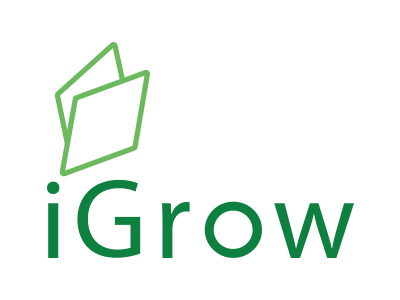
Welcome to iGrow News, Your Source for the World of Indoor Vertical Farming
Artemis Releases 2020 State of Indoor Farming Report
The purpose of this report is to look at where the indoor agriculture industry is today as well as to give growers an industry voice around the latest trends, biggest challenges, and the immense opportunities in this rapidly expanding industry.
We are excited to release our third State of Indoor Farming report. Since their inception in 2016, the State of Indoor Farming reports have been downloaded by millions of people and used as a trusted resource on the industry.
The purpose of this report is to look at where the indoor agriculture industry is today as well as to give growers an industry voice around the latest trends, biggest challenges, and the immense opportunities in this rapidly expanding industry.
The report includes a high-level overview of the industry, as well as a deep dive on key topics such as expenses, sales channels, growth, cannabis, and projections for the future of the industry.
To learn more, you can access the report here.
You can also access our 2016 and 2017 State of Indoor Farming reports.
Ready to see how Artemis can help your operation?
Reach out to our team today. GET STARTED
Artemis, 718 The Hideout, Lake Ariel, PA 18436
© 2020 Artemis Contact Privacy Policy
Polygreens Podcast Episode: 30 - Richard Vollebregt - Part 1
In this episode Joe and Nick interview Richard Vollebregt, President & CEO of Cravo Equipment Ltd, a company that develops retractable roof production systems to enhance berry, cherry, cannabis, and vegetable production for growers worldwide
In this episode Joe and Nick interview Richard Vollebregt, President & CEO of Cravo Equipment Ltd, a company that develops retractable roof production systems to enhance berry, cherry, cannabis, and vegetable production for growers worldwide.
His background in economics combined with 30+ years of experience designing automated retractable roof greenhouses, knowledge of plant physiology and my worldwide experience in many crop industries allows me to be very effective in designing crop production systems and then creating financial models which benchmarking again conventional greenhouses, tunnels, and open field production.
Latest Episode
CANADA: Firefly: A Bug Early Warning System / Precision Crop Health Monitor
LEAN Systems and its technology partner, Proxilogica, are pleased to announce the start of pre-production testing of “Firefly” in collaboration with Agriculture and Agri-Food Canada at the Lethbridge Research Development Center (LeRDC)
Delivering unprecedented crop state comprehension through innovative high-density instrumentation and the power of the cloud
Canada – LEAN Systems and its technology partner, Proxilogica, are pleased to announce the start of pre-production testing of “Firefly” in collaboration with Agriculture and Agri-Food Canada at the Lethbridge Research Development Center (LeRDC).
The Firefly is a wireless and self-powered IoT imager the size of a credit card, purpose-built for early detection of disease and pest outbreaks in the cereal crops and horticulture industry.
The LEAN/Proxilogica team has worked in collaboration with AAFC-LeRDC for almost two years to explore economical digital imaging systems for indoor plant phenotyping pursuant to a three-year material development agreement.
Dr. Anne Smith, a research scientist at LeRDC, together with her colleagues Drs. Jonathan Neilson and Charles Geddes have been developing inexpensive imaging platforms for digital image capture and image analysis protocols for plant phenotyping in growth rooms, greenhouses, and laboratories. Drs. Smith and Neilson, over the last two years, have been collaborating with LEAN Systems to test their technology. The early systems, which were installed less than one month prior to reducing on-site presence in response to COVID-19 restrictions, showed:
· effective image capture over greenhouse plants
· the ability to upload images remotely to a central server
· provide regular downloadable images to the user
· apply image analysis protocols to automatically extract information on plant growth over time
Dr. François Eudes, Director of Research and Technology, LeRDC, says “digital imaging solutions in controlled growth environments have supported research programs during the pandemic and have given us a view of the future of distributed teamwork and data-intensive plant science.”
Dr. Keshav Singh, who recently joined the team at LeRDC, says “diversified applications of Firefly sensing technology over traditional agricultural industry will facilitate the digital ag revolution for global food security. It will involve further development of ground-sensing Firefly technology and possibly aerial platform (drone) applications for rapid field scouting. In the future, this technology will help growers make critical decisions related to identifying types of pests and tracking micro-climates within a field much faster than ever before.”
AAFC is excited to continue working with LEAN Systems on the Firefly technology for automated image capture and extraction of plant phenotyping information relevant to rapid assessment of new varieties, the impacts of abiotic and biotic stresses, and for screening herbicide resistance in a variety of weed species.
Dr. David Southwell, CEO of Proxilogica Corporation, says behind the Firefly architecture are “large fleets of tiny imagers that maximize space coverage with enough onboard intelligence to pre-process and securely transmit data to the cloud where bird’s eye maps are then assembled. AI-boosted analytics functions may be performed at both edge and core, drastically reducing network traffic thereby enabling fleet scaling. We start in CEA spaces and will soon be ruggedizing and adapting the imagers for more demanding open field horticulture applications, including UAV platforms.”
“We are very excited about this technology and see the opportunity for a range of strategic B2B relationships to accelerate commercial evaluation and deployment as well as additional initiatives with research partners globally to expand the Firefly’s useful purpose,” said Bill Halina, managing director of LEAN Systems.
About AAFC:
The Lethbridge Research and Development Centre (LeRDC) was established in 1906 in Lethbridge, Alberta, and is one the largest facilities within Agriculture and Agri-Food Canada's (AAFC) network of 20 research and development centres. LeRDC leads research on beef cattle production systems, crop production, and sustainable production systems under dryland and irrigated conditions associated with farming in a semi-arid climate.
Dr. Anne Smith is a research scientist at LeRDC who specializes in remote sensing applications for agriculture. Over the last 25 years she has conducted studies in cropping systems and grasslands using satellite, airborne, drone and ground-based multispectral, hyperspectral, and radar systems.
Dr. Keshav Singh is a research scientist at LeRDC who specializes in high-throughput proximal and aerial imaging technologies to study canola, legume, and cereal crop phenomics. His work mainly involves agronomic data processing, image-cube analysis, algorithm development, crop mapping and analytics.
For more information:
https://profils-profiles.science.gc.ca/en/research-centre/lethbridge-research-and-development-centre
About Proxilogica:
Proxilogica was incorporated in 2017, built around a team of engineers with more than two decades of experience in technical computing with a vision to develop edge analytics devices. Firefly is the first technology to emerge from this campaign, aimed at improving productivity in precision horticulture.
For more information:
The Proxilogica Corporation
contact@proxilogica.com
www.proxilogica.com
About LEAN Systems:
LEAN Systems Limited Partnership (LP) was registered in the Province of Alberta on July 19, 2018 to help The Proxilogica Corporation fund development of proprietary technologies in the field of horticulture. The LP is managed by LEAN Systems GP Inc. who also provides business development support/advice to Proxilogica's leadership.
For more information:
LEAN Systems LP
contact@LEAN-Systems.ca
www.lean-systems.ca
VIDEO: Russia's Vertical Farm Experiment
"Such technological progress gives the possibility of having 3 harvests in a year.” When #Covid19 restrictions caused border closures with Russia, scientists in Moscow developed these LED-powered vertical farms to solve import problems
June 9, 2021
"Such technological progress gives the possibility of having 3 harvests in a year.” When #Covid19 restrictions caused border closures with Russia, scientists in Moscow developed these LED-powered vertical farms to solve import problems (Source: Quicktake)
When COVID-19 restrictions caused border closures with Russia, scientists in Moscow developed these LED-powered vertical farms to solve import problems. The imported products were received in a bad condition. "We started substituting imports by turning to vertical farming," she said.
Click on the video below to get to know more about the farm.
Green Skyscrapers That Add A Touch of Nature + Sustainability To Modern Architecture!
Polish designers Pawel Lipiński and Mateusz Frankowsk created The Mashambas Skyscraper, a vertical farm tower, that is in fact modular!
06/09/2021
Skyscrapers have taken over most of the major cities today. They’re symbols of wealth and power! And most of the skylines today are adorned with glistening glass skyscrapers. They are considered the face of modern architecture. Although all that glass and dazzle can become a little tiring to watch. Hence, architects are incorporating these tall towers with a touch of nature and greenery! The result is impressive skyscrapers merged with an element of sustainability. These green spaces help us maintain a modern lifestyle while staying connected to nature. We definitely need more of these green skyscraper designs in our urban cities!
Zaha Hadid Architects designed a pair of impressive skyscrapers that are linked by planted terraces, for Shenzhen, China. Named Tower C, the structure is 400 metres in height and is supposed to be one of the tallest buildings in the city. The terraces are filled with greenery and aquaponic gardens! They were built to be an extension of a park that is located alongside the tower and as a green public space.
Polish designers Pawel Lipiński and Mateusz Frankowsk created The Mashambas Skyscraper, a vertical farm tower, that is in fact modular! The tower can be assembled, disassembled and transported to different locations in Africa. It was conceptualised in an attempt to help and encourage new agricultural communities across Africa. The skyscraper would be moved to locations that have poor soil quality or suffer from droughts, so as to increase crop yield and produce.
