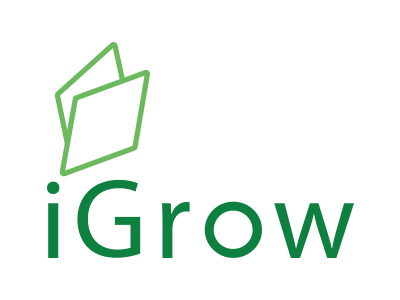
Welcome to iGrow News, Your Source for the World of Indoor Vertical Farming
Direct Delivery
With its fresh delivery service and strategic retail partnerships, Great Lakes Growers is building a business for the modern consumer.
May 28, 2019
Chris Manning | Photos by Allison Krieg
Great Lakes Growers, based in Burton, Ohio, produces leafy greens and herbs hydroponically in glass greenhouses.
Great Lakes Growers wants to change the way people buy and think about salad. The hydroponic greens and herbs operation is capitalizing on changing consumer tastes and sending its products straight to customers’ doorsteps with a new initiative called Great Lakes Growers Express.
Located in Burton, Ohio — a village with a total population of less than 1,500 — the operation was founded in 2011. But through relationships with restaurants and regional grocery store chains such as Buehler’s, Giant Eagle and Heinen’s, the business can reach a customer base in Ohio and neighboring states that would make up several dozen Burtons. And if its home delivery service goes according to plan, the company’s reach will extend even further.
“There’s about 80 million people we can reach,” says John Bonner, owner and founder.
“There are home delivery services out there for food, but we’ve always heard the complaints about, well it’s the produce that is really bad,” says Tim Ward, who does marketing for Great Lakes Growers and helped develop the Great Lakes Growers Express concept. “The other food is fine; the produce doesn’t hold up because they’re really packaging it and shipping it in traditional methods, the way you might find in a traditional grocery store. They’re getting it from out West. Everything’s being shipped directly from the source here.”
Through Great Lakes Growers Express, which officially launched in March, consumers can order combinations of living lettuce, fresh-cut herbs and other leafy greens from the grower online, and have them shipped directly to their home via UPS. Currently, there are four different combinations to pick from and each is available for delivery weekly or every other week for $29.99 per delivery.
According to Bonner, the logic behind the delivery service is two-fold. First, it opens new markets in urban and rural communities that don’t have grocery stores nearby — like inner-city Cleveland or a small town in Pennsylvania.
Second, Bonner believes that by shipping fresh greens directly to the consumer, he can tap into a younger customer base that seeks out instant gratification and is already ordering other goods like pet food, razors and toothbrushes online with pre-determined shipping (and payment) dates. It’s also a customer base, Bonner says, that wants fresh produce and worries about the quality of food they are consuming.
“Even if you’re getting it from a local guy like me, it’s still three or four days old at the store, which there’s probably not much difference in freshness,” Bonner says. “So it had to be fresh, had to be good, and the cost had to be no more money than they’re going to pay when they go the grocery store.”
John Bonner, left, and Tim Ward
Bonner’s beginnings
Bonner grew up in Burton, where his entire family is connected to the horticulture industry. On his father’s side, the main family profession has been traditional field farming. On his mother’s side, his grandfather founded BFG Supply, a greenhouse supply company based in Burton. Additionally, his father founded Dillen Products (later renamed HC Companies), a manufacturer of injected molded pots whose clients included many members of the Van Wingerden family, several of whom own large-scale ornamental operations.
“That’s how I got into farming,” Bonner says.
Additionally, his sister owns Eagle Creek Nursery, a wholesale ornamental producer. Originally, though, horticulture was not the path Bonner pursued. After graduating high school, Bonner attended Capital University in Columbus and earned a bachelor’s degree in finance. From there, he took a job at Merrill Lynch. But according to Bonner, it wasn’t work that fit him.
Bonner worked at Eagle Creek Nursery for a time after leaving Merrill Lynch, gaining notoriety in the industry for implementing sustainable business practices. In 2011, he left the family business and founded Great Lakes Growers.
The business started out small. He tested out his concept with 300 square feet of poly greenhouses and a basic hydroponic system constructed from supplies at Home Depot — but expansion came quick. From there, he was able to get his greens into local restaurants and eventually local grocery chains.
Today, Great Lakes Growers has 80,000 square feet of production space and is currently in the middle of an expansion that will double its size. Down the line, Bonner sees a need to hire growers. (Currently, he’s hands-on with the plants seven days a week.) But he can’t envision a future where he doesn’t spend at least some time in the greenhouse working directly with the crops.
“I cannot see myself not coming in here at least one day a week and watering everything and taking care of everything,” he says. “I can call everybody up in an hour and find out, ‘Hey, where do we want to do this, do that?’ But it’s just got to have more structure as we get bigger. And that’s what we’re doing. We’re expanding as an organization; we’re broadening out. So it’s fun. It’s challenging.”
Great Lakes Growers is in the midst of an expansion but it's already mapping out its next building project.
Fresh deliveries
Bonner and Ward, another Burton native and someone Bonner has known for years, started working on the delivery service about a year ago. According to Bonner, Great Lakes Growers Express and has been rolled out slowly on purpose in order to solve any potential logistical issues. The idea appealed to Bonner as a way to diversify outside of traditional retail methods.
“We told our retail partners we were doing it and they said, ‘Spot on man.’ Because they’re seeing it, too,” he says. “We’re doing meal kits and things for them, but their product development, this whole convenience thing, is what I was seeing when I started. This whole feeling of instant gratification — well it’s getting on steroids now. And I think we see it in all these subscription services and things like that. It’s not going to stop.”
To start, the company sent out greens and herbs via UPS and FedEx to friends and family. When the packages arrived, those friends and family sent back pictures of the greens to see how they held up. Bonner says that they sent out packages in a variety of weather conditions from extreme heat to extreme cold to make sure the greens would remain fresher than what they could buy at the store.
“We were testing so many things and looking at the variables,” Ward says. “I think we got it down to where anything within basically 24 hours is doable. So in any place that UPS can ship within a day is perfect.”
A key to the service is that Great Lakes Growers offers living lettuce with the roots still attached — allowing the lettuce to last longer once its in the customer’s fridge. Each order is also checked by hand in Burton to ensure that the greens are fresh and the order is correct. According to Ward, word-of-mouth and rave reviews from customers on social media are the driving factor as the business continues to grow organically and expand into new areas.
“We want to make sure that we can check every single box and we’ve had zero complaints so far of anything that we’ve shipped out to consumers,” Ward says. “And frankly I expect that to continue.”
Offering fresher products than the local grocery store is the main selling point for Great Lakes Growers Express. Say a customer orders greens on a Sunday. On Tuesday of that week, the greens are harvested, packaged and shipped out. The next day, the greens arrive at the customer’s doorstep via UPS. That’s even faster than the same greens, harvested the same day, would arrive at the local grocery store.
“It’s more units than you might find on a trip on a Monday to a grocery store, but it’s also got a shelf life that’s two weeks plus,” Bonner says. “So that whole process of training people that say, ‘Hey wow, got five heads of lettuce or six heads of lettuce, whatever it is, I can’t eat all that.’ But then if you leave it in your fridge for a week, two weeks, and you look at it, you’re going to go, ‘Damn, that still looks better than anything I’ve put in there.’”
Great Lakes Growers Express launched in April 2019 as part of Bonner's effort to better engage with modern consumers.
A key part of Great Lakes Growers' labor force is workers from the neighboring Amish communities.
Growing into the future
Right next door to the greenhouses filled with greens and herbs in Burton, Great Lakes Growers is in the process of expanding. Walk through one door and instead of greens, you’ll find construction crews building glass greenhouses and setting up the space for a concrete floor to be poured. Each greenhouse will be outfitted with LED lighting, environmental control systems, boom irrigation and other technologies since Bonner believes embracing technology and its possible benefits is key to keeping the business moving forward.
“I’m a big believer that ultimately, we have to get the cost inside the greenhouse down in the space or an area where we’re competitive with the field-grown stuff,” he says.
The plan, Bonner says, is to have enough growing space that products shipped via Great Lakes Growers Express have their own production area. He adds that the additional space is already “sold out” — meaning he already knows what will be grown there. And another expansion in the near future isn’t out of the question either.
There are also plans to continue diversifying the business. In addition to the delivery service — which Bonner and Ward hope to expand to new areas in the coming months — Great Lakes Growers products are now sold at Giant Eagle under the grocery store’s Market District branding. And other retailers are selling the product with the Great Lakes Growers logo on the package.
Outside of that, Bonner says selling greens to the food service sector is the business’ largest growing market share.
The key for whatever comes next, however, is still freshness. Regardless of what is next for Great Lakes Growers, and for Bonner, he says that must remain the core principle of the business.
“I look at it as we need to have stuff there that tastes better, looks better, grows better,” he says. “We need to give our customers the best price, so they can compete with their competitors. But ultimately, we’ve got to give the consumer the best price and the best quality.”
To learn about Great Lakes Growers' Amish workforce, search 'Amish' at producegrower.com
Hydroponics Leafy greens Herbs Grocery Harvesting
Career Opportunity: Head Hydroponics Grower - Grand Rapids, Michigan
Career Opportunity: Head Hydroponics Grower
Company: Mac & Fulton Talent Partners
Location: Grand Rapids, MI
Career Opportunity:
M&F Talent has a client in CEA crop production that is looking to onboard a new Head Grower. The position will focus on the commercial production of leafy greens and herbs in hydroponics systems. Our client is passionate about sustainable development as well as the creation of more nutritious food sources Moreover, they are on the cutting-edge of greenhouse cultivation techniques and have plans for exponential growth in the coming years.
