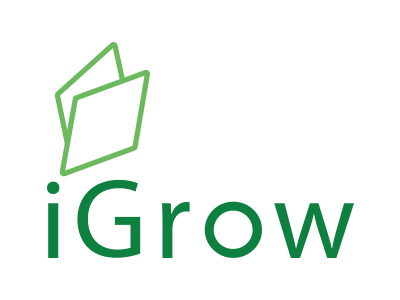
Welcome to iGrow News, Your Source for the World of Indoor Vertical Farming
USA: WASHINGTON - Lacey Is Home To The Largest Vertical Farm On The West Coast
Here they can grow 6 million heads of lettuce a year, using just 2 percent of the water an outdoor farm would need
The Future of Farming Is Happening
Right Now In This 25,000 Square Foot Warehouse.
Author: Saint Bryan
May 6, 2021
LACEY, Wash. — Though it looks like the set of some far-out science fiction fantasy, with bright walls of light and characters dressed in medical gowns, this is actually a farm growing six different kinds of lettuce inside a 25-thousand square foot warehouse located in a Lacey Business Park.
“In the beginning, it was always our goal to find a better way to grow healthier and more nutritious food for families,” says Bryce Clemmer who owns NW Farms with his wife Andrea. It’s the largest vertical farm in the Northwest.
Here they can grow 6 million heads of lettuce a year, using just 2 percent of the water an outdoor farm would need.
“This is a unique combination of robotics, software but also hardware that ultimately makes growing food at large scale possible,” says Clemmer, who is an engineer. He’s invented a few proprietary systems that make this vertical farm unlike any other.
“We've created a perfect environment for plants to grow,” he says.
Everything is monitored here: the temperature, the humidity, the light, the nutrients that go into the water. The result is produce that grows three times faster indoors than outside. The lettuce needs just 20 days from planting to be ready for your table.
“We have experimented with growing everything from strawberries and blueberries to edamame and any type of herbs that you can imagine,” says Clemmer. The only produce he can't imagine growing here are pineapples and pumpkins.
A NW Farms employee prepares to plant lettuce. Credit: KING TV
There are no overalls or John Deere caps here. All farmhands are gowned up, with hairnets and food handling gloves.
“So food safety, the handling, and the overall environment is the cleanest in which it can be,” says Clemmer.
“It's all-natural and healthy,” adds Andrea Clemmer.
She says other farms may rely on pesticides. And with farms so far away from our supermarkets, half of all produce gets thrown out. That doesn’t happen here.
“When our product is pulled off the towers it goes right into the bag, and it's in the store the same day so it's fresh same day and it is still living,” she says.
As the world’s population grows and more pressure is put on natural resources vertical farmers say they may have the key that prevents hunger and famine in the future.
“We have to figure out how to grow reliably and sustainably fresh food that's nutritious for everybody,” says Bryce Clemmer.
KING 5's Evening celebrates the Northwest. Contact us: Facebook, Twitter, Instagram, Email.
CANADA: Startup Bets 'Vertical Farms' Can Boost Quebec's Winter Berry Output
Standing about six metres tall, the indoor Vaudreuil facility will cover about 1,250 square metres and eventually produce 15 to 18 tons of strawberries a month, according to founder and chief operating officer Yves Daoust
Brossard-Based Ferme d’Hiver Has Just Raised $5 million
In A So-Called "Seed Round" To Help Accelerate Its Expansion.
Frédéric Tomesco
May 05, 2021
Ferme d'Hiver president Alain Brisebois, right, and founder and COO Yves Daoust in the vertical farming grow room at their operation in Brossard. PHOTO BY JOHN MAHONEY /Montreal Gazette
A South Shore startup is going live with a technology it says will help Quebec growers produce tasty strawberries year-round and reduce the province’s wintertime reliance on imports.
Brossard-based Ferme d’Hiver said Wednesday it has begun building a “vertical farm” in Vaudreuil to produce pesticide-free berries starting in October. The three-year-old company has just raised $5 million in a so-called “seed round” from investors such as Investissement Québec to help accelerate its expansion, while the Quebec government chipped in with $1.7 million in loans and loan guarantees.
Standing about six metres tall, the indoor Vaudreuil facility will cover about 1,250 square metres and eventually produce 15 to 18 tons of strawberries a month, according to founder and chief operating officer Yves Daoust. That would double Quebec’s current winter berry output, he said.
Known as precision farming, Ferme d’Hiver’s technology optimizes climate conditions for indoor gardening, resulting in production and crop density per square metre that’s 15 times greater than that of a traditional greenhouse, the company says.
“This is a game-changer for the growers,” chief executive Alain Brisebois said in an interview Wednesday. “Instead of only producing seven months a year, they can now produce year-round. Our goal in Vaudreuil is to prove to the industry that our technology is not only viable, but profitable and that it can work on a large scale.”
While most growers typically use propane to produce fruits and vegetables, Ferme d’Hiver’s technology relies on electricity. As a result, the company says its solution is 30 percent more energy efficient than a typical greenhouse, which cuts capital costs by 40 percent.
When it strikes a deal with a grower, Ferme d’Hiver commits to buying 100 percent of the production and acting as a wholesaler. It has a long-term contract with IGA in Quebec to deliver at least 25 tons of strawberries every week, Daoust said.
Ferme d’Hiver has signed partnership agreements with about a dozen Quebec growers thus far, and talks are underway with additional producers to buy their output, according to Brisebois.
Within three years, the company is aiming to replace 10 percent of Quebec’s strawberry imports with the production of its grower partners.
Premier François Legault has singled out food production as one of the areas in which he wants Quebec to become self-sufficient to better insulate the province from disruptions in the global supply chain — such as the current pandemic. His government unveiled plans to invest $157 million to increase the province’s “food autonomy” in November.
“The government was very clear when they started financing us two years ago: the goal here is not to become the Amazon.com of strawberry production, but rather to create an industrial cluster around agri-foods,” Daoust said. “We want to help create a nexus of Quebec growers with specific skills in the production of winter fruits and vegetables.”
Although it’s currently unprofitable, Ferme d’Hiver plans to break even when it hits 5,000 square metres of total production capacity, the CEO said.
“Given all the discussions we’re having with producers, we’re very confident of getting to 5,000 square metres next year. Then we can start covering our expenses,” said Brisebois, a former Metro Inc. and Alimentation Couche-Tard executive. “As a startup, I would say we’ve just finished childhood. Now we’re entering adolescence.”
AmplifiedAg Increases Better Fresh Farms Production 50% With New Indoor Farm And AmpEDGE Operating System
AmplifiedAg hydroponic container farm and technologies increased leafy green production over 50% for Better Fresh Farms
By AmplifiedAg
May 6, 2021
AmplifiedAg hydroponic container farm and technologies increased leafy green production over 50% for Better Fresh Farms.
AmplifiedAg, Inc. is an agtech visionary on a mission to provide global access to safe food. (PRNewsfoto/AmplifiedAg)
CHARLESTON, S.C., May 6, 2021 /PRNewswire/ -- AmplifiedAg, Inc.®, holistic indoor farming leader with a mission to provide global access to safe food, has increased leafy green production over 50% for Metter, Georgia-based Better Fresh Farms with its automated hydroponic container farm and AmpEDGE™ proprietary Operating System.
AmplifiedAg farms sustainably grow consistent yields of 800-1000 pounds of full head leafy greens per harvest every 3 weeks.
Founded in 2016 by Grant Anderson, Better Fresh Farms is expanding its hyperlocal produce throughout Georgia with the addition of its first AmplifiedAg farm, the company's exclusive producer of leafy greens.
Anderson said, "Our AmplifiedAg farm replaced two existing models that were fairly inefficient for our goals. The new system has optimized our production in the same square footage,"
"The software is going to help us get our arms around the whole operation; there's nothing out there really like it," added Anderson. "To have tracking processes that follow produce from growth all the way through to the sale is huge. It's been cumbersome up until now, and it will save us money in the long run to have one efficient system instead of multiple programs."
AmpEDGE uniquely combines farm production and business management for an end-to-end system. 24/7 environment controls, detailed analytics, and traceability features allow farmers to easily optimize crop growth, mitigate risk, while also tracking sales forecasts, revenue streams, and daily operations. Multi-tenant software with data-driven learning capabilities, AmpEDGE can operate any type of controlled environment.
"We grow 52 weeks a year in Georgia where the majority of the time weather is extremely hot and humid," added Grant. "We're constantly trying to adapt our systems to work in an environment that they weren't designed for. AmplifiedAg understands how to adapt their containers to different weather."
Manufactured from upcycled shipping containers, AmplifiedAg's enterprise-scale farms are built to the highest global food safety certifications. The resilient architecture allows for farming in any region regardless of resources and climate. A compact 320-square feet container design promotes ultimate segmentation and risk mitigation for reliable production.
AmplifiedAg farms sustainably grow consistent yields of 800-1000 pounds of full head leafy greens per harvest every 3 weeks. The company deploys farms 70% faster and at a fraction of the cost of other CEA implementations
"This has given us a chance to start exploring larger and more legitimate sales opportunities," added Anderson.
David Flynn is the General Manager of AmplifiedAg and leader behind the company's farm and technology production. He and his team have built and deployed over 180 farm containers that services farms across the country. This includes AmplifiedAg's Vertical Roots hydroponic container farm, with produce in nearly 1,500 stores nationwide.
"We've spent the last five years developing a platform that proves our technology and shipping container farms can be used to operate a profitable produce business at scale," said Flynn.
"We're excited to share our technologies and farms with other indoor farming experts like Grant and Better Fresh Farms, and continue to refine the indoor farming process for the future."
Learn more at www.amplifiedaginc.com.
Myths Surrounding ‘White Light’ Part 2 – Do You Need ‘White’ Light To Grow Better Crops?
This article is the second in a series of interviews with Signify’s Esther de Beer, manager of the team of plant specialists at Philips Horticulture
May 6, 2021
Myths surrounding ‘white light’ – Do you need ‘white’ light to grow better crops?
An interview with our plant specialist
· There are several myths surrounding the specific light spectra used for growing crops and, more specifically, the use of white, green, or broad-spectrum light.
· This article is the second in a series of interviews with Signify’s Esther de Beer, manager of the team of plant specialists at Philips Horticulture.
· In this interview, we asked the question: Do you need ‘white’ light to grow better crops?
Eindhoven, the Netherlands – Light is perhaps the most important consideration for optimizing plant growth in a greenhouse or vertical farm. There are several myths surrounding the specific light spectra used for growing crops and, more specifically, the use of white, green, or broad-spectrum light. This article is the second in a series of interviews with Signify’s Esther de Beer, manager of the team of plant specialists at Philips Horticulture. In this interview we asked the question: Do you need ‘white’ light to grow better crops?
Interested in the first interview with Esther, where she answers the question if green light penetrates deeper into the canopy? Read it here.
First of all, what do we mean with white and green light?
When talking about light for plants, we often distinguish four basic colors: blue (400-499nm), green (500-599nm), red (600-699nm), and far-red (700-799nm). Purple light is actually a combination of red and blue light. Basically, you will get white light when you add enough green light to this red/blue light. Therefore, we will focus on the question of whether you need green light to grow better crops.
How efficient does a plant use green light for growth?
In the first interview it is explained that blue, red and green light are absorbed equally by a plant canopy and only far-red light is absorbed significantly less. But are all these colors used equally for growth?
