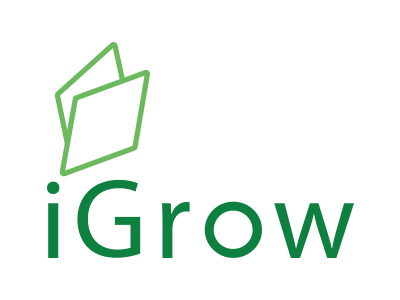
Welcome to iGrow News, Your Source for the World of Indoor Vertical Farming
Urban Home For High Tech Horticulture In Australia
A feasibility study will be conducted to identify the opportunities and challenges for high technology horticulture in urban Australia
RMCG has kicked off 2021 with a new project for the Australian horticulture industry, which aims to assess the potential of emerging production technology and its application in the urban landscape.
Vertical farms, aquaponics, floating farms – these are just some of the many possibilities of high technology horticulture in urban areas across the globe. But are they feasible for Australian growers?
RMCG is excited to lead a consortium in partnership with the University of Technology Sydney (UTS) and global urban agriculture consultancy ugritecture to answer that very question. The six-month project, funded by Hort Innovation, will assess the potential of emerging production technology and its application in the Australian urban landscape, which will also cover regional areas and hubs.
High technology horticulture and emerging production technology can benefit Australian growers and industry by developing food production and delivery systems that have the potential to optimize yield, quality and supply. Examples of this technology include vertical farm systems, hydroponics, aquaponics, nearly fully automated production as well as rooftop, underground and floating farms.
Project approach
A feasibility study will be conducted to identify the opportunities and challenges for high technology horticulture in urban Australia. It will identify a range of high technology systems and assess their applicability to urban Australia by considering: regulation and planning, farm input and waste, supply chain logistics, and social, environmental, and economic aspects.
The project will include a high-level literature review and modeling of the social and environmental impacts. The economics of high technology systems for urban horticulture will also be analyzed.
The study is being guided by an industry-led reference group including growers and emerging commercial leaders engaged in urban high technology horticulture in Brisbane and Sydney, members of local city councils, and subject-matter experts in protected cropping.
The outcomes of the study will identify future priorities for research, development and extension activities and investment into Australian high technology horticulture in urban areas.
For more information:
RMCG
www.rmcg.com.au
28 Jan 2021
What Are The Emerging Trends Affecting Indoor Farming? State of Indoor Farming Survey
Artemis Ag has opened its third annual State of Indoor Farming Survey, and is looking for your input
By Artemis Ag
January 9, 2021
Photo: Kalera
Artemis Ag has opened its third annual State of Indoor Farming Survey, and is looking for your input. The survey will provide insights on emerging trends and challenges in the greenhouse and vertical farming industries.
“We’re looking forward to learning how growers are facing new challenges such as COVID-19,” says Allison Kopf, CEO of Artemis Ag. “In the past, expansion was one of the prime goals for growers, and we’ve asked some new questions around the topic. We will be sharing even more information related to technology usage, the evolution of the industry, and how growers are working with lenders.”
In the past few years, more than 500 growers have participated in Artemis’ annual State of Indoor Farming Surveys. Past reports have been downloaded more than 2 million times and are one of the most widely circulated and respected sources of industry data.
More and better data collected means more insights for growers. Growers can participate in the 2020 State of Indoor Farming survey here.
The survey will be open for a few weeks and Artemis expects to launch the 2020 report immediately following.
Learn more here.
How Vertical Farms Could Be Ready To Take-Off
Carried out by the John Innes Centre, the University of Bristol, and the aeroponic technology provider LettUs Grow, the study identifies future research areas needed to accelerate the sustainable growth of vertical farming using aeroponic systems
12-01-2021 | LettUsGROW
Vertical farms with their soil-free, computer-controlled environments may sound like sci-fi, but there is a growing environmental and economic case for them, according to new research laying out radical ways of putting food on our plates.
The interdisciplinary study combining biology and engineering sets down steps towards accelerating the growth of this branch of precision agriculture, including the use of aeroponics which uses nutrient-enriched aerosols in place of soil.
Carried out by the John Innes Centre, the University of Bristol, and the aeroponic technology provider LettUs Grow, the study identifies future research areas needed to accelerate the sustainable growth of vertical farming using aeroponic systems.
Dr. Antony Dodd, a Group Leader at the John Innes Centre and senior author of the study, says: “By bringing fundamental biological insights into the context of the physics of growing plants in an aerosol, we can help the vertical farming business become more productive more quickly while producing healthier food with less environmental impact.”
Jack Farmer, Chief Scientific Officer at LettUs Grow and one of the authors of the study, adds: “Climate change is only going to increase the demand for this technology. Projected changes in regional weather patterns and water availability are likely to impact agricultural productivity soon. Vertical farming offers the ability to grow high-value nutritious crops in a climate-resilient manner all year round, proving a reliable income stream for growers.”
Vertical farming is a type of indoor agriculture where crops are cultivated in stacked systems with water, lighting and nutrient sources carefully controlled.
It is part of a rapidly growing sector supported by artificial intelligence in which machines are taught to manage day to day horticultural tasks. The industry is set to grow annually by 21% by 2025 according to one commercial forecast (Grand View Research, 2019).
Green benefits include better use of space because vertical farms can be sited in urban locations, fewer food miles, isolation from pathogens, reduction in soil degradation and nutrient and water recapturing and recycling.
Vertical farms also allow product consistency, price stabilization, and cultivation at latitudes incompatible with certain crops such as the desert or arctic.
“Vertical systems allow us to extend the latitude range on which crops can be grown on the planet, from the deserts of Dubai to the 4-hour winter days of Iceland. In fact, if you were growing crops on Mars you would need to use this kind of technology because there is no soil,” says Dr Dodd.
The study, which appears in the journal New Phytologist, lays out seven steps – strategic areas of future research needed to underpin increased productivity and sustainability of aeroponic vertical farms.
These seek to understand:
Why aeroponic cultivation can be more productive than hydroponic or soil cultivation
The relationship between aeroponic cultivation and 24-hour circadian rhythms of plants
Root development of a range of crops in aeroponic conditions
The relationship between aerosol droplet size and deposition and plant performance
How we can establish frameworks for comparing vertical farming technologies for a range of crops
How aeroponic methods affect microbial interactions with plant roots
The nature of recycling of root exudates (fluids secreted by the roots of plants) within the nutrient solutions of closed aeroponic systems
The report argues that a driver of technological innovation in vertical farms is minimising operation costs whilst maximising productivity – and that investment in fundamental biological research has a significant role.
Dr. Dodd’s research area covers circadian rhythms – biological clocks that align plant physiology and molecular processes to the day to day cycle of light and dark. He recently completed a year-long Royal Society Industry Fellowship with LettUs Grow.
This involved combining Dr Dodd’s expertise in circadian rhythms and plant physiology with the work of LettUs Grow’s team of biologists and engineers to design optimal aeroponic cultivation regimens. This is a key area of investigation as these molecular internal timers will perform differently in vertical farms.
Aeroponic platforms are often used to grow high-value crops such as salads, pak choi, herbs, small brassica crops, pea shoots, and bean shoots. LettUs Grow are also working on growth regimens for fruiting and rooting crops such as strawberries and carrots, as well as aeroponic propagation of trees for both fruit and forestry.
John Innes Centre researchers have bred a line of broccoli adapted to grow indoors for a major supermarket and one of the aims of research will be to test how we can genetically tune more crops to grow in the controlled space of vertical farms.
Bethany Eldridge, a researcher at the University of Bristol studying root-environment interactions and first author of the study adds: “Given that 80% of agricultural land worldwide is reported to have moderate or severe erosion, the ability to grow crops in a soilless system with minimal fertilizers and pesticides is advantageous because it provides an opportunity to grow crops in areas facing soil erosion or other environmental issues such as algal blooms in local water bodies that may have been driven by traditional, soil-based, agriculture.”
Lilly Manzoni, Head of Research and Development at LettUs Grow and one of the authors of the study says, “This paper is unique because it is broader than a typical plant research paper, it combines the expertise of engineers, aerosol scientists, plant biologists, and horticulturalists. The wonderful thing about controlled environment agriculture and aeroponics is that it is truly interdisciplinary”
The study ‘Getting to the Roots of Aeroponic Indoor Farming‘ appears in the New Phytologist journal.
Source and Photo Courtesy of LettUsGROW
Japan: Operating Rate of 99% In Large-Scale Automated Farm
Stable production at a large-scale automated vertical farm, with a production capacity of 30,000 heads of lettuce per day, and running at full strength, is an achievement yet to be demonstrated at any other facility worldwide
Spread Reaches High Operating Rate At Techno Farm Keihanna
Spread Co., Ltd. has reached the operating rate of 99% at Techno Farm Keihanna, a large-scale automated vertical farm. This percentage is based on the number of harvested heads compared to the maximum capacity of the farm. Stable production at a large-scale automated vertical farm, with a production capacity of 30,000 heads of lettuce per day, and running at full strength, is an achievement yet to be demonstrated at any other facility worldwide. This will further support Spread’s expansion, as it strives to establish a model for sustainable agriculture.
The challenge of large-scale vertical farming
Stable production at a large-scale is considered one of the toughest challenges in vertical farming. Spread’s Kameoka Plant claims to achieve profitability and an operating rate of 97% within 6 years. Techno Farm Keihanna started operating in November 2018. It has now achieved a stable operating rate of 99% and has delivered a monthly average product weight of over 3 tons since October 2020.
Stable production and environmentally sustainable
Spread’s Technologies are implemented at the Techno Farm Keihanna, which is a high-level synergy of automated cultivation and human operations. Accordingly, Spread succeeded in automating most of the labor-intensive processes, to make the whole process inside the farm more efficient and cost-saving. Next to that, they make use of precise environmental control technology for large spaces Spread’s technology ensures there is little variation in temperature and humidity, even at a large scale. Analysis of the actual cultivation environment allows for stable production and consistent high quality.
