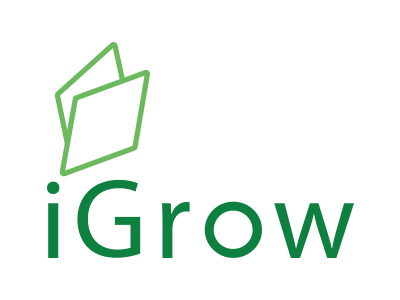
Welcome to iGrow News, Your Source for the World of Indoor Vertical Farming
Vertical Farming and the Future of Automation in Agriculture
Vertical farming is by no means a new idea. However, recent supply chain disruptions coupled with the falling price of produce, is opening new doors for a farming method previously deemed unviable by many.
August 10, 2021
Vertical farming is by no means a new idea. However, recent supply chain disruptions coupled with the falling price of produce, is opening new doors for a farming method previously deemed unviable by many. Here, John Young, APAC country manager at automation parts supplier EU Automation, highlights the renewed interest in vertical farming among a new generation of farmers, and explores the advantages it offers in tackling some of the biggest challenges facing the sector.
Turn the clock back approximately 1000 years, and less than four per cent of the world's habitable land was used for farming — that is the equivalent of four million square kilometres. Today, farmland takes up more than half of the world's habitable land, which equates to a landmass larger than South America.
Our World in Data reports the alarming facts associated with industrialized livestock farming, involving climate change, extinction of species, widespread destruction of habitat, and 80 per cent of cropland grown to feed livestock. With the population of the Asia Pacific region expected to reach 5 billion by 2050, the responsibility to supply food to an ever-growing population is becoming difficult.
A new generation of farmers are rising to the sustainability challenge. This agricultural revolution presents the transition from traditional farming to futuristic high-tech artificial intelligence (AI) and robotics. Whether it's weed-killing robots, harvesting and picking robots, or autonomous tractors, the farming landscape is evolving. In this age of robotic farming, producers believe incorporating automation and data will enable farmers to produce more, while damaging the environment less.
One major process change that is currently on the rise is the shift to vertical farming. Currently, 16.55 million square feet (sq ft) of indoor farms operate across the globe. However, the State of Indoor Farming report suggests this figure will increase to 22 million sq ft by 2022. The demand is high, and the AI journey is only getting started.
Why are farmers suddenly interested in vertical farming?
Vertical farming is the practice of producing food in vertically stacked layers. The climate-controlled indoor farms contain rows of plants situated next to each other, growing vertically, and hanging from the ceiling. Robotics help manoeuvre the products around, and AI can monitor the different parameters that are required for the crops to grow, such as the levels of water, temperature, and light.
Indoor agriculture is at an exciting point in its development. Key technologies used in farming systems today range from perception technologies which use cameras and sensors to detect and monitor various factors of the lifecycle. AI processes the data from sensors and provides solutions, while automated and autonomous mechatronics that use robotics and automated machines collect products when ready to dispatch to the market and recover the crops from ailments during the growing cycle.
Right now, the focus is to take vertical farming to the next level by developing smart robots which can increase precision and productivity, while minimizing environmental impact and risk. Agriculture, one of humankind’s oldest inventions, is merging with the latest technology, and farmers will soon be looking to pair with a reliable automation parts supplier to make the step up to vertical farming.
Vertical farming offers a unique set of advantages. Farmers understand there are many urgent and practical reasons to grow upwards rather than outwards. This farming method has huge potential for sustainability and food security, while protecting the environment, economy, and ecosystems.
In addition, the inclusion of AI and robotics ensures high-quality growth of products all year round, while preserving water, nutrients, and land consumption by 95 per cent. The controlled process of indoor farming with the help of AI and robotics also protects crops against pest invasions, and ensures they are well insulated — this is an aspect field farming cannot guarantee since it requires amenable weather conditions and labour.
Vertical farms can operate anywhere with no geographical constraints and are not subject to the limitations presented in outdoor farming, such as extreme conditions. This not only protects the crops, but also provides a safer working environment for labourers. What’s more, labour costs can be significantly reduced due to the automated indoor growing systems; thus, there is no longer a need for manual labour all year long.
In addition, energy consumption can be drastically reduced in vertical farming by implementing LED lighting to mimic the sun as a light source. A minor change like this can limit heat waste while increasing energy efficiency and cutting energy costs. Not only can LED lighting be used as an alternative, but renewable energy generated from wind turbines can be paired with vertical farming to ensure 100 per cent of its energy is produced from renewable sources. It is a win-win situation.
How will it boost the economy?
This sector is expecting a huge boom in investment and interest and manufacturers, suppliers and retailers are therefore preparing for this shift through early adoption. In the past, vertical farming was viewed as theoretical, but now the vertical farming market in the APAC region is expected to grow at a compound annual growth rate (CAGR) of 29 percent, rising from its current value of $0.78 billion to $2.77 billion by 2026. This is largely due to the advancement in technology such as sensors and smart energy systems that have improved the efficiency of growing products.
Although vertical farms will not replace traditional ways of farming, they hold great potential to revamp the future of agriculture in the APAC region by pushing towards a sustainable, environmentally conscious, tech savvy, economically rational, and health-sensitive world.
Source and Photo Courtesy of Agritech Tomorrow
Blue Radix & Ecoation Join Forces With The World's 1st Autonomous Find & Fix Solution
May 19, 2021, Rotterdam, Netherlands and North Vancouver, Canada
Blue Radix, an independent Dutch AI-tech specialist for the international greenhouse industry, and Ecoation Innovative Solutions Inc. (ecoation), a Canadian developer of automated greenhouse management and crop health monitoring technologies, have signed an agreement.
The collaboration aims to identify new ways to automate decision-making and action in the greenhouse, using vision technology and algorithms. ecoation and Blue Radix are using the data collected by ecoation’s OKO and platform to enhance the impact of Blue Radix’ algorithms for autonomous growing. By combining data sets, algorithms, and analytical efforts the companies are able to create new insights and applications that help growers worldwide to improve their crop strategy, quality and yield.
Blue Radix and ecoation look forward to ongoing collaborative efforts where the duo explores the multitude of innovation opportunities that become available when you combine ecoation’s OKO and platform with Blue Radix’ Crop Controller. Collaborating across data and algorithms has the potential to create value across many avenues, including optimizing crop strategy, autonomous steering, IPM enhancement, and understanding spatial climate distribution.
The World’s 1st Autonomous Find & Fix Solution
The first project the duo is working on is enhanced autonomous growing with crop data visualization. ecoation’s OKO collects sensory data and information about climate, integrated pest management, and crop work at every row and post to an SqM granularity. These insights greatly contribute to a complete and accurate view on the state of the crop. The broad range of data points, including fruit count, fruit colouring, and stem density, will be combined with the smart steering algorithms of Blue Radix’ Crop Controller. Crop Controller will actively, continuously and autonomously control the greenhouse conditions with the grower’s crop strategy as its starting point and the optimal crop status as its goal. E.g. by optimizing the plant load, plant stress is reduced avoiding weak plants that are vulnerable to pests and diseases. In this way ecoation and Blue Radix find and fix imperfections before they impact yield or crop quality.
Support growers
“Collaborating with Blue Radix means pioneering the future of ag more effectively, at a pace that would be difficult to reach if we carried on separately,” shared ecoation CEO Dr. Saber Miresmailli. “Both teams are committed to the same goal: to support growers in making the best possible decisions. Working together means unlocking new ways to get the most from the data and providing better insights to our customers that inform their decisions.”
“Ecoation offers solutions which are important components in a fully autonomous greenhouse. Optimization and steering with algorithms depends on high quality data and a robust crop strategy. Vision technology and enhanced analytics from ecoation provides this data and the necessary input to improve the grower’s crop strategy even further,” emphasizes Blue Radix CEO Ronald Hoek. “We strive for open collaboration and partnerships. Growers should always be able to choose freely what they want to do with their data and benefit from the best combination of services & products for their greenhouse.”
The duo will only work with greenhouse data retrieved from the customers of ecoation and Blue Radix who provide full consent. Transparency and data security is paramount, and this collaboration will rely on growers who are looking to optimize their greenhouse operations with autonomous processes and are interested in contributing to the future of ag with their facility data and insights.
About Blue Radix
Blue Radix is an independent Dutch AI-tech specialist for the international greenhouse industry. Blue Radix creates solutions with artificial intelligence for daily decisions and actions in greenhouses. Greenhouses offer an efficient way to produce food and flowers in a sustainable manner. But the number of skilled people with expertise of growing crops in greenhouses is declining every year. This has a direct and negative impact on yield, costs, continuity, and product quality. Blue Radix offers solutions for these challenges: smart algorithms which optimize and steer climate, irrigation, and energy continuously and autonomously, supported by off-site
Autonomous Greenhouse Managers. Blue Radix offers growers a digital brain for their greenhouse. More information at blue-radix.com. Find Blue Radix on LinkedIn, Twitter, and Instagram.
About ecoation
ecoation is an award-winning grower-centric platform that combines Human knowledge and experience with Machine precision and automation to increase operational visibility, assist growers, and enhance their decisions. Commercially available since September 2019, ecoation products can be found in greenhouses across the United States, Canada, Mexico, and Europe. With an experienced team of 60+ growers, scientists, engineers, and business professionals from all over the globe, ecoation is passionate about enabling a cleaner future and supporting growers in making the best possible decisions. At ecoation, we are on a mission to empower growers because we believe in doing so, we win together.
More information at ecoation.com. Find ecoation on LinkedIn, Twitter, and Instagram.
For media inquiries, please contact:
Blue Radix
Marijke van Rongen
Manager Global Marketing & Communications
marijke.vanrongen@blue-radix.com
+31 6 53 43 38 39
ecoation
Marketing and Media Contact
Cameron Lust
Signify Adds Automatic Intensity Adjustment Plus Year-Long Recipe Modulations To Horticultural Controls
There’s something for both the greenhouse and the vertical farm in the GrowWise tweaks, which in some cases rely on tying to other systems’ sensors.
