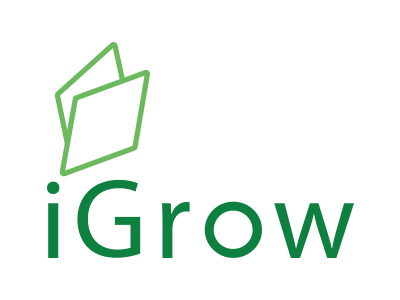
Welcome to iGrow News, Your Source for the World of Indoor Vertical Farming
Wageningen Researches Efficiency of Vertical Farming
Researchers of Wageningen University & Research are looking at how vertical farming can be more efficient
14 Jan 2020
Researchers of Wageningen University & Research are looking at how vertical farming can be more efficient.
“In a high-rise building – on a surface area about the size of a soccer field – you can grow enough vegetables for 100,000 people who each eat 250 grams of vegetables a day. You have complete control over the production process, so you are not dependent on the weather, the temperature, the daylight and the season. This makes vertical farming possible everywhere – also in infertile areas, in the desert or on Mars”, says Leo Marcelis, professor of Horticulture, in his blog on the website of Wageningen University & Research.
Vertical farming 1 of the solutions to the global food issue
“Vertical farming will not solve food shortages. It does not lend itself to rice and cereal production, but it is good for healthy, fresh vegetables, packed with fiber and vitamin C, and grown without contamination by pesticides or harmful microorganisms. That makes vertical farming one of the solutions to the global food issue”, says Marcelis.
Vertical farming takes place in buildings – the crops are grown on top of each other in several layers. - Photo: AFP
2 to 4 litres of water to grow a kilo of tomatoes
Vertically grown vegetables can make do with much less water. “We can recycle all the water and recover most of the water that the plants evaporate. As a result, we only need 2 to 4 litres of water to grow a kilo of tomatoes, whereas we use 17 litres of water in a Dutch greenhouse and in theory at least 60 litres for soil cultivation in for example southern Europe, and in practice often 200 litres,” says Marcelis.
In the closed cultivation system, nutrients such as nitrates and phosphates are also retained, while outside cultivation they end up in the soil, groundwater and surface water.
Pesticides a thing of the past
The use of pesticides is also a thing of the past, the professor emphasises. “By ensuring high hygiene levels, we can prevent insects and diseases from entering the building with employees, materials, seeds or air.”
Marcelis says the fact that the vegetables are not sprayed is good for our health, the environment and the preservation of plant and animal species. Moreover, thanks to local production, no shipping over long distances is required, which means that the CO2 footprint for transport is a lot smaller.
LED light healthy for plants?
The vegetables are grown on multiple floors of a high-rise building without daylight using special LED lamps, which often emit purple or bright pink light. Is LED light healthy for plants? “If we adjust the amount, colour and duration of the light, the amount of water and the temperature and composition of the air very precisely, we can give the crops much more nutritional value. I am absolutely convinced of that; there is already evidence that these factors influence nutritional value. In addition, we can also improve taste and shelf life.”
High energy consumption
Even though LED lamps are economical, a quarter of the costs goes to energy consumption says Marcelis in his blog. “If you can make substantial savings on this, the investment will become more affordable,” he says. Together with colleagues, he is studying options for reducing energy consumption. “We want to ensure that the light is used more efficiently by the plant. If we can optimize the temperature, humidity, the concentration of carbon dioxide and availability of water and fertilizers and can determine the optimum intensity and color of the light for every moment of the day, we can produce much more per unit of light,” says Marcelis. He also wants to improve the efficiency of climate control technologies.
Improve the crops
Current crops have been bred for outdoor cultivation and greenhouse cultivation. “We can also breed crops for these indoor circumstances, but that is a long-term task. Plant breeding projects easily take ten years.” And finally, the buildings can also be made more energy-efficient, for example by using the heat generated by the light for the heating of houses and offices.”
5 million euros for research into vertical farming
The Netherlands Organization for Scientific Research (NWO) has awarded 5 million euros to Wageningen research into vertical farming. “Our greenhouse horticulture sector is leading and has a lot of technology and knowledge that the Netherlands exports worldwide, also in the field of vertical farming. That is why it is important that we stay ahead,” says professor Marcelis.
Greenhouse cultivation is very efficient in the Netherlands and therefore much cheaper than vertical farming. In many places in the world, however, it is too cold in the winter or too hot in the summer to keep growing vegetables all year round. And sometimes there is simply not enough land available, for example in the city-state of Singapore. Singapore, but also the US, countries from the Middle East and Japan, are interested in vertical farming, according to the professor. “In Japan, food safety has become very important since the Fukushima nuclear disaster, and vertical farming is very safe,” explains Marcelis.
"Lack of Knowledge One of The Biggest Issues In Indoor Ag"
Lack of knowledge is one of the biggest issues in indoor agriculture, says Eric Stein, Executive Director of the Center of Excellence for Indoor Agriculture. "Lack of knowledge of the market place, lack of knowledge of growing, lack of knowledge of how to be profitable," he sums up
Eric Stein, e3garden
Lack of knowledge is one of the biggest issues in indoor agriculture, says Eric Stein, Executive Director of the Center of Excellence for Indoor Agriculture. "Lack of knowledge of the market place, lack of knowledge of growing, lack of knowledge of how to be profitable," he sums up. "In addition, there is confusion about the best technologies to use." With the launch of the Center, he hopes to help growers get over these challenges. From an online platform, it will grow eventually to a headquarters and a technology demo facility.
"Our goal is to provide a place for connection and exchange to take place every day of the year", says Eric. He is Associate Professor of Business at Penn State and CEO of Barisoft Consulting Group and advised businesses interested in setting up indoor farms, run workshops for the USDA on indoor farming and designed and operated an indoor vertical farm himself (e3garden) to conduct applied research on the economics of indoor farms.
Eric believes there's a lack of knowledge-sharing in the industry. "You have to go to the industry-specific conferences such as Indoor Ag-Con and Agtech NYC, which are great but bring together people for only a few days of the year."
The new center wants to connect growers with universities and investors to facilitate those relationships. "For example, we are working to bring in a Silicon Valley investment group that is interested in funding agtech start-ups. We also offer an energy savings program for our members, esp. growers, who want to cut operating costs. We are in the process of populating an Amazon-like multi-vendor marketplace just for indoor ag. We are also developing discount programs for members to receive reduced rates to key conferences like Indoor Ag-Con."
This all takes place at the newly launched website, indooragcenter.org. “The site offers an opportunity to create a highly networked community for indoor agriculture that is available to the members throughout the year. We expect it will help investors find farms to invest in, help growers find the products and services they need, highlight key conferences and events, and develop a knowledge base of best practices, solutions, cases, and research. We invite all types of indoor growers to participate regardless of technology or product type; e.g., from greenhouses to plant factories and from leafy greens to mushrooms", says Eric.
In the near future, the Center of Excellence for Indoor Agriculture wants to go offline as well. Phase two of its development includes raising capital and building a COE headquarters and technology demo facility in the greater Philadelphia area.
"Every industry has grown through bench-marking and knowledge sharing. The pharmaceutical industry is a case in point. I think we are reaching the point where indoor ag investors want accountability and transparency. We think the Center can help in this regard", Eric concludes.
"As we have seen recently, several companies have gone out of business. For instance, the container farms seem to not be doing well. I am not surprised because the logistics for growing in spaces like this are not optimal and the wild claims of profitability were not realistic, esp. given the high price of these units. We need to ground the business model for indoor ag on fundamentals, and that just is not happening in many cases. We think the investors will drive the need for better, curated knowledge, which is what the Center is all about."
For more information:
Indoor Ag Centerindooragcenter.org
Publication date: Wed 18 Dec 2019
© HortiDaily.com / Contact
€5 Million For Dutch Vertical Farming Research
"The increasing world population needs to be fed, while more and more people live in cities, there is often too little water, and we want our vegetables to have more and more nutritional value”
Wageningen University & Research (WUR) is to receive more than €8 million from the Dutch Research Council (NWO) and participating bodies for two major research programs, one involving tower garden systems using LEDs and the other focusing on improvements in the welfare of pigs and chickens. A third project, with WUR as a partner, is about sustainable freshwater management in the Dutch delta.
The recipients of the so-called Perspectief round 2019 funding were announced during the annual ‘Teknowlogy’ event hosted by NWO’s Applied and Engineering Sciences domain.
Tower gardens using LEDs
Sky High, a research program led by Professor of Horticulture & Product Physiology Leo Marcelis, which aims to bring about a revolution in vertical farming, received a total grant of €5 million.
"The increasing world population needs to be fed, while more and more people live in cities, there is often too little water, and we want our vegetables to have more and more nutritional value. By growing plants in layers on top of each other and illuminating them with special LED lights, you can produce fresh vegetables all year round, anywhere in the world, and under all weather and climate conditions," says program leader Prof. Leo Marcelis.
