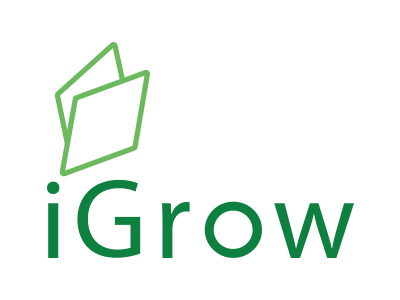
Welcome to iGrow News, Your Source for the World of Indoor Vertical Farming
Fresh Produce, Brought To You By Robots
IN SAN CARLOS, CALIFORNIA, UNDER LED lighting in a controlled, 8,000-square-foot environment, a team of autonomous robots is whirring night and day between rows of leafy greens
A Family-Owned Market In California
Is Now Selling Robot-Reared Leafy Greens
BY LUKE FATER AUGUST 08, 2019
An industrial robotic arm with custom gripper and sensors constantly reorganizes plants as they grow. IRON OX
IN SAN CARLOS, CALIFORNIA, UNDER LED lighting in a controlled, 8,000-square-foot environment, a team of autonomous robots is whirring night and day between rows of leafy greens. There is no dirt, there are no pesticides, and on this indoor farm, the only humans work behind screens. This is one of the world’s first autonomously operated commercial farms, and their produce is now flying off the shelves.
As a child, roboticist Brandon Alexander spent summers in Oklahoma helping his grandfather grow potatoes, peanuts, and cotton on a 6,000-acre farm. But as CEO of Iron Ox, the start-up company behind the automated farm, he says traditional farming is now his biggest competition—and granddad understands. “He knows that for farming to survive, this is almost inevitable,” says Alexander.
At Bianchini’s Market, a family-owned grocery in the San Francisco Bay Area, the two worlds are competing for the first time. As it stands, the robots are holding their own: Between retail buyers and several local restaurants, including San Francisco’s Trace, Iron Ox saw sales more than double last quarter.
Compact spacing techniques unique to hydroponic farms allow Iron Ox to grow 30 times the yield per acre compared to outdoor farming, according to Alexander. IRON OX
The San Carlos operation is not completely automated just yet. Human staff still plant the initial seed and handle post-harvest packaging. But the rest is left to robots.
Angus, a half-ton aluminum porter, roams the “field” of trays, or pallets, 24/7 with an overhead camera. On traditional farms, plants need space for their roots to absorb nutrients; on hydroponic farms, however, seeds can be planted in their trays mere inches apart. As they grow and begin crowding each other, though, this does require more attention from, say, a sleepless robot. Angus carries the 800-pound pallets in need of rearranging to a separate, industrial robotic arm that gently re-shuffles the growing pods into new compact rows. Angus is also responsible for IPM (integrated pest management) and scanning for aphids, mildew, and browning.
The robotic arm’s stereo-camera (“two cameras that kind of mimic your eyes,” Alexander casually explains) creates a 3-D model of at-risk produce that’s run through a machine algorithm to diagnose the issue and quarantine or prune accordingly. “The Brain,” a cloud-based AI software, coordinates all these autonomous functions while monitoring light, nitrogen, and water levels. “It’s a neighborhood farm,” says Alexander.
A 1,000-pound aluminum porter named Angus scans for crowding, carrying plant pallets to a separate robotic arm for rearranging. IRON OX
He’s not wrong. Produce from Iron Ox travels less than a mile to reach Bianchini’s—itself a mere 25 miles from downtown San Francisco. In fact, evening shoppers at Bianchini can buy produce robo-picked that morning, and at price points that compete with outdoor farms: A bunch of basil sells for $2.99; four heads of baby lettuce for $4.99; and a bunch of red-veined sorrel for $2.99.
Typically, the cost of human labor required for indoor hydroponic farms has made their produce inaccessibly expensive. Jake Counne of Backyard Fresh Farms, a similarly autonomously assisted farm in Chicago, told the Chicago Tribune that employing robotics reduced his labor costs by 80 percent. For this reason, building a farm around robotics and A.I. could crack the code of making indoor farms feasible. And while Alexander’s leafy greens remain local, the consequences of Iron Ox’s success may not.
Using robotics to make indoor hydroponic farms practical could alleviate a host of agricultural problems. In 2016, World Water Forum cited farming as a major contributor to global water scarcity. But farms like Iron Ox use 90 percent less water than outdoor farms. In a 2019 report on the challenges of feeding 10 billion people by 2050, The World Resources Institute cites concern over “the difference between global agricultural land area in 2010 and the area required in 2050 … if crop yields continue to grow at past rates.” According to Alexander, Iron Ox yields 30 times more produce per acre over the course of a year than conventional farms, and without using any arable land. A 2016 report from the National Center for Biotechnology on Chemical Pesticides urged a “drastic reduction in the use of agrochemicals,” and indoor farms alleviate the need for herbicides and pesticides.
This vision-enabled robot runs 3-D scanned models of the plants through a machine learning algorithm for quality control. IRON OX
For now, Iron Ox’s goals are more pointed. “How can we make your salad pop? We try to prioritize that,” Alexander says. Following the success of the San Carlos location, he does plan to set up robotic farms near other U.S. cities, though he’s not announcing anything yet. Iron Ox is, however, hiring humans for plant science and growing teams.
Gastro Obscura covers the world’s most wondrous food and drink.
Sign up for our email, delivered twice a week
Building A 2.76M Square Foot Sustainable Greenhouse In Job Starved Appalachia
The UN's Intergovernmental Panel on Climate Change just released a report highlighting the alarming effect climate change and the rise in global temperatures are having on fertile soil—and on the world's ability to produce enough food to feed the planet's growing population
Anne Field Contributor Entrepreneur
AppHarvest facility rendering | APPHARVEST
The UN's Intergovernmental Panel on Climate Change just released a report highlighting the alarming effect climate change and the rise in global temperatures are having on fertile soil—and on the world's ability to produce enough food to feed the planet's growing population. There’s also an increasing depletion of the global water supply.
Jonathan Webb, founder of two-year-old startup AppHarvest, thinks his company can help address those urgent crises. Specifically, he plans to produce more food with less water using massive controlled-environment, sustainable greenhouses. In the process, Webb, a native of Kentucky who also worked in renewable energy, also hopes to help revive the struggling Appalachian economy.
“There are technical solutions to many of these problems,” says Webb. “But much of it is a matter of execution at scale and at a rapid pace.”
His plan: build a 2.76 million-square-foot controlled-environment agricultural facility on 60-acres in Morehead, Kentucky, using hydroponic growing techniques, which rely on a nutrient solution, instead of the usual soil. As a result, according to Webb, it will be able to grow pesticide-free tomatoes and cucumbers year-round using 90% less water than traditional farming—and do so in the middle of coal country. Water will come from rainwater kept in a retention pool and there will be circular irrigation systems. The whole project takes its inspiration from the Netherlands, which is a top exporter of tomatoes, potatoes and onions, among other food, thanks to its pioneering work in climate-controlled agriculture.
The facility is also in a strategically-situated location that’s within a day’s drive of 70% of the U.S. population, according to the company. That should slash the amount of gas used in transportation compared to imports trucked across the country to the East Coast, while supplying markets with fresher produce. The company is working with distribution partner Mastronardi Produce.
In job-starved Appalachia, where one in four residents live in poverty, according to the U.S. Census Bureau, the facility also could provide a boost to the economy. While AppHarvest is buying components from the Netherlands, Webb estimates that the project will create 285 full-time positions, plus 100 construction jobs. The company will also work with local universities to add job training classes.
Webb recently closed an $82 million all-cash deal with Equilibrium Capital to build its greenhouse. Plus, it raised more money in a Series A round led by Value Act Spring Fund and joined by existing investor Revolution’s Rise of the Rest Seed Fund.
The mega-greenhouse is projected to be up and running by mid-2020. As for building similar facilities in other parts of the country, Webb says he wants to see that happen, but by different parties. “We’re in Appalachia,” he says. “But I hope other people will be building throughout the country.”
I'm an award-winning journalist with a particular interest in for-profit social enterprise, as well as entrepreneurship and small business in general. I've covered those areas for many many places, including The New York Times, Bloomberg Businessweek, Crain's New York Business, Inc. and Business Insider. As an entrepreneurial journalist--ie, a freelancer--I work from my home office in Pelham, NY.
Indoor Farming New Buzz Across Globe
Urban farming is taking over from conventional farming at many across the globe. A BBC report states that ten shipping containers dominate a corner of the Brooklyn parking area, each full of climate control tech, growing herbs that are distributed to local stores on bicycles
Representative image. Courtesy: MarketWatch
Urban farming is taking over from conventional farming at many across the globe.
A BBC report states that ten shipping containers dominate a corner of the Brooklyn parking area, each full of climate control tech, growing herbs that are distributed to local stores on bicycles.
The containers are owned by Square Roots, part of America’s fast-expanding vertical farming industry, a sector run by many tech entrepreneurs who believe food production is ripe for disruption.
The world’s best basil reputedly comes from Genoa, Italy. Square Roots grows Genovese seeds in a container that recreates the city’s daylight hours, humidity, Co2 levels – and all fed hydroponically in nutrient-rich water, the report added.
An artificial intelligence expert, Peggs founded Square Roots with investor Kimball Musk (Elon’s brother) two years ago.
They’ve signed a deal with one of America’s big distribution companies, Gordon Food Service, to locate herb-growing containers at some its 200 warehouses.