The Signify toplights at Belgium’s De Glastuin lettuce greenhouse automatically dim or brighten as daylight levels changes. (Photo credit: All images courtesy of Signify.)
Signify has enhanced the control system for its greenhouse LED lighting so that toplights can react immediately to changes in daylight conditions and adjust brightness accordingly. The company has also added year-long control settings intended to allow vertical farmers — but not greenhouses — to program seasonal variations in LED spectral content over a 365-day period.
Both upgrades are intended to reduce manual labor and improve overall cost efficiencies, Signify said.
Until now, greenhouse farmers could dim or brighten their Signify toplights by instructing the lights to do so via the control system, called GrowWise. Signify has now modified GrowWise software so that it can take readings from daylight sensors that are part of separate systems. GrowWise then instantly and automatically adjusts artificial light intensity emitted by the toplights, called Philips GreenPower LED.
“The lighting can be used much more efficiently since it gives us the flexibility to reduce light levels at any moment we need to,” said Wouter de Bruyn, the owner of Belgian lettuce grower De Glastuin, an early user of the new automatic feature.
Whereas Signify is known in office settings to build sensors into its smart luminaires, the GrowWise controls make use of sensors that are part of climate control systems and greenhouse management systems from companies such as Priva, Hoogendern Growth Management, and Ridder, all based in Holland.
Planet Farms’ Luca Travaglini backs up Signify’s point that prescribing a year of spectral content improves efficiency and helps keep down manual labor costs in controlled environment agriculture (CEA) operations such as vertical farms.
“The climate computer is equipped with a daylight sensor that sends actual light measurements to the GrowWise Control System so we can adapt our light levels automatically to ensure an even light level throughout the day and season,” de Bruyn said at De Glastuin, based in Kontich.
“Dynamic lighting in a greenhouse is the next step in improving the cost efficiency and quality for the cultivation process,” said Udo van Slooten, business leader, horticulture LED solutions at Signify. “It allows growers to effortlessly maintain a consistent level of light throughout the day to produce the best possible crops. The system compensates for cloudy weather and creates a more controlled growing environment for your crop.”
In another upgrade to GrowWise, vertical farmers who want to prescribe modulations in spectral content are no longer limited to 24 hours of looped recipe cycles. Rather, they can order up a year’s worth of shifts for controlled environment agriculture (CEA) operations.
The year-long programming feature is aimed at vertical farmers rather than at greenhouses because the lights that Signify provides for vertical farms support controllable spectral changes, whereas the greenhouse toplights do not. Signify refers to its GreenPower LED vertical farm lights as “production modules” rather than as “toplights.” Toplights and production modules can both be programmed for intensity over a year, but the intention of the year-long feature is oriented toward spectral content.
Compared to greenhouses, vertical farms tend to make much less, if any, use of natural light. In vertical farms, the lights are mounted much closer to the crop in stacked shelves.
One of the first users of the year-round feature is Italy’s greens and lettuce grower Planet Farms.
“Now we can easily create custom light recipes and set them to run year-round to provide the right light recipe with the right light intensity at the right time throughout the crop’s growth cycle,” said Planet Farms co-founder Luca Travaglini. “By automating our full light strategy during the growth cycle, for the whole year, we can run our operations very efficiently and keep our manual labor costs low. That makes it easier for us to maintain consistent quality as we scale up our production.”
The horticultural market is a key growth sector for Signify, especially as it maps out a strategy to maintain profits in the pandemic economy, in which last week it reported a yearly rise amid rigorous cost controls that now include a small number of layoffs. CEO Eric Rondolat is targeting a big chunk of what he has quantified as a $2 billion general horticultural lighting market by 2023.
MARK HALPER is a contributing editor for LEDs Magazine, and an energy, technology, and business journalist (markhalper@aol.com).
“Agriculture Doesn’t Lack For Data – It Needs Better Organisation of Data to Feed 10 Billion”
"At Sensei Ag, we believe that indoor agriculture can transform the way we capture data about edible plants, help transform land and water usage at least tenfold through better use of that data, and be part of the critical new infrastructure of post-pandemic economies
As we look ahead to 2021, the challenge of overcoming Covid-19 still stands before us. The primary focus is on rolling out vaccines, but as worries about new variants come to the fore, we really do need to act at warp speed to get shots in arms and take additional measures if necessary.
To look at some of the challenges we face and some of the solutions we have in place, we asked a number of the world’s leading thinkers what their “moonshots” would be, and what grand visions for society we should pursue today.
Sonia Lo says: "Data is collected in the millions of data points every second around the world, in food and agriculture systems. In lesser developed economies, informational offers abound, to help even the smallest small-hold farmer. However, this is not relevant or helpful in the absence of the attendant ecosystem infrastructure of financing; robust, weather-resistant, and inexpensive physical facilities in which to farm; and real-time feedback for the farmers about their critical inputs. The world today is capable of imaging and analyzing every edible plant on the planet and yet there isn’t an international data infrastructure to be able to do that."
"At Sensei Ag, we believe that indoor agriculture can transform the way we capture data about edible plants, help transform land and water usage at least tenfold through better use of that data, and be part of the critical new infrastructure of post-pandemic economies. Organizing data across countries and providing unified data sets across climates and crops not only helps individual farmers but also enables a new generation of “agricultural fintech” which helps those farmers with much needed, but now, well-informed capital. Our vision is to enable the building of a multitude of indoor farm types – to stabilize food supply around the world but also t
Abandoned Spaces And Automation: What To Expect For Indoor Farming in 2021
Controlled-environment agriculture — also simply known as indoor farming — had a big year both in terms of activity and investment dollars
Controlled-environment agriculture — also simply known as indoor farming — had a big year both in terms of activity and investment dollars. While once we might have questioned the sector’s economic viability and ability to actually feed a growing global population, a lot of those doubts have diminished and indoor ag in its many forms now has an important role in our future food system.
What that role is, however, will continue to evolve over time. Here are a few thoughts on how that will happen over the next 12 months.
More automation.
Automation isn’t new to controlled-environment agriculture, but its presence as a part of indoor farming operations has increased over the last several months and will continue to in the next year.
In the context of controlled-environment farming, automation can refer to any kind of technology that removes manual human labor from the growing process. In some cases that includes robots that plant and harvest greens or move trays of produce around the farm. More often, though, automation refers to software that can calculate the optimal environmental temperature for each plant, know when plants need to be fed and harvested, and handle many other calculations that would otherwise require a person to have horticultural and technological (hardware and software) expertise.
Moving into 2021, we’ll definitely see a few more robots buzzing around the indoor farm. But the bulk of automation will be about software.
More grocery store partnerships.
Many large-scale indoor farms started out selling their leafy green wares to restaurants and hotels. The pandemic, of course, put a hold on that in 2020, and controlled-environment agriculture operations had to look elsewhere for customers.
Enter the grocery store. From container farms at local markets to Kalera’s partnership with Publix stores across the U.S., more indoor farming companies are growing their greens either onsite at grocery stores or within throwing distance of them.
This could in turn help bring the cost of greens grown on high-tech farms down, since the shipping and distribution steps will be less resource intensive in many cases and nonexistent in others.
More underutilized space.
One of my favorite stories from 2020 was this one, about a company called Wilder Fields that turned an abandoned Target store in south Chicago into a massive indoor farm.
Many companies are constructing their own facilities from the ground up, while others stick to smaller scale container farms that are a bit more mobile. Finding existing space, such as an abandoned big box retailer, seems a logical middle ground, and one we’ll likely see more of as companies work to lower costs and keep their environmental footprint down.
Predictions pieces, of course, are always a bit of a crapshoot, and even if the above forecasts turn out to be true, they’ll be but a smattering of the activity that will happen for controlled-environment ag in 2021.
FILED UNDER: AG TECH BUSINESS OF FOOD DELIVERY & COMMERCE FEATURED FOODTECH
Food Trends Suppliers Should Know to Stay Ahead of the Curve in 2021
With growing concerns about climate change, sustainability and healthy living, 2021 will bring new trends to the food industry. Plant based foods are expected to increase in popularity as more people try to consciously live a more sustainable life.
From insects and pumpkin-seed oil to Brad Pitt-branded wine and transparent packaging, these are the food trends expected to take the U.S. by storm in 2021.
What Will People Be Eating in 2021?
It’s predicted that Americans will be consuming a lot more of the following foods and drinks in 2021:
Insects — According to Forbes, 2.5 billion people around the world eat cooked or raw insects regularly. Many in the U.S. still consider the concept of insect consumption a little grotesque, but attitudes are expected to shift in the coming months with several startups, including Exo cricket protein bars in New York, securing significant funding from investors.
Boxed wine — It’s hard to believe that boxes of wine were considered classy before they were tacky. But in 2021, consumer appreciation for boxed wine is predicted to return. It’s easier to store, cheaper to transport, generates half the carbon dioxide emissions, and has a longer shelf life than its glass-bottled counterparts.
Alternative oils — Whole Foods Market predicts that consumers will become more experimental in their use of oil, choosing walnut, pumpkin seed, and sunflower seed oil over traditional options like olive oil.
Celebrity alcohol — There was an arguably better time when everyone knew someone who wore the Britney Spears perfume. But in 2021, it’s all about Brad Pitt’s rosé and Cara Delevingne’s prosecco, as alcohol brands and vineyards look to drive revenue through partnering with big-name celebrities.
Kombucha — Kombucha is a fermented, lightly effervescent, sweetened black or green tea drink that first hit the mainstream in 2018. Since then, its health benefits have been lauded, and the drink has been growing in popularity. It’s gluten-free and can be filled with live probiotic cultures.
