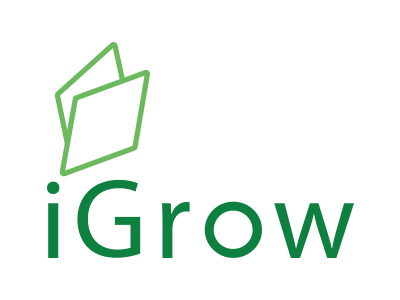
Welcome to iGrow News, Your Source for the World of Indoor Vertical Farming
It Is Time To Grow!
In an Urban farming pilot project, we grow leafy greens in a nutritious fluid, in a container powered with 100% renewable energy outside the IKEA Malmö store in Sweden
2ndProject portfolio Leader på IKEA, Ingka, Group Sustainability
The majority of IKEA visitors enjoy the IKEA food offer and today we enable millions of people to eat healthier and more sustainably by choosing our plant-based options. We are continuously exploring how we can contribute to a better, greener, and tastier future making healthier and more sustainable food accessible and affordable for many people.
In an Urban farming pilot project, we grow leafy greens in a nutritious fluid, in a container powered with 100% renewable energy outside the IKEA Malmö store in Sweden. This will not only result in delicious, fresh, locally grown greens that IKEA visitors can enjoy but what is more important this contributes to our ambition to become people and planet positive by 2030 by using fewer natural resources compared to conventional growing methods:
90% less water
No pesticides
No farmland
Less food waste
Together with Urban Crop Solutions we have installed a controlled-environment vertical farm where plants are grown in a closed system. Water and nutrients are used instead of soil and LED-light is used instead of sunlight.
We believe that every action that enables and inspires people to live more sustainably matters and perhaps we can change the world together, one plant at the time.
Urban Crop Solutions
Fresh Fruit In February: Quebec's Premier About To Test A Cherished Commandment of Economics
Quebec has put more than $150 million towards becoming self-sufficient in all four food groups, all year around
Kevin Carmichael
May 06, 2021
Quebec Premier François Legault, who earned a master’s degree in business administration and co-founded Transat A.T. Inc. before entering politics, is about to test one of the most cherished commandments of economics.
David Ricardo (1772-1823) popularized the idea at the core of all trade agreements: comparative advantage. Ricardo observed that it was ridiculous for England to produce wine when plentiful Portuguese vintages were both cheaper and better. Conversely, Portugal had no business making its own cloth, since its textile industry was no match for Britain’s cotton spinners. Everyone would be better off if England imported its wine from Portugal, and if Portugal obtained its cotton from England.
It took some time, but eventually, politicians saw the wisdom of Ricardo’s teachings. It helped that attempts to defy the rule of comparative advantage tend to go badly: the Newfoundland government’s embarrassing attempt in the late 1980s to become self-sufficient in cucumbers, for example. Free-trade agreements replaced tariff walls, culminating in China’s addition to the World Trade Organization in 2001.
Ricardo wouldn’t like many of the current trends in trade. Protectionism is back, thanks to the Great Recession and Donald “Tariff Man” Trump’s four years in the White House. Now, the COVID-19 crisis has some policymakers thinking that an inefficient textile industry might be better than no textile industry if the country with the comparative advantage in the making of masks and medical gowns refuses to send you any at the outset of a deadly pandemic.
The federal budget promises hundreds of millions of dollars for bioengineering, as Canada’s embrace of globalization left it without the manufacturing capacity necessary to make COVID-19 vaccines. Several provinces have initiated programs aimed at boosting home-grown supplies of food, none more aggressively than Quebec, which has put more than $150 million to become self-sufficient in all four food groups, all year around.
Folly? Advances in greenhouse technology combined with cheap hydro-generated electricity and shifts in spending habits suggest that it’s possible. Still, even if the cost of heating a state-of-the-art greenhouse in Quebec during the winter might be relatively cheap, it’s still not as cheap as in sunny Mexico, where fruit and vegetable farmers warm their crops for free. Legault’s bet will come down to whether Quebecers are willing to pay more for their food. Modern industrial agriculture is built on the notion that consumers only care about price. We’re about to see if that’s true.
Lead photo: A worker harvests strawberries at the Ferme d'hiver vertical farm in Brossard, Quebec, Canada, on Wednesday, Jan. 6, 2021. PHOTO BY CHRISTINNE MUSCHI/BLOOMBERG
New Hydroponic Farm, Vittone Farms, Is Welcomed To The Smith Mountain Lake Regional Chamber of Commerce With Ribbon Cutting
“What is great about hydroponic growing is that we can serve the local community with safe, nutritional food 365 days a year, additionally local farming removes the extended transportation of produce from the equation
May 12, 2021
Vittone Farms, Inc., a true-agricultural start-up that uses hydroponic farming to grow thousands of plants a month and host of the Smith Mountain Lake (SML) Farmers Market, celebrated the ribbon cutting with the Smith Mountain Lake Regional Chamber of Commerce on Wednesday, May 5, 2021. As an official member of the region’s growing business community, Vittone Farms looks forward to supporting the local and seasonal community.
10 local businesses attended the ribbon cutting and each attendee was provided with a hydroponic salad lunch created by a local Smith Mountain Lake restaurant, The Landing Restaurant, with salad ingredients provided by Vittone Farms.
The 40-foot farming container uses advanced vertical farming techniques using every inch of space for effective, indoor, all-season, all-weather growing and sits on land once known in the community for the Mayberry Diner & Drive-In. In 2007 the Diner burned down and for the past several years the prominent land remained vacant and unusable. Vittone Farms plans to make this land useful once again through the use of the farm and farmers market, making Vittone Farms a viable member of the Smith Mountain Lake Regional Chamber of Commerce. The SML Farmers Market features local growers and producers from within a 100-mile radius of its location in Moneta, VA and for the 2021 season, all members of 4-H, FFA, or any young farmer or producer under the age of 18 is eligible to receive free booth space at the up-and-coming farmers market.
The Vittone Farms team consists of Jeff Vittone, the founder of Vittone Farms and SML Famers Market and a U.S. Air Force Veteran, Jordan Gudely, a lifelong farmer who attained his Argibusiness Management Degree from North Carolina State University gained unique experience with organic fruit and vegetable production from the NC State sweet potato breeding program also has 1.5 years’ experience in different forms of farming works alongside part-time worker Kevin Painchaud, a local high school student, and future Horticultural Science Major at Virginia Tech. The Vittone Farms team is preparing for the farmer’s market season by growing a variety of plants and herbs inside the container farm and will continue to learn how to optimize the unique sustainable farming technique.
Vittone Farms offers a variety of produce derived from organic seeds and pesticide-free nutrients from its initial harvest including: Butter Lettuce, Romaine, Bibb Lettuce, Red and Green Salanova Sweet Crisp, Basil, Cilantro, Dill, Parsley, and Radish. Soon, Vittone Farms plans to include Microgreens and eggs from free-range, cage-free, organically fed chickens.
“What is great about hydroponic growing is that we can serve the local community with safe, nutritional food 365 days a year, additionally local farming removes the extended transportation of produce from the equation. When food is shipped over extended distances it loses its quality and nutritional value. We are grateful to be part of this beautiful community and welcomed by the local chamber of commerce. We are honored to make use of a once treasured land by not only growing on the land but inviting others to join us each weekend by selling their local meats, produce, or designs,” adds Jeff Vittone.
AeroFarms CEO Rosenberg Kicks Off Indoor Ag-Con 2021 Keynote Address
“We are thrilled to have an industry leader like David Rosenberg join us as we kick off our return to the live event format,” says Brian Sullivan, co-owner, Indoor Ag-Con LLC
Rosenberg Headlines Full Roster of Keynotes, Panels, Networking & Expo Floor Innovations For In-Person October 4-5, 2021 Edition In Orlando
MAY 6, 2021 -- AeroFarms CEO David Rosenberg will lead the opening morning keynote address for the 8th annual edition of Indoor Ag-Con, scheduled for October 4-5, 2021 at the Hilton Orlando, Florida.
Themed “Growing Your Business,” the premier trade show and conference for the indoor |vertical farming industry will give attendees the opportunity to explore new resources on the expo floor and hear from Rosenberg, other CEOs, thought leaders and industry experts from today’s cutting-edge farms and other innovative companies.
“We are thrilled to have an industry leader like David Rosenberg join us as we kick off our return to the live event format,” says Brian Sullivan, co-owner, Indoor Ag-Con LLC along with other event industry veterans Nancy Hallberg and Kris Sieradzki. “We look forward to gathering with our industry colleagues again and are working hard to bring the best possible combination of networking, education and exhibition opportunities together in Orlando.”
Scheduled for opening morning, October 4, Rosenberg’s address will be held from 8:30 am – 9:20 am. Rosenberg co-founded and leads AeroFarms. AeroFarms has been leading the way for indoor vertical farming and championing transformational innovation for agriculture overall. On a mission to grow the best plants possible for the betterment of humanity, AeroFarms is a Certified B Corp Company with global headquarters in Newark, New Jersey, United States. Named one of the World’s Most Innovative Companies by Fast Company three years in a row and one of TIME's Best Inventions, AeroFarms patented, award-winning indoor vertical farming technology provides the perfect conditions for healthy plants to thrive, taking agriculture to a new level of precision, food safety, and productivity while using up to 95% less water and no pesticides vs. traditional field farming. Grown for flavor first, AeroFarms enables local production to safely grow flavorful baby greens and microgreens all year round.
