
The Verdesian ETV team was expanded in the first quarter of 2018, with the additions of Biology Laboratory Technician, Sandra Paa, and Greenhouse Technician, Beth Waller.
For more information:
Verdesian
1001 Winstead Drive, Suite 480
Cary, NC 27513
919.825.1901
www.vlsci.com
Publication date : 10/8/2018
"Producing More With Less Water And Nutrients"
Stefanie van Wienhoven, Grodan
The concept of 'Precision Growing' stipulates that optimal growing conditions can be achieved during an entire growing season. In precision cultivation the plants are supplied with the exact amount of water and fertilizers they need. Excess water and fertilizers can be collected efficiently and be reused. And while less resources are needed, the crop yield per square meter increases.
Water management
Precision cultivation literally translates into more growth with less input. In this context, Grodan focuses on water management in the root environment of the mat. By using water and nutrients more efficiently and in a more targeted manner, crop yield and fruit quality improves. This can be achieved by carefully aligning the water content (WG) of the substrate and the electrical conductivity (EC) in accordance with the current climatic conditions and generative/vegetative plant balance.
Extra attention for root environment
"By matching the needs of the plant in a smart way with the characteristics of the substrate mat, a strong and productive plant can be planted without waste of water and nutrients," says Stefanie Wienhoven of Grodan.
In greenhouse horticulture, much more efficient use is made of water than with (uncovered) open field crops. However, large amounts of water and fertilizers are lost in freely draining substrate systems. Water use efficiency can be improved by collecting the drain water and bringing it back to the crop. In this way glasshouse horticulturists can further improve their efficiency of water use and become more sustainable producers.
Careful management
Careful management of water and nutrients in combination with re-use of the drain water in the cultivation can have the following benefits according to Wienhoven:
Reducing total fertilizer use
Saving costs
Optimizing crop growth
Ensuring sufficient and clean irrigation water
Keeping a sufficiently wide range of crop protection products available
Protecting the environment
Complying with the legislation
Sustainable cultivation methods
According to the stone wool manufacturer, precision cultivation is an interesting concept for helping with current and future challenges in the area of water management. They continue to think about even better and smarter ways to grow crops in a sustainable way. They want to cooperate with growers, retailers and scientists for this.
The drought of this summer and the consequences of climate change motivate the company even more to think again about the best methods for efficient cultivation and the saving of even more water. This should be possible with newer, innovative techniques in water management.
Source: Glastuinbouw Waterproof
For more information:
Vertical Farming: Bursting With Promise -- But Unknown Costs
By Dr. Michael Evans - - Wednesday, October 10, 2018
The production of food crops such as fresh greens (like lettuce and arugula) and herbs (such as basil) in vertical production facilities is part of a larger field of agriculture often referred to as controlled environment agriculture (CEA). In addition to production of these types of crops in vertical facilities, production also occurs in such facilities as greenhouses and plant factories inside of converted warehouses and shipping containers. The types of crops most commonly grown in CEA production include tomatoes, peppers, cucumbers, strawberries and fresh greens and herbs.
Depending on the crops being grown, different types of production systems might be used in CEA, but the most common systems are nutrient film technique, floating beads, Dutch bucket systems and various types of gutter systems. These systems might be true hydroponic systems — in which the plant roots are suspended in a static or recirculating fertilizer solution — or a system that uses an artificial soil or substrate in which the plant roots grow.
Across all of the types of controlled environment structures, systems and crops, the production of food crops in CEA has been experiencing rapid growth in the U.S. In fact, Rabobank, a Dutch multinational banking and financial services company, reported that the value of U.S. greenhouse-grown food crops exceeded $3 billion in 2013 and is expected to exceed $4 billion by 2020.
The U.S. Department of Agriculture’s statistics also support the conclusion that greenhouse-grown produce production has been rapidly increasing. Many factors have been reported to be responsible for the growth in greenhouse food crop production including reducing water and fertilizer inputs needed to grow crops, an ability to better program and have predictability of crops in CEA versus open fields, the ability to grow crops year-round and thus better serve the local markets, the ability to potentially better use biorational disease and pest control, the ability to grow food crops on nonarable land, the ability to produce higher volumes of produce on limited land (especially with vertical farms), and the potential for reducing food safety issues as compared to open field production.
In addition to these factors, the growth of CEA was reported as being fueled by market and human factors. Karen Halliburton Barber of Rabobank noted in a report that, “There is a growing preference among U.S. retail and food service buyers for greenhouse produce.” She also noted that, “The buyers are seeking the quality and reliability of supply that greenhouse products provide.”
As a type of CEA, vertical farming affords the opportunity to produce larger volumes of these crops per area than traditional field production. This is achieved by both the potential for year-round production and the multiple levels of production systems employed. Vertical systems also allow for the production of produce crops in areas where land is very limited or very expensive as is often the case with highly urbanized areas. However, compared to both field production and even traditional greenhouse (single level production) hydroponic production, the fixed costs and variable costs of production will be different for vertical farming. Some costs are likely to be significantly higher while others might be lower. Costs are likely to be spread over higher levels of crop production.
It is important to understand these costs. It is important also to understand the market. What is the target market? What crops does the market want? How large is that market and what are the prices for a given product that the market will tolerate are all important questions before deciding to move forward with any type of CEA operation — including vertical farms. Having a strong understanding of the crops to be grown, the level of production achievable, the costs of production and the market will increase the chances for a successful CEA business venture.
• Michael Evans, Ph.D., is director of the School for Plant and Environmental Sciences in the College of Agriculture and Life Sciences at Virginia Tech (@VTCals).