The report quoted him as saying that the deal represents everything about indoor farming’s potential – locally grown, quick-to-market, fresh produce that can be harvested year-round and is free of pesticides and harsh weather.
Jeffery Landau, director of business development at Agritecture Consulting estimates the global value of the vertical farming market will rise to about $ 6.4 bn by 2023, from $ 403 m in 2013, with almost half that attributed to growth in the US.
Plenty, another major US player, raised funds from Softbank chief executive Masayoshi Son and former Google head Eric Schmidt.
The company has ambitions to build hundreds of vertical farms in China. In the UK, food delivery and robotics company Ocado is investing in indoor farming.
In neighbouring New Jersey, however, Bowery Farming, takes a different approach. The five-year-old company runs industrial-sized farms.
Outside one huge, grey windowless warehouse a heat haze shimmers off the concrete.
It’s a sharp contrast to the chilly interior where an aroma of fresh farm produce hits you immediately, the report added.
Sustainable Living: Hydroponic Mobile Farms To Let Anyone Grow Vegetables In Hong Kong, Slashing Carbon Footprints
Shops, restaurants, schools, and households could grow their own fresh produce, reducing need for imports, if mobile farming trial is successful. Technology is the latest brainchild of team of University of Hong Kong MBAs behind urban farm that supplies restaurants vegetables and herbs grown without soil
Shops, restaurants, schools, and households could grow their own fresh produce, reducing need for imports, if mobile farming trial is successful
Technology is the latest brainchild of team of University of Hong Kong MBAs behind urban farm that supplies restaurants vegetables and herbs grown without soil
13 Aug, 2019
Farmacy grows vegetables and herbs hydroponically in Causeway Bay, and is trialling mobile farms. Co-founder Raymond Mak talks about cutting Hong Kong’s carbon footprint and delivering fresh produce. Photo: Jonathan Wong
As a social movement gathers pace on the city streets this summer, there’s another growing revolution – a green movement.
This one is all about groundbreaking farming technology that cuts lengthy supply chains to allow easy access to fresh produce rich in nutrients and bursting with flavour.
Farmacy (farmacyhk.com), an urban farming technology company launched in January 2018, has been offering herbs, micro greens, and edible flowers to restaurants, hotels and home cooks. It will take things to the next level in a couple of weeks with the launch of its first “mobile farm”.
“That’s a farm that is so mobile it can be stored in your home, restaurant, school or supermarket. In the future, supermarkets won’t need to import vegetables, you can grow the vegetables fresh – lettuce, pak choi, choi sum, whatever,” says Raymond Mak, Farmacy’s CEO and co-founder.
Farmacy grows vegetables and herbs hydroponically. Photo: Jonathan Wong
Using hydroponic technology, the greens will grow in-store so that consumers know exactly where their food is coming from – they can actually see their vegetables as they grow. The pilot mobile farm will be launched in mid-August at the organic convenience store JustGreen in Sai Kung.
“They want to first roll it out at the Sai Kung store because there’s more room and they have a good relationship with clients who are open to trying new things and are more demanding about sustainability and freshness,” says Mak.
Customers will be able to order vegetables that can be harvested and delivered within minutes or hours, instead of the usual four-day minimum for imported goods. Photo: Jonathan Wong
We are in the firm’s hydroponics farm in Fashion Walk, Causeway Bay, a 200 sq ft space with two glass walls that allow the curious a peek at the herbs, micro greens, and edible flowers growing in their shallow blue tubs. There’s no air-conditioning in here – the plants like it warm – and just a fan to cool things down a bit if necessary. At 11am it’s time to turn on the lights and “wake up” the greens. “They need eight hours sleep, just like humans,” says Mak.
Hydroponic basically refers to the way that the plants absorb nutrients, which is through water instead of soil. Farmacy uses organic nutrients bought from the United States which has US Federal Drug Administration approval, and adds it to water. An advantage of indoor farming is that it’s very “clean” – there are none of the pesky insects and pests you get with soil and outdoors – and it also saves water.
“Compared with soil-based farming, where a lot of water is lost, goes underground, hydroponic farming saves 90 per cent more water,” says Mak.
Tastes like chicken? Why maggots might be the future of food
Hong Kong imports an astounding 98.3 per cent of its vegetables, with 70 per cent of the imports coming from China and 28 per cent flown in from around the world. All the emissions involved in getting our greens into Hong Kong is a massive black mark in terms of sustainability – and it’s also bad for our health. As soon as produce is harvested, the roots stop supplying water to the leaves and stem and the plant starts leaking goodness, with much of the nutrition going as the plant’s water evaporates.
“University of California studies show that vegetables can lose 15 to 55 per cent of vitamin C within a week and some spinach can lose 90 per cent of vitamin C within the first 24 hours after harvest,” says Mak, one of five University of Hong Kong MBA graduates who teamed up to found Farmacy.
The beauty of a mobile farm is the ability to buy your greens with the roots still intact, take the produce home and cut it up and cook it while it’s still super fresh and packed with goodness.
Raymond Mak co-founded Farmacy with four other HKU MBA graduates. Photo: Jonathan Wong
He notes the irony of consumers forking out high prices at high-end supermarkets for organic goods from Italy and France when the long travel time seriously affects its nutritional value. The four days minimum it takes to get from farm to supermarket represents a huge loss of nutrients. Even produce from Yunnan in southwest China – where much of Hong Kong’s vegetables are grown – takes one to two days to reach Hong Kong, Mak says.
The longer it takes to transport produce, the more flavour it loses. Mak proposes an impromptu tasting session.
First, we try a purple flower, oxalis, which is super sour, then a yellow cucumber flower, followed by lime basil, and a nasturtium (known as Empress of India) which knocks our socks off with a powerful wasabi hit. Harvested just moments before we ingested them, the flavours are full of zing, so it’s easy to understand why Michelin-starred chefs want to get their hands on them. French restaurant Le Salon de Thé de Joël Robuchon was an early adopter.
University of California studies show that vegetables can lose 15 to 55 per cent of vitamin C within a week and some spinach can lose 90 per cent of vitamin C within the first 24 hours after harvestRaymond Mak, Farmacy’s CEO and co-founder
But Farmacy isn’t about just catering to celebrity chefs – it’s got a bigger mission in mind.
“We don’t want this to be a small, niche thing, we want it to be accessible to the public, to all citizens, we want to make it a movement,” says Mak.
The movement is taking hold elsewhere. In Germany, the Berlin-based Infarm (infarm.com), founded in 2013 by two brothers, has partnered with 25 major food retailers and deployed more than 200 in-store farms, and is harvesting 150,000-plus plants monthly. Farmshelf (farmshelf.com), started by Andrew Shearer in a San Francisco garage in 2015, is now leading the urban farming pack in the US.
Closer to home, the idea has taken root in Singapore. Earlier this year the city state announced its intention to have all the island state’s needs home-grown by 2030, including vegetables cultivated in climate-controlled greenhouses under special LED lighting to maximise yields.
“Singapore has quite aggressive targets. Hong Kong needs to catch up and we want to play a role in it,” says Mak.
The Farmacy team – nine staff, including the five founders – have been using the Causeway Bay operation for research and development and a base in Cyberport to develop the mobile farm technology. Beyond the hydroponic technology, Mak says the team is developing even more sustainable and efficient farming technology, but they’ve taken it slow the first year to develop their green thumbs.
“You have to understand the plants before moving to the technology, or else it has no soul,” he says.
This article appeared in the South China Morning Post print edition as: green movement to turn city slickers into farmers
Sustainable Living Health and wellness Veganism Food and agriculture Singapore Environment
FARMPRO: Fully Automated And Climate Controlled 40' Container Farming
The Urban Crop Solutions FarmPro is a 40 ft fully automated freight container with a state-of-the-art leafy green growing system. This system gives you a fully automated 4-layer growing solution
FARMPRO by Urban Crop Solutions
A FULLY AUTOMATED AND
CLIMATE CONTROLLED 40' FREIGHT CONTAINER
The Urban Crop Solutions FarmPro is a 40 ft fully automated freight container with a state-of-the-art leafy green growing system. This system gives you a fully automated 4-layer growing solution.
HYDROPONICS AND OWN GROWTH RECIPES FOR 200+ CROPS
To deliver healthy crops, our closed-loop irrigation system:
Minimizes the use of fresh water
Increases plant nutrient uptake and can work with up to 70 organic nutrients and minerals
Provides optimal root growth, aeriation and nutrient delivery
Allows to grow microgreens and super-large crops
CLIMATE CONTROLLED ENVIRONMENT
In/outflow of air is controlled to limit unwanted elements while optimizing climate conditions.
Closed production plants have minimal external elements influencing the indoor climate
Monitoring the in- and outflow of air allows for the best possible crops
Flavour can be tailored to market demand by influencing climate, light and nutrients
CUSTOM-MADE LED TECHNOLOGY
Our own LED lights provide the optimal spectrum for your plants, using limited energy.
The photosynthetic active radiation (PAR) range, enables photosynthesis in the 400-700nm range
Using energy-efficient LEDs, our crops receive just the right light spectrum to grow efficiently
ROBOTIZED AND CONTROLLED PROCESS
Our top-notch industrial standards allow full control over monitoring and automation.
