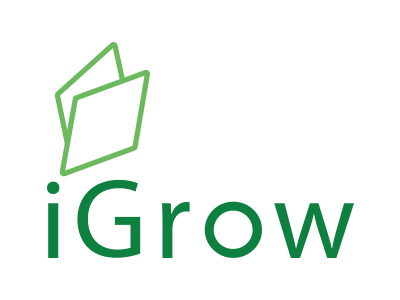
Welcome to iGrow News, Your Source for the World of Indoor Vertical Farming
What’s Real And What’s Hype With Controlled Environment Agriculture?
The flourishing development of Controlled Environment Agriculture and how retailers and consumers view this emerging segment of fresh produce production will be the topic of an educational session at Organic Produce Summit 2021.
July 27, 2021
The flourishing development of Controlled Environment Agriculture and how retailers and consumers view this emerging segment of fresh produce production will be the topic of an educational session at Organic Produce Summit 2021. The Growth of CEA—What’s Real and What’s Hype from a Retail and Consumer Perspective will feature leadership from a pair of recognized retailers and one of the fresh produce industry’s most progressive grower-shippers, offering their insight on how indoor-grown fresh produce items come to market, pricing and marketing challenges, and how consumers are reacting to them.
Moderated by Walter Robb, former CEO of Whole Foods, the session is the second of a two-part educational series at OPS offering a retailer and consumer perspective on the growth of indoor growing. Among the topics to be discussed in the session are the impact of indoor-grown products on the supply chain, the messaging and labeling of these various items, and the ramifications of what CEA production means for the organic fresh produce industry.
Panelists for the session include Frances Dillard, vice president of brand and product marketing at Driscoll’s; Victor Savanello, vice president produce and floral at Spartan Nash; and Shawn Peery, vice president produce and floral at Albertsons.
Production of fresh produce in CEA has become a $100 billion-plus industry, showcasing how growing indoors uses less water and no pesticides, while incorporating innovative and efficient technologies to provide fresher produce to consumers. “CEA is changing the landscape of food production and providing consumers a variety of new items that will continue to evolve in the years ahead,” said Susan Canales, president of Organic Produce Summit. “OPS attendees will have the chance to hear from retail leadership on how these products are marketed and learn about the challenges and opportunities these new items offer consumers.”
This second educational workshop follows a session exploring the growth of CEA from leaders actively involved in the production of indoor growing. The panelists for the first session include Philip Karp, president of Shenandoah Growers; Marc Oshima, co-founder of AeroFarms; and Caitlin Tierney, director of business development for Mastronardi Produce.
“Indoor agriculture is increasingly playing a more meaningful role in our fresh produce supply, in terms of volume, variety, and geographical footprint,” said Robb. “The ability of indoor ag to provide predictability and resiliency for supply, coupled with its lower impact on both the environment and resource use, is drawing substantial interest from both investors and consumers. Clearly, the future will be a hybrid one and our panels will explore how quickly and responsibly this will happen.”
Organic Produce Summit 2021 is a live and in-person two-day event specifically designed to bring together organic fresh produce growers, shippers, and processors with retailer and buying organizations from across North America. Over 1,000 attendees will meet Sept. 15-16 in Monterey, CA, to exchange ideas, information and insights into the organic fresh produce industry.
In addition to the educational sessions focused on CEA, a session looking at the organic industry in a post-COVID-19 environment and a keynote presentation by Jim Donald, co-chairman of Albertsons, have also been announced. OPS 2021 also includes a selection of field tours for retailers and buyers, a gala opening night reception, and a sold-out trade show floor featuring over 150 producers and processors of organic fresh produce from across North America and the globe.
iUNU Meets U.S. House Agriculture Committee & Highlights Importance of CEA To U.S. Food Supply
Chairman David Scott (GA) held a Congressional Hearing Thursday morning to increase public awareness of the critical importance of the CEA (Controlled Environment Agriculture) industry to promote food safety, nutritious produce, and food security for the American people
Chairman David Scott (GA) held a Congressional Hearing Thursday morning to increase public awareness of the critical importance of the CEA (Controlled Environment Agriculture) industry to promote food safety, nutritious produce, and food security for the American people.
Adam Greenberg | CEO | IUNU LLC
“While a global pandemic certainly magnified our food supply chain issues, one of the issues we can cover today is how to ensure a supply of fresh fruits and vegetables from all sources,” Chairman Scott asserted in his opening statement. “Controlled environment agriculture has the ability to fill in gaps where there are food deserts, reduce emissions from transportation of produce, and very importantly, limit our reliance on imports to fill our needs for fresh produce. We have an opportunity today to be on the cutting edge of technologies and the ability to provide affordable food to more households that need it.”
iUNU, an AI and computer vision-based technology platform that is employed by large commercial growers to enhance productivity is working with Congress and the USDA to ensure nutritious produce is available to all Americans.
“iUNU is an integral part of the solution to these issues as the leading provider of Artificial Intelligence and machine learning to help indoor growers rapidly expand their operations,” stated CEO Adam Greenberg at the Hearing. “The fact that 87% of the imported tomatoes come from one country, Mexico, leaves the U.S. population highly susceptible to food insecurity whether it is from a pandemic or other forces we can’t control. The CEA industry can significantly reduce these risks.”
Representative Jim McGovern (MA) expressed deep concerns about the need to recognize that food security is a national security issue in terms of ensuring the availability of healthy, nutritious produce for all Americans. “Every child in America deserves fresh, nutritious, contaminant-free fruits and vegetables they can trust.”
iUNU provides indoor growers with an AI and machine learning technology that gives growers the ability to see a plant from the time it sprouts until the time it is harvested in real-time.
“Our LUNA system can see where a problem is when it is happening and what is causing it, which significantly reduces the time it takes to identify any potential outbreak,” Mr. Greenberg said. “By catching a pest or pathogen issue as early as possible, we help growers reduce the need for pesticides. In short, we help reduce a grower’s risks and increase their productivity.”
Representative Jim Costa (CA) reiterated his concern with the nation’s food supply. “The sustainability of our food supply is critical,” he stated. “Focusing on protecting America's food supply chain is a national security issue. We need to focus on innovation as we move forward.”
Later in the afternoon, both Chairman Scott (GA) and Ranking Member Thompson (PA) issued a joint statement urging Congress to address the expansion of Broadband Internet so Americans living in rural areas and food deserts will have the same access as those living in urban areas. The lack of access hampers the ability of businesses such as growers to optimize their facilities through the use of AI and computer vision.
How To Maximize Resource Efficiency In Controlled Environment Ag Operations
Join Meena Sankara, KETOS CEO, and Tinia Pina, Re-Nuble CEO, for a discussion about the most significant challenges and opportunities facing Controlled Environment Agriculture operations
Tuesday, August 3 @ 12:30 pm ET / 9:30 am PT
Wednesday, August 4 @ 9:00 am ET / 1 pm GMT
Meena Sankara, KETOS CEO
Join Meena Sankara, KETOS CEO, and Tinia Pina, Re-Nuble CEO, for a discussion about the most significant challenges and opportunities facing Controlled Environment Agriculture operations. In this webinar you will learn:
Tinia Pina, Re-Nuble CEO
Why water management is important in the CEA industry
Challenges soilless/indoor farms face when improving water management efficiency
How soilless operations (including vertical farms and greenhouses) can be more resource-efficient
Strategies for the nutrient wastewater recovery
Which waste recovery solutions are best for your operation
August 3rd Webinar Registration
August 4th Webinar Registration
Optimizing Resource Use Efficiency In CEA System
An important factor affecting the profitability of vertical farming is a grower’s ability to consistently deliver a predictable product
Date: July 29, 2021
Time: 2 p.m. - 3 p.m. EDT
Presented by: Murat Kacira (The University of Arizona)
Click Here To Register
Webinar Description
An important factor affecting the profitability of vertical farming is a grower’s ability to consistently deliver a predictable product. To achieve this, growers must create an environment that supplies all the crop’s needs over its entire growth cycle by identifying and co-optimizing environmental variables such as CO2, light, humidity, airflow, and other parameters. This presentation will focus on real-time sensing, monitoring, and climate control strategies with system designs for environmental uniformity leading to enhanced resource use efficiency in CEA system.
Dr. Murat Kacira (Professor)
Murat Kacira is director of the Controlled Environment Agriculture Center and he is a professor in the Biosystems Engineering Department at the University of Arizona. He received his B.S. degree in Agricultural Engineering in Cukurova University in Turkey and M.Sc. and Ph.D. degrees from Food, Agricultural and Biological Engineering from The Ohio State University in USA. His research involves automation, environmental control, alternative energy integrated CEA systems and resource use optimization in controlled environment agriculture systems including greenhouses and vertical farming-based plant factories with artificial lighting. He is a member of American Society of Agricultural and Biological Engineers (ASABE), American Society of Horticultural Sciences (ASHS), and International Society for Horticultural Science (ISHS). He serves as Chair of the Division Precision Horticulture Engineering under ISHS.
Special thanks to our Industry partners
Join Today
If you have any questions or would like to know more about GLASE, please contact its executive director Erico Mattos at em796@cornell.edu
No Soil. No Growing Seasons. Just Add Water And Technology
A New Breed of Hydroponic Farm, Huge And High-tech, is Popping Up in Indoor Spaces All Over America, Drawing Celebrity Investors And Critics
A New Breed of Hydroponic Farm, Huge And High-tech, is Popping Up in Indoor Spaces All Over America, Drawing Celebrity Investors And Critics.
By Kim Severson
July 6, 2021
MOREHEAD, Ky. — In this pretty town on the edge of coal country, a high-tech greenhouse so large it could cover 50 football fields glows with the pinks and yellows of 30,600 LED and high-pressure sodium lights.
Inside, without a teaspoon of soil, nearly 3 million pounds of beefsteak tomatoes grow on 45-feet-high vines whose roots are bathed in nutrient-enhanced rainwater. Other vines hold thousands of small, juicy snacking tomatoes with enough tang to impress Martha Stewart, who is on the board of AppHarvest, a start-up that harvested its first crop here in January and plans to open 11 more indoor farms in Appalachia by 2025.
In a much more industrial setting near the Hackensack River in Kearny, N.J., trays filled with sweet baby butterhead lettuce and sorrel that tastes of lemon and green apple are stacked high in a windowless warehouse — what is known as a vertical farm. Bowery, the largest vertical-farming company in the United States, manipulates light, humidity, temperature, and other conditions to grow produce, bankrolled by investors like Justin Timberlake, Natalie Portman, and the chefs José Andrés and Tom Colicchio.
“Once I tasted the arugula, I was sold,” said Mr. Colicchio, who for years rolled his eyes at people who claimed to grow delicious hydroponic produce. “It was so spicy and so vibrant, it just blew me away.”
The tomatoes at AppHarvest were delicious enough to attract an investment from Martha Stewart.Credit...Luke Sharrett for The New York Times
The two operations are part of a new generation of hydroponic farms that create precise growing conditions using technological advances like machine-learning algorithms, data analytics and proprietary software systems to coax customized flavors and textures from fruits and vegetables. And they can do it almost anywhere.
