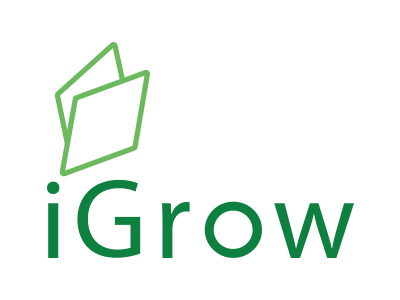
Welcome to iGrow News, Your Source for the World of Indoor Vertical Farming
USA: Local Farm Brings Hope To Food Desert
A hydroponic produce farm in Indianapolis is filling a need in food deserts around the city. Food deserts are areas where grocery stores aren’t easily accessible. More than 200,000 people live in food deserts in Indy, according to a study published by SAVI
Q&A: Mario Vitalis
April 13, 2021
Mario Vitalis, farmer, owner, and founder of New Age Provisions, holds plants grown on his farm.
INDIANAPOLIS — A hydroponic produce farm in Indianapolis is filling a need in food deserts around the city.
Food deserts are areas where grocery stores aren’t easily accessible. More than 200,000 people live in food deserts in Indy, according to a study published by SAVI.
Mario Vitalis, farmer, owner, and founder of New Age Provisions farm, uses advanced hydroponics and vertical planting to grow year-round.
It all starts inside a shipping container on an old car lot on East 10th Street. A step inside transports visitors to a lush, green garden of produce. A variety of herbs, leafy greens, microgreens, and hemp are grown inside.
The location allows Vitalis to provide fresh produce to the community, one of the city’s many food deserts. The farm also provides produce to restaurants in Indianapolis.
“I’ve always known the city life — but there is a nagging desire to get back to my roots,” Vitalis said. “As an African American, my roots made it from slaves in the field, to sharecroppers in the South, to farming in the city.
“As a descendent of slaves, this farm enables me to get back to the type of living where our people once lived off the land. Having an urban farm allows me to connect to a long history of farming that has been forgotten.”
Vitalis shared his story with AgriNews.
Tell me a little bit about your farm.
“We are a hydroponic commercial farm. We officially started farming in August 2020.”
What was your inspiration to grow things?
“I wanted to be involved in agriculture, to be able to provide fresh food to the community independent of the supply chain, and independent of herbicides, pesticides, and contaminants.”
Indiana has several food deserts. Did that inspire you to fill a need in the community?
“Yes, it did. It provides us with the equipment to do so, as well. We’re the first company in Indiana to own this piece of equipment, the Freight Farms Greenery. We’re currently the only African American owner of the equipment. We want to be able to provide food and also provide a new way of farming. We want people to see it and have access to it.”
How does the farming system work?
“It’s called a Greenery and it’s built by Freight Farms, based in Boston. It’s essentially a hydroponic farming system in a 40-foot shipping container. If you can imagine those shipping containers that go up and down the highway, you go inside of one of these and grow vegetables. It has everything you need to do that. It has a seedling table and growth tower with different types of hydroponic methods.”
Basil grows at a hydroponic produce farm in Indianapolis.
What are some of the features of the technology?
“It has its own dosing system to control nutrients. You can control humidity, temperature and pH levels. You can check your settings and programming on a computer. There’s an app that goes with it, as well. So, you can control your farm from your phone. The technology is state of the art.”
What are some of the challenges you’ve faced as a new farmer?
“I think the biggest challenge is developing a market and getting our name out there. There’s also a learning curve to farming. I didn’t have any experience. So, I had to learn what to do and how to operate.”
What do you enjoy most about growing things?
“Seeing the plant life cycle from seed to seedling into a full plant. I also enjoy the environment. Since we’re in an enclosed environment, we can grow year-round and it’s always 65 degrees.”
Do you have any advice for minorities interested in farming?
“Right now there are so few minority farmers in general. For African American farmers, the best thing they can do is get land and find ways to cultivate the land or make use of it. Good land is becoming a scarce resource. If they’re interested in farming, there’s funding available from USDA for Black and minority farmers. There are different avenues out there. But it all starts with land and a business plan. After that you just have to have motivation and knowledge to do it.”
Anything else you’d like to share about your farm?
“Our farm is local on the east side of Indianapolis. We grow hydroponically without herbicides, pesticides or contaminants.”
How can people purchase your products?
“They can go online to our website www.newageprovisions.com. We deliver. Or, you can purchase through Market Wagon or Hoosier Harvest Market.”
Explore The Sixth Edition of Clima, Powered by IGS
In this edition, we look at why precision farming and Controlled Environment Agriculture (CEA) techniques are becoming more mainstream, and the skills and talent required to make this approach a success
In this edition, we look at why precision farming and Controlled Environment Agriculture (CEA) techniques are becoming more mainstream, and the skills and talent required to make this approach a success. Technology is having a greater impact on agriculture than ever before, and this is only set to increase. It will bring with it a wider and more advanced agricultural ecosystem that requires a skilled, knowledgeable, and committed workforce, with as great an appetite for innovation and capacity to problem solve as any generation before.
Discover more on this topic in the sixth edition of Clima today.
Bringing future talent to Agriculture 4.0
We discuss the emerging influences on education and skills development across Agriculture and Horticulture with two senior leaders from Scotland’s Rural College (SRUC). We spoke to Professor Fiona Burnett, Head of Connect for Impact in SRUC’s Knowledge and Information Hub, and Ruth Vichos, Lecturer in Horticulture, about the evolution of Agriculture 4.0, and how technology is impacting skills evolution and teaching mechanisms.
Listen To The Full Interview
Vertical Farming: A Solution To Waste And Inefficiency In The Food Supply Chain?
The global food supply chain is in trouble. The coronavirus pandemic is only the latest crisis to highlight the inefficiencies and spotty reliability of the traditional model for getting food from farm to consumer
April 12, 2021
Robert J. Bowman, SupplyChainBrain
The global food supply chain is in trouble. The coronavirus pandemic is only the latest crisis to highlight the inefficiencies and spotty reliability of the traditional model for getting food from farm to consumer. Repeated instances of contamination reveal inadequacies in quality control and the tracking of product throughout the supply chain. And environmental concerns are raising serious questions about the impact of large-scale farming on the land, water, and air.
There’s a clear need for alternative methods of food production. One is vertical farming, a system of growing crops in stacked layers, spaced 24 to 36 inches apart, usually in greenhouse environments. Vertical farms can be constructed within any type of confined space, including dedicated buildings, shipping containers and even abandoned mineshafts. The equivalent of 60 acres of produce can be squeezed into a single greenhouse, with layers stacked six levels or more high.
Further advantages of vertical farming include complete protection from weather and crop pests, without the need for pesticides or other chemicals, and drastic reductions in water use. A pound of lettuce that requires 41 gallons of water with conventional farming needs just two gallons with vertical farming — in all, up to 99% less water than field-grown produce.
One such system is in operation outside Boston, Massachusetts by Crop One, which markets its products under the FreshBox Farms brand. In business for eight years, Crop One claims to be the oldest vertical farmer in North America, in terms of continuous commercial production.
Crop One grows a wide variety of leafy produce, including lettuce, arugula, basil, and spinach. From its location in Millis, Massachusetts, it supplies sellers within a radius of approximately 100 miles, with a presence in more than 35 grocery stores in the Northeast, according to chief executive officer Craig Ratajcyzk.
The location was chosen to cut down on the large volumes of produce that are typically shipped into the Boston area from California, Arizona, Texas, and South and Central America. “Those are really long supply chains,” Ratajcyzk says. “Right now, we’re within an hour’s drive of all the markets we serve.” Crop One also sources its seed stock locally, he adds, although he acknowledges the need to diversify supply in order to reduce the risk of supply-chain disruptions.
Indoor farming allows Crop One to grow to produce all year round, Ratajcyzk says. Currently, its output stands at around three tons a day, serving 10 customers in the Boston area and an overseas account that in turn sells to some 20 retailers.
The company has big ambitions to expand its production and marketing reach, and Ratajcyzk sees no problem in scaling up. Currently, he says, “the whole CEA [controlled environmental agriculture] industry represents a small fraction of the global demand market.” But recent storms and cold weather in large portions of the U.S. have highlighted the need for a method of farming that isn’t susceptible to the whims of Mother Nature.
“The industry is growing substantially,” Ratajcyzk declares, with producers increasingly being drawn to a method of farming that dramatically boosts crop yield within a limited space.
The technology can even extend to fruit-bearing trees. “A traditional orange tree maybe 15 or 20 feet,” Ratajcyzk says. “Why not a 10-foot tree producing twice as many oranges?”
The chief downside of vertical farming at the moment is one of cost. The price of an initial building containing the equivalent of a 60-hectare farm has been estimated at $100 million. Expenses include heavy energy consumption for supplemental lighting, temperature and humidity controls, fertilizer, and maintenance of proper carbon dioxide levels.
A Cornell University study from 2014 called vertical farms “pie in the sky,” estimating that a single loaf of bread containing wheat grown in a vertical farm would cost $27. Current economics would therefore appear to limit vertical farming to high-end products, although producers are banking that costs will plummet as the technology catches on. The net environmental advantages should also serve to boost its popularity in the coming years.
Vertical farming is “small, but growing every day,” says Ratajcyzk. “It’s a difficult model to establish, but if you’ve been around for five years-plus, then you have a higher probability of success.” He’s hoping for federal, state, and local support of the fledgling technique.
“I can’t really think of a downside to this industry,” he says.
Lead photo: Photo: Bloomberg
How Square Roots Is Meeting Unprecedented Post-Pandemic Demand For Fresh, Healthy, Locally-Grown Food
Square Roots is expanding fast—deploying its latest indoor farm in Michigan in just three months
Square Roots Is Expanding Fast—Deploying Its Latest
Indoor Farm In Michigan In just Three Months.
To meet rapidly increasing demand for our locally-grown produce, today we’re announcing our newest indoor farm in Grand Rapids, Michigan. We broke ground in late December and planted the first seeds in March—just three months later. Now we're preparing for the first harvest, and our delicious, fresh produce will be available at grocery stores, eCommerce platforms, and restaurants across the Great Lakes region in the coming weeks.
Kimbal Musk, our Co-founder and Executive Chairman, says: “COVID-19 exposed major weaknesses in the industrial food supply chain, and accelerated the already fast-growing local farming movement. Square Roots can now deploy commercial-scale, controlled-climate farms, fast, in locations across America to meet the demand for local food, all year round. My wider mission is to bring responsibly-grown, local food to everyone in America. With Square Roots, we’re going to do it fast.”
From shovels-in-the-ground to first-seeds-planted, we built our new farm in just three months.
Growing Reliable, Fresh Produce Throughout the COVID-19 Pandemic
While COVID-19 wreaked havoc across the industrial food system, consumers increasingly valued local food, which in turn accelerated the adoption of indoor-grown produce. Consumers, forced to stay at home and cook, were able to experience the consistent peak-season flavor of our locally-grown greens. Meanwhile, retailers appreciated the reliability, longer shelf life, and complete traceability of all Square Roots’ products. As a result, we’ve seen a big increase in retail demand this year, and we’re now available in more than 200 stores (including Fresh Thyme Market, D&W Fresh Market, Whole Foods Market, FreshDirect, and more!).
