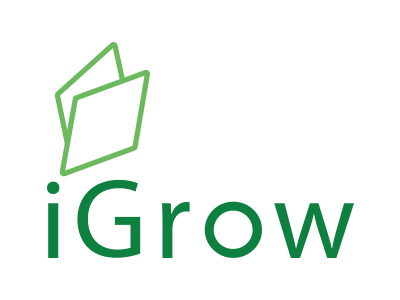
Welcome to iGrow News, Your Source for the World of Indoor Vertical Farming
Is CEA-Grown Produce REALLY Better For You?
As a lifelong farmer - one who has grown commercially using conventional field techniques, organic soil methods, as well as Controlled Environment ("CEA") technologies, I hope to shed a bit more light on the subject. Maybe you'll like what you hear, maybe you won't. But in either case, I'd love to hear from you
August 18, 2019
Joe Swartz
Vice President/Lead Horticulturalist at AmHydro
I get this question a lot.
More than you might think!
Strong opinions are plentiful.......and misinformation abounds.
As a lifelong farmer - one who has grown commercially using conventional field techniques, organic soil methods, as well as Controlled Environment ("CEA") technologies, I hope to shed a bit more light on the subject. Maybe you'll like what you hear, maybe you won't. But in either case, I'd love to hear from you.
In recent years, the general public has been inundated with media stories about the various Controlled Environment Agriculture ("CEA") technologies. Stories of monumental financial investments and "futuristic" growing technologies seem to have permeated every news cycle and public interest storyline. A quick online search of terms such as "food miles," "climate change," "sustainability," or "urban farming" will likely fill your screen with headline after headline about the latest quest to produce more and better quality food. In fact, if that weren't true......you'd likely not be reading this now.
"Indoor food factories? Shipping container farms? Automated greenhouses? Outdoor fields?..........So what really does grow the best food for myself and my family?"
The simple fact is this:
Whether a crop is grown using CEA techniques in a greenhouse, outdoors in a field, or on the Moon, for that matter, is NOT what will determine it's nutritional value.
The actual nutritional content of any crop is simply a function of 3 basic parameters -
3 and only 3!
They are:
- 1. The particular crop/cultivar - Every plant has a genetic predisposition and physiology - the grower has control of external parameters, but not the internal ones.
- 2. The physical environment the plant was grown in - This is either supplied by nature and/or the grower and includes light quantity and quality, temperature, humidity/ VPD, C02 levels, air movement, etc etc)
- 3. The nutritional/microbial environment available to the plant's root zone - This includes not only the nutrients readily available to the plant, but also root temperature, pH, dissolved Oxygen and the beneficial microbial life in the root zone. This microbial flora is constantly stimulating plant growth, metabolizing waste products, breaking down chemical compounds, and inhibiting harmful pathogens. People tend to underestimate the importance of managing the rooting environment and developing and maintaining these microbes.
That's it! Nothing more and nothing less.
However, even a slight deviation (be it a natural occurrence of an error in your growing) can have HUGE consequences in your crop performance.
This is why many high value producers are moving into using Controlled Environment Ag (“CEA”) growing techniques. CEA allows them to produce crops that are undoubtedly more nutritious and flavorful than many of their conventionally grown counterparts. The ability to optimize these 3 factors is unmatched in appropriate CEA growing techniques - mind you, there are some amazing growers out there on conventional farms, growing fantastic and nutritious food too!
Proper design and application make all the difference in the world!
Using CEA, we can select appropriate varieties (selected for taste and nutrition, rather than the ability to ship thousands of miles and sit on supermarket shelves for days!), provide a near-perfect growing environment, and manage both nutrition and biological activity in the root zone to a very high degree. This also underscores the need to utilize APPROPRIATE CEA technologies! Greenhouse hydroponic, indoor vertical, shipping container farming and more are NOT created equal! Each situation is different, so the choices of the correct technologies are of critical importance.
So, when I am asked, "Is CEA-grown produce really better for you?" I always answer - "It's not quite as simple as that." However, when considering the above-mentioned factors, it is certainly MY preferred method to grow the highest quality, most nutritious and best tasting produce.
There are many ways to grow nutritious, healthy, and sustainable food. This is just one of the many great techniques we use. The more that we can do to support and nurture the PLANT........the better that it will provide for US!
Joe Swartz
VP AmHydro Joe @Amhydro.com
https://twitter.com/HydroConsultant
https://twitter.com/amhydro
https://www.instagram.com/joeswartz1325/
https://www.instagram.com/amhydro/
Published by
Joe Swartz Vice President/Lead Horticulturalist at AmHydro - 35 years as Controlled Environment Ag Consultant and Commercial
#hydroponics #sustainability #green #urbanfarming #urbanag #farming #food #CEA #indoorag #indoo
HAREDI HYDROPONICS: Technology And Sustainability Meet At The Diaspora Yeshiva
“Probably many of these guys have never had kale before,” comments Robin Katz, founder and CEO of Start-Up Roots, the nonprofit that runs hydroponic gardens here and at two haredi (ultra-Orthodox) schools in Jerusalem
JACOB SCHONZEIT checks the roots of greens growing in the hothouse. (Photos: Jordana Benami)
• JORDANA BENAMI
AUGUST 16, 2019
In the courtyard of a 2,000-year-old stone building on Mount Zion, a sign taped to a tiny black door announces the unlikely scene found within: The Diaspora Yeshiva Hydroponic Garden.
Inside, two agronomists in white shirts and black kippot tend tiers of vibrant kale, basil and romaine lettuce. The strings of their tzitzit gently sway as they climb up and down, adjusting nutrient and pH levels, preparing new seedlings and checking lights and filters.
The hyper-local and hyper-fresh greens, grown in a soil-less medium bathed in nutrient-enriched water, will be harvested and carried across the courtyard to the yeshiva’s kitchen to find their way into a variety of dishes.
“Probably many of these guys have never had kale before,” comments Robin Katz, founder and CEO of Start-Up Roots, the nonprofit that runs hydroponic gardens here and at two haredi (ultra-Orthodox) schools in Jerusalem. “I’ve had some kids look at let- tuce and say, ‘Are you sure this is kosher? I’ve never seen it in my house.’”
Katz, a Chicago émigré, is a lawyer and teacher by profession. Since 2015, her organization has been installing hydroponic systems in schools and providing a multidisciplinary curriculum that teaches how to care for the produce, how to incorporate it into nutri- tious meals and how to monetize the bounty. A photo-journalism element allows the students to create visual documentation of the growth process.
The Diaspora Yeshiva setup was donated by Irving Backman of Massachusetts, an international benefac tor of sustainability and advanced technology initiatives through his DATT (Developers of Advanced Technology Today) group. Backman’s grandson, Rabbi Yaakov Kent, is the son-in-law of the Rosh Yeshiva of the Diaspora Yeshiva and the study partner of Katz’s son, Rabbi Zechariah Kaplan, at the nearby Yeshivas Bircas HaTorah.
“Irving Backman & Associates sent over the equipment for a hydroponic garden at the Diaspora Yeshiva, and Mr. Backman’s assistant, Ameth Alzate, asked me to help shepherd it through customs,” says Katz, who had worked with him previously.
With Backman’s blessing, she took the project under the wing of Start-Up Roots, and the garden was inaugurated on her birthday, June 12.
The site is professionally managed by Ari Waldman, chief operating officer of Start-Up Roots, with daily assistance from Jacob Schonzeit, another study partner of Katz’s son at Bircas HaTorah. “Jacob had a background in permaculture, so we trained him in hydroponics,” says Katz.
Diaspora Yeshiva students, who range in age from 17 to 70-plus, may choose to spend an hour or two every day helping to tend the system.
Daniel Levin, 36, found out about the garden when he saw Katz carrying supplies in the courtyard and offered to help. Now he volunteers regularly.
“When Robin showed me what was happening here, I thought it was cool because in South Africa I lived on a farm where we tried growing different plants and trees. It also combines other experiences I’ve had working with electricity and water pumps and salts and nutrients. We’re looking at what works well and could be most viable to grow efficiently and that would most benefit the yeshiva menu,” says Levin.
SEEDLINGS ARE started in a growing medium called rock wool, and incubated before being planted in the trays.
RABBI YOSEF GOLDSTEIN: Spending time in the hydroponic garden ‘helps our students get close to God.’
KATZ SEES all the Start-Up Roots projects as a strategy toward ensuring a healthier future.
“Chemical pesticides are killing us,” she says. “Israel has the highest chemical pesticide usage in the OECD.
We also have a high poverty rate and a high malnutrition rate, and we’re right behind America with a rising obesity rate. I really believe that schools can be a great agent for change.”
Katz discovered hydroponics several years ago and realized it could solve multiple problems at once: The veggies provide vitamins, minerals and fiber often missing in impoverished families’ diets; the plants don’t leave carbon footprints since they are grown on premises and aren’t trucked in; and the students work- ing in the enterprise gain valuable skills they could use to earn a living.
Moreover, during the shmita (agricultural sabbatical) year, when most haredi Israelis buy only imported pro- duce, the greens raised in the school gardens can be cultivated, harvested and consumed without worry because they don’t grow in the ground. The absence of soil and the indoor environment adds another benefit year-round in keeping the plants largely insect-free.
START-UP ROOTS CEO Robin Katz with the greens growing in the hydroponic garden at the Diaspora Yeshiva.
“You don’t need chemical pesticides. The idea is to control the environment so that insects aren’t such a problem,” says Katz. Before entering the growing area, all visitors cover their shoes with paper booties so as not to track in bugs or other contaminants.
She also explains that in a water-stressed region, growing in water actually makes good ecological sense.
“Hydroponics saves 90% of the water of regular agriculture because the water goes directly to the roots and not into the ground,” explains Katz.
Speaking of roots, the word in the name of the organization has more than one layer of meaning. “Many children think that lettuce comes from the grocery store. They have no concept of the chain behind it. So we try to connect kids with the source of their food,” says Katz.
Beyond that are the roots of Torah teachings involving agriculture. Religious schoolchildren learn the laws of tithing, for example, but rarely or never have the opportunity to pick fresh produce and perform the ceremony. It’s all been done at a distant packing house.
And on a more spiritual level, Katz adds, “By watching how the tiny seeds develop, kids learn that the universe is more complicated and bigger and more awesome than they ordinarily take time to stop and think about. They learn that if they don’t put in the effort nothing will grow, but there are also aspects that are beyond their control.”
Rabbi Yosef Goldstein, spiritual adviser at the Diaspora Yeshiva and son of its founder, says spending time in the hydroponic garden “helps our students get close to God.
It’s a way to clean their minds and to be surrounded by nature. Even learning next to the plants for an hour in the morning helps them grow spiritually. I love to come in here and see what’s growing and breathe in all the oxygen. And afterward, we get to eat this healthy nutritious food.”
GOLDSTEIN, WHO is also a practitioner of Chinese medicine, hopes the garden will raise herbs in the future. In only a few months, the site has produced vegetables including cucumbers, radishes, green beans and chard.
“We have 200 students from all over the world from many different backgrounds, and I believe this project can also be a way to build a future source of parnassa [income] especially in the shmita year,” adds Goldstein. “It will be nice for religious people to go into agriculture.”
Levin says that volunteering in the garden “gives me a new dimension of looking at what I am learning in the Torah.”
The connection between faith and farming is entrenched in Judaic sources. The 13th century Tosafist Talmudic commentators expressed it like this: “The farmer who sows seeds places his faith in the life-giver of all the worlds, for he trusts that God will provide all that is needed for his crops to grow.”
The Torah also admonishes against waste, Levin points out. “When you know where food comes from and how much goes into growing something that takes five minutes to eat, you are motivated not to waste anything.”
Katz extracts additional lessons from the hydroponic growing experience.
“In an indoor controlled environment, we’re putting nutrients directly into the water exactly what the plant needs – and we measure it every day along with the pH of the water because that affects how the plants absorb the nutrients,” she says.
“We use that as a metaphor for absorbing information in the learning environment. We encourage kids to think how they can optimize their own ‘pH level.’ They see that if you take care of something it thrives, and they can apply the same principle to themselves.”
Aside from the project at the Diaspora Yeshiva, Start-Up Roots has established hydroponic gardens at two haredi girls’ schools in Jerusalem. The schools’ science teachers present the science part of the curriculum, while a Start-Up Roots dietitian presents hands- on sessions to enable students to discover the impact of the food choices they can make.
“The students enjoy the nutritious food that they are growing, which enables them to incorporate the greens into their own diets in tasty ways,” says Katz.
Shiran Iluz, vice chairman of the IDC Entrepreneurship Club, came to one of these schools to help the students develop a viable business plan around the veggies.
“One girl thought of selling a green drink. Initially, the others thought it sounded awful but when they tried making it with our nutritionist, they discovered that they loved it. Then they named it and learned how to pitch it and sell it to their classmates. They had to learn how to network with kids outside their social circles, and this project totally changed the social dynamics of the school.”
In the fall, Start-Up Roots will implement a hydroponic garden at a pluralistic school in the Sharon region.
“Food is a great unifier and our environment is a great unifier,” says Katz. “I’m very happy that every segment of Israeli society is embracing our initiative and our curriculum.”