Furthermore, the farm has a Techno Farm Cloud implemented. Meaning, a unified IoT-based management system for all farm operations. The visualization of cultivation data has brought efficiency improvements to farm management. Through analysis of the cultivation and post-harvest data, Spread maximizes cultivation efficiency and achieves truly smart agriculture.
The Techno Farm Keihanna
The environmentally sustainable factors used are water recycling technology and LED lights, optimized for vertical farming. Techno Farm Keihanna recycles over 90% of the water used in cultivation, allowing for savings of 16,000 liters/day. (This is equal to more than 10 million 500ml water bottles saved every year). Spread’s unique LED lights allow for a reduction in energy consumption by 30% compared to conventional LED lights. Implemented at both Kameoka Plant and Techno Farm Keihanna.
Sales performance
According to the Spread team, the demand for vertically farmed vegetables among consumers and the foodservice industry has been rising. Spread has been steadily increasing shipment volume since the start of operations at its Techno Farm Keihanna. Together with the utilization of an in-house logistics system, this has helped Spread to expand its presence among major Japanese retailers. At the moment, Spread supplies 3,600 stores across Japan.
Future developments
Using the validated technology of the Techno Farm TM, Spread is pursuing further business opportunities through technological innovation and collaboration with stakeholders, both in
Japan and overseas. Spread aims to provide solutions for the global problems of climate change and food security, and to deliver the SDGs through the creation of a truly sustainable society.
For more information:
Spread Co., Ltd.
www.spread.co.jp/en
Sustainable Food Leads £6m Research Project To Transform The UK food System
Food security and sustainability are among the greatest challenges facing the world today, and traditional approaches of intensifying food production are coming under criticism for not looking at the whole picture of how we produce, and supply food to the nation
By India Education Diary Bureau Admin
January 10, 2021
A new £6m research project titled Healthy soil, healthy food, healthy people (H3) seeks to transform the UK food system from the ground up via an integrated programme of interdisciplinary research.
Social and natural scientists from the Institute for Sustainable Food at the University of Sheffield will collaborate on a whole-system approach to emphasise the links between production and consumption and identify practical paths towards food system transformation.
Food security and sustainability are among the greatest challenges facing the world today, and traditional approaches of intensifying food production are coming under criticism for not looking at the whole picture of how we produce, and supply food to the nation.
The Covid-19 pandemic also shone a light on the fragility of the UK’s food systems resilience and how its reliance on foreign imports during a global crisis meant people in the UK experienced empty shelves, and shortages of basic staples such as flour and pasta.
The H3 consortium – which draws on the combined strength of researchers from the University of Sheffield, University of Leeds, University of Bristol, University of Cambridge and City, University of London as well as a wide range of stakeholders from government, business and civil society – will focus its research on horticulture, hydroponics and hybrid farms, and on the health benefits of biofortification and increased fibre consumption.
This is an exciting, once-in-a-lifetime, opportunity to use cutting-edge research to have a genuinely transformative effect on the health and sustainability of the UK food system.
“We are delighted that the Institute for Sustainable Food will be leading one of the four consortia to be funded by the UK Research and Innovation’s Transforming the UK Food System for Healthy People and a Healthy Environment programme.
Professor Peter Jackson
Co-director of the Institute for Sustainable Food at the University of Sheffield
The project will identify practical paths towards food system interventions: on farm, in food manufacturing and retail, and improve dietary health and environmental sustainability of the agri-food industry in the UK.
This will include finding ways to increase the production of health-promoting vegetables while reducing reliance on harmful agricultural inputs and imported food by integrating hydroponic production systems within conventional soil-based farms. The project will also look at how improving the microbiomes of growing mediums has the potential to increase nutrients in our food systems and reduce our reliance on pesticides.
We are absolutely delighted by this award and excited to apply the food systems-level thinking we’ve developed at the Institute for Sustainable Food to the real world.
“Backed up by our world-leading research, this work has huge transformational potential to improve the sustainability, the quality, and the equity of our agri-food system here in the UK. Working closely with our external partners will add a real world perspective to shape how our initiatives are applied.
“In terms of fighting the climate crisis, this kind of transformational research is sorely needed. We are delighted that the Institute for Sustainable Food will be leading the way in developing and applying that research.”
UK: £5m Funding Award For John Innes Centre To Modernize Horticultural Facilities
A little over £3m of the investment will provide new Controlled Environment Rooms (CERs) for plant and microbial experiments. CER’s offer scientists precise control of environmental factors such as light, temperature, and humidity
A multi-million-pound project to modernize the horticultural facilities at John Innes Centre has been approved.
The £5.1m upgrade is funded by UKRI-BBSRC. Work will begin in Autumn 2020, and the project set to be completed by March 2021.
The company's Horticultural Services support the world-renowned science of the John Innes Centre and The Sainsbury Laboratory and occupies a large site on the Norwich Research Park.
A little over £3m of the investment will provide new Controlled Environment Rooms (CERs) for plant and microbial experiments. CER’s offer scientists precise control of environmental factors such as light, temperature, and humidity. The upgrade will also improve the containment measures required for experiments that investigate plant pathogens, or for growing genetically modified plants.
The new infrastructure offers energy efficiency and sustainability gains due to LED lighting, wastewater treatment, and rainwater harvesting. The reduction in utility costs from installing these technologies is estimated to be £116,000 per year.
Further savings will be achieved by more efficient use of glasshouse space (£200,000 per year) and reduced reliance on off-site horticultural facilities (£240,000) per year.
The current glasshouses (which cover an area of 5,775m2) is mostly single-span structures designed and built several decades ago. This investment is the start of a long-term move away from using glasshouses and towards controlled environments which better enable consistency of inputs and experimental results.
Head of Horticultural Services at the John Innes Centre, John Lord said: “World-class science needs world–class, market-leading technology. This investment is timely because there is a desperate need for our scientists to work on solutions to the challenges that face us. From understanding pathogens that cause plant diseases, to creating climate-resilient, nutritious crops that feed the world.
“This investment will bring a much-needed upgrade, providing facilities that are relevant and appropriate for the world-leading plant and microbial science that takes place on the Norwich Research Park. It also future proofs the site to fit with longer-term ambitions to redevelop the infrastructure here.”
Features of the new modernization include 30m2 of large walk-in growth space which offers LED lighting, nutrient enrichment, climate control, and state-of-the-art irrigation systems. The spaces will be configurable, it can be divided into multiple layers or used as a large open space, offering the next step towards bigger trials for crops.
The new facility will also benefit from a sustainable water supply, as it will harvest rainwater. The rainwater will be monitored and treated onsite to ensure it is free from phytopathogens, and that it has the correct pH. This soft, nutrient-rich harvested rainwater means that scientists will be able to minimize the use of fertilizers, and the consistent, monitored water supply will ensure that scientific experiments are reliable and repeatable.
“This is the start of a wider, long term project to update horticultural services at the John Innes Centre to ensure that it continues to meet the needs of science of today while being flexible enough to meet the needs of tomorrow as problems and new technologies arise,” said John.
For more information:
John Innes Centre
www.jic.ac.uk
Publication date: Thu 8 Oct 2020
Vertical Farming: IDTechEx Research Asks How Big Is Too Big
An ongoing argument within the industry is a question of size – is it better to focus on building a large, highly automated plant factory to minimize production costs, or is a small, more flexible approach the best way to set up a vertical farm?
NEWS PROVIDED BY IDTechEx
Oct 05, 2020
BOSTON, Oct. 5, 2020,/PRNewswire/ -- Vertical farming is growing quickly. The concept of vertical farming, the idea that crops can be grown far more efficiently indoors under controlled environmental conditions than would be possible on conventional farmland, has captured the imagination of entrepreneurs and investors alike, with dozens of start-ups being founded across the world raising ever-increasing amounts of investor capital. The recent IDTechEx report, "Vertical Farming 2020-2030" explores the technologies and market factors that are shaping this rapidly expanding industry.
An ongoing argument within the industry is a question of size – is it better to focus on building a large, highly automated plant factory to minimize production costs, or is a small, more flexible approach the best way to set up a vertical farm?
This question stems from some of the challenges facing the vertical farming industry. Setting up and running a vertical farm is not cheap and many vertical farming companies have struggled to overcome spiraling labor and power costs, alongside unforeseen logistical complexities, and issues with maintaining an optimum growing environment.
A potential solution to some of these problems is to build a very large vertical farm, which allows the power costs to be averaged out over a large quantity of crops. Additionally, large vertical farms make it easier to justify using advanced automation systems that can help reduce labor costs, with the cost of the automated systems also being spread out over large quantities of crops. These sorts of economies of scale can help a vertical farm begin to reach price parity with a conventional farm, something which has long eluded smaller vertical farms, which are often forced to sell produce in premium categories. Large vertical farms producing large quantities of crops can also be more easily incorporated into existing food supply chain structures, for example, next to a supermarket's main distribution center.
One company attempting to use this scale-based approach is Jones Food Company, a British vertical farming start-up that currently operates Europe's largest vertical farm. The company believes that the only way that vertical farming will be successful in the long term is by reaching price parity with conventional farming, which it hopes to achieve through automation and by operating large scale facilities close to distribution centers.
The company takes its inspiration from car factories – it is far more cost-effective to produce cars in a large central facility than it would be to produce them in small facilities near the dealerships and Jones Food Company believes this same logic applies to vertical farming. Crops grown in distribution centers are still able to reach consumers rapidly, often within a day of harvest, and the company doesn't believe that the hyper-local model promoted by certain competitors is worth the inefficiencies and costs of many small facilities located in city centers.
