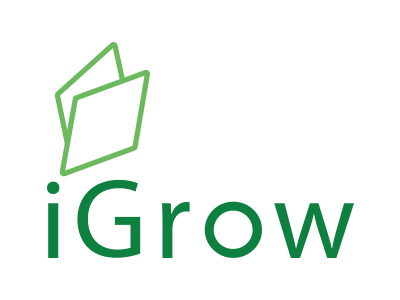
Welcome to iGrow News, Your Source for the World of Indoor Vertical Farming
Light Company LumiGrow Has Ceased Operations
The company has not shared specific information as to why operations have been ceased.
The lighting company LumiGrow has ceased operations and is now out of business.
LumiGrow was a company focused on LED lights, and it hit the headlines at the beginning of 2020 for the purple glow that illuminated the sky over Navajo County, Arizona, which was coming from a cannabis greenhouse where LumiGrow LEDs were installed.
The company has not shared specific information as to why operations have been ceased. For sure, the global pandemic together with the fierce competition in the LED sector of horticulture have had an impact.
Publication date: Tue 2 Feb 2021
VIDEO: Kentucky Greenhouse Company AppHarvest Goes Public On Nasdaq As It Prepares To Grow
AppHarvest has estimated it will generate net revenue of $21 million in 2021. The company is expected to produce 45 million pounds of tomatoes annually. AppHarvest employs 300 Eastern Kentuckians
FEBRUARY 03, 2021
AppHarvest has estimated it will generate net revenue of $21 million in 2021.
The company is expected to produce 45 million pounds of tomatoes annually. AppHarvest employs 300 Eastern Kentuckians.
David Wicks, Nasdaq’s vice president of new listings, said he was “incredibly proud to be your partner and look forward to supporting your innovation as a NASDAQ listing company” in a video message Monday.
Founder and CEO Jonathan Webb eats an AppHarvest tomato in a video message displayed in Times Square on Monday.
Two weeks ago, AppHarvest shipped its first bundle of tomatoes from its flagship location in Morehead.
“All this noise that is happening around us — listing on the Nasdaq and being shown in Times Square, selling our tomatoes to the largest grocers in the U.S. — all that is resonating back on the ground inside of our facility where our employees are feeling the positive impact of the work we’re all doing together,” Webb said.
The beefsteak tomatoes are selling out at grocers around the country.
“We can’t grow fast enough,” he said. “Our tomatoes are hitting store shelves and flying off the store shelves. It’s not just Kentucky, it’s everywhere from Indiana, all the way down to Florida.”
Webb said the company’s job now is to build faster and grow more vegetables to get on store shelves.
The company continues to look throughout Eastern Kentucky for building sites, Webb said, but there are challenges.
“We just have to find a place to build,” he said. “We have the capital. We want to build there, but building on these reclaimed coal mine sites are incredibly challenging and very expensive to try to make work. We would love to be there.”
The first greenhouse was originally planned for Pikeville, but AppHarvest said the site, a reclaimed strip mine, was not feasible for construction. After about two years of delays, AppHarvest announced its decision to relocate to a 350-acre parcel about two miles off I-64 near the Sharkey community of Rowan County.
Webb said they continue to invest in Pike County with a container farm at Shelby Valley High School. AppHarvest has two other farms at schools in Rowan and Breathitt counties.
The company aims to have 12 facilities growing and supplying fruits and vegetables by 2025. AppHarvest already announced a Berea facility to grow leafy greens and a Richmond facility to grow vine crops.
“One massive impact of 12 facilities is we’re going to have hundreds of millions of pounds of fresh fruits and vegetables pouring out of our region,” Webb said. “Not only the economic benefits of that, but the health benefits are tremendous. We’re in a situation where not many companies can say they feel incredibly proud of the product they produce and we do that.”
The first AppHarvest tomatoes will be in grocery stores by Wednesday, Jan. 20, 2021.
Photos: COURTESY OF APPHARVEST
Liz Moomey is a Reporter for America Corps member covering Eastern Kentucky for the Lexington Herald-Leader. She is based in Pikeville.
Pure Flavor® Receives International Taste Award For New Cloud 9® Tomato
Strategically grown in high-tech greenhouses in Canada, USA, and Mexico, Cloud 9® Bite-Sized Fruity Tomatoes are available year-round
Leamington, ON (February 1st, 2021) – While consumers continue to look for more healthy snacks in the fresh produce aisle, greenhouse vegetable grower Pure Flavor® is launching their new Cloud 9® Bite-Sized Fruity Tomatoes to help meet the growing demand for consistently flavorful options. After extensive product trials and consumer taste testing, many are heralding the new tomato variety as an everyday snack game changer.
“We taste hundreds of tomatoes every year searching for something special - unique colors, shapes, sizes, but most importantly flavor. From the first taste of the Cloud 9® variety, we knew we had found it”, said Jamie Moracci, President. With fruit like flavor, the new Cloud 9® Tomatoes are going to redefine what snacking tomatoes should taste like as an everyday item, not just as color in a salad. “We have created the Cloud 9® Standard for quality and look forward to consumers enjoying this premium and hand-selected bite-sized tomato every day”, said Moracci.
Strategically grown in high-tech greenhouses in Canada, USA, and Mexico, Cloud 9® Bite-Sized Fruity Tomatoes are available year-round. With a distinct color, unique shape, and a fruit-like flavor profile, Pure Flavor® has conducted extensive product trials in key growing regions to create the appropriate growing formula to consistently produce an exceptional snacking tomato.
“From the first bite, you know this will be memorable: it’s a fresh snacking experience that comes from an unwavering commitment to quality”, commented Matt Mastronardi, Executive Vice-President. Available in a variety of formats, Pure Flavor®’s award-winning Cloud 9® Tomato is available starting February 1st to be shipped throughout North America. “We hand-select a limited quantity of the most vibrant tomatoes so you can enjoy bold, balanced flavor that sweetens any snack or homecooked meal”, said Mastronardi.
Pure Flavor® recently received the prestigious Superior Taste Award Certification from the International Taste Institute (Brussels, Belgium) for the Cloud 9® Tomato. The reviewing Jury, consisting of more than 200 renowned European Chefs & Sommeliers from over 20 countries, critically tested & analyzed the Cloud 9® Tomato and highlighted these characteristics to award the product the Superior Taste designation:
Very clear, ripe tomato flavor with a marked sweetness; the taste lingers for a long time on your palate
These tomatoes have an original shape, and the size makes them ideal as a snack or for use in the kitchen
An intense red color with a soft texture and sweet taste; nice and juicy – good balance between sweetness & acidity
The product is very versatile; can be used in numerous different recipes and types of cuisines, suitable as a snack, in pasta, salads, stews, with various proteins (beef, poultry, fish), or even a Gazpacho
“It’s a strict process where all products are blind tasted; this means that the samples are anonymized, we do not see the packaging and do not know the brand name nor the producers’ name - we don’t even know from which country the product comes from. This forces us to be completely objective as we do the sensory analysis. Only truly good products are certified”, stated Stijn Roelandt – Sous-Chef at Hof van Cleve, 3 Michelin stars and member of the Jury, International Taste Institute.
The launch of a sweeter snacking tomato comes at a time when consumers are looking to enjoy a wider variety of healthy foods to eat at home. Cloud 9® offers consumers a healthy new snack option that will “make life’s sweetest moments even sweeter” – figuratively and of course, quite literally.
Video #1: https://youtu.be/CrsCQTszdp0
Video #2: https://youtu.be/hQIwq8M2Tfs
“The award-winning Cloud 9® tomatoes burst with a fruity sweetness that enriches any dish or eating occasion, every recipe you create deserves to be a showstopper”, said Chris Veillon, Chief Marketing Officer.
In anticipation of the new product launch, Pure Flavor® spent the last 16+ months developing the Cloud 9® brand to ensure that consumers could go beyond the package to enjoy all aspects of the tomato.
