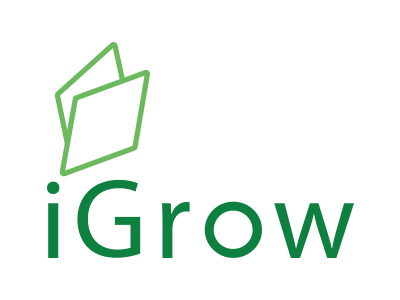
Welcome to iGrow News, Your Source for the World of Indoor Vertical Farming
AeroFarms: An Unproven Business With Enormous Risk
AeroFarms's mission is to grow the best plants possible for the betterment of humanity
June 13, 2021
Written by Jamie Louko
Spring Valley Acquisition Corp. (SV) APPHSVSVU
Summary
AeroFarms is a SPAC that is being brought to the market by Spring Valley Acquisition Corp. The deal was announced on March 26.
AeroFarms runs and operates vertical greenhouse farms. Unlike most greenhouses, AeroFarms' greenhouses take up little horizontal space, which allows them to pay less in expenses.
AeroFarms's mission is to grow the best plants possible for the betterment of humanity.
Currently, AeroFarms is not a buy, but it should be on a watchlist for investors to watch closely to see how well they can execute.
sompong_tom/iStock via Getty Images
Investment Thesis
AeroFarms (SV will become NASDAQ: ARFM) is a business that has high hopes, but with little edge from their other tech-savvy competitors, I struggle to see how they will be able to achieve the immense growth they are claiming. With poor financials and only $2.5 million in revenue, this business has not yet shown that it can achieve these expectations. Until AeroFarms can consistently show investors they are able to meet the guidance they set for themselves, it should be avoided by long-term investors.
SPAC Details
AeroFarms is being brought to the market by Spring Valley Acquisition Corp. This was announced on March 26. AeroFarms is expected to receive $317 million in cash from the deal, and the deal is expected to close in the second quarter of 2021, which would assume that AeroFarms would branch off into their Nasdaq listing, ARFM, within the month. However, SPACs usually take 4-6 months from announcement to go public, which would pin AeroFarms around July-September. September is on the longer side of this estimate, and considering estimates from Spring Valley and AeroFarms, a September target is likely inaccurate. I would expect that AeroFarms will go public sometime between late June and late July.
This process would estimate AeroFarms' equity value to be roughly $1.2 billion, which is slightly lower than another competitor that recently SPAC'ed in 2021, AppHarvest (NASDAQ: APPH). After the SPAC process, AeroFarms expects to nominate two of Spring Valley's existing directors, Debora Frodl and Patrick Wood, III, to its Board of Directors. Now that we have the basic details of the SPAC out of the way, let us dive into what AeroFarms does and why they are coming to the public markets.
AeroFarms' Mission
AeroFarms is a vertical greenhouse that is trying to change how Americans create sustainable food. This Certified B-Corp uses vertical farming, AI, and biological sciences to improve the way fresh produce is grown and distributed locally and globally. Their product, Dream Greens, "wins on quality, flavor, taste, and texture," and they sell in many major distributors like Whole Foods, ShopRite, Amazon Fresh, and FreshDirect.
AeroFarms was founded in 2004, and it became a B Corp in 2017. AeroFarms is trying to solve issues brought on by the megatrends of population growth, water scarcity, arable land loss, and climate change.
Source: Analyst Day Presentation
Currently, AeroFarms focuses on leafy greens, primarily bok choy, kale, micro broccoli, and arugula. AeroFarms' reason for existing today is to meet the need to solve issues brought on by climate change and other environmental issues. Due to strong droughts and water scarcity, water will be needed more and more if our world continues to use water at the pace we do today. AeroFarms uses 95% less water than traditional farms, which allows them to be less reliant on these problems, as well as open up water that would have been used to go towards other needs. This lack of water has also caused droughts, which can, in turn, lead to food shortages. Because AeroFarms' greenhouses are not as reliant on water, as well as the fact that they are indoors, these droughts are not as impactful to AeroFarms' business.
Source: Analyst Day Presentation
Simply put, AeroFarms sees great problems with our future if we continue to farm the way we do today, and they are trying to preemptively solve these problems.
Both co-founders are still involved, one as the CEO and the other as the CMO. Considering that AeroFarms was founded in 2004, it is clear that the founders are very dedicated to the vision and the mission of AeroFarms, and they will likely stay with the business for the long haul. If they founded this business simply to make a quick buck, the founders likely would have moved on already instead of dedicating 17 years of their lives to this business. This is a very good sign in my book. However, management is still extremely important for a business like this. If management were to cash out within a year of coming public, that would show me that the founders were not as dedicated as I thought, which would lower my conviction in this business to a more bearish conviction.
Being a SPAC, they were allowed to project revenues and estimates out to 2026. Therefore, it should come as no surprise that this company sees massive growth potential. They expect that vertical farming alone will be a $12.7 billion business by 2026, growing at over 22% 5-year CAGR. They also expect global fresh produce to become a $1.8 trillion industry by 2023, and leafy greens alone will contribute $108 billion to that large TAM. Clearly, this sort of farming is going to grow due to increases in demand (as the population increases). I have some skepticism as to whether it will be this large come 2023, but there is no doubt that the industry will be growing.
Quite frankly, it is near-impossible to correctly estimate how big this market will get. If it gets as big as AeroFarms claims it will, then AeroFarms will definitely have room to fight for market share and they will have vast opportunities to grow and become an amazing business. However, a 22% 5-Year CAGR in vertical farming is definitely aggressive. I worry that AeroFarms may be estimating on the extreme side, and that vertical farming will not grow that fast. If this is the case, then AeroFarms' potential will noticeably decrease, and it would make it a much less interesting investment.
Also, I am a firm believer that the world is going to need more greenhouses as it becomes harder to grow outdoors due to climate change and other sub-optimal weather conditions. There have been many recent droughts and other disasters that make it hard to count on reliable crops from outdoor farms, and greenhouses can minimize the impact that Mother Nature is having on our crop yields.
The sustainability of greenhouses is also a major benefit to society. The water usage is drastically lowered in greenhouses like AeroFarms, and so are emissions. These negative impacts are greatly reduced compared to traditional farms, so AeroFarms is not only helping create a sustainable supply of food, but they are also doing in a very environmentally friendly manner.
Their mission and drive to make our world better is the reason that I am writing about this stock today. I believe that AeroFarms and companies like it are trying to solve a major future problem for our world, and I am happy to give them attention for it. As I have mentioned a few times already, they have tons of competition. This competition is fierce, and it definitely has the potential to make AeroFarms fight for this market share.
Competition Concerns
As I have mentioned many times already, AeroFarms has some steep competition in the greenhouse space they are playing in. Although no major competitors are actively engaging in vertical farming (excluding one), they still have plenty of competition in the sustainable farming space.
Probably the company that first comes to mind is AppHarvest. I have written an article that dives deep into AppHarvest, but I will go over it quickly for anyone who is not extremely interested in AppHarvest. AppHarvest is a business that is based out of Kentucky and Appalachia. Unlike AeroFarms, which primarily focuses on growing leafy greens, AppHarvest's current focus is tomatoes. AppHarvest has plans in place to expand into leafy greens in a major way in the next 5 years, however. With their 60-acre farm (and 9 more facilities on the way), AppHarvest is planning to ramp up production in a major way.
AeroFarms is not expected to grow as fast as AppHarvest. Currently, the only things they are building is an R&D farm facility in Abu Dhabi, and another farm in Danville. The Abu Dhabi facility plans on breaking ground this month. They do, however, have a total of 3 farms, their biggest and only cash-generating farm bring their vertical farm headquarters in Newark, New Jersey. On April 29, 2021, AeroFarms announced that they are breaking ground and starting construction of their second farm, located in Danville, Virginia. Their third farm is the new facility in Abu Dhabi.
Clearly, both of these businesses are growing at a very fast rate. and there is no doubt that it will continue. Although they are not directly competing currently, they will likely be competing in the leafy greens area quite soon. In terms of technology, they are using similar kinds of tech, although I believe that AppHarvest has a very slight edge.
Source: Investor Presentation
The main thing that gives AeroFarms an edge over AppHarvest is how they commercialize their product. One of the weaknesses I have with AppHarvest is how they sell their product. Simply, AppHarvest partners with a distributor, Mastronardi, who then is the sole buyer of AppHarvest's product and they distribute it out to larger companies. This results in a customer concentration for them. AeroFarms does not do this, but rather they partner directly with large businesses like Whole Foods. I like AeroFarms' distribution model much more than AppHarvest's.
I would be remiss if I did not briefly mention some of the private competitors. First, Bowery Farms, another vertical farming company that is private, is a major threat to AeroFarms. First, they are roughly double the size of AeroFarms. Second, they are operating in the same rough geographical region that AeroFarms is selling in. Bowery operates in New York, with plans to expand into Pennsylvania.
Source: Bowery Website
Bowery has 2 operating farms compared to just one for AeroFarms, and they are building one more today. These farms are in New Jersey and Maryland, which is quite intrusive on AeroFarms' market. Bowery also is planning on expanding into berries, tomatoes, and carrots, while they currently grow leafy greens. Due to greater size, they have been able to reach better economies of scale than AeroFarms, so their prices are actually lower currently. Bowery also sells in 850 grocery stores. Like AppHarvest and AeroFarms, Bowery is using a similar structure of technology that enables sustainability and limits pesticides in their farming.
Another strong (and private) competitor is Gotham Greens. They operate a very unique business model: instead of building large facilities, Gotham builds its greenhouses on the rooftops of its customers. This enables extreme freshness for its customer and nearby customers.
Source: Gotham Greens Website
Gotham Greens obviously has more greenhouses built and producing crops than any of the businesses mentioned. They have 8 greenhouses, encapsulating the Northeast, as well as the West of the U.S. Currently, they are operating and selling in 40 U.S. states. Freshness is clearly Gotham's edge over AeroFarms, however, their business model can be both a blessing and a curse. Gotham is limited to small greenhouses, whereas large, 60-acre greenhouses like AppHarvest's are much more cost-effective. AeroFarms sits in the middle of these sizes for its facilities.
All of these businesses have their own edge, and it is still unknown which will make the greatest difference. However, farming is by no means a winner-take-all market. There will be many winners in this space, and potentially even all of these competitors could be successful along with AeroFarms. To quickly summarize, each company has benefits that separate them from the pack. AppHarvest has its central location (Kentucky), Bowery has strong economies of scale due to its size, and Gotham has its ability to deliver the freshest products. Now, I am going to take a look at what makes AeroFarms special compared to some of its competitors.
The Edge
Compared to traditional farming, AeroFarms' technology and sustainability is what separates them. Due to the nature of greenhouses, AeroFarms can have tight control on conditions that the plants experience, so AeroFarms can create the most optimal environment for the plants to grow faster, and be of the highest quality. They also excel at full automation of their farm. Everything from seeding to packaging their produce is fully automated.
Source: Investor Presentation
AeroFarms uses data science and a fully-controlled technology platform that enables it to better understand plants and optimize farms while improving quality and reducing costs. Simply, they are analyzing plant biology to optimize the growth of these plants.
Teams of plant scientists develop custom algorithms to precisely define the conditions each plant needs to thrive. This understanding allows AeroFarms to optimize performance, cultivate new varieties, improve quality, lower costs and optimize efficiency.