In the early 1970’s, McCree measured the photosynthetic efficiency as a function of wavelength for a large number of plants. These data show a large commonality between the plants and has been averaged to what is now known as the “McCree curve”, see figure 1 below.
Figure 1 McCree curve: the photosynthetic efficiency of light as a function of wavelength
This shows that green light is used for photosynthesis, but at a lower efficiency when compared to red light. Since this early work, many researchers have found similar results. [Hogewoning 2012, Paradiso 2011]
For overall plant growth, not only the process of photosynthesis is important, but also other processes which, for instance, influence the shape of the crop. Therefore, for practical applications it is relevant to evaluate the total crop growth rather than only zooming in on photosynthesis.
So, what is the effect of green light on the crop?
We have found that several crops have significantly higher fresh weight when actually grown without green light. For other crops, however, the amount of green light has no effect on the fresh weight. Also, we have found that to steer the shape of the crop, blue and far-red light are far more effective than green. Let me share some examples from our research.
At the Philips GrowWise Center, we have run a trial where we have grown eight RijkZwaan Salanova lettuce varieties under light spectra with both 0 and 20% green light, but with the same photon flux and percentage of blue light. The graph below shows the relative fresh weight of these crops, comparing the growth under both spectra with 0% green and 20% green light.
As you can see in this graph, not all lettuce varieties react the same. There are two varieties (RZ1 and RZ2) that grow slightly better under the spectrum with 20% green. However, most varieties have significantly higher fresh weight (even up to 20% more fresh weight for RZ8) when grown without green light.
Figure 2 Significantly higher fresh weight for lettuce varieties when grown without green light
The small effect which green light has on the growth of a crop is confirmed by an extensive academic study by Snowden, who compared the growth of 7 diverse plant species under 8 different spectral compositions: “In contrast to the significant effects of blue light, increasing green light in increments from 0 to 30% had a relatively small effect on growth, leaf area and net assimilation at either low or high PPF”. [Snowden 2016]
A second example from our own research is related to medicinal cannabis. In this trial, two different cultivars were grown under three different light spectra with 0%, 6% and 36% green at the same supplemental light level (600 µmol/m2/s). Here, in addition to looking at the flower weight, we also looked at the quality of the crops.
The graph on the right in Figure 3 below shows the dry flower weight for two different cultivars, whereas the graph on the left shows the percentage of active compounds, which are the key factor in determining the product quality for medicinal cannabis.
Figure 3 Higher active compounds of medicinal cannabis with lower percentages of green light.
The graph on the right shows that the dry weight remains the same for all three spectra, again confirming that the amount of green light has little effect on growth. However, the active compounds reduce substantially when the green content increases. Since these crops are grown specifically for their medicinal compounds, this leads to a preference of light spectra which contain little or no green.
To summarize: in our studies, we find that different crops require different light spectra for optimal growth. However, in most cases there is no benefit in adding more than a few percent of green; both for the yield and for the quality of the crop.
So, if green light has so little benefits, why use it?
That needs some further clarification; all of the above results describe the use of light by the crop, comparing yields at the same photon flux. However, they do not take into account how much electrical energy is needed to create this light. Since there are big differences in efficacy (mmol/Joule), this of course has a huge impact on the total energy usage.
Red LEDs give far more photons per electrical Watt (μmol/W) compared to blue and green LEDs.
Our research shows that a spectrum with approximately 6% green light is sufficient for good color recognition by people and is 30% more energy efficient when compared to a ‘sun-like’ spectrum, which contains approximately 40% green light.
At Signify, we want to provide our end customers with the optimal lighting solution to grow their crops in the most sustainable way. Green light is much less efficient than blue and red LEDs. Only a limited amount of green can be considered for most lighting applications as only a small amount of green light is required for good color recognition by people and as crops do not need a high amount of green light to grow well.
Esther de Beer is the manager of the plant specialist team at Signify horticulture LED solutions. She spends her days trying to make LED grow lights more effective. In this series of articles, she explains facts and fiction with regards to white light and how research has shown which light spectrum helps crops grow better.
References:
Hogewoning S.W., Wientjes E., Douwstra P., Trouwborst G., Van Ieperen W., Croce R. and Harbinson J., 2012.
Photosynthetic Quantum Yield Dynamics: From photosystems to Leaves. The Plant Cell 24: 1921-1935.
Paradiso, R., Meinen, E., Snel, J.F.H., De Visser, P.H.B, Van Ieperen, W., Hogewoning, S.W., Marcelis, L.F.M., 2011.
Spectral dependence of photosynthesis and light absorptance in single leaves and canopy in rose. Scientia Horticulturae 127: 548-554.
McCree, K.J., 1972.
The action spectrum, absorptance, and quantum yield of photosynthesis in crop plants. Agricultural Meteorology 9: 191-216.
Snowden, M.C., Cope, K.R, Bugbee, B., 2016
Sensitivity of seven diverse species to blue and green light: interactions with photon flux. Plos One 11(10): e0163121. Doi: 10.1371/journal.pone.0163121
--- END ---
For more information:
Global Marcom Manager Horticulture at Signify
Daniela Damoiseaux
Tel: +31 6 31 65 29 69
Email: daniela.damoiseaux@signify.com
About Signify
Signify (Euronext: LIGHT) is the world leader in lighting for professionals and consumers and lighting for the Internet of Things. Our Philips products, Interact connected lighting systems, and data-enabled services, deliver business value and transform life in homes, buildings, and public spaces. With 2020 sales of EUR 6.5 billion, we have approximately 37,000 employees and are present in over 70 countries. We unlock the extraordinary potential of light for brighter lives and a better world. We achieved carbon neutrality in 2020, have been in the Dow Jones Sustainability World Index since our IPO for four consecutive years, and were named Industry Leader in 2017, 2018, and 2019. News from Signify is located at the Newsroom, Twitter, LinkedIn, and Instagram. Information for investors can be found on the Investor Relations page.
VIDEO: Ottawa Startup Plantaform Hopes To Harvest Profits From Indoor Gardening Technology
Ottawa biotech startup Plantaform's system, dubbed Rejuvenate, uses a concept called fogponics to grow herbs and leafy vegetables indoors
Ottawa biotech startup Plantaform's system, dubbed Rejuvenate, uses a concept called fogponics to grow herbs and leafy vegetables indoors.
A Carleton University business grad says his new startup is planting the seeds of a flourishing global horticulture enterprise with a soil-free system that grows herbs and leafy vegetables in a container small enough to sit on a kitchen countertop.
Alberto Aguilar launched fledgeling biotech startup Plantaform last spring with longtime friend Kiwa Lang, an industrial designer who attended high school with Aguilar in Dubai and now lives in Australia.
Lang was looking for sustainable alternatives to traditional horticulture and discovered a concept called fogponics, a technique pioneered by NASA that nourishes plants with nutrient-enriched water vapour rather than soil. He immediately reached out to his old pal, and a truly international startup was born.
“It’s extremely efficient,” Aguilar says of the technology, explaining that it uses 95 per cent less water than traditional soil-based horticulture operations.
Unlike more well-established hydroponics systems, Plantaform’s product – dubbed Rejuvenate – doesn’t submerge plant roots in water. Rather, it circulates a fine mist loaded with nutrients throughout an egg-shaped device roughly 60 centimetres high by 60 centimetres wide.
The high-tech indoor garden can grow up to 15 plants at a time, ranging from herbs such as basil and oregano to leafy greens including lettuce and kale.
35-day growing cycle
Customers set the proper lighting and nutrient mix on a smartphone app. Aguilar says the system can effectively run itself for up to three weeks before the water supply needs to be replenished, and it takes roughly 35 days to harvest a crop from the time seeds are “planted” in the device.
Plantaform’s own growth path has been a little rockier.
Backed by about $100,000 in funding from the founders’ family and friends as well as investors in Aguilar’s previous startups, the company stumbled out of the gate early last year.
The initial design for Rejuvenate failed, and it’s taken about half a dozen iterations to get the concept just right. In addition, Aguilar notes ruefully, the firm’s original team “collapsed” after several employees quit last summer because the founders couldn’t afford to pay them full-time salaries.
Supply-chain disruptions
Meanwhile, the pandemic wreaked havoc with the startup’s supply chain, forcing Aguilar and Co. to abandon foreign suppliers in China and elsewhere and manufacture the bulk of the components for the prototypes in their own homes on 3D printers.
But the plucky grow-op persevered, overhauling its development staff and bringing on veteran Ottawa-based engineer Georges Hamoush as chief operating officer. Plantaform eventually signed a Chinese contractor to manufacture most of the components, which will be assembled locally at Stittsville’s L-D Tool & Die.
If all goes according to plan, the first units will be shipped to customers this fall – and Aguilar plans to personally deliver as many as he can.
“We’ve made a lot of mistakes, but you know what? We’re not giving up,” says the budding biotech magnate, who grew up in Barcelona, spent some of his teenage years in Dubai and moved to Ottawa in 2014 to finish high school at Lisgar Collegiate before studying international business at Carleton.
"I’m really trying to put Ottawa on the map."
Alberto Aguilar - CEO and co-founder of biotech startup Plantaform
“We’re confident that if we keep trying, it’ll eventually work out.”
The 24-year-old Aguilar boasts an accomplished entrepreneurial resume. Plantaform is already his third startup, and he earned spots in Invest Ottawa’s pre-accelerator and Ottaw’’s Startup Garage with his previous ventures.
He’s hoping to secure additional seed funding for Plantaform later this year, with an eye to landing a series-A round early in 2022. The company also has its sights set on even bigger markets – it’s currently working with the Vineland Research and Innovation Centre, a non-profit organization based near Niagara Falls, on a system to grow cannabis using fogponics technology.
The worldly Aguilar says he’s hoping his venture can elevate his adopted hometown on the international biotech stage.
“I’m really trying to put Ottawa on the map,” he says. “We want to go global.”
VIDEO: Tortuga Raises $ 20m To Build Hundreds of Harvesting Robots
Last year Tortuga launched a strawberry harvesting robot. This platform is flexible, according to Tortuga it can be adapted to work on other crops like indoor-grown tomatoes or outdoor table grapes
23-04-2021
Harvest automation start-up Tortuga completed a $ 20 million Series A funding. The money will be used to build hundreds of robots to deploy in 2022.
Last year Tortuga launched a strawberry harvesting robot. This platform is flexible, according to Tortuga it can be adapted to work on other crops like indoor-grown tomatoes or outdoor table grapes.
Picking robots
“For many years, the story behind harvesting robotics has been a lot of promise but really companies have struggled to deliver on that promise for the customer. That’s because this is one of the hardest problems there is to solve,” Eric Adamson, co-founder of Tortuga AgTech told AgFunder News. “Not only are we doing autonomous robotics but we are also doing picking robotics and we are doing them together in really unstructured environments.”
Robots-as-a-service
The $ 20 million in new capital will be used to build hundreds of robots to deploy in 2022. Some of the funding will also go towards building out the operating model and making sure there are enough employees to operate the robot fleets.
Tortuga currently offers its technology through a robots-as-a-service model, getting paid by the kilo for the produce that its robots pick.
Additional services
“On top of that, as we provide other services that are close to harvest, like data-driven forecasting and other types of cultivation services, those will also be service-based although they may not be quite so specific to a kilogram. We are charging for some of these additional services on a monthly or per-hectare basis,” Adamson told AFN.
