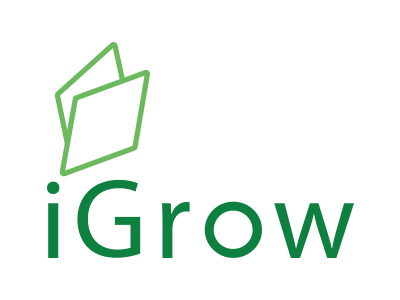
Welcome to iGrow News, Your Source for the World of Indoor Vertical Farming
Hydroponics Giant Hydrofarm Plans New Northern California HQ After IPO, 3 Acquisitions
Becoming a publicly-traded company, moving its headquarters from Petaluma temporarily to the East Coast, spending $343 million to acquire three more companies, prepping to return to a larger North Bay hub. It’s been a busy seven months for indoor farming equipment maker and distributor Hydrofarm
THE NORTH BAY BUSINESS JOURNAL
June 25, 2021
Becoming a publicly-traded company, moving its headquarters from Petaluma temporarily to the East Coast, spending $343 million to acquire three more companies, prepping to return to a larger North Bay hub. It’s been a busy seven months for indoor farming equipment maker and distributor Hydrofarm.
On Dec. 14, nearly 10 million shares of Hydrofarm Holding Group stock started trading on the Nasdaq Global Select Market under the ticker symbol “HYFM,” harvesting proceeds of $182.3 million, according to the March 31 annual report. The company did a follow-on offering of 5.5 million shares ended May 3, netting $309.8 million more.
After peaking at $92 in mid-February, the share price was $56.96 at the close of trading Friday.
Then early this year, Hydrofarm shifted its headquarters to its Philadelphia-area distribution center. It’s one of nine totaling 900,000 square feet that the 4-decade-old company operates in the U.S., Canada, and Spain. Hydrofarm also has offices in China.
That happened because Hydrofarm was lining up a larger location elsewhere in the North Bay, something it has been looking for over the past few years.
Hydrofarm had planned to relocate its headquarters from Petaluma to the 250,000-square-foot Victory Station warehouse south of Sonoma, but that deal didn’t materialize amid the rapid cooling of demand for real estate from the newly legal cannabis industry, according to real estate sources.
Hydrofarm couldn’t be reached for comment on its North Bay plans.
While cannabis has become a key driver of demand for controlled environment agriculture products, Hydrofarm got its start in Marin County during the disastrous drought of 1977-1978, the Business Journal reported in 2010. Founder Stuart Dvorin developed water-saving hydroponics that gained traction among gardeners.
The product line expanded to energy-efficient grow lights and germination kits. Then Hydrofarm moved into manufacturing and distributing indoor gardening equipment for both professional growers and hobbyists.
Today, key markets are growers of cannabis, flowers, fruits, plants, vegetables, grains and herbs. The portfolio now includes 26 internally developed, proprietary brands with about 900 product variations under 24 patents and 60 registered trademarks. The company also has over 40 exclusive and preferred brands totaling another 900 stock-keeping units.
Company brands account for about 60% of sales. The total catalog, which carries products from over 400 suppliers, includes over 6,000 SKUs.
“Our revenue mix continues to shift towards proprietary brands as we continue to innovate, improving overall margins,” the annual report said. “Further, our revenue stream is highly consistent as, in our estimation, we believe that approximately two-thirds of our net sales are generated from the sale of recurring consumable products including growing media, nutrients and supplies.”
Net sales last year were $342.2 million, up 45.6% from 2019. The company speculated in its annual report that the coronavirus pandemic shelter-at-home public health orders contributed to this jump in sales. Net revenue the previous year grew only 11.0% from 2018.
First-quarter net sales were $111.4 million, up 66.5% from a year before. The company attributed that to a 59.6% increase in the volume of products sold plus a 6.9% increase in price and mix of those products.
A sign of its commitment to remain in the North Bay, Hydrofarm earlier this year secured a lease for a 175,000-square-foot new distribution warehouse at 2225 Huntington Drive in Fairfield. Meanwhile, Hydrofarm founder Stuart Dvorin was preparing to sell the 110,000-square-foot main Petaluma facility at 2249 S. McDowell Blvd. Extension, a $17.5 million deal that closed June 7.
“We also intend to relocate our existing distribution operations in Northern California from the existing Petaluma building to a larger distribution center in the surrounding area,“ the company wrote in its annual report.
Started in Marin County in 1977 as Applied Hydroponics, Hydrofarm moved the headquarters to Petaluma in 1994, employing 65 at the time. It gradually expanded to 150,000 square feet there with a staff of more than 150 employees by 2010 and then to 195,000 square feet in the city in 2017. The company employed 327 full-time in all locations as of the end of February, it reported.
2017 is when Hydrofarm made a big expansion into Canada with the acquisition of Eddi’s Wholesale and Greenstar Plant Products. That deal helped Hydrofarm become a top supplier of hydroponics gear in Canada, the company said.
This year, Hydrofarm has acquired three more companies. Los Angeles-area premium nutrient maker Heavy 16 was picked up for $78.1 million, and Humboldt County’s House & Garden portfolio of brands for $125 million. A $161 million deal was announced this month for Aurora International Inc. and Gotham Properties LLC, Oregon-based manufacturers and suppliers of organic hydroponic products.
“We view M&A as a significant driver of potential growth as the hydroponics industry is fragmented and primed for consolidation,“ Hydrofarm wrote in its annual report.
Hydrofarm also has been fertilizing its C-suite with acumen in the past couple of years. At the beginning of 2019, Bill Toler came in as CEO, bringing with him over 3 decades of senior executive experience at major consumer packaged goods companies, including most recently seven years as CEO and president of Hostess Brands. B. John Lindeman came in as chief financial officer in March 2020 with 25 years of agriculture and finance executive experience.
Inside The Deals
Lease: Fairfield Commerce Center, 2225 Huntington Drive, Fairfield
Property type: Industrial
Size: 175,404 square feet
Tenant: Hydrofarm
Owner: TreaJP Venture Fairfield LLC
Date: Early 2021
Sale: 2249 S. McDowell Blvd. Extension, Petaluma
Property Type: Industrial
Size: 110,000 square feet
Buyer: Scannell Properties 531 LLC
Seller: Stuart Robert and Emily Alice Dvorin LDGT Grantor Trust
Agents: Cushman & Wakefield represented the buyer, and Meridian Commercial the seller.
Date: June 7, 2021
Price: $17.5 million
Sources: Cushman & Wakefield and Business Journal research
Lead photo: Hydrofarm's former headquarters on South McDowell Boulevard Extension in Petaluma (Facebook.com/Hydrofarm)
Jeff Quackenbush covers wine, construction, and real estate. Before the Business Journal, he wrote for Bay City News Service in San Francisco. He has a degree from Walla Walla University. Reach him at jquackenbush@busjrnl.com or 707-521-4256.
FRANCE: In The Jungle Vertical Farm, The Aromatic Herbs See Life In Pink
Founded in 2016 by former financier Gilles Dreyfuss and a founder Nicholas Segui, this young growth launched the first site in chateau-theory. It plans to open two more by the end of 2022 and become the number one vertical vegetable farm in the country
June 26, 2021
Pascal Mollard-Chenebenoit
France Media Agency
Founded in 2016 by former financier Gilles Dreyfuss and a founder Nicholas Segui, this young growth launched the first site in chateau-theory. It plans to open two more by the end of 2022 and become the number one vertical vegetable farm in the country.
This agriculture works on hydroponics, i.e. without soil, the plants grow on a surface and receive water rich in nutrients. In all warm and humid weather, the garden is lit by LEDs.
Two production “towers” operate with platforms ten meters high. “By the end of this year, we will have nineteen,” Jungle president Gilles Dreyfus told AFP.
A tower can produce 400,000 plants a year. When all is said and done, the 38-year-old former financier explained that the annual production would be 8 million plants.
Taste
Jungle grows aromatic herbs (basil, parsley, cilantro, chives), microgreens (mustard, ple da radish, red shiso, wasabi) and salads (lettuce, arugula).
Playing in Ultra-Fresh its products are intended for mass distribution and its herbs are already available in some Parisian stores.
“Keeping the power of industrial innovation in the service of plant life”: this is the motto of the Jungle. “With pesticide-free plants we meet consumer uses and new needs, they taste, they are alive, they are recognizable and most of all they are produced very close to where they are sold and eaten,” says Gilles Dreyfus.
In the warehouse, the seed course, mounted on a tray, begins on an automated belt. Sow them accurately in a small container filled with surface.
Then to the germination rooms, with tropical climates, the plants stay for a few days. Before joining cultivation tours to thrive and reach maturity.
In the tower, a computer controls all the parameters (water, nutrients, lighting, temperature, humidity, CO2, Ventilation) and constantly adjusts them according to the desired target.
“By playing with the light spectrum and different color ratios, we can make a plant flower faster, more compact, have larger leaves, and change its morphology,” explained Michael Mittrand, agronomist and research and culture administrator.
Robot
A robot has the maneuver to manipulate the trays set up at fifteen levels and control their health condition.
“We have a lot more productivity because we optimize all the parameters,” Gilles Dreyfus stressed. “On earth, you will have a maximum of 3 to 5 crops of basil a year. We have 14 ”.
It aims for profitability by the end of 2022, with the second site at half its capacity.
Jungle also relies on plant production for perfume manufacturers and cosmetic brands. This activity already represents 30% of its turnover, but the company is silent on the flowers produced.
Product area is hidden from visitors. It grows there “rare flower”, which enters into the recipe for perfume, Gilles Dreyfus has the content to say.
After ten years in finance, he decided to change his life in 2015 after reading an article about vertical farming and went to New York to meet the “Father of Concept”, Professor Emeritus Dixon Despomier at Columbia University. He goes to a world conference on vertical agriculture in California.
“When I got back to Paris, I quit my job. I went all over the world to see what was already there ”. On the way, he meets Nicholas Dupuy, who has become his partner.
The Jungle raised just 42 million euros for takeoff.
Logan Leo
Experienced Media Personality skilled in Breaking News, Television, Intelligence Gathering, News Analysis, and Social Media. Strong media and communication professional with a Master of Science (MSc) focused in Economics from Harward University.
Robots Take Vertical Farming To New Heights
Braddock, Pa., is where Andrew Carnegie first mass-produced steel. The city, now one-tenth its former size, is home to a new kind of industry: robotic farms that grow greens inside buildings
Braddock, Pa., Is Where Andrew Carnegie First Mass-Produced Steel. The City, Now One-Tenth Its Former size, Is Home To A New Kind Of Industry: Robotic Farms That Grow Greens Inside Buildings.
June 28, 2021
A decades-long decline of industry in Braddock has left the western Pennsylvania town in ruins. Ten miles upriver from Pittsburgh in the Mon (Monongahela) Valley, most of the city’s factories, businesses and homes were abandoned long ago and leveled. Among the ruins, a sprawling steel mill, built by Andrew Carnegie in 1874, is still producing slabs of steel, 24 hours a day, seven days a week. It’s stained blue walls and maze of giant, rust-colored pipes and vents stand in contrast to the brand-new, block-long, gleaming white structure directly across the street. The mill’s neighbor is Fifth Season, a vertical farm growing greens indoors by stacking racks of plants on top of each other.