CEA Food Safety Coalition Creates Board of Directors, Elects Officers And Seeks Members
The CEA Food Safety Coalition, comprised of leading controlled environment leafy greens producers, recently completed the formation of its governance structure and is taking steps to accept new members
By urbanagnews - August 13, 2019
Press Release – New York, NY – The CEA Food Safety Coalition, comprised of leading controlled environment leafy greens producers, recently completed the formation of its governance structure and is taking steps to accept new members. Controlled environment agriculture (“CEA”) is agricultural food production in environments that are indoors (such as in greenhouses and vertical farms) and controlled, providing crops with ideal growing conditions and protection from outdoor elements (such as weather and animals). The Coalition’s objective is to establish food safety standards, educate, and protect consumer health.
The Coalition, a tax exempt 501(c)(6), recently filed its articles of incorporation, adopted bylaws and elected the following individuals as the initial members of its board of directors: Michele Kubista (Revol Greens), Paul Lightfoot (BrightFarms), Christopher Livingston (Bowery Farming), Daniel Malech (Plenty), Marc Oshima (Aerofarms), Jack Seaver (Plenty), and Paul Sellew (Little Leaf Farms).
In addition, the Coalition elected the following officers:
Board Chairman – Paul Lightfoot (BrightFarms)
Acting Executive Director – Jack Seaver (Plenty)
Board Vice Chairman – Marc Oshima (AeroFarms)
Board Secretary – Christopher Livingston (Bowery Farming)
Board Treasurer – Paul Sellew (Little Leaf Farms)
Until the position is filled permanently, Jack Seaver of Plenty will serve as Acting Executive Director.
“The growing methods in our industry are different as compared to field-grown produce,” said the Coalition’s Chairman Paul Lightfoot. “This coalition provides an opportunity for all brands in the space to collaborate to further protect consumers by establishing standards and sharing insights.” “This is a critically important step in maintaining consumer confidence and supporting the growth of our industry,” he added.
“We frequently get questions from growers and buyers as to what food safety means in a CEA environment” said Dr. Jennifer McEntire, vice president for food safety at United Fresh Produce Association. “We look forward to helping the coalition develop appropriate food safety standards for this growing segment”
The Coalition is developing an enrollment process for admitting new members. All leafy greens growers employing controlled environment methods (including hydroponics, aquaponics and aeroponics), and who are willing to submit to third party food safety auditing, are encouraged to join the Coalition.
Interested parties can contact membership@ceafoodsafety.org. In addition, the Coalition seeks great candidates for a permanent Executive Director, and welcomes applications at info@ceafoodsafety.org.
With Founder Gone, U. Vertical Farming Project's Main Farm Closes, But Forbes Offshoot Will Remain
After two years of operation, the Princeton Vertical Farming Project (PVFP), which introduced students to sustainable farming practices and provided fertile ground for research, has come to an end
By Katie Tam | August 12, 2019
A taste test set up at the Forbes College vertical farm for Akiti's thesis project.
Photo Courtesy of Kor Akiti
After two years of operation, the Princeton Vertical Farming Project (PVFP), which introduced students to sustainable farming practices and provided fertile ground for research, has come to an end.
The PVFP was launched in April of 2017 by Paul Gauthier, who served as an associate research scholar in plant physiology and environmental plant metabolism in the Department of Geosciences beginning in 2012, in a windowless room in Moffett Laboratory. With support from the Office of Sustainability, Gauthier and student collaborators built and maintained the hydroponic vertical farm, where peppers, strawberries, herbs, and other plants were grown only with water and nutrient solutions—no soil.
At the end of June, Gauthier left for Delaware Valley University in Doylestown, PA, where he will start an appointment as Professor of Plant Science. Although an offshoot in Forbes College will remain, the main farm has been shuttered, with equipment in Moffett Laboratory dismantled and placed in storage.
As the global population continues to rise, vertical farming has grown in popularity, as the practice requires less water, space, and energy than traditional farms. Vertical farms can yield several harvests of fresh produce a year, which could help to feed growing urban centers.
According to Gauthier, although many start-ups have tried vertical farming, few have succeeded. Many have been forced to close after a few years due to lack of revenue and funding. In addition, he said, little research has been conducted on best practices, such as how water, nutrients, and the environment influence plant growth.
One of the primary motivations of the PVFP was to identify the problems and challenges associated with the technique and learn how to solve them — much like in traditional agriculture.
“People tend to forget that there is a ‘farming’ in ‘vertical farming,’” Gauthier said. “You are a farmer first.”
To that end, the farm experimented with different techniques, seeking to determine how to feed a family of four by quantifying nutrient usage, testing new technologies, and planting a variety of crops.
Another goal of the project was to create an on-campus “food hub,” where students could gain experience with farming and learn about food sustainability. Gauthier said that he wanted students to understand the commitment and responsibility that vertical farming entails.
“We want to train the next generation of vertical farmers,” he said.
Several students have taken on the burdens of both research and responsibility by conducting senior thesis projects with the PVFP. In the PVFP’s first year, projects ranged from a Department of Ecology and Evolutionary Biology (EEB) thesis comparing environmental impacts of vertical and conventional farming to a Wilson School thesis on the economic costs of running a vertical farm.
In her EEB thesis, Kor Akiti ’19 compared the palatability and nutritional quality of crops grown in the Vertical Farm to organic, soil-grown crops from a local grocer.
Akiti performed several “taste tests” in the Forbes dining hall and Frist Campus Center, asking passersby to taste and rank the produce – kale, peppers, and strawberries – on appearance, taste, and texture. She then asked tasters: which would you buy at the supermarket?
Using a technique called mass spectrometry, she was able to conclude that nutrient profiles of vertical farm and soil-grown crops were similar, but the hydroponic crops lacked visual appeal.
“One of the main takeaways was that the appearance of the hydroponic crops was significantly less satisfying than the appearance of the soil-grown crops across the board,” she said. “If vertical farming is going to be competitive, whether it’s in the context of Princeton, on campus, or in the larger urban market, farmers are going to have to find a way to make their produce more appealing, because appearance is such a critical point of purchase.”
Overall, her findings suggested the complexity of consumer choice and preference, hinting at challenges to come in not only growing crops in vertical farms but also in marketing them.
The impact of the PVFP has been considerable, not only in advancing research but also in contributing to outreach and education.
In September 2018, Gauthier partnered with Hopewell Elementary School in Hopewell, N.J., to develop a farm-to-cafeteria program. The initiative provides students with the opportunity to grow their own fresh produce, almost all of which is then used in school lunches.
Gauthier also co-founded his own indoor farming company, Ker Farms (pronounced “care”), in Hamilton, N.J., which grows and sells a variety of fruits and vegetables. According to Gauthier, the company is also training local educators in the hope of bringing vertical farming to more schools in the area.
“There is no question about it,” Gauthier said. “Vertical farming will be part of our lives.” Thus, Gauthier continued, it is essential that young people know how to grow, interact, and experiment with plants from a young age, so they can be prepared for the future.
Similar concerns motivated the establishment of an offshoot of the PVFP in the lobby of Forbes College in the fall of 2018. This mini-vertical farm was intended as a different kind of experiment – to see how farming could integrate into the daily life of a busy Princeton student, as Gauthier put it.
The conclusion, he said, was that taking care of plants was harder than it seemed.
Kaylin Xu ’22 played a leading role in maintenance of the Forbes College farm, changing the water, checking nutrient levels, and making adjustments to optimize conditions for growth. It was a labor-intensive job, Xu admitted, and although other students cycled in and out to help, she was one of the only people to consistently care for the plants. Xu hopes that the maintenance of the Forbes “farm” will become more communal.
“I want to get more of the Forbes community involved in having a hand in creating this green space, because I feel like that is really unique,” Xu said.
“Unfortunately, students are busy,” Xu continued, making it difficult to find dedicated members to join the team.
Gauthier also emphasized how important it was for future farmers to be dependable. “Plants are like babies,” Gauthier said. Just as a parent cannot ignore the cries of a hungry child, so a plant cannot go without water.
This past year, products from the Forbes offshoot and the main farm were featured in several “Meet What You Eat” dinners in the dining halls, where students could sample fresh produce incorporated into pastas, flatbreads, and more. In the fall, the Forbes farm will continue to grow crops for use in the Forbes kitchen and the Pink House food-share.
“I hope [the vertical farm in] Forbes will continue the spirit of sustainability,” Xu said, as the torch is passed from the original farm.
In his new position at Delaware Valley, Gauthier hopes to continue the work he started at Princeton, reproducing the vertical farm model on a larger scale and developing local projects and collaborations.
Although the Hopewell ES program and the Forbes offshoot will continue, the PVFP in its official capacity has ended – much like the start-ups and companies Gauthier was interested in when he began.
“I would have loved to continue,” Gauthier said of the project. “It’s important to start thinking and finding solutions for the future.” The University was a unique place for such an undertaking, he said, as it allowed for cross-pollination from a variety of fields of study.
“All different departments – computer science, MAE [Mechanical and Aerospace Engineering], EEB, business, architecture – students from all these departments were working on the vertical farm,” Gauthier said. “We can tackle the problem from very different disciplines.”
Gauthier did not rule out the possibility of reviving the PVFP.
“If there is demand, maybe the project will come back,” he said.
Lead Photo: Kor Akiti ’19 poses beside plants at the vertical farm in Moffet Laboratory. Photo Courtesy of Kor Akiti
Artificial Intelligence And Controlled Environment Agriculture
As the role of controlled environment growing increases in agriculture, so does the opportunity for artificial intelligence. But can AI replace the human touch? Kent Gruetzmacher investigates
Kent Gruetzmacher | July 15, 2019
Takeaway: As the role of controlled environment growing increases in agriculture, so does the opportunity for artificial intelligence. But can AI replace the human touch? Kent Gruetzmacher investigates.
As both a process and vocation, controlled environment agriculture (CEA) is intimately entwined with technology. As CEA gets increasingly sophisticated through technological advancements, how these developments will affect horticultural processes and, in turn, world food supplies, remains largely unknown. At the forefront of new frontiers in CEA technology lies artificial intelligence (AI), which can potentially forever change the way humankind procures fresh produce, largely by replacing human labor with mechanized production.
We live in a world increasingly dependent upon, and defined by, technology. This notion rings true in almost every facet of day-to-day life in the 21st century, including communication, entertainment, and work. Similarly, for those living in the Western world, this same technology contributes to meeting our general human needs, as food is readily available for most people at grocery stores and beyond. Yet, our current food subsistence patterns are far from infallible and the technologies that make commercial agriculture possible are falling short on several fronts.
These shortcomings are evident in pesticide- and preservative-laden food sources as well as hungry human populations in less-fortunate regions of the globe.
Over the last few decades, CEA production has grown leaps and bounds in its scale and capabilities. Many believe CEA practices such as urban agriculture and vertical farming will eventually help resolve global food crises. This positive outlook is largely because of technological advancements in “smart” environmental controls and LED lighting, which have made CEA production viable, as well as profitable, on a commercial scale for the first time.
Sophisticated irrigation systems have also drastically reduced the amount of human labor required in propagating crops. For many CEA advocates and technology authorities, AI is the next phase in streamlining and sophisticating agricultural procedure as well as global subsistence patterns.
Why Artificial Intelligence?
There are several reasons why AI has so much potential in the world of CEA. These reasons mainly have to do with notions of horticultural processes and labor efficiency. Today, automation is already an essential element in most CEA growing, and its benefits are related to both consistency and efficiency in operations. For example, smart controllers take much of the guesswork out of troubleshooting environmental issues, while fertigation systems accomplish irrigation in a controlled and effective fashion.
Artificial intelligence has the capabilities to take these advancements even further.
Technology authorities postulate that AI can potentially circumvent human interaction with horticultural processes and garden maintenance almost in their entirety. According to agfundernews.com: “Hypothetically, it is possible for machines to learn to solve any problem on Earth relating to the physical interaction of all things within a defined or contained environment… by using artificial intelligence and machine learning.” The important take away here is the idea AI systems can learn as well as make choices based on the objective constraints that dictate rational human decision making.
Concerning both production and labor, this avant garde theory pushes notions of CEA automation to their absolute extremes. This AI learning concept postulates robots would be at the controls of environmental and irrigation systems that currently require human intervention in the way of fine tuning and decision making. Also, AI could circumvent human error from these processes by removing the human labor needed to grow CEA crops.
While these ultramodern appraisals of AI and CEA cultivation can seem somewhat alarming, many see a real potential benefit in the technology, namely because humans are, well, undependable. The industry is traditionally plagued by labor shortages in jobs that aren’t very attractive to even the most entry-level employees. Many companies, in CEA and beyond, understand the struggles of finding dependable help for their businesses, with tech retail giant Amazon currently employing more than 40,000 robots in its warehouse operations.
In agriculture, there are several robots being developed that can handle more rudimentary CEA garden chores such as leaf pruning. When it comes to AI learning applications and high-level jobs in CEA, it’s worth noting even the most rudimentary human error in fertilization or irrigation can have devastating effects on crops. Large vertical farming companies are aware of this and are currently implementing AI help in certain facets of their operations.
Read also: Automation Options for Outdoor Soil Gardens
Sensors and Data Analytics
Artificial intelligence applications in CEA are entirely data driven — machines both gather, as well as use, this information as the basis of machine learning. This sort of remote sensing, data compiling technology is already widely popular in more advanced CEA operations, especially regarding soil and air sensors. These technological advancements are used to measure moisture levels in grow mediums, and temperature and humidity levels in the air, and give cultivators real-time updates on the working analytics of their operations.