Company Bio:
Mac & Fulton Talent Partners is the most knowledgeable and attentive recruiting agency in cannabis, hydroponics, and horticulture. As such, our business aligns itself with those individuals passionate about pushing the industry forward with skill, knowledge, and integrity.
M&F Talent approaches each of our business relationships with a partnership mentality based on trust and transparency. Looking to the future, we will continue to push for progression in the industry by setting high standards of follow-through and timeliness. With both clients and candidates, this level of excellence will help lay a solid foundation for growth and progress.
Our client is looking for a passionate and dedicated Head Grower to compliment their already growing team. This key position is responsible for all growing operations including water chemistry, food safety, biologicals, and growth strategies.
Contact & Info:
If you, or someone you may know, would like to learn about these exciting job opportunities in more detail, please follow this link:
Head Hydroponics Grower: https://mandfconsultants.com/jobs/head-grower-hydro-produce-michigan/.
To learn more about Mac & Fulton Talent Partners, please visit their website at www.mandfconsultants.com or contact them at info@mandfconsultants.com.
Competitors Join Forces to Push The Industry Forward
“FarmRoadTM was conceived to fulfil two broad purposes. A platform for autonomous farming and secondly as a way of bringing together all disparate technologies that farmers use into one unified management tool,” explains Darryn
Autogrow and Ridder
In order for the industry to move forward, collaboration is necessary. That’s what Darryn Keiller, CEO with Autogrow, is convinced of. “Everybody is innovating, but innovating in silos. There’s no real sharing of advantages created for the broader industry - and that’s the only way of speeding up innovation.”
Launching FarmRoad on the Indoor AgTech yesterday!
To change this, Autogrow launched a new farm management platform: FarmRoad. The new platform was launched yesterday at the Indoor AgTech Summit in New York.
“FarmRoadTM was conceived to fulfil two broad purposes. A platform for autonomous farming and secondly as a way of bringing together all disparate technologies that farmers use into one unified management tool,” explains Darryn.
Autogrow aren’t just talking - they are doing what they say they are - and have also announced a collaboration with their competitor Ridder Group, which will make it possible for growers to connect their Ridder climate control and irrigation systems to the FarmRoadTM platform.
“To be truly unified you need to be open and work collaboratively across the industry with buy-in from existing major players. It’s a concept we advocated two years ago when we came out with the first open API (Application Programming Interface) and I’m pleased to be in a position to say the dream is now tangible.”
“We are ecstatic that Ridder has shown the foresight and faith in us, to support what we are doing and join us in showing the industry what is possible when true collaboration occurs.”
Both Autogrow and Ridder market automation solutions for Controlled Environment Agriculture (CEA) and both will be able to integrate with FarmRoadTM. Ridder Group, will make it possible for growers to connect their Ridder climate control and irrigation systems to the FarmRoadTM platform.
“The Ridder Group, developer of the HortiMaX greenhouse control systems for over 40 years, supports the initiative of Autogrow,” says Joep van den Bosch, Chief Innovation Officer, Ridder Group. “Ridder believes strongly in a connected future where systems and data is shared for the benefit of optimizing the plants growing conditions and more efficient and sustainable greenhouse operations.”
There are various developments in the industry causing Autogrow to start innovating in this direction. Darryn explains how there are roadblocks in the way when it comes to the adoption of Agtech including the knowledge base – with the average age of the farming community going up and limited knowledge sharing tools available.
In order to transfer knowledge and systemise it, making it possible to utilise new technology, they developed FarmRoadTM, making it possible to share knowledge and collaborate.
Autogrow CEO Darryn Keiller at the Auckland, NZ office
“There are many applications growers have to deal with at their farm. If it’s the cultivars or heating, or energy consumption - traceability, environmental effects, finance, labor. Part of our journey is unifying farm information and data for different farms and crops, including machine learning techniques, into one platform.”
Alongside Ridder Group, Autogrow will also be collaborating with New York based Start-Up NATIVE.
“Equally as important as an established player showing vision, is new entrants to the industry who are also bringing innovation. What NATIVE are creating delivers a fundamental industry building block, which we will integrate with FarmRoadTM,” says Darryn.
The NATIVE platform connects farms with local buyers, maximizing the value of their harvests and helping both buyers and restaurants deliver on the promise and demand of locally sourced food.
“Our partnership with Autogrow will most benefit the growers and the farmers,” says Frank Pica, co-founder, NATIVE. “FarmRoadTM users can provide NATIVE with real-time data that verifies the quantity and quality of their harvests, and Native will return the true market value of the products. NATIVE then provides an outlet for growers to bring their products to premium markets within their region.”
Autogrow will work closely with Ridder Group and NATIVE over the coming months during the pilot phase. The beginning of the journey in working collaboratively with producers and growers.
“The next iterations of FarmRoadTM include flower and fruiting identification through Machine Vision and AI to provide pollination rates and flower to fruit conversion performance. We will be extending the 3rd party integration to include finance, labor management, food security and more,” says Darryn.
For more information:
Kylie Horomia
Autogrow
kylie.horomia@autogrow.com
www.farmroad.io
NatureFreshTM Farms Takes Home Accolades for Best Overall Pepper, Tomato & Cucumber at Leamington Greenhouse Vegetable Awards
Leamington, ON (June 16th, 2019) – The Tomato Capital of Canada, Leamington, Ontario, hosted its annual Greenhouse Vegetable Awards this past weekend at the Leamington Fair. Showcasing the best greenhouse-grown produce from leading North American growers, family-owned NatureFreshTM Farms was awarded many top accolades, including best overall Pepper, Tomato & Cucumber.
NatureFreshTM Farms took home top awards in the following categories:
-Best English Cucumber
- Best Speciality Mini Pepper
- Best Beefsteak Tomato
- Best Cluster Tomato
- Best Speciality Tomato for their TOMZ Orange Cherry Tomato
- People’s Choice Tomato for their TOMZ Tomberry® Tomato
- Kid’s Choice Tomato for their TOMZ Tomberry® Tomato
- Overall Best Cucumber for their Long English Cucumber
- Overall Best Tomato for their TOMZ Orange Cherry Tomato
- Overall Best Pepper for their Red Mini Pepper
Accepting the awards on behalf of NatureFreshTM Farms was Executive Retail Sales Account Manager Matt Quiring, “We have an amazing team who works very hard to ensure our produce has top-notch flavor paired with consistency.
Winning the highest overall honors across the board is a great testament to what our team can accomplish; it is more than just about showcasing the best that we grow, it is about our commitment to continuing to push our categories in the right direction.”
This is the second year in a row that NatureFreshTM Farms has won the Peoples Choice Award for Hottest Tomato and the Kids’ Choice Award for Hottest Tomato for their Tomberry® Tomato, an outstanding accomplishment considering the strong competition from other varieties in the market place. The Tomberry® Tomato, with a unique flavor profile & dubbed the World’s Smallest Tomato is one that has seen great response from consumers & continues to grow in demand.
Done under secret ballot, consumers get a true blind taste test on selecting the best varieties. NatureFreshTM Farms has proven themselves deserving of the awards with their continuous efforts toward perfecting flavor and growing the best vegetables they can. With such strong competition, NatureFreshTM Farms is very proud to be
taking home these meaningful awards voted and judged by the locals of Leamington.
All funds raised from the Greenhouse Vegetable Awards go to R.E.A.C.H International.
This local charity has continuously hosted this annual competition which celebrates Essex County as being the largest greenhouse industry in North America. As a recognized and registered Canadian charity, R.E.A.C.H International’s humanitarian efforts assist the poor all over the world with their main project currently in Uganda.
-30-
About NatureFreshTM Farms
NatureFreshTM Farms has grown to become one of the largest independent, vertically integrated greenhouse vegetable growers in North America. Growing in Leamington, ON and Delta, OH, NatureFreshTM Farms prides itself on exceptional flavor & quality. Family owned NatureFreshTM Farms ships fresh greenhouse grown produce year-round to key retailers throughout North America.
SOURCE: NatureFreshTM Farms | info@naturefresh.ca T: 519 326 1111 | www.naturefresh.ca
Can Giant Greenhouses Help Feed Consumers? AppHarvest Wants to Find Out
AUTHOR Christopher Doering@cdoering
May 28, 2019
Jonathan Webb grew up in Kentucky, where coal production once dominated the landscape. But while the region and its economy have fallen on hard times as mines have shuttered and workers laid off, the 34-year old is optimistic that it can rebound through a business typically not associated with the hilly area: agriculture.
Webb's company AppHarvest is expected to start shipping its first crop — tomatoes — to 25 major U.S. grocers in the second half of 2020. It will eschew the outdoor fields typically associated with agricultural production, instead embracing controlled environmental agriculture by working indoors with sprawling glass-enclosed greenhouses using rainwater to grow food that will be non-GMO and chemical-free.
Discover how you can apply real-time, predictive and historical traffic data and leverage location intelligence to improve and optimize your on-demand delivery service.
