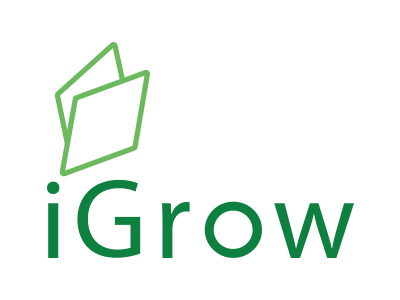
Welcome to iGrow News, Your Source for the World of Indoor Vertical Farming
KSA-Based Natufia Makes It Easy To Grow Food In Your Home With Its Hydroponic Tech
Founded in 2015 by Gregory Lu and Nadim Taoubi, Natufia is a multi-awarded research lab specializing in hydroponic kitchen appliances. With its fully integrated and automated indoor smart hydroponic kitchen garden, especially created for restaurant kitchens and households, Natufia enables people to grow an assortment of the freshest plants, vegetables, flowers and herbs all year round right in the heart of their kitchen.
By Pamella de Leon
August 10, 2021
Can you imagine growing your own salad in your kitchen? This is what KSA-based enterprise Natufia is daring to achieve. Founded in 2015 by Gregory Lu and Nadim Taoubi, Natufia is a multi-awarded research lab specializing in hydroponic kitchen appliances. With its fully integrated and automated indoor smart hydroponic kitchen garden, especially created for restaurant kitchens and households, Natufia enables people to grow an assortment of the freshest plants, vegetables, flowers and herbs all year round right in the heart of their kitchen.
Offering a holistic solution to healthy living, this smart garden nestled in your kitchen provides the optimal combination of water, lighting, nutrients, and even music (as the team’s research found that it helps to stimulate more growth). The fridge-sized appliance is easy to use: seed pods -which can be compared to the size of Nespresso capsules- are placed in the nursery drawer where it will grow for about 10 days, after which, the pod will be moved to grow in another cabinet. After 20-30 days, you are ready to harvest, and every 3-4 months, you just need to refill the nutrients. All other steps are automated as the Natufia smart kitchen garden creates the perfect environment needed to grow plants. It can grow 32 different types of plants, such as basil, lettuces, cilantro, kale, dill, cherry tomatoes, mint, and more, simultaneously, producing 1-2 plants per day.
Gregory Lu, co-founder and CEO, explains how the startups aims to solve the huge multifaceted problem in the food industry. “The plants that will grow in your kitchen are free of pesticides, preservatives, and because of [its] freshness, they will give you up to 400% more vitamins.” He adds, “Because they are grown right where they are consumed, you will rediscover a wider biodiversity, true original taste of the greens vegetable, whilst they are being accessible anywhere and from the proximity of one’s kitchen." The startup aims to minimize the prevalent environmental impact by reducing food waste, packaging, pollution, and food miles. It also addresses the gaps of food security and traceability awareness, a prevalent issue for the region’s food security sector. “We are disrupting the way people relate to their food and reinventing the consumer meal journey by allowing communities to take control of their food- produce where it is consumed," Lu says, explaining the startup’s mission. "By using Natufia, we encourage people to change their food habits by consuming a diet rich in vitamins and nutrition-dense vegetables and greens, improving their health and helping our planet.”
Source: Natufia
For Lu, taking on the path to entrepreneurship was inevitable, he says. “I have been an entrepreneur from a young age, so that’s something that’s always been inside of me.” Beginning his career in the property development and investment sector, the entrepreneur accumulated over 25 years of experience in the real estate sector and decided to diversify his businesses by diving into the food industry. Upon buying an olive plantation in Sicily to produce olive and tomato sauce, Lu faced the common issues of needing to use pesticides and fertilizers, which contradicted his views on healthy food and showcased the significance of the organic food industry. “I felt people needed to experience what I experienced in these hills of Sicily- the freshness, the connection of growing your own food and the quality,” adds Lu. “My real estate background also thrusted me into following up the idea. If people could grow food in their own homes, offices, schools, or hotels, all year around having fresh quality food easily accessible, then the world would be a much better place.” Lu is joined by co-founder and COO Nadim Taoubi, whose background includes advising tech companies at Deloitte and LD&A, as well as founding his own Estonia-based e-commerce platform, Ooolala which has been sold to an undisclosed buyer in 2016.
Originally launched in Estonia, the co-founders bootstrapped the concept and built a basic prototype to show to a few European fairs and evaluate initial reception. It kickstarted the first phase of their journey, which was focused on developing the technology: “It took us years to do that, but we accumulated over 20 patents.” This was followed by proof of concept and field-testing phase, wherein the duo invested in R&D and grew its team. “We have sold dozens of our Natufia [product] to the US, Europe and the Middle East to receive feedback and analyze large amounts of data.” As the company grew, the co-founders looked outside Estonia for investment partners. In 2018, the startup was accepted into the Techstars Dubai accelerator program, held in partnership with GINCO Investments. This proved to be an advantageous step, as the startup was able to raise US$1.2 million in a seed funding round, led by Butterfly Ventures, Techstars, and GINCO Investments, as well as several angel investors from US, Europe and the Middle East. The capital was set to pave its expansion plans to Europe and the US. “We spent a lot in Dubai with Techstars and understood that the region is a great market for Natufia,” says Lu. Later on, the CEO met representatives from the King Abdullah University of Science and Technology (KAUST) at a conference in London. After months of discussions, KAUST announced it would lead a $3.5 million investment in a Series A funding round, though its venture capital investment arm KAUST Innovation Fund, with Butterfly Ventures also participating in the round. This puts Natufia’s total funding to $4.7 million, with previous investors Butterfly Ventures, Techstars and GINCO Investments, remaining as minority shareholders.
As part of the new capital infusion, the startup is also relocating to Saudi Arabia, basing itself at the KAUST Research and Technology Park (KRTP) to help grow its R&D capabilities. Lu explains, “We felt it would be a huge opportunity being in the heart of the region to develop the market, but also being at KAUST on campus could give us the possibility to keep working on our technology to make it even better and advanced.” Lu commends KAUST’s distinctive infrastructure and tools, which can be greatly beneficial for the startup’s innovative solutions. “I give you an example: for us, it is very important to test the quality of our plants -the vitamins, nutrients, minerals, etc. In Estonia, it was a long and complex process. We had to reserve the test well in advance, transport the plants, which come with a lot of paperwork, expensive fees and long waiting times, before getting the result without being sure it was fully accurate.” He continues, “Today, at KAUST, we simply have to go across the street and get the result the same day. It means our research is more efficient. The other major factor is the community we continuously interact with, exchanging ideas with professors on pertinent topics like sensors, biology, botany, technology and so on- and that’s extremely enriching for new ideas and technology developments. We might even use KAUST technology in our future developments.”
Natufia botany lab
Besides furthering its R&D development, Lu is also keen to help create job opportunities and align themselves with Saudi’s Vision 2030, which inevitably establish the Kingdom’s status as a top choice for businesses in the Middle East. “And we want to be a part of that,” Lu points out. At the moment, Lu notes that it’s all about the production of the newly upgraded Natufia smart kitchen garden model in Saudi and scaling its distribution locally and internationally. Next up, the team hopes to move towards mass production and develop new Natufia models. Having partnered with KAUST and Jumeirah Group, today, the startup now consists of a team of 12 people and is focused on its prime model, the Natufia smart kitchen garden, retailed at $7,955 and is available worldwide. With distributors in the USA, Europe, Australia and Saudi Arabia, the team have more lined up for next year- a model for those keen on a smaller budget, and another model to cater for commercial settings. On facing hurdles, Lu comments, “I personally work and build companies in different countries and contrary to what people might think, a lot of things are online and work smoothly. The biggest challenge was to get the residency for the core team who were not Saudi native and a bank setup for the company. It takes perseverance and patience.” However, the key benefit that the co-founders found (“and a pleasant surprise”) was the quality of local talent they found to work at Natufia, “The young generation is very well-educated, studied abroad and eager to work in the type of environment that Natufia creates- high tech, fast-moving and with big growth potential.”
As newcomers join the industry, Lu is focused on its USP: “Compared to our competition, we offer automation, quality and design. Our robust technology runs the whole process automatically and its high-end design that can be integrated into any kitchen design." And as for the future, Lu states it’s just the beginning of agritech. “We are just scratching the surface, because in the last 60 years, the industry was only focusing on quantity, price, shelf life and transportability. Since organic products came on the scene, people started to understand the importance of food quality, we opened up a new horizon. Freshness, taste and nutrient value is something that [people] will follow.” He dreams of having Natufia’s product everywhere, “We want to see Natufia in every home, in every school, in every office, hospital, airport. We want people to be able to experience the real taste of greens and vegetables and connect with nature on a daily basis from everywhere they are.”
Lead Photo: Gregory Lu, co-founder and CEO, Natufia
Technology Is Shaping The Future of Food But Practices Rooted In Tradition Could Still Have A Role To Play
Its executive summary said the food we consume — and the way we produce it — was “doing terrible damage to our planet and to our health.”
By Anmar Frangoul
August 6, 2021
From oranges and lemons grown in Spain to fish caught in the wilds of the Atlantic, many are spoiled for choice when it comes to picking the ingredients that go on our plate.
Yet, as concerns about the environment and sustainability mount, discussions about how — and where — we grow our food have become increasingly pressing.
Last month, the debate made headlines in the U.K. when the second part of The National Food Strategy, an independent review commissioned by the U.K. government, was released.
The wide-ranging report was headed up by restaurateur and entrepreneur Henry Dimbleby and mainly focused on England’s food system. It came to some sobering conclusions.
Its executive summary said the food we consume — and the way we produce it — was “doing terrible damage to our planet and to our health.”
The publication said the global food system was “the single biggest contributor to biodiversity loss, deforestation, drought, freshwater pollution and the collapse of aquatic wildlife.” It was also, the report claimed, “the second-biggest contributor to climate change, after the energy industry.”
Dimbleby’s report is one example of how the alarm is being sounded when it comes to food systems, a term the Food and Agriculture Organization of the UN says encompasses everything from production and processing to distribution, consumption and disposal.
According to the FAO, food systems consume 30% of the planet’s available energy. It adds that “modern food systems are heavily dependent on fossil fuels.”
All the above certainly provides food for thought. Below, CNBC’s Sustainable Future takes a look at some of the ideas and concepts that could change the way we think about agriculture.
Growing in cities
Around the world, a number of interesting ideas and techniques related to urban food production are beginning to gain traction and generate interest, albeit on a far smaller scale compared to more established methods.
Take hydroponics, which the Royal Horticultural Society describes as “the science of growing plants without using soil, by feeding them on mineral nutrient salts dissolved in water.”
In London, firms like Growing Underground are using LED technology and hydroponic systems to produce greens 33-meters below the surface. The company says its crops are grown throughout the year in a pesticide free, controlled environment using renewable energy.
With a focus on the “hyper-local”, Growing Underground claims its leaves “can be in your kitchen within 4 hours of being picked and packed.”
Another business attempting to make its mark in the sector is Crate to Plate, whose operations are centered around growing lettuces, herbs and leafy greens vertically. The process takes place in containers that are 40 feet long, 8 feet wide and 8.5 feet tall.
Like Growing Underground, Crate to Plate’s facilities are based in London and use hydroponics. A key idea behind the business is that, by growing vertically, space can be maximized and resource use minimized.
On the tech front, everything from humidity and temperature to water delivery and air flow is monitored and regulated. Speed is also crucial to the company’s business model.
“We aim to deliver everything that we harvest in under 24 hours,” Sebastien Sainsbury, the company’s CEO, told CNBC recently.
“The restaurants tend to get it within 12, the retailers get it within 18 and the home delivery is guaranteed within 24 hours,” he said, explaining that deliveries were made using electric vehicles. “All the energy that the farms consume is renewable.”
Grow your own
While there is a sense of excitement regarding the potential of tech-driven, soilless operations such as the ones above, there’s also an argument to be had for going back to basics.
In the U.K., where a large chunk of the population have been working from home due to the coronavirus pandemic, the popularity of allotments — pockets of land that are leased out and used to grow plants, fruits and vegetables — appears to have increased.
In September 2020 the Association for Public Service Excellence carried out an online survey of local authorities in the U.K. Among other things it asked respondents if, as a result of Covid-19, they had “experienced a noticeable increase in demand” for allotment plots. Nearly 90% said they had.
“This alone shows the public value and desire to reconnect with nature through the ownership of an allotment plot,” the APSE said. “It may also reflect the renewed interest in the public being more self-sustainable, using allotments to grow their own fruit and vegetables.”
In comments sent to CNBC via email, a spokesperson for the National Allotment Society said renting an allotment offered plot holders “the opportunity to take healthy exercise, relax, have contact with nature, and grow their own seasonal food.”
The NAS was of the belief that British allotments supported “public health, enhance social cohesion and could make a significant contribution to food security,” the spokesperson said.
A broad church
Nicole Kennard is a PhD researcher at the University of Sheffield’s Grantham Centre for Sustainable Futures.
In a phone interview with CNBC, she noted how the term “urban agriculture” could refer to everything from allotments and home gardens to community gardens and urban farms.
“Obviously, not all food is going to be produced by urban agriculture, but it can play a big role in feeding local communities,” she said.
There were other positives, too, including flood and heat mitigation. “It’s … all those benefits that come with having green spaces in general but then there’s the added plus, [which] is that you’re producing food for local consumption.”
On urban farming specifically, Kennard said it provided “the opportunity to make a localized food system” that could be supported by consumers.
“You can support farms that you know, farmers that you know, that are also doing things that contribute to your community,” she said, acknowledging that these types of relationships could also be forged with other types of farms.
