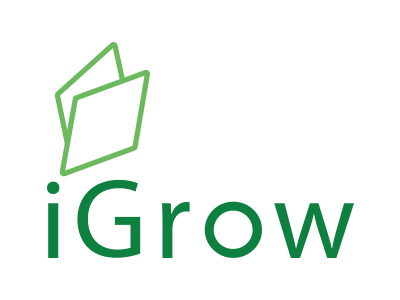
Welcome to iGrow News, Your Source for the World of Indoor Vertical Farming
Applying Automated Warehouse Systems To Indoor Farming
“At Swisslog, we don’t have standard solutions in place for vertical farms yet. But due to our long-lasting expertise both in the food industry and in the distribution of fresh products to the point of sale, we understand the supply chain processes and linked to that shelf life considerations.”
“History is written in circles as we observe similar drive for automation in indoor farming, as we saw years ago in the intralogistics sector. There are yet few important differences,” says Timo Landener, product innovator at Swisslog.
Swisslog, with the vision to shape the future of intralogistics, not only develops warehouse automation and software solutions to reduce costs and introduce flexibility to warehouse-based operations but also looks into innovative future-proof approaches. In March 2021, Swisslog announced its foray into the vertical farming market. While Swisslog has not specifically designed systems for vertical farming, its vast portfolio of automation solutions can be adapted to vertical farms, whether pre-existing or purpose-built.
Timo Landener
“At Swisslog, we don’t have standard solutions in place for vertical farms yet. But due to our long-lasting expertise both in the food industry and in the distribution of fresh products to the point of sale, we understand the supply chain processes and linked to that shelf life considerations. Moreover, our portfolio can be easily adapted to indoor farming since the payload is fairly light, the throughput is not critical and the automation operations demand low power compared to the needs of the intralogistics automation,” explains Timo. “Nevertheless, we already learned, that we can't just adopt the same requirements, because plants are living organisms. And we have to respect that.”
Although unable to reveal their clients, Swisslog has reportedly demonstrated its technologies in the vertical farming industry with success to allow growers to reduce operational costs and increase scalability. Examples of innovative systems applicable to vertical farming include the PowerStore high-density storage system, the AGV based good-to-person order fulfillment solution CarryPick, the Tornado mini-load crane and the Vectura stacker crane.
When does automation become economically feasible?
Automation can be applied to multiple processes in an indoor farm including seeding, harvesting, packaging, tray manipulation, etc. However, Timo explains that automation is capital-intensive and best suited for large-scale indoor farms. A higher production level introduces more opportunities to increase operational efficiency and reduce labor requirements.
“Even Amazon began in a small space with little automation. Then, they reached a level where automation made sense. In the vertical farming industry, we need to discuss with clients where the tipping point is for needing automation,” says Timo.
To determine which automation solutions are right for the grower, Swisslog’s automation experts work directly with clients to identify opportunities for increased operational efficiency and customize solutions according to the farm’s architecture. Additionally, the close relation with KUKA as the parental company allows collaboration opportunities to automate and incorporate the sub-processes in an Indoor Farm to a more turnkey solution.
Harvest-on-demand
Timo explains that despite the relatively short distance between urban indoor farms and retailers, a major challenge to indoor farming is the logistics of transporting farm-grown products to retailers while maintaining crop quality.
“After the plants have grown in a perfect environment, they are cut and immediately begin to lose quality. The current challenge is to speed up the process of getting the products to the retailer. Pursuing the innovative approach of harvesting-on-demand, we can make sure that the end customer receives fresh and rich nutrition vegetables. With a palette of automated solutions this is finally possible,” says Timo.
Swisslog’s ties with global retailers started long ago as the Swiss Company delivered solutions for huge automated projects (distribution centers) as well as smaller, more local applications, known as Micro-Fulfillment Centers. Harvesting-on-demand differs from mainstream distribution models by supplying retailers with living plants, which can continue growing until they are purchased.
This process can be carried out in retailers’ “back shops” and would support additionally retailers to fulfill three major sales channels: in-store sales, home delivery and BOPIS (buy online, pick up in-store). Swisslog is certain that we are at the edge of a revolution in food the supply chain: There will be the need for Indoor Farms at the point of sales: a “fresh food on the demand-supply grid”. We see automation as a means for leveraging the indoor farms and help them deliver efficiency that will lower the entry threshold for further investments.
Retailers are a fundamental part of this revolution. “Many indoor farms are currently selling to retailers. Due to the fact, that the retailers sell the crops, they determine how the supply chain will look like. Thus, the power of re-designing the process of the supply chain and ensuring consistency in the circular economy lies in their hands. As for today, the complexity and ramifications of the matter inspire us to join forces with retailers and find out how to react in the best way to changing needs of the customers and the industry. We are on the verge of something new and powerful. Swisslog, an intralogistics automation leader, together with retailers and farming experts, we can deliver a great added value for consumers” explains Timo.
For more information:
Timo Landener, product innovator
Swisslog
timo.landener@swisslog.com
www.swisslog.com
Publication date: Thu 3 Jun 2021
Author: Rebekka Boekhout
© VerticalFarmDaily.com
A Fully Automated Three-Dimensional Vertical Farm Comes Into Operation
Eponic Agriculture Co. Ltd is a supplier of indoor farming equipment. Alice, the company's director, introduced the recently fully automated production system of a stereochemical vertical farm
Eponic Agriculture Co. Ltd is a supplier of indoor farming equipment. Alice, the company's director, introduced the recently fully automated production system of a stereochemical vertical farm.