The Living Skyscraper was chosen among 492 submissions that were received for the annual eVolo competition that has been running since 2006. One of the main goals of the project is to grow a living skyscraper on the principle of sustainable architecture. The ambitious architectural project has been envisioned for Manhattan and proposes using genetically modified trees to shape them into literal living skyscrapers. It is designed to serve as a lookout tower for New York City with its own flora and fauna while encouraging ecological communications between office buildings and green recreation centers. The building will function as a green habitable space in the middle of the concrete metropolis.
ODA’s explorations primarily focus on tower designs, in an attempt to bring versatility and a touch of greenery to NY’s overtly boxy and shiny cityscape. Architectural explorations look at residential units with dedicated ‘greenery zones’ that act as areas of the social congregation for the building’s residents. Adorned with curvilinear, organic architecture, and interspersed with greenery, these areas give the residents a break from the concrete-jungle aesthetic of the skyscraper-filled city. They act as areas of reflection and of allowing people to connect with nature and with one another.
Heatherwick Studio built a 20-storey residential skyscraper in Singapore called EDEN. Defined as “a counterpoint to ubiquitous glass and steel towers”, EDEN consists of a vertical stack of homes, each amped with a lush garden. The aim was to create open and flowing living spaces that are connected with nature and high on greenery.
Designed by UNStudio and COX Architecture, this skyscraper in Melbourne, Australia features a pair of twisting towers placed around a ‘green spine’ of terraces, platforms, and verandahs. Called Southbank by Beulah, the main feature of the structure is its green spine, which functions as the key organizational element of the building.
Mad Arkitekter created WoHo, a wooden residential skyscraper in Berlin. The 98-meter skyscraper will feature 29 floors with different spaces such as apartment rentals, student housing, a kindergarten, bakery, workshop, and more. Planters and balconies and terraces filled with greenery make this skyscraper a very green one indeed!
Algae as energy resources are in their beginnings and are seen as high potential. Extensive research work has dealt with algae as an energy source in recent decades. As a biofuel, they are up to 6 times more efficient than e.g. comparable fuels from corn or rapeseed. The Tubular Bioreactor Algae Skyscraper focuses on the production of microalgae and their distribution using existing pipelines. Designed by Johannes Schlusche, Paul Böhm, Raffael Grimm, the towers are positioned along the transalpine pipeline in a barren mountain landscape. Water is supplied from the surrounding mountain streams and springs, and can also be obtained from the Mediterranean using saltwater.
Tesseract by Bryant Lau Liang Cheng proposes an architecture system that allows residents to participate in not just the design of their own units; but the programs and facilities within the building itself. This process is inserted between the time of purchase for the unit and the total time required to complete construction – a period that is often ignored and neglected. Through this process, residents are allowed to choose their amenities and their communities, enhancing their sense of belonging in the process. Housing units will no longer be stacked in repetition with no relation whatsoever to the residents living in it – a sentimental bond between housing and men results.
In a world devoid of greenery, Designers Nathakit Sae-Tan & Prapatsorn Sukkaset have envisioned the concept of Babel Towers, mega skyscrapers devoted to preserving horticultural stability within a single building. The Babel towers would play an instrumental role in the propagation of greenery in and around the area. These towers would also become attraction centers for us humans, like going to a zoo, but a zoo of plants. Seems a little sad, saying this, but I do hope that we never reach a day where the Babel Tower becomes a necessity. I however do feel that having towers like these now, in our cities, would be a beautiful idea. Don’t you think so too?
Farm Tech Startup Iron Ox Appoints Impossible Foods and Tesla Veteran Rachel Konrad as First Independent Board Member
Iron Ox growing facilities use advanced robotics to precisely cultivate perfect, nutritious produce by giving each plant the specific attention it needs, and then getting it on a store shelf nearby within about a day of harvest
-- Konrad, who spent the past five years at Impossible Foods, joins the board of Iron Ox during a period of rapid manufacturing scale-up and retail expansion.
-- Iron Ox growing facilities use advanced robotics to precisely cultivate perfect, nutritious produce by giving each plant the specific attention it needs, and then getting it on a store shelf nearby within about a day of harvest.
-- The Series B-stage company, whose products are already a breakout seller in California, is also hiring plant scientists, engineers, greenhouse operators, and roboticists.
SAN CARLOS, Calif., June 10, 2021 /PRNewswire/ -- Iron Ox, a farming innovation company with deep expertise in robotics and artificial intelligence, has appointed former Impossible Foods and Tesla executive Rachel Konrad as its first independent board member. This appointment further demonstrates the food tech startup's growth trajectory as they scale up operations and expand their commercial footprint.
Iron Ox, which launched the world's first autonomous farm, has an industry-leading intellectual property portfolio to automate farming and produce that's fresher, cleaner, and locally grown. Thanks to the company's groundbreaking robotics, Iron Ox farms require 90% less water than traditional farms — generating 30 times more produce per acre of land.
Konrad joins Iron Ox after spending the past five years as Chief Communications Officer and a member of the senior leadership team at Impossible Foods, reporting directly to CEO Pat Brown. She previously held senior management roles at Renault-Nissan-Mitsubishi and Tesla, where she reported directly to Elon Musk as the company scaled up operations.
"We can't solve our planet's climate crisis without radical changes to the way we make food," said Konrad, who lives in the San Francisco Bay Area and enjoys cooking for her family and hiking with her rescue German Shepherd. "Iron Ox's intellectual property portfolio can usher in a new era of farming that produces food sustainably and ethically. But honestly, I was sold after my first whiff of Iron Ox basil."
"Rachel understands the unique power of disruptive startups to shift entire industries and force even the most entrenched incumbents to do the right thing for people and the planet," said Brandon Alexander, Iron Ox CEO and Co-Founder. "Her unique perspective will help Iron Ox refine and execute our ambitious strategy. As our first independent board member, we expect Rachel to help us set a new standard for inclusive governance in corporate America."
The Series B-stage company operates farms in Northern California and recently broke ground on a new 535,000 sq. ft. indoor farm in Lockhart, Texas. Today, California consumers can buy Iron Ox food throughout California at Whole Foods and at San Francisco Bay Area's upscale Biancchini's markets. Sales in Texas are expected to begin in late 2021.
The company is also hiring plant scientists, engineers, greenhouse operators and roboticists who are passionate about solving food insecurity, which is at the root of our environmental and public health crises.
For more information, and to view the job openings, visit the Iron Ox jobs page.
About Iron Ox:
Iron Ox is a farming innovation company with deep expertise in robotics and artificial intelligence, and a vision to solve global climate through food. Their approach redesigns every step of the farming process, achieving levels of precision that are impossible through traditional farming. Iron Ox produce is both local and sustainable by design, greatly reducing systemic food waste and minimizing the ecological impact of farming. For more information, visit www.ironox.com.
SOURCE: Iron Ox
Scottish Agritech Business IGS Appoints First CFO To Enhance Leadership Team And Support Global Expansion
With many countries developing national food security strategies there is an increasing emphasis on sustainable food production
Appointment of Sarah Willis Will Bolster Readiness For Rapid Growth
Edinburgh, Scotland – 31 May 2021 – Intelligent Growth Solutions (IGS), the Edinburgh-headquartered agritech business, continues to enhance its executive talent as it welcomes Sarah Willis into the role of Chief Financial Officer. Sarah’s appointment reflects the company’s need for substantial transactional and commercial financial experience to support IGS’ global growth strategy in the vertical farming market.
With many countries developing national food security strategies there is an increasing emphasis on sustainable food production. This is driving a rapid maturing of the vertical farming industry, generating significant levels of momentum from customers, consumers, and investors. IGS’s strategic position fits very well with these developments enabling the company to enter multiple regional markets this year.
Sarah’s role will be pivotal as the company looks to expand its operating base over the coming 12 months, ensuring operational support, corporate governance, and reporting structures are fit for purpose. She will be responsible for the company’s financial management, HR, admin support, and new office development, working closely with IGS CEO David Farquhar and the Board.
Sarah joins IGS from Spirit Energy, where, as Head of Finance Operations, she was responsible for the financial integrity of the company which generated over £1bn of revenues. Prior to that, Sarah was in senior management overseeing operational and financial performance at Centrica E&P in the UK and Europe. Sarah is a qualified Chartered Accountant, starting her career with KPMG and latterly Deloitte in Aberdeen, before joining Wood.
Working with highly regulated industries throughout her career, Sarah brings a strong commitment to due diligence, risk management and governance. She brings broad, multi-national M&A experience which will boost IGS’ ability to roll out across its global markets. Her financial and stakeholder management experience will further enhance the relationship with the IGS investment and shareholder community helping transition to a capacity expansion phase in this exciting industry.
Talking about her decision to join IGS, Sarah commented: “The opportunity to be part of a business like IGS is really exciting. The combination of the talented team, the incredibly innovative technology, and the prodigious industry growth was compelling for me.
“The company has achieved remarkable progress to date, reflecting its purposeful approach and hugely passionate team. I believe strongly in the guardianship of the planet – we must leave it in a better place for the next generation - and businesses like IGS are genuinely committed to this belief and have embedded this in its approach so well. I am delighted that I can be part of this ambitious team to help support a positive evolution in food production for the future.”
David Farquhar commented: “Sarah is a hugely welcome addition to the leadership team at IGS, as we seek to further diversify and expand the talent across our organization. She joins our business at a crucial and pivotal point in our evolution, bringing us a fresh perspective from the energy industry particularly, whilst expanding her own capabilities and leadership skills in her first CFO role.
David continued: “The IGS growth curve is steepening sharply and Sarah’s appointment demonstrates our commitment to deliver optimum results for our investors, customers, and partners. Sarah’s international experience is world-class, given her career in highly regulated, quoted companies across multiple geographies. Her leadership will be vital in helping us efficiently manage significant expansion.”
