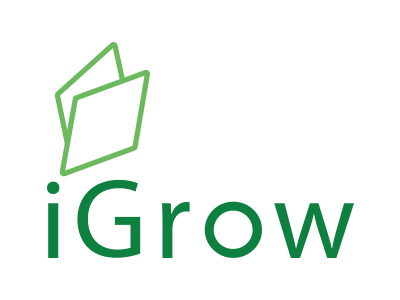
Welcome to iGrow News, Your Source for the World of Indoor Vertical Farming
SINGAPORE - VIDEOS: How IoT And Machine Learning Are Automating Agriculture
A new generation of farmers is tapping the internet of things and machine learning to operate self-sustaining urban farms with minimal supervision
A New Generation of Farmers Is Tapping The internet of Things And Machine Learning To Operate Self-Sustaining Urban Farms With Minimal Supervision
By Aaron Tan, TechTarget
21 Jul 2021
A new generation of farmers is turning to technologies such as the internet of things (IoT) and machine learning to automate agricultural production, alleviating the need to toil on the land while keeping a watchful eye on their crops.
Joining their ranks is Phoebe Xie, director, and co-founder of Singapore-based agrotechnology startup AbyFarm. Teaming up with technology service provider SPTel, Xie is building a smart hydroponics farm in a greenhouse that uses a plethora of IoT sensors, including video cameras, to keep the farm humming around the clock.
“To run a self-regulating farm at the optimal temperature with optimal water and nutrient supply, and to control the quality and taste of vegetables and fruits, we need IoT sensors,” she said, adding that the farm and its sensors collect and monitor thousands of data points, including humidity and temperature.
With the data and in certain environmental conditions, processes and actions are automatically triggered to protect crops from the elements. For instance, if the temperature or humidity gets too high, fans, water curtains, and roof shades are activated in the greenhouse.
Xie said the smart farm, located at a rooftop carpark in Singapore, is also equipped with sensors that monitor the pH and electrical conductivity levels of water. Among the sensors, which are connected to a Lora low-power wide area network, is a dozer that automatically releases acidic or alkaline nutrients to maintain optimal pH levels.
Whereas the farmers of old had to physically inspect their crops, AbyFarm’s agronomists and farmers can do so remotely using video cameras and image recognition technology to identify crops that might be succumbing to disease.
“If the image recognition finds that a plant is likely to be sick, the farmer will be alerted to go onsite to check how the plant is right now,” said Xie, adding that agronomists will also advise farmers on taking corrective actions to prevent disease or restore the health of their crops.
Like any machine learning system, AbyFarm’s algorithms get smarter over time. Each time a crop is affected by disease, data about the occurrence and corrective action is fed into the system, enabling its algorithms to formulate solutions for other farmers with similar crop issues – without consulting an agronomist.
With that, said Xie, even those who are new to the field can use the system to guide them on treating diseased crops, which can be isolated from other crops to prevent cross-infections.
AbyFarm’s automated farming system, which is hosted on SPTel’s private cloud, can also advise farmers on the best time to transplant their crops after germination and harvest them later for sale, said Xie.
Heng Kwee Tong, vice-president for engineering and customer solutions at SPTel, said the company has built up a software-defined platform to help companies like AbyFarm overcome the challenges of deploying applications such as IoT.
“The common struggle that companies like AbyFarm face with building an IoT solution is that it is quite intensive in terms of ICT infrastructure,” said Heng. “You’ve got to find the radio connectivity like Lora, subscribe to a service provider, and connect your sensors to a sensor collector.
“We make it easy by investing in a platform and because we are a service provider with edge hub assets for deploying radio connectivity, all AbyFarm needs to do is to bring their sensors onboard.”
Going forward, Heng said SPTel is looking to support next-generation video analytics capabilities through edge cloud services that can be used to crunch workloads closer to where they reside, reducing latency.
AbyFarm was one of six companies to win contracts from the Singapore Food Agency last year to build urban farms at nine rooftop carparks in public housing estates across Singapore.
The goal is to collectively produce about 1,600 tonnes of vegetables a year in a bid by the city-state – where less than 1% of the land is used for agriculture – to become more self-sufficient in meeting the nutritional needs of its people.
That could well be achievable with technology that makes farming more efficient, scalable, and less labor-intensive than before. “We are willing to train and educate the next generation in agrotechnology because now you don’t need 10 farmers to take care of one farm,” said Xie. “It’s just looking at the dashboard and, with the alerts, doing what is required.”
Signify and RIAT Pioneer Growing Tomatoes and Cucumbers In A Vertical Farm Without Daylight
Signify (Euronext: LIGHT), the world leader in lighting, and RIAT, an innovative farming enterprise located in Russia, have together pioneered the growing of tomatoes and cucumbers in a vertical farm without daylight.
April 30, 2020
Eindhoven, the Netherlands – Signify (Euronext: LIGHT), the world leader in lighting, and RIAT, an innovative farming enterprise located in Russia, have together pioneered the growing of tomatoes and cucumbers in a vertical farm without daylight. During the research phase in 2019, RIAT achieved a yield comparable to advanced traditional greenhouses using Philips GreenPower LED grow lights.
We already had facilities of sufficient height at our disposal, therefore there was no need to invest in building a glass construction. But as the building had no windows, we needed a high-quality lighting system to fulfill the intensive lighting requirements of tomatoes and cucumbers. In 2019, Signify provided its Philips GreenPower LED grow lighting, helping us to achieve a yield performance comparable to traditional greenhouse operations."
Vladimir Bukharev
Director at RIAT
RIAT’s indoor farm is located in the center of the Ivanovo region, enabling the company to distribute its tomatoes, cucumbers and 19 types of green crops to its own RIAT stores within an hour after harvesting. RIAT has a special technique to fold the long stems, allowing it to grow the 3.5m high plants indoors.
“With a harvest of 2.7 to 3.2 kg of cucumbers per m2 every week, and 1.7 kg per m2 of tomatoes, we started making a profit as of the second year of operation,” Bukharev added. “In addition to that, the quality of the product is very high, there’s hardly any waste and we sell 99% of what is being grown.”
“To mimic nature as much as possible, RIAT has chosen a combination of different kinds of Philips GreenPower LED toplighting and interlighting, bringing light both from the top and right in the canopy where the light is needed the most for photosynthesis. While using different kinds of lights, the light recipe can be adjusted based on the crop that is grown,” said Sergey Khokhrin, business Development Manager CEE/Russia & CIS at Signify.