Fifth Season is the brainchild of brothers Austin and Brac Webb, and co-founder Austin Lawrence. “We view vertical farming as really a smart manufacturing system,” says Austin Webb. “We just happen to manufacture living organisms.”
The partners consider their fledgling enterprise as more than a means to feed people, but also a chance to work with a community in need. Almost none of the old steel plant’s employees live in Braddock. Conversely, everyone hired to work at Fifth Season lives close by and in the surrounding communities. “We’re creating a workforce of the future,” Webb says. “It’s an entirely new ag-manufacturing job that hasn’t existed before.”
Since the collapse of the steel industry in Braddock, the borough has struggled to attract new business and residents.(David Kidd/Governing)
Automated City Farming
Two shifts of 20 people oversee operations at the vertical farm. And like the steel maker across the road, the work never stops. Dressed in blue scrubs and lab coats, with heads covered and gloves on their hands, workers inside the plant look more like medical research professionals than farmers. The entire process, from seed to harvest, is controlled robotically. “What we have built is the industry first, and industry only, end-to-end automated platform,” says Webb.
Fifth Season’s proprietary software allows efficiencies otherwise not attainable. Spinach, arugula and other greens move around the 60,000-square-foot facility in plastic trays, each with its own unique ID. Sensors are constantly monitoring everything from nutrient mix, carbon dioxide levels and light spectrum, in order to ensure that the greens follow their prescribed grow recipe. Every plant can be traced from any point in the process, at any time.
Webb is quick to tout the advantages of vertical farming. Fifth Season uses up to 95 percent less water and 98 percent less land than conventional farming. Water from the municipal system is filtered and proprietary nutrients added before getting to the plants directly through their roots. “It means you can replicate any form of soil environment,” he says. Whatever water is not used by the plants is retreated and recirculated, with nutrients added as needed. A peat mix is used to support the roots, but all the nutrients are in the water, not the “soil.”
“We use no herbicides and no pesticides,” Webb says. “And that’s because we have hermetically sealed environments.” The possibility of contamination is all but eliminated. Fifth Season recently received a perfect score from the Safe Quality Food (SQF) program, an international, independent body that certifies food safety management. “The second time in 25 years they gave 100 percent,” he says.
With only their faces exposed, employees work among the various conveyor belts that crisscross the high, white-walled rooms of Fifth Season’s production floor. But there are no humans in the adjacent grow room, where tightly spaced racks, supporting trays of plants, are stacked 30 feet high, bathed in an otherworldly purple-magenta glow. The dramatic color comes from the LEDs that replicate the most useful parts of the spectrum of sunlight. “You can’t control the sun,” Says Webb. “But what you can control are LEDs.”
Fifth Season’s proprietary systems allow more plants to be grown in less space. The purple-magenta LED lighting replicates the most useful parts of the spectrum of sunlight, improving growth of the greens.(Fifth Season)
Every few minutes, a robot glides forward and back along a raised guideway that runs down the center of the room, dividing the stacks in half. The machine is not much more than a plain box, just a few feet tall. A metal beam rises from its back, extending to the ceiling. Its task is to place and remove trays of plants, taking its instructions from the all-knowing software. Because they are so tightly spaced, more trays can be stacked on top of each other, resulting in greater production.
“Compared to some other vertical farms out there, we have a lot more density,” says Webb. “We’re able to have more racks that grow inside the same space.” Moving trays is a task well-suited to a machine. Not only does the robot fit into places no human could, it always knows where every tray of greens should be, and for how long.
Vertical Farming Comes to Braddock
After a five-year career in finance, Austin Webb enrolled in an MBA program at Carnegie Mellon University in Pittsburgh. “I believe that robotics will possibly disrupt every industry in the world,” he says. “And so I went to C.M.U., specifically because it’s the No. 1 school in computers, science and robotics.”
There he met Austin Lawrence, who shared his interest in controlled environment agriculture. Together they visited a few vertical farms, coming to the conclusion that what was needed was an entire robotic platform, something the two of them could not accomplish on their own. Webb’s brother Brac, a self-described engineer and entrepreneur, was soon recruited to help. Their new business was incorporated in 2016, initially as RoBotany, which later morphed into Fifth Season.
With financial backing in hand, the partners looked for a place to build, quickly settling on nearby Braddock. They broke ground in May of 2019, were installing equipment less than a year later and were at full production before the end of 2020. “I think there’s a lot of opportunity for resurgence in a place like this,” says Webb. “A lot of folks that stayed are passionate around Braddock being able to grow and thrive and we want to be a part of that.”
In the foreground, Fifth Season’s new structure stands in contrast to the steel plant behind it that still dominates the town.(David KIDD/Governing)
Andrew Carnegie’s mill was the first of many that would proliferate in the Mon Valley, making it the nation’s steel capital. The churches, schools, stores and restaurants that served the town’s 20,000 inhabitants are mostly gone now. Shops and services are few and far between for the 2,000 that remain. “The nearest grocery store is up the hill, two towns over,” says Braddock Mayor Chardae Jones. “And most people don’t have cars.” It’s a hot day in June when a few of the locals gather in a brand-new park along Braddock Avenue. Everyone agrees the park is nice, but it’s no consolation for the hospital that used to stand on the site.
Many years ago, steelworkers and their families lived close to the mill.(David Kidd/Governing)
A few blocks away, an ever-present din still emanates from Carnegie’s steel mill, and a parade of trucks continues to roll past the boarded-up stores and empty lots that line the borough’s main thoroughfare. “We have a lot of vacant buildings,” says Mayor Jones. “That’s our biggest issue.” But there are signs of a revival among the ruins.
Present Day Braddock
Against the backdrop of empty and dilapidated storefronts, “The Ohringer,” a former furniture store built in the streamline moderne style of the 1940s, has recently been completely rebuilt and modernized as apartments and studio space for artists. Applicants are expected to present their work for review and answer a few questions, one of which is “why are you interested in becoming part of Braddock’s resurgence?”
Not only does Braddock lay claim to Andrew Carnegie’s first steel mill, but also the first Carnegie library, dedicated in 1889. Narrowly escaping demolition in the 1970s, the impressive stone structure is today undergoing a comprehensive restoration and modernization. Bright yellow notices of this year’s street sweeping schedule are affixed to telephone poles near the library and all over town, an indication that the local government is still functioning.
A repurposed furniture store now provides updated living and studio space to area artists.(David Kidd/Governing)
Further up the avenue, more official-looking signs are attached to random telephone poles. “NOTICE, WRITE MORE LOVE LETTERS” says one. “NOTICE, LOVE IS FREE,” says another. The signs were placed there, unofficially, by Gisele Fetterman, wife of former mayor and current Lt. Governor John Fetterman. Among her many initiatives to improve the lives of people in Braddock, she founded the Free Store nine years ago, a place where “surplus and donated goods are received and redistributed to neighbors in need.”
Fifth Season is a regular contributor to the Free Store, having recently given them a new refrigerator and donating 100 pre-packaged salads every Thursday. “We’re treated like we’re a customer,” says Gisele Fetterman. “We’re not getting things that didn’t sell, or surplus. Our families get to come in and choose. They can feel like they are at a grocery store. There is great dignity in the process of being able to choose.”
Offering “produce grown in soil by humans in Braddock,” workers at Braddock Farms do it the old-fashioned way.(David Kidd/Governing)
There are more signs along Braddock Avenue. “BE ALERT: VEGETABLES AHEAD.” Another simply says “TURNIPS.” Back in 2007, when John Fetterman was the mayor, he encouraged a nonprofit group of community gardeners to establish a farm in Braddock. Bisected by a side street, the organic farm has expanded to a little less than an acre in size, growing greens, tomatoes, onions, peppers and eggplant. This is Nick Lubecki’s fourth year as manager of the farm. “We’re here in Braddock, so the people in Braddock are our main focus,” he says. “We want to be useful.”
At best, the little farm on Braddock Avenue can produce 13 plantings of greens in a year. It is entirely different from the computer-controlled, machine-driven, non-stop production that takes place a few blocks away at Fifth Season, where a half-acre indoors can produce the equivalent of nearly 100 acres of farmland. But higher yields don’t matter as much if a significant portion is ultimately lost in transit to the table.
Serving a Market
Localized food production means less spoilage and waste. “If it takes anywhere from five to eight days to go from California to Pittsburgh, you’ve just lost five to eight days of shelf life,” says Austin Webb. Most of what Fifth Season produces is consumed in the Pittsburgh area. “The day after it was cut, not 10 days later.” Their ready-to-eat salads can be purchased at a local supermarket chain, or delivered directly to the consumer at home, a direct response to the pandemic. Local restaurants, hospitals and universities are also customers.
Convinced they have successfully demonstrated the viability of their proprietary technology, the three partners are looking to expand beyond western Pennsylvania. “We can build these anywhere… even larger than what we have here today,” says Austin Webb. “And we don’t have to re-create the wheel. It’s not like it would take us another five years.”
Conversations are already taking place about licensing the technology, proceeding in partnership with someone else, or going it alone. “That will allow us to build a facility just like we built in Braddock, in other parts of the U.S., and other parts of the world, even faster.”
A Job You Can Walk to
Andrew Carnegie built his steel mill in the Mon Valley because he needed the river, the raw materials, and access to labor. His plant was expressly designed to use the Bessemer Process, the first method to inexpensively mass-produce steel. Nearly 150 years later, the Webb brothers and their partner Austin Lawrence chose the exact same location to showcase their own new manufacturing technology and to fill a need in the community. “Knowing that we could build these anywhere, we wanted to build in Braddock because we knew that we could create jobs,” says Austin Webb. “That we could create this new workforce of the future.”
Employed since January, John Davis lives less than a block away from Fifth Season. “I have family in Braddock. They’re very happy I’ve got a job.”(David Kidd/Governing)
Braddock resident John Davis may or may not think of himself as part of the workforce of the future. But he’s happy to have a good job. Covered head to toe in his surgical outfit, he works in the seeding department at Fifth Season, a job he’s held since January. He’s lived here for 20 years, and this is the first job he’s had that didn’t involve a commute. He walks to work from his house, half a block away.
Davis is 32 years old and anxious to put the past behind him. “To have a job that you like, where you live, it’s comfortable,” he says. “And you can see that this is going to change Braddock for the better because it gives the residents jobs and new innovations. It’s going to bring life.”
While awaiting their fate, many of Braddock’s empty buildings provide space for murals and artwork.(David Kidd/Governing)
Lead photo: Greens leave the grow room at robot farm Fifth Season, ready for harvest. (Fifth Season)
Tags: Economic DevelopmentFood AssistanceTechnology
David Kidd is a photojournalist and storyteller for Governing. He can be reached at dkidd@governing.com.