Sarah graduated from the University of Edinburgh and Dauphine Université de Paris where she studied International Business with French. Sarah is an advocate of diversity in its many forms and was involved closely in supporting Spirit Energy’s initiatives to create a more inclusive culture across the oil and gas industry.
Sarah is based in Aberdeen where she lives with her husband and daughter. A fluent French speaker, she is also very interested in music and plays golf.
Ends
Notes to editors:
For more information: please contact Kate Forster or Georgia Lea, IGS, on either kate@intelligentgrowthsolutions.com / +44 7787 534 999 or georgia@intelligentgrowthsolutions.com / +44 7897 539 954.
About Intelligent Growth Solutions (IGS):
Founded in 2013, IGS brought together decades of farming and engineering experience to create an agritech business with a vision to revolutionise the indoor growing market. Its commitment to innovation has continued apace and it has evolved the applications of its technology beyond indoor agriculture to create solutions for a wide variety of farming applications which enhance life for plants and people alike.
IGS launched its first vertical farm crop research centre in August 2018.
For more information visit www.intelligentgrowthsolutions.com or connect with us on Twitter and LinkedIn.
CEA Food Safety Coalition Details First Indoor-Farming Standards
Inspired by rising food safety concerns after the 2018 Thanksgiving romaine recalls, the CEA Food Safety Coalition is launching the first-ever food safety certification program specifically designed for indoor-grown leafy greens.
By AMY SOWDER June 2, 2021
(Photos courtesy CEA Food Safety Coalition)
Inspired by rising food safety concerns after the 2018 Thanksgiving romaine recalls, the CEA Food Safety Coalition is launching the first-ever food safety certification program specifically designed for indoor-grown leafy greens.
“The new standard champions CEA-grown produce as a critical component of safe and secure domestic food supply, especially in times of business disruption as experienced during the COVID-19 pandemic,” Marni Karlin, executive director of the CEA Food Safety Coalition, said in a news release.
Controlled Environment Agriculture, or CEA, has exploded with investment and sales the last few years, as more urban, indoor farms crop up to meet demand.
Soon after organizing in 2019, the coalition educated the Centers for Disease Control and Prevention and Food and Drug Administration about the limited risk of contamination from indoor-produced leafy greens, Karlin said.
“During the Thanksgiving 2019 romaine recall, those government agencies were transparent that CEA leafy greens were safe and did not extend the recall to them. This enabled retailers to keep CEA-produced greens on the shelves and consumers to safely buy CEA leafy greens for their families,” she said in the release.
The team had to create a standard that made sense across the board for the variety of production processes included in CEA — from greenhouses and vertical farming to aeroponic, hydroponic and aquaponic.
“Current food safety standards were written for the field, and many don't adequately address the unique attributes of controlled indoor environments,” Karlin said in the release. “Traditional food-safety risk profiles associated with conventional farming include examining the physical hazards and microbial hazards from water use, herbicide, and pesticide use, and impact from animals and animal byproducts. These do not impact CEA growers in the same way, if at all.”
As a result, a separate set of guidelines is needed.
This new certification process and the accompanying on-pack seal will spread awareness about CEA and unify these growers while differentiating them from traditional field growers, she said.
“It will allow producers to adhere to a standard tailored to indoor production and give incoming entrepreneurs guidance on the measures they'll need to meet to align with the existing industry,” Karlin said in the release.
The certification program is available to all CEA food safety coalition members for a small fee, and an external audit to the standard must be completed on an annual basis.
Growers are assessed across four key areas:
Hazard analysis: All potential hazards associated with a producer’s practices, including use of water, nutrients, growing media, seeds, inputs, and site control;
Water: Often used by CEA producers, recirculated water requires a continuing hazard analysis throughout its life cycle and zone-based environmental monitoring based on company-specific risk assessment, she said;
Site control: All food contact surfaces and adjacent food contact surfaces, including plant containers, must be considered and associated with potential farm physical hazards, including lighting, robotics, sensors, equipment, and utensils; and
Pesticide and herbicide use: Even though CEA-produced greens generally don’t use pesticides or herbicides, this module evaluates the potential risk of pesticide contamination and addresses if residue testing is required, she said.
“Consumer interest in food labels is high and shows a genuine desire to shop smarter,” Karlin said. “For consumers to truly make informed purchasing decisions, we need to explain what the labels mean, the process of certification and which labels they can trust.”
PinDuoDuo: Building A More Resilient Food System With Technology - July 14 -15
Join us virtually for our inaugural Food Systems Forum, which will convene experts from around the world to share their insights and spark further connections and potential collaborations
The pandemic has shone a light on how fragile and intertwined our global agri-food supply chain is, making it even more pressing to push for food systems innovation and change. Can we leverage technology to build a more resilient food system that feeds more people and feeds them better?
Join us virtually for our inaugural Food Systems Forum, which will convene experts from around the world to share their insights and spark further connections and potential collaborations.
Register To Join The Conversation
North America’s Indoor Farms Plan To Add 500-Plus Acres Over Next 5 Years
“Now that the market has established itself, you’re going to see a lot of technology in the next few years come on to the market. New hardware, new sensors, new control systems, new lighting, new physical structures, new growing system automation, robotics, AI — you name it.”
June 7, 2021 Lauren Manning
Indoor farming analytics provider Artemis has just released its annual State of Indoor Farming report, which reflects a survey of 205 enterprise horticulture facilities across the US and Canada. Put together in partnership with research firm Startle, the report’s goal is to assess where the region’s industry is today – as well as giving growers a voice around the latest trends, challenges, and opportunities it presents.
It covers everything from container farms to high-tech glass greenhouses and vertical farms.
“One thing we did this year that was different from last time was asking things like, ‘How are you actually getting capital? How are you getting contracts with buyers? How did the mechanics work to make sure that you can actually expand and build projects?'” Artemis co-founder and CEO Allison Kopf tells AFN.
“There are some really interesting tidbits that might go unnoticed, like the small number of people who indicated that part of their expansion plan includes packing operations. I think this is probably driven by Covid-19 and the supply chain holes that we saw. Doing more on-site packing and increasing on-site capacity is very different from field ag.”
A few other notable findings from the report include:
77% of respondents are growing multiple crops while 23% are growing a single crop.
The three most commonly cultivated crops indoors are leafy greens (26% of total), herbs (20%), and microgreens (16%). Tomatoes (10%), cucumbers (8%), peppers (8%), ornamentals (6%), and strawberries (6%) round out the list.
The average revenue reported by growers selling the leading indoor crop, leafy greens, is $7.82 per pound.
Inputs remain one of the biggest drivers of operational costs for indoor growers with average annual costs for seeds ($24,989), grow media ($19,190), and nutrients ($17,510) among the most expensive.
Retail and grocery outlets (28%) remain the dominant sales channel for indoor growers, followed by direct-to-consumer outlets (26%) and wholesale accounts (17%).
Indoor growers are also eager to expand their footprints. Roughly three-quarters have expansion plans that they aim to execute in the next five years. If they are successful in their endeavors, they’ll add a predicted 544 acres to North America’s indoor farming industry.
Technology adoption indoors
The indoor farming industry has a big appetite for technology, according to the Artemis report. Just over a third of respondents are using mainly tablets and mobile phones to run their daily operations, with 24% using desktop computers. Six percent have adopted barcode scanners.
When considering new technologies, 39% of indoor growers are eager to find solutions to manage operations more efficiently. Lowering the cost of production (20%) and increasing yields (19%) are also high on the tech discovery list.
Investing in technology and understanding it is a critical ingredient for success, according to Kopf.
“Now that the market has established itself, you’re going to see a lot of technology in the next few years come on to the market. New hardware, new sensors, new control systems, new lighting, new physical structures, new growing system automation, robotics, AI — you name it,” she says.
But the increase in choice comes with its own problems. Some growers may find themselves overwhelmed by the flood of new offerings, or lack the time to research the optimal products for them.
“Being able to find the right stuff to operate the facility the way you want for the crops that you are growing is going to be really, really critical. [Tech vendors] that differentiate based on product are going to stand above the rest,” Kopf suggests.
This could include products that help indoor farms prove they are carbon neutral or negative, opening up a new world of branding and marketing opportunities.
Advancements in breeding technology are also starting to open the door to new types of crop cultivation. As developments in genetics unlock the right varieties for indoor conditions, the industry will be better equipped to move beyond leafy greens and herbs.
Suited for public markets
As more indoor farming startups raise substantial rounds or take their companies public — like AppHarvest and Aerofarms have done recently through SPAC mergers — questions are bubbling up around whether the momentum can last.
For Kopf, the fact that indoor farms are producing tangible products differentiates them from some of the other hyped subsectors within agrifoodtech. Indoor farming operations can also involve substantial physical infrastructure, making them well suited for public markets, she says – while they can also tick the increasingly important ESG box for investors. As a result, she sees more SPAC deals and IPOs on the horizon.
There’s also room left for indoor farming to expand in certain geographies where massive consumer markets await.
“If you look at the Netherlands or Spain, markets where greenhouse production is commonplace, we’re really behind in the US. If you’ve got plenty of room to grow – that changes the dynamic,” Kopf says.
“I don’t think we are anywhere near where we will be in the next five to 10 years, which to me indicates you’re not in a bubble. You’re in the early stages of a transitional period for an industry as a whole.”
Growfoam Is Gearing Up For The Next Revolution In Controlled Environment Agriculture
The agricultural market stands on the verge of a true revolution and Growfoam is destined to pave the way for growers around the globe. Their mission? Enable growers to grow Greener, Safer and Faster
The agricultural market stands on the verge of a true revolution and Growfoam is destined to pave the way for growers around the globe. Their mission? Enable growers to grow Greener, Safer and Faster.