Signify, in collaboration with several research partners, discovered that the red spectrum in light stimulates growth of plant cells and tissues, while the blue spectrum influences the processes of cytodifferentiation (racemes initiation, bines and root formation, flowering). The combination of red and blue with the addition of white and other colors in Philips LED grow lights creates lighting conditions that are as close to natural daylight as possible. Additionally, RIAT is using bumblebees for pollination, as in traditional greenhouses. The bees don’t experience difficulties due to the absence of natural light.
When choosing a lighting supplier, RIAT tested LED modules from different manufacturers from around the globe. “By using Philips LED lighting modules, we managed to achieve maximum stability and a light output of 18 g/mol. This is why we chose Signify. The area equipped with LED lamps is currently 3,800 m2. Soon, we are going to launch a new area of 700 m2 to grow lettuce which will also be equipped with Philips LED lighting,” Bukharev added.
For further information, please contact:
Global Marcom Manager Horticulture at Signify
Daniela Damoiseaux
Tel: +31 6 31 65 29 69
E-mail: daniela.damoiseaux@signify.com
Signify Corporate Communications and Government Affairs in Russia
and CIS
Natalia Neverskaya
Tel.: +7 (495) 937-93-30; fax +7 (495) 937-93-59
E-mail: natalia.neverskaya@signify.com
About Signify
Signify (Euronext: LIGHT) is the world leader in lighting for professionals and consumers and lighting for the Internet of Things. Our Philips products, Interact connected lighting systems and data-enabled services, deliver business value and transform life in homes, buildings and public spaces. With 2019 sales of EUR 6.2 billion, we have approximately 38,000 employees and are present in over 70 countries. We unlock the extraordinary potential of light for brighter lives and a better world. We have been named Industry Leader in the Dow Jones Sustainability Index for three years in a row. News from Signify is located at the Newsroom, Twitter, LinkedIn and Instagram. Information for investors can be found on the Investor Relations page.
A Whole Season of Hybrid Tomato Cultivation Den Berk Delice & Bryte Confirm: “LED Ensures Controllability”
A stronger plant, higher fruit weight, and more uniformity in growth; these are the results of a lit tomato crop when combining Philips GreenPower LED toplighting compact and HPS lighting in a hybrid lighting solution
September 9, 2020
A stronger plant, higher fruit weight, and more uniformity in growth; these are the results of a lit tomato crop when combining Philips GreenPower LED toplighting compact and HPS lighting in a hybrid lighting solution. The growers, the world-renowned tomato cultivators Bryte from the Netherlands and Den Berk Délice from Belgium share their experiences with hybrid lighting during the first cultivation season in this article. Both projects were installed at the end of 2019
Both entrepreneurs were very positive about their experiences after a year of tomato cultivation with hybrid grow light. The combination, which resulted in a more uniform fruit and crop growth and a more controllable greenhouse climate, asks for more. Cultivation with hybrid lighting, in which LED lighting is combined with HPS lighting, however, requires a different approach than cultivation with only HPS lighting. “The big advantage of LED lighting is that there is much less radiant heat from the light, which gives us more control over the climate in the greenhouse. Since light and temperature can be controlled more independently from each other with hybrid lighting, we have to change the way we approach the climate differently and that requires a new way of thinking, where the experience of the Signify plant specialists comes in handy, ”says Zwinkels.
Heat differences in the greenhouse
Where heat is mostly the deciding factor with traditional HPS illumination - but also plays a major role as an unavoidable by-product for cultivation control - this is no longer the case with hybrid illumination. LED leads to much less excess heat in the greenhouse, which makes it possible to control light and temperature separately. It is thus easier to control the growing conditions. For example, Den Berk Délice chooses to grow generatively up to 28° C in winter and from March more vegetatively to keep a strong crop. Lucas: "We noticed that we are much more in control with LED." The cultivation experts at both companies carefully thought about how they could anticipate on the changing temperature situation in the greenhouse. Erik: "With us, the position of the growth tube could be at the expense of the fruit weight. In our case, the best solution was to introduce extra heat from the bottom of the greenhouse. We also noticed that control errors were less likely to be made due to better control over the climate and that the climate became more constant. We saw positive crop development and were satisfied with the fruit weight and the crop growth."
Illuminate longer
“A big advantage of hybrid cultivation in comparison with HPS is the possibility to light the crop for a longer period of time", said Koen. “Especially in the winter months, a high crop yield is important to us; it is a period that we want to make the most of. We have seen that with hybrid cultivation you can illuminate earlier in the fall, but also until deeper in the spring, up to thirteen or fourteen hours a day. Of course, you have to keep looking at what extra lighting brings in terms of production and costs.”
Light advice
The plant experts of Signify are experts in using LED and know better than anyone else what LED lighting means for crop growing and climate. In the past growing season, they assisted the companies with light and climate advice. Both companies now have 180 µmol/s/m2 light, distributed across 90 µmol/s/m2 LED toplighting compact and 90 µmol/s/m2 HPS lighting. The Philips GreenPower LED toplighting compact was introduced to the market during the last growing season. "Signify talks a clear language", said Erik. "They are the right discussion partner for me, who regularly visits and discusses what we encounter in practice." Koen adds: “The specialists also have a large network. Via them, I managed to get into contact with other growers who also use LED. I look forward to the annual Tomato Community Event organized by Signify, where cultivators from around the world get together. This not only gives me the opportunity to share experiences with LED lighting, but also to expand my network that I can take advantage of in the future. We always see talking to like-minded people as very valuable.”
Does LED toplighting have a future?
Firstly, LED saves up to 60% on energy costs, but there is more. Erik: "As cultivator, I would like to bring the winter to the summer. LED lighting makes it possible to go to higher light levels and is the right way to do that. I prefer a hybrid solution with HPS, and then look at how we can regulate the heat in the greenhouse.” For Koen, the ideal cleaning conditions, where the modules do not have to be shielded, and the simple scaling options are reasons to choose a combination of HPS with LED toplighting compact luminaires. He refers to the plug-and-play ease of installation of the Philips GreenPower LED toplighting. Both consider future investments in a larger portion of LED in their greenhouses. They look forward to the development of LED in combination with higher light levels.
Create the correct balance to control your crops
Erik wondered if he, at his company, as he said, maybe loved the plants too much. In passing, he refers to the learning curve that you as a grower with LED go through. "You control it differently with hybrid lighting and that requires experience that you will gain through the years. You become wiser. Light and heat become more tangible and you are better able to control the right balance in your crop. I see it as an added value in which we can develop ourselves year after year, with better end results. Let the summer come during the winter!"