In parallel, working hand-in-hand with our strategic partner Gordon Food Service—one of the largest food distributors in North America—we've been supporting and supplying restaurants throughout the pandemic. We’re as excited as anyone to see diners begin to venture out once more, and the restaurant industry bounce back strong.
Square Roots' new Michigan farm
This new farm in Michigan, our third commercial facility, is co-located with Gordon Food Service and represents another step towards a larger shared ambition to build indoor farms together across the continent—enabling local food at a national scale.
Our produce can be found at more than 200 stores across the Midwest and New York City area.
Square Roots’ Modular Farm-Tech Platform
Central to our ability to move fast and meet demand is our modular farm-tech platform. Capital-efficient and pre-fabricated inside upcycled shipping containers, ready-to-go farms can be shipped and deployed just-in-time to any site in the world, immediately creating the perfect conditions for growing the highest quality food, regardless of local climate conditions or time of year. The overall growing capacity of any Square Roots farm can seamlessly scale up or down depending on demand in the local market.
Our new two-story farm in Michigan also includes all of the necessary infrastructures to run a state-of-the-art, food-safe, and people-safe commercial operation. This includes cold storage, biosecurity, climate-controlled packaging space, distributor loading docks, and more. Meanwhile, all of our farms are Harmonized Good Agricultural Practices (GAP) certified, in line with the USDA’s standards, and operate to strict COVID-19 safety protocols to keep farmers and the local community safe.
Our farms are also cloud-connected and managed by a combination of skilled Square Roots farmers and sophisticated in-house software. Known as The Square Roots Farmer Toolbelt, our proprietary OS provides day-to-day guidance to farmers while capturing millions of data points throughout growing cycles across our network. This data can then be analyzed to determine how changes in certain environmental parameters impact factors like yield, taste, and texture. Our system learns faster as we deploy more farms and our network gets larger, all while helping farmers determine how to grow more, better-tasting food with fewer resources. Training new farmers—and empowering the next generation of leaders in indoor agriculture—has always been core to our mission, and the Farmer Toolbelt is a key enabler in our ability to offer accessible pathways for young people to enter the high-tech farming industry.
Farmers are guided through day-to-day operations by The Square Roots Farmer Toolbelt.
Responsibly-Grown, Local Food, Available Everywhere
We’ve always designed our farms to provide responsibly-grown food in areas close to the end consumer. Our hydroponic system uses 95% less water than conventional agriculture, our farms require zero pesticides, and the location of our facilities cuts down dramatically on food miles and food waste by enabling delivery of fresh produce within 24 hours of harvest, all year round. Meanwhile, our latest farm design is easily configured for both vertical and horizontal-stacked growing formats—a new and unique capability that means we can grow a wide range of crops to meet a variety of local market needs. To date, we've grown over 200 different varieties of herbs, microgreens, leafy greens, fruits, and even root vegetables—and we’re just getting started!
Keep an eye on this blog for announcements about more new farms soon. For more information about Square Roots check out our website, squarerootsgrow.com. And for daily updates, follow us on social media @squarerootsgrow.
Your Quick Guide To Grow Room Controllers
A grow room controller brings together all the moving parts of your cultivation facility and allows you to automate your operation
March 5, 2021
What is a Grow Room Controller?
A grow room controller brings together all the moving parts of your cultivation facility and allows you to automate your operation. With a grow room controller, you can monitor and control your climate, lighting, irrigation, fertigation, and track your crop’s success to adjust and improve each cycle. These control systems can connect to existing equipment or come with their own set of sensors to track your environment, and adjust according to your set parameters, ultimately saving you time and money.
Grow room controllers integrate with existing systems, or can be purchased with sensors and equipment for larger operations. Some systems need only a few sensors and an application for your phone or computer, while others require larger computing and monitoring devices. Which option you choose will largely depend on the size of your greenhouse or indoor growing operation.
Being able to monitor and control your indoor or greenhouse facility is crucial for consistent and desired results. These systems are a huge benefit to all crop types, including cannabis, and can be adjusted to fit your cultivation style and desired outcomes. Not only will you be able to more accurately track and monitor your crop’s progress, but you can then take that learning and replicate it or improve upon it for your next growth cycle.
The Benefits
Grow room controllers offer you complete control and oversight of your crop. Any environmental aspect that you wish to control can be monitored and adjusted with a grow room control system. More advanced systems offer automation for your whole system, allowing you to pull yourself out of the weeds (pun intended) of trying to control everything manually. Grow room controllers are also scalable, especially if you purchase a setup with that in mind, allowing you to expand your facility but keep the same environmental parameters and automation.
All greenhouse and indoor growers know that having control over your environment is crucial to achieving desired results. This means monitoring and adjusting your lighting, climate, irrigation, and fertigation to ensure consistency, which can be time-consuming. A greenhouse control system does the monitoring and adjusting for you, ensuring all of the environmental controls work together and are adjusted accurately.
With advanced control systems, you can program light preferences for your greenhouse, so if light falls below a certain threshold your lights will adjust and will turn off if it exceeds that threshold. Indoor growing can also benefit from lighting such as timers and spectrum controls. Hydroponic sensors in your medium can tell you if you need to increase or decrease water durations. Ultimately being as efficient as possible with water and electricity, which is both environmentally and economically beneficial.
This monitoring and automation are incredibly cost-effective in the long run for your greenhouse or indoor facility. The more automation you have, the less labor you need to support your cultivation, and labor is one of the most, if not the most costly aspect of a cultivation facility. Grow room and greenhouse control systems can also schedule timers and alarms for preventative maintenance so that your equipment can receive proper downtime, preventing blowouts and loss of productivity.
How to Select a Grow Room Controller
Figure 1 from GroAdvisor Webinar
The above worksheet is an example of how you can select the right grow room controller for your needs. While many focus on cost, it’s also important to take into account which system will integrate with and enhance your facility the most. Take stock of your equipment and current manual system to ensure that your new grow room controller will add value to your operation.
Finding a grow room controller that is right for your facility will help you realize your fullest growth potential. Once you have compared and found a system that can accommodate the environmental controls you’d like to track and automate, all that’s left is the installation. Once the grow room controller is installed and your parameters are set you will no longer have to manually adjust your elements, saving time and labor, which ultimately saves money.
How Square Roots Is Training Next-Gen Farmers During A Pandemic
The average age of the American farmer is 58 years old. If we're going to change the food system, we need to create more pathways for young people to launch successful careers in agriculture
Square Roots
10.08.20
The average age of the American farmer is 58 years old. If we're going to change the food system, we need to create more pathways for young people to launch successful careers in agriculture.
One of the many ways Square Roots invests in the future of farming is through our Next-Gen Farmer Training Program—aimed at new farmers or those at early stages in their careers. Farmers initially join Square Roots as Apprentice Growers. Through our proprietary training methodology—supported by our intuitive technology platform—Apprentice Growers rapidly learn the essential farm skills needed to move into permanent roles on the farm team and accelerate their careers.
We continuously evolve our training program to zero in on the skills and experiences that help employees become the best indoor farmers they can be. Throughout COVID-19, we have been committed to prioritizing people safety and plant safety which has led to changes in our day-to-day farming operations, as well as rewiring our in-flight farmer training programs in May and adapting how we run the Square Roots Next-Gen Farmer Training Program going forward. Also, after several years of training farmers, we’ve listened and learned to what farmers value from their experience at Square Roots and have incorporated that into our program going forward. Read more about what it’s like to be a grower at Square Roots and how the program has evolved:
Individual Pathways
Based on the needs of our farm production teams, apprentices are hired and onboarded, either individually or in pairs, on a rolling basis. By spacing out onboarding and training, our team is able to provide more attention and support to apprentices, allowing them to move more quickly through the training program and into permanent positions on our team. We expect most apprentices will complete their training in three to six months, but each will advance at their own pace.
Foundational Remote Learning
We have moved our training materials onto a virtual learning platform, which houses videos, interactive presentations, animated diagrams, virtual tours, and other types of content that can be brought to life beyond a typical presentation. Since COVID-19 restricts our ability to hold classroom-style learning, online learning can be self-serve, supporting different types of learning styles. It also drives consistency in training and terminology, reducing the burden on managers responsible for administering it.
Intensive ‘Boot-Camp’ Style Farm Immersion
Training for Apprentice Growers is laser focused on the skills required for new farmers to quickly become the best indoor farmers they can be. After the initial foundational onboarding, apprentices will jump into production, and, in parallel, will be equipped with the necessary context and complementary training to support expanded learning and competency much sooner. Apprentices will be supported by our software operating system the Farmer Toolbelt, empowering them to get up to speed much faster, engaging with data, and ultimately helping them become better growers. Throughout the training process, farmers will receive direct supervision by one of our experienced farm team members who will act as their training guide and provide professional and moral support.
Pathway to Permanent Employment at Square Roots
Central to Square Roots is our mission to empower Next-Gen leaders in urban farming, and the Next-Gen Farmer Training Program is one of the most direct ways we do that. The program is designed to bring young people with little or no experience up to speed in our proprietary indoor farms as quickly as possible and on to their careers in indoor farming—acting as an internal training program for permanent full-time employees on the Square Roots farm team.
The Apprentice Grower role is the first step in a career path to indoor farming at Square Roots. To start, apprentices will earn an hourly rate indexed to the area’s living wage, and receive 100% covered health benefits and equity in Square Roots. Once they’ve successfully mastered indoor growing fundamentals (we expect this to take three to six months), apprentices will be eligible to move into Associate Grower positions.
For more information and to learn about new open positions on our farm teams, follow us on social media and sign up for our newsletter for updates.
Tags: Next-Gen Farm / Farmer Training / COVID-19 Response / Updates
PODCAST: Vertical Farming Podcast - Season 3 Episode 29 - Nicholas Dyner. Nick Is The CEO of Moleaer
In this episode, Harry and Nick discuss Nick’s extensive background working in the water treatment industry
Join Harry Duran, host of Vertical Farming Podcast, as he welcomes to the show Nicholas Dyner. Nick is the CEO of Moleaer, an organization that produces commercial nanobubble generators to deliver sustainable, chemical-free water quality improvement for agriculture, reservoirs, lakes, ponds, and more.
In this episode, Harry and Nick discuss Nick’s extensive background working in the water treatment industry. Nick expounds on nanobubble technology, what it is and how it can be used to improve vertical farming and the agricultural industry as a whole. Finally, Harry and Nick talk about the ongoing struggle for universal access to safe water and how advancements in technology can help restore and improve the quality of sea life.
Listen & Subscribe
VIDEOS: How To Design A Successful Vertical Farm
Vertical farming provides a practical and cost-effective way to bring food production to congested spaces. Getting a vertical farm off the ground requires more than just a green thumb and some warehouse space, though
March 26, 2021
Vertical farming provides a practical and cost-effective way to bring food production to congested spaces. Getting a vertical farm off the ground requires more than just a green thumb and some warehouse space, though. Read on to find out how to design a successful vertical farm and start harvesting crops indoors in city environments.
What Is Vertical Farming?
Vertical farming is an indoor cultivation technique that maximizes the use of space for plant production. It involves layering multiple crops or types of crops in a highly controlled vertical hydroponic or container-based system. Those who are already familiar with indoor growing can think of it like a traditional hydroponic or container garden but on multiple levels.