Commercial agriculture operations are taking notions of remote sensors and data analytics to the extreme by way of drone sensing. Some commercial farms use drones to fly over fields of crops and take precise readings of growth patterns and environmental conditions. This data informs growers, in real time, what sort of elements their garden is lacking or burdened with — allowing them to make proactive decisions in counteracting potential problems.
For the time being, drone technology in commercial agriculture is still being utilized to inform rational decision-making in the human mind — but many feel these processes would be integral with informing data matrices in the “minds” of AI machines.
Artificial Intelligence and Machine Learning
Potential advances, as well as drawbacks, of AI applications for CEA can be drawn from current mainstream research — such as with IBM — into the technology’s capabilities regarding commercial agriculture. agfundernews.com reports: “Interviews with some of the IBM project team members … revealed that the team believed it was entirely possible to ‘algorithm’ agriculture, meaning that algorithms could solve any problem in the world.”
While IBM’s claims are grandiose and positive in nature, they are not entirely unreasonable. Major computer tech companies such as Google and Pandora already utilize algorithms to isolate relevant data, make decisions, and cater to human needs. However, all these algorithmic applications depend upon objectively derived, predictable points of data in informing the machine learning process.
When it comes to creating algorithms for agriculture, researchers have been running into countless problems stemming from the unpredictability of the natural world. There are countless variables contributing to weather patterns around the globe; the nuances of these factors are far beyond the scope of human understanding. This notion is relevant because humankind cannot program machines to learn about environmental systems that we don’t yet understand, and AI cannot make the critical step in accounting for anomalous factors in weather or crop production. Therefore, our technology is only as strong as the data we supply it with via our own knowledge.
While issues with environmental predictability that plague AI applications in traditional agriculture may not seem to affect CEA production as intensely, there are still factors that make AI fall short in controlling CEA growing in its entirety. For instance, many greenhouse gardens are still largely at the mercy of Mother Nature and present challenges with anomalous weather patterns.
Similarly, indoor growing operations experience problems with such irregularities as equipment failure and power outages, which only human intervention can fix.
Controlled environment agriculture crop production is only as strong as the equipment and human labor supporting it, so the balance between these two continues to shift under the pressures of new advancements with technology such as AI. This notion presents an interesting crux in modern cultivation processes, as automation can provide a more efficient platform for consistency than with human labor. However, machines cannot account for the rhythms of the natural world or other operational variances.
Many accomplished horticulturists understand the intuitive touch it takes to produce exceptional crops — this intuition comes as a feeling rather than as a form of objective knowledge or data. AI and other technological advancements in CEA growing have their place in today’s horticultural processes, yet cannot match the capacity for creativity explicit in the human mind.
Written by Kent Gruetzmacher
Kent Gruetzmacher is a California-based freelance writer and the west coast director of business development at Mac & Fulton Executive Search and Consulting, an employment recruiting firm dedicated to the indoor gardening and hydroponics industries. He is interested in utilizing his Master of Arts in humanities to explore the many cultural and business facets of this emerging industry by way of his entrepreneurial projects.
"Global CEA Census Ending - Last Day To Participate - Monday July 22"
3 June 2019 (NEW YORK): Global automation specialist Autogrow and New York based Agritecture Consulting are appealing to growers to take part in the inaugural Global CEA Census.
The Census seeks to understand the scale and nature of Controlled Environment Agriculture (CEA) to better determine the roadblocks to accelerating the industry. This includes greenhouses, vertical farms, indoor rooms and hoop or tunnel houses.
Both Agritecture and Autogrow believe a great deal of CEA activity worldwide is not well documented, with data being fragmented and often unreliable, making it difficult to provide support or solutions on a larger scale.
“We do a lot of work with city leaders around the world and the conversations are about how the infrastructure needs to be in place in order to use new technology, drive costs down and operate sustainably. Through the Census we hope to highlight who is growing, what they’re growing, where they are growing and what they need to take it to the next level,” notes Agritecture Founder Henry Gordon-Smith.
“Based on that information both Autogrow and Agritecture can then work closer with governments, growers and city planners on where they can focus their efforts and utilize valuable resources.”
One of the biggest known roadblocks to adoption of new technology today is internet connection on the farm. Without connectivity growers are unable to join the growing trend of cloud-based software and remote access.
Autogrow CEO, Darryn Keiller says “We need to understand whether growers are ready for innovation, and if they aren’t, how we can get them there.”
“New crop production technologies are heavily reliant on growers having multi-modal internet to the farm and commercial grade onsite network infrastructure. If this isn’t addressed, and supported at a government level, then we will see an ever widening ‘digital divide’ at the farm level.”
“All the best technology in the world is of no use if it can’t be connected to the farm.”
Additionally, the Census hopes to record best practice solutions to share across the industry.
“There are some amazing growers around the world who are using creative solutions for things like water usage, labor shortages, energy consumption or improved marketing activities using social media. We want to capture that and share to the wider community. Only by banding together can we hope to push our industry forward in a positive way,” explains Henry.
The Census will run until 22 July with a report on the findings published in September. All submissions will remain confidential and only anonymized data will be reported.
WIN A TRIP TO NYC: Submissions will also go in a draw to win a trip to New York to attend this year’s NYC AgTech Week running from 21-26 September.
Take the survey, enter the draw and have your say -
https://www.surveymonkey.com/r/global-cea-census
Survey Terms and Conditions - https://www.agritecture.com/cea-census-terms-conditions
About Autogrow
Autogrow leverages the power of technology, data science and plant biology to provide indoor growers affordable, accessible and easy-to-use innovation – 24/7, anywhere in the world.
Our hardware, software and data solutions support growers and resellers in over 40 countries producing over 100 different crop types.
With over 25 years in business, we have a depth of experience and passionate, fun people creating original ideas and making them a reality for our growers.
About Agritecture Consulting
Agritecture Consulting provides a comprehensive approach to CEA project development.
In operation since 2014, Agritecture has helped more than eighty organizations determine the feasibility of their ideas, validate their business strategies, recruit talent for their projects, and manage operational challenges.
Our job is to jumpstart your knowledge of CEA, help you navigate barriers to entry, make industry connections, and mitigate risk. Our consulting services are backed by several years of operations data and a team of experienced growers, engineers, and sustainability managers.
Glase Uses Outreach Activities To Inform And Educate Growers, Manufacturers And Suppliers
The goal of the Greenhouse Lighting and Systems Engineering (GLASE) consortium is to create a more sustainable and profitable greenhouse industry
Greenhouse Lighting and Systems Engineering (GLASE) consortium is using outreach activities to provide controlled-environment growers, lighting manufacturers and service companies with pertinent information to increase energy efficiency and improve their products and operating procedures.
By David Kuack
The goal of the Greenhouse Lighting and Systems Engineering (GLASE) consortium is to create a more sustainable and profitable greenhouse industry. The consortium is a partnership between Cornell University in Ithaca, N.Y., and Rensselaer Polytechnic Institute (RPI) in Albany, N.Y. GLASE is supported by the New York State Energy Research and Development Authority (NYSERDA) and by industry partners.
The consortium is conducting research to improve controlled environment agriculture (CEA) operations. Research activities include improving lighting fixtures and systems that synergistically control lighting and developing plant lighting and carbon dioxide control strategies. These strategies would ultimately reduce energy consumption to create a more sustainable and profitable greenhouse industry. Although the focus of GLASE research is on greenhouse production, the findings are expected to have application to other controlled-environment production systems including vertical farms and warehouses.
Information for the CEA industry
In addition to the research being conducted by GLASE, the consortium is also offering a variety of outreach activities to provide growers, lighting manufacturers and service suppliers with information that can assist them in improving their business operations. These activities include webinars, technical meetings and trade journal articles.
“The webinar series is the one activity that GLASE has been doing the longest,” said Neil Mattson, horticulture professor and greenhouse extension specialist at Cornell University and GLASE principal investigator. “The webinars are open to the entire industry. Some have been more oriented towards growers. Others have more application to the supply side, including manufacturers and service providers.”
Improving energy efficiency through benchmarking
“One of the webinar topics we covered is our energy efficiency benchmarking platform, Mattson said. “GLASE worked with sustainability solutions service supplier EnSave Inc.. The company does farm energy audits and also helps farms to apply for grants to make energy efficiency improvements. What the company found working with other agricultural commodities, including dairy farms and poultry producers, is there are more solid benchmarks on how much energy those industries use. The greenhouse industry is highly fragmented in regards to the crops grown and the numerous geographic locations of growing operations. What’s lacking is a unified data bank or benchmarks of typical energy usage numbers for heating and lighting relative to the crops that are grown.”
Neil Mattson at Cornell University said GLASE is using a variety of outreach activities to provide CEA industry members with information that can assist them in improving their business operations.Photo courtesy of Neil Mattson, Cornell Univ.
Because of the diversification of the horticulture industry, Mattson said it has been more difficult to collect energy-use data.
“Through this collaboration with EnSave we are hoping that growers will use this benchmarking database,” he said. “We’ve tested it and we’re trying not to make it too onerous for the growers so it’s as easy as inputting their monthly utility bills. The growers would also input their productivity units, which could be heads of lettuce, pounds of tomatoes or number of 6-inch ornamental plants. We are looking to collect information from both greenhouse vegetable and ornamental plant growers. The data base could accommodate both types of crops.”
“The real strength of this data base would lie in having a critical mass of users. For the individual users of the data base, they would be able to see how their operations compare to other industry benchmarks. Growers would be able to compare their businesses to an anonymous group of similar operations. If growers find they are using more energy per output, they could try to determine why they are using more energy. Nationally this could be useful to growers who are trying to obtain federal funds from grant programs for adopting energy-efficient systems. We would also like to be able to share with the industry some of this anonymous benchmark data that is collected.”
Horticultural lighting label
Another GLASE webinar topic was on a horticultural lighting label. The webinar was presented by A.J. Both, a professor and extension specialist at Rutgers University and member of the GLASE research team.
One of the GLASE webinar topics was the horticultural lighting label which has helped to educate growers about lighting fixtures. Photo courtesy of A.J. Both, Rutgers Univ.
“This webinar was oriented toward greenhouse growers, educating them as to what to look for and what questions to ask lighting manufacturers when they are considering adding lights or looking to make changes to their lighting systems,” Mattson said. “The webinar was also aimed at the lighting manufacturers that potentially would adopt the label.”
Mattson said the lighting label has helped educate growers about lighting fixtures.
“Growers are learning the lighting units to use when comparing lighting fixtures,” he said. “Although lighting manufacturers haven’t adopted the entire label yet, they have incorporated elements of it. Lighting manufacturers have become much better at providing technical specifications. They are talking about lighting units in terms of plant lighting not human lighting. They are talking about micromoles of light instead of lumens of light. Rarely are footcandles used anymore by growers and lighting manufacturers.”
Lighting fixture analysis
Another one of GLASE’s outreach activities is to drive adoption of the horticultural lighting label. GLASE has partnered with Intertek, a total quality assurance provider, to work with its lighting company members.
“Intertek has the specialized equipment for quantifying light output and light distribution,” Mattson said. “Each lighting company that is a GLASE member can submit one lamp a year for testing by Intertek. Intertek conducts a series of measurements with each lamp. GLASE then takes the raw data generated by Intertek and we provide the lighting companies with a lighting label for each lamp that is analyzed.
“There are currently six lighting companies that are GLASE members. This spring we had the first companies take advantage of the lamp analysis. The companies decide whether they want to share the lighting label GLASE provides them. This is a good way to introduce the GLASE lighting company members into the process of what it takes to generate the information that is needed to prepare a lighting label.”
Informational conference calls
GLASE has been offering its members periodic informal conversations on industry-related topics.
“These industry talks enable GLASE members to learn in a more informal setting where there is not a large audience,” Mattson said. “This provides GLASE members more time to have their questions answered by the speakers which could directly help them with their business.”
The first industry talk was a video conference call with lighting researchers Kevin Folta at the University of Florida and Bruce Bugbee at Utah State University who discussed the potential benefits of green light in plants.
“The green light conference call was geared more towards the growers, but GLASE manufacturer and supplier members were also able to participate,” Mattson said. “The informal format for these calls has been conducive to discussion between members and the speakers. There are 20 minutes during which the thought leaders talk about the topic and then that evolves into a question and answer period with the members. The program format enables the participants to have their questions answered.”
One of the informal industry talks offered by GLASE to its members discussed the potential benefits of green light on plants. Photo courtesy of Kevin Folta, Univ. of Fla.
Another industry talk covered power supply and power distribution options for CEA. This call was geared more to the lighting manufacturers. The speakers included Bahram Barzideh, principal engineer of LED lighting components at Underwriters Laboratories (UL), and Frank Cirolia, systems and application engineer at Artesyn Embedded Technologies.
“For LED lights some of the energy is used by the diode,” Mattson said. “This is the energy used to produce the light. Some of the energy is used by the power supply as well as the driver. There have numerous developments in power supplies, which have helped to improve the energy efficiency of the new generation of lights. Regarding power distribution, there are opportunities for improving energy efficiency related to the way power is delivered to the fixtures.”
Articles on research findings
Technical articles about GLASE research results are the newest outreach activity.
“GLASE will be rolling out these articles this summer,” Mattson said. “Some of these articles will be geared more to the growers. Other articles will have application to suppliers and lighting manufacturers.
“Topics will include the plant research and the lighting control studies that we have conducted at Cornell. There will also be articles on designing more energy-efficient lights, which is what researchers at RPI are working on.”
The following articles will appear in CEA-related magazines in the coming months.