Source: Investor Presentation
This understanding of the biology of plants is extremely important for AeroFarms. One of the primary benefits they have over traditional farming is that they can create the best-looking and tasting produce. Understanding exactly how plants thrive and do this is crucial. If they were to expand into different products, such as berries or tomatoes, they would have to do this again. This knowledge may take time to learn, and if they are testing environments to see which one produces the best crops, it could take a while. However, once learned, this can be easily replicated in dozens, if not hundreds, of other facilities. Once AeroFarms learns that leafy greens thrive under (and these numbers/metrics are not accurate but for the example) 75-degree heat with high sun exposure and light water levels, they can replicate those conditions in whatever facility they grow leafy greens in. This intellect is somewhat time-consuming to learn, but once it is learned, it gives the company a massive advantage.
Through the integration of these disciplines, AeroFarms achieves up to 390 times greater productivity per square foot annually versus traditional field farming while using up to 95% less water and zero pesticides. Therefore, due to the productivity, clearly the knowledge that they learned from the data and plant biology is paying off.
Source: Investor Presentation
Another thing that most traditional famers do not have is data. AeroFarms can create lasting network effects and benefit greatly from scale if they can efficiently use and act on data they receive from their facilities.
Lastly, AeroFarms has been creating a strong library of IP since its founding. With over 250 invention disclosures and a vast library of data collected over 15 years of operations, AeroFarms is continually improving its systems to understand plants at unprecedented levels and solve agriculture-related supply chain issues. Currently, AeroFarms has 15 granted patents, with 38 more pending approval. They also have 46 designated trade secrets. The vast amount of trade secrets show that they want to keep its operations relatively unknown to its competitors, so they do not elaborate much on what those secrets entail. However, their strong number of patents show that they have actual technology that is working effectively and it is independent to them. No other greenhouse or direct competitor could do the same thing AeroFarms is doing in some of its capacities.
AeroFarms plans on bringing these trade secrets to future facilities, with plans to start construction on three farms, none of which have been announced or actually planned yet, by the start of 2023. AeroFarms also sees strawberries as a major growth avenue. Strawberries are highly cyclical due to growing conditions and they carry lots of pesticides, both of which AeroFarms is trying to solve in the farming universe.
AeroFarms has a clear edge above traditional farming, just as AppHarvest, Gotham, and Bowery do. Where I struggle to find an edge is between the technology of these businesses. After looking at the technology for all of these businesses, the results seem to be the same: more efficient production and productivity, better tasting produce, less use of water, greater sustainability. Also, all of these businesses have some sorts of patents that make their business stand out. Personally, I believe that it is not the technology that gives AeroFarms an edge over its competition, nor do I think it is vertical farming (itself).
Vertical farming alone does not provide any greater benefits over non-vertical farms in terms of quality of produce. However, I believe the optionality that comes from vertical farming when it comes to growth is the edge for AeroFarms. Unlike AppHarvest, where they need 60 acres of land to have a 60-acre farm, AeroFarms only needs a small portion of that land. With even a 48-towered farm, AeroFarms could theoretically create the same sized farm in a fraction of the horizontal size of one of AppHarvest's farms. This is beneficial in one primary way: AeroFarms would be able to go to places AppHarvest would not. For example: AeroFarms' HQ is in Newark, New Jersey. AppHarvest could never find a large enough space in that city to build a farm, but AeroFarms can.
Simply, AeroFarms has the agility in its farms to travel to cities and more urbanized geographies that competitors like AppHarvest cannot. This can give them an edge, for if both AppHarvest and AeroFarms are selling in the same city, but AeroFarms actually has a greenhouse in the city, grocers would likely sell more AeroFarms' products because of locality and freshness.
Financials and Valuation
Financially, AeroFarms is quite lacking. AeroFarms has over $48 million in cash and no long-term debt, which is wonderful, but that is just about where the good news stops. Their net revenues were $2.5 million for the FY 2020, yet their cost of goods sold was almost $8 million, resulting in a gross profit loss of $5.4 million. As they continue to scale, at least for a while, this number can get worse too. AeroFarms is spending a whopping $17 million in SG&A compared to only $1 million in R&D. This is exactly the opposite of what I want to see in a business. I want their R&D expenses to be high, because it shows me that they are heavily investing in the future of their business.
All of this combines for a grand net income loss of over $25 million. However, as most SPACs do, they are projecting monstrous growth.
Source: Investor Presentation
They are expecting their current one farm to grow to 16 farms and their revenue to grow to $553 million (from the $4 million today) by 2026. They also expect their gross margins to be roughly 50% by 2026, which is high for any farming business. EBITDA margin is also expected to reach a whopping 35%. AeroFarms is clearly spinning an optimistic story with these growth projections, and I am not sure how confident I am that they can get that done. Transitioning from negative to positive gross margin is going to be hard enough for them, and I think it will take at least until 2023 for them to do that. Therefore, the fact that they believe that they will have margins of 50% just 3 years after turning their gross profit positive is a bit of a stretch to me. I have no doubt that this company will grow, but I do doubt that they will be able to grow at such a high rate.
Also, they project that they will be able to get 3 new farms up and running and producing every single year until 2026. That is extremely optimistic growth. AeroFarms only broke ground on 2 farms recently, and they are expecting to build both of those up to production capacity in 1.5 years? That is quite aggressive. Not to mention that they would still need to find another area to build a farm, build it, and start producing crops in that same time frame. That is an extremely tall order, just to meet 2022 estimates. Then they have to do that again, and again, until 2026, just to meet guidance. Not exceed, just meet.
Clearly, I am quite skeptical about how rapidly they will be able to grow. Personally, I do not think they will be able to do this, and for me, a company that does not meet their own expectations is not worth an investment. For me, missing expectations gives me a lack of confidence in the ability of management, and therefore I lose trust. AeroFarms has not missed any expectations yet, but they have a tall order ahead of them, and any small slip in any form would likely cause consistent misses on growth estimates.
Considering that this business has not become its own public company yet, the valuation metrics are slim. Also considering that this business is gross profit negative, operating income negative, EBITDA negative, and net income negative, the only valuation metric available is Price-to-Sales Ratios.
Valued at $1.2 billion, AeroFarms has $2.5 million in sales (let's say $3 million to be super generous). At these metrics, AeroFarms' P/S Ratio would be 400. This is absolutely ludicrous. Even at AppHarvest's insanely optimistic revenue estimates, their forward 2023 P/S Ratio is over 22.
It does not help that I am skeptical on AeroFarms' own estimates for the success of their business, but 22x forward sales is quite an expensive multiple. At those high forward multiples, I would stay far away and make sure they execute and (hopefully) beat their expectations. If they can meet or beat their revenue guidance, maybe these valuations can be justified, but until they prove my skepticism wrong, this company is extremely highly valued for no good reason at all.
Why I'm Not Buying Today
Today, this business should not be touched with a 10-foot pole. The reasoning for this ultimately comes down to two concepts: Their technology is not drastically different than its direct competitors, and their financial situation is simply miserable. The first one is going to be hard to fix, which is why I am likely to remain bearish on the business, but the second one could change within the next 2-3 years. In which case, I would likely take another look at this business and rethink my thesis. For the meantime, while they are still gross profit negative, investors should definitely stay away.
Lastly, I must mention again that the valuation and AeroFarms' guidance are insane. AeroFarms' guidance assumes some of the largest growth we have seen in any modern day company, within only 5 years. These growth estimates might be accurate if they were placed out 7-10 years in the future, but 5 years for this business to go from its first sales to fully-scaled economics is highly unlikely. Even if we assume these drastic growth rates, their valuation is still quite high.
Investors should stay away from AeroFarms for now, but watch it closely for the next 2-3 years. As this business operates, we can watch to see how they prove themselves out. If they can consistently meet their own guidance and expectations, then AeroFarms' might be investment material. Until, however, they have some time to prove themselves out, AeroFarms is merely a company with little edge that is hopeful to grow at astronomical rates. Today, this business is not worth the high risk of investment.
This article was written by
Long Only, Growth, Long-Term Horizon, Tech
Contributor Since 2021
I am a college student who has found a deep thirst for learning and investing. Being very young, I have leaned toward very long-term investments and growth stocks, primarily in tech. I do, however, love consumer goods companies as well. Currently, I am studying International Business and Economics.
Disclosure: I am/we are long APPH. I wrote this article myself, and it expresses my own opinions. I am not receiving compensation for it (other than from Seeking Alpha). I have no business relationship with any company whose stock is mentioned in this article.
Airgarden Uses NASA-Designed Technology To Give Sustainable Produce An Easy Win
Airgarden, Australia’s very first vertical soilless gardening system, is making use of the technology for the benefit of anyone obsessed with sustainable design – or for those who just want access to more home-grown produce, faster
Does Your Home Benefit From The Use
of Astronaut Technology?
No. Let’s Change That, Shall We?
Airgarden, Australia’s very first vertical soilless gardening system, is making use of the technology for the benefit of anyone obsessed with sustainable design – or for those who just want access to more home-grown produce, faster.
The game-changing gardening system is said to sprout 5 times more home-grown produce, 3 times faster, with 95% percent water. What’s more, is that the Airgarden takes up 1sqm of space so your petite inner-city apartment is no excuse to not get your green thumb on.
“The idea stemmed from wanting to grow fresh produce that was good for us, and the environment while living in the inner city,” said co-founder Prue Bauer, who started Airgarden with her brother Tom. “We were sick of throwing out so much of what we bought and wanted quality produce that didn’t cost an arm and a leg. More and more people are thinking about what they are putting in their bodies and the cost of organic food was unsustainable long term, so we knew there has to be a better solution.”
NASA-developed aeroponics technology – which has been approved by horticulturalists – is typically used to grow plants in space. Tom and Prue wisely repurposed that to allow anyone to grow their own urban farms with no digging, weeding, or watering required.
Even if the game-changing potential for giving life to your inner-city apartment doesn’t win you over. The money-saving potential surely will. With Airgarden, budding home-gardeners can sprout up to 150 different types of fruits and vegetables to feed a family of four each week. That is a significant cut to the weekly grocery run, and an easy way to incorporate more lush, leafy greens in your diet.
Airgarden is already being picked up in some sustainably-minded restaurants across Australia, including Halcyon House’s Paper Daisy restaurant, Manly Boathouse, and Wild Canary. Undoubtedly that list is going to be growing in no time, especially given as it’s a way for a restaurant to grow their own on-site garden without actually having the space (or rooftop) to do so.
USA: WASHINGTON STATE - Ummah Sustained Agroecology Center - Long Time! We Have Been Getting Things Started Here On The West Coast. We Opened!
Ummah Sustained AgroEcology Center - U.S.A.C. features Washington States 1st Certified Jr Master Gardener, Youth Agroecology, and Discover through Hydroponic K8 Farm School programs
Ummah Sustained Agroecology Center, a unique opportunity for your K-8 child to be creative, and confident while building lasting friendships. Our youth development program nurtures a child’s instinctive curiosity through informal exploration learning experiences
Ummah Sustained AgroEcology Center - U.S.A.C. features Washington States 1st Certified Jr Master Gardener, Youth Agroecology, and Discover through Hydroponic K8 Farm School programs.
Our Certified Urban Permaculture center houses three hydroponic systems including Freight Farm, a greenhouse, raised beds, community garden, small session classroom, and Afrocentric resource library.
We offer volunteer opportunities through WSU Extension Snohomish County 4-H and AmeriCorp.
Vertical Roots Opens Third Indoor Hydroponic Container Farm
Vertical Roots, a vertical farming company which grows its leafy greens in repurposed shipping containers year-round, has opened its third indoor farm in Atlanta, Georgia, reducing produce transportation and expanding access to fresh, locally-grown leafy greens.