These farms arrive at a pivotal moment, as swaths of the country wither in the heat and drought of climate change, abetted in part by certain forms of agriculture. The demand for locally grown food has never been stronger, and the pandemic has shown many people that the food supply chain isn’t as resilient as they thought.
But not everyone is on board. These huge farms grow produce in nutrient-rich water, not the healthy soil that many people believe is at the heart of both deliciousness and nutrition. They can consume vast amounts of electricity. Their most ardent opponents say the claims being made for hydroponics are misleading and even dangerous.
“At the moment, I would say the bad guys are winning,” said Dave Chapman, a Vermont farmer and the executive director of the Real Organic Project. “Hydroponic production is not growing because it produces healthier food. It’s growing because of the money. Anyone who frames this as food for the people or the environment is just lying.”
The sprawling Kentucky farm is one of a dozen that AppHarvest hopes to open across Appalachia.Credit...Luke Sharrett for The New York Times
The technical term for hydroponic farming is controlled environmental agriculture, but people in the business refer to it as indoor farming. What used to be simply called farms are now referred to as land-based farms or open-field agriculture.
“We’ve perfected mother nature indoors through that perfect combination of science and technology married with farming,” said Daniel Malechuk, the chief executive of Kalera, a company that sells whole lettuces, with the roots intact, in plastic clamshells for about the same price as other prewashed lettuce.
In March, the company opened a 77,000-square-foot facility south of Atlanta that can produce more than 10 million heads of lettuce a year. Similar indoor farms are coming to Houston, Denver, Seattle, Honolulu, and St. Paul, Minn.
The beauty of the process, Mr. Malechuk, and other executives say, is that it isn’t limited by seasons. The cost and growing period for a crop can be predicted precisely and farms can be built wherever people need fresh produce.
“We can grow in the Antarctic,” he said. “We can be on an island. We can be on the moon or in the space station.”
That’s easy to picture: The farms are staffed by a new breed of young farmers who wear lab coats instead of overalls and prefer computers to tractors.
Today, the more than 2,300 farms growing hydroponic crops in the United States make up only a sliver of the country’s $5.2 billion fruit and vegetable market. But investors enamored of smart agriculture are betting heavily on them.
Lettuces at a Kalera vertical farm destined for nutrient-filled water begin in small plugs of growing medium.
Credit...Courtesy of Kalera
In 2020, $929 million poured into U.S. indoor-farming ventures, more than double the investments in 2019, according to PitchBook data. Grocery chains and California’s biggest berry growers are partnering with vertical farms, too.
“There is no question we are reinventing farming, but what we are doing is reinventing the fresh-food supply chain,” said Irving Fain, the founder, and chief executive of Bowery, which is based in Manhattan and has the indoor farm in New Jersey and one in Maryland, another under construction in Pennsylvania, and two research farms in New Jersey.
Mr. Fain said his farms are 100 times as productive as traditional ones and use 95 percent less water. Other companies claim they can grow as much food on a single acre as a traditional farm can grow on 390.
Vertical farms can be built next to urban centers, so lettuce, for example, doesn’t have to sit inside a truck for days as it makes its way from California to the East Coast, losing both quality and nutritional value. Vegetables can be bred for flavor rather than storage and yield.
The new systems are designed to produce a sanitary crop, grown without pesticides in hygienic buildings monitored by computers, so there is little risk of contamination from bacteria like E. coli, which forced large recalls of romaine lettuce in 2019 and 2020.
Bowery, the largest vertical-farm company in the United States, is growing hydroponic vegetables that have attracted the attention of chefs. Credit...Brian Fraser for The New York Times
Still, many farmers and scientists remain unpersuaded. Mr. Chapman, of the Real Organic Project, served on a U.S. Department of Agriculture hydroponics task force five years ago, and is leading an effort to get the agency to stop allowing hydroponic farmers to certify their produce as organic. The very definition of organic farming, he and others say, rests on building healthy soil. In May, the Center for Food Safety, an environmental advocacy group, led an appeal of a federal court ruling that upheld the agency’s policy.
Although the nutritional profile of hydroponic produce continues to improve, no one yet knows what kind of long-term health impact fruits and vegetables grown without soil will have. No matter how many nutrients indoor farmers put into the water, critics insist that indoor farms can never match the taste and nutritional value, or provide the environmental advantages, that come from the marriage of sun, a healthy soil microbiome, and plant biology found on well-run organic farms.
“What will the health outcomes be in two generations?” Mr. Chapman asked. “It’s a huge live experiment, and we are the rats.”
The divide between soil loyalists and ag-tech futurists is playing out on a much more intimate scale between two influential brothers: Dan and David Barber, who founded and own the organic farm Blue Hill and its restaurants in Greenwich Village and at Stone Barns in Pocantico Hills, N.Y.
In 2018, David Barber created an investment fund to support new food tech companies, including Bowery. But Dan Barber, a chef whose 2014 book “The Third Plate: Field Notes on the Future of Food” devotes an entire section to soil, believes that truly delicious food can come only from the earth.
“I am not buying any of it,” Dan Barber said of the hydroponic fever.
The chef Dan Barber, a soil loyalist, is skeptical of the claims made for hydroponic farms.
Credit...James Estrin/The New York Times
Trying to enhance water with nutrients to mimic what soil does is virtually impossible, he said, in part because no one really knows how the soil microbiome works.
“We know more about the stars and the sky than we do about soil,” he said. “We don’t know a lot about nutrition, actually.”
There is a cultural cost, too. For centuries, cuisines have been developed based on what the land and the plants demanded, he said. Regional Mexican diets built on corn and beans came about because farmers realized that beans fixed nitrogen in soil, and corn used it to grow strong.
“The tech-farming revolution is turning this equation on its head,” Mr. Barber said. It aids efficiency in the name of feeding more people but divorces food from nature.
His brother, David, had long been skeptical of hydroponics, too. “Most of my career was about good soil leads to good agriculture and good systems and ultimately good flavor,” David Barber said.
But the environmental advantages of next-generation hydroponic food production can’t be ignored, he said. Nor can the improvements in taste over earlier hydroponic produce. “They are combining outdoor and indoor thinking, and science and history, to create something special,” he said. “There are not going to be many winners in this space, but it is going to be a part of our food system.”
At Bowery, “there is no question we are reinventing farming, but what we are doing is reinventing the fresh-food supply chain,” said Irving Fain, its founder, and chief executive. Credit...Brian Fraser for The New York Times
Indoor farm companies view their competition as the large, industrial growers that produce fruits and vegetables bred to withstand processing and shipping — not smaller farmers using more natural growing techniques. The battle, they say, is against monoculture, not farmers who maintain healthy soil and feed their communities. Hydroponic farms can help develop new and more diverse plants, and reduce overall pesticide use.
“The only thing we are trying to do is get as good as farmers were 100 years ago,” said Mr. Malechuk, the hydroponic lettuce grower.
Indoor farming is a bet on the nation's agriculture, said Jonathan Webb, the Kentucky-born founder and chief executive of AppHarvest.
“The American farmer is already obsolete,” he said, pointing out that the United States imports four billion pounds of tomatoes from Mexico every year. “Our hope is we can get farmers back on U.S. shelves.”
Even Mr. Colicchio, who led a campaign against genetically modified food and has long been a champion of small farmers, said the two styles of farming can coexist. “We’re going to need a lot of tools in the toolbox,” he said.
Ouita Michel, a chef in Kentucky, likes AppHarvest because the company is creating jobs and growing tomatoes she is happy to use in her restaurants.
But technology, she said, will never trump the magic of soil. “Nothing will ever replace my summer Kentucky tomatoes.”
Lead photo: AppHarvest, the nation’s largest hydroponic greenhouse, opened in January in Morehead, Ky. — one in a new breed of huge indoor produce farms that use technology to fine-tune flavor, texture, and other attributes. Credit...Luke Sharrett for The New York Times
Can Vertical Farms Be Profitable?
Basically, we’re skeptical of both the economics and the save-the-world ethos that many companies preach. We enlisted an industry insider to help us separate the wheat from the chaff
Earlier this year, we covered a couple of indoor farming companies going public through mergers with special purpose acquisition companies (SPACs). Neither seemed very appetizing for retail investors, with negligible revenues to date. As we predicted, more indoor farming startups (referring to both large-scale greenhouses and vertical farming operations) are jumping on the SPAC crazy train. The latest is a Montana company called Local Bounti that had generated little buzz until this month’s announcement, which included news that Cargill is providing $200 million in debt financing in the deal.
In this article, we want to take a step back and look a little more closely at the indoor farming industry, sometimes referred to as controlled environment agriculture (CEA), particularly on the vertical farming side of things. Basically, we’re skeptical of both the economics and the save-the-world ethos that many companies preach. We enlisted an industry insider to help us separate the wheat from the chaff.
Saving the World from BS
Mark Korzilius
Mark Korzilius is the founder and chief strategy officer of &ever, a vertical farming startup based in Germany, with its first mega-farm located in the desert of Kuwait. Korzilius was also the co-founder in 2002 of a chain of fast-casual Italian restaurants, Vapiano, with more than 200 locations in about 30 countries. He reached out to us, as founders sometimes do after reading a story that didn’t include them, to tell us about all of the cool things their company is doing. In the case of Korzilius, he also wanted to set the record straight on all of the things that competitors like AeroFarms and other indoor vertical farming companies aren’t doing despite claims to the contrary.
Obviously, Mr. Korzilius is biased, but he also confirmed one of our chief suspicions: Many indoor farming companies claim they are on a mission to help feed the world, which seems incongruous with the fact that most are growing leafy greens, herbs, berries, and maybe tomatoes. Hardly the sorts of staples that are going to keep the estimated 800 million people in the world from going hungry at the end of the day. He also argues that claims of automation using artificial intelligence and sensor-rich environments are also overblown.
“We truly believe to become farmers and to be successful farmers for some crops, we can prove that [vertical farming] is, in the end, a way forward,” he says. “Hopefully, we can find some technologies to really overcome some issues that have been created by others … that will help solve problems that have been the result of technologies that have been created 50 years ago.”
In the second half of that comment, Korzilius is obviously referring to the modern industrial farming system, with its reliance on pesticides, herbicides, and fertilizers that deplete and poison soils and water supplies. That’s why you see so many companies developing natural fertilizers using microbes or biomanufacturing solutions for non-chemical pesticides. Outdoor agriculture is also water intensive, especially for products like almonds, which require one gallon of water per nut. Various technologies are in development to use water more efficiently, from soil sensors to aerial imagery from drones and satellites. Vertical farming gets at the root of the problem by moving the growing operation indoors, employing LED lights and hydroponics to deliver nutrients using only water rather than soil. That eliminates both pesticides and many traditional fertilizers, and reportedly cuts down on water usage by as much as 95%. Let’s take a look at the specific technology behind Korzilius’ company.
Creating the Right Climate for Vertical Farms
Founded in 2015, &ever (formerly known as Farmers Cut) has raised an undisclosed amount of money, originally through bootstrapping and Seed funding, before raising a Series A from partners in Kuwait for its mega-farm, a joint venture with a local investment company called NOX Management. Korzilius said &ever is currently raising a Series B but declined to offer any details.