July: Multi-spectrum research LED lights
August: Greenhouse light and shade system implementation controls
September: Light distribution measurements in tall canopies
October: Spectral acquisition systems for greenhouses
November: Plant responses to integrated light and CO2 controls
December: Horticultural lighting fixtures analyses
For more: Neil Mattson, Cornell University, School of Integrative Plant Science, Horticulture Section, Ithaca, (607) 255-0621; NY 14853; nsm47@cornell.edu; http://www.cornellcea.com; http://www.greenhouse.cornell.edu
Editor’s note: Neil Mattson will be doing three educational presentations at this year’s Cultivate’19, July 13-16, in Columbus, Ohio
Biostimulants: Another Tool for the Grower’s Toolbox
Sunday, July 14, 2:45 p.m.-3:45 p.m.
Greenhouse Light and Carbon Dioxide Management to Enhance Crop Yield
This educational session will include information related to GLASE research.
Monday, July 15, 11:30 a.m.-12 p.m.
Lighting Approaches to Maximize Profits (LAMP)
Tuesday, July 16, 9:30 a.m.-10:30 a.m.
David Kuack is a freelance technical writer in Fort Worth, Texas; dkuack@gmail.com
Posted in Interviews
Power REIT Announces Acquisitions As Part of A New Investment Focus and Publishes Updated Investor Presentation
Power REIT is expanding its focus to include agricultural real estate with a focus on Controlled Environment Agriculture (“CEA”)
New Investment Focus on
Controlled Environment Agriculture (”CEA”)
New Focus For Acquisitions
Old Bethpage, NY, July 15, 2019, Power Reit (NYSE American: PW) is announcing an expanded focus for acquisitions. In addition to its existing high quality real estate related to transportation infrastructure and alternative energy, Power REIT is expanding its focus to include agricultural real estate with a focus on Controlled Environment Agriculture (“CEA”). CEA is an innovative method of growing plants that involves creating optimized growing environments for a given crop indoors. Power REIT intends to focus on CEA related real estate for growing food as well as cannabis.
Controlled Environment Agriculture
Power REIT believes agricultural production is ripe for technological transformation and that we are at the early stages of a boom in agricultural venture capital that, among other things, will shift food production for certain crops from traditional outdoor farms to CEA “food factories.” Since a significant portion of any given CEA enterprise is real estate, Power REIT sees an opportunity to participate in the trend towards indoor agriculture.
CEA facilities are generally greenhouses or industrial properties specifically designed to efficiently grow crops. Power REIT will primarily focus on greenhouses as opposed to other forms of indoor agriculture properties based on a thesis that for many crops, greenhouses should be the most cost competitive producer given the higher capital and operating costs associated with other indoor growing facilities that do not benefit from sunlight for their crops.
Controlled Environment Agriculture for Food Production
CEA for food production is widely adopted in parts of Europe and is becoming an increasingly competitive alternative to traditional farming for a variety of reasons. CEA caters to consumer desires for sustainable and locally grown products. Locally grown indoor produce will have a longer shelf life as the plants are healthier and also travel shorter distances thereby reducing food waste. In addition, a controlled environment produces high-quality pesticide free products that eliminates seasonality and provides highly predictable output that can be used to simplify the supply chain to the grocer’s shelf.
As the amount of productive farmland continues to decline, CEA can provide a sustainable and economic solution to feed our growing population. Climate change is having a negative impact on traditional farming and is making once rich areas for farming arid and inhospitable. Hydroponic growing use 95% less water and can grow more than twenty-times traditional farming in the same area. Simply put, CEA can lower the carbon footprint associated with our food supply.
Power REIT has an active pipeline of CEA projects it is pursuing.
Controlled Environment Agriculture for Cannabis
The legal cannabis industry in the United States is projected to hit $25 billion of revenue by the year 2025.
With the passage of the 2018 Farm Bill, the cultivation of hemp was legalized and regulated across the United States. Hemp is produced from the Cannabis Sativa strain and has properties that contain almost no THC, the federally illegal hallucinogenic compound found in marijuana. Hemp has many industrial uses including textiles, animal bedding and mulch. Hemp is also commonly used to produce CBD which is used in a variety of skincare and homeopathic products ranging from oils and moisturizers to sleep and relaxation aids.
Currently 34 states have legalized marijuana for medical purposes and 11 of those states have also legalized adult recreational use of marijuana. Many other states have decriminalized marijuana use even without formally changing laws and many remaining States continue to evaluate legalization. In addition, there is the potential for federal legalization across the United States at some point in the future given the momentum generated at the State level.
Power REIT is focused on investing in the cultivation and production side of the cannabis industry through the ownership of real estate. As such it is not directly in the cannabis business and also not even indirectly involved with facilities that sell cannabis directly to consumers. By serving as a landlord, Power REIT believes it can generate attractive risk adjusted returns related to the fast growing cannabis industry and that this offers a safer approach than investing directly in cannabis operating businesses.
Acquisition of greenhouse properties in Colorado for cultivation and processing of Cannabis
On July 15, 2019, through wholly owned subsidiaries, Power REIT is announcing that it has completed the acquisition of two greenhouse properties in southern Colorado. One property was acquired for $1,075,000 and is 2.11 acres and has an existing greenhouse and processing facility totaling 12,996 square feet. The other property was acquired for $695,000 and is 5.2 acres and has an existing greenhouse and processing facility totaling 5,616 square feet. The total combined purchase price of $1,770,000 plus acquisition expenses was paid with existing working capital.
Concurrent with the closing on the acquisitions we entered into leases with a tenant that is licensed for the production of medical marijuana at the facilities. The tenant is an affiliate of a company that is active in the Colorado cannabis market and currently has two indoor cultivation facilities and five dispensary locations. The tenant has also received a preliminary approval to operate a dispensary in the town where the properties are located. The leases require the tenant to maintain a medical marijuana license and operate in accordance with all Colorado and local regulations with respect to their operations and also prohibits the retail sale of its products from the properties.
The leases provide that tenant is responsible for paying all expenses related to the properties including maintenance expenses, insurance and taxes. The term of each of the Leases is 20 years and provides two options to extend for additional five-year periods. The Leases also have financial guarantees from affiliates of the tenant.
The rent for each of the leases is structured whereby after a six-month free-rent period, the rental payments provide a full return of invested capital over the next three years in equal monthly payments. After the 42nd month, rent is structured to provide a 12.5% return on the original invested capital amount which increases at a 3% rate per annum. At any time after year 6, the rent level will be readjusted down to an amount equal to a 9% return on the original invested capital amount and will increase at a 3% rate per annum based on a starting date of the start of year seven.
The combined straight-line annual rent will be approximately $331,000 although, as described above, the rental payments are accelerated such that we receive a full return of capital over the first 42 months of the lease. David Lesser, Power REIT’s Chairman and CEO, commented, “These acquisitions represent a starting point for our new focus on greenhouse based Controlled Environment Agriculture projects and will be immediately accretive to earnings. We have an active pipeline of potential acquisitions that we are pursuing. Given the small size of our company, we believe that we can deploy capital for real estate focused on Controlled Environment Agriculture on a highly accretive basis.”
Both properties have plans to expand the greenhouse growing and processing space and the leases provide that we have the right to fund such projects on comparable terms to the original leases. Mr. Lesser commented that “this creates the built-in ability for us to deploy additional capital on risk adjusted terms that should prove to be attractive and on a highly accretive basis.”
The greenhouse properties are located in a very favorable plant-growing environment that benefits from over 360 days of sunlight annually and offers a dry climate. In addition the local communities are supportive of cannabis growing facilities unlike places which are confronted with “not in my backyard” pressures. Both properties have been granted “use by right” authority from the county to grow cannabis which provides long-term stability to allow the facility to grow cannabis. In addition, both properties are located in an Opportunity Zone. Opportunity Zones were created by the Tax Cuts and Jobs Act of 2017 and provide a deferral of and potentially an elimination of capital gains related to qualified investments.
Updated Investor Presentation
On July 15, 2019, Power REIT is announcing that an updated version of its investor presentation is available on its website: www.pwreit.com
About Power REIT
Power REIT is a real estate investment trust that owns real estate related to infrastructure assets including properties for Controlled Environment Agriculture, Renewable Energy and Transportation. Power REIT is actively seeking to expand its real estate portfolio related to Controlled Environment Agriculture and Renewable Energy.
Cautionary Statement about Forward-Looking Statements
This document includes forward-looking statements within the meaning of the U.S. securities laws. Forward-looking statements are those that predict or describe future events or trends and that do not relate solely to historical matters. You can generally identify forward-looking statements as statements containing the words "believe," "expect," "will," "anticipate," "intend," "estimate," "project," "plan," "assume", "seek" or other similar expressions, or negatives of those expressions, although not all forward-looking statements contain these identifying words.
All statements contained in this document regarding our future strategy, future operations, future prospects, the future of our industries and results that might be obtained by pursuing management's current or future plans and objectives are forward-looking statements. You should not place undue reliance on any forward-looking statements because the matters they describe are subject to known and unknown risks, uncertainties and other unpredictable factors, many of which are beyond our control. Our forward-looking statements are based on the information currently available to us and speak only as of the date of the filing of this document.
Over time, our actual results, performance, financial condition or achievements may differ from the anticipated results, performance, financial condition or achievements that are expressed or implied by our forward-looking statements, and such differences may be significant and materially adverse to our security holders.
Contact:
David H. Lesser, Chairman & CEO
(212) 750-0371
301 Winding Road
Old Bethpage, NY 11804
212-750-0371
Global CEA Census Launched to Help Drive Agriculture Industry Forward
3 June 2019 (NEW YORK): Global automation specialist Autogrow and New York based Agritecture Consulting are appealing to growers to take part in the inaugural Global CEA Census.
The Census seeks to understand the scale and nature of Controlled Environment Agriculture (CEA) to better determine the roadblocks to accelerating the industry. This includes greenhouses, vertical farms, indoor rooms and hoop or tunnel houses.
Both Agritecture and Autogrow believe a great deal of CEA activity worldwide is not well documented, with data being fragmented and often unreliable, making it difficult to provide support or solutions on a larger scale.
“We do a lot of work with city leaders around the world and the conversations are about how the infrastructure needs to be in place in order to use new technology, drive costs down and operate sustainably. Through the Census we hope to highlight who is growing, what they’re growing, where they are growing and what they need to take it to the next level,” notes Agritecture Founder Henry Gordon-Smith.
“Based on that information both Autogrow and Agritecture can then work closer with governments, growers and city planners on where they can focus their efforts and utilize valuable resources.”
One of the biggest known roadblocks to adoption of new technology today is internet connection on the farm. Without connectivity growers are unable to join the growing trend of cloud-based software and remote access.
Autogrow CEO, Darryn Keiller says “We need to understand whether growers are ready for innovation, and if they aren’t, how we can get them there.”
“New crop production technologies are heavily reliant on growers having multi-modal internet to the farm and commercial grade onsite network infrastructure. If this isn’t addressed, and supported at a government level, then we will see an ever widening ‘digital divide’ at the farm level.”
“All the best technology in the world is of no use if it can’t be connected to the farm.”
Additionally, the Census hopes to record best practice solutions to share across the industry.
“There are some amazing growers around the world who are using creative solutions for things like water usage, labor shortages, energy consumption or improved marketing activities using social media. We want to capture that and share to the wider community. Only by banding together can we hope to push our industry forward in a positive way,” explains Henry.
The Census will run until 15 July with a report on the findings published in September. All submissions will remain confidential and only anonymized data will be reported.
WIN A TRIP TO NYC: Submissions will also go in a draw to win a trip to New York to attend this year’s NYC AgTech Week running from 21-26 September.
Take the survey, enter the draw and have your say -
https://www.surveymonkey.com/r/global-cea-census
Survey Terms and Conditions - https://www.agritecture.com/cea-census-terms-conditions
About Autogrow
Autogrow leverages the power of technology, data science and plant biology to provide indoor growers affordable, accessible and easy-to-use innovation – 24/7, anywhere in the world.
Our hardware, software and data solutions support growers and resellers in over 40 countries producing over 100 different crop types.
With over 25 years in business, we have a depth of experience and passionate, fun people creating original ideas and making them a reality for our growers.
About Agritecture Consulting
Agritecture Consulting provides a comprehensive approach to CEA project development.
In operation since 2014, Agritecture has helped more than eighty organizations determine the feasibility of their ideas, validate their business strategies, recruit talent for their projects, and manage operational challenges.
Our job is to jumpstart your knowledge of CEA, help you navigate barriers to entry, make industry connections, and mitigate risk. Our consulting services are backed by several years of operations data and a team of experienced growers, engineers, and sustainability managers.
Program Provides A Low-Cost Way For Businesses To Obtain The Advanced GrowPod Cultivation System
CORONA, Calif.
June 18, 2019 /PRNewswire/
GP Solutions (GWPD), a leading developer of automated micro-farms, announced it is now offering financing to provide businesses with a quick, low-cost pathway to begin growing profitable herbs and vegetables with the advanced "GrowPod" system.
GrowPods are portable, automated, perfectly-tuned cultivation environments that use significantly less space and water than conventional methods. The proprietary plug-and-play system allows a business to have a sustainable, efficient, and environmentally-friendly farm located virtually anywhere.
GP Solutions' new financing plans offer a variety of options for businesses to enter the highly profitable world of micro-farming.
GrowPods can be customized to provide the perfect environment for a wide variety of cash-crops, herbs and vegetables.