"The current three-dimensional indoor farms on the market are based on semi-automated workflow, with some links requiring additional equipment configuration and no continuity in the whole planting system. In order to solve this problem, we developed and designed a complete automated planting system, including the processes from sowing to planting, full-spectrum planting light control, fertilization, harvesting, and cleaning. Which are all done by automated equipment. Whereas all procedures can be controlled by intelligent software with real-time monitoring, data collection, and many other functions."
Benefits of an automated farm
When talking about the advantages of the automated equipment, Alice said, "Take our recently built 20-layer vertical farm as an example. First of all, the mechanical sowing time is 10 times-30 times faster than manual sowing. And on top of that, the use of automated equipment can realize precise planting and efficient communication of multi-layer planting surfaces. The 20-layer vegetable trays are automatically transferred to the ground for uniform watering, harvesting, and cleaning. This greatly improves productivity.
Secondly, the use of lift trucks is required when handling high-level crops. There are certain safety hazards in using lift trucks in a small space. While operating the automated equipment, only a tablet computer is needed to control the whole planting process, which is much safer and more convenient."
Although automated vertical farm systems have many advantages, their application in China is not yet popular. "In terms of production design, we have gone through countless experiments to design the most suitable software program. As well as hardware equipment for practical planting applications. Luckily after a long period of research, we finally chose the most cost-effective and suitable materials. The R&D investment is large and time-consuming.”
From a cost point of view, according to Alice, a fully automatic system is 2-3 times higher in costs than the semi-automatic system which is currently used more often. Most traditional agricultural companies find it difficult to accept such high initial costs. Thirdly, the automated system requires high technical requirements for farm managers. Managers need to have an understanding of both planting technology and software. Alice adds: “It is for these three reasons that the application of fully automated stereoscopic systems is not very common in China and other countries."
Automated planting
"Although the application is not yet widespread, I think fully automated stereoscopic planting is a trend. Urbanization has led to a reduction in arable land and soil pollution has triggered problems with pests and pesticide residues in fruits and vegetables, and the development of three-dimensional agriculture is the only way to maximize and optimize output in a limited area. Currently, stereoscopic planting plants still require a lot of manual labor to operate. As labor costs rise and planting techniques require more precision, the use of automated equipment will be a future trend," Alice notes.
"Automated systems are a trend, not only in China but also globally. Urbanization has been moving forward, in the face of soil pollution, pesticides and pests, etc. The planting area is gradually reduced and three-dimensional agriculture must be developed in order to quantify planting. Three-dimensional agriculture can be located near the city, and reduce the transport distance, people can eat the freshest vegetables, to achieve local supply. Therefore it is necessary to promote automated, intelligent planting systems in order to achieve efficient planting and sustainable development." Alice said.
Industry experience
Eponic Agriculture Co. Ltd's head office, Dahua Intelligent Electronics, has a twenty-five-year history division. The team has been focusing on the development and production of intelligent control systems and industrial lighting. Alice said that based on years of technical foundation, we developed full-spectrum LED planting lights which have been approved and applied by the USDA. Over the years, we have received technical support and affirmation from several agricultural doctors from Europe and the United States, focusing on the development and production of automated stereoscopic planting equipment.
According to Alice, the company has laboratories and showrooms in the US, Australia and Africa. This year, the company is planning on opening new showrooms and laboratories in Europe. “We are expanding our global reach and continue to optimize our growing systems to be a better supplier of fully automated growing equipment."
For more information:
Eponic Agriculture Co. Ltd
Alice Ou, Director
aliceou@eponicagriculture.com
www.eponicagriculture.com
Author: Rebekka Boekhout
© VerticalFarmDaily.com
This Startup Wants Vertical Farmers To Hire A Robot Gardener
“By automating the production with robotics and remote monitoring, we can lower labor costs and offer solutions for food producers that are economically viable and environmentally sustainable,” the company claims on their website.
Arugula micro greens are grown at AeroFarms on February 19, 2019, in Newark, New Jersey.
Photo: Photo by Angela Weiss (Getty Images)
In recent years, vertical farming has emerged as a futurist’s solution to the world’s agricultural problems. The growing trend seeks to use controlled environments to boost food production, leveraging indoor labs where temperature, light, and nutrients can be mechanically controlled.
Yet while vertical farms have gained in popularity, they are also still very expensive. When compared to conventional farming, these farms necessitate the purchase of pricey equipment to aid human labor—a fact that, when paired with other economic pressures, has apparently led to an industry “littered with bankruptcies.”
One company hopes to change this dire picture. Enter Watney the robot.
Watney was designed by start-up Seasony. The company, which was featured today at this year’s Alchemist Accelerator’s Demo Day, has sought to make the tech-farming trend more accessible by automating away some of the more difficult labor involved.
Image: Screenshot: Youtube/TV2LORRY
“By automating the production with robotics and remote monitoring, we can lower labor costs and offer solutions for food producers that is economically viable and environmentally sustainable,” the company claims on their website.
Indeed, Watney is designed to augment (and, in many ways, replace) a human labor force—currently one of the biggest expenditures for vertical farms. Essentially an intelligent, automated cart, the robot was designed to “move and transport plant trays” within a farming hub. In techno-jargon, it is an autonomous mobile manipulation robot (AMMR), a type of machine known for moving and manipulating items on its own. It is also equipped with a camera that captures image data and sends it back to farm management software for human analysis. Watney also gathers valuable horticultural data to help farmers optimize yields, said Christopher Weis Thomasen, Seasony’s CEO and Co-Founder, in an email.