14-June-2021
By Mary Ellen Shoup
Vertical Roots, a vertical farming company which grows its leafy greens in repurposed shipping containers year-round, has opened its third indoor farm in Atlanta, Georgia, reducing produce transportation and expanding access to fresh, locally-grown leafy greens.
To Continue Reading, Please Click Here
Source Courtesy of Food Navigator-usa.com
What Is Aeroponics?
Aeroponics is an advanced variation of hydroponics where plants are suspended in the air; their roots dangle down and are periodically misted with water from a timed sprinkler system connected to the main nutrient reservoir
How Aeroponics Works,
Types, And Pros, And Cons
June 14, 2021
Aeroponics is an advanced variation of hydroponics where plants are suspended in the air; their roots dangle down and are periodically misted with water from a timed sprinkler system connected to the main nutrient reservoir. This soilless growing method is best for plants that need more oxygenation since aeroponic roots aren’t hampered by dense soil or thick growing mediums. Depending on the plant and specific type of aeroponics system, the grower typically uses little to no growing media at all.
In aeroponics, a specially designed pump and spray system is submerged into the nutrient-water solution and timed to release short mists of water to the plants’ roots throughout the day. Because roots will have more access to oxygen and humidity in an aeroponics system, they often grow two to three times larger and yield far bigger numbers than traditional farming methods. Generally, it also uses less water over time since excess water not absorbed by the roots is drained back into the nutrient tank, and the mist allows for higher concentrations of nutrients with less liquid.
Most of the plants that work with hydroponics will thrive in an aeroponics system, from leafy greens and herbs to tomatoes, cucumbers, and strawberries, but with additional perks. Because of the exposed root qualities of aeroponics systems, root vegetables like potatoes that would otherwise be ill-suited for hydroponics systems will flourish as they’ll have more room to grow and be easier to harvest.
Neznam / Getty Images
Aeroponics in Space
NASA began experimenting with aeroponics as early as 1997, planting adzuki beans and seedlings aboard the Mir space station in zero gravity and comparing them to controlled aeroponic gardens on Earth treated with the same nutrients. Amazingly, the zero gravity plants grew more than the plants on Earth. Aeroponics can not only provide long-mission deep-space NASA crews with fresh food, but it also has the potential to provide them with fresh water and oxygen.
How Does Aeroponics Work?
The seeds are planted somewhere they’ll stay in place, such as pieces of foam, pipes, or foam rings, which are then wedged into small pots or a perforated panel with a tank full of nutrient solution below. The panel elevates the plants so they’ll be exposed to the natural (or artificial) light and circulating air, providing light on the top and nutrient mist on the bottom, and an enclosure around the roots helps keep the moisture in. A timed pump rests inside the tank or reservoir, pumping solution up and through spray nozzles that mist the roots, with excess liquid draining straight down through an outflow chamber back into the reservoir. At the next timed interval, the entire cycle starts again.
Neznam / Getty Images
Nutrients for aeroponics systems, like hydroponics, come packaged in both dry and liquid forms. Depending on the plant and growth stage, primary nutrients may include nitrogen, phosphorus, and potassium, while secondary nutrients can range from calcium and magnesium to sulfur. It is also important to consider micro-nutrients, such as iron, zinc, molybdenum, manganese, boron, copper, cobalt, and chlorine.
In aeroponics systems where the nutrient solution is continuously recycled, the pH measurements need to be taken regularly to ensure that enough nutrients are getting absorbed into the plants.
Natural Aeroponics
Aeroponics occurs in nature, specifically in more humid and wet regions like the tropical islands of Hawaii. Near waterfalls, for example, plants will grow vertically on the rocks with their roots openly hanging in the air, the spray from the waterfall moistening the roots under the right conditions.
Types of Aeroponics
There are two types of commonly used aeroponics: low pressure and high pressure. Low pressure is the most used by home growers since it is low cost, easy to set up, and its components are easier to find. However, this type of aeroponics often uses a plastic spray nozzle and a typical fountain pump to deliver nutrients, so the droplet sizes are not exact and can sometimes waste more water.
High-pressure aeroponics, on the other hand, distributes nutrients through a highly pressurized nozzle that can deliver smaller water droplets to create more oxygen in the root zone than low-pressure techniques. It is more efficient, but much more costly to set up, so it tends to be reserved for commercial production rather than hobbyists.
High-pressure systems typically mist for 15 seconds every 3 to 5 minutes, while low-pressure systems may spray for 5 minutes straight every 12 minutes. Experienced growers will adjust the spraying interval according to the time of day, watering more frequently at night when the plants are less focused on photosynthesis and more focused on taking up nutrients. With both types, the reservoir solution is kept at a temperature range between 60 F and 70 F in order to maximize the absorption rate of the plant. If the water becomes too hot, it is more susceptible to algae and bacteria growth, but if it gets too cold, the plants may start to shut down and not take as many nutrients as they would at a more optimal temperature.
Aeroponics at Home
While some growers choose to use horizontal aeroponic systems similar to traditional soil farming, vertical systems can save more space. These vertical systems come in all shapes and sizes, even small enough to be used on a back porch, balcony, or even inside an apartment with the appropriate lighting setup. In these smaller systems, misting devices are placed on top, allowing gravity to evenly distribute the nutrient solution as it spreads downward.
Neznam / Getty Images
Aeroponics kits are available to make the setup process easier for beginners, but it is also possible to design and build your own system at home, similar to hydroponics, with tools found at most local gardening stores. Due to the complicated and expensive nature of high-pressure aeroponics, it is always prudent for beginners to start off with a low-pressure system before working their way up to more technical operations.
Fun Fact
The first recorded use of aeroponics happened in 1922 when B.T.P. Barker developed a primitive air plant-growing system and used it to research plant root structure in a laboratory setting. By 1940, researchers were frequently using aeroponics in plant root studies, as the dangling roots and lack of soil made it much easier to observe changes.
Pros and Cons
One of the most significant advantages of aeroponics systems is the fast and high crop yield and the fact that it uses the least amount of water over time compared to hydroponics and aquaponics. Roots are exposed to more oxygen, helping them absorb more nutrients and grow faster, healthier, and larger. Also, the lack of soil and growing medium means that there are fewer threats of root zone diseases.
On the flip side, aeroponic system chambers are constantly being sprayed with mist, keeping them wet and prone to bacteria and fungi; this can be remedied by cleaning and sterilizing misters and chambers regularly.
Affordability Factor
Studies show that the cost of growing a tuber (such as potatoes, jicama, and yams) using aeroponics is about one-quarter less than the cost of a conventionally grown tuber.
Due to the circular nature of the watering system and the higher nutrient absorption rate, aeroponics uses considerably less water than similar farming systems. Aeroponic equipment is also easier to move and requires much less space (nurseries can even be stacked on top of each other like a modular system). In a study comparing lettuce growth aeroponics, hydroponics, and substrate culture, results showed that aeroponics significantly improved root growth with greater root biomass, root-shoot ratio, length, area, and volume. The study concluded that aeroponics systems may be better for higher-valued crops.
surabky / Getty Images
Because the plants aren’t submerged in water, aeroponics is completely dependent on the misting system. If anything malfunctions (or in the event of power outages), then the plants will quickly dry up and die without water or nutrients. Seasoned growers will think ahead and have some sort of backup power and misting system waiting in storage in case the primary one fails. The system’s pH and nutrient density ratio is sensitive, and will require plenty of hands-on experience to understand how to properly balance them; as there is no soil or media to absorb the excess nutrients, proper knowledge about the perfect amount of nutrients is essential to aeroponics systems.
Lead photo: surabky / Getty Images
Eco-Friendly Smart Farms Based On Nutrient Solution Recirculation
UV sterilization and microbial stability analysis used to recycle nutrient solution; proposed method minimizes the use of fertilizers and water by hydroponic farms
15-JUN-2021
UV sterilization and microbial stability analysis used to recycle nutrient solution; proposed method minimizes the use of fertilizers and water by hydroponic farms
NATIONAL RESEARCH COUNCIL OF SCIENCE & TECHNOLOGY
The development of new urban agriculture technologies, such as vertical and smart farms, has accelerated rapidly in recent years. These technologies are based on hydroponic cultivation in which plants are grown using nutrient-rich solutions rather than soil. Approximately 20-30% of the nutrient solutions used during hydroponic cultivation are discharged without being absorbed by the crops, and because most farmers in South Korea do not treat the discharged solutions, hydroponic farms contribute significantly to environmental pollution.
This problem can be reduced if hydroponic farms use a recirculating hydroponic cultivation method that reuses the nutrient solutions after sterilizing them with ultraviolet (UV) light, instead of discharging them. However, two main issues complicate the implantation of such recirculation systems. First, the potential for diseases and nutrient imbalances to develop owing to microbial growth in the recycled nutrient solutions must be eliminated. Second, the initial investment required to set up a recirculating hydroponic cultivation system is often prohibitive, costing hundreds of millions of Korean won per hectare.
However, a new study conducted by researchers at the Korea Institute of Science and Technology (KIST) proposes a method that can stably manage the microbial population in recirculating hydroponic cultivation systems. The research team, led by Drs. Ju Young Lee and Tae In Ahn of the Smart Farm Research Center, KIST Gangneung Institute of Natural Products, conducted an integrated analysis of the microbial growth characteristics by constructing a model that simulates the flow of water and nutrients, and the inflow, growth, and discharge of microorganisms in recirculating and non-circulating hydroponic cultivation systems. Their simulations revealed that the microbial population in recirculating hydroponic cultivation systems can be controlled by adjusting the UV output and the water supply. On the contrary, in non-circulating hydroponic cultivation, the microbial population fluctuates considerably depending on the amount of water used, increasing sharply if there is too little water.
KIST researchers are experimenting with a circulating hydroponic cultivation system. Credit: Korea Institute of Science and Technology (KIST)
High cost has restricted the use of UV sterilization systems in hydroponic farming in Korea And prompted the research team to develop their own UV sterilization system, with further studies underway to commercialize this system as an economical alternative to imported systems.
The results of the study have already received strong interest: the rights to the operation and management software technology for recirculating hydroponic cultivation has been acquired by Dooinbiotech Co., Ltd. for an advance fee of 80 million won (8.5% of the operating revenue), while an agreement is in place with Shinhan A-Tec Co., Ltd. for the advanced recirculating hydroponic cultivation technology for an advance fee of 200 million won (1.5% of the operating revenue). Commercializing the recirculating hydroponic cultivation system is expected to reduce fertilizer costs by approximately 30~40%, which equates to 30 million won per year based on a 1-hectare farm.
Commenting on the envisaged impacts of the study, Dr. Ju Young Lee said, "The developed system makes the transition to eco-friendly recirculating hydroponic cultivation systems an affordable option for many more farmers." Dr. Tae In Ahn added, "We are also developing software and operation manuals to guide farmers in managing the nutrient balance in the solutions to increase the number of farms using the recirculating hydroponic cultivation system."
Lead photo: THE INTEGRATED MODEL DESCRIPTION. view more
CREDIT: KOREA INSTITUTE OF SCIENCE AND TECHNOLOGY(KIST)
###
The study was supported by the Ministry of Agriculture, Food, and Rural Affairs (Institute of Planning and Evaluation for Technology in Food, Agriculture, and Forestry) and the Innovative Smart Farm Technology Development Program of Multi-agency Package. The research results are published in the latest issue of the Journal of Cleaner Production (IF: 7.24, ranked in the top 6.9% by JCR), a highly respected international journal in the field of environmental science.