Sweet and Umami — The Green Seed Group suggests that the big flavor combination of 2021 will be umami and sweet. Think rice infused with fish sauce caramel and nori and pork floss.
How Will People Be Eating in 2021?
It’s not just what people eat and drink that will change in 2021, but the entire culture surrounding it.
COVID-19 has contributed to a rise in passionate amateur chefs. With so many people spending much of 2020 stuck at home with extra time on their hands, cooking has become something of an outlet. Indeed, 74% of respondents to a Sensodyne/OnePoll survey said they used cooking as a coping mechanism to manage the stress of being at home, 44% have learned a new recipe, and 32% have taken online cooking classes.
Reduced access to on-the-go, takeout food has seen breakfast truly become the most important meal of the day, and the demand for interesting and diverse breakfast recipes will increase into 2021. Cooking enthusiasts are also investing more time and effort in making baby food and looking for creative takes on staple meals.
Coupled with this newfound enthusiasm for cooking is, unsurprisingly, a newfound enthusiasm for health and wellbeing. Forbes reports that 54% of American consumers care more about the healthfulness of their food and beverage choices in 2020 than they did in 2010. This will see demand for superfoods, probiotics, and supplements grow in 2021, with many food suppliers already incorporating functional ingredients like vitamin C which promise to support the immune system. In a June 2020 survey conducted by GlobalData, 23% of global consumers confessed to stockpiling vitamins and supplements.
COVID-19 has certainly driven Americans to evaluate the relationship they have with food and drink but, fortunately, extreme diets and food fads are expected to lose popularity in 2021. Instead, people are expected to take a healthier and more sustainable approach to healthy living by embracing balance and moderation.
How Will Food and Drink Be Packaged in 2021?
Before COVID-19, food and drink packaging was headed in a very sustainable direction, with consumers increasingly concerned about excess waste and ocean-bound plastics.
But the pandemic has led to increased concerns about biosafety, particularly surrounding the packaging of food and drink. In recent years, many retailers have committed to eliminating unnecessary packaging, but some of these efforts will likely be undone in 2021 due to health and safety concerns and retailers’ desire to reassure their customers. Starbucks, for example, banned the use of reusable cups at the beginning of the coronavirus outbreak.
Despite these setbacks, developments in sustainable and environmentally friendly packaging will continue in 2021.
Other trends will include an increase in transparent windows within food packaging that allow consumers to assess product quality, and QR codes, which can verify product and ingredient claims.
How Will Attitudes to Sustainable Living Change in 2021?
More than two-thirds of consumers want to ensure their everyday actions have a positive impact on the environment. This includes an interest in sustainably produced items, and a shift towards the consumption of plant-based proteins: in 2020, 28% of Americans ate more proteins from plant sources than they did in 2019. Another sustainability trend will see food suppliers up-cycling underused ingredients in a bid to reduce food waste.
Although the year 2021 won’t include a country-wide shift to veganism, retailers can expect increased demand for plant-based food as consumers commit to a more balanced diet and look to reduce their meat and dairy intake.
Image Credit: Rido / Shutterstock.com
Laura Ross Dec 15, 2020
AppHarvest’s Mega-Indoor Farm Offers Economic Alternative To Coal Mining For Appalachia
AppHarvest is taking advantage in the new wave of high-tech agriculture to help feed a growing population and increase domestic work opportunities in a sustainable manner.
Inside AppHarvest's 60 acre state-of-the art indoor farm in Morehead, KY.
In the first year of business, Jonathan Webb and his growing team at AppHarvest are riding high on what he calls the “third wave” of sustainable development: high-tech agriculture, following the waves of solar energy and electric vehicles. Since launching the concept in 2017, Webb and AppHarvest have raised more than $150 million in funding while building and opening one of the largest indoor farms in the world on more than 60 acres near the Central Appalachian town of Morehead, Kentucky.
For Webb, who grew up in the area and has a background in solar energy and other large-scale sustainable projects, AppHarvest is both a homecoming and a high-profile, purpose-driven venture that addresses the need for additional production to feed a growing population and reduce imported produce.
Webb’s vision for AppHarvest was inspired in part by a National Geographic article on sustainable farming in the Netherlands, where indoor growing is part of a national agriculture network that relies on irrigation canals and other innovations. He traveled across the Atlantic Ocean to see the farmers in action, then decided it was a venture he wanted to pursue — in his home state of Kentucky, where the coal industry is in decline and unemployment levels are on the rise.
“Seeing that the world needs 50% to 70% more food by 2050, plus seeing that we’ve shifted most of our production for fruits and vegetables down to Mexico — produce imports were tripled in the last 10 to 15 years,” he says. “I would go to a grocery store, pick up a tomato, and it could be hard, discolored. That’s because it’s been sitting for two weeks on a semi truck, being bred for transportation. So first it was seeing the problem, then asking, ‘How do we solve the problem?’”
As part of my research on purpose-driven businesses and stakeholder capitalism, I recently talked with Webb about AppHarvest’s whirlwind initial year in business, successful investor fundraise, plans to go public, and B Corp Certification.
Good for Business, Good for Community
Jonathan Webb, founder and CEO of AppHarvest
“Where we’re doing what we’re doing is incredibly important. One of our biggest competitive advantages, frankly, is doing it here,” he says. “Some of the hardest-working men and women are the people in this region that power the coal mines, and all we’re trying to do is tap into that and harness that passion. It’s good for our business, but it's good for communities.”
The location has been central to AppHarvest’s benefit in another way, Webb says, as local enthusiasm for the project enabled swift construction that likely would’ve been a challenge in some other regions.
“It's all about economies of scale. We have to build a really big facility to get our costs on materials down so that we can compete with products that are being imported into the country from Mexico,” he says. “We built one of the largest facilities in about a year, so speed and scale are definitely advantages for the company, and a lot of that’s possible based on where we’re operating here in this region.”
While the Bluegrass State has been a good home for AppHarvest, Webb wants the business to be a resource for nearby communities and a beneficial workplace for residents.
“A fundamental part of the way we’re building and growing this company is that every entry-level employee gets full health care, full benefits, living wage, paid time off. So we’re not just creating jobs, we’re creating a lifestyle for your career path,” he says. “We want to see people with high school degrees in this region grow with the company and be assistant growers and head growers three, four years from now. I know this region, and I know what people can do here. Those are the success stories that I look forward to having happen.”
Creating Positive Stakeholder Impact
Producing needed food and building a stronger workforce aren’t the only goals at AppHarvest; Webb says growing produce sustainably, with minimal impact on the environment, also is paramount.
“We’re land constrained in the world, and water constrained. And we have to grow a lot more food and use fewer resources,” he says. “It’s simple in theory; it’s complex in scale. Just the fact that the place is so big is what makes this challenging. But we’re collecting rainwater on the roof and using it directly on the root of the plants. We’re growing hydroponically, and as a result we can use 90% less water than open field agriculture.
“The way we treat water and handle water and how we use rainwater efficiently is the really biggest driver of resiliency long term for us.”
In building a business to have a positive impact on workers, community, and environment, Webb also created a company that is a natural fit for the B Corporation community made up of businesses that achieve a certification based on how well they incorporate all stakeholders into their policies and practices.
“The impact side of this is incredibly important. We didn’t chase certifications,” he says. “We just did the right things: We’re paying a living wage, we're offering health care. It’s the right way to do business. And as a result, we get a huge ROI on our dollar.”
Thanks to its bottom-line success and future promise, AppHarvest has found favor with investors, including Martha Stewart and venture capitalists; and is part of a growing cohort of businesses with a social purpose that are finding traction in the public markets. The company announced in September that it’s going public through a combination with special purpose acquisition company Novus Capital Corp. (Nasdaq: NOVS).
“Why are we going public now? Because full transparency in agriculture is desperately needed,” Webb says. “We want the people who buy our fruits and vegetables to also have the ability to buy into our company. We want the record. We want the institutional rigor. It’s hard to have this spotlight this early, but it’s making us stronger.”
Christopher Marquis, Contributor
Babylon Microfarms Bets On Automation For The Future of Vertical Farming
What started as a humble tabletop farm at the University of Virginia has since evolved into a major company to watch in the vertical farming space, particularly when it comes to the software piece of the process
What started as a humble tabletop farm at the University of Virginia has since evolved into a major company to watch in the vertical farming space, particularly when it comes to the software piece of the process. Babylon Microfarms has over the last few years garnered quite a bit of attention for its controlled-environment farms the company now licenses to hospitals, cafeterias, and other other foodservice operations.
Based in Charlottesville, Virginia (though soon moving HQ to Richmond, VA) Babylon makes a “plug-and-play” system for hydroponic farming that automates much of the grow process and makes controlled-environment farming more accessible. The company raised a $2.3 million seed round in January of this year and, its current product is a standalone farming unit that grows leafy greens.
Of late, however, the bulk of founders Alexander Olesen and Graham Smith’s focus is on software: namely, using it to automate the growing process, which removes the more complicated aspects of vertical farming that would be off-putting to the average user.
“Growing is a cumbersome experience for many,” Olesen explained to me over the phone this week. “Removing the friction of the user experience and combining that will some of the remote management [will make] smaller forms of vertical farming possible.”
Were the average person to try and build their own high-tech grow system, it would require significant expertise in horticulture, hardware infrastructure, and software development. To name just a few examples, that would include calculating one’s one LED light recipe (which takes the place of sunlight in controlled-environment ag), controlling the temperature of the farm, and understanding how much nutrient to feed each crop and when to do that. Everyday would require a certain amount of trial and error for every plant variety.
All of this makes for prohibitively high costs when it comes to commercial greenhouse production. Olesen noted that for controlled-environment farming to go mainstream, it has to be less technically complicated for the user.