There are two key parts to the company’s technology, as we understand it: Dryponics and climate cells.
Dryponics is a new riff on hydroponics, which involves growing plants without soil. The company uses a proprietary growth substrate to keep the roots dry. In effect, the root system stays on top of the substrate, while absorbing the nutrients in the water. This setup reportedly has several advantages, including using 68% less water than common hydroponic systems and 37% less water than aeroponic systems, which grow plants in the air using a mist environment or similar system. Less water means the basins underneath the substrates are flatter, allowing more compact layering of crops.
Each crop requires different growing conditions, Korzilius explains, so his team developed climate cells – microenvironments optimized for temperature, light, humidity, and CO2, among other factors. Controlling the environment also helps control energy costs, especially in the large structures that house many of today’s vertical farms, including the company’s flagship facility in Kuwait.
Credit: &ever
“Within the same premises, we can create different climates. In our Kuwait farm, we have four climate cells next to each other. So, we could potentially create California climate next to Denmark climate next to Singapore climate,” he explains. “By creating climate cells within one premise, we save energy [and] only climatize what needs to be climatized.”
Take spinach, a notoriously difficult plant to grow indoors that took the company two years to figure out the right combination of substrate and climate. But that work has paid off by reducing the amount of growth time by 15%, which translates into 18 grow cycles a year, which is good enough for Popeye to be an investor (if only he hadn’t blown his retirement on canned spinach).
Betting the Farm on Indoor Farming
The value proposition is that products from &ever leave the farm as living plants with the roots intact, continuing to grow while staying fresh and retaining maximum freshness, according to Korzilius. The Kuwait farm is the first large-scale effort to prove the business model, though the company also has smaller grow towers for on-site retail locations like grocery stores, including one in Munich. A second mega-farm is in development in Singapore.
A &ever grow tower. Credit: &ever
The Kuwait farm, which went live shortly before the Rona hit, is designed to grow up to 250 varieties of greens and herbs. The 30,000-square-foot facility can reportedly produce up to 1,200 pounds of green stuff. Korzilius says the pandemic continues to hinder full-scale operations of the farm, which is overseen by just six employees. However, he claims the vertical farm is profitable from an operations standpoint (in other words, without accounting for the original capital expenditure). “So, we are not selling below cost. Yes, it’s a prototype, but it’s working nicely.”
Tasty greens from a vertical farm in Kuwait. Credit: &ever
However, there is a reason why the mega-farm is located in Kuwait and not in Munich or elsewhere in Europe. Energy is simply cheaper in the Middle East, so it was a no-brainer to plug into the grid there. In Singapore, where electricity doesn’t come as cheaply, the local government has stepped in with grant money to subsidize the project. Currently, Singapore imports more than 90% of its food, so the government is motivated to find ways to be more self-sufficient, especially in the wake of the pandemic.
The bigger implication is that vertical farms will require cheap sources of energy to be economically viable. That goes against the current narrative of locating large-scale operations in the middle of big urban centers where electricity is usually pretty expensive. Of course, there are other economics to consider: Centrally located growing facilities will incur lower shipping costs and can theoretically deliver fresher, tastier products to consumers, who may be willing to pay the premium for what Korzilius calls harvest on demand.
“I strongly believe in consumers being at the center of all activities,” he says. “The consumer, in the end, has to pay for this. And, if he doesn’t, then all of this is just a stupid bubble.”
Conclusion
The bubble is certainly ballooning. The three indoor farming companies that are going (or have gone) public that we are aware of are valued at nearly $4 billion. Last year, the top three indoor farming startups in 2020 funding brought in more than $400 million between them, according to AgFunder News. These companies claim to be building a sustainable food system, but it seems unlikely that a business built on microgreens can be sustainable at that scale and cost. As always, the market will decide which model will succeed.
Tech investing is extremely risky. Minimize your risk with our stock research, investment tools, and portfolios, and find out which tech stocks you should avoid. Become a Nanalyze Premium member and find out today!
Sweden: Opening of New In-Store Vertical Farm At ICA Maxi
The opening event of the in-store vertical farm, a service provided and managed by Swedish technology company Swegreen, gained lots of traction from surprised and sometimes confused shoppers.
“We are actually making a difference here, because we grow next to the consumer, literally,” says Andreas Dahlin, CEO of Swegreen. “There are still many vertical farms that claim to produce sustainable, located close to the consumer, but they don’t mention the last mile. If logistics are needed to get the product to the consumer, they can still make a much bigger difference. That’s why we think this hyper-local model really makes an impact in the supply chain.”
It was all laughs and surprised faces during the opening at the ICA Maxi supermarket in Linköping this week. The opening event of the in-store vertical farm, a service provided and managed by Swedish technology company Swegreen, gained lots of traction from surprised and sometimes confused shoppers. Andreas opened the event by giving a toast to invitees. After explaining the concept, the crowd was allowed a visit to the farm.
Andreas leading the tour. Photo credit: Vertical farm daily.
Click here to view the photo report.
Biggest in Sweden
After successfully launching an in-store farm at ICA Focus, Gothenburg late 2020, the Swedish, fast-growing vertical farming enterprise Swegreen is now rolling out its Farming-as-a-Service concept in Scandinavia. First to get the installation in place is Ica Maxi in Linköping. The 60m2 farm supplies 10 different lettuces and herbs to the store – and more sorts are coming up – which makes this in-store growing facility the biggest in Sweden. Another share of the crops will be used in the store's own kitchen. Every day, several hundreds of crops are harvested that will end up on the shelves very soon after that.
Andreas adds, “The excessive heat from the farm is brought into the supermarket to optimally use all energy of the farm. We’re constantly looking at how we can optimize the cultivation processes up to energy use.”
Andreas explaining on vertical technologies. Photo credit: Verticalfarmdaily.
Full control
All technology is supplied and developed by Swegreen, such as the cultivation room and the AI-based control system which controls and optimizes the environment remotely. The farm is fully equipped with sensors, taking a huge relief off the farm operator who normally visits the facility 3-4 hours a day. Robot arms enable the gutters to be automatically moved from the beginning to the end-stage.
All processes are done on the farm, from seeding, breeding, cultivation and harvesting to packing the products. Everything in the farm is visible to the naked eye of store visitors.
Sepehr Mousavi, Chief Innovation Officer, and Innovation Lead at Swegreen explains that all technology is automated. “We can prevent any kind of error in the farm because the sensors will notify our technical services team immediately if something goes wrong to prevent any downtime.”
Click here to view the photo report.
Lead photo: Photo report: Swegreen launches event to celebrate project launch
For more information:
Swegreen
Andreas Dahlin, CEO of Swegreen
andreas.dahlin@swegreen.se
www.swegreen.se
Publication date: Wed 16 Jun 2021
Author: Rebekka Boekhout
© FreshPlaza.com
Certhon Wraps Up 7th Raspberry Trial Successfully
After successfully growing strawberries in the Certhon Innovation Centre (CIC), the company has decided to take on another trial of growing fruits indoors.
“Raspberry isn’t the first crop that comes to mind when figuring out which crops to grow indoors,” Andrea Huegler, R&D Engineer and Agronomist at Certhon said. “However, we accepted the challenge and decided to go for it as there are a lot of benefits to growing it in a controlled environment.”
After successfully growing strawberries in the Certhon Innovation Centre (CIC), the company has decided to take on another trial of growing fruits indoors. Certhon has been doing lots of research on indoor farming for a long time now. This has allowed them to investigate how to grow more complex crops in a controlled environment without daylight.
Andrea Huegler
Trial results
The main advantage of growing this crop indoors is having higher yields and consistent quality year-round. Certhon sees great opportunities ahead for the crop, due to its premium status and short shelf life. “It makes it a perfect candidate to be grown indoors.” During this trial, common raspberry cultivars were chosen. Certhon used chilled raspberry canes from a propagator, pollination by bumblebees and top and interlighting was used to flourish the crops. The harvesting period comprises 10 weeks, out of a total cultivation cycle of 21 weeks and is expected to end in July 2021.
Cultivation risks
The research was mainly about investigating the right transition of the vegetative state of the crop to the generative state. Andrea says that balancing the climate and light with energy consumption is the trickiest part here. “Ever since the first raspberry trial we’ve been trying to balance out the reduction of energy use, having an X amount of yield at a great quality and extending the harvesting period. Throughout the trials, we have obtained nearly twice as much yield compared to the traditional Dutch polytunnel producers in the summer,” Andrea notes.
However, raspberry cultivation isn’t without challenges. “One of the risks that could come up is growing grey mold,” explains Andrea. “If nectar isn’t removed well from the flower, the fruit can grow mold or have a grey undertone. However, if you manage your humidity wisely, the incidence is severely reduced. That’s the idea behind the CIC, optimizing growing recipes and eventually expanding the product portfolio because we want to provide a wide selection of product options to our clients.”
Greenhouse application
The knowledge that is generated in the CIC can also be applied to the cultivation of raspberries in greenhouses. Growing these crops indoors allows Certhon to generate ideal growing conditions and maximum potential for raspberry cultivation. With this knowledge, Certhon generates a blueprint that growers can follow in greenhouse cultivation as well.
Andrea explains, “For instance, the blueprint can be followed when growers want to know when to: provide extra lighting, shading, or adjust the humidity. In this way, ideal growing conditions can be mimicked to achieve the highest quality and yield possible in a greenhouse.”
Cane risk
Another, very important aspect is the quality of the raspberry canes. In order to have good production, your raspberry canes need to be of good quality and pest-free. “This cannot always be guaranteed, '' says Andrea, “since they are propagated outdoors and therefore bound to the pressures of external influences, such as climate. Although we have not tried it ourselves yet, we think the next step is to also propagate raspberry canes in a controlled environment without daylight.”
For more information:
Andrea Huegler, R&D Engineer and Agronomist
Certhon
andrea.huegler@certhon.com
ABC Westland 555
P.O. Box 90
2685 ZH Poeldijk
The Netherlands
Tel: +31 174 22 50 80
www.certhon.com
Publication date: Mon 7 Jun 2021
Author: Rebekka Boekhout
© HortiDaily.com
Aspara’s High-Tech At-Home Farm Launches In The U.S.
This official U.S. launch makes the device available to all U.S. consumer
Hong Kong-based Aspara, which makes high-tech, tabletop-sized farming units for homes, is now shipping devices across the U.S. through retailers like Home Depot, Wayfair, and via its own website.
The Spoon flagged Aspara back in January as a company to watch in the up-and-coming at-home farming space because of the device’s small size, lowish price point, and approach to hydroponics. At the time, the company was selling its system, which can fit easily on a countertop, to customers in Hong Kong and in very, very limited quantities via Amazon to other parts of the world.
This official U.S. launch makes the device available to all U.S. consumers. Speaking on the phone today, Rob Alexander, the Owner of Conducted Sales, the sales agent for Aspara in North American markets, said that Aspara has another eight retailers in the works, though he couldn’t at this point use specific names.