Web editor for Future Farming
Green Bronx Machine’s New TV Series on PBS/WNET In Partnership With NYC Schools
Stay tuned for more episodes in the coming weeks, with characters like Bobby the Bear, Sammy the Shark, and General Sequoia! And a very special episode in which the one and only Mr. Met teaches me how to dance
I’m so proud of Green Bronx Machine’s new TV series on PBS/WNET in partnership with NYC Schools. In fact, the New York State Education Department has been showcasing our content. Even the new Chancellor of New York City Department of Education has seen the show! Have you?
WATCH THE EPISODES!
Stay tuned for more episodes in the coming weeks, with characters like Bobby the Bear, Sammy the Shark, and General Sequoia! And a very special episode in which the one and only Mr. Met teaches me how to dance!
Every episode has a Big Word Alert, and we’d love to hear yours — give us some feedback about the show so far.
I’m excited to read your thoughts, and I’m even more excited for you to watch the new episodes on April 28th, May 5th, May 10th, and May 11th!
With love, your pal,
Recording of Indoor Ag Science Cafe April 20th
"Plant Factories And Indoor Farming Innovations in Japan"
April Indoor Ag Science Cafe
Thank You For Participating In This Month's Cafe!
Recording Is Now Available
"Plant Factories And Indoor
Farming Innovations in Japan"
by: Eri Hayashi
Japan Plant Factory Association
Indoor Ag Science Cafe is an open discussion forum, planned and organized by OptimIA project team supported by USDA SCRI grants.
US: KENTUCKY - AppHarvest Continues To Expand Operations, Adds New Container Farm In Madison County
Some Central Kentucky high school students will soon be able to help grow food not only for themselves but the entire region
AppHarvest (WYMT)
By Brandon Robinson
Apr. 22, 2021
RICHMOND, Ky. (WYMT) - Some Central Kentucky high school students will soon be able to help grow food not only for themselves but the entire region.
On Thursday, officials with Morehead-based AppHarvest announced the expansion of their container farm program to Madison County High School in Richmond.
Watch Live Below:
Gov. Andy Beshear, who attended the event, appropriately held on Earth Day, said the move will not only provide food but help students prepare for possible careers in a field with growing demand.
“AppHarvest has been reimagining and reinventing sustainable food production at its state-of-the-art facility in Morehead. With the opening of the company’s container farm classroom at Madison Central High School, AppHarvest is showing its commitment to the Commonwealth runs both strong and deep,” said Gov. Andy Beshear. “This living, teaching lab will inspire and engage Kentucky students to learn about cutting-edge technology that will become the basis of the jobs of the future. Thank you to Founder & CEO Jonathan Webb and his team for making education and Kentucky students a priority in his plans for success.”
The container farm is 2,880 cubic feet, weighs 7.5 tons and includes space to grow up to 4,608 seedlings and 8,800 mature plants all at once using 440 vertical crop columns.
Each retrofitted shipping container serves as a hands-on agricultural classroom for students, allowing them to grow and provide fresh leafy greens to their classmates and those in need in their communities. The company has previously opened container farms in Eastern Kentucky at Breathitt High School in Jackson, Shelby Valley High School in Pikeville, and Rowan County Senior High School in Morehead, the site of the company’s flagship farm.
AppHarvest Founder & CEO Jonathan Webb said the latest expansion will not only help feed Kentuckians but will help Eastern Kentucky’s struggling economy.
“We knew long before opening our Morehead farm that we wanted to invest in the region to help grow our growers and build on the many outstanding community and education programs focused on creating a more resilient Appalachian economy,” Webb said. “The technology in each of these container farms is a good example of what AppHarvest’s modern farmers use daily on a larger scale.”
The Madison Central High School container program will be led by agriculture teacher and FFA adviser Derek Adams.
“Our students are looking forward to getting hands-on experience with state-of-the-art technology that will better prepare them for career opportunities in the agriculture industry,” Adams said. “They are especially eager to see the leafy greens come full circle from farm to table in their own school cafeteria.”
USA: This Colorado Company Is Building Farms In Shipping Containers To Help Feed People In Need
FarmBox Foods wants people to be able to farm anywhere, allowing them to access fresh food they otherwise wouldn't be able to
Author: Jeremy Moore
April 19, 2021
FarmBox Foods Wants People To Be Able To Farm
Anywhere, Allowing Them To Access Fresh Food
They Otherwise Wouldn't Be Able To
SEDALIA, Colo. — A three-year-old Colorado company has an ambitious goal: to bring food security, safety, and sustainability to communities in need around the world.
FarmBox Foods aims to achieve that goal by connecting those communities to sustainably sourced food that's grown locally inside one of their container farms.
Their first product was a vertical hydroponic farm, or VHF, built inside a shipping container.
The company has since developed a second product: a gourmet mushroom farm, or GMF.
So far, customers in Colorado include Centura Health, Vitamin Cottage Natural Food Markets, and the C Lazy U Ranch in Granby.
FarmBox CEO Rusty Walker and COO Jake Savageau joined 9NEWS to talk about how they hope to change the way the world thinks about farming.
9NEWS also spoke with a prospective customer of FarmBox, Cori Hunt of the Denver restaurant group Edible Beats.
(Editor’s note: Responses have been edited for context and clarity.)
As a mission-driven company, what is the mission of FarmBox Foods?
Walker: Our goal and our mission is to get our products out into the communities where we can help develop food security programs. We’re looking to get into food deserts, opportunities where folks in the world might not have access to good, clean nutritional food. And so we kind of strive as a company that’s driven to feed the world one container at a time. And we’re ready to go out and manufacture thousands of these if we can.
We’re able to decentralize growing food by being mobile – being able to deploy these by just having a semi come in. We can then lift it up on a flatbed and take it to anywhere in the world. We’ve got two containers going to islands. We’ve got our first container that took off for the island of Jamaica. It’s going to Montego Bay where it’s going to be used behind mega marts on the island. And then we have another container which is our gourmet mushroom farm that’s going to be going to Tahiti where they’re going to be using that to feed the island population which does not have access to that type of food.
One big area that we’re really focusing on is the urban areas throughout the U.S. where they don’t have a lot of land to grow. These farms can go right into the parking lots, behind a church for example. We’re working with a community church on the south side of Chicago that’s looking at placing two of these containers – a vertical hydroponic farm and a mushroom farm – right outside in the parking lot outside the church.
And we think we could bring an educational spin to this where we can have the community grow their own food and supply the community themselves with highly nutritional food that ordinarily they just would not be able to get their hands on. So, we’re thinking that if this pilot program goes well this would be an application that would apply to every inner city throughout the U.S.
Farmbox Foods grows vegetables in shipping containers. Credit: Jeremy Moore, KUSA
Savageau: The mission’s always been to create products that are for the decentralized food insecurity industry. So, we want to create a product that can be deployed anywhere in the world, can run off-grid, and can feed communities. So, we have two different products – the VHF and the GMF. Every product that we develop gets us one step closer to being able to feed a community with everything they need, because you can’t feed communities forever just on leafy greens.
So mushrooms, they’re more nutrient dense, that gets us one step closer. There’s other products that we’re going to develop to get us to that point. But, I think the mission for the company is to be able to deploy these farms into communities where they’re needed, whether that’s a rural area, a food desert in the U.S., an inner city, or somewhere in Africa like Ghana or the Sudan.
We want to align with big ag and we want to help the industry get better. So we want to get food to where it’s needed. We’re looking at doing stuff with food insecurity and food inequality. That’s big with what we’re doing. So, that kind of aligns with our mission. If you look at our food system – just take for instance – you know if you look at a SNAP program or food subsidy program – you’re taking food and giving it to somebody or they’re purchasing it.
But, a lot of that food that they’re purchasing is processed, sugar – I mean, it’s poison. And if you go on a military base anywhere in the U.S., there’s fast food on the base. It’s really what you see. So, there’s a lot of reasons why we’re doing this I think. We can help fix our food system. And we can help educate the youth on how they should eat. We’re doing some stuff with an Inuit community in Alaska. They don’t necessarily know how to fix this food or prepare it or use it. So, I think education is a big part of what we’re doing.
How do these container farms work?
Savageau: When people think of farms, they don’t think of agriculture like this. Vertical hydroponics and indoor ag and controlled environments – it’s been around for a long time. I think that the way that this one works is pretty simple. The water gets fed into a tube system and the water trickles down and goes back into the tank. And where you’re standing – the seedling tray area – the water goes into a tank, into the seedling trays, gets flooded, and then back into the tank.
There’s a software that we use called Agrotech that monitors the temperature, the humidity, the lights – basically, all automated. So, it’s fairly easy to run. You need about 15 to 20 hours a week to run one farm. The GMF farms takes about 25 hours a week. It’s a little bit more intensive. The VHF is the vertical hydroponic farm and that’s the farm that we’re standing in. The GMF is the gourmet mushroom farm, which is the one that you went through earlier. You want to just keep things as clean as possible. The cleaner that you keep it the better it’s going to run.
So, we have a standard SOP, you know, that we implement with our training. Cleaning the floors. Cleaning the tubes. You don’t clean them every time. But, usually, every couple harvests you’ll take the tubes out, wash them out. You’re cleaning the tanks about every 60 days.
But, on average it’s pretty easy to maintain if you’re doing the daily checklist. The seeds are going to be in the seedling tray for about two weeks. Then, they go into the wall. And then they get harvested about 60 days after they start in the seedling tray. So, on average you’re about 60 days from seedling to harvest depending on what you’re growing.
And this farm is really setup for vertical hydroponics. So, it’s leafy greens. You can do hundreds of different types of lettuce. You can do cherry tomatoes, strawberries and peppers. There’s a lot of different things that you can grow in here. Most of our clients are only growing a couple things at one time. You don’t have to worry about weather. You don’t have to worry about if this is in a cold climate like the arctic. You know, they can’t grow food. If it’s in a desert, they can’t grow food. If it’s on an island, they can’t grow food. So, these can be deployed anywhere. And they grow 365, all day, every day. Also, the yield is very high for the square footage. So, you can put these on top of a building, inside of a building. It only takes up 320-square feet. You don’t have any pesticides. So, you don’t have to worry about pests, bugs, mildew, stuff like that’s going to effect the plant as it’s growing. It’s also decentralizing the food system.
So, you’re not having to ship food hundreds of thousands of miles from point A to point B. So, the food is right there. And the nutrients that we use are organic plant-based nutrients. And there’s no pesticides. So, the nutrient density is extremely high compared to something that you would buy – even organic – in a store.
Walker: We grow a variety of vegetables and lettuces. I believe that we’re somewhere in the area of 30 to 40 different types of vegetables and lettuces that we can grow in our farms. And, then of course we’ve got our gourmet mushroom farm which we’re currently growing anywhere from eight to nine different varieties of mushrooms. We’re in the startup phase of running that farm ourselves. So, we’re exploring the different types of mushrooms that we can grow. But, we’re very proud of the folks that are actually running these farms – our staff, very knowledgeable and they do a great job. We’re going upwards to 300 to 400 pounds a week now. We’re not competing with traditional farming. We’re actually a compliment.
Who are your customers?
Walker: One of our first customers is Centura Health. They purchased their first container – which is now sitting at St. Mary’s in Pueblo. They ordered two more containers after seeing how the first container behind their hospital worked. We actually started up a pilot program with Centura Health where we’re now running them as the FarmBox family.
We’re working with Centura Health in identifying not only their hospitals and the patients who are going to be fed through our vertical farm – but then we’re also identifying where the food deserts are and Centura Health will then help us with what we’re going to be growing, and then the communities that we’re going to be serving from those, those particular crops.