Its first greenhouse, which will be 60 acres, costs $82 million to build. AppHarvest recently secured funding for the 2.76 million square-foot facility from Equilibrium Capital. It separately raised an undisclosed amount from ValueAct Spring Fund and Revolution’s Rise of the Rest Seed Fund, led by AOL co-founder Steve Case and author J.D. Vance, to run its operations.
The company's location in Appalachia is no accident. AppHarvest is less than a day's drive to more than two-thirds of the U.S. population — including cities such as New York, Philadelphia and Boston — lowering transportation costs by 75% and enabling it to compete against foreign imports. The inspiration for the project came after Webb noticed how high-tech greenhouses in the Netherlands produce much as 10 outdoor acres on just one acre.
As the population around the world increases and many consumers demand healthier foods produced in a more sustainable and transparent way, Webb said companies such as AppHarvest will be ideally positioned to benefit. Webb spoke with Food Dive about AppHarvest's future and how it is planning to tap into these trends while helping the local community and posting a profit at the same time. The interview has been edited for brevity and clarity.
FOOD DIVE: Why did you pick Appalachia to start this business?
WEBB: Building a produce hub from the ground up that we can all be proud of is going to be a lot easier than trying to untangle a mess that frankly some folks in the food business are currently operating. And if you walk into a grocery store and a majority of what's in the grocery store is not real food, you know, that's a problem. And, I mean, if healthcare is bankrupting our country, how do you get to the root of the problem? Well, in many cases, that's food, and it's unacceptable that healthy, fresh food is not accessible and available to everybody.
Jonathan Webb
Credit: AppHarvest
There's a lot of different complexity to our business and our approach and how we're doing this. But in essence, we're building in a region of the country that got walloped on the decline of coal, and we think these are some of the hardest working men and women of the country.
This region has been kind of lambasted by national media. ...We would like to think that our region is well positioned to be a solution in agriculture.
So [we are] going from that transition of an energy economy in this region to hopefully ... a major producer for fresh fruits and vegetables for the U.S. It's an area of the country that powered the country, and we'd like to think it's going to be an area of the country that will be able to feed large segments of the U.S. Being a part of a solution is an important thing for this region and we think growing indoors, growing in a controlled environment, has extreme benefits from a lot of different levels.
What are the benefits of growing fruits and vegetables this way?
WEBB: It uses 80% to 90% less water than open-field agriculture. We're able to use integrated pest management to where we don't need to use the harsh chemical pesticides. And then a big one is the trucking. I mean, it doesn't matter if you're on the left or the right side of the aisle, it's unacceptable that food gets trucked five days in this country to make it to a plate. That's not good for anybody. It's not good for the environment. It's not good for the quality of the food itself. We're blessed by our geographic position, where we can get to roughly 70% of the U.S. population in one day's drive.
Has your unconventional approach made it difficult to convince people to invest?
WEBB: The first investors were Steve Case and J.D. Vance, and since then we've taken on significant follow-on investment over the course of the year. ... Attracting investment is very hard ... but if you look at the macro trends in how we're set up differently than many of the other players in this business, as people peel back the onion, it (conversation) has become increasingly, "Wow, this is a really good strategy and a very good geographic location, both from labor and from how we can get access to markets with transportation."
And then there's the macro trends of 600% more people said they were vegan over the last five years and ... more plant-based foods sold in the U.S. year over year. It's a good time to be in the fresh fruit and vegetable business, and it's a really good time to get into controlled agriculture. I mean, look at the scares with lettuce. ... Look at Wendy's, how they announced all tomatoes need to be purchased from greenhouse production. There's many layers to the business that just are attaching onto these macro trends. ... We think we're in a good segment and we're pretty optimistic on what the next five to 10 years look like in this industry.
"[We are] going from that transition of an energy economy in this region to hopefully ... a major producer for fresh fruits and vegetables for the U.S. It's an area of the country that powered the country, and we'd like to think it's going to be an area of the country that will be able to feed large segments of the U.S."
Jonathan Webb
Founder and CEO, AppHarvest
How did you come up with this idea?
WEBB: I was in D.C. and kept having and hearing conversations about the Netherlands. ... As we peeled back and looked at the Netherlands, it was pretty shocking. I mean, to see a country that is one-third the size of Kentucky in landmass — I can fit the entire country of the Netherlands in eastern Kentucky — and they have the second most agricultural exports in the world is just completely shocking. ... It's a very robust, proven industry in Holland. ... Our planet is at a real peril point on many different places and we need to take the best ideas and deploy those ideas around the world as quickly as possible.
... By 2050, we might need 50% to 70% more food to feed our growing population. You know, people are saying we might need two planet Earths ... to have enough land and water to grow enough food. ... We have one planet Earth, so we have to figure out how to grow significantly more food with significantly less land and significantly less water. And we can do that with all the proven technology that's in the Netherlands.
If you look at the rapid build out in the solar and wind energy industries, I mean, solar was nearly the No. 1 job creator in the U.S. because of the construction jobs. And so, if we're able to replicate that ... and build at scale with controlled environment agriculture, there's no reason why $10 billion to $15 billion of development does not go in the U.S. over the next five to 10 years. There's a market for it. Grocers want regional production. Groceries and food service want food safety with controlled ag. And I think there's an opportunity to bring a lot of these specialty crops indoors, regionalized production, and build out at scale all across the country. ... There's an opportunity for many of us to kind of get together at the table and figure out how we can collectively push the industry.
Your first greenhouse is slated to open next year. What's next and when?
WEBB: We're trying to be somewhat quiet about the strategy in general, but you know, that's a big facility for us. It's a first flagship, one of the largest connected under roof. ... It's actually about 70 acres fully connected with the (area to pack the produce) and everything. ... We have a very, very, very large strategy. I mean, we are looking at sites all across the region. Phase one of development is that first project and we have a phase two development that we're going to be pretty aggressive on.
Credit: AppHarvest
Do you have plans to look outside of Appalachia and maybe consider other parts of the country?
WEBB: We're going to completely focus on central Appalachia. We want it to be the largest indoor produce hub of the U.S. and we think, "Look at what happened with the Netherlands." ... We've tried to, again, just talk to operators, talk to growers. Why is the Netherlands so successful? Why do they get so much efficiency? Because it's such a tight-knit community and they've done it in such a close tight-knit environment.
We're going to leave the West off the table. Let everybody else fight for that 30% of market where you've got a ton of production. We're going to focus on the 70% of the U.S. on the Eastern Seaboard, the Midwest and Southeast. And we can get to all of that in a day's drive from central Appalachia.
What crops are you planning to grow in your facility? Are you going to focus on specialty crops?
WEBB: Wheat, corn, soy, all those row crops will stay outdoors in the U.S. We believe everything else is going to come indoors and it's going to become regionalized. Is it going to take five years, 10 years, 15 years, 20 years? We'll see. We're going to focus on tomatoes, cucumbers, bell peppers, anything on the vine and then the specialty crops, the leafy greens, the herbs, the berries and strawberries. All can be grown inside these facilities. But for us out of the gate, we're going to completely focus on tomatoes. ... People are really paying attention that produce imports from Mexico have nearly tripled in the last 10 to 15 years.
Will the prices for your crops be competitive with other so-called conventionally grown methods?
WEBB: We're going to be selling to the largest ... 25 grocers in the U.S., and we're going to compete with conventional pricing. Our goal is to get fresh, healthy produce to the table of the majority of Americans. But we're bound and determined to make it affordable. Price is important, and we were going to be competitive with everything else that's on the market.
You plan to open the first facility in 2020. When do you anticipate having produce arriving in stores?
WEBB: It'll be in 2020. We'll be breaking ground on this first facility here in the very near future, and then we'll be operational in the second half of 2020, and we'll be on store shelves in 2020. We're going to be able to grow produce all year round, 24/7, 365 (days a year) in a controlled environment. We might go offline some in the summer to clean out the facility, but you know, we'll have the ability to run year round if that's what we choose to.
What do farmers think of your endeavor?
WEBB: We've tried to meet with local farmers and made it very clear that local farmers are not our competition. Our competition is 2,000 miles in the other direction (in Mexico), but we also want to be cognizant of the market in the U.S. ... There's a lot of production that goes online due to seasonality during those (summer) months. And so for us, we see the best price benefit and the best market opportunity in the winter months. ... We want to to situate ourselves best to satisfy market demands where a lot of the produce is not available in those colder fall and winter months.
I think for us there's been some big names that have announced, indoor growers that have gotten a lot of attention in New York and San Francisco and some of those big VC-backed companies. I'm huge fan of what they're doing. I think there's going to be a lot of winners in this market and anybody that can grow fresh food, whether it be hyperlocal or ... urban environments. There's a lot of excitement around indoor growing and controlled environment agriculture. I think there's a lot of opportunity in different segments of the market, but when it comes to production at scale, we don't really think it's going to be one of those companies in New York City or San Francisco ... that's going to feed the country.
"Our goal is to get fresh, healthy produce to the table of the majority of Americans. But we're bound and determined to make it affordable. Price is important, and we were going to be competitive with everything else that's on the market."
Jonathan Webb
Founder and CEO, AppHarvest
At the end of the day, are you a for-profit entity?