“Our team has developed dozens of recipes, conducted in person tasting surveys before the pandemic and hundreds of digital preference surveys during the Love For Fresh campaign late last fall, to creating engaging web & social content in lifestyle situations – we needed to effectively communicate that Cloud 9® is not just another salad topper, it’s the sweetness you crave with the quality you deserve. We think it’s a tiny taste of heaven™”, said Veillon.
To learn more about Cloud 9® Bite-Sized Fruity Tomatoes, please visit: https://www.pure-flavor.com/cloud9/
-30-
About Pure Flavor® -
Pure Flavor® is a family of greenhouse vegetable growers who share a commitment to bringing A Life of Pure Flavor™ to communities everywhere. Our passion for sustainable greenhouse growing, strong support for our retail & foodservice customers, and focus on engaging consumers is built on a foundation drawn from generations of growing expertise.
We are the next generation of vegetable growers, inspired to put quality, flavor, and customers first by providing greenhouse-grown vegetables from our farms that are strategically located throughout North America.
About the International Taste Institute –
The International Taste Institute, founded in 2005 and based in Brussels, Belgium, evaluates and certifies the taste of food and drink from all over the world. Its jury is composed of over 200 renowned Chefs and Sommeliers from 15 European culinary or sommeliers associations.
The Taste Institutes performs objective sensory evaluation: its jury follows a rigorous blind tasting methodology in which product samples are anonymized to avoid any bias in the scoring. In addition to the scoring of the various sensory analysis criteria, the jury provides comments and eventually suggestions for further product improvement or food pairing suggestions.
Elevated Vertical Farming: Vaisala Sensors And The Story of Fifth Season
“When you don’t have to worry about outdoor conditions, you have the benefit of going vertical. We can grow plants year-round in urban areas close to the dense part of a city,” said Fifth Season Cofounder and CTO/COO Brac Webb
Vertical farming is looking up – quite literally. No sun, no soil, no vast expanse of land? No problem. At least not for indoor vertical farming company Fifth Season.
“When you don’t have to worry about outdoor conditions, you have the benefit of going vertical. We can grow plants year-round in urban areas close to the dense part of a city,” said Fifth Season Co-founder and CTO/COO Brac Webb
Every minute, we’re collecting Vaisala sensor data to measure and maintain the conditions most important for plant growth and using that information to build something special.
-Brac Webb, Fifth SeasonUsing a sophisticated mix of artificial intelligence (AI), sensors, data modeling and robotics, Fifth Season’s technology tends to each plant’s individual needs at high levels of efficiency and precision. But sensors and their data play the most pivotal role. “The plants are telling us exactly what they want. We just have to adjust to that,’ said Webb. “Every minute, we’re collecting Vaisala sensor data to measure and maintain the conditions most important for plant growth and using that information to build something special.”
Background
The story of Fifth Season is very much the story of the American Dream.
The startup began with three friends and entrepreneurs: cofounders Brac Webb, Austin Webb, and Austin Lawrence. Originally founded in 2016 as RoBotany Ltd., the company was incubated at Carnegie Mellon University’s (CMU) Swartz Center for Entrepreneurship.
“We really started as a tech company and looked at the vertical farming problem at first and wondered what we can do to help solve some tech problems there,” Webb said. “Much of our evolution is due to the advances of HVAC sensors and LED lights. We already had the programming. So, we said, heck, let’s just do the whole thing.”
Fifth Season is now a 60,000-square-foot, solar-powered vertical farm in the Pittsburgh borough of Braddock, PA. The company’s 25,000 square-foot grow room is equipped with 40 different robots and has 12 levels with more than 125,000 square feet of production capacity. Compared to conventional produce, which can travel thousands of miles by truck or plane, fresh produce grown in local vertical farms need only travel a few miles to reach consumers. The company produces an assortment of leafy greens, arugula, and spinach as well as ready-to-eat salads that are sold to a local clientele including Giant Eagle and numerous other retailers. They have also launched a Direct-To-Consumer model on their website.
The company uses its small army of 40 robots to streamline almost every aspect of the vertical growing operation, including storage, retrieval, harvesting, integrated pest, and disease management, scouting, seeding, media packaging, and more, according to Webb. Humans are minimally involved in the process, mostly to coordinate the robotic army to execute specific growing recipes or other tasks – which also cuts labor costs from 40% in traditional farms to just 20%.
“We have cutting-edge technology - not using traditional methods, using more of a robotics approach - and a ton of data collection with Vaisala sensors, not only for closed-loop control but also for alerting us to changes in plant growth or the environment,” Webb said.
Industry Overview
Total control of the growing environment – 24/7/365 – in small spaces governed by known and emerging technologies are farming’s oft-cited competitive advantages over other types of farming. Vertical farming also is known for efficient resource management. For example, with its hydroponics approach, growing plants in a solution of water and nutrients, Fifth Season uses 97% less land and up to 95% less water than traditional farming.
Vertical farming attempts to take the uncertainties of agriculture – pests, sunlight, soil, etc. – and makes them controllable through various combinations of AI, artificial light, sensor monitoring, climate control systems, etc. Crops are stacked in layers or rows sometimes 20 to 30 feet high. LED lights are used by all vertical farms to create a specific light recipe for each plant, giving the greens the exact spectrum, intensity, and frequency needed for photosynthesis. LEDs offer several benefits, such as: exceptional color range, longevity, low radiated heat, and energy-efficiency. They can also be recycled and don’t contain any toxic compounds or elements like mercury. Different types of crops prefer different types of lighting. For example, leafy greens and vegetative crops prefer light towards the blue side of the spectrum; whereas fruiting and flowering crops may need something more along the red spectrum.
Vaisala Sensors
The peace of mind factor is huge. You get that from Vaisala.... I never once questioned the reading that I’m getting, or that it will be just as consistent tomorrow.
-Brac Webb, Fifth Season
So, why Vaisala? “The peace of mind factor is huge. You get that from Vaisala. If we have issues with our growing environments, all our plants can die. I mean, it could kill our business,” Webb said. “I never once questioned the reading that I’m getting, or that it will be just as consistent tomorrow. But, more than that, it was also the support we received to quickly integrate your technology into our engineering and get everything up and running fast,” Webb added. In fact, tightly controlling and monitoring light, humidity, CO2, and the temperature is critically important to Fifth Season. So, data, data, data….
“We have, gosh, probably 360 of Vaisala’s HMP110 humidity and temperature probes and 36 GMP252 CO2 probes distributed throughout the entire growing environment. It’s not just about gathering data in real-time. With post-analysis of big data, we can review the growth history of those plants and learn something about them. We may learn, for example, what we thought was the best growing environment for those plants to achieve optimal conditions for taste, quality, and yield isn’t the best after all,” Webb said. “And we can course-correct.”
Future
As the world’s population expands, projected to reach 9 billion by 2050, so too does the amount of fruits and vegetables needed to sustain it. There is only so much farmland to accommodate the increase in fresh food required for life. The U.S. Department of Agriculture, investors, and entrepreneurs alike are acknowledging vertical farming as having the potential to strengthen the global food system. And startups like Fifth Season, backed by significant venture capital, are paving the way to deliver new solutions that efficiently deliver fresh and healthy food to people.
“The more we learn, the more we can improve vertical farming,” Webb said, jokingly adding: “If only we can get to the point that the computer could taste the plant.”
The story of Fifth Season is just beginning.
“We’d like to replicate these hyper-local farms. So, it isn’t just about solving the problems of having fresh produce available in Pittsburgh and making sure we can run it here. This farm is a product that we want to be able to deploy in multiple locations all over the United States, all over the world at some point, you know. That’s our grand vision.”
For Fifth Season and Webb, there’s also an underlying humanitarian goal of vertical farming that transcends business.