Babylon’s software is one solution addressing those complications. The company’s “seed-to-sale” system automatically dispenses the right amount of nutrients, light, and water for each crop, simultaneously collecting data on the plants so that the system can make adjustments as needed. The entire system can be controlled remotely via a mobile app.
Up to now, the company has drawn comparisons to the likes of Farmshelf, Farm.One, and InFarm, all companies that license a hardware-software farming combination out to foodservice and hospitality operations.
But Babylon’s founders told me they aren’t necessarily interested in the hardware aspect going forward. Smith says they would prefer something like teaming up with a hardware manufacturer that wants to make vertical farms but perhaps needs more expertise in software to complement their hardware capabilities.
Such a scenario is actually on its way to becoming a reality. At CES this past year, hardware giant LG announced plans for a smart-farming appliance for the consumer kitchen. At the same time, GE Appliances showcased its Home Grown concept, which featured grow systems using hydroponics and soil-based methods. Prior to CES, Miele acquired Agrilution in another play for smart farms in the appliance space.
All of these hardware developments suggest great opportunity for the accompanying software. While many companies in the vertical farming space try to do both right now, Babylon’s future focus on being “an enabling company” that offers software and services may prove a wiser bid for the long term. Besides building out distribution of its own farms, Babylon is currently interested in working with other businesses, particularly those making hardware, that want to enter the vertical farming space.
There will be no one product that wins, Olesen said, adding that instead, it will be a combination of tools working together to make vertical farming more accessible to everyone.
FILED UNDER: AG TECH BUSINESS OF FOOD EDUCATION & DISCOVERY FEATURED FOODTECH
MODERN FARMER VERTICAL FARMING
“If We Really Want To Make A Change, We Should Intensively Invest In Innovation and Technique In Africa”
Christine Zimmerman discusses vertical farming trends
Christine Zimmerman Discusses Vertical Farming Trends
Vertical farming is a rapidly growing industry, and there are many challenges and opportunities. In this interview with Christine Zimmermann-Loessl, Chairwoman at the Association for Vertical Farming, she discusses the latest trends and developments within the vertical farming sector worldwide.
What are the latest trends within vertical farming?
Zimmermann-Loessl stated that there is a very clear trend in automation and fully automated systems. Especially in the USA, Japan, and Europe. “The main trend here is that we see robotics and AI machine learning that will even play a bigger role than it does now. Another trend is scaling, as people start to understand the necessity of vertical farming. I still hear from the majority of greenhouse growers, to have a fully automated greenhouse, the vertical farmers say: no we can be more efficient and it can be much more controlled. However, there are so many input factors that cannot be perfectly controlled in a greenhouse. In order to have reliable minimal resources and yield, vertical farming is a better solution.”
Zimmermann stated that once the energy problem issue is solved, they can connect the issue with solar and teach students about it in the AVF demonstration center. Using solar is possible and there are the costs to have the proof of concept.
Have you seen positive developments in vertical farming regarding COVID-19?
As there are strict hygiene standards, higher than in any other farm, there is a very clean environment. “We are beyond ahead COVID-19 measurements and this needs to be communicated even better.” According to Zimmermann, a great advantage of indoor farming the high hygiene standards. Working with a hygiene room quality and improving these standards. “We have seen a lot of growth, also at the AVF as we gained 11 members. Start-ups have the ambition to grow out of that start-up phase.”
She also notes that vertical farming has had more understanding of politics and politicians, but also on a national- and municipal level. They understand that there is a need to secure the future, being less dependent on external factors. “We had to communicate all these advantages even better. The majority doesn’t know them yet and we have to improve that”, she adds.
What is the quickest growing country in terms of vertical farming techniques?
“That’s a tough question. I think that in Germany really took off in the past two years. We have Fraunhofer Institute in Aachen with two brand new systems that haven’t been on the market before with that high level of innovation. The Orbiplant, from Fraunhofer, shows how economical VF can be today. It is built from material on the market for automation or transport systems highly automated and allows cheap production prices. Another company, Lite+Fog, where I see innovation at a level of experience with a new system design and water-saving fog for the roots instead of hydroponics.
Zimmermann continues that Japanese farming company Spread, its Techno farm, is really the state of the art. It’s a proven operation and they produce for the market. “However, Orbiplant and Lite+Fog are still in a demo size compared to the commercial farms of SPREAD and the fully on-demand farms now. We have a differentiation to make between these three.”
And in terms of newly constructed farms?
"I have visited Farminova, Turkey, and it’s very interesting to see how in such an agricultural country a company takes on the innovative food business. Cantek Turkey, the owner Hakan Karaca decided to go into vertical farming and built a system in one of his warehouses, near Antalya, to bring the topic forward. They see the need for sustainability and innovation.” Zimmermann said that Italy is also becoming an interesting country for vertical farming. Companies such as Planet Farms and Ono Exponential Farms that have fully automated new constructions. “People need to build up their trust in technology and the produce from it. In Europe, they have a prejudice against artificial environment by technology, but in Asian countries such as Japan and Singapore they don’t. They’re much more open to it, also in the new farming technology because it offers safe, fresh, local products. They see the shrinking traditional farming in their countries and growing imports."
Are we at a maturity stage in vertical farming yet?
“Not at all. When we started we were in an infant stage. Now we are at age 12 to 14. From an age perspective, we are not mature enough yet. It would be really good to have official government backing. Not just money-wise, but also policy-wise. We want more agriculture sustainable methods. One of these is indoor vertical farming. Once that statement comes, it would help VF implementation a lot.”
Why do you think that governments haven’t done that yet?
“It’s all about the necessity. ‘Why do we need it? We have greenhouses. We have industrial agriculture. Now, with severe droughts, even in Europe, more politicians see the need. I am part of the dialog forum for the 'Future of Agriculture', where all major stakeholders gather in Berlin twice a year. I get to meet all the associations from traditional farming and few of them have heard of vertical farming. Not to talk about embracing, saying it could be a part of agriculture production. However, it’s still a long way to go for communication, marketing, and raising awareness.
"We need more innovation- and vertical farming centers around the cities and rural areas to enable our hands-on learning and demonstration. If we do that, farmers will see it and understand it better. We start with the farmers. More young people are coming in the industry. We will rely on vertical farming systems to maintain reliable food production. It will play a major role if we want to protect the ecosystem when we have over 10 billion people on this planet.”
What would you address as the most frequent struggles within the industry?
“Investment is still a major struggle. Either banks don’t understand the business model of high-tech farms, because they have only know traditional agriculture business models. Or investors don’t have a sufficient understanding of vertical farming. They want a quick ROI and don’t know that they need patience. So, in order to find the right investor and money, it’s not that easy. If you want to scale, you have to have a proof of concept. But more money is needed to go to that next level.
"It ‘seems easier’ in the USA and Asia. Looking at the UAE, which is taking off with vertical farming, partially because the government is supporting it now too. Their food supply chain is in the hand of a couple of people and they were used to importing all food. It takes time to build a new food chain and trust in new suppliers."
In what underdeveloped countries do you see the most potential for vertical farming?
“Absolutely, we just founded our regional chapter by our team. We cannot serve the interest in India anymore, so we decided to have a local team there. It’s taking off like crazy. Now, we have two members in Africa and we get at least two requests per week. In South Africa, it can be seen that there’s a lot of equipment development. Which gives them the highest level of technology compared to the rest of Africa.
"We see a lot of the need to train farmers and really implement vertical farming in Africa. We just received new proposals from Cameroon to train 1200 farmers on vertical farming in the Northwest. So far, our partner in Cameroon has built the center already and we only need the equipment yet and training can start. It’s great to see what they do. If we really want to make a change, we should intensively invest in innovation and technology in Africa. We can grow forest there, instead of turning more land into agriculture and reduce CO2 even more. They are willing to do that and know what they need. It’s not up to us to tell them what they do. If AVF would have the financial power, we’d be there tomorrow to help them."
Where do you see the most positive reactions towards vertical farming?
"In Asia, we can find mature markets, especially in Singapore and Japan. People are willing to buy and understand the concept. China is an important market from a global perspective. A lot of projects in vertical farming are happening there, but the government policy to protect traditional agriculture has such a big importance for the government. Therefore, it’s very tricky to launch vertical farming in the right way. They have megacities and over 1.3 bln people so the demand is huge. But, they only have 12% of land and so there are many opportunities for farming. However, there’s a huge challenge for vertical farming as it’s very hard to implement it on a bigger scale."
For more information:
Association for Vertical Farming
Christine Zimmermann-Loessl, Chairwoman
czl@vertical-farming.net
www.vertical-farming.net
Publication date: Wed 26 Aug 2020
Author: Rebekka Boekhout
© HortiDaily.com
45 Years Logiqs: From Container Systems to Vertical Farming and Warehouse Automation
Nowadays Logiqs supports most horticulture crops grown in greenhouses as well as a large variety of hydroponic crops
45 years ago, on July 1st, 1975, the Logiqs journey began, together with the founding of Intransit B.V. (the company’s initial name).
And even though the company name and shareholders may have changed since then, they still look back at this date as the very beginning of the company.
"At the start, the main goal of our company was to design and build innovative and reliable benching systems for potted plant growers, that add true value to the customer’s business.
"This initial focus has held up very well throughout the years and has produced amazing results for our customers, with thousands of acres of Logiqs benching systems operational in greenhouses all over the world.
"This success has allowed us to expand our area of expertise to serve a much wider range of growers as well as a couple of new industries."
Nowadays Logiqs supports most horticulture crops grown in greenhouses as well as a large variety of hydroponic crops.
"Our experience working with some of the most successful growers in the world, encouraged us to also apply our know-how and expertise to the Vertical Farming industry. This amazing collaboration with our customers allowed us to quickly become one of the industry leaders and trendsetters in automated vertical farming.