ROBUST 2021 CONFERENCE SCHEDULE NOW IN DEVELOPMENT
In addition to Rosenberg’s keynote, look for additional announcements coming soon on other CEO keynote presentations planned for the October event. The 2021 conference will also include a full roster of panel discussions, fireside chats and presentations offering a deep dive into three core tracks – Business & Marketing, Science & Technology and Alternative Crops.
In addition to the extensive educational component, attendees will find more new initiatives and show highlights to explore, including:
NEW LOCATION: HILTON ORLANDO – DISCOUNTED HOTEL RATES, TOO
Indoor Ag-Con’s Hilton Orlando venue makes it the perfect opportunity for a business vacation. Centrally located to all major theme parks and attractions, it is just minutes from the eclectic dining scene and entertainment of International Drive. What’s more, the Hilton Orlando resort sits on more than 26 acres of lush landscaping and tropical inspirations making it a true destination of its own. Indoor Ag-Con has arranged for discounted hotel rates for attendees and exhibitors starting as low as $129/night. Complete details are available on the show website.
NEW ASSOCIATION ALLIANCES
Indoor Ag-Con is also forging new alliances with other events, industry associations/groups that will play an integral role in its marketing outreach and conference programming. Look for partnership announcements coming soon.
EXPANDED EXHIBIT FLOOR & NETWORKING OPPORTUNITIES
The Indoor Ag-Con team is working to bring even more resources for farmers/growers to explore across all sectors – everything from IT, energy, AI and lighting solutions to substrates, vertical farming solutions, business services and much more. Attendees and exhibitors alike will also have even more networking opportunities with daily luncheon sessions and receptions on the show floor.
QUICK FACTS:
WHEN: Monday, October 4 – Tuesday, October 5
WHERE: Hilton Orlando, 6001 Destination Pkwy, Orlando, FL 32819
INFO: For information on exhibiting or attending visit www.indoor.ag
ABOUT INDOOR AG-CON LLC
Founded in 2013, Indoor Ag-Con has emerged as the premier trade event for vertical farming | indoor agriculture, the practice of growing crops in indoor systems, using hydroponic, aquaponic and aeroponic techniques. Its events are crop-agnostic and touch all sectors of the business, covering produce, legal cannabis |hemp, alternate protein, and non-food crops. In December 2018, three event industry professionals – Nancy Hallberg, Kris Sieradzki, and Brian Sullivan – acquired Indoor Ag-Con LLC, setting the stage for further expansion of the events globally. More information: https://indoor.ag
USA: INDIANA - 5 Acres of Food In 80 Feet: Urban Farmer Grows A Garden In The Heart of Indianapolis
An unassuming plot of land sits on the eastside of Indianapolis on 30th Street. From the outside, it looks like an empty lot with a couple of shipping containers on it. But inside those containers is an entire garden
May 6, 2021
An unassuming plot of land sits on the eastside of Indianapolis on 30th Street. From the outside, it looks like an empty lot with a couple of shipping containers on it. But inside those containers is an entire garden.
And among the plants, you can find DeMario Vitalis.
Vitalis is the first in Indiana to own a hydroponic farm inside of a shipping container. The unique method involves planting seedlings of plants such as herbs and lettuces on vertical panels and feeding them controlled levels of water, nutrients, and light — no soil required.
It’s a mode of farming uniquely suited for urban environments. Vitalis is able to produce almost 5 acres of food a year from two 40-foot shipping containers. It also uses 99% less water than traditional farming, according to the company that makes the containers.
Vitalis sells his fresh herbs, lettuces, and more to people in the community through online platforms such as Market Wagon.
The climate control is a huge advantage for Vitalis, who set up his farm, called New Age Provisions, in the latter half of last year. Regardless of the outside weather, he can grow anything he wants.
“It can be 30 degrees outside and raining,” he said, “but inside it’s 65 degrees. In here I’m watching Netflix and planting seeds.”
Even though he now spends much of his time dedicated to plants, Vitalis wasn’t a farmer when he started all of this. He was just an entrepreneur looking for his next project, and farming — which connected to his history as a descendent of enslaved people and Southern sharecroppers — felt like the right choice.
“It was just a way to become an entrepreneur,” he said, “and also get back into the type of occupation my ancestors once had.”
‘It’s in his blood’
Vitalis was looking for something that would put a piece of property he owned to use, and he had a hunch shipping containers were key.
At first, he thought he would set up some modular tiny homes built out of containers. But then he came across Freight Farms, a Boston-based company that could cram 2.5 acres of production into one shipping container, and the decision was made.
Although born in San Francisco, Vitalis’ family is originally from the South, and he moved around quite a bit before settling in Indiana.
“Three of my four grandparents started off from the South,” Vitalis said, “So we were part of that Black migration when we moved eventually from the South to San Francisco on the West Coast.”
After living in Germany, Kansas, and other places as his stepfather moved around with the military, Vitalis’ mother decided to move him to Indianapolis, where he stayed and attended Arlington High School and Purdue University.
Vitalis’ mother Barbara Johnson is a cook, so food has always been important to the family. And the herbs and vegetables grown by her son, she said, are “absolutely wonderful.”
“I just believe that you can always inspire a person with a good meal,” she said.
Even so, farming or food production was never anything they did at home, she said. But she knows it’s something he feels close to because of the family’s history.
“I guess it was just in his blood,” she said.
Vitalis was one of the first Black owners of a Freight Farms shipping container in the country, said Caroline Katsiroubas, marketing, and communications director for the company.
“He, in particular, wanted to be a catalyst for more Black farmers to join the Freight Farming community,” she said, “and I’ve definitely seen the impact.”
Overcoming learning, funding hurdles
It wasn’t easy learning how to grow food.
Despite two degrees from Purdue University, Vitalis doesn’t have a background in farming and had to put himself through some education before diving into his urban farm. He took online classes and even visited Freight Farms in Boston to learn about the equipment and process.
“It does take a learning curve,” he said. “It’s not easy to learn how to farm; you have to learn how to react to the plants.”
Sometimes his daughter will help him with the planting. Johnson, too, will help out and trim plants, clean or help with planting, and occasionally brings her grandson along. Understanding how the farm works was a learning curve for her, too.
“I didn’t know anything about hydroponic farming,” she said. “When I saw that wall of plants, I didn’t think it was possible.”
Funding was another obstacle. The farms cost $100,000 each.
After some research, Vitalis found that the U.S. Department of Agriculture will supply loans for these types of businesses, so he requested $50,000 to help him pay for one container and was promptly denied.
The people evaluating the profitability of these containers simply didn’t understand how it worked or how much it could produce, he said. But instead of giving up, he pushed back. Black farmers have historically been discriminated against when trying to obtain USDA loans, and he was motivated to make sure his business plan was being fairly evaluated.
“There’s a history behind that,” he said. “I was just one of many.”
Vitalis appealed the decision and won. Then, he turned around and asked for $200,000 instead — and got it.
Finally one day, a semi-trailer pulled up outside his property with the containers, picked them up with an enormous crane, and plopped them right down behind the nearby building.
“It was pretty interesting to see a big old 40-foot container fly over a building,” Vitalis said. “It was not easy, but you know, God was on my side and I was able to get through the hurdles that were put in my way.”
How hydroponics works
In a hydroponic farm, everything is vertical — and everything is controlled.
At first, the plants start as seedlings or seeds and are placed on shelves under LED lights, and water flushed with nutrients is dispensed to them with attached machines.
After a few weeks, the plants are large enough to transfer to a series of vertical panels that roll along tracks. These panels are also connected to machines for dosing water and nutrients and placed in between LED lights. The water circulating through the plants is saved and re-cycled through the system, conserving water and nutrients.
Although space may seem tight, one container can output the equivalent of 1,000 heads of lettuce each week, Katsiroubas said.
And throughout the whole process, Vitalis controls the light, temperature, nutrients, and water. The plants live in a perfectly contained ecosystem that’s never under threat from drought, flooding or pests.
“It has its own brain,” Vitalis said.
It’s a big advantage, he said, because he can grow food year-round and he doesn’t have to worry about pesticides or herbicides. It’s also “hyper-local,” he said. When he gets an order, the food comes from the planter into the customer’s hands within a matter of hours.
David Bosley, Vitalis’ former boss at Cummins, Inc., used Vitalis’ greens for his Thanksgiving meal and said he was impressed by the packaging and freshness. At first, he said, the idea of a hydroponics farm was surprising.
“I thought it was rather novel,” he said, “but I also thought, well that’s just like DeMario.”
Nobody was surprised that Vitalis made New Age Provisions happen.
He’s always been one to tackle a project without giving up, Bosley said. And he’s always been a trailblazer and hard worker, his mother said. She thinks it’s something he may have picked up from her, since she worked multiple jobs and attended school while caring for him and his siblings.
“I’m even more amazed with my son,” Johnson said. “He‘s satisfying a need in the community and following a dream. It was his vision and he brought it to fruition.”
Contact IndyStar reporter London Gibson at 317-419-1912 or lbgibson@gannett.com. Follow her on Twitter @londongibson.
Connect with IndyStar’s environmental reporters: Join The Scrub on Facebook.
IndyStar's environmental reporting project is made possible through the generous support of the nonprofit Nina Mason Pulliam Charitable Trust.
HighQuest Events – Global AgInvesting, WIA Summit, Organic & Non-GMO Forum – Return To In-Person
It’s time to reconnect! Global ag event, consulting and media firm HighQuest Partners has announced that it will return to in-person events in the second half of 2021
BOSTON (May 5, 2021) – It’s time to reconnect! Global ag event, consulting and media firm HighQuest Partners has announced that it will return to in-person events in the second half of 2021.