From left to right: Erkan Tosti Taskiran, Servet Coskun and Christopher Weis Thomasen.
Photo: Photo from Seasony.
“We are doing for vertical farming what the integration of autonomous mobile robots did to amazon. We are able to decrease the costs of growing food in a vertical farm by alleviating the logistics pains of working from scissor lifts,” said Thomasen.
Thomasen, a mechanical engineer, and his two co-founders electrical engineer Servet Coskun and business specialist Erkan Tosti Taskiran, were inspired to create the business while brainstorming what it would take to sustain life in outer space (Watney the robot is named after Mark Watney, the astronaut in the movie The Martian, who, after being stranded on the Red Planet, fertilizes potatoes with his own poop to survive).
“It quickly evolved to Seasony setting up a vertical farming lab and exploring the technical challenges facing the new industry. Reducing the costs related to labor is key in order to scale vertical farming and make agriculture more sustainable,” Thomasen said.
There is, of course, some debate in the farming community about the social costs incurred through the large-scale displacement of human labor.
Presumably, we will have to wait to see what that cost-saving process looks like. Seasony, which is still getting off the ground, plans to do a pilot trial with the largest vertical farm in Europe in April. It has plans to conduct further testing with several smaller vertical farms, as well, Thomasen said.
Lucas Ropek
Staff writer at Gizmodo
VIDEO: Common Mistakes When Setting Up Hydroponics
Even if you have a lot of guidance in setting up your grow space, you may make mistakes in the initial development stages
January 4, 2021 | By Joy King
Starting a hydroponics garden is thrilling. It's an exciting project where you can enjoy the progress your plants make over time. However, producing perfect plants requires some skill and attention to detail that take time to develop. Even if you have a lot of guidance in setting up your grow space, you may make mistakes in the initial development stages.
What is hydroponics?
Wikipedia describes hydroponics as "a type of horticulture as a method of growing plants, usually crops, without soil. It's become popular in vertical and indoor farming. Let's examine some common errors to avoid when setting up a hydroponics grow:
Ignoring plants
New growers may not devote the amount of time necessary to grow hydroponically. Some mistakenly believe that they can check in on plants on the weekend. But, a lot can go wrong if you're not regularly checking on them. Even if your system is fully automated through a grow controller, it's essential to check on your plants daily to ensure that everything is going smoothly.
Check that your automation system isn't clogged or failed in some other way. Once you are a more experienced grower, it will become easier for you to identify failures in your systems and problems with your plants since you're dedicating time to their wellbeing.
Going overboard
More is not always better, particularly in regards to plant growth. Often, problems arise in the grow room from a lack of experience in tending to plants grown hydroponically. It usually takes time to understand how to irrigate and fertilize plants properly. Overwatering is often detrimental to plants, and beginners often do not realize they are overwatering before it is too late. Excessive nutrients, or nutrient burn as it's referred to, is also a common problem for beginners.
Overcrowding plants
It is common for beginners to overestimate how many plants will fit in their grow space. When you first plant them, it may seem that your plants have a lot of room, but once they grow up, they will need that extra space to maintain growth. Be vigilant about removing excess plants and pruning if overcrowding seems like it will be a problem. When in doubt, err on the side of caution and plant fewer plants.
Sudden changes to the environment
You need to give your plants time to adjust when you make changes. One of the most common problems that beginners face is when they suddenly change the grow room's light levels or room temperature. Any sudden increase in light may cause leaf bleaching and burning. It's better that you make changes gradually, giving your plants time to adjust.
Final thoughts
There are many scholarly books on starting hydroponics grow room or space. Do your research and enjoy your hydroponic garden! It's a rewarding way to grow food, cannabis, or flowers.
Source: Growlink
Tags: Hydroponics, Nutrient Dosing System, Wireless Automation, Automated Grow System, Customer Service, Automated Grow Systems, Nutrient Delivery System, nutrients, automation
Iron Ox Announces Next Robotic Farm In Lockhart, TX
Iron Ox has purchased nearly 25 acres of land and plans to build a new, state-of-the-art facility on the property
November 6, 2020
LOCKHART, TX, — Iron Ox, a leader in robotics and AI-enabled farming with a mission to solve food insecurity, and the City of Lockhart, Texas today announced that Iron Ox will expand their operations to the city with plans to break ground on a new facility this December, bringing new tax revenue and jobs to Lockhart.
Since 2015, Iron Ox has developed hybrid robotic greenhouses that support a range of produce offerings. To bring those produce offerings to new communities, the company identified Texas as the next state in their national expansion plan with its favorable business environment and rich history of agriculture.
“We’re proud to make Lockhart our next farm outside of California,” said Brandon Alexander, Iron Ox CEO & Co-founder. “Lockhart’s city government, as well as their planning and development staff, worked diligently with us throughout this process and made us feel right at home. In addition, the city's central location within the Texas triangle and short drive from Austin, allows for strong distribution lanes of same-day grown and harvested products throughout the entire state of Texas, making the city the ideal choice for our robotic greenhouse growing platform”.
Iron Ox has purchased nearly 25 acres of land and plans to build a new, state-of-the-art facility on the property. This new facility will house the company’s natural light greenhouses, processing operations and AI-enabled robots to bring fresh, clean and healthy food to new customers and communities throughout Texas.