The system features a number of advanced technologies, including optimized photosynthesis, high level security, 24/7 remote control, video monitoring via a cloud-based platform, and precision environmental controls for temperature, humidity, and other vital factors.
Unlike other growing systems that use fixed greenhouses or require enormous capital for large indoor "warehouse farms," GrowPods are modular, scalable, indoor micro-farms that can be placed virtually anywhere. The pods have been shown to outperform other methods of cultivation, providing quicker harvest times with higher yields and greater consistency.
GrowPod farmers are provided with data, insights and other tools to further refine and improve their crops. As a sealed environment, GrowPods give farmers the ability to keep crops and strains separated, eliminating contaminants, pathogens, and pesticides.
For more information on GP Solutions' financing options or the GrowPod system, visit: www.growpodsolutions.com, or call (855) 247-8054.
ABOUT GP SOLUTIONS:
GP Solutions developed "GrowPods" – portable, modular, automated indoor micro-farms that provide optimum conditions for plant cultivation with total environmental control.
Forward-Looking Statements
This release includes predictions or information that might be considered "forward-looking" within securities laws. These statements represent Company's current judgments, but are subject to uncertainties that could cause results to differ. Readers are cautioned to not place undue reliance on these statements, which reflect management's opinions only as of the date of this release. The Company is not obligated to revise any statements in light of new information or events.
Connect:
Email: info@growpodsolutions.com
Website: www.growpodsolutions.com
Facebook: facebook.com/GrowPodTechnology
Twitter: @GrowPodSolution
Media:
hello@inov8.us
FarmTech Society Held First Constitutional Annual General Meeting
The Farm Tech Society (FTS) is an international non-profit industry association that unites and supports the Controlled Environment Agriculture (CEA) industry, seeking to strengthen the sector through the development and implementation of resilient and future proof methods and technologies for indoor growing
The Farm Tech Society (FTS) is an international non-profit industry association that unites and supports the Controlled Environment Agriculture (CEA) industry, seeking to strengthen the sector through the development and implementation of resilient and future proof methods and technologies for indoor growing.
The FarmTech Society (FTS) held its first constitutional annual general meeting at Greentech Amsterdam 2019. Also, FTS entered into a partnership with the vertical farm institute (vfi). Both organizations focus on value generation for the CEA industry and help the sector to grow together.
FTS members also elected a new board of directors, as well as its new board of advisors. The new boards are elected for a period of two years, and the board of directors also appointed the daily management team:
Board of Directors
Chairman: Gus Van der Feltz (founding member)
Vice-chair: Yanni Garcia (founding member)
Vice-chair: Penny McBride (founding member)
Director: Adam Rosenbaum (founding member)
Director: Daniel Podmirseg - vertical farm institute
Director: Wythe Marschall - PhD candidate Harvard University
Director: Stefan Frey - FREYconsult
Board of Advisors
Maren Schoormanns - PRIVA
Nicole Thorpe - Cultinova
Enrico Costanzo - ILab AirLiquide
Stefanie Linzer - Valoya
Pierre Grootscholten - Grootscholten Consultancy
Ian Kanski - INTAG Systems
Daily management
Secretary-General: Thomas Zoellner (founding member)
Treasurer: Yanni Garcia (founding member)
Communication: Mark Horler - Soya Project / UKUAT
For more information:
FarmTech Society
Tom Zoellner
BREAKING NEWS: Autogrow Announces First Industry Collaboration With Ridder Group And NATIVE
The collaboration is made possible with the launch of Autogrow’s new farm management platform, FarmRoadTM, which was announced by CEO Darryn Keiller at the Indoor AgTech Summit in New York today
June 20, 2019 (NEW YORK): Global automation expert Autogrow has announced a collaboration with competitor Ridder Group and New York agriculture software firm NATIVE.
The collaboration is made possible with the launch of Autogrow’s new farm management platform, FarmRoadTM, which was announced by CEO Darryn Keiller at the Indoor AgTech Summit in New York today.
“FarmRoadTM was conceived to fulfil two broad purposes. A platform for autonomous farming and secondly as a way of bringing together all disparate technologies that farmers use into one unified management tool,” explains Mr. Keiller.
“To be truly unified you need to be open and work collaboratively across the industry with buy-in from existing major players. It’s a concept we advocated two years ago when we came out with the first open API (Application Programming Interface) and I’m pleased to be in a position to say the dream is now tangible.”
“We are ecstatic that Ridder has shown the foresight and faith in us, to support what we are doing and join us in showing the industry what is possible when true collaboration occurs.”
Both Autogrow and Ridder market automation solutions for Controlled Environment Agriculture (CEA) and both will be able to integrate with FarmRoadTM.
“The Ridder Group, developer of the HortiMaX greenhouse control systems for over 40 years, supports the initiative of Autogrow,” says Joep van den Bosch, Chief Innovation Officer, Ridder Group.
“Ridder believes strongly in a connected future where systems and data is shared for the benefit of optimizing the plants growing conditions and more efficient and sustainable greenhouse operations.”
“As an industry partner, Ridder will make it possible for growers to connect their Ridder climate control and irrigation systems to the FarmRoadTM platform.”
Alongside Ridder Group, Autogrow will also be collaborating with New York based Start-Up NATIVE.
“Equally as important as an established player showing vision, is new entrants to the industry who are also bringing innovation. What NATIVE are creating delivers a fundamental industry building block, which we will integrate with FarmRoadTM,” says Mr. Keiller.
The NATIVE platform connects farms with local buyers, maximizing the value of their harvests and helping both buyers and restaurants deliver on the promise and demand of locally sourced food.
“Our partnership with Autogrow will most benefit the growers and the farmers,” says Frank Pica, co-founder, NATIVE. “FarmRoadTM users can provide NATIVE with real-time data that verifies the quantity and quality of their harvests, and NATIVE will return the true market value of the products. NATIVE then provides an outlet for growers to bring their products to premium markets within their region.”
Autogrow will work closely with Ridder Group and NATIVE over the coming months during the pilot phase. The beginning of the journey in working collaboratively with producers and growers.
“The next iterations of FarmRoadTM include flower and fruiting identification through Machine Vision and AI to provide pollination rates and flower to fruit conversion performance. We will be extending the 3rd party integration to include finance, labor management, food security and more,” says Mr. Keiller.
More information can be found on www.farmroad.io
QUERIES
General queries: (e) info@farmroad.io
Media queries: Kylie Horomia, Autogrow Head of Communications (e) Kylie.horomia@autogrow.com
(w) www.farmroad.io
About Autogrow
Autogrow leverages the power of technology, data science and plant biology to provide indoor growers affordable, accessible and easy-to-use innovation – 24/7, anywhere in the world.
Our hardware, software and data solutions support growers and resellers in over 40 countries producing over 100 different crop types.
With over 25 years in business, we have a depth of experience and passionate, fun people creating original ideas and making them a reality for our growers.
About Ridder Group
Farmers and growers worldwide need to be able to adopt their own individual approach to efficient and sustainable controlled environment agriculture. This is the promise that Ridder, as an international family-owned company, fulfils by translating more than 65 years of Dutch agri-food expertise into adaptive technology and know-how that is tailored precisely to local needs and conditions.
At Ridder, the drive to innovate is in our DNA. We are also committed to finding the best possible solution. The balanced combination of these two characteristics has enabled Ridder to evolve into the experienced market leader in technical solutions for the horticulture, intensive livestock and crop storage sectors. Today, Ridder has customers in more than 100 countries, who receive support from international offices and a global partner network.
About NATIVE
NATIVE’s mission is to empower local growers by maximizing the value of their harvests and meet the rising demand for local, transparently sourced food. NATIVE integrates real-time technology throughout the agricultural supply chain to accelerate traceability, waste mitigation, and return on investment. For more information, please visit www.nativeag.io
Global CEA Census Launched to Help Drive Agriculture Industry Forward
3 June 2019 (NEW YORK): Global automation specialist Autogrow and New York based Agritecture Consulting are appealing to growers to take part in the inaugural Global CEA Census.
The Census seeks to understand the scale and nature of Controlled Environment Agriculture (CEA) to better determine the roadblocks to accelerating the industry. This includes greenhouses, vertical farms, indoor rooms and hoop or tunnel houses.
Both Agritecture and Autogrow believe a great deal of CEA activity worldwide is not well documented, with data being fragmented and often unreliable, making it difficult to provide support or solutions on a larger scale.
“We do a lot of work with city leaders around the world and the conversations are about how the infrastructure needs to be in place in order to use new technology, drive costs down and operate sustainably. Through the Census we hope to highlight who is growing, what they’re growing, where they are growing and what they need to take it to the next level,” notes Agritecture Founder Henry Gordon-Smith.
“Based on that information both Autogrow and Agritecture can then work closer with governments, growers and city planners on where they can focus their efforts and utilize valuable resources.”
One of the biggest known roadblocks to adoption of new technology today is internet connection on the farm. Without connectivity growers are unable to join the growing trend of cloud-based software and remote access.
Autogrow CEO, Darryn Keiller says “We need to understand whether growers are ready for innovation, and if they aren’t, how we can get them there.”
“New crop production technologies are heavily reliant on growers having multi-modal internet to the farm and commercial grade onsite network infrastructure. If this isn’t addressed, and supported at a government level, then we will see an ever widening ‘digital divide’ at the farm level.”
“All the best technology in the world is of no use if it can’t be connected to the farm.”
Additionally, the Census hopes to record best practice solutions to share across the industry.
“There are some amazing growers around the world who are using creative solutions for things like water usage, labor shortages, energy consumption or improved marketing activities using social media. We want to capture that and share to the wider community. Only by banding together can we hope to push our industry forward in a positive way,” explains Henry.
The Census will run until 15 July with a report on the findings published in September. All submissions will remain confidential and only anonymized data will be reported.
WIN A TRIP TO NYC: Submissions will also go in a draw to win a trip to New York to attend this year’s NYC AgTech Week running from 21-26 September.
Take the survey, enter the draw and have your say -
https://www.surveymonkey.com/r/global-cea-census
Survey Terms and Conditions - https://www.agritecture.com/cea-census-terms-conditions
About Autogrow
Autogrow leverages the power of technology, data science and plant biology to provide indoor growers affordable, accessible and easy-to-use innovation – 24/7, anywhere in the world.
Our hardware, software and data solutions support growers and resellers in over 40 countries producing over 100 different crop types.
With over 25 years in business, we have a depth of experience and passionate, fun people creating original ideas and making them a reality for our growers.
About Agritecture Consulting
Agritecture Consulting provides a comprehensive approach to CEA project development.
In operation since 2014, Agritecture has helped more than eighty organizations determine the feasibility of their ideas, validate their business strategies, recruit talent for their projects, and manage operational challenges.
Our job is to jumpstart your knowledge of CEA, help you navigate barriers to entry, make industry connections, and mitigate risk. Our consulting services are backed by several years of operations data and a team of experienced growers, engineers, and sustainability managers.
The Future of CEA And Urban Farming
Gearing up to the second Indoor AgTech Innovation Summit on June 19-20 in New York, the event organizers found out what the summit’s Research Partner Cornell University has been working on, with insights from Neil Mattson, CEA Director & Associate Professor, School of Integrative Plant Science, Horticulture.
Gearing up to the second Indoor AgTech Innovation Summit on June 19-20 in New York, the event organizers found out what the summit’s Research Partner Cornell University has been working on, with insights from Neil Mattson, CEA Director & Associate Professor, School of Integrative Plant Science, Horticulture.
What’s been your focus this year about CEA and Urban Farming?
A key project has been a collaboration between our FCEA group and Cornell economists Charles Nicholson and Miguel Gómez. Together we’ve produced a report focused on the economic and environmental footprint and viability to scale urban farming.
We looked at scenarios of producing leafy greens locally in New York and Chicago. For each city our three scenarios were:
Field production in CA and shipping to the city
Greenhouse production in a hypothetical facility with 1-acre crop canopy
Vertical farm production in a hypothetical warehouse facility with 1-acre crop canopy
In the New York City scenarios, we considered CEA production in the middle of the city and in the Chicago peri-urban CEA production about 50 miles outside the city.
The comparison led to some interesting discussion points around bottlenecks and priorities for the sector to scale. I’ll share more on that below, and in my presentation at the summit.
Aside from that important study, from a plant-science standpoint, Cornell CALS has also continued its work to improve energy-efficient leafy greens, tomatoes and strawberries using LED lighting strategies and CO2 enrichment to photosynthesize through its Greenhouse Lighting and Systems Engineering (GLASE) research efforts.
We’re also collaborating with Rensselaer Polytechnic Institute (RPI) to understand the nutritional content of CEA-grown kale vs field-grown kale.
How do the Greenhouse and Plant Factory compare economically with open field farming?
In terms of economics, our study found it was cheapest to produce in a field and ship thousands of miles with a landed cost of $3 per kilo of lettuce. The New York city greenhouse scenario cost $8 per kilo, including production and short shipping distance. Plant factory was slightly cheaper. In peri-urban Chicago, with cheaper land rates, greenhouse production gave a cost of $7 per kilo. Again, the plant factory cost came in slightly cheaper.
The lower plant factory cost in both scenarios unlocks potential opportunities in urban areas where a high land cost is a significant contributor to the overall cost. Plant factory is more efficient use of land due to its vertical stacking, with a smaller footprint overall.