Looking ahead
Discussions about how and where we produce food are set to continue for a long time to come as businesses, governments and citizens try to find ways to create a sustainable system that meets the needs of everyone.
It’s perhaps no surprise then that some of the topics covered above are starting to generate interest among the investment community.
Speaking to CNBC’s “Squawk Box Europe” in June, Morgan Stanley’s global head of sustainability research, Jessica Alsford, highlighted this shift.
“There’s certainly an argument for looking beyond the most obvious … ways to play the green theme, as you say, further down the value and the supply chain,” she said.
“I would say as well though, you need to remember that sustainability covers a number of different topics,” Alsford said. “And we’ve been getting a lot of questions from investors that want to branch out beyond the pure green theme and look at connected topics like the future of food, for example, or biodiversity.”
For Crate to Plate’s Sainsbury, knowledge sharing and collaboration will most likely have a big role to play going forward. In his interview with CNBC, he emphasized the importance of “coexisting with existing farming traditions.”
“Oddly enough, we’ve had farmers come and visit the site because farmers are quite interested in installing this kind of technology … in their farm yards … because it can supplement their income.”
“We’re not here to compete with farmers, take business away from farmers. We want to supplement what farmers grow.”
Lead Photo: Fruit and vegetable allotments on the outskirts of Henley-on-Thames, England.
AeroFarms and Nokia Unveil Partnership for Next Generation AI-Enabled Plant Vision Technology
AeroFarms and Nokia Bell Labs today unveiled a groundbreaking multi-year partnership to combine their expertise and expand their joint capabilities in cutting-edge networking, autonomous systems, and integrated machine vision and machine learning technologies to identify and track plant interactions at the most advanced levels.
August 5, 2021
NEWARK, N.J.--(BUSINESS WIRE)--AeroFarms and Nokia Bell Labs today unveiled a groundbreaking multi-year partnership to combine their expertise and expand their joint capabilities in cutting-edge networking, autonomous systems, and integrated machine vision and machine learning technologies to identify and track plant interactions at the most advanced levels.
As part of this partnership, AeroFarms, a Certified B Corporation and global leader in indoor vertical farming, contributes its commercial growing expertise, comprehensive environmental controls, an agriculture-focused data platform, and machine vision core foundation. Nokia Bell Labs, the world-renowned industrial research arm of Nokia, contributes its groundbreaking autonomous drone control and orchestration systems, private wireless networks, robust image and sensor data pipelines, and innovative artificial intelligence (AI) enabled mobile sensor technologies. This combination of innovative technologies allows AeroFarms to reach the next level of imaging insights that further enhance its capabilities as an industry leading operator of world-class, fully-connected smart vertical farms that grow the highest quality plants all year round.
AeroFarms and Nokia Bell Labs have been working together since 2020 and have reached an important milestone of achieving a proof of concept for this state-of-the-art integrated system and testing the technologies with AeroFarms’ current commercial crop varieties. Together, they are now ready to scale this system to all of AeroFarms’ crops and future indoor vertical farms, including the next ones in Danville, Virginia and Abu Dhabi, UAE.
The integration of Nokia Bell Labs’ AI-enabled drone-based sensors and advanced machine learning, computer vision and data analytics technologies with AeroFarms’ existing machine vision tools enhances and elevates AeroFarms’ position as an agriculture platform and capabilities organization dedicated to solving food and agriculture supply chain challenges.
David Rosenberg, CEO at AeroFarms, said: “With Nokia Bell Labs, we have developed the next-generation system that can image every plant every day in a cost-effective way at scale. This level of detailed imaging and insights helps us be better farmers by monitoring our plant biology dynamically and allowing us to course correct as needed to ensure the highest level of quality all year round. When I watch the drones autonomously imaging our plants, I am blown away by how this truly represents the power of harnessing leading-edge technologies and bringing brilliant problem solvers together from diverse groups to grow the best plants possible.”
Roger Buelow, CTO at AeroFarms, said: “AeroFarms’ expert team of plant scientists and engineers have been working together for two years with Nokia Bell Labs’ top researchers and engineers to train these complex learning systems with a nuanced understanding of plant biology. We have created a cross-disciplinary understanding at an industrial scale to develop the latest imaging technology to help accelerate our ability to introduce new crops and ensure the highest quality for our commercial operations.”
Nokia Bell Labs’ machine vision technology has enabled the most precise data capture yet, down to the level of individual plants, using leaf size segmentation, quantification, and pixel-based scanning to identify consistency and variation. Going beyond what even the human eye can perceive, this state-of-the art imaging technology enables the gathering of immense insights about a plant including its leaf size, stem length, coloration, curvature, spotting, and tearing. The end-to-end system is flexible and robust, built to take advantage of Nokia’s industry-leading 5G private wireless network with cloud processing technology, designed for low latency and high privacy in an on-premises network. It also provides intelligent industrial analytics capabilities as an integrated service that can be deployed quickly and efficiently anywhere.
Thierry Klein, VP, Integrated Solutions and Experiences Research Lab at Nokia, said: “Nokia Bell Labs is driven to solve hard and impactful problems, and together with AeroFarms, we are building the ability to see and identify plant interactions at unprecedented levels. The fundamental technologies of this partnership are our strength, and vertical farming is just the beginning. With the AeroFarms platform, we are exploring the power of network driven intelligence for industrial outcomes. These capabilities can expand into a multitude of indoor industrial operations, including logistics, warehousing, distribution hubs, and manufacturing.”
The multi-year partnership between AeroFarms and Nokia is anchored on shared values as mission-driven companies with the vision to scale technologies for the greater good. AeroFarms’ vertical farming platform is more sustainable than traditional farming with up to 390 times greater productivity per square foot annually, while using up to 95% less water and zero pesticides. In addition, vertical farming provides local food options for communities, reducing the environmental impact of trucking and shipping produce long distances and helping combat food waste.
Additional resources
AeroFarms website
Nokia Bell Labs website
About Nokia
At Nokia, we create technology that helps the world act together. As a trusted partner for critical networks, we are committed to innovation and technology leadership across mobile, fixed and cloud networks. We create value with intellectual property and long-term research, led by the award-winning Nokia Bell Labs. Adhering to the highest standards of integrity and security, we help build the capabilities needed for a more productive, sustainable and inclusive world.
About AeroFarms
Since 2004, AeroFarms has been leading the way for indoor vertical farming and championing transformational innovation for agriculture. On a mission to grow the best plants possible for the betterment of humanity, AeroFarms is a Certified B Corporation with global headquarters in Newark, New Jersey. Named one of the World’s Most Innovative Companies by Fast Company two years in a row and one of TIME’s Best Inventions in Food, AeroFarms patented, award-winning indoor vertical farming technology provides the perfect conditions for healthy plants to thrive, taking agriculture to a new level of precision, food safety, and productivity while using up to 95% less water and no pesticides ever versus traditional field farming. AeroFarms enables local production to safely grow all year round, using vertical farming for elevated flavor. In addition, through its proprietary growing technology platform, AeroFarms has grown over 550 varieties and has developed multi-year strategic partnerships ranging from government to major Fortune 500 companies to help uniquely solve agriculture supply chain needs. For additional information, visit: https://aerofarms.com/.
On March 26, 2021, AeroFarms announced a definitive business combination agreement with Spring Valley Acquisition Corp. (Nasdaq: SV). Upon the closing of the business combination, AeroFarms will become publicly traded on Nasdaq under the new ticker symbol "ARFM". Additional information about the transaction can be viewed here: https://aerofarms.com/investors/.
No Offer or Solicitation
This press release does not constitute an offer to sell or a solicitation of an offer to buy, or the solicitation of any vote or approval in any jurisdiction in connection with a proposed potential business combination among Spring Valley and AeroFarms or any related transactions, nor shall there be any sale, issuance or transfer of securities in any jurisdiction where, or to any person to whom, such offer, solicitation or sale may be unlawful. Any offering of securities or solicitation of votes regarding the proposed transaction will be made only by means of a proxy statement/prospectus that complies with applicable rules and regulations promulgated under the Securities Act of 1933, as amended (the “Securities Act”), and Securities Exchange Act of 1934, as amended, or pursuant to an exemption from the Securities Act or in a transaction not subject to the registration requirements of the Securities Act.
Forward Looking Statements
Certain statements included in this press release that are not historical facts are forward-looking statements for purposes of the safe harbor provisions under the United States Private Securities Litigation Reform Act of 1995. Forward-looking statements generally are accompanied by words such as “believe,” “may,” “might,” “will,” “estimate,” “continue,” “contemplate,” “anticipate,” “intend,” “expect,” “should,” “would,” “could,” “plan,” “predict,” “project,” “potential,” “seem,” “seek,” “future,” “outlook,” and similar expressions that predict or indicate future events or trends or that are not statements of historical matters. All statements, other than statements of present or historical fact included in this press release, including those regarding the expected benefits of the partnership, improvement of plant yields and quality and Spring Valley’s proposed acquisition of AeroFarms are forward-looking statements. These statements are based on various assumptions, whether or not identified in this press release, and on the current expectations of the respective management of AeroFarms and Spring Valley and are not predictions of actual performance. These forward-looking statements are provided for illustrative purposes only and are not intended to serve as, and must not be relied on as, a guarantee, an assurance, a prediction, or a definitive statement of fact or probability. Actual events and circumstances are difficult or impossible to predict and will differ from assumptions. Many actual events and circumstances are beyond the control of AeroFarms and Spring Valley. These forward-looking statements are subject to a number of risks and uncertainties, including changes in domestic and foreign business, market, financial, political, and legal conditions; the inability of the parties to successfully or timely consummate the proposed transaction, including the risk that any regulatory approvals are not obtained, are delayed or are subject to unanticipated conditions that could adversely affect the combined company or the expected benefits of the proposed transaction or that the approval of the stockholders of Spring Valley or AeroFarms is not obtained; failure to realize the anticipated benefits of the proposed transaction; risks related to the expansion of AeroFarms’ business and the timing of expected business milestones; the effects of competition on AeroFarms’ business; the ability of Spring Valley or AeroFarms to issue equity or equity-linked securities or obtain debt financing in connection with the proposed transaction or in the future, and those factors discussed in Spring Valley’s Annual Report on Form 10-K, Quarterly Report on Form 10-Q, final prospectus dated November 25, 2020 and definitive proxy statement/prospectus dated July 26, 2021 under the heading “Risk Factors,” and other documents Spring Valley has filed, or will file, with the SEC. If any of these risks materialize or our assumptions prove incorrect, actual results could differ materially from the results implied by these forward-looking statements. There may be additional risks that neither Spring Valley nor AeroFarms presently know, or that Spring Valley nor AeroFarms currently believe are immaterial, that could also cause actual results to differ from those contained in the forward-looking statements. In addition, forward-looking statements reflect Spring Valley’s and AeroFarms’ expectations, plans, or forecasts of future events and views as of the date of this press release. Spring Valley and AeroFarms anticipate that subsequent events and developments will cause Spring Valley’s and AeroFarms’ assessments to change. However, while Spring Valley and AeroFarms may elect to update these forward-looking statements at some point in the future, Spring Valley and AeroFarms specifically disclaim any obligation to do so. These forward-looking statements should not be relied upon as representing Spring Valley’s and AeroFarms’ assessments of any date subsequent to the date of this press release. Accordingly, undue reliance should not be placed upon the forward-looking statements.
Contacts
AeroFarms Contacts
Investor Relations:
Jeff Sonnek
ICR
Jeff.Sonnek@icrinc.com
1-646-277-1263
Media Relations:
Marc Oshima
AeroFarms
MarcOshima@AeroFarms.com
1-917-673-4602
The Art Of Growing Plants Without Soil – Aeroponics, And Hydroponic
Historically, humans have grown crops in soil and they could not think of growing them in the air or a liquid but the advent of modern science and technology has made it possible
Jenna Walter
July 12, 2021
The post-apocalyptic scenario depicted in Wall-E shows that the planet earth had turned into a barren wasteland, although the movie shows a seedling growing out of a shoe, a possible solution would have been the use of aeroponics and hydroponics. These processes of growing plants without soil as a medium are mind-boggling for many.
Historically, humans have grown crops in soil and they could not think of growing them in the air or a liquid but the advent of modern science and technology has made it possible.
Hydroponics:
Hydroponics requires an aqueous solvent to grow a plant. The hydroponic system will control the environmental conditions of the plant. These conditions include the temperature and the pH balance. Simultaneously it also maximizes plants’ exposure to nutrients and water.
Hydroponics has a simple philosophy that is to provide the exact things the plant needs to grow. The administration of nutrient solutions is tailored to the needs of the particular plant being grown. The system will let the researchers control the exact amount of sunlight needed and for how long it is needed. These conditions are customized and controlled to accelerate the growth of the plant. The controlling of these factors helps reduce the chances of diseases or stunted plant growth.
On the contrary, plants that are grown in conventional conditions are more susceptible to growth issues. The soil of these plants can have fungus which can spread to the plants. Conventional plantations are also vulnerable to wildlife. Locusts attacks are also common on crops. They are known to consume whole fields in a day.
The hydroponics system can end the uncertainty that comes with growing plants outdoors. The soil only acts as a barrier for the seed while a hydroponic system allows a plant to grow vigorously.
If you are into trying out hydroponics you can buy a hydroponic garden kit. It will help you grow your favorite plants within your home.
Aeroponics:
Aeroponic systems will use the nutrient-laden mist to provide the plant necessary nourishment. It is based on the above-mentioned hydroponics systems in which the roots are submerged in a soilless growing medium.