High-tech, hydroponic farms have historically been the territory of industrial-scale indoor farming companies — the AeroFarms and Plentys of the world. But following this past January’s CES show, both major appliance makers like LG and Miele along with smaller startups began to heavily publicize a new kind of indoor farm, one created for the at-home consumer. These devices are typically quite small and meant to feed a single household, rather than supply a grocery retailer.
Alexander said Aspara’s homegrown system differs from others on the market in the way it tackles the hydroponic element of farming. It uses what he calls an “ebb and flow” design, where water for the plant roots is constantly replenished from the side unit (see image above), making the water supply easier to refill than many at-home farms. Aspara’s also has sensors that determine nutrient levels in the water, the current level of humidity in the air, and whether a plant is getting too much light. An accompanying app notifies the user when any of these elements need attention.
“It’s trying to give you feedback to create the optimum growing environment,” Alexander said.
Another differentiation: the device is repairable. While that might first sound like a weird selling point (no one wants to buy tech that might break), it actually speaks to how seriously Aspara is pursuing the idea of making its high-tech grow system the kind of kitchen appliance that’s on par with a dishwasher or refrigerator. You don’t throw out a dishwasher the second something goes wrong. In the same way, Aspara users can replace parts like sensors and light canopies, rather than having to go out and buy a whole new farm.
The company’s approach recently won them the Green Product Audience Award.
Price-wise, Aspara is on the lower end of the at-home farming spectrum.
The device goes for $349 right now at Home Depot online.
Of course these days you can’t have a conversation about at-home food production without bringing COVID-19 up. Since Apsara wasn’t available to North Americans at the height of shelter-in-place mandates, the company wasn’t measuring demand for its product in that region. However, Alexander told me they did see a spike in Hong Kong, where the device has been available for some time.
My guess is that with the product available Stateside, that demand will surface quickly. Other at-home farming systems have seen huge jumps in demand recently as the pandemic, panic-buying sprees, and other factors have made many consumers question their total reliance on the traditional food supply chain.
Next up, Aspara wants to do a widespread launch in Canada, and also broaden the types of plants its system can grow to include other types of plants, including fruits and vegetables.
CEA Food Safety Coalition Details First Indoor-Farming Standards
Inspired by rising food safety concerns after the 2018 Thanksgiving romaine recalls, the CEA Food Safety Coalition is launching the first-ever food safety certification program specifically designed for indoor-grown leafy greens.
By AMY SOWDER June 2, 2021
(Photos courtesy CEA Food Safety Coalition)
Inspired by rising food safety concerns after the 2018 Thanksgiving romaine recalls, the CEA Food Safety Coalition is launching the first-ever food safety certification program specifically designed for indoor-grown leafy greens.
“The new standard champions CEA-grown produce as a critical component of safe and secure domestic food supply, especially in times of business disruption as experienced during the COVID-19 pandemic,” Marni Karlin, executive director of the CEA Food Safety Coalition, said in a news release.
Controlled Environment Agriculture, or CEA, has exploded with investment and sales the last few years, as more urban, indoor farms crop up to meet demand.
Soon after organizing in 2019, the coalition educated the Centers for Disease Control and Prevention and Food and Drug Administration about the limited risk of contamination from indoor-produced leafy greens, Karlin said.
“During the Thanksgiving 2019 romaine recall, those government agencies were transparent that CEA leafy greens were safe and did not extend the recall to them. This enabled retailers to keep CEA-produced greens on the shelves and consumers to safely buy CEA leafy greens for their families,” she said in the release.
The team had to create a standard that made sense across the board for the variety of production processes included in CEA — from greenhouses and vertical farming to aeroponic, hydroponic and aquaponic.
“Current food safety standards were written for the field, and many don't adequately address the unique attributes of controlled indoor environments,” Karlin said in the release. “Traditional food-safety risk profiles associated with conventional farming include examining the physical hazards and microbial hazards from water use, herbicide, and pesticide use, and impact from animals and animal byproducts. These do not impact CEA growers in the same way, if at all.”
As a result, a separate set of guidelines is needed.
This new certification process and the accompanying on-pack seal will spread awareness about CEA and unify these growers while differentiating them from traditional field growers, she said.
“It will allow producers to adhere to a standard tailored to indoor production and give incoming entrepreneurs guidance on the measures they'll need to meet to align with the existing industry,” Karlin said in the release.
The certification program is available to all CEA food safety coalition members for a small fee, and an external audit to the standard must be completed on an annual basis.
Growers are assessed across four key areas:
Hazard analysis: All potential hazards associated with a producer’s practices, including use of water, nutrients, growing media, seeds, inputs, and site control;
Water: Often used by CEA producers, recirculated water requires a continuing hazard analysis throughout its life cycle and zone-based environmental monitoring based on company-specific risk assessment, she said;
Site control: All food contact surfaces and adjacent food contact surfaces, including plant containers, must be considered and associated with potential farm physical hazards, including lighting, robotics, sensors, equipment, and utensils; and
Pesticide and herbicide use: Even though CEA-produced greens generally don’t use pesticides or herbicides, this module evaluates the potential risk of pesticide contamination and addresses if residue testing is required, she said.
“Consumer interest in food labels is high and shows a genuine desire to shop smarter,” Karlin said. “For consumers to truly make informed purchasing decisions, we need to explain what the labels mean, the process of certification and which labels they can trust.”
Robotic Warehouse Farms Will Save The World
CEA technology is just getting started. Like the Tesla Cybertruck, we have a working concept that promises a more-than-Jetson’s-level future many of us can see the benefits of and actively want―it’s just not quite available to the masses yet
by Elle Griffin
Four years ago, Ritch Wood was looking for a better way to grow plants. As the CEO of global skincare company Nu Skin, he ran into ingredient shortages every winter when fields went dormant―and when he moved grow operations to the equator he ran into water and land shortages, along with a host of quality control issues.
Nu Skin needed reliable, quality ingredients for their skincare products. But farming was too unpredictable an industry. “If there was a way to grow indoors,” he thought, “and be able to do that 24 hours a day, 365 days a year―if we could guarantee that it was grown without any herbicides or pesticides and in a sustainable way that uses less water and land―that would be really helpful.”
At the time, controlled-environment agriculture (CEA) was in its infancy and grow-light technology had yet to take a turn for the more affordable. When he learned of an agricultural system that promised to use a fraction of the land and water used by traditional agriculture methods and had the potential to make it more affordable, Wood made an investment.
Nu Skin paid $3 million for 70 percent of the company and rights to its IP―and Grōv Technologies was born.
Grōv grass grown in the Olympus machine at the Bateman Mosida Farms. Photo from Grōv Technologies
Controlled-environment agriculture is on the rise
The theory behind CEA is that by controlling the environment in which it grows, we can control everything about a plant and what it grows into by micro-tweaking one of a thousand different characteristics―including temperature, humidity, light duration, light wavelength, dissolved oxygen in the water, and carbon dioxide saturation in the air. By tweaking the growing cycle, we can control the caloric content as well as the nutrient content and density of the plant.
“What we’ve learned through controlled-environment agriculture,” Benjamin Swan, co-founder and CEO at Sustenir in Singapore, once told National Geographic, “[is] we can actually emphasize certain characteristics of the plants. So, without using GMO, we can make our kale softer, we can actually make it sweet.”
The theoretical use cases for this technology are endless―from being able to grow in places where water is scarce (like in much of Africa), or where water is overly abundant (like Hawaii), or in places where labor is scarce (like in parts of Asia), or even in places that have long winters (like Northern Europe). Theoretically, we could have grow towers in every town and feed the whole of it no matter its natural environment.
We could even grow those foods to those cities’ exact nutritional needs―more vitamin D-rich foods in wintery places, for example. Dr. Lee Mun Wei, a senior manager at the Food Innovation and Resource Centre (FIRC) in Singapore aims to predict and prevent illness in a given population by tracking their biometric data using Apple watch-like wearables, then 3D printing nutrient-specific foods that could mitigate imbalances.
Though these technologies exist, they are still in their infancy. Singapore leads much of the research and development out of necessity. With limited land and water resources, the county is forced to import 90 percent of their food and 40 percent of their water from outside the country. As a result, they have no option but to grow vertically and desalinate water from the ocean.
Elsewhere, the industry has been slow to catch on, largely due to exorbitant startup costs, low returns, and lack of urgent need. According to a 2017 State of Farming report by L.E.K., only 27 percent of indoor, vertical farms are profitable compared with 50 percent of container farms and 75 percent of greenhouses. But one thing has spurred the industry on in recent years: cannabis.
Legalized in 39 states, demand for cannabis has created a $13.6 billion industry and enough capital to fund CEA-enabled grow operations. “When you have a crop that fetches up to $2,400 or $2,500 a pound, you need to be able to dial everything in and make it consistent and repeatable,” says Dashiel Kulander, co-founder and CEO at Boojum Group. “If the temperature swings five to 10 degrees on a cannabis plant, that will change the plant’s various cannabinoids. The goal is to create a medicine that is consistent batch after batch.”
It’s only recently that there has been some financial incentive to use CEA technologies for food use―largely driven by Big Ag players hoping to hedge out the competition. Berry farming giant Driscoll’s, for one, led a $500 million round to fund Plenty, a 2.2-acre vertical farm in California they hope will help them fulfill a contract with Albertsons. The Ingka Group, for another, led a $100 million round to fund AeroFarms, a 2.4-acre vertical farm in New Jersey that will help them fulfill a contract with Singapore Airlines.
Grōv tent at the Bateman Mosida Farms. Photo from Grōv Technologies
Grōv Tech is building CEA prototypes in Utah
By investing in Grōv Tech, Nu Skin hopes to do something similar, getting ahead of the supply chain that fuels their skincare products before the competition can beat them to it, or before climate change makes traditional methods more difficult, all while shoring up technology that could provide a farming model that is more sustainable―if only it were more economical.
“The purpose was always, can we build a better product for Nu Skin?” Wood says. “We think there’s a huge story around the ingredient sustainability, and there were a lot of ingredients we felt we could grow, but the challenge was: could we do it in an economical way?”
Grōv Tech started out with a prototype: a tower that pairs hydroponic growing technology with grow lights. But like all CEA startups, a lot of the growing process was manual and the technology was prohibitively expensive. To make something that was scalable and profitable the whole thing needed to be automated and it needed to be cheap.
With this goal in mind, Wood decided they would start by growing animal feed for Bateman’s Dairy farm. Having grown up on a dairy farm himself, Wood figured this would allow the company to scale the product while refining and automating the technology to the point that it could be replicated. And all of this would have a fortuitous effect on Nu Skin’s bottom line.
“One of our bestselling products is a weight-loss protein powder which uses whey protein,” Wood says. “So again, a very nice connection there is if the animal is eating a more sustainable product and producing better milk with better protein and it’s being done in a sustainable way―certainly that can be a benefit to Nu Skin down the road.”
One year into feeding the 20,000 animals at Bateman, the company has learned a lot. For instance: cows need a lot of magnesium, but they don’t like eating it. Now, Grōv Tech puts magnesium in the water so it’s directly absorbed into the plant and then becomes bioavailable to the cow upon eating it. And because the growing process only takes seven days, data scientists can analyze the results in real-time and adjust the components to optimize production for the next batch of feed.