“The addition of Iron Ox to the Lockhart business community represents synergy between our city’s storied history in agriculture and our growing technology sector,” said Lockhart Mayor Lew White. “The food and beverage processing industry is one of four business sectors Lockhart has targeted in its 5-year economic growth plan because our city’s unique advantages align perfectly with the needs of companies like Iron Ox.”
Mike Kamerlander, Director, Economic Development, represented the Lockhart Economic Development Corporation (CEcD) on this project.
“As Lockhart continues to grow, Iron Ox and companies like it are essential to our economic vitality and future. We thank them for their investment and commitment to Lockhart.”
About Iron Ox
Iron Ox launched the world’s first autonomous farm in October 2018, leveraging advancements in plant science, machine learning, and robotics. The Iron Ox team develops AI-enabled, autonomous technology that enables fresher, more consistent produce to be grown and distributed globally. The company’s goal is to service thousands of communities with the freshest and healthiest products, while establishing global reach and impact on food security.
For more information, visit www.ironox.com.
About Lockhart Economic Development Corporation
The Lockhart Economic Development Corporation, a department within the City of Lockhart, is designed to provide a range of business and economic development assistance. To learn more about opportunities in Lockhart, visit www.lockhartedc.com.
Contact Info:
Taylor Aldredge
570-534-4754
CANADA: Automated Guelph Vertical Farm Supplies Retailers With Local, Leafy Greens
An automated vertical farm in south Guelph is now fully operational. GoodLeaf Farms has the capacity to produce 800,000 units of locally grown leafy greens for Ontario retailers — including Loblaw banners, Longo’s, and Whole Foods — 12 months of the year
By Lilian Schaer
October 14, 2020
The Newly Opened Farm Grows Crops
40 to 50 Percent Faster Than Traditional Crops
There are 50 workers employed at the GoodLeaf Farms facility in Guelph. Photo: Lilian Schaer
An automated vertical farm in south Guelph is now fully operational. GoodLeaf Farms has the capacity to produce 800,000 units of locally grown leafy greens for Ontario retailers — including Loblaw banners, Longo’s, and Whole Foods — 12 months of the year.
“It’s really unique for Canada that we can grow 365 days of the year, and we can fill a gap in the market without going up against traditional farming,” said account manager Jacquie Needham during a tour of the facility on Sept. 15.
Why it matters:
The pandemic has heightened demand for locally grown foods less dependent on sometimes fragile global supply chains.
GoodLeaf’s crops include baby arugula and baby kale, along with four types of microgreens: pea shoots, Asian blend, spicy mustard medley, and arugula. While consumers are familiar with “baby” leafy greens, they’re less comfortable with what to do with microgreens, admits Needham.
“Micros are a learning curve for consumers, but they can be used to add nutritional elements to meals as garnishes, in salads or sandwiches, or as something you add to a smoothie,” she said.
“People are cooking more at home right now and experimenting more.”Vertical farming is an innovative process that naturally grows plants with hydroponics under specialized LED lights designed to maximize photosynthesis. In the GoodLeaf facility, carbon dioxide, water, nutrition, and light are carefully programmed and monitored for each specific crop.
Jacquie Needham, of GoodLeaf Farms, talked about the company’s products during a recent tour at the facility.’ photo: Lilian Schaer
According to Needham, that makes their growth cycles an estimated 40 to 50 percent shorter than traditional crops. From seed to store takes about 12 days for the microgreens and about 22 days for the baby leafy greens. That includes testing every crop for contaminants before shipping to ensure they’re safe — important at a time when North American produce recalls make headlines and can have far-reaching economic and health consequences.
Needham also pointed to the sustainability of vertical farming production. The GoodLeaf facility uses 95 percent less water than a traditional farm, doesn’t use pesticides, herbicides, or fungicides, and has no run-off issues that could impact local water supplies. The production is not organic, however.
“We are not certified organic because our production does not use soil, but we feel we have a cleaner product than organic because, in addition to being pesticide-free, it’s not exposed to wind or rain, for example,” she said. “It’s an education piece for consumers.”
GoodLeaf Farms was founded in 2011 in Nova Scotia by Gregg Curwin. That original Nova Scotia farm has now been converted into a research and development centre for the company.
The new Guelph facility employs about 50 people who work seven days a week and it’s the city’s research expertise and proximity to the Greater Toronto Area that brought GoodLeaf to the region.
The GoodLeaf building is located in an industrial area in south Guelph. photo: Lilian Schaer
“Ontario is a big hub for consumers, retail and foodservice, so we were looking for a place close to the market so we can get product to people as quickly as possible,” said Executive Director of Operations Juanita Moore. “And the University of Guelph has been a great help with research.”
Research conducted in controlled environments
GoodLeaf is working with university researchers on a number of horticulture and food safety projects, including studies on controlled environments and light spectrums. The company received $4.4 million in start-up innovation funding from Agriculture and Agri-Food Canada’s AgriInnovation Program.
“I’ve been the mayor (of Guelph) for six years now and this is one of my “wow” moments,” said Guelph Mayor Cam Guthrie following the tour. “Guelph is embracing the circular food economy and we are seeing it in action here. It’s a testament to what Guelph has to offer.”
Guelph MP Lloyd Longfield, who was also on the tour, pointed to vertical farming’s potential to help address climate change and food security issues in both urban and northern or Indigenous communities.
“This type of agriculture is consistent and gives predictability to the producers and it would be interesting to see if it could be used more widely,” he said.