The Four Key Design Factors
There are four key design factors that future vertical farmers must keep in mind if they want to bring down large, high-quality yields. They mimic processes that occur in nature but would otherwise be absent in a man-made system. The four factors are:
Lighting
Climate control
Nutrient control
Vertical integration
There’s little sense in purchasing seeds or rootstock until future farmers know exactly how they will provide for all the plants’ needs, so this is a good place to start. Let’s take a look at what factors farmers need to take into account before they start the design phase.
Adequate Lighting
All indoor farms and gardens require some form of artificial lighting. Farmers and growers who are still in the beginning stages of taking their operations indoors can get the basics down by visiting Agron and reading through their educational materials. However, vertical farming is a little more complicated than a normal hydroponic or container-based garden.Since plants will be grown on multiple levels, hanging lights from the ceiling isn’t always the best solution. Most vertical farmers purchase specialized ballasts and use LED lights that emit very little heat so they can keep their lighting as close to the plants’ canopies as possible. Some modern farmers also go in for more advanced options like installing rotating beds or utilizing smart lights, but they won’t make up for inadequate lighting for all levels of the vertical farm.
Climate Control
Plants can only grow and thrive under the right climate conditions. Vertical farms need good temperature, humidity, and air handling systems. In most cases, the building’s HVAC system will be able to handle heating and cooling demands. Without adequate ventilation and air handling systems in place, though, high humidity can negatively impact plants’ cellular respiration processes and create a perfect environment for the spread of fungal diseases. It’s worth taking the time to investigate options like dehumidification systems, exhaust fans, or specialized HVAC systems that manage humidity and airflow as well as temperature control.
Nutrient Control
Plants don’t get all the energy they need from photosynthesis alone. They require nutrients as well as light and water. Every species has a different set of requirements, but all terrestrial plants need macronutrients like nitrogen (N), phosphorous (P), and potassium (K) along with a smaller amount of micronutrients to fuel healthy growth and crop production. How they get those nutrients is largely a matter of farmers’ preferences.
There are four types of systems that are appropriate for vertical farming. On a small scale, container farming using soil, amendments, and fertilizers can work. However, most large-scale vertical farms eschew this traditional practice in favor of hydroponic or aeroponic systems. Hydroponic and aeroponic setups remove soil from the equation entirely. They’re similar systems, but while hydroponics gives plants access to nutrients via a water-based solution, aeroponics involves leaving the roots exposed and spraying them with nutrients.
Finally, some more sustainability-minded vertical farmers introduce elements of aquaponics into their farms. Aquaponics involves cultivating both plants and fish. The fish provide beneficial nutrients via a hydroponic system, while the plants filter the water so the fish can thrive. The benefits of vertical aquaponics systems include improved sustainability, water conservation, and added crop value.
Vertical Integration
Not all indoor farms are vertical farms. To qualify as a vertical farm, the plants must be cultivated on multiple levels in the same room. Warehouses are perfect for this approach since they have high ceilings that can accommodate tall towers of plants and all the equipment required to maintain optimal temperatures, humidity levels, light, and nutrient delivery. The key in designing a vertically integrated farm is to maximize crop production by ensuring that the plants have just enough space to grow and thrive and receive as much light as possible.
Crop Selection for Vertical Farming
It may be tempting to assume that since vertical farming occurs indoors in a highly controlled environment, that means it’s suitable for all crops. While it’s true that vertical farmers can grow almost any kind of annual plants, and even some perennials, that doesn’t mean they should. Farmers need to consider these factors when selecting crops:
Local demand
Time to harvest
Climate requirements
Revenue margins
If the idea is to get crops out to market as fast as possible, farmers may want to stick with fast-turn crops like lettuce, potherbs, and other greens. Most of these crops will be ready for harvest in six weeks or less. Slow turn crops have higher revenue margins but require more inputs and time to grow than leafy greens. It’s also perfectly fine to plant a combination of crops as long as they all have similar climate requirements.
Vertical Farming Is the Future
With climate change poised to wreak havoc on agricultural lands across the globe and the costs associated with water scarcity on the rise, vertical farming poses a viable solution. A well-designed system can help to conserve water, avoid the impacts of inclement weather, and provide reliable, year-long access to fresh food.
The best part is, designing sustainability features like LED lighting, aquaponic systems, or even wind turbines into the vertical farm from the beginning can help to offset both the financial and environmental costs of producing food for city-dwellers, often right in their backyards. It takes a large initial investment to get started, but the payoffs will be worth it.
Related Videos about How to Design a Successful Vertical Farm :
Vertical Farms | Design, and Innovation
Growing Up: How Vertical Farming Works
Designing the vertical farm
Vertical Farming
Tags: vertical farming design pdf, vertical farming business plan, vertical farming technology, vertical farm for home, vertical farming in india, hydroponic vertical farming, vertical farming equipment, how to start vertical farming,
USA: ILLINOIS - Glenview's Wiseacre Farm To Be Featured On History Channel
"We were connected to this opportunity through Freight Farms, a hydroponic farming container company in Boston. Our farm was built and distributed by Freight Farms," said Yael Sheinfeld, whose father, Aviad, founded Wiseacre Farm
This Sunday's Episode of "Modern Marvels"
Will Highlight Innovative Hydroponic Techniques
March 23, 2021
The Wiseacre Farm crew (left to right): Sam Sheinfeld, Yael Sheinfeld and Aviad Sheinfeld. (Photo by Wiseacre Farm)
GLENVIEW, IL — Back in December of last year, a television production crew from the History Channel made a special visit to Glenview. Wiseacre Farm, a family-owned hydroponic farm, will be featured this Sunday as part of the network's "Modern Marvels" program.
Yael Sheinfeld, who handles marketing for the farm at 1975 N Lake Terrace, said the team at Wiseacre hasn't seen the episode titled, "Future of Food," yet. It is set to air at 9 p.m.
"We were connected to this opportunity through Freight Farms, a hydroponic farming container company in Boston. Our farm was built and distributed by Freight Farms," said Yael Sheinfeld, whose father, Aviad, founded Wiseacre Farm. "We're so grateful for the experience, and are very excited for the episode to air."
Aviad Sheinfeld shows off Wiseacre Farm during an episode of "Modern Marvels" on The History Channel. (Courtesy of Wiseacre Farm)
Sunday's episode of "Modern Marvels," hosted by food author and culinary entrepreneur Adam Richman, showcases Wiseacre's innovative hydroponic farming process as the future of food, highlighting the farm's mission to grow clean, fresh produce within the community that it serves.
"It was exciting for the film crew to visit the farm. Our farming team (Aviad Sheinfeld and his dad, Sam Sheinfeld) talked through each step of the plant life cycle and delivery process while the crew filmed," Yael Sheinfeld said. "[We also] participated in sit-down interviews where we discussed the concept behind the farm, how we started it, etc."
Yael Sheinfeld said that due to COVID-19 restrictions, the entire film crew for the episode was local.
Founder Aviad Sheinfeld talks about Wiseacre Farm during the episode of "Modern Marvels" titled, "Future of Food." (Photo by Wiseacre Farm)
Wiseacre Farm works to shorten the path from farm to table, promote and practice environmental sustainability, and educate consumers about the origins of their food.
"We're a family-owned hydroponic farm in Glenview that provides fresh, hyperlocal greens to the community," Yael Sheinfeld said. "We currently offer home delivery and farmside pickup options."
Wiseacre greens are available through home delivery subscriptions and weekly farmside pickup. Wiseacre Farm also makes frequent donations to local food pantries, working to ensure that fresh greens are accessible to all.
More information about Wiseacre Farm can be found here: https://www.wiseacre.farm/.
AUSTRALIA: VIDEO - Shipping Container Farms: Check Out This Craze In Modified Containers
Greenhouses, hydroponics, and mushroom farms – converted shipping containers can produce protein and vegetables for all your needs
Greenhouses, hydroponics, and mushroom farms – converted shipping containers can produce protein and vegetables for all your needs. Even if you’re not an environmentalist, there are business opportunities to be had in delivering extremely fresh food to people in urban environments like Brisbane. Given the changing climate and topsoil loss we are facing, shipping container farms could well be an answer to these issues.
Over the years in the Gateway Gazette, we have published a number of stories that look at producing food in converted shipping containers. Reflecting on what we have published and looking at the detail of what can be done, let’s consider the possibilities that come with shipping container farms.
Open Top Container Greenhouse
One of the most cost-effective ways of using a shipping container as a food-producing unit is by attaching a glass top to an open-top shipping container.
In this video, Urban Farm Units looked at the concept of a greenhouse-container. An open-top 20-foot container would have a greenhouse attached to the top with shelving units directly under the glass. This allows photosynthesis to take place in the normal way.
Seedlings can be started in the lower part of the unit, which is warmed by the light and heat from the outside.
One step down from slapping a greenhouse on top of an open-top container would be to use a flat rack container and to have the greenhouse on the base (Gateway Containers can supply both open-top and flat rack containers).
The concept is an improvement on the one in the video, as long as you keep the greenhouse within the dimensions of a 20ft standard or high-cube container, it would be possible to lift and move the container farm from place to place.
This might be useful where you have an agreement with property developers or a council to use vacant plots of land in a city for agriculture. When the site is ready to be developed you can stick it all on a truck and move it to the next plot.
The concept of a shipping container greenhouse is:
Cheap to buy
Mobile
And often won’t need planning permission for a permanent site
Could this be something you’d consider? Contact us at Gateway Containers to discuss your needs!
Mushie Container Farm!
Image source: King Oyster Mushrooms Facebook
In 2019 we reported how Belgrave, Vic-based John Ford has developed a shipping container mushroom farm. This could produce protein for people as an alternative to meat or for anyone who loves the taste of freshly cut shrooms.
Mushrooms of any kind don’t store well and are best eaten as soon as possible after cutting. This is why having a mushroom farm close to restaurants could be a money-spinner.
This requires no modification from a basic shipping container, you could even install the racking inside the container yourself.
In their lifecycle, mushroom mycelium live out of sight of the world until they are stressed and get the impression that they are facing death. When stressed they flower to produce spores – those flowers are the mushrooms that many of us love to eat.
A shipping container is perfect to take advantage of such a lifecycle. Logs or other media are infected with the mycelium and left to rot for a certain time. By altering the environmental conditions, so you deliberately stress the fungi and they flower.
In our article, we reported how John Ford is producing mushroom species that are famed for their delicate taste but don’t travel well at all – shiitake and oyster mushrooms. As a sideline to his main income as a marine biologist restoring seagrass habitats near Belgrave, he produces freshly cut shrooms for local people and restaurants.
For you as an entrepreneur, mushroom growing would require buying a used shipping container and setting it up as a mushroom farm. If you are planning an urban mushroom container farm, you can take advantage of the fact that you can treat the container as a mobile unit and not as a permanent base. Shipping containers are also pretty inexpensive to buy and convert.
Hydroponics – The Rolls Royce of Shipping Container Farms
Image source: ABC
The hydroponics concept is highly developed for the use of fresh food and can be set up for high density vegetable farming in shipping containers. This requires a fair bit more modification than the two systems we describe above.
Unlike the Urban Farm Units company, several companies have managed to survive over the years selling their hydroponic container farm businesses to entrepreneurs and restaurants around the world.