The company will once again bring together the communities of Global AgInvesting, Women in Agribusiness, and the Organic & Non-GMO Forum for unparalleled onsite networking and engagement at its next events, all while respecting current safety guidelines and instituting unique ways of bridging relationships and partnerships in the agribusiness and investing sectors. Most events also will offer a virtual option for those who are not able to attend the live events.
Global AgInvesting On the Green
Just outside NYC, July 13-15
“Despite an extraordinary year of challenges, the GAI community did not waver in its commitment to agricultural advancements and investments,” said Kate Westfall, chief operating officer for the Ag Investing Division. “We are very excited to bring everyone together again this summer in a safe and unique way, and have had an overwhelming response from attendees eager to join us and reconnect.”
The 13th annual Global AgInvesting conference will be held July 13-15 at the Sleepy Hollow Country Club, just an hour north of NYC. Sessions and networking will take place in a professional, covered outdoor setting overlooking the Hudson River and a top 50 golf course,
with plenty of opportunities for al fresco meetings. Preliminary agenda topics include international deal flow in the ag sector, the growth of carbon sequestration/monetization, regenerative farming, agtech investment and adoption, the role of PE and a broad range of agriculture investment vehicles, and many more current themes in the burgeoning sector. Visit globalaginvesting.com to register or for more details.
Women in Agribusiness Summit
Minneapolis, September 21-23
Women in Agribusiness initiatives have fostered a year-round community of engaged executives, leaders and professional women through its distinctive virtual event offerings, its WIA Meet Ups, and informative webinars. “
Our goal is always to provide as much value to as much of our community as possible, so, for our 10th anniversary Summit, we’ve decided to host it both in-person and virtually to ensure that anyone who wants to attend can,” said Joy O’Shaughnessy, chief operating officer for HighQuest’s Agribus
The 10th anniversary Women in Agribusiness Summit, September 21-23, will be held at the Hyatt Regency Minneapolis on Nicollet Mall. Discussions will ensue on innovations in the sector, the supply chain crisis and sustainability, as well as the annual highlights of the executive profiles panel and industry tour. Register and learn more at womeninag.com.
Organic & Non-GMO Forum
Minneapolis, December 1-2
The Organic & Non-GMO Forum is the event that is the source for conventional food and ag businesses to learn about the opportunities in the organic and non-GMO industries. Now in its seventh year, the event returns to Minneapolis at the Hyatt Regency on December 1-2.
Producers, processors, manufacturers, buyers and more will convene to consider the potential in these growing sectors, where sales of certified organic food products in the U.S. alone more than doubled to $7.6 billion from 2011 to 2016. Likewise, the global non-GMO food market is expected to reach $2.76 billion by 2025, growing at a CAGR of 16.5 percent. A plethora of current topics will be presented and examined by expert industry speakers. Learn more at ongforum.com.
A 10 percent discount on registration is offered to all of these events by using the code: HQ10 at check out.
###
USA: WASHINGTON - Lacey Is Home To The Largest Vertical Farm On The West Coast
Here they can grow 6 million heads of lettuce a year, using just 2 percent of the water an outdoor farm would need
The Future of Farming Is Happening
Right Now In This 25,000 Square Foot Warehouse.
Author: Saint Bryan
May 6, 2021
LACEY, Wash. — Though it looks like the set of some far-out science fiction fantasy, with bright walls of light and characters dressed in medical gowns, this is actually a farm growing six different kinds of lettuce inside a 25-thousand square foot warehouse located in a Lacey Business Park.
“In the beginning, it was always our goal to find a better way to grow healthier and more nutritious food for families,” says Bryce Clemmer who owns NW Farms with his wife Andrea. It’s the largest vertical farm in the Northwest.
Here they can grow 6 million heads of lettuce a year, using just 2 percent of the water an outdoor farm would need.
“This is a unique combination of robotics, software but also hardware that ultimately makes growing food at large scale possible,” says Clemmer, who is an engineer. He’s invented a few proprietary systems that make this vertical farm unlike any other.
“We've created a perfect environment for plants to grow,” he says.
Everything is monitored here: the temperature, the humidity, the light, the nutrients that go into the water. The result is produce that grows three times faster indoors than outside. The lettuce needs just 20 days from planting to be ready for your table.
“We have experimented with growing everything from strawberries and blueberries to edamame and any type of herbs that you can imagine,” says Clemmer. The only produce he can't imagine growing here are pineapples and pumpkins.
A NW Farms employee prepares to plant lettuce. Credit: KING TV
There are no overalls or John Deere caps here. All farmhands are gowned up, with hairnets and food handling gloves.
“So food safety, the handling, and the overall environment is the cleanest in which it can be,” says Clemmer.
“It's all-natural and healthy,” adds Andrea Clemmer.
She says other farms may rely on pesticides. And with farms so far away from our supermarkets, half of all produce gets thrown out. That doesn’t happen here.
“When our product is pulled off the towers it goes right into the bag, and it's in the store the same day so it's fresh same day and it is still living,” she says.
As the world’s population grows and more pressure is put on natural resources vertical farmers say they may have the key that prevents hunger and famine in the future.
“We have to figure out how to grow reliably and sustainably fresh food that's nutritious for everybody,” says Bryce Clemmer.
KING 5's Evening celebrates the Northwest. Contact us: Facebook, Twitter, Instagram, Email.
Robotic Warehouse Farms Will Save The World
CEA technology is just getting started. Like the Tesla Cybertruck, we have a working concept that promises a more-than-Jetson’s-level future many of us can see the benefits of and actively want―it’s just not quite available to the masses yet
by Elle Griffin
Four years ago, Ritch Wood was looking for a better way to grow plants. As the CEO of global skincare company Nu Skin, he ran into ingredient shortages every winter when fields went dormant―and when he moved grow operations to the equator he ran into water and land shortages, along with a host of quality control issues.
Nu Skin needed reliable, quality ingredients for their skincare products. But farming was too unpredictable an industry. “If there was a way to grow indoors,” he thought, “and be able to do that 24 hours a day, 365 days a year―if we could guarantee that it was grown without any herbicides or pesticides and in a sustainable way that uses less water and land―that would be really helpful.”
At the time, controlled-environment agriculture (CEA) was in its infancy and grow-light technology had yet to take a turn for the more affordable. When he learned of an agricultural system that promised to use a fraction of the land and water used by traditional agriculture methods and had the potential to make it more affordable, Wood made an investment.
Nu Skin paid $3 million for 70 percent of the company and rights to its IP―and Grōv Technologies was born.
Grōv grass grown in the Olympus machine at the Bateman Mosida Farms. Photo from Grōv Technologies
Controlled-environment agriculture is on the rise
The theory behind CEA is that by controlling the environment in which it grows, we can control everything about a plant and what it grows into by micro-tweaking one of a thousand different characteristics―including temperature, humidity, light duration, light wavelength, dissolved oxygen in the water, and carbon dioxide saturation in the air. By tweaking the growing cycle, we can control the caloric content as well as the nutrient content and density of the plant.
“What we’ve learned through controlled-environment agriculture,” Benjamin Swan, co-founder and CEO at Sustenir in Singapore, once told National Geographic, “[is] we can actually emphasize certain characteristics of the plants. So, without using GMO, we can make our kale softer, we can actually make it sweet.”
The theoretical use cases for this technology are endless―from being able to grow in places where water is scarce (like in much of Africa), or where water is overly abundant (like Hawaii), or in places where labor is scarce (like in parts of Asia), or even in places that have long winters (like Northern Europe). Theoretically, we could have grow towers in every town and feed the whole of it no matter its natural environment.
We could even grow those foods to those cities’ exact nutritional needs―more vitamin D-rich foods in wintery places, for example. Dr. Lee Mun Wei, a senior manager at the Food Innovation and Resource Centre (FIRC) in Singapore aims to predict and prevent illness in a given population by tracking their biometric data using Apple watch-like wearables, then 3D printing nutrient-specific foods that could mitigate imbalances.
Though these technologies exist, they are still in their infancy. Singapore leads much of the research and development out of necessity. With limited land and water resources, the county is forced to import 90 percent of their food and 40 percent of their water from outside the country. As a result, they have no option but to grow vertically and desalinate water from the ocean.
Elsewhere, the industry has been slow to catch on, largely due to exorbitant startup costs, low returns, and lack of urgent need. According to a 2017 State of Farming report by L.E.K., only 27 percent of indoor, vertical farms are profitable compared with 50 percent of container farms and 75 percent of greenhouses. But one thing has spurred the industry on in recent years: cannabis.
Legalized in 39 states, demand for cannabis has created a $13.6 billion industry and enough capital to fund CEA-enabled grow operations. “When you have a crop that fetches up to $2,400 or $2,500 a pound, you need to be able to dial everything in and make it consistent and repeatable,” says Dashiel Kulander, co-founder and CEO at Boojum Group. “If the temperature swings five to 10 degrees on a cannabis plant, that will change the plant’s various cannabinoids. The goal is to create a medicine that is consistent batch after batch.”
It’s only recently that there has been some financial incentive to use CEA technologies for food use―largely driven by Big Ag players hoping to hedge out the competition. Berry farming giant Driscoll’s, for one, led a $500 million round to fund Plenty, a 2.2-acre vertical farm in California they hope will help them fulfill a contract with Albertsons. The Ingka Group, for another, led a $100 million round to fund AeroFarms, a 2.4-acre vertical farm in New Jersey that will help them fulfill a contract with Singapore Airlines.
Grōv tent at the Bateman Mosida Farms. Photo from Grōv Technologies
Grōv Tech is building CEA prototypes in Utah
By investing in Grōv Tech, Nu Skin hopes to do something similar, getting ahead of the supply chain that fuels their skincare products before the competition can beat them to it, or before climate change makes traditional methods more difficult, all while shoring up technology that could provide a farming model that is more sustainable―if only it were more economical.