How A Malaysian Company Born During The Pandemic Is Championing Harvest-To-Table In Kuala Lumpur
The brainchild of founders Shawn Ng, 28, and Sha G.P., 27, The Vegetable Co. aims to deliver fresh greens within three to four hours after harvest to their customers in various parts of Klang Valley
27 June 2021
BY KENNY MAH
Harvest-to-table vegetables have arrived in Malaysia, courtesy of The Vegetable Co. — Picture courtesy of The Vegetable Co.
PUCHONG, June 27 — The vegetables we eat and where we get them from can be a quagmire of questions: Is it organic? Local or imported? Is it safe? Is it fresh?
Getting your daily intake of healthy greens shouldn’t be this stressful, I reckon.
Enter The Vegetable Co. This fledgling harvest-to-table startup was launched early last year and is based on sustainable vertical farming concepts and in-house, customized technology.
The Vegetable Co. founders Shawn Ng (left) and Sha G.P. (right). — Picture courtesy of The Vegetable Co.
The brainchild of founders Shawn Ng, 28, and Sha G.P., 27, The Vegetable Co. aims to deliver fresh greens within three to four hours after harvest to their customers in various parts of Klang Valley.
Quality is a major differentiator. Ng explains, “Our vegetables are meant to be better than what’s available in the market due to their freshness and growing method. The indoor farming method ensures that they are delicious and pesticide-free while still reaching optimal size, taste, and nutritional value.”
Through their Controlled-Environment Agriculture farming method, the startup has devised and built an indoor, environment-controlled chamber that saves significantly on land and water consumption.
This indoor environment approach differs from conventional farming practices as they grow vegetables utilizing LED lights, vertical stacks, hydroponic systems, and environmental control to keep the internal atmosphere at an optimal constant that encourages optimal plant growth.
Ng adds, “The chamber is also an isolated environment, which prevents external contaminants from entering and as such mitigates the need for pesticide usage. Basically, we are farmers in lab coats, or plant scientists. Our aim is to grow food in the best possible environment to get the most nutrition and freshness onto your table.”
As with many startups, The Vegetable Co.’s overall ambitions and strategy are heavily influenced by the founders. The duo first met when they were doing their A-levels, and have been friends for well over a decade.
This meant they understood each other’s strengths and differences — Sha has a BSc in Economics from The University of Manchester while Ng received a Masters in Green Management and Sustainability from the University of Bocconi in Italy — and how best to complement each other.
Ng recalls, “Since college, we have always been young idealists who spent countless nights debating on the many ways in which we could contribute to the nation’s development. Generally, Sha is always pragmatic in nature, while I’m a bit of an optimist who dreams of a better future for the Malaysian people.”
Therefore, unlike many businesses that are driven solely by profit making, the two friends started their venture due to their burning need to drive change in a significant and tangible manner.
A sense of purpose was crucial, as Ng observes: “We both had work experiences prior to this, and they never fully aligned to our overarching goals and principles. By working on the business, we were given the opportunity to pursue and craft our own paths forward.”
But why vegetables?
Loyal customers have the 2015 film The Martian to thank. Ng explains, “It really intrigued Sha as the astronaut had to find a way to grow food in an extreme environment to survive. He began considering whether it could be feasible and commercially viable in the Malaysian context. He approached me with the idea, and the rest is history.”
Assembling their team was another piece of the puzzle they had to solve early on.
Ng says, “One of our most important hires remains our first farm operator, Bryan Lee. We hired him back in late 2019 when he was 19, and he has been with us since. Combining his love for plants with his mechanical and electrical engineering skills has made him essential for the work here, especially during the early stages.”
Plenty of care is taken in growing the vegetables, with the latest vertical farming technology. — Picture courtesy of The Vegetable Co.
The Vegetable Co. also has an in-house Research & Technology team — comprising young Malaysians below the age of 30 from varying backgrounds — working to optimise their automated systems, fit-for-purpose farm designs, as well as the quality and nutritional value of their produce.
That last attribute, Ng notes, is a crucial factor to market acceptance: “Our customers can smell the fragrance of the basil when they first open the box. This, combined with the springiness of our lettuce, really drives a good impression on people.”
The key to the freshness of their produce lies in their harvest-to-table approach, typically within a three- to four-hour window.
Ng explains, “Our intention is to move away from mass industrial agriculture and long supply chains. Research has shown that vegetables travelling far distances tend to lose nutritional value over time, some as fast as within 48 hours. There are also the concerns of food waste, as a third of all food stuff is usually discarded in the beginning, generating methane through open decomposition and exacerbating climate change.”
A typical subscription box contains seven types of freshly harvested vegetables. — Picture courtesy of The Vegetable Co.
As a result, The Vegetable Co. strives to grow within 20 kilometres of high populated districts within the Klang Valley, such as Kuala Lumpur, Petaling Jaya, Subang, Puchong, and Shah Alam.
In doing so, Ng claims this will help preserve the maximum nutrients possible, cut down on transport emissions and increase transparency as they minimise the number of unknown variables between the farm and the consumers.
He adds, “During the past year, we also observed interruptions in supply and knee-jerk reaction price hikes due to inter-state logistical issues associated with Covid-19 restrictions and we believe our solution helps address these challenges by farming right in the middle of population centres.”
By growing in vertical stacks within urban areas, The Vegetable Co. purportedly mitigates around 95 times the land use through conventional farming methods. In the future, the duo also plans to activate unused urban spaces to further increase land use efficiency.
Given the constraints of each individual farm being able to only service a certain radius around it, The Vegetable Co. will leverage both localisation and decentralisation to scale up in a sustainable manner.
Ng explains, “The modularity of our farms enables us to install farms in every urban centre where there is demand. This is how we envision the growth of our company and the vertical farming sector here in Malaysia.
Sounds like a reasonable and promising business model, no? But as any seasoned entrepreneur would tell you, the journey is never a smooth nor swift one.
The Vegetable Co. was self-funded by the two co-founders at the beginning. Ng says, “We really had to dig deep into our coffers and commit all our resources into the start of the company — scraping for whatever savings or equipment we have in order to make things work.”
Harvesting time. — Picture courtesy of The Vegetable Co.
Beyond a startup tendency to stay lean and agile, part of the scramble came from launching the business barely a month before the first movement control order (MCO) last year. Initial plans for pop-up booths and taste testing as a market education tool were immediately shelved.
With only a small number of early adopters, they decided to focus solely on promoting their subscription model. Ng explains, “This was what truly appealed to our first base of customers — those who were concerned about regular access to freshly-grown produce without needing to brave the supermarkets or fearing a shortage of supply.”
That gamble paid off handsomely as revenue grew by 300 per cent in the first few weeks alone. Both co-founders realised that customer satisfaction and confidence were critical for pushing the product to market, and have since made it part of their company promise: To reduce the time and distance for quality produce to reach their customers.
“Customers who took the chance on us in the early stages could immediately tell the difference,” Ng says, “From there the product sold itself by word-of-mouth. The popularity of the subscription service drove demand and allowed us to expand and to increase our capacity as we prepare for the launch of our next phase in July.”
Packing the just-harvested vegetables into subscription boxes. — Picture courtesy of The Vegetable Co.
Since then, the duo has gotten the support of an angel investor as they expanded their operations. Ng adds, “Although we have no immediate fundraising plans, we’re looking at raising a bridging round sometime Q3/Q4 this year to continue our business expansion and technology consolidation.”
Part of that expansion would include gradually doubling the number of their produce variants as production capacity increases. Currently The Vegetable Co. has about 10 variants; a standard box comes with about seven variants, making every delivery a little surprise, not unlike CSA (Community Supported Agriculture) boxes.
The Vegetable Co. aims to deliver fresh greens within three to four hours after harvest to their customers. — Picture courtesy of The Vegetable Co.
According to Ng, by having fresh vegetables delivered to them on a frequent basis, many of their customers have changed their diets for the better: “Some of our customers have taken to snacking on our veggies and moving away from the bad habit of eating junk food. Fundamentally, we are in the business of encouraging healthy habits and lifestyles.”
Are vertical farming and vegetable subscription boxes the future of our dining tables? It is early days yet but The Vegetable Co. certainly makes a strong and admirable case for Malaysian harvest-to-table.
To borrow from a classic jingle: Any fresher and you’d have to pick these greens yourself.
The Vegetable Co.
Lead photo: A typical subscription box contains seven types of freshly harvested vegetables. — Picture courtesy of The Vegetable Co.
Web: thevegetable.co
Vertical Harvest Collaborates Directly With Chefs Across Jackson
Since its inception, Vertical Harvest Farms has had a special relationship with the chefs of Jackson. The farm works closely with chefs to grow micro and petite greens specifically curated to each restaurant’s menus
06-21-21
Vertical Harvest Collaborates Directly With Chefs,
Finding Fresh Flavor To Elevate Any Dish
JACKSON, Wyo. — Chef Alejandra Peña nibbles a small green leaf and the spark in her eyes is unmistakable. Her customers at Persephone Westbank will soon find a similar tiny stalk in their morning granola bowl. “They’ll be surprised at the pop of citrus with their oats and yogurt,” said Peña. “ Tangerine cress is something people haven’t experienced as a taste before and it is really exciting to use microgreens like these in unexpected ways.”
Chef Alejandra Peña of Persephone Wesbank. Photo: Lindley Rust
It’s a fun day at the farm when a chef stops by the Vertical Harvest greenhouse. Geeking out over a microgreen’s flavor profile rings deeply sincere coming from the person who places it precisely on the plate. “Seeing the colors, tastes and textures helps me brainstorm my menus with something that is very tangible,” said Peña. “This is such a different experience than looking at a product list because being in the greenhouse and talking through the flavors with the growers helps the dish in my head come to life.”
Since its inception, Vertical Harvest Farms has had a special relationship with the chefs of Jackson. The farm works closely with chefs to grow micro and petite greens specifically curated to each restaurant’s menus. Chefs are welcome to book time to come and “shop” the greens with the Vertical Harvest grow and sales teams.
Persephone West Bank Chef Alejandra trying microgreens with Hannah Bouline (Product Manager) and Emily Peterson (Sales Director). Photo: Kyra Foley
“It’s satisfying to see the look in chefs eyes when we sample a new green with them. We always do a deep dive into how the flavors and textures can make other ingredients come alive,” said Hannah Bouline, Vertical Harvest Product Manager.
On her recent greenhouse visit, Peña was preparing for Persephone Westbank’s new 5-9 p.m. dinner service, which just started on June 17, 2021. She tasted radish microgreens, mustard frills, rock chive, and red veined sorrel. While the sorrel and tangerine cress are already breakfast and lunch menu staples, she was excited to play with the mustard frills for the dinner menu.
According to Peña, it’s important to have microgreens and petite greens that she can use for breakfast, lunch, and dinner but still have very different flavors and textures throughout the day. “Our goal is to avoid waste and use the freshest product possible.”
The overall vibe of the new dinner menu is fresh, floral, and citrus-like a French bistro, she says. “We’ll offer vegan dinner options and provide an experience that is casual and kid-friendly with a specific kid’s menu. I don’t want anything to be too heavy, but instead, have the entire family leave feeling like they could really enjoy the dishes and not be too full.”