"Beyond greenhouse cultivation systems and Vertical Farming, we have also made incredible steps in warehouse automation by developing the innovative iCUBE Automated Storage and Retrieval System.
"We are grateful to all of our wonderful customers and partners who have influenced us to get better, and we hope that we can continue to repay their trust in the coming decades.
"We would also like to take this opportunity to thank all Logiqs team members that have devoted their time, energy, and passion to our common goals in the past 45 years.
"Without these devoted and talented individuals, Logiqs could have not evolved into the company it is today.
"We are extremely excited to think of the impact that our talented colleagues will have moving forward on the future of Logiqs, and on the future of horticulture, agriculture, and logistics."
For more information:
Publication date: Thu 2 Jul 2020
CubicFarm Systems Corp Announces Completion of $5M Private Placement With Ospraie Ag Science
Net proceeds to be used for R&D to expand machine capabilities and crop varieties
Net proceeds to be used for R&D to expand machine capabilities and crop varieties
Vancouver, BC – (AccessWire – May 13, 2020) – CubicFarm® Systems Corp. (TSXV:CUB) (“CubicFarms” or the “Company”) is pleased to announce that further to its press release dated May 1, 2020, the Company has completed the non-brokered private placement with Ospraie Ag Science, LLC (“Ospraie”), involving the issuance of 21,739,130 common shares of CubicFarms at a price of C$0.23 per share for gross proceeds of approximately C$5.0 million (the “Offering”). Ospraie now holds an approximate 18.8% interest in the Company on a non-diluted basis (see Early Warning Disclosure below).
“We are very excited to complete this transaction with Ospraie, all the more so amid the current economic and travel challenges,” said CubicFarms CEO Dave Dinesen.
“Ospraie’s strategic investment will allow CubicFarms to execute on our vision of providing technology to feed a changing world, by driving our R&D efforts to further optimize our machine yields, automation and functionality, as well as expand the crop varieties that can be grown in our machines – all with a view of capturing more market share and adding value to our grower-customers.
“We look forward to working closely with Ospraie as they add incredible value to CubicFarms through their industry expertise, and exploring potential technological and commercial synergies with the other ag-tech companies in their portfolio and network.”
The shares issued in connection with the Offering are subject to a statutory four-month hold period.
Early Warning Disclosure
Prior to the Offering, Ospraie held 99,500 common shares of the Company, representing approximately 0.1% of the then current issued and outstanding common shares on a non-diluted basis. After giving effect to the Offering, Ospraie holds 21,838,630 common shares, representing approximately 18.8% of the issued and outstanding common shares on a non-diluted basis.
The Company has been advised by Ospraie that the common shares were acquired under the Offering by Ospraie for investment purposes and that Ospraie reviews its holdings in the Company from time to time and may, based on such review, market and other conditions and subject to compliance with applicable hold periods, increase or decrease its ownership of common shares, other securities of the Company or related financial instruments, whether in the open market, by privately negotiated transaction or otherwise.
A copy of Ospraie’s early warning report will appear with the Company’s documents on the System for Electronic Document Analysis and Retrieval and may also be obtained by contacting Scott Baglio at +212-602-5090.
Ospraie’s address is c/o Ospraie Management, LLC, 437 Madison Avenue, 28th Floor, New York, NY 10022.
This press release does not constitute an offer to sell or the solicitation of an offer to buy, nor shall there be any sale of these securities, in any jurisdiction in which such offer, solicitation or sale would be unlawful prior to registration or qualification under the securities laws of such jurisdiction. The securities have not been and will not be registered under the United States Securities Act of 1933, as amended (the “U.S. Securities Act”), or any state securities laws, and may not be offered or sold within the United States unless an exemption from such registration is available.
Neither the TSX Venture Exchange nor its Regulation Services Provider (as that term is defined in the policies of the TSX Venture Exchange) accepts responsibility for the adequacy or accuracy of this release.
About CubicFarm® Systems Corp.
CubicFarm Systems Corp. (“CubicFarms”) is a technology company that is developing and deploying technology to feed a changing world. Its proprietary technologies enable growers around the world to produce high-quality, predictable crop yields. CubicFarms has two distinct technologies that address two distinct markets. The first technology is its patented CubicFarm™ System, which contains patented technology for growing leafy greens and other crops. Using its unique, undulating-path growing system, the Company addresses the main challenges within the indoor farming industry by significantly reducing the need for physical labour and energy, and maximizing yield per cubic foot. CubicFarms leverages its patented technology by operating its own R&D facility in Pitt Meadows, British Columbia, selling the System to growers, licensing its technology and providing vertical farming expertise to its customers.
The second technology is CubicFarms’ HydroGreen System for growing nutritious livestock feed. This system utilizes a unique process to sprout grains, such as barley and wheat, in a controlled environment with minimal use of land, labour and water. The HydroGreen System is fully automated and performs all growing functions including seeding, watering, lighting, harvesting, and re-seeding – all with the push of a button – to deliver nutritious livestock feed without the typical investment in fertilizer, chemicals, fuel, field equipment and transportation. The HydroGreen System not only provides superior nutritious feed to benefit the animal, but also enables significant environmental benefits to the farm.
Information contact
Kimberly Lim
kimberly@cubicfarms.com
Phone: +1-236-858-6491
www.cubicfarms.com
Cautionary statement on forward-looking information
Certain statements in this release constitute "forward-looking statements" or "forward-looking information" within the meaning of applicable securities laws, including, without limitation, statements with respect to the use of proceeds of the Offering and the potential benefits of Ospraie’s investment to the Company. Such statements involve known and unknown risks, uncertainties, and other factors including evolving market conditions, which may cause the actual results, performance, or achievements of CubicFarm Systems Corp., or industry results, to be materially different from any future results, performance, or achievements expressed or implied by such forward-looking statements or information including the Company obtaining the approval of the Offering from the TSX Venture Exchange. Such statements can be identified by the use of words such as "may", "would", "could", "will", "intend", "expect", "believe", "plan", "anticipate", "estimate", "scheduled", "forecast", "predict", and other similar terminology, or state that certain actions, events, or results "may", "could", "would", "might", or "will" be taken, occur, or be achieved.
These statements reflect the Company's current expectations regarding future events, performance, and results and speak only as of the date of this news release. Consequently, there can be no assurances that such statements will prove to be accurate and actual results and future events could differ materially from those anticipated in such statements. Except as required by securities disclosure laws and regulations applicable to the Company, the Company undertakes no obligation to update these forward-looking statements if the Company's expectations regarding future events, performance, or results change.
Kimberly Lim
VP, Corporate Communications & Investor Relations
Mobile: 236.858.6491
Office: 1.888.280.9076
Email: kimberly@cubicfarms.com
Marcel Koolen, Codema; "Food Safety, Automation And Reliability Are More Critical Than Ever"
“In this changing market, it is crucial that we provide the investor and what we call the 'corporate horticulturist' with the right information, knowledge and the proper perspective
Since 2017, Marcel Koolen has been at the head of Codema as CEO. He took over from founder Maarten de Jager, who meticulously merged various horticultural specialists into the Netherlands' leading supplier of horticultural solutions. It is his task to realize the international ambitions and at the same time, realize his own vision.
Market for horticultural solutions is changing
“We come from a world in which our customers, experienced growers who took over the company from their parents, know all about the technology. They exactly know what they need. These people choose the best solution for each individual aspect of their operation, for example, a logistics system from Hawe or a water solution from B-E De Lier. These critical cultivation systems can now be found under one roof: at Codema. This fits in well with the changing market. An increasing part of the market requires a conversation partner who comes up with a total solution.”
In recent years, horticulture has been a popular destination for the money of investors who want to invest on a large scale in, for example, medicinal cannabis, food production, and vertical farming. Floriculture and traditional growers also continue to develop and grow. Partly due to size, technical innovation must ensure higher efficiency or yield.
Conversation partner from the start
“In this changing market, it is crucial that we provide the investor and what we call the 'corporate horticulturist' with the right information, knowledge and the proper perspective. After which, we arrive at the delivery of critical cultivation systems. In the first place, this means that, from the beginning of their trajectory, we are a full conversation partner for these organizations. Our organization is now geared up for this.
Secondly, this requires an international presence. We are always building projects in America, Europe and the Asia-Pacific region with a particular emphasis on China. This goes beyond a simple sales organization, our "license to operate" depends on our ability to provide after-sales service and maintenance."
Due to these developments and continuing growth, the organization of Codema has grown strongly. "From the Netherlands, we serve and supply all over the world and on location we work as much as possible with local workers. Many beliefs converge in the latter; cost control from the customer and the influence of Nordian Capital. For example, on sustainability." However, Koolen's personal motives also make their mark:
“That does not mean that I make many difficult considerations or want to impose these on my customers. By applying new technological developments and continuing to work on both design and engineering, we already are more economical with raw materials.
Of course, it starts by considering if we can make better decisions in everything we think about and everything we do. Think about choosing green energy, solar panels, limiting flight movements, a hybrid fleet, and so on. Good business decisions that are simply better for our planet. It is no coincidence that this is also essential for our investor, Nordian Capital. Nordian’s entire investment portfolio compensates for all of its emissions through certified contracts with Land Life Company. This foundation is committed to the reforestation of around 2 billion hectares of land around the world.’’
A shared vision for the future
Originally, Marcel Koolen was an Electrical Engineer. However, he soon discovered that a wider field of vision suits him better. That theme had been a common thread in his entire career. Paired with his passion for what he calls ‘public interest’. With every step, his playing field grew larger.
‘The first time that it actually connected was with an electrical family business. There I quickly built up a department whose turnover was equal to that of the parent company and was allowed to slim it down a few years later. I have been able to face these kinds of challenges at an increasingly higher level. First at VolkerRail, during the privatization of the railways, and then at Spitzke and ABB.