WEBB: We're a registered benefit corporation, so I don't just have fiduciary responsibility to our shareholders, but I also am able to do what I think are frankly just smart long-term business decisions. For example, we've made a significant investment at a high school in Eastern Kentucky and we put a container farm there. And why did we do it? We're pre-revenue, we don't even have tomatoes on the shelf.
In Holland, that culture of growing is so ingrained in society. ... You have to start early and have kids dreaming of what this industry can be. So for us, investing in more of these programs. It's not steel and glass or infrastructure that's going to define AppHarvest, it's the people of the region. And so for us, investing in communities in the region to create a culture of growing is critically important.
When do you expect to be profitable?
WEBB: We plan to be profitable in our first year. ... In order to have impact and be mission oriented, we've got to have a return for our investors, and so as long as I can show that this business is profitable, we're going to be able to do all of this other impact work. It's very important to us.
You operation seems to check a lot of the boxes popular with consumers such as chemical-free, non-GMO, less water consumption.
WEBB: Consumers are becoming more aware of what they're buying at the grocery. I think mothers and fathers are becoming more aware of what they're putting on their table. ... A lot of people in the agriculture industry do not want you to know the way your food is produced and they don't want you to know where your food comes from because it is dirty, it is messy.
With what we're doing, we want to be as transparent as possible, and we think the way we farm is going to sell our produce more than anything. I want people in New York City or in D.C., or wherever they're at, to know they're voting with their dollar. And by voting with your dollar, you can put healthy food on the table for your family and you're also supporting very important work in our community.
We want people to know how we're running our operation. And so it's important to us that minimum wage in our greenhouse for even entry-level employees is going to be $13 an hour, plus health benefits. And we're going to have upskilling classes in the nights and weekends. That's the way farming should be.
We've got a farming system in the U.S. where it's messy and we can't be proud of it. And I think you look at some of the labor practices that go on around the country and some of the labor practices south of the border and some of the chemicals. There's harsh chemical pesticides that are legal in the U.S. that are being used on farms and other countries. ... App Harvest is certainly not going to be perfect, but we're going to try our hardest to be very intentional about our growing practices and allow people to be proud of what it is they're putting on the table for their families.
Follow Christopher Doering on Twitter
Wageningen University Proves Viability of Fluence by OSRAM LEDs
Five-month growing trial on high-wire tomatoes conducted by Wageningen and Vortus demonstrates full-spectrum LEDs from Fluence by OSRAM are a viable solution to replace legacy HPS fixtures
June 11, 2019
ROTTERDAM, Netherlands & AUSTIN, Texas--(BUSINESS WIRE)--Wageningen University and Research (WUR), in cooperation with Fluence by OSRAM and Vortus, has released initial results of a cultivation trial analyzing the viability of full-spectrum LED lighting solutions, using Fluence PhysioSpec Greenhouse™ spectrum, in comparison to legacy high-pressure sodium (HPS) greenhouse lighting fixtures. Preliminary data shows PhysioSpec Greenhouse is up to 11% more effective than HPS in yield for certain tomato cultivars, with the added benefit of being more energy efficient than HPS fixtures.
“The initial results of this trial show growers can cultivate tomatoes as effectively with PhysioSpec Greenhouse as you can under HPS, possibly with a better yield, and with shorter stems,” said Dr. Ep Heuvelink, associate professor, WUR. “Of the tomatoes grown under PhysioSpec Greenhouse, when compared to the HPS control environment, the WUR team saw the crop developed well and fruits had similar dry matter content. In fact, fruit yield is a bit higher in the LED sections for the Tomagino cultivar, which is a welcome benefit when considering the energy reduction LEDs naturally exhibit over HPS technology.”
Dr. Heuvelink, and his team at WUR, tested PhysioSpec Greenhouse in comparison to HPS lighting from a recognized vendor. The research was conducted on Tomagino and Merlice tomato cultivars. WUR will publish the full data set later this year.
“Current practices use HPS technology as the sole source for supplemental lighting in greenhouses and the WUR trial proves this should not be the case,” said Barend Lobker, director and owner, Vortus. “Growers have been reluctant to transition to LEDs because they are uncertain if LEDs can be as effective for cultivation and the WUR trial eliminates any doubts around the capabilities of full spectrum LEDs.”
“This is a very exciting result for the application of full-spectrum LED technology in greenhouse tomato production. It demonstrates that even without any other environment optimization for LED solutions, LEDs can match, or even out-perform legacy lighting fixtures for commercial growers,” said Haris Ouzounis, horticulture service specialist and senior photobiologist, Fluence by OSRAM. “Upcoming studies from Fluence into the influences of light quality, distribution, and intensity, as well as optimizations to the rest of the environment should demonstrate improvements in productivity compared to legacy production practices.”
Further Collaborations in Science and Research
Cooperating with recognized thought leaders around the world is a top priority for Fluence by OSRAM. This initial trial with WUR is the first in a series of results Fluence will release over the coming months. Additionally, Fluence is advancing several other initiatives with research centers, universities, and organizations around the world to further develop best practices and forward-looking applications for the industry.
“Basing our solutions on research and science are fundamental differentiators which sets Fluence apart,” said David Cohen, chief executive officer, Fluence by OSRAM. “We are proud to be working with Wageningen University and to join the WUR Club of 100, to further extend the world’s understanding of critical and fundamental horticultural research. Greenhouses are a significant source of nutritious fruits and vegetables and WUR’s ground-breaking research will empower more countries to cultivate high-quality crops in an energy-efficient way.”
To learn more about the preliminary results, meet with the Fluence team at Green Tech in Amsterdam, or visit https://fluence.science/wageningen for more information.
About Fluence by OSRAM
Fluence Bioengineering, Inc., a wholly-owned subsidiary of OSRAM, creates the most powerful and energy-efficient LED lighting solutions for commercial crop production and research applications. Fluence is the leading LED lighting supplier in the global cannabis market and is committed to enabling more efficient crop production with the world’s top vertical farms and greenhouse produce growers. Fluence global headquarters are based in Austin, Texas, U.S.A., and its EMEA HQ in Rotterdam, Netherlands. https://fluence.science
About Wageningen University and Research
The mission of Wageningen University and Research is “To explore the potential of nature to improve the quality of life.” Under the banner Wageningen University & Research, Wageningen University and the specialized research institutes of the Wageningen Research Foundation have joined forces in contributing to finding solutions to important questions in the domain of healthy food and living environment. With its roughly 30 branches, 5,000 employees and 10,000 students, Wageningen University & Research is one of the leading organizations in its domain. The unique Wageningen approach lies in its integrated approach to issues and the collaboration between different disciplines.
About Vortus bv
Established in 1982, Vortus bv is an independent greenhouse consulting firm which services clients from around the world. The team is comprised of ten consultants, which specializes in providing technical advice regarding climate, irrigation, nutrition, energy management, and labor management for greenhouse environments. The Vortus bv office is based in Honselersdijk, The Netherlands. For more information on Vortus bv services, visit www.vortus.eu.
Is The United States "Under Greenhoused"?
Peter Tasgal: The author is a consultant focused on the agriculture space with previous experience as CFO and board member of a $100 million CPG business headquartered in Montreal, Canada prior to which he was an investment banker for over 10 years.
US Greenhouse Trends - Comparison to Netherlands and Finland
May 28,2019
Peter Tasgal: The author is a consultant focused on the agriculture space with previous experience as CFO and board member of a $100 million CPG business headquartered in Montreal, Canada prior to which he was an investment banker for over 10 years.
His contact information is as follows: Peter Tasgal, ptasgal1@gmail.com, 617-794-4058.
The United States has over 10,000 vegetable and herb growing greenhouses according to the 2017 US Census of Agriculture. However, the majority of production occurs in only a small slice of these. A mere 296 of these greenhouses (2.7% of the category), make up what is termed as the “Large Commercial Greenhouses” category - characterized as being 40,000 square feet or larger. However, the Large Commercial Greenhouse category represents 68% of total square footage and sales. United States production is highly concentrated and much of the growth in vegetable greenhouses has been in “Small Greenhouses” – characterized as being less than 10,000 square feet. As of 2017, there are 9,658 greenhouses of less than 10,000 square feet, a 3.5x increase from 2002, when there were just 2,726.
The United States is “under-greenhoused” when it comes to vegetable production. Below is a comparison of the United States, The Netherlands, and Finland’s greenhouse vegetable production on a per capita basis:
United States: 0.35 square feet of greenhouse per capita
Finland: 4.12 square feet of greenhouse per capita
Netherlands: 31.4 square feet of greenhouse per capita
The reasons for the significant discrepancies among countries include Finland’s climate being much less conducive to outdoor farming than the US, and in the case of The Netherlands, it is a significant exporter around the world. However, these discrepancies are massive. Finland has 12x the production of the US per capita and The Netherlands has 90x the production of the US per capita. Why is this and more importantly how do we increase US production in a significant way?