Researchers working on the Sky High program will cooperate with lighting specialists, plant breeding companies, growers, horticultural technology companies, architects and food suppliers to make vertical agriculture systems cheaper and more energy-efficient. Another aim is to produce vegetables and herbs that taste better, have longer shelf lives and provide more nutritional value, while using the absolute minimum of water and fertilizers and no pesticides.
Other participants
Amsterdam Institute for Advanced Metropolitan Solutions (AMS), Bayer, Bosman Van Zaal, Certhon, Fresh Forward, Grodan, GrowX, HAS University of Applied Sciences, OneFarm, Own Greens, Priva, Signify (Philips Lighting), Solynta, TU Delft, Eindhoven University of Technology, Unilever, Leiden University, Utrecht University, University of Amsterdam, and Van Bergen Kolpa Architecten.
Source: Wageningen University & Research
Publication date: Tue 12 Nov 2019
Vertical Farming Reaches New Heights In Germany With Fraunhofer IME
The AVF was invited to visit its member Fraunhofer IME in Aachen, Germany, one of 72 institutes of the Fraunhofer-Gesellschaft, the leading organization for applied science in Europe with over 26,000 employees and various international branches around the world
OCTOBER 22, 2019 | KYLE BALDOCK | Indoor Vertical Farming - Association
Visit to the Fraunhofer IME in Aachen: On September 4th, the AVF was invited to visit its member IME and experience their groundbreaking, innovative vertical farming technologies live on the spot.
Aachen, 04. September 2019: The AVF was invited to visit its member Fraunhofer IME in Aachen, Germany, one of 72 institutes of the Fraunhofer-Gesellschaft, the leading organization for applied science in Europe with over 26,000 employees and various international branches around the world.
The Fraunhofer Institute for Molecular Biology and Applied Ecology IME has six different sites in Germany and conducts research in the field of applied life sciences from the molecular level to entire ecosystems. Its division “Molecular Biotechnology” is located in Aachen, Germany and conducts R&D in the field of biotechnology with a strong focus on plant-based applications.
Over the last 10 years, the IME has developed and established two different vertical farming systems at the Aachen site in cooperation with the Fraunhofer IPT and IIS (à VertiPharm) as well as the Fraunhofer IML (à OrbiPlant™):
VertiPharm, a fully automated vertical farm with a strong focus on different research applications (e.g. plant cultivation, plant phenotyping, biopharmaceutical production) and OrbiPlant™, a novel and cost-efficient approach to vertical farming of food crops. These two vertical farming systems are complemented by LEDitGrow, an innovative multi-chamber system for the rapid development of plant growth protocols and the optimization of specific plant target values.
The design of the two IME vertical farming systems, their degree of automation, data management, efficiency and productivity, as well as their application and research possibilities go beyond the current state of the art of indoor farming technology. The systems provide an unprecedented basis to promote vertical farming, not only in Germany but worldwide. The different technology platforms are available for cooperation projects. Potential cooperation partners are encouraged to get in contact with IME (see below).
During a facility tour AVF had the opportunity to visit the different systems that are outlined below.
Fig.1: LEDitGROW plant cultivation unit for the accelerated multi-parameter development of plant growth protocols (© Ann-Katrin Beuel, IME).
LEDitGROW – Multi-parameter single plant cultivation system
A LEDitGROW unit comprises 24 single plant cultivation chambers, each equipped with various different LED-based light spectra including UVA. The unit has been designed to fit into a phytotron to run experiments at defined temperature, humidity and CO2 concentration. Each plant chamber can hold a single plant or several tissue culture petri dishes and can be individually supplied with nutrient solution.
The parallelization of cultivation conditions together with a statistical multi-parameter design of experiment (DoE) approach allows the rapid establishment of species-specific growth recipes as well as the optimization of specific target values such as biomass, secondary plant metabolites or morphology.
VertiPharm – Automated multifunctional research platform for vertical farming
Fig. 2: Top view on VertiPharm’s vertical farming unit (above, © AVF) and N. benthamiana plants under LED lighting in one layer of the vertical farm unit (below, © Andreas Reimann, IME).
The highlight of the IME in Aachen is the fully automated, pilot-scale vertical farming research platform featuring core functionalities such as multi-tier-based vertical farming, single plant handling, sensor-based in-process control, 2D/3D plant scanning, vacuum plant infiltration, downstream processing and central data management.
The impressive construction of the vertical farm unit consists of eight cultivation levels and provides ~550m2 of net cultivation area for the continuous or batch-wise cultivation of plants under highest reproducibility.
Different parameters such as temperature, humidity, CO2-concentration, LED-based lighting and composition of the plant nutrient solution can be defined and monitored in the central control system. Each plant receives a unique ID during seeding and is tracked individually throughout the entire cultivation time until harvest. Movement, sensor and measurement data are continuously recorded and can be used for in-process control or retrospective analysis of cultivation parameters and specific plant characteristics.
The fully automated facility can be used to produce food and non-food plants of different varieties and sizes. In addition to the vertical farming of plants a separate vacuum-infiltration unit connected to a fermentation suite allows the rapid production of recombinant biopharmaceuticals (e.g. vaccines, antibodies or enzymes) in plants by Agrobacterium-mediated gene transfer. Thanks to this multifunctionality the plant production research platform at Fraunhofer IME enables a broad spectrum of applications in different plant-based fields but also in the field of engineering, for instance:
Cultivation of food plants
Cultivation of medicinal/ specialty plants
Cultivation of ornamental plants
Production of recombinant biopharmaceuticals
Plant breeding and plant phenotyping
Software-based applications (e.g. digitization of production, artificial intelligence, augmented reality-assisted maintenance)
OrbiPlant™ – groundbreaking vertical farming system for the cost-efficient production of food crops
Fig. 3: OrbiPlantTM pilot-scale system with various leafy greens and herbs on a conveyor belt. The plant size gradually increases along the four conveyor belt loops (© Andreas Reimann, IME).
OrbiPlant™ represents an innovative approach to vertical farming of food crops that can truly make a difference to the spread and market penetration of vertical farming.
The major difference to classical tier-based approaches is a continuous conveyor belt system that is flexibly arranged in vertical loops allowing the easy placement of seeds or seedlings on one end of the conveyor system and the easy harvest on the other end. In between plants grow self-sufficiently under specific LED lighting conditions that can be adapted to the respective growth stage.
The conveyor belt movement can be specifically adjusted to a plant’s growth cycle and takes advantage of a growth-stimulating orbitropal effect on the plant, which is stemming from the changing gravitational orientation of the plant on the conveyor belt. The water-nutrient supply is ensured by aeroponic nozzles inside the belt loops. The innovative OrbiPlant system has several key improvements over current vertical farming systems:
High plant biomass yields and short growth cycles
Low production costs (e.g. <0.40 € per lettuce head)
Optimal cost-efficiency due to minimal hardware and personnel costs
Modular conveyor belt concept easily adaptable to different plants and growth cycles as well as to different building geometries
Improved vertical heat convection
Low LED lighting requirement
Flexible degree of automation depending on customer need
OrbiPlant is not only providing a cost-effective, optimized production platform for food crops with minimal space and resource requirements, but its unique design and flexibility has the potential to take vertical farming to a new level. It overcomes the shortcomings of today’s most commonly used horizontal rack systems, saves energy, utilizes intelligent automation, and enables easy handling and operation.
The AVF in cooperation with the Fraunhofer IME welcomes company and stakeholder inquiries on the presented systems.
Contacts:
Christine Zimmermann-Lössl, AVF Chairwoman
Email: czl@vertical-farming.net
Marvin Spence, AVF Project Manager
Email: ms@vertical-farming.net
Andreas Reimann, Senior Acquisition and Project Manager at Fraunhofer IME, Business Field Indoor Farming/Vertical farming
Email: andreas.reimann@ime.fraunhofer.de
Visit Fraunhofer IME’s website to learn more about them.
Saving Land With Vertical Farming Food Production
The Innovation Hub for Controlled-Environment Agriculture (IHCEA) at the James Hutton Institute is a collaboration between government agri-tech centre Crop Health and Protection (CHAP), and Liberty Produce, a London-based farming technology company with expertise in horticultural lighting and fertigation systems
By Rohese Devereux Taylor @hellorohese Senior Digital Reporter | October 11, 2019
A new research centre for vertical farming technologies that aims to enable Scottish farmers to transition to sustainable growing techniques opens in Dundee next week.
The Innovation Hub for Controlled-Environment Agriculture (IHCEA) at the James Hutton Institute is a collaboration between government agri-tech centre Crop Health and Protection (CHAP), and Liberty Produce, a London-based farming technology company with expertise in horticultural lighting and fertigation systems.
The centre has been purpose built for research and development and will help the industry to understand and tackle barriers to the adoption of hydroponic production systems.
The aim of the centre, which houses Liberty Produce's Future Farming Hub, is to drive innovations that reduce operational costs and improve the yields from controlled-environment farms, providing benefits to growers, food processors and consumers, as well as help farmers meet food requirements and limit further damage to the environment.
Director of Liberty Produce, Zeina Chapman said: "What we do is develop technology with a focus on trying to reduce the operational costs and the capital costs of running these systems, as well as improving the yield.