“As a person and an engineer, I always like reading about how (US President) Thomas Jefferson thought agriculture and engineering are intertwined: that agriculture is humanity’s first and foremost engineering problem to solve. You’re helping create jobs in that local area and we have seen how important that is to the economy. Thanks to the technology from Vaisala, you can create an environment that is perfect for the plants and help people too.”
For more information, please Contact Us.
Download the complete Customer Story below.
Elevated vertical farming: Vaisala sensors and the story of Fifth Season
The Indoor Farms Disrupting The Produce Industry
If you don't already, chances are you'll soon be eating produce from indoor farms
If you don't already, chances are you'll soon be eating produce from indoor farms. FORWARD GREENS:
Known as 'America's salad bowl,' Yuma County, Arizona grows much of the iceberg lettuce and other leafy greens consumed in the United States. During the winter months, the area grows as much as 90 percent of America's leafy greens. Yet, over the past decade, indoor vertical farms popping up in cities throughout the country have begun to decentralize the produce market. But can they scale enough to provide consumers with local vegetables and even fruits year-round while still being able to compete with the price of conventionally grown produce?
"By remotely monitoring and analyzing the data across our global network of modular farms in real-time, we're not only able to offer a closer, more sustainable alternative to industrial farming, but we're able to improve the way our produce grows to offer a fresher, tastier product year-round," said Emmanuel Evita of Global Communications Director of Infarm which has more than 1200 indoor farms in stores and distribution centers in the United States, Canada, and Europe.
Vertical farms like Washington-based Forward Greens use soilless farming techniques, technology and constant data monitoring to grow their crops. PHOTO: FORWARD GREENS
If you don't already, chances are you'll soon be eating produce from indoor farms. While outdoor farms rely on water, sun, and sometimes luck to produce leafy greens and other produce, most indoor farms use soilless farming techniques, technology, and constant data monitoring to grow their crops.
"We believe that vertical farming will play an instrumental role in the future of local, pesticide-free, sustainable food production year-round in nearly any location in the world," said Hiroki Koga, Co-Founder &CEO of Oishii, which figured out how to vertically farm strawberries, growing the Omakase Berry. "The industry is in its infancy, and over time yields will increase and production costs will decrease. There truly is a roadmap to reaching cost parity with greenhouse and conventional production systems."
There's no doubt that vertical farms will play a role in feeding the growing worldwide population, especially as increasing climate disruptions make outdoor farming more unpredictable. However, much of the indoor farming industry is still trying to figure out the best model, whether that looks like distributed or centralized indoor farms to produce food efficiently and sustainably.
"Where an indoor farm is built is just as important as who it's being built by," Ken Kaneko, the founder of Washington-based Forward Greens. "It requires a consumer that is willing to try new things."
Ken Kaneko got introduced to vertical farming while working at Apple AAPL -3.7%. With a goal of simplifying the indoor farm process to be more affordable and scalable, he launched Forward Greens (then known as West Village Farms) in 2017.
Forward Greens currently provides leafy greens throughout southwest Washington-state and is working to expand to a larger demographic PHOTO: FORWARD GREENS
"When you build smaller farms even multiple farms within a city you can enjoy fresh local produce made in your neighborhood," said Kaneko.
Forward Greens currently provides leafy greens throughout southwest Washington-state and is working to expand to a larger demographic while focusing on making sure all the business fundamentals are accounted for before growing.
"In addition to creating and marketing a product we're also creating a demand for how a product is being made," Kaneko said.
Like Forward Greens, Oishii is currently working to build out its farms to expand to new locations within the US.
"Oishii has set its sights on creating a paradigm shift in indoor vertical farming," Koga.
It may not be long before consumers start to pay attention to and create the demand for specific brands of lettuce or strawberries the way they might for a brand of tomato sauce.
I’m a NY-based freelance writer covering food, technology, and the environment. My work has appeared in Martha Stewart Living, Civil Eats, PBS NewsHour, and more. As the former digital strategy at Edible Brooklyn I worked closely with the Editor-in-Chief to develop editorial content around the magazine’s annual Food Loves Tech event, reporting on urban farms, food waste, and other issues relating to how technology is changing our food system. When not editing, reporting, or writing, you will often find me exploring new places through their food markets, dreaming about the beach, and attempting to wrangle my golden retriever into proper behavior.
Tips On How To Set Up Large Hydroponics Farms
The need for large-scale hydroponics farms will increase as urban areas get more populated each year
The need for large-scale hydroponics farms will increase as urban areas get more populated each year. Hydroponics is an innovative farming method that will solve present and future issues surrounding urban areas. Operators of large-scale hydroponics farms can sell their goods to local restaurants, businesses, and individuals so people can get their food in the same city rather than from rural farming areas. This article is going to cover the basics of how to set up a large-scale hydroponics farm.
Step 1: Flesh Out Your Business Idea
Great, you want to start a hydroponics farm. But you’ll need to plan out your business venture to ensure it is set up for success! Configure the costs associated with starting a hydroponics farm, the ongoing costs. Who’s going to be your target market? Are you trying to sell to individuals, grocery stores, or local restaurants? How are you planning to sell your products? In bulk? What is the name of your business? Does it align with your company’s values and beliefs?
Step 2: Choose a Location
When it comes to a large-scale hydroponics farm, you’ll need to decide where you want to set up shop. Since the future of farming is appealing to major cities, you may want to set up your business nearby or inside a major city. The location of your business also depends on your target audiences.
Step 3: Decide What Crops You Want to Grow
Choosing the crops you want to grow is one of the most critical factors for your hydroponics farm. Check to see if there are other hydroponics farms in the area, and if so, what are they selling? See if you can offer a product that’s not only easy to grow but also will have demand amongst your audiences. Are you planning on growing one single crop to cut costs, or do you want to grow a variety of crops to appeal to various target markets?
Step 4: Pick a Hydroponics Growing System
Look at the space you’re planning to have your hydroponics farm in and determine what kind of system will work best depending on the location and the crop. If you’re growing crops like lettuce or spinach, then an NFT setup will suffice because these crops grow fast and short, which allows for easy pickings. Larger crops such as tomatoes or fruits will benefit from vertical hydroponics growing systems. Compare the prices for various hydroponics growing systems depending on the materials, crops, location, and setup.
Step 5: Lighting
Now you’ll want to determine the light source to use to grow your plants. Lighting can lead to expensive costs, especially when powering large-scale hydroponics farms. From LEDs to HID lamps to HPS bulbs, lighting is an important factor in hydroponics farming. Each lighting source has its pros and cons, and you’ll need to study each one to determine which option best suits your needs.
Hydroponics farms are the key to the future of farming. To learn more about hydroponics and farming, subscribe to the Nick Greens YouTube channel and join our microgreens group on Facebook. We look forward to helping you reach your goals!
#hydroponicsfarm #hydroponicsfarming #hydroponicsgrowing #hydroponicfarm #hydroponicfarming
PODCAST: Season 2 Episode 22
In this episode, Harry and Kyle discuss the varying facets of ponics, from deep water culture and NFTs to vertical farming and aquaponics
Join Harry Duran, host of Vertical Farming Podcast, as he welcomes to the show founder of Ponic Jobs and co-host of the CropTalk Podcast, Kyle Barnett. Kyle is currently serving as Account Manager in the horticulture division at WestRock, focusing on helping growers create superior packaging, labels, and merchandising solutions.
In this episode, Harry and Kyle discuss the varying facets of ponics, from deep water culture and NFTs to vertical farming and aquaponics. They talk about the vital role distribution plays in the AgTech industry, what inspired Kyle to create the Ponic Jobs website, as well as his collaboration with CropTalk Media. His podcast segment, Kyle Talks AgTech, focuses on CEA, vertical farms, greenhouse technology as well as industry leaders.