“The purpose was always, can we build a better product for Nu Skin?” Wood says. “We think there’s a huge story around the ingredient sustainability, and there were a lot of ingredients we felt we could grow, but the challenge was: could we do it in an economical way?”
Grōv Tech started out with a prototype: a tower that pairs hydroponic growing technology with grow lights. But like all CEA startups, a lot of the growing process was manual and the technology was prohibitively expensive. To make something that was scalable and profitable the whole thing needed to be automated and it needed to be cheap.
With this goal in mind, Wood decided they would start by growing animal feed for Bateman’s Dairy farm. Having grown up on a dairy farm himself, Wood figured this would allow the company to scale the product while refining and automating the technology to the point that it could be replicated. And all of this would have a fortuitous effect on Nu Skin’s bottom line.
“One of our bestselling products is a weight-loss protein powder which uses whey protein,” Wood says. “So again, a very nice connection there is if the animal is eating a more sustainable product and producing better milk with better protein and it’s being done in a sustainable way―certainly that can be a benefit to Nu Skin down the road.”
One year into feeding the 20,000 animals at Bateman, the company has learned a lot. For instance: cows need a lot of magnesium, but they don’t like eating it. Now, Grōv Tech puts magnesium in the water so it’s directly absorbed into the plant and then becomes bioavailable to the cow upon eating it. And because the growing process only takes seven days, data scientists can analyze the results in real-time and adjust the components to optimize production for the next batch of feed.
According to Grōv Tech president Steven Lindsley, it’s not far off that we’ll be looking at milk production (butter, fats, and proteins) and optimizing a herd’s diet for taste, quality, and nutritional value―not to mention the wellbeing of the animal. We’ll be able to look at how many trips from the veterinarian an animal gets when they’re fed certain nutrients in their diet, and whether they can have more calves and produce the same amount of dairy on less, better quality feed. (So far, the answer to this last question is yes. When animals are fed better quality food they need less of it―just like humans.)
And if we hook all of the cows up to robotic milking equipment and connect everything to artificial intelligence, machine learning, and the Internet of Things―Lindsley’s far-flung goal―then we might be able to collect enough data to not only feed cows to their optimum health and performance ability, but humans too. And that could have ramifications not only for feeding the world, but nourishing it― just like Dr. Wei hopes to do in Singapore.
“Last year was about starting to feed animals and get data and prove out the hypothesis we have while continuing to perfect the technology and get confidence there,” Wood says. “And now we’re really to a point where we’ve got data that proves that it works and that financially it’ll be a good thing for a farmer. So now we can really take that proposition to farmers and start to scale.”
Olympus Tower Farm at Bateman Farms in Mosida, UT. Photo from Grōv Technologies
CEA technology could feed the world
Right now, Grōv Tech is focused on refining its technology right here in our own backyard. But once they do that, the plan is to expand internationally.
“Saudi Arabia has actually passed a law where you cannot use water to grow fodder or feed for animals, so all of that now has to be imported. China imports one-third of their alfalfa feed for their dairy animals because they don’t have the capability of growing it,” Wood says. “So there are countries that will probably benefit more than the US would. But we’ve got to refine the technology and get that built to where it’s ready to scale before we start spreading ourselves all around the globe.”
CEA technology is just getting started. Like the Tesla Cybertruck, we have a working concept that promises a more-than-Jetson’s-level future many of us can see the benefits of and actively want―it’s just not quite available to the masses yet. But with more than a billion dollars invested in the technology in just the past few years alone―we’re getting there. And the “there” we are heading toward is rosy indeed.
“To put it in perspective, one tower that is about 875 square feet on the ground will replace 35 to 50 acres of land,” says Lindsley. “And that will feed the animals on roughly five percent of the amount of water. The UN says that that the world will add about 2.5 billion people in the next 30 years. And we have to find a way to feed them on arguably less arable land and water. The good news is the technology is coming along to help solve that equation.”
If COVID-19 taught us anything, it’s that our food supply chain is fragile. But that’s only because our supply chain was built to grow food in California, refrigerate it so it stays fresh, then transport it 1,500 miles so we can eat a salad in the winter in Chicago. In the future, that might not be a thing. “We’re having a dry year now,” Lindsley tells me in February. “But a year ago we were in a blizzard, and even in the middle of a blizzard in February in Utah, we’re pumping out fresh, beautiful, safe green grass for animals. It’s a paradigm shift.”
“Four years ago it was a good idea,” Wood tells me of his company’s investment in CEA technology, “But four years from now it’s going to be required.”
Elle Griffin
Elle is the editor-in-chief of Utah Business and a freelance writer for Forbes, The Muse, and The Startup. She is also a literary novelist and the author of a weekly newsletter called The Novelleist. Learn more at ellegriffin.com.
AmplifiedAg Increases Better Fresh Farms Production 50% With New Indoor Farm And AmpEDGE Operating System
AmplifiedAg hydroponic container farm and technologies increased leafy green production over 50% for Better Fresh Farms
By AmplifiedAg
May 6, 2021
AmplifiedAg hydroponic container farm and technologies increased leafy green production over 50% for Better Fresh Farms.
AmplifiedAg, Inc. is an agtech visionary on a mission to provide global access to safe food. (PRNewsfoto/AmplifiedAg)
CHARLESTON, S.C., May 6, 2021 /PRNewswire/ -- AmplifiedAg, Inc.®, holistic indoor farming leader with a mission to provide global access to safe food, has increased leafy green production over 50% for Metter, Georgia-based Better Fresh Farms with its automated hydroponic container farm and AmpEDGE™ proprietary Operating System.
AmplifiedAg farms sustainably grow consistent yields of 800-1000 pounds of full head leafy greens per harvest every 3 weeks.
Founded in 2016 by Grant Anderson, Better Fresh Farms is expanding its hyperlocal produce throughout Georgia with the addition of its first AmplifiedAg farm, the company's exclusive producer of leafy greens.
Anderson said, "Our AmplifiedAg farm replaced two existing models that were fairly inefficient for our goals. The new system has optimized our production in the same square footage,"
"The software is going to help us get our arms around the whole operation; there's nothing out there really like it," added Anderson. "To have tracking processes that follow produce from growth all the way through to the sale is huge. It's been cumbersome up until now, and it will save us money in the long run to have one efficient system instead of multiple programs."
AmpEDGE uniquely combines farm production and business management for an end-to-end system. 24/7 environment controls, detailed analytics, and traceability features allow farmers to easily optimize crop growth, mitigate risk, while also tracking sales forecasts, revenue streams, and daily operations. Multi-tenant software with data-driven learning capabilities, AmpEDGE can operate any type of controlled environment.
"We grow 52 weeks a year in Georgia where the majority of the time weather is extremely hot and humid," added Grant. "We're constantly trying to adapt our systems to work in an environment that they weren't designed for. AmplifiedAg understands how to adapt their containers to different weather."
Manufactured from upcycled shipping containers, AmplifiedAg's enterprise-scale farms are built to the highest global food safety certifications. The resilient architecture allows for farming in any region regardless of resources and climate. A compact 320-square feet container design promotes ultimate segmentation and risk mitigation for reliable production.
AmplifiedAg farms sustainably grow consistent yields of 800-1000 pounds of full head leafy greens per harvest every 3 weeks. The company deploys farms 70% faster and at a fraction of the cost of other CEA implementations
"This has given us a chance to start exploring larger and more legitimate sales opportunities," added Anderson.
David Flynn is the General Manager of AmplifiedAg and leader behind the company's farm and technology production. He and his team have built and deployed over 180 farm containers that services farms across the country. This includes AmplifiedAg's Vertical Roots hydroponic container farm, with produce in nearly 1,500 stores nationwide.
"We've spent the last five years developing a platform that proves our technology and shipping container farms can be used to operate a profitable produce business at scale," said Flynn.
"We're excited to share our technologies and farms with other indoor farming experts like Grant and Better Fresh Farms, and continue to refine the indoor farming process for the future."
Learn more at www.amplifiedaginc.com.
Sri Lanka: “Ever Since We Started, Costs Have Dropped And Economics Have Improved"
“Even greenhouses are relatively new here,” says Aneeshan, one of the co-founders of Honest Greens. “There were no high-tech greenhouses to be found, until five to ten years ago
“Even greenhouses are relatively new here,” says Aneeshan, one of the co-founders of Honest Greens. “There were no high-tech greenhouses to be found, until five to ten years ago. Our farm, therefore, is something rather odd here. Many people are trying to work with hybrid systems, but the main problem is high humidity and erratic weather patterns. During the monsoon seasons, humidity could hit 100%.” According to Aneeshan, this causes many problems for greenhouse farmers, therefore the company wanted to come up with something consistent and controllable.
Boosted by critics
Sanuja explains that “compared to local lettuce grown by traditional farmers, we are more expensive. However, their prices fluctuate drastically, whereas our prices are always stable.” Sanuja notes that vertical farming is new to the country and that people were initially skeptical about it. “People think that our choices are unwise, given electricity is very costly here whereas the sun can be used as a free resource. However, we also notice that many others are fascinated about the concept, as it’s something completely new and unexpected here.”
One of the co-founders, Sanuja, explains: “We’re cultivating varieties that are frequently used in the Sri Lankan cuisine. As our country is an island, there are many fluctuations in product availability and price. With our technology, we want to cater to this inconsistent supply.”