"The biggest challenge growers have at the moment is that vertical farming is really only on the cusp of commercial viability and that's because the cost of the capital expenditure required to build these systems is enormous, the operational costs are still very high, they're still quite labour intensive."
Because of this, most producers can only grow high-value crops such as microgreens, which can be sold for up to £40 per kilogram, and herbs.
But Liberty Produce, founded in 2018, wants to change that by developing new technologies with a focus on reducing costs these systems can be adopted globally.
Vertical farming grows produce in layers indoors in sometimes soil-less systems aided by LED lights either by hydroponics, where roots are continuously in moisture in the growing medium, or aeroponics, where the produce is misted and doesn't rely on a growing medium.
They are seen as a sustainable alternative to cultivating land not currently used for food, can withstand variable and increasingly extreme weather, eliminate the use of agrichemicals and reduce water use.
Liberty Produce will lead a £1.3 million project with eleven partners to accelerate the development of the UK vertical farming sector.
Using the funds, awarded by Innovate UK, the farming hub will support the creation of an integrated technology system focused on reducing operational costs by 25 percent, improving crop yield by 30 percent and reducing necessary grower intervention through improved decision support and automation in lighting, nutrient and environmental control technologies.
Some of the innovations that will be carried out at the centre will include designing high-efficiency LED lighting systems; test growing regimes, lighting applications and nutrient mixes in a variety of crops.
Vertical farming crops will complement traditional arable farming but Ms Chapman believes that more produce will be grown via the method as technologies advance and natural resources struggle to cater to growing populations.
She said: "I think they will become more mainstream for crops that are currently grown in fields or in glass houses. I think we'll start to see a more broadening of the crop types growing in these systems."
Growers are looking to produce baby leaves commonly found in salad bags with the vertical farming method, moving away from polytunnels and indoor track systems. But utilising the vertical method for wheat, barley and potatoes has a way to go yet.
Ms. Chapman said: "I think we'll start to see a patchwork of new growing systems coming in to help support and take over some of the more traditional growing systems."
Vertical crops are grown in a controlled environment with light levels, temperature, carbon dioxide, and applied nutrients all closely monitored and as an indoor crop, no pesticides are required.
Ms. Chapman said: "Improved technology in this sector will increase the adoption of these sustainable food growing systems, reduce the environmental impact of crop production, improve food security and create opportunities for the growth and export of UK agricultural technologies.”
Innovation Hub For Controlled Environment Agriculture Launched In Dundee
CHAP partnered with Liberty Produce to develop and build the IHCEA facility with funding from Innovate UK. The facility is a series of self-contained units housing state-of-the-art equipment with a modular structure designed to create a flexible environment for research and development
10th October 2019
London, UK
Agri-tech centre Crop Health and Protection (CHAP) and farming technology company Liberty Produce have launched the Innovation Hub for Controlled Environment Agriculture (IHCEA) at the James Hutton Institute’s site in Invergowrie near Dundee.
CHAP partnered with Liberty Produce to develop and build the IHCEA facility with funding from Innovate UK. The facility is a series of self-contained units housing state-of-the-art equipment with a modular structure designed to create a flexible environment for research and development. With integrated cutting-edge LED lighting systems and patented nutrient delivery technologies, this unique research facility will enable collaboration between industry, academia, and government to effectively tackle the barriers to widespread adoption of vertical farming. Its purpose is to accelerate the development of sustainable food production year-round through resource-efficient, fully-controlled systems.
The IHCEA is a key part of Liberty Produce’s Future Farming Hub, which will offer a wide range of services, including research and development and CEA training programmes within a commercial demonstrator system, as well as industry and academic collaboration opportunities.
The James Hutton Institute has welcomed the location of CHAP’s IHCEA and Liberty Produce’s Future Farming Hub in Invergowrie, in the context of the Institute’s drive for the establishment of Open Science campuses at its sites and this has been facilitated by the creation of the Advanced Plant Growth Centre at Invergowrie as part of the Tay Cities Deal.
Fraser Black, CHAP Chief Executive, said: “We are excited to be partnering with Liberty Produce and the James Hutton Institute to establish the Innovation Hub for Controlled Environment Agriculture (IHCEA), in Invergowrie. This is a prime example of CHAP’s mission to harness game changing ideas from our creative and innovative partners to solve the problems industry is facing today and tomorrow. This is a progressive step in our ambition is enable the United Kingdom to become a global leader in CEA and augment the production of healthy food in a sustainable way.”
Zeina Chapman, Liberty Produce Co-Founder and Director, added: “Vertical farming is not yet sustainable; this partnership which has established the IHCEA and Future Farming Hub at the James Hutton Institute marks an advancement of our collective journey towards creating truly sustainable vertical farming technologies. The greater vision of Liberty Produce remains driving innovation that will enable us to meet our global crop requirements without harming the planet.”
Professor Colin Campbell, Hutton Chief Executive, commented: “This collaboration with Liberty Produce and CHAP marks the next step in the growth of the Institute's Open Science Campus initiative and brings new innovative companies to work closely with world-leading science. This has been facilitated by Tay Cities Deal announcement to create an Advanced Plant Growth centre at Invergowrie and our other new investments there and builds on our track record of engaging with industry, research partners and the public.”
UK Government Minister Colin Clark said: “I am pleased to see the opening of this new Innovation Hub at the James Hutton Institute. We know that technological innovation is the future of sustainable agriculture and Scotland is home to world-leading resources and expertise in this field. The UK Government recognises the importance of this work and remains committed to funding research and development through our modern Industrial Strategy.”
It is hoped that the synergy between CHAP, Liberty Produce and the James Hutton Institute will provide a better understanding of total controlled environment technologies, drive innovation and accelerate the growth of the vertical farming sector in the UK.
**Ends**
About CHAP
Crop Health and Protection (CHAP), funded by Innovate UK, is one of four UK Agri-Tech Centres. CHAP’s vision is for the UK to be a global leader in the development of applied agri-technologies, to help secure our future by nourishing a growing population sustainably while delivering economic, environmental and health benefits to society.
CHAP acts as a unique, independent nexus between UK government, researchers and industry, building innovation networks to identify and accelerate the development of cutting-edge solutions to drive incremental, transformative and disruptive changes in sustainable crop productivity and to establish controlled environment agriculture (CEA) as a core competency.
www.chap-solutions.co.uk/
For further information contact:
Darren Hassall
Darren.hassall@chap-solutions.co.uk
+44 (0)1904 462062
About Liberty Produce:
Liberty Produce is a farming technology company, enabling the growth of local produce year-round, using a fully-controlled, industry-leading, indoor vertical farming system. With expertise in lighting and nutrient delivery technology, Liberty develops and builds systems that reduce operational costs and improve yields of crops grown in controlled-environment farms. Their vision is to drive innovations that will enable the UK to meet our crop requirements over the next century, without harming the planet. Liberty Produce established the Future Farming Hub to enhance UK technology development and commercialization in the Controlled Environment Agriculture (CEA) sector. www.liberty-produce.com
For further information contact:
Benita Rajania
+44 20 3290 8801
About the James Hutton Institute
The James Hutton Institute is a world-leading scientific organization encompassing a distinctive range of integrated strengths in land, crop, waters, environmental and socio-economic science. It undertakes research for customers including the Scottish and UK governments, the EU and other organizations worldwide. The ongoing collaboration between the James Hutton Institute and Scottish-based vertical farm technology business Intelligent Growth Solutions Ltd resulted in the opening of Scotland’s first vertical farm at the Hutton Invergowrie campus in August 2018, and continues to be a major strength in developing the Advanced Plant Growth Centre initiative, which has been backed by a £27m transformational investment from the Tay Cities Deal. www.hutton.ac.uk
More information from Bernardo Rodriguez-Salcedo, Media Manager, James Hutton Institute, Email Bernardo.RodriguezSalcedo@hutton.ac.uk, Tel: +44 (0)1224 395089 (direct line), +44 (0)344 928 5428 (switchboard) or +44 (0)7791 193918 (mobile).
Inside Indoor AgTech
In order to better foster thought leadership through The Mixing Bowl and gain a deeper perspective for investment opportunities at Better Food Ventures, we have created a landscape of Indoor AgTech (Download Landscape Here)
Chris Taylor and Michael Rose provide a deep-dive analysis of Indoor Agriculture, tracking more than 1,000 companies to capture the technology ecosystem of controlled-environment agriculture: vertical farms, greenhouses, urban farms, plant factories, and container farms...
Understanding the Landscape
Controlled Environment Agriculture (CEA) or, Indoor Ag, as it is more commonly known, has been garnering tremendous attention because of the compelling benefits of growing indoors in a controlled environment. In order to better foster thought leadership through The Mixing Bowl and gain a deeper perspective for investment opportunities at Better Food Ventures, we have created a landscape of Indoor AgTech (Download Landscape Here). As with our partners’ landscape maps from Brita Rosenheim and Seana Day on FoodTech and AgTech (field production), this landscape focuses on the technology of the Indoor Ag market.