When I started at Codema, significant changes were to come and therefore was an excellent fit. However, the main reason for my choice is our shared vision for the future. When I worked on the mobility of the Netherlands at VolkerRail, I noticed that serving the ‘public interest’ motivates me enormously. And at Codema we go further: we help feed the world. A good and efficient food production not only ensures that everyone has food but also makes it a lot less harmful to the environment. That is a challenge, which I would like to put my efforts into.’
Future and strategy Codema: food production
The herb cultivation market has boomed in recent years, and the legalization of the cultivation of medicinal cannabis has created a large capital inflow, which also benefited Codema. Codema realized critical cultivation systems in the largest, most advanced cannabis greenhouses in the world. These are greenhouses in which food safety and reliability, as well as automation, are more critical than ever. Codema also works in the floriculture with large cultivation organizations to apply the latest technology in areas such as software, water, lighting, and logistics. This provides knowledge and experience that Codema can directly apply to food cultivation.
“Investing in food production is a good business decision. The world population is growing, and with it, the demand for food. There are many challenges in this area that require a technical solution and where Codema can make the difference. That makes it a good investment for both investors and Codema. Since we are now active in the three major time zones, we reduce the risk of economic volatility further. That makes us future-proof.”
Cooperation in the chain
“That does not mean that Codema can do that alone. We work together with greenhouse builders and engineering -and consultancy firms, such as scientific researchers, educational institutions and market researchers. Partly because of this, Codema is able to present the final solution to the customer. This means that we go further than ever in our services. That is also what the market demands.”
When asked whether he is satisfied if, in Codema 2024 anchored her international position as a food production specialist, Koolen replies:
“We should always keep growing, but that doesn't mean it's always about financial growth. This could, for instance, be growth in the impact you have on the world. Or growth in knowledge and skills, the development of new technologies. We need to keep moving and ensure that Codema can continue to offer its customers the best proposition in the future.”
For more information:
Codema Systems Group
Oosteindsepad 8
2661 EP Bergschenhoek
The Netherlands
+31105212755
info@codemasystemsgroup.com
www.codemasystemsgroup.com
Publication date: Wed 8 Apr 2020
FINLAND: New Chairman of The Board Appointed For Netled
Mr. Rintamäki brings solid key experience to Netled. In his previous career, he has acted in leading financial positions in various operations of Kone Oy and later in Konecranes PLC in Finland and overseas
Netled announced that Teuvo Rintamäki (M.Sc. Econ) has been elected as Netled’s new Chairman of the Board. Mr. Rintamäki brings solid key experience to Netled. In his previous career, he has acted in leading financial positions in various operations of Kone Oy and later in Konecranes PLC in Finland and overseas. Last eight in Konecranes he held a position of CFO.
Rintamäki has also next to 10 years of experience in guiding and leading start-ups as a Board Member and Chairman of the Board. He has a history of successful company listings and sales. Currently he operates as a Chairman of the Board in, for example, companies like Safedo Oyj, PowerProfPartners Oy and Saunaranta Invest Oy, as well as a Board Member and Board Advisor in various companies. In the 2000s, he also served as a member of the Committee on Strategic and Economic Affairs of the Technology in Finland.
Teuvo Rintamäki
”I´m very excited about this new position. Netled is currently in a very interesting growing phase; the company is taking off as an internationally recognised technology provider and notable player in the global market. In addition, Netled operates in a rapidly growing business field. Vertical farming is more efficient compared to traditional ways of cultivation, and it’s also more ecological and sustainable way of farming”, says Teuvo Rintamäki.
Netled’s CEO Niko Kivioja comments: ”We are extremely pleased to have Teuvo Rintamäki as our new Chairman of the Board. He has a vast know-how of globally operating technology companies as well as experience in working successfully with start-ups. We are certain that his professional background will give our company the boost for future growth.”
For more information:
Netled
netled.fi
Publication date: Tue 29 Oct 2019
Green Automation Is Bringing Automation And Efficiency To New Greenhouse Operation In Texas
Green Automation Group is proud to announce the latest project realization in the North American market – hydroponic lettuce producer TrueHarvest Farms in Belton, Texas. The 50,000 square feet greenhouse is equipped with growing automation technology from Green Automation
October 24, 2019, Wellington, FL, USA
Green Automation Group is proud to announce the latest project realization in the North American market – hydroponic lettuce producer TrueHarvest Farms in Belton, Texas. The 50,000 square feet greenhouse is equipped with growing automation technology from Green Automation. Riding on the steadily increasing demand for locally grown produce, TrueHarvest Farms will grow fresh and pesticide-free head lettuce locally in the controlled environment of a greenhouse 365 days a year. The farm is strategically located in the “Texaplex Triangle”, which is formed between the cities, Dallas-Fort Worth, Houston, San Antonio, and Austin. With a population of around 20 million people and having 80% of the state’s population growth since 2000 as well as generating up to 70% of the Texas economy, this area is the ideal location for new, innovative and sustainable production of leafy greens.
“The climate here in Texas makes year-round field growing of leafy greens impossible and the area has so far, as the rest of the USA, relied heavily on having lettuce trucked into the state from California and Arizona for a substantial part of the year”, says Marshall McDaniel, Managing Member at TrueHarvest Farms. “We will be distributing truly fresh, nutritious, safe and locally grown lettuce to stores within a 250 miles radius of our operations. The lettuce will be available to the customer in less than 24 hours of harvesting”.
TrueHarvest Farms, rooted in Belton, TX, is ready to supply fresh, nutritious and safe leafy greens to the Texaplex Triangle.
Recent food safety scares in the lettuce industry has led to an increased interest in and call for safe and clean lettuce produced in a controlled environment. The greenhouse is a closed system, controlling what comes into the greenhouse, making it possible to not only keep the lettuce clean but also to grow them without using any chemical pesticides. The irrigation water, the air, and the growing medium are controlled, monitored and clean - keeping consumers safe and the environment protected.
“There is an enormous demand for locally grown and safe lettuce today”, confirms Jason Maks, Managing Member, and Grower at TrueHarvest Farms. “Our facility is in the final stage of obtaining PrimusGFS certification and we are dedicated to meeting the highest safety standards in the food industry. TrueHarvest Farms will be a reliable source for locally grown and safe produce for the Texas markets. We are ramping up our production right now and expect to reach full capacity in January 2020. At the moment we are growing Butterhead, Crisp and Romaine varieties”, explains Maks.
TrueHarvest Farms is using the automated growing system optimized for head lettuce production. “When growing leafy greens in tough climates it is imperative to operate the greenhouse with the highest efficiency and to generate the highest yields per square foot, therefore TrueHarvest Farms decided to use the automated growing system from Green Automation”, says Patrik Borenius, CEO, Green Automation Americas. “Throughout the entire growing process maximal space efficiency is achieved through automatic movement and adjustment of gutters, giving the plants as much space as needed, but as little as possible”.
In addition to maximizing yield through space efficiency, labor efficiency is an essential key component in a profitable operation. The system has a highly automated and versatile medium filling and seeding line arrangement using stackable trays and supporting both net pots as well as Ellepots. After seeding and germination, the plants are placed onto the automatic growing system, featuring adjustable and movable growing lines, where they will soak up the natural sunlight. As the plants grow, they are moved automatically through the greenhouse toward the harvesting station.
TrueHarvest Farms did multiple trips to reference operators in Europe, including to such remote locations as Joensuu, Finland, before making a decision. “It is a proven system and on par with our earth-conscious commitment. We are looking forward to growing and providing the Texas market with the highest quality lettuce”, says Marshall McDaniel. “This is only the beginning, we have room to grow and our head house as well as the irrigation system are designed for future expansions,” McDaniel explains.
Contact:
Patrik J. Borenius
Green Automation Americas LLC
13833 Wellington Trace, Suite #E4-203
Wellington, Florida 33414
About Green Automation Group
Green Automation Group Ltd, headquartered in Finland, and it’s subsidiary Green Automation Americas LLC, based in Florida, develop, manufacture and market the most advanced greenhouse automation systems for lettuce and herb production. The systems are designed for commercial greenhouse operations with a growing area of 1 acre / 0.4 hectares and above. www.greenautomation.com
About TrueHarvest Farms
TrueHarvest Farms, LLC is a controlled environment hydroponic farm specializing in leafy greens. Founded in 2017, the company is focused on rapid growth through the production and distribution of high-quality lettuce and other leafy greens. TrueHarvest Farms is the evolution of a family hay and pecan farm now 40 years old. So, whether it is the “family roots” or the “plant roots,” we are truly “Rooted in Belton, Texas”.
https://www.facebook.com/trueharvestfarms
Indoor Farming Technology Leader SANANBIO (R) Debuts UPLIFT (TM) Vertical Farming System
SANANBIO firmly believes that agriculture technology should be based on science paired with input from farmers
10/02/19
SANANBIO®, a leading provider in LED horticulture lighting and vertical farm technology, announces the commercial release of its fully automated vertical farming system: UPLIFT™ (Unmanned Platform of Lean and Intelligent Farming Technology). Decades of manufacturing and automation experience, combined with successful multi-year vertical farm operations through parent company Sanan Optoelectronics, have given SANANBIO the expertise necessary to design and prove the concept of UPLIFT.
SANANBIO firmly believes that agriculture technology should be based on science paired with input from farmers. Michael Yates, Sananbio VP of Sales, said, "With over one million square feet of commercial vertical farms currently using RADIX, farmers and investors in more than 10 countries believe in our company's highly engineered grow technology. The proof is in the plants as our customers like to say."
Sananbio UPLIFT
Fully automated vertical farming system
UPLIFT is based on RADIX™, SANANBIO's highly successful manual vertical grow system being used in farms today. "Farmers and investors in more than 10 countries and a combined one million square feet of commercial space believe in our company's highly engineered grow technology. The proof is in the plants as our customers like to say," said Yates.