Starting in 2015, Honest Greens has been cultivating several greens inside their farm, which is based in Colombo, Sri Lanka. As the team was new to the industry, they literately took the time to experiment, improve and build up the growing system by themselves. Ever since 2019, their products can be found in local supermarkets around Sri Lanka. The growing facility is 930m2 comprises, with a cultivation area of 370m2. This floor area consists of 10 stacked layers, upon which plants can be grown.
Entrepreneurial approach
Ashish, one of the other co-founders, adds: “We all know it normally takes a lot of time before greens end up on the shelves. We’re glad that we can now render more stability to the market and a guaranteed supply to consumers.” With the home delivery platform, Honest Greens delivers directly to customers, a feature that came in handy during the lockdown. According to Sanuja, the company is looking to expand and increase its product lines. “We already launched pak choi and are working on growing coriander and spinach.”
Besides national expansion, Honest Greens is also planning on taking an international approach in the future. “Once we’ve created a profitable and stable business here, we will scale our company to countries with a large population such as India and Bangladesh,” says Sanuja.
As Ashish Advani explains, their main goal is to give consumers better options in fresh produce available. “People need to eat and food insecurity is becoming a bigger issue worldwide. Countries should own their entire supply chain."
Opportunities ahead
To balance everything out, the team is constantly working on bringing down the unit costs. Unlike in other parts of the world, labor is cheap in South East Asia, so automatization isn’t a high priority, says Sanuja. “Ever since we started the costs have dropped and the economics have improved. We are also looking into solar energy, to lower our electricity costs.”
Ashish notes that the company can do better on CapEx, whereas in Sri Lanka there are many options for industries to use the roof space. “By doing so, solar systems and electricity can be put up back to the grid. However, it’s not really used so far, but as time goes on, in terms of energy, unique economics are ahead of us.“
Lead photo: The co-founders
For more information:
Honest Greens
Sanuja Cooray, co-founder
sanuja.c@urbanagri.co
Aneeshan Tyagarajah, co-founder
aneeshan.t@urbanagri.co
Ashish Advani, co-founder
ashish.a@urbanagri.co
+94 11 702 4251
www.honestgreens.asia
Publication date: Tue 4 May 2021
Author: Rebekka Boekhout
© VerticalFarmDaily.com
2021 CEA Awards
We are excited to announce the winners of the 2021 CEA Awards. The awards were established to recognize distinguished individuals and organizations in the Controlled Environment Agriculture industry across North America
We are excited to announce the winners of the 2021 CEA Awards. The awards were established to recognize distinguished individuals and organizations in the Controlled Environment Agriculture industry across North America.
The winners were selected by a prestigious, independent awards committee comprised of agriculture professionals from Artemis, Cargill, Fluence by OSRAM, and Schneider Electric. The committee received over 130 qualified nominations for the awards and selected 11 category winners and 3 honorable mention awards.
“It has been inspiring to see our industry step up through the pandemic and continue innovating in every facet of the value chain. I am privileged to honor the outstanding contributors via the 2021 CEA Awards,” said Steve Graves, Vice President of Business Development at Fluence by OSRAM and Committee Member.
“All of the winners have had a tremendous impact on our industry this past year. It’s an honor to acknowledge the work of these companies and individuals,” said Allison Kopf, CEO of Artemis and Committee Member.
Top Employer Award
This award honors an employer who has created a great workplace environment.
Winner - AppHarvest, Inc.
Honorable Mention - NatureSweet
Brand Excellence Award
This award honors a brand that has recently dominated on store shelves.
Winner - Dream Greens by AeroFarms
Health and Safety Award
This award honors a company or individual who has gone above and beyond to create a safe and healthy workplace, as well as safe and healthy products in the wake of COVID-19.
Winner - Sudeshna Nambiar, Lakeside Produce
Sustainability Award
This award honors a company or individual who has focused on operating a sustainable facility.
Winner - Legion of Bloom
Produce Person of the Year
This award honors an individual who has made an immeasurable impact on the produce industry in the past 12 months.
Winner - Daniel Malechuk, Kalera
Honorable Mention - Hiroki Koga, Oishii
Cannabis Person of the Year
This award honors an individual who has made an immeasurable impact on the cannabis industry in the past 12 months.
Winner - Wanda James, Simply Pure
Innovative New Packaging Award
This award honors innovation in packaging and highlights new packaging concepts that have launched in the past 12 months.
Winner - Mucci Farms
Honorable Mention - Nature Fresh Farms
Innovative New Product Award
This award honors a new product launched in the past 12 months.
Winner - Wendy’s Sandwich Leaves & Salad Blend by Inspired Greens
Disruptor Award
This award honors an individual who has a spirit of innovation and is constantly looking to disrupt the status quo.
Winner - Stephen Ritz, Green Bronx Machine
Rising Star Award
This award honors an individual with < 3 years of experience in the CEA industry.
Winner - Cory Roof, Ogallala Greens
Industry Connector Award
This award honors a consultant or advisor who helps growers make the best decisions possible.
Winner - Agritecture
Congratulations to all of the winners for having an incredible impact on the CEA industry this past year. Stay tuned as we will be sharing each winners’ story on our website over the next few weeks.
“We Believe That The Time Has Come To Harness Innovative Technologies”
"The extreme African weather conditions make this market a perfect candidate for controlled environmental growth," says Francois Duvenage, R&D researcher at CAN Agri.
"The extreme African weather conditions make this market a perfect candidate for controlled environmental growth," says Francois Duvenage, R&D researcher at CAN Agri. “From wet tropical to extreme desert conditions, it especially means we can enable African countries to successfully grow their produce and sell a marketable product.”
Francois says the company has “two extremely exciting projects coming up, one project in Namibia starting in the next few months and the other is an international collaboration that we established and are strengthening.” According to him, the company is not only targeting Africa but also areas such as Eurasia and North America.
Value proposition
CAN-Agri has developed a multi-faceted solution to ensure our client’s overall support to successfully commission and sustain a CAN-Agri hybrid vertical-greenhouse. “We employ a six-phase approach where each phase is developed to ensure the client’s requirements are accommodated by detailed consultation agreements," says Francois.
“We believe that the time has come to harness innovative technologies to enable responsible and efficient food production, meeting the challenges and demands of the years to come,” says Francois. CAN-Agri’s operational procedure allows an advantage, that a farming unit is flexible in design and scalable to suit client needs. The vertical tower growing units allow for improved product quality and quantity through all seasons. Rows of fresh produce are harvested daily, opening space for new seedlings to be planted, forming a continuous daily production cycle.
Upcoming projects
As the travel restrictions are lifted, CAN Agri has encountered visitors both diplomats and private investors from several African countries. The interested parties are currently in negotiation processes and according to Francoise, the company foresees that its units will be established in these countries. “The earliest construction of a CAN-Agri greenhouse will probably start early August 2021, in our close desert neighboring country, Namibia.
This year, CAN-Agri has worked closely with a major retailer in the development of an additional market to amplify the supply and demand of its lettuce produce. Francois adds, “We have grown the sales of private markets to the extent that we are currently at full capacity. Our long shelf life, no-wash technique, and clean, great quality produce have been openly accepted by all of our clients, the demand keeps growing daily.”
Hybrid benefits
According to Francois, CAN-Agri’s patented technology allows providing an unmatched scalable, commercially viable farming solution that is grounded in both scientific research and credible data. The company has developed an innovative hybrid farming system. In this way, they can share the knowledge and technical support to allow their clients around the world to create a successful farm. “We continue to prove that our system provides better yields through our enhanced methods.”
As of now, the company does not make use of additional lighting. “We have done in-depth studies with regards to the implementation of lighting coupled with the installment and operation of additional lighting, mainly for use in other parts of the world with low solar radiation. Operating in sunny South Africa it is currently unnecessary to implement additional lighting as ample solar radiation is available to the plants,” says Francois.
In terms of cost-efficient production, the company identified common limiting factors and found solutions to the challenges of successful production in hybrid greenhouses. “Our extensive research and development on operation specifics are always ongoing. We have our commercial-scale testing facility CAN-AGRI Greenhouse RSA and continuously produce and record empirical data to support our model.”
For more information:
Francois Duvenage, R&D plant propagationist
CAN-Agri
info@can-agri.com
https://can-agri.com
3 May 2021
Author: Rebekka Boekhout
© HortiDaily.com
Lead photo: Francois Duvenage
Freight Farms Releases Next Generation of Container Farming
Freight Farms released the 10th generation of their container farming system – Greenery S, which has several key improvements on its predecessors
4 May 2021
Freight Farms released the 10th generation of their container farming system – Greenery S, which has several key improvements on its predecessors.
Since its founding in 2013, Freight Farms has been dedicated to making modular vertical farming technology accessible to more communities around the globe in a sustainable fashion. Their systems use a hybrid of hardware, software and services to make food production possible for anyone of any background, anywhere in the world.
“Greenery S represents the apex,” Jon Friedman, COO and co-founder tell Future Farming, “leveraging the excellent design and intuitive automation to streamline workflow while driving up yields.”
LED technology
Greenery S has several key improvements on its predecessors. This includes the new Dynamic Lighting Control, which uses LED technology that allows farmers to customize the lighting spectrum, intensity and duration for optimal plant yields. It also features a brand new user-centric Workstation design making for a sleek, self-contained and multi-functional farm command center.
Text continues underneath image
LED technology allows farmers to customise the lighting spectrum, intensity and duration for optimal plant yields. - Photo: Freight Farms
More consistent harvests
This new generation also brings with it an update to Freight Farms’ farmhand software that includes a new feature called “Recipes.” This update allows farmers to obtain more consistent harvests.
