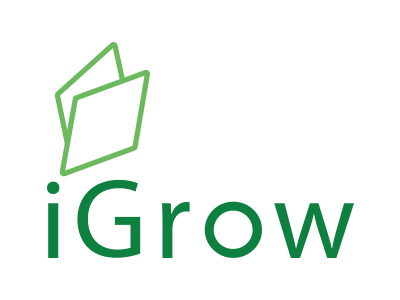
Welcome to iGrow News, Your Source for the World of Indoor Vertical Farming
Hi-Tech Vertical Farm Could Produce A Third of Leafy Greens And Create 30 Jobs
Wayne Furbert, the Cabinet Office minister, said the state-of-the-art farm could also reduce the cost of food production and create up to 30 jobs
November 13, 2020
Wayne Furbert, the Minister for the Cabinet Office (Photograph by Blaire Simmons)
A vertical farm could produce almost one-third of Bermuda’s demand for leafy greens – the equivalent of 200 acres of farmland, it was revealed today.
Wayne Furbert, the Cabinet Office minister, said the state-of-the-art farm could also reduce the cost of food production and create up to 30 jobs.
Mr. Furbert added the Government was close to finalizing plans for the development and finance for the project.
He said: “Vertical farming will utilize the latest technology to grow leafy greens in a controlled environment.”
“The aim of this venture is to reduce the cost of food to the general public, reduce the reliance on imported leafy greens, and boost employment in Bermuda.”
Vertical farming involves the production of crops in a controlled environment, usually indoors.
It also uses techniques such as hydroponics instead of soil and the crops grow in stacked layers.
Mr. Furbert said the hi-tech farm would be “environmentally sound”, use 95 percent less water than conventional production, and no pesticides.
He added: “A key component of this project, and in line with the Government’s vision to create a nation of owners, will be to allow Bermudians to invest in this entity so that they can enjoy the benefits of ownership of local food production.”
According to environmental studies, there are about 760 acres of land available for farming in Bermuda, although only 365 were being actively worked.
The plans will be presented to the Cabinet Committee for Economic Development next week.
Mr. Furbert also fleshed out plans for a proposed fish processing center, a drive to attract technology companies to the island, and a bid to expand the intellectual property industry.
He said: “The shoreside fisheries complex will be the operational center of a new, long-anticipated enterprise that will transform and reposition Bermuda’s commercial fisheries sector.
“It will be a purpose-built facility where fish will be cleaned and processed for sale to the Bermuda market.
“This facility is just the start of our ambitions and while targeted towards local consumption, it has the potential to grow into international exports.”
Mr. Furbert said that the aim of technology companies was to “create a hub wherein technology companies can set up and conduct their business right here in Bermuda in a business-friendly environment”.
He added: “We have recently been engaged in very fruitful discussions with global tech companies about relocating to Bermuda.”
Mr. Furbert said that Government was examining how to overhaul legislation “to remove bureaucracy and red tape”.
He highlighted that changes had already meant the arrival of 58 technology workers from Pakistan.
Mr. Furbert said: “They are part of a very large and successful technology company and it is our hope that this will be the genesis of their setting up business long-term in Bermuda and training and hiring Bermudians.”
He added further amendments to legislation would make Bermuda an attractive location for international companies that wanted to register trademarks and copyrights.
Mr. Furbert said: “We have adopted a phased approach to overhauling our intellectual property legislation and by the Spring of 2021 we shall have achieved significant enhancements in this realm.
“These are just a few of the major initiatives the Cabinet Ministry is forging ahead with in the next year or so, and I am very optimistic that we shall succeed in generating positive economic activity as a result.”
WEBINAR: The Importance of Light Quality In CEA Systems
Spectrum has an important impact on plant growth, morphology, and development. Plants have evolved a sophisticated photoreceptor system capable of perceiving small changes on the light spectrum
Date: November 19, 2020
Time: 2 p.m. - 3 p.m. EDT
Presented by: Ricardo Hernandez (NCSU)
Click Here to Register
Spectrum has an important impact on plant growth, morphology, and development. Plants have evolved a sophisticated photoreceptor system capable of perceiving small changes on the light spectrum. Plants use spectral changes as information to adapt and increase survival and reproduction. Therefore, by understanding plant-light interactions, we are able to use light as a tool to change plant responses to meet human needs. This presentation will outline the importance of light quality and provide examples of the commercial applicability of spectral manipulation.
Dr. Ricardo Hernandez is an assistant professor at North Carolina State University focused on Controlled Environment Agriculture research and teaching (https://ceh.cals.ncsu.edu/). He has worked in the field of spectral optimization for over 10 years. In addition to his academic appointment, Ricardo is also a co-founder of two start-ups focused on the use of controlled environment technology and strategies to produce young plants.
Special thanks to our Industry partners
Join today
If you have any questions or would like to know more about GLASE, please contact its executive director Erico Mattos at em796@cornell.edu
Advancing Indoor Farming In Asia – Intelligent Growth Solutions Ltd - Interview
Ahead of the virtual Asia-Pacific Agri-Food Innovation Summit, we caught up with David Farquhar, CEO at IGS about advancing indoor farming systems in Asia, new projects on the horizon, and working with governments to scale up controlled environment agriculture.
Ahead of the virtual Asia-Pacific Agri-Food Innovation Summit, we caught up with David Farquhar, CEO at IGS about advancing indoor farming systems in Asia, new projects on the horizon, and working with governments to scale up controlled environment agriculture.
FIND OUT MORE
David Farquhar, CEO, IGS
What role can indoor farming play in delivering greater sustainability and resilience to Asia’s urban food systems, especially post-COVID?
The resilience of food supply chains has been tested to the limit throughout 2020 in the wake of COVID-19 and has brought very quickly to the fore the food security challenges Asia and most other regions will face with climate change. Now is the time to be focusing very clearly on local (urban and peri-urban) food production to ensure greater self-sufficiency and less reliance on imports. Greater adoption of agricultural technologies is imperative to ensure optimum use of available space, be it urban, industrial or uncultivatable land, all of these are spaces that can be used to introduce more indoor farming methods. As part of the agricultural ecosystem, this will deliver a far more controlled and sustainable method for producing fresh, homegrown crops, probably amounting to something like 25-30% of a fully balanced diet.
Does the APAC market offer particular opportunities or challenges for scaling urban/indoor farming, compared to other global markets? What particular projects is IGS excited about in this region? What progress has already been made?
Asia-Pacific has a very different climate across its expanse, which makes it hard to compare easily with other regions. The population in these regions is significant and growing substantially which puts food security very high on the agenda, highlighting the importance of finding new ways to produce and complement the existing agricultural ecosystem. In addition to growing populations, land and water scarcity are also becoming significant in certain geographies and this makes indoor farming – which requires a much smaller footprint and utilizes a fraction of the water typically required to produce crops – a very interesting proposition. This has led to some exciting collaborations between commercial and government bodies. For example, in Singapore and Hong Kong, where land is very scarce and expensive, there is a demand for alternative options of producing food. The appetite for indoor and alternative growing methods is highlighted in Singapore’s 30 by 30 initiative, aiming to reduce import reliance and expand food self-sustainability.
In terms of exciting projects, we are delighted to be working with Eden Towers (https://eden-towers.com/) a very ambitious new entrant to the national and regional food chains that are re-localizing across APAC. Based in Jakarta and privately financed, they have major plans for regional expansion with sites planned already in Singapore, Australia, and Indonesia. The first location will be Perth, Western Australia, and the initial farm is under manufacture for imminent deployment. This is what we believe to be the first of many in this region. We are in advanced discussions across the APAC region with existing growers and other prospects and are currently trialing a range of crops specific to the cuisine and tastes of the population. These are progressing very well in our system and producing some very tasty results. We have other customers in the pipeline with projects in Singapore, India, and Polynesia.
What partnerships and collaborations are needed to scale controlled environment agriculture in Asia? What types of organizations are you keen to connect with at the Asia-Pacific Agri-Food Innovation Summit in November?
In this wider region, we recognize the important role that governments more broadly have to play in supporting and driving the food security and sustainability agenda. In Singapore for example we have talked closely with the Economic and Development Board (EDB) and the Singapore Food Agency (SFA), who are aiming to draw investment, research, and development into Singapore-based companies.
At November’s event, we hope to connect with existing and established growers, as well as entrepreneurs looking to set up farms or expend their existing horticulture operations. We also welcome further interaction with the EDB and SFA, as well as those operating in real estate and commercial property investment.
Finally, we are keen to identify regional sources of investment capital and asset finance on behalf of our customers seeking to establish agri-tech operations.
What key insights will you be looking out for personally at the summit?
I am very interested to know what emphasis is being put on clear and open data-driven discussions about payback timescales from investment in agri-food technologies. We know that there are technologies with varying approaches, sizes, and challenges to address, but ultimately these solutions need to be sustainable, scalable, and operationally reliable. However, they need to be commercially sound and that is something I am very keen to discuss further.
Join David online at the virtual Asia-Pacific Agri-Food Innovation Summit and watch his panel debate on ‘Success Factors for Scaling Vertical Farming Operations’ on November 19.
For more information about IGS, follow them on LinkedIn, Twitter, and YouTube.
The Future of Farming Is Inside This Bomb Shelter
The farm is known as Growing Underground (GU), and it’s located 108 feet below the main street in Clapham, a south London suburb
Ten Stories Underneath London,
Thousands of Plants Are growing
BY ROB KEMP
PHOTOGRAPHY BY KATE PETERS
NOV 12, 2020
Deep beneath the streets of London, in a complex of bomb shelters left abandoned since World War II, something is growing. Thousands of green sprouts burst from their hydroponic trays, stretching toward glowing pink lights that line the arched ceilings. These plants, along with tens of thousands of other salad crops, are being grown from seed without soil or sunlight, in tunnels transformed into a high-tech commercial farm.
The farm is known as Growing Underground (GU), and it’s located 108 feet below the main street in Clapham, a south London suburb. Every year, in 6,000 square feet of old bomb shelter, more than 100 tons of pea shoots, garlic chives, cilantro, broccoli, wasabi mustard, arugula, fennel, red mustard, pink stem radishes, watercress, sunflower shoots, and salad leaves are sown, grown, and prepared for dispatch.
London’s unique move toward re-localizing agriculture—feeding its growing population while cutting the environmental impact of producing and transporting crops—is the brain-child of entrepreneur Richard Ballard and his business partner Steve Dring.
The tunnels consist of two portions - a larger upper level, where growing and processing takes place, and a smaller lower level, shown here, which is used for storage. KATE PETERS
“The United Nations predicts that we need 70 percent more food by 2050,” says Ballard. “But how are we going to achieve this when only 10 percent of the Earth’s surface is suitable for agriculture and we use a third of that to grow livestock feed?”
Ballard’s journey to becoming a pioneering subterranean farmer is an unusual one. After his ethical garden furniture business went bust in 2008, he moved closer to his old friend, Dring, and the pair would regularly sit in the pub and discuss ideas for start-ups. Both men were intrigued by the idea of vertical farming as an efficient way to feed people, especially in urban areas.
These farms are not susceptible to weather, and crops can be protected from food contamination and grown without herbicides and pesticides. Transport costs are minimal, harvesting is often automated, and much of the water used to grow crops can be recycled.
But the question of how to build it in a city where living space is at such a high premium presented their first major challenge.
At that time, London’s Crossrail line was in its construction stages. The excavations for the 73-mile-long high-speed railway across the city regularly featured on the TV news—especially as secrets to the city’s past were being unearthed, including plague pits, Roman artifacts, and unexploded World War II bombs. It led Ballard and Dring to consider going underground.
Cilantro sprouts under the pink growing lights. KATE PETERS
They worked with the management company for the city’s underground railway network, Transport for London (TfL), to find the Clapham site. “As long as we weren’t building an underground nightclub, they were happy for us to trial a small farm to see if a tunnel could work as a growing environment,” Dring says.
A crowdfunded campaign raised more than $900,000 to develop the site. After a successful trial in one small section of the shelters, Ballard and Dring negotiated a nearly 20-year lease from TfL and began operating in 2015.
The entrance to GU is within an unassuming brick office at street level. In here sit four of the site’s seven aboveground staff; they work at computers taking orders from retailers and arranging deliveries. It’s also the spot where visitors are asked to remove any jewelry and sign a consent form confirming that they are in good health, have never carried typhoid, and are not bringing any nuts onto the site.
From there, it’s a trip into a cramped elevator with barely enough room for two people. It descends slowly, 10 stories belowground, to where visitors step out into a tunnel of whitewashed corrugated arches that contrast brightly with the eerie elevator shaft. Through a row of rubber strips hanging from a tunnel entrance, the kind you see in an industrial refrigerator, a bright pink light glows. Coupled with a sound of hard-core punk music coming from another passageway, this farm has the feel of the illicit nightclub their landlords had feared.