We do have a couple that’s looking at doing some farming right here in Sedalia. They’re going to use it to supplement their traditional farming, which will be an interesting pilot program for us to work with them on. We’re working with C Lazy U Ranch out of Granby, Colorado. They’ve ordered a hydroponic farm and we’re going to be manufacturing that. And they’re going to place that at the ranch. They don’t really have access to a lot of good food as far as having it grown right there on the property. So, this will be a nice compliment to the services and the customer experience that they provide their customers by having one of our farms right on site.
Centura Health is one of FarmBox Foods' first customers. Credit: Jeremy Moore, KUSA
One big area that we’re really focusing on is the urban areas throughout the U.S. where they don’t have a lot of land to grow. These farms can go right into the parking lots, behind a church for example. We’re working with a community church in the south side of Chicago that’s looking at – we’re looking at placing two of these containers – a vertical hydroponic farm and a mushroom farm right outside in the parking lot outside the church.
We can have the community grow their own food and supply the community themselves with highly nutritional food that ordinarily they just would not be able to get their hands on. So, we’re thinking that if this pilot program goes well this would be an application that would apply to every inner city throughout the United States.
Savageau: We have a customer here in Lakewood that’s going to put one in their backyard. They run a small organic farm. We’re looking all the way up into federal government and military, and everything in between.
So, Rusty was talking about FEMA, the UN, UNICEF, those are the big customers that take a long time to build a relationship with. And then we have customers that are all the way down to just an individual that wants one for their property or maybe a couple of people are going to run one for a restaurant or a developer wants one for a small development that he’s doing.
We’re working with a group in New Mexico and they’re building a huge development of about 45,000 houses. So, we’re talking about 100 of these units that are going to be deployed in that area right outside Albuquerque to feed those communities within that area over the course of about two years. We work with a grocer that’s regional. And we work with some other customers that are kind of at a government, federal government level.
I think we’ve done a lot in the last three years. I mean we haven’t gone out and raised any capitol. So, we’ve self-funded it. And I think from that point of view you know we’ve done a lot. We’re kind of at the point right now where we’re just starting to scale. So, we’ve just started our social media. You know SEO (search engine optimization), SEM (search engine marketing). We have a sales team. And orders are starting to come in. We’ve partnered with RK which is manufacturing our units. That’s giving us the ability to scale. Because before that we were building these one or two at a time in Sedalia and now we can build 100 of them. So, that’s really been a huge part of us being able to scale is the manufacturing side.
How much does it cost to purchase and operate the farms?
Jake: This VHF farm – vertical hydroponic farm – starts at $140,000. The GMF starts at $150,000. Then, you have training and deploy, getting it there. So, usually, you’re over $150,000 for a farm. So, your ROI (return on investment) in this product is going to be about 12 months to 24 months depending on what you’re growing and where it is in the world.
The GMF is going to be closer to 12 months because mushrooms tend to be more expensive – again – depending on where it’s going. We have a unit that’s going to Tahiti for example. That ROI is going to be extremely fast because they ship everything in. If there’s a market for mushrooms there, which there is with a grocer, it’s going to be quick. So, the cost of running it with labor and everything you need to grow the plants, usually around $20,000 to $40,000 a year. We’re a mission-driven company. So, money isn’t the first thing that’s important. We want to build a certain amount of these and then every x amount that we build, we build one for free and we send it to a community that maybe our social media has engaged with or given us an idea that ‘hey, this would be a good community.’ And then, we send it there. We pay for it. We train people. And that’s something that we want to do. We can’t do it yet. But, I think that’s coming in the next year.
Why is Edible Beats interested in working with FarmBox?
Hunt: We try to be as local and organic as possible and that’s what brought us here to FarmBox. We can put a box behind a restaurant and have lettuces cut and washed and put on the plate the next day.
Just to have that connection with our food and know exactly where it’s coming from and how it was produced. It’s going to be better quality because it’s not traveling. It’s not ripening in a truck coming from Mexico. Economically, what we can do to not pay the mileage on the vehicles and the gas, the inputs, the emissions, the extra packaging, the plastics.
That’s one of the best things about FarmBox – that what we can do is – if we produce food for our restaurant group – I’m not going to have to buy packaging that’s going to go into a landfill or even need to be recycled. It’ll go directly into the vessels that we’re going to store them in the cooler. We don’t have to worry about marketing and labeling and you know stickers and plastics and all this extra stuff – this hoopla that we don’t need – because FarmBox is a possibility now.
The Farmbox Foods containers allow leafy greens to grow vertically, maximizing space.
Credit: Jeremy Moore, KUSA
We are looking at lettuces and herbs, leafy greens. So yeah, like basils, sage, leaf lettuces, butter lettuces, arugula – these kinds of things that we use that could greatly help our impact. Essentially it’s a self-contained box that you can grow fruits and vegetables in – most likely leafy greens – and it’s a soilless or near soilless medium.
So, essentially you plant your seed in a very small amount of coconut core or soil or peat moss – something to hold the root structure – and that, according to with FarmBox, they’re system is a vertical farming.
So, they have vertical towers and then they put the lettuces in the towers in their small soil medium and then they drip water with enhanced nutrients mixed into the water specifically built for those vegetables. It doesn’t have a lot of soil waste.
For the amount of the surface area you can get way more production out of it and the water that goes through is recycled. Per plant, it uses far less water than any other type of growing system.
RELATED: Why Colorado agriculture groups oppose Initiative 16, an animal cruelty proposal
US: VIRGINIA - Senior Project Brings Daily Salads For School Lunches
Students Set Up A Hydroponic System In The School Lab
Two Upper School Seniors at the Hampton Roads Academy (HRA) constructed a hydroponic unit for the school's hydroponics lab. About a year ago two students, Ava and Cooper, were asked to construct a new hydroponics unit for the school. They immediately agreed to work on the project, with their first task to create a new system for the school's 1,000 sq. ft. 'Martha H. Patten Hydroponics Lab'. After approval, they picked up the supplies needed and set up the system.
Ava and Cooper set up the hydroponic system by themselves, making use of the additional growing lights, nutrient dosers, Rockwool, and water pumps. However, the project wasn't without struggles. At one point, the system turned out to have some leaks and a PCV pipe was disconnected from the system. They later improved the system to remedy the problems.
The first harvest was successfully done and enough for 200 salads. Throughout the year, all harvested produce went directly to HRA's school lunches. During their project, Ava and Cooper made it their goal to educate other students at the HRA on hydroponic farming. After a while, many students had expressed their interest in the hydroponic lab. Given that response, the seniors held information sessions to teach students how they could get involved.
Ava and Cooper have said to be thankful for the opportunity to create a hydroponic lab for the school. Their main goal to keep educate and inspire others to create their own hydroponic system as they see it as 'the future of sustainable farming.'
Click on the video below to see the complete story.
For more information:
Hampton Roads Academy
739 Academy Lane
Newport News, VA 23602
+1 (757) 884-9100
admissions@hra.org
www.hra.org
6 April 2021
Author: Rebekka Boekhout
© VerticalFarmDaily.com
Lead photo:
Ava and Cooper at the 'Martha H. Patten Hydroponics Lab
USA: Delaware Entrepreneurs Start Growing Crops In Water. Will Hydroponic Farms Catch On?
Bill Jordan of Millsboro is an accidental farmer who's growing crops without soil. “I was going to make alcohol from corn or peaches to supplement fuel when fuel prices got stupid,” Jordan recalled, but he quickly realized that was not profitable
Delaware News Journal
Bill Jordan of Millsboro is an accidental farmer who's growing crops without soil.
“I was going to make alcohol from corn or peaches to supplement fuel when fuel prices got stupid,” Jordan recalled, but he quickly realized that was not profitable.
As part of his research, though, he saw that some hydroponic farms use what’s left of the corn or peaches from the alcohol-making process as a fertilizer.
“That’s what led me to it,” he said.
About 15 years ago when he lived in Maryland, he started taking courses on hydroponics and visiting hydroponic farms. He built his own greenhouse and supplemented his income by building greenhouses for others.
After moving to Delaware, he started Fresh Harvest Hydroponics in Millsboro, specializing in a variety of hydroponically-grown lettuces and herbs that are pesticide-free and herbicide-free.
The plants are raised in three climate-controlled greenhouses. The largest has the capacity to grow 50,000 heads of lettuce at one time.
Before the pandemic, he was selling to wholesalers like Sysco and Teddy Bear Fresh, along with Hocker’s grocery stores in Sussex County and restaurants like Fager’s Island in Ocean City, Maryland.
“COVID really hurt us,” Jordan said. “A lot of restaurants just are not buying. Right now, we’re just doing farmers markets and onsite sales, trying to keep our head above water.”
He and one employee are able to maintain the operation, but before the pandemic, the business had several other employees.
However, Jordan said hydroponics has been a profitable business.
“It’s done well for me. It cost me a certain amount to start, but I had it paid off in about a year,” he said. “If COVID ever lifts enough, if people aren’t scared to go back to restaurants, I’ll do pretty well.”
He’s convinced that the indoor crop is superior to field grown.
“Hydroponics can grow bigger, faster, and healthier plants,” he said. “The taste is better. My basil is much stronger than field-grown because it has the right nutrients every day. We test our water on a daily basis.”
Christel Folke is an applied agriculture instructor at the Owens Campus of Delaware Technical and Community College in Georgetown. She said while hydroponic start-up and maintenance costs are the main hurdles, the process has a long list of advantages.
“It’s a controlled environment. The grower has complete control of the lighting, heat, humidity, water, and nutrients. A lot of diseases usually come from the soil, but with hydroponics, you eliminate most of that risk. You still have some pests and disease, but it is easier to control, and we use natural methods,” Folke said, speaking about the college’s hydroponic system.
Saving water is another plus because the water is targeted at the roots, with much less evaporation compared to overhead irrigation outdoors.
The plants have a longer shelf life, Jordan said. Some hydroponic growers like him sell plants with the roots.
“With the root system attached, lettuce can last two weeks or more,” he said. “The shelf life on hydroponics crushes anything else.”
Fuel your hometown's passion and plug into the stories that define it.
Like with other greenhouse operations, farmers can grow year-round if they have heating and cooling systems.
Hydroponics is starting to attract more attention in Delaware.
‘Life-changing experience’ turns hobby into a business
In Dover, Doug Wood was a special education teacher in the Capital School District who started aquaponics as a hobby, raising fish to supply nutrient-rich water which is filtered and used to grow crops like lettuce.
“I was selling mainly to my fellow teachers. They really liked it and they said, ‘You should do this for real.’ Then I went through a life-changing event when I lost my mother to cancer, and I started thinking, ‘You only go around once,’ and decided to pursue it as a career,” Wood said.
He also wanted to help people eat a healthier diet in an effort to prevent cancer.
“I’ve always known we consume more chemicals, more man-made stuff, than we ever have," Wood said. "What really sparked me was trying to grow with no chemicals, no pesticides."
After attending a seminar at an aquaponics company, he decided to jump in, starting 302 Aquaponics with his wife, Katie.
With the help of another former teacher, Jomelle Bowen, who majored in plant science in college, they set up the two-part operation. One section is for fish tanks and water filtration systems, and the other is for dozens of shallow “table tanks” in which the lettuce floats in containers with the roots dangling in the water below.
No soil is used. A man-made, rock-like granular material is used to help anchor the roots.