Listen & Subscribe
AVF FREE PUBLIC WEBINARS: AVF Annual General Meeting Day
AVF members will convene at the annual general meeting on the 29th of January 2021 at 5 p.m. CET to review 2020 and plan for the new year
AVF members will convene at the annual general meeting on the 29th of January 2021 at 5 p.m. CET to review 2020 and plan for the new year. All members are required to register for this session:
Register For The Meeting (Only for Members)
On the same day, we plan to provide a platform for our members to present their innovations and introduce their companies to a wider audience in the format of roundtable talks and short presentations.
AVF members have time until the 25th of January to either send us a short recording (10-15 minutes) introducing your company’s vision or express their interest in presenting live for the second webinar.
Send Us Your Recordings (Only for Members)
Please bear in mind that if you wish to attend all sessions you need to register for them separately.
Webinars are free and open to the public
There are only a limited number of seats available
Webinar 1
AVF Roundtable: Vertical Farming Startups’ Challenges, Solutions & Opportunities in the Time of COVID-19
Friday, 29 January 2021, 11-12:30 CET
Featuring YASAI, Organifarms, and Urban Greens
Register for Webinar 1
Webinar 2:
AVF Focus on Leading Vertical Farming Innovations
Friday, 29 January 2021, 14-17 CET
Interested members: AgricUltra, IFCO Systems, VeggiTech, Seoul Semiconductor, iFarm, Innovation Agri-Tech Group, Urban Crop Solutions, CDVTA, and maybe your company!
Register for Webinar 2
Contact us for more information: re@vertical-farming.net
AppHarvest, USDA Partner To Expand Educational Container Farm Program
Located at Breathitt High School in Jackson, Ky., the retrofitted shipping container allows students to grow and provide fresh leafy greens to their classmates and those in need in their community
In partnership with the U.S. Department of Agriculture, we’ve opened a new high-tech educational container farm in Eastern Kentucky to offer students a hands-on AgTech experience.
Located at Breathitt High School in Jackson, Ky., the retrofitted shipping container allows students to grow and provide fresh leafy greens to their classmates and those in need in their community. The U.S. Department of Agriculture provided a majority of funding for the container farm through its Community Facilities grants program.
The Breathitt County container farm is the third in our program, which started in 2018 in Eastern Kentucky to excite students about growing their own food.
“This amazing project will not only put fresh vegetables on the table but, more importantly, it will teach tomorrow’s agribusiness leaders — and do all of that right here in Eastern Kentucky,” said U.S. Department of Agriculture Rural Development State Director Hilda Legg.
Click here to learn more and here for coverage of the container farm’s opening.
Seattle Architect Is Helping The Fast-Growing Field of Indoor Ag Take Root
Seattle architect Melanie Corey-Ferrini is launching a controlled-environment business with assists from Sabey Corp., and Microsoft. The multifaceted, to-be-named enterprise includes a training program at Alan T. Sugiyama High School at South Lake in Seattle, where she is pictured in the cafeteria with a grow tower. Anthony Bolante | PSBJ
By Marc Stiles – Senior Staff Writer, Puget Sound Business Journal
January 16, 2021
Seattle architect Melanie Corey-Ferrini’s kiosk-style lobby pop-up concept called G2 is the ultimate in farm-to-fork dining. Protein-rich grains and greens are grown on-site in the unmanned, transparent kiosk and combined with other veggies, roots, spices and dairy to make custom bowls ordered on a mobile app. G2 last summer was named best pioneering food service concept in a national contest.
It’s one small example of the possibilities of controlled-environment agriculture (CEA), which is at the heart of Corey-Ferrini’s latest endeavor: a multifaceted, urban ag project largely centered in Tukwila, where Sabey Corp. is providing warehouse space for hydroponic growing equipment that Microsoft donated.
Corey-Ferrini will use space at Sabey’s Intergate East data center campus to build and launch CEA education and business development programs this year.
CEA is a technology-based approach to food production that allows indoor farmers to maximize use of water, energy and labor. Worldwide in the third quarter, venture capitalists invested $1.6 billion in ag tech companies, bringing the 2020 total to $4.2 billion, according to PitchBook. Alexandria Real Estate Equities, a developer of life science office and lab space, offers early-stage companies move-in-ready space at its Center for AgTech in Durham, North Carolina.
The sector has struggled to put down roots in the Seattle region, where there has been one unsuccessful attempt. Now comes not only Corey-Ferrini’s to-be-named enterprise but also Kalera, a Florida-based company that plans to open a facility in 70,000 square feet of leased space in Lacey this year.
Several years ago, Corey-Ferrini consulted with Microsoft on a CEA project in Redmond. Contract farmers used Microsoft’s PowerBI and Azure platforms to grow in hydroponic towers lettuce and micro-greens for company cafeterias.
“I was like, why aren’t more people doing this? It seems like it should be a programmatic feature in all food-related spaces,” said Corey-Ferrini. “I’ve learned it’s really a little bit of robotics, a little bit of AI, a little bit of automation.”
As a member of Soroptimist Seattle, which works to empower women and girls, she is establishing a program at Alan T. Sugiyama at South Lake, an alternative public high school in the Rainier Valley. She is working with other groups like New Roots, an International Rescue Committee program that provides land and other support in South King County to around 150 immigrant and refugee families.
Deepa Iyer, senior program coordinator for New Roots, said a pilot indoor ag tech and business class will be offered at the Sabey building through Corey-Ferrini’s enterprise. She said it will provide pathways not only to a year-round growing platform but training for tech careers.
The experience of a Seattle indoor ag business, UrbanHarvest, shows the challenges of such an endeavor. Six years ago, it worked with Seattle’s Millionair Club Charity (now Uplift Northwest) during its launch, but the program shut down after about a year when it couldn’t raise additional funds, said founder Chris Bajuk.
Corey-Ferrini is approaching it with a long-term view and plans to build a multipronged enterprise with multiple income streams. Kara Anderson, director of architecture at Sabey, said Corey-Ferrini has a good shot at pulling this off.
“She’s got endless energy,” said Anderson, who added that, like Sabey, Corey-Ferrini is known for outside-the-box thinking.
“She’s not afraid to pick up an idea without knowing really how she’s going to pull it together. She just starts marching down the path to get partners and grab people into her extensive network to brainstorm,” said Anderson.
Sabey, a developer and operator of data centers nationwide, sees opportunities in the project for both its business and community.
“We’re interested in what’s going on in our backyard and opportunities to help out and make some lives better if we can,” Anderson said “At some point these indoor facilities will be monitored by computers and that, in turn, ends up feeding into the data center world.”
Melanie Corey-Ferrini
Position: Chief experience architect
Company: Dynamik Space, a design and branding company
Founded: 2000
Career: Also currently CEO of 3.14DC, which programs food and retail spaces
Lessons Learned
Use your sense of humor.
Be curious.
Don’t fear failure.
Agri Matters Podcast: Interview With AquaFarms Africa Co-Founder On Empowering Women With Aquaponics
In the latest episode of the Agri Matters Podcast, we spoke to Wiatta Thomas, co-founder of AquaFarms Africa, an agritech startup based in Conakry, Guinea
In the latest episode of the Agri Matters Podcast, we spoke to Wiatta Thomas, co-founder of AquaFarms Africa, an agritech startup based in Conakry, Guinea. She told us about implementing aquaponics technology, a combination of fish farming and soilless vegetable growing, in Africa.
In this ecosystem, the fish excrete waste that is converted by beneficial bacteria to nutrients for the plants, which purify the water in return.
"The focus of AquaFarms Africa was to locally produce fruits and vegetables that normally are imported because they're not able to be produced in Guinea," said Thomas. The produce would be sold to high-end restaurants and hotels that offer higher margins.
Aquaponics is also generally considered more efficient than conventional farming. It is more productive on a per square meter basis and requires 95% less water than traditional agriculture. It is also completely organic.