Disclaimer: AAAS and EurekAlert! are not responsible for the accuracy of news releases posted to EurekAlert! by contributing institutions or for the use of any information through the EurekAlert system.
CANADA: The Value of Hyper-Local Produce
At Yellowknife Co-op, produce is grown steps away from the store in a container farm!
The hyper-local food trend is more than just a fad: there’s a reason that hyper-local food is catching on in a big way. If you’re thinking about growing hyper-local food, it’s important to understand the value of the product and its market position.
At Yellowknife Co-op, produce is grown steps away from the store in a container farm!
BUT FIRST, WHAT IS HYPER-LOCAL FOOD?
Where does that ‘local’ head of lettuce you pick up from the grocery store actually come from? The Canadian Food Inspection Agency (CFIA) defines ‘local food’ as being grown in the province where it’s being sold, or within 50km of the border. But hyper-local food is even more local than being from the same province or being Canadian-grown. It is usually grown within the same town or city, or a short distance from where it’s being sold (sometimes even right behind the store!).
BENEFITS OF HYPER-LOCALLY GROWN FOOD
LOWER FOOD MILES
Hyper-local produce is usually grown within the same town or city, or a short distance from where it’s being sold.
As consumers are becoming more and more aware of the environmental impact of our food choices, the demand to lower food miles is also growing. A food mile can be thought of as the distance that food travels from the grower to the consumer. As a metric, it helps to assess the environmental impact of the foods we consume. A 2012 study showed that on average, 30% of food is imported in Canada, leading to annual emissions of 3.3 million metric tonnes of CO2.
Growing food hyper-locally can result in significantly lower food miles (and as few as zero food miles!) in both urban centres and rural communities. This reduces the carbon footprint of what you eat.
SUSTAINABLY GROWN
Growing hyper-locally in a hydroponic farming system has further benefits. Water in a closed hydroponic system is captured and reused, resulting in 90% less water use, and 95% less land than conventional farming.
TRACEABLE FOOD CHAIN
Growing hyper-local is completely traceable. This means you know exactly what’s going into your product. There are no synthetic pest control products, less risk for E.Coli, and a shorter supply chain to manage.
FRESHER PRODUCE WITH A LONGER SHELF LIFE
Growing food hyper-locally also means fresher produce and a longer shelf-life. Instead of wilting in a truck for hundreds of kilometers, hyper-local produce is shelf-ready immediately. This has a marked effect on the quality, as most produce loses 30 percent of nutrients just three days after harvest.
Life Water Gardens, a container garden project in Norway House Cree Nation, sells locally-grown produce at the Northern Store. Click here to learn more about the project and hear from its growers!
“When you get your hands on the fresh produce and taste it, you know it’s a good thing for your community in general. It’s really easy to get excited and pumped about [this project].” - Ian Maxwell from Norway House.
“When you get your hands on the fresh produce and taste it, you know it’s a good thing for your community. It’s really easy to get excited and pumped about [this project].”
— Ian Maxwell, co-manager of Life Water Gardens
WHERE IS HYPER-LOCAL PRODUCE POSITIONED IN THE MARKET?
For growers, it’s important to keep in mind that hyper-local food isn’t competing with foreign produce that you typically find in grocery stores. Between locally-grown vs imported food, the wholesale price for foreign produce is cheaper than local produce.
Keep in mind that grocery stores buy produce at wholesale prices, which means that they may buy produce from you at a certain cost, and then sell it with a 30% margin added to the price. When you walk into a grocery store and see produce being sold for $4.99, the reality is that the grocery store-bought it for $3.50 and added a mark up to the final price to help cover their costs of operations.
To find price-compatible products for market research in your area, look for products that will match your future products, such as living lettuce, other hydroponic greens, and other hyper-local, organic produce. Growcer greens belong in the hyper-local, value-added produce category.
GETTING STARTED WITH HYPER-LOCAL FOOD
Growing hyper-local food has many benefits: not only is it fresher, healthier, and better for the planet, it can also be a profitable investment for growers. When crafting your financial projections, keep in mind the value of hyper-local produce and where it sits in the market.
Interested in learning more about our hyper-local hydroponic growing systems? Find out more.
Is A Vertical Farm Cost Effective To Build And Operate?
A common question we’re often asked is a vertical farm cost effective to build and operate? There is no categorical answer to this complex question, which often requires a detailed feasibility study to resolve.
Author: Robert Colangelo.
Founding Farmer at Green Sense Farms Holding, INC.
A common question we’re often asked is a vertical farm cost-effective to build and operate? There is no categorical answer to this complex question, which often requires a detailed feasibility study to resolve.
The answer Starts With The 4 Cs -
Crop, Capacity, Climate, and Capital Budget.
Crop: What is the intended crop and how many varieties will be grown? At this time vertical farms can economically grow leafy greens (lettuces, baby greens, herbs, and microgreens), starter plants, and cannabis. To grow a cultivar well its best to design a farm with individual grow rooms where set points can be optimized to the monocrop. Many customers ask us to build farms that can grow a wide range of crops. We suggest specializing in growing large volumes of a few crops, that you can grow well and build a brand. This will also make production more efficient increasing the profitability.
Capacity: What is the desired output and frequency of harvest? The answer to this question is key to sizing a farm design. Understanding the production schedule and how many crop rotations a farm will hold will assist in laying out the farm. Capacity is also key to calculating the unit production cost. The bigger the farm typically the lower the unit cost.
Climate: One of the advantages of a vertical farm is that it can be built anywhere from the cold-dry climate in the South Pole to the hot- humid climate in Southeast Asia. The more humid the climate the more expensive mechanical equipment will be required to control Temperature and Relative Humidity. A good farm design can take into consideration the outside cool-dry climate and use it to reduce capital and operating expenses. In addition, cooler drier climates tend to have less bugs which will reduce operating costs when it comes to Integrated Pest Management (IPM) programs.
Capital Budget: A rule of thumb is that if you spend more on capital expense then you will reduce your operating expense. A well-built farm that is designed to optimize crop growth will lower the daily operating cost. To do this it greatly helps to have an anchor customer identified, define the crop (s) that will be grown, the harvest frequency/delivery and how it will be packaged so that these variables all be factored into the farm design.
Many other factors play a role in setting and building a farm. This includes location, automation, and labor. The 4C’s will get you off to a good start and will allow the development of an initial financial proforma so that you can predict the size of the farm, output, and the capital required to build and operate the farm profitably. I have learned that sometimes the best projects are the “ones not done.” Building a farm too big or too small can be a disaster. Starting backwards to first identify and understand the customers’ needs is a good way to begin. With adequate research and planning a vertical farm can be built to operate profitably and be a project worth doing!
VIDEO: Can An Indoor Smart Garden Beat Outdoor Gardening? We Tested It
Can smart gardens really grow delicious vegetables inside your apartment? WSJ asked Timothy Hammond, an urban gardener, and educator in Houston, to test out Rise Gardens
Can smart gardens really grow delicious vegetables inside your apartment? WSJ asked Timothy Hammond, an urban gardener, and educator in Houston, to test out Rise Gardens hydroponic smart garden to see how the vegetables compare with his own outdoor garden.
Photo: Ben Hallock for The Wall Street Journal
MIT Engineers Have Discovered A Completely New Way of Generating Electricity
A new material made from carbon nanotubes can generate electricity by scavenging energy from its environment
By ANNE TRAFTON
MASSACHUSETTS INSTITUTE OF TECHNOLOGY
JUNE 7, 2021
MIT engineers have discovered a way to generate electricity using tiny carbon particles that can create an electric current simply by interacting with an organic solvent in which they’re floating. The particles are made from crushed carbon nanotubes (blue) coated with a Teflon-like polymer (green). Credit: Jose-Luis Olivares, MIT. Based on a figure courtesy of the researchers.
Tiny Particles Power Chemical Reactions
A new material made from carbon nanotubes can generate electricity by scavenging energy from its environment.
MIT engineers have discovered a new way of generating electricity using tiny carbon particles that can create a current simply by interacting with liquid surrounding them.
The liquid, an organic solvent, draws electrons out of the particles, generating a current that could be used to drive chemical reactions or to power micro- or nanoscale robots, the researchers say.
“This mechanism is new, and this way of generating energy is completely new,” says Michael Strano, the Carbon P. Dubbs Professor of Chemical Engineering at MIT. “This technology is intriguing because all you have to do is flow a solvent through a bed of these particles. This allows you to do electrochemistry, but with no wires.”
In a new study describing this phenomenon, the researchers showed that they could use this electric current to drive a reaction known as alcohol oxidation — an organic chemical reaction that is important in the chemical industry.
Strano is the senior author of the paper, which appears today (June 7, 2021) in Nature Communications. The lead authors of the study are MIT graduate student Albert Tianxiang Liu and former MIT researcher Yuichiro Kunai. Other authors include former graduate student Anton Cottrill, postdocs Amir Kaplan and Hyunah Kim, graduate student Ge Zhang, and recent MIT graduates Rafid Mollah and Yannick Eatmon.
Unique properties
The new discovery grew out of Strano’s research on carbon nanotubes — hollow tubes made of a lattice of carbon atoms, which have unique electrical properties. In 2010, Strano demonstrated, for the first time, that carbon nanotubes can generate “thermopower waves.” When a carbon nanotube is coated with layer of fuel, moving pulses of heat, or thermopower waves, travel along the tube, creating an electrical current.
That work led Strano and his students to uncover a related feature of carbon nanotubes. They found that when part of a nanotube is coated with a Teflon-like polymer, it creates an asymmetry that makes it possible for electrons to flow from the coated to the uncoated part of the tube, generating an electrical current. Those electrons can be drawn out by submerging the particles in a solvent that is hungry for electrons.
To harness this special capability, the researchers created electricity-generating particles by grinding up carbon nanotubes and forming them into a sheet of paper-like material. One side of each sheet was coated with a Teflon-like polymer, and the researchers then cut out small particles, which can be any shape or size. For this study, they made particles that were 250 microns by 250 microns.
When these particles are submerged in an organic solvent such as acetonitrile, the solvent adheres to the uncoated surface of the particles and begins pulling electrons out of them.
“The solvent takes electrons away, and the system tries to equilibrate by moving electrons,” Strano says. “There’s no sophisticated battery chemistry inside. It’s just a particle and you put it into solvent and it starts generating an electric field.”
“This research cleverly shows how to extract the ubiquitous (and often unnoticed) electric energy stored in an electronic material for on-site electrochemical synthesis,” says Jun Yao, an assistant professor of electrical and computer engineering at the University of Massachusetts at Amherst, who was not involved in the study. “The beauty is that it points to a generic methodology that can be readily expanded to the use of different materials and applications in different synthetic systems.”
Particle power
The current version of the particles can generate about 0.7 volts of electricity per particle. In this study, the researchers also showed that they can form arrays of hundreds of particles in a small test tube. This “packed bed” reactor generates enough energy to power a chemical reaction called an alcohol oxidation, in which alcohol is converted to an aldehyde or a ketone. Usually, this reaction is not performed using electrochemistry because it would require too much external current.
“Because the packed bed reactor is compact, it has more flexibility in terms of applications than a large electrochemical reactor,” Zhang says. “The particles can be made very small, and they don’t require any external wires in order to drive the electrochemical reaction.”