According to Grōv Tech president Steven Lindsley, it’s not far off that we’ll be looking at milk production (butter, fats, and proteins) and optimizing a herd’s diet for taste, quality, and nutritional value―not to mention the wellbeing of the animal. We’ll be able to look at how many trips from the veterinarian an animal gets when they’re fed certain nutrients in their diet, and whether they can have more calves and produce the same amount of dairy on less, better quality feed. (So far, the answer to this last question is yes. When animals are fed better quality food they need less of it―just like humans.)
And if we hook all of the cows up to robotic milking equipment and connect everything to artificial intelligence, machine learning, and the Internet of Things―Lindsley’s far-flung goal―then we might be able to collect enough data to not only feed cows to their optimum health and performance ability, but humans too. And that could have ramifications not only for feeding the world, but nourishing it― just like Dr. Wei hopes to do in Singapore.
“Last year was about starting to feed animals and get data and prove out the hypothesis we have while continuing to perfect the technology and get confidence there,” Wood says. “And now we’re really to a point where we’ve got data that proves that it works and that financially it’ll be a good thing for a farmer. So now we can really take that proposition to farmers and start to scale.”
Olympus Tower Farm at Bateman Farms in Mosida, UT. Photo from Grōv Technologies
CEA technology could feed the world
Right now, Grōv Tech is focused on refining its technology right here in our own backyard. But once they do that, the plan is to expand internationally.
“Saudi Arabia has actually passed a law where you cannot use water to grow fodder or feed for animals, so all of that now has to be imported. China imports one-third of their alfalfa feed for their dairy animals because they don’t have the capability of growing it,” Wood says. “So there are countries that will probably benefit more than the US would. But we’ve got to refine the technology and get that built to where it’s ready to scale before we start spreading ourselves all around the globe.”
CEA technology is just getting started. Like the Tesla Cybertruck, we have a working concept that promises a more-than-Jetson’s-level future many of us can see the benefits of and actively want―it’s just not quite available to the masses yet. But with more than a billion dollars invested in the technology in just the past few years alone―we’re getting there. And the “there” we are heading toward is rosy indeed.
“To put it in perspective, one tower that is about 875 square feet on the ground will replace 35 to 50 acres of land,” says Lindsley. “And that will feed the animals on roughly five percent of the amount of water. The UN says that that the world will add about 2.5 billion people in the next 30 years. And we have to find a way to feed them on arguably less arable land and water. The good news is the technology is coming along to help solve that equation.”
If COVID-19 taught us anything, it’s that our food supply chain is fragile. But that’s only because our supply chain was built to grow food in California, refrigerate it so it stays fresh, then transport it 1,500 miles so we can eat a salad in the winter in Chicago. In the future, that might not be a thing. “We’re having a dry year now,” Lindsley tells me in February. “But a year ago we were in a blizzard, and even in the middle of a blizzard in February in Utah, we’re pumping out fresh, beautiful, safe green grass for animals. It’s a paradigm shift.”
“Four years ago it was a good idea,” Wood tells me of his company’s investment in CEA technology, “But four years from now it’s going to be required.”
Elle Griffin
Elle is the editor-in-chief of Utah Business and a freelance writer for Forbes, The Muse, and The Startup. She is also a literary novelist and the author of a weekly newsletter called The Novelleist. Learn more at ellegriffin.com.
Sustainable Impacts Indoor Farming May Have On Environment
This article identifies the potential environmental effects large-scale indoor farming may have on air, water, and soil. We begin with an overview of what indoor farming is with a focus on greenhouses and indoor vertical farms (eg, plant factories)
Mar 18, 2021, | Knowledge Base, Learning, Research Paper
By Center of Excellence
Figure 1. Map of research and knowledge domain of indoor farming.
Abstract
This article identifies the potential environmental effects large-scale indoor farming may have on air, water, and soil. We begin with an overview of what indoor farming is with a focus on greenhouses and indoor vertical farms (eg, plant factories). Next, the differences between these 2 primary methods of indoor farming are presented based on their structural requirements, methods of growing, media, nutrient sources, lighting requirements, facility capacity, and methods of climate control. We also highlight the benefits and challenges facing indoor farming. In the next section, an overview of research and the knowledge domain of indoor and vertical farming is provided. Various authors and topics for research are highlighted. In the next section, the transformative environmental effects that indoor farming may have on air, soil, and water are discussed. This article closes with suggestions for additional research on indoor farming and its influence on the environment.
Citation
Stein EW. The Transformative Environmental Effects Large-Scale Indoor Farming May Have On Air, Water, and Soil. Air, Soil and Water Research. January 2021. doi:10.1177/1178622121995819
Introduction
Open field farming has been practiced the same way for centuries as the primary means of growing food. Its origins can be traced back to wheat production 11 000 years ago in the Middle East, which later spread to the Mediterranean, North Africa, and elsewhere.1 Given limitations on the amount of arable land, water scarcity, increased awareness of sustainable development, and the well-documented environmental effects of open-field agriculture, other farming methods have been developed in the past few decades. The primary alternative to open field farming is referred to as indoor farming, which has received relatively little attention in terms of environmental impacts. The goal of this article is to introduce indoor farming in its many forms to environmental scientists, outline key areas of research, and highlight the effects large-scale indoor farming could have on the environment. Research needs to be done to better understand the cumulative and transformative environmental effects indoor farming methods may have on water, air, and soil as it realizes its potential to supply a significant portion of the population with fresh food.
What Is Indoor Farming?
Indoor farming is a relatively new method of growing vegetables and other plants under controlled environmental conditions. These farm systems are variously referred to as indoor farms, vertical farms, vfarms, zfarms, greenhouses, controlled environment agriculture (CEA), and plant factories.2,3 Indoor farms are sometimes confused with urban farms, which typically represent small outdoor farms or gardens to grow vegetables that are located in urban areas. It also should be noted that mushrooms have been grown indoors in compost under controlled conditions without light for more than one hundred years.4 For the purposes of this article, we will focus on characteristics of controlled environment indoor vertical farms and greenhouses, which are the primary architectures used for the large-scale production of leafy greens and other vegetables that require natural or artificial light.
The many faces of indoor farming
Greenhouses have been the workhorse for indoor growers for decades, especially in the production of flowers and ornamental plants. The modern high-tech greenhouse designs were pioneered in the Netherlands and have since been embraced all over the world. Several examples of these farms are evident throughout the United States and the largest span hundreds of acres. For example, according to Greenhouse Grower,5 Altman Plants (CA) has almost 600 acres under glass followed by Costa Farms (FL) with 345 acres. These are mainly used in the production of ornamental plants.
For vegetables, greenhouses were originally designed for tomatoes but now are used in the production of kale, microgreens, lettuces, herbs, squash, and other types of fresh produce. These greenhouses, formerly located in rural areas, are now being positioned near urban and peri-urban areas to bring operations closer to population centers to save money and reduce the carbon footprint associated with transportation miles. For example, BrightFarms (brightfarms.com) has greenhouse operations located just outside of Philadelphia and Cincinnati to produce lettuces and other leafy greens. Gotham Greens (gothamgreens.com) situated its first greenhouse on top of a warehouse in Brooklyn, NY and has since expanded to other cities. AppHarvest (appharvest.com) is a venture located in Kentucky whose greenhouses cover more than 60 acres to produce tomatoes and other vegetables. What is common to greenhouse design is that all growing takes place on a single level, they are clothed in materials such as glass that transmit natural sunlight, and include climate control and irrigation equipment. They may also use a modest amount of supplemental artificial lighting during winter months.6
Growing leafy greens and other plants in buildings has emerged in the past 25 years whereby plants are grown vertically and hydroponically using artificial lights. Indoor vertical farms are typically located in warehouses or similar structures that have been retrofitted to provide superior heating, ventilation, and cooling (HVAC) for the benefit of plant production and racking systems to support the production systems.7-9 The PVC grow systems transport nutrient-rich water to the root zone of the plants, and the water is then returned to the main reservoir. Designed as closed re-circulating systems, indoor vertical farms only use a fraction of the amount of water as greenhouses or open-field methods (see also section “Water Use”). The advent of cost-effective LED lighting technologies has allowed farmers to provide the plants with just the right wavelengths of light, intensity, and photo-period to optimize growth.10 Other advances include automation, IoT, and artificial intelligence; ie, all of the information technologies that contribute to “smart farming.”11
Although modern LEDs are very efficient compared to HID, high-pressure sodium, or florescent lamps, the capital and operating costs of these artificial lighting systems are significant,10 as are the climate control systems that are also required. Greenhouses, for example, require significant investment in heating and cooling equipment to maintain stable temperatures and humidity, which results in significant operating costs in buildings with low R-value membranes (eg, glass). The chief benefit of this design is that the light comes free, although growing is limited to a single level. Indoor vertical farms, however, can benefit from well-insulated structures that reduce heating and cooling costs and growing can take place on multiple levels. That said, these savings come at the expense of relatively high electricity usage for artificial lighting.10 These operating costs can be mitigated with the increasing efficiencies of LED’s, sensing systems that modulate light to the maximum required for the plants, pairing indoor farms with renewable energy sources such as solar and geo-thermal, and architectures that favor energy efficiency.9
Methods of indoor farms
Indoor farms are characterized by several parameters:
Growing Method and Media
Source of Nutrients
Lighting Requirements
Facility Capacity
Climate Control
Economics
Most indoor farms use hydroponic methods of growing; i.e, plants are grown in water. Seeding takes place in an inert material such as stone-wool or peat, which is irrigated with nutrient–rich water. Water is administered using a variety of techniques ranging from fine mist sprayers (aeroponics), to shallow water (NFT) irrigation, to deep water culture (DWC) immersion to flood and drain methods.9 All are effective and have their pros and cons. Nutrients for larger-scale hydroponic production systems typically come from dissolved salts that ionize in the water. In some smaller systems, the nutrients come from the nutrient-rich water of fish farms (ie, aquaponic systems) that are proximate to and coupled with the plant production system.
In greenhouse production facilities, most lighting comes from the sun, which may be supplemented with artificial light, especially in the northern latitudes during winter. Plant factories and vertical farms, however, use only artificial lighting but are designed to maximize growing area using stacking methods. One common design is characterized by horizontal multi-tier growing systems starting at ground level that may include up to a dozen growing levels or tiers. Aerofarms (aerofarms.com) and Bowery Farms (boweryfarming.com) use this type of design for their production processes. An alternative is to use vertical drip irrigation grow systems. This design is characterized by vertical multi-site growing systems starting at ground level that extend upwards of 8 ft. In these systems, plants grow “sideways” toward artificial lights that are positioned at a right angle. Plenty, Inc. (plenty.ag) uses systems like these obtained in the acquisition of Bright Agrotech. Several examples of vertical farming ventures can also be found in Al-Kodmany.