After a little over a year in business, they now have almost 20,000 square feet in greenhouses. Together with 10 other employees, they harvest about 600 heads of lettuce a day, close to 220,000 per year, with the capacity to raise 350,000 heads per year, all in under a quarter acre.
“We are basically turning over nine crops per year,” Wood said.
They raise fish to supply the nutrients for the lettuce. The water the fish are in goes through several filtration steps and then is used to grow the plants. After the solids are filtered out, “good bacteria” are added to break down the fish waste that has dissolved in the water, creating a natural fertilizer in the water.
They raise tilapia, a tropical fish that grows well in the warmer temperatures inside the greenhouse.
Lettuce is a profitable crop. But those profits came after more of a challenge than he expected.
“When we first started production, it was three weeks before COVID struck. After that, our sales were a fourth of what they should’ve been,” he said. “We were giving a lot of [lettuce] away, to the Food Bank and shelters.”
So he went to farmers’ markets, locally-owned grocery stores and offered sales directly to customers for pickup at his farm or at a variety of locations throughout the state.
“I have a refrigerated delivery van. If I didn’t have that, I don’t know what I would have done,” he said. “A lot of people didn’t want to go in stores, but they would preorder and I’d deliver to them in my van.”
Business at restaurants started picking up as capacity restrictions eased, and schools reopened.
“Sales have done really well in the last four months,” Wood said.
He sells lettuce to restaurants, three school districts – Smyrna, Caesar Rodney, and Colonial – and grocery stores like Janssen’s Market in Greenville and Hocker’s Supermarkets in Bethany Beach and Clarksville.
“My big market is at the beach with restaurants and independently-owned grocery stores,” he said.
So far, he hasn’t sold to wholesalers because the profits would be too small. But he thinks he’s on the ground floor of what could be a big business.
“Consumers are becoming much more aware of the product they’re buying, where it’s coming from, and they’re willing to pay a little more for a cleaner, more sustainable product,” he said.
Why isn’t it more widespread?
While the hydroponics business is starting to sprout in Delaware, there are some big operations in other states.
AppHarvest in Morehead, Kentucky began trading on the Nasdaq stock exchange Feb. 1. Already operating a 60-acre high-tech indoor facility, the company plans to use funds from the stock offering to build 12 more large-scale indoor farms. In February, the company broke its record by harvesting more than 120,000 pounds of tomatoes in a single day.
Another major operation is AeroFarms in Newark, New Jersey, with a 70,000 square-foot greenhouse in a former steel mill, a 30,000 square-foot growing space in a former paintball and laser tag arena and a 5,500 square-foot research and development farm in a former nightclub. The company reports it can grow more than 2 million pounds of produce a year.
AppHarvest and AeroFarms confirm the advantages of hydroponics: saving land, saving water, a year-round growing season and eliminating man-made pesticides and herbicides, opting for natural solutions.
However, the high start-up costs can be demonstrated in AppHarvest’s financial forecasts. It estimates 2021 net revenue of $21 million, but a loss of $41 million because of expenses which include building more indoor farming systems.
Another reason hydroponics hasn’t taken off: “Not every crop can be grown that way,” said Kellie Michaud, agriscience teacher at Smyrna High School. “It’s a niche.”
Some plants grow well when they’re constantly in water, but others don’t. Some are just too large to be practical in a greenhouse. Indoor farmers need crops that take up little space and reach maturity quickly.
Michaud said some of the best performers are lettuce, greens, herbs, tomatoes, peppers, celery, and strawberries.
What could turn the tide?
Smyrna High agriscience teacher Keith Shane said scarcity of land could spur more hydroponic operations.
“If the state of Delaware continues at the rate of development we have seen, I could see hydroponics becoming a little bit more mainstream,” Shane said. “I don’t know if that future will be in our lifetime, but I honestly think it will be a niche – a pretty sustainable niche. I don’t see it going away.”
At Delaware Technical Community College in Georgetown, Dr. Daniele Kidd agrees.
“We’ve got to figure out how to feed the growing population,” said Kidd, the chair of the college’s applied agriculture department. “Other countries where land is scarce like Japan, they have skyscrapers that are basically indoor greenhouses.”
In Delaware, even with farm preservation programs, many farms have been sold to developers.
“It would be very difficult to start a farm in our area, to buy 50 acres,” Kidd said. “It would be expensive and might not make financial sense, but with hydroponics, you can make a living on three to four acres.”
Jordan, at Fresh Harvest Hydroponics, believes this system of farming will become much more widespread.
“There are tons of advantages to hydroponics, and they’re not making any more land,” he said.
Ben Mace covers real estate and business news. He can be reached at rmace@gannett.com.
Green Bronx Machine and Stephen Ritz - Our New PBS TV Show Featuring Leslie Ladybug And Tower Garden
This week we debut our friend Leslie Ladybug, who moves into a new Tower Garden home - Basil Towers - teaching all about seeds, vertical farming, healthy living, and growing food with children all year long - using 90% less water and 90% less space
I could not be more proud of Green Bronx Machine and our new series: Let's Learn debuting on PBS today. This series, designed to inspire healthy living, healthy learning, equity, empathy, compassion, and wellness features a series of diverse and inclusive characters right from our Bronx classroom!
This week we debut our friend Leslie Ladybug, who moves into a new Tower Garden home - Basil Towers - teaching all about seeds, vertical farming, healthy living, and growing food with children all year long - using 90% less water and 90% less space. Leslie teaches us that you too can grow food all year long and have fun doing it!
WATCH THE EPISODE NOW
AND SHARE IT!
And, you can find teacher and student resources to accompany all the fun and learning right on the GBM website.
We hope you'll tune in and share all the learning! Stay tuned to meet Patti the Pigeon, Sammy the Shark, Bobby the Bear, Sam the Squirrel, Artie the Ant, Mr. Met, and General Sequoia - the world's biggest tree - in weekly episodes coming soon!
With love from the Bronx, to the world, your pal,
Continuing Education: Urban Agriculture
It’s been 10,000 years since the agricultural revolution gave rise to cities. Agriculture now covers more than half of the world’s habitable land and is spreading at a rate of about 15 million acres annually
April 1, 2021
It’s been 10,000 years since the agricultural revolution gave rise to cities. Agriculture now covers more than half of the world’s habitable land and is spreading at a rate of about 15 million acres annually. Cities, meanwhile, now comprise more than half the global population (over 80 percent in developed countries), and the numbers are rising. Using current farming methods to feed a global population expected to hit 10 billion by midcentury would require adding new farmland equal in size to the continental United States.
This alarming situation is not even factoring in the impact of the climate crisis, which is expected to alter growing seasons and disrupt the phenological cycles that keep plants and their pollinators in sync. What’s more, new agricultural land mostly comes from felling biodiverse, carbon-sequestering forests to make room for mono-crops that stash very few greenhouse gases and for livestock that actually generate them. That makes the climate crisis worse and farming more difficult.
READ MORE ABOUT
In addition to land consumption, agriculture guzzles three-quarters of the fresh water used globally each year, while runoff from fields treated with herbicides, pesticides, and fertilizers contaminates significant amounts of the water that’s left. Then there’s transportation. As farms extend farther and farther from the cities they supply, food is trucked, shipped, and flown vast distances: farm to plate, the ingredients in a typical American meal travel an average of 1,500 miles. From a security perspective, the fact that most of the world’s food production is controlled by just a handful of corporations is unnerving. And from a public health perspective, the emergence of Covid-19 and other new diseases offers yet another indicator of ecological imbalance. It’s time to rethink the way we farm.
Food security, as defined by the United Nations, means that all people, at all times, have physical, social, and economic access to sufficient, safe, and nutritious food that serves their food preferences and dietary needs for an active and healthy life. Key to achieving food security in a way that’s more sustainable than current practices is urban agriculture—not as an outright replacement for rural farming, but as a crucial component in a balanced system.
Urban agriculture can take many forms: rooftop greenhouses, raised beds, and community-farming initiatives such as the City of Atlanta’s “Aglanta” program, which turns underused parcels in utility rights-of-way into farm plots eligible for U.S. Department of Agriculture certificates and associated loans. Ultimately, though, horizontal strategies are not productive enough to make a real dent in the food needs of a city. (If raised beds covered every rooftop in Manhattan, the produce grown would feed only about 2 percent of the borough’s population.) Just as cities grow vertically, so too must urban agriculture, and that means bringing it indoors.
“Controlled environments have been used for many years,” says Chieri Kubota, a professor of controlled environment agriculture (CEA) in the Department of Horticulture and Crop Science at Ohio State University. “Now that multiple issues are making conventional production outdoors more difficult, putting controlled environments in and near cities brings food production closer to potential markets—and also to younger generations of potential farmers who want to live in urban centers.”
Vertical agriculture is a type of CEA that—like high-rise buildings—stacks layers to provide usable area many times the footprint of the site. Instead of growing in soil, which is a heavy way to deliver nutrients, plants in vertical farms are grown hydroponically, aquaponically, or aeroponically. In hydroponics, plants are cultivated in nutrient-enriched water, which is captured and reused so that the system uses as little as a tenth of the water conventional agriculture needs. An aquaponic system pairs hydroponics with fish production, circulating the nutrients in the fish waste to feed the vegetables, and using the plants as a biofiltration system that returns clean water to the fish. Reducing water consumption even further—by as much as 98 percent, compared to field growing—aeroponic systems deliver nutrients in a fine mist to plant roots that are just hanging in the air. And because controlled environments exclude the weeds and pests that trouble field-grown produce, the use of herbicides and pesticides is all but eliminated.
Stacked plants may need to be rotated to make the most of available sunlight, which can be supplemented (or even substituted altogether) with LED grow lights. These can be calibrated to provide blue and red light in optimal doses for each type of plant, and timed to increase plant growth with extended days and growing seasons. (While it’s technically possible to grow any type of crop this way, for now it’s mainly leafy greens and tomatoes that are economically viable.) Cool enough to be strung right in among the plants without burning them, LEDs reduce site electricity consumption (and costs) per square foot of grow area by about a third compared to older technologies, such as high-pressure sodium. “Energy is a game-changer,” says Dickson Despommier, an emeritus professor of microbiology and public health at Columbia University, whose seminal 2010 book, The Vertical Farm: Feeding the World in the 21st Century, is widely credited with kick-starting vertical agriculture in North America. Cost-effective LED lighting opens up the possibility of converting urban and urban-adjacent building types such as parking garages, big-box stores, and shopping malls into productive local farms, he says.
With productivity rates that are orders of magnitude greater than conventional farming, high-rise growing is gaining traction worldwide. The world’s first such system began operations in 2012 in Singapore. The land-strapped city-state, which imports about 90 percent of its food, aims to grow a third of its produce locally by 2030. Indoor vertical farms in the country now produce about 80 tons of greens a year, and the Singapore Food Agency is supporting research into and development of the method as its main bet on the future.
In China, great swaths of arable land have been lost to development (more than 30 million acres between 1997 and 2008) and 20 percent of what’s left is contaminated. At the same time, the country has a strong tradition of urban-adjacent farming. When a 247-acre agricultural site, midway between Shanghai’s main international airport and the megacity’s center, recently came up for redevelopment, global design firm Sasaki proposed that, rather than create yet another tech park, the client take its agricultural mission to the next level. As a result, the Sunqiao Urban Agricultural District is slated to become one of China’s first comprehensive national agricultural zones. Sasaki’s master plan, which has received approval from the Pudong District and is now proceeding for formal approval from the City of Shanghai, expands the district’s role in Shanghai’s food network, integrating vertical agricultural production, research, and education into a dynamic public domain. In addition to research and development facilities and an agriculture production zone, the plan provides for a civic plaza showcasing productive landscapes, a science museum, an interactive greenhouse, an aquaponics display, and a destination market. “It’s urban agriculture on steroids,” says Michael Grove, chair of landscape architecture, civil engineering, and ecology at Sasaki.