Netled And SweGreen Collaborate In Sweden – Netled’s Vertical Farming System Delivered To In-Store Farm In ICA Focus Supermarket
Netled is specialized in developing and selling high-technology vertical farming systems
7th September 2020 by johannak
We have delivered a vertical farming system to our partner SweGreen’s project in Sweden. SweGreen has agreed on providing ICA Focus, one of Sweden’s biggest supermarkets in Gothenburg, an automated in-store farming solution. The greens are grown within the store and harvested directly off the shelf. This kind of in-store farm is first-of-its-kind in Sweden and globally unique in size as well as production capacity.
Netled is specialized in developing and selling high-technology vertical farming systems. Our mission is to enhance vertical farming by providing the best technology, expertise, and guidance for vertical farming projects and actors all around the world. The collaboration with SweGreen has been outstanding and produced valuable next steps towards hyper-local vertical farming.
Netled’s CEO Niko Kivioja comments: “We have followed the markets for ultra-local vertical farming for quite some time now and seen that our technology has clearly many opportunities for the current markets. This first project we have executed with and according to the wishes of our Swedish partner SweGreen is a great reference for us. Their business model, Farming as a Service, is elegant and easy to implement by supermarkets. Our team is proud to be partners with SweGreen, making fresh production close to consumers possible.”
Photos: SweGreen & Netled
More photos in SweGreen’s post on LinkedIn >
Watch a video by ICA Gruppen on LinkedIn >
Read more from the article in Gothenburg’s local paper Göteborg’s Posten (in Swedish) >
Facebook Twitter LinkedIn Share
Filed Under: NewsTagged With: agtech, autonomous farming, indoor farming, indoor farming technology, indoor growing, vertical farming, vertical farming expertise, vertical farming technology
Chinese Startup Gets In On Ground Floor Of High-Rise Farms
Looking ahead, the costs associated with conventional farming will match those of vertical farming around 2025, according to Zhan Zhuo, Sananbio's general manager. If this forecast is accurate, opportunities for vertical farms to spread quickly would explode, Zhan said
Sananbio Develops Techniques And
Hardware To Drive Indoor Agriculture
Sananbio has successfully grown more than 300 types of plants without the help of the sun. (Photo courtesy of Sananbio)
XIAO YAN, 36kr
August 17, 2020
BEIJING -- A Chinese company expects the future of high-rise farming to arrive in 2025. That's when the costs of conventional farming are expected to match those of vertical farming, when growing food inside urban towers will be able to address population and environmental issues in a more economical way, and when the indoor agriculture market is expected to be worth $9.9 billion.
Sananbio is the vertical farm leader in China, and the market estimate is from Grand View Research of the U.S.
The sector is still getting off the ground, but overseas startups have succeeded in raising large amounts of money.
Sananbio was created in 2015 by the Institute of Plant Research at the Chinese Academy of Sciences and the Fujian Sanan Group. It inherited the Institute of Plant Research's plant technology and Fujian Sanan's capabilities in optoelectronics, a field concerned with the use of electronics and light. With these tools, it conducts research into biotechnology, photobiology, indoor agriculture, and other areas.
It currently holds 416 patents, nearly 60% of which have been filed with the Patent Cooperation Treaty, an international organization that helps patent holders gain international protection for their inventions.
Sananbio has set up research facilities in Fujian and Anhui provinces and operates large indoor farms in Beijing, Shanghai, and other major cities.
In the U.S. state of Nevada, it is developing cultivated varieties for the North American market. In Singapore, it is developing indoor farming technologies for desert and island countries.
In 2015, Sananbio worked with another research institute to build a 10,000 sq. meter indoor farm that grows leafy vegetables with artificial light, the first such facility in the world.
Its latest triumph is Uplift, a system for unmanned agricultural factories that can create construction plans for factories based on internal layouts so that sowing, dividing roots, and daily management can be automated. The system also can reduce the use of pesticides.
The company has successfully grown more than 300 types of leafy vegetables, fruits, herbs, edible flowers, and medicinal herbs.
Sananbio's business model is to provide hardware and vertical farming solutions to farmers who want to innovate and companies looking to enter agriculture. It also provides ongoing technical support. Its research facilities in Fujian, Anhui, and the U.S. already supply technology, and globally the company either owns or services 120,000 sq. meters worth of indoor farms. More than 50 indoor agricultural facilities in the U.S., Canada, Japan, South Korea, Singapore, the United Arab Emirates, the U.K., Saudi Arabia, and Germany use Sananbio facilities.
Looking ahead, the costs associated with conventional farming will match those of vertical farming around 2025, according to Zhan Zhuo, Sananbio's general manager. If this forecast is accurate, opportunities for vertical farms to spread quickly would explode, Zhan said.
The company says it is also making progress in other areas, such as plant-based bioreactors, planters for home use, and exhibition indoor farms for educational purposes.
36Kr, a Chinese tech news portal founded in Beijing in 2010, has more than 150 million readers worldwide. Nikkei announced a partnership with 36Kr on May 22, 2019.
For the Japanese version of this story, click here.
For the Chinese version, click here.
Swegreen Vertical Farm Goes In-Store in Gothenburg, Sweden
Swegreen's first automated farming unit takes place at ICA Focus in Gothenburg
Swegreen's first automated farming unit takes place at ICA Focus in Gothenburg
Swegreen inks contract with ICA Focus in Gothenburg, to become the exclusive producer of hyper-locally grown vegetables via an automated cultivation system inside the store itself. The agreement is based on Swegreen's subscription-based Farming-as-a-Service, which gives food retailers and restaurants the opportunity to offer their customers fresh crops all year round – harvested directly on-site or in-store.