Several other vertical farming companies are following this approach, with New Jersey start-up AeroFarms announcing in 2019 that it was investing $42 million to construct a 150,000 square foot facility in Danville, Virginia, which the company claims will be the largest in the world. Jeff Bezos-backed Plenty operates a 52,000 square foot facility in South San Francisco, with the company aiming to maximize production efficiency to improve the economics of vertical farming.
Not everyone agrees with this large-scale approach, however. Large facilities and automation are expensive, with large scale facilities costing tens of millions of dollars to set up. Whilst this approach might make sense for a factory producing cars or other high-margin products, for low margin products such as fresh produce, it can take decades to pay back this initial investment.
Additionally, supply and demand for fresh produce is not always consistent and pricing can change frequently, making it difficult to accurately predict returns on investment, which can be very problematic for a vertical farm that cost several million dollars to build. Furthermore, many of the processes required to grow crops cannot yet be addressed through off-the-shelf automation solutions, creating difficult engineering challenges that can make scale-up very complicated.
A further problem for very large-scale vertical farms is that operational complexity can increase vastly for larger farms. Plants are living organisms that can behave in unpredictable ways, making it difficult to grow them in a manner resembling a factory production line. Plants give out heat and water vapor as they grow, whilst also needing a supply of carbon dioxide and oxygen, in addition to nutrients. Keeping the crop inputs consistent across the whole vertical farm and managing waste heat and water vapor can also be very difficult in a high-density growing space. Careful consideration of the plant science, alongside planning the logistical workflow to maximize efficiency are needed to successfully operate a large-scale vertical farm.
Because of these challenges, some companies have chosen instead to focus on smaller vertical farming facilities, choosing to focus on flexibility instead of economies of scale. For example, Freight Farms, which manufactures turnkey modular vertical farms inside 40' containers, believes that smaller vertical farms enable a more flexible and targeted business model than large, centralized facilities. Small vertical farms can be tailored to certain markets with gaps, such as crops that can't be imported, transient falls in supply for high-demand crops, and restaurants or food suppliers that need a specific ingredient. These are all markets in which large, warehouse-like vertical farms cannot easily access.
Rather than focusing on mass-produced, wholesale crops, where vertical farms will always struggle to compete on price with traditional farms and greenhouses, it may make more sense for vertical farm operators to focus on high-value crops that command a price premium, perhaps within niche markets or specialized applications.
The debate over the best size for a vertical farm is still ongoing. There is no easy answer on which model is best, and a would-be vertical farm operator should carefully consider their options and target market before starting a business. For more information and discussion over business models in vertical farming, as well as industry evaluations and 10-year market forecasts, see the recent IDTechEx report "Vertical Farming 2020-2030".
For more information on this report, please visit www.IDTechEx.com/VertFarm or for the full portfolio of AgTech research available from IDTechEx please visit www.IDTechEx.com/Research/AgTech.
IDTechEx guides your strategic business decisions through its Research, Consultancy and Event products, helping you profit from emerging technologies. For more information on IDTechEx Research and Consultancy, contact research@IDTechEx.com or visit www.IDTechEx.com.
Media Contact:
Natalie Moreton
Digital Marketing Manager
press@IDTechEx.com
+44(0)1223 812300
SOURCE IDTechEx
Valoya Announces Its Spectrum Technology Licensing Program
Valoya’s extensive patent portfolio in the field of horticultural LED lighting is a result of significant innovation and investments into R&D over the past 11 years
Valoya, the research-driven LED grow light manufacturer has today announced a licensing program making their patented technology available to LED manufacturers and horticultural LED fixture providers.
Valoya’s extensive patent portfolio in the field of horticultural LED lighting is a result of significant innovation and investments into R&D over the past 11 years. The patents are in the field of light spectra for plant cultivation and lighting applications. At the moment, the portfolio consists of over 100 patents, all of which can be reviewed at valoya.com/patents.
'We have always been curious about the possibilities of light and how its potential could be pushed further to make cultivation of crops we use for food or medicine production more efficient. When we started in 2009, LED meant piercing purple light produced by red and blue chips. We were the first to apply wide spectrum LED light to plants in our experiments and to introduce wide spectrum light to the market. We are now in a business phase where we can extend this intellectual property and know-how to other companies wishing to produce premium quality horticultural LED luminaires through our licensing program' comments Lars Aikala, the CEO and Co-Founder of Valoya.
The research and development at Valoya does not stop. ‘After having conducted over 600 plant trials on over 300 plant varieties/species, we have an understanding of plant response to light, unmatched by other LED companies in the market. The focus remains on advancing horticulture through developing even better spectra and helping our customers grow. We are happy we get to share this expertise with other companies now’, comments Nemanja Rodic, Marketing Director of Valoya.
To learn more about Valoya's patent licensing program,
please click here.
About Valoya
Valoya is a provider of high end, energy-efficient LED grow lights for use in crop science, vertical farming, and medicinal plants cultivation. Valoya LED grow lights have been developed using Valoya's proprietary LED technology and extensive plant photobiology research. Valoya's customer base includes numerous vertical farms, greenhouses, and research institutions all over the world (including 8 out of 10 world’s largest agricultural companies).
Additional information:f
Valoya Oy, Finland
Tel: +358 10 2350300
Email: sales@valoya.com
Web: www.valoya.com
Facebook: https://www.facebook.com/valoyafi/
Twitter: https://twitter.com/valoya
Aquaponics AI, A US-Based Aquaponic Technology Research Company, Just Unleashed Their Software Into The Wild
In addition to being the forerunner in Aquaponic technology, they also have invaluable libraries for fish, plants, and diseases, as well as calculators for managing your system
Aquaponics AI, a US-based aquaponic technology research company, just unleashed its software into the wild. It’s the system every aquaponic grower has been waiting for. It has traditionally been difficult to get started in Aquaponics because of the steep learning curve but they are making it easy to get started and maintain a system with features like a project template that gets your system running with recommended maintenance schedules by big players in Aquaponics.
They’re bringing innovative usage of artificial intelligence and big data to Aquaponics for the betterment of the global aquaponics community. Their vision is to unleash your Aquaponic growing powers. You’re the beneficiary of high-quality produce and revenue streams created from your system.
In addition to being the forerunner in Aquaponic technology, they also have invaluable libraries for fish, plants, and diseases, as well as calculators for managing your system.
“We’re about empowering people to be the best aquaponic growers possible. Tech is what gives people the tools to do awesome things.” - Jonathan Reyes, CEO, and Co-founder of Aquaponics AI
You can see the latest developments on their website https://aquaponics.ai alongside invaluable resources and calculators that are available for free.
Tags: Aquaponics, Dashboard, IoT, Sensors, Cloud
Texas A&M AgriLife Expands Urban Agriculture Research
Niu’s research is in urban horticulture specifically. This can conjure images of community and backyard gardens, or rooftop and balcony plant installations, but her focus is producing quality food in controlled environments
A living, vertical salad bar in the employee break room is more than just a novelty at the Texas A&M AgriLife Center at Dallas. It is a small, and delicious, sign of the comprehensive urban agriculture research ramping up at the center in 2020.
Genhua Niu, Ph.D. Texas A&M AgriLife Research professor of controlled environment agriculture, with an indoor vertical garden system at the Texas A&M AgriLife Center at Dallas (Texas A&M AgriLife photo by Patricia Moran)
The purple-glowing installation arrived at Dallas with Genhua Niu, Ph.D., and Texas A&M AgriLife Research professor of controlled environment agriculture. Her research team represents one component of an overarching push by Texas A&M AgriLife to realize sustainable production of nutritious food within cities — the next frontier in commercial agriculture.
Niu’s research is in urban horticulture specifically. This can conjure images of community and backyard gardens, or rooftop and balcony plant installations, but her focus is producing quality food in controlled environments. Her studies are especially relevant in Dallas — of which certain communities are urban food deserts — and they carry promising implications for agriculture industries across rural Texas, too.
“AgriLife’s substantial investments in urban agriculture innovation reflect our commitment to better human nutrition and health at every interval along the food supply chain,” said Patrick Stover, Ph.D., vice chancellor and dean of Texas A&M’s College of Agriculture and Life Sciences and director of AgriLife Research. “In addressing these obstacles, we can bring to bear the considerable research and extension resources of the Texas A&M University System.”
Bringing urban horticulture to Dallas
Niu comes to Dallas from the AgriLife Center at El Paso, where her work since 2004 hinged on research conducted in varying greenhouse settings. Now, controlled environments at the renovated urban center at Dallas allow her to direct innovation toward vertical farming systems housed fully indoors.
Niu earned her doctorate in horticultural engineering at Chiba University in Japan as controlled environment agriculture there gained momentum in the 1980s. The research area has seen rapid growth in recent years on the heels of climate change concern and increasing limitations of global open-field production.
Greenhouses, the focus of much of Niu’s research to date, also pose obstacles to agricultural economics and environmental sustainability.
Niu said plants utilize about 43% of sunlight to grow; the surplus becomes heat. And glass and clear plastics — typical greenhouse covers — can make temperature control difficult during harsher outdoor conditions. Consequently, these systems require energy-intensive heating and cooling in winter and summer.
“There are still problems to economic feasibility, like very high upfront investment and operational expenditures,” Niu said.
But opportunity for controlled environment agriculture, or CEA development, is ripe across Texas.
Niu peers into vertical grow rack. (Texas A&M AgriLife photo by Patricia Moran)
On the horizon: Seedlings
For example, she said, many open-field crop producers — who comprise the majority of Texas farmers — acquire transplant seedlings from out-of-state sellers who grow them in controlled environments. Valuable Texas examples include tomato and pepper transplants produced in winter. Dollars for out-of-state seedlings might be kept in Texas down the line by bolstering the state’s own urban production capacity, and by delivering emerging knowledge to farmers and urban upstarts via the Texas A&M AgriLife Extension Service.