Commercial Greenhouses – US
The focus of this document is commercial greenhouses, which I classify as those 10,000 square feet or greater. 10,000 square feet was chosen as the US Census shows an average sales figure of just over $6 per square foot for greenhouses of 10 to 20 thousand square feet, implying a minimum $60,000 revenue per greenhouse in the category. Please note this is a minimum and there are farmers doing hundreds of thousands of dollars in revenue in greenhouses less than 10,000 square feet. For analytic purposes it is useful to delineate those greenhouses which are 10 to 40 thousand square feet (“Medium Commercial Greenhouses”) as compared to Large Commercial Greenhouses, those over 40 thousand square feet. The following table summarizes data from the 2017 Census of Agriculture for:
“Total greenhouse vegetables and fresh cut herbs”:
The 1,191 commercial greenhouses represent 81% of greenhouse vegetable production. Within commercial greenhouses, those defined as medium sized are quite small, averaging less than 17 thousand square feet. A 17 thousand square foot greenhouse selling product at a rate of $6 per square foot is generating in the range of $100,000 in revenue per annum. As in any analysis, these figures are averages, and many greenhouses are doing far more in revenue on a per square foot basis. Like anything else, greenhouses are not all the same. Revenues are dependent on crop types, cycles per annum, efficiency of farm, location and sales method.
Benchmarking “Best of Breed”
Finland
Given that Finland is one of the world’s northernmost countries, outdoor vegetable growth is limited. This makes Finland ideally suited for greenhouse production, as well as imported products. Finland imports significant amounts of outdoor grown produce from the likes of Spain, Italy, Greece and other parts of the world. However, there is a significant concern from the Finnish people regarding pesticide levels of imported fruits and vegetables. According to the Luke Natural Resources Institute of Finland, the country is more independent in terms of greenhouse vegetables than it was 10 to 15 years ago.
According to the Natural Resources Institute of Finland, as of 2018, there were 484 enterprises involved in greenhouse vegetable production. This represents 2.1 million m2 of production. 2.1 million m2 equates to 22.8 million square feet of production and an average of over 47 thousand square feet per enterprise. As a comparison, the average vegetable producing greenhouse in the US is just over 10 thousand square feet.
The Netherlands
The Netherlands has been the leader in greenhouse production for decades. In a September 2017 article in the National Geographic it was noted that The Netherlands is the “globe’s number two exporter of food as measured by value, second only to the United States, which has 270 times its landmass.” Comparing US greenhouse production to The Netherlands’ is difficult as the Dutch made a national commitment toward sustainable agriculture in the early 2000’s. However, it does give the US direction as to production and methodologies for the future.
According to Statistics Netherlands, there were 4,990 hectares (approximately 537 million square feet) of vegetable production under glass in 2018 across 1,180 greenhouses. This represents an average of over 455 thousand square feet per greenhouse. For comparison purposes, the average size of a Large Commercial Greenhouse in the US is about 257,000 square feet, just over half the size of the average of all vegetable greenhouses in The Netherlands.
Trends in the US Compared to Best of Breed Countries
When analyzing 10 and 20-year trends in the US vegetable greenhouse industry, findings show them to be in almost direct contrast to the trends for a similar period in Finland and The Netherlands. In the US there has been a rapid increase in the number of greenhouses and total production space, but the average size of each greenhouse has gotten smaller. Similar trends exist relating to commercial vegetable greenhouses in the US, those 10,000 square feet and greater. The number of greenhouses and production space has increased, but the average size of each greenhouse is smaller. In 2007 the average size of a commercial vegetable greenhouse was 118 thousand square feet and in 2017 averaged 76 thousand square feet, a 35% decrease over the decade.
In Finland and The Netherlands the number of enterprises have decreased dramatically. There is a slight discrepancy in terms of average production space. In the Netherlands average production space has increased nominally and in Finland it has decreased, but these trends are much more moderate than those trends in the US. In both the Netherlands and Finland the average size of each greenhouse has risen dramatically over the period. The tables on the following page highlight the long-term trends:
Table 1. US Vegetable Greenhouse Industry
The contrast between countries is quite staggering. The Dutch are the clear industry leaders, distantly followed by the Finnish, and even more distantly followed by the US. Additionally, the trends in each of Finland and the Netherlands are highly consistent on a year-over-year basis over the long-term. Looking to the future of the US commercial vegetable greenhouse industry, similar trends are expected to those that Finland and The Netherlands have experienced over the past 10 to 20 years. Looking forward 10 years from now, I would expect the average commercial greenhouse in the US to be significantly larger than 76 thousand square feet.
Basis for Trends in The Netherlands and Finland
Some of the underlying reasons for the trends outlined above for the Finnish and Netherlands greenhouse industries are outlined below:
Aging Farmers – The farmer population is aging. Those next generation farmers who have chosen to remain farmers have invested in larger greenhouses with more modern cultivation technology which will allow them to compete on a global scale.
Professionalism – Maintaining a competitive presence requires professional operations, especially in the highly competitive export market.
Mergers / Alliances – Given that economies of scale are reached through larger facilities; there has been significant merger / alliance activity. In Finland, for example, there are currently 3 to 4 entities representing 70 to 80% of the production of lettuce and herbs.
Desire for Local – In Finland there is less dependence on imported produce than 10 to 15 years ago. People want local produce. At those times when local is not accessible, consumers still want to know the origin of their produce. There is a major concern in Europe regarding levels of pesticide use by outdoor farmers in the major European growing areas - Spain, Italy, Greece.
Renewable Energy Sources – The latest technology in greenhouses is expected to utilize “renewable energy resources”, potentially making greenhouse production carbon neutral. This would quell a lot of the discussion regarding the balancing act between greenhouses using less water than outdoor growing; but using more energy resources for lighting and temperature maintenance.
The basis for trends in The Netherlands and Finland are directly relevant to the United States applying to:
Aging farmers
Desire for locally grown food
Concerns as to farming practices of food exporters
Pesticides
Energy usage / Ability to use renewable energy
Environmental volatility
Population growth
Water scarcity
A significant number of these could be mitigated through the building of technologically advanced greenhouses and other forms of CEA within the United States. There are highly experienced commercial greenhouse manufacturers in the United States, The Netherlands and around the world who can bring the latest technology to the US market (See Appendix A – Overview of Greenhouse Manufacturers).
Summary:
Currently the United States is “under-greenhoused”. There are many reasons why it is important and possible for the United States to have more greenhouses over the near and long-term. The United States can be an efficient operator of greenhouses, similar to best of breed countries - The Netherlands and Finland, if some trends over the past two decades are steadily reversed. Growth in vegetable greenhouses will need to be focused on Large Commercial Greenhouses as compared to Small Greenhouses. The technology and capital needed to build large greenhouses is expensive. However, the end result of building such greenhouses will help mitigate some of the biggest issues of our time – energy usage, water scarcity, consumer knowledge of food origin, and growth inputs.
© 2019 - The Under-Greenhoused U.S. - Peter Tasgal
Waste Heat From Berlin Biomass Plant Will Help Grow Hydroponic Greens
The biomass power plant in Berlin is getting half a million dollars from the state to build a waste heat recovery system that will soon power a new greenhouse
PHOTO: Wood chips wait to be turned into electricity – and excess thermal energy – at the Burgess BioPower plant in Berlin.
Photo By CORI PRINCELL / NHPR
By ANNIE ROPEIK • 05-17-19
The biomass power plant in Berlin is getting half a million dollars from the state to build a waste heat recovery system that will soon power a new greenhouse.
The Burgess Biopower plant burns wood chips to make steam, which turns turbines and generates electricity.
It also makes a lot of excess heat – 500 million BTUs an hour, enough to keep roughly 10 million square feet warm. Right now, that heat is released to the atmosphere.
Burgess operations manager Dammon Frecker says the new grant, from the state Public Utilities Commission, will help them build a system to harness that waste heat and put it to good use.
"We're very excited about not only the economic development, but in doing something novel with Burgess BioPower,” he says. “Not only producing electrical renewable energy, but thermal renewable energy."
One application for that thermal energy will be a hydroponic greenhouse that’ll grow more than a million pounds a year of baby leafy greens – like spinach, kale and arugula – for sale locally.
"Particularly in a Northern climate, a greenhouse will need heat ... for growing the produce,” he says. “So this thermal energy recovery system has been designed just to meet those heating demands in the cooler weather."
The 4-acre greenhouse is set to be built next year and will be operated by a third party, which Frecker declined to name.
The city of Berlin also wants to use some waste heat to melt snow and ice on its sidewalks. Frecker says these kinds of “synergies” have been one of Burgess’ goals since it was built.
And he says even these two projects combined will only use about 20 percent of the heat the power plant generates.
Burgess has space left on its campus for future businesses that could use the heat. Frecker says it could also theoretically be distributed beyond their facility, with other infrastructure upgrades.
TAGS: BERLIN BURGESS BIOPOWER BIOMASS
RELATED CONTENT
Berlin City Manager Hopes To Harness Steam From Biomass Plant To Melt Sidewalk Snow
By SARAH GIBSON • JAN 18, 2019
SARAH GIBSON FOR NHPR
On cold days, Berlin City manager Jim Wheeler can stand on the steps of city hall and see plumes of steam billowing from the wood chip burning plant Burgess BioPower.
The plant sits on the former site of the city’s pulp mill factory on the Androscoggin River.
“One of the things about biomass plants is that they make a lot of steam, and that's energy that goes to the sky,” Wheeler says.
Now, Wheeler wants to harness the heat that makes this steam for a snowmelt system.
Student Design for Space Colony Greenhouse Wins NASA Praise
Student-designed inflatable dome folds and collapses for transport, racks plants vertically.
IMAGE COURTESY OF DARTMOUTH THAYER SCHOOL OF ENGINEERING
May 8, 2019
A radiation-shielded, inflatable greenhouse with a hydroponic growing system designed by undergraduate students at Dartmouth College’s Thayer School of Engineering could sustain four astronauts on a 600-day mission to Mars as soon as 2030.