With the first release of this Indoor AgTech Landscape, we believed it was important to start with an ecosystem of the market as opposed to an investment heat map. As part of this effort, we are tracking more than 1,000 companies in the indoor space. This landscape is a subset of those companies, and others, that are active in the space. While some market assessments, including the notable AgFunder AgriFood Tech Investment Report, include cannabis, algae, and insect production, this landscape is limited to traditional food crop production, from seed to immediate post-harvest activities, and utilizes a lens focused on digital and information technology.
The landscape is segmented into broad categories of component technologies, production growing systems, and actual growers. Some other important components of indoor operations, such as the structures themselves, energy systems, and traditional or tangential equipment and supplies are not part of the map. Additionally, many companies in this space, particularly established vendors, offer products in multiple categories but are only represented once. Also, tools that are often shared with field farmers, such as supply-chain platforms and other downstream applications, are captured on the AgTech Landscape created by our colleague Seana Day.
Greenhouses as part of the Indoor Ag Landscape
While there has been much media attention on growing indoors with artificial lights in “Sunless” environments (sometimes referred to urban, vertical, indoor, plant factory,…), greenhouses, as an indoor farming approach, need to be included in the discussion and we have made a point to include them in this landscape. Greenhouses provide similar compelling benefits as a complete Sunless approach and have been utilized to enhance crop production for decades. They have evolved to become technically sophisticated, large in scale and widely deployed while incorporating a broad range of innovations in energy, sustainability, lighting, environmental control, irrigation, monitoring and automation. There are a number of greenhouse operations where production is already fully automated such as Little Leaf Farms in Massachusetts.
Component Technology
Indoor AgTech component technologies are represented on the left half of the landscape map segmented into environment, monitoring, management, and automation. In general, these technologies may be applicable to both sunless and greenhouse environments.
The landscape includes vendors of systems that are used to maintain an optimal growing environment, namely environmental control, irrigation/fertigation, and lighting. Environmental control and fertigation are not new technologies, but as they encapsulate and effectuate a grower’s decisions, they have enabled greater precision and scale in operations. Lighting, the third component, has seen more change in recent years as LEDs have emerged as a viable alternative to traditional lighting technologies. Lighting systems, most obvious in sunless environments, are also applied in greenhouse operations.
Companies offering monitoring solutions, including sensors and imaging systems to gather data on the environment, crop health and pests and disease pressure are also included. Environmental Monitoring companies measure conditions such as indoor and outdoor weather, soil moisture, and nutrient, CO2 and light levels; data that has been used historically to drive decisions and control at a relatively macro level. Newer innovations in Pest/Disease and Crop Monitoring like automated scouting, stress detection, and growth monitoring can shift focus from maintaining external conditions to a plant’s real-time response to a grower’s decisions.
The Management and Analytics segment, including crop and farm management solutions, may hold the most promise of all the component technologies. With more extensive deployment of sensors and associated big-data analytics, the growth environment will be increasingly managed by predictive, proactive, real-time, and autonomous optimization by AI that can recognize complex interactions beyond a grower’s capabilities. However, as with field farming, maximizing yield does not necessarily equate to maximizing the success of the overall operation. Forecasting, labor and overall farm management solutions address that greater requirement.
Production Growing Systems
In addition to individual component technologies being marketed to the Indoor Ag market, companies are also selling production growing systems in various formats and configurations: appliances, containers, and sunless and greenhouse production systems. These systems extend almost linearly in size and features from countertop consumer units to acres-scale installations, many being provided as complete growing environments. While one can find countless consumer and hobbyist growing systems on Amazon, Alibaba, and Walmart.com, the landscape does not capture them due to our commercial growing focus.
Industrial Appliances
A step up from the consumer growing systems are Industrial Appliances. These standalone units, intended for restaurants, grocery stores or corporate/school foodservice, are designed for volume production and can be located in the front of the store and in the “back of the house”. While primarily focused on greens and herbs, they provide retailers and foodservice with the freshest produce available, virtually eliminating the carbon footprint of distribution. Some questions do arise around food safety and challenges of adding new operational roles to this labor impacted sector. These appliances not only contain all the requisite elements of a growing environment and operating software, but many are offered with a service/supply program that included seeds, nutrient inputs, grow recipes and even remote monitoring and operation, i.e., remote growing by the appliance vendor.
Container Systems
Like the Industrial Appliances, Container Systems offer a complete growing environment but typically enclosed in a shipping-like container. In general, these units provide a significant increase in production volume and great flexibility in location, including and typically outdoors. Available for a moderate investment (roughly $100,000) they can produce tons of greens and herbs annually. This combination of benefits has made this approach appealing to a broad range of customers from retailers or food service locating units at their distribution centers to rural field farmers wanting to try their hand at indoor growing on a yearly basis.
Sunless and Greenhouse Production Systems
Manufacturers can deploy production systems at industrial scale. They are usually modular and allow purchasers to expand a system footprint as needed. Typically these systems are complete growing environments that include all the necessary components for production, often configured to be site-specific. These systems are specifically designed to reduce labor and maximize yield for the space allocated, often through the use of automation. As with other segments of the landscape, many of these system manufacturers are building products for both the sunless and greenhouse markets.
The growing environment of Sunless Production Systems is vertically oriented and typically configured as stacked horizontal trays or vertical growing panels/walls. Most of these systems deliver nutrients utilizing hydroponics though some providers are offering aeroponics approaches such as the Mobile Aeroponics system from the CombaGroup in Switzerland. Currently, most systems deployed are producing leafy greens and herbs, and in some cases strawberries. While generally smaller in footprint compared to greenhouses, they are capable of large production per floor area due to the system’s vertical orientation, such as at the Jones Food Company facility with its 17 levels stacked to a height of 36 feet. In some instances though, Sunless Production Systems have been deployed with larger footprints such as SananBio’s Chinese installation covering more than two acres and producing 1.5 tons of leafy greens a day. These systems are being offered with various business models. This can range from a simple equipment sale to a turnkey offering where a provider such as Infinite Acres will partner with the purchaser and provide operational expertise.
Greenhouse Production Systems are typically horizontally oriented with nutrients delivered through various approaches such as deep water with floating rafts, Nutrient Film Technique, or drip irrigation. The systems will operate in environments with ambient light, and supplemental lighting purchased separately. They are available for a range of crops from leafy greens and herbs to vining crops such as tomatoes, cucumbers and peppers and increasingly, strawberries. The footprint of a typical Greenhouse Production System is quite large with installation increments characterized in acres, or even tens of acres. Automation within systems varies and is usually crop dependent with a minimal amount in systems for vining crops and an extensive level in leafy greens and herbs. A number of providers such as Hortiplan and Viscon have extensive deployments of fully automated systems that handle seeding to harvest.
Growers
As mentioned above, we thought it was important to highlight indoor growers in addition to Indoor Ag technologies in this year’s landscape. While it is still farming at its core, technology is the essence of modern Indoor Ag and its operations. Not only do indoor producers leverage technology to farm, in many instances growers such Plenty, Bowery and aquaponics grower, Edenworks, are developing their own technology.
The landscape captures as a subset of the growers operating in the market today. Those represented are noted for the respective scale and scope of technology used in their operations, innovative systems integration, novel approaches, or that they are currently pioneering technical growing practices in their country or region.
Modern Sunless Growers, catching the spotlight in the last few years, are standing on the shoulders of early Plant Factories built in Asia where they began over 25 years ago. While most of the publicly identified funding for Sunless Growers over the last few years has been in the U.S., there are now more than 500 Plant Factories in operation throughout Asia according to New Bean Capital. Operating economics remains a key challenge and criticism for these facilities and sunless operations in general, although the Japanese grower Spread, which opened their second facility in late 2018, claims that through the use of technology, scale, and automation they are not only profitable but can be cost-competitive with field farming.
Greenhouses are the larger and more developed growing method. Cuesta Roble Consulting estimates that there are more than one million acres of vegetable production inside permanent structures worldwide. Though, most of the technically advanced and greatest concentration can be found in the Netherlands where there are more acres “under glass” than the size of Manhattan. While already well established as an indoor-growing approach, it appears the recent attention on Sunless farming and cannabis has stimulated additional activity in the sector. Since the beginning of 2018 more than $500 million has been invested in Sunless growers. During that same time period, the Greenhouse sector has seen the likes of Equilibrium raise and deploy its new Controlled Environment Foods Fund of $336 million, Gotham Greens and Bright Farms raise $84 million and investors such as ValueAct Capital Management and Revolution invest in AppHarvest, which is building one of the country’s largest greenhouse in Eastern Kentucky.
There are many impressive and much needed community-based and social impact organizations focused on indoor growing. These efforts range from Teens for Food Justice working on urban access of fresh produce to increasing employment opportunities for veterans by Veterans to Farmers. These are important entities but are not captured on the landscape as it focuses on commercial-scale businesses and production.
The Changing Landscape
For the purpose of this first Indoor AgTech Landscape, we make the distinction of Greenhouse and Sunless as a growing approach or market. This segmentation is done only to raise awareness, to ensure the entire market and various approaches are represented.