Rising demand for fresh & healthy vegetable crops.
With an increasing global population and rising global welfare, the fruit & vegetable market is expected to increase towards 260% in 2050, compared to current levels.
This rise in demand for fresh & healthy crops has resulted in a boom of investments towards greenhouse projects (e.g. in China and the US) and a steep rise in VC investments in AgTech Scale-ups. Such a swift market development offers the AgTech industry both a challenge, as well as an opportunity: we need to push ourselves in growing Greener, Safer and Faster.
Growfoam knows it is possible to sustainably feed a growing population. They contribute to this goal by continuously innovating their growing media and collaborate with growers around the world. This way Growfoam enables growers in cultivating their crops Greener, Safer and Faster.
Future-proof farms aim for de-risking the value chain
The horticultural industry continues to offer consumers fresh produce at increasing quality standards while maintaining efficient pricing. This trend will be further enabled by emerging technologies such as vertical farming, hydroponic cultivation, big data, and autonomous greenhouse cultivation. The next big leap for farms across the globe will be to de-risk the entire fruit & vegetable value chain.
Vertical Farms and other Controlled Environment Agriculture technologies are already enabling this by growing their produce locally near end-consumers while utilizing stable and predictable year-round cultivation methods. And it doesn’t stop at just predictable year-round cultivation, improved technologies such as automation and completely clean starting materials (e.g. clean Growfoam growing media) enable growers to further de-risk the value chain by offering traceable, pathogen-free and thus fully safe healthy greens.
These de-risked and highly efficient future-proof farms offer added value for the entire value chain by producing safer produce.
Reducing operational costs (OPEX) is key to farm success
The last major hurdle for vertical farms and hydroponic cultivation techniques is to increase production efficiency and reduce OPEX.
Although many important breakthroughs (e.g. lowered CAPEX/m2 farm, optimized growing methods, increased automation) have been realized in overcoming this hurdle, there is still much to win. One major enabler in reducing OPEX is the correct choice in growing media: most of the growing media available on the market today are less suited for vertical farms and hydroponic cultivation techniques.
Loose-fill growing media offer significant challenges in automation, increasing labor costs as well as maintenance costs. Growing media consisting of organic components such as peat and coir offer significant safety challenges by introducing potential pathogens into the farm and are destined to be banned completely over time. They increase risks of crop failure due to high variation in batch-to-batch consistency and increase logistical risk due to limited resource availability due to swift expansion of the horticulture industry.
Non-degradable growing media increase waste disposal costs when disposing of the growing media after crop cultivation. These waste disposal costs can be easily reduced and sometimes even be avoided by utilizing biodegradable alternatives such as Growfoam..
New website and brand identity
Today Growfoam unveiled its new brand identity. This premiere marks the start of a new era for Growfoam, to match the ambitious and innovative nature of the Growfoam products and signifying the evolution of the company from an innovative startup to an exponentially growing scale-up. Growfoam has created a cross-platform brand experience that is future-proof and authentic, focusing on their main client groups; vertical- and hydroponic farmers.
‘The new Growfoam brand design marks the start of great things to come,’ says Martin Tietema, CEO and one of the founding partners of Growfoam. ‘By formulating new content, sharing knowledge and with out-of-the-box solutions for growers all over the world, Growfoam is enabling a fast transformation towards a future with full circular possibilities for every vertical- or hydroponic farm. Now is the right time to make the new attitude of our brand visible to the outside world.’
The brand promise ‘grow greener, grow safer, grow faster’ can be seen and experienced in the design and production of the Growfoam products, in customer contacts, and the brand presentation as a whole.
Growfoams Chief Commercial Officer, Niels Steenvoorden, explains: ‘We have created a new global brand experience on all channels and across all touchpoints.. Our aim is to truly connect with our clients, grow with them, share knowledge and enable them to do what they do best; grow great crops.’ ‘We invite growers to contact us and join us on our journey to establishing the perfect grow zone for their crops. Enabling them in growing Greener, Safer and Faster.’
The new visual brand language will be very different from that presented by Growfoam to date. It will be bolder, more colorful and the focus will be on real-life situations and actual challenges of the controlled environment farmers.
An abstract representation of the foam bubbles they produce is incorporated in their new logo. The bold and bright colors they use are a direct link to both the RGB lights in vertical farms as well as the water used in hydroponic farms.
The strategic foundations for the new brand identity were laid by a joint team of Foamplant and JEEN, a marketing agency in Agri and food, over the last few months.
Atoomweg 19
9743 AJ Groningen
The Netherlands
Email: info@growfoam.ag
Tel: +31 6 4487 4093
HOURS
MONDAY - FRIDAY 08:00 - 17:30
IBAN: NL26 RABO 0361898924
BIC: RABONL2U
CoC: 80987516
VAT: NL861878127B01
USA - Orlando, Florida: No Better Time Than Now
Kalera, one of 2020’s biggest headline makers in vertical farming, has even bigger plans for its still-under-construction nationwide network, and there’s nothing that can slow it down.
Kalera, one of 2020’s biggest headline makers in vertical farming, has even bigger plans for its still-under-construction nationwide network, and there’s nothing that can slow it down.
May 21, 2021
Matthew J. Grassi || Photos by Connor Barber
Kalera, based in Orlando, Florida, is taking the local indoor farming concept and stretching it from coast to coast during a nationwide pandemic. This all while turning out flavor and nutrient-packed and conventional crop price-competitive lettuce and leafy greens in a zero-pesticide, 95% less water-requiring closed-loop automated production system.
The highly automated vertical grower (with the slogan The Science of Great Greens) operates three indoor vertical farms, two of which are situated near its corporate headquarters in Central Florida.
The operation’s third vertical farm, located in Forest Park, Georgia, recently completed its inaugural lettuce harvest. This farm is one of the largest indoor farms in the U.S. Southeast at 77,000 square feet and is reportedly capable of churning out 10 million heads of lettuce to local Atlantans and foodservice distributors annually. Heads of lettuce pulled out of the new Atlanta facility have already made their way to local operators like Publix, Sysco and Fresh Point.
With the first harvest in Atlanta now under its belt, the nationwide farm network rollout rolls on into the summer.
The latest scoop: Kalera is pursuing a whirlwind agenda for the home stretch of 2021 and into the next year, opening new, modular farms in places like St. Paul, Houston, Denver, Columbus, Seattle and Hawaii. There, the company says the farm will be the island’s first operable commercial indoor farm when launched.
The new farm building campaign is not the only big news with Kalera. The group recently made waves by acquiring Vindara, an up-and-coming disruptor in the plant breeding world. The operation says it leverages machine learning and AI alongside traditional breeding techniques to drastically shorten the development window of new seed varieties and traits bred specifically for indoor vertical farming.
Leading and innovating
While the Kalera name is fairly new, the group is not some fly-by-night operator that just sprang up in a retrofitted warehouse one day. CEO Daniel Malechuk says the group worked for 10 years “behind the scenes in stealth mode” to develop the coast-to-coast indoor farm network concept.
“For the first time ever, an indoor farming company can offer you something from Hawaii to Seattle to Florida, and everywhere in between — which is exactly what the foodservice companies want — and it’s a consistent, quality product,” he says. “We’re bringing scale and unit economics and high yields unseen to this point in the vertical farming world, a couple of years ago people laughed at this concept, but clearly this is no longer a pipe dream.”
Malechuk has been with Kalera for just about a year now, having spent the bulk of his career in supply chain and retail purchasing across the food industry. The former VP of the supply chain for Mastronardi Produce has a firm grasp on what consumers want from an indoor produce company, and how to make that a reality in today’s world of segmented supply chains and COVID-closed borders.
“I have a lot to learn [about vertical farming] and I still do, and honestly that is what is most exciting for me — solving some of these challenges of ‘this is how we do it now, but can we do it this way’,” he says. “Can this be done at scale and with profitability? Those are the burning questions in this industry right now, and at Kalera we are answering those questions in a big way.”
Answering those questions by staying focused on providing a phenomenal produce product at a reasonable price is what sets Kalera apart in a crowded segment, according to Malechuk. “[Growing] something people can afford and not have to splurge to purchase this premium product, that is really what drives. Of course, our robotics and advanced technology is part of that focus, too, but our customer and what they care about — quality grown and sustainably produced, and at what price — that’s what gets us out of bed every morning.”
Kalera's closed-loop growing system produces crops with 95% less water used than field growing, according to the company.
Building out during a shutdown
Austin Martin is Kalera’s chief operating officer, based at the group’s first farm outside Orlando. The former big-box retail logistics professional oversees all of the far-reaching tentacles of the Kalera nationwide expansion strategy, managing the various farm buildouts as well as many aspects of the farm operations themselves.
“For those that were willing to work really hard and push the envelope to make things happen, [COVID] was actually a great opportunity for us to focus and get ahead,” Martin says when asked what it has been like managing such an ambitious rollout throughout the pandemic.
COVID did in fact alter Kalera’s go-to-market slightly. Initially, management was keenly focused on the food service retail segment as its primary customer. Then COVID hit and the bars, restaurants and local distribution networks that serve them practically grounded to a halt. Martin and his team had to quickly pivot to consumer-facing food retail to ensure a mixed-channel distribution strategy which the company will stick with once normalcy returns.
“These food retailers want to partner with a more sophisticated provider who can guarantee continuity in supply across a wide geography, yet still maintain that same level of focus on food safety,” Martin says. “They deal with a lot of regional growers and that’s really just because they don’t have another choice. They want the redundancy that a larger-scale operation can provide.”