Modular Farms is a company we featured in our blog originally based in Canada, but who recently set up shop over here in Australia. According to their website, they “design and manufacture container farm systems that can be used to grow food in most locations on earth.”
These systems strive to get around some of the issues we face here. Cities like Brisbane get far too much water sometimes and then face droughts for years on end. The Australian Food Services News reported, “With a focus on sustainability, Modular Farms’s hydroponic, closed-loop system uses 95% less water than a typical outdoor farm.”
Topsoil erosion is a problem, especially in prolonged droughts when it gets blown away as dust. Hydroponics use media like rock wool and even used mattresses to house the plants’ root systems and feed them nutrients via a watering system.
With our ever more extreme climate, food often has to be imported into cities from hundreds or thousands of miles away. A hydroponic container farm can enable you to grow many vegs very close to markets and restaurants.
This has been observed by global homewares retail giant IKEA, which in 2019 announced it was piloting growing vegetables in its stores for use at its restaurants. We reported, “While selling hydroponic indoor growing equipment to customers, IKEA is feeding its staff with lettuce and other vegetables grown in a container outside its Malmö and Helsingborg stores.”
Image source: ABC
There are a few downsides to hydroponics. Firstly, while some types of plants are happy enough growing in hydroponics – the simpler ones producing leaves and flowers (like broccoli!) – others aren’t so happy, such as cassava, wheat, and potatoes.
The next big issue is that for a high-intensity farm, not unlike factory farming chickens, you need to be ultra-clean in your production as the arrival of a destructive disease or fungus could wipe you out very quickly.
Container Fish Farm Too?
In theory, it is possible to run a fish farm connected to the hydroponics container farm, with you largely feeding the fish and collecting their feces and other waste to feed the plants. The plants would clean the fishes’ water and make it habitable for them as reed beds do in nature. This a concept that is in development but hasn’t caught on commercially yet.
How Can Gateway Containers Help?
We can provide and convert an insulated container for you to get started with and advise you how to best make further additions without compromising the overall structure.
If any or all of these ideas have caught your interest – or you just know about these concepts and need a shipping container to make it possible – then get in touch with us today to discuss your needs!
Posted on February 22, 2021
By Mark FinneganOtherShipping ContainerModified Shipping ContainersLeave a comment
UAE: “Hydroponic Farming Is Not Yet Deployed At A Meaningful Scale”
Greener Crop was founded in September last year with the goal of enabling hydroponic farming in the Middle East and Africa
“While hydroponic farming is extremely relevant to the water-poor Middle East, and incentives for agriculture such as energy and water subsidies have been put in place, the technology has not been deployed at a meaningful scale yet,” Alexander Kappes, founder of Greener Crop states.
Greener Crop was founded in September last year with the goal of enabling hydroponic farming in the Middle East and Africa. Alexander was working at an investment office prior to Greener Crop which brought his attention to the long-existing problem: the country is too dependent on food imports. “We wanted to enable local sustainable farming here as well.” Greener Crop offers farm management solutions, removing entry barriers.
The company offers four key solutions for existing or aspiring farmers: development of crop strategy, input management, physical farm management, and crop marketing. From Container farms to greenhouses and indoor vertical farms, Greener Crop supports their clients from finding the right supplier and setup, to selling the crops in the market. “It’s a great solution if you’re looking for an experienced partner to get your farm up and running, whether it’s short or long term,” says Alexander.
Alexander Kappes
There has been a strong push from local governments to develop alternative farming methods. The government in the UAE has invested over $200 million to support the development of growing facilities. This is a highly valuable approach, however, it is important to keep in mind that even a $40m indoor vertical farm can only contribute 0.03% of the local annual fruit & vegetable consumption. Farming is a highly democratized industry and requires not only a handful of a large farm but thousands of small and medium-sized farms that enable a country to be self-sufficient,” Alexander claims.
Removing barriers
Whether farmers want to expand or convert their farm into a hydroponic farm or an outsider investor, Greener Crop is here to help. The company connects farmers to suppliers and manufacturers, they can either run the farm, handle the supply chain and in some cases, handle the sales. “Clients no longer have to figure out everything on their own – we are here to support them with the operations and even sale of their crops. In many cases, clients are self-consumers such as hotels and restaurants,” Alexander explains.
The company sits together with their clients, comes up with a plan, ticks off the boxes, and starts setting things up, given the customer budget. Based on the expected yield, an approximate selling price per kg can be provided to clients. “We can always predict with a certain degree of accuracy. In this way, we can sketch revenue, utility costs, including labor, etc., which eventually leaves us to the expected profits. After the preliminary proposal is given, we reach out to potential suppliers as we understand what they offer in terms of yield, cycles, crop analyses, costs, and input.”
Green Crop has the ability to run a farm completely independently, however, the client can decide how hands-on they want the company to be. Clients can set foot on the farm at any time. “We can also operate certain parts of the operation such as maintenance for instance. Our benefit is that we come in, with trained staff, they do the work and go out.
Finding a suitable market
Alexander says, “The difficulty is not in selling all of the produce, but whether you are able to sell it at the right price. The smaller the farm, the higher the production costs. Being able to sell something at the price where it covers all costs is the main goal.” The challenge this therefore to gauge the available client-base for your produce, as well as the competition and their prices. Similarly, a thorough crop strategy must account for seasonal price fluctuations and ensure that we seed to harvest at the right time.
Often, the biggest challenge, according to Alexander, for smaller individual farmers is sourcing the right seeds and nutrients. Finding suppliers of quality products is often a challenge, and in most cases, they require you to buy large quantities that exceed the farms' annual consumption. “There are large differences in quality between suppliers and often when farmers choose the most affordable solution, this results in high costs for maintenance and replacements. For many new manufacturers, hydroponic farming looks like an easy enough industry to get into, but they underestimate the complexity of fine-tuning an indoor farm for efficient farming, and it’s often the farmers that pay the price for this,” Alexander notes.
Greener Crop started operations in the UAE and is now expanding into Saudi Arabia and Qatar, with the rest of the Middle East and all of Africa in their sights. Alexander adds: “As the region in the world most under threat from water stress and shortages, conventional farming is often not a sustainable option. It is for that reason that we chose to focus on enabling hydroponic farming in this area.”
For more information:
Alexander Kappes, Founder and CEO
Greener Crop
alexander@greenercrop.com
www.greenercrop.com
Publication date: Mon 22 Mar 2021
Author: Rebekka Boekhout
© VerticalFarmDaily.com
FRANCE: How To Grow Food In A Concrete Jungle
Building flourishing farms in the heart of cities used to be just a utopian fantasy. Now it's an important step towards developing a smart, diversified food system capable of feeding a growing world population
22-03-2021 | BBC
FRANCE - Building flourishing farms in the heart of cities used to be just a utopian fantasy. Now it's an important step towards developing a smart, diversified food system capable of feeding a growing world population. Guillaume Fourdinier has lived in Paris for six years, but he still misses the taste of the fresh cereal grains, beets, carrots, and more that grow on his family's farm in Verton. There, in northern France's countryside, eating locally is a way of life – not simply a trend or a sticker on an apple at the grocery store.
“Local food is everywhere when you are in the countryside. You get fruits and vegetables with better taste, more nutritional value,” he says. “When you are in Paris, what is local food? There is nothing coming from a local farm. I think for quality of life for people living in big cities this is a big problem.”
In 2015, Fourdinier co-founded Agricool, an urban farm that's now comprised of 11 recycled shipping containers on the north side of the city. Eight farmers plant, harvest, pack, and deliver the pesticide-free lettuces, herbs, and strawberries to 60 supermarkets (though Fourdinier expects that number to grow to at least 200 retailers by the end of 2021).
Urban farms like Agricool are part of a broad collection of metropolitan agricultural efforts including everything from vertical farms to greenhouses to aquaponics to community gardens. The idea of cultivating food in or near cities is not new (see the victory gardens of both world wars, for example), but these ventures have become increasingly popular in recent years as the local food movement strengthens. After the rise of the supermarkets led many people to feel disconnected from food production, consumers are again paying more attention to how and where their food is grown, along with how far ingredients must travel between field and plate.
From Brussels to Nigeria, entrepreneurs and farmers are reimagining what farms are and conceiving innovative technology to help grow food in smaller spaces and in more sustainable ways. They're attempting to fix existing food supply chain concerns, which we've all became intimately familiar with in the past year. Images of picked-over grocery shelves and farmers tossing out produce early in the Covid-19 pandemic broadcast the failures and fragility of our current systems.
Click here to read the full article.
Photo Courtesy of BBC
US: NEW YORK - 21st Century Fund Awards FeedMore WNY $100,000 For Expanded Freight Farms Greenery
In 2020, FeedMore WNY served more than 16 million meals to WNYers who were homebound due to quarantine
by queenseyes
March 17, 2021
Recognizing the needs of the community is an integral component of the 21st Century Fund. Making sure that those needs are met is another. The Fund – “a giving circle open to anyone who wants to give back in Western New York” – designates significant awards to worthy organizations that submit applications for consideration. This year, FeedMore WNY is the recipient of $100,000, which will allow the non-profit to continue on with its efforts to feed those struggling during the pandemic.
In 2020, FeedMore WNY served more than 16 million meals to WNYers who were homebound due to quarantine. This was accomplished via the group’s 300 pantries, soup kitchens, emergency shelters, etc., throughout Erie, Niagara, Cattaraugus, and Chautauqua counties.
FeedMore WNY will be using the significant funds to expand its GrowMore for Good project, by allowing the organization to double its capacity, which in turn will ensure that fresh produce will be available to over 129,000 individuals. The expansion of a FeedMore-operated Freight Farms Greenery™ (the organization’s second hydroponic container farm) means that FeedMore will be able to produce 200 lbs. of produce each week. The group’s initial hydroponic “container farm” will supplement the effort. This food will be harvested and distributed within 24 to 48 hours, according to FeedMore.
This is an incredible effort that will allow more people to access healthy foods, instead of relying upon less wholesome canned foods.
In order to receive the crucial funding, FeedMore WNY made it to the final four, out of a streamlined pool of 30 applicants, before coming away with top honors. Homespace, Jericho Road, and OLV Charities were the other three finalists – all four projects can be found here.
Members* from across the country ended up casting their votes for FeedMore WNY, knowing how imperative it is to get healthy foods into the hands and onto the tables of disadvantaged households. The existence of ‘food deserts’ and the fight for ‘food justice’ go hand-in-hand. Compounded by the pandemic, it’s more important than ever to offer people food security, for healthier futures.
“FeedMore and all the clients we serve across Erie, Niagara, Cattaraugus and Chautauqua counties are overwhelmingly grateful for the generous support from the 21st Century Fund which will allow us to purchase our second container farm. The indoor, vertical growing, hydroponic farm will allow us to double our output of crops to enable us to put fresh, nutritious and fragile produce into our clients’ hands within 48 hours of harvest,” said Tara A. Ellis, FeedMore president and CEO.
“Our giving circle is a great way to introduce people to philanthropy,” said Ted Borowiak, 21st Century Fund Co-Chair. “We are always accepting members and encourage anyone including families, school groups or organizations to learn more about our membership options. Once you are a member, you are a member for life, allowing you to stay informed on new projects underway and make an impact in our community over and over again.”
The next 21st Century Fund grant process will open in the fall of 2021. For more information about the 21st Century Fund and membership details, visit www.21stcenturyfund.org.