All indoor farming methods share the characteristic of offering CEA. Controlled environment agriculture offers the grower complete control over several environmental variables including, but not limited to: light intensity and wavelength, photo-period, wind velocity, temperature, and humidity. Water culture is further managed to obtain optimal results based on nutrient levels, PH, and dissolved oxygen.9,12 In most cases, pesticides and herbicides are eliminated. More advanced farms such as Fifth Season (fifthseasonfresh.com) benefit from extensive use of sensors, IoT, robotics, automation, and control systems designed to optimize yields and minimize labor. Another valuable aspect of CEA farms is their ability to produce plants with certain desired morphologies and nutritional profiles based on the control of lighting wavelength, temperature, and nutrient levels. Sharath Kumar et al13 go so far as to suggest that with CEA, we are moving from genetic to environmental modification of plants.
Benefits and challenges of indoor vertical farms
Several benefits are associated with vertical farming,9 although the industry is not without its challenges (see Table 1). The principal sustainable benefits of indoor vertical farming are a large reduction in the use of water (see also section “Water Use”), the reduction or elimination of pesticides, and mitigation of the effects of excess fertilizer run-off. From an economic perspective, the ability to control the environment results in a stable supply chain, price stability, long-term contracts with distributors and retail markets, and high yields per square foot. The elimination of pesticides puts produce grown this way on par with organics, which command premium pricing. Indoor farms, if designed correctly, can reduce labor costs and may be located closer to urban centers. Some see a role for indoor farms to ameliorate food deserts, unemployment, and as a means to re-purpose abandoned buildings and lots.3,9,14-16 Finally, vertical farms provide resilience to climate change, flooding, droughts, etc.
However, the vertical farming industry is facing some key challenges. For instance, currently only a very small portion of fresh vegetables are produced indoors. The one exception is the mushroom industry, which represents a US$1.15 billion industry.17 Second, the USDA does not clearly identify vegetable production by method; eg, greenhouse, open field, vertical farm, etc, so data are not readily available. Third, profits have been elusive, especially for vertical farms.18 According to the 2019 Global CEA Census Report only 15% of shipping container farms and 37% of indoor vertical farms were profitable vs. 45% for greenhouse operations.19 Another limitation of indoor farming is that a relatively small number of cultivars can be grown using indoor farming methods.
The primary ones are leafy greens, herbs, microgreens, tomatoes, and peppers, although berries, root vegetables, and other more exotic plants are being trialed.19 Another challenge for indoor farm start-ups are the high capital costs, which can range from US$50-150/ft2 for greenhouses to US$150-400/ft2 for vertical farms. For example, AppHarvest had to raise over US$150 million to fund its 60-acre greenhouse complex.20 Aerofarms raised US$42 million for a 150 000 ft2 vertical farm,21 which equates to over US$280/ft2. Cosgrove22 further reports that access to capital is impeding the growth of indoor farming, especially for smaller farms. One reason that indoor vertical farms are not easily profitable is that they have to compete against conventional farms, which still enjoy a cost advantage.
As a result, indoor farms typically price product toward the high end and along the lines of pricing for organics,2 which limits market penetration. The 2 major factors contributing to the high costs of indoor and vertical farm operations are energy10,23,24 and labor, which account for nearly 3 quarters of the total.2,24 Despite these challenges, venture capital continues to pour money into indoor farming and agtech in the hopes of driving cost down and maintaining growth. Dehlinger25 reported that US$2.8 billion was invested by venture capitalists in Agtech companies in 2019.
Finally, the industry is struggling to share knowledge, establish standards, and create best practices, although progress is being made. For example, the Center of Excellence for Indoor Agriculture established a “Best in Class” award for growers and manufacturers (indoorgacenter.org). Indoor Ag-Con (indoor.ag) and the Indoor Agtech Innovation Summit (rethinkevents.com) hold online events and annual conferences to help promote knowledge sharing. Several specialized industry news outlets now exist including Vertical Farm Daily (verticalfarmdaily.com), Urban Ag News (urbanagnews.com), iGrow (igrow.news), Hortidaily (hortidaily.com), AgFunder Network (agfundernews.com), and others.
Read more >>>
Keywords: Indoor farming, vertical farming, vfarm, zfarm, plant factory, water, air, soil, sustainability, carbon cycles, drought, information technology, greenhouse gases, climate change, environment, agtech
Explore The Sixth Edition of Clima, Powered by IGS
In this edition, we look at why precision farming and Controlled Environment Agriculture (CEA) techniques are becoming more mainstream, and the skills and talent required to make this approach a success
In this edition, we look at why precision farming and Controlled Environment Agriculture (CEA) techniques are becoming more mainstream, and the skills and talent required to make this approach a success. Technology is having a greater impact on agriculture than ever before, and this is only set to increase. It will bring with it a wider and more advanced agricultural ecosystem that requires a skilled, knowledgeable, and committed workforce, with as great an appetite for innovation and capacity to problem solve as any generation before.
Discover more on this topic in the sixth edition of Clima today.
Bringing future talent to Agriculture 4.0
We discuss the emerging influences on education and skills development across Agriculture and Horticulture with two senior leaders from Scotland’s Rural College (SRUC). We spoke to Professor Fiona Burnett, Head of Connect for Impact in SRUC’s Knowledge and Information Hub, and Ruth Vichos, Lecturer in Horticulture, about the evolution of Agriculture 4.0, and how technology is impacting skills evolution and teaching mechanisms.
Listen To The Full Interview
Can Vertical Farming Be A Viable Method Of Controlled Environment Production?
Fifth Season is using its fully integrated, automated operating system to crack the economics code for vertical farming with the potential to integrate with greenhouse operations.
Fifth Season is using its fully integrated, automated operating system to crack the economics code for vertical farming with the potential to integrate with greenhouse operations.
To say that controlled environment agriculture is drawing a lot of interest and dollars from the investment world would be an understatement. Austin Webb, co-founder, and CEO at Fifth Season, a vertical farm operation in Pittsburgh, Pa., estimates that over $3 billion has been invested in the CEA industry during the last four years alone, excluding debt and merger and accusations activities for greenhouse operations.
“For indoor ag overall, including both vertical farming and greenhouse, about half that equity investment has been for vertical farming,” Webb said. “There were a lot of dollars that came into this space early on. The unfortunate piece to that is there was a lot of overhype and false promises made in this space. A lot of those dollars came in too early for some of these companies and overall were wasted.
“There has been an industry-wide struggle to make the economics of vertical farming work. All of these companies talk about what they are going to do in the future, but the issue is they have negative unit economics. They lose money for every pound of produce they sell. In many cases, they will say that they will make the economics work in the future, but only after they build more production facilities.”
Webb said negative economics has had a major impact on the vertical farm industry.
“The false promises and the negative economics have held the industry back, overshadowed companies that are building substantial vertical farming solutions that work and pushed additional dollars to incremental greenhouse solutions,” he said. “Moving forward we will continue to see more dollars come into CEA and into vertical farming specifically. This will include public markets and SPAC (special purpose acquisition company) activity.
“Overall, there will be more money invested in CEA. This will include investments that are mediocre. The important element will be investments made into tech platforms designed for scalability and repeatability. This is the only way that volume requirements for wholesale buyers can be met to unlock indoor ag as a material participant in overall market share.”
Need for a mindset change
Even with additional investment dollars coming into the CEA industry, Webb doesn’t expect it to be enough to make traditional vertical farming companies a success.
“Unfortunately, even though significant dollars have been invested in vertical farming, much of it has been wasted,” he said. “The incremental mindset a lot of people in this industry have had is to simply convert farming from outdoors to indoors. In doing so, all they inevitably did was bring people from outdoors and put them indoors. The mindset was to create a growing platform to produce leafy greens and then sprinkle on some technology. The technology was sort of an afterthought.
“There were a lot of companies throwing out buzz words without having actual practicality in regards to robotics, artificial intelligence, and automation. All the money that has been invested has been going toward continued R&D, but at a level which has companies creating technical debt.”
The thing that has helped Fifth Season avoid the technology issues other vertical farms have encountered is the way the company developed and designed its operating system.
Fifth Season has created a manufacturing platform that is fully automated from end-to-end including growing, processing, and packaging.
“We had a completely different mindset,” Webb said. “We took a blank slate to really design this holistically from beginning to end. We think of this as manufacturing a living organism. As a result, we’ve created an IoT–connected smart manufacturing platform that is an industry-first, industry-only, fully end-to-end automated platform—not just growing, but also processing and packaging. There are other operations that have automation here or there, but nothing else truly automated from beginning to end.
“More importantly, we have integrated the system so it is completely run by our proprietary software platform. We don’t have a bunch of automated equipment that runs on its own controls. Instead, we have a combination of our own proprietary tech and some off-the-shelf equipment such as conveyors. All of the electromechanical systems sit within our software skin and are run by our in-house built firmware and software brain. We have a pathfinding algorithm where when we receive an order from a customer, our system is sequencing out the schedule completely on a daily, weekly and monthly basis.”
Fifth Season worked with Hort Americas and GE Current, a Daintree company, to develop its automated grow room.
“Partnering together on our solution helped us validate that there was a path for our vertical farm to have favorable economics,” Webb said. “Being able to bounce ideas and technologies off of the Hort Americas team allowed us to push the boundaries of innovative thinking in terms of our approach and how we wanted to use technology to solve the complex issues that are limiting vertical farming. We were able to think differently, knowing we had the Hort Americas team as both a check and enabler, which ultimately created a successful collaboration.”
Partnering with Hort Americas also gave Fifth Season the opportunity to incorporate Current’s LED technology into its unique growing platform.
“We did a lot of things differently with our proprietary design and in so doing there were certain things that we couldn’t necessarily handle ourselves,” Webb said. “Working with Hort Americas and Current enabled us to move very quickly while making smart, capital-efficient decisions, as opposed to designing the LEDs ourselves or over-paying for unnecessary functionality.
“We worked with Current in key areas that made big differences related to the integration of our design. We leveraged Current’s significant expertise in regards to light spectrum strategy and the corresponding impact on plant science and quality.”
Creating an economic advantage
Webb said Fifth Season’s unique platform has allowed the company to unlock positive unit economics where it can offer a market price that works for wholesalers and consumers.
“We have been able to make money per pound and make vertical farming economically sustainable,” he said. “Our platform has enabled us to make a stepwise function change in labor costs and efficiency and in energy costs. For labor, we have 2x+ less labor costs than other companies in this space. We also measure and track energy down to every individual bot. We have over 60 bots that are all integrated into one robotics system. We measure and track how to optimize energy utilization to all of those bots.
Fifth Season’s unique operating platform has allowed the company to unlock positive unit economics enabling it to offer a market price that works for wholesalers and consumers.
“Finally we have made a stepwise function change in pounds to fixed costs ratio. That’s because we have been able to remove large aisle ways and manual inefficient storage and retrieval. We have created a patent-pending solution around our automated storage retrieval, which ties to the rest of our system. In the end, we are able to remove all human involvement from the grow room and are able to achieve 2x+ the growing capacity.”
Another advantage of the platform Fifth Season has created is the need for raising additional capital compared to some other vertical farms.
“We have raised just over $40 million to date,” Webb said. “There are multiple vertical farm companies that have raised $200 to $400 million+. The reason we haven’t had to raise that much capital is because of our mindset about engineering, grow science, and operations in the same R&D pipeline. It has allowed us to catch up and to surpass the rest of the industry in a fraction of the time with a fraction of the capital.