The indoor farm's acquisition of a vertical farming genetics startup allows for customized hybrids brimming with nutrients, taste, and texture.
Seed acquisition
While Kalera’s scale and approach to vertical farming are attention-worthy attributes, what put the operation over the top was the acquisition of indoor seed genetics provider Vindara. It’s not every day that a farm can buy the company and infrastructure that provides arguably the most crucial link in the production chain.
The collaboration was born out of both familiarity and need: both companies have close ties to North Carolina State University’s ag programs — Malechuck is an alumnus — and Kalera’s leadership had realized a glaring need for genetics tailored specifically to indoor production systems.
Add Vindara president and co-founder Jade Stinson to the list of Kalera-connected executives with an interesting background. Stinson has worked in agriculture for decades, having helped with uncovering the link between mad cow disease and humans in the United Kingdom before joining BASF after college.
Vindara was founded in 2018 on the back of Stinson’s vision of becoming the premier provider of elite genetics for the vertical farming space. The fact that they figured out how to accelerate the seed trait breeding cycle from a ten-year lead time down to 18 months, while maintaining and even offering customizable yield and flavor profiles, simply cannot be oversold.
We're bringing scale and unit economics and high yields unseen to this point in vertical farming ..."
“Say we develop a new indoor lettuce seed variety today with higher yield. Ok, that’s great, but that can’t be it,” Stinson says. “LED lighting technology will evolve, there’ll be more automation and more hands-off growing style, different plant architectures. This industry is moving too fast for traditional breeding to keep up, and when you can leverage deep machine learning and analytics, you can really dive into the genetics and really start leveraging genetic diversity.”
What today’s vertical farming space requires is what Stinson calls a “systems approach” to breeding. “It’s not a one seed fits all approach. The production systems from grower to grower are so disparate, one seed in one system won’t move the needle,” she adds.
The partners share a focus on democratizing their own corners of the ag universe. Vindara is wholly-owned by Kalera, yet operates autonomously and will continue serving genetics to the entire CEA industry. Kalera wants more access to fresh, nutritious and affordable food, and Vindara wants the same for the breeding innovations side of the coin, too.
“Let’s democratize and have growers be able to call us up and say ,‘Ok I want a lettuce with dark purple color, high yield and nutrition, and it has to stay crispy in transport,” she envisions. “The Kalera vision is why should just the top 5% of the world population have access to the most nutritious food? And that’s what we believe in, too.”
Automation and technology
Having launched its first facility located at Orlando, Florida’s Marriott World Center convention area (which has a commercial irrigation and climate control system) Kalera’s chief technology officer and co-founder knew the operation required more precision and customization.
“Development and implementation of our automated HyCube growing system has been a tremendous advantage for our production cycles,” says Cris Toma, co-founder, and chief science officer. “It’s something we started to develop a couple of years ago because those off-the-shelf systems didn’t meet the requirements of our vertical farming operation and it was too difficult to extract the data.”
Today, the system is a cloud-based, mobile-optimized ecosystem of sensors and controllers and irrigation modules that are in constant interaction with the group’s closed-loop production systems.
By developing and launching its own system, the operation has cultivated a unique approach to technology via its experiences thus far.
“We like to say that we are farmers who use technology, rather than being a technology provider looking for an application in farming,” Toma says. “And that’s coming from somebody like myself with a machine learning and digital imaging processing background.”
By establishing indoor farms from coast to coast (and beyond) Kalera can offer its customers a consistent product from California to Maine.
“We do not make these statements because we do not understand technology, or have trepidation in dealing with it, rather it’s been my entire professional life,” he continues. “Yet, at the same time we need to be very careful that we don’t destroy the ROI and economic performance of each project with how we integrate technology.”
Once Kalera’s farm network is built and fully operational, the built-in advantage provided by all that aggregated production data will be a massive enablement piece for the head growers at each facility.
“We’ll create a digital data warehouse and implement big data analytics and algorithms, and those activities will drive our sensors with computer visions and AI for tracking plant health and development across all facilities,” Toma says.
While that data is important to what Kalera plans to do in 2021 and beyond, it will still rely on the tried-and-true head grower structure.
“The AI is not quite there yet for full automation, but the trend is there and will only continue to grow. And yet we still need a human in the loop for certain tasks, for the more complex tasks you still need the expert in there monitoring and making adjustments, and then you hope to build on the expert with data and analytics,” Toma says.
Bottom line
Kalera isn’t settling down anytime soon.
“I envision our expansion plans are going to continue, and we are also looking at international expansion in the years ahead,” Toma replies when asked what’s next for the operation. “We’ve got a deep pipeline of opportunities to capitalize on.”
For the CEO, it’s all about continuous improvement and never growing complacent.
“We never want to be flat organizationally, we are constantly striving to get better, learn, refine, and innovate within our business model,” Toma says. “And, if it adds value to our customers, then we’re going to do it.”
How AgriTech Is Playing A Key Role In Greenhouse Vegetable Production
In this exclusive interview with Greenhouse Grower, Gov. Beshear provides a closer look at the AgriTech Initiative and how companies like Kentucky Fresh Harvest are building a brighter future for the commonwealth
June 2, 2021
Editor’s Note: This is the last of a four-part series covering of growth of Kentucky Fresh Harvest as it prepares for its first crop. Check out the previous parts of the series here.
In support of Kentucky Gov. Andy Beshear’s vision of a diverse and resilient agricultural industry in Kentucky, one of the keys to the long-term growth plan of Kentucky Fresh Harvest is its involvement with the Kentucky AgriTech Initiative. This initiative is designed to highlight Kentucky’s unique position to offer an environment that can attract, develop, and sustain agritech-related enterprises.
In this exclusive interview with Greenhouse Grower, Gov. Beshear provides a closer look at the AgriTech Initiative and how companies like Kentucky Fresh Harvest are building a brighter future for the commonwealth.
Greenhouse Grower: Can you give an overview of the Kentucky AgriTech Initiative, why it was formed, and its goals?
Gov. Beshear: Last June, I took several steps, including creating an AgriTech Advisory Council, to keep my promise to build America’s AgriTech capital in Kentucky. The council includes representatives from farming, education, labor, civic life, and representatives from leading companies in the commonwealth such as Alltech, AppHarvest, Black Soil, and Kentucky Fresh Harvest.
Your readers are familiar with Kentucky Fresh Harvest, which cares about where our food comes from, how our food is grown, and who grows our food. These are all elements that align with the Kentucky AgriTech Initiative. Because of this, they have been able to revolutionize the protected agriculture industry and become an authority on vegetable production in Kentucky.
Kentucky Fresh Harvest already has been through the growing pains associated with building a greenhouse of this scale. So, it made sense for them to join the AgriTech Advisory Council nearly a year ago in our collective mission to highlight and develop Kentucky’s tremendous potential to help solve one of the greatest challenges of our generation: producing reliable, safe, and accessible food for the world. While that challenge is prevalent today, the expected global population surge in between now and 2050 will only amplify its severity. Team Kentucky is addressing this by combining three signature strengths: Kentucky’s prowess as a national leader in both manufacturing and logistics, along with our deep roots as an agricultural state.
The initiative will attract and cultivate good-paying, private-sector jobs and companies that create technologies, services and produce to help feed the world.
Our AgriTech Advisory Council’s goals for the initiative:
Create good jobs and strengthen Kentucky’s economy;
Attract local and global technologies and partners that support the development of innovative agriculture in the commonwealth;
Craft policies that spur the development of our agritech ecosystem;
Develop local supply and demand for technologies and agricultural products grown and manufactured here in Kentucky;
Develop and attract the necessary workforce to sustain the agritech ecosystem;
Help develop access to capital for new and innovative businesses in this sector; and
Build necessary cooperation channels between interested players.
Greenhouse Grower: What are the benefits of the initiative to both consumers and growing operations?
Gov. Beshear: By harnessing the assets in our backyard, the AgriTech Advisory Council seeks to develop an environment in which consumers gain better access to healthy food, obtain a more thorough understanding of where their food comes from, and realize the benefits of supporting local, sustainable farms. Relative to growing operations, the initiative focuses on helping them do what they do best – run their businesses while relying on Team Kentucky as a partner that shares their vision for a more sustainable, equitable, and resilient food system based right here in the Bluegrass State.
Greenhouse Grower: How can growers get involved?
Gov. Beshear: We want to hear from growers, no matter the size of their operations. We believe there are a number of opportunities for collaboration among growers and other innovators from all sectors – from greenhouse vegetable producers to our advanced manufacturing and logistic sectors. We even offer opportunities on all levels of the educational and workforce training system so that some of our youngest minds can look forward to becoming a part of the industry. If you are in a position to showcase your work or engage with Kentucky students, please contact us. Visit www.agritech.ky.gov.
Greenhouse Grower: What has been Kentucky’s experience of working with Kentucky Fresh Harvest?
Gov. Beshear: Kentucky Fresh Harvest has been a great partner of the commonwealth and true pioneers in the state’s high-tech greenhouse sector. Rocky Adkins, my Senior Advisor, and I visited the site in Lincoln County recently, and it was great to see the rich promise of agritech in Kentucky on display. The company’s scientific approach shows us that certain obstacles of large-scale agritech are no longer relevant. Kentucky Fresh Harvest’s dedication to education and inclusivity are great examples of excellent corporate citizenship and ambassadorship for the industry as a whole.
Source and Photo Courtesy of Greenhouse Grower
Introducing Our Earthbag - Biodegradable and Compostable!