The Sunqiao project will include a civic plaza with productive landscapes (top), a science museum, and an interactive greenhouse (above), among other elements. Image courtesy Sasaki, click to enlarge.
Grove identifies three primary drivers for prioritizing urban agriculture globally: the need to curtail agricultural sprawl and thereby protect ecosystems, to reclaim economic agency by diversifying control of food production, and to build community: “Food brings us together,” he says. Behind Asia’s early adoption of urban agriculture, he sees a historic understanding among the region’s societies that the well-being of the population requires systemic support. That may also be a factor in Europe, where the Netherlands is a global leader in controlled-environment technology, and Denmark is home to the world’s latest and largest vertical farm, a partnership between a Taiwanese CEA tech company and a local start-up: with growing shelves stacked 14 deep, the 75,000-square-foot wind-powered facility has the capacity to produce 1,000 metric tons of greens a year.
A hub for teaching, research, and community engagement, located within sight of downtown Columbus and designed by Erdy McHenry Architecture, supports Ohio State’s CEA efforts. Brad Feinknopf
North America has been slower to adopt vertical farming, a lag that Ohio State’s Kubota attributes in large part to the year-round, nationwide availability of produce from California, Arizona, and Florida. But now, she says, climate disruptions and shortages of viable farmland in those states, along with the increasing urbanization of the workforce, strengthen the rationale for controlled environment agriculture. To support Ohio State University’s multidisciplinary research into CEA, a one-acre vertical greenhouse is under construction within sight of downtown Columbus. As part of the facility, the recently completed Kunz-Brundige Franklin County Extension Office serves as a hub for teaching, research, and community engagement around food, health, agricultural production, and sustainability. Both buildings are designed by Philadelphia-based Erdy McHenry Architecture.
Although still tiny, vertical farming is the fastest-growing sector in U.S. agriculture. A projected compound annual growth rate (CAGR) of more than 20 percent from 2020 to 2026 is expected to bring sales to around $10 billion a year. And while significant numbers of start-ups in the capital-intensive sector have failed—as indicated by the track record of several initiatives profiled in this magazine eight years ago —experts say that’s an inevitable aspect of an emerging technology.
Among the growing number of enterprises going strong, however, is Vertical Harvest, the first vertical hydroponic greenhouse in North America. Cofounded by architect Nona Yehia, principal at GYDE Architects, the company began operations in 2016 in Jackson Hole, Wyoming. Jackson is a rural town, but it performs like a city in relevant ways: 97 percent of its developable land is already in use, and, with a four-month growing season, 98 percent of its food is imported. Inspired by Despommier’s work, the need for a local food supply, and the opportunity to provide meaningful work for community members with intellectual and physical challenges, Yehia designed a three-story greenhouse for a 30-by-100-foot municipally owned lot next to a parking garage. “The town councilor who showed us the property thought we’d put up a plastic hoop structure to extend the growing season a couple of months, employ a few people, and call it a day,” recalls Yehia. But she and her business partners wanted to grow as much food as possible, to employ as many people as possible, and to do both year-round. “That’s where the idea to grow up came from,” she says.
Vertical Harvest’s three-story CEA facility in Jackson Hole, Wyoming, produces as much food on a tenth of an acre as on a 10-acre conventional farm. Photos © Vertical Harvest (1), Hannah Hardaway (2 & 3)
With a footprint of a tenth of an acre, the greenhouse produces as much food as would a 10-acre conventional farm. It employs 30 people, more than half of whom have a disability. And it’s profitable. “It would have been easier as a nonprofit,” Yehia says, “but we were committed to creating a replicable model that is not about charity: it’s about empowerment.”
After five years of operation, Vertical Harvest is ready to expand. Construction is scheduled to start this year on a second location that incorporates affordable housing and municipal parking in Westbrooke, Maine. The new 70,000-square-foot greenhouse is expected to provide the equivalent of 50 full-time jobs and to produce 1.3 million pounds of produce a year, supplying hospitals, corporate cafeterias, schools, chefs, restaurants, and caterers, as well as individual customers. “These ecosystems can put out a lot of food,” says Yehia. “Making sure you have customers who can buy at scale is as essential to success as growing plans.”
Vertical Harvest intends to build up to 15 farms in the next five years, with agreements already in place for projects in Philadelphia and Harrisburg, Pennsylvania, and Chicago, and discussion is underway for five other locations. Like the Wyoming and Maine projects, they will integrate social value and community engagement with their agricultural mission. “It’s the perfect intersection to show what architecture can achieve in its social role in our communities,” Yehia says. And while she has run Vertical Harvest as designer, entrepreneur, and urban farmer, it’s entirely possible for architects to advocate for urban agriculture in their more usual role as prime consultants, coordinating the work of other experts.
As CEA picks up speed, the time may not be far off when every municipality will incorporate vertical farming into its civic infrastructure, valued the way public libraries and recreation centers are. “It should be something that we all expect to see when we go to cities,” Yehia says: “infrastructure that grows food and futures, and bolsters the sustainability of the community.”
Continuing Education
To earn one AIA learning unit (LU), including one hour of health, safety, and welfare (HSW) credit, read the article above and watch this video.
Then complete the quiz. Upon passing the test, you will receive a certificate of completion, and your credit will be automatically reported to the AIA. Additional information regarding credit-reporting and continuing-education requirements can be found at continuingeducation.bnpmedia.com
Learning Objectives
Explain how conventional agricultural methods contribute to climate change.
Define terms such as urban agriculture, controlled environment agriculture (CEA), and vertical agriculture.
Describe technologies relevant to CEA, such as hydroponics, aeroponics, and aquaponics.
Discuss how CEA can enhance food security and bring social value to underserved communities.
AIA/CES Course #K2104A
Lead photo: Sunqiao Urban Agricultural District has been designed by Sasaki for a site midway between Shanghai’s city center. Image courtesy Sasaki
KEYWORDS cities / climate change / urban planning
How CubicFarms Is Feeding A Changing World With Its Automated Indoor Growing Technology
The global supply chain today is facing significant, costly disruptions. A shipping container crisis has upended the global food trade. Devastating winter weather has impacted the U.S., and ongoing labour shortages within the farming industry show no sign of relenting as border crossings remain shut
April 7, 2021
Mark Shelling, Market One Media
CubicFarms provides sustainable and profitable commercial-scale automated indoor growing systems for local produce and fresh livestock feed. , Image courtesy of Market One Media
Supply chain – CubicFarms Garden – Foodservice – HG cattle
In an already tumultuous year, agriculture is facing supply chain disruptions and unpredictable climate changes
To combat this, CubicFarms offers new automated indoor farming systems that could revolutionize global food supplies
With multiple patents in the ag-tech space, CubicFarms is poised for further expansion
The global supply chain today is facing significant, costly disruptions. A shipping container crisis has upended the global food trade. Devastating winter weather has impacted the U.S., and ongoing labour shortages within the farming industry show no sign of relenting as border crossings remain shut.
The ability to move people and goods across long distances will always be at risk of disruption because the longer the supply chain, the more chances there are for things to go wrong.
The farming industry was already in the midst of a labour crisis even before this year, with fewer and fewer workers available to tend to fields. Now with borders being shut, it's unclear how many foreign workers will be able to return to their jobs, despite some having been issued flight exemptions.
Because of this continued downward trend, Canada is currently projected to lose 123,000 workers within a decade, according to a report done by RBC. That represents a loss of $11 billion in GDP, if the labour gap continues to widen.
Couple this labour shortage with changing weather patterns like the devastating cold snap in Texas, the shipping container crisis, and the ongoing demand for fresh produce, and you’ve got a perfect storm against the food industry.
These stacked variables have revealed just how vulnerable the global food supply chain is. Farmers are now scrambling to find sustainable alternatives to what appears to be a crumbling framework.
"We believe long food supply chains are dangerous. As a technology company in the agriculture business, we’ve seen the challenges with growing outdoors. The solution is in using technology to make locally grown produce more widely accessible, 365 days a year, not just here, but anywhere in the world.”
— Dave Dinesen, CEO, CubicFarm® Systems Corp.
Innovative new agriculture technologies like indoor vertical farming are more attractive to farmers who want the stability and consistency that come from harvesting indoor crops. Innovators in the agriculture space have already anticipated this shift and are now offering ways to safeguard against further threats to cultivation.
The technology is improving rapidly with automated, commercial-scale indoor growing systems that grow fresh produce in a controlled environment. These crops can be harvested with less labour than traditional farming, addressing the need to do more during labour shortages.
By creating the ideal indoor environment onsite, growers use LED lighting, less land, significantly less water, and less energy. In Canada and the U.S., in particular, the ability to grow fresh produce during the winter months allows farmers to expand the growing season to 12-months a year.
Disruptions to the supply chain during the ongoing pandemic have sent food distribution centres searching for more local produce. We can expect that demand to rise as the number of growers using indoor vertical farming systems increases.
A new leader in agricultural automation
For a better look at these automated indoor growing systems, Canadian ag-tech company, CubicFarm® Systems Corp. (TSXV:CUB), offers insights into how this technology is the future of agriculture.
Different from other companies in the ag-tech space, CubicFarms began with the farmers themselves. Jack Benne and his son Leo Benne visited a farm in Puerto Rico after a hurricane when they had an idea for an automated indoor growing system that could grow produce in any weather.
Being the principles behind Bevo Farms, one of the largest propagation greenhouse systems in North America, they put their considerable expertise to work on this important problem.
CubicFarms’ produce is grown onsite in an indoor, controlled environment, for delicious greens harvested at the peak of freshness, bringing food production closer to home.
The automated systems they created are now at the forefront of solving the supply chain woes of countries that must rely on outside suppliers for their fresh produce. The potential for this shift is massive.
A local supply chain would reduce long distance shipping/flights, the indoor controlled environment is pesticide and herbicide-free so there would be fewer shortages due to recall (think of the recent romaine E. coli scares), and there would be less food waste, as produce is harvested at peak freshness instead of days or even weeks in advance.
Under traditional supply chains, there is an expected amount of rot, unnecessary waste of food and profits in each shipment, and it’s a wonder that’s considered tolerable.
The CubicFarm System technology is housed within modules that are 40 ft by 8 ft, standing 9.5 ft tall. The beauty of their structure is that farmers can buy as many modules as they need and place them together, creating indoor fields with the ideal controlled environment year-round.
A patented undulating path is used to move crops throughout the module. Plants are cycled through each module on suspended trays, which periodically pass an artificial LED light source along with regulated CO².
This is different than the typical ‘rack and stack’ vertical farming setups which need more space to allow people through to seed, monitor, and harvest plants. The CubicFarm System brings the plants in a full circle once every 90 minutes.
Each module is custom-built, stainless steel container. Trays move along a patented undulating path.
This allows for harvesting to easily take place at the front of the module, while sensors monitor the plants from the inside. This also prevents leaf burning, sometimes seen in vertical farms when the plants are too close to the light and heat source, or those suffering the ill-effects of their position too high or too low in the rack for the ideal amount of CO² necessary for healthy growth.