Erik and Mark Zwinkels are co-owners of Bryte; with 40 hectare - of which 60% is lit - one of the biggest players in the Dutch tomato cultivation. Koen Lauwerysen is one of the four business managers at Den Berk Délice, where Lucas Aertsen is the cultivation manager. With 60 hectares tomatoes - of which half is lit - their company is also one of the bigger ones in Belgium. Both share their experiences during the past cultivation season where they used the combination LED and HPS for the first time. Bryte installed it on eight hectares, and Den Berk Délice on ten.
For further information, please contact:
Global Marcom Manager Horticulture at Signify
Daniela Damoiseaux
Tel: +31 6 31 65 29 69
E-mail: daniela.damoiseaux@signify.com
Signify Global Media relations - Professional Lighting
Wendy Schellens
Tel: +31 6 51 863 401
Email: wendy.schellens@signify.com
About Signify
Signify (Euronext: LIGHT) is the world leader in lighting for professionals and consumers and lighting for the Internet of Things. Our Philips products, Interact connected lighting systems and data-enabled services, deliver business value, and transform life in homes, buildings, and public spaces. With 2019 sales of EUR 6.2 billion, we have approximately 36,000 employees and are present in over 70 countries. We unlock the extraordinary potential of light for brighter lives and a better world. We have been named Industry Leader in the Dow Jones Sustainability Index for three years in a row. News from Signify is located at the Newsroom, Twitter, LinkedIn, and Instagram. Information for investors can be found on the Investor Relations page.
Could Urban Agriculture Feed The Cities of The Future?
Vertical farms, rooftop farms and computer-controlled growing environments are an emergent phenomenon in cities around the world, which are eager to take advantage of the many benefits of urban agriculture
03 Sep 2020
By Agency
Vertical farms, rooftop farms, and computer-controlled growing environments are an emergent phenomenon in cities around the world, which are eager to take advantage of the many benefits of urban agriculture.
Drawing on new technologies and enthusiasm for locally sourced organic produce, these promising initiatives have raised hopes for greater sustainability that will reduce the environmental impact of cities and agricultural production required to meet the needs of their citizens.
However, the question remains: will urban farms be able to produce enough food to make cities self-sufficient?
The vast majority of fruit and vegetables sold in cities are picked before they are ripe, and are produced using intensive farming methods, which do extensive damage to the environment.
In contrast, urban agriculture offers the hope that we will one day be able to meet the global challenge of feeding cities in a much more sustainable manner. At the same time, it also provides a solution to the need for high-quality and locally sourced fresh food.
Recent successes in the field speak for themselves, notably the US$4mil (RM16.6mil) in funding raised by IFarm, which provides software and technology to the vertical farming sector.
The Helsinki-based company manages heavily automated indoor farms in which produce is grown in vertically stacked beds with a host of technologies that include a wide range of sensors, computer vision, and machine learning.
It currently has some 50 farms that are in development and is hoping to manage one million square meters of vertical farms and provide support for 500 different crops by 2026.
Is food self-sufficiency within reach?
It could be, notably with regard to vertical farms and certain crops. A recent publication in the interdisciplinary scientific journal PNAS has drawn attention to the potential of vertical farming to generate enormous yields of wheat.
Researchers have calculated, on the basis of theoretical values for the growth of wheat under optimal conditions, that a 10-story building on a one-hectare site could provide up to 1,940 tonnes of wheat per year, 600 times more than the average yield from traditional agriculture.
One of the reasons for this is because vertical farming provides conditions that would allow for five harvests per year instead of one. With the added advantages of doing away with the need for herbicides and pesticides, low water use, and land depletion, vertical farms may well fulfill their promise.
Questions remain about the viability of projects
However, as it stands, urban farms are very expensive to set up, and only a very few are actually profitable. Taking advantage of their situation in cities, most of those that are now operating are sustained by revenue from sources other than food production: notably income generated by cultural events, workshops, and renting plots to private individuals. – AFP Relaxnews
Related stories:
Community farm brings residents together
Getting ready for Agriculture 4.0
Lead photo: Urban agriculture is increasingly common in cities. This picture shows one of six farms created by the New York City Housing Authority in Brooklyn, New York. Photo: Leticia Barboza/AFP
TAGS / KEYWORDS: Urban Farming , Food Security , Vertical Farming , Rooftop Farms
Smart Acres CEO on The launch of The UAE’s Latest Vertical Smart Farm
The launch of Smart Acres, the UAE’s latest addition to the hydroponic vertical farming industry, this week means that a line of the freshest, most nutrient-dense greens for UAE residents and businesses alike is now being produced in containers on the Armed Forces Officers Club in Abu Dhabi, with the aim to expand across the UAE
Smart Acres Is Here With Lettuce At The Helm. In An Exclusive Interview With Abu Dhabi World, Smart Acres CEO Abdulla al Kaabi Reveals What This Means To Abu Dhabi And The Farming Community On The Whole.
words Derek Issacs
If you love healthy produce, and who doesn’t, then this news is going to please you and your tastebuds no end. The only draw back at the moment is they’re not for sale in supermarkets just yet, but it won’t be long before they are.
The launch of Smart Acres, the UAE’s latest addition to the hydroponic vertical farming industry, this week means that a line of the freshest, most nutrient-dense greens for UAE residents and businesses alike is now being produced in containers on the Armed Forces Officers Club in Abu Dhabi, with the aim to expand across the UAE.
So we headed over to the St. Regis Abu Dhabi to meet Smart Acres CEO Abdulla al Kaabi to find out more.
Tell us about your background?
I am from tech and farm background. My father has a passion for farming and gardening; he’s very strict about anybody who messes around with his garden or farm. My father has a few farms across the UAE, where he grows crops and dates. When he heard that I was pursuing a project in the agriculture sector he got excited and actually gifted me a farm, which I am grateful for and will keep. However, Smart Acres, rather than the farm my father gifted me, is an urban farm.
How was Smart Acres first developed?
CEO Abdulla al Kaabi (centre)
Smart Acres was founded in 2017 and local testing began in July 2019. Smart Acres was developed by a team of experts, including myself, Director Sean Lee and Lead Project Manager, Aphisith Phongsavanh with the aim of improving food security within the United Arab Emirates and developing the country’s farming capabilities, providing a solution to potential socioeconomic threats such as pandemics and climate limitations the Middle East currently endures.
Tell us more
We planted lettuce and after a few harvests, we decided to expand from two containers to eight containers. From the two insulated containers the yield was 3.5 tons annually, which was our proof of concept. For the proof of concept, our target weight for each lettuce head was 140g. However, we have reached an average of 200g per head. I don’t think any other vertical farm here reached that quality or weight in terms of vegetables at this size.
How would you describe Smart Acres?