*Members pay a one-time fee to join the 21st Century Fund and come together every other year to vote on awarding a $100,000 grant to one deserving organization for a specific project that will benefit the community. The 2018 winner chosen by members was the Niagara Falls Boys & Girls Club’s 17th Street Clubhouse Revitalization Project.
Tagged with:21st Century Fund, FeedMore WNY, food deserts, Freight Farms Greenery, GrowMore for Good, Tara A. Ellis, Ted Borowiak
Providing A Sustainable Growing Solution For Farmers, Using Renewable Energy in Container Farming
Recently, Freight Farms and Arcadia have partnered to provide Freight Farms' U.S. customers with access to clean energy for their everyday operations
“The past year has really proved our proposition as it has never been proven before,” says Rick Vanzura, CEO at FreightFarms. “The pandemic put a huge focus on supply chain security, local food access, and how to handle disruption to a supply chain, and we saw that having a modular farming solution that can be put next to people where they need food fits in perfectly. Some segments have suffered, while our farms have proven to be a great solution.” The company has seen demand going up, with 2020 being a record year: Freight Farms tripled revenue versus the prior year and set a record for orders.
Recently, Freight Farms and Arcadia have partnered to provide Freight Farms' U.S. customers with access to clean energy for their everyday operations. With this partnership, Freight Farms and Arcadia are taking strides to align their respective industries, moving indoor farming into a more sustainable future. Freight Farms’ customers can now connect the utility for their container farm to Arcadia to match 100% of the farm’s electrical usage with clean energy.
Tackling sustainability pillars
“We already have a number of current farmers that have signed up with the Arcadia energy offering. It was a really important milestone for us as sustainability has been a core mission since the founding of the company.” Rick identifies the sustainability pillars in farming as soil conservation, water conservation, food miles, and energy usage. “At Freight Farms, we have always performed very strongly in the first three categories. Our farms have no effect on soil; they use very little water (5 gallons/day, or 19 L/day), and they reduce food miles significantly, sometimes to zero. What remained for us to solve and why the Arcadia partnership is so crucial is energy,” Rick notes.
Before the Arcadia partnership, energy was the only unsolved part of the sustainability pillars Freight Farms hadn’t tackled yet. The recent partnership has given access to clean energy to all small business farmers. “With the presence of clean energy, we believe there hasn’t been a more sustainable farming solution similar to this one before.
Freight Farms looks at sustainability through the triangle of labor, yield, and power. They are increasing the output per unit of input. According to Rick, Freight Farms is far down the road in the development of greater efficiencies in their farms, focusing on optimizing for yield per unit of power and continuing to research renewable energy options. Rick says that “Everybody’s success is a collective success as we’re all relying on the industry as a whole... We’re all bound by this mission to create a more sustainable planet. Therefore, anything we can do in our own small way, we’re ready to do.”
Improving farm efficiency
On the product side, the company is doing updates to everything. “We made our farms more efficient, delivering value in several aspects, working on different renewable energy in all forms. The ROI has never been better than this farm, because of the intersection of output and efficiency gains. As we’re big believers in helping the industry as a whole for good, our ultimate goal is to be NET zero ultimately.”
While Freight Farms customers already span 46 U.S. states and 32 countries, Rick believes that the company will expand into more locations this year. This growth is stimulated by recent investment and team expansion. “By the end of 2021, we’re expecting to be in every US state and several other countries. Ospraie Ag Science led our last fundraising round, where they invested heavily in our ability to do research. Therefore, we’ve added lots of strength to the team over the last year.”
Collaborations
As a plug of vertical farming, Freight Farms is collaborating with MIT sustainability lab students together on a project. The project is about working in conjunction with the government, and public- and private partnerships around sustainability. “The goal is to be part of something where brilliant people are willing to donate their time and energy. This is just one example of many where people want to pitch in and help as we all want to have a more sustainable planet,” Rick notes.
“We’re not trying to solve for renewable energy on a location by location basis. That would be the route to go with today, but it’s a solution limited to the United States as of now,” Rick affirms. Freight Farms is always on the lookout for partners worldwide where its services can be made available.
For more information:
Rick Vanzura, CEO
Freight Farms
+1 877 687 4326
info@freightfarms.com
www.freightfarms.com
Publication date: Wed 17 Mar 2021
Author: Rebekka Boekhout
© VerticalFarmDaily.com
Eeden Farms Sees Phenomenal Market Response To Pioneering Concept
Lincoln Deal II, the founder of Eeden Farms, said: “The response has been phenomenal. Most days, we are combing growing and facilitating tours because the interest level is so high among restaurants and hotels
An Eeden Farms worker plants seeds for a sustainable future. (PHOTO: EEDEN FARMS)
NASSAU, BAHAMAS — A tech-enabled containerized farming company has seen a “phenomenal” response to its offering, according to its founder, who told Eyewitness News “the demand is definitely there”.
Lincoln Deal II, the founder of Eeden Farms, said: “The response has been phenomenal. Most days, we are combing growing and facilitating tours because the interest level is so high among restaurants and hotels.
Lincoln Deal II.
“A lot of the restaurants and hotels are enamored by how fresh the produce is, that they can get it farm-to-table and it’s Bahamian. The demand is definitely there.”
Eeden Farms, located in the BRON Business Centre, Airport Industrial Park, officially launched back in February.
The company currently utilizes three repurposed shipping containers equivalent to 15 acres of farmland and offers fresh organic produce year-round. Its farm system was created by Boston-based Freight Farms, the world’s leading manufacturer of container farm technology.
Deal defended the containerized farming concept, noting that Eeden Farms is the first company to have Freight Farm’s newest model of containerized farms.
“The technology that we are utilizing has never been used here before,” said Deal.
“We are the pioneers of this technology here in The Bahamas despite what misinformation may put out there. We were the first to receive this model from Freight Farms and they own the patent on this particular technology.”
Caroline Katsiroubas, director of marketing and community relations at Freight Farms, told Eyewitness News: “Eeden Farms represents the first entry of our technology into that region and that market. It began in 2020 but the journey didn’t start there. We have been working with him (Deal) for quite a few years, having first met at a conference in 2016.
“We’re in 32 countries right now. In terms of who our client base is, we have a very diverse kind of network of people who are interested in operating the system and it has infinite applications.”
Tags Always a headline ahead, Bahamas news, ewnews, ewnews.com, Eyewitness News, Eyewitness News Online, Nassau Bahamas, www.ewnews.com
About Natario McKenzie
View all posts by Natario McKenzie →
Lead photo: Eeden Farms. (BIS PHOTO/KRISTAAN INGRAHAM)
US: SOUTH CAROLINA - Indoor Farm Provides Fresh Lettuce To Charleston County Schools
Vertical Roots’ goal is to revolutionize the way communities grow, distribute and consume food
Indoor Farm Provides Fresh Lettuce
To Charleston County Schools
03-16-21
Vertical Roots, a hydroponic farm in Charleston, looks different compared to a traditional farm. Inside the upcycled shipping containers, individual heads of bright green and red lettuce line the walls as they complete the growing process without touching the outdoors.
Vertical Roots’ goal is to revolutionize the way communities grow, distribute and consume food.
“All the founders of the company have always been very inspired and motivated by feeding the community healthy, nutritious food,” said Jessica Diaz, the sales manager at Vertical Roots.
Students at Chicora Elementary School taste-tested Vertical Roots lettuce. PROVIDED
The school system is no exception to the organization’s mission. At the end of February, Vertical Roots began providing all of Charleston County schools with fresh lettuce from the farm.
“They’ve never been in the position where they could have a local lettuce provider,” said Diaz. “You have to be able to provide that product year-round for it to be an option for the farm-to-school program.”
In order to provide food to the schools, a farm has to meet the requirements of the Fresh Fruits and Vegetables Order Receipt System Catalog from the Department of Agriculture, which includes sufficient quantity and ability to produce a consistent supply.
Since Vertical Roots’ lettuce is grown indoors in a controlled environment, the lettuce is not impacted by environmental factors, like flooding, droughts or even seasonal changes. This means the lettuce can be produced year-round with each container growing 3,400 heads of lettuce per harvest.
Vertical Roots’ two farms in Charleston and Columbia produced approximately 3 million pounds of lettuce in 2020.
Diaz said it’s taken several years to scale up to the capacity that the farm is currently at; Vertical Roots began in 2016 and currently, it’s the largest hydroponic container farm in the country. The farm provides lettuce to over 1,200 retail locations across 11 states in the Southeast.
Vertical Roots farmers checking on the lettuce in one of the storage containers. PROVIDE
Vertical Roots initially connected with the CCSD in January 2020 during its Harvest of the Month program. Each month, CCSD’s Nutrition Services, in partnership with the Green Heart Project, provides students with nutrition education with a focus on locally grown produce.
“Based on the success of that program, we started having conversations about what would it look like to service the school district in a more meaningful way,” Diaz said.
Each school district is allocated a specific amount of money from the government that goes towards fresh fruits and vegetables based on the number of students and school sizes, according to Kerrie Hollifield, a registered dietitian with the CCSD Office of Nutrition.
She said it’s up to the district on how the funds are spent and CCSD is committed to providing fresh, local produce to students and staff so partnering with Vertical Roots became a natural fit.
The current lettuce options at the schools are the Green Butter lettuce and a cut spring mix. Each day, the schools offer an entrée salad that includes Vertical Roots lettuce, grilled chicken and fresh vegetables including tomatoes, cucumbers, and carrots. There is also a side salad option. Occasionally, the schools will offer other options like a lettuce wrap sandwich.
Hollifield said all of the lettuce in Charleston County schools is from Vertical Roots, which means over 50,000 students from 84 schools have a fresh lettuce option. “It’s been awesome to see the kids get excited about salads,” she said.
Since the initiative began, Emily Trogdon, the public relations specialist for Vertical Roots, said the farm has received positive feedback from teachers and parents who are excited that fresh, local lettuce is now available at the schools.
“Children, in general, are always geared towards sweets and candies, salty snacks, but to see them genuinely enjoying the vegetable is just a testament to the product quality itself and to the amazing work that the nutrition program has been doing in the schools,” said Trogdon.
Typically, lettuce that is consumed on a food service or retail level is grown in California or Arizona, so most lettuce travels 2,000 miles before reaching a restaurant or grocery store.
Vertical Roots’ goal is to close the “farm-to-table gap” by providing lettuce with close to zero food miles.
The lettuce growing in an indoor, controlled environment. PROVIDED
Charleston County schools have not had a local lettuce option until the partnership with Vertical Roots because lettuce cannot be grown year-round in South Carolina on a traditional, outdoor farm.
In addition to being grown locally, Vertical Roots’ lettuce is not treated with chemicals or pesticides. Trogdon said she likes to tell people the produce is 100 percent lettuce.
“The produce is incredibly clean and safe to consume,” Trogdon said. “That’s a barrier that the school system doesn’t have to jump over with our produce.”
Vertical Roots controls the entire environment as the lettuce matures from propagation to harvest. The temperature, humidity, amount of light, and water are optimized in order to provide the safest and most productive growing environment.
Vertical Roots’ system speeds up the harvest time to 35 days, versus the 45 to 60 days for traditionally grown lettuce.