On the practical side of implementation, Niu said, “In my opinion, it would be easier to do in Texas because we have high temperatures, which means lower heating costs in winter than northern states.”
Better technology: Controlled environment agriculture
She also seeks opportunities for improving controlled environmental agriculture technology.
“How can we design lighting systems in a way that the plants use most efficiently?” she asked. “How do we use less energy and produce more lumens? Can we reduce labor costs through automation? Do we need to heat the whole greenhouse or just the nutrient solution? How do we control temperature efficiently while improving quality and productivity?”
These are the questions her team works to answer in Dallas. At the same time, the second edition of Niu’s co-edited and co-authored textbook, Plant Factory: An Indoor Vertical Farming System for Efficient Quality Food Production, is available following its publication in late 2019.
LED light fixtures in a vertical grow rack at Dallas (Texas A&M AgriLife photo by Patricia Moran)
The 33-chapter text is a collaboration with Niu’s Chiba University mentor Toyoki Kozai, Michiko Takagaki and other contributors to the CEA field. It covers the latest information on each area of controlled environment horticulture: plant-light responses, advances in LED technology, environmental effects on plants as well as production for pharmaceuticals and transplant production among a range of other CEA topics.
Niu’s research in Dallas over the next year aims to expand emerging knowledge in these areas. Her laboratories now house controlled environment studies of leafy greens, and she will pursue future research on specialty greens, pharmaceutical-grade plant production and a range of other controlled environment agriculture systems.
“It is a field of innumerable possibilities,” Niu said.
Find urban horticulture program information, a curriculum vitae and listing of Niu’s publications at dallas.tamu.edu/urbanhort.
Source: AgriLife Today (Gabe Saldana)
Publication date: Wed 19 Feb 2020
Institute For Advanced Learning And Research And Virginia Tech Launch The Controlled Environment Agriculture Innovation Center in Danville
The Institute for Advanced Learning and Research (IALR) is partnering with the Virginia Tech School of Plant and Environmental Sciences and the Virginia Seafood Agricultural Research and Extension Center to launch a Controlled Environment Agriculture Innovation Center on IALR’s campus in Danville, Virginia
By urbanagnews
February 17, 2020
The partnership will create a hub of innovation and economic development in an industry expected to grow to $4 billion
The Institute for Advanced Learning and Research (IALR) is partnering with the Virginia Tech School of Plant and Environmental Sciences and the Virginia Seafood Agricultural Research and Extension Center to launch a Controlled Environment Agriculture Innovation Center on IALR’s campus in Danville, Virginia.
The Innovation Center will leverage technology and research to accelerate advancements, economic development, and regional participation in the developing industry of indoor farming. The value of U.S. greenhouse-grown food crops is expected to exceed $4 billion this year.
“We are delighted that the Institute for Advanced Learning and Research and Virginia Tech’s College of Agriculture and Life Sciences have combined their expertise to create a top program in controlled environment agriculture. This collaborative effort is creating tremendous energy and excitement because of its potential to provide innovative solutions to the agricultural community,” said Alan Grant, dean of the College of Agriculture and Life Sciences. “Partnerships like this will help us realize the vision of the SmartFarm Innovation Network Initiative to support the agriculture industry.”
Convening industry, academia and producers, the Innovation Center will be housed primarily within a modern greenhouse complex on IALR’s campus. Features will include various hydroponic systems, which grow plants in a soilless root medium with optimal amounts of water and nutrients. Vertical growing racks will maximize space, and high-tech engineering and technology will be integrated and on display throughout the center.
High-value demonstration crops will include lettuce, herbs, strawberry, blackberry, hemp, and more. In addition, faculty and staff involved in the center will research and educate on raising fish in controlled environments using aquaponics, or recirculating aquaculture systems that integrate plant and fish production. While traditionally viewed as separate fields, plant and fish production share many similar technologies, issues, and needs.
“We are excited to partner with Virginia Tech, a fellow champion of cutting-edge innovation, to expand the impact of agriculture in promising new ways,” said Mark Gignac, executive director of IALR. “While agriculture is a longtime industry of Southern Virginia, economic factors have demanded a new identity. We believe controlled environment agriculture is one of the defining solutions, and we are proud to work with Virginia Tech to introduce the concept to our region’s growers and attract industry.”
According to Michael Schwarz, director of the Virginia Seafood Agricultural Research and Extension Center, this new collaboration will further bolster domestic seafood production.
“The U.S. currently has a national seafood trade deficit in excess of $15 billion, with more than 50 percent of the seafood we consume originating from aquaculture,” he said. “Through this new programming and leveraging of expertise and infrastructure, we have the opportunity to drastically increase domestic seafood and produce production within the state, region, and country, enhancing food safety, security, sustainability, and, most importantly, socioeconomically within our agriculture economies.”
Controlled environmental agriculture helps protect plants from disease and stress while providing ideal growing conditions for high-quality, quick-to-harvest food products — sometimes in as fast as two weeks depending on the crop. In addition to hydroponic systems, the Innovation Center will use data management, sensors, and vertical structures to ensure ideal distribution of water, energy, capital, and labor. Plus, strict entry protocols will prevent pests. Together these factors result in a high-quality, consistent product with significantly more harvests than outdoor conventional production methods. Other advantages of controlled environmental agriculture include uniform, year-round production, potentially pesticide-free agriculture, and greatly reduced land and water requirements.
AeroFarms, a leading controlled environmental commercial producer based in New Jersey, recently announced the world’s largest indoor farm to be located in Cane Creek Centre in Pittsylvania County, just minutes from IALR. While this industrial-sized operation demonstrates scalability, Michael Evans, director of Virginia Tech’s School of Plant and Environmental Science, believes the technology is accessible to even small farmers in the region.
To encourage market growth, and in line with IALR’s role as a regional catalyst for economic transformation, the Innovation Center will introduce controlled environmental technologies to regional parties interested in entering the market. Conferences, workshops, site visits, and a web presence will comprise part of the outreach and educational activities. According to Evans, controlled environment agriculture is a rapidly growing sector that offers many potential opportunities in Southern Virginia.
“We are excited to house this facility on the Institute for Advanced Learning and Research’s campus and to benefit from both the technology developed and the associated economic development opportunities it provides for the region,” said Scott Lowman, director of applied research at IALR. “Consumer demand for healthy, local, and pesticide-free produce is high and will continue to increase in the coming decades. We look forward to serving this need through controlled environment agriculture.”
The Institute for Advanced Learning and Research serves Virginia as a regional catalyst for economic transformation with applied research, advanced learning, advanced manufacturing, conference center services, and economic development efforts. IALR’s major footprint focuses within Southern Virginia, including the counties of Patrick, Henry, Franklin, Pittsylvania, Halifax, and Mecklenburg, along with the cities of Martinsville and Danville. For more information, visit www.ialr.org.
For more information on IALR, contact Allison Moore at allison.moore@ialr.org or 434.766.6766
Researchers Tackling Viability of Leafy Greens In Vertical Farming Production
To better serve this burgeoning industry, researchers hope to integrate the indoor vertical growers within the specialty crop segment of agriculture, with the ultimate goal of increasing sustainability and profitability
Posted by Brian Sparks
February 19, 2020
Murat Kacira, University of Arizona. Photo: Rosemarie Brandt/College of Agriculture and LIfe SciencesA research team from the University of Arizona, Michigan State University, Purdue University, and The Ohio State University is using a $2.7 million grant from USDA’s Specialty Crops Research Initiative to study indoor leafy green production, with the goal of improving the quality, quantity, efficiency, and cost-effectiveness of indoor vertical farming production.
The initiative — called Optimizing Indoor Agriculture, or OptimIA — has caught the eye of more than 25 industry leaders, whose matching financial support brings the project total to $5.4 million.
“We’re privileged to work with a team of powerhouse scientists, engineers, economists, and industry partners to collectively address the significant challenges faced by the indoor vertical farming industry,” says Murat Kacira, a Professor of Biosystems Engineering and Director of the University of Arizona Controlled Environment Agriculture Center. “Controlled environmental agriculture is one piece of the puzzle, combining plant science, engineering, and computer-controlled production systems to enhance the yield and quality of our crops and optimize resource use.”
To better serve this burgeoning industry, researchers hope to integrate the indoor vertical growers within the specialty crop segment of agriculture, with the ultimate goal of increasing sustainability and profitability.
To do that, the multi-university team plans to assess variable environmental conditions, such as humidity, air movement, temperature, light, and carbon dioxide concentration, and then provide a more complete picture of best practices for indoor farming stakeholders.
Kacira and his team will be using computer simulations, modeling, and experimental studies to design and test more effective localized air-distribution methods, environmental monitoring, and control strategies for indoor vertical farms
.Michigan State University will lead final economic modeling, with Erik Runkle collaborating with co-principal investigators Roberto Lopez and Simone Valle de Souza. Chieri Kubota will take the reins testing environmental condition variables at The Ohio State University, and Cary Mitchell will lead closed canopy and phasic lighting tests at Purdue University.
Learn more about the research here.
Brian Sparks is senior editor of Greenhouse Grower and editor of Greenhouse Grower Technology.
See all author stories here.
Light4food And Moleaer Announce Indoor Farming & Research Partnership
Light4Food expertise is in indoor growing, and consequently, they have experience in medicinal plants. “Moleaer’s nanobubble technology is the most efficient method to dissolve oxygen in the water
Moleaer has expanded their position in the high tech horticulture sector by partnering up with Light4Food. Light4Food gains knowledge by using their own research facilities, the so-called Indoor GrowHow Facilities, which exist of multiple climate chambers for conducting research to the most optimum growing conditions to cultivate plants in an indoor environment. Both for own research and in collaboration with a client.