Too often we hear declarative statements that “this” is the “right” approach for Indoor Ag or is “the” future of farming. It is more appropriate to start with the question “what problem are you trying to solve?” The unique environmental, climate, economic, and market factors will inform the growing approach. It is doubtful that a one-size-fits-all solution will dominate, but rather utilization of the most appropriate growing structures, systems, and technologies for the desired crop, location and business goal. The challenges, needs, and parameters in Singapore are not going to be the same as St Louis, or Dubai. It is not always an either-or question.
Not only are we seeing vendors and technology providers offering products and systems for both the Sunless and Greenhouse segments, some growers are now utilizing or combining the two approaches. Veteran indoor grower Green Sense Farms is now designing combined facilities and Shenadoah Growers, a long time field and greenhouse grower, has added Sunless production to their operations. Deliscious, a Dutch lettuce grower has seamlessly integrated sunless seeding and propagation into the automation workflow before plants are transported and finished in a greenhouse mobile gutter system. Even on the financing front, start-up Contain is providing a leasing and insurance platform for all indoor farming approaches from “container farms and warehouse farms to the most sophisticated greenhouses and plant factories.”
Moving Forward
To meet its promise and continued expansion, particularly to those locations underserved by traditional production methods, Indoor Ag needs to drive down its cost of operations. Sunless production, especially, has further to go on this front mainly due to a lack of efficiencies from scale and energy use. While indoor costs need to be closer to field production, no one will benefit from a race to the bottom on cost. Indoor and field production are both working on some of the same challenges including labor, sustainability, safety, traceability, and profitability. Technology has an important role in meeting those challenges and we look forward to seeing further advances, innovations, and implementations in data capture and analytics, automation, and predictive and autonomous control.
We welcome your thoughts and reactions and look forward to following the Indoor AgTech landscape together for the coming years.
Bios:
Chris Taylor, a Senior Consultant on The Mixing Bowl team, has spent more than 20 years on global IT strategy and development innovation in manufacturing, design and healthcare, focusing most recently on Indoor AgTech.
Michael Rose is a Partner at The Mixing Bowl and Better Food Ventures where he brings more than 25 years immersed in new venture creation and innovation as an operating executive and investor across the Internet, mobile, restaurant, and Food Tech and AgTech sectors.
These UMD Researchers Are Helping Farmers Grow Crops on Urban Roofs
With the help of University of Maryland researchers, farms across Washington, D.C., are taking watermelons, cucumbers and cherry tomatoes to the next level: the roof
September 6, 2019
The green roof at the top of the Physical Sciences Complex is just one among many around campus that serve as drainage and an ecosystem. (Joe Ryan/The Diamondback)
With the help of University of Maryland researchers, farms across Washington, D.C., are taking watermelons, cucumbers and cherry tomatoes to the next level: the roof.
John Lea-Cox, a plant science and landscape architecture professor at this university, and Andrew Ristvey, an affiliate faculty in the department, are working with the D.C.-based farming foundation Up Top Acres to grow crops on urban rooftops.
Kristof Grina, co-founder and farm director of Up Top Acres, said he initially connected with Lea-Cox and Ristvey a few years ago for help with research and data collection surrounding stormwater management and water retention on their rooftop farms.
Lea-Cox and his team monitor the rainfall, soil temperature and soil moisture on Up Top Acres’ rooftop farms, Grina said. Lea-Cox said he was impressed by the quality of the rooftop produce, which grows across eight farms in Maryland and D.C. The crops are delivered to restaurants downstairs or sold in a community-supported agriculture system.
“There’s like a little bit of Little Italy on the roof down in D.C.,” Lea-Cox said.
Relish Catering, a catering company in North Bethesda, started working with Up Top Acres about a year ago. The company operates about half a mile away from the rooftop farm at Pike and Rose.
The rooftop farm cuts transportation costs for the company, said chef Laura Calderone, since it’s both walkable and bikeable. When she needs ten pounds of pea shoots, for example, she can just load them in her backpack.
“They will literally pick it that morning, and it is going out to our clients that afternoon for the following day,” Calderone said. “Sometimes there are still bugs in it that are moving around, but that’s okay.”
Calderone said Relish Catering has incorporated local rooftop ingredients into salads, salsa verde and tarts, among other dishes.
“Their greens are sweeter and they are not as fibrous,” Calderone said. “You don’t have to manipulate it much. We can let it shine as it is.”
This university’s researchers collect data that gives the farm’s operators “better insight” into how the systems are functioning, Grina said. It lets them know how they’re doing with irrigation practices, and can spur ideas for design improvement.
Lea-Cox and his team also monitor nitrogen and phosphorus levels in the crops. An excess of these nutrients can runoff into local waterways and trigger excessive algae growth. When algae grows too quickly and too abundantly, oxygen levels decline, ultimately killing the fish.
La Betty, an American-style restaurant on K Street in D.C., featured wild rooftop-sourced bouquets on the tabletops. Owner and head of operations Tessa Velazquez said that the flowers last longer than alternatives.
“The story behind it is great,” Velazquez said. “To say that we’re featuring local farmed flowers makes us feel good, makes our customers excited … they’re beautiful and they’re colorful and you really just get that sense of how natural and fresh that they are.”
La Betty is located about two miles from Up Top Acres’ 55 M Street farm in the Capitol Riverfront neighborhood, which opened in 2016. Soon, Velazquez said, she hopes to feature produce from a rooftop farm on her menu.
“I love that they’re actually engaged with the community, as well as really trying to bring that fresh farm-to-table experience — which is a fuzzy term, but they’re really doing it,” Velazquez said. “They’re your neighbors. They’re down the street. They’re not two hours away in Pennsylvania, they are really here.”
GP Solutions Installs State-of-the-Art Growth Chamber at University of California, Riverside
Specially configured “GrowPod” will be used to expand knowledge into advanced agricultural methodologies
Corona, CA – May 14, 2019 – GP Solutions (OTC: GWPD), developer of GrowPod modular automated micro-farms, announced it has installed one of its state-of-the-art Growth Chambers at the University of California, Riverside. The growth chamber will be utilized for agricultural and horticultural research at the University.
Grow Pod Solutions developed the specialized system to meet the need for a large walk-in growing system that offers researchers a precision-controlled environment to conduct sophisticated research at laboratories and universities across the country.
Grow Pod Solutions offers one of the finest walk-in growth chambers available, and features a number of advanced technologies, including optimized photosynthesis, high level security, 24/7 remote control and video monitoring via a cloud-based platform, and precision environmental controls for temperature, humidity, and other vital factors.
The GrowPod system provides an optimum solution for research with a clean environment that is free of contaminants, pathogens, and pesticides.
The University of California, Riverside, College of Natural and Agricultural Sciences, is one of preeminent institutions of its kind in the world. Known for its cutting-edge research, the campus is at the forefront of ag-science and operates several prominent institutions, including The California Agriculture and Food Enterprise, The Citrus Research Center, The Center for Conversation Biology, and The Center for Integrative Biological Collections.
GP Solutions is proud to be a provider of technology and expertise to the University, and looks forward to becoming an integral partner in the ongoing development of advanced cultivation methodologies.
For more information, visit: www.growpodsolutions.com, or call (855) 247-8054.
ABOUT GP SOLUTIONS:
GP Solutions is at the forefront of clean agriculture. The company developed “GrowPods” – innovative indoor clean micro farms that provide optimum conditions for plant cultivation with total environmental control. GrowPods are modular and automated for ease of use and scalability.
Forward-Looking Statements
This release includes information considered “forward-looking” within securities laws. These statements represent Company’s current judgments, but are subject to uncertainties that could cause results to differ. Readers are cautioned to not place undue reliance on these statements, which reflect management’s opinions only as of the date of this release. Company is not obligated to revise statements in light of new information.
Connect:
Email: info@growpodsolutions.com
Website: www.growpodsolutions.com
Facebook: facebook.com/GrowPodTechnology
Twitter: @GrowPodSolution
The Urban Farming ‘Revolution’ Has A Fatal Flaw
Commercial urban agriculture in New York City has provided questionable environmental gains, and has not significantly improved urban food security
By Emma Bryce
April 15, 2019
Commercial urban agriculture in New York City has provided questionable environmental gains, and has not significantly improved urban food security.
These are the findings of a recent case study of New York City which shows that, despite the fanfare over commercial urban farming, it will need a careful re-evaluation if it’s going to play a sustainable role in our future food systems.
The rise of commercial controlled-environment agriculture (CEA)—comprised of large scale rooftop farms, vertical, and indoor farms—is a bid to re-envision cities as places where we could produce food more sustainably in the future. Proponents see CEA as a way to bring agriculture closer to urban populations, thereby increasing food security, and improving agriculture’s environmental footprint by reducing the emissions associated with the production and transport of food.
But the researchers on the new paper wanted to explore whether these theoretical benefits are occurring in reality.
They focused on New York City, where CEA has dramatically increased in the last decade. Looking at 10 farms that produce roof- and indoor-grown vegetables at commercial scales, they investigated how much food the farms are producing, who it’s reaching, and how much space is available to expand CEA into.