The organization is committed to sustainability, specifically with water and land conservation. Indoor farming uses up to 95 percent less water compared to traditional farming due to the ability to recycle and re-filter water throughout the system.
The company is also socially sustainable when it comes to providing fair wages for employees.
While part of Vertical Roots’ mission is to revolutionize the produce industry, Diaz said their goal is not to eliminate traditional farming. She said there are many heritage crops in South Carolina that could not be grown in an indoor system, so the organization fully supports the local farming industry.
When it comes to buying locally, Diaz said ultimately it benefits the county and state. “When you’re buying from a local farm, you’re employing local people who spend that money in the local economy,” Diaz said.
Lead Photo: The lettuce growing in a controlled upcycled shipping container. PROVIDED
LONDON: New Vertical Farm Offers Eco-Friendly Greens Picked And Delivered Within 24 Hours
London’s first delivery service for vertically-farmed, eco-friendly greens has launched from its base in the Docklands. Vertical farming is a fast-growing trend, with the global market size that was valued at $2.23 billion in 2018, projected to reach $12.77 billion by 2026
Lettuces growing vertically at Crate to Plate, a new farm in London's docklands | CRATE TO PLATE
London’s first delivery service for vertically-farmed, eco-friendly greens has launched from its base in the Docklands. Vertical farming is a fast-growing trend, with the global market size that was valued at $2.23 billion in 2018, projected to reach $12.77 billion by 2026. Crate to Plate is a clever new vertical farming venture founded by Sebastien Sainsbury who is a firm advocate of the concept of "15-minute cities" where everyone has access to fresh produce within a 15-minute walk of home. Crate to Plate offers consumers a wide range of super fresh organic lettuces, leafy greens and herbs, all picked within 24 hours, available by home delivery or at select greengrocers throughout London.
Recycled shipping containers house Crate to Plate, a vertical farm in London | ALISTAIR CARMAN
The eco-friendly farm is located in a parking lot owned by international property company Lendlease on the Isle of Dogs (Canary Wharf) inside three recycled shipping containers kitted out with LED lighting and an automated nutrient delivery system. Each 40-foot container achieves the same production as over an acre of farmland, with the site projecting to produce around six tonnes of greens each year. Not only does the urban farm use far less land but the pesticide-free produce is grown using hydroponic technology that uses 96% less water than traditional farming.
Crate to Plate, a new vertical farming initiative |. CRATE TO PLATE
Scientists and farmers at Crate to Plate carefully control the environment inside the shipping containers. Meticulously monitored vertical farming ensures that greens can be grown locally in urban environments, all year round, using minimal water, allowing produce to be delivered to consumers within 24 hours of harvest, with zero carbon footprint in transporting from farm to customer. As a result, the produce is as fresh as possible and has the highest possible nutrient value, completely free of pesticides and toxic chemicals. Lettuce, rocket, kale, pak choi, herbs, microgreens and more are harvested and delivered twice a week. The difference in taste between Crate to Plate’s greens and those you can buy from a supermarket is astonishing and delicious. And dynamite options like wasabi rocket and basil Genovese are already proving to be customer favorites.
Basil growing vertically at Crate to Plate | JOANNE SHURVELL
Produce from Crate to Plate is available in select greengrocers like Artichoke in North London and direct to consumers via their website. A £15 mixed box includes three types of lettuce, three bags of greens, and three herbs. Crate to Plate also sells to restaurants and have recently become Chef Ollie Dabbous's exclusive distributor of greens for his Michelin-starred Mayfair restaurant Hide. Crate to Plate has an ambitious UK expansion plan. A second site will open near Elephant and Castle this month, followed by other London sites and farms in other cities (Manchester, Birmingham, etc). And further ahead will be expansion to the United States.
Seedlings before they are transferred to the walls of the farm | CRATE TO PLATE
Crate to Plate’s new site in Elephant Park is part of a £2.5 billion regeneration project headed by the local council and Lendlease. One of the key aims of the development is to create a local, community-oriented ecosystem, with businesses from the area supplying residents and other retailers in the nearby community. Crate to Plate slots nicely into this concept, aiming to sell direct to local residents and to the new food businesses that are opening. Crate to Plate’s next London site is already in the works: the International Quarter London development near the 2012 Olympic Park in Stratford, east London.
With the global covid-19 pandemic fueling home deliveries and such a high-quality product on offer, it’s no surprise that Crate to Plate’s greens have sold-out every week since launching. Founder Sebastien Sainsbury says he wants “everyone to be able to get fresh leafy greens no more than a mile away from where they live.” It appears he’s off to a good start at achieving that goal and it will be fascinating to follow the progress of this sustainable new business.
Crate to Plate London home delivery boxes range from £6 to £28 depending on the selection and quantity, with no delivery charge on orders of £20 or more.
I've been writing on travel, food, fashion and culture for the past decade or so for a variety of publications. I co-founded PayneShurvell, a contemporary art gallery in London which is now an art consultancy in London and Suffolk. My photographer partner Paul Allen supplies photos for my features that often include a music or art event and our travels have taken us to under the radar music and art festivals in France, Italy, Portugal and Spain. I am the co-author of the Citysketch series of books that includes London, Paris and New York, published by Race Point and I'm the author of Fantastic Forgeries: Paint Like Van Gogh. Follow our adventures on Twitter at @jshurvell and on Instagram at @joshurvell and @andfotography
Kimbal Musk’s Quest To Start One Million Gardens
The tech veteran and restaurateur (and brother of Elon) has been preaching the ‘real food’ gospel for years — and his newest project may be his most ambitious yet
MARCH 20, 2021
The tech veteran and restaurateur (and brother of Elon) has been preaching the ‘real food’ gospel for years — and his newest project may be his most ambitious yet
By ALEX MORRIS
Million Gardens Movement
On the day he almost died, Kimbal Musk had food on the brain. The internet startup whiz, restaurateur, and younger brother of Tesla’s Elon had just arrived in Jackson Hole, Wyoming, from a 2010 TED conference where chef Jamie Oliver had spoken about the empowerment that could come from healthy eating. This was something Musk thought about a lot — food’s untapped potential, how he might be a disruptor in the culinary space — but beyond expanding his farm-to-table ethos along with his restaurant empire, Musk hadn’t yet cracked the code. Then he went sailing down a snowy slope on an inner tube going 35 miles an hour and flipped over, snapping his neck. The left side of his body was paralyzed. Doctors told the father of three that he was lucky: Surgery might bring movement back.
“I remember telling myself, ‘It’s all going to be fine,’ and then realizing that tears were streaming down the side of my face,” he says. “I was like, ‘Yeah, OK. I don’t really know what’s going on. I’m just going to, you know, let things go.’”
Musk, 48, eventually made a full recovery, but it involved spending two months on his back, which gave him plenty of time to think about the intersections of food, tech, and philanthropy. Since then, he has launched an initiative to put “learning gardens” in public schools across America (now at 632 schools and counting); courted Generation Z into the farming profession by converting shipping containers into high-tech, data-driven, year-round farms; spoken out vociferously against unethical farming practices and vociferously for the beauty and community of slow food; and this year, on the first day of spring, is kicking off a new campaign with Modern Farmer’s Frank Giustra to create one million at-home gardens in the coming year.
Aimed at reaching low-income families, the Million Gardens Movement was inspired by the pandemic, as both a desire to feel more connected to nature and food insecurity have been at the forefront of so many people’s lives. “We were getting a lot of inquiries about gardening from people that had never gardened before,” says Giustra. “People were looking to garden for a bunch of reasons: to supplement their budget, because there was a lot of financial hardship, to help grow food for other people, or just to cure the boredom that came with the lockdown. To keep people sane, literally keep people sane, they turned to gardening.”
The program offers free garden kits that can be grown indoors or outdoors and will be distributed through schools that Musk’s non-profit, Big Green, has already partnered with. It also offers free curriculum on how to get the garden growing and fresh seeds and materials for the changing growing seasons. “I grew up in the projects when I was young, in what we now call food deserts,” says EVE, one of the many celebrities who have teamed up with the organization to encourage people to pick up a free garden or to donate one. “What I love about this is that it’s not intimidating. Anyone can do this, no matter where you come from, no matter where you live. We are all able to grow something.”
Rolling Stone recently talked with Musk about the Million Gardens Movement, why shipping containers can grow the most perfect basil, and how he is channeling his family’s trademark disruptor drive to change America’s relationship with food.
How did you first get interested in food and then how did that grow into an interest in agricultural innovation?
I’ve always loved food. I started cooking for my family when I was 12, maybe even 11.
What was the first meal you made? Do you remember?
It’s actually funny. My mother is a wonderful person, great dietitian, but because she’s a dietitian, the food we ate was brown bread and yogurt or bean soup. I mean, as a kid, it drove me crazy. So I asked my mom, “If I could cook, could we get something else?” And so I went to the butcher, and I asked them, “How do you roast a chicken?” And he said, “Put it in a really hot oven for one hour.” And I was like, “Oh, how hot is hot?” He was like, “Make it as hot as your oven goes for one hour, and if it starts to burn, then just take it out.” And he gave me the chicken, and that was it. I’ve kept that recipe forever. 450, 500 degrees, one hour. That’s a great straight-up recipe.
And then my mother insisted on a vegetable, so I decided to do French fries, which was my funny way of convincing her that I’m doing a vegetable.
It is a vegetable.
I totally screwed up the French fries. I didn’t heat up the oil ahead of time, and if you don’t do that, the potatoes actually soak in the oil so you’re eating basically a sponge of oil. I made everyone throw up. But the roast chicken was delicious. Everyone loved that. And so I was encouraged to cook more. I cooked for my friends in university. I didn’t have any money, so I figured out how to cook for 40 cents a person. It was a Kraft dinner with weiner sausages. And if someone chipped in an extra dollar, I’d get actually real cheese instead of the powdered cheese.
Anyway, I studied business, and then went down to California to start a company with my brother building maps and door-to-door directions for the internet.
I read that you and your brother were sleeping in your office and showering at the YMCA and that sort of startup lifestyle made you appreciate food.
Yeah, that’s totally right. We only had enough money for rent for either an office or an apartment, so we rented an office. I had a little minibar fridge and put one of those portable cooktops above it, and that was our kitchen. But we also ate at Jack in the Box all the time because it was the only place that was open late. Ugh, 25 years later, I can still remember the items on that menu. It was just really, really not great — a huge inspiration to go focus on real food after that.
And I just did not like the lack of social connection. It’s a work-hard-go-to-sleep-and-work-hard-again culture with not much socializing in the way that I enjoy, which is eating food, eating together over a meal, talking about ideas. I kind of was suffocating a little bit.
It’s a Soylent culture.
Yeah, exactly. They actually want food to be a pill. So I kind of needed to leave. We ended up selling [our company] for a gazillion dollars when I was 27, and I had this sort of opportunity to do whatever I wanted. So I went to New York to enroll at the French Culinary Institute.
Was culinary school as brutal as people make it out to be?
Absolutely brutal. It was Full Metal Jacket, but cooking. They just totally break you down. They make sure you don’t have any faith in your own abilities — within a few months, you’re like, “I am a completely useless fool” — and then after that, they start building you up with the skills they want you to have. It was very, very hard on the ego. I managed to graduate, but I would say 70 percent of the people that start don’t finish — and you pay upfront.