Minimize human intervention to achieve higher levels of pro
STANDARD FUNCTIONS
40 ft insulated container
Climate control
SIZE: 40” - LAYERS: 4
1 irrigation system
Continuous monitoring
Custom-made LEDs
4 cultivation layers
Handling area and technical room
Fully automated growing process
Online crop and process management
OPTIONS
Custom outside colour
Personalized logo on container
Up to 2 different water systems
1 or multiple windows
1 or multiple webcams
Back-up power system
WHAT YOU GET
80 M² GROWING SURFACE
1.6K- 3.6K CROPS PER GROWING CYCLE
24K - 54K CROPS PER YEAR
To View Our Videos, Please Click Here
ARE YOU INTERESTED IN A FARMPRO?
Would You Like To Receive Additional Information?
US: Purdue University Workshop To Feature Hydroponic Technology - September 5, 2019
The fourth annual Greenhouse and Indoor Hydroponics Workshop will be from 8 a.m. to 3 p.m. Sept. 5 on the Purdue University campus
Ashley Langreck AgriNews Publications
JulY 31, 2019
Krishna Nemali examines hydroponically grown lettuce in the horticulture and landscape architecture greenhouse at Purdue University. Provided photo/Purdue University
WEST LAFAYETTE, Ind. — The fourth annual Greenhouse and Indoor Hydroponics Workshop will be from 8 a.m. to 3 p.m. Sept. 5 on the Purdue University campus.
The workshop, which is sponsored by Purdue Extension, Purdue’s Department of Horticulture and Landscape Architecture and the Indiana State Department of Agriculture, will focus on teaching attendees about hydroponic production technology.
Lori Jolly-Brown, who is serves as the Extension events and communications coordinator for the horticulture and landscape architecture department, said the morning session of the workshop will focus on how to get started in hydroponics, where to purchase and find materials, how to fertilize plants, ways to keep bugs away and a wide variety of other topics.
After lunch, Jolly-Brown said, attendees will have the chance to tour one of Purdue’s state-of-the-art greenhouses and indoor hydroponic facilities, while also having the opportunity to participate in hands-on activities.
Jolly-Brown said individuals will be able to interact with workshop organizer Krishna Nemali, a Purdue assistant professor and a controlled environment agriculture Extension specialist.
“They will get to see Nemali’s hydroponic research and vertical farming displays,” Jolly-Brown said.
Jolly-Brown said the workshop is geared toward commercial producers and growers, those just getting started in hydroponics, as well as those who are involved in hydroponics production technology as a hobby.
To register for the workshop, visit https://bit.ly/2OjqTBn.
Ashley Langreck can be reached at 800-426-9438, ext. 192, or alangreck@agrinews-pubs.com.
Follow her on Twitter at: @AgNews_Langreck.
Choosing Your First Hydroponic System
For growers trying out hydroponics for the first time, choosing the best system can be a daunting task. Are you up for the challenge? Take our quiz to find out, then read on to learn about several low-maintenance hydro systems and determine which one is right for you.
Lacey Macri | August 13, 2019
Takeaway: For growers trying out hydroponics for the first time, choosing the best system can be a daunting task. Are you up for the challenge? Take our quiz to find out, then read on to learn about several low-maintenance hydro systems and determine which one is right for you.
As laws and climates change and mentalities shift towards living more sustainably, an increasing number of people are joining the grow revolution and bringing things indoors so they can grow year-round. Selecting your first indoor garden set-up can be difficult with all the options available, each with its own set of pros and cons.
Depending on your unique set of circumstances, certain set-ups may be more valuable to you than others. Take this short quiz to find out if you’re ready for hydroponics, then read on to dial in the specifics.
1) Do you have limited start-up cash?
a) Yes
b) Not necessarily
2) Do you see this as a long-term hobby or just temporary?
a) Temporary
b) Long-term hobby
3) Do you have plenty of time available to spend on this each day?
a) Yes
b) No
4) Do you live in a region with frequent power outages?
a) Yes
b) No
5) Do you want to grow organically or in a sterile environment?
a) Organic
b) Sterile
6) Are you eager to get started right away?
a) Yes
b) No rush
7) Will the growroom be in a rural area subject to many pest infestations?
a) Not sure
b) Yes
8) Is it important to you to keep your growroom as clean as possible at all times?
a) Not a factor
b) Definitely
Results
Tally up the number of answers you responded to with A versus B. If you answered more questions with A, you might be better off with a traditional, soil-based system. If you answered more questions with B, hydroponics may be for you. Even if your answers were mixed, there might be a hydro system listed here that fits your bill perfectly.
Read also: Hydroponics: Pros and Cons of Hydroponic Gardening
Ebb & Flow
Ebb and flow systems have long been recognized as classic hydroponic systems. An ebb and flow system consists of a shallow table with a centralized flood and drain system that is hooked up to timers to control the feed schedule. An overflow valve is also installed to control the height of the water that is flooded onto the tray that holds the plants.
Once the plant tray is flooded for a set amount of time, the water drains back into the reservoir, which is usually placed beneath the table. There are many benefits to choosing this type of system, including the ability to move plants around if they become crowded, and how easy it is to set up and customize your system based on spatial and financial limitations.
Drawbacks include a few slightly higher risk factors than other methods. If you live in a region with frequent power outages, this might be the least desirable option for you, as plants rely solely on the pump delivering the nutrient-rich water to them on a strict time schedule.
If you are out and about and are unable to get to your growroom in a timely manner, plants can die in a matter of hours. However, many plants are resilient, so if you open up your tent to see wilted, sad-looking plants, it is worth trying to resuscitate them by watering them immediately, as you may be pleasantly surprised.
Water Culture
Some water culture systems are visually similar to ebb and flow systems, but they operate somewhat differently. A traditional water culture system consists of a vessel that is flooded but never drained.
The plants may float around in the water in Styrofoam rafts, or they might be held in net pots positioned directly above the water with their roots suspended indefinitely in the water below, which is usually referred to as deep water culture. Plants are exposed to a nutrient-enriched water source at all times. To avoid suffocating plants, the water must be properly oxygenated with air pumps and air stones.
One benefit to water culture is being able to run your nutrient solution at a lower concentration, since the food source is ever-present and plants are free to feed as they need. One of the most serious drawbacks is the threat of diseases.
Because roots are constantly exposed to the solution, whatever is in that solution—good or bad—will propagate quickly. Some common, serious threats include fusarium, root rot and pythium. You can use products like hypochlorous acid, or H2O2, to help prevent the development of water-borne pathogens.
Aeroponics
Similar to water culture, the roots of plants in aeroponic systems are also suspended, but instead of being immersed in the water, they are hanging in the air. The nutrient-rich solution is then misted periodically from a reservoir onto roots. Plants are often held up by flexible, firm neoprene collars instead of grow media.
Aeroponics is one of the cleanest, most sterile ways to grow. Without grow media, there aren’t as many locations for bacteria to hide. The absence of grow media also allows the plants to grow as quickly as possible without any limits to the span of their root mass. These conditions make aeroponics one of the most preferred cloning options available, as fresh cuttings are highly susceptible to various diseases and prone to failure.
One limitation is that many plants will eventually outgrow their original system, so they will have to be transplanted. Unless you’re growing lettuce or basil, you will have to have something lined up for when that happens. While it is possible to grow mature plants in an aeroponic system, some plant strains may have higher demands for water and nutrients than the misting environment can viably deliver.
Nutrient Film Technique
Most hydroponic systems are hybrids, and nutrient film technique (NFT) systems are no different. This set-up may require a bit more experience than the rest, but its results are typically superior. Every system has its shortcomings, which usually evolve from a lack of one of three things: air, water or nutrients. The beauty of NFT is that all three of these essentials are abundantly available at all times.
Typically, people think of NFT as a hollowed-out, cylindrical tube on a downward slope that houses the channels that carry nutrients and water. Plants are spaced proportionally and placed in the holes on the upper surface of the tube. Grow media is not necessary and like aeroponics, growers may use neoprene collars or something similar to hold plants in place.
Nutrient-rich solution is pumped from a reservoir, usually located at the base of the channel and then directed up to the highest part of the channels and allowed to flow continuously downstream through the roots. The unused water may then drain directly back into the reservoir for recirculation. When NFT is done right, it can be the best in its class. However, dialing in all the details is something that only comes from experience.
Drip System
Drip systems are one of the most popular hydroponic methods. Similar to NFT, plants on a drip system may be placed on a slanted table to direct nutrient solution overflow into a recovery or non-recovery system. In recovery drip systems, the solution not absorbed by plants will ultimately drain directly back into the original reservoir, while the water that drains into a non-recovery system is considered wastewater.
The dripline is controlled by a submersible pump that supplies nutrient solution around the base of each plant directly onto the grow media. Common grow media used in this technique include stonewool, clay pebbles and coco. Stonewool and coco allow growers to irrigate less frequently, as they tend to hold enough moisture to keep plants adequately hydrated in between drip cycles. Clay pebbles make nutrient management easier in situations where the drip is more constant.
Drip systems are popular for their easy and affordable set-ups, and high level of control over how plants are fed. On the other hand, drip systems are more prone to fluctuations in pH and EC, as these levels are less stable in recirculating systems.
One of the goals of hydroponics is running a fully automated system. With all the plug-and-play systems available, there is bound to be something for everyone. When selecting a system, keep in mind it isn’t always about which method is best overall, but rather which method will work best for you. Don’t be afraid to try something new.