The working farm currently occupies an eighth of its potential 45,000 square feet of growing space. The entire site is two parallel tunnels, each 1,640 feet in length. Built at the height of the Blitz between 1940 and 1942 and capable of accommodating 8,000 people, the space was already connected to electricity and the London water supply before Growing Underground moved in.
Pea shoots are planted in the recycled growing medium. KATE PETERS
Belowground the next set of safety precautions sees visitors putting on white rubber boots, disposable hair nets, another net to cover any facial hair, and white lab coats.
“It’s a controlled environment. We don’t need pesticides but we can’t afford contamination,” says Jess Moseley, GU’s operations coordinator and tour guide. “We ask visitors to remove their jewelry to prevent any possibility of any foreign body contamination. We don’t want tiny gemstones in our salad.” Visitors wash their hands thoroughly with soap and use an alcohol-based sanitizer on them, and then are free to enter the farm.
Moseley works alongside a team of growers, all wearing the same hair net and rubber boots combo. Four of them, dressed in blue, stand in a line at polished-metal weighing scales picking bunches of harvested herbs and packing them for distribution.
“There are 16 production staff and two growers who organize the sowing,” Moseley explains, as the electronic scales beep and another box of fresh herbs is sealed and stacked. These micro greens are the intensely flavored early stages of plants that are usually harvested later in their life cycle. They’re especially popular with restaurants that serve dishes with very little on the plate. “We switched pea shoots to tendril pea shoots, which are frillier, because the chefs prefer them,” says Moseley.
The trays in the foreground hold crops that are ready for the harvest, while those under the lights are still growing. KATE PETERS
Most of GU’s crops are micro herbs—there are only two larger crops, pea shoots and sunflower shoots. Most full-size produce such as carrots or bok choy could be grown here, but they take too long to grow to make them profitable. However, more research into alternative lighting spectrums may make these a possibility, says GU operations manager Alex Hamilton-Jones.
"OUR PEA SHOOTS CAN BE HARVESTED UP TO 60 TIMES IN A YEAR. OUTDOORS YOU GET THREE OR FOUR HARVESTS A YEAR; IN A GREENHOUSE, AROUND 30."
“Larger crops require a change to the growing equipment, like the height of the stacks and light intensity,” Moseley says. “This is going to be a part of the next iteration of the farm.”
Within its short existence, Growing Underground’s team has expanded its variety and reduced turnaround time on crops. That’s due in no small part to a number of technological innovations that optimize growing conditions on the farm.
“Our pea shoots can be harvested up to 60 times in a year,” Ballard says. “Outdoors you get three or four harvests of those in a year; in a greenhouse, around 30.”
To help plants grow quickly, the correct lights are key. Ballard and Dring tried seven different LEDs during their R&D and found that the system they settled on—spectrum AP673L LEDs from Valoya of Finland—produced the best yield and greatest flavors.
These LEDs utilize a red:far-red (R:Fr) spectrum ratio that targets the red and far-red light-absorbing photoreceptors on the plant leaf. The light resembles sunlight at its peak level, which delays the flowering of herbs and allows the plant to focus its energy into fast biomass development.
The result is a compact, intensely flavored product grown in a short time in conditions that not only suit the plant but meet the needs of the growers, too. “The cycle for growing coriander has gone from 21 to 14 days,” explains Riley Anderson, the site’s team leader. “Some plants can be harvested after just six days in the growing tunnel, which beats anything a farm aboveground can achieve consistently through the year.” They toyed with duller tones than the vivid pink that now illuminates the growing tunnel, but found that the reduction in visibility meant having to lift each plant tray out off of its bench to do quality checks. It slowed the process and didn’t enhance the crop.
Jess Moseley, GU’s operations coordinator and tour guide, checks on some of the crops. KATE PETERS
“We wanted to source the lowest energy-consuming lighting system we could find,” explains Ballard. “The LEDs do not use the same amount of energy nor do they create the high direct heat that conventional (high-pressure sodium) lights do, which means we’re able to grow the plants in shelves closer together.”
The power comes from Good Energy, which only uses renewable sources. “As it’s a closed-loop system of farming, anything that’s added—nutrients or fertilizers—stays within the circuit,” says Ballard. The only farm waste—the substrate recycled carpet leftover from harvesting the herbs—is sent to SELCHP, a waste-to-energy converter in southeast London. “Zero carbon output has been the Key Performance Indicator we chose to work to from the very start because any business starting today needs to think about its impact on the environment,” says Ballard.
This 700-recipe cookbook will have you eating every last bit of your bounty. This is an actual problem at our house. Cooking everything takes creativity.
In addition to high-tech lighting, there are several other adaptations that allow plants in the tunnels to grow so quickly. It starts when the seeds are sown, without the aid of conventional soil: Workers place two-inch-thick rectangular growing mats—called Growfelt and made from pulped floor carpet—into shallow trays. The mats are sprinkled with seeds by hand.
Once sown, the seed trays are stacked onto carts and left in a dark section of the same tunnel for propagation. For a short time, they sit in complete darkness, covered with plastic wrap. This “fools” the seeds into thinking they’re beneath the earth. This is where germination begins. Within a day or two, the seed shoots appear. By the fourth day, the trays are transferred to shelves known as benches under the banks of LEDs in the crop-growing tunnel.
Garlic chive seeds are sewn into the recycled carpet seed bed. KATE PETERS
There’s no music playing in the growing area—workers seldom spend much time in here, as the plants are doing all the work on their own. Instead, the only noise in this long, flamingo-pink chamber is the whirring of the axial fans dangling from the ceiling. Although the fans help keep the farm at a settled temperature of around 59°F, the plants beneath the glare of the LEDs feel the warmth of up to 77°F.
“There’s a slight variance throughout the farm,” says Anderson. “We place the crops strategically to optimize growth. Our radishes prefer to be right at the front of the farm, where it is coolest. Our most robust crop, the pea shoot, grows well wherever it is positioned within the farm.”
On either side of the tunnel are trays bristling with herbs at different stages of growth. In each tray, a handwritten sign identifies the type of crop, along with a P date of propagation, an L for the day it was put under the lights (when transferred to the farm from propagation), and B for the bench the tray is assigned to.
The warming glow provides “sunlight” for 18 hours a day. Rain comes in the form of hydroponics. A faucet fills each tray of plants with a water-and-nutrient mix five times a day. The roots in the trays grow down through the matting to absorb the mix and then water is filtered through tanks beneath the benches. “We use 70 percent less water than conventional field farming,” says Moseley.
The garlic chive crop is harvested and ready for packing. KATE PETERS
The night before a harvest, workers put the plants on carts in the middle of the farm, which has the best airflow, Anderson says. That dries them overnight to the point of being packable without them breaking down quicker.
CROPS HERE CAN BE HARVESTED, PACKED, DELIVERED, AND SERVED ON A PLATE ALL WITHIN FOUR HOURS.
To harvest, fresh herbs are sliced from their roots, shaken off of the matting that served as their soil bed, and placed into a blue bowl. From there the crop is weighed and packed into transparent tubs made from rPET—recycled plastic—and labeled with the GU logo and contents.
Above each growing bench is a round, yellow sensor the size of a large coin that records temperature, humidity, and illumination, and sends the data to the University of Cambridge’s engineering department. The results are fed back to GU, which compares them with the crop yields to determine which conditions are working best for growth.
“We monitor yields every day when we cut,” says Ballard. “A platform with machine learning capability collects the data from all the sensors and alerts you to any anomalies. It gives us access to the sort of technology being used in big agricultural projects, but that would be too expensive for us to put together.”
Crops here can be harvested, packed, delivered, and served on a plate all within four hours. The reduced time spent in transit means GU products have a longer shelf life than those grown outside of the capital. As a result, they’re sold in some of the U.K.’s major food retailers and wholesalers.
A number of renowned London chefs use GU produce, too, including Michelin-starred Michel Roux Jr. He not only uses their herbs in his dishes at Le Gavroche, a French restaurant in the Mayfair area of London, but he also came on board as a founding supporter. He describes the shoots and leaves that it provides as “mind-blowingly good.”
For distribution to smaller restaurants, GU goes underground as well. “We send our delivery guys off with all these bags of orders onto the subway trains,” says Anderson. “Food that’s been grown in a Tube tunnel is delivered through one as well, further reducing the carbon footprint.”
Tours of the tunnels take place outside of the production cycle, with chefs, students, and potential investors visiting during the week and members of the public shown around on Saturday afternoons. “We’ve had farmers from Scotland, mainland Europe, and as far as America come and visit us,” adds Anderson. In the past five years that the farm has been operating, technology has improved a lot—more efficient LED lighting, water recycling, and air management systems, Anderson says. “But the principle of what we’re doing is remarkably simple, giving crops the nutrients they need and a medium to grow in.”
Ballard is now busy sourcing funding to expand farther into the tunnels while investigating sites for other controlled-environment farms in other parts of the world and in different structures.
“When we started, the plan was to produce a supply for London,” Ballard says. “But as the retailers have taken an interest, we’re now looking to serve their distribution centers beyond the M25 [London’s encircling motorway].”
As GU grows, it looks to similar farms for inspiration. In South Korea, subterranean vegetable farms are cropping up at underground stations on the Seoul metro, thanks to a start-up called Farm8, while in Tokyo, abandoned utility tunnels built to service a skyscraper city that never materialized have also been converted into GU-style farms. In Hamburg, Germany, a vertical farm called &ever uses methods similar to GU’s to harvest salad crop using just 5,920 square feet of indoor growing space. Producing an equivalent yield outdoors would require 161,458 square feet of open field.
Increasingly crowded cities are getting imaginative when it comes to farmland. “But these farms don’t have to be underground at all,” says Ballard. “It can be in an abandoned factory or disused warehouse aboveground. The model is simply redundant space.” Even so, with at least six more abandoned tunnels beneath London alone, GU’s subterranean farm may not be the only game of its type in town, or underneath it, for much longer.
How Family Investors Can Reap What They Sow In Vertical Farming With Vertical Future
Issues surrounding the increasing population of the world combined with water scarcity in a changing climate and the security of food and supply chains exposed by the coronavirus pandemic have all seeded minds on the possibilities of vertical farming
12 NOVEMBER, 2020 | BY JAMES BEECH
Vertical farming is being planted as the future of agriculture and the blossoming sector’s long-term growth could be a good fit for family investors and their patient capital.
Issues surrounding the increasing population of the world combined with water scarcity in a changing climate and the security of food and supply chains exposed by the coronavirus pandemic have all seeded minds on the possibilities of vertical farming.
CampdenFB asked Jamie Burrows, co-founder, and chief executive of Vertical Future, what the nascent sector really means for family investors looking to harvest returns, how his company is innovating in the field, and if families could host a vertical farm on their own property.
Why should families which are not directly involved in or have knowledge of crop health and food production consider investing in Vertical Future and vertical farming?
Families should consider investing in Vertical Future because without sustainable, scalable vertical farming—which is one of the solutions required to deal with the rising global food challenge—the future of our food, crop health, human health, and planetary health are all at risk.
Scientific literature, prominent scientists, and leading figures such as Sir David Attenborough, building on decades of research and lived experience, have shown the gravity and complexity of the issues that we face as a global, interconnected ecosystem.
Over the past 50 years, there has been a significant decrease in biodiversity, a significant increase in population growth, density, and physical expansion, an overall reduction in the quality of food, and an increase in the intensification of farming and use of pesticides. To contextualize this, one of every eight species of plants face extinction, one-third of soil faces degradation, and insect populations, which form a vital part of the food system, are seriously under threat. For these reasons and many others, food, next to water and sustainable forms of energy, must surely be the investment classes of today. Without these, the future is at risk.
Vertical Future is also, at its core, a family business, established by a husband and wife couple in 2016. My wife Marie-Alexandrine, as chief people officer, and I as chief executive, both came from careers in health and life sciences, with no prior knowledge of farming, let alone vertical farming. We believed in the importance of using technology to bring about health improvement and this is our main reason for establishing the company, which constantly strives to achieve this goal. Marie and I simply want a better and healthier future for our children, Gabrielle and Caspien, and a healthy planet for all.
What is vertical farming, how does it work and what does it achieve?
Vertical farming is the practice of growing crops indoors under controlled conditions in stacked layers or on vertical walls, typically using high-efficiency LED lighting and an either hydroponic or aeroponic method of irrigation, instead of soil.
Growing in this type of environment means that produce can be grown sustainably without the use of pesticides, herbicides, or fungicides. It also means that crops can be grown in an optimal manner, increasing output/yield, also relieving pressure on increasingly scarce farmland, encouraging rewilding, and an overall increase in biodiversity. Technological approaches continue to improve, meaning lower water utilization, less energy, and less waste. Moreover, automation, clever systems design, and robotics are allowing vertical farming systems to grow a broader variety of produce, aligning with customer demands.