In future work, Strano hopes to use this kind of energy generation to build polymers using only carbon dioxide as a starting material. In a related project, he has already created polymers that can regenerate themselves using carbon dioxide as a building material, in a process powered by solar energy. This work is inspired by carbon fixation, the set of chemical reactions that plants use to build sugars from carbon dioxide, using energy from the sun.
In the longer term, this approach could also be used to power micro- or nanoscale robots. Strano’s lab has already begun building robots at that scale, which could one day be used as diagnostic or environmental sensors. The idea of being able to scavenge energy from the environment to power these kinds of robots is appealing, he says.
“It means you don’t have to put the energy storage onboard,” he says. “What we like about this mechanism is that you can take the energy, at least in part, from the environment.”
Reference: “Solvent-induced electrochemistry at an electrically asymmetric carbon Janus particle” by Albert Tianxiang Liu, Yuichiro Kunai, Anton L. Cottrill, Amir Kaplan, Ge Zhang, Hyunah Kim, Rafid S. Mollah, Yannick L. Eatmon, and Michael S. Strano, 7 June 2021, Nature Communications.
DOI: 10.1038/s41467-021-23038-7
The research was funded by the U.S. Department of Energy and a seed grant from the MIT Energy Initiative.
Vertical Roots Expands To Atlanta, Partners With Two Wholesalers
The company partnered with two of the leading Southeastern produce suppliers, Collins Brothers Produce BB #:128652 and Phoenix Wholesale Foodservice BB #:134241, to place the farm directly at their facilities
June 11, 2021
CHARLESTON, S.C., June 10, 2021 /PRNewswire/ — Vertical Roots, the largest hydroponic container farm in the U.S. sustainably growing fresh leafy greens year-round, opened its third indoor farm in Atlanta, Georgia this June.
The company partnered with two of the leading Southeastern produce suppliers, Collins Brothers Produce BB #:128652 and Phoenix Wholesale Foodservice BB #:134241, to place the farm directly at their facilities.
The new Atlanta farm site will eliminate the need for produce transportation to the distributor and allow Vertical Roots lettuce to be delivered to local customers the same day it’s harvested.
Located within the Atlanta State Farmers Market, this is phase one of the company’s Atlanta expansion. With farm production underway, Vertical Roots Georgia Grown™ lettuce will be available in grocery stores in July 2021.
Crisp, sweet, tender, or buttery, Vertical Roots lettuces are nutritious, pesticide-free, and come in a wide variety of flavors, colors, and textures for culinary masterpieces and everyday meals. With long lasting freshness, produce is in the hands of consumers within one to three days of being harvested and has up to a 21-day shelf life.
Vertical Roots’ mission is to revolutionize the ways communities grow, distribute, and consume food. Farming directly at distribution hubs is a part of Vertical Roots’ distinctive strategy to eliminate a massive leg of produce transportation in order to reduce emissions and provide communities with fresh, locally-grown produce.
The new Atlanta farmsite will reduce produce transportation by an estimated 300 miles per delivery and will help meet the company’s retail demand that services thousands of grocery stores across the Southeast and Mid-Atlantic, as well as restaurants, universities, and schools.
“A large part of our mission is to grow food as close to the point of consumption as possible, and this farmsite accomplishes just that,” said Andrew Hare, co-founder, and general manager of Vertical Roots. “The Collins family are esteemed produce industry leaders for three generations, and we’re ecstatic about the unique grower-supplier partnership that we’ve cultivated.”
David Collins, President of Collins Brothers & Phoenix Wholesale Foodservice, said, “At Collins Brothers and Phoenix Wholesale, we’ve had the privilege to work with dedicated farmers across the country for decades. We’re thrilled to partner with Vertical Roots as they bring an innovative way of farming to the agriculture industry. We look forward to this relationship as we share a like-minded mission in providing our customers with high quality, fresh, local produce.”
Vertical Roots’ state-of-the-art indoor farms are manufactured from upcycled shipping containers at the company’s headquarters in Charleston, SC. The farm containers made their way to Atlanta on June 8, where farmers started seeding and transplanting to produce Vertical Roots lettuce within weeks.
A small footprint with a large output, the new farm will produce half a million heads of lettuce this year. Each 320-square-foot container maximizes the growing space with 3,400 plants per harvest, and up to 17 harvests per year.
Vertical Roots farms operate with the highest globally recognized food safety standards, eliminating the need for pesticides of any kind.
An AmplifiedAg, Inc.® company, Vertical Roots operates farms with proprietary software and technology. The farms don’t rely on soil, use up to 95% less water and grow crops 25% faster, compared to traditional farming methods.
About Vertical Roots:
An AmplifiedAg, Inc. company, Vertical Roots is the country’s largest hydroponic container farm and is revolutionizing the ways communities grow, distribute and consume food. Sustainably-grown indoors and pesticide-free, Vertical Roots leafy greens are fresh, clean, nutritious, and delivered to your local grocery store within one to three days of being harvested. Vertical Roots produce is available at thousands of leading grocery stores in 12 Southeastern states, educational institutions, restaurants, and other food service organizations. Vertical Roots operates farms in Charleston, S.C., Columbia, S.C. and Atlanta, Ga.
Tagged greenhouse, lettuce, vertical farming
FOR SALE - Surplus Turnkey Propagation Equipment
We have surplus equipment available that will allow you to plug and play so that you can begin sowing seeds, germ, and nurse your starter plants to transplant into the field, greenhouse, or vertical farm
We have surplus equipment available that will allow you to plug and play so that you can begin sowing seeds, germ, and nurse your starter plants to transplant into the field, greenhouse, or vertical farm. Great for year-round propagation of plants, vegetables, or cannabis. This is a low-cost way for you to begin growing, all you need is water, electricity, and a room.
$10,000 Seeding Line
Seeder Seederman GS3-8 ft, Needle Seeder with sowing kit and dibbler for 105 and 72 cell propagation trays. Compressor & hose, and coco coir blocks available
The GS3-HD automatic Needle Seeder was developed with the larger growing operation in mind. The GS3-HD machine is easy to operate it can be mastered in less than a day. The GS3-HD is capable of direct seeding into bedding flats and pots up to 4" square.
- 100 % Pneumatic - Requires 5 cfm / 80 psi compressed air source
- 8ft Machine size 96"L X 36"W X 72"H
- Weight approx 200 lbs
- Aluminum and stainless-steel construction (where possible)
- Dibble bar
- Vibrating seed pan
- Seed collector
- Air blow gun for cleaning
- Oversize air filter
- Adjustable leveling feet
- Adjustable guide rails
- Two sowing kit included – 105 cell and 72 cell
- Can sow up to 60 trays per hour
$7,500 Germ /Nursery Equipment
This equipment will fit in a 15 L x 15 W x 15 T room and can germ up to 1600 plantlets at a time. With climate control system and LED lights, the room can be used as both a germ room and a nursery.
$1,000 2- Towers with 5 levels each, enough for 160 - 1020 propagation trays
Unarco white power coated, tear drop, quick release pallet racking
4 - 12 ft uprights
20 - 8ft beams
20 - wire mesh decks
$500 500-gallon water tank with two pumps (for each tower)
$250 Reverse Osmosis System
$500 1-ton AC unit and Dehumidifier
$250 1 greenhouse, electric heater fan
Finned steel tubular heating element.
Internal manual reset thermal cut-out.
Chord for hard-wire installations.
Base with wall, floor, or ceiling mount.
Temperature control thermostat with 35F to 85F range.
10' air throw, 262 CFM.
5,600/4,200 Watts. 240/208 V. Single phase, 19,000/14,000 maximum BTUs.
$500 Timer with sensor to control T and RH
$3,000 30-GE Horticulture LED grow lights with connectors
Light intensity for typical indoor farming applications
P66 rated and UL wet rated for easy watering and cleaning
Daisy chain end to end making installation easier
8 ft. light bar
Uniform light for even plant growth
Operating Environment: 0°C to +40°C
L90/36000 hours per TM-21
5-year limited warranty
$1,500 20- plastic grow tubs, with drains, can hold 16 -1020 propagation trays
For more information, please contact:
Robert Colangelo at robert@greensensefarms.com
How UAE Produce Is Taking Over The Dining Table: 'We Are Growing All This On Our Doorstep'
Local farms are reporting a rise in demand, while Atlantis, The Palm resort has introduced an initiative to put UAE produce on its restaurants' tables
Local farms are reporting a rise in demand, while Atlantis, The Palm resort has introduced an initiative to put UAE produce on its restaurants' tables
Oasis Greens is a hydroponic farm located in the Jebel Ali free Zone. All photos by Antonie Robertson / The National unless otherwise mentioned
The concept of a “farm tour” is not what it once was.
Instead of the smell of open mud and fertilizer that I used to equate with a farm, I’m standing inside a pristine, temperature-controlled room that contains rows of herbs and leafy greens stretching out to the ceiling.
I am at Oasis Greens, one of many hydroponic, vertical farms to have cropped up in Dubai over the past few years. In this high-tech environment, seeds are planted into foam, which is placed in a solution that provides plants with all the nutrients they need, while LED lights overhead mimic the rays of the run.
The process involves no messy soil or pests and, by default, no need for pesticides either, while 90 percent less water is used than required by traditional farms. The result is sustainably grown, organic and local produce – from varieties of lettuce (be it butterheads and icebergs) to kale, rocket, and bok choy.
Why buy UAE-grown fruits and veggies?
Oasis Green hydroponic farm, located in Jebel Ali Free Zone. Antonie Robertson / The National
Whether it’s a hydroponic or traditional farm, there are indisputable benefits of opting for local over imported produce, which is being noticed by both consumers and big brands.
Among the latter is Atlantis, The Palm, which has launched a sustainability initiative titled the Atlantis Atlas Project.
One of the cornerstones of this campaign is a pledge to give diners access to dishes that are made with locally sourced and organic ingredients, grown and harvested in the UAE. Kelly Timmins, director of conservation, education and corporate social responsibility at the hotel, says the reason for this is two-fold.
“One of the key focuses for Atlantis is to look at increasing our use of local suppliers and vendors as part of our commitment to drive the whole local economy."
She says using local produce is better for the environment as it reduces freight and the carbon footprint involved with bringing in goods from across the world.
Plants are grown in foam rather than soil in hydroponic farms like Oasis Greens. Antonie Robertson / The National
“We are trying to see how we can source perishable products responsibly. Sustainability is a journey and to get there we need the involvement of our community,” she explains.
To procure fresh ingredients on a daily basis, Atlantis, The Palm has teamed up with Fresh on Table, which works as a facilitator between UAE farms and consumers. The company, which launched in Dubai in 2019, takes orders from hotels, stores and customers online, and co-ordinates with farms to ensure that the product is harvested, packaged and delivered the next day.
According to commercial manager Garima Gambhir, the company has grown month-on-month, and currently works with more than 1,000 farms, as well as big hotel groups.
Home-grown company Fresh on Table supplies products from farms to consumers. Supplied
“Chefs realise that local produce is just fresher and going to last longer on the shelf, as opposed to something that has, say, been imported from [the Netherlands] and passed through three days of transit before reaching the kitchen,” she says.
The pandemic has also had an invariable role to play in the rising demand for local produce.
“When borders and hotels started closing last year, the supply food chain was disrupted. With distributors unable to fulfil contracts from international suppliers, we were able to pitch in because everything was local, reliable, and could be picked up from a farm and delivered in a few hours,” says Gambhir.