The aeroponic eliminates the growing medium, the roots are left mid-air hanging from the pieces of foam stuffed into tiny pots. The roots are sprayed with nutrient-rich mist from time to time using specially designed devices that let you control the amount of mist, its pressure, and direction.
The seeds are planted in the foam stuffed tiny pots. On one side of the seed is light and on the other side is the mist. The foam helps to hold the plant as it grows over time.
The Use Of This Technology In Future
In the future use of these technologies will only increase. Climate change and global warming are making it difficult to grow crops using conventional methods. The earth is becoming barren due to aggressive farming practices.
The only solution left would be to use hydroponics and aeroponics. They offer more control over the growth of the plant. They can help increase crop production and they are safer because they do not use pesticides or insecticides.
There is No Soil. There Is No Growth Period. Just Add Water and Technology.
Inside, nearly £3 million of beefsteak tomatoes grow on 45-foot-high vines without a teaspoon of soil, and their roots are submerged in nutrient-rich rainwater. Other vines hold thousands of small, juicy snack tomatoes with enough pepper to impress Martha Stewart on the board. AppHarvest, a start-up company that harvests its first crop here in January and plans to open 11 more indoor farms in Appalachia by 2025.
Scott Krantz
July 10, 2021
Morehead, Kentucky — In this beautiful town on the edge of the coal country, a high-tech greenhouse large enough to cover 50 soccer fields glows pink and yellow with 30,600 LEDs and high-pressure sodium lamps.
Inside, nearly £3 million of beefsteak tomatoes grow on 45-foot-high vines without a teaspoon of soil, and their roots are submerged in nutrient-rich rainwater. Other vines hold thousands of small, juicy snack tomatoes with enough pepper to impress Martha Stewart on the board. AppHarvest, a start-up company that harvests its first crop here in January and plans to open 11 more indoor farms in Appalachia by 2025.
In a much more industrial environment near the Hackensack River in Kearny, NJ, trays filled with sweet baby butterhead lettuce and sorrel flavored with lemon and green apple are piled up in a windowless warehouse. This is known as vertical farming. Bowery, The largest vertical farming company in the United States, manipulates light, humidity, temperature and other conditions to grow produce and is funded by investors such as: Justin Timberlake, Natalie Portman, chefs Jose Andre and Tom Colicchio.
“If you taste arugula, it’s sold,” said Koricchio, who has turned to people who claim to grow delicious hydroponic produce for years. “It was very spicy and lively and surprised me.”
The two operations use technological advances such as machine learning algorithms, data analysis, and proprietary software systems to create accurate growing conditions and bring out customized flavors and textures from fruits and vegetables in a new generation of hydroponics. It is part of a cultivation farm. And they can do it almost anywhere.
These farms arrive at crucial moments. The country’s strips have withered due to the heat and drought of climate change, partly supported by certain forms of agriculture. Demand for locally sourced foods is higher than ever, and pandemics have shown that many people are not as resilient as their food supply chains may have been.
However, not everyone is participating. These huge farms grow their produce in nutrient-rich water, rather than in healthy soil, which many believe is central to both deliciousness and nutrition. They can be consumed A huge amount of electricity. Their most ardent opponents say that the claims made to hydroponics are misleading and even dangerous.
“At this point, I think the bad guys are winning,” said a Vermont farmer. Real organic project.. “Hydroponics isn’t growing because it produces healthier foods. It’s growing thanks to money. Anyone who sees this as food for people or the environment is lying. I’m just there. “
The jargon of hydroponics is controlled environmental farming, but business people call it indoor farming. What used to be simply called a farm is now called an onshore farm or field farming.
“We have perfected Mother Nature indoors by combining science and technology with agriculture,” said Daniel Malechuk, CEO of. Carrera, A company that sells whole lettuce in plastic clamshells, leaving the roots intact, at about the same price as other washed lettuce.
In March, the company opened a 77,000-square-foot facility south of Atlanta, capable of producing more than 10 million lettuce annually. Similar indoor farms in Houston, Denver, Seattle, Honolulu St. Paul, Minnesota.
According to Malechuk and other executives, the beauty of this process is not limited by the seasons. You can accurately predict the cost and growth period of your crops and build farms wherever people need fresh produce.
“We can grow in Antarctica,” he said. “We can be on the island. We can be on the moon or on the space station.”
It’s easy to imagine. There are new breeds of young farmers on the farm who wear lab coats instead of overalls and prefer computers to tractors.
Today, more than 2,300 farms growing hydroponic crops in the United States make up just part of the country’s $ 5.2 billion fruit and vegetable market. But investors who are crazy about smart farming are betting big on them.
In 2020, $ 929 million was invested in US indoor farming ventures, more than double the investment in 2019. PitchBook data. The grocery chain and California’s largest berry producer Alliance with vertical farming, also.
“There is no doubt that we are reinventing agriculture, but what we are doing is reinventing the fresh food supply chain,” said Manhattan-based indoor farm in New Jersey. Irving Fain, founder and chief executive officer of Bowery, said. One is under construction in Maryland and the other in Pennsylvania, and two research farms are in New Jersey.
Mr. Fine said his farm is 100 times more productive than traditional farms and uses 95% less water. Other companies claim that one acre can grow as much food as a traditional farm can grow at 390.
Vertical farming can be built next to the city center, so lettuce, for example, doesn’t have to sit in a truck for days when heading from California to the east coast, losing both quality and quality. Nutritional value. Vegetables are grown for flavor, not storage and yield.
The new system was designed to produce pesticide-free sanitary crops in computer-monitored sanitary buildings, forcing a major recall of Romain Lettuce in 2019 and 2020. There is little risk of contamination by bacteria such as E. coli.
Still, many farmers and scientists remain unconvincing. Chapman of the Real Organic Project was engaged in hydroponics at the US Department of Agriculture Taskforce. Five years ago, he led an effort to encourage distributors not to allow hydroponics farmers to certify their produce as organic produce. According to him and others, the very definition of organic farming depends on creating healthy soil. May, Food Safety Center, Environmental groups, led Appeal of Federal Court Decision. It upheld the policy of government agencies.
The nutritional profile of hydroponics continues to improve, but no one yet knows what long-term health implications for fruits and vegetables grown without soil. No matter how many nutrients an indoor farmer puts in water, critics say that an indoor farmer can rival the taste and nutritional value that comes from a combination of sun, healthy soil microbes, and common phytobiology. They can’t and claim they can’t offer environmental benefits-run an organic farm.
“What are the health consequences of the second generation?” Chapman asked. “This is a huge live experiment and we are mice.”
The gap between soil lovers and ag-tech futurists has spread on a much closer scale between two influential brothers, Dan and David Barber, who found and own organic farms. Masu Blue Hill Restaurants in Greenwich Village and Stoneburn, Pocantico Hills, NY
Created by David Barber in 2018 Investment fund To support new food technology companies, including Bowery. But the 2014 book “Third plate: Field notes on the future of food” dedicates the entire section to the soil and believes that truly delicious food can only come from Earth.
“I haven’t bought it,” said Dan Barber about the heat of hydroponics.
It is virtually impossible to try to fortify water with nutrients to mimic what the soil does, he said.
“We know more about the stars and the sky than the soil,” he said. “In fact, we don’t know much about nutrition.”
There are also cultural costs. For centuries, he said, cooking has been developed based on what the land and plants demand. The Mexican diet in the corn and bean-based region was born out of farmers’ awareness that corn grows better in the presence of beans that fix nitrogen in the soil.
“The technological agricultural revolution is changing this equation head-on,” Barber said. It helps efficiency in the name of feeding more people but divorces food from nature.
His brother, David, was also skeptical of hydroponics for a long time. “Most of my career has been that good soil leads to good agriculture, good systems, and ultimately good flavors,” said David Barber.
But the environmental benefits of next-generation hydroponics cannot be ignored, he said. It also does not taste better than previous hydroponic produce. “They combine outdoor and indoor thinking, and science and history to create something special,” he said. “There aren’t many winners in this area, but they will be part of our food system.”
Indoor farmers see competition as a large industrial producer producing fruits and vegetables grown to withstand processing and shipping, rather than small farmers using more natural cultivation techniques. They say the fight is against monoculture, not the farmers who maintain healthy soil and feed the community. Hydroponic farms can help develop new and more diverse plants and reduce the overall use of pesticides.
“All we’re trying to do is be as good as a farmer 100 years ago,” said hydroponic lettuce grower Malechuk.
Kentucky-born founder and CEO of App Harvest, Jonathan Webb, said indoor farming is a bet on national farming.
“American farmers are already out of date,” he said, noting that the United States imports £ 4 billion of tomatoes from Mexico each year. “Our hope is to be able to bring farmers back to US shelves.”
Coriccio also leads the campaign opposed to genetically modified foods and long advocate for smallholders, he said the two farming styles could coexist. “The toolbox needs a lot of tools,” he said.
Uita Michel Kentucky chef App Harvest likes App Harvest because the company creates jobs and grows tomatoes that they are happy to use in restaurants.
But technology will never beat the magic of the soil, she said. “There is no substitute for my summer Kentucky tomatoes.”
There is no soil. There is no growth period. Just add water and technology.
"Resilience Is Going To Become A Key Element of Food Security"
A little over two years ago they formed AgroUrbana, a startup dedicated to vertical agriculture, which consists of producing food in vertically stacked layers, in their case using LED lights and hydroponic cultivation, to provide the light and water necessary to harvest vegetables with nutrition. very accurate in spaces with controlled climates.
July 5, 2021
When it comes to rethinking agriculture to create better products with much less impact 365 days a year on a large scale, Cristián Sjögren and Pablo Bunster, two professionals from the renewable energy sector, left their jobs behind to bring sustainable farming to cities.
A little over two years ago they formed AgroUrbana, a startup dedicated to vertical agriculture, which consists of producing food in vertically stacked layers, in their case using LED lights and hydroponic cultivation, to provide the light and water necessary to harvest vegetables with nutrition. very accurate in spaces with controlled climates.
In 2020, despite the fact that its creators consider that much more work needs to be done to advance in a country where traditional agriculture prevails, they have managed to expand their distribution channels. “Our investors and clients are excited. We have seen a very positive reception from the markets ”explains Bunster, who points out that last August they began to sell their vegetables in Jumbo, and since last week they have been in the North American multinational Walmart.
“The new generations read the label in the supermarket more than any other. The sophistication of the consumer is demanding more from the producers, and the way agriculture has been done until today has not been able to cope with these consumption conditions. This is part of the value of bringing vertical agriculture to Chile ”, says Pablo Bunster, who sees in the startup a possible solution by automating food production.
In March 2020, AgroUrbana closed its second round of financing, which was led by the CLIN fund of ChileGlobal Ventures, the Venture Capital area of Fundación Chile. To date, the startup adds USD 1.5 million in financing, in which funds from Venture Capital, Family Offices, and individuals have participated, which has allowed them to reach an advanced stage of the AgroUrbana Series A round for USD $ 4 million, to finance the construction of a much larger scale vertical farm.
Read the complete article at: Vertical Farm Daily
PinDuoDuo: Building A More Resilient Food System With Technology - July 14 -15
Join us virtually for our inaugural Food Systems Forum, which will convene experts from around the world to share their insights and spark further connections and potential collaborations
The pandemic has shone a light on how fragile and intertwined our global agri-food supply chain is, making it even more pressing to push for food systems innovation and change. Can we leverage technology to build a more resilient food system that feeds more people and feeds them better?
Join us virtually for our inaugural Food Systems Forum, which will convene experts from around the world to share their insights and spark further connections and potential collaborations.
Register To Join The Conversation
RotoGro (ASX:RGI) Updates Market On Vertical Farming Tech
The RotoGro Garden System is the core of the company's technology with the ability to maximize plant surface growing area by situating a spherical garden around a centrally placed lighting system
Source: RotoGro
RotoGro (RGI) provides an update of its vertical farming technology with encouraging results from recent trials
The company says recent data indicates its garden systems produce more yield per square meter when compared to other indoor vertical farming methods
Further, trials of RotoGro 710 are said to be progressing well and the team is trialing how to further reduce water and energy usage
RGI is also encouraged by its studies and customer feedback for its RotoGro 420 system which it says validates commercial-scale cultivation of lawful cannabis
Shares were trading 2.3 percent higher at 4.4 cents apiece
RotoGro designs and manufactures cultivation solutions for indoor vertical farming, operating in perishable foods and lawful cannabis.
The RotoGro Garden System is the core of the company's technology with the ability to maximize plant surface growing area by situating a spherical garden around a centrally placed lighting system.
The systems can be stacked, maximizing the yields per square meter when compared to the ground space occupied.
RGI said data collected from recent crop trials conducted in collaboration with agriculture company Verity Greens and herb grower and distributor Fresh Leaf indicates its garden systems produce more yield per square meter when compared to other indoor vertical farming methods.
Specifically, RotoGro projects yields 3.8 to 15.3 times the yield per square meter compared to industry-leading farming producers and greater in contrast to greenhouse and conventional farming.
CEO Michael Di Tommaso said ventures like the ones with Verity Greens and Fresh Leaf will "strengthen RotoGro’s market presence by successfully penetrating the burgeoning indoor vertical farming industry with its technology offerings".
Further, internal trials of the company's most recently developed garden system, the RotoGro 710, are said to be progressing well with cultivation of 48 kilograms of basil and 26.5 kilograms of cilantro in a single harvest cycle.
After multiple trials cultivating leafy greens, the agronomy team repeatedly achieved yields of 124 kilograms in a fully planted RotoGro 710, indicating single harvest yields of 372 kilograms could be achieved when the technology is at full capacity, stacked three-high.