They found that the biggest of these 10 commercial farms is around a third of an acre in size. Most are on roofs spread across New York City, and some are inside buildings and shipping containers. Mainly, these farms are producing impressive amounts of leafy greens such as lettuce, and herbs; some also produce fish.
But while rooftop farms rely on natural sunlight to feed the crops, indoor farms use artificial lights. These farms potentially have a greater energy footprint even than conventional outdoors farms, the researchers say–challenging the assumption that urban farms are less impactful than conventional ones.
Some farms also embraced high-tech systems, such as wind, rain, temperature, and humidity detectors and indoor heating, to enhance growing conditions in environments that aren’t naturally suited to agriculture. These elevate the energy costs of the food produced, and may be giving CEA an unexpectedly high carbon footprint, the researchers say.
Furthermore, the predominantly grown foods—such as lettuce—aren’t of great nutritional value for the urban population, especially those threatened by food insecurity. Most produce from CEAs is sold at a premium, something that partly reflects the cost of the real estate used to grow the food. Consequently, that produce is typically grown for high-end food stores and restaurants, meaning it’s unlikely to reach low-income urban populations who need it most.
The researchers also think it’s unlikely that CEA—which currently occupies just 3.09 acres in New York City—could expand into the roughly 1,864 acres they estimate is still suitable for urban farming in New York City.
The rising cost of real estate might put these urban acres beyond the reach of new farming start ups, they think. These companies also face increasing competition from a growing number of farms springing up on the outskirts of cities—where land is cheaper and there’s space to produce more food, while also benefiting from urban proximity.
With its one-city focus, the research isn’t representative of what might be unfolding in other places around the world. Other cities may be having more success—for instance, Tokyo has gained global attention for its large scale vertical farming efforts. Yet as a case study, it does reveal useful lessons—especially for cities wanting to meet the original twin goals of urban agriculture: equitably increasing access to food, at a lower environmental cost.
The researchers note first of all that CEA is optimal in places where less supplemental heat and light is needed to grow food. More thought might also be given to the nutritional value and cost of foods grown, to generate benefits for all the city’s residents, not just high-income ones. The researchers question whether smaller, community-driven plots of urban agriculture—like community gardens, school, and prison farms—might actually do a better job of providing food to at-risk city residents, compared to commercial urban farms that inevitably have to focus on profits.
Based on the study of New York, the researchers caution: “CEA may be touted as an exciting set of technologies with great promise, but it is unlikely to offer a panacea for social problems or an unqualified urban agricultural revolution.”
It’s easy to be drawn in by the dystopian allure of vertical farms and underground greens nestled into our cities. But until we’ve streamlined its role, we should perhaps not overstate what commercial urban agriculture can do—or, instead be guided by cities where there are stronger signs of social and environmental success.
Source: Goodman et. al. “Will the urban agricultural revolution be vertical and soilless? A case study of controlled environment agriculture in New York City.”Land Use Policy. 2019.
This piece was originally published on Anthropocene Magazine, a publication of Future Earth dedicated to creating a Human Age we actually want to live in.
Scientists Made Better-Tasting Basil Through “Cyber Farming”
A better basil exists, but it’s being grown in an environment that resembles something more likely to show up on an episode of Star Trek than in any backyard garden
REUTERS/TOM MIHALEK
By Chase Purdy April 5, 2019
PESTO, CHANG-O
A better basil exists, but it’s being grown in an environment that resembles something more likely to show up on an episode of Star Trek than in any backyard garden.
The team of MIT scientists behind it are calling their process “cyber agriculture,” a method of growing plants in shipping containers retrofitted with lots of high-tech gear that brings crazy levels of precision control to the environment. That entails using complex computers to track a plant’s minor genetic and epigenetic changes over time while searching for the right balance of temperature, humidity, level of ultraviolet light, and light-exposure time, among other things, to create the conditions that will encourage the basil to producer a richer, tastier version of itself. They call it a “climate recipe,” but really it’s using machine learning technology to farm. The details of their work were published April 3 in the journal PLOS ONE.
“We’re really interested in building networked tools that can take a plant’s experience, its phenotype, the set of stresses it encounters, and its genetics, and digitize that to allow us to understand the plant-environment interaction,” said researcher Caleb Harper in a statement.
Most of this research is being conducted in Middleton, Massachusetts, a small town about 20 miles (32 km) north of Boston. It’s there that the MIT team tends to a hydroponic farm of basil plants. They’ve discovered some interesting details: For instance, the plants tend to taste better when they have exposure to light all 24 hours of the day.
“You couldn’t have discovered this any other way. Unless you’re in Antarctica, there isn’t a 24-hour photoperiod to test in the real world,” said John de la Parra, a co-author of the study.
The scientists are making their data available to the public at no charge. Right now, there are companies working on similar high-tech hydroponic farming. Toshiba is churning out lettuce, it’s happening on rooftops in China, and a company called Farm.One is growing food out of basements in Manhattan. But most of these companies keep their techniques under wraps, making it hard for more people to enter the market or for nonprofit initiatives to get off the ground.
“Our tools being open-source, hopefully they will get spread faster and create the ability to do networked science together,” Harper said.
And that could lead to an interesting new era of urban farming, in which cities can more efficiently feed themselves without relying on the costly supply chain networks that currently exist to ship herbs, fruits, vegetables into municipalities from faraway farms.
Photo: Halcyon hydroponics.
Climate Labels On Food To Become A Reality In Denmark
Research from the University of Technology Sydney and Duke University suggests that using labels that are easy to understand may create demand for responsibly produced food. Lead author of the research
The Danish Government has announced that a climate labeling system on food products will accompany its plan to become carbon neutral by 2050. Officials from the Danish Ministry of Energy, Utilities, and Climate stated that the Government is proposing to work with supermarkets to place stickers on all food products that clearly indicate their carbon footprint. The proposal would help consumers make informed choices, with Denmark’s Minister for the Environment, Lars Christian Lilleholt, explaining, “We want to give consumers the means to assess in supermarkets the environmental impact of products.”
Research from the University of Technology Sydney and Duke University suggests that using labels that are easy to understand may create demand for responsibly produced food. Lead author of the research, Dr. Adrian Camilleri, describes the current lack of transparency, “With an appliance such as a heater you can feel the energy used and see an electricity bill at the end of the month, so the impact is quite salient, whereas the impact of food production is largely invisible.”
Minister Lilleholt says that giving consumers easy access to information is important, but accurate labeling comes with a long list of challenges. The labels may have to consider water and land usage, life-cycle analysis, greenhouse gas emissions, and carbon footprint from transport. Director of the Danish Agriculture & Food Council, Morten Høyer, approves of the proposal, but notes a challenging component: nutritional value. “It might be necessary to weigh up the environmental impact against the nutritional value of the product. A bottle of soda may have a low environmental impact, but it is not a product you can live on,” says Høyer.
Developing a comprehensive labeling system that spans all food products in Denmark’s supermarkets may take time, and a formal launch date has not yet been set. If successful, climate labeling could shed light on which practices produce healthy food more sustainably and may even inspire competitive innovation from producers. “My impression is that there is a demand for knowledge about how individual consumers can contribute to improving world climate,” Lilleholt says.
Denmark, which ranked 17th in the world in the Climate Change Performance Index, announced the proposal last year in the wake of the Intergovernmental Panel on Climate Change report highlighting the consequences of global warming
Agriculture and Food Research Initiative - Sustainable Agricultural Systems
Program:
Agriculture and Food Research Initiative (AFRI) | AFRI Sustainable Agricultural Systems
Applications to the FY 2019 Agriculture and Food Research Initiative - Sustainable Agricultural Systems (SAS) Request for Applications (RFA) must focus on approaches that promote transformational changes in the U.S. food and agriculture system within the next 25 years.
NIFA seeks creative and visionary applications that take a systems approach, and that will significantly improve the supply of abundant, affordable, safe, nutritious, and accessible food, while providing sustainable opportunities for expansion of the bioeconomy through novel animal, crop, and forest products and supporting technologies.
These approaches must demonstrate current and future social, behavioral, economic, health, and environmental impacts.
Additionally, the outcomes of the work being proposed must result in societal benefits, including promotion of rural prosperity and enhancement of quality of life for those involved in food and agricultural value chains from production to utilization and consumption. See AFRI SAS RFA for details.
APPLY FOR GRANT(LINK IS EXTERNAL)VIEW RFA
ELIGIBILITY DETAILS
Who Is Eligible to Apply:
1862 Land-Grant Institutions, 1890 Land-Grant Institutions, 1994 Land-Grant Institutions, Other or Additional Information (See below), Private Institutions of Higher Ed, State Controlled Institutions of Higher Ed
More on Eligibility:
Note: This RFA invites only integrated project (must include research, education, and extension) applications. Please see Part III, A. of the this AFRI SAS RFA for more specific eligibility requirements for integrated projects. Applications from ineligible institutions will not be reviewed.