From left: Andreas Dahlin, CEO at Swegreen. Elsa Adlersson, ICA Focus' responsible for the In-Store greenhouse. Marcus Petersson, chairman at Swegreen.
The contract between Swegreen and ICA Focus concludes that the Gothenburg-based store will be the first in Sweden to offer its customers hyper-locally produced greens grown from seed to fully-grown size inside a store itself. The cultivation facility, which is provided by the Swedish startup company Swegreen, is based on so-called hydroponic cultivation technology that is both resource-efficient and climate-smart. The technical solution also includes the company's special lighting and nutrient recipe, air conditioning system for control of heat, humidity, and CO2 content plus a complete digital monitoring – as well as a data-driven intelligent system for optimization of all cultivation processes.
Through Swegreen's subscription-based business model, Farming-as-a-Service (FaaS), the cooperation between the parties is based on a long-term commitment where Swegreen ensures efficient production at agreed volumes and quality.
- Our FaaS model means that every store and restaurant owner can offer hyper-local, fresh and high-quality crops that are fantastically nutritious and tasty – at very competitive prices, says Swegreen's CEO, Andreas Dahlin.
- We are very proud and happy to start this collaboration with ICA Focus. It is a store that has the will to be at the forefront, and we think there are going to be many who desire to follow their footsteps.
ICA Focus is located in the Gårda district in central Gothenburg, just a stone’s throw away from the famous amusement park, Liseberg, and the Swedish Exhibition and WTC. A flagship store that always has a large assortment of environmental-friendly products.
- Our customers have demanded more locally produced and sustainable greens in our assortment – and it will not be more local and greener than this! Says Daniel Åkerhage, Store Manager at ICA Focus.
- Now we look forward to our first on-site harvest, which we expect to take place later this month.
At full capacity, it is possible to deliver and harvest around 300 units of fresh salad heads and herbs per day in the cultivation facility in the ICA Focus store.
With hydroponic cultivation technology, where the crops grow without soil with lighting from special LED lamps, it is possible to grow vegetables in an urban environment – and thus produce food very close to the consumer. It also removes unnecessary, expensive, and climate-damaging transportations. In addition, the crops do not need to be sprayed by pesticides or herbicides – they are ready to be eaten directly off the growing system. Up to 95% of the irrigation water is reused via the recycling system. Nutrients are also recycled, while the plants receive carbon dioxide through a filtered air intake from the store itself.
Swegreen has developed the cultivation module to be able to create integrated plant environments together with partners in the food and restaurant sector. Therefore, Swegreen has developed a cloud-based control- and monitoring system to make production easy to manage. Through data collection of current factors in the cultivation environment, the system can continuously refine and further optimize the cultivation processes by the use of artificial intelligence.
For more information contact:
Andreas Dahlin, CEO of Swegreen, +46 70-924 00 32, andreas.dahlin@swegreen.se
Daniel Åkerhage, store manager ICA Focus, +46 76-117 16 20, daniel@icafocus.se
Swegreen is a Swedish FoodTech company that combines advanced technology, data science, and agricultural knowledge to be able to efficiently produce high-quality and climate-smart crops in an urban environment. The company offers a subscription-based cultivation service called Farming-as-a-Service (FaaS). It gives food retailers and restaurants the opportunity to offer their customers hyper-locally produced, fresh, nutritious, and tasty greens all year round. www.swegreen.com
ICA Focus is a unique grocery store that has been a rendezvous place for food-loving Gothenburgers for over 25 years. With an assortment of over 35,000 items, you have about twice as much to choose from as in an ordinary ICA store. ICA Focus also has its own bakery, charcuterie and restaurant. The store also has one of Gothenburg's best fish delicate retailers, Fisk i Focus. ICA Focus is located in Focushuset, Gårda, in central Gothenburg.
An Aussie Vertical Farm Company Has Gained International Interest Amid Concerns About Food Supply Chain During The Coronavirus Pandemic
Aussie company Stacked Farm, a fully automated vertical indoor farm, has been gaining international interest amid the coronavirus pandemic
By Sharon Masige | Business Insider | 5 June 2020
Stacked Farm, an Australian automated vertical indoor farm, has received international interest during the coronavirus pandemic amid concerns about the continuity of food supplies.
The farm produces salad greens and has the capacity for tomatoes and strawberries.
CEO Conrad Smith told Business Insider Australia Stack Farm received significant interest from the Middle East.
Aussie company Stacked Farm, a fully automated vertical indoor farm, has been gaining international interest amid the coronavirus pandemic.
Stacked Farm, founded in 2017, produces salad greens and herbs like lettuce and rocket and has the capacity to produce tomatoes and strawberries. It's even looking at testing out a type of blueberry next year.
The company has been receiving a lot of interest during the coronavirus pandemic amid concerns about virus clusters breaking out in the food supply chain. Back in May, a coronavirus cluster broke out at Melbourne's Cedar Meats abattoir, which was linked to 62 cases, according to the ABC.
"People are more concerned than ever about who is handling their food, where it’s coming from and how many stops it made before arriving on supermarket shelves," Stacked Farm CEO Conrad Smith said in a statement.