Written by Lacey Macri
Lacey Macri works as head of sales at CleanGrow, focusing her time on business development within the company. She received a bachelor’s degree in communications and psychology from the University of California, Davis, in 2011, where she worked at the California Aggie student newspaper on campus. Full Bio
Hydroponic Farms Use Less Land, Water To Grow Vegetables
Growing lettuce and other leafy greens indoors is gaining traction nationwide, as such big players as New Jersey-based Aero Farms and Bowery, are producing huge quantities in giant warehouses fueled by millions of dollars in investment
By Susan Salisbury For The Palm Beach Post
August 12, 2019
Green Life Farms’ hydroponic greenhouse occupies nearly 3 acres. It expects to yield 750,000 pounds of premium leaf green produce throughout the year, said Mike Ferree, vice president. The greens are grown, harvested and packaged onsite. [CONTRIBUTED BY HYDRONOV}
Greenhouses Allow Year-Round Growing
And Protection From Freezes And Extreme Rainfall.
Growing lettuce and other leafy greens indoors is gaining traction nationwide, as such big players as New Jersey-based Aero Farms and Bowery, are producing huge quantities in giant warehouses fueled by millions of dollars in investment.
The push comes as farmland becomes increasingly expensive and in short supply, and consumers demand locally grown produce that’s fresher because it hasn’t been transported hundreds of miles.
In Palm Beach County two new hydroponic farms—Green Life Farms and Patagonia Green Leaf— are being launched in greenhouses off U.S. 441 west of the Lake Worth Beach/Boynton Beach area. Hydroponic farming uses no soil. Instead, crops are grown in perlite, coconut fiber or nutrient-rich water in a controlled and enclosed environment.
Art Kirstein, agricultural economic development coordinator with the Palm Beach County Cooperative Extension Service, said that hydroponic farming offers advantages such as year-round growing, increased capacity on a smaller amount of land and protection from freezes and weather events such as extreme rainfall.
Green Life Farms harvested its first crop of baby arugula, baby romaine and baby spinach in mid-July. Its greenhouse occupies nearly 3 acres and will yield approximately 750,000 pounds of premium leaf green produce throughout the year, said Mike Ferree, vice president.
Baby romaine lettuce grows in the Green Life Farms hydroponic greenhouse off U.S. 441 west of Lake Worth Beach. The company has spent $15 million on the facility.
The greens are grown, harvested and packaged onsite, then picked up or shipped directly from the farm. They are also GMO and pesticide-free.
Green Life’s head grower, Greg Graft, said the produce is mechanically harvested using an automated system.
The first crop is not available for sale. Once Green Life begins official commercial production, products will be available at local grocery stores, restaurants and other locations, Graft said.
Green Life chose Palm Beach County for its large consumer market, proximity to sales partners and an agriculture-friendly environment, Graft said. It has invested $15 million so far.
Green Life uses a deep-water floating raft technology from Hydronov, an Ashley, Ind.-based leader in the hydroponic industry with more than 30 years of experience.
The floating raft system helps to conserve water, using the oxygenated clean water in which the plants grow as a conveyor system. Green Life will be able to produce 18 harvests each year and use 90 percent less water than conventional farming.
Patagonia Green Leaf, about a mile south of Green Life, is a hydroponic farm on a former plant nursery. It’s owned by the Canosa family. They’ve farmed in the traditional way in Argentina for 10 years.
The first phase of 10 greenhouses totaling 30,000 square feet is completed. The initial crop of baby greens will be planted soon, with harvesting expected by late September.
“The idea is to harvest and deliver the product within 24 hours,” said Juan Ignacio Canosa, who lives in Boca Raton.
After visiting Miami and Fort Lauderdale on vacations, the family started coming to Boca Raton. Last year they bought 5 acres from Boynton Botanicals, whose owner was retiring.
Plants will be grown pesticide-free using a system known as NFT, (nutrient film technique) from Arcata, Calif.-based AmHydro. A pump delivers fertilized water to the growing trays, flows over the plants’ roots, then drains back into the reservoir and is recycled.
Robert Hochmuth, regional extension agent with the University of Florida’s North Florida Research and Education Center, said since the early 2000s, the number of acres of produce grown in greenhouses and other structures in Florida has increased five-fold to more than 500 acres.
Producing in protected structures extends the season and reduces insects and diseases, Hochmuth said.
“You can be a consistent supplier in the marketplace over a long period of time,” Hochmuth said.
Most of the hydroponic farms in Florida are less than an acre and tend to cater to local markets.
Hochmuth said hydroponic growing is attracting people who are new to farming.
“Because they are going with high-value specialty crops, the likelihood of profitability makes sense,” Hochmuth said.
Of course, greenhouses and other facilities are at risk of being destroyed during hurricanes or high winds. Hochmuth advises removing the plastic from the structures prior to storms because it acts as a sail.
Hydroponic farming isn’t new to Palm Beach County. Walter Ross founded Farmhouse Tomatoes west of Lake Worth in 1996 and grows heirloom tomatoes in 160,000-square-feet of greenhouses from Nov. 1 through June 30.
Eco Convergence Group Announces Corporate Name Change To Kalera, Breaks Ground On Largest Indoor Vertical Farming Facility In The Southeast
Last year, the company opened the first of several planned hydroponics HyCube growing centers with the completion of a facility located on the premises of the Orlando World Center Marriott
GlobeNewswire August 20, 2019
ORLANDO, Fla., Aug. 20, 2019 (GLOBE NEWSWIRE) -- Eco Convergence Group, a leader in indoor vertical farming, announces its official name change to Kalera today. In addition, Kalera also announces that it has begun construction of a state-of-the-art indoor growing facility in Orlando, which will provide an abundance of healthy, tasty greens for the hospitality, grocery, and food service industries.
Last year, the company opened the first of several planned hydroponics HyCube growing centers with the completion of a facility located on the premises of the Orlando World Center Marriott. Kalera is now scaling operations to include a new growing facility, which will be the single largest indoor vertical farm of its kind in the Southeastern United States. Kalera will begin production at the new indoor farm sometime in Q4 of 2019 and is projected to grow over 5 million heads of lettuce annually.
“Our goal at Kalera is to harness plant and data science to deliver new economies of scale in agriculture, making it possible for more people to have access to high-quality, non-GMO, clean, nutritious food, locally grown without the use of pesticides—no matter the season,” said Cristian Toma, CEO of Kalera. “We have proven the technology and refined our production methods to a point where we are ready to scale up.”
Each plant grown in Kalera’s precisely controlled hydroponic facilities receives just the right amount of nutrients, filtered water and air, light, temperature, and humidity to achieve its dense, crisp, colorful, and delectable state. Kalera never uses any pesticides, insecticides, hormones, or GMOs. Unlike traditional farms, Kalera plants aren’t at risk for exposure to contaminants and pathogens in the soil, water, or air.
“Kalera produce is like none other—it’s not just delicious, it’s also clean and beautiful,” said Eric Martinez, Executive Chef, Orlando World Center Marriott Resort & Convention Center. “Having access to Kalera’s exceptional produce year-round opens up limitless possibilities to expand our menu and create new dishes that delight patrons. Many restaurants pride themselves on sourcing ingredients from farms 50 to 100 miles away. We are thrilled to say that we are sourcing our greens from 50 feet away."
Central to Kalera’s business is the idea of good science. The company is planting non-GMO seed, and has perfected over the past years plant and data science driven methods to optimize nutrient mixtures, light recipes, and environmental controls resulting in highly nutritious vegetables with consistent high quality year-round. Kalera is simply working with nature to give plants what they need to thrive, ensuring they reach their full growing and nutritive potential.
By using a closed loop irrigation system, Kalera’s plants grow while consuming 95% less water compared to field farming. Furthermore, the company utilizes cleanroom technology and processes to eliminate the use of chemicals and remove exposure to pathogens. With indoor facilities situated right where the demand is, Kalera is able to supply an abundance of produce locally, eliminating the need to travel long distances when shipping perishable products and ensuring the highest quality and freshness.
The new Orlando facility will deliver this high level of quality in abundance to the local market. The company plans for accelerated growth and will build additional facilities as production capacity is further expanded in the US and internationally.
About Kalera
Kalera is a technology-driven vertical farming company that excels in creating optimal conditions to grow delicious, nutritious, non-GMO produce that is free from pesticides and environmental pathogens. Kalera’s high-yield hydroponic production systems are automated, clean-room standard facilities. By utilizing unique methodologies that leverage plant and data technologies, Kalera creates optimal growing conditions for a variety of micro greens, year-round. The company is focused on reducing environmental impact and supplying produce to customers as close to the source as possible.
Elka Karl
Phone: 510-508-7328
Email: elka@dadascope.com
Hong Kong Start-Ups Are Using Hydroponic Technology And Vertical Farming To Bring Fresh And Healthy Food To Citizens
The green movement is a growing revolution across the world and particularly Hong Kong. A part of this change is the ground-breaking farming technology that cuts lengthy supply chains to allow easy access to fresh produce rich in nutrients and bursting with flavour
Hong Kong Growing Urban Farming Tech
The green movement is a growing revolution across the world and particularly Hong Kong. A part of this change is the ground-breaking farming technology that cuts lengthy supply chains to allow easy access to fresh produce rich in nutrients and bursting with flavour.
A Hong Kong-based urban farming technology company launched in January 2018, has been offering herbs, microgreens, and edible flowers to restaurants, hotels and home cooks. It will take things to the next level in a couple of weeks with the launch of its first “mobile farm”.
Using hydroponic technology, the greens will grow in-store so that consumers know exactly where their food is coming from – they can actually see their vegetables as they grow. The pilot mobile farm will be launched in mid-August at an organic convenience store in Sai Kung.