The team is trialing shorter full crop cycle lengths while maintaining yields and aims to refine the plant irrigation schedules to further minimize water usage and refine the environmental controls to ensure enhanced energy efficiencies.
In other news, RotoGro has enabled full automation of its lawful cannabis cultivator, RotoGro 420.
The company's software controls the wheel revolution speed, lighting cycles, and spectrum variations, direct CO2 injection as well as the plant irrigation processes and environmental controls including temperature, air conditioning, and humidification.
Notably, the 420-garden system has been able to consistently produce 10.2 kilograms of dried cannabis flower in a single 56-day crop cycle when stacked three-high.
RGI said its studies in combination with its customer’s data validates the commercial viability of RotoGro 420 in the commercial-scale cultivation of lawful
cannabis.
Mr Di Tommaso said RotoGro is continuing to develop relationships globally to expand its presence in both the perishable foods and lawful cannabis markets.
Shares were trading 2.3 percent higher at 4.4 cents apiece at 1:31 pm AEST.
PinDuoDuo: Building A More Resilient Food System With Technology - July 14 -15
Join us virtually for our inaugural Food Systems Forum, which will convene experts from around the world to share their insights and spark further connections and potential collaborations
The pandemic has shone a light on how fragile and intertwined our global agri-food supply chain is, making it even more pressing to push for food systems innovation and change. Can we leverage technology to build a more resilient food system that feeds more people and feeds them better?
Join us virtually for our inaugural Food Systems Forum, which will convene experts from around the world to share their insights and spark further connections and potential collaborations.
Register To Join The Conversation
VIDEO: Japanese University Looks Abroad
Researchers hope to promote technologies for things like breeding vegetables that grow well indoors
June 3, 2021
A Japanese university is turning overseas to find new customers for farming and medical technologies developed by its staff.
Chiba University has teamed up with the Japan External Trade Organization, or JETRO. They signed an agreement last month.
The push abroad will mainly be online for now as the coronavirus pandemic pulls the plug on conferences and other trade events.
Researchers hope to promote technologies for things like breeding vegetables that grow well indoors.
They are already making progress in China.
The university's technology is helping a next-generation plant-growing facility in the city of Shenzhen.
Watch the video at www.nhkj.or.jp.
CANADA - MONTREAL: Indoor Farming Technology Seeks To Localize Agriculture
“The goal is to have the first crops in the system in August of this year,” Zeman said. “It’s going to take a pretty serious pull from everyone involved to get us there.” Whereas traditional agriculture grows in outdoor fields or gardens, Interius Farms uses hydroponics and vertical farming to grow plants indoors, offering a climate-controlled environment and artificial lighting in place of sunlight.
A Canadian company is pioneering new technology for growing produce indoors, utilizing hydroponics to provide year-round, cost-effective food production. Interius Farms, based in Montreal, developed the innovative system as a means to localize agriculture in a country where fresh produce is imported at least seven months a year from other parts of the U.S. and North America.
Founded in 2018 by longtime friends Jonnie Lawson and Tristan Zeman, the company is taking vertical farming to the next level with its 8-foot rotating rack design—exposing plants to a single light fixture saving on both space and energy demand.
More efficiency
While the project is currently in its beta stage, Interius Farms is ambitiously ramping up to commercial scale, moving into a 14,000-square-foot facility to grow leafy greens, including lettuce, kale, cilantro, parsley, and basil.
The rotating rack eliminates the need for additional lighting systems, maximizing energy efficiency. Zeman said the system requires 40-80% less lighting and 92% less land than traditional agriculture. The original proof of concept was done in the corner of Zeman’s Chicago apartment. Now, he said they are zeroing in on a commercial facility where Interius Farms can grow a significant amount of food. “5,000 square feet of growing space produces over a million heads of lettuce,” he said.
Growing with hydroponics is inherently more expensive, Zeman said, with higher costs of inputs. He knows they cannot compete on direct cost with field lettuce. However, where the technology proves especially valuable is how it insulates against seasonal price fluctuations of produce and other shocks in the supply chain, such as disease outbreaks and natural disasters in other parts of the world.
Collaboration
Interius Farms is also working with urban-gro, a Colorado-based company that focuses on engineering efficient and profitable controlled environment agriculture facilities. Though urban-gro is traditionally rooted in cannabis, the business is expanding its expertise to work with innovators in other areas of farming. “We are excited to be working with Interius Farms and their innovative and patented approach to growing fresh and sustainable foods for the Canadian market,” said Jim Dennedy, urban-gro’s president and chief operating officer.
The mission of Interius Farms, according to Zeman, is to localize Canadian agriculture through its platform. Buyers will have access to locally grown food even in harsh winter months while at the same time giving themselves an “insurance policy” against volatile prices caused by supply chain disruptions.
“We offer a fresher and more sustainable product, and we introduce price and business sustainability into the Canadian food market, especially in those import months,” Zeman said.
Seasonal fluctuations can increase the price of field lettuce by as much as 85% during the non-growing months, Zeman said. “When the vast majority of the Canadian supply chain in the winter is coming from the American Southwest, you’re very exposed, and you’re not getting very high-quality produce by the time it’s been shipped up here,” Zeman added.
The fresh produce
More control
Looking ahead, Zeman said he has heard from some consumers who question whether indoor agriculture produces healthy, natural food. That is a perception the company will battle, he said, though he points out Interius Farms can offer enhanced traceability with its design. “Everyone wants to know exactly where their food came from,” he said. “And we can tell you, from the seed, exactly what nutrients it has received. For every second of the plant’s life, we can tell you exactly what the plant has received, whereas if you’re in the field, many factors are out of your control.”
Over the next six months, Zeman said Interius Farms and urban-gro will be joined at the hip, testing their commercial facility’s design, vendors, lighting fixtures and other options. “Through our engagement with urban-gro, we gain the advantage of supplementing our internal expertise with the urban-gro team that has spent decades working with complex systems. We can rely on urban-gro to guide us in developing the right solutions for our unique application. The ultimate goal is to be in that facility, to have that anchor customer—which we feel like we’re very close to having in place—and growing very soon in our first facility,” Zeman said.
Lead photo: From the left: Brady Deslippe (Chief Technology Officer) and Tristan Zeman (Founder/President)
For more information:
Publication date: Thu 27 May 2021
Author: Andrea Di Pastena
© HortiDaily.com
USA: NEW JERSEY - AeroFarms Expands Global Headquarters To Support Growth And Innovation
Indoor vertical farming leader continues commitment to Newark as it expands presence within the community
April 23, 2021
Indoor vertical farming leader continues commitment to Newark as it expands presence within the community
Co-Founder & CEO David Rosenberg recognized as ROI-NJ Top Technology Influencer
AeroFarms, a certified B Corporation and leader in indoor vertical farming, today announced that the Company has received its certificate of occupancy for expansion of its global headquarters in Newark, New Jersey. To support its corporate expansion, AeroFarms recently completed the build-out of an additional 25,000 square feet at its headquarters for new office space and more expansive R&D and Innovation Centers of Excellence.
In 2015, AeroFarms partnered closely with the City of Newark and the New Jersey Economic Development Authority (NJEDA), to relocate its headquarters to Newark from the Finger Lakes region of New York with the goal of creating more than 75 year-round jobs in the local community. Today, AeroFarms employs in Newark more than 150 team members, and the Company is delivering on its vision of not only serving the broader New York metro area but also serving as the global epicenter for large scale commercial indoor vertical farming and the latest in breakthrough proprietary technologies addressing some of the world’s most pressing agricultural challenges.
AeroFarms has been leading the way for innovation and technology breakthroughs since its inception and will continue to build on this legacy through continued R&D and infrastructure to maintain its leadership position as the Company scales. Earlier this week, AeroFarms Co-Founder and CEO David Rosenberg was recognized as a Top Technology Influencer by New Jersey media outlet ROI-NJ, further demonstrating the Company’s leadership in technology and innovation.
"New Jersey and Newark have been the perfect home for AeroFarms to recruit the best talent for horticulture, engineering, data science, operations, and food safety enabling us to reimagine agriculture in the Garden State," said Rosenberg. "We are scaling farms around the world, partnering closely with major multi-national retailers, and our newly expanded global headquarters will be a showcase for our transformative work and innovation that will further drive our mission to grow the best plants possible for the betterment of humanity."
AeroFarms has a long history of community involvement, including partnering with Ironbound Community Corporation and NJ Reentry Program, which offers career opportunities to those previously incarcerated. In addition, AeroFarms has made an impact with its Community Farms, working with partners such as Newark-based Philips Academy Charter School and their EcoSpaces program. The Company also partnered with the City of Jersey City and the World Economic Forum’s Healthy Cities and Communities initiative for the first-ever municipal indoor vertical farming program, consisting of ten vertical farms throughout Jersey City located in senior centers, schools, public housing complexes, and municipal buildings. The ten sites will grow 19,000 pounds of vegetables annually, using targeted aeroponics water mist and minimal electricity, and the food will be provided to the community for no cost.
About AeroFarms
Since 2004, AeroFarms has been leading the way for indoor vertical farming and championing transformational innovation for agriculture. On a mission to grow the best plants possible for the betterment of humanity, AeroFarms is a Certified B Corporation Company with global headquarters in Newark, New Jersey, United States. Named one of the World’s Most Innovative Companies by Fast Company two years in a row and one of TIME’s Best Inventions, AeroFarms patented, award-winning indoor vertical farming technology provides the perfect conditions for healthy plants to thrive, taking agriculture to a new level of precision, food safety, and productivity while using up to 95% less water and no pesticides versus traditional field farming. AeroFarms enables local production to safely grow all year round for its commercial retail brand that offers peak flavor always®. In addition, through its proprietary growing technology platform, AeroFarms has developed multi-year strategic partnerships ranging from government to major Fortune 500 companies to help uniquely solve agriculture supply chain needs. For additional information, visit: https://aerofarms.com/.
On March 26, 2021, AeroFarms announced a definitive business combination agreement with Spring Valley Acquisition Corp. (Nasdaq: SV). Upon the closing of the business combination, AeroFarms will become publicly traded on Nasdaq under the new ticker symbol "ARFM". Additional information about the transaction can be viewed here: https://aerofarms.com/investors/
No Offer or Solicitation
This press release does not constitute an offer to sell or a solicitation of an offer to buy, or the solicitation of any vote or approval in any jurisdiction in connection with a proposed potential business combination among Spring Valley and AeroFarms or any related transactions, nor shall there be any sale, issuance or transfer of securities in any jurisdiction where, or to any person to whom, such offer, solicitation or sale may be unlawful. Any offering of securities or solicitation of votes regarding the proposed transaction will be made only by means of a proxy statement/prospectus that complies with applicable rules and regulations promulgated under the Securities Act of 1933, as amended (the "Securities Act"), and Securities Exchange Act of 1934, as amended, or pursuant to an exemption from the Securities Act or in a transaction not subject to the registration requirements of the Securities Act.
Forward-Looking Statements
Certain statements included in this press release that are not historical facts are forward-looking statements for purposes of the safe harbor provisions under the United States Private Securities Litigation Reform Act of 1995. Forward-looking statements generally are accompanied by words such as "believe," "may," "will," "estimate," "continue," "anticipate," "intend," "expect," "should," "would," "plan," "predict," "potential," "seem," "seek," "future," "outlook," and similar expressions that predict or indicate future events or trends or that are not statements of historical matters. All statements, other than statements of present or historical fact included in this presentation, regarding Spring Valley’s proposed acquisition of AeroFarms, Spring Valley’s ability to consummate the transaction, the benefits of the transaction, and the combined company’s future financial performance, as well as the combined company’s strategy, future operations, estimated financial position, estimated revenues and losses, projected costs, prospects, plans and objectives of management are forward-looking statements. These statements are based on various assumptions, whether or not identified in this press release, and on the current expectations of the respective management of AeroFarms and Spring Valley and are not predictions of actual performance. These forward-looking statements are provided for illustrative purposes only and are not intended to serve as, and must not be relied on as, a guarantee, an assurance, a prediction, or a definitive statement of fact or probability. Actual events and circumstances are difficult or impossible to predict and will differ from assumptions. Many actual events and circumstances are beyond the control of AeroFarms and Spring Valley. These forward-looking statements are subject to a number of risks and uncertainties, including changes in domestic and foreign business, market, financial, political, and legal conditions; the inability of the parties to successfully or timely consummate the proposed transaction, including the risk that any regulatory approvals are not obtained, are delayed or are subject to unanticipated conditions that could adversely affect the combined company or the expected benefits of the proposed transaction or that the approval of the stockholders of Spring Valley or AeroFarms is not obtained; failure to realize the anticipated benefits of the proposed transaction; risks relating to the uncertainty of the projected financial information with respect to AeroFarms; risks related to the expansion of AeroFarms’ business and the timing of expected business milestones; the effects of competition on AeroFarms’ business; the ability of Spring Valley or AeroFarms to issue equity or equity-linked securities or obtain debt financing in connection with the proposed transaction or in the future, and those factors discussed in Spring Valley’s final prospectus dated November 25, 2020 under the heading "Risk Factors," and other documents Spring Valley has filed, or will file, with the SEC. If any of these risks materialize or our assumptions prove incorrect, actual results could differ materially from the results implied by these forward-looking statements. There may be additional risks that neither Spring Valley nor AeroFarms presently knows, or that Spring Valley nor AeroFarms currently believe are immaterial, that could also cause actual results to differ from those contained in the forward-looking statements. In addition, forward-looking statements reflect Spring Valley’s and AeroFarms’ expectations, plans, or forecasts of future events and views as of the date of this press release. Spring Valley and AeroFarms anticipate that subsequent events and developments will cause Spring Valley’s and AeroFarms’ assessments to change. However, while Spring Valley and AeroFarms may elect to update these forward-looking statements at some point in the future, Spring Valley and AeroFarms specifically disclaim any obligation to do so. These forward-looking statements should not be relied upon as representing Spring Valley’s and AeroFarms’ assessments of any date subsequent to the date of this press release. Accordingly, undue reliance should not be placed upon the forward-looking statements.