“As we move forward and look at raising additional capital, what’s different is we don’t have to use our equity capital to build more farms for all the hard costs associated with real estate, equipment and building facilities. We can if we want to and if it makes sense for our equity partners, but it is not required. We have been able to unlock positive unit economics which means we have been able to unlock non-dilutive capital to build additional facilities more capital efficiently. Overall, we have built a scalable, repeatable platform, which is what investors need to see.”
What’s ahead for vertical farming?
Webb said there will be a few select companies that have approached indoor ag and vertical farming with a solution that works and will thrive. There will also be a number of companies that are large and excessive that will eventually disappear.
“There will be some consolidation in this industry,” he said. “Some companies won’t be consolidated because they don’t have a tech platform that is investable in terms of the synergies of wanting to acquire that footprint. Consolidation will be selective in some cases.
“There is a lot of production regardless of footprint and money going into leafy greens. There are companies in this space that have no intention of doing anything different than that. I think that focus will run them into a leafy greens race to the bottom. It all comes down to no sustainable competitive advantage.”
Webb also sees the potential for synergy between vertical farms and greenhouses.
“We have built a scalable system that allows us to do a number of crops and then do asset management across different applications,” he said. “We also have the technology that is applicable from an asset management production operations standpoint that works for greenhouses as well.
“We will be able to unlock with this technology what many others won’t necessarily be able to do. Fifth Season will not only be a company that has vertical farm and greenhouse footprints but also is one that uses those footprints in a collaborative way for specific crops. For example, a crop could be in a vertical farm environment for part of its life and in a greenhouse for another part of its life. This will create cross-category and cross footprint combinations.”
For more: Fifth Season, (412) 899-2268; hello@fifthseasonfresh.com; https://www.fifthseasonfresh.com/
Lead photo: Austin Webb, co-founder, and CEO at Fifth Season, said even though significant dollars have been invested in vertical farming, much of it has been wasted. Photos courtesy of Fifth Season
This article is property of Urban Ag News and was written by David Kuack, a freelance technical writer in Fort Worth, Texas.
CHINA: $500 Billion To Bring All World Crop Farming Indoors
China will build 2 Million hectares (20 billion square meters) of controlled environment greenhouses by 2025 and this will produce half of their vegetables and crop needs
Brian Wang | April 3, 2021
China will build 2 Million hectares (20 billion square meters) of controlled environment greenhouses by 2025 and this will produce half of their vegetables and crop needs. Temperature, humidity, lighting would all be under controlled conditions. It would not matter if there were new extreme temperature swings outside or if there was drought. The needed food and water would be immune to any projected climate change over the next 500-1000 years.
Alibaba sells greenhouses for as little as 70 cents per square meter. The bulk, high volume cost to the manufacturer is about 50 cents per square meter. If installation labor costs are 50% of the 2 million hectare project then it would cost about $20 billion for the 2 million hectare project. $40 billion would be sufficient for China to make 40 billion square meters of climate-controlled greenhouses which could produce all vegetables and crops. It would cost $260 billion to make greenhouses for the food production of the entire world.
Indoor climate-controlled agriculture has almost no need for pesticides and uses 7% of the water. This would take up 3-5% of the total land area of open-air farming.
Additional funds could be provided for higher demand from population growth and for some level of automation, sensors and other systems.
There is an economic analysis of smaller scale greenhouse and vertical farming. The all-in delivered cost of a pound of greens grown in a commercial greenhouse is estimated to be $2.33 per pound. It cost $18.3 million to build 280,000 square feet (2.6 hectares) of commercial greenhouse in the USA. The total cost to grow would be just over $3.0 million per year for 2 million pounds of greens or $1.52 per pound. BrightFarms employs 165 people for the three greenhouses. $1.10 per pound consists of employee costs.
The cost estimates for greenhouses could be brought down to $1 per pound or less with large-scale construction. Below are costs for 2.8 hectare systems in the USA.
There is value to having national food security and not having to depend on imported food. Ten billion to twenty billion dollars per year in indoor farm subsidies closes the cost gap with open-air farming.
China’s controlled environment system will have a lot of automation and lower construction costs because of the massive scale and lower costs in China.
PNAS – Wheat yield potential in controlled-environment vertical farms
Wheat growing is vastly more land and water-efficient but costs are not yet competitive with open-air farming.
Wheat is the most important food crop worldwide, grown across millions of hectares. Wheat yields in the field are usually low and vary with weather, soil, and crop management practices. We show that yields for wheat grown in indoor vertical farms under optimized growing conditions would be several hundred times higher than yields in the field due to higher yields, several harvests per year, and vertically stacked layers. Wheat grown indoors would use less land than field-grown wheat, be independent of climate, reuse most water, exclude pests and diseases, and have no nutrient losses to the environment. However, given the high energy costs for artificial lighting and capital costs, it is unlikely to be economically competitive with current market prices. Wheat grown on a single hectare of land in a 10-layer indoor vertical facility could produce from 700 ± 40 t/ha (measured) to a maximum of 1,940 ± 230 t/ha (estimated) of grain annually under optimized temperature, intensive artificial light, high CO2 levels, and a maximum attainable harvest index. Such yields would be 220 to 600 times the current world average annual wheat yield of 3.2 t/ha. Independent of climate, season, and region, indoor wheat farming could be environmentally superior, as less land area is needed along with reuse of most water, minimal use of pesticides and herbicides, and no nutrient losses.
Meat production could also be brought under climate control. The feed for cows, pigs, chicken and fish could be either brought into greenhouses or converted to insects. Insect feed can be twenty to one hundred times more space and water-efficient.
Meat can be converted into cell-based production in large vats. This would be similar to the industrial production of beer.
There would be zero risk of mass starvation caused by temperature or drought-induced crop failure.
There may not be a need to bring all crops indoors. But if China brings half of all of their crops indoors in five years it clearly shows that civilization can bring all crops and farming indoors at any time. The cost as I have shown is less than 0.5% of global GDP for the crops and a few percent to deal with the meat and feed as well.
It is likely only truly economical (even with China’s mass production) to bring vegetable and fruit farming indoors. If China has indoor vegetable and fruit production at $1 per pound then other countries could follow at different levels based upon how cost-competitive indoor farming is against open-air farming for a particular crop. There is also the question if people will pay more for greenhouse crops. Greenhouses allow for year-round crop production. This means consistent prices and availability for fruits and vegetable year round. It also means indoor farms can be inside of cities for fruit and vegetables that are fresh from the tree and vine. The greenhouse crops would also be mostly or completely free of pesticides. Indoor farming share will grow as efficiency and costs are improved.
I think 20-60% of all crops (mainly higher-value fruits and vegetables) globally will go indoors by 2030 and gradually more as indoor becomes a lower cost and superior product to outdoor farming. Greenhouse farmed fruits and vegetables can have a higher quality versus outdoor grown fruits and vegetables.
Some of the advantages of protected culture greenhouse crops are:
Season extension is just one of the advantages gained from greenhouse growing. Protected crops are less apt to be damaged by wind, rain, and hail so the percentage of marketable products is higher. Yield is often higher as well, if you can provide optimum growing conditions for each crop. Greenhouses protect crops from many diseases, particularly those that are soilborne and splash onto plants in the rain. And greenhouse crops may be protected from common field pests. Of course, greenhouse crops have their own particular problems such as foliar disease, aphids, and whiteflies, so vigilance is still required.
SOURCES- Alibaba, PNAS, agfunder news
How Can The World Benefit From Indoor Vertical Farming
Due to urbanization and enormous industrial development, we are losing our natural sources and farming land each year, bit by bit
by Bhok Thompson in Lifestyle
Have you ever sat down and wondered about the uncertainty of our future? With the world population growing and expanding each day, will we reach a point where we might face a scarcity of food? It has been speculated that three decades later, our world population will reach nearly 10 billion people. And feeding such a massive population is nothing less than a challenge.
Due to urbanization and enormous industrial development, we are losing our natural sources and farming land each year, bit by bit. As a matter of fact, according to a report published in 2015, our planet has lost 1/3 of its cultivable lands, which is quite alarming given the fact that our population is expanding each year.
That said, nothing can be predicted for sure about how much more arable land humanity will lose in the upcoming decades. Nonetheless, food demands will continue to grow proportionally to the growth of the world population. Many believe that vertical farming and indoor vertical farming software installation is the ultimate solution to our potential world hunger problems.
Read on to find out more about vertical farming and the future of our agriculture. Let us cover the basics first:
What Exactly is Vertical Farming?
You might have already figured out that vertical farming is all about producing and cultivating food on specifically vertically inclined surfaces. Instead of the traditional food cultivation methods of farming veggies and other food items on horizontally inclined surfaces, such as greenhouses and agriculture fields, the method of vertical farming intends to produce foods in vertically established layers with structures resembling a skyscraper. Nonetheless, the structures can also identify a shipping container and a warehouse.
For the effective production of foods in the vertical farming method, the integration of technology is mandatory. This is where the indoor vertical farming software comes in. With the integration of CEA (Controlled Environment Agriculture) technology, indoor vertical farming has been made possible.
The integration of the technology includes induced control of humidity, light, climate, temperature, and artificial gases that contribute to the possibility of growing indoor foods, herbs, and medicine. In this way, you can think of vertical farming in terms of a greenhouse where natural sunlight is induced with the help of metal reflectors and artificial light sources.
Nonetheless, indoor vertical farming’s primary goal is the optimization of food production within a limited space.
Why The World Needs Indoor Vertical Farming Software?
Vertical farming is the ultimate solution that can save us from hunger and starvation in the long run. Vertical farming allows more output and food production while using a small area of cultivation. The below-given list includes the essential benefits of vertical farming:
Preparing for The Future
As we mentioned earlier, four decades from now, our world population is more likely to expand to 10 billion. Not to mention that nearly 70% of the world population is expected to live in industrialized and urbanized areas, which will also peak food demand. The proficient use of vertical farming will prepare us for any upcoming challenges related to food scarcity.
All-Season Crop Production
Vertical farming enables us to produce more crops while using the limited square footage of the production area. If we were to make a rough estimation about the potential crop production, you could think of it in the following ways. For example, one acre of the indoor vertical farming area will allow you to produce crops worth four to six acres of outdoor capacity. Suppose you are running an indoor vertical farm inside a 30-story skyscraper that includes a basal area of five acres. With the integration of vertical farming software, you will produce food/ crops worth 2500 acres.
Unaffected by Weather and Climate Issues
Amongst the top benefits of indoor vertical farming is that this farming method is explicitly unaffected by unfavorable outside temperatures and weather conditions. Since everything is controlled and monitored inside, the crops and foods cultivated with indoor vertical farming are least affected by natural calamities. That said, indoor vertical farming allows you to produce food throughout the year without worrying about favorable weather conditions.
Indoor vertical farming is also good for biodiversity. This method is essentially environment friendly and exposes farmers to lesser risks and diseases.