Hydroponic basically refers to the way that the plants absorb nutrients, which is through water instead of soil. The start-up uses organic nutrients bought from the United States which has US Federal Drug Administration approval and adds it to water. An advantage of indoor farming is that it is extremely sanitary and water-saving.
Soil-based farming often sees the loss of a lot of water (which goes underground), hydroponic farming saves 90 per cent more water.
Hong Kong imports an astounding 98.3 per cent of its vegetables, with 70 per cent of the imports coming from China and 28 per cent flown in from around the world. All the emissions involved in getting our greens into Hong Kong is a massive black mark in terms of sustainability – and it’s also bad for health.
Another issue is that as soon as produce is harvested, the roots stop supplying water to the leaves and stem and the plant start losing their nutrient content. A benefit of a mobile farm is the ability to buy greens with the roots still intact, take the produce home and use it while it’s still fresh.
The start-up’s team have been using the Causeway Bay operation for research and development and a base in Cyberport to develop the mobile farm technology.
Beyond the hydroponic technology, the team is developing even more sustainable and efficient farming technology, but they’ve taken it slow the first year to develop their understanding of the crops they are growing.
According to an earlier report, a hi-tech vegetable farm in Hong Kong’s Tai Po district is thriving inside a converted factory building and produces four tonnes of lettuce, wild rocket, endive and cabbage for salads each month.
Its workers, most of them in their 20s and 30s, tend to neat rows of racks, each 30cm tall and 10 tiers high, filled with potted greens lit by low-energy light-emitting diode (LED) lamps and connected to fish tanks on the floor.
Instead of shovels and hoes, they work with computers and drones. The farm’s co-founder noted that they farm with technology, not ploughs. This is farming 4.0.
This start-up offers a glimpse of the future of farming by harnessing technology and using less space than traditional, long regarded a sunset industry in Hong Kong.
Primary industries, mainly comprising farming, fishing, mining and quarrying, accounted for HK$502 million last year, a tiny fraction of the city’s total gross domestic product of HK$2.65 trillion.
But the start-up’s co-founder, who is optimistic about the prospects for aqua-farming, said that Hong Kong is a service-based city, but still needs healthy food. This is a viable business in Hong Kong because of the demand for healthy produce and the growing awareness of food safety.
The Urban Agriculture Startup
As consumers grow tired of contamination risk, and their tastes broaden to include fresher produce, the opportunity exists for startups to disrupt their local food supply chain
NFT (Nutrient Film Technique) Hydroponic Vertical Farm
As consumers grow tired of contamination risk, and their tastes broaden to include fresher produce, the opportunity exists for startups to disrupt their local food supply chain.
The age-old job of the farmer has been replaced by a new wave of local small footprint farmers. These farmers are able to grow and deliver to market high-quality food with very little waste. These farmers sell directly to restaurants, grocery stores, or at farmers markets around the world.
Most small footprint growers use a form of hydroponics to grow their product. Hydroponics is simply growing plants in water rather than soil, allowing the farmer to give the plant the perfect conditions for growth.
The return on investment for a crop of herbs can be quite high. For leafy greens like lettuce, it's entirely possible to keep your cost at around $1 while selling retail for $4. Big restaurants and hotels can do 10,000 plates a night or more, supply deals with companies of this size will net a lower price but provide a higher volume. If space is a concern, its best to grow out of your local farmers market and have the ability to get more space before taking on high volume.
There are a variety of places you can grow — from shipping containers to greenhouses. The darker the place the higher the cost of electricity. Greenhouses use less energy, but if you live in the north you will still have to run supplemental lighting and heat.
Most people believe the future of this industry is vertical.
Vericle gardening is growing plants on top of plants in a warehouse. Some are stacked on verticle walls, but most are horizontal systems stacked on top of each other. Many believe that this is the future of farming, particularly for leafy greens. Most real estate is valued by the square footage, the vertical footage provides “free expansion” to the indoor farm.
The most popular hydroponics system for leafy greens is the NFT system (Nutrient film technique). It is a system of pipes typically made of PVC or metal gutters that continuously flow water over the roots of the plant. The water drains into a reservoir where a pump pushes the water back up into the system in a continuous cycle.
There is a massive opportunity in flowering plants, though the equipment can be very specific. If you are interested in growing Tomatoes , your costs will be significantly higher as light and smell usually need to be contained. You may be able to excel at flowering plants — particularly if they are heritage varieties, but they represent a small section of the industry right now. Lighting, ventilation and nutrient formulas can drive up the price of flowering plants and may be why only specific flowing crops like Tomatoes or Cannabis are grown in significant quantity — and nursery plants are largely ignored.
Lettuce grown in a hydroponic system uses 2% the water it would if grown in a field 3000 miles away. It's a great plant to start out with because almost everyone eats it — and there is constantly outbreaks of food born illness related to Romaine and other leafy lettuce which only helps your marketing. It's also easy to grow.
Romaine Lettuce would take a week or two longer than most varieties that finish in about 30 days. On a perpetual system, you can be delivering fresh produce weekly to the farmers market or restaurant.
Indoor agriculture, particularly urban agriculture, is the future of our civilization. Opportunities rarely exist where it is possible to disrupt an industry with relatively little money.
What many farmers lack are branding and marketing strategies. By catering to local markets it's quite possible to establish strong local ties. Many people are making the switch to plant-based diets and ideas like the 50-mile diet are really starting to take hold.
Our food supply is currently at natures mercy. Climate change, draining aquifers, and man-made dams are devastating water supplies in many cities around the world. Crops are wiped out by weather in dramatic fashion every single year. It seems every week there is some new warning about the food we eat.
Getting started with indoor agriculture is as easy as building your own system and feeding your own needs. For those who fall in love with it — every city in the world needs indoor farms providing nutritious local foods. Someone will become a household name because of this industry — if you start now — it could be you.
WRITTEN BY Ryan Geddes
Entrepreneur, Writer, Digital Strateg
The Future of Arctic Farming – Infographic
Despite difficult growing conditions, the number of vegetable farms in Alaska, Norway, Canada and other Arctic regions appears to have increased
Green Iglus, solar retention greenhouses in Nunavut, aim at producing greenery and produce for the community. Photo: Mike Beauregard
Greenhouses and Hydroponic Systems are Becoming Ripe with Possibility
Despite difficult growing conditions, the number of vegetable farms in Alaska, Norway, Canada and other Arctic regions appears to have increased. The hope is that a better, more affordable supply of vegetables in Arctic communities will help battle public health issues, improve food security and decrease the economy’s dependence on oil and imports.
This infographic designed by Jennifer Cook illustrates the challenges of vegetable production in the Arctic as well as possible solutions offered by Arctic farming. Lower temperatures and permafrost result in short growing seasons and slow down the growing process.
A frequent solution, the import of vegetables, is often unreliable and expensive. Combined with other factors, this can affect the food security, health, well-being, and financial situation of communities. In recent years, the number of Arctic farming projects based on greenhouses, hydroponics, or other technologies has developed rapidly, offering the potential for a better, more affordable, and more sustainable supply of fresh vegetables.
DOWNLOAD
INDIA: Urban Kisaan Brings Commercial Hydroponic Farming To Visakhapatnam
The Hyderabad-based startup, Urban Kisaan, specialises in soil-less gardening also known as hydroponics that is particularly popular in urban centres as it allows people to grow fresh vegetables even if they don’t have a garden
AUGUST 02, 2019
With Hydroponic Farming, Even Those
Without Gardens Can Grow Their Own Greens
As soon as you enter the office of Urban Kisaan in MVP Colony, you are swamped by the greenery and the sound of flowing water. The Hyderabad-based startup, Urban Kisaan, specialises in soil-less gardening also known as hydroponics that is particularly popular in urban centres as it allows people to grow fresh vegetables even if they don’t have a garden.
The fresh palak, methi and gongura shrubs at their office make a compelling case of why one should consider trying farming at home. The objective of hydroponic farming is to cultivate vegetables with minimal use of soil and water.
Urban Kisaan has come lately to Visakhapatnam. It provides the infrastructure to grow plants at home. The base model has three hydroponic channels in tiers on a metal stand. Above them, there are six plants growing in plastic nets that allows the roots to reach to the water in the channels below them. The water is circulated into in the channels through a 20 litre-reservoir tank. The water is mixed with a nutrient solution for maintaining its acidic content. (see infobox)
Set up the plants and channels in an area that gets eight to 10 hours of sunlight
Check pH/EC values once in three days
Ensure that reservoir tank is sealed; flush the tank every three months
Top up the tank with water and add nutrient each week
The kit needs to be placed where plants get eight to 10 hours of sunlight. Depending on the plant and climatic conditions, you get the yield once in two weeks. For instance each plant of palak gives a yield of 250 grams once in two weeks. They are also prototyping a set-up where plants can be grown in artificial light. Any numner of leafy vegetables can be cultivated. Basil, Bok choy , lettuce , parsley, kale, spinach, sorrel leaves, coriander, mint, and fenugreek are some that have done well with hydroponics.
The kit comprises two bottles of nutrient solution, a digital pH scale (to determine the pH balance of the water-based solution) and an electrical conductivity metre. There are instructions on how to set up and dismantle the structure. The smallest set-up which can hold 18 plants costs around ₹10,000.
Urban Kisaan has managed to sell about 10 kits in July. Says its CEO Vihari Kanukollu, “In coming months, we plan to set up a farm in Visakhapatnam where people can harvest vegetables before purchasing them.” Urban Kisaan has expanded its operations to Bengaluru as well.