View source version on businesswire.com: https://www.businesswire.com/news/home/20210423005283/en/
Contacts
AeroFarms Contacts
Investor Relations:
Jeff Sonnek
ICR
Jeff.Sonnek@icrinc.com
1-646-277-1263
Media Relations:
Marc Oshima
AeroFarms
MarcOshima@AeroFarms.com
1-917-673-4602
VIDEO: Indoor Farming Powered By Robotics And Technology - Plenty
Indoor farming powered by robotics and technology is enabling one California company to grow 'Plenty' of flavorful nutrient-rich and pesticide-free produce
Author: abc10.com
April 6, 2021
How CubicFarms Is Feeding A Changing World With Its Automated Indoor Growing Technology
The global supply chain today is facing significant, costly disruptions. A shipping container crisis has upended the global food trade. Devastating winter weather has impacted the U.S., and ongoing labour shortages within the farming industry show no sign of relenting as border crossings remain shut
April 7, 2021
Mark Shelling, Market One Media
CubicFarms provides sustainable and profitable commercial-scale automated indoor growing systems for local produce and fresh livestock feed. , Image courtesy of Market One Media
Supply chain – CubicFarms Garden – Foodservice – HG cattle
In an already tumultuous year, agriculture is facing supply chain disruptions and unpredictable climate changes
To combat this, CubicFarms offers new automated indoor farming systems that could revolutionize global food supplies
With multiple patents in the ag-tech space, CubicFarms is poised for further expansion
The global supply chain today is facing significant, costly disruptions. A shipping container crisis has upended the global food trade. Devastating winter weather has impacted the U.S., and ongoing labour shortages within the farming industry show no sign of relenting as border crossings remain shut.
The ability to move people and goods across long distances will always be at risk of disruption because the longer the supply chain, the more chances there are for things to go wrong.
The farming industry was already in the midst of a labour crisis even before this year, with fewer and fewer workers available to tend to fields. Now with borders being shut, it's unclear how many foreign workers will be able to return to their jobs, despite some having been issued flight exemptions.
Because of this continued downward trend, Canada is currently projected to lose 123,000 workers within a decade, according to a report done by RBC. That represents a loss of $11 billion in GDP, if the labour gap continues to widen.
Couple this labour shortage with changing weather patterns like the devastating cold snap in Texas, the shipping container crisis, and the ongoing demand for fresh produce, and you’ve got a perfect storm against the food industry.
These stacked variables have revealed just how vulnerable the global food supply chain is. Farmers are now scrambling to find sustainable alternatives to what appears to be a crumbling framework.
"We believe long food supply chains are dangerous. As a technology company in the agriculture business, we’ve seen the challenges with growing outdoors. The solution is in using technology to make locally grown produce more widely accessible, 365 days a year, not just here, but anywhere in the world.”
— Dave Dinesen, CEO, CubicFarm® Systems Corp.
Innovative new agriculture technologies like indoor vertical farming are more attractive to farmers who want the stability and consistency that come from harvesting indoor crops. Innovators in the agriculture space have already anticipated this shift and are now offering ways to safeguard against further threats to cultivation.
The technology is improving rapidly with automated, commercial-scale indoor growing systems that grow fresh produce in a controlled environment. These crops can be harvested with less labour than traditional farming, addressing the need to do more during labour shortages.
By creating the ideal indoor environment onsite, growers use LED lighting, less land, significantly less water, and less energy. In Canada and the U.S., in particular, the ability to grow fresh produce during the winter months allows farmers to expand the growing season to 12-months a year.
Disruptions to the supply chain during the ongoing pandemic have sent food distribution centres searching for more local produce. We can expect that demand to rise as the number of growers using indoor vertical farming systems increases.
A new leader in agricultural automation
For a better look at these automated indoor growing systems, Canadian ag-tech company, CubicFarm® Systems Corp. (TSXV:CUB), offers insights into how this technology is the future of agriculture.
Different from other companies in the ag-tech space, CubicFarms began with the farmers themselves. Jack Benne and his son Leo Benne visited a farm in Puerto Rico after a hurricane when they had an idea for an automated indoor growing system that could grow produce in any weather.
Being the principles behind Bevo Farms, one of the largest propagation greenhouse systems in North America, they put their considerable expertise to work on this important problem.
CubicFarms’ produce is grown onsite in an indoor, controlled environment, for delicious greens harvested at the peak of freshness, bringing food production closer to home.
The automated systems they created are now at the forefront of solving the supply chain woes of countries that must rely on outside suppliers for their fresh produce. The potential for this shift is massive.
A local supply chain would reduce long distance shipping/flights, the indoor controlled environment is pesticide and herbicide-free so there would be fewer shortages due to recall (think of the recent romaine E. coli scares), and there would be less food waste, as produce is harvested at peak freshness instead of days or even weeks in advance.
Under traditional supply chains, there is an expected amount of rot, unnecessary waste of food and profits in each shipment, and it’s a wonder that’s considered tolerable.
The CubicFarm System technology is housed within modules that are 40 ft by 8 ft, standing 9.5 ft tall. The beauty of their structure is that farmers can buy as many modules as they need and place them together, creating indoor fields with the ideal controlled environment year-round.
A patented undulating path is used to move crops throughout the module. Plants are cycled through each module on suspended trays, which periodically pass an artificial LED light source along with regulated CO².
This is different than the typical ‘rack and stack’ vertical farming setups which need more space to allow people through to seed, monitor, and harvest plants. The CubicFarm System brings the plants in a full circle once every 90 minutes.
Each module is custom-built, stainless steel container. Trays move along a patented undulating path.
This allows for harvesting to easily take place at the front of the module, while sensors monitor the plants from the inside. This also prevents leaf burning, sometimes seen in vertical farms when the plants are too close to the light and heat source, or those suffering the ill-effects of their position too high or too low in the rack for the ideal amount of CO² necessary for healthy growth.
The CubicFarm System uses a propagator, which grows seeds into seedlings, and a cultivator that takes crops from seedlings to harvest.
This is all while being provided with the necessary nutrients and using up to 95 per cent less water than traditional farming. This line can replicate the exact growing conditions to yield the perfect leafy greens, herbs, and microgreens every time.
"When you provide the optimal environment every day for a crop, it won't only reward you by growing as fast as possible, but it will also be more delicious and nutritious," Dinesen notes.
Global food distribution giant, Sysco, recently announced on their Sysco Vancouver Facebook page that they’re purchasing fresh produce from growers using the CubicFarm System.
This significant relationship is appealing to anyone looking to get into the supply chain, which can be challenging for smaller farming operations.
A new division of CubicFarms is an expert brokerage called CubicFarms Garden. This expert team provides business consulting services for growers using the CubicFarm System onsite, helping them enter the local supply chain and fostering relationships with food distribution centres.
Farmers have long been at the forefront of technology when it comes to new machinery and systems. “Farmers are the most innovative people we know,” explains Dinesen. “In technology terms, this is the Tractor 2.0. After the invention of the tractor, no one would plow a field without one. With the automated, onsite, and commercial scale of the CubicFarm System, no one would want to grow indoors without us.”
While it might sound complex, farmers who use CubicFarm System will immediately notice its simplicity. When a new unit arrives on site, it's already 90 per cent ready to go, and the remaining set up is assisted by a hands-on customer experience team.
Farmers are trained on how to maximize each module's potential and are given resources for developing new crops. With the recently announced addition of Edoardo De Martin, former Microsoft Vancouver GM, to the executive team as Chief Technology Officer, we can expect the next generation of growing technologies to use more artificial intelligence and robotics to enhance their existing automations and efficiencies.
From fresh food to livestock feed
In January of 2020, the company's success and expertise led to the acquisition of a second farmer-founded innovative company called HydroGreen Inc. Another patented indoor farming system, the HydroGreen Grow System is focused solely on the production of fresh, nutritious livestock feed. Feed that would once be grown across acres of grazing land is now produced in a module that's a fraction of that size.
It is a necessary innovation for ranchers who are facing land and water scarcity issues. Dihl Grohs developed the technology for growing nutritious livestock feed for his ranches in South Dakota, Utah, and Missouri. The concept of low-maintenance feed growing was in direct response to the areas where his cattle had limited precipitation.
Recently published university research confirms greenhouse gas reductions using HydroGreen’s hydroponic fodder system. The university study results came from a HydroGreen Grow System operating in British Columbia, the latest market for the system in CubicFarms’ backyard.
At the EcoDairy in Abbotsford, British Columbia, where they produce milk and use agritourism to educate people about where their food comes from, owner Bill Vanderkooi is using HydroGreen for his dairy cattle.
In a video interview, Vanderkooi talks about incorporating HydroGreen livestock feed into the current mixture and replacing some grain and forage in the cattle diet, measuring against a control group for differences in performance, production, and health. “At the early stage of the trial we’re seeing some positive benefits on performance.” Ongoing research into the nutritional benefits will be combined with land, water, and energy usage as factors for farmers.
The HydroGreen Grow System uses 92 percent less water and less land than traditional farming, so it’s expected that this technology will be widely embraced by the livestock industry in the future.
The fresh livestock feed can be used for a variety of animals, but it’s mainly used for dairy and beef cattle. For those facing labour shortages, the HydroGreen module operates with the push of a button and is self-cleaning. Growing predictable amounts of fresh livestock feed indoors and onsite will allow farmers to reduce the unpredictability that can be costly and dangerous to their animals and livelihoods.
The HydroGreen Grow System’s automated seeder spreads half an inch of small grain seed on the growing surface, growing from seed to feed in six days, with less land, water, labour, and energy.
CEO Dave Dinesen considers the HydroGreen Grow System to be the most automated livestock feed growing technology on the planet.
He explains, "When it comes to animal health and nutrition, the HydroGreen Grow System is giving the most nutritious and delicious livestock feed to these animals. They’re healthier, the feed is more consistent, and ranchers can become more self-sufficient.”
“It’s also automated and scalable because we have the technology to make this possible and profitable,” he adds.
“At the end of the day, we’re a technology company, not a produce or livestock feed company, so we don’t compete with farmers. They become our farmer partners and it’s our job to advance the technologies that support their businesses.”
With a $5 million investment from a top ag-tech investor, Ospraie, and a 100-module sale (their largest yet) to a farm in Surrey, B.C., CubicFarms’ momentum is only growing. It's this momentum that will continue to cultivate new acquisitions, like HydroGreen, and propel the company into an expanding market.
CubicFarms also has an R&D Innovation Centre that is continuously creating new crops and streamlined growing practices to benefit the growers using their technologies, including the CubicFarm System and the HydroGreen Grow System. It's a hopeful progression in a time when there seems to be a new crisis emerging every month. With technology like this positioned to revolutionize global food supply and essentially end hunger, it's one fewer crisis we have to face in 2021.
Learn more about CubicFarms by visiting their website here.
For more information about the CubicFarm System, watch this overview video to see it in action.
VIDEO: Device Communicates With Plants Using Electric Signals
Researchers envision a future where farmers can take preventive steps to protect their crops, using the plant ‘communication’ device they have developed
24 March 2021
Researchers envision a future where farmers can take preventive steps to protect their crops, using the plant ‘communication’ device they have developed.
A team of scientists led by Nanyang Technological University, Singapore (NTU Singapore) has developed a device that can deliver electrical signals to and from plants, opening the door to new technologies that make use of plants.
The NTU team developed their plant ‘communication’ device by attaching a conformable electrode (a piece of conductive material) on the surface of a Venus flytrap plant using a soft and sticky adhesive known as hydrogel.
Pick up and transmit electric signals
With the electrode attached to the surface of the flytrap, researchers can achieve two things: pick up electrical signals to monitor how the plant responds to its environment, and transmit electrical signals to the plant, to cause it to close its leaves.
According to the scientists, the ability to measure the electrical signals of plants could create opportunities for a range of useful applications, such as plant-based robots that can help to pick up fragile objects or to help enhance food security by detecting diseases in crops early.
Text continues underneath the video
Monitor crop health
The research team envisions a future where farmers can take preventive steps to protect their crops, using the plant ‘communication’ device they have developed.
Lead author of the study, Chen Xiaodong, President’s Chair Professor in Materials Science and Engineering at NTU Singapore said: “Climate change is threatening food security around the world. By monitoring the plants’ electrical signals, we may be able to detect possible distress signals and abnormalities. When used for agriculture purpose, farmers may find out when a disease is in progress, even before full‑blown symptoms appear on the crops, such as yellowed leaves. This may provide us the opportunity to act quickly to maximise crop yield for the population.”
Smartphone
The device has a diameter of 3 mm and is harmless to the plant. The researchers say it does not affect the plant’s ability to perform photosynthesis while successfully detecting electrical signals from the plant. Using a smartphone to transmit electric pulses to the device at a specific frequency, the team elicited the Venus flytrap to close its leaves on demand, in 1.3 seconds.
The researchers have also attached the Venus flytrap to a robotic arm and, through the smartphone and the ‘communication’ device, stimulated its leaf to close and pick up a piece of wire half a millimetre in diameter.