The CubicFarm System uses a propagator, which grows seeds into seedlings, and a cultivator that takes crops from seedlings to harvest.
This is all while being provided with the necessary nutrients and using up to 95 per cent less water than traditional farming. This line can replicate the exact growing conditions to yield the perfect leafy greens, herbs, and microgreens every time.
"When you provide the optimal environment every day for a crop, it won't only reward you by growing as fast as possible, but it will also be more delicious and nutritious," Dinesen notes.
Global food distribution giant, Sysco, recently announced on their Sysco Vancouver Facebook page that they’re purchasing fresh produce from growers using the CubicFarm System.
This significant relationship is appealing to anyone looking to get into the supply chain, which can be challenging for smaller farming operations.
A new division of CubicFarms is an expert brokerage called CubicFarms Garden. This expert team provides business consulting services for growers using the CubicFarm System onsite, helping them enter the local supply chain and fostering relationships with food distribution centres.
Farmers have long been at the forefront of technology when it comes to new machinery and systems. “Farmers are the most innovative people we know,” explains Dinesen. “In technology terms, this is the Tractor 2.0. After the invention of the tractor, no one would plow a field without one. With the automated, onsite, and commercial scale of the CubicFarm System, no one would want to grow indoors without us.”
While it might sound complex, farmers who use CubicFarm System will immediately notice its simplicity. When a new unit arrives on site, it's already 90 per cent ready to go, and the remaining set up is assisted by a hands-on customer experience team.
Farmers are trained on how to maximize each module's potential and are given resources for developing new crops. With the recently announced addition of Edoardo De Martin, former Microsoft Vancouver GM, to the executive team as Chief Technology Officer, we can expect the next generation of growing technologies to use more artificial intelligence and robotics to enhance their existing automations and efficiencies.
From fresh food to livestock feed
In January of 2020, the company's success and expertise led to the acquisition of a second farmer-founded innovative company called HydroGreen Inc. Another patented indoor farming system, the HydroGreen Grow System is focused solely on the production of fresh, nutritious livestock feed. Feed that would once be grown across acres of grazing land is now produced in a module that's a fraction of that size.
It is a necessary innovation for ranchers who are facing land and water scarcity issues. Dihl Grohs developed the technology for growing nutritious livestock feed for his ranches in South Dakota, Utah, and Missouri. The concept of low-maintenance feed growing was in direct response to the areas where his cattle had limited precipitation.
Recently published university research confirms greenhouse gas reductions using HydroGreen’s hydroponic fodder system. The university study results came from a HydroGreen Grow System operating in British Columbia, the latest market for the system in CubicFarms’ backyard.
At the EcoDairy in Abbotsford, British Columbia, where they produce milk and use agritourism to educate people about where their food comes from, owner Bill Vanderkooi is using HydroGreen for his dairy cattle.
In a video interview, Vanderkooi talks about incorporating HydroGreen livestock feed into the current mixture and replacing some grain and forage in the cattle diet, measuring against a control group for differences in performance, production, and health. “At the early stage of the trial we’re seeing some positive benefits on performance.” Ongoing research into the nutritional benefits will be combined with land, water, and energy usage as factors for farmers.
The HydroGreen Grow System uses 92 percent less water and less land than traditional farming, so it’s expected that this technology will be widely embraced by the livestock industry in the future.
The fresh livestock feed can be used for a variety of animals, but it’s mainly used for dairy and beef cattle. For those facing labour shortages, the HydroGreen module operates with the push of a button and is self-cleaning. Growing predictable amounts of fresh livestock feed indoors and onsite will allow farmers to reduce the unpredictability that can be costly and dangerous to their animals and livelihoods.
The HydroGreen Grow System’s automated seeder spreads half an inch of small grain seed on the growing surface, growing from seed to feed in six days, with less land, water, labour, and energy.
CEO Dave Dinesen considers the HydroGreen Grow System to be the most automated livestock feed growing technology on the planet.
He explains, "When it comes to animal health and nutrition, the HydroGreen Grow System is giving the most nutritious and delicious livestock feed to these animals. They’re healthier, the feed is more consistent, and ranchers can become more self-sufficient.”
“It’s also automated and scalable because we have the technology to make this possible and profitable,” he adds.
“At the end of the day, we’re a technology company, not a produce or livestock feed company, so we don’t compete with farmers. They become our farmer partners and it’s our job to advance the technologies that support their businesses.”
With a $5 million investment from a top ag-tech investor, Ospraie, and a 100-module sale (their largest yet) to a farm in Surrey, B.C., CubicFarms’ momentum is only growing. It's this momentum that will continue to cultivate new acquisitions, like HydroGreen, and propel the company into an expanding market.
CubicFarms also has an R&D Innovation Centre that is continuously creating new crops and streamlined growing practices to benefit the growers using their technologies, including the CubicFarm System and the HydroGreen Grow System. It's a hopeful progression in a time when there seems to be a new crisis emerging every month. With technology like this positioned to revolutionize global food supply and essentially end hunger, it's one fewer crisis we have to face in 2021.
Learn more about CubicFarms by visiting their website here.
For more information about the CubicFarm System, watch this overview video to see it in action.
March Indoor Ag Science Cafe Recording Is Now Available!
This presentation 'USDA SBIR Grants Program Overview' was given by Dr. Steven Thomson & Melinda Coffman (USDA NIFA) during our 28th cafe forum on March 30th, 2021
"USDA SBIR Grants Program Overview"
Dr. Steven Thomson & Melinda Coffman
USDA NIFA
SBIR = Small Business Innovation Research
Please contact Melinda Coffman for SBIR questions.
This presentation 'USDA SBIR Grants Program Overview' was given by Dr. Steven Thomson & Melinda Coffman (USDA NIFA) during our 28th cafe forum on March 30th, 2021. Indoor Ag Science Cafe is organized by the OptimIA project team funded by USDA SCRI grant program.
Upcoming Cafes:
Tuesday, April 20th, 10 AM Eastern - 'Plant Factories and Indoor Farming Innovations in Japan' by Eri Hayashi (Japan Plant Factory Association)
Tuesday, May 18th, 11 AM Eastern - 'Smart Sensors for Indoor Farming' by Dr. Krishna Nemali (Purdue University)
Interested in giving a talk to share your thoughts and experiences? Please contact us!
Invitation To F&A Next 2021: The Impact of Innovation!
While our aim was to physically host the upcoming edition of F&A Next at the Campus of Wageningen University & Research, another virtual summit is today’s reality. Postponing is definitely not an option. Irrespective of Covid-19, a great deal happened in 2020. Investments in global food- and agtech were increased by over 30% to some USD 26 bilion!
F&A Next invites investors, entrepreneurs, and experts to address the next challenges of our sector on Wednesday, 26 May 2021 at the 6th annual F&A Next Summit. We look forward to showcasing the next scaling food and agtech companies. Yes, we‘ll miss meeting you in person, but we’ll make sure that dialing in will be as close as possible to the real thing!
During this year's 3-hour live, virtual summit we will
bring you up to speed on the Impact of Innovation in the agrifood industry,
present eight 'Next Heroes in Food- & Agtech', and
offer you ample opportunity to virtually connect and meet with (other) startups, scale-ups, investors, and corporates in the agrifood space.
GET YOUR EARLY-BIRD TICKET WITH A 25% DISCOUNT
Book your ticket before 12 April to get a 25% discount! Apply the code: FaN@21
Stay safe, stay healthy!
The partners of F&A Next
2021 Theme: "The impact of Innovation"
Get Your eTicket to F&A 2021, 26 May
Food & Ag Innovation only started around 2014 and has definitely gained momentum ever since. in 2020 investments in global food and agtech have risen, irrespective of Covid-19 influences. The pandemic did, however, trigger changes in consumer behavior. Has ‘life as we know it’ irrevocably changed? And what about the much-needed innovation earlier in the value chain?
At F&A Next, Rob Leclerc, founding Partner of Agfunder and Nick Ferreday, Executive Director Food & Agribusiness at Rabobank, will compare notes.
Continuing Education: Urban Agriculture
It’s been 10,000 years since the agricultural revolution gave rise to cities. Agriculture now covers more than half of the world’s habitable land, and is spreading at a rate of about 15 million acres annually
April 1, 2021
It’s been 10,000 years since the agricultural revolution gave rise to cities. Agriculture now covers more than half of the world’s habitable land, and is spreading at a rate of about 15 million acres annually. Cities, meanwhile, now comprise more than half the global population (over 80 percent in developed countries), and the numbers are rising. Using current farming methods to feed a global population expected to hit 10 billion by midcentury would require adding new farmland equal in size to the continental United States.
This alarming situation is not even factoring in the impact of the climate crisis, which is expected to alter growing seasons and disrupt the phenological cycles that keep plants and their pollinators in sync. What’s more, new agricultural land mostly comes from felling biodiverse, carbon-sequestering forests to make room for mono-crops that stash very few greenhouse gases and for livestock that actually generate them. That makes the climate crisis worse and farming more difficult.
In addition to land consumption, agriculture guzzles three-quarters of the fresh water used globally each year, while runoff from fields treated with herbicides, pesticides, and fertilizers contaminates significant amounts of the water that’s left. Then there’s transportation. As farms extend farther and farther from the cities they supply, food is trucked, shipped, and flown vast distances: farm to plate, the ingredients in a typical American meal travel an average of 1,500 miles. From a security perspective, the fact that most of the world’s food production is controlled by just a handful of corporations is unnerving. And from a public health perspective, the emergence of Covid-19 and other new diseases offers yet another indicator of ecological imbalance. It’s time to rethink the way we farm.
Food security, as defined by the United Nations, means that all people, at all times, have physical, social, and economic access to sufficient, safe, and nutritious food that serves their food preferences and dietary needs for an active and healthy life. Key to achieving food security in a way that’s more sustainable than current practices is urban agriculture—not as an outright replacement for rural farming, but as a crucial component in a balanced system.
Urban agriculture can take many forms: rooftop greenhouses raised beds, and community-farming initiatives such as the City of Atlanta’s “Aglanta” program, which turns underused parcels in utility rights-of-way into farm plots eligible for U.S. Department of Agriculture certificates and associated loans. Ultimately, though, horizontal strategies are not productive enough to make a real dent in the food needs of a city. (If raised beds covered every rooftop in Manhattan, the produce grown would feed only about 2 percent of the borough’s population.) Just as cities grow vertically, so too must urban agriculture, and that means bringing it indoors.
“Controlled environments have been used for many years,” says Chieri Kubota, a professor of controlled environment agriculture (CEA) in the Department of Horticulture and Crop Science at Ohio State University. “Now that multiple issues are making conventional production outdoors more difficult, putting controlled environments in and near cities brings food production closer to potential markets—and also to younger generations of potential farmers who want to live in urban centers.”
Vertical agriculture is a type of CEA that—like high-rise buildings—stacks layers to provide usable area many times the footprint of the site. Instead of growing in soil, which is a heavy way to deliver nutrients, plants in vertical farms are grown hydroponically, aquaponically, or aeroponically. In hydroponics, plants are cultivated in nutrient-enriched water, which is captured and reused so that the system uses as little as a tenth of the water conventional agriculture needs. An aquaponic system pairs hydroponics with fish production, circulating the nutrients in the fish waste to feed the vegetables, and using the plants as a biofiltration system that returns clean water to the fish. Reducing water consumption even further—by as much as 98 percent, compared to field growing—aeroponic systems deliver nutrients in a fine mist to plant roots that are just hanging in the air. And because controlled environments exclude the weeds and pests that trouble field-grown produce, the use of herbicides and pesticides is all but eliminated.