Saras Chandra, learnt about hydroponics after a YouTube algorithm guided him towards hydroponic videos while he was searching for gardening tips. He is now growing 24 varieties of plants using this technique in his balcony. “I was fascinated with the technology. I now grow palak, methi and gongura. Over the last two weeks, he has harvested palak twice. So taken is Saras with his success in growing his own food that he has left his full time job at a bank to explore business opportunities in hydroponic farming.
The Urban Kisaan technology also flourishes on the rooftop of Karuna Shree, a city based lawyer. She says, “My terrace not only looks green but also gives me fresh vegetables.” According to her, the set up is sturdy and can easily endure few days of heavy rainfall.
Each drop counts
Vertical farming uses 70-95 percent less water as compared to traditional cultivation method.
Her Farm’s Mission: Empowering People With Disabilities
Nona Yehia is CEO and Co-founder of Vertical Harvest, a company in Jackson, Wyoming, that cranks out roughly 100,000 pounds of produce each year in a three-story, state-of-the-art, hydroponic greenhouse.
By Claire Elise Thompson on July 27, 2019
Nona Yehia is CEO and Co-founder of Vertical Harvest, a company in Jackson, Wyoming, that cranks out roughly 100,000 pounds of produce each year in a three-story, state-of-the-art, hydroponic greenhouse. Bumble Bee tomatoes, rainbow chard, butterhead lettuce — the company’s 34 employees generate as much bounty as a 10-acre traditional farm while using only one tenth of an acre of land.
And there’s something else: Many of those employees have developmental disabilities. Including this underserved population in such an innovative endeavor “is about empowerment,” Yehia says. “It’s about exposing ability.”
We caught up with Yehia, (who, along with Co-founder Penny McBride, was featured on Grist’s annual list of “Fixers” in 2016) to talk about a new documentary that follows the “tumultuous” first 15 months of Vertical Harvest’s endeavor, and the company’s journey in the years since it was filmed.
Here are some snippets from our conversation.
Yehia on reliving the early days of Vertical Harvest:
I like to call it adventures in sleep deprivation and weight gain. Anyone in the startup world can understand. [The film is] actually very hard for us to watch. But at the same time, it’s great to recognize how hard we’ve worked and how far we’ve come. Where it really shines is in telling the stories of our employees and their role in the startup.
On the origins of the company, and its employment model:
It was three women — myself, Penny McBride, and Caroline Croft Estay. I’m an architect. Penny McBride was a sustainability consultant, and Caroline Croft Estay was working as an employment facilitator, trying to find meaningful work for her clients with disabilities. The project was born out of those interests meeting.
I have a brother with different abilities. This country has come a long way in education, providing an inclusive and supportive environment for people with disabilities in the classroom, but when it comes to employment, the opportunities are few and far between.
On befriending a member of the Tea Party who wanted to kill the project:
This guy had seen our business plan, and he basically said, “You’re using public funding. You’re designed like a nonprofit but you’re not a nonprofit. I’m going to kill your project.” And we said, “Hey, let’s talk.”
We started going to lunch with him every month, and he actually became one of our biggest advocates. He spoke on our behalf many times, and I believe he was really pivotal to our success. I learned from that process to embrace your detractors as much as your supporters, because you’ve got a lot to learn from them.
On being pioneers in vertical farming:
When we started, the Dutch were the only people doing hydroponic farming. We had consultants who were heavily involved in choreographing the building — and we love our Dutch counterparts, but it was really difficult not having domestic support. Our building is a very complex ecosystem. Every part affects a whole. You don’t know what you don’t know, and you have to move forward despite that fact. There were many places where we kind of looked at each other and said, maybe this isn’t going to work.
On the greenhouse design:
We stacked three greenhouses on top of each other, so that each level has a different microclimate. The middle level has a lot of airflow, so it stays cool. Lettuces like a cool environment. The third level gets much hotter, which is a perfect climate for viney crops.
It’s hard to develop multiple microclimates to grow different crops — [that’s why] so much of the [vertical farming] industry is growing microgreens. But we are very invested in growing a diversity of crops. You can’t feed a community on lettuce alone.
On fighting the bad bugs:
We have an integrated pest management system — bug-on-bug warfare. We have parasitic wasps that are right now patrolling to take care of white flies and aphids.
On the future of Vertical Harvest:
This week we received eight requests for facilities in cities around the world, and that’s a pretty common week for us. We are in the midst of developing a plan to own, operate, and develop seven greenhouses in different communities over the next several years. We have also gotten a contract from Fannie Mae to look at the feasibility of including a vertical farm in an affordable housing plan.
On the power of the work they’re doing:
One of our employees, who was washing dishes all her life, is now in charge of creating 200 pounds of lettuce a week, and has learned a vital skill in a new industry. Another employee can now create and repair vertical farming equipment, which is a totally rare and important skill. He will be a teacher in tomorrow’s farms. We’ve been able to expand what their future would look like, by lightyears.
Hearts of Glass has made the festival route, and had its premiere in Jackson at the start of June. It’s not available to the public yet, but you can catch a free screening in Chicago or Wyoming in the coming months.
Workshop To Feature Hydroponic Technology - September 5, 2019
The workshop, which is sponsored by Purdue Extension, Purdue’s Department of Horticulture and Landscape Architecture and the Indiana State Department of Agriculture, will focus on teaching attendees about hydroponic production technology
Ashley Langreck | AgriNews Publications
July 31, 2019
Krishna Nemali examines hydroponically grown lettuce in the horticulture and landscape architecture greenhouse at Purdue University. Provided photo/Purdue University
WEST LAFAYETTE, Ind. — The fourth annual Greenhouse and Indoor Hydroponics Workshop will be from 8 a.m. to 3 p.m. Sept. 5 on the Purdue University campus.
The workshop, which is sponsored by Purdue Extension, Purdue’s Department of Horticulture and Landscape Architecture and the Indiana State Department of Agriculture, will focus on teaching attendees about hydroponic production technology.
Lori Jolly-Brown, who is serves as the Extension events and communications coordinator for the horticulture and landscape architecture department, said the morning session of the workshop will focus on how to get started in hydroponics, where to purchase and find materials, how to fertilize plants, ways to keep bugs away and a wide variety of other topics.
After lunch, Jolly-Brown said, attendees will have the chance to tour one of Purdue’s state-of-the-art greenhouses and indoor hydroponic facilities, while also having the opportunity to participate in hands-on activities.
Jolly-Brown said individuals will be able to interact with workshop organizer Krishna Nemali, a Purdue assistant professor and a controlled environment agriculture Extension specialist.
“They will get to see Nemali’s hydroponic research and vertical farming displays,” Jolly-Brown said.
Jolly-Brown said the workshop is geared toward commercial producers and growers, those just getting started in hydroponics, as well as those who are involved in hydroponics production technology as a hobby.
To register for the workshop, visit https://bit.ly/2OjqTBn.
Ashley Langreck can be reached at 800-426-9438, ext. 192, or alangreck@agrinews-pubs.com. Follow her on Twitter at: @AgNews_Langreck.
Tags Lori Jolly-brown Agriculture Economics Department Of Agriculture Indiana
Dave Riddell Grows Greens In A Storage Container
Riddell grew up in Needham, Massachusetts outside Boston. Both his mom and his aunt were passionate gardeners. His fascination began early with the plant world. He graduated from the University of Maine after a course of study that included communications and forest recreation management
August 7, 2019
Owner Dave Ridill holds a tower of growing lettuce inside his hydroponic farm, housed in an upcycled, 40-foot shipping container in Tetonia, Idaho. Riddell has been in business for three years and grows a variety of hardy greens like lettuce, Swiss chard, arugula and others. It happens 365 days a year.
Greens sprout from towers in Riddell’s hydroponic farm at Clawson Greens.
REBECCA NOBLE / NEWS&GUIDE photos
It was quite a while back, actually, that my dear friend Ken retired from Grand Targhee Resort’s ski patrol and moved to Salt Lake City. It was then that he told me it would be a good idea for me to become acquainted with his fellow patroller, Dave Riddell. Ridill had started a new business, Clawson Greens, growing greens inside shipping containers in Tetonia, Idaho. Now just how unlikely is that scenario?
Ridill and I spoke on the phone a few times before I met him, with me repeatedly promising it would be soon that I would come check out his scene. Around Christmas time of 2017 we met while he was delivering his beautiful produce to Hand Fire Pizza as I was interviewing the chef and manager for a column. Hand Fire serves one simple and delicious salad. It is made of Clawson Greens.
Ridill grew up in Needham, Massachusetts outside Boston. Both his mom and his aunt were passionate gardeners. His fascination began early with the plant world. He graduated from the University of Maine after a course of study that included communications and forest recreation management.
One college spring break Riddell accompanied his brother and some friends to Jackson Hole to ski. While in the neighborhood he applied for a summer job at Grand Targhee on the wilderness crew of the U.S. Forest Service in the Jedediah Smith Forest. That continued until 2018, when Clawson Greens began consuming more of his time.
That winter of 2007 Ridill started a winter job of as ski patroller at Grand Targhee that he still enjoys. He was later a bike patrolman for six years but, after breaking his back in four places, he decided that job was not for him. He also worked as part of Teton County, Idaho’s fire department.
In 2016 he was about to attend paramedic school in Boston when his neighbors approached him with an outlandish proposal. They had discovered a company that used shipping containers to grow food in a controlled environment. They loved the idea and yet believed it more appropriate for someone much younger than they were to embark on such project of that scope. Thus they shared the idea with their favorite neighbor.