Technology Is Key To Feeding The World - Celebrating National Ag Day On March 23: We've Come A Long Way From Plows To Agbots
High-Tech Farm Trends: A Glossary
March 18, 2021
By: Steve Foster
Extension Educator Pershing County, University of Nevada, Reno Extension
High-Tech Farm Trends: A Glossary
Over the years, I have listened to many speakers predict what the future of agriculture will look like. One of the biggest challenges for agriculture is to feed 9.6 billion people by 2050. To do so, food production must increase 70% by 2050.
One way to address these issues and increase the quality and quantity of agricultural production is to use sensing technology to make farms more intelligent and connected through so-called "precision agriculture," also known as “smart farming.”
I came across an article the other day, Five High-Tech Farming Trends, by JoAnn Alumbaugh, that shares British author and Labour Party politician Anthony Crosland’s most cited sentence: “What one generation sees as a luxury, the next sees as a necessity." History has shown this to be true – just look at the use of cell phones, televisions, hand-held devices, and computers. Then look at how living conditions and diets have changed as societies have become more affluent.
Below are technologies related to agricultural and natural manufacturing under four key areas of accelerating change, many of which are already in use today: sensors, food, automation, and engineering.
Sensors
Air & soil sensors: Enable a real-time understanding of current farm, forest or body of water conditions.
Equipment telematics: Allow mechanical devices, such as tractors, to warn mechanics that a failure is likely to occur soon.
Livestock biometrics: Collars with GPS, radio frequency identification systems (RFIDs), and biometrics identify and relay vital information about livestock in real-time. Also, farmers and ranchers are using virtual fencing to control the movement of livestock, similar to invisible fences for pets.
Crop sensors: Instead of prescribing field fertilization before application, high-resolution crop sensors inform application equipment of correct amounts needed. Drones or optical sensors, such as infrared light, identify crop health across the field.
Food
Genetically designed food: The creation of entirely new strains of food animals and plants to better address biological and physiological needs. A departure from genetically modified food, genetically designed food is engineered from the ground up.
In vitro meat: Also known as cultured meat, in vitro meat is muscle tissue grown in a lab and therefore never part of a live animal. These products have already entered the market, including the plant-based hamburgers sold by Burger King.
Automation
Agricultural robots: Also known as “agbots,” these are used to automate agricultural processes, including harvesting, fruit picking, plowing, soil maintenance, weeding, planting, and irrigation, among others.
Precision agriculture: Farming management based on observing and responding to intra-field variations. With satellite imagery and advanced sensors, farmers can optimize returns on crop resources, such as irrigation and fertilizer, while preserving natural resources at ever-larger scales. Further understanding of crop variability, geo-located weather data, and precise sensors should allow improved automated decision-making and complementary planting techniques.
Robotic farm swarms: The combination of dozens or hundreds of agbots with thousands of microscopic sensors that would monitor, predict, cultivate and extract crops from the land with practically no human intervention. Small-scale implementations are already on the horizon.
Variable-rate swath control: Building on existing geo-location technologies such as GPS, future swath control could save on seeds, minerals, fertilizer, and herbicides by reducing overlapping resources. By pre-computing the shape of the field where the resources are to be used, and by understanding the relative productivity of different areas of the field, tractors or “Agbots” can procedurally apply resources at variable rates throughout the field.
Engineering
Closed ecological systems: Ecosystems that do not rely on matter exchange outside the system. Such closed ecosystems would theoretically transform waste products into oxygen, food, and water to support life-forms inhabiting the system. Such systems already exist in small scales, but existing technological limitations prevent them from scaling.
Synthetic biology: Programming biology using standardized parts in the same way computers are programmed using standard libraries today. Includes the broad redefinition and expansion of biotechnology, with the ultimate goals of being able to design, build and remediate engineered biological systems that process information, manipulate chemicals, fabricate materials and structures, produce energy, provide food, and maintain and enhance human health and our environment.
Vertical farming: A natural extension of urban agriculture, vertical farms would cultivate plant or animal life within dedicated or mixed-use skyscrapers in urban settings. Using techniques similar to glass houses, vertical farms could augment natural light using energy-efficient lighting. The advantages are numerous, including year-round crop production, protection from the weather, support for urban food autonomy, and reduced transport costs.
The information revolution ties global and local producers and consumers together in ways not possible just a decade ago. As the speed and capacity of computers continue to increase, the ability to gather and use the information on all aspects of production agriculture will explode. Some of these technological advances have already been developed and are just waiting to become financially viable before they transition from a luxury to a necessity.
Sources:
“15 Emerging Agriculture Technologies That Will Change The World,” Michell Zappa, Policy Horizons Canada.
“Five High-Tech Farming Trends,” JoAnn Alumbaugh.
By: Steve Foster
Extension Educator Pershing County, University of Nevada, Reno Extension
Space: A Hi-Tech Vegetable Garden To Grow On The Moon And At The Poles
The future is already here! This is demonstrated by Enea, which is working on a hi-tech garden to grow micro-vegetables on the moon and in extreme terrestrial environments, such as polar ones
ENEA: The Experimental Campaign Between Real And Virtual Begins
The future is already here! This is demonstrated by Enea, which is working on a hi-tech garden to grow micro-vegetables on the moon and in extreme terrestrial environments, such as polar ones. The cultivation is set up inside a special igloo greenhouse designed to withstand very low temperatures.
Luca Nardi
Simulated space missions are also contemplated, thanks to advanced immersive virtual reality techniques. These are the challenges of V-GELM (Virtual Greenhouse Experimental Lunar Module), the experimental project that kicks off in the Casaccia Research Center with the aim of developing a lunar cultivation module by combining innovative hydroponic cultivation techniques with virtual experiments to support the life of astronauts in future long-term missions. The project will be carried out by a team of Enea researchers and by students from CITERA (Centro Interdipartimentale Territorio Edilizia Restauro Ambiente) and from the Tuscia University and Sapienza University of Rome.
A virtual reconstruction of some activities
V-GELM has been selected among the best projects conducted by university teams from all over the world in the context of the IGLUNA 2020 mission of the European Space Agency (ESA), presented yesterday 09/07/2020 by the coordinator Swiss Space Center.
The project is divided into two phases: the first involved students and researchers, in collaboration with Mars Planet Society, in the architectural and functional design of the spaces simulated through immersive virtual reality technologies. The second phase will involve Hort3, the innovative Enea garden where the hydroponic cultivation of two particular varieties of radish, Daikon and Rioja, will be tested, inside a particular tent called "EGG" for its particular egg shape, designed by the University of Milan.
The EGG tent
"The virtual experiment - stresses Luca Nardi of the Enea Biotechnology Laboratory - allows you to offer to the public a realistic interactive perspective suitable for simulating the environments and the operations to be performed and also carrying out ergonomic analyzes. In this way, it is possible to identify from the beginning any critical issues and reduce the costs of developing space modules and of astronaut training times".
The module developed by Enea as part of the Hortspace project, funded by the Italian Space Agency, consists of a closed-cycle hydroponic multi-level cultivation system of one cubic meter with LED lighting where different species of micro-vegetables are grown, purposefully selected to reach the ideal growth stage for consumption within 10-15 days.
The laboratory
"It is a soilless cultivation system - explains Nardi - with the recycling of water, without the use of agrochemicals, able to guarantee the members of the crew engaged in space missions high-quality fresh food and correct nutritional intake, without forgetting the psychological benefit given by the growth of plants in confined environments - such as those of future extraterrestrial bases or in extreme environments, such as hot and cold deserts".
US - SOUTH CAROLINA: VIDEO: Columbia Vertical Farm Uses Technology To Cut Plastic Pollution And Boost Sustainability
With the use of agricultural technology, Vertical Roots farm in West Columbia created a packaging system for its leafy greens that cut down the company’s plastic usage by 30% and extends the shelf life of the lettuce
FEBRUARY 01, 2021
Vertical Roots is the largest hydroponic container farm in the country. They grow and package lettuce varieties and have recently implemented a packaging process that reduces plastic with a resealable film. TRACY GLANTZ TGLANTZ@THESTATE.COM
With the use of agricultural technology, Vertical Roots farm in West Columbia created a packaging system for its leafy greens that cut down the company’s plastic usage by 30% and extends the shelf life of the lettuce.
In 2015, high school friends Andrew Hare and Matt Daniels created the idea for Vertical Roots, now the largest hydroponic container farm in the country. Hare is the general manager of the company and Daniels acts as the chief horticulturist.
The first Vertical Roots opened in Charleston and expanded with its second farm site in West Columbia in 2019. Vertical Roots parent company, AmplifiedAg, manufactures the container farms and farm technology of which Vertical Roots operates.
The farms are part of a growing industry called controlled environmental agriculture (CEA) that uses technology to ramp up nutrient-rich food production year-round.
Hydroponics helps the farm uses 98% less water than traditional farming, according to Hare. Their technology creates an indoor environment to grow lettuce on the East Coast. Most lettuce in the U.S. comes from California and Arizona, where temperatures do not fluctuate much throughout the year, traveling 2,000 miles from farm to table. Vertical Roots offers a solution for local lettuce.
“Our mission is to revolutionize the way communities grow, distribute and consume food,” said Hare. As populations grow, Hare said the ability to produce enough food is a global concern.
VERTICAL ROOTS AGRICULTURAL INNOVATION
As a company committed to sustainability, Vertical Roots had to address its plastic usage and the consumer demand for environmentally friendly products.
“I think everyone can agree that the amount of plastic that’s consumed and used globally is a bit of a problem,” said Hare.
If Vertical Roots were to completely opt-out of using plastics, as much as 40% of the lettuce would be damaged in transportation to the retailers, Hare said. So the company decided to still use plastic containers in order to cut out food waste, but it changed the amount and type of plastic used.
By replacing the conventional “clamshell” plastic lids that you see on a container of lettuce at the grocery store, Vertical Roots cut down more than 30% of plastic usage by creating a resealable film lid. The new packaging comes at no extra cost to the customer and will be cheaper in the long-run for Vertical Roots, according to Hare.
The farm also uses recycled plastic that can also be recycled again after use. Tiny perforations in the film lid of the packaging allows air to leave the lettuce container and extends the product’s freshness, making Vertical Roots lettuce last around 14 days on the shelf.
“We tested respiration and condensation with each lettuce variety, and ultimately found that we could extend the freshness and shelf life of our salad mixes even more,” said Hare.
GROWTH IN THE AGRICULTURAL TECHNOLOGY INDUSTRY
In the first three quarters of 2020, a record $754 million of venture capital was invested in the vertical farming industry, according to PitchBook data. This was a 34% increase from the entire previous year, Bloomberg reported in a January article.
A 2019 report from Global Market Insights showed that the vertical farming market size, or the number of potential customers or unit sales, surpassed $3 billion in 2018 and said it, “will exhibit a massive compound annual growth rate (CAGR) of over 27% from 2019 to 2026.”
In vertical farms, crops are harvested on several vertical layers indoors, where farmers can grow year-round by controlling light, temperature, water, and other factors, according to the U.S. Department of Agriculture.
Vertical agriculture is also seen as a growing industry because it “could help increase food production and expand agricultural operations as the world’s population is projected to exceed 9 billion by 2050,” according to the USDA.
However, some are skeptical about the future of vertical farming for several reasons. The farms use LED light bulbs to grow the crops, which require a lot of energy and money to operate.
Also, the farms mostly produce greens, which are low in calories because they take less water and light. The new farming technology is marketed as a way to combat world hunger, but in poorer countries, low-calorie greens are not as beneficial, according to Bloomberg.
THE FUTURE OF VERTICAL ROOTS
Despite a tough year due to COVID-19, Vertical Roots will open two more indoor, container farms in Georgia and Florida in 2021.
The company lost revenue from foodservice customers like restaurants, schools, and universities during the pandemic, said Hare.
Those food service customers accounted for about half of Vertical Roots’ business, Hare said. Grocery store business stayed steady and even grew during the pandemic. As schools and restaurants are slowly reopening, Vertical Roots is gaining business back.
The West Columbia farm location produces about $1.5 million pounds of produce per year, said Hare. Vertical Roots lettuce is in 1,200 different grocery stores in 11 states, including Lowes Foods stores, Publix, Harris Teeter, and Whole Foods Market chains.
Hare said the company is constantly working on sustainable initiatives, including figuring out a way to reduce light energy consumption by 20-25%, thinking about compostable packaging systems and finding ways to use less water at the farms.
In the future, Vertical Roots hopes to offer a larger variety of produce. The team is experimenting with growing foods like tomatoes, cucumbers, peppers, herbs and mushrooms to see if they could be viable products.
Cultivatd Launches As A New Vertical Farming Technology Brokerage
Co-founded by two former executives at ZipGrow Inc, Cultivatd will represent over 30 different vertical farming and greenhouse growing technologies to better help people select which tools and tech are best suited for their project needs
JANUARY 1st, 2021: Cultivatd Inc, a startup based in Canada, is announcing it has begun operations and launched an indoor farming technology brokerage.
Co-founded by two former executives at ZipGrow Inc, Cultivatd will represent over 30 different vertical farming and greenhouse growing technologies to better help people select which tools and tech are best suited for their project needs.
“We were seeing a lot of people come to us in the past, asking for solutions that required more than one technology, so we decided to launch Cultivatd to fill that gap in the marketplace,” says Eric Bergeron, a serial entrepreneur who is now on his fourth AgTech startup. “We use our expertise as growers, manufacturers, and consultants to make recommendations on the proper setup and agtech solutions.”
Added co-founder Eric Levesque, the former VP of Business Development at ZipGrow, “We work with manufacturers and technology providers to help sell their products to customers that are best suited to their needs. Our brokerage services are free to the end-user as we work on behalf of our partners”.