I actually graduated just a few weeks before 9/11 and woke up to the sounds of the plane hitting the building. That’s how close we were. Fourteen days later, I started volunteering to feed the firefighters. We would do 16-hour days, every day — there was never a reason not to work because the alternative is you sit at home during the nightmare after 9/11, where no one was on the streets or anything. I started peeling potatoes and eventually got to the point where I would drive the food down to Ground Zero. The firefighters would come in completely gray in their face and gray in their eyes, covered in dust. And then they’d start eating, and you’d see the color come back in their face, the light in their eyes.
And you worked as a line cook after that?
Yeah, for Hugo Matheson, at his restaurant. He was the chef of a popular restaurant in Boulder, and I just wanted to learn. I was a line cook for $10 an hour for probably 18 months. And loved it. You know, it’s a submarine culture. And you get in there and everything you do in the moment is measured in the moment. It’s very much the opposite of [building] software.
You and Hugo eventually started a restaurant [The Kitchen] that practiced the farm-to-table thing before it was even really a term. Why was it so important to you to have local suppliers and organic methods? At that point, was it mainly about flavor, or was there a bigger ethic behind it?
For sure flavor was the driver. But I think that the thing that I resonated with more was the sense of this concept of community through food. You know, when I was feeding the firefighters, it was all about community. The fishermen would come and give us their fish, so we got the best fish you can imagine. The cooks were all volunteers. We were going through this really tough time. So for me, the community through food was what I loved about it.
[At The Kitchen], we literally had a basic rule to farmers saying we’ll buy whatever you grow. We said that if you can deliver by 4 p.m., then we will get it on the menu that evening.
Oh, wow.
We would get fiddlehead ferns at 4 p.m. and be trying to think, “OK, what can we do with this?” If you turn the food around that quickly, it really does show up in the flavor.
Food that had potentially been in the ground that morning.
Not potentially. Every day was working with the harvest of that day. We had 43 different farmers coming to the back door. It was awesome.
Let’s move ahead to the part of the story, after your accident, when you’re like, “All right, I’ve gotten this new lease on life and now what am I going to do with it?” Obviously, within the food space, there are a lot of choices you could have made. So how did you decide where to go from there?
So when I came out of that hospital, I resigned as CEO of my software company. I told my wife I wanted a divorce. The spiritual message I got was: Work with a way to connect kids to real food, to get kids to understand what real food is. And real food for me is food that you trust to nourish the body, trust to nourish the farmer, trust to nourish the planet. It’s very simple. Processed food would be the opposite of that. There’s no nourishment there. The farmer gets hosed and it’s terrible for the planet. So I [looked into] farm-oriented work and cooking-skills training. Turned out giving kids knives isn’t a good idea.
What? [laughter]
Yeah. Exactly. But the thing that came back to me was the value of a school garden. I actually was pretty frustrated with school gardens. I had been a philanthropic supporter of them for a few years and found them to be expensive, hard to maintain — a passionate parent would put it in, and then their kid would graduate, and it would become this mess in the corner of the schoolyard. So we [created] learning gardens. They’ve got a beautiful Fibonacci sequence layout. They’re made in a factory, but they have a natural look and feel. These are totally food-safe and can go on any school ground. They’re [wheelchair] accessible, easy to teach in, and built into the irrigation system of the school. We go in and we do 100 of them at a time. Pre-COVID we got to almost 700 schools in Denver, Chicago, Detroit, Pittsburgh, Indianapolis, Memphis, L.A.
How did you decide which cities to go into?
I believe this is useful anywhere, but what I found was low-income communities were the areas where you really needed it. Private schools or wealthier schools, they all have gardens — there’s not a private school out there that doesn’t embrace having a school garden. It’s actually the low-income schools that don’t have it. And that is also, coincidentally or not, where the obesity is. And so what I wanted to do is take what existed in private schools and put it into low-income schools and to do it in a way where it would be the most beautiful thing in the school. So instead of that sort of eyesore that was in the backyard, we said, “These have to be right next to the classroom, right next to the playground. You’re not allowed to build a fence around it. And if you don’t want to do that, great, we’ll just find another school. But these are the rules for learning garden.” And because we were doing 100 at a time, the districts would work with us, including maintenance and installation and curriculum and teacher training. Pre-COVID we were teaching almost 350,000 kids every school day.
And are there measurable effects?
Absolutely. Studies show that fifth grade in particular is the most effective grade. If you teach science in fifth grade to a kid, the exact same lesson in the garden versus in the classroom, you will get a 15-point increase on a 100-point score on their test scores.
And then if you teach kids 90 minutes a week in school, which is not hard to do because it’s beautiful and fun to be outside, you’ll double their intake of fruits and vegetables. Now they’re not eating a lot of fruits and vegetables, so the base is low, but you’re still doubling. The way I like to look at it is you’re really not trying to make them eat vegetables all the time — that’s too hard — you just try to change the course of their life by a few degrees; if you can do it by third, fourth, fifth grade, they’re going to be a different adult when they grow up. We’re not here to claim that what we do changes everything. We believe that the cafeteria needs to improve, that we need grocery stores to exist in these food deserts. There are many legs of the stool, but the school garden movement is a critical leg.
Are there any other technological innovations in this space that are really giving you hope?
I think there’s a lot of cool things going on around carbon capture with regenerative farming, because if you do farming correctly, you’ve become a wonderful carbon sink. And there needs to be an economy around it. So what is the value of a carbon credit? They’ve got value for that in Europe, but they haven’t valued it in America. So I think there’s a lot of government policy that needs to work there. But it’s a fascinating area to look at.
It’s interesting, the concept of bringing innovation to agriculture, which is—
So old school! Yeah, it’s fun. I do get frustrated that it doesn’t move fast enough. Then I’m reminded of how big this is and I’ve got my whole life to work on it. So I’m learning to embrace going a little slower. If you are in the software world, it’s more “move fast and break things,” and I think with food, it’s something in between.
Yeah, you don’t want to break the food chain.
No, people need to eat. Exactly.
And I know you’ve been advocating, too, for policies that help farmers shift to organic methods.
Yeah, I’ve been a supporter of that, but I really have pushed my energy now to work with young farmers of any kind. I’m not against organic at all. I love organic. But I’ve kind of said, “You know, we just need young farmers.” Real food doesn’t require it to be organic. If it’s a zucchini that happens to be grown conventionally, I’m still in favor of that.
It’s still a zucchini.
Right. That being said, organic is better. Farmers make more money on it. But it’s really about young farmers getting them into the business.
If you don’t mind, let me take one minute to just talk about [another initiative called] Square Roots. So there was a sort of a turning point in indoor farming technology around 2014, where you could really do quality food. Indoor farming’s been around forever, but the quality was really terrible. It would taste like water. No real flavor. But the technology of lighting really changed in 2014, and so by 2016 we said, “You know, there is a way here.” And what got me going was I really wanted to create this generation of young farmers. I love technology and I love food. And I think that if we bring the two together, we will get young people interested in farming again. And so we started out Square Roots as really a training entity.
And with Square Roots, you’re growing food in shipping containers? There’s no soil?
Yeah, we refine the nutrients [through the water]. We’ve gotten very, very thoughtful about what the nutrients are so that we can re-create as best we can the soil that they would get normally. The shipping containers, what’s beautiful about them is the fact that we can totally control the climate. For example, we have found that Genoa in Italy is where the best basil in the world is grown. It’s four weeks in June that are the best, and actually, 1997 was the best June. And so we re-create the climate of 1997 Genoa, Italy, in each of those containers to create the tastiest basil you can possibly imagine. Using data, we can monitor the growth and how they work. And every square meter of the air in there is exactly the same. That’s why containers are so valuable. Plants factories have to grow basil or cilantro or whatever all in the same climate. We get to grow arugula, basil, parsley, cilantro or whatever each in their own climate. For example, we’ve discovered that mint grows best in the Yucatan Peninsula — superhuman, grows like a weed, delicious. And we re-create that climate.
Square Roots Basil Farm in Brooklyn.
Square Roots
And the shipping containers, the idea for that was, “Let’s use things that we can recycle”?
Well, they are recycled. But no, it wasn’t that. It was actually climate control. They’re actually like refrigerators. We can drop that temperature in there to 40 degrees Fahrenheit for a particular growth cycle. If we have any pests, we don’t use pesticides, we have something called Mojave mode where we turn it into the Mojave Desert for four days. We bring the temperature up to 120 degrees, drop the humidity down to four percent and nothing can survive. That’s how we remove pests. No one else can do that unless you use these kind of containers. So it’s really a technology solution.
You’ve referred to food as being the new Internet. Do you still feel that way?
Oh, my god. Absolutely. It’s showing itself. Food is different to social media and so forth. It takes a long time to build up supply chains, get consistent growing. It’s not as fast-moving, but it is a much bigger business. Software is a $400 billion business. Food is an $18 trillion business. So the opportunity is much, much bigger in food than it is in software.
What are the top two or three things that really bother you about the industrial food system right now?
The processing of food. For some reason back in the ’70s, America just started to idolize processed food. And so what you have is a high-calorie hamburger, for example, that is nutritionally irrelevant. In other words, people were just not thinking about nutrition. And they used laboratories to adjust the flavor, chemicals to adjust the flavor, artificial ingredients. The result was a very high-calorie, highly processed kind of a Frankenstein burger that did please the pallet, but it made you feel awful afterwards.
The other one that is absolutely ludicrous is ethanol. Forty percent of our corn fields are growing ethanol. That’s 25 million acres of land that could be used to grow real food. People keep feeding us bullshit that we need to try and feed the world. We have so much food that we are turning 40 percent of it into ethanol. It takes a gallon of oil to make a gallon of ethanol. So it’s just a total boondoggle for the corn farmers and it’s terrible for the environment. In fact, it’s hilarious: It’s the only thing that both the oil industry and the environmentalists hate. Can you imagine there’s something that those two can agree on? And it’s ethanol.
Why the hell are we doing it?
It’s a subsidy for farmers. We do it because old people vote, and they control the farms, and they would all be devastated right now if the true demand of corn is what they had to deal with. And until a politician has the courage to make those hard decisions, we’re going to be stuck growing ethanol. Now, the good thing is we are all switching to electric cars, so ethanol is going to go away anyway. But for a while, the next five to 10 years, ethanol is going to be a part of what we do.
Let’s talk about the Million Gardens Movement. How did you get the idea that you wanted to do it?
Frank [Giustra] and his team pitched us on joining forces and doing the Million Gardens Movement. And we loved it. We thought it was a great idea. Because of Covid, we had been forced to pivot our model from the learning gardens because we couldn’t really teach people in the gardens anymore. And so we had done this trial of what we call little green gardens, which are round, beautiful sort of beige sacks, and you can come in and pick these up from a local school in your community. You can grow them on a windowsill as long as there’s some light. You can grow them indoors, which enables any city to be able to use them.
Say you get to a million gardens, are there any projections on what the environmental impact of that might be?
What we would be doing with these little green gardens is inspiring people to garden and empowering them to garden. The average garden generates about $600 to $700 worth of food a year. So it provides actual food to your family. You’re having a lower carbon footprint because you’re not shipping food around. It’s great for mental health. Think about Covid and how crazy we all are. This gets you out there. It connects you to your kids. Gardening is such a beautiful thing to do for yourself, for the community, for the environment.