Ridill became more intrigued and educated about the possibilities. There are countless shipping containers all over the planet. Many are abandoned or fallen into disuse. Why not repurpose, up-cycle these already existing units in a productive manner?
Ridill connected with Freight Farms. As fate would have it, the founder of the company grew up a couple miles from Ridill’s family home. They went to the same high school although five years apart. It was as if it was meant to be.
After he returned from training with Freight Farms the first shipping container grow room arrived at its final home in Tetonia, Idaho. In the winter of 2017 Ridill had his first restaurant customer.
It’s simple to check out Freight Farms’ website online. It is amazing to look at the possibilities of the future of farming and food, though it’s much more impressive in person.
The system uses a fraction of the water used in most agriculture. The drip irrigation waters the vertical tube, and it all recycles. The environment is temperature and humidity controlled for a growing season of 52 weeks a year. Beautiful organic produce is available mud- and insect-free using no pesticides.
It is an eight-week process from planting the seeds in tiny plugs to harvesting the heads of greens with their root ball attached. The variety of plants ranges from red-veined sorrel and wasabi arugula to rainbow chards and many lettuce varieties. All are vibrantly alive and remain in excellent condition for use for a couple weeks. As chefs plan their seasonal menus, Ridill provides specialty greens in a timely fashion.
There are now three grow room containers that supply 10 local restaurants. Last winter the customers at Phoenix and Dragon were impressed enough that they requested greens for home use. Eric and Zarina Sakai, who own Phoenix and Dragon, put together a little CSA. Ridill brought greens and everyone was happy. I hope they do it again next winter. It is true that the salads at the restaurant are particularly tasty. The small plate of summer rolls and their KFC, or Korean Fried Chicken, sent me into a dreamy state the other evening. Their summer schedule serves lunch Monday through Friday and dinner Tuesday through Saturday.
Ridill has not become a paramedic and yet he is caring for our health in a different way. It’s pretty exciting. 
Where to find Clawson Greens
The Phoenix and the Dragon
Hand Fire Pizza
Forage Bistro & Lounge (Driggs, Idaho)
Butter Cafe (Victor, Idaho)
Citizen 33 Brewery (Driggs)
Warbirds Cafe (Driggs)
Huntsman Springs (Driggs)
Royal Wolf (Driggs)
Branding Iron Cafe (Bondurant)
Visit ClawsonGreens.com or FreightFarms.com for more information.
Bru, who cooks for private clients, writes about the valley’s talented chefs.
OId MacDonald Had A Farm…And A Robot, And Racks of plants, And Lots of Plastic To grow Plants In…
How about farms that go up vertically – measured in stories high, instead of in acres wide? How about farms that are inside buildings, instead of outdoors? How about farms that are in a city, instead of out in the country? How about farms that use water, instead of dirt?
The future of farming?
How about farms that go up vertically – measured in stories high, instead of in acres wide? How about farms that are inside buildings, instead of outdoors? How about farms that are in a city, instead of out in the country? How about farms that use water, instead of dirt? How about farms that use plastic, instead of dirt? Not to mention robots and drones working the crops.
All possible. All happening, in fact. And perhaps, the future of farming.
Over the year to come, we’ll tell you more in detail about these innovations, and other changes in how we grow our food. But the future of farming has more in common with the past and the present than you might think. Petrochemicals, for instance. Past, present or future, you can’t farm without the products made from them: from the strong, lightweight plastics used to build the racks (and even the “ground”) plants grow on, to the carbon fiber-reinforced resin used to make many of those drones and robots and other equipment used on the indoor farms of the future – to the fuels that move the tractors, combines and other equipment used on the outdoor farms of today, as well as the fuels that move the food those farms grow to us – farming has deep petrochemical roots.
*****
Today, we’ll start with an introduction, and we’ll start in – in San Carlos, California.
That’s where Iron Ox has turned a warehouse into a grow house: a dirt-free indoor farm growing romaine lettuce, kale and other leafy greens. What replaces dirt at Iron Ox, is water (water supercharged with nutrients) – and racks, rows and rows of horizontal and vertical racks of plants…
(Photo from Iron Ox)
…fresh food grown for people living in cities (like so many of us), grown in the cities where we live, and grown year round (which even in California, isn’t possible outdoors).
And the “Iron Ox”? Much of the work on this farm is done by robots (like the one in that picture, lifting and moving racks of plants). Those robots can move in any direction, so they can place those racks closer together and get the most out of those indoor spaces. The robots move on Mecanum wheels made from a high-tech synthetic rubber derived from petrochemicals like ethylene, propylene and toluene. Even the robot arm that plants seeds and transfers plants? That bends and flexes thanks to polypropylene joints.
*****
In Houston, Moonflower Farms has replaced the dirt with vermiculite that contains a mineral blend. In their mini-warehouse (more of a shack really), their micro-greens are racked vertically…
(Photo from Moonflower Farms)
…under hot pink lights.
That meant, after Hurricane Harvey swept over the Gulf Coast, Moonflower had 10 inches of water on the floor – but almost all of their crop was just fine (since it was up above the ground, and the flood water).
(Those racks, by the way, must be light-weight and strong, which requires engineered polymers like high-density polyethylene, ABS and HIPS. And yes, those high-tech polymers are made from petrochemicals such as ethylene, propylene, butadiene and benzene.)
*****
Also in Houston is Acre in a Box. In this case, the “box” is an old shipping container. And inside that 320 square feet, is an acre (and a half, actually) of produce…
(Photo from Acre in a Box)
…growing hydroponically day and night, come rain or come shine, or even come hurricane.
*****
At Urban Organics, in St. Paul, Minnesota – it’s easy to see one advantage of indoor farming. The average high temperature in January is 23 degrees. And unless you like a hot bowl of pine needle soup (think Euell Gibbons), there’s not much of anything growing fresh in that weather.
Urban Organics is an aquaponics farm – meaning they also grow their plants in a nutrient-rich water – but in this case, the fertilizer comes from fish (fish poop, that is). In turn, the plants filter the water as they absorb those nutrients, the clean water goes back to the fish, and round and round the system goes.
(Photo from Urban Organics)
And this type of advanced agriculture wouldn’t be possible without the engineered plastics made from petrochemicals. Companies like Pentair Aquatic Eco-Systems use polyethene and fiber-reinforced resins, made from the petrochemical ethylene, to make fish tanks and filter tanks. Ethylene is also used in the polyethylene and vinyl liners. And the advanced membrane technology that allows for water recycling depends on petrochemicals as well (like the xylene, that makes the polyamide, that makes those membranes).
*****
But maybe the most far-out farming is going on in Japan – where Mebiol Research and Development is growing tomatoes – indoors – on a plastic sheet.
(Photo from Mebiol)
This plastic (polymer) sheet is a hydrogel called polyvinyl acetate – a material like a super sponge which soaks up water and nutrients. The tomatoes (and there are other plants too), grow ON the polymer, spreading their roots across the surface, and absorbing the nutrient-steeped water. That polymer starts with ethylene, again – which as you know by now, is a critical part of future farming.
*****
Oh, and those drones? Drones nowadays inspect crops – check for plants that are underwatered – spot diseased plants – evaluate smoke contamination after a fire. And after a fire, drones can plant new trees (as seeds), to help restore burned-over wilderness areas (and since they are drones, getting into a wilderness to plant is not a problem).
(Photo from DroneSeed)
The drones, by the way, don’t dig holes and plant seeds – these drones “shoot” seed pods into the ground. The pods are packed with nutrients, and coated with capsaicin (the stuff in chili peppers), to keep animals from eating the seeds.
(These sophisticated, seed-planting drones have to be tough, to withstand a wide variety of weather conditions and constant stress from the multiple blades – so fiber-reinforced resins are used because they are as strong as steel and much lighter in weight. The resins are a special type of plastic called epoxy, and the petrochemical propylene is their foundation.)
*****
All of these methods of farming use far less water (as much as 90 percent less water) as conventional farming – they take up far less land – they can grow food year round – and they can grow food in the same place where most of it is being eaten, our cities. All good, and all important at a time when there is less and less good farmland, and more and more of us needing to be fed. And as we told you at the beginning of this peek at the future, all of this depends on farming’s deep petrochemical roots.
*****
Right after World War I, there was a hit song: “How ya gonna keep ‘em down on the farm (after they’ve seen Paree)?”
Millions of American soldiers came home after the war, having left their home town for the first time, their state for the first time, their country for the first time – and maybe, so the song went, soldiers who’d left small towns across America, might have a taste now for big city life, and wouldn’t want to go home.
That might be different in years to come though. Because “down on the farm” might be very much a part of big city life. And it won’t be “down” on the farm anyhow. Those future farms will go up, up into the air. Skyscrapers filled with vegetables? Stay tuned throughout the year as we follow this story.
AeroFarms Raises $100 Million In New Capital
Last year, AeroFarms raised $40 million in Series D funding with the INGKA Group, chef David Chang and retired U.S. general David Petraeus among the investors. At that time, AeroFarms had raised over $130 million; the new investment pushes its total over $230 million
Photo courtesy of AeroFarms
The New Jersey-Based grower Is Valued At $500 Million
According To Its Latest Round of Funding
July 19, 2019
According to an article in the Financial Times, Newark, New Jersey-based indoor farming company AeroFarms has raised $100 million in its latest round of funding. The lead investor is the INKGA Group, the parent company of furniture company IKEA. After this round, AeroFarms is valued at $500 million.