At current, Cultivatd works with several known AgTech partners including long-time industry companies such as ZipGrow, Cubic Farms, Moleaer, AutoGrow, Ceres Greenhouses, Nelson & Pade Aquaponics, Modular Farms Australia, Growfilm, Iluminar, Hydrogreen, and Intravision Group as well as new technology providers such as GroStack, AmplifiedAg, GROV, Canobi Technologies, Auto Greenhouse, Just Vertical, Grobo and ATOM Controllers,.
Cultivated is also announcing two new service offerings;
Farming As A Service and Cultivatd Consultants.
Farming As A Service (FAAS) is a program where Cultivatd will send a farm manager to operate your indoor farm, removing the difficulties in getting a farm up-and-running and eliminating the barrier-to-entry for most new farmers. The service is contract-based and meant to get your farm to full operational efficiency with an experienced grower by your side. Once the team is trained and using the SOPs put in place, the farmer will move on or remain on as a consultant.
The Cultivatd Consultants service will be a brokerage of experienced master growers looking to share knowledge with indoor farm operators. Cultivatd currently has 6 consultants with expertise in cannabis, vertical farming, greenhouse production, operations, and sales & marketing for vertical farming. “We are always looking to expand our network of consultants as demand for this service is already outweighing our ability to connect experts to projects in need of support..” added Levesque.
“We continue to add new partnerships every day and want to work with the world’s best agtech technology solutions so we can offer our clients a true, unbiased, assessment of the right solution to solve their need”. added Bergeron.
Visit cultivatd.com for more details and to see the growing list of partnerships.
FOR MORE INFORMATION
Eric Levesque
Managing Partner, Cultivatd Inc.
+1 (613) 360-5195
Things To Think About Before Purchasing A Freight Farm
In this article, I will detail all the steps, hurdles, and bureaucracy I endured trying to start and bring a Freight Farm into my local community in Canada
Connor McGoran
In this article, I will detail all the steps, hurdles, and bureaucracy I endured trying to start and bring a Freight Farm into my local community in Canada. While this may not be the same experience for everybody, I will share what I learned and how I failed at starting a Freight Farming business. This process took me approximately three months to go through. The goal of this article is not to dissuade anyone from trying to start a Freight Farm business but to learn from my shortcomings so that the next individual who embarks on this journey will succeed and know what to expect.
Background
I had just finished my degree in Technology Management from NAIT and the early phase of COVID-19 hit which caused community lockdowns across Canada. During the lockdown, I stumbled upon an article from the MIT Technology Review about a unique way to grow roughly 1.5 acres of food in a retrofitted sea-can using LEDs, hydroponics, and specialized HVAC. My curiosity got the best of me and I asked myself if there was a feasible business case for this type of innovation in my home town. This to me seemed like a well-timed idea due to the broken food supply chain across North America due to COVID-19. With further research, I even found that Elon Musk’s younger brother Kimbal used multiple Freight Farm’s to grow his produce for his restaurants. This led me to read more to see if this magic box would be feasible from an economics and business perspective.
Step 1 : Research
The first thing I did was reach out to Freight Farms in Boston where I had a wonderful experience dealing with the Freight Farm Team. They gave me all the documentation I would need to get started detailing the cost of a brand new unit to be 115,000 USD. I also reached out to another company called FarmBoxFoods to see how their technology differed and what their price was set at 125,000 USD. Due to the high cost and the poor CAD-USD currency conversion (1.4), I looked at purchasing a used Freight Farm from the iGrow Group which re-sells used units online.
LGM Freight Farm Operating Costs
Step 2: Business Spreadsheet
I then created my own spreadsheet-based upon the numbers provided to me by the Freight Farm team and my own research to see if it would be feasible from a business perspective. There are some numbers included in this spreadsheet which I will talk about later in the article.
LGM Calculator Tab 1
LGM Calculator Tab 2
LGM Calculator Tab 3
After building my spreadsheet, I determined that the only way for me to make money and pay off any debt in Canada with the CAD-USD conversion rate was to purchase a used unit through the iGrow Group. Different brands of hydroponic growing sea-cans and units ranged from 55,000 USD to 150,000 USD depending on the model and year.
Step 3: Business Plan
After creating my spreadsheet I called other Freight Farmers within Canada to ask about their experience running a company. The expertise of people who already operated their own Freight Farms was extremely insightful because they were able to share their difficulties, what they learned, and what I should anticipate. This helped me write a modified version of the business plan below. I decided to call my company KLC Greens.
KLC Greens Business Plan
KLC Greens is a hydronic farming company that would provide the highest quality local produce to the local industry in Canada 365 days a year! It has the capability to turn around over 1000 heads of lettuce or other leafy greens after a 6-week initial phase.
Demand for local produce is booming and KLC Greens would be perfectly positioned to increase the availability of “hyper local” foods for our customers. By utilizing the very best hydroponic farming technology, Freight Farms’ Leafy Green Machine would grow high value cash crops year-round with consistent high quality that is not possible with outdoor farming in the local community.
Marketing Strategy:
KLC Greens marketing strategy would focus on selling their produce to wholesale grocery stores, a retail CSA program, and local restaurants that want the best produce available year-round. KLC Greens has been in contact with different local grocery stores that have shown interest to our product.
Company Description
KLC Greens is a hydroponic farming company that would provide fresh produce to the local vegetable industry in Canada. We will grow different lettuce varieties for restaurants, wholesalers, and retail through CSA that would aim to support the growing local food movement in Canada.
Our world is changing. More people than ever are now living in tightly populated, urban areas, and there’s an increasing demand for locally grown and sustainably produced food. People want to know the story behind the meal on their plates. And even city dwellers want their food to be fresh and full of nutrients, not pre-packaged and shipped from thousands of miles away.
Our climate is also continuing to evolve. Extreme weather conditions are becoming more common, and land and water are becoming scarcer. Large-scale food production and distribution has had a significant impact on the earth’s ecosystem, and it’s continuing to affect our water levels and biodiversity.
Transparency is key to understanding where and how food is produced and KLC Greens is committed to improving transparency in the produce industry by growing ‘hyper-local’ produce in one of the most innovative hydroponic system available, Freight Farms’ Leafy Green Machine. Growing in the Leafy Green Machine enables us to provide unparalleled transparency in all operations from seed to harvest and provides our customers with the certainty that they are eating, receiving, buying Okanagan produce grown via the best agricultural practices available.
Our Product
We will initially grow different lettuce varieties and sell it to wholesalers and restaurants at an expected price of 2$ per head of lettuce. This type of cash crop takes 6 weeks to reach maturity and we estimate harvesting 4044 heads per month. For details on harvest volumes, see Appendix A for revenue calculation data and assumptions.
Our lettuce is hyper-local, meaning that our lettuce is grown in the community where it will be consumed, and is thus considered a premium and differentiated product by the market, commanding a higher price point than even organic foods. This differentiation is what enables us to command the higher price of 2$ as opposed to the general wholesale price of 1.50–1.75$.
Market Breakdown
KLC Greens will specifically target high-end restaurants in the Canada area. Our target customers are chefs and restaurant owners in the farm-to-table movement who already provide information to customers about their sourcing policies and chefs and restaurant
owners in the ethnic cuisine space who require specific fresh greens for their dishes that are not available year-round through traditional farming.
Our competitors in the restaurant industry include direct competition from other local farmers, and wholesalers who source exclusively from local farms but are constrained by seasonality, and indirect competition from larger wholesalers who bring in low cost produce from around the world and in all seasons. KLC Greens will compete by providing “hyper local” produce to the restaurant industry regardless of season.
KLC Greens plans to sell its lettuce into the wholesale market in Canada. We will target smaller wholesale companies who specialize in local produce as opposed to working with the larger, national companies where we will struggle to meet sufficient volumes to be a relevant partner.
Our competitors for local wholesale are other local farmers growing vegetables and different varieties of vegetables (traditionally or hydroponically). During the summer months, traditional farmers will be KLC Greens greatest competition as the supply of local Lettuce is significantly increased and the price is driven down. During the non-summer months, regional, large-scale hydroponics producers are the greatest competitors for KLC Greens. In both instances, KLC Greens will rely on its freshness and consistent availability to appeal to our wholesale partners.
KLC Greens will sell its produce in farmers markets in the Canada area. We will target markets in middle to upper-middle class areas in order to gain access to consumers who are dedicated to eating fresh, local produce and have the disposable income to purchase our premium Lettuce.
Our competitors fall into two categories, direct competitors from the farmers market community and indirect competitors from outside the farmers market. To date, KLC Greens does not know of another hydroponic farmer participating in farmers markers in the Canada area, meaning that our primary direct competitors will be local farmers growing Lettuce in the traditional way. Outside of the farmers market, our competitors are traditional food retailers who may or may not stock local Lettuce. In both instances, KLC Greens has an advantage as we can differentiate on freshness and availability all year.
KLC Greens will also target middle to upper-middle class customers who already participate in CSA programs and demonstrate a commitment to eating local produce.
While most of KLC Greens competitors are not “hyper local” producers, it is worth briefly discussing the different methods of urban farming that may eventually enter the market as direct competitors. The four main competitors to KLC Greens Leafy Green Machine growing method in the urban farming space are indoor warehouses farms, urban greenhouses, rooftop farms, and small plots of land transformed into farms. Each have their benefits, however KLC Greens firmly believes that the Leafy Green Machine provides the best combination of protection from natural elements, cost effective production, and reliable crop yields that will make urban farming a profitable venture now and into the future.
Competitive Advantage
KLC Greens main competitive advantages are the farming technology we will use to produce our lettuce and the support of a network of small business hydroponic farmers.
We are in the process of purchasing a Leafy Green Machine from Freight Farms to use as our primary farming tool. A Leafy Green Machine is a turnkey hydroponic farm built inside of an insulated shipping container, enabling it to produce fresh vegetables in any climate for a full 365 days per year. To help ensure success, the Leafy Green Machine is equipped with sophisticated environmental controls which allow KLC Greens to easily grow consistently high-quality lettuce while simultaneously eliminating the guesswork inherent in traditional farming. The Leafy Green Machine only requires 20 hours a week to operate.
In addition to the benefits of the Leafy Green Machine itself, our purchase of a Leafy Green Machine provides us with access to the many resources Freight Farms offers to its extensive and ever-growing network of small business farmers. Freight Farms’ commitment to KLC Greens success includes:
· Comprehensive in-farm and online training
· A resident plant expert who is available to all beginning farmers
· Monthly shipments of customized nutrients and seeds
· Software designed to optimize harvest yields and allow remote monitoring of crops and control of the Greenery
· And most importantly, access to Freight Farms’ very active network of small business farmers who are available for assistance and advice
The strength of the Freight Farms network cannot be overstated. Each small business farmer has faced similar business challenges to those that KLC Greens will inevitably face. By leveraging the solutions of fellow Greenery farmers, KLC Greens can significantly reduce the risk associated with a new venture and move through challenges quickly and successfully.
Marketing and Sales Plan
KLC Greens sales plan is to target Restaurants, Retail (CSA) and wholesalers. Our company will target chefs and owners of high-end farm-to-table restaurants who have already demonstrated a desire to provide customers with transparency in food sourcing. Our Retail CSA program will target middle to upper-middle class customers who already participate in CSA programs and demonstrate a commitment to eating local produce. KLC Greens will also target wholesalers who are looking for consistent quality produce that can be supplied year-round.
KLC Greens has discussed our hyper-local lettuce with Natures Fare, Sysco, and Valley Green Foods and they are very excited about the possibility of buying year-round, local lettuce.
In order to obtain customers KLC Greens will implement the following marketing strategies of utilizing digital marketing tools, word of mouth, social media campaigns, and attending local regional industry events. KLC Greens will use a combination of digital marketing, via add words and a company website, and networking at industry events to identify and network with farm to-table restauranteurs, grocery chains and wholesalers. We will operate a booth at local conferences to better spread the word about our hyper-local lettuce, give potential customers the opportunity to try the lettuce for themselves, and direct further inquiries to our website for more information about the benefits of hydroponic produce.
KLC Greens will have a variety of different packaging for products depending on industry or consumer needs. If wholesalers require clam shell or hard plastic containers for packaging, our business will source that out. KLC Greens will package its lettuce in grams or kg in either rectangular clamshell packages or hard plastic containers for it’s wholesale partners.
Management Team
Key Partners:
· Accounting/Tax Partner: TBD
· Legal Advisor: TBD
· Insurance Provider: TBD
Use of Funds
KLC Greens is requesting $150,000 CAD for the purchase, transportation, and installation of a Greenery and for the cash flow necessary to get started. In addition to the requested loan amount, Farm Credit Canada has granted KLC Greens 80% of the funds to purchase the Leafy Green Machine. The 80% of the funds provided by Farm Credit Canada would be paid back to the loan.
A detailed breakdown of our planned use of funds is below:
· Greenery Purchase: $88,000
· Greenery Transportation: $9000
· Customs Tax (5%): $4375
· Greenery Installation: $3000
o Leveling: $1000
o Electric: $1000
o Plumbing: $1000
· Training: $4000
o Cost of training: $2500
o (if applicable) Cost of flight to Boston: $1000
o (if applicable) Cost of hotel in Boston: $500
· Business Materials Purchase: $1000
Financial Projections
KLC Greens financial projections are derived from the proven operations and profit models of fellow Leafy Green Machine small business farmers. Based on their experiences, collected, and consolidated by Freight Farms, we have constructed the following financial projections forecasting our first five years of operations.