Niels Jacobs, Project Engineer at Light4Food, says, “we are using the Moleaer Bloom nanobubble generator for half a year now. In our Indoor GrowHow facilities, we dissolve oxygen in the form of nanobubbles into the cultivation water. Multiple cultivations of lettuce and herbs are grown with nanobubble technology were compared with traditional aeration systems. The results are very positive, not only in the deepwater hydroponic system but also in tests with high wire crops grown on rock wool substrate."
Michiel de Jong, Moleaer: “The findings corresponded with what we see in practice. Nanobubbles provide cleaner water with more available oxygen for the roots, this makes them less susceptible to molds and bacteria. Lack of oxygen is less generally known as a limiting factor for plant growth in comparison to lack of light or CO2. We can already assume that in spring and especially in summer, oxygen is the limiting factor for plant growth whether using rock wool, cocos or hydroponic systems. This is also the case when the substrate is too wet during cultivation. Not only the roots are negatively influenced, but also the microclimate in the root environment."
Left without Moleaer, Right with Moleaer
Light4Food expertise is in indoor growing, and consequently, they have experience in medicinal plants. “Moleaer’s nanobubble technology is the most efficient method to dissolve oxygen in the water. Therefore, we are looking forward to discussing this technology with our clients, eventually to realize the most viable indoor growing concepts”, says Rene van Haeff, managing director Light4Food.
For more information:
Light4Food
Expeditiestraat 11
5961 PX Horst
+31 77 207 0008
info@light4food.com
www.light4food.com
Moleaerinfo@moleaer.com
moleaer.com
Publication date: Mon 27 Jan 2020
Wageningen Researches Efficiency of Vertical Farming
Researchers of Wageningen University & Research are looking at how vertical farming can be more efficient
14 Jan 2020
Researchers of Wageningen University & Research are looking at how vertical farming can be more efficient.
“In a high-rise building – on a surface area about the size of a soccer field – you can grow enough vegetables for 100,000 people who each eat 250 grams of vegetables a day. You have complete control over the production process, so you are not dependent on the weather, the temperature, the daylight and the season. This makes vertical farming possible everywhere – also in infertile areas, in the desert or on Mars”, says Leo Marcelis, professor of Horticulture, in his blog on the website of Wageningen University & Research.
Vertical farming 1 of the solutions to the global food issue
“Vertical farming will not solve food shortages. It does not lend itself to rice and cereal production, but it is good for healthy, fresh vegetables, packed with fiber and vitamin C, and grown without contamination by pesticides or harmful microorganisms. That makes vertical farming one of the solutions to the global food issue”, says Marcelis.
Vertical farming takes place in buildings – the crops are grown on top of each other in several layers. - Photo: AFP
2 to 4 litres of water to grow a kilo of tomatoes
Vertically grown vegetables can make do with much less water. “We can recycle all the water and recover most of the water that the plants evaporate. As a result, we only need 2 to 4 litres of water to grow a kilo of tomatoes, whereas we use 17 litres of water in a Dutch greenhouse and in theory at least 60 litres for soil cultivation in for example southern Europe, and in practice often 200 litres,” says Marcelis.
In the closed cultivation system, nutrients such as nitrates and phosphates are also retained, while outside cultivation they end up in the soil, groundwater and surface water.
Pesticides a thing of the past
The use of pesticides is also a thing of the past, the professor emphasises. “By ensuring high hygiene levels, we can prevent insects and diseases from entering the building with employees, materials, seeds or air.”
Marcelis says the fact that the vegetables are not sprayed is good for our health, the environment and the preservation of plant and animal species. Moreover, thanks to local production, no shipping over long distances is required, which means that the CO2 footprint for transport is a lot smaller.
LED light healthy for plants?
The vegetables are grown on multiple floors of a high-rise building without daylight using special LED lamps, which often emit purple or bright pink light. Is LED light healthy for plants? “If we adjust the amount, colour and duration of the light, the amount of water and the temperature and composition of the air very precisely, we can give the crops much more nutritional value. I am absolutely convinced of that; there is already evidence that these factors influence nutritional value. In addition, we can also improve taste and shelf life.”
High energy consumption
Even though LED lamps are economical, a quarter of the costs goes to energy consumption says Marcelis in his blog. “If you can make substantial savings on this, the investment will become more affordable,” he says. Together with colleagues, he is studying options for reducing energy consumption. “We want to ensure that the light is used more efficiently by the plant. If we can optimize the temperature, humidity, the concentration of carbon dioxide and availability of water and fertilizers and can determine the optimum intensity and color of the light for every moment of the day, we can produce much more per unit of light,” says Marcelis. He also wants to improve the efficiency of climate control technologies.
Improve the crops
Current crops have been bred for outdoor cultivation and greenhouse cultivation. “We can also breed crops for these indoor circumstances, but that is a long-term task. Plant breeding projects easily take ten years.” And finally, the buildings can also be made more energy-efficient, for example by using the heat generated by the light for the heating of houses and offices.”
5 million euros for research into vertical farming
The Netherlands Organization for Scientific Research (NWO) has awarded 5 million euros to Wageningen research into vertical farming. “Our greenhouse horticulture sector is leading and has a lot of technology and knowledge that the Netherlands exports worldwide, also in the field of vertical farming. That is why it is important that we stay ahead,” says professor Marcelis.
Greenhouse cultivation is very efficient in the Netherlands and therefore much cheaper than vertical farming. In many places in the world, however, it is too cold in the winter or too hot in the summer to keep growing vegetables all year round. And sometimes there is simply not enough land available, for example in the city-state of Singapore. Singapore, but also the US, countries from the Middle East and Japan, are interested in vertical farming, according to the professor. “In Japan, food safety has become very important since the Fukushima nuclear disaster, and vertical farming is very safe,” explains Marcelis.
"Lack of Knowledge One of The Biggest Issues In Indoor Ag"
Lack of knowledge is one of the biggest issues in indoor agriculture, says Eric Stein, Executive Director of the Center of Excellence for Indoor Agriculture. "Lack of knowledge of the market place, lack of knowledge of growing, lack of knowledge of how to be profitable," he sums up
Eric Stein, e3garden
Lack of knowledge is one of the biggest issues in indoor agriculture, says Eric Stein, Executive Director of the Center of Excellence for Indoor Agriculture. "Lack of knowledge of the market place, lack of knowledge of growing, lack of knowledge of how to be profitable," he sums up. "In addition, there is confusion about the best technologies to use." With the launch of the Center, he hopes to help growers get over these challenges. From an online platform, it will grow eventually to a headquarters and a technology demo facility.
"Our goal is to provide a place for connection and exchange to take place every day of the year", says Eric. He is Associate Professor of Business at Penn State and CEO of Barisoft Consulting Group and advised businesses interested in setting up indoor farms, run workshops for the USDA on indoor farming and designed and operated an indoor vertical farm himself (e3garden) to conduct applied research on the economics of indoor farms.
Eric believes there's a lack of knowledge-sharing in the industry. "You have to go to the industry-specific conferences such as Indoor Ag-Con and Agtech NYC, which are great but bring together people for only a few days of the year."
The new center wants to connect growers with universities and investors to facilitate those relationships. "For example, we are working to bring in a Silicon Valley investment group that is interested in funding agtech start-ups. We also offer an energy savings program for our members, esp. growers, who want to cut operating costs. We are in the process of populating an Amazon-like multi-vendor marketplace just for indoor ag. We are also developing discount programs for members to receive reduced rates to key conferences like Indoor Ag-Con."
This all takes place at the newly launched website, indooragcenter.org. “The site offers an opportunity to create a highly networked community for indoor agriculture that is available to the members throughout the year. We expect it will help investors find farms to invest in, help growers find the products and services they need, highlight key conferences and events, and develop a knowledge base of best practices, solutions, cases, and research. We invite all types of indoor growers to participate regardless of technology or product type; e.g., from greenhouses to plant factories and from leafy greens to mushrooms", says Eric.
In the near future, the Center of Excellence for Indoor Agriculture wants to go offline as well. Phase two of its development includes raising capital and building a COE headquarters and technology demo facility in the greater Philadelphia area.
"Every industry has grown through bench-marking and knowledge sharing. The pharmaceutical industry is a case in point. I think we are reaching the point where indoor ag investors want accountability and transparency. We think the Center can help in this regard", Eric concludes.
"As we have seen recently, several companies have gone out of business. For instance, the container farms seem to not be doing well. I am not surprised because the logistics for growing in spaces like this are not optimal and the wild claims of profitability were not realistic, esp. given the high price of these units. We need to ground the business model for indoor ag on fundamentals, and that just is not happening in many cases. We think the investors will drive the need for better, curated knowledge, which is what the Center is all about."
For more information:
Indoor Ag Centerindooragcenter.org
Publication date: Wed 18 Dec 2019
© HortiDaily.com / Contact
€5 Million For Dutch Vertical Farming Research
"The increasing world population needs to be fed, while more and more people live in cities, there is often too little water, and we want our vegetables to have more and more nutritional value”
Wageningen University & Research (WUR) is to receive more than €8 million from the Dutch Research Council (NWO) and participating bodies for two major research programs, one involving tower garden systems using LEDs and the other focusing on improvements in the welfare of pigs and chickens. A third project, with WUR as a partner, is about sustainable freshwater management in the Dutch delta.
The recipients of the so-called Perspectief round 2019 funding were announced during the annual ‘Teknowlogy’ event hosted by NWO’s Applied and Engineering Sciences domain.
Tower gardens using LEDs
Sky High, a research program led by Professor of Horticulture & Product Physiology Leo Marcelis, which aims to bring about a revolution in vertical farming, received a total grant of €5 million.
"The increasing world population needs to be fed, while more and more people live in cities, there is often too little water, and we want our vegetables to have more and more nutritional value. By growing plants in layers on top of each other and illuminating them with special LED lights, you can produce fresh vegetables all year round, anywhere in the world, and under all weather and climate conditions," says program leader Prof. Leo Marcelis.