Labor costs are a significant 50% of the high cost in our un-automated CEA scenarios. As a follow up to this study we’re looking at a scenario with automated production for seeding plants, moving channels through the greenhouse and harvest. We can reduce labor cost by two thirds to three quarters, bringing us much closer to field production costs overall.
Another option is to move to cheaper land rural production within a couple hundred miles outside the city. In this scenario, we can reduce cost of production by a further $1 per kilo. Taking automation and site selection into account CEA greenhouse production down to $4 per kilo may be possible which is very close field-grown and cuts 2,800 miles from transportation.
In all scenarios, CEA was much more water-efficient than any other field, of course really important in this time of climate change. Hydroponic systems are far more water-efficient by design, with water recapture and reuse.
Agtech Startup Agrilyst Is Now Artemis, Raises $8M Series A
May 22, 2019
Artemis, the agtech startup formerly known as Agrilyst, today announced that it has raised an $8 million Series A funding round. The round was co-led by Astanor Ventures and Talis Capital, with participation from iSelect Fund and New York State’s Empire State Development Fund. With this, the company, which won our 2015 Disrupt SF Battlefield competition, has now raised a total of $11.75 million.
When Agrilyst launched, the company mostly focused on helping indoor farmers and greenhouse operators manage their operations by gathering data about their crop yields and other metrics. Over the course of the last few years, that mission has expanded quite a bit, and today’s Artemis sees itself as an enterprise Cultivation Management Platform (CMP) that focuses on all aspects of indoor farming, including managing workers and ensuring compliance with food safety and local cannabis regulations, for example.
The expanded platform is meant to give these businesses a single view of all of their operations, and integrates with existing systems that range from climate control to ERP tools and Point of Sale systems.
Compliance is a major part of the expanded platform.
“When you look at enterprise operations, that risk is compounded because it’s not just that risk across many, many sites and many acres, so in 2018, we switched to almost entirely focusing on those operations and have gained a lot of momentum in that space,” CEO and founder Allison Kopf said. “And now we’re using the funding to expand from mainly focusing on managing that data to help with profitability to using that data to help you with everything from compliance down to the profitability element. We want to limit that exposure to controllable risk.”
With this new focus on compliance, the company also added Dr. Kathleen Merrigan to its board. Merrigan was the deputy secretary of Agriculture in the Obama administration and is the first executive director of the Swette Center for Sustainable Food Systems at Arizona State University . She is also a venture partner at Astanor Ventures .
“Technology innovation is rapidly transforming the agriculture sector. Artemis’ approach to using data as a catalyst for growth and risk management provides the company a significant advantage with enterprise-level horticulture operations,” said Merrigan.
Cannabis, it’s worth noting, was not something the company really focused on in its early years, but as Kopf told me, it now accounts for about half of the company’s revenue. Only a few years ago, many investors were also uncomfortable investing in a company that was in the cannabis business, but that’s far less of an issue today.
“When we raised our seed round in 2015, we were pitching to a lot of funds and a lot of funds told us that they had LPs that can’t invest in cannabis. So if you’re pitching that you’re going to eventually be in cannabis, we’re going to have to step away from the investment,” Kopf said. “Now, folks are saying: ‘If you’re not in cannabis, we don’t want to invest.’ ”
Today, Artemis’ clients are worth a collective $5 billion. The company plans to use the new funding to scale its sales and expand its team.
Image Credits: Ben McLeod / Getty Images
Meet Mexico’s Biggest Producer of Hydroponically Grown Food
When you meet Leo Lobato, co-founder of Karma Verde Fresh, the first thing that you will notice is his charisma and warm-hearted charm
When you meet Leo Lobato, co-founder of Karma Verde Fresh, the first thing that you will notice is his charisma and warm-hearted charm. Leo’s energy for life and his well-earned passion for indoor growing has not only allowed him to start what may prove to become Mexico’s biggest producer of hydroponically grown food but has also allowed him to create some great allies along the way.
by Jens Ruijg
May 17, 2019
I sat down with Leo at NCERA-101, meeting in May to learn more about the newest Farmtech Society member.
Leo grew up in the farming and ranching community of Durango, Colorado, where he learned the balance of life eating produce grown in his Irish grandfather’s garden. His journey took Leo to Jalapa, Veracruz, Mexico in 1974, as a study abroad student from the University of Colorado. In 2004 Leo launched his atmospheric science business which is now a major contractor to the country’s National Weather Service, with exclusive representation of some of the World Meteorological Organization’s largest technology committee members. His post as the President of the Membership Committee for the American Chamber of Commerce of Mexico, and as a founding board member of the Ag-Industry Sector of CANACINTRA (Mexico’s largest industrial chamber) he has fostered many connections; it was a thoughtful conversation with a fellow member that inspired him to begin his exploration into indoor farming.
Beginning in 2015 until 2018, Lobato Kelly headed abroad to understand the landscape of indoor farming. Starting at the agriculture focused Milan World Fair, followed with trips to Rome and Munich, and finally landing at the Japanese Plant Factory Association summit, he consulted with some of the world’s best indoor farming experts. In order to understand the impact of hunger on violence in society Lobato Kelly visited the Peace Institute in Washington.
This long journey resulted in Leo securing a critical location for production in Mexico, a head grower, and essential industry connections that helped him to Karma Verde Fresh’s proof of concept site in 2018.
Truly embodying the spirit of the Farmtech Society, Karma Verde Fresh began collaborating with key universities throughout the region and has donated GrowRacks sourced from Hort Americas to expand educational opportunities. Thanks to the Enterprise-University-Enterprise (E-U-E) Collaboration Model and key industry guidance, Karma Verde Fresh has carried out 5 separate training courses preparing 163 local students, professionals and citizens for indoor growing.
Lobato is marketing lilies grown with his university partners to 10 Home Depot stores to help generate funding for ag school student food and transportation scholarships and for funding further vertical agriculture R&D.
Thanks to the success of the E-U-E at the UANL in Monterrey, and the university interest in further development of Mexico as a thought leader in Controlled Environment Agriculture, in 2019 the team at Karma Verde begins their Proof of Production phase of 10,000 square feet at the Marin Campus, within 30 minutes of the Central Distribution Centers of the major grocery store chains. The company has plans to expand into full production into the first of 2 of 30, 100,000 sq ft facilities between Monterrey and Mexico City beginning in 2020.
With an undeniable knack for creating community, the Farmtech Society is excited to partner with this growing company to help expand Ponics VET, which is based on the Erasmus+ vocational training credentials, and will serve to augment the course materials for certifying students in controlled environment agriculture across Mexico.
FarmTech Society will organize a series of panel discussions during Greentech Amsterdam 2019. On Tuesday June 11, Tom Zöllner will host a discussion on Plant Nutrition – Extra Natura, focusing on how we can grow the best possible plants in a controlled environment with speakers from Rijk Zwaan, Valoya, INTAG and Signify.
On Wednesday the 12th, Daniel Podmirseg of the Vertical Farming Institute will host speakers from The European Commission, Priva, Liberty Produce, Cultinova and Vertimis to discuss Energy and Building Topology for controlled environment agriculture.
Finally on Thursday June 13, Gus van der Feltz will host a discussion on Vertical Farming Business cases and Consumer Acceptance with speakers from Valoya, 80 Acres, Wageningen University, and Innovation Quarter.
For more information:
FarmTech Society
Place du Champs de Mars 5, 1050 Ixelles
+32 487 90 79 54
contact@farmtechsociety.org
farmtechsociety.org
Publication date: 5/16/2019
Relationships And Trust Help Hort Americas Mark 10 Years In Controlled Environment Agriculture
Horticultural distributor Hort Americas is celebrating its 10th anniversary of working with controlled environment growers. General manager Chris Higgins said it has been 10 years of forming trusting relationships with the growers and vendor suppliers that Hort Americas works with
Hort Americas 10 years of providing controlled environment growers with timely technical information and innovative products to solve their problems.
Horticultural distributor Hort Americas is celebrating its 10th anniversary of working with controlled environment growers. General manager Chris Higgins said it has been 10 years of forming trusting relationships with the growers and vendor suppliers that Hort Americas works with.
“Hort Americas doesn’t make a single product,” Higgins said. “What Hort Americas does do is we use our technical expertise to assist in the development of new products used to solve growers’ problems. This process takes a lot of trust. Our customers have to trust us about sharing their information. Some of that information could be proprietary. It could be information about their business that they need to be comfortable sharing. It could be information that allows us to look into the future and identify problems growers see coming up. By partnering with our grower customers and vendor suppliers, Hort Americas has been able to develop the technology, products and services that help controlled environment growers.”
At the same time that growers have to be able to trust Hort Americas, Higgins said a similar relationship has to exist between Hort Americas and its suppliers.
“Whether it’s working with our suppliers to develop new substrates or lighting fixtures, Hort Americas often has to share sensitive information. We need to have trust that sensitive information is going to turn into products that are going to be equitable in terms of helping everyone along the supply channel grow their businesses profitably.
“There is a lot of trust involved and that trust can’t be built off of non-disclosure agreements. That trust needs to be built off of years of experiences, cooperation and deliverables. If someone can’t deliver what they say they are going to deliver when they say they are going to deliver it, then trust is going to be lost. And the desire to want to cooperate is going to be lost too.”
Forming trusting business relationships
Higgins said forming a trusting business relationship should not have anything to do with the size of the company whether it’s a grower or supplier.
“Many businesses find themselves on a one-way street,” he said. “Many business people today only care about the value they create for their own business. And while it has probably always been this way, it feels this is more the case today than ever before.
“Trust takes years to build, seconds to break, and forever to repair.” – Author unknown
“This can happen with suppliers that haven’t set up a true supply channel management strategy. Distribution partnerships may seem needed, but are truly not necessary. Therefore some suppliers don’t really care about the health or well-being of their partners or partnerships. They just want to get as much of their product out the door as possible. Fortunately for Hort Americas we have been able to find those suppliers that are exceptions to the rule. Hort Americas must then remember that it is on a two-way street. We must create a situation that is not only good for our grower customers, but are vendor partners as well.”
Chris Higgins, general manager at Hort Americas, with Daniel Lee, sales development manager at Current, powered by GE.
Partnerships in the Information Age
Higgins said today’s Information Age also creates challenges for companies trying to form strong partnerships.
“In this Information Age companies don’t necessarily see the value of networking,” he said. “They don’t see the value of how long it takes to build trust along the supply channel.
“Hort Americas goes out on a limb every time it takes on a new business relationship whether it’s with a grower or supplier. Every time we begin to build a new partnership we have to expect we may never receive the invested money or time back. There’s two to three years of never knowing whether all of the resources we have invested are going to take on any sort of return.”
Higgins said there is an inherent amount of risk that one takes when forming business relationships.
“Sometimes companies build these relationships and they go very well for five to six years,” he said. “Then one person at the top changes the management strategy of an entire company and everything implodes. This could be a change in personnel. This could be a stress fracture created by the need to find increased profitability. There could be a change in market dynamics such as competition, demand or price. Based on this list of changing conditions, companies need to be able to find the ability to trust each other.
“Partnerships are based on trust and that takes time. Hort Americas and GE have been working together for 5 years and we could not be happier with what we have been able to accomplish together.” —Dan Lee, Current, powered by GE
“Just like in a marriage, if something drastic happens, the marriage can end in divorce. Being able to maintain that relationship has to do with the ability to change and adapt. The way you treat somebody, the professionalism and the ability to be empathetic to the position that a customer might be in, those are going to speak volumes in terms of one’s ability to create strong business relationships.”
From bicycles to horticulture
William Fry, who is Hort Americas longest serving employee, started as the customer service manager in 2012.
“I came from the world of bicycles, Fry said. “Bicycles were a passion of mine, including riding bikes all the time. That led me to the business side of bicycles. I owned a bicycle shop and worked with a bicycle parts distribution company. That experience translated well into horticultural distribution when I came to Hort Americas. It doesn’t really matter what the commodity is that you are trying to get from one side of the world to the other, it’s very similar.
“Coming to Hort Americas I had no knowledge of greenhouse technology–what went where, what was needed for each crop, etc. But since I had learned about thousands of bicycle parts, I figured I could learn anything I needed to know about what goes inside a greenhouse.”
Fry, who is now Hort Americas operations manager, said the reasons he has stayed with the company is it’s a fun place to work and he really enjoys working in the horticulture industry.
“Hort Americas and the industry constantly challenge me, both by the technology that is coming out and how they are ever evolving,” he said. “I have to constantly educate myself from a product standpoint.
“From a logistics standpoint, our products are shipped from all over the world. The challenge is to bring them in in a logical way. I’m constantly trying to beat myself as to how I can do things more efficiently and bring costs down for us and for our customers.”
Trying to grow its customers’ business
Fry said one of the major reasons that growers enjoy working with Hort Americas is the company is constantly trying to bring new technology to market.
“We’re trying to bring proven technology to market,” he said. “We aren’t just going to have an idea that a product might work and then offer it to growers. We are going to test it in a research greenhouse first. We are going to send it to growers who we have great relationships with for them to trial. And we are going to work with universities to prove that these products will serve a purpose in this market and work before we bring them to market. That has been fun and interesting.”
Hort Americas general manager Chris Higgins (center) with the Hort Americas team look to provide their grower customers with the expertise they have acquired on controlled environment production.
Another benefit that Hort Americas offers its grower customers is its efforts to be very economical.