It is a one-of-a-kind agriculture system that is designed to produce some of the highest yields of crops within the UAE’s vertical farming industry, while introducing a new future for clean foods and allowing both business to business (B2B) and business to consymer (B2C ) sectors to locally source produce.
Tell us about the containers
We invested heavily in the containers, not just financially, and it took us a while to partner up with n.thing, a South Korean vertical farming technology company, to bring the best vertical farm here in the UAE. We had talks with other companies before and we decided to go with this one, in terms of risk, in terms of technology they are using. And the system we are using in the containers is hydroponics (growing plants without soil) which has been used by growers for hundreds of years. Techno advancements means we were able to implement the Internet of Things for operations, which helps us to monitor the entire farm in terms of humidity, temperature, and even the nutrients that goes inside the plants. Now we have our expansion plan from eight to 78 containers, which eventually will produce more than 140 tons of produce annually. We are currently in talks with private and public entities in terms of the expansion. We are also planning to have a research and development centre in order to start growing our own potato seeds in a controlled environment.
Will Smart Acres just be growing lettuce?
In our current eight containers, we grow four types of lettuce; Lolo rosso , green glace, oakleaf Batavia, but we are able to grow 30 types of lettuce. Currently we are testing new methods to improve quality and weight of the existing lettuce. The results of last month’s test resulted in lettuce whose individual heads weighed more than 200 grams on average. However, we aim to grow more than just lettuce. We have plans to eventually grow baby spinach, mature spinach, and baby arugula. Smart Acres’ vision is to expand to meet the demand of popular produce in the region such as strawberries, and, as I previously mentioned, a shift and emphasis on cultivating potato seeds.
Where can we buy your smart lettuces?
We are now supplying restaurants and hotels for free to get ourselves known, and we have had great feedback from them. We have also partnered with several restaurants and cafes around the country including Inked and Fae Cafe, and have plans to have our produce in the kitchen of dozens of other F&B outlets. The recent initiative by HH Sheikh Mansour bin Zayed, Deputy Prime Minister, Minister of Presidential Affairs, and Abu Dhabi Agriculture and Food Safety Authority (ADAFSA), stating that all major grocery stores in the capital must allocate space for local produce means we are perfectly poised to enter local supermarkets. We have had lots of offers from Abu Dhabi Holding and other government entities that are members in the food security committee to buy our whole produce. Currently we are focused on our actual produce itself, in terms of quality, weight.
Posted in Features, Food, Life, News
Tagged agriculture system Abu Dhabi, CEO Abdulla al Kaabi, Clean foods UAE, food security UAE, SMART ACRES Abu Dhabi, st regis abu dhabi, UAE Climate Change Risks and Resilience, UAE farms, UAE’s vertical farming industry, vertical farming Abu Dhabi
UAE: Smart Acres Plans To Open R&D Lab For Local Produce Amid AgTech Growth
Abu Dhabi vertical farming start-up Smart Acres is looking to raise at least Dh20 million to fund a research and development center to produce a local variety of potato as agriculture technology gathers pace in the UAE
Vertical farming start-up aims to raise as much as Dh20m to fund the project
Abu Dhabi vertical farming start-up Smart Acres is looking to raise at least Dh20 million to fund a research and development center to produce a local variety of potato as agriculture technology gathers pace in the UAE.
“The future is green. The Hope probe has headed to Mars, why shouldn’t the UAE be the first to put a container farm on the planet?” Abdulla Al Kaabi, founder and chief executive, told The National.
The entrepreneur is part of a team of three working in partnership with a Korean AgTech platform called N.thing, to adapt the technology to the harsh arid climate of the Emirates on an Abu Dhabi farm gifted to him two years ago by his father.
Smart Acres has designed vertical farms in shipping containers using the IoT-based technology system that monitors water, carbon dioxide, and nutrient levels. The system sends a push notification to one of the team's iPhones or iPads if levels need to be adjusted, but it allows the process to happen largely unmonitored. The farm is empty most of the time, Mr. Al Kaabi said. The growing process also consumes up to 90 percent less water than traditional farming methods and grows premium and cost-competitive lettuces.
Food security and innovation in agriculture is a priority of the Abu Dhabi government, which has earmarked Dh1 billion for an agri-tech incentive program as part of the government’s Ghadan 21 accelerator initiative.
In April, Abu Dhabi Investment Office (Adio) invested $100 million (Dh367m) to bring four agriculture technology companies to the emirate as part of government efforts to attract high-skilled talent and cutting-edge research. The country’s 24,000 farms are set to benefit if new technology can be applied to drive efficiencies in crop yield and water usage.
The Covid-19 pandemic has only underscored the need to achieve greater food security in the UAE. Between 80 and 90 percent of the food in the GCC is imported, according to Chatham House.
While the figure is high, UAE residents are starting to see signs of progress: locally-harvested tomatoes and greens at the market or on dining menus are now a common sight. All of this has sprung up in the last several years as vertical and hydroponic farming ventures and research, as well as cloud-seeding, bear fruit.
Mr Al Kaabi wants the Smart Acres Institute of Food Security & Agriculture “to have Emirati hands” build the project. He is looking to attract recent graduates in environmental sciences and technology to the R&D lab to customize seeds to grow in this region in a controlled environment.
Potatoes, one of the most common crops in the world with consistent growing demand year-on-year, will be his first target. The team also wants to develop robots to help with harvesting and packing.
In addition to the R&D lab, Mr. Al Kaabi is aiming to increase the annual yield capacity at the farm more than tenfold, from the 40 tonnes of lettuces that it currently produces.
Mr. Al Kaabi was well-versed with the food industry even before he struck out on his own. His family owns the exclusive distribution license for a popular Korean ramen brand called Samyang Noodles as well as Tom’s Farm almonds.
While he learned a lot from the family trading business, his father encouraged him to build something on his own. After seeing how difficult the last several months have been on the imported food business, he is glad he did so.
With Smart Acres, Mr. Al Kaabi said, "I'm finally doing something right. Now my father asks me every two weeks what is going on at the farm”.
Updated: July 21, 2020 06:52 PM
Lead Photo: Farming via smartphone in Abu Dhabi. Courtesy Smart Acres
VIDEO: The Supermarkets That Grow Their Own Food
There's a food-tech revolution happening in our supermarkets, and it could change the way we eat forever
Jul-2020
Ian Dickson
There's a food-tech revolution happening in our supermarkets, and it could change the way we eat forever.
To View The Video, Please Click Here.
From romaine lettuce to curly parsley, salads and herbs are leaving the fields behind to be grown in-store in front of customers' eyes.