For the last nine years, Thomas has lived in Guinea and worked across West Africa in youth economic development, giving her a deep understanding of entrepreneurial ecosystems and promising agricultural value chains. She has also built a business incubator called Dare-to-Innovate. She actively promotes economic development and African diaspora investment in the continent, with agriculture being a priority sector.
To Listen To The Podcast, Please Click Here
Here are some of the highlights from the interview:
Pinduoduo: How did the idea of AquaFarms Africa come about?
Thomas: What I found is that it's very, very difficult on the continent for young people especially to start agribusinesses, for several reasons. One is that there's a lack of capital. So the idea was that rather than just start an aquaponics farm ourselves, what we would do is create or design a franchise system.
Pinduoduo: Why did you or your partner choose aquaponics?
Thomas: The main reason was that we needed a way to have a closed system that would allow us to control the temperature in order to produce some things that wouldn't normally grow in a tropical climate or very intense weather conditions. So aquaponics gave us a way to control the entire environment in which we're growing our produce.
(In the aquaponics system,) you can't put chemicals because it'll kill the fish. So automatically, you're going to have organic produce. And so it's really an all-natural system. We really wanted to recreate an environment inside of our greenhouses.
Pinduoduo: What kind of yield can we expect?
Thomas: One farm (12 by 12 foot) will produce somewhere around one ton of vegetable and fruit product that doesn't include fish product. We haven't included that yet in our total revenue system — it's more just to keep the system going. But we will be selling fruit shrimp and tilapia fish later on.
Pinduoduo: Do you work with local lending partners to provide loans to franchisees?
Thomas: Part of the loan system is provided by investments from the diaspora. Some of it is with partnerships with local banking systems that we've already started forging. So it's a combination of all of that. Because it's very, very hard for a young person to come off the bat and be able to get loans in Guinea.
Pinduoduo: What are the training and technical support provided?
Thomas: We are building an app that we haven't deployed yet. But in 2021, we're going to be deploying it that will allow our franchisees to be able to monitor their system so all of the indicators, such as the nutrient levels, or the temperature in the system, through IoT devices that will be placed in their systems, and will be able to monitor or to track growing schedules, harvesting and planting with an app.
Pinduoduo: Does this technology gives women more opportunities than traditional farming?
Thomas: It's actually more geared toward women. And the great thing is that because it's not as strenuous of work, and because it's in urban areas, we can give a lot more opportunities to women who are in urban areas and who are unemployed.
In case you missed our end-of-year newsletter, here's the link where you can find the best of Agri Matters podcasts of 2020.
Agri Matters is a podcast about cutting-edge technology and innovation in agriculture. From scientists, venture capitalists to startup founders, we talk to the people responsible for bringing food from farm to table. Subscribe to Agri Matters on Spotify, Apple Podcasts, Google Podcasts, and other major podcast platforms.
For more stories about the latest in agriculture and technology, visit us at https://stories.pinduoduo-global.com/category/agriculture. Subscribe to our YouTube channel and follow us on Twitter, LinkedIn and Facebook.
US: Public Oral Argument In Hydroponically-Grown Organic Food Lawsuit
CFS filed a petition requesting USDA to prohibit organic certification of hydroponic operations that do not work with or build soil in 2019
Source: Vertical Farming Daily
On Thursday, January 21st, the United States District Court for the Northern District of California will hear arguments in Center for Food Safety's (CFS) ongoing lawsuit challenging the U.S. Department of Agriculture's (USDA) "soil-less" loophole that permits the labeling of hydroponically-grown foods as USDA Certified Organic, even though the Organic statute and regulations clearly mandate all organic crop producers foster soil fertility in order to obtain organic certification.
WHAT: Oral Argument in Center for Food Safety's Lawsuit Challenging the Labeling of Hydroponically-Grown Foods as Organic
WHEN: Thursday, January 21, 2021, at 1:30 PM PST
(Note: the Court's afternoon session starts at 1:30 PM and is currently listed as the first of the two cases scheduled for hearing that afternoon, but the Court can hear the cases in any order it wishes).
WHERE: District Judge Richard Seeborg's Virtual Courtroom via Zoom.
CFS filed a petition requesting USDA to prohibit organic certification of hydroponic operations that do not work with or build soil in 2019. After USDA denied the petition, CFS, along with a coalition of organic farms and stakeholders, filed a lawsuit challenging USDA's decision to allow hydroponic operations to continue to be certified organic in March 2020. The lawsuit claims that hydroponic operations violate organic standards for failing to build healthy soils, and asks the Court to stop USDA from allowing hydroponically-produced crops to be sold under the USDA Organic label.
Hydroponic operations, or "hydroponics," describes methods of growing crops using water-based nutrient solutions without any soil. CFS's lawsuit cites the federal Organic Foods Production Act, which requires farms to build soil fertility in order to be certified organic. Hydroponics cannot comply with federal organic standards because hydroponic crops are not grown in soil. Allowing hydroponics to be certified organic is another attempt to weaken the integrity of the Organic label, and has resulted in market confusion and inconsistent organic certifications.
Thursday's hearing on summary judgment will be the only time the Court will hear oral arguments on whether hydroponic operations that do not work with soil meet the mandatory requirements to be sold under the USDA Organic label, and whether USDA violated the federal Organic Foods Production Act when it decided to exempt hydroponic operations from the Organic Label's soil-building requirements.
The plaintiff coalition in the lawsuit includes some of the longest-standing organic farms in the United States, including Swanton Berry Farm, Full Belly Farm, Durst Organic Growers, Terra Firma Farm, Jacobs Farm del Cabo, and Long Wind Farm, in addition to organic stakeholder organizations, such as organic certifier OneCert and the Maine Organic Farmers and Gardeners Association.
Publication date: Wed 20 Jan 2021
The Mexican Tec Graduates Who Are Using Vertical Farming To Eradicate Hunger
Vertical farms use 90% less water than traditional agriculture and can meet the challenge of feeding more than 9 billion people
Vertical farms use 90% less water than traditional agriculture and can meet the challenge of feeding more than 9 billion people
Por Susan Irais
January 11, 2021
Not all fruit and vegetables can be grown using this technique, but a great variety can. (Photo: Courtesy of Verde Karma Fresh)
Every night, seven million people go to bed hungry in Mexico. It is estimated that the coronavirus pandemic will cause that figure to increase. According to the latest report by the United Nations Food and Agriculture Organization (FAO), 130 million people will be affected by chronic hunger worldwide by the end of 2020.
Unfortunately for Mexico, the traditional agricultural industry uses a lot of resources and wastes a large amount of what it takes from the land.
For example, 34% of total production ends up in landfills due to inefficiencies during processing, storage, and transportation. What’s more, 40 billion liters of water are wasted annually due to poor irrigation.
“Fresh” products travel 300 to 1,000 kilometers and have already lost 45% of their nutritional value by the time they hit the shelves. But there is a complementary option for agriculture: vertical gardens.
Vertical Farming
“Vertical farming –in controlled environments– is a method of growing in vertically stacked layers, optimizing growing conditions and soil-less cultivation techniques, such as hydroponics,” says Leo Lobato Kelly, CEO of Verde Karma Fresh, a vertical farming company from Monterrey, Nuevo León.
The modern concept of vertical farming was proposed in 1999 by Dickson Despommier, Professor of Public and Environmental Health at Columbia University in the United States.
Due to climate change, this method has become a real alternative for countries like Japan, Taiwan, Singapore, South Korea, Saudi Arabia, the Netherlands, Germany, France, the United Kingdom, the United States, Canada, and now, Mexico.
Karma Verde Fresh (KVF) has spent the last five years developing farming systems and growing a variety of vegetables, sprouts, and seedlings in Monterrey, Nuevo León. “This has been achieved through an association with two universities and Tec graduate agronomists, using natural substrates, in this case: tezontle (volcanic rock). This substrate can be washed without contaminating the soil. By substituting mineral products, you allow fields to regenerate themselves, which is highly beneficial to the soil,” says the CEO of Karma Verde Fresh.