What makes Vertical Future the market leader in vertical farming?
The global vertical farming market is beginning to receive a significant amount of interest and investment however, much of this is focused on older, first-generation technologies, and models that are not futureproof, and some will potentially fail. Like many other young and nascent markets, there is a tendency for investors to back brands that are perceived to be likely to grow the fastest instead of investing in sustainable technology solutions. Vertical farming, from Vertical Future’s standpoint, should be considered as a medium-to-long-term infrastructure investment. Much like building a hospital to care for the betterment of health and wellbeing, a vertical farm does much the same thing, growing healthy, local food that forms a vital part of the local circular economy.
Leveraging its years of running vertical farms in central London, where the Vertical Future team were at the time used other companies’ technologies, the company has developed a clear and concise understanding of what works, what needs improving, and what innovations are required to grow and succeed in the sector. The last 18 months have focused on building a holistic, integrated, fully-automated vertical farming system—integrating hardware and software—that is future proof, addressing all the issues that exist with other competitors’ systems.
Importantly, the Vertical Future team is built on experience, with more than 200 years of senior-level experience across the engineering and plant science teams alone. Several talented developers lead the company’s software efforts, with data forming an important part of the vertical farming opportunity. The leadership team is also supported by an experienced board, including the former head of the National Health Service, which is the second-largest health organization in the world, and the former chief marketing officer of Deliveroo.
Despite Covid, in the past six months alone the company has already begun to sell its systems through technology sale and software licensing and has generated more than £300 million ($397 million) of prospective pipeline opportunities, across four continents. This adds to ongoing support and recognition from the UK Department for International Trade, with the company winning numerous national and international competitions and being a part of the London Mayor’s International Business Programme.
Research and development (R&D), which is engrained throughout Vertical Future’s activities, shows a 75% success rate in grant funding applications and more than half a million pounds in revenue for the next 18 months alone. This includes collaborative projects ranging from seed sterilization through plasma treatment through to the growing of root extracts for the phytopharmaceutical industry, targeting the development of a novel respiratory drug.
The combination of Vertical Future’s technologies, growing experience, R&D program, experienced team, and pipeline put it in a market-leading position. Considering the importance of the underlying issues that vertical farming aims to address, Vertical Future believes that it is important that investors back sustainable models that are likely to succeed and grow the market.
Where are you vertical farming, is it scalable and where is the produce being supplied?
Vertical Future’s operations to date have been based out of a converted space in Deptford, located about 10 minutes from London Bridge station. The company grew its consumer-focused brand MiniCrops, which today supplies more than 110 restaurants across London and thousands of homes. This was an initial proof of concept, using other companies’ technologies before the company built out its technology proposition. The resulting proprietary technology solution is modular, scalable, affordable, and recognized for its differentiating factors in comparison to other vertical farming systems globally.
How will Vertical Future invest the capital it is looking for?
The focus is on scaling the company to realize the full potential of the vertical farming market. This starts with the build-out of the largest vertical farm in the world, located in London, building on Vertical Future’s client network and existing growing operations.
The second aspect of scale focuses on expanding Vertical Future’s physical footprint in key target geographies, including the development of manufacturing facilities to further improve margins and deployment of sales, technical, and marketing teams. The final element of the round focuses on the improvement of Vertical Future’s existing hardware and software technologies.
What kind of returns are expected for family investors?
The company’s sales model has been built for profitability, with a positive EBITDA [earnings before interest, taxes, depreciation, and amortization] expected in 2022. The Vertical Future team expects there to be an opportunity for a Series B round in several years’ time, in advance of a potential exit, or partial exit, in 2024/25, likely through an Initial Public Offering (IPO) or trade sale. With the growing popularity of vertical farming and the evident need for sustainable food solutions, the company expects there to be ample interest from prospective buyers in a variety of sectors. A trade sale or partial exit would be expected to be at a price 3-5x (minimum) of the current round, with an IPO potentially offering substantially higher returns.
How can families incorporate vertical farming on their own real estate?
As this is a very new industry, Vertical Future is not aware of any examples of families incorporating vertical farming in their own real estate. However, there are clearly massive opportunities to do so.
Families that have access to or own retail-focused assets, manufacturing capabilities, or assets in strategically positioned areas can both benefit and add value to Vertical Future’s growth plans. For example, commercial real estate located in urban areas can provide opportunities for systems integration, effectively eradicating food miles and providing a constant, year-round supply of fresh produce to local buyers. Similarly, real estate located close to target geographies could be used to increase the rate of expansion, providing land for development of manufacturing sites, or if manufacturing facilities already exist, eradicate the need for new sites.
Where do you want to see Vertical Future’s vertical farming venture in five years?
Food, water, and sustainable energy are—in Vertical Future’s view—the main investment categories of the future. In five years, the Vertical Future team wants to be an internationally recognized brand with its technologies and sites spread across the world. Each site will be sustainable and purpose-driven, producing healthy, affordable food for local inhabitants and improving their quality of life, job opportunities, and level of education. Through their connection via smart data infrastructure, the sites will be on a path of continual improvement. For rural locations, energy independence, accomplished through integrated, off-grid solutions, will be a reality.
RELATED CONTENT:
Future portfolio success will be built on impact
Why impact investors don’t have to sacrifice financial returns
About the Author
Editor
James Beech is the multimedia Editor of CampdenFB, with 21 years of international experience in daily newspapers, B2B and consumer magazines, online, social media, photographic and video journalism, in addition to editorial management, marketing, public relations and client relations, in the United Kingdom, Australia and New Zealand. He graduated from Bournemouth University in 1999.
University of Arizona CEAC Hydroponic Online Intensive Workshop
Taught by Dr. Stacy Tollefson, this two-day event is perfect for novice growers and will be packed with tons of critical information and research discoveries that UA-CEAC has assembled into their courses and programs for over 20 years
Are you interested in growing tomatoes hydroponically? Join the University of Arizona Controlled Environment Agriculture Center for the Hydroponic Online Intensive Workshop – November 16 & 17 via Zoom.
Taught by Dr. Stacy Tollefson, this two-day event is perfect for novice growers and will be packed with tons of critical information and research discoveries that UA-CEAC has assembled into their courses and programs for over 20 years. You will get access to numerous lecture materials, personal question follow-ups, certificate of completion, and tons of knowledge!
Click Here to Register!
Limited seats are available. For questions, please email arizona.ceac@gmail.com
Tags Online Events Online Classes #agriculture #tomato #greenhouse #tomatoes #hydroponics #controlledenvironment #controlled_environment_ag #indoor_agriculture
Why Are British People Protesting U.S. Farm Imports?
10.28.2020
Cow costumes, tractor caravans, and Great British Bake Off support: U.K. farmers and their allies are registering opposition to a new agriculture bill.
This weekend, lawmakers in the U.K. were greeted with a strange sight. Costumed demonstrators—one dressed like President Trump carrying a syringe, others dressed like farm animals—gathered in London to protest the passage of a new agriculture bill.
At issue was the government’s failure to codify British food standards as the country exits the European Union. Activists fear this omission would crack open the door for an influx of food imports from the United States as part of a trade deal between the two nations. They argue that allowing imports of U.S. products like beef raised with hormones (hence the syringe) and chicken washed in chlorine would compromise food safety and animal welfare.
A similar battle is playing out across Europe: The EU recently issued a green farming plan that blocks these products and signals a shift away from chemical pesticides and fertilizers. U.S. trade representative Ted McKinney called the plan a “diss.” And the EU once faced fierce opposition over imports of hormone-raised beef and chlorine chicken from the U.S., leading to an eventual ban—which Britain may abandon.
Elsewhere in the country, protestors have staged tractor parades down city streets and enlisted the support of celebrities including Jamie Oliver and Great British Bake Off judge Prue Leith in support of their cause. (Leith actually voted in favor of Brexit, so her tweets promoting British food standards were met with backlash from opponents who said she should have considered the consequences for farmers before voting to leave the European Union.)
“In this country, we’ve been through some major food crises with foot and mouth 20 years ago. We had the horsemeat scandal. We had the egg scandal in the 80s, with salmonella.” says Liz Webster, a self-described “farmer’s wife” and campaign organizer with Save British Farming, a group that advocates for British food standards. “We’ve got stricter standards about how many animals you can have in an area.”
Jamie Oliver put it another way in a video with the BBC: “Imagine being a British beef farmer and all of a sudden someone across the pond who uses hormones—those cows have never seen grass—they can sell you a product much cheaper.”
The messaging in these campaigns is a little muddled: They’re claiming that loosening import rules is bad for animal welfare, and also that it’s bad for farmers’ bottom lines, and, perhaps most alarmingly, that imported food threatens the health of the people who eat it. And it is true that the European Union has adopted food standards that ban some potentially harmful products used in animal production and food processing in the U.S., including bovine growth hormone. If the U.K. adopts its own agriculture policy without banning the same products, activists worry they’ll find their way into the food supply. It’s also true that Europe has adopted some stricter animal welfare laws, including rules that give chickens a bit more space than their American counterparts.
“They’re trying to imply that food imported from America isn’t safe somehow, or that it’ll poison them or something—they don’t spell it out because it’s not true.”
Yet the implication in many of these campaigns that U.S. food imports are less safe than homegrown beef is not backed up by acknowledgment from the U.S. or the World Trade Organization. “They’re trying to imply that food imported from America isn’t safe somehow, or that it’ll poison them or something—they don’t spell it out because it’s not true. What they’re really talking about is the way the food is produced,” said Sean Rickard, an economic analyst who advises clients on food and farming.
Of course, there’s a deeper set of issues at play here: This bill, which represents the government’s foray into post-Brexit agricultural policy, has been a wake-up call for farmers, half of whom voted in favor of leaving the EU, Rickard said. “What farmers realized as it was going through the Houses of Parliament was that it wasn’t actually the sort of milk and honey that they had been expecting,” he added. The bill removes direct payments to farmers and replaces them over the next several years, though the details are hazy. More concerning to some are the trade implications.
“Farmers suddenly woke up to the fact that one of the dangers was that if this bill didn’t protect them against imports of cheaper food, they were going to be completely screwed,” Rickard said. “They were not only going to lose their support systems, but they were also going to face imports from countries that can produce food more cheaply.”
Over time, the food service sector will slowly start purchasing imported meat, and Britons will start eating chicken grown in the U.S. at KFC.
Rickard is cynical about the potential inclusion of food standards language in the agriculture bill because such a move could jeopardize a trade deal with the U.S. “[Representatives] made abundantly clear there will be no trade deal with us if we are not prepared to accept American standards,” Rickard said. That puts politicians in a bind: Some of Prime Minister Boris Johnson’s key supporters are farmers, but a bilateral trade deal with the U.S. is not compatible with a policy that limited American farm imports.
U.K. legislators have promised not to allow imports of the two most incendiary products—beef raised with growth hormones and chicken washed with chlorine—but The Guardian notes that the proof will be in the pudding. Under pressure to sign a trade deal with the U.S., these assurances may fall by the wayside.
In the long run, Rickard envisions a slow, grudging acceptance of U.S. food imports. “I think in the short run, the supermarkets will say, ‘Oh, we’re going to put big labels up. None of our food will be produced in the way Americans do,’” he said. But over time, the foodservice sector will slowly start purchasing imported meat, and Britons will start eating chicken grown in the U.S. at KFC. Slowly, the grocery stores will follow suit. “The truth is that when it comes to buying food—and we have a lot of people, unemployed, single-parent families, in this country—cheaper food will find its way into the supermarkets,” he added.
Lead photo: AP Photo/Alberto Pezzali
Also tagged farmers, food imports, trade, trump administration, united kingdom
H. Claire Brown is a senior staff writer for The Counter.
How iFarm Vertical Farms Save Water
In many places around the world, for example in the Middle East, water resources are limited and their price is high. Reducing water consumption on a vertical farm in such regions can have a very positive economic and environmental impact
Generally, vertical farming uses 95% less water than traditional farming. At iFarm we have improved this indicator.
In many places around the world, for example in the Middle East, water resources are limited and their price is high. Reducing water consumption on a vertical farm in such regions can have a very positive economic and environmental impact. iFarm engineers have recently developed and patented a dehumidification system allowing to reuse the water that farm plants evaporate during growth.
How does it work? Let's take a look at a vertical farm with a cultivation area of 1000 m2. It produces 2.5 tons of fresh salads and herbs every month. To get such a yield, you need 2020 liters of water daily, most of which — 1400 liters — is used for plant nutrition. However, the daily actual water consumption is almost three times less. 2020 liters are poured into the system once, and then the "engineering magic" begins.