The company is headquartered in Burleigh Heads, Queensland and has plans to open up farms across Australia as well. "A scaled-up farm in Victoria will be our first major commercial farm," Smith told Business Insider Australia. Its farm is fully automated, with the produce packed and sealed once its harvested by robotic farming.
"It doesn’t pass through the usual supply chains either – greens and herbs can go directly to wholesalers, retails, hotels and restaurants, unlike traditional produce which passes through a number of hands before reaching our shelves," Smith said in a statement.
Stacked Farm has a partnership with fresh produce supplier Morco Fresh and counts Dnata as one of its clients as well, which provides aircraft services like flight catering.
"We are not too dissimilar to a normal farm where we go through markets and we go through wholesalers and food service distributors," Smith said.
And while it mainly supplies to the food service industry, Stacked Farm is looking at a move into retail so people can grab its produce from supermarket shelves as well. "We haven't got the capacity to do that at the moment," Smith said. "But when we scale up to our Victorian farm, we will certainly have the capacity to do that and we'll be looking for retail partners to jump on the journey that we're on."
The farms are temperature controlled and automated
Stacked Farm grows its produce 12 months a year, without relying on different seasons. Its products are grown in a temperature-controlled environment that is fully automated from seeding to harvesting. The company is looking at post-harvest automation as part of its next business phase.
Stacked Farm also makes barley-based livestock feed. "In a drought-vulnerable country like Australia, there's a lot of opportunity there because while we all think about human consumption, animals are a massive part of the food chain that needs to be considered," Smith said.
The company's employees are mainly in the science and tech field rather than traditional farm labourers.
"We're not like traditional farms where we require pickers, packers and harvesters," Smith said. "We employ more labour leaning towards engineering, software engineering, mechanical engineering, CAD designers [and] horticultural scientists."
The company has been receiving interest from the Middle East
Stacked Farm has received international interest in its farm during the coronavirus pandemic, mainly thanks to concerns over food safety, quality and security.
"There's a lot of food chains that have been broken throughout this COVID-19 pandemic, and we've had interest from the Middle East to set up farms there," Smith said.
"We have been very enthused by the interest from particularly a couple of states in the Middle East that have governments that really support local industry and local farming." Smith gave the example of Dubai which relies predominantly on imports. According to Bloomberg, the United Arab Emirates imports up to 90% of its food.
Smith explained that in Dubai, "a lot of produce can't travel by sea".
"They've immediately recognised that there's a problem in their food chain and they need to bring tech businesses to their country to support feeding their people." And, in the case of Stacked Farm, can help feed livestock too.
Smith added that Stacked Farm can support the future of food production, particularly in extremely hot and dry or extremely cold climates. He explained that one in nine people go hungry around the world. According to the Food and Agriculture Organisation of the United Nations, by 2050 world food demand is expected to rise by 70%.
"Having urban indoor vertical farms is definitely [an] exciting prospect for the future," Smith said. "We can literally shave days off out of the logistics process, we can extend the shelf life of products so there's less wastage and that in turn will benefit the community."
Bowery Is Sprouting In Baltimore With A New Automated Indoor Farm
Using technology that allows farming to go beyond the limits that the land imposes, the company has a mission to democratize access to fresh produce. It initially opened two farms in Kearney, New Jersey, serving the tri-state area
With a mission to democratize food access, the indoor farming startup sees the White Marsh location as a mid-Atlantic hub.
By Stephen Babcock / STAFF / 2/20/20
Inside Bowery's indoor farming operation. (Courtesy photo)
On land in White Marsh that was once associated with a working farm, new growth is taking root. But it didn’t require clearing away the building on the site: All of the growing is done inside.
“We are turning what was once an industrial warehouse back into a modern farm,” said Katie Seawell, chief marketing officer of Bowery Farming.
In early November, Bowery Farming opened a new indoor farming operation inside the warehouse on Franklin Square Drive and has been ramping up operations.
First flagged by Fast Company, it’s the third and largest farm for the New York-based startup, which in 2018 raised $90 million in a round led by Google Ventures.
Using technology that allows farming to go beyond the limits that the land imposes, the company has a mission to democratize access to fresh produce. It initially opened two farms in Kearney, New Jersey, serving the tri-state area.
With the expansion to Baltimore, the company is seeking a wider foothold in the mid-Atlantic. Seawell said the White Marsh location will open up distribution into a 150-mile radius where it can reach a potential 25 million people.
The company looks to hire locally even as it thinks regionally, and Seawell said White Marsh proved to be a transit-accessible location.
When it is fully-staffed, Bowery Farming expects to have about 80 farmers working at the space, in a mix of hourly and supervisory roles. Even for folks with no prior farming experience, Bowery looks to offer opportunities for farmers to move up within the organization as they gain skills. The farmers rotate through different roles on the farm, learning different aspects. Seawell recalled one farmer whom she met in the early days of the Kearney farm when he had a role in the packing section.
“I just ran into him last week and he was now in a support role for the ag science team,” she said.
They also seek out opportunities to support growth. In New York, the engineering team recently taught a coding class.
Inside the farm itself, hydroponics — the process of growing plants without soil — is key to the vertical farming operation, and technology plays a big role, too. CEO Irving Fain teamed with cofounders to apply technology to a big mission area. The team devised a system called BoweryOS to run the farm, which uses visual systems, sensory systems and automation. With data-gathering techniques and machine learning, the company sees its farms as a network, so the data is helping to build on what’s been done at the other two locations.
“Even though it’s the newest farm, it’s the smartest farm we’ve ever had,” Seawell said.