UPLIFT offers a full suite of automation for growing vertically. From seeding and germination to transplanting and harvesting, the high-stack, high-cube configuration offers the latest advancements in vertical farming solutions that reduce labor while achieving higher yields. The UPLIFT farming platform also benefits from an industry-standard production and inventory management system facilitating crop management, farm production planning, and crop traceability.
"Labor costs continue to be a major challenge for vertical farm operators while also maintaining profitability," stated Dr. Charlie Wang, Sananbio U.S. CEO. "The UPLIFT system will help operators significantly reduce labor costs so they can sell more fresh and healthy produce and, therefore, receive better returns on their investment. The system also provides an open platform to integrate technology that enables farms with more intelligence and controls, allowing for maximized yields and profitability."
SANANBIO's is prepared to work with leading farmers and investors in the industry who share the same passion to build ground-breaking projects in controlled environment agriculture using this cutting-edge technology.
ABOUT SANANBIO®
SANANBIO^® is a trademark carried and backed by Sanan Sino-science Photobiotech, a company invested in by Sanan Optoelectronics, one of the world's largest LED chip manufacturers. Supported by an elite R&D team comprised of plant scientists, researchers, and engineers, SANANBIO utilizes state-of-the-art technology that enables growers in the horticulture industry to increase the quality and quantity of their yields. Years of extensive research and real-world deployment and operations allow SANANBIO to offer its customers proven, scalable, efficient and cost-effective solutions in LED horticulture lighting and Controlled Environment Agriculture (CEA) vertical farming grow systems. SANANBIO empowers growers with the technology and knowledge to achieve unprecedented results in farming operations. Learn more at https://sananbious.com/.
This Startup Is Building A Massive Indoor Farm In A Rust Belt Steel Town
The farm, from a startup called Fifth Season, will begin selling spinach, lettuce, and other leafy greens early next year, using a robot-based system that the founders say is cost-competitive with growing and transporting the same crops from a traditional farm
Fifth Season will begin selling spinach, lettuce, and other leafy greens—all grown inside with the help of robots—early next year.
[Photo: courtesy Fifth Season]
10.22.19
In a vacant lot next to one of the last remaining steel mills in Braddock, Pennsylvania, a town just south of Pittsburgh, a massive new indoor farm is taking shape. The farm, from a startup called Fifth Season, will begin selling spinach, lettuce, and other leafy greens early next year, using a robot-based system that the founders say is cost-competitive with growing and transporting the same crops from a traditional farm.
It’s more affordable, they argue than some others in the vertical farming industry. “We looked at vertical farming and realized that the industrywide struggle to make the economics work was a huge factor, and something that would really prevent the industry from truly taking off,” says Austin Webb, co-founder, and CEO of Fifth Season, which incubated its first farm at Carnegie Mellon University. “The per-unit economics don’t work. Companies are losing money for every pound that they sell. And that obviously needs to change.”
[Photo: courtesy Fifth Season]
Like others in the space, the startup touts the advantages of growing indoors. It’s possible to use only a tiny fraction of the water that’s used to grow greens in fields; most lettuce is currently grown in drought-prone California and Arizona. (In Arizona, farmers will also soon start losing access to water from the Colorado River.) Growing indoors eliminates the need for pesticides. It eliminates food safety hazards like E. coli contamination. And if crops are grown close to end markets—in this case, restaurants and stores in Pittsburgh—it also eliminates the emissions from trucks traveling thousands of miles and the problem of less-than-fresh produce that may be more likely to be thrown out because it’s already starting to wilt. “When we look at the food distribution system, we looked at it and saw an overly complicated broken system, where no one’s connected to their food, and there’s a lot of food waste,” Webb says.
[Photo: courtesy Fifth Season]
Some past efforts at indoor farming have failed because of high costs, such as FarmedHere, near Chicago, which shut down in 2017 in part because of the cost of labor. “When you look at vertical farms and labor is 40% to 60% of their cost—labor for them is actually more than the all-in delivered cost of Western-grown field produce—it’s just not going to work,” he says. The company’s system, which it has running now at another location and which it’s recreating at the new location, uses around 40 robots. “Together, they’re completely integrated so that our facility is, in a sense, one robotic system.”
Robots plant seeds in trays and deliver trays to grow rooms, where automated systems control everything from the amount of nutrients the plants receive to the schedule of lighting and the amount of carbon dioxide in the air. When a crop is ready, it goes into an automated harvesting system, and then to an automated packaging system, and the trays are sent back to be automatically cleaned and sanitized and then replanted. “We essentially looked at it and said that we should create an automated fulfillment center,” says Webb. “The difference being that instead of pallets of boxes, it should be trays of plants.” Solar panels on the roof and a battery backup system means that the facility can continue operating even if extreme weather takes out the electric grid.
[Photo: courtesy Fifth Season]
Other companies in the industry are also developing automated systems, including Plenty, a Softbank-funded Silicon Valley startup that now has a suite of state-of-the-art custom robotics. Plenty hasn’t shared the details of the cost of its system. But Fifth Season estimates, as an example, that its own robot used for storing and retrieving plants may cost two to three times less. It also uses space more efficiently than some other companies; because everything is automated and humans don’t need to access rows of produce on scissor-lift equipment, the aisles between plants can shrink, growing more produce in the same amount of space. (The new farm is 60,000 square feet, a little smaller than the 69,000-square-foot farm run by another company called Aerofarms.) During its first full year of operation, it expects to grow half a million pounds of greens and herbs, with prices in line with organically grown produce. At that price point, the payback period of the full system will be less than two years.
[Photo: courtesy Fifth Season]
In Braddock, where the population has shrunk more than 90% since its high point in the 1920s to around 2,000 people today, the new farm can provide some new jobs, despite the automation. Three shifts a day will employ 20 workers each. “These are manufacturing-like jobs where we’ve got folks that are helping us operate our machinery,” Webb says. “We’ve got folks that are monitoring the health of the equipment. All of that is something where someone can come from a previous job and you’re not necessarily saying you’re going to do something that’s totally completely different, such as sit at a computer and write code.” As the company expands, it will also hire more engineers and plant scientists.
The startup hopes to replicate the new facility, designed as a modular system, throughout the country. “We’re able to take what we’re building in Braddock and take those blueprints and really hit the repeat button quickly,” he says.
ABOUT THE AUTHOR
Adele Peters is a staff writer at Fast Company who focuses on solutions to some of the world's largest problems, from climate change to homelessness. Previously, she worked with GOOD, BioLite, and the Sustainable Products and Solutions program at UC Berkeley, and contributed to the second edition of the bestselling book "Worldchanging: A User's Guide for the 21st Century."
You Might Also Like:
Robots are already farming crops inside this Silicon Valley warehouse
Live in your own farm in the sky in this plant-covered apartment building
Video: The most crucial advice Patreon CEO Jack Conte has for any struggling creator
SPONSORED: OLD DOMINION
How Old Dominion is using technology to better serve its customers
Shenandoah Growers Opens Next Generation USDA Certified Indoor Biofarms In Virginia
The new BioFarms will solve persistent problems in the fresh product supply chain – delivering peak freshness, longer shelf life, enhanced food safety, reduced food miles, and year-round organic supply.
ROCKINGHAM, Va. — Shenandoah Growers, Inc., the US leader in indoor USDA certified organic agriculture, has begun harvests at its next generation BioFarm facilities in Rockingham and Elkwood, Virginia. The company will now grow, pack and ship locally grown, premium quality organic produce from its sustainable indoor farms to its customers in the Mid-Atlantic region 365 days a year.
Shenandoah Growers BioFarm Basil Plants
The new BioFarms will solve persistent problems in the fresh product supply chain – delivering peak freshness, longer shelf life, enhanced food safety, reduced food miles, and year-round organic supply. Shenandoah’s sustainable growing technology uses bioactive soil and fresh water, just like in nature, producing healthy organic plants and delivering on the company’s mission to reduce its carbon footprint and lead in environmental stewardship.
The Rockingham BioFarm will supply 100% of Shenandoah’s basil in the Mid-Atlantic region, marking the transition away from traditional field production. Basil is not only the best-selling herb, but it is also the most difficult to grow and ship nationally due to its vulnerability to weather volatility, disease and temperature damage. The Elkwood BioFarm will supply the company’s new line of local organic lettuces to Mid-Atlantic customers.
“Being able to grow the totality of our basil demand inside our pack house and not fly or truck hundreds or thousands of miles from the field was inconceivable when I entered the business over 20 years ago,” says Tim Heydon, CEO.
While Shenandoah Growers are pioneers in indoor organic agriculture, they are quick to emphasize that the company has been farming and operating in the industry for over 30 years. Chief Customer Officer Steven Wright intoned, “It’s one thing to be able to grow indoors, it’s quite another to harvest, pack and deliver with consistent quality 7 days a week, 52 weeks a year while meeting demand during peak seasons.”
The company points out that its indoor production units, many of which have been in operation for over 4 years, are proven efficient. According to company President, Phillip Karp, “Fundamentally we are about the democratization of sustainably grown organic produce, and for the promise of indoor agriculture to truly unlock its great potential, it must achieve cost parity with traditional farming. Anything we launch from our indoor farms will be scalable and profitable for us and our customers and affordable for the shopper.”
The company is in the process of accelerating its indoor farming capacity with a clearly defined plan to deploy additional next generation USDA certified organic Biofarms across its entire national platform of operating locations.
About Shenandoah Growers, Inc.
Founded in 1989, Shenandoah Growers is the leading grower and marketer of fresh organic culinary herbs in the United States, providing sustainable, USDA certified organic, regionally grown produce to retailers coast-to-coast. The Rockingham, Virginia-based company has developed the nation’s largest commercial indoor organic growing systems and continues to redefine how to bring fresh, organic, and sustainably farmed produce to market—operating across a nationally integrated platform of farms, production, and logistics facilities. For more information, please visit www.shenandoahgrowers.com.