The students’ Deployable, Enclosed Martian Environment for Technology, Eating and Recreation (DEMETER) concept—the acronym is also the name of the Greek goddess of the harvest—won first place in the 2019 NASA Breakthrough, Innovative and Game Changing (BIG) Idea Challenge, the agency announced on April 24.
The team pitched their idea to scientists at NASA and the National Institute of Aerospace (NIA) in competition with four other finalist teams.
NASA and NIA are seeking innovative ideas for the design, installation and sustainable operation of a habitat-sized Mars greenhouse, with the primary purpose of food production, according to NASA. The agency says an efficient and safe greenhouse design could assist with Mars missions and long-term lunar missions.
The 8-meter-high by 16-m-wide DEMETER includes an automated hydroponic growing system that uses a 3-m-tall cylinder inside of a torus, with the cylinder storing the water and nutrient delivery and recycling systems. A running track for astronaut recreation circles the vertically integrated assembly of growing trays.
The team used a 1⁄6-scale prototype to show folding methods for 1.5-m-long hydroponic growing trays, which nest against the central cylinder during transport. It also tested growing crops in a nutrient film technique hydroponic system to refine their design.
Dartmouth edged ahead when scored on the completeness of the proposed design, low system mass, optimization for food production and design simplicity, says Kevin Kempton, NASA program element manager and one of seven judges.
The team used “top-notch systems engineering throughout,” Kempton says. “That began with a systems overview that identified their system of interest relative to external systems, such as sunlight, heat, and water in the Martian environment.”
Kempton says another strength is that the components all appear relatively low risk and are based largely on a habitat design developed in a 2017 NASA feasibility study, which was the basis for the competition. “The team estimates it would take three to four missions to become a cost-effective option,” versus the cost of transporting food from Earth, Kempton says.
The team also scored high marks for innovation for the proposed concept of operations and for system deployment, which begins with robotic transport of the packaged greenhouse payload from the landing site to the deployment site. The design “seemed to have the highest level of technical maturity and it would likely require less technology development effort to get a DEMETER-base design up and running for the initial Martian outpost,” Kempton says.
NASA plans to send astronauts to the moon by 2024, with future missions in the 2030s, when a Mars greenhouse concept would potentially be viable, says Drew Hope, NASA program manager.
MIT placed second for its Biosphere Engineered Architecture for Viable Extraterrestrial Residence (BEAVER) concept. Plans include a spiral hydroponic design track in a multilevel facility featuring an enclosed waterfall for astronaut relaxation. Other finalists included designs from three state universities, California Davis, Colorado Boulder and Michigan Ann Arbor.
The finalist teams receive a shot at five NASA internships, recognition and a $6,000 stipend to travel to NASA’s Langley, Va., research center to present. All original ideas and concepts are credited to the student teams, but NASA has the option to take any portion of the ideas for use in future NASA mission planning, Hope says.
KEYWORDS Greenhouse /Hydroponic / Mars / NASA /Space Colony
Swiss Retail Migros: "All Greenhouses To Be Heated Fossil-Free By 2025"
Retailer Migros is serious: From 2025 onwards, the greenhouses supplying the Swiss retail chain are only to be heated with renewable energy. "With this pioneering work, Migros and its producers are showing that it is possible to phase out heating oil and fossil gas," said WWF CEO Thomas Vellacott earlier this year. "We need this kind of joint effort to meet the Paris Climate Agreement and curb climate change, which sets an example for Migros - also for other sectors."
Nowadays, the greenhouses are mostly heated by oil or natural gas. An estimated 100 companies supply the various cooperatives of Migros throughout Switzerland. "In the future, every company should use the optimum mix of renewable energy sources for its location", Migros explained. "Heat pumps, wood heaters, bio-gas, geothermal energy and solar energy are in the foreground."
Heating swiss horticulture
Greenhouses are heated especially at the beginning and end of the Swiss season to extend the domestic season. Since most growers have improved the insulation and energy use of their greenhouses in recent years, they have reduced their emissions. Nevertheless, greenhouse production continues to be one of the most carbon intensive sectors in Switzerland. "With annual savings of up to 75,000 tonnes of CO2 thanks to the use of renewable-heated greenhouses, regional production in cultivation is significantly strengthened",
The schedule to heat all greenhouses from 2025 fossil-free is ambitious. For this reason, the conversion takes place in close cooperation between Migros and the producers. Migros invests one million francs a year in the project. "With the money producers are financially supported in the conversion. In addition, thanks to clear commitments regarding the future scope of supply, producers are given planning certainty. Migros welcomes the commitment of all those involved to work together for a climate-friendly future", the retailer explained.
These energy changes in the glasshouses, however, have their price. There is a rumbling in the vegetable industry. Nobody wants to comment publicly, but behind the scenes, the very short deadline that the largest retailer in the country poses to its producers is being criticized, says SRF.ch.
Climate friendly lettuce
On the other hand, Migros' demand did not catch all producers cold. Patrick Forster, Managing Director and owner of the Forster Group, has already taken all kinds of steps by himself.
Hydroponic lettuce. The vegetable garden of the future?
When he built a modest new greenhouse a few years ago, he installed a waste heat installation instead of a conventional one. According to Forster, the greenhouse emits around 700 tonnes less CO2 per year. That's as many greenhouse gases as about 700 single households emit annually.
Sustainable Hydro Lettuce
In the Forster's greenhouse, lettuces are lined up next to other lettuces. Forster delivers them to the Migros. This so-called Hydro Lettuce production facility is already very sustainable, because it functions with a minimum use of water, pesticides and fertilizer, says Forster. The climate-friendly heating mode completes this sustainable project.
His greenhouse is situated next to a waste incineration plant in the district of Oftringen in the canton of Aargau. A special pipeline transports warm water to the greenhouse, where it creates the necessary temperatures. This heating system was twice as expensive as a conventional heating system, says Forster. However, the vegetable growers will have earned back the investment costs within five years.
After that, the heating system is quite a bit cheaper: "This way, we have realized an economically and environmentally sensible project," says the vegetable grower and entrepreneur. But not everyone can build a greenhouse like him, next to a waste incineration plant. "For some companies it will be almost impossible to find a solution," Forster thinks.
For more information:
A. Trachsel AG - Forster Gruppe
Inh. Patrick Forster
Gewerbe Brunnmatt 7
6264 Pfaffnau (CH)
+41 62 746 93 00
www.trachsel.ch
Publication date: 5/8/2019
Northern Italian Trial Greenhouse To Test Floating Systems In Winter
"Water temperature essential element in growing on floating systems"
"Growers have been using floating systems for years, but not always in the right way. We verified that an essential element is the temperature of water." Speaking is Gian Paolo Menarello with Idromeccanica Lucchini. The company set up a testing area in a company located in northern Italy to grow lettuce using a floating system in winter. "They proved that it is not so much air temperature, but rather the water temperature that determines crop development."
Idromeccanica Lucchini is continuously experimenting with hydroponic cultivation and, specifically, with floating systems.
Non-heated greenhouse
Tests are still being carried out in a non-heated greenhouse (45 meters long, 8 meters wide and 3.5 meters high) protected with a plastic film. A heat exchanger helps maintain the temperature within a suitable range without wasting too much energy, so that the crop can be economically viable.
"Another fundamental aspect is the monitoring of oxygenation. While the floating system technique helps make a better use of the space, it cannot be improvised and all materials must be chosen accurately. For example, supports are made of PVC suitable for young plants."
Lucchini focuses on innovation working alongside entrepreneurs to make sure all steps are verified and all components are checked. For example, while the temperature in tanks must be regulated in winter to obtain sustainable productivity, the environment needs to be cooled down in summer.
"The first winter harvest was excellent and economic results were very positive for growers. Heads were large, weighing around 450 grams each. Thanks to our tests, we proved that, in theory, lettuce could be cultivated throughout the year in northern Italy too, but the cycle becomes too long in central winter months, so it is not worthwhile. Anyway we are also carrying out tests with parsley, celery and endive."
This type of cultivation leads to many advantages: there are no soil fatigue problems, a lot of water can be saved and there is no need to weed or prepare the soil. In addition, producers can make more precise plans and spend less money on labor.
Contacts:
Idromeccanica Lucchini S.p.a.
Via Cavriana 4B
46040 Guidizzolo (MN)
Tel.: (+39) 0376 818433
Fax: (+39) 0376 819498
Email: info@lucchiniidromeccanica.it
Website: www.lucchiniidromeccanica.it
Publication date: 5/8/2019
© HortiDaily.com
Boston, MA - It Happens Here: Hands-Off, Year Round Farming At Little Leaf Farms In Devens
By Kate Merrill April 26, 2019 Filed Under: Boston News, Devens News, It Happens Here, Little Leaf Farms
DEVENS (CBS) – It happens here in Devens, a region made up of sections of Shirley and nearby Ayer. It’s a decommissioned army base named for Union Army General Charles Devens. It is now a residential and business community that is home to a small company helping New Englanders eat fresh, locally grown greens year-round.
Welcome to Little Leaf Farms. It’s not what most of us picture when we think of farming.
“It’s an automated system,” explained founder and CEO Paul Sellew.