Researchers working on the Sky High program will cooperate with lighting specialists, plant breeding companies, growers, horticultural technology companies, architects and food suppliers to make vertical agriculture systems cheaper and more energy-efficient. Another aim is to produce vegetables and herbs that taste better, have longer shelf lives and provide more nutritional value, while using the absolute minimum of water and fertilizers and no pesticides.
Other participants
Amsterdam Institute for Advanced Metropolitan Solutions (AMS), Bayer, Bosman Van Zaal, Certhon, Fresh Forward, Grodan, GrowX, HAS University of Applied Sciences, OneFarm, Own Greens, Priva, Signify (Philips Lighting), Solynta, TU Delft, Eindhoven University of Technology, Unilever, Leiden University, Utrecht University, University of Amsterdam, and Van Bergen Kolpa Architecten.
Source: Wageningen University & Research
Publication date: Tue 12 Nov 2019
Vertical Farming Reaches New Heights In Germany With Fraunhofer IME
The AVF was invited to visit its member Fraunhofer IME in Aachen, Germany, one of 72 institutes of the Fraunhofer-Gesellschaft, the leading organization for applied science in Europe with over 26,000 employees and various international branches around the world
OCTOBER 22, 2019 | KYLE BALDOCK | Indoor Vertical Farming - Association
Visit to the Fraunhofer IME in Aachen: On September 4th, the AVF was invited to visit its member IME and experience their groundbreaking, innovative vertical farming technologies live on the spot.
Aachen, 04. September 2019: The AVF was invited to visit its member Fraunhofer IME in Aachen, Germany, one of 72 institutes of the Fraunhofer-Gesellschaft, the leading organization for applied science in Europe with over 26,000 employees and various international branches around the world.
The Fraunhofer Institute for Molecular Biology and Applied Ecology IME has six different sites in Germany and conducts research in the field of applied life sciences from the molecular level to entire ecosystems. Its division “Molecular Biotechnology” is located in Aachen, Germany and conducts R&D in the field of biotechnology with a strong focus on plant-based applications.
Over the last 10 years, the IME has developed and established two different vertical farming systems at the Aachen site in cooperation with the Fraunhofer IPT and IIS (à VertiPharm) as well as the Fraunhofer IML (à OrbiPlant™):
VertiPharm, a fully automated vertical farm with a strong focus on different research applications (e.g. plant cultivation, plant phenotyping, biopharmaceutical production) and OrbiPlant™, a novel and cost-efficient approach to vertical farming of food crops. These two vertical farming systems are complemented by LEDitGrow, an innovative multi-chamber system for the rapid development of plant growth protocols and the optimization of specific plant target values.
The design of the two IME vertical farming systems, their degree of automation, data management, efficiency and productivity, as well as their application and research possibilities go beyond the current state of the art of indoor farming technology. The systems provide an unprecedented basis to promote vertical farming, not only in Germany but worldwide. The different technology platforms are available for cooperation projects. Potential cooperation partners are encouraged to get in contact with IME (see below).
During a facility tour AVF had the opportunity to visit the different systems that are outlined below.
Fig.1: LEDitGROW plant cultivation unit for the accelerated multi-parameter development of plant growth protocols (© Ann-Katrin Beuel, IME).
LEDitGROW – Multi-parameter single plant cultivation system
A LEDitGROW unit comprises 24 single plant cultivation chambers, each equipped with various different LED-based light spectra including UVA. The unit has been designed to fit into a phytotron to run experiments at defined temperature, humidity and CO2 concentration. Each plant chamber can hold a single plant or several tissue culture petri dishes and can be individually supplied with nutrient solution.
The parallelization of cultivation conditions together with a statistical multi-parameter design of experiment (DoE) approach allows the rapid establishment of species-specific growth recipes as well as the optimization of specific target values such as biomass, secondary plant metabolites or morphology.
VertiPharm – Automated multifunctional research platform for vertical farming
Fig. 2: Top view on VertiPharm’s vertical farming unit (above, © AVF) and N. benthamiana plants under LED lighting in one layer of the vertical farm unit (below, © Andreas Reimann, IME).
The highlight of the IME in Aachen is the fully automated, pilot-scale vertical farming research platform featuring core functionalities such as multi-tier-based vertical farming, single plant handling, sensor-based in-process control, 2D/3D plant scanning, vacuum plant infiltration, downstream processing and central data management.
The impressive construction of the vertical farm unit consists of eight cultivation levels and provides ~550m2 of net cultivation area for the continuous or batch-wise cultivation of plants under highest reproducibility.
Different parameters such as temperature, humidity, CO2-concentration, LED-based lighting and composition of the plant nutrient solution can be defined and monitored in the central control system. Each plant receives a unique ID during seeding and is tracked individually throughout the entire cultivation time until harvest. Movement, sensor and measurement data are continuously recorded and can be used for in-process control or retrospective analysis of cultivation parameters and specific plant characteristics.
The fully automated facility can be used to produce food and non-food plants of different varieties and sizes. In addition to the vertical farming of plants a separate vacuum-infiltration unit connected to a fermentation suite allows the rapid production of recombinant biopharmaceuticals (e.g. vaccines, antibodies or enzymes) in plants by Agrobacterium-mediated gene transfer. Thanks to this multifunctionality the plant production research platform at Fraunhofer IME enables a broad spectrum of applications in different plant-based fields but also in the field of engineering, for instance:
Cultivation of food plants
Cultivation of medicinal/ specialty plants
Cultivation of ornamental plants
Production of recombinant biopharmaceuticals
Plant breeding and plant phenotyping
Software-based applications (e.g. digitization of production, artificial intelligence, augmented reality-assisted maintenance)
OrbiPlant™ – groundbreaking vertical farming system for the cost-efficient production of food crops
Fig. 3: OrbiPlantTM pilot-scale system with various leafy greens and herbs on a conveyor belt. The plant size gradually increases along the four conveyor belt loops (© Andreas Reimann, IME).
OrbiPlant™ represents an innovative approach to vertical farming of food crops that can truly make a difference to the spread and market penetration of vertical farming.
The major difference to classical tier-based approaches is a continuous conveyor belt system that is flexibly arranged in vertical loops allowing the easy placement of seeds or seedlings on one end of the conveyor system and the easy harvest on the other end. In between plants grow self-sufficiently under specific LED lighting conditions that can be adapted to the respective growth stage.
The conveyor belt movement can be specifically adjusted to a plant’s growth cycle and takes advantage of a growth-stimulating orbitropal effect on the plant, which is stemming from the changing gravitational orientation of the plant on the conveyor belt. The water-nutrient supply is ensured by aeroponic nozzles inside the belt loops. The innovative OrbiPlant system has several key improvements over current vertical farming systems:
High plant biomass yields and short growth cycles
Low production costs (e.g. <0.40 € per lettuce head)
Optimal cost-efficiency due to minimal hardware and personnel costs
Modular conveyor belt concept easily adaptable to different plants and growth cycles as well as to different building geometries
Improved vertical heat convection
Low LED lighting requirement
Flexible degree of automation depending on customer need
OrbiPlant is not only providing a cost-effective, optimized production platform for food crops with minimal space and resource requirements, but its unique design and flexibility has the potential to take vertical farming to a new level. It overcomes the shortcomings of today’s most commonly used horizontal rack systems, saves energy, utilizes intelligent automation, and enables easy handling and operation.
The AVF in cooperation with the Fraunhofer IME welcomes company and stakeholder inquiries on the presented systems.
Contacts:
Christine Zimmermann-Lössl, AVF Chairwoman
Email: czl@vertical-farming.net
Marvin Spence, AVF Project Manager
Email: ms@vertical-farming.net
Andreas Reimann, Senior Acquisition and Project Manager at Fraunhofer IME, Business Field Indoor Farming/Vertical farming
Email: andreas.reimann@ime.fraunhofer.de
Visit Fraunhofer IME’s website to learn more about them.
Saving Land With Vertical Farming Food Production
The Innovation Hub for Controlled-Environment Agriculture (IHCEA) at the James Hutton Institute is a collaboration between government agri-tech centre Crop Health and Protection (CHAP), and Liberty Produce, a London-based farming technology company with expertise in horticultural lighting and fertigation systems
By Rohese Devereux Taylor @hellorohese Senior Digital Reporter | October 11, 2019
A new research centre for vertical farming technologies that aims to enable Scottish farmers to transition to sustainable growing techniques opens in Dundee next week.
The Innovation Hub for Controlled-Environment Agriculture (IHCEA) at the James Hutton Institute is a collaboration between government agri-tech centre Crop Health and Protection (CHAP), and Liberty Produce, a London-based farming technology company with expertise in horticultural lighting and fertigation systems.
The centre has been purpose built for research and development and will help the industry to understand and tackle barriers to the adoption of hydroponic production systems.
The aim of the centre, which houses Liberty Produce's Future Farming Hub, is to drive innovations that reduce operational costs and improve the yields from controlled-environment farms, providing benefits to growers, food processors and consumers, as well as help farmers meet food requirements and limit further damage to the environment.
Director of Liberty Produce, Zeina Chapman said: "What we do is develop technology with a focus on trying to reduce the operational costs and the capital costs of running these systems, as well as improving the yield.
"The biggest challenge growers have at the moment is that vertical farming is really only on the cusp of commercial viability and that's because the cost of the capital expenditure required to build these systems is enormous, the operational costs are still very high, they're still quite labour intensive."
Because of this, most producers can only grow high-value crops such as microgreens, which can be sold for up to £40 per kilogram, and herbs.
But Liberty Produce, founded in 2018, wants to change that by developing new technologies with a focus on reducing costs these systems can be adopted globally.
Vertical farming grows produce in layers indoors in sometimes soil-less systems aided by LED lights either by hydroponics, where roots are continuously in moisture in the growing medium, or aeroponics, where the produce is misted and doesn't rely on a growing medium.