It’s what eco-conscious consumers want
Pontus Files International Patent Application For Automated Vertical Farm Harvesting Robot
Pontus' initial crop, water lentils, is the fastest-growing leafed plant.* Pontus' CEVAS helps accelerate the growth of Pontus' water lentils, requiring the plant to be harvested every 24 hours
NEWS PROVIDED BY
Jun 09, 2021, VANCOUVER, BC, June 9, 2021 /CNW/ - Pontus Protein Ltd. (TSXV: HULK) (OTCQB: HLKKF) (FSE: 8YC) ("Pontus" or the "Company"), is pleased to announce that it has filed an international patent application through the Patent Coordination Treaty with the World Intellectual Property Organization for Pontus' proprietary Harvesting Automated Robotic Vehicle or "HARV" for short. HARV is a vertical farm rack system and automated plant tending and harvesting robot designed to work alongside and assist Pontus' Closed Environment Vertical Aquaponics System or CEVAS system.
Pontus' Harvesting Automated Robotic Vehicle or “HARV” for short. HARV is a vertical farm rack system and automated plant tending and harvesting robot (CNW Group/Pontus Protein Ltd.)
Pontus' initial crop, water lentils, is the fastest-growing leafed plant.* Pontus' CEVAS helps accelerate the growth of Pontus' water lentils, requiring the plant to be harvested every 24 hours. Pontus developed the HARV technology to allow the crop to be automatically harvested daily. In addition, due to its low profile, HARV will enable Pontus to stack nine levels of vertical farming at its Surrey, British Columbia production facility.
Steve McArthur, Chief Technology Officer, Pontus, stated, "Talking with the experienced team at Automation Experts (an automation and innovation company based in Calgary, Canada), we were able to identify that there was no robot out there that handled everything we needed it to do. By harvesting the crop in situ, using HARV, we will reduce the space between the water beds and increase the number of levels, increasing efficiency and the yield. We are beyond excited about pairing HARV with our CEVAS system, as we see CEVAS as a greener, more ecologically sustainable way of producing high nutrition food products."
Stephen Bruce Wong, CEO, Automation Experts, added, "HARV is more than a mechanical tool for harvesting. It will manage the farm and give us critical insight and data regarding the optimization of the growing environment. The robotics in HARV will allow Pontus to eliminate moving parts from the structure thus lowering the cost to build Pontus' vertical farms as the water beds can be dumb and do not need the technology built into them. It also uses machine learning and artificial intelligence to support all aspects of the growing process."
The patent filing is part of the technology leadership in the aquaponic space that Pontus continues to secure.
About Pontus Protein Ltd.
Pontus Protein Ltd. is a Vancouver, B.C. based technology company that grows water lentil protein for commercial use. Pontus is reinventing agriculture with their proprietary Closed Environment Vertical Aquaponic System (CEVAS) – the farming of the future. Pontus specializes in the indoor vertical farming of water lentils that use 95% less water than traditional agriculture and no pesticides or chemicals. Pontus is committed to solving the global food crisis by providing access to sustainable indoor biosecure pure plant-based proteins. Pontus' water lentils can be harvested every 24 hours, exceed organic certification, and can be grown in any climate in a relatively small area. Our water lentil protein is filled with antioxidants, minerals, vitamins, and all the amino acids, making a complete protein food source. Pontus aims to revolutionize the plant-based sector as the entire sector is currently based on two main protein sources: soy and pea. Water lentil protein is far superior to pea and soy protein. It contains over 40% protein vs. 5-36% protein*, and Pontus aims to be the base protein for nutrition-rich plant-based food products and nutraceuticals to support the movement transitioning the world from meat-based to plant-based proteins.
To learn more, please visit pontuswaterlentils.com.
*https://www.infood.net/visitor/collection/75?portion_size=100
*https://www.zmescience.com/science/fastest-growing-plant-02022021/
On behalf of the Board of Directors
"Connor Yuen"
Connor Yuen, CEO
Pontus Protein Ltd.
Contact Information
For more information, please contact:
Connor Yuen
Chief Executive Officer
https://pontuswaterlentils.com/company/#contact
Forward-Looking Information
Certain statements in this release are forward-looking statements, which reflect the expectations of management regarding the Company. Forward-looking statements consist of statements that are not purely historical, including any statements regarding beliefs, plans, expectations or intentions regarding the future, including but not limited to Pontus' ability to revolutionize the plant based sector. Such statements are subject to risks and uncertainties that may cause actual results, performance or developments to differ materially from those contained in the statements, including risks related to factors beyond the control of the Company. These risks include, but are not limited to, the following: the unknown magnitude and duration of the effects of the COVID-19 pandemic, the failure of Pontus to receive the necessary approvals from the Canadian Food Inspection Agency for its products and facilities, the inability to complete Pontus' Surrey-based production facility, as well as other general business, economic, or market related risks beyond the director control of the Company and which may affect the Company's business, operations, or products. No assurance can be given that any of the events anticipated by the forward-looking statements will occur or, if they do occur, what benefits the Company will obtain from them. The Company undertakes no obligation to update forward-looking information if circumstances or management's estimates or opinions should change, unless required by law. The reader is cautioned not to place undue reliance on forward-looking information.
Neither the TSX Venture Exchange nor its Regulation Services Provider (as that term is defined in policies of the TSX Venture Exchange) accepts responsibility for the adequacy or accuracy of this release.
SOURCE Pontus Protein Ltd.
For further information: Investor Relations or Media enquiries: invest@pontuswaterlentils.com, (403) 589-7992
Organization Profile
Pontus Protein Ltd.
TAIWAN: Environmental Impact Assessment: Will Vertical Farms Upend Conventional Agriculture?
In a country that has limited agricultural land and commonly endures floods, droughts, and typhoons, controlled-environment agriculture may be an ideal alternative to traditional farming
June 09, 2021
By Steven Crook
In a country that has limited agricultural land and commonly endures floods, droughts, and typhoons, controlled-environment agriculture may be an ideal alternative to traditional farming
For millennia, the plants that humans have eaten absorbed light energy from the sun, and water from the soil through their roots. Farmers hoped and prayed for just the right amount of rain, temperatures that would make their crops thrive, and an absence of pests.
Now, consumers in Taiwan and many other countries can buy vegetables that have never come into contact with soil, been exposed to sunlight or been made wet by falling rain.
Indoor farms — often called vertical farms, because they occupy small pieces of land but feature multi-level growing areas — bypass the unpredictability of nature.
Curl leaf lettuce growing indoors at YesHealth’s vertical farm.
Photo courtesy of YesHealth Group
In few places does indoor farming, also known as controlled-environment agriculture (CEA), makes more sense than in Taiwan. Farmers here lack space (according to official statistics, households engaged in agriculture have on average less than one hectare of farmland each), endure floods and droughts, and worry typhoons might destroy their crops. What’s more, Taiwan has scores of disused industrial sites that could be repurposed into vertical farms.
GOING VERTICAL
A vertical farm in Taoyuan City’s Lujhu District (蘆竹) is the most productive example of CEA in Taiwan, according to Jesper Hansen, chief commercial officer of YesHealth Group, the company that designed and operates it.
YesHealth Group founder and CEO Winston Tsai.
Photo courtesy of YesHealth Group
The farm, inaugurated in 2017, yields 1.5 to 1.6 metric tonnes of lettuces, cruciferous vegetables and herbs every day of the year. Its growing chambers, which cover 3,000 square meters, are dominated by 10m-high, 14-level sets of shelves on which 50 farming staff nurture leafy greens.
The various types of leafy greens grown by YesHealth take between 21 and 32 days to grow from a seed to a harvestable product. The company doesn’t currently grow tomatoes or cucumbers on a commercial basis, because they take a relatively long time to grow from seed, Hansen says.
YesHealth Group founder and CEO Winston Tsai (蔡文清) comes from a technology background. His passion for pesticide-free food dates from his battle with a liver tumor several years ago.
YesHealth CCO Jesper Hansen shows how the company’s greens grow on polystyrene boards.
Photo: Steven Crook
The company’s first hydroponics facility, set up in 2013, produced 200kg of produce per day.
“At that time, it was considered quite a sizable vertical farm,” says Kevin Lin (林威立), YesHealth’s director of business development.
That site, superseded in terms of efficiency as well as size, now functions as the company’s R&D center.
Construction underway last year at the vertical farm in Copenhagen developed by YesHealth Group in partnership with Nordic Harvest.
Photo: Jesper Palermo, courtesy of YesHealth Group
IDEAL GROWING CONDITIONS
Identifying and recreating the ideal conditions for a particular plant isn’t easy. Lin gives as an example the constant breeze that blows over YesHealth’s lettuces.
“Getting the windspeed exactly right took us several years,” he says, adding that, by mixing the air, wind helps plants to absorb more carbon dioxide.
Some vertical farms are airtight. One advantage of a closed system is that the amount of carbon dioxide in the air can be enhanced so as to boost photosynthesis levels. In places that are exceptionally hot or unusually cold, closed systems are more energy-efficient, because they reduce the need for cooling or heating.
The Taoyuan facility has an open system. As air is drawn in, it’s filtered to keep out dust and insects.
Different crops thrive best in different light spectrums, and the farm’s LED arrays can be adjusted to achieve these conditions.
Compared to conventional farming, hydroponic agriculture uses tiny amounts of water, because the rate of evaporation is far lower. In YesHealth’s Taoyuan farm, water is recirculated for 45 to 60 days, then discarded.
A biofertilizer solution made from soybeans, brown sugar, oyster shells and other components is added to the water. Antagonist microorganisms are used to combat fungi and algae, which may arrive in the air or on the seeds themselves.