It’s a massive greenhouse where green leaf, red leaf, and arugula are neatly planted in gutters. They are irrigated with rainwater collected from the roof, and an automatic shading system on the roof makes sure it doesn’t get too hot.
Lettuce grows in gutters at Little Leaf Farms in Devens. (WBZ-TV)
Each gutter slowly moves across the massive greenhouse at a pace so slow, you don’t even notice it. After about three weeks, the gutter drops onto a conveyer belt where it heads into the packing room where it feeds through a pair of circular cutters and then through a sorting system before it’s packaged into plastic bins.
While not officially organic, Sellew says there are no chemical pesticides.
“We use something called biological control,” he explains.
Little Leaf Farms uses lady bugs to eat the insects that threaten crops. (WBZ-TV)
They use lady bugs to eat the insects that threaten the crop.
“Because no human hands touch it, there’s no need to wash it. It’s ready to eat,” Sellew said.
With a farming background, (he also created Backyard Tomatoes from Maine) Sellew built a massive greenhouse back in 2015. His goal was to provide New England shoppers with an alternative to produce that’s shipped from the west coast.
“They were relying on stuff that’s grown in California that is trucked across the country and by the time we get it, it’s 10 days old,” he said.
Little Leaf Farms products are boxed at their Devens facility. (WBZ-TV)
The company believes the hydroponic method of growing also cuts down on the risk of disease like the romaine E.coli outbreak last fall.
“What we are doing has nothing in common with that is being done in California where they have cattle ranches and dairy farms next to lettuce fields,” Sewell said.
Greens from Little Leaf are packaged within minutes of harvest and can be at the store that same day.
Sellew says customers are loyal and demand is constantly increasing which is why they are building another massive greenhouse on their Devens campus.
Their next project? A new romaine variety. No word on when you’ll see it in your local supermarket.
KATE MERRILL
Emmy award winning journalist Kate Merrill is a news anchor for WBZ-TV News weekday morning and noon newscasts.
Gotham Greens To Open New Greenhouse In Rhode Island
A rendering of Gotham Greens' forthcoming greenhouse in Providence
Photo courtesy of Gotham Greens
The 110,000-Square-Foot
Facility Will Open In Fall 2019
April 25, 2019
According to a press release, urban grower Gotham Greens is opening a new 110,000-square-foot facility in Providence, Rhode Island. The facility, according to Gotham Greens will produce 10 million heads of lettuce and leafy greens annually for customers in Providence and the greater New England region.
The greenhouse, located on the site of a former General Electric facility that has sat vacant for two decades, is set to open in fall 2019.
"We are thrilled to partner with the City of Providence and State of Rhode Island on this project," said Gotham Greens Co-Founder and CEO Viraj Pur, according to the release. "Providence is the perfect location for us, strategically located at the gateway to New England, the city has a rich legacy of manufacturing, world-class institutes of higher education, and a thriving local food culture. Geographically, New England is farthest from the West Coast, where the majority of leafy greens distributed across the U.S. today are grown. Once we're operational, Gotham Greens will be able to supply this region's supermarket retailers and foodservice operators with a consistent and reliable supply of fresh produce grown right here in New England year-round."
Pur announced the new greenhouse alongside Rhode Island Governor Gina Raimondo, Providence Mayor Jorge Elorza, Rhode Island Commerce Secretary Stefan Pryor and other community leaders. An estimated 60 full-time jobs at the greenhouse and 100 construction jobs are expected to be created by the project, which will cost $12.5 million. The Rhode Island Commerce Corporation has committed up to $2.3 million in tax credits, payable over a 10-year period contingent on job created.
US - Pennsylvania - BrightFarms To Open Hydroponic Greenhouse in Snyder County
BY MELINA DRUGA | APRIL 25, 2019
New York-based BrightFarms recently announced plans to open a 250,000-square-foot hydroponic greenhouse in Snyder County.
© Shutterstock
The greenhouse will serve the company’s four primary facilities and will grow leafy greens and herbs. BrightFarms will invest more than $20 million, and the project is expected to create 54 jobs over the next three years.
“BrightFarms is extremely grateful for the support we have received while searching for our next location in Pennsylvania,” Paul Lightfoot, BrightFarms CEO, said. “This is an exciting chapter for our company as we push forward with our mission of providing more Americans access to the freshest, tastiest and most responsibly grown local produce through their supermarkets. Our next step will be recruiting members of the community to fill over 50 ‘green-collar’ jobs at the greenhouse. These employees will receive competitive pay, industry-leading benefits and world-class training from our team members.”
The Department of Community and Economic Development submitted a $24,300 grant proposal to BrightFarms for workforce training.
The Pennsylvania Industrial Development Authority has encouraged BrightFarms to apply for a $2.95 million low-interest loan to assist with the purchase of land, machinery, and equipment.
BrightFarms grows using sustainable farming methods in four states: Pennsylvania, Ohio, Virginia, and Illinois.
Italy: Thirteen Hectares of Lettuce Grown On A Floating System
All types of lettuce are grown with the floating system on an area of 13 hectares. The whole system is automated to produce salad marketed under the brand name Ninfa. The location is Standiana, (Ravenna), near the large amusement park Mirabilandia, famous in Italy. "Here we also have fun with water - and we produce lettuce with water", entrepeneur Gianluca Rossi says.
The owner Gianluca Rossi
High quality
A production site of this size, with these technologies is not often seen in Europe. According to Rossi he gets positive responds on his systems, even from the major seed companies in the world.
"The 13 hectares are part of a 100-hectare farm. The design took more than six years to complete and I did it myself together with the leading experts. I made many trips abroad before it was done", he recalls.
Here is how the roots appear in the support, just removed from the water
On the track, oriented in the direction of the processing warehouse, the panels with the lettuce.
Gianluca shows how everything is done with utmost care. "Our greenhouses only serve as protection, not to anticipate cycles. The production runs from mid-April to December, while in the winter months it is suspended."
The cultivation takes place with floating panels certified for contact with food. The roots are immersed in water. Nutrition is carried out with the classic triad of elements N, K, P and microelements. Weed killers are not needed, of course. Defence follows the technique of integrated control.
Watch the video!
The positioning of the panels with lettuce on the railroad.
180 hectare land
"With traditional methods, adds Rossi - considering also the rotations, in the open field - it would take 180 hectares of land to produce what we can do in 13 hectares of floating system. In our case, the rotation is nothing more than the replacement of the "old" water that is not wasted but returned to the fields of the remaining 87 hectares of our company".
No water waste
At first glance, it might seem that there is a waste of water, but that is not the case. "Careful management allows for prolonged and waste-free use. With the same number of plants produced, the reduction in water consumption varies between 70 and 80% compared to a traditional method".
Here are some other numbers: 9 million cultivated plants expected in 2019, 4000 tons of products and 169,000 floating support panels. "Our history goes back a long way, Rossi points out, because it was my father, from a very young age, who dedicated himself to the trade in vegetables. At a national level, we are already known for our activity as traditional producers, and now we want to make ourselves known for this new reality".
Aerial view of the Standiana farm. There are 13 hectares of greenhouses with lettuce grown in floating systems
Minerals
Water, like the earth, does not of itself, contain enough nutrients, but they are both a means of mixing, holding and conveying them. Unlike traditional methods, in the tank, the mineral salts are available only to plants that absorb according to their daily needs, excluding leaching, waste and dispersion into the surrounding environment or in the aquifers.
"More yields, less waste of nutrients, less water consumption, no forcing, concludes Rossi. There is a difference, even from an organoleptic point of view. The panel tests carried out on the Ninfa salad have shown a higher percentage of mineral salts than traditional crops, with a significant increase in shelf life.
The Research of The Investment Potential of Russian Greenhouse Complexes 2019
The team of analysts from Vostock Capital is preparing a report on the research of Investment Potential of Greenhouse Complexes in Russia 2019. The report will feature:
new investment projects (greenhouse complexes construction and modernisation)
development perspective and challenges of the Russian greenhouse industry
greenhouse products potential at the domestic market in the upcoming future
global mega-trends, influencing Russian greenhouse industry and a lot more outcomes significant for the industry
Get the report by taking part in a 5-minute survey.
Fill in the questionnaire here
The report will be prepared prior to the upcoming Forum Greenhouse Complexes Russia 2019 to be held on 4-5 December in Moscow.
4th Annual Forum and Exhibition Greenhouse Complexes Russia 2019 – is an established professional international platform for attracting investment in the Greenhouse Industry of Russia, discussion of industry development strategies, exchanging of experience between key market players and signing new win-win contracts.
Over 700 leaders and senior executives of agricultural holdings, greenhouse complexes, initiators of investment projects, investors, retail chains, government officials, producers and providers of equipment and related services for the greenhouse industry took part in the Greenhouse Complexes Russia Forum 2018. Delegates from more than 20 countries participated in the event. 500+ business meetings were conducted at the Forum.
Date: 4-5 December 2019
Organised by: Vostock Capital
Website: https://www.greenhousesforum.com/
Contacts: Elvira Sakhabutdinova, Project Director
+7 495 109 9 509
Urban Farming: Gotham Greens Sees ‘Continued Rise’ In Demand
Gotham Greens said its Chicago facility is “the world’s largest” rooftop farm. © Gotham Greens/Julie McMahon
Posted By: Jules Scully
April 8, 2019
Following the recent romaine lettuce E coli outbreak across North America, US authorities called on the leafy greens supply chain to adopt emerging technologies to trace produce from field to fork.