IMPORTANT DATES
Posted Date:
Friday, March 29, 2019
Closing Date:
Thursday, September 26, 2019
Other Due Date:
Letter of Intent Due:
Tuesday, June 4, 2019
ADDITIONAL INFORMATION
For More Information Contact:
AFRI Sustainable Agricultural Systems Team
Contact for Electronic Access Problems:
electronic@nifa.usda.gov(link sends e-mail)
Funding Opportunity Number:
USDA-NIFA-AFRI-006739
CFDA number:
10.310
Previous fiscal year(s) RFA:
FY 2018 AFRI SAS FINAL RFA (431.48 KB)
Estimated Total Program Funding:
$90,000,000
Percent of Applications Funded:
10%
Cost Sharing or Matching Requirement:
See RFA
Range of Awards:
$5,000,000 - $10,000,000
Six Spectral Channels: Osram Unveils Grow Light System For Horticulture Research
Phytofy RL is already being used by NASA and Michigan State University. Osram is using it to carry out research of growth, anthocyanins and taste, conducted in a climate chamber at the TU Munich.
Osram has developed a research luminaire to meet the growing demands of researchers at universities, private institutes and plant production in greenhouses and vertical farms. Researchers and modern agriculturists can use the LED-based plant luminaire system Phytofy RL in the lab or in climatic chambers in order to develop new plant-specific light and growth recipes. These recipes can lead to desired outcomes in plant quality, yield and flavor.
Each of the six spectral channels can be addressed individually with Phytofy RL and the intensity planned and managed precisely in real time.
Selective intervention
"Various light wavelengths and intensities allow selective intervention in the metabolic processes of agricultural crops and ornamental crops", Claudia Zehnpfennig, Global Product Manager with Osram explains. "Yield, coloration and taste as well as other features can be influenced in this way. The latest research shows that not only is this process impacted by photosynthetically active radiation (PAR) – in the range of 400 to 700 nanometers (nm) – but that shorter and longer wavelengths also influence plant development."
With Phytofy RL, six spectral channels – from a natural far-red end-of-day light to UV light – can be addressed individually and the photosynthetic photo flux density (PPFD) planned and controlled precisely in real time: 385 nm, 450 nm, 521 nm, 660 nm, 730 nm as well as a warm white channel with 2,700 Kelvin. At the same time, the large number of LEDs in the fixture allows a higher photosynthetic photon flux (PPF).
Claudia Zehnpfennig & her colleague Kelcey Trecartin last year on the Cultivate
Light recipes
According to Claudia, the highly uniform light distribution is a special feature of the system. "The calibrated system furthermore supplies a precise irradiance map, calculated by the software with no quantum flux measurements required. Use of Phytofy RL allows for evaluation of the most varied light recipes, without having to change luminaires between individual tests. Diverse combinations of wavelengths also can be programmed, in different light profiles and across the entire photoperiod." In addition, users get five light recipes following registration, which have been specially developed by Osram.
Use of Phytofy RL allows the researchers to evaluate the most varied light recipes, without having to change luminaires between individual tests.
Climate chambers
The system software was developed by Osram together with plant biologists and can be used intuitively via the graphical user interface. Manufacturers of climate chambers benefit too, with integration possible in their systems. "The flat and robust design (667 x 299 x 44 mm, just under 9 kilos) is optimized for vertical farms, rack systems and growth chambers."
Phytofy RL is already being used by NASA and Michigan State University. Osram is using it to carry out research of growth, anthocyanins and taste, conducted in a climate chamber at the TU Munich.
For more information:
Claudia Zehnpfennig
horticulture@osram.com
Osram
Marcel-Breuer-Strasse 6
80807 Munich, Germany
Phone +49 89 6213-0
Fax +49 89 6213-2020
www.osram.com/phytofy
Publication date : 2/27/2019
"Clean Growing Solutions For Hospitals And Research Laboratories"
Seedo, a high-tech company providing fully automated and controlled indoor growing machines for the cannabis and agriculture markets, has signed a memorandum of understanding for mutual research and development with SYS Technologies, a company specializing in the development and manufacture of innovative indoor and portable clean environment technologies, to deploy next-generation containerized clean growing solutions for commercial use. The systems will be applied to technology used in hospitals and research laboratories, resulting in high-quality yield of both medical cannabis and vegetables.
SYS Technologies will provide Seedo's commercial indoor growing machines with positive air pressure clean environment technologies, resulting in pressurized growing containers that have more filtered air then the surrounding space outside the containers. The protected containers will be bacteria-free with zero environmental influence, allowing commercial operators to cost-effectively generate high yields of lab-grade, pesticide-free product. Even in the harshest environments or with limited space, cultivators can use Seedo's intelligent systems and cloud-enabled app for secure remote monitoring and controlling to harvest the leading-edge of precision agriculture.
"We're honored to be working in alignment with Seedo to design the future of commercial indoor growing technologies," said Mr. Yossi Zur, CEO of SYS Technologies. "With quality standards and environmental stressors rising in cannabis and agricultural markets, our mission to provide the cleanest and highest yield of product for commercial growers is well on track in our partnership with Seedo."
SYS Technologies offers a variety of innovative solutions and breakthrough technology in the field of indoor clean environment systems as well as portable solutions. Its clean air environment systems allow the creation of a defined space that is free of contaminants such as particles, bacteria, microbes, and more. These systems have broad applications, both in the medical field such as operating rooms and isolation facilities, and in the high-tech industry such as cleanrooms that have a variety of purposes.
"We are looking forward to the successful development and deployment of our future containerized clean growing solutions for commercial use," said Zohar Levy, CEO of Seedo. "By adopting cutting edge technology that is already in use by governments, non-profits, hospitals and research institutes all over the world, we will meet the highest quality standards and comply with international health regulations."
For more information:
Seedo
+972-546-642-228
info@seedolab.com
www.seedolab.com
EDEN ISS Antarctic Grower Paul Zabel Returns
365 days on the eternal ice flows.
365 days in the Antarctic, of which 257 days cut off from the outside world. Antarctic grower Paul Zabel from the German Aerospace Center (DLR) has tested vegetable cultivation, suitable for Moon and Mars environments in the EDEN-ISS greenhouse. There, he harvested peppers, tomatoes, cucumbers and various lettuces and herbs, grown with the use of artificial light.
Now Paul Zabel has returned to Germany and, at a press conference at the DLR Bremen site, he spoke for the first time since his arrival of his efforts and deprivations of recent months, as well as the joys of plant breeding in extreme situations and his life on the seventh continent.
"The Antarctic is a fascinating place and I am very happy that I could be one of the few people who had the opportunity to spend the winter there, having experienced many unique impressions and challenges over the past 12 months. Now it is great to be back home, seeing family, friends and colleagues again," said Zabel.
"Antarctic grower" Paul Zabel returned after a stopover at the Antarctic Novo Airbase and a short stay in Cape Town shortly before celebrating Christmas in his home in the Brandenburg Spreewald. "Having spent Christmas 2017 in the Antarctic, it was very special to spend Christmas Eve and New Year's Eve at home." Zabel left for the Antarctic on 16 December 2017, with three other members of the EDEN-ISS team. After a two-month build-up phase, he remained there from February 18, 2018 on German Antarctic station Neumayer III with nine other overwinterers of the AWI.
Working in the Antarctic cold
Day by day, Zabel set off on the commute to the EDEN-ISS greenhouse, about 400 meters from the station. Only during the strongest storms, of which Zabel experienced many during the Antarctic winter, the greenhouse was monitored and controlled automatically by people in the Bremen control center. "From Bremen, we were in daily contact with Paul," reports EDEN-ISS's Daniel Schubert from the DLR Space Systems Institute. "He has done a great job over the past months. Although it has taken up quite a lot of his time, the EDEN-ISS project and he himself will be thanked by future astronauts."
Other members of the AWI hibernation team also helped Paul Zabel with his work. They aided him with the sowing of the plants and supported him with the numerous experiments. "After more than a year in the Antarctic, we can look back on successful overwintering." The work in the greenhouse and the fresh vegetables have enriched our time at the Neumayer Station III," says station manager Bernhard Gropp.
Rich harvest
A detailed evaluation of the studies on plant breeding in Antarctica is currently in full swing. The extensive results, including technical, botanical, microbiological and psychological analysis, are expected in May 2019. It is already clear that Paul Zabel has repeatedly been able to harvest a rich harvest, again supported by the other AWI overwinterers. For example, on Neumayer III over the past year, the crew wwere able to eat 67 kilograms of cucumbers, 46 kilograms of tomatoes, 19 kilograms of kohlrabi, 8 kilograms of radishes, 15 kilograms of herbs and 117 kilograms of lettuce.
The station continues to be open to researchers from all over the world. In the next two years, DLR, AWI and other research partners will further develop the production processes in the EDEN-ISS greenhouse, with the goal to offer future stations on the Moon and Mars an optimized greenhouse concept. The continuation of the project is open to researchers from all over the world. "Soon we will hand over the greenhouse to the new overwinterers who will continue the EDEN-ISS project in the Antarctic and look after the crop," says dr. Daniel Schubert. "We will monitor and control the greenhouse from Bremen." Schubert and his team will again travel to the Antarctic in mid-January 2019 to maintain the EDEN-ISS greenhouse and update it technically for the continuation.