Vegetables are grown in the manmade substrate (previously plastic foam, now a biodegradable gel) on thin polystyrene boards that are reused. Polystyrene has a reputation for being bad for the environment because it decomposes so slowly if at all. However, it tends to release toxins only when heated or exposed to sunlight; inside a vertical farm, this is unlikely to happen.
SUSTAINABILITY
Visitors to YesHealth are educated as to the sustainability advantages of CEA, “But here in Taiwan, our USP continues to be that our produce is healthy and pesticide-free,” says Hansen.
Posters around the facility highlight the company’s promise of “Four No’s, Two Lows.” This represents produce free of pesticides, heavy metals, insects, and E. coli, with low nitrate and bacteria levels.
Some visitors say that the farm’s produce — which is sold on-site, through chains like Carrefour and Jasons Market Place and supplied to several high-end hotels — is attractive yet pricey.
“We shouldn’t benchmark vertical-farm produce with crops grown outside,” Hansen insists, while lamenting that few consumers in Taiwan appreciate that vegetables that cost more may well be better for you — and better for the creatures with which humans share the planet.
“We can produce perfect-looking vegetables without contaminating them with chemicals or harming the environment,” he says.
Hansen explains that while YesHealth will continue to supply Taiwanese consumers with produce so clean it can be eaten raw without washing, its global role is now that of a technology provider for overseas partners.
“We’ve realized that our technology is superior to many of our foreign counterparts. This has a lot to do with the R&D mindset here and the supply chains in Taiwan and China,” says Hansen. “Our technology is all in-house. We don’t buy any third-party solutions.”
Hansen says it’s unfair to pass judgment on vertical farming, to say it’s too expensive.
“Of course, it’s more expensive than using free sunlight and free rainwater, but in five years or 10 years, I believe our produce will be competitive with produce from traditional farms,” Hansen says.
The cost of setting up and operating a vertical farm is dropping.
“The technologies we use — LEDs, automation, robotics, software — are becoming much more efficient over time,” Hansen says.
At the end of last year, YesHealth Group, working in partnership with Nordic Harvest, completed what’s said to be Europe’s largest indoor farm on the outskirts of Copenhagen. Hansen describes the Danish facility as “massively more efficient” than YesHealth’s main Taoyuan farm.
Conventional farmers in Taiwan and Denmark have nothing to fear from YesHealth.
“In every project, we try first to substitute imports, not locally-grown food,” Hansen stresses.
The Copenhagen farm will be able to supply three metric tonnes of greens per day when it reaches its full production capacity.
“Because we’re able to grow locally all year round, we’re doing away with a huge number of food miles,” says Hansen, who points out that perishables are often flown several thousand kilometers from farms to supermarkets in Europe and Asia.
Taiwanese scientists have developed space-efficient devices that permit the automated monitoring of a plant’s weight, accurate to 0.1g. However, rather than track the progress of each lettuce, YesHealth aims to develop a perfect standard operating procedure for each crop.
“We don’t need lots of sensors, because our R&D team has worked out what conditions are needed to get the best results. The only monitoring we need to do is to ensure that the temperature or another variable doesn’t stray beyond the normal range. We control these parameters tightly, so the plants grow the same way every time. We’ve never lost a harvest,” Hansen says.
LONGER SHELF LIFE
YesHealth’s way of farming can be likened to baking. If the ingredients are mixed in the right proportions, and the temperature and timing are spot on, the cake — or the kale — will come out just right.
“If you harvest and wash a leafy green, it’s almost impossible to dry it properly. When you wrap it, because of moisture on the leaves, it’ll have a short shelf-life,” says Hansen. He says that YesHealth’s salad products last twice as long on the shelf as traditionally outdoor-grown produce, because they are “extremely clean, dry and ready to eat.”
Asked if YesHealth will ever grow GM crops, Hansen replies that when crops undergo genetic modification, it’s usually to protect them against pests or to enhance fertilizer takeup.
“We don’t need those attributes,” he says.
The rapid growth of CEA isn’t likely to diminish the use of GM crops, however, because currently there’s no feasible way to produce indoors the cassava, maize, potatoes, rice and wheat that meet most of humanity’s food needs.
Vertical farms are almost certainly a good thing. But even in crowded and industrialized Taiwan, conventional agriculture isn’t going away. The rise of CEA shouldn’t distract farmers or consumers from understanding and managing the ecological impacts of rice paddies, fruit orchards and chicken farms.
Steven Crook, the author or co-author of four books about Taiwan, has been following environmental issues since he arrived in the country in 1991. He drives a hybrid and carries his own chopsticks.
This column does not necessarily reflect the opinion of the Taipei Times.
Lead Photo: YesHealth Group founder and CEO Winston Tsai.
Photo courtesy of YesHealth Group
Dickson Despommier, Professor Emeritus - Contributor To The New Book "The Economics of Sustainable Food: Smart Policies For Health And The Planet "
In The Economics of Sustainable Food, co-authored by Dr. Charles Knirsch, I discuss, as agrotechnology advances rapidly, consumers will no longer have their produce shipped months in advance and from thousands of miles away
I contributed to the new book The Economics of Sustainable Food: Smart Policies for Health and the Planet , Co-Authored by Dr. Charles Knirsch, and am excited to say that it is now available!
In The Economics of Sustainable Food, I discuss, as agrotechnology advances rapidly, consumers will no longer have their produce shipped months in advance and from thousands of miles away. Vertical farming uses a fraction of the resources of conventional farming and allows farmers to grow locally and bring fresh produce to the mass market within days or even hours, reducing the carbon footprint associated with transporting food. Additionally, as climate change brings dramatic weather changes, CEA allows constant conditions regardless of weather patterns. VF thus promises substantial environmental and economic gains, and policy should incentivize vertical farms to grow increasing shares of produce both domestically and across the world.
If you’d like to purchase a copy from Island Press, which ships worldwide, use the code BATINI, which is good for a 20% discount. You can also order the book from Amazon, Barnes and Noble, and your local independent bookseller.
I hope you will consider sharing the book with your own networks.
You can help in a few ways:
Forward this message to your own contacts or
share the news on your social media networks.
Feel Free To Include The Discount Code, BATINI.
· If you’d like to review it for a publication or website, you can request a review copy from press@islandpress.org.
· If you’d like to use it in a class, you can request an exam copy
at www.islandpress.org/request-exam-copy.
· Encourage your organization to contact info@islandpress.org
for details about a discounted bulk purchase.
· Review the book on Amazon, Goodreads, or another review site.
If you have any questions or ideas for how to use the book in your own work, please don’t hesitate to get in touch. I hope you enjoy the book.
All the best,
Dickson
Natural Gas Liquids Drive Geothermal Tech
A Canada-based firm has developed geothermal technology that removes water from the equation
A Canada-based firm has developed geothermal technology that removes water from the equation.
Commonly associated with water via hot springs, geysers, or plumes of steam, geothermal energy relies on underground heat. A Canada-based firm has developed geothermal technology that removes water from the equation, potentially expanding where the renewable resource can be tapped.
“Geothermal, derived from its Greek roots, means ‘earth’ and ‘hot’ and quite literally means that we bring heat up from the ground,” Chris Cheng, a senior development engineer with Eavor, told Rigzone. “This heat can then be used directly or converted to electricity with a power generation unit.”
Unlike conventional approaches to harness geothermal energy, Eavor’s technology uses a closed-loop energy system that eliminates the need to find hot water or steam resources, Cheng continued.
“Since there is heat under the ground everywhere, Eavor technology is applicable in many more places than traditional geothermal, places where that hot water or steam resource may not exist,” he said.
Cheng explained that his company’s technology generates electricity by bringing heat up to the earth’s surface with a working fluid inside the “Eavor-Loop” system, exchanging heat with the working fluid – often one of two natural gas liquids – used by the power-generating unit.
“For an Organic Rankine Cycle application, this working fluid is usually butane or pentane, shown in the red loop and is chosen for its lower-than-water boiling temperature,” Cheng said, referencing the diagram below that illustrates Eavor’s closed-loop technology. “The working fluid is allowed to vaporize and expand in the power turbine which turns this into rotational energy, making electricity. The working fluid is cooled and condensed back to a liquid and is ready to collect heat from the Eavor-Loop once again.”
This diagram outlines how Eavor's closed-loop geothermal technology works. IMAGE SOURCE: Eavor
“While the power generation unit is not unique to Eavor, Eavor’s novelty in its closed-loop design reduces exploration risk – no need for hot aquifers – and allows for more predictability and operational control, including dispatchability,” Cheng said.
The geothermal technology’s novelty evidently appeals to two major oil and gas players, which have steered investment dollars to Eavor. Find out which companies are supporting the technology developer in the following excerpts from Rigzone’s conversation with Cheng.
Rigzone: Where in North America is there sufficient geothermal potential to sustainably diversify the energy mix?
Chris Cheng: The average geothermal gradient around the world is about 30 degrees Celsius (86 degrees Fahrenheit) per kilometer (0.6 miles), which means that, on average, the temperature increases by 30 degrees for every kilometer you drill into the earth.
It all comes down to price, and Eavor believes there is geothermal potential in most places in the world, including all of North America, for both heat and electricity. For now, while the technology is new and costs are high, Eavor is targeting locales where the price for heat and electricity is also high, such as in Germany, the Netherlands, or Japan. These countries have what we call feed-in tariffs in place to help support the transition to renewables.
Eavor is working hard to reduce the cost of its technology so that it can be economic anywhere, comparable to the prices we see now for wind and solar but with the added benefit of dispatchability and small footprint.
Rigzone: What makes geothermal stand out as a renewable resource?
Cheng: Compared to wind and solar, geothermal has a relatively small surface footprint which is important in jurisdictions where surface space may be at a premium.