Oasis Greens currently grows varieties of lettuce, leafy greens and microgreens. Antonie Robertson / The National
Local farms have also witnessed a spike in demand over the past year. Nikita Patel, founder of Oasis Greens, says despite the pandemic, business has been good, with a notable rise in online orders.
“Everyone has been at home, cooking. And even though we didn’t have a lot of tourists come in, residents weren’t leaving, either,” she says.
“I think the pandemic made people realise that food security isn’t a theoretical thing. In a lot of countries, people were having issues with grocery items running out, but the UAE did a very good job ensuring that didn’t happen. Over the past year, more companies are looking inwards and seeing how they can source local. We are just riding the wave.”
Hydroponic farms in the UAE
At UNS Hydroponic, custom LED lights mimic the rays of the sun, helping plants grow. Antonie Robertson / The National
Oasis Greens grows approximately 12 to 15 types of herbs and leafy greens, and has started cultivating microgreens. “The aim is to get into fruits and vegetables, too,” says Patel. “We want to grow cherry tomatoes, chillies and more.”
Within the industrial area of Al Quoz, meanwhile, grows one of the largest, most lush indoor vertical farms in the region. UNS Farms is home to 16 varieties of leafy greens and 16 varieties of micro greens across a space of 5,600 square metres.
During a tour, executive director Mehlam Murtaza asks us to dip our feet in a solution to ensure we don’t track any crop-destroying bacteria or germs inside, before explaining how different elements can affect the growth of plants.
“Our LED lights are a custom design with a special spectrum. Each colour actually has a different effect on the crop – they can widen the leaf size, make them longer or have another indirect effect,” he says.
The nutritional value of the plant remains unchanged, though, with a lot depending on the quality of the seeds used. The seed also plays a role in the taste – at USN Farms, I’m given two types of basil leaves, Thai and Italian. Despite the fact that both varieties are grown in the UAE, the Italian version is subtle in taste and smell, while the Thai is sharper.
UNS Farms in Al Quoz is spread over 5,600 square metres. Antonie Robertson / The National
“We have just scratched the surface about what we can do,” says Murtaza. In the future, research and development may be able to further tweak the taste of plants, he adds. "Who knows what's next? Maybe cotton-candy-flavoured herbs."
With a number of perks of buying local, it does beg the question: why haven’t hotels been doing this all along?
Murtaza says it’s only in the past couple of years that vertical farms have developed to deal with the volume they need. Even then, the maintenance and power required to run hydroponic farms means only certain crops can be grown at financially feasible rates.
Locally 'farmed' seafood in the UAE
Fish Farm in Jebel Ali grows organic and regular salmon, sea bass, sea bream, yellow tail kingfish and hammour. Antonie Robertson / The National
Supporting local goes beyond leafy greens. While the UAE is blessed with an abundance of seafood, there is still a reliance on imports.
That's something home-grown company Fish Farm is aiming to change. Launched in 2013, the company identified the most in-demand fish species being imported and sought to change this by growing them within the country. It currently produces organic and regular salmon, sea bass, sea bream, yellowtail kingfish, and hammour.
“It’s all part of building our food security,” says chief executive Bader bin Mubarak. “At the moment, less than 10 percent of the fish is locally acquired. We want to be able to cover the entire UAE market.”
The company plans on doing this with the help of three facilities: a caged farming facility in Dibba, a hatchery in Umm Al Quwain, and a land farming facility in Jebel Ali.
At the facility in Jebel Ali, Mubarak explains how juveniles and eggs were first sourced from different parts of the globe to ensure the right genetics.
“But since then, we have been hatching our own fish eggs,” he says. The Fish Farm was the first establishment in the world to grow Atlantic salmon on land, from eggs, Mubarak says.
Fish Farm has recreated ideal marine conditions for various species of fish. Antonie Robertson / The National
Business development manager Edmund Broad agrees that it is all about growing and harvesting seafood in the most sustainable manner possible.
“One of the biggest problems with the seafood industry is the pressure it puts on wild fish stocks, through commercial hunting using huge nets. We are a substitute for this. By growing fish on land in a controlled and secure environment, we are not taking anything from the sea. We’re leaving the oceans alone.”
The farm has recreated the ideal environments required by fish, many of which stem from cold-water countries, such as Scotland and Iceland. The fish swim in an area with appropriate salinity, currents, temperature, pH level, and even lighting.
“We’ve recreated the ideal marine conditions suitable to each species: the Atlantic for the salmon, the Pacific for the yellowtail kingfish, the Gulf for the hammour and the Mediterranean for the sea bass,” explains Broad.
The farm currently produces 3,000 metric tonnes of fish per year. “By 2030, we want 50 per cent of seafood consumed to be produced within the country,” says Broad.
From farm to table
UAE residents can get a taste of these sustainable and local ingredients in some of the best restaurants in the country. Thanks to its sustainability pledge, nine of Atlantis, The Palm's signature restaurants are serving dishes with ingredients grown and harvested in Dubai.
Locally hand picked mushrooms, pecorino and truffle at Bread Street Kitchen. Courtesy Atlantis, The Palm
Guests can tuck into locally produced burrata from Bread Street Kitchen or an organic salmon carpaccio from Seafire Steakhouse. Hakkasan is offering dim sum with locally handpicked chestnut mushrooms while Nobu has a crispy hand-picked shiitake mushroom truffle salad.
Ronda Locatelli, The Shore, Wavehouse, and White Restaurant are some other restaurants offering dishes with sustainable ingredients.
Seven-day dry-aged organic Atlantic salmon, grown in the UAE, is available at Seafire Steakhouse. Courtesy Atlantis, The Palm
Raymond Wong, chef de cuisine at Seafire Steakhouse, says the difference between imported and local ingredients is staggering.
“As a chef, an import order is always challenging as you need to place it three to four days in advance for your produce to come in time. But with this initiative, we can order just a day in advance from sustainable farms in Dubai and the produce is as fresh as it can be.”
He hopes this will encourage other restaurants and hotels to follow suit. “I think it will bring a lot of awareness. A lot of people don’t even know we are growing all this on our doorstep.”
June 13, 2021 07:48 AM
Click & Grow 25 Is An Efficient, Self-Monitoring Indoor Garden
“I started the company with a dream to make fresh food available and accessible for everyone and with the Click & Grow 25, we finally made it happen in a sustainable way,” said Mattias Lepp, founder, and CEO of Click & Grow
Written by Dawn Hammon
June 9, 2021
In a world struggling to find balance between busy lifestyles and healthy living, Click and Grow 25 aims to offer an easy-to-use way to grow organic food inside your home.
The smart indoor garden only takes up as much space as a microwave, yet with stacking trays, you can grow fresh produce for one person, two people or an entire family. With such a compact design, anyone can incorporate the Click & Grow 25 into their apartment, home or office.
The system is intuitive and does most of the work for you. Simply select your proprietary biodegradable Smart Soil plant pods, which are similar to the design used in single-serve coffee machines. Each pod is pre-loaded with seeds and soil. Once planted, the built-in technology takes over, monitoring the growth of leafy greens, fruits, and herbs.
This self-growing garden takes care of plants automatically by maintaining optimal levels of moisture, nutrients, root oxygen and pH. The device ensures perfect conditions needed to grow lush produce at a faster rate than you will find in an outdoor garden. Plus, the direct garden-to-table aspect offers a higher nutrient content than store-bought food, often pulled from the field weeks before. All plants are organic without the need for fertilizers and pesticides.
Click & Grow 25 not only provides convenience, but its energy-efficient design consumes just 200 kWh of electricity per year, which equates to about $40 in large urban areas. An associated app lets users know when it is time to add more water and offers harvesting tips as well as recipes.
“I started the company with a dream to make fresh food available and accessible for everyone and with the Click & Grow 25, we finally made it happen in a sustainable way,” said Mattias Lepp, founder and CEO of Click & Grow. “With the impact of population growth and the demand on our natural resources, it is inevitable for us to become more self-sufficient. I believe we are all going to be growing some of our food at home soon and I’m certain we’ve developed the best solution to do just that.”
Click & Grow 25 recently launched via Kickstarter, where it was fully funded in the first 20 minutes. At the time of writing, it had raised over $500,000 of the $35,000 goal.
Images via Click & Grow
Another Week, Another Webinar! You are Invited To Join Us on The 17th of June For The: FTS Virtual Round Table Talks HR in CEA
Agriculture, as a whole, has a wide range of labor and HR challenges. How can CEA help the horticulture industry overcome these problems? Join FarmTech, Ponic Jobs, and more experts from the field in this webinar to find out
Agriculture, as a whole, has a wide range of labor and HR challenges. How can CEA help the horticulture industry overcome these problems? Join FarmTech, Ponic Jobs, and more experts from the field in this webinar to find out!
Register For The Webinar >>
The webinar will be interactive, hosted via Zoom, and there is time reserved for a Q&A directly with the experts. Can't join live? Register now and you'll be able to watch the recording of the webinar at your convenience.
Join us on Thursday 17 June!
FTS virtual round table talks HR in CEA
Thursday 17 June 15:00 – 16:30 (GMT +2)
Kyle BarnettFounder/Owner, Ponic Jobs
Moderator
Todd DowningManaging Partner, Best Human Capital & Advisory Group
Table guest
Charlotte VisserCOO, Viscon Group
Table guest
Lisanne MeulendijksSpecialist Vertical Farming, Delphy Improvement Center
Table guest
Kate BrunswickStrategic Relationship Manager, Innovation AgriTech Group
Table guest
Clement CardonAgriculture Policy Assistant, FarmTech Society
Table guest
See The Program>>
RotoGro (ASX:RGI) Updates Market On Vertical Farming Tech
The RotoGro Garden System is the core of the company's technology with the ability to maximize plant surface growing area by situating a spherical garden around a centrally placed lighting system
Source: RotoGro
RotoGro (RGI) provides an update of its vertical farming technology with encouraging results from recent trials
The company says recent data indicates its garden systems produce more yield per square meter when compared to other indoor vertical farming methods
Further, trials of RotoGro 710 are said to be progressing well and the team is trialing how to further reduce water and energy usage
RGI is also encouraged by its studies and customer feedback for its RotoGro 420 system which it says validates commercial-scale cultivation of lawful cannabis
Shares were trading 2.3 percent higher at 4.4 cents apiece
RotoGro designs and manufactures cultivation solutions for indoor vertical farming, operating in perishable foods and lawful cannabis.
The RotoGro Garden System is the core of the company's technology with the ability to maximize plant surface growing area by situating a spherical garden around a centrally placed lighting system.
The systems can be stacked, maximizing the yields per square meter when compared to the ground space occupied.
RGI said data collected from recent crop trials conducted in collaboration with agriculture company Verity Greens and herb grower and distributor Fresh Leaf indicates its garden systems produce more yield per square meter when compared to other indoor vertical farming methods.
Specifically, RotoGro projects yields 3.8 to 15.3 times the yield per square meter compared to industry-leading farming producers and greater in contrast to greenhouse and conventional farming.
CEO Michael Di Tommaso said ventures like the ones with Verity Greens and Fresh Leaf will "strengthen RotoGro’s market presence by successfully penetrating the burgeoning indoor vertical farming industry with its technology offerings".
Further, internal trials of the company's most recently developed garden system, the RotoGro 710, are said to be progressing well with cultivation of 48 kilograms of basil and 26.5 kilograms of cilantro in a single harvest cycle.
After multiple trials cultivating leafy greens, the agronomy team repeatedly achieved yields of 124 kilograms in a fully planted RotoGro 710, indicating single harvest yields of 372 kilograms could be achieved when the technology is at full capacity, stacked three-high.