They are seen as a sustainable alternative to cultivating land not currently used for food, can withstand variable and increasingly extreme weather, eliminate the use of agrichemicals and reduce water use.
Liberty Produce will lead a £1.3 million project with eleven partners to accelerate the development of the UK vertical farming sector.
Using the funds, awarded by Innovate UK, the farming hub will support the creation of an integrated technology system focused on reducing operational costs by 25 percent, improving crop yield by 30 percent and reducing necessary grower intervention through improved decision support and automation in lighting, nutrient and environmental control technologies.
Some of the innovations that will be carried out at the centre will include designing high-efficiency LED lighting systems; test growing regimes, lighting applications and nutrient mixes in a variety of crops.
Vertical farming crops will complement traditional arable farming but Ms Chapman believes that more produce will be grown via the method as technologies advance and natural resources struggle to cater to growing populations.
She said: "I think they will become more mainstream for crops that are currently grown in fields or in glass houses. I think we'll start to see a more broadening of the crop types growing in these systems."
Growers are looking to produce baby leaves commonly found in salad bags with the vertical farming method, moving away from polytunnels and indoor track systems. But utilising the vertical method for wheat, barley and potatoes has a way to go yet.
Ms. Chapman said: "I think we'll start to see a patchwork of new growing systems coming in to help support and take over some of the more traditional growing systems."
Vertical crops are grown in a controlled environment with light levels, temperature, carbon dioxide, and applied nutrients all closely monitored and as an indoor crop, no pesticides are required.
Ms. Chapman said: "Improved technology in this sector will increase the adoption of these sustainable food growing systems, reduce the environmental impact of crop production, improve food security and create opportunities for the growth and export of UK agricultural technologies.”
Innovation Hub For Controlled Environment Agriculture Launched In Dundee
CHAP partnered with Liberty Produce to develop and build the IHCEA facility with funding from Innovate UK. The facility is a series of self-contained units housing state-of-the-art equipment with a modular structure designed to create a flexible environment for research and development
10th October 2019
London, UK
Agri-tech centre Crop Health and Protection (CHAP) and farming technology company Liberty Produce have launched the Innovation Hub for Controlled Environment Agriculture (IHCEA) at the James Hutton Institute’s site in Invergowrie near Dundee.
CHAP partnered with Liberty Produce to develop and build the IHCEA facility with funding from Innovate UK. The facility is a series of self-contained units housing state-of-the-art equipment with a modular structure designed to create a flexible environment for research and development. With integrated cutting-edge LED lighting systems and patented nutrient delivery technologies, this unique research facility will enable collaboration between industry, academia, and government to effectively tackle the barriers to widespread adoption of vertical farming. Its purpose is to accelerate the development of sustainable food production year-round through resource-efficient, fully-controlled systems.
The IHCEA is a key part of Liberty Produce’s Future Farming Hub, which will offer a wide range of services, including research and development and CEA training programmes within a commercial demonstrator system, as well as industry and academic collaboration opportunities.
The James Hutton Institute has welcomed the location of CHAP’s IHCEA and Liberty Produce’s Future Farming Hub in Invergowrie, in the context of the Institute’s drive for the establishment of Open Science campuses at its sites and this has been facilitated by the creation of the Advanced Plant Growth Centre at Invergowrie as part of the Tay Cities Deal.
Fraser Black, CHAP Chief Executive, said: “We are excited to be partnering with Liberty Produce and the James Hutton Institute to establish the Innovation Hub for Controlled Environment Agriculture (IHCEA), in Invergowrie. This is a prime example of CHAP’s mission to harness game changing ideas from our creative and innovative partners to solve the problems industry is facing today and tomorrow. This is a progressive step in our ambition is enable the United Kingdom to become a global leader in CEA and augment the production of healthy food in a sustainable way.”
Zeina Chapman, Liberty Produce Co-Founder and Director, added: “Vertical farming is not yet sustainable; this partnership which has established the IHCEA and Future Farming Hub at the James Hutton Institute marks an advancement of our collective journey towards creating truly sustainable vertical farming technologies. The greater vision of Liberty Produce remains driving innovation that will enable us to meet our global crop requirements without harming the planet.”
Professor Colin Campbell, Hutton Chief Executive, commented: “This collaboration with Liberty Produce and CHAP marks the next step in the growth of the Institute's Open Science Campus initiative and brings new innovative companies to work closely with world-leading science. This has been facilitated by Tay Cities Deal announcement to create an Advanced Plant Growth centre at Invergowrie and our other new investments there and builds on our track record of engaging with industry, research partners and the public.”
UK Government Minister Colin Clark said: “I am pleased to see the opening of this new Innovation Hub at the James Hutton Institute. We know that technological innovation is the future of sustainable agriculture and Scotland is home to world-leading resources and expertise in this field. The UK Government recognises the importance of this work and remains committed to funding research and development through our modern Industrial Strategy.”
It is hoped that the synergy between CHAP, Liberty Produce and the James Hutton Institute will provide a better understanding of total controlled environment technologies, drive innovation and accelerate the growth of the vertical farming sector in the UK.
**Ends**
About CHAP
Crop Health and Protection (CHAP), funded by Innovate UK, is one of four UK Agri-Tech Centres. CHAP’s vision is for the UK to be a global leader in the development of applied agri-technologies, to help secure our future by nourishing a growing population sustainably while delivering economic, environmental and health benefits to society.
CHAP acts as a unique, independent nexus between UK government, researchers and industry, building innovation networks to identify and accelerate the development of cutting-edge solutions to drive incremental, transformative and disruptive changes in sustainable crop productivity and to establish controlled environment agriculture (CEA) as a core competency.
www.chap-solutions.co.uk/
For further information contact:
Darren Hassall
Darren.hassall@chap-solutions.co.uk
+44 (0)1904 462062
About Liberty Produce:
Liberty Produce is a farming technology company, enabling the growth of local produce year-round, using a fully-controlled, industry-leading, indoor vertical farming system. With expertise in lighting and nutrient delivery technology, Liberty develops and builds systems that reduce operational costs and improve yields of crops grown in controlled-environment farms. Their vision is to drive innovations that will enable the UK to meet our crop requirements over the next century, without harming the planet. Liberty Produce established the Future Farming Hub to enhance UK technology development and commercialization in the Controlled Environment Agriculture (CEA) sector. www.liberty-produce.com
For further information contact:
Benita Rajania
+44 20 3290 8801
About the James Hutton Institute
The James Hutton Institute is a world-leading scientific organization encompassing a distinctive range of integrated strengths in land, crop, waters, environmental and socio-economic science. It undertakes research for customers including the Scottish and UK governments, the EU and other organizations worldwide. The ongoing collaboration between the James Hutton Institute and Scottish-based vertical farm technology business Intelligent Growth Solutions Ltd resulted in the opening of Scotland’s first vertical farm at the Hutton Invergowrie campus in August 2018, and continues to be a major strength in developing the Advanced Plant Growth Centre initiative, which has been backed by a £27m transformational investment from the Tay Cities Deal. www.hutton.ac.uk
More information from Bernardo Rodriguez-Salcedo, Media Manager, James Hutton Institute, Email Bernardo.RodriguezSalcedo@hutton.ac.uk, Tel: +44 (0)1224 395089 (direct line), +44 (0)344 928 5428 (switchboard) or +44 (0)7791 193918 (mobile).
Inside Indoor AgTech
In order to better foster thought leadership through The Mixing Bowl and gain a deeper perspective for investment opportunities at Better Food Ventures, we have created a landscape of Indoor AgTech (Download Landscape Here)
Chris Taylor and Michael Rose provide a deep-dive analysis of Indoor Agriculture, tracking more than 1,000 companies to capture the technology ecosystem of controlled-environment agriculture: vertical farms, greenhouses, urban farms, plant factories, and container farms...
Understanding the Landscape
Controlled Environment Agriculture (CEA) or, Indoor Ag, as it is more commonly known, has been garnering tremendous attention because of the compelling benefits of growing indoors in a controlled environment. In order to better foster thought leadership through The Mixing Bowl and gain a deeper perspective for investment opportunities at Better Food Ventures, we have created a landscape of Indoor AgTech (Download Landscape Here). As with our partners’ landscape maps from Brita Rosenheim and Seana Day on FoodTech and AgTech (field production), this landscape focuses on the technology of the Indoor Ag market.
With the first release of this Indoor AgTech Landscape, we believed it was important to start with an ecosystem of the market as opposed to an investment heat map. As part of this effort, we are tracking more than 1,000 companies in the indoor space. This landscape is a subset of those companies, and others, that are active in the space. While some market assessments, including the notable AgFunder AgriFood Tech Investment Report, include cannabis, algae, and insect production, this landscape is limited to traditional food crop production, from seed to immediate post-harvest activities, and utilizes a lens focused on digital and information technology.
The landscape is segmented into broad categories of component technologies, production growing systems, and actual growers. Some other important components of indoor operations, such as the structures themselves, energy systems, and traditional or tangential equipment and supplies are not part of the map. Additionally, many companies in this space, particularly established vendors, offer products in multiple categories but are only represented once. Also, tools that are often shared with field farmers, such as supply-chain platforms and other downstream applications, are captured on the AgTech Landscape created by our colleague Seana Day.
Greenhouses as part of the Indoor Ag Landscape
While there has been much media attention on growing indoors with artificial lights in “Sunless” environments (sometimes referred to urban, vertical, indoor, plant factory,…), greenhouses, as an indoor farming approach, need to be included in the discussion and we have made a point to include them in this landscape. Greenhouses provide similar compelling benefits as a complete Sunless approach and have been utilized to enhance crop production for decades. They have evolved to become technically sophisticated, large in scale and widely deployed while incorporating a broad range of innovations in energy, sustainability, lighting, environmental control, irrigation, monitoring and automation. There are a number of greenhouse operations where production is already fully automated such as Little Leaf Farms in Massachusetts.