Under the glare of artificial light and computer-controlled temperatures, these pioneering plants are part of an ambitious vertical farming project. One that could fundamentally change how fresh food is grown and help dramatically reduce food miles (the distance food travels to get to your plate) and the use of natural resources.
Behind the revolution is Germany-based Infarm, one of a growing number of companies weaving technology and food production together.
Infarm sells supermarkets a modular growing chamber, a bit like a giant fridge, with plants stacked in rows to ceiling height, where they're remotely controlled through a cloud-based and "internet of things" enabled farming platform.
Currently, Infarm supplies more than 700 local "farms" across the world, from The Netherlands to Japan, and harvests in excess of 250,000 plants a month.
So far, these farms have saved 2.4 million kilometers of transport, 27 million liters of water and 38,000 square kilometers of land.
Infarm are based in Berlin, and were founded in 2013. /Infarm
Emmanuel Evita is the global communications director at Infarm and he says it's vital to grow fresh produce as close as you can to where it will be consumed because of the environmental burden of agriculture supply chains.
He tells CGTN Europe: "At Infarm, we want to find another way. We want to practice a form of agriculture that is resilient, sustainable and beneficial to our planet."
The farms are designed to easily "plug into any urban space." As Evita says: "Our in-store farms each occupy less than 2 square meters of ground. When these plants are purchased, they are so fresh they are still living."
Over in the UK, supermarket chain M&S has been trialing Infarm at seven of its London branches. It says that each of its micro-farms produces a crop equivalent to 400 square meters of farmland.
And because they are controlled by self-learning internet of things technology, the plants are continually monitored and receive only the optimum level of light, water and nutrients.
As a result, M&S says its store-grown plants use 95 percent less water and 75 percent less fertilizer than traditional soil-grown plants.
"Infarm's innovative farming platform is a fantastic example of what can happen when passionate agricultural, food and technology experts work together," said Paul Willgoss, director of food technology at M&S Food. "We operate as part of a complex global food supply chain and want to understand the emerging technologies that could help provide more sustainable solutions, while also delivering fantastic products."
Infarm's vertical farms specialise in herbs. /Infarm
In May, Infarm partnered with Germany's ALDI SUD to grow chives, parsley, basil, mint, and coriander in stores across Frankfurt and Dusseldorf. Additionally, ALDI SUD is providing 300 more stores with fresh Infarm produce from centralized distribution centers.
"Our customers can watch the herbs grow. They are grown and harvested in our stores – they couldn't be more fresh," says David Labinsky, group buying director at ALDI SUD.
While customers can watch the plants grow, they can't pick their own. Instead, they're harvested on a regular basis and packaged in-store where they're at their freshest.
Could vertical farms be the future of food? That's certainly what Paul Gauthier, professor of plant science at Delaware Valley University, believes. As he told The Daily Princetonian newspaper: "There is no question about it, vertical farming will be part of our lives. It's important to start thinking and finding solutions for the future."
Video editor: David Bamford
VIDEO: IGS Intelligent System Design – FTS Finds Out More
IGS has, as a company, focused from the outset on automation, intelligent system design, and the energy equation of CEA vertical farming
July 6, 2020
IGS has, as a company, focused from the outset on automation, intelligent system design, and the energy equation of CEA vertical farming. This has garnered them a reputation as one of the leading and most innovative companies in the industry. We took some time to have a chat with them and find out a bit more about how this all works in practice.
FTS: Hello and thanks for taking the time to talk with us. Can you briefly introduce IGS, its history as well as its outlook?
IGS: IGS was founded in 2013 bringing together decades of farming and engineering experience with a vision to revolutionize the indoor growing market. The two founders, farmer Henry Aykroyd and our CTO Dave Scott had an appetite for innovation and realized that there were significant gaps in the provision of scalable technology for the sector.
Henry knew how to grow and understood the challenges which faced traditional farming: Dave knew how to manage automation and power controls in an industrial environment. The opportunity to bring greater climate control to a growing environment was significant. The ability to manage power consumption was revolutionary. The simplicity of its implementation and use is pivotal.
We opened our first vertical farm demonstrator in Scotland in 2018. Artificial intelligence determines optimal nutritional input and the exact combination or ‘recipes’ of weather: lighting, watering, and ventilation. Data is collected continuously and machine learning used to make iterative adjustments, all of which is monitored through a web-based app. The whole Intelligent Growth platform is IOT-enabled to automate system control and management. Our degree of control is so fine that each 6m2 growth tray has its own microclimate. Technical simplicity is at the heart of our mechanical design.
Our commitment to innovation has continued apace and we have evolved the applications of our technology beyond agriculture to create solutions for a wide variety of indoor environments, developing the Intelligent Grid platform.
The Intelligent Grid uses the same IOT-enabled power and controls platform to manage and monitor lights, sensors, cameras, and communications for complete climate control and reporting. It too has a very simple, clean, and elegant design for application in any commercial building, greenhouse or livestock shed. In contrast to the vertical farm, we use our same core technology through the Intelligent Grid to create whole-space macroclimates.
Both IGS demonstrators are based at the James Hutton Institute, a world-renowned crop, and plant science research facility. IGS and the Hutton collaborate closely to help advance the understanding of plant science for indoor growing.
Until 2018 IGS had invested approximately £7m in R&D to ensure that its platforms offered the greatest levels of control and achieved levels of economic viability, scale, and minimal environmental impact compared to other systems on the market. In 2019 IGS raised £7 million in institutional capital to enter production and take its systems to global markets. We continue to invest over £1m per annum in R&D.
FTS: You have recently shared news of two reseller partnerships – one in the Middle East and one in the UK and Italy with TEP Renewables. Can you tell us briefly a bit more about them?
IGS: We have been talking to International Real Estate Partners (IREP), the international facilities management firm for some time in the Middle East, and we’re really pleased to recently sign this referral agreement which is specifically focused on indoor vertical farming for the UAE and Saudi Arabian markets.
We also have an opportunity to extend into Asian markets in the future. It gives us a greater capacity to service the Middle East market and secure and deploy vertical farming platforms across the region. IREP’s presence in this market is well established with many existing customers across agriculture, retail, and construction and it is a very positive development for both companies we believe.
The agreement with TEP Renewables is an MOU (Memorandum of Understanding) or a reseller-type partnership if we identify customers who would like to operate solar-powered vertical farms in Italy or the United Kingdom that we will work with them.
FTS: Fantastic! In the end, any vertical farm (indeed any farm!) is only as environmentally sustainable as its energy equations. But it is also only as financially sustainable as its energy cost. You have focused quite intensely on this energy cost question. As we see this dramatic collapse of fossil fuel energy production return on investment, it seems that NOW is the time to have renewable energy options on hand for CEA. Do you believe that renewable energy can be cost-competitive – both in terms of installation, sustainable life-cycle and with regard to the price of the final product for the consumer?