The Salmon Tartine. Photo: Kyra Foley
Peña’s plan is to pair Vertical Harvest’s red-veined sorrel with dishes such as salmon tartine and use the tangerine cress across many dishes on the menu. She also hopes to make Vertical Harvest edible flowers a key part of the restaurant’s cocktail program.
She is most excited about the ½ roasted chicken with seasonal vegetables. “It’s so juicy and has a light yet flavorful cardamom glaze,” she said. “I’m so excited for everyone to try it!”
A group of Vertical Harvest team members visited opening night and were impressed with the atmosphere and the food. “It was so lovely to enjoy the light, yet flavorful, food on a warm afternoon,” said Emily Peterson, Vertical Harvest Sales Director. “The cocktails were spot on and I loved the salmon tartine with its pop of citrus supplied by the red-veined sorrel. The menu perfectly balances rich dimensions of flavor without being too heavy. Even the usually deep and earthy ratatouille had a fresh essence.”
Try the chicken, salmon tartine, and other wonderful new dinner menu items yourself this season. Dine at Persephone Westbank at 3445 N Pines Way in the Aspens, Wilson WY. Learn more about Vertical Harvest Farms and its freshly, locally grown produce on the company’s website here.
Lead photo: Vertical Harvest collaborates directly with chefs, finding fresh flavor to elevate any dish. Photo: Shannon Corsi
Sponsored by Vertical Harvest - Jackson Hole, Wyoming
Meet The Woman Reconnecting African Communities With Locally-Grown Food
Whilst small in scale (only 10 meters in diameter), La Ferme Urbaine Okoume’s hydroponic microfarm produces an astonishing 300 lettuces and herbs per week. Claudia S. Ondo comments that the farm produces “mostly lettuces, romaine and iceberg, alongside parsley, coriander, basil, oregano, and arugula.”
Editor’s note: The following information is derived from an interview Agritecture conducted with Claudia S. Ondo, Owner & General Manager at La Ferme Urbaine Okoume. Visit their website or contact the team to learn more about or to partner with La Ferme Urbaine Okoume.
From College To Agricultural Entrepreneur
After completing her studies in Political Science at the University of Montreal, Claudia S. Ondo was contemplating the next phase of her adventure in order to make a positive impact on global politics, the environment, and on communities.
After spending that summer in Libreville, she was dumbfounded with the discovery that her native country of Gabon was extremely dependent on food imports. She highlights that “local agricultural production covers less than 35% of [the population’s] needs, and food imports are growing by 11% each year.”
Image sourced from La Ferme Urbaine Okoume
Claudia shares that “Gabon is a very small country - small population, only about 2 million inhabitants - but, a rich country in terms of resources. We have lots of wood and oil, so most of the working population is directed to the public and private sectors. The agriculture sector is left out.”
Drawing from her political science education, she saw an opportunity to offer the Gabonese people a sustainable agricultural model that not only “met this need for local fruits and vegetables, but also offered up a solution for youth unemployment and encouraged the Gabonese people to take an interest in agriculture.”
Whilst small in scale (only 10 meters in diameter), La Ferme Urbaine Okoume’s hydroponic microfarm produces an astonishing 300 lettuces and herbs per week. Claudia comments that the farm produces “mostly lettuces, romaine, and iceberg, alongside parsley, coriander, basil, oregano, and arugula.”
Alongside this technological approach, the team at La Ferme also wanted to take advantage of Gabon’s rich soil and weather conditions. “We have an experimental garden in which we grow tomatoes, green onions, lettuces, and now zucchinis too.” This garden is experimental because the team is still testing out rotating crops throughout the year, depending on the seasons.
The team not only prioritizes local production, they also want to deliver organic produce. With a mix of hydroponic and greenhouse set-ups, the farm is also still able to utilize natural sunlight and collect rainwater for the crops.
Claudia shares that produce brought into Gabon is not supervised, and, as a result, you can’t trust the quality. “We don't know where it comes from. We don't know what has been used. What is the process? How has it been cleaned?” This is a huge reason that customers come to La Ferme Urbaine Okoume.
The key was to form a stronger relationship between the Gabonese people and urban agriculture. To Claudia, hydroponics seemed to be the perfect combination to achieve these goals, and to build greener cities and communities for future generations.
Image sourced from La Ferme Urbaine Okoume
The team calls it their “little green paradise.”
So far, the farm has been able to add to the neighborhood a place for relaxation, and positive thinking. “It allows many city dwellers to reconnect with nature, agriculture, and the process of growing a plant. What does a tomato plant look like? What does a seedling look like? How are in-soil crops like carrots, potatoes or onions harvested?”
The construction of this farm is encouraging curiosity. Today, more and more people are contacting La Ferme Urbaine for viewings, schools are desiring workshops, individuals are coming in to learn how to grow their own plants at home, and restaurant owners are delighted to know where their products come from.”
Claudia and the La Ferme Urbaine team are grateful to Agritecture for making their dream a practical reality.
Having studied agribusiness in university, Claudia had tons of practical knowledge on how to transform an idea into a business. But, what she didn’t have was the agricultural knowledge and expertise in hydroponics and urban agriculture.
Image sourced from La Ferme Urbaine Okoume
After being awarded a grant by The World Bank, Claudia knew she needed more agricultural expertise to tackle this vast mission of transforming Gabon. Whilst Claudia initially looked for a local company, after stumbling across Agritecture in a newsletter, she felt an instant connection. She not only found a team with shared values, but also one with international agricultural expertise. This was key to her given the Gabonese context.
With over 6 years of experience in agriculture, specifically between the North American and MENA-GCC region, Agritecture’s Director of Operations, Yara Nagi, shares her experience working with La Ferme Urbaine. “Agritecture guided Claudia on equipment selection, the bill of materials for the farm, and management planning. The model was to grow fresh, local lettuces and herbs that are not available in that same quality to restaurants, hotels, and public markets. Guiding clients on making the best use of their grant money and avoiding costly mistakes fits within our social mission to help young farmers make a positive impact on their community.”
On her experience working with Agritecture, Claudia adds that “as someone who had a political & agribusiness background, but no prior agricultural experience, Agritecture really gave me the assurance and guidance I needed in this new business and adventure.”
Image sourced from La Ferme Urbaine Okoume
Since being hit by the pandemic, the farm still runs 24/7. However, they’ve changed their primary clientele. Today, they serve more restaurants than hotels. Claudia adds that “95% of our customers are restaurants. 5% are just individuals who want fresh products.”
Additionally, the team has come into contact with the Sylvia Bongo Ondimba Foundation run by the First Lady of Gabon, Sylvia Bongo Ondimba. The two teams have come together to scale up urban farming in the region and create more revenue streams for locals.
Not only this, their partnership empowers women by highlighting how young women in Gabon can run their own businesses.
Claudia shares that “this field was thought to be exclusively for a certain category of people, so, the fact that it’s a women-led business speaks volumes. We’re often congratulated by our customers when we deliver lettuce in stores or to restaurants, because they’re surprised to see women in farmer outfits.
Yara shares that what makes this farm and team unique is “the vision of the entrepreneur, Claudia. It is always incredibly inspiring to see women of our generation lead agricultural projects like these, but this project in specific has a vision of shifting the local food system and making produce more accessible. I think there are many more projects like these to come.”
New AeroMax Growing Media From OASIS Grower Solutions Increases Hydroponic Crop Growth by Up to 30%
Engineered with a unique open matrix, the increased porosity of the new Horticubes® AeroMax growing media leads to greater airflow and maximizes the opportunity for oxygen to get to a plant’s root zone
(Kent, OH) – OASIS Grower Solutions, a worldwide leader in propagation and division of Smithers-Oasis Company, understands the importance of propagation. Not only helping plants grow but generating big ideas as well. The most recent of which is the revolutionary new substrate engineered for precision hydroponic farming called Horticubes® AeroMax.
New Horticubes® AeroMax growing media introduces a higher level of porosity for faster, healthier hydroponic crop root growth.
Before creating a new media to support the production of leafy greens, herbs, and other crops for hydroponic farming, Vijay Rapaka Ph.D., Global Research Manager set a rather lofty goal: “To create a smart substrate designed for today’s precision growing systems. Through extensive research over the last 24 months, we’ve achieved an ultra-low density that allows unrestricted root growth of young plants, so they can express their full growth potential of up to 30%. This innovative purpose is precisely why we named it AeroMax.”
Engineered with a unique open matrix, the increased porosity of the new Horticubes® AeroMax growing media leads to greater airflow and maximizes the opportunity for oxygen to get to a plant’s root zone. This helps crops grow faster and stronger, allowing young plants to prosper in the maximum air-filled substrate. Due to its enhanced porosity, air and nutrients constantly replenish a plant’s root zone, promoting stronger and healthier roots through each watering cycle.
The maximum airflow created with new Horticubes® AeroMax substrate helps get this young lettuce off to a great start.
Created with support from John Bonner of Great Lakes Growers, AeroMax has already delivered some impressive results. “The more porosity, the greater opportunity for air to contact the root zone,” begins Bonner. “And that happens more often with AeroMax, so we get fuzzy, almost hairy-looking roots. And when you get that type of growth, the plants simply grow faster. Since we started using AeroMax, we’ve seen faster crop growth upwards of 15%,” grins Bonner.
In addition to delivering greater oxygen to the crop’s root zone, AeroMax’s increased porosity and airflow enables it to drain more easily. This improved drainage keeps the top of the AeroMax growing media drier, dramatically reducing algae blooms and subsequent disease – creating a wonderfully clean and pathogen-free environment for young plants to grow.
Dr. Vijay Rapaka of OASIS® Grower Solutions and John Bonner of Great Lakes Growers review the incredible success of the new Horticubes® AeroMax.
AeroMax has a multitude of other functional benefits that support improved propagation. Its rich black color was strategically selected to increase the surface temperature and synergize well with photosynthetic light spectrum to produce more well-toned young plants. Plus, the less dense, almost spongy nature of AeroMax minimizes dust generation throughout the production process, making it easy to work with.
AeroMax has also been designed to separate easily at transplant through a unique etching around each cube, which also supports uniformity and precision growing. AeroMax growing media works well in NFT, Deepwater, and Vertical hydroponic systems, and is available in single-seed and multi-seed dibbled sheets of 50ct, 104ct, 162ct, and 276ct. The 50ct, 104ct, and 162ct sheets are top-grooved for easier separation.
For more information on Horticubes® AeroMax, contact Shannon Enoch, at Senoch@smithersoasis.com, customer service at 855.585.4769, or visit us online at www.oasisgrowersolutions.com/aeromax.
FOR SALE - Surplus Turnkey Propagation Equipment
We have surplus equipment available that will allow you to plug and play so that you can begin sowing seeds, germ, and nurse your starter plants to transplant into the field, greenhouse, or vertical farm
We have surplus equipment available that will allow you to plug and play so that you can begin sowing seeds, germ, and nurse your starter plants to transplant into the field, greenhouse, or vertical farm. Great for year-round propagation of plants, vegetables, or cannabis. This is a low-cost way for you to begin growing, all you need is water, electricity, and a room.