At iFarm vertical farms we use flow hydroponics, i.e the roots of plants are constantly placed in the nutrient solution and consume it whenever they need, getting all the macro- and microelements in the right ratio and concentration.
From 1400 liters of the water, plants use only 80 liters for weight gain (consumption of nutrients from a larger volume is a prerequisite). The remaining 1 320 liters the plants simply evaporate. In the process of transpiration, a lettuce leaf can evaporate an amount of water that exceeds its own weight many times. We collect this water with air conditioners and dehumidifiers, purify it and reuse it in production, maintaining the optimal humidity inside at 70%.
The second "source" of water on the farm is the water supply system — another 700 liters are collected from it and then run through a special filtration unit, resulting in 560 liters of purified and 140 liters of untreated water. The latter is collected in a special tank for technical needs (washing hands, pallets, floors, etc.).
Thus in order to save water, we started collecting it from air conditioners and dehumidifiers that were originally designed to maintain optimal moisture on the farm. This approach allows the production to use only 700 liters of tap water per day, which is three times less than growing plants in conventional hydroponic greenhouses.
We are currently improving the automation of the nutrient solution replacement. The system will determine what macro- and microelements are missing in the trays at a given time and adjust them. According to the calculations of engineers, this will reduce the number of times the sewerage has to be drained completely and almost halve its consumption — from 360 liters to 150 liters. The amount of tap water required by a vertical farm to produce delicious and reach yields then will be just 440 liters, which is five times less than what a hydroponic greenhouse needs.
16.10.2020
A Couple of Showrooms In Europe Need To Get The Ball Rolling For Verde Compacto - Shipping Container Farm
"People Are Immediately Enthusiastic When They See It"
"People Are Immediately Enthusiastic When They See It"
He, partly joking, calls himself ‘a born and raised’ city dweller from the heart of Amsterdam: Olivier Kappetein. As a representative of Mexican vertical farming company Verde Compacto in Europe, this is not ideal; will people be willing to listen to him given his background and his not yet widely undisputed product?
"Unfortunately not always, but that is why I’m looking for partners to start showrooms within Europe where we can display our cultivation systems. If people could actually see what we do, they would also see the potential in it. Of this, I’m sure. And yes, I know very well that vertical farming is not the solution to the global food problem, but I do believe there are many situations in which our systems would come in handy.”
The team of Verde Compacto that develops the container farm Huvster and the smaller Veggiebox cultivation variety
Advancing a Mexican family-run company
Before going further into the systems (such as the cultivation containers), we need to go back to where it all began. How does a young man from Amsterdam end up at a Mexican company active in vertical farming? “I was introduced to a Mexican through my dad a few years ago. It turns out he worked at Verde Compacto where he developed fertilizers. Through those fertilizers, they came into contact with vertical farming and decided to continue in that field.
I went to Mexico myself and got to know the family-run business better. They are ambitious and want to expand their brand in Europe and were looking for someone who could help them with that. With my degree in Business Administration, I can take on that role, and after doing my research to understand the relatively young market better, I now want to take some real steps forward.”
Opportunities, among others for apocalyptic bunkers
In the beginning, Olivier planned to aim all of his efforts in the Netherlands at first, but due to, among other things, the coronavirus, getting to know the market better, and the reservations against vertical farming in the Netherlands, he had to look in other places as well. “I want to build a couple of showrooms where people can see our products both in the Netherlands and in other European countries. We make cultivation systems in various sizes, from container to fridge-sized systems, always according to the vertical farming principle with a high productivity per square meter of 253 kilograms. I see a potential for these systems in, for example, Scandinavia, Germany, and the United Kingdom, countries with large urban areas or difficult growing climates. The younger generations in those places have a demand for sustainable, local products.”
But Olivier also has his eyes set outside of Europe, like in the Middle East. He is also looking into bunkers. Actual bunkers. “It is currently trendy for rich people worldwide to build apocalypse bunkers out of fear for the end of the world. Those people want to be self-sufficient in those bunkers, which is where our systems come into play. A great niche market with requests from the United States, Australia, and New Zealand, to name a few.”
Realistic due to size
In any case, Olivier is a realist: replacing large, traditional cultivation companies with vertical farms in whatever way can not be justified anywhere. “To give you an indication of our system size: recently, we started working together with The Goat Project, an Italian vertical farming project. Up to an investment amount of 30 million euros, we will be delivering together, but after that, they take on everything up to an investment amount of 3 billion euros.”
That is why Olivier aims first and foremost on restaurants and supermarkets, where the consumer can choose how the product they will eat is grown. But, the systems can just as well be used for ornamental cultivation or cannabis cultivation, both medical and recreational. “For that latter type of cultivation, we developed a specialized system which could also be used to cultivate tomatoes, though on such a small scale that would not be very profitable.”
Strawberry yogurt
However, it would be profitable for an Icelandic producer of strawberry yogurt. Importing fresh strawberries to the island is more expensive than growing them yourself in a vertical farm. “The energy comes from the earth in Iceland due to the geysers, but there are many more situations in which, with a bit of thinking and using the local circumstances, a generally more expensive system works. The ROI of our systems is about one to three years, with a very high productivity per square meter (5700 plants in a 12-meter container named Huvster), the second-highest for container cultivation on the market.”
Rotating LED lighting increases energy efficiency
Critics often point out the high energy input of vertical farming. Olivier recognizes that, but refers to the clever use of local circumstances, and the technological innovations developed by Verde Compacto meant to increase efficiency. Rotating lights, for instance, a unique system compared to many other vertical farming systems. “Instead of cultivating in layers, we work with cultivating in standing tubes with LED strips rotating around them so that every plant gets the light it needs, but the energy input in kilowatt-hours is 50% lower per square meter and the production per square meter higher.”
Make them enthusiastic
Back to the restaurants, which is what Olivier focuses on in Europe first. He imagines one of the cultivation containers walls being see-through so that the consumers can take a peek at the cultivation facility. “Especially large groups of young consumers who want to, for instance, eat vegetarian or vegan, I expect will be very enthusiastic, and so will the investors. It is also easier to talk about something if it is physically there and allows fresh and healthy foods to be sourced closer to home.”
However, Olivier is aware of the disadvantage that European supermarkets are not yet able to sell products grown in vertical farms under an organic quality mark. According to him, that hampers the growth of vertical farming. “At the moment, they lose their organic quality mark as soon as they cultivate on water because the standards are pretty outdated when compared to the technological cultivation developments.”
Win-win situation
But it is not an insurmountable problem, especially given the worldwide increase in demand for local products during the pandemic. But is this true given the fact that Verde Compacto is Mexican, and in the Netherlands, many well-known players are active in offering cultivation solutions? “I don’t think that matters all too much these days. Price-wise we don’t differ much from European or North American systems. Every system has its pros and cons. I am very open about that. A well-thought-out calculation is always required, but both parties can create a win-win situation when it happens. Of this, I, and hopefully my future partners as well, am sure. I'm looking forward to discussing it with them.”
For more information:
Verde Compacto
www.verdecompacto.com
Olivier Kappetein
olivier.kappetein@verdecompacto.com
+316 14 62 13 10
SOUTH AFRICA: 'We See Hydroponics As The Future of Farming’
Getting children to learn how to grow vegetables at school is an idea that is growing in popularity across Mzansi
By Terry van der Walt
November 10, 2020
Getting children to learn how to grow vegetables at school is an idea that is growing in popularity across Mzansi.
The topic is close to the heart of Branden Gee and his business partner Cameron Blair, who also have a hydroponic set-up in Pinetown outside Durban, as well as an e-commerce business.
“Our major ambition is to get either a hydroponic system or a 100 percent organic and sustainable vegetable patch in every school in the country. That’s the reason we do it for free. We want everyone to learn how to grow their own food and self-sustain.
“Each project deals with a different aspect that contributes to a greater goal, and that goal is sustainable living,” said Gee.
This past Friday they visited Curro Hillcrest Independent School and taught learners the basic building blocks of permaculture, and introduced a worm farm to the school.
“Worms are arguably the most important organisms to life on our planet. They convert organic matter into valuable nutrients that your plants will thank you for later,” he said.
The worm farm makes use of vegetable scraps which the worms feed on, which creates a nutrient-rich liquid - worm wee - which helps build fertile soil, resulting in thriving crops.
On Saturday the duo hosted Thomas More College learners at their Geeshydro hydroponic farm and grow store.
“We use the farm as an educational tool to teach anyone and everyone who is wanting to learn more about hydroponics.
“We see hydroponics as the future of farming since it uses 90% less water than traditional farming, and it can grow a surplus of food in a smaller area using vertical grow towers,” he said.
Brenden Gee and Cameron Blair, in front, are getting learners to grow food. Picture: Supplied
Their e-commerce website called Our Local Market is free to vendors in the upper highway area and was set up to create and support opportunities for young entrepreneurs to thrive by offering them a platform to sell their products with no risk.
“We want the next generation to not only learn how the natural world works, but also how to use it to create a business.
“By using nature the kids can learn how to create a vegetable garden that can thrive. We teach them how to build soil, how to harvest worm wee, how to grow seedlings to sell, growing chickens and learning how to harvest the eggs, as well as selling their produce,” he said.
Learners from Thomas More College get the low-down on hydroponics. Picture: Supplied
Their business is structured around three major principles: Earth care, People care, Fair share.
Gee hopes to adopt more schools and relies on donations to make it happen.
If you want to help go to: https://gf.me/u/y6gtkm
“I know money has been harder to come by this year but I’ve been getting a little from all over, so any donation makes a huge difference, every little bit helps,” he said.
Lead photo: The hydroponic set-up uses a fraction of water and is used as an educational tool for visiting schools. Picture: Supplied
Featured Project: Jakob Factory Saigon
Proposing an environmentally friendly alternative to the typically horizontally spread manufacturing buildings, the Jakob Factory offers an innovative vertical densification strategy, stacking the usable zones on superimposed slats
November 10, 2020
Jakob Factory Saigon
Ho Chi Minh City, Vietnam
Approximately 39,288 of
Living Walls & Green Façades
Greenroofs.com Featured Project November 10, 2020
When referring to acting responsibly and specifying green architecture, don’t we all say, “Put your money where your mouth is?”
Well, Jakob Rope Systems has certainly done that with its beautifully and sensitively designed second factory in the former Saigon. Plus, it’s a great way to showcase your own products!
Image: Jakob Rope Systems
Taking its cue from nature, the factory has been designed to increase workers’ comfort and decrease its environmental footprint by creating the first project in Vietnam with completely naturally ventilated manufacturing halls. Kudos to Jakob Rope Systems and its designers!
Image: Oki Hiroyuki, courtesy G8A Architects and rollimarchini Architekten
Excerpt from Greenroofs.com Project Profile:
Located in the center of an industrial park 50 kilometers north of Ho Chi Minh City, the new Jakob Factory Saigon opened in late 2019. The factory houses steel rope producers Jakob Rope Systems, specializing in custom made steel meshing.
Designed by rollimarchini Architekten and G8A Architects, the highly innovative manufacturing space boasts completely naturally ventilated manufacturing halls.
Image: Oki Hiroyuki, courtesy G8A Architects and rollimarchini Architekten
Ever since Vietnam’s economic reform in 1986 the country has experienced industries and populations moving from a primarily agricultural industry to a focused industrial practice. Priorities have focused on economic gain rather than environmental impact and the past ten years have seen the doubling of industrial parks.
The design of the new Jakob Factory Saigon offers an alternative to these detrimental practices, presenting a strategically land saving project with focus elements of passive design.
Image: Oki Hiroyuki, courtesy G8A Architects and rollimarchini Architekten
Proposing an environmentally friendly alternative to the typically horizontally spread manufacturing buildings, the Jakob Factory offers an innovative vertical densification strategy, stacking the usable zones on superimposed slats. This robust design avoids unnecessary ground usage negating needless land development, while also offering workers agreeable outdoor spaces.
Taking reference from the traditional tropical architecture of the region, the design has a porous façade devised as a lush-planted skin. The suspended structure is supported by a two-layer rope network stretched from the ground to the roof. The horizontal planters not only filter rain and sun, but also contribute to lowering the atmospheric temperature through evaporation, acting as air purifiers and dust particle binders as well as allowing the air to circulate.
Image: Oki Hiroyuki, courtesy G8A Architects and rollimarchini Architekten
Image: Jakob Rope Systems
More
Covered in a wide variety of tropical plants, two types of greenwalls are found at the Jakob Factory Saigon. The multilayer system on the façades of the production and office building are sustained by Jakob ropes and stainless steel RHS frames, and living walls are planted in custom horizontal planters consisting of a geotextile, HDPE, and Jakob Webnet. Green façades cover the parking area using Jakob Webnet with climbing plants planted in the ground.