The team is trialing shorter full crop cycle lengths while maintaining yields and aims to refine the plant irrigation schedules to further minimize water usage and refine the environmental controls to ensure enhanced energy efficiencies.
In other news, RotoGro has enabled full automation of its lawful cannabis cultivator, RotoGro 420.
The company's software controls the wheel revolution speed, lighting cycles, and spectrum variations, direct CO2 injection as well as the plant irrigation processes and environmental controls including temperature, air conditioning, and humidification.
Notably, the 420-garden system has been able to consistently produce 10.2 kilograms of dried cannabis flower in a single 56-day crop cycle when stacked three-high.
RGI said its studies in combination with its customer’s data validates the commercial viability of RotoGro 420 in the commercial-scale cultivation of lawful
cannabis.
Mr Di Tommaso said RotoGro is continuing to develop relationships globally to expand its presence in both the perishable foods and lawful cannabis markets.
Shares were trading 2.3 percent higher at 4.4 cents apiece at 1:31 pm AEST.
Spread, Chubu Electric Power And ES-CON JAPAN Enter An Investor Agreement, Plan To Construct Techno Farm Fukuroi, World’s Largest Vertical Farm To Produce 10 Tons Daily
Spread is excited to enter the investor agreement with Chubu Electric Power and ES-CON JAPAN, as all partners share the same vision and values of sustainable agriculture, and each partner is bringing their own unique strengths to the partnership
Spread Co., Ltd., Chubu Electric Power Co., Inc., ES-CON JAPAN Ltd., announced today that they have entered into an investor agreement regarding the establishment of TSUNAGU Community Farm LLC to construct and operate vertical farms.
Expectations are high for vertical farms for stable production of pesticide-free agricultural products through precise control of the cultivation environment.
Many hope that vertical farms will provide a solution for a number of problems, such as growing consumer needs for food safety, a decrease in farming population, as well as food supply instability, and price fluctuations due to extreme weather.
Based on the agreement, Spread, Chubu Electric Power, and ES-CON JAPAN will jointly establish the new company that will construct and operate vertical farms, in July 2021.
As its first initiative, the new company is planning to build an automated vertical farm Techno Farm Fukuroi” in Fukuroi city (Shizuoka, Japan), which will be the world’s largest automated vertical farm, capable of producing 10 tons of lettuce per day.
The construction will start in October this year, while the production start is planned for January 2024.
The integration of Chubu Electric Power’s energy management know-how, ES-CON JAPAN’s real estate development capabilities, and Spread’s cultivation technologies will allow for the efficient and stable production of pesticide-free, safe and clean vegetables.
Spread, Chubu Electric Power, and ES-CON JAPAN aim to solve the issues affecting food and agriculture through vertical farming, while actively utilizing renewable energy and effectively using CO2 in the cultivation process to achieve a sustainable society and the delivery of SDGs through decarbonization.
About Spread
Since its establishment in 2006, Spread has been promoting vertical farming with the goal of creating a sustainable society.
In 2018, Spread started shipping from the large-scale automated Techno Farm Keihanna in Kizugawa, Kyoto which is the first facility to employ Spread’s next-generation food production system Techno Farm?. In less than 2 years from the start, Techno Farm Keihanna reached a stable operating rate of 99%. Spread will further refine Techno Farm? technologies that allow stable production anywhere at any time, and plans to reach 100 tons of daily production domestically by 2030, while pursuing various business opportunities both in Japan and overseas. Under the concept of “Sustainable Vegetable”, Spread delivers its own vertically farmed vegetables brand Vegetus to approximately 4,000 stores in Japan. Since the start of the brand in 2008, Spread has sold over 70 million packs in total*1.
Spread is excited to enter the investor agreement with Chubu Electric Power and ES-CON JAPAN, as all partners share the same vision and values of sustainable agriculture, and each partner is bringing their own unique strengths to the partnership.
Unique Features of Techno Farm Fukuroi
Largest vertical farm in the world, capable of producing 10 tons of lettuce per day
Standardized, efficient operations via automated cultivation
Even more precise environmental control
Recycling of the water used for cultivation
Energy-saving due to in-house developed LED lighting specifically for vertical farming
IoT-based cultivation management system
Pesticide-free, stable production, not influenced by the weather
Utilization of renewable energy
Spread will continue to pursue further business opportunities through technological innovation both in Japan and overseas.
Spread aims to provide solutions for the global problems of climate change and food security and the delivery of a truly sustainable society.
Techno Farm Fukuroi’s Specification
Construction site: Fukuroi-shi, Shizuoka Prefecture, Japan Farm type: Indoor Vertical Farm using Artificial Lighting Site area: Approximately 24,400㎡
Product: Leafy greens(Lettuce)
Production capability: 10 tons per day / 3,650 tons per year Production start: January 2024
Overview of TSUNAGU Community Farm LLC
Established: July 2021 (scheduled)
Location: 1, Higashi-shincho, Higashi-ku, Nagoya-shi, Aichi Prefecture Managing partners: Chubu Electric Power (representative member), ES-CON JAPAN, Spread
Investment: Chubu Electric Power: 51%, ES-CON JAPAN: 48%, Spread: 1%
Business: Production and sale of agricultural products through the operation of vertical farms, utilizing fully artificial light
Overview of Chubu Electric Power Co., Inc.
President & Director:Kingo Hayashi
Business:Renewable energy business, Nuclear power business, Overseas business, Community support infrastructure-related business, Etc.
Overview of ES-CON JAPAN Ltd.
President & Representative Director:Takatoshi Ito
Business:Real estate sale, Real estate leasing, Real estate planning, brokerage, and consultation
Overview of Spread Co., Ltd.
Chief Executive Officer :Shinji Inada
Business:Vertical farming operation, management, and sales of the products
"We Store CO2 From The Outside Air To Make Plants Grow Faster"
“Our ultimate goal is to make greenhouses independent of fossil fuels while improving their crop yield”, says Jarle. This ambitious goal is the main motivation behind their unique, yet a straightforward new product: an environmental climate system that provides plants inside of the greenhouse with outside CO2.
Bringing captured CO2 into the greenhouse with zeolites
“In short, we capture CO2 from the air outside and then release it inside the greenhouse. As our system includes the greenhouse to be a closed system, all the CO2 inside will increase plant growth. This new technology does not give any emissions to its surroundings while in use and the solution is 100% climate-neutral”, Jarle Skjæveland with GreenCap Solutions explains. The company recently launched their product, and they are working on several projects in Norway and abroad.
“Our ultimate goal is to make greenhouses independent of fossil fuels while improving their crop yield”, says Jarle. This ambitious goal is the main motivation behind their unique, yet straight forward new product: an environmental climate system that provides plants inside of the greenhouse with outside CO2. On top of that, it allows for the reuse of condensed water, which further reduces costs for growers.
GreenCap Solution’s technical team combines decades of energy in the oil and gas industry, which is now taken to the greenhouse industry. For the past four years, they have been working on the carbon-capturing technique. Last year, they started working with the first greenhouse company to apply the technique: Lauvsnes Gartneri, a tomato greenhouse in Finnøy, Norway. The second project they started this year is with a Norwegian cucumber grower.
Zeolites: a tried method
For the capturing of the CO2 molecules, the company uses zeolites, a porous mineral that can adsorb large quantities of gas. Zeolites occur naturally but are also produced industrially. “Using zeolites as carbon adsorbent is nothing new. It was already used in the 1960s for industrial applications. Our invention is effectively using the energy and storing the CO2 for greenhouse application, in combination with climate control within the greenhouse,” Jarle explains.
Inside the greenhouse, the CO2 is transported by a constant air flow. “With the greenhouse closed on a sunny day, the temperature might get too high. For that reason, we have a circulation system that shifts the air every 10 minutes. Air tubes underneath the plants produce a constant low-speed airflow. This way, the temperature inside can be a comfortable 24 C even in a hot climate,” Jarle adds.
Vertical farming in Saudi Arabia
This technique comes in handy as the company recently started a new project in Saudi Arabia. This time not with a greenhouse but with a vertical farm that grows eight layers of lettuce. “When we visited Saudi Arabia some months ago, we noticed that some people were skeptical as to our technology would work in a hot climate too. With this new project, we are proving that our technique works, not only for different crops in different growing systems but also in different climates. And the additional benefit is that there we can make better use of solar power as well, taking advantage of the natural resources available.”
In many European countries, growers generally have a combined heat power (CHP) that already provides additional CO2 to growers. But according to Jarle, the systems can be combined easily. “Our technique is twofold: either we replace the current CO2 source or we add it to the closed growth environment. Both work fine together, but with our system, growers can stop using fossil fuels completely while still giving that beneficial CO2 to their plants. Besides, many countries do not need the extra heat provided by the CHP, at least not year-round. In that case, working with a CHP is not cost-effective.”
Already within the horticultural industry, GreenCap’s environmental climate control system can have many different applications. But the company is already investigating other possible usages of their carbon adsorbent technique. “CO2 is used in other industries too, so we are investigating other expansion already, such as companies absorbing their CO2 emission. However, horticulture is such a vast and rapidly growing industry. Imagine this huge industry, that is so essential for the food production of the entire world, being totally emission-free. That is what we’re working for.”
A promotional video of GreenCap Solution's system can be watched here.
For more information:
GreenCap Solutions
www.greencap-solutions.com
Publication date: Fri 4 Jun 2021
Author: Jenneken Schouten
© HortiDaily.com
These High-Tech Strawberries Cost $6 Apiece. Here’s What They Taste And Smell Like
The Omakase Berry, a Japanese variety grown by the New Jersey-based company called Oishii, bills itself as an entirely different strawberry experience
By Hannah Selinger
June 11, 2021
Some months ago, a curious new strawberry began appearing in my social media feeds. The berry, which comes in packages of three, six, or eight, was a uniform pale red. Each berry in each plastic carton looked almost exactly the same — heart-shaped, symmetrical, and indented on the surface where, in a store-bought strawberry, yellow seeds would appear. One more notable thing: They cost between $5 and $6.25 apiece.
The Omakase Berry, a Japanese variety grown by the New Jersey-based company called Oishii, bills itself as an entirely different strawberry experience. The website even offers advice when it comes to eating them: Allow berries to sit at room temperature for 10 to 15 minutes; let the berries’ aromatics “fill the room”; inhale the “bouquet”; eat.
Oishii grows its berries indoors vertically, leveraging technology that its co-founder and CEO, Hiroki Koga, 34, explored in Japan. “I got my first start in the vertical farming industry as a consultant in Japan, where it took off before anywhere else in the world,” he said. “But the whole industry failed pretty quickly, you know, in the early 2010s in Japan, because it was too expensive to grow leafy greens in a very tech-savvy, costly environment.” The technology, he said, was there; someone just needed to find the right way to use it.
The first run of berries (the Omakase cultivar) has been geared toward the luxury market and is available only in the New York City area. But the company is in the process, Koga said, of expanding its market share. Some of the varieties the company is experimenting with can be grown in a much more cost-efficient way, he said, “which means that we should be able to place these into the market at a significantly affordable, reasonable price, compared to what it is today.”
Koga came to the United States in 2015, first to California, where, he said, the quality of produce was unexpectedly good, though not as good as in Japan. The strawberries he selected for the company’s first vertical farms in New Jersey are known as “short-day cultivars.” In Japan, “They’re grown during the winter in a greenhouse environment in a little more wet environment,” Koga said.