$10,000 Seeding Line
Seeder Seederman GS3-8 ft, Needle Seeder with sowing kit and dibbler for 105 and 72 cell propagation trays. Compressor & hose, and coco coir blocks available
The GS3-HD automatic Needle Seeder was developed with the larger growing operation in mind. The GS3-HD machine is easy to operate it can be mastered in less than a day. The GS3-HD is capable of direct seeding into bedding flats and pots up to 4" square.
- 100 % Pneumatic - Requires 5 cfm / 80 psi compressed air source
- 8ft Machine size 96"L X 36"W X 72"H
- Weight approx 200 lbs
- Aluminum and stainless-steel construction (where possible)
- Dibble bar
- Vibrating seed pan
- Seed collector
- Air blow gun for cleaning
- Oversize air filter
- Adjustable leveling feet
- Adjustable guide rails
- Two sowing kit included – 105 cell and 72 cell
- Can sow up to 60 trays per hour
$7,500 Germ /Nursery Equipment
This equipment will fit in a 15 L x 15 W x 15 T room and can germ up to 1600 plantlets at a time. With climate control system and LED lights, the room can be used as both a germ room and a nursery.
$1,000 2- Towers with 5 levels each, enough for 160 - 1020 propagation trays
Unarco white power coated, tear drop, quick release pallet racking
4 - 12 ft uprights
20 - 8ft beams
20 - wire mesh decks
$500 500-gallon water tank with two pumps (for each tower)
$250 Reverse Osmosis System
$500 1-ton AC unit and Dehumidifier
$250 1 greenhouse, electric heater fan
Finned steel tubular heating element.
Internal manual reset thermal cut-out.
Chord for hard-wire installations.
Base with wall, floor, or ceiling mount.
Temperature control thermostat with 35F to 85F range.
10' air throw, 262 CFM.
5,600/4,200 Watts. 240/208 V. Single phase, 19,000/14,000 maximum BTUs.
$500 Timer with sensor to control T and RH
$3,000 30-GE Horticulture LED grow lights with connectors
Light intensity for typical indoor farming applications
P66 rated and UL wet rated for easy watering and cleaning
Daisy chain end to end making installation easier
8 ft. light bar
Uniform light for even plant growth
Operating Environment: 0°C to +40°C
L90/36000 hours per TM-21
5-year limited warranty
$1,500 20- plastic grow tubs, with drains, can hold 16 -1020 propagation trays
For more information, please contact:
Robert Colangelo at robert@greensensefarms.com
RotoGro (ASX:RGI) Updates Market On Vertical Farming Tech
The RotoGro Garden System is the core of the company's technology with the ability to maximize plant surface growing area by situating a spherical garden around a centrally placed lighting system
Source: RotoGro
RotoGro (RGI) provides an update of its vertical farming technology with encouraging results from recent trials
The company says recent data indicates its garden systems produce more yield per square meter when compared to other indoor vertical farming methods
Further, trials of RotoGro 710 are said to be progressing well and the team is trialing how to further reduce water and energy usage
RGI is also encouraged by its studies and customer feedback for its RotoGro 420 system which it says validates commercial-scale cultivation of lawful cannabis
Shares were trading 2.3 percent higher at 4.4 cents apiece
RotoGro designs and manufactures cultivation solutions for indoor vertical farming, operating in perishable foods and lawful cannabis.
The RotoGro Garden System is the core of the company's technology with the ability to maximize plant surface growing area by situating a spherical garden around a centrally placed lighting system.
The systems can be stacked, maximizing the yields per square meter when compared to the ground space occupied.
RGI said data collected from recent crop trials conducted in collaboration with agriculture company Verity Greens and herb grower and distributor Fresh Leaf indicates its garden systems produce more yield per square meter when compared to other indoor vertical farming methods.
Specifically, RotoGro projects yields 3.8 to 15.3 times the yield per square meter compared to industry-leading farming producers and greater in contrast to greenhouse and conventional farming.
CEO Michael Di Tommaso said ventures like the ones with Verity Greens and Fresh Leaf will "strengthen RotoGro’s market presence by successfully penetrating the burgeoning indoor vertical farming industry with its technology offerings".
Further, internal trials of the company's most recently developed garden system, the RotoGro 710, are said to be progressing well with cultivation of 48 kilograms of basil and 26.5 kilograms of cilantro in a single harvest cycle.
After multiple trials cultivating leafy greens, the agronomy team repeatedly achieved yields of 124 kilograms in a fully planted RotoGro 710, indicating single harvest yields of 372 kilograms could be achieved when the technology is at full capacity, stacked three-high.
The team is trialing shorter full crop cycle lengths while maintaining yields and aims to refine the plant irrigation schedules to further minimize water usage and refine the environmental controls to ensure enhanced energy efficiencies.
In other news, RotoGro has enabled full automation of its lawful cannabis cultivator, RotoGro 420.
The company's software controls the wheel revolution speed, lighting cycles, and spectrum variations, direct CO2 injection as well as the plant irrigation processes and environmental controls including temperature, air conditioning, and humidification.
Notably, the 420-garden system has been able to consistently produce 10.2 kilograms of dried cannabis flower in a single 56-day crop cycle when stacked three-high.
RGI said its studies in combination with its customer’s data validates the commercial viability of RotoGro 420 in the commercial-scale cultivation of lawful
cannabis.
Mr Di Tommaso said RotoGro is continuing to develop relationships globally to expand its presence in both the perishable foods and lawful cannabis markets.
Shares were trading 2.3 percent higher at 4.4 cents apiece at 1:31 pm AEST.
These High-Tech Strawberries Cost $6 Apiece. Here’s What They Taste And Smell Like
The Omakase Berry, a Japanese variety grown by the New Jersey-based company called Oishii, bills itself as an entirely different strawberry experience
By Hannah Selinger
June 11, 2021
Some months ago, a curious new strawberry began appearing in my social media feeds. The berry, which comes in packages of three, six, or eight, was a uniform pale red. Each berry in each plastic carton looked almost exactly the same — heart-shaped, symmetrical, and indented on the surface where, in a store-bought strawberry, yellow seeds would appear. One more notable thing: They cost between $5 and $6.25 apiece.
The Omakase Berry, a Japanese variety grown by the New Jersey-based company called Oishii, bills itself as an entirely different strawberry experience. The website even offers advice when it comes to eating them: Allow berries to sit at room temperature for 10 to 15 minutes; let the berries’ aromatics “fill the room”; inhale the “bouquet”; eat.
Oishii grows its berries indoors vertically, leveraging technology that its co-founder and CEO, Hiroki Koga, 34, explored in Japan. “I got my first start in the vertical farming industry as a consultant in Japan, where it took off before anywhere else in the world,” he said. “But the whole industry failed pretty quickly, you know, in the early 2010s in Japan, because it was too expensive to grow leafy greens in a very tech-savvy, costly environment.” The technology, he said, was there; someone just needed to find the right way to use it.
The first run of berries (the Omakase cultivar) has been geared toward the luxury market and is available only in the New York City area. But the company is in the process, Koga said, of expanding its market share. Some of the varieties the company is experimenting with can be grown in a much more cost-efficient way, he said, “which means that we should be able to place these into the market at a significantly affordable, reasonable price, compared to what it is today.”
Koga came to the United States in 2015, first to California, where, he said, the quality of produce was unexpectedly good, though not as good as in Japan. The strawberries he selected for the company’s first vertical farms in New Jersey are known as “short-day cultivars.” In Japan, “They’re grown during the winter in a greenhouse environment in a little more wet environment,” Koga said.
Long-day cultivars — American summer berries — are, he said, “optimized for mass production,” at the expense of flavor. Koga says Oishii’s low yields are guided by the same principles as fine wine production: An intentionally depleted crop, achieved by such tactics as crop-thinning, forces the plant to push more of its nutrients and flavor into fewer berries, yielding a more concentrated flavor. The growing environment, according to Koga, is also optimized so that berries yield the maximum amount of nutrients and sweetness.
“We constantly were testing and tweaking to find the perfect environment for the unique Omakase berry,” Koga said. That meant, he said, finding the optimal temperature and breeze; controlling plant management, water frequency, and pruning; and leveraging artificial intelligence to help predict yields.
I wanted to know how the Omakase Berry — billed by Koga as a berry with no American equal — would stand up to other domestic fruit. I arranged my own taste comparison, using three different strawberries: Oishii’s Omakase Berry, available only in the New York City area; widely available Driscoll’s strawberries, produced by a network of more than 900 independent growers around the world, in such places as North America, Europe, China and Australia; and first-of-the-season strawberries from Balsam Farms, in Amagansett, N.Y., down the road from where I live. (Full disclosure: My yearly CSA box comes from Balsam.)
Driscoll's organic strawberries. (Jennifer Beeson Gregory/The Washington Post)
The appearance
Perhaps most striking about the Omakase Berry is its utter uniformity. Each orangy berry — I purchased a package of eight for $50 — looks exactly the same. Glance quickly and you might mistake the berries for marzipan candies, their exterior is so flawless.
The Driscoll’s berries ($3.99 for the company’s standard 16-ounce plastic clamshell) were far deeper in pigment — the company aims for “deep red,” said Scott Komar, 58, the company’s senior vice president for global research and development — and were larger, overall, than the Omakase, though there was variability in size. They were covered in tiny yellow seeds. In selecting berry plants, Komar said, Driscoll’s considers “the color of the strawberry, the shape, the size, and the mouth texture.”
My local strawberries (a quart for $9) were smaller, deeply pigmented and visually much less consistent. The traditional heart shape that is associated with the fruit became more triangular here on Long Island, where conditions are unpredictable. Balsam Farms, said Ian Calder-Piedmonte, 41, the farm’s co-owner, uses a technique called plasticulture. A barrier between plants and the ground is formed using plastic, aiding farmers with weed control, assisting with water management and keeping berries cleaner.
Plasticulture, Calder-Piedmonte said, combined with pruning runners, keeps the plants compact and the berry placement concentrated. Without the plastic, he said, berries can “try to set down roots between rows, and actually will take away from the growth of the mother plants.” Still, holding in my hand the tiny first berries of the Long Island season, it was hard not to consider how much work had gone into producing just a pint of fruit.
Strawberries for sale at the Kuhn Orchards booth at the Fairlington Farmers Market in Arlington, Va. (Jennifer Beeson Gregory/The Washington Post)
The aroma
Oishii isn’t lying when it says the aroma of its berries will fill the room. When I unearthed my plastic container from its refrigerator pack, I could already smell them. Opening the box, I was assaulted with the most strawberry-smelling fruit I’d ever encountered. Aroma, Koga said, is one of the classic characteristics of the Omakase Berry.
In this category, there was no competition. My Driscoll’s berries did not have much of a scent, but aroma may not be at the top of the list in breeding priority. “We conduct quantitative measurements on the sugars, acids, and aromatics of our berries,” said Komar of Driscoll’s berries. “Then that information helps us pick the berry varieties we will commercialize for our brand.” Driscoll’s places a high premium on flavor and color, and the variety I tried may not have been bred, specifically, for aroma.