Based on passive climatic strategies adapted to its tropical region, amenities for staff, and the intelligent distribution of work spaces, the pioneering initiative of the Jakob Factory Saigon is set to become a design reference for sustainable, tropical living architecture.
Image: Oki Hiroyuki, courtesy G8A Architects and rollimarchini Architekten
Year: 2019
Owner: Jakob Rope Systems
Location: Ho Chi Minh City, Vietnam
Building Type: Industrial
Type: Living Walls & Green Façades
System: Single-Source Provider
Size: Approximately 32,292 sq.ft. Living Walls & 6,996 sq.ft. Green Façades
Slope: Living Walls: 1-2% & Green Façades: 100%
Access: Private
Image: Oki Hiroyuki, courtesy G8A Architects and rollimarchini Architekten
Credits:
ARCHITECTS:
G8A ARCHITECTS & ROLLIMARCHINI ARCHITEKTEN
STAINLESS STEEL, WEBNET, STAINLESS STEEL ROPES AND ACCESSORIES FOR LIVING WALLS & GREEN FAÇADES:
JAKOB ROPE SYSTEMS
WATER SAVING APPLIANCES:
DELABIE
Image: Oki Hiroyuki, courtesy G8A Architects and rollimarchini Architekten
See the Project Profile
See the Jakob Factory Saigon Project Profile to view ALL of the Photos and Additional Information about this particular project in the Greenroofs.com Projects Database.
Image: Oki Hiroyuki, courtesy G8A Architects and rollimarchini Architekten
Did we miss your contribution? Please let us know to add you to the Project Profile.
Would you like one of your projects to be featured on Greenroofs.com? Read how, and remember we have to have a profile first! Submit Your Project Profile.
Love the Earth, Plant a Roof (or Wall)!
By Linda S. Velazquez, ASLA, LEED AP, GRP
Greenroofs.com Publisher & Greenroofs & Walls of the World™ Virtual Summits Host
Watch #VirtualSummit2019 Speaker Videos and EXPO and Speaker Q&A Videos on demand through 2020 with FREE Registration!
Tags: ARCHITECTURE, BIODIVERSITY, GREEN INFRASTRUCTURE, GREEN WALLS, STORMWATER MANAGEMENT, SUSTAINABILITY
Novel Coronavirus (COVID-19) News Updates
Find the latest news and updates on how the coronavirus COVID-19 is affecting you, the world and the produce industry
Long-Haulers Are Redefining COVID-19
Read More
Covid-19 Just Passed Another Horrible Milestone in the U.S. From ‘It’s Going To Disappear’ To ‘WE WILL WIN THIS WAR’
Read More
Covid-19 is Here to Stay. People Will Have to Adapt
Read More
What We Know About Coronavirus And Water Treatment
Read More
COVID-19: Cargill Closes Pennsylvania Plant
Read More
INDIA
New Lockdown Guidelines: Here's A List of Economic Activities That Will Be Allowed After April 20
Read More
Smithfield Foods Warns of Shortage As it Closes Major Pork Plant Indefinitely
Read More
Turning Your Home Into Your Main Food Producer
Read More
Coronavirus Resource Center
Read More
Fears grow over Covid-19 impact
Read More
Study Shows How Long COVID-19 Virus Lives On Different Materials: Plastic, Steel, Copper, Cardboard, Air
Read Here
Thirteen Science Questions About COVID-19 From Teens
Read Here
A food crisis looms as coronavirus forces farms to stay idle and countries hoard supplies
Read Here
A Visual History of Pandemics
Read More
Shipping Firms Warn of Risk to Food Supplies
Read More
Shocking Coronavirus Study Says People Could Be Locked Down For 18 Months
Read More
MIT Researchers Create a Reusable Silicone Mask to Replace The N95
Read More
Copper Masks Are The Latest Craze. Should You Buy One?
Read More
You May Be Stocking Up On Toilet Paper. Others Are Out Buying Guns
Read More
How Our Cellphone Location Data Can Save Us From A COVID-19 Recession
Read More
Copper Kills Coronavirus. Why Aren’t Our Surfaces Covered In It?
Read More
Find the latest news and updates on how the coronavirus COVID-19 is affecting the produce industry, and add your insights by taking our survey.
Read More
A Guide For Local Producers To Navigate The COVID-19 Outbreak
Read More
Soap And Water 101: Why It’s Best For COVID-19 Coronavirus (And Everyday Practice)
Read More
COVID-19: The Perils of a ‘Just Enough, Just in Time’ Food System
Read More
Coronavirus And Supply Chain Disruption: What Firms Can Learn
Read More
The ‘Chinese Flu’ Is Part of a Long History of Racializing Disease
Read More
In Honolulu, a fire started by health authorities in an effort to "sanitize" the city's Chinatown in 1900 raged out of control, destroying much of the city. Gabriel Bertram Bellinghausen via Wikimedia Commons
A President Unfit For A Pandemic
Much of The Suffering And death coming was preventable.
The President Has Blood On His Hands
Read More
What Happens To Our Food Supply If American Farmers Can't Farm?
Read More
Mobile Vaccination Centres in Shipping Containers Could Immunise 60 million People in Four Months, says Waugh Thistleton Architects
Read More
41 Million Dollar Investment To Boost Abu Dhabi's Agriculture Technology
The Abu Dhabi Investment Office, ADIO, announced today individual partnerships with Pure Harvest Smart Farms, Pure Harvest, FreshToHome, and Nanoracks that will see the companies receive financial and non-financial incentives totaling AED 152 million (USD 41 million)
Three innovative agriculture companies will develop cutting-edge projects in Abu Dhabi to boost the emirate’s agriculture technology, AgTech, capabilities across land, sea, and space.
The Abu Dhabi Investment Office, ADIO, announced today individual partnerships with Pure Harvest Smart Farms, Pure Harvest, FreshToHome, and Nanoracks that will see the companies receive financial and non-financial incentives totaling AED 152 million (USD 41 million). The research and technologies developed by these companies will expand existing capabilities in Abu Dhabi’s AgTech ecosystem and promote innovation in the sector to address global food security challenges.
New partnerships
The new partnerships are a continuation of ADIO’s efforts to accelerate the growth of Abu Dhabi’s AgTech ecosystem through the AgTech Incentive Programme, which was established under Ghadan 21, Abu Dhabi’s accelerator program. The Programme is open to both local and international AgTech companies. The partnerships follow ADIO’s AED 367 million (USD 100 million) investment earlier this year to bring four AgTech pioneers – AeroFarms, Madar Farms, RNZ, and Responsive Drip Irrigation, RDI, – to the emirate to develop next-generation agriculture solutions in arid and desert climates.
Dr. Tariq Bin Hendi, Director General of ADIO, said: "Abu Dhabi is pressing ahead at full steam with our mission to ‘turn the desert green’ and solve long-term global food security issues. We have created an environment where innovative ideas can flourish and this has enabled the rapid expansion of our AgTech sector. Innovations from the companies we partnered with earlier this year are already propelling the growth of Abu Dhabi’s 24,000 farms. Partnering with Pure Harvest, FreshToHome and Nanoracks adds a realm of new capabilities to the ecosystem across land, sea, and space."
Bin Hendi continued: "We are driving innovation across the entire agriculture value chain and this is producing a compounding effect that is benefiting farmers, innovators, and companies in our region and beyond."
Pure Harvest, FreshToHome, and Nanoracks have been awarded financial and non-financial incentives to expand operations in Abu Dhabi. The competitive incentive packages include rebates on innovation-linked high-skilled payroll, high-tech CAPEX, as well as land, utility, and intellectual property support.
Since the beginning of 2020, ADIO has attracted seven AgTech companies to Abu Dhabi, each bringing a complementary skill to expand the ecosystem. ADIO’s new partnerships with Pure Harvest, FreshToHome, and Nanoracks will build on the achievements made by AeroFarms, Madar Farms, RNZ and RDI, the AgTech pioneers ADIO partnered with earlier this year to establish R&D and production facilities in Abu Dhabi.
Pure Harvest is a home-grown, tech-enabled farming venture that uses cutting-edge food production systems to grow fresh fruits and vegetables in a climate-controlled environment, enabling year-round production anywhere, while using seven times less water compared to traditional farming methods.
Pure Harvest will invest in smart farming and infrastructure technologies at its new farms in Al Ain, Abu Dhabi, to optimize growing conditions through hardware design innovations, artificial intelligence, autonomous growing and robotics, plant science research, and desert-optimized machines. The company will also progress R&D and deployment of a commercial-scale algae bioreactor production facility that will grow higher quality, healthier Omega-3 fatty acids without the limitations and challenges of traditional animal sources.
Sky Kurtz, Co-Founder, and CEO of Pure Harvest, said: "We are delighted to have received the support of ADIO to further invest in our home-grown, innovative growing solutions. It also serves as a powerful endorsement of our business case and mission as we pursue innovation to address food security locally and internationally. As one of the pioneering champions in the region’s emerging AgTech sector, this commitment will give us the resources we need to drive and expand our R&D capabilities and will position us for international expansion from our strategic base in Abu Dhabi. This partnership further demonstrates how committed the government is in supporting and enabling innovative technology companies, providing them with the tools, resources, and support to thrive and make a large-scale impact in the region."
FreshToHome is an e-grocery platform for fresh, chemical-free produce. The company maintains complete control over its supply chain, inventory, and logistics by obtaining produce directly from the source through an AI-powered auction process. ADIO’s partnership will aid the expansion of FreshToHome’s land and sea operational and processing capabilities in the UAE, bringing expertise in aquaculture, contract farming for marine and freshwater fish species, and precision agriculture to Abu Dhabi. It will also invest in innovative fish farming technologies and cold chain.
Shan Kadavil, CEO and Co-Founder of FreshToHome, said: "At FreshToHome we use cutting-edge research in AI and precision aquaculture for furthering food security in a sustainable manner while also giving better value to consumers, fishermen, and farmers. To this end, we intend to bring our US patent pending AI-powered Virtual Commodities Exchange technology, our e-grocery platform, and our nano farm aquaculture technology to Abu Dhabi, enhancing food production and distribution for the region. ADIO has been a terrific partner to us and we are thankful for their support in helping us be part of the vision."
US-based Nanoracks is the single largest commercial user of the International Space Station and is building the first-ever commercial AgTech space research program. Nanoracks’ ‘StarLab Space Farming Center’ in Abu Dhabi will be a commercial space research facility focused on advancing knowledge and technology for organisms and food produced in space and in equally extreme climates on Earth. The space-based technology will be applied to desert agriculture to address pressing environmental and food security challenges and to benefit long-term human space exploration.
Allen Herbert, SVP of Business Development and Strategy, and Head of Nanoracks, UAE, said: "Much of today’s technology used for vertical, urban and closed environment agriculture initially came from space research from 30 years ago, and Nanoracks is ready to synergize these technologies back to in-space exploration. We firmly believe that space research holds the keys to solving major challenges on Earth from climate change to food security. And our StarLab Space Farming Center in Abu Dhabi is just the beginning.
We’re building a global research and development team that will produce and commercialize organisms, technology, and innovative products that will not only revolutionize farming in Earth’s deserts and harsh environments but also change the way humans are able to explore deeper into our universe."
For more information:
www.wam.ae
11 Nov 2020
RII And ACEEE Awarded USDA Grant To Transform Controlled Environment Agriculture Toward Resource Conservation And Efficiency
“As an industry-leading indoor vertical farming company with two farms and over 126,000 sq. ft. of growing space which can produce over 500,000 lbs. of fresh food each year, Fifth Season is committed to this exciting project,” said Grant Vandenbussche, Chief Category Officer, Fifth Season
Washington, D.C. (November 9, 2020) – Resource Innovation Institute (RII) and the American Council for an Energy-Efficient Economy (ACEEE) will receive nearly $600,000 over three years from the Conservation Innovation Grants (CIG) program at the United States Department of Agriculture’s Natural Resources Conservation Service. The project was one of 24 projects selected for the 2020 program. RII and ACEEE will jointly implement the project through 2023.
Authorized by the 2002 Farm Bill, the CIG program helps develop the tools, technologies, and strategies to support next-generation conservation efforts on working lands and develop market-based solutions to resource challenges.
The awarded proposal, titled Data-Driven Market Transformation for Controlled Environment Agriculture, will characterize key performance indicators, baseline data, and facility-level benchmarking for controlled environmental agriculture facilities. The project will develop a comprehensive suite of data tools, coupled with a market intervention strategy to address barriers to energy conservation, adoption of energy-efficient technologies, access to energy use data, and best practices.