Not all fruit and vegetables can be grown using this technique, but a great variety can be (Photo: courtesy of Karma Verde Fresh).
Vertical farming systems use 90% less water and 95% less space than traditional farming and are 100% herbicide and pesticide-free. “Our crops can be adapted to any space, which allows us to be closer to the consumer, reduce our carbon footprint, and promote local purchases that are fresher,” says Leo Lobato.
Vertical farms keep crops fresh for longer, so they don’t lose any nutrients, using state-of-the-art LEDs that are extremely energy efficient. Energy can also be generated from renewable sources and this creates job opportunities.
Traditional Agriculture Plus Vertical Farming
“Vertical farming is another option within the agricultural industry, though it is intended as a way of complementing rather than replacing traditional agriculture,” adds Tagino Lobato from KVF.
Not all fruit and vegetables can be grown using this technique, but a great variety can be, “enough to have a balanced diet,” according to Leo Lobato.
For example, KVF produces lettuce, microgreens (mustard), Ballerina lettuce, Alexandria lettuce, peas, beetroot, large-eared lettuce, radish, Italian lettuce, and sunflowers, as well as others such as astro arugula, rocket arugula, spinach, coriander, chard, strawberries, and tomato seedlings.
Vertical farms are very beneficial. For example, they use 90% less water than traditional agriculture and they can be built anywhere, which means many spaces could be repurposed. (Infographic: Karma Verde Fresh)
This type of initiative hopes to feed the 150 million people who will be living in Mexico by 2050, of whom approximately will be in 80% urban areas, according to FAO estimates.
Karma Verde Fresh saw a great entrepreneurial opportunity in vertical technology. “We need this in all communities because we all need to eat better without damaging the planet. Vertical farming in a controlled environment has many possibilities. We can take it to schools or food bank centers,” says the co-founder of Verde Karma Fresh.
The company wants to make this innovation in agriculture available to everyone, so they are looking to make the technology accessible. For example, “we already have one of these vertical farms in Dr. Adriana Elizondo’s house in the Linda Vista neighborhood of Guadalupe in Monterrey. She’s farming with this prototype from her bedroom,” says Leo.
Karma Verde Fresh has two versions of the growing system: one for crops (KVF-AG6) and one for seedlings (KVF-AG10). (Photo: Karma Verde Fresh)
Mexico, The Land of Opportunity
The Lobato technology has already made deals with 20 international universities to take their equipment and establish laboratories. “By involving universities, we are hoping to find Mexican ingenuity that will produce better technology and create more employment opportunities in all Spanish-speaking countries,” he says.
KVF doesn’t just want to sell the technology but also to lower the costs by using Mexican technology. Sources of financing are being set up for all of the entrepreneurs who wish to take vertical farms to different levels.
The end product from vertical farms promotes local purchases that are more nutritious (Photo: Courtesy)
VIDEO: What's The Difference? Aeroponics Vs. Hydroponics
With a large portion of the world’s farmland shrinking, and food shortages affecting countries all over the world, newer farming methods like aeroponics and hydroponics allow crops to be grown where traditional farming cannot
Nate Klingler | January 11, 2021
With a large portion of the world’s farmland shrinking, and food shortages affecting countries all over the world, newer farming methods like aeroponics and hydroponics allow crops to be grown where traditional farming cannot. As these alternative farming systems increase in popularity, more misconceptions arise about the design, environmental impact, and the overall health of the plants grown using aeroponics and hydroponics.
This list will compare and contrast the differences between the two methods, and show how aeroponic and hydroponic farming technology can be used to grow some of the tastiest, healthiest, and greatest greens on the planet!
Aero Vs Hydro
Many people often confuse aeroponic farming with hydroponics, another form of farming that has gained plenty of popularity over recent years. While both methods are similar in that they don’t require soil, the way nutrients are delivered to plants is much different. In hydroponics, plants may be suspended in water full-time or fed by an intermittent flow of water. Aeroponic plants are never placed into water, instead being given nutrients from a mist that’s sprayed onto their roots.
This key difference is what gives each method their unique name. The term ‘Aeroponics’ stems from the Greek word aero, meaning air, and ponos, meaning work. Hydroponics, on the other hand, uses the Greek term hydro, meaning water, and is translated to the term ‘‘working water’!
The Method
Another major distinction between Aeroponics and Hydroponics lies in the design and methodology of the farming setup.
Aeroponic farms are completely controlled and enclosed environments, with crops growing suspended in air. The plants are contained in a humid atmosphere where frequent misting delivers a nutrient-rich solution right to the roots, keeping the crop from drying out. Because the entire process is enclosed, the mist is able to remain around the plants for longer, helping them grow much quicker than in a traditional outdoor farm.
Hydroponic farming also utilizes nutrient-rich water, but the process of delivering these nutrients is different. Instead of spraying the solution onto the roots, the plants are either grown in containers of nutrient solution, or the solution is circulated past the roots.
Plant Growth and Health
As far as the overall health of the plant goes, aeroponics takes a slight advantage. These crops grow in a completely sealed and protected environment, meaning there is a very small chance that the roots will be exposed to foreign objects and bacteria. Hydroponic plants on the other hand, are at a much greater risk of bacterial exposure, due to the high humidity levels in their growing environment.
Another important aspect that contributes to a plant’s health is the aeration or the amount of oxygen the plant receives while growing. During aeroponic growing the plant’s roots are completely suspended for the entire growing process, allowing them to take in air at a much greater rate. In hydroponics, the roots are submerged and do not receive nearly as much oxygen, contributing to a generally smaller plant and crop yield.
The Environmental Impact
Both aeroponics and hydroponics are regarded to be less harsh on the earth than traditional ‘geoponic’ farming, with neither requiring the use of chemical fertilizers or pesticides. However, there are some differences in the number of resources used between both systems. Hydroponics requires much larger quantities of water to operate, as well as four times the amount of nutrients needed to grow a plant using the aeroponics method.
Because of this, aeroponics has been developed to compete with the problems that arise from climate change, diminishing farmland, and the building of large housing and urban centers. It uses 98% less land than traditional farming methods, 95% less water, and is 100% controlled, allowing for crops to be grown year-round using fewer resources.
Living Greens Farm & The Future of Aeroponics
Living Greens Farms started with a simple goal to build a sustainable, next-generation farm, and has now expanded into the largest vertical-plane, indoor aeroponic farm in the world! Follow our journey as we look to expand into other areas of the country, where we can make a difference in communities that have little access to fresh produce. Changing the world for the better starts with one person, one bite, and one Living Greens salad at a time.
USA VIRGINIA: Regional Board Approves Agreement For AeroFarms To Receive $200,000 Grant
The company plans to build the largest indoor growing facility to date in Cane Creek Centre, a joint industrial park owned by Danville and Pittsylvania County via the Danville-Pittsylvania Regional Industrial Facility Authority
January 11, 2021
AeroFarms, the company that announced in December 2019 it would bring 92 jobs to the region and invest $42 million over three years, will get a $200,000 state grant if it meets up to a performance agreement approved Monday by the Danville-Pittsylvania Regional Industrial Facility Authority.
The RIFA board unanimously passed a resolution during its meeting Monday to sign a performance agreement with the company for a $200,000 grant from the Virginia Department of Agriculture and Consumer Services.
Matt Rowe
"They have all intention of moving forward with the project in the near future," said Pittsylvania County Economic Director Matt Rowe. "I think you will see some activity out there soon."
The company plans to build the largest indoor growing facility to date in Cane Creek Centre, a joint industrial park owned by Danville and Pittsylvania County via the Danville-Pittsylvania Regional Industrial Facility Authority.
AeroFarms specializes in chemical-free vertical farming and announced in December 2019 that it plans to bring 92 jobs and invest about $42 million in the Dan River Region over three years.