Expanding Controlled Environment Agriculture Beyond 'The Big 4'
Greenhouses, vertical farms, and hybrid systems (collectively known as controlled environment agriculture or CEA) continue to attract investment at a much greater scale than in previous decades
By PETER TASGAL
March 29, 2021
Greenhouses, vertical farms, and hybrid systems (collectively known as controlled environment agriculture or CEA) continue to attract investment at a much greater scale than in previous decades. In each of the past five years, there have been multiple nine-figure capital raises. Capital has been deployed across farm types:
Large-scale greenhouses (e.g., AppHarvest, Mastronardi Produce),
Regional greenhouses (e.g., Gotham Greens, Bright Farms),
Localized vertical farms (e.g., InFarm – Berlin, Kalera).
Sources of funding have expanded from almost exclusively highly-specialized private equity investors to include public equity, mezzanine debt and even commercial banks. Within these funding sources, the breadth of investors has expanded beyond agriculture-focused investors to more mainstream investors, especially those with an interest in Environmental, Social and Corporate Governance (ESG) investing.
More from The Packer: Deep dive on the economics of greenhouse growing
Despite all of the investment, the vast majority of produce grown in CEA’s across North America consists of tomatoes, cucumbers, peppers, and lettuce, and leafy greens (“The Big 4”). Most of the lettuce and leafy greens are coming from CEA’s in the U.S. In Canada, The Ontario Greenhouse Vegetable Growers include 220 members producing tomatoes, cucumbers, and peppers on over 3,000 acres of greenhouse.
In my opinion, the next leap for the industry will be expanding the breadth of products. Specifically, focusing on products the taste of which is highly important to the consumer. A strawberry, for example, is a more important purchasing decision to the average consumer compared to lettuce. Lettuce is much more likely to be eaten as part of a salad along with a variety of other ingredients. Today, you can buy at mainstream retail locations a greenhouse-grown strawberry likely grown by Mucci Farms in Ontario or Mastronardi’s Green Empire Farms in New York.
Consumer demand will continue to drive product expansion. Meeting that demand will be possible through further investment in the CEA space. Although investment has been growing, it has not met the levels of other industries where many billions of dollars have been invested on an annual basis. Investment levels in CEA are likely to become far greater over the near future as some of the largest investors in the world are focused on investments that meet and exceed ESG standards.
More from The Packer: On tour with AeroFarms
Efficient vertical farms and greenhouses meet and exceed ESG standards. The farms are closed-loop systems where everything that goes into the farm is contained and recycled. Additionally, as the environment is fully controlled, only the precise amounts of inputs are added so as to limit excess waste. Lastly, a controlled environment allows for plants to grow without chemicals and pesticides.
Combining consumers’ desire for more locally-grown produce throughout all seasons of the year with increased investor appetite should drive great growth across the industry for years to come. I believe the biggest leap will be new and exciting products coming from indoor farms. This will all be enhanced with incremental improvements in product taste, farm efficiency, and additional varieties within The Big 4 and other products to come.
Peter Tasgal is a Boston-area food agriculture consultant focused on controlled environment agriculture.
Evaluating Real Estate For Indoor Agriculture
Several factors need to be evaluated before purchasing or leasing a piece of real estate for CEA. Will you build new construction or rehabilitate a vacant building? Are you building a large-scale greenhouse or a small, urban vertical farm?
March 17, 2021
Traditionally, buyers of agricultural real estate have focused on rural land where primary considerations for their farm include things such as soil quality, annual rainfall amounts, and adequate drainage. Increasingly, however, agriculture start-ups are moving indoors. Compared to field-based agriculture, indoor farming allows for more crop cycles, less water usage, and the farms can be located closer to the consumer. The considerations for an indoor, or controlled environment agriculture (CEA) operation are considerably different than for outdoor farms.
Assessing Potential Real Estate for CEA
Several factors need to be evaluated before purchasing or leasing a piece of real estate for CEA. Will you build new construction or rehabilitate a vacant building? Are you building a large-scale greenhouse or a small, urban vertical farm?
Environment
Weather and terrain are important for natural light greenhouse projects. The primary limiting factor to crop production in a greenhouse is low light intensity during the winter so consult with an Ag-extension service or other resource to get that information for a proposed location. Adequate acreage is a must for not only the greenhouses themselves but, also shipping and receiving space, a retention pond (if needed), and potentially even worker housing.
Spacing
For a vertical or urban farm in an enclosed building, important factors to consider include adequate square footage to allow for proper spacing between growing systems and enough room to move the towers (if mobile) for cleaning or maintenance. Additionally, a building should have a sufficient water supply and potentially drainage, a robust HVAC system and humidity controls, and a ceiling which is high enough for the growing towers. Although indoor farms using high efficiency LED lighting, these systems, combined with pumps, humidifiers, and HVACs can use significant amounts of electricity, a developer should carefully and conservatively estimate those costs prior to negotiating those terms with a landlord or electric company. Finally, the farm should be in close enough proximity to allow for routine delivery to local customers, be they restaurants, groceries, farmers markets, or Community Supported Agriculture distributors.
Labor
In both types of farms, labor availability and cost is a critically important consideration. The cost of wages for urban farms, even for unskilled workers, will likely be higher than that of rural areas. And in the case of any real estate development, ensure prior coordination with relevant agencies has been done on permits, licenses, and zoning regulations prior to signing any leases or closing on a land contract. Prior to starting a search for a CEA project, it’s wise to seek expert help from outside consultants who can save an indoor farm developer time, money, and aggravation.
Tags real estate, indoor agriculture, cea
FRANCE: Jungle Says It’s Cracked How To Make Vertical Farms Profitable
“No matter how good your product is, if the price is higher than the alternative, then you’re dead.”
“No Matter How Good Your Product Is,
If The Price Is Higher Than The Alternative,
Then You’re Dead.”
BY FREYA PRATTY
22 MARCH 2021
Jungle, a French vertical farming company that says it can produce ten to 30 times more food than traditional greenhouses, has raised €42m in new funding.
The company also says its focus on large-scale farms will help it overcome one of the biggest challenges facing vertical farming: how to make a profit.
Jungle’s new funding, €7m of which is in equity and €35m of which is debt financing, comes from Founders Future, a French investment firm focused on impact startups. Jungle is the firm’s first investment.
The company’s funding comes as the wider industry continues to grow fast. It was worth $2.2bn in 2018 but is expected to reach $12.8bn by 2026. Investor appetite is clearly there: vertical farming giant Infarm raised $170m at the end of last year.
Jungle is building a 5,500m2 farm 80km from Paris, where crops will grow on stacked platforms. The site is already partly operational and the company has secured contracts with French supermarkets Monoprix and Intermarche.
At present, it’s growing a mixture of aromatic herbs, greens and, unlike other vertical farms, flowers. It’ll be fully operational by the end of 2021.
Less pesticides, more local and a greater yield
Gilles Dreyfus, cofounder of Jungle.
“We don’t claim to be instigating a revolution, we are part of an equation that wants to be a solution,” explains Gilles Dreyfus, who cofounded Jungle in 2015.
For Dreyfus, vertical farming has several advantages. Crops can be grown close to cities, where the majority of consumers are, thereby reducing the environmental costs of transit.
Plants can also be grown on more frequent cycles than on traditional farms because they’re not seasonally dependent, and they’re also grown without using pesticides.
“Our most popular product, Green Basil, gives 14 harvests a year in the vertical farm, compared to 3 or 4 in the South of France, where the crop grows best outdoors.”
National food sovereignty
Being able to grow crops out of season means vertical farming can help countries achieve better food sovereignty, Dreyfus says.
“We have to go further and further from the country to get crops when they’re out of season,” he says. “Brexit import taxes on food have shown the complicated situations this can lead to.”
“If the price is higher, you’re dead”
Despite the benefits, vertical farming has often struggled with how to make a profit. “Having a viable financial model and an efficient farm is the main hurdle for vertical farming,” Dreyfus says.
“No matter how good your product is, if the price is higher than the alternative, then you’re dead.”
The company believes that bigger farms is the answer.
German company Infarm, which is aiming at profitability by 2023, places microunits into supermarkets. Jungle, which is aiming at profitability in 18 months time, will focus on large-scale production facilities that then supply a whole area.
“Price depends on scale and we’re not aiming for small-scale farms, we’re aiming for less farms but a lot bigger. If you activate the economies of scale you can get a very reasonable product,” he says.
The company’s aiming to sell food at 5% more than the cost of conventional alternatives, but at 20% less than organic foods grown on farms.
For Valentine Baudouin, partner at Founders Future which has invested in Jungle, the focus on large-scale farms is the key to profitability, and what makes Jungle stand out.
“They’ve answered the economic question of vertical farming, which is very important because you have many similar enterprises that haven’t done so.”
Jungle’s vertical farm warehouse.
Beyond salad?
A criticism often leveled at the vertical farming industry is whether it can grow beyond just salad leaves and herbs.
Unlike other farms, Jungle also grows flowers for the perfume industry, but Dreyfus says the other crops its working on, including cherry tomatoes and mushrooms, won’t be in supermarkets until 2023.
“You can grow virtually anything you want, except truffles — which is a real shame actually,” says Dreyfus. “But the question shouldn’t be, can we grow it, it should be, do we have the financial model to make it work?”
Jungle’s currently got a team of 25 people based in France, but will use the new funding to double its workforce by 2022. It also plans to open two new large-scale farms in France, including one in the south that’ll be twice as big as its first site.
Freya Pratty is Sifted’s news reporter. She tweets from @FPratty
GrowGroup IFS Introduces Their Own Grow Container Systems GCS 40HQ
The GCS 40HQ is available in different models. All models are in a 40ft container and includes LED technology, climate computers with remote control, and extensive control on water, temperature, humidity, CO2, and lighting
March 12, 2021
GrowGroup IFS Introduces Their Own Grow Container Systems GCS 40HQ
GrowGroup IFS introduces the GrowGroup Grow Container Systems “GCS 40HQ” for small container cluster farms, research & development, schools & universities, and pilots for new indoor farms. With this new solution now GrowGroup IFS can support also small farms in an accessible way with their unique and full approach including support with the operation through their partners GaaS Wageningen and Hoogendoorn Growth Management.
Grow Container Systems “GCS 40HQ”
The GCS 40HQ is available in different models. All models are in a 40ft container and includes LED technology, climate computers with remote control, and extensive control on water, temperature, humidity, CO2, and lighting. The basic model has a very low entry-level and is upgradeable on different levels. The client can choose for example for an upgrade to the highest quality of climate computers of partner Hoogendoorn Growth Management or the highest quality of LED technology of Signify. The client can even choose for the support with the operation through partner GaaS Wageningen.
“We support the bigger farmers with our unique and full approach on indoor farming for some time already but noticed also that smaller farmers, in particular, have a great need for this. That’s why we launch our own GCS solution right now, so all farmers can use the newest technology of indoor farming for year-round cultivation all over the world”, John Breedveld, CEO GrowGroup IFS.
GaaS Wageningen
Partner GaaS Wageningen from the Netherlands has access to a pool of more than 200 agricultural specialists. Its core business is supporting the operation of high-tech indoor farms from the small ones as the container farms up to the large ones as the big indoor factories. They have high knowledge of indoor farming and sharing their knowledge with the farmers by supporting and training them but also with schools and universities.