“We’ve been assessing energy and water use in the energy-intensive cannabis cultivation sector for years and have built a set of vetted tools and resources that will now be extended to the broader controlled environment agriculture marketplace,” said Derek Smith, Executive Director of Resource Innovation Institute. “We appreciate the support of the USDA as well as leading producers, supply chain actors, universities, utilities, governments, standards organizations, and other project partners.”
“Market transformation is a proven strategy for creating and sustaining energy efficiency improvements in energy-intensive market sectors,” said Jennifer Amann, ACEEE’s Buildings Program Director. “With USDA’s support, we’ll engage leading CEA market actors, utilities, and policymakers to demonstrate market transformation’s potential to drive resource efficiency in the fast-growing and innovative CEA market.”
“Agricultural innovation has long played a key role in Oregon’s rural economy, and has made countless contributions to our state for generations,” said Oregon’s U.S. Senator Jeff Merkley, who serves as the top Democrat on the Senate Appropriations subcommittee that funds the USDA. “I’m pleased that this funding will help Oregonians keep us at the cutting edge of the newest technology in sustainable agriculture, and I will continue to partner with our state’s researchers and farmers to make sure Oregon agriculture continues to thrive.”
“The world’s population is increasing, but available agricultural land is decreasing. Through science and innovation, we can help farmers improve the health of their operations and productivity on their lands while protecting the natural resources we all depend on,” said Natural Resources Conservation Service Acting Chief Kevin Norton. “The new systems, tools, and technologies being developed through CIG are helping us ensure the longevity of American agriculture.”
Additional support includes:
Fifth Season
“As an industry-leading indoor vertical farming company with two farms and over 126,000 sq. ft. of growing space which can produce over 500,000 lbs. of fresh food each year, Fifth Season is committed to this exciting project,” said Grant Vandenbussche, Chief Category Officer, Fifth Season. “We will benchmark the resource efficiency performance of our facilities, evaluate potential efficiency upgrades, and be featured in case studies demonstrating the financial and environmental results of our projects.”
Fluence by OSRAM
Fluence is a leading global provider of energy-efficient LED lighting solutions for commercial agriculture production. Fluence regularly contributes to RII’s cultivation guidance and serves as an industry-leading voice for RII on efficient energy consumption for LED lighting in CEA facilities. “We are increasingly observing global growers commit to more energy-efficient cultivation solutions at their facilities,” said Corinne Wilder, Vice President of Global Business Operations for Fluence. “This grant underscores the important work RII has already done for growers and we will enthusiastically recruit cultivators to engage with this project to not only help improve the efficiency of their own operations but those of the entire CEA industry.”
Grodan
“For more than 50 years, Grodan has developed Precision Growing methods proven to reduce water and nutrient use while maximizing crop quality and yield. Vertical farms and greenhouses are critical to the future of global food and medicine production as well as minimizing resource usage with technologies such as recirculation,” said Gonneke Gerkema, North American Business Director, Grodan. “This project collaboration brings together several key companies who share the same vision of industry benchmarking combined with Data-Driven decision making to generate water-use efficiencies that will benefit the cultivators, the industry, and indeed the environment.”
Northwest Power & Conservation Council
“Indoor agriculture is a significant part of the driving force behind forecast growing electric loads in agriculture,'' said Ben Kujala, Director of Power Planning, Northwest Power & Conservation Council. “The Council supports looking for opportunities for cost-effective energy efficiency and demand management within the growing indoor agriculture sector as part of its power planning and conservation responsibilities. As project advisor, Council staff commit to engage and educate stakeholders.”
For more information, go to ResourceInnovation.org/CEA. To schedule an interview with an RII representative, please contact Ellie Malone at ellie@themaverickpr.com or 262-337-3312.
About Resource Innovation Institute: Advancing Resource Efficiency to Cultivate a Better Agricultural Future
Resource Innovation Institute (RII) is a non-profit organization whose mission is to advance resource efficiency to cultivate a better agricultural future. Founded in 2016 to address the resource impacts of cannabis cultivation, RII is extending its services to other energy-intensive horticultural sectors. Its PowerScore benchmarking platform represents the world’s largest dataset on indoor agriculture energy use. RII’s Technical Advisory Council, which includes a Policy Working Group and a Utility Working Group, is the leading multi-disciplinary body assessing the environmental impacts and best practices associated with cultivation resource issues. RII’s Board of Directors includes the American Council for an Energy Efficient Economy (ACEEE) and a former board member of the US Green Building Council. RII is funded by utilities, foundations, governments and industry leaders. Visit our website at ResourceInnovation.org. Follow us on LinkedIn, Facebook, Twitter and Instagram.
# # #
VIDEO: We Use An Exceptional Amount of Land To Grow Food For Sows. Vertical Farms Could Change That If We Used Them To Grow Cow Feed
While most other vertical farms focus on growing salad greens for city dwellers, the new system is designed to tackle another challenge: the environmental footprint of growing feed for livestock
[Photo: Grōv Technologies]
Inside a new tent-like building on a large dairy farm west of Provo, Utah, tall towers stacked with trays of wheatgrass grow food for the cows outside. While most other vertical farms focus on growing salad greens for city dwellers, the new system is designed to tackle another challenge: the environmental footprint of growing feed for livestock.
A single tower in the growing system, from a startup called Grōv Technologies, takes up a little more than 850 square feet on the ground. But it can grow as much wheat or barley grass as 35 to 50 acres of farmland, the company says. Right now, an inordinate amount of land in the contiguous U.S.—around 780 million acres, or 41% of the total area—is used to grow feed for farm animals, either on pastures or through growing crops. And the demand continues to grow. “The availability of arable land, especially for animal feed, is shrinking,” says Steve Lindsley, president of Grōv Technologies.
[Photo: Grōv Technologies]
In some areas, that means forests are being cut or burned down to make room for crops to feed cows or chickens. “There’s clearly an environmental benefit that we think can be profound when you think about deforestation around the world,” Lindsley says. Grōv’s technology also significantly saves water, using around 5% of what is used in conventional farming. Additionally, it can reduce the distance to transport animal feed—China, for example, which has been buying agricultural land all over the world to grow food for its own animals, including in the U.S., is one of the startup’s key markets. The company plans to sell its systems to farms raising dairy and beef cattle to grow feed directly for their own animals.
[Photo: Grōv Technologies]
The farm in Utah, called Bateman’s Dairy Farm, is the first to test the new technology. Inside the new building, 10 towers, each around 25 feet tall, are filled with wheatgrass. Everything is automated: A robot plants four pounds of seeds in each tray and then sends it into the system, where sensors monitor conditions to give the crop the light and water it needs until it’s harvested automatically. “In an average of six and a half days, we have the crop,” Lindsley says.
Grōv provides support, but the system is designed to operate on its own, without any additional labor needed from the farmer. The system is also designed to minimize operating costs. The startup’s custom lights, for example, don’t put out heat, avoiding the large air-conditioning bills that are necessary in some other indoor farms. (The company says that the system can also run on renewable energy, and it plans to reach net-zero emissions by 2025.)
In early tests with hundreds of cows in 2019, the dairy found that the feed was more nutritious than its standard feed; the cows ate less, helping save money while producing the same amount of milk. Grōv estimates that farmers can break even on their investment in the technology in three years. As climate change progresses, growing indoors can also help mitigate risk from increasing droughts, heatwaves, floods, wind storms, and other extreme weather conditions.
The technology isn’t intended to fully replace conventional farming, but to provide one portion of the mix of food that cattle eat. At the farm in Utah, the new pilot system will provide 15% of the food for around 2,000 cows. But even replacing a fraction of conventional farming has the potential to make a meaningful difference. (That’s especially true if some farmland could be reforested, helping suck up excess carbon from the atmosphere to fight climate change.)
Lindsley argues that the environmental benefits could help dairy and beef farmers compete in a world where an increasing number of consumers are turning to plant-based foods. “The industry can utilize this technology as a counterpunch, really, to some of the lab-based protein efforts or the competitive efforts that are trying to pull people away from beef and/or dairy products,” he says.
ABOUT THE AUTHOR
Adele Peters is a staff writer at Fast Company who focuses on solutions to some of the world's largest problems, from climate change to homelessness. Previously, she worked with GOOD, BioLite, and the Sustainable Products and Solutions program at UC Berkeley, and contributed to the second edition of the bestselling book "Worldchanging: A User's Guide for the 21st Century."
NYPA Collaborates On Shipping Container Project To Advance Indoor Farming & Increase Food production For Needy Western New York Families
A pilot project was launched Monday in Buffalo to help New York state advance indoor farming and increase the year-round production of fresh fruits and vegetables in areas where they are not readily available
November 9, 2020
Partnership with Electric Power Research Institute to help address challenges of decreased availability, affordability of fresh produce year-round
A pilot project was launched Monday in Buffalo to help New York state advance indoor farming and increase the year-round production of fresh fruits and vegetables in areas where they are not readily available. Through a research collaboration funded by the New York Power Authority’s environmental justice program and led by the National Electric Power Research Institute (EPRI), The project will study optimum growing in a shipping container farm environment and address environmental and energy impacts that could help reduce costs and expand crop production.
The demonstration will provide produce for FeedMore WNY nutrition programs, help address climate change in communities that host NYPA facilities, and support New York’s clean energy and greenhouse gas reduction goals by using this low-energy indoor farming method.
“The New York Power Authority is pleased to be part of this national collaboration with the Electric Power Research Institute that will improve indoor farming methods while supporting our neighbors in need in Western New York,” NYPA Chairman John R. Koelmel said. “Under Gov. Andrew Cuomo’s continued climate leadership, we will find new and sustainable ways to grow affordable and fresh produce all year while prioritizing New York state’s greenhouse gas reduction goals.”
NYPA is collaborating with EPRI to demonstrate and monitor the indoor production facility at FeedMore WNY’s offices on James E. Casey Drive in Buffalo. For the first year, the specially outfitted 40-foot shipping container, branded “Rooting for Our Neighbors,” will be used to harvest kale that will be distributed to food pantries and soup kitchens that rely on FeedMore WNY for nutritious food and support. Fresh kale, and kale dishes, also will be delivered directly to hungry community members served through its mobile food pantry and Meals on Wheels programs.
A press release stated, “Using shipping containers makes it possible to increase the availability and affordability of fresh fruits and vegetables year-round in urban and rural areas where they are not readily available. By growing indoors in a controlled, pesticide-free, 'sunless' environment, indoor farming uses far less water and land than conventional farming. Farms can be built anywhere, reducing both costs and carbon emissions from transportation of produce to consumers, and increasing food security. New York state’s Climate Act requires the state to reduce greenhouse gas emissions 85% by 2050 from 1990 levels.
“Indoor agriculture is essential to future food production, and we need to understand its implications for the electric power industry,” said Gil C. Quiniones, NYPA’s president and CEO. “NYPA is eager to demonstrate a replicable, sustainable indoor farming solution that helps to address climate change in the communities that host our facilities. If utilities have solid knowledge about how lighting, water use, and other systems impact plant production, we can be good partners in helping to provide food resources to disadvantaged communities in our respective regions through these innovative farming methods.”
State Agriculture Commissioner Richard A. Ball said, “This indoor farming project is a unique and creative way to support urban agriculture and to increase access to healthy food in our communities. Building on the work the state has been doing through initiatives like Nourish to deliver fresh foods to families in need, this pilot program will allow FeedMore WNY to provide local agricultural products year-round. I thank NYPA, EPRI and FeedMore WNY for their participation in this forward-thinking project, and look forward to the first harvest.”
NYPA is one of eight utilities nationwide to participate in a two-year EPRI study designed to help utilities better understand and engage in commercial-scale indoor food production, which is reliant on efficient energy and water consumption. Other demonstration sites are in Delaware, Tennessee, Minnesota, South Dakota, and Colorado. Through site/operator engagement and automated monitoring, researchers will evaluate how energy loads, water use, innovative technologies, rate design, and sustainability considerations vary across different facilities and locations. Other trackable data will include water consumption and reuse and the impact of seasonal climate variance on production and operations.
EPRI President Arshad Mansoor said, “Against the backdrop of increasing weather events and a global pandemic, there’s been an increasing appetite for indoor food production. EPRI engineers and scientists have been at the nucleus of this development, advancing technology to run container farm demonstrations across the country. This is a worldwide movement toward sustainable communities. Indoor agriculture also is an important part of efficient electrification, which is critical to enabling decarbonization throughout the economy.”
Tara A. Ellis, president and CEO of FeedMore WNY, said, “FeedMore WNY is incredibly excited for this opportunity to work with New York Power Authority and the Electric Power Research Institute in order to grow nutritious produce for distribution to our hungry community members, NYPA and EPRI are the true definition of good neighbors and we are so fortunate to have their support as we work to make sure our neighbors in need have access to nutritious food, including fresh produce.”