Component Technology
Indoor AgTech component technologies are represented on the left half of the landscape map segmented into environment, monitoring, management, and automation. In general, these technologies may be applicable to both sunless and greenhouse environments.
The landscape includes vendors of systems that are used to maintain an optimal growing environment, namely environmental control, irrigation/fertigation, and lighting. Environmental control and fertigation are not new technologies, but as they encapsulate and effectuate a grower’s decisions, they have enabled greater precision and scale in operations. Lighting, the third component, has seen more change in recent years as LEDs have emerged as a viable alternative to traditional lighting technologies. Lighting systems, most obvious in sunless environments, are also applied in greenhouse operations.
Companies offering monitoring solutions, including sensors and imaging systems to gather data on the environment, crop health and pests and disease pressure are also included. Environmental Monitoring companies measure conditions such as indoor and outdoor weather, soil moisture, and nutrient, CO2 and light levels; data that has been used historically to drive decisions and control at a relatively macro level. Newer innovations in Pest/Disease and Crop Monitoring like automated scouting, stress detection, and growth monitoring can shift focus from maintaining external conditions to a plant’s real-time response to a grower’s decisions.
The Management and Analytics segment, including crop and farm management solutions, may hold the most promise of all the component technologies. With more extensive deployment of sensors and associated big-data analytics, the growth environment will be increasingly managed by predictive, proactive, real-time, and autonomous optimization by AI that can recognize complex interactions beyond a grower’s capabilities. However, as with field farming, maximizing yield does not necessarily equate to maximizing the success of the overall operation. Forecasting, labor and overall farm management solutions address that greater requirement.
Production Growing Systems
In addition to individual component technologies being marketed to the Indoor Ag market, companies are also selling production growing systems in various formats and configurations: appliances, containers, and sunless and greenhouse production systems. These systems extend almost linearly in size and features from countertop consumer units to acres-scale installations, many being provided as complete growing environments. While one can find countless consumer and hobbyist growing systems on Amazon, Alibaba, and Walmart.com, the landscape does not capture them due to our commercial growing focus.
Industrial Appliances
A step up from the consumer growing systems are Industrial Appliances. These standalone units, intended for restaurants, grocery stores or corporate/school foodservice, are designed for volume production and can be located in the front of the store and in the “back of the house”. While primarily focused on greens and herbs, they provide retailers and foodservice with the freshest produce available, virtually eliminating the carbon footprint of distribution. Some questions do arise around food safety and challenges of adding new operational roles to this labor impacted sector. These appliances not only contain all the requisite elements of a growing environment and operating software, but many are offered with a service/supply program that included seeds, nutrient inputs, grow recipes and even remote monitoring and operation, i.e., remote growing by the appliance vendor.
Container Systems
Like the Industrial Appliances, Container Systems offer a complete growing environment but typically enclosed in a shipping-like container. In general, these units provide a significant increase in production volume and great flexibility in location, including and typically outdoors. Available for a moderate investment (roughly $100,000) they can produce tons of greens and herbs annually. This combination of benefits has made this approach appealing to a broad range of customers from retailers or food service locating units at their distribution centers to rural field farmers wanting to try their hand at indoor growing on a yearly basis.
Sunless and Greenhouse Production Systems
Manufacturers can deploy production systems at industrial scale. They are usually modular and allow purchasers to expand a system footprint as needed. Typically these systems are complete growing environments that include all the necessary components for production, often configured to be site-specific. These systems are specifically designed to reduce labor and maximize yield for the space allocated, often through the use of automation. As with other segments of the landscape, many of these system manufacturers are building products for both the sunless and greenhouse markets.
The growing environment of Sunless Production Systems is vertically oriented and typically configured as stacked horizontal trays or vertical growing panels/walls. Most of these systems deliver nutrients utilizing hydroponics though some providers are offering aeroponics approaches such as the Mobile Aeroponics system from the CombaGroup in Switzerland. Currently, most systems deployed are producing leafy greens and herbs, and in some cases strawberries. While generally smaller in footprint compared to greenhouses, they are capable of large production per floor area due to the system’s vertical orientation, such as at the Jones Food Company facility with its 17 levels stacked to a height of 36 feet. In some instances though, Sunless Production Systems have been deployed with larger footprints such as SananBio’s Chinese installation covering more than two acres and producing 1.5 tons of leafy greens a day. These systems are being offered with various business models. This can range from a simple equipment sale to a turnkey offering where a provider such as Infinite Acres will partner with the purchaser and provide operational expertise.
Greenhouse Production Systems are typically horizontally oriented with nutrients delivered through various approaches such as deep water with floating rafts, Nutrient Film Technique, or drip irrigation. The systems will operate in environments with ambient light, and supplemental lighting purchased separately. They are available for a range of crops from leafy greens and herbs to vining crops such as tomatoes, cucumbers and peppers and increasingly, strawberries. The footprint of a typical Greenhouse Production System is quite large with installation increments characterized in acres, or even tens of acres. Automation within systems varies and is usually crop dependent with a minimal amount in systems for vining crops and an extensive level in leafy greens and herbs. A number of providers such as Hortiplan and Viscon have extensive deployments of fully automated systems that handle seeding to harvest.
Growers
As mentioned above, we thought it was important to highlight indoor growers in addition to Indoor Ag technologies in this year’s landscape. While it is still farming at its core, technology is the essence of modern Indoor Ag and its operations. Not only do indoor producers leverage technology to farm, in many instances growers such Plenty, Bowery and aquaponics grower, Edenworks, are developing their own technology.
The landscape captures as a subset of the growers operating in the market today. Those represented are noted for the respective scale and scope of technology used in their operations, innovative systems integration, novel approaches, or that they are currently pioneering technical growing practices in their country or region.
Modern Sunless Growers, catching the spotlight in the last few years, are standing on the shoulders of early Plant Factories built in Asia where they began over 25 years ago. While most of the publicly identified funding for Sunless Growers over the last few years has been in the U.S., there are now more than 500 Plant Factories in operation throughout Asia according to New Bean Capital. Operating economics remains a key challenge and criticism for these facilities and sunless operations in general, although the Japanese grower Spread, which opened their second facility in late 2018, claims that through the use of technology, scale, and automation they are not only profitable but can be cost-competitive with field farming.
Greenhouses are the larger and more developed growing method. Cuesta Roble Consulting estimates that there are more than one million acres of vegetable production inside permanent structures worldwide. Though, most of the technically advanced and greatest concentration can be found in the Netherlands where there are more acres “under glass” than the size of Manhattan. While already well established as an indoor-growing approach, it appears the recent attention on Sunless farming and cannabis has stimulated additional activity in the sector. Since the beginning of 2018 more than $500 million has been invested in Sunless growers. During that same time period, the Greenhouse sector has seen the likes of Equilibrium raise and deploy its new Controlled Environment Foods Fund of $336 million, Gotham Greens and Bright Farms raise $84 million and investors such as ValueAct Capital Management and Revolution invest in AppHarvest, which is building one of the country’s largest greenhouse in Eastern Kentucky.
There are many impressive and much needed community-based and social impact organizations focused on indoor growing. These efforts range from Teens for Food Justice working on urban access of fresh produce to increasing employment opportunities for veterans by Veterans to Farmers. These are important entities but are not captured on the landscape as it focuses on commercial-scale businesses and production.
The Changing Landscape
For the purpose of this first Indoor AgTech Landscape, we make the distinction of Greenhouse and Sunless as a growing approach or market. This segmentation is done only to raise awareness, to ensure the entire market and various approaches are represented.
Too often we hear declarative statements that “this” is the “right” approach for Indoor Ag or is “the” future of farming. It is more appropriate to start with the question “what problem are you trying to solve?” The unique environmental, climate, economic, and market factors will inform the growing approach. It is doubtful that a one-size-fits-all solution will dominate, but rather utilization of the most appropriate growing structures, systems, and technologies for the desired crop, location and business goal. The challenges, needs, and parameters in Singapore are not going to be the same as St Louis, or Dubai. It is not always an either-or question.
Not only are we seeing vendors and technology providers offering products and systems for both the Sunless and Greenhouse segments, some growers are now utilizing or combining the two approaches. Veteran indoor grower Green Sense Farms is now designing combined facilities and Shenadoah Growers, a long time field and greenhouse grower, has added Sunless production to their operations. Deliscious, a Dutch lettuce grower has seamlessly integrated sunless seeding and propagation into the automation workflow before plants are transported and finished in a greenhouse mobile gutter system. Even on the financing front, start-up Contain is providing a leasing and insurance platform for all indoor farming approaches from “container farms and warehouse farms to the most sophisticated greenhouses and plant factories.”
Moving Forward
To meet its promise and continued expansion, particularly to those locations underserved by traditional production methods, Indoor Ag needs to drive down its cost of operations. Sunless production, especially, has further to go on this front mainly due to a lack of efficiencies from scale and energy use. While indoor costs need to be closer to field production, no one will benefit from a race to the bottom on cost. Indoor and field production are both working on some of the same challenges including labor, sustainability, safety, traceability, and profitability. Technology has an important role in meeting those challenges and we look forward to seeing further advances, innovations, and implementations in data capture and analytics, automation, and predictive and autonomous control.
We welcome your thoughts and reactions and look forward to following the Indoor AgTech landscape together for the coming years.
Bios:
Chris Taylor, a Senior Consultant on The Mixing Bowl team, has spent more than 20 years on global IT strategy and development innovation in manufacturing, design and healthcare, focusing most recently on Indoor AgTech.
Michael Rose is a Partner at The Mixing Bowl and Better Food Ventures where he brings more than 25 years immersed in new venture creation and innovation as an operating executive and investor across the Internet, mobile, restaurant, and Food Tech and AgTech sectors.