Long-day cultivars — American summer berries — are, he said, “optimized for mass production,” at the expense of flavor. Koga says Oishii’s low yields are guided by the same principles as fine wine production: An intentionally depleted crop, achieved by such tactics as crop-thinning, forces the plant to push more of its nutrients and flavor into fewer berries, yielding a more concentrated flavor. The growing environment, according to Koga, is also optimized so that berries yield the maximum amount of nutrients and sweetness.
“We constantly were testing and tweaking to find the perfect environment for the unique Omakase berry,” Koga said. That meant, he said, finding the optimal temperature and breeze; controlling plant management, water frequency, and pruning; and leveraging artificial intelligence to help predict yields.
I wanted to know how the Omakase Berry — billed by Koga as a berry with no American equal — would stand up to other domestic fruit. I arranged my own taste comparison, using three different strawberries: Oishii’s Omakase Berry, available only in the New York City area; widely available Driscoll’s strawberries, produced by a network of more than 900 independent growers around the world, in such places as North America, Europe, China and Australia; and first-of-the-season strawberries from Balsam Farms, in Amagansett, N.Y., down the road from where I live. (Full disclosure: My yearly CSA box comes from Balsam.)
Driscoll's organic strawberries. (Jennifer Beeson Gregory/The Washington Post)
The appearance
Perhaps most striking about the Omakase Berry is its utter uniformity. Each orangy berry — I purchased a package of eight for $50 — looks exactly the same. Glance quickly and you might mistake the berries for marzipan candies, their exterior is so flawless.
The Driscoll’s berries ($3.99 for the company’s standard 16-ounce plastic clamshell) were far deeper in pigment — the company aims for “deep red,” said Scott Komar, 58, the company’s senior vice president for global research and development — and were larger, overall, than the Omakase, though there was variability in size. They were covered in tiny yellow seeds. In selecting berry plants, Komar said, Driscoll’s considers “the color of the strawberry, the shape, the size, and the mouth texture.”
My local strawberries (a quart for $9) were smaller, deeply pigmented and visually much less consistent. The traditional heart shape that is associated with the fruit became more triangular here on Long Island, where conditions are unpredictable. Balsam Farms, said Ian Calder-Piedmonte, 41, the farm’s co-owner, uses a technique called plasticulture. A barrier between plants and the ground is formed using plastic, aiding farmers with weed control, assisting with water management and keeping berries cleaner.
Plasticulture, Calder-Piedmonte said, combined with pruning runners, keeps the plants compact and the berry placement concentrated. Without the plastic, he said, berries can “try to set down roots between rows, and actually will take away from the growth of the mother plants.” Still, holding in my hand the tiny first berries of the Long Island season, it was hard not to consider how much work had gone into producing just a pint of fruit.
Strawberries for sale at the Kuhn Orchards booth at the Fairlington Farmers Market in Arlington, Va. (Jennifer Beeson Gregory/The Washington Post)
The aroma
Oishii isn’t lying when it says the aroma of its berries will fill the room. When I unearthed my plastic container from its refrigerator pack, I could already smell them. Opening the box, I was assaulted with the most strawberry-smelling fruit I’d ever encountered. Aroma, Koga said, is one of the classic characteristics of the Omakase Berry.
In this category, there was no competition. My Driscoll’s berries did not have much of a scent, but aroma may not be at the top of the list in breeding priority. “We conduct quantitative measurements on the sugars, acids, and aromatics of our berries,” said Komar of Driscoll’s berries. “Then that information helps us pick the berry varieties we will commercialize for our brand.” Driscoll’s places a high premium on flavor and color, and the variety I tried may not have been bred, specifically, for aroma.
My Long Island berries smelled very much like strawberries, although their scent was not nearly as potent as the Omakases. “I think there’s probably more variation on local strawberries, as there are with probably everything that’s locally produced,” Calder-Piedmonte said. Other berries that come from “incredibly controlled” environments “where it’s sunny every day” are more likely to be consistent in size, shape, flavor, and even aroma. On Long Island, he said, “I think there are a lot more variables.”
The taste
Oishii’s Omakase Berries cost $50 for a package of eight. (Oishii)
Do you prefer a tart berry that’s firm to the tooth? Are you enamored by sweetness? What type of berry the average consumer perceives as “best” depends on such personal preference. The Omakase Berry was, without question, the sweetest that I sampled. (However, Driscoll’s grows a trademarked, premium fresh berry segment called the Sweetest Batch for strawberries, blueberries, raspberries and blackberries, which Komar said are “unique selections” from the company’s breeding program; I did not try these.)
The Driscoll’s berries were the firmest of the three, with a consistent mouthfeel and flavor. It seemed to me that the objective in their breeding was a distinct balance between sweet and tart — and that balance certainly came through on each bite. In some ways, the acid, a quality in food and drink that compels you to keep consuming, makes sense: You’re unlikely to eat only a single strawberry, but Driscoll’s berries come in large, satisfying packages. It’s okay to keep eating.
As for my local berries, there was something compelling about the unpredictability. They were not the sweetest berries I’d ever tasted, but they varied between sweet and tart. Pop a strawberry in your mouth and come alive with the surprise of how sweet it is. Get a slightly underripe berry and pucker in delight. That contrast might make you wish that berries at the farm stand were sold by more than just the quart.
And, as Ian Calder-Piedmonte pointed out, the distinct advantage of a local strawberry is that you’re eating it the day it’s picked. “They really are harvested that day or the day before,” he said. Many berries are picked and then held in refrigerators (or refrigerated trucks) for days before they reach the consumer, and flavor can diminish each day. A fresh-picked berry tastes far different from a berry that has been off the plant for a few days or, as happens in some cases, a week.
Then came the Omakase Berry. The berry, Koga said, was “specifically selected out of 250 cultivars that exist in Japan,” optimizing for “very strong aroma and high sweetness level.” “Because most of the conventional strawberries here in the U.S. have a very high acidity and very low sweetness level, we just wanted to differentiate our product,” he added. This berry, with its heightened sweetness, is the type of berry that sits heavy on the tongue. Eat one, consider it, let the sugar coat the palate. That’s more than enough. The point isn’t to keep eating. The point, in fact, is to stop. So I did.
Selinger is a writer based in East Hampton, N.Y.
Lead photo: The Omakase Berry, a Japanese varietal grown indoors by Oishii in New Jersey. (Oishii)
USA - ALABAMA: Auburn College of Agriculture Using High-Tech Shipping Containers To Grow Produce For Campus Dining
Unique ‘Vertical’ Farms part of Planned 16-Acre Transformation Garden On Campus
High-tech Horticulture
Unique ‘Vertical’ Farms part of Planned 16-Acre Transformation Garden On Campus
June 10, 2021
Josh Woods | College of Agriculture
Recycled shipping containers have gained popularity in recent years, being converted into everything from houses to small stores—but the Auburn University College of Agriculture, in partnership with Campus Dining, is using them as self-contained “vertical” farms to grow produce to serve to students.
In April, the college acquired two Freight Farms shipping containers that have been converted into technologically advanced hydroponic growing stations in which plants grow vertically indoors without soil, getting their nutrition from water and light energy from powerful LEDs.
Now, the farms are producing the first crop of lettuce.
“This is state of the art,” said Desmond Layne, head of the Department of Horticulture. “We're talking growing from seed to fork in four to six weeks, depending on whether it is lettuce, arugula or another vegetable crop that can grow in there. And we can produce 15 times as much per year as we could outside in the same exact spot.”
Associate Professor of Horticulture Daniel Wells taught a vertical farming course this spring and leads operations of the vertical farms.
Wells said the containers are outfitted with a complete climate control system, which includes air conditioning and humidity control. Because they are highly insulated, the system ensures the same climate 365 days a year.
The converted containers also have an elaborate lighting system, giving all the light the plants need from two color LEDs.
“We can do any number of colors of lights,” he said. “But it turns out for photosynthesis, plants use mostly red and blue light. What’s neat about that is you can cut out a lot of the other color spectrum, creating far less heat energy. That's very efficient. It means more of the energy used is turned into light than heat.”
The containers also allow for controlled carbon dioxide levels, which accelerates plant growth.
“Ambient CO2, what you and I are exposed to every day, is about 400 ppm [parts per million],” he said. “And that’s fine, plants can grow there. But if we boost the CO2 to 1,000 ppm, they’ll grow faster. And because we’re containing the CO2, the plants can really use it. And it’s not dangerous for humans at all.”
Wells and Director of Dining and Concessions Glenn Loughridge first initiated a partnership between the College of Agriculture and Campus Dining five years ago through the Auburn Aquaponics Project, which uses hydroponics and aquaculture technologies to provide a system in which nutrient-laden wastewater from fish production is used as a food source for plant growth. Today, fish from this effort are served in dining facilities on the Auburn campus.
The new vertical farms build on that effort.
“We're in the process of finishing a $26 million dining hall in the center of campus,” Loughridge said. “It has always been foremost in my mind that we would have the opportunity to feature produce grown here on campus in that dining hall. In our biggest location, our biggest asset, we want to bring our A-game.
“This is hyper-local, on-campus sourcing,” he added. “Can you imagine being a potential student coming to tour, seeing where these products are grown, and then going to eat there? It’s incredible. We truly believe this elevates our dining experience.”
The converted shipping containers were manufactured by Freight Farms, a Boston-based company operating in 45 states and 28 countries.
“There are a few different companies out there doing this,” Layne said. “But Freight Farms is the most sophisticated. They’re the ones who have both the best product on the market and the largest production of these containers. It’s really a best-case scenario.”
Adam Lenhard, a rising senior majoring in biological agricultural technology management, said Wells’ course has been one of the most influential courses he’s taken at Auburn.
“It has been very helpful, not just in preparation for the arrival of the freights, but also in learning all about new hydroponic technologies and growing techniques,” Lenhard said. “Post-graduation, I plan to continue to work with these types of indoor, LED hydroponic systems. My primary goal after college is to normalize urban hydroponic farming, provide large, consistent yields of fresh vegetables and provide food to those in need who do not have as much access to fresh produce.”
Transformation Garden
The vertical farms are located on the College of Agriculture’s planned 16-acre Transformation Garden on the south end of the university’s campus, near the intersection of Lem Morrison Drive and Duncan Drive. The goal of the garden is to encompass every aspect of plant-based agriculture, including everything from fruits and vegetables to ornamentals to grow crops and more.
The Transformation Garden will showcase new technology and the history of agriculture, as it envelops Auburn’s Old Rotation, a single-acre research plot created in 1896. Continuously since that year, the historic landmark has been the site for testing and advancing transformative ideas that are now commonplace—ideas like crop rotation, cover crops, and low- and no-till farming.
(Written by: Kristen Bowman)
HELP DEVELOP THE TRANSFORMATION GARDEN
To help develop the new Transformation Garden, you can give online or contact Phillip Cowart, College of Agriculture director of development, at poc0001@auburn.edu or 334-844-1198.
Auburn University is a nationally ranked land grant institution recognized for its commitment to world-class scholarship, interdisciplinary research with an elite, top-tier Carnegie R1 classification, life-changing outreach with Carnegie’s Community Engagement designation and an undergraduate education experience second to none. Auburn is home to more than 30,000 students, and its faculty and research partners collaborate to develop and deliver meaningful scholarship, science and technology-based advancements that meet pressing regional, national and global needs. Auburn’s commitment to active student engagement, professional success and public/private partnership drives a growing reputation for outreach and extension that delivers broad economic, health and societal impact.
Latest Newsroom Articles