“We try to buy at the best price, sell at the best price and ship at the best price,” Fry said. “We are constantly working to provide excellent customer service and to save people money. We are trying to help our customers grow their business so that our business can grow. We try to be a cheerleader for our customers. I have always tried to value every single sale that we have made and try to make our customers that much better so that as they grow we grow.
“Developing our own network of logistics partners has given Hort Americas the ability to cherry-pick the best combination of price vs. speed depending on the situation. With this network we feel confident that we can respond to whatever needs our customers have, whether it is saving money on shipping or delivering an emergency order to them ASAP. We can lean not only on our logistics network, but also on our network of vendors who have much larger buying power.
Looking for supportive suppliers
Fry said good vendor/suppliers provide a consistent, high quality product in a timely manner with logistical excellence.
“Good vendors back us with sales and marketing materials and trial materials for our customers who want to try a product to prove it will work for them,” he said. “They also have a good customer service team on their end as well.
“I’m looking for vendors who treat us as a customer and as a partner, not as a middleman. The same thing that I expect Hort Americas to deliver to our customers, I expect from our vendors. Offer good products, deliver them to us in the best manner possible and help us market and promote them. Be there as a partner and work with us as a team to accomplish a goal. The training that has been by provided by GE lighting engineers along with the hands-on installation of new GE fixtures and factory tours with Grodan representatives to understand the rockwool production process have been invaluable.”
Kyle Barnett (left), regional sales manager at Hort Americas, talks with Bruno D’Amico, design and product manager at GE, about the lighting company’s newest LED fixtures.
Fry said Hort Americas tries to pull from its staff’s experiences when developing new products and working with its vendors to develop these products.
“Sometimes we find a product and it really works well,” he said. “Sometimes we decide the market just isn’t big enough for a product. Or a product may not work in trials as well as we thought it would and we scrub it before ever bringing it to market. We are always looking for those products that make us special to our grower customers. We have also been much more responsive in how we bring on new products in order to lower costs for our customers and for Hort Americas.
“The other half of this product development is training our staff to work with the products. Our staff has a lot of hands-on experience with the products. Depending on the supplier, they may not have the employees who understand the niche industry that we’re in. That is where Hort Americas comes in with staff members who are experts in controlled environment agriculture.”
This article is property of Hort Americas and was written by David Kuack, a freelance technical writer in Fort Worth, TX.
Controlled Environment Agriculture Carbon Dioxide Injection
Indoor production of leafy greens, Part III: Is carbon dioxide enrichment beneficial for indoor production of basil seedlings?
March 25, 2019
Indoor vertical production of basil seedling under sole-source light-emitting diodes (LED)Photo: Roberto G. Lopez
In this third article of a four-part series, researchers from Michigan State University share science-based information about indoor production of leafy greens and herbs.
To read part one, click here. To read part two, click here.
In recent years, researchers and growers have been mainly focused on quantifying the effects of sole-source light quality on crops grown in indoor CEA warehouses and containers. However, one commonly overlooked environmental parameter that has the potential to increase growth and yield is carbon dioxide (CO2). Atmospheric (ambient) CO2 concentration has been increasing over the years from below 320 µmol·mol-1 (or parts per million, ppm) in 1960 to current values where CO2 levels outdoors comprise 0.04% of atmospheric volume, or around 400 µmol·mol-1. However, CO2 concentrations in a “tightly sealed” greenhouse or indoor growing operation can quickly dip down to 200 µmol·mol-1 as plants use CO2 during photosynthesis.
You may think that maintaining the CO2 concentration at ambient levels is as easy as venting or introducing fresh air. It can be during certain times of the year, but this can be difficult when outdoor temperatures are very low. Increasing CO2 to concentrations above ambient and up to 1,200 µmol·mol-1 has been shown to increase photosynthetic rates, growth and yield. There are several commercial methods to increase CO2 concentrations above atmospheric levels. However, these methods should be deployed during periods when ventilation is minimal to reduce the loss of the added CO2 outside of the growing area.
For CO2 enrichment above ambient, growers can deploy CO2 burners that produce CO2. This method produces some heat, moisture and CO2 by burning natural gas or propane. Incomplete combustion or contaminated fuels can lead to the introduction of toxic gases for both plants and humans. To improve CO2 uniformity, burners should be dispersed throughout and horizontal air flow (HAF) fans can be deployed to circulate air. Another method of CO2 enrichment for both greenhouses and indoor farms is injecting compressed or liquid CO2 from a tank. The compressed CO2 is converted from a liquid to a gas and then released into the growing area. These tanks can be rented or purchased through local gas distributors. When delivered in this form, CO2 is often dispersed through polyethylene tubes. Remember that CO2 is heavier than the other air components, so concentrations tend to be greater closer to the floor.
Fig. 1. Sweet Basil ‘Nufar’ grown in growth chambers with either 500 or 1,000 µmol·mol-1 CO2 and light intensities of 100, 200, 400 or 600 µmol·m–2·s–1 two weeks after sowing.
Fig 2. Sweet Basil ‘Nufar’ grown in growth chambers with either 500 or 1,000 µmol·mol-1 and light intensities of 100, 200, 400 or 600 µmol·m–2·s–1 two weeks after sowing.
Fig. 3. Limitations to photosynthesis include carbon dioxide (CO2; blue line), light intensity (red line) and biochemical (phosphate; purple line). The green line represents a theoretical photosynthetic response curve.Photos and Graphics courtesy of Kellie Walters
Experimental protocol
The goal of our research program is to develop indoor and greenhouse environmental management protocols for different stages of culinary herb production. Given that CEA production is energy-intensive, we have focused our efforts on young plant production since inputs such as light and CO2 can be delivered across more plants at the seedling stage when plant density is greater compared to the finished stage when plant density is lower. The objectives of our research were to determine if indoor CO2 enrichment during the seedling stage influences: 1) sweet basil seedling growth and development; 2) morphology, growth, and yield at harvest in the greenhouse; and 3) volatile oil content and flavor (this research is in progress and we will report the results in an upcoming article).
Sweet basil ‘Nufar’ seeds were sown in Grodan rock-wool cubes and placed in walk-in growth chambers with an average daily temperature (ADT) set point of 73° F (23° C) and CO2 set points of 500 or 1,000 µmol·mol-1 throughout the day and night. We maintained these concentrations by injecting compressed CO2 into the chambers, and by scrubbing CO2 with soda lime when concentrations were too high. In each chamber we had four light intensity treatments of 100, 200, 400 and 600 µmol·m–2·s–1 that operated 16 h per day to create daily light integrals (DLIs) of 6, 12, 23 or 35 mol·m–2·s–1. This allowed us to determine whether there was an interaction between CO2 concentration and light intensity. The seedlings were grown for two weeks, after which plants were transplanted into deep flow technique (DFT) hydroponic systems in a greenhouse with an ADT of 73° F (23° C) and a DLI of 14 mol·m–2·s–1. With the plants growing in a common greenhouse environment, we could evaluate if differences or higher inputs at the seedling stage would result in increased yields down the road.
In theory, by increasing CO2 concentration, we should have seen increased growth; however, this was not the case. As can be seen in Figs. 1 and 2, light intensity had a much larger impact on seedling growth than CO2, but we will discuss that in the next article of this series. Increasing CO2 concentration did not influence growth and development. Why would increasing CO2 from 500 to 1,000 µmol·mol-1 not actually improve growth and development of basil seedlings?
Cross-merchandising of fresh-cut basil and tomatoesPhoto: Kellie Walters
There are three main limitations to photosynthesis: the supply or utilization of CO2, of light, or of phosphate (also referred to as biochemical limitation; Fig 3.). Theoretically, if CO2 concentration starts at 0 and increases, you will hit a CO2 compensation point above which plants have positive net photosynthesis. As the CO2 concentration further increases, the photosynthetic rate will increase until the CO2 concentration reaches a species or cultivar-dependent saturation point. In our case, 500 µmol·mol-1 CO2 may have been near the saturation point for basil seedlings. Therefore, increasing the concentration to 1,000 µmol·mol-1 did not significantly increase growth. In addition, if photosynthesis is light-limited, increasing CO2 concentration will not result in large increases in photosynthesis. Conversely, if photosynthesis is CO2-limited, increasing light intensity will not result in large increases in photosynthesis. However, increasing CO2 can have some other positive effects, including reducing oxygenation and photorespiration. In our case, increasing the light intensity further or growing the plants past the transplant stage may have resulted in differences between CO2 treatments.
Do our results mean we should write off CO2 enrichment as a means of increasing photosynthesis and ultimately growth and yield? No. We are currently evaluating several other culinary herbs at lower and higher CO2 concentrations and a range of light intensities to see if there is a species-dependent response. In addition, it is possible that elevating CO2 concentration would have a larger impact during the finish stage. More studies are needed to parse out which horticultural crops and at what stage of production CO2 enrichment would be the most beneficial to improving growth and yield.
Take-home message
Other environmental factors besides CO2 concentration may have a larger impact during the seedling stage. Read the last article in this four-part series to understand the benefits of increasing indoor CEA light intensity during propagation on subsequent yield in the greenhouse.
Kellie is a PhD student and Roberto is assistant professor and controlled environment/floriculture extension specialist in the Department of Horticulture at Michigan State University.
The authors gratefully acknowledge Sean Tarr and Nate DuRussel for assistance, Fluence Bioengineering for LEDs, JR Peters for fertilizer, Grodan for substrate, Hydrofarm for hydroponic production systems, Dramm for irrigation equipment and MSU AgBioResearch, MSU Graduate School and the USDA-NIFA for funding.
Seeds Lighting Ventilation CO2 Basil Photosynthesis Temperature
The Trouble With The Urban Farming ‘Revolution’
by Emma Bryce | April 5, 2019
Commercial urban agriculture in New York City has provided questionable environmental gains, and has not significantly improved urban food security. These are the findings of a recent case study of New York City which shows that, despite the fanfare over commercial urban farming, it will need a careful re-evaluation if it’s going to play a sustainable role in our future food systems.
The rise of commercial controlled-environment agriculture (CEA)–comprised of large scale rooftop farms, vertical, and indoor farms–is a bid to re-envision cities as places where we could produce food more sustainably in the future. Proponents see CEA as way to bring agriculture closer to urban populations, thereby increasing food security, and improving agriculture’s environmental footprint by reducing the emissions associated with the production and transport of food.
But the researchers on the new paper wanted to explore whether these theoretical benefits are occurring in reality.
They focused on New York City, where CEA has dramatically increased in the last decade. Looking at 10 farms that produce roof- and indoor-grown vegetables at commercial scales, they investigated how much food the farms are producing, who it’s reaching, and how much space is available to expand CEA into.
They found that the biggest of these 10 commercial farms is around a third of an acre in size. Most are on roofs spread across New York City, and some are inside buildings and shipping containers. Mainly, these farms are producing impressive amounts of leafy greens such as lettuce, and herbs; some also produce fish.
But while rooftop farms rely on natural sunlight to feed the crops, indoor farms use artificial lights. These farms potentially have a greater energy footprint even than conventional outdoors farms, the researchers say–challenging the assumption that urban farms are less impactful than conventional ones.
Some farms also embraced high-tech systems, such as wind, rain, temperature, and humidity detectors and indoor heating, to enhance growing conditions in environments that aren’t naturally suited to agriculture. These elevate the energy costs of the food produced, and may be giving CEA an unexpectedly high carbon footprint, the researchers say.
Furthermore, the predominantly grown foods–such as lettuce–aren’t of great nutritional value for the urban population, especially those threatened by food insecurity. Most produce from CEAs is sold at a premium, something that partly reflects the cost of the real estate used to grow the food. Consequently, that produce is typically grown for high-end food stores and restaurants, meaning it’s unlikely to reach low-income urban populations who need it most.
The researchers also think it’s unlikely that CEA–which currently occupies just 3.09 acres in New York City–could expand into the roughly 1,864 acres they estimate is still suitable for urban farming in New York City.
The rising cost of real estate might put these urban acres beyond the reach of new farming start ups, they think. These companies also face increasing competition from a growing number of farms springing up on the outskirts of cities–where land is cheaper and there’s space to produce more food, while also benefiting from urban proximity.
With its one-city focus, the research isn’t representative of what might be unfolding in other places around the world. Other cities may be having more success–for instance, Tokyo has gained global attention for its large scale vertical farming efforts. Yet as a case study, it does reveal useful lessons–especially for cities wanting to meet the original twin goals of urban agriculture: equitably increasing access to food, at a lower environmental cost.
The researchers note first of all that CEA is optimal in places where less supplemental heat and light is needed to grow food. More thought might also be given to the nutritional value and cost of foods grown, to generate benefits for all the city’s residents, not just high-income ones. The researchers question whether smaller, community-driven plots of urban agriculture–like community gardens, school, and prison farms–might actually do a better job of providing food to at-risk city residents, compared to commercial urban farms that inevitably have to focus on profits.
Based on the study of New York, the researchers caution: “CEA may be touted as an exciting set of technologies with great promise, but it is unlikely to offer a panacea for social problems or an unqualified urban agricultural revolution.”
It’s easy to be drawn in by the dystopian allure of vertical farms and underground greens nestled into our cities. But until we’ve streamlined its role, we should perhaps not overstate what commercial urban agriculture can do – or, instead be guided by cities where there are stronger signs of social and environmental success.
Source: Goodman et. al. “Will the urban agricultural revolution be vertical and soilless? A case study of controlled environment agriculture in New York City.” Land Use Policy. 2019.