“Operators simply choose the crop they wish to grow and farmhand automatically adjusts in-farm settings for that crop production,” explains Friedman. “In-farm cameras and sensors gather information and continuously improve the precision of the recipes over time, aggregating data from the entire farmer network to determine patterns that lead to exceptionally successful harvests.”
Of all their systems, Greenery S combines Freight Farms’ most optimized combination yet to allow farmers the highest possible yields at the highest quality with the fastest rates.
Lower startup costs
With lower startup costs, Freight Farms reports that their Greenery S farm system can grow an equivalent of 2.5 acres of traditional farmland with 12 harvests per year. According to Friedman, it typically takes their farmers two to three years to see returns on their initial investments.
Greenery S is now available for purchase worldwide.
Jaclyn Krymowski
Correspondent for North America
Read more about: Vertical Farming Indoor Farming Container Farming
Strategic Partnership Between Oreon And Enersavings, Inc.
The energy savings possibilities of Oreon’s LED grow lights made EnerSavings recognize the advantages of the sustainable water-cooling technology
IJsselstein, 4 May 2021. Oreon and the Canadian company EnerSavings Inc. have come to an agreement for a strategic partnership. EnerSavings is a leader in customized lighting retrofits throughout Canada with a presence in 7 provinces. As a lighting engineering firm, they continuously work on improvement and innovation. EnerSavings expertise in providing the most sustainable and energy-saving solutions to its customers, fits perfectly with the sustainable water-cooling technology of Oreon’s LED grow lights.
Energy saving solutions
In EnerSavings, Oreon sees a strong partner for the Canadian market. EnerSavings is based in Toronto, Ontario, and has over a decade of experience in the ever-increasing market demand for efficient lighting technologies. The energy savings possibilities of Oreon’s LED grow lights made EnerSavings recognize the advantages of the sustainable water-cooling technology. They see lots of opportunity for growers in the fixture’s high efficiency and the ability to reuse the gained heat and save on cooling costs. The active water-cooling makes it possible for the LED fixtures to efficiently produce a large amount of light without heating up the greenhouse or grow facility. Revenues are increased by lowering operating costs, and growers get full control over the climate in their facility. This results in high-quality yields year-round.
"EnerSavings is excited to partner with Oreon and expand its presence in the North American LED plant grow light market. The Oreon water-cooled fixture is by far the best grow light in the market today, bringing the highest value proposition to growers. Oreon was the first to bring an LED grow light to market in 2009 and its fixtures are the best built, and cheapest per micromole. The water-cooling ensures productive longevity second to none. The first install over a decade ago still has over 90 percent light output today!" – Jason Beer, Business Development Director of EnerSavings.
“With EnerSavings Inc. as a new dealer, Oreon creates a better connection to the Canadian market. Both Oreon and EnerSavings share the fact that we are both committed to providing sustainable LED solutions and tailored energy-saving solutions, so customers can reduce operating expenses and increase profits. With the expertise of EnerSavings in commercial horticulture projects, we see a promising future in this rapidly growing market,” says Bill Whittaker (North-American Sales Manager) of Oreon.
US: TEXAS - Awty Unveils Carbon-Neutral Container Farm Thanks to Sustainability Grant From Green Mountain Energy Sun Club
Incorporating a container farm into Awty’s current operations and curriculum reinforces the school’s commitment to sustainability while providing a real-life example of environmentally sound sourcing practices to their international student body
Source: GREEN MOUNTAIN ENERGY
05/03/21
Teachers and students alike at The Awty International School are excited about the possibilities a carbon-neutral container farm brings to their campus. Awty received a $135,000 sustainability grant from the Green Mountain Energy Sun Club to implement the container farm that now provides fresh produce to the school’s cafeteria and hands-on education for students through a newly formed urban farming elective class. The school installed a 20-foot hydroponics shipping container, a 20-foot aquaponics shipping container, and a 14.4-kilowatt solar system with 48 panels to power both containers to achieve the carbon-neutral status.
Incorporating a container farm into Awty’s current operations and curriculum reinforces the school’s commitment to sustainability while providing a real-life example of environmentally sound sourcing practices to their international student body. The farm serves to demonstrate how to reduce the carbon footprint of a food operation by shortening the supply chain and reducing fuel emissions. The innovative container farm and solar-powered equipment provides Awty a year-round steady supply of fresh produce, regardless of the outside climate. The closed-loop hydroponic system also uses 98 percent less water than traditional agriculture, significantly reducing the environmental impact of food production.
“While our school community has already started to reap the benefits from the farm, one of our many goals for the container project is sharing what we have achieved with others,” stated Robert Sload, STEAM coordinator at The Awty International School. “As an international school, we certainly want to help other international, national, and local schools introduce their communities to the wonderful community-wide lessons this project provides. A larger goal is to deconstruct our efforts and refashion a much simpler and cost-effective model that could be recreated anywhere with a particular eye to school communities located in food deserts.”
Green Mountain Energy, the nation’s longest-serving renewable energy retailer, founded Sun Club in 2002 to advance sustainability by partnering with nonprofit organizations engaged in meaningful work to support the communities the company serves. Awty is one of more than 130 projects to receive a sustainability grant since Sun Club’s founding. The grants are awarded to nonprofits seeking to implement projects promoting renewable energy, energy efficiency, resource conservation, and environmental stewardship.
“Green Mountain Energy’s goal with Sun Club grants is to promote sustainability in the community, and we were excited about this project from the start as it amplifies the message to future generations through education,” said Mark Parsons, vice president, and general manager of Green Mountain Energy. “Container farming will allow Awty students the opportunity to explore innovative new approaches to food production. Farming fresh produce directly on campus powered by solar energy makes it easy to captivate students and facilitate a dialogue around farming and solar energy at the same time.”
The respect of self, of individuals, and of the environment, and the importance of contributing to the community, are the fundamental principles of Awty’s sustainability program. The program’s mission is to reduce the school’s environmental impact and become more sustainable while inspiring and challenging students to come up with innovative solutions to environmental problems. Initiatives like composting, recycling, collecting water from HVAC units, and working toward becoming a zero-waste school have allowed the school to become a Bronze Award recipient of the Eco-Schools program, an international organization that accredits schools demonstrating a commitment to sustainability.
Tags: Indoor & Vertical Farming, Processing & Supply Chain | Containers
What Is A Container Farm?
A container farm is usually a vertical farming system built inside a shipping container. The benefits of placing a farm within a container, rather than a building, are that it is transportable and can be squeezed into existing spaces, such as in car parks or on farmland
30-04-2021 LettUs
Container farming, vertical farming, indoor farming… What do they all mean? Are they all the same thing? In this blog, we’re going to explain exactly what a container farm is and what the benefits of growing crops in this way are.
The controlled environment agriculture club
Controlled environment agriculture (CEA) is a term for using different technologies to grow food indoors. In CEA, these technologies ensure the best growing conditions and protection for specific crops. This is slightly different to just indoor farming - by nature, indoor farms simply protect crops from external forces such as weather and pests. A container farm would be an example of CEA, as would other indoor farms such as vertical farms and high-tech commercial greenhouses.
A container farm is usually a vertical farming system built inside a shipping container. The benefits of placing a farm within a container, rather than a building, are that it is transportable and can be squeezed into existing spaces, such as in car parks or on farmland.
Since it is classified as a temporary structure, you typically don’t need planning permission for a shipping container. This can be particularly useful for those who rent their farmland. However, there are always exceptions and the necessary checks should always be made before making arrangements. As long as there is level ground, access to electricity, water & wifi, a shipping container can fit into a range of different settings.
Serving communities, big or small
Since they’re easy to transport, container farms can be easily deployed as and when they are needed. This means they could be used for research or social-impact projects, without needing to build a permanent facility. Shipping containers are also modular, which means multiple containers can be used to build a larger facility and businesses can scale their operations appropriately. They also have the potential to be bedded into existing container parks - these are dotted around the UK and are usually shipping containers made up of independent shops, cafes, and restaurants. One container farm could supply fresh produce to all of these.
In this way, container farms have the potential to be a positive disruptor within our food supply networks and strengthen our local food security by reducing our dependence on imported produce. Food waste and carbon caused by food transportation would also be reduced by strategically placing containers in key locations within communities.
The DROP & GROW container farm
LettUs Grow’s container farms are powered by aeroponic technology. This is a soil-less system that uses a nutrient-dense mist to irrigate crops - boosting oxygen levels and encouraging healthy root stock. Whilst hydroponic container farms are more common, DROP & GROW uses aeroponics to optimise crop health and increase growth rates.
Our container farms have also been designed with the grower in mind. DROP & GROW:24 includes a separate preparation area, providing ample space for the grower to do their job. Our farms have also been designed to be easy to maneuver within and check on your crops.
Celebrating vertical farming technology
DROP & GROW wasn’t designed to be inconspicuous. Quite the opposite! We think urban farming, new technologies and feeding local communities is something to shout about, so a DROP & GROW on your site is an opportunity to start a conversation and encourage your customers to learn more about the benefits of vertical farming.
If you want to take a positive step towards a more sustainable and resilient food supply chain in the UK, then talk to LettUs business development team about why a container farm might be in the right choice for you. Find out more...
Source and Photo Courtesy of LettUs Grow
New Greenhouse Design Shines With More Growing Capacity
Lettuces, Asian greens, herbs, and more. These are just a few types of produce that Shayne Johnson of Grampa G’s farm in Pillager has experimented with growing in the middle of winter in Central Minnesota
30-04-2021
University of Minnesota Extension
Lettuces, Asian greens, herbs, and more. These are just a few types of produce that Shayne Johnson of Grampa G’s farm in Pillager has experimented with growing in the middle of winter in Central Minnesota.