According to the Financial Times, the company's latest round of investment included no new backers. The company has not yet publicly disclosed the new funding.
Last year, AeroFarms raised $40 million in Series D funding with the INGKA Group, chef David Chang and retired U.S. general David Petraeus among the investors. At that time, AeroFarms had raised over $130 million; the new investment pushes its total over $230 million.
As of 2019, AeroFarms has two commercial farms in the U.S. - its flagship 70,000 square foot facility 30,000 square foot farm. The locations opened in 2016 and 2015, respectively.
In March of this year, it was announced that AeroFarms greens would be served on Singapore Airlines flights from Newark to Singapore. It also hired Roger Post, formerly of Danone Foods and Kraft Nabisco,as its new COO in February.
FOR SALE - Two - 2015.5 Freight Farm - Computer Controlled Hydroponic Grow Systems - Location: Colorado
Manufacturer - Freight Farms
Model - (2) 2015.5 Leafy Green Machine (LGM) - Winterized" for Cold Climates.
Price - $50,000 Each - Can be sold individually
Location: Colorado
The Leafy Green Machine is a complete hydroponic growing system built entirely inside a shipping container with all the components needed for commercial food production. The system is designed and engineered for easy operation, allowing users of all backgrounds to immediately start growing.
Current Uses
• Perfect for starting a small produce business, growing for restaurants or supplementing existing produce production.
• Restauranter who wants to grow custom greens for rotating menus 365 days a year. Farm to Table? How about Parking Lot to Table!
• Universities and schools have created programs for students to learn to grow while supplementing dining facilities with fresh greens.
The Highest Standard in Controlled Environment Agriculture
• Pre-built system designed to maximize operational efficiency and streamline workflow
• Perfect environment is achievable 365 days a year, regardless of geographic location
• Automated scheduling reduces the amount of labor required to operate
• Remote monitoring & control capabilities through the Farmhand AppTM
Operation Requirements
Space- The LGM dimensions are 40’ x 8’ x 9.5’. We suggest putting the farm on either trap rock or a concrete pad.
Electrical- 60 amp, 120/240-volt single phase or 120/208V three phase connection.
Water- A designated water source is suggested such as a garden hose or hardline water plumbing.
Labor- 15 to 20 hours a week for farming and upkeep.
It is recommended growing smaller compact crops with a high turnover rate, like head and loose leaf lettuces, herbs and heartier greens like kale and swiss chard.
Crop Examples
Butterhead lettuce, Oakleaf lettuce, Swiss Chard, Mustard Greens, Cabbage Leaves, Arugula, Cilantro, Mint, Dill, Oregano, Kale, Endive, Basil, Chives and Thyme
Yields
800+ heads of lettuce weekly
12 heads per tower (256 vertical towers)
1 LGM= 1.8 acres
LGM Included Accessories:
Zebra Printer and Bar Code System + Case of Ribbons & Paper
Numerous additional extras included.
Numerous warranties still in effect
Training, website and ongoing support available through Freight Farms.
Visit www.freightfarms.com for more information.
<br/>
Attached Documents:
LGM Cut Sheets
See All Photos And Videos Here
Indoor Vertical Farming, Electronically - Consumer Electronics Giants Such As Panasonic Are Expanding Into Indoor Agriculture
When the news first broke several years ago that Panasonic was growing lettuce in a warehouse in Singapore, it was tempting to think of it as a kind of lark—an exotic branding exercise meant to show the ever-expanding depth and breadth of new electronics technologies. The results have proven otherwise
When the news first broke several years ago that Panasonic was growing lettuce in a warehouse in Singapore, it was tempting to think of it as a kind of lark—an exotic branding exercise meant to show the ever-expanding depth and breadth of new electronics technologies.
The results have proven otherwise. Panasonic is now an established and growing player—if still a small one—in Asia’s agricultural marketplace, selling primarily to local grocers and restaurants. And it is not alone. Several of its rivals are engaged in similar experiments in diversification into vertical agriculture far beyond their core electronics businesses. What’s driving these high-tech high-fliers into this low-margin business? And what’s in it for them?
Not business as usual
A look inside Panasonic’s hydroponic operation reveals that there are indeed the predictable high-tech bells and whistles: automated farming systems do the seeding, potting, and irrigation. Plants grow under intelligent LED grow lights in a room whose temperature, humidity, and carbon dioxide settings are electronically controlled at levels that hasten and maximize plant growth.
But the electronics company is taking the enterprise seriously. It has more than quadrupled the farm’s square footage and output in the past few years. Its lab-coated farmer engineers now run a facility of almost 13,000 square feet that yields more than 80 tons of produce annually.
Meanwhile, in 2016, Fujitsu joined forces with Masuda Seed and Orix, a private equity firm, to use cloud-based technology to grow produce indoors in a facility in Japan, while Toshiba has also dabbled in leaf-vegetable production. In Dubai, Sharp recently debuted a high-tech strawberry-growing operation built around its Plasmacluster air-disinfecting technology. Many of these efforts are supported by governments in Asia that are looking for solutions to concerns about the scarcity of arable land and food sustainability. One estimate places the market for vertical indoor farming in Asia at $4 billion by 2024.
“It’s super interesting to see these companies starting to play in farming, where you go from the highest tech margins to the lowest margins possible,” says Allison Kopf, founder and CEO of Agrilyst, a tech company that harnesses data to help indoor farm operators build their businesses. The depth and intensity of the connection between the electronics companies and agriculture crystallized for her last year in China, when she toured a facility operated by BOE Technology Group, a Chinese maker of intelligent interface products like cell phone displays that, in a not-unrelated development, is also in the LED business. “The carryover opened up a new market for them,” she says. “And it makes sense—the technology definitely overlaps.”
Neil Mattson, associate professor at Cornell’s School of Integrative Plant Science in the department of horticulture, studies indoor growing. He points out that the factories are eerily suited to what growers need—predictability in an increasingly unpredictable world. These companies already produce electronic components in clean rooms with tight environmental controls that ensure impeccable air quality, lest any floating contaminants end up in motherboards or other highly sensitive equipment. “A clean-room protocol is really good in terms of food safety and infectious-disease issues,” Mattson says.
Climate, controlled
The indoor factories also mitigate food-supply issues arising from the changing climate. California’s unusually wet winter several years ago, for example, triggered shortages in spinach crops, causing the vegetable to virtually disappear for a time from stores on the East Coast. “The thought is that as the climate changes, we’re going to have to be more conscious of transportation and water and so on,” says Mattson. “And we don’t have to worry about wild animals, we don’t have surface-water irrigation sources, so there’s a lot less potential for contamination, and it’s a lot easier to control checkpoints.”
Growing in these kinds of controlled conditions is also several times more efficient than conventional farming in terms of water and fertilizer use and the use of space, Mattson notes. In 2015, researchers from Arizona State University found that lettuce grown in a hydroponic system used about a tenth of the water required with conventional methods. Scientists at the University of Nevada-Reno came up with a similar finding in a study focused on strawberries. These kinds of results prompted the authors of the Arizona study to note that hydroponics “could become a strategy for sustainably feeding the world’s growing population, if the high energy consumption can be overcome through improved efficiency and/or cost-effective renewables.”
Mattson concurs that the main issue right now is the power required for the lighting systems—and that research into LEDs may hold the solution. “Energy is the current sticking point,” he says.
All of these overlaps in technology and marketplace demand have made for some intense buzz. Back in the U.S., for example, the indoor farming startup Plenty recently announced it had raised $200 million in funding. A Panasonic spokesman told one media outlet: “We foresee this business to be a potential growth portfolio, given the global shortage of arable land, increasing populations, climate change, and demand for high-quality and stable food supply.”
But can it scale?
For all the deserved excitement, though, there are good reasons the electronics companies so far have mostly only dabbled in their respective enterprises. Serious questions remain about whether vertical farming is viable at any sort of significant scale. One problem is energy: indoor farms use twice as much as a greenhouse in the same climate, Mattson says, and significantly more than it takes to grow crops in a field and to ship them thousands of miles.
There are reasons why no dominant company has emerged, and they have to do with climate and geography, and the challenges inherent in shipping delicate foods like lettuce and strawberries. “Globally, you’ve got an industry that’s been around for decades and decades, but it looks very, very different in different regions,” Kopf says. “There are similarities that carry through, but as far as technology goes it looks very different because of geography. There’s no real standardization, which makes it hard for a clear market winner to evolve.”
In China, Kopf saw companies dabbling in agriculture using government subsidies, or opening farms on a one-off basis as a kind of experiment in ways to build market advantage, she says. The farming enterprises essentially amount to elaborate R&D programs—experimental efforts to determine whether produce can become a high-value product. “It feels very much like the Wild West,” Mattson says. “I like to say the hardware of intelligent lighting is farther advanced than our physiological understanding of plants. So a company can deliver these lights to the market, but we don’t truly know the best way to operate or use those lights.”
The learning curve
The reasons to bet on these counterintuitive types of business expansions? One is simply that these companies are deeply experienced at manufacturing and shipping products at scale. Mattson also says to expect improvements in LEDs and the understanding of how to use them—refining what companies refer to as their “light recipes.” Meanwhile, the continued evolution of robotics will drive down overhead.
One key question that remains is whether electronics companies really want to own and run the farms, or just provide the technology to run them. Either way, it’s safe to say that if you live in Asia in the not-so-near future, your lettuce and your Bluetooth headphones might very well have something very much in common.