FeedMore WNY, the largest hunger-relief organization in WNY serving Cattaraugus, Chautauqua, Erie, and Niagara counties, is assisting thousands more community members than ever before, primarily due to the COVID-19 pandemic. As many as one in six individuals in FeedMore WNY’s service area may be at risk of hunger.
The press release explained, “Fresh fruits and vegetables are vitally important components of a healthy diet. However, for food-insecure community members, fresh produce can be challenging to access due to financial constraints, lack of transportation, and lack of nearby grocery stores, farmers’ markets or bodegas.
“Kale was chosen as the initial crop because of its high nutrient value and short harvest cycle. After the first year, FeedMore WNY will grow a variety of produce to benefit its food-insecure community members.”
The initiative is part of NYPA’s environmental justice program, which offers educational programs about clean, renewable energy and sustainability, and provides resources to meet the needs of underrepresented communities located near NYPA’s power assets. NYPA’s largest hydroelectric power plant – the Niagara Power Project – is located in Lewiston.
“NYPA uses its expertise and resources to help benefit residents who live and work in areas near our facilities,” said Lisa Payne Wansley, NYPA vice president of environmental justice and sustainability. “This indoor food production initiative aligns with and supports NYPA’s sustainability plan goals to demonstrate sustainable solutions to addressing climate change in local communities where we operate.”
Through its corporate responsibility efforts, the environmental justice program provides science, technology, engineering, and math (STEM) education, mentorship, and energy-efficiency initiatives to empower neighbors to make life choices that will improve the quality of their lives. Every year, the environmental justice team participates in “Rock the Block,” a one-day, annual event aimed at improving curb appeal in the South End of Niagara Falls, led by the Levesque Institute. Workshops teaching residents how to weatherize their homes are also offered to various community groups in Buffalo and Niagara Falls.
New York State Sen. Tim Kennedy said, "For years, FeedMore WNY has served as a critical resource for many, and that important role has only been magnified throughout the COVID-19 pandemic. Through this partnership, WNY families will have increased access to fresh, locally grown food, which will in turn fuel healthier communities and provide nutritious support to those who need it most."
Majority Leader Crystal Peoples-Stokes said, “This collaboration is a major step forward in bringing healthy food options, mainly fresh fruits, and vegetables, to some of our city’s food deserts. We thank the NYPA and the state for dedicating its expertise and resources to EPRI and FeedMore WNY to help advance year-round indoor farming in areas that need it the most.”
Mayor Byron Brown said, “Low-income communities, and especially Black and brown communities, have historically faced difficulties with food security and access to fresh, healthy fruits and vegetables. The COVID-19 pandemic has only heightened those challenges, either through a loss of income, decreased mobility or more limited access to supportive nutritional programs. Today's announcement of this new partnership is a bold step in helping to address these systemic problems. I am confident that this collaboration between Gov. Andrew Cuomo’s office, the New York Power Authority’s environmental justice program, the Electric Power Research Institute, and FeedMore WNY will help advance indoor farming in our community and further strengthen Buffalo’s year-round production of fresh produce in the neighborhoods with residents who have had the most trouble accessing them.”
Lead Image courtesy of the New York Power Authority
SANANBIO ARK, The Mobile Farm For All Climates That Supplies Communities With Fresh Local Food
SANANBIO, a leading vertical farming solution provider announces the availability of its climate-controlled mobile farm for growers globally
November 4th, 2020—SANANBIO, a leading vertical farming solution provider announces the availability of its climate controlled mobile farm for growers globally.
“3,300-4,400 lbs of cucumbers, 7,700 lbs of arugula, and 8,000 lbs of lettuce. These are the proven annual yields that we’re confident to announce,” said Zhan Zhuo, co-founder and CEO of SANANBIO, “We ‘produce’ turnkey farms and this one is mobile.” It adapts to any climate thanks to its thermal insulation systems with a thermal conductivity below 0.024w/(m·K). One of the mobile farms operated as usual in a coldness of -40℉ in northern China, sustaining local communities with local produces at a reduced carbon footprint. It is shocking to find that our food travel 1,500 miles on average before reaching our plate.
The CO2 generated, and the nutrients lost during the transportation, can’t be good for the planet or human beings. That’s why local food is advocated. “The ready-to-use farm is the solution we offer to regions where the environment is too harsh to support stable agricultural production,” said Zhan.
To streamline the farming experience, the designer simplifies the start-up procedures to a single plug-in motion: power it up through a connector on the exterior and then even hydroponic beginners are set to grow. Moreover, growers can monitor and control farm metrics simply by moving fingertips on their phone.
“By simplifying modern agriculture, we offer more farming opportunities for kids and urban dwellers. We have a mobile farm deployed in a Malaysian suburb where kids from the neighborhood frequent the farm for hands-on hydroponic experience. It’s a perfect bonding time when families go there to pick their own salad ingredients. As a Photobiotech company, we’re nurturing a new generation of growers,” said Zhan.
For more info about the mobile farm, please visit www.sananbio.com/ark.
About SANANBIO
SANANBIO is a joint-venture by Sanan Optoelectronics, one of the world’s largest LED manufacturers, and the Institute of Botany of Chinese Academy of Sciences, a leading institute in plant science. Comprised of LED experts and plant scientists, SANANBIO is able to provide simple CEA solutions for growers globally. The RADIX, a Reddot award winner, has been widely endorsed by growers in more than twenty countries.
Thrive Containers Launched Operations With Its New Intelligent Container Technology - Shipping Container Farm
Our vision is to not only bring accessibility to farming but to offer a great return on investment for the AgTech industry.”
Thrive Containers launched operations today with its new intelligent container technology, aiming to disrupt the commercial farming industry. COVID-19 and climate change have accelerated existing strains in global food accessibility and supply chains, highlighting the need to rethink the world’s agriculture systems.
Our founder and CEO Shannon O'Malley has been at the forefront of this change through six years of container farm innovation here at Brick Street! O’Malley observed “Thrive Containers is redefining shipping container farming technology.
Our vision is to not only bring accessibility to farming but to offer a great return on investment for the AgTech industry.” Thrive Container's farm system uniquely excels in software automation, customer experience ease of use, and adaptability engineered by industry-leading experts. The result is maximized, year-round crop growth, reducing up to 90% of freshwater resources used in traditional agriculture practices. Shannon Quotes
Thrive Launch
“Thrive Containers is redefining shipping container farming technology. Our vision is to not only bring more accessibility to farming but to offer a great return on investment for the AgTech industry.”
“We want to bring this cutting-edge technology to the masses, to build a farm whose technology is firmly centered on the grower experience.”
Ohio Container
“The Ohio Container is the first breakthrough container model that focusses on leafy greens and herbs providing industry leading yields to the shipping container farms market.”
“Rivers are the inspiration for our model naming convention. Since Thrive container technology supports cleaner, healthier waterways, we want to celebrate, acknowledge, and highlight our commitment to our planet.”
Industry Evolution
“The Agtech industry is currently situated where the .com legacy once was. We are in an industry that is in a race to define who the main players are.”
Investment opportunity
“In the Agtech industry, shipping container farming is wide open, with key competitors that are raising and looking for market share. Each competitor has its own unique business model and approach, focused on different paths to success. Our focus is decentralizing the commercial food system at the point of consumption while utilizing large scale grocers in minimal spaces.”
Supply chain
“By growing the highest producing yield containers, we are bringing production to the point of consumption to provide access to the masses. We are mobile and focused on the urban core. Vs competitors buying large acreage and trucking produce out.”
THE LINE-UP
Thrive Containers provide a multitude of container farm systems for all types of growing solutions. Our in house manufacturing continues to explore the endless possibilities of technology + agriculture.
The most efficient leafy green hydroponic container on the planet. Built for ROI, Ohio’s production efficiencies and low reliability on resources yield higher, while maximizing profit and planet.
COMING SOON: The most efficient micro green hydroponic container on the planet. Built for ROI, Yukon’s production efficiencies and low reliability on resources yield higher, while maximizing profit and planet.
COMING SOON: The most efficient cannabis/hemp hydroponic container on the planet. Built for ROI, Colorado’s production efficiencies and low reliability on resources yield higher, while maximizing profit and planet.
Thrive Container Website!
Follow us on Instagram @thrivecontainers
Click the link below to check out the Thrive website!
Linkedin
Twitter
America Is Hungrier Than Ever For Sustainable Food Systems. Can We Build Them?
In the spring of 2020, many small farms across the U.S. found themselves in a bittersweet predicament. Restrictions aimed at slowing the spread of the coronavirus were forcing restaurants — major buyers for the local farms that serve urban areas — to shut down
November 2, 2020
In the spring of 2020, many small farms across the U.S. found themselves in a bittersweet predicament. Restrictions aimed at slowing the spread of the coronavirus were forcing restaurants — major buyers for the local farms that serve urban areas — to shut down. The loss of these key customers might have wiped out many of these local growers, if not for another COVID-19-induced phenomenon: individual shoppers started calling — and calling — and calling.
"The farms we work with are seeing a huge spike in demand [for direct sales]," Dan Miller, CEO, and founder of the crowdfunding platform Steward, told me when we spoke by phone in early April. "But now they have to quickly switch their businesses to meet that demand." So Miller, who launched the platform in the fall of 2019 to provide funding to small, sustainably run farms — operations often underserved by traditional finance — soon found himself expanding Steward’s services to help these same farmers shift their business model.
Stories of small farms pivoting their operations on a dime were easy to find in the early months of the pandemic: these farmers worked overtime to meet customer demand, added services such as online ordering and home delivery, and jumped into action to prop up community food banks struggling to serve an influx of the newly unemployed. Compared to the industrialized and supersized food system most Americans live with — represented by rivers of wasted milk and COVID-19 outbreaks at meat-packing plants that killed more than 200 people — these distributed systems looked healthier, safer, and more environmentally sustainable than ever. They also looked more agile and resilient.
Crises often present an opportunity to reimagine current systems, so I wondered: Would that happen here, with food? Would the food consumption trends driven by the pandemic wind up as a paragraph in the history books — like the "victory gardens" of World War II — or could it lead to lasting change? And how do we transform this moment of crisis into a more resilient, sustainable, healthy, and just food system?
Crises often present an opportunity to reimagine current systems.
At GreenBiz Group’s virtual clean economy conference, VERGE 20, last week, speakers and participants addressed questions such as these, discussed how to make sure that these changes stick and identified what challenges stand in the way. During a session delving into lessons from the pandemic, panelists agreed that the No. 1 barrier to changing the current food system is financing.
"The financial services that are out there … are really not calibrated for the moment we’re in," said Janie Hipp, CEO of the Native American Agriculture Fund. "If we’re going to actually build an agile and resilient system going forward, then we have to invest in it."
One example of the financial challenges sustainable farms face comes in the form of crop insurance. If a farmer wants to transition a farm from conventional practices to organic or regenerative ones, costs are associated with that transition. However, insurance policies typically do not cover them, so the farmer is forced to take on the extra up-front costs and risk. The same holds true for traditional agriculture financing, developed for conventional farming. Loans are typically underwritten based on the equipment, inputs, volume, prices, and insurance coverage of conventional growers. These factors are different for organic and regenerative farmers, so the numbers often don’t work, resulting in loans being denied or unaffordable.
This increased access to capital could help scale the market, which hopefully would bring down the cost and make this more nutritious food more widely available, said Matthew Walker, managing director at S2G Ventures, a food systems-focused venture fund and mission investor.
"There’s a lot of work to be done to provide affordable nutrition … and allow those who are seeking to grow organic, or use any tech-enabled process that might be better for soil health, better for nutrition, to at least get started," he said.
This increased access to capital could help scale the market.
Making healthy food available in disadvantaged neighborhoods, where affordable, fresh vegetables are hard to come by, is the mission of the Green Bronx Machine, but founder Stephen Ritz — a VERGE keynote speaker — didn’t wait for systems change. Established in 2012, the program uses hydroponic and vertical farming technology at its indoor teaching farm at a South Bronx school, where kids learn how to grow and cook vegetables themselves.
Each week throughout the school year, the kids take home bags of groceries to their families. Green Bronx Machine also operates a "food for others" outdoor garden and summer youth employment program in the Bronx, which serves food-insecure families in the community. And it has various other partnerships and serves as a model for schools in other districts, including a program in more than 60 Chicago schools, sponsored by the foundation of Chicago Blackhawks captain Jonathan Toews, who joined Ritz on VERGE’s Building a Better Food System for America’s Cities panel.
Like the farmers who work with Steward, the Green Bronx Machine’s student farmers pivoted when the pandemic hit, Ritz said in his keynote.