IGS: We consider a variety of power distribution and supply methods. Renewables can have considerable benefits from an environmental perspective and also specific to grants and other financial support for utilizing renewable energy resources.
The “virtual power plant” capabilities of our systems indicate strong Demand Side Response (DSR) potential. We can manipulate our growth cycles to respond to power availability and respond to inherent instabilities in power networks. This is already having an influence on our engagement in circular energy projects to utilize spare energy for growing and allows for more renewable power sources to be adopted.
FTS: Labor cost is the other biggest outlay for any vertical farm. You have invested heavily in automation. Is the trade-off of increased capital expenditure for automation worth the reduction in operational expenditure for labor, in your experience?
IGS: Absolutely. Driving down the farm gate price is the ultimate goal and while labor costs vary from region to region, we believe that this investment in the automation (and indeed the associated patents) within our growing operations is imperative and differentiates our systems considerably.
FTS: You’ve set about designing modular and intelligent systems. Such a bespoke system offers advantages of course, as we’ve seen above. But it can also present challenges if it cannot be integrated with other equipment and systems later. Do you future-proof your systems to be able to accommodate such updates and integrations over time?
IGS: We have thought about this from the outset, and our systems are designed in a plug and play model, rather than being bespoke as such. Scalability is paramount for our customers and this has been a consideration throughout our R&D development. Rather than using proprietary systems for processes such as sowing and harvesting, we use off-the-shelf equipment and components. This means we can keep startup and maintenance costs down by providing items with which farmers are already familiar. If a section of the vertical farming system needs to be replaced or upgraded, such as a water filter, a lighting panel or a tray, it can be done with almost no interruption.
However, what is also imperative to think about in terms of future proofing, and a hugely important part of our approach, is how we work so closely with the science community to better understand plant light interactions. The level of control we have designed into our hardware systems allows us to flex and adapt as we need to deploy the most up to date plant light information through our software development, which is continuously evolving.
The approach of our software development has also involved maximising security of our systems and ensuring simplicity of operation. This will be continuously updated, but with seamless integration for our customers.
FTS: Along with FTS, you’ve joined a number of other associations and similar collaborative groups. Why is this important to you as a company, and how do you balance the proprietary needs of your company against this desire to cooperate?
IGS: Collaboration and cooperation across this sector is essential. Our vision is that sustainable change will only be delivered not only when we collaborate, but when we are all open and honest about the limitations, as well as the opportunities for this sector. We want to work alongside technology vendors with complementary products, and with growers and producers, supported by science and greater understanding of growing plants indoors, all backed by far-sighted investors.
We firmly believe that through innovation, collaboration and investment we can create an economically and environmentally sustainable global indoor food industry.
FTS: Thanks so much for taking the time to talk with us today. We wish you every success and look forward to working with you in the future.
IGS: Thanks very much indeed. We look forward very much to be part of Farmtech Society as we all move forward in the development and innovation of agricultural technology.
For IGS
David Farquhar
CEO
VIDEO: Vertical Farming: The Only Way Is Up
Just like we've grown accustomed to living in compartments stacked directly on top and beside each other so too are lettuce and herbs
by Jasmine Reimer
Trends - /March 2, 2020
Just like we've grown accustomed to living in compartments stacked directly on top and beside each other so too are lettuce and herbs.
Agriculture is going vertical. Why? Because it saves water, increases efficiency, and provides us with fresh, local produce.
Vertical farming is the practice of producing food on upright surfaces. Instead of farming in a field, vertical farming grows plants stacked in layers, in structures like shipping containers or warehouses.
If this seems like an insignificant shift, unlikely to produce much effect, consider this: by 2050 the world's population is expected to grow by another 2 billion people.
Feeding everyone will be challenging. Vertical farming could be a solution.
What is vertical farming?
Assembled layer by layer under candy-colored lights, vertical farming has become an increasingly popular way for food producers to reduce costs related to space and energy consumption while increasing growth rates and nutrient values.
Of the many companies that are testing out this innovative farming method, Urban Crops uses a conveyor-like system to hold baby plants under LED ultraviolet lights. Their system is automated and relies on technology to program lighting and growing conditions specific to each species. And because they don't heat up, the bulbs can be placed closer to the leaves to encourage optimal light absorption.
In addition to not having to maintain an entire plot of land, Urban Crops boasts that vertical farming yields more crops per square meter than traditional farming or greenhouses. It also grows plants faster and can be used year-round. In theory, vertical farming can be practiced anywhere, which means that water-restricted locations can still harvest produce. Vertical farming uses up to 95% less water than traditional methods.
As Urban Crops' Chief Executive Maartin Vandecruys points out:
“Basically… every day is a summer's day without a cloud in the sky."
CES 2020: LG are launching exciting new indoor gardening technology.
While vertical farming could be the future of large-scale agriculture, companies like Urban Crops are also hoping that non-farming folk like yourself will be interested in investing in DIY versions. Because, while it makes sense to grow salad greens and edible flowers, trying to grow other foods like wheat for bread isn't yet an option: “At 10 cents a kilowatt-hour, the amount of energy it would take to produce wheat would [translate to] something like $11 for a loaf of bread," states, Vandecruys. Nonetheless, vertical farming could mean big changes in the way you think about “local" produce.
Vertical farming helps reduce the amount of questions for the consumer including its provenance, growing conditions and harvest date.
Data is useless unless you put it to work
Around the world, data-driven technologies are being used to keep indoor farming afloat. Detailed, real-time data collected via artificial intelligence, location services and IoT technology is used to analyze and produce better feeding models and optimal configurations, i.e. the concentration and scheduling of light and ratio of nutrients. Most recent is IoT company n.thing's Planty Cube, launched at this year's CES 2020.
Leo Kim, n.thing's CEO, came up with the idea for Planty Cube after creating an IoT-enabled smart pot called “Planty Square."
Planty Cube is a smart hydroponic vertical farm that relies on data from farming logs, which are fed back into a database called the “Cube Cloud" and analyzed with AI to help farmers determine optimal growing conditions. As the user adds more Planty Cubes to the vertical farm, this real-time, cloud-based system makes it easier for the grower to manage the overall farm, even remotely.
But even prior to sowing seeds, technology can help vertical farmers and consumers alike.
Automation, tracking and AI technology also opens up the potential to locate farms in urban, industrial, and even domestic spaces that can produce crops all year round.