The company must meet the jobs and investment goals before it gets the $200,000 from the state’s Agriculture and Forestry Industries Development Fund, Rowe said during an interview with the Danville Register & Bee Monday afternoon.
"It's guaranteeing to them that if they do those things, they'll get the money," Rowe said. "The company signed the agreement two weeks ago."
The agreement is among the company, Danville, Pittsylvania County, RIFA, and the state.
The Newark, New Jersey-based company's process involves growing such crops as leafy green vegetables in stacks at a rate said to be 390 times more productive than field-grown plants. It uses no soil, sunlight or chemicals and takes place indoors, where the environment is brought to the crops.
AeroFarms co-founder and CEO David Rosenberg points to an illustration of what the company’s vertical farming process looks like at the Institute for Advanced Learning and Research in December 2019. The company announced then that it was bringing 92 jobs and $42 million in investment to Cane Creek Centre. File photo
Vertical growing uses LED lighting and aeroponic mist on leafy greens in stacks that can reach as high as 40 feet. It mists the greens’ roots with nutrients, water, and oxygen, using 95% less water than field farming and 40% less than hydroponics, according to the company’s website.
The Virginia Economic Development Partnership worked with the Virginia Department of Agriculture and Consumer Services, Pittsylvania County, Danville, and the Southern Virginia Regional Alliance to secure the project for Virginia.
Incentives for the company include $190,000 in grant money from the Virginia Tobacco Commission, $200,000 from the Governor’s Commonwealth Opportunity Fund, and the $200,000 that's part of the agreement approved by RIFA.
No money will go to the company until it meets its obligations, Rowe said.
Rowe said he was not sure when construction would start on the 150,000-square foot building for AeroFarms.
"Given the COVID situation, I don't want to go on the record for a specific time," Rowe said.
Lead photo: Alina Zolotareva, marketing director and product champion at AeroFarms, offers some of the company’s leafy greens for sampling at the Institute for Advanced Learning and Research in December 2019. The company announced then that it was bringing 92 jobs and $42 million in investment to the Dan River Region. File photo
Tags Grant Aerofarms Rifa Agreement Matt Rowe Economics Agriculture Commerce
Finance Industry Danville And Pittsylvania County Money Danville
AVF Presents Advisory Board For 2021
The Advisory Board will support and advise AVF Board of Directors in all strategic developments, oversee the implementation of annual objectives and create a valuable ecosystem for the members to advance the Vertical Farming industry globally
AVF is honored to introduce our Advisory Board members for the year 2021, they are experts in their own fields and represent different sections of the indoor farming industry and academia.
The Advisory Board will support and advise AVF Board of Directors in all strategic developments, oversee the implementation of annual objectives and create a valuable ecosystem for the members to advance the Vertical Farming industry globally. AVF’s board and staff are pleased to have the support of this esteemed group going forward.
Ali Ahmadian is the CEO of Heliospectra and the chair of AVF’s Advisory Board for 2021.
Ali combines his passion for people and technology with 20 years of international business leadership experience to his position at the helm of Heliospectra.
Ali is globally recognized for his successful track record of developing new business and delivering profitable growth in a multitude of geographies. He has lived and worked in five different countries on three different continents over the course of his career. Highly skilled in integrating cultural and commercial experiences, he excels in establishing partnerships with different stakeholders and driving diverse teams to peak performance. Prior to joining Heliospectra, Ali was Vice President of Tetra Pak in Asia Pacific and served as a member of Tetra Pak’s global executive team.
Luis Trujillo is an Area Sales Manager at Hoogendoorn Growth Management.
He has more than 25 years of experience in markets with a strong focus on innovation and technology. He is currently with Hoogendoorn America.
Jasper den Besten is a professor at HAS University of Applied Sciences in the Netherlands.
He is researching new cultivation systems, with a focus on cultivation without daylight. Since 2009, HAS University has been involved in very applied LED-lit climate cell research.
Hemant Julka is the Co-founder and COO at Veggitech in the UAE, a professional with over 3 decades of experience in business and technology.
He is a social entrepreneur with a vision to make a positive impact in transforming communities at the grass-root level. The Agro-Tech startup company, VeggiTech, is disrupting the Agriculture industry with protected Hydroponics and grow light-based Hydroponics.
Max Loesel is the CEO of Agrilution and one of the Co-founders of the AVF.
He is a young entrepreneur and has been engaging with activists for sustainable living to preserve our planet for years. He has pioneered a fully automated Vertical Farming home system with Agrilution.
For more information:
Association for Vertical Farming
info@vertical-farming.net
www.vertical-farming.net
Publication date: Wed 6 Jan 2021
Bottom of Fresh Herbs Bag Becomes Growing Pot
Bottom of Fresh Herbs Bag Becomes Growing Pot
Danish Company Launches New Package Solution
Danish-based growing company Grow Up FARM is launching a new product, named Eat-Grow-Repeat: Small pea plants that grow in hemp in a bag. Refrigerated and bagged, the pea sprouts keep fresh for a week. "Rip off the upper section of the bag, and the bottom of the bag is now the pot," they explain. "Place the bottom of the bag with pea plants on your windowsill and care for it with light, water, and a little love. The growth will continue, and after a few days you can cut completely fresh pea sprouts for your salad bowl."
"Usually, bean sprouts are packed in a tray and then flow wrapped, so the consumer would have to repack any sprouts that may be leftover. But now this is history," they explain.
The corner stone of the Greenow family business was laid back in 1966, when the first generation pioneered the professional cultivation of bean sprouts. It turned into a success and still is - who does not regularly add the crisp and healthy bean sprouts to the shopping cart? Sales of organic bean sprouts are growing steadily, and this has led Greenow to seek a more efficient packaging solution, also since their pea sprouts dependance Grow Up FARM is growing as well.
Fresh produce
Initially, the Schur®Star Packaging Machine they use for this new packaging was only planned for packing bean sprouts fully automatically into reclosable bags. "Often, one does not eat all the sprouts at once; but in a reclosable bag, the sprouts do not desiccate in the refrigerator, but will retain their crispness for up to eight days. Hereby, the consumer can make his contribution to reducing problematic food waste, which is today an issue in both the retail outlet and the home," they say.
Capacity for new project
With its large capacity, the Schur®Star Packaging Machine has given Greenow & Grow Up FARM the opportunity to realize the Eat-Grow-Repeat project. The pea plants are initially grown in an entirely new, vertical greenhouse – on five floors, in a 100% controlled climate, with recirculated water, under artificial light and completely without soil. And to match the 100% compostable contents, the bag is produced of PE, a single-layer material that does not require separation to be processed in a recycling system.
Convenient packing
”Bean sprouts are our core product, for which we chose the Schur®Star Concept,” says Lasse Vilmar, CEO and third generation in the company. ”But because of the versatility of the packaging machine and its high capacity, we decided to speed up the new Eat-Grow-Repeat project. When starting up a new project, flexibility is of the utmost importance, as you must be able to quickly adapt to market reactions”.
Lasse Vilmar continues: ”Now we can change from a fully automatic to a manual packing process in a few minutes – e.g. if we want to pack meal salads with different elements. Also in terms of bag constructions we are not at all limited to the two bag types that we started up with. We are excited about the new flexibility and the many options, and we feel convinced that the market will welcome our novelties: Healthy and tasty produce in convenient packaging.”
With its rectangular fill opening in the entire width of the bag, the Schur®Star Packaging Machine is ideal for filling of light and unevenly shaped products, such as a portion of bean sprouts or small pea plants. With more than 500 companies around the world, the concept packs all types of products – including a broad range of fresh produce, into a comprehensive range of bag constructions.