"As COVID-19 brought the world to a standstill, it became the ultimate manifestation of three larger illnesses: racism; greed; and corruption," Ritz said. "And we found new ways to secure and distribute food to those who needed it most."
This has included providing weekly grocery delivery for 26 food-insecure patients at Memorial Sloan Kettering Hospital, who are recovering from cancer, and for 55 of the most vulnerable families in the Bronx, across a 26-mile route that includes walk-up buildings.
"The truth is children want to be part of the conversation. The truth is children don’t let differences divide them. The truth is children are smarter than you think," Ritz said.
As COVID-19 brought the world to a standstill, it became the ultimate manifestation of three larger illnesses: racism; greed; and corruption.
When New York was the epicenter of the pandemic — a place whereby May, the virus had killed more than 20,000 people, primarily in underprivileged neighborhoods such as the South Bronx — food grown by a bunch of kids was delivered to families who may not have eaten otherwise.
The Green Bronx Machine joined community farms, urban farms, and small family farms in offering a lifeline to their communities. They proved themselves resilient in a crisis, and their numbers are growing, but they remain a teeny, tiny part of the gargantuan American food system.
In 2017, there were 16,585 certified organic farms, a 17 percent increase from just a year earlier, according to the National Agricultural Statistics Service’s latest Organic Survey, released this month. These farms accounted for 5.5 million certified organic acres, an increase of 9 percent over 2016.
This impressive growth marks the continuation of a decade-long trend. And yet, certified organic acres still represent less than 1 percent of the total 911 million acres of American farmland. (Although I should add that the survey’s three-year lag does not provide an up-to-date picture, and farms that use organic or regenerative practices but have not been certified don’t get counted.)
The main challenges for these farms is getting the infrastructure and operational capacity in place to support a growing customer base.
Curious to see whether the direct sales demand Steward’s farmers saw in the spring was continuing to hold, I checked back in with Miller. By email, he told me that demand had held and offered an example from Fisheye Farms, an urban farm in Detroit. Fisheye, he reported, already has sold out their entire winter CSA and is fielding inquiries for spring. CSA stands for "community-supported agriculture," a system where customers buy "a share" of the farm. They pay a fixed rate to receive regular boxes of whatever’s in season. Every other week, from November through February, members of Fisheye’s winter CSA will receive spinach, kale, carrots, turnips, radishes, microgreens, and more. The cost is $300, or about $38 a week.
"The main challenges for these farms is getting the infrastructure and operational capacity in place to support a growing customer base," Miller said in his email. "Even the farmers with the most demand still need capital to run better, as they can’t finance everything they need just on cash flow."
In other words, to replicate and scale what these farms do, and build distributed food systems that are resilient, sustainable, healthy, and just, will take time, cooperation, and a lot of green.
Lead photo: by Oleg Demakov on Unsplash.
Infarm Raises $200 Million To Add “Farm” to Cities
heir environment-controlled and automated growing chambers grow food such as leafy greens inside the supermarket, so it’s fresh, without your food accumulating food miles
Infarm’s Israeli founders take on Berlin and the farm to table movement with high-tech farms.
Infarm, a company that grows fresh produce inside supermarkets, has recently announced a $170 million USD funding round to help the company expand across Europe. Their environment-controlled and automated growing chambers grow food such as leafy greens inside the supermarket, so it’s fresh, without your food accumulating food miles.
The company was founded by three Israelis in Berlin in 2013, and they announced this astounding investment achievement despite the Covid plague destroying global markets. Food, we understood, is something that must stay constant. The need for food which is grown locally, and available fresh now resonates at a time of uncertainty and the basic need for survival.
The company has raised $200 million USD total in their Series C round funding which was by LGT Lightstone, Hanaco, Bonnier, Haniel, and Latitude, Atomico, TriplePoint Capital, Mons Capital, and Astanor Ventures.
With a mix of equity and debt financing, the fresh capital brings Infarm’s total funding to date to more than $300 million, underscoring consumer and retailer appetite for Infarm’s approach to fresh, sustainable, and local food production in the wake of this year’s pandemic.
By 2025, Infarm’s farming fridge network is expected to reach more than 5,000,000 square feet to become the largest distributed hydroponic network in the world as it builds towards helping cities become self-sufficient in their food production. Competition includes Freight Farms in the US, and BrightFarms, also American.
“The coronavirus pandemic has put a global spotlight on the urgent agricultural and ecological challenges of our time,” says Erez Galonska, Co-founder and CEO of Infarm. His brother Guy Galonska is also a founder: “At Infarm, we believe there’s a better, healthier way to feed our cities: increasing access to fresh, pure, sustainable produce, grown as close as possible to people,” adds Erez.
The investment will be used to deepen the regional and local penetration of Infarm’s global farming network and complete development of Infarm’s new generation of vertical cloud-connected farms, capable of generating the crop-equivalent of acres of farmland and amplifying the diversity of produce currently available through vertical farming. Vertical farming is also known as hydroponic farming or controlled environment agriculture.
The technology has become developed and well-known over the years thanks to cannabis growers who used this energy-intensive and “stealth” mode of farming to grow cannabis with high concentrations of the active ingredient THC. When it was illegal to grow in Canada, young entrepreneurs were inspired by early blueprints from NASA and farming in space and found ways to set up a soil-less system in basements and closets. To their surprise, they could grow better quality cannabis, faster as inputs such as lighting, humidity, and nutrients could be tightly controlled.
And growing food became the next natural step for people who wanted to grow fresh food year-round even though it’s usually not cost-effective to grow tomatoes or lettuce this way unless you do it at scale.
Hydroponics and variations of it, using just water, a semi-solid coir medium or Styrofoam and/or with fish added, has become the promise for growing food in far-flung locations like Antarctica and food deserts where chocolate bars are available at bodegas, but fresh greens are not. This is according to mothers I have met in Harlem, New York. The hydroponic method is not that complicated at all in theory but in practice, it is hard to achieve good results without know-how in chemistry, engineering, and biology.
An integration of advanced engineering, software, and farming technology, the Infarm farms will save labour, land, water, energy, and food-miles, while contributing to a more sustainable food system, the company proposes.
Partnering with Aldi, Marks & Spencer, Sobeys
While companies like Farmigo founded in New York (also by an Israeli) wanted to put supermarkets out of business, in the past year Infarm has been working to keep them relevant and formed new partnerships with the world’s largest retailers, including Albert Heijn (Netherlands), Aldi Süd (Germany), COOP/Irma (Denmark), Empire Company Ltd (Sobeys, Safeway, Thrifty Foods – Canada), Kinokuniya (Japan), Kroger (United States), Marks & Spencer (United Kingdom) and Selfridges (United Kingdom).
With operations across 10 countries and 30 cities worldwide, Infarm harvests 500,000+ plants monthly, while using 99.5% less space than soil-based agriculture, some 95% less water, 90% less transport, and zero chemical pesticides. Today, 90% of the electricity use throughout the Infarm network is from renewable energy and the company has set a target to reach zero emissions from their production next year.
With the cost of lighting typically very high in hydroponics systems, I’d be curious to know how they will do that without buying carbon credits. Consider this Stanford research paper that mentioned the cost of hydroponic lettuce to be about 8KG of carbon compared to 150g if grown conventionally. The research is a few years old and certainly, there can be ways to improve energy efficiencies.
What organic farmers think?
Proponents of organic farming, regenerative agriculture, and permaculture don’t love hydroponics farming because it relies on petroleum-based fertilizers and nutrients as additives, and while there may be no or few bugs in the grow chambers, there is a risk of fungus and bacteria; in nature, there is always free natural sun (unless you are in Finland in the winter) and natural interactions between plant, soil; and even among small biota like mycorrhizal fungi which play a role in the uptake of micronutrients to the roots and the overall essence of what we call a plant. There is one school of thought that says the “organic” label can only be applied to soil-based farming. Lawyers are debating the issue now.
The answer will be somewhere in the middle. Like most things in life the middle way will help us. The dream is many one-acre regenerative farms to feed us healthily and to feed the planet too but meanwhile there is a gap. How do we feed everyone else who can’t afford to buy at Whole Foods?
We need to improve our local supply chain for food. When you live in a country like Israel, Egypt or Jordan with ample sun, growing food inside a supermarket fridge makes no sense, although hydroponics does. See this project in Jordan, funded by the USAID. Or the one that has changed lives in Harlem.
I had a hydroponics robotics venture (see this article on Bloomberg) and I took it to New York a few years ago and found myself running in circles trying to explain why eating local is good for the planet, it’s good for a circular economy that might one day be about survival. Venture Capitalists laughed at me. They said my technology and vision was a vitamin and not a bandaid –– “a nice to have” but not “a necessary to have”, especially in cities like New York. Then Covid thinking happened.
Here is what investors in Infarm say now (and kudos to the team who worked hard building physical farms and maintaining the pilots):
“We are excited to partner with the Infarm team to accelerate their urban vertical farm vision, ultimately creating a more sustainable food system for a growing population,” says Dharmash Mistry, Partner of LGT Lightstone: “With over $1bn of customer demand, partnerships with 17 of the top 50 global grocers, Infarm is set to revolutionise the market behind a unique ‘demand led’ modular business model.”
Let’s hope. Another Israeli called Benzi Ronen came from Silicon Valley and started a farm-to-table venture in New York and was on top of the world. He had just raised $26 million to grow Farmigo into the Amazon for fresh food and I spoke with him at one point when he warned me to stay in Israel and work there locally for a couple of years before moving stateside. That’s me in the biodome below, growing bok choy for future Martians on my roof in Tel Aviv. I didn’t listen.
I had a venture in robotics to help cannabis farmers (even Mars farmers grow cannabis in space – see this article in Fast Company) and city hydroponic farmers. Farmigo was trying to eliminate supermarkets, by connecting farmers to consumers at drop off points throughout the city. The model was valorous –– who doesn’t want the freshest farm picked veggies every morning? The modern CSA? And it supported local farming, just like what Michael Pollan wants us to do. And to compete with Amazon? Yes. Yes. Yes.
Farmigo raised millions and then the company’s vision to be the Amazon of fresh food could not compete with Amazon. Farmigo changed its business model and now sells software.
I saw the challenges of the business in supplying fresh food. The mechanics of the machines, the lack of willing labor, software needed, the logistics, the importance of food safety. The fungus, the bacteria. The good bacteria. The bad. The responsibility. The chemicals needed to feed the plants, to keep the systems “clean” and safe. So much is hard to control when you are talking about living things.
I always said that if hydroponics or farmers that come from Microsoft want to make city farming work the model will look like the cellphone industry: different players supplying various parts like Qualcomm, Verizon, 3M, Broadcom, and Texas Instruments does. Even to make iPhones work.
Can and will Infarm do it all?
“We see a massive demand in the market for sustainable, environment-friendly, and healthy food – and Infarm has just the right team in place to make this happen,” says Pasha Romanovski, Co-founding Partner of Hanaco Ventures.
More about Infarm
Founded in Berlin in 2013 by Osnat Michaeli and the brothers Erez and Guy Galonska, Infarm is dedicated to creating a future where local super fresh produce is available for everyone. The farms are placed in various locations in the city, like supermarkets, restaurants, and distribution centers, so that vegetables grow and are harvested close to the moment of purchase or consumption. People like Elon Musk’s brother Kimbal Musk has been doing this in New York with a project called Square Roots. They train young entrepreneurs to dream up all sorts of business models inside the shipping container farms built by Freight Farms.
Some in the VC world I have talked with question the viability of the business model of these containers. While it’s a nice idea it’s hard to get the return on the upfront investment.
But when it comes to specialty products and “farms” you can find the Infarm service model in all sorts of permutations in the United States. I got to spend some ample time in meetups with a pile of entrepreneurs building an urban farming project in New York. There I met Andrew Carter, now growing mushrooms in a warehouse in Williamsburg. There is also Farm.One which grows papalo, minutina and all the boutique and hipster greens any chef could dream up in the center of New York City. They deliver.
Lastly and most easily is to try out growing fresh greens at home without the supermarket, or less of the supermarket. I met the founder of Hamama when she was in Israel via MIT helping kids in Israel grow their own food using hydroponics at The Greenhouse. (After I wrote this story in 2008 <— kids from the US were writing me about how to donate their Bar Mitzva money to Noam Geva).
Over at The Greenhouse Camille had her head inside an aeroponics system she’d rigged up last time I saw her. She brought a few of her MIT geek friends over to my house in Jaffa and we talked about hydroponics changing the world. And now she helps people in the easiest way to grow microgreens at home. That’s a hyper simplified way to do hydroponics. She was one of the most inspiring people I met in hydroponics and urban farming.
In fact many in the business are. They are people who want to change the world. Have you met Henry?
Go out and meet someone, start a farm. Grow something. That’s how we change the world.
Now over to Infarm: good luck!