From October to December, a total of 63 people were infected with the same strain of E coli. While no one died, 25 people were hospitalised and two developed kidney failure.
Following the romaine recall, prices of other lettuce varieties more than doubled at one point due to surging demand. The outbreak – which saw authorities warn consumers to avoid eating romaine lettuce – has heightened consumer demands for traceability, as they aim to ensure the food they purchase is safe to eat.
US urban agriculture pioneer Gotham Greens believes the scare, and resulting supply chain and traceability issues, served to validate its business model of growing produce in a secure environment that can reduce the risk of food-borne pathogens. Indeed, during the incident, the company saw a surge in orders of its romaine lettuce.
“Customers were confident in the origin of Gotham Greens produce and they knew they could rely on our products to be safe and grown locally in sterile greenhouses,” said CEO Viraj Puri, who co-founded the company in 2009.
The firm opened its first facility in 2011, located in Brooklyn, New York, and it now operates more than 180,000 square feet of greenhouse across four sites in New York and Chicago – and currently has an additional 500,000 square feet of development underway across five US states.
Viraj Puri, Gotham Greens CEO and co-founder. © Gotham Greens/Julie McMahon
Last June, the company secured $29 million in a funding round, as it aims to continue transforming urban real estate and promoting sustainable agriculture.
Supplying retail, restaurant, and institutional customers, Gotham Greens’ non-GMO, pesticide-free produce is grown using sustainable methods in climate-controlled urban greenhouses using 100% renewable electricity.
The firm sells produce such as iceberg lettuce, basil, baby kale, rocket, a range of leaf blends, as well as a selection of salad dressings and dips.
“When we built our first rooftop greenhouse, there was really no precedent for what we were trying to construct and we faced our fair share of scepticism from landlords,” Puri said. “Over the last ten years, urban farming has become commonplace in cities across the country, utilising space that wouldn’t traditionally be used for agriculture such as former industrial sites, rooftops, backyards, and parking lots.”
“Over the last decade, we’ve seen a major shift in consumer preferences towards local and sustainably produced food products. The rise in recent foodborne illness has underscored the need for greater traceability and transparency in the supply chain. As a result, we’ve seen a continued rise in demand for greenhouse-grown produce. There is an incredible value proposition of growing highly perishable fresh food in close proximity to large population centres while using fewer natural resources.”
Last week, Gotham Greens revealed plans for a new $12.5 million site in Providence, Rhode Island, which is expected to open its doors in early autumn 2019, creating 60 jobs. Geographically, New England is farthest from the West Coast, where the majority of leafy greens distributed across the US are currently grown.
Using growing methods such as recirculating hydroponics, data-driven climate control intelligence, and renewable energy, the facility is expected to produce approximately “30 times the yield of conventional agriculture per acre”.
The company offers produce such as iceberg lettuce, basil, baby kale, and rocket. © Gotham Greens.
The company’s technology enables it to capture irrigation water for re-use, which allows it to use “90% less water” than conventional farming, while eliminating all agricultural runoff. The greenhouses let it to grow year-round in regions that typically have much shorter growing seasons.
While it serves large foodservice operators and retailers such as Whole Foods Market and Target, Gotham strives to be community-minded and collaborates with local businesses, schools, and community partners where its facilities are situated.
“By locating our greenhouse farms in cities, Gotham Greens not only eliminates the environmental footprint and food waste linked to shipping produce long distances but also advocates for improved healthy food access, environmental education, and community development,” Puri said.
“We want to bring farming closer to city residents while simultaneously addressing supply chain issues for the food industry at large. We think globally but act locally.”
With seven years of data and experience to help inform growing decisions at future sites, the Gotham team believe they are ready to expand their project in 2019, with plans in place to more than double the workforce.
With the food traceability market predicted to surge in the coming years, the future looks positive for Gotham as it meets consumer demands for more sustainable, locally grown produce. Puri concluded: “The challenge is of course that the larger and more successful we get, the more complex scaling the business becomes.”
Tags:Gotham Greens sustainability Urban agriculture US
Qatar Academy Visit Dutch Greenhouse Tech Firm
Eight students of the Qatar Academy for Science and Technology (QAST), a new Science, Technology, Engineering, and Mathematics (STEM) school visited Certhon recently. The students visited the Dutch company because of their curriculum focus on reducing the need for imported food with a specific focus on growing fruits. The academy aims at honing the abilities of talented students to be the leaders and innovators, as well as building a distinctive generation in different paths that is innovative and in line with the requirements of the 21st century in facing the challenges of local and global reality, as well as to prepare students to succeed in institutions of higher education excellence.
This visit gave the students the opportunity to ask everything about the SuprimAir technology Certhon implemented in the UAE. Almost one hectare semi closed greenhouse for the production of tomatoes was built in the desert of Abu Dhabi. And with the first successful harvest in November 2018, a major step towards actual food security has been taken: the step towards the production of fresh and healthy vegetables with sustainable use of water, energy and raw materials in the Gulf region.
For more information:
Certhon
ABC Westland 555
P.O. Box 90
2685 ZH Poeldijk
The Netherlands
Tel: +31 174 22 50 80
Fax: +31 174 22 50 81
www.certhon.com
Publication date: 4/8/2019
Signify Expands In Belgian Horticulture Market With New TOMCO Project
Signify today announced its second horticulture project with tomato grower Luc Coghe to install full LED lighting in a newly built 10 hectares greenhouse in Roeselare, Belgium. Since 2014, Luc Coghe, Owner of TOMCO and his wife, Greet Biesbrouck, have increased yields and improved the quality and taste of high wire tomatoes grown under a combination of Philips GreenPower LED interlighting and high-pressure sodium (HPS) lighting at their Biesbrouck Company. Based on this success, they are moving to a full Philips LED lighting system for their newest greenhouse.
The new greenhouse is equipped with a combination of Philips LED toplighting and interlighting that produces a total of 225 µmol/m2/s. LEDs produce little heat so planting can start earlier and therefore the plants can be given more light in the spring and summer. “I expect this system to bring in higher yields and more predictable production for my customers. LEDs should also help us differentiate ourselves in terms of quality and taste, as we have experienced at our Biesbrouck location,” said Coghe. “More importantly, my greenhouse is future proof with full LED.”
“We are seeing a great demand for our Philips GreenPower LED solutions in the Belgian market,” said Udo van Slooten, Business Leader Horticulture at Signify. “Not only has Luc Coghe decided to reinvest in LEDs. Other companies in Belgium that have made that move recently include Den Boschkant and Tomaline with hybrid toplighting combining LED and HPS and Ceulemans. That is because they trust that our Philips products will help them achieve higher yield and a better-quality crop.”
TOMCO is planning to grow the variety Xandor in the new greenhouse. The project is being carried out with Philips LED Horti Partner MAIS AUTOMATISERING NV and the plants are expected to go in in June 2019
DelFresco Pure Goes Vertical With CubicFarm
April 10, 2019
Jo-Ann Ostermann, of CubicFarm and Carl Mastronardi of DelFresco Produce demonstrated the vertical farming system by CubicFarm at CPMA in Montreal.
MONTRÉAL—Vertical farms are all over the news as players want to cash in on consumer demand for local fresh produce, but it’s not as easy as dropping a container next to a supermarket.
That’s where a background in greenhouse growing comes in.
Kingsville, ON-based DelFresco Produce Ltd. is working with CubicFarm Systems, Milner, BC, to expand the company’s product line and footprint with container farms.
“We’re starting with 14 units, and we’re going to see how quickly we can get this going,” said DelFresco President Carl Mastronardi. “Once we see that it’s going well, we’re going to expand it.”
Mastronardi envisions nationwide expansion over the next five years and is drawing on decades of experience growing greenhouse produce in Canada.
Growing in containers is a hot trend right now, but not everyone’s up for the challenge.
“A lot of people are getting into it, and a lot are failing,” he said.
Part of that is the technology, and part is the high cost of labor – two things for which CubicFarm and DelFresco believe they have the solution. CubicFarms’ system is fully automated, instead of relying on racks that have to be manually rotated. That cuts down tremendously on labor, Mastronardi said.
The technology has evolved over the past decade and a half. Most growers wouldn’t consider lights for vegetables because the energy cost is too high.
Nowadays, the LED lights are highly specific, emitting only the light necessary for optimal plant growth, with new tech constantly coming online, said Jo-Ann Ostermann, vice president of CubicFarm.
“We’re getting better and better at it every day,” she said.
Mastronardi is no stranger to taking risks with a new technology. DelFresco launched greenhouse strawberries in Ontario several years ago, and Mastronardi was recognized by the Ontario Produce Marketing Association as its Produce Person of the Year for the endeavor in 2018.
With this new venture, DelFresco is aimed at flavor and safety.
“What we’re trying to do is give the consumer a real safe product, and a taste experience,” he said.
Products planned for launch include living garden lettuces, which consumers can buy with roots intact and continue growing at home, as well as living microgreens that stay fresher longer.
“The biggest advantage is a better flavor profile whether it’s 120 degrees outside or 20 degrees outside,” Mastronardi said.
Tagged cpma, greenhouse
Pamela Riemenschneider is Retail Editor for Blue Book Services