For more information:
Schur Star Systems GmbH
Tel:+49 (0) 461 99 750
Email: sfg@schur.com
www.schur.com/en/
11 Jan 2021
The Farm of The Future Could Be Hiding Inside This Shipping Container
It's called The Cube and could bring farming to urban environments
It's Called The Cube And Could Bring Farming To Urban Environments
The Cube's crops are powered by LED lights. N.Thing
As we head into 2021 facing a number of dire existential threats -- pandemics and climate change to name a few -- one of humanity's encroaching issues is population rise.
How on earth (literally) are we going to feed all these people?
Traditional farming methods could be problematic in the long term. It's not just an issue of space but a problem of sustainability. We're currently damaging our environment with current farming techniques -- and eradicating existing species and their habitats to the point where many are calling it the sixth extinction event.
In short, we have some problems to solve. Part of the solution could be found inside this 40-foot refrigerated shipping container.
They call it The Cube: A modular smart farm, designed to be built in urban spaces in pretty much any configuration you like.
The containers can be stacked vertically or horizontally, with potentially dozens or even hundreds of Cubes fitting together to make one giant farming system, capable of cultivating and growing tonnes of produce. The hope is to bring sustainable, efficient, year-round farming to spaces that can't traditionally support agriculture.
"The human populations are growing quite fast," explains Seungsoo Han, the COO at N.thing, "and we need to come up with some kind of very efficient solution that can actually support that fast-growing population, also at the same time, we shouldn't actually damage the environment that that population lives in."
At the heart of the Cube, the farm is an automated operating system known as Cube OS. The system takes in data from sensors inside each farm, measuring readings like humidity, ph levels in the water, temperature, carbon dioxide -- everything that's needed to grow a healthy plant. And each of these variables can be tweaked and optimized, depending on the plants you're growing.
N.Thing has already partnered with Korea's largest supermarket chain to supply greens and, last year, it rolled out a farm in the United Arab Emirates, where summer temperatures regularly climb over 100. Next, N.Thing plans to expand into other territories like Singapore and Qatar.
Improving The Profitability And Economic Sustainability of Vertical Farms
“According to our research, most vertical farms are focused on lighting as a means of improving yield and growth speed,” says Rob Agterberg, Partner at Back of the Yard Algae Sciences (BYAS)
“According to our research, most vertical farms are focused on lighting as a means of improving yield and growth speed,” says Rob Agterberg, Partner at Back of the Yard Algae Sciences (BYAS).
“However, not enough vertical farms are looking at innovative ways of growing faster and better. Through our research, we’ve discovered that certain algal proteins improve the photosynthetic process and this results in a biostimulant effect and also improves taste, aroma, shelf life and nutrient value in vertically farmed crops such as lettuce."
The biostimulant research
Algae biostimulant
“At BYAS we’re creating ingredients such as alternative proteins, food colorants, made from microalgae. We have a patented, unique, zero-waste production process that enables us to extract food ingredients and alternative proteins from microalgae,” says Marc Peter Geytenbeek, Partner at BYAS. The company has been researching its biostimulant for vertical farming the past 2 years and recently published a scientific article outlining a number of breakthrough results. Currently, the biostimulant is being tested by vertical farming companies, including across the world.
Saving time and money
Rob states that about two-thirds of vertical farms are struggling to be economically viable, due to their high capital expenditures. He says: “Our research has shown that lettuce growth increases after adding the biostimulant. This increase results in up to 20% shorter growth cycles, saving on lighting and therefore energy and labor costs. We think that our biostimulant can be a huge boost to make vertical farms more economically sustainable.”
Sustainable works
“Surprisingly, the biostimulant can be made from algae grown on agriculture waste streams,” says Rob. The biostimulant is organic and GRAS (generally recognized as safe). What is particularly interesting to vertical farming is the fact that the biostimulant is an extract, so there is no need to administer a live bacteria or fungus into a hydroponic system. BYAS is committed to the circular economy - sustainable re-use of resources. This can be found in the production processes that are zero-waste and use very little energy.
For more information:
Back of the Yard Algae Sciences
Marc Geytenbeek, Partner
marc.geytenbeek@algaesciences.com
www.algaesciences.com
Rob Agterberg, Partner
rob.agterberg@algaesciences.com
www.algaesciences.com
Publication date: Wed 6 Jan 2021
Author: Rebekka Boekhout
© VerticalFarmDaily.com
Standardization To Build A Vertical Farming Industry or Building Customized Farms That Keep Cost High?
“Are we thinking about standardization so we can build a vertical farming industry or are we going to build a bunch of customized farms that keep costs unnecessarily high?
There are a lot of new ideas being trialed within the indoor farming space. “One of the hurdles I see is that it’s expected that there are standardized products available that will fit the new vertical farming systems being developed. Many farmers request that manufacturers develop custom components and equipment to meet the specifications of their system and their requirements, assuming that their systems will be the ones adopted by the industry and standardized,” says Chris Higgins, CEO of Hort Americas.”
According to Chris vertical farmers mostly don’t always take into account the required size and scale needed for custom made products. As an example, many of the new farming systems don’t fit the current substrate industry models. And that in itself is ok. Unfortunately, many of these farms aren’t large enough to afford the customizations needed to keep their produce profitable. That then creates additional work for these new farming businesses. Instead of being able to focus on growing, they’re trying to figure out the best way to manage a non-existent supply channel. “Growers keep designing new irrigation models and growing systems without thought of how they are going to source a substrate, consistently and cost-effectively.”
Chris Higgins
Chris says that there is a lot to learn from the Dutch greenhouse industry. Over the years they have built a great model that supports the commercial greenhouse industry really well. Namely, building a commercial vegetable greenhouse around a single crop, with the scale required to manage cost, labor, and the supply channel. “They are focused on reducing labor by using automation and getting as much efficiency out of the system and supply channel as possible. Dutch and other northern European farms grow several vegetable crops in greenhouses that are quite similar to each other. Here in the USA, the vertical farming industry is new. We are still finding ourselves. Defining our plan, and building learning to build out an industry that will support potential growth.”
“Are we thinking about standardization so we can build a vertical farming industry or are we going to build a bunch of customized farms that keep costs unnecessarily high? Factories are all about processes and standardization. Plant factories should be no different.” Chris wonders whether it’s really a problem to treat an indoor farm as a factory when building it. He states that substrates requirements are a simple yet good example of how there has not been much thought to standardization. But, how planning and simple changes could help farmers be more successful sooner.
A second hurdle Chris sees is a desire to become organic. “Building a new farm is challenging enough! Building a successful indoor hydroponic organic farm with new growers is even more challenging.” Indoor and vertical farmers are rightfully focused on food safety issues. Much of a successful food safety program is based on the ability to have tracking, tracing, consistencies and guarantees. This requires growers to need input products that can fit that model. Unfortunately truly organic products do not always fit that mold. Organics inputs can be hard to standardize as they are often not manufactured in a traditional way causing them to be influenced by outside variables in which only mother nature controls.
This can be seen within the peat moss substrate industry. “The vertical farming industry needs organic substrates to be delivered in a customized fashion, timely and in the highest of qualities. However, the peat moss industry has not necessarily evolved over time with this focus in mind. The industry has evolved to provide a very cost-competitive product to ‘large’ greenhouse growers. A smaller footprint farm that needs the highest of quality in a custom package may simply not have the volume needed to interest a supplier. However, many small farms using a similar product can work together to create the volume that will encourage the suppliers to change their strategies and put the energy and effort needed into new product development.”
So how can an industry be formed in such a competitive time where entrepreneurs are fighting for investor dollars? “Simple, focus on the business practices that truly make your new farming business unique. Then leverage the supporting horticulture industries and use what's available to you in a standardized package. This will allow you to grow quickly and focus on what makes you successful.”
For more information:
Hort Americas
Chris Higgins, CEO
chiggins@hortamericas.com
www.hortamericas.com
Publication date: Fri 8 Jan 2021
Author: Rebekka Boekhout
© VerticalFarmDaily.com