Secondly, as previously mentioned, Eavor’s closed-loop design allows for improved operational control, making the Eavor-Loop both load following and dispatchable. The heat in the ground is always present, while the wind and the sun may not always be there.
Rigzone: Where do you see geothermal contributing to the energy transition, particularly in North America?
Cheng: Eavor sees itself fitting into the energy mix alongside other renewables. It can fill in the gaps where wind, solar and traditional geothermal are less effective, such as during the night, when the weather is unfavorable, or where the geology doesn’t support traditional geothermal.
Rigzone: What are the biggest misconceptions you hear about geothermal energy, perhaps from the oil and gas community? How do you overcome them?
Cheng: We get a lot of questions about induced seismicity or fracing, which can be a non-starter in some places. With Eavor’s closed-loop system, there is no fracing and a very, very low probability of induced seismicity, so it’s important that we educate potential clients and partners about what separates our technology from the incumbents.
While we are adopting technology from oil and gas, Eavor’s technology eliminates some of the perceived negative aspects that may be associated with enhanced geothermal systems or hydrocarbon extraction, such as fracing.
In the grand scheme of things, the misconceptions are not that major – something that a few technical meetings can overcome – and the overall reception has been positive. Our latest round of investment back in February of 2021, which included bp (NYSE: BP) and Chevron (NYSE: CVX), are a good indicator that we have been embraced by at least some major players in the oil and gas industry as a viable solution.
Rigzone: Where do you see geothermal market opportunities for oil and gas industry players such as operating companies, drilling companies, service and equipment providers, etc.?
Cheng: One of the reasons Eavor is based in Calgary is because of the vast amount of geoscience and engineering expertise that exists due to the oil and gas roots of this city. There is a lot of opportunity for technical staff, service and equipment providers to pivot into geothermal due to the amount of overlap between the two industries.
For example, as a development engineer, the work that I do is remarkably similar to oil and gas. We have to select a good place to drill an Eavor-Loop, which begins with good geological and geophysical work, then we have to design the well and spend capital to drill the well and construct the facility, and finally sell a commodity for a forecasted price over many years.
Sound familiar? For geothermal, instead of oil and gas, the commodity is heat and power, but the development process and the financial modeling is very similar!
To contact the author, email mveazey@rigzone.com. Find out more about geothermal energy in recent Rigzone articles discussing orphaned oil and gas wells, market opportunities and collaboration, and ultra-deep drilling technology.
USA: DENVER, COLORADO: Is Urban Farming The Next Big Condo Trend?
Lakehouse is home to a 3,000-square-foot urban farm, from which residents can pluck herbs and lettuce for dinner
May 17, 2021 | By: LX Collection
Judy Weingarten doesn’t live in a rural cottage, but in a newly opened condo at Lakehouse in Denver. Aside from the perks, you might expect from a development like this—70-foot lap pool, yoga studio, elegant residents’ lounge—Lakehouse is home to a 3,000-square-foot urban farm, from which residents can pluck herbs and lettuce for dinner.
Photo Credit: Lakehouse
“I love looking out my window at the garden, contemplating what vegetable I am going to have with my dinner tonight,” Weingarten says. “I enjoy trying new recipes based on what is harvested at the time, as well as having fresh-cut flowers throughout the summer!”
The Condo with Its Own Urban Farm
Flourishing with green beans, poblano, oregano, carrots, and eggplant, Lakehouse’s raised vegetable and herb beds are overseen by Agriburbia. The company describes itself as “an innovative and growing design movement that integrates aspects of agrarianism with land development.” While Agriburbia oversees planting, irrigation, and harvesting, residents can weigh in on what gets planted—and are encouraged to chip in with the farming too.
Brian Levitt, co-founder and president of NAVA Real Estate Development, which developed Lakehouse, tells LX Collection: “Notices will go out on harvest days inviting residents to come to the harvest room and help themselves. They are able to cull herbs from the farm for their cooking at any time. Crops are also used for community events and cooking demonstrations.”
In 2020, Lakehouse’s urban farm turned over 1,600 pounds of produce. That’s enough to provide almost four Americans with their vegetable quota for the entire year.
The Growth of Condo Gardens
Outdoor space is increasingly desirable for potential condo buyers, and while this partly stems from the pandemic and the demand for residential space en plein air, the trend began before 2020 and made outdoor space a precious commodity.
Innovative outdoor spaces have been finding their way into condominiums for years. Sky gardens have shot up from London to Ho Chi Minh City. Courtyards, lawns, and pergolas are now commonplace. In New York City, condos like 70 Charlton and 565 Broome maximize greenery with living walls. Architects and designers are looking at every last inch of space, asking, “could this be a garden?”
Until now, designers of these spaces have focused on aesthetics and creating outdoor entertaining areas, but a movement in growing vegetables, fruits, and herbs is now underway. You can see it in the sheer number of articles and explainer videos showing how to grow microgreens on the windowsill or dwarf apple trees in patio containers.
In response, some new condo developments are sowing the seeds for a genre of urban gardening where edible produce is grown and harvested in a community environment.
Ambitious Plans in Europe
In the Netherlands, a particularly ambitious urban farm concept is in the offing. MARK Green Vertical Village is a proposed complex of three towers in the city of Utrecht. Taking its inspiration from the traditional Dutch villages in the area, plans for this Vertical Village show roofs with greenhouses growing the likes of tomatoes, cucumbers, mushrooms, and apples. These year-round gardens would be owned and operated by a collective of farmers and financed by inhabitants of the 1,128 apartments via a monthly service fee. An on-site restaurant and area residents would also have access to harvests.
As with Lakehouse, MARK’s residents needn’t dig for their supper: “Participation is encouraged but not vital to the food production,” says Darius Reznek, a partner at Karres en Brands, the firm behind the plans.
But vertical villages face steep challenges. The biggest, says Reznek, is competing with traditional and industrial farming practices on cost and yield. “The farming concept/system needs to have additional benefits,” Reznek says, “community spaces, community building, soundproofing.”
While MARK is on track for completion by 2025, the urban farming aspect of it remains up in the air: “It is a vital part of the entire concept but currently under feasibility studies,” explains Reznek. He is in no doubt that a condo garden like this can happen—and be self-sustaining, too—but in the first instance, it requires an initial financial investment.
An Enhanced Sense of Community
Lakehouse’s success shows that baby steps will get you places. And while its urban farm doesn’t produce enough crops to feed residents at every meal, Brian Levitt explains it has already grown something else in abundance: community spirit.
“Our goal was to create an enhanced sense of community through education and access to good food that is grown on-site,” says Levitt. “It provides a way for residents to come together either to help in the garden or to cook together in the collaborative kitchen and outdoor grills.”
Reznek agrees that community farms and gardens sow the seeds for healthy relationships, as well as sustainability: “Common spaces are the places that tie these communities together,” he says, “where you meet your neighbors, get to know them, and are more likely to share things such as food, energy, and space.”
The urban condo farm isn’t a trend just yet. But Lakehouse is a beacon of what can be achieved, while MARK Green Vertical Village is an ideal of what might.
As residents seek sustainability, wellbeing, and community in their daily lives, expect to see the green shoots of more urban farms appearing in condos near you.
Lead Photo: Photo Credit: Chuttersnap
Ontario Greenhouse Installs Combined Heat Power
"We look forward to expanding our energy-efficient and sustainable system"
With the demand for greenhouse-grown produce continuing to increase, DelFrescoPure is consistently looking for ways to become more sustainable. "Ensuring high-quality produce is available year-round. Implementing a Cogeneration power plant is the most efficient way to achieve that goal," they say. As of fall 2021, DelFrescoPure will be increasing their pre-existing Cogen system by 6.5 MW, for a total of 10+ MW across their facilities.
Cogeneration or combined heat and power (CHP) is the onsite generation of electricity from the use of natural gas. The byproducts of CHP are the heat that can be stored and used to create the desired microclimate within the greenhouse and CO2 that is used to fertilize the crops. The CHP units will additionally produce the electricity required to power the grow lights as well as the mechanical load of the facility. While electricity generation alone is typically 40% efficient in converting fuel to power, adding heat recovery to the equation can bring that efficiency to 90%, a reality that suits greenhouses well.
Year-round production
DelFrescoPure intends to use the electricity to power the lights at Via Verde Hydroponics. These grow lights allow for an extended growing season, making produce that would originally be grown in the summer available all year round. The heat harnessed by CHP will also be recycled to heat the greenhouses and meet all daily power needs. Being able to produce electricity more cost-effectively onsite also means DelFrescoPure does not have to worry about voltage fluctuation from the area maxing out the local grid. With electricity no longer being a concern DelFrescoPure is primed and ready for the 25-acre expansion currently underway.
“DelFrescoPure is excited to increase our Cogeneration Power units. We are very pleased to be working with Martin Energy again to install the new CHP technology and solutions they offer. The results from using the Cogeneration technology over the past three years have been great. We look forward to expanding the system so we can continue to provide fresh produce all year long.” said Carl Mastronardi, President of Del Fresco Produce.
Along with the financial benefits, CHP power is better for the environment. This method ensures that fewer resources are wasted and required to produce electricity. The extended growing season also reduces our carbon footprint by decreasing the need for local retailers to import high milage commodities. DelFrescoPure is taking a sustainable approach to providing consumers with the freshest items possible. CHP is perfectly suited for the greenhouse environment since it is able to harness all three attributes of the technology (electricity, heat & CO2). DelFrescoPure® will never have to worry about where their energy is coming from and can continue to expand as market demand increases.
For more information:
DelFresco Pure
www.delfrescopure.com