Photo: Shayne (left) and Louise Johnson of Grampa G’s farm in Pillager, outside their deep winter greenhouse prototype, 2018. Courtesy of University of Minnesota Extension
“Nothing we’ve tried to grow has failed,” said Johnson, who sells the farm’s product to local food co-ops and customers in the area by word of mouth.
How does Grampa G’s do it? With the help of a prototype deep winter greenhouse made possible by a collaboration with the University of Minnesota Extension Regional Sustainable Development Partnerships (RSDP) and the College of Design Center for Sustainable Building Research (CSBR).
In fall 2020, this collaboration released new designs for a farm-scale winter greenhouse (FSWG v1.0). These new solar winter greenhouse designs seek to improve both the productivity and profitability of extended season vegetable and produce production in Minnesota, creating a more resilient, local food system.
“Our partnerships with Minnesota farmers and the Center for Sustainable Building Research to develop these farm-scale winter greenhouse designs will make winter production more accessible to small- and mid-sized farmers in Minnesota and beyond,” said Greg Schweser, statewide co-director of RSDP’s Sustainable Agriculture and Food Systems program who has helped lead related research and outreach with Daniel Handeen, winter greenhouse designer and CSBR research fellow.
Evolution in solar winter greenhouse design
The farm-scale winter greenhouse designs rely on passive solar principles, similar to the earlier deep winter greenhouse design (DWG 2.0), but build on and incorporate lessons learned from the deep winter greenhouse prototypes in the field. The deep winter greenhouse at Grampa G’s farm is one of five prototypes in Greater Minnesota, supported by RSDP.
Farm scale winter greenhouse under construction at Appetite for Change in Minneapolis, 2021. Photo credit: Daniel Handeen.
The new farm-scale designs have a larger footprint that increases growing capacity. They also include variations in foundations and thermal storage specifications to accommodate different budgets.
“These designs keep evolving and getting better. That’s what I find so cool about them,” Johnson said. “The University adjusts based on our experiences and feedback with the technology.”
RSDP and CSBR partners iteratively developed the farm-scale winter greenhouse designs with input from growers like Johnson and Carol Ford, Extension project coordinator, and an early winter greenhouse pioneer. Ford has helped spread the word and grow a network of deep winter greenhouse adopters and enthusiasts.
“It’s always been about not just making this technology effective for me, but then having it be something that other farmers would feel engaged to do,” Ford said, during a recent podcast interview about this work.
Since their release in November 2020, the farm scale winter greenhouse designs have had more than 1,150 downloads. Solar winter greenhouse designs are freely available and can be downloaded from the RSDP Deep Winter Greenhouse resource website.
Farm scale designs ripe for testing
Schweser noted the designs are now ripe for testing and recommends a similar, regional prototype approach that proved successful with the earlier deep winter greenhouse design.
Open house at the Lake City Catholic Worker Farm deep winter greenhouse, 2018.
In the earlier prototyping process, university and community partners prioritized both research and education, testing the design’s performance and hosting outreach events that have attracted hundreds of participants.
“It’s turned out to be so much more than just the prototype and initial support,” Johnson said. “It’s now this long-standing relationship. We connect with other greenhouse operators and are regularly in touch with our university partners throughout the year.”
Schweser hopes to see similar results with prototypes of farm-scale winter greenhouses in the coming years. University and community partners could then evaluate their performance in the field and improve existing cost estimates before encouraging more widespread adoption.
After field testing, Schweser believes the new structures could open up opportunities for smaller and more diverse farmers to grow more produce and be more profitable.
“The new farm-scale design, more so than the smaller deep winter greenhouses, is far more affordable to construct, and is an appropriate scale for most small direct-market farmers,” Schweser said. “It has the potential to be an equity-building, level-playing field technology to sustainably and profitably grow produce in the winter.”
Johnson is also optimistic about the potential of the new farm-scale winter greenhouse designs.
“I love to see the evolution of these greenhouses taking shape,” Johnson said. “We are learning from our accomplishments and defeats, and then we make them better. That’s what’s exciting about this work and these partnerships—if anyone can make these designs better, this initiative is the one to do it.”
Those with questions about the University of Minnesota's farm scale winter greenhouse designs and related work can contact RSDP's Greg Schweser (schwe233@umn.edu), statewide co-director of the Sustainable Agriculture and Food Systems program.
From Passenger Plane To Vertical Farm – Repurposing Old Aircraft
Recently iFarm’s engineers began designing a custom vertical farm that could flourish inside the body of a commercial airplane, with the potential to extend the life of decommissioned aircraft
By MATT PESKETT
April 19, 2021
iFarm (Intellectual Farms Oy) is a Helsinki-based international company that develops solutions, platforms, and technologies for indoor farming and agribusiness. Recently iFarm’s engineers began designing a custom vertical farm that could flourish inside the body of a commercial airplane, with the potential to extend the life of decommissioned aircraft.
Experts from iFarm were approached by a European airline with the brief. In response, they proposed converting a passenger plane’s cabin into a salad bar and designed a vertical farm with a total growing area of 135 m² in the aft section of the aircraft so that the bar can offer 14 kg of fresh salad daily.
The partition between the cafe and the farm can be made transparent, and the equipment zone moved to the tail end of the plane [Image source: iFarm]
For the airline, this project would serve as a demonstration of its forward-thinking approach and the increased focus on customer service, including the provision of fresh and healthy meals on board.
For iFarm, the project demonstrates another innovative way of integrating agrotechnology into seemingly unsuitable infrastructure and the versatility of vertical farming.
While contemplating additional ways of using the wide-body aircraft to grow plants, engineers suggested a number of configurations that make such refitting not only useful for advertising purposes but also commercially viable. For example, a farm located in the body of a decommissioned cargo jumbo jet can produce up to 1.5 tons of greens per month.
“Vertical farms are good because they can be installed in a wide variety of spaces, from abandoned subway stations to airplanes that no longer serve their intended purpose. We will be happy to cooperate with companies that think outside the box and consider such high-tech repurposing options. This project does not yet have a deadline, but it has already drawn the attention of specialized design bureaus as an easily scalable example of old aircraft upcycling.” commented Kirill Zelensky, CEO of iFarm Europe.
Not all obsolete aircraft are recycled. The airline industry has long used conservation methods to repurpose aircraft, such as sending airliners to spare airfields in dry climates, where they essentially serve as containers of spare parts. Each aircraft includes about 350,000 individual components, and many of these planes remain useful long after their last flight.
But some owners prefer upcycling to disposal in an attempt to provide “second life” old aircraft, especially those with some historical value (e.g., the first airplane of the airline). There are existing examples of creative airliner usage, including dozens of on-board cottages, offices, cafes, and hotels all over the world, and even an old soviet Yak in Georgia that hosts a kindergarten.
For airline companies, the opportunity to upcycle planes into highly sustainable vertical farms is an enticing one. When an industry known for its high carbon footprint can find new ways to support sustainable practices, it could offset emissions, enhance a brand’s image and have a genuine impact on the environment.
USA: NEW YORK - When A Shipping Container Becomes A Farm
Compact, enclosed vertical farms are making their way to Hudson Valley's urban areas
Compact, Enclosed Vertical Farms Are Making Their
Way To Hudson Valley's Urban Areas
May 3, 2021
John Lekic is the chef and owner of Farmers & Chefs in Poughkeepsie and vertically grows his own produce for his restaurant in a shipping container on site. He came across the concept of shipping container farming at an exhibition at the Culinary Institute of America in 2019. Aaron Lacan
The Hudson Valley is quite familiar with what it means to be farm-to-table, but what if the farm is also practically right next to the table, even in the more urban and metro areas?
Vertical farming via high-tech shipping containers is emerging as a new solution for businesses seeking to grow their own produce in a way that shrinks the necessary agricultural footprint while maximizing yield and reducing produce travel time. Here in the Hudson Valley, a 20 by 20-foot shipping container is being used to grow up to 400 pounds of fresh produce a month at Farmers & Chefs restaurant in Poughkeepsie.
Last year, the restaurant partnered with an Israel-based agro-tech company Vertical Field to grow herbs and vegetables for its dishes in a new and innovative way. The startup, established in 2006, uses technology to create innovative growing methods to improve food supplies in urban areas around the world, working mostly in the Middle East and Europe but also recently in the United States — including right here in Dutchess County.
Poughkeepsie's Farmers & Chefs is one of the first businesses in the Hudson Valley to try shipping container farming. The restaurant's 20 by 20-foot climate-controlled container (pictured above) produces about 400 pounds of fresh produce a month. Aaron Lacan
John Lekic, chef and owner of Farmers & Chefs, grows everything from buttercrunch lettuce, kale and baby arugula to herbs like rosemary, sage and basil in his enclosed vertical farm. The container is divided into four growing fields and is set on the restaurant’s property for customers to see, which has drawn even more interest to Farmers & Chefs as of late.
So why vertical farming?
Vertical Field is just one manufacturer specializing in reimagining steel shipping containers into enclosed, climate-controlled farms that are powered by LED lights instead of the sun, essentially supercharging a growing environment. Freight Farms and Grow Pod Solutions, other manufacturers, also tout this farming approach for its lower burden on farm labor and land, and for the higher output per square foot.
Shipping container farming is climate-controlled, powered by LED lights instead of the sun, and can produce high yield in a small space. But humidity and start-up infrastructure costs can be challenges. Aaron Lacan
“It’s a dream come true for chefs to be involved from the seed to the plate,” said Lekic. “It’s a great experience when you grow your own ingredients.”