Bowery Farming from above. (Courtesy photo)
When it comes to the crops themselves, the farm has leafy greens and herbs in the market now. They’re available through Amazon Fresh, and Bowery is working on developing retail partnerships in the region to bring produce in the spring and summer. The company is also working to move beyond the “leafy green” category, which is often a staple of indoor farms and is testing other crops. It also has a partnership to regularly deliver hundreds of pounds of produce to the Maryland Food Bank.
Vertical farming doesn’t only upend the traditional growing model. With a wider food system that often involves food being shipped long distances, Bowery’s indoor farming approach yields lots of promise to bring production closer to where it’s eaten, employ local folks and offer a pesticide-free product.
Still, indoor farming remains new, and it’s entering an existing market with plenty of other produce players. As such, it has to make a product that’s attractive to folks, as well, and Seawell said the company has also put a lot of time and care into not just the operations, but also how it tastes.
“We believe we have a great-tasting product,” Seawell said.
BREAKING NEWS: Autogrow Announces First Industry Collaboration With Ridder Group And NATIVE
The collaboration is made possible with the launch of Autogrow’s new farm management platform, FarmRoadTM, which was announced by CEO Darryn Keiller at the Indoor AgTech Summit in New York today
June 20, 2019 (NEW YORK): Global automation expert Autogrow has announced a collaboration with competitor Ridder Group and New York agriculture software firm NATIVE.
The collaboration is made possible with the launch of Autogrow’s new farm management platform, FarmRoadTM, which was announced by CEO Darryn Keiller at the Indoor AgTech Summit in New York today.
“FarmRoadTM was conceived to fulfil two broad purposes. A platform for autonomous farming and secondly as a way of bringing together all disparate technologies that farmers use into one unified management tool,” explains Mr. Keiller.
“To be truly unified you need to be open and work collaboratively across the industry with buy-in from existing major players. It’s a concept we advocated two years ago when we came out with the first open API (Application Programming Interface) and I’m pleased to be in a position to say the dream is now tangible.”
“We are ecstatic that Ridder has shown the foresight and faith in us, to support what we are doing and join us in showing the industry what is possible when true collaboration occurs.”
Both Autogrow and Ridder market automation solutions for Controlled Environment Agriculture (CEA) and both will be able to integrate with FarmRoadTM.
“The Ridder Group, developer of the HortiMaX greenhouse control systems for over 40 years, supports the initiative of Autogrow,” says Joep van den Bosch, Chief Innovation Officer, Ridder Group.
“Ridder believes strongly in a connected future where systems and data is shared for the benefit of optimizing the plants growing conditions and more efficient and sustainable greenhouse operations.”
“As an industry partner, Ridder will make it possible for growers to connect their Ridder climate control and irrigation systems to the FarmRoadTM platform.”
Alongside Ridder Group, Autogrow will also be collaborating with New York based Start-Up NATIVE.
“Equally as important as an established player showing vision, is new entrants to the industry who are also bringing innovation. What NATIVE are creating delivers a fundamental industry building block, which we will integrate with FarmRoadTM,” says Mr. Keiller.
The NATIVE platform connects farms with local buyers, maximizing the value of their harvests and helping both buyers and restaurants deliver on the promise and demand of locally sourced food.
“Our partnership with Autogrow will most benefit the growers and the farmers,” says Frank Pica, co-founder, NATIVE. “FarmRoadTM users can provide NATIVE with real-time data that verifies the quantity and quality of their harvests, and NATIVE will return the true market value of the products. NATIVE then provides an outlet for growers to bring their products to premium markets within their region.”
Autogrow will work closely with Ridder Group and NATIVE over the coming months during the pilot phase. The beginning of the journey in working collaboratively with producers and growers.
“The next iterations of FarmRoadTM include flower and fruiting identification through Machine Vision and AI to provide pollination rates and flower to fruit conversion performance. We will be extending the 3rd party integration to include finance, labor management, food security and more,” says Mr. Keiller.
More information can be found on www.farmroad.io
QUERIES
General queries: (e) info@farmroad.io
Media queries: Kylie Horomia, Autogrow Head of Communications (e) Kylie.horomia@autogrow.com
(w) www.farmroad.io
About Autogrow
Autogrow leverages the power of technology, data science and plant biology to provide indoor growers affordable, accessible and easy-to-use innovation – 24/7, anywhere in the world.
Our hardware, software and data solutions support growers and resellers in over 40 countries producing over 100 different crop types.
With over 25 years in business, we have a depth of experience and passionate, fun people creating original ideas and making them a reality for our growers.
About Ridder Group
Farmers and growers worldwide need to be able to adopt their own individual approach to efficient and sustainable controlled environment agriculture. This is the promise that Ridder, as an international family-owned company, fulfils by translating more than 65 years of Dutch agri-food expertise into adaptive technology and know-how that is tailored precisely to local needs and conditions.
At Ridder, the drive to innovate is in our DNA. We are also committed to finding the best possible solution. The balanced combination of these two characteristics has enabled Ridder to evolve into the experienced market leader in technical solutions for the horticulture, intensive livestock and crop storage sectors. Today, Ridder has customers in more than 100 countries, who receive support from international offices and a global partner network.
About NATIVE
NATIVE’s mission is to empower local growers by maximizing the value of their harvests and meet the rising demand for local, transparently sourced food. NATIVE integrates real-time technology throughout the agricultural supply chain to accelerate traceability, waste mitigation, and return on investment. For more information, please visit www.nativeag.io