My Long Island berries smelled very much like strawberries, although their scent was not nearly as potent as the Omakases. “I think there’s probably more variation on local strawberries, as there are with probably everything that’s locally produced,” Calder-Piedmonte said. Other berries that come from “incredibly controlled” environments “where it’s sunny every day” are more likely to be consistent in size, shape, flavor, and even aroma. On Long Island, he said, “I think there are a lot more variables.”
The taste
Oishii’s Omakase Berries cost $50 for a package of eight. (Oishii)
Do you prefer a tart berry that’s firm to the tooth? Are you enamored by sweetness? What type of berry the average consumer perceives as “best” depends on such personal preference. The Omakase Berry was, without question, the sweetest that I sampled. (However, Driscoll’s grows a trademarked, premium fresh berry segment called the Sweetest Batch for strawberries, blueberries, raspberries and blackberries, which Komar said are “unique selections” from the company’s breeding program; I did not try these.)
The Driscoll’s berries were the firmest of the three, with a consistent mouthfeel and flavor. It seemed to me that the objective in their breeding was a distinct balance between sweet and tart — and that balance certainly came through on each bite. In some ways, the acid, a quality in food and drink that compels you to keep consuming, makes sense: You’re unlikely to eat only a single strawberry, but Driscoll’s berries come in large, satisfying packages. It’s okay to keep eating.
As for my local berries, there was something compelling about the unpredictability. They were not the sweetest berries I’d ever tasted, but they varied between sweet and tart. Pop a strawberry in your mouth and come alive with the surprise of how sweet it is. Get a slightly underripe berry and pucker in delight. That contrast might make you wish that berries at the farm stand were sold by more than just the quart.
And, as Ian Calder-Piedmonte pointed out, the distinct advantage of a local strawberry is that you’re eating it the day it’s picked. “They really are harvested that day or the day before,” he said. Many berries are picked and then held in refrigerators (or refrigerated trucks) for days before they reach the consumer, and flavor can diminish each day. A fresh-picked berry tastes far different from a berry that has been off the plant for a few days or, as happens in some cases, a week.
Then came the Omakase Berry. The berry, Koga said, was “specifically selected out of 250 cultivars that exist in Japan,” optimizing for “very strong aroma and high sweetness level.” “Because most of the conventional strawberries here in the U.S. have a very high acidity and very low sweetness level, we just wanted to differentiate our product,” he added. This berry, with its heightened sweetness, is the type of berry that sits heavy on the tongue. Eat one, consider it, let the sugar coat the palate. That’s more than enough. The point isn’t to keep eating. The point, in fact, is to stop. So I did.
Selinger is a writer based in East Hampton, N.Y.
Lead photo: The Omakase Berry, a Japanese varietal grown indoors by Oishii in New Jersey. (Oishii)
USA - ALABAMA: Auburn College of Agriculture Using High-Tech Shipping Containers To Grow Produce For Campus Dining
Unique ‘Vertical’ Farms part of Planned 16-Acre Transformation Garden On Campus
High-tech Horticulture
Unique ‘Vertical’ Farms part of Planned 16-Acre Transformation Garden On Campus
June 10, 2021
Josh Woods | College of Agriculture
Recycled shipping containers have gained popularity in recent years, being converted into everything from houses to small stores—but the Auburn University College of Agriculture, in partnership with Campus Dining, is using them as self-contained “vertical” farms to grow produce to serve to students.
In April, the college acquired two Freight Farms shipping containers that have been converted into technologically advanced hydroponic growing stations in which plants grow vertically indoors without soil, getting their nutrition from water and light energy from powerful LEDs.
Now, the farms are producing the first crop of lettuce.
“This is state of the art,” said Desmond Layne, head of the Department of Horticulture. “We're talking growing from seed to fork in four to six weeks, depending on whether it is lettuce, arugula or another vegetable crop that can grow in there. And we can produce 15 times as much per year as we could outside in the same exact spot.”
Associate Professor of Horticulture Daniel Wells taught a vertical farming course this spring and leads operations of the vertical farms.
Wells said the containers are outfitted with a complete climate control system, which includes air conditioning and humidity control. Because they are highly insulated, the system ensures the same climate 365 days a year.
The converted containers also have an elaborate lighting system, giving all the light the plants need from two color LEDs.
“We can do any number of colors of lights,” he said. “But it turns out for photosynthesis, plants use mostly red and blue light. What’s neat about that is you can cut out a lot of the other color spectrum, creating far less heat energy. That's very efficient. It means more of the energy used is turned into light than heat.”
The containers also allow for controlled carbon dioxide levels, which accelerates plant growth.
“Ambient CO2, what you and I are exposed to every day, is about 400 ppm [parts per million],” he said. “And that’s fine, plants can grow there. But if we boost the CO2 to 1,000 ppm, they’ll grow faster. And because we’re containing the CO2, the plants can really use it. And it’s not dangerous for humans at all.”
Wells and Director of Dining and Concessions Glenn Loughridge first initiated a partnership between the College of Agriculture and Campus Dining five years ago through the Auburn Aquaponics Project, which uses hydroponics and aquaculture technologies to provide a system in which nutrient-laden wastewater from fish production is used as a food source for plant growth. Today, fish from this effort are served in dining facilities on the Auburn campus.
The new vertical farms build on that effort.
“We're in the process of finishing a $26 million dining hall in the center of campus,” Loughridge said. “It has always been foremost in my mind that we would have the opportunity to feature produce grown here on campus in that dining hall. In our biggest location, our biggest asset, we want to bring our A-game.
“This is hyper-local, on-campus sourcing,” he added. “Can you imagine being a potential student coming to tour, seeing where these products are grown, and then going to eat there? It’s incredible. We truly believe this elevates our dining experience.”
The converted shipping containers were manufactured by Freight Farms, a Boston-based company operating in 45 states and 28 countries.
“There are a few different companies out there doing this,” Layne said. “But Freight Farms is the most sophisticated. They’re the ones who have both the best product on the market and the largest production of these containers. It’s really a best-case scenario.”
Adam Lenhard, a rising senior majoring in biological agricultural technology management, said Wells’ course has been one of the most influential courses he’s taken at Auburn.
“It has been very helpful, not just in preparation for the arrival of the freights, but also in learning all about new hydroponic technologies and growing techniques,” Lenhard said. “Post-graduation, I plan to continue to work with these types of indoor, LED hydroponic systems. My primary goal after college is to normalize urban hydroponic farming, provide large, consistent yields of fresh vegetables and provide food to those in need who do not have as much access to fresh produce.”
Transformation Garden
The vertical farms are located on the College of Agriculture’s planned 16-acre Transformation Garden on the south end of the university’s campus, near the intersection of Lem Morrison Drive and Duncan Drive. The goal of the garden is to encompass every aspect of plant-based agriculture, including everything from fruits and vegetables to ornamentals to grow crops and more.
The Transformation Garden will showcase new technology and the history of agriculture, as it envelops Auburn’s Old Rotation, a single-acre research plot created in 1896. Continuously since that year, the historic landmark has been the site for testing and advancing transformative ideas that are now commonplace—ideas like crop rotation, cover crops, and low- and no-till farming.
(Written by: Kristen Bowman)
HELP DEVELOP THE TRANSFORMATION GARDEN
To help develop the new Transformation Garden, you can give online or contact Phillip Cowart, College of Agriculture director of development, at poc0001@auburn.edu or 334-844-1198.
Auburn University is a nationally ranked land grant institution recognized for its commitment to world-class scholarship, interdisciplinary research with an elite, top-tier Carnegie R1 classification, life-changing outreach with Carnegie’s Community Engagement designation and an undergraduate education experience second to none. Auburn is home to more than 30,000 students, and its faculty and research partners collaborate to develop and deliver meaningful scholarship, science and technology-based advancements that meet pressing regional, national and global needs. Auburn’s commitment to active student engagement, professional success and public/private partnership drives a growing reputation for outreach and extension that delivers broad economic, health and societal impact.
Latest Newsroom Articles
Artemis Releases 2020 State of Indoor Farming Report
The purpose of this report is to look at where the indoor agriculture industry is today as well as to give growers an industry voice around the latest trends, biggest challenges, and the immense opportunities in this rapidly expanding industry.
We are excited to release our third State of Indoor Farming report. Since their inception in 2016, the State of Indoor Farming reports have been downloaded by millions of people and used as a trusted resource on the industry.
The purpose of this report is to look at where the indoor agriculture industry is today as well as to give growers an industry voice around the latest trends, biggest challenges, and the immense opportunities in this rapidly expanding industry.
The report includes a high-level overview of the industry, as well as a deep dive on key topics such as expenses, sales channels, growth, cannabis, and projections for the future of the industry.
To learn more, you can access the report here.
You can also access our 2016 and 2017 State of Indoor Farming reports.
Ready to see how Artemis can help your operation?
Reach out to our team today. GET STARTED
Artemis, 718 The Hideout, Lake Ariel, PA 18436
© 2020 Artemis Contact Privacy Policy
Polygreens Podcast Episode: 30 - Richard Vollebregt - Part 1
In this episode Joe and Nick interview Richard Vollebregt, President & CEO of Cravo Equipment Ltd, a company that develops retractable roof production systems to enhance berry, cherry, cannabis, and vegetable production for growers worldwide
In this episode Joe and Nick interview Richard Vollebregt, President & CEO of Cravo Equipment Ltd, a company that develops retractable roof production systems to enhance berry, cherry, cannabis, and vegetable production for growers worldwide.
His background in economics combined with 30+ years of experience designing automated retractable roof greenhouses, knowledge of plant physiology and my worldwide experience in many crop industries allows me to be very effective in designing crop production systems and then creating financial models which benchmarking again conventional greenhouses, tunnels, and open field production.
Latest Episode
CEA Food Safety Coalition Details First Indoor-Farming Standards
Inspired by rising food safety concerns after the 2018 Thanksgiving romaine recalls, the CEA Food Safety Coalition is launching the first-ever food safety certification program specifically designed for indoor-grown leafy greens.
By AMY SOWDER June 2, 2021
(Photos courtesy CEA Food Safety Coalition)
Inspired by rising food safety concerns after the 2018 Thanksgiving romaine recalls, the CEA Food Safety Coalition is launching the first-ever food safety certification program specifically designed for indoor-grown leafy greens.
“The new standard champions CEA-grown produce as a critical component of safe and secure domestic food supply, especially in times of business disruption as experienced during the COVID-19 pandemic,” Marni Karlin, executive director of the CEA Food Safety Coalition, said in a news release.
Controlled Environment Agriculture, or CEA, has exploded with investment and sales the last few years, as more urban, indoor farms crop up to meet demand.
Soon after organizing in 2019, the coalition educated the Centers for Disease Control and Prevention and Food and Drug Administration about the limited risk of contamination from indoor-produced leafy greens, Karlin said.
“During the Thanksgiving 2019 romaine recall, those government agencies were transparent that CEA leafy greens were safe and did not extend the recall to them. This enabled retailers to keep CEA-produced greens on the shelves and consumers to safely buy CEA leafy greens for their families,” she said in the release.
The team had to create a standard that made sense across the board for the variety of production processes included in CEA — from greenhouses and vertical farming to aeroponic, hydroponic and aquaponic.