This has the possibility to truly change the way cities source food. Most urban supermarkets are supplied from distributors around the world. Local indoor farms could decrease reliance on imports and reduce carbon emissions from transportation.
In the future, I hope to see supermarkets filled with vertical farms of their own.
The ups and downs of growing up
The vertical farming industry is booming. However, there are realities to consider before growing on a professional scale:
What are you growing and for whom?
Before you invest, do some market research. Get a sense of who your customers will be and your price point. Basically, if you can't sell it, you shouldn't grow it.
What is your distribution plan?
How will you physically get your produce to your customers? Find out who your end customers are and keep your farm as close to them as possible. Being local is an integral component to your success but this may present further challenges such as high cost of land, poor soil quality, and resource restrictions.
Will your building meet your needs?
Remember, indoor farming requires substantial amounts of power: lighting, pumps, HVAC, automation equipment, fans, computers etc. Not all buildings are equipped with the type of electricity you require. And if you're serious about getting into the vertical farming industry, you need to plan for future expansions.
Fortunately, vertical farming is being supported by more than just salad-starved individuals like me; location services and tracking technology are helping farmers retain high yields and prepare for the future.
Tech-Driven Vertical Farming Company Kalera Announces New CIO, VP of Sales
Today, technology-driven vertical farming company Kalera announced that it has hired two new executives to fill the positions of CIO and VP of Sales. New Chief Information Officer Jeremy Johnston brings over 15 years of experience in a broad range of fields, including technology, manufacturing, and retail
The appointment of these executives coincides with Kalera’s recent expansion into new markets
ORLANDO, Fla., June 02, 2020 (GLOBE NEWSWIRE) | Source: Kalera
Today, technology-driven vertical farming company Kalera announced that it has hired two new executives to fill the positions of CIO and VP of Sales. New Chief Information Officer Jeremy Johnston brings over 15 years of experience in a broad range of fields, including technology, manufacturing, and retail. The newly appointed VP of Sales Jeff Larsen brings with him 23 years of sales experience from a diverse set of industries with Fortune 100 companies.
With over 15 years of experience, Jeremy Johnston has spent his career leading information technology for the world’s largest companies including Deloitte, Amazon, and National Oilwell Varco. Most recently, Johnston worked in technology as the CTO of Qoreboard and PH6 Labs. He has also worked with global technology at Deloitte, where he managed several massive technology transformations in the oil & gas and healthcare verticals.
New Chief Information Officer Jeremy Johnston brings over 15 years of experience in a broad range of fields, including technology, manufacturing, and retail.
At Amazon, Johnston led the design and implementation of Amazon’s internal HRIS system responsible for the timekeeping and payroll for over 250,000 employees across nine countries. Johnston spent eight years at National Oilwell Varco early in his career where he oversaw custom application development, data warehousing, and ERP implementation for over 40,000 employees in 21 countries. Johnston will manage Kalera’s Information Technology policies, procedures, strategies, standards, and roadmap. At Kalera, being a data-driven company, advanced automation and data collection with IoT, Big Data Analytics and AI capabilities are essential.
“I am thrilled to be joining a company as forward-thinking and exciting as Kalera. I believe my global experience with diverse, complex companies will inform and accelerate Kalera’s rapid growth plans as we change the way produce is grown around the world,” said Jeremy Johnston, Kalera’s new Chief Information Officer.
Kalera has also named Jeff Larsen the Vice President of Sales. A multi-faceted and seasoned sales professional, Larsen has achieved many awards and accolades across a diverse range of industries. Larsen has over 20 years of experience in sales across various industries with Fortune 100 companies. Larsen has excelled at both regional and national levels in large scale distribution, business development, and account management.
The newly appointed VP of Sales Jeff Larsen brings with him 23 years of sales experience from a diverse set of industries with Fortune 100 companies.
“From foodservice and hospitality to grocery, I am excited to be supporting this groundbreaking business with my years of sales expertise,” noted Jeff Larsen, Kalera’s new Vice President of Sales. “People need safe, delicious and affordable produce now more than ever. Kalera is leading the charge in supplying the public with the freshest, most delicious lettuce on the market.”
"As Kalera continues to focus on our rapid national and international expansion, building a world-class executive team has been among our top priorities, and we are beyond excited to welcome Jeremy and Jeff to the Kalera family,” noted Kalera CEO Daniel Malechuk.
Kalera has experienced significant growth in recent months, with plans of its new growing facility in Atlanta being announced only months after the opening of its facility in Orlando. Its Orlando facility is currently the single largest indoor vertical farm in the Southeastern United States, and the Atlanta facility will be even larger. Kalera also made headlines after pivoting their business strategy amidst the COVID-19 crisis, shifting from a foodservice-focus to land their produce in the aisles of Publix. During this time, Kalera also organized giveaways for the Orlando community, giving away tens of thousands of heads of lettuce to provide access to fresh, local, produce to residents.
Central to Kalera’s business is good science. The company is planting non-GMO seed, and over the past several years has perfected plant and data science-driven methods to naturally optimize the factors that make plants thrive. Kalera manages these natural factors in a way that makes plants reach their maximum potential, resulting in the highest quality produce, grown locally with consistent high yields year-round.
By using a closed-loop irrigation system, Kalera’s plants grow while consuming 95% less water compared to field farming. While a head of lettuce grown in a field may use as much as 60 gallons of water, Kalera’s systems result in a healthier plant with less than five gallons.
The company utilizes cleanroom technology and processes to eliminate the use of chemicals and remove exposure to pathogens. With indoor facilities situated right where the demand is, Kalera is able to supply an abundance of produce locally, eliminating the need to travel long distances when shipping perishable products and ensuring the highest quality and freshness.
About Kalera
Kalera is a technology-driven vertical farming company with unique growing methods combining optimized nutrients and light recipes, precise environmental controls, and cleanroom standards to produce safe, highly nutritious, pesticide-free, non-GMO vegetables with consistent high quality and longer shelf life year-round. The company’s high-yield, automated, data-driven hydroponic production facilities have been designed for rapid rollout with industry-leading payback times to grow vegetables faster, cleaner, at a lower cost, and with less environmental impact.
Elka Karl
Phone: 510-508-7328
Email: elka@dadascope.com
A High-Yield Indoor Farming System Ideal For The City
According to Pollard, the evolution of new technology, such as LED grow lighting and the Internet of Things (IoT), has complemented the development of indoor soilless cultivation systems
As prolonged droughts occur more frequently in South Africa, some entrepreneurs are investing in and developing new technology and farming methods, such as indoor growing systems, that ensure consistent, high-quality food production. Juan-Griffith Pollard, CEO of Urban Cultivation International, spoke to Pieter Dempsey about his scaleable hydroponic farming system.