Image: Pixabay
The Future of Container Farming & Controlled-Environment Agriculture
There are positives and negatives of growing produce far from the end consumer, but most would agree that all else being equal, local is better
Peter Tasgal: The author is a consultant focused on the agriculture space with previous experience as CFO and board member of a $100 million CPG business headquartered in Montreal, Canada prior to which he was an investment banker for over 10 years.
His contact information is as follows: Peter Tasgal, ptasgal1@gmail.com, 617-794-4058.
Over the past two decades many industries including the auto industry and the retail environment have seen drastic evolutions. At first glance, the agricultural space seems to be lagging behind. Produce at your local grocery store largely comes from seasonally favorable climates. For example, tomatoes from Canada during summer and peppers from Mexico during winter. Increasingly, produce is coming from areas of the world in close proximity of the equator to limit seasonality. Today, more than half of the fresh fruit and over one-third of the fresh vegetables that Americans buy is grown outside of the United States. This share has been growing steadily for decades and is expected to continue to grow over the future decade and beyond. 1
There are positives and negatives of growing produce far from the end consumer, but most would agree that all else being equal, local is better. Chilean grapes stored in refrigerated containers for 1 to 5 months at a temperature of 30 to 32 degrees Fahrenheit and which have traveled 5000 miles are not going to taste as good as freshly picked grapes from your local farmers market.
Community desire for local produce, combined with improvements in hydroponic, lighting and other technologies, have attracted participants looking to grow in controlled environments. Controlled environments include greenhouses – both ground level and rooftop, buildings, and 40 to 53-foot shipping containers re-purposed for growing.
The table below provides a high-level comparison of some prominent forms of farming today:
Please click on the above to enlarge
The fundamental reliance on rain and sun makes traditional farming the most efficient and environmentally friendly form of agriculture. However, generally it is furthest from the end consumer. Shipping containers on the other hand can be located at or are very close to the consumer but are the least efficient in terms of cost per delivered pound. Greenhouses and contained structures are in the middle of the two. Depending on their locations, greenhouses and other contained structures can be close to the consumer. Also, they can deliver produce at a competitive price for certain items.
1 https://www.nytimes.com/2018/03/13/dining/fruit-vegetables-imports.html
Technological innovation is happening in all areas of agriculture. The biggest evolutions are happening in environmental control systems, data collection, material handling/logistics , traceability/food safety and crop management.
Examples of innovators in the agricultural space include:
2 companies founded out of Boston based Flagship Pioneering, Indigo Ag, Inc. and Inari have raised $600 million and $40 million respectively. Indigo Ag is using natural microbiology and digital technologies to improve grower profitability, environmental sustainability and consumer health. Inari is building the world’s first seed foundry to reintroduce genetic diversity to achieve desired field experiences.
New Zealand based BioLumic is introducing Ultraviolet light to transplant crops at nursery stage to increase crop yield.
Philips recently introduced its GreenPower LED production module, optimized for closed, climate- controlled cultivation facilities. The module allows for a dedicated combination of spectrum, intensity, timing, uniformity and positioning of light to optimize production.
Let’s make the assumption that assumption that the consumer prefers locally grown produce, and that locally grown produce tastes best. The question I am then posing is: Can produce grown in a shipping container be priced competitively with traditional farm grown produce? Or, alternatively, does the consumers’ mindset need to be changed for them to be willing to pay a large premium for local products to enable container farming to work? Essentially, does the industry need a “Starbucks model” to motivate people to pay a premium price for a premium product when lower cost, albeit less quality product is available?
The University of California Cooperative Extension Agricultural and Natural Resources – Agricultural Issues Center did a complete analysis in 2015 of a range of crops. One of these crops was romaine hearts from the Central Coast Region (Monterey, Santa Cruz & San Benito Counties). They determined that based on a range of assumptions it costs an average of $0.65 to deliver a pound of romaine hearts to a blend of regions across the United States (See Appendix A for Cost Analysis – Conventional Farming). Traditional retailers in the United States look for 40 to 45% gross margins in their produce departments. This allows retailers to sell a pound of romaine hearts for just over a dollar to meet their return targets.
Grown in a container farm, the cost to deliver a similar product as described above is at best 3.6x the cost of conventional farming ($2.38 per pound), and more realistically 10.9x ($7.14 per pound - See Appendix B for Cost Analysis – Container Farming). This is impressive for container farming, especially given the square footage of a container is equal to approximately 1% of the square footage of an acre of land.
To determine the viability of selling container grown produce at the retail store level, I did a store check on a range of greens at a local supermarket. Greens were chosen as they are the easiest to grow in a container because they stay at a vegetative stage and do not go to a flowering stage. The flowering stage requires additional lighting of different color for optimum growth.
The chart below depicts pricing for a range of greens at a recent store check of a Whole Foods Market in Newton, Massachusetts. A 40% store level gross margin is assumed for the analysis below:
Please click on the above to enlarge
As shown above, container farming can provide a competitively priced source for many of the locally grown items, as well as small packages of specialized herbs. The items for which container farming can be competitive are largely niche products. Examples of this are products sold in low volumes at a Whole Foods Market in an affluent Boston suburb. For example, there were 30 small boxes of organic herbs on the shelf during my visit, equating to less than 2 total pounds of herbs.
Where are likely efficiencies to be found in container farms?
There are 4 high-level variables that determine the efficiency of a container farm:
Product yield
Cost of the container
Labor
Power
Product Yield
According to American Hydroponics (“AmHydro”) the maximum number of plants per year that can be grown in a container are 46,592. This is based on the assumption of 3,584 plant sites are turned 13x per year. This case assumes a 2oz plant, which equates to 5,824 pounds of annual production. This is the most aggressive yield case and assumes each of the following: (i) 4-week grow time; (ii) No loss; and (iii) no downtime. A much more realistic yet still aggressive yield case would be closer to 4,000 pounds of production. This is based on a 5 to 6 week grow period, 10 turns per year, and some downtime for container maintenance and cleaning. After discussions with container farmers, their estimation of actual yields are closer to 3,000 pounds per year. Efficiency improvements are likely to be limited in terms of yield, given the size constraints of a container.Container Cost
Freight Farms is listing its containers at $85,000 prior to delivery and set-up. AmHydro projects a delivered figure of $87,000. Each of these figures assume use of a container typically purchased from shipping lines and/or container lessors once determined the containers are no longer seaworthy, retrofit for hydroponic farming. CAI International, a major container lessor, published in its 2017 annual report a 3-year average residual price for a 40-foot standard dry van container of $1,101 and $4,045 for a 40-foot high cube refrigerated container. Therefore, the vast majority of the cost of a container ready for farming lies in its retrofitting and profit margin to the container farm seller / lessor.
Determining the true cost of retrofit for a container is difficult. Dan Backhaus, the number 2 person at now defunct PodPonics, a company which had raised $14 million in funding, estimated the cost of retrofit at approximately $20,000. Additionally, a Google search of container farms for sale depicted several Freight Farm units originally purchased in 2016 and now being listed for sale between $55,000 and $68,000.
Efficiencyimprovementsarelikelytobegreatestintheareaofcontainercosts. Ifthemarketgrowsthere will be additional container farm suppliers which will bring prices down. In Appendix B, under the likely scenario, the amortization of the cost of the container represents $2.25 per pound of production.
Labor
The amount and cost of labor is a function of several variables:
Proximity – For example, if one person is going to be responsible for several containers which are far
apart, this will require more staffing hours than if containers are clustered together;
Product type (s) being grown – Certain crops require more care than others and growing multiple crops
will require more labor;
Singular vs multiple cycles – One consistent cycle where an entire containers’ crop is ready at one time
will be more efficient compared to staggering the cycle so that product is being harvested on a more
frequent basis.;
Container layout – More efficient container layout could optimize labor efficiency, although the
efficiency may come with the cost of lower production levels; and
Cost of labor in the region.
Improvements in labor efficiencies are likely to be a function of what is trying to be achieved in the container farm. As the popularity of container farming increases, labor is likely to become more skilled and containers will be in closer proximity. Technological advancements have been very effective in reducing labor costs (eg. viewing plants and monitoring pH levels and other internal variables from a distance). However, most of these technological advancements are what has made container farming viable today. Most of these technological enhancements are not since but rather prior to the advent of the container farm. There has been limited research on the use of robotics to improve harvesting and seeding in container farms. This could potentially have a great impact on labor efficiency but will be very expensive.
Power
Based on my discussions, the item that farmers underestimate the most is the cost to provide heating and cooling to the container farm. The containers themselves are solid steel masses but then are being modified for an alternate function. Modifications are frequently made to provide multiple entrances and exits. Additionally, provisions for ventilation, heating and cooling are needed to achieve optimal temperatures and humidity levels for plant growth. Each of these modifications reduces the solidity of the container and can require further power. Additionally, as high levels of lighting are required for growth, these lights can generate significant levels of heat.If the container is expected to be mobile, there may be limitations to types of power which can be used. Copious work has been done on the use of solar, with limited benefits to date. The limiting factor largely is the square footage of the container (typically 8ft x 40ft). Increased lighting efficiency, predominantly within LED, has improved power efficiency. These improvements are likely to increase steadily.
Summary of Efficiencies
The greatest cost improvement will be the pricing of the retrofit container. In a blog posting in March of 2018 by the Indoor-Ag Conference, it was estimated that branded containers cost in the range of $50,000 and $120,000 to purchase (our analysis uses $85,000 to $87,000) and those which were “homegrown” cost between $15,000 and $20,000. The cost of the branded containers should come closer to those which are homegrown. In the same blog, it was estimated that the cost of LED lighting, representing 25% of the fixed cost of a container, is expected to fall 40% from 2017 to 2020.
Labor is a second area where efficiencies will likely occur. However, gaining short term efficiencies in labor will likely be capital intensive. Given there are an estimated 500 container farms in the world, the incentive to infuse large amounts of dollars into container farms by R&D focused entities, is likely limited. The efficiencies will likely initially come to greenhouses and other contained environments; then the technology will be transferred to container farms.
Container Farms vs. Other Types of Controlled Environments
One of the many benefits of a container farm is related to being close to the customer. Another is that production is occurring in a fully contained environment. However, what are the benefits of container farming as compared to other forms of farming in controlled environments? The Indoor-Ag Conference Blog from March 2018 described the 5 most important benefits of container farms (paraphrased below):
The typical farmer is aging and 80% of container farmers are new to growing – Therefore, this brings new farmers into industry.
Investors have shown interest in providing funding to the industry.
Container can be in place and ready to grow in a few months, versus many months to over a year for
a fixed structure.
Containers can be placed almost anywhere due to size and having been retrofit offsite.
Comparatively low priced to set-up.
However, the question still remains, why choose a container instead of other forms of controlled environment farming facilities. This is a complex question because the constraints of the container footprint can impact the efficiencies of the container. I outlined 2 major reasons that could spur the growth of the container farm industry, as outlined below.
Reason 1: The primary reason that I can see for growth in container farms is that new farmers want to get into the industry with a limited investment. In no other form can one own a farm and all the necessary equipment for less than $100,000, and be up and running within a few months. This is an enticing motivator for an individual interested in going into farming. However, why the need for container farming. If a product can be grown in an alternative contained environment at a location within a day’s transport from the end consumer, at a cost that is far below that of produce grown in an on-site container farm; then there seems limited need for the container form for farming. Potentially container farming would be practical in an extremely cold location, where building a solid structure would be problematic.
Reason 2: Marketing! Wouldn’t it be a great marketing tool for a high-end restaurant or other type of food establishment to tell customers that the food they are eating was grown on-site and picked just prior to serving. An interesting example is the Boston based Cultivar restaurant, that touted on their homepage “Chef Dumont’s menu is informed by the restaurant’s on-site Freight Farm hydroponic garden, enabling fresh food production year-round, along with seasonal market produce, foraged ingredients, sustainable seafood and dry-aged meats”. In this example and others, the container was a great marketing tool and provided a premium product. However, it required great amounts of time and expense. I visited Cultivar l
to see the container and noted that it was covered in a fine wood exterior (see picture below) and was seeming less than a 20-foot container (less than 160 square feet). The container was located in a very public and expensive location and has a singular entrance point outside of the restaurant requiring an individual to go outside of the restaurant to harvest. Per Cultivar’s website, the container produced 225 heads of lettuce, brassicas and herbs a week.2
Summary:
Following a full analysis herein, my conclusion is that container farming is and will continue to be a niche product. It appears that fewer new farmers will buy container farms as they learn the results others have experienced. I believe container farming will become an increasingly niche product focusing on area’s that cannot get recently harvested produce at a reasonable price as well as niche restaurants and other food establishments that are willing to invest their resources to tout the growth of produce on-site.
The benefits of growing in a container, versus growing in an alternative contained environment are largely supply-side benefits: (i) Need for more farmers in the market; (ii) Investors seeking returns in the space; (iii) Entry into market with limited capital; (iv) Time to market; and (v) Limited footprint. It is on the demand side that the viability of the business comes into question. What do you get by growing right next to your location, versus, growing within a short distance of your location? The answer lies in the marketing of the container farm. It is my belief that the entities whom are willing to invest time and money to gain this marketing appeal will be very limited.
2 Please note that in January of 2019 it was announced that Cultivar was closing after being opened for less than 2 years. Speaking to Cultivar’s owner, Mary Dumont, she stated that the farm would be for sale in the near future.
Please click on the above to enlarge
Please click on the above to enlarge
Please click on the above to enlarge