“Current food safety standards were written for the field, and many don't adequately address the unique attributes of controlled indoor environments,” Karlin said in the release. “Traditional food-safety risk profiles associated with conventional farming include examining the physical hazards and microbial hazards from water use, herbicide, and pesticide use, and impact from animals and animal byproducts. These do not impact CEA growers in the same way, if at all.”
As a result, a separate set of guidelines is needed.
This new certification process and the accompanying on-pack seal will spread awareness about CEA and unify these growers while differentiating them from traditional field growers, she said.
“It will allow producers to adhere to a standard tailored to indoor production and give incoming entrepreneurs guidance on the measures they'll need to meet to align with the existing industry,” Karlin said in the release.
The certification program is available to all CEA food safety coalition members for a small fee, and an external audit to the standard must be completed on an annual basis.
Growers are assessed across four key areas:
Hazard analysis: All potential hazards associated with a producer’s practices, including use of water, nutrients, growing media, seeds, inputs, and site control;
Water: Often used by CEA producers, recirculated water requires a continuing hazard analysis throughout its life cycle and zone-based environmental monitoring based on company-specific risk assessment, she said;
Site control: All food contact surfaces and adjacent food contact surfaces, including plant containers, must be considered and associated with potential farm physical hazards, including lighting, robotics, sensors, equipment, and utensils; and
Pesticide and herbicide use: Even though CEA-produced greens generally don’t use pesticides or herbicides, this module evaluates the potential risk of pesticide contamination and addresses if residue testing is required, she said.
“Consumer interest in food labels is high and shows a genuine desire to shop smarter,” Karlin said. “For consumers to truly make informed purchasing decisions, we need to explain what the labels mean, the process of certification and which labels they can trust.”
PinDuoDuo: Building A More Resilient Food System With Technology - July 14 -15
Join us virtually for our inaugural Food Systems Forum, which will convene experts from around the world to share their insights and spark further connections and potential collaborations
The pandemic has shone a light on how fragile and intertwined our global agri-food supply chain is, making it even more pressing to push for food systems innovation and change. Can we leverage technology to build a more resilient food system that feeds more people and feeds them better?
Join us virtually for our inaugural Food Systems Forum, which will convene experts from around the world to share their insights and spark further connections and potential collaborations.
Register To Join The Conversation
SpaceFarms Successfully Trialed With Grapes, Now Opts Almonds And Tomatoes
When Tusya first heard about vertical farming, she imagined a new generation of high-tech farming in Georgia. “I was fascinated when I heard about the possibilities of growing crops indoors in urban areas. Unfortunately, there’s little agricultural production in Georgia and lots of produce is imported from other countries.”
Introducing vertical farming to Georgia
Georgian vertical farming company SpaceFarms their product portfolio contains many different products such as salad greens, microgreens, herbs, and edible flowers. However, the company isn’t limiting itself to (leafy) greens only. “We’ve already grown three different grape varieties indoors because it’s a product we’re proud of here,” says Tusya Gharibashvili, Project author, and CEO. Tusya explains that Georgia is quite famous for its wine and its first wine was discovered 8000 years ago, research showed.
When Tusya first heard about vertical farming, she imagined a new generation of high-tech farming in Georgia. “I was fascinated when I heard about the possibilities of growing crops indoors in urban areas. Unfortunately, there’s little agricultural production in Georgia and lots of produce is imported from other countries.”
Crop trials
It’s important to us that we know how to enable grape cultivation indoors. Tusya noted they’re using cocopeat for the roots, and the results are promising thus far. “It gave us so much validation because we put so much effort into this and hopefully by rolling out more and more products, it will become more familiar to the Georgian (agri)culture,” Tusya affirms. Next to grapes, they’ve experimented with tomatoes and almond seedlings in a one-layer cultivar.
“We are now conducting strawberry trials so we still have supplied during the winter period. We’re constantly looking at opportunities for new crops to grow in our farm. We think it’s important to make people aware of the possibilities of growing in urban areas. We started experimenting with different crops in order to set the right growing parameters were.”
In 2017, Tusya started to dive into the concept of urban farming, together with her partner. Their first production facility comprised a 15 m2 cultivation area where various microgreens were grown. Produce was delivered to restaurants and other organizations in the catering sector. “It was something completely new for everyone and people were amazed by the concept of growing indoors.”
Government backing
After the initial success, Tusya started to follow up on more research in indoor vertical farming when she stumbled upon container growing. “After writing a motivation plan, I presented my ideas to Georgian investor to Mr. Temuri Ugulava the founder and the main driving force behind Adjara Group, decided to give it a try,” says Tusya.
At first, she started production inside a former Sovjet printing press building, now the award-winning Stamba Hotel., in order to supply fresh greens for the entire building. This was the first indoor farm space in Georgia. We had quite a tough time there, but with the help and support of Adjara Group, we made it through the first year.”
Nowadays, Space Farms produces 5000 plants per month and 30-kilo Microgreens in a 150m2 area, using seven layers. We grow our greens in the most efficient way possible. SpaceFarms applies 75% less water than traditional farming. Don’t use pesticides, using disruptive technologies, we fully control the environment (light intensity, nutrient intake, humidity, carbon dioxide emissions, and temperature) to yield optimal plant growth. Regardless of the season, we’re able to deliver fresh micro and leafy greens.
“It’s such a small effort, and yet such a big step towards sustainability. CEA growing is a great innovation that I think will change lots of the meaning of agriculture in combination with modern technology,” says Tusya.
Introducing modern agriculture
Space Farms collaborates with students from the University of Agriculture. The students are introduced to hands-on learning on the farm, from sowing to harvesting. Tusya says, “It’s a unique opportunity to have these students working on our farm, so they can get familiar with this new type of agriculture. In this way, we’re hoping to increase awareness on vertical farming throughout the country and eventually to neighboring countries.”
Next to running a farm, Spacefarms also working on a new project SpaceFarms spot, a farm growing kit that can be applied in any room. It’s the size of a fridge, which allows consumers or businesses to grow their own greens on location. “This will be something completely new in Georgia, so we hope to make a lasting impact. We might be a small country, but we can do big things with the help of technology. We’re backed by several programs from which we’ve received funding so we can further develop our Farm Pods,” adds Tusya.
Space Farms has received support from several programs. The programs are focusing on innovation and women in agriculture.
Lead photo: Tusya Gharibashvili
For more information:
Tusya Gharibashvili, Project author, and CEO Space Farms
1 Jun 2021
Author: Rebekka Boekhout
© VerticalFarmDaily.com
VIDEO: World Food Prices Rise At Fastest Pace In A Decade As Inflation Concerns Continue In U.S.
What's driving the increase? Drought in key growing regions including the western U,S. and Brazil, slowing vegetable oil production in Southeast Asia along with increasing costs for livestock producers and soaring Chinese demand
AgDay 06/04/21 - Food Prices
By AGDAY TV June 4, 2021
The United Nations issued a warning this week as world food prices are rising at their fastest pace in a decade.
The data comes from the UN's Food and Agriculture Organization (FAO)'s Food Price Index for May. The Index surged in May with prices rising at their fastest monthly pace since October of 2010. Global food prices have risen for 12 consecutive months and now sit at their highest level since September of 2011.
What's driving the increase? Drought in key growing regions including the western U,S. and Brazil, slowing vegetable oil production in Southeast Asia along with increasing costs for livestock producers and soaring Chinese demand.
Arlan Suderman of StoneX Group says inflation is also part of the equation.
"It definitely is a factor," says Suderman. "And we saw after the Beige Book report [Federal Reserve] came out this past week talking about inflation pressures, how money came into the commodity sector in the overnight trade following that report's release, and it's a hedge against inflation. However, whenever that causes the dollar to rise sharply because interest rates start to go up, then they start to pull back because the fear factor takes hold, we're not going to compete. Longer-term, though, the trend is inflation tends to be positive for the commodity sector, particularly those with a story."
Suderman says data indicates wage inflation is also having an impact. He says wage inflation is increasing at rates the U.S. hasn't seen since the 12th Federal Reserve Chair Jimmy Volcker held his position from 1979 to 1987, under U.S. presidents Jimmy Carter and Ronald Reagan.
"I still see momentum building on the flip inflation pressures right now," Suderman adds. "And a lot of people talk about it being transitory, the Fed talks a lot about that supply lines refilling, that's not what we're seeing in ag, this is a build up a demand that's been building up over time. And then when you look at wage inflation, the last four quarters in a row combined, the strongest wage inflation we've seen in four decades going back to the Paul Volcker era."
FAO says the world food price surge comes with a warning as it echoes similar moves in 2008 and 2011, when high costs led to food riots across some 30 nations.
USA - INDIANA: Planning A $1.7 Million Expansion Spread Over Four Years
GroPod, a Heliponix LLC brand, announced plans to grow its operations in southern Indiana, with plans to create up to 30 new, high-wage jobs in Vanderburgh County by the end of 2025
GroPod, a Heliponix LLC brand, announced plans to grow its operations in southern Indiana, with plans to create up to 30 new, high-wage jobs in Vanderburgh County by the end of 2025.
GroPod will invest more than $1.7 million over the next four years to expand its operations in downtown Evansville in order to support the production of its primary product, the GroPod system, which is a smart garden appliance that allows consumers the ability to grow vegetables, herbs and specialty plants in their homes.
“With our strong agricultural tradition and booming tech sector, Indiana offers an ideal environment for companies like GroPod that are at the intersection of ag and technology to flourish,” said Interim Indiana Secretary of Commerce Jim Staton. “Choosing to plant its roots in Evansville, GroPod will not only create high-skilled, high-wage jobs, but it will also bolster a growing industry that is developing innovative solutions, improving agricultural products consumed around the world, and providing consumers with a sustainable food source.”
Massey co-founded GroPod in 2016 with Ivan Ball, and the pair initially funded the business through pitch competition awards, including Gold and Black Awards totaling $100,000 from the Elevate Purdue Foundry Fund in 2018. Since then, the company has raised more than $1 million from investors. GroPod’s parent company, Heliponix, was recently awarded a National Science Foundation Small Business Innovation Research grant for $256,000 with a $50,000 Elevate match to research an LED lighting system to maximize the production of leafy vegetables.
“The city of Evansville is honored to be the home of GroPod,” said Evansville Mayor Lloyd Winnecke. “I’m grateful to the commitment of Scott and his team for their innovation and entrepreneurial spirit.”
For more information:
GroPod
www.gropod.io
Publication date: Wed 26 May 2021
Sadarah Partners With iFarm To Advance The Next Generation of Sustainable Vertical Farming in Qatar
A multi-year partnership will optimize indoor growing of leafy greens, strawberries and edible flowers, contributing to the implementation of Qatar’s National Food Security Strategy
Doha (Qatar), Helsinki (Finland), Moscow (Russia) - Sadarah (Qatar), owner of Agrico Organic Farm, and iFarm, a Finland-headquartered AgTech company with operations in Russia, Europe and globally, joined forces to build and collaboratively manage a commercial-scale indoor farm based on iFarm’s latest vertical farming technology in the State of Qatar. The multi-year partnership will optimize the growing of leafy greens, strawberries, and edible flowers and help ensure a steady year-round supply of fresh produce to the tables of Qatari people.