Key Assumptions of Projected Financial Statements
· One month is 31 days (the Leafy Green Machine operates every day) or four weeks
· Year 1 begins on the day of Leafy Green Machine purchase
· Tax payments are not included in our calculations
· KLC Greens is a cash-based business so we will not offer terms to our customers and pay our bills upon receipt, therefore we have not calculated for Accounts Receivable or Accounts Payable
· We have elected to exclude inventory from our asset calculations however, there will be a nominal amount of work-in-progress and materials inventory at any given time
Step 5: Finding a Freight Farm
After creating my business plan I was ready to try and find a used unit that would fit within my budget through the iGrow Group. The team at iGrow was also super helpful and narrowed down the best unit that was close to where I lived to reduce shipping costs and help pair me with another business owner. I had to WhatsApp call the seller multiple times to ask questions and to inspect the unit due to COVID-19 as I was unable to cross the border. I was able to put a down payment on the unit until I secured further funding.
Step 6: Finding Capital (Funding)
In order to fund my business venture, I had to try and find different avenues for funding which led me on a rabbit trail for approximately two months. At the time of trying to obtain funding I was 22 and had no assets in my name but actually had little difficulty in getting approved funding. The only problem that occurred was that no bank in Canada would give me a bridge loan to bring the used Freight Farm into Canada. I called every single bank over the span of two months that I could possibly think of and tried to brainstorm creative ways to bypass the process. My seller was growing impatient so this led the seller to agree to send the unit across the border on the condition I would pay the remaining 90% and provide letters from the different financial institutions that I was approved for funding. I was able to obtain funding three different financial institutions called Farm Credit Canada, Community Futures, and RBC. Farm Credit Canada is a farm lender that is subsidized by the government which has a special young farmers loan for ages under 40 that can approve loans of up to a million dollars. Community Futures is a community-based organization that helps aspiring entrepreneurs within the Okanagan and RBC is a bank within Canada.
I reached an agreement with Farm Credit Canada after dealing with their business analyst’s and scrutinizing my business plan they would grant me 80% funding for the Freight Farm once it crossed the border, Community Futures would provide the operating expenses and other equity, and RBC would provide me a business account with an operating line of credit. Once I obtained the letters from all three financial institutions I was able to bring the Freight Farm across Canada.
Step 7: Logistics, Logistics, Logistics
Growing up in the Okanagan Valley in Canada which has an abundance of agriculture land and plenty of farming, I did not think I would have such a difficult time finding a place to put the Freight Farm. I reached out to numerous farmers, tried my contacts, and tried door knocking to try and find some land. What I found was that majority of old farmers did not want the hassle of having this on their property, did not understand the technology or it was not worth their time for the money. Being on a budget and knowing where I wanted my profit margins it was proving to be quite difficult. The Leafy Green Machine I was purchasing also required a certain power supply, access to water and it has to be leveled. If the land did not have these pre-requisites I would have to pay to have a sub-meter installed, the piping for water, and a contractor to have the unit leveled.
I ended up using a service called Young Agrarians which is a farmer educational resource network for new and young ecological, organic, and regenerative farmers in Canada. They had a local representative that assisted me with their land matching program and helped guide me through making a lease agreement. I ended up finding a landowner by door knocking who would allow me to put my Freight Farm on his land for a reasonable price and had the Young Agrarian Organization help build the lease agreement.
Step 8: Incorporation and Accounting
Due to my limited expertise and from the wisdom of other mentors I thought it would be best to get the advice from an accountant and lawyer to help me best set up my business. I know from other experiences that the CRA is not the most forgiving and can cause major headaches if you do not submit the proper paperwork. I consulted my local accountant where he advised me on the pros and cons of doing a sole proprietorship or incorporating and helped draft me a letter to my lawyer. I chose to incorporate and then sent the letter to my lawyer who set up the business to best suit my companies needs. A few weeks later KLC Greens was approved and incorporated.
Step 9: Website and Logos
While I was trying to find suitable land and was waiting for my business to be incorporated I decided to design my company logo and build a website. I utilized Fiverr as a platform to build my logo as it cost 60 CAD and was created within 48 hours. These were some of the designs created within 48 hours.
To build my website I decided to go through Wix. I used Wix because it was the most reasonably priced 25 USD and it had the best functionality for what I needed. I was able to create this website.
Step 10: Apply for a City Business License
Applying for a city license was an easy process as there was an online portal where I had to describe my business and what I was planning on selling. The estimated time to obtain a response was approximately 48 hours. I contacted my local city a few months prior to ask if there would be any concerns with having a Freight Farm within the city limits. So I expected my business license to be approved without any obstacles.
Step 11: Customs Broker/Shipping/Crane
While completing the last few steps I had to find a customs broker that would deal with the transaction so that the Freight Farm would come across the border without any difficulty. I also contacted numerous shipping companies with the IGrow Group to find the best deal. Once this was secured I could then schedule the crane companies in the seller's city and my home town. Now that everything was set, my Freight Farm was scheduled to come in three weeks' time.
Step 12: Bureaucracy
My assumption that obtaining a city business license was going to be easy proved to be wrong due to my city’s bylaws and bureaucracy. My application was forwarded to the agriculture department, the city planner, and the building inspector where I was met with the following response. I had numerous conversations about if there was any variance that could happen and how someone at the city three months ago told me they did not see anything wrong with my Freight Farming idea.
Hi Connor,
I was forwarded your email to help answer. The Planning Department and ALC both allow hydroponics to be grown on site (A1/ALR), however, the sea-can is not permitted. We only allow sea-cans/shipping containers on a permitted basis if they meet BC Building Code, which will require an engineer or an architect to make the sea-can structural sound. Sea-can’s are not permitted structures and won’t be given a Building Permit unless they are altered to meet the BC Building Code.
Please let me know if you have any other questions, I’m happy to help.
This was my response to the email above
To whom it may convern,
I talked with an associate at the city of Canada about three months ago about my business plan and any concerns I should foresee in the future, this associate saw no problems with my business and freight farm being in Canada. When I went to apply for a business license a week ago I ran into a few hurdles with the City about the freight farm meeting the BC Building Code and certain bylaws and obtaining a building permit. My understanding was that this container would be deemed a temporary unit on ALR land and should not need a building permit.I have reached an agreement with the business license team at the City and planners that this will be deemed a temporary structure for 6 months (as it can be moved readily at any time).
My container will be delivered in the next two weeks and I did not foresee these hurdles and I am looking for guidance on what to do next. I am a young entrepreneur and have taken a loan to start this business and would love to reach an agreement with the City and make the necessary legal changes to make my business work. I really appreciate how supportive the City has been and the amazing staff I have dealt with.
I have attached a pdf describing the leafy green machine, as well as the bylaw pdf on steel containers.
Here was the city’s reply;
Hi Connor,
I see from the web site link that you provided that this product comes from a USA based manufacturer. Do you have any support documentation from the supplier/manufacturer that references a Canadian standard for the electrical system, water system and building standard(s) that these are built to? We will require this information as part of a Building Permit & Plumbing Permit application along with a site plan showing where this container will be installed on the property
The bulletin that you have copied and referenced as allowable under exception, clearly identifies the exception for the use of the container as storage and not as an occupied/semi occupied building for the production of plants with a dedicated water system and electrical system. The British Columbia Building Code (2018 edition) is the Provincial standard that needs to be meet once the structure is being used as a building, which is what you are proposing. The A277 standard in BCBC 2018 is for factory built units, similar to modular homes that are factory inspected for compliance during construction and certified as compliant. The storage container can be stored on the site if approved by City of planning staff for 6 months, but would not be allowed connection to city water or electrical without meeting the minimum standard set by BC BC 2018. I would suggest that you reach out to the modular factory representatives to see if they can have a factory inspector come to do an on-site evaluation of the container unit to certify it or help provide information to cross reference Canadian to the USA based standards, so that you can apply for a building permit. https://www.kelowna.ca/homes-building/agricultural-land/dwellings is the link to the requirements for Building Permit application. A plumber will be required to apply for a plumbing permit if/when the building permit is issued and a proper back flow preventor will be required to protect the city water source.
This process may seem overwhelming but is no different than importing a USA built car into the Canadian market. The car would need to meet the standards set in Canada for the car to be registered and used in Canada. If the USA company has built these containers to meet or exceed Canadian standards and can prove this with valid documentation, the application process should be straight forward. An application for building permit can be made at 2nd floor city hall and the permit would be for an accessory building on farm land.
This response led me on another rabbit trail of trying to figure out if the Freight Farm I was purchasing would meet any of the building standards in Canada and so forth. At this point in time, my container was two weeks away, I had already purchased all my supplies for the Freight Farm and was going to sign my lease agreement. Freight Farm’s provided me with the following information below through an email and was able to confirm their shipping containers were ISO certified.
All LGMs are upcycled reefer containers. What this means is that they were previously used to ship produce to and from other countries. Once the refrigeration unit no longer worked, they were decommissioned. We would remove that unit, and retrofit our equipment. I bring this up, because the container itself will likely have some dents and marks from its usage as a freight container. This does not impact the structural integrity of the container at all. We have frequently had these container re-certified to be seaworthy, and safe for use from a structural standpoint. Additionally, the company that would have manufactured the farm has a number of certifications (CE, UL, etc.) that would apply to the actual assembly.
With this information, I called a few inspection agencies about what it would cost to bring the Freight Farm up to the BC Building Code or CSA standards where I got numerous replies saying it would cost thousands of dollars and be a very time-consuming process. On top of this, I would then have to be certified by the local building inspector and make sure the Freight Farm was conforming to any local bylaws.
Where it all went wrong
Just as I was confident about my business and thought I had everything prepared, I was hit with the bombshell from the city about bringing the container up to the BC Building Code and the numerous inspections I would have to go through. Also last minute the landowner of the farmland I was going to lease decided he did not want me on his land anymore or to sign a lease. This led me to call off the shipment 10 days before my container was supposed to arrive which caused me to call of the shipment. From my further conversations with the BC Building Inspectors and other consultants who specialized in shipping container homes, they said that any other Freight Farms located in BC that were not CSA approved or up to the BC Building code were illegal. They further elaborated that the only reason they were operating was that the local city or bylaw was turning a blind eye. This was the turning point where I had to decide if the current risks were worth taking with the knowledge that it would cost much more than expected to get the Freight Farm certified and if I didn’t it could be shut down by the city. I went back to crunch the numbers and realized I could not financially risk having the Freight Farm nonoperational for a few months due to the loans payments from the bank. I could not wait to have my container certified by the proper governing bodies and inspections to take place. This led me to painfully decide to not pursue my business plan anymore. I had to contact my seller and the IGrow Group about my situation and unfortunately, three months' progress was now void.
Where I Failed
I did not properly do my due diligence in contacting all the necessary channels in my local city to ask about the local bylaws. I trusted one individual's opinion at the city who did not have the proper knowledge to give me the advice that I relied on.
I did not think of the construction standards of the Freight Farm at the early phase of my business plan. This led to more hurdles when I was asked for information by the city.
I put a 10% down payment on the container before I had secured funding from other financial institutions. This caused the process to take longer than expected and caused my seller to wait over two months to get my finances in order only to have to cancel last minute.
Due to my limited assets, I had to borrow from numerous financial institutions to obtain the financial capital to purchase the Freight Farm. In the last two weeks, before my Freight Farm was expected to arrive, RBC called to inform me that there was too much conflict between the financial agreements between Farm Credit Canada, Community Futures, and RBC. This caused me to have to re-negotiate all my letters with my lenders delaying the purchase further.
I did not sign a lease agreement before arranging the shipment of the container causing the landowner to back out the last minute.
I purchased supplies for the container before it arrives.
I rushed the entire process in three months, leaving little time to carefully think out everything.
What I learned
Before starting the process make sure you know what your city’s bylaws are and talk to a few local representatives to make sure the information you are being told is true.
Read the bylaws to ensure your Freight Farm is up to local standards.
Obtain financing early on before contacting a seller if you have limited assets or can only afford a small down payment.
Make sure that if you borrow from numerous financial institutions there is no conflict of interest between them if they require equity of your Freight Farm until the loan is paid off.
Sign a lease agreement from a landowner, do not go off of their word.
If you want to disregard the city bylaws the best scenario would be to know someone who has land or own it yourself. That way you can hide the Freight Farm and won’t have any complaints, thus reducing the risk of your business being shut down in British Columbia.
Have more certainty of your business before purchasing supplies, creating logos, or a website.
Leave more time to think through each step, because once you are in the chaos it is harder to take a bird’s eye view of your business
Do not be dissuaded by hurdles that come out of nowhere, this is a natural occurrence in business. Learn how to navigate them and reflect on how to make sure they do not happen again. I went through what seemed hundreds of hurdles and learned how to navigate them. Even though I had to decide to give up in the end it was due to huge financial risk and my limited access to capital. The risk of not running my business for four months while making bank payments and the uncertainty of the financial amount to bring the Freight Farm up to BC building code were my deciding factors.
You learn 110% more when you stick your neck out and go through the process. Going into business is not easy and requires a certain mental fortitude and resilience.
Know when to give up and know when to keep on persevering. At certain times you may feel like giving up but that is also where the most learning can be achieved and later on you’ll laugh at the thought that you almost gave up. The flip side is don’t let your ego cause you to make bad business decisions, use logic, and periodically review your business plan and current state of affairs.
Even though I failed to start my company the amount of learning I went through the last three months was invaluable.
Conclusion
My hope is that this article will help the next entrepreneurs who embark on purchasing a Freight Farm and help them build off of my experience. I still believe there is a strong business case for a Freight Farm within my community but currently, I lack the financial capital and political power to cut through the bureaucracy. I hope my three months of trials and tribulations will save you time or help you in your journey.
WRITTEN BY
Connor McGoran
Edumacated Writer, Aspiring Blogger
Technology Farming Hydroponics Farming Startup Entrepreneurship