More frequent and long-lived droughts. Global warming. Water scarcity. Higher input costs.
These are some of the factors driving the growing interest in new technology that enables a farmer to produce the same quality and yields as conventional farming, but using indoor farming systems instead.
Hydroponics, or indoor soilless cultivation, as Urban Cultivation International (UCI) calls it, is a method of growing plants in a water-based, mineral- and nutrient-rich solution instead of soil, and under artificial LED lights instead of sunshine.
According to Juan-Griffith Pollard, the CEO of UCI, indoor farming uses up to 90% less water than traditional farming practices, and far less space. In addition, plants can be grown pesticide-free and closer to high-consumption areas, such as densely populated cities.
These reasons, and more, explain why an increasing number of growers have begun exploring indoor soilless cultivation.
Precision growing
The system provides the optimal growing conditions for plants, enabling them to develop much faster and be far healthier than is the case with traditional outdoor cultivation.
According to Pollard, the evolution of new technology, such as LED grow lighting and the Internet of Things (IoT), has complemented the development of indoor soilless cultivation systems.
“IoT can be used to automate and regulate indoor farming by monitoring water levels, nutrient levels, pH levels, and temperature and light requirements of plants. “A farmer can be in control of the harvest at all times, wherever he or she is physically present.
“One of the biggest benefits of indoor farming is that produce can be farmed at any time of the year. Thus, a farmer can sell produce at out of season prices, and supermarkets can stock fresh local produce all year around,” says Pollard.
No-soil farming
Pollard started investigating various methods of indoor soilless cultivation in 2016 and fine-tuned them in 2019 to create a healthy, productive indoor farming system.
An entrepreneur by nature, he took note of the various challenges in traditional South African agriculture, including water scarcity and security risks. He also noticed the demand for certain leafy greens and microgreens in cities.
Thereafter, he traveled to the US, Europe and Asia to research systems that could be applied in the South African agricultural environment.
He went on to establish UCI at the N4 Gateway Industrial Park in Pretoria East.
“What makes UCI’s technology different from most other indoor systems is that a farmer can start small and expand by adding additional racks to the system. So there’s no need to commit to a huge capital investment to get started,” Pollard explains.
The UCI model enables the farmer to control the light hours, nutrients and moisture. It is automated to produce rapid harvest cycles with predictable results, and can be used in a small space. Crucially, it is also affordable.
A key advantage is that the plants can be grown without the use of insecticides and herbicides, as the crops are grown in a controlled environment.
Pollard predicts that farms of the future will be urban-based, and crop cultivation will have to become far more sensitive to water and energy usage. There are many cost-effective options for indoor, soilless cultivation, and these allow farmers to move from the fields to the city.
Indoor production is also an easier entry into farming; it can be started by any entrepreneur, or even a retiree, he adds.
A wide range
The options offered by UCI range from small household units to large-scale commercial systems. Regardless of size, they can deliver crop yields of up to 10kg/m2.
The household units are small, with just enough space to service the average household and to plant a variety of crops, such as leafy greens, microgreens and berries.
The household system was also developed for educational purposes and can be used as an entry into indoor soilless cultivation before a large capital investment is made in a commercial unit. UCI has developed a curriculum that explains the A to Z of indoor hydroponic farming.
The company’s industrial units include climate control and a lift system, which makes harvesting easier.
Depending on the type of crop, the return on investment is between two-and-a-half and five years, while high-value crops such as microgreens have a payback period of less than a year on capital investment.
Growing with ease
Plants can be grown from seed to harvest in 28 days, three times faster than that achieved with traditional farming.
“The plants are grown in a controlled environment under 12 to 16 hours of LED lights, giving you optimal harvest and zero wastage,” explains Pollard. In addition, produce grown in UCI’s systems has proved to be of excellent quality and offer good taste.
The entry commercial turnkey solution system contains a 10m-long and 1,9m-wide row, and the buyer can choose to fit between three and 12 levels.
For example, a 10m-row, five-level-high farm enables 100m2 to be planted in a floor space of only 20m2. “The higher you go, the more your yield per square metre,” says Pollard. The grow trays and spacing between plants are designed for optimal growing and yield. No sunlight is needed for this method; all the systems use LED grow lighting.
“LED technology provides the best energy efficiency, which saves you money in the long term,” says Pollard.
Production
A 10m-long unit can handle 54 plants per tray. At 12 trays per level and at five levels, this equates to 3 240 plants per unit.
The lighting is usually kept on for between 12 and 16 hours a day, depending on the requirements of the plants.
“The more light they get, the faster they grow,” says Pollard.
The system can handle a variety of crops such as lettuce, spinach, baby spinach, marog (imfino), cherry tomatoes, strawberries, basil, watercress, sage, zucchini, beans, fodder and a range of microgreens and herbs.
To illustrate potential crop yields, Pollard and his team have used the five-level demonstration system at UCI’s premises to grow 250g lettuce heads in 28 days under optimal growing conditions. A yield of more than 18kg per tray has been achieved.
“Compared with traditional farming, the only major cost drivers are electricity and wages,” he says.
Each tray contains about 20ℓ of constantly recirculated water, and total water use is approximately 1 250ℓ/month. The system is extremely water-friendly, as almost all the water is absorbed by the plant.
“No water is wasted, hence the saving of 90% compared with traditional farming,” says Pollard.
He adds that climate and temperature control is a key factor in the grow room, and even the water temperature is cooled or heated as the plants require.
“We can mimic the controlled growing environment of certain crops as they require. “The system works with any water, and tests are routinely conducted to see what nutrients the plants need, and all variables can be adjusted according to the needs of the plants.
“We have a nursery system that grows the plants from seed to seedlings. After about seven days, the seedlings can be transported into the commercial system; the fully grown plant is then ready to be harvested after another 21 days,” Pollard says.
Due to the way in which the system operates, the chances of a pest infestation are very low.
“Biosecurity is crucial and we prevent any pathogens and pests from entering the facility.”
Harvesting a system that is 10m long and has five levels requires about three hours with two people.
With rapid urbanization increasing the demand for food, UCI’s system offers a number of key advantages.
It brings the farm closer to the people, thereby improving food security, and it reduces transport costs, in turn lowering the carbon footprint of supplying food. The system also offers good potential as a job creator.
“Our aim is to get entrepreneurial farmers to start utilizing the empty spaces in cities, such as empty buildings in city centres. Such spaces can be used to grow food, provide jobs and supply retailers directly,” says Pollard.
Visit urbancultivation.co.za.
By Pieter Dempsey | Farmer’s Weekly | May 6, 2020