“This partnership brings one of the world’s most advanced vertical farming technologies to our country. Combining Agrico and iFarm’s capability will deliver consumers even more of the freshest produce on the same day,” said Mr Ahmed Hussain Al-Khalaf, Chairman of Sadarah/Agrico. “Strawberries and most lettuce varieties are now 100% imported and in many cases of a low quality and lacking freshness. Once the development is ready we will jointly be delivering the freshest strawberries and lettuces available anywhere in the world.”
The first phase of Sadarah-iFarm partnership involves developing a commercial trial farm at Sadarah’s Agrico Farm in Al Khor, Qatar. This will be the first deployment in the countries of Gulf Cooperation Council of an AI managed vertical farm that uses drones to monitor crop health and manage yields. Thus, combining Agrico's know-how and technology for farming in arid environments with iFarm’s state-of-the-art vertical farming solution will enable to improve the quality of crops and to maximize the yield in one of the world’s harshest environments.
The second phase of the joint project entails commercial distribution of the produce to the local Qatar market and the expansion of the vertical farming technology to other farms in Qatar and its regional neighbours. Both Sadarah and iFarm are focused on delivering the most flavourful, nutritious, fresh leafy greens, strawberries, and edible flowers at any time throughout the year. The partnership will also help Qatar reduce its heavy reliance on food imports and bring the country closer to achieving the goal of reaching a 70% self-sufficiency in food production by 2023, as outlined in Qatar’s National Food Security Strategy.
“Vertical farming is a key to boosting food security in Qatar, where conventional agricultural production is extremely challenging due to the country’s hot and arid climate. We are excited to tap into Agrigo’s long-standing expertise in the region and work together toward helping Qatar achieve its ambitious goals of food independence”, said Kirill Zelenski, CEO of iFarm - Intellectual Farm, OY. “I believe that it's the beginning of a long-term and fruitful collaboration. The role of iFarm won’t be limited to simply supplying equipment and software at the construction phase, but we will help oversee the farm after it’s up and running and provide support to our partners in managing iFarm’s cutting-edge technology.”
Qatar-Russia Investment and Trade Advisory (QRITA) acted as an advisor in establishing the partnership and will continue to work with iFarm and Sadarah to develop their joint venture further.
Oleg Chizh, Managing Director and CEO of QRITA, said: “We are pleased to facilitate the integration of the advanced agricultural technology by iFarm into the food security framework in Qatar and the MENA region, in partnership with Sadarah - one of the leading diversified conglomerates in the region, with a long-standing history in the food and agriculture space. This is consistent with QRITA’s mission to enable impactful cross-border partnerships between the Russia/CIS and GCC regions. We look forward to supporting the partners in launching this pilot project and, hopefully, many subsequent projects. We are honored to contribute to promoting sustainable urban farming in Qatar.”
About Sadarah LLC (Qatar): Established in 2005, Al Sadarah Group has established itself as one of the leading family-owned conglomerates in the region. A business enterprise built around traditional family values and an uncompromising commitment to integrity, premium service, and social responsibility. Al Sadarah Group has created new benchmarks of excellence within its diverse portfolio which has grown to include ventures in F&B, real estate development, education, constructions, engineering, and investment.
Agrico Qatar is a private Qatari Agricultural Development Company that was founded on the principle of sustainable long-term agricultural production with an eye on the National target of achieving food security. AGRICO has achieved this through combining local innovation, international expertise, and the best available technology in the world. Agrico is one of the first and largest organic smart farms in Qatar, with 100,000 sqm of organic greenhouses. Production more than 10,000 ton/year and distribution over 1,400 supermarkets, restaurants, and cafes in Qatar. Using the most cutting-edge locally developed technology and turnkey solution system.
About iFarm — Intellectual Farm, OY (Finland): Established in 2017, iFarm provides innovative technologies for growing fresh greens, berries, and vegetables. iFarm has farms operating and under construction in Europe, Middle East, Russia, and CIS, with a total planting area of more than 30.000 m². iFarm technologies are recognized worldwide: the project is included in the TOP 500 food startups of the world and is a member of the EIT Food Accelerator Network; iFarm also became the best agricultural startup in Europe in The Europas Awards 2020, the winner in the category of the best social impact startup of Nordic Startup Awards 2019. Recently, iFarm received a Solar Impulse Efficient Solution label that certifies environment-friendly technologies that have proven to be profitable and economically viable.
About QRITA (Russia): QR Investment and Trade Advisory is a specialist cross-border advisory and business development firm that supports and facilitates the proactive development of business transactions between the markets of Qatar and Russia, as well as between the broader Gulf and Russia/CIS regions. QRITA is a subsidiary of the Qatari-Russian Center for Cooperation (QRCC).
Vertical Farming Startup Hopes To Make Fresh, Healthy Greens More Affordable Across America
Forward Greens, a Vancouver, Washington-based vertical farm is re-envisioning and repurposing existing machinery, technology, and traditional farming methods. Founder Ken Kaneko who previously worked in tech at Intel and Apple is now looking at how to make indoor farming an accessible resource across the nation
May 28, 2021
Vertical farming startup from Vancouver, Washington, hopes to transform the "greens" industry.
FORWARD GREENS
With land expensive to buy, and farmers facing weather-related changes constantly and a push towards more eco-friendly and local production of food, could indoor (and vertical) farming be part of the answer?
Forward Greens, a Vancouver, Washington-based vertical farm is re-envisioning and repurposing existing machinery, technology, and traditional farming methods. Founder Ken Kaneko who previously worked in tech at Intel and Apple is now looking at how to make indoor farming an accessible resource across the nation.
Here’s more on his unique journey from tech to agriculture and his new mission to get us growing more green vertically.
Chhabra: You were inspired in Japan. Tell me what you saw there and how it got your wheels turning.
Kaneko: When I was working at Apple, I went to Japan on business to look for real estate for manufacturing electronics components for phones and other devices. Japan used to have many semiconductor and hard-disk manufacturing sites before much of it got off-shored, much like America. We took a look at many of these older sites, which were oftentimes empty or repurposed for other activities. One of the sites was operating as an indoor farm, and that piqued my interest.
My background is in R/D for semiconductors, and the fact that there were plants growing in an old semiconductor fabrication made me think, “Maybe I can try this.” So I did.
Founder Ken Kaneko | FORWARD GREENS
Chhabra: Why don't we do more vertical farming? It makes a lot of sense from various angles — space, water, cost, etc.
Kaneko: There’s a capital intensity that is not easy to manage. That’s in part due to the fact that a strong vendor and sub-vendor network has not yet matured, so getting the right equipment in place can require big up-front costs. While vertical farming is poised to transform the future of agriculture because of its multiple benefits across the environment, food safety and supply chain, starting a farm can be expensive, especially if it’s built to scale. Production has yet to be formalized so that it can be replicated and used as a template to build multiple vertical farms across the country, and this would help the industry deliver a cost-effective product to consumers in a financially sustainable way.
Another key component is that introducing something new takes time. The idea of vertical farming is gaining traction, but most consumers require education to understand what exactly it is, how it works, its benefits, the things that can be grown, etc. Without that knowledge, it can be an intimidating industry. Produce itself is also heavily commoditized. So many marketing dollars have gone into different brands, farming methodologies, cultivars, etc. Overcoming that, especially as a new entrant, takes time.
Chhabra: How did you fund this venture?
Kaneko: Forward Greens was funded through a mixture of capital from friends, acquaintances and from my own savings.
Chhabra: What challenges did you face in your first harvest? Any big learning curves?
Kaneko: Everything about this experience has been humbling. For the first harvest, things went surprisingly well with respect to product formulation, product packaging, quality assurance and food safety. The part that was the trickiest was learning how the distribution business works with respect to retailer preference and margin expectations.
Chhabra: Is vertical farming getting enough traction and support, in your opinion?
Kaneko: I think vertical farming is beginning to gain traction as a number of facilities are opening up across the country. Vertical farms, in conjunction with controlled environment greenhouses, will likely create a unique market category known for never using pesticides, herbicides or fungicides. Alongside the environmental benefits, these farms provide a significant safety factor that outdoor farming has difficulties in controlling, especially with fresh produce.
Chhabra: How do you think you can make vertical farming more cost-effective and easier to replicate?
Kaneko: From an idealistic engineering perspective, I would like to think anything is possible in terms of making vertical farming more cost-effective. The difficult part is executing this possibility at a reasonable cost. To do it, the industry requires the collective learnings built on the successes and mistakes of everyone involved. You see something similar with the recent technologies in electronics and automobiles. As companies start iterating on others’ ideas, innovations happen. And when more companies build on these solutions it actually helps drive down costs associated with those solutions.
Forward Greens is highly focused on the costs related to delivering a fantastic product to the consumer. We aim to optimize the cost of the whole process by using existing machinery, technology and methods already tried and tested in agricultural and packaging industries. Our focus is on streamlining production to spend more time pushing the practice toward its intended use: using less land, less water, zero pesticides and prioritizing the environment. Efficiencies in how to use technology lead to new ways to apply the technology.
Chhabra: What do you make of all this chatter around regenerative agriculture? Where does vertical farming fit into this?
Kaneko: Agriculture heavily impacts greenhouse gas emissions, in addition to the space utilization, deforestation, water and chemical discharge in the environment. And many people are now noticing these effects. Any practice or methodology that helps in mitigating impacts on the environment should be considered as part of the portfolio of solutions. Regenerative agriculture, organic farming, controlled environment agriculture and vertical farming should all be pursued as they optimize on varying impacts.
Much like negotiating problems spanning science, politics, etc, there is rarely a single solution that addresses all of the issues. I think this is especially true for something as complex as climate change and repairing the environment.
Chhabra: Do you have to have a branded product to make it a profitable venture or can you just be a classic farmer (albeit vertically) and sell the crop to distributors/ CSAs/ markets?
Any of these models can work. Forward Greens opted to brand our greens because we hope to educate the consumers about the benefits of our methodologies and products. Because we’re indoors, we use no pesticides, herbicides or fungicides. We use 97% less land and 95% less water than traditional outdoor agriculture. As a company and brand, Forward Greens is also able to build local partnerships within our own community through employment opportunities and food donations. These benefits and possibilities are due in large part because we grow our products and distribute them under our brand.
Because farm products traditionally trade many hands, the integrity of the product is oftentimes diluted at each node of the supply chain. The farms, packers, distributors, etc. all have competing interests, so messaging and communication can be inconsistent to the end consumer. Forward Greens believes in what we’re doing and how we’re doing it, so we want to keep a channel of communication open directly with our consumers.
I cover a new taxonomy that looks at the crossroads of business and impact, particularly brands and individuals who are developing solutions for social and environmental problems. As a freelance journalist, I’ve written for numerous publications, including the San Francisco Chronicle, New York Times, Atlantic, Economist, and The Guardian. In recent years, the Pulitzer Center for Crisis Reporting has supported my reporting from Asia, which looks at sustainable fashion, global health, and technology for development. Follow me on Twitter @esh2440 or on Instagram at @eshatravels.