Under the THAT’S TASTY® BRAND, Shenandoah Growers provides USDA organic, non-GMO, regionally grown, and sustainably farmed fresh culinary herbs and greens. Launched in 2017, the THAT’S TASTY BRAND offers consumers ways to add Pure Organic Flavor™ to their everyday cooking by offering a full line of products including living organic herb plants, fresh cut herbs, herb purees, lettuces and microgreens. www.thatstasty.com
Indoor Farming Technology Leader, SANANBIO®, Debuts UPLIFT Vertical Farming System
SANANBIO firmly believes that agriculture technology should be based on science paired with input from farmers. Michael Yates, SANANBIO's VP of Sales said, "Advanced knowledge of plant physiology and photobiology are fundamental to success in the vertical farming industry
The System Offers Customers A Fully
Automated Indoor Growing Process
LAS VEGAS, NEVADA (September 25, 2019) – SANANBIO®, a leading provider in LED horticulture lighting and vertical farm equipment and technology, announces the commercial release of its fully automated vertical farming system, UPLIFT (Unmanned Platform of Lean and Intelligent Farming Technology). Decades of manufacturing and automation experience, combined with successful multi-year vertical farm operations through parent company Sanan Optoelectronics has given SANANBIO the expertise in designing and operating the UPLIFT system to offer its customers a proven, fully automated indoor growing process.
SANANBIO firmly believes that agriculture technology should be based on science paired with input from farmers. Michael Yates, SANANBIO's VP of Sales said, "Advanced knowledge of plant physiology and photobiology are fundamental to success in the vertical farming industry. Through employing one of the world's largest teams focused on advancing vertical farming technology, UPLIFT is the solution born from the efforts of over 100 plant scientists and engineers."
The UPLIFT automated solution is based on SANANBIO's highly successful manual vertical farming grow system being used in farms today, RADIX. "With over 1M square feet of commercial vertical farms currently using RADIX, farmers and investors in more than 10 countries believe in our company's highly engineered grow technology. The proof is in the plants as our customers like to say," said Yates.
SANANBIO designed and installed the first pilot UPLIFT farm in April 2018 at its facility in Xiamen, China. After 18 months of operation and optimization, the UPLIFT system is now available for commercial deployment globally.
UPLIFT offers a full suite of automation for growing vertically. From seeding and germination to transplanting and harvesting, the high-stack, high-cube configuration offers the latest advancements in vertical farming solutions that reduce labor while achieving higher yields. The UPLIFT farming platform also benefits from an industry-standard production and inventory management system facilitating crop management, farm production planning, and crop traceability.
"Labor costs continue to be a major challenge for vertical farm operators while also maintaining profitability," stated Dr. Charlie Wang, SANANBIO CEO. "The UPLIFT system will help operators significantly reduce labor costs so they can sell more fresh and healthy produce, and therefore receive better returns on their investment. The system also provides an open platform to integrate technology that enables farms with more intelligence and controls allowing for maximized yields and profitability," said Wang.
SANANBIO's engineers and sales teams are prepared to work with leading farmers and investors in the industry who share the same passion to build ground-breaking projects in controlled environment agriculture using this cutting-edge technology.
SANANBIO® is a trademark carried and backed by Sanan Sino-science Photobiotech, a company invested in by Sanan Optoelectronics, one of the world’s largest LED chip manufacturers. Supported by an elite R&D team comprised of plant scientists, researchers, and engineers; SANANBIO utilizes state-of-the-art technology that enables growers worldwide in the horticulture industry to increase the quality and quantity of their yields. Years of extensive research and real-world deployment and operations allow SANANBIO to offer its customers proven, scalable, efficient and cost-effective solutions in LED horticulture lighting and Controlled Environment Agriculture (CEA) vertical farming grow systems. SANANBIO empowers growers with the technology and knowledge to achieve unprecedented results in farming operations.
To learn more visit: https://sananbious.com/
###
The Scottish Innovations Tackling The World’s Food Shortage
Invergowrie-based Intelligent Growth Solutions (IGS) has created Scotland’s first vertical farm, pictured here, and the company has recently harvested a £5.4 million cash boost from the Scottish Investment Bank, agri-food investor S2G and online venture capital firm AgFunder
Intelligent Growth Solutions' purpose-built facility is being constructed at the James Hutton Institute near Dundee.
SARAH DEVINE
19 September 2019
Scotland’s agriculture sector is changing rapidly, with rural businesses across the country driving forward groundbreaking innovations in attempts to address the myriad challenges of the land.
Globally, some 113 million people across 53 countries reportedly experienced food poverty last year, and it is expected that the world’s population will reach 9.8 billion by 2050, according to the UN.
However, inventive organizations across Scotland are devising new and creative ways to tackle the global food shortage.
Invergowrie-based Intelligent Growth Solutions (IGS) has created Scotland’s first vertical farm, pictured here, and the company has recently harvested a £5.4 million cash boost from the Scottish Investment Bank, agri-food investor S2G and online venture capital firm AgFunder.
The firm, which is based at the James Hutton Institute situated on the outskirts of Dundee, provides vertical farming technology to enable efficient food production through indoor crops around the world, having built its demonstration facility at Invergowrie last year.
It features stacked layers, LED lights and app-controlled air vents to create the perfect conditions for crops to thrive all year round.
The early-stage company states that its patented Internet of Things-enabled power and communications platform is able to reduce an organization’s energy usage by up to 50 percent and labor costs by up to 80 percent, in comparison to other indoor growing environments, and can produce yields of 225 percent compared to crops that have been grown under glass.
IGS experimented with colored LED lights, growing basil plants at the indoor facility in an impressive 20 days.
Its chief executive, David Farquhar, explains that such developments are urgently needed because at present an astonishing 30 percent of the world’s food is put to waste.
“Vertical farming allows experimentation to take place in order to impact the yield or cost of production, flavor, nutrients, appearance or a combination of those things,” he says.
“Producers want consistency, assurance of supply, and to know they are going to fill supermarket shelves or supply those Michelin-starred restaurants every day of the week. Those are things that farmers struggle with all the time.”
Farquhar adds: “If there is a forecast for bad weather and a supermarket decides to only take half of their delivery, what are they going to do with the rest of the produce?”
Using the vertical farm, a crop’s growth can be slowed down or sped up to prevent waste.
“People have been talking about vertical farms for several years, but we are now at the starting point. Over the next six months, we will get going with the first technology in the world that is capable of delivering this on an industrial scale.”
The firm, which was formed in 2013, plans to use this recent funding to create jobs in areas such as software development, engineering, robotics, and automation.
Investment into such areas is also needed across Scotland because dietary demand is changing, according to David Ross, chief executive of Edinburgh-based Agri-EPI Centre.
“Environmental sustainability is personal now for everyone and therefore there are challenges for primary producers to adapt to the needs of the consumer, the needs of society and the overall sustainability of the planet,” he says.
DASCOM Americas Announces Contained Environment Horticulture Systems To Be Globally Marketed And Jointly-Branded As HYVETM and EPONICTM
According to Ken Bryant, Marketing Director for DASCOM Americas: “The joint-branding effort will provide consistency and logistical advantages for our clients and prospects worldwide
August 22, 2019, Verona, Virginia – DASCOM Americas, a worldwide diversified technology leader today announced a joint branding initiative for its complete indoor hydroponic farming systems. Going forward the systems will be developed, marketed, and sold as either HYVETM (www.growhyve.com) or EPONICTM (www.eponicagriculture.com) depending on the geographic region of the globe.
HYVETM is led by Ron Acorn, President of DASCOM Americas and has its offices and grow lab facilities approximately 2 1⁄2 hours southwest of Washington, D.C.
EPONICTM is a brand of Eponic Agriculture Company, Ltd. Based in Zhuhai, Guangdong, China. Eponic Agriculture is led by Liu Guowei, a noted developer, engineer, entrepreneur, and horticulture system specialist. The company has enjoyed success throughout Asia and Europe with its innovative hydroponic growing systems and has developed a branded following with the EPONICTM name.
The respective farming systems consist of scalable product offerings including a comprehensive solution for commercial growing which includes vertical racking, irrigation, fertigation, LED grow lighting, robotics, programmable logic control, and other ancillary system components that provide industrial growers with a “complete solution” from one source.
Acorn says of the commercial vertical system: “Our complete solution is different than any system in the market because we combine all elements of contained environment horticulture into one product system offering. Our vertical racking offering is designed to provide growers with a great return on investment and consumers with a choice for the healthiest and freshest plants in the market. Indoor farming cuts down on transportation and spoilage costs, limits the exposure to diseased plants, and is safer largely because of no need for herbicides or pesticides.”
The brands are also offering a smaller home hydroponic unit that is a solid offering for education, residential, or small business use. The “LF-ONE” allows users to grow up to 54 mature plants per grow cycle and is programmable and automated much like the larger system. It is easy to assemble and use and provides fresh produce and the opportunity to grow 365 days a year.
Going forward HYVETM will direct its primary focus and brand in the North America and LAT regions of the globe. EPONICTM will be the brand name for systems marketed in EMEA and most of China and select other Asia-Pacific Regions. The exception in the China market will be that XiaMen New Green Ecological Technology Company LTD will utilize the HYVETM brand name as part of an exclusive distributorship agreement.
According to Ken Bryant, Marketing Director for DASCOM Americas: “The joint-branding effort will provide consistency and logistical advantages for our clients and prospects worldwide. EPONIC Agriculture is an expert company in development of products for contained horticulture systems. Our collaboration from day one has been extremely strong. Together this will allow us to capitalize on the strong EPONICTM brand in select markets while we build the HYVETM brand in our region of the world, while assuring our combined customers and prospects will experience consistency in equipment advances, customer service, and pricing.”
####