Stacked plants may need to be rotated to make the most of available sunlight, which can be supplemented (or even substituted altogether) with LED grow lights. These can be calibrated to provide blue and red light in optimal doses for each type of plant, and timed to increase plant growth with extended days and growing seasons. (While it’s technically possible to grow any type of crop this way, for now it’s mainly leafy greens and tomatoes that are economically viable.) Cool enough to be strung right in among the plants without burning them, LEDs reduce site electricity consumption (and costs) per square foot of grow area by about a third compared to older technologies, such as high-pressure sodium. “Energy is a game-changer,” says Dickson Despommier, an emeritus professor of microbiology and public health at Columbia University, whose seminal 2010 book, The Vertical Farm: Feeding the World in the 21st Century, is widely credited with kick-starting vertical agriculture in North America. Cost-effective LED lighting opens up the possibility of converting urban and urban-adjacent building types such as parking garages, big-box stores, and shopping malls into productive local farms, he says.
With productivity rates that are orders of magnitude greater than conventional farming, high-rise growing is gaining traction worldwide. The world’s first such system began operations in 2012 in Singapore. The land-strapped city-state, which imports about 90 percent of its food, aims to grow a third of its produce locally by 2030. Indoor vertical farms in the country now produce about 80 tons of greens a year, and the Singapore Food Agency is supporting research into and development of the method as its main bet on the future.
In China, great swaths of arable land have been lost to development (more than 30 million acres between 1997 and 2008) and 20 percent of what’s left is contaminated. At the same time, the country has a strong tradition of urban-adjacent farming. When a 247-acre agricultural site, midway between Shanghai’s main international airport and the megacity’s center, recently came up for redevelopment, global design firm Sasaki proposed that, rather than create yet another tech park, the client take its agricultural mission to the next level. As a result, the Sunqiao Urban Agricultural District is slated to become one of China’s first comprehensive national agricultural zones. Sasaki’s master plan, which has received approval from the Pudong District and is now proceeding for formal approval from the City of Shanghai, expands the district’s role in Shanghai’s food network, integrating vertical agricultural production, research, and education into a dynamic public domain. In addition to research and development facilities and an agriculture production zone, the plan provides for a civic plaza showcasing productive landscapes, a science museum, an interactive greenhouse, an aquaponics display, and a destination market. “It’s urban agriculture on steroids,” says Michael Grove, chair of landscape architecture, civil engineering, and ecology at Sasaki.
The Sunqiao project will include a civic plaza with productive landscapes (top), a science museum, and an interactive greenhouse (above), among other elements. Image courtesy Sasaki.
Grove identifies three primary drivers for prioritizing urban agriculture globally: the need to curtail agricultural sprawl and thereby protect ecosystems, to reclaim economic agency by diversifying control of food production, and to build community: “Food brings us together,” he says. Behind Asia’s early adoption of urban agriculture, he sees a historic understanding among the region’s societies that the well-being of the population requires systemic support. That may also be a factor in Europe, where the Netherlands is a global leader in controlled-environment technology, and Denmark is home to the world’s latest and largest vertical farm, a partnership between a Taiwanese CEA tech company and a local start-up: with growing shelves stacked 14 deep, the 75,000-square-foot wind-powered facility has the capacity to produce 1,000 metric tons of greens a year.
A hub for teaching, research, and community engagement, located within sight of downtown Columbus and designed by Erdy McHenry Architecture, supports Ohio State’s CEA efforts. Brad Feinknopf
North America has been slower to adopt vertical farming, a lag that Ohio State’s Kubota attributes in large part to the year-round, nationwide availability of produce from California, Arizona, and Florida. But now, she says, climate disruptions and shortages of viable farmland in those states, along with the increasing urbanization of the workforce, strengthen the rationale for controlled environment agriculture. To support Ohio State University’s multidisciplinary research into CEA, a one-acre vertical greenhouse is under construction within sight of downtown Columbus. As part of the facility, the recently completed Kunz-Brundige Franklin County Extension Office serves as a hub for teaching, research, and community engagement around food, health, agricultural production, and sustainability. Both buildings are designed by Philadelphia-based Erdy McHenry Architecture.
Although still tiny, vertical farming is the fastest-growing sector in U.S. agriculture. A projected compound annual growth rate (CAGR) of more than 20 percent from 2020 to 2026 is expected to bring sales to around $10 billion a year. And while significant numbers of start-ups in the capital-intensive sector have failed—as indicated by the track record of several initiatives profiled in this magazine eight years ago —experts say that’s an inevitable aspect of an emerging technology.
Among the growing number of enterprises going strong, however, is Vertical Harvest, the first vertical hydroponic greenhouse in North America. Cofounded by architect Nona Yehia, principal at GYDE Architects, the company began operations in 2016 in Jackson Hole, Wyoming. Jackson is a rural town, but it performs like a city in relevant ways: 97 percent of its developable land is already in use, and, with a four-month growing season, 98 percent of its food is imported. Inspired by Despommier’s work, the need for a local food supply, and the opportunity to provide meaningful work for community members with intellectual and physical challenges, Yehia designed a three-story greenhouse for a 30-by-100-foot municipally-owned lot next to a parking garage. “The town councilor who showed us the property thought we’d put up a plastic hoop structure to extend the growing season a couple of months, employ a few people, and call it a day,” recalls Yehia. But she and her business partners wanted to grow as much food as possible, to employ as many people as possible, and to do both year-round. “That’s where the idea to grow up came from,” she says.
Vertical Harvest’s three-story CEA facility in Jackson Hole, Wyoming, produces as much food on a tenth of an acre as on a 10-acre conventional farm. Photos © Vertical Harvest (1), Hannah Hardaway (2 & 3)
With a footprint of a tenth of an acre, the greenhouse produces as much food as would a 10-acre conventional farm. It employs 30 people, more than half of whom have a disability. And it’s profitable. “It would have been easier as a nonprofit,” Yehia says, “but we were committed to creating a replicable model that is not about charity: it’s about empowerment.”
After five years of operation, Vertical Harvest is ready to expand. Construction is scheduled to start this year on a second location that incorporates affordable housing and municipal parking in Westbrooke, Maine. The new 70,000-square-foot greenhouse is expected to provide the equivalent of 50 full-time jobs and to produce 1.3 million pounds of produce a year, supplying hospitals, corporate cafeterias, schools, chefs, restaurants, and caterers, as well as individual customers. “These ecosystems can put out a lot of food,” says Yehia. “Making sure you have customers who can buy at scale is as essential to success as growing plans.”
Vertical Harvest intends to build up to 15 farms in the next five years, with agreements already in place for projects in Philadelphia and Harrisburg, Pennsylvania, and Chicago, and discussion is under way for five other locations. Like the Wyoming and Maine projects, they will integrate social value and community engagement with their agricultural mission. “It’s the perfect intersection to show what architecture can achieve in its social role in our communities,” Yehia says. And while she has run Vertical Harvest as designer, entrepreneur, and urban farmer, it’s entirely possible for architects to advocate for urban agriculture in their more usual role as prime consultants, coordinating the work of other experts.
As CEA picks up speed, the time may not be far off when every municipality will incorporate vertical farming into its civic infrastructure, valued the way public libraries and recreation centers are. “It should be something that we all expect to see when we go to cities,” Yehia says: “infrastructure that grows food and futures, and bolsters the sustainability of the community.”
Continuing Education
To earn one AIA learning unit (LU), including one hour of health, safety, and welfare (HSW) credit, read the article above and watch this video.
Then complete the quiz. Upon passing the test, you will receive a certificate of completion, and your credit will be automatically reported to the AIA. Additional information regarding credit-reporting and continuing-education requirements can be found at continuingeducation.bnpmedia.com.
Learning Objectives
Explain how conventional agricultural methods contribute to climate change.
Define terms such as urban agriculture, controlled environment agriculture (CEA), and vertical agriculture.
Describe technologies relevant to CEA, such as hydroponics, aeroponics, and aquaponics.
Discuss how CEA can enhance food security and bring social value to underserved communities.
AIA/CES Course #K2104A
Complete the Quiz
Lead Image: KEYWORDS cities / climate change / urban planning
Underground Agriculture In London Is Gearing Up
By 2022, Growing Underground aims to produce 60 metric tons of vegetables across an area of 528 square meters. That should be enough for 10,000 households and is 12x more than what is produced on a regular farm
Growing Underground In London Is One
of The Largest Underground Vertical Farms
In the World That is Controlled Entirely
By A Digital Twin At The University of Cambridge.
29 March 2021
All the good things an old World War II bunker can bring, right? Thirty meters below ground, near the London New Covent Garden food market, two entrepreneurs have been working together for several years with the British University of Cambridge on an underground farm that has great ambitions.
Their intention is not only to significantly increase production on-site over the coming years. The project also serves as an example for the whole world, according to co-founder Richard Ballard,
By 2022, Growing Underground aims to produce 60 metric tons of vegetables across an area of 528 square meters. That should be enough for 10,000 households and is 12x more than what is produced on a regular farm.
Energy and water
Vegetable cultivation takes place without soil, as the plants thrive on a kind of ‘woolen carpet’ that uses very little water. “70% less than on a conventional farm,” claims Growing Underground. Energy consumption is also low due to the great depth – which ensures few temperature fluctuations – and thanks to the energy-efficient LED lighting.
Nevertheless, energy is the one thing that still stands in the way of a global breakthrough. Ballard: “Vertical agriculture is on the verge of exponential growth due to ever-improving LED technology, the Internet of Things, cloud computing, and wireless sensors. But the really big breakthrough will come once more and cheaper renewable energy becomes available that can also be stored.”
Ballard believes vertical agriculture can make a significant contribution to the food problem we undoubtedly have in store as a result of an ever- growing global population. For a techie, the fun part is that it also requires a lot of high-end sensor technology.
Melanie Jans-Singh
A digital twin
There are 25 sensors in the underground farm that constantly track how the plants are doing. E.g., whether something needs to be done with the amount of CO2 in the air, nutrients, temperature, humidity and light. In total, 89 variables are involved. Even the speed at which the plants grow is measured, says researcher Melanie Jans-Singh from the University of Cambridge.
Jans-Singh: “The digital twin provides us with a 3D representation of the situation in London here in Cambridge. That image is even better than if you were there on site yourself. The digital twin can do much more than a human being. It can monitor, learn, give feedback and make predictions. All factors that will help increase productivity.”
A great deal of research into vertical farming is also being done in the Netherlands, such as by the company Plantlab.
ABOUT THE AUTHOR
Maurits Kuypers graduated as a macroeconomist from the University of Amsterdam, specializing in international work. He has been active as a journalist since 1997, first for 10 years on the editorial staff of Het Financieele Dagblad in Amsterdam, then as a freelance correspondent in Berlin and Central Europe. When it comes to technological innovations, he always has an eye for the financial feasibility of a project.
VIDEOS: AppHarvest CEO On Building The Third Wave of Sustainable Infrastructure
AppHarvest founder and CEO Jonathan Webb broke down what goals the agriculture technology is seeking to achieve by building a homegrown food supply in the U.S.
AppHarvest founder and CEO Jonathan Webb broke down what goals the agriculture technology is seeking to achieve by building a homegrown food supply in the U.S.