Lekic pursued vertical farming after coming across Vertical Field during an exhibition showcasing a number of Israeli-based companies involved in food and agriculture at the Culinary Institute of America in late 2019.
Before the shipping container arrived at the Poughkeepsie restaurant, Lekic sourced vegetables from nearby farms and grew herbs in small outdoor gardening beds on site. However, Lekic found that it wasn’t enough yield, especially in the summer, and he often collaborated with additional farms to fill the gap. With a shipping container for growing, the restaurant is able to produce enough of what they need and on site – a key benefit for Lekic.
“There is a huge importance of having urban farms where the demand is,” said Lekic. “The problem with today’s agriculture is that everything has to travel. Most people are not aware of it, but depletion of the nutrients in our food is a huge issue.”
If you harvest spinach, it would be full of vitamin C that same day, Lekic said. But that changes dramatically just 48 hours later, when that nutrient is mostly gone. (A 2013 study by the University of California showed that spinach could lose as much as 90 percent of vitamin C in a single day.)
Farmers & Chefs restaurant grows everything from buttercrunch lettuce, kale, and baby arugula to rosemary and sage in its on-site shipping container. Aaron Lacan
By growing the restaurant’s produce steps away from the kitchen, “it’s as fresh as it gets,” said Lekic.
Farmers & Chefs received its shipping container farm right around the same time that COVID-19 hit last year, which Lekic said actually worked out well, as it gave him a chance to learn the ins and outs of vertical farming during a period that was quiet for his restaurant. By April, he was harvesting the first crops.
“Overall, the goal of vertical farming is to reduce the cost of healthy and fresh food to the retailer and to the end buyer as well,” said Vertical Field marketing director Noa Winston. “Since vertical farming reduces transportation costs, food losses, inventory inconsistencies, and price fluctuations due to climate, natural disasters, and other crises that create shortages, the retailer with vertical farming can benefit from consistency, security, and ownership over the entire supply chain.”
In another regional example, Evergreen Market, a grocery store in Monsey in Rockland County, partnered with Vertical Field to grow vegetables that ultimately stocked the store’s produce aisles, while also inviting customers to view its micro-farm when they visit the store.
Cost and maintenance concerns
This farming approach isn’t for everyone and there are drawbacks. “While it does offer some solutions to things like land access — which is, frankly, a huge barrier to the farming we advocate for here in the Hudson Valley — there is a lot of infrastructure needed,” said Kathleen Finlay, president of Glynwood, a center for regional food and farming based in Cold Spring.
“That brings a whole other set of challenges — how to create enterprises with a high capital upfront cost, how to get sustainable systems. It’s a different suite of challenges than more land-based production.”
Indeed, the start-up costs for an on-site shipping container farms aren’t cheap, although businesses say savings can be realized downstream by the reduced costs of paying produce purveyors for food that a restaurant or business is now growing itself.
Freight Farms' 2021 Greenery S model costs $149,000, which doesn’t include the shipping fee. Additional start-up costs can vary depending on where its being shipped, training packages selected, and any extras. Vertical Field would not disclose the fees associated with its model.
Plus, there is a bit of a learning curve when farming in a shipment container. Lekic played around with different variables, like what was best to grow at the same time, to see what would produce the highest yield.
"It's as fresh as it gets," said John Lekic of Farmers & Chefs, pictured above, about the new way of farming. Aaron Lacan
“For my purposes, I learned to stick with only two to four items – mostly greens,” said Lekic about his growing. “It makes the most sense based on my demand.”
Maintenance is an ongoing effort with an enclosed growing system that requires constant electricity and temperature controls to assure optimal growing conditions. “It’s always work,” said Lekic.
Over the past year, Lekic had to work out some kinks and issues, like making sure the air conditioning and heat levels were favorable to growing produce year-round. Just like traditional farming, some seasons might require more work — a vertical farm in the summer, for example, would have increased humidity that could negatively affect plants if not properly controlled.
While some growers may need back-up plans for electricity outages, Lekic doesn't foresee issues there because he is connected to the main restaurant building, which runs on a hospital-grid electricity system. Just in case, he has two generators that he could connect to if needed.
These drawbacks are outweighed by the ability to grow such consistent produce yield himself on site, he said, and the built-in technology features like being able to water plants by pushing a button on his phone. Lekic said overall it’s pretty easy to operate and monitor, so much so that the restaurant is looking into upgrading its original container to the newer version of the same size, and purchasing a second container.
“I’m interested in doing a mushroom container,” said Lekic. “There is the possibility of that. It’s a completely different kind of experience, but we would be super excited.”
DIY shipping container farming
While the hefty price tag of some farming shipping containers might be too prohibitive for some, others are riffing off of elements of tech-first farming for their own DIY growing methods.
KC Sullivan, a New Jersey-based mushroom farmer, created his own vertical farming environment out of an abandoned 40-foot-length shipping container that was used for storage at the Whitechapel Projects in Long Branch. Sullivan, who often collaborates with Tivoli Mushrooms here in the Hudson Valley, decided to create his own container farm by spray foaming it, sealing the floors, putting in an HVAC system, adding lighting and installing a misting mechanism.
He estimated the costs to be between $15,000 and $20,000 — not insignificant but far cheaper than a new shipping container already turbo-charged for farming.
“It was challenging,” said Sullivan. “There is no real guidebook or instruction manual on how to create a container mushroom farm. It was all about brainstorming how we wanted it to be.”
While it’s only been a year since mushrooms have been grown out of this urban shipping container, Sullivan is happy with the high-yield results: he's growing around 400 to 500 pounds of mushrooms a week. Mushroom container farming is slightly different from growing vegetables or herbs; for example, Sullivan doesn’t grow compost mushrooms, so there is no dirt necessary.
“We grow hardwood varieties, so it’s exclusively on red oak saw dust that is supplemented with agricultural byproducts,” said Sullivan. “You mix the two together with water, pasteurize it to kill off any pathogens, inoculate it with the strain of mushroom you’re looking to grow. It goes through an incubation period in a separate room [outside of the container], and then it goes to the fruiting room, which is the container and where it will be harvested.”
Just like Lekic, Sullivan also has run into some maintenance hiccups. The waterlines froze during the winter, which was a “big challenge and setback,” leading to a starved off humidification system, costing him around 100 to 150 pounds of crop.
Despite that hurdle, Sullivan also says the container can stand up against storms because it’s “built like a tank,” while regular farmland could be vulnerable to severe thunderstorms and potential flooding.
“One tool in the toolbox”
While an exciting option for some, vertical farming is “one tool in the toolbox” and it’s important to not forget about the benefits of traditional farming, said Finlay of Glynwood.
Finlay applauds any effort to produce food “that aligns with environmental sustainability,” but doesn’t think vertical farming will ever replace traditional farming or even fix the lack of land available for production.
Still, any effort to grow fresh food for more people is a win overall.
“We need more healthy food, accessible and affordable to more people,” said Finlay. “As much as vertical farming can play a role to that, I think that’s wonderful.”
Written By
Cloey Callahan is a lifelong Hudson Valley resident who was born and raised in Brewster, lived in New Paltz for four years while she attended college, and now resides in Newburgh on Liberty Street. On a sunny day, she strolls through Newburgh enjoying the 19th-century architecture on her way to the Hudson River waterfront. You can reach her at cloey.callahan@hearst.com to say hi or with pitches.
Vertically Grown Salads And Fresh Herbs In Føtex And Bilka Across Denmark
Danske Nordic Harvest has entered into a strategic partnership with Salling Group
Danske Nordic Harvest has worked at high pressure to get one of the world's largest vertical farms, fitted with the ground-breaking technology, ready for production for Danish consumers, and now the products are landing on Danish shelves for the first time: "The products from Nordic Harvest are unique in taste and quality. They are made without the use of pesticides, with an approx. 250 times less water consumption and through completely optimal land use.
We have believed in Nordic Harvest's innovative products for several years and are pleased that it has now become a reality," says Stephan Bruhn, category director at Salling Group, and continues: "We know that consumers are interested in the green transition, food security, and goods without chemicals, and we are convinced that sustainable products in this form will be a hit. That's why we also go out and launch in all føtex and Bilka's for a start."
With the agreement, Nordic Harvest will deliver almost three tonnes of salads and herbs a week to the Salling Group. At the same time, the plan is to test new products in Salling Group's chains on an ongoing basis.
On Nordic Harvest's vertical farm in Taastrup, the crops are grown on floors, which utilizes space. On 14 floors, the salads and herbs are grown in water in a closed and controlled environment that gives the plants the optimal conditions for growth, taste and nutritional content."
From harvest until they are in the package in the fridge, it takes about 10 minutes. From seeds to supermarkets, they have never been in contact with soil, human hands, bacteria, fungal spores or pests. And they, therefore, do not need to be rinsed, either when packed or before being used at home at the dining table. So there is nothing along the way that degrades the plant, and therefore the products have an impressive shelf life that minimizes food waste.
"We could not have found a better launch partner than Salling Group. Our common values around sustainable production and their skilled sense of taste and quality have meant that we have had a fantastic dialogue and a good collaboration from our very beginning. I am looking forward to seeing how Danish consumers receive our products," says Anders Riemann, CEO of Nordic Harvest.
The prices of Nordic Harvest products will be at the same level as similar organic products. All the products from Nordic Harvest are delivered cut and in boxes that do not crush the leaves, and which can also be easily closed again if you do not use it all at once. The packaging is made from 100 percent recyclable recycled plastic.
Source: https://via.ritzau.dk/
Photo source: Dreamstime.com
Publication date: Fri 30 Apr 2021