It’s easy to think about what has been lost during this time, but I do like this idea of using COVID as an opportunity for change.
It’s obviously one of the worst things we’ve gone through as a society, but if we do this correctly, if we take this opportunity well, it could be one of the best things that’s happened to society — in a few years, we’ll look back and say, “OK, this was a good way to restart and focus more on climate change, focus more on gardening with your family, being connected to each other.” I think it has a lot of potential, as long as we take that potential and we leverage it. So the Million Gardens Movement is a part of that.
VIDEO: Farming In A Shipping Container
Transforming Unused Spaces Into Vertical Farms
Transforming Unused Spaces Into Vertical Farms
Indoor Agtech: An Evolving Landscape of 1,300+ Startups
Our Indoor AgTech Landscape 2021 provides a snapshot of the technology and innovation ecosystem of the indoor food production value chain
March 17, 2021
Editor’s note: Chris Taylor is a senior consultant on The Mixing Bowl team and has spent more than 20 years on global IT strategy and development innovation in manufacturing, design, and healthcare, focussing most recently on indoor agtech.
Michael Rose is a partner at The Mixing Bowl and Better Food Ventures where he brings more than 25 years immersed in new venture creation and innovation as an operating executive and investor across the internet, mobile, restaurant, food tech and agtech sectors.
The Mixing Bowl released its first Indoor AgTech Landscape in September 2019. This is their first update, which you can download here, and their accompanying commentary.
Since the initial release of our Indoor AgTech Landscape in 2019, the compelling benefits of growing food in a controlled indoor environment have continued to garner tremendous attention and investment.
One of the intriguing aspects of indoor agriculture is that it is a microcosm of our food system. Whether within a greenhouse or a sunless (vertical farm) environment, this method of farming spans production to consumption, with many indoor operators marketing their produce to consumers as branded products. As we explore below, the indoor ag value chain reflects a number of the challenges and opportunities confronting our entire food system today: supply chain, safety, sustainability, and labor. Of course, the Covid-19 pandemic rippled through and impacted each aspect of that system, at times magnifying the challenges, and at others, accelerating change and growth.
Invest with Impact. Click here.
Our Indoor AgTech Landscape 2021 provides a snapshot of the technology and innovation ecosystem of the indoor food production value chain. The landscape spans component technology companies and providers of complete growing systems to actual tech-forward indoor farm operators. As before, the landscape is not meant to be exhaustive. While we track more than 1,300 companies in the sector, this landscape represents a subset and serves to highlight innovative players utilizing digital and information technology to enhance and optimize indoor food production at scale.
Supply chain & safety: Where does my food come from?
The pandemic highlighted the shortcomings of the existing supply chain and heightened consumer desires to know where their food comes from, how safely it was processed and packaged, and how far it has travelled to reach them. A key aspect of indoor farming is its built-in potential to respond to these and other challenges of the current food system.
Indoor farmers can locate their operations near distribution centers and consumers, reduce food miles and touch points, potentially deliver consistently fresher produce and reduce food waste, and claim the coveted “local” distinction. The decentralized system can also add resiliency to supply chains overly dependent on exclusive sources and imports.
Growing local has many forms. Greenhouse growers tend to locate their farms outside the metropolitan area while sunless growers may operate in urban centers, such as Sustenir Agriculture in Singapore and Growing Underground in London. Growers like Square Roots co-locate their indoor farms with their partner’s regional distribution centers, and Babylon deploys its micro-farms solution on site at healthcare and senior living facilities and universities. Recently, Infarm announced it was expanding beyond its growing-in-a-grocery store model, to include decentralized deployments of high-capacity “Growing Centers” across a number of cities. Additionally, the value of “growing local” might take on a much larger meaning if your country imports most of its produce from other countries; a number of the Gulf region countries have announced major indoor growing initiatives and projects with AeroFarms, Pure Harvest, and &ever to address the region’s food dependence on other countries.
Organic produce sales jumped to double digit growth in 2020 as consumers are increasingly mindful of the healthiness of their food. The additional safety concerns due to the pandemic only accelerated this trend. While not typically organic, crops produced in the protection of indoor farms are isolated from external sources of contamination and are often grown with few or no pesticides. Human touch points are reduced as supply chains shorten and production facilities become highly automated. Through the CEA Food Safety Coalition, the industry has recently taken steps to establish production standards with a goal to keep consumers safe from foodborne illness.
Indoor farmers market their products as local, fresh, consistent and clean. This story is resonating with consumers as the growers seem to be selling everything they can produce, with many reporting significant sales growth in 2020. The direct connection to consumer concerns is also a key part of their ability to sell their branded products at a premium, which has been critical to financial viability for some growers. This connection can also enable them to collapse the supply chain further, at least at smaller scales, through direct sales and creative business models, e.g., sunless grower Willo allows subscribers to have their own “personal vertical farm plot” and watch their plants grow online.
Sustainability: Is my food part of the problem or part of the solution?
Farming, as with most industries, has been under increasing pressure to operate more sustainably, and indoor growers, with their efficient use of resources, have rightfully incorporated sustainability prominently into their narratives.
We are well aware of the impacts of climate change, including greater variability in weather patterns and growing seasons. The UN’s Food and Agriculture Organization projects that over the coming decades climate change will cause a decrease in global crop production through traditional farming practices, causing greater food insecurity. Indoor growing, which provides protection from the elements, consistent high yields per land area, and the ability to produce food year-round in diverse locations, including those unsuitable for traditional agriculture, can help mitigate this trend.
Water scarcity is projected to increase globally, presenting a national security issue and serious quality of life concerns. According to the World Bank, 70% of the global freshwater is used for agriculture. Indoor agriculture’s efficient use of water decreases use by more than 90% for the current crops under production. It is also common practice for greenhouses to capture rainwater and reuse drainage as does Agro Care, the Netherlands’ largest greenhouse tomato grower.
On the flip side, energy use, particularly in sunless facilities, is indoor growing’s sustainability challenge. Efficiency will continue to improve, but as recent analysis on indoor soilless farming from The Markets Institute at WWF indicated, there is an industry-wide opportunity to integrate alternative energy sources. Growers recognize this opportunity to decrease impact and improve bottom-line and are already utilizing alternative approaches such as cogeneration, geothermal sources, and waste heat networks. H2Orto tomatoes are grown in greenhouses heated with biogas generated hot water. Gotham Greens’ produce is grown in 100% renewable electricity-powered greenhouses, and Denmark’s Nordic Harvest will be running Europe’s largest indoor farm solely on wind power.
Labor: We’re still hiring!
There are labor challenges and opportunities throughout the food system value chain, and this couldn’t be more acute than on the farm. Farm operators—both in-field and indoor—find it difficult to attract labor for the physically demanding work. Even before the pandemic, the hardening of borders in Europe and the US created a shortage of farmworkers for both field and greenhouse production. In addition, grower and farm manager-level expertise is in short supply, exacerbated by an aging workforce and the rapid addition of new indoor facilities. While operators would like to see more trained candidates coming from university programs, they are also looking to technology and automation to relieve their labor challenges.
Automation of seedling production and post-harvest activities is already well established for most crops in indoor farming. In addition, the short growth cycle and contained habit of leafy greens lends them to mechanization. For example, the fully automated seed-through-harvest leafy green systems from Green Automation and Viscon have been deployed in major greenhouse operations like Pure Green Farms and Mucci. On the sunless side, Urban Crop Solutions has uniquely implemented automation in shipping containers, and Finland’s NetLed has developed a fully automated complete growing system. Note that many of the larger-scale sunless growers have developed their own technology stacks and have designed labor-saving automation into their systems. For example, Fifth Season has robotics deployed throughout the entire production process.
Despite numerous initiatives, the challenging daily crop care tasks and harvesting for certain crops (tomatoes, peppers, cucumbers, and berries) have not yet been automated at scale. However, planned, near-term commercial deployments of de-leafing and harvesting robots offer the promise of significantly altering labor challenges. Software technologies, like those from Nitea and Hortikey address labor management, crop registration, yield prediction, and workflow/process management for the indoor sector and strive to improve operational efficiencies for a smaller workforce.
Technologies that provide, monitor, and control climate, light, water, and nutrients are already deployed in today’s sophisticated indoor growing facilities and are fundamental to maintaining optimal conditions in these complex environments. They also form the base for the next innovation layer, i.e., crop optimization and even autonomous control of the growing environment based on imaging and sensor platforms (like from Ecoation, iUNU, and 30MHz), data analysis, machine learning, digital twins and artificial intelligence. Recent events like the Autonomous Greenhouse Challenge have successfully explored the potential of AI to “drive horticultural productivity while reducing resource use and management complexity”. Emerging commercialized autonomous growing innovations, such as the Blue Radix Crop Controller and Priva’s Plantonomy, promise to extend and enhance the reach of available grower expertise, particularly in large and multi-site operations.
Where do we go from here?
Since we created our initial Indoor AgTech Landscape, there has been positive change and reason to be optimistic about the future. But, as with any evolving market and sector of innovation, it can be a bumpy ride. Some believe CEA is not the answer to our food problems because not everything can be economically grown indoors today. We see indoor ag as just one of the approaches that can help fix our food system and it should be applied when it makes sense. For example, tomatoes sold through retail are already more than likely grown in a greenhouse. Expect more crops to be grown indoors more economically with further advancements.
One aspect of our previous landscape was to increase awareness that, despite the fervor surrounding novel sunless farming, greenhouse growing was already well-established. Dutch greenhouse growers have demonstrated the viability of indoor growing with 50-plus years of experience and more acres “under glass than the size of Manhattan.” The recent public offering and $3 billion market cap of Kentucky-based greenhouse grower AppHarvest also clearly raised awareness! Other high-profile and expanding greenhouse growers, including BrightFarms and Gotham Greens, have also attracted large investments.
The question is often asked, “which is the better growing approach, sunless or greenhouse?”. There is no proverbial “silver bullet” for indoor farming. The answer is dictated by location and the problem you are trying to solve. A solution for the urban centers of Singapore, Hong Kong and Mumbai might not be the same as one deployed on the outskirts of Chicago.
Regardless of approach, starting any type of sizable tech-enabled indoor farm is capital intensive. A recent analysis from Agritecture indicates that it can range from $5 to $11 million dollars to build out a three-acre automated farm. Some of the huge, advanced greenhouse projects being built today can exceed $100 million. Given the capital requirements for these indoor farms, some question the opportunity for venture-level returns in the sector and suggest that it is better suited to investors in real assets. Still, more than $600 million was raised by the top 10 financings in 2020 as existing players vie for leadership and expand to underserved locales while a seemingly endless stream of new companies continue to enter the market.
Looking forward, indoor farming needs to address its energy and labor challenges. In particular, the sunless approach has work to do to bring its operating costs in line and achieve widespread profitability. Additionally, to further accelerate growth and the adoption of new technologies in both greenhouse and sunless environments, the sector needs to implement the sharing of data between systems. Waybeyond is one of the companies promoting open systems and APIs to achieve this goal.
As we stated in the beginning of this piece, the indoor ag value chain reflects some of the challenges and opportunities confronting our entire food system today: supply chain, safety, sustainability, and labor. Indoor agriculture has tremendous opportunity. While it is still early for this market sector overall, it can bring more precision and agility to where and how food is grown and distributed.