EDEN-ISS: Food supply of the future
World food production is one of the key societal challenges of the 21st century. An increasing world population and simultaneous upheavals caused by climate change call for new ways of cultivating crops, even in climatically unfavorable regions. For deserts and areas with low temperatures, as well as space missions to the Moon and Mars, a greenhouse, closed of from the weather, the sun and the seasons, will allow independent harvests, less water consumption and the abandonment of pesticides and insecticides. With the project EDEN-ISS, such a greenhouse of the future can be tested under Antarctic extreme conditions.
Source: www.gemuese-online.de
Publication date : 1/15/2019
Netherlands: Additional Research Facilities At Delphy
The facility has now been extended with the addition of two climate cells.
For years, Delphy Improvement Centre in Bleijswijk and Certhon have shared the same ambition: to contribute to global solutions in the field of health, food safety and sustainability, through knowledge sharing and knowledge development. This is reflected in the Improvement Centre, which was opened a few years ago and has been used for various research projects since. The facility has now been extended with the addition of two climate cells.
Following the research facilities in the greenhouse, Delphy wanted to make an in-depth study of research and research methods. With the two climate cells realized by Certhon last summer, Delphy can gain more knowledge about daylight-free cultivation and physiological aspects of plants. This knowledge can also be applied in the greenhouse.
The two climate cells can be found in the reception area of the research centre. The doors of the cells are equipped with two small windows, so visitors can see which test set-up with which crops are inside. A few weeks ago, the first tomato and cucumber plants were placed and the research started. During the cultivation process there will be frequent consultation between Delphy and Certhon, to share advice and knowledge.
For more information:
Certhon
www.certhon.com
Publication date : 12/17/2018
Digestate As Alternative Substrate For Soil-Less Lettuce Farming
Researchers from Modena University and Reggio Emilia University – in collaboration with the Foggia’s CRA – evaluated the digestate as an alternative and sustainable substrate for farming and as a nutritive solution in the hydroponic farming of lettuce.
The consumption of ready-to-eat salad has been growing over the last 20 years in the European market. The annual growth rate is at 4%. That's why this food category is renowned as one of the most profitable horticultural segments.
As a result of a growing trend, the lettuce and chicory are farmed over a 1.2 million hectares surface globally. The global production is of 27 million tons, almost.
Italy occupies the fourth place in the world, with 38.542 hectares farmed with lettuce and chicory (31.7% in the north, 10% in the Centre, and 58,3% in the South) for a total production of 8.1 million tons. Additionally, greenhouse production is important as well, for a total surface of 4.549 hectares (37.3% in the North, 31.9% in the Centre and 30.8 in the South).
Leafy produce is considered to be one of the most exposed to microbiological risks. The ready-to-eat lettuce is often connected to food poisoning. The Escherichia Coli O157: H7 has been often associated with lettuce.
Researchers from Modena University and Reggio Emilia University – in collaboration with the Foggia’s CRA – evaluated the digestate as an alternative and sustainable substrate for farming and as a nutritive solution in the hydroponic farming of lettuce. In three different experiments, nine hydroponic combinations of substrate and fertilization (agriperlite + standard solution, agri-perlite + liquid digestate, solid digestate + standard solution, solid digestate + liquid digestate, soil + standard solution, peat + standard solution, peat + liquid digestate, digested pelleted + standard solution and digested pelleted + liquid digestate) were tested and compared for the cultivation of baby leaf lettuce.
During crop cycles, the yield and other agronomic and microbiological parameters have been studied. In all the experiments, the combination of agri-perlite + liquid digestate, solid digestate + standard solution and pelleted digestate + standard solution improved the plant growth by influencing roots (+ 32%), buds (+ 40%), total dry weight (+ 29%) and SPAD parameters (+ 17%).
As the results illustrate, the digestate represents a nutritive sustainable solution and an alternative for the soilless baby leaf lettuce farming.
Source: Domenico Ronga, Leonardo Setti, Chiara Salvarani, Riccardo De Leo, Elisa Bedin, Andrea Pulvirenti, Justyna Milc, Nicola Pecchioni, Enrico Francia, 'Effects of solid and liquid digestate for hydroponic baby leaf lettuce (Lactuca sativa L.) cultivation', 2019, Scientia Horticulturae, Vol. 244, pag. 172-181.
Publication date : 12/12/2018
You're Invited Tuesday, February 5, 2019 - Ronald Reagan Building - Washington, DC
The Foundation for Food and Agriculture Research invites you to explore food and agriculture research at our all day event, Foster Our Future. Join FFAR to:
Demonstrate game-changing research technology and innovation
Bring scientific breakthroughs to life
Celebrate the impact food and agriculture has on consumers and producers
Showcase research talent
Highlight the importance of continued research investment
For event and registration information:
REGISTER NOW!
CLICK HERE to add event to calendar.
FFAR thanks our current sponsors as of January 7, 2019.
AgLaunch Initiative, Conagra Brands, Institute for Feed Education & Research, Select Milk Producers
Agritecture Consulting
American Society of Agronomy, Crop Science Society of America, Soil Science Society of America
Association of American Veterinary Medical Colleges
Biotechnology Innovation Organization
Commonwealth Scientific and Industrial Research Organization (CSIRO)
Corn Refiners Association
Food Marketing Institute Foundation
The Grange Foundation
International Fertilizer Development Center
McDonald's Corporation
Meridian Institute | AGree
National Pork Producers Council
NOBLE RESEARCH INSTITUTE, LLC
Potomac Grange #1
Soil Health Institute
The Sugar Association
Supporters of Agricultural Research (SoAR) Foundation
Weed Science Society of America
Special thanks to the American Dairy Science Association
and the American Society of Animal Science.
For more information on how to sponsor contact:
Renée Bullion, rbullion@foundationfar.org.
Foundation for Food and Agriculture Research | 401 9th St NW, Suite 630, Washington , DC 20004
The Vegetable Farmer from the Antarctic
Paul Zabel from the German Aerospace Center operates a greenhouse in the Antarctic, where tomatoes, lettuce and cucumbers flourish
By Dirk Asendorpf
The greenhouse EDEN: tomatoes, cucumbers and lettuce grow up to -40 degrees outside. (DLR)
Paul Zabel from the German Aerospace Center operates a greenhouse in the Antarctic, where tomatoes, lettuce and cucumbers flourish. For future space missions, plant cultivation is to be tested under difficult conditions.
"Zabel. Hello. "- A call in Antarctica. Just started there the polar day.
"We have 24 hours of sunshine when we have no clouds. Today it is very nice. We have the second right summer week. It's only
about minus 13 degrees. " In recent months, Paul Zabel had to cope with significantly worse weather conditions. For one polar winter, he was responsible for the research greenhouse of the German Aerospace Center. This is located 300 meters from the German Neumeyer Station in a container.
"We had the lowest temperature with minus 43.4 degrees in August. There were a few days where there were stronger storms, and I did not go because that was just too dangerous. "
He has a satellite connection at all times in the greenhouse 13,500 kilometers away in the view. A dozen screens fill a wall of the control room.
"We can not touch the plant itself. But we could say for example: The container is now two degrees warmer, we put this here and then the container would be up to two degrees warmer. We could control the light and, for example, we could also give a different nutrient mix to the plant. We can control everything from here. "
A full greenhouse for the first visitors to Mars
The complete remote control of vegetable cultivation in a hermetically sealed container is the prerequisite for its application to future interplanetary space missions.
"Scenarios provide that the greenhouse system flies to Mars in advance, unfolds there automatically and already plants are grown automatically. And when the first humans come to Mars, they can almost find a fully grown greenhouse. That's the theory. "
The tomatoes and salad are well grown. Only the strawberries and peppers did not really thrive in the EDEN greenhouse. (DLR)
However, the practice was still a long way away. Almost every day Paul Zabel had to look to the right in the Antarctic greenhouse.
"For example, we had a broken LED lamp from the plant LEDs relatively early in the year. I could then replace it with a spare part. We had several failures of electrically controlled valves and pumps in our cooling system, which are now being replaced by other models. "
The repairs will be carried out by project manager Daniel Schubert personally in January. Then he also brings the seeds for the next test run, including seeds for ten different types of lettuce that Nasa has already tested on the International Space Station. In the Antarctic container they should germinate and grow as independently as possible. A gardener will not exist in the next polar winter.
The greenhouse should be completely remotely controlled
"We could not find anyone who would like to hibernate again. And then we thought: Could we do a self-sufficient mission? So really just observe and control the greenhouse system only from Bremen, out of our mission control center. And we say to the overwinterers: Only go in an emergency - or to harvest. "
Paul Zabel flies back in mid-December to Bremen. There he missed a century summer.
"I also talked regularly with my colleagues and then I was a bit jealous here and there. But I was just a year in the Antarctic. But chirping birds and being able to go out into the forest again, these are things that you just can not